
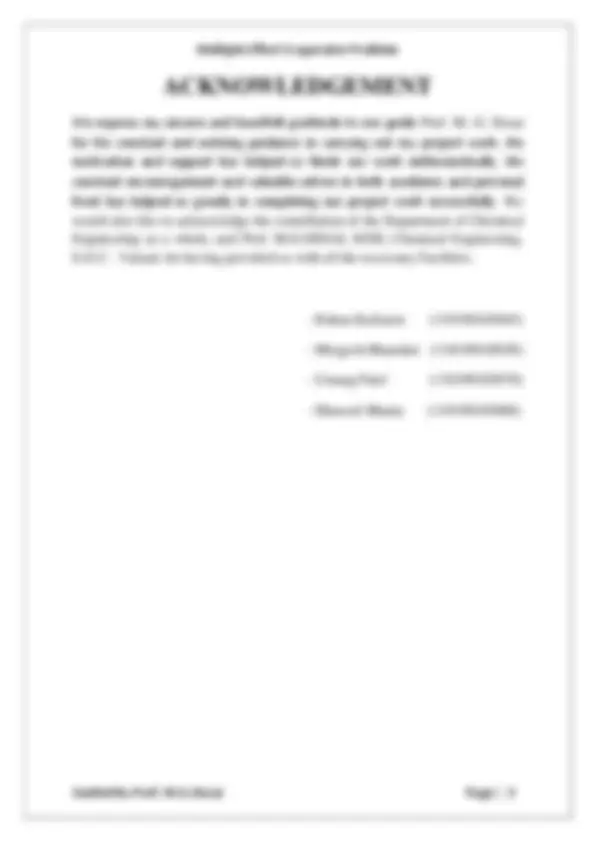
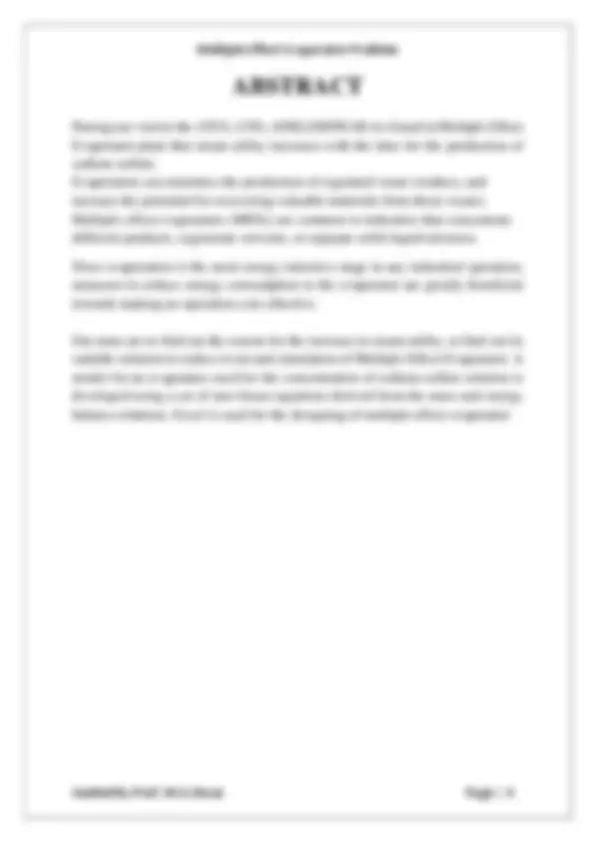
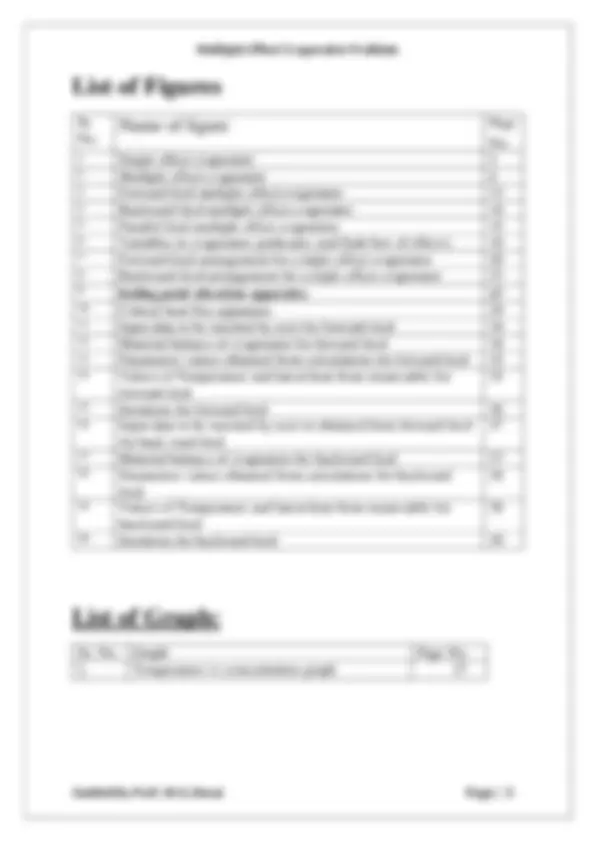
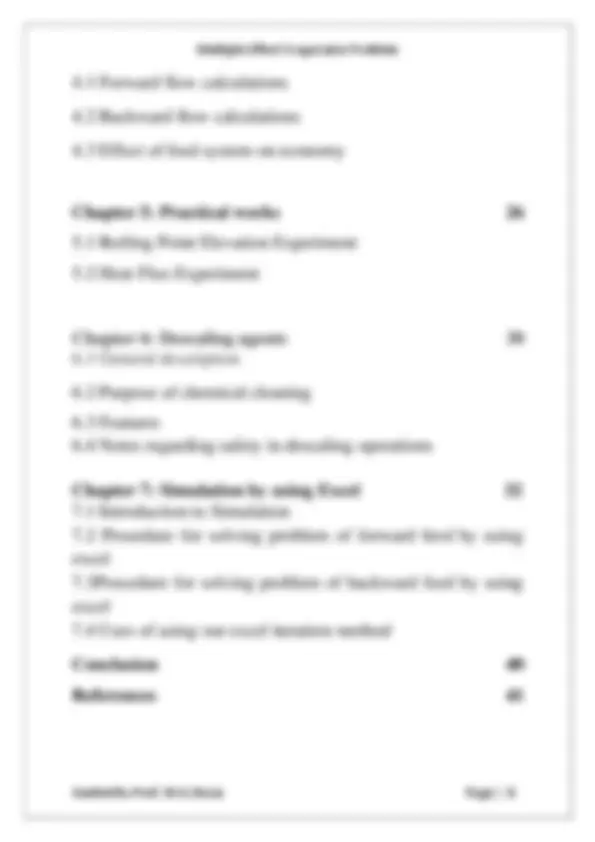
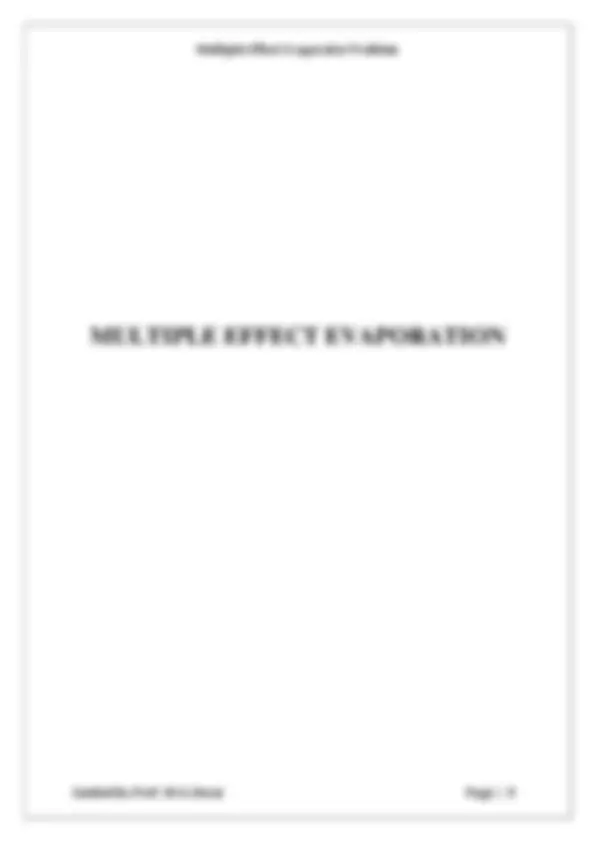
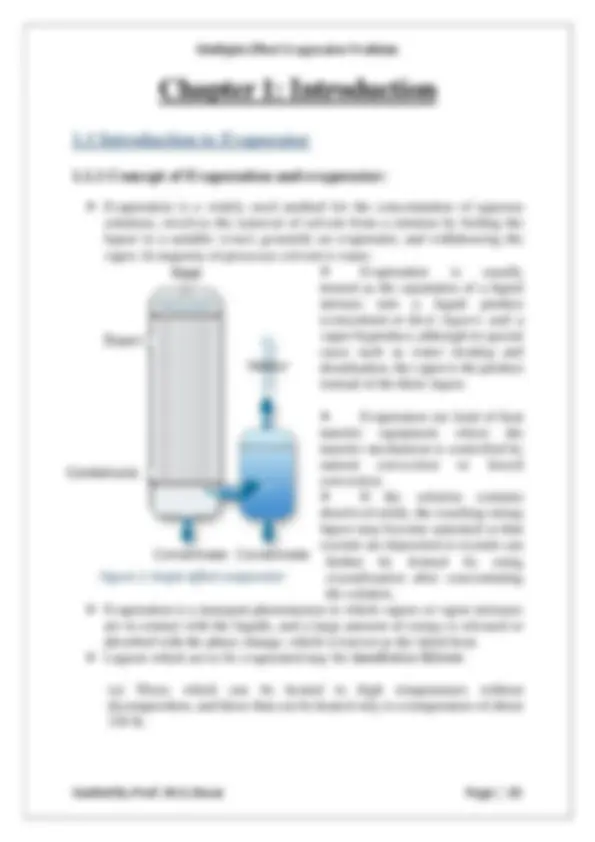
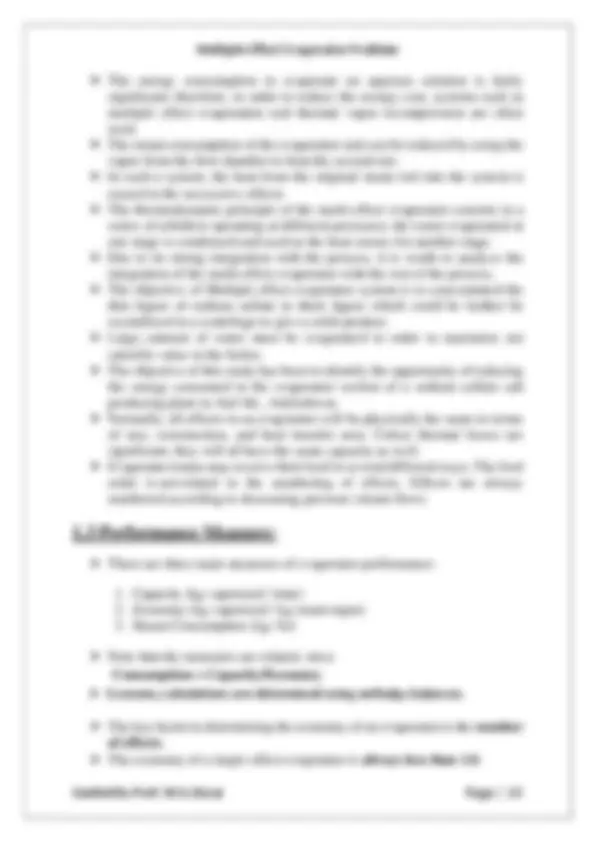
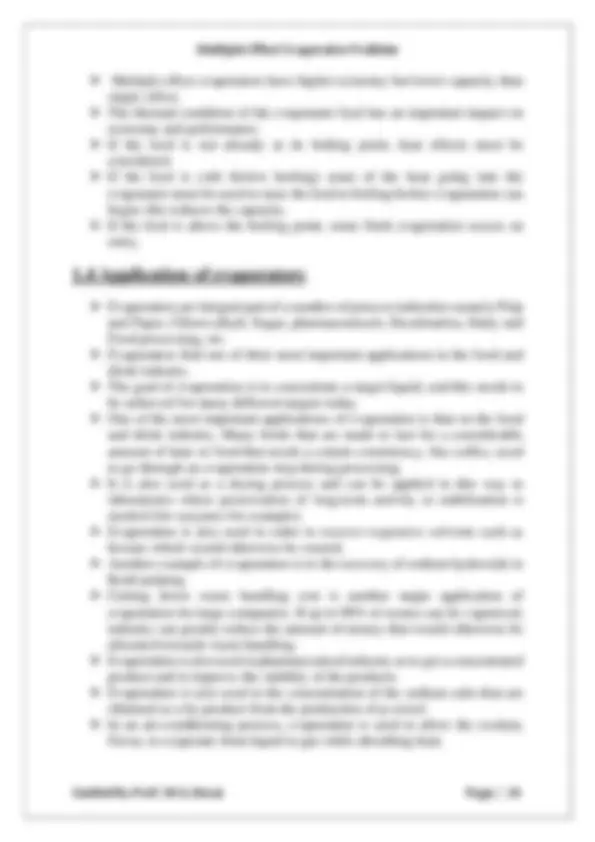
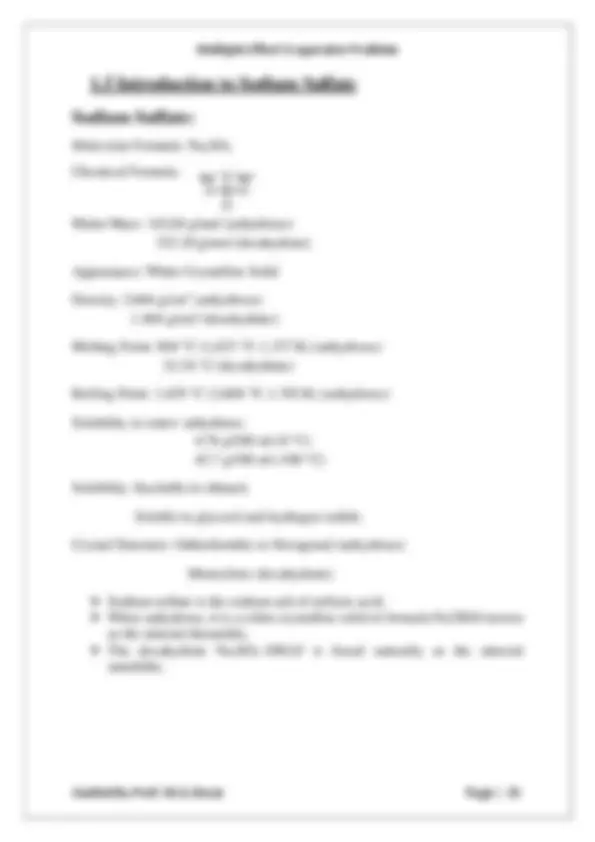
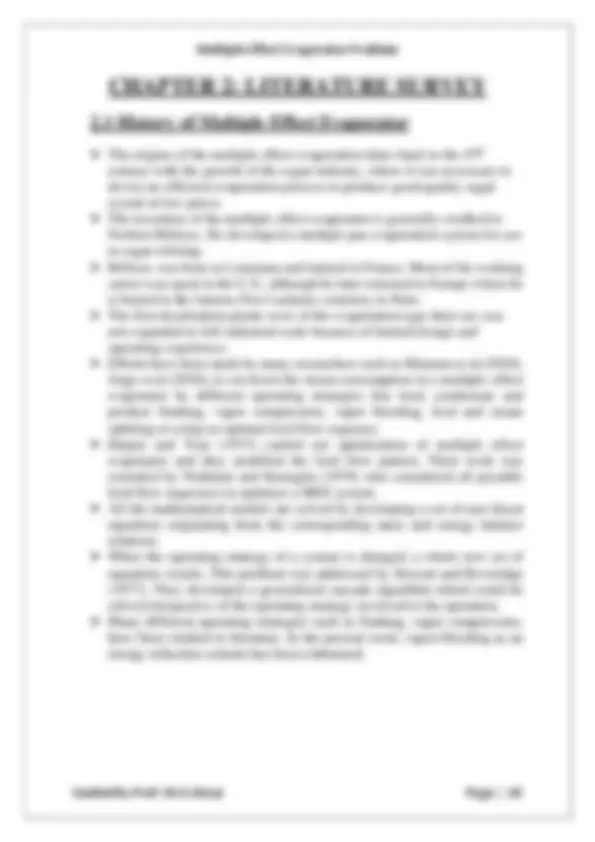
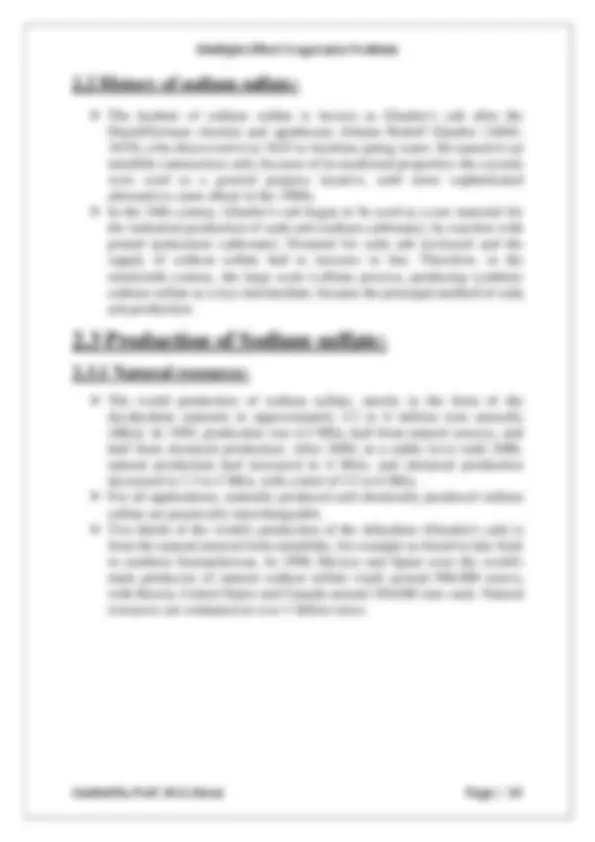
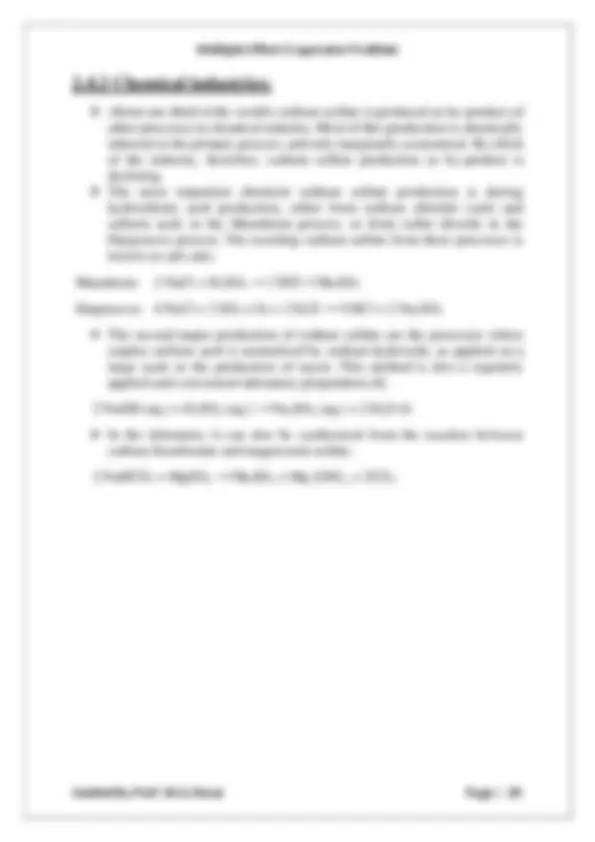
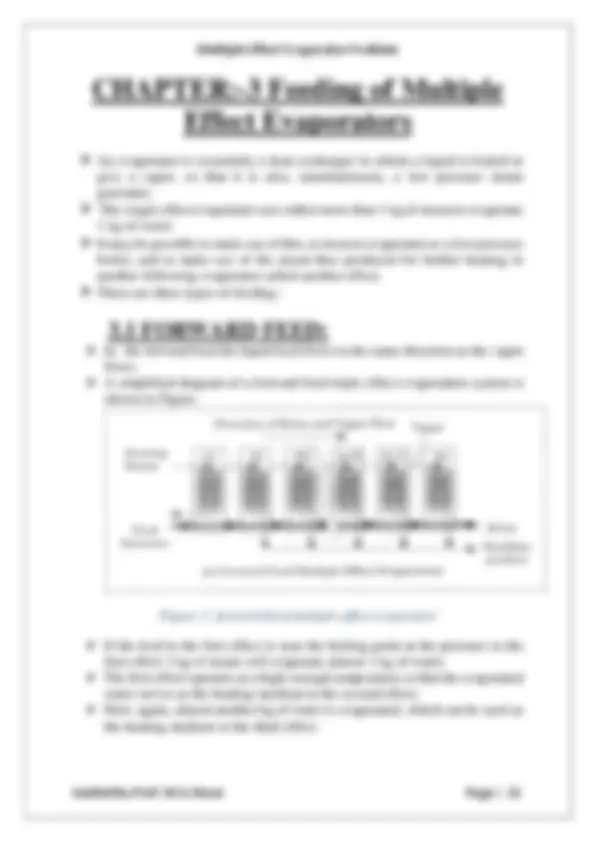
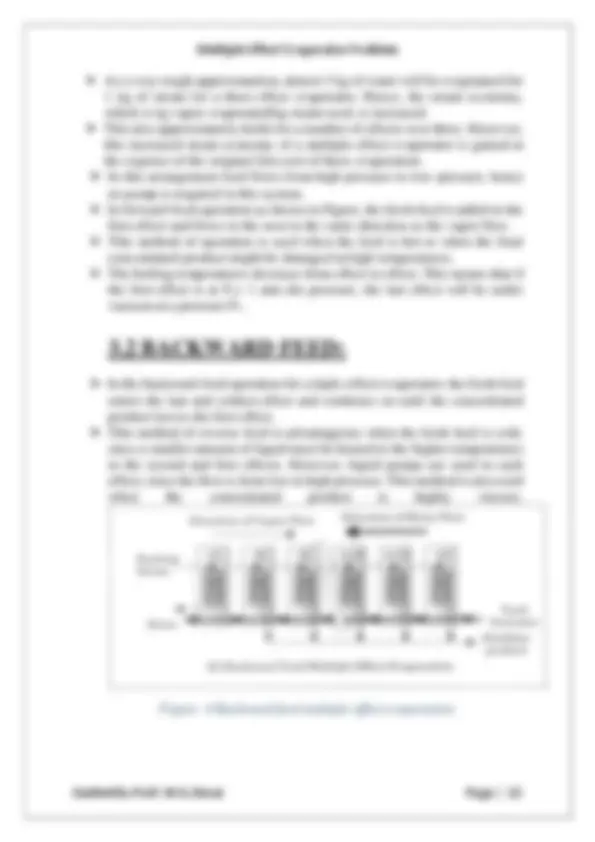
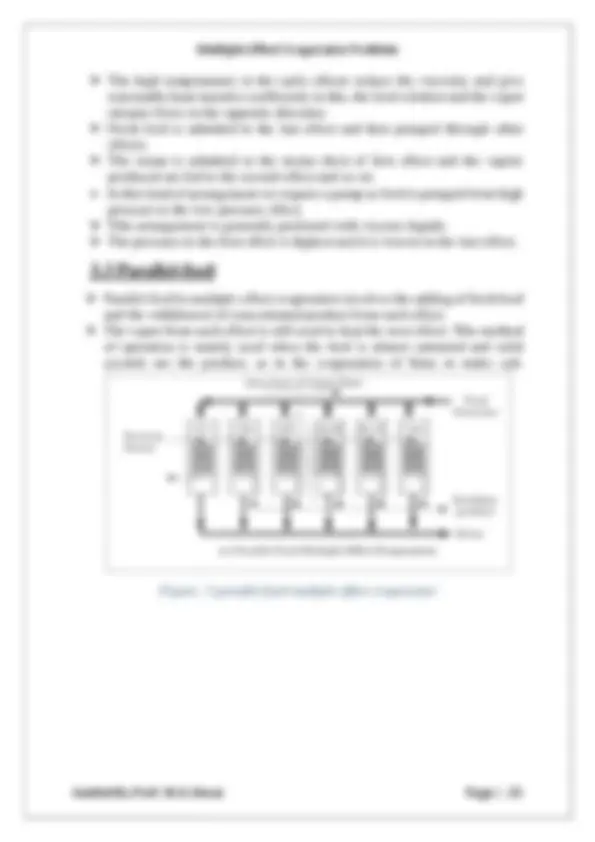
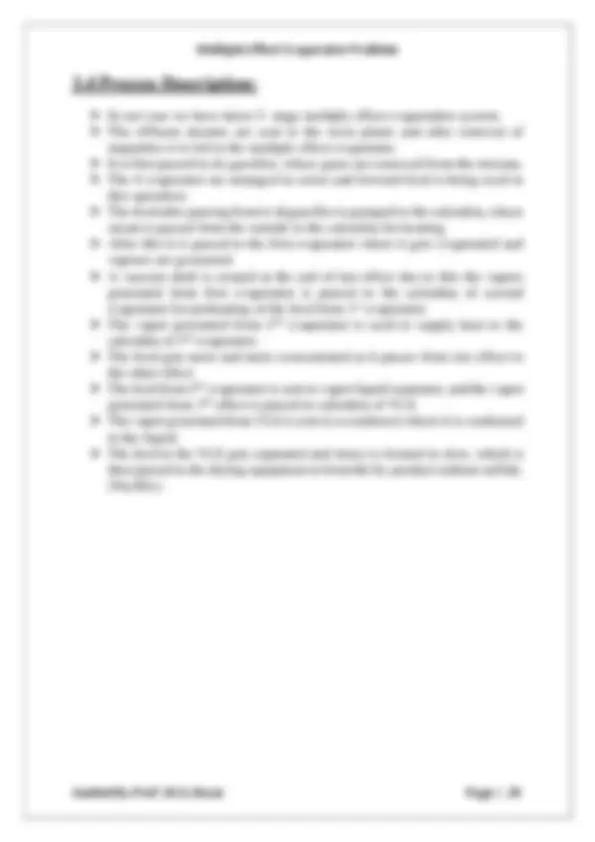


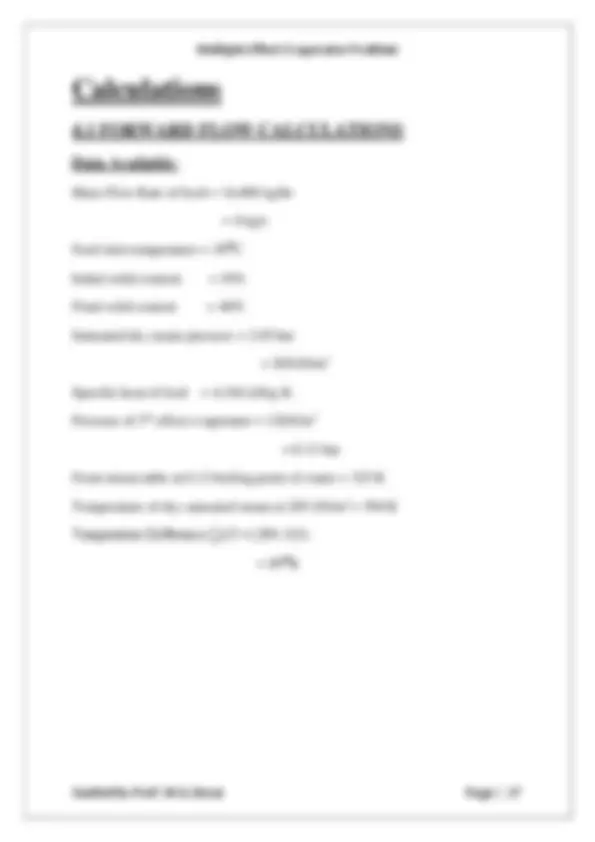
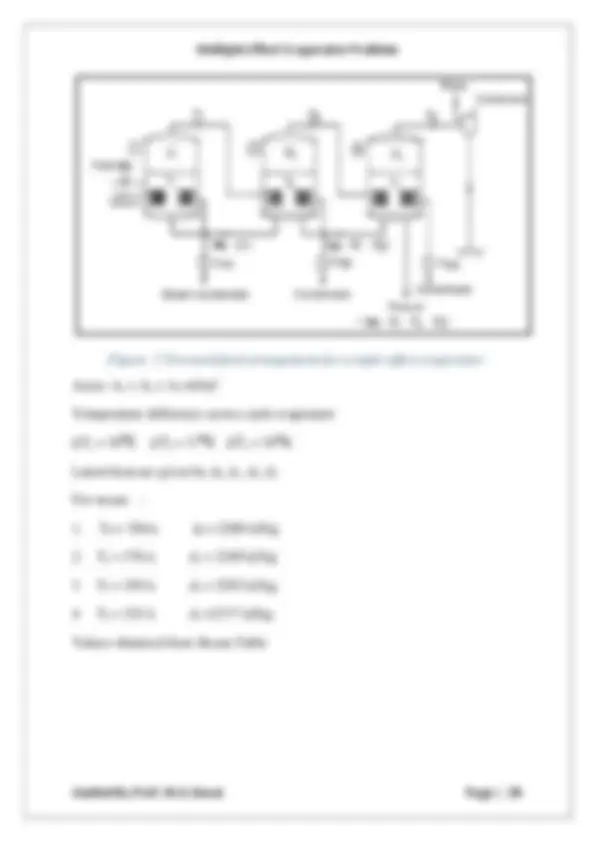
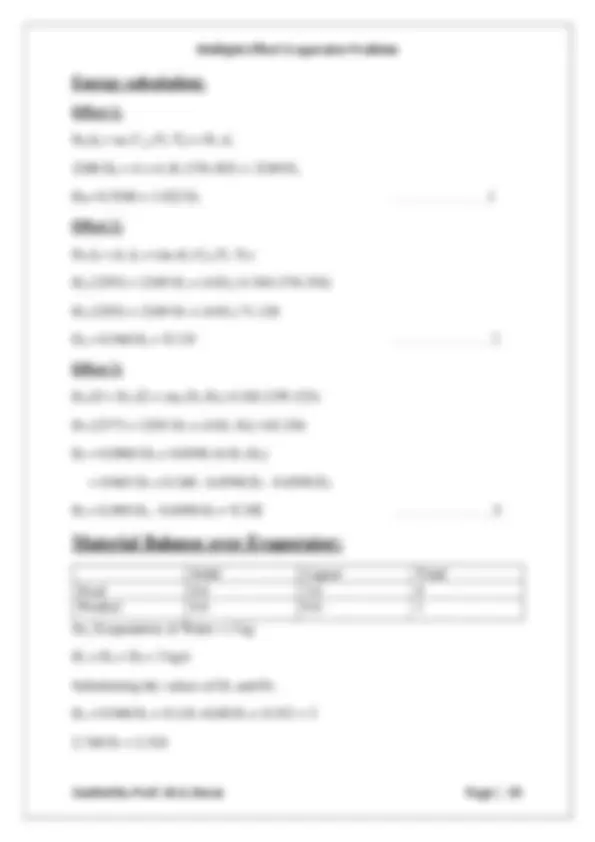
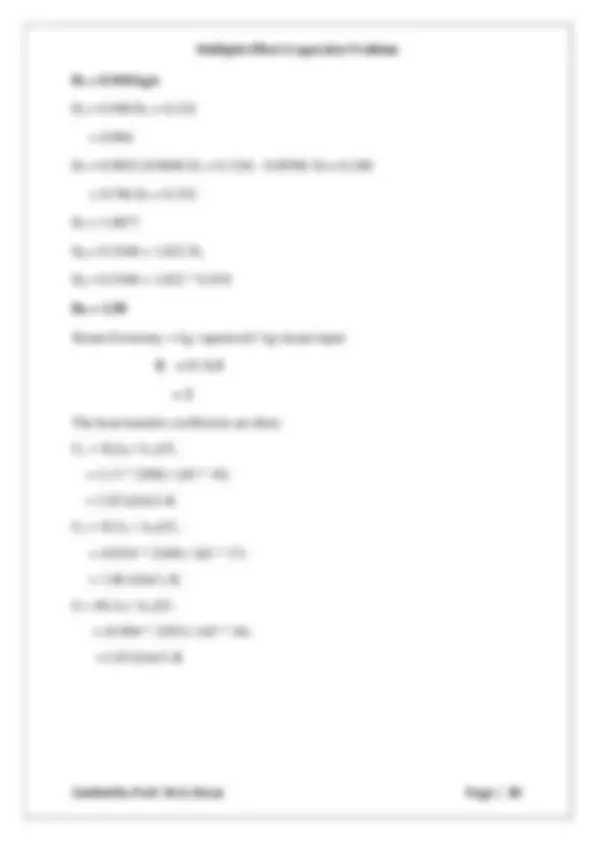
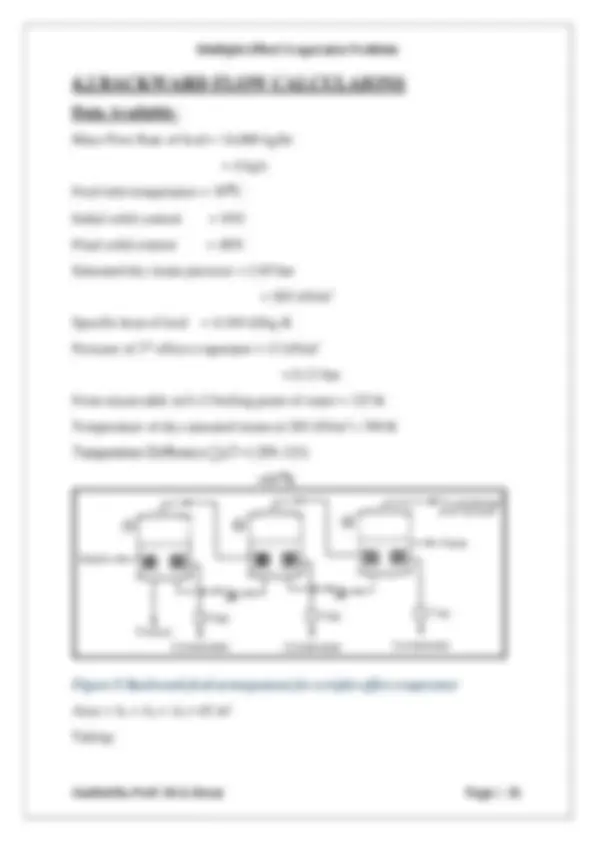
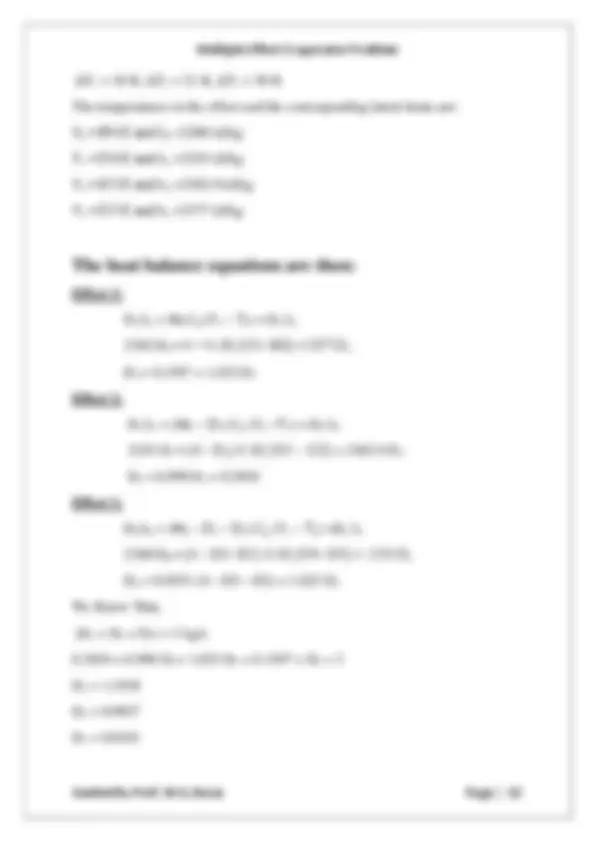
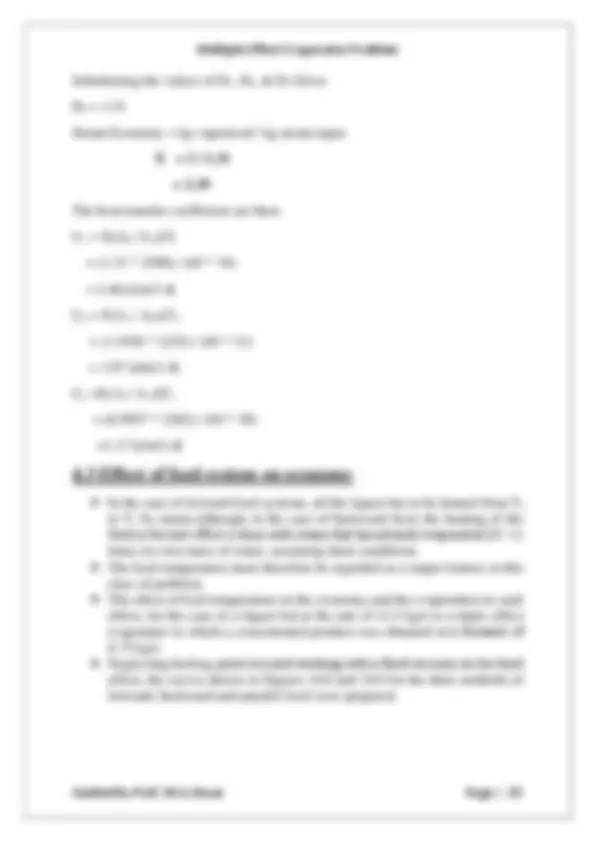
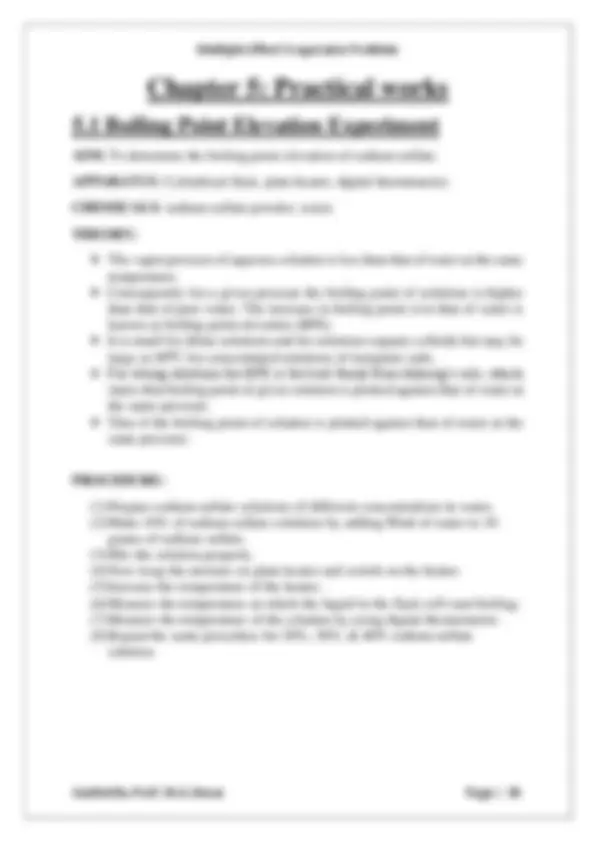
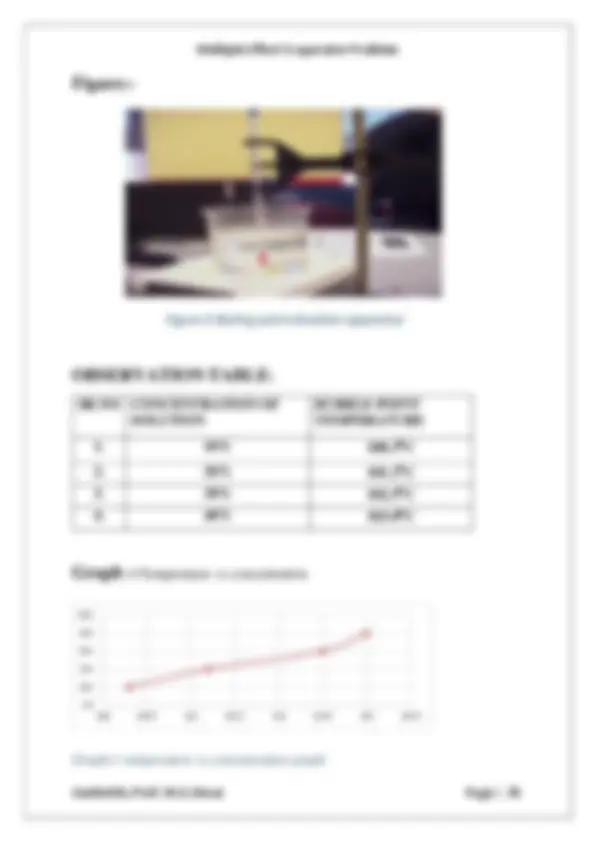
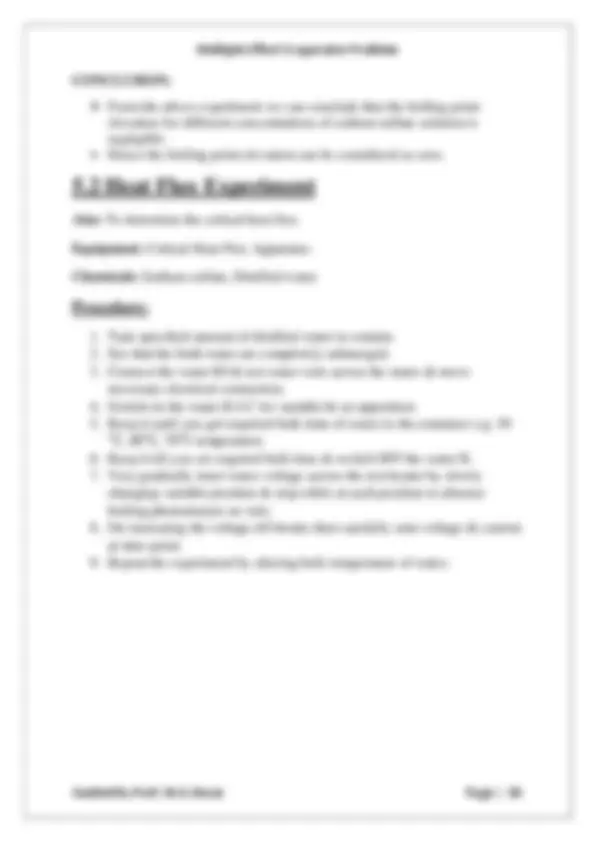
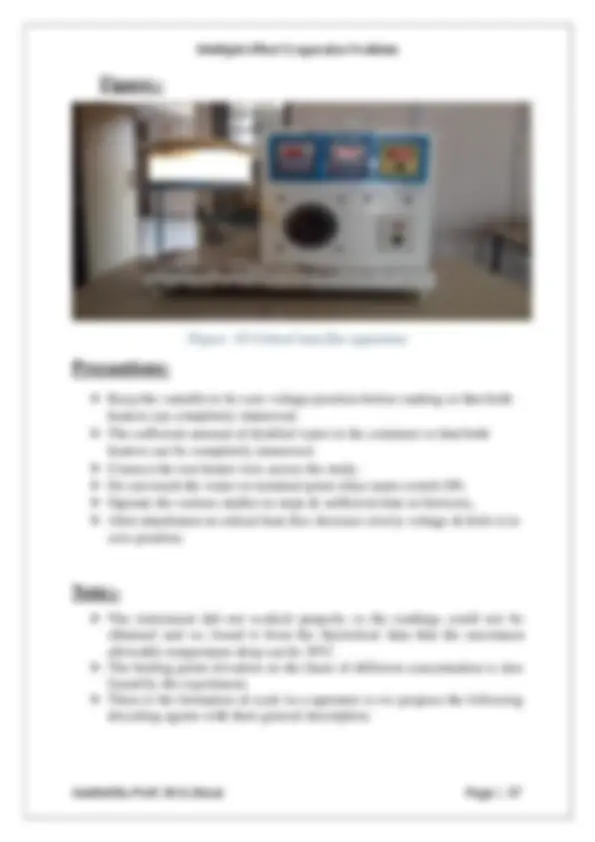
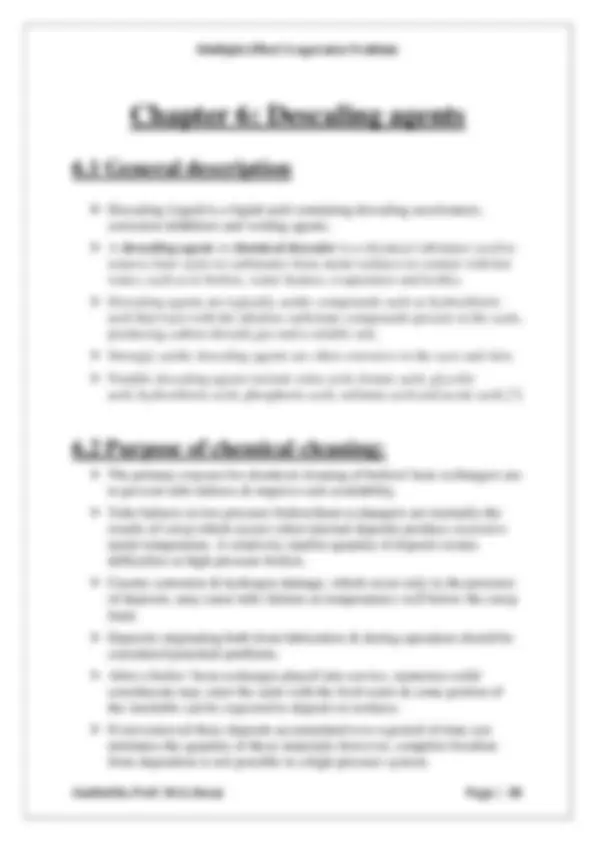
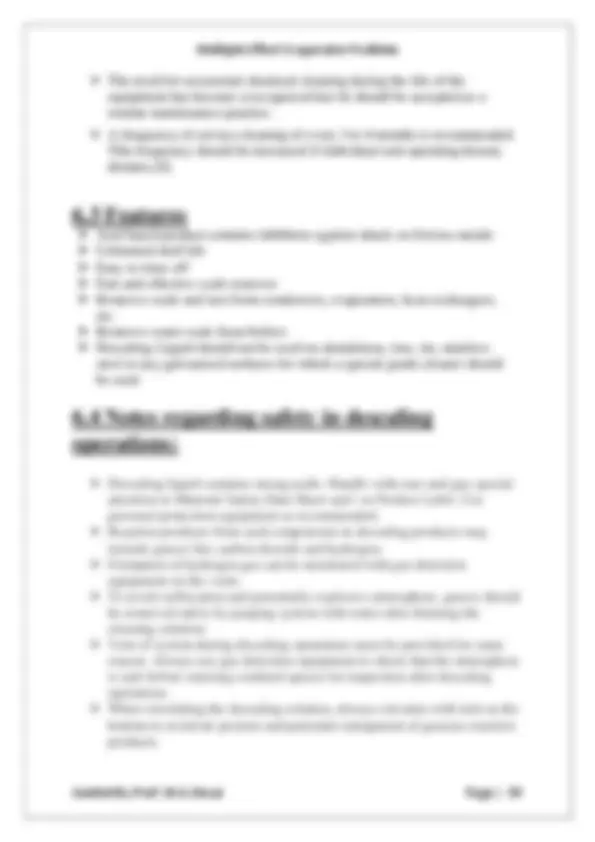
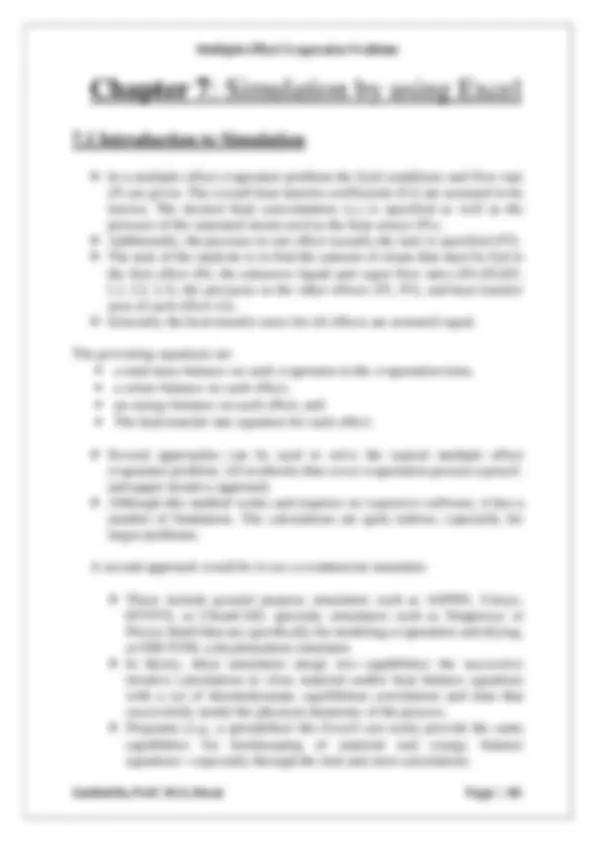
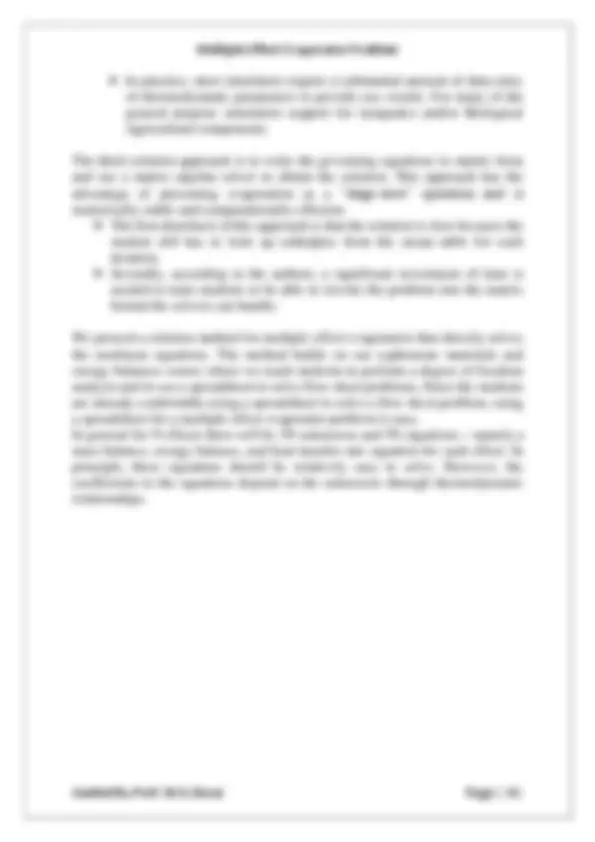
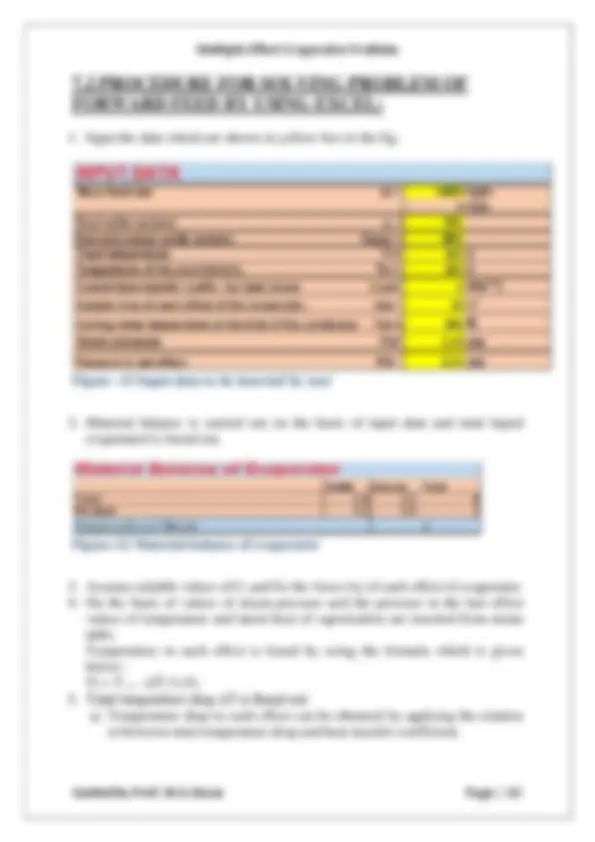
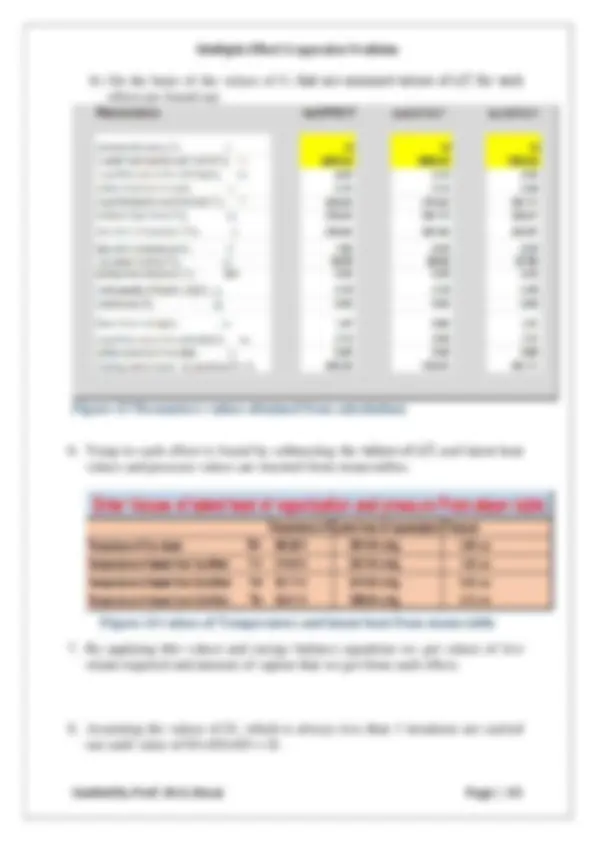

