
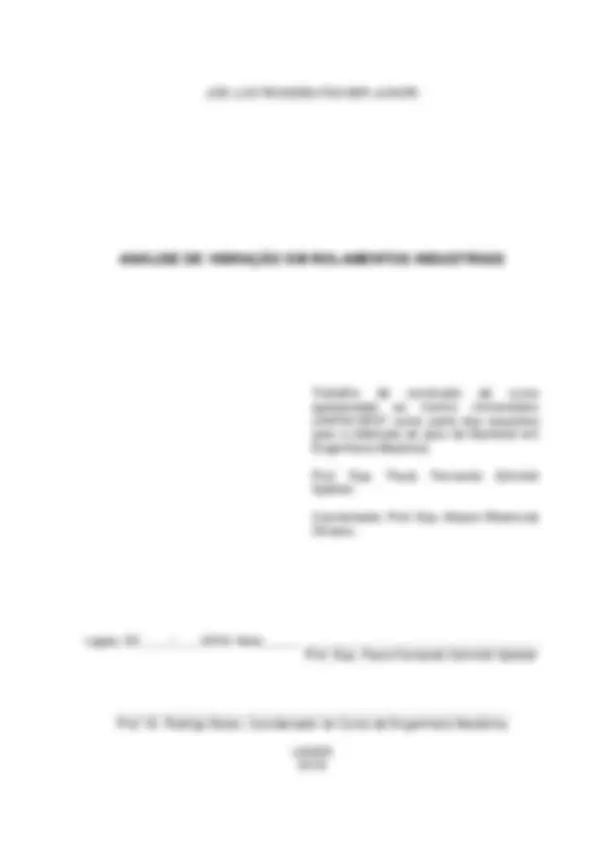
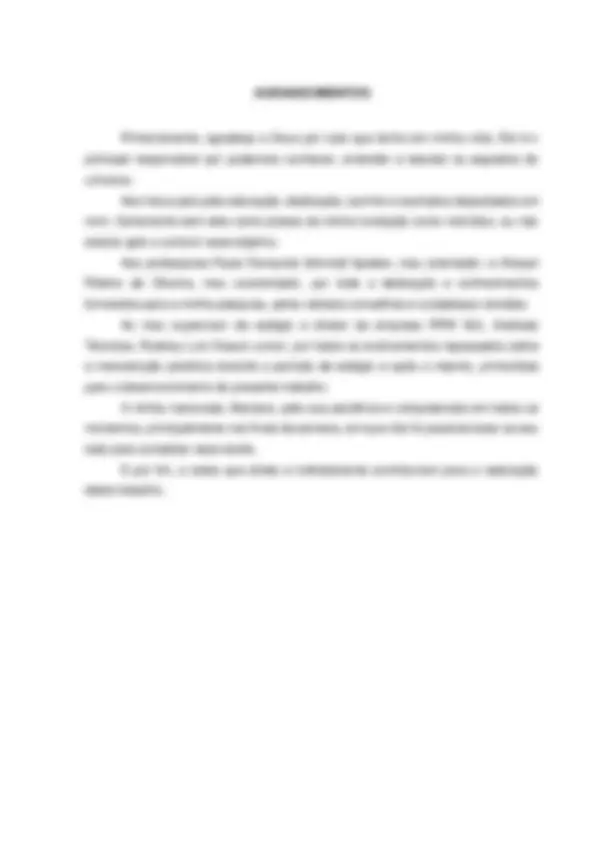
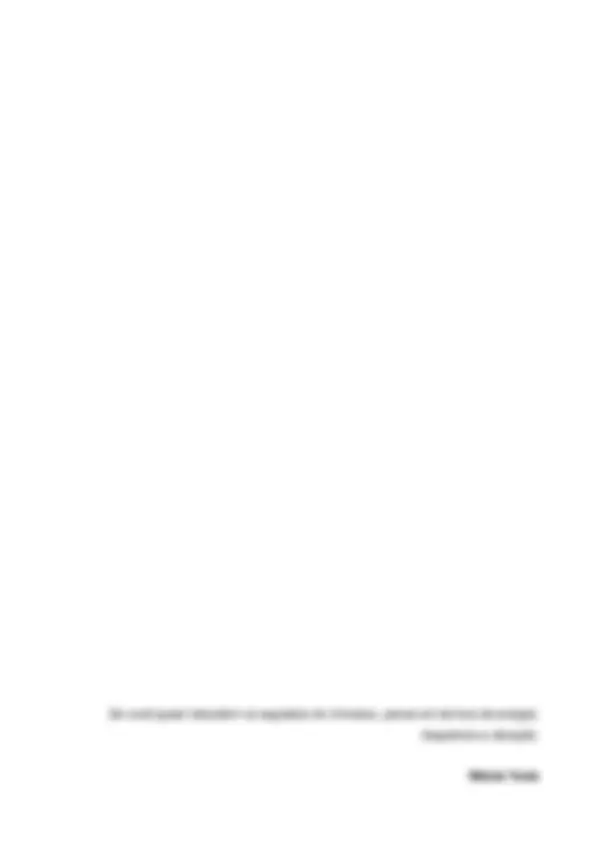
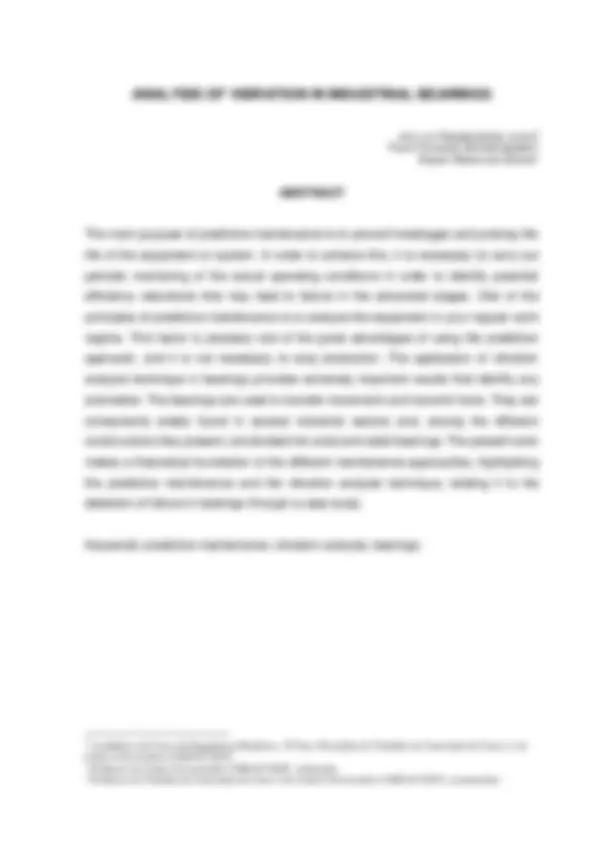
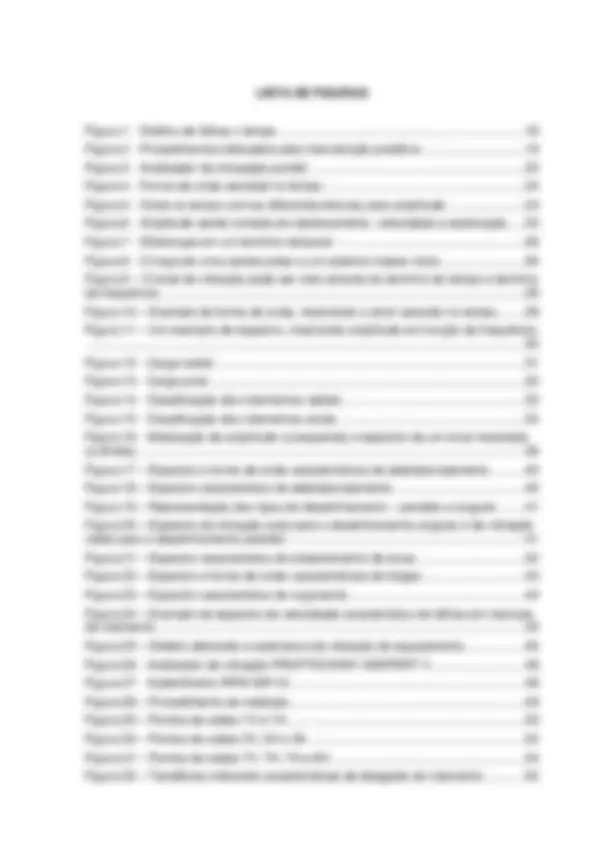
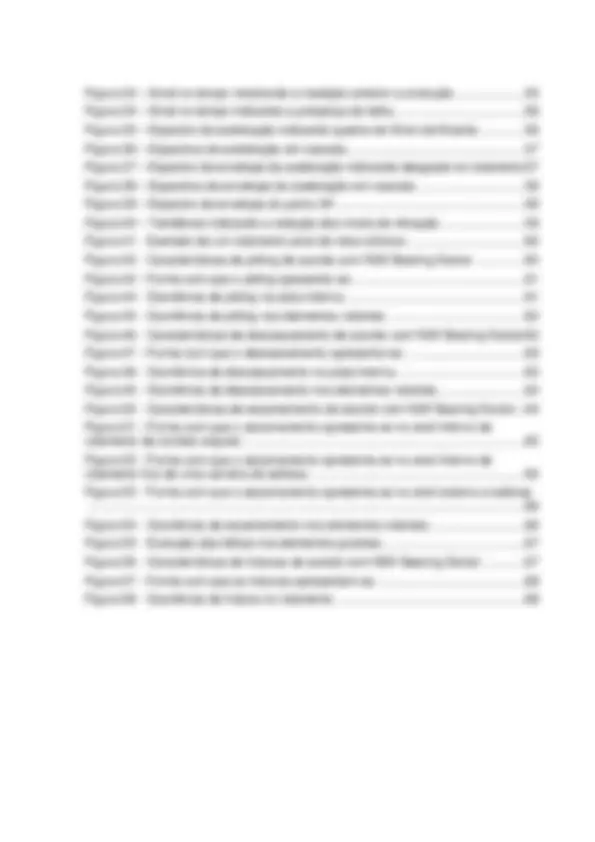
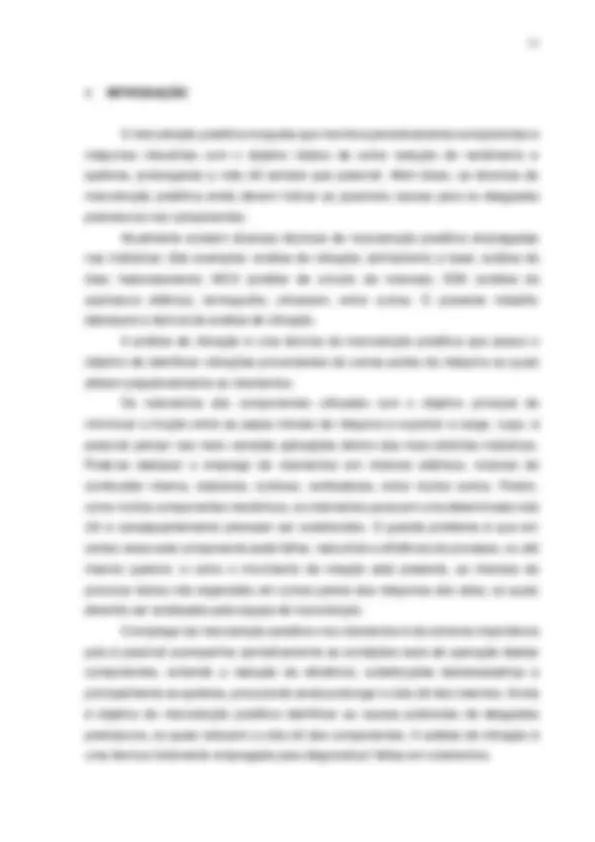
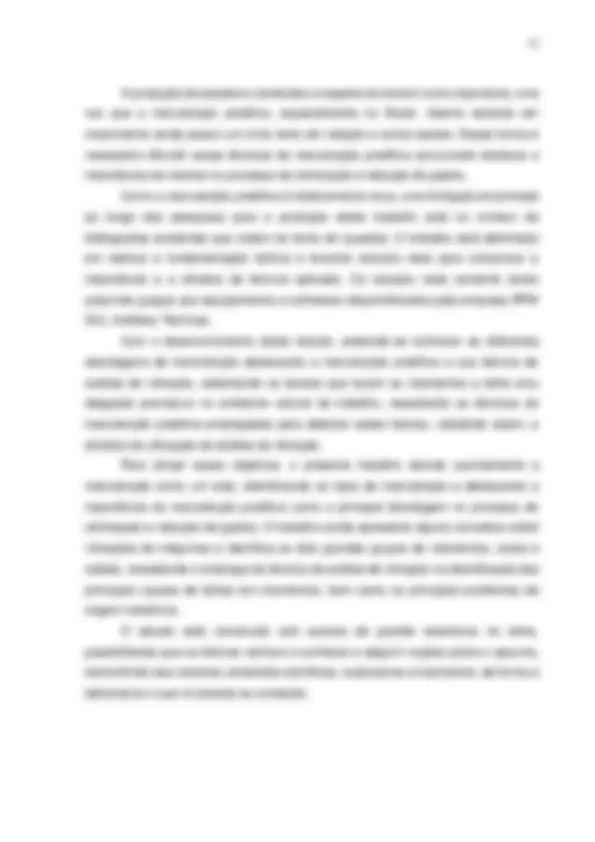
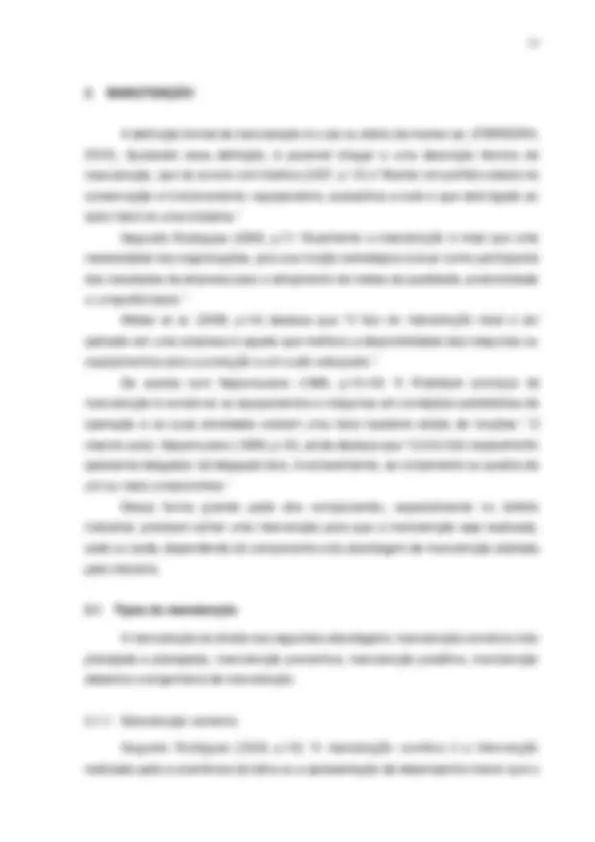
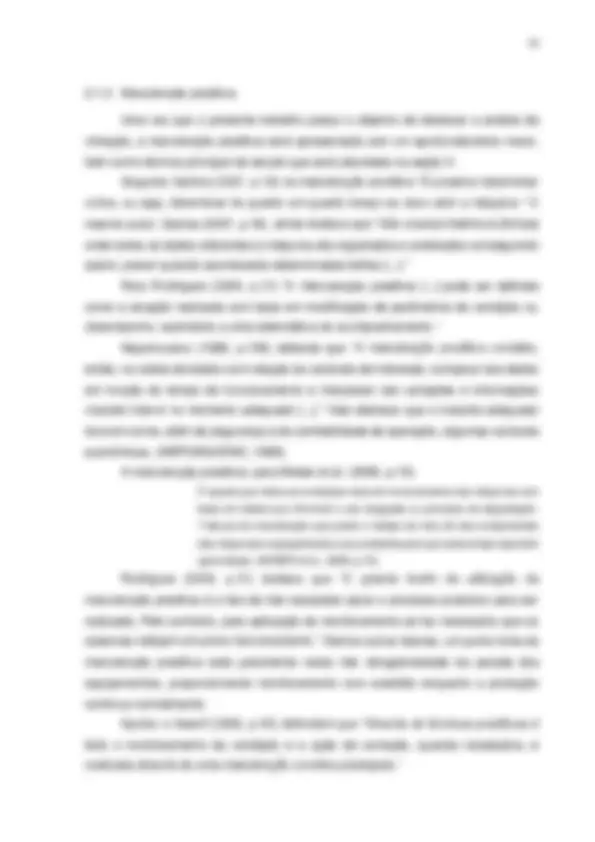
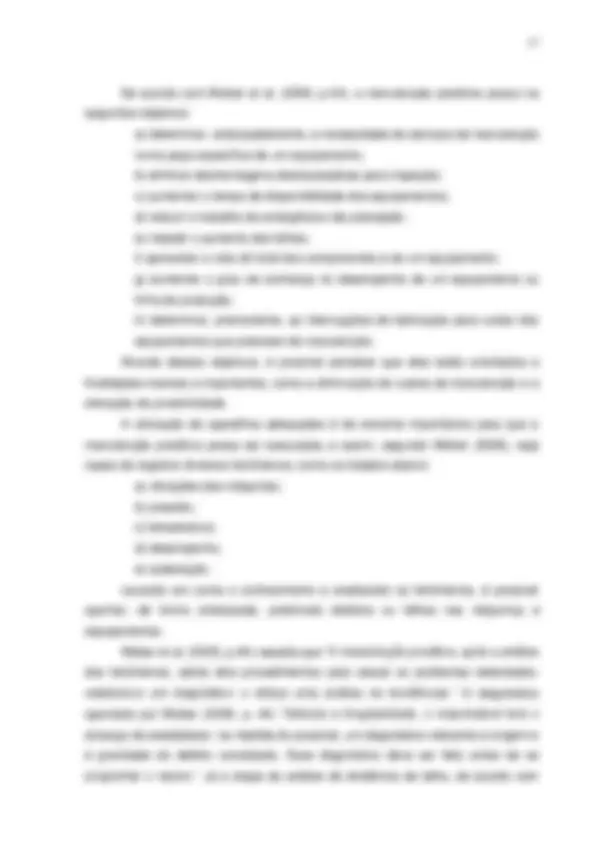
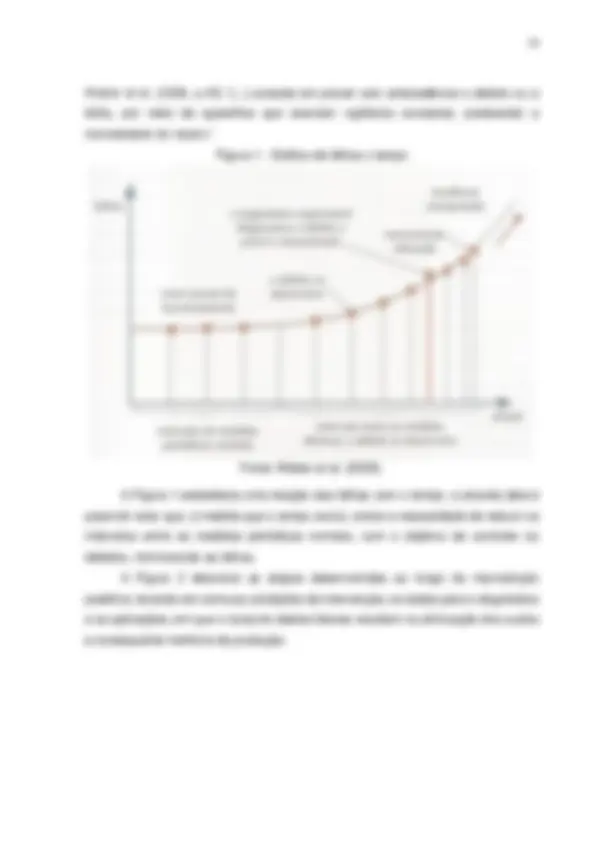
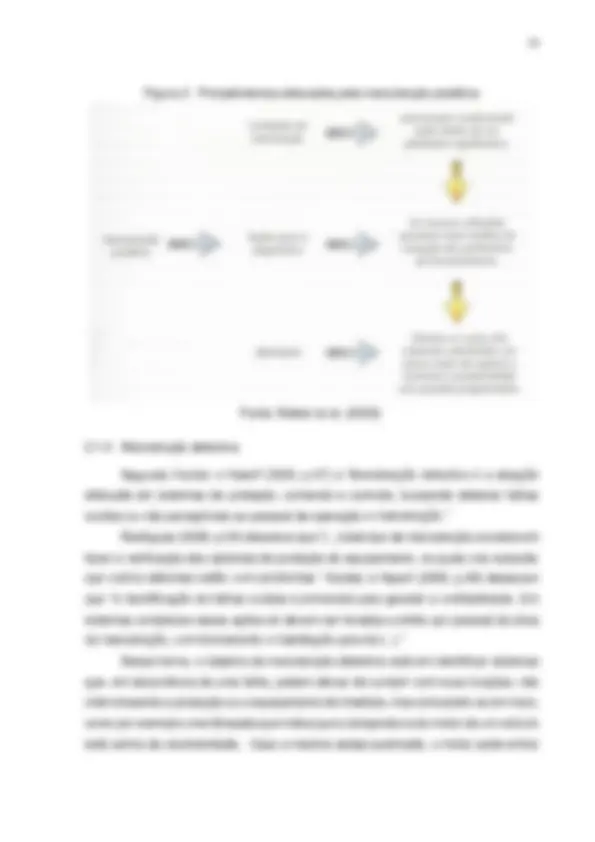
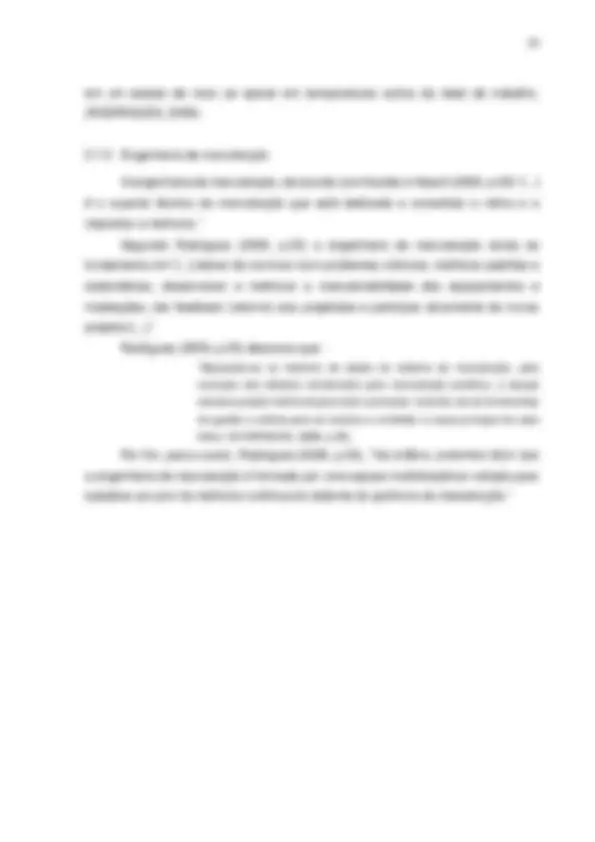
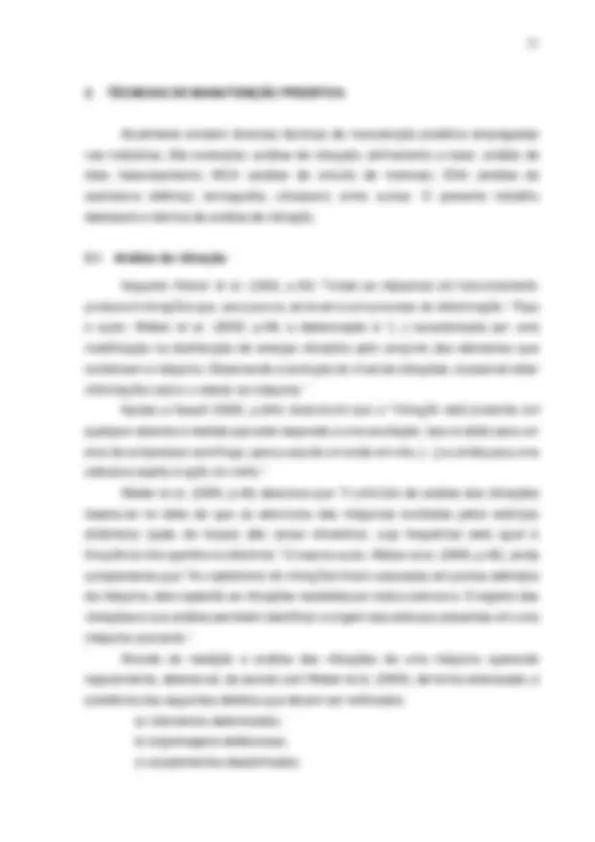
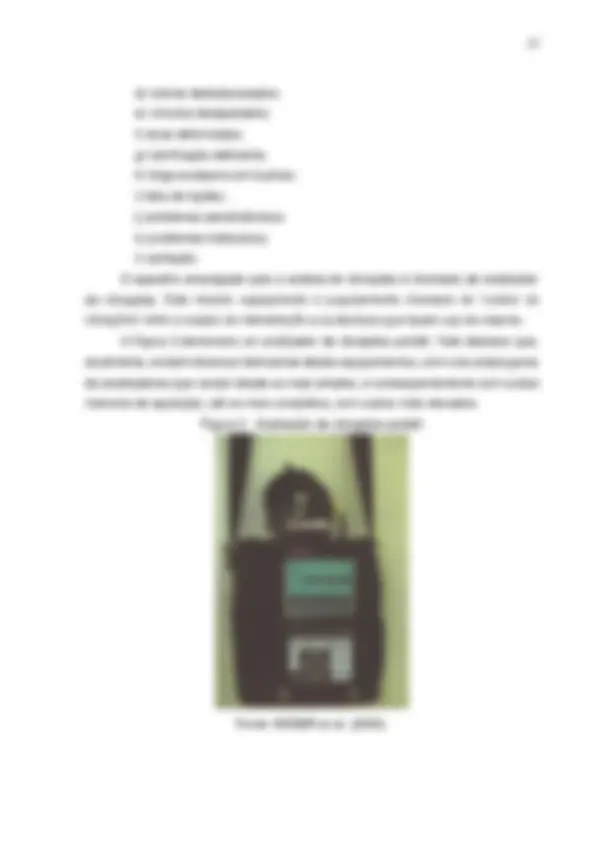
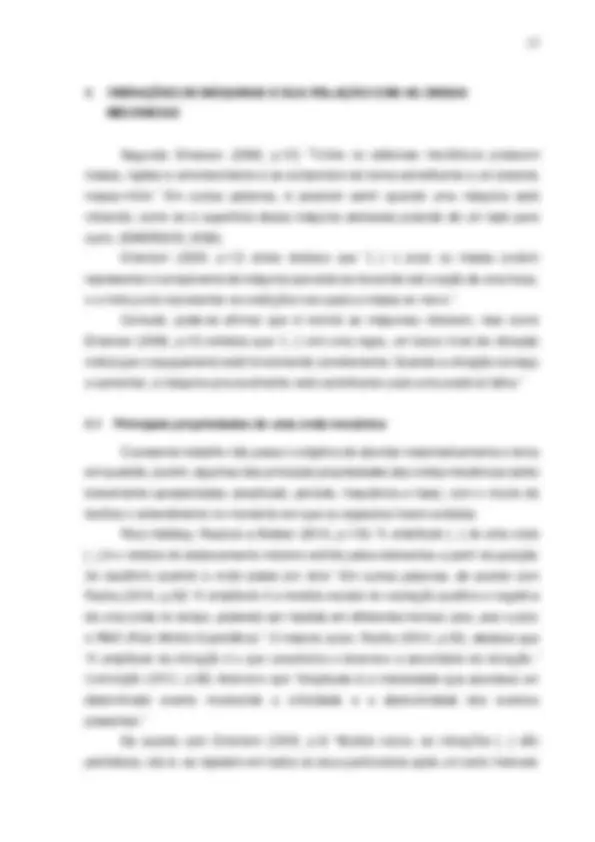
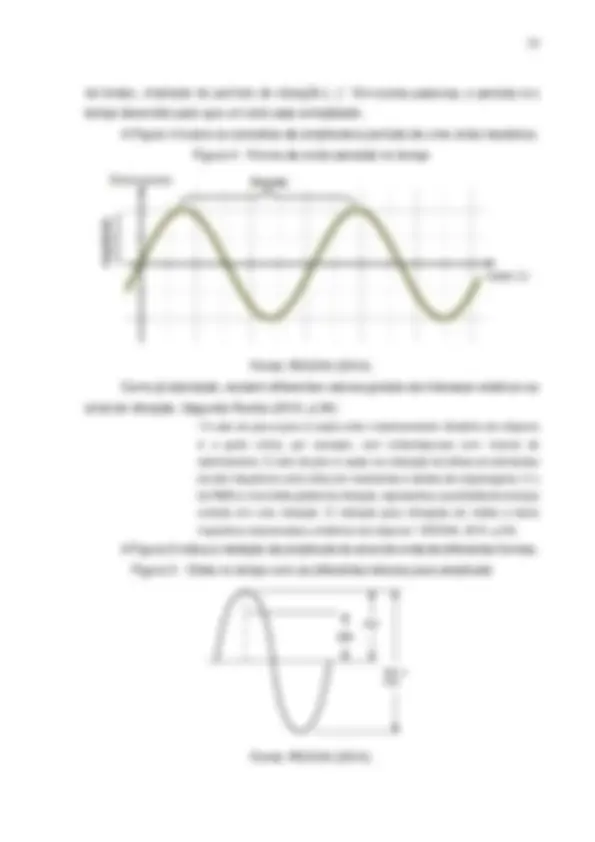
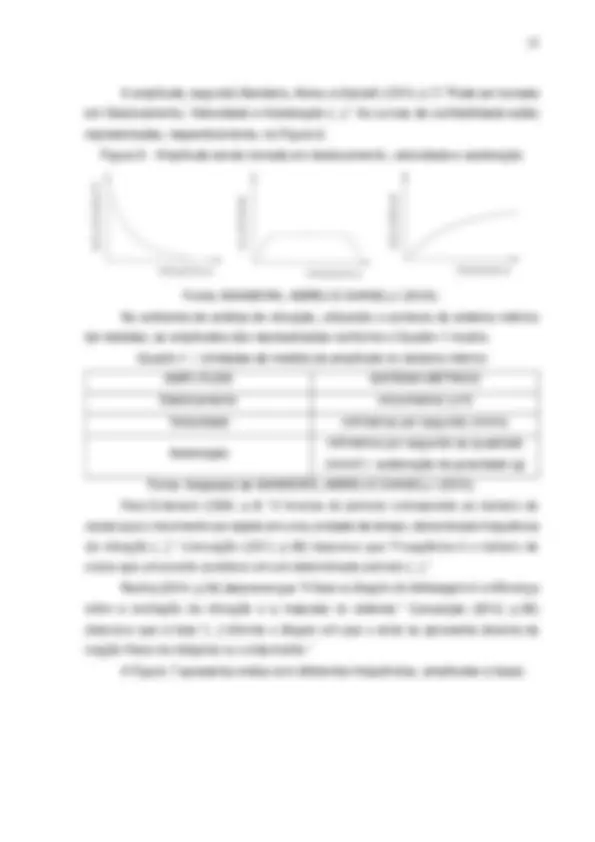
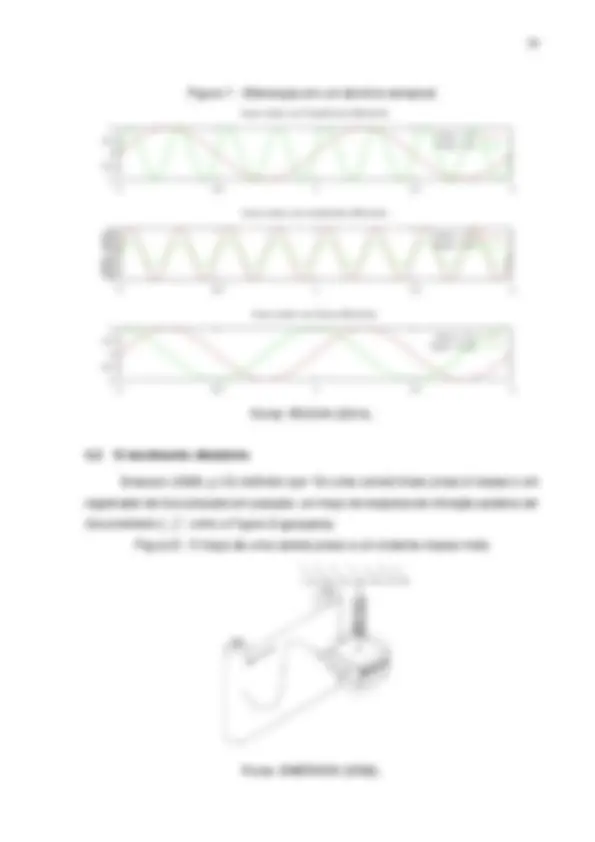
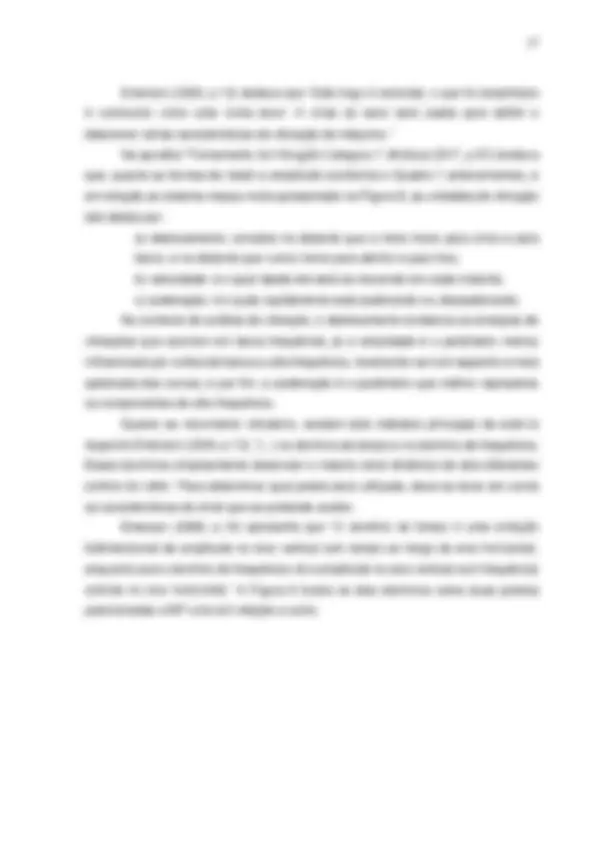
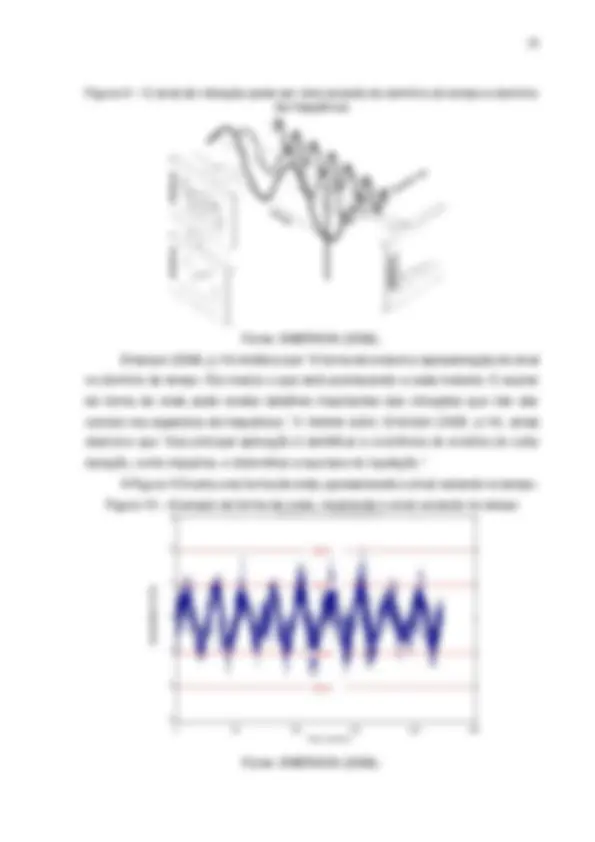
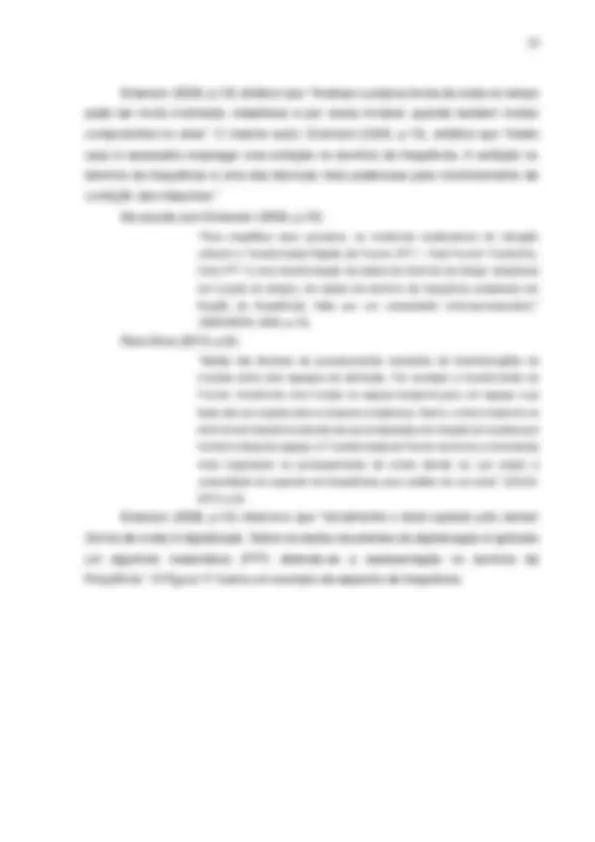
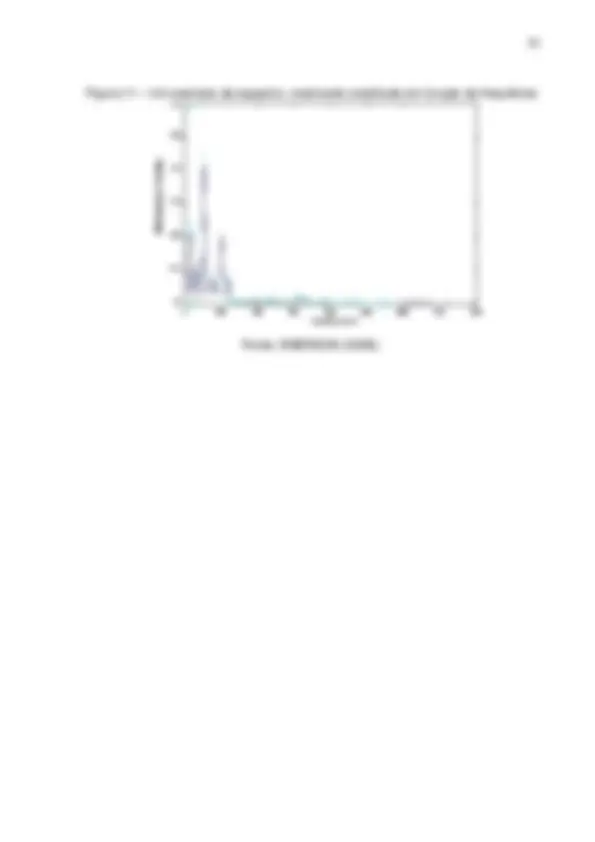
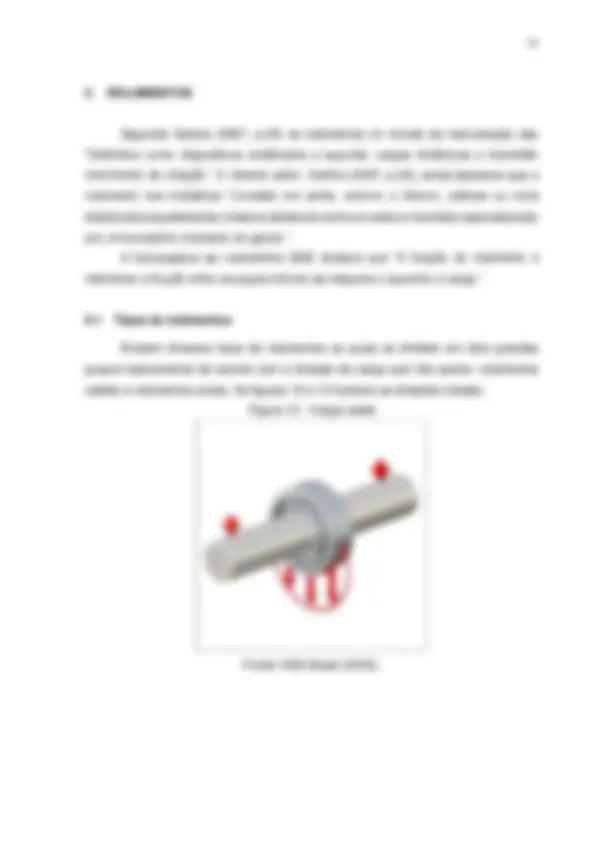
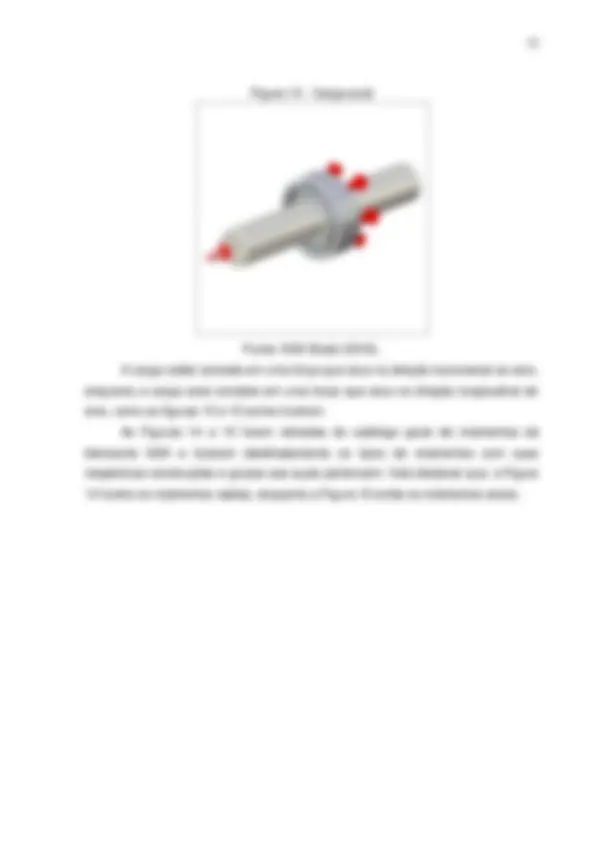
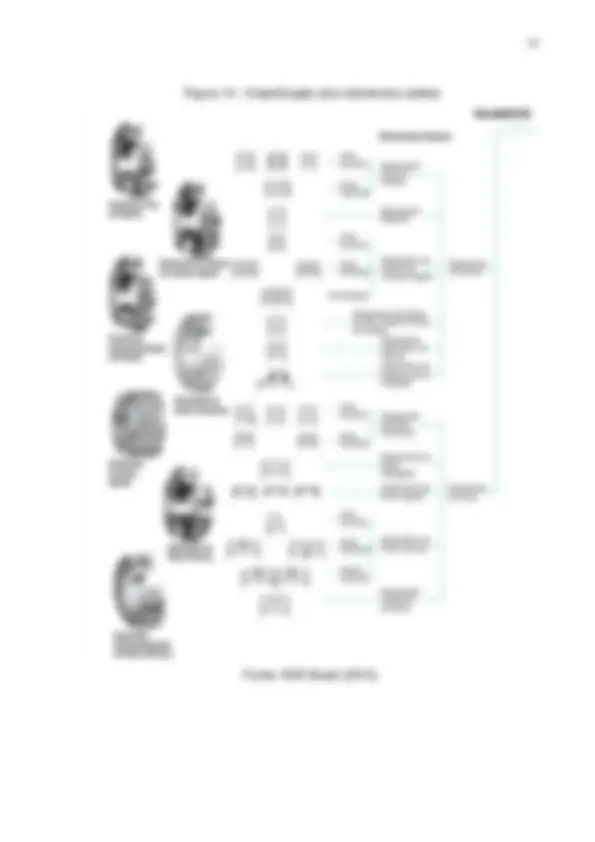

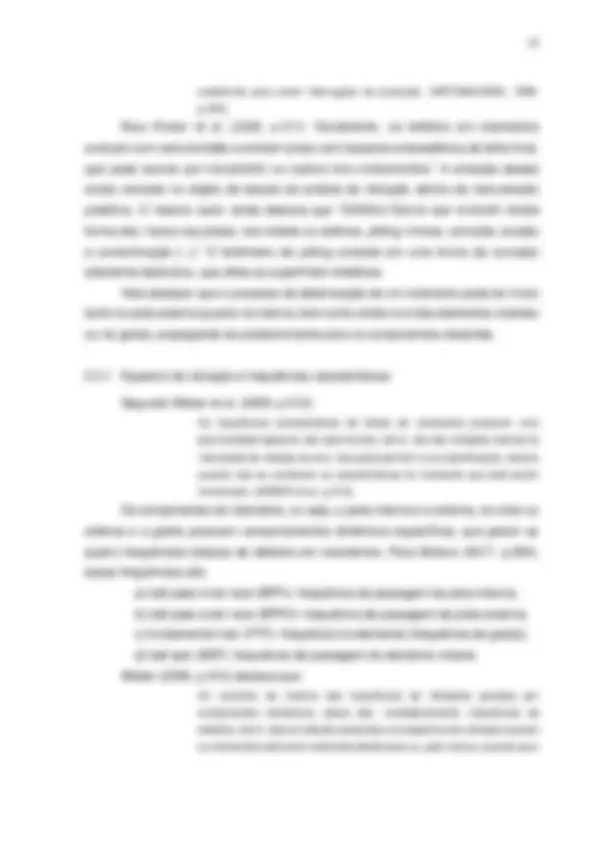
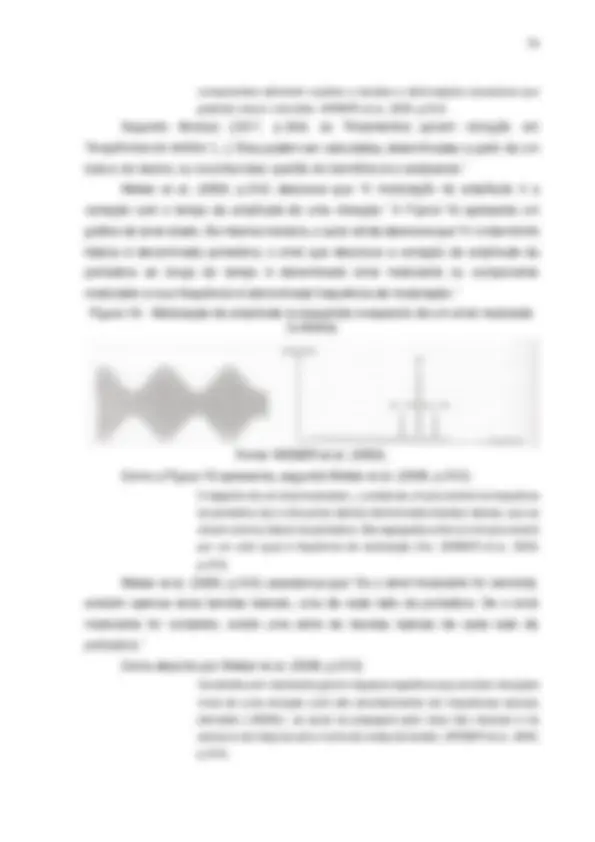
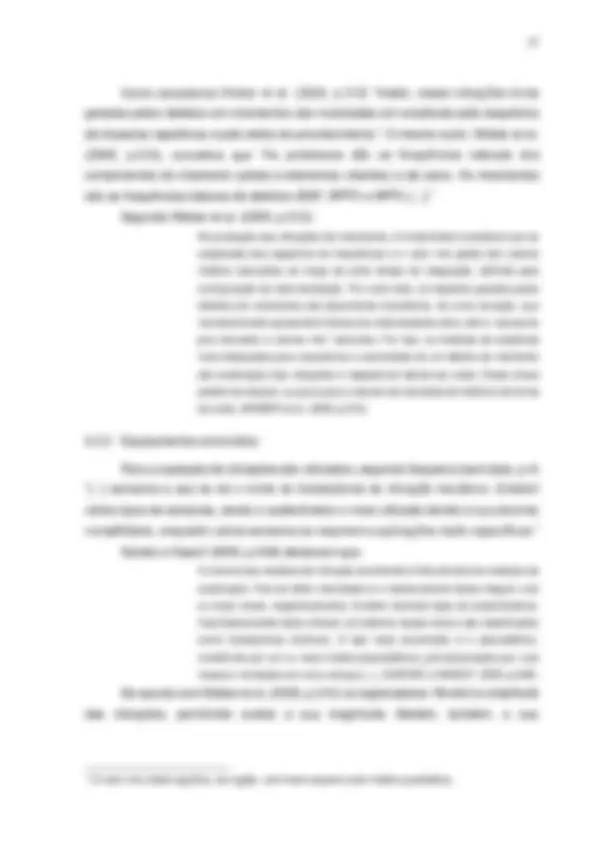
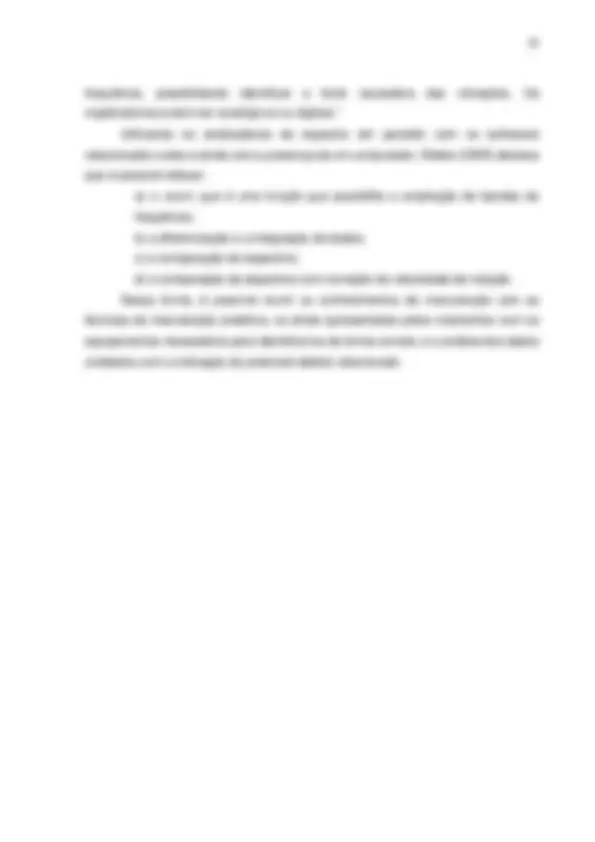
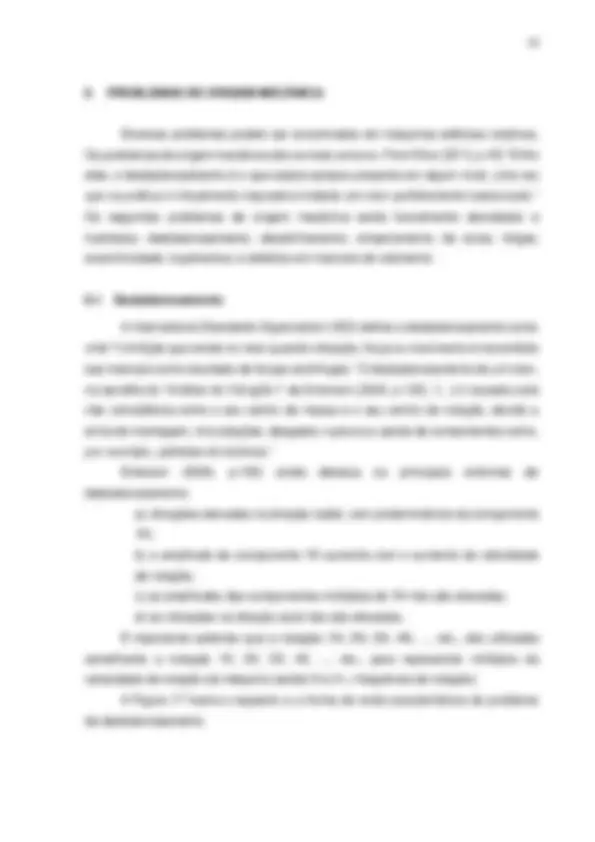
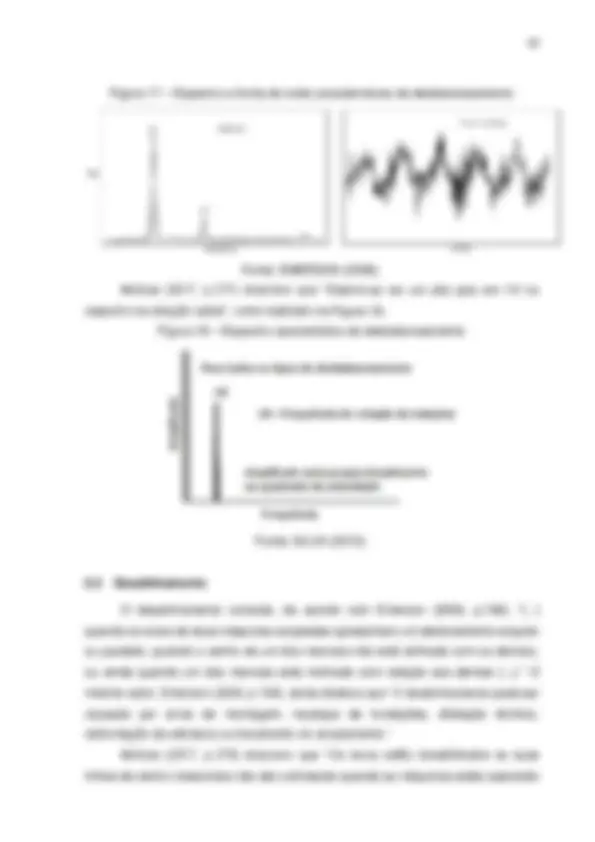
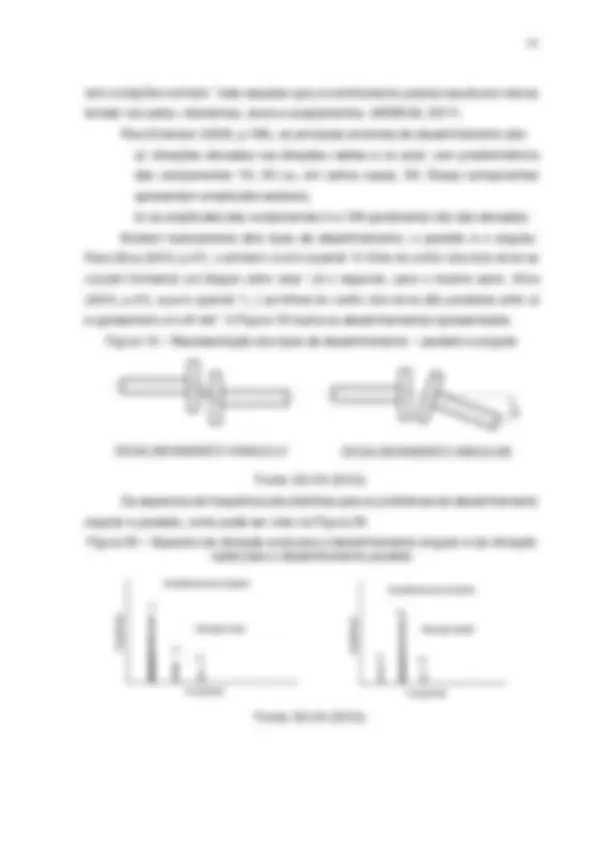
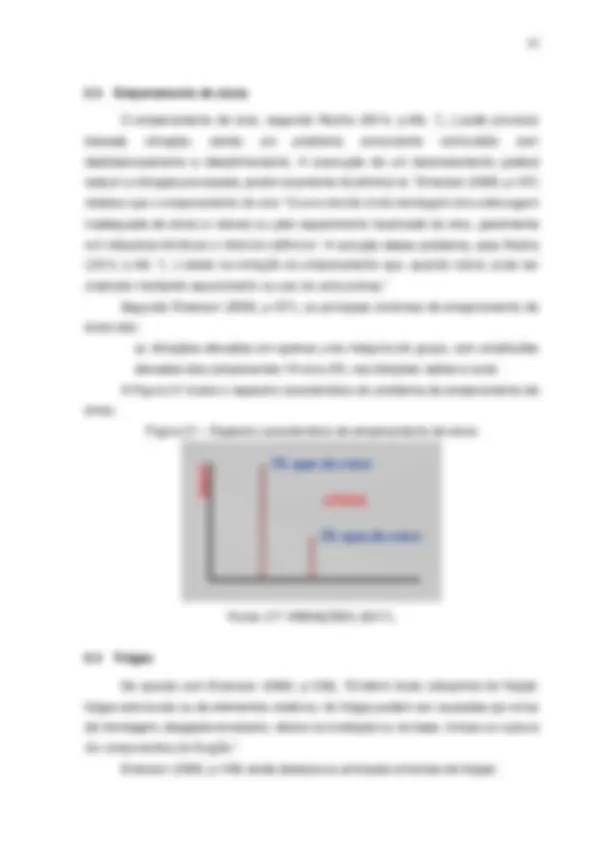
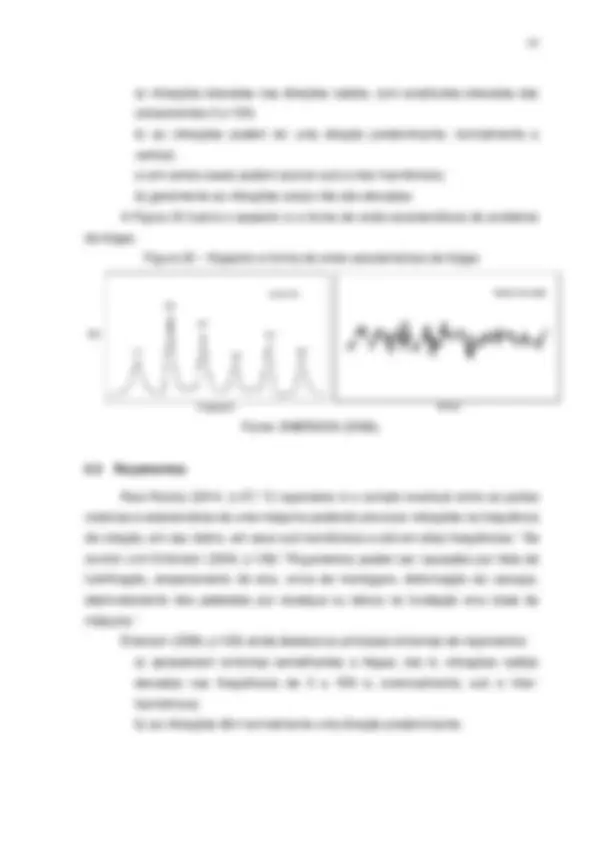
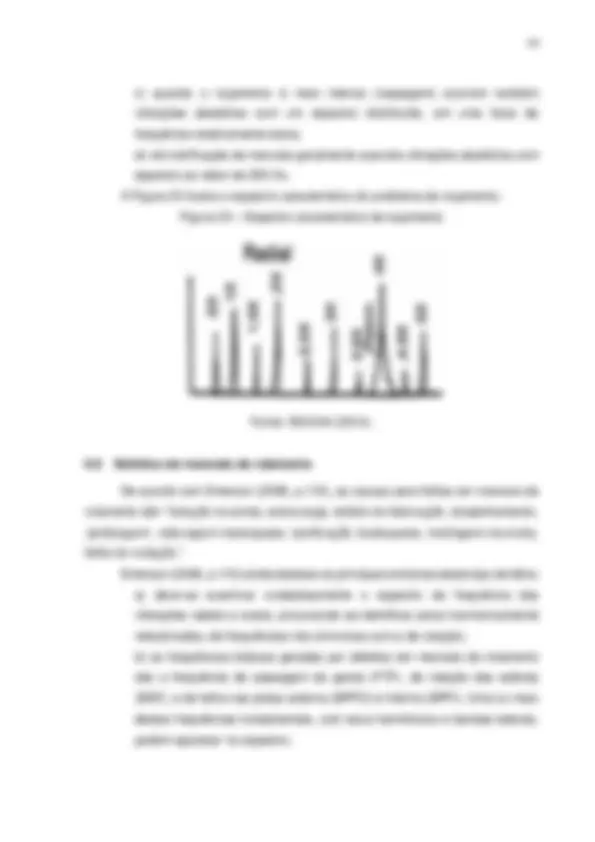
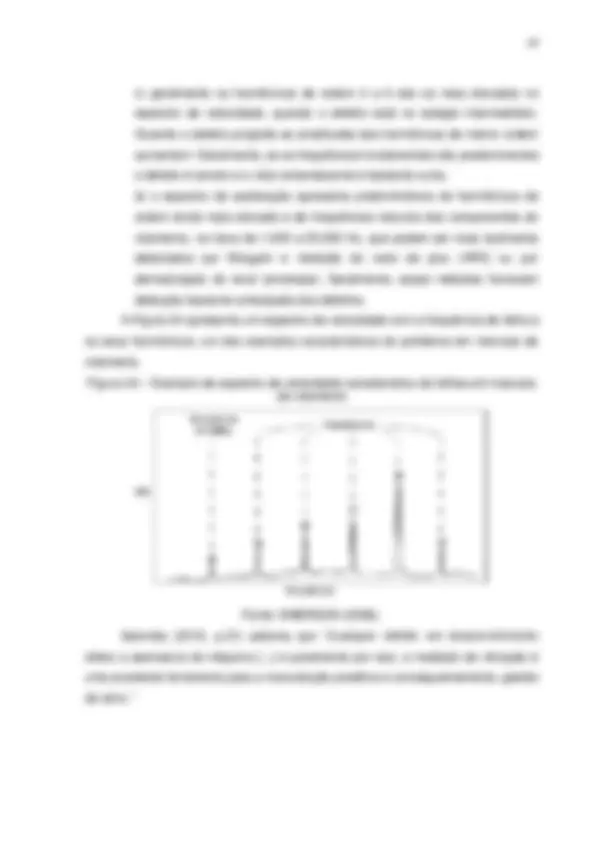
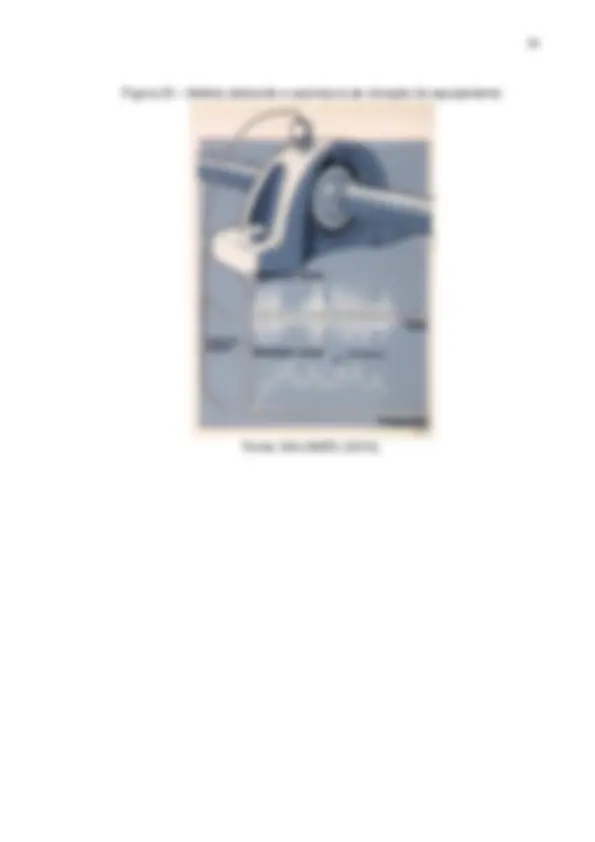
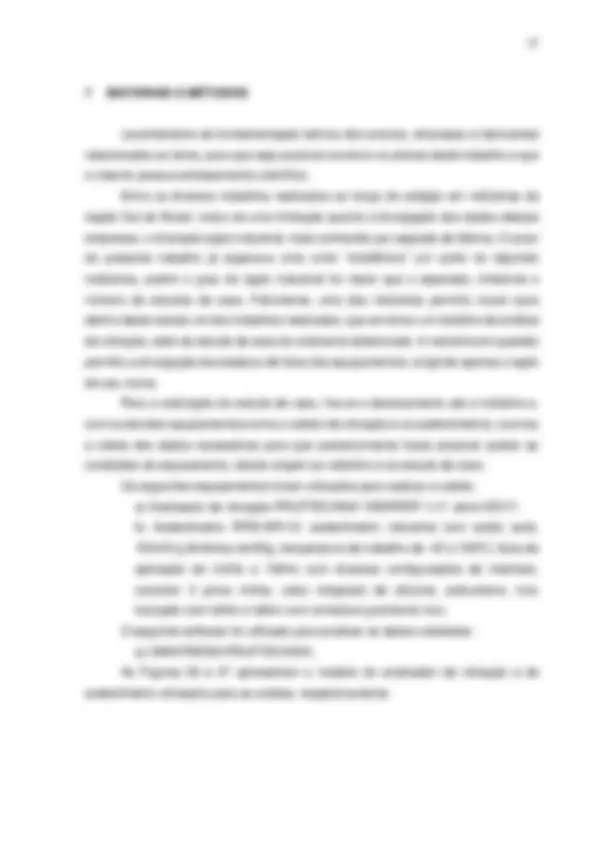
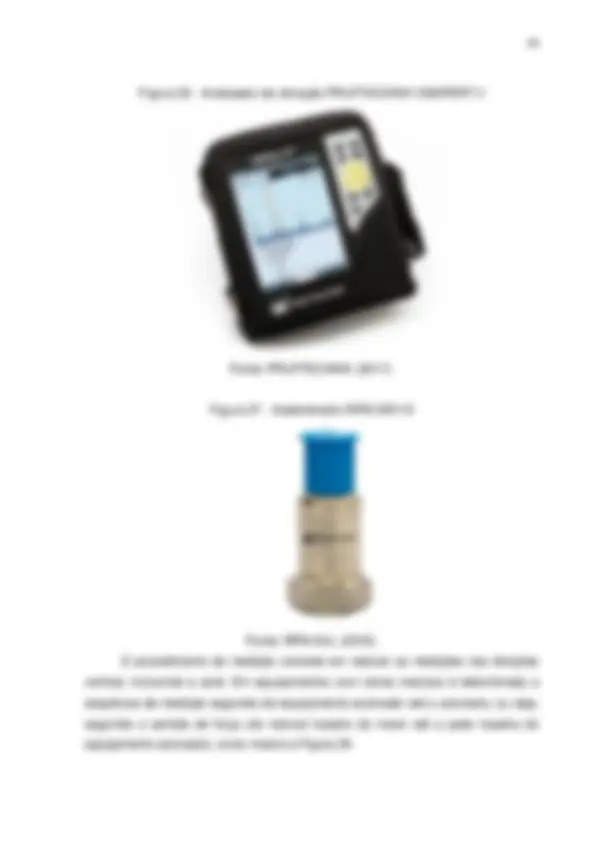
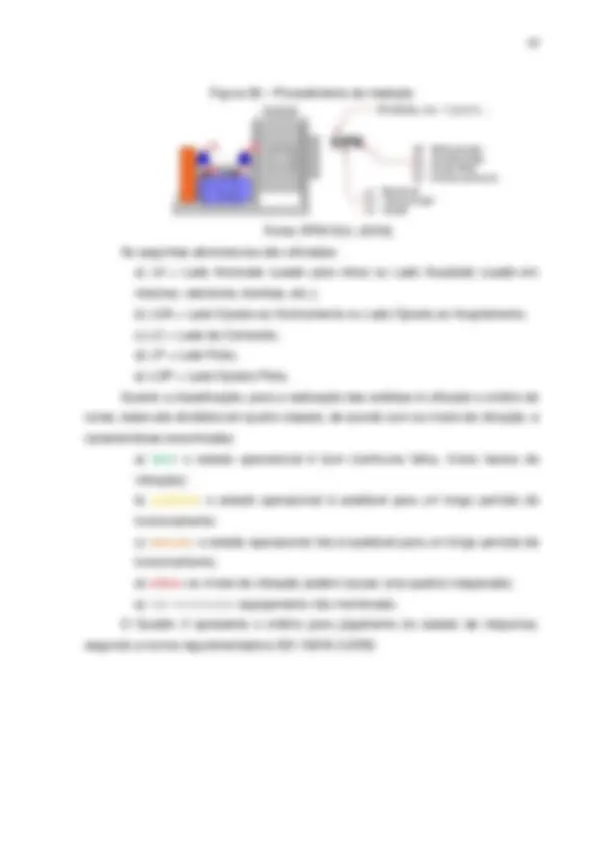
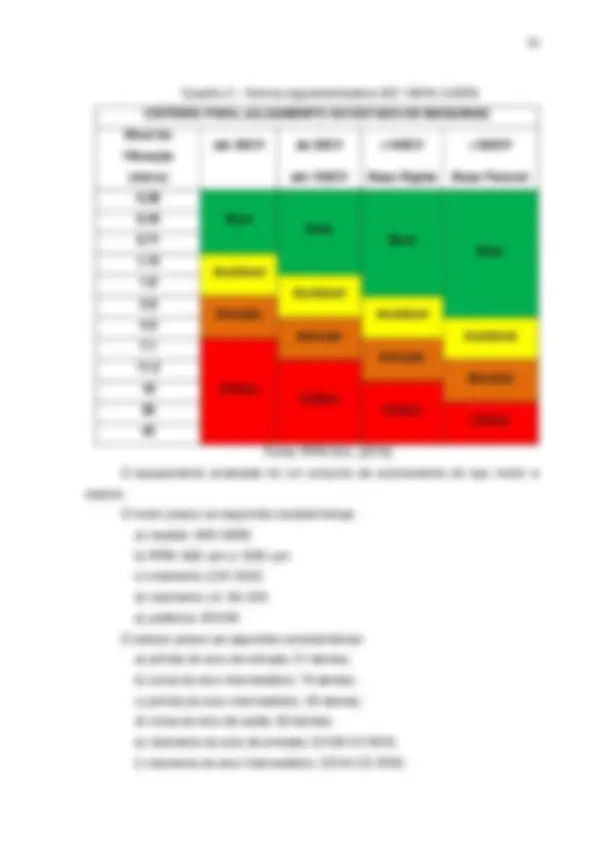
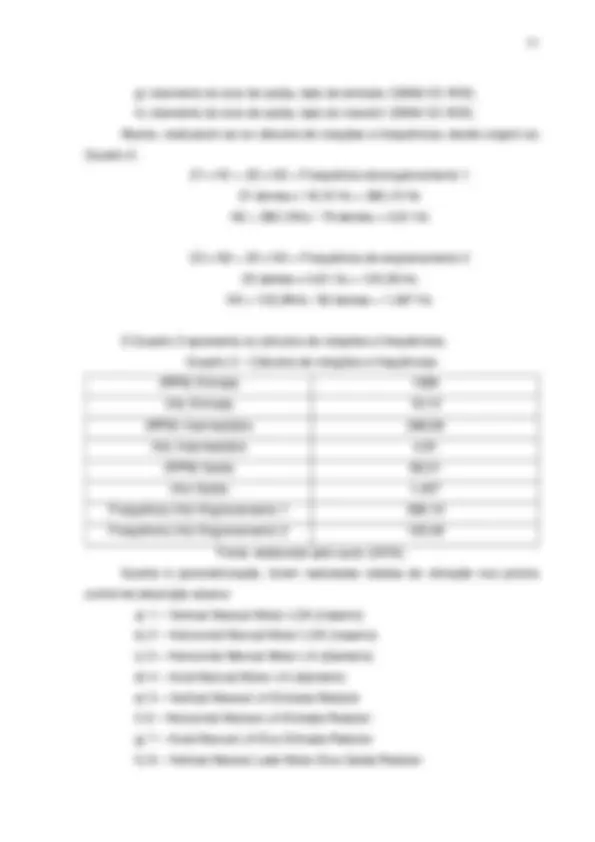
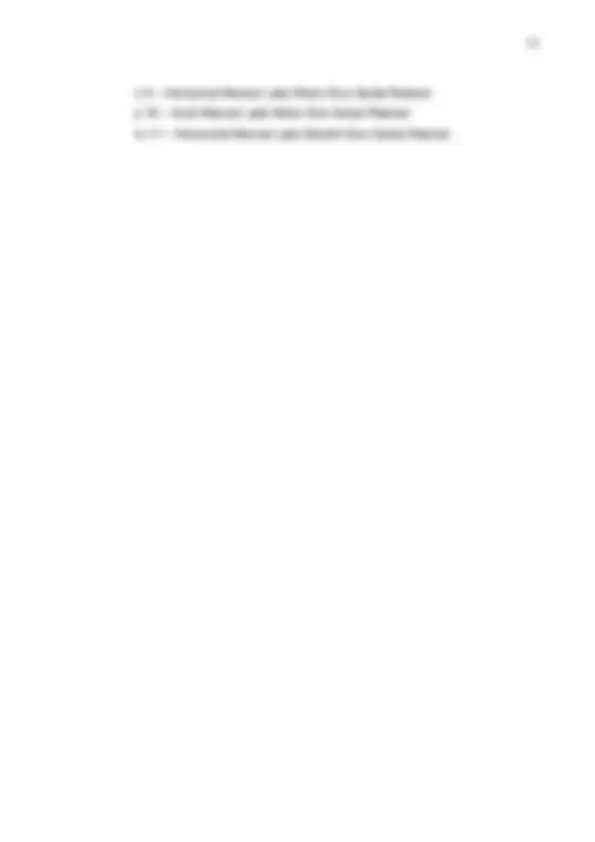
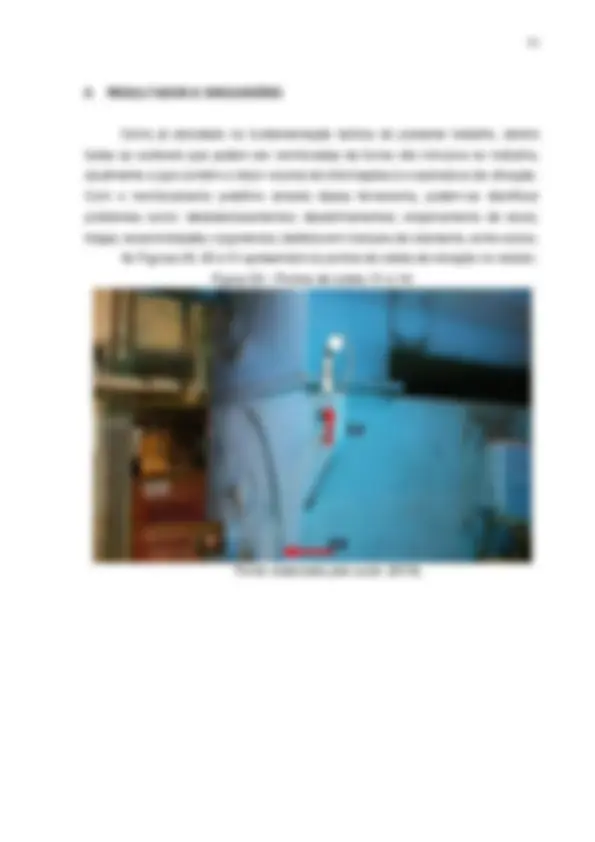
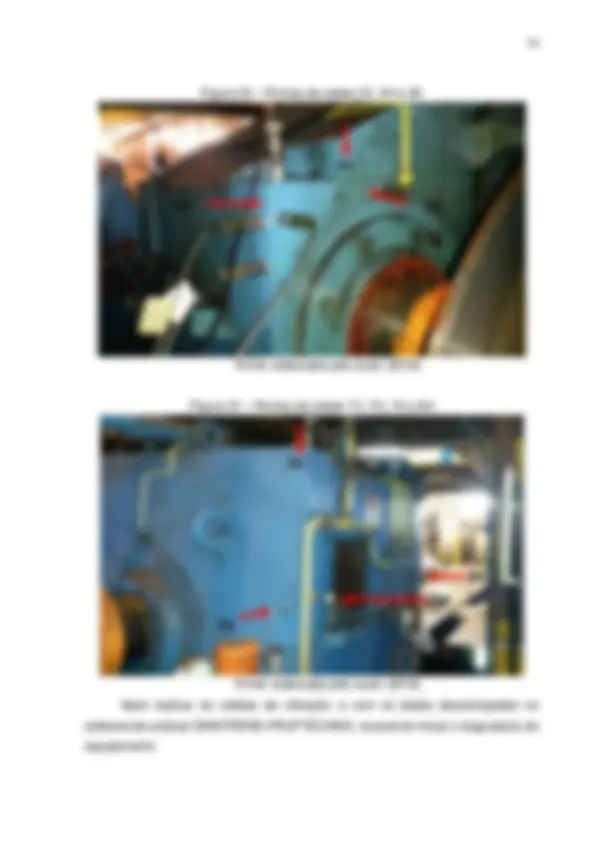
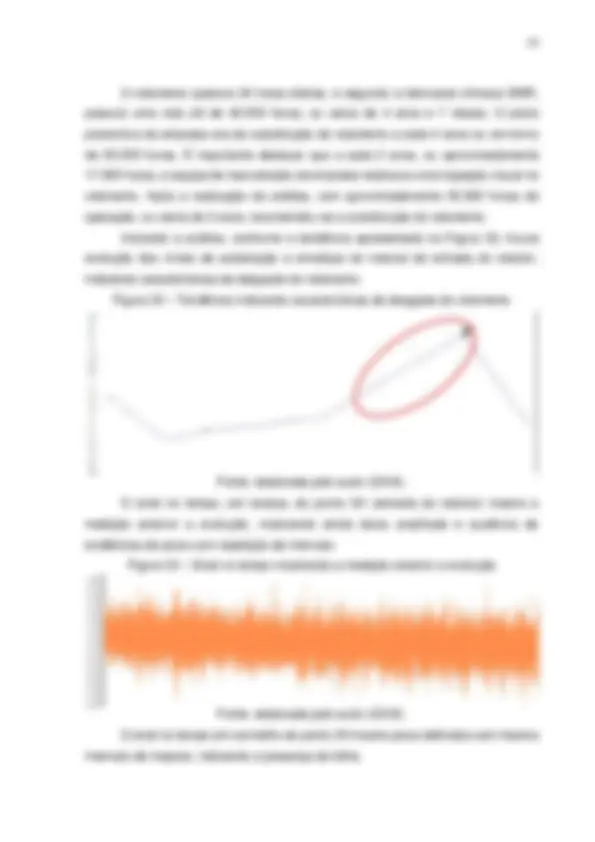
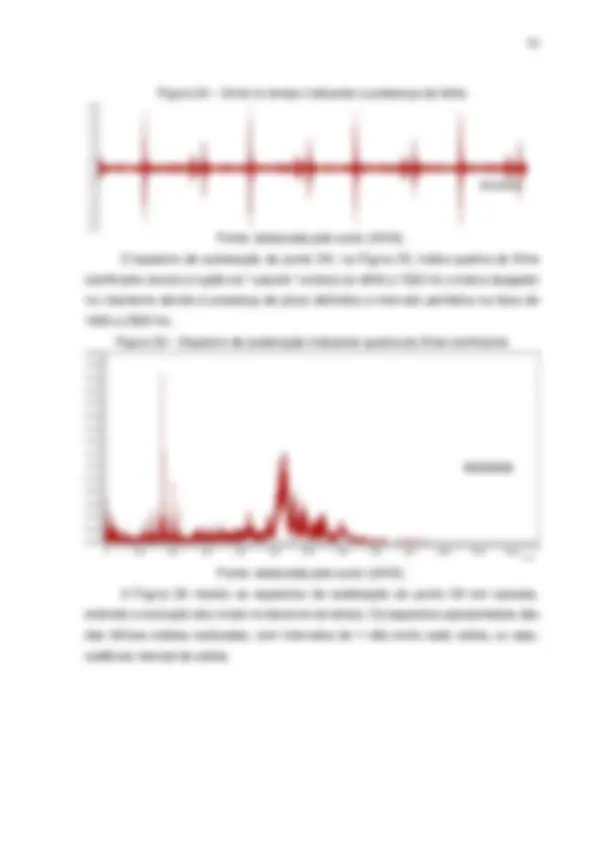
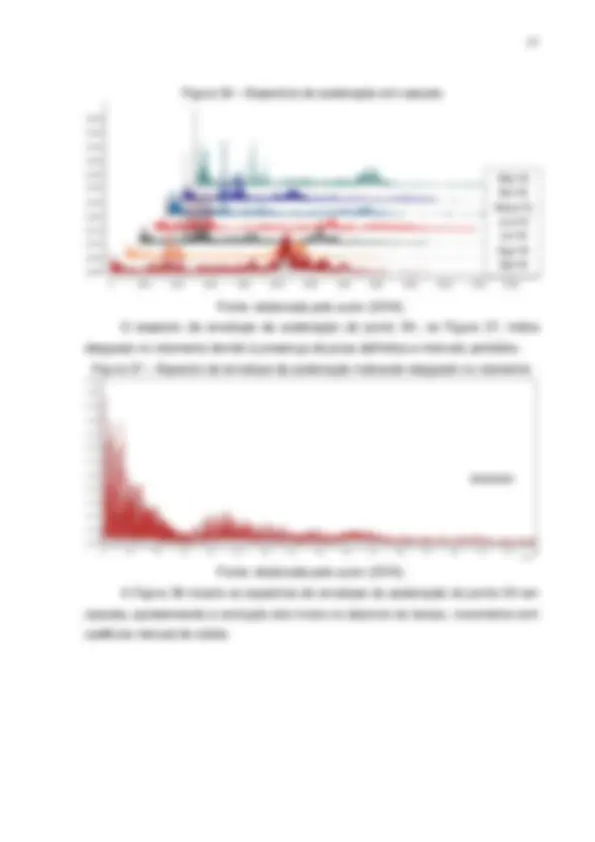
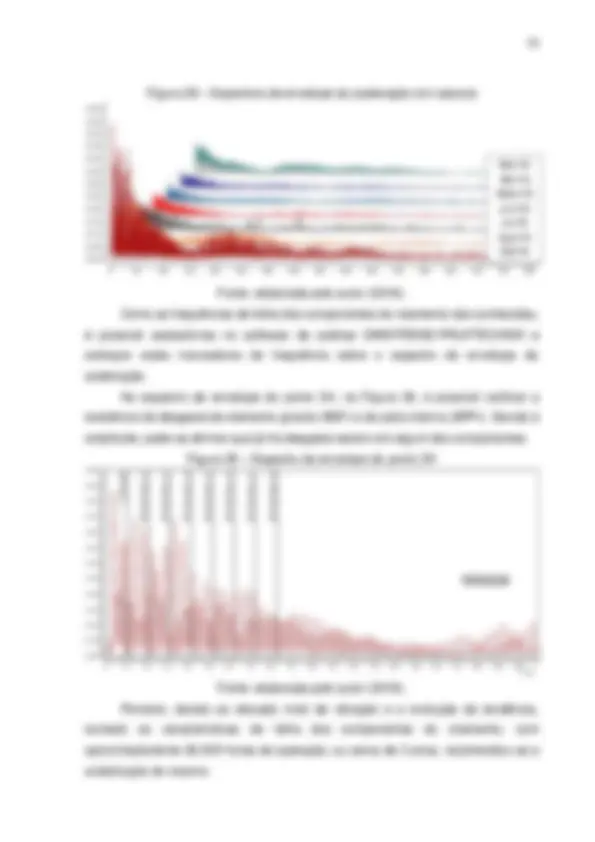
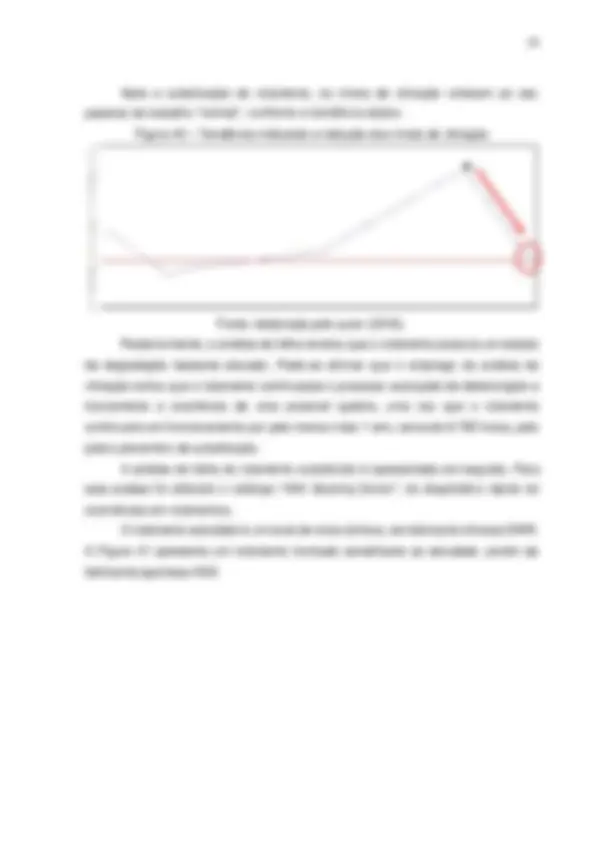
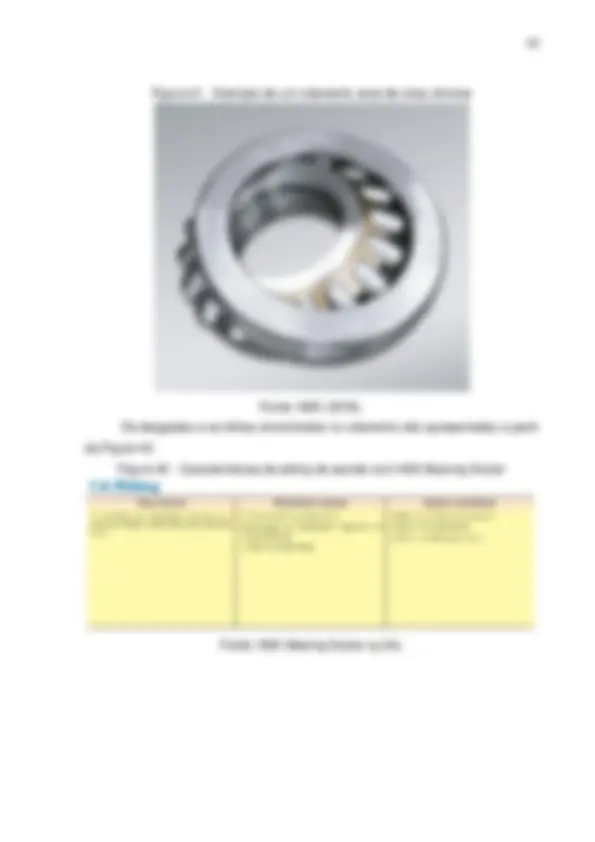
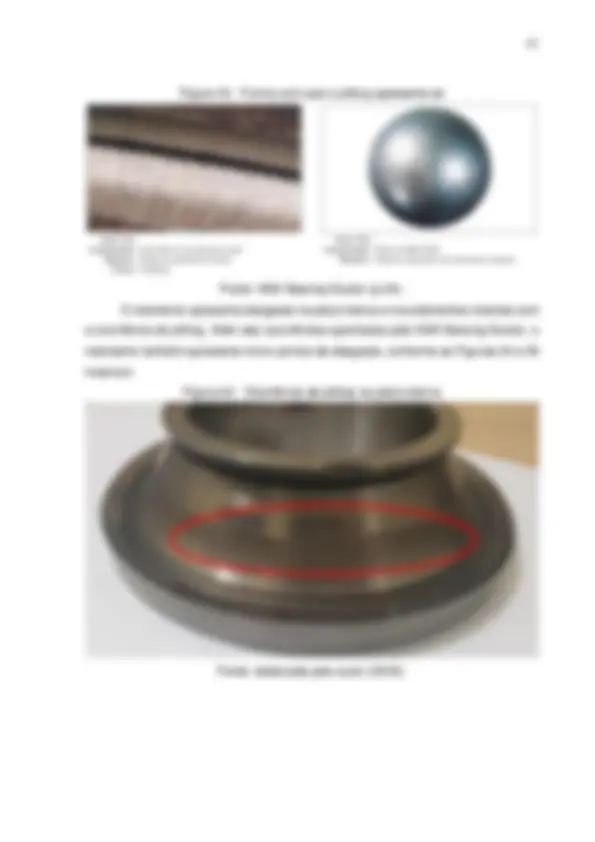
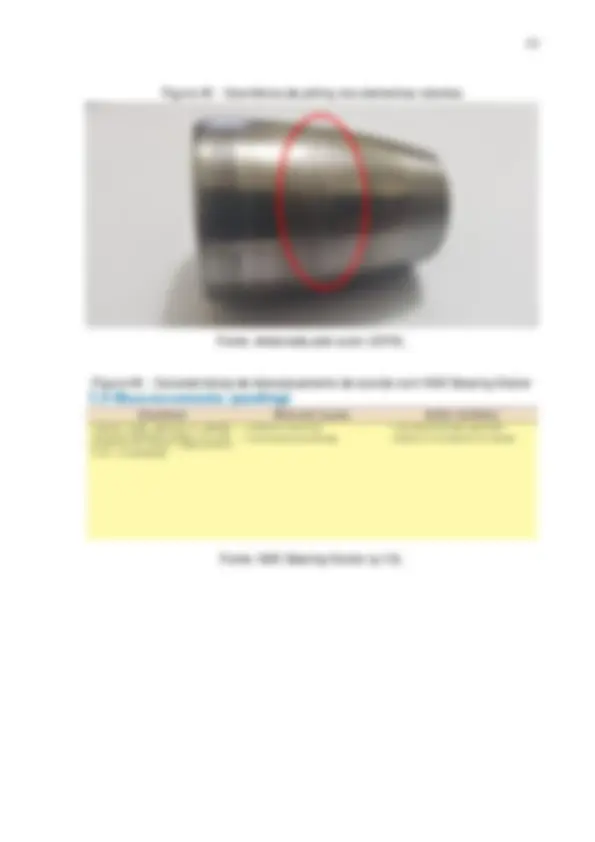
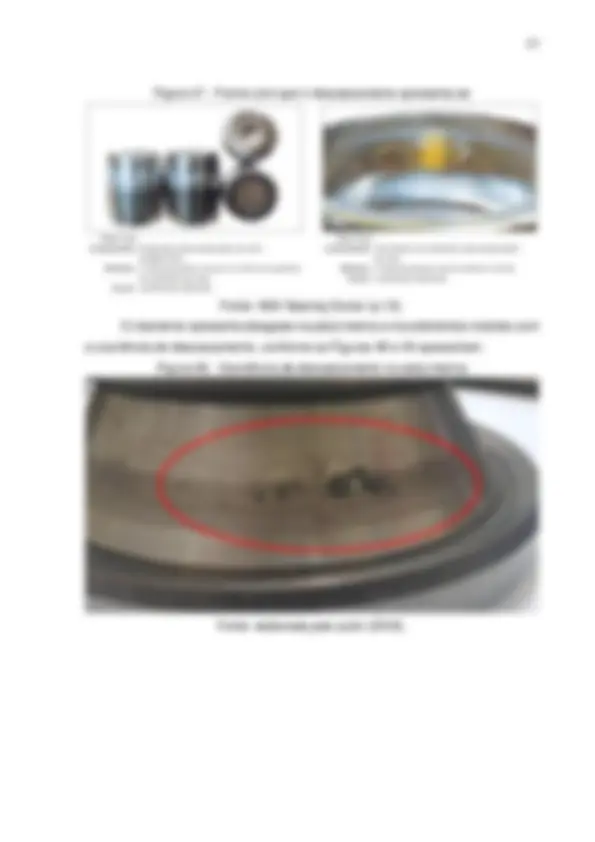
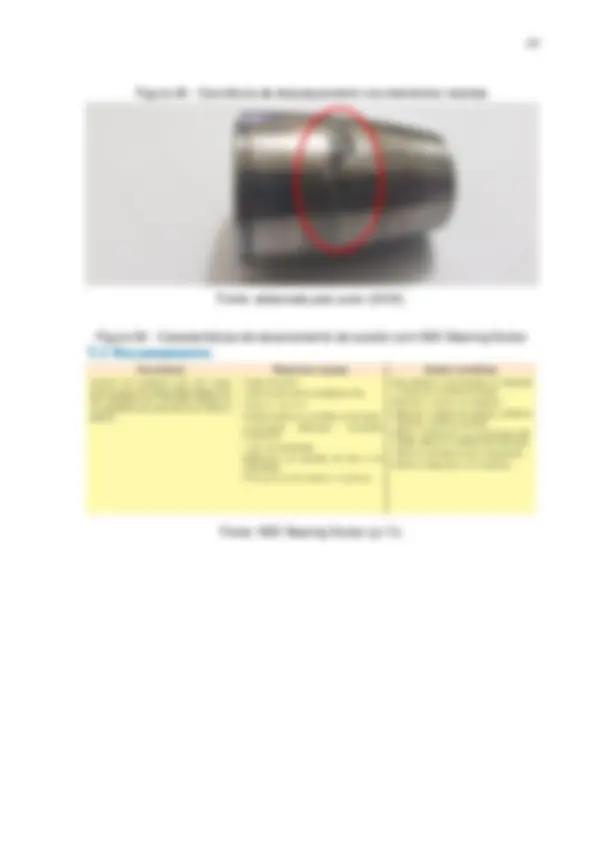
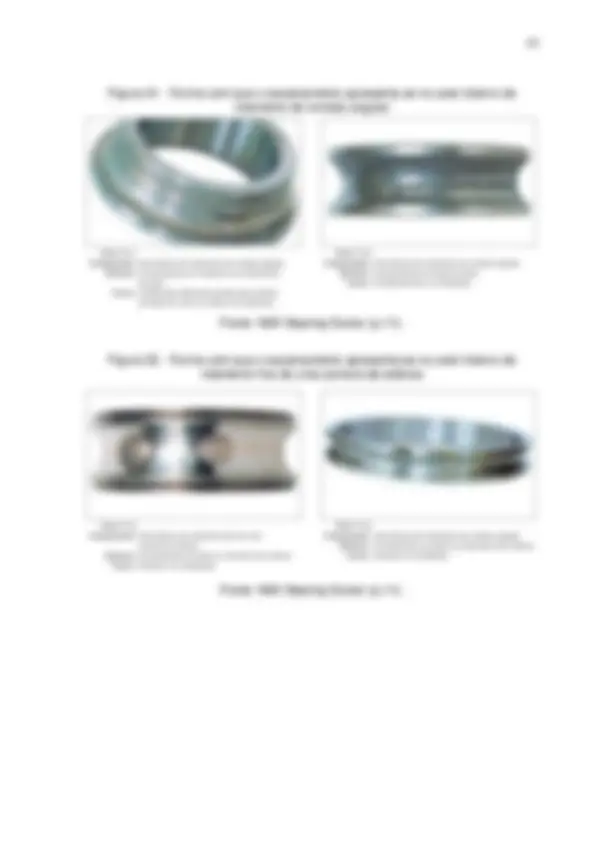
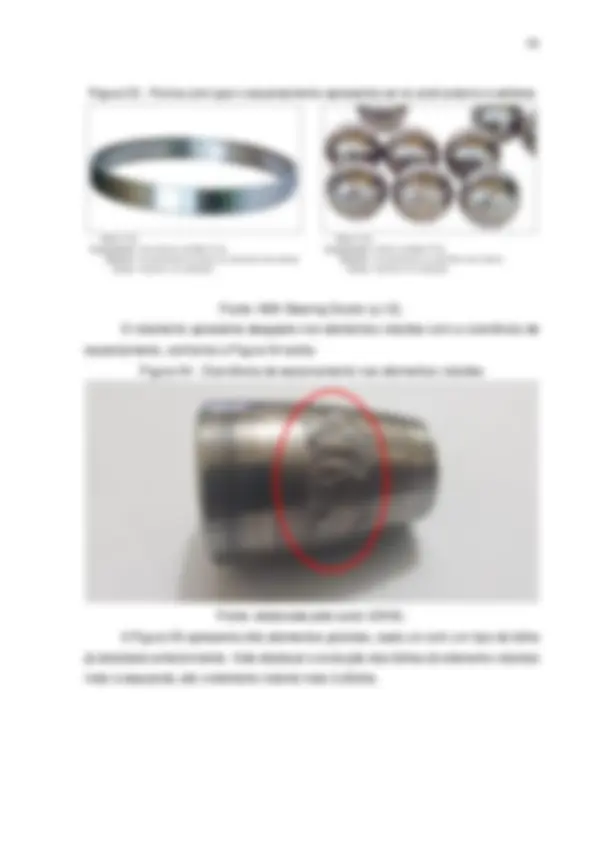
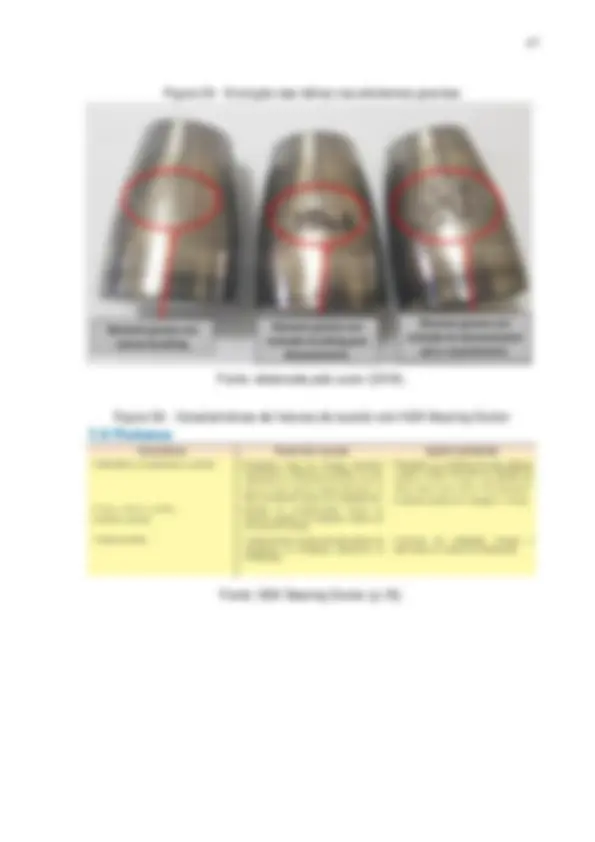
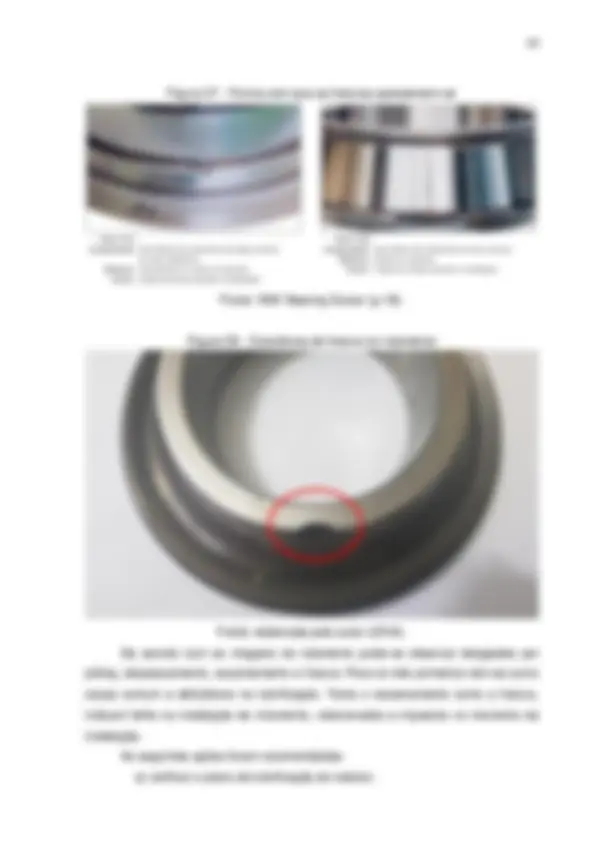
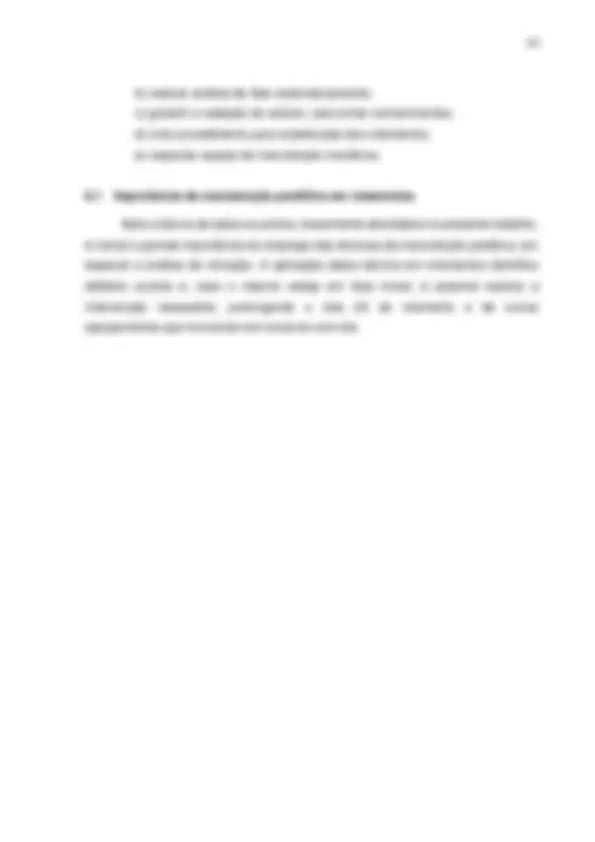
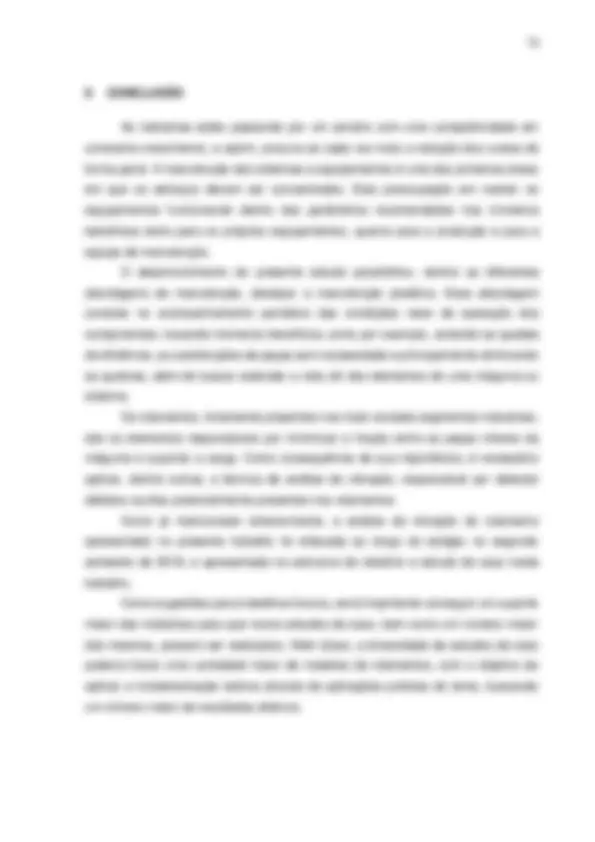
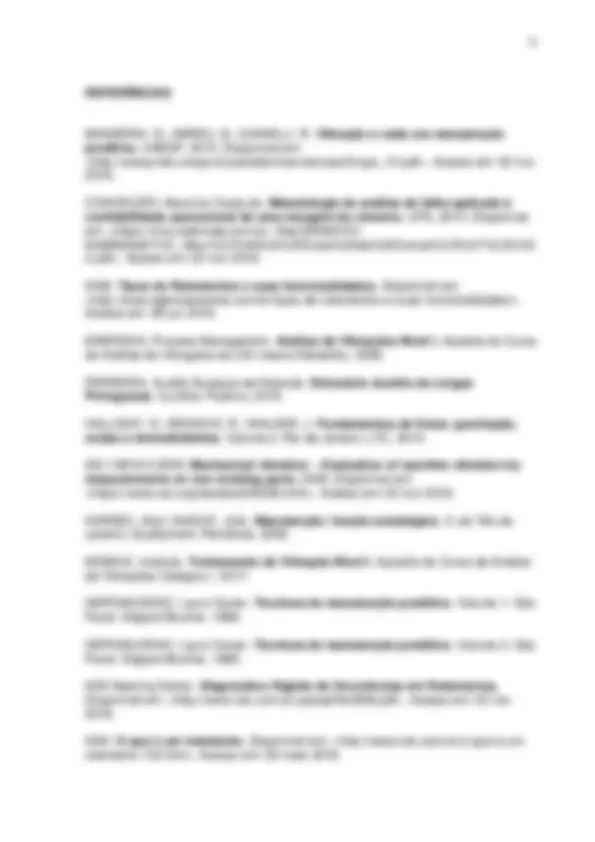
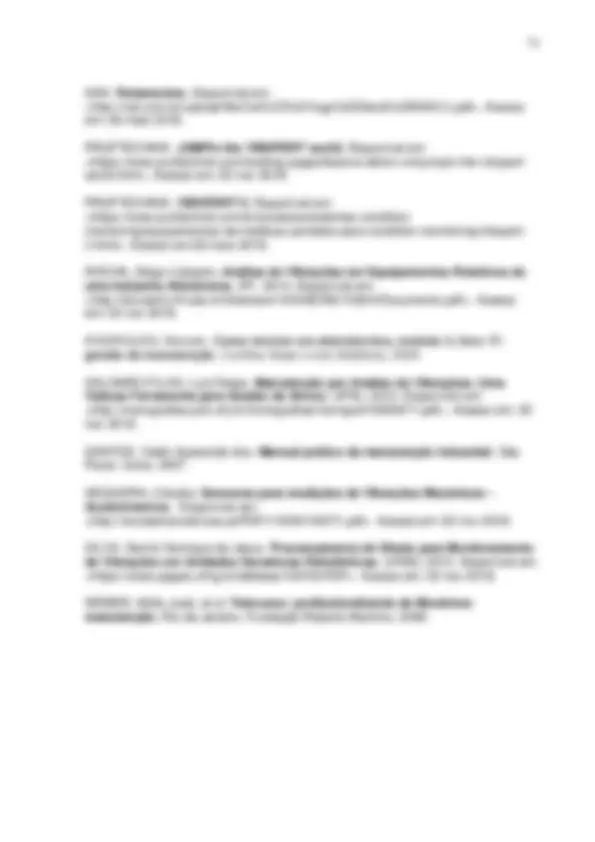
Estude fácil! Tem muito documento disponível na Docsity
Ganhe pontos ajudando outros esrudantes ou compre um plano Premium
Prepare-se para as provas
Estude fácil! Tem muito documento disponível na Docsity
Prepare-se para as provas com trabalhos de outros alunos como você, aqui na Docsity
Os melhores documentos à venda: Trabalhos de alunos formados
Prepare-se com as videoaulas e exercícios resolvidos criados a partir da grade da sua Universidade
Responda perguntas de provas passadas e avalie sua preparação.
Ganhe pontos para baixar
Ganhe pontos ajudando outros esrudantes ou compre um plano Premium
Comunidade
Peça ajuda à comunidade e tire suas dúvidas relacionadas ao estudo
Descubra as melhores universidades em seu país de acordo com os usuários da Docsity
Guias grátis
Baixe gratuitamente nossos guias de estudo, métodos para diminuir a ansiedade, dicas de TCC preparadas pelos professores da Docsity
tcc de mecânica da manutenção sobre analise de vibração e importância da lubrificação
Tipologia: Esquemas
1 / 74
Esta página não é visível na pré-visualização
Não perca as partes importantes!
Trabalho de conclusão de curso apresentado ao Centro Universitário UNIFACVEST como parte dos requisitos para a obtenção do grau de Bacharel em Engenharia Mecânica. Prof. Esp. Paulo Fernando Schmidt Spieker. Coorientador: Prof. Esp. Alisson Ribeiro de Oliveira. LAGES 2018
Primeiramente, agradeço a Deus por tudo que tenho em minha vida. Ele é o principal responsável por podermos conhecer, entender e estudar os segredos do universo. Aos meus pais pela educação, dedicação, carinho e exemplos depositados em mim. Certamente sem eles como pilares da minha fundação como indivíduo, eu não estaria apto a concluir esse objetivo. Aos professores Paulo Fernando Schmidt Spieker, meu orientador, e Alisson Ribeiro de Oliveira, meu coorientador, por toda a dedicação e conhecimentos fornecidos para a minha pesquisa, pelos valiosos conselhos e cuidadosas revisões. Ao meu supervisor de estágio e diretor da empresa RPM SUL Análises Técnicas, Rodney Luis Vissoci Junior, por todos os ensinamentos repassados sobre a manutenção preditiva durante o período de estágio e após o mesmo, primordiais para o desenvolvimento do presente trabalho. A minha namorada, Mariana, pela sua paciência e compreensão em todos os momentos, principalmente nos finais de semana, em que não foi possível estar ao seu lado para completar essa tarefa. E por fim, a todos que direta e indiretamente contribuíram para a realização deste trabalho.
Se você quiser descobrir os segredos do Universo, pense em termos de energia, frequência e vibração. Nikola Tesla
Joe Luiz Rossdeutscher Junior^4 Paulo Fernando Schmidt Spieker^5 Alisson Ribeiro de Oliveira^6 ABSTRACT The main purpose of predictive maintenance is to prevent breakages and prolong the life of the equipment or system. In order to achieve this, it is necessary to carry out periodic monitoring of the actual operating conditions in order to identify potential efficiency reductions that may lead to failure in the advanced stages. One of the principles of predictive maintenance is to analyze the equipment in your regular work regime. This factor is precisely one of the great advantages of using the predictive approach, and it is not necessary to stop production. The application of vibration analysis technique in bearings provides extremely important results that identify any anomalies. The bearings are used to transfer movement and transmit force. They are components widely found in several industrial sectors and, among the different constructions they present, are divided into axial and radial bearings. The present work makes a theoretical foundation of the different maintenance approaches, highlighting the predictive maintenance and the vibration analysis technique, relating it to the detection of failure in bearings through a case study. Keywords: predictive maintenance; vibration analysis; bearings. (^4) Acadêmico do Curso de Engenharia Mecânica, 10ª fase, Disciplina de Trabalho de Conclusão de Curso 2, do Centro Universitário UNIFACVEST. (^5) Professor do Centro Universitário UNIFACVEST, orientador. (^6) Professor de Trabalho de Conclusão de Curso 2 do Centro Universitário UNIFACVEST, coorientador.
Figura 53 - Forma com que o escamamento apresenta-se no anel externo e esferas
A manutenção preditiva é aquela que monitora periodicamente componentes e máquinas industriais com o objetivo básico de evitar redução de rendimento e quebras, prolongando a vida útil sempre que possível. Além disso, as técnicas da manutenção preditiva ainda devem indicar as possíveis causas para os desgastes prematuros nos componentes. Atualmente existem diversas técnicas de manutenção preditiva empregadas nas indústrias. São exemplos: análise de vibração; alinhamento a laser; análise de óleo; balanceamento; MCA (análise de circuito de motores); ESA (análise da assinatura elétrica); termografia; ultrassom; entre outras. O presente trabalho destacará a técnica de análise de vibração. A análise de vibração é uma técnica da manutenção preditiva que possui o objetivo de identificar vibrações provenientes de outras partes da máquina as quais afetam prejudicialmente os rolamentos. Os rolamentos são componentes utilizados com o objetivo principal de minimizar a fricção entre as peças móveis da máquina e suportar a carga. Logo, é possível pensar nas mais variadas aplicações dentro das mais distintas indústrias. Pode-se destacar o emprego de rolamentos em motores elétricos, motores de combustão interna, redutores, turbinas, ventiladores, entre muitos outros. Porém, como muitos componentes mecânicos, os rolamentos possuem uma determinada vida útil e consequentemente precisam ser substituídos. O grande problema é que em certas vezes este componente pode falhar, reduzindo a eficiência do processo, ou até mesmo quebrar, e como o movimento de rotação está presente, as chances de provocar danos não esperados em outras partes das máquinas são altas, os quais deverão ser analisados pela equipe de manutenção. O emprego da manutenção preditiva nos rolamentos é de extrema importância pois é possível acompanhar periodicamente as condições reais de operação destes componentes, evitando a redução da eficiência, substituições desnecessárias e principalmente as quebras, procurando ainda prolongar a vida útil dos mesmos. Ainda é objetivo da manutenção preditiva identificar as causas potenciais de desgastes prematuros, os quais reduzem a vida útil dos componentes. A análise de vibração é uma técnica fortemente empregada para diagnosticar falhas em rolamentos.
A produção de estudos e conteúdos a respeito do tema é muito importante, uma vez que a manutenção preditiva, especialmente no Brasil, mesmo estando em crescimento ainda possui um ritmo lento em relação a outros países. Dessa forma é necessário difundir essas técnicas da manutenção preditiva procurando destacar a importância da mesma no processo de otimização e redução de gastos. Como a manutenção preditiva é relativamente nova, uma limitação encontrada ao longo das pesquisas para a produção deste trabalho está no número de bibliografias existentes que tratem do tema em questão. O trabalho está delimitado em realizar a fundamentação teórica e levantar estudos reais para comprovar a importância e a eficácia da técnica aplicada. Os estudos reais somente serão possíveis graças aos equipamentos e softwares disponibilizados pela empresa RPM SUL Análises Técnicas. Com o desenvolvimento deste estudo, pretende-se conhecer as diferentes abordagens de manutenção destacando a manutenção preditiva e sua técnica de análise de vibração, salientando os fatores que levam os rolamentos a falha e/ou desgaste prematuro no ambiente natural de trabalho, ressaltando as técnicas de manutenção preditiva empregadas para detectar esses fatores, validando assim, a eficácia da utilização de análise de vibração. Para atingir esses objetivos, o presente trabalho aborda sucintamente a manutenção como um todo, identificando os tipos de manutenção e destacando a importância da manutenção preditiva como a principal abordagem no processo de otimização e redução de gastos. O trabalho ainda apresenta alguns conceitos sobre vibrações de máquinas e identifica os dois grandes grupos de rolamentos, axiais e radiais, ressaltando o emprego da técnica de análise de vibração na identificação das principais causas de falhas em rolamentos, bem como os principais problemas de origem mecânica. O estudo está construído sob autores de grande relevância no tema, possibilitando que os leitores venham a conhecer e adquirir noções sobre o assunto, transmitindo aos mesmos conteúdos científicos, explicativos e ilustrativos, de forma a demonstrar o que é inerente ao conteúdo.
esperado.” Esta forma é a que representa quase que a totalidade das operações de manutenção industrial, desde que a primeira fábrica entrou em funcionamento. (Rodrigues, 2009). A manutenção corretiva, segundo Santos (2007, p.13) “Representou o princípio, em que os mecânicos simplesmente consertavam o que estava quebrado, não se preocupando com as causas ou efeitos que ocasionaram o defeito.” 2.1.1.1 Manutenção corretiva não planejada Segundo Rodrigues (2009, p.1 7 ) “Esta é a forma mais reativa que a manutenção pode ter. Uma planta industrial usando este modelo de gerência em sua manutenção corretiva não gasta qualquer valor com manutenção, até que uma máquina ou sistema pare de operar.” A palavra reativa destaca que este tipo de abordagem provoca uma reação que muitas vezes passa despercebida pela empresa, reação esta que consiste na elevação do custo final, pois quando ocorre uma falha inesperada, além dos danos com o próprio equipamento que falhou, ainda é necessário avaliar os danos causados em outras partes da máquina, que possivelmente foram afetadas. De acordo com Kardec e Nascif (2009, p.39) a “Manutenção corretiva não planejada é a correção da falha de maneira aleatória. [...] Caracteriza-se pela atuação da manutenção em fato já ocorrido, seja este uma falha ou um desempenho menor do que o esperado.” Após o deslocamento da equipe de manutenção, uma nova etapa de análise é iniciada, levando em conta a dimensão dos danos, a verificação de peças no almoxarifado que serão utilizadas na substituição ou ainda a emissão de ordens de compra de emergência. Dessa forma, segundo Kardec e Nascif (2009, p.39), “Normalmente, a manutenção corretiva não planejada implica altos custos, pois a quebra inesperada pode acarretar perdas na produção, perda da qualidade do produto e elevados custos indiretos de manutenção.” 2.1.1.2 Manutenção corretiva planejada Segundo Rodrigues (2009, p.18) “Esta forma de manutenção é realizada quando o equipamento apresentou um defeito que foi identificado pelas práticas
preventivas ou preditivas.” Em outras palavras, esta técnica possui custos significativamente inferiores se comparada com a técnica não planejada, justamente em decorrência do planejamento. Kardec e Nascif (2009, p.41) descreve que “Um trabalho planejado é sempre mais barato, mais rápido e mais seguro do que um trabalho não planejado. E será sempre de melhor qualidade.” 2.1.2 Manutenção preventiva A manutenção preventiva, segundo Santos (2007, p.1 4 ), é aquela em que “[...] o mecânico deve prever a vida do equipamento.” O mesmo autor, Santos (2007, p.14), destaca que “Para este tipo de manutenção exige-se do mecânico uma ‘intuição’ e um conhecimento técnico maior. Os mecânicos deixam de ser meros trocadores de peças, tornando-se profissionais realmente qualificados.” Weber et al. (2009, p.35) salienta que: A manutenção preventiva obedece a um padrão previamente esquematizado, que estabelece paradas periódicas com a finalidade de permitir a troca de peças que apresentam desgaste, ou não, por novas, assegurando, assim, o funcionamento perfeito da máquina por um período predeterminado. (WEBER et al., 2009, p.35). A garantia de um certo ritmo de trabalho, além do equilíbrio necessário ao bom desenvolvimento das atividades, são fatores proporcionados pelo método preventivo. (WEBER et al. 2009). Para Rodrigues (2009, p.19), a “Manutenção preventiva é a intervenção realizada de forma a evitar a falha ou queda no desempenho do equipamento, obedecendo a um plano previamente elaborado, baseado em intervalos definidos de tempo.” Kardec e Nascif (2009, p. 43 ) destaca que “Evidentemente, ao longo da vida útil do equipamento não pode ser descartada a falha entre duas intervenções preventivas, o que, obviamente, implicará uma ação corretiva.” Dessa forma, em comparação com a manutenção corretiva, a abordagem preventiva traz um número notavelmente maior de benefícios, tanto para os equipamentos, quanto para a produção e para a equipe de manutenção.
De acordo com Weber et al. (2009, p.43), a manutenção preditiva possui os seguintes objetivos: a) determinar, antecipadamente, a necessidade de serviços de manutenção numa peça específica de um equipamento; b) eliminar desmontagens desnecessárias para inspeção; c) aumentar o tempo de disponibilidade dos equipamentos; d) reduzir o trabalho de emergência não planejado; e) impedir o aumento das falhas; f) aproveitar a vida útil total dos componentes e de um equipamento; g) aumentar o grau de confiança no desempenho de um equipamento ou linha de produção; h) determinar, previamente, as interrupções de fabricação para cuidar dos equipamentos que precisam de manutenção. Através desses objetivos, é possível perceber que eles estão orientados a finalidades maiores e importantes, como a diminuição de custos de manutenção e a elevação da produtividade. A utilização de aparelhos adequados é de extrema importância para que a manutenção preditiva possa ser executada, e assim, segundo Weber (2009), seja capaz de registrar diversos fenômenos, como os listados abaixo: a) vibrações das máquinas; b) pressão; c) temperatura; d) desempenho; e) aceleração. Levando em conta o conhecimento e analisando os fenômenos, é possível apontar, de forma antecipada, potenciais defeitos ou falhas nas máquinas e equipamentos. Weber et al. (2009, p.44) ressalta que “A manutenção preditiva, após a análise dos fenômenos, adota dois procedimentos para atacar os problemas detectados: estabelece um diagnóstico e efetua uma análise de tendências.” O diagnóstico apontado por Weber (2009, p. 44) “Detecta a irregularidade, o responsável terá o encargo de estabelecer, na medida do possível, um diagnóstico referente à origem e à gravidade do defeito constatado. Esse diagnóstico deve ser feito antes de se programar o reparo.” Já a etapa da análise da tendência da falha, de acordo com
Weber et al. (2009, p.45) “[...] consiste em prever com antecedência o defeito ou a falha, por meio de aparelhos que exercem vigilância constante, predizendo a necessidade do reparo.” Figura 1 - Gráfico de falhas x tempo Fonte: Weber et al. (2009). A Figura 1 estabelece uma relação das falhas com o tempo, e através dela é possível notar que, à medida que o tempo evolui, existe a necessidade de reduzir os intervalos entre as medidas periódicas normais, com o objetivo de controlar os defeitos, minimizando as falhas. A Figura 2 descreve as etapas desenvolvidas ao longo da manutenção preditiva, levando em conta as condições de intervenção, os dados para o diagnóstico e as aplicações, em que o conjunto destes fatores resultam na otimização dos custos e consequente melhoria da produção.