
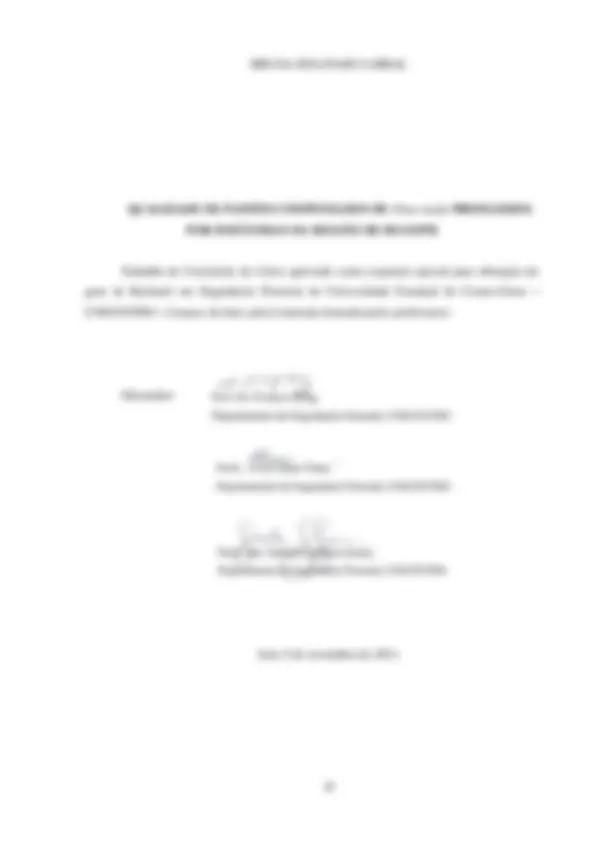
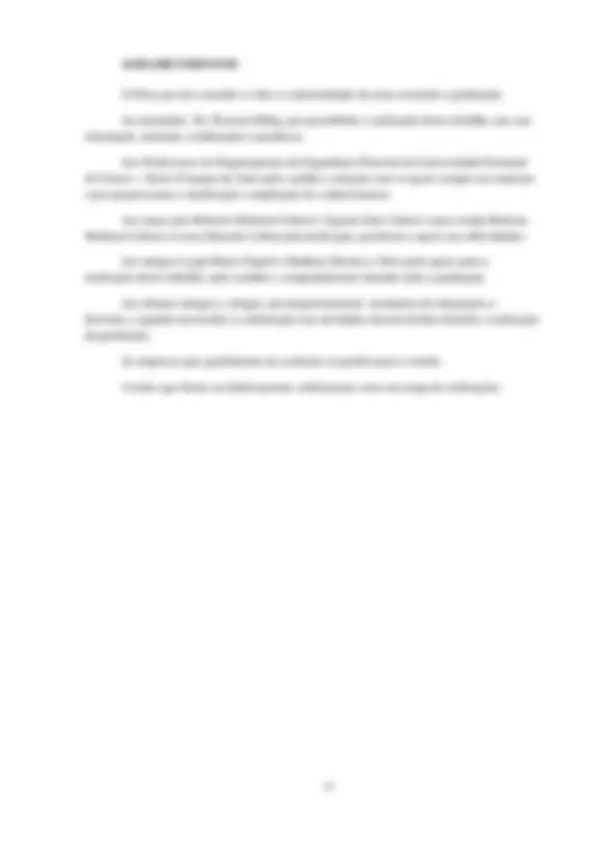
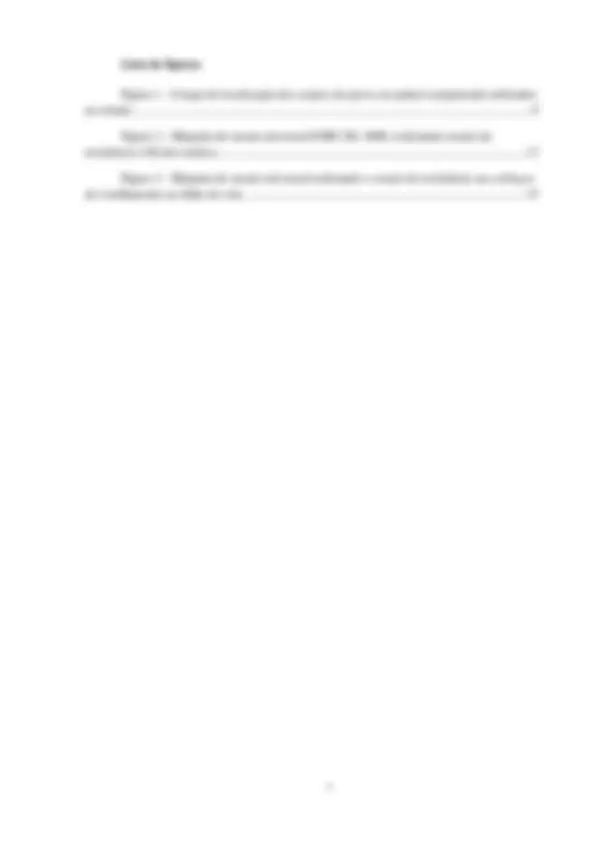
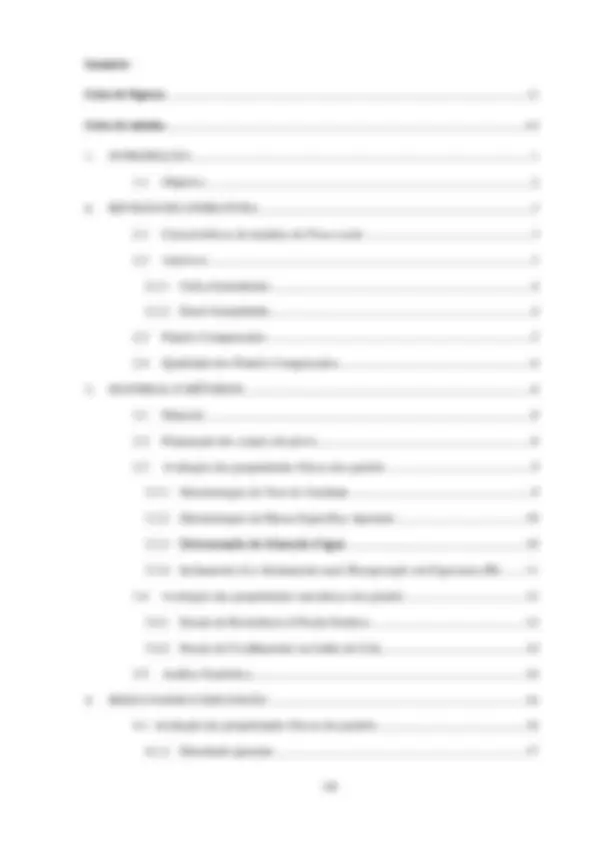
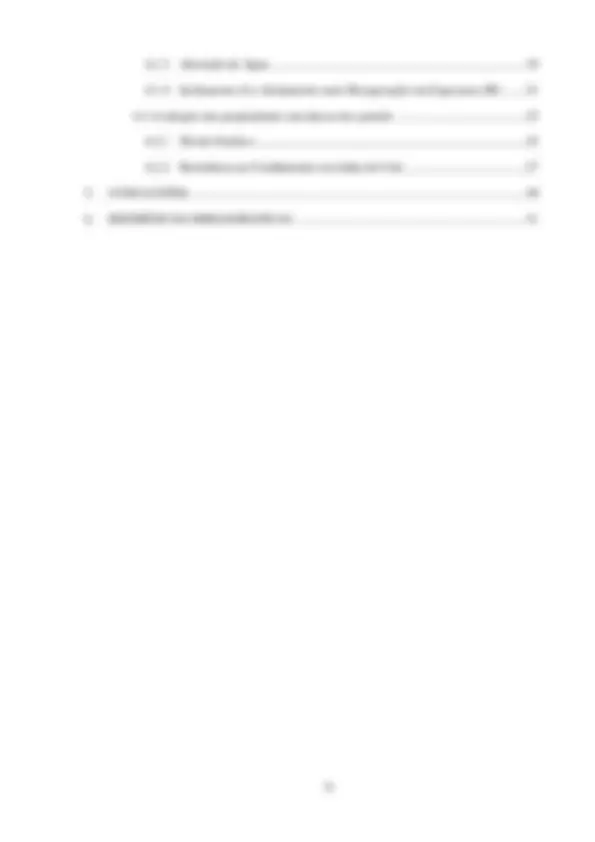
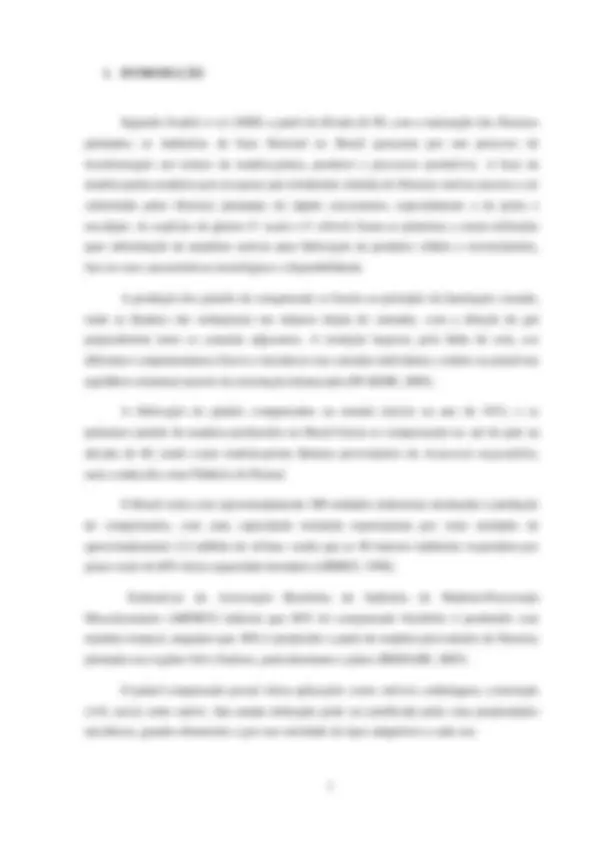
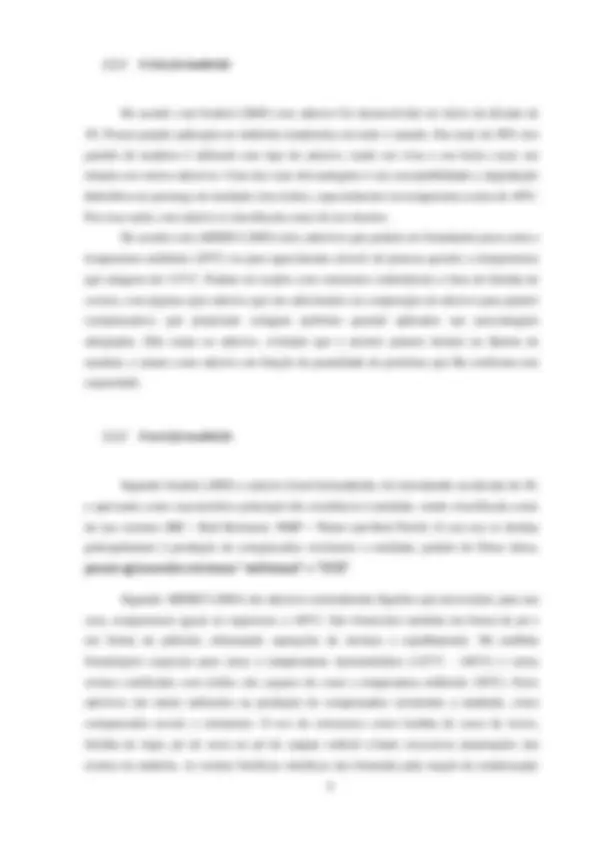
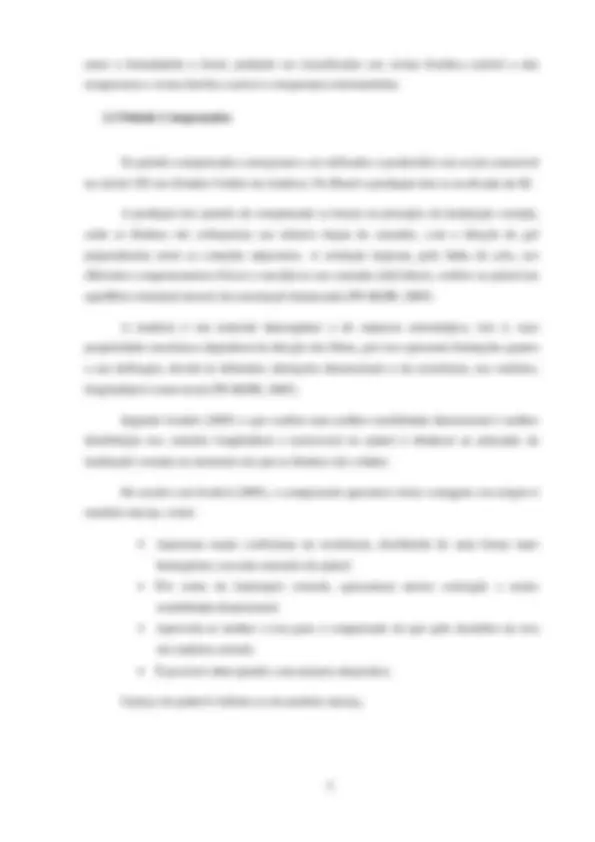
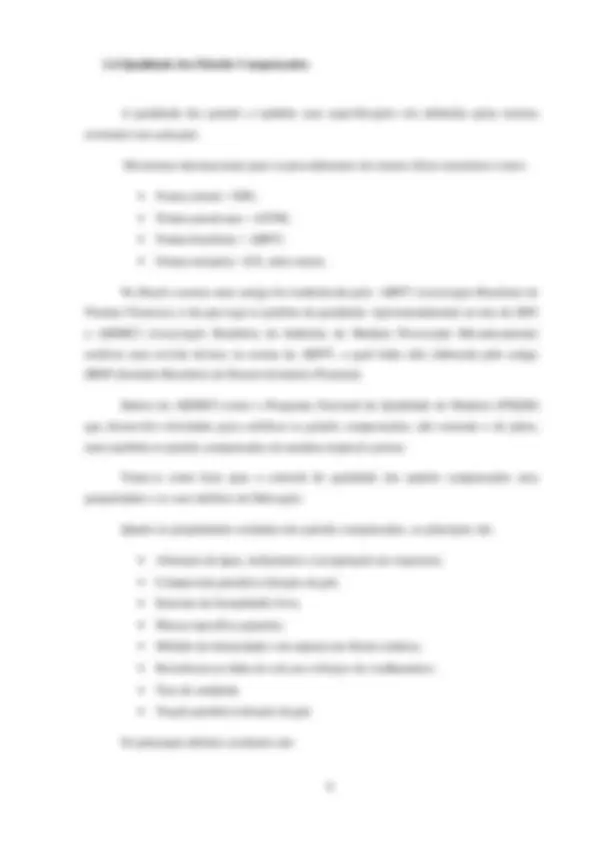
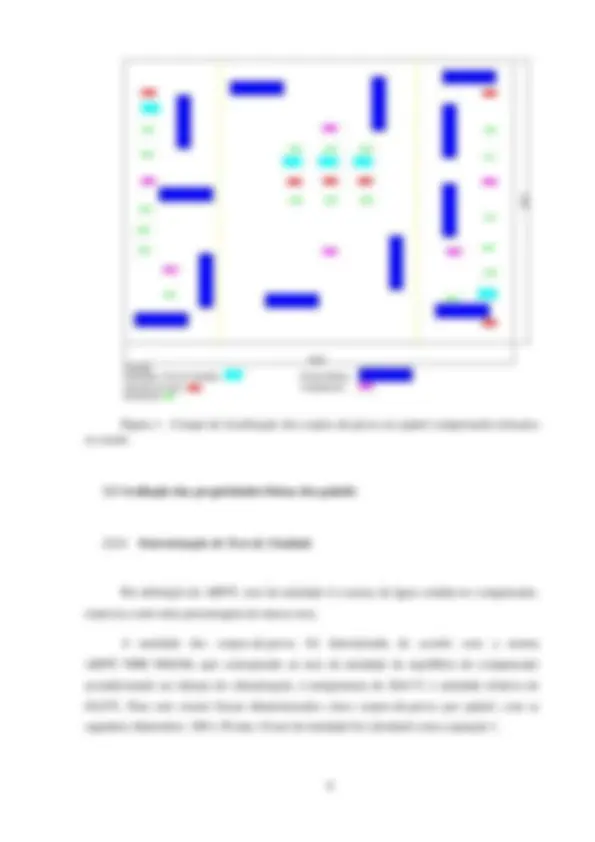
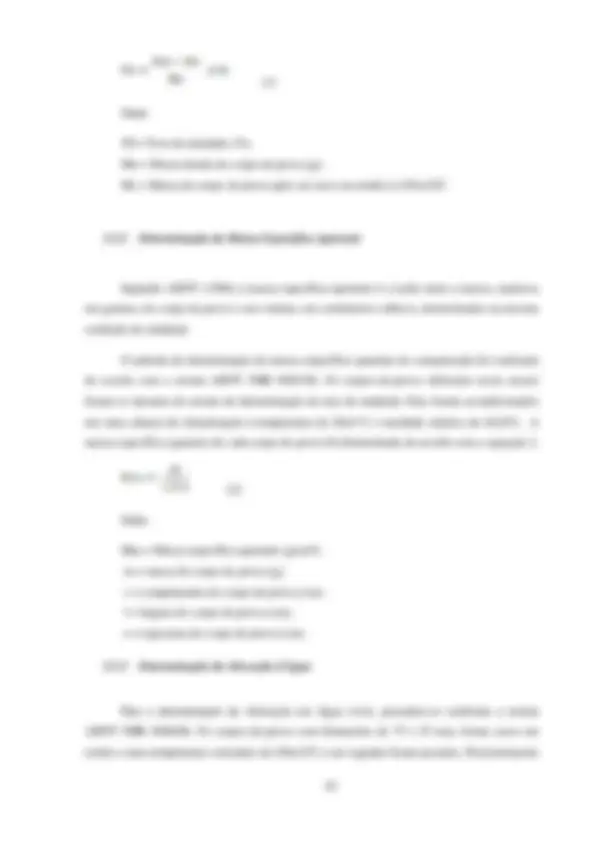
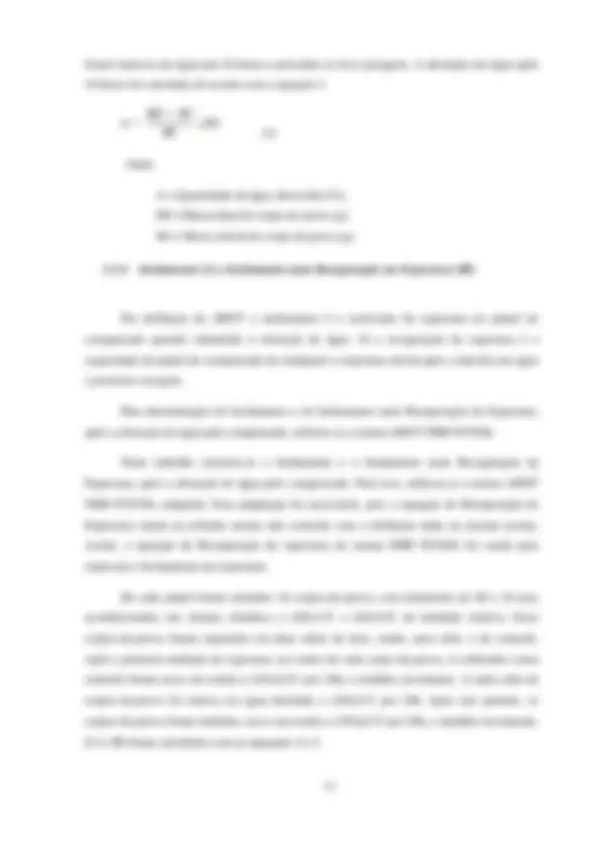
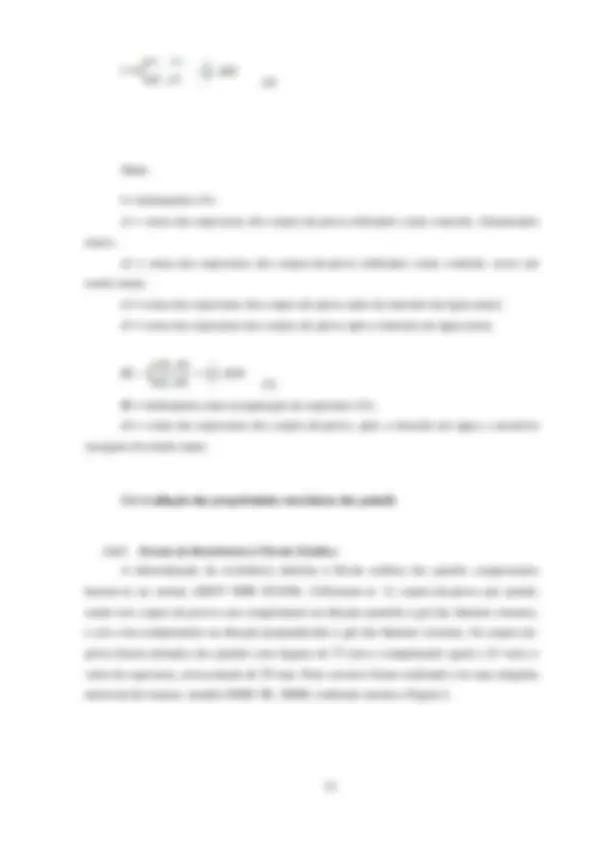
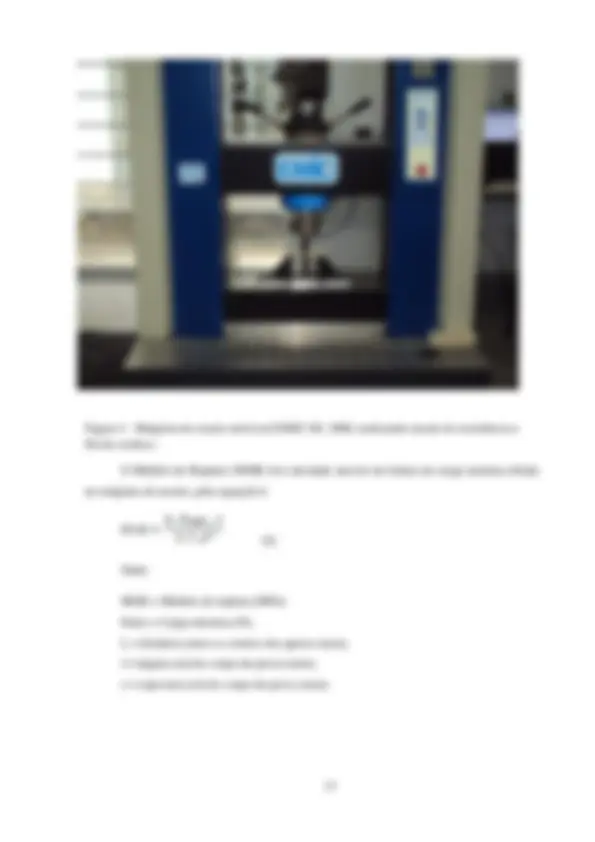
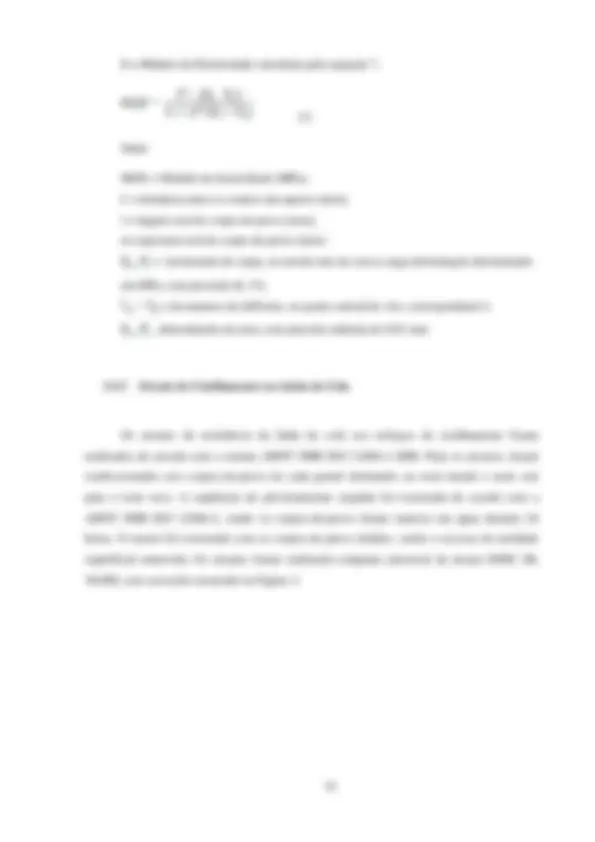
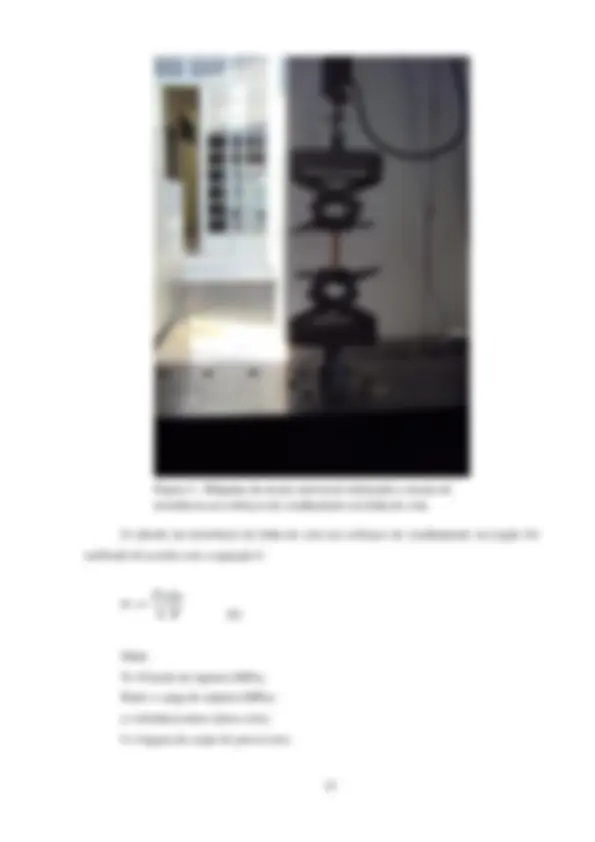
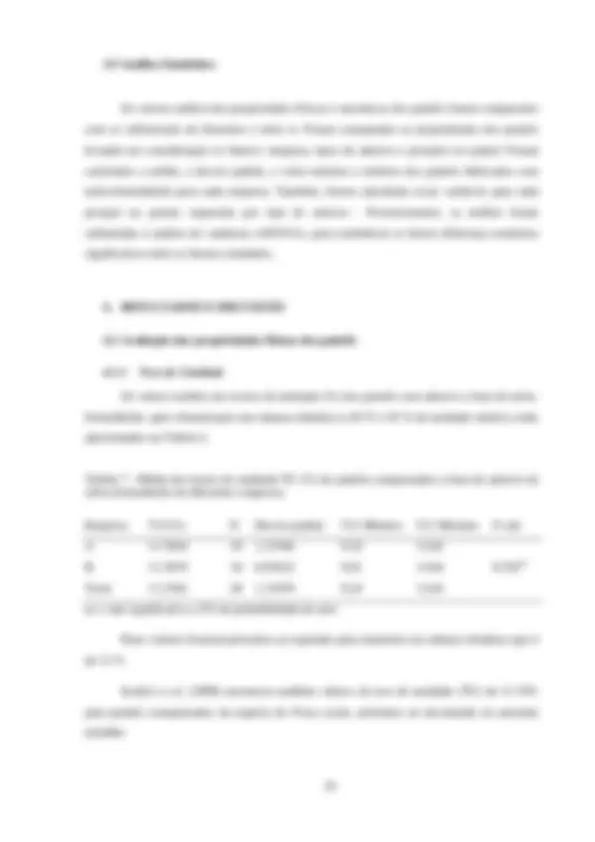
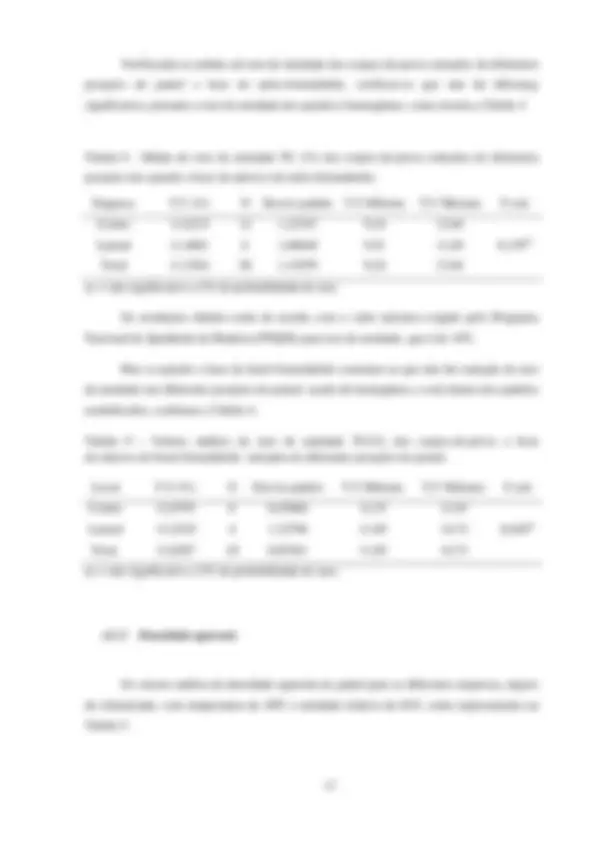
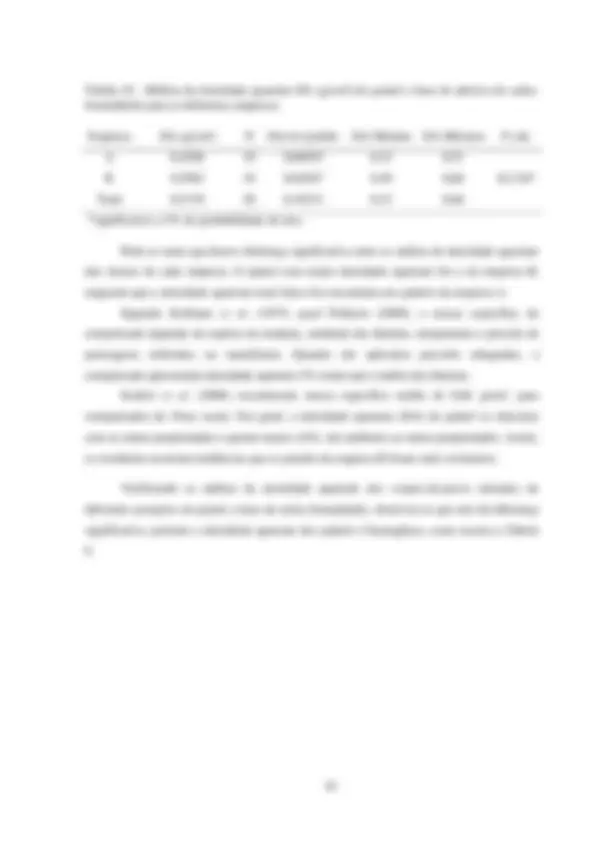
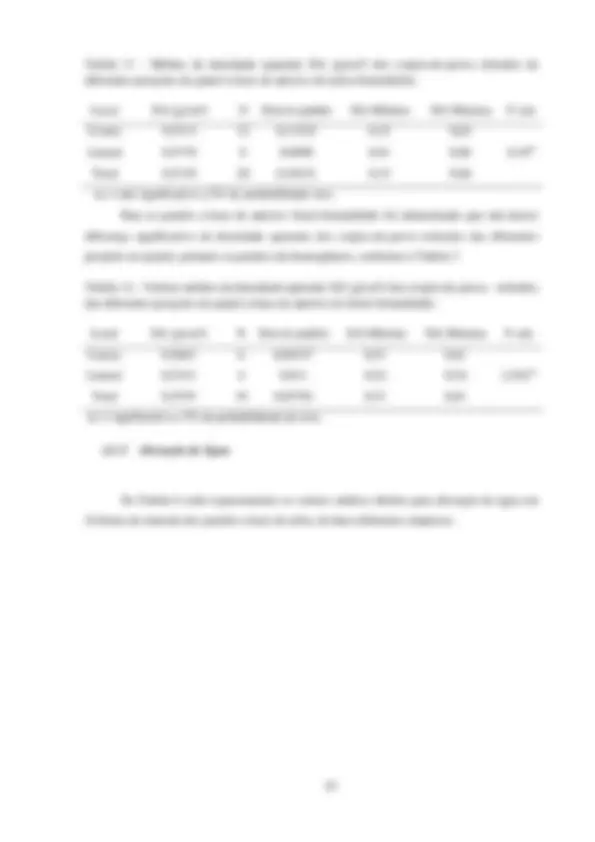
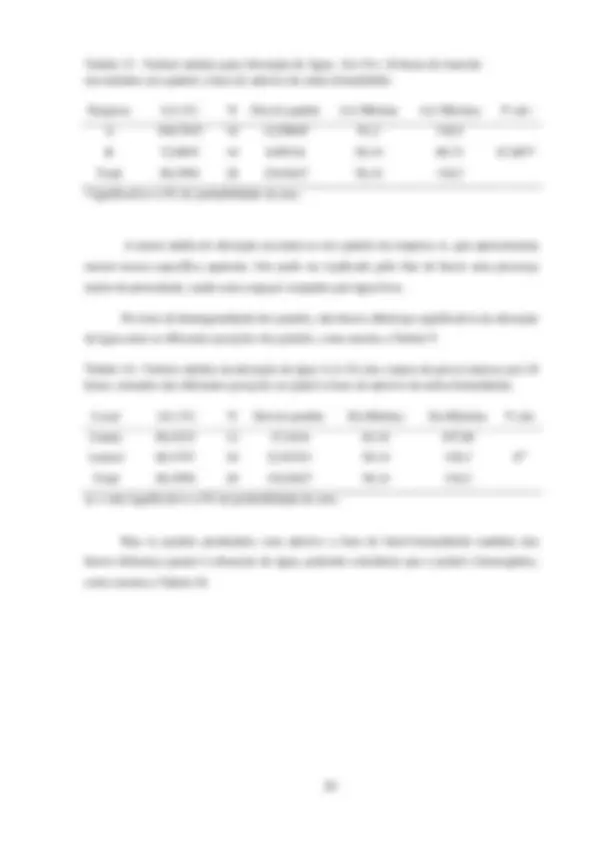
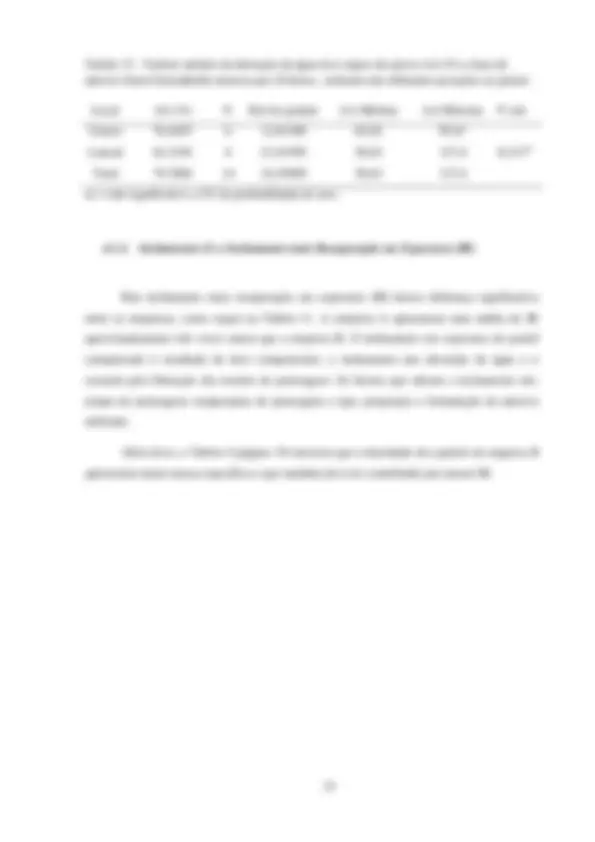
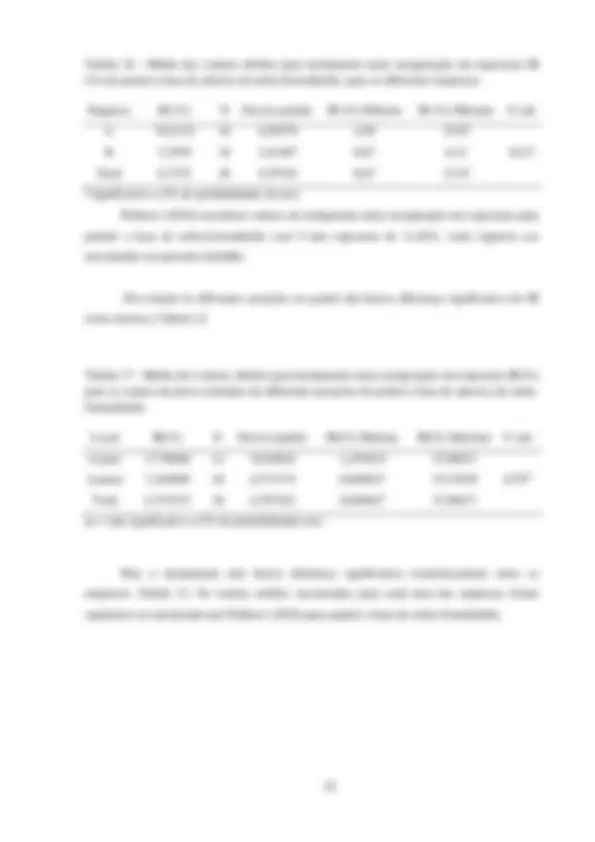
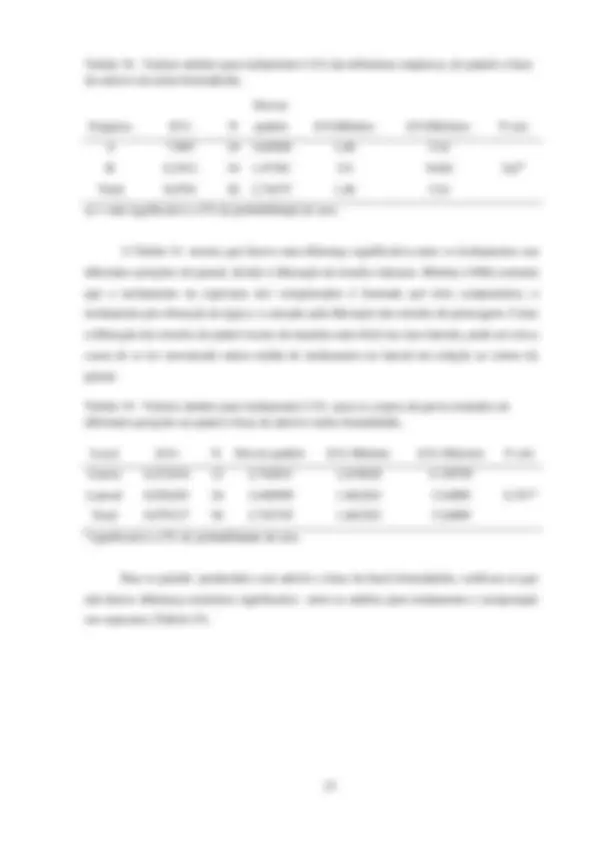
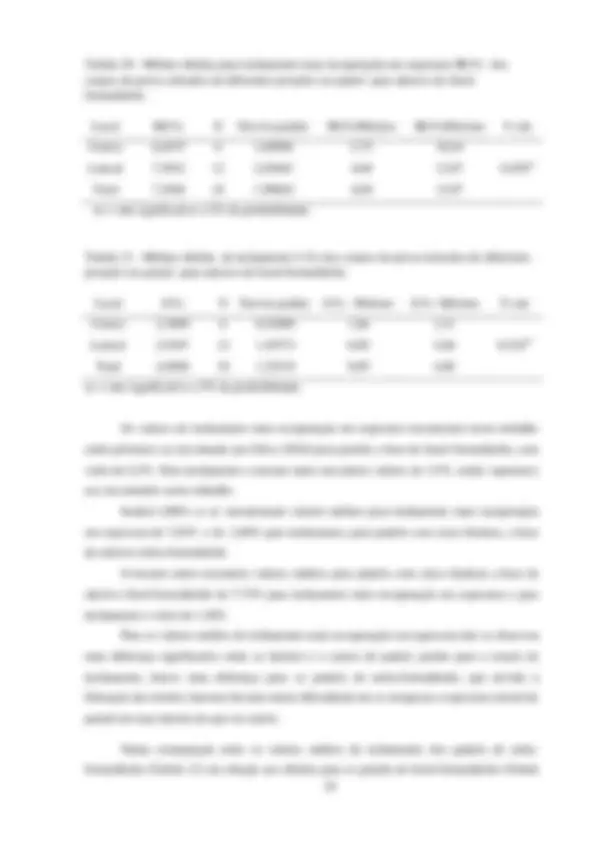
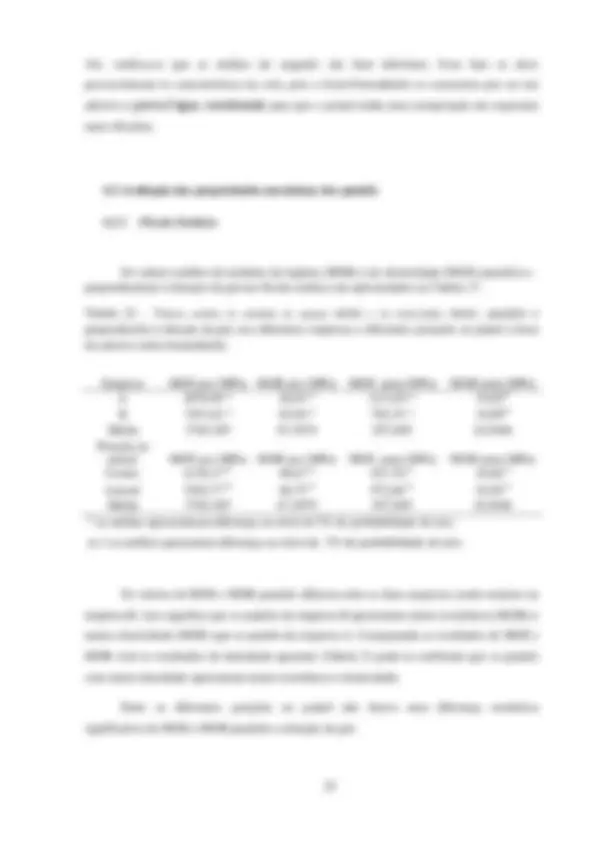
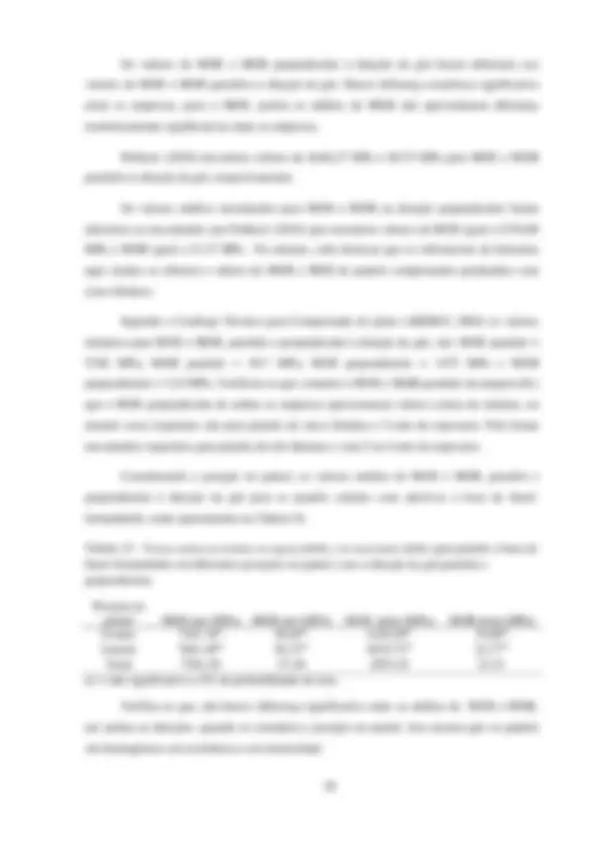
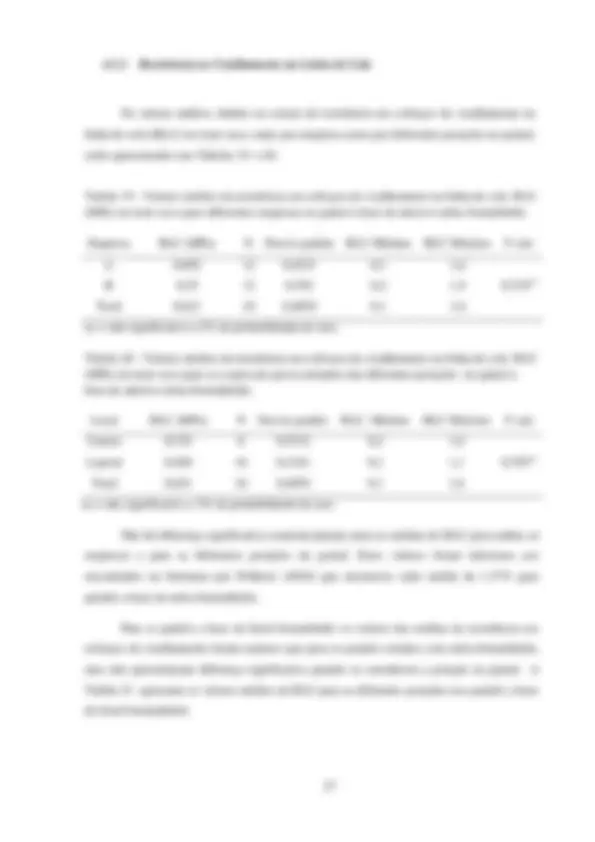
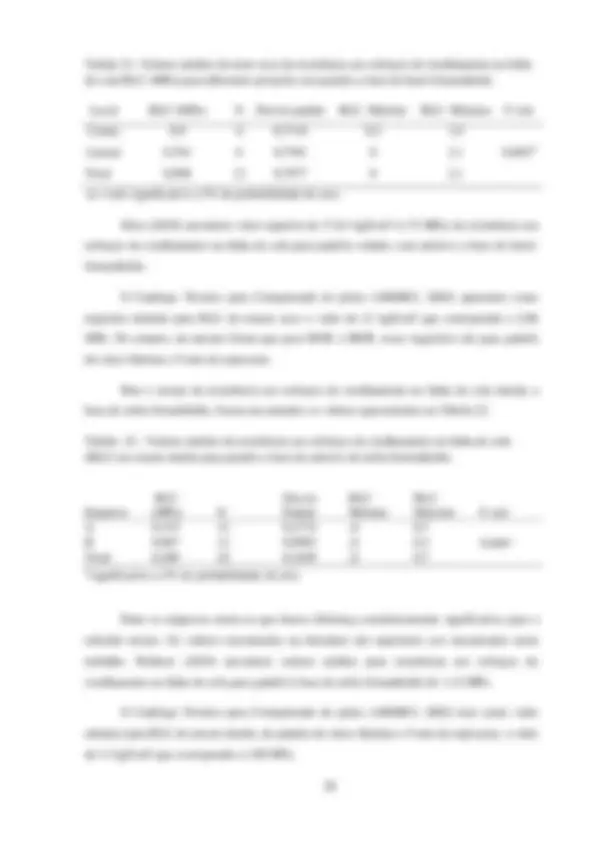
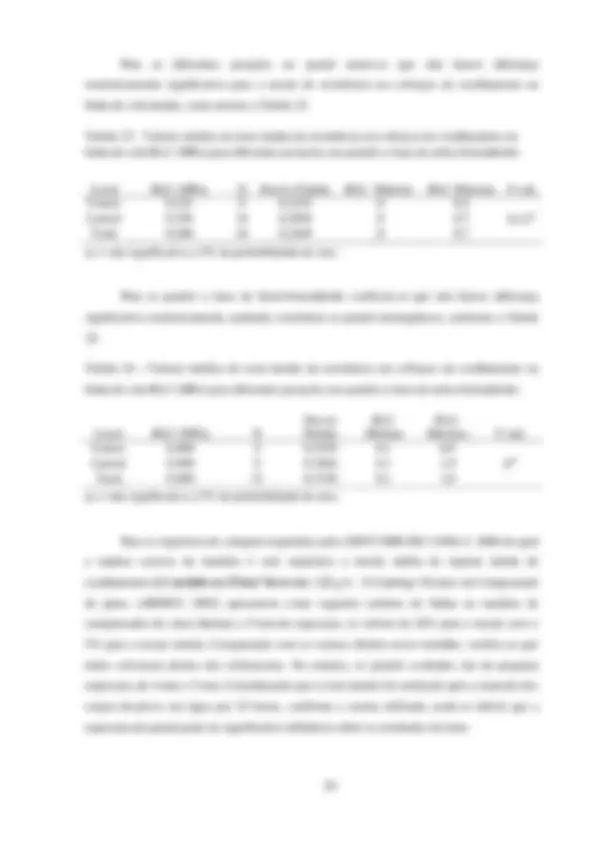
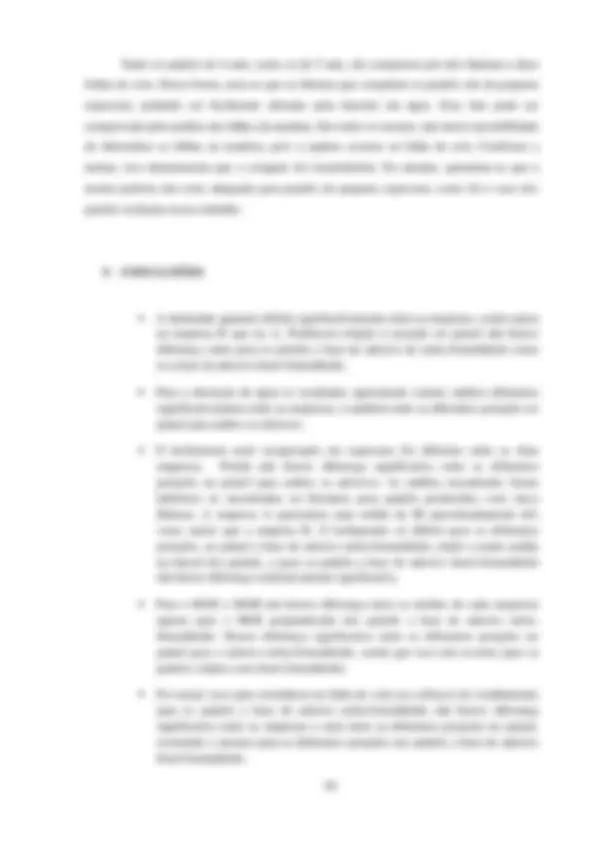
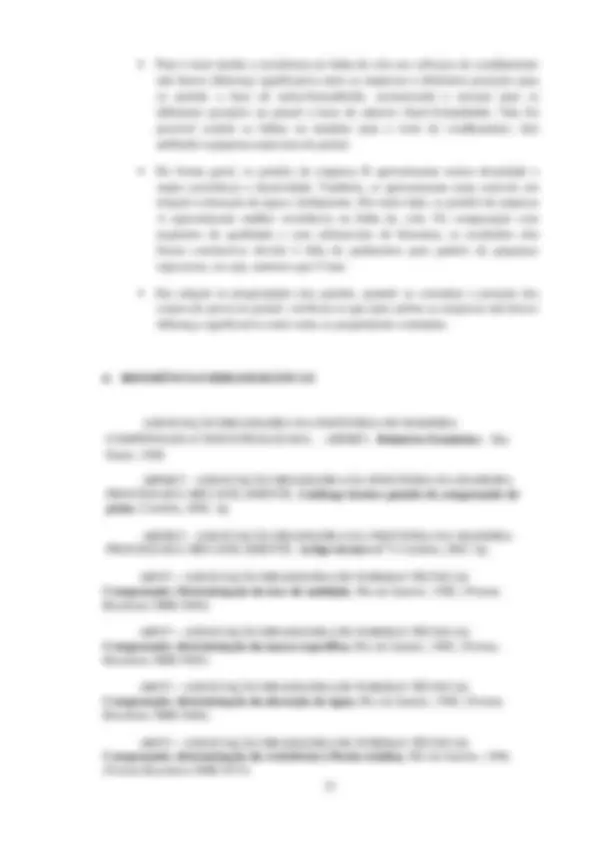
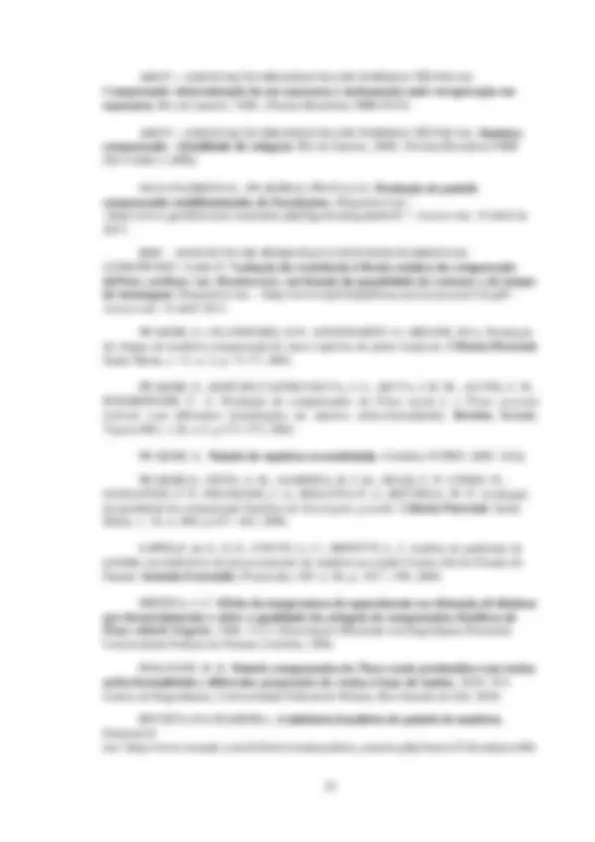
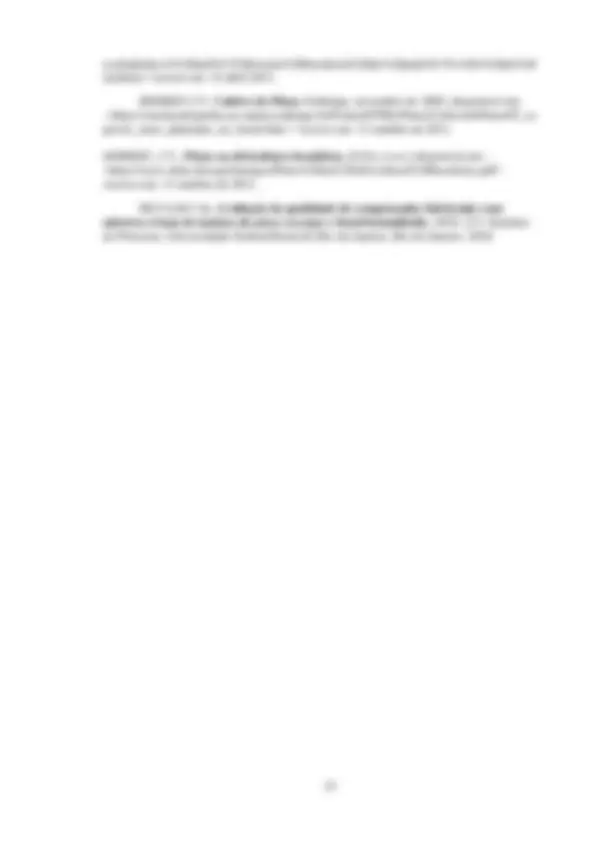
Estude fácil! Tem muito documento disponível na Docsity
Ganhe pontos ajudando outros esrudantes ou compre um plano Premium
Prepare-se para as provas
Estude fácil! Tem muito documento disponível na Docsity
Prepare-se para as provas com trabalhos de outros alunos como você, aqui na Docsity
Os melhores documentos à venda: Trabalhos de alunos formados
Prepare-se com as videoaulas e exercícios resolvidos criados a partir da grade da sua Universidade
Responda perguntas de provas passadas e avalie sua preparação.
Ganhe pontos para baixar
Ganhe pontos ajudando outros esrudantes ou compre um plano Premium
Comunidade
Peça ajuda à comunidade e tire suas dúvidas relacionadas ao estudo
Descubra as melhores universidades em seu país de acordo com os usuários da Docsity
Guias grátis
Baixe gratuitamente nossos guias de estudo, métodos para diminuir a ansiedade, dicas de TCC preparadas pelos professores da Docsity
Trabalho de Conclusão de Curso
Tipologia: Trabalhos
1 / 42
Esta página não é visível na pré-visualização
Não perca as partes importantes!
QUALIDADE DE PAINÉIS COMPENSADOS DE Pinus taeda PRODUZIDOS POR INDÚSTRIAS DA REGIÃO DE IRATI/PR
QUALIDADE DE PAINÉIS COMPENSADOS DE Pinus taeda PRODUZIDOS POR INDÚSTRIAS DA REGIÃO DE IRATI/PR
Monografia apresentada ao Curso de Engenharia Florestal, como requisito parcial para obtenção do Título de Engenheiro Florestal, Setor de Ciências Agrárias e Ambientais, Universidade Estadual do Centro-Oeste – UNICENTRO – Campus de Irati. Orientador: Prof. Dr. Éverton Hillig
iv
À Deus por me conceder a vida e a oportunidade de estar cursando a graduação. Ao orientador Dr. Éverton Hillig, por possibilitar a realização deste trabalho, por sua orientação, amizade, colaboração e paciência.
Aos Professores do Departamento de Engenharia Florestal da Universidade Estadual do Centro – Oeste (Campus de Irati) pelo carinho e atenção com os quais sempre me trataram e por proporcionar a atualização e ampliação de conhecimentos.
Aos meus pais Roberto Mulinari Cabral e Águeda Inês Cabral e meus irmão Roberta Mulinari Cabral e Lucas Eduardo Cabral pela dedicação, paciência e apoio nas dificuldades.
Aos amigos Lygia Maria Napoli e Matheus Moraes e Silva pelo apoio para a realização deste trabalho, pelo carinho e companheirismo durante toda a graduação.
Aos demais amigos e colegas, por proporcionarem momentos de integração e diversão, e quando necessário a colaboração nas atividades desenvolvidas durante a realização da graduação.
Às empresas que gentilmente me cederam os painéis para o estudo. A todos que direta ou indiretamente colaboraram com esta etapa de realizações.
v
Lista de figuras Figura 1 - Croqui de localização dos corpos-de-prova no painel compensado utilizados no estudo. .................................................................................................................................... 9
Figura 2 - Máquina de ensaio universal EMIC DL 3000, realizando ensaio de resistência à flexão estática....................................................................................................... 13
Figura 3 - Máquina de ensaio universal realizando o ensaio de resistência aos esforços do cisalhamento na linha de cola. ............................................................................................. 15
vii
Tabela 15 - Médias obtidas para inchamento mais recuperação em espessura IR(%) dos corpos-de-prova retirados de diferentes posições no painel para adesivo de fenol- formaldeído. .............................................................................................................................. 24
Tabela 5 - Médias obtidas de inchamento I (%) dos corpos-de-prova retirados de diferentes posições no painel para adesivo de fenol-formaldeído........................
Tabela 17 - Valores médios de módulos de ruptura (MOR) e de elasticidade (MOE), paralelo e perpendicular à direção da grã, nas diferentes empresas e diferentes posições no painel a base de adesivo uréia-formaldeído. ............................................................................. 25
Tabela 18 - Valores médios de módulos de ruptura (MOR) e de elasticidade (MOE) para painéis a base de fenol-formaldeído em diferentes posições no painel, com a direção da grã paralela e perpendicular. ..................................................................................................... 26
Tabela 19 - Valores médios da resistência aos esforços do cisalhamento na linha de cola RLC (MPa) no teste seco para diferentes empresas no painel a base de adesivo uréia- formaldeído.............................................................................................................................. 27
Tabela 20 - Valores médios da resistência aos esforços do cisalhamento na linha de cola RLC (MPa) no teste seco para os corpos-de-prova retirados das diferentes posições no painel a base de adesivo uréia-formaldeído. ............................................................................. 27
Tabela 21- Valores médios do teste seco da resistência aos esforços do cisalhamento na linha de cola RLC (MPa) para diferentes posições nos painéis a base de fenol-formaldeído. .................................................................................................................................................. 28 Tabela 22 - Valores médios de resistência aos esforços do cisalhamento na linha de cola (RLC) no ensaio úmido para painéis a base de adesivo de uréia- formaldeído...............................................................................................................................
Tabela 23 - Valores médios do teste úmido da resistência aos esforços do cisalhamento na linha de cola RLC (MPa) para diferentes posições nos painéis a base de uréia-formaldeído. .................................................................................................................................................. 29 Tabela 24 - Valores médios do teste úmido da resistência aos esforços do cisalhamento na linha de cola RLC (MPa) para diferentes posições nos painéis a base de uréia-formaldeído ...................................................................................................................................................
Sumário
Lista de figuras .........................................................................................................................vi
Segundo Iwakiri et al. (2008) a partir da década de 80, com a maturação das florestas plantadas, as indústrias de base florestal no Brasil passaram por um processo de transformação em termos de matéria-prima, produtos e processos produtivos. A base da matéria-prima madeira que era quase que totalmente oriunda de florestas nativas passou a ser substituída pelas florestas plantadas de rápido crescimento, especialmente a de pinus e eucalipto. As espécies do gênero P. taeda e P. elliottii foram as primeiras a serem utilizadas para substituição de madeiras nativas para fabricação de produtos sólidos e reconstituídos, face às suas características tecnológicas e disponibilidade.
A produção dos painéis de compensado se baseia no princípio da laminação cruzada, onde as lâminas são sobrepostas em número ímpar de camadas, com a direção da grã perpendicular entre as camadas adjacentes. A restrição imposta, pela linha de cola, aos diferentes comportamentos físicos e mecânicos nas camadas individuais, confere ao painel um equilíbrio estrutural através da construção balanceada (IWAKIRI, 2005).
A fabricação de painéis compensados no mundo iniciou no ano de 1913, e os primeiros painéis de madeira produzidos no Brasil foram os compensados no sul do país na década de 40, tendo como matéria-prima lâminas provenientes da Araucaria angustifolia , mais conhecida como Pinheiro do Paraná.
O Brasil conta com aproximadamente 300 unidades industriais destinadas à produção de compensados, com uma capacidade instalada representada por estas unidades de aproximadamente 2,2 milhões de m³/ano, sendo que as 40 maiores indústrias respondem por pouco mais de 60% desta capacidade instalada (ABIMCI, 1998).
Estimativas da Associação Brasileira da Indústria de Madeira Processada Mecanicamente (ABIMCI) indicam que 60% do compensado brasileiro é produzido com madeira tropical, enquanto que 40% é produzido a partir de madeira proveniente de florestas plantadas nas regiões Sul e Sudeste, particularmente o pinus (REMADE, 2003).
O painel compensado possui várias aplicações como: móveis, embalagens, construção civil, naval, entre outros. Sua ampla utilização pode ser justificada pelas suas propriedades mecânicas, grandes dimensões e por sua variedade de tipos adaptáveis a cada uso.
Atualmente, a madeira de pinus é utilizada na produção de serrados e de painéis compensados.
Os painéis compensados podem ser destinados para uso interno e externo, dependendo do adesivo que será usado e do local de utilização. Compensados produzidos com adesivos pouco resistentes a umidade, são recomendados para uso interno, como é o caso dos adesivos a base de uréia-formaldeído. Os compensados produzidos com adesivos a base de fenol- formaldeído são resistentes a umidade, portanto são adequados ao uso externo. Estes dois adesivos são os mais utilizados na colagem da madeira e dos seus subprodutos.
Segundo Jankowsky (1980) a qualidade do painel compensado relaciona-se com a qualidade das lâminas utilizadas e com as variáveis envolvidas no processamento, principalmente a espécie de madeira, o adesivo (tipo, qualidade e formulação), e tempo de montagem do painel.
Segundo ANCESPAR^1 (2001) apud Lopes et al. (2004) a região Centro-Sul do Paraná é caracterizada por possuir extensos reflorestamentos e inúmeras indústrias de base florestal, com destaque para as serrarias e as indústrias de laminação, compensados, aglomerados e moveleiras.
Nesse cenário, é importante que se desenvolvam trabalhos junto às indústrias de base florestal, procurando auxiliar as empresas na busca por produtos de melhor qualidade e na eficiência do processo produtivo.
1.1 Objetivo
O objetivo geral do trabalho foi avaliar a qualidade dos painéis compensados de pequenas espessuras produzidos por duas empresas da região de Irati – PR.
Os objetivos específicos foram: Avaliar as propriedades físico-mecânicas de painéis compensados produzidos por duas indústrias;
(^1) ANCESPAR – Associação dos Municípios da Região Centro – Sul do Estado do
Paraná. Relatório interno. Curitiba, 2001. (não publicado)
2.2.1 Uréia-formaldeído
De acordo com Iwakiri (2005) esse adesivo foi desenvolvido no início da década de
2.2.2 Fenol-formaldeído
Segundo Iwakiri (2005) o adesivo fenol-formaldeído, foi introduzido na década de 30, e apresenta como característica principal alta resistência à umidade, sendo classificada como de uso exterior (BR – Boil Resistent, WBP – Water and Boil Proof). O seu uso se destina principalmente à produção de compensados resistentes a umidade, painéis de fibras duras, painéis aglomerados estruturais “waferboard” e “OSB”.
Segundo ABIMCI (2003) são adesivos normalmente líquidos que necessitam, para sua cura, temperaturas iguais ou superiores a 140°C. São fornecidos também em forma de pó e em forma de película, eliminando operações de mistura e espalhamento. Há também formulações especiais para curas a temperaturas intermediárias (125°C - 140°C) e certas resinas catalizadas com ácidos são capazes de curar a temperatura ambiente (20°C). Estes adesivos são muito utilizados na produção de compensados resistentes a umidade, como compensados navais e estruturais. O uso de extensores como farinha de casca de nozes, farinha de trigo, pó de serra ou pó de sangue solúvel evitam excessivas penetrações das resinas na madeira. As resinas fenólicas sintéticas são formadas pela reação de condensação
entre o formaldeído e fenol, podendo ser classificadas em: resina fenólica curável a alta temperatura e resina fenólica curável a temperatura intermediária.
2.3 Painéis Compensados
Os painéis compensados começaram a ser utilizados e produzidos em escala comercial no século XX nos Estados Unidos da América. No Brasil a produção deu-se na década de 40.
A produção dos painéis de compensado se baseia no princípio da laminação cruzada, onde as lâminas são sobrepostas em número ímpar de camadas, com a direção da grã perpendicular entre as camadas adjacentes. A restrição imposta, pela linha de cola, aos diferentes comportamentos físicos e mecânicos nas camadas individuais, confere ao painel um equilíbrio estrutural através da construção balanceada (IWAKIRI, 2005).
A madeira é um material heterogêneo e de natureza anisotrópica, isto é, suas propriedades mecânicas dependem da direção das fibras, por isso apresenta limitações quanto a sua utilização, devido às diferentes alterações dimensionais e da resistência, nos sentidos, longitudinal e transversal (IWAKIRI, 2005).
Segundo Iwakiri (2005) o que confere uma melhor estabilidade dimensional e melhor distribuição nos sentidos longitudinal e transversal no painel é obedecer ao princípio da laminação cruzada no momento em que as lâminas são coladas.
De acordo com Iwakiri (2005), o compensado apresenta várias vantagens em relação à madeira maciça, como:
Apresenta maior coeficiente de resistência, distribuído de uma forma mais homogênea, em toda extensão do painel; Por conta da laminação cruzada, apresentam menor contração e maior estabilidade dimensional; Aproveita-se melhor a tora para o compensado do que pelo desdobro da tora em madeira serrada; É possível obter painéis com maiores dimensões; O preço do painel é inferior ao da madeira maciça.
Bolha; Delaminação; Defeitos abertos; Encavalamento; Ultrapassagem de cola. De acordo com Iwakiri (2005) a classificação dos painéis compensados pode ser realizada com base na qualidade das lâminas que irão compor a capa e contracapa do painel. As lâminas são previamente classificadas em:
Pinus: A, B, C+, C, D. A classificação genérica é realizada com base no local de utilização e de acordo com o adesivo que foi utilizado:
Interior (IR): Utilizado em locais protegidos da ação d’água ou alta umidade, colados com adesivo a base de uréia-formaldeído; Intermediário (IM): Utilizado em locais com alta umidade relativa podendo algumas vezes receber a ação de água, colados com adesivos a base de melamina-uréia-formaldeído; Externo (EX): Utilizados em ambientes externos ou fechados que são submetidos a umedecimento e secagem ou ação d’água, colados com adesivos a base de fenol-formaldeído. Segundo Medina (1986) durante a prensagem dos painéis compensados produz-se um incremento da densidade e tensões internas, fatores estes que afetam a estabilidade dimensional na direção da compressão. Quando o produto absorve água e incha, parte das tensões internas é liberada, e é a causa disto que quando o produto é seco não consegue retornar a sua espessura original. O inchamento na espessura dos compensados é formado por dois componentes, o inchamento por absorção de água e o causado pela liberação das tensões de prensagem.
De acordo com Wellons^2 (1983) apud Medina (1986) et al. o aumentando do tempo de prensagem aumenta a compressão, e por consequência crescem as tensões internas.
(^2) WELLONS, J. D.; KRAHMER, R.L.; SANDOE', M.D.; JOKERST, R.W. Thickness loss in hot- pressed plywood. For. Prod. J. , 33(1): 27-34, 1983.
3.1 Material
Para o desenvolvimento do trabalho, foram utilizados seis painéis compensados, cedidos por duas empresas da região de Irati – PR e montados com lâminas provenientes de madeira de Pinus taeda. Quatro painéis foram colados com adesivo a base de uréia- formaldeído e dois com fenol-formaldeído, conforme a Tabela 1.
Tabela 6 - Caracterização do material utilizado para o estudo.
Empresa Chapa Adesivo A 1 Uréia - fomaldeído A 2 Fenol - formaldeído A 3 Uréia - fomaldeído A 4 Fenol - formaldeído B 1 Uréia - fomaldeído B 2 Uréia - fomaldeído
Os painéis compensados cedidos pela empresa A, de três camadas, apresentaram dimensões de 1.220 mm de comprimento e 2.400 mm de largura, com espessura de 5 mm. Os painéis da empresa B, também de três camadas, possuíam dimensões de 1.600 mm de comprimento e 2.200 mm de largura, com espessura de 4 mm.
3.2 Preparação dos corpos-de-prova
Os cortes dos corpos-de-prova foram realizados com serra circular manual, para posteriormente serem acondicionados em uma câmara climática à temperatura de 20 ± 1°C e umidade relativa de 65 ± 5%, até atingirem umidade de equilíbrio à aproximadamente 12%, conforme as normas da Associação Brasileira de Normas Técnicas (ABNT, 1986).
Foram realizados cortes para obtenção de corpos-de-prova para os ensaios físicos de determinação da massa específica, determinação do teor de umidade, absorção de água, inchamento em espessura e para os ensaios mecânicos de flexão estática e cisalhamento na linha de cola. Foram retirados corpos-de-prova da região central e das regiões laterais de cada painel, conforme esquema de corte apresentado na Figura 1.
Onde: TU= Teor de umidade (%); Mu = Massa úmida do corpo de prova (g); Ms = Massa do corpo de prova após ser seco em estufa à (103±2)ºC.
3.3.2 Determinação da Massa Específica Aparente
Segundo ABNT (1986) a massa específica aparente é a razão entre a massa, expressa em gramas, do corpo de prova e seu volume, em centímetros cúbicos, determinados na mesma condição de umidade.
O método de determinação da massa específica aparente do compensado foi realizado de acordo com a norma ABNT NBR 9485/86. Os corpos-de-prova utilizados neste ensaio foram os mesmos do ensaio de determinação do teor de umidade. Eles foram acondicionados em uma câmara de climatização à temperatura de 20±1°C e umidade relativa de 65±5%. A massa específica aparente de cada corpo de prova foi determinada de acordo com a equação 2.
Onde: Mea = Massa específica aparente (g/cm³); m = massa do corpo de prova (g); c = comprimento do corpo de prova (cm); l = largura do corpo de prova (cm); e = espessura do corpo de prova (cm).
3.3.3 Determinação da Absorção d’água
Para a determinação da Absorção em Água (AA), procedeu-se conforme a norma ABNT NBR 9486/86. Os corpos-de-prova com dimensões de 75 x 25 mm, foram secos em estufa a uma temperatura constante de (50±2)ºC e em seguida foram pesados. Posteriormente
foram imersos em água por 24 horas e procedeu-se nova pesagem. A absorção em água após 24 horas foi calculada de acordo com a equação 3.
Onde: A = Quantidade de água absorvida (%); Mf = Massa final do corpo de prova (g); Mi = Massa inicial do corpo de prova (g).
3.3.4 Inchamento (I) e Inchamento mais Recuperação em Espessura (IR)
Por definição da ABNT o inchamento é o acréscimo da espessura do painel de compensado quando submetida à absorção de água. Já a recuperação da espessura é a capacidade do painel de compensado de readquirir a espessura inicial após a imersão em água e posterior secagem.
Para determinação do Inchamento e do Inchamento mais Recuperação da Espessura, após a absorção de água pelo compensado, utilizou-se a norma ABNT NRB 9535/86.
Neste trabalho calculou-se o Inchamento e o Inchamento mais Recuperação da Espessura, após a absorção de água pelo compensado. Para isso, utilizou-se a norma ABNT NRB 9535/86, adaptada. Essa adaptação foi necessária, pois a equação de Recuperação de Espessura citada na referida norma não coincide com a definição dada na mesma norma. Assim, a equação de Recuperação de espessura da norma NBR 9535/86 foi usada para expressar o Inchamento em espessura.
De cada painel foram retirados 18 corpos-de-prova, com dimensões de 60 x 10 mm, acondicionados em câmara climática a (20±1)°C e (65±5)% de umidade relativa. Estes corpos-de-prova foram separados em duas séries de dois, sendo, uma série, a de controle. Após a primeira medição de espessura, no centro de cada corpo-de-prova, os utilizados como controle foram secos em estufa a (103±2)°C por 24h, e medidos novamente. A outra série de corpos-de-prova foi imersa em água destilada a (20±2)°C por 24h. Após este período, os corpos-de-prova foram medidos, secos em estufa a (103±2)°C por 24h, e medidos novamente. O I e IR foram calculados com as equações 4 e 5.