
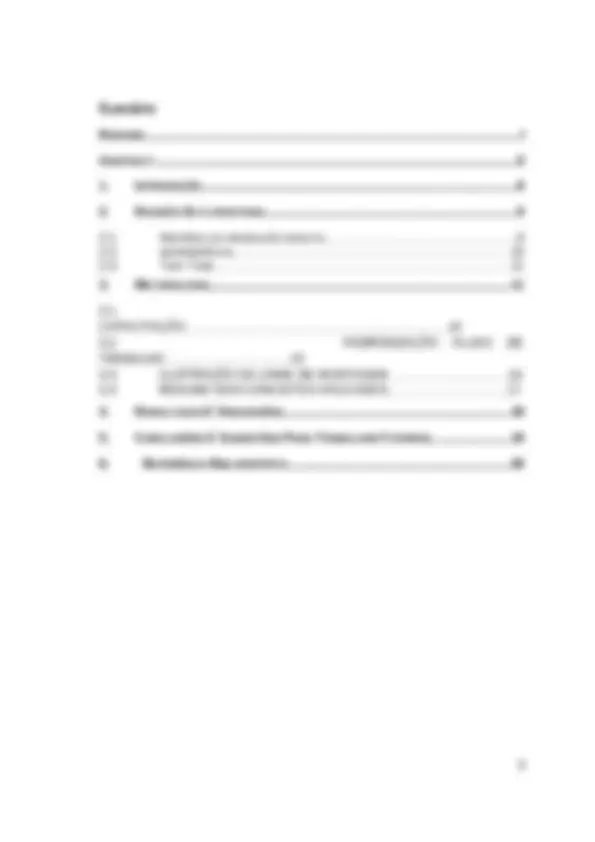
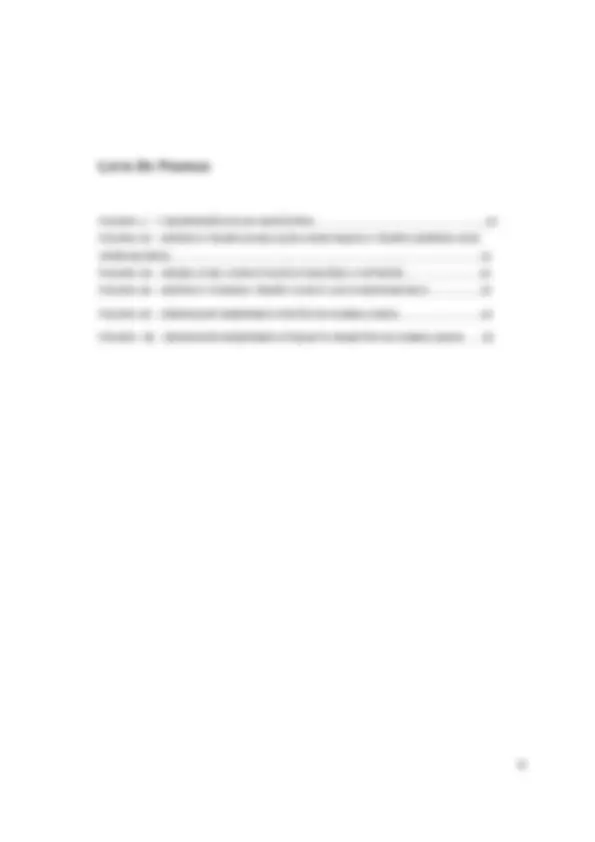
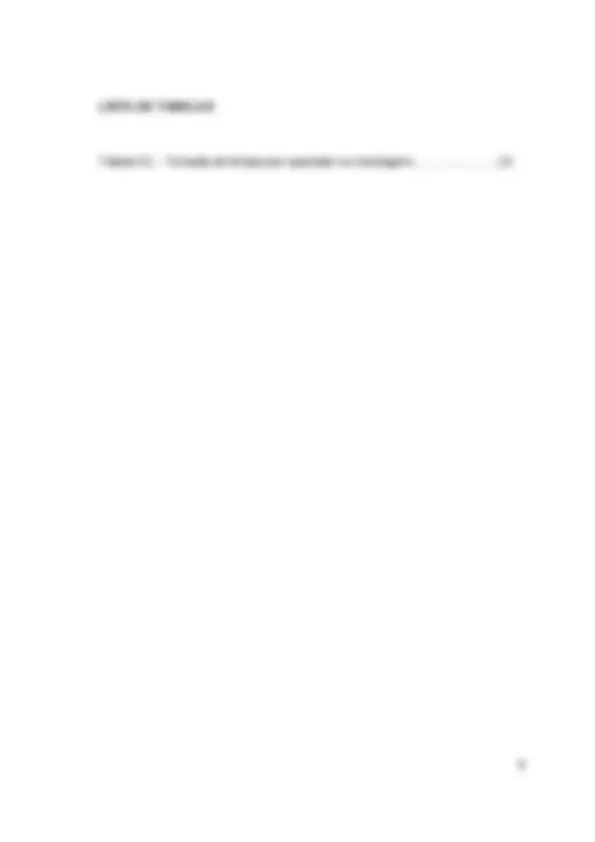
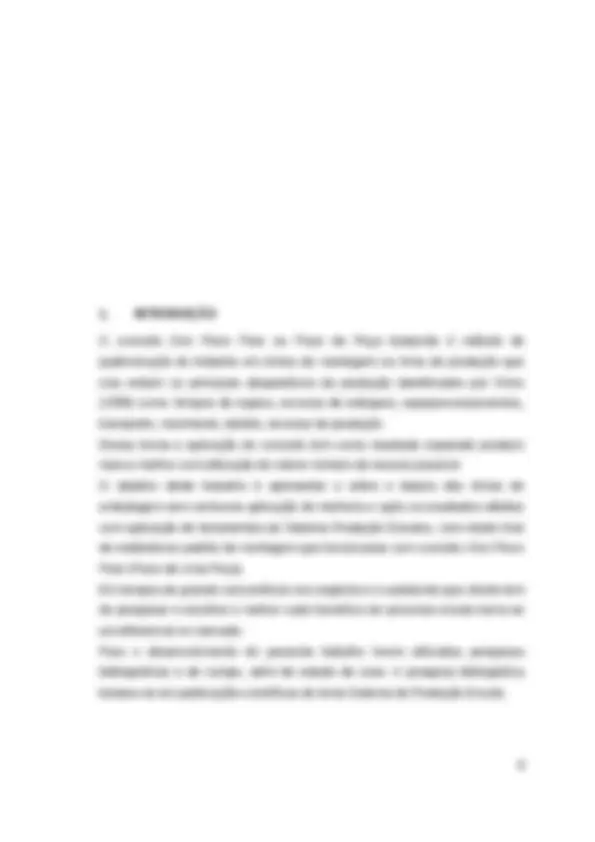
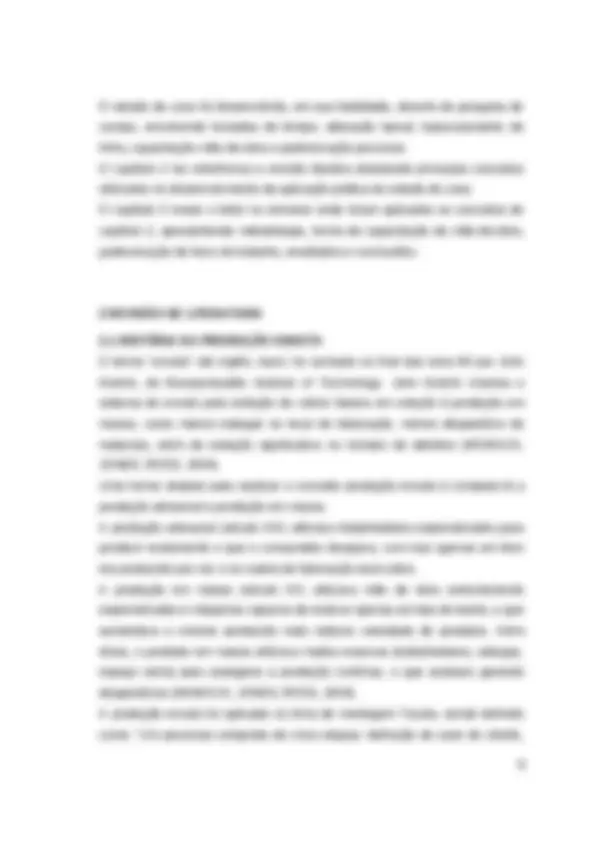
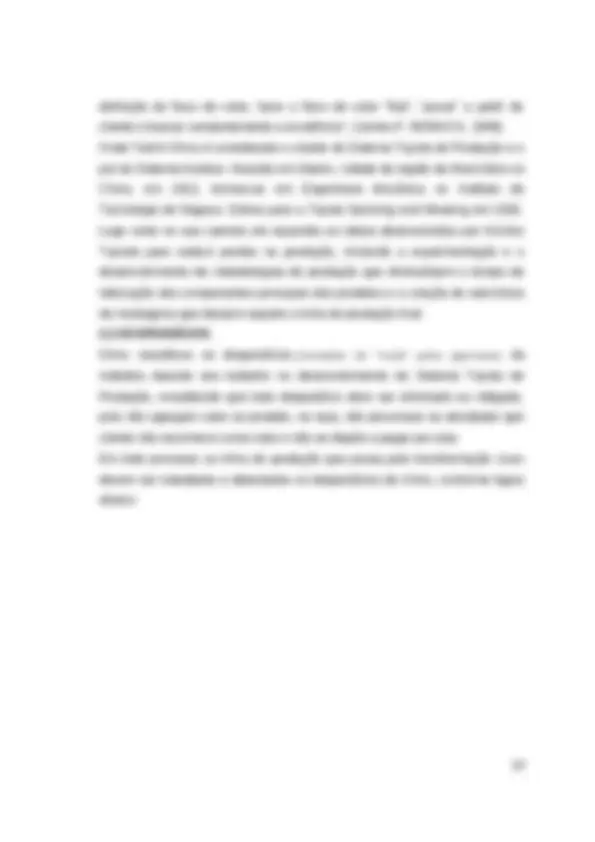
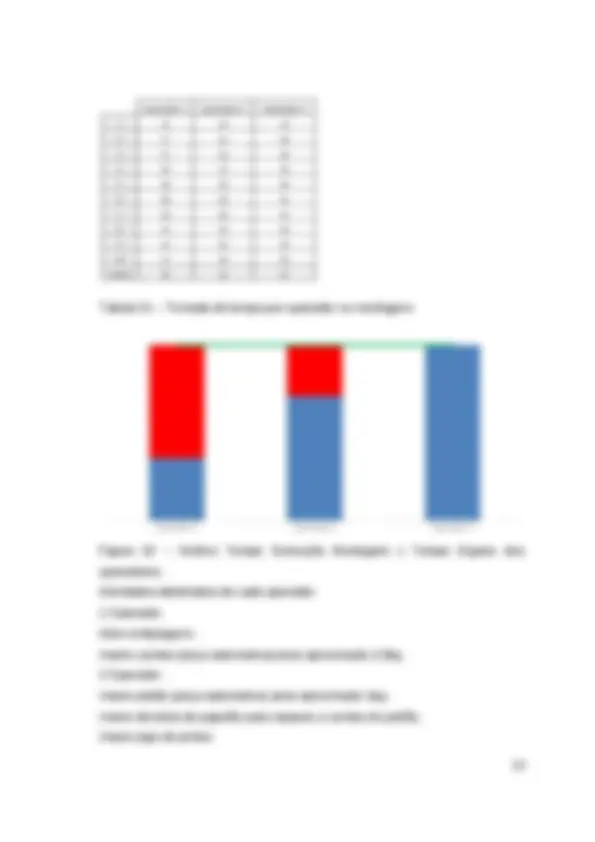
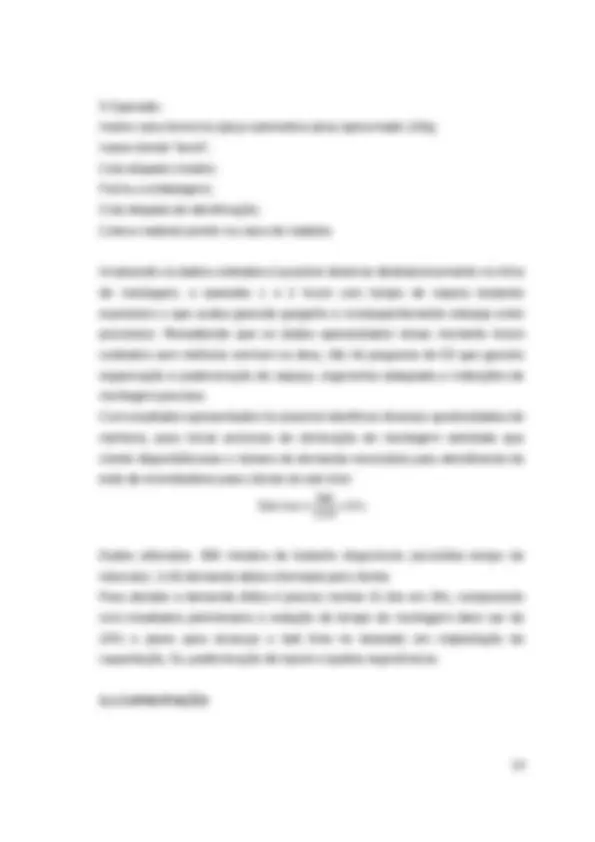
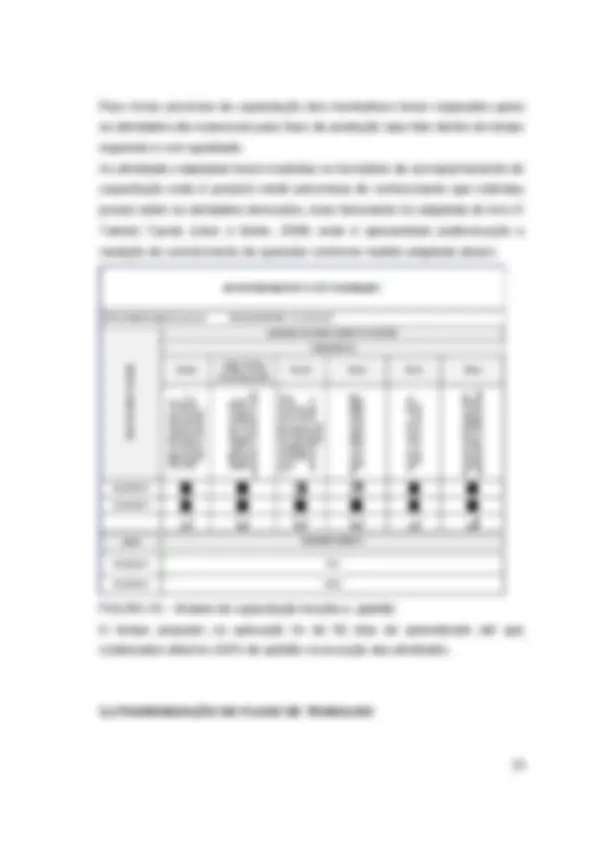
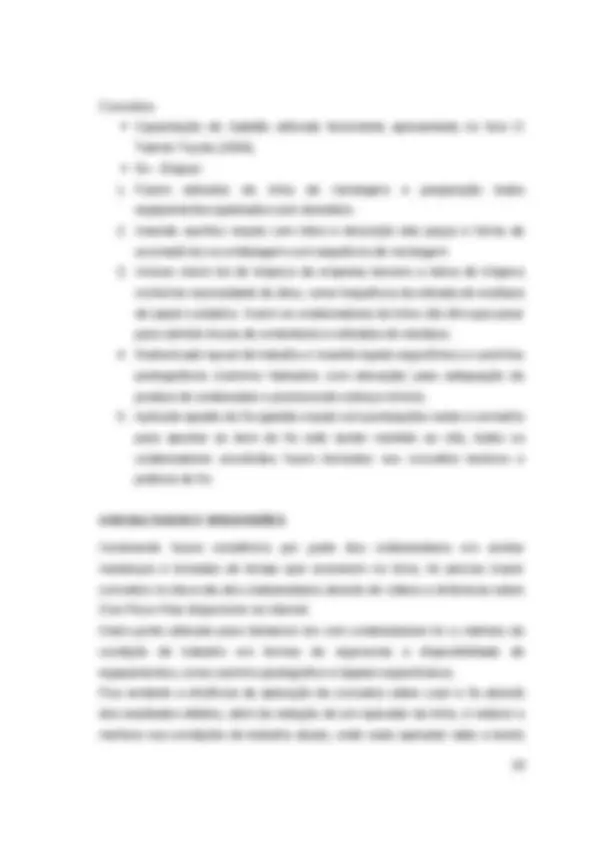
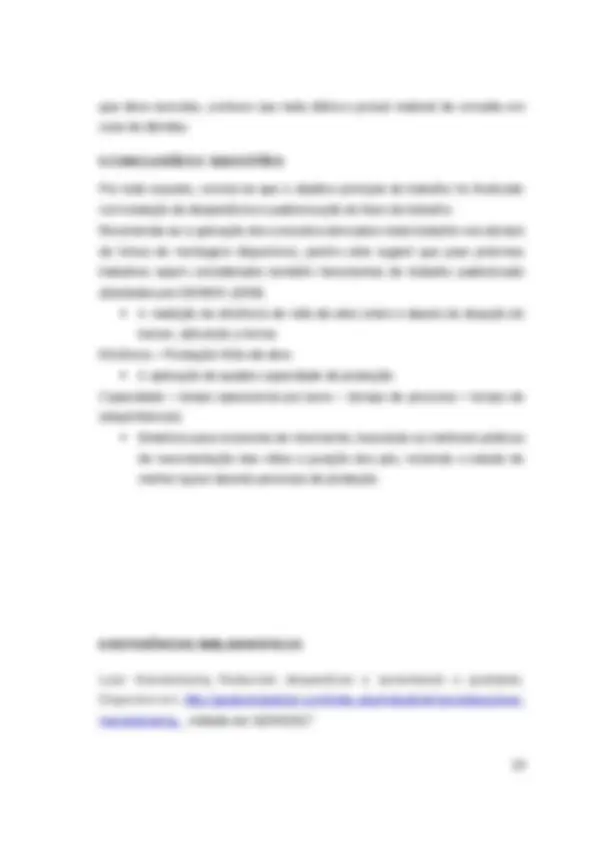
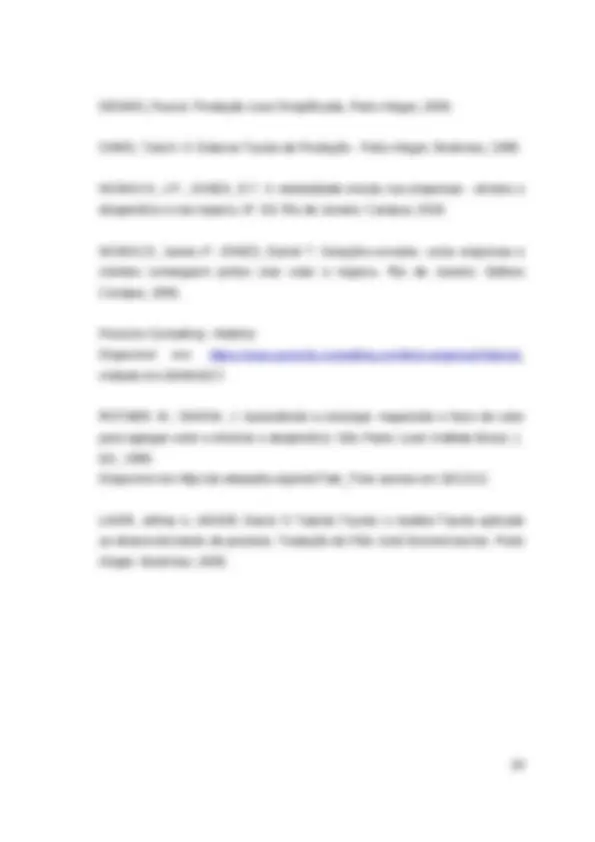
Estude fácil! Tem muito documento disponível na Docsity
Ganhe pontos ajudando outros esrudantes ou compre um plano Premium
Prepare-se para as provas
Estude fácil! Tem muito documento disponível na Docsity
Prepare-se para as provas com trabalhos de outros alunos como você, aqui na Docsity
Os melhores documentos à venda: Trabalhos de alunos formados
Prepare-se com as videoaulas e exercícios resolvidos criados a partir da grade da sua Universidade
Responda perguntas de provas passadas e avalie sua preparação.
Ganhe pontos para baixar
Ganhe pontos ajudando outros esrudantes ou compre um plano Premium
Comunidade
Peça ajuda à comunidade e tire suas dúvidas relacionadas ao estudo
Descubra as melhores universidades em seu país de acordo com os usuários da Docsity
Guias grátis
Baixe gratuitamente nossos guias de estudo, métodos para diminuir a ansiedade, dicas de TCC preparadas pelos professores da Docsity
Lean e melhoria continua em linha de embalagem de peças automotivas e montagem de kit.
Tipologia: Teses (TCC)
1 / 20
Esta página não é visível na pré-visualização
Não perca as partes importantes!
Faculdade de Jaguariúna - FAJ Programa De Pós-Graduação Em Engenharia De Produção
Monografia apresentada ao Programa de Pós-Graduação em Gestão da Qualidade Lean Seis Sigma , da Faculdade de Jaguariúna - FAJ, como requisito para obtenção do Título de especialização. Jaguariúna, São Paulo
Monografia apresentada ao Programa de Pós-Graduação em Gestão da Qualidade Lean Seis Sigma, para obtenção do título de especialização.
FIGURA 1 – 7 DESPERDÍCIOS DA INDÚSTRIA.............................................................. FIGURA 02 - GRÁFICO TEMPO EXECUÇÃO MONTAGEM X TEMPO ESPERA DOS OPERADORES................................................................................................................ FIGURA 03 – MODELO DE CAPACITAÇÃO FUNÇÕES X APTIDÃO........................... FIGURA 04 - GRÁFICO TOMADA TEMPO COM FLUXO PADRONIZADO................... FIGURA 05 - OPERADOR INSERINDO PISTÃO NA EMBALAGEM.............................. FIGURA 06 - OPERADOR INSERINDO ETIQUETA INMETRO NA EMBALAGEM.......
Tabela 01 – Tomada de tempo por operador na montagem..........................
IN LINES OF PACKAGING OF AUTOMOTIVE PARTS. 2017 Monograph presented to the Post-Graduate Program in Quality Management Lean Six Sigma, focus on Production Engineering -, Jaguariúna -São Paulo
Applying Lean concepts in automotive parts assembly lines is now essential to ensure production targets are met and assembly errors are reduced. To begin the process of Lean deployment in the Jundiaí parts distribution center, the line selected to start was kit assembly line, where significant results were obtained with concepts of standardization workflow, training tools and 5S. It is recommended that concepts be replicated in the other assembly lines and for future applications are considered the measurement of labor efficiency and application of the production capacity table. KEYWORDS: Kaizen, Takt time, One Piece Flow, production line.
O conceito One Piece Flow ou Fluxo de Peça traduzido é método de padronização do trabalho em linhas de montagem ou linha de produção que visa reduzir os principais desperdícios da produção identificados por Ohno (1999) como: tempos de espera, excesso de estoques, superprocessamentos, transporte, movimento, defeito, excesso de produção. Dessa forma a aplicação do conceito tem como resultado esperado produzir mais e melhor com utilização do menor número de recurso possível. O objetivo deste trabalho é apresentar o antes e depois das linhas de embalagem sem nenhuma aplicação de melhoria e após os resultados obtidos com aplicação de ferramentas do Sistema Produção Enxutos, com intuito final de estabelecer padrão de montagem que funcionasse com conceito One Piece Flow (Fluxo de Uma Peça). Em tempos de grande concorrência nos negócios e a autotomia que cliente tem de pesquisar e escolher o melhor custo benefício ter processo enxuto torna-se um diferencial no mercado. Para o desenvolvimento do presente trabalho foram utilizadas pesquisas bibliográficas e de campo, além de estudo de caso. A pesquisa bibliográfica baseou-se em publicações científicas do tema Sistema de Produção Enxuta.
definição do fluxo de valor, fazer o fluxo de valor “fluir”, “puxar” a partir do cliente e buscar constantemente a excelência”. (James P. WOMACK, 1996). Onde Taiichi Ohno é considerado o criador do Sistema Toyota de Produção e o pai do Sistema Kanban. Nascido em Dairen, cidade da região da Manchúria na China, em 1912, formou-se em Engenharia Mecânica no Instituto de Tecnologia de Nagoya. Entrou para a Toyota Spinning and Wearing em 1932. Logo cedo na sua carreira ele expandiu as ideias desenvolvidas por Kiichiro Toyoda para reduzir perdas na produção, iniciando a experimentação e o desenvolvimento de metodologias de produção que diminuíssem o tempo de fabricação dos componentes principais dos produtos e a criação de sub-linhas de montagens que dessem suporte a linha de produção final. 2.2 DESPERDÍCIOS Ohno classificou os desperdícios (chamados de "muda" pelos japoneses) da indústria durante seu trabalho no desenvolvimento do Sistema Toyota de Produção, ressaltando que todo desperdício deve ser eliminado ou mitigado, pois não agregam valor ao produto, ou seja, são processos ou atividades que cliente não reconhece como valor e não se dispõe a pagar por elas. Em todo processo ou linha de produção que passa pela transformação Lean devem ser estudados e detectados os desperdícios de Ohno, conforme figura abaixo:
Figura 01 – 7 Desperdícios da Indústria 2.3 TAKT TIME O takt time é balanceamento da linha, onde calculamos o tempo que se deve produzir uma peça ou produto, baseado no ritmo de vendas, para atender a demanda dos clientes. Calculado dividindo-se o volume da demanda do cliente por turno (necessidade programada) pelo tempo disponível de trabalho por turno, subtraindo-se os tempos de perdas, interrupções, setups , refeição, etc. (ROTHER, 1998)
Operador 1 Operador 2 Operador 3 1 15 29 43 2 17 31 46 3 15 32 46 4 16 37 50 5 16 33 39 6 18 30 44 7 16 30 45 8 15 32 40 9 15 33 46 10 17 32 46 Média 16 32 45 Tabela 01 – Tomada de tempo por operador na montagem Operador 1 Operador 2 Operador 3 Figura 02 – Gráfico Tempo Execução Montagem x Tempo Espera dos operadores. Atividades detalhadas de cada operador: 1 Operador: Abre embalagem; Insere camisa (peça automotiva) peso aproximado 2,5kg. 2 Operador: Insere pistão (peça automotiva) peso aproximado 1kg; Insere divisória de papelão para separar a camisa do pistão; Insere jogo de juntas.
3 Operador: Insere caixa bronzina (peça automotiva peso aproximado 100g; Insere brinde “boné”; Cola etiqueta Inmetro; Fecha a embalagem; Cola etiqueta de identificação; Coloca material pronto na caixa de madeira. Analisando os dados coletados é possível observar desbalanceamento na linha de montagem, o operador 1 e 2 ficam com tempo de espera bastante expressivo o que acaba gerando gargalho e consequentemente estoque entre processos. Ressaltando que os dados apresentados nesse momento foram coletados sem melhoria nenhum na área, não há programa de 5S que garanta organização e padronização do espaço, ergonomia adequada e instruções de montagem precisas. Com resultados apresentados foi possível identificar diversas oportunidades de melhoria, para iniciar processo de otimização de montagem solicitado que cliente disponibilizasse o número de demanda necessária para atendimento da rede de revendedores para cálculo do takt time: Takt time =
= 34 s Dados utilizados: 398 minutos de trabalho disponíveis (excluídos tempo de intervalo), 1143 demanda diária informada pelo cliente. Para atender a demanda diária é preciso montar 01 kits em 34s, comparando com resultados preliminares a redução de tempo de montagem deve ser de 24% o plano para alcançar o takt time foi baseado em implantação de capacitação, 5s, padronização de layout e ajustes ergonômicos. 3.1 CAPACITAÇÃO
O trabalho padronizado é essencial para entender o melhor jeito de executar as tarefas de forma segura, ágil e prática com mínimo esforço do operador. Segundo Pascal Dennis no capitulo 4 – Trabalho Padronizado (DENNIS, 2008) para entender o trabalho padronizado são aplicados determinados conceitos e benefícios, sendo ressaltados alguns que foram aplicados nesse case : Estabilidade de processos; Pontos de start e paradas pré-definidos; Envolvimento dos colaboradores na melhoria do processo; Treinamento e mapeamento de aptidão. Após estabelecido um fluxo padronizado foram tomados novos tempos conforme gráfico abaixo: Operador 1 Operador 2 FIGURA 04 – GRÁFICO TOMADA TEMPO COM FLUXO PADRONIZADO Atividades detalhadas de cada operador: 1 Operador: Abre embalagem; Insere camisa (peça automotiva) peso aproximado 2,5kg. Insere pistão (peça automotiva) peso aproximado 1kg; Insere divisória de papelão para separar a camisa do pistão; Insere jogo de juntas.
2 Operador: Insere caixa bronzina (peça automotiva peso aproximado 100g; Insere brinde “boné”; Cola etiqueta Inmetro; Fecha a embalagem; Cola etiqueta de identificação; Coloca material pronto na caixa de madeira. 3.3 ILUSTRAÇÃO DA LINHA DE MONTAGEM Para apresentar ao leitor uma noção mais didática sobre conceitos discutidos nesse trabalho, segue abaixo imagens da execução de parte das tarefas: Trata-se de uma linha de montagem 100% manual onde os materiais são dispostos em caixas e cada operador tem determinado número de componentes para inserir na embalagem e etiqueta-las. Figura 05 - Operador inserindo pistão na embalagem. Figura 06 - Operador inserindo etiqueta Inmetro na embalagem. 3.4 RESUMO DOS CONCEITOS APLICADOS Após conceitos de capacitação, 5S serem aplicados na área e definido o fluxo de trabalho padronizado foi notável a melhoria obtida foi possível reduzir um operador da linha e equalizar as atividades de forma que houvesse redução do tempo de espera entre processos.
que deve executar, conhece sua meta diária e possui material de consulta em caso de dúvidas. 5 CONCLUSÕES E SUGESTÕES Por todo exposto, conclui-se que o objetivo principal do trabalho foi finalizado com redução de desperdícios e padronização do fluxo de trabalho. Recomenda-se a aplicação dos conceitos elencados neste trabalho nas demais de linhas de montagem disponíveis, porém cabe sugerir que para próximos trabalhos sejam considerados também ferramentas de trabalho padronizado abordados por DENNIS (2008). A medição da eficiência de mão-de-obra antes e depois da atuação do kaizen, utilizando a forma: Eficiência = Produção/ Mão-de-obra A aplicação do quadro capacidade de produção: Capacidade = tempo operacional por turno ÷ (tempo de processo + tempo de setup/intervalo) Diretrizes para economia de movimento, buscando as melhores práticas de movimentação das mãos e posição dos pés, incluindo o estudo de melhor layout durante processo de produção. 6 REFERÊNCIAS BIBLIOGRÁFICAS Lean Manufacturing Reduzindo desperdícios e aumentando a qualidade. Disponível em: http://gestaoindustrial.com/index.php/industrial/manufatura/lean- manufacturing, visitado em 16/04/
DENNIS, Pascal. Produção Lean Simplificada, Porto Alegre, 2008. OHNO, Taiichi. O Sistema Toyota de Produção. Porto Alegre: Bookman, 1999. WOMACK, J.P.; JONES, D.T. A mentalidade enxuta nas empresas - elimine o desperdício e crie riqueza. 8ª. Ed. Rio de Janeiro: Campus, 2004. WOMACK, James P. JONES, Daniel T. Soluções enxutas: como empresas e clientes conseguem juntos criar valor e riqueza. Rio de Janeiro: Editora Campus, 1996. Porsche Consulting - História Disponível em: https://www.porsche-consulting.com/br/a-empresa/historia/, visitado em 26/06/2017. ROTHER, M.; SHOOK, J. Aprendendo a enxergar: mapeando o fluxo de valor para agregar valor e eliminar o desperdício. São Paulo: Lean Institute Brasil, 1. Ed., 1998. Disponível em http://pt.wikipedia.org/wiki/Takt_Time acesso em 18/12/12. LIKER, Jeffrey k.; MEIER, David. O Talento Toyota: o modelo Toyota aplicado ao desenvolvimento de pessoas. Tradução de Félix José Nonnenmacher. Porto Alegre: Bookman, 2008.