
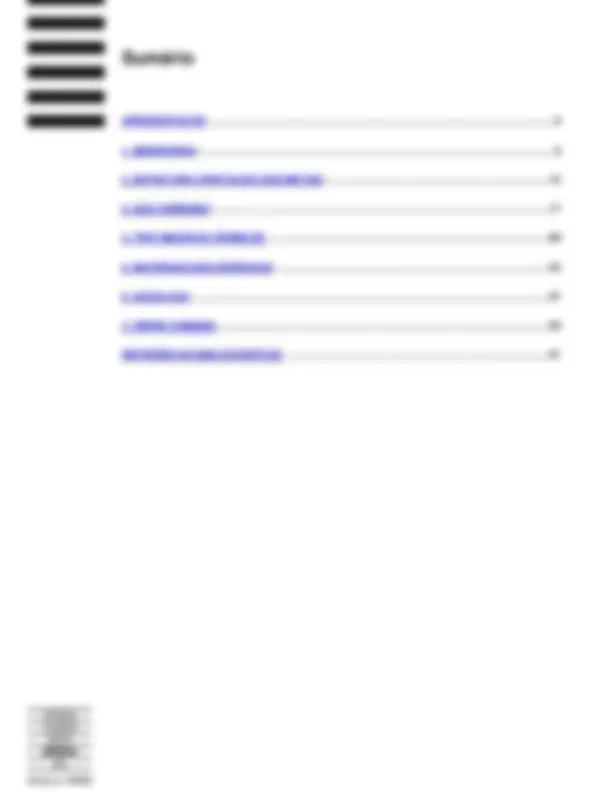
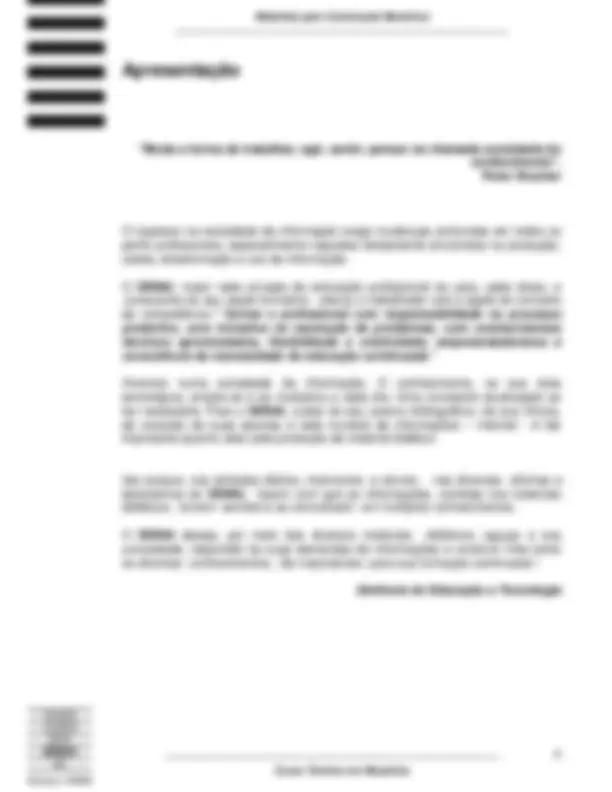
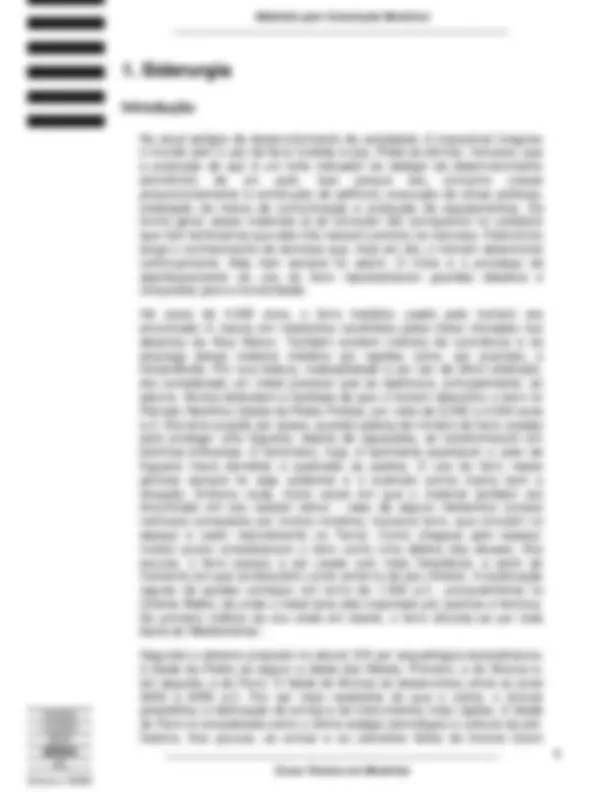
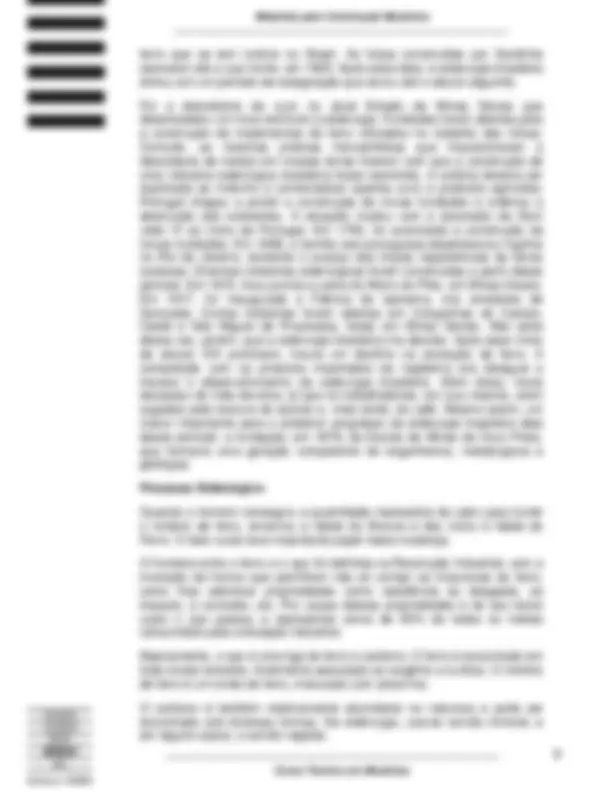
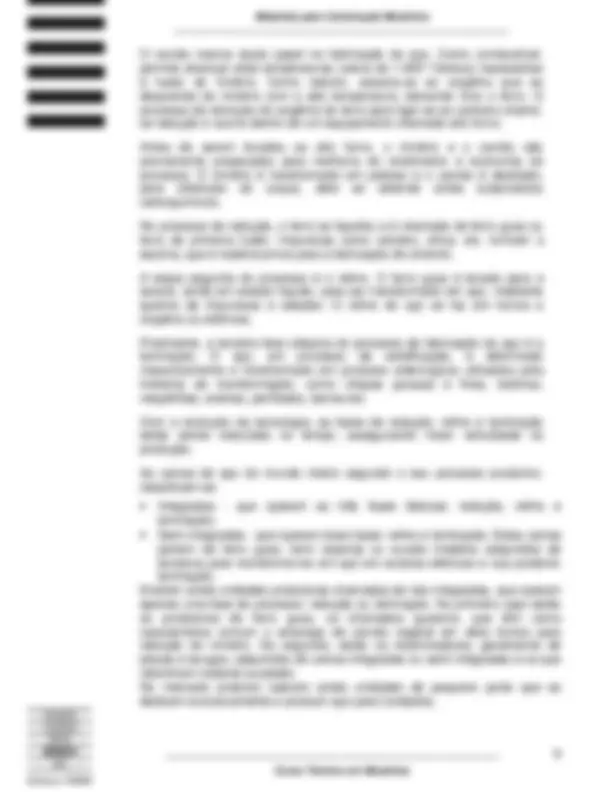
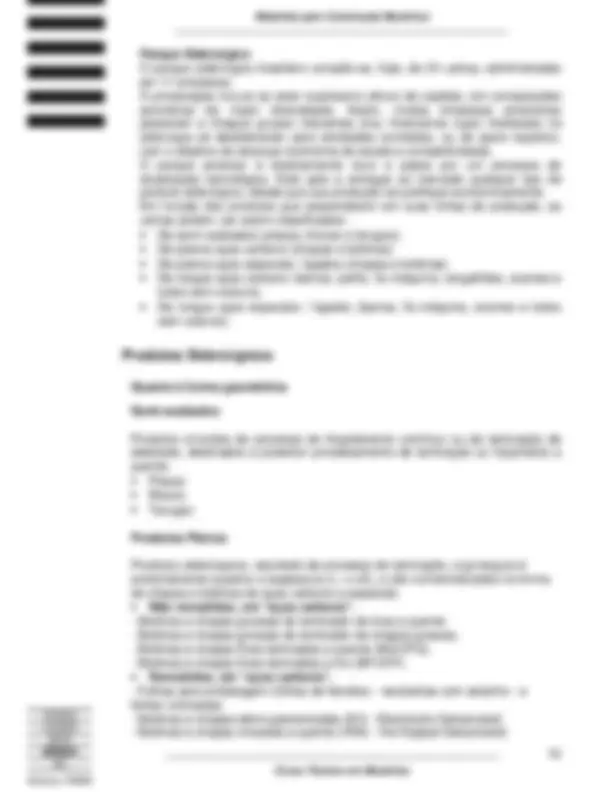
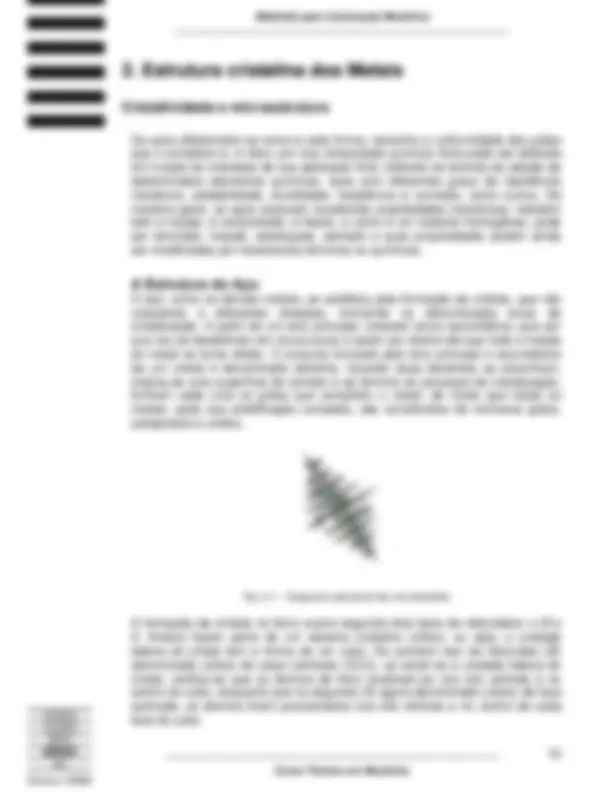
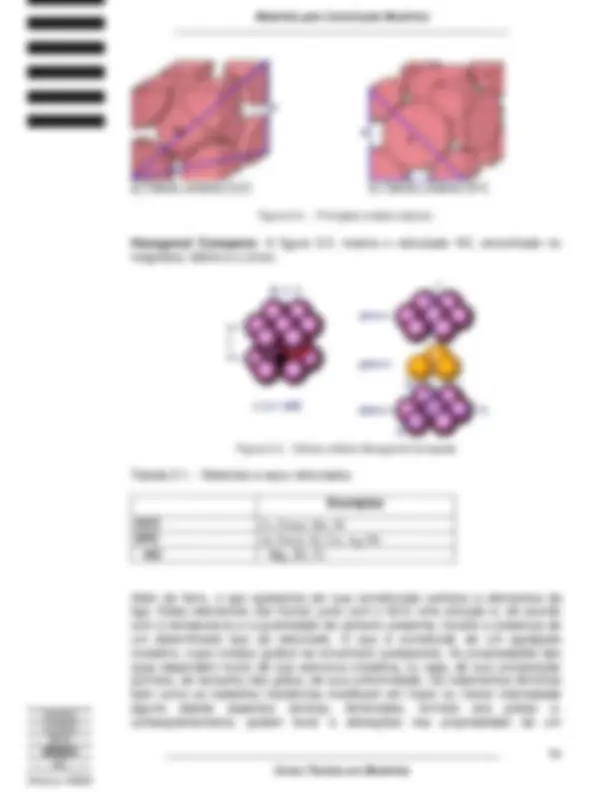
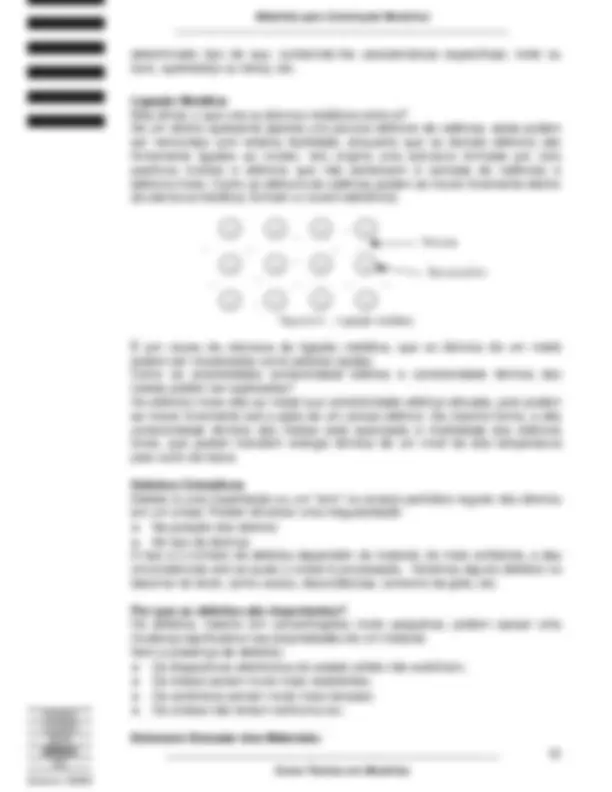
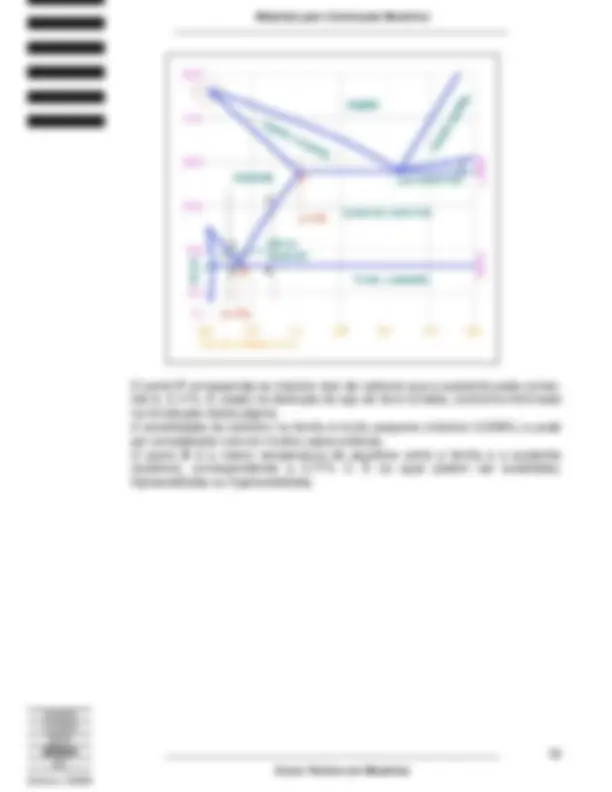
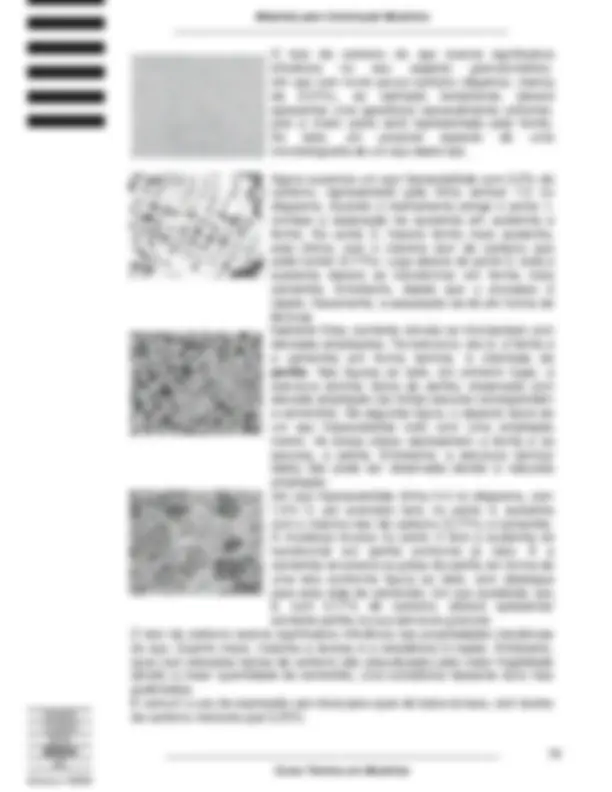
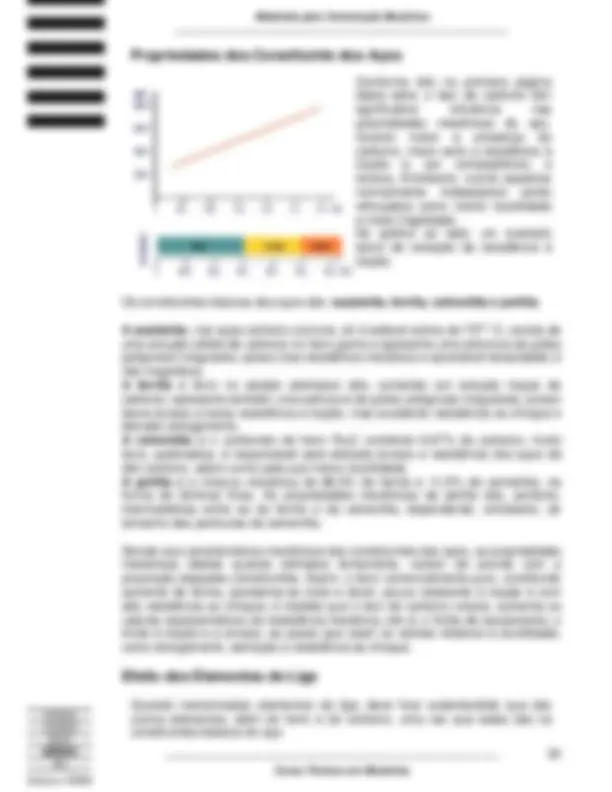
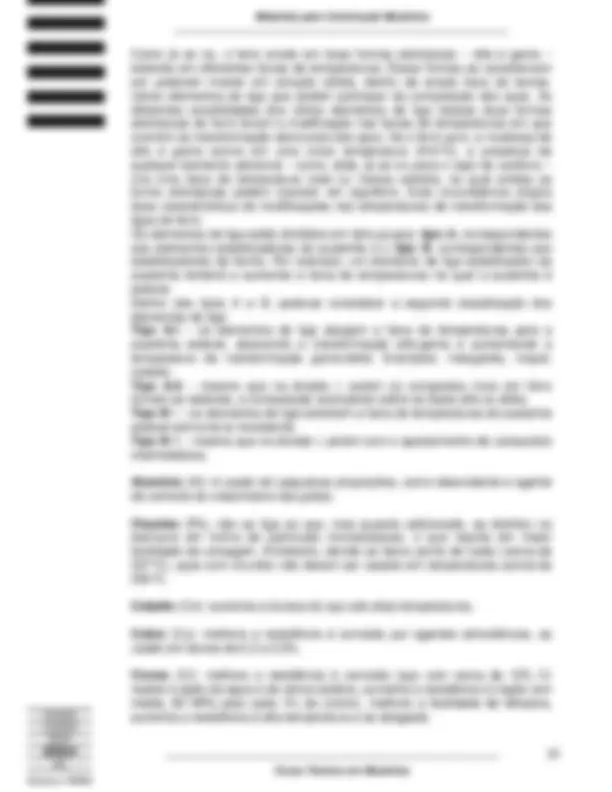
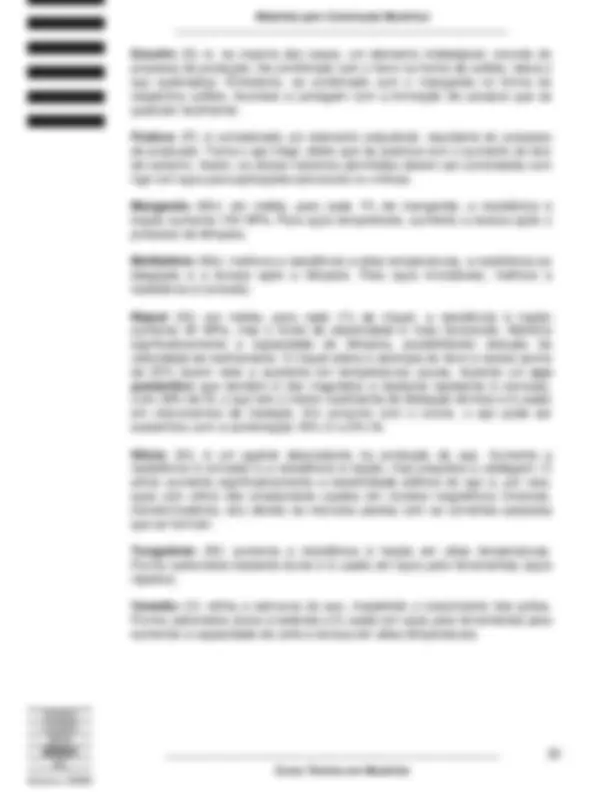
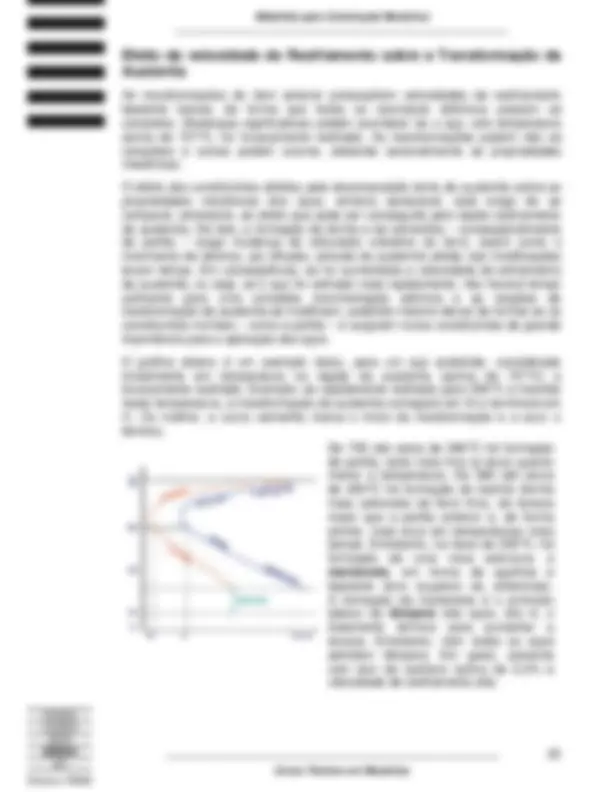
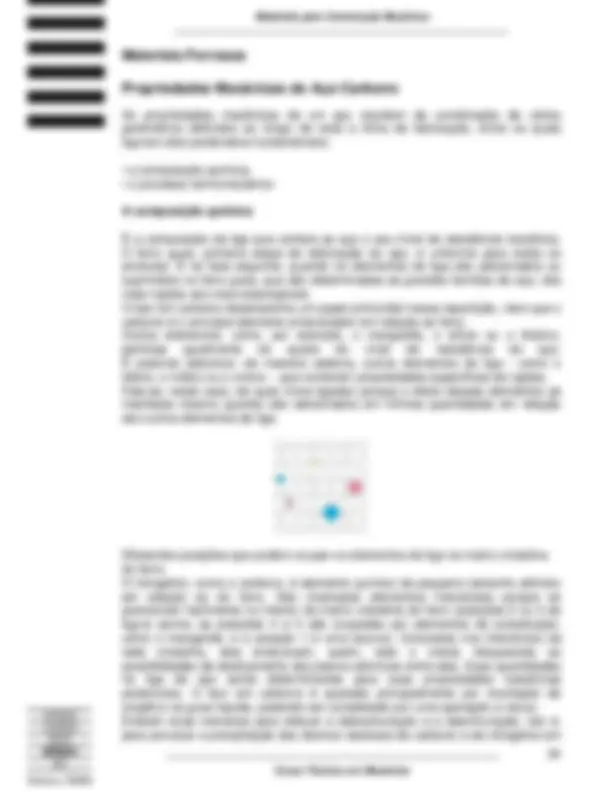
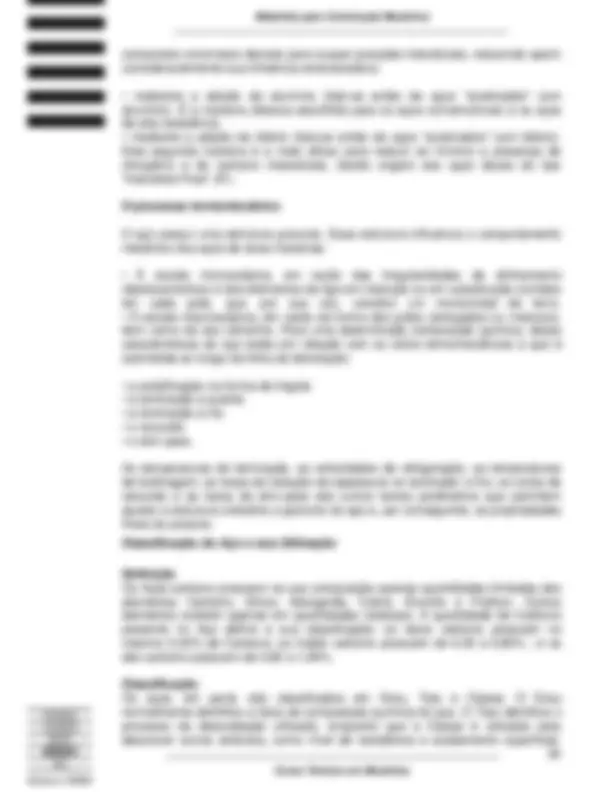
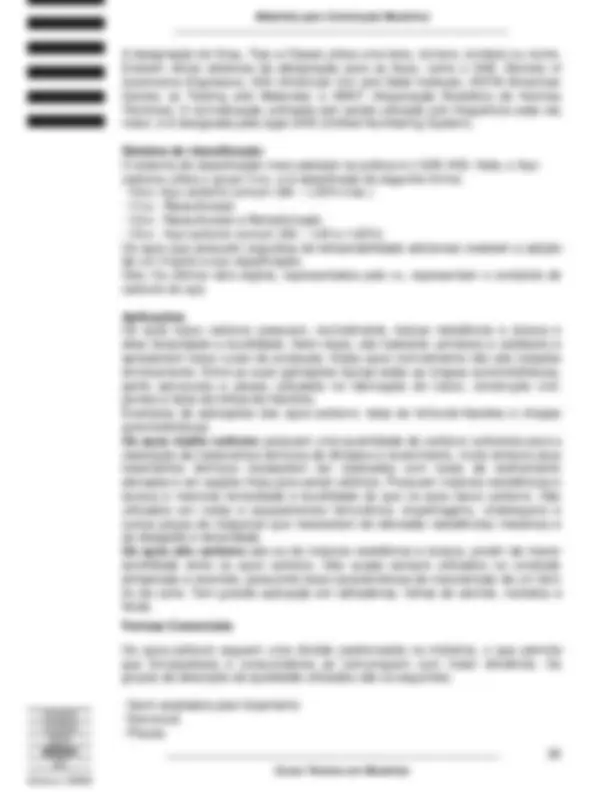
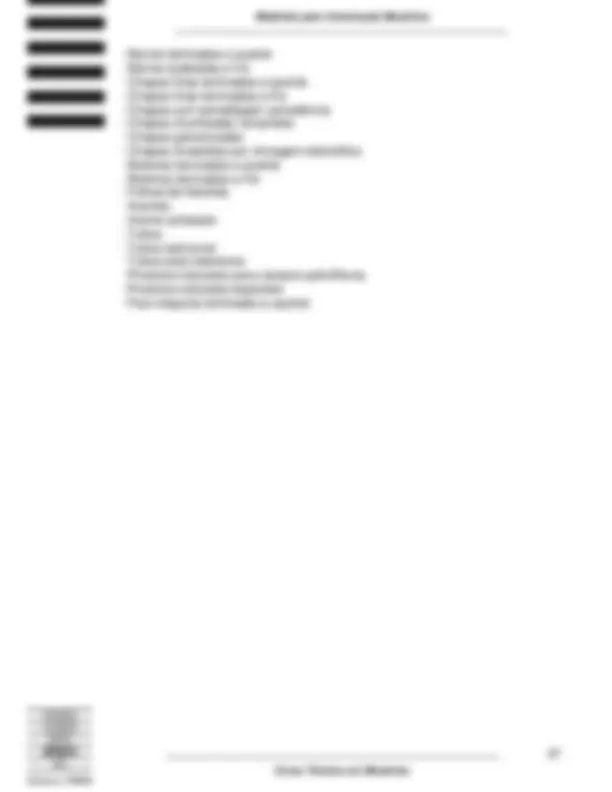
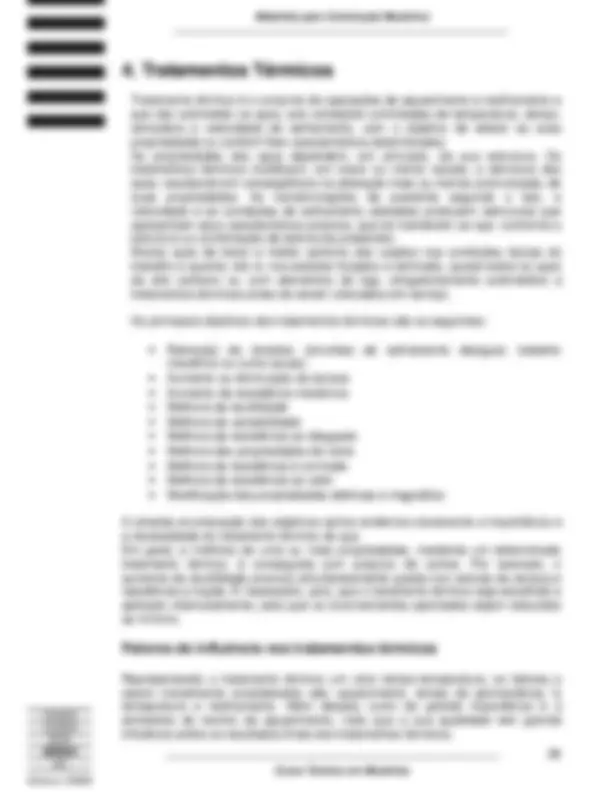
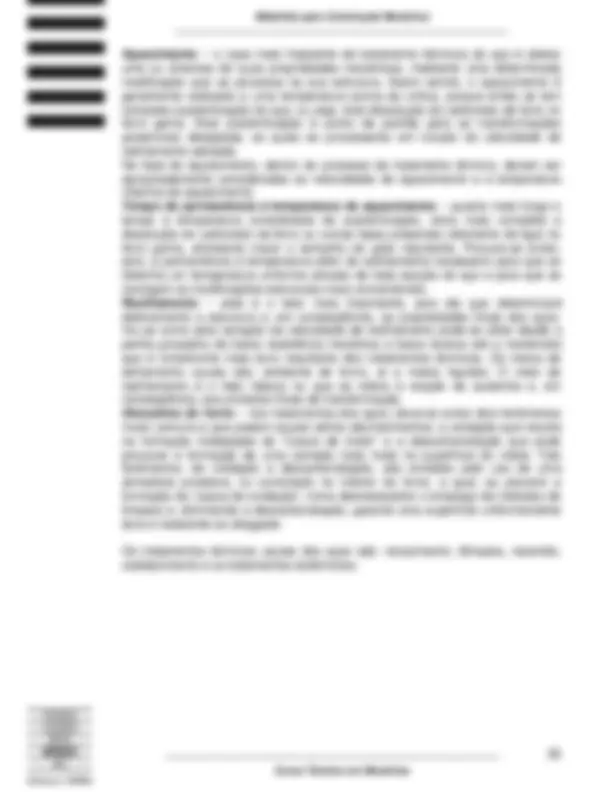
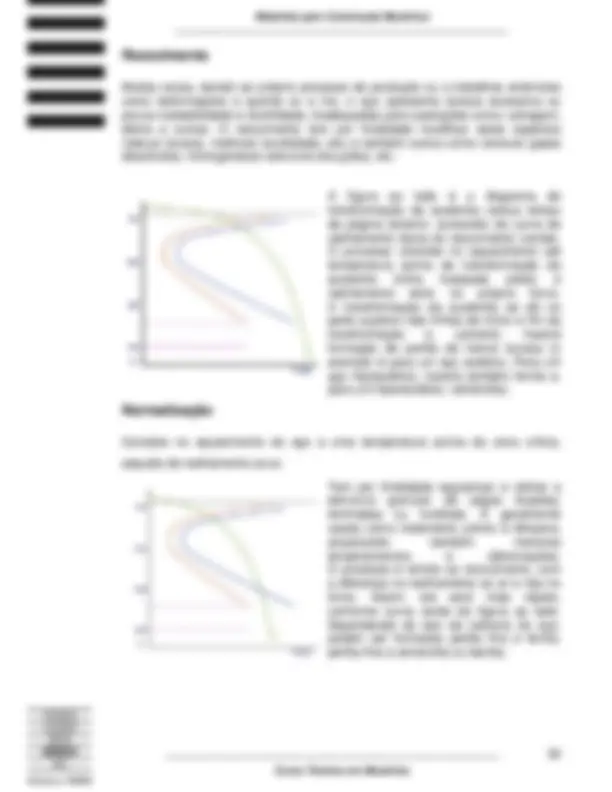

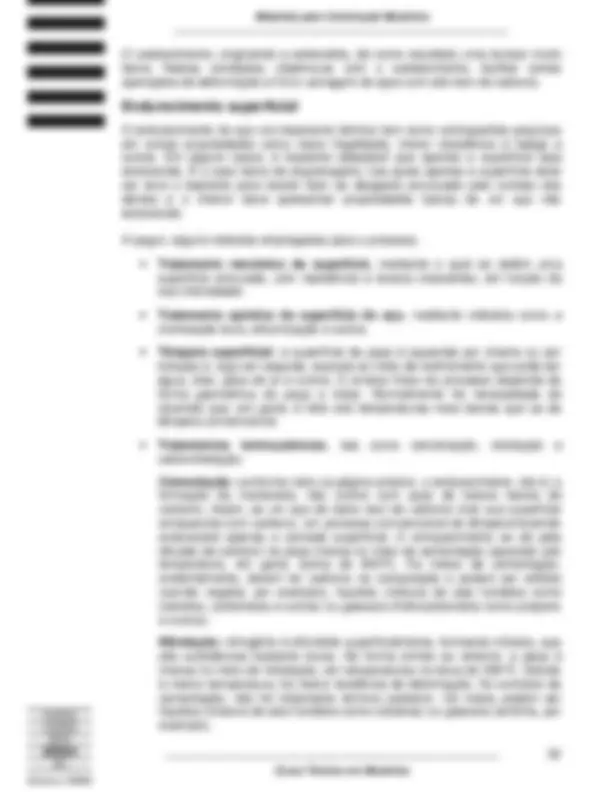
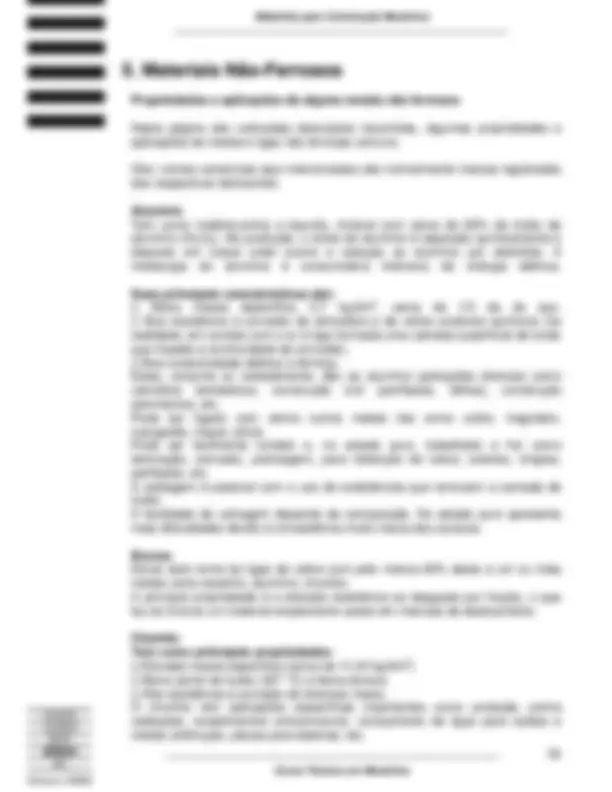
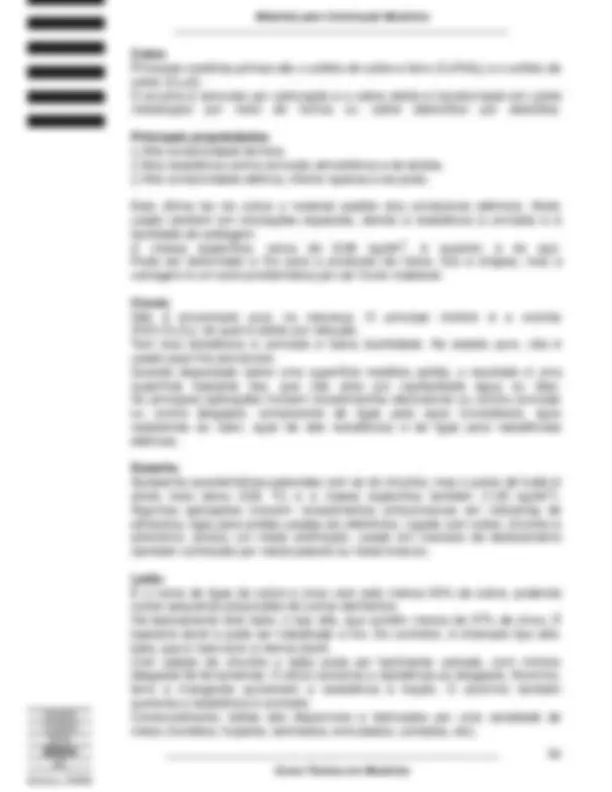
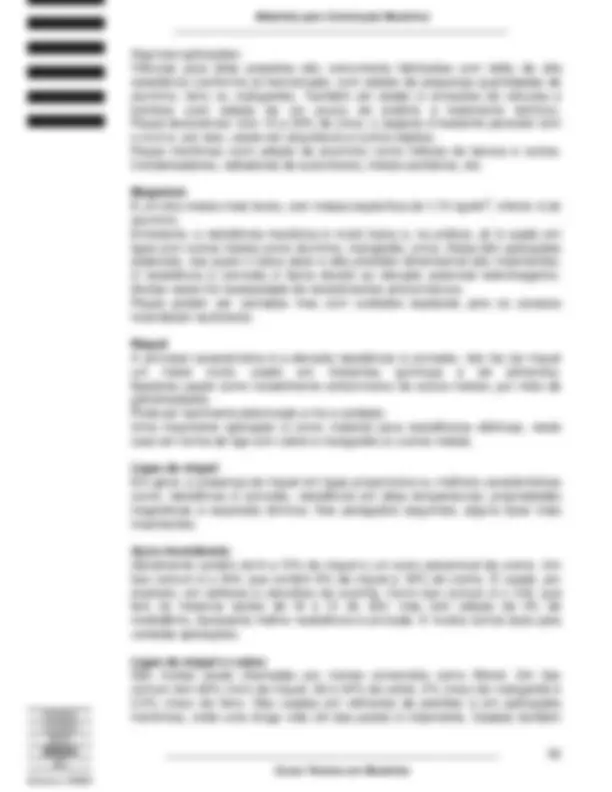
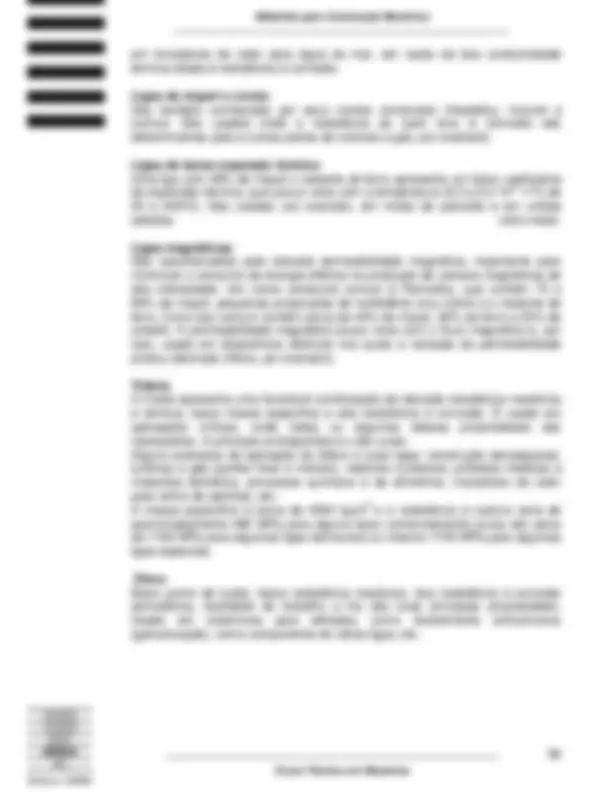
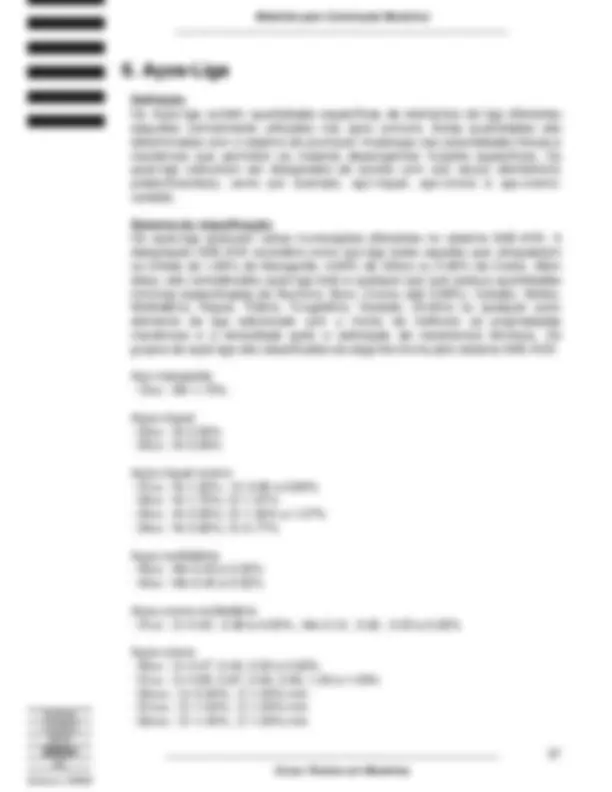
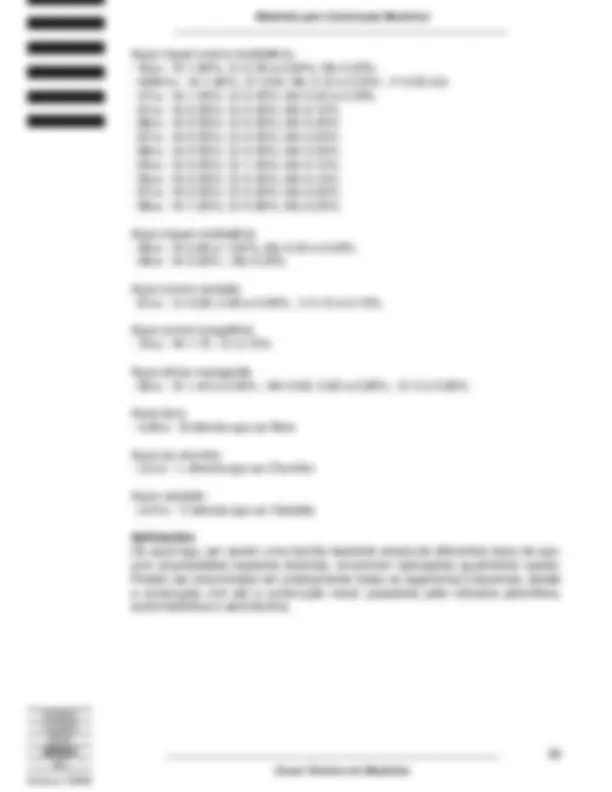
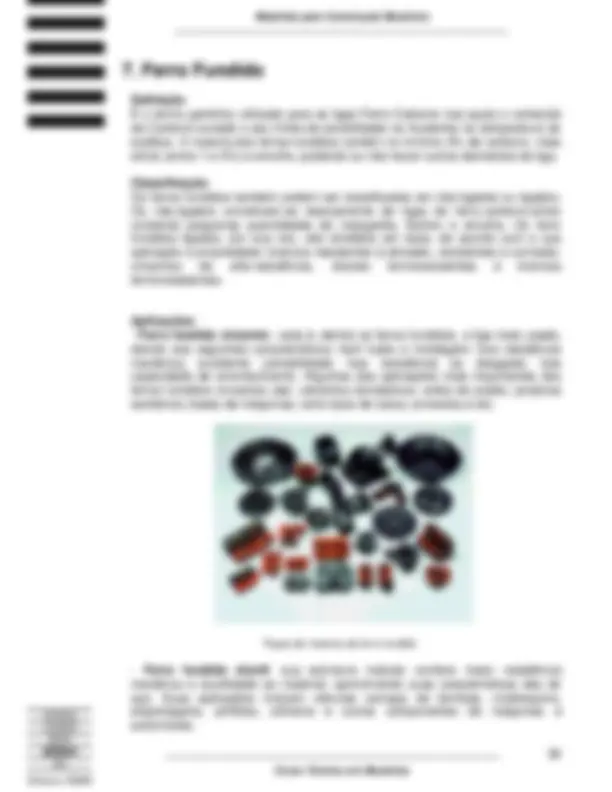
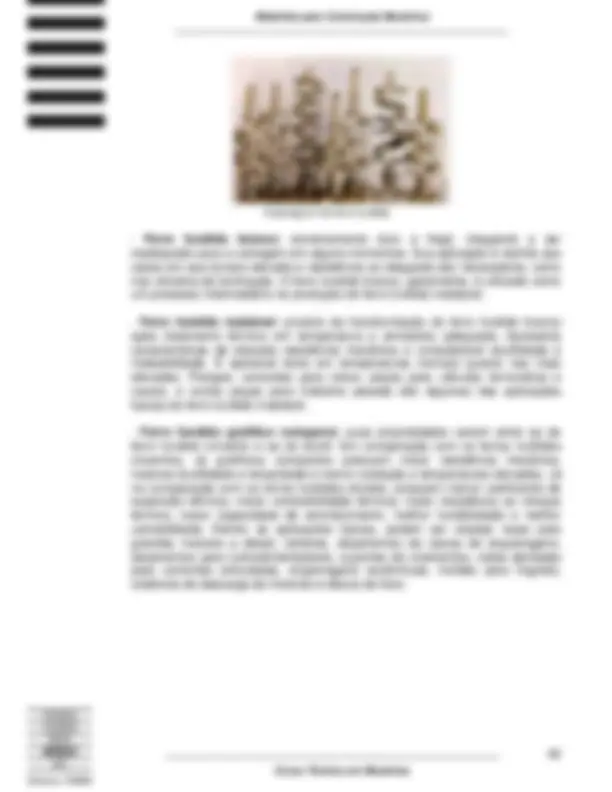
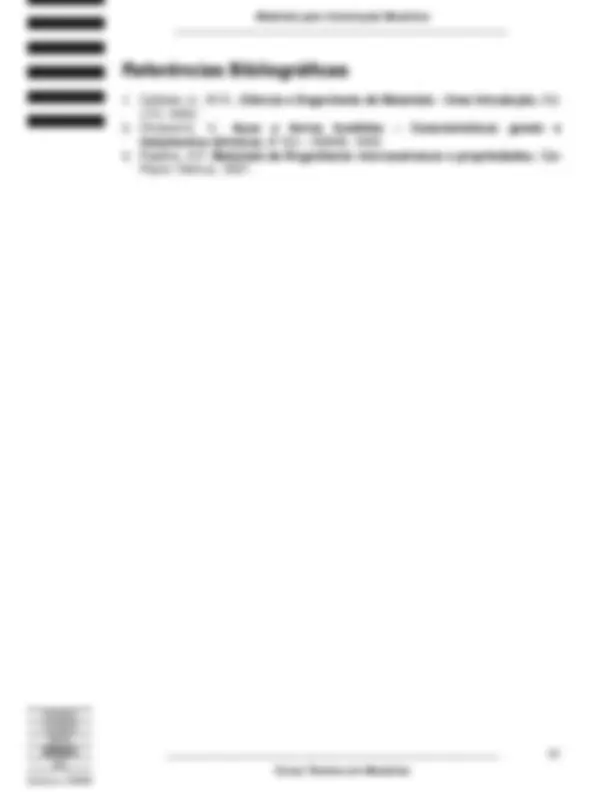
Estude fácil! Tem muito documento disponível na Docsity
Ganhe pontos ajudando outros esrudantes ou compre um plano Premium
Prepare-se para as provas
Estude fácil! Tem muito documento disponível na Docsity
Prepare-se para as provas com trabalhos de outros alunos como você, aqui na Docsity
Os melhores documentos à venda: Trabalhos de alunos formados
Prepare-se com as videoaulas e exercícios resolvidos criados a partir da grade da sua Universidade
Responda perguntas de provas passadas e avalie sua preparação.
Ganhe pontos para baixar
Ganhe pontos ajudando outros esrudantes ou compre um plano Premium
Comunidade
Peça ajuda à comunidade e tire suas dúvidas relacionadas ao estudo
Descubra as melhores universidades em seu país de acordo com os usuários da Docsity
Guias grátis
Baixe gratuitamente nossos guias de estudo, métodos para diminuir a ansiedade, dicas de TCC preparadas pelos professores da Docsity
Materiais para construção mecânica e suas tecnologias.
Tipologia: Notas de aula
1 / 41
Esta página não é visível na pré-visualização
Não perca as partes importantes!
Presidente da FIEMG
Robson Braga de Andrade
Gestor do SENAI
Petrônio Machado Zica
Diretor Regional do SENAI e
Superintendente de Conhecimento e Tecnologia
Alexandre Magno Leão dos Santos
Gerente de Educação e Tecnologia
Edmar Fernando de Alcântara
Elaboração
Adelides Antonio de Oliveira
Unidade Operacional
Centro de Formação Profissional “Fidélis Reis” Uberaba – MG 2004
______________________________________________________________
______________________________________________________________ 4
Apresentação
“Muda a forma de trabalhar, agir, sentir, pensar na chamada sociedade do conhecimento". Peter Drucker
O ingresso na sociedade da informação exige mudanças profundas em todos os perfis profissionais, especialmente naqueles diretamente envolvidos na produção, coleta, disseminação e uso da informação.
O SENAI , maior rede privada de educação profissional do país, sabe disso, e ,consciente do seu papel formativo , educa o trabalhador sob a égide do conceito da competência :” formar o profissional com responsabilidade no processo produtivo, com iniciativa na resolução de problemas, com conhecimentos técnicos aprofundados, flexibilidade e criatividade, empreendedorismo e consciência da necessidade de educação continuada .”
Vivemos numa sociedade da informação. O conhecimento, na sua área tecnológica, amplia-se e se multiplica a cada dia. Uma constante atualização se faz necessária. Para o SENAI , cuidar do seu acervo bibliográfico, da sua infovia, da conexão de suas escolas à rede mundial de informações – internet - é tão importante quanto zelar pela produção de material didático.
Isto porque, nos embates diários, instrutores e alunos , nas diversas oficinas e laboratórios do SENAI , fazem com que as informações, contidas nos materiais didáticos, tomem sentido e se concretizem em múltiplos conhecimentos.
O SENAI deseja, por meio dos diversos materiais didáticos, aguçar a sua curiosidade, responder às suas demandas de informações e construir links entre os diversos conhecimentos, tão importantes para sua formação continuada!
Gerência de Educação e Tecnologia
______________________________________________________________
______________________________________________________________ 5
11 ..^ SSiiddeerruurrggiiaa
No atual estágio de desenvolvimento da sociedade, é impossível imaginar o mundo sem o uso de ferro fundido e aço. Pode-se afirmar, inclusive, que a produção de aço é um forte indicador do estágio de desenvolvimento econômico de um país. Isso porque seu consumo cresce proporcionalmente à construção de edifícios, execução de obras públicas, instalação de meios de comunicação e produção de equipamentos. De forma geral, esses materiais já se tornaram tão corriqueiros no cotidiano que nem lembramos que eles não nascem prontos na natureza. Fabricá-los exige o conhecimento de técnicas que, hoje em dia, o homem desenvolve continuamente. Mas nem sempre foi assim. O início e o processo de aperfeiçoamento do uso do ferro representaram grandes desafios e conquistas para a humanidade.
Há cerca de 4.500 anos, o ferro metálico usado pelo homem era encontrado in natura em meteoritos recolhidos pelas tribos nômades nos desertos da Ásia Menor. Também existem indícios da ocorrência e do emprego desse material metálico em regiões como, por exemplo, a Groenlândia. Por sua beleza, maleabilidade e por ser de difícil obtenção, era considerado um metal precioso que se destinava, principalmente, ao adorno. Muitos defendem a hipótese de que o homem descobriu o ferro no Período Neolítico (Idade da Pedra Polida), por volta de 6.000 a 4.000 anos a.C. Ele teria surgido por acaso, quando pedras de minério de ferro usadas para proteger uma fogueira, depois de aquecidas, se transformaram em bolinhas brilhantes. O fenômeno, hoje, é facilmente explicável: o calor da fogueira havia derretido e quebrado as pedras. O uso do ferro nesse período sempre foi algo acidental e o exemplo acima ilustra bem a situação. Embora raras, havia vezes em que o material também era encontrado em seu estado nativo - caso de alguns meteoritos (corpos rochosos compostos por muitos minérios, inclusive ferro, que circulam no espaço e caem naturalmente na Terra). Como chegava pelo espaço, muitos povos consideravam o ferro como uma dádiva dos deuses. Aos poucos, o ferro passou a ser usado com mais freqüência, a partir do momento em que se descobriu como extraí-lo de seu minério. A exploração regular de jazidas começou em torno de 1.500 a.C., provavelmente no Oriente Médio, de onde o metal teria sido importado por assírios e fenícios. Do primeiro milênio da era cristã em diante, o ferro difundiu-se por toda bacia do Mediterrâneo.
Segundo o sistema proposto no século XIX por arqueólogos escandinavos, à Idade da Pedra se seguiu a Idade dos Metais. Primeiro, a do Bronze e, em seguida, a do Ferro. A Idade do Bronze se desenvolveu entre os anos 4000 e 2000 a.C. Por ser mais resistente do que o cobre, o bronze possibilitou a fabricação de armas e de instrumentos mais rígidos. A Idade do Ferro é considerada como o último estágio tecnológico e cultural da pré- história. Aos poucos, as armas e os utensílios feitos de bronze foram
______________________________________________________________
______________________________________________________________ 7
A Revolução Industrial iniciada na Inglaterra, no final do século XVIII, tornaria a produção de ferro ainda mais importante para a humanidade. Nesse período, as comunidades agrária e rural começavam a perder força para as sociedades urbanas e mecanizadas.
Mas a grande mudança só ocorreu realmente em 1856, quando se descobriu como produzir aço. Isso porque o aço é mais resistente que o ferro fundido e pode ser produzido em grandes quantidades, servindo de matéria-prima para muitas indústrias.
Quem fabrica o aço é a indústria siderúrgica. A origem dessa palavra está associada à história da descoberta do minério de ferro: sidur é uma palavra grega que significa astro.
Com o avanço tecnológico dos fornos e a crescente demanda por produtos feitos de ferro e aço, as indústrias siderúrgicas aumentavam a produção. Isso gerava problemas, devido aos gases poluentes liberados na atmosfera pela queima de carvão vegetal. Em meados do século XIX, a produção diária de um alto-forno chegava a cerca de três toneladas, o que elevava ainda mais o consumo de carvão vegetal.
Atualmente, as indústrias siderúrgicas são de extrema importância para as nações e representam um dos alicerces de um país desenvolvido. Não é à toa que são chamadas de indústrias de base, já que fornecem equipamentos e produtos para todas as outras. O ferro e o aço são encontrados na agricultura (ceifadeiras, colheitadeiras, semeadores, arados etc.), nos transportes (caminhões, carros, navios, aviões etc.), na construção civil, na indústria automobilística, em embalagens, aparelhos domésticos e muitas outras utilidades.
A produção mundial de aço bruto, em 2003, foi de cerca de 965 milhões de toneladas anuais. Para 2004, a expectativa é de que ela ultrapassará um bilhão de toneladas. Os dez maiores produtores mundiais de aço são, em ordem decrescente, China, Japão, Estados Unidos, Rússia, Coréia do Sul, Alemanha, Ucrânia, Índia, Brasil e Itália.
A Siderurgia no Brasil
Quando as terras brasileiras foram descobertas, as ações dos colonizadores portugueses já indicavam que o Brasil construiria uma sólida história da siderurgia. As práticas mercantilistas imperavam na Europa e a chegada dos portugueses ao Brasil trazia a esperança da extração de metais como ouro, prata e bronze. Os portugueses não encontraram nem ferro, nem outros metais nesse primeiro momento. Os poucos ferreiros que vieram para o Brasil utilizavam o ferro originário da Europa para produzir os instrumentos usados na lavoura. Em 1554, o padre jesuíta José de Anchieta relatou, em um informe ao rei de Portugal, a existência de depósitos de prata e minério de ferro no interior da capitania de São Vicente (atual estado de São Paulo). Quem primeiro trabalhou na redução desse minério de ferro foi Afonso Sardinha. Em 1587, ele descobriu magnetita na atual região de Sorocaba, no interior de São Paulo, e iniciou a produção de ferro a partir da redução do minério. É a primeira fábrica de
______________________________________________________________
______________________________________________________________ 8
ferro que se tem notícia no Brasil. As forjas construídas por Sardinha operaram até a sua morte, em 1629. Após essa data, a siderurgia brasileira entrou em um período de estagnação que durou até o século seguinte.
Foi a descoberta de ouro no atual Estado de Minas Gerais que desencadeou um novo estímulo à siderurgia. Fundições foram abertas para a construção de implementos de ferro utilizados no trabalho das minas. Contudo, as mesmas práticas mercantilistas que impulsionaram a descoberta de metais em nossas terras fizeram com que a construção de uma indústria siderúrgica brasileira fosse reprimida. A colônia deveria ser explorada ao máximo e comercializar apenas ouro e produtos agrícolas. Portugal chegou a proibir a construção de novas fundições e ordenou a destruição das existentes. A situação mudou com a ascensão de Dom João VI ao trono de Portugal. Em 1795, foi autorizada a construção de novas fundições. Em 1808, a família real portuguesa desembarcou fugitiva no Rio de Janeiro, temendo o avanço das tropas napoleônicas às terras lusitanas. Diversas indústrias siderúrgicas foram construídas a partir desse período. Em 1815, ficou pronta a usina do Morro do Pilar, em Minas Gerais. Em 1817, foi inaugurada a Fábrica de Ipanema, nos arredores de Sorocaba. Outras indústrias foram abertas em Congonhas do Campo, Caeté e São Miguel de Piracicaba, todas em Minas Gerais. Não seria dessa vez, porém, que a siderurgia brasileira iria decolar. Após esse início de século XIX promissor, houve um declínio na produção de ferro. A competição com os produtos importados da Inglaterra era desigual e travava o desenvolvimento da siderurgia brasileira. Além disso, havia escassez de mão-de-obra, já que os trabalhadores, em sua maioria, eram sugados pela lavoura do açúcar e, mais tarde, do café. Mesmo assim, um marco importante para o posterior progresso da siderurgia brasileira data desse período: a fundação, em 1876, da Escola de Minas de Ouro Preto, que formaria uma geração competente de engenheiros, metalúrgicos e geólogos.
Processo Siderúrgico
Quando o homem conseguiu a quantidade necessária de calor para fundir o minério de ferro, encerrou a Idade do Bronze e deu início à Idade do Ferro. O fator custo teve importante papel nesta mudança.
A fronteira entre o ferro e o aço foi definida na Revolução Industrial, com a invenção de fornos que permitiam não só corrigir as impurezas do ferro, como lhes adicionar propriedades como resistência ao desgaste, ao impacto, à corrosão, etc. Por causa dessas propriedades e do seu baixo custo o aço passou a representar cerca de 90% de todos os metais consumidos pela civilização industrial.
Basicamente, o aço é uma liga de ferro e carbono. O ferro é encontrado em toda crosta terrestre, fortemente associado ao oxigênio e à sílica. O minério de ferro é um óxido de ferro, misturado com areia fina.
O carbono é também relativamente abundante na natureza e pode ser encontrado sob diversas formas. Na siderurgia, usa-se carvão mineral, e em alguns casos, o carvão vegetal.
______________________________________________________________
______________________________________________________________ 10
Parque Siderúrgico O parque siderúrgico brasileiro compõe-se, hoje, de 24 usinas, administradas por 11 empresas. A privatização trouxe ao setor expressivo afluxo de capitais, em composições acionárias da maior diversidade. Assim, muitas empresas produtoras passaram a integrar grupos industriais e/ou financeiros cujos interesses na siderurgia se desdobraram para atividades correlatas, ou de apoio logístico, com o objetivo de alcançar economia de escala e competitividade. O parque produtor é relativamente novo e passa por um processo de atualização tecnológica. Está apto a entregar ao mercado qualquer tipo de produto siderúrgico, desde que sua produção se justifique economicamente. Em função dos produtos que preponderam em suas linhas de produção, as usinas podem, ser assim classificadas:
Quanto à forma geométrica
Semi-acabados
Produtos oriundos de processo de lingotamento contínuo ou de laminação de desbaste, destinados a posterior processamento de laminação ou forjamento a quente.
Produtos Planos
Produtos siderúrgicos, resultado de processo de laminação, cuja largura é extremamente superior a espessura (L >>>E), e são comercializados na forma de chapas e bobinas de aços carbono e especiais.
______________________________________________________________
______________________________________________________________ 11
Produtos Longos
Produtos siderúrgicos, resultado de processo de laminação, cujas seções transversais têm formato poligonal e seu comprimento é extremamente superior à maior dimensão da seção, sendo ofertados em aços carbono e especiais.
Quanto ao tipo de aço
Aços Carbono
São aços ao carbono, ou com baixo teor de liga, de composição química definida em faixas amplas.
Aços Ligados / Especiais
São aços ligados ou de alto carbono, de composição química definida em estreitas faixas para todos os elementos e especificações rígidas.
Aços construção mecânica:
São aços ao carbono e de baixa liga para forjaria, rolamentos, molas, eixos, peças usinadas, etc.
Aços ferramentas.
São aços de alto carbono ou de alta liga, destinados à fabricação de ferramentas e matrizes, para trabalho a quente e a frio, inclusive aços rápidos.
______________________________________________________________
______________________________________________________________ 13
22 ..^ EEssttrruuttuurraa^ ccrriissttaalliinnaa^ ddooss^ MMeettaaiiss
Os aços diferenciam-se entre si pela forma, tamanho e uniformidade dos grãos que o compõem e, é claro, por sua composição química. Esta pode ser alterada em função do interesse de sua aplicação final, obtendo-se através da adição de determinados elementos químicos, aços com diferentes graus de resistência mecânica, soldabilidade, ductilidade, resistência à corrosão, entre outros. De maneira geral, os aços possuem excelentes propriedades mecânicas: resistem bem à tração, à compressão, à flexão, e como é um material homogêneo, pode ser laminado, forjado, estampado, estriado e suas propriedades podem ainda ser modificadas por tratamentos térmicos ou químicos.
O aço, como os demais metais, se solidifica pela formação de cristais, que vão crescendo a diferentes direções, formando os denominados eixos de cristalização. A partir de um eixo principal, crescem eixos secundários, que por sua vez se desdobram em novos eixos e assim por diante até que toda a massa do metal se torne sólida. O conjunto formado pelo eixo principal e secundários de um cristal é denominado dendrita. Quando duas dendritas se encontram, origina-se uma superfície de contato e ao término do processo de cristalização, formam cada uma os grãos que compõem o metal, de modo que todos os metais, após sua solidificação completa, são constituídos de inúmeros grãos, justapostos e unidos.
Fig. 2.1 – Esquema estrutural de uma dendrita
A formação de cristais no ferro ocorre segundo dois tipos de reticulados: o Ø e ß. Ambos fazem parte de um sistema cristalino cúbico, ou seja, a unidade básica do cristal tem a forma de um cubo. No primeiro tipo de reticulado (Ø) denominado cúbico de corpo centrado (CCC), ao isolar-se a unidade básica do cristal, verifica-se que os átomos de ferro localizam-se nos oito vértices e no centro do cubo, enquanto que no segundo (ß) agora denominado cúbico de face centrada, os átomos ficam posicionados nos oito vértices e no centro de cada face do cubo.
______________________________________________________________
______________________________________________________________ 14
a) Célula unitária CCC b) Célula unitária CFC
Figura 2.2. – Principais cristais cúbicos.
Hexagonal Compacto : A figura 2.3. mostra o reticulado HC, encontrado no magnésio, titânio e o zinco.
Figura 2.3. - Célula unitária Hexagonal Compacta
Tabela 2.1. - Materiais e seus reticulados
Exemplos CCC (^) Cr, Fe(α), Mo, W CFC (^) Al, Fe(γ), Ni, Cu, Ag, Pb HC Mg, Zn, Ti.
Além do ferro, o aço apresenta em sua constituição carbono e elementos de liga. Estes elementos vão formar junto com o ferro uma solução e, de acordo com a temperatura e a quantidade de carbono presente, haverá a presença de um determinado tipo de reticulado. O aço é constituído de um agregado cristalino, cujos cristais (grãos) se encontram justapostos. As propriedades dos aços dependem muito de sua estrutura cristalina, ou seja, de sua composição química, do tamanho dos grãos, de sua uniformidade. Os tratamentos térmicos bem como os trabalhos mecânicos modificam em maior ou menor intensidade alguns destes aspectos (arranjo, dimensões, formato dos grãos) e, conseqüentemente, podem levar a alterações nas propriedades de um
4r a
a
______________________________________________________________
______________________________________________________________ 16
Estrutura interna é definida como o arranjo de elétrons e átomos dentro do metal. Deve-se observar que um dado material com determinada composição química, a estrutura interna não é constante, podendo variar grandemente, dependendo de: (1) como o material foi fabricado (condições de processamento); (2) sob que condições o material se encontra em serviço (temperatura, pressão, agentes corrosivos, etc.). A análise da estrutura é feita, em geral, ao nível da resolução de microscópios ópticos (10-1200x) ou de microscópios eletrônicos (2000-100.000x). Esta estrutura observada é chamada de microestrutura. Um conjunto de células unitárias forma o cristal com contornos geométricos, o qual, ao adquirir os contornos irregulares pelo seu crescimento e devido aos pontos de contato de cada conjunto, passa a chamar-se grão. Esses grãos são ligados entre si por um limite, denominado contorno de grão.
Figura 2.5. - estrutura granular de uma material puro.
As propriedades mecânicas dos metais dependem fortemente do tamanho do grão, por isto a American Society for Testing of Materials (ASTM) criou um índice do tamanho de grão dos aços, através da seguinte equação: N = 2n- onde: N é o número de grãos observados por polegada quadrada, quando o metal é examinado ao microscópio com um aumento de 100x n é o número do tamanho de grão ASTM. Considerando os grãos, as microestruturas dos metais monofásicos podem ser diferenciadas de três maneiras: ♦ Tamanho de grão ♦ Forma do grão ♦ Orientação preferencial
Tamanho de grão diferente
Com e sem orientação preferencial
Forma de grão diferente
______________________________________________________________
______________________________________________________________ 17
33 ..^ AAççoo^ CCaarrbboonnoo
Alguns elementos químicos apresentam variedades alotrópicas , isto é, estruturas cristalinas diferentes que passam de uma para outra em determinadas temperaturas, chamadas temperaturas de transição. O ferro apresenta 3 variedades, conforme a seguir descrito.
Ao se solidificar (temperatura de aproximadamente 1540°C), o ferro apresenta estrutura cúbica de corpo centrado, chamada de ferro delta ( Fe d ). Permanece nesta condição até cerca de 1390ºC e, abaixo desta, transforma-se em ferro gama ( Fe g ), com estrutura cúbica de face centrada. Abaixo de 912°C, readquire a estrutura cúbica de corpo centrado, agora chamada de ferro alfa ( Fe a ). Continuando o resfriamento, a 770°C ocorre o ponto de Curie , isto é, ele passa a ter propriedades magnéticas. Entretanto, isto não se deve a um rearranjo da disposição atômica, mas sim à mudança do direcionamento da rotação dos elétrons (spin). Em outras épocas, tal fato não era conhecido e se julgava corresponder a uma variedade alotrópica, chamada de ferro beta.
Ligado com o carbono, o comportamento das variedades alotrópicas do ferro e a solubilidade do carbono nele variam de forma característica, dependendo da temperatura e do teor de carbono. Isto pode ser visto em forma de gráfico, chamado diagrama de equilíbrio ferro-carbono.
Abaixo, definições dos termos usados no diagrama:
Austenita : é a solução sólida do carbono em ferro gama. Ferrita : é a solução sólida do carbono em ferro alfa. Cementita : o carboneto de ferro (Fe3C). Grafita : a variedade alotrópica do carbono (estrutura cristalina hexagonal).
Obs: próximas ao ponto marcado com (*), existem na realidade linhas de equilíbrio com o ferro delta, mas não são exibidas por razões de clareza e de pouco interesses práticos.
A adição do carbono altera as temperaturas de transição das variedades alotrópicas em relação ao ferro puro, dependendo do seu teor. Exemplo: para um aço com cerca de 0,5% C, representado pela linha vertical 1-2 no diagrama, o ferro gama contido na austenita começará a se transformar em alfa no ponto 1 e estará totalmente transformado no ponto 2, a 727°C, inferior aos 912°C do ferro puro. Importante lembrar que, abaixo de 727°C, não poderá haver ferro gama. Somente a variedade alfa está presente.
______________________________________________________________
______________________________________________________________ 19
O teor de carbono do aço exerce significativa influência no seu aspecto granulométrico. Um aço com muito pouco carbono (digamos, menos de 0,01%), se resfriado lentamente, deverá apresentar uma aparência razoavelmente uniforme, pois a maior parte será representada pela ferrita. Ao lado, um possível aspecto de uma microfotografia de um aço deste tipo.
Agora supomos um aço hipoeutetóide com 0,5% de carbono, representado pela linha vertical 1-2 no diagrama. Quando o resfriamento atinge o ponto 1, começa a separação da austenita em austenita e ferrita. No ponto 2, haverá ferrita mais austenita, esta última, com o máximo teor de carbono que pode conter (0,77%). Logo abaixo do ponto 2, toda a austenita deverá se transformar em ferrita mais cementita. Entretanto, desde que o processo é rápido, fisicamente, a separação se dá em forma de lâminas bastante finas, somente visíveis ao microscópio com elevadas ampliações. Tal estrutura, isto é, a ferrita e a cementita em forma laminar, é chamada de perlita. Nas figuras ao lado, em primeiro lugar, a estrutura laminar típica da perlita, observada com elevada ampliação (as linhas escuras correspondem a cementita). Na segunda figura, o aspecto típico de um aço hipoeutetóide visto com uma ampliação menor. As áreas claras representam a ferrita e as escuras, a perlita. Entretanto, a estrutura laminar desta não pode ser observada devido à reduzida ampliação. Um aço hipereutetóide (linha 3-4 no diagrama, com 1,5% C, por exemplo) terá, no ponto 4, austenita com o máximo teor de carbono (0,77%) e cementita. A mudança brusca no ponto 4 fará a austenita se transformar em perlita conforme já visto. E a cementita envolverá os grãos de perlita em forma de uma teia conforme figura ao lado, com destaque para esta rede de cementita. Um aço eutetóide, isto é, com 0,77% de carbono, deverá apresentar somente perlita na sua estrutura granular. O teor de carbono exerce significativa influência nas propriedades mecânicas do aço. Quanto maior, maiores a dureza e a resistência à tração. Entretanto, aços com elevados teores de carbono são prejudicados pela maior fragilidade devido à maior quantidade de cementita, uma substância bastante dura mas quebradiça. É comum o uso da expressão aço doce para aços de baixa dureza, com teores de carbono menores que 0,25%.
______________________________________________________________
______________________________________________________________ 20
Conforme dito na primeira página desta série, o teor de carbono tem significativa influência nas propriedades mecânicas do aço. Quanto maior a presença do carbono, maior será a resistência à tração e, por conseqüência, a dureza. Entretanto, outros aspectos normalmente indesejáveis serão reforçados como menor ductilidade e maior fragilidade. No gráfico ao lado, um exemplo típico da variação da resistência à tração.
Os constituintes básicos dos aços são: austenita, ferrita, cementita e perlita.
A austenita , nos aços-carbono comuns, só é estável acima de 727° C; consta de uma solução sólida de carbono no ferro gama e apresenta uma estrutura de grãos poligonais irregulares; possui boa resistência mecânica e apreciável tenacidade; é não magnética. A ferrita é ferro no estado alotrópico alfa, contendo em solução traços de carbono; apresenta também uma estrutura de grãos poligonais irregulares; possui baixa dureza e baixa resistência à tração, mas excelente resistência ao choque e elevado alongamento. A cementita é o carboneto de ferro Fe 3 C contendo 6,67% de carbono; muito dura, quebradiça, é responsável pela elevada dureza e resistência dos aços de alto carbono, assim como pela sua menor ductilidade. A perlita é a mistura mecânica de 88,5% de ferrita e 11,5% de cementita, na forma de lâminas finas. As propriedades mecânicas da perlita são, portanto, intermediárias entre as da ferrita e da cementita, dependendo, entretanto, do tamanho das partículas de cementita.
Devido aos característicos mecânicos dos constituintes dos aços, as propriedades mecânicas destes quando esfriados lentamente, variam de acordo com a proporção daqueles constituintes. Assim, o ferro comercialmente puro, constituído somente de ferrita, apresenta-se mole e dúctil, pouco resistente à tração e com alta resistência ao choque; à medida que o teor de carbono cresce, aumenta os valores representativos da resistência mecânica, isto é, o limite de escoamento, o limite à tração e a dureza, ao passo que caem os valores relativos à ductilidade, como alongamento, estricção e resistência ao choque.
Quando mencionados elementos de liga , deve ficar subentendido que são outros elementos, além do ferro e do carbono, uma vez que estes são os constituintes básicos do aço.