
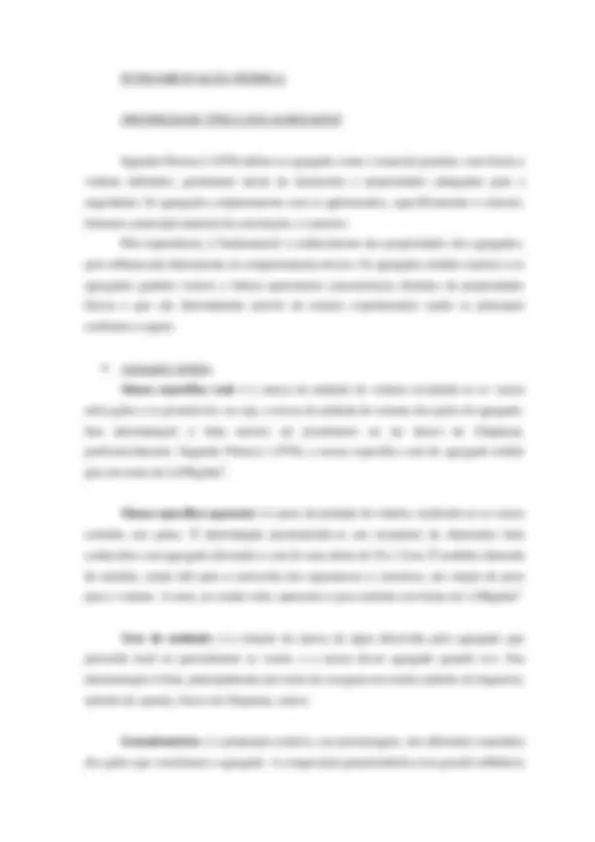
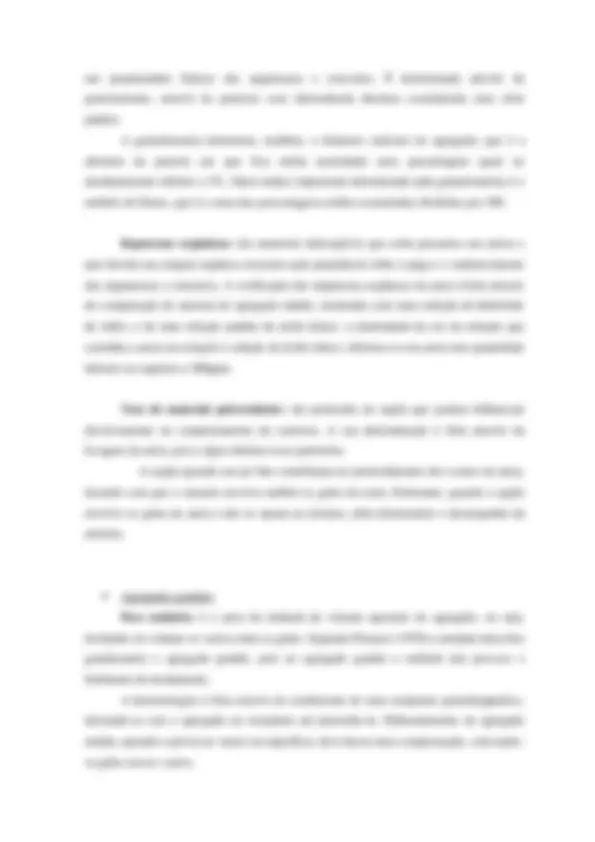
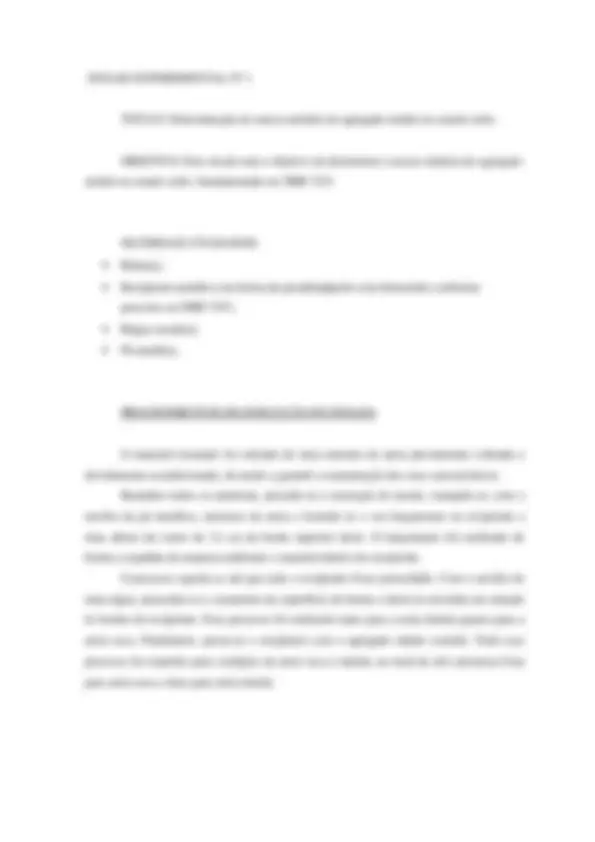
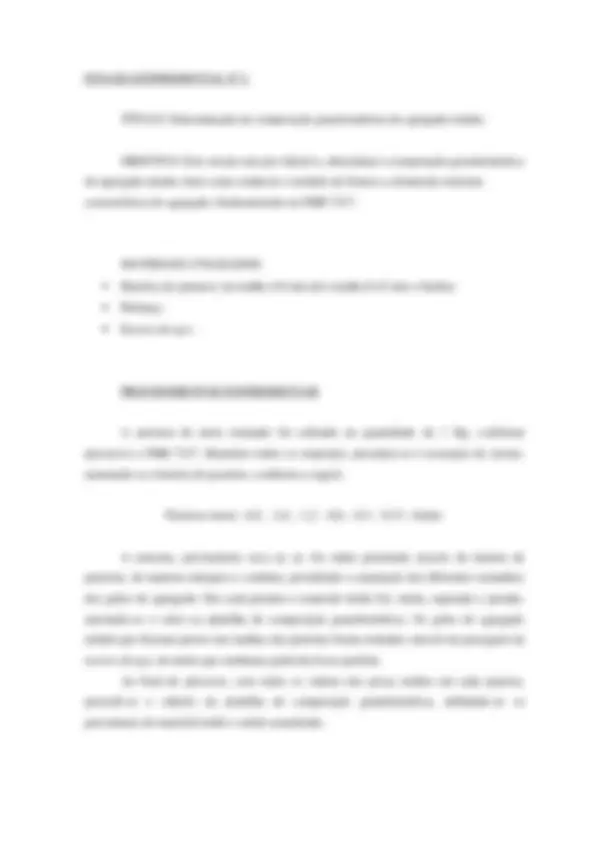
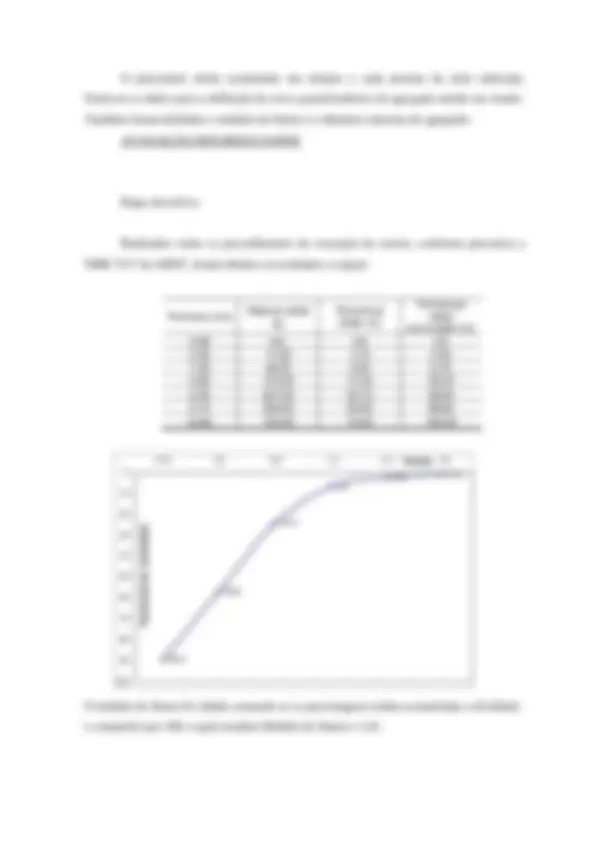
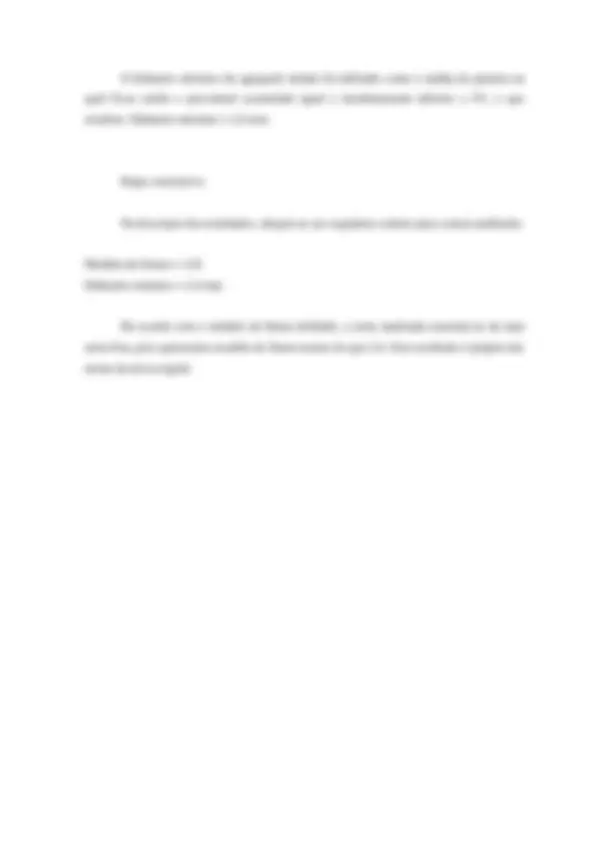
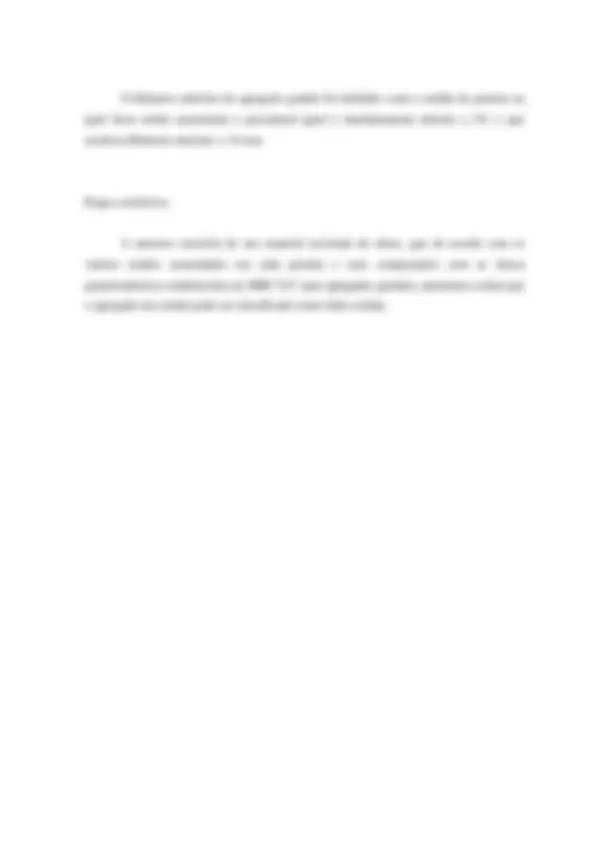
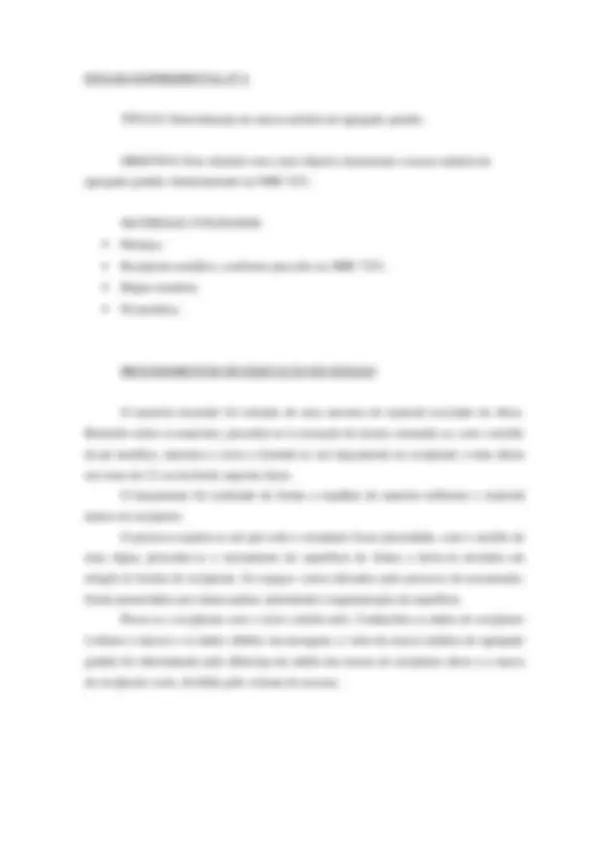
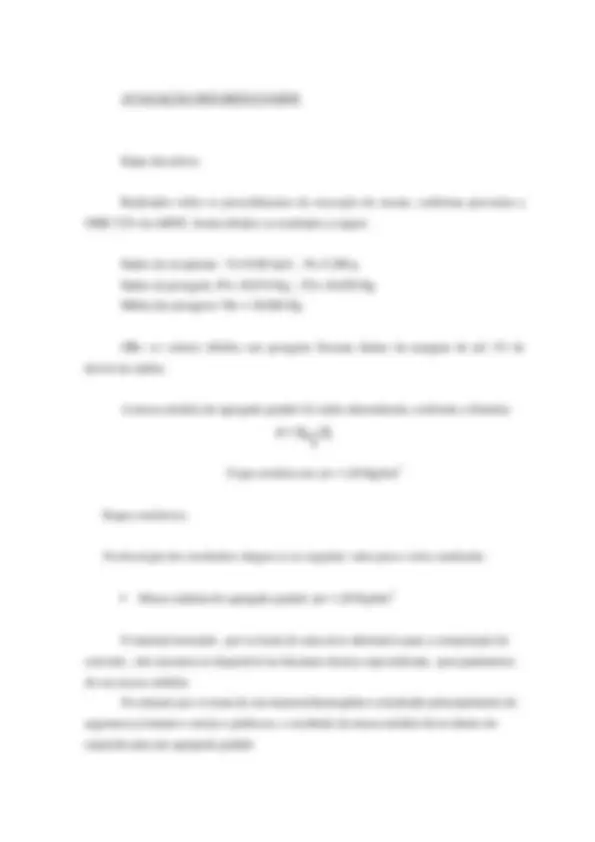
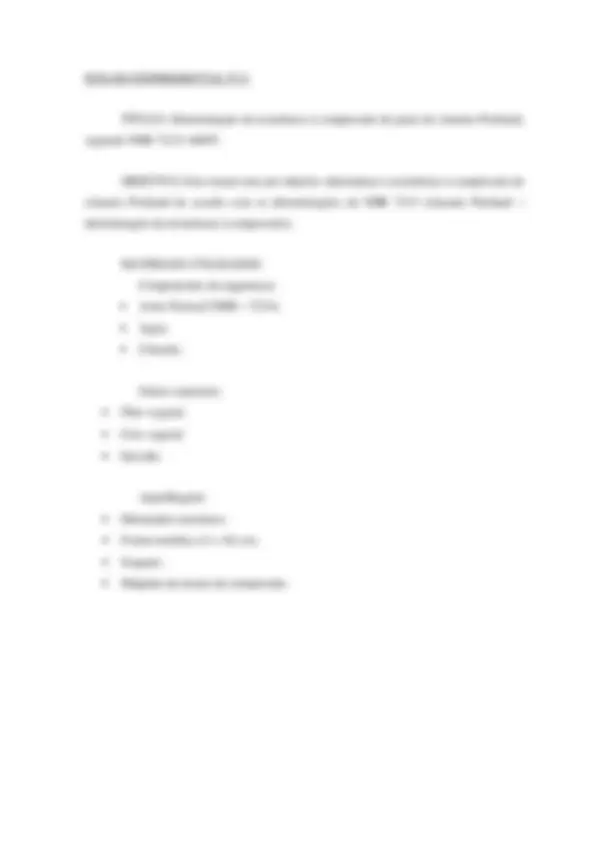
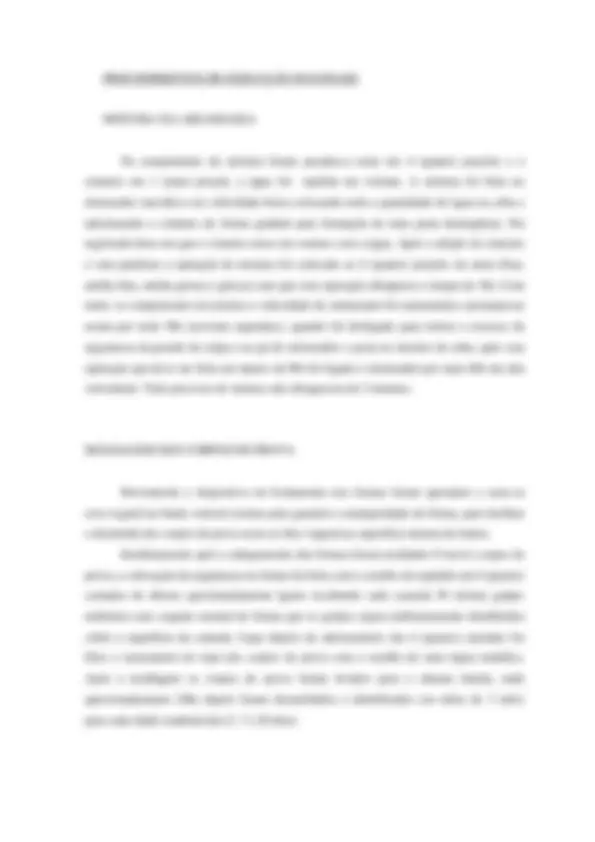
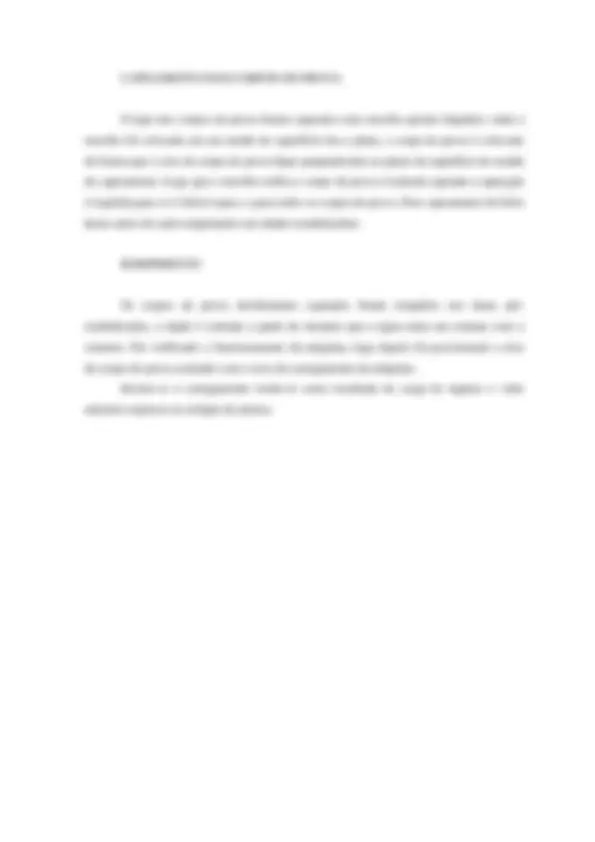
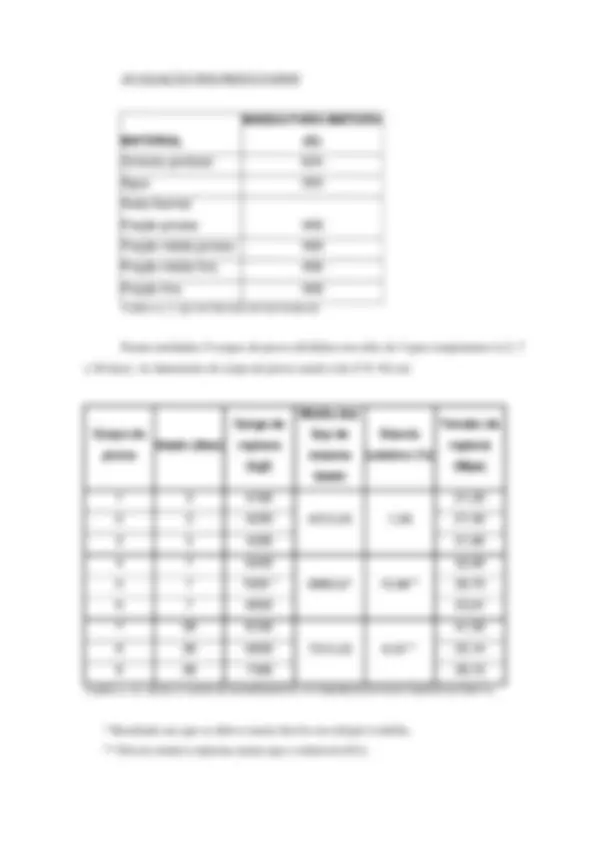
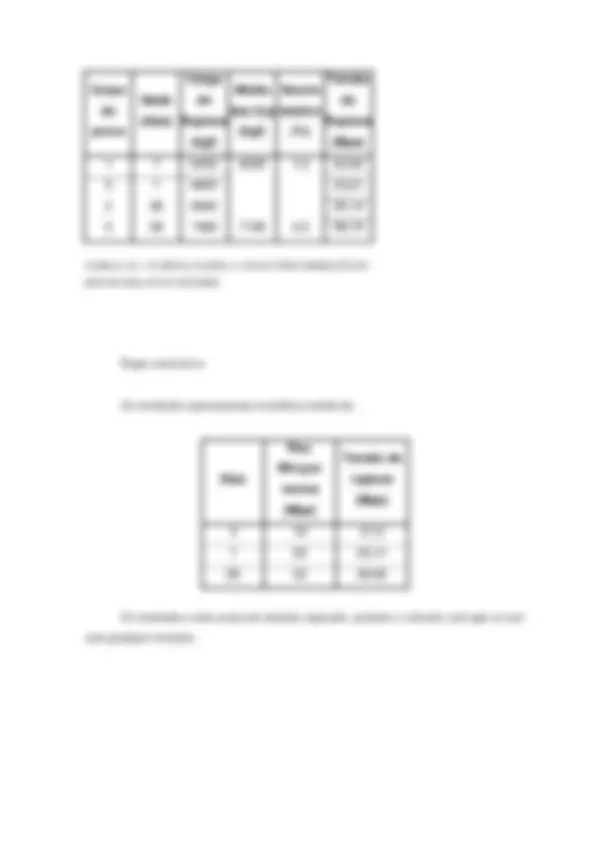
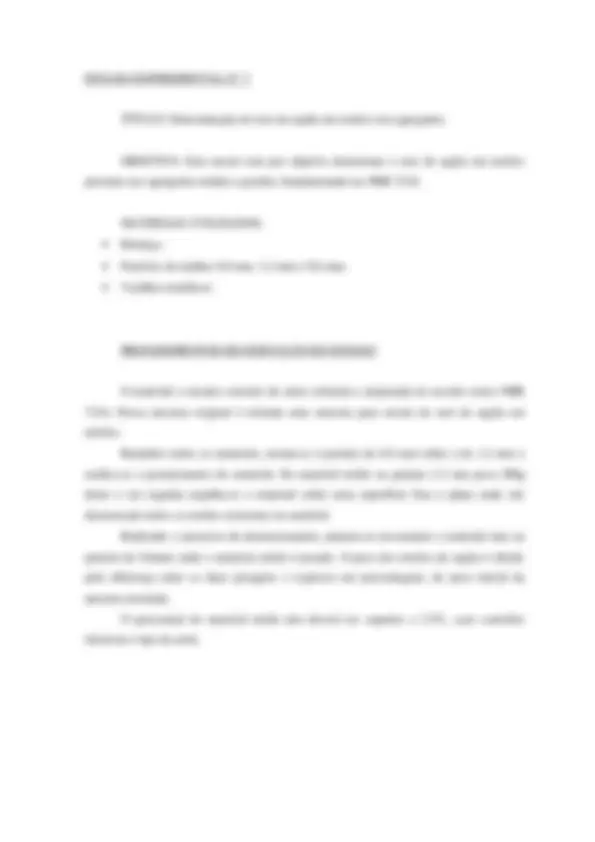
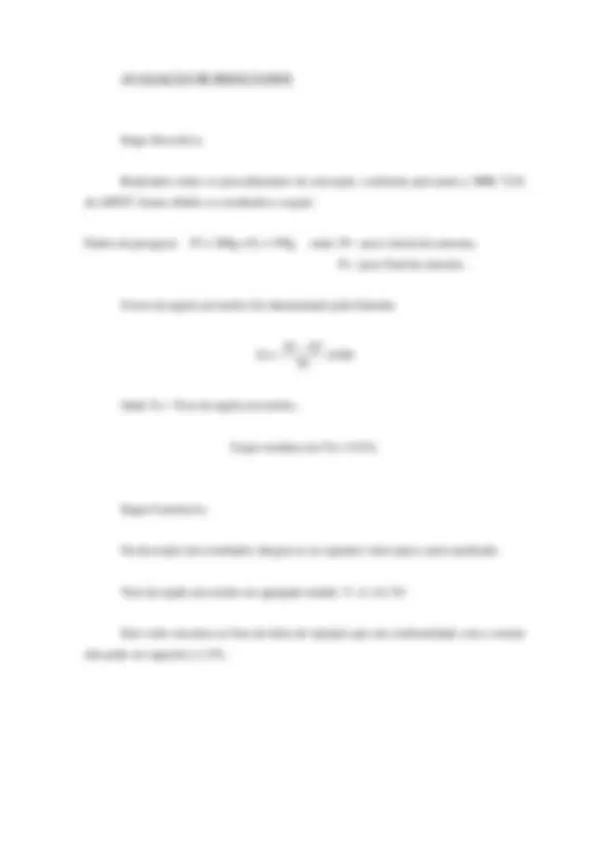
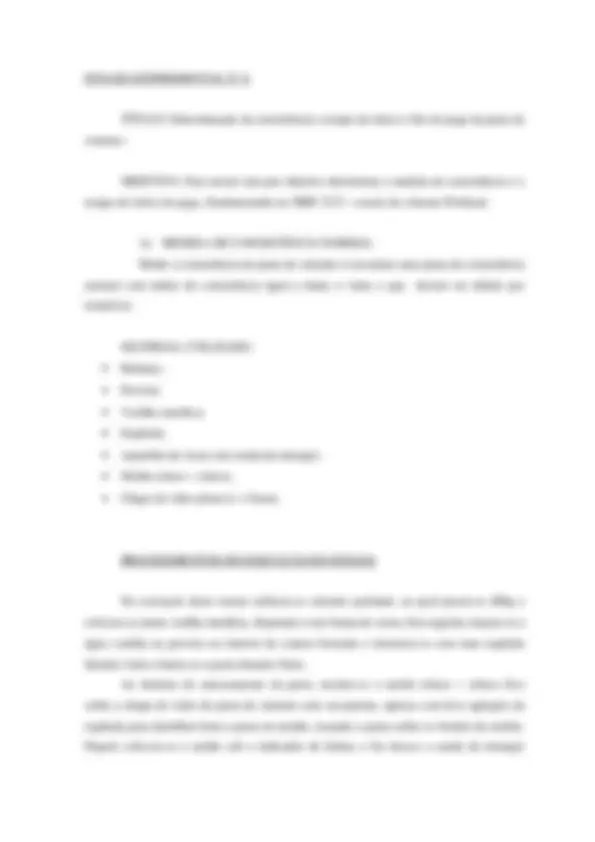


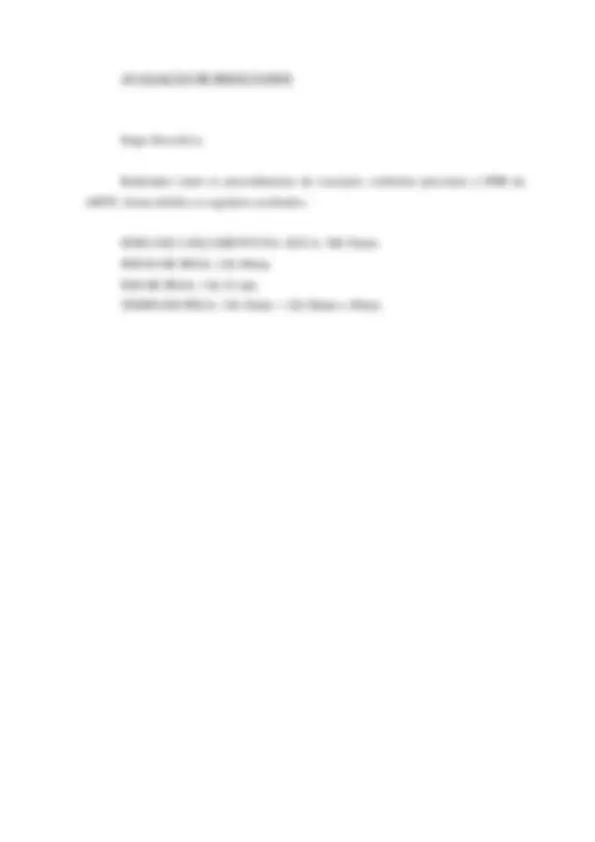
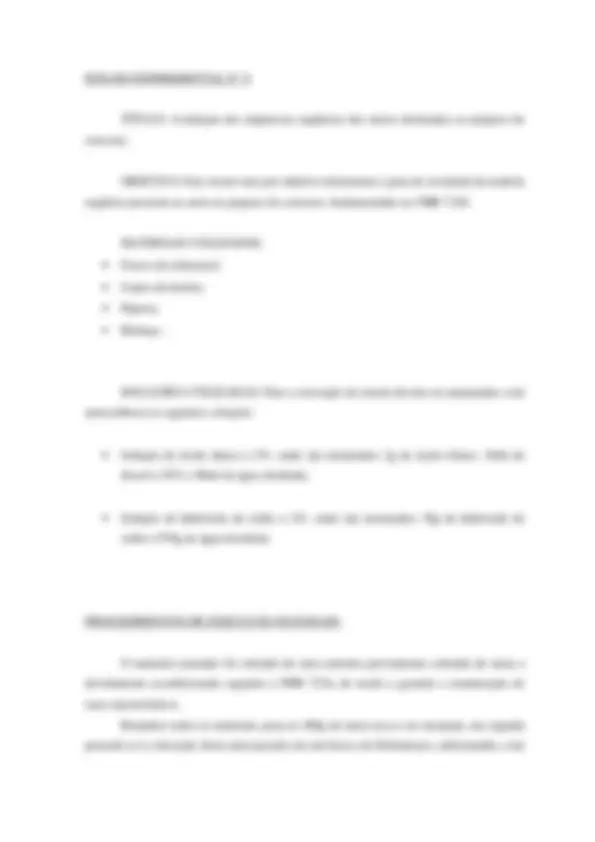
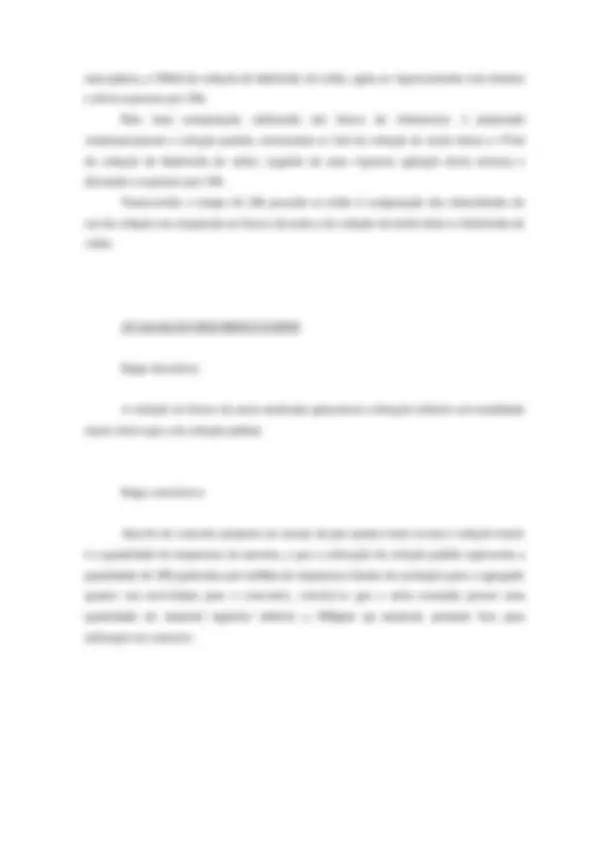
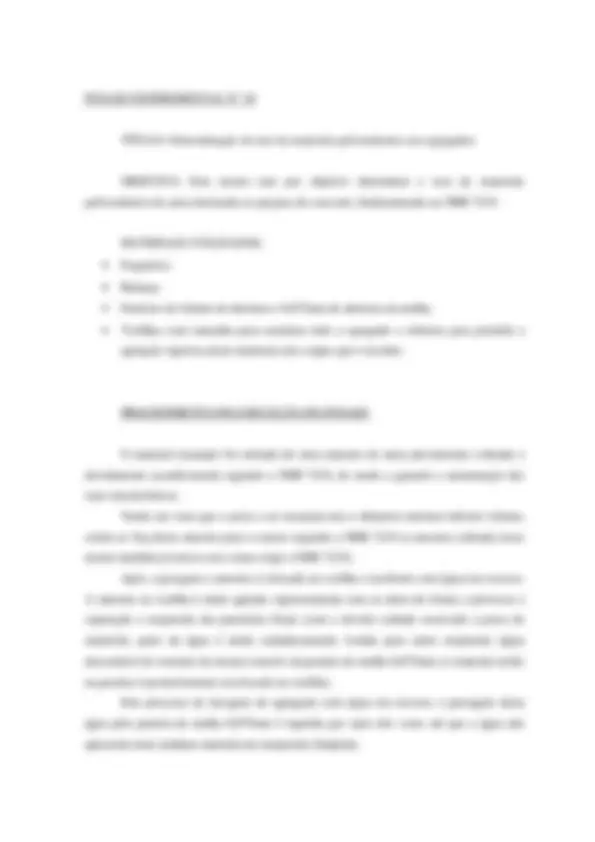
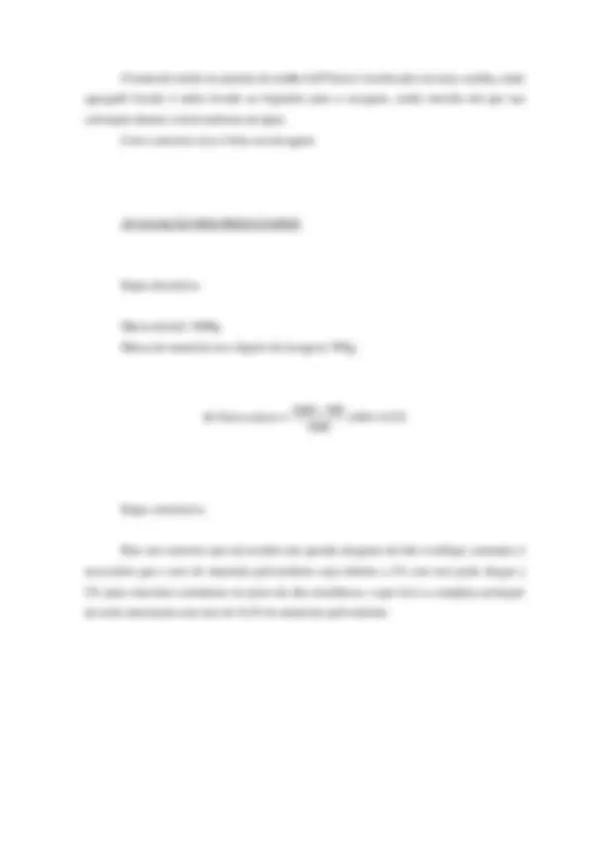
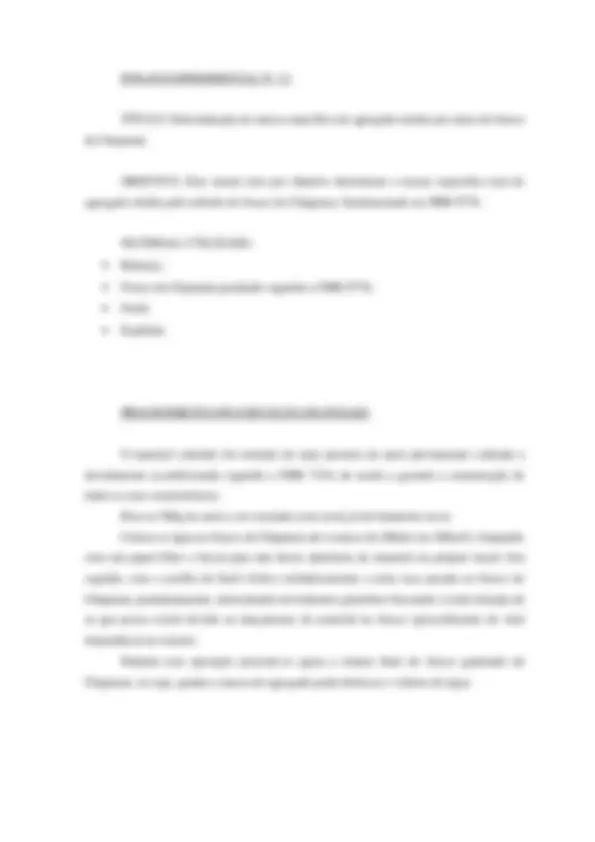
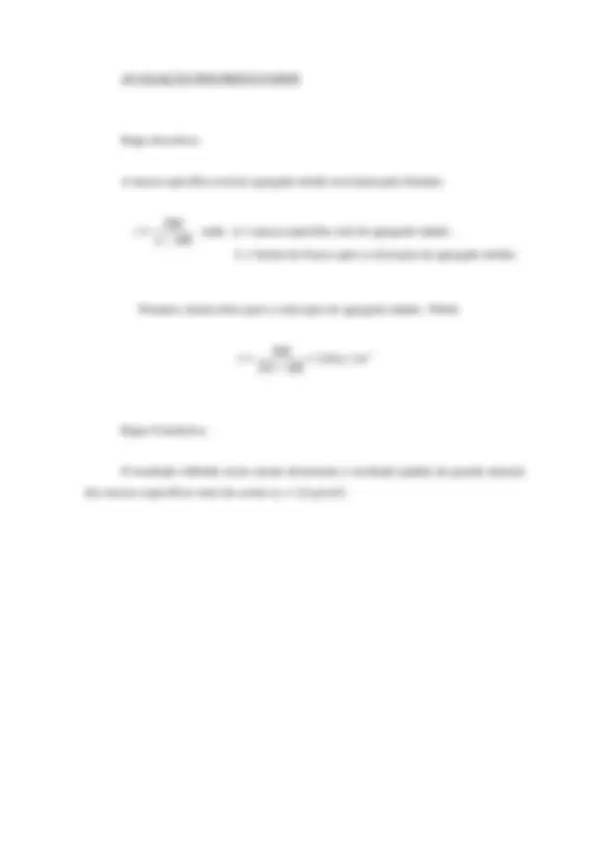
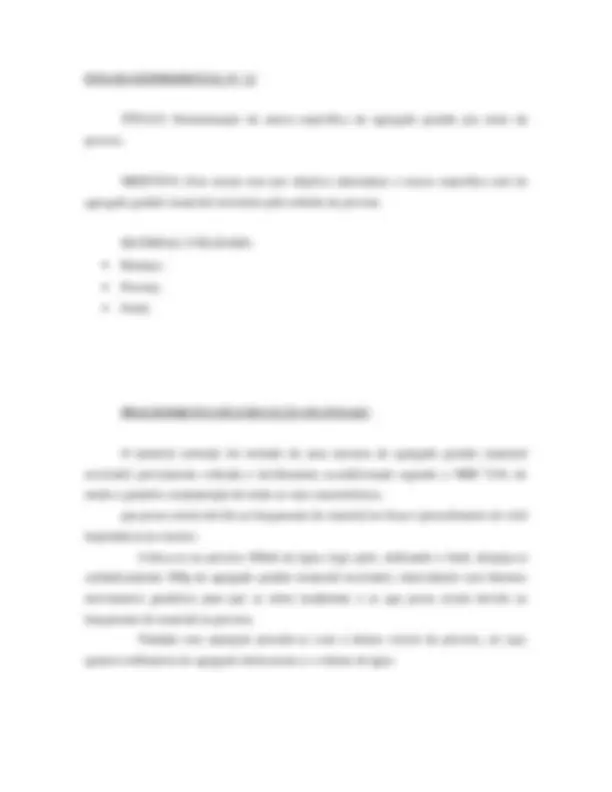

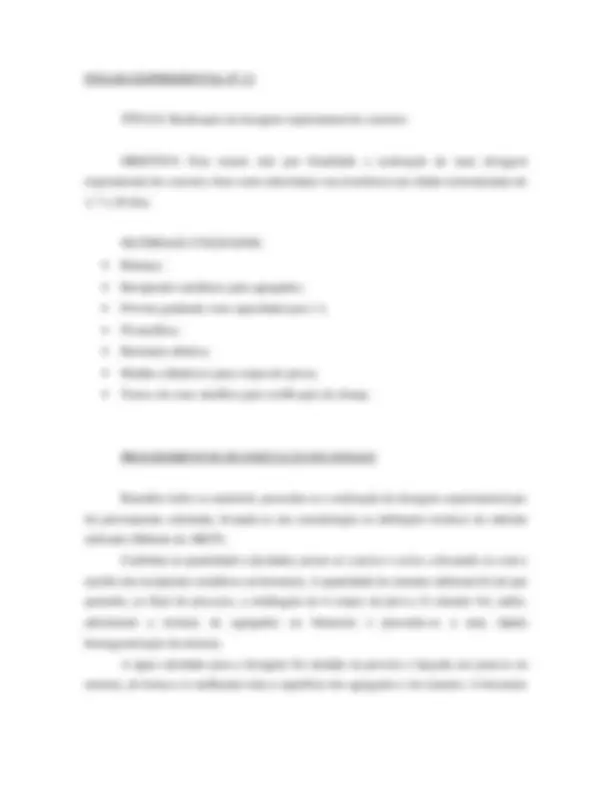
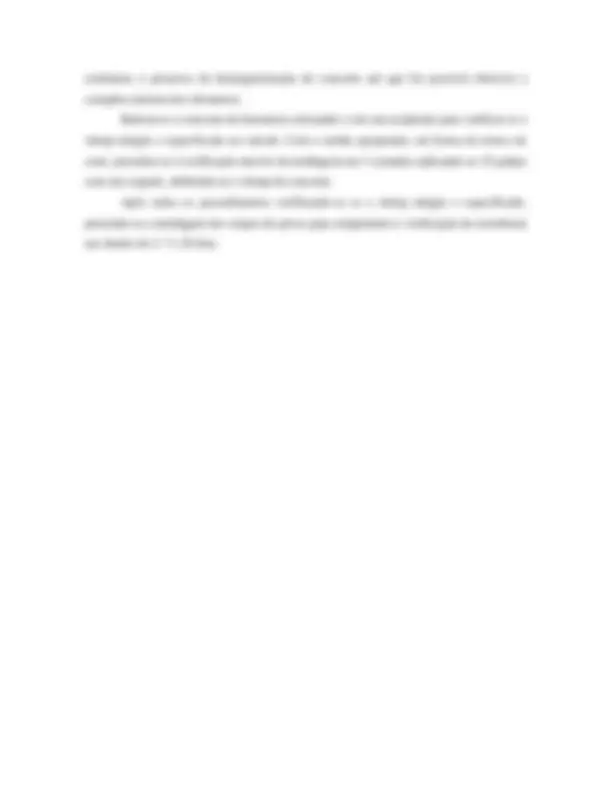
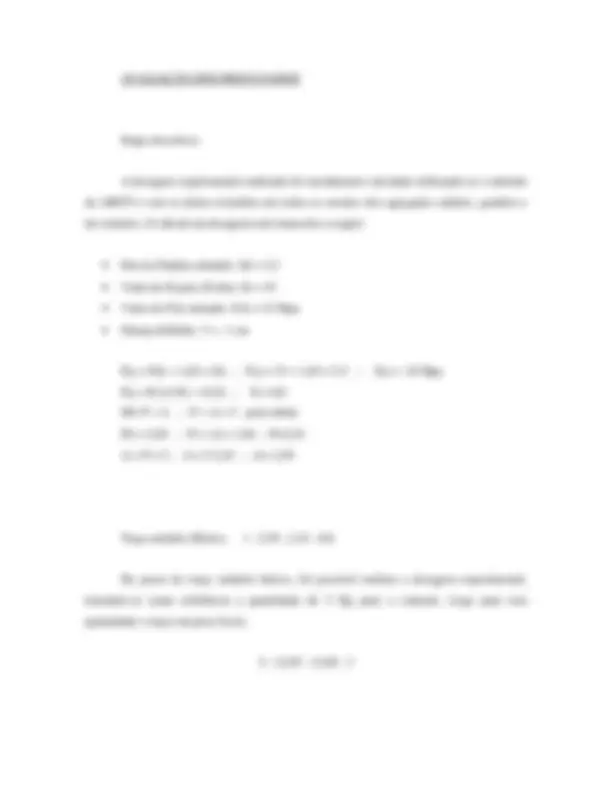
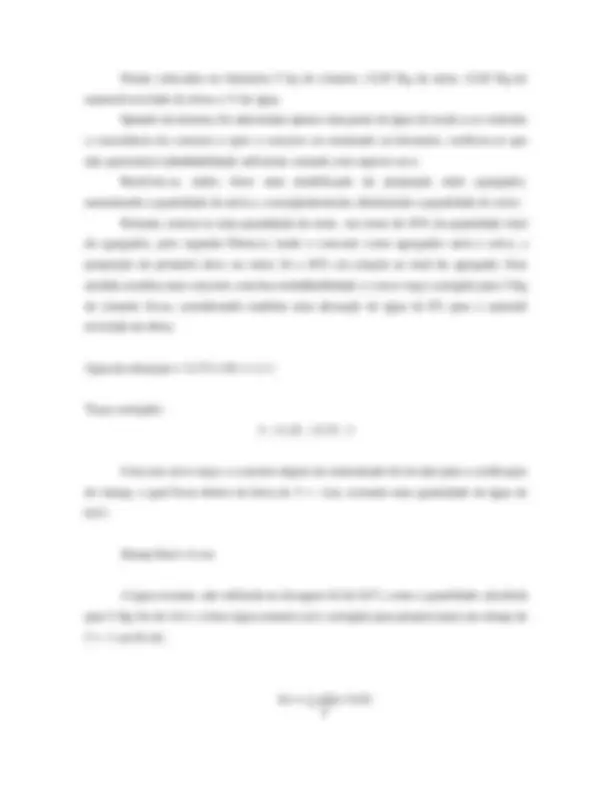
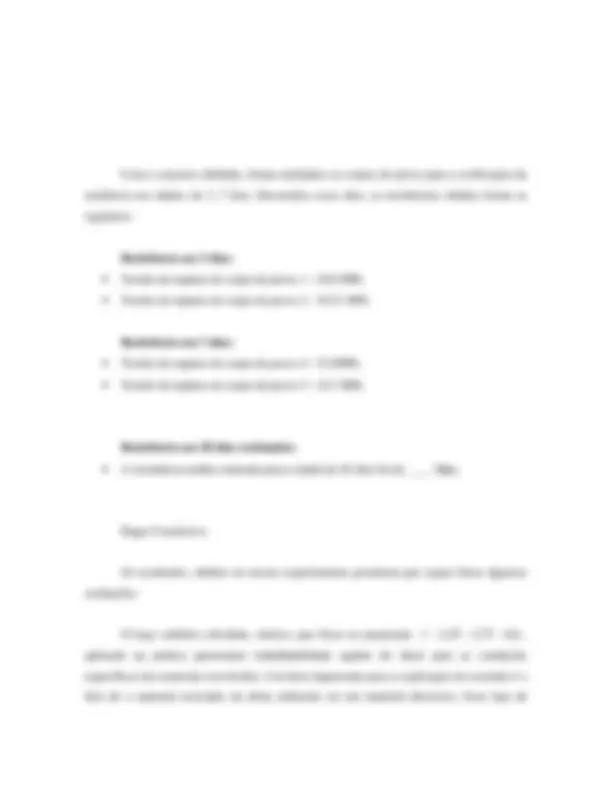
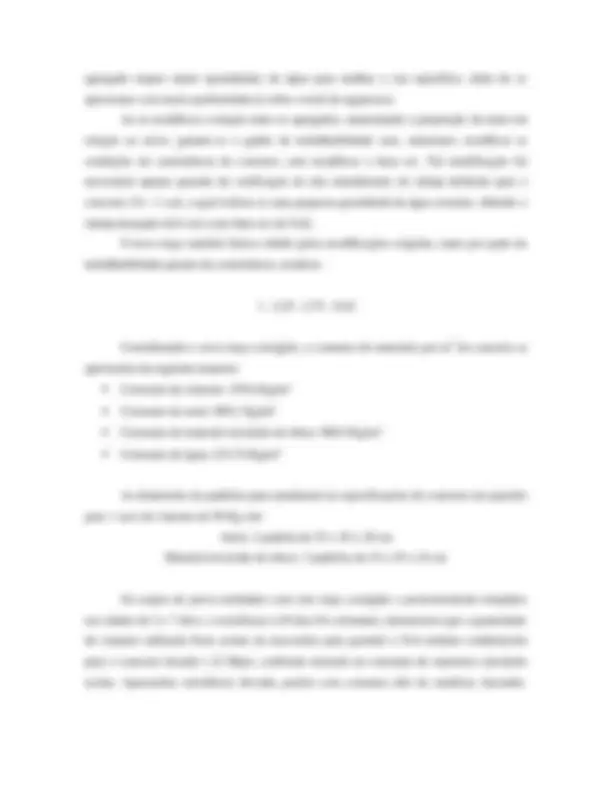
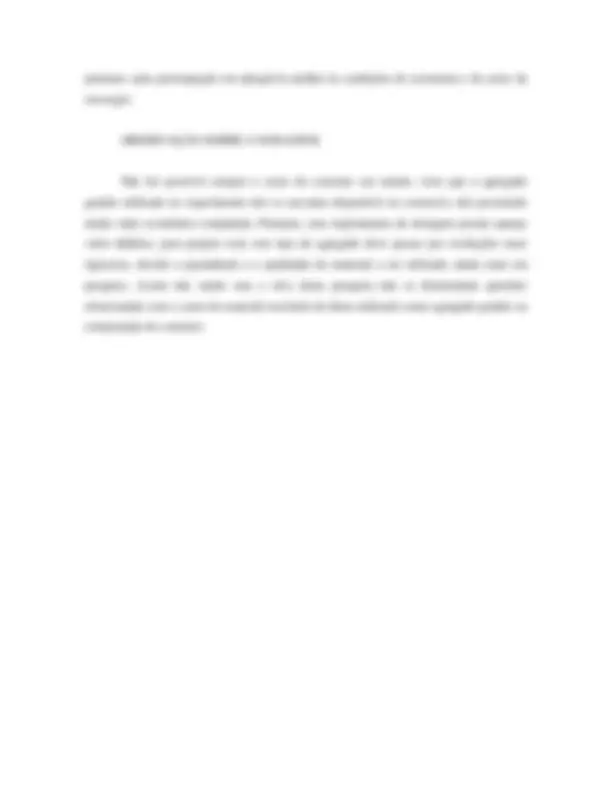
Estude fácil! Tem muito documento disponível na Docsity
Ganhe pontos ajudando outros esrudantes ou compre um plano Premium
Prepare-se para as provas
Estude fácil! Tem muito documento disponível na Docsity
Prepare-se para as provas com trabalhos de outros alunos como você, aqui na Docsity
Os melhores documentos à venda: Trabalhos de alunos formados
Prepare-se com as videoaulas e exercícios resolvidos criados a partir da grade da sua Universidade
Responda perguntas de provas passadas e avalie sua preparação.
Ganhe pontos para baixar
Ganhe pontos ajudando outros esrudantes ou compre um plano Premium
Comunidade
Peça ajuda à comunidade e tire suas dúvidas relacionadas ao estudo
Descubra as melhores universidades em seu país de acordo com os usuários da Docsity
Guias grátis
Baixe gratuitamente nossos guias de estudo, métodos para diminuir a ansiedade, dicas de TCC preparadas pelos professores da Docsity
"Os produtos cerâmicos são obtidos pela moldagem, secagem e queima de argila. A
Tipologia: Exercícios
1 / 43
Esta página não é visível na pré-visualização
Não perca as partes importantes!
O processo experimental é o modo racional e otimizado de se avaliar os fenômenos ocorrentes do meio natural de se avaliar os fenômenos ocorrentes do meio natural e possibilita, acima de tudo, analisar seus comportamentos. Nesse relatório estão compilados os processos experimentais dos ensaios de índices físicos dos agregados e dos ensaios de caracterização do cimento, utilizados na composição de concreto. Esses ensaios dividem-se em dois grupos distintos: ensaios de agregados e ensaios de cimento, conforme o que segue:
Ensaios de agregados:
Determinação da massa unitária do agregado miúdo unido em estado solto; Determinação da massa unitária do agregado miúdo seco em estado solto; Determinação da massa unitária do agregado graúdo; Determinação da composição granulométrica do agregado miúdo; Determinação da composição granulométrica do agregado graúdo; Determinação do teor de argila em torrões no agregado miúdo; Avaliação das impurezas orgânicas das areias; Determinação do teor de material pulverulento; Determinação da massa específica real do agregado miúdo e graúdo; Ensaios de cimento; Determinação da finura do cimento; Determinação da consistência normal da pasta; Determinação do início e fim de pega; Determinação da resistência à compressão; Dosagem experimental.
Além do supracitado, este relatório descreve o processo experimental de dosagem de concreto, resultado dos conhecimentos preliminares de caracterização dos índices físicos. A importância desses tópicos na atividade prática decorre da necessidade de se conhecer as especificidades dos materiais constituintes do concreto, a fim de se compor, ao
final do processo, sua eficiente e necessária dosagem e assim garantir seu padrão técnico – qualitativo. Portanto, os processos experimentais apresentados objetivam demonstrar os resultados obtidos nos diversos ensaios e assim possibilitar suas análises.
nas propriedades futuras das argamassas e concretos. É determinada através de peneiramento, através de peneiras com determinada abertura constituindo uma série padrão. A granulometria determina, também, o diâmetro máximo do agregado, que é a abertura da peneira em que fica retida acumulada uma percentagem igual ou imediatamente inferior a 5%. Outro índice importante determinado pela granulometria é o módulo de finura, que é a soma das porcentagens retidas acumuladas divididas por 100.
Impurezas orgânicas: são materiais indesejáveis que estão presentes nas areias e que devida sua origem orgânica exercem ação prejudicial sobre a pega e o endurecimento das argamassas e concretos. A verificação das impurezas orgânicas da areia é feita através de comparação da amostra de agregado miúdo, misturado com uma solução de hidróxido de sódio, e de uma solução padrão de ácido tânico. a intensidade da cor da solução que continha a areia em relação à solução de ácido tânico, informa se esta areia tem quantidade inferior ou superior a 300ppm.
Teor de material pulverulento: são partículas de argila que podem influenciar decisivamente no comportamento do concreto. A sua determinação é feita através da lavagem da areia, pois a água elimina essas partículas. A argila quando em pó fino contribuem no preenchimento dos vazios da areia, fazendo com que o cimento envolva melhor os grãos da areia. Entretanto, quando a argila envolve os grãos de areia e não se separa na mistura, afeta diretamente o desempenho da mistura.
Agregados graúdos Peso unitário: é o peso da unidade de volume aparente do agregado, ou seja, incluindo no volume os vazios entre os grãos. Segundo Petrucci (1970) a unidade nãoa feta grandemente o agregado graúdo, pois no agregado graúdo a unidade não provoca o fenômeno do inchamento. A determinação é feita através do enchimento de uma recipiente paralelepípedico, deixando-se cair o agregado no recipiente até preenche-lo. Diferentemente do agregado miúdo, quando o provocar vazios na superfície, deve haver uma compensação, colocando- se grãos nesses vazios.
TITULO: Determinação da massa unitária do agregado miúdo no estado solto.
OBJETIVO: Este ensaio tem o objetivo de determinar a massa unitária do agregado miúdo no estado solto, fundamentado na NBR 7251
Balança; Recipiente metálico em forma de paralelepípedo com dimensões conforme prescrito na NBR 7251; Régua rasadora; Pá metálica.
O material ensaiado foi retirado de uma amostra de areia previamente coletada e devidamente acondicionada, de modo a garantir a manutenção das suas características. Reunidos todos os materiais, procede-se a execução do ensaio, tomando-se, com o auxílio da pá metálica, amostras da areia e fazendo-se o seu lançamento no recipiente a uma altura em torno de 12 cm da borda superior deste. O lançamento foi realizado de forma a espalhar de maneira uniforme o material dentro do recipiente. O processo repetiu-se até que todo o recipiente fosse preenchido. Com o auxílio de uma régua, procedeu-se o rasamento da superfície de forma a deixá-la nivelada em relação às bordas do recipiente. Esse processo foi realizado tanto para a areia úmida quanto para a areia seca. Finalmente, pesou-se o recipiente com o agregado miúdo contido. Todo esse processo foi repetido para condição da areia seca e úmida, no total de três amostras.Uma para areia seca e duas para areia úmida.
Por se tratar de areia úmida, determinou-se através do método do fogareiro, o valor dessa umidade, obtendo-se: Mo = 100g (inicial) ; Mf = 98g (final) .: H = Mo – Mf x 100 Mo Sendo, portanto, a umidade de: H% = 2 % A massa unitária da areia úmida no estado solto foi determinada conforme a fórmula: u = Pm – Po V O que resultou em: u = 1,22 Kg/dm^3
Etapa conclusiva:
Na descrição dos resultados chegou-se aos seguintes valores para a areia analisada:
Massa unitária da areia seca no estado solto: s = 1,69 Kg/dm^3 Massa unitária da areia úmida no estado solto: u = 1,22 Kg/dm^3 Umidade: H% = 2 %
Estes valores apresentam-se próximo aos valores de referência indicados pela norma, e, portanto, são resultados coerentes e satisfatórios, o que permitem avaliar que o material analisado está em conformidade com os padrões que são escopo deste ensaio.
TÍTULO: Determinação da composição granulométrica do agregado miúdo.
OBJETIVO: Este ensaio tem por objetivo, determinar a composição granulométrica do agregado miúdo, bem como conhecer o módulo de finura e a dimensão máxima característica do agregado, fundamentado na NBR 7217.
Baterias de peneira ( da malha 4,8 mm até a malha 0,15 mm e fundo); Balança; Escova de aço;
A amostra de areia ensaiada foi coletada na quantidade de 1 Kg, conforme prescreve a NBR 7217. Reunidos todos os materiais, procedeu-se à execução do ensaio, montando-se a bateria de peneiras, conforme a seguir:
Peneiras (mm) : 4,8 ; 2,4 ; 1,2 ; 0,6 ; 0,3 ; 0,15 ; fundo.
A amostra, previamente seca ao ar, foi então peneirada através da bateria de peneiras, de maneira enérgica e contínua, permitindo a separação dos diferentes tamanhos dos grãos do agregado. Em cada peneira o material retido foi, então, separado e pesado, anotando-se o valor na planilha de composição granulométrica. Os grãos de agregado miúdo que ficaram presos nas malhas das peneiras foram retirados através da passagem da escova de aço, de modo que nenhuma partícula fosse perdida. Ao final do processo, com todos os valores dos pesos retidos em cada peneira, procede-se o cálculo da planilha de composição granulométrica, definindo-se os percentuais de material retido e retido acumulado.
O diâmetro máximo do agregado miúdo foi definido como a malha da peneira na qual ficou retido o percentual acumulado igual o imediatamente inferior a 5%, o que resultou Diâmetro máximo = 2,4 mm.
Etapa conclusiva:
Na descrição dos resultados, chegou-se aos seguintes valores para a areia analisada:
Modulo de finura = 1, Diâmetro máximo = 2,4 mm
De acordo com o módulo de finura definido, a areia analisada constituí-se de uma areia fina, pois apresentou modulo de finura menor do que 2,4. Este resultado é próprio das areias da nossa região.
TÍTULO: Determinação da composição granulométrica do agregado graúdo.
OBJETIVO: Este ensaio tem por objetivo, determinar a composição granulométrica do agregado graúdo, bem como conhecer o módulo de finura e a dimensão máxima característica do agregado, fundamentado na NBR 7217.
MATERIAL UTILIZADO: Bateria de peneiras 25 / 19 / 9,5 / 4,8 / 2,4 / 1,2 / 0,6 / 0,3 / 0,15 / FUNDO Balança; Escova de aço.
A amostra ensaiada consistiu num material reciclado de obras coletada na quantidade de 5 Kg conforme prescreve a NBR 7217. Reunidos todos os materiais, procedeu-se à execução do ensaio, montando-se a bateria de peneiras, conforme a seguir:
Peneiras (mm): 25 / 19 / 9,5 / 4,8 / 2,4 / 1,2 / 0,6 / 0,3 / 0,15 / FUNDO
A amostra foi peneirada através da bateria de peneiras, de maneira enérgica e contínua, permitindo a separação dos diferentes tamanhos de grãos do agregado. Em cada peneira o material retido foi separado e pesado, anotando-se o valor na planilha de composição granulométrica. Os grãos de agregado graúdo que porventura ficaram presos nas malhas das peneiras, foram retirados com a passagem da cerdas de aço da escova.Ao final do processo, com todos os valores dos pesos retidos em cada peneira, procedeu-se o cálculo da planilha de composição granulométrica, definindo-se os percentuais de material retido e retido acumulado.
O diâmetro máximo do agregado graúdo foi definido como a malha da peneira na qual ficou retido acumulado o percentual igual o imediatamente inferior a 5% o que resultou Diâmetro máximo = 19 mm.
Etapa conclusiva:
A amostra consistiu de um material reciclado de obras, que de acordo com os valores retidos acumulados em cada peneira e suas comparações com as faixas granulométricas estabelecidas na NBR 7217 para agregados graúdos, permitem avaliar que o agregado em estudo pode ser classificado como brita corrida.
TÍTULO: Determinação da massa unitária do agregado graúdo.
OBJETIVO: Este relatório tem como objetivo determinar a massa unitária do agregado graúdo, fundamentado na NBR 7251.
MATERIAIS UTILIZADOS: Balança; Recipiente metálico, conforme prescrito na NBR 7251; Régua rasadora; Pá metálica;
O material ensaiado foi retirado de uma amostra de material reciclado de obras. Reunidos todos os materiais, procedeu-se à execução do ensaio, tomando-se, com o auxílio da pá metálica, amostras o seixo e fazendo-se seu lançamento no recipiente a uma altura em torno de 12 cm da borda superior deste. O lançamento foi realizado de forma a espalhar de maneira uniforme o material dentro do recipiente. O processo repetiu-se até que todo o recipiente fosse preenchido, com o auxílio de uma régua, procedeu-se o razoamento da superfície de forma a deixa-la nivelada em relação às bordas do recipiente. Os espaços vazios deixados pelo processo de razoamento, foram preenchidos por outras pedras, permitindo a regularização da superfície. Pesou-se o recipiente com o seixo contido nele. Conhecidos os dados do recipiente (volume e massa) e os dados obtidos nas pesagens, o valor da massa unitária do agregado graúdo foi determinado pela diferença da média das massa do recipiente cheio e a massa do recipiente vazio, dividida pelo volume do mesmo.
TÍTULO: Determinação da finura do cimento
OBJETIVO: Este ensaio tem por objetivo determinar a finura do cimento, fundamentado na NBR 7215.
MATERIAL UTILIZADO: Balança com respectivos pesos; Peneira de malha 0,075 mm; Pincel de cerdas macias.
Reunidos todos os materiais, inicialmente, pesou-se 50 g do cimento a ser analisado. Esse material foi colocado na peneira de malha 0,075 mm com seu respectivo fundo. Iniciou-se o processo de peneiramento contínuo do cimento, permitindo que todo o material se espalhasse por igual na tela da peneira para facilitar o peneiramento. Esse processo foi realizado através de movimentos na direção horizontal, sendo a peneira constantemente girada de forma que todo o material fosse peneirado por igual. Após colocou-se a tampa no conjunto e imprimiu-lhe um peneiramento contínuo, estando a peneira ligeiramente inclinada, dando-se cerca de 25 golpes com a palma da mão na peneira e girando-a ao fim disso, até um total de 150 golpes. Realizado esse processo, retirou-se o material retido na peneira, limpando-a com o pincel de forma não perder material pesando-se o cimento em seguida. Todos os procedimentos descritos acima foram repetidos até que o peso do cimento que passou na peneira registrou um valor inferior a 0,05 g.
Etapa descritiva:
Realizados todos os procedimentos de execução do ensaio, foram obtidos os seguintes resultados:
A massa inicial de cimento do ensaio foi de P=50g. Após todo o processo de peneiramento e pesagem do material retido na peneira, o resultado final foi:
Massa retida na peneira: R=2,02 g
O índice de finura do cimento foi então obtido aplicando-se a fórmula:
F= R x 100 P
O qual resultou F= 4,04 %
Etapa conclusiva:
O cimento analisado apresentou finura igual a 4,04 %.
Os componentes da mistura foram pesados,a areia em 4 (quatro) porções e o cimento em 1 (uma) porção, a água foi medida em volume. A mistura foi feita no misturador mecânico em velocidade baixa colocando toda a quantidade de água na cuba e adicionando o cimento de forma gradual para formação de uma pasta homogênea. Foi registrada hora em que o cimento entra em contato com a água. Após a adição do cimento e sem paralisar a operação de mistura foi colocado as 4 (quatro) porções de areia (fina, média fina, média grossa e grossa) sem que esta operação ultrapasse o tempo de 30s. Com todos os componentes da mistura a velocidade do misturador foi aumentada e permaneceu assim por mais 90s (noventa segundos), quando foi desligado para retirar o excesso de argamassa da parede da culpa e na pá do misturador e posta no interior da cuba, após esta operação que deve ser feita em menos de 90s foi ligado o misturador por mais 60s em alta velocidade. Todo processo de mistura não ultrapassou de 5 minutos.
Previamente o dispositivo de fechamento das formas foram apertados e usou-se cera vegetal na fenda vertical externa para garantir a estanqueidade da forma, para facilitar o desmolde dos corpos de prova usou-se óleo vegetal na superfície interna da forma. Imediatamente após o adequamento das formas foram moldados 9 (nove) corpos de prova, a colocação da argamassa na forma foi feita com o auxílio da espátula em 4 (quatro) camadas de alturas aproximadamente iguais recebendo cada camada 30 (trinta) golpes uniforme com soquete normal de forma que os golpes sejam uniformemente distribuídos sobre a superfície da camada. Logo depois do adensamento das 4 (quatro) camadas foi feito o razoamento do topo dos corpos de prova com o auxílio de uma régua metálica. Após a moldagem os corpos de prova foram levados para a câmara úmida, onde aproximadamente 24hs depois foram desmoldados e identificados em séries de 3 (três) para cada idade estabelecida (3, 7 e 28 dias).
O topo dos corpos de prova foram capeados com enxofre quente (líquido), onde o enxofre foi colocado em um molde de superfície lisa e plana, o corpo de prova é colocado de forma que o eixo do corpo de prova fique perpendicular ao plano da superfície do molde de capeamento. Logo que o enxofre resfria o corpo de prova é retirado capeado a operação é repetida para os 2 (dois) topos, e para todos os corpos de prova. Este capeamento foi feito horas antes de cada rompimento nas idades estabelecidas.
ROMPIMENTO
Os corpos de prova devidamente capeados foram rompidos nas datas pré- estabelecidas, a idade é contada a partir do instante que a água entra em contato com o cimento. Foi verificado o funcionamento da máquina, logo depois foi posicionado o eixo do corpo de prova centrado com o eixo de carregamento da máquina. Iniciou-se o carregamento tendo-se como resultado da carga de ruptura o valor máximo expresso no relógio da prensa.