
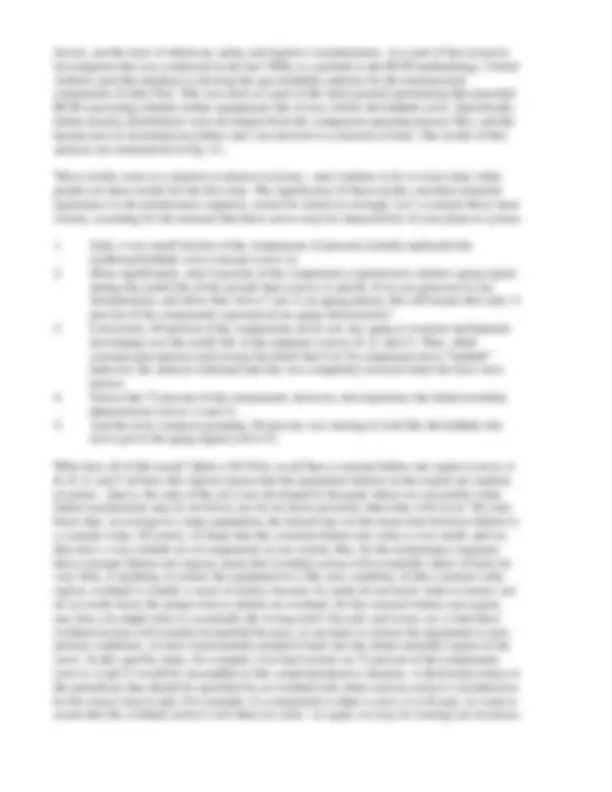
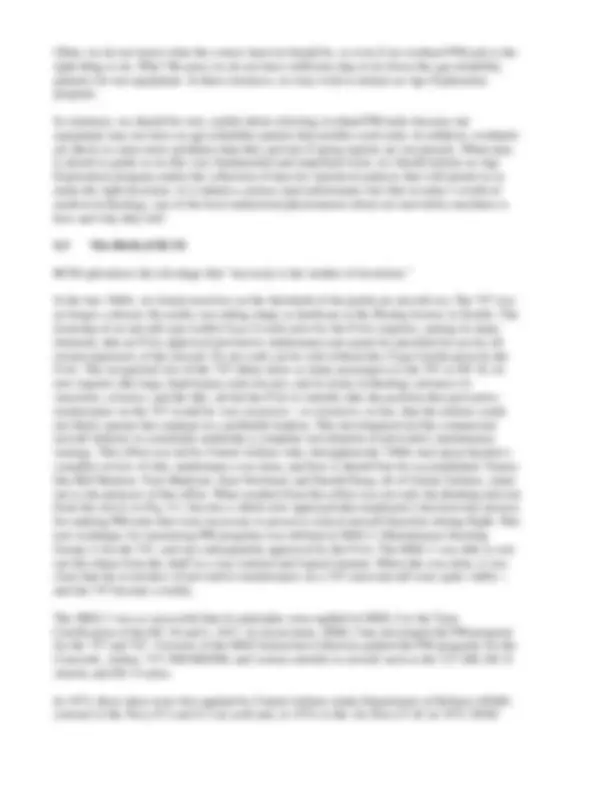
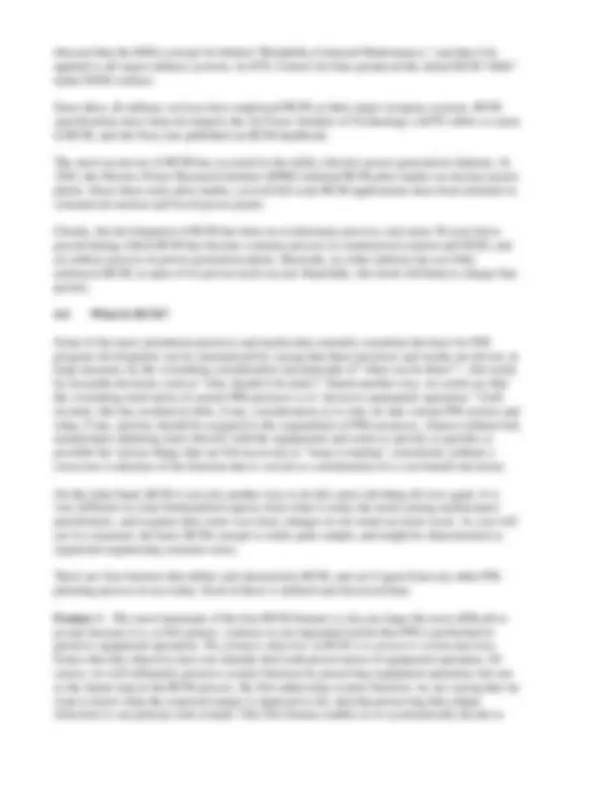
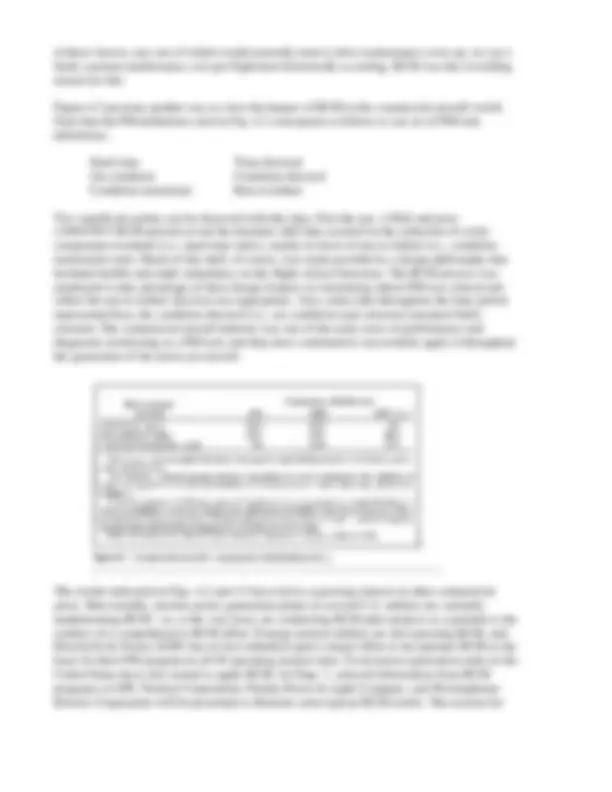
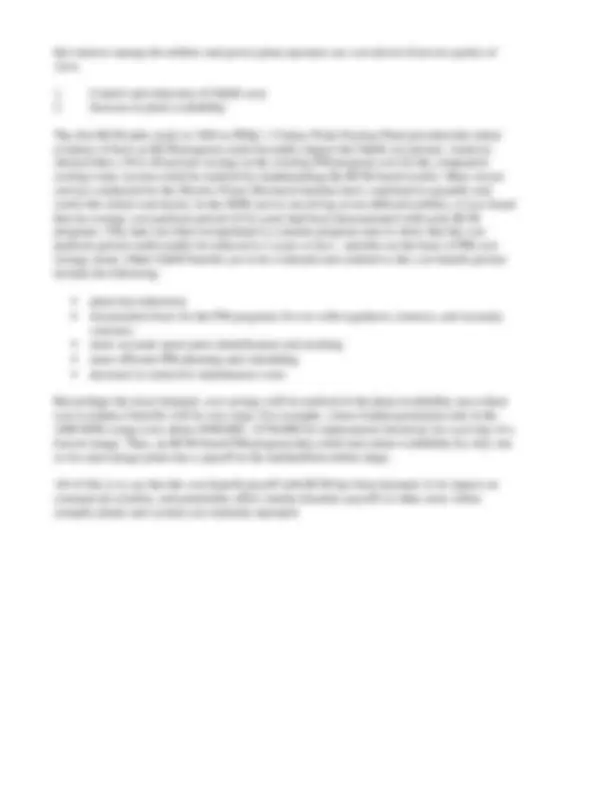
Estude fácil! Tem muito documento disponível na Docsity
Ganhe pontos ajudando outros esrudantes ou compre um plano Premium
Prepare-se para as provas
Estude fácil! Tem muito documento disponível na Docsity
Prepare-se para as provas com trabalhos de outros alunos como você, aqui na Docsity
Os melhores documentos à venda: Trabalhos de alunos formados
Prepare-se com as videoaulas e exercícios resolvidos criados a partir da grade da sua Universidade
Responda perguntas de provas passadas e avalie sua preparação.
