
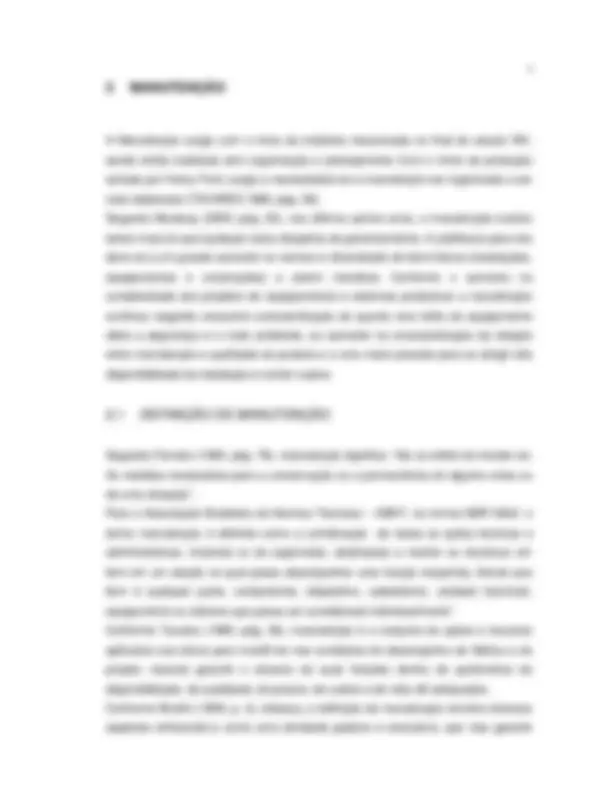
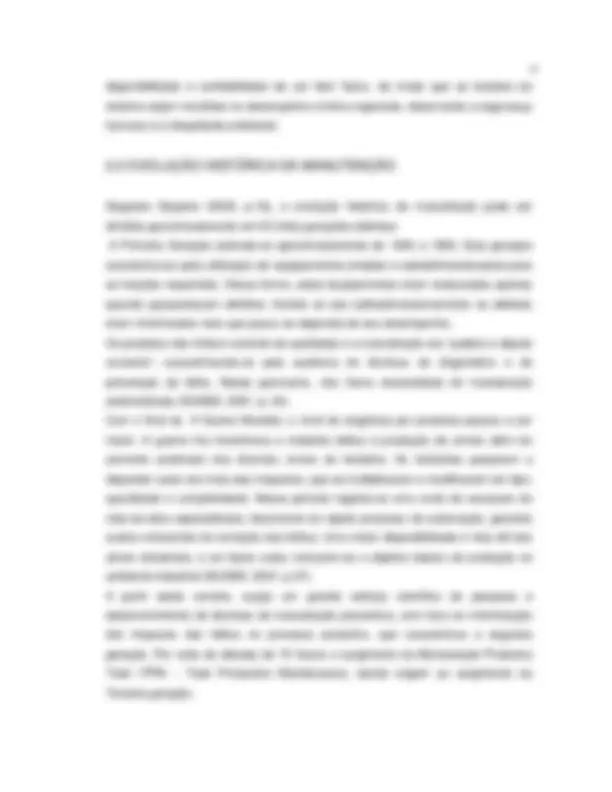
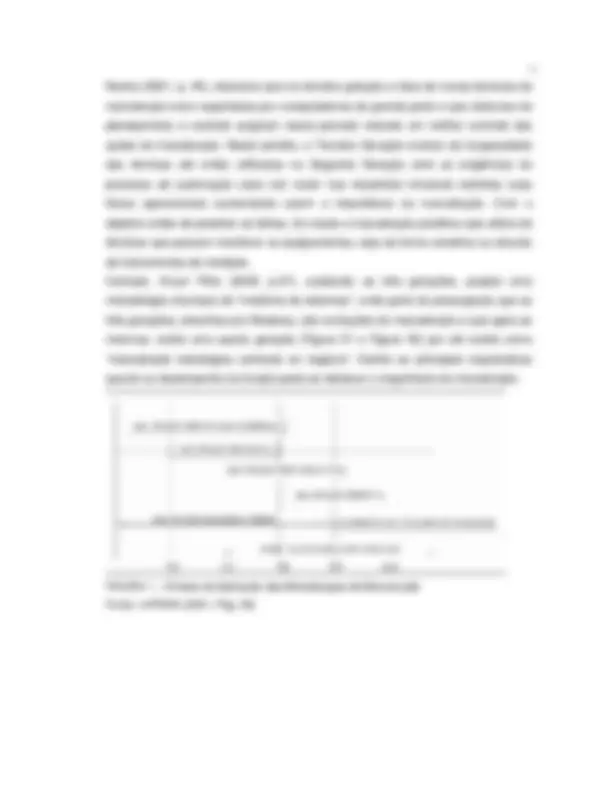
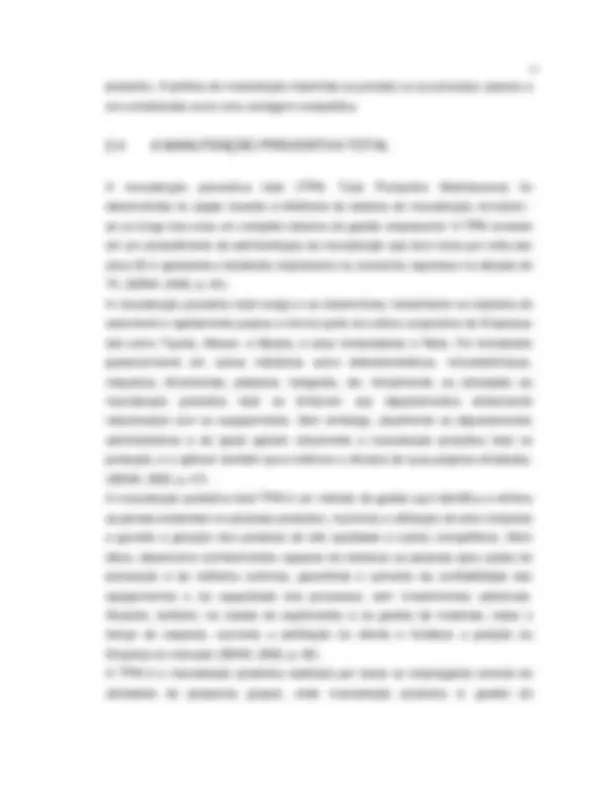
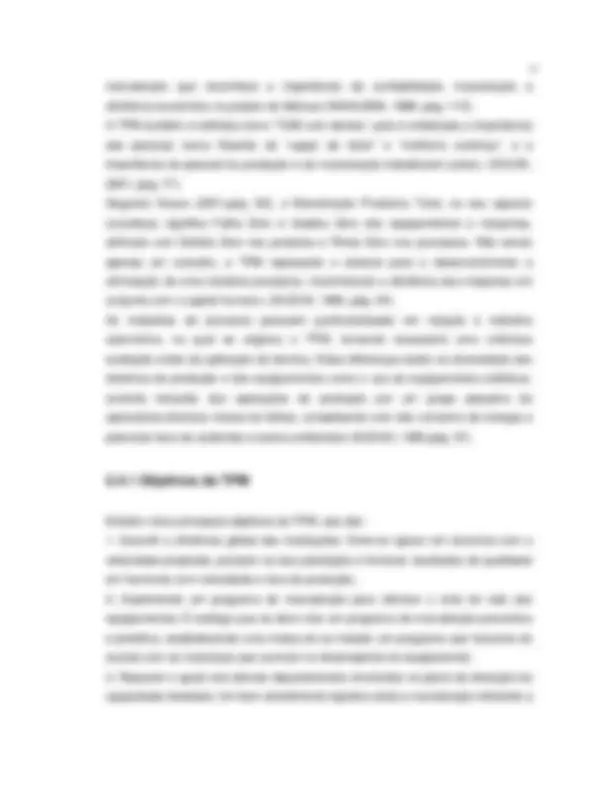
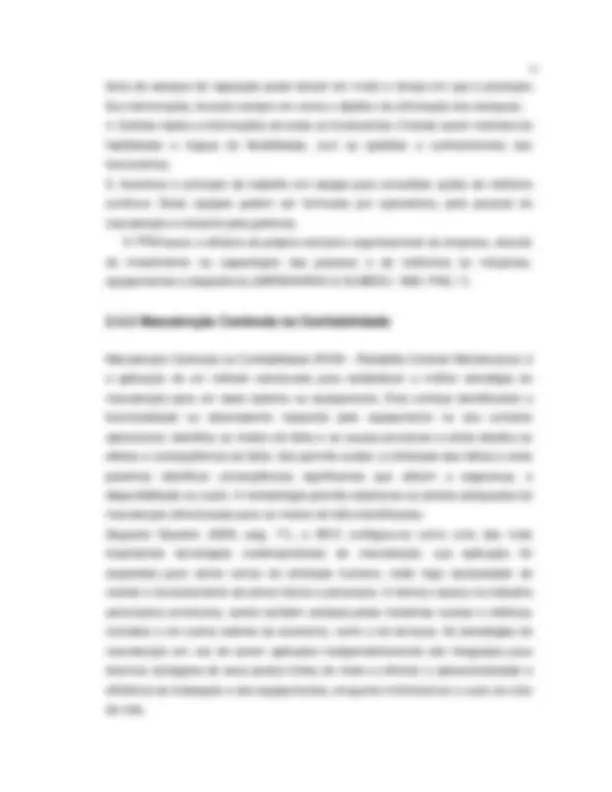
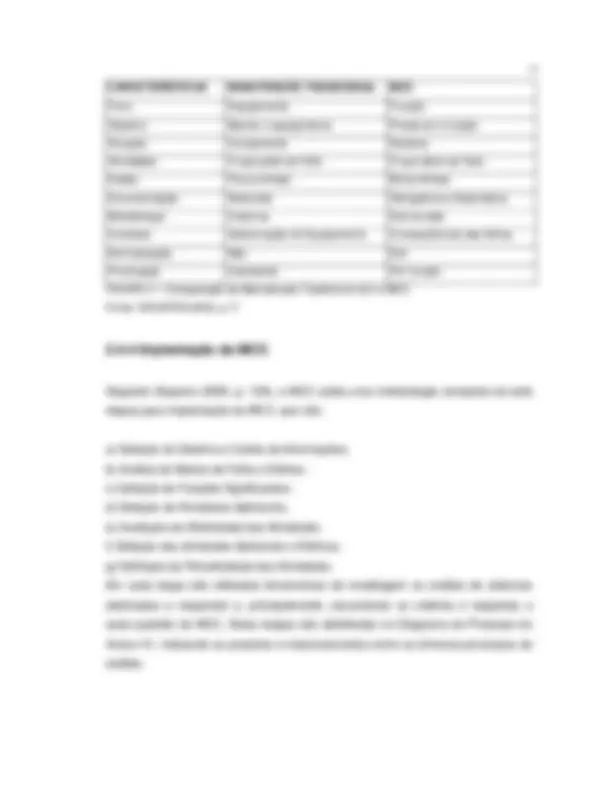
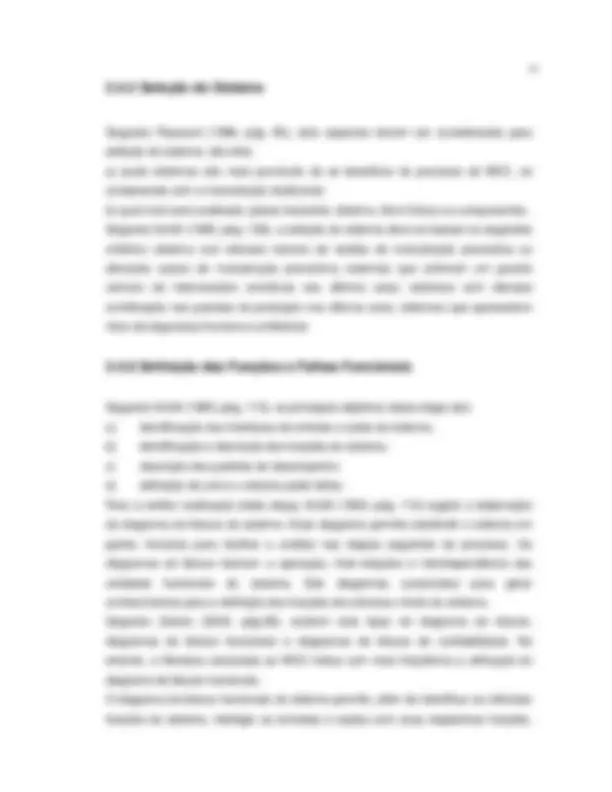
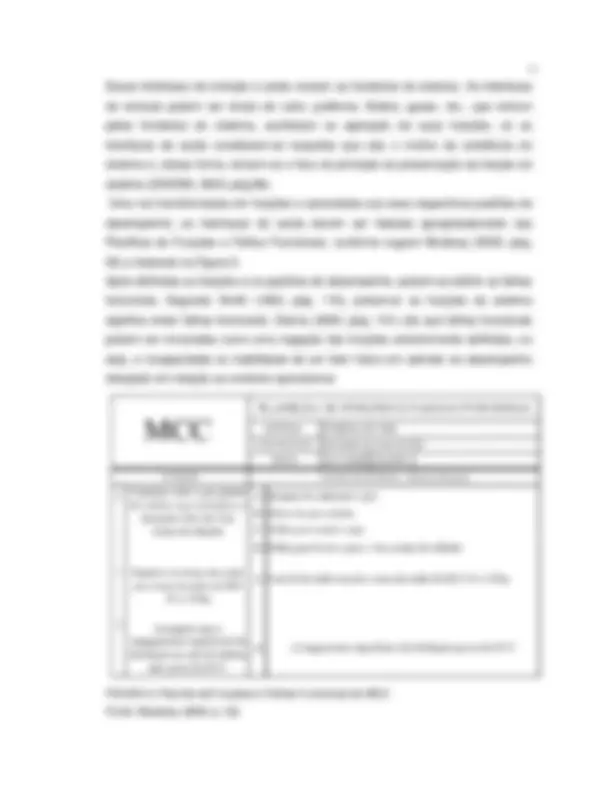
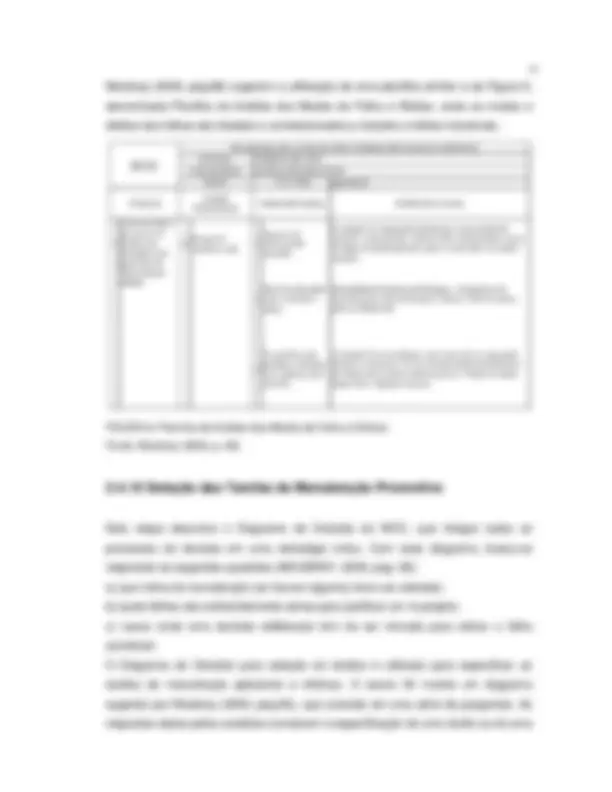
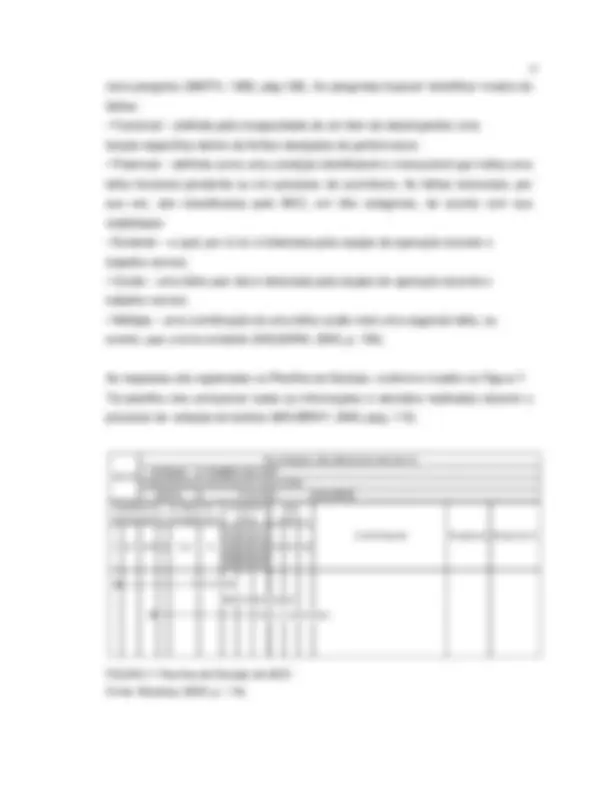
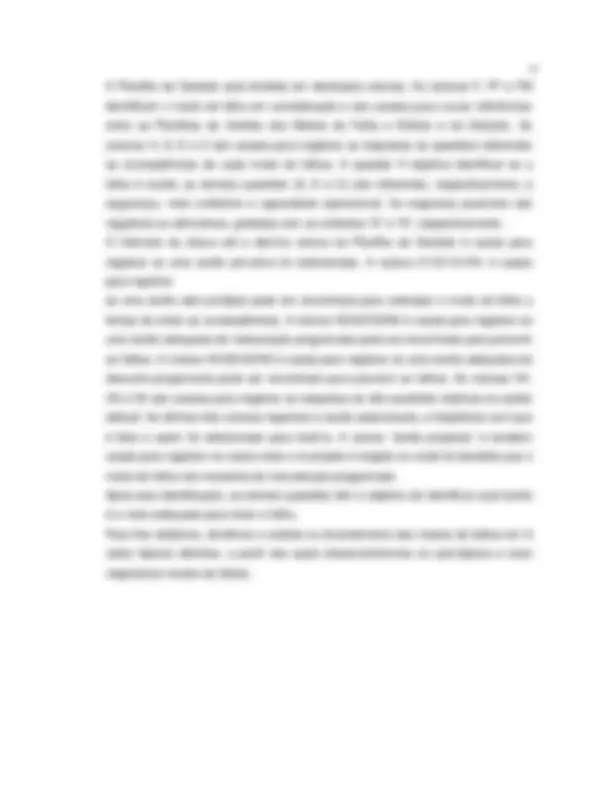
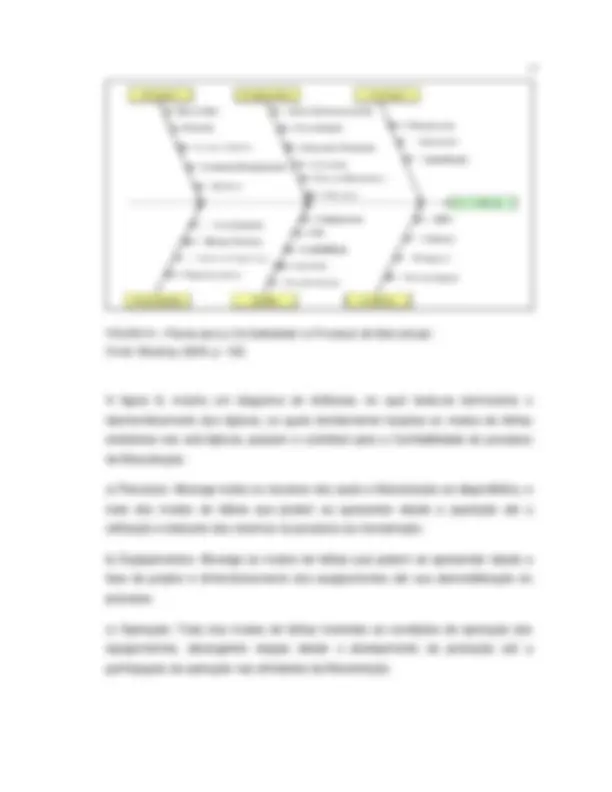
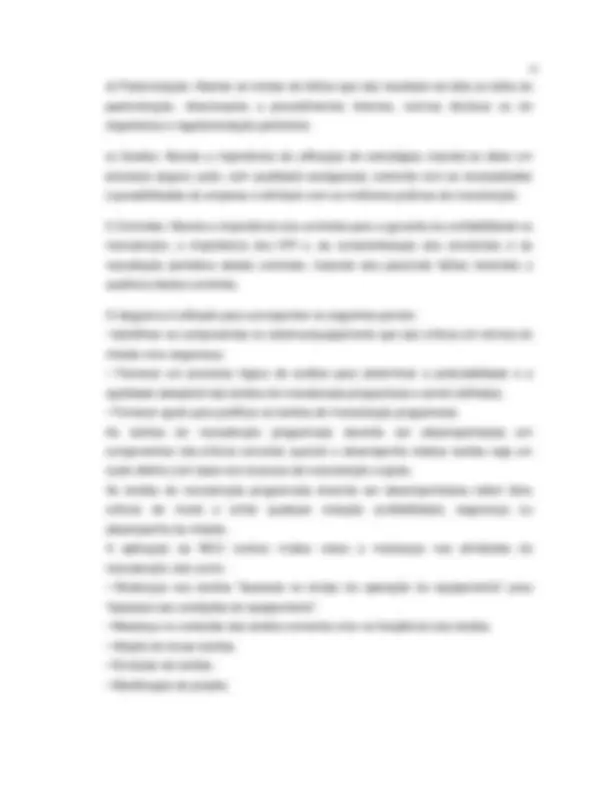
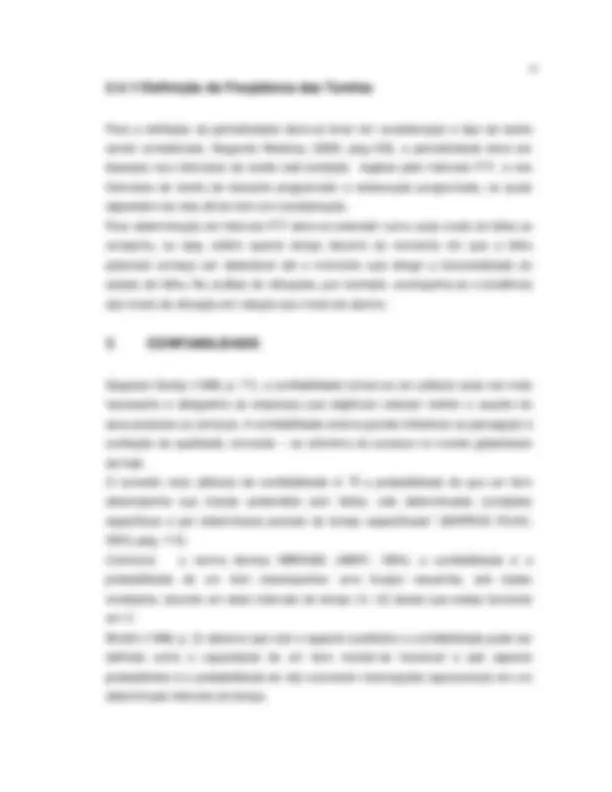
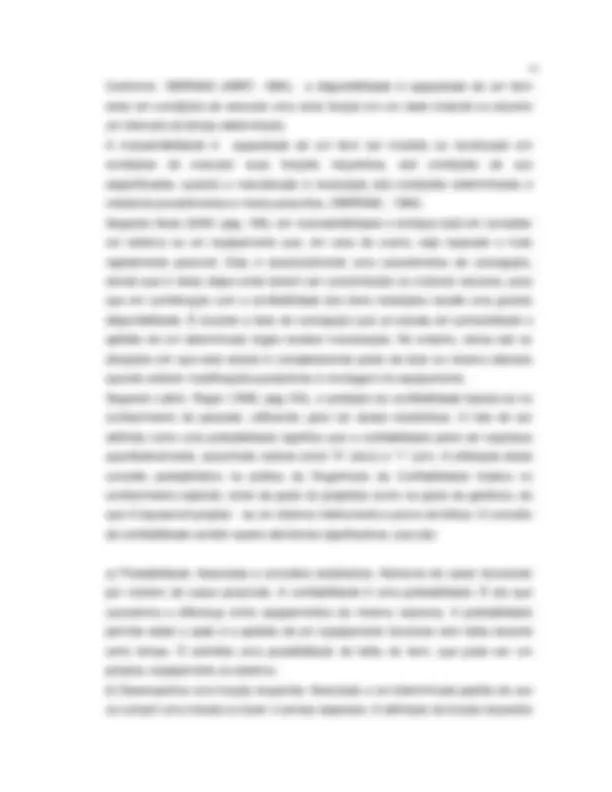
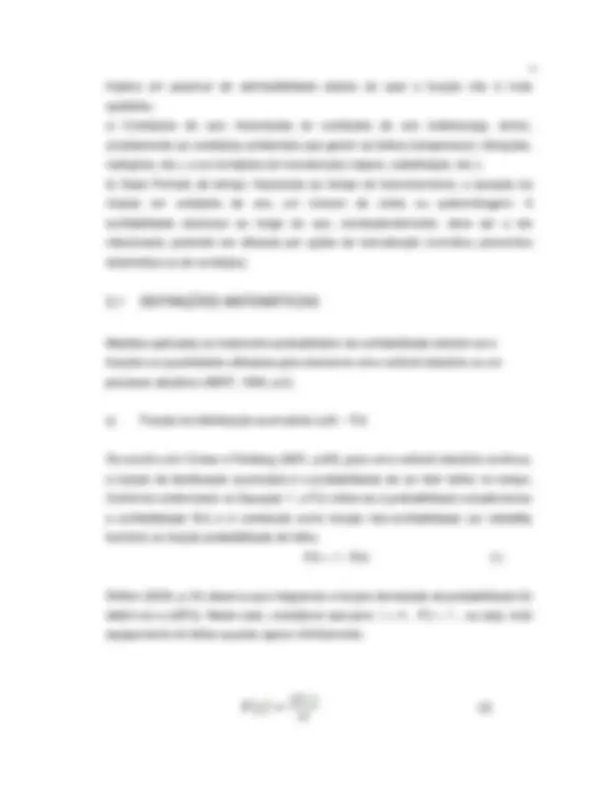
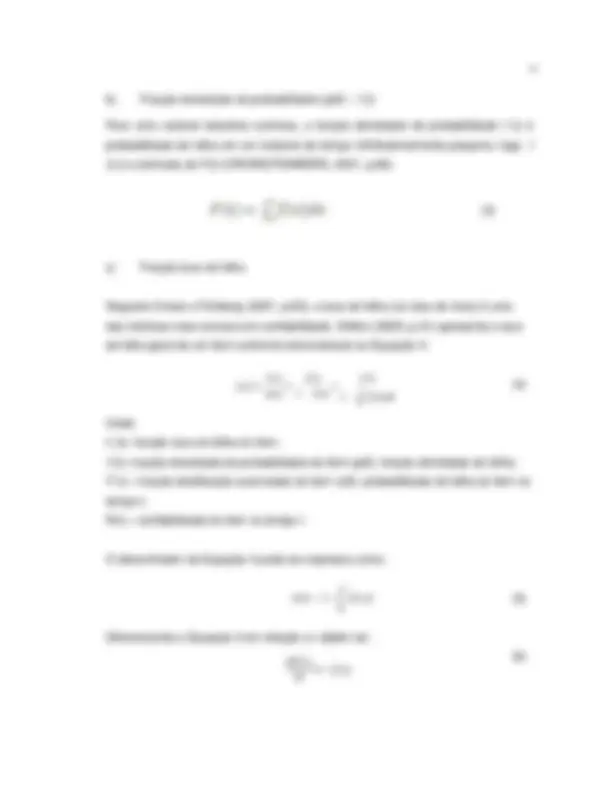
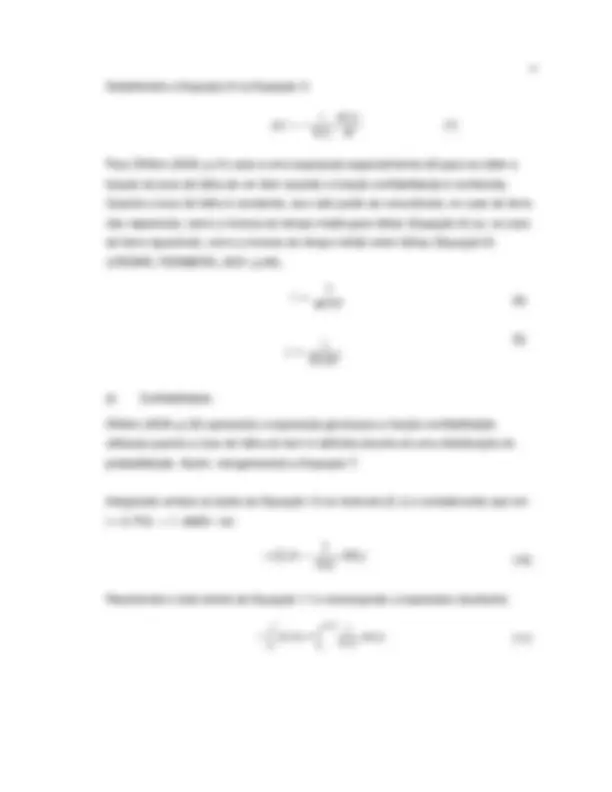
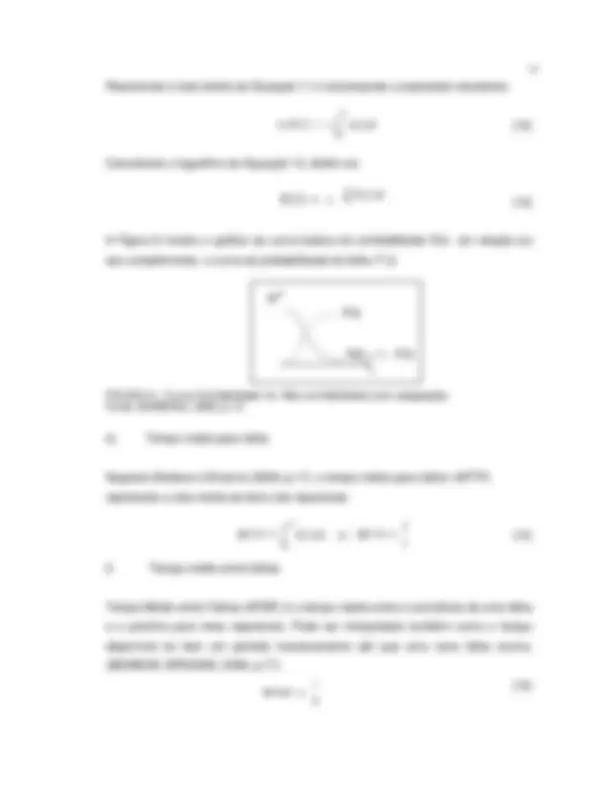
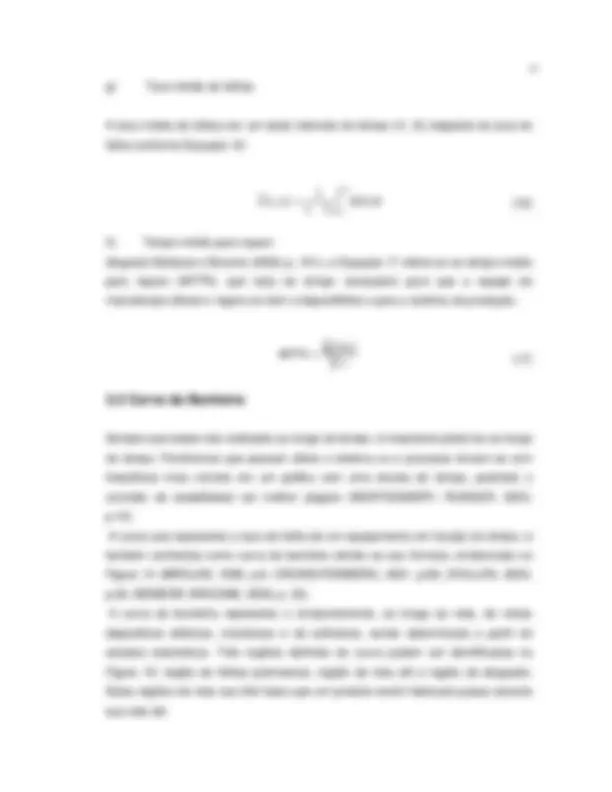
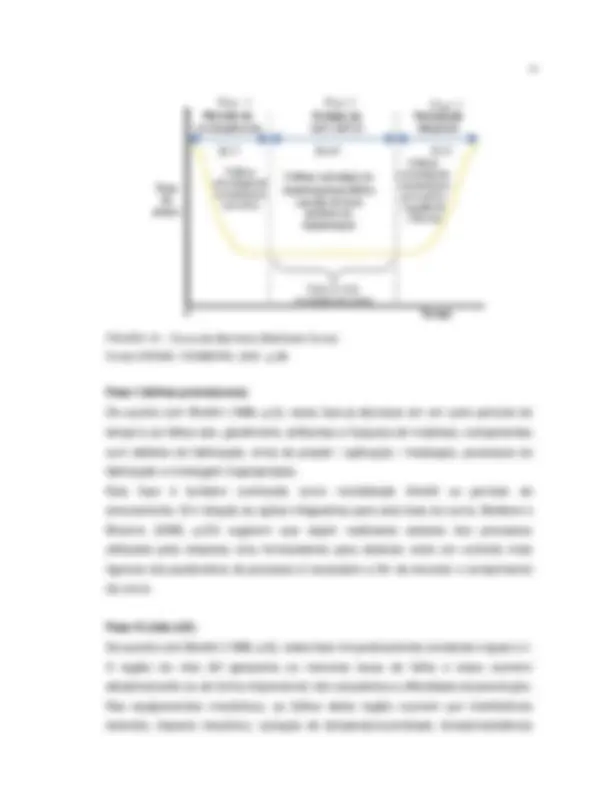
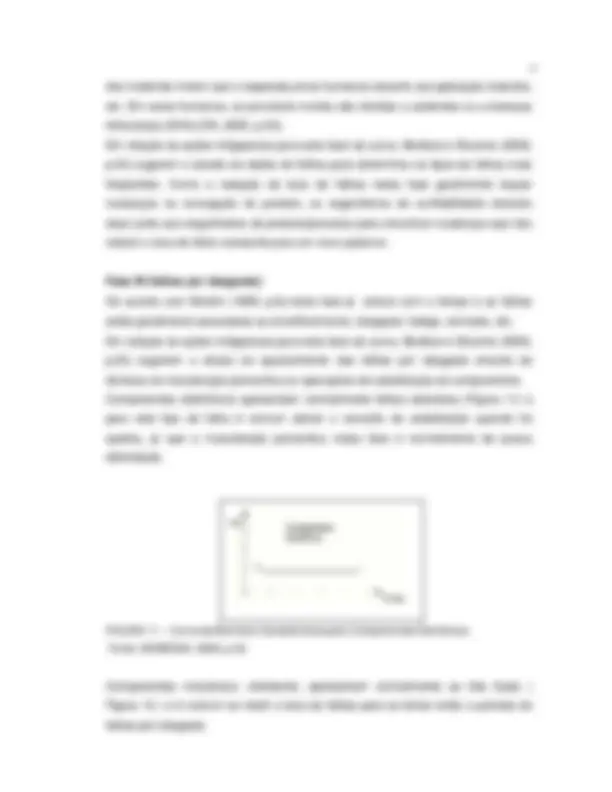
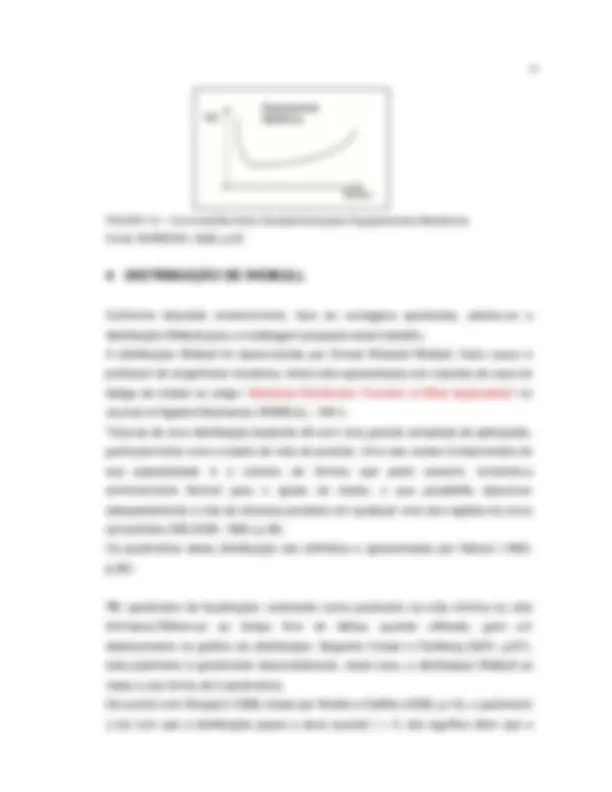
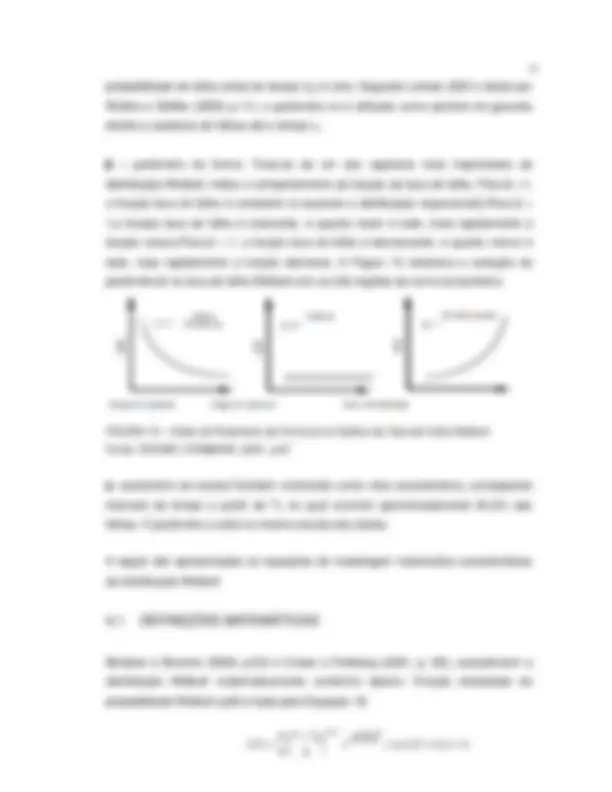
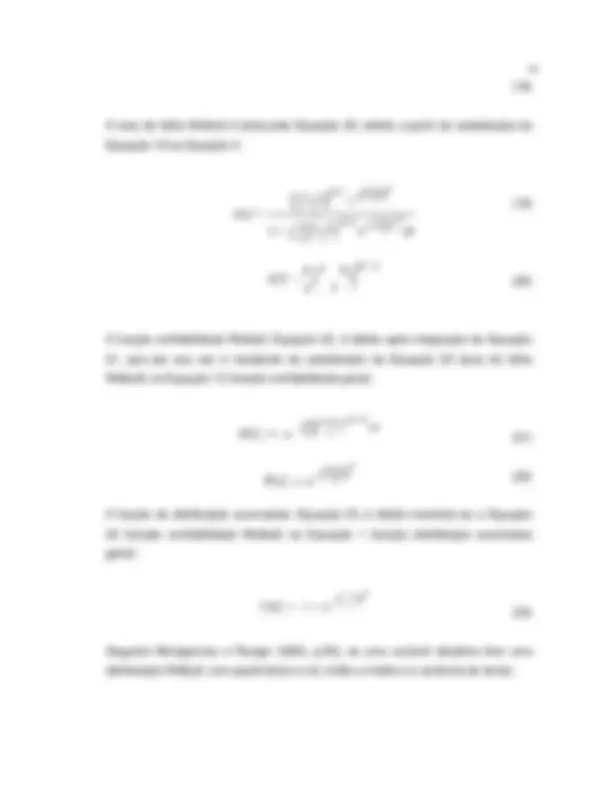
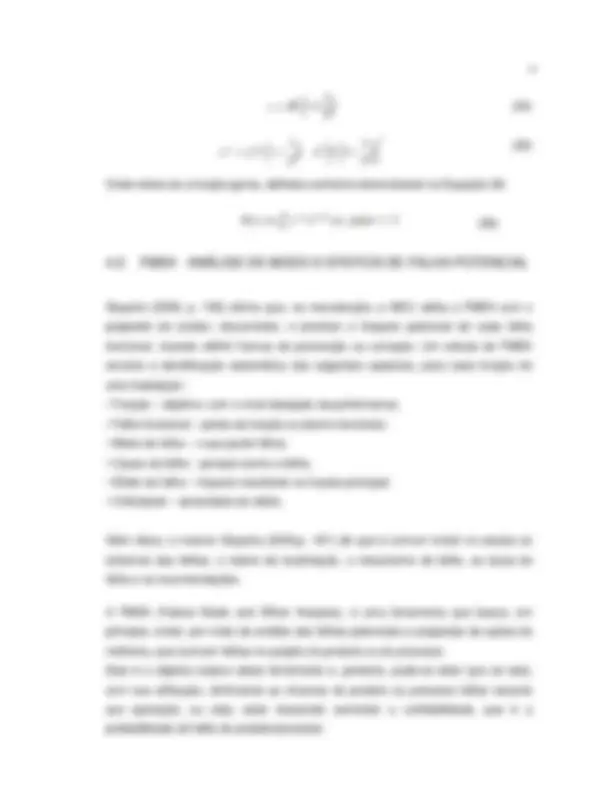
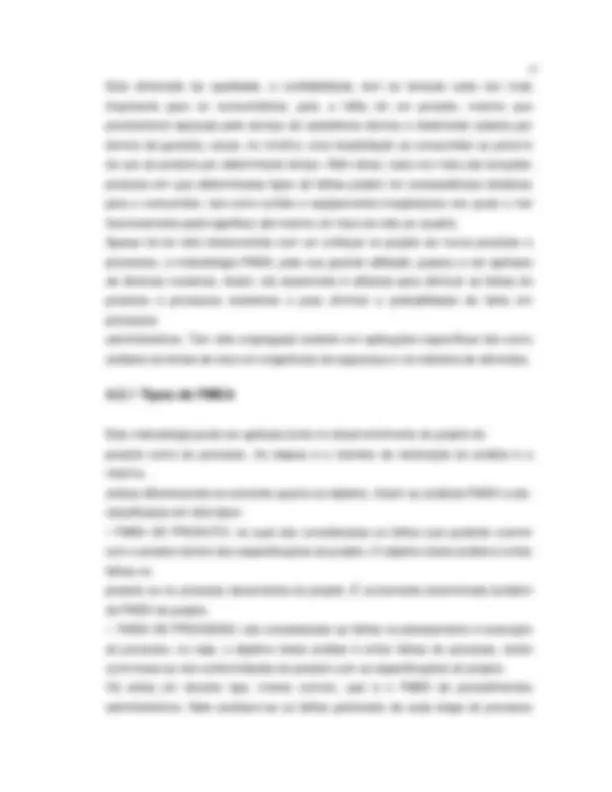

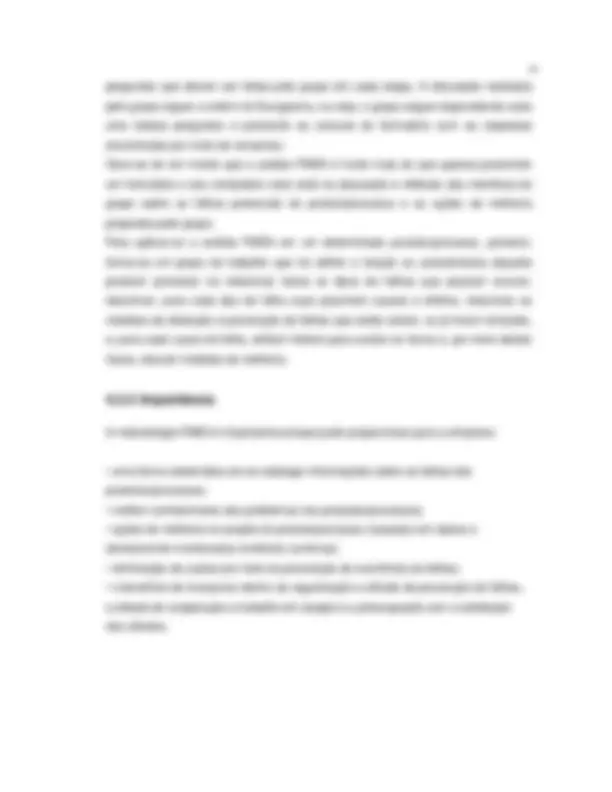
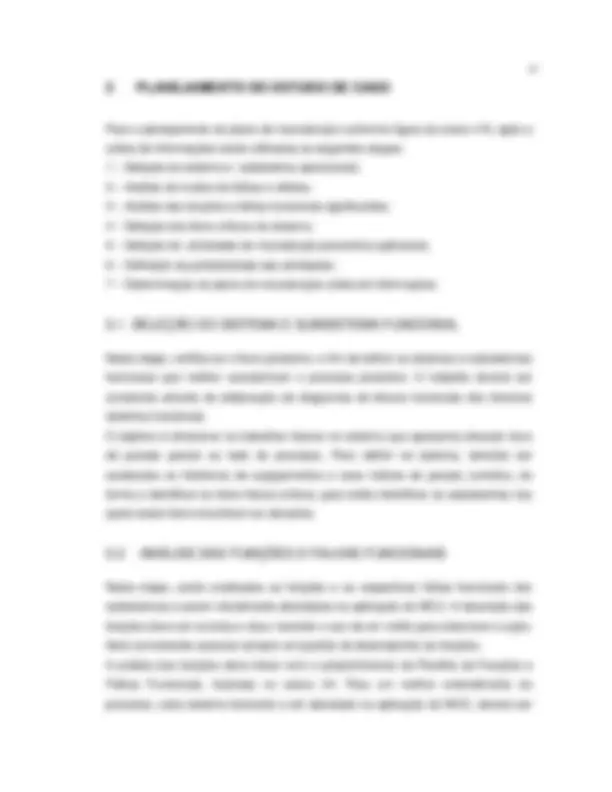
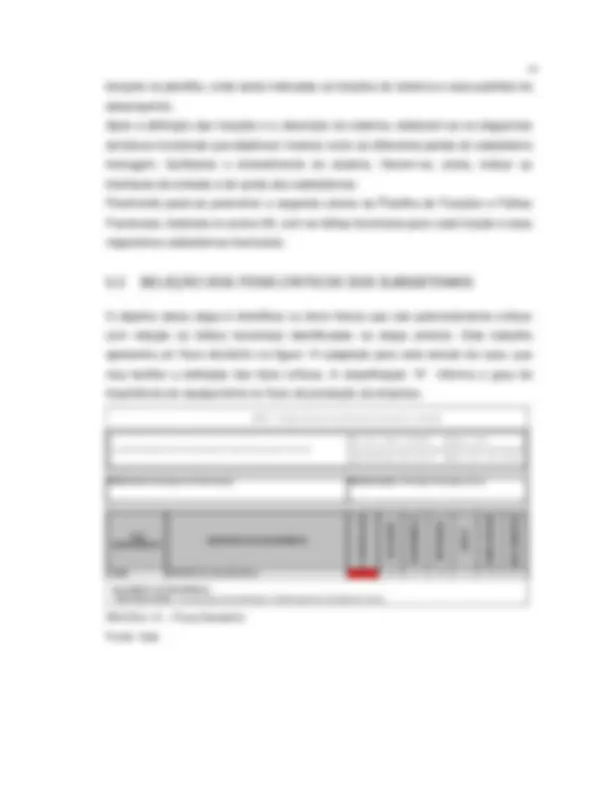
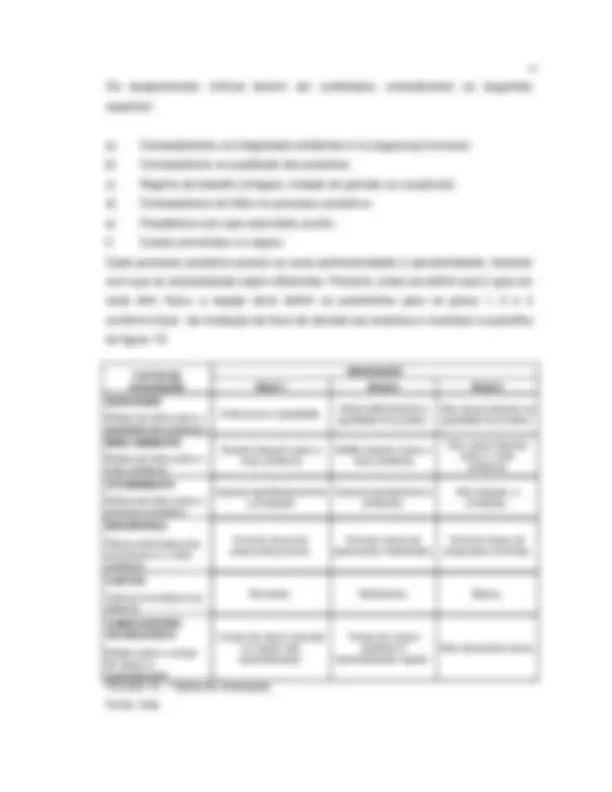

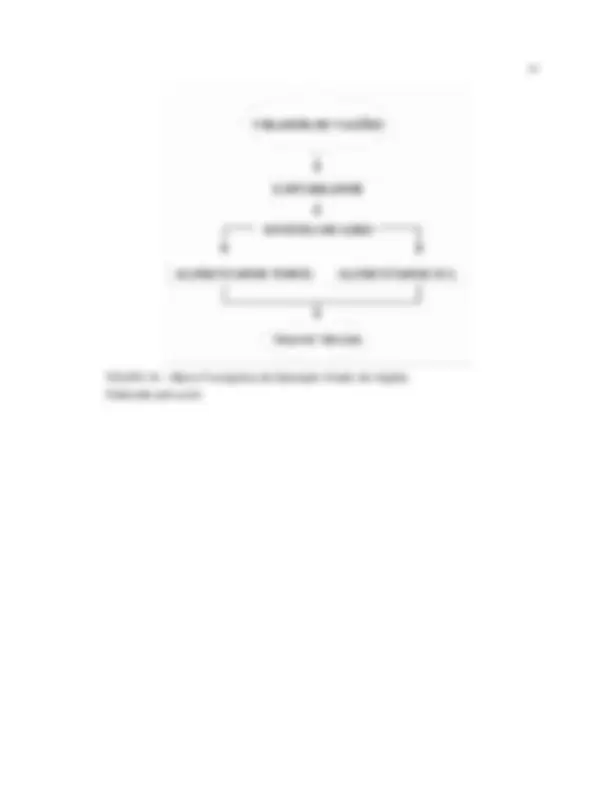
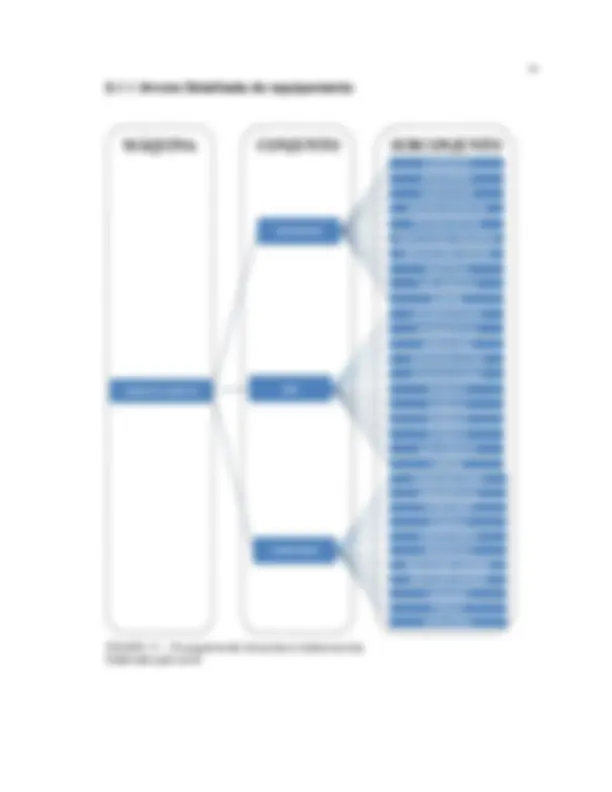
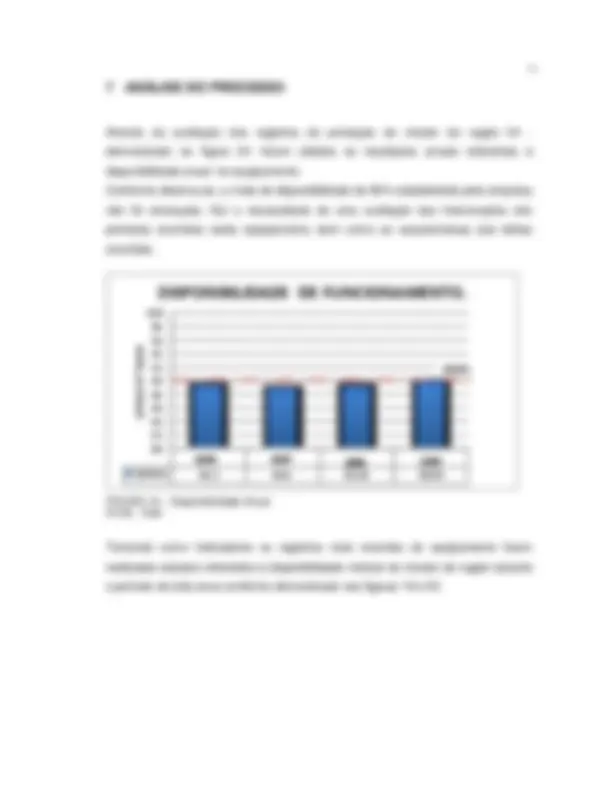
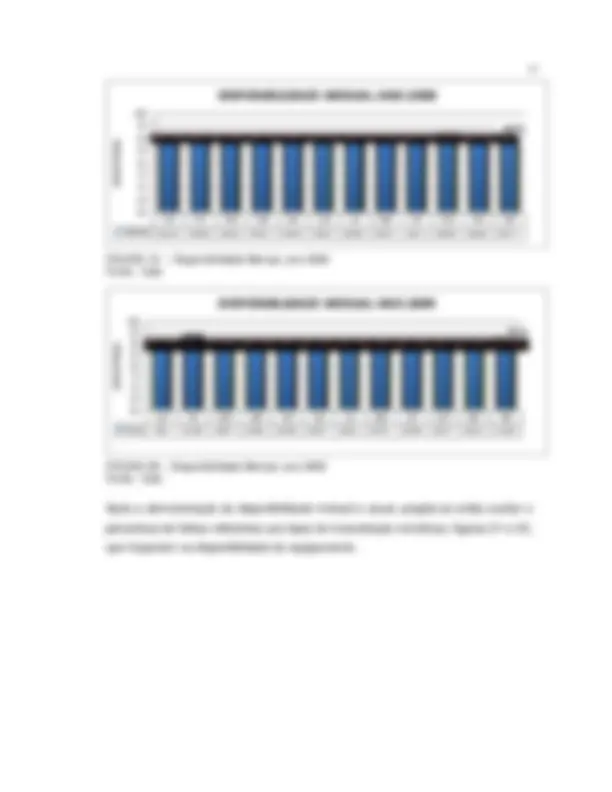
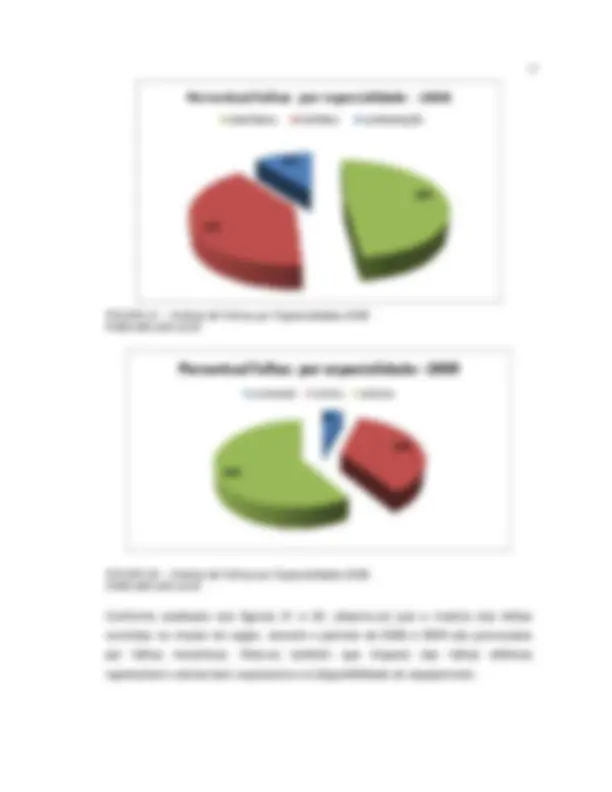
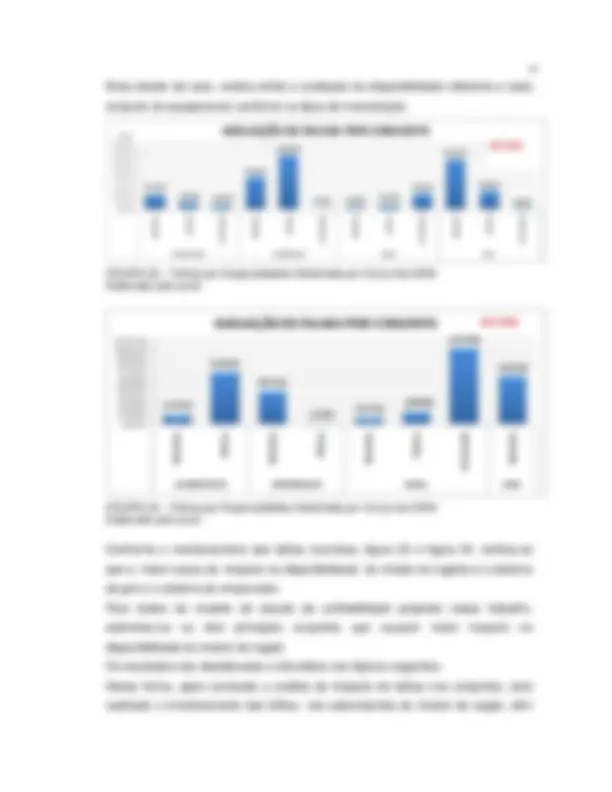
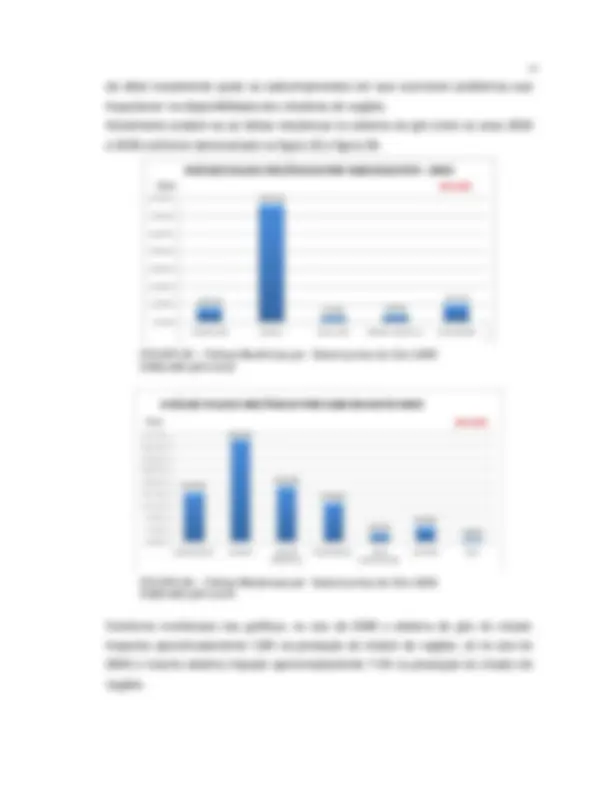
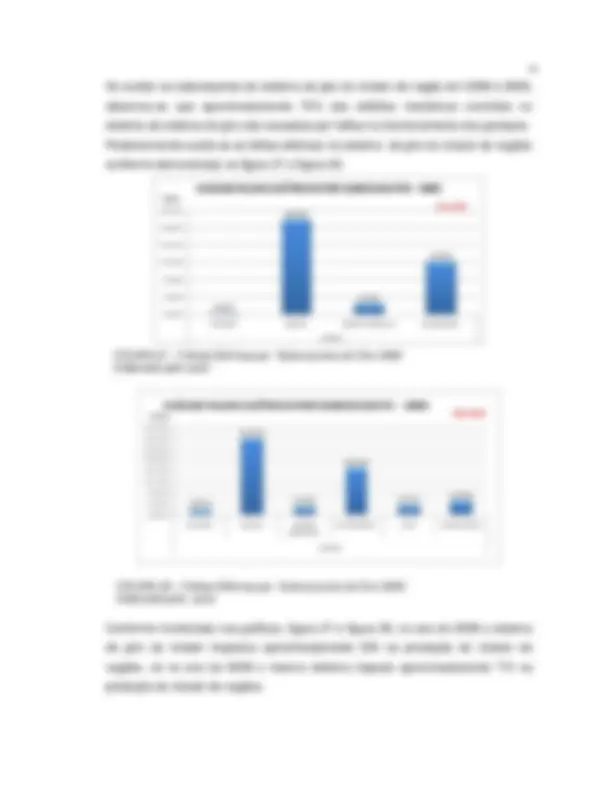
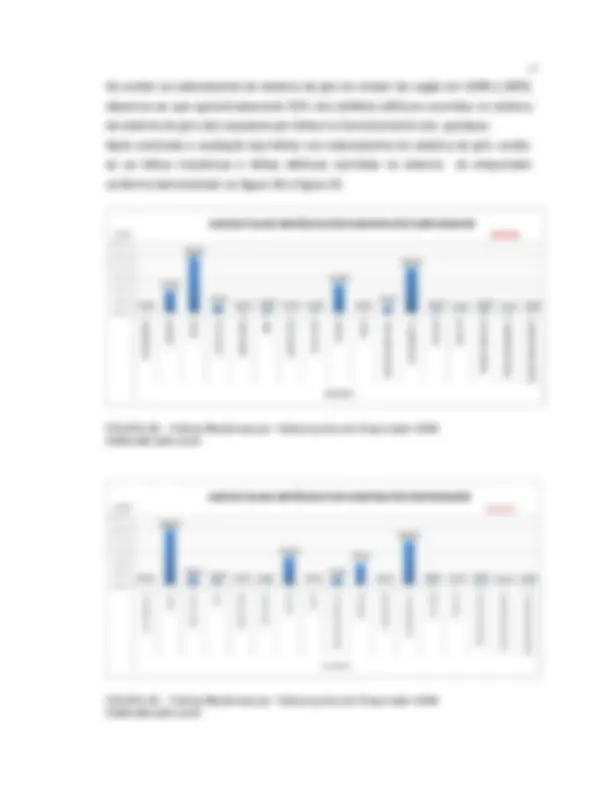
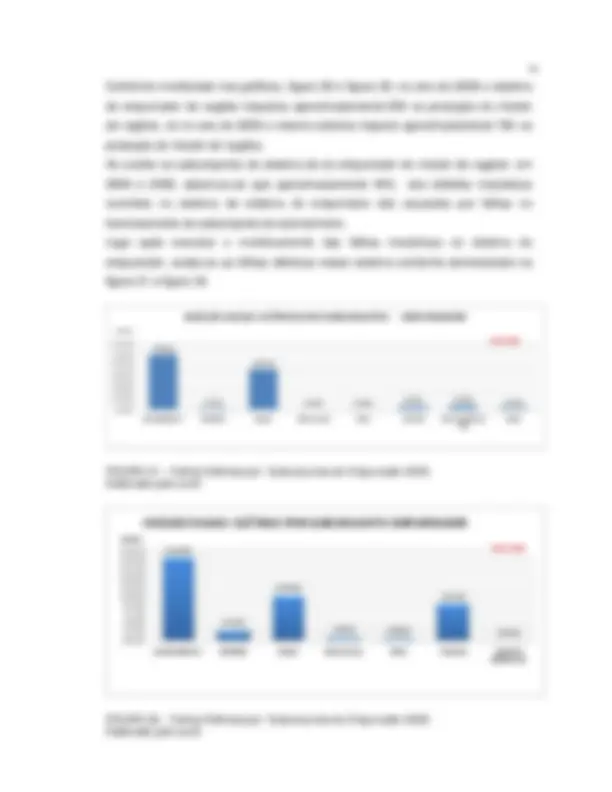
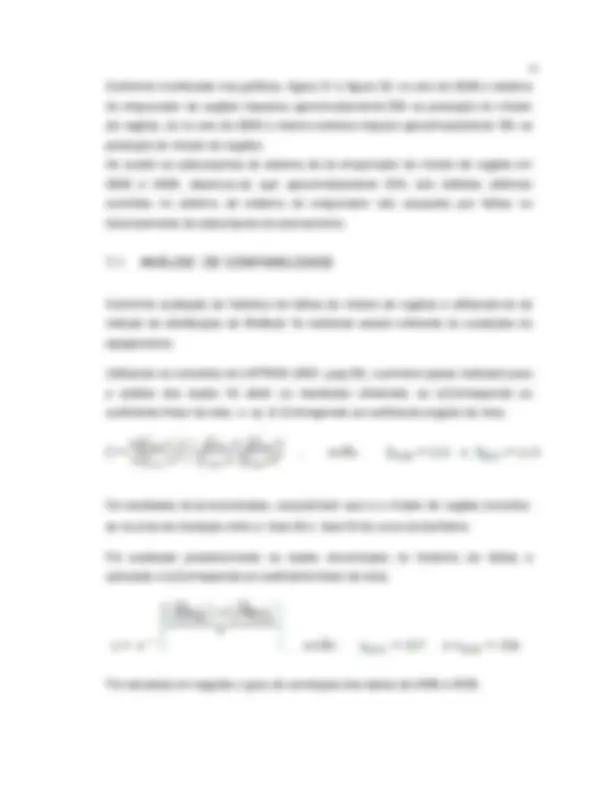
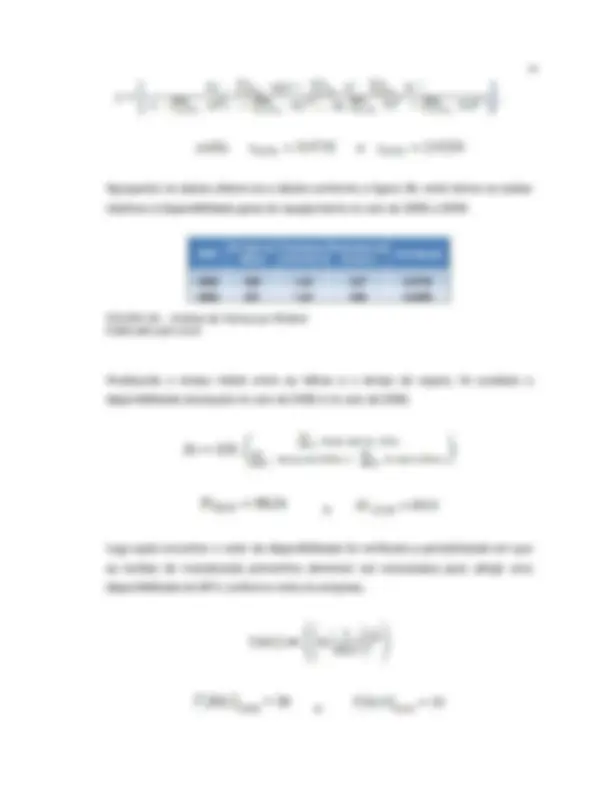
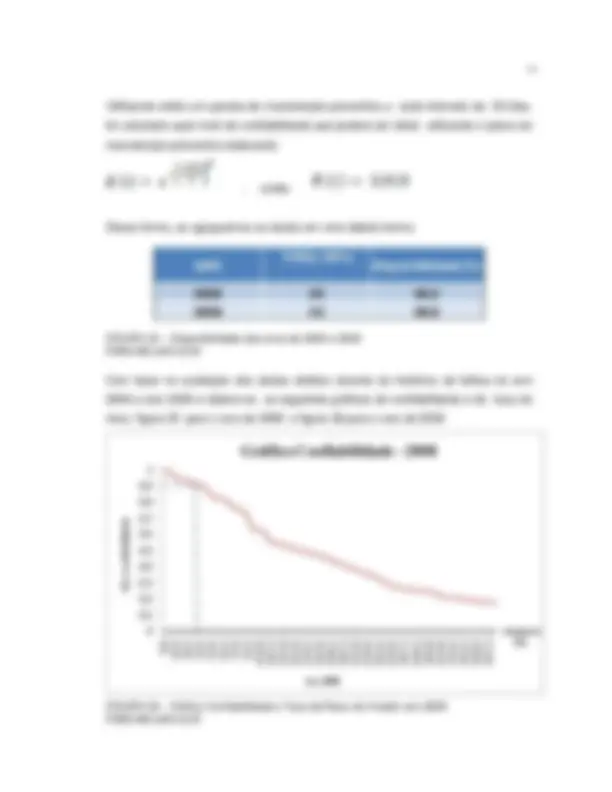
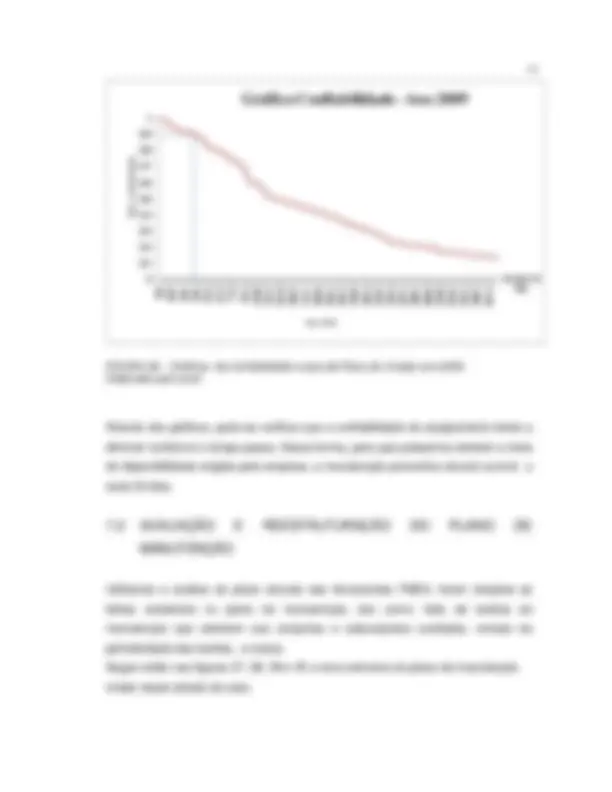
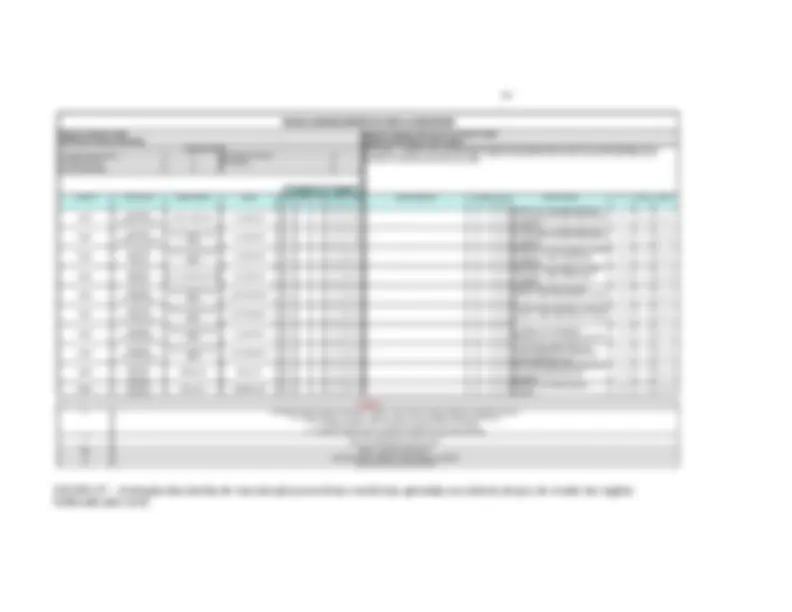
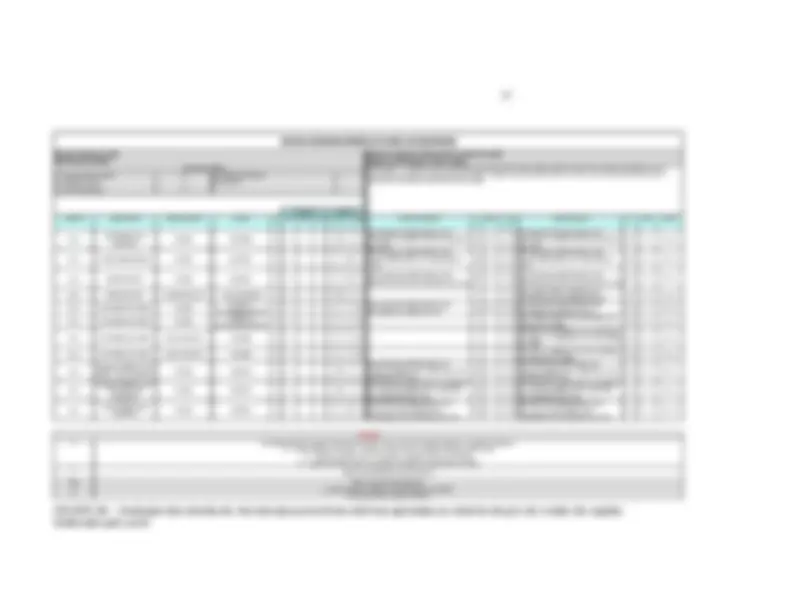
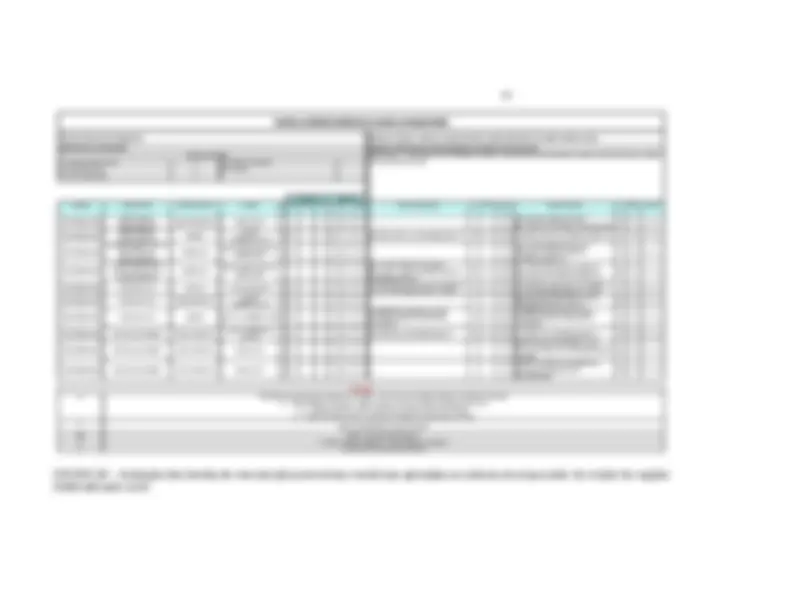
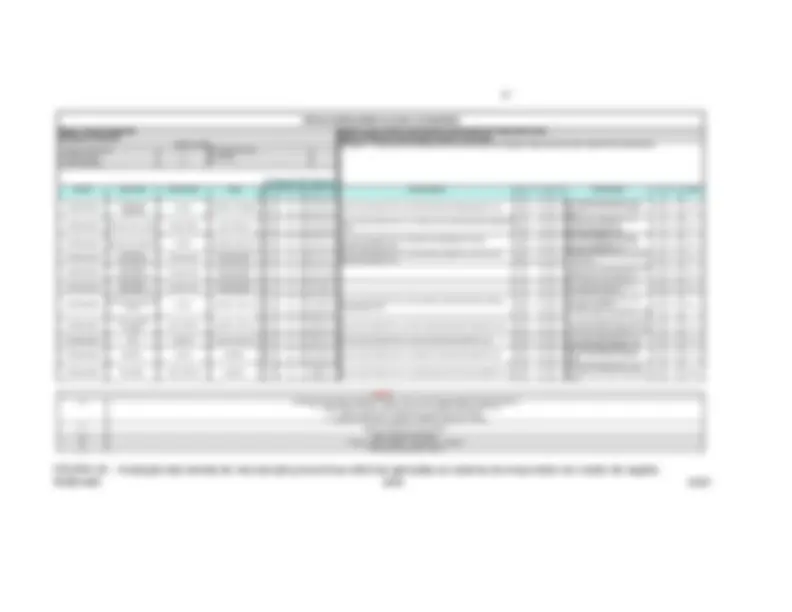
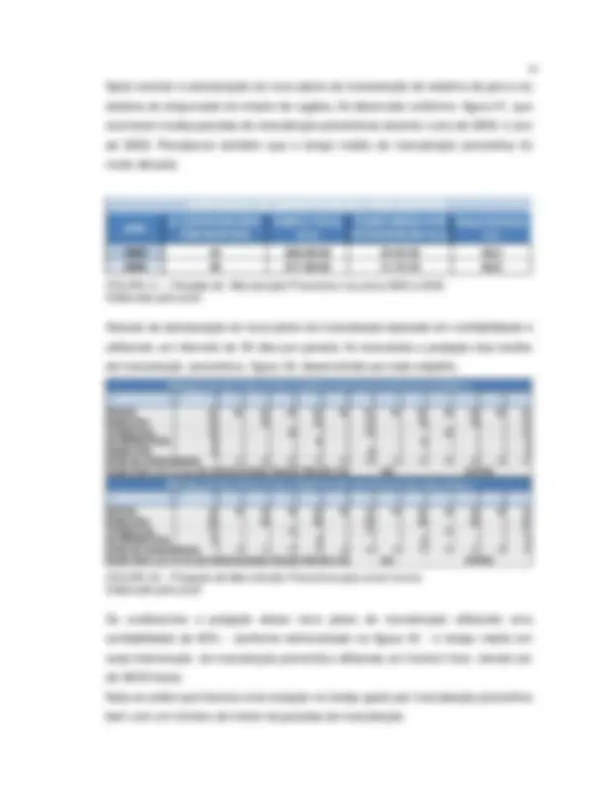
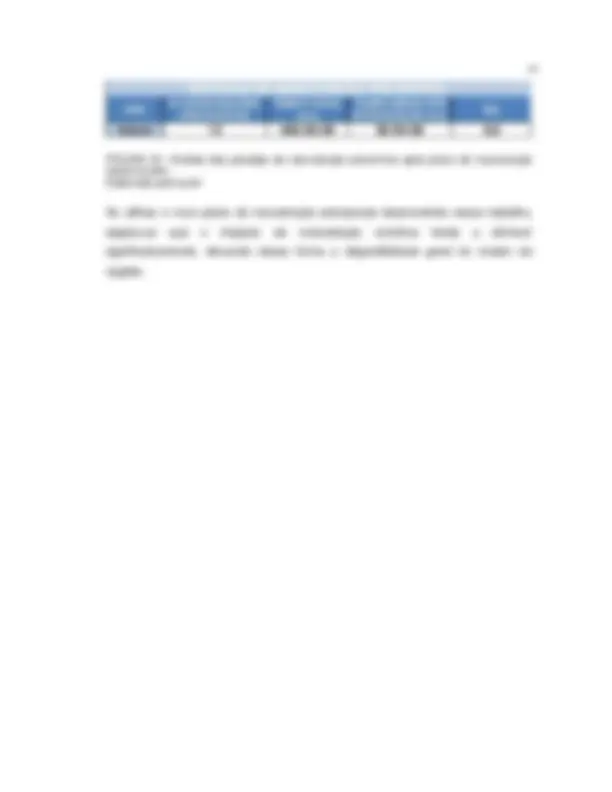
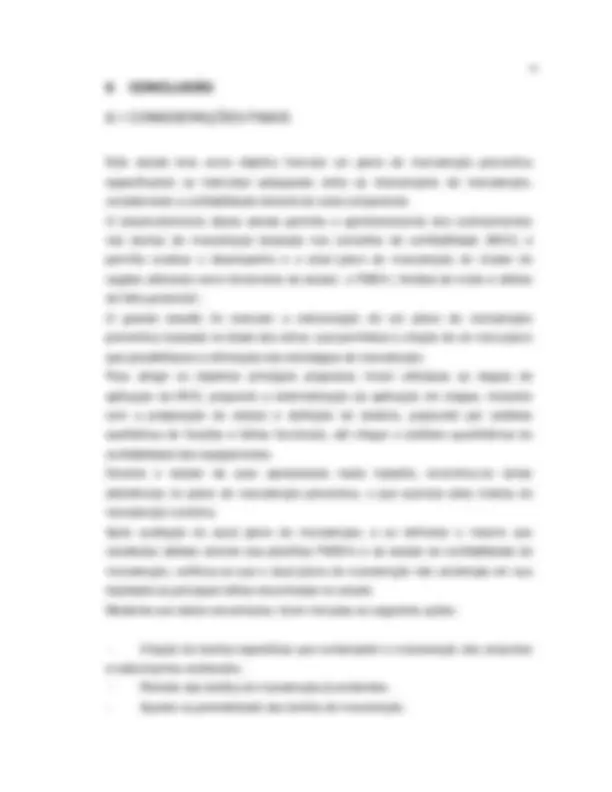
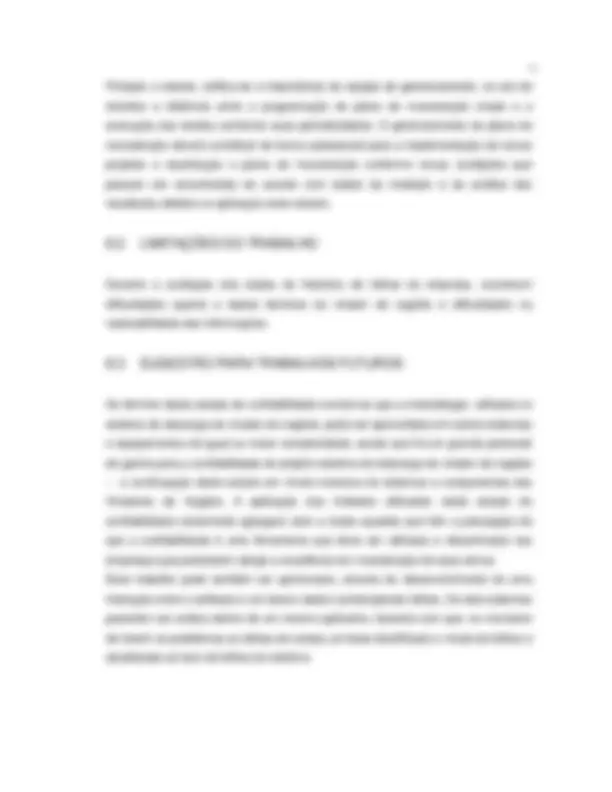
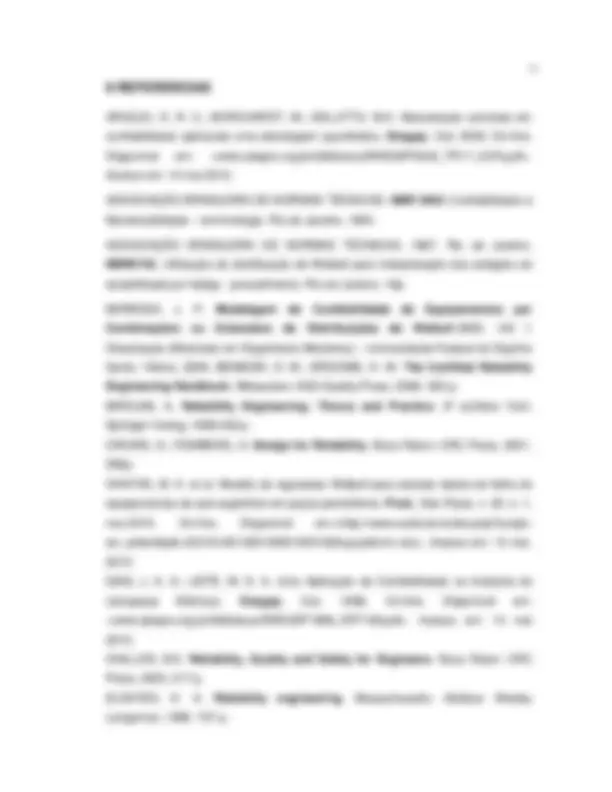
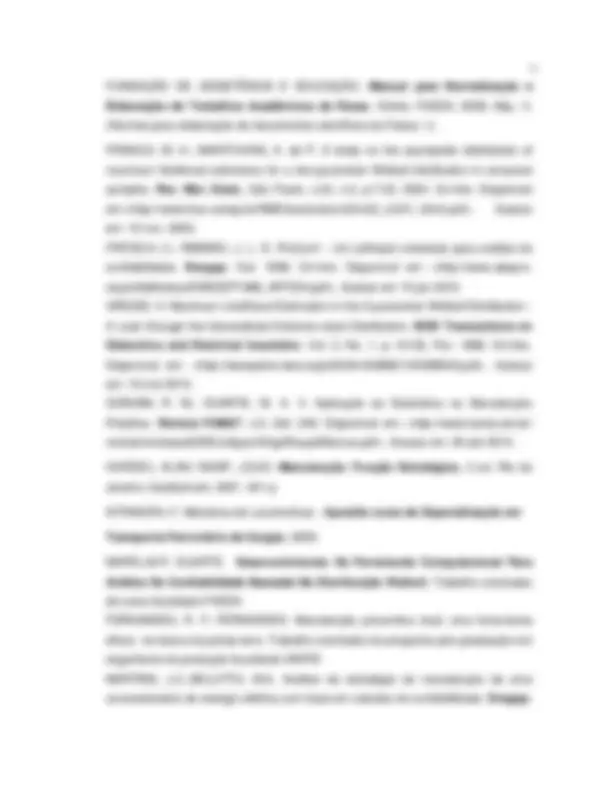
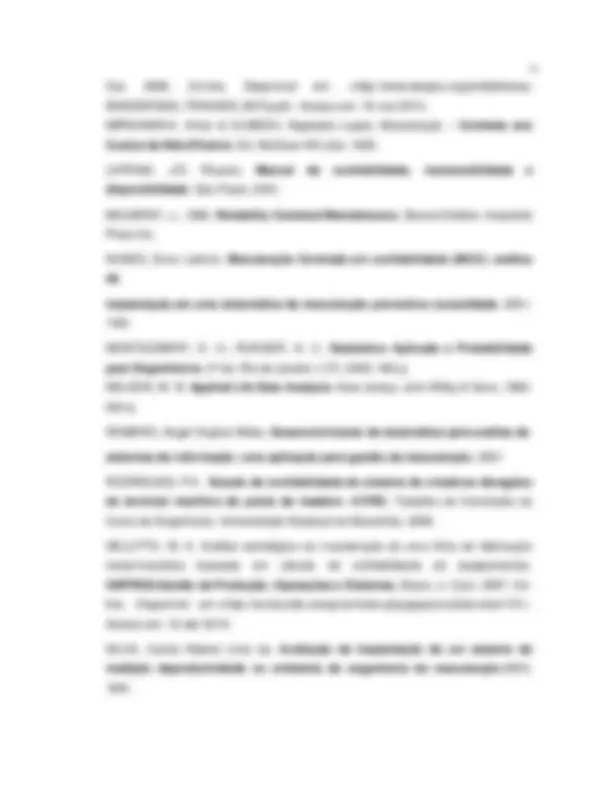
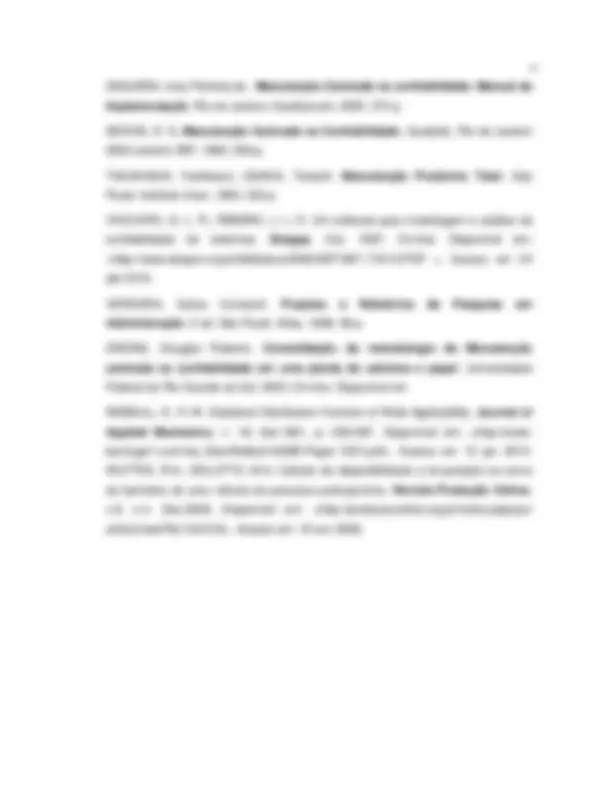
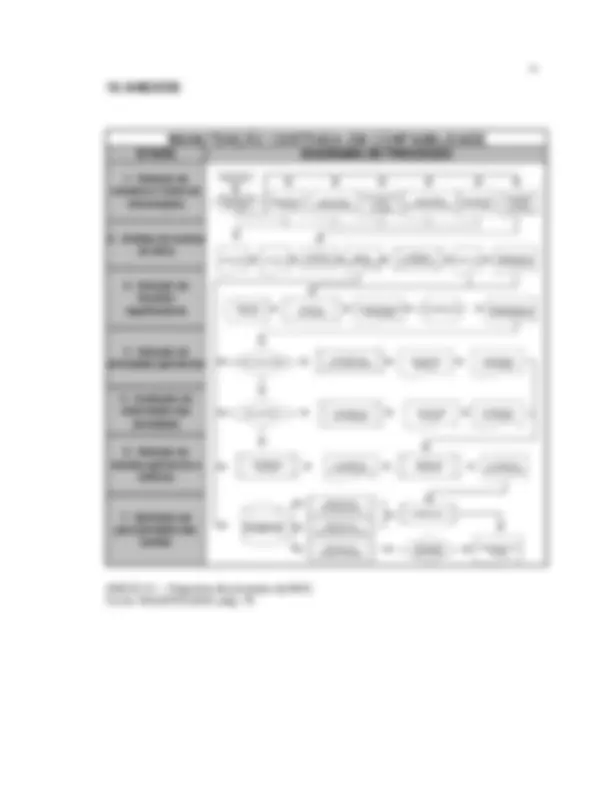
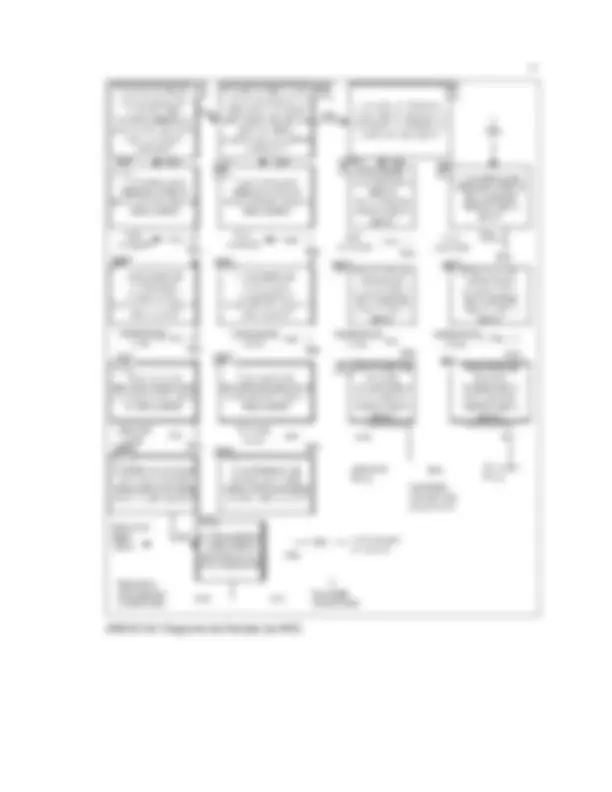
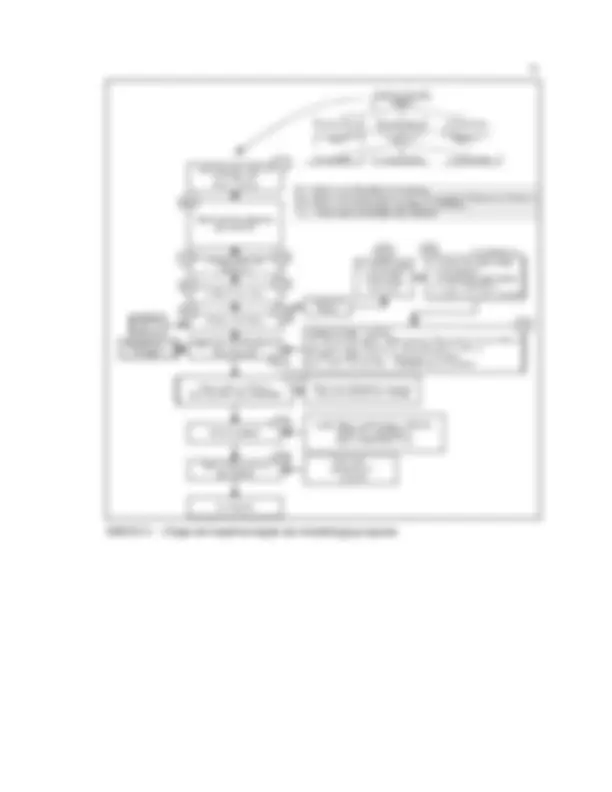
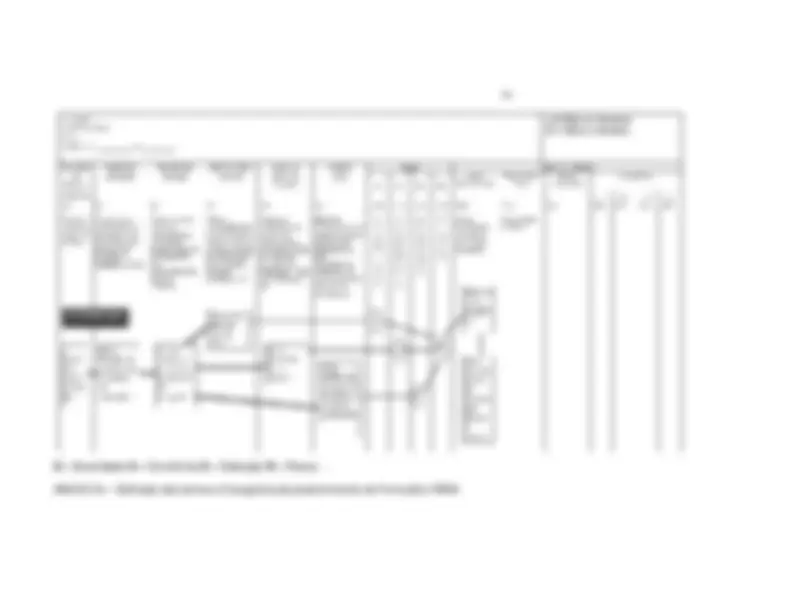
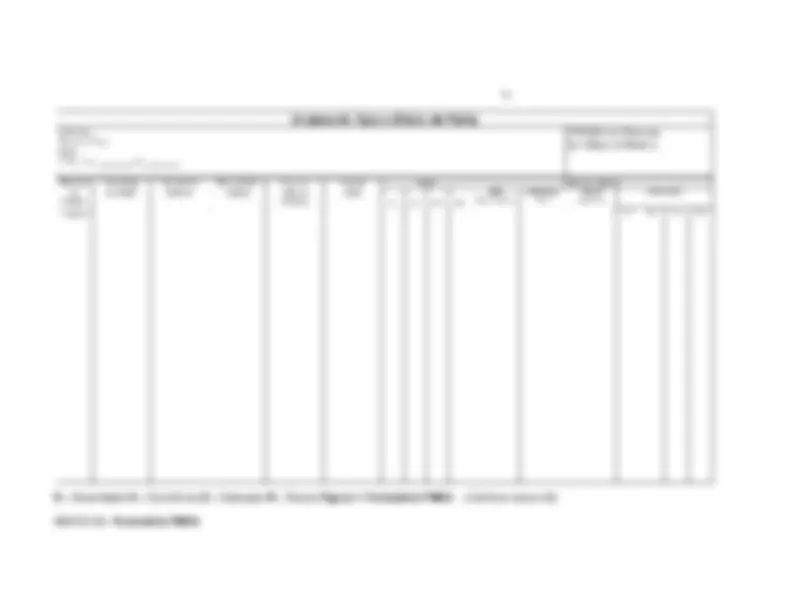
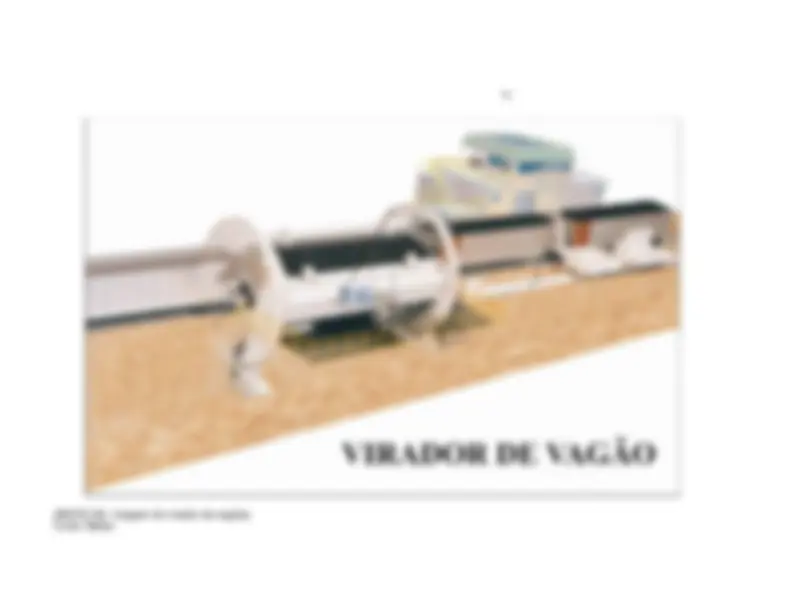
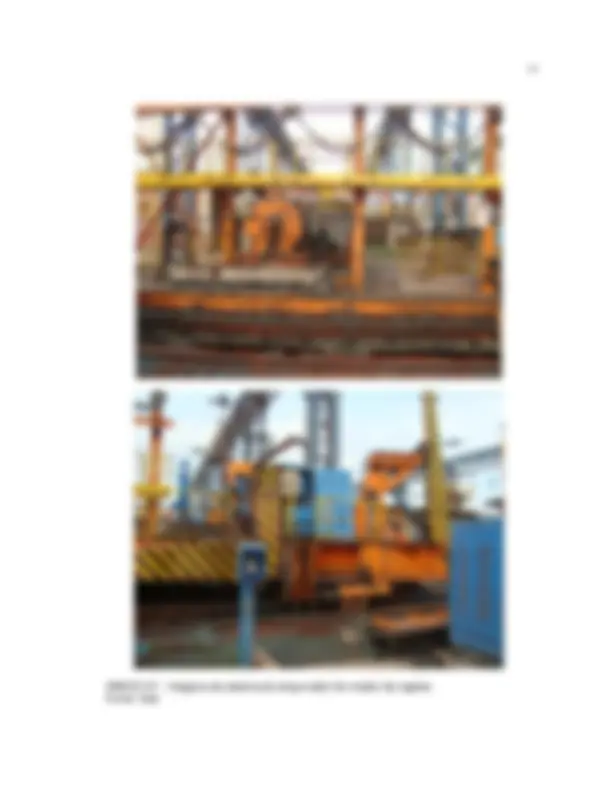
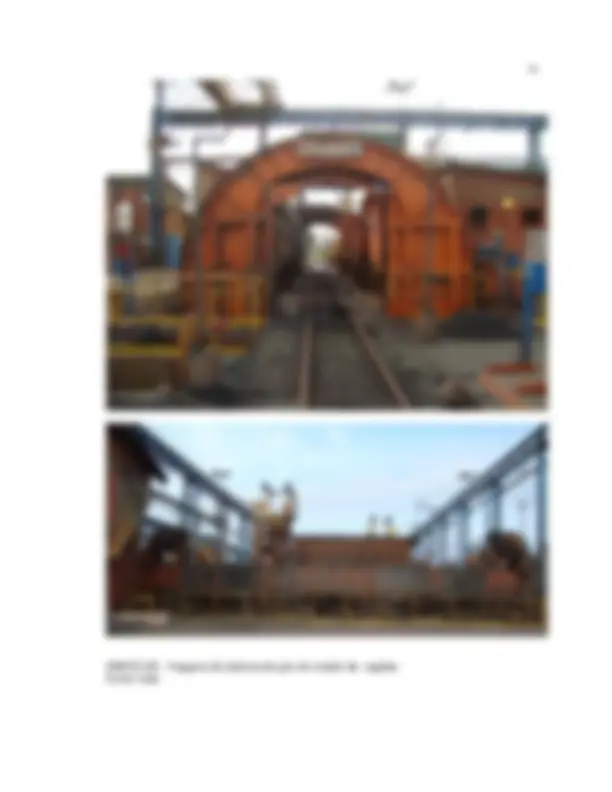

Estude fácil! Tem muito documento disponível na Docsity
Ganhe pontos ajudando outros esrudantes ou compre um plano Premium
Prepare-se para as provas
Estude fácil! Tem muito documento disponível na Docsity
Prepare-se para as provas com trabalhos de outros alunos como você, aqui na Docsity
Os melhores documentos à venda: Trabalhos de alunos formados
Prepare-se com as videoaulas e exercícios resolvidos criados a partir da grade da sua Universidade
Responda perguntas de provas passadas e avalie sua preparação.
Ganhe pontos para baixar
Ganhe pontos ajudando outros esrudantes ou compre um plano Premium
Comunidade
Peça ajuda à comunidade e tire suas dúvidas relacionadas ao estudo
Descubra as melhores universidades em seu país de acordo com os usuários da Docsity
Guias grátis
Baixe gratuitamente nossos guias de estudo, métodos para diminuir a ansiedade, dicas de TCC preparadas pelos professores da Docsity
Manutenção Centrada na Confiabilidade
Tipologia: Notas de estudo
1 / 77
Esta página não é visível na pré-visualização
Não perca as partes importantes!
O principal desafio de qualquer empresa, nos dias atuais, é otimizar o desempenho da planta produtiva, controlar e reduzir os custos de produção, aumentar ou pelo menos manter a lucratividade. Nesse sentido a atividade de manutenção passa a ter como objetivo fundamental, a garantia de patamares, cada vez mais altos, da disponibilidade do sistema produtivo. Sem essa visão, os resultados da atividade de manutenção ficam restritos ao desempenho de cada ação, perdendo a visão global. A manutenção tornou-se o diferencial de sobrevivência para algumas empresas no atual mercado competitivo. Muitas vezes tratado como um processo coadjuvante, o Processo de Manutenção dentro de uma empresa tem um relevante papel que influi em vários aspectos tais como: a segurança, a saúde, o meio ambiente, a produtividade, a lucratividade, a qualidade final do produto, entre outros aspectos. Para aprimorar a Manutenção com a conseqüente melhoria da disponibilidade das plantas com um custo cada vez mais reduzido, níveis de segurança cada vez mais aprimorados e atendimento as demandas de saúde ocupacional e meio ambiente, o mundo da manutenção vem desenvolvendo estratégias de gerenciamento e controle, uma das quais trata da aplicação de princípios de Confiabilidade para os seus sistemas, equipamentos ou componentes. O próprio processo da Manutenção, com suas atividades, etapas, prerrogativas, filosofias, estratégias, e demais nuances, é um processo no qual pode-se aplicar as ferramentas da Confiabilidade, identificando seus modos de falhas e aplicando as ações preventivas cabíveis. Com base neste cenário apresentado, a empresa do setor de mineração e logística localizada no porto de minérios de Vitória-ES, tem o interesse em elaborar um plano de Manutenção Centrada na Confiabilidade que poderá ser utilizada na melhoria no sistema de gestão de ativos industriais permitindo assim aumento na disponibilidade dos viradores de vagões.
O plano de manutenção servirá como guia para o planejamento de testes mais eficientes, economia nos custos e tempo de desenvolvimento, além de fornecer uma referência rápida para resolução de problemas e redução nas mudanças de engenharia – como um subdimensionamento de um componente do equipamento. Dessa forma há captura e manutenção do conhecimento do produto e de seu
processo na organização, reduzindo eventos não previstos, dando a possibilidade de identificação de problemas na segurança.
Os objetivos deste trabalho são:
a) apresentar os conceitos, métodos e tarefas de manutenção, com ênfase no MCC; b) desenvolver e avaliar os resultados da utilização preceitos da Manutenção Centrada na Confiabilidade para otimizar as estratégias de manutenção dos viradores de vagões c) apresentar os conceitos, métodos e tarefas de manutenção, para implementação do MCC;
Para o desenvolvimento do trabalho pesquisou-se amplamente referências sobre distribuições de probabilidade aplicadas a análise de confiabilidade, censura de dados, método de estimação de parâmetros, bem como, artigos, dissertações e teses relacionadas. Este trabalho está estruturado em nove capítulos, sendo o primeiro relativo à introdução e os próximos capítulos, de 1 a 5, dedicados ao referencial teórico onde se encontra a fundamentação teórica necessária para a discussão do tema em estudo. A análise e estudo de caso é explorada no capitulo 6 e 7, onde é apresentado o resultado da avaliação dos dados e proposto novo plano de manutenção. No capítulo 8 encontra-se a conclusão geral do trabalho e a limitações do trabalho.
disponibilidade e confiabilidade de um item físico, de modo que as funções do sistema sejam mantidas no desempenho mínimo esperado, observando a segurança humana e a integridade ambiental.
Segundo Siqueira (2005, p.18), a evolução histórica da manutenção pode ser dividida aproximadamente em 03 (três) gerações distintas: A Primeira Geração estende-se aproximadamente de 1940 a 1950. Esta geração caracteriza-se pela utilização de equipamentos simples e sobredimensionados para as funções requeridas. Dessa forma, estes equipamentos eram restaurados apenas quando apresentavam defeitos. Devido ao seu sobredimensionamento os defeitos eram minimizados visto que pouco se dependia de seu desempenho. Os produtos não tinham controle de qualidade e a manutenção era “quebra e depois conserta”, caracterizando-se pela ausência de técnicas de diagnóstico e de prevenção da falha. Nesse panorama, não havia necessidade de manutenção sistematizada (NUNES, 2001, p. 34). Com o final da II Guerra Mundial, o nível de exigência por produtos passou a ser maior. A guerra fria incentivava a indústria bélica á produção de armas além do aumento acelerado dos diversos ramos da indústria. As indústrias passaram a depender cada vez mais das máquinas, que se multiplicaram e modificaram em tipo, quantidade e complexidade. Nesse período registra-se uma onda de escassez de mão-de-obra especializada, decorrente do rápido processo de automação, gerando custos crescentes de correção das falhas. Uma maior disponibilidade e vida útil dos ativos industriais, a um baixo custo, tornaram-se o objetivo básico de avaliação no ambiente industrial (NUNES, 2001, p.37). A partir deste cenário, surgiu um grande esforço científico de pesquisa e desenvolvimento de técnicas de manutenção preventiva, com foco na minimização dos impactos das falhas no processo produtivo, que caracterizou a segunda geração. Por volta da década de 70 houve o surgimento da Manutenção Produtiva Total (TPM – Total Productive Maintenance), dando origem ao surgimento da Terceira geração.
Nunes (2001, p. 40), descreve que na terceira geração a fase de novas técnicas de manutenção eram suportadas por computadores de grande porte e que sistemas de planejamento e controle surgiram nesse período visando um melhor controle das ações de manutenção. Neste sentido, a Terceira Geração evoluiu da incapacidade das técnicas até então utilizadas na Segunda Geração ante as exigências do processo de automação cada vez maior nas industriais tornando estreitas suas faixas operacionais aumentando assim a importância da manutenção. Com o objetivo então de predizer as falhas, foi criada a manutenção preditiva que utiliza de técnicas que possam monitorar os equipamentos, seja da forma sensitiva ou através de instrumentos de medição. Contudo, Arcuri Filho (2005, p.27), avaliando as três gerações, propõe uma metodologia chamada de “medicina de sistemas”, onde parte do pressuposto que as três gerações, descritas por Moubray, são evoluções da manutenção e que após as mesmas, existe uma quarta geração (Figura 01 e Figura 02) por ele aceita como “manutenção estratégica centrada no negócio”. Dentre as principais expectativas quanto ao desempenho da função pode-se destacar a engenharia de manutenção.
FIGURA 1 – Síntese da Aplicação das Metodologias de Manutenção Fonte: LAFRAIA (2001, Pág. 38)
Segundo Kardec (2002, p. 81), a missão da manutenção nos dias atuais se resume em “garantir a disponibilidade da função dos equipamentos e instalações de modo a atender a um processo produtivo ou de serviços, com confiabilidade, segurança, preservação do meio ambiente e custos adequados". Segundo a NBR 5462:1994, disponibilidade é a capacidade de um item estar em condições de executar uma certa função em um dado instante ou durante um intervalo de tempo determinado, levando-se em conta os aspectos combinados de sua confiabilidade, mantenabilidade e suporte de manutenção, supondo que os recursos externos requeridos estejam assegurados (ABNT,1994). A mantenabilidade é um parâmetro de projeto. A manutenção é uma conseqüência do projeto. A mantenabilidade é uma característica inerente ao projeto de um sistema ou de um produto. Então, atributos como precisão, segurança e economia relativa às ações de manutenção, devem estar contidos em cada item (componente, subsistema ou sistema) e em todas as fases do projeto. Isso significa que o produto deve ser projetado na perspectiva de que cada item que o constitui, quando do processo de perda da funcionalidade ou mesmo após a falha da função, seja recuperado para a condição de “tão bom quanto novo”, qualquer que seja a ação de manutenção executada: corretiva, preventiva ou preditiva (ABNT,1994). A contribuição da manutenção dentro de um sistema produtivo, segundo Kardec e Nascif (1998, p. 103), pode ser resumida como a maior disponibilidade confiável da planta industrial ao menor custo, isto é, quanto maior esta disponibilidade menor a demanda de serviços e, conseqüentemente, redução de custos, favorecendo o crescimento da produtividade da função manutenção. Essas ações de manutenção têm algumas variantes, e tem evoluído no tempo. A adoção do projeto para a mantenabilidade do produto, melhora os procedimentos, o acesso aos itens, a detecção das falhas, a instrumentação associada, os materiais, as ferramentas, o treinamento da mão de obra e os procedimentos para executar a manutenção (BLANCHARD,1995, p. 65). A exigência de disponibilidade proporcionou à manutenção, um destaque em relação ao grau de importância para o projeto do produto e para a gestão do processo
produtivo. A política de manutenção imprimida ao produto ou ao processo, passou a era considerada como uma vantagem competitiva.
A manutenção preventiva total (TPM- Total Productive Maintenance) foi desenvolvida no Japão visando à eficiência do sistema de manutenção, tornando - se ao longo dos anos um completo sistema de gestão empresarial. A TPM consiste em um procedimento de administração da manutenção que teve início por volta dos anos 50 e apresentou resultados expressivos na economia Japonesa na década de
itens de estoque de reposição pode reduzir em muito o tempo em que à produção fica interrompida, levando sempre em conta o objetivo da otimização dos estoques;
Manutenção Centrada na Confiabilidade (RCM – Reliability Centred Maintenance) é a aplicação de um método estruturado para estabelecer a melhor estratégia de manutenção para um dado sistema ou equipamento. Esta começa identificando a funcionalidade ou desempenho requerido pelo equipamento no seu contexto operacional, identifica os modos de falha e as causas prováveis e então detalha os efeitos e conseqüências da falha. Isto permite avaliar a criticidade das falhas e onde podemos identificar conseqüências significantes que afetam a segurança, a disponibilidade ou custo. A metodologia permite selecionar as tarefas adequadas de manutenção direcionadas para os modos de falha identificados. Segundo Siqueira (2005, pág. 71), a MCC configura-se como uma das mais importantes tecnologias contemporâneas de manutenção; sua aplicação foi expandida para vários ramos de atividade humana, onde haja necessidade de manter o funcionamento de ativos físicos e processos. A técnica nasceu na indústria aeronáutica americana, sendo também adotada pelas indústrias nuclear e elétricas mundiais e em outros setores da economia, como o de serviços. As estratégias de manutenção em vez de serem aplicadas independentemente são integradas para tirarmos vantagens de seus pontos fortes de modo a otimizar a operacionalidade e eficiência da instalação e dos equipamentos, enquanto minimizamos o custo do ciclo de vida.
PREVENTIVA
PREDITIVA
PRÓ-ATIVA
MCC –Manutenção centrada em confiabilidade
FIGURA 3 – Componentes de um Programa de MCC Fonte: Nascif (2001, p. 36).
Segundo Siqueira (2005), a origem da MCC provém da necessidade de certificação da linha de aeronaves Boeing 747, pela Federal Aviaton Authority (FAA), nos Estados Unidos. O Boeing 747 foi um marco em níveis de automação para a aviação comercial, com a triplicação do número de assentos em relação à maior aeronave existente na época. A metodologia tradicional de manutenção seria inviável para máquinas com tamanha complexidade, as companhias aéreas não seriam capazes de operar economicamente as aeronaves. Sendo assim, era necessário reduzir a probabilidade de ocorrência de uma falha significativa. Isto motivou a criação de uma Força-Tarefa na United Airlines, em 1968, conhecida pela sigla de MSG- (Maintenance Steering Group), encarregada de rever a aplicabilidade dos métodos existentes a estas aeronaves. O relatório desta comissão introduziu os conceitos de manutenção centrada em confiabilidade (RCM - Reliability-Centered Maintenence), atendendo a solicitação do Departamento de Defesa americano.
CARACTERÍSTICAS MANUTENÇÃO TRADICIONAL MCC Foco Equipamento Função Objetivo Manter o equipamento Preservar a função Atuação Componente Sistema Atividades O que pode ser feito O que deve ser feito Dados Pouca ênfase Muita ênfase Documentação Reduzida Obrigatória e Sistemática Metodologia Empírica Estruturada Combate Deterioração do Equipamento Conseqüências das falhas Normalização Não Sim Priorização Inexistente Por função FIGURA 4 – Comparação da Manutenção Tradicional com a MCC Fonte: SIQUEIRA,2005, p.
Segundo Siqueira (2005, p. 128), a MCC adota uma metodologia composta de sete etapas para implantação da MCC, que são:
a) Seleção do Sistema e Coleta de Informações; b) Análise de Modos de Falha e Efeitos; c) Seleção de Funções Significantes; d) Seleção de Atividades Aplicáveis; e) Avaliação da Efetividade das Atividades. f) Seleção das atividades Aplicáveis e Efetivas. g) Definição da Periodicidade das Atividades. Em cada etapa são utilizadas ferramentas de modelagem ou análise de sistemas destinadas a responder e, principalmente, documentar os critérios e respostas a cada questão da MCC. Estas etapas são detalhadas no Diagrama de Processo do Anexo 01, indicando os produtos e relacionamentos entre os diversos processos de análise.
Segundo Rausand (1998, pág. 85), dois aspectos devem ser considerados para seleção do sistema, são eles: a) quais sistemas são mais prováveis de se beneficiar do processo de MCC, se comparando com a manutenção tradicional; b) qual nível será analisado: planta industrial, sistema, itens físicos ou componentes. Segundo Smith (1993, pág. 108), a seleção do sistema deve-se basear os seguintes critérios: sistema com elevado número de tarefas de manutenção preventiva ou elevados custos de manutenção preventiva; sistemas que sofreram um grande número de intervenções corretivas nos últimos anos; sistemas com elevada contribuição nas paradas de produção nos últimos anos; sistemas que apresentam risco de segurança humana e ambiental.
Segundo Smith (1993, pág. 112), os principais objetivos desta etapa são: a) identificação das interfaces de entrada e saída do sistema; b) identificação e descrição das funções do sistema; c) descrição dos padrões de desempenho; d) definição de como o sistema pode falhar. Para a melhor realização desta etapa, Smith (1993, pág. 113) sugere a elaboração do diagrama de blocos do sistema. Esse diagrama permite subdividir o sistema em partes menores para facilitar a análise nas etapas seguintes do processo. Os diagramas de blocos ilustram a operação, inter-relações e interdependência das unidades funcionais do sistema. São diagramas construídos para gerar conhecimentos para a definição das funções dos diversos níveis do sistema. Segundo Zaions (2003, pág.95), existem dois tipos de diagrama de blocos: diagramas de blocos funcionais e diagramas de blocos de confiabilidade. No entanto, a literatura associada ao MCC indica com mais freqüência a utilização do diagrama de blocos funcionais. O diagrama de blocos funcionais do sistema permite, além de identificar as referidas funções do sistema, interligar as entradas e saídas com suas respectivas funções.
Segundo Rausand (1998, pág. 88), o objetivo desta etapa é identificar os itens físicos que são potencialmente críticos com relação às falhas funcionais identificadas na etapa anterior. Segundo Smith (1993, pág.125), a separação em itens físicos críticos não deve ser feita, pois pode excluir alguns itens físicos importantes do foco de atenção. Barnard (1998, pág. 80) afirma que a seleção de itens críticos é importante para direcionar a análise a itens que trarão um retorno financeiro significativo. Nas etapas de implementação definidas por Moubray (2000, pág. 60), não consta a etapa de seleção dos itens críticos. O autor, porém, cita, na etapa de preparação, que um dos elementos chave do processo de planejamento é decidir quais os ativos são mais prováveis de se beneficiar do processo de MCC, havendo assim uma forma de seleção de itens críticos. Segundo Castro (2003, pág.72), os equipamentos críticos devem ser escolhidos considerando a sua relevância no processo, seu grau de redundância e impacto nos custos de manutenção, além da experiência dos especialistas. Westbrook (2001, pág. 145) cita que a Boeing selecionou os sistemas com maior potencial de melhoria nas práticas de manutenção e utilizou a regra do 80-20, onde 80% das perdas da produção e custos de manutenção são gerados por 20% dos sistemas. A regra 80-20 também é conhecida como Princípio de Pareto. Este princípio foi desenvolvido por Vilfredo Pareto, economista e sociólogo do século XIX. Pareto notou que 80% dos recursos de um povo pertence a 20% das pessoas. Posteriormente, este princípio foi intensamente utilizado na indústria japonesa através de J.M. Juran. Em linha gerais, esta regra diz que 80% dos problemas se devem a 20% das causas (ISHIKAWA, 1985, pág. 168). Smith (2003, pág.130) sugere a elaboração de uma planilha que correlacione falhas funcionais e itens físicos. A matriz de equipamentos versus falhas funcionais visa relacionar as falhas funcionais com os equipamentos e classificá-los em ordem de criticidade, a fim de estabelecer prioridades para aplicar a metodologia do MCC. Essa conexão entre as falhas funcionais e os itens físicos é avaliada pela opinião dos especialistas que definem a criticidade levando em consideração os seguintes aspectos:
a) Conseqüências na segurança humana; b) Conseqüências na integridade ambiental; c) Conseqüências econômicas e operacionais; d) Dificuldade de realizar a manutenção.
De acordo com Rausand (1998, 95), as informações para a análise do MCC podem ser divididas em três categorias: informações de projeto, informações operacionais e informações de confiabilidade. Em algumas situações, têm-se poucas informações sobre os equipamentos, principalmente quando os equipamentos são novos. Nesses casos, devem-se procurar informações com os fabricantes de máquinas ou através de máquinas similares. O sucesso da implantação do MCC depende muito do volume de informações disponíveis, tanto qualitativamente como quantitativamente. Segundo Wireman (1998, pág.180), para obter sucesso na implantação do MCC, é fundamental dispor de históricos dos tipos de falhas, freqüência das falhas e as causas básicas das falhas, para que a implantação não seja baseada em suposições.
Esta etapa visa identificar os modos de falha que são provavelmente a causa de cada falha funcional e apurar os efeitos da falha associados a cada modo de falha. Isto é feito realizando as análises de modos e efeitos de falha (MOUBRAY, 2000, pág. 87). Segundo Zaions (2003, pág.105), há no mínimo três fontes de informações às quais o analista poderá recorrer para determinar os modos de falha de um item físico: a) histórico dos equipamentos; b) experiência das pessoas envolvidas com o equipamento; c) a FMEA de projeto ou literatura especializada que contenha informações sobre os modos de falha normalmente associados ao item em estudo.
nova pergunta (SMITH, 1993, pág.138). As perguntas buscam identificar modos de falhas:
As respostas são registradas na Planilha de Decisão, conforme modelo na Figura 7. Tal planilha visa armazenar todas as informações e decisões realizadas durante o processo de seleção de tarefas (MOUBRAY, 2000, pág. 115).
FIGURA 7: Planilha de Decisão do MCC Fonte: Moubray (2000, p. 119)
A Planilha de Decisão está dividida em dezesseis colunas. As colunas F, FF e FM identificam o modo de falha em consideração e são usadas para cruzar referências entre as Planilhas de Análise dos Modos da Falha e Efeitos e de Decisão. As colunas H, S, E e O são usadas para registrar as respostas às questões referentes às conseqüências de cada modo de falhas. A questão H objetiva identificar se a falha é oculta; as demais questões (S, E e O) são referentes, respectivamente, à segurança, meio ambiente e capacidade operacional. As respostas possíveis são negativas ou afirmativas, grafadas com os símbolos “S” e “N”, respectivamente. O intervalo da oitava até a décima coluna da Planilha de Decisão é usado para registrar se uma tarefa pró-ativa foi selecionada. A coluna H1/S1/O1/N1 é usada para registrar se uma tarefa sob-condição pode ser encontrada para antecipar o modo de falha a tempo de evitar as conseqüências. A coluna H2/S2/O2/N2 é usada para registrar se uma tarefa adequada de restauração programada pode ser encontrada para prevenir as falhas. A coluna H3/S3/O3/N3 é usada para registrar se uma tarefa adequada de descarte programado pode ser encontrado para prevenir as falhas. As colunas H4, H5 e S4 são usadas para registrar as respostas às três questões relativas às ações default. As últimas três colunas registram a tarefa selecionada, a freqüência com que é feita e quem foi selecionado para fazê-la. A coluna “tarefa proposta” é também usada para registrar os casos onde o re-projeto é exigido ou onde foi decidido que o modo de falha não necessita de manutenção programada. Após esta identificação, as demais questões têm o objetivo de identificar qual tarefa é a mais adequada para tratar a falha. Para fins didáticos, dividimos a análise ou levantamento dos modos de falhas em 6 (seis) tópicos distintos, a partir dos quais desenvolveremos os sub-tópicos e seus respectivos modos de falhas.