
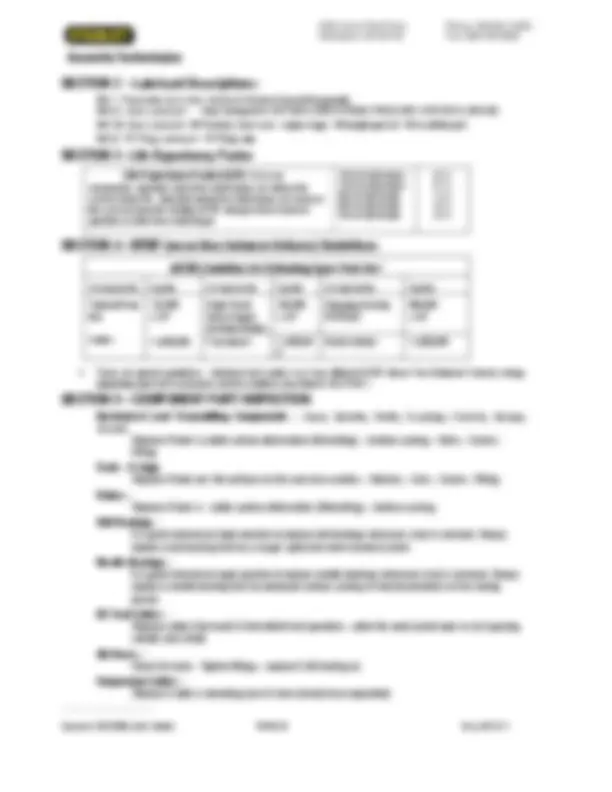
Estude fácil! Tem muito documento disponível na Docsity
Ganhe pontos ajudando outros esrudantes ou compre um plano Premium
Prepare-se para as provas
Estude fácil! Tem muito documento disponível na Docsity
Prepare-se para as provas com trabalhos de outros alunos como você, aqui na Docsity
Os melhores documentos à venda: Trabalhos de alunos formados
Prepare-se com as videoaulas e exercícios resolvidos criados a partir da grade da sua Universidade
Responda perguntas de provas passadas e avalie sua preparação.
Ganhe pontos para baixar
Ganhe pontos ajudando outros esrudantes ou compre um plano Premium
Comunidade
Peça ajuda à comunidade e tire suas dúvidas relacionadas ao estudo
Descubra as melhores universidades em seu país de acordo com os usuários da Docsity
Guias grátis
Baixe gratuitamente nossos guias de estudo, métodos para diminuir a ansiedade, dicas de TCC preparadas pelos professores da Docsity
Manual detalhado de preventivas
Tipologia: Esquemas
1 / 2
Esta página não é visível na pré-visualização
Não perca as partes importantes!
5335 Avion Park Drive Phone: 440-461- Cleveland, OH 44143 Fax: 866-239-
Document: 20Z101800, Vault: Intralink PCN12215 Rev-J, 09-15-
Stanley assembly tools are designed for tightening threaded fasteners. Application variables such as torque level, free run time, joint type, operator practices and maintenance procedures can affect assembly tool durability. The following guidelines recommend maintenance intervals for specific tool types and components. Use the table at the bottom to adjust the intervals for actual torque level. Special assembly tools such as crowfoot and tubenut tools are used where space is limited. To fit into these spaces, typical robust design standards cannot apply, and these tools require more frequent maintenance than standard tools.
Monthly Safety inspection:^ Inspect condition of all air hoses or power cables and connections, Inspect tool suspension components and torque reaction devices. Replace worn or damaged components. Replace worn or damaged safety labels. REFERENCE SECTION 5 Note: Failure to perform this inspection could result in unsafe and hazardous conditions being present
First 5, cycles
High Torque Crowfoot tools (250 NM and up): Inspect tool using external transducer every 1000 cycles to ensure calibration is accurate. Recalibrate if required.
25,000 cycles Or Weekly
Tubenut tools: Lubricate gear head 2-3 pumps (Ref. 2a) Note: Failure to perform this maintenance will result in damage to socket journals and mating housing surfaces causing undue expense and down time. Inspect housing, baseplate, socket, & socket bushings and replace any visibly worn components.
75,000 cycles Crowfoot tools:^ Lubricate gear head 2-3 pumps (Ref. 2a)^ Note: Failure to perform this maintenance could result in damage to socket journals and mating housing surfaces causing undue expense and down time. Inspect housing, baseplate, socket, & socket bushings and replace any visibly worn components.
150,000 cycles Angle heads:^ Lubricate angle head gears 2-3 pumps (Ref. 2a)^ Note: Failure to perform this maintenance could reduce gear life 20 to 50%. Inspect packing cap to ensure tight; inspect pin and ball retainer to ensure they are in good operating condition.
250,000 cycles Pneumatic tools: Disassemble motor; replace rotor blades and motor bearings. Inspect all valves and seals and replace any worn components. Ref 2c Inspect clutch and replace any worn components. Electric and Pneumatic tools: Disassemble output (angle head, crowfoot head, spindle support, etc.), inspect for wear, replace bearings and any worn parts. Replace grease (Ref 2a) covering all tooth spaces. Or replenish Gear Oil (Ref 2b)
500,000 cycles Electric tools: Inspect switches, cables and connectors and replace any worn components. Electric and Pneumatic tools: Disassemble gear case and output (angle head, crowfoot head, spindle support, etc.), inspect for wear, replace bearings and any visibly worn parts Replace grease (Ref 2a) covering all tooth spaces. Or replenish Gear Oil (Ref 2b)
5335 Avion Park Drive Phone: 440-461- Cleveland, OH 44143 Fax: 866-239-
Document: 20Z101800, Vault: Intralink PCN12215 Rev-J, 09-15-
Ref. 1: Pneumatic tool motor lubricant: Air tool oil (emulsifying grade) Ref.2a : Gear Lubricant – Dow Corning MOLYCOTE® G-4700 EXTREME PRESSURE SYNTHETIC GREASE Ref. 2b: Gear Lubricant - #5 Planetary Gear case – output stage – 90 weight gear oil - fill to outflow port. Ref 2c: “ O” Ring Lubricant – “ O” Ring Lube
components, operation above the rated torque can reduce the cycle to failure life. Operation below the rated torque can increase the cycle to failure life. Multiply MTBF rating by these factor for operation at other than rated torque
120% of rated torque 110% of rated torque 90% of rated torque 80% of rated torque 70% of rated torque
0.5 X 0.7 X 1.3 X 2.0 X 2.5 X
Components Cycles Components Cycles Components Cycles
Tubenut/Crow foot
x LEF
Angle Heads Other Outputs Air Motor Blades
x LEF
Planetary Gearing Air Motors
x LEF
Cables (^) >1,000,000 Transducers >1,000, 0
Electric Motors >1,000,
Sockets