
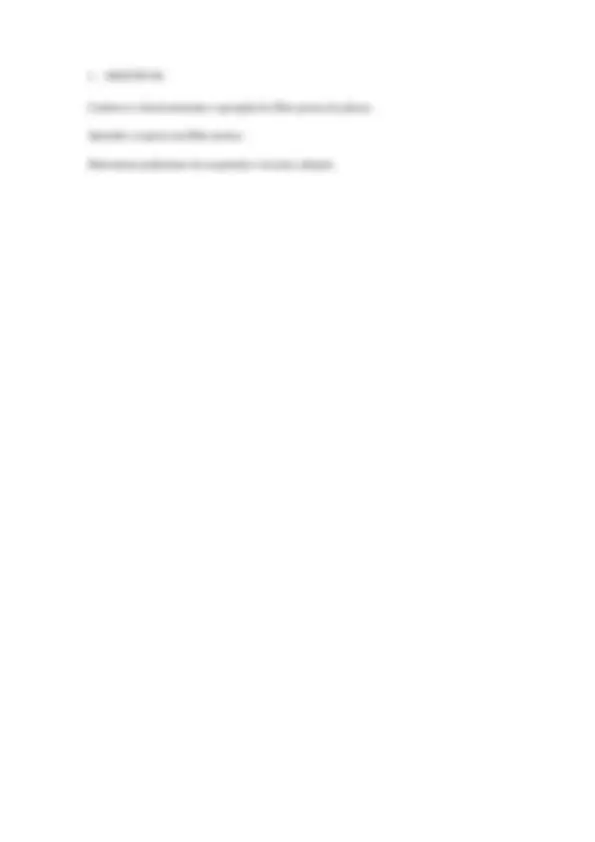
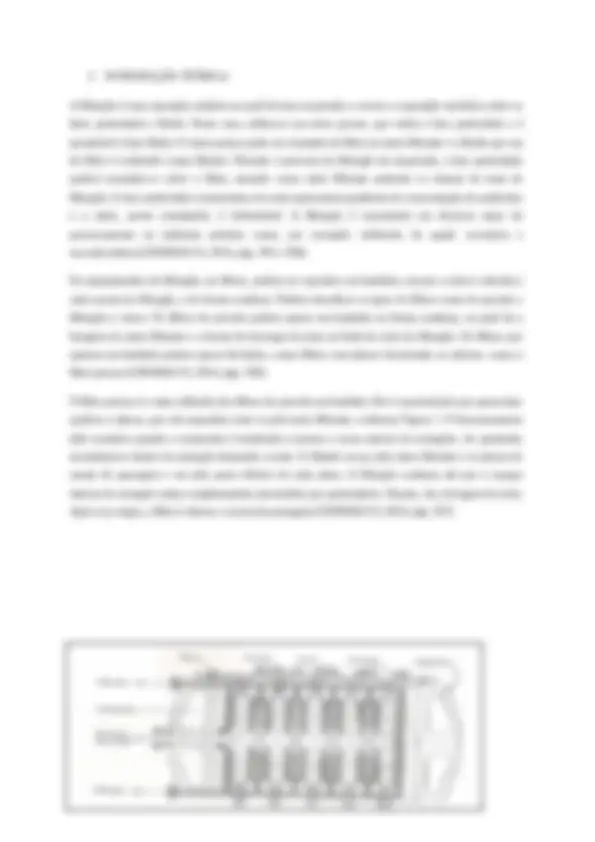
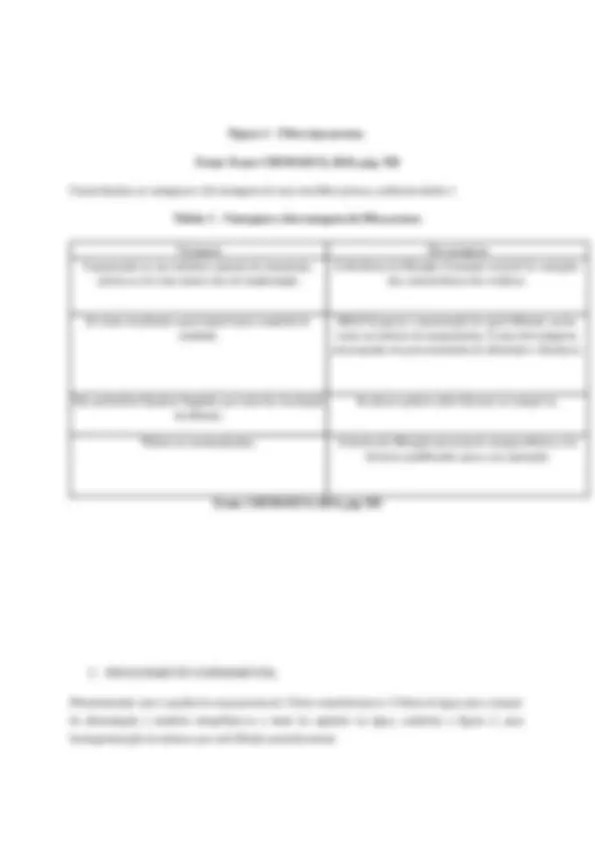
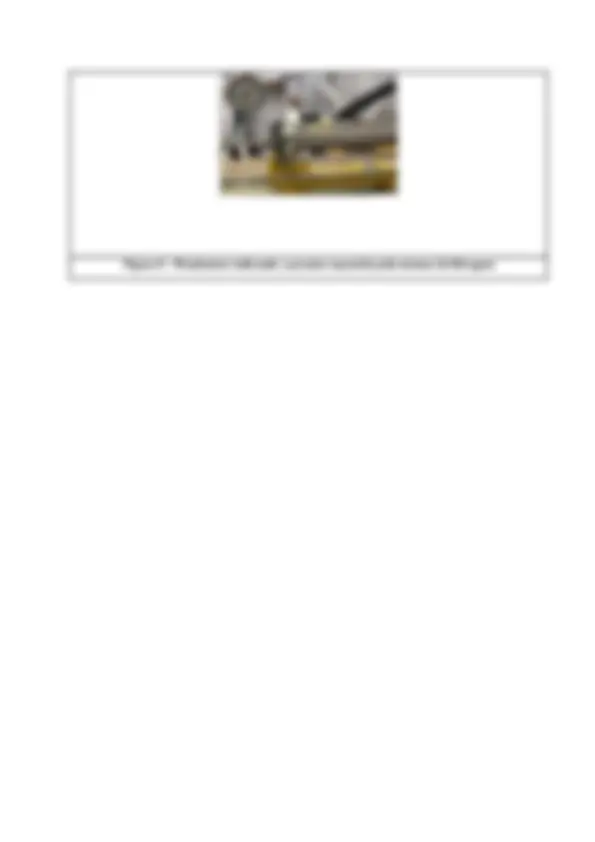
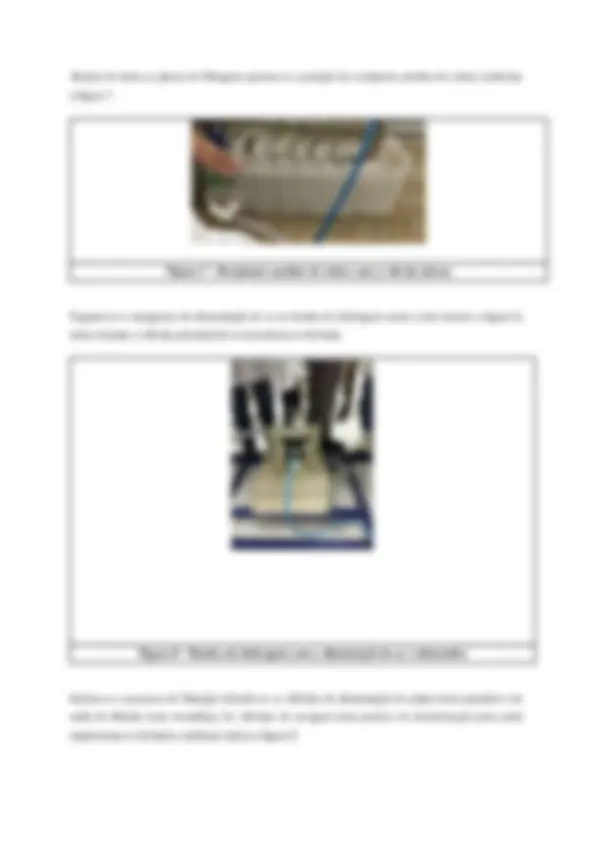
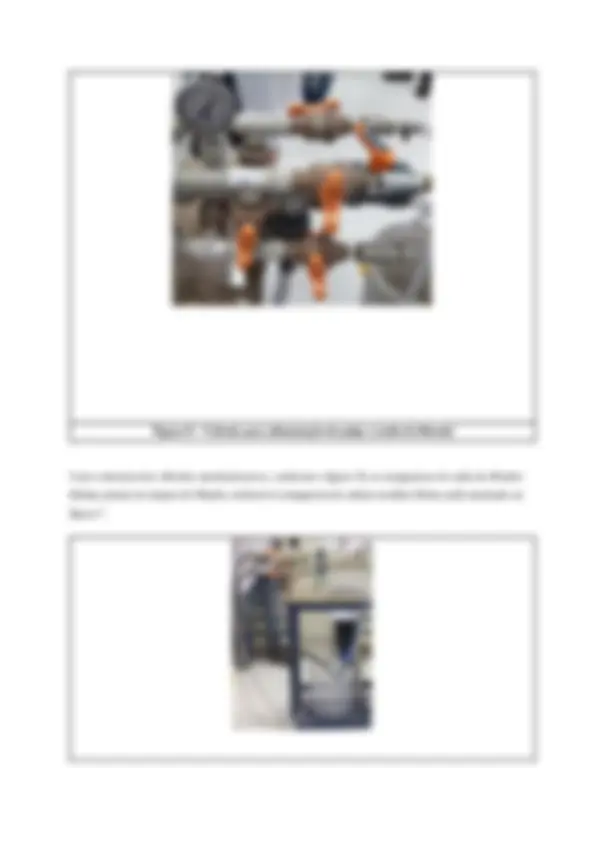
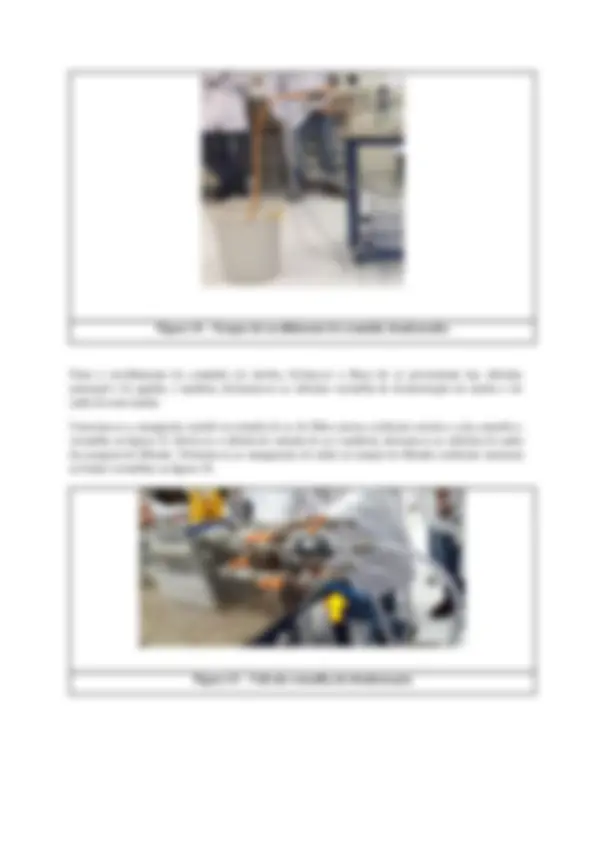
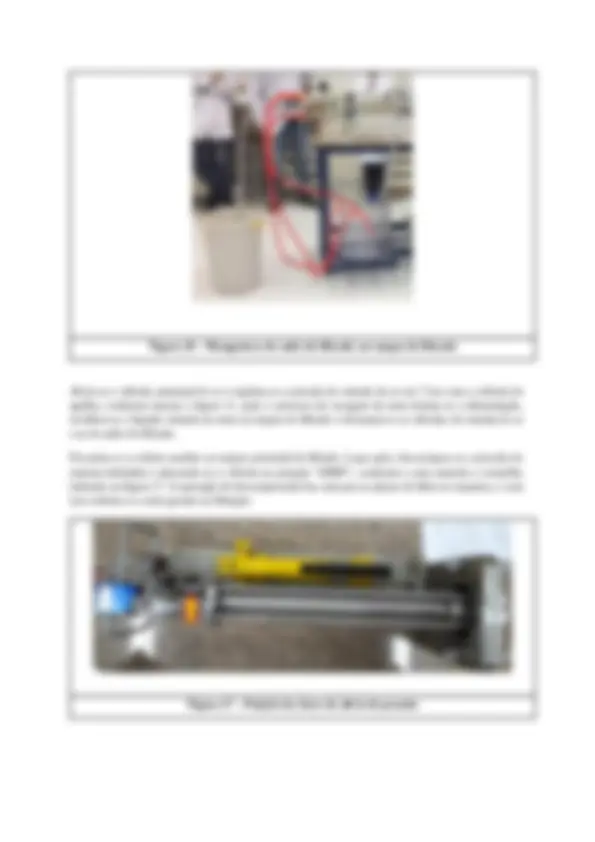
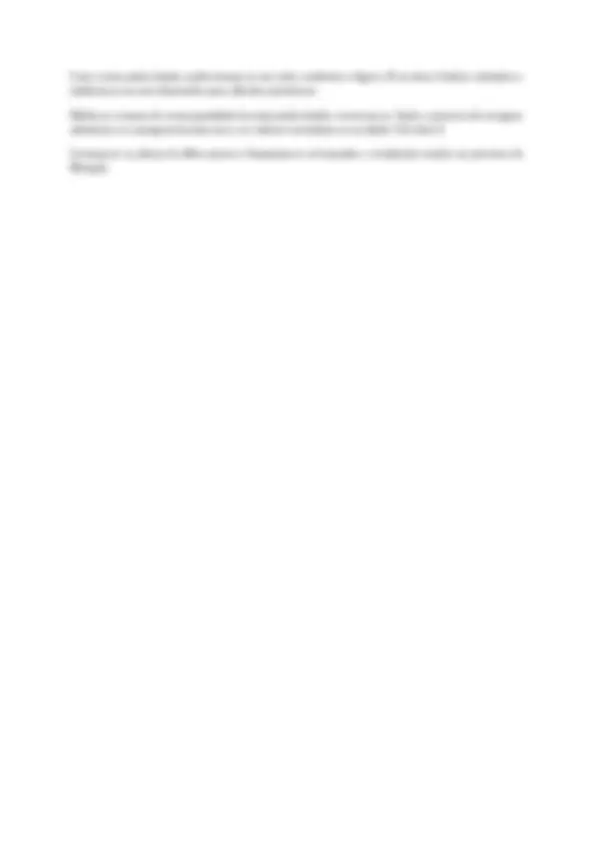
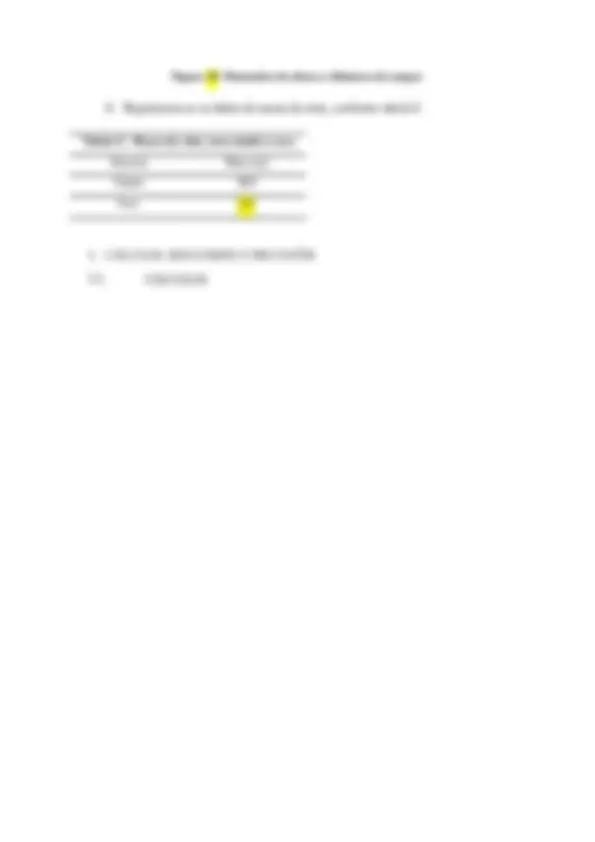
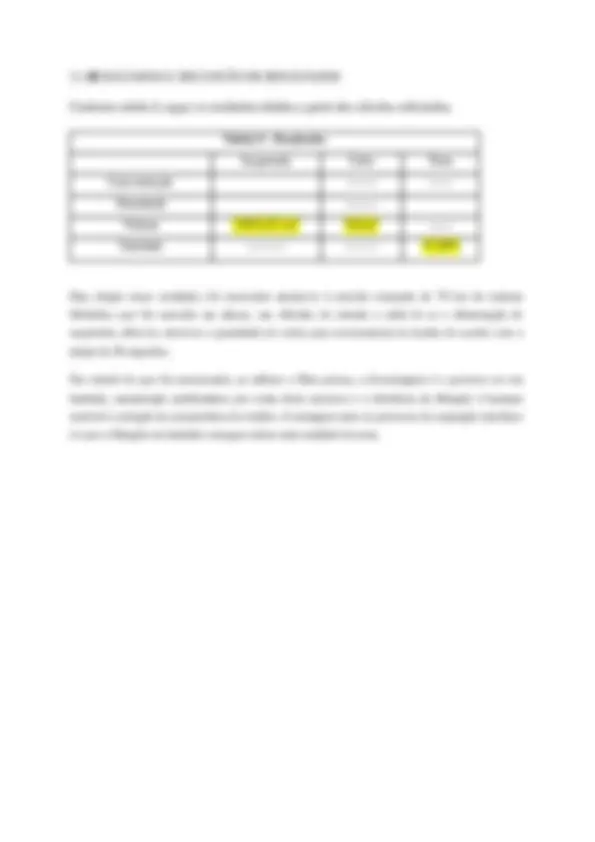
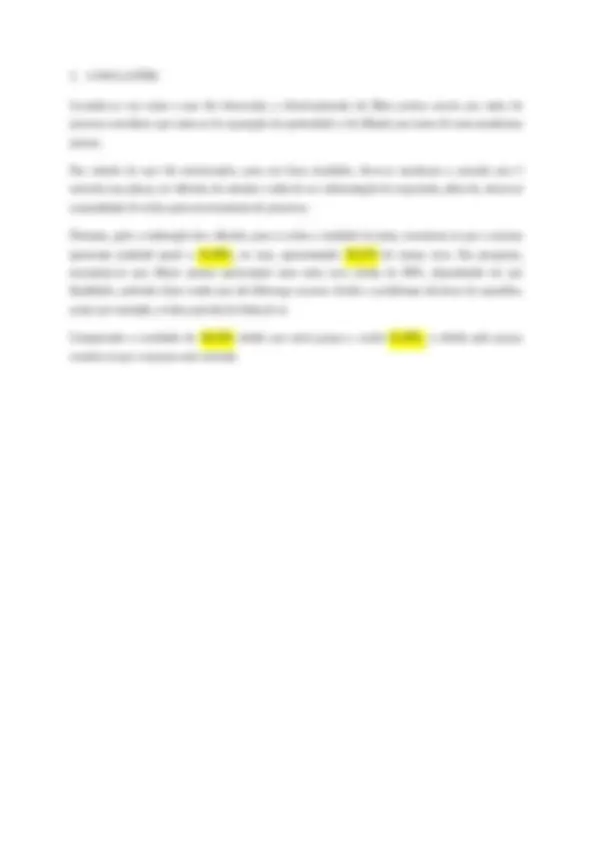
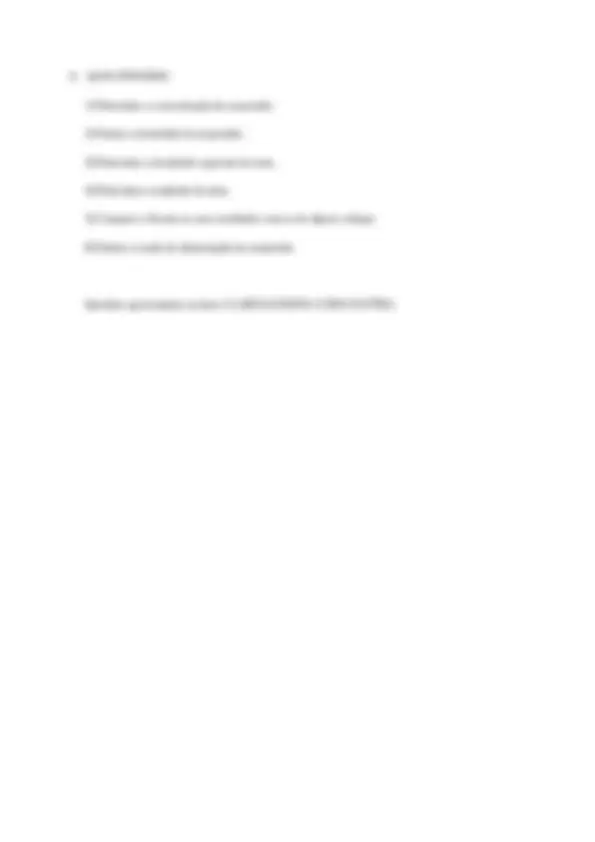
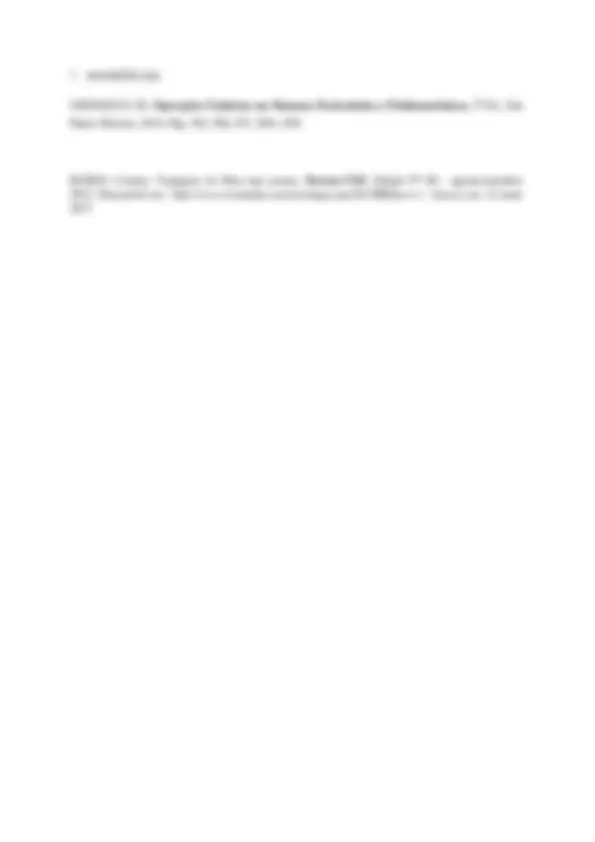
Estude fácil! Tem muito documento disponível na Docsity
Ganhe pontos ajudando outros esrudantes ou compre um plano Premium
Prepare-se para as provas
Estude fácil! Tem muito documento disponível na Docsity
