
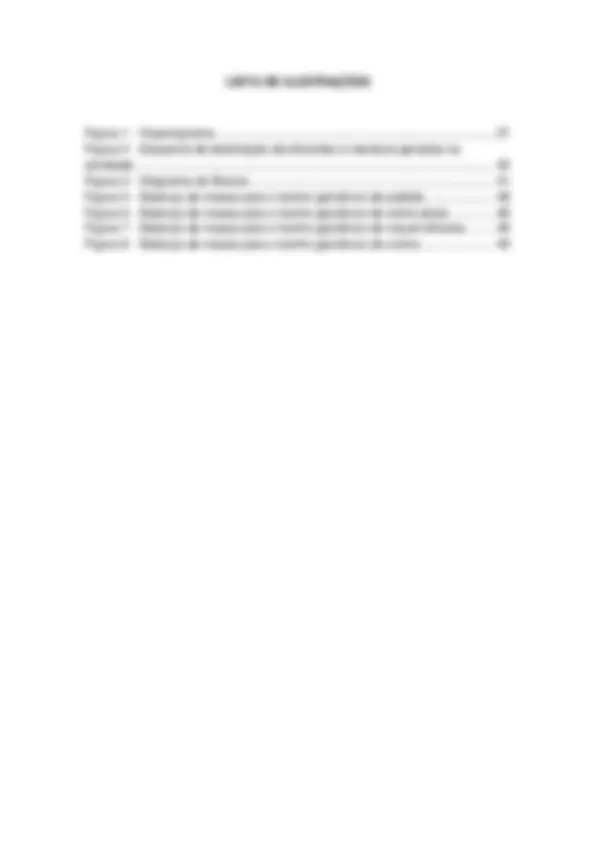
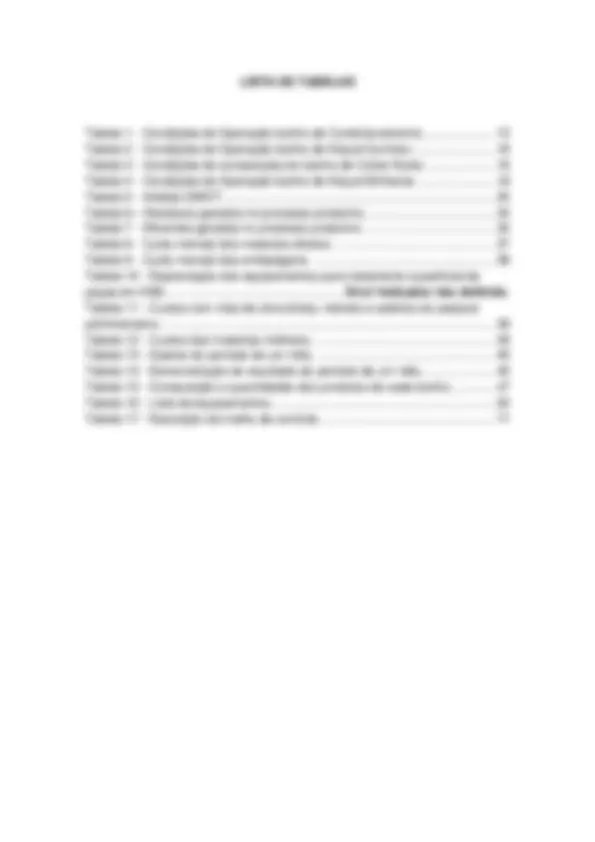
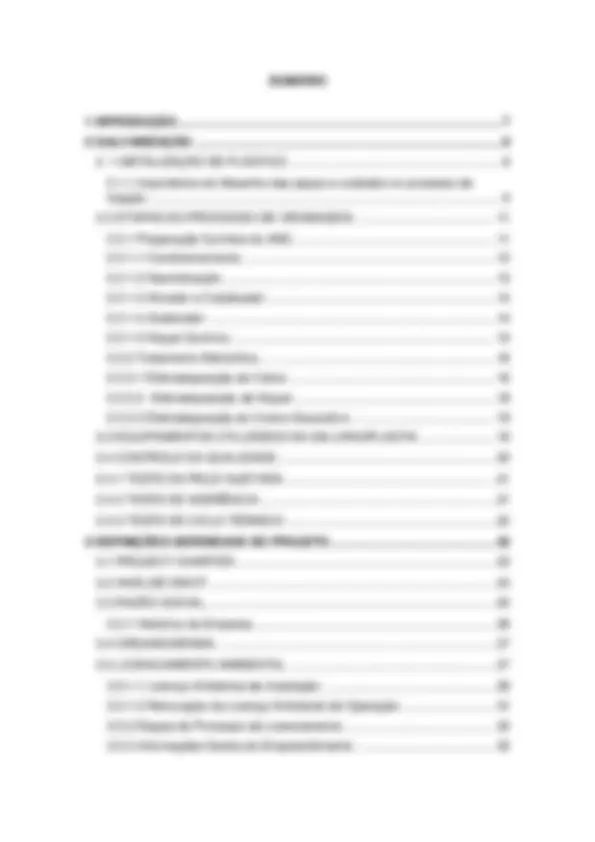
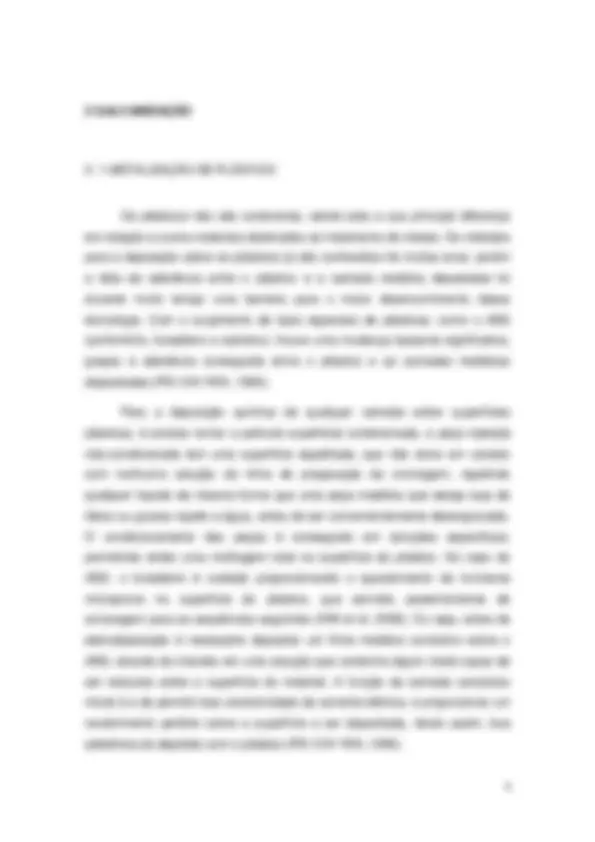
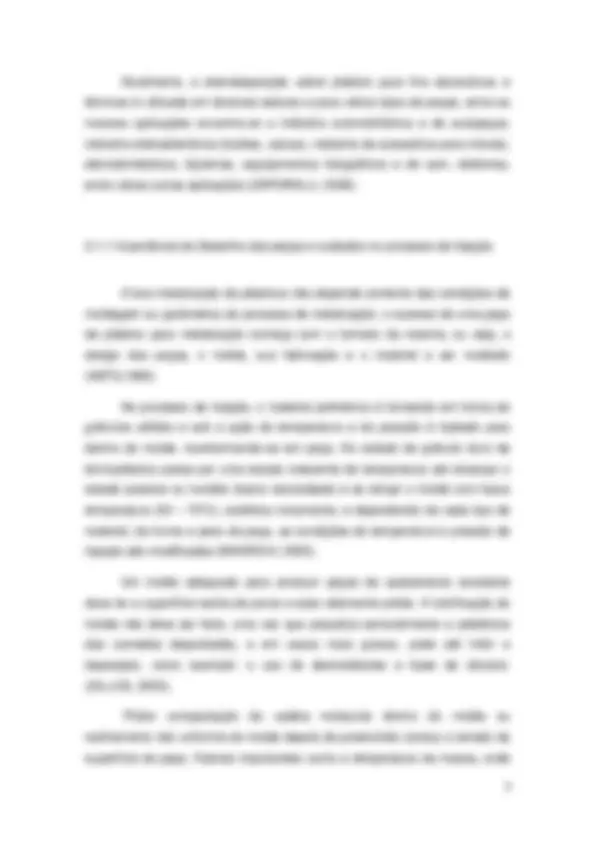
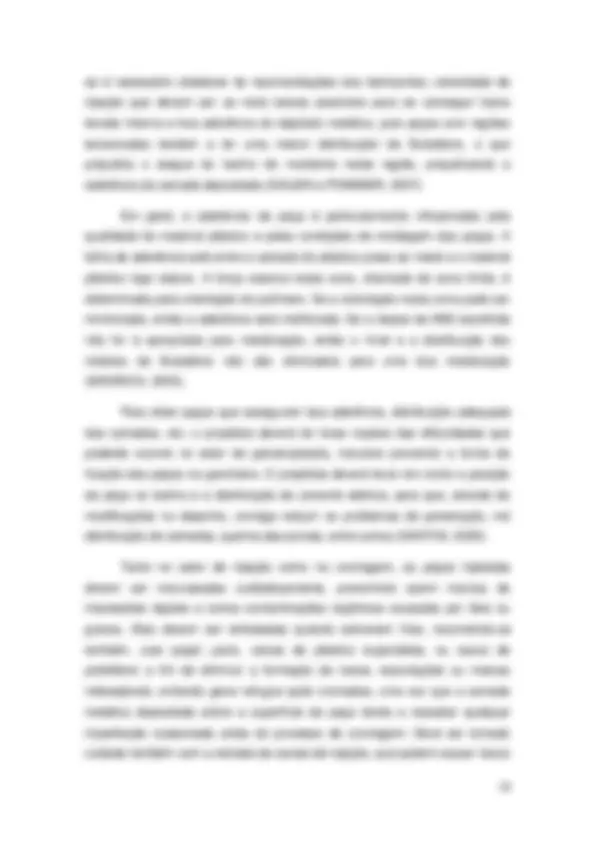
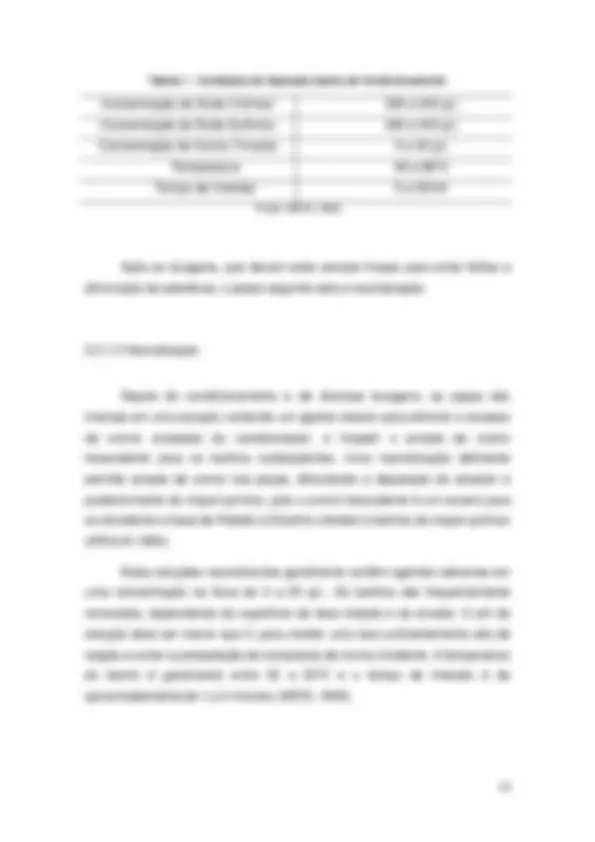
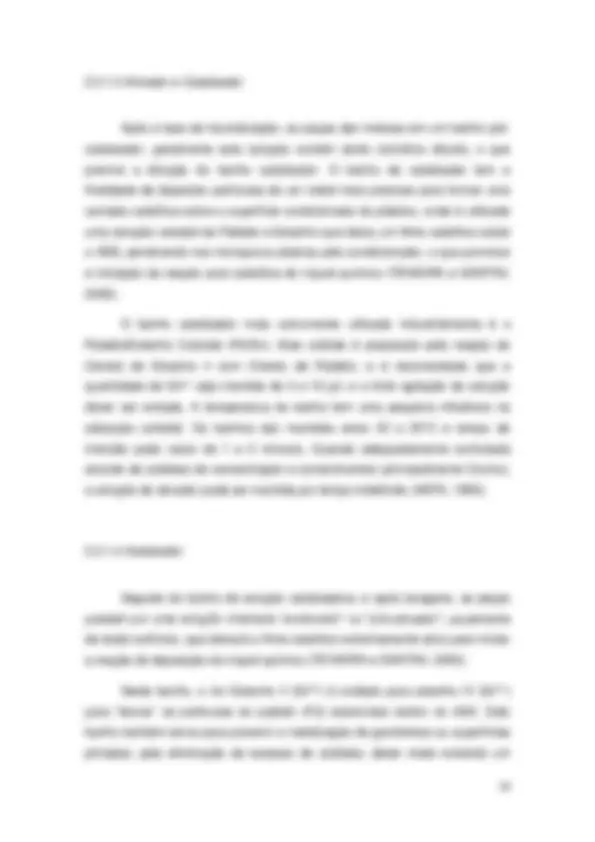

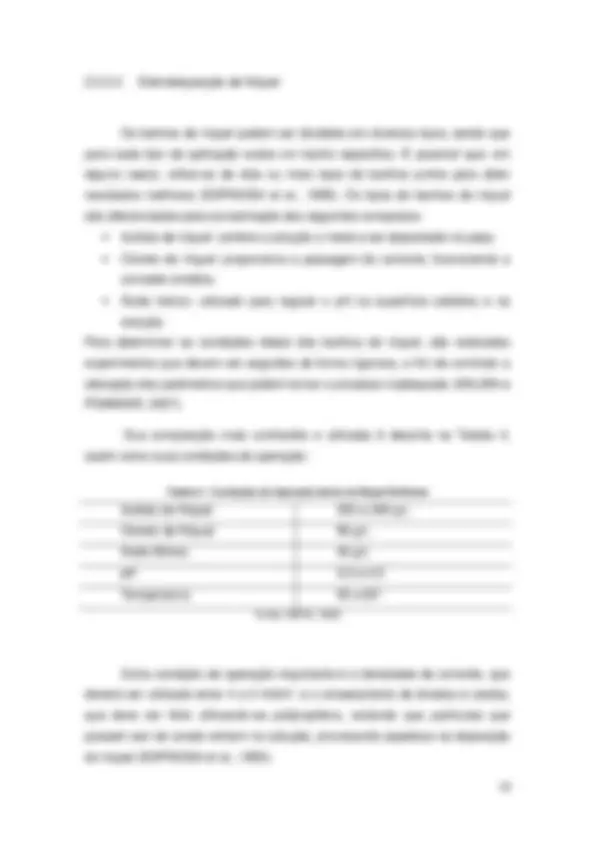
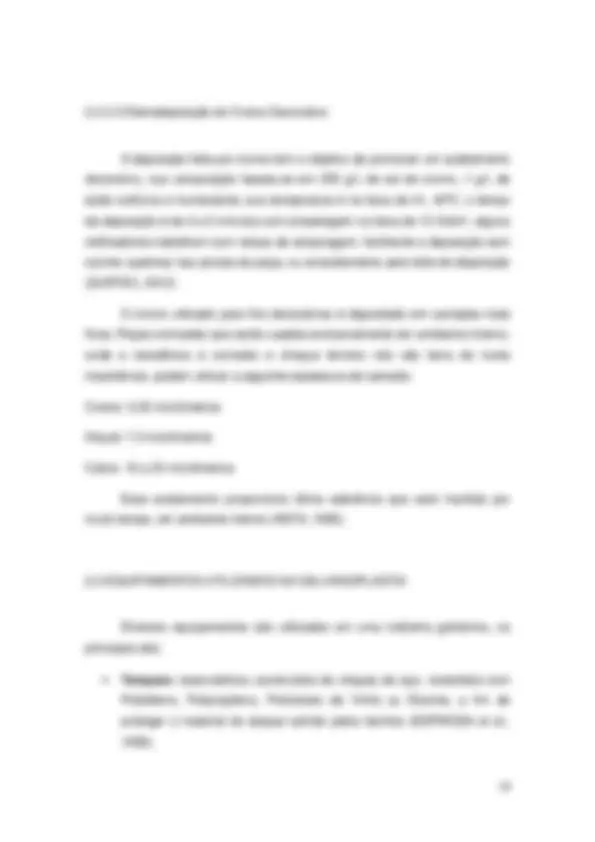
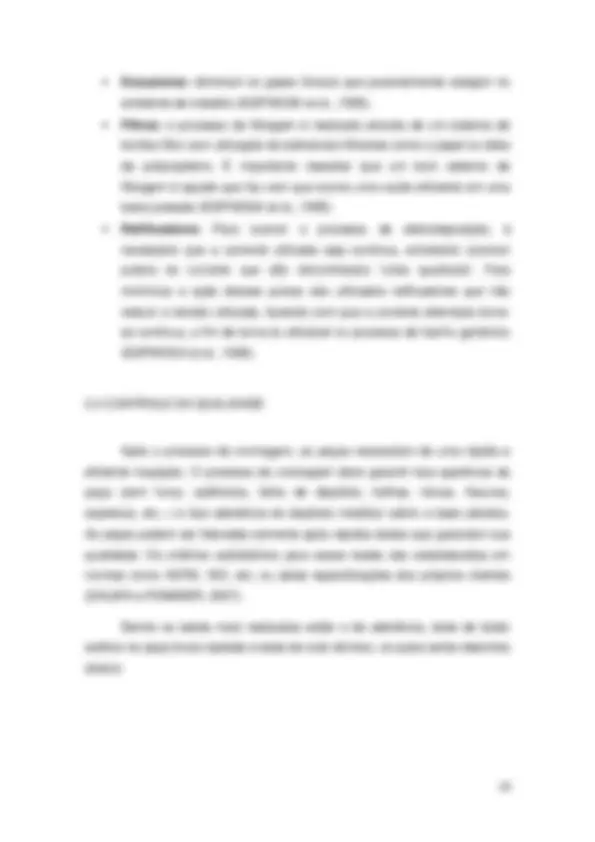
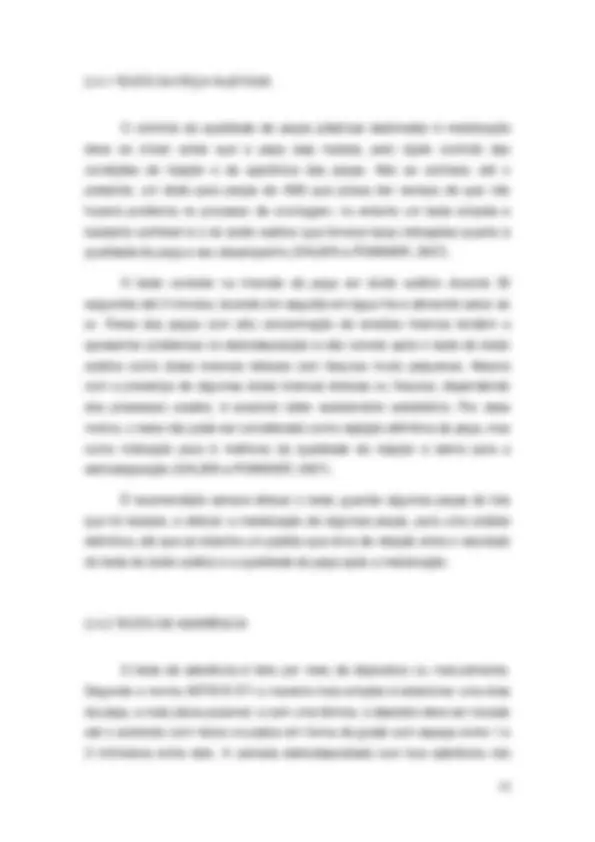
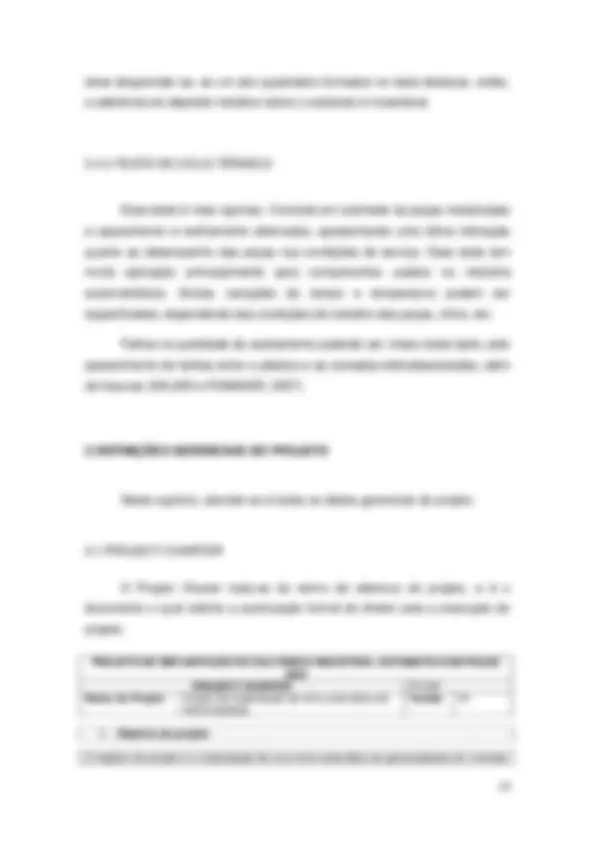
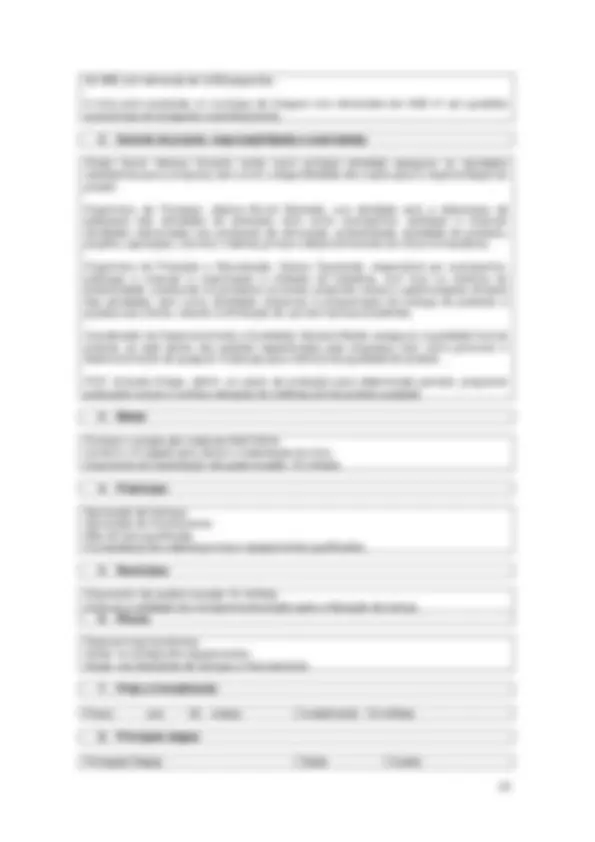
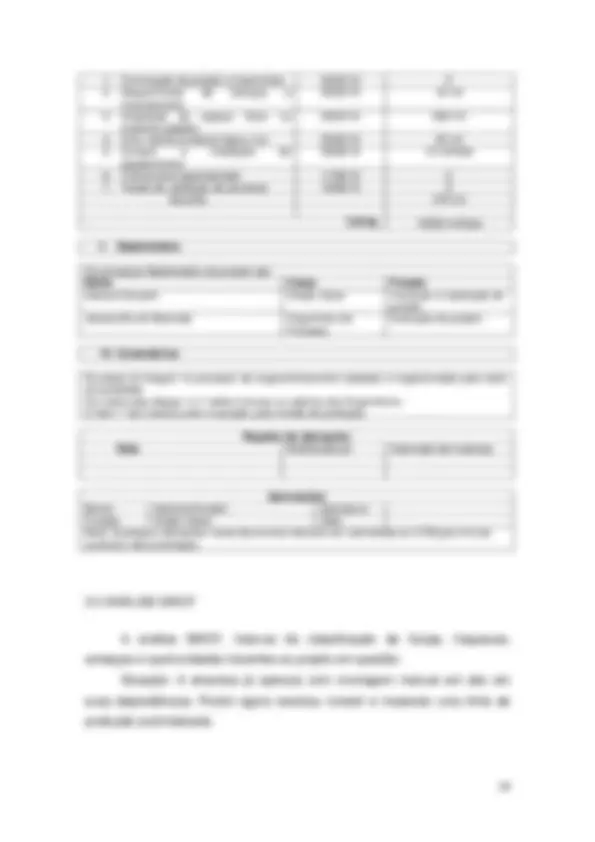
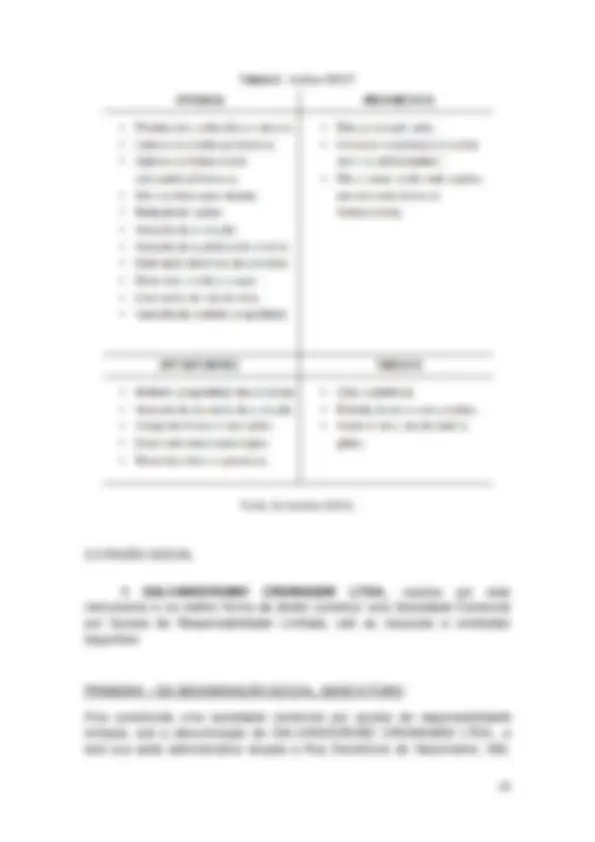
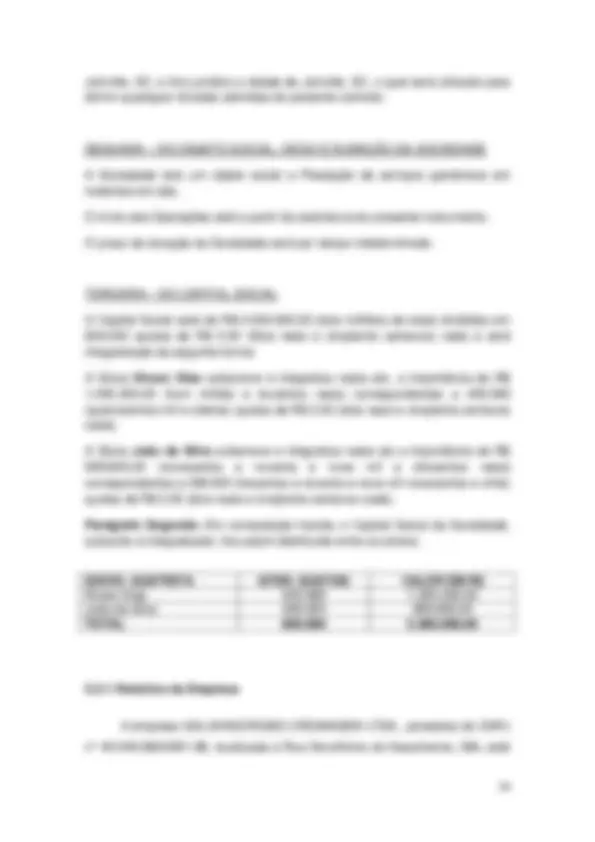
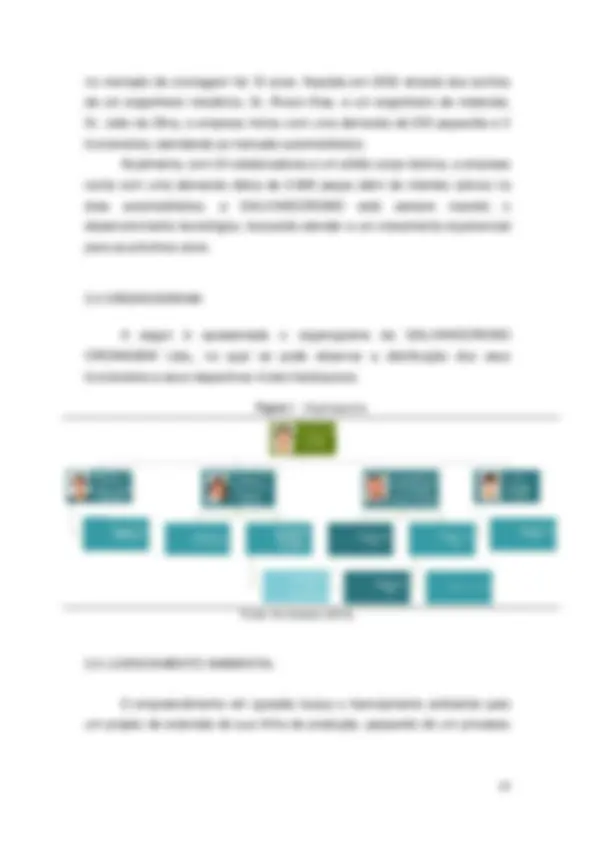
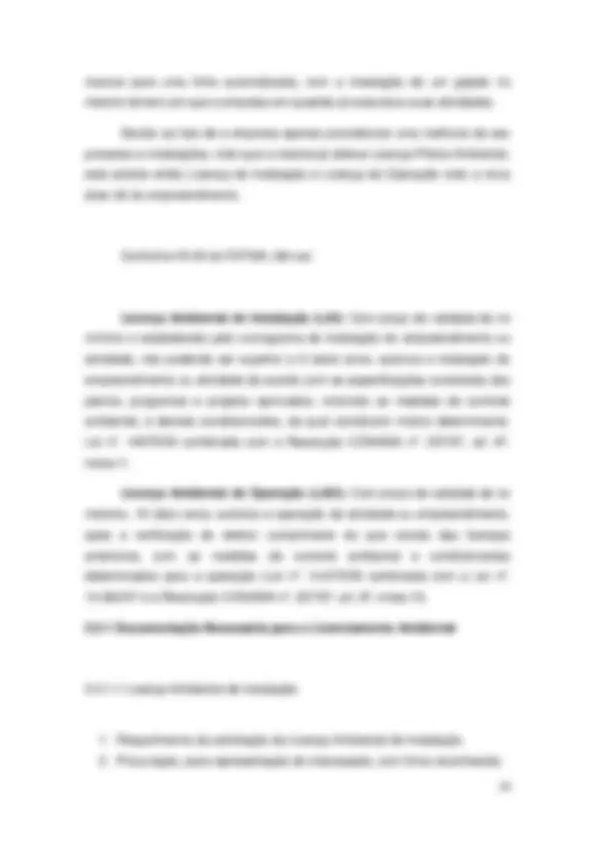
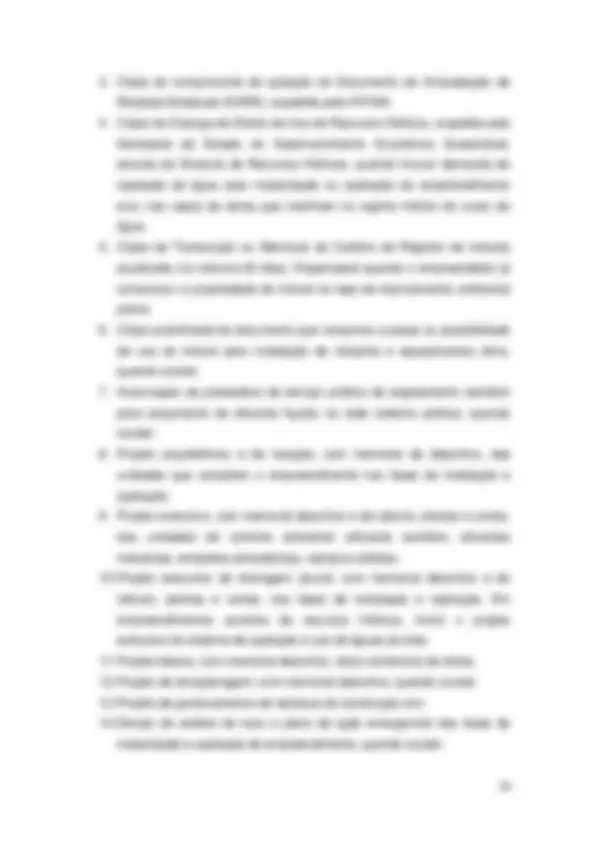
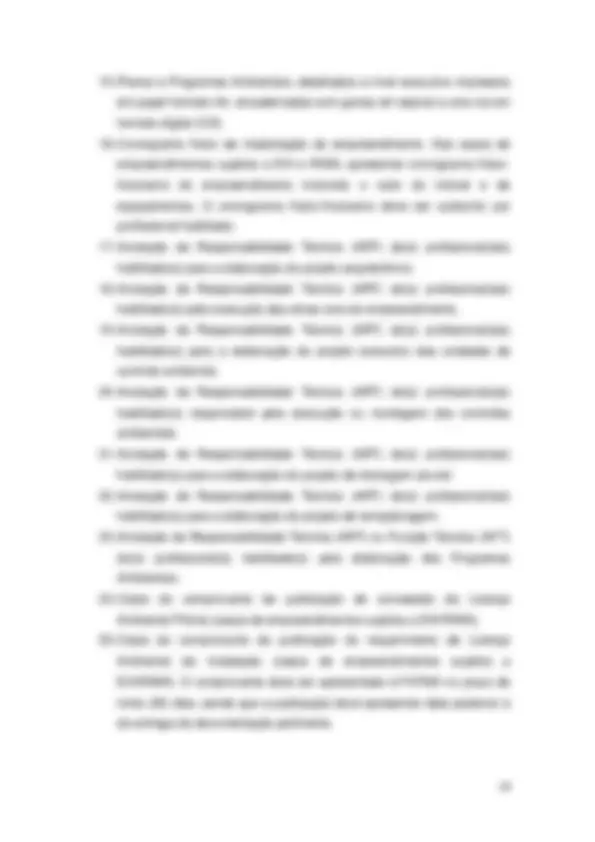
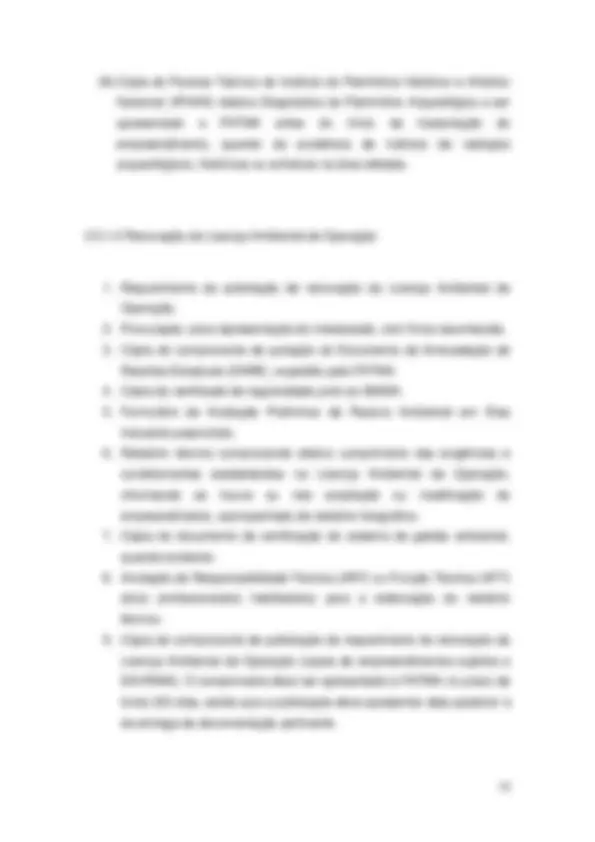
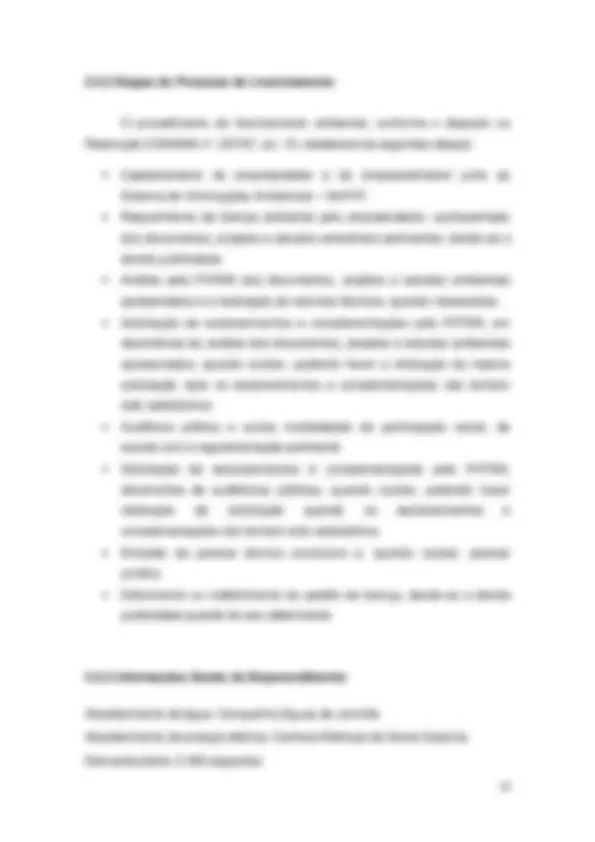
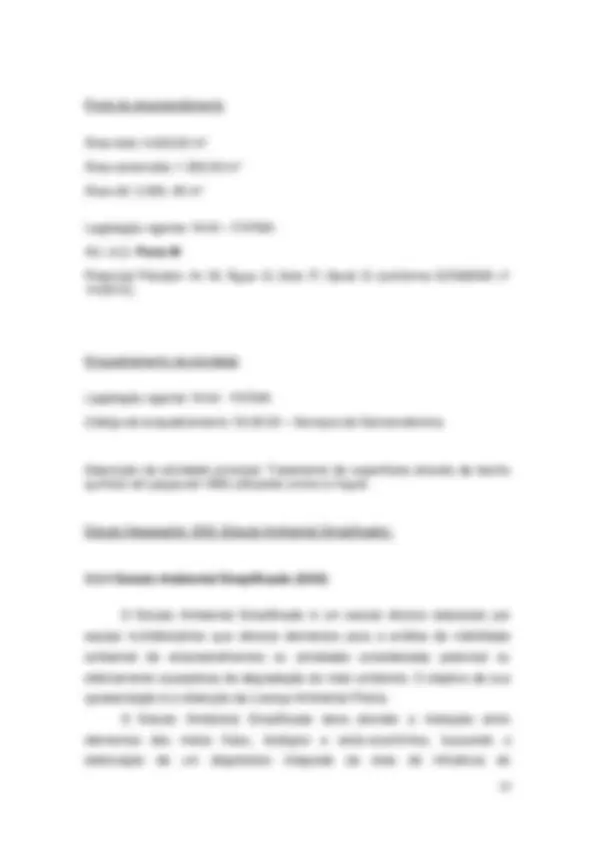
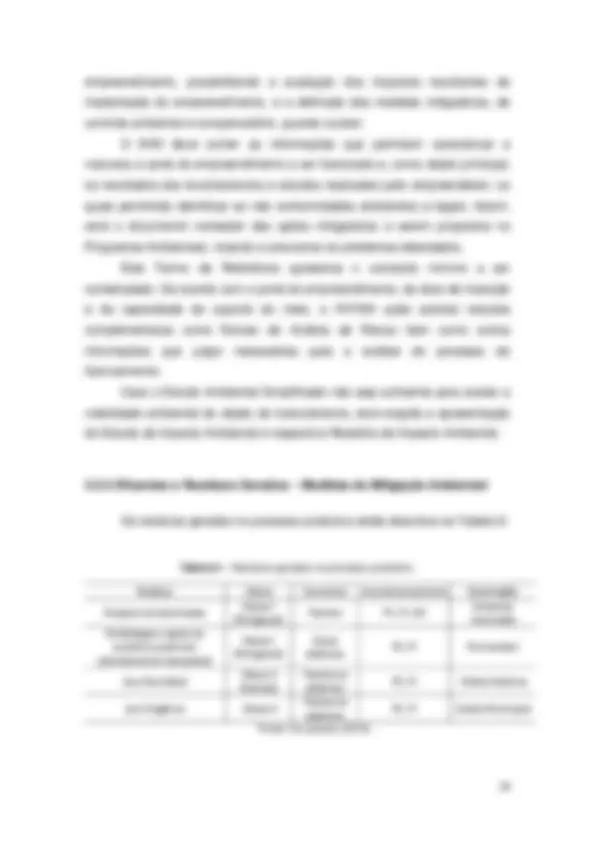
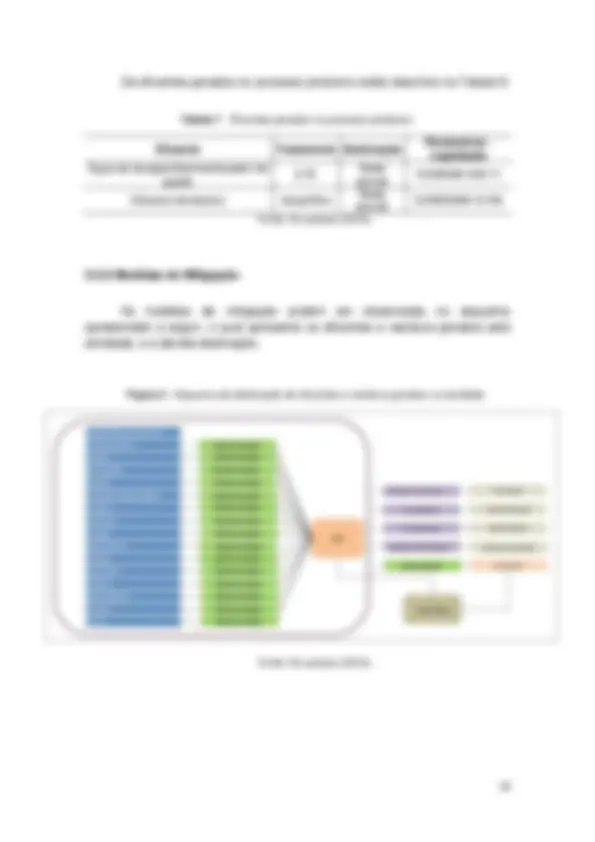
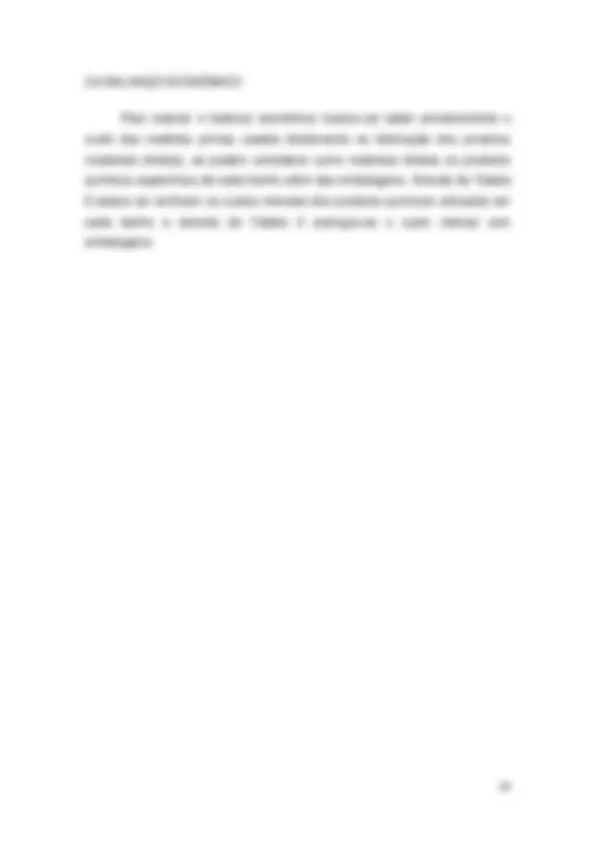
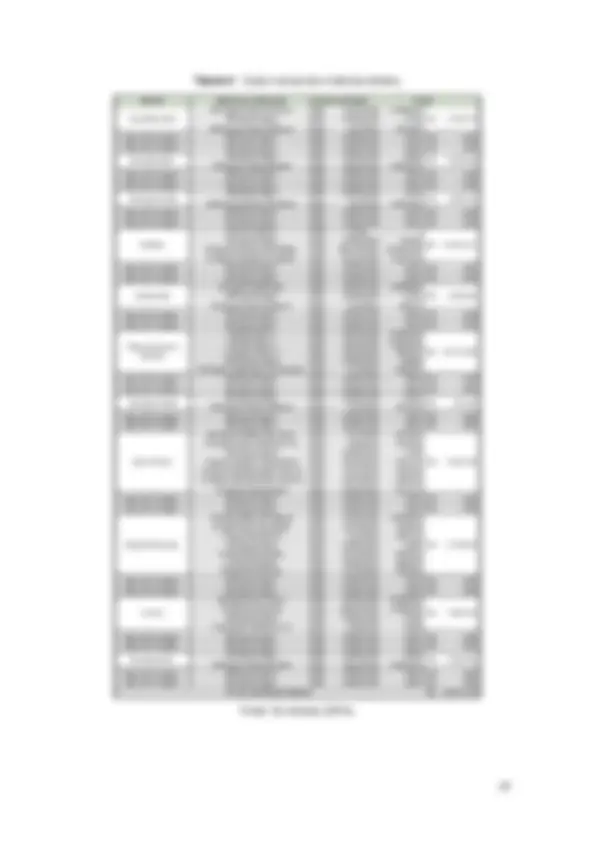
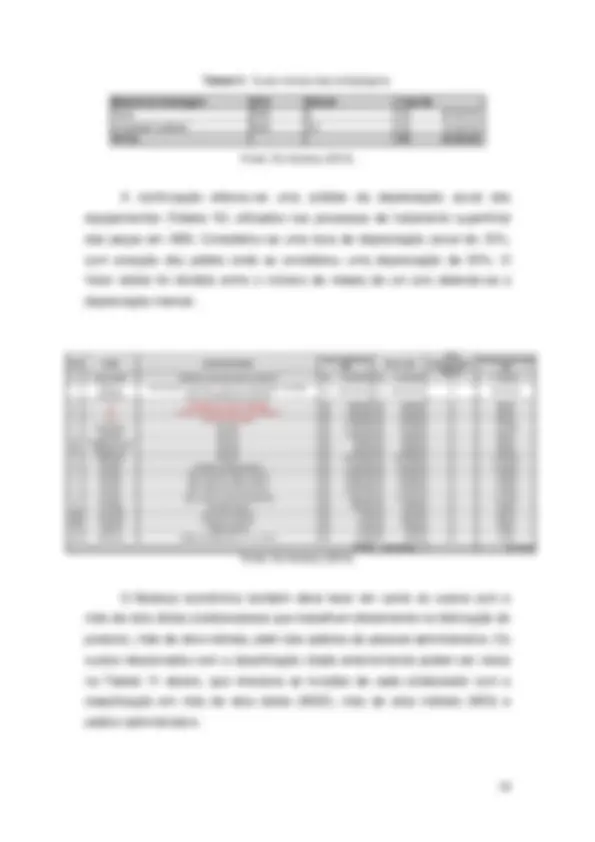
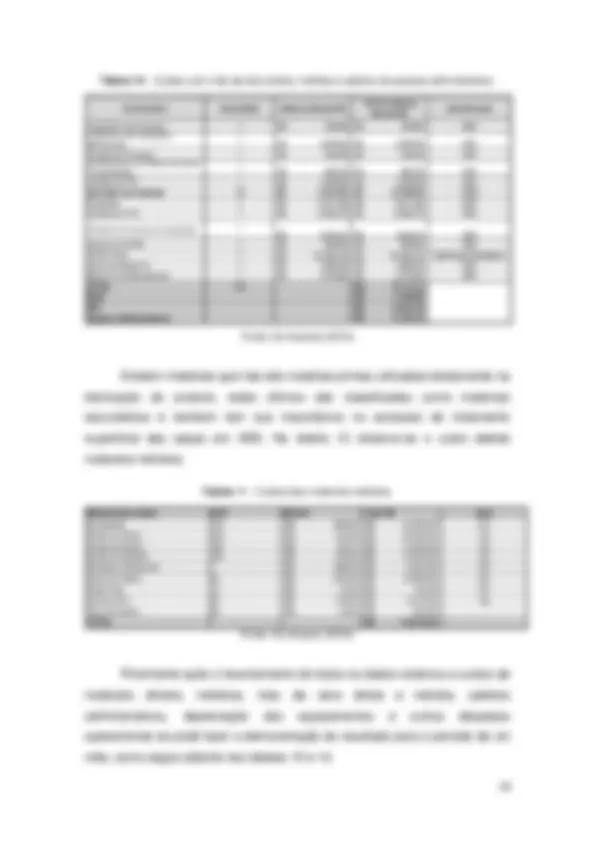
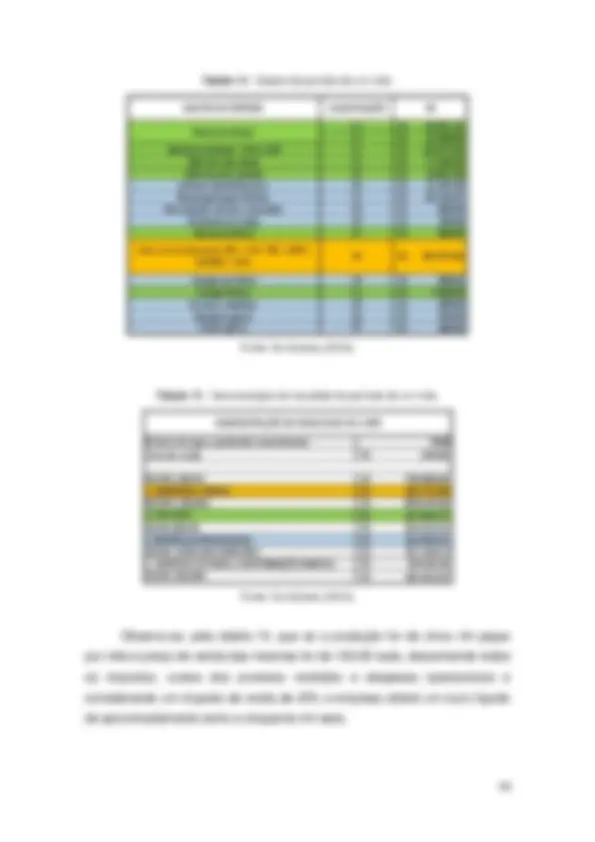
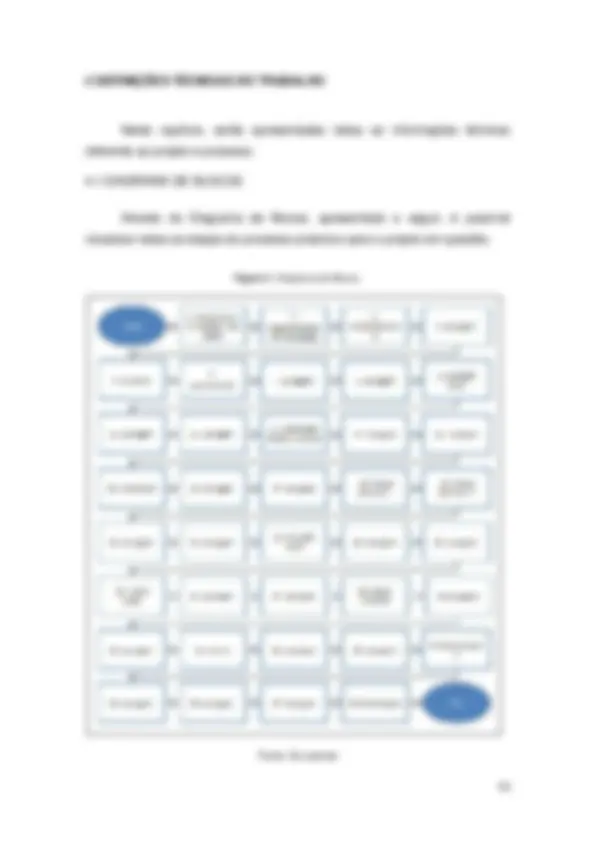
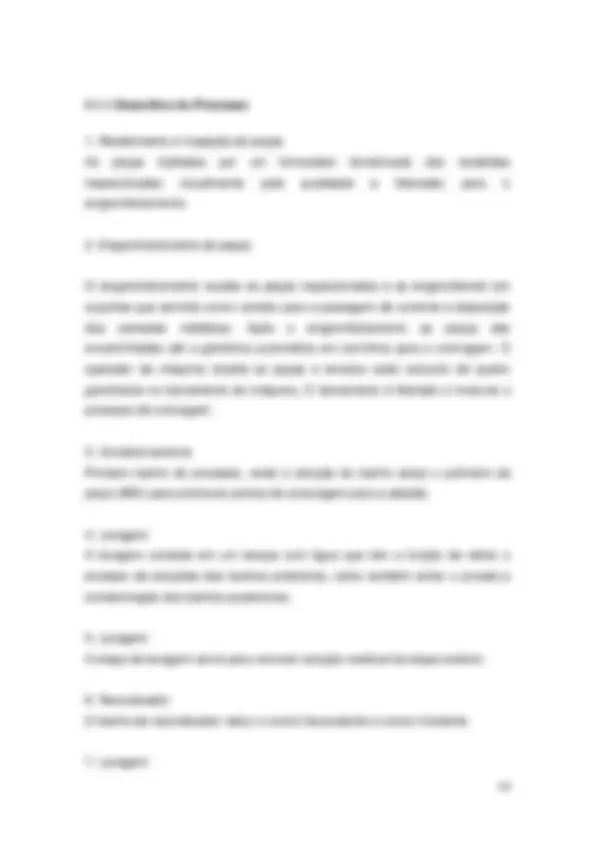
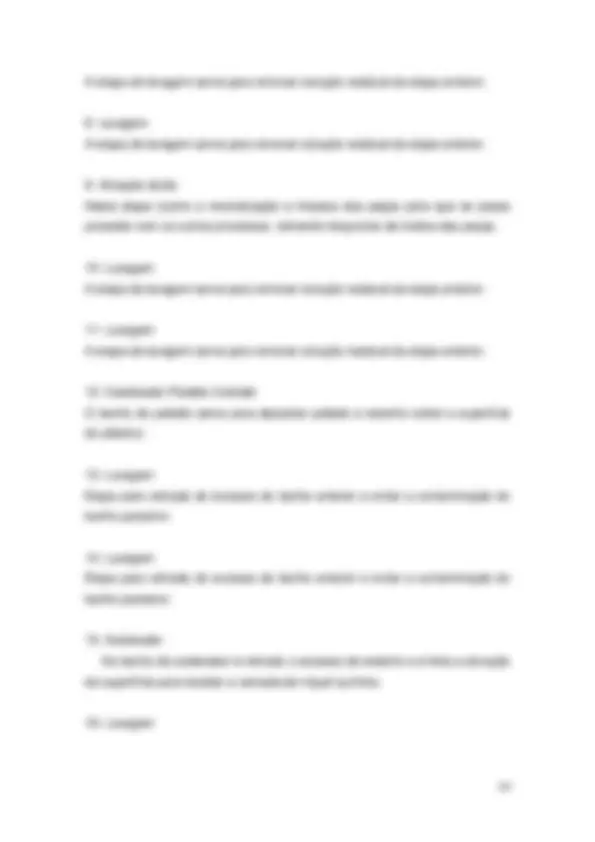
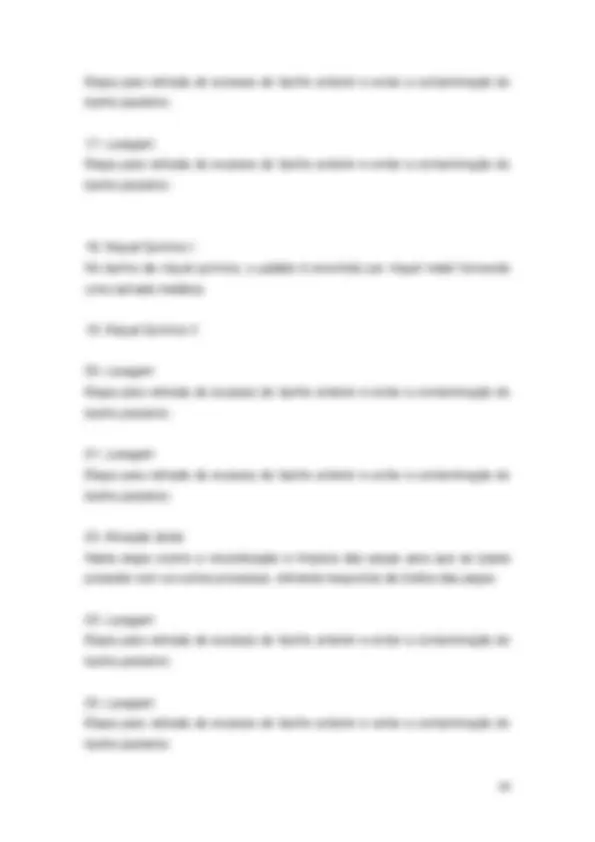
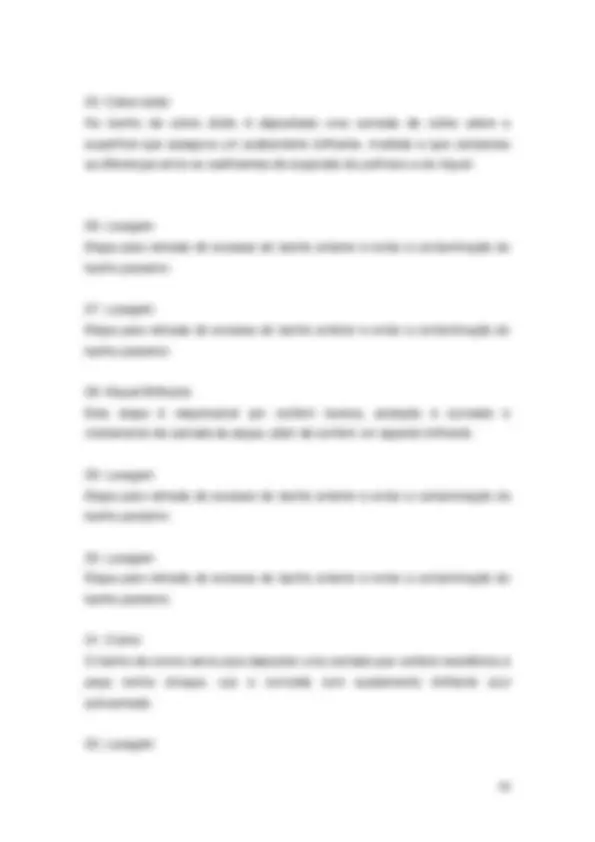
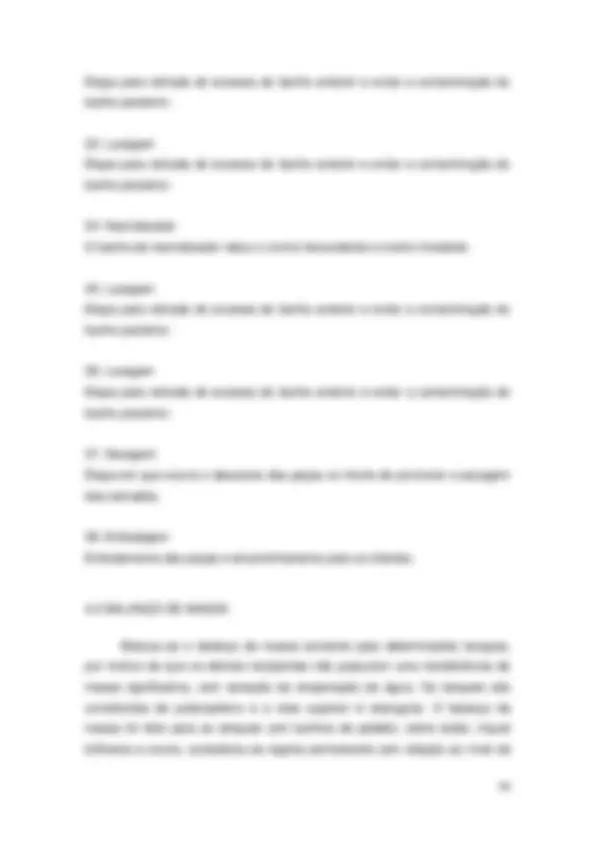
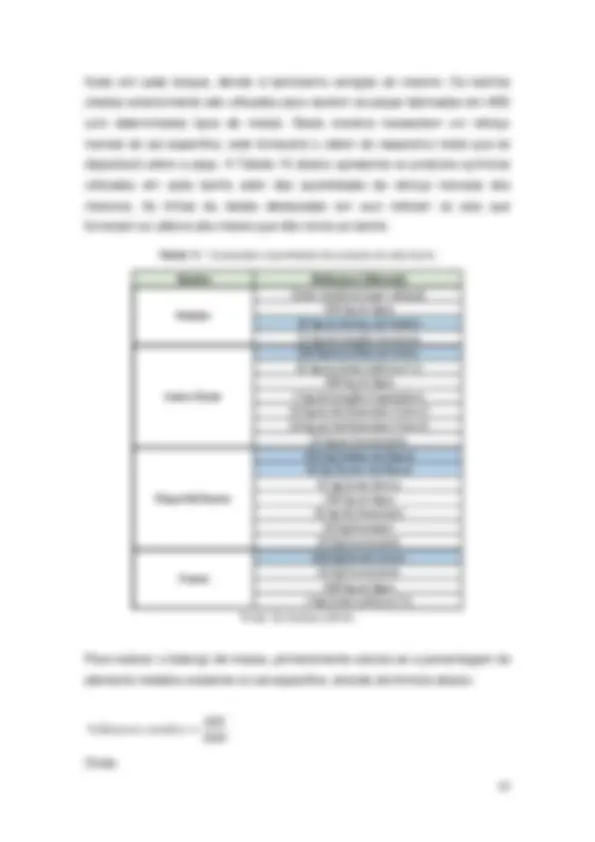
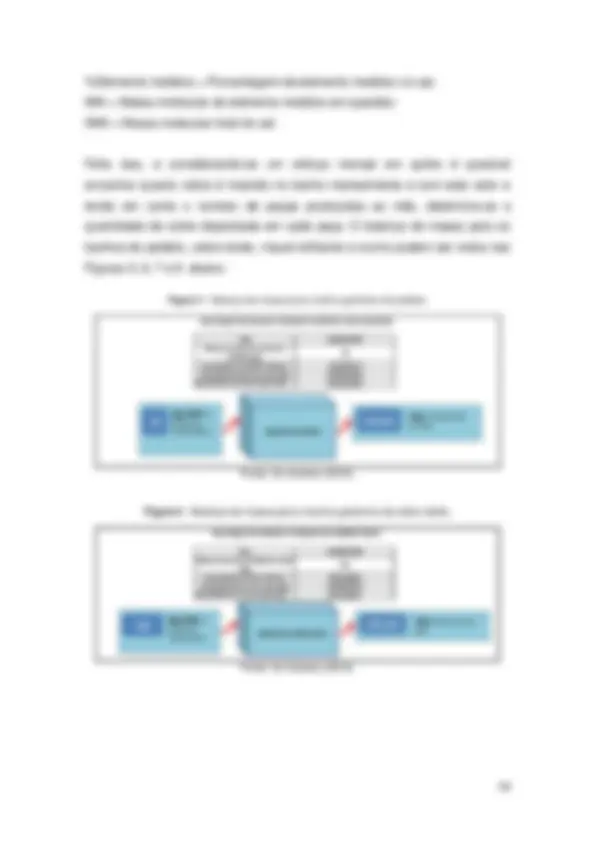
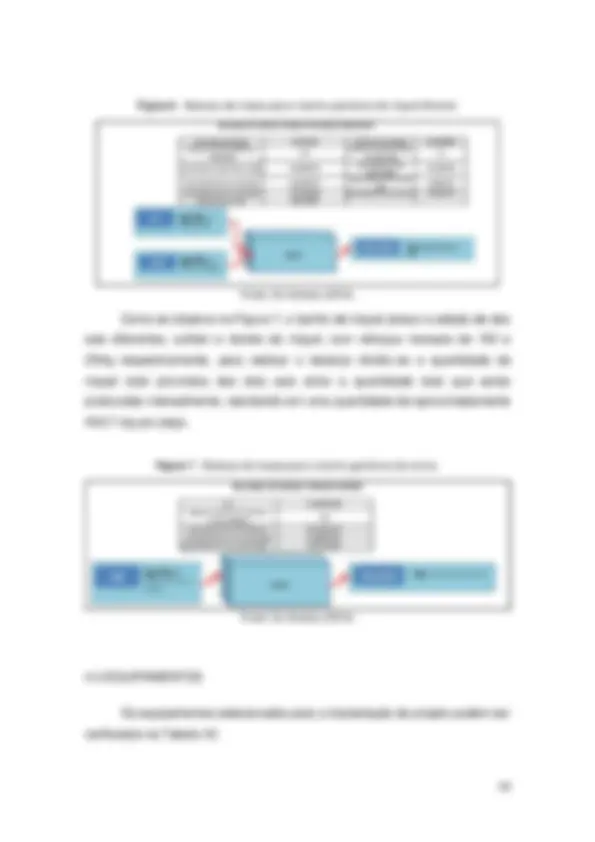
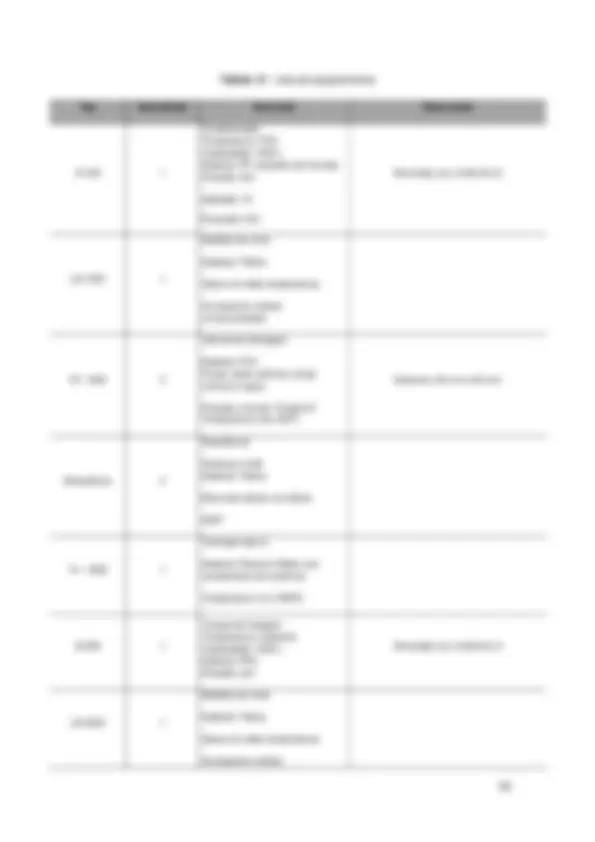
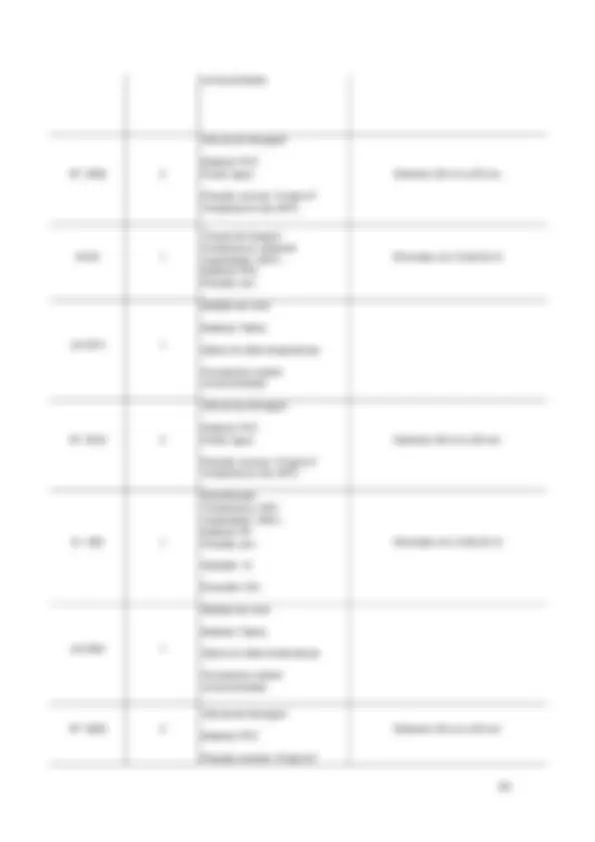
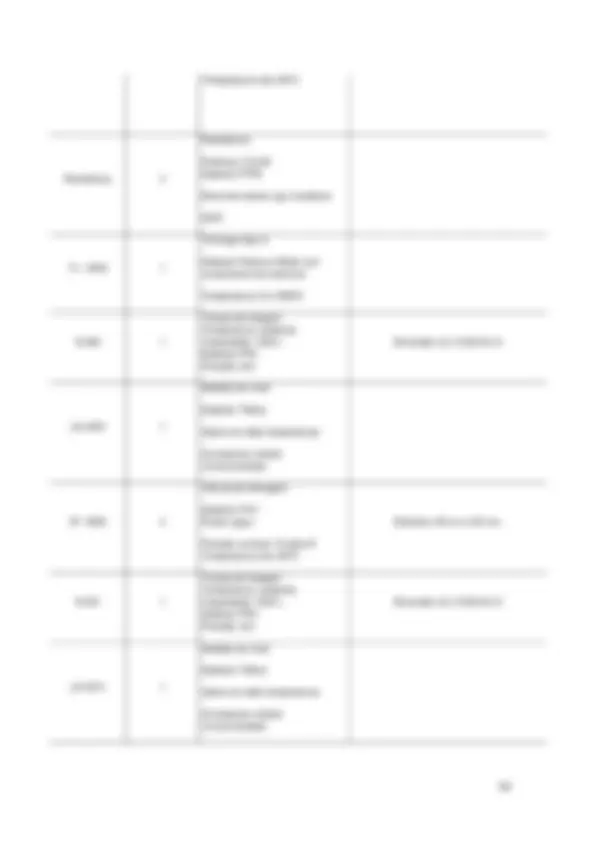
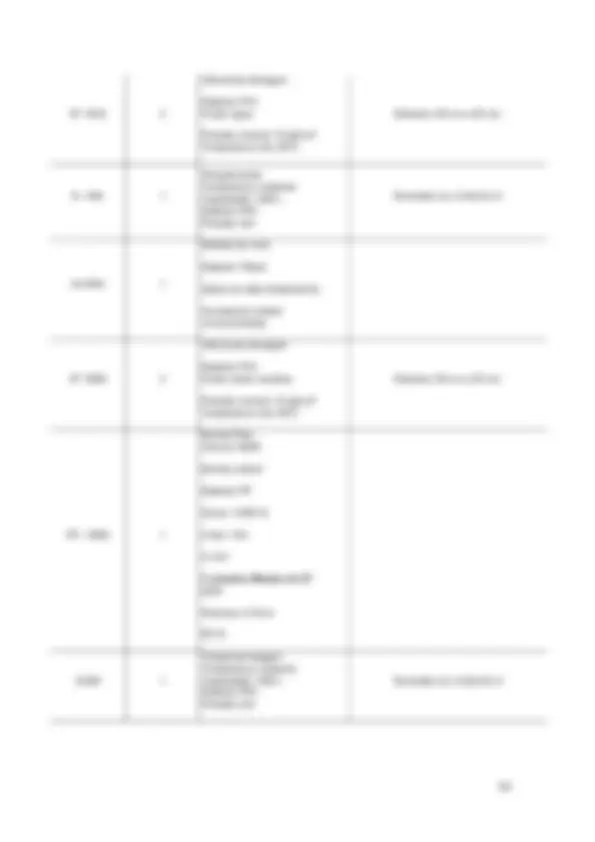
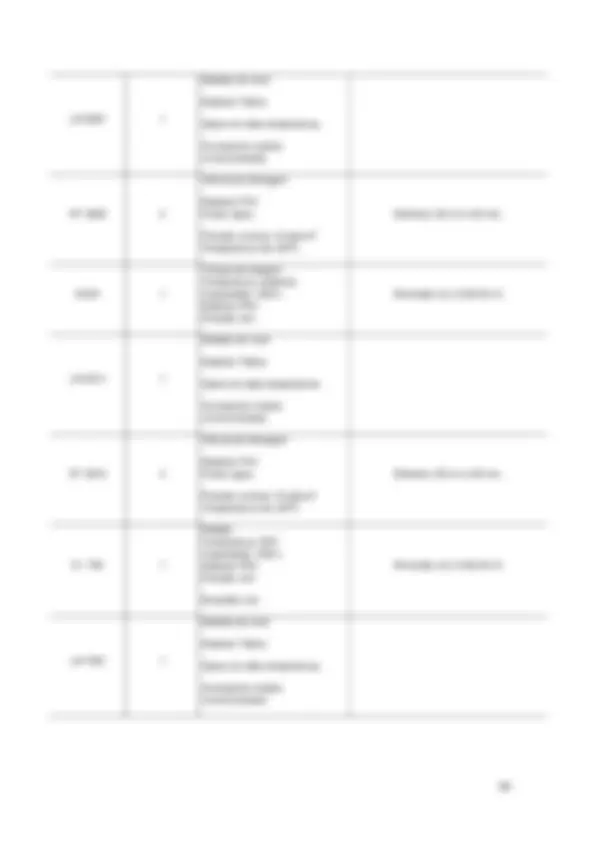
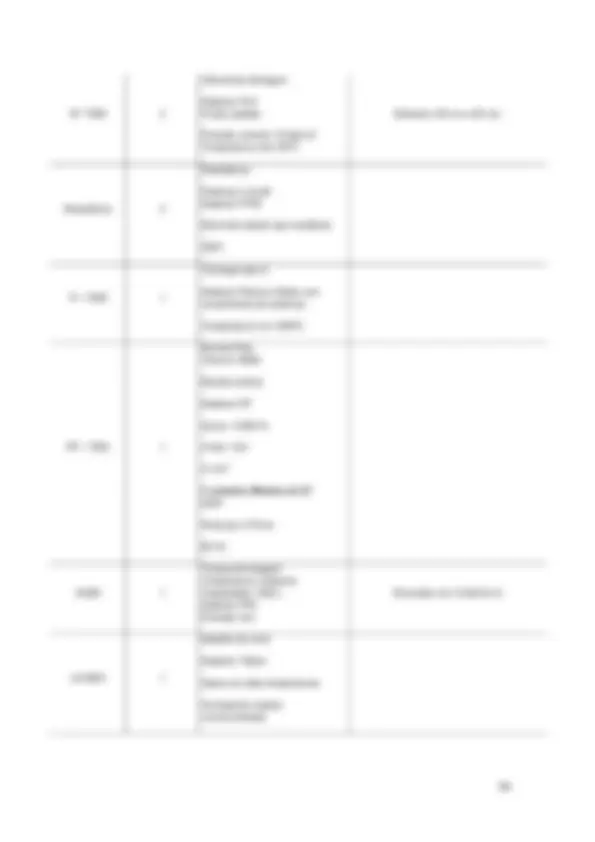
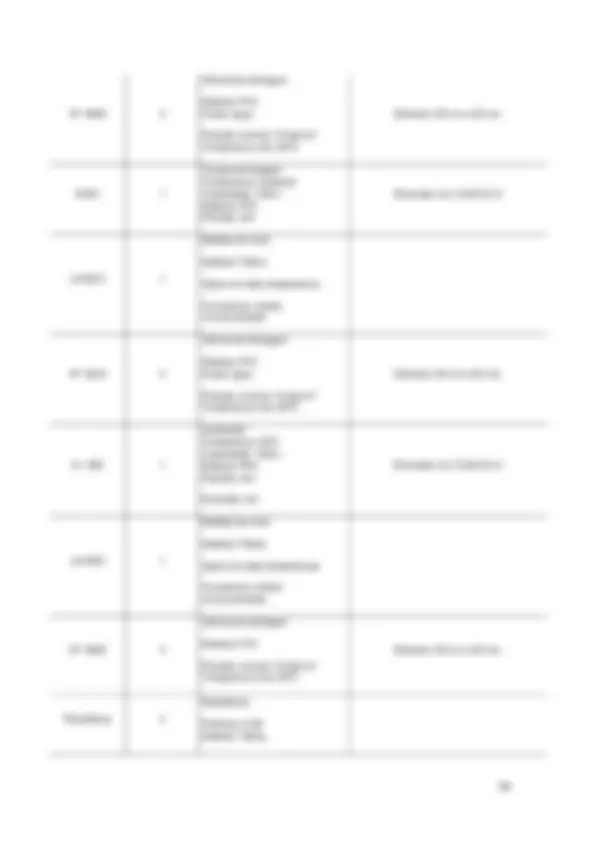
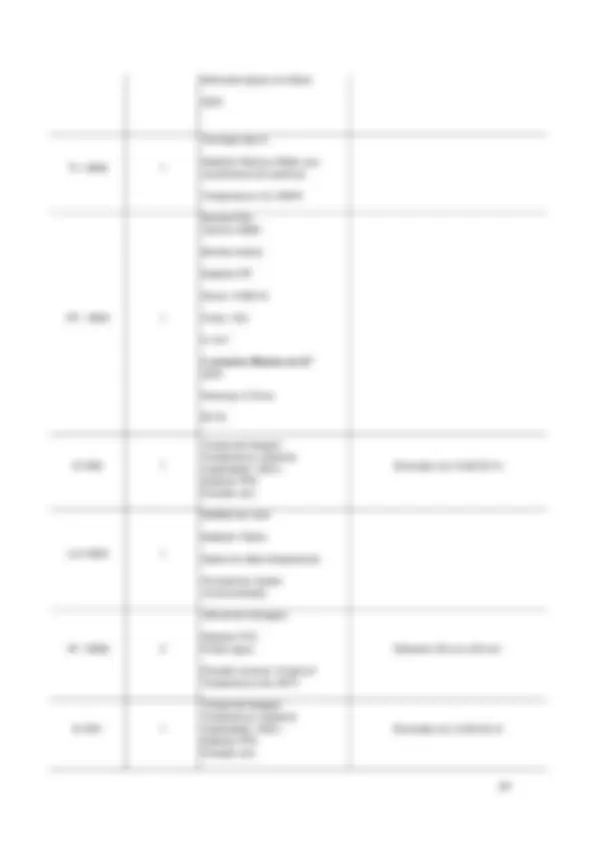
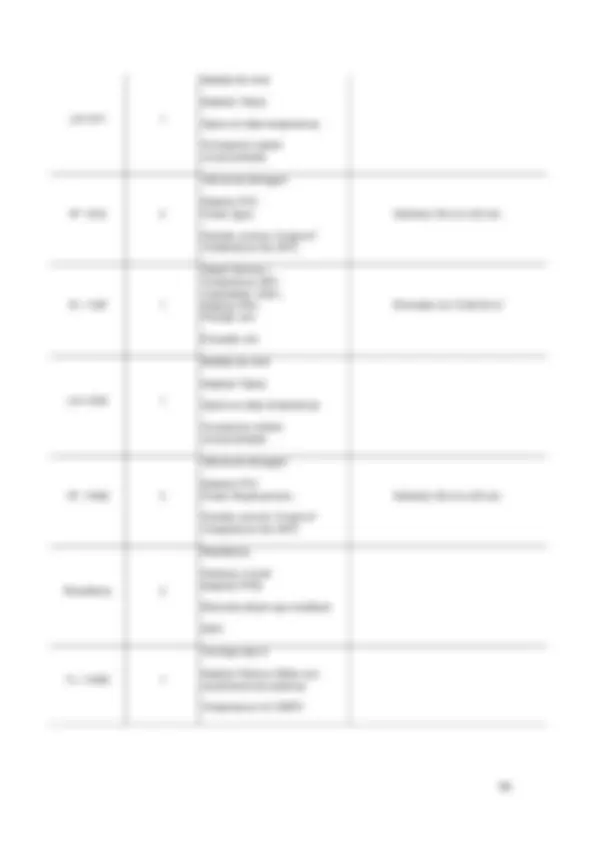
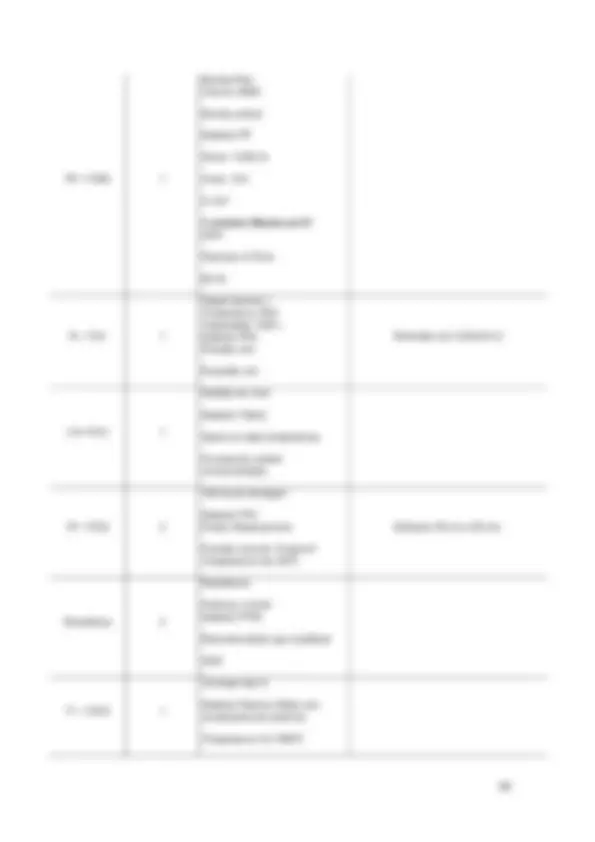
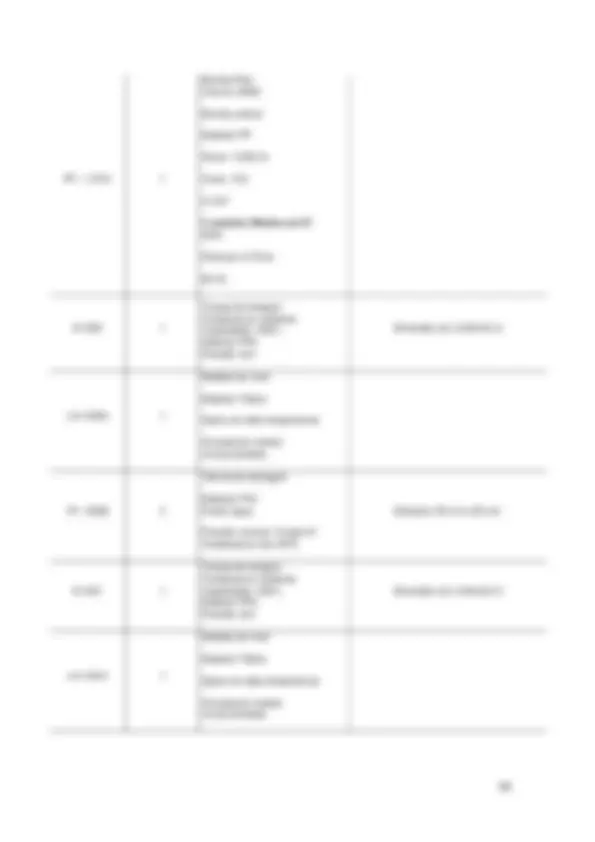
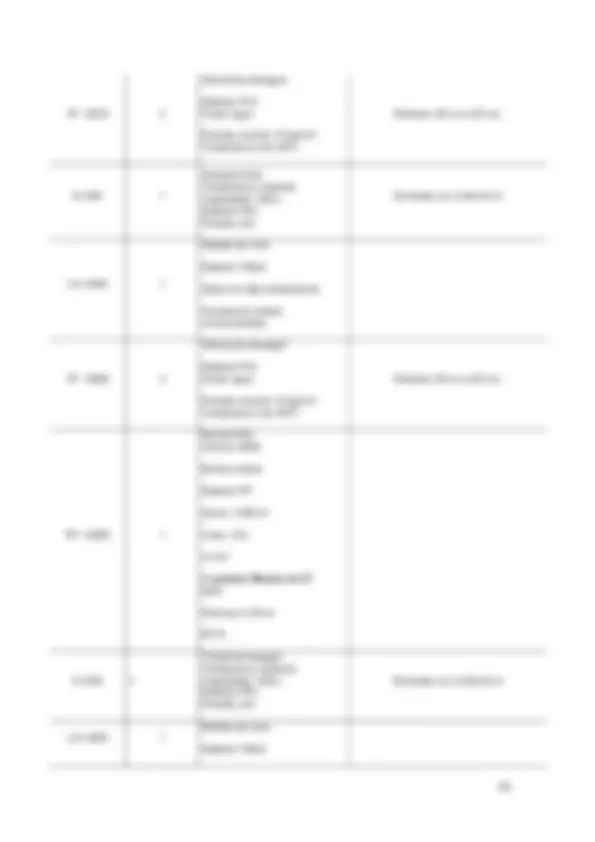
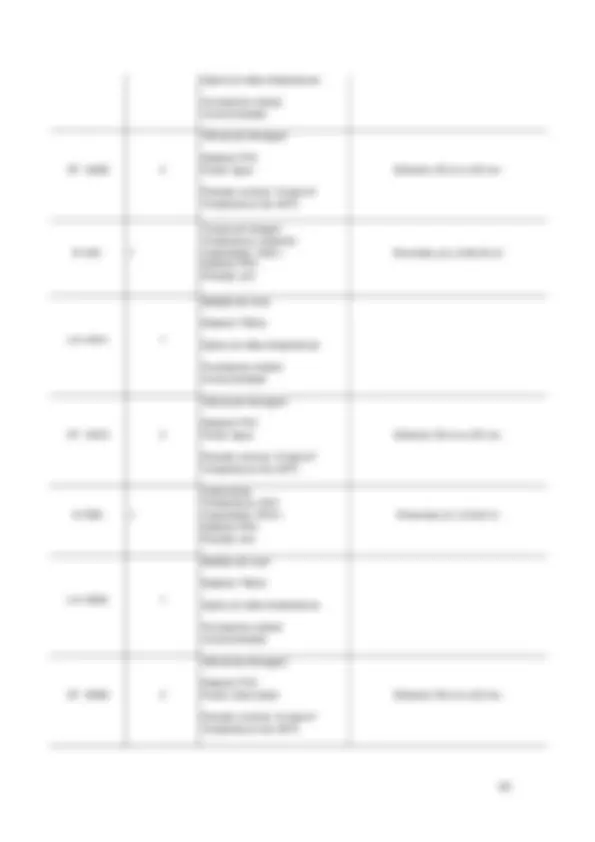
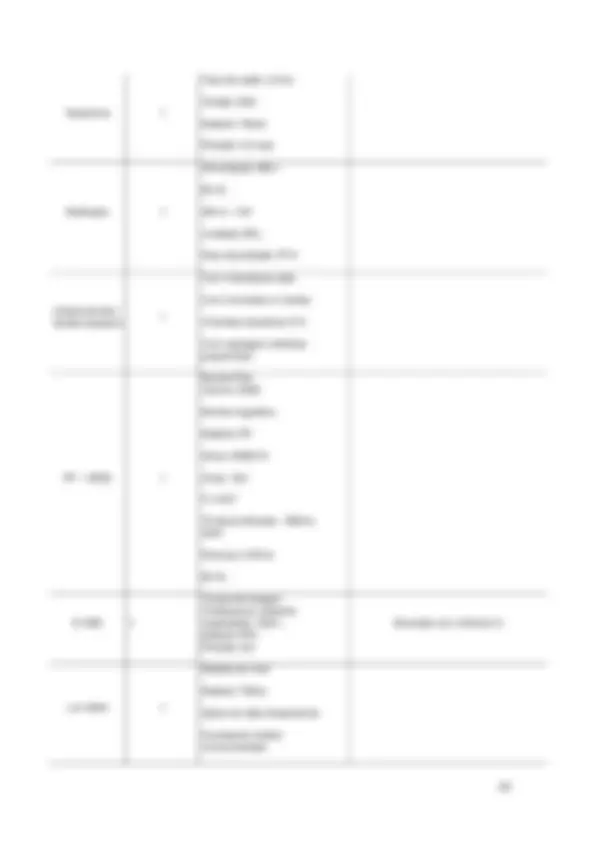
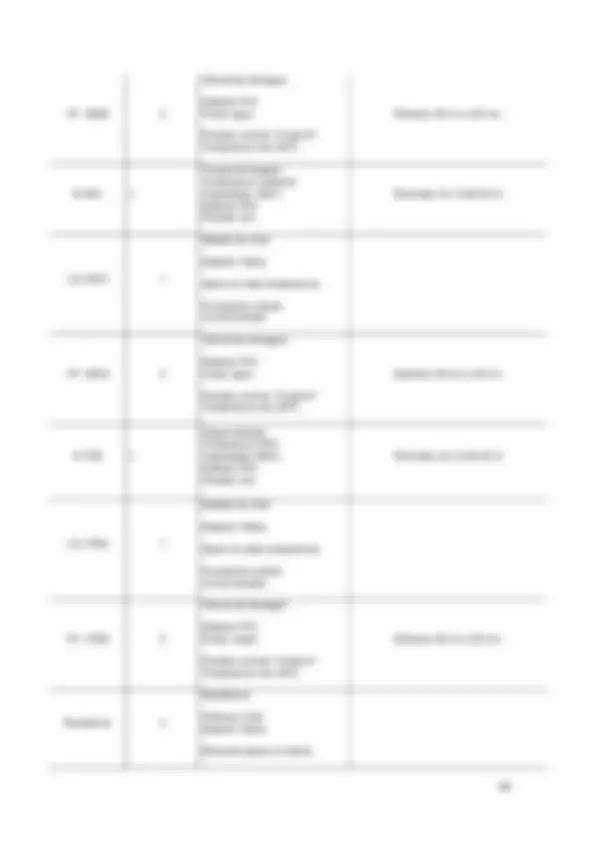
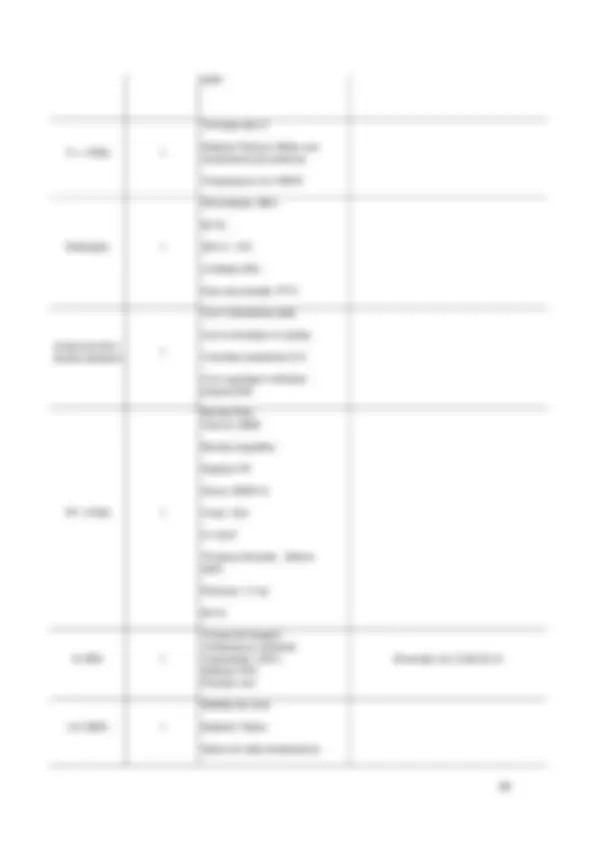
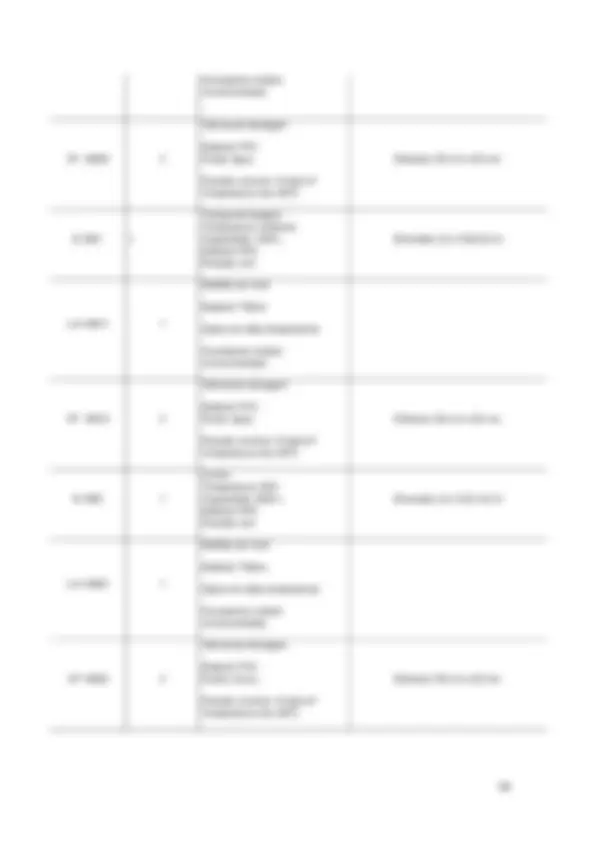
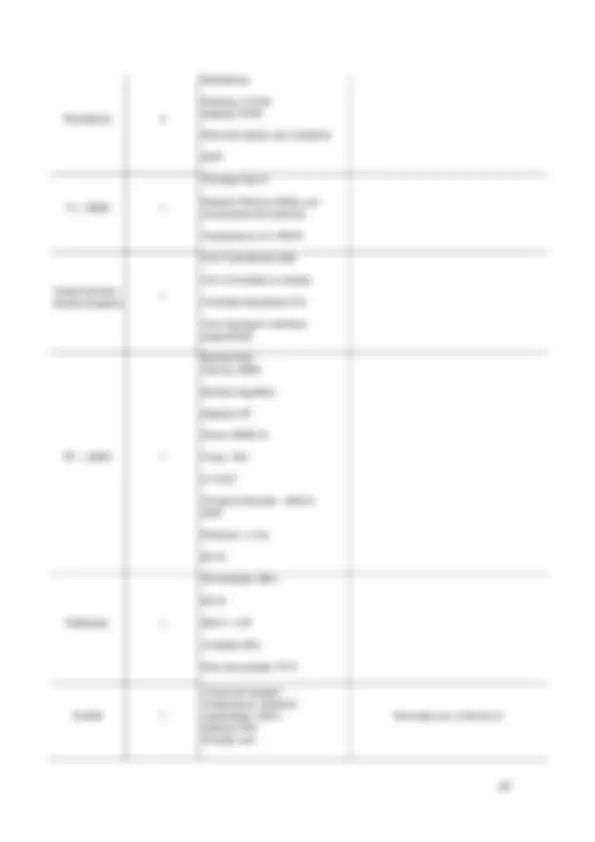
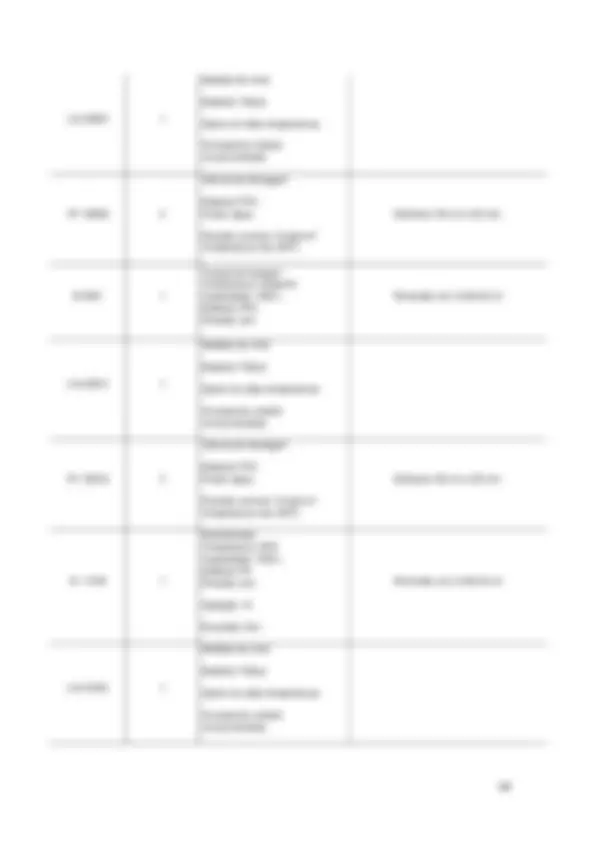
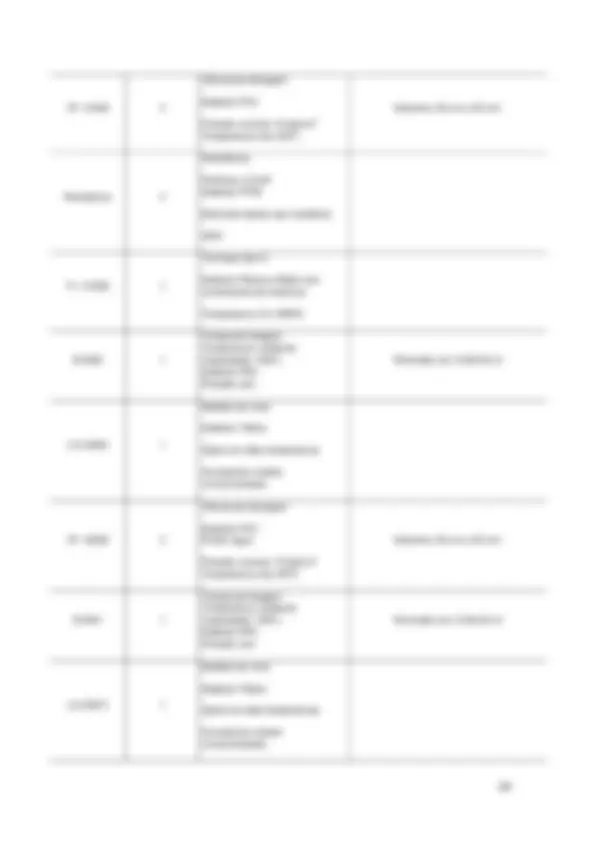
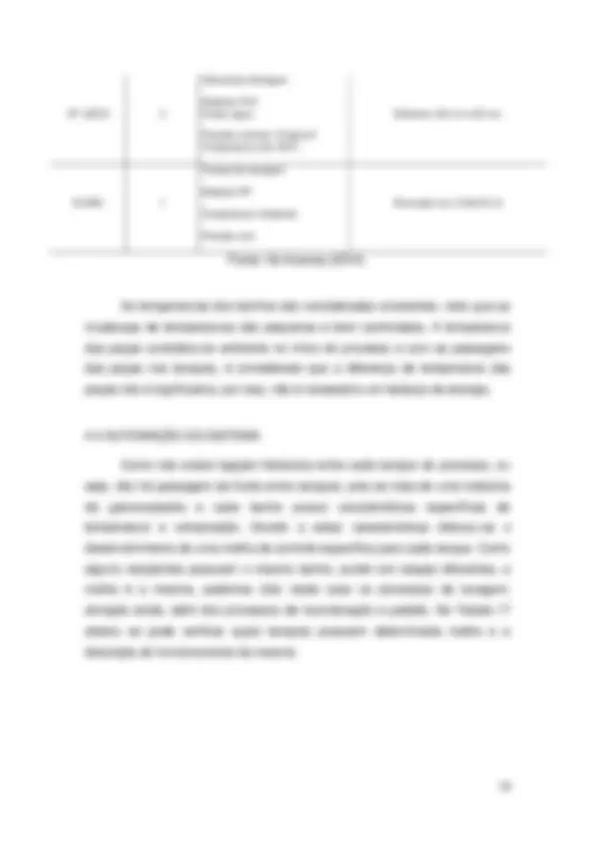
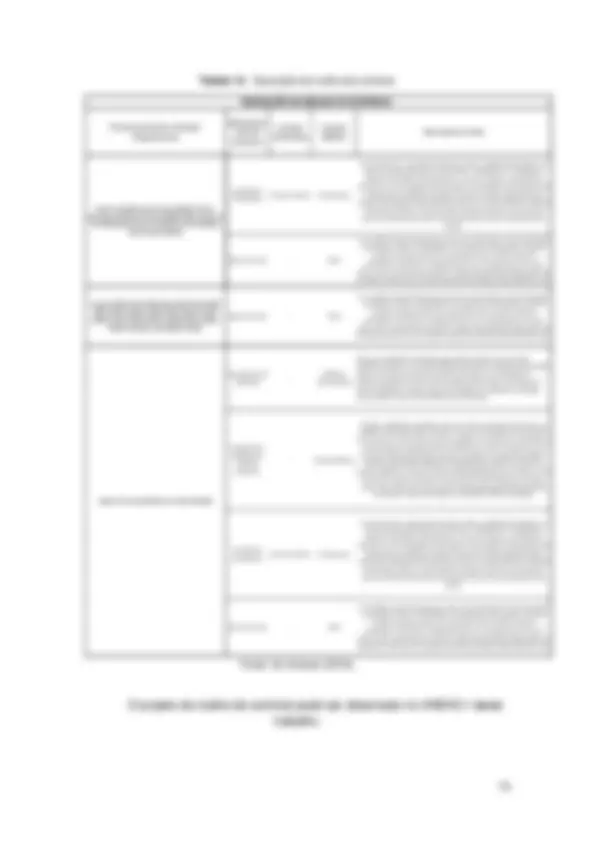
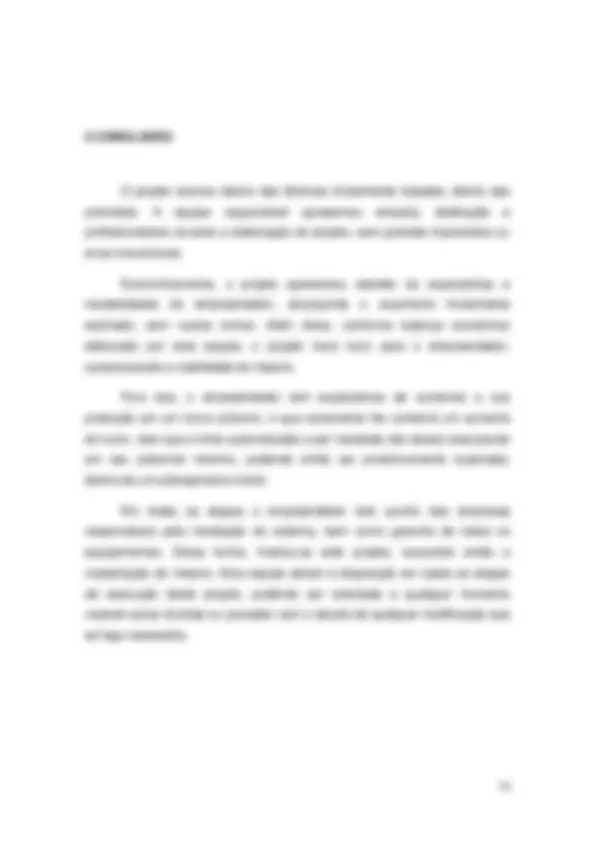
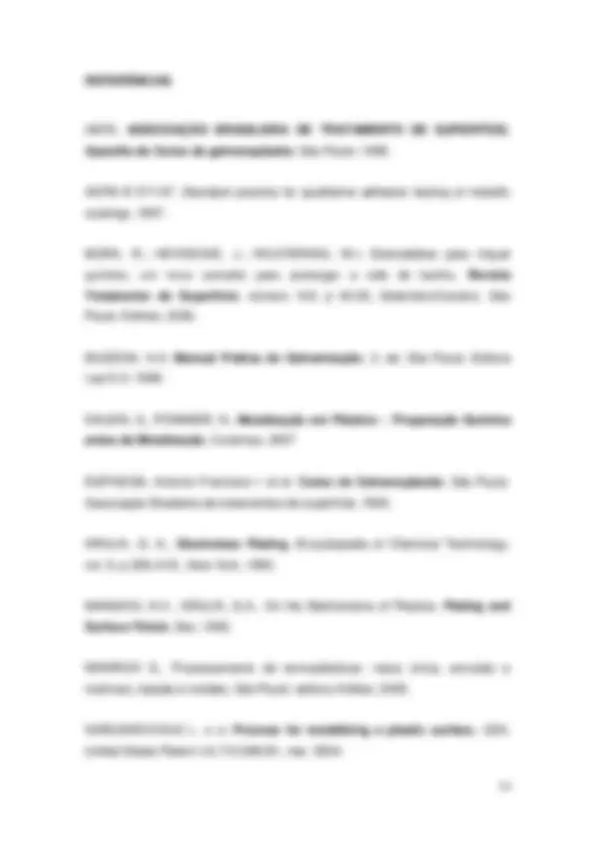
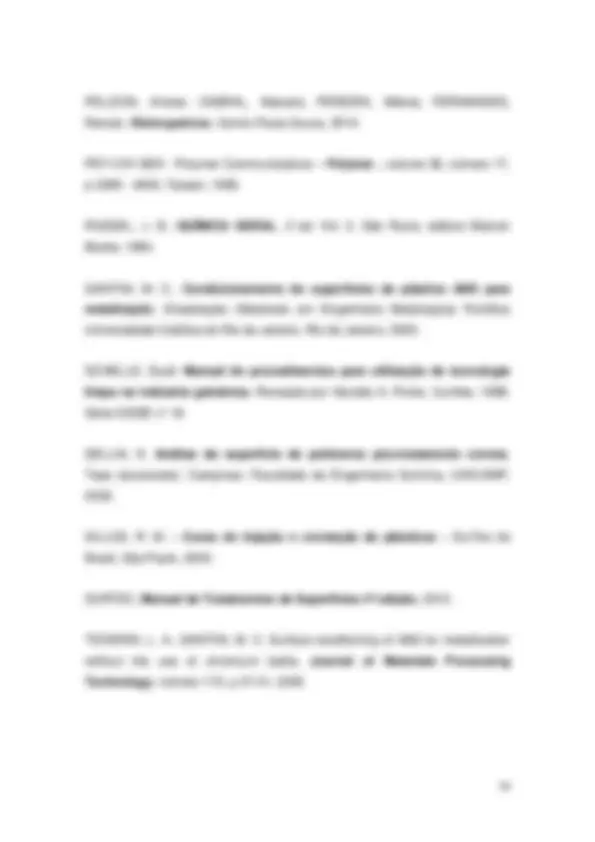
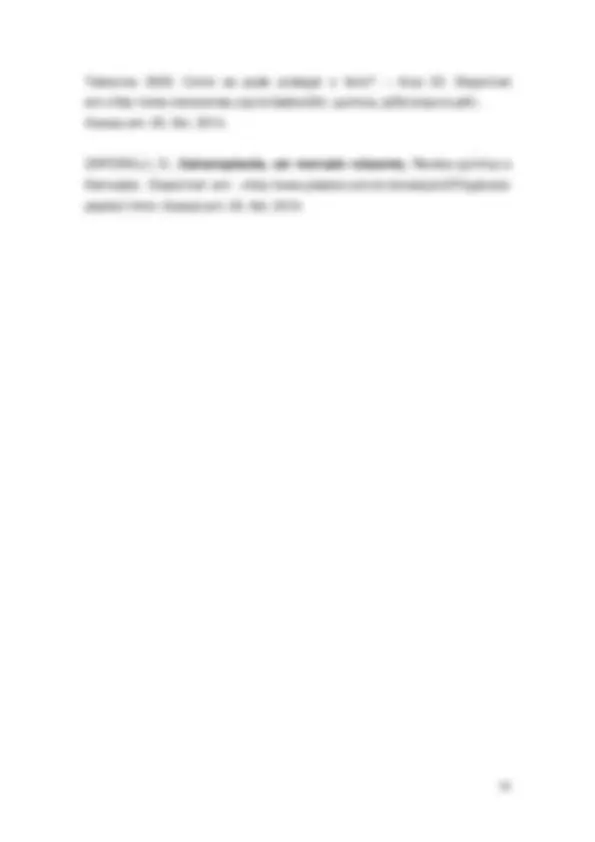
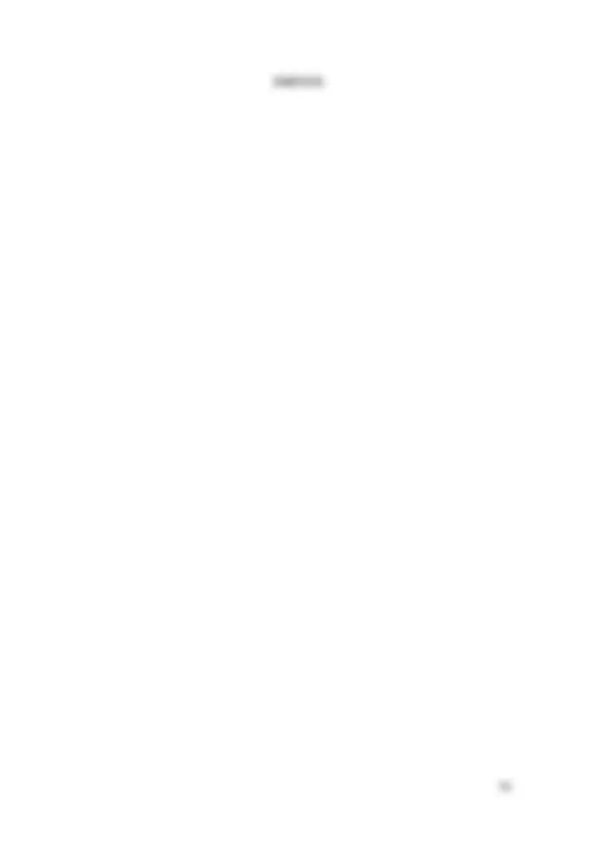
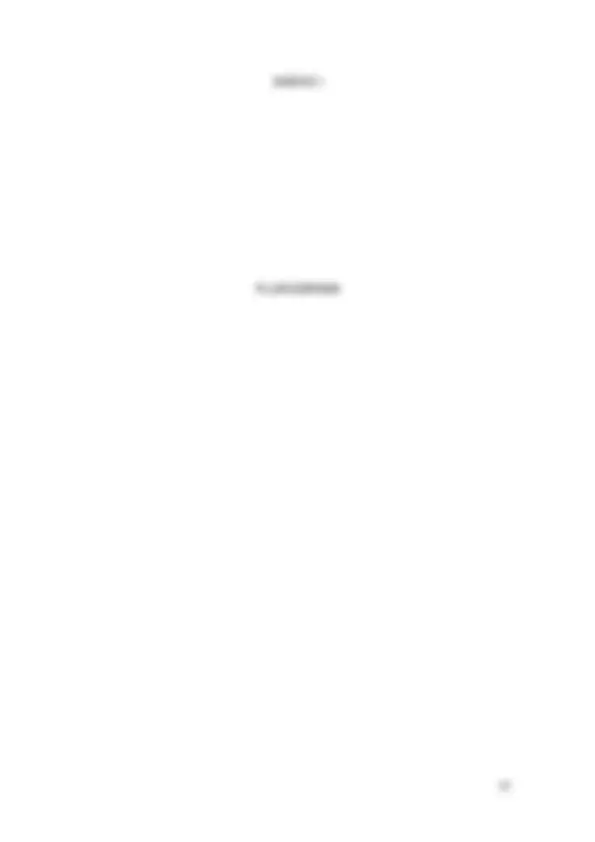
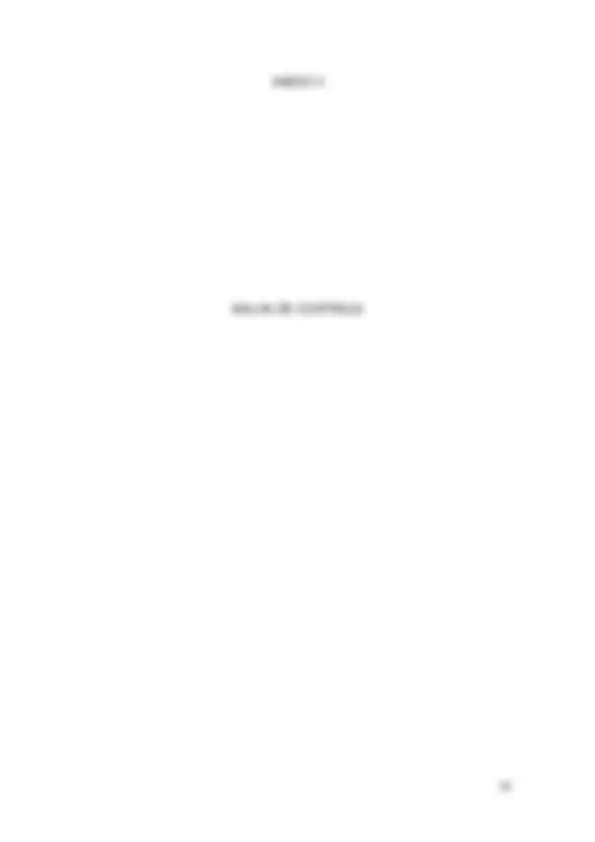

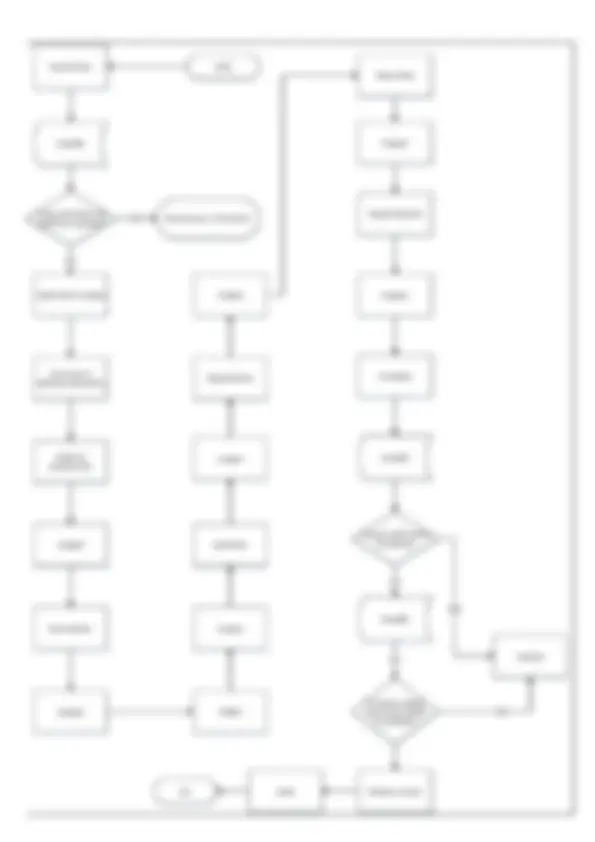
Estude fácil! Tem muito documento disponível na Docsity
Ganhe pontos ajudando outros esrudantes ou compre um plano Premium
Prepare-se para as provas
Estude fácil! Tem muito documento disponível na Docsity
Prepare-se para as provas com trabalhos de outros alunos como você, aqui na Docsity
Os melhores documentos à venda: Trabalhos de alunos formados
Prepare-se com as videoaulas e exercícios resolvidos criados a partir da grade da sua Universidade
Responda perguntas de provas passadas e avalie sua preparação.
Ganhe pontos para baixar
Ganhe pontos ajudando outros esrudantes ou compre um plano Premium
Comunidade
Peça ajuda à comunidade e tire suas dúvidas relacionadas ao estudo
Descubra as melhores universidades em seu país de acordo com os usuários da Docsity
Guias grátis
Baixe gratuitamente nossos guias de estudo, métodos para diminuir a ansiedade, dicas de TCC preparadas pelos professores da Docsity
Projeto de implantação de Galvânica Cromagem de peças ABS
Tipologia: Trabalhos
1 / 80
Esta página não é visível na pré-visualização
Não perca as partes importantes!
Joinville 2014/
Orientador: Prof. Msc. Salvelino Aparecido Nunes
Joinville 2014/
Tabela 10 - Depreciação dos equipamentos para tratamento superficial de peças em ABS..................................................... Erro! Indicador não definido.
O processo de galvanoplastia consiste no processo de revestimento de uma peça com uma camada metálica fina de maneira eletrolítica, protegendo a peça contra oxidações e também conferindo um acabamento decorativo à mesma. Para se aplicar a galvanização é necessário analisar alguns fatores como a categoria de corrosividade do ambiente, custo da manutenção do revestimento, custo de aplicação do revestimento em cada peça e vida útil do revestimento (BUZZONI, 1957). Basicamente, o processo de galvanoplastia envolve uma sequência de banhos consistindo de etapas de pré-tratamento, de revestimento e de conversão de superfície. Entre estas etapas, a peça sofre um processo de lavagem (SCHEELE, 1998). A cromagem (galvanização que utiliza cromo como revestimento) é considerada um importante tipo de banho eletrolítico, pois é resistente a temperatura e dureza. A técnica dos banhos de cromo é utilizada, pois o cromo é resistente ao ataque de sais e outros ácidos orgânicos e inorgânicos, sendo que o ácido sulfúrico aquecido e o ácido clorídrico são os únicos que podem atacá-lo. O cromo conserva a cor e o brilho mesmo quando o material é exposto ao ambiente externo, é resistente à oxidação, possui uma dureza maior do que a do ferro (quando precipitado por meios eletrolíticos) (BUZZONI, 1957). O mercado de galvanoplastia abrange os mais diferenciados segmentos e tem crescido de maneira considerável nos últimos anos, visto que já não trata-se apenas de um tratamento de proteção superficial, mas também adquiriu caráter decorativo, o qual tem ganho grande parcela do mercado. Visto o considerável aumento da demanda, este trabalho visa a instalação de uma linha automática de galvânica, buscando maior produção sem perder a qualidade de suas peças.
Os plásticos não são condutores, sendo esta a sua principal diferença em relação a outros materiais destinados ao tratamento de metais. Os métodos para a deposição sobre os plásticos já são conhecidos há muitos anos, porém a falta de aderência entre o plástico e a camada metálica depositada foi durante muito tempo uma barreira para o maior desenvolvimento dessa tecnologia. Com o surgimento de tipos especiais de plásticos, como o ABS (acrilonitrilo, butadieno e estireno), houve uma mudança bastante significativa, graças à aderência conseguida entre o plástico e as camadas metálicas depositadas (PEI-CHI YEN, 1995).
Para a deposição química de qualquer camada sobre superfícies plásticas, é preciso tornar a película superficial condicionada, a peça injetada não-condicionada tem uma superfície espelhada, que não entra em contato com nenhuma solução da linha de preparação da cromagem, repelindo qualquer líquido da mesma forma que uma peça metálica que esteja suja de óleos ou graxas repele a água, antes de ser convenientemente desengraxada. O condicionamento das peças é conseguido em soluções específicas, permitindo então uma molhagem total na superfície do plástico. No caso do ABS, o butadieno é oxidado proporcionando o aparecimento de inúmeros microporos na superfície do plástico, que servirão posteriormente de ancoragem para as sequências seguintes (KIM et al, 2006). Ou seja, antes da eletrodeposição é necessário depositar um filme metálico condutivo sobre o ABS, através da imersão em uma solução que contenha algum metal capaz de ser reduzido sobre a superfície do material. A função da camada condutora inicial é a de permitir boa condutividade da corrente elétrica, e proporcionar um recobrimento perfeito sobre a superfície a ser depositada, tendo assim, boa aderência do depósito com o plástico (PEI-CHI YEN, 1995).
se é necessário obedecer às recomendações dos fabricantes; velocidade de injeção que devem ser as mais baixas possíveis para se conseguir baixa tensão interna e boa aderência do depósito metálico, pois peças com regiões tensionadas tendem a ter uma menor distribuição de Butadieno, o que prejudica o ataque do banho de mordente neste região, prejudicando a aderência da camada depositada (DALBIN e POMMIER, 2007).
Em geral, a aderência da peça é particularmente influenciada pela qualidade do material plástico e pelas condições de moldagem das peças. A falha de aderência está entre a camada do plástico presa ao metal e o material plástico logo abaixo. A força coesiva nesta zona, chamada de zona limite, é determinada pela orientação do polímero. Se a orientação nesta zona pode ser minimizada, então a aderência será melhorada. Se a classe de ABS escolhida não for à apropriada para metalização, então o nível e a distribuição dos nódulos de Butadieno não são otimizados para uma boa metalização (MANRICH, 2005).
Para obter peças que asseguram boa aderência, distribuição adequada das camadas, etc, o projetista deverá ter boas noções das dificuldades que poderão ocorrer no setor de galvanoplastia, inclusive prevendo a forma de fixação das peças na gancheira. O projetista deverá levar em conta a posição da peça no banho e a distribuição de corrente elétrica, para que, através de modificações no desenho, consiga reduzir os problemas de penetração, má distribuição de camadas, queima das pontas, entre outros (SANTINI, 2000).
Tanto no setor de injeção como na cromagem, as peças injetadas devem ser manuseadas cuidadosamente, prevenindo assim marcas de impressões digitais e outras contaminações orgânicas causadas por óleo ou graxas. Elas devem ser embaladas quando estiverem frias, recomenda-se também, usar papel, pano, caixas de plástico expandidas, ou sacos de polietileno a fim de diminuir a formação de riscos, escoriações ou marcas indesejáveis, evitando gerar refugos após cromadas, uma vez que a camada metálica depositada sobre a superfície da peça tende a ressaltar qualquer imperfeição ocasionada antes do processo de cromagem. Deve ser tomado cuidado também com a retirada de canais de injeção, que podem causar riscos
na superfície da peça. Em alguns casos é interessante deixar o canal de injeção, que servirá de ponto de fixação nas gancheiras, retirando-o depois da metalização (ABTS, 1995).
O processo de cromagem em peças de ABS ocorre basicamente em duas etapas, o pré-tratamento químico e o tratamento eletrolítico, descritos a seguir.
2.2.1 Preparação Química do ABS
A maioria dos polímeros apresenta superfícies quimicamente inertes, não porosas e com baixa energia livre superficial, o que os tornam não receptivos à adesão de outras substâncias (tintas, metais, adesivos). Por esses motivos, os materiais poliméricos são tratados com técnicas específicas com o intuito de alterar suas propriedades de superfície favorecendo a interação e a adesão com outras substâncias (SELLIN, 2002). No caso da deposição metálica em superfícies de terpolímeros ABS, é necessário, previamente a esse processo, modificar a superfície por meio do pré tratamento químico para que haja adesão entre a camada metálica e o terpolímero (SANTINI, 2000). Esta modificação pode ser realizada pelo condicionamento, favorecendo a retenção do metal ao polímero. A adesão, neste caso, se dá pela mudança física da superfície proporcionando ancoramento mecânico do metal nas microcavidades formadas (MANDICH e KRULIK , 1993)
A seqüência do pré-tratamento químico mais utilizada industrialmente é constituída pelas seguintes etapas: condicionador, neutralizador, reativador, paládio, acelerador e níquel químico (MANDICH e KRULIK , 1993).
Tabela 1 - Condições de Operação banho de Condicionamento Concentração de Ácido Crômico 300 a 400 g/L Concentração de Ácido Sulfúrico 300 a 400 g/L Concentração de Cromo Trivante 5 a 30 g/L Temperatura 60 a 68°C Tempo de Imersão 5 a 20min Fonte: ABTS, 1995
Após as lavagens, que devem estar sempre limpas para evitar falhas e diminuição da aderência, o passo seguinte será a neutralização.
2.2.1.2 Neutralização
Depois do condicionamento e de diversas lavagens, as peças são imersas em uma solução contendo um agente redutor para eliminar o excesso de cromo arrastado do condicionador, e impedir o arraste de cromo hexavalente para os banhos subseqüentes. Uma neutralização deficiente permite arraste de cromo nas peças, dificultando a deposição do ativador e posteriormente do níquel químico, pois o cromo hexavalente é um veneno para os ativadores a base de Paládio e Estanho coloidal e banhos de níquel químico (KRULIK,1993).
Estas soluções neutralizantes geralmente contêm agentes redutores em uma concentração na faixa de 5 a 20 g/L. Os banhos são frequentemente renovados, dependendo da superfície da área tratada e do arraste. O pH da solução deve ser menor que 2, para manter uma taxa suficientemente alta de reação e evitar a precipitação de compostos de cromo trivalente. A temperatura do banho é geralmente entre 25 e 35°C e o tempo de imersão é de aproximadamente de 1 a 3 minutos (ABTS, 1995).
2.2.1.3 Ativador e Catalisador
Após a fase de neutralização, as peças são imersas em um banho pré- catalisador, geralmente esta solução contém ácido clorídrico diluído, o que previne a diluição do banho catalisador. O banho de catalisador tem a finalidade de depositar partículas de um metal mais precioso para formar uma camada catalítica sobre a superfície condicionada do plástico, onde é utilizada uma solução coloidal de Paládio e Estanho que deixa um filme catalítico sobre o ABS, penetrando nos microporos abertos pelo condicionador, o que promove a iniciação da reação auto-catalítica do níquel químico (TEIXEIRA e SANTINI, 2005).
O banho catalisador mais comumente utilizado industrialmente é o Paládio/Estanho Coloidal (Pd/Sn). Este colóide é preparado pela reação do Cloreto de Estanho II com Cloreto de Paládio, e é recomendado que a quantidade de Sn2+^ seja mantida de 5 a 10 g/L e a forte agitação da solução dever ser evitada. A temperatura do banho tem uma pequena influência na adsorção coloidal. Os banhos são mantidos entre 20 a 35°C e tempo de imersão pode variar de 1 a 5 minutos. Quando adequadamente controlada através de análises de concentração e contaminantes (principalmente Cromo), a solução de ativador pode ser mantida por tempo indefinido (ABTS, 1995).
2.2.1.4 Acelerador
Seguido do banho de solução catalisadora, e após lavagens, as peças passam por uma solução chamada “acelerador" ou "pós-ativador", usualmente de ácido sulfúrico, que deixará o filme catalítico extremamente ativo para iniciar a reação de deposição do níquel químico (TEIXEIRA e SANTINI, 2005).
Neste banho, o íon Estanho II (Sn2+) é oxidado para estanho IV (Sn4+) para “liberar” as partículas de paládio (Pd) adsorvidas dentro do ABS. Este banho também serve para prevenir a metalização de gancheiras ou superfícies pintadas, pela eliminação de excesso de colóides, deste modo evitando um
Tabela 2 - Condições de Operação banho de Níquel Químico Sulfato de níquel.6H20 8 - 30 g/L Hipofosfito de sódio 10 - 50 g/L Amônia (33%) 50 - 100 g/L pH 8 - 10 Temperatura 20 - 40°C Fonte: ABTS, 1995
2.2.2 Tratamento Eletrolítico
Após a metalização em banho de níquel químico, as peças seguem para a segunda fase do processo: metalização eletrolítica, de maneira similar às peças metálicas. As peças são lavadas e ativadas, seguindo o primeiro banho eletrolítico: cobre ácido, seguido de níquel brilhante e finalizando com o cromo (RUSSEL,1994).
2.2.2.1 Eletrodeposição de Cobre
O depósito de cobre nivela a superfície para assegurar um acabamento mais brilhante possível. O cobre cria uma camada elástica que compensa a diferença do coeficiente de expansão entre o substrato plástico e o níquel químico. Esta camada é essencial para suportar os esforços gerados durante os choques térmicos ou ciclos térmicos (ABTS, 1995). O banho de sulfato de cobre é quimicamente um banho simples. Existem diversas fórmulas, sendo a mais usada às condições de composição conforme a Tabela 3:
Tabela 3 - Condições de composição do banho de Cobre Ácido Sulfato de Cobre 180 a 250 g/L Acido Sulfúrico P.A 40 a 75 g/L Íon Cloro 30 a 80 mg/L Fonte: ABTS, 1995
Os banhos brilhantes de cobre ácido, ainda necessitam de certos aditivos: abrilhantadores, niveladores e humectantes. O sucesso dos banhos de cobre ácidos brilhantes de base de sulfato de cobre baseia-se sobre as seguintes características: alta velocidade de eletrodeposição; alto nivelamento; camadas dúcteis e alto brilho de camada de cobre. O rendimento máximo destas soluções é conseguido usando a agitação com ar e um bom controle da temperatura. Temperaturas acima de 30°C afetam negativamente o poder de nivelamento e a formação do brilho (ABTS, 1995).
Para os banhos de cobre ácidos foram desenvolvidos ânodos de cobre especiais chamados anodos "fosforados". Estes anodos têm uma especificação rígida em relação à cristalização, teor de fósforo e impurezas de outros metais. O teor do fósforo em geral se encontra entre 0,02 e 0,07% (0,2-0,7g/kg). Os anodos de cobre fosforado em condições normais de trabalho formam um filme preto durante a eletrólise, o qual não aumenta a resistência elétrica e permite ao anodo se dissolver uniformemente. Os banhos de cobre ácido têm uma eficiência catódica perto de 100%, assim, o cálculo da camada formada deste banho é simples. Na prática pode ser usada a regra que com 5 Âmperes/dm^2 será formada uma camada de 1 micrômetro de cobre por minuto (ABTS, 1995).
Sob condições normais, os banhos de cobre ácido brilhante precisam de poucos reforços. Se o arraste do banho for muito baixo, a concentração do cobre metal lentamente aumentará e será necessário a diluição ocasional do banho ou a substituição dos anodos de cobre fosforados por anodos de chumbo. Porém, na maioria dos casos, pequenas adições de sulfato de cobre e ácido sulfúrico se tornam necessárias. O íon cloro é um componente necessário no banho de cobre ácido, a manutenção deste íon dentro das especificações do processo é de alta importância, pois em casos de baixo teor de cloro como também alto teor de cloro, o banho torna-se inoperante pela formação de diversos defeitos, como estrias e fosqueamento da camada. A análise do cloro deve ser feita regularmente. No caso de falta de cloro pode-se adicionar uma quantidade calculada de ácido clorídrico (SURTEC, 2012).
2.2.2.3 Eletrodeposição do Cromo Decorativo
A deposição feita por cromo tem o objetivo de promover um acabamento decorativo, sua composição baseia-se em 250 g/L de sal de cromo, 1 g/L de ácido sulfúrico e humectante, sua temperatura é na faixa de 41, 42ºC, o tempo de deposição é de 3 a 5 minutos com amperagem na faixa de 12 A/dm², alguns retificadores trabalham com rampa de amperagem, facilitante a deposição sem ocorrer queimas nas pontas da peça, ou amarelamento pela falta de deposição (SURTEC, 2012)
O cromo utilizado para fins decorativos é depositado em camadas mais finas. Peças cromadas que serão usadas exclusivamente em ambiente interno, onde a resistência à corrosão e choque térmico não são itens de muita importância, podem utilizar a seguinte espessura de camada:
Cromo: 0,25 micrômetros
Níquel: 7,5 micrômetros
Cobre: 15 a 20 micrômetros
Esse acabamento proporciona ótima aderência que será mantida por muito tempo, em ambiente interno (ABTS, 1995).
Diversos equipamentos são utilizados em uma indústria galvâniva, os principais são:
Tanques: reservatórios construídos de chapas de aço, revestidos com Polietileno, Polipropileno, Policloreto de Vinila ou Ebonite, a fim de proteger o material do ataque sofrido pelos banhos (ESPINOSA et al., 1995).
Exaustores: eliminam os gases tóxicos que possivelmente estejam no ambiente de trabalho (ESPINOSA et al., 1995). Filtros: o processo de filtragem é realizado através de um sistema de bomba filtro com utilização de elementos filtrantes como o papel ou telas de polipropileno. É importante ressaltar que um bom sistema de filtragem é aquele que faz com que ocorra uma vazão eficiente em uma baixa pressão (ESPINOSA et al., 1995). Retificadores: Para ocorrer o processo de eletrodeposição, é necessário que a corrente utilizada seja continua, entretanto ocorrem pulsos na corrente que são denominados “onda quadrada”. Para minimizar a ação desses pulsos são utilizados retificadores que irão reduzir a tensão utilizada, fazendo com que a corrente alternada torne- se continua, a fim de torna-la utilizável no processo de banho galvânico (ESPINOSA et al., 1995).
Após o processo de cromagem, as peças necessitam de uma rápida e eficiente inspeção. O processo de cromagem deve garantir boa aparência da peça (sem furos, saliências, falha de depósito, bolhas, névoa, fissuras, aspereza, etc...) e boa aderência do depósito metálico sobre a base plástica. As peças podem ser liberadas somente após rápidos testes que garantam sua qualidade. Os critérios satisfatórios para esses testes são estabelecidas em normas como ASTM, ISO, etc, ou pelas especificações dos próprios clientes (DALBIN e POMMIER, 2007).
Dentre os testes mais realizados estão o de aderência, teste de ácido acético na peça bruta injetada e teste de ciclo térmico, os quais serão descritos abaixo: