
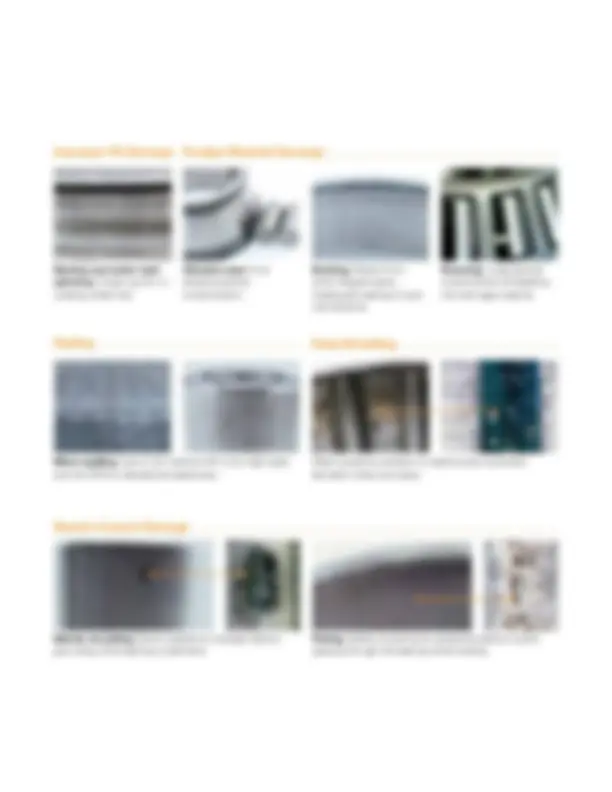
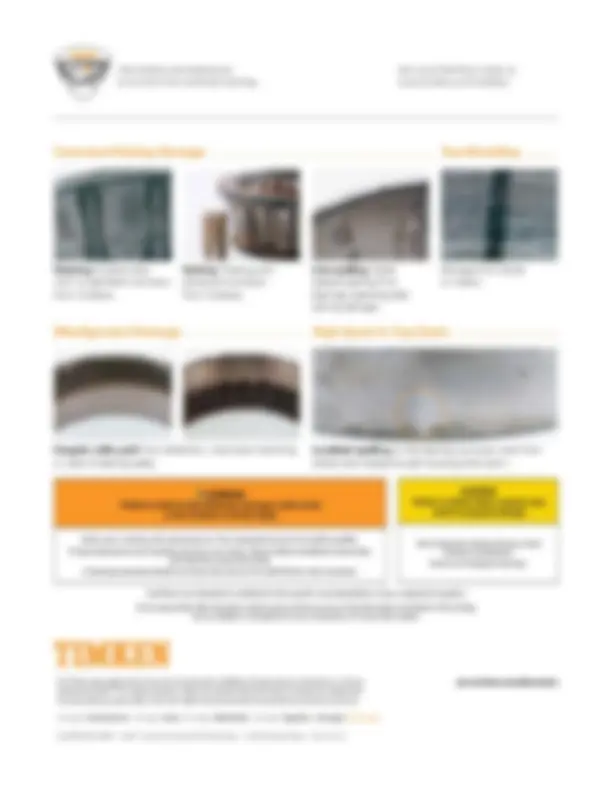
Estude fácil! Tem muito documento disponível na Docsity
Ganhe pontos ajudando outros esrudantes ou compre um plano Premium
Prepare-se para as provas
Estude fácil! Tem muito documento disponível na Docsity
Prepare-se para as provas com trabalhos de outros alunos como você, aqui na Docsity
Os melhores documentos à venda: Trabalhos de alunos formados
Prepare-se com as videoaulas e exercícios resolvidos criados a partir da grade da sua Universidade
Responda perguntas de provas passadas e avalie sua preparação.
Ganhe pontos para baixar
Ganhe pontos ajudando outros esrudantes ou compre um plano Premium
Comunidade
Peça ajuda à comunidade e tire suas dúvidas relacionadas ao estudo
Descubra as melhores universidades em seu país de acordo com os usuários da Docsity
Guias grátis
Baixe gratuitamente nossos guias de estudo, métodos para diminuir a ansiedade, dicas de TCC preparadas pelos professores da Docsity
An overview of various types and causes of bearing damage, including oxide inclusions, point surface origin damage, geometric stress concentration, total bearing lock-up, and handling damage. It also discusses commercial vehicle tapered roller bearing damage, scoring, improper fit damage, foreign material damage, false brinelling, and corrosion/etching damage. The document emphasizes the importance of recognizing bearing damage to prevent further damage and improve bearing life and performance.
Tipologia: Manuais, Projetos, Pesquisas
1 / 4
Esta página não é visível na pré-visualização
Não perca as partes importantes!
Skill Level: Easy | Special Tools: None
Inclusion origin: Oxides or other hard inclusions in bearing steel.
Point surface origin (PSO): Debris and raised metal exceeding the lubricant film thickness.
Geometric stress concentration (GSC): Misalignment, system deflections and heavy loading.
Total bearing lock-up: Rollers skew and slide sideways.
Bearing cone (inner race) large rib face deformation: Metal flow from excessive heat generation.
Bearing cup (outer race) -face denting: Indentations from hardened driver.
Roller nicking and denting: Rough handling or installation damage.
Roller spaced nicking: Raised metal on races from contact with roller edges.
COMMERCIAL VEHICLE
CV
Rollers binding and skewing: Cage ring compressed or interfered with during installation or service.
Cage deformation: Improperly installed or dropped bearing.
Bearing cone (inner race) bore polishing: Contact wear and creeping on shaft caused by lack of lubrication and cone bore contraction from excessively tight setting (preload).
Full race width fatigue spalling: caused by heavy loads creating a thin lubricant film and elevated temperatures.
Scalloping: Uneven localized wear resulting from excessive end play.
Cage pocket wear: Heavy contact between rollers and cage pocket surfaces caused by bearing operating too loosely.
*Damage caused by excessive preload can appear similar to damage caused by inadequate lubrication.
Bearing cone (inner race) large rib face scoring: ‘Welding’ and heat damage from metal-to-metal contact.
Roller end scoring: Metal- to-metal contact from breakdown of lubricant film.
Bearing cone (inner race) bore damage: Fractured cone due to out-of-round or oversized shaft.
The Timken team applies their know-how to improve the reliability and performance of machinery in diverse www.timken.com/aftermarket markets worldwide. The company designs, makes and markets high-performance mechanical components, including bearings, gears, belts, chain and related mechanical power transmission products and services. Stronger. Commitment. Stronger. Value. Stronger. Worldwide. Stronger. Together. | Stronger. By Design. 2-16: 29 Order No. 10308 |^ Timken ®^ is a registered trademark of The Timken Company. |^ © 2016 The Timken Company |^ Printed in U.S.A.
Line spalling: Roller spaced spalling from bearings operating after etching damage.
Etching: Rusting with pitting and corrosion from moisture.
Staining: Surface stain with no significant corrosion from moisture.
Damage from shock or impact.
Irregular roller path from deflection, inaccurate machining or wear of bearing seats.
Localized spalling on the bearing cup (outer race) from stress riser created by split housing pinch point.
WARNING Failure to observe the following warnings could create a risk of death or serious injury.
Never spin a bearing with compressed air. The components may be forcefully expelled. Proper maintenance and handling practices are critical. Always follow installation instructions and maintain proper lubrication. A bearing/component should not be put into service if its shelf life has been exceeded.
CAUTION Failure to follow these cautions may result in property damage
Use of improper bearing fits may cause damage to equipment. Do not use damaged bearings.
TechTips is not intended to substitute for the specific recommendations of your equipment suppliers. Every reasonable effort has been made to ensure the accuracy of the information contained in this writing, but no liability is accepted for errors, omissions or for any other reason.
Visit timken.com/techseries to enroll in free technical training.
Get more TechTips online at www.timken.com/techtips