
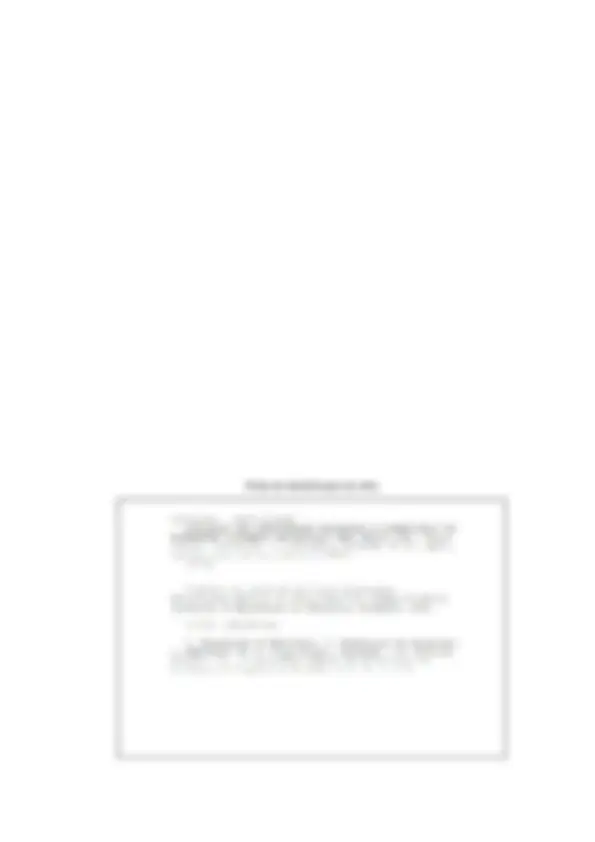
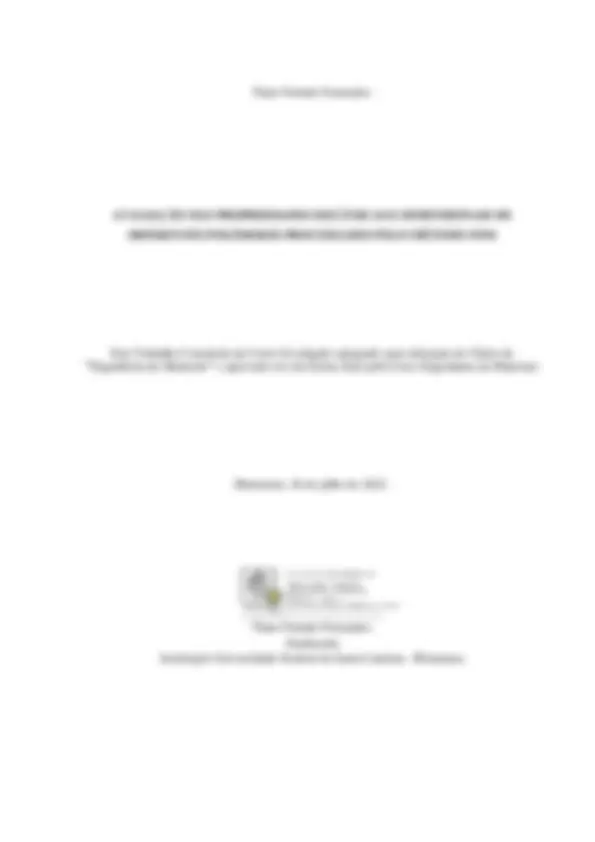
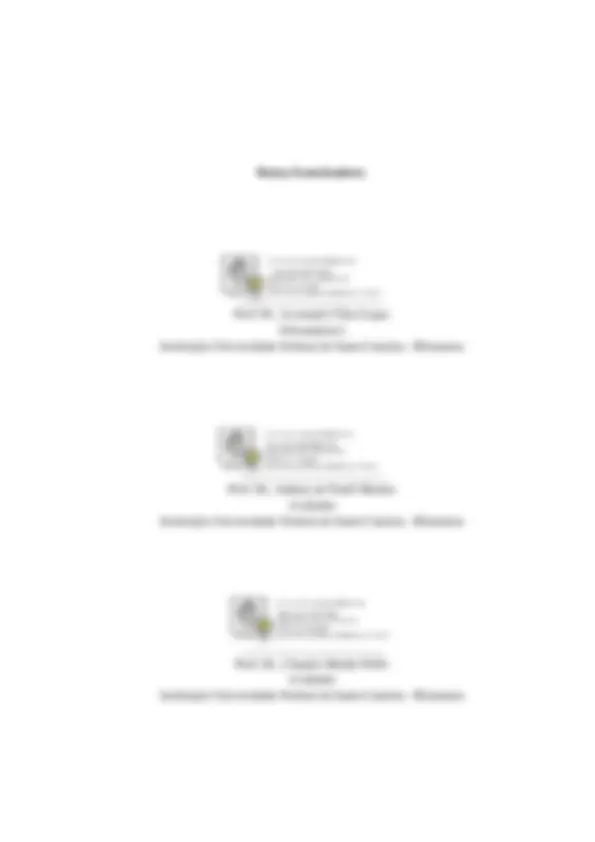
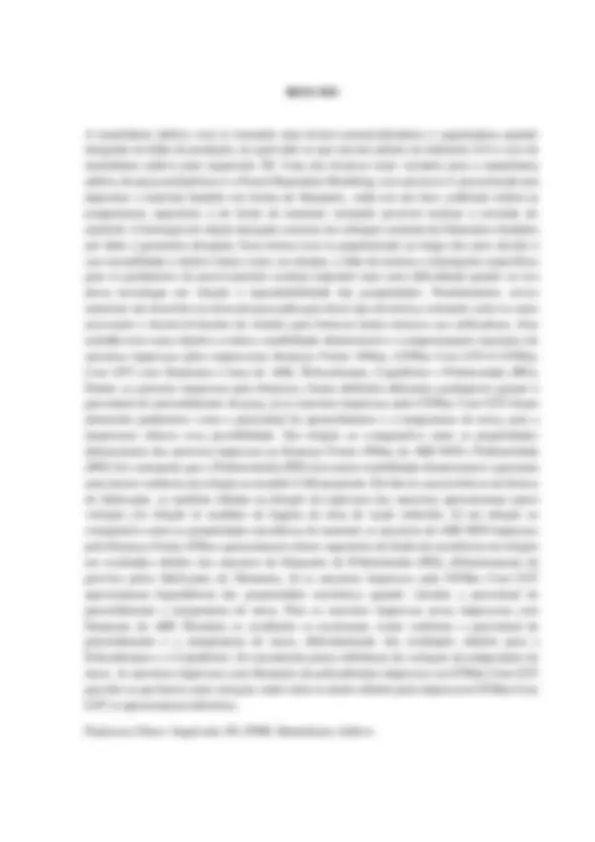
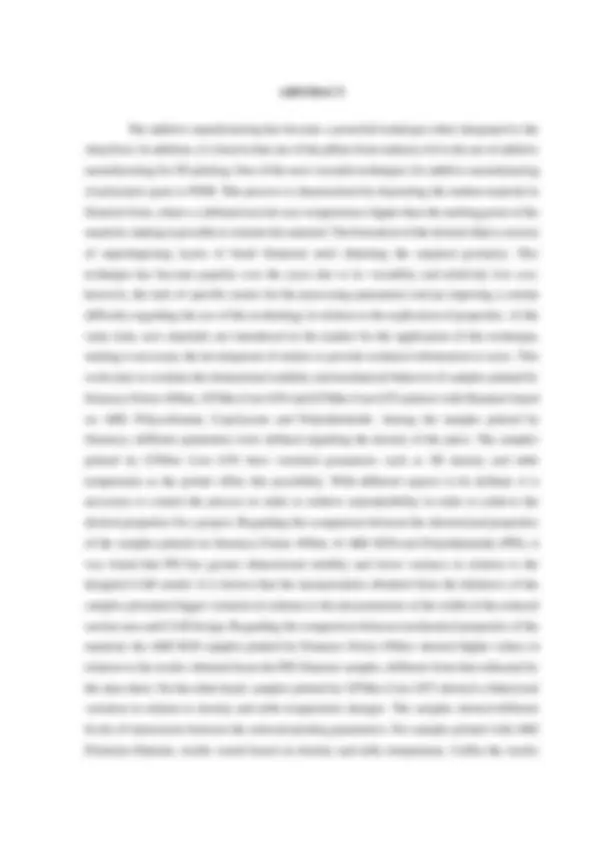
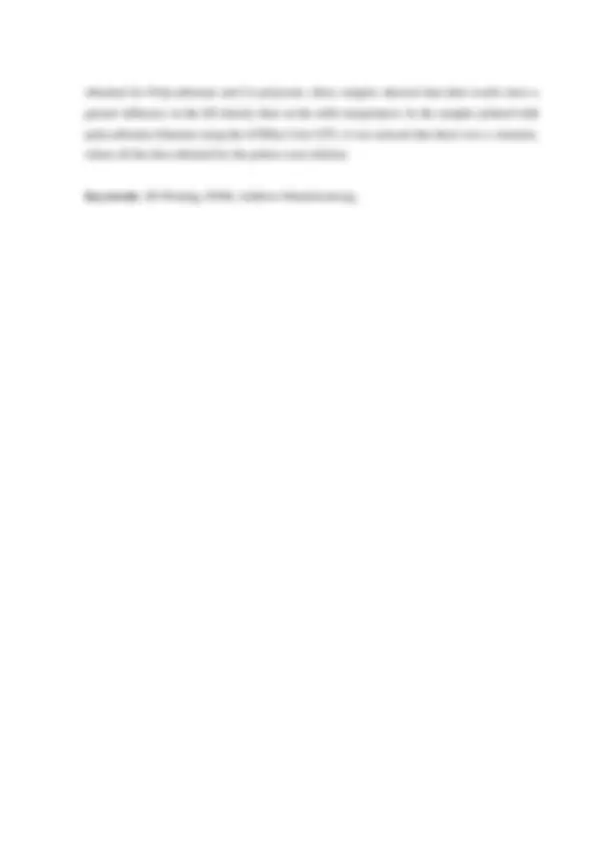
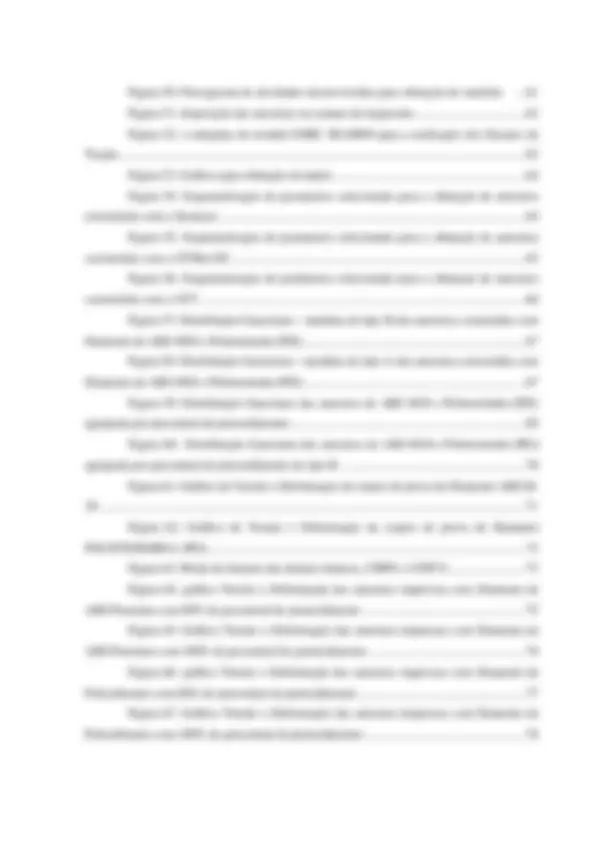
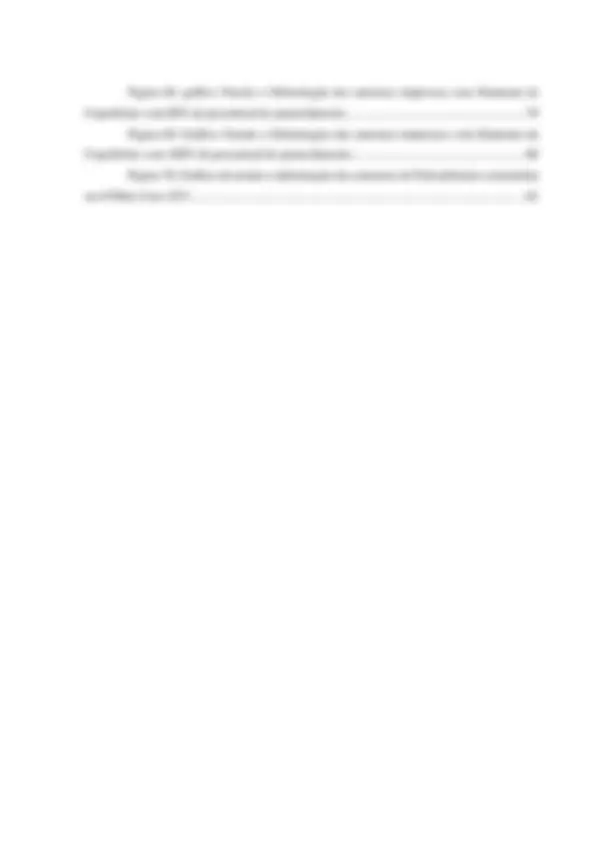
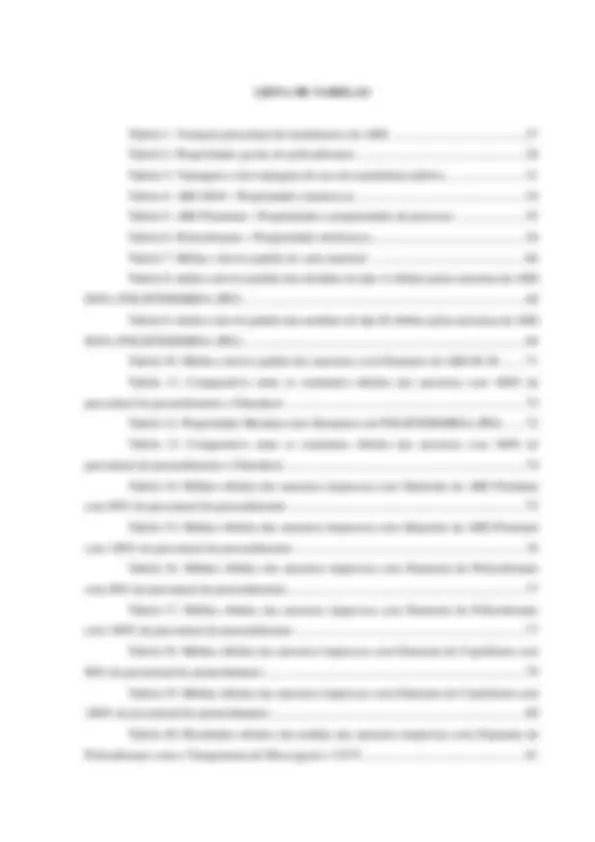
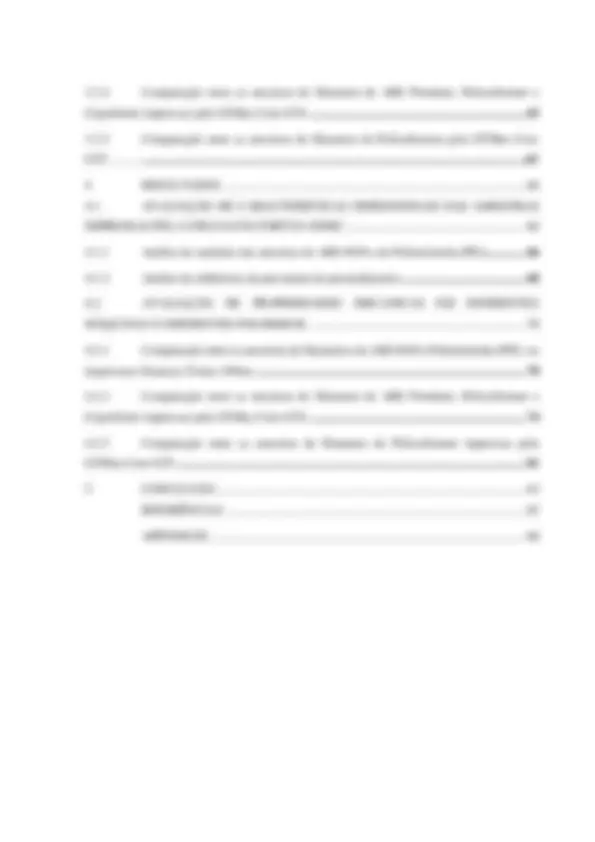
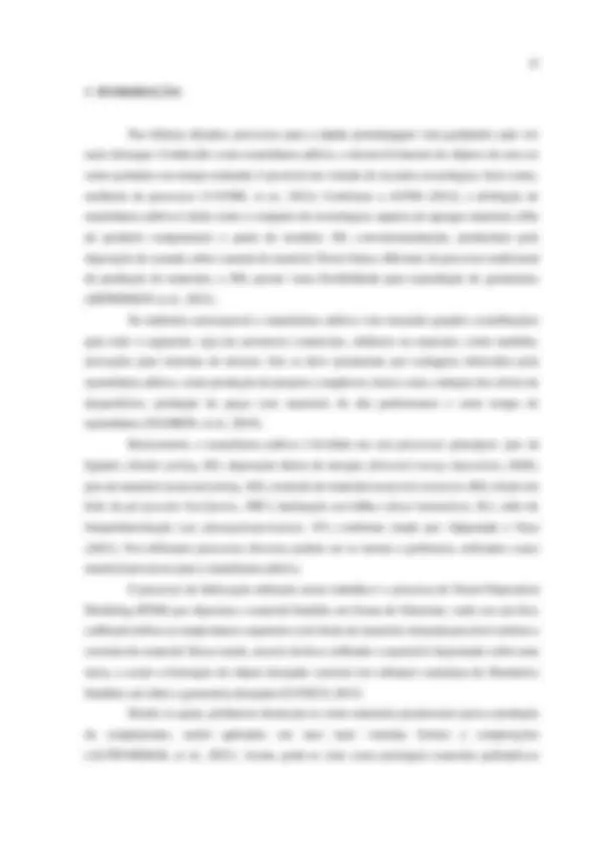
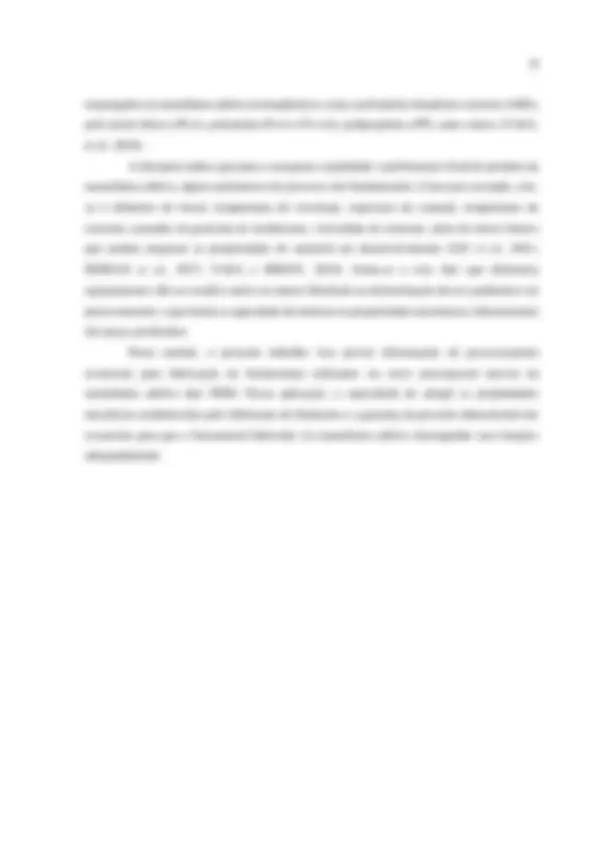
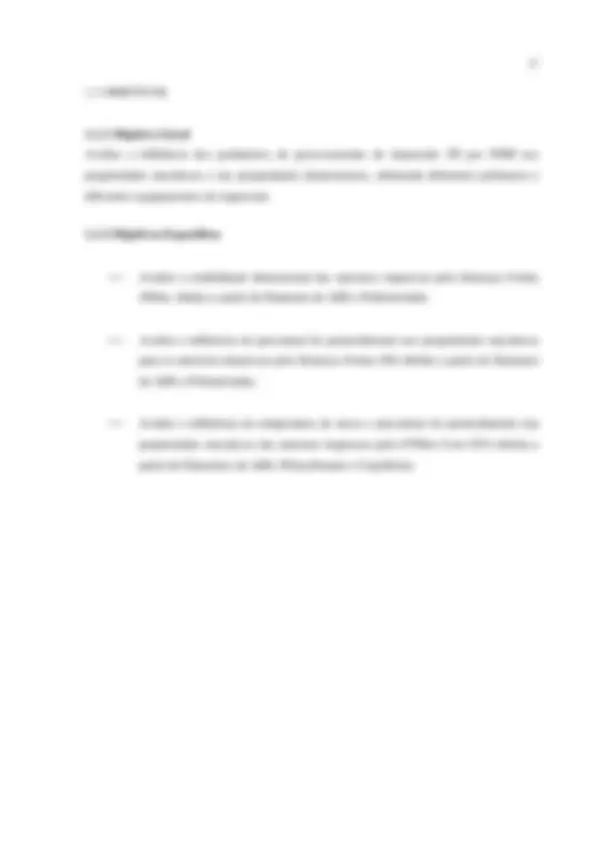
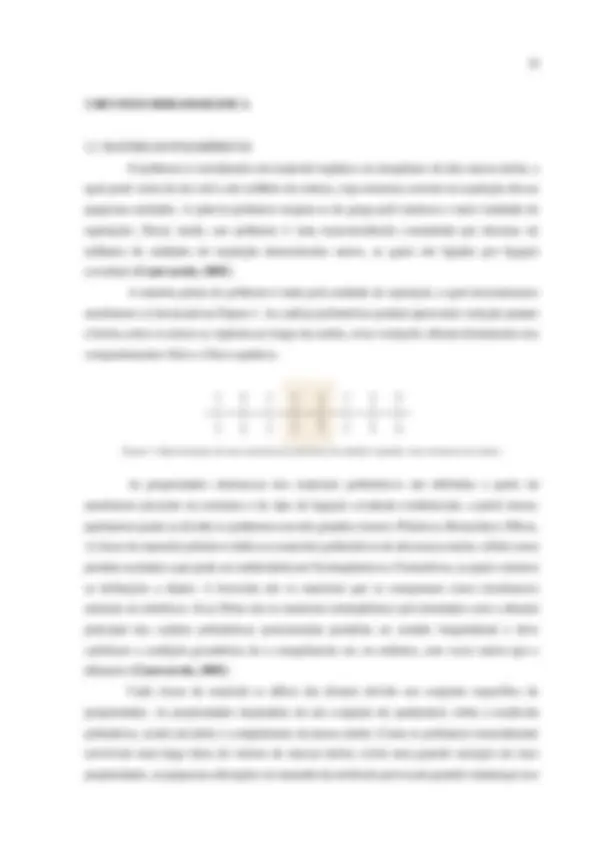
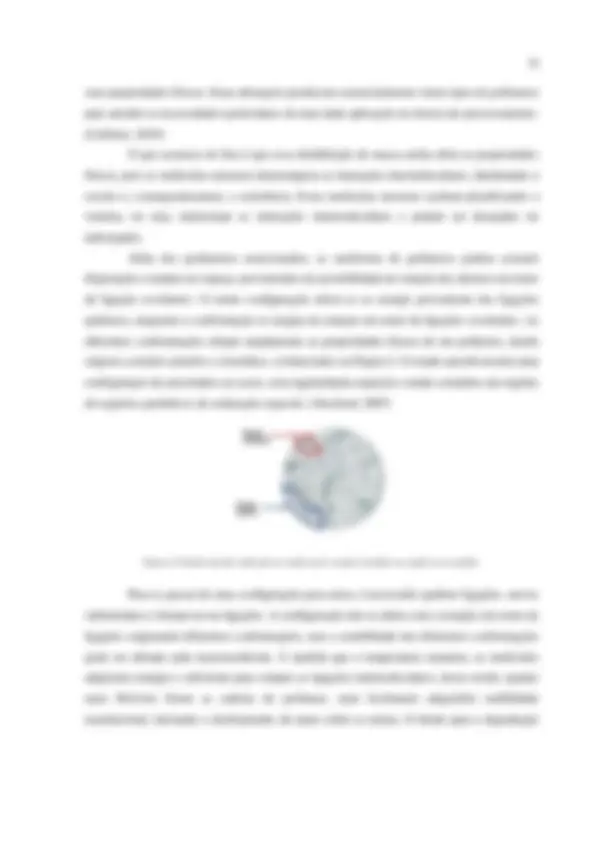
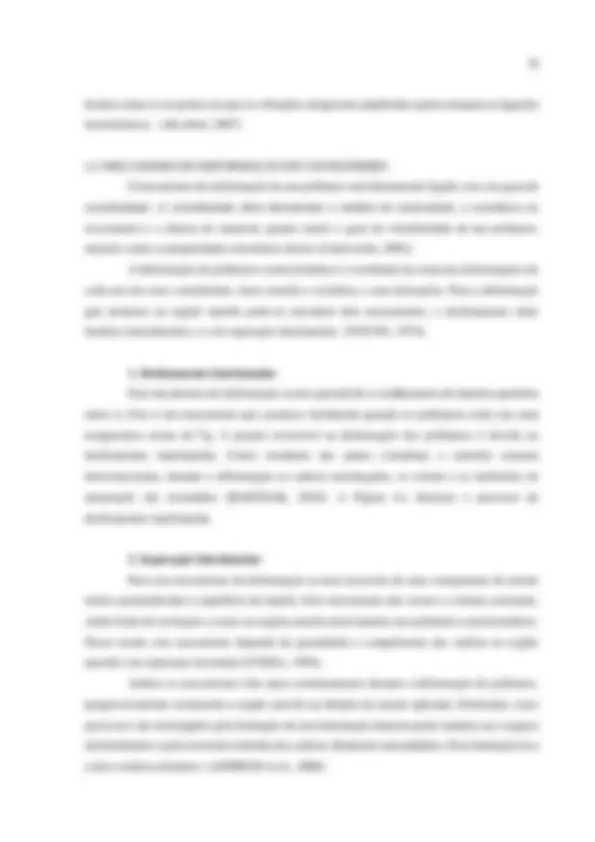
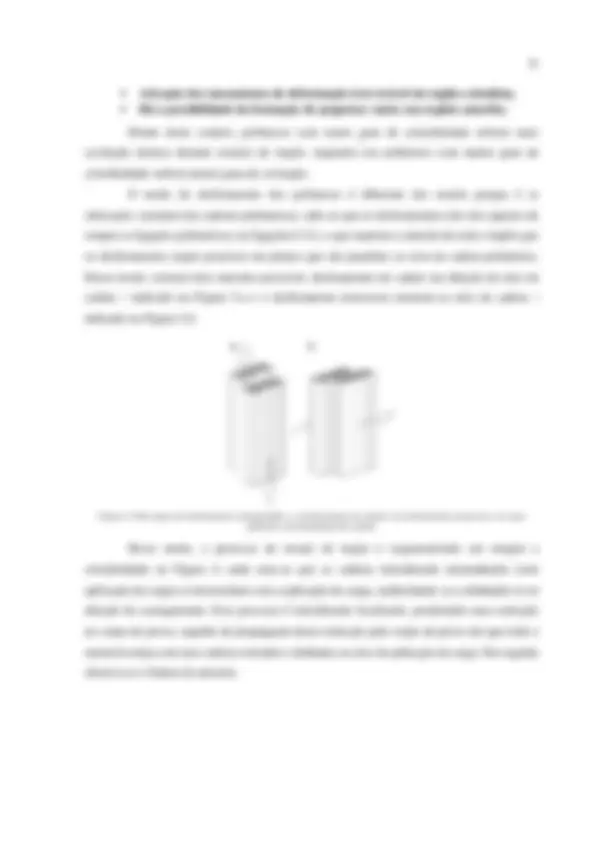
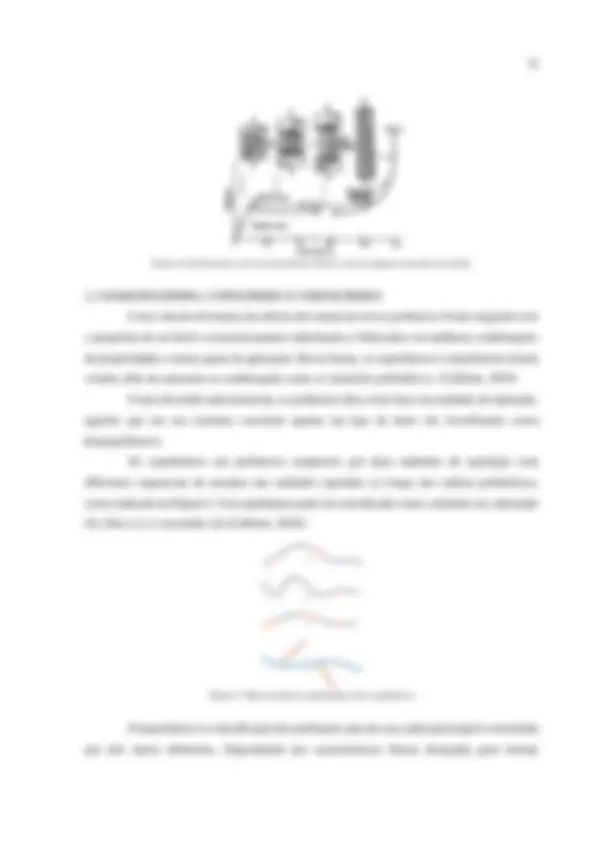
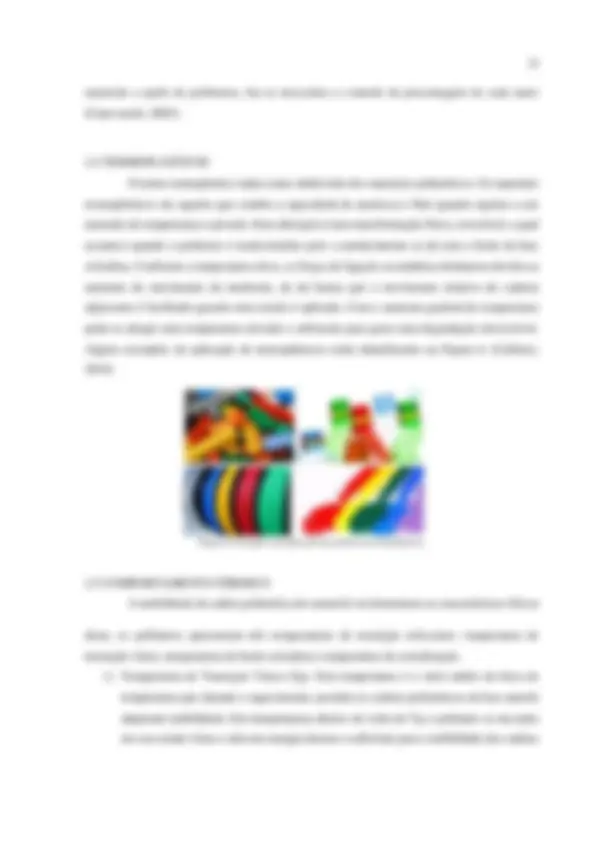
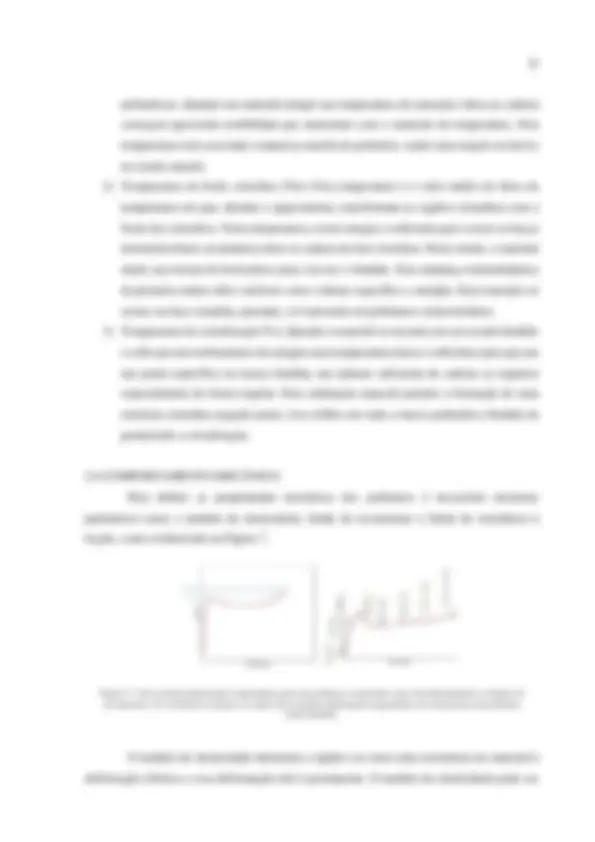
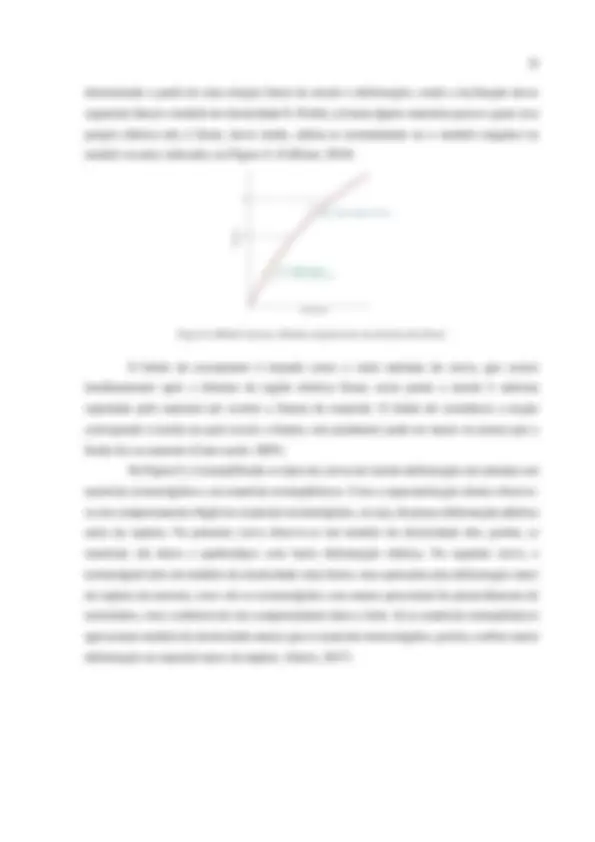
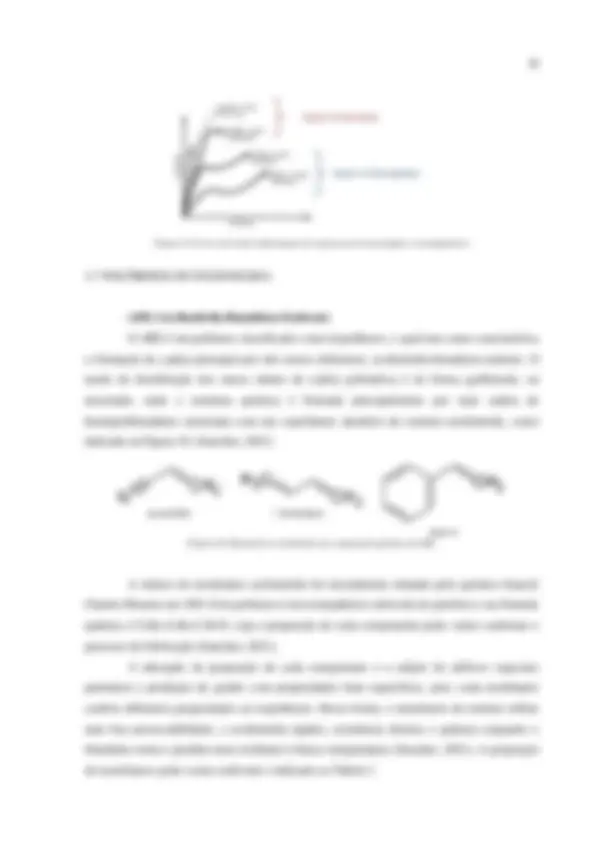
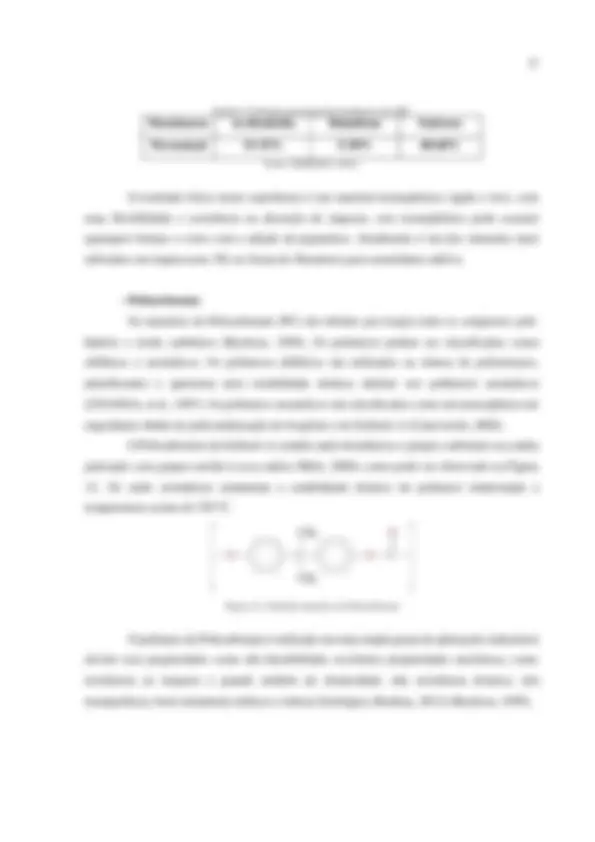
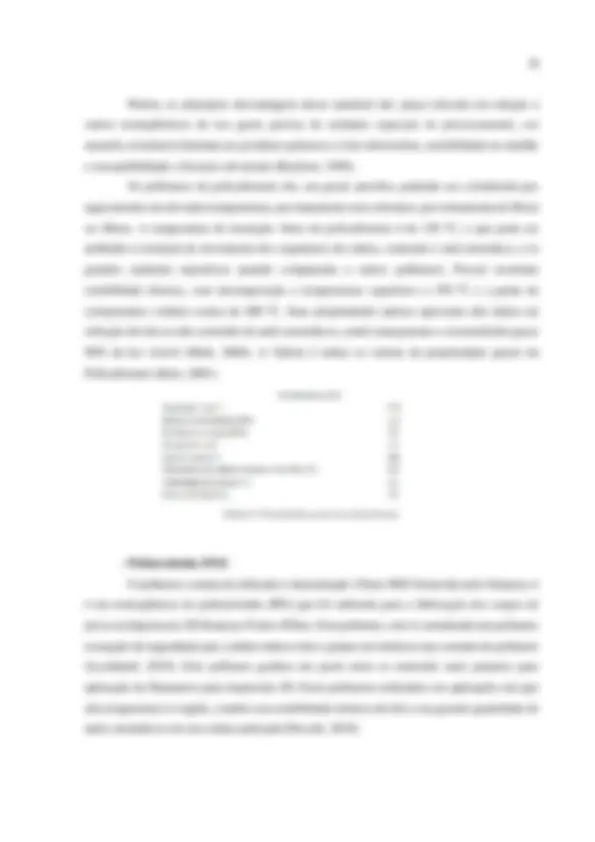
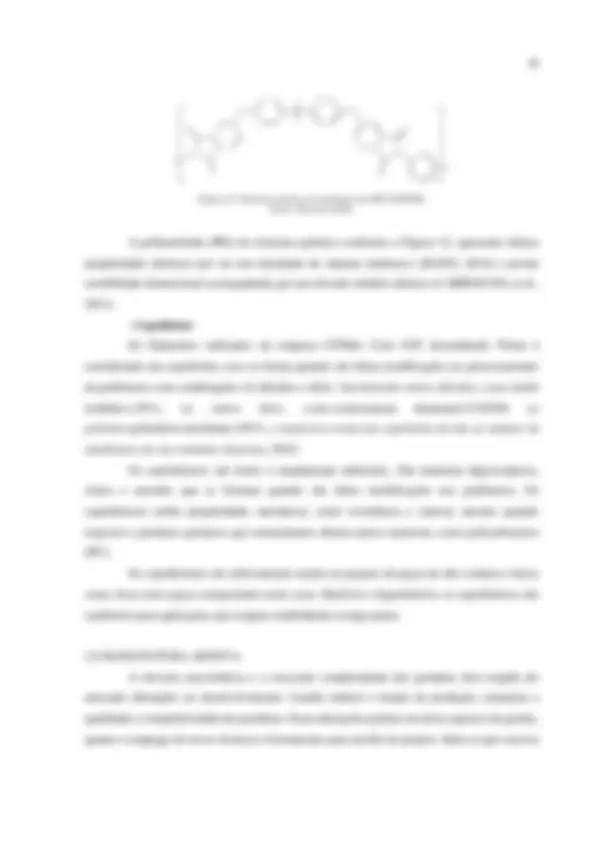
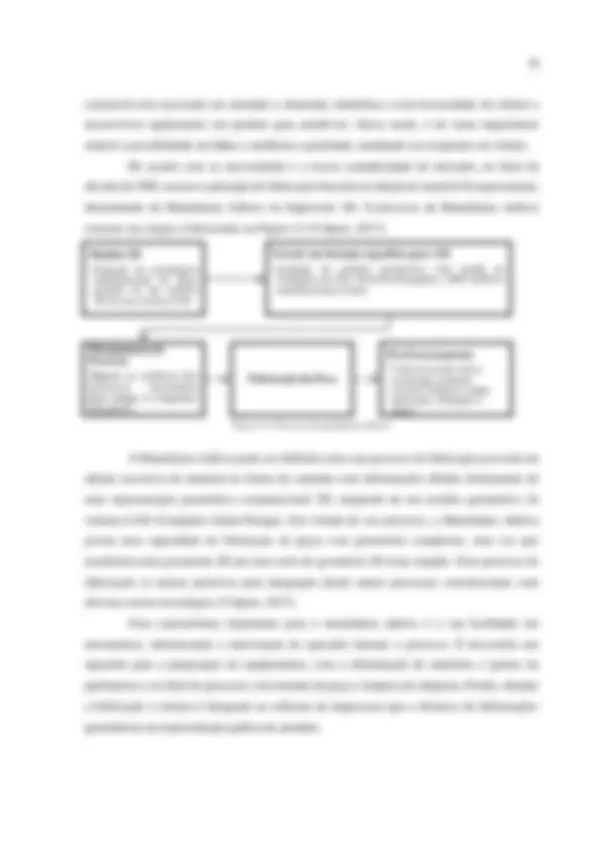
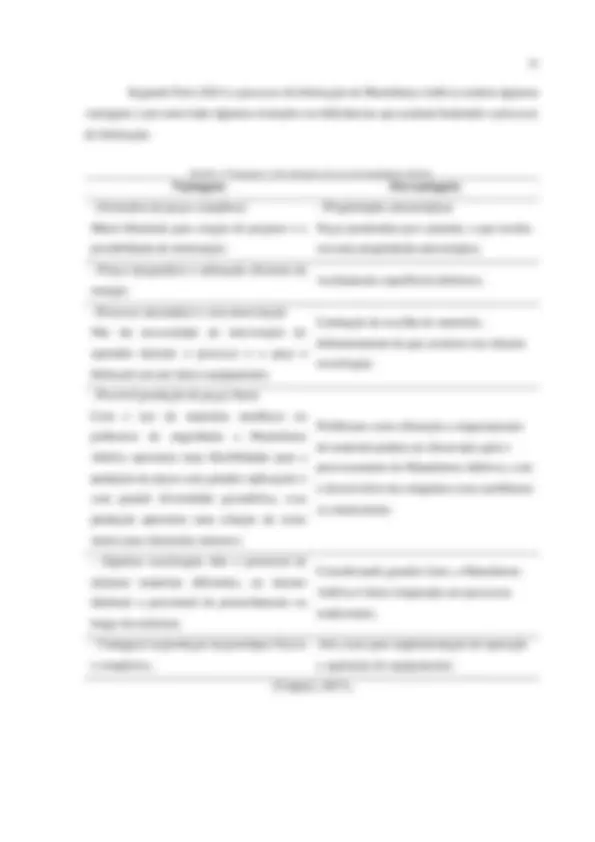
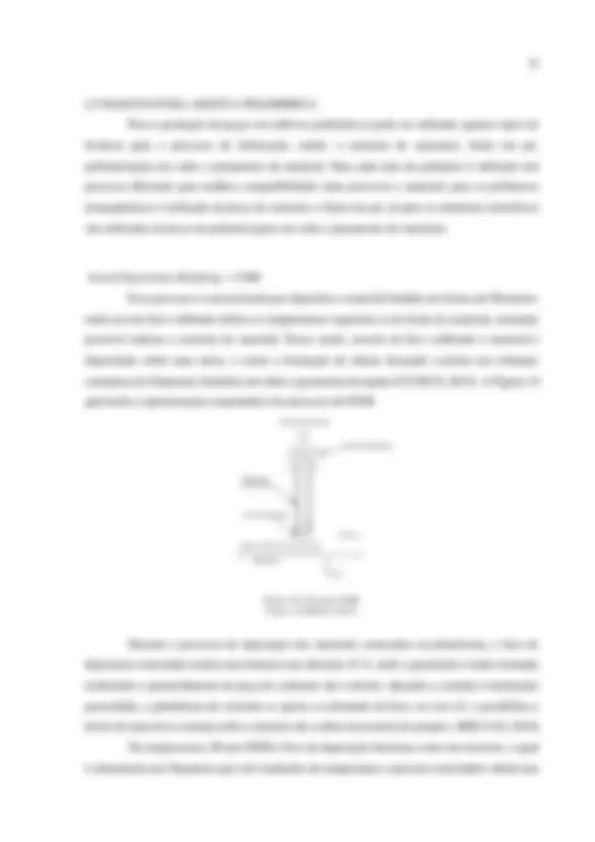
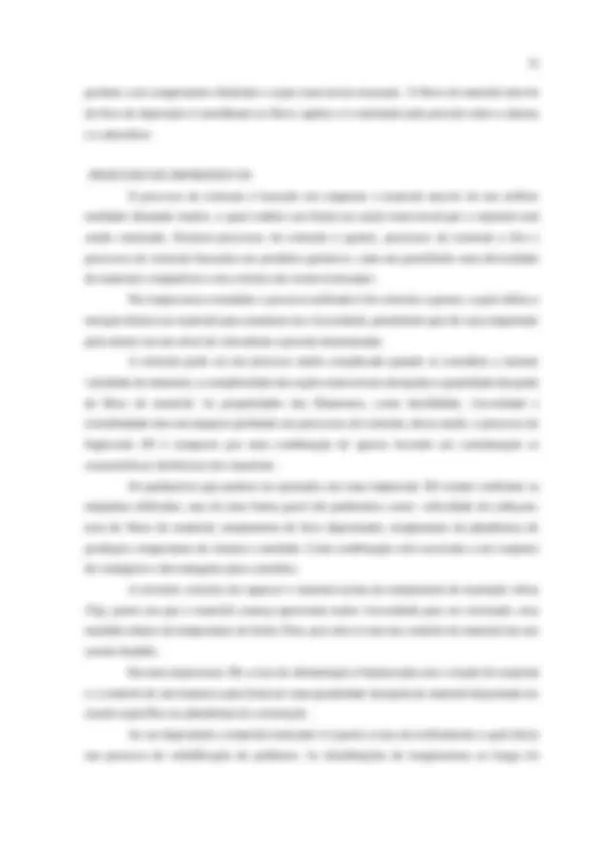
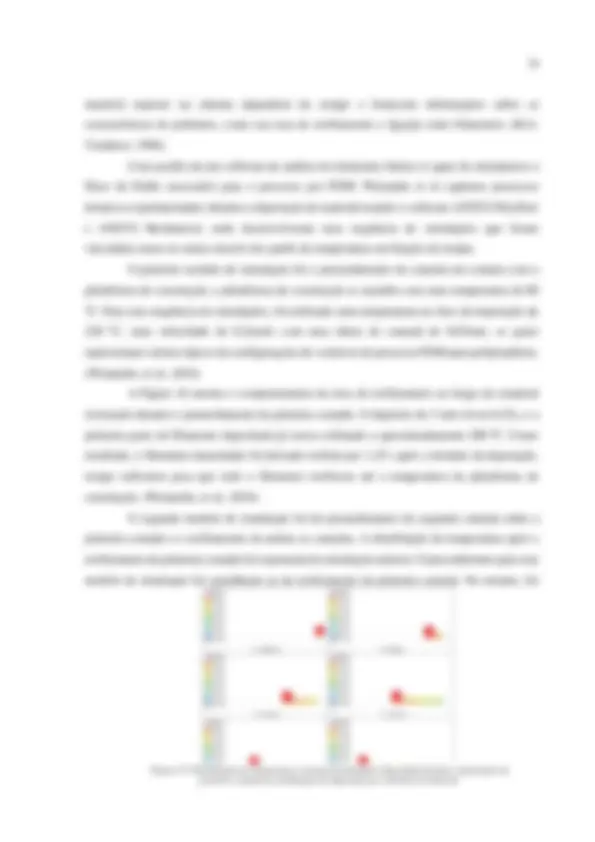
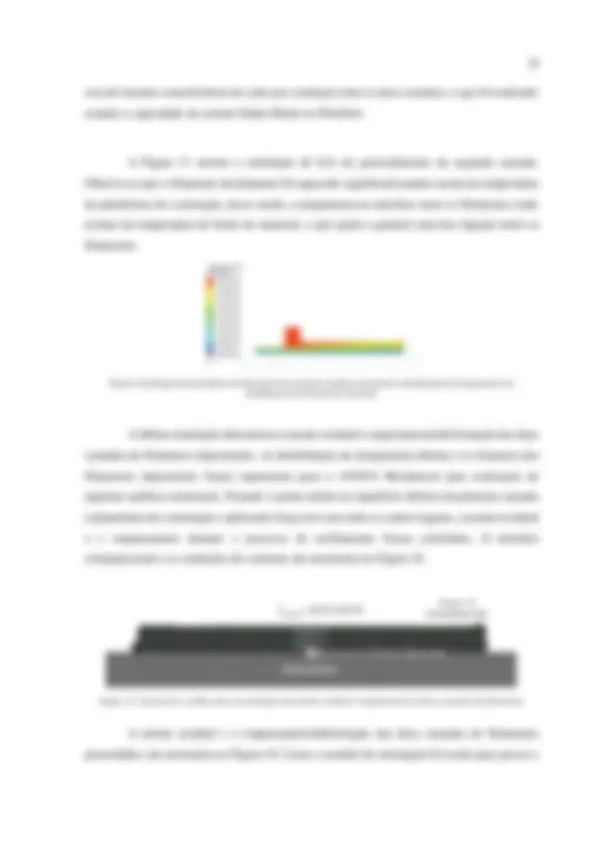
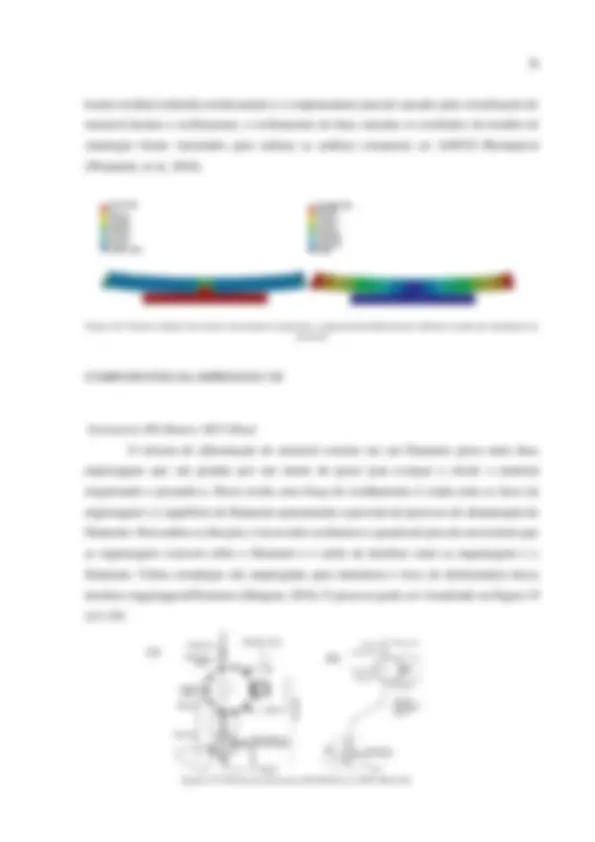
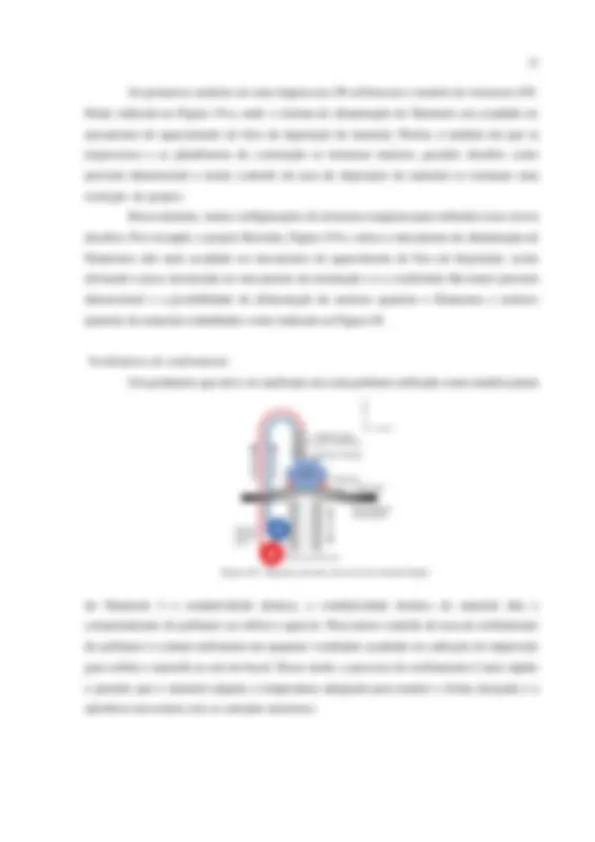
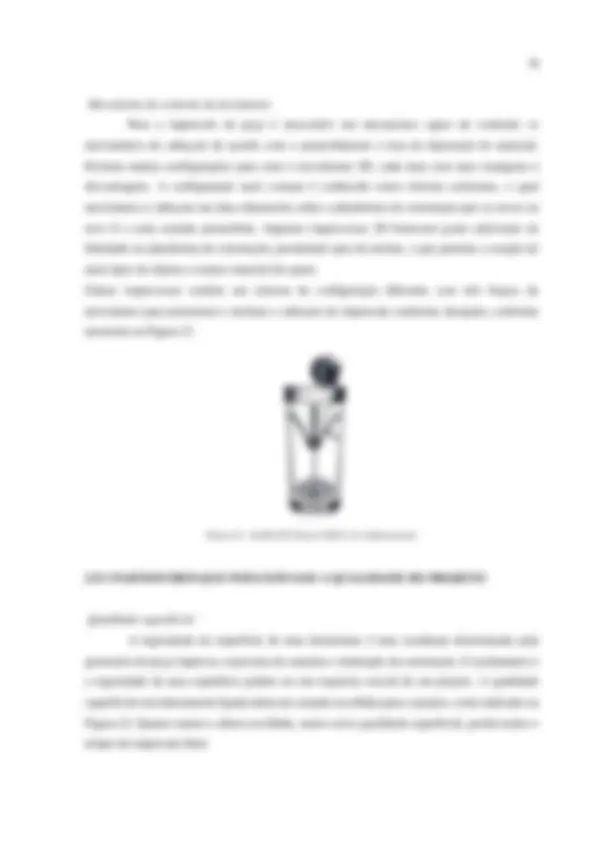
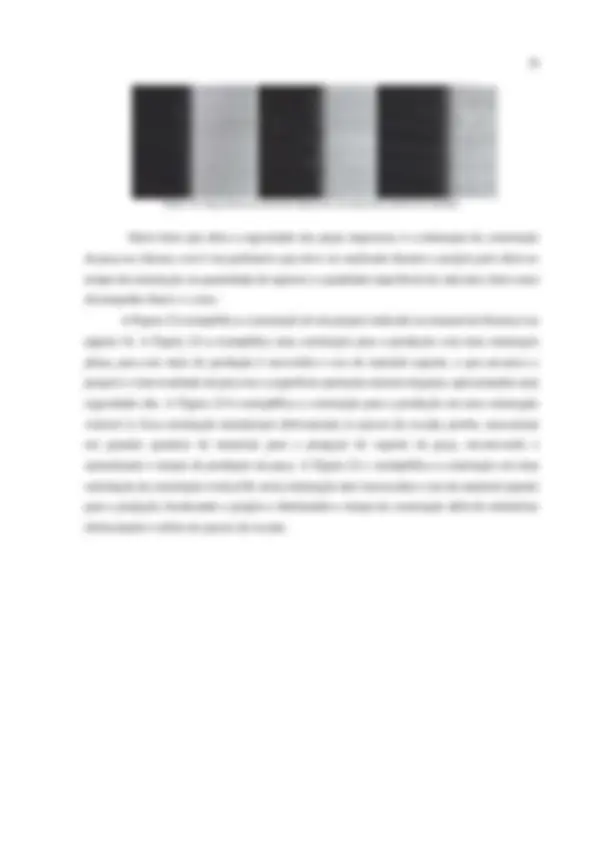
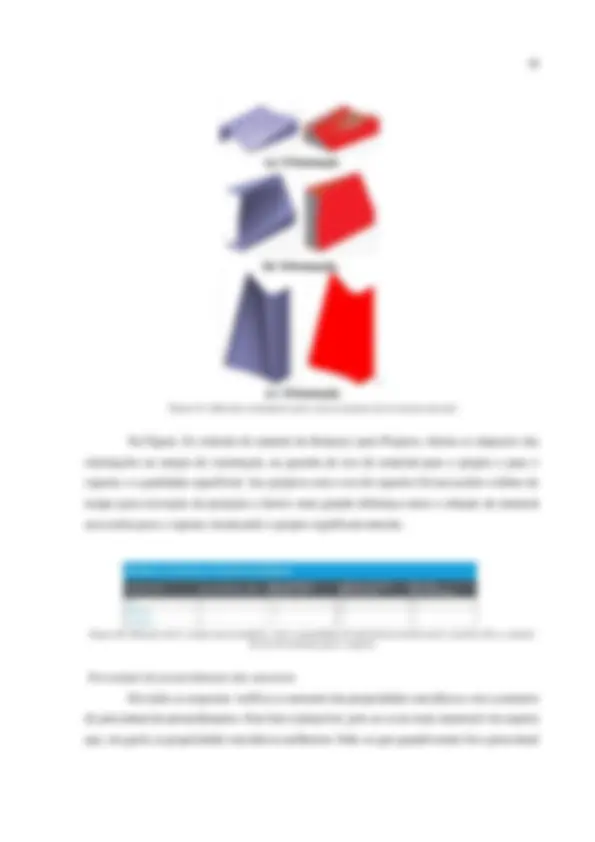
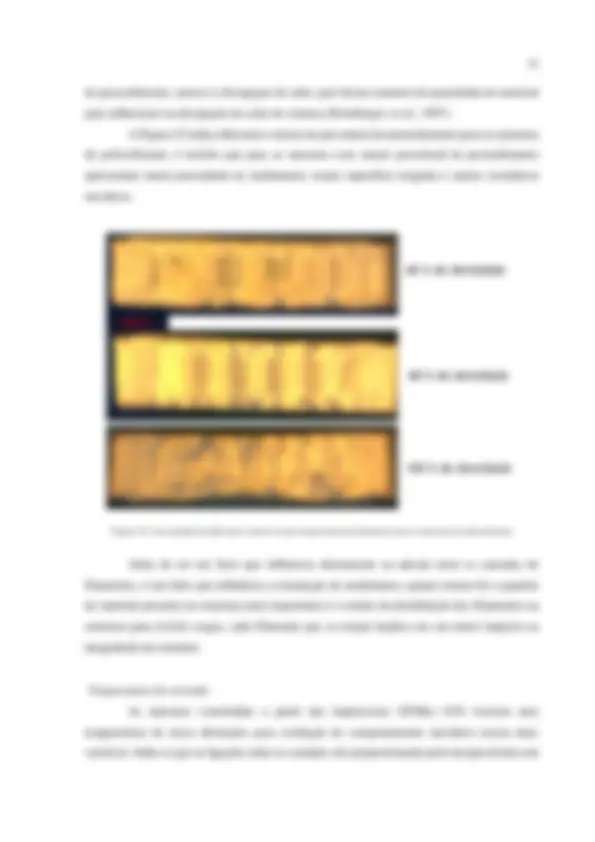
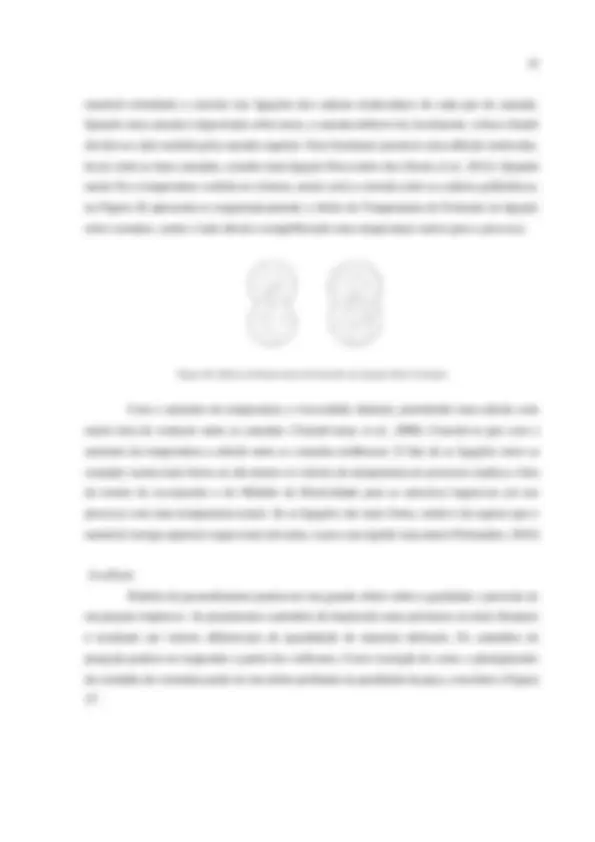
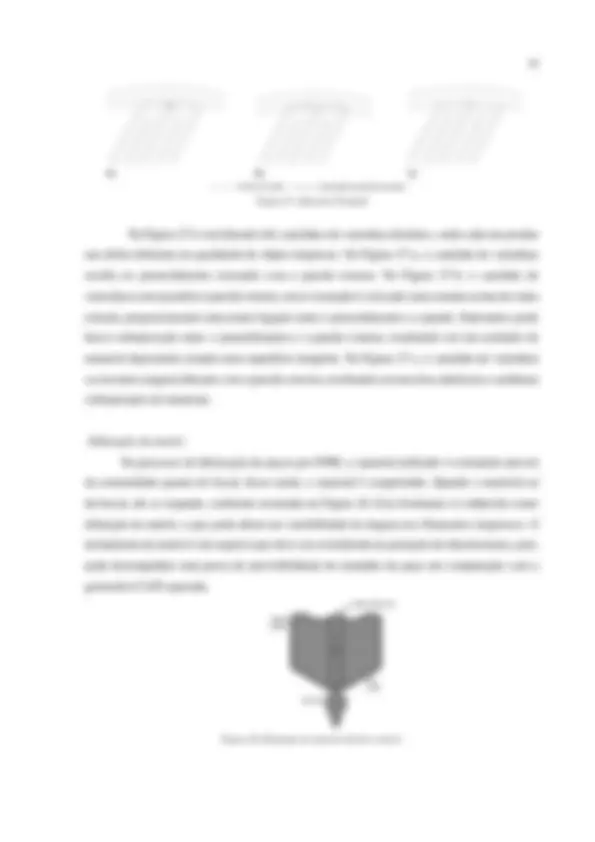
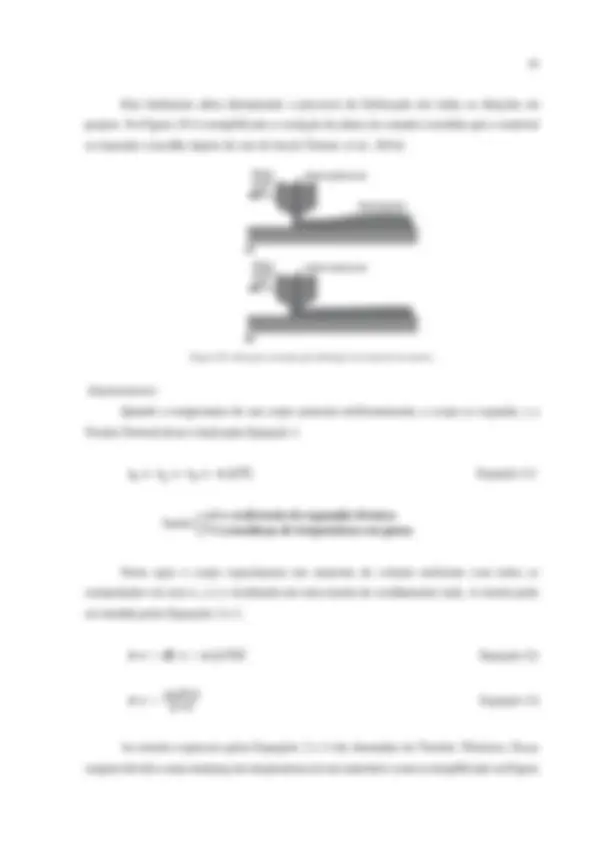
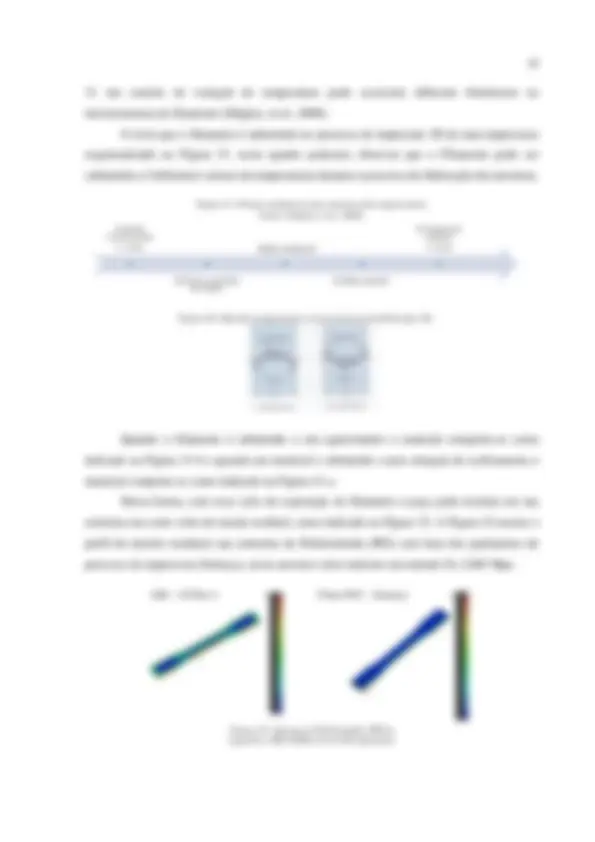
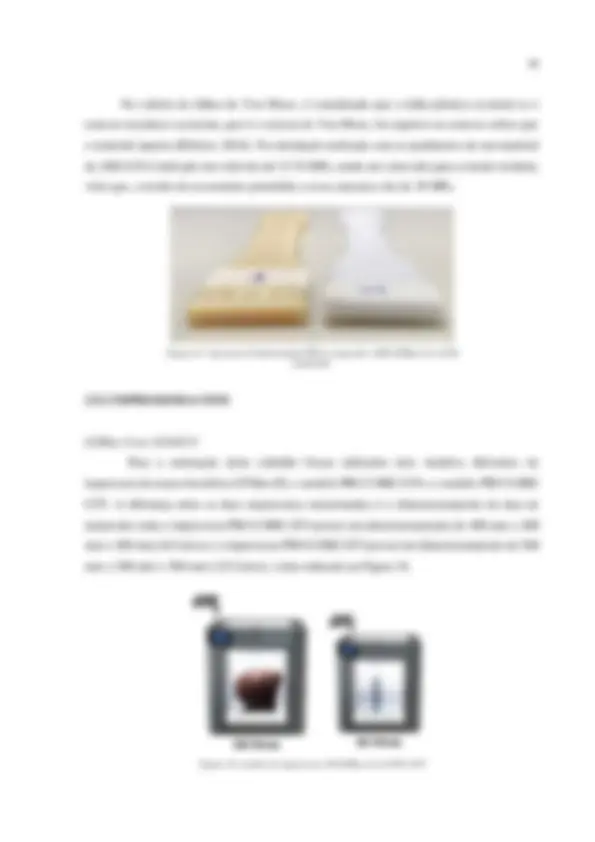
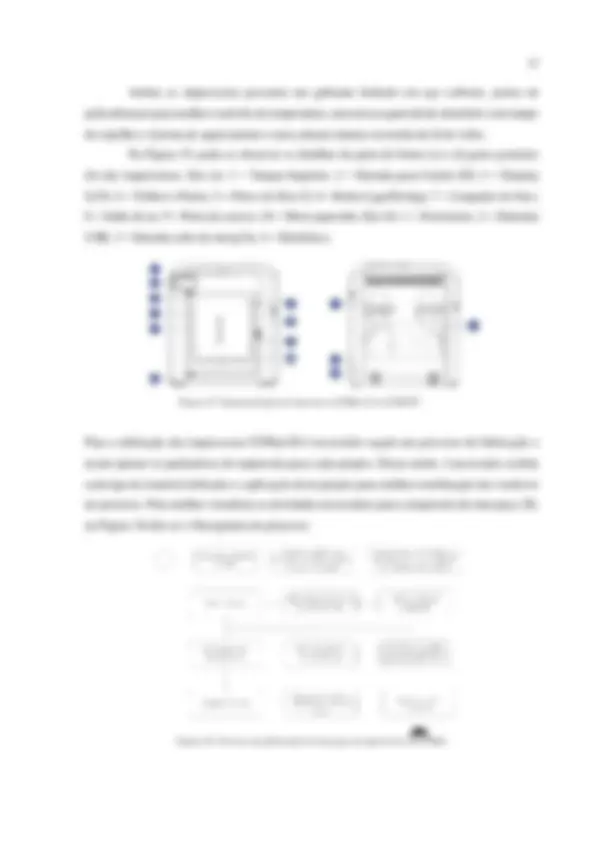
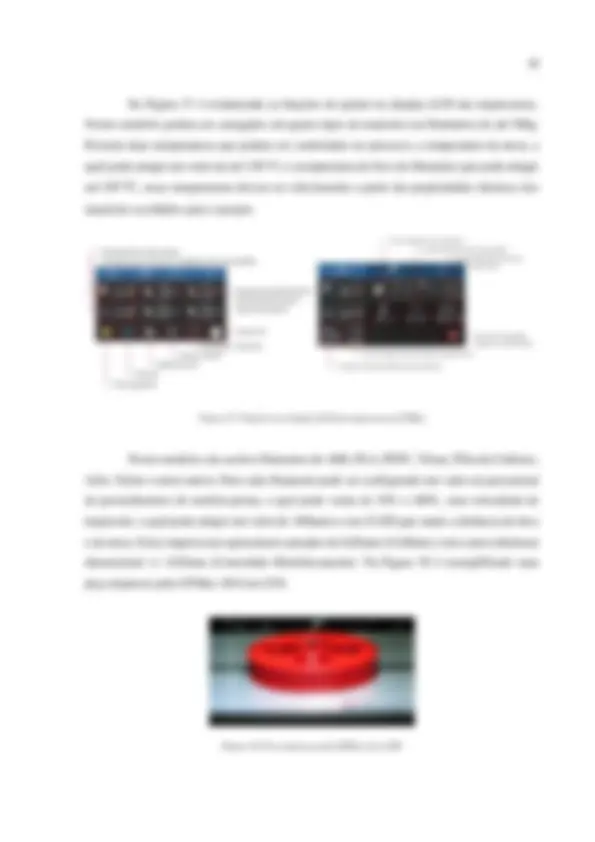
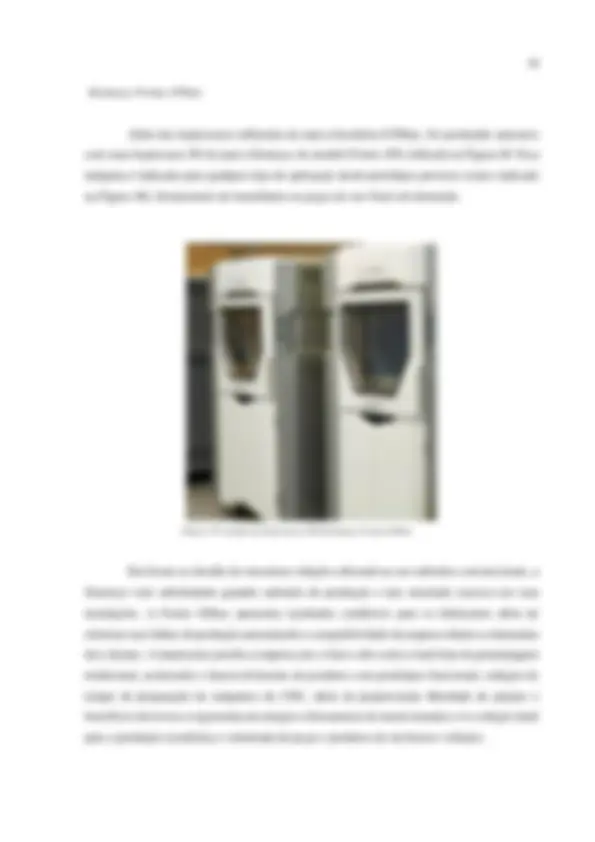
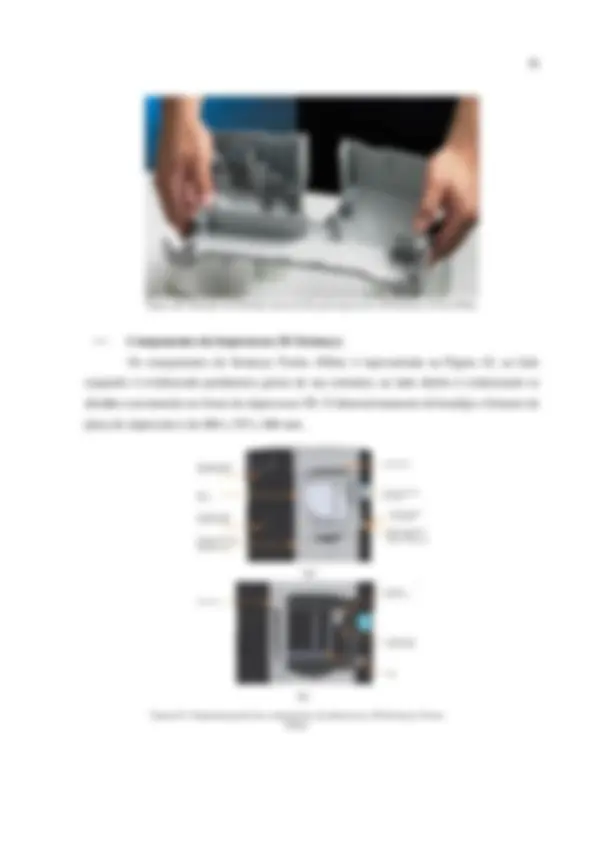
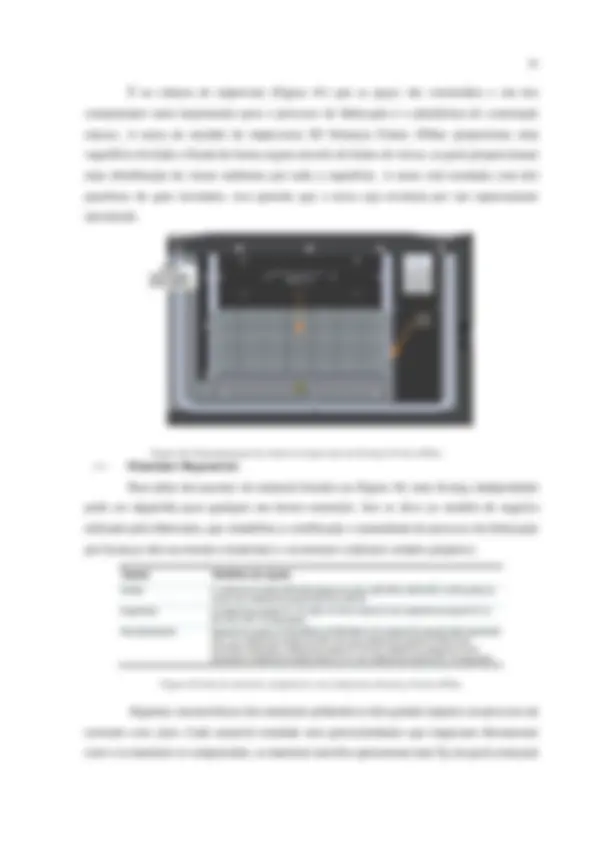
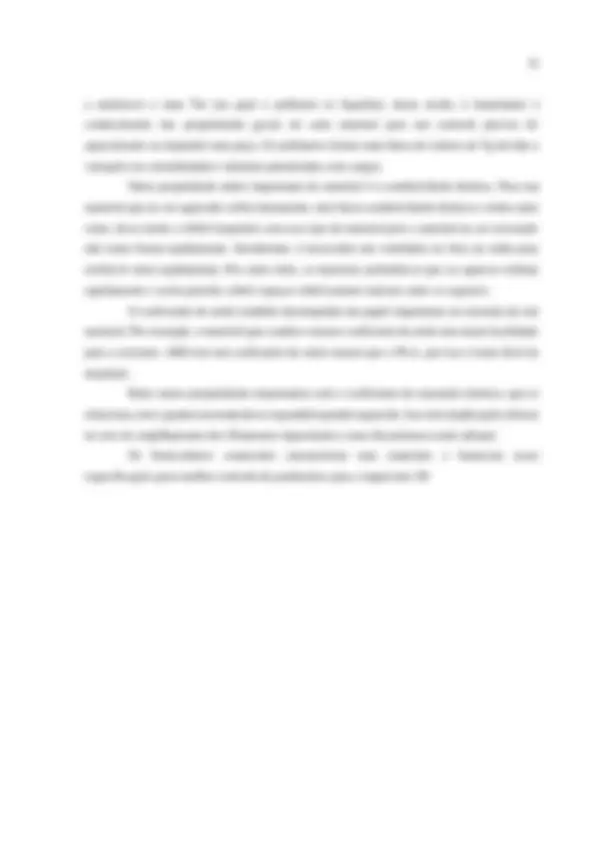
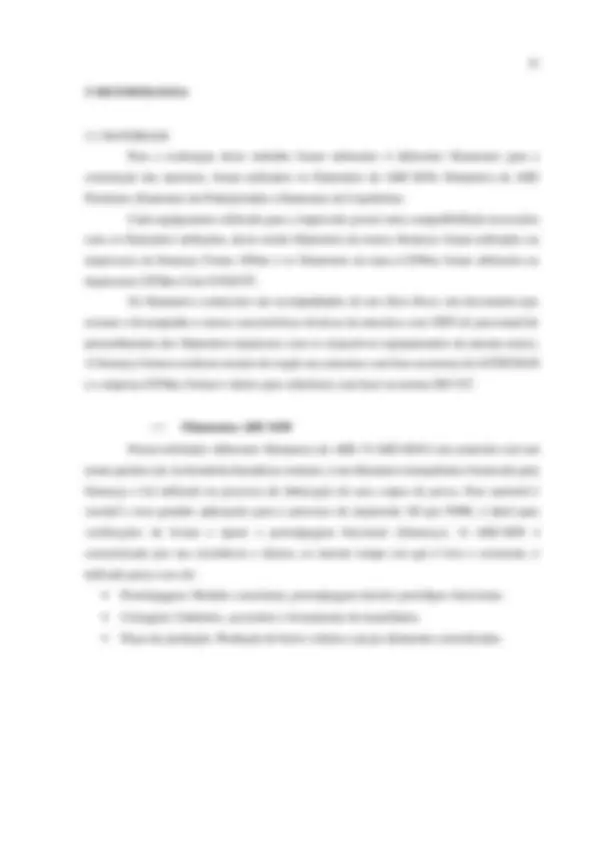
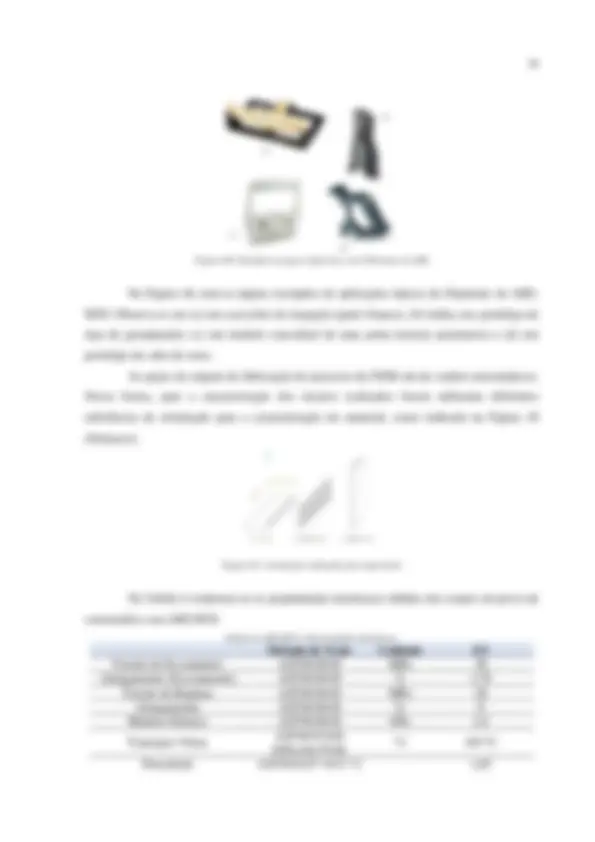
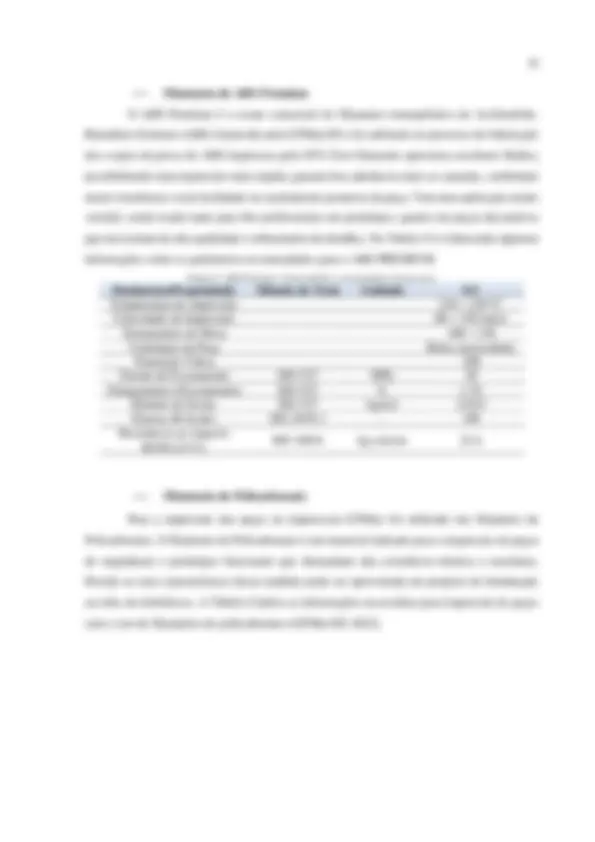
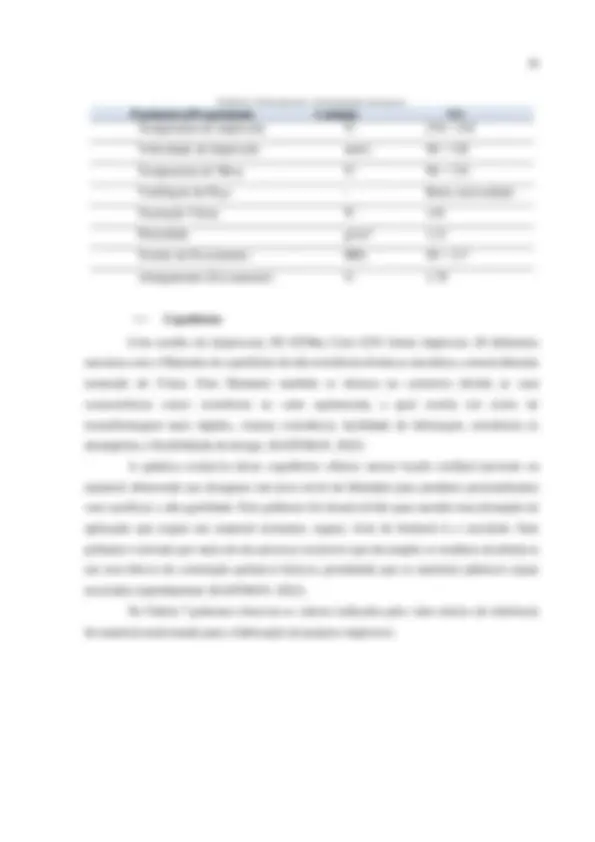
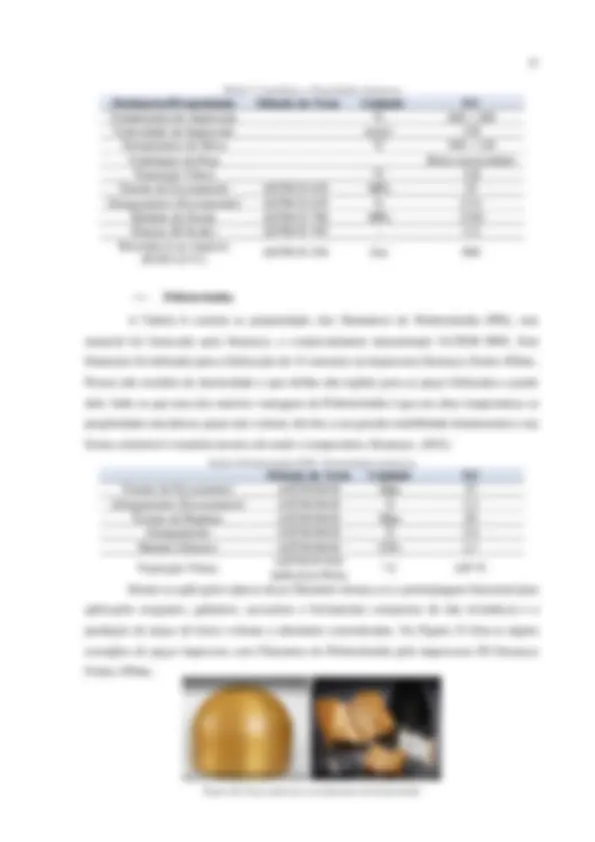
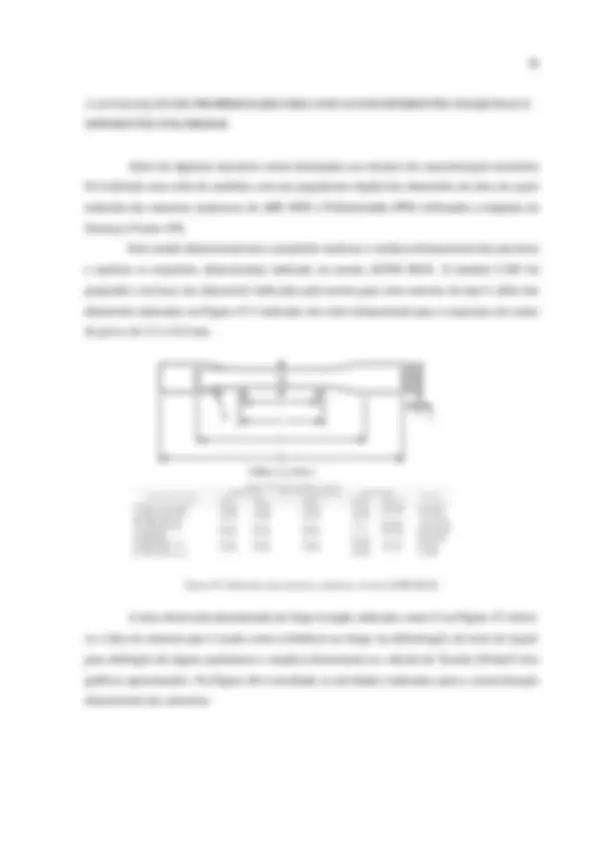
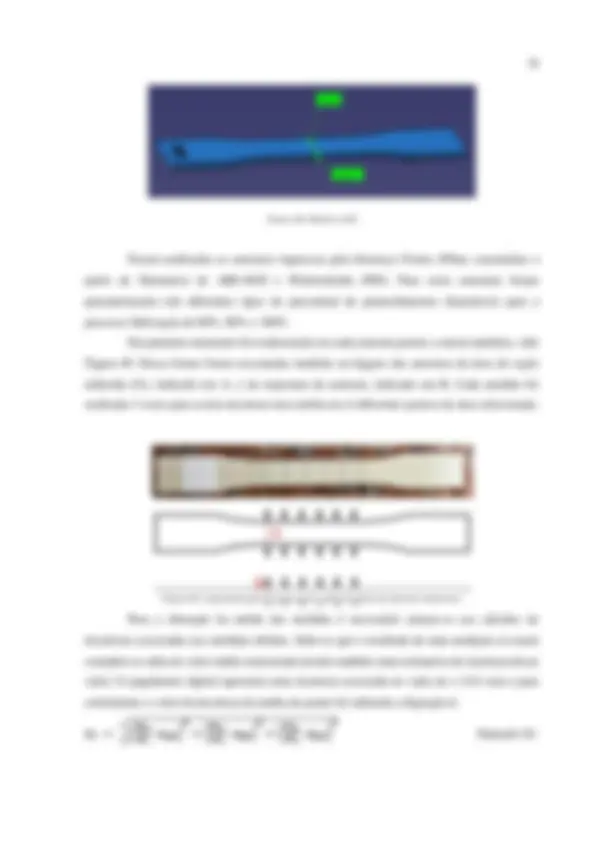
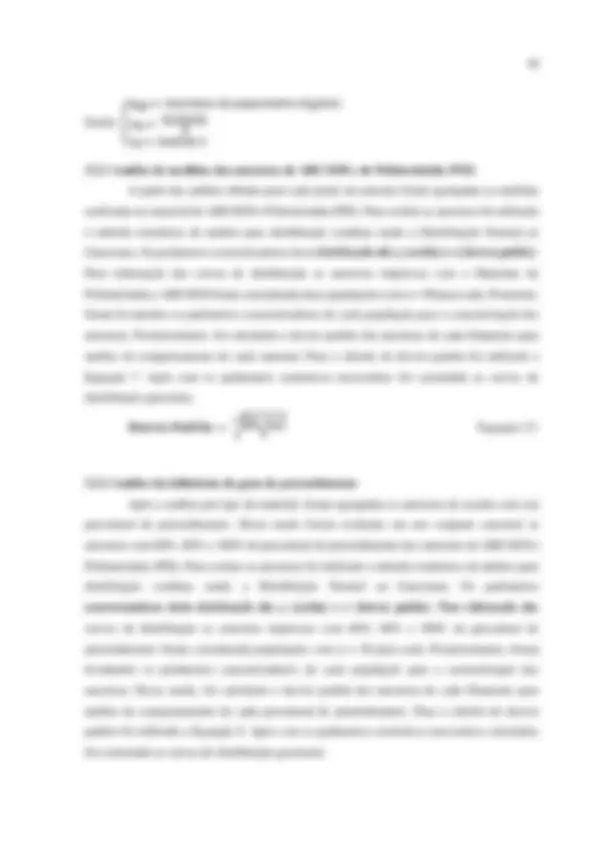
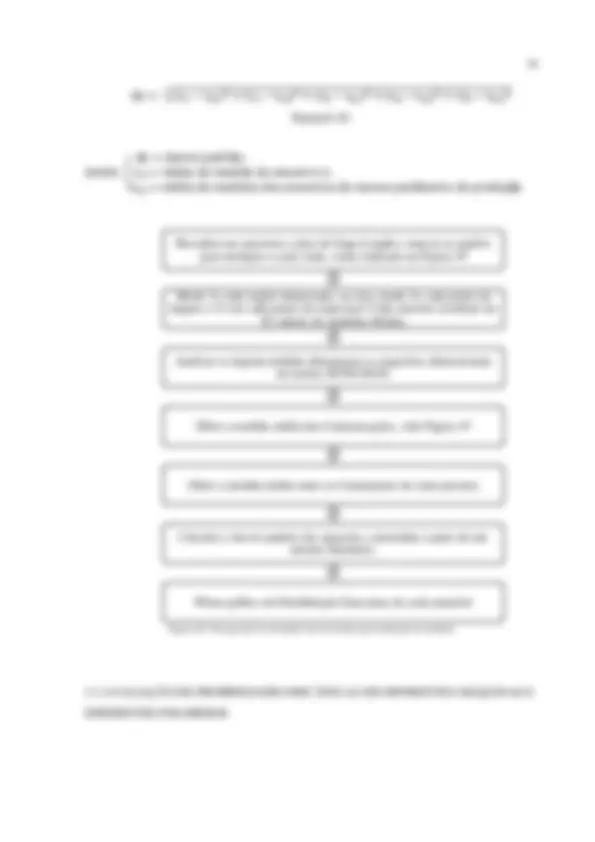
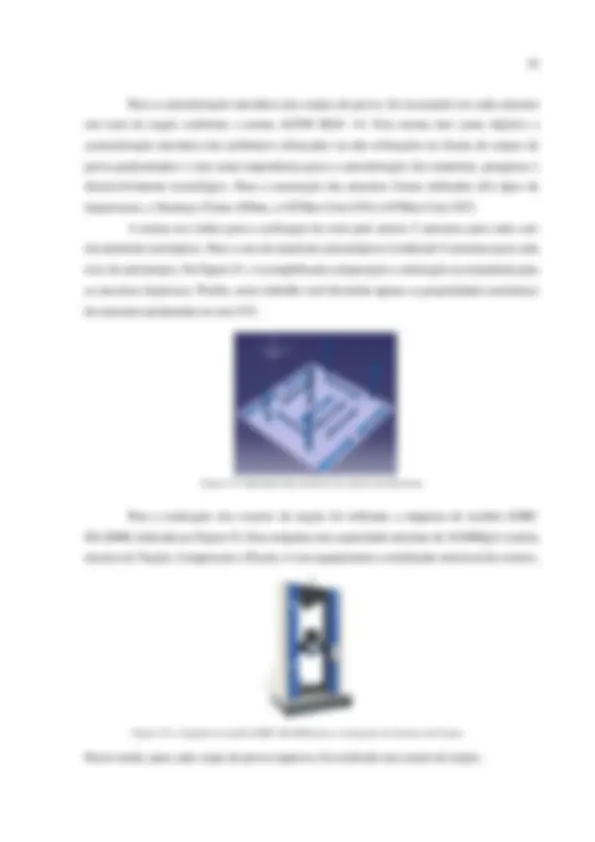
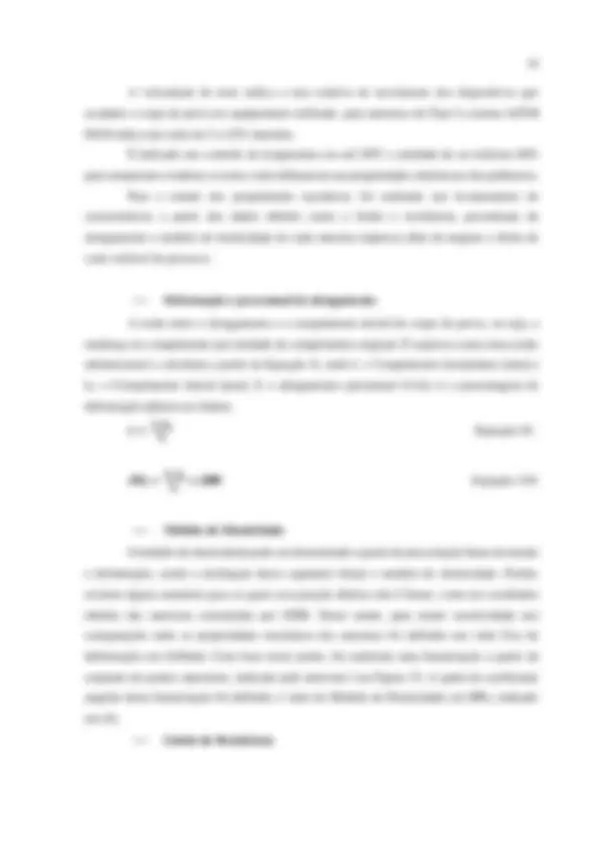
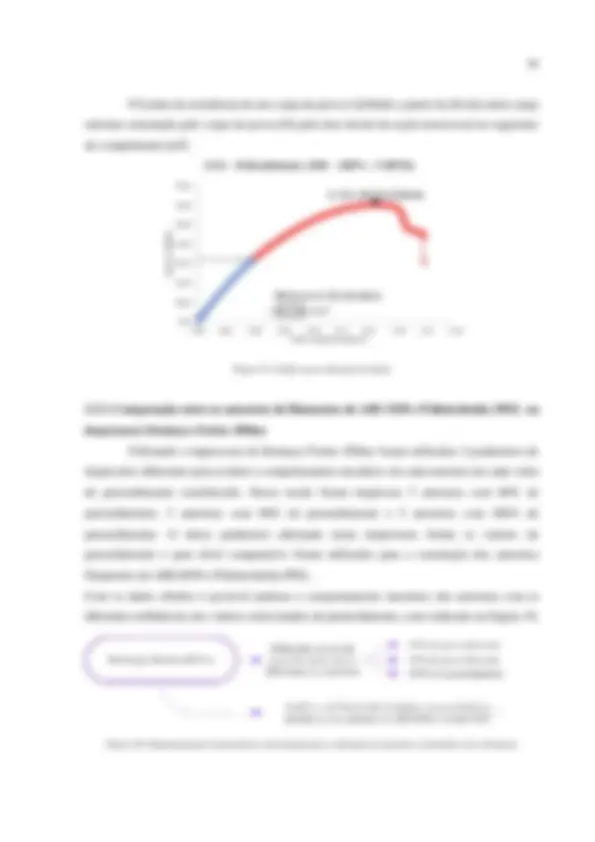
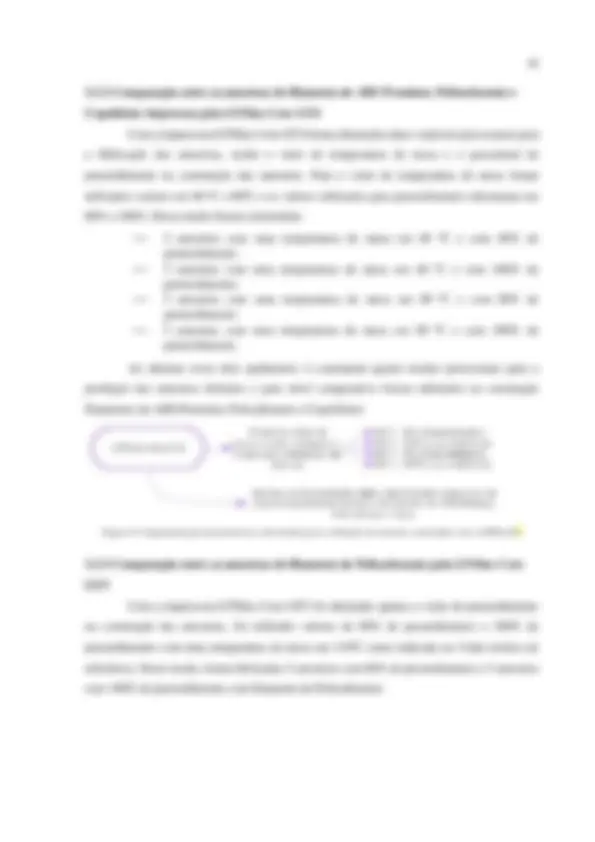
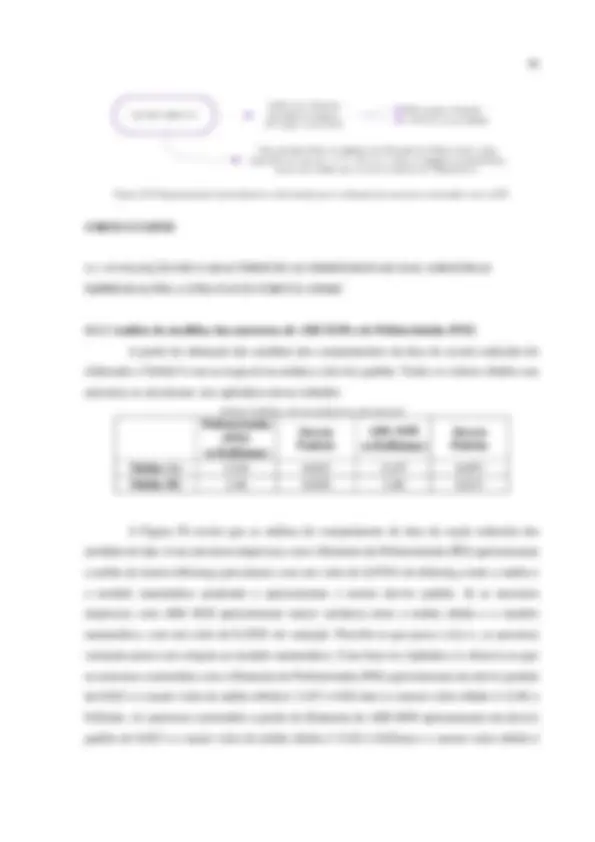
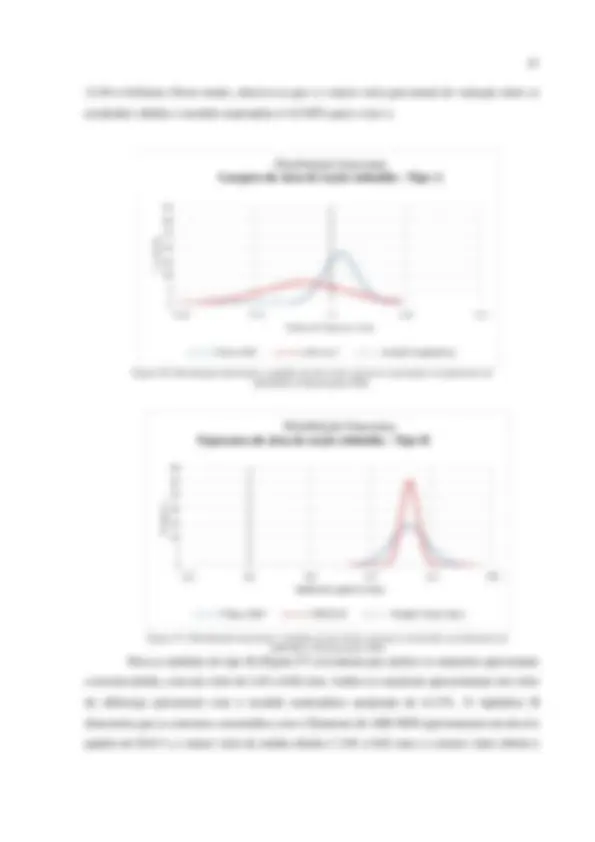
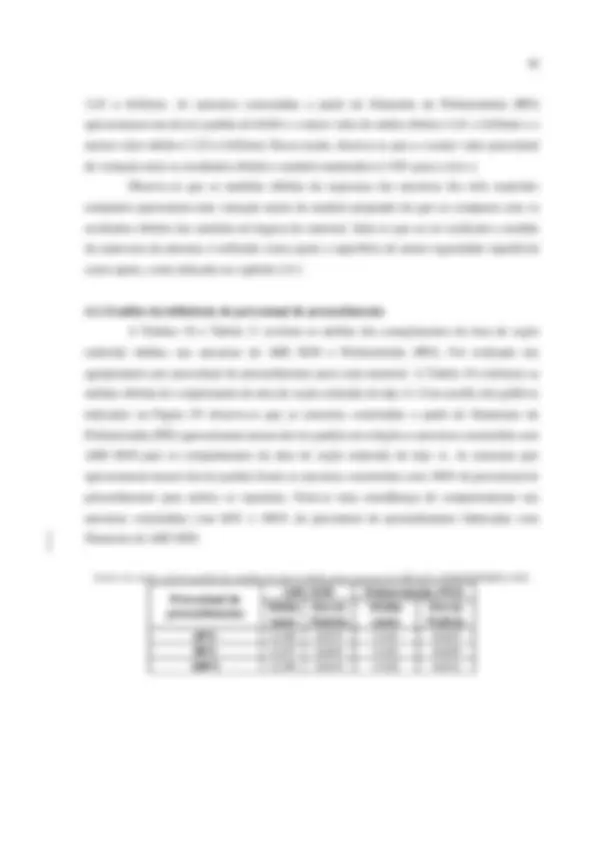
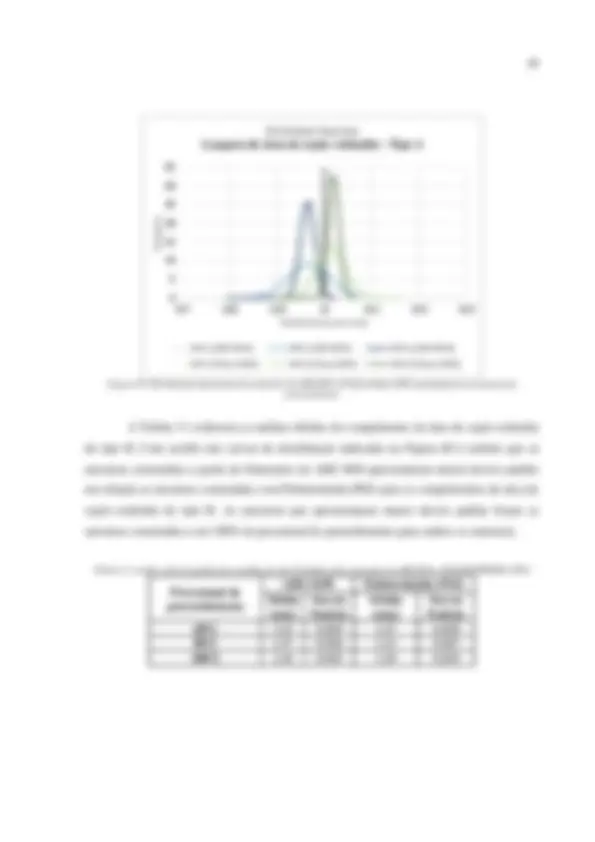
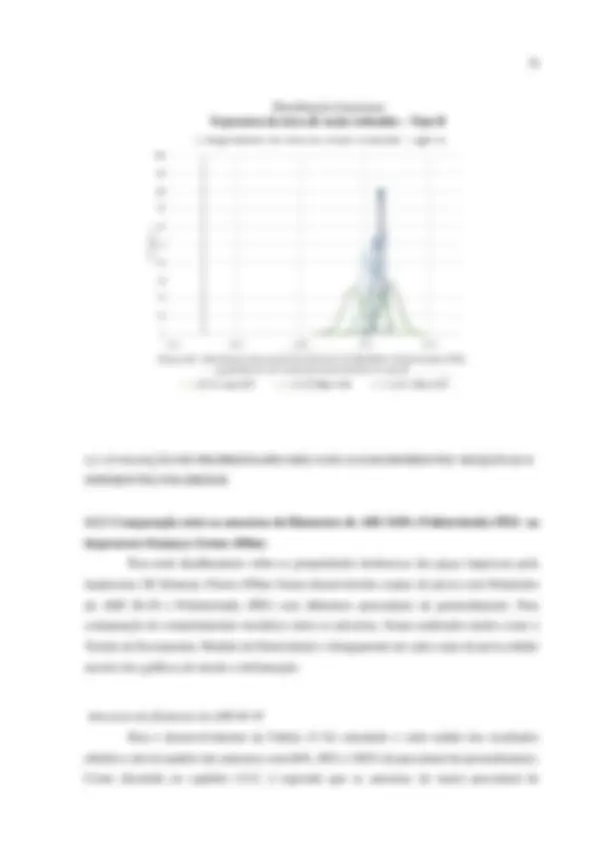
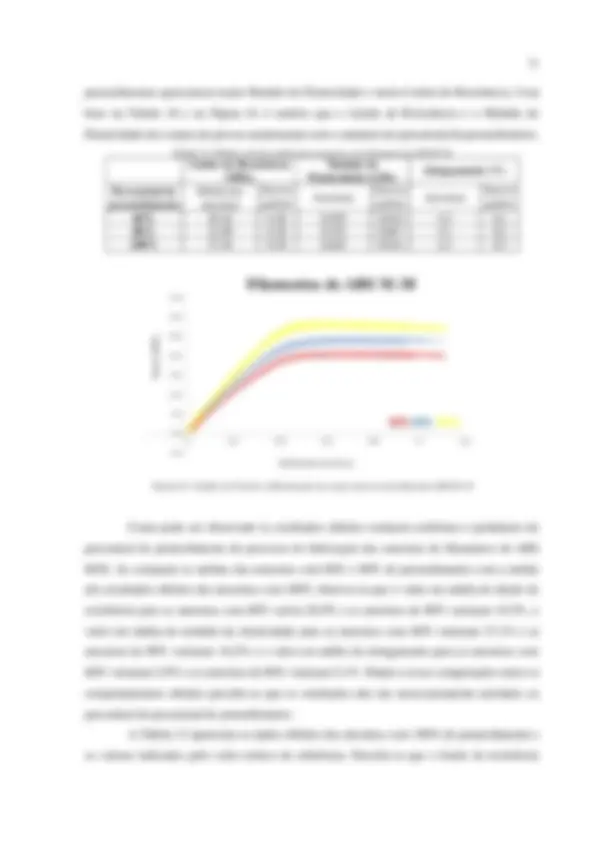
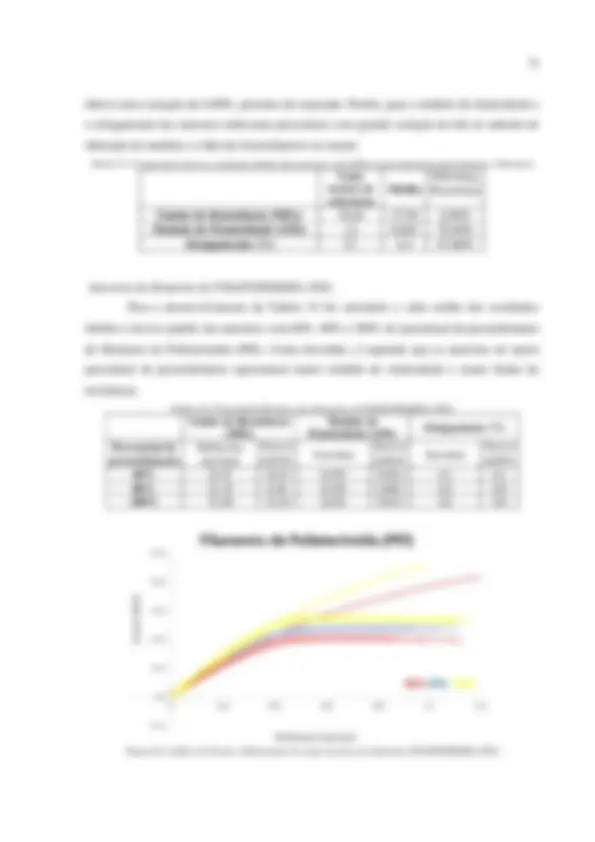
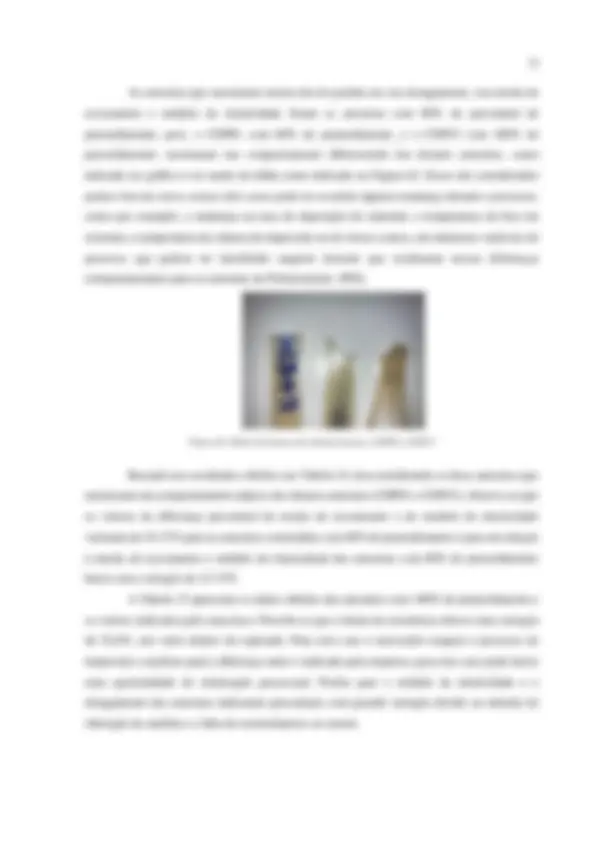
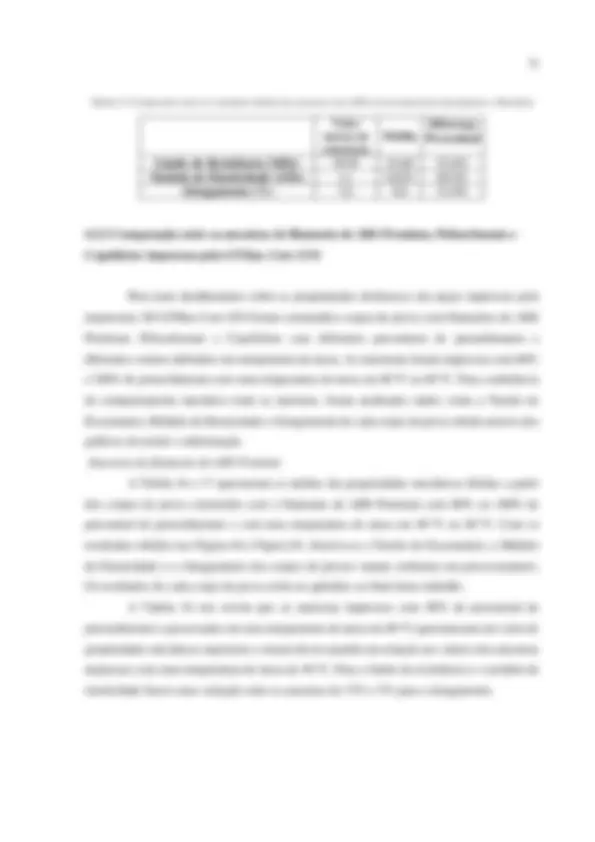
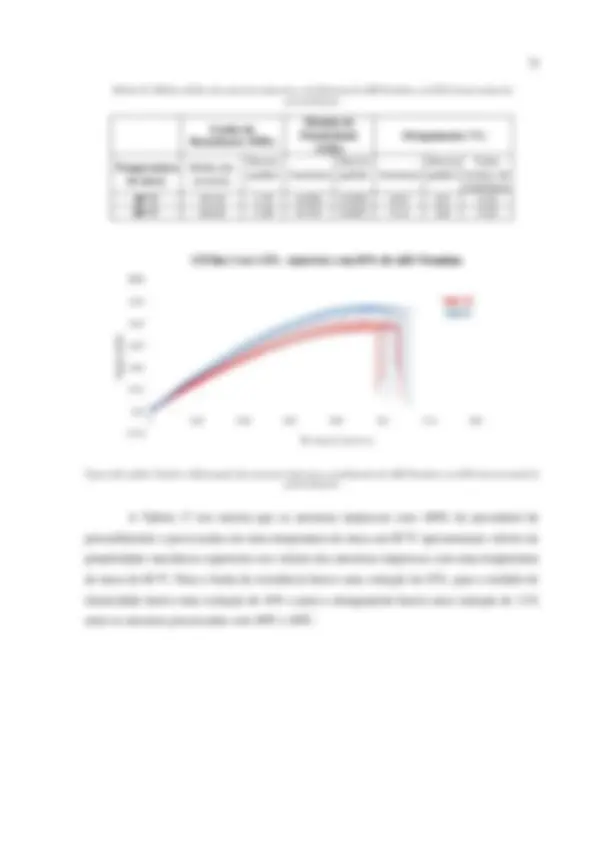
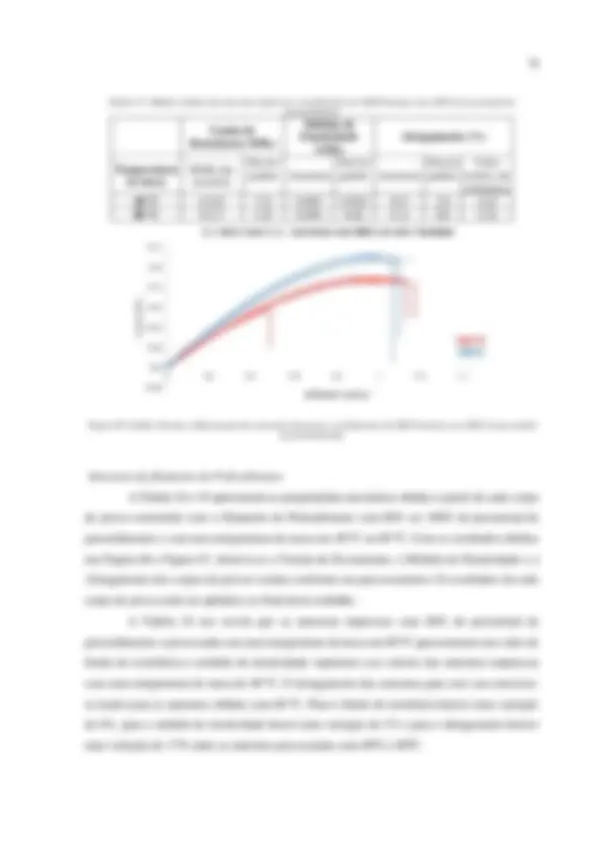
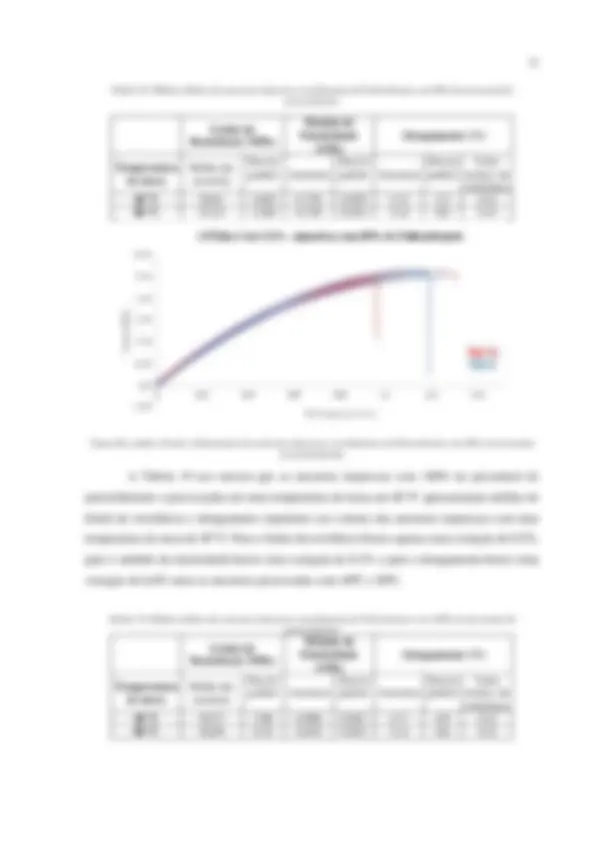
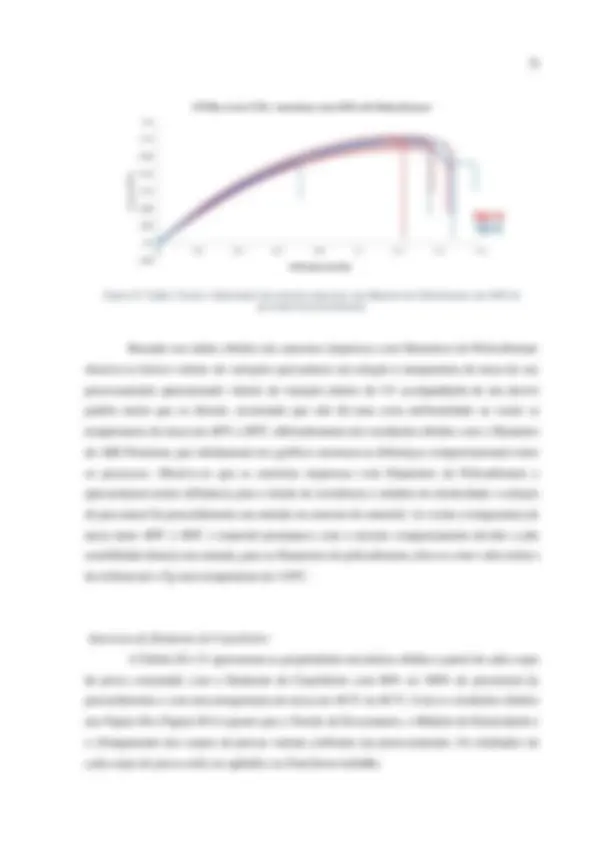
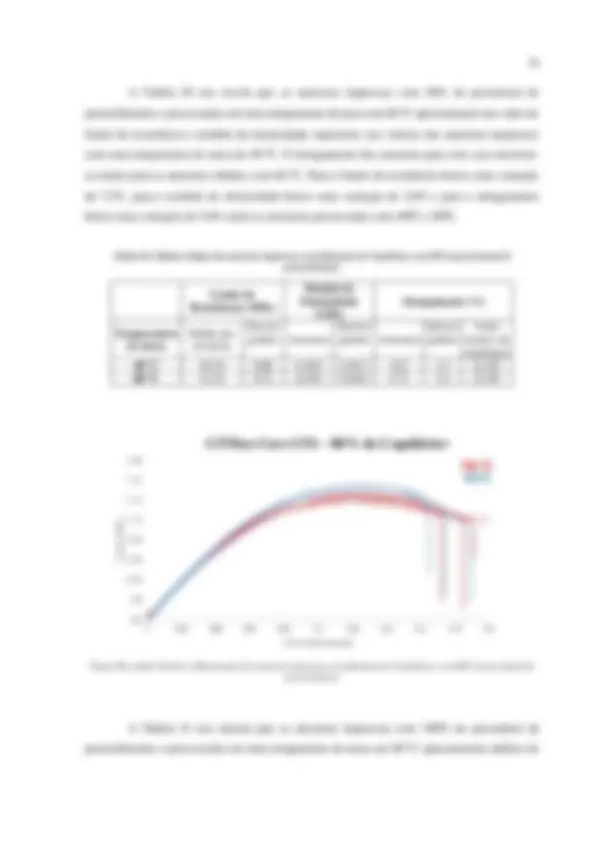
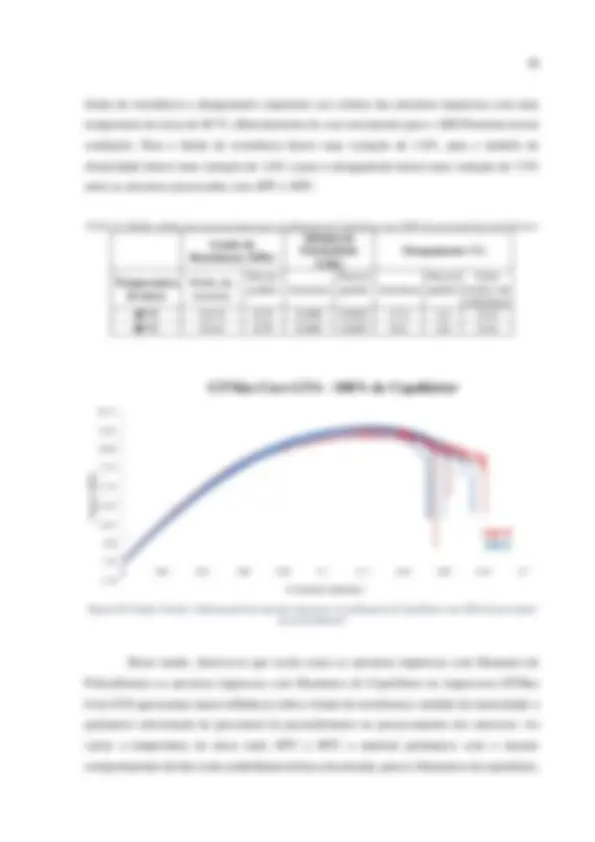
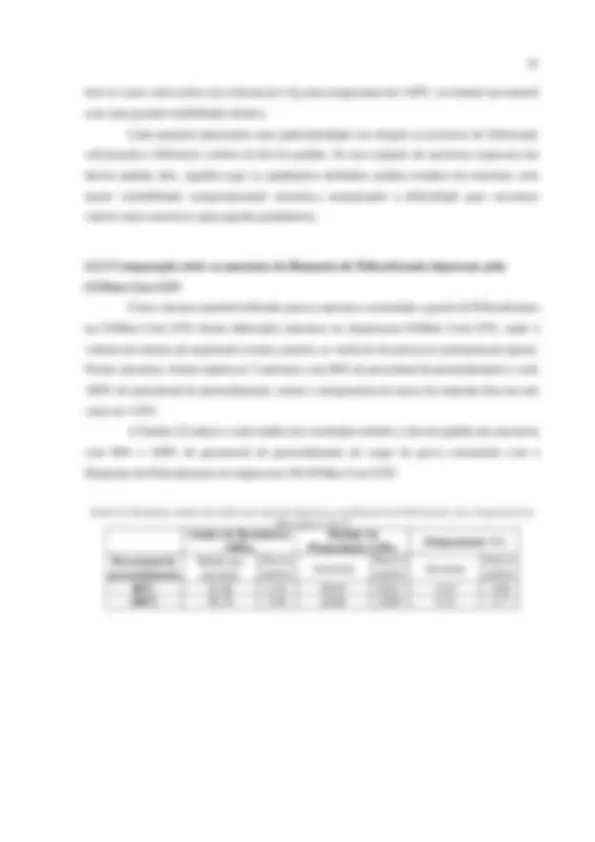
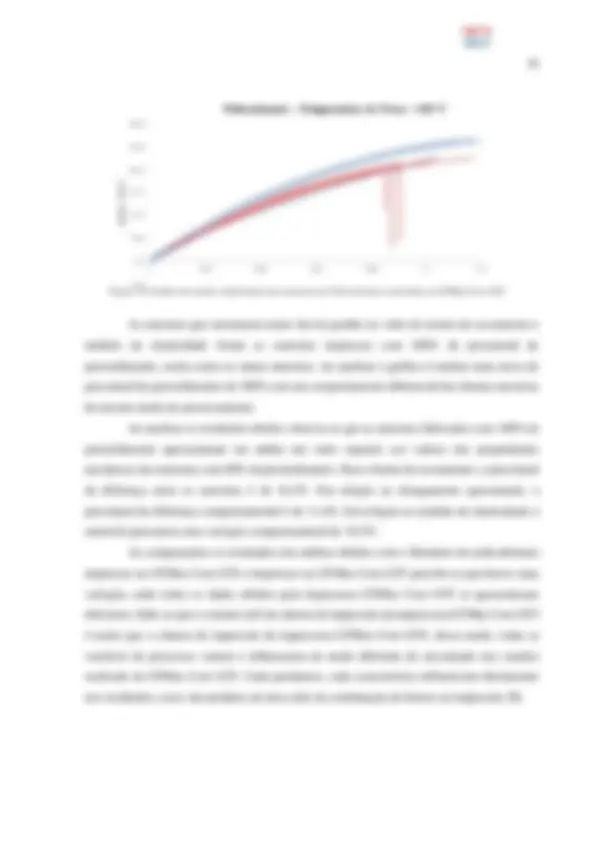
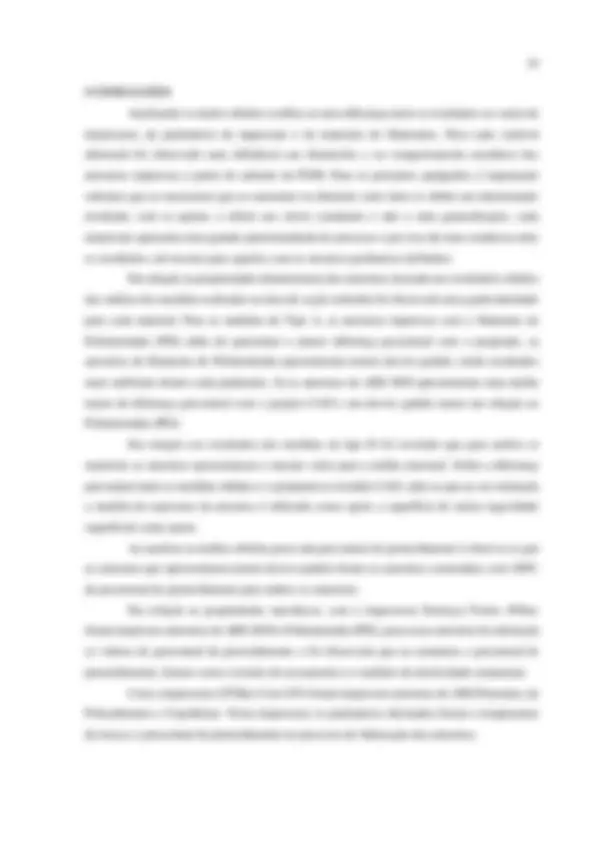
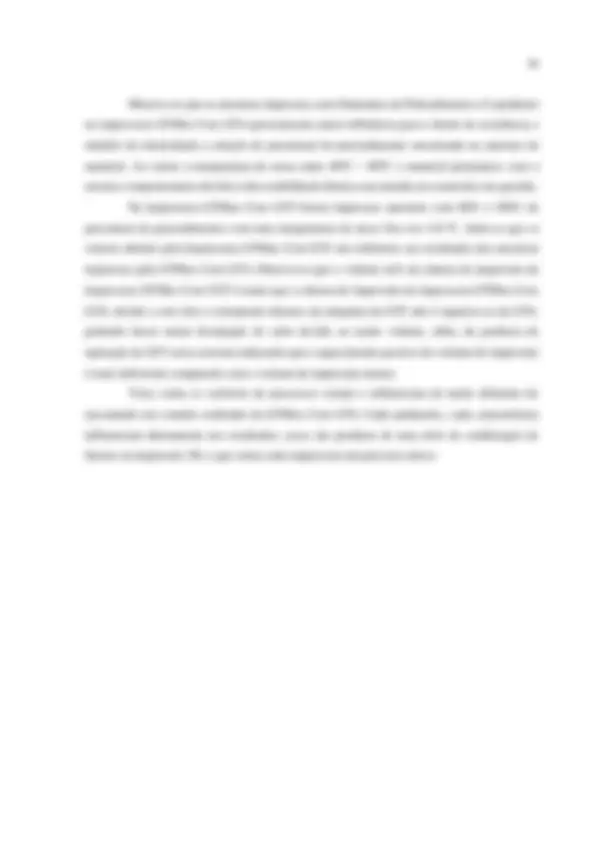
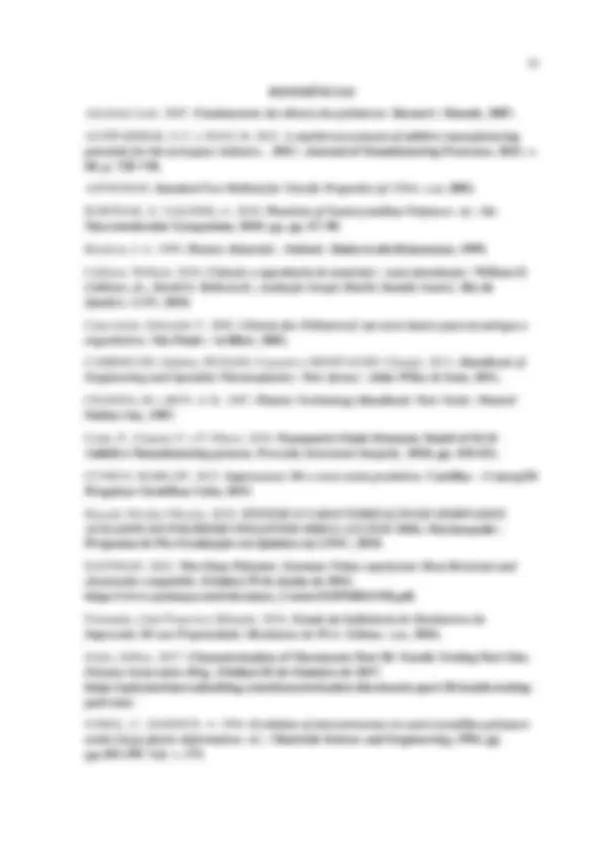
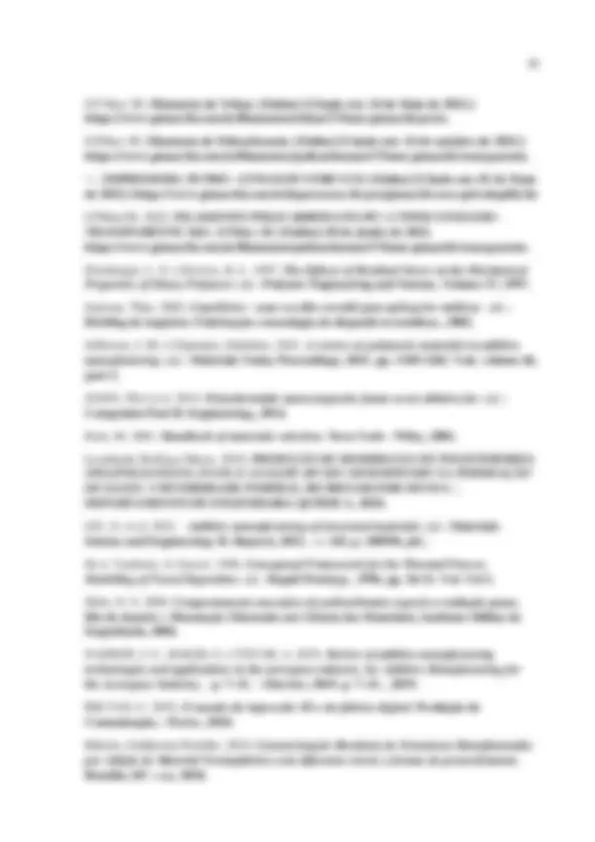
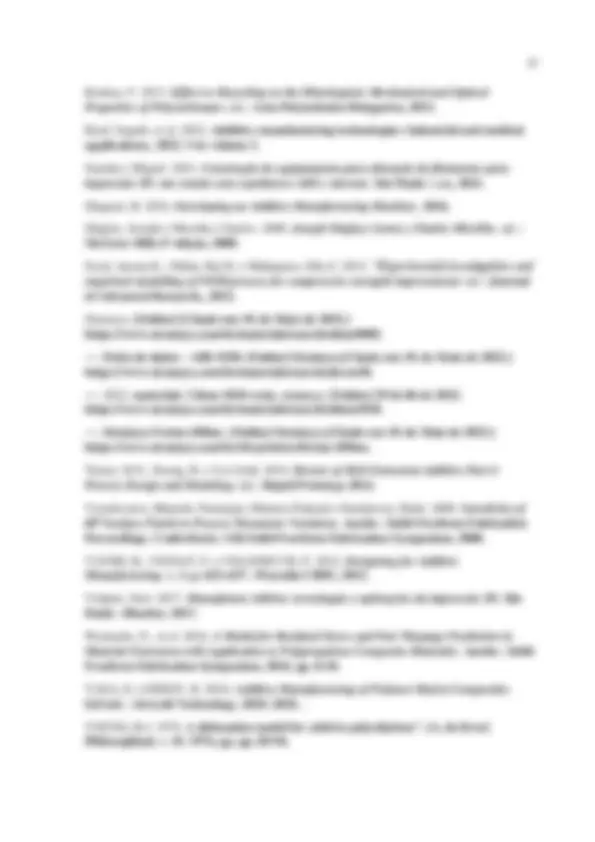
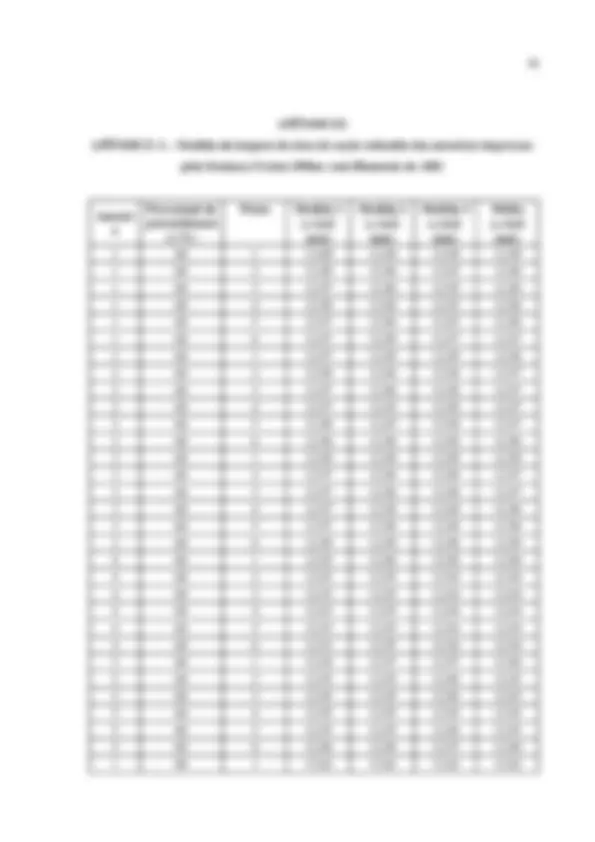
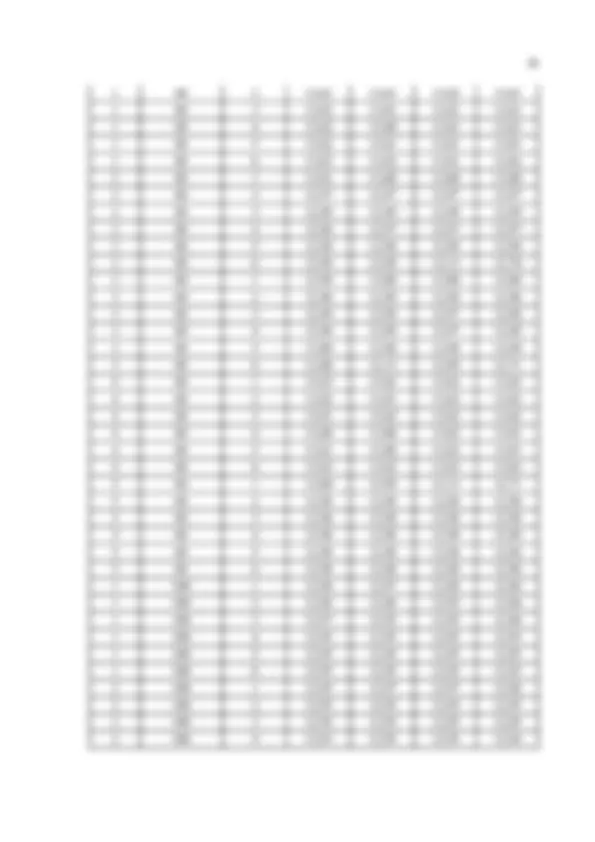
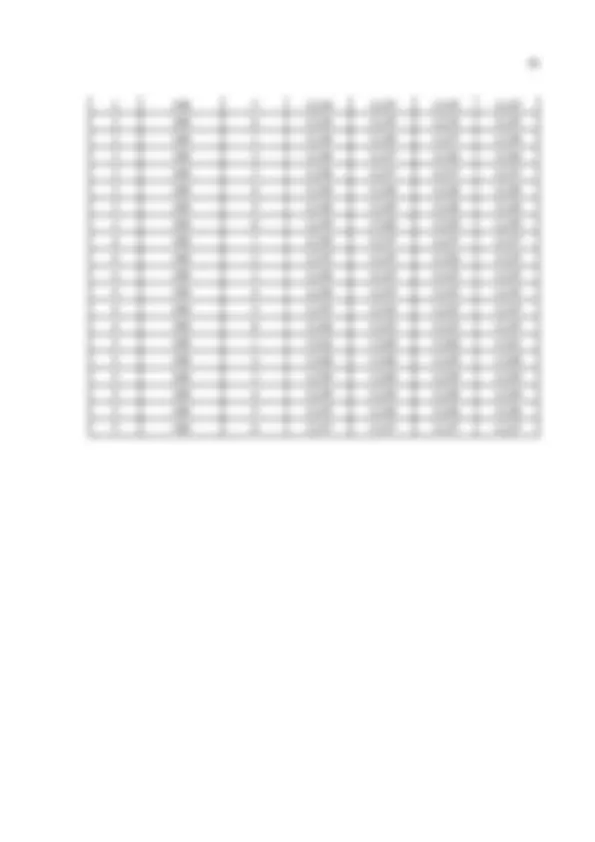
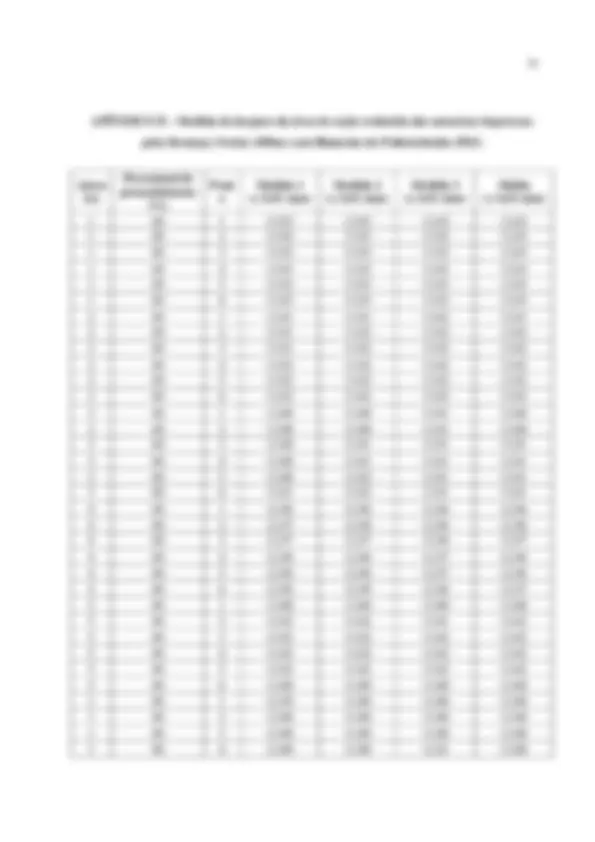
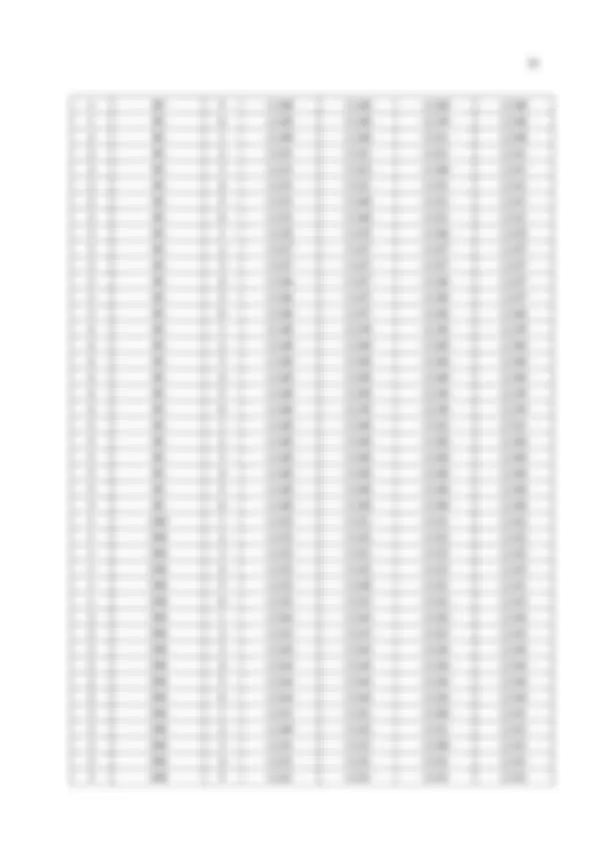
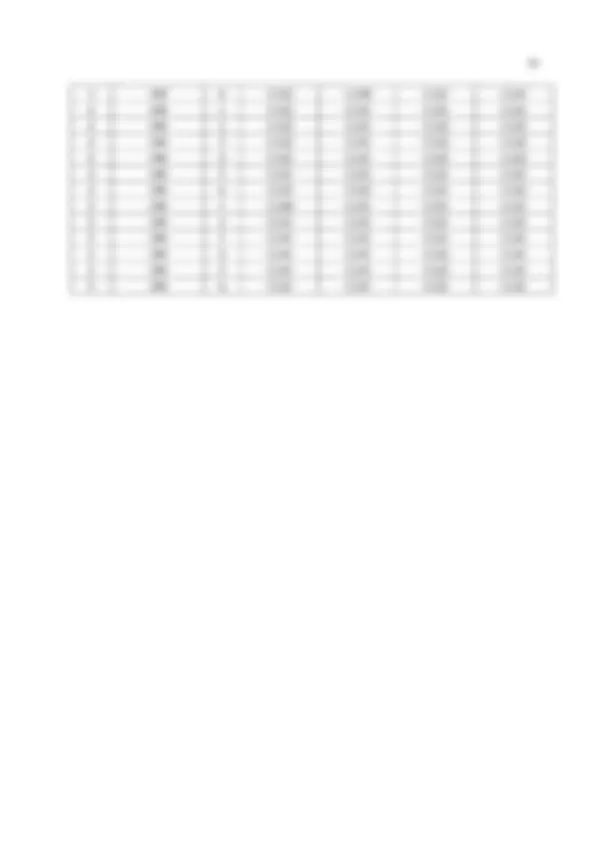

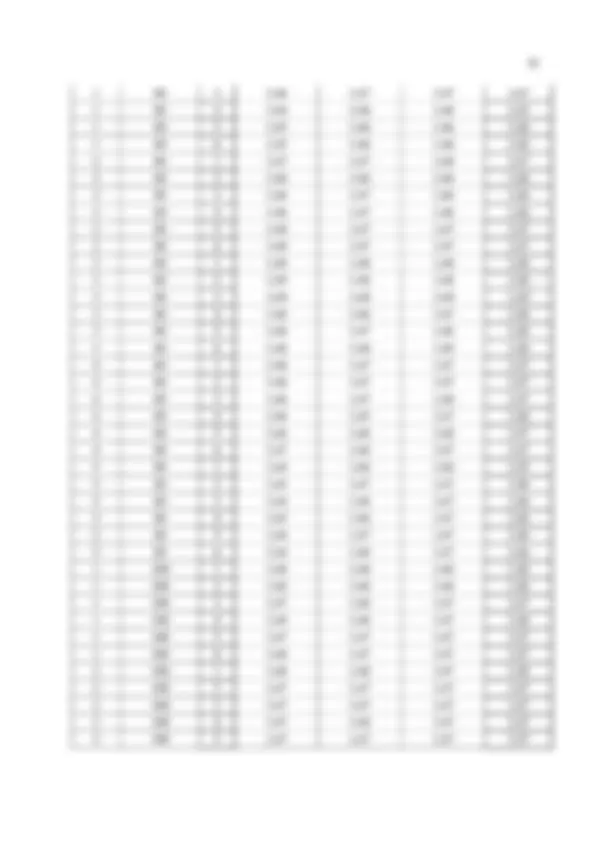
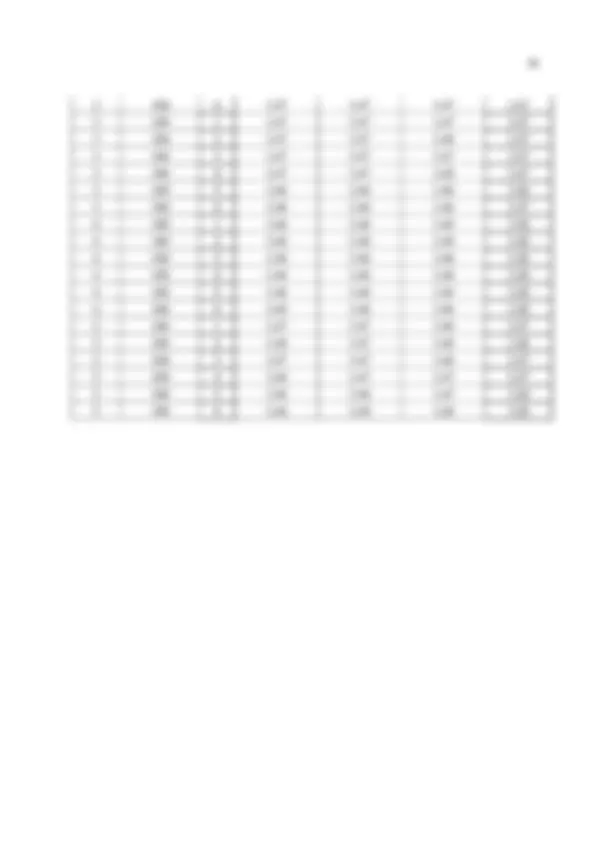
Estude fácil! Tem muito documento disponível na Docsity
Ganhe pontos ajudando outros esrudantes ou compre um plano Premium
Prepare-se para as provas
Estude fácil! Tem muito documento disponível na Docsity
Prepare-se para as provas com trabalhos de outros alunos como você, aqui na Docsity
Os melhores documentos à venda: Trabalhos de alunos formados
Prepare-se com as videoaulas e exercícios resolvidos criados a partir da grade da sua Universidade
Responda perguntas de provas passadas e avalie sua preparação.
Ganhe pontos para baixar
Ganhe pontos ajudando outros esrudantes ou compre um plano Premium
Comunidade
Peça ajuda à comunidade e tire suas dúvidas relacionadas ao estudo
Descubra as melhores universidades em seu país de acordo com os usuários da Docsity
Guias grátis
Baixe gratuitamente nossos guias de estudo, métodos para diminuir a ansiedade, dicas de TCC preparadas pelos professores da Docsity
Engenharia de Materiais do Centro de Blumenau da ... Blumenau, 26 de julho de 2022. ... ASA - Acrilonitrila estireno e acrilato.
Tipologia: Slides
1 / 109
Esta página não é visível na pré-visualização
Não perca as partes importantes!
Blumenau 2022
Thais Furtado Fernandes AVALIAÇÃO DAS PROPRIEDADES MECÂNICAS E DIMENSIONAIS DE DIFERENTES POLÍMEROS PROCESSADOS PELO MÉTODO FDM Trabalho Conclusão do Curso de Graduação em Engenharia de Materiais do Centro de Blumenau da Universidade Federal de Santa Catarina como requisito para a obtenção do título de Engenheira de Materiais. Orientador: Prof, Dr. Leonardo Ulian Lopes Coorientador: M.Sc Adriano Passini Blumenau 2022
Thais Furtado Fernandes AVALIAÇÃO DAS PROPRIEDADES MECÂNICAS E DIMENSIONAIS DE DIFERENTES POLÍMEROS PROCESSADOS PELO MÉTODO FDM Este Trabalho Conclusão de Curso foi julgado adequado para obtenção do Título de “Engenheira de Materiais” e aprovado em sua forma final pelo Curso Engenharia de Materiais Blumenau, 26 de julho de 2022.
Thais Furtado Fernandes Graduanda Instituição Universidade Federal de Santa Catarina - Blumenau
Banca Examinadora:
Prof. Dr., Leonardo Ulian Lopes Orientador(a) Instituição Universidade Federal de Santa Catarina - Blumenau
Prof. Dr., Johnny de Nardi Martins Avaliador Instituição Universidade Federal de Santa Catarina - Blumenau
Prof. Dr., Claudio Michel Poffo Avaliador Instituição Universidade Federal de Santa Catarina - Blumenau
Primeiramente, à Deus por toda a força e conhecimento nessa trajetória. Ao meu querido pai, por todo esforço, amor e apoio que me deu durante todos estes anos. Essa conquista também é dele. À minhas irmãs que foram fonte de inspiração e força para a realização desta jornada. À Universidade Federal de Santa Catarina pelos anos de aprendizagem e pelos amigos colecionados. À Embraer pelo apoio e aprendizado concebido Ao meu orientador pelo apoio e ensinamentos. Ao meu coorientador e amigo, Adriano Passini, pelo apoio, força e conhecimento passados diariamente. Ao time da Manufatura Ágil da Embraer por viabilizar todos os processos necessários para a realização deste trabalho. Aos meus amigos, Caio, Ghabriell e Larissa por me apoiarem em toda a jornada da graduação e me ajudando a ser cada vez melhor. Ao meu amigo Renan pela paciência, ajuda e incentivo durante a realização deste trabalho.
A manufatura aditiva vem se tornando uma técnica potencializadora e capacitadora quando integrada na linha de produção, na qual sabe-se que um dos pilares da Industria 4.0 é o uso de manufatura aditiva para impressão 3D. Uma das técnicas mais versáteis para a manufatura aditiva de peças poliméricas é a Fused Deposition Modeling, esse processo é caracterizado por depositar o material fundido em forma de filamento, onde em um bico calibrado utiliza-se temperaturas superiores à de fusão do material, tornando possível realizar a extrusão do material. A formação do objeto desejado consiste em sobrepor camadas de filamentos fundidos até obter a geometria desejada. Essa técnica tem se popularizado ao longo dos anos devido à sua versatilidade e relativo baixo custo, no entanto, a falta de normas e orientações específicas para os parâmetros de processamento acabam impondo uma certa dificuldade quanto ao uso dessa tecnologia em relação à reprodutibilidade das propriedades. Paralelamente, novos materiais são inseridos no mercado para aplicação deste tipo de técnica, tornando cada vez mais necessário o desenvolvimento de estudos para fornecer dados técnicos aos utilizadores. Este trabalho tem como objetivo avaliar a estabilidade dimensional e o comportamento mecânico de amostras impressas pelas impressoras Stratasys Fortus 450mc, GTMax Core GT4 E GTMax Core GT5 com filamentos à base de ABS, Policarbonato, Copoliéster e Polietermida (PEI). Dentre as amostras impressas pela Stratasys, foram definidos diferentes parâmetros quanto à percentual de preenchimento da peça, já as amostras impressas pela GTMax Core GT4 foram alternadas parâmetros como a percentual de preenchimento e a temperatura de mesa, pois a impressora oferece essa possibilidade. Em relação ao comparativo entre as propriedades dimensionais das amostras impressas na Stratasys Fortus 450mc de ABS M30 e Polieterimida (PEI) foi constatado que o Polieterimida (PEI) tem maior estabilidade dimensional e apresenta uma menor variância em relação ao modelo CAD projetado. Devido às características da técnica de fabricação, as medidas obtidas na direção da espessura das amostras apresentaram maior variação em relação às medidas da largura da área de seção reduzida. Já em relação ao comparativo entre as propriedades mecânicas do material, as amostras de ABS M30 impressas pela Stratasys Fortus 450mc apresentaram valores superiores de limite de resistência em relação aos resultados obtidos das amostras de filamento de Polieterimida (PEI), diferentemente do previsto pelos fabricantes do filamento. Já as amostras impressas pela GTMax Core GT apresentaram dependência das propriedades mecânicas quando variadas a percentual de preenchimento e temperatura de mesa. Para as amostras impressas nessa impressora com filamento de ABS Premium os resultados se mostraram variar conforme a percentual de preenchimento e a temperatura de mesa, diferentemente dos resultados obtidos para o Policarbonato e o Copoliéster, foi encontrada pouca influência da variação da temperatura de mesa. As amostras impressas com filamento de policarbonato impressos na GTMax Core GT percebe-se que houve uma variação, onde todos os dados obtidos pela impressora GTMax Core GT5 se apresentaram inferiores. Paalavras-Chave: Impressão 3D, FDM, Manufatura Aditiva
obtained for Polycarbonate and Co-polyester, these samples showed that their results have a greater influence on the fill density than on the table temperature. In the samples printed with polycarbonate filament using the GTMax Core GT5, it was noticed that there was a variation, where all the data obtained by the printer were inferior. Keywords: 3D Printing, FDM, Additive Manufacturing.
Figura 1: Representação de uma molécula de polietileno da unidade repetida e das estruturas da cadeia. .................................................................................................................. 18 Figura 2: Estado amorfo, indicado na região azul e estado cristalino na região em vermelho. .................................................................................................................................. 19 Figura 3: Dois tipos de deslizamento cristalográfico. a) deslizamento de cadeia e b) deslizamento transverso. As setas indicam a movimentação da cadeia. .................................. 21 Figura 4: Estiramento a frio de um polímero linear com um pequeno aumento da tensão. ....................................................................................................................................... 22 Figura 5: Representações esquemáticas dos copolímeros .......................................... 22 Figura 6: Exemplos de aplicação de polímeros termoplásticos. ................................ 23 Figura 7: Curva tensão-deformação esquemática para um polímero, mostrando como são determinados os limites de escoamento e de resistência à tração e ao lado Curva tensão- deformação esquemática em tração para um polímero semicristalino. .................................... 24 Figura 8: Módulo Secante e Modulo tangencial de um material não linear. .............. 25 Figura 9: Curvas de tensão-deformação de tração para termorrígidos e termoplásticos .................................................................................................................................................. 26 Figura 10: Monomeros constituídos na composição química de ABS. ..................... 26 Figura 11: Unidade repetitiva do Policarbonato......................................................... 27 Figura 12: Estrutura química do monômero da PEI ULTEM®. ................................ 29 Figura 13: Processo de manufatura aditiva. ............................................................... 30 Figura 14: Processo FDM........................................................................................... 32 Figura 15: Distribuição de temperatura e formato do filamento depositado durante a deposição da primeira camada na modelagem de deposição por extrusão de material. ........... 34 Figura 16:Estágio intermediário de deposição da segunda camada mostrando a distribuição de temperatura na modelagem de extrusão do material........................................ 35 Figura 17: Geometria e malha antes da simulação de tensão residual e empenamento de duas camadas de filamentos................................................................................................. 35 Figura 18: Tensão residual em estado estacionário (esquerda) e empenamento/deformação (direita) resulta da simulação em material. ................................... 36 Figura 19: Sistema de Extrusora ON-Head (a) e OFF-Head (b). ............................... 36 Figura 20: Esquema de uma extrusora de material duplo. ........................................ 37
Figura 50: Fluxograma de atividades desenvolvidas para obtenção de medidas. .. 61 Figura 51: disposição das amostras na camara de impressão ..................................... 62 Figura 52: a máquina de modelo EMIC DL10000 para a realização dos Ensaios de Tração ....................................................................................................................................... 62 Figura 53: Gráfico para obtenção de dados ................................................................ 64 Figura 54: Esquematização de parametros selecionado para a obtenção de amostras construidas com a Stratasys ...................................................................................................... 64 Figura 55: Esquematização de parametros selecionado para a obtenção de amostras construidas com a GTMax3D. .................................................................................................. 65 Figura 56: Esquematização de parâmetros selecionado para a obtenção de amostras construidas com a GT5. ............................................................................................................ 66 Figura 57: Distribuição Gaussiana – medidas do tipo B das amostras construídas com filamento de ABS M30 e Polieterimida (PEI) .......................................................................... 67 Figura 58: Distribuição Gaussiana – medidas do tipo A das amostras construídas com filamento de ABS M30 e Polieterimida (PEI). ......................................................................... 67 Figura 59: Distribuição Gaussiana das amostras de ABS M30 e Polieterimida (PEI) agrupada por percentual de preenchimento .............................................................................. 69 Figura 60: Distribuição Gaussiana das amostras de ABS M30 e Polieterimida (PEI) agrupada por percentual de preenchimento do tipo B .............................................................. 70 Figura 61: Gráfico de Tensão x Deformação de corpos de prova de filamento ABS M- 30 .............................................................................................................................................. 71 Figura 62: Gráfico de Tensão x Deformação de corpos de prova de filamento POLIETERIMIDA (PEI) .......................................................................................................... 72 Figura 63: Modo de fraturas das demais fraturas, CDP01 e CDP15 .......................... 73 Figura 64: gráfico Tensão x Deformação das amostras impressas com filamento de ABS Premium com 80% de percentual de preenchimento ...................................................... 75 Figura 65: Gráfico Tensão x Deformação das amostras impressas com filamento de ABS Premium com 100% de percentual de preenchimento..................................................... 76 Figura 66: gráfico Tensão x Deformação das amostras impressas com filamento de Policarbonato com 80% de percentual de preenchimento ........................................................ 77 Figura 67: Gráfico Tensão x Deformação das amostras impressas com filamento de Policarbonato com 100% de percentual de preenchimento ...................................................... 78
Figura 68: gráfico Tensão x Deformação das amostras impressas com filamento de Copoliéster com 80% de percentual de preenchimento............................................................ 79 Figura 69: Gráfico Tensão x Deformação das amostras impressas com filamento de Copoliéster com 100% de percentual de preenchimento.......................................................... 80 Figura 70: Gráfico de tensão e deformação das amostras de Policarbonato construídas na GTMax Core GT5 ................................................................................................................ 82
ABNT - Associação Brasileira de Normas Técnicas ABS - Acrilonitrila-butadieno-estireno ASA - Acrilonitrila estireno e acrilato ASTM - American Society for Testing and Materials CAD - Computer Aided Design CDP - Corpo de prova DSC - Differential scanning calorimetry FDM - Fused Deposition Modeling IBGE - Instituto Brasileiro de Geografia e Estatística MA - Manufatura aditiva PC - Policarbonato PETG - Polietileno tereftalato glicol PEI – Polieterimida PLA - Poli ácido lático PP - Polipropileno Tc - Temperatura de cristalização Tg - Temperatura de transição vítrea Tm - Temperatura de fusão cristalina TMA - Thermomechanical Analysis
15 1 INTRODUÇÃO Nas últimas décadas, processos para a rápida prototipagem vem ganhando cada vez mais destaque. Conhecido como manufatura aditiva, o desenvolvimento de objetos do zero ou semi-acabados em tempo reduzido é possível em virtude de recentes tecnologias, bem como, melhoria de processos (VAYRE, et al., 2012). Conforme a ASTM (2012), a definição de manufatura aditiva é dada como o conjunto de tecnologias capazes de agregar materiais afim de produzir componentes a partir de modelos 3D, convencionalmente, produzidos pela deposição de camada sobre camada de material. Desta forma, diferente do processo tradicional de produção de materiais, a MA possui vasta flexibilidade para reprodução de geometrias (JEFFERSON et al., 2021). Na indústria aeroespacial a manufatura aditiva vem trazendo grandes contribuições para todo o segmento, seja em aeronaves comerciais, militares ou espaciais, como também, inovações para sistemas de mísseis. Isto se deve justamente por vantagens oferecidas pela manufatura aditiva, como produção de projetos complexos, baixo custo, redução dos níveis de desperdícios, produção de peças com materiais de alta performance e curto tempo de manufatura (NAJMON, et al., 2019). Basicamente, a manufatura aditiva é dividida em sete processos principais: jato de ligantes ( binder jetting , BJ ), deposição direta de energia ( directed energy deposition , DEB ), jato de material ( material jetting , MJ ), extrusão de material ( material extrusion , ME ), fusão em leito de pó ( powder bed fusion , PBF ), laminação em folhas ( sheet lamination , SL ), cubo de fotopolimerização ( vat photopolymerization , VP ), conforme citado por Altparmak e Xiao (2021). Nos diferentes processos diversos podem ser os metais e polímeros, utilizados como material precursor para a manufatura aditiva. O processo de fabricação utilizado nesse trabalho é o processo de Fused Deposition Modeling (FDM) por depositar o material fundido em forma de filamento, onde em um bico calibrado utiliza-se temperaturas superiores à de fusão do material, tornando possível realizar a extrusão do material. Desse modo, através do bico calibrado o material é depositado sobre uma mesa, e assim a formação do objeto desejado consiste em sobrepor camadasa de filamentos fundidos até obter a geometria desejada (CUNICO, 2015) Dentre os quais, polímeros destacam-se como materiais promissores para a produção de componentes, sendo aplicados em suas mais variadas formas e composições (ALTIPARMAK, et al., 2021). Assim, pode-se citar como principais materiais poliméricos
16 empregados na manufatura aditiva termoplásticos como acrilonitrila-butadieno-estireno (ABS), poli (ácido lático) (PLA), poliamida (PA 6 e PA 6.6), polipropileno (PP), entre outros (YASA, et al., 2018). A literatura indica que para a assegurar a qualidade e performance final do produto da manufatura aditiva, alguns parâmetros de processo são fundamentais. Como por exemplo, cita- se o diâmetro do bocal, temperatura do envelope, espessura da camada, temperatura de extrusão, tamanho da partícula de enchimento, velocidade de extrusão, além de outros fatores que podem impactar as propriedades do material em desenvolvimento (LIU et al ., 2021; MOHAN et al ., 2017; YASA e ERSOY, 2018). Soma-se a esse fato que diferentes equipamentos dão ao usuário maior ou menor liberdade na determinação desses parâmetros de processamento, o que limita a capacidade de otimizar as propriedades mecânicas e dimensionais das peças produzidas. Neste sentido, o presente trabalho visa prover informações de processamento essenciais para fabricação de ferramentais utilizados no setor aeroespacial através da manufatura aditiva tipo FDM. Nessa aplicação, a capacidade de atingir as propriedades mecânicas estabelecidas pelo fabricante do filamento e a garantia da precisão dimensional são essenciais para que o ferramental fabricado via manufatura aditiva desempenhe suas funções adequadamente.