Prepare-se para as provas com trabalhos de outros alunos como você, aqui na Docsity
Os melhores documentos à venda: Trabalhos de alunos formados
Prepare-se com as videoaulas e exercícios resolvidos criados a partir da grade da sua Universidade
Responda perguntas de provas passadas e avalie sua preparação.
Ganhe pontos para baixar
Ganhe pontos ajudando outros esrudantes ou compre um plano Premium
Comunidade
Peça ajuda à comunidade e tire suas dúvidas relacionadas ao estudo
Descubra as melhores universidades em seu país de acordo com os usuários da Docsity
Guias grátis
Baixe gratuitamente nossos guias de estudo, métodos para diminuir a ansiedade, dicas de TCC preparadas pelos professores da Docsity
Laboratório de Engenharia química
Tipologia: Trabalhos
1 / 22
Esta página não é visível na pré-visualização
Não perca as partes importantes!
A filtração é uma operação unitária na qual há uma suspensão e ocorre a separação mecânica entre as fases particulada e fluida. Neste caso, utiliza-se um meio poroso, que retém a fase particulada e é permeável à fase fluida. O meio poroso pode ser chamado de filtro ou meio filtrante e o fluido que sai do filtro é conhecido como filtrado. Durante o processo de filtração da suspensão, a fase particulada poderá acumular-se sobre o filtro, atuando como meio filtrante podendo se chamar de torta de filtração. A fase particulada característica da torta apresentará gradiente de concentração de partículas e o meio, assim constituído, é deformável. A filtração é encontrada em diversos tipos de processamento na indústria química como, por exemplo: indústrias de papel, cervejeira e sucroalcooleira (CREMASCO, 2014, pág. 355 e 356).
Os equipamentos de filtração, ou filtros, podem ser operados em batelada, em que a torta é retirada a cada ensaio de filtração, e de forma contínua. Podem classificar os tipos de filtros como de pressão e filtração a vácuo. Os filtros de pressão podem operar em batelada ou forma contínua, na qual há a lavagem do meio filtrante e a forma de descarga da torta ao final do ciclo de filtração. Os filtros que operam em batelada podem operar fechados, como filtros com placas horizontais ou abertos, como o filtro prensa (CREMASCO, 2014, pág. 356).
O filtro prensa é o mais utilizado dos filtros de pressão em batelada. Ele é caracterizado por apresentar quadros e placas, que são separadas entre si pelo meio filtrante, conforme Figura 1. O funcionamento dele acontece quando a suspensão é bombeada à prensa e escoa através de armações. As partículas acumulam-se dentro da armação formando a torta. O filtrado escoa pelo meio filtrante e as placas de canais de passagem e sai pela parte inferior de cada placa. A filtração continua até que o espaço interno da armação esteja completamente preenchido por particulados. Depois, há a lavagem da torta. Após essa etapa, o filtro é aberto e a torta descarregada (CREMASCO, 2014, pág. 357).
Figura 1 – Filtro tipo prensa.
Fonte: Fonte: CREMASCO, 2014, pág. 358
Foram listadas as vantagens e desvantagens de usar um filtro prensa, conforme tabela 1:
Tabela 1 – Vantagens e desvantagens do filtro prensa
Vantagens Desvantagens Comparando-se aos métodos naturais de tratamento, precisa-se de uma menor área de implantação.
A eficiência da filtração é bastante sensível às variações das características dos resíduos.
As tortas resultantes apresentam baixo conteúdo de umidade.
Difícil lavagem e manutenção do meio filtrante, assim como no interior do equipamento. É uma desvantagem preocupante em processamento de alimentos e fármacos.
São produzidos líquidos límpidos por meio da circulação do filtrado.
As placas podem sofrer fissuras ou romper-se.
Podem ser automatizados. A técnica de filtração necessita de energia elétrica e de técnicos qualificados para a sua operação.
Fonte: CREMASCO, 2014, pág 359
Primeiramente com o auxilio de uma proveta de 2 litros transferiram-se 12 litros de água para o tanque de alimentação e também mergulhou-se a haste do agitador na água, conforme a figura 2, para homogeneização da mistura que será filtrada posteriormente.
Conforme a figura 4 organizaram-se as placas do filtro respeitando-se a sequência alternada, 2 – 1 dos orifícios de identificação de cada placa, a começar da direita para esquerda.
Figura 4 – Sequencia alternada das placas do filtro prensa
Ajustaram-se as placas de filtragem com o sistema hidráulico do filtro mostrado na figura 5, primeiramente fechou-se a válvula do sistema e conforme solicitado no procedimento prensaram-se as placas ate a pressão 70 bar, como mostra a figura 6. A pressão não se mantem constante e, portanto ao decorrer da filtração ajustou-se a pressão sempre que necessário.
Figura 5 – Sistema Hidráulico do filtro prensa
Figura 6 – Manômetro indicando a pressão requerida pelo sistema de filtragem
Figura 9 – Válvula para alimentação de polpa e saída de filtrado
Com a abertura das válvulas introduziram-se, conforme a figura 10, as mangueiras de saída do filtrado (linhas pretas) no tanque de filtrado, inclusive à mangueira do coletor auxiliar (linha azul) mostrado na figura 7.
Figura 10 – Linhas de saída de filtrado para o tanque de coleta do filtrado
Com as válvulas da figura 9 abertas, as mangueiras da figura 10 no tanque de filtrado e a mangueira de ar conectada a bomba conforme a figura 8 abriu-se a válvula de ar principal e com a válvula de agulha, conforme a figura 11, ajustou-se a pressão de entrada da bomba em 7 bar. Para evitar problemas na sucção manteve-se a todo o tempo a mangueira de sucção submersa por inteiro na polpa.
Figura 11 – Válvula principal e válvula de agulha
Registraram-se a altura da suspensão no tanque de alimentação em função do tempo, a pressão do manômetro do filtro em função do tempo e por ultimo a altura de filtrado coletado em função do tempo dados esses apresentados no item 4 dados coletados nas tabelas 2, 3 e 4.
Atingiu-se a condição de 30 segundos/ciclo, onde nesse momento fechou-se a válvula principal de ar e logo após a válvula de agulha.
É necessário desobstruir o núcleo das placas do filtro e para isso abriu-se a válvula de desobstrução do núcleo indicada na figura 12 pela seta cinza e vermelha e fecharam-se todas as outras válvulas. Após conectou-se a mangueira de ar na válvula vermelha de desobstrução indicada pela seta amarela e vermelha na figura 13 e abriu-se a mesma.
Figura 14 – Tanque de recolhimento de conteúdo desobstruído
Feito o recolhimento do conteúdo do núcleo, fechou-se o fluxo de ar proveniente das válvulas principal e de agulha, e também, fecharam-se as válvulas vermelha de desobstrução do núcleo e de saída da torta úmida.
Conectou-se a mangueira espiral na entrada de ar do filtro prensa conforme mostra a seta amarela e vermelha na figura 15. Abriu-se a válvula de entrada de ar e também, abriram-se as válvulas de saída da secagem do filtrado. Verteram-se as mangueiras de saída no tanque de filtrado conforme mostram as linhas vermelhas na figura 16.
Figura 15 – Válvula vermelha de desobstrução
Figura 16 – Mangueiras de saída de filtrado no tanque de filtrado
Abriu-se a válvula principal de ar e regulou-se a pressão de entrada de ar em 7 bar com a válvula de agulha, conforme mostra a figura 11, após o processo de secagem da torta fechou-se a alimentação, recolheu-se o líquido retirado da torta no tanque de filtrado e fecharam-se as válvulas de entrada de ar e as de saída do filtrado.
Esvaziou-se o coletor auxiliar no tanque principal de filtrado. Logo após, descarregou-se a pressão do sistema hidráulico colocando-se a válvula na posição “ABRE”, conforme a seta amarela e vermelha indicada na figura 17. A operação de descompressão faz com que as placas do filtro se separem, e com isso coletou-se a torta gerada na filtração.
Figura 17 – Posição da chave de alivio de pressão
Dados dinâmicos registrados
Tabela 2 – Altura da suspensão no tanque
Tempo (s) Altura (cm) 0 25, 6’23’’ 23, 15’36’’ 20, 23’57’’ 17, 36’17’’ 13, 47’35’’ 13, 54’18’’ 12,
Tabela 3 – Altura do líquido filtrado coletado Altura (cm)
12,
Tabela 4 – Temperatura da água Temperatura (ºC)
20
Figura 18- Dimensões de altura, largura e comprimento do cubo
Tabela 6 – Resultados
Para chegar nesse resultado, foi necessário atentar-se à pressão constante de 70 bar do sistema hidráulico que foi exercida nas placas, nas válvulas de entrada e saída de ar e alimentação de suspensão, além de, observar a quantidade de ciclos para encerramento da bomba de acordo com o tempo de 30 segundos.
Em virtude do que foi mencionado, ao utilizar o filtro prensa, a desvantagem é o processo ser em batelada, manutenção problemática por conta deste processo e a eficiência da filtração é bastante sensível a variação da característica do resíduo. A vantagem entre os processos de separação mecânica é a que a filtração em batelada consegue retirar mais umidade da torta.
Levando-se em conta o que foi observado, o funcionamento do filtro prensa ocorre por meio de processo mecânico que trata-se da separação do particulado e do filtrado por meio de uma membrana porosa.
Em virtude do que foi mencionado, para um bom resultado, deve-se monitorar a pressão que é exercida nas placas, às válvulas de entrada e saída de ar e alimentação de suspensão, além de, observar a quantidade de ciclos para encerramento do processo.
Portanto, após a realização dos cálculos para se achar a umidade da torta, encontrou-se que a mesma apresenta umidade igual a 41,68%, ou seja, apresentando 58,32% de massa seca. Em pesquisas, encontrou-se que filtros prensa apresentam uma torta seca acima de 60%, dependendo de sua finalidade, podendo dizer então que tal diferença ocorreu devido a problemas técnicos do aparelho, como por exemplo, a baixa pressão da linha de ar.
Comparando o resultado de 40,50% obtido por outro grupo e, sendo 41,68%, o obtido pelo grupo, conclui-se que o mesmo está coerente.