
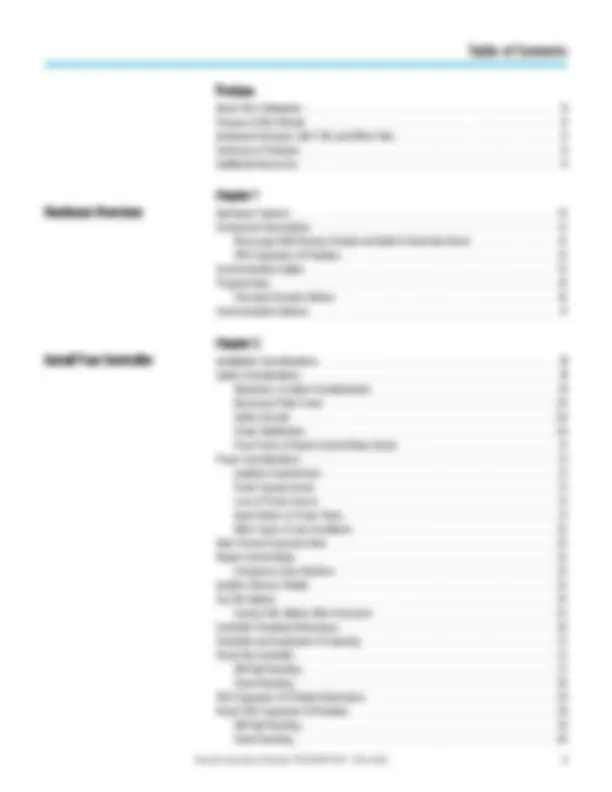
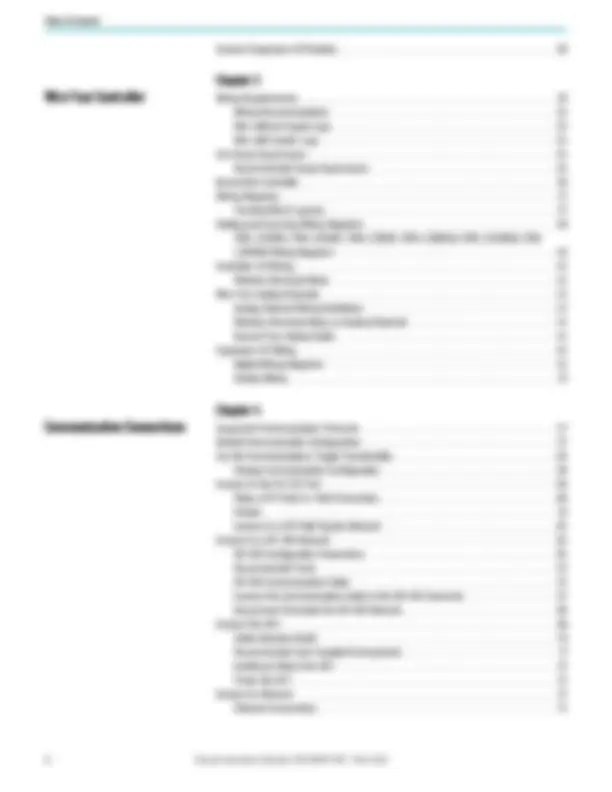
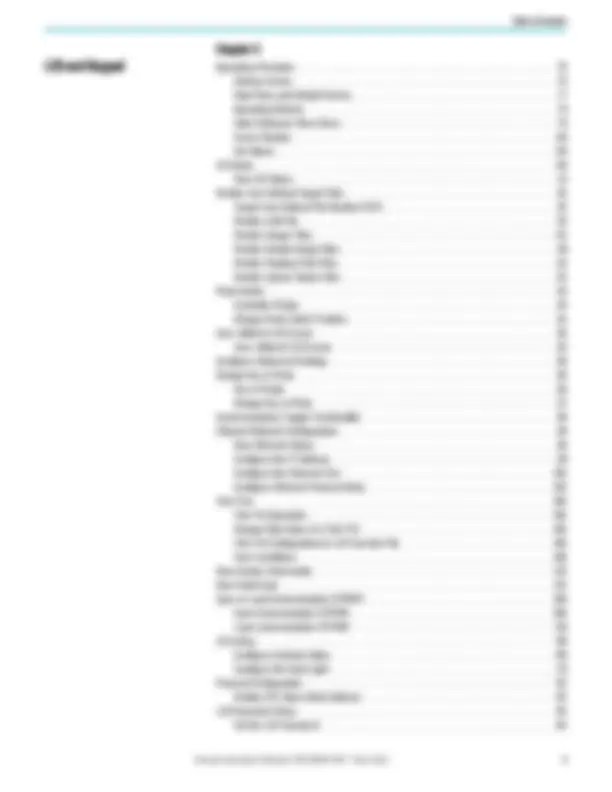
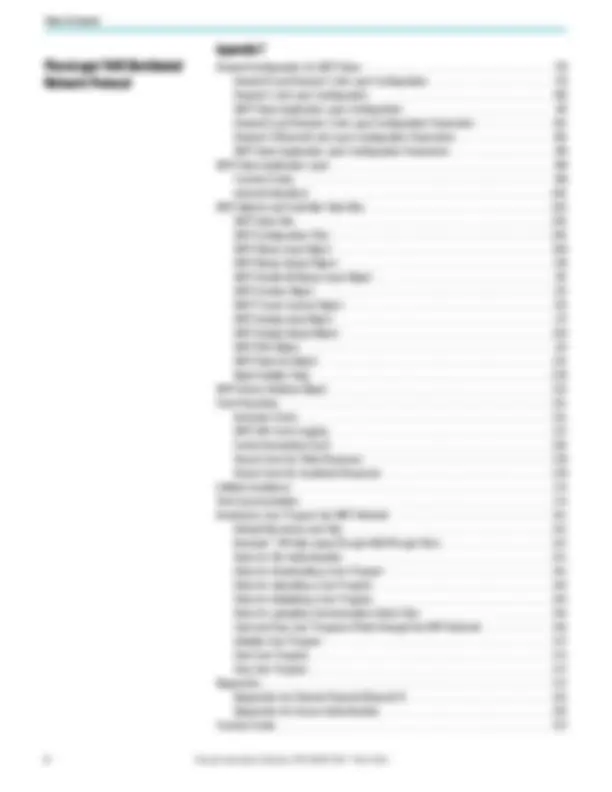
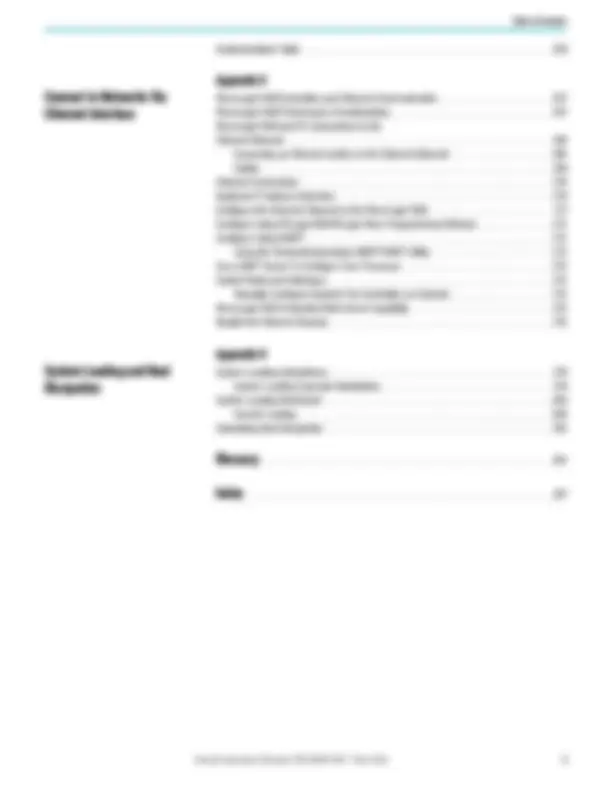
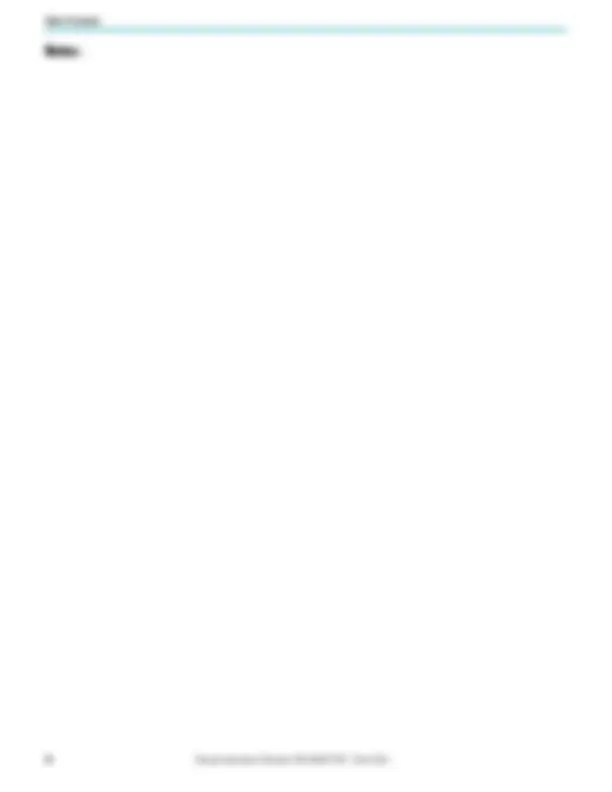
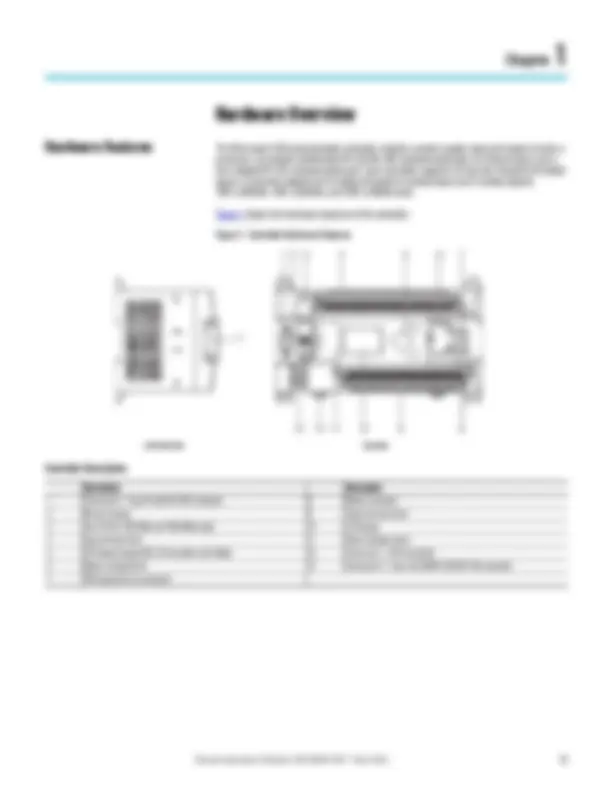
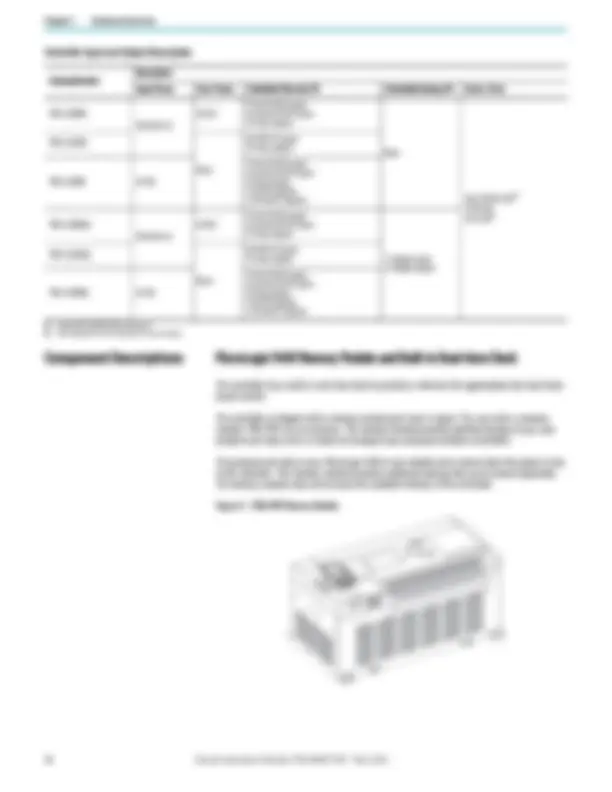
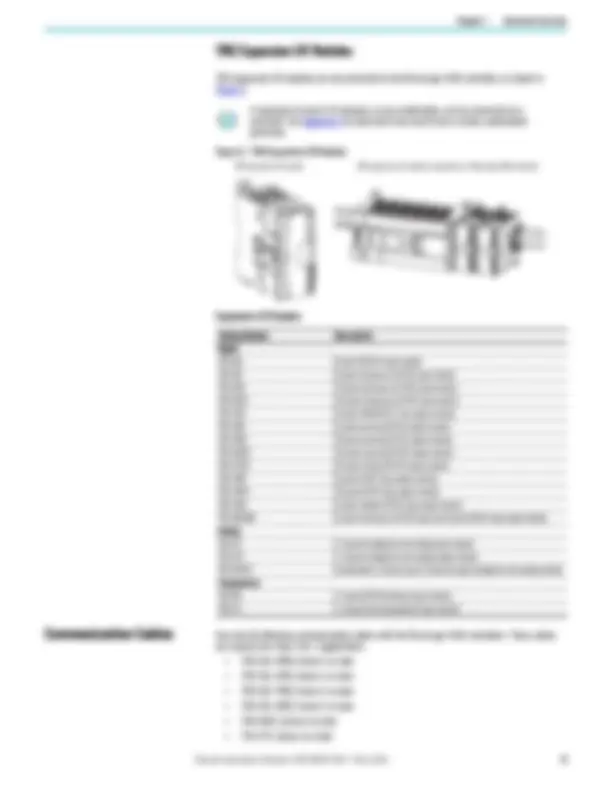
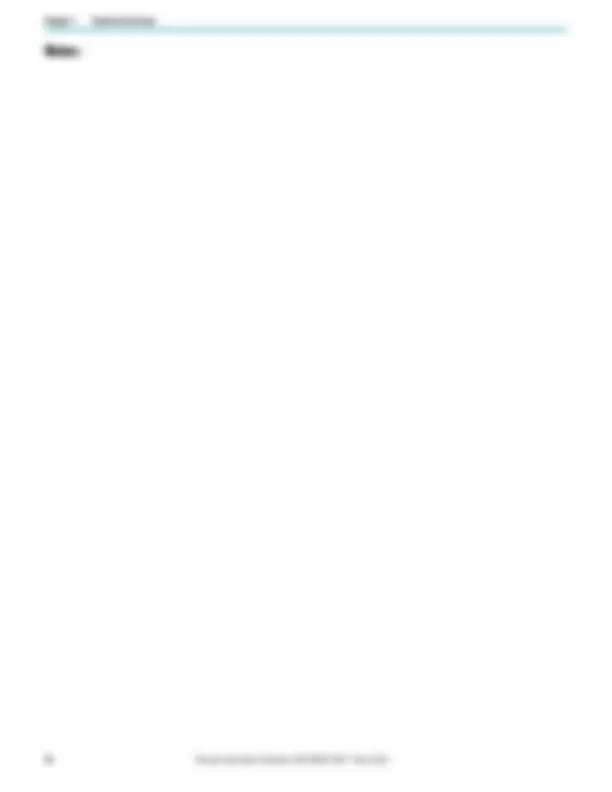
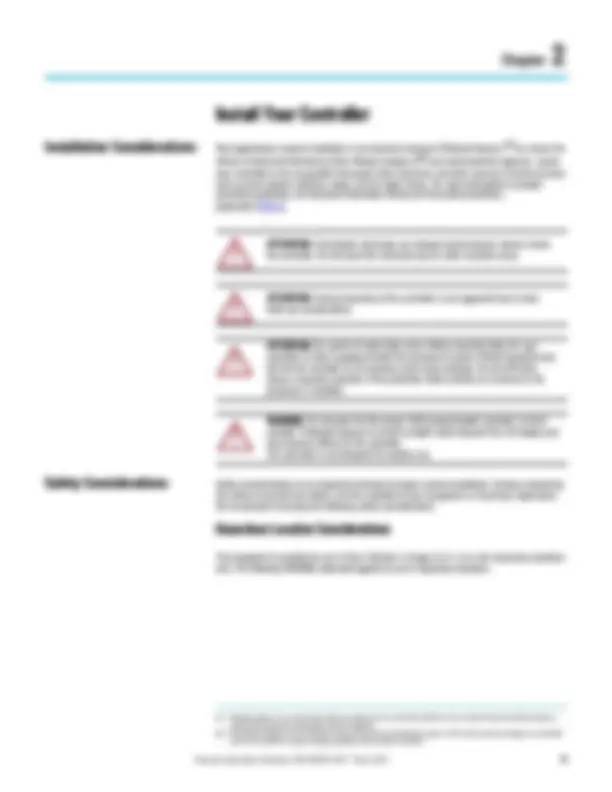


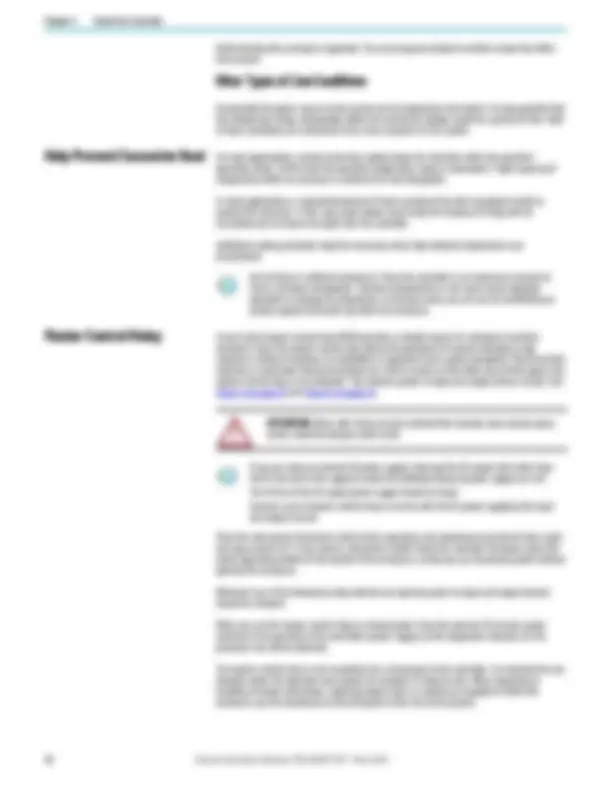
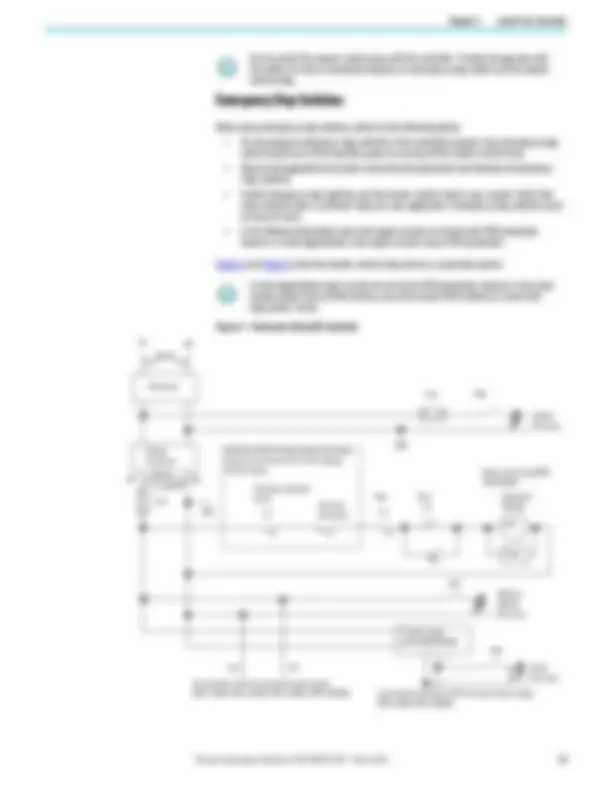
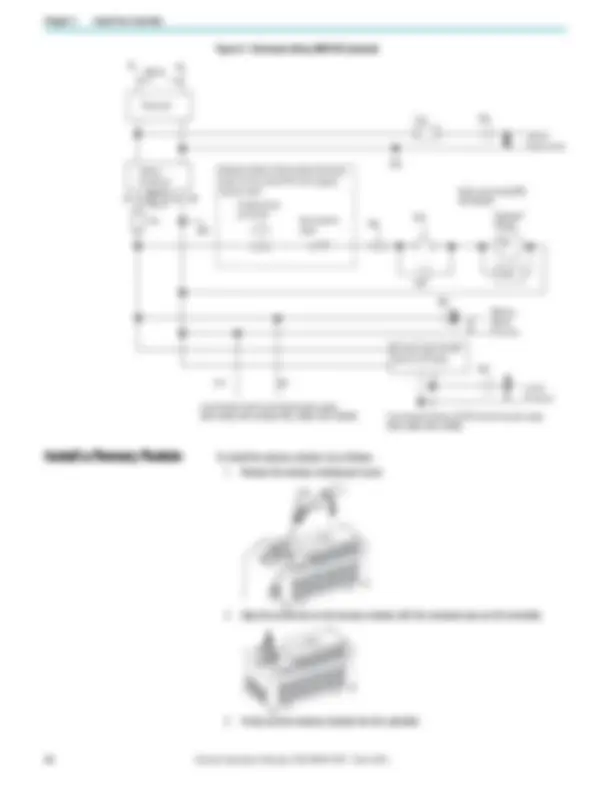
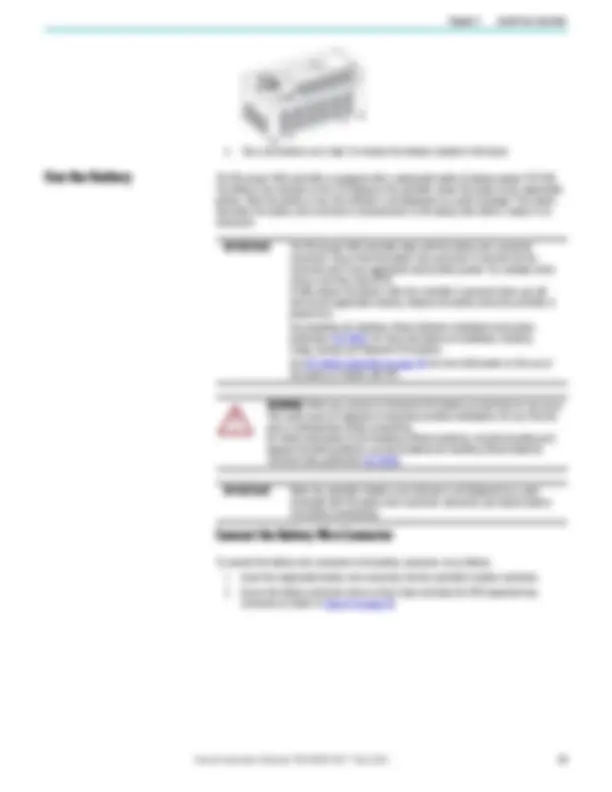
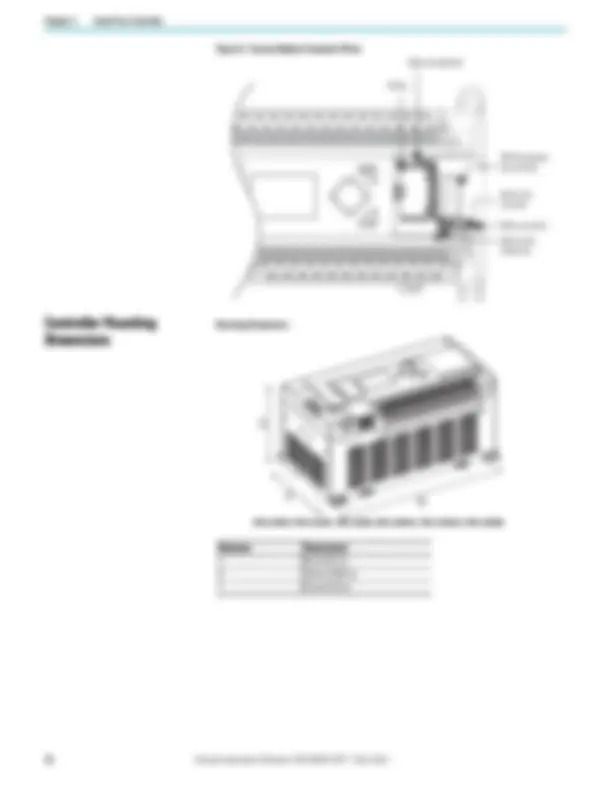
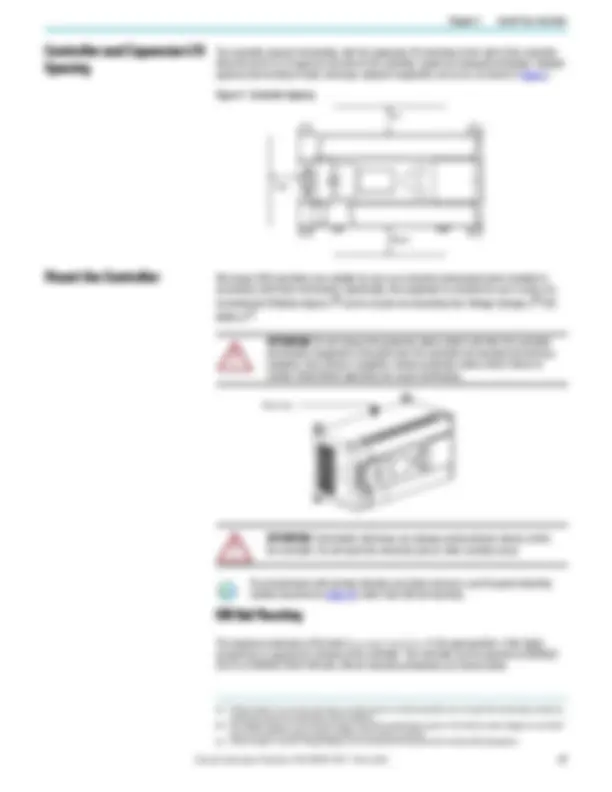
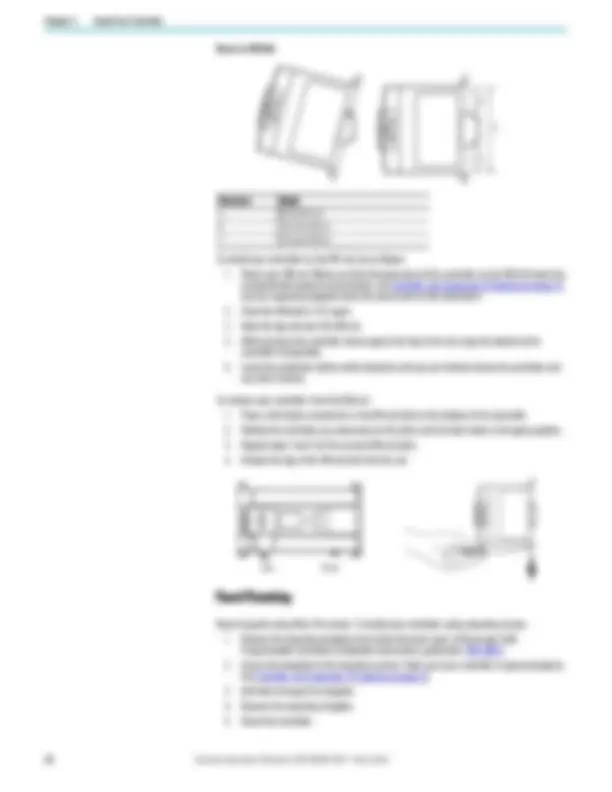
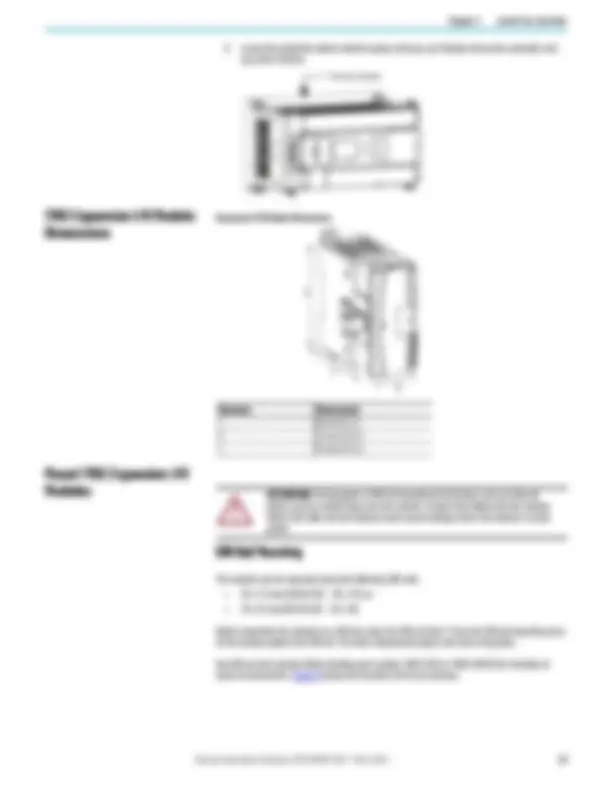
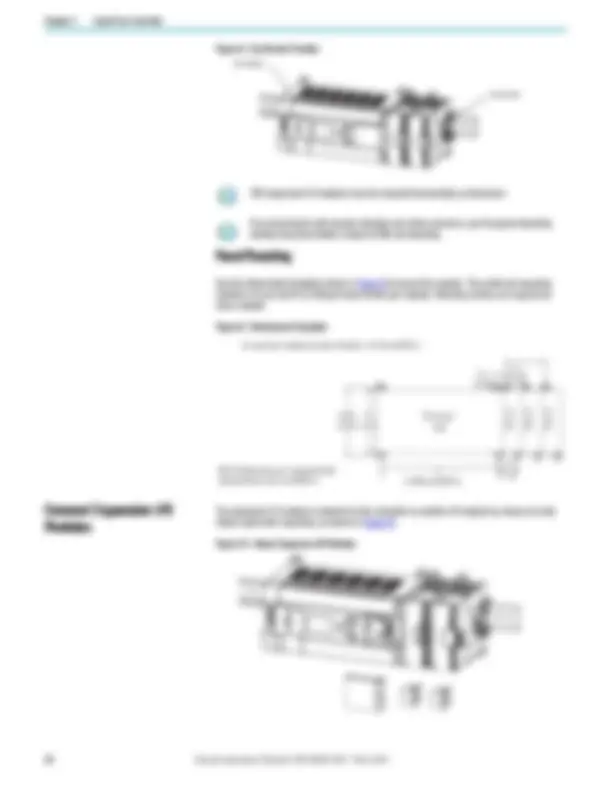
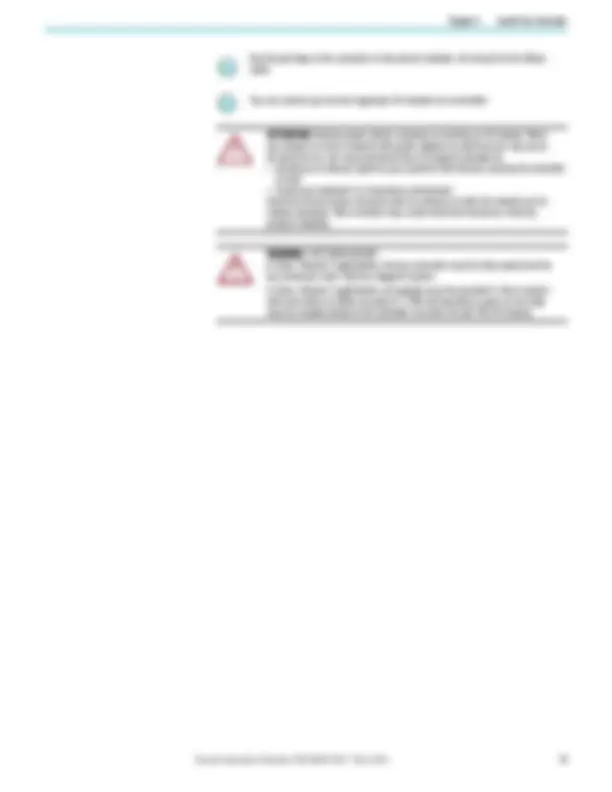
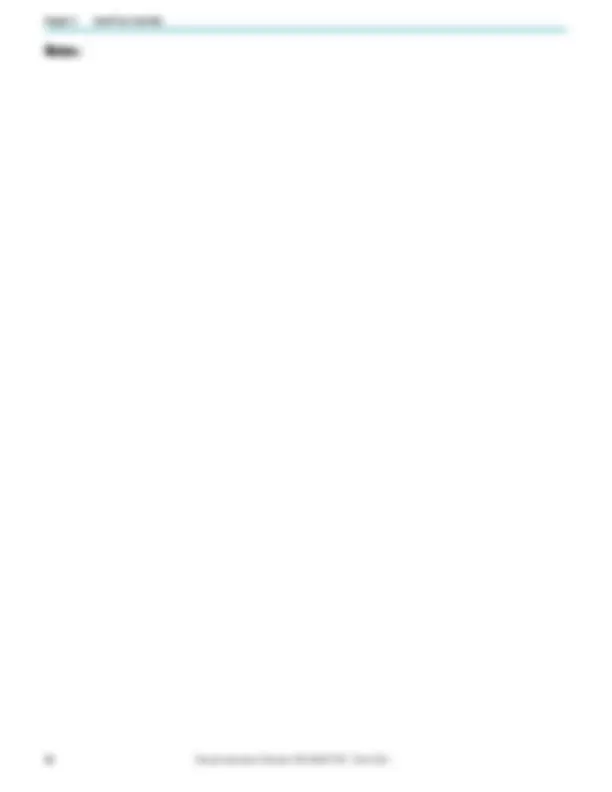
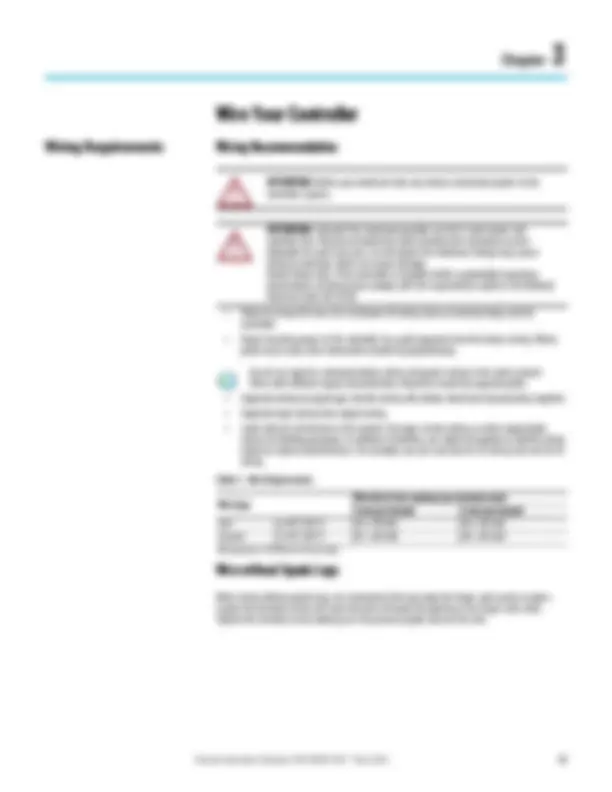
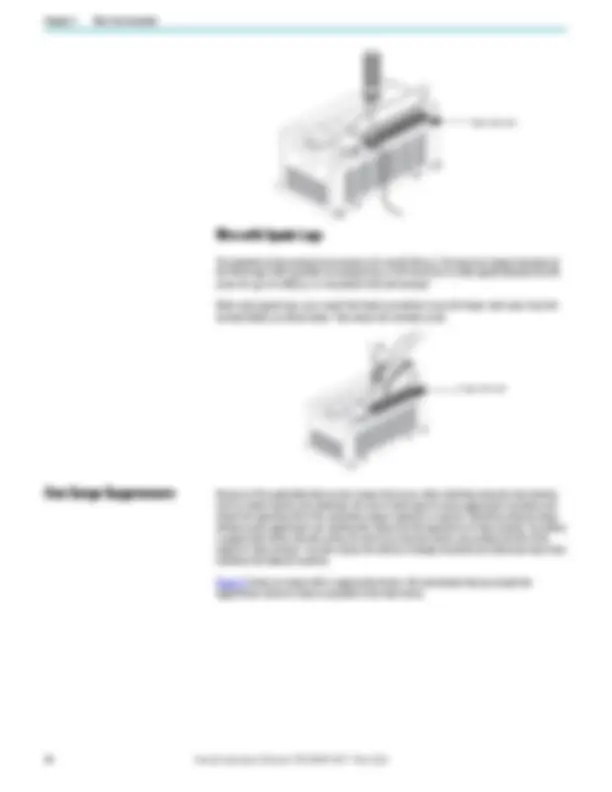
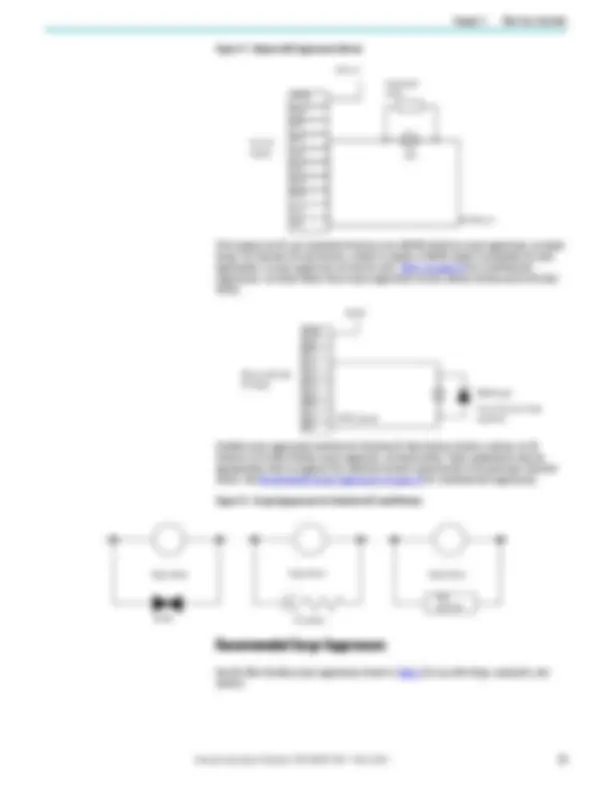
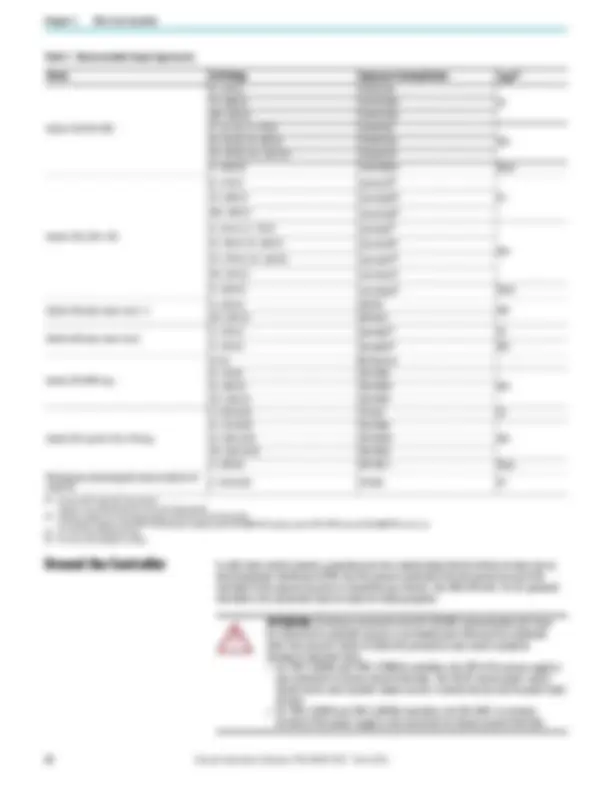
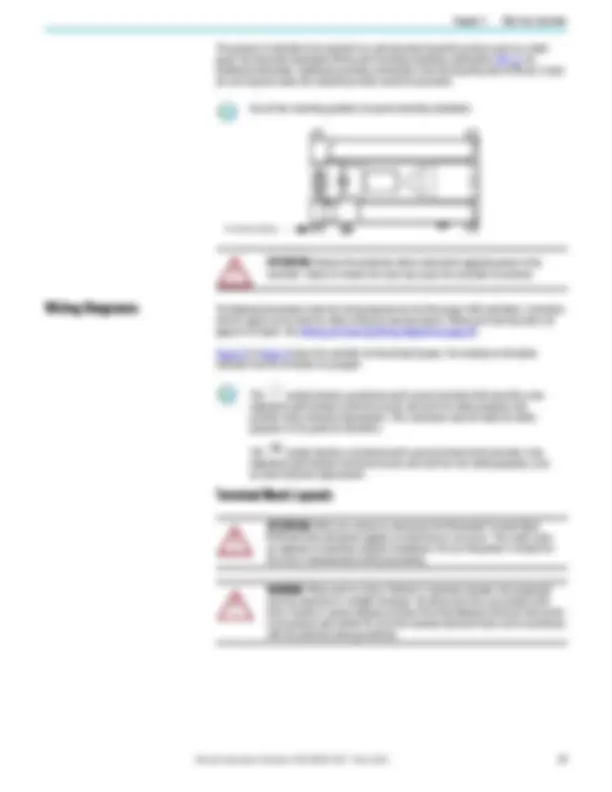
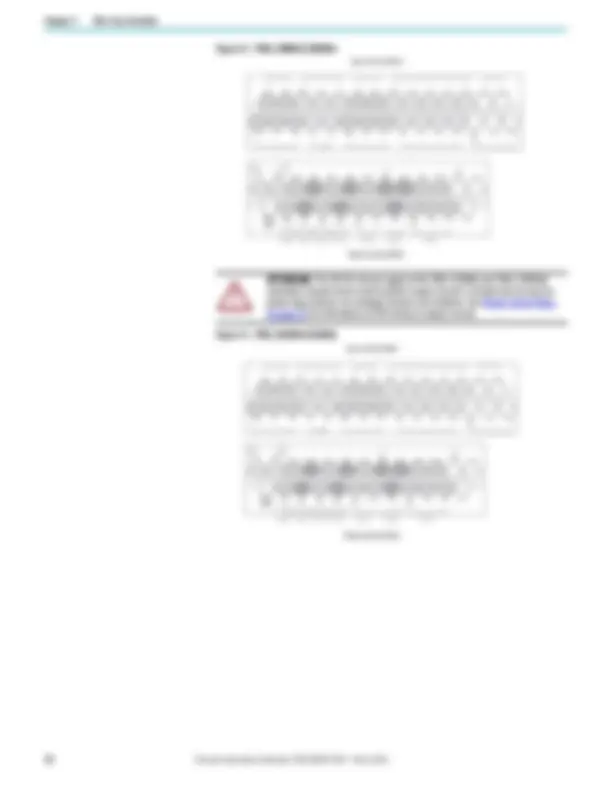
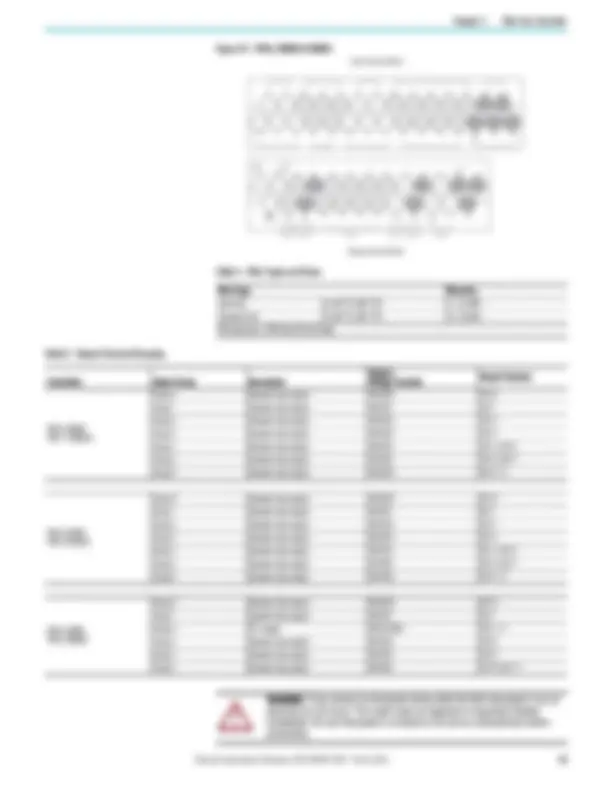
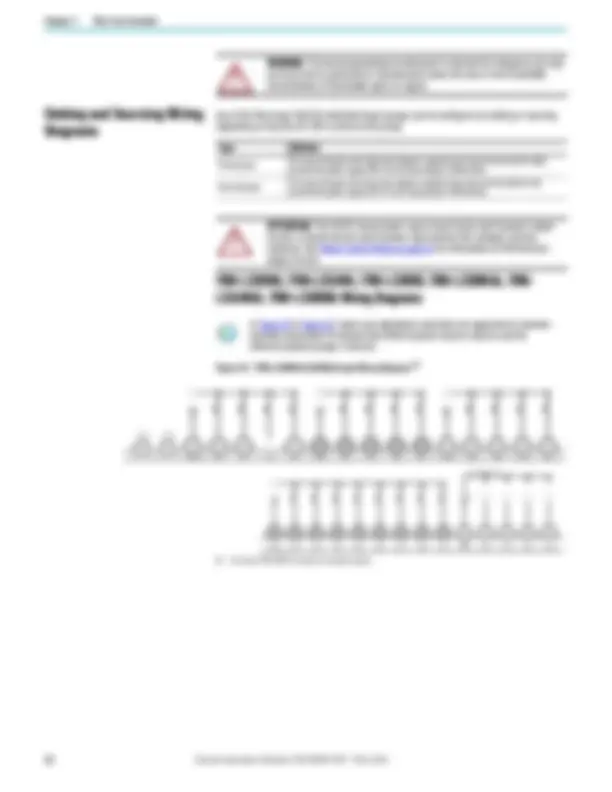
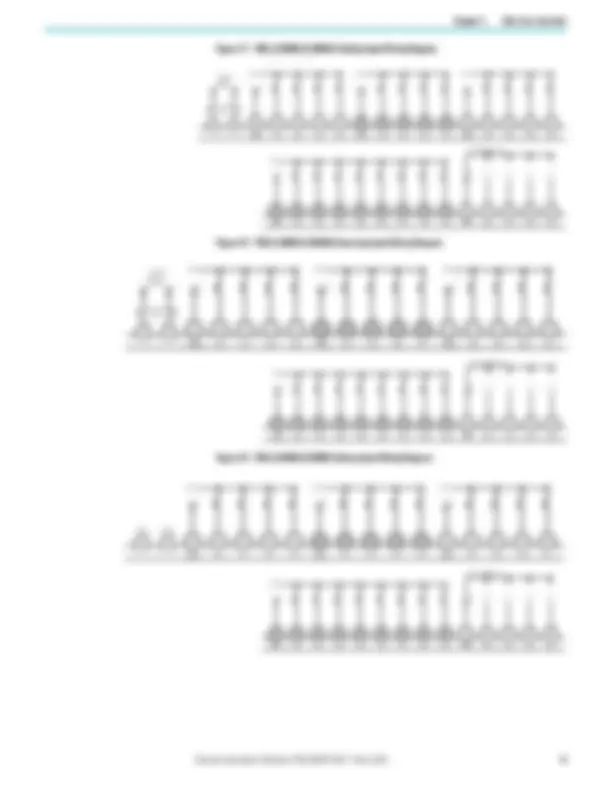
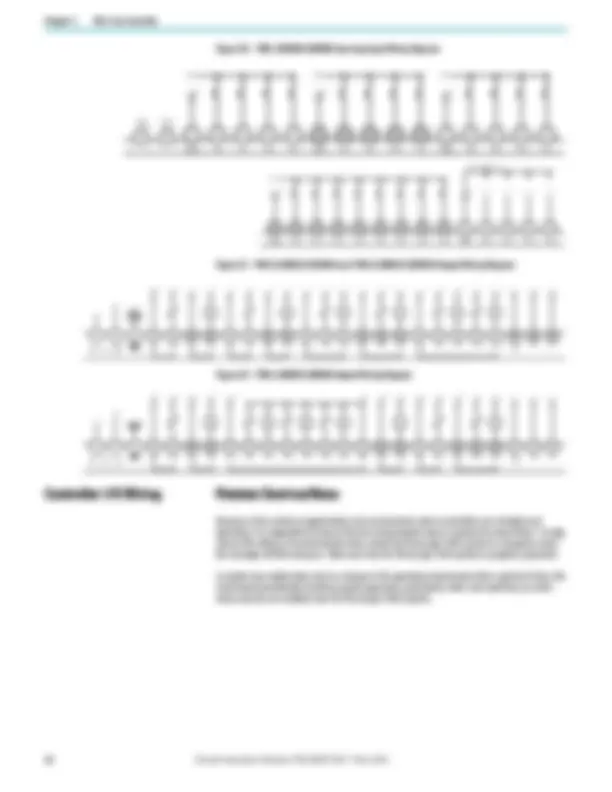
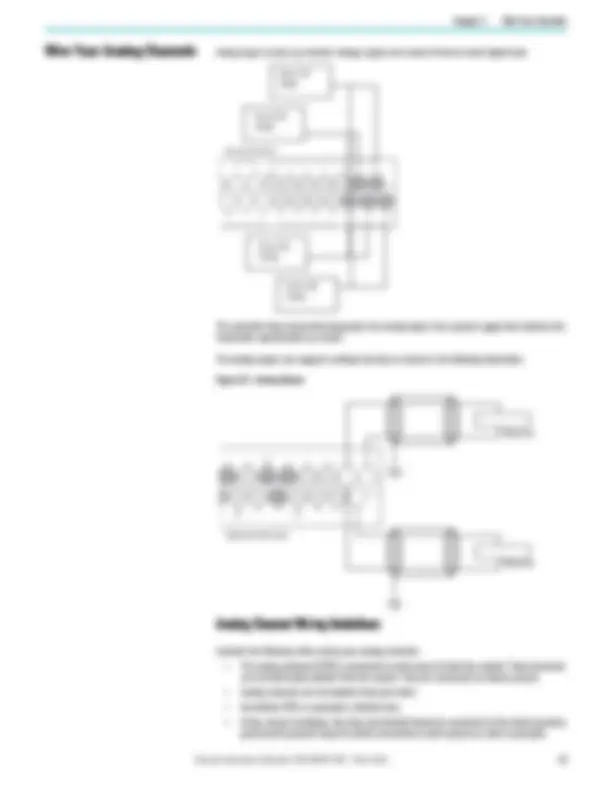
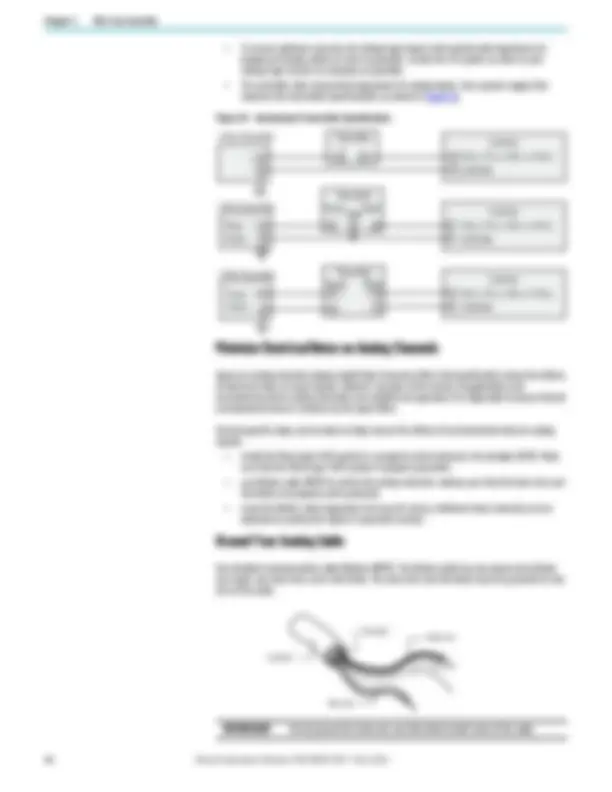
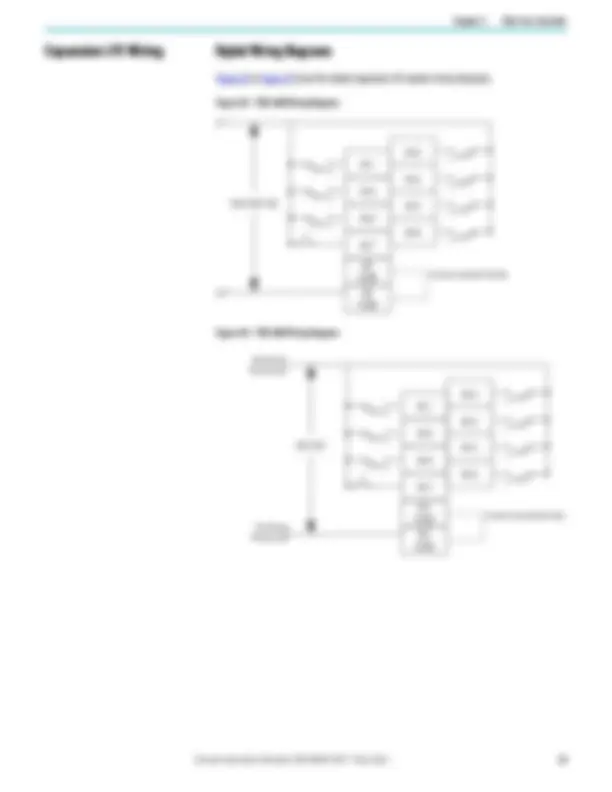
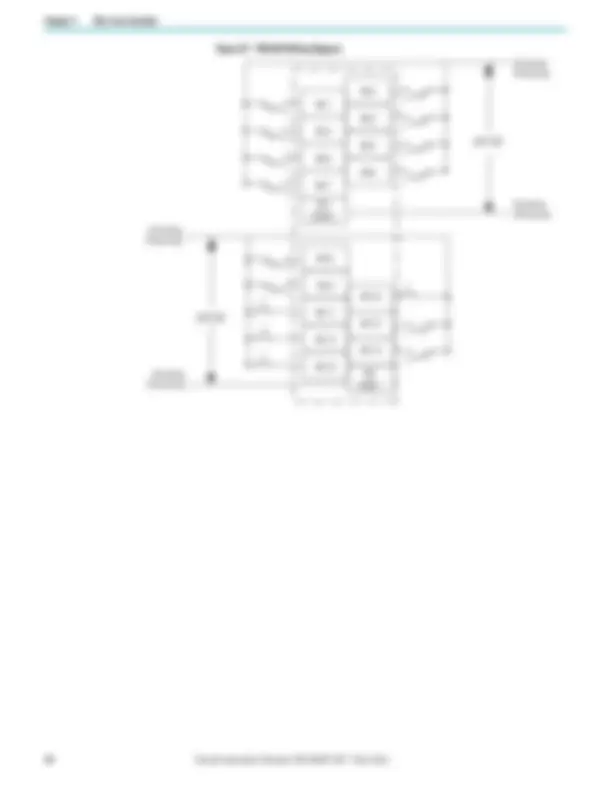
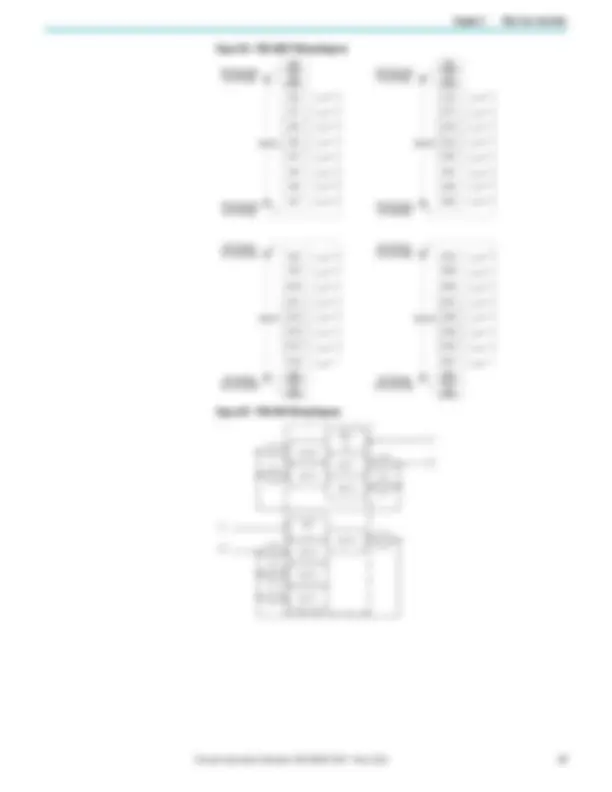
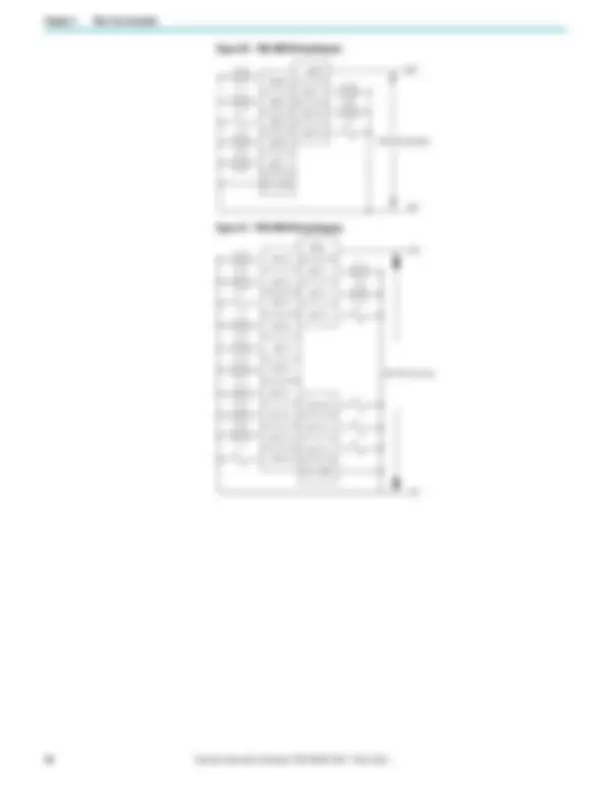
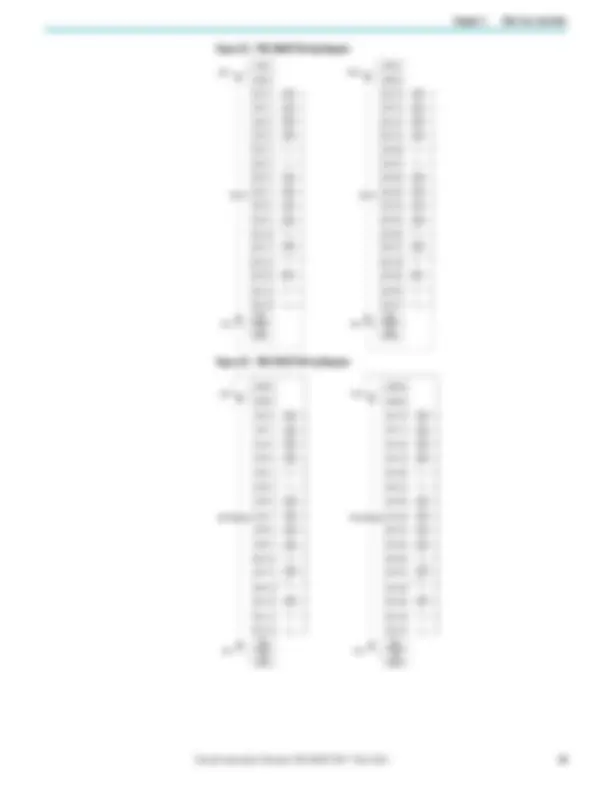
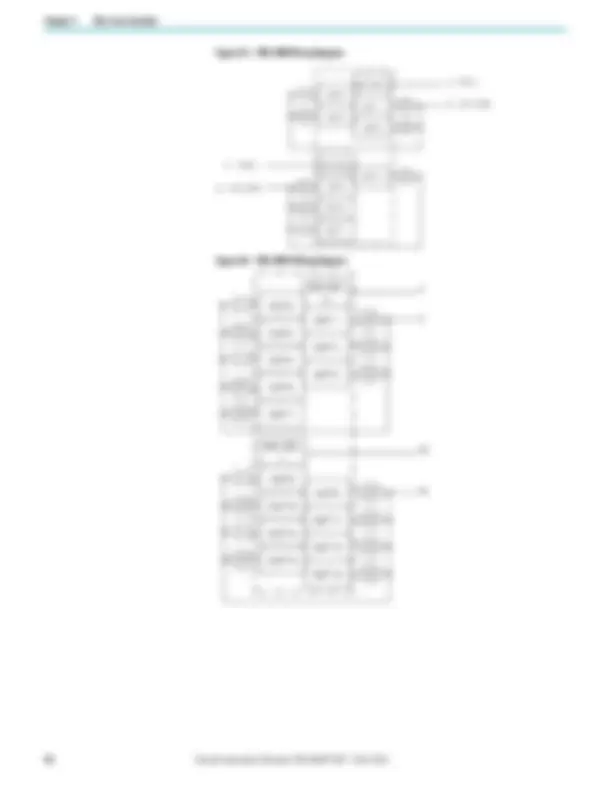
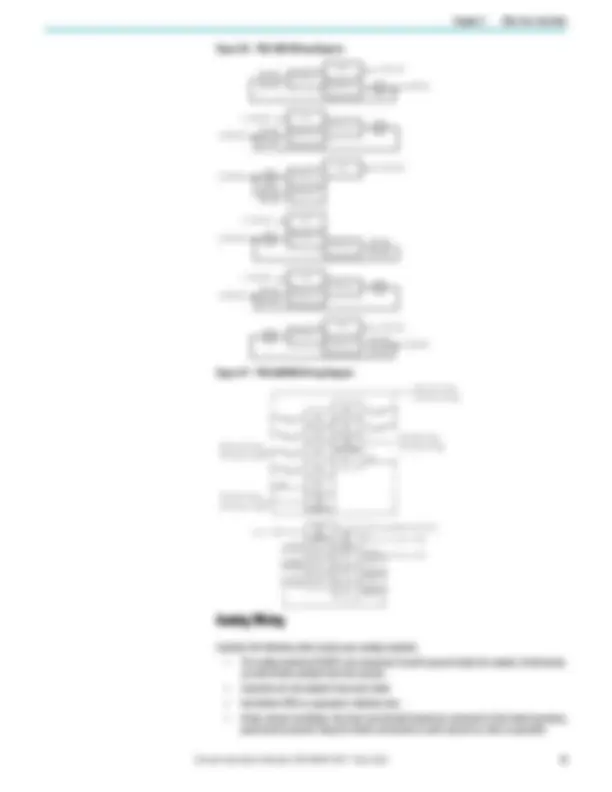
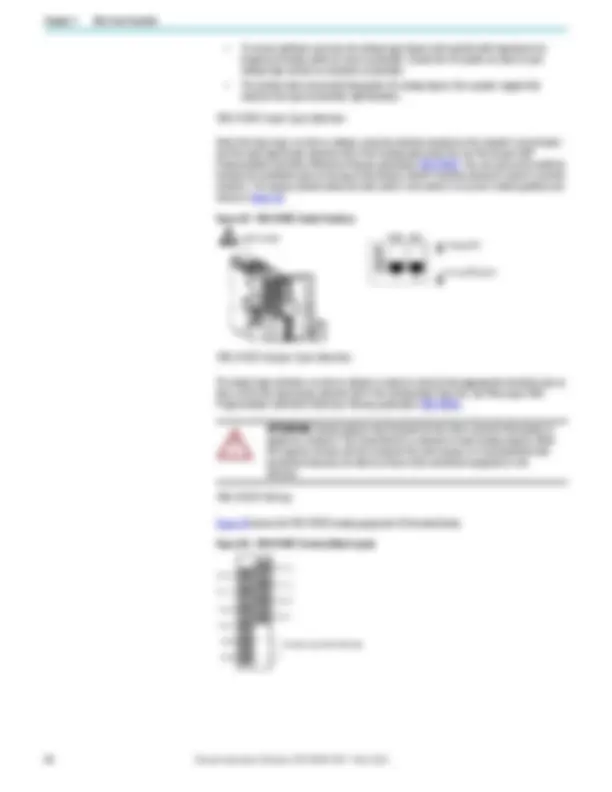
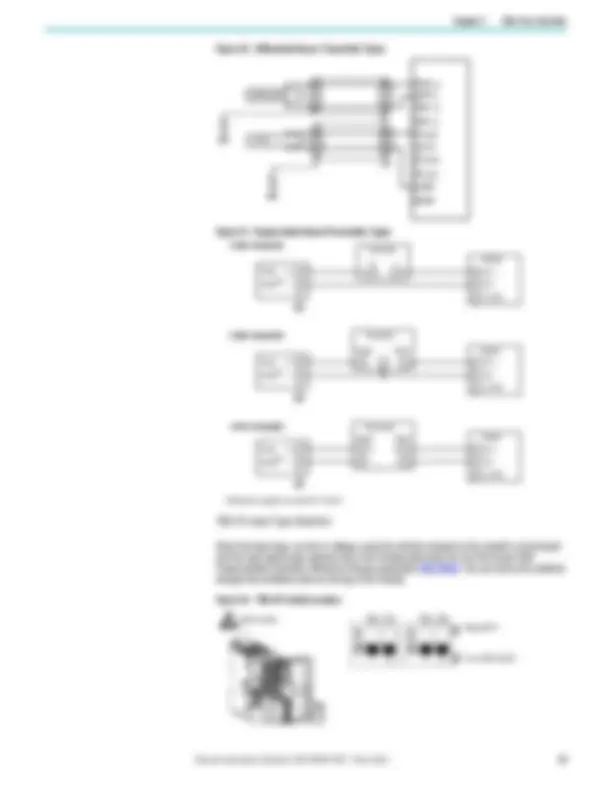
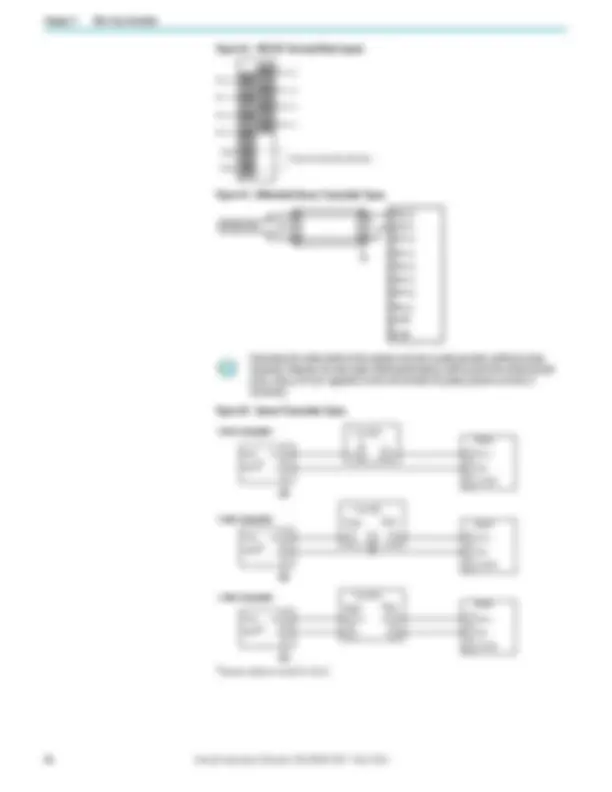
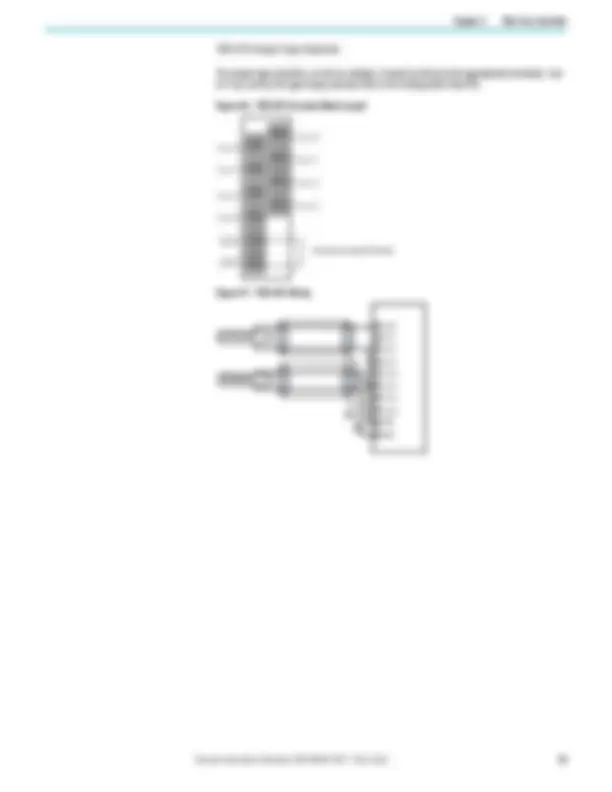
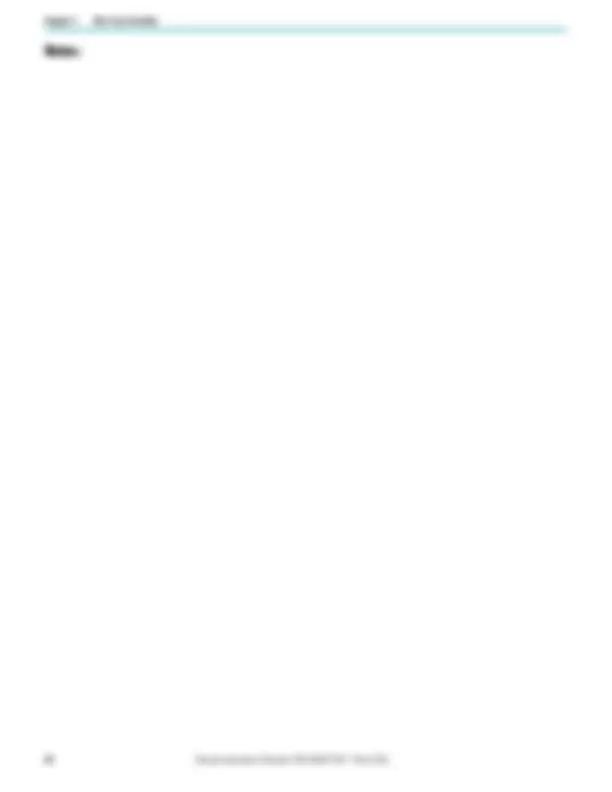
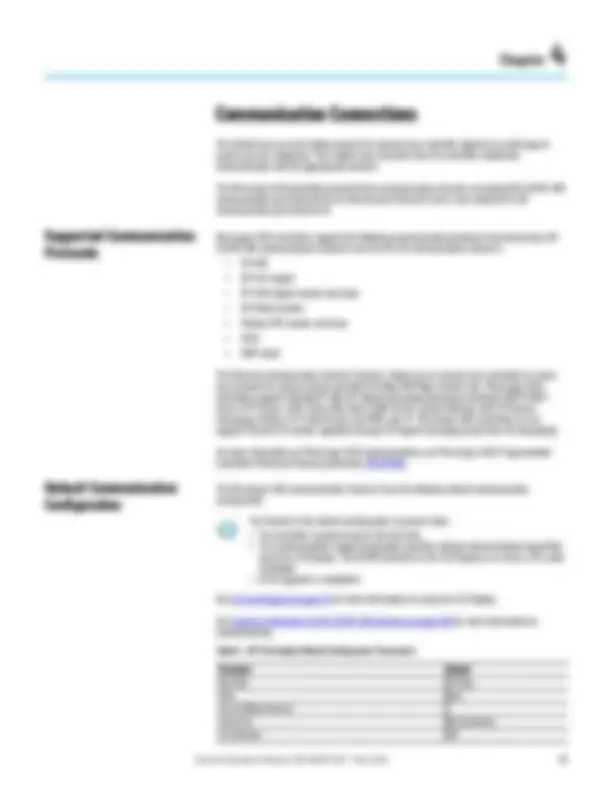
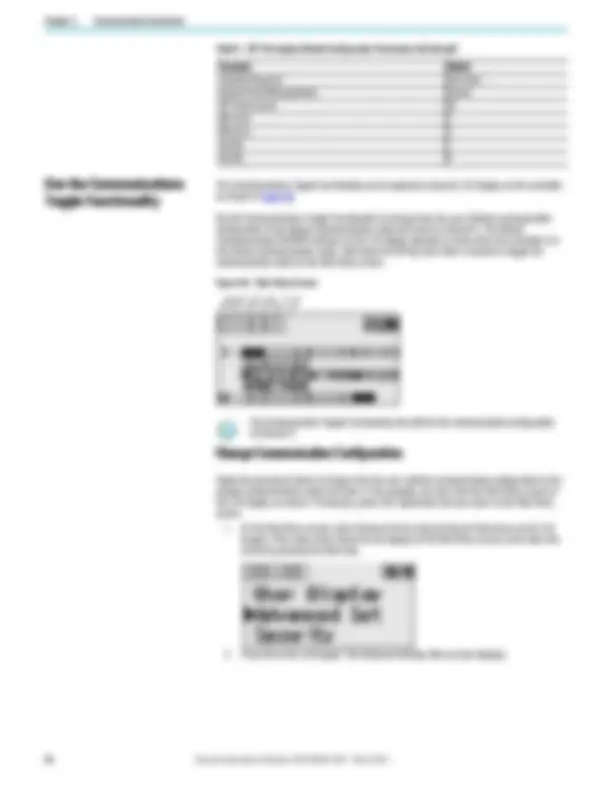
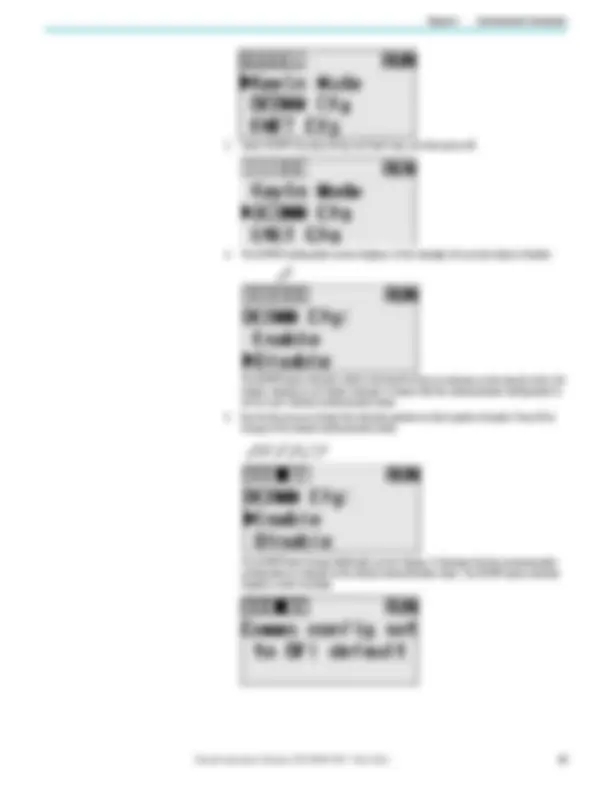
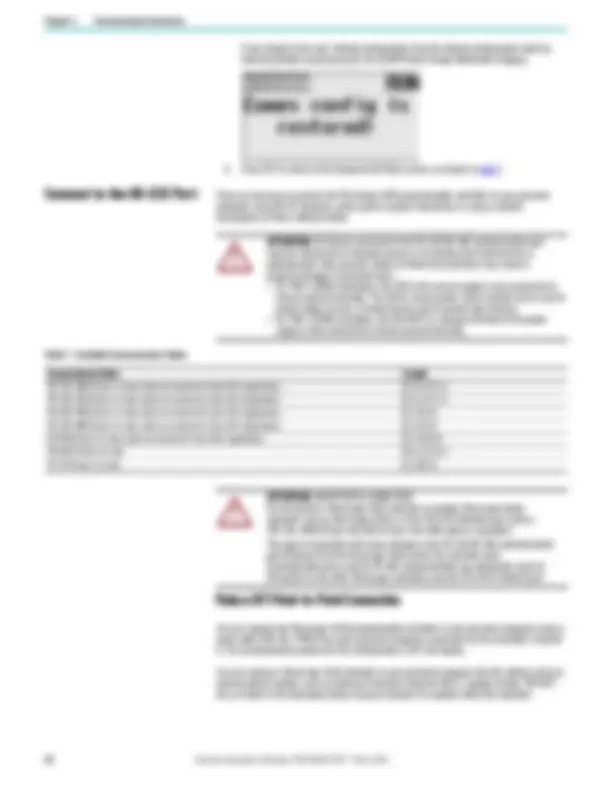
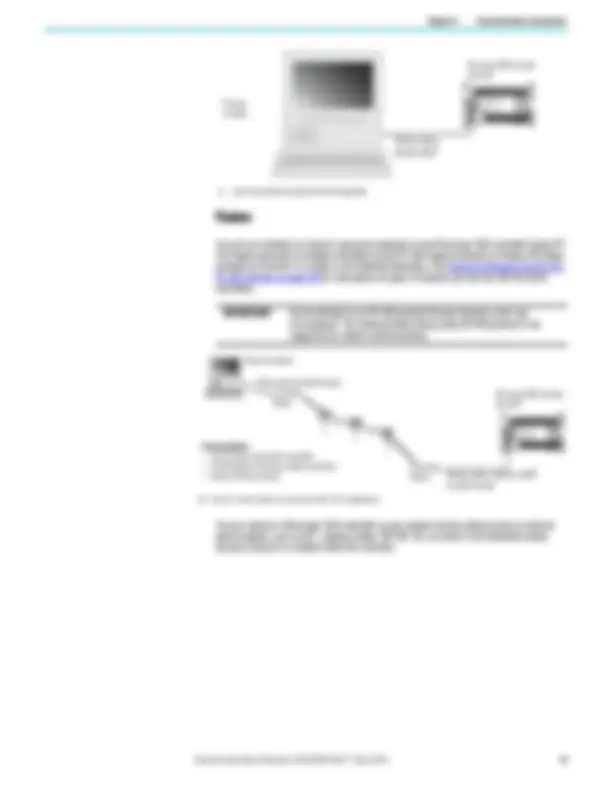
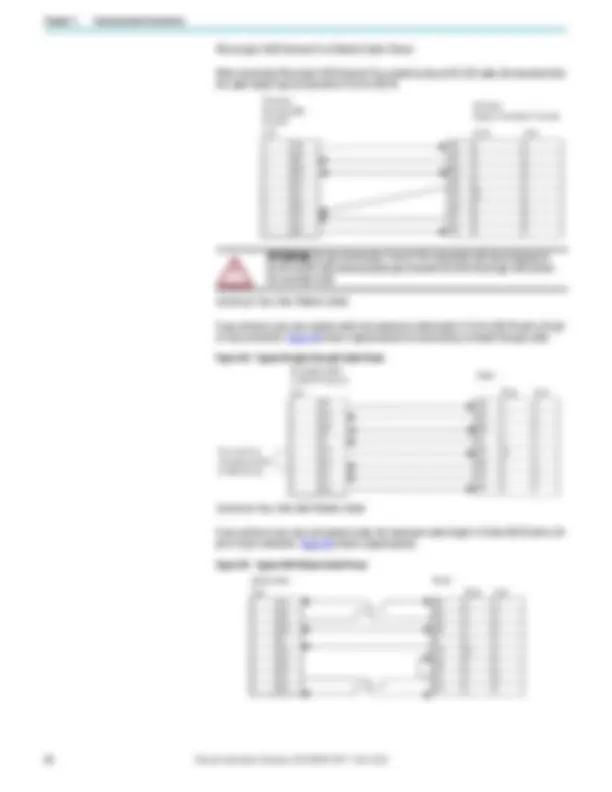
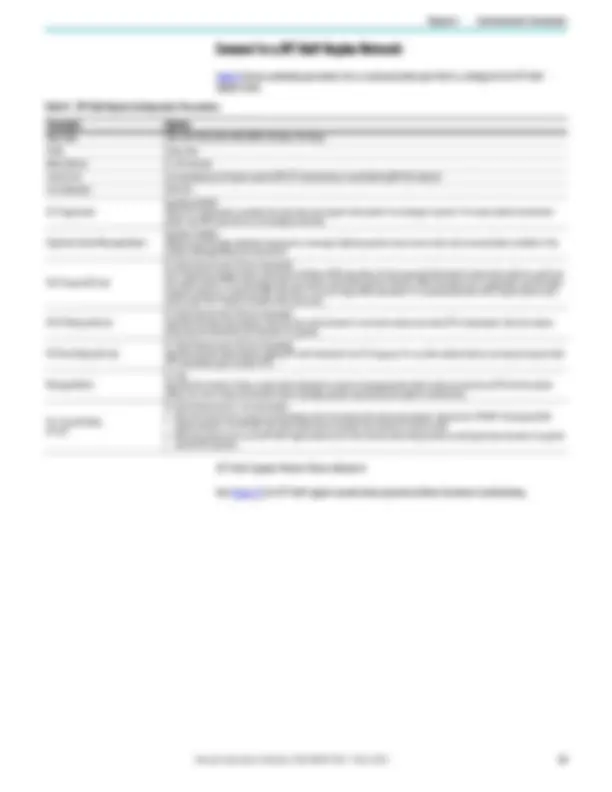
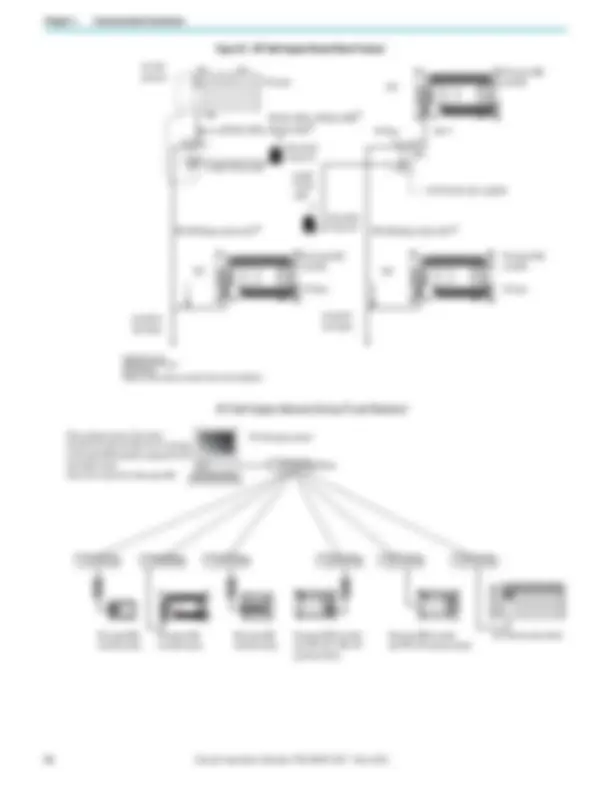
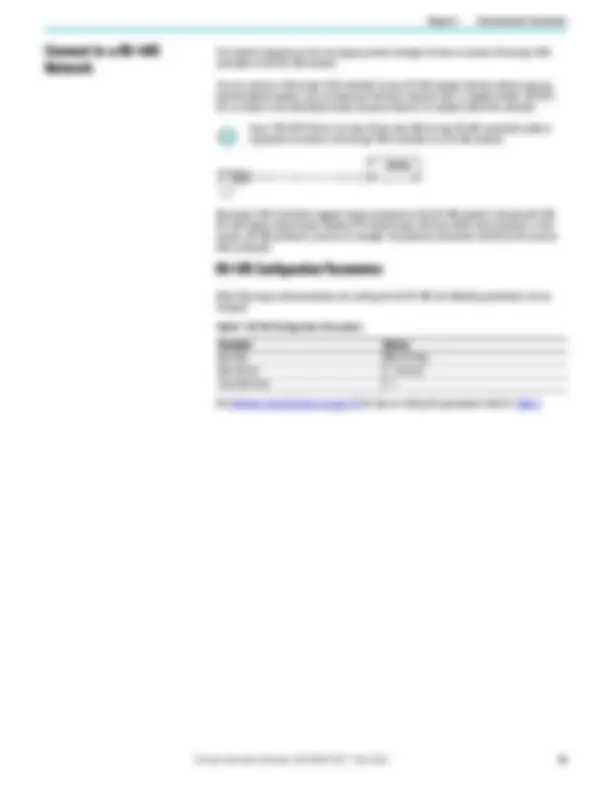
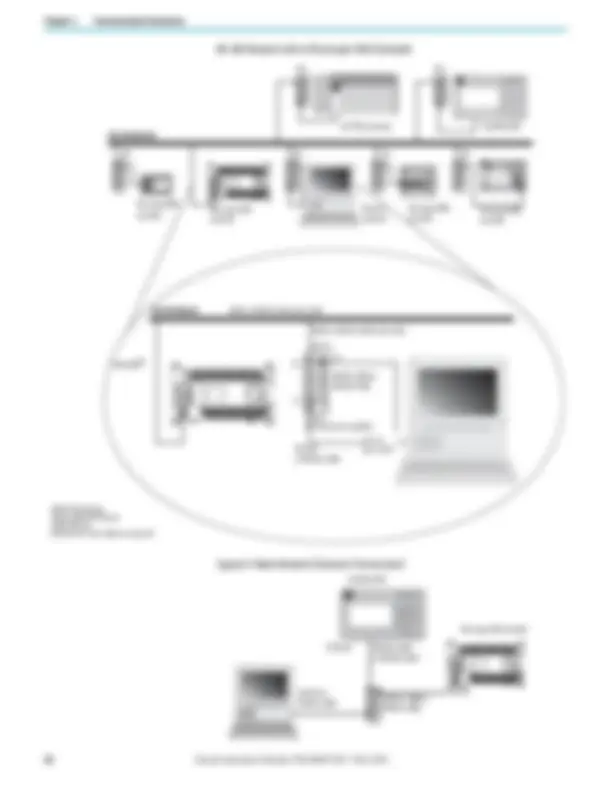
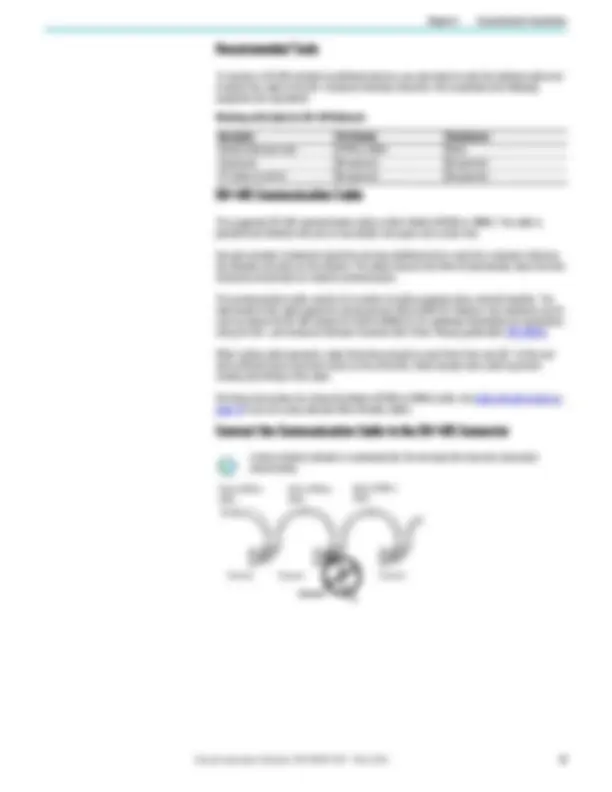
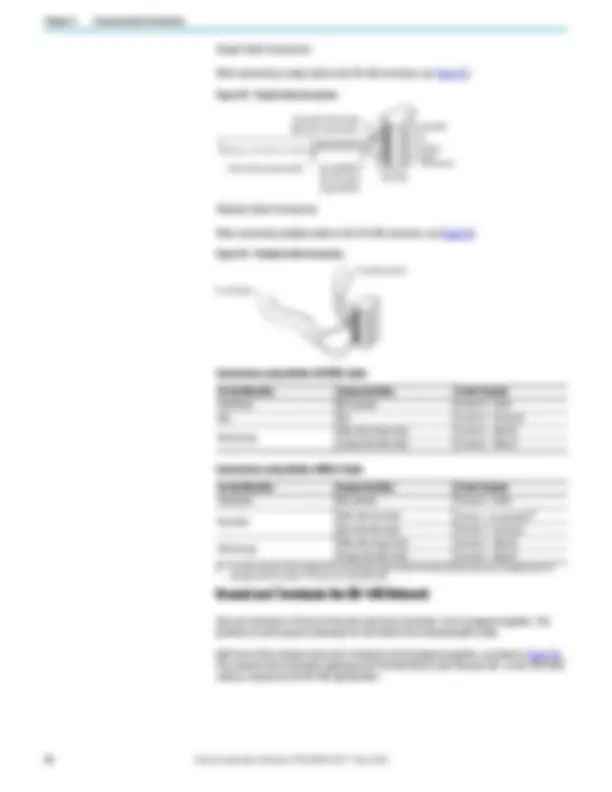
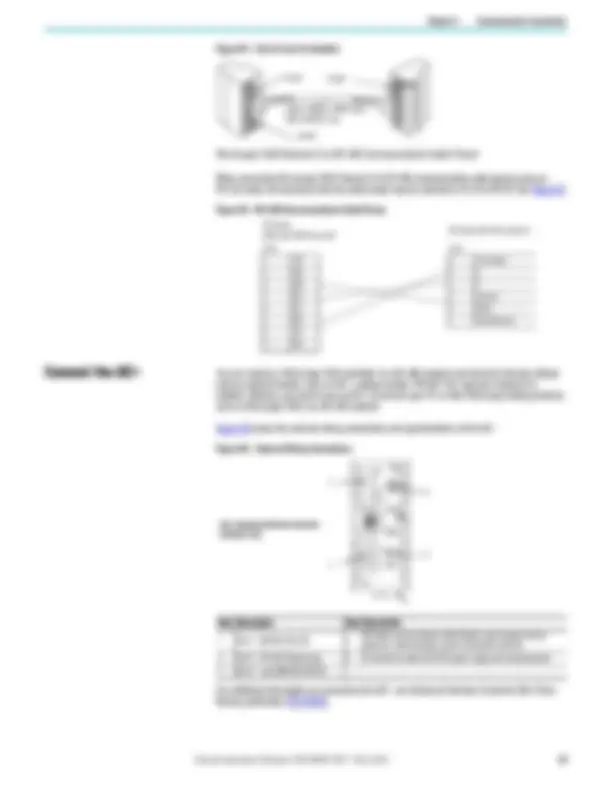
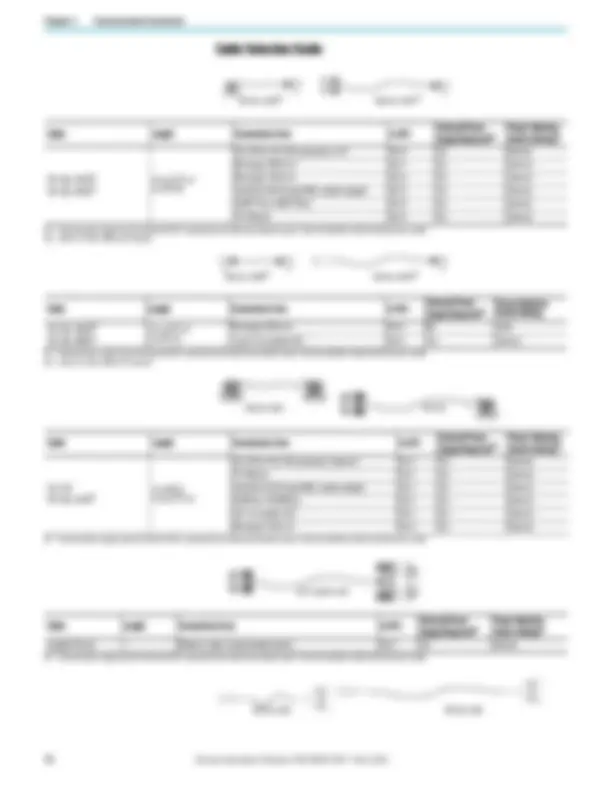
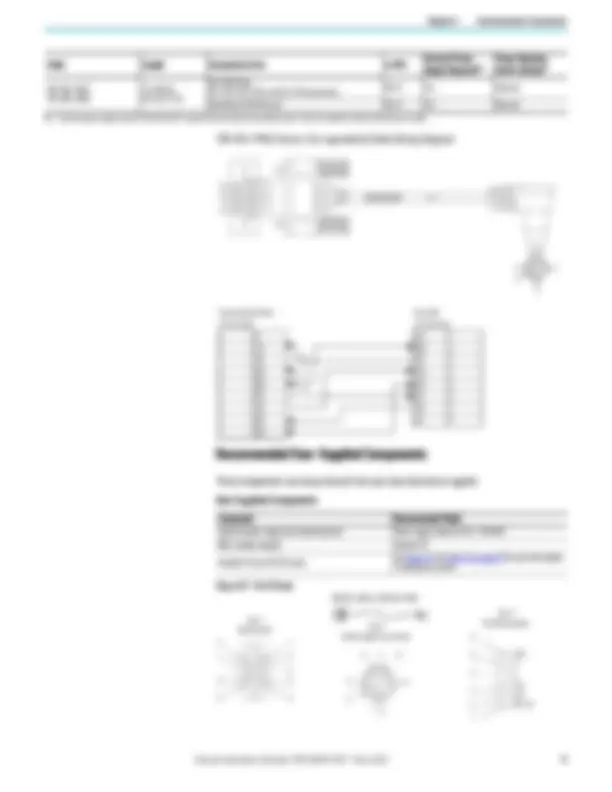
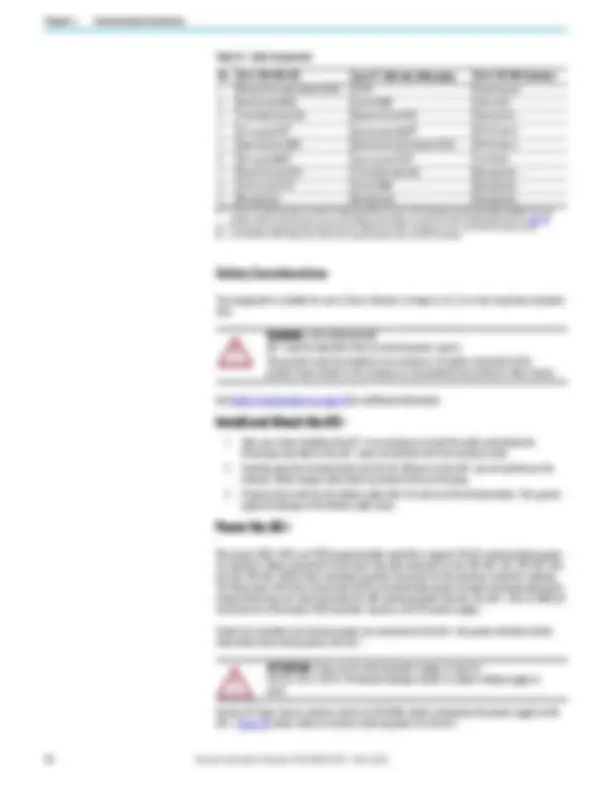
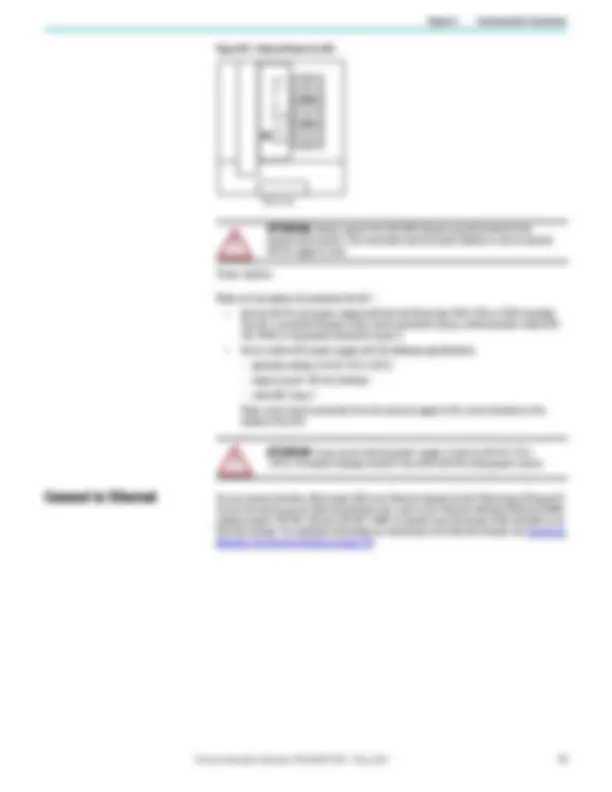
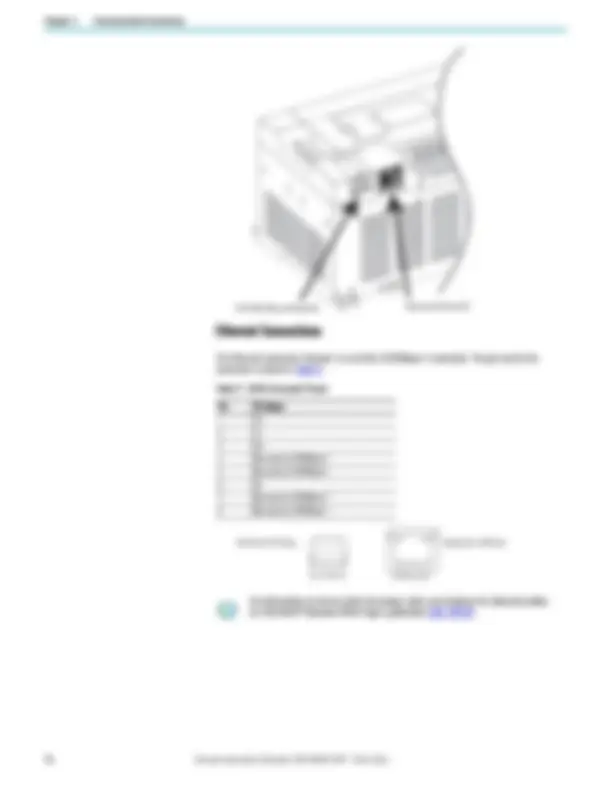
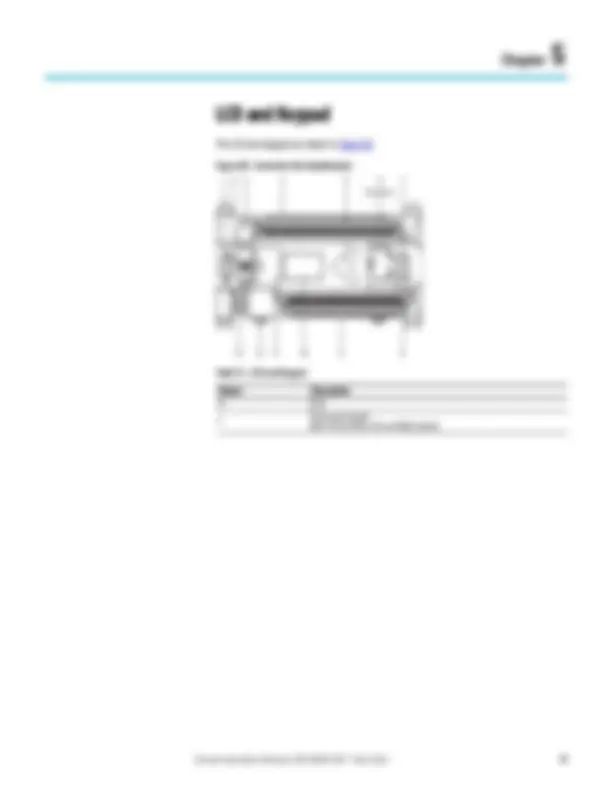
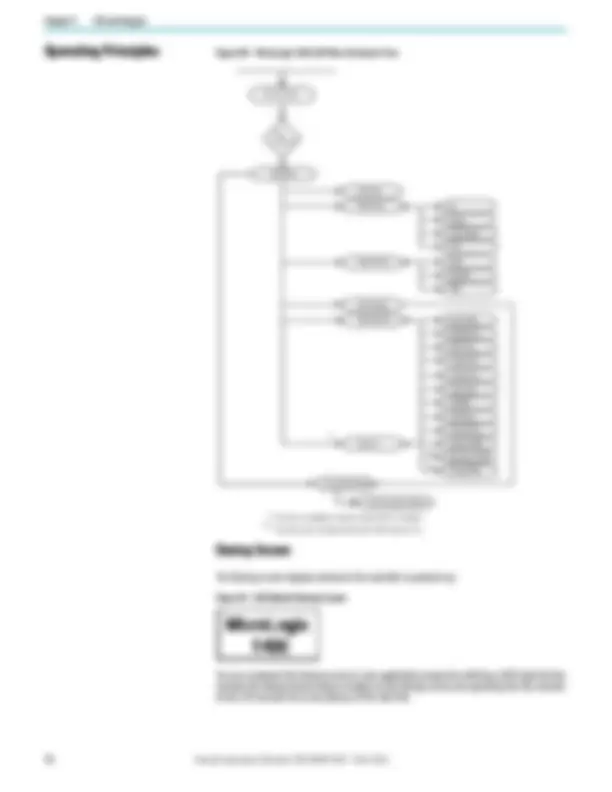
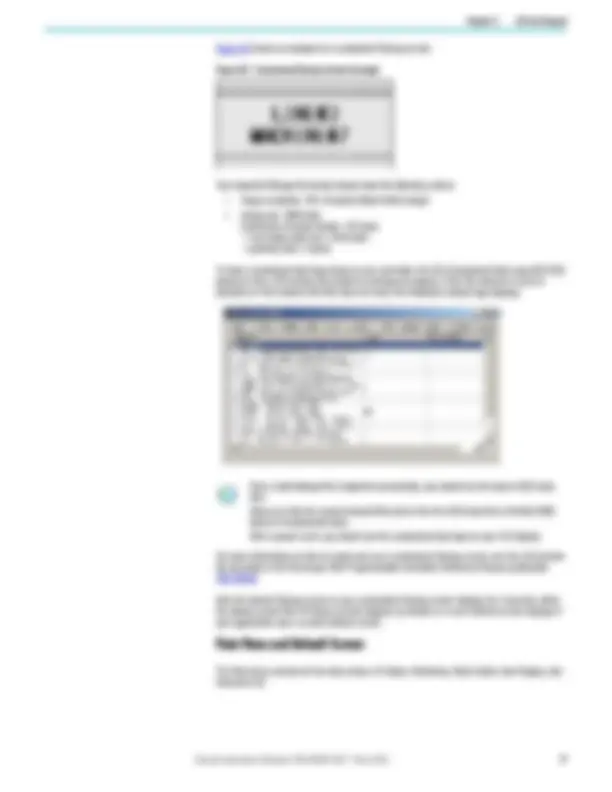
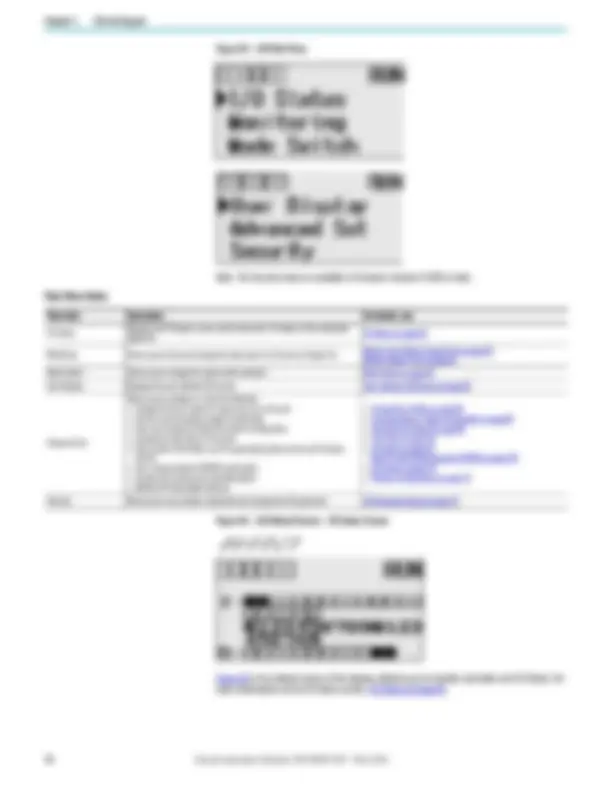
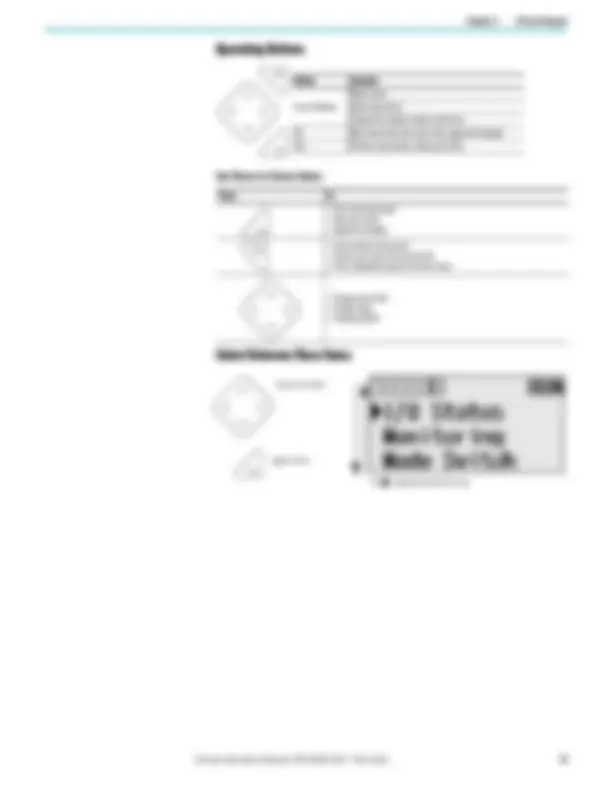
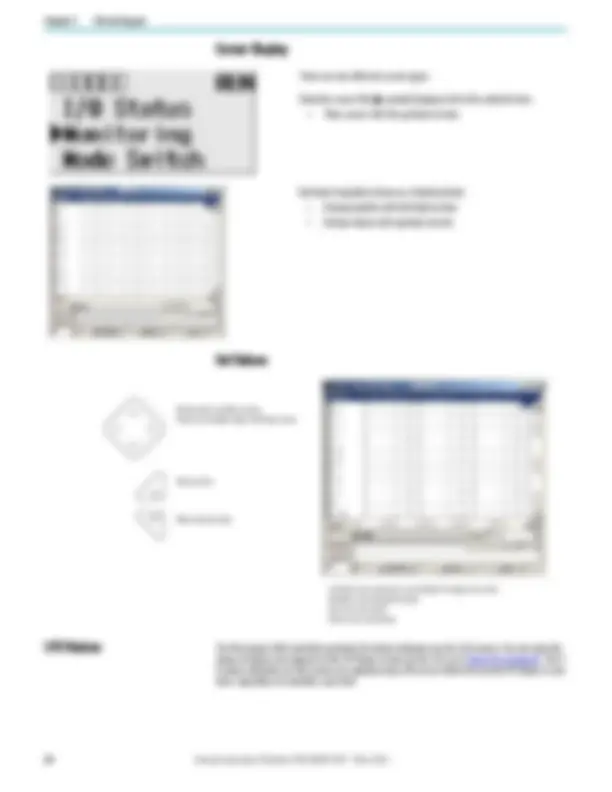
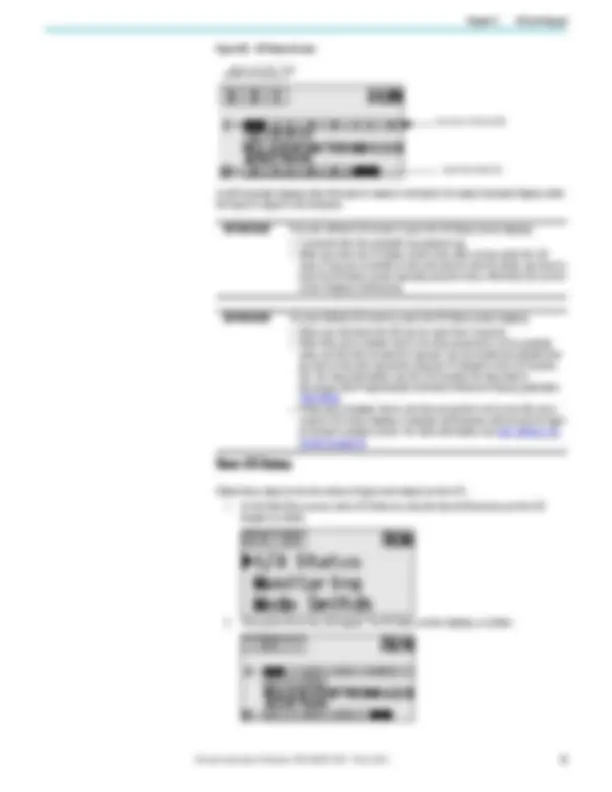
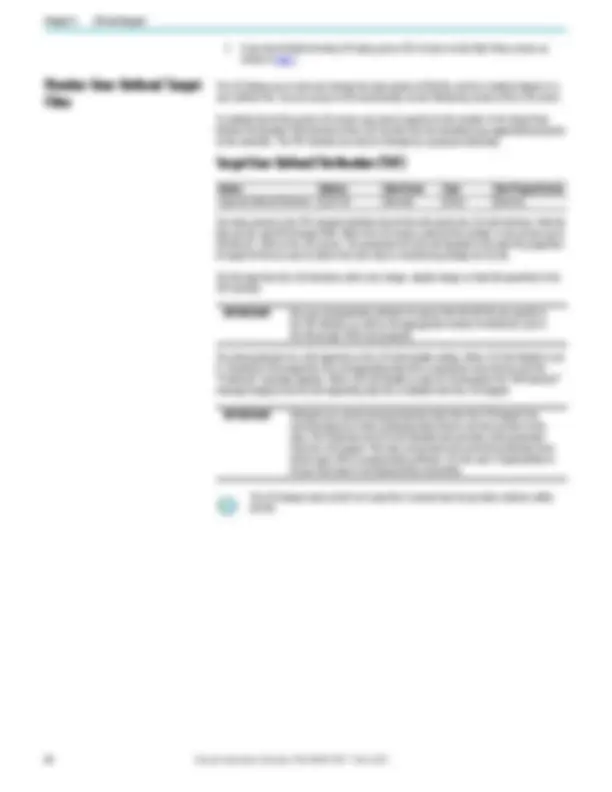
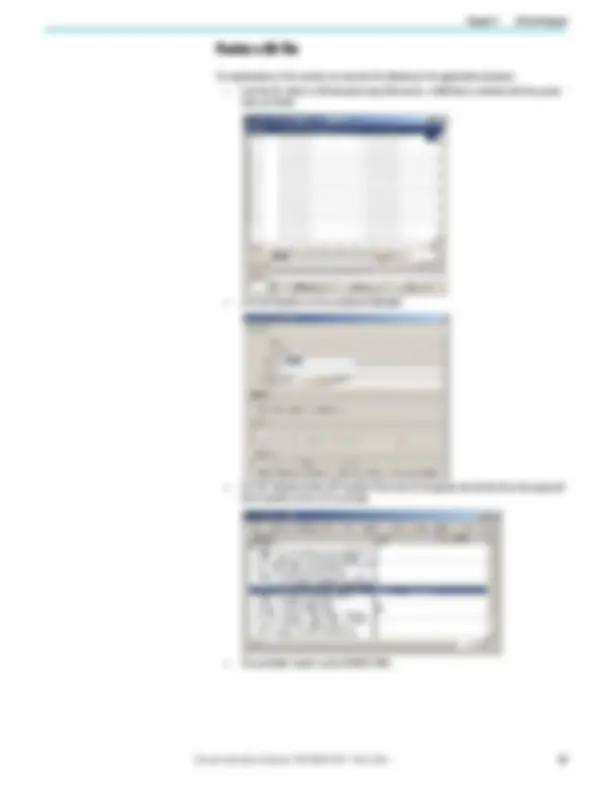
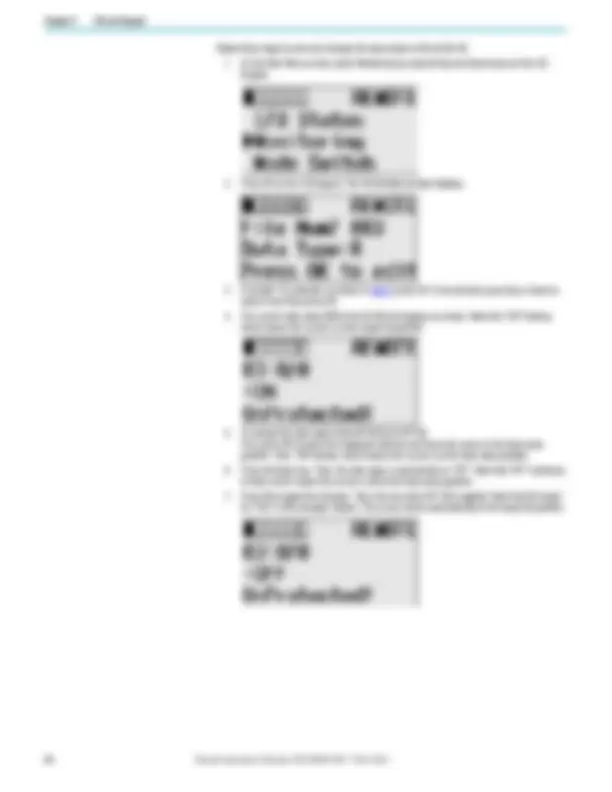
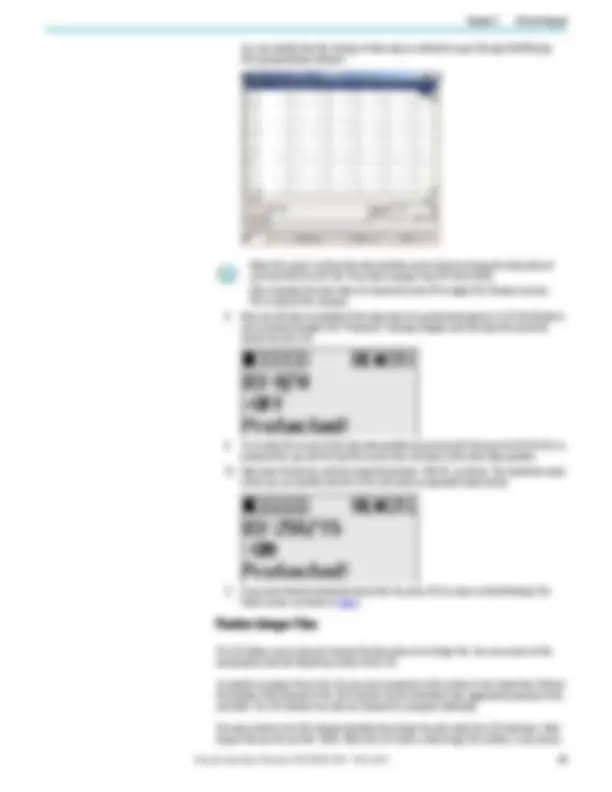
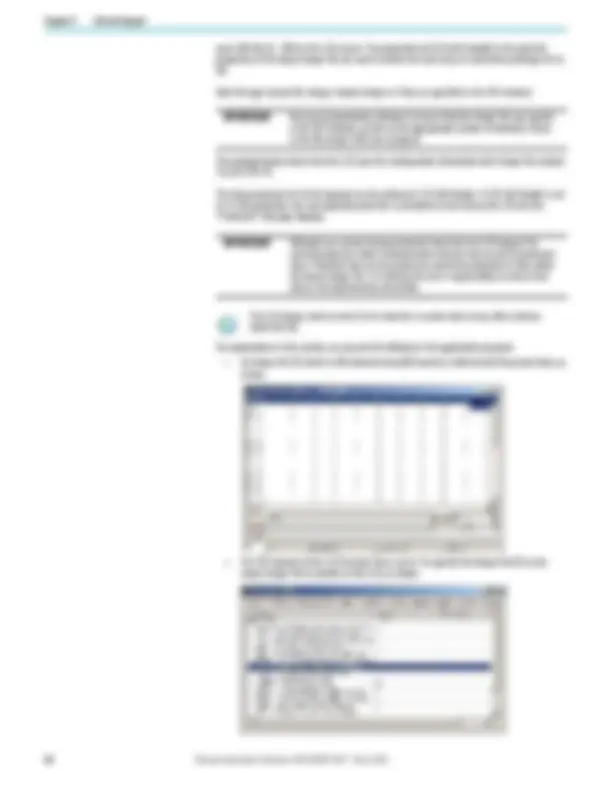
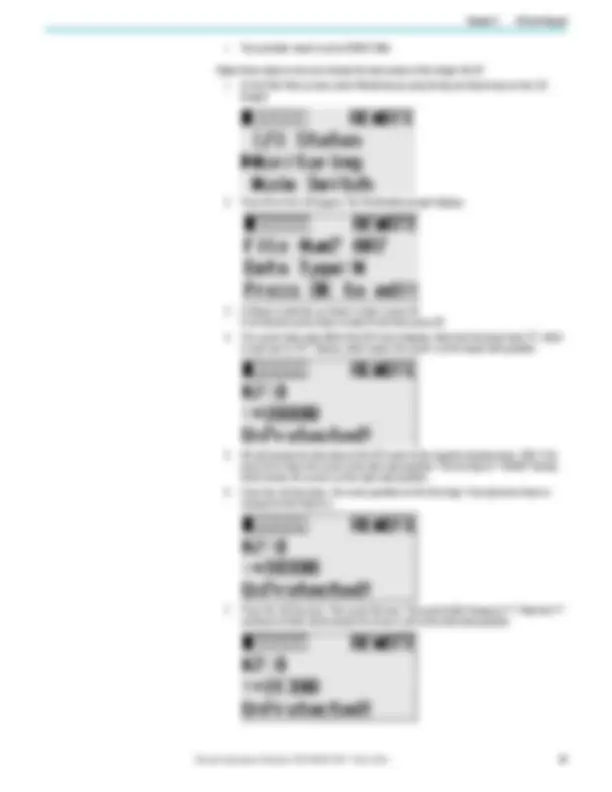
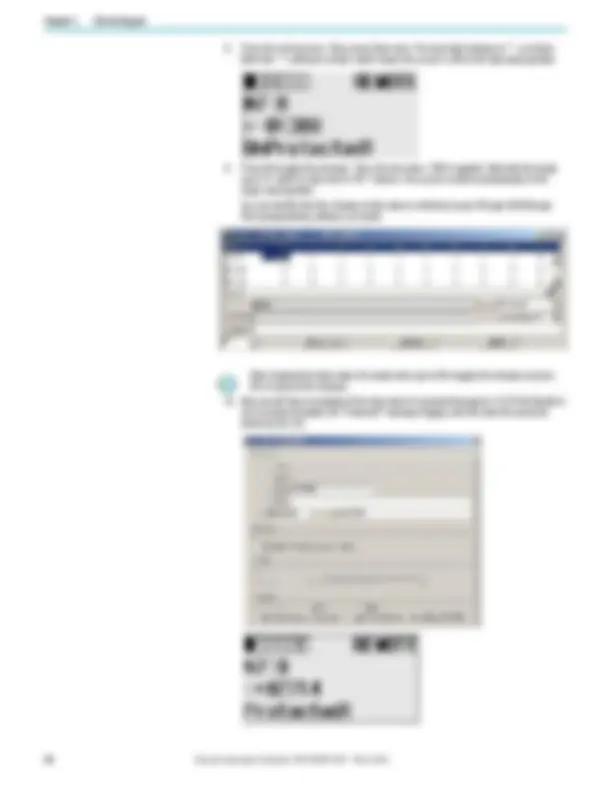
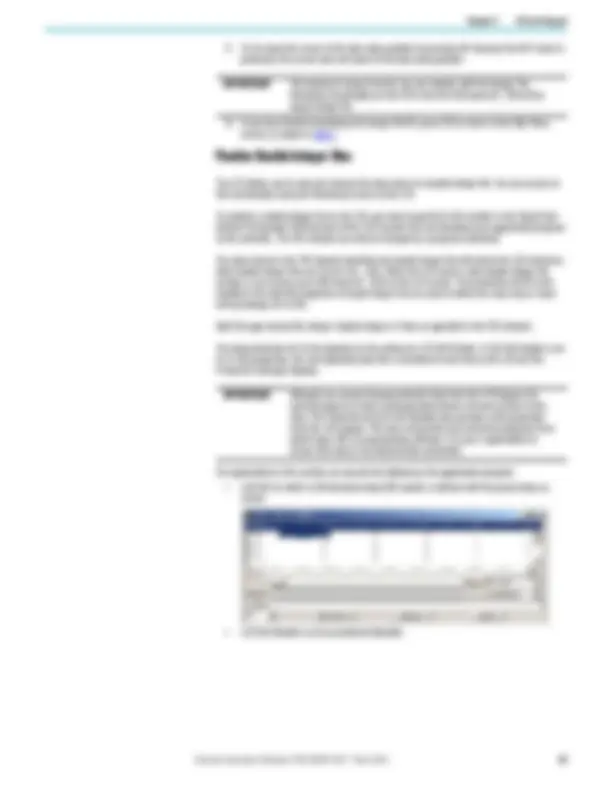
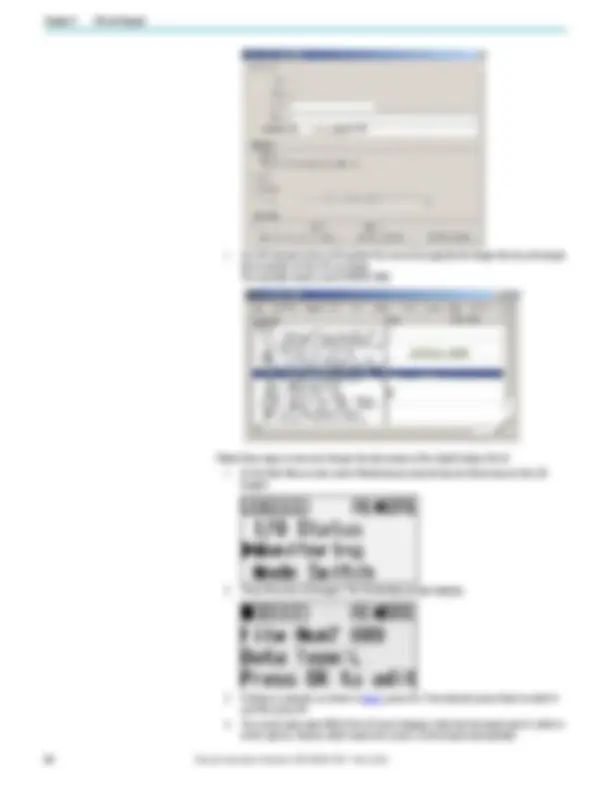
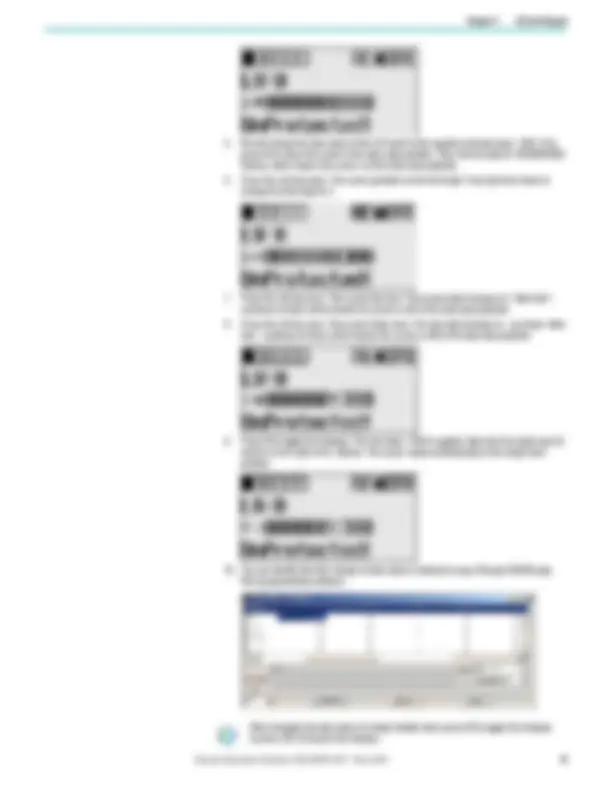
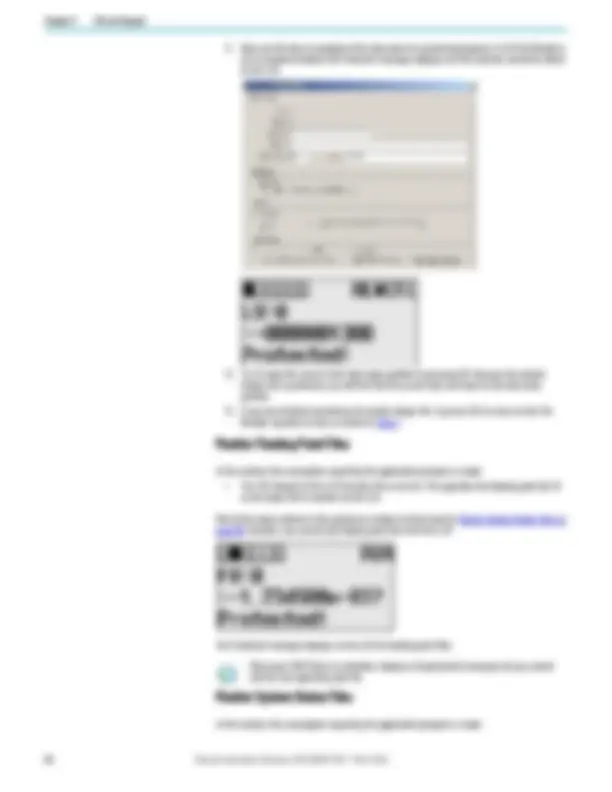
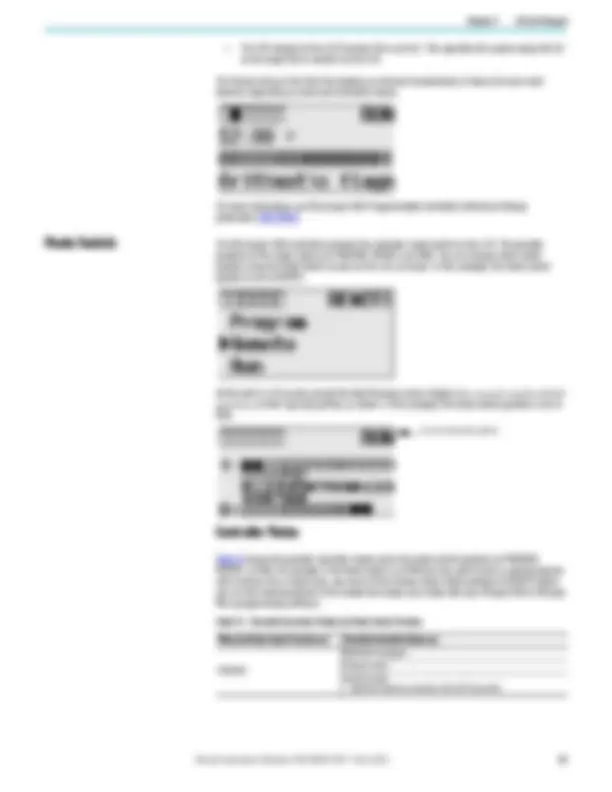
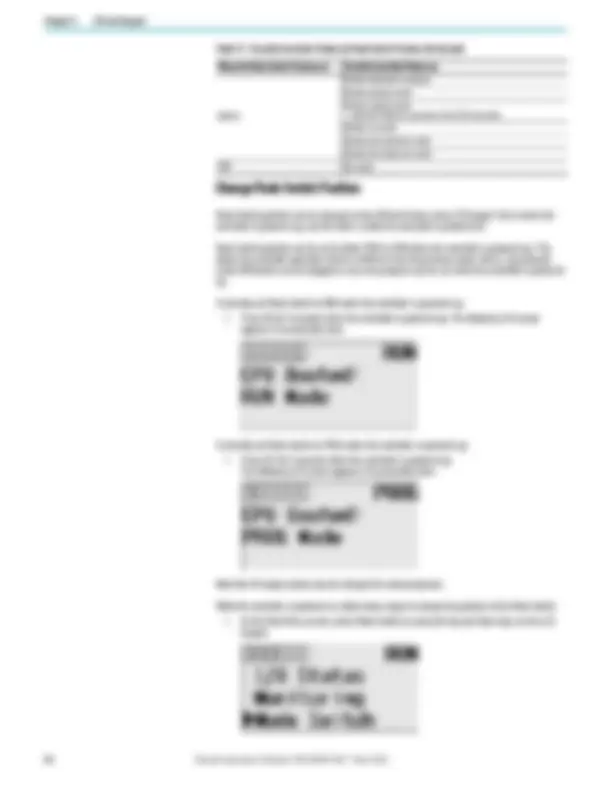
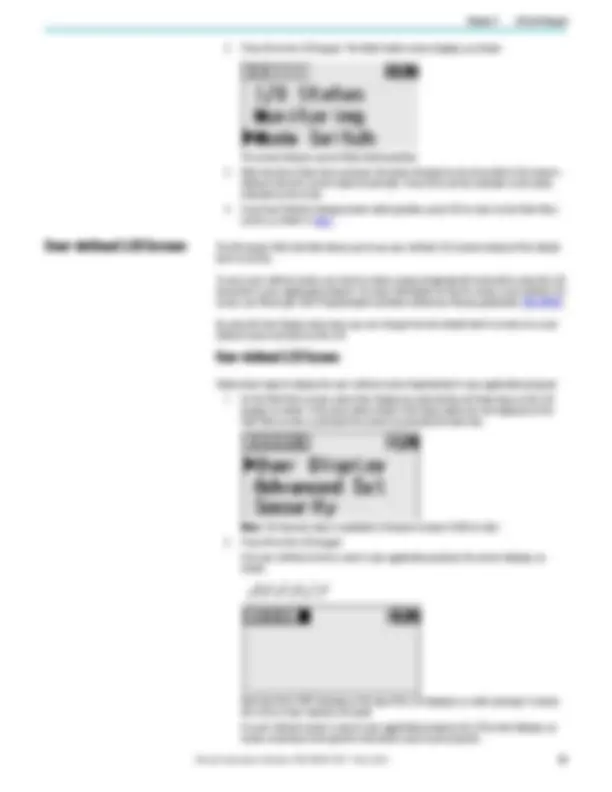
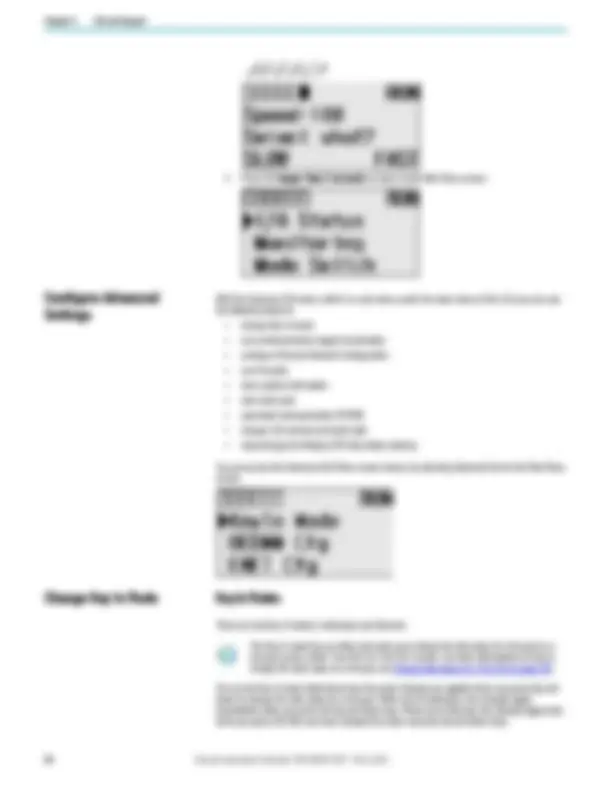
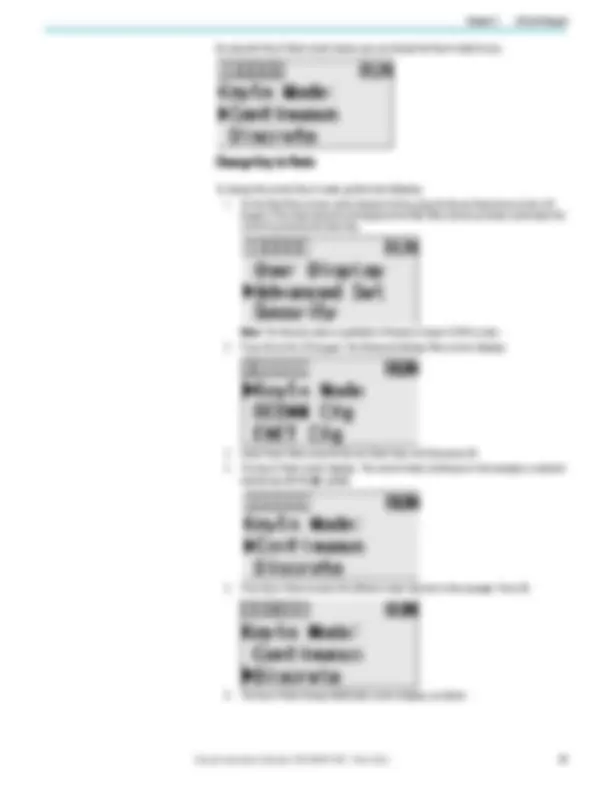
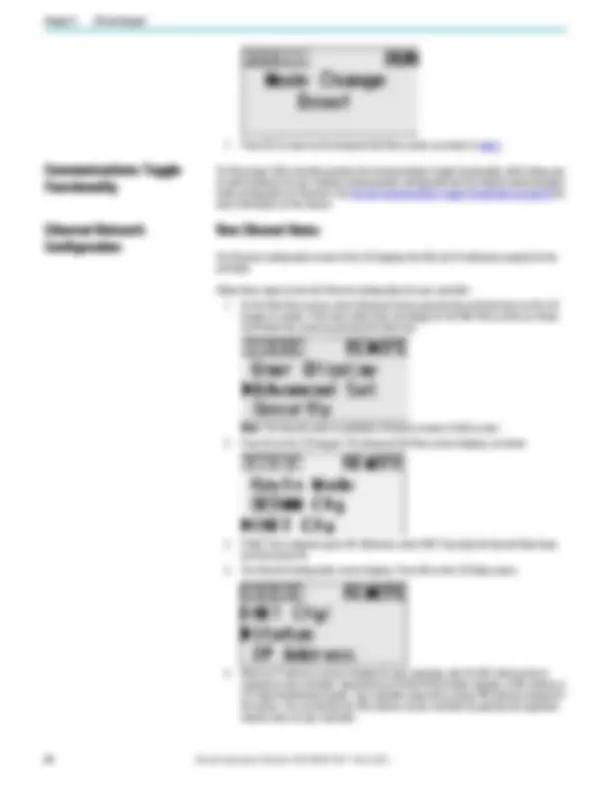
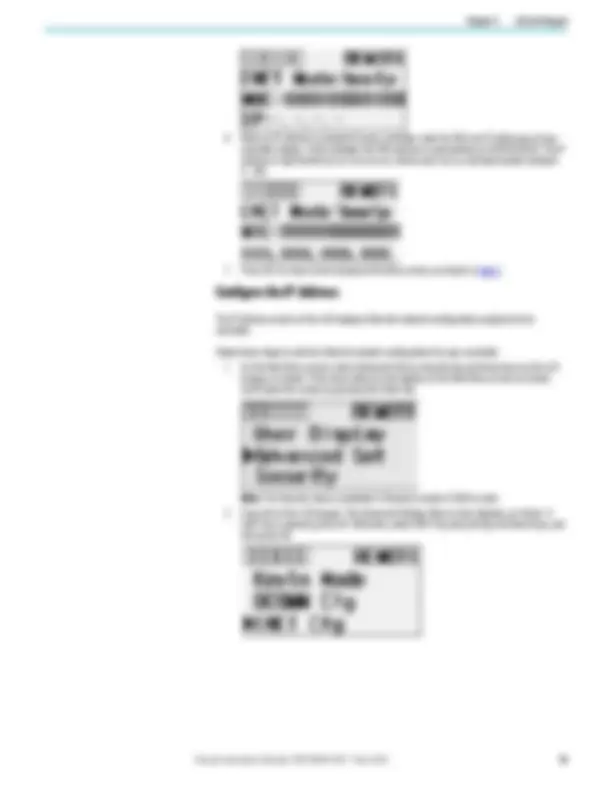
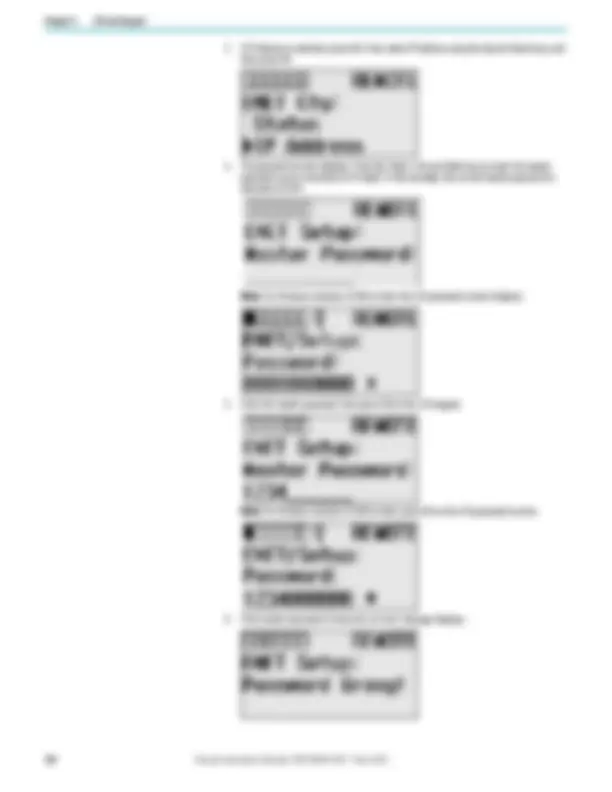
Estude fácil! Tem muito documento disponível na Docsity
Ganhe pontos ajudando outros esrudantes ou compre um plano Premium
Prepare-se para as provas
Estude fácil! Tem muito documento disponível na Docsity
Prepare-se para as provas com trabalhos de outros alunos como você, aqui na Docsity
Os melhores documentos à venda: Trabalhos de alunos formados
Prepare-se com as videoaulas e exercícios resolvidos criados a partir da grade da sua Universidade
Responda perguntas de provas passadas e avalie sua preparação.
Ganhe pontos para baixar
Ganhe pontos ajudando outros esrudantes ou compre um plano Premium
Comunidade
Peça ajuda à comunidade e tire suas dúvidas relacionadas ao estudo
Descubra as melhores universidades em seu país de acordo com os usuários da Docsity
Guias grátis
Baixe gratuitamente nossos guias de estudo, métodos para diminuir a ansiedade, dicas de TCC preparadas pelos professores da Docsity
RSLogix 5000 manual de programação
Tipologia: Esquemas
1 / 294
Esta página não é visível na pré-visualização
Não perca as partes importantes!
MicroLogix 1400 Programmable Controllers User Manual
WARNING: Identifies information about practices or circumstances that can cause an explosion in a hazardous environment, which may lead to personal injury or death, property damage, or economic loss.
ATTENTION: Identifies information about practices or circumstances that can lead to personal injury or death, property damage, or economic loss. Attentions help you identify a hazard, avoid a hazard, and recognize the consequence.
IMPORTANT Identifies information that is critical for successful application and understanding of the product.
SHOCK HAZARD: Labels may be on or inside the equipment, for example, a drive or motor, to alert people that dangerous voltage may be present.
BURN HAZARD: Labels may be on or inside the equipment, for example, a drive or motor, to alert people that surfaces may reach dangerous temperatures.
ARC FLASH HAZARD: Labels may be on or inside the equipment, for example, a motor control center, to alert people to potential Arc Flash. Arc Flash will cause severe injury or death. Wear proper Personal Protective Equipment (PPE). Follow ALL Regulatory requirements for safe work practices and for Personal Protective Equipment (PPE).
Identifies information that is useful and can help to make a process easier to do or easier to understand.
Appendix D
Use ControlFLASH to Upgrade
Appendix E
Connect to Networks Via RS-
Table of Contents Appendix F MicroLogix 1400 Distributed
Table of Contents
Notes:
Preface
About This Publication Use this manual if you are responsible for designing, installing, programming, or troubleshooting
control systems that use MicroLogix™ 1400 controllers.
You should have a basic understanding of electrical circuitry and familiarity with relay logic. If you do not, obtain the proper training before using this product.
Rockwell Automation recognizes that some of the terms that are currently used in our industry and in this publication are not in alignment with the movement toward inclusive language in technology. We are proactively collaborating with industry peers to find alternatives to such terms and making changes to our products and content. Please excuse the use of such terms in our content while we implement these changes.
Purpose of this Manual This manual is a reference guide for MicroLogix 1400 controllers and 1762 expansion I/O. It describes the procedures you use to install, wire, and troubleshoot your controller. This manual:
See MicroLogix 1400 Programmable Controllers Reference Manual, publication 1766-RM001, for the MicroLogix 1400 instruction set and for application examples to show the instruction set in use. See your RSLogix 500®/RSLogix™ Micro programming software user documentation for more information on programming your MicroLogix 1400 controller.
Download Firmware, AOP,
EDS, and Other Files
Download firmware, associated files (such as AOP, EDS, and DTM), and access product release notes from the Product Compatibility and Download Center at rok.auto/pcdc.
Summary of Changes This publication contains the following new or updated information. This list includes substantive
updates only and is not intended to reflect all changes.
Additional Resources These documents contain additional information concerning related products from Rockwell
Automation.
Topic Page Updated template throughout Added 1762 Expansion I/O Specifications 134 Updated Certifications 135
Resource Description MicroLogix 1400 Programmable Controllers Reference Manual, publication 1766-RM
Information on the MicroLogix 1400 Controllers instruction set.
MicroLogix 1400 Programmable Controllers Installation Instructions, publication 1766 -IN
Information on mounting and wiring the MicroLogix 1400 Controllers, including a mounting template for easy installation.
Advanced Interface Converter (AIC+) User Manual, publication 1761-UM004 A description on how to install and connect an AIC+. This manual also contains information on network wiring. DeviceNet Interface User Manual, publication 1761-UM005 Information on how to install, configure, and commission a DeviceNet® Interface. DF1 Protocol and Command Set Reference Manual, publication 1770-6.5.16 Information on DF1 open protocol. Modbus Protocol Specifications available from www.modbus.org Information about the Modbus protocol. Distributed Network Protocol (DNP3) Specifications Available from www.dnp.org Information about the Distributed Network Protocol.
System Security Design Guidelines Reference Manual, publication SECURE-RM
Provides guidance on how to conduct security assessments, implement Rockwell Automation® products in a secure system, harden the control system, manage user access, and dispose of equipment.
UL Standards Listing for Industrial Control Products, publication CMPNTS-SR002 Assists original equipment manufacturers (OEMs) with construction of panels, to help ensure that they conform to the requirements of Underwriters Laboratories. American Standards, Configurations, and Ratings: Introduction to Motor Circuit Design, publication IC-AT
Provides an overview of American motor circuit design based on methods that are outlined in the NEC.
Chapter 1
Hardware Features The MicroLogix 1400 programmable controller contains a power supply, input and output circuits, a
processor, an isolated combination RS-232/RS-485 communication port, an Ethernet port, and a non-isolated RS-232 communication port. Each controller supports 32 discrete I/O points (20 digital inputs, 12 discrete outputs) and 6 analog I/O points (4 analog inputs and 2 analog outputs: 1766-L32BWAA, 1766-L32AWAA, and 1766-L32BXBA only).
Figure 1 shows the hardware features of the controller.
ESC
OK
Left side view Top view
Controller Description
Description Description 1 Comm port 2 – 9-pin D-shell RS-232C connector 8 Battery connector 2 Memory module 9 Output terminal block 3 User 24V (for 1766-BWA and 1766-BWAA only) 10 LCD display 4 Input terminal block 11 Status indicator panel 5 LCD display keypad (ESC, OK, Up, Down, Left, Right) 12 Comm port 1 – RJ45 connector 6 Battery compartment 13 Comm port 0 – 8-pin mini DIN RS-232C/RS-485 connector 7 1762 expansion bus connector
Chapter 1 Hardware Overview
Component Descriptions MicroLogix 1400 Memory Module and Built-in Real-time Clock
The controller has a built-in real-time clock to provide a reference for applications that need time- based control.
The controller is shipped with a memory module port cover in place. You can order a memory module, 1766-MM1, as an accessory. The memory module provides optional backup of your user program and data, and is a means to transport your programs between controllers.
The program and data in your MicroLogix 1400 is non-volatile and is stored when the power is lost to the controller. The memory module provides additional backup that can be stored separately. The memory module does not increase the available memory of the controller.
Controller Input and Output Description
Catalog Number
Description
Input Power User Power Embedded Discrete I/O Embedded Analog I/O Comm. Ports
12 fast 24V DC inputs 8 normal 24V DC inputs 12 relay outputs
None
1 Ethernet 1 RS-232(2)
None
20 120V AC inputs 12 relay outputs
12 fast 24V DC inputs 8 normal 24V DC inputs 6 relay outputs 3 fast DC outputs 3 normal DC outputs
12 fast 24V DC inputs 8 normal 24V DC inputs 12 relay outputs
4 voltage inputs 2 voltage outputs
None
20 120V AC inputs 12 relay outputs
12 fast 24V DC inputs 8 normal 24V DC inputs 6 relay outputs 3 fast DC outputs 3 normal DC outputs
(1) Isolated RS-232/RS-485 combo port. (2) Non-isolated RS-232. Standard D-sub connector
M Mod ule em^ o^ ry
Chapter 1 Hardware Overview
Programming Program the MicroLogix 1400 controller using RSLogix 500/RSLogix Micro software, version 8.10.
or later for Series A controllers and version 8.30.00 or later for Series B and Series C controllers. Communication cables for programming are available separately from the controller and software.
Firmware Revision History
Features are added to the controllers through firmware updates. Use the listing in Table 1 to be sure that your controller’s firmware is at the level you need. Firmware updates are not required, but they allow you to access to the new features.
ATTENTION: UNSUPPORTED CONNECTION Do not connect a MicroLogix 1400 controller to another MicroLogix family controller such as MicroLogix 1000, MicroLogix 1200, MicroLogix 1500, or the network port of a 1747-DPS1 port splitter with a 1761-CBL-AM (8-pin mini-DIN to 8-pin mini-DIN) cable or equivalent. This type of connection damages the RS-232/RS-485 communication port (Channel 0) of the MicroLogix 1400 and/or the controller itself. The communication pins that are used for RS-485 communications on the MicroLogix 1400 are alternately used for 24V power on the other MicroLogix controllers and the network port of the 1747-DPS1 port splitter.
Catalog Number
Series Letter
OS Revision Letter
Firmware Release Number
Release Date Enhancement
A A FRN1 August 2005 Initial product release
A B FRN2 October 2005 According to the SRAM component, MicroLogix 1400 could cause Hard-fault at the start of the Operating System in a very high temperature environment. Corrected. A C FRN3 February 2006 Added Data file write feature through web server.
B A FRN4 February 2007
B B FRN5 May 2007
1766-L32DWD B B FRN5 May 2007 • Initial Product release. Supports the features that are listed above for the 1766- L32AWA, 1766-L32BWA, and 1766-L32BBB controllers.
(1) OS = Operating system
Chapter 1 Hardware Overview
Communication Options MicroLogix 1400 controllers provide three communications ports: an isolated combination RS-232/
RS-485 communication port (Channel 0), an Ethernet port (Channel 1), and a non-isolated RS- communication port (Channel 2).
You can connect Channel 0 and Channel 2 ports on the MicroLogix 1400 controller to the following:
When connecting to an RS-485 network with DH-485, DF1 half-duplex master/slave, Modbus RTU master/slave, or DNP3 slave protocols, you can connect the MicroLogix 1400 controller directly via Channel 0 without an Advanced Interface Converter, catalog number 1761-NET-AIC. The Channel 0 combo port provides both RS-232 and RS-485 isolated connections. The appropriate electrical interface is selected through your choice of communication cable. The existing MicroLogix 1761 communication cables provide an interface to the RS-232 drivers. The 1763-NC01 cable provides an interface to the RS-485 drivers.
You can also connect the controller to serial devices, such as barcode readers, weigh scales, serial printers, and other intelligent devices, using ASCII. See Default Communication Configuration on page 57 for the configuration settings for Channel 0. MicroLogix 1400 controller can be connected directly to the RS-485 network via channel 0, using ASCII.
The MicroLogix 1400 supports EtherNet/IP™ communication via the Ethernet communication Channel 1. In addition, either Modbus TCP or DNP3 over IP can be enabled for Channel 1. You can connect your controller to a local area network that provides communication between various devices at 10 Mbps or 100 Mbps. This port supports CIP explicit messaging (message exchange) only. The controller cannot be used for CIP implicit messaging (real-time I/O messaging). The controller also includes an embedded web server that allows viewing of not only module information, TCP/IP configuration, and diagnostic information, but also includes the data table memory map and data table monitor screen using a standard web browser.
See Chapter 4 for more information on how to connect to the available communication options.
Chapter 2
Installation Considerations Most applications require installation in an industrial enclosure (Pollution Degree 2
(a) ) to reduce the effects of electrical interference (Over Voltage Category II(b)^ ) and environmental exposure. Locate your controller as far as possible from power lines, load lines, and other sources of electrical noise such as hard-contact switches, relays, and AC motor drives. For more information on proper grounding guidelines, see Industrial Automation Wiring and Grounding Guidelines, publication 1770-4.1.
Safety Considerations Safety considerations are an important element of proper system installation. Actively considering
the safety of yourself and others, and the condition of your equipment, is of primary importance. We recommend reviewing the following safety considerations.
Hazardous Location Considerations
This equipment is suitable for use in Class I Division 2, Groups A, B, C, D, or non-hazardous locations only. The following WARNING statement applies to use in hazardous locations.
(a) Pollution Degree 2 is an environment where normally only non-conductive pollution occurs except that occasionally temporary conductivity caused by condensation shall be expected. (b) Overvoltage Category II is the load level section of the electrical distribution system. At this level, transient voltages are controlled and do not exceed the impulse voltage capability of the products insulation.
ATTENTION: Electrostatic discharge can damage semiconductor devices inside the controller. Do not touch the connector pins or other sensitive areas.
ATTENTION: Vertical mounting of the controller is not supported due to heat build-up considerations.
ATTENTION: Be careful of metal chips when drilling mounting holes for your controller or other equipment within the enclosure or panel. Drilled fragments that fall into the controller or I/O modules could cause damage. Do not drill holes above a mounted controller if the protective debris shields are removed or the processor is installed.
WARNING: Do not place the MicroLogix 1400 programmable controller in direct sunlight. Prolonged exposure to direct sunlight could degrade the LCD display and have adverse effects on the controller. The controller is not designed for outdoor use.
Chapter 2 Install Your Controller
Use only the following communication cables in Class I Division 2 hazardous locations.
Disconnect Main Power
The main power disconnect switch should be located where operators and maintenance personnel have quick and easy access to it. In addition to disconnecting electrical power, all other sources of power (pneumatic and hydraulic) should be de-energized before working on a machine or process that is controlled by a controller.
Safety Circuits
Circuits installed on the machine for safety reasons, like overtravel limit switches, stop push buttons, and interlocks, should always be hard-wired directly to the master control relay. These devices must be wired in series so that when any one device opens, the master control relay is de- energized, which removes power to the machine. Never alter these circuits to defeat their function. Serious injury or machine damage could result.
Power Distribution
There are some points about power distribution that you should know:
WARNING: EXPLOSION HAZARD
Environment Classification Communication Cables
Class I Division 2 Hazardous Environment
1761-CBL-AC00 Series C or later 1761-CBL-AM00 Series C or later 1761-CBL-AP00 Series C or later 1761-CBL-PM02 Series C or later 1761-CBL-HM02 Series C or later 2707-NC9 Series C or later 1763-NC01 Series A or later 1747-CP3 Series
WARNING: Explosion Hazard Do not replace components, connect equipment, or disconnect equipment unless power has been switched off.
WARNING: Explosion Hazard Do not connect or disconnect connectors while the circuit is live.