
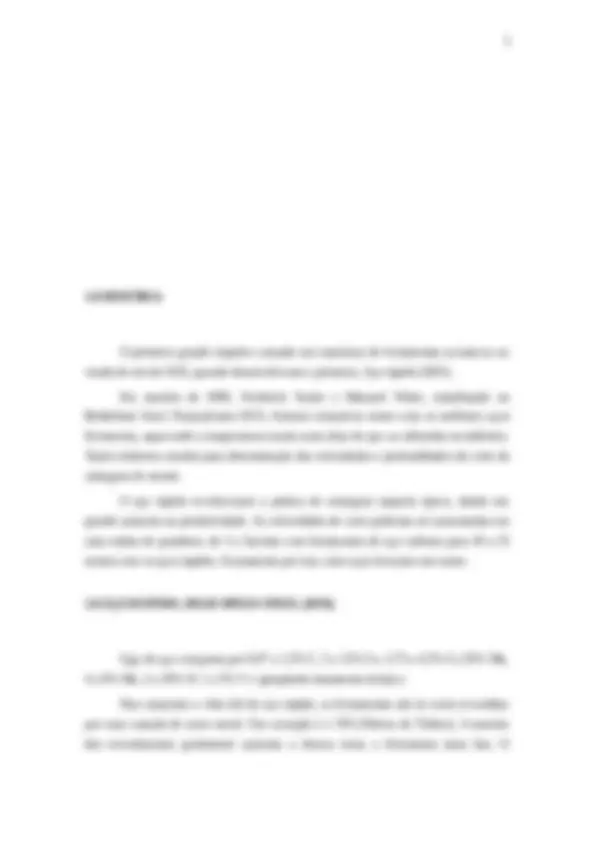
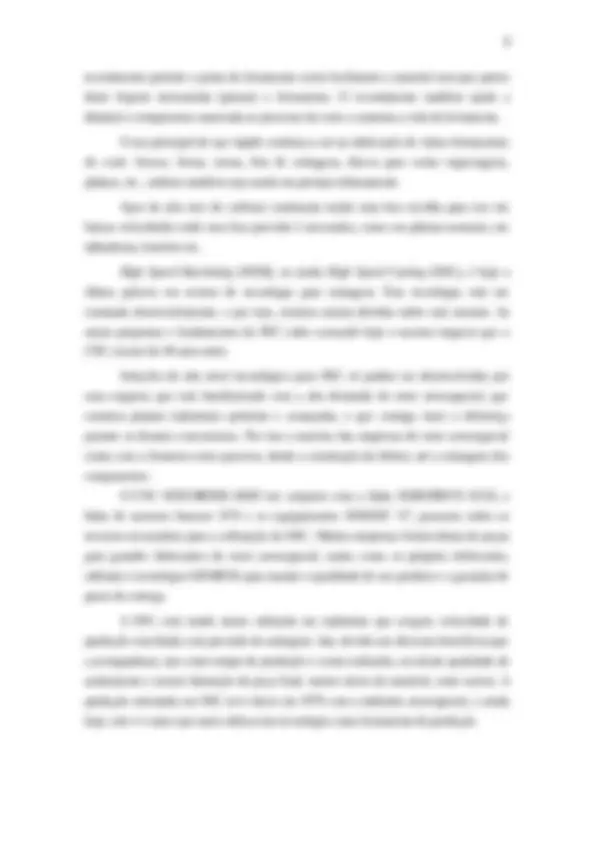
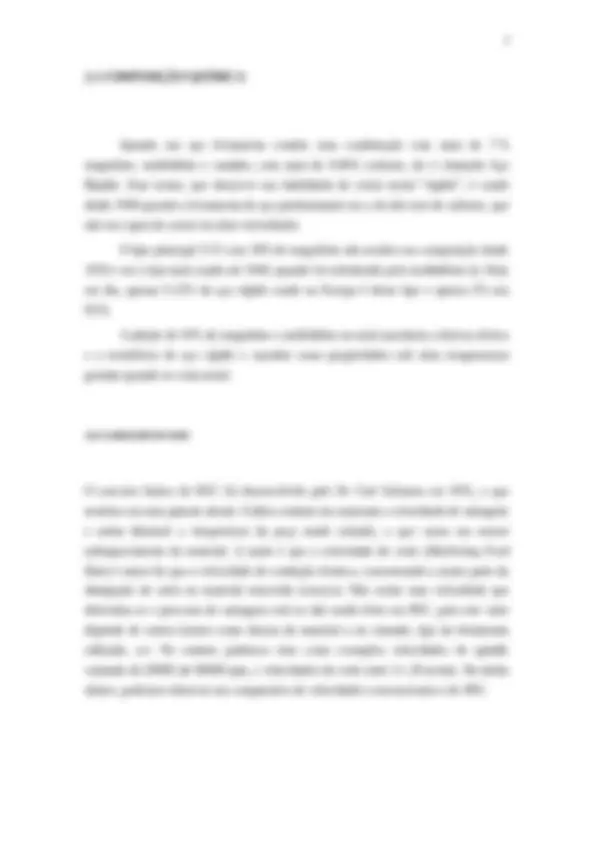
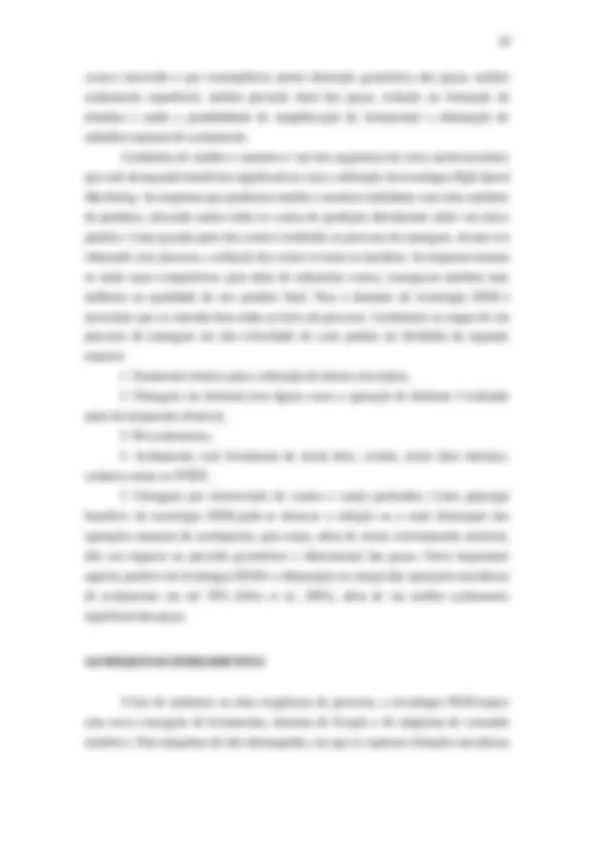
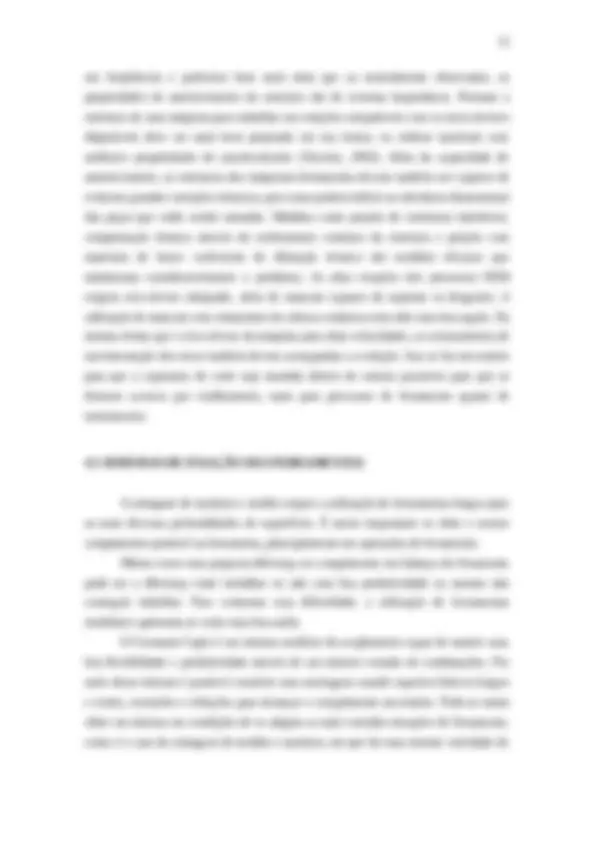
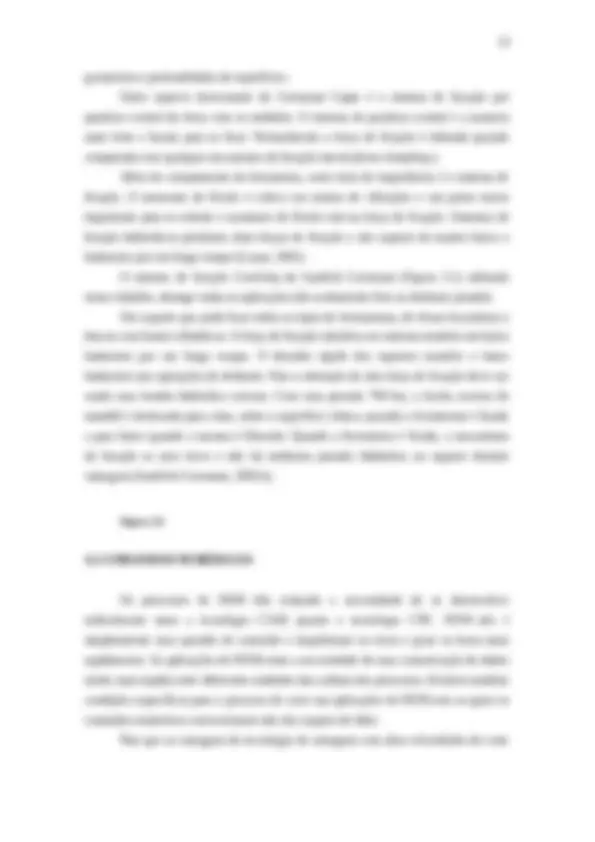
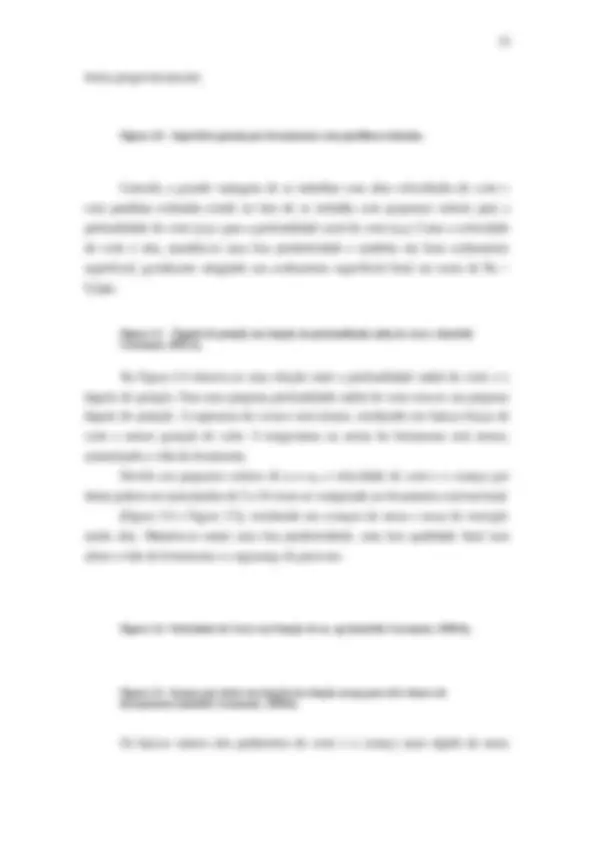
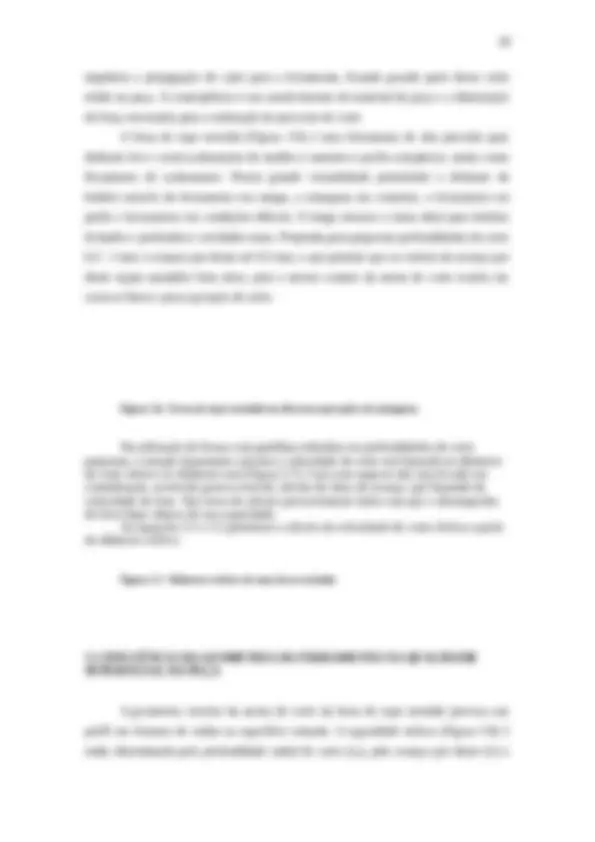
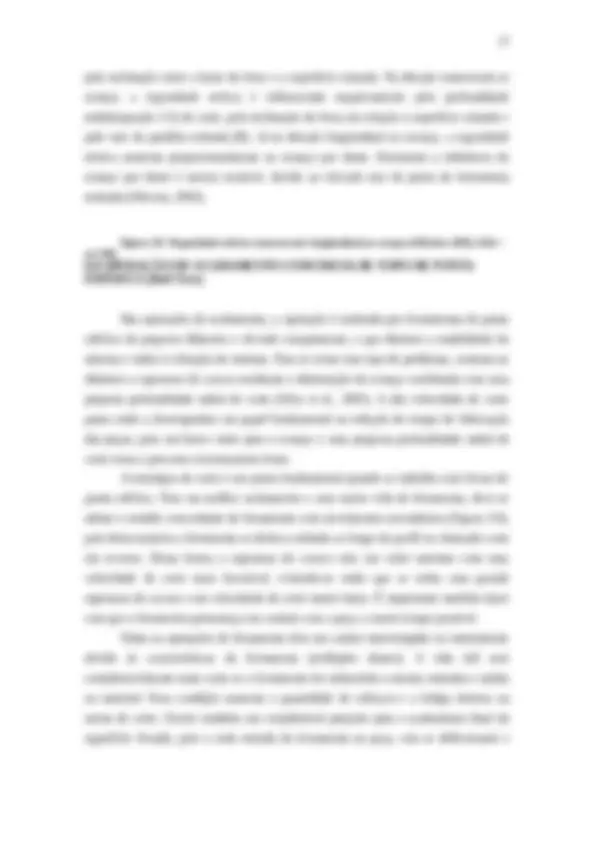
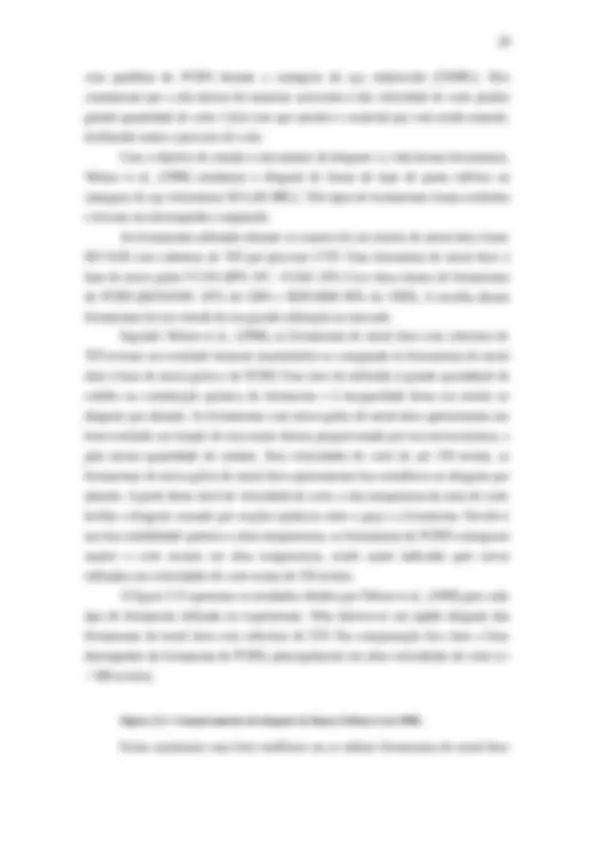
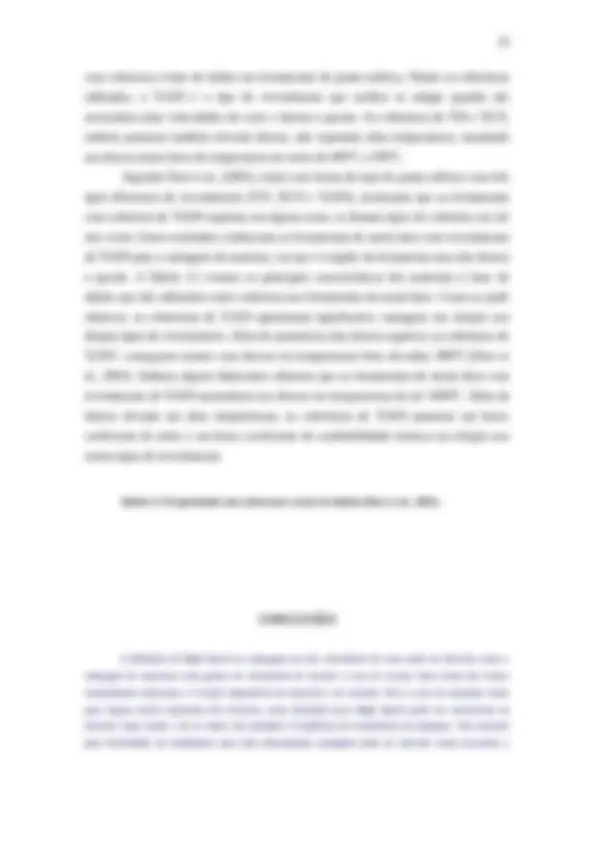
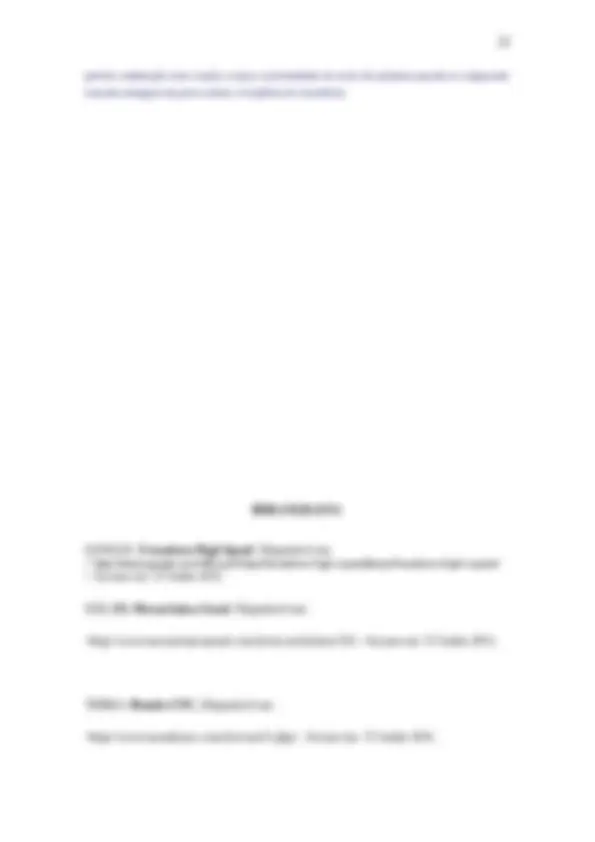
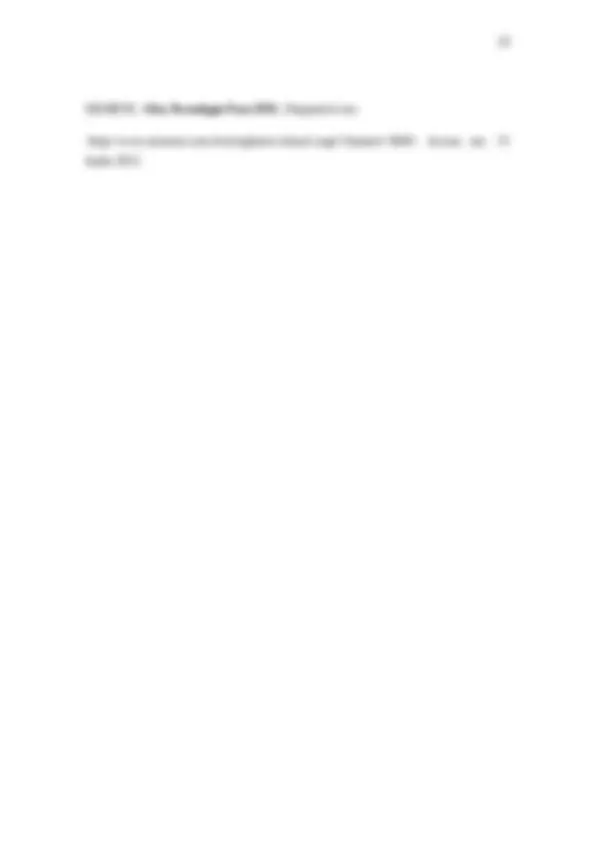
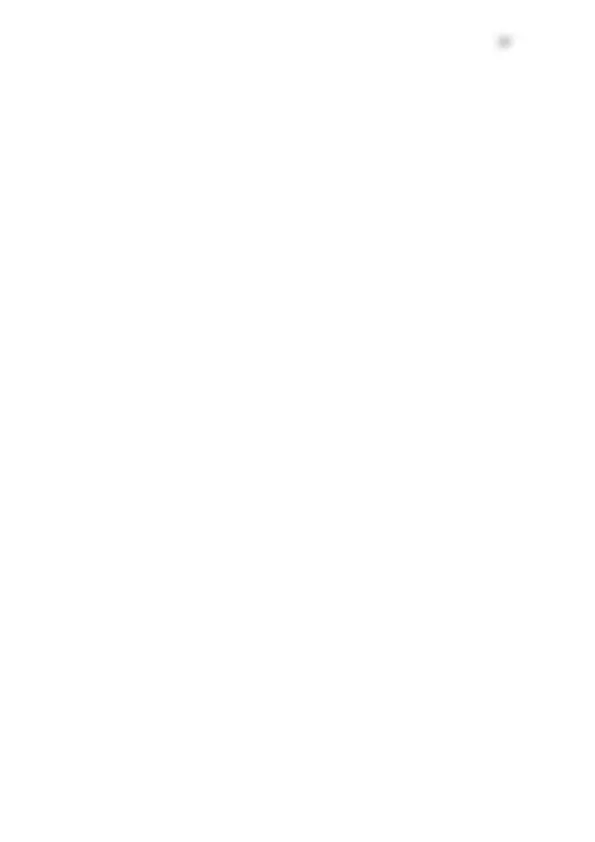
Estude fácil! Tem muito documento disponível na Docsity
Ganhe pontos ajudando outros esrudantes ou compre um plano Premium
Prepare-se para as provas
Estude fácil! Tem muito documento disponível na Docsity
Prepare-se para as provas com trabalhos de outros alunos como você, aqui na Docsity
Os melhores documentos à venda: Trabalhos de alunos formados
Prepare-se com as videoaulas e exercícios resolvidos criados a partir da grade da sua Universidade
Responda perguntas de provas passadas e avalie sua preparação.
Ganhe pontos para baixar
Ganhe pontos ajudando outros esrudantes ou compre um plano Premium
Comunidade
Peça ajuda à comunidade e tire suas dúvidas relacionadas ao estudo
Descubra as melhores universidades em seu país de acordo com os usuários da Docsity
Guias grátis
Baixe gratuitamente nossos guias de estudo, métodos para diminuir a ansiedade, dicas de TCC preparadas pelos professores da Docsity
Trabalho falando sobre a tecnologia high speed
Tipologia: Trabalhos
1 / 22
Esta página não é visível na pré-visualização
Não perca as partes importantes!
2
- INTRODUÇÃO - 1.0 HISTÓRIA - 2.0 AÇO RÁPIDO, HIGH SPEED STEEL (HSS) - 2.1 COMPOSIÇÃO QUÍMICA - 3.0 A ORIGEM DO HSC - 3.1 O QUE É NECESSÁRIO? - 3.2 GENERALIDADES - 4.0 MÁQUINAS FERRAMENTAS - 4.1 SISTEMAS DE FIXAÇÃO DAS FERRAMENTAS - 4.2 COMANDOS NUMÉRICOS
INTRODUÇÃO
Neste trabalho iremos apresentar algumas características de composição da fabricação da higt speed, sua história, trazendo os primórdios e também evolução durante o inicio em que se começou a usá-la até as tecnologias que a incorporam agora. O trabalho traz ainda alguns exemplos gráficos comparativos do material em que a se é forjada e o tipo de usinagem em que aplica para cada caso, detalhando a velocidade de avanço, profundidade de corte, quebra de cavaco e outros itens que são fundamentais na hora em que deseja usinar determinado material.
revestimento permite a ponta da ferramenta cortar facilmente o material sem que partes deste fiquem incrustadas (presas) a ferramenta. O revestimento também ajuda a diminuir a temperatura associada ao processo de corte e aumenta a vida da ferramenta.
O uso principal do aço rápido continua a ser na fabricação de várias ferramentas de corte: brocas, fresas, serras, bits de usinagem, discos para cortar engrenagens, plainas, etc., embora também seja usado em prensas ultimamente.
Aços de alto teor de carbono continuam sendo uma boa escolha para uso em baixas velocidades onde uma boa precisão é necessária, como em plainas manuais, em talhadeiras, formões etc.
High Speed Machining (HSM), ou ainda High Speed Cutting (HSC), é hoje a última palavra em termos de tecnologia para usinagem. Esta tecnologia está em constante desenvolvimento, e por isso, existem muitas dúvidas sobre este assunto. As atuais propostas e fundamentos da HSC estão causando hoje o mesmo impacto que o CNC causou há 40 anos atrás.
Soluções de alto nível tecnológico para HSC só podem ser desenvolvidas por uma empresa que está familiarizada com a alta demanda do setor aeroespacial, que construa plantas industriais perfeitas e avançadas, e que consiga fazer a diferença perante os demais concorrentes. Por isso a maioria das empresas do setor aeroespacial conta com a Siemens como parceira, desde a construção da fábrica até a usinagem dos componentes. O CNC SINUMERIK 840D em conjunto com a linha SIMODRIVE 611D, a linha de motores lineares 1FN e os equipamentos SIMATIC S7, possuem todos os recursos necessários para a utilização da HSC. Muitas empresas fornecedoras de peças para grandes fabricantes do setor aeroespacial, assim como os próprios fabricantes, utilizam à tecnologia SIEMENS para manter a qualidade de seu produto e a garantia de prazo de entrega.
A HSC está sendo muito utilizada em indústrias que exigem velocidade de produção conciliada com precisão de usinagem. Isto, devido aos diversos benefícios que a acompanham, tais como tempo de produção e custos reduzido, excelente qualidade de acabamento e menor distorção da peça final, menor stress do material, entre outros. A produção orientada em HSC teve início em 1976 com a indústria aeroespacial, e ainda hoje, este é o ramo que mais utiliza esta tecnologia como ferramenta de produção.
Quando um aço ferramenta contém uma combinação com mais de 7 % tungstênio, molibdênio e vanádio, com mais de 0.60% carbono, ele é chamado Aço Rápido. Esse termo, que descreve sua habilidade de cortar metal “rápido”, é usado desde 1940 quando a ferramenta de aço predominante era a de alto teor de carbono, que não era capaz de cortar em altas velocidades.
O tipo principal T-15 com 18% de tungstênio não mudou sua composição desde 1910 e era o tipo mais usado até 1940, quando foi substituído pelo molibdênio-2). Hoje em dia, apenas 5-12% do aço rápido usado na Europa é desse tipo e apenas 2% nos EUA.
A adição de 10% de tungstênio e molibdênio no total maximiza a dureza efetiva e a resistência do aço rápido e mantém essas propriedades sob altas temperaturas geradas quando se corta metal.
3.0 A ORIGEM DO HSC
O conceito básico da HSC foi desenvolvido pelo Dr. Carl Salomon em 1931, o que resultou em uma patente alemã. A idéia consiste em aumentar a velocidade de usinagem e assim diminuir a temperatura da peça sendo usinado, o que causa um menor enfraquecimento do material. A razão é que a velocidade de corte ( Machining Feed Rate ) é maior do que a velocidade de condução térmica, concentrando a maior parte da dissipação de calor no material removido (cavaco). Não existe uma velocidade que determina se o processo de usinagem está ou não sendo feito em HSC, pois este valor depende de outros fatores como dureza do material a ser usinado, tipo da ferramenta utilizada, ect. No entanto podemos citar como exemplos velocidades de spindle variando de 20000 até 60000 rpm, e velocidades de corte entre 2 e 20 m/min. Na tabela abaixo, podemos observar um comparativo de velocidades convencionais e de HSC.
controlar alguns itens essenciais para a HSC: -Processamento rápido de blocos de movimento (block cycle time) -Pré-processamento
Define-se fresamento em HSM ( High Speed Machining ) como sendo o fresamento de topo com elevadas velocidades de corte (altas rotações) e elevada velocidade de avanço. Na realidade o conceito de HSM é algo bem mais abrangente do que simplesmente girar um eixo em altas rotações. O conceito HSM envolve a redefinição de parâmetros como máquinas com alta rotação e elevada rigidez, sistema de fixação bem balanceado, ferramentas capazes de suportar as condições de corte extremamente severas, tecnologia CAD/CAM e funções de comandos CNC com 47 processamento look-ahead. Há contudo algumas limitações e dificuldades que devem ser lembradas ao se trabalhar com HSM: excessivo desgaste das ferramentas, necessidade de máquinas extremamente caras, balanceamento do sistema de fixação das ferramentas e a necessidade de materiais para ferramentas e revestimentos cada vez mais sofisticados, além de programas computacionais e capacidade de processamento e armazenamento de dados das máquinas de comando numérico (Fallböhmer et al., 2000). O desenvolvimento da tecnologia HSM ocorreu principalmente pela necessidade da indústria de moldes e matrizes obter produtos com melhor acabamento superficial, em um menor espaço de tempo. A eliminação de trabalhos manuais em decorrência de um melhor acabamento final conseguido por HSM é de extrema importância para as empresas que trabalham com essa tecnologia. Há inúmeras vantagens na utilização de processos HSM, quais sejam: alta taxa de remoção de material, redução do tempo de fabricação das matrizes, baixas forças de corte, dissipação do calor com a alta taxa de
cavaco removido e por conseqüência menor distorção geométrica das peças, melhor acabamento superficial, melhor precisão final das peças, redução na formação de rebarbas e ainda a possibilidade de simplificação do ferramental e eliminação de trabalhos manuais de acabamento. A indústria de moldes e matrizes é um dos segmentos do setor metal-mecânica que está alcançando benefícios significativos com a utilização da tecnologia High Speed Machining. As empresas que produzem moldes e matrizes trabalham com lotes unitários de produtos, alocando assim todos os custos de produção diretamente sobre um único produto. Como grande parte dos custos é atribuído ao processo de usinagem, 48 uma vez otimizado esse processo, a redução dos custos se torna-se imediata. As empresas tornam se então mais competitivas, pois além de reduzirem custos, conseguem também uma melhoria na qualidade de seu produto final. Para o domínio da tecnologia HSM é necessário que se entenda bem todas as fases do processo. Geralmente as etapas de um processo de usinagem em alta velocidade de corte podem ser divididas da seguinte maneira:
A fim de satisfazer as altas exigências do processo, a tecnologia HSM requer uma nova concepção de ferramentas, sistemas de fixação e de máquinas de comando numérico. Para máquinas de alto desempenho, em que se esperam vibrações mecânicas
geometrias e profundidades de superfícies. Outro aspecto interessante do Coromant Capto é o sistema de fixação por parafuso central da fresa com os módulos. O sistema de parafuso central é a maneira mais forte e barata para se fixar. Normalmente a força de fixação é dobrada quando comparada com qualquer mecanismo de fixação lateral ( front clampling ). Além do comprimento da ferramenta, outro item de importância é o sistema de fixação. O momento de flexão é crítico em termos de vibrações e um ponto muito importante para se reduzir o momento de flexão está na força de fixação. Sistemas de fixação hidráulicos permitem altas forças de fixação e são capazes de manter baixo o batimento por um longo tempo (Layne, 2001). O sistema de fixação CoroGrip da Sandvik Coromant (Figura 3.1) utilizado nesse trabalho, abrange todas as aplicações (do acabamento fino ao desbaste pesado). Um suporte que pode fixar todos os tipos de ferramentas, de fresas faceadoras a brocas com hastes cilíndricas. A força de fixação simétrica no sistema mantém um baixo batimento por um longo tempo. O desenho rígido dos suportes mantém o baixo batimento nas operações de desbaste. Para a obtenção de alta força de fixação deve ser usada uma bomba hidráulica externa. Com uma pressão 700 bar, a bucha externa do mandril é deslocada para cima, sobre a superfície cônica, quando a ferramenta é fixada e para baixo quando a mesma é liberada. Quando a ferramenta é fixada, o mecanismo de fixação se auto trava e não há nenhuma pressão hidráulica no suporte durante usinagem (Sandvik-Coromant, 2002/a).
Figura 2.
4.2 COMANDOS NUMÉRICOS
Os processos de HSM têm realçado a necessidade de se desenvolver radicalmente tanto a tecnologia CAM, quanto a tecnologia CNC. HSM não é simplesmente uma questão de controlar e impulsionar os eixos e girar os fusos mais rapidamente. As aplicações de HSM criam a necessidade de uma comunicação de dados muito mais rápida entre diferentes unidades das cadeias dos processos. Existem também condições específicas para o processo de corte nas aplicações de HSM com os quais os comandos numéricos convencionais não são capazes de lidar. Para que as vantagens da tecnologia de usinagem com altas velocidades de corte
possam ser alcançadas, os comandos numéricos presentes nas máquinas devem possuir características técnicas não necessariamente exigidas, até o momento, para máquinas ferramentas. O primeiro requisito é a velocidade de processamento de blocos (linhas de comando). Programas CNC para fresamento de superfícies complexas, muito comuns em moldes e matrizes, geralmente consistem de uma longa seqüência de comandos de interpolação que determinam a posição da ponta da fresa. Neste caso, o tempo de processamento de bloco pode representar uma limitação à velocidade de avanço. Outro recurso necessário é a capacidade de interpolação simultânea de até cinco eixos. Para a usinagem de superfícies complexas é necessário que uma fresa de topo possa fresar com ângulos de até 90 graus trabalhando perpendicularmente à superfície gerada. Isso só é possível com capacidade de movimentação em 5 eixos, movendo-se a mesa (peça) ou o eixo-árvore. Nesse caso o CNC deve compensar a geometria da máquina bem como o comprimento e diâmetro da fresa. Além disso, o CNC deve garantir que a velocidade de avanço comandada seja mantida para a ponta da ferramenta. São ainda desejáveis recursos mais sofisticados, permitindo que se modifique a inclinação da fresa em relação à normal da superfície fresada durante a interpolação. Isto permite a otimização da usinagem durante a operação, através da eliminação de vibrações (Teixeira, 2002).
4.3 BALANCEAMENTOS EM ALTA VELOCIDADE DE CORTE.
Define-se desbalanceamento como sendo a condição em que o eixo de massa principal de um corpo giratório, também conhecido como eixo de inércia, não coincide com seu eixo de rotação (Layne, 2001). Há diferentes tipos de desbalanceamento; desbalanceamento estático quando o eixo de massa de um rotor não coincide com o eixo de rotação e é paralelo ao eixo de rotação, desbalanceamento conjugado, quando o eixo de massa não coincide com o eixo de rotação, porém o intercepta no centro de gravidade do rotor. Finalmente têm-se o desbalanceamento dinâmico como sendo a condição em que o eixo de massa não coincide com o eixo de rotação, não é paralelo a ele e não o intercepta. Quando se trabalha com velocidades acima de 8000 rpm, um desbalanceamento relativamente pequeno pode produzir forças extremamente altas sobre os mancais do eixo árvore à medida que a rotação aumenta. Essas forças certamente afetam as peças que estão sendo produzidas assim como as máquinas-ferramentas. Na peça o desbalanceamento produz ondulações na superfície do metal como
forma progressivamente.
Figura 3.0 - Superfície gerada por ferramentas com pastilhas redondas.
Contudo, a grande vantagem de se trabalhar com altas velocidades de corte e com pastilhas redondas reside no fato de se trabalha com pequenos valores para a profundidade de corte (a e) e para a profundidade axial de corte (a p). Como a velocidade de corte é alta, mantêm-se uma boa produtividade e também um bom acabamento superficial, geralmente atingindo um acabamento superficial final em torno de Ra = 0,2μm.
Figura 3.1 - Ângulo de posição em função da profundidade axila de corte. (Sandvik- Coromant, 2002/a).
Na Figura 3.4 observa-se uma relação entre a profundidade radial de corte e o ângulo de posição. Para uma pequena profundidade radial de corte tem-se um pequeno ângulo de posição. A espessura do cavaco será menor, resultando em baixas forças de corte e menor geração de calor. A temperatura na aresta da ferramenta será menor, aumentando a vida da ferramenta. Devido aos pequenos valores de a e e ap, a velocidade de corte e o avanço por dente podem ser aumentados de 5 a 10 vezes se comparado ao fresamento convencional (Figura 3.4 e Figura 3.5), resultando em avanços de mesa e taxas de remoção muito alta. Mantém-se assim uma boa produtividade, uma boa qualidade final sem afetar a vida da ferramenta e a segurança do processo.
Figura 3.4- Velocidade de Corte em Função de ae, ap (Sandvik-Coromant, 1999/b).
Figura 3.5- Avanço por dente em função da relação ae/ap para três classes de ferramentas (Sandvik-Coromant, 1999/b).
Os baixos valores dos parâmetros de corte e o avanço mais rápido da mesa
impedem a propagação de calor para a ferramenta, ficando grande parte desse calor retido na peça. A conseqüência é um amolecimento do material da peça e a diminuição da força necessária para a realização do processo de corte. A fresa de topo toroidal (Figura 3.6) é uma ferramenta de alta precisão para desbaste leve e semi-acabamento de moldes e matrizes e perfis complexos, assim como fresamento de acabamento. Possui grande versatilidade permitindo o desbaste de bolsões através do fresamento em rampa, a usinagem em contorno, o fresamento em perfis e faceamento em condições difíceis. O longo alcance a torna ideal para bolsões fechados e profundos e cavidades rasas. Projetada para pequenas profundidades de corte 0,2 - 1 mm e avanços por dente até 0,5 mm, o que permite que os valores do avanço por dente sejam mantidos bem altos, pois o menor contato da aresta de corte resulta em cavacos finos e pouca geração de calor.
Figura 3.6- Fresa de topo toroidal em diversas operações de usinagem.
Na utilização de fresas com pastilhas redondas em profundidades de corte pequenas, é sempre importante calcular a velocidade de corte real baseada no diâmetro de corte efetivo ou diâmetro real (Figura 3.7). Caso esse aspecto não seja levado em consideração, ocorrerão graves erros de cálculo da faixa de avanço, que depende da velocidade do fuso. Tais erros de cálculo provavelmente farão com que o desempenho da fresa fique abaixo de sua capacidade. As equações 3.1 e 3.2 permitem o cálculo da velocidade de corte efetiva a partir do diâmetro efetivo.
Figura 3.7- Diâmetro efetivo de uma fresa toroidal.
SUPERFICIAL DA PEÇA
A geometria circular da aresta de corte da fresa de topo toroidal provoca um perfil em formato de ondas na superfície usinada. A rugosidade teórica (Figura 3.8) é então determinada pela profundidade radial de corte (ae ), pelo avanço por dente (f z) e
haverá uma marca e um excesso de material na superfície usinada. Quando a ferramenta sai da peça, as forças de corte e a flexão da ferramenta diminuirão e haverá também uma marca e uma leve rebaixo de material na superfície usinada.
Figura 3.9- Fresamento concordante e ascendente.
Devido à sua grande versatilidade, as fresas de topo de ponta esférica (Figura 3.10) são também bastante utilizadas na usinagem de superfícies curvas em processos de fabricação de moldes e matrizes. Utilizadas principalmente para operações de acabamento e semi-acabamento com altas velocidades de corte (V c > 220 m/min), as fresas de topo de ponta esférica têm apresentado resultados bastante satisfatórios quanto ao acabamento superficial, à vida das ferramentas e às forças presentes no processo.
Figura 3.10- Fresa de topo de ponta esférica (Aspinwall et. al. (2000/a)).
O cálculo da velocidade de corte é feito em relação ao diâmetro efetivo da ferramenta, conforme nos indicam as equações
A Figura 3.11 ilustra o mecanismo de formação do cavaco durante o corte de um material com fresa de topo de ponta esférica. Como mostra a Figura 3.12, a geometria da ferramenta produz um cavaco curto, em forma de cunha.
Figura 3.11- Formação do cavaco durante o corte com ferramenta de topo de ponta esférica (Fallbohmer, 1996).
Figura 3.12- Cavaco em forma de cunha (Fallbohmer, 1996). Diversos autores têm estudado o comportamento das fresas de topo de ponta esférica sob a influência de vários fatores como: tipo de cobertura da ferramenta, posição da ferramenta em relação à peça, utilização de fluido de corte e variação dos parâmetros de corte. Aspinwall et al., (2000/b) analisaram o comportamento dessas
fresas ao usinarem Inconel 718 ( 53% Ni , 19 % Cr , 18% Fe , 5 % Nb 3%Mo , 0,9% Ti , 0,5 % Al , 45 HRC). Ferramentas com coberturas de TiAlCrN e com cobertura de TiAlN (mono e multi-camadas) foram avaliadas sob várias condições de corte. As ferramentas com cobertura de TiAlCrN apresentaram melhores resultados quando se avaliou a vida das ferramentas e o acabamento superficial. A Figura 3.13 mostra o efeito do tipo de cobertura no comprimento de corte. A operação foi realizada sem fluido de corte.
Figura 3.13- Comprimento de corte obtido em função do tipo de cobertura (Aspinwall et al., 2000/b).
Devido à complexidade das superfícies a serem usinadas, as fresas de topo de ponta esférica têm sido amplamente utilizadas na usinagem de acabamento de aços endurecidos empregados na confecção de moldes e matrizes. Utilizando fresas na usinagem de aço ABNT 1045 e velocidade de corte variando de 100 m/min a 1600 m/ min, Fallbohmer et al., (1996) testaram vários tipos de cobertura de ferramenta. A Figura 3.14 mostra o comportamento do desgaste de flanco em função do comprimento de corte. Observou-se que as ferramentas de PCBN apresentaram um desempenho consideravelmente superior em relação às demais ferramentas. As ferramentas de metal duro com cobertura de TiN apresentaram um desempenho superior aos outros tipos de cobertura mais avançados, como TiCN e o TiAlN. Segundo Fallbohmer et al., 1996, para se tirar maior proveito de ferramentas com uma cobertura mais avançada, é necessário que se utilize ferramenta com grande rigidez, o que às vezes é extremamente difícil de se conseguir em fresamento de matrizes, já que esse tipo de processo exige ferramentas longas para a usinagem de raios, reentrâncias e cavidades, o que acaba reduzindo a rigidez do sistema.
Figura 3.14- Comportamento do desgaste de flanco para várias ferramentas (Fallbohmer et al., 1996).
Elbestawi et al., (1997) analisaram o desgaste de fresa de topo de ponta esférica
com cobertura à base de titânio em ferramentas de ponta esférica. Dentre as coberturas utilizadas, o TiAlN é o tipo de revestimento que melhor se adapta quando são necessárias altas velocidades de corte e dureza a quente. As coberturas de TiN e TiCN, embora possuam também elevada dureza, não suportam altas temperaturas, mantendo sua dureza numa faixa de temperatura em torno de 400ºC a 450ºC. Segundo Dorr et al., (2001), testes com fresas de topo de ponta esférica com três tipos diferentes de revestimento (TiN ,TiCN e TiAlN), mostraram que as ferramentas com cobertura de TiAlN superam em alguns casos, os demais tipos de cobertura em até sete vezes. Esses resultados credenciam as ferramentas de metal duro com revestimento de TiAlN para a usinagem de matrizes, em que é exigido da ferramenta uma alta dureza a quente. A Tabela 3.1 resume as principais características dos materiais à base de titânio que são utilizados como cobertura nas ferramentas de metal duro. Como se pode observar, as coberturas de TiAlN apresentam significativa vantagem em relação aos demais tipos de revestimento. Além de possuírem uma dureza superior, as coberturas de TiAlN conseguem manter essa dureza em temperaturas bem elevadas, 800ºC (Dorr et al., 2001). Embora alguns fabricantes afirmem que as ferramentas de metal duro com revestimento de TiAlN mantenham sua dureza em temperaturas de até 1000ºC. Além da dureza elevada em altas temperaturas, as coberturas de TiAlN possuem um baixo coeficiente de atrito e um baixo coeficiente de condutibilidade térmica em relação aos outros tipos de revestimento.
Tabela 3.1 Propriedades das coberturas a base de titânio (Dorr et al., 2001).
A definição de High Speed ou usinagem em alta velocidade de corte pode ser descrita como a usinagem de materiais com gamas de velocidade de rotação e taxa de avanço bem acima das faixas normalmente utilizadas e é função dependente do material a ser usinado. Para o caso do alumínio como para alguns outros materiais não ferrosos, outra definição para High Speed pode ser encontrada ou descrita como sendo a de se usinar tão próximo à freqüência de ressonância da máquina. Um conceito para efetividade ou rendimento para uma determinada usinagem pode ser descrita como encontrar a
perfeita combinação entre rotação, avanço e profundidade de cortes tão próximas quando se comparadas à mesma usinagem um pouco abaixo a freqüência de ressonância.
BIBLIOGRAFIA
GOOGLE. Fresadora High Speed. Disponível em: < http://www.google.com/#hl=pt-R&q=fresadora+high+speed&oq=fresadora+high+speed
Acesso em: 15 Junho 2011.
UOL.BR. Mecatrônica Atual. Disponível em:
<http://www.mecatronicaatual.com.br/secoes/leitura/331 >Acesso em: 15 Junho 2011.
TERRA. Mundo CNC. Disponível em:
http://www.mundocnc.com.br/avan11.php. Acesso em: 15 Junho 2011.