Ganhe pontos para baixar
Ganhe pontos ajudando outros esrudantes ou compre um plano Premium
Comunidade
Peça ajuda à comunidade e tire suas dúvidas relacionadas ao estudo
Descubra as melhores universidades em seu país de acordo com os usuários da Docsity
Guias grátis
Baixe gratuitamente nossos guias de estudo, métodos para diminuir a ansiedade, dicas de TCC preparadas pelos professores da Docsity
rcm - reliability centered mainte
Tipologia: Notas de estudo
1 / 9
Esta página não é visível na pré-visualização
Não perca as partes importantes!
By: Anthony M. Smith, PE.
Chapter 4
RCM—A Proven Approach
In this chapter, we will introduce the basic concepts that constitute what is known as Reliability- Centered Maintenance. Initially, however, we will briefly discuss how PM has evolved in the industrial world, and most importantly, we will look at how one of the basic tenets of reliability engineering—the “bathtub curve”—can and should influence the formulation of PM tasks. Next, we will look at how the commercial aviation industry was historically the motivating force behind the creation of the RCM methodology during the Type Certification process for the 747 aircraft in the 1960s. Finally, we will itemize the four basic features that constitute the necessary and sufficient conditions or principles that define RCM, and discuss some of the cost-benefit considerations that can accrue through the use of RCM.
4.1 Some Historical Background
If we look back to the days of the Industrial Revolution, we find that the designers of the new industrial equipment were also the builders and operators of that equipment. At the very least, they had a close relationship with the hardware that evolved from their creative genius, and as a result they truly did “know” their equipment—what worked, how well, and for how long; what broke, how to fix it, and, yes, how to take certain reasonable (not too expensive) actions to prevent it from breaking. In the beginning, then, experience did in fact play the major role in formulating PM actions. And, most importantly, these experience-based actions derived from those people who had not just maintenance experience, but also design, fabrication, and operation knowledge. Within the limits of then available technology, these engineers were usually correct in their PM decisions.
As industry and technology became more sophisticated, corporations organized for greater efficiency and productivity. This, of course, was necessary and led to numerous advantages that ultimately gave us the high-volume production capability that swept us into the twentieth century. But some disadvantages occurred also. One of these was the separation of the design, build, and operate roles into distinct organizational entities where virtually no one individual would have the luxury of personally experiencing the entire gamut of a product cycle. Thus, the derivation of PM actions from experience began to lose some of its expertise.
Not to worry! Another technology came along to help us—reliability engineering. The early roots of reliability engineering trace back to the 1940s and 1950s. Much of its origin resides in the early work with electronic populations where it was found that early failures (or infant mortalities) occurred for some period of time at a high but decreasing rate until the population would settle into a long period of constant failure rate. It was also observed that some devices (e.g., tubes) would finally reach some point in their operating life where the failure rate would
again sharply increase, and aging or wearout mechanisms would start to quickly kill off the surviving population. (This scenario, of course, also very accurately describes age-reliability characteristics of the human population.) Engineers, especially in the nonelectronic world, were quick to pick up on this finding, and to use it as a basis for developing a maintenance strategy. The picture we have just described is the well-known bathtub curve. Its characteristic shape led the maintenance engineer to conclude that the vast majority of the PM actions should be directed to over-hauls where the equipment would be restored to like-new condition before it progressed too far into the wearout regime.
Thus, until the early 1960s, we saw equipment preventive maintenance based in large measure on the concept that the equipment followed the bathtub shape, and that overhaul at some point near the initiation of the increasing failure-rate region was the right thing to do.
4.2 The “Bathtub Curve” Fallacy
As this title suggests, all may not be totally well with the bathtub curve. True, some devices may follow its general shape, but the fact is that more has been assumed along those lines than has actually been measured and proven to be the case. As those with even a cursory knowledge of statistics and reliability theory can attest, this is not surprising, because large sample sizes are
required in order to accurately develop the population age-reliability characteristics of any given device, component, or system. And such large samples, with recorded data on operating times and failures, are hard to come by.
The commercial aviation industry, however, does have fairly large populations of identical or similar components in their aircraft fleets— components that are common to several aircraft types. And, as an industry, they have made some deliberate and successful efforts to accumulate a database of operating history on these components. Such a database is driven by several
Often, we do not know what the correct interval should be, or even if an overhaul PM task is the right thing to do. Why? Because we do not have sufficient data to tie down the age-reliability patterns for our equipment. In these instances, we may wish to initiate an Age Exploration program.
In summary, we should be very careful about selecting overhaul PM tasks because our equipment may not have an age-reliability pattern that justifies such tasks. In addition, overhauls are likely to cause more problems than they prevent if aging regions are not present. When data is absent to guide us on this very fundamental and important issue, we should initiate an Age Exploration program and/or the collection of data for statistical analyses that will permit us to make the right decisions. It is indeed a curious (and unfortunate) fact that in today’s world of modern technology, one of the least understood phenomenon about our marvelous machines is how and why they fail!
4.3 The Birth of RCM
RCM epitomizes the old adage that “necessity is the mother of invention.”
In the late 1960s, we found ourselves on the threshold of the jumbo jet aircraft era. The 747 was no longer a dream; the reality was taking shape as hardware at the Boeing factory in Seattle. The licensing of an aircraft type (called Type Certification by the FAA) requires, among its many elements, that an FAA-approved preventive maintenance pro-gram be specified for use by all owners/operators of the aircraft. No air-craft can be sold without this Type Certification by the FAA. The recognized size of the 747 (three times as many passengers as the 707 or DC-8), its new engines (the large, high bypass ratio fan jet), and its many technology advances in structures, avionics, and the like, all led the FAA to initially take the position that preventive maintenance on the 747 would be very extensive—so extensive, in fact, that the airlines could not likely operate this airplane in a profitable fashion. This development led the commercial aircraft industry to essentially undertake a complete reevaluation of preventive maintenance strategy. This effort was led by United Airlines who, throughout the 1960s, had spear-headed a complete review of why maintenance was done, and how it should best be accomplished. Names like Bill Mentzer, Tom Matteson, Stan Nowland, and Harold Heap, all of United Airlines, stand out as the pioneers of this effort. What resulted from this effort was not only the thinking derived from the curves in Fig. 4.1, but also a whole new approach that employed a decision-tree process for ranking PM tasks that were necessary to preserve critical aircraft functions during flight. This new technique for structuring PM programs was defined in MSG-1 (Maintenance Steering Group-1) for the 747, and was subsequently approved by the FAA. The MSG-1 was able to sort out the wheat from the chaff in a very rational and logical manner. When this was done, it was clear that the economics of preventive maintenance on a 747-sized aircraft were quite viable— and the 747 became a reality.
The MSG-1 was so successful that its principles were applied in MSG-2 to the Type Certification of the DC-10 and L-1011. In recent times, MSG-3 has developed the PM program for the 757 and 767. Versions of the MSG format have likewise guided the PM programs for the Concorde, Airbus, 737-300/400/500, and various retrofits to aircraft such as the 727-200, DC- stretch, and DC-9 series.
In 1972, these ideas were first applied by United Airlines under Department of Defense (DOD) contract to the Navy P-3 and S-3 air-craft and, in 1974, to the Air Force F-4J. In 1975, DOD
directed that the MSG concept be labeled “Reliability-Centered Maintenance,” and that it be applied to all major military systems. In i978, United Air-lines produced the initial RCM “bible” under DOD contract.
Since then, all military services have employed RCM on their major weapons systems. RCM specifications have been developed, the Air Force Institute of Technology (AFIT) offers a course in RCM, and the Navy has published an RCM handbook.
The most recent use of RCM has occurred in the utility (electric power generation) industry. In 1983, the Electric Power Research Institute (EPRI) initiated RCM pilot studies on nuclear power plants. Since these early pilot studies, several full-scale RCM applications have been initiated in commercial nuclear and fossil power plants.
Clearly, the development of RCM has been an evolutionary process, and some 30 years have passed during which RCM has become a mature process in commercial aviation and DOD, and an embryo process in power generation plants. Basically, no other industry has yet fully embraced RCM, in spite of its proven track record. Hopefully, this book will help to change that picture.
4.4 What Is RCM?
Some of the more prominent practices and myths that currently constitute the basis for PM program development can be summarized by saying that these practices and myths are driven, in large measure, by the overriding consideration and principle of “what can be done?”—but rarely by traceable decisions such as “why should it be done?” Stated another way, we could say that the overriding motivation of current PM practices is to “preserve equipment operation.” Until recently, this has resulted in little, if any, consideration as to why we take certain PM actions and what, if any, priority should be assigned to the expenditure of PM resources. Almost without fail, maintenance planning starts directly with the equipments and seeks to specify as quickly as possible the various things that are felt necessary to “keep it running” (sometimes without a conscious evaluation of the function that is served or consideration of a cost-benefit decision).
On the other hand, RCM is not just another way to do this same old thing all over again. It is very different in some fundamental aspects from what is today the norm among maintenance practitioners, and requires that some very basic changes in our mind-set must occur. As you will see in a moment, the basic RCM concept is really quite simple, and might be characterized as organized engineering common sense.
There are four features that define and characterize RCM, and set it apart from any other PM planning process in use today. Each of these is defined and discussed here.
Feature 1. The most important of the four RCM features is also per-haps the most difficult to accept because it is, at first glance, contrary to our ingrained notion that PM is performed to preserve equipment operation. The primary objective of RCM is to preserve system function. Notice that this objective does not initially deal with preservation of equipment operation. Of course, we will ultimately preserve system function by preserving equipment operation, but not as the initial step in the RCM process. By first addressing system function, we are saying that we want to know what the expected output is supposed to be, and that preserving that output (function) is our primary task at hand. This first feature enables us to systematically decide in
establish specific PM tasks. We thus address each failure mode, in its prioritized order, to identify candidate PM actions that could be considered. And here, RCM again has one last unique feature that must be satisfied. Each potential PM task must be judged as being “applicable and effective.” Applicable means that if the task is performed, it will in fact accomplish one of the three reasons for doing PM (i.e., prevent or mitigate failure, detect onset of a failure, or discover a hidden failure). Effective means that we are willing to spend the resources to do it. Generally, if more than one candidate task is judged to be applicable, we would opt to select the least expensive (i.e., most effective) task. Recalling, that when describing a run-to-failure task category, there are three reasons for making such a selection - failure of a task to pass either the applicability or effectiveness test results in two of the run-to-failure decisions, while the third would be associated with a low-priority ranking and a decision not to spend PM resources on such insignificant failure modes.
In summary, then, the RCM methodology is completely described in four unique features:
4.5 Some Cost-Benefit Considerations
As noted earlier, the primary driving force behind the invention of RCM was the need to develop a PM strategy that could adequately address system availability and safety without creating a totally impractical cost requirement. This has clearly been successfully achieved by commercial aircraft; however, quantitative data in the public arena on this cost picture is rather scarce.
Figure 4.2 presents maintenance cost per flight hour in the first 10 years of RCM use. What we see in Fig. 4.2 is a maintenance cost that is essentially constant from the late 1960s to the early 1980s. This is precisely the period during which the 747, DC-10, and L-1O11 were introduced into revenue service on a large scale. These jumbo jets not only introduced the large increase in passenger capability per aircraft (about 3 times over the 707 and DC-8), but also a higher daily usage rate and the deployment of several advanced technologies into everyday use. In spite of all
of these factors, any one of which would normally tend to drive maintenance costs up, we see a fairly constant maintenance cost per flight hour historically occurring. RCM was the overriding reason for this.
Figure 4.3 presents another way to view the impact of RCM in the commercial aircraft world. Note that the PM definitions used in Fig. 4.3 correspond as follows to our set of PM task definitions:
Hard-time Time-directed On-condition Condition-directed Condition-monitored Run-to-failure
Two significant points can be observed with this data. First the pre- (1964) and post- (1969/1987) RCM periods reveal the dramatic shift that occurred in the reduction of costly component overhauls (i.e., hard-time tasks), mainly in favor of run-to-failure (i.e., condition- monitored) tasks. Much of this shift, of course, was made possible by a design philosophy that included double and triple redundancy in the flight-critical functions. The RCM process was employed to take advantage of these design features in structuring where PM was critical and where the run-to-failure decision was appropriate. Also, notice that throughout the time period represented here, the condition-directed (i.e., on-condition) task structure remained fairly constant. The commercial aircraft industry was one of the early users of performance and diagnostic monitoring as a PM tool, and they have continued to successfully apply it throughout the generation of the newer jet aircraft.
The results indicated in Figs. 4.2 and 4.3 have led to a growing interest in other commercial areas. Most notably, nuclear power generation plants in several U.S. utilities are currently implementing RCM—or, at the very least, are conducting RCM pilot projects as a prelude to the conduct of a comprehensive RCM effort. Foreign nuclear utilities are also pursuing RCM, and Electricité de France (EDF) has in fact embarked upon a major effort to incorporate RCM as the basis for their PM program in all 50 operating nuclear units. Fossil power generation units in the United States have also started to apply RCM. In Chap. 7, selected information from RCM programs at GPU Nuclear Corporation, Florida Power & Light Company, and Westinghouse Electric Corporation will be presented to illustrate some typical RCM results. The reasons for