
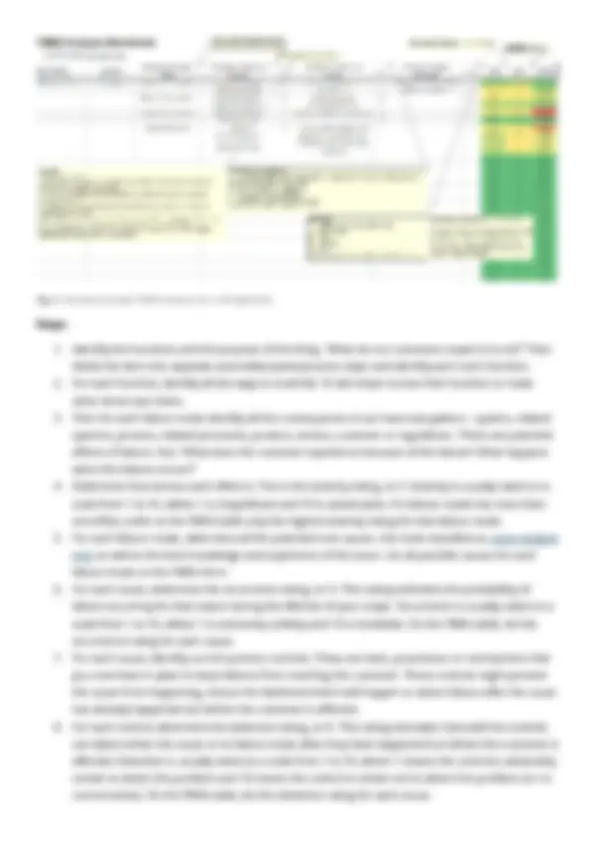
Estude fácil! Tem muito documento disponível na Docsity
Ganhe pontos ajudando outros esrudantes ou compre um plano Premium
Prepare-se para as provas
Estude fácil! Tem muito documento disponível na Docsity
Prepare-se para as provas com trabalhos de outros alunos como você, aqui na Docsity
Os melhores documentos à venda: Trabalhos de alunos formados
Prepare-se com as videoaulas e exercícios resolvidos criados a partir da grade da sua Universidade
Responda perguntas de provas passadas e avalie sua preparação.
Ganhe pontos para baixar
Ganhe pontos ajudando outros esrudantes ou compre um plano Premium
Comunidade
Peça ajuda à comunidade e tire suas dúvidas relacionadas ao estudo
Descubra as melhores universidades em seu país de acordo com os usuários da Docsity
Guias grátis
Baixe gratuitamente nossos guias de estudo, métodos para diminuir a ansiedade, dicas de TCC preparadas pelos professores da Docsity
Failure modes and effects analysis (fmea) is a systematic approach used to identify potential failures in design, manufacturing, or assembly processes, products, or services. By analyzing the ways in which something might fail (failure modes) and the consequences of those failures, fmea helps prevent failures and improve overall system performance. A summary of the fmea process, including steps, examples, and rating scales.
O que você vai aprender
Tipologia: Exercícios
1 / 2
Esta página não é visível na pré-visualização
Não perca as partes importantes!
A summary by André Duarte B. L. Ferreira Last edit: 16 th May 2017 FMEA = Failure Modes and Effects Analysis. FMEA is an approach to identify all possible failures in a design, a manufacturing or assembly process, or a product or service. “Failure modes” means the ways, or modes, in which something might fail. FMEA is used during design to prevent failures. Fig. 1 Example of FMEA table of an ATM machine.
Fig. 2 Example of simple FMEA analysis for a LED light bulb. Steps: