
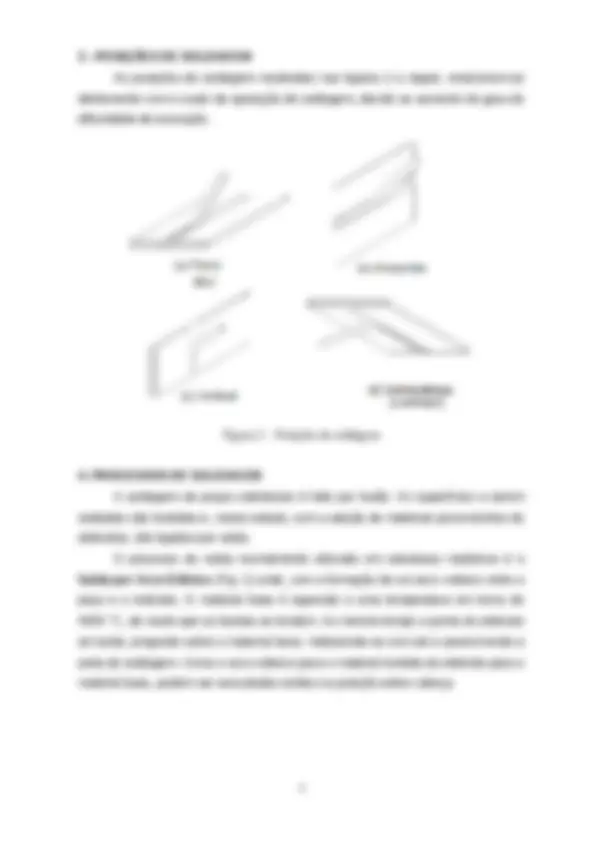
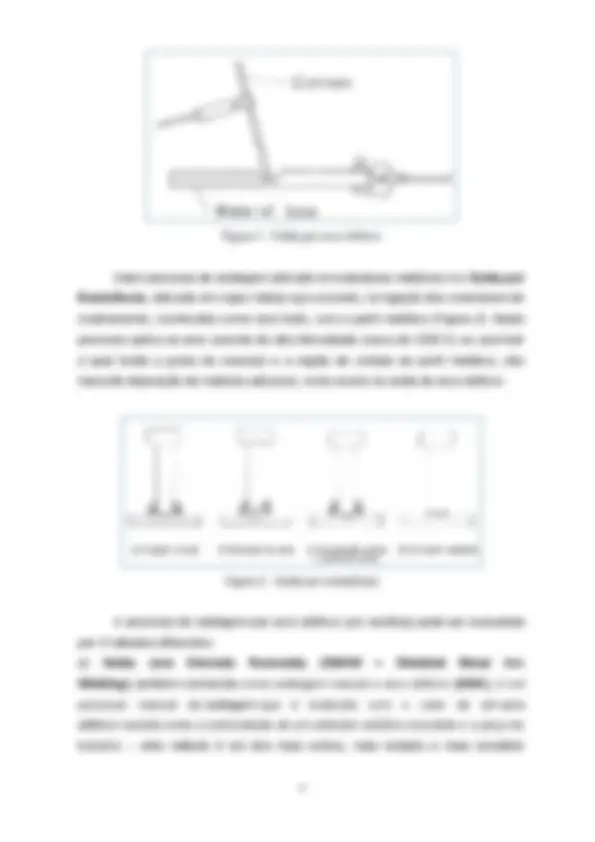
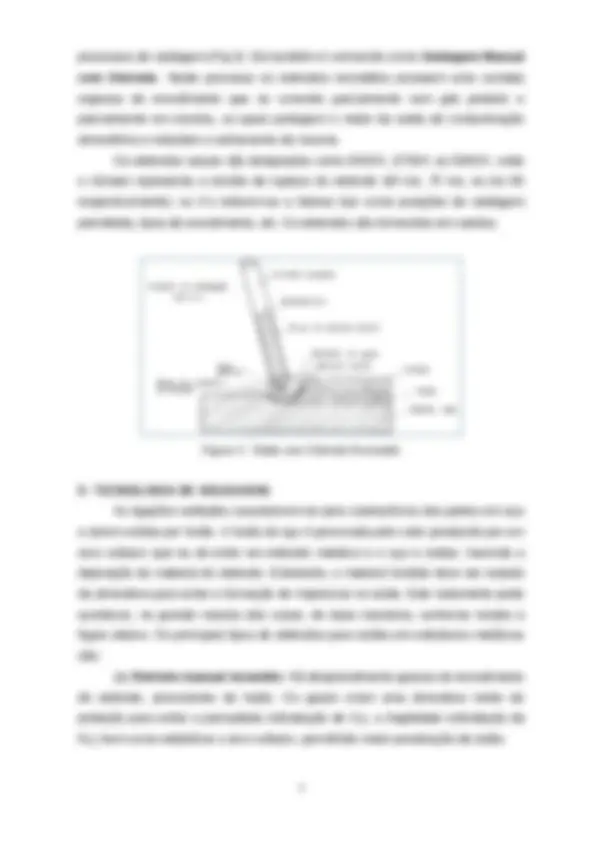
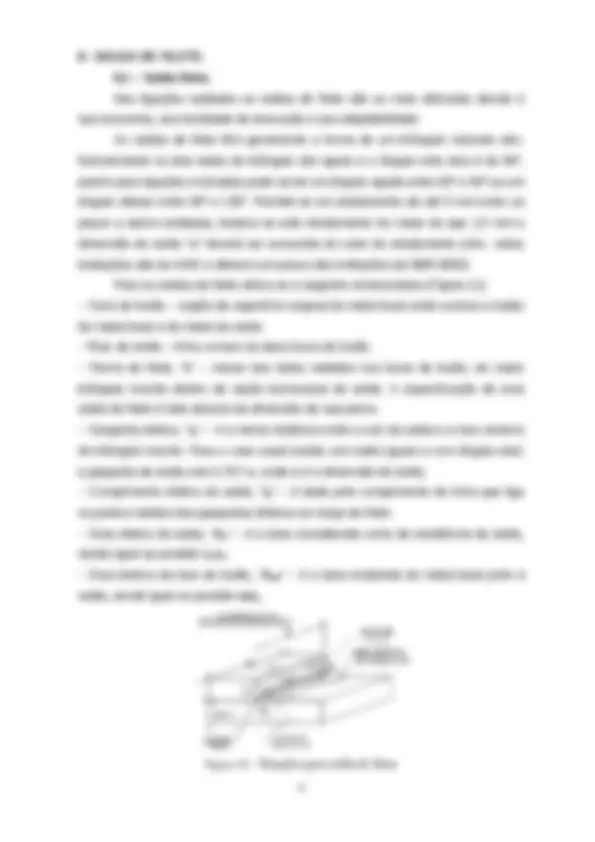
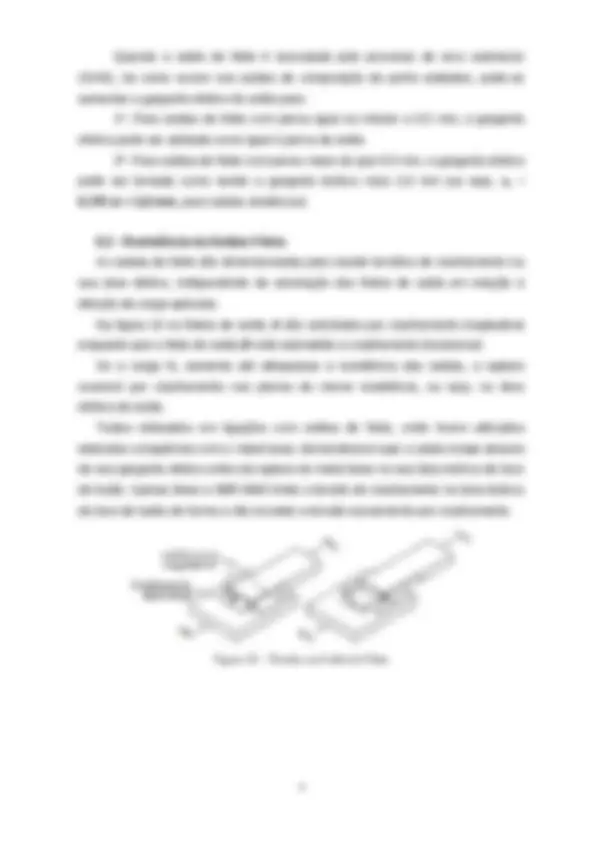
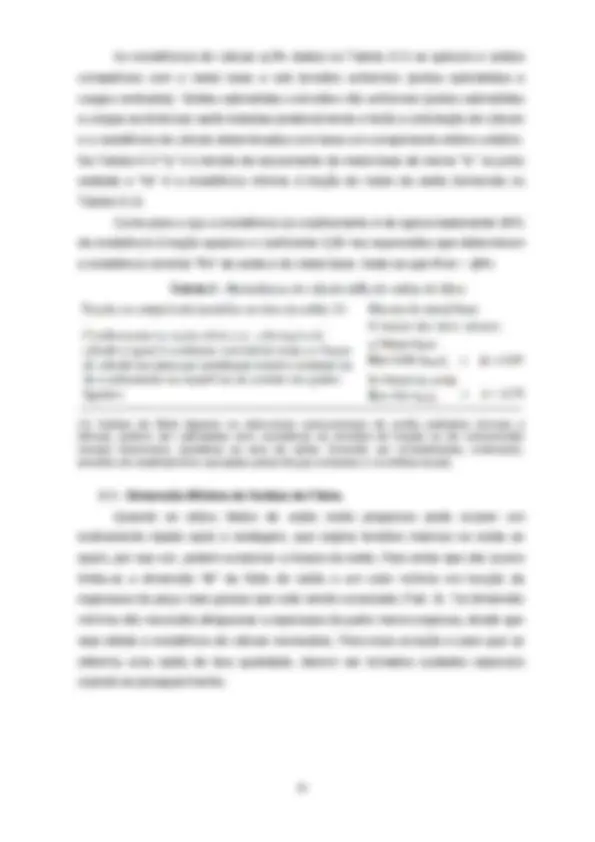
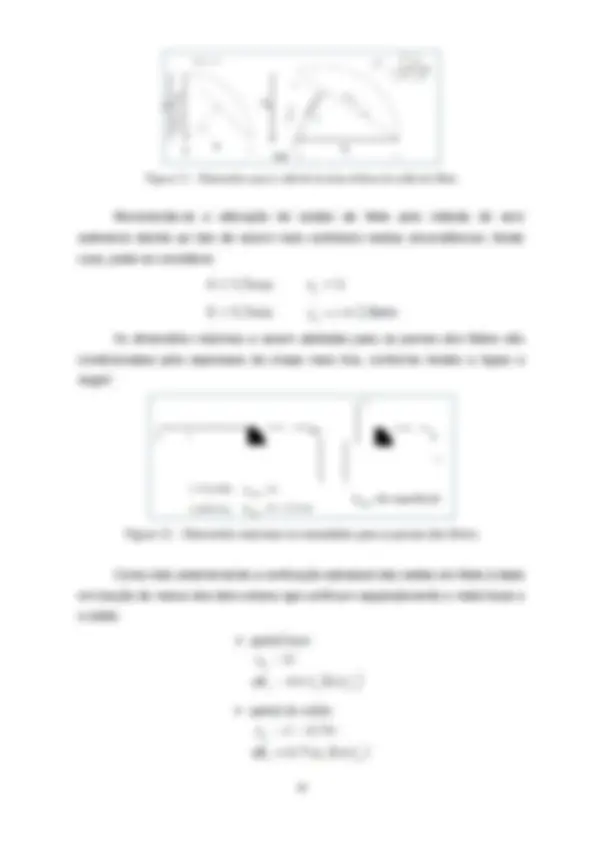
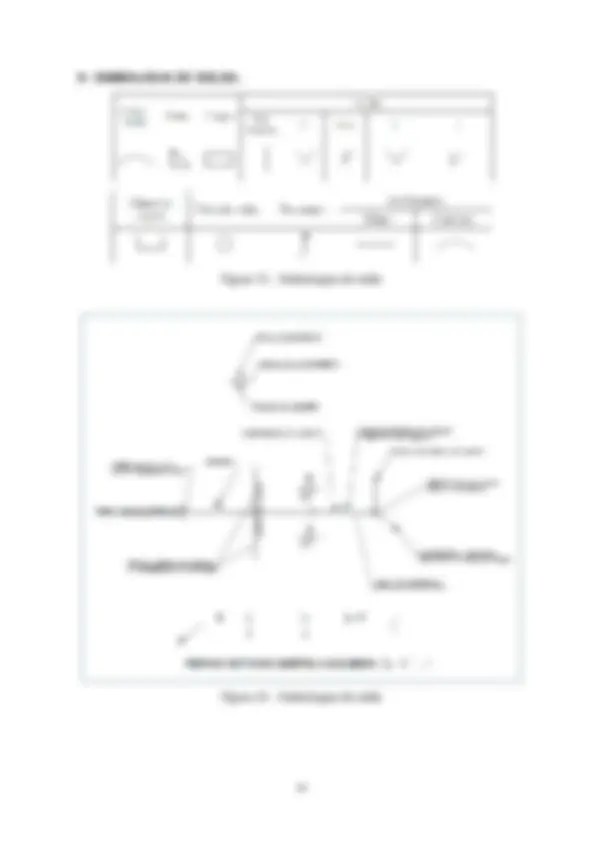
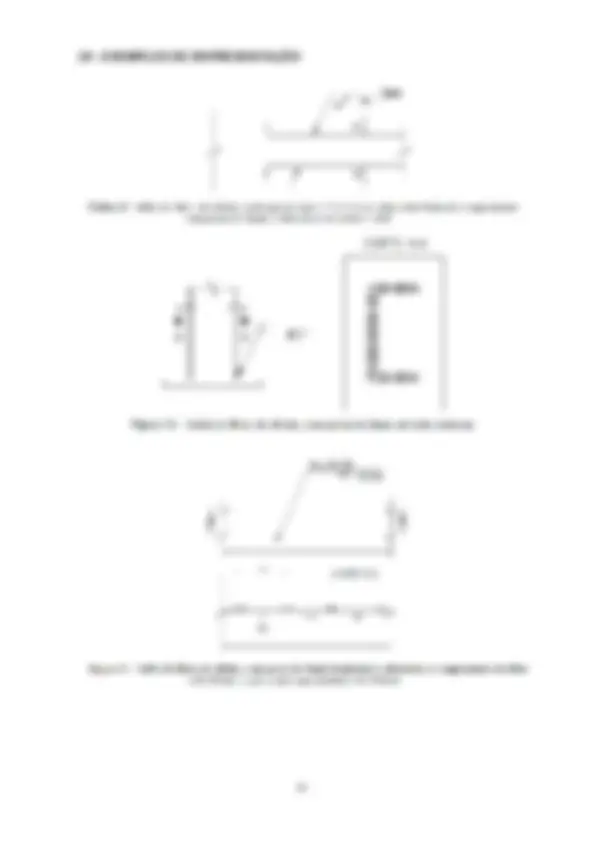
Estude fácil! Tem muito documento disponível na Docsity
Ganhe pontos ajudando outros esrudantes ou compre um plano Premium
Prepare-se para as provas
Estude fácil! Tem muito documento disponível na Docsity
Prepare-se para as provas com trabalhos de outros alunos como você, aqui na Docsity
Os melhores documentos à venda: Trabalhos de alunos formados
Prepare-se com as videoaulas e exercícios resolvidos criados a partir da grade da sua Universidade
Responda perguntas de provas passadas e avalie sua preparação.
Ganhe pontos para baixar
Ganhe pontos ajudando outros esrudantes ou compre um plano Premium
Comunidade
Peça ajuda à comunidade e tire suas dúvidas relacionadas ao estudo
Descubra as melhores universidades em seu país de acordo com os usuários da Docsity
Guias grátis
Baixe gratuitamente nossos guias de estudo, métodos para diminuir a ansiedade, dicas de TCC preparadas pelos professores da Docsity
Ligação é todo detalhe construtivo que promove a união de partes da estrutura entre si, ou a união da estrutura com elementos externos a ela. As ligações devem representar o mais fielmente possível os vínculos idealizados na análise estrutural
Tipologia: Notas de aula
1 / 15
Esta página não é visível na pré-visualização
Não perca as partes importantes!
Instituição: Faculdade Martha Falcão Curso: Engenharia Civil Disciplina: Aço e Madeira Professor: Lourival Paula de Góes, MSc. Assunto: Metálica: Notas de Aula 7
As ligações soldadas apresentam a grande vantagem de simplificar as ligações. Em contrapartida elas exigem mão-de-obra qualificada, condições de execução controladas e necessidade de inspeção. De acordo com o processo fabril pode-se ter a quase totalidade das ligações de fábrica como sendo soldadas, ficando as ligações parafusadas para ligações de campo. Deve-se evitar a utilização de soldas nas ligações de campo devido às dificuldades de acesso ao local da soldagem, necessidade de andaimes, posições desfavoráveis ou inadequadas para soldagem, necessidade de proteção do local da solda contra vento e chuva, e dificuldade do controle de qualidade da solda. Alguns fabricantes com processos produtivos automatizados dão preferências às ligações parafusadas, inclusive na fábrica. Mesmo nestes casos inúmeros elementos de ligações são soldados devido à complexidade que seria torná-los parafusados (por exemplo, placas de base de colunas, enrijecedores de alma de colunas, placas de topo de vigas, etc.). Vantagens: Maior rigidez das ligações; Redução de custos de fabricação (elimina furações, redução da quantidade do aço, pois as conexões são mais compactas); Melhor acabamento final facilidade de limpeza, pintura e estanqueidade; Facilidade de execução em estruturas existentes. Desvantagem Dificuldade para desmontagem; Dificuldade para controle de qualidade na obra
As ligações soldadas caracterizam-se pela coalescência das partes em aço a serem unidas por fusão. A fusão do aço é provocada pelo calor produzido por um arco voltaico que se dá entre um eletrodo metálico e o aço a soldar, havendo a deposição do material do eletrodo. Entretanto, o material fundido deve ser isolado da atmosfera para evitar a formação de impurezas na solda. Este isolamento pode se dar, na grande maioria dos casos, por duas maneiras, conforme mostra a figura abaixo. Os principais tipos de eletrodos para soldas em estruturas metálicas são: (a) Eletrodo manual revestido : Há desprendimento gasoso do revestimento do eletrodo, proveniente da fusão. Os gases criam uma atmosfera inerte de proteção para evitar a porosidade (introdução de O 2 ), a fragilidade (introdução de N 2 ), bem como estabilizar o arco voltaico, permitindo maior penetração da solda. (b) Arco submerso em material granular fusível : O eletrodo nu é acompanhado de um tubo de fluxo com material granulado, que funciona como isolante térmico, garantindo assim proteção quanto aos efeitos da atmosfera. O fluxo granulado funde-se parcialmente, formando uma camada de escória líquida que posteriormente se solidifica. A figura 1 mostra tipos de eletrodos. Os principais eletrodos utilizados na indústria da construção metálica são:
comum);
Obs: ksi , uma antiga unidade inglesa de tensão (e, conseqüentemente de pressão), significa kilo pound per square inch , ou seja kilo libras por polegada quadrada. Figura 1– Tipos de eletrodo
Figura 1 - Solda por arco elétrico Outro processo de soldagem utilizado em estruturas metálicas é a Solda por Resistência , utilizada em vigas mistas aço-concreto, na ligação dos conectores de cisalhamento, conhecidos como stud bolts , com o perfil metálico (Figura 2). Neste processo aplica-se uma corrente de alta intensidade (cerca de 1500 A) ao stud bolt a qual funde a ponta do conector e a região de contato do perfil metálico, não havendo deposição de material adicional, como ocorre na solda de arco elétrico. Figura 2 - Solda por resistência A processo de soldagem por arco elétrico ( arc welding ) pode ser executado por 4 métodos diferentes: a) Solda com Eletrodo Revestida (SMAW = Shielded Metal Arc Welding), também conhecida como soldagem manual a arco elétrico (MMA) , é um processo manual de soldagem que é realizado com o calor de um arco elétrico mantido entre a extremidade de um eletrodo metálico revestido e a peça de trabalho – este método é um dos mais velhos, mais simples e mais versáteis
processos de soldagem (Fig.3). Ele também é conhecido como Soldagem Manual com Eletrodo. Neste processo os eletrodos revestidos possuem uma camada espessa de revestimento que se converte parcialmente num gás protetor e parcialmente em escória, os quais protegem o metal da solda de contaminação atmosférica e retardam o esfriamento da mesma. Os eletrodos usuais são designados como E60XX, E70XX ou E80XX, onde o número representa a tensão de ruptura do eletrodo (60 ksi, 70 ksi, ou ksi 80 respectivamente); os X’s referem-se a fatores tais como posições de soldagem permitidas, tipos de revestimento, etc. Os eletrodos são fornecidos em varetas. Figura 3 - Solda com Eletrodo Revestido 5 - TECNOLOGIA DE SOLDAGEM. As ligações soldadas caracterizam-se pela coalescência das partes em aço a serem unidas por fusão. A fusão do aço é provocada pelo calor produzido por um arco voltaico que se dá entre um eletrodo metálico e o aço a soldar, havendo a deposição do material do eletrodo. Entretanto, o material fundido deve ser isolado da atmosfera para evitar a formação de impurezas na solda. Este isolamento pode acontecer, na grande maioria dos casos, de duas maneiras, conforme mostra a figura abaixo. Os principais tipos de eletrodos para soldas em estruturas metálicas são: (a) Eletrodo manual revestido : Há desprendimento gasoso do revestimento do eletrodo, proveniente da fusão. Os gases criam uma atmosfera inerte de proteção para evitar a porosidade (introdução de O 2 ), a fragilidade (introdução de N 2 ), bem como estabilizar o arco voltaico, permitindo maior penetração da solda.
Os quatro tipos usuais de soldas são conforme figura 6: Solda de filete Solda de entalhe de penetração total Solda de entalhe de penetração parcial Solda de tampão (em furos e em rasgos) O tipo de solda mais utilizado é a solda de filete. Para cargas leves a solda de filete é a mais econômica por não precisar de preparação no metal base. Para cargas elevadas, as soldas de entalhe se revelam mais eficientes, pois com elas consegue-se atingir a resistência do metal base facilmente. A utilização de soldas de tampão é limitada às situações especiais onde não é prático utilizar soldas de filete ou de entalhe. De uma maneira aproximada os quatro tipos de solda representam a seguinte porcentagem nas ligações soldadas em estruturas metálicas: soldas de filete = 80%, soldas de entalhe = 15%, soldas de tampão e outras soldas especiais = 5%. Figura 6 – Tipos usuais de soldas
8.1 – Solda filete. Nas ligações soldadas as soldas de filete são as mais utilizadas devido à sua economia, sua facilidade de execução e sua adaptabilidade. As soldas de filete têm geralmente a forma de um triângulo isóscele reto. Normalmente os dois lados do triângulo são iguais e o ângulo ente eles é de 90º, porém para ligações inclinadas pode-se ter um ângulo agudo entre 60º e 90º ou um ângulo obtuso entre 90º e 135º. Permite-se um afastamento de até 5 mm entre as peças a serem soldadas, todavia se este afastamento for maior do que 1,5 mm a dimensão da solda “w” deverá ser acrescida do valor do afastamento (obs.: estas limitações são da AWS e diferem um pouco das limitações da NBR 8800). Para as soldas de filete utiliza-se a seguinte nomenclatura (Figura 11): − Face de fusão – região da superfície original do metal base onde ocorreu a fusão do metal base e do metal da solda. − Raiz da solda – linha comum às duas faces de fusão. − Perna do filete, “b” – menor dos lados medidos nas faces de fusão, do maior triângulo inscrito dentro da seção transversal de solda. A especificação de uma solda de filete é feita através da dimensão de sua perna. − Garganta efetiva, “ tw ” – é a menor distância entre a raiz da solda e a face externa do triângulo inscrito. Para o caso usual (solda com lados iguais e com ângulo reto) a garganta da solda vale 0,707.w, onde w é a dimensão da solda. − Comprimento efetivo da solda, “ lw ” – é dado pelo comprimento da linha que liga os pontos médios das gargantas efetivas ao longo do filete. − Área efetiva da solda, “ Aw ” – é a área considerada como de resistência da solda, sendo igual ao produto tw.lw. − Área teórica da face de fusão, “ AMB ” – é a área resistente do metal base junto à solda, sendo igual ao produto w.lw. Figura 10 – Notações para solda de filete
As resistências de cálculo φ.Rn dadas na Tabela III.3 se aplicam a soldas compatíveis com o metal base e sob tensões uniformes (juntas submetidas a cargas centradas). Soldas submetidas a tensões não uniformes (juntas submetidas a cargas excêntricas) serão tratadas posteriormente e terão a solicitação de cálculo e a resistência de cálculo determinadas com base em comprimento efetivo unitário. Na Tabela III.3 “fy” é a tensão de escoamento do metal base de menor “fy” na junta soldada e “fw” é a resistência mínima à tração do metal da solda (fornecida na Tabela III.2). Como para o aço a resistência ao cisalhamento é de aproximadamente 60% da resistência á tração aparece o coeficiente 0,60 nas expressões que determinam a resistência nominal “Rn” da solda e do metal base. Sabe-se que Rnd =ϕRnRn (1) Soldas de filete ligando os elementos componentes de perfis soldados (mesas e almas), podem ser calculadas sem considerar as tensões de tração ou de compressão nesses elementos, paralelas ao eixo da solda. Deverão ser consideradas, entretanto, tensões de cisalhamento causadas pelas forças cortantes e os efeitos locais. 8.3 - Dimensão Mínima de Soldas de Filete. Quando se utiliza filetes de solda muito pequenos pode ocorrer um resfriamento rápido após a soldagem, que origina tensões internas na solda as quais, por sua vez, podem ocasionar a fissura da solda. Para evitar que isto ocorra limita-se a dimensão “ b” do filete de solda a um valor mínimo em função da espessura da peça mais grossa que está sendo conectada (Tab. 3). Tal dimensão mínima não necessita ultrapassar a espessura da parte menos espessa, desde que seja obtida a resistência de cálculo necessária. Para essa exceção e para que se obtenha uma solda de boa qualidade, devem ser tomados cuidados especiais usando-se preaquecimento.
Tabela II – Dimensões mínimas da perna de filete em função da espessura da chapa mais grossa. (1). 8.4 - Dimensão Máxima de Soldas de Filete. As soldas de filete executadas ao longo de bordas das peças soldadas devem ter sua dimensão limitada a um máximo. A dimensão máxima de uma solda de filete que pode ser usada ao longo de bordas de partes soldadas é a seguinte: 1- Ao longo de bordas de material com espessura inferior a 6,35 mm, não mais do que a espessura do material; 2- Ao longo de bordas de material com espessura igual ou superior a 6, mm, não mais do que a espessura do material subtraída de 1,5 mm. O objetivo desta limitação é evitar que seja fundida a borda de chapas com espessura de 6,35 mm ou mais, o que levaria a avaliações erradas da garganta efetiva da solda. Portanto, para chapas com espessura maior ou igual a 6,35 mm a borda da chapa deve ser facilmente identificada. Figura 11 – Identificação da Borda da Chapa 8.5 - Comprimento das Soldas de Filete. O comprimento efetivo mínimo de uma solda de filete, dimensionada para uma solicitação de cálculo qualquer, não pode ser inferior a 4 vezes sua dimensão nominal ou, então, essa dimensão nominal não pode ser considerada maior que 25% do comprimento efetivo da solda. Adicionalmente, o comprimento efetivo de uma solda de filete sujeita a qualquer solicitação de cálculo não pode ser inferior a 40 mm.
Figura 11 – Dimensões para o cálculo da área efetiva da solda de filete Recomenda-se a utilização de soldas de filete pelo método do arco submerso devido ao fato de serem mais confiáveis nestas circunstâncias. Neste caso, pode-se considerar: As dimensões máximas a serem adotadas para as pernas dos filetes são condicionadas pela espessura da chapa mais fina, conforme mostra a figura a seguir: Figura 12 – Dimensões máximas recomendadas para as pernas dos filetes Como visto anteriormente a verificação estrutural das soldas em filete é dada em função do menor dos dois valores que verificam separadamente o metal base e a solda:
Figura 13 – Simbologias de solda Figura 14 – Simbologias de solda