
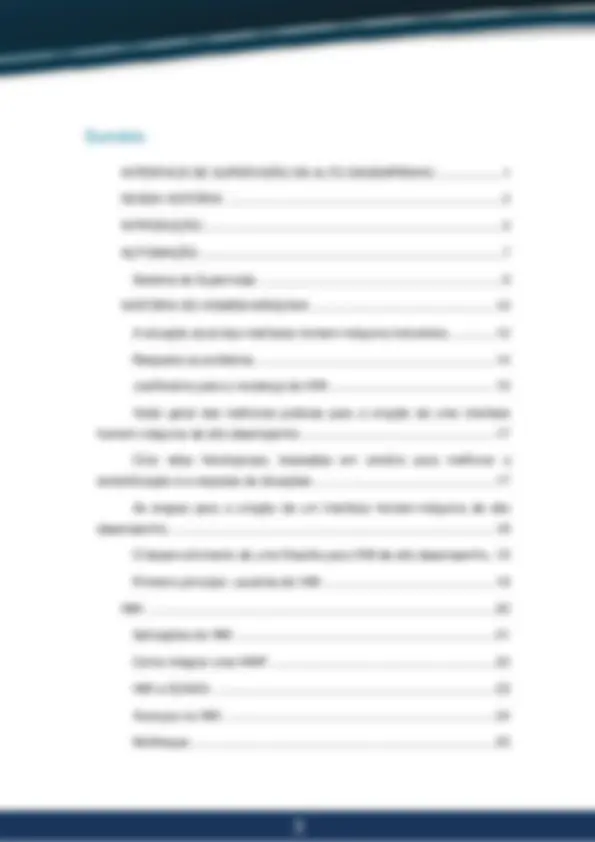
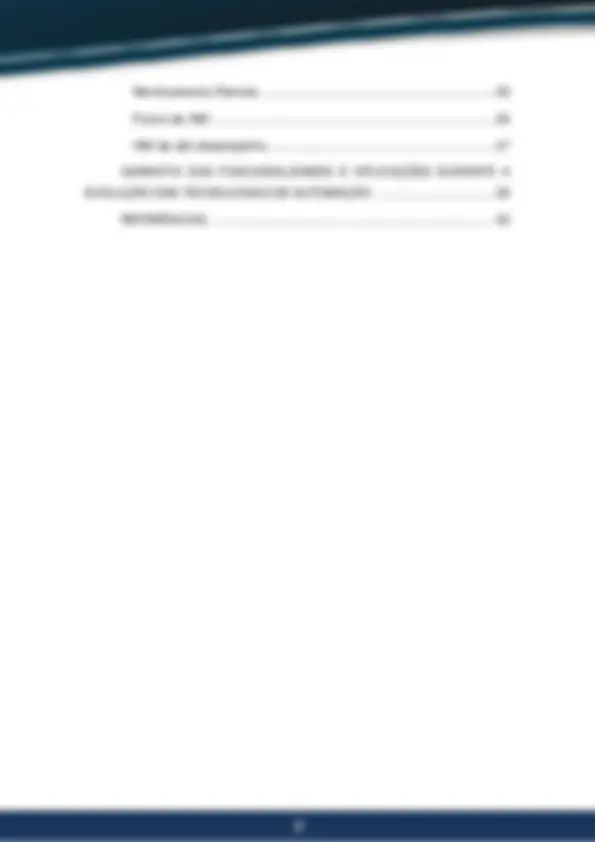
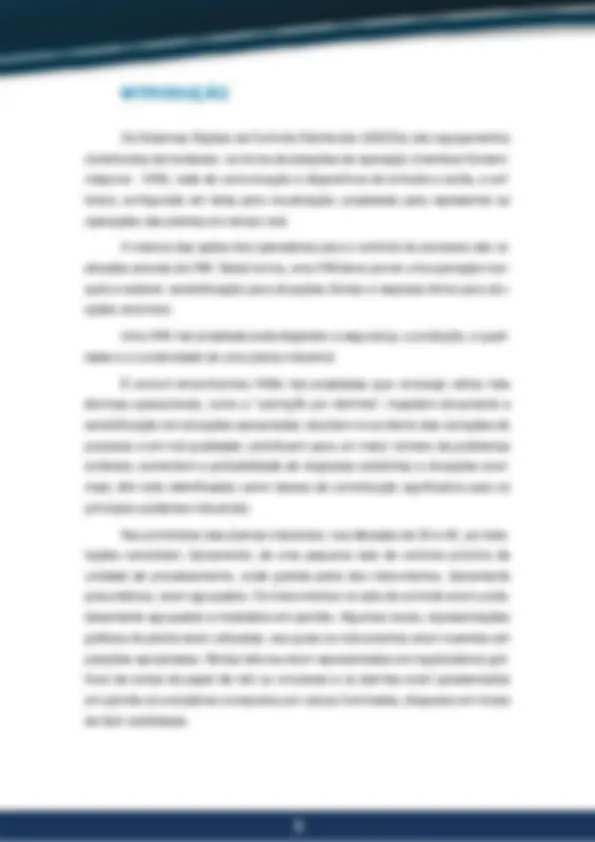
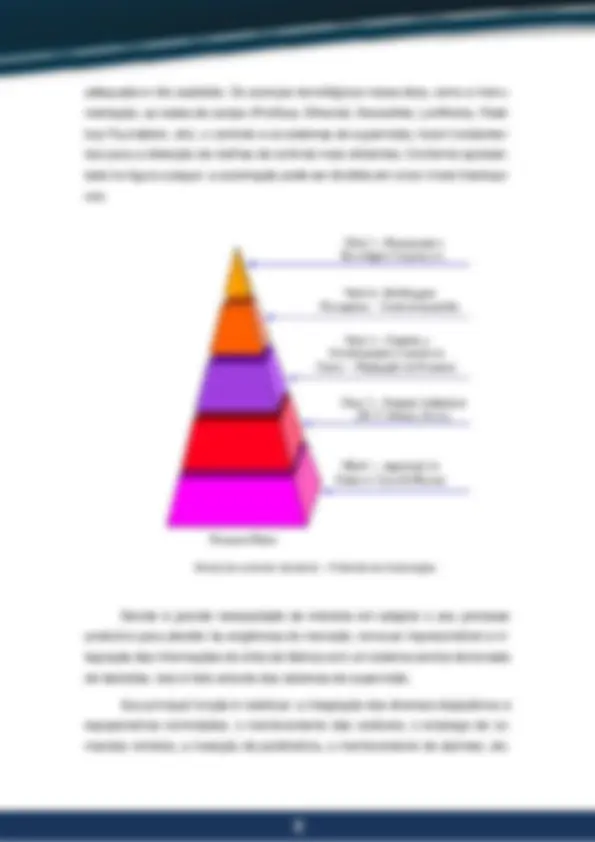
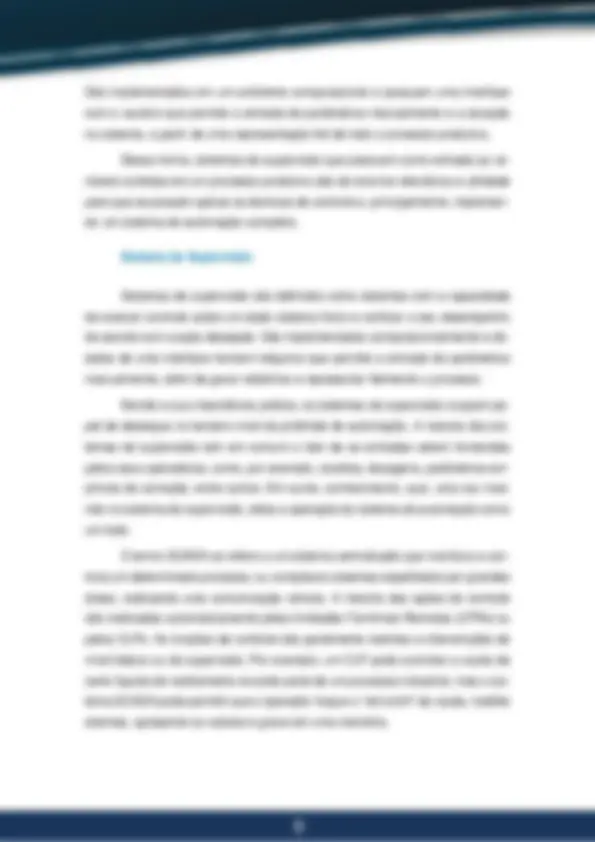
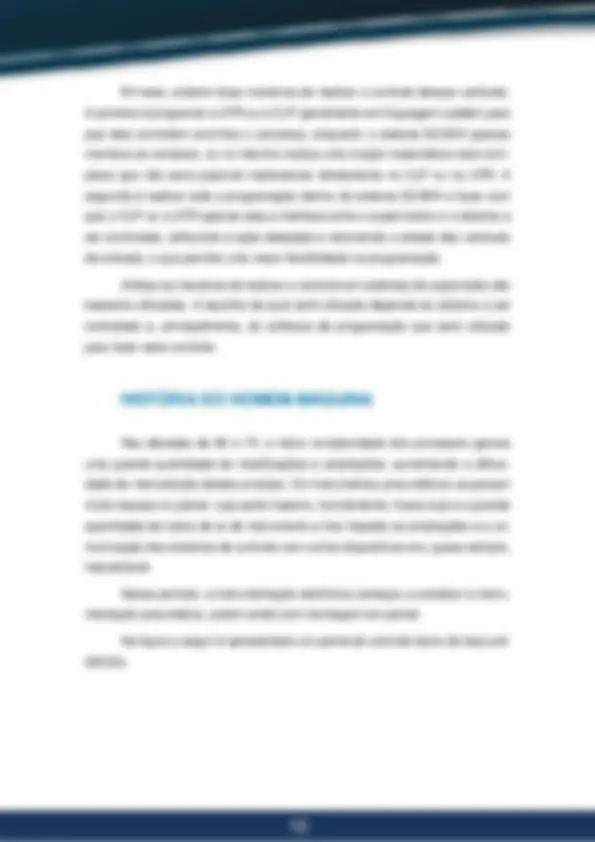
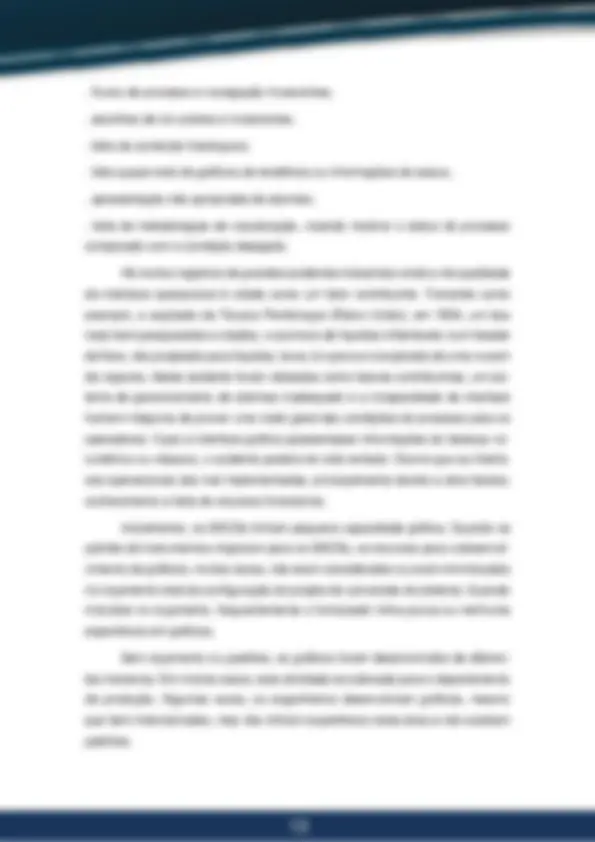
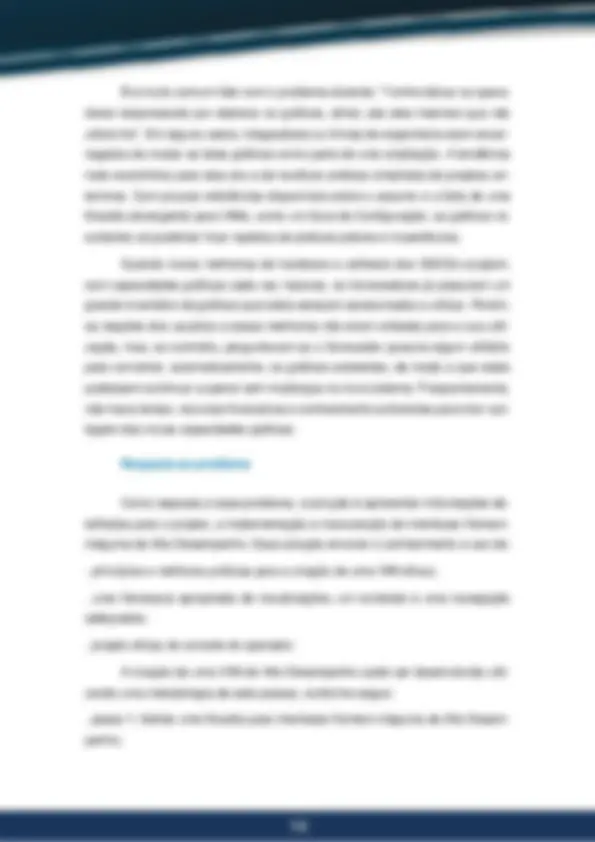
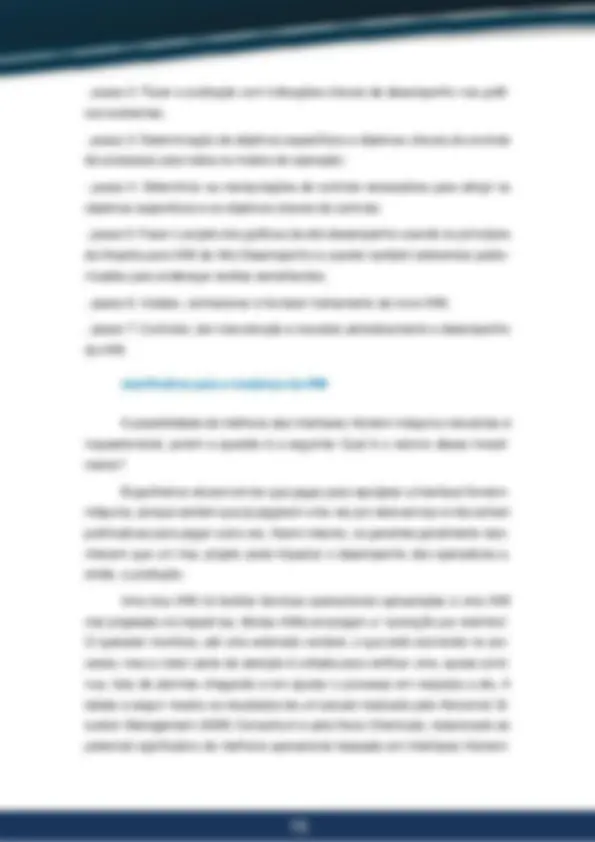
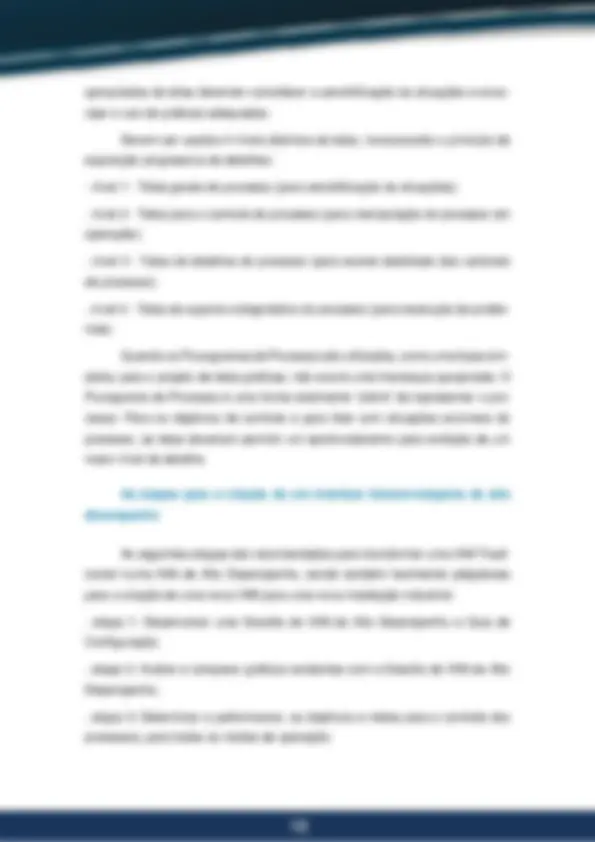
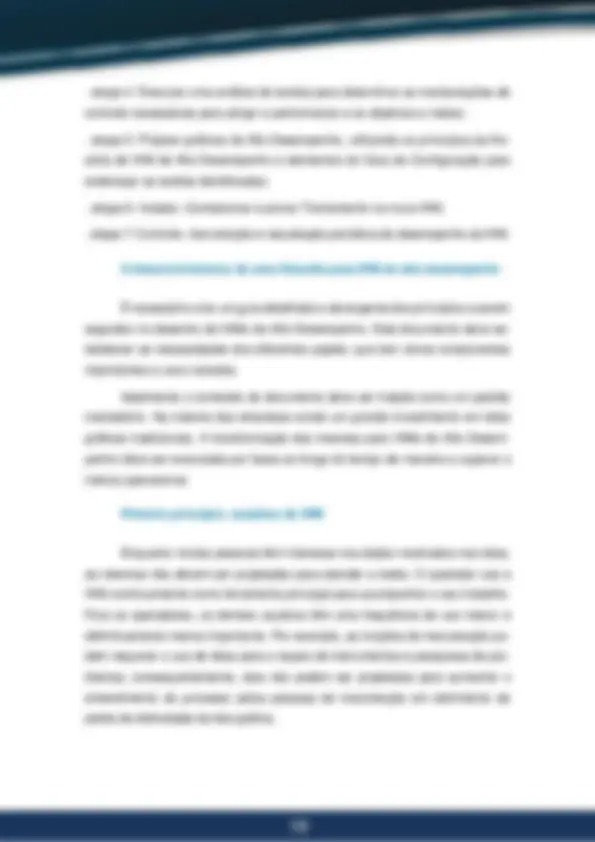
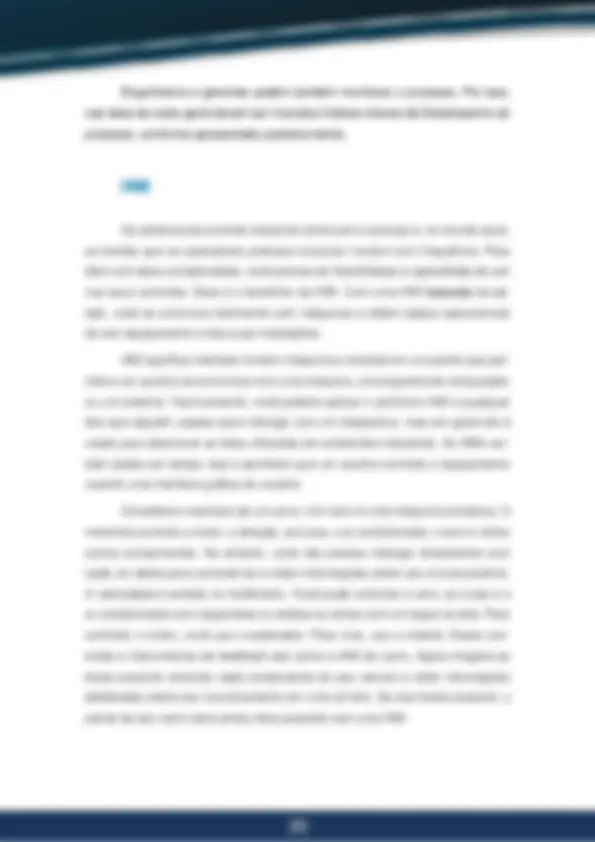
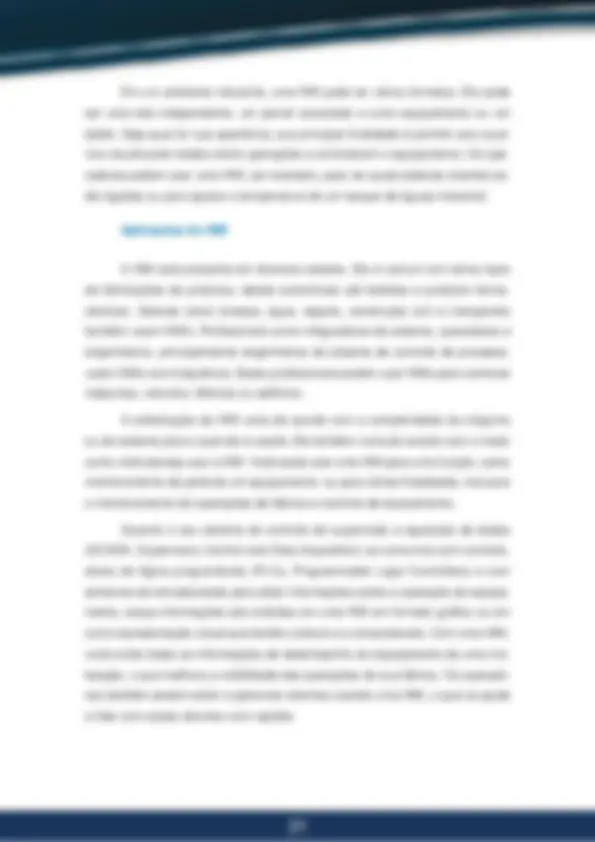
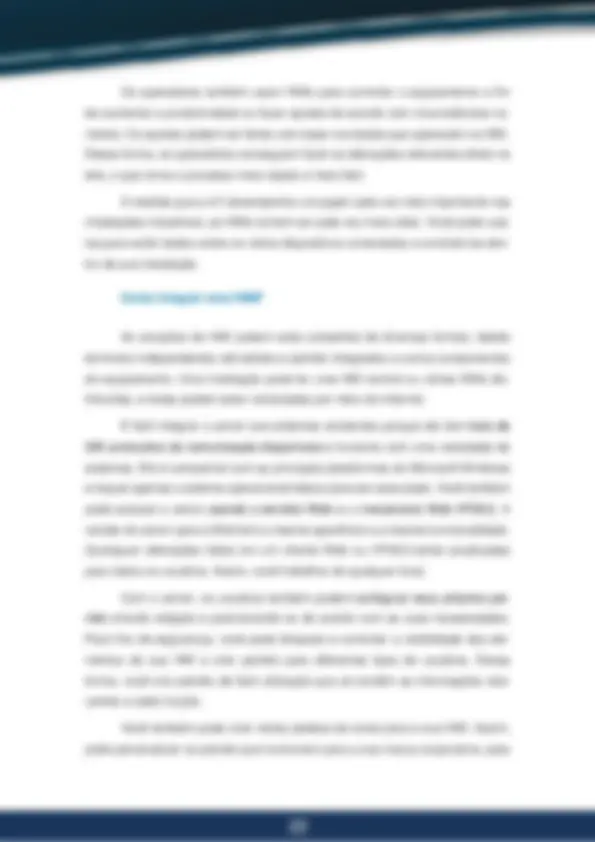
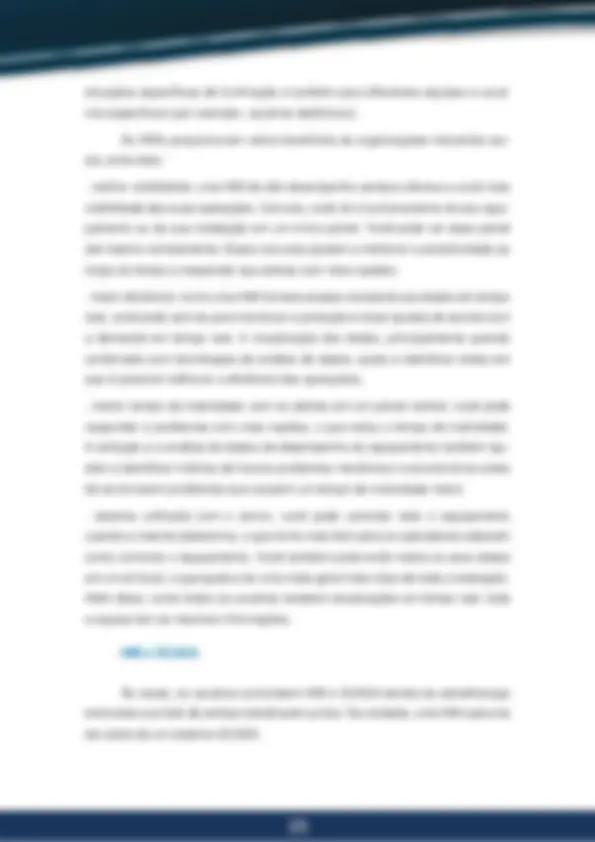
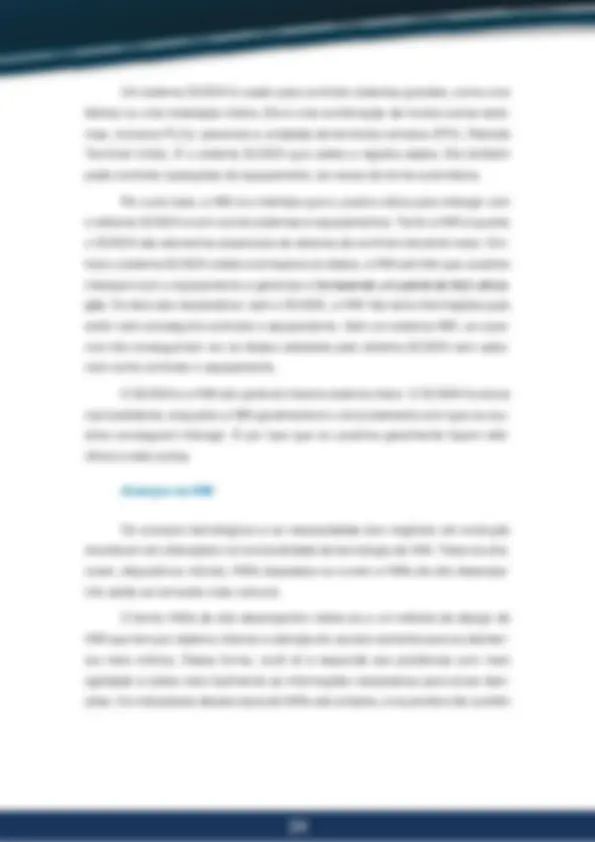
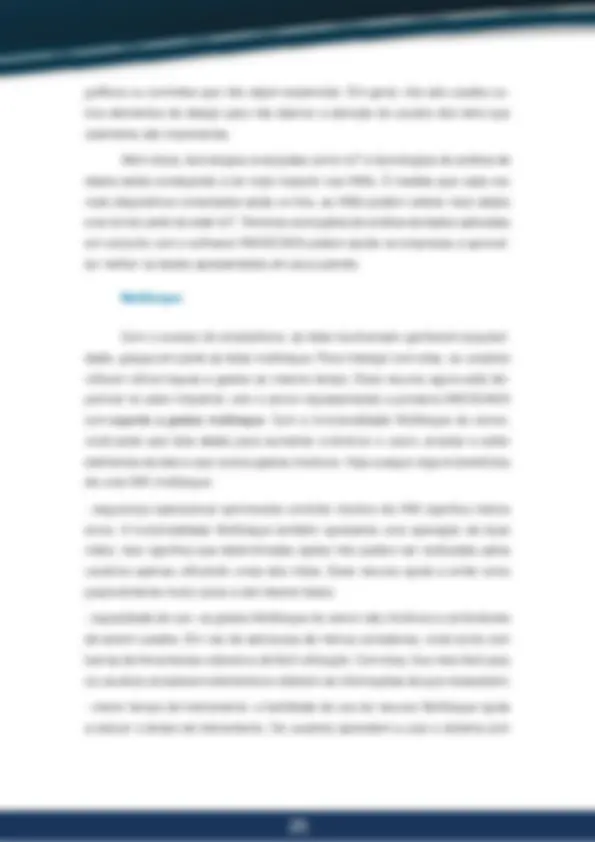
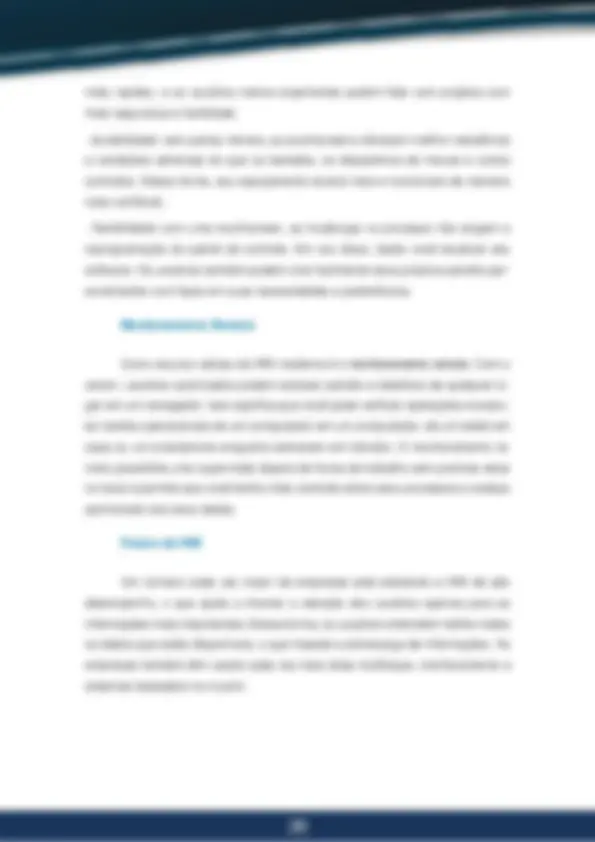
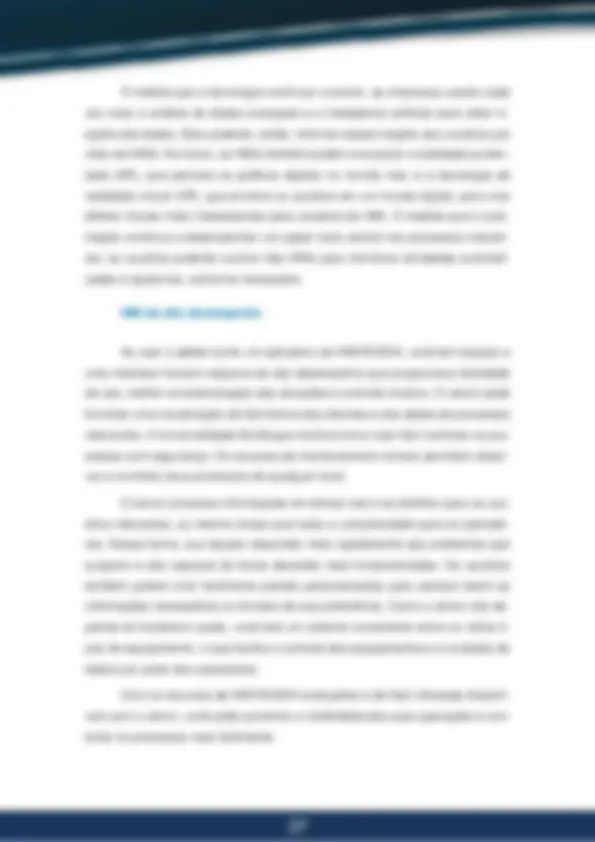
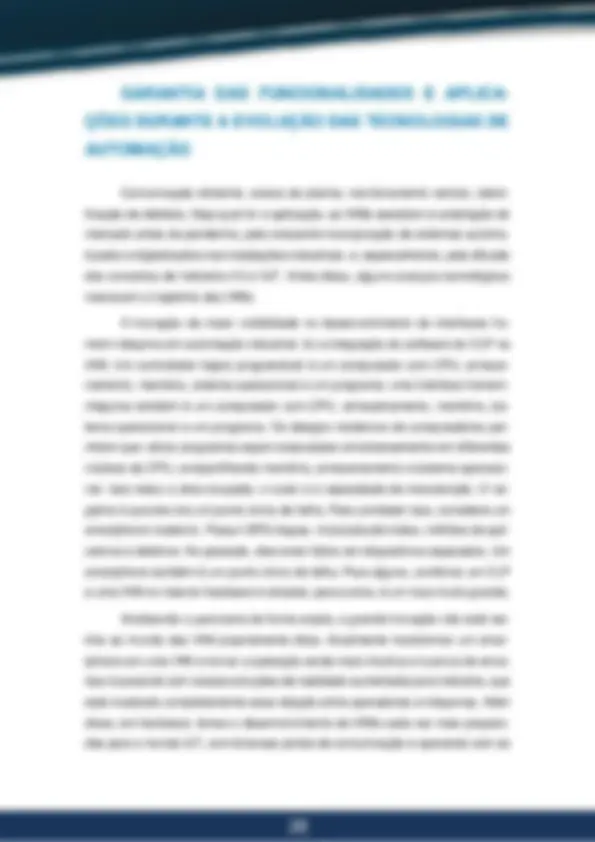
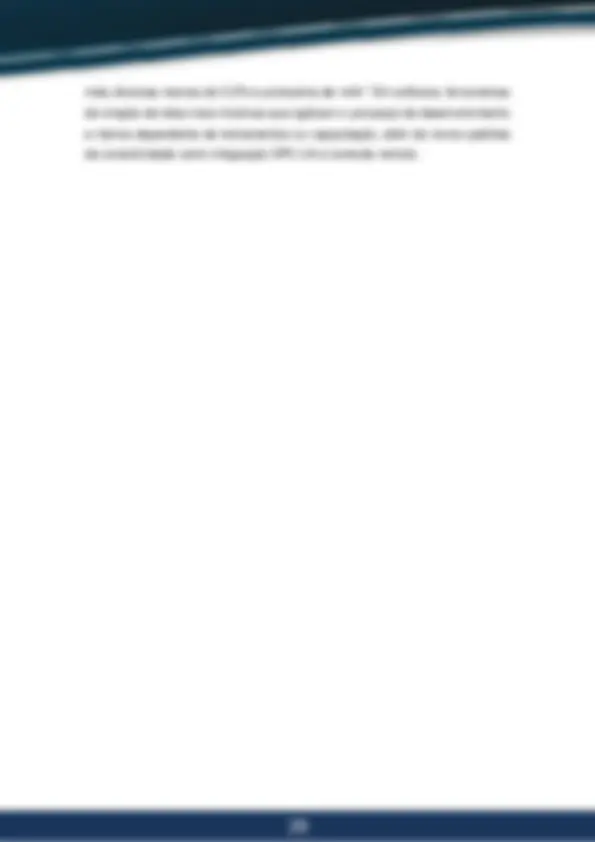
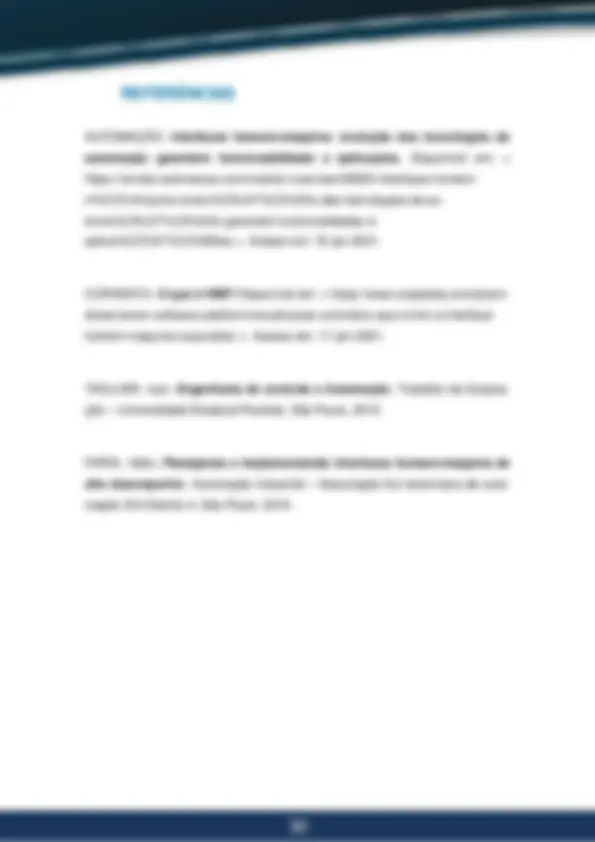
Estude fácil! Tem muito documento disponível na Docsity
Ganhe pontos ajudando outros esrudantes ou compre um plano Premium
Prepare-se para as provas
Estude fácil! Tem muito documento disponível na Docsity
Prepare-se para as provas com trabalhos de outros alunos como você, aqui na Docsity
Os melhores documentos à venda: Trabalhos de alunos formados
Prepare-se com as videoaulas e exercícios resolvidos criados a partir da grade da sua Universidade
Responda perguntas de provas passadas e avalie sua preparação.
Ganhe pontos para baixar
Ganhe pontos ajudando outros esrudantes ou compre um plano Premium
Comunidade
Peça ajuda à comunidade e tire suas dúvidas relacionadas ao estudo
Descubra as melhores universidades em seu país de acordo com os usuários da Docsity
Guias grátis
Baixe gratuitamente nossos guias de estudo, métodos para diminuir a ansiedade, dicas de TCC preparadas pelos professores da Docsity
Os sistemas digitais de controle distribuído (sdcds) e a importância das interfaces homem-máquina (ihms) de alto desempenho na indústria. Explora a evolução dos sistemas de controle, a necessidade de integração de informações e a importância de ihms eficazes para a tomada de decisões e a otimização de processos. O documento destaca os princípios de design de ihms de alto desempenho, as etapas para transformar uma ihm tradicional em uma ihm de alto desempenho e os benefícios de usar uma hmi de alto desempenho, como melhor visibilidade, maior eficiência e flexibilidade.
Tipologia: Notas de estudo
1 / 30
Esta página não é visível na pré-visualização
Não perca as partes importantes!
A nossa história inicia com a realização do sonho de um grupo de empre- sários, em atender à crescente demanda de alunos para cursos de Graduação e Pós-Graduação. Com isso foi criado a nossa instituição, como entidade ofere- cendo serviços educacionais em nível superior.
A instituição tem por objetivo formar diplomados nas diferentes áreas de conhecimento, aptos para a inserção em setores profissionais e para a partici- pação no desenvolvimento da sociedade brasileira, e colaborar na sua formação contínua. Além de promover a divulgação de conhecimentos culturais, científicos e técnicos que constituem patrimônio da humanidade e comunicar o saber atra- vés do ensino, de publicação ou outras normas de comunicação.
A nossa missão é oferecer qualidade em conhecimento e cultura de forma confiável e eficiente para que o aluno tenha oportunidade de construir uma base profissional e ética. Dessa forma, conquistando o espaço de uma das instituições modelo no país na oferta de cursos, primando sempre pela inovação tecnológica, excelência no atendimento e valor do serviço oferecido.
Os Sistemas Digitais de Controle Distribuído (SDCDs) são equipamentos constituídos de hardware, na forma de estações de operação (Interface Homem- máquina - IHM), rede de comunicação e dispositivos de entrada e saída, e sof- tware, configurado em telas para visualização, projetadas para representar as operações das plantas em tempo real.
A maioria das ações dos operadores para o controle do processo são re- alizadas através da IHM. Desta forma, uma IHM deve prover uma operação tran- quila e estável, sensibilização para situações ótimas e resposta ótima para situ- ações anormais.
Uma IHM mal projetada pode degradar a segurança, a produção, a quali- dade e a lucratividade de uma planta industrial.
É comum encontrarmos IHMs mal projetadas que: encoraja várias más técnicas operacionais, como a “operação por alarmes”; impedem ativamente a sensibilização em situações apropriadas; resultam no aumento das variações do processo e em má qualidade; contribuem para um maior número de problemas evitáveis; aumentam a probabilidade de respostas subótimas a situações anor- mais; têm sido identificadas como fatores de contribuição significativa para os principais acidentes industriais.
Nos primórdios das plantas industriais, nas décadas de 30 e 40, as insta- lações consistiam, tipicamente, de uma pequena sala de controle próxima da unidade de processamento, onde grande parte dos instrumentos, tipicamente pneumáticos, eram agrupados. Os instrumentos na sala de controle eram cuida- dosamente agrupados e instalados em painéis. Algumas vezes, representações gráficas da planta eram utilizadas, nas quais os instrumentos eram inseridos em posições apropriadas. Muitas leituras eram representadas em registradores grá- ficos de cartas de papel de rolo ou circulares e os alarmes eram apresentados em painéis anunciadores compostos por caixas iluminadas, dispostos em locais de fácil visibilidade.
É sabido que a automação é a ciência que estuda e aplica metodologias, ferramentas e equipamentos, objetivando definir quando e como converter o con- trole de um processo manual para automático. Com isso, uma coleta metodoló- gica e precisa de dados pode ser empregada para se obter a otimização de um processo.
Atualmente, existe grande interesse por sistemas de automação, especi- almente onde a presença humana é insalubre ou perigosa, e também, por siste- mas de segurança, que necessitam que os tempos de resposta sejam extrema- mente curtos. Mais especificamente, existe grande demanda de automação no setor industrial, devido aos seguintes motivos:
. redução dos custos de produção; . rápida resposta ao atendimento da produção; . redução dos volumes, tamanhos e custos dos equipamentos; . restabelecimento mais rápido do sistema produtivo; . repetibilidade e maior qualidade na produção; . possibilidade de introdução de sistemas produtivos interligados.
Paralelamente a esses pontos positivos, a automação industrial traz a ne- cessidade de investimentos iniciais mais elevados, além de maiores custos de manutenção dependentes de mão-de-obra mais qualificada. Em geral, esses en- traves são compensados pela garantia da qualidade da produção que, dessa forma, torna-se mais homogênea. Deve-se destacar que a automação por si só não tem a capacidade de melhorar um produto final, mas sim, de torná-lo mais homogêneo de acordo com um padrão pré-estabelecido.
Em suas primeiras implantações, os projetos de automação de instala- ções industriais visavam apenas ao monitoramento e controle automático local de parâmetros mais importantes, voltados à garantia de uma operação remota
adequada e não assistida. Os avanços tecnológicos nessa área, como a instru- mentação, as redes de campo (Profibus, Ethernet, DeviceNet, LonWorks, Field- bus Foundation, etc), o controle e os sistemas de supervisão, foram fundamen- tais para a obtenção de malhas de controle mais eficientes. Conforme apresen- tado na figura a seguir, a automação pode ser dividida em cinco níveis hierárqui- cos.
Níveis de controle industrial – Pirâmide de Automação
Devido à grande necessidade da indústria em adaptar o seu processo produtivo para atender às exigências do mercado, torna-se imprescindível a in- tegração das informações do chão de fábrica com um sistema central de tomada de decisões. Isso é feito através dos sistemas de supervisão.
Sua principal função é viabilizar: a integração dos diversos dispositivos e equipamentos controlados, o monitoramento das variáveis, o emprego de co- mandos remotos, a inserção de parâmetros, o monitoramento de alarmes, etc.
Em tese, existem duas maneiras de realizar o controle dessas variáveis. A primeira é programar a UTR ou o CLP (geralmente em linguagem Ladder) para que eles controlem sozinhos o processo, enquanto o sistema SCADA apenas monitora as variáveis, ou no máximo realiza uma função matemática mais com- plexa que não seria possível implementar diretamente no CLP ou na UTR. A segunda é realizar toda a programação dentro do sistema SCADA e fazer com que o CLP ou a UTR apenas seja a interface entre o supervisório e o sistema a ser controlado, atribuindo a ação desejada e retornando o estado das variáveis de entrada, o que permite uma maior flexibilidade na programação.
Ambas as maneiras de realizar o controle em sistemas de supervisão são bastante utilizadas. A escolha de qual será utilizada depende do sistema a ser controlado e, principalmente, do software de programação que será utilizado para fazer esse controle.
Nas décadas de 60 e 70, a maior complexidade dos processos gerava uma grande quantidade de modificações e ampliações, aumentando a dificul- dade de manutenção destes arranjos. Os instrumentos pneumáticos ocupavam muito espaço no painel, cuja parte traseira, normalmente, ficava suja e a grande quantidade de tubos de ar de instrumento e fios impedia as ampliações e a co- municação dos sistemas de controle com outros dispositivos era, quase sempre, impraticável.
Nesse período, a instrumentação eletrônica começou a substituir a instru- mentação pneumática, porém ainda com montagem em painel.
Na figura a seguir é apresentado um painel de controle típico da fase pré- SDCDs.
Um típico painel de controle pré-SDCD
Com a chegada dos sistemas digitais de controle distribuído (SDCDs) na década de 70, os sinais de processo passaram a ser monitorados por uma es- trutura computadorizada. Os instrumentos físicos foram substituídos por janelas gráficas configuradas por software. As vantagens comerciais dos SDCDs eram enormes. Ficou fácil configurar e reconfigurar as estratégias de controle e pro- gramas para alterar o comportamento do sistema. A melhoria e a otimização dos processos foram facilitadas, não somente pela facilidade de configuração, mas também pelo aumento da quantidade e da diversidade de algoritmos disponíveis. Entretanto, essa facilidade também trouxe muitos problemas para a administra- ção dos SDCDs. De qualquer forma, as vantagens dos SDCDs superaram em muito as suas deficiências, tais como lidar com os milhares de alarmes que es- ses sistemas têm a capacidade de gerar.
. fluxos de processo e navegação incoerentes; . escolhas de cor pobres e incoerentes; . falta de conteúdo hierárquico; . falta quase total de gráficos de tendência ou informações de status; . apresentação não apropriada de alarmes; . falta de metodologias de visualização, visando mostrar o status do processo comparado com a condição desejada.
Há muitos registros de grandes acidentes industriais onde a má qualidade da interface operacional é citada como um fator contribuinte. Tomando como exemplo, a explosão da Texaco Pembroque (Reino Unido), em 1994, um dos mais bem pesquisados e citados, o acúmulo de líquidos inflamáveis num header de flare, não projetado para líquidos, levou à ruptura e à explosão de uma nuvem de vapores. Neste acidente foram relatados como fatores contribuintes, um sis- tema de gerenciamento de alarmes inadequado e a incapacidade da interface homem-máquina de prover uma visão geral das condições do processo para os operadores. Caso a interface gráfica apresentasse informações do balanço vo- lumétrico ou mássico, o acidente poderia ter sido evitado. Ocorre que as interfa- ces operacionais são mal implementadas, principalmente devido a dois fatores: conhecimento e falta de recursos financeiros.
Inicialmente, os SDCDs tinham pequena capacidade gráfica. Quando os painéis de instrumentos migraram para os SDCDs, os recursos para o desenvol- vimento de gráficos, muitas vezes, não eram considerados ou eram minimizados no orçamento total da configuração do projeto de conversão do sistema. Quando incluídos no orçamento, frequentemente o fornecedor tinha pouca ou nenhuma experiência em gráficos.
Sem orçamento ou padrões, os gráficos foram desenvolvidos de diferen- tes maneiras. Em muitos casos, esta atividade era deixada para o departamento de produção. Algumas vezes, os engenheiros desenvolviam gráficos, mesmo que bem intencionados, mas não tinham experiência nesta área e não existiam padrões.
Era muito comum lidar com o problema dizendo: “Vamos deixar os opera- dores responsáveis por elaborar os gráficos, afinal, são eles mesmos que vão utilizá-los”. Em alguns casos, integradores ou firmas de engenharia eram encar- regados de mudar as telas gráficas como parte de uma ampliação. A tendência mais econômica para elas era a de reutilizar práticas simplistas de projetos an- teriores. Com poucas referências disponíveis sobre o assunto e a falta de uma filosofia abrangente para IHMs, como um Guia de Configuração, os gráficos re- sultantes só poderiam ficar repletos de práticas pobres e incoerências.
Quando novas melhorias de hardware e software dos SDCDs surgiam, com capacidades gráficas cada vez maiores, os fornecedores já possuíam um grande inventário de gráficos que todos estavam acostumados a utilizar. Porém, as reações dos usuários a essas melhorias não eram voltadas para a sua utili- zação, mas, ao contrário, perguntavam se o fornecedor possuía algum utilitário para converter, automaticamente, os gráficos existentes, de modo a que estes pudessem continuar a operar sem mudanças no novo sistema. Frequentemente, não havia tempo, recursos financeiros e conhecimento suficientes para tirar van- tagem das novas capacidades gráficas.
Resposta ao problema
Como resposta a esse problema, a solução é apresentar informações de- talhadas para o projeto, a implementação e manutenção de interfaces Homem- máquina de Alto Desempenho. Essa solução envolve o conhecimento e uso de:
. princípios e melhores práticas para a criação de uma IHM eficaz; . uma hierarquia apropriada de visualizações, um conteúdo e uma navegação adequados; . projeto eficaz do console do operador.
A criação de uma IHM de Alto Desempenho pode ser desenvolvida utili- zando uma metodologia de sete passos, conforme segue:
. passo 1: Adotar uma filosofia para Interfaces Homem-máquina de Alto Desem- penho;
máquina de Alto Desempenho, na qual 21 operadores experientes foram testa- dos utilizando gráficos tradicionais e gráficos projetados de acordo com muitos dos princípios das Interfaces Homem-máquina de Alto Desempenho, utilizando um simulador de processos sofisticado.
Benefícios das interfaces homem-máquina de alto desempenho
Existe um evidente retorno financeiro do investimento para os esforços de mudança de uma IHM Tradicional para uma IHM de Alto Desempenho, além da capacidade potencial para evitar incidentes e acidentes. Com base em taxas de incidentes e problemas operacionais numa Planta de Etileno, os ganhos da mu- dança para uma Interface Homem-máquina de Alto Desempenho foram estima- dos em US$ 800,000 por ano (2).
O ASM Consortium estima que as situações anormais contribuam para perdas de mais de US$ 20 milhões por ano, somente na economia americana. De 3 a 8% da capacidade industrial é perdida nessas situações e estima-se que 20 a 25% dessa perda pode ser recuperada com a implementação apropriada de Interfaces Homem-máquina de Alto Desempenho e métodos apropriados de gerenciamento de alarmes.
O propósito de uma Interface Homem-máquina de Alto Desempenho é permitir que você opere, de forma tranquila e eficaz, e responda às situações anormais, o mais cedo possível, e com o mínimo de consequências adversas.
Visão geral das melhores práticas para a criação de uma interface homem-máquina de alto desempenho
Uma IHM de Alto Desempenho permite a um operador monitorar e geren- ciar uma planta de processamento com segurança e eficácia.
Com os antigos painéis de controle, os operadores experientes podiam utilizar técnicas de reconhecimento de padrões para rapidamente verificar as condições operacionais do processo. A maioria das variáveis possuíam gráficos de tendência e a detecção de eventos anormais era muito rápida. Durante uma perturbação importante, cada operador na sala de controle podia facilmente ver o status da planta, numa única passada de olhos, examinando o painel de ins- trumentos.
Com o surgimento do SDCD, gerentes, engenheiros e operadores de campo muitas vezes têm que questionar o operador do console para conhecer o status da planta, ou pior, assumir o console e começar a chamar outras telas. Durante as situações anormais, essa é uma distração desnecessária que so- mente acrescenta stress a uma situação já estressante.
Existem várias práticas para possibilitar a criação de uma Interface Ho- mem-máquina de Alto Desempenho. Essas práticas são as seguintes:
. trazer de volta o Painel de Controle; . criar telas hierárquicas, baseadas em cenários para melhorar a sensibilização e a resposta às situações; . reprojetar telas para dar ênfase às informações mais importantes; . executar projetos adequados de Salas de Controle e Consoles de Operação; . minimizar as distrações na Sala de Controle.
Criar telas hierárquicas, baseadas em cenário para melhorar a sen- sibilização e a resposta às situações
Sensibilização às situações tem por significado um entendimento preciso e, em tempo hábil, das condições e do comportamento do processo. Projetos
. etapa 4: Executar uma análise de tarefas para determinar as manipulações de controle necessárias para atingir a performance e os objetivos e metas; . etapa 5: Projetar gráficos de Alto Desempenho, utilizando os princípios da filo- sofia de IHM de Alto Desempenho e elementos do Guia de Configuração para endereçar as tarefas identificadas; . etapa 6: Instalar, Comissionar e prover Treinamento na nova IHM; . etapa 7: Controle, manutenção e reavaliação periódica do desempenho da IHM.
O desenvolvimento de uma filosofia para IHM de alto desempenho
É necessário criar um guia detalhado e abrangente dos princípios a serem seguidos no desenho de IHMs de Alto Desempenho. Este documento deve es- tabelecer as necessidades dos diferentes papéis, que tem vários componentes importantes e usos variados.
Idealmente o conteúdo do documento deve ser tratado como um padrão mandatório. Na maioria das empresas existe um grande investimento em telas gráficas tradicionais. A transformação das mesmas para IHMs de Alto Desem- penho deve ser executada por fases ao longo do tempo de maneira a superar a inércia operacional.
Primeiro princípio: usuários de IHM
Enquanto muitas pessoas têm interesse nos dados mostrados nas telas, as mesmas não devem ser projetadas para atender a todos. O operador usa a IHM continuamente como ferramenta principal para acompanhar o seu trabalho. Fora os operadores, os demais usuários têm uma frequência de uso menor e definitivamente menos importante. Por exemplo, as funções de manutenção po- dem requerer o uso de telas para o reparo de instrumentos e pesquisas de pro- blemas, consequentemente, elas não podem ser projetadas para aumentar o entendimento do processo pelas pessoas de manutenção em detrimento da perda de efetividade da tela gráfica.
Engenheiros e gerentes podem também monitorar o processo. Por isso, nas telas de visão geral devem ser incluídos Índices-chaves de Desempenho do processo, conforme apresentado posteriormente.
Os sistemas de controle industrial continuam a avançar e, no mundo atual, as tarefas que os operadores precisam executar mudam com frequência. Para lidar com essa complexidade, você precisa ter flexibilidade e capacidade de uso nos seus controles. Esse é o benefício da HMI. Com uma HMI baseada no ze- non, você se comunica facilmente com máquinas e obtém dados operacionais do seu equipamento e das suas instalações.
HMI significa interface homem-máquina e consiste em um painel que per- mite a um usuário se comunicar com uma máquina, um programa de computador ou um sistema. Tecnicamente, você poderia aplicar o acrônimo HMI a qualquer tela que alguém usasse para interagir com um dispositivo, mas em geral ele é usado para descrever as telas utilizadas em ambientes industriais. As HMIs exi- bem dados em tempo real e permitem que um usuário controle o equipamento usando uma interface gráfica do usuário.
Considere o exemplo de um carro. Um carro é uma máquina complexa. O motorista controla o motor, a direção, as luzes, o ar condicionado, o som e vários outros componentes. No entanto, você não precisa interagir diretamente com cada um deles para controlá-los e obter informações sobre seu funcionamento. A velocidade é exibida no hodômetro. Você pode controlar o som, as luzes e o ar condicionado com maçanetas ou botões ou talvez com um toque na tela. Para controlar o motor, você usa o acelerador. Para virar, usa o volante. Esses con- troles e instrumentos de feedback são como a HMI do carro. Agora imagine se fosse possível controlar cada componente do seu veículo e obter informações detalhadas sobre seu funcionamento em uma só tela. Se isso fosse possível, o painel do seu carro seria ainda mais parecido com uma HMI.