
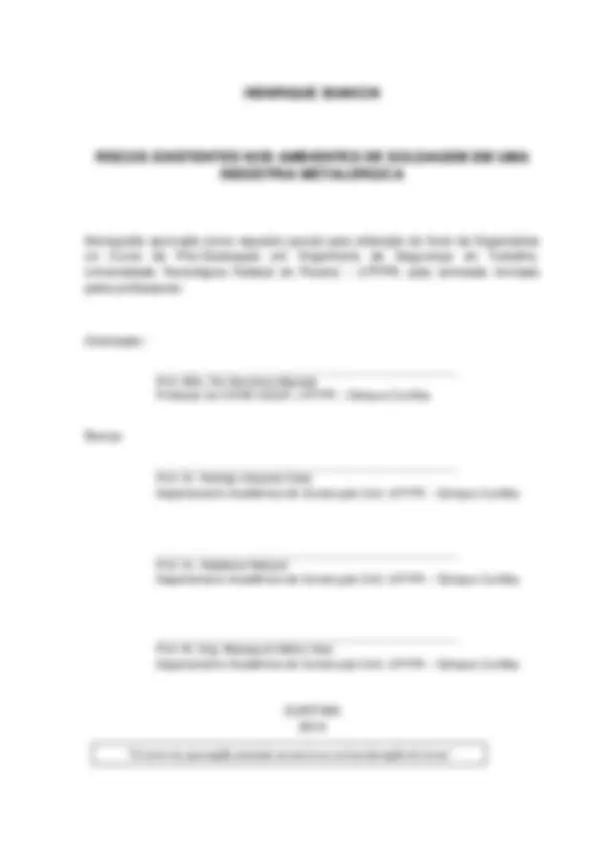
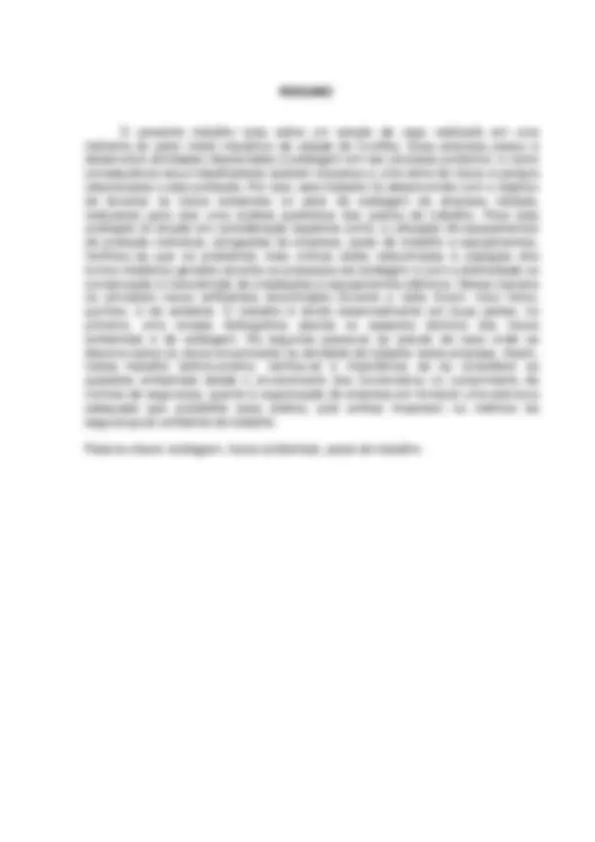
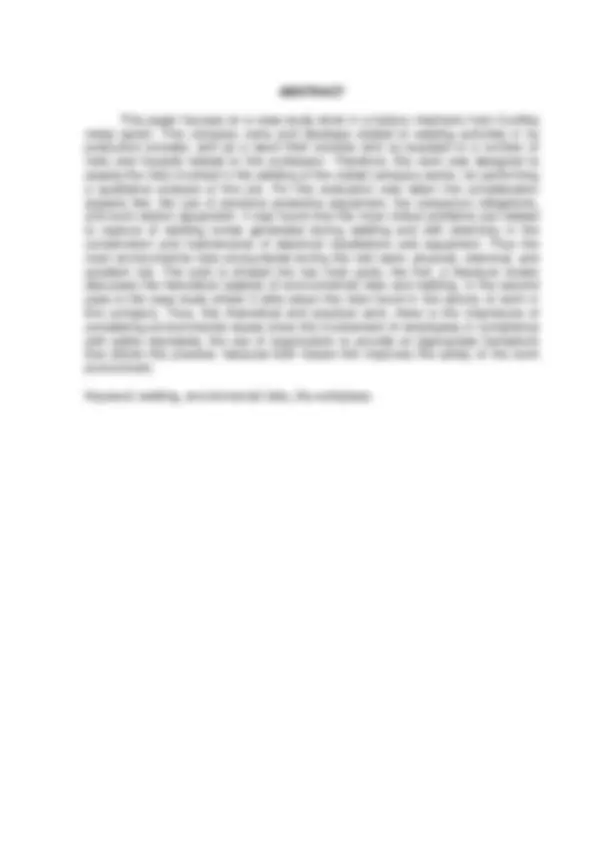
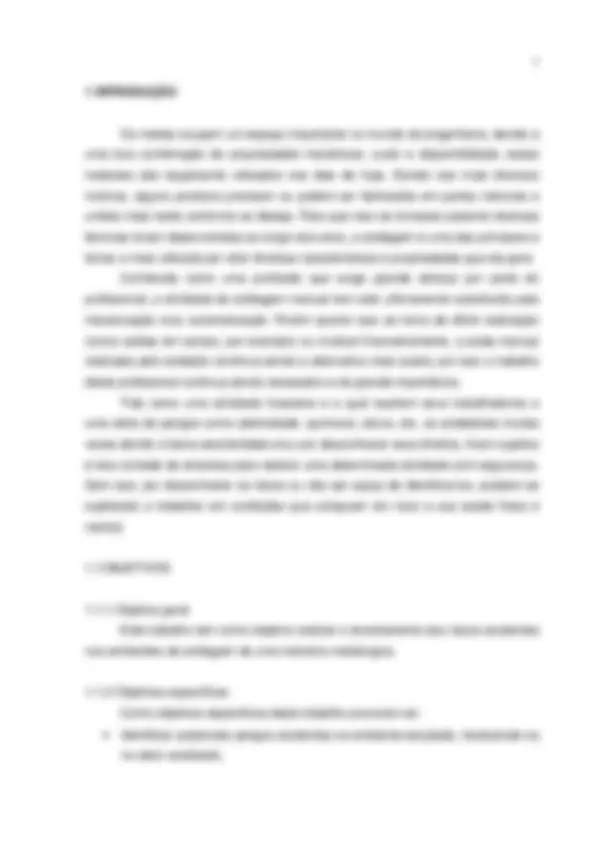
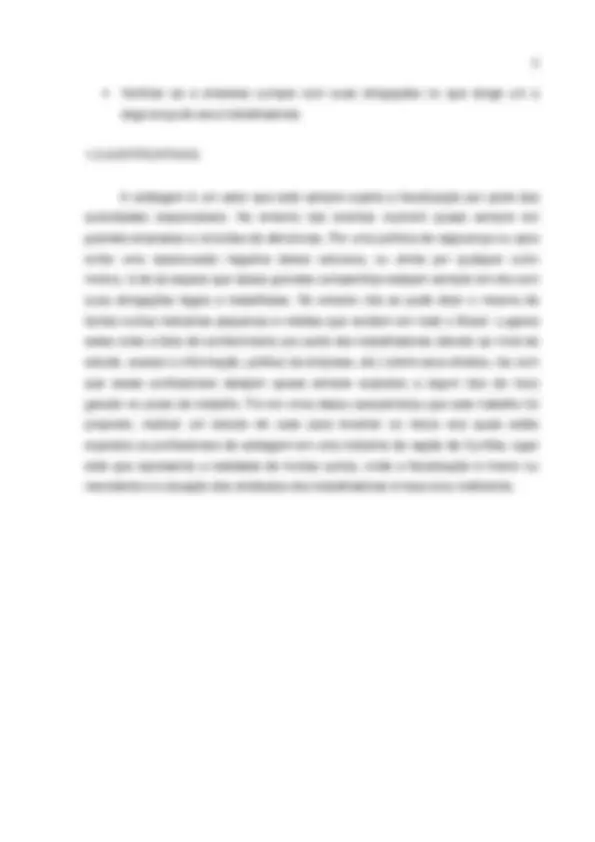
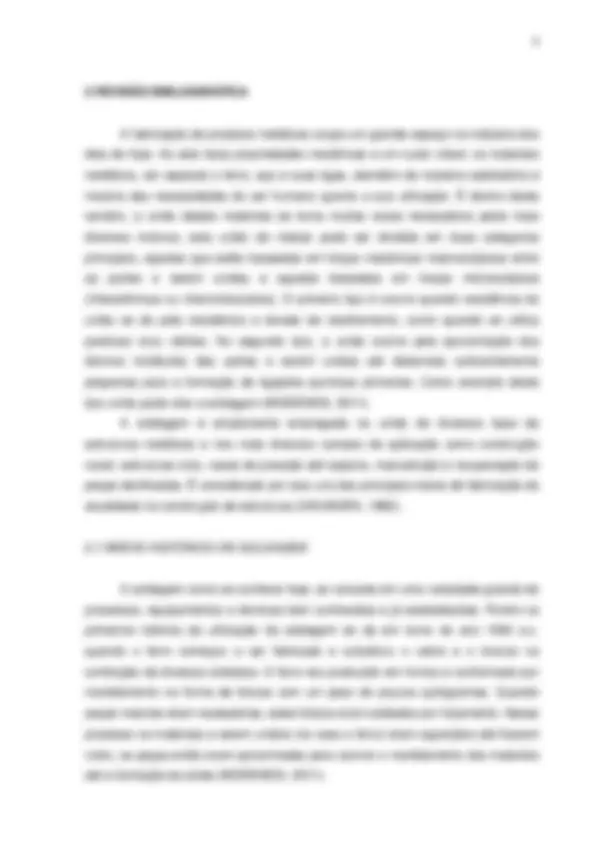
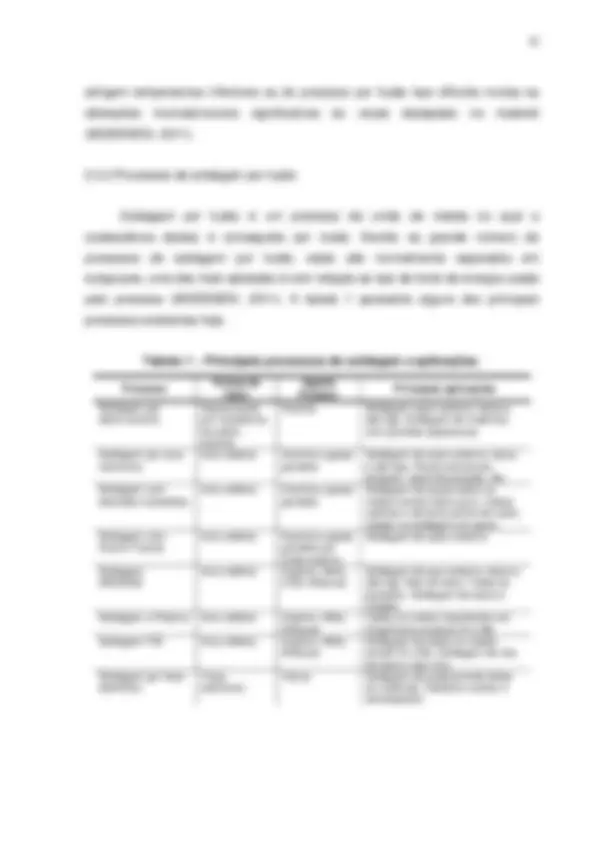
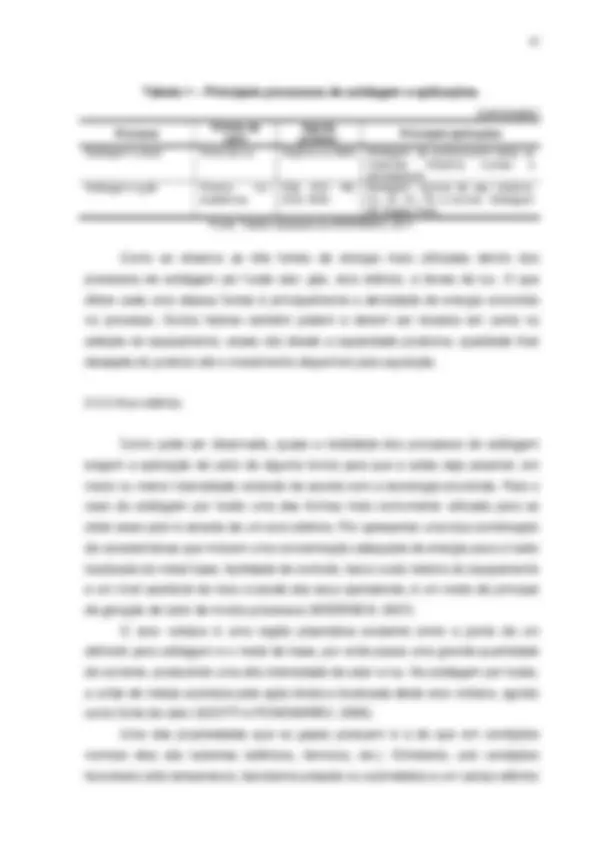
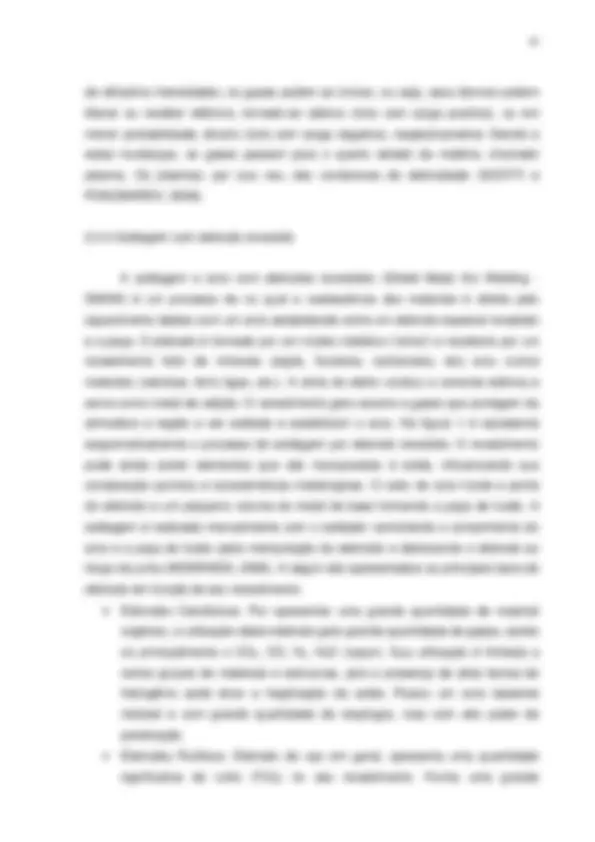
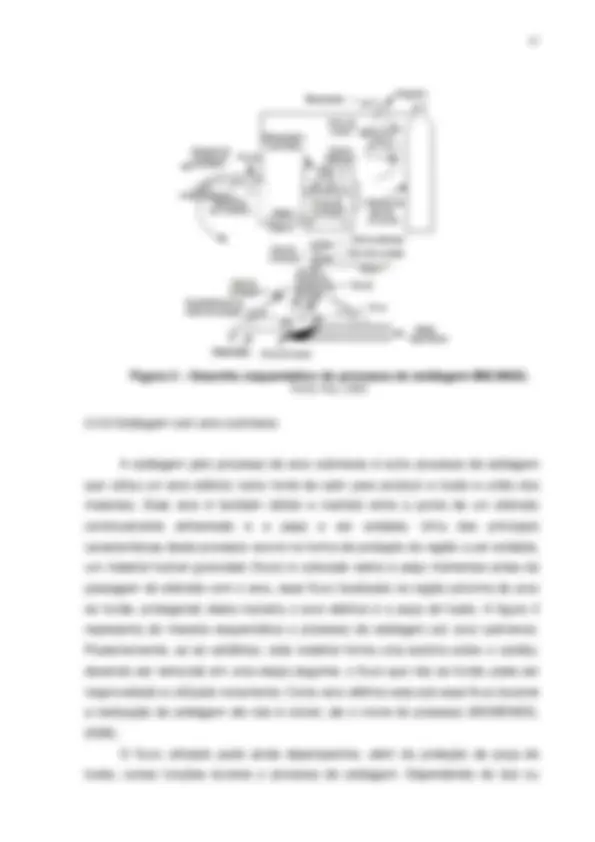
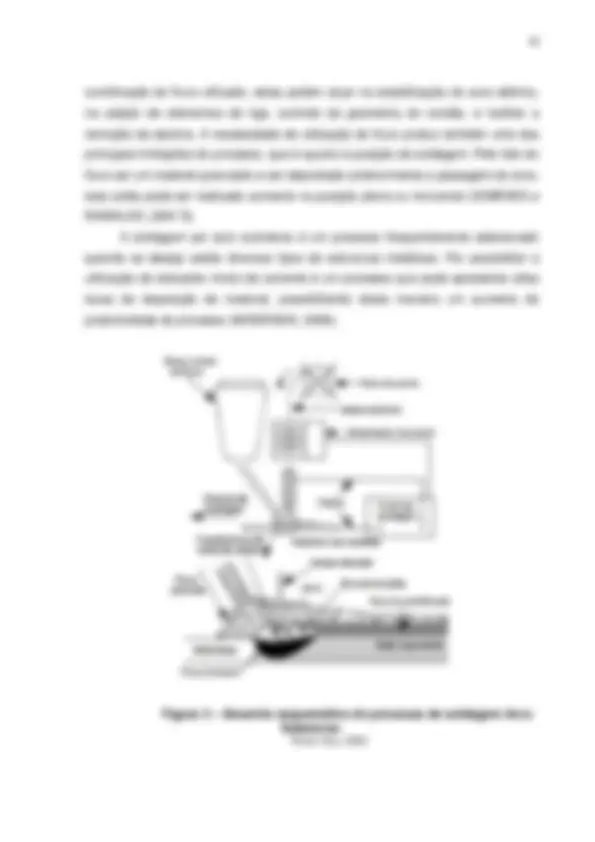
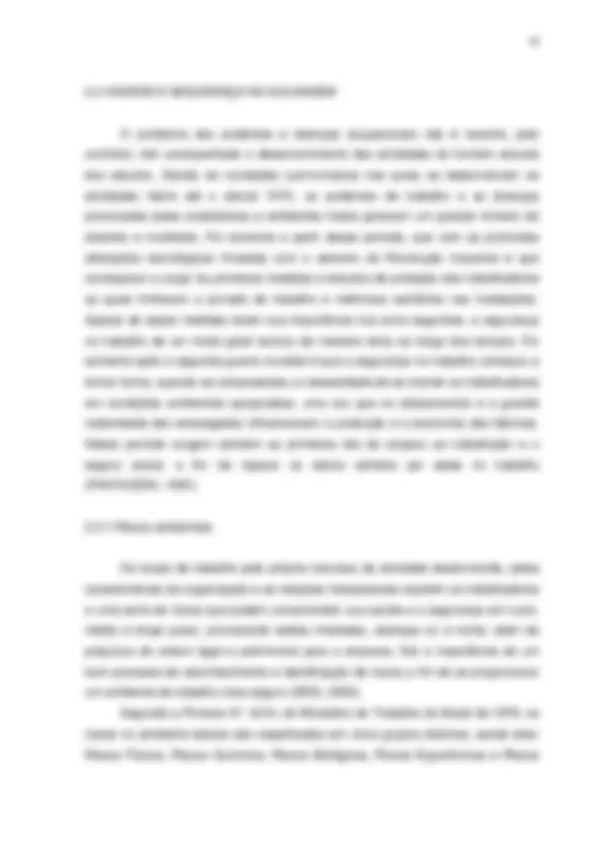
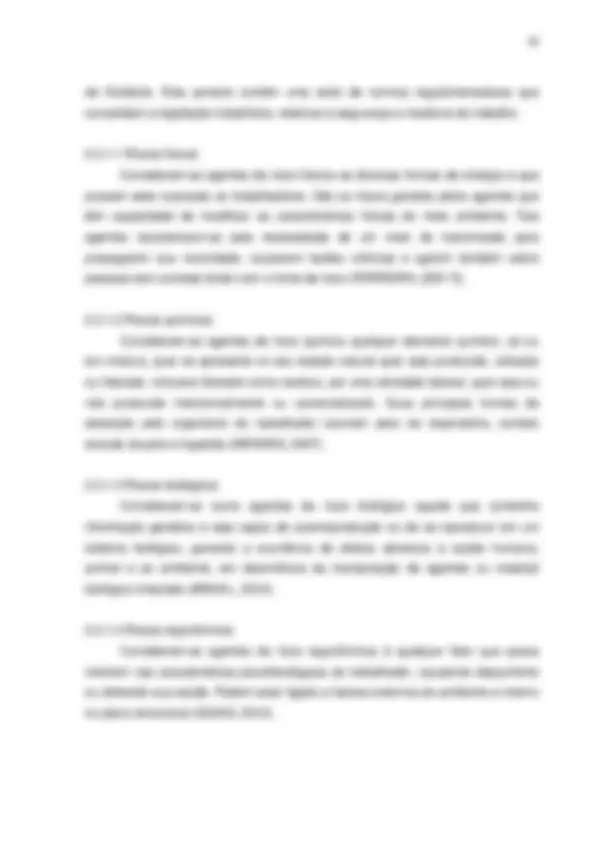
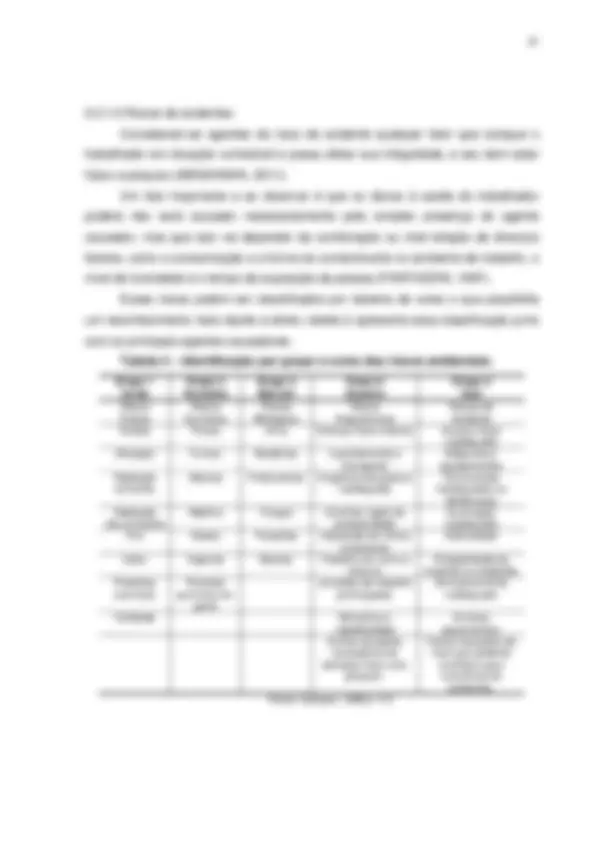
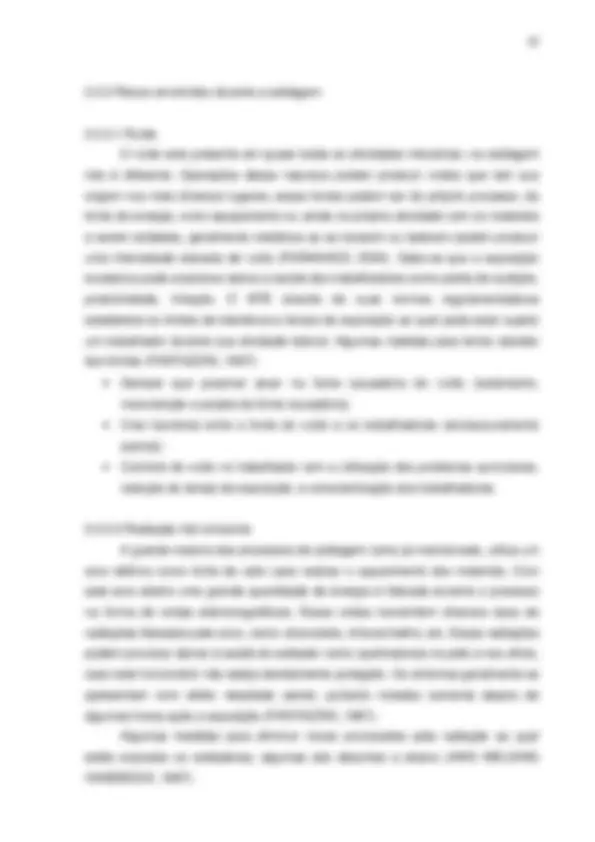
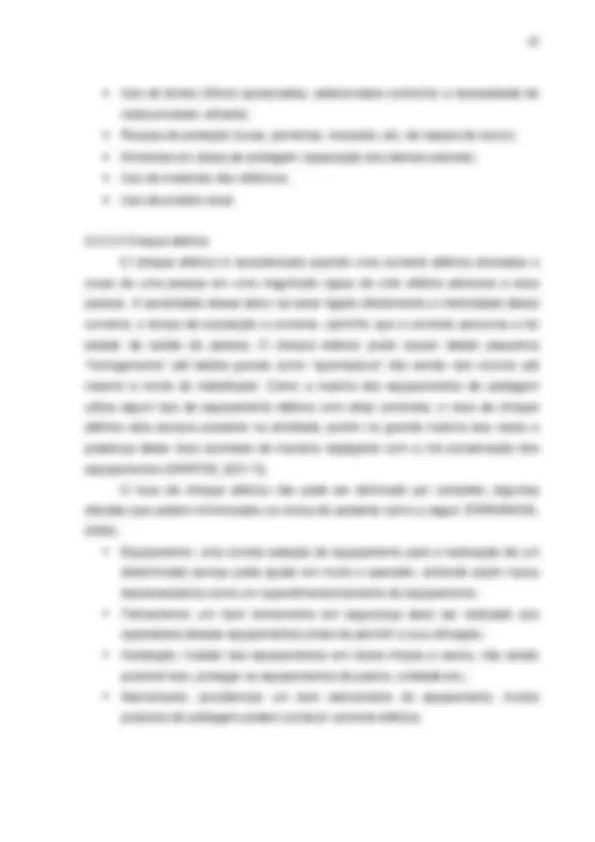
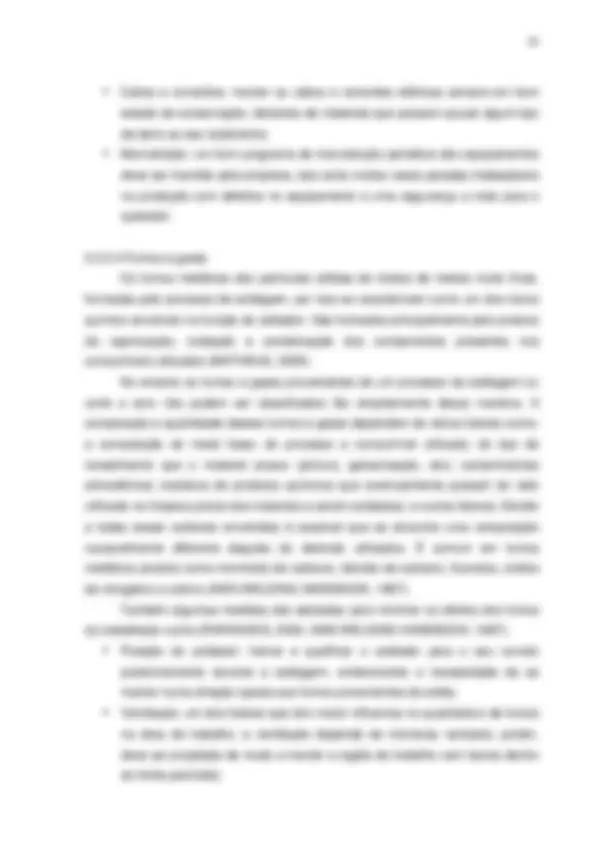
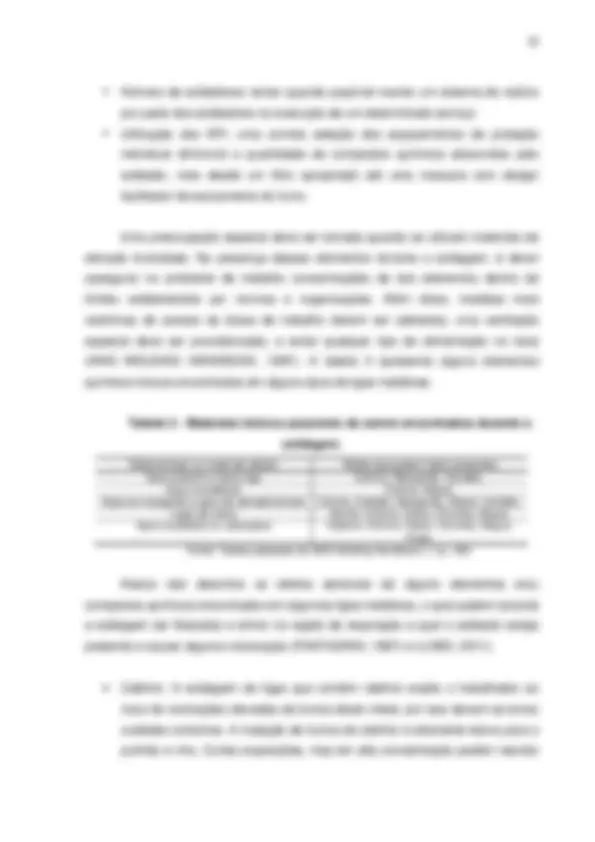
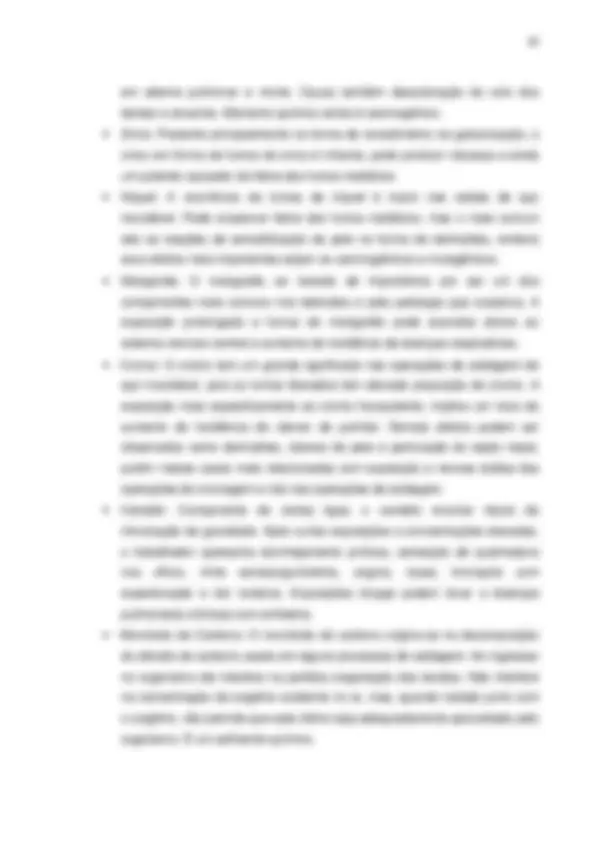
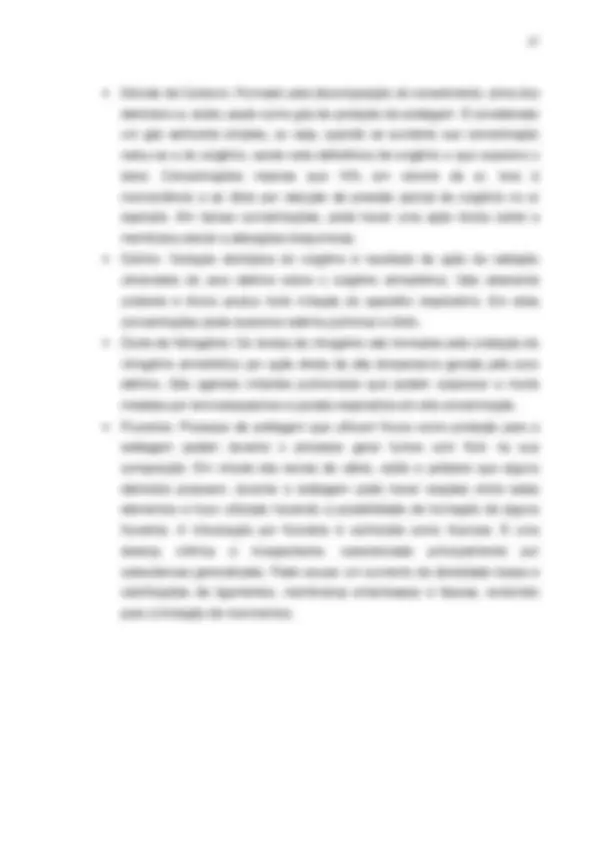
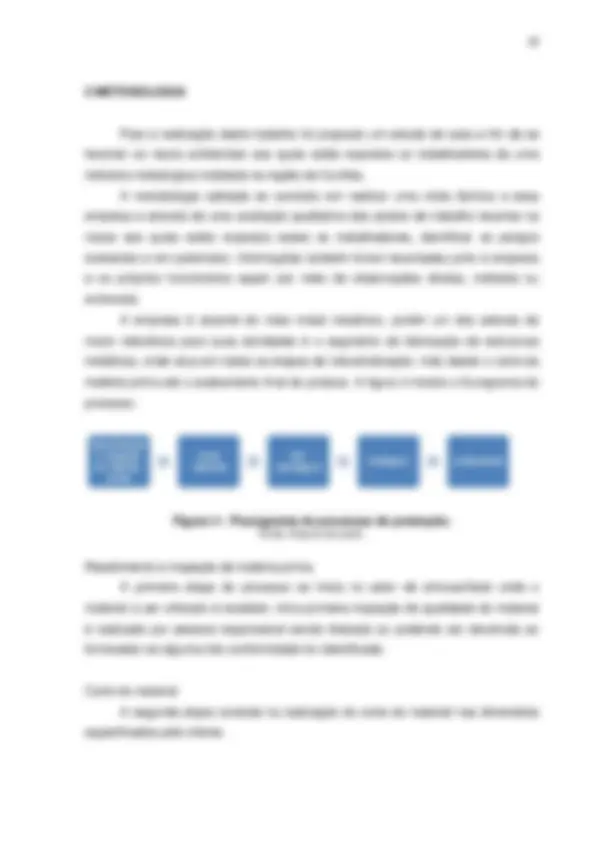
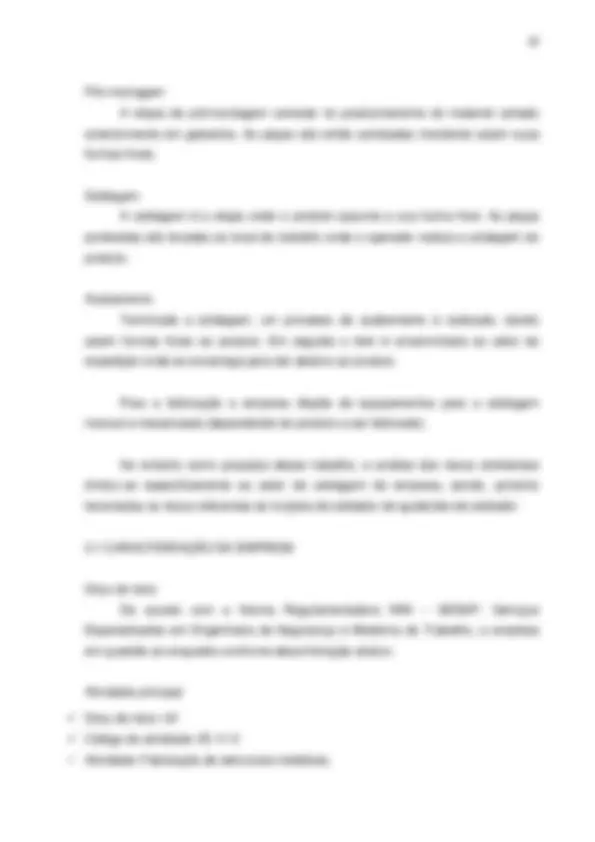
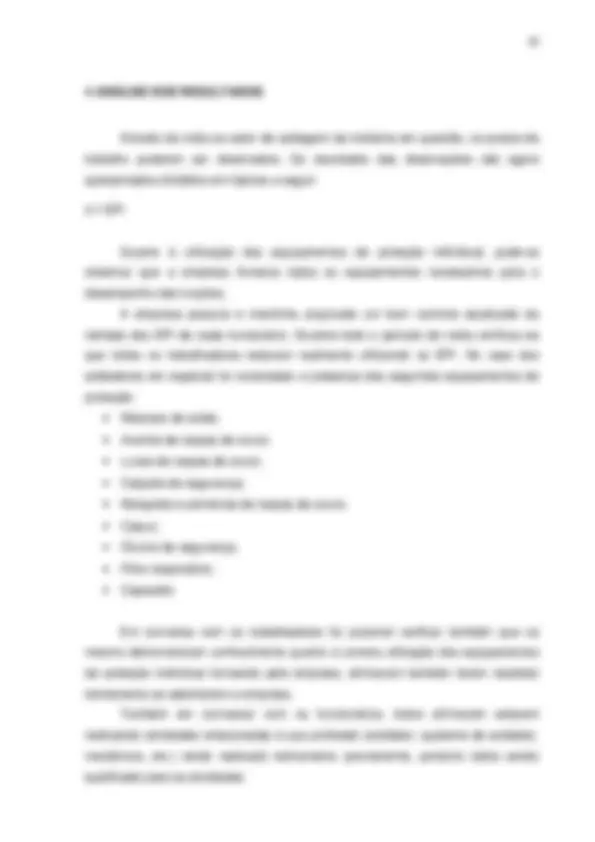
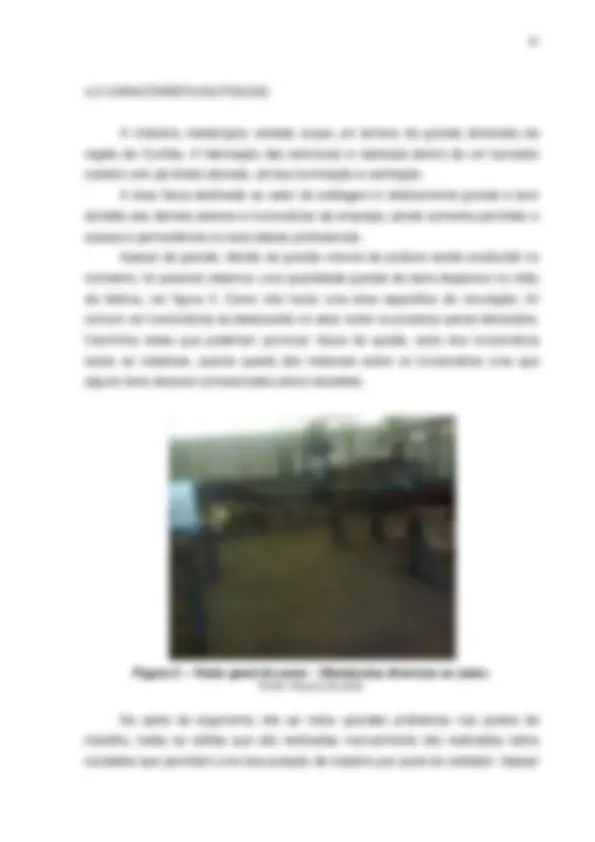
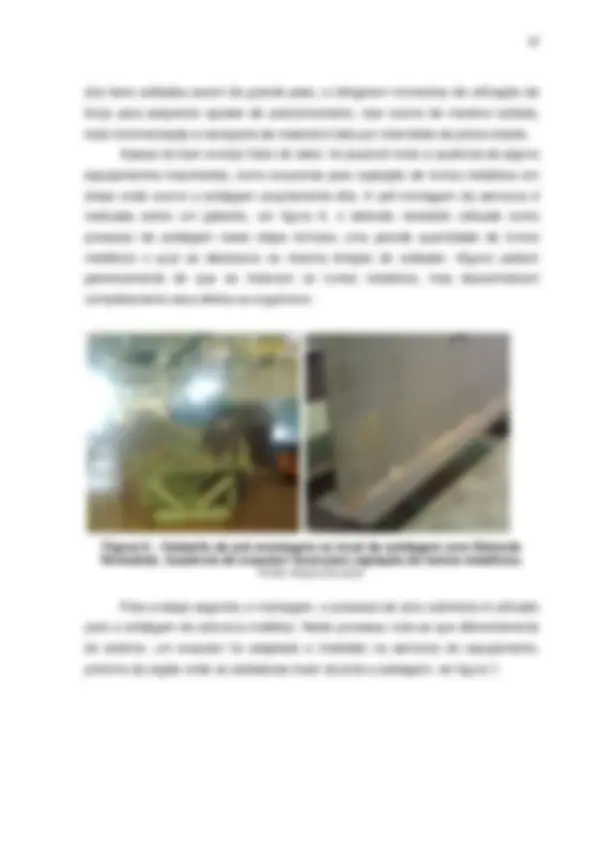
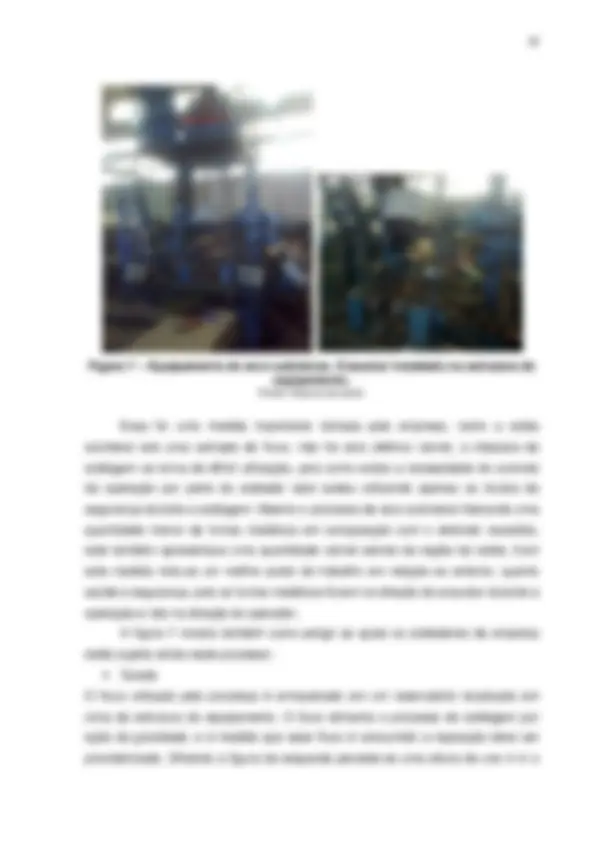
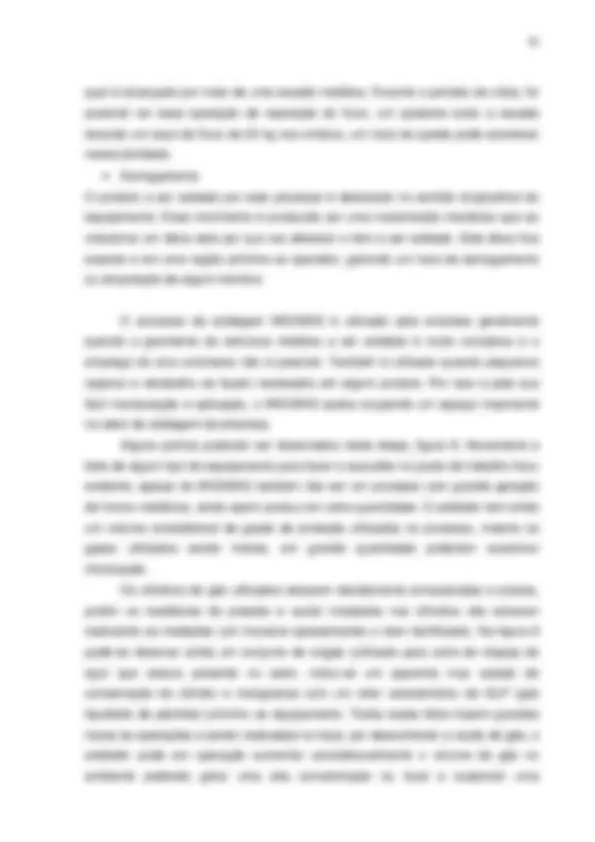
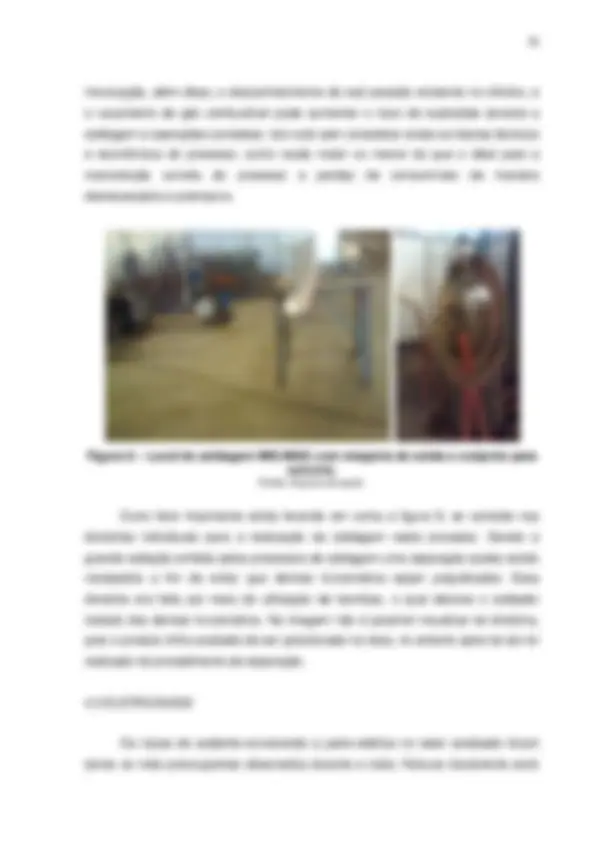
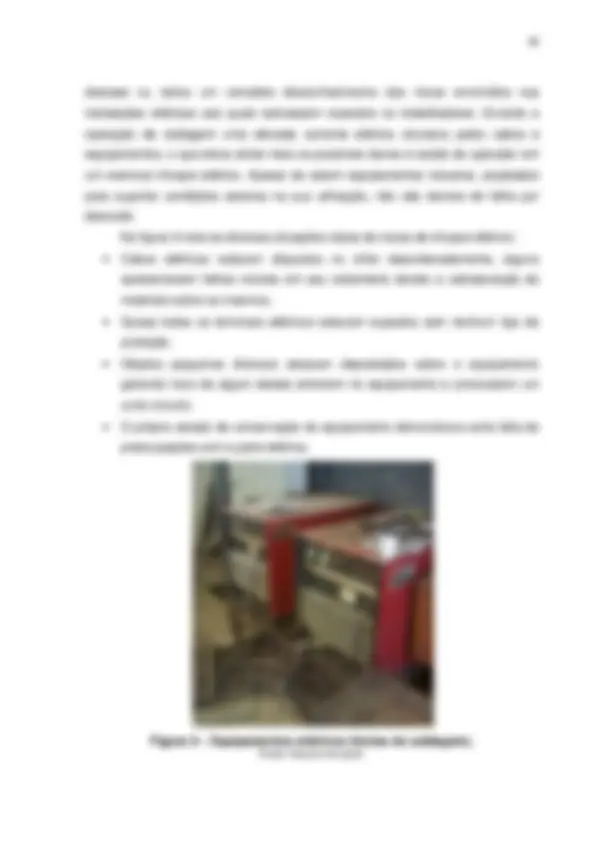
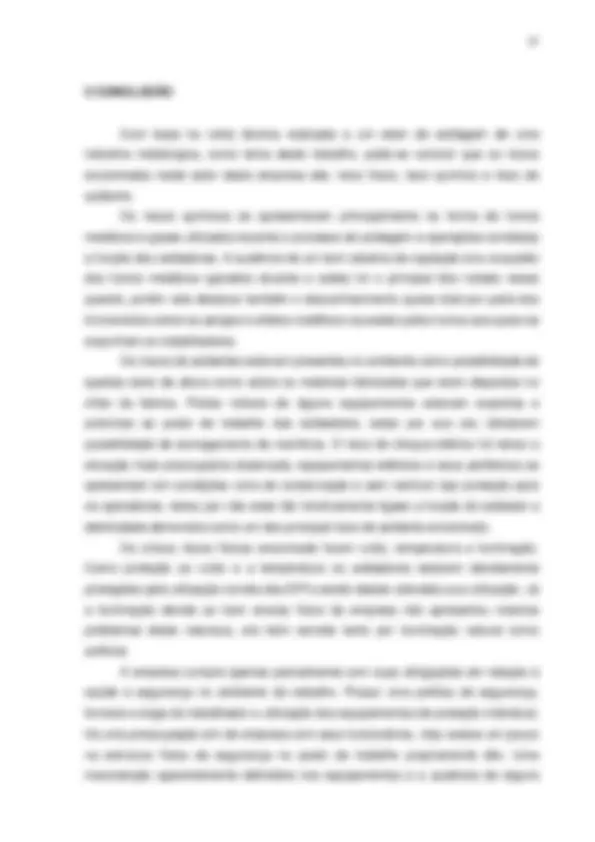
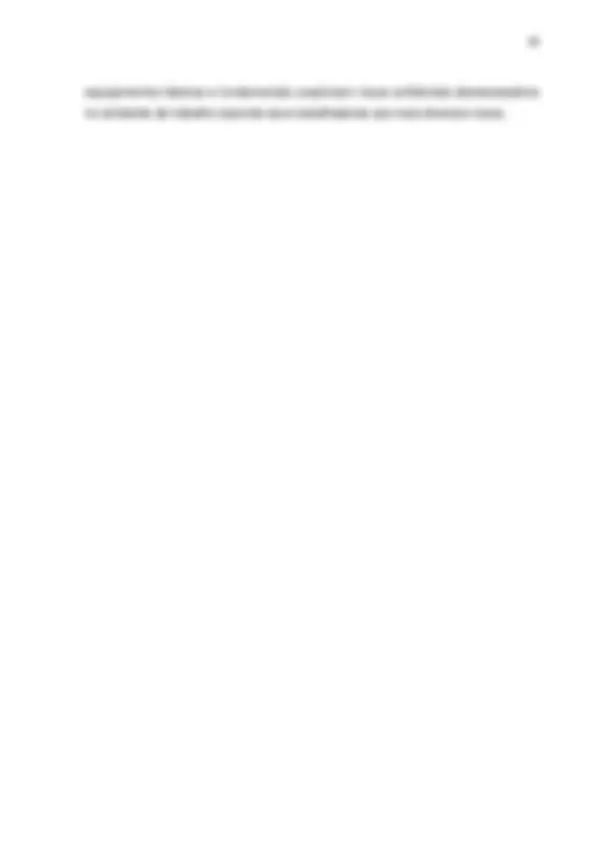
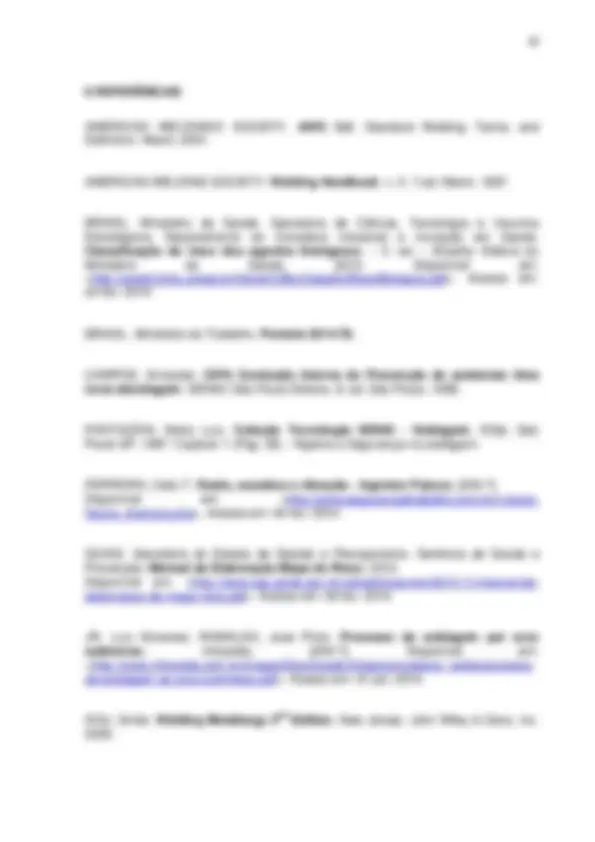
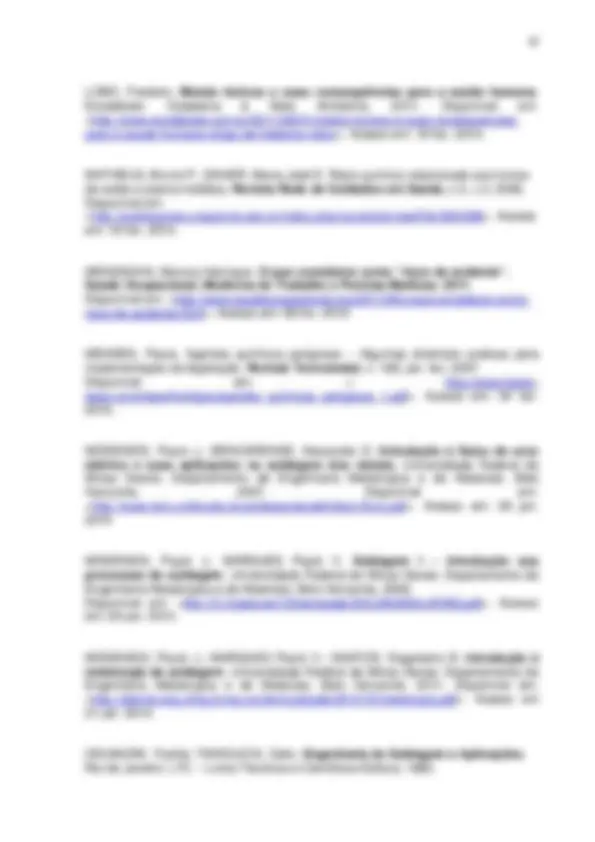
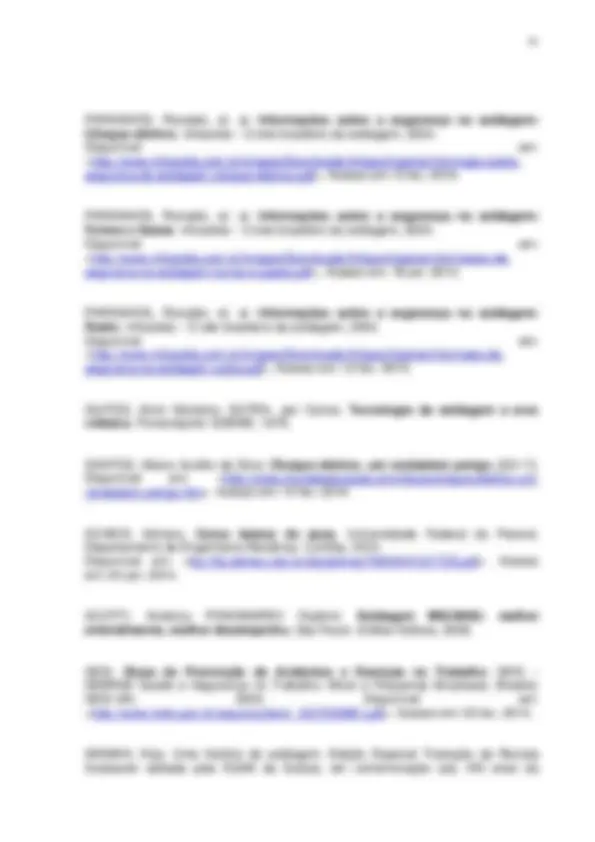
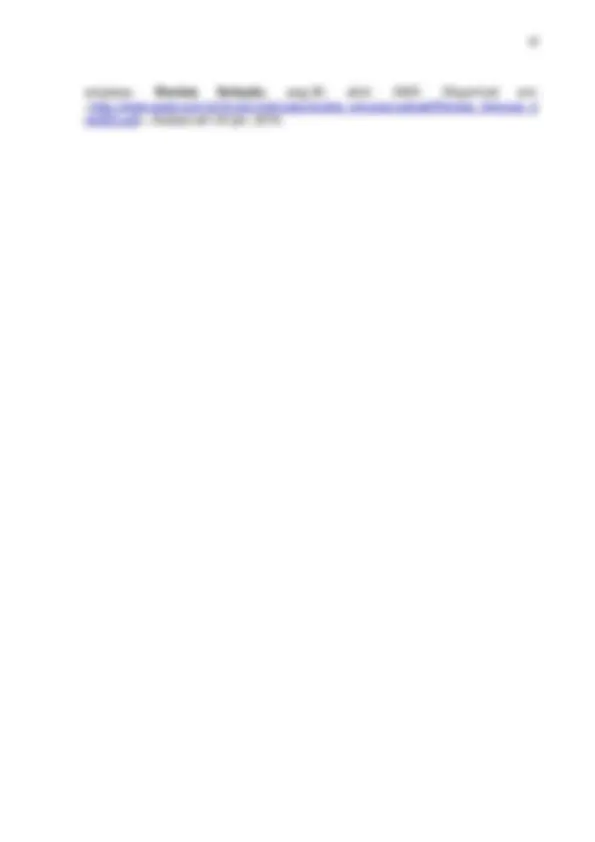
Estude fácil! Tem muito documento disponível na Docsity
Ganhe pontos ajudando outros esrudantes ou compre um plano Premium
Prepare-se para as provas
Estude fácil! Tem muito documento disponível na Docsity
Prepare-se para as provas com trabalhos de outros alunos como você, aqui na Docsity
Os melhores documentos à venda: Trabalhos de alunos formados
Prepare-se com as videoaulas e exercícios resolvidos criados a partir da grade da sua Universidade
Responda perguntas de provas passadas e avalie sua preparação.
Ganhe pontos para baixar
Ganhe pontos ajudando outros esrudantes ou compre um plano Premium
Comunidade
Peça ajuda à comunidade e tire suas dúvidas relacionadas ao estudo
Descubra as melhores universidades em seu país de acordo com os usuários da Docsity
Guias grátis
Baixe gratuitamente nossos guias de estudo, métodos para diminuir a ansiedade, dicas de TCC preparadas pelos professores da Docsity
Uma análise qualitativa dos riscos existentes no setor de soldagem de uma indústria metalúrgica, com ênfase na captação de fumos metálicos e na eletricidade na conservação e manutenção de instalações e equipamentos elétricos. O texto aborda os processos de soldagem por pressão e por fusão, incluindo esquemas esquemáticos e aplicações. A soldagem se consolidou como processo de fabricação durante a 1ª guerra mundial e é definida como um processo de união que produz a coalescência de materiais aquecendo-os até a temperatura de soldagem. Os principais processos de soldagem são separados em subgrupos com base no tipo de fonte de energia usada.
Tipologia: Notas de aula
1 / 43
Esta página não é visível na pré-visualização
Não perca as partes importantes!
Monografia apresentada para obtenção de titulo de Especialista no Curso de Pós Graduação em Engenharia de Segurança do Trabalho, Departamento Acadêmico de Construção Civil, Universidade Tecnológica Federal do Paraná, UTFPR. Orientador: Prof. MSc. Rui Bocchino Macedo
O presente trabalho trata sobre um estudo de caso realizado em uma indústria do setor metal mecânico da cidade de Curitiba. Essa empresa possui e desenvolve atividades relacionadas à soldagem em seu processo produtivo, e como consequência seus trabalhadores acabam expostos a uma série de riscos e perigos relacionados a esta profissão. Por isso, este trabalho foi desenvolvido com o objetivo de levantar os riscos existentes no setor de soldagem da empresa visitada, realizando para isso uma análise qualitativa dos postos de trabalho. Para esta avaliação foi levado em consideração aspectos como: a utilização de equipamentos de proteção individual, obrigações da empresa, posto de trabalho e equipamentos. Verificou-se que os problemas mais críticos estão relacionados à captação dos fumos metálicos gerados durante os processos de soldagem e com a eletricidade na conservação e manutenção de instalações e equipamentos elétricos. Dessa maneira os principais riscos ambientais encontrados durante a visita foram: risco físico, químico, e de acidente. O trabalho é divido essencialmente em duas partes, na primeira, uma revisão bibliográfica aborda os aspectos teóricos dos riscos ambientais e de soldagem. Na segunda passa-se ao estudo de caso onde se discorre sobre os riscos encontrados na atividade de trabalho nesta empresa. Assim, nesse trabalho teórico-pratico, verifica-se a importância de se considerar as questões ambientais desde o envolvimento dos funcionários no cumprimento de normas de segurança, quanto à organização da empresa em fornecer uma estrutura adequada que possibilite essa prática, pois ambas impactam na melhora da segurança do ambiente de trabalho.
Palavra-chave: soldagem, riscos ambientais, posto de trabalho.
This paper focuses on a case study done in a factory mechanic from Curitiba metal sector. This company owns and develops related to welding activities in its production process, and as a result their workers end up exposed to a number of risks and hazards related to this profession. Therefore, this work was designed to assess the risks involved in the welding of the visited company sector, for performing a qualitative analysis of this job. For this evaluation was taken into consideration aspects like: the use of personal protective equipment, the company's obligations, and work station equipment. It was found that the most critical problems are related to capture of welding fumes generated during welding and with electricity in the conservation and maintenance of electrical installations and equipment. Thus the main environmental risks encountered during the visit were: physical, chemical, and accident risk. The work is divided into two main parts, the first, a literature review discusses the theoretical aspects of environmental risks and welding. In the second pass is the case study where it talks about the risks found in the activity of work in this company. Thus, this theoretical and practical work, there is the importance of considering environmental issues since the involvement of employees in compliance with safety standards, the use of organization to provide an appropriate framework that allows this practice, because both impact the improves the safety of the work environment.
Keyword: welding, environmental risks, the workplace.
Figura 1 - Desenho esquemático do processo de soldagem por eletrodo revestido............................................................................................................... Figura 2 - Desenho esquemático do processo de soldagem MIG/MAG.............. Figura 3 - Desenho esquemático do processo de soldagem Arco Submerso..... Figura 4 - Fluxograma do processo de produção................................................ Figura 5 - Visão geral do setor. Obstáculos diversos no setor............................. Figura 6 - Gabarito de pré-montagem no local de soldagem com eletrodo Revestido. Ausência de exaustor local para captação de fumos metálicos......... Figura 7 - Equipamento de arco submerso. Exaustor instalado na estrutura do equipamento......................................................................................................... Figura 8 - Local de soldagem MIG/MAG com máquina de solda e conjunto para oxicorte......................................................................................................... Figura 9 - Equipamentos elétricos. Fontes de soldagem.....................................
Tabela 1 – Principais processos de soldagem e aplicações............................... Tabela 2 – Identificação por grupo e cores dos riscos ambientais...................... Tabela 3 – Materiais tóxicos possíveis de serem encontrados durante a soldagem..............................................................................................................
7
1 INTRODUÇÃO
Os metais ocupam um espaço importante no mundo da engenharia, devido a uma boa combinação de propriedades mecânicas, custo e disponibilidade, esses materiais são largamente utilizados nos dias de hoje. Devido aos mais diversos motivos, alguns produtos precisam ou podem ser fabricados em partes menores e unidas mais tarde conforme se deseja. Para que isso se tornasse possível diversas técnicas foram desenvolvidas ao longo dos anos, a soldagem é uma das principais e talvez a mais utilizada por aliar diversas características e propriedades que ela gere. Conhecida como uma profissão que exige grande esforço por parte do profissional, a atividade de soldagem manual tem sido ultimamente substituída pela mecanização e/ou automatização. Porém quanto isso se torna de difícil realização (como soldas em campo, por exemplo) ou inviável financeiramente, a solda manual realizada pelo soldador continua sendo a alternativa mais aceita, por isso o trabalho deste profissional continua sendo necessário e de grande importância. Tida como uma atividade insalubre e a qual expõem seus trabalhadores a uma série de perigos como eletricidade, químicos, altura, etc. os soldadores muitas vezes devido à baixa escolaridade e/ou por desconhecer seus direitos, ficam sujeitos à boa vontade da empresa para realizar uma determinada atividade com segurança. Sem isso, por desconhecer os riscos ou não ser capaz de identifica-los, acabam se sujeitando a trabalhar em condições que coloquem em risco a sua saúde física e mental.
1.1 OBJETIVOS
1.1.1 Objetivo geral Este trabalho tem como objetivo realizar o levantamento dos riscos existentes nos ambientes de soldagem de uma indústria metalúrgica.
1.1.2 Objetivos específicos Como objetivos específicos deste trabalho procuram-se:
9
A fabricação de produtos metálicos ocupa um grande espaço na indústria dos dias de hoje. Ao aliar boas propriedades mecânicas e um custo viável, os materiais metálicos, em especial o ferro, aço e suas ligas, atendem de maneira satisfatória à maioria das necessidades do ser humano quanto a sua utilização. È dentro deste cenário, a união destes materiais se torna muitas vezes necessários pelos mais diversos motivos, esta união de metais pode ser dividida em duas categorias principais, aquelas que estão baseadas em forças mecânicas macroscópicas entre as partes a serem unidas e aquelas baseadas em forças microscópicas (interatômicas ou intermoleculares). O primeiro tipo é ocorre quando resistência da união se da pela resistência a tensão de cisalhamento, como quando se utiliza parafuso e/ou rebites. No segundo tipo, a união ocorre pela aproximação dos átomos moléculas das partes a serem unidas até distancias suficientemente pequenas para a formação de ligações químicas primarias. Como exemplo deste tipo união pode citar a soldagem (MODENESI, 2011). A soldagem é amplamente empregada na união de diversos tipos de estruturas metálicas e nos mais diversos campos de aplicação como construção naval, estruturas civis, vasos de pressão até reparos, manutenção e recuperação de peças danificadas. È considerado por isso uns dos principais meios de fabricação da atualidade na construção de estruturas (OKUMURA, 1982).
2.1 BREVE HISTÓRICO DE SOLDAGEM
A soldagem como se conhece hoje, se consiste em uma variedade grande de processos, equipamentos e técnicas bem conhecidas e já estabelecidas. Porém os primeiros indícios da utilização da soldagem se da em torno do ano 1500 a.c. quando o ferro começou a ser fabricado e substituiu o cobre e o bronze na confecção de diversos artefatos. O ferro era produzido em fornos e conformado por martelamento na forma de blocos com um peso de poucos quilogramas. Quando peças maiores eram necessárias, estes blocos eram soldados por forjamento. Nesse processo os materiais a serem unidos (no caso o ferro) eram aquecidos até ficarem rubro, as peças então eram aproximadas para ocorrer o martelamento dos materiais até a formação da solda (MODENESI, 2011).
10
Durante muito tempo a soldagem foi mantida como um processo de fabricação secundário devido ao desenvolvimento de inúmeros outras técnicas e processos tidos como melhores para a época, mantendo-se aplicada apenas em pequenos aplicações e reparos. Foi nos anos 1800 que esta história começou a mudar, com a descoberta do acetileno e o aparecimento das primeiras fontes produtoras de energia elétrica se tornou possível a soldagem por fusão. Diversas técnicas começaram a surgir em cima dessas descobertas e expandiram o campo de soldagem, no entanto foi a partir da 1ª guerra mundial que a soldagem se consolidou como processo de fabricação, devido à necessidade da época, a soldagem passou a ser utilizada mais intensamente na fabricação por sua flexibilidade de manuseio e resultados satisfatórios obtidos. Mais recentemente com avanço da eletrônica, diversas variações e técnicas de soldagem surgiram, novos equipamentos possibilitam cada vez mais um maior controle e precisão sobre a solda, assegurando assim uma maior qualidade em seu produto final. Existem hoje dezenas de diferentes processos de soldagem nos mais diversos segmentos da indústria desde segmentos de baixa tecnologia até aqueles com elevada tecnologia e complexidade por isso estudos relativos a eles se tornam cada vez mais e mais necessário e importante (WEMAN, 2004).
2.2 FABRICAÇÃO DE AÇO
A principal utilização da soldagem se consiste na união de materiais metálicos. Esses em sua grande maioria possuem o ferro como sua matéria-prima em maior ou menor grau. Por isso, uma boa compreensão dos processos de soldagem passa pelo conhecimento do seu principal elemento. O ferro, principal elemento de diversas ligas de aço, não existe na natureza como é conhecido, o que existe de fato é o minério de ferro, que até chegar à indústria passa por diversas transformações nas usinas. A ciência que trabalha e estuda este segmento da engenharia é a siderurgia. O processo siderúrgico está subdivido em três grandes etapas: Redução, Refino, e Conformação Mecânica. A redução envolve a transformação do minério de ferro em ferro gusa, o refino a transformação dos produtos da redução até a composição desejada e adequada e a conformação mecânica a transformação dos aços em produtos para utilização (SCHEID, 2010). Um estudo mais detalhado e aprofundado pode ser realizado nesses processos em
12
atingem temperaturas inferiores as do processo por fusão isso dificulta muitas as alterações microestruturais significativas às vezes desejadas no material (MODENESI, 2011).
2.3.2 Processos de soldagem por fusão
Soldagem por fusão é um processo de união de metais no qual a coalescência destes é conseguida por fusão. Devido ao grande número de processos de soldagem por fusão, estes são normalmente separados em subgrupos, uma das mais adotadas é com relação ao tipo de fonte de energia usada pelo processo (MODENESI, 2011). A tabela 1 apresenta alguns dos principais processos existentes hoje.
Tabela 1 – Principais processos de soldagem e aplicações. Processo Fontes de Calor Protetor^ Agente Principais aplicações Soldagem por eletro-escória
Aquecimento por resistência da eletro- escória
Escória Soldagem aços carbono, baixa e alta liga. Soldagem de materiais com grandes espessuras. Soldagem por arco submerso
Arco elétrico Escória e gases gerados
Soldagem de aços carbono, baixa e alta liga. Peças estruturais, tanques, vasos de pressão, etc. Soldagem com eletrodos revestidos
Arco elétrico Escória e gases gerados
Soldagem de quase todos os metais exceto cobre puro, metais reativos e de baixo ponto de fusão. Usado na soldagem em geral. Soldagem com Arame Tubular
Arco elétrico Escória e gases gerados por fonte externa
Soldagem de aços carbono
Soldagem MIG/MAG
Arco elétrico Argônio, Helio, CO2, Misturas
Soldagem de aço carbono, baixa e alta liga. Não ferrosos. Todas as posições. Soldagem de tubos e chapas. Soldagem a Plasma Arco elétrico Argônio, Hélio, Misturas
Todos os metais importantes em Engenharia excesso Zn e Be Soldagem TIG Arco elétrico Argônio, Hélio, Misturas
Soldagem de todos os metais exceto Zn e Be. Soldagem de não ferrosos e aço inox. Soldagem por feixe eletrônico
Feixe eletrônico
Vácuo Soldagem de praticamente todos os materiais. Indústria nuclear e aeroespacial.
13
Tabela 1 – Principais processos de soldagem e aplicações. (conclusão) Processo Fontes de calor protetor^ Agente Principais aplicações Soldagem a laser Feixe de luz Argônio ou Hélio Soldagem de praticamente todos os materiais. Indústria nuclear e aeroespacial Soldagem a gás Chama oxi- acetilênica
Gás (CO, H2, CO2, H20)
Soldagem manual de aço carbono, Cu, Al, Zn, Pb e bronze. Soldagem de chapas finas. Fonte: Tabela adaptada de MODENESI, 2011.
Como se observa as três fontes de energia mais utilizadas dentro dos processos de soldagem por fusão são: gás, arco elétrico, e feixes de luz. O que difere cada uma dessas fontes é principalmente a densidade de energia envolvida no processo. Outros fatores também podem e devem ser levados em conta na seleção do equipamento, esses vão desde a capacidade produtiva, qualidade final desejada do produto até o investimento disponível para aquisição.
2.3.3 Arco elétrico
Como pode ser observada, quase a totalidade dos processos de soldagem exigem a aplicação de calor de alguma forma para que a solda seja possível, em maior ou menor intensidade variando de acordo com a tecnologia envolvida. Para o caso da soldagem por fusão uma das formas mais comumente utilizada para se obter esse calor é através de um arco elétrico. Por apresentar uma boa combinação de características que incluem uma concentração adequada de energia para a fusão localizada do metal base, facilidade de controle, baixo custo relativo do equipamento e um nível aceitável de risco à saúde dos seus operadores, é um modo de principal de geração de calor de muitos processos (MODENESI, 2007). O arco voltaico é uma região plasmática existente entre a ponta de um eletrodo para soldagem e o metal de base, por onde passa uma grande quantidade de corrente, produzindo uma alta intensidade de calor e luz. Na soldagem por fusão, a união de metais acontece pela ação direta e localizada deste arco voltaico, agindo como fonte de calor (SCOTTI e PONOMAREV, 2008). Uma das propriedades que os gases possuem é a de que em condições normais eles são isolantes (elétricos, térmicos, etc.). Entretanto, sob condições favoráveis (alta temperatura, baixíssima pressão ou submetidos a um campo elétrico
15
quantidade de escoria, porém de fácil remoção. São eletrodos de fácil manuseio em soldagem, produzindo cordões de bom acabamento e de média penetração.
Figura 1 – Desenho esquemático do processo de soldagem por eletrodo revestido. Fonte: Kou, 2002.
16
2.3.5 Soldagem MIG/MAG
O processo de soldagem conhecido como MIG/MAG é mais um processo que utiliza o arco elétrico como fonte de calor para fusão dos materiais a serem soldados. Porém a maior diferença entre os processos apresentados até agora esta na forma de manutenção do arco elétrico propriamente dito. Na soldagem MIG/MAG o arco é estabelecido entre um eletrodo continuamente alimentado e a peças a ser soldada. Esta característica do processo permite algumas vantagens em relação aos demais como: um alto fator de ocupação do soldador, alta densidade de corrente e apresenta uma elevada produtividade (MODENESI, 2006). O processo MIG/MAG apesar de ser genericamente conhecido desta maneira, é na verdade dois processos distintos. A diferença entre eles esta no tipo de gás utilizado na proteção da poça de fusão, caso um gás inerte seja usado na soldagem temos MIG (Metal Inert Gas), por outro lado se o gás for ativo temos o MAG (Metal Active Gas). Essa diferenciação é fundamental na soldagem, pois estes influenciam de maneira significativa a soldabilidade e qualidade do produto final. Os gases utilizados devem ser selecionados de acordo com os materiais a serem soldados. Gases inertes puros são, em geral, usados na soldagem de metais e ligas não ferrosas, misturas de gases inertes com pequenas quantidades de gases ativos são usadas, em geral com aços ligados, enquanto que misturas mais ricas em gases ativos ou CO 2 puro são usados na soldagem de aços carbonos. Os dois processos são conhecidos desta maneira principalmente pelo fato utilizarem o mesmo equipamento de soldagem (fonte, alimentador, tocha, etc). Na figura 2 é representado esquematicamente o processo de soldagem MIG/MAG. Utilizado normalmente de forma semi-automática, pode ser facilmente mecanizado e automatizado, sendo também o principal processo de soldagem a arco usado com robôs industriais. Por essa e outras característica o MIG/MAG se tornou um processo largamente utilizado em vários setores da indústria aliando produtividade, custo e simplicidade de utilização (MODENESI, 2006).
18
combinação do fluxo utilizado, estes podem atuar na estabilização do arco elétrico, na adição de elementos de liga, controle da geometria do cordão, e facilitar a remoção da escória. A necessidade de utilização do fluxo produz também uma das principais limitações do processo, que é quanto à posição de soldagem. Pelo fato do fluxo ser um material granulado e ser depositado anteriormente a passagem do arco, esta solda pode ser realizado somente na posição plana ou horizontal (GIMENES e RAMALHO, [200-?]). A soldagem por arco submerso é um processo frequentemente selecionado quando se deseja soldar diversos tipos de estruturas metálicas. Por possibilitar a utilização de elevados níveis de corrente é um processo que pode apresentar altas taxas de deposição de material, possibilitando desta maneira um aumento de produtividade do processo (MODENESI, 2006).
Figura 3 – Desenho esquemático do processo de soldagem Arco Submerso. Fonte: Kou, 2002.
19
O problema dos acidentes e doenças ocupacionais não é recente, pelo contrário, tem acompanhado o desenvolvimento das atividades do homem através dos séculos. Devido às condições sub-humanas nas quais se desenvolviam as atividades fabris até o século XVIII, os acidentes de trabalho e as doenças provocadas pelas substâncias e ambientes hostis geravam um grande número de doentes e mutilados. Foi somente a partir desse período, que com as profundas alterações tecnológicas iniciadas com o advento da Revolução Industrial é que começaram a surgir às primeiras medidas e estudos de proteção dos trabalhadores as quais limitavam a jornada de trabalho e melhorias sanitárias nas instalações. Apesar de essas medidas terem sua importância nos anos seguintes, a segurança no trabalho de um modo geral evoluiu de maneira lenta ao longo dos tempos. Foi somente após a segunda guerra mundial é que a segurança no trabalho começou a tomar forma, quando se compreendeu a necessidade de se manter os trabalhadores em condições ambientais apropriadas, uma vez que os afastamentos e a grande rotatividade dos empregados influenciavam a produção e a economia das fábricas. Nesse período surgem também as primeiras leis de amparo ao trabalhador e o seguro social, a fim de reparar os danos sofridos por estes no trabalho (FANTAZZINI, 1997).
2.2.1 Riscos ambientais
Os locais de trabalho pela própria natureza da atividade desenvolvida, pelas características da organização e as relações interpessoais expõem os trabalhadores a uma serie de riscos que podem comprometer sua saúde e a segurança em curto, médio e longo prazo, provocando lesões imediatas, doenças ou a morte, além de prejuízos de ordem legal e patrimonial para a empresa. Daí a importância de um bom processo de reconhecimento e identificação de riscos a fim de se proporcionar um ambiente de trabalho mais seguro (SESI, 2005). Segundo a Portaria N°. 3214, do Ministério do Trabalho do Brasil de 1978, os riscos no ambiente laboral são classificados em cinco grupos distintos, sendo eles: Riscos Físicos, Riscos Químicos, Riscos Biológicos, Riscos Ergonômicos e Riscos