
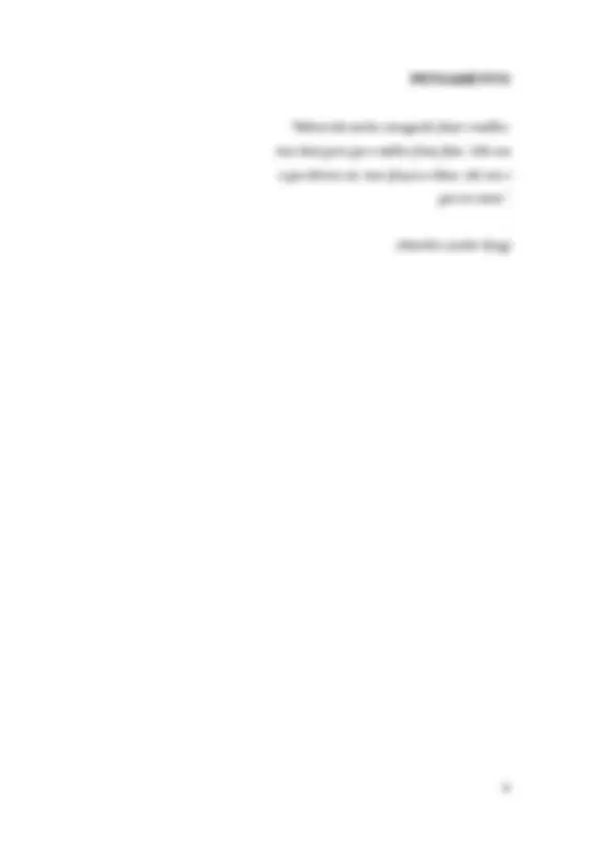
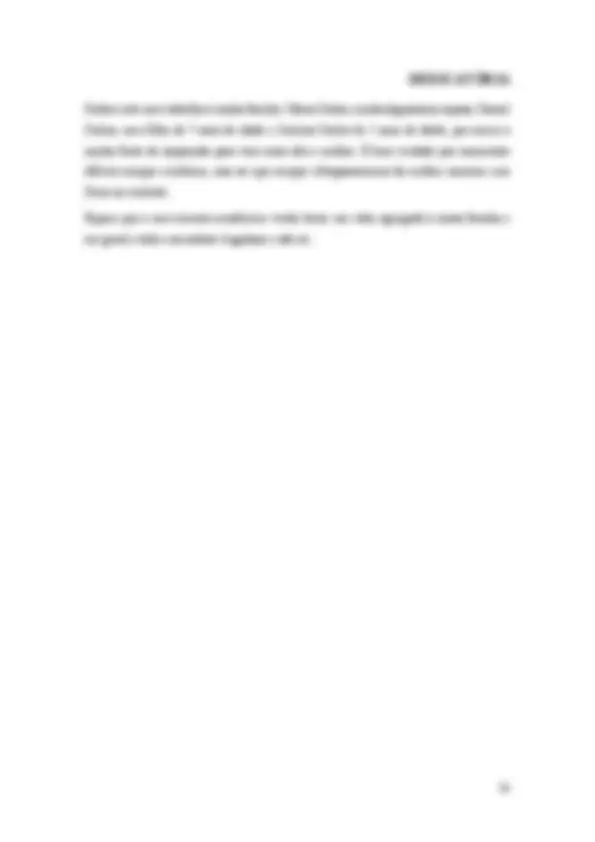
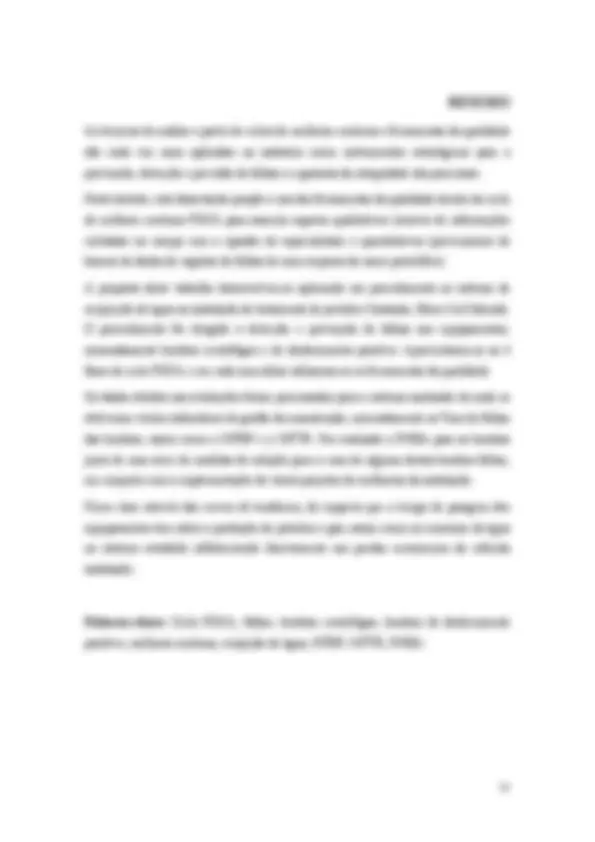
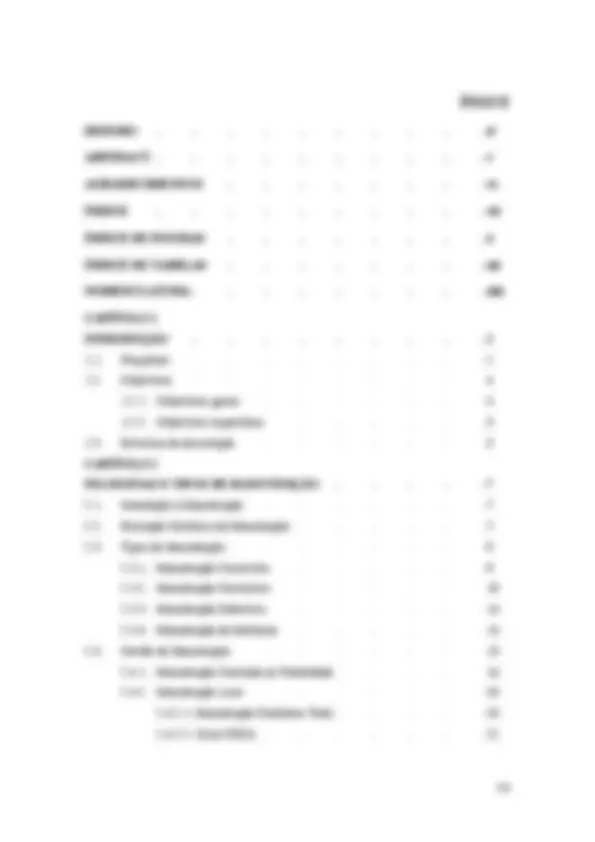
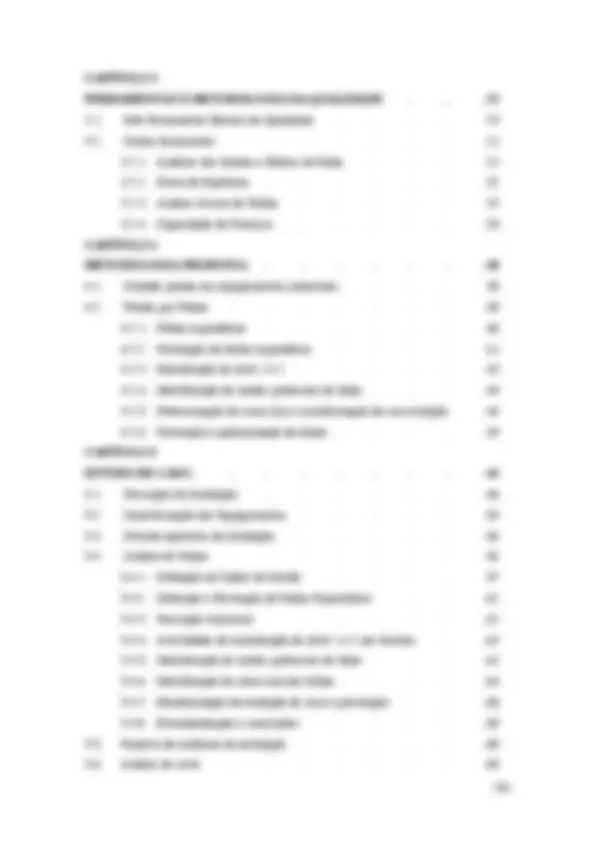
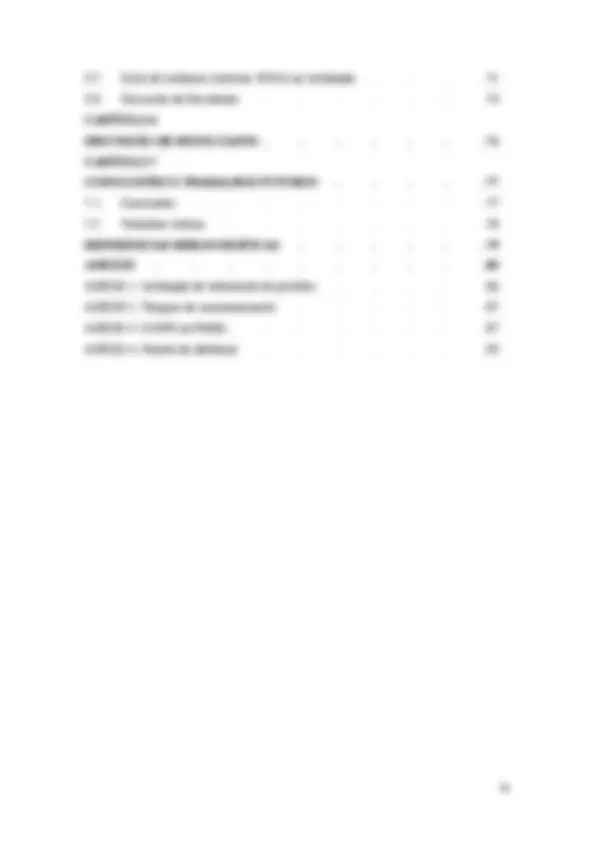
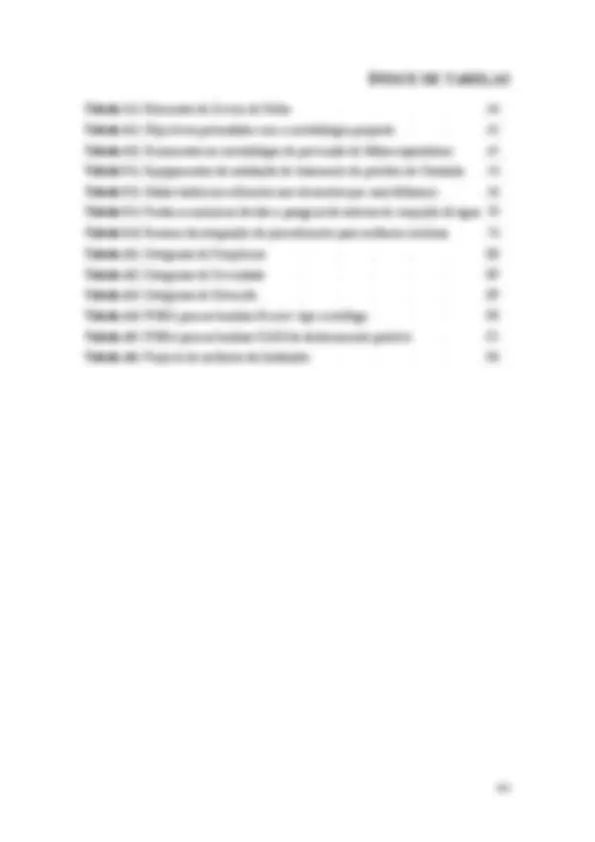
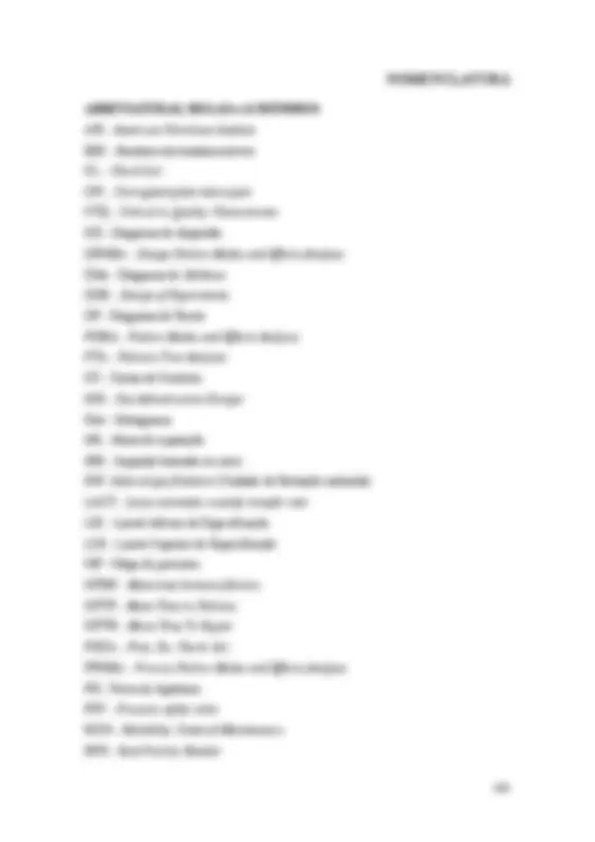
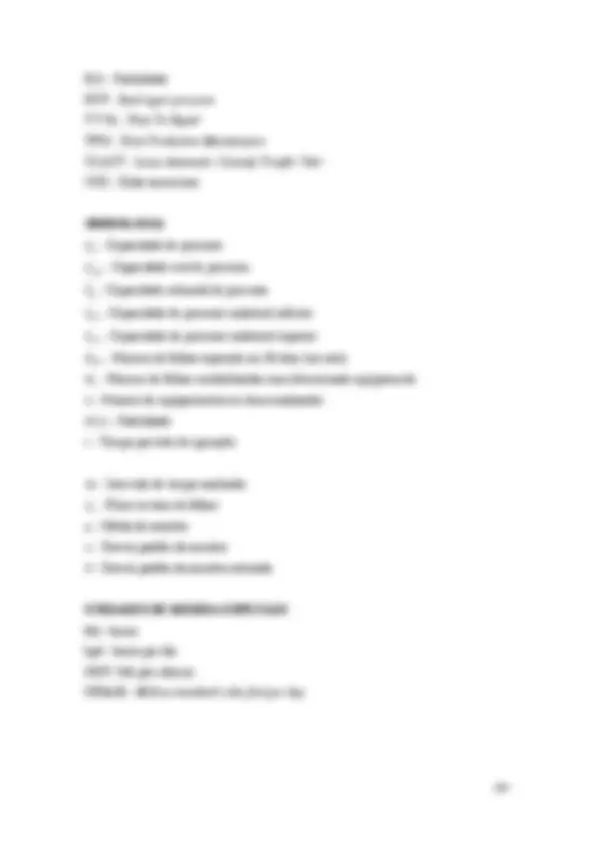
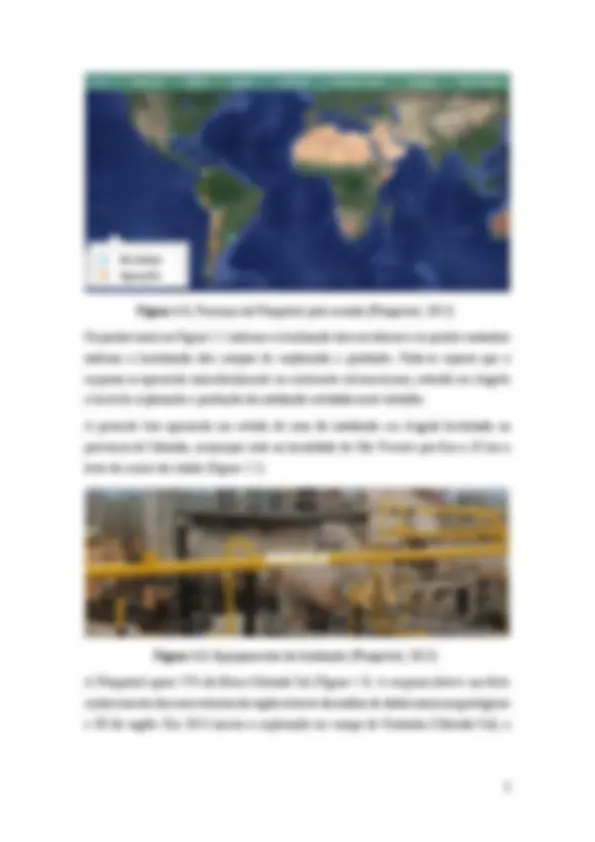
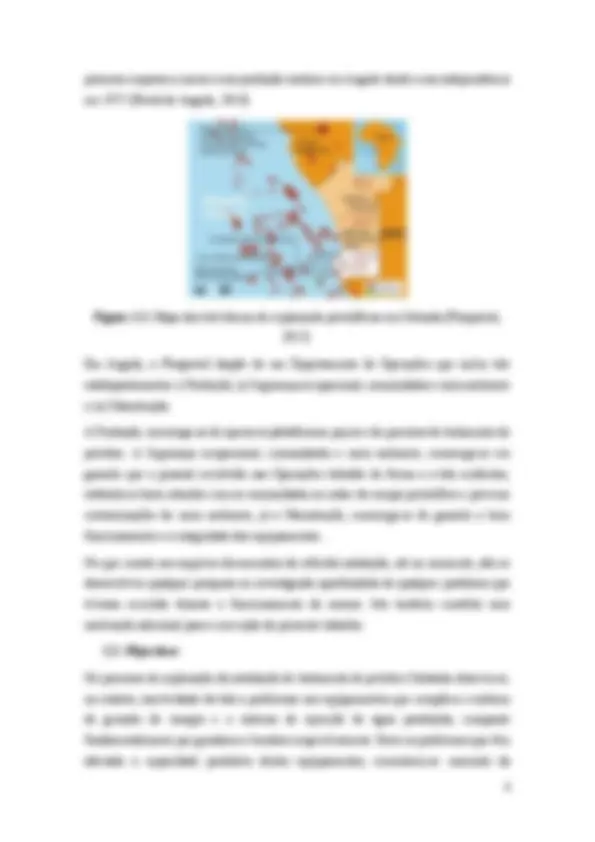
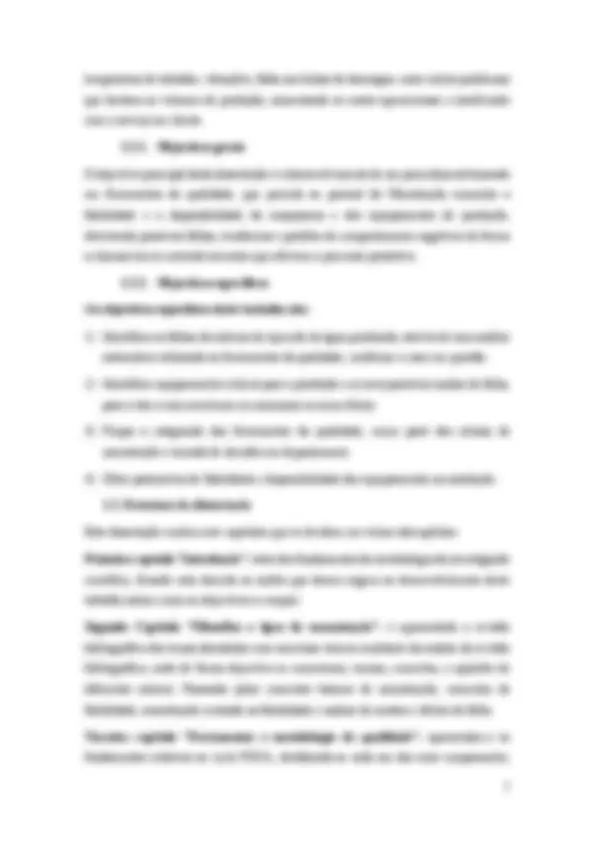
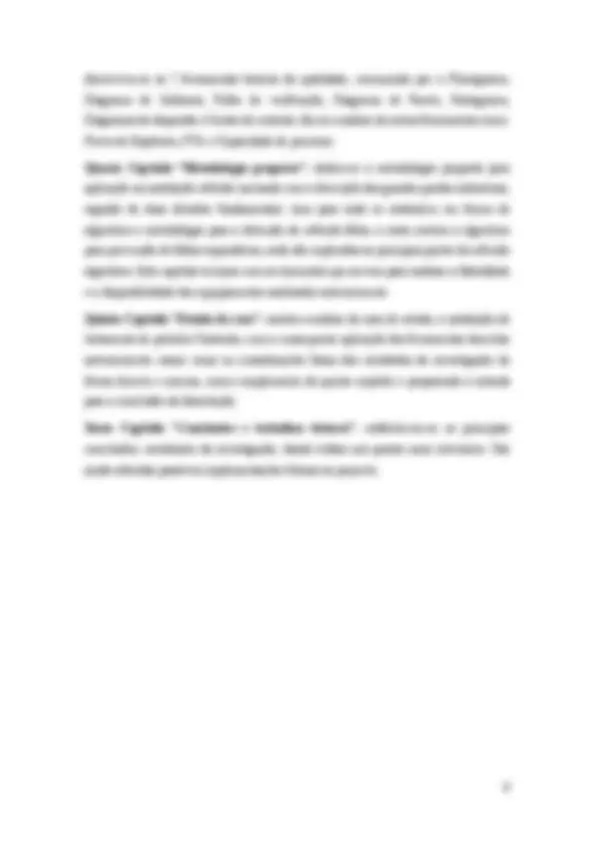
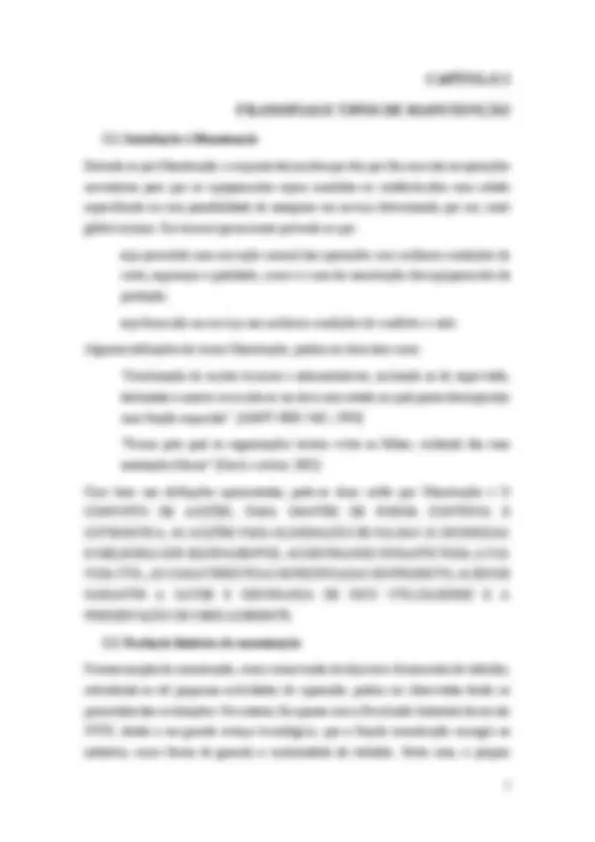
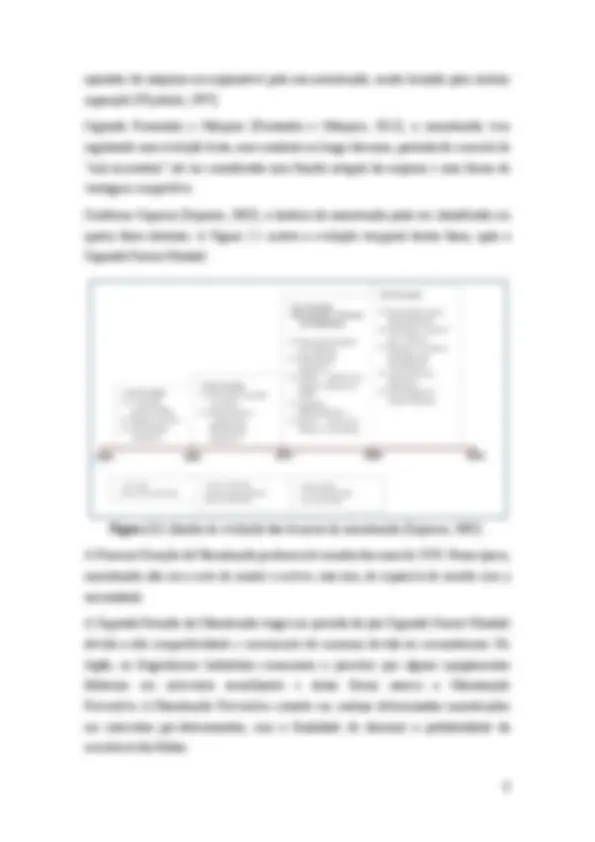
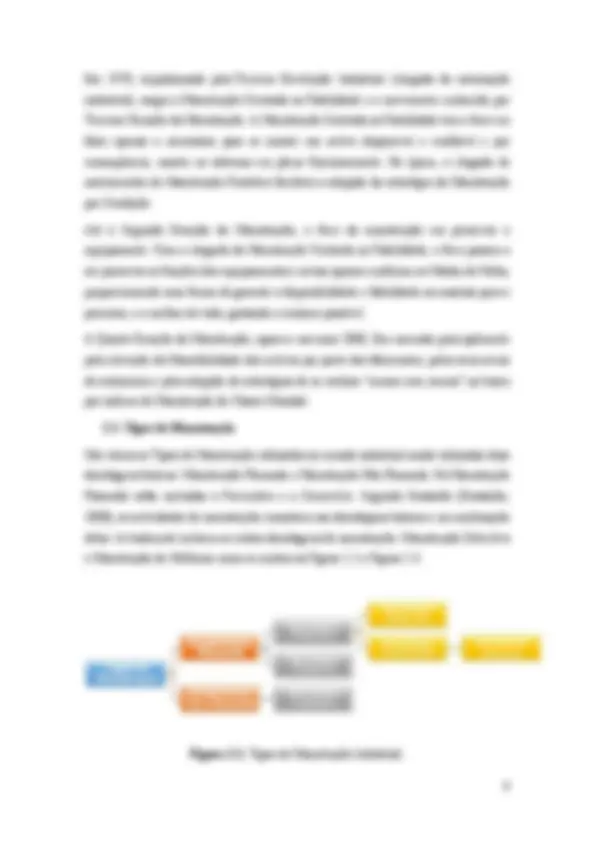
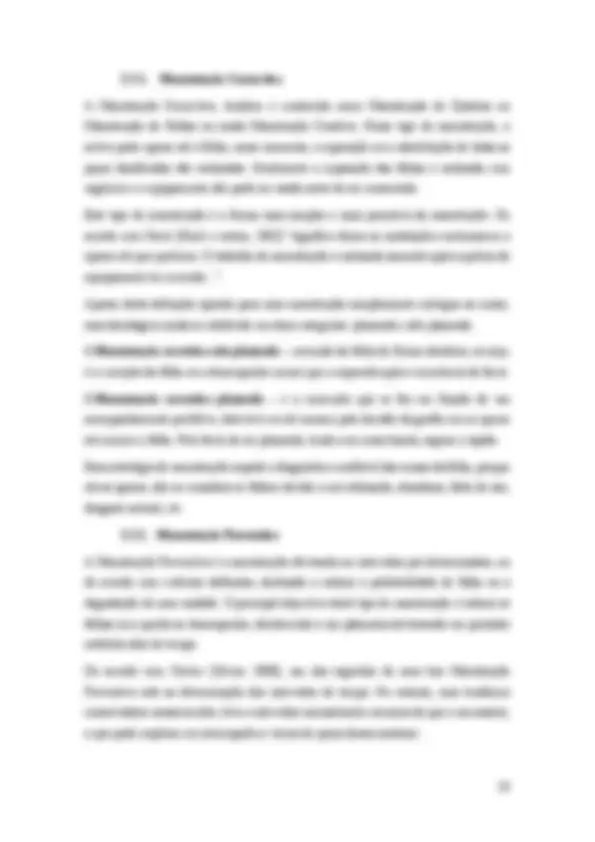
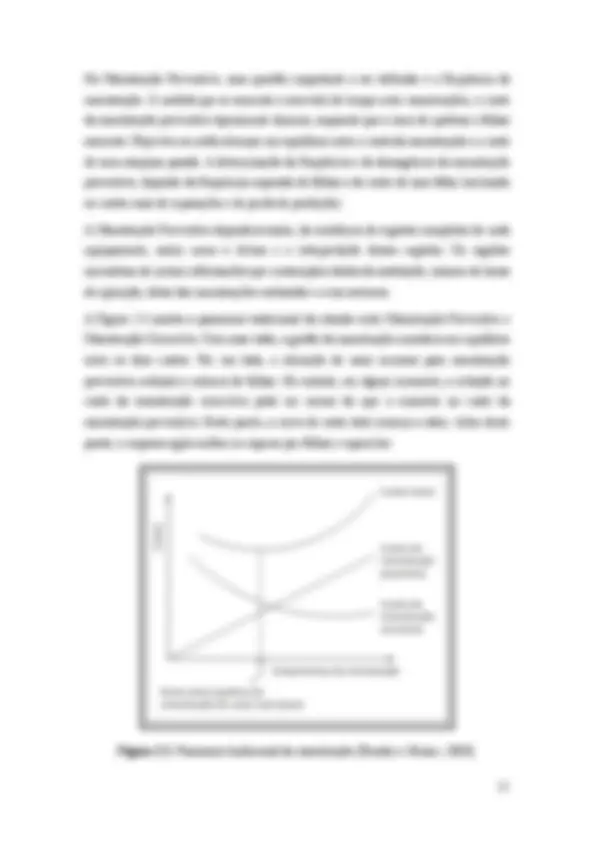
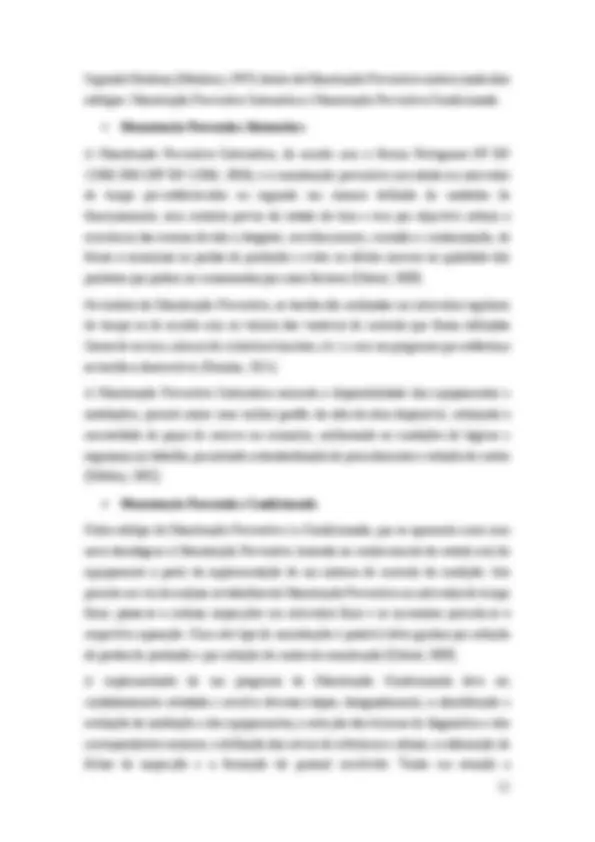
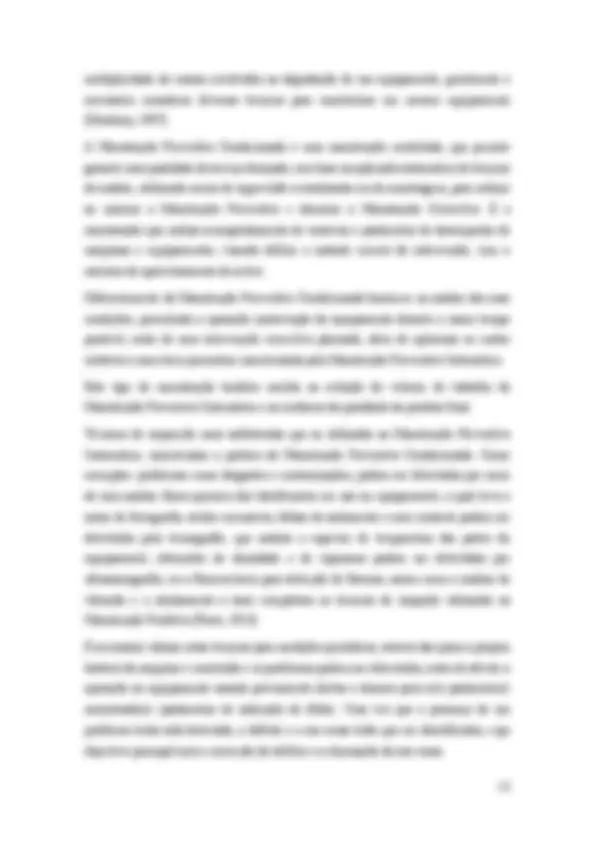
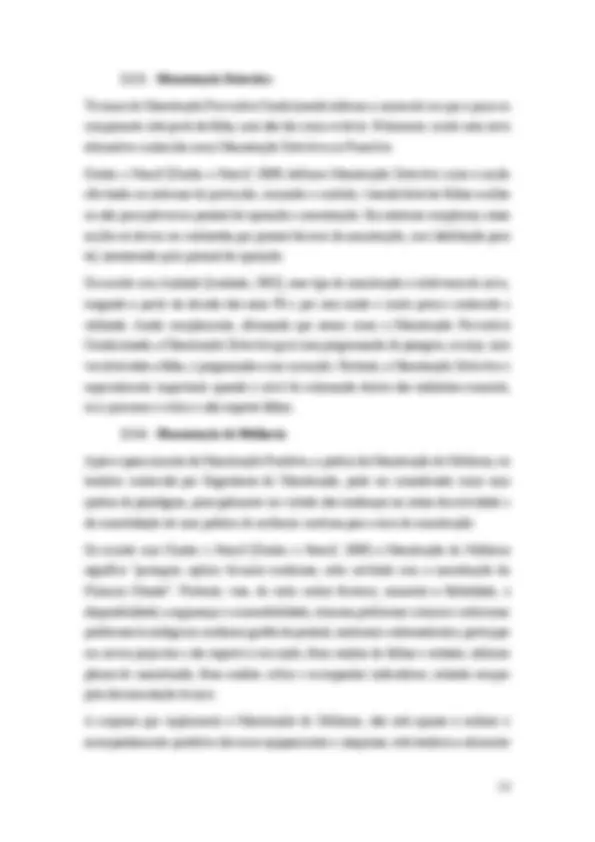
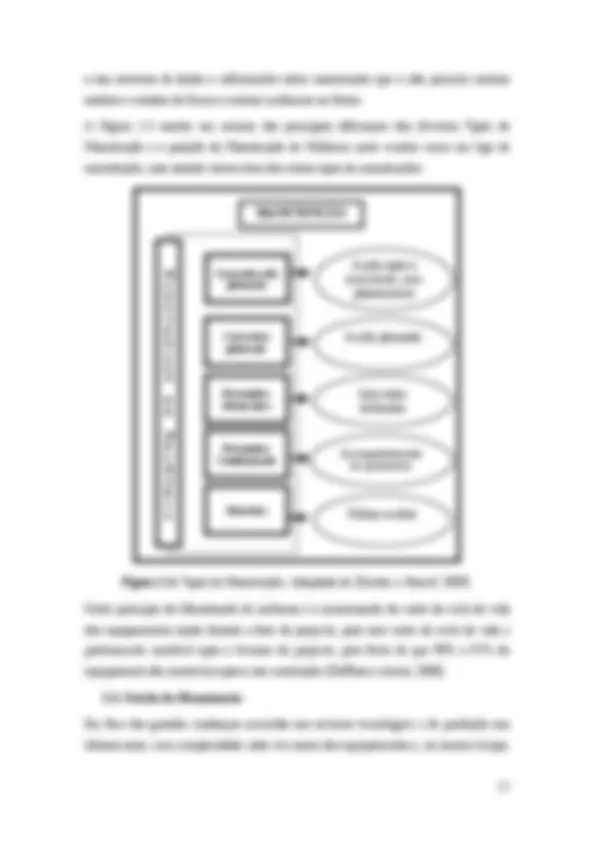
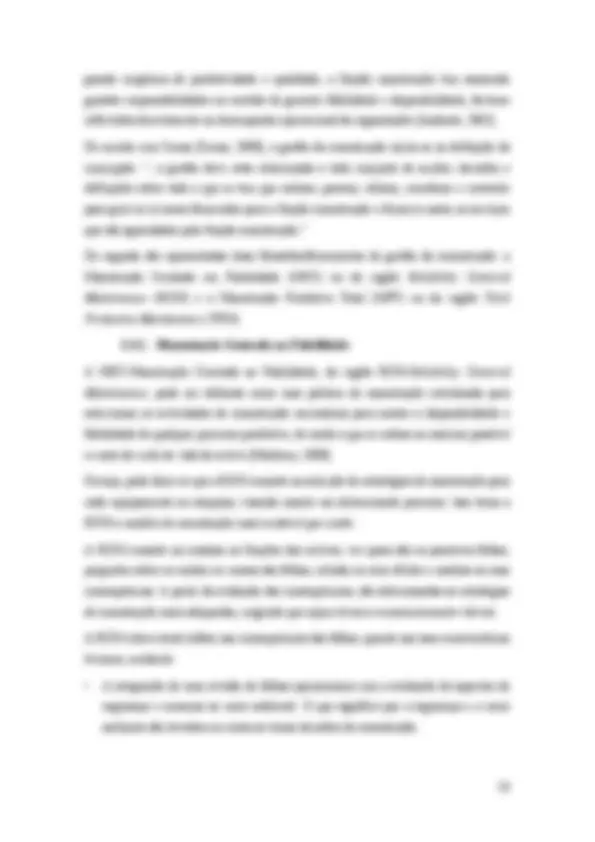
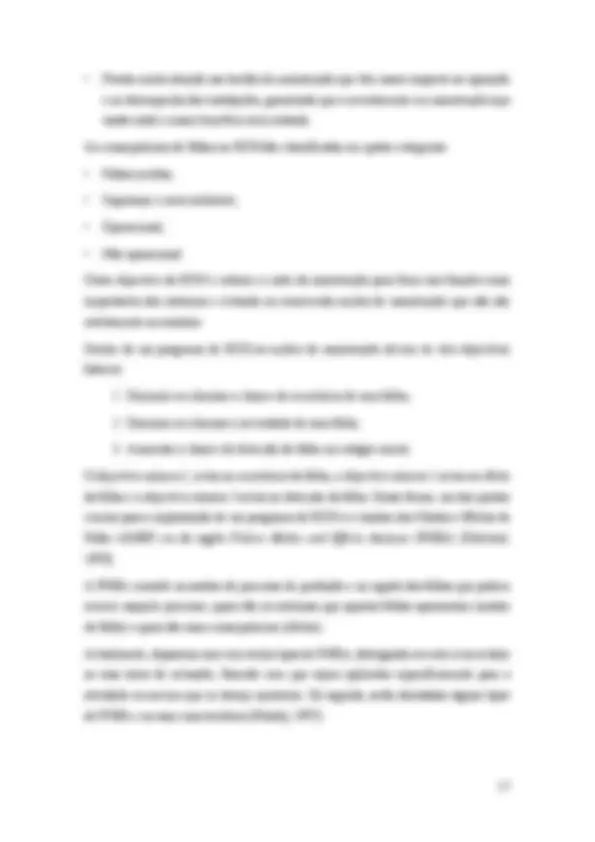
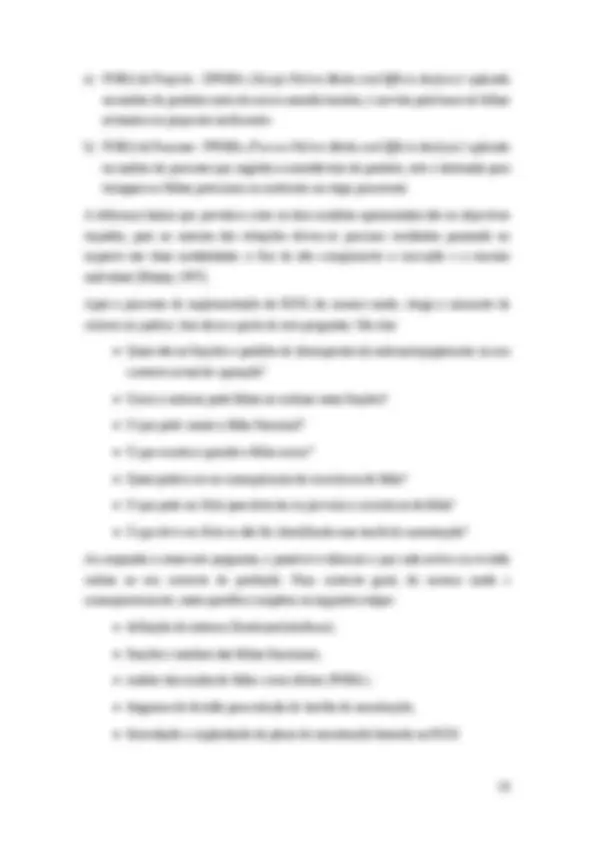
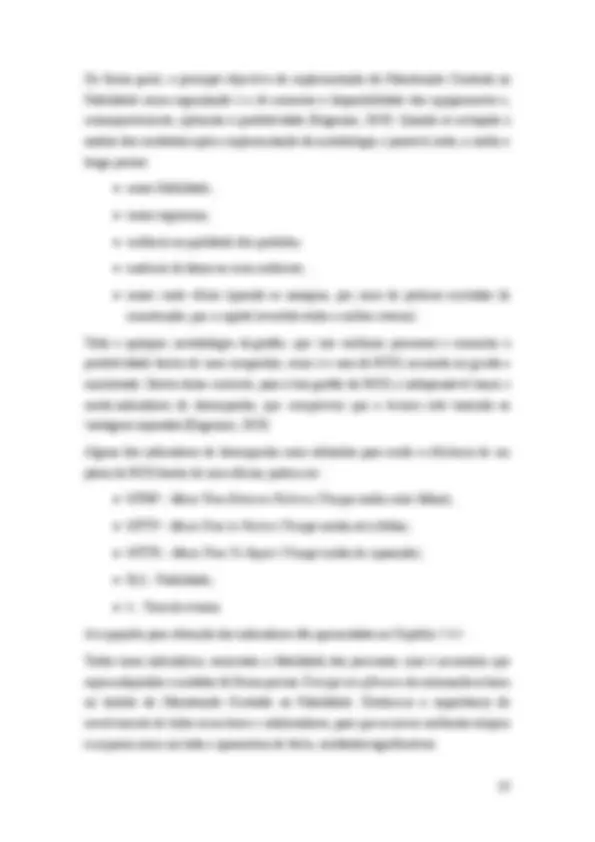
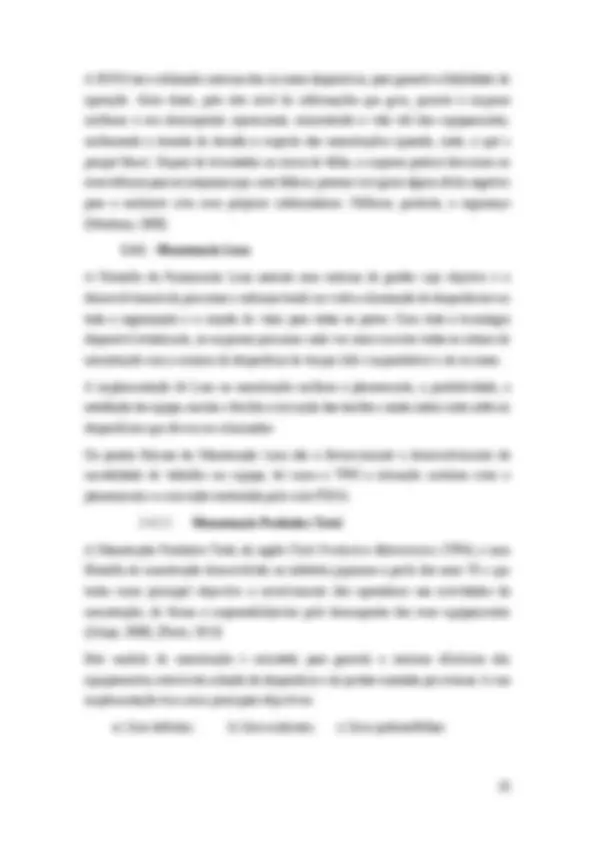
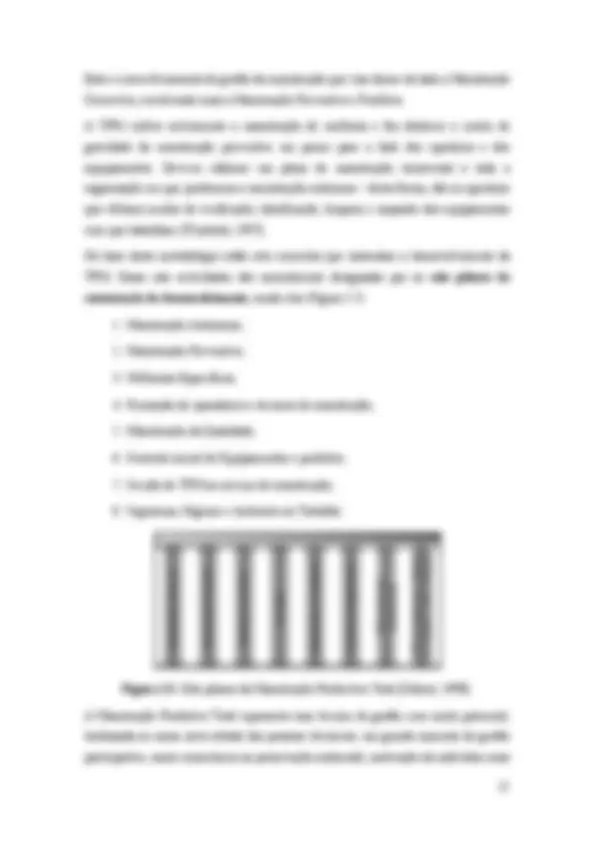
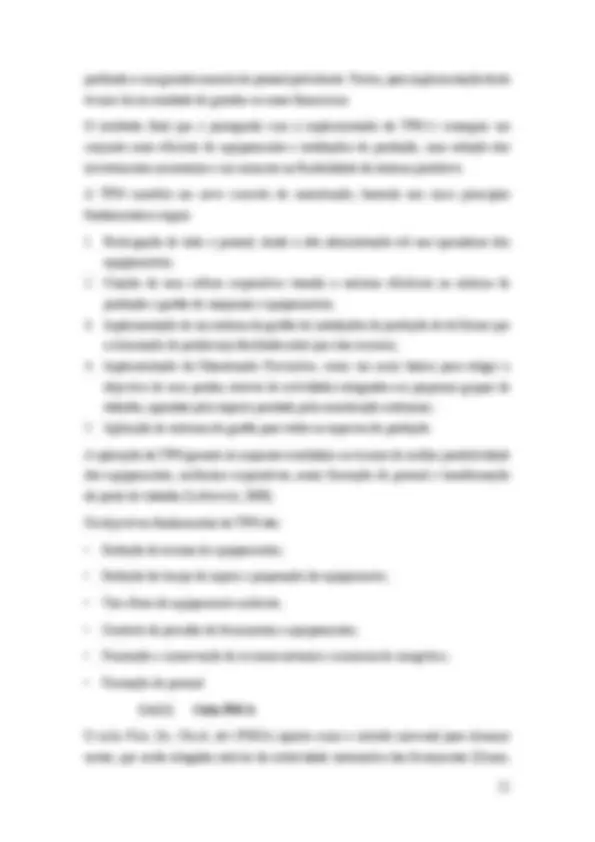
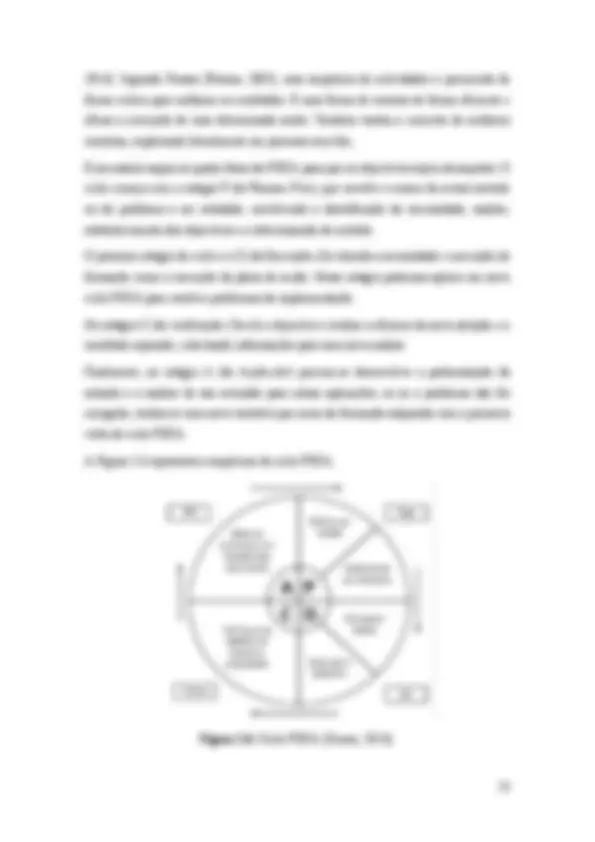
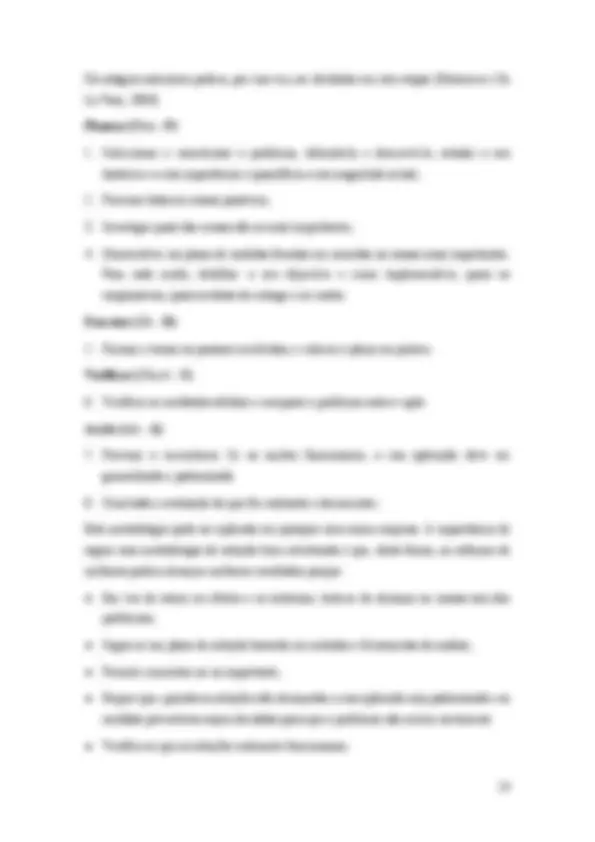
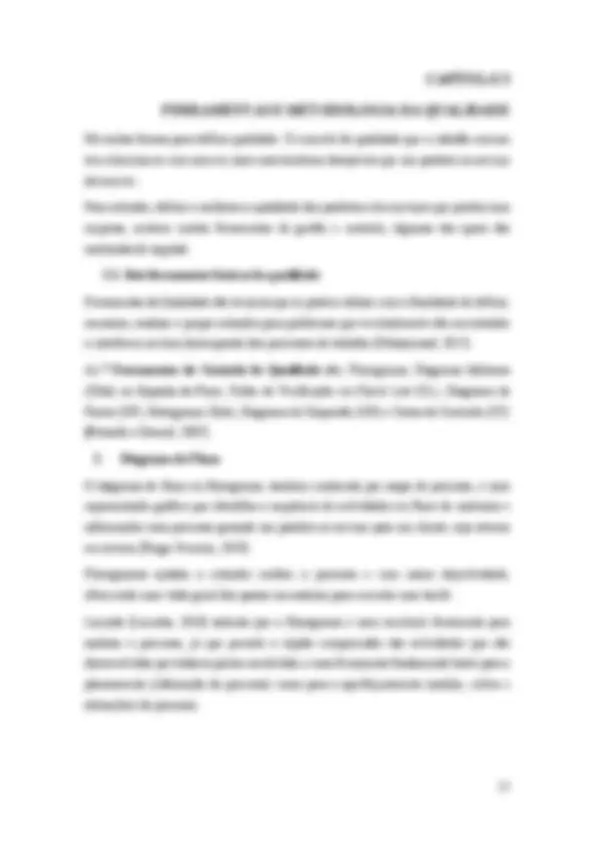
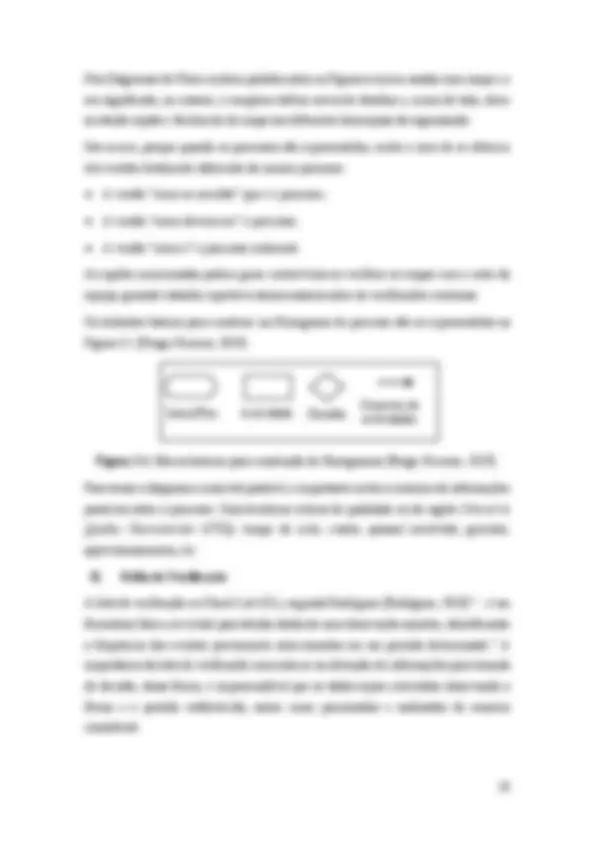
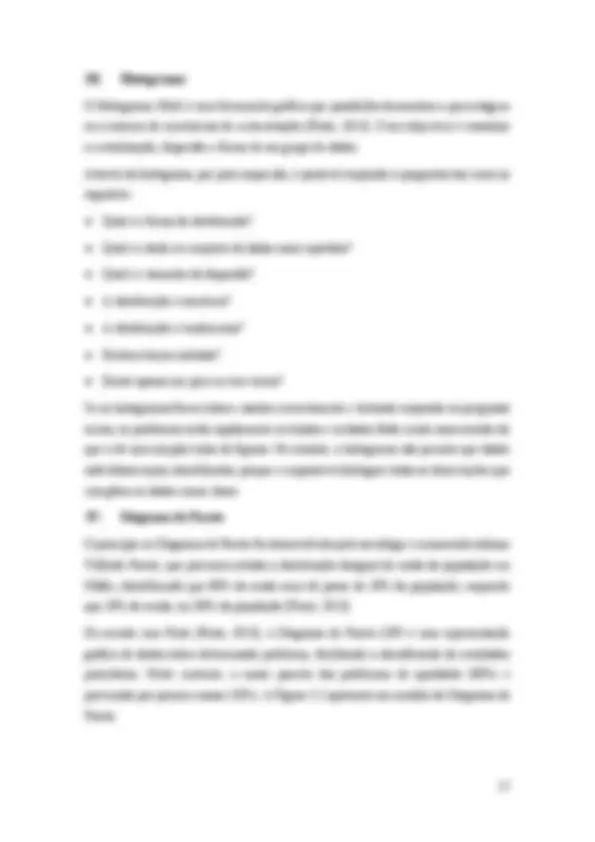
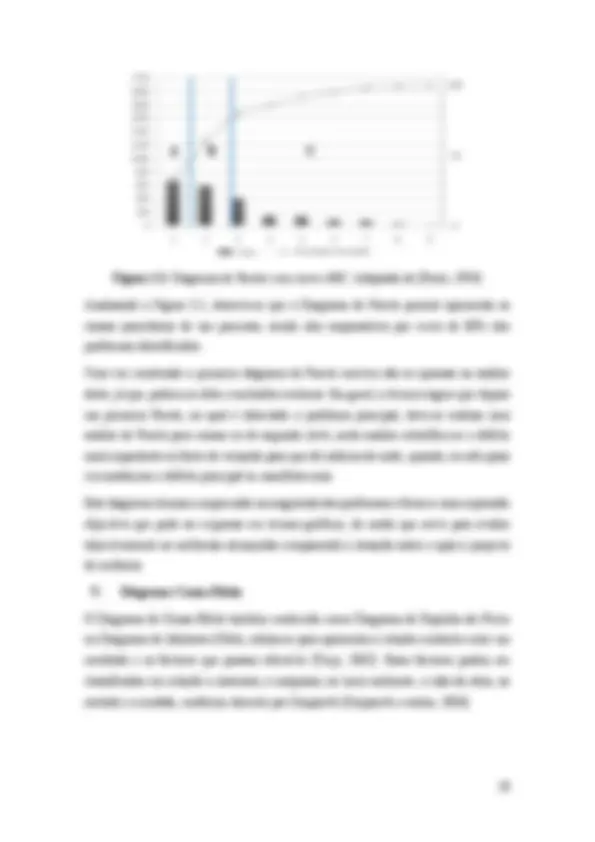
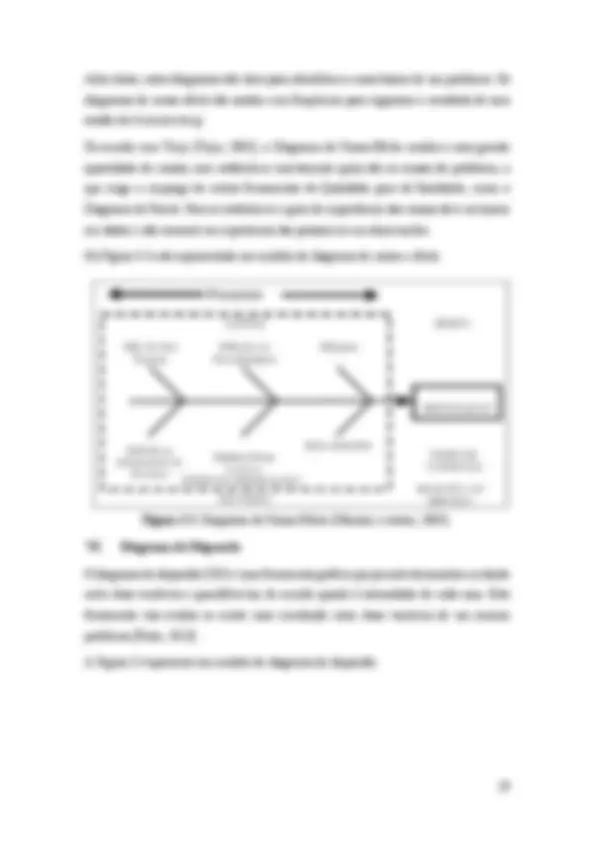
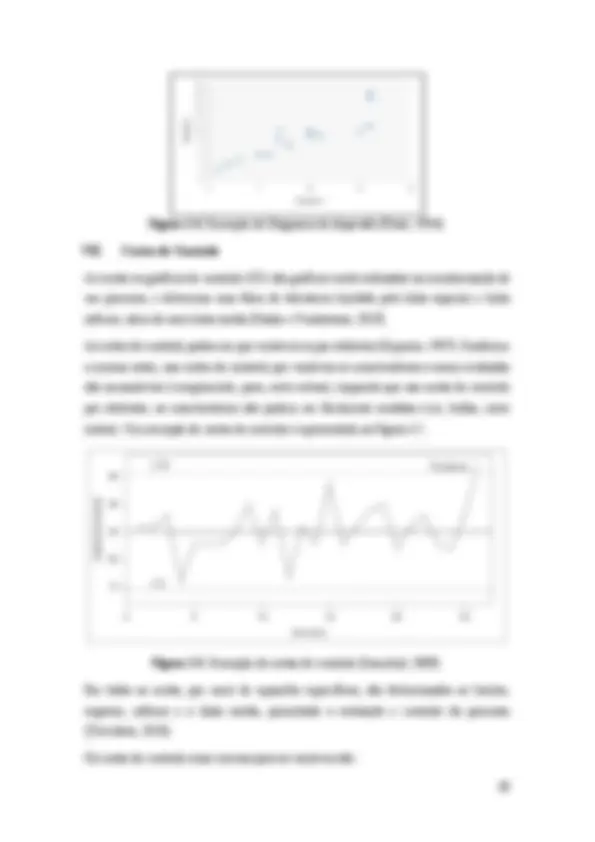
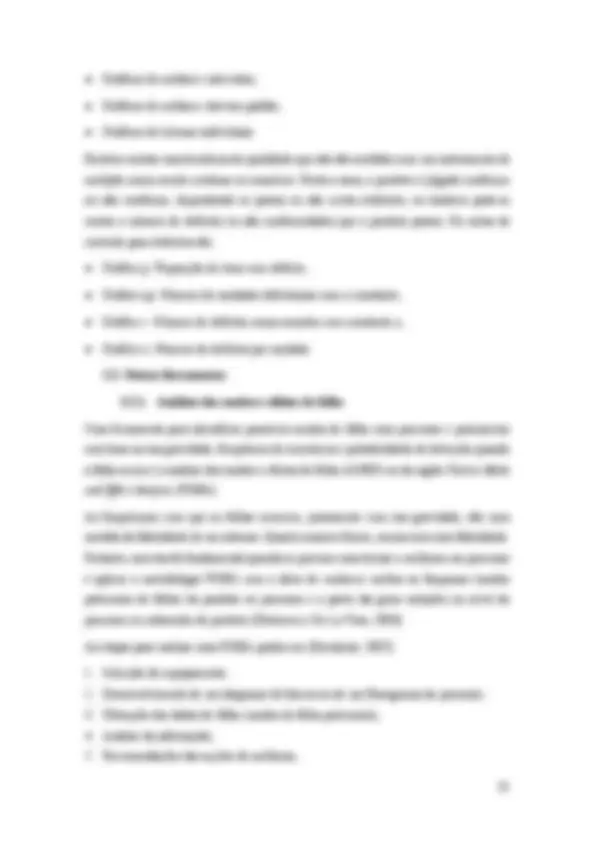
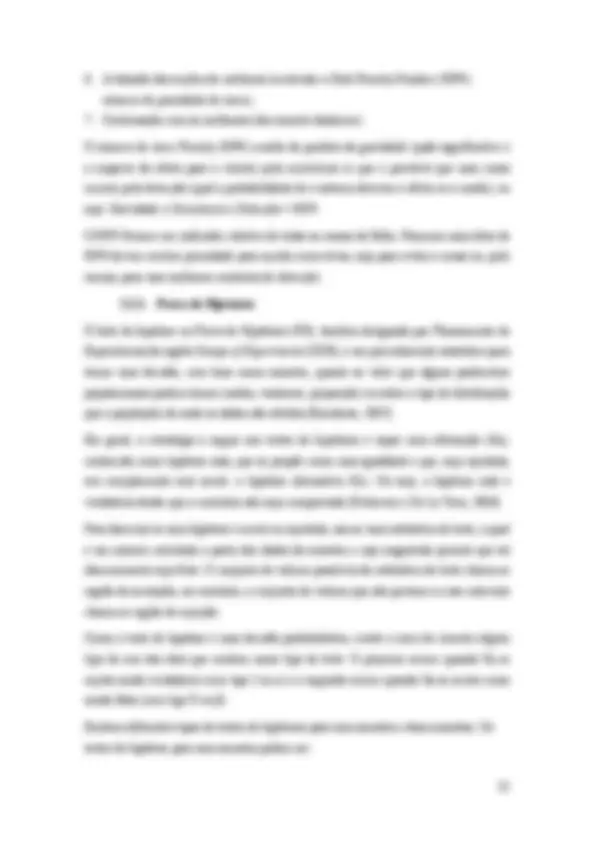
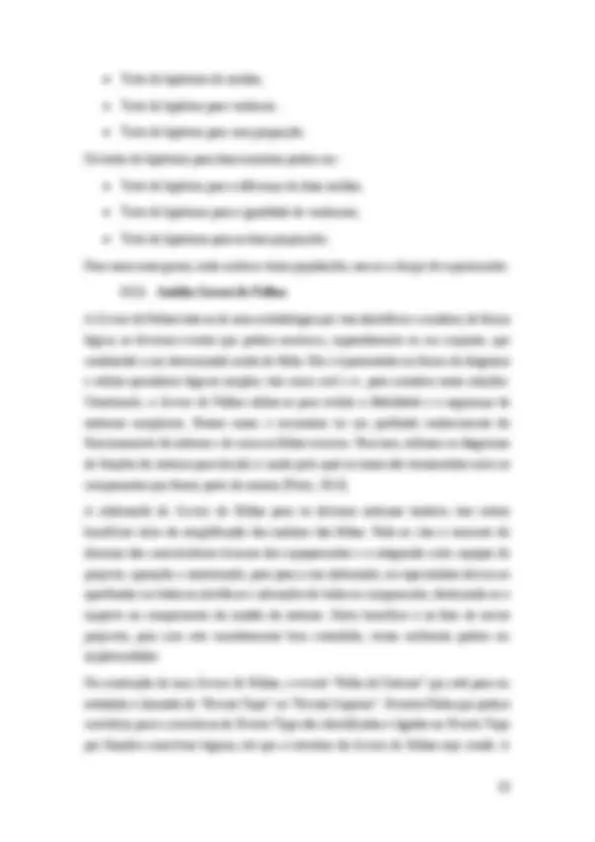
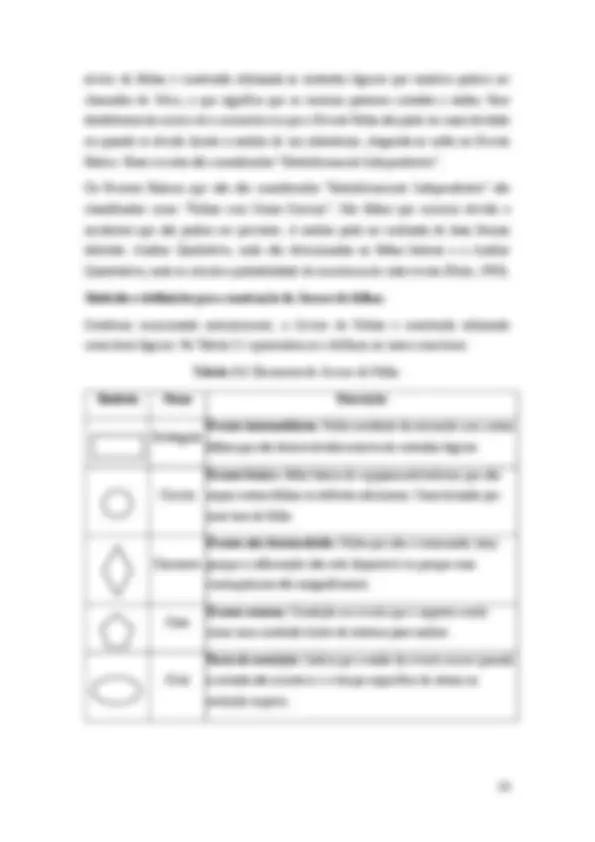
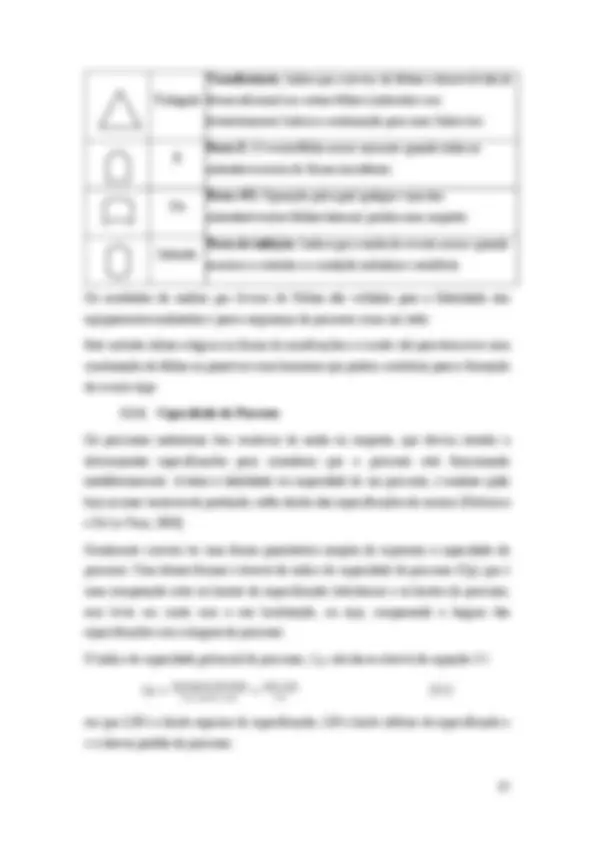
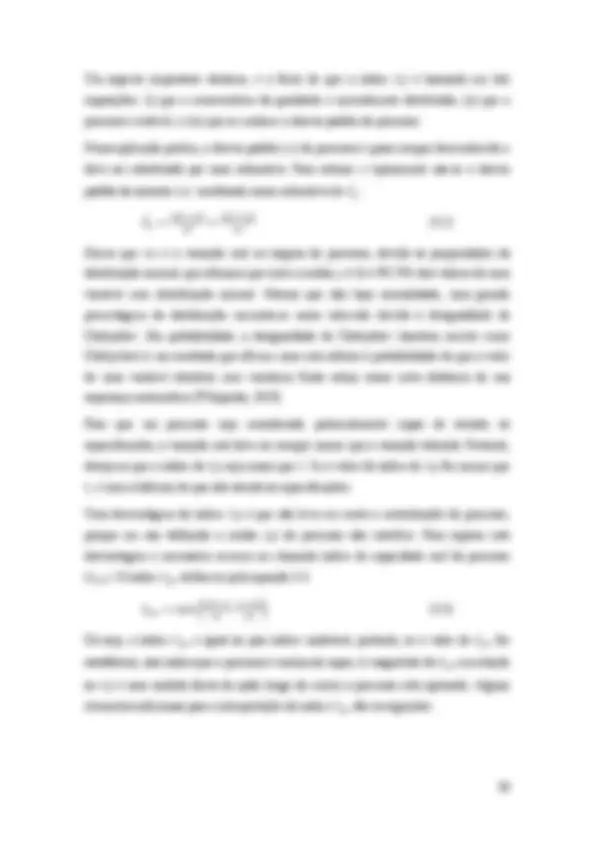
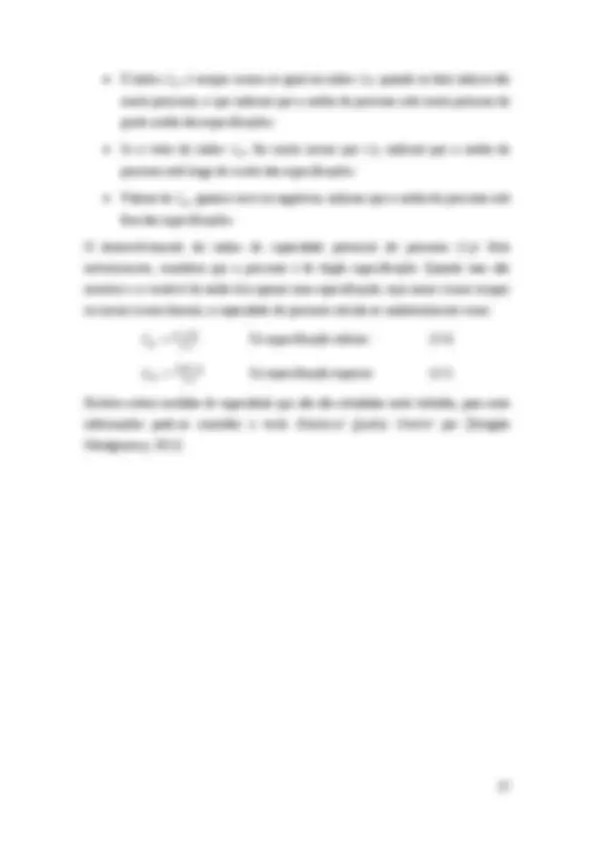
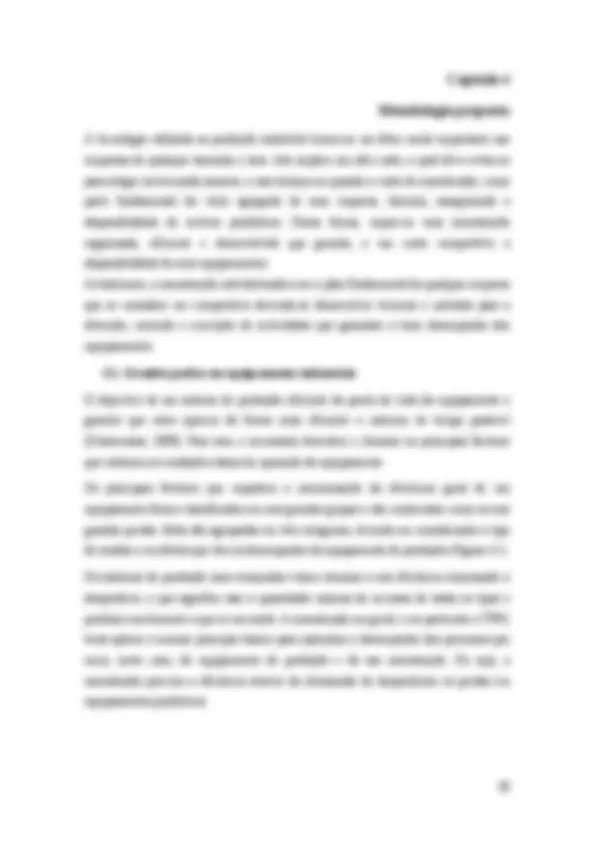
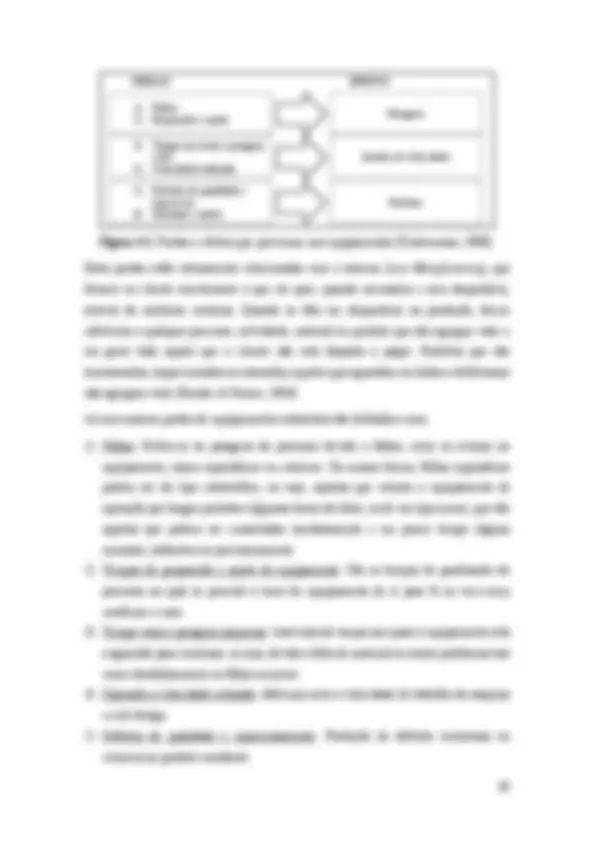
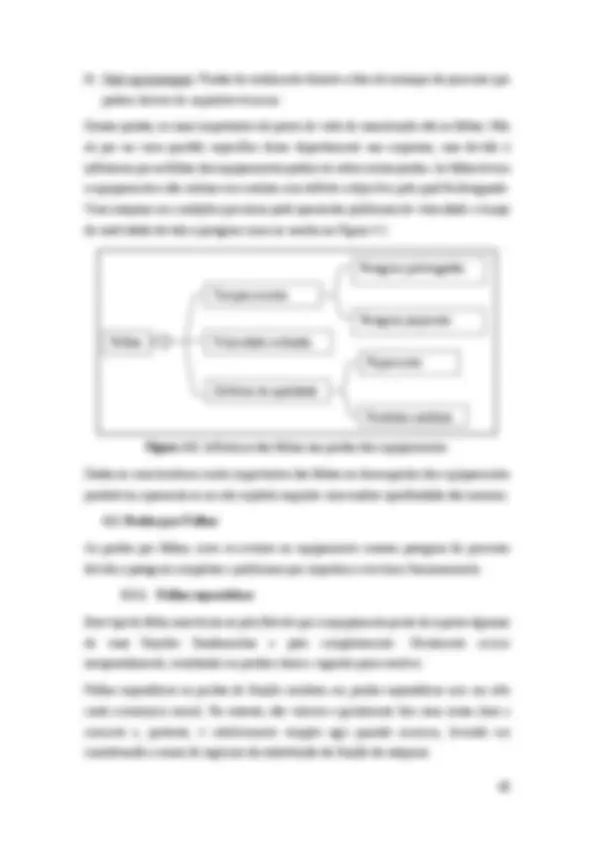
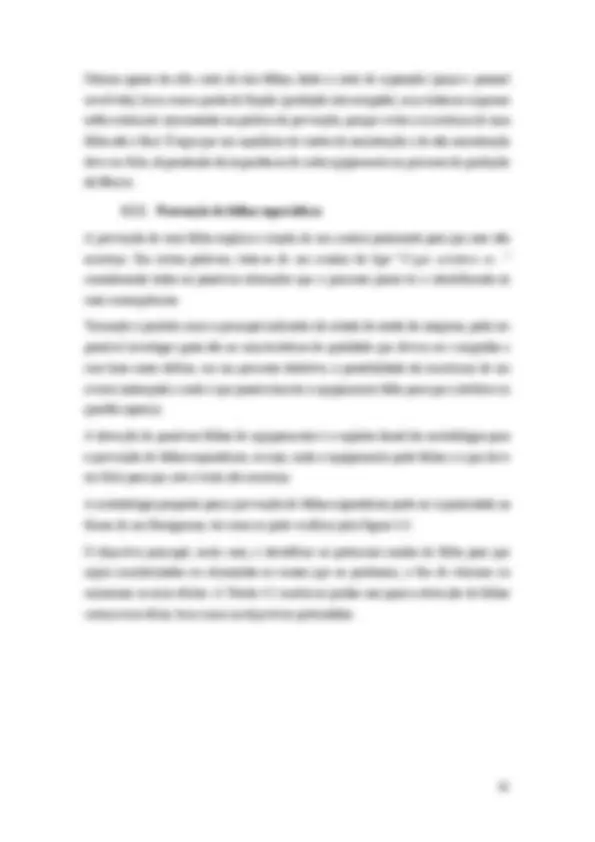
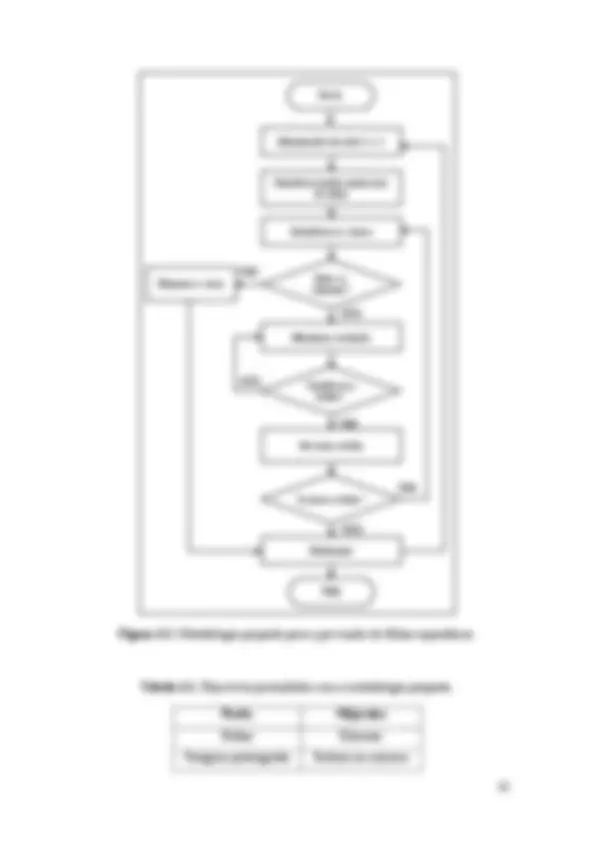
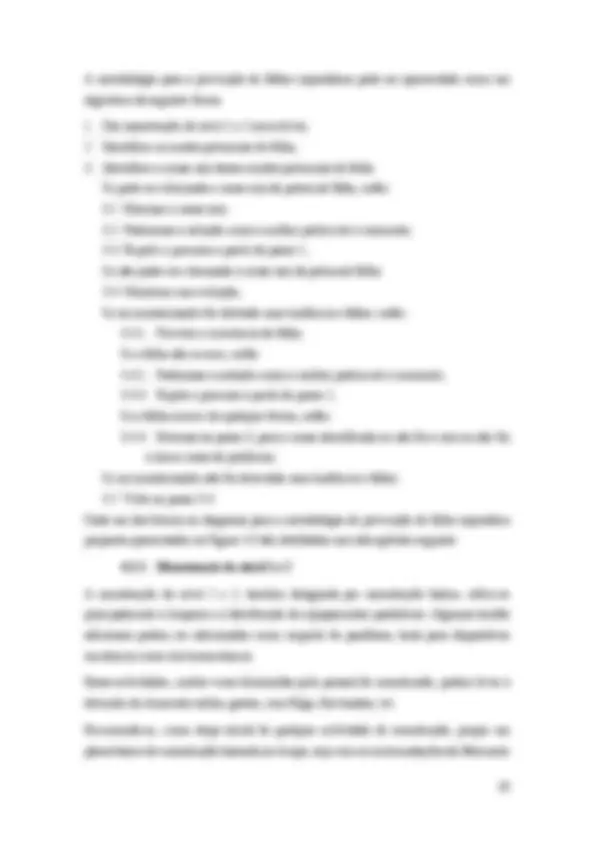
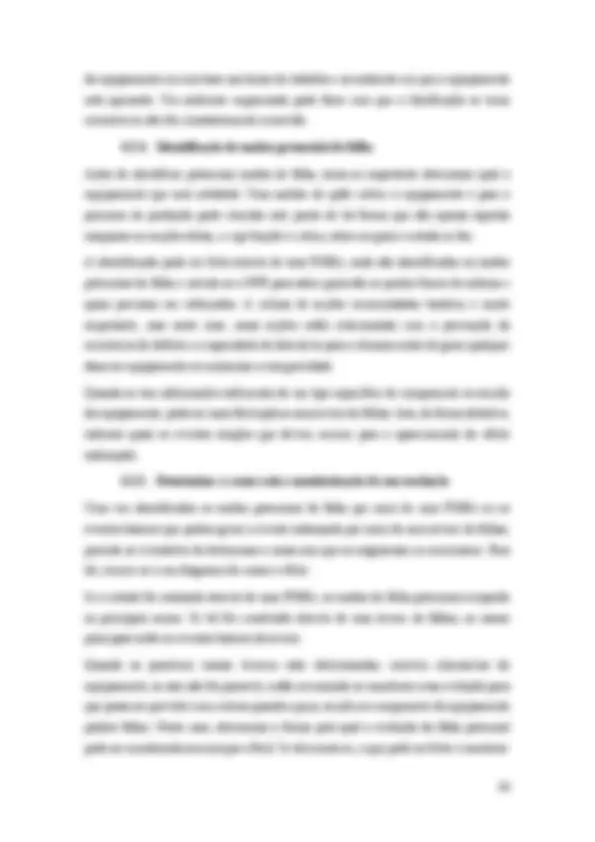
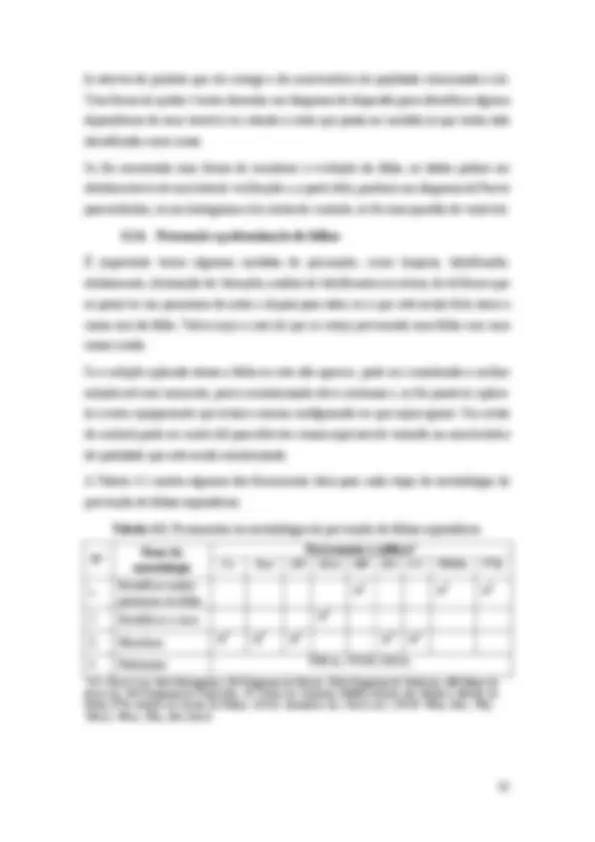
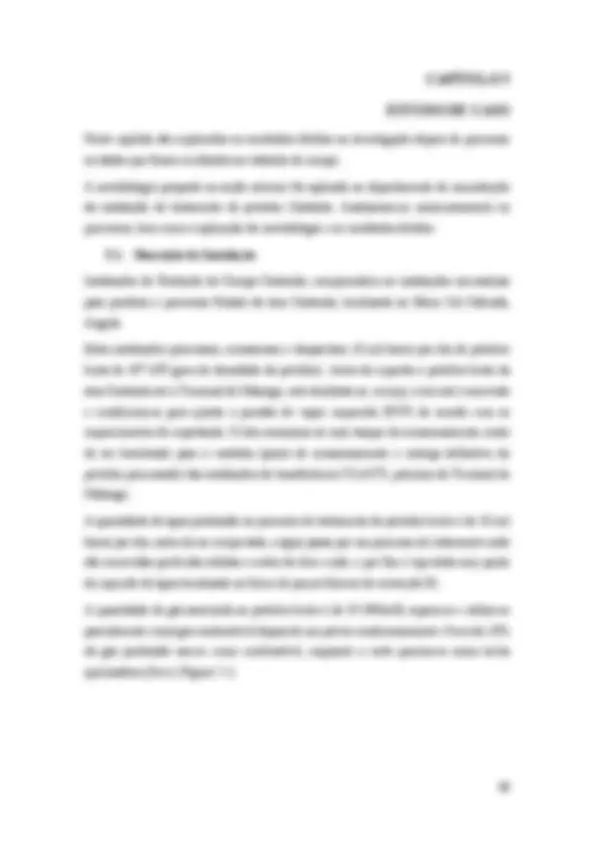
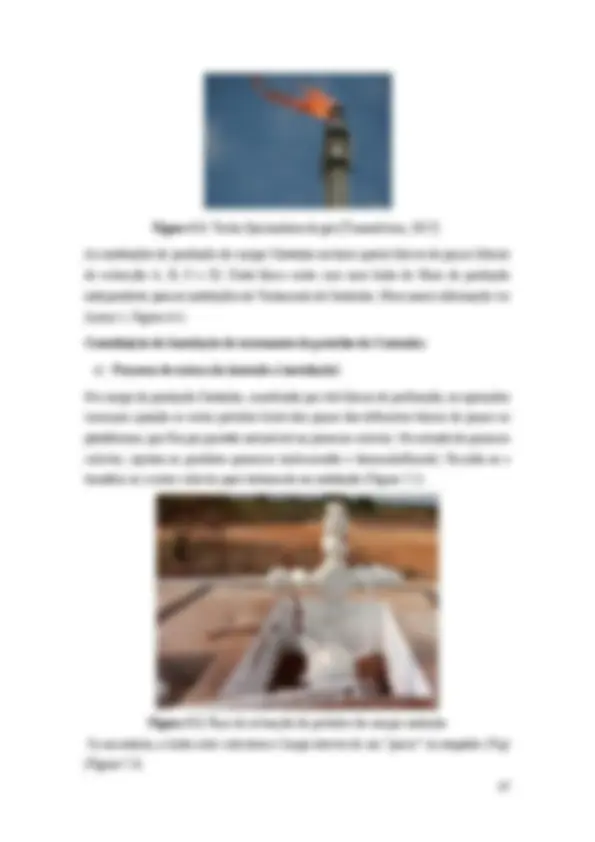
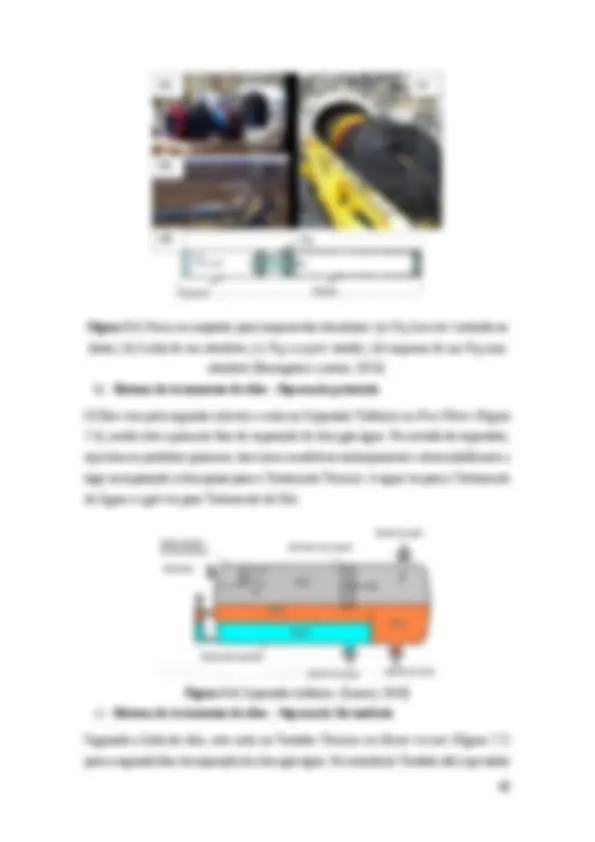
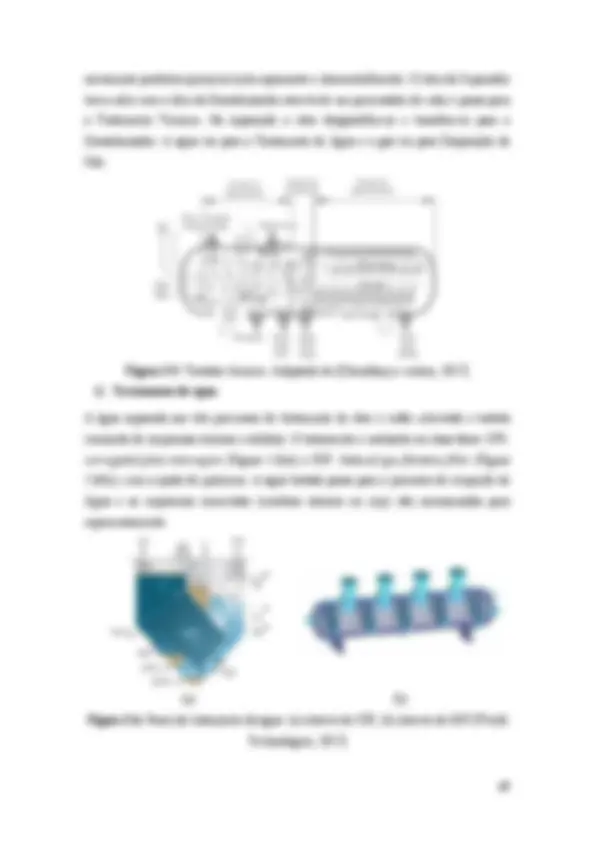
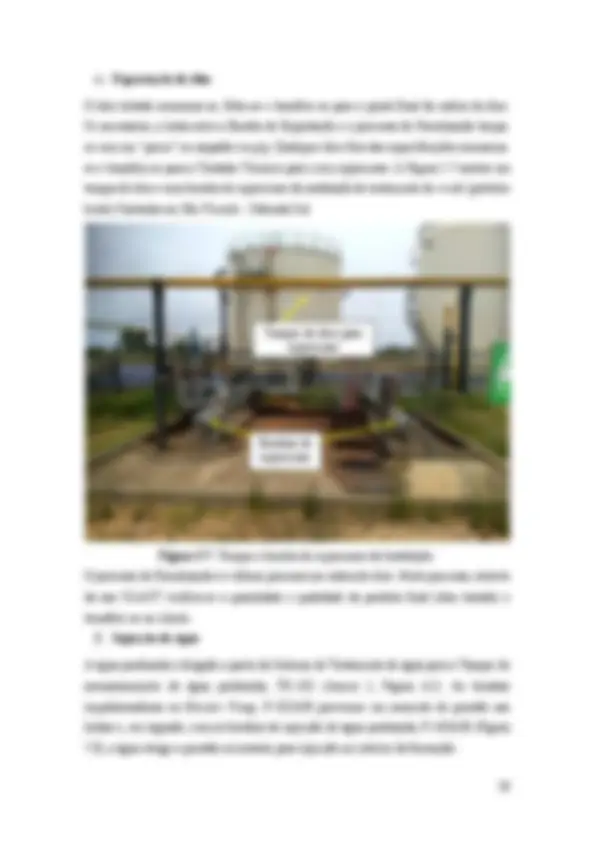
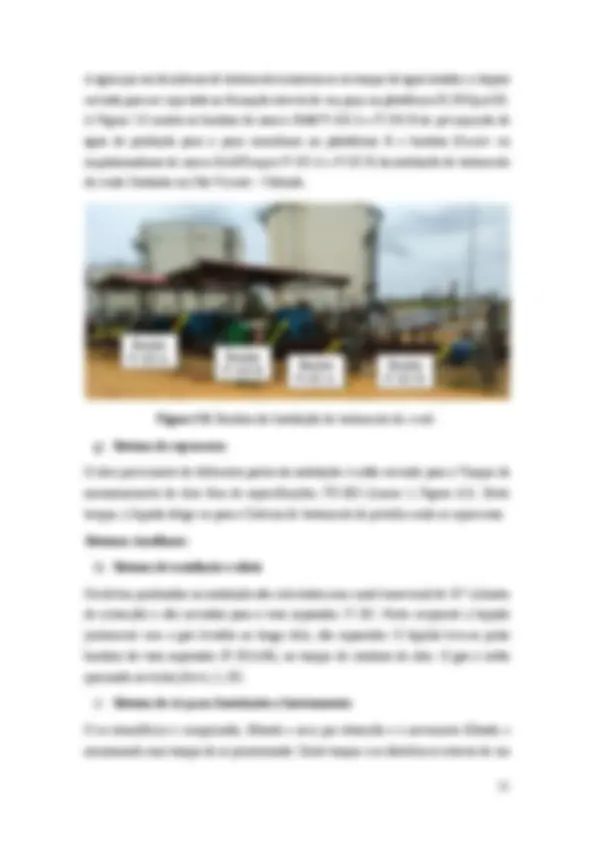
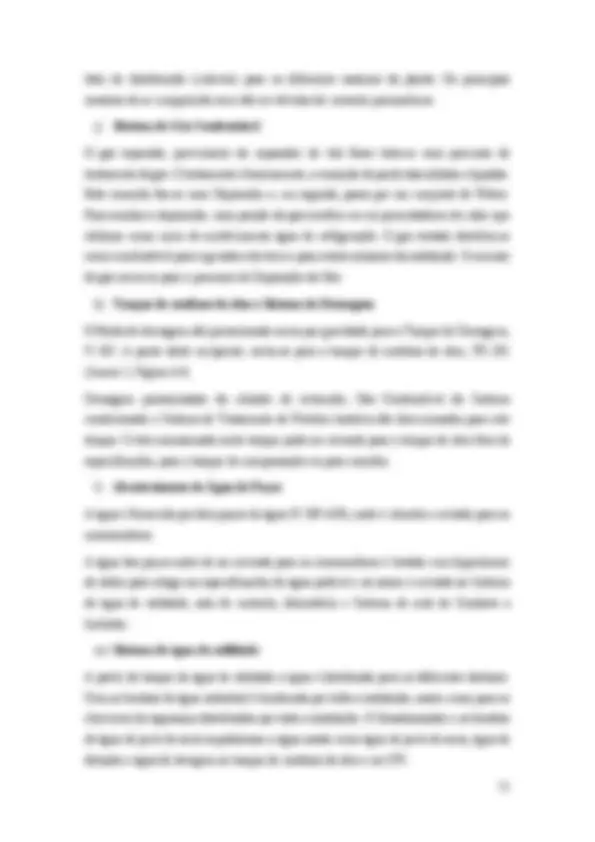
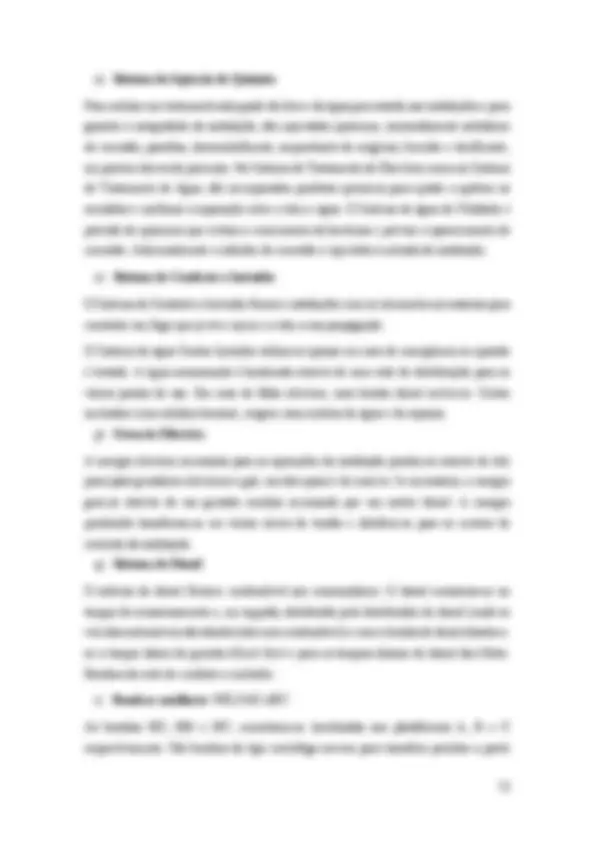
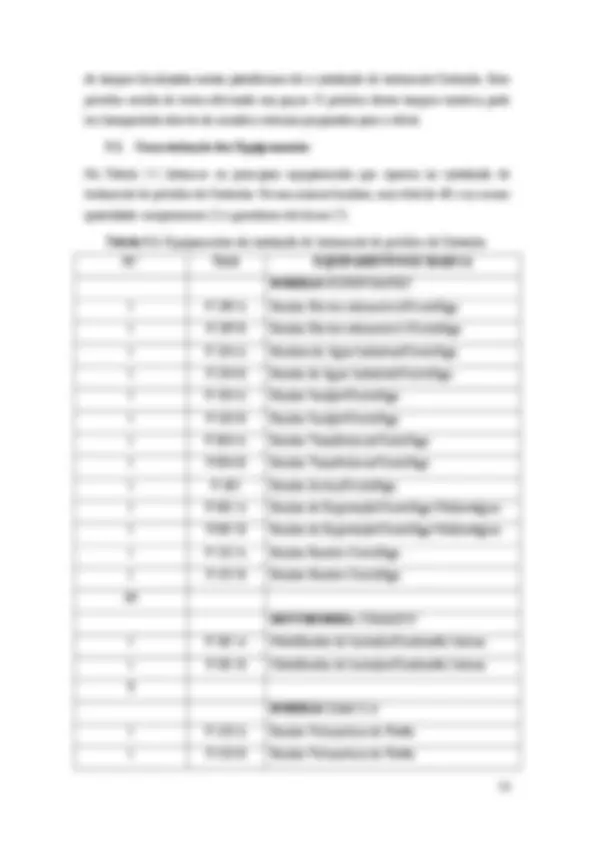
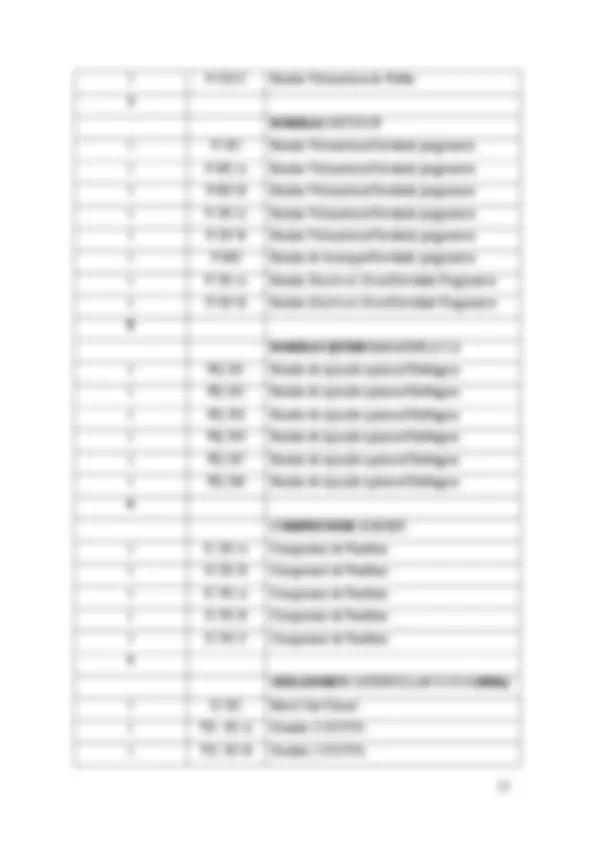
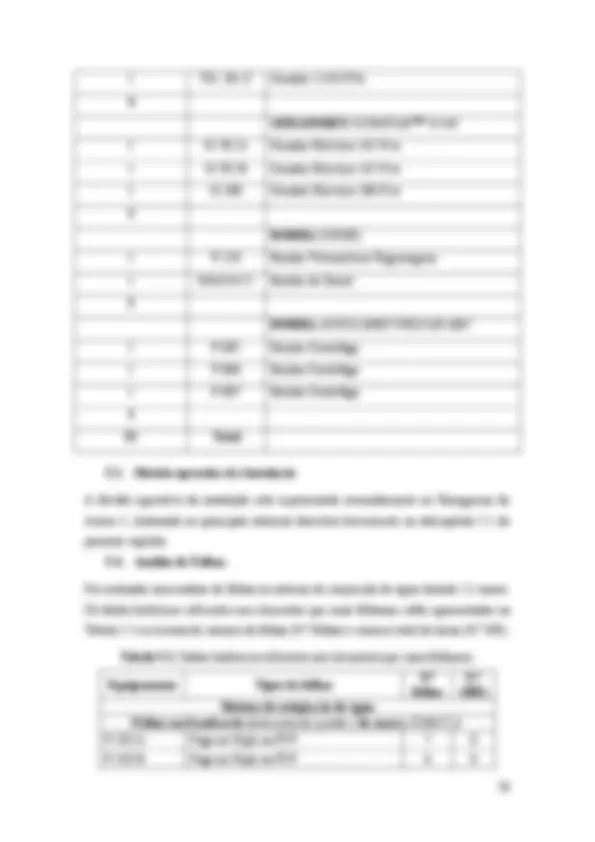

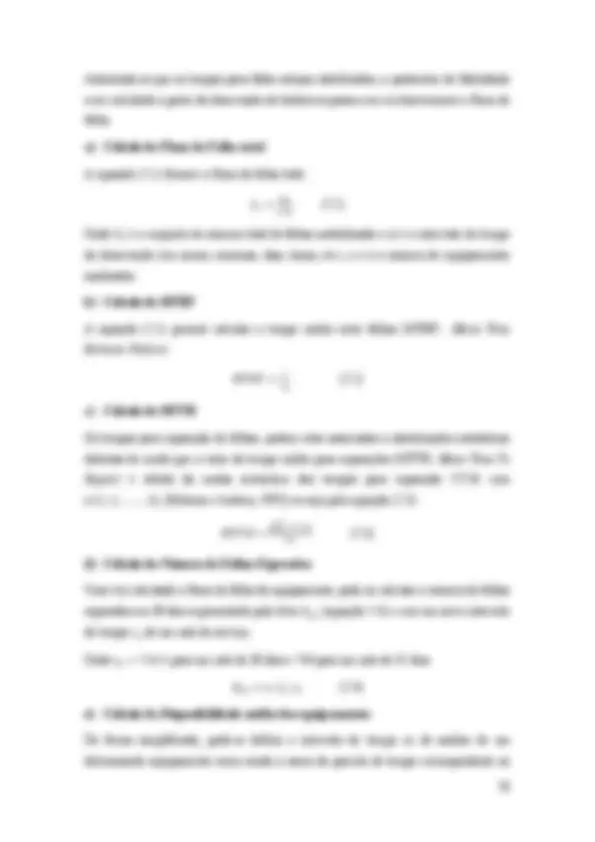
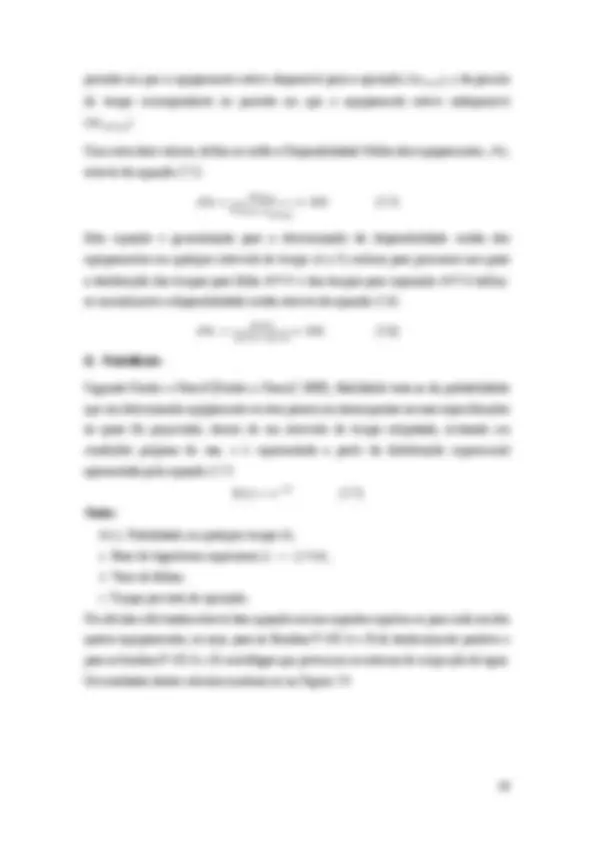
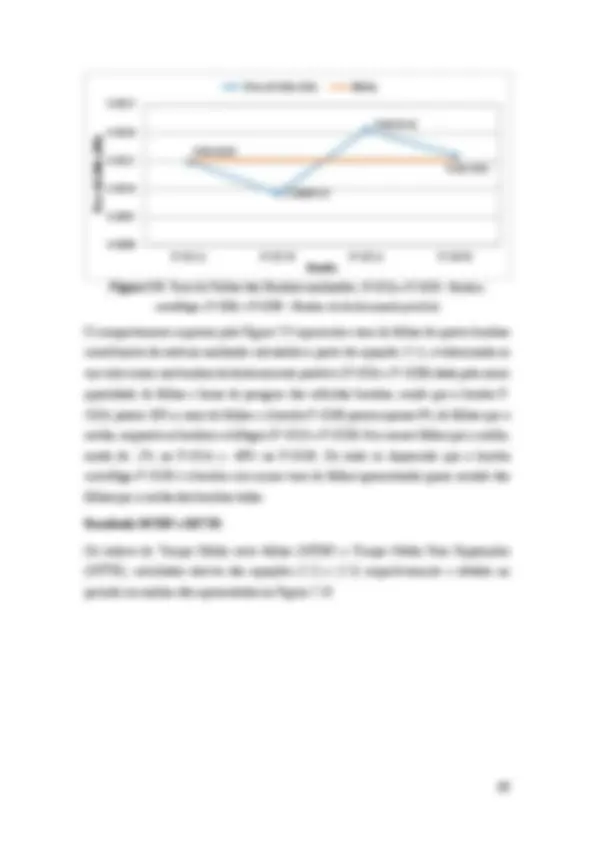
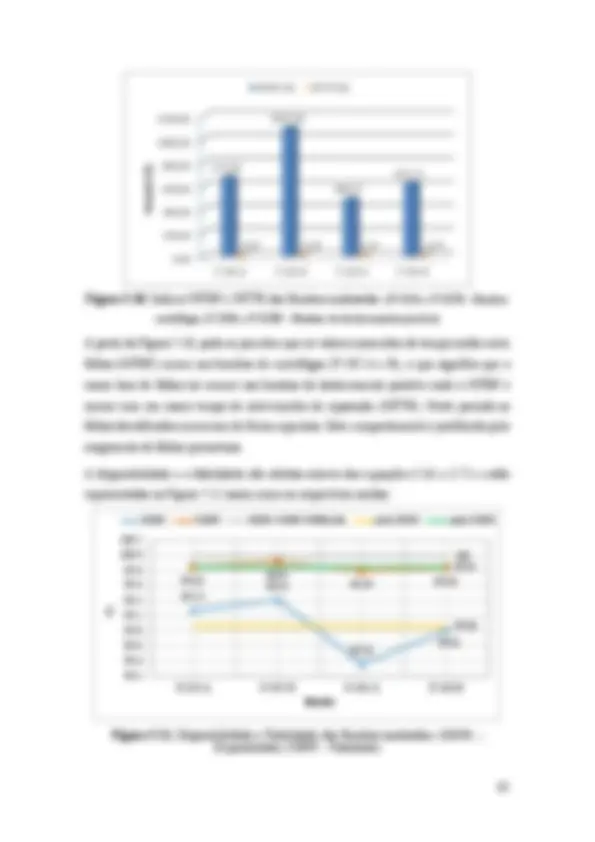
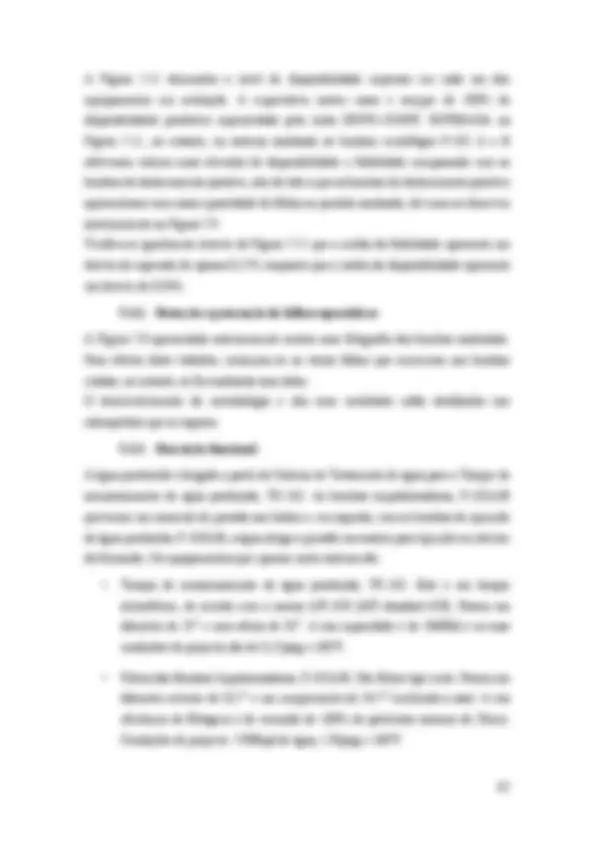
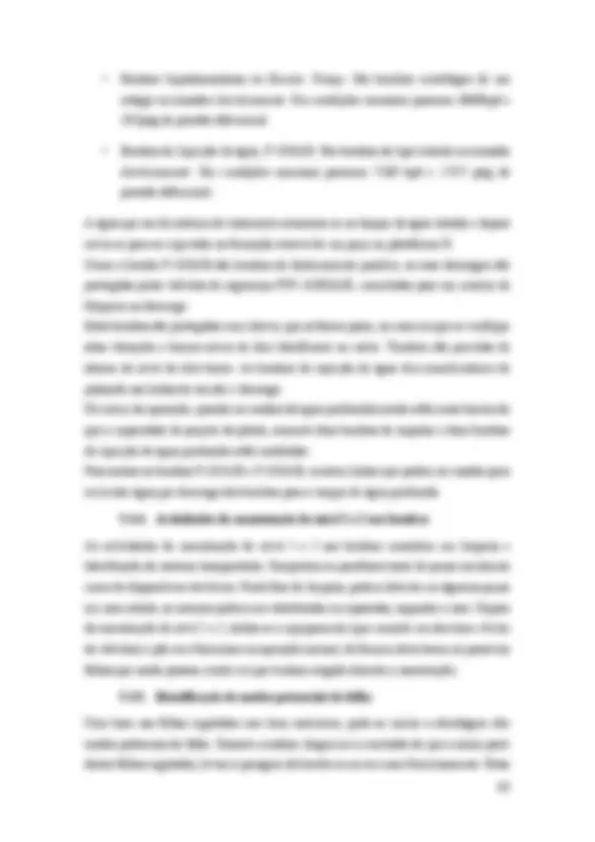
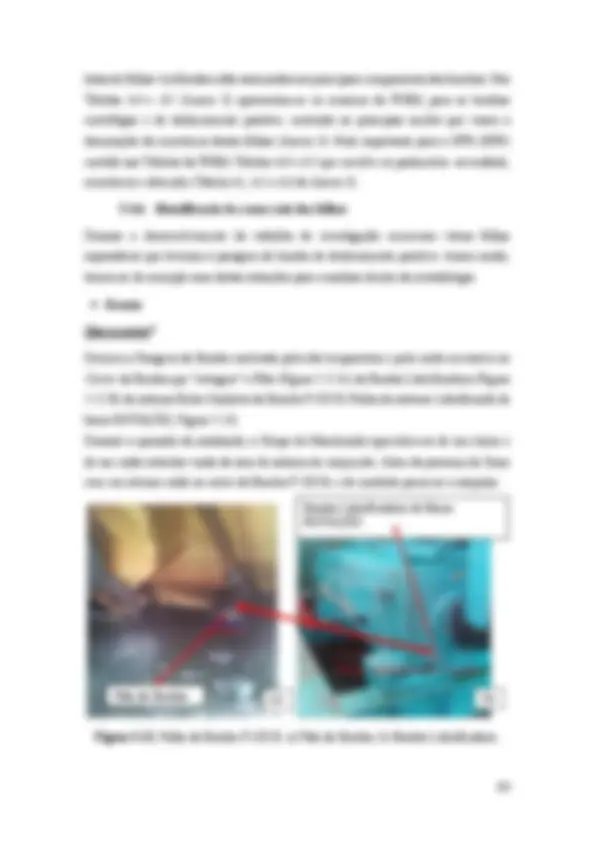
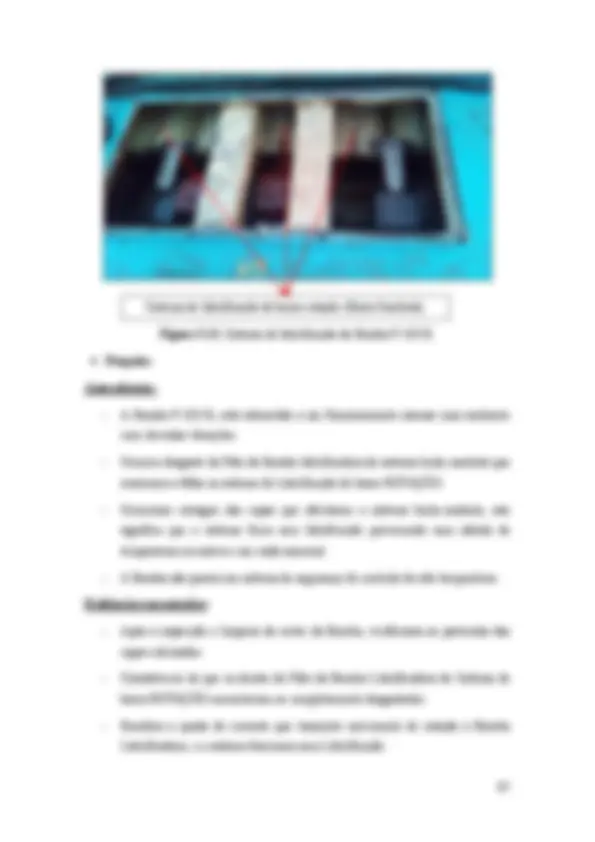
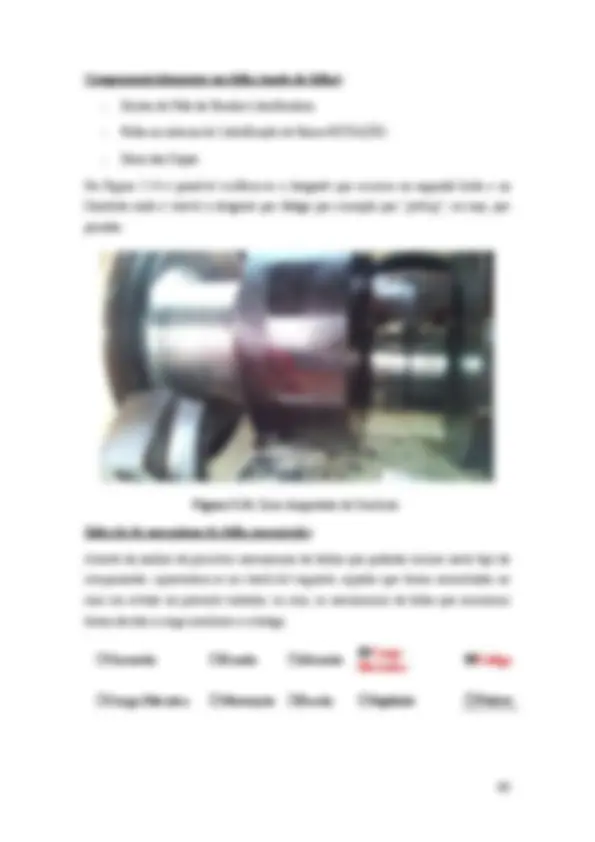
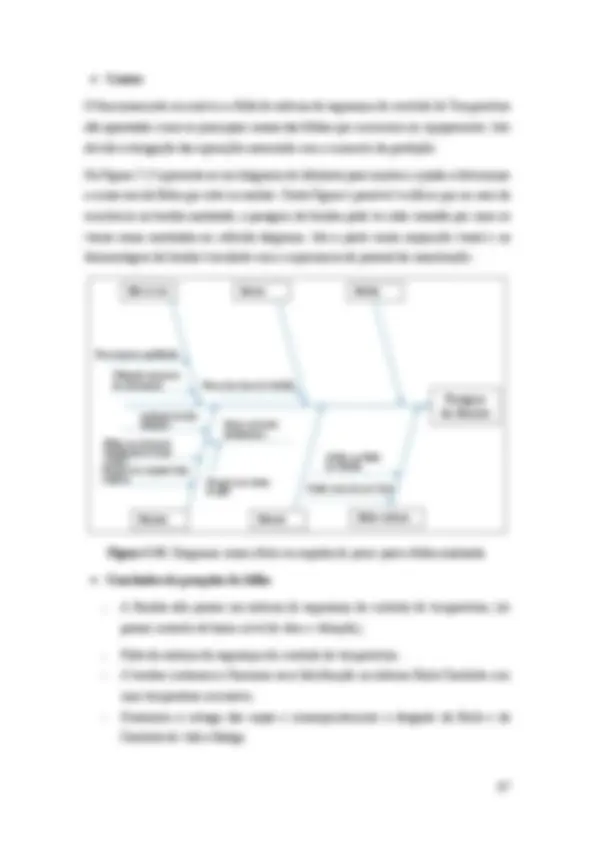
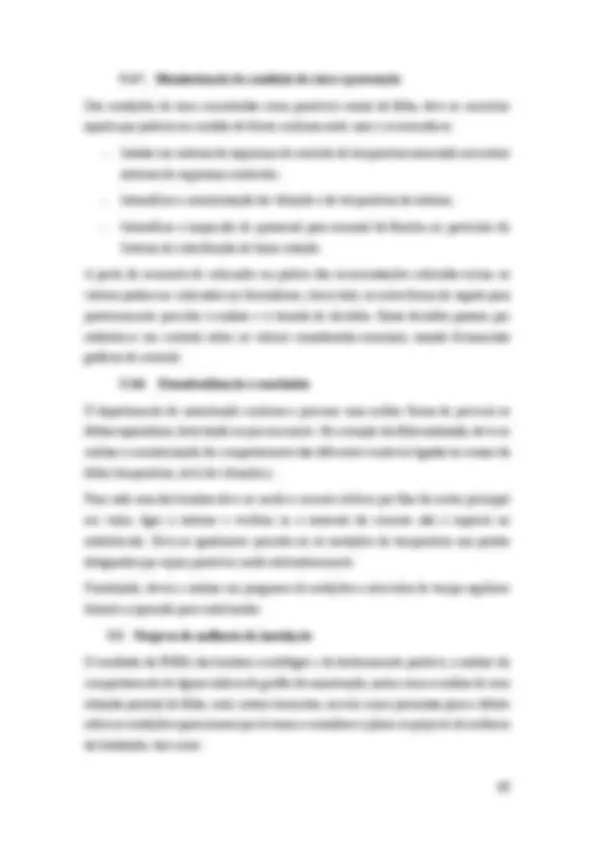
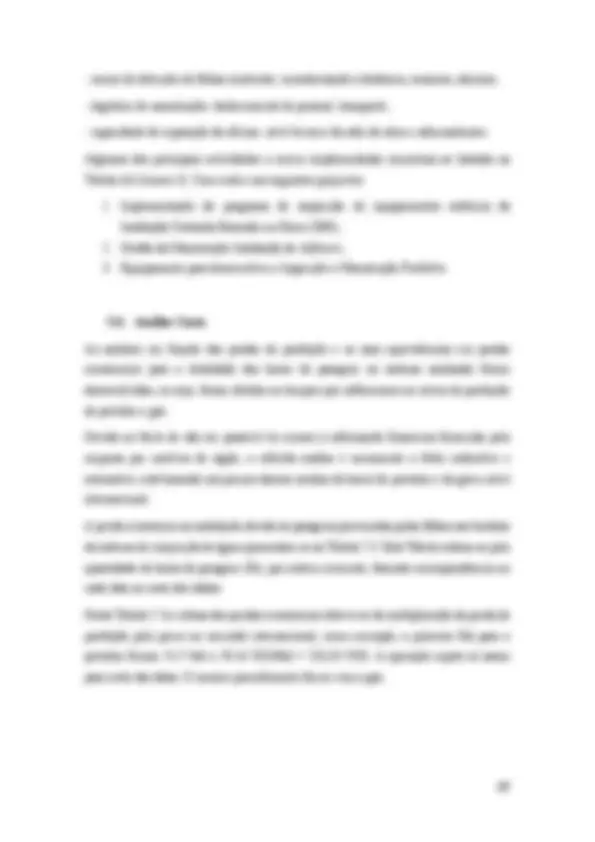
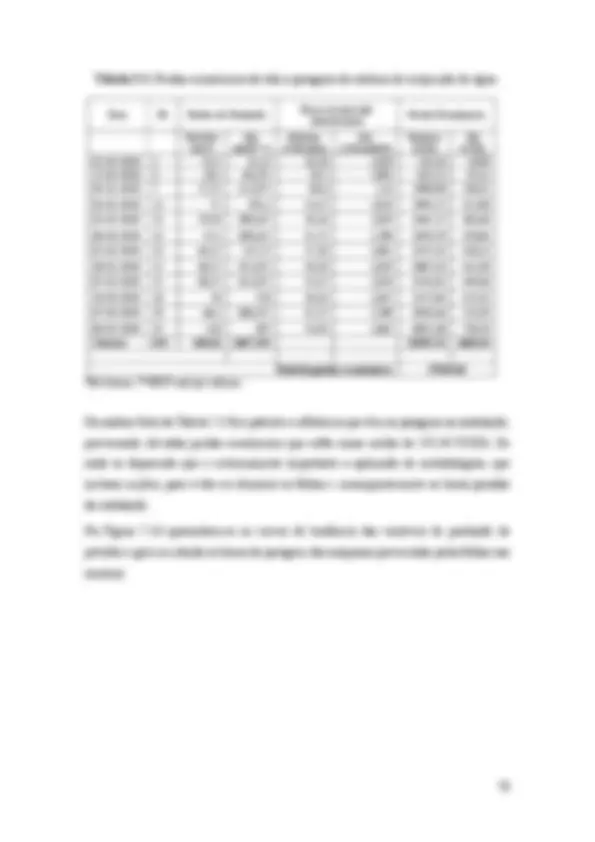
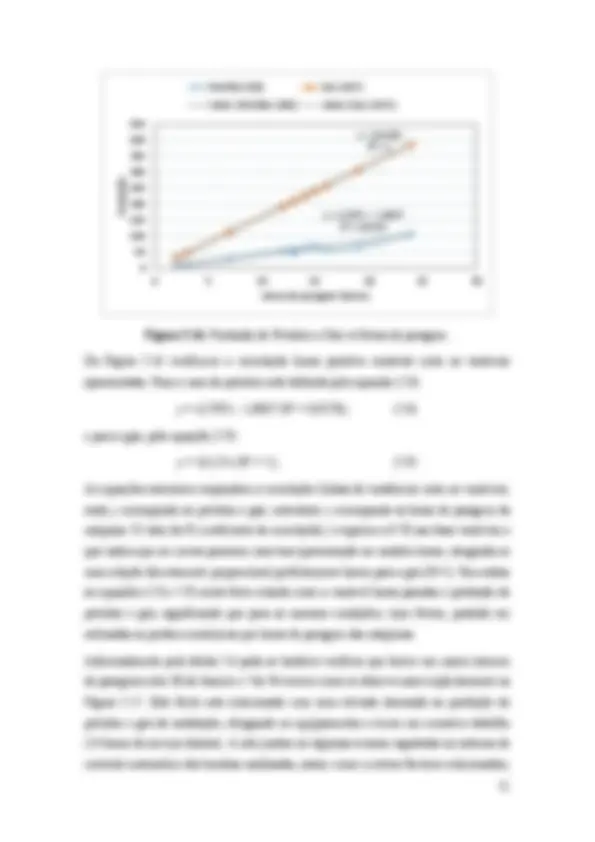
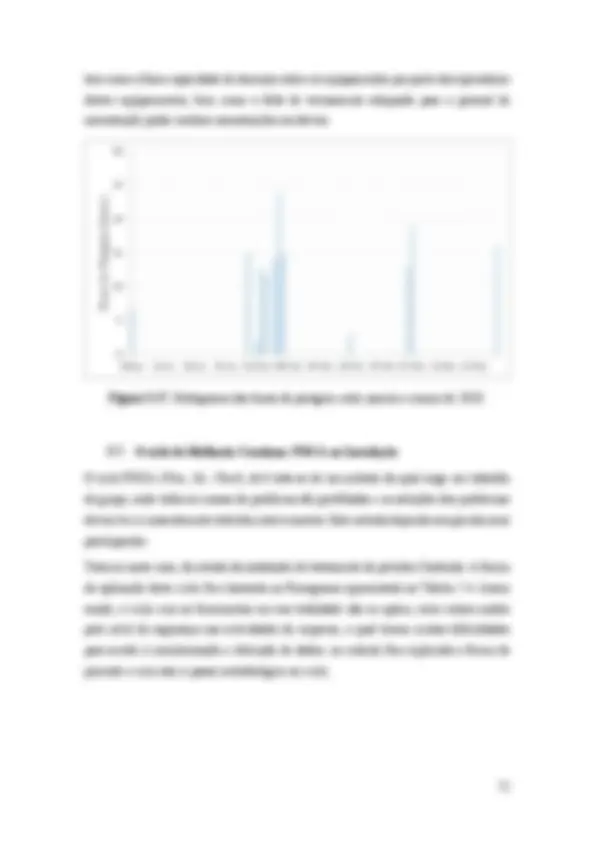
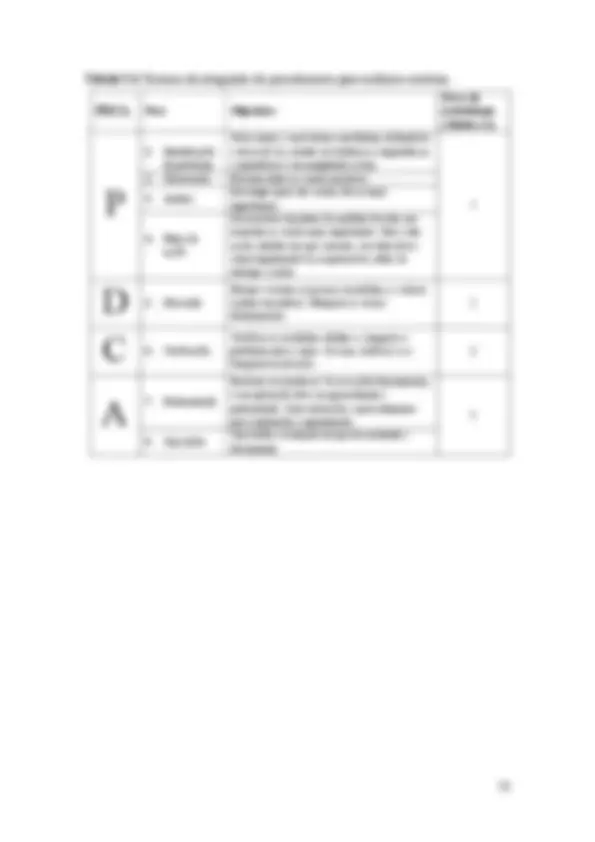
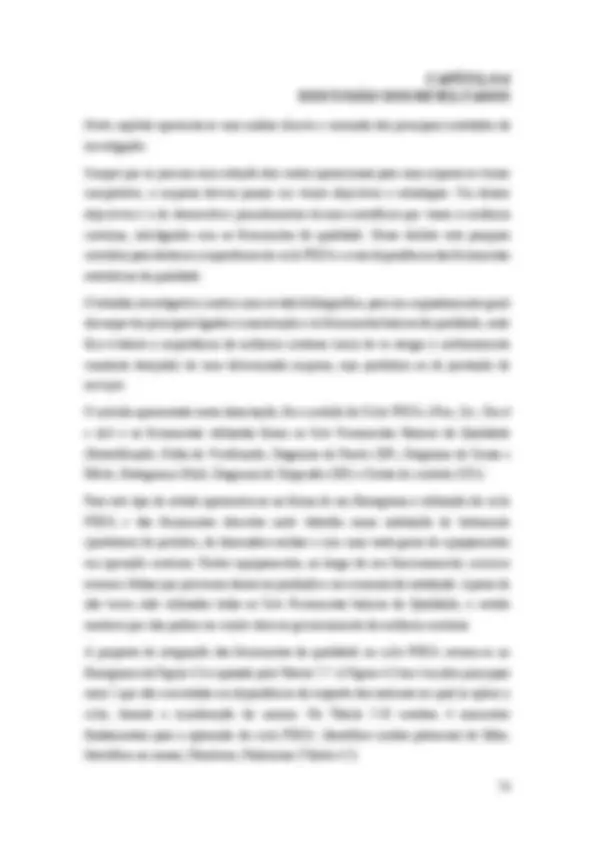
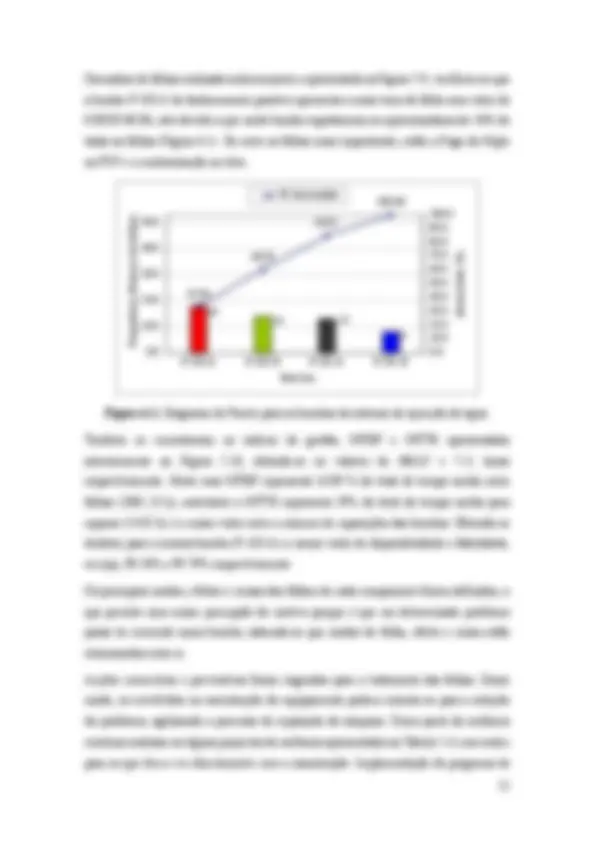
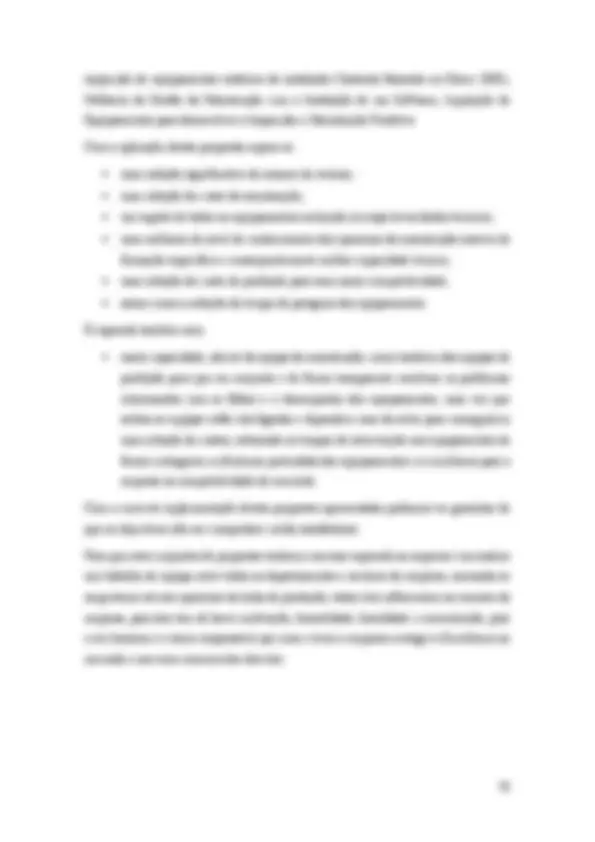
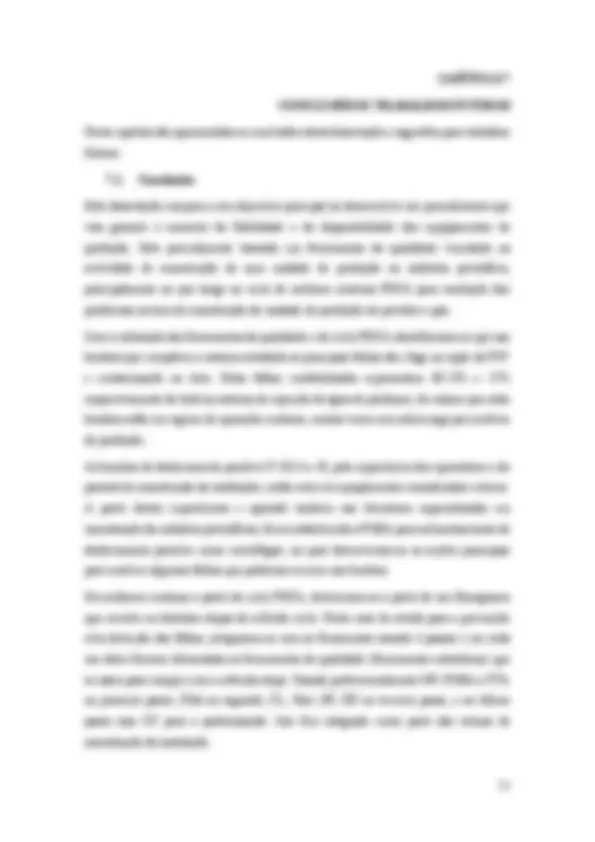
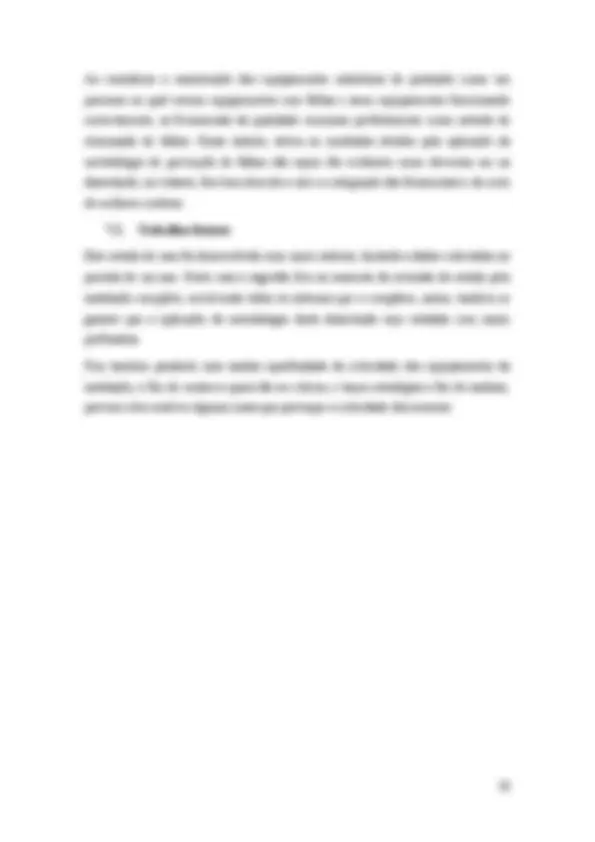
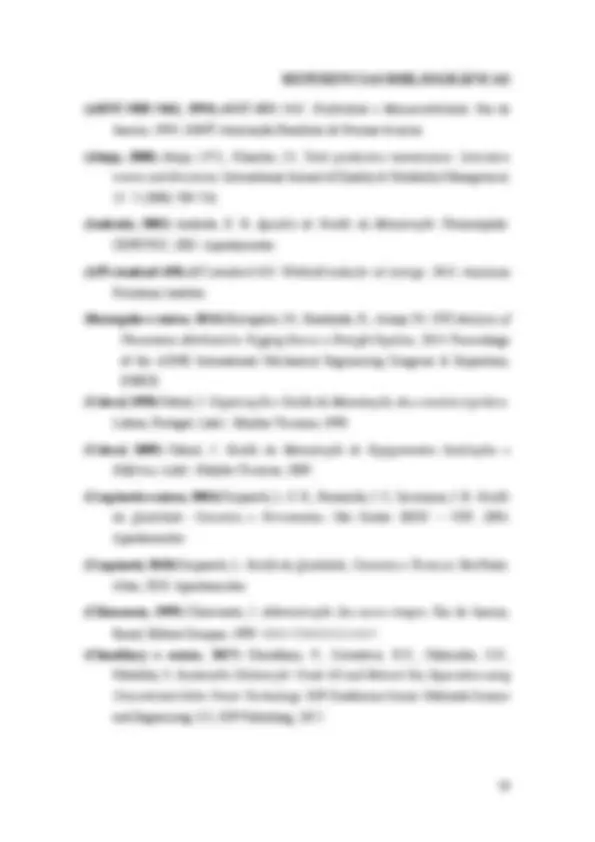
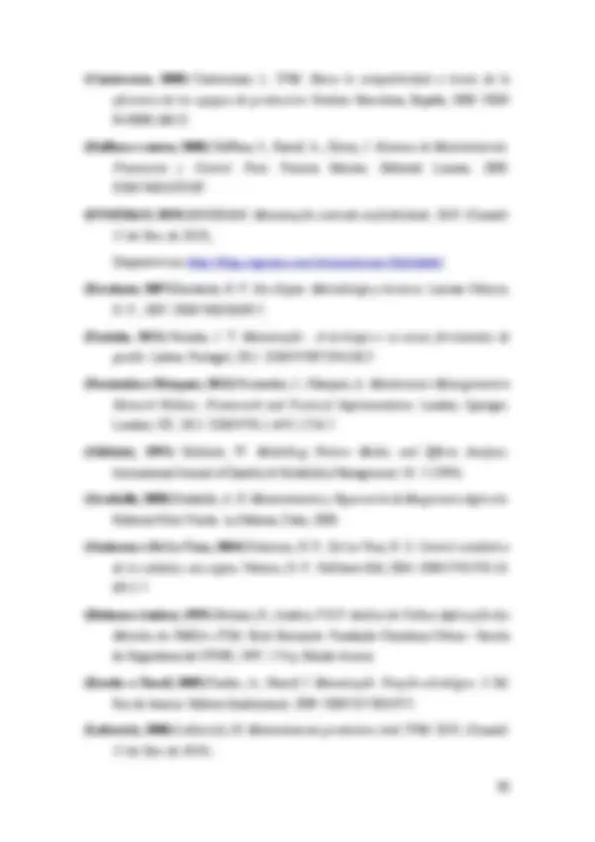
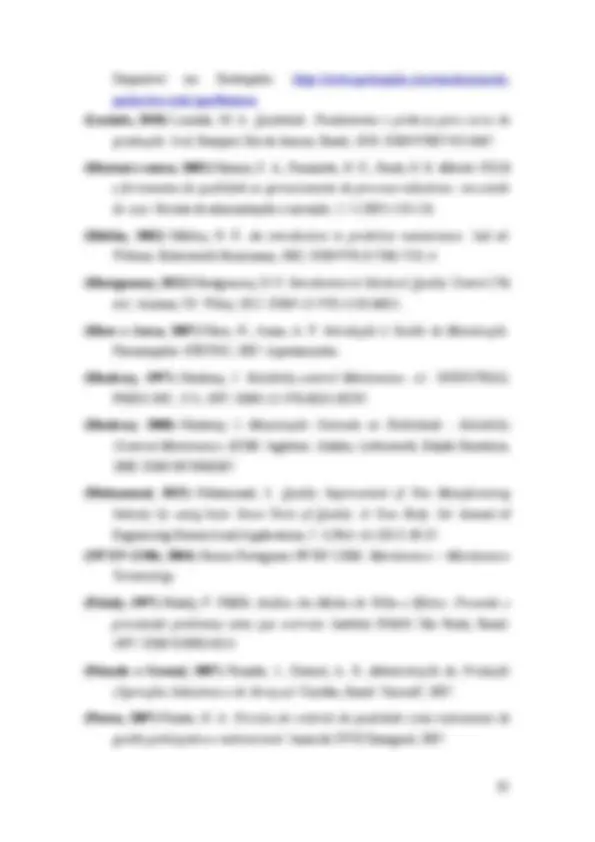
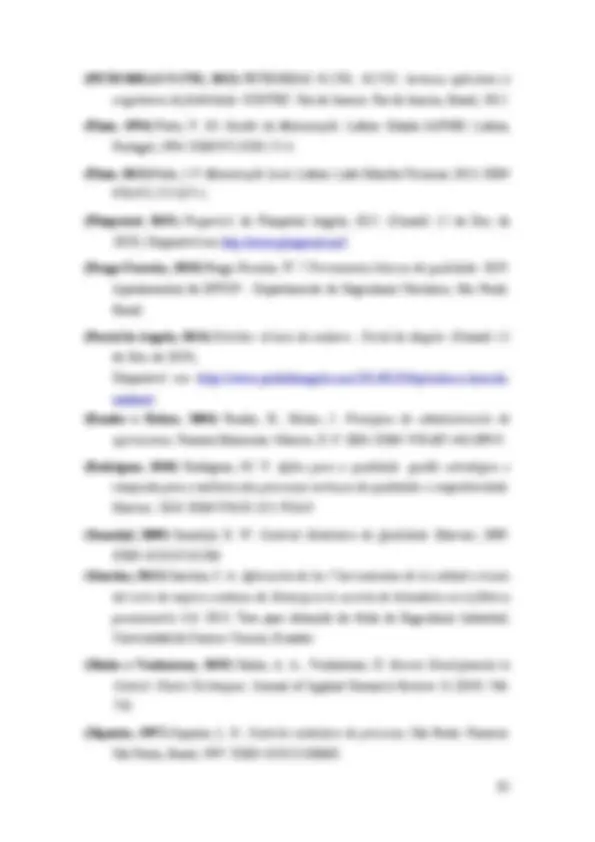
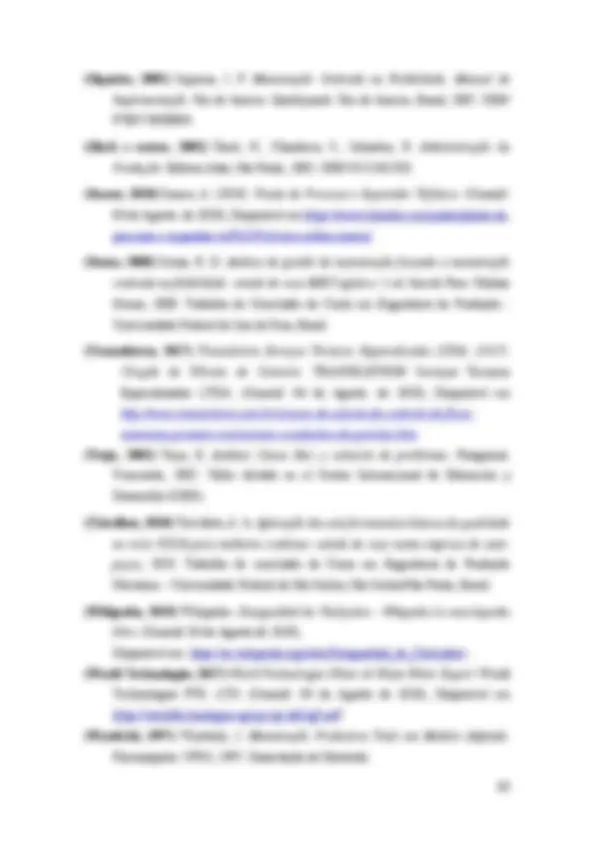
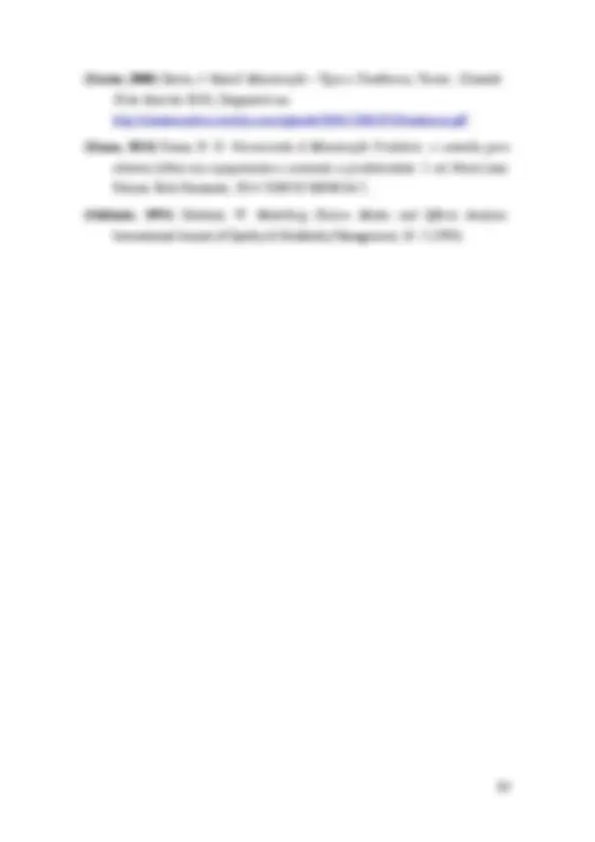
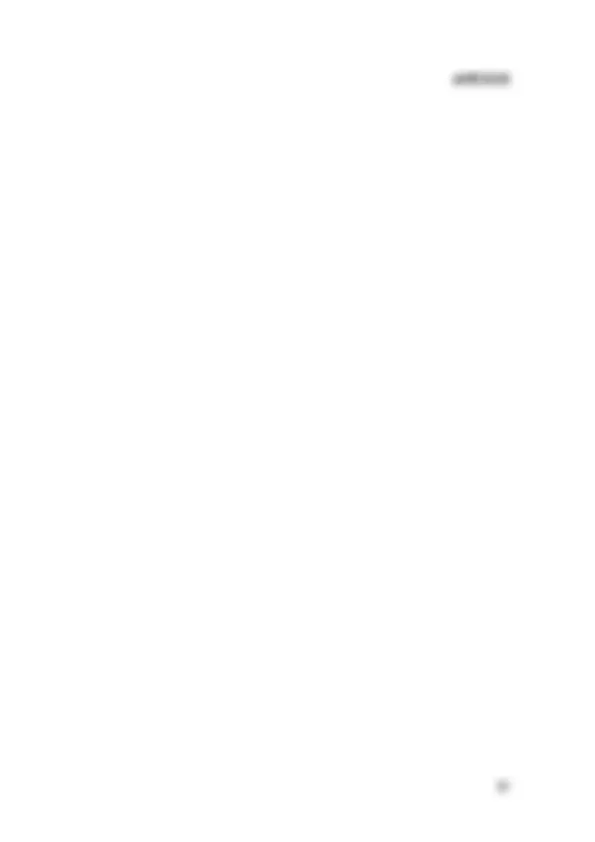
Estude fácil! Tem muito documento disponível na Docsity
Ganhe pontos ajudando outros esrudantes ou compre um plano Premium
Prepare-se para as provas
Estude fácil! Tem muito documento disponível na Docsity
Prepare-se para as provas com trabalhos de outros alunos como você, aqui na Docsity
Os melhores documentos à venda: Trabalhos de alunos formados
Prepare-se com as videoaulas e exercícios resolvidos criados a partir da grade da sua Universidade
Responda perguntas de provas passadas e avalie sua preparação.
Ganhe pontos para baixar
Ganhe pontos ajudando outros esrudantes ou compre um plano Premium
Comunidade
Peça ajuda à comunidade e tire suas dúvidas relacionadas ao estudo
Descubra as melhores universidades em seu país de acordo com os usuários da Docsity
Guias grátis
Baixe gratuitamente nossos guias de estudo, métodos para diminuir a ansiedade, dicas de TCC preparadas pelos professores da Docsity
leia, compreenda, aprenda, reflicta, discuta, reformule, pense, repense, crie, inove, invente, ria, sorria, durma, sonhe, ressone e faz também o teu trabalho.
Tipologia: Trabalhos
1 / 112
Esta página não é visível na pré-visualização
Não perca as partes importantes!
iii
Dedico este meu trabalho à minha família: Maria Carlos, minha dignissima esposa, Daniel Carlos, meu filho de 7 anos de idade e Jemima Carlos de 5 anos de idade, por serem a minha fonte de inspiração para voar mais alto e melhor. É bem verdade que momentos dificeis sempre existiram, mas sei que sempre ultrapassaremos da melhor maneira com Deus no controlo... Espero que o meu sucesso académico venha trazer um valor agregado à nossa família e em geral a toda a sociedade Angolana e não só...
iv
As técnicas de análise a partir de ciclos de melhoria contínua e ferramentas da qualidade são cada vez mais aplicadas na indústria como instrumentos estratégicos para a prevenção, detecção e previsão de falhas e a garantia da integridade dos processos. Neste âmbito, esta dissertação propõe o uso das ferramentas da qualidade dentro do ciclo de melhora contínua PDCA para associar aspetos qualitativos (através de informações coletadas no campo com a opinião de especialistas) e quantitativos (provenientes de bancos de dados de registos de falhas de uma empresa do ramo petrolífero). A proposta deste trabalho desenvolveu-se aplicando um procedimento ao sistema de reinjecção de água na instalação de tratamento de petróleo Castanha, Bloco Sul Cabinda. O procedimento foi dirigido à detecção e prevenção de falhas nos equipamentos, nomeadamente bombas centrífugas e de deslocamento positivo. Aproveitaram-se as 4 fases de ciclo PDCA e em cada uma delas utilizaram-se as ferramentas da qualidade. Os dados obtidos nas avaliações foram processados para o sistema analisado de onde se obtiveram vários indicadores de gestão da manutenção, nomeadamente as Taxa de falhas das bombas, assim como o MTBF e o MTTR. Foi realizada a FMEA para as bombas junto de uma série de medidas de solução para o caso de alguma destas bombas falhar, em conjunto com a implementação de vários projetos de melhorias da instalação. Ficou claro através das curvas de tendência, do impacto que o tempo de paragem dos equipamentos tem sobre a produção de petróleo e gás, assim como no consumo de água no sistema estudado influênciando directamente nas perdas económicas da referida instalação. Palavras-chave: Ciclo PDCA, falhas, bombas centrífugas, bombas de deslocamento positivo, melhoria contínua, reinjeção de água, MTBF, MTTR, FMEA.
vi
O fôlego da vida a Deus pertence, sendo assim agradeço e agradecerei sempre a Deus pela saudável protecção, pois só assim foi possível atingir este objectivo. Aos meus colegas, ex-colegas que dum modo geral contribuíram directa ou indirectamente durante a longa jornada de formação extendendo-se até aos dias de hoje em que nos tornamos profissionais, não posso deixar de mencionar os colegas Engenheiros Gaspar Dalas Jungo e Miclino Dário Carlos Mendes a vocês o meu respeito e o meu muito obrigado. À empresa Pluspetrol Angola Coorporation o meu muito obrigado por me terem acolhido como funcionário desde Junho de 2012 e me darem a possibilidade de ter acesso a todos os dados que se achou necessário para a elaboração deste trabalho. À Escola Superior Náutica Henfante D. Henrique em Oeiras, Paço de Arcos, na pessoa do Coordenador do Mestrado em Engenharia de Máquinas Marítimas (MEMM), Professor Manuel Nogueira, com o qual mantive os primeiros contactos para a elaboração do trabalho que aqui se apresenta. No final, não por serem menos importantes, mas pelo contrário, sem vocês, meus
Yodelkis Delgado Drubey seria simplesmente impossivel a realização deste trabalho, a vocês, meus caríssimos Orientadores, os meus sinceros agradecimentos, não haverá maneira de pagar o esforço demandado por vós para me orientarem de forma incansável, mesmo em gozo de férias da vossa parte recebi as ajudas em tempo e hora, muito além do esperado. Ao corpo de jurados presentes e todos que no ar da sua graça ajudaram para este trabalho para que a conclusão do MEMM fosse uma realidade, os meus agradecimentos.
vii
RESUMO.......... iv ABSTRACT.......... v AGRADECIMENTOS........ vi ÍNDICE.......... vii ÍNDICE DE FIGURAS........ x ÍNDICE DE TABELAS........ xii NOMENCLATURA......... xiii CAPÍTULO 1 INTRODUÇÃO......... 1 1.1. Pluspetrol......... 2 1.2. Objectivos......... 4 1.2.1. Objectivos gerais....... 5 1.2.2. Objectivos específicos...... 5 1.3. Estrutura da dissertação....... 5 CAPÍTULO 2 FILOSOFIAS E TIPOS DE MANUTENÇÃO..... 7 2.1. Introdução à Manutenção....... 7 2.2. Evolução Histórica da Manutenção...... 7 2.3. Tipos de Manutenção........ 9 2.3.1. Manutenção Correctiva...... 9 2.3.2. Manutenção Preventiva...... 10 2.3.3. Manutenção Detectiva...... 14 2.3. 4. Manutenção de Melhoria...... 14 2.4. Gestão da Manutenção....... 15 2.4.1. Manutenção Centrada na Fiabilidade..... 16 2.4.2. Manutenção Lean....... 20 2.4.2.1. Manutenção Produtiva Total..... 20 2.4.2.2. Ciclo PDCA....... 2 2
x
xii
xiii
ABREVIATURAS, SIGLAS e ACRÓNIMOS API - American Petroleum Institute BES - Bombas electrosubmersíveis CL - Check List CPI - Corrugated plate interceptor CTQ - Critical to Quality Characteristic DD - Diagrama de dispersão DFMEA - Design Failure Modes and Effects Analysis DIsh - Diagrama de Ishikawa DOE - Design of Experiments DP - Diagrama de Pareto FMEA - Failure Modes and Effects Analysis FTA - Failures Tree Analysis CC - Cartas de Controlo GIE - Gas Infrastructure Europa Hist - Histograma. HR - Horas de reparação IBR - Inspeção baseada em risco IGF- Induced gas flotation (Unidade de flutuação induzida) LACT - Lease automatic custody transfer unit LIE - Limite Inferior de Especificação LSE - Limite Superior de Especificação MP - Mapa de processo. MTBF - Mean time between failures MTTF - Mean Time to Failures MTTR - Mean Time To Repair PDCA - Plan, Do, Check. Act PFMEA - Process Failure Modes and Effects Analysis PH - Prova de hipóteses. PSV - Pressure safety valve RCM - Reliability Centered Maintenance RPN - Risk Priority Number
Desde o advento das máquinas, muitos empresários dedicaram-se a estudar e a propor formas mais eficientes de organizar o processo fabril. Todas elas visavam atingir o máximo grau de produtividade. Os sistemas produtivos mais importantes criados nesta filosofia foram o Taylorismo e o Fordismo. Fazendo uma rápida retrospectiva, pode-se identificar no Taylorismo uma pretensão em submeter o trabalhador ao ritmo da máquina, com o mínimo de interrupções, predominando neste sistema de produção a divisão e a subdivisão de tarefas, bem como a valorização de procedimentos mecânicos que dispensavam o raciocínio dos trabalhadores. O Fordismo surgiu numa tentativa de aperfeiçoar este primeiro sistema, havendo em ambos os casos, como exigência, o domínio de habilidades específicas. Só que mais avanços e mudanças tecnológicas continuaram a ocorrer e assim estes modelos ficaram ultrapassados, uma vez que não conseguiram satisfizer as novas exigências do mercado justamente por não se preocuparem com a qualificação dos trabalhadores [Moro e Auras, 2007]. Actualmente na prática, em muitas empresas os directores de manutenção precisam pensar que é um bom negócio investir na manutenção dos equipamentos e não considerar a manutenção como uma despesa. Nos últimos anos, rigorosos padrões de qualidade que devem ser cumpridos, assim como a intensa pressão da concorrência entre as indústrias na mesma categoria para se manterem nos mercados nacionais e internacionais, foi forçando os responsáveis pela manutenção nessas indústrias a implementarem mudanças necessárias e deixar de ser um departamento que realize somente reparações e mudanças de peças, convertendo-se assim numa unidade estratégica de alto nível, contribuindo dessa forma para o aumento dos níveis de produção. Portanto, é necessário notar que a actividade da manutenção se for realizada da melhor forma, poderá gerar um melhor produto; originando assim uma melhor qualidade de produção e maior quantidade com menores custos. Nenhuma filosofia ou política da qualidade como Lean Manufacturing , Kaizen , Zero Defeitos, etc., faria sentido numa empresa onde a maquinaria apresenta um
funcionamento deficiente. É por essa razão que estas filosofias e técnicas nunca devem esquecer o desempenho e a manutenção dos seus equipamentos de produção. Qualidade não é apenas separar produtos bons de produtos maus no fim da actividade de produção. A qualidade não é controlada, fabrica-se, evitando que os defeitos ocorram nos processos de produção, criando uma nova cultura, mantendo a liderança, desenvolvendo o pessoal e trabalhando em equipa. Para garantir a qualidade na gestão da manutenção, existem várias ferramentas de qualidade, especificamente um grupo chamado Sete Ferramentas Básicas que são aplicadas para a melhoria da qualidade e resolução de problemas. Cada organização, adopta aquelas ferramentas que podem ajudar a melhorar a sua gestão; o sucesso dessas ferramentas está na capacidade que demonstram ao ser aplicadas numa ampla gama de problemas, desde o controlo de qualidade até às áreas de produção, marketing, recursos humanos e administração [Sánchez, 2013]. Depois da Segunda Guerra Mundial, por volta de 1950, com a preocupação dos japoneses em reconstruir o país, conquistar novos mercados e recuperar a reputação dos produtos, o sindicato japonês de cientistas e engenheiros convidou o estatístico americano Willian Edwards Deming para se deslocar ao Japão e ministrar palestras para lideres, ele dizia: “ elimine defeitos, analise os erros até encontrar a fonte dos erros, fazer correcções e registrar os acontecimentos posteriores à correcção ” [Chiavenato, 1999]. Com esse cuidado, a qualidade tornou-se uma preocupação prioritária na base das organizações japonesas, dando origem à fase de conceituação e conscientização da qualidade, o que provocou o surgimento da melhoria contínua da qualidade. A melhoria de desempenho de produtos e processos pode ser obtida a partir de duas abordagens, melhoria contínua e melhoria radical [Carpinetti, 2010]. 1.1. Pluspetrol A instalação estudada no trabalho que aqui se apresenta, pertence à indústria petrolífera, mais especificamente à empresa Pluspetrol. A Pluspetrol é uma empresa internacional privada e independente com mais de 40 anos de experiência na exploração e produção de petróleo e gás. A Pluspetrol está presente em Angola, Argentina, Bolívia, Colômbia, Estados Unidos, Holanda, Peru e Uruguai, e promove o desenvolvimento de energia (Figura 1.1) [Pluspetrol, 2015].
primeira empresa a iniciar a sua produção onshore em Angola desde a sua independência em 1975 [Portal de Angola, 2014 ]. Figura 1.3. Mapa dos três blocos de exploração petrolíferas em Cabinda [Pluspetrol, 2015 ]. Em Angola, a Pluspetrol dispõe de um Departamento de Operações que inclui três subdepartamentos: i) Produção; ii) Segurança ocupacional, comunidades e meio ambiente e iii) Manutenção. A Produção, encarrega-se de operar as plataformas, poços e do processo de tratamento do petróleo. A Segurança ocupacional, comunidades e meio ambiente, encarrega-se em garantir que o pessoal envolvido nas Operações trabalhe de forma a evitar acidentes, estabelecer boas relações com as comunidades ao redor do campo petrolífero e prevenir contaminações do meio ambiente, já a Manutenção, encarrega-se de garantir o bom funcionamento e a integridade dos equipamentos. No que consta nos arquivos documentais da referida instalação, até ao momento, não se desenvolveu qualquer pesquisa ou investigação aprofundada de qualquer problema que tivessm ocorrido durante o funcionamento da mesma. Isto também constitui uma motivação adicional para a execução do presente trabalho. 1.2. Objectivos No processo de exploração da instalação de tratamento de petróleo Castanha observa-se, no entanto, inactividade devido a problemas nos equipamentos que compõem o sistema de geração de energia e o sistema de injecção de água produzida, composto fundamentalmente por geradores e bombas respectivamente. Entre os problemas que têm afectado a capacidade produtiva destes equipamentos, encontram-se: aumento da
temperatura de trabalho; vibrações; falha nas linhas de descargas; entre outros problemas que limitam os volumes de produção, aumentando os custos operacionais e interferindo com o serviço ao cliente. 1.2.1. Objectivos gerais O objectivo principal desta dissertação é o desenvolvimento de um procedimento baseado em ferramentas da qualidade, que permita ao pessoal da Manutenção aumentar a fiabilidade e a disponibilidade da maquinaria e dos equipamentos de produção, detectando possíveis falhas, tendências e padrões de comportamento negativos de forma a eliminá-los ou controlá-los antes que afectem o processo produtivo. 1.2.2. Objectivos específicos Os objectivos específicos deste trabalho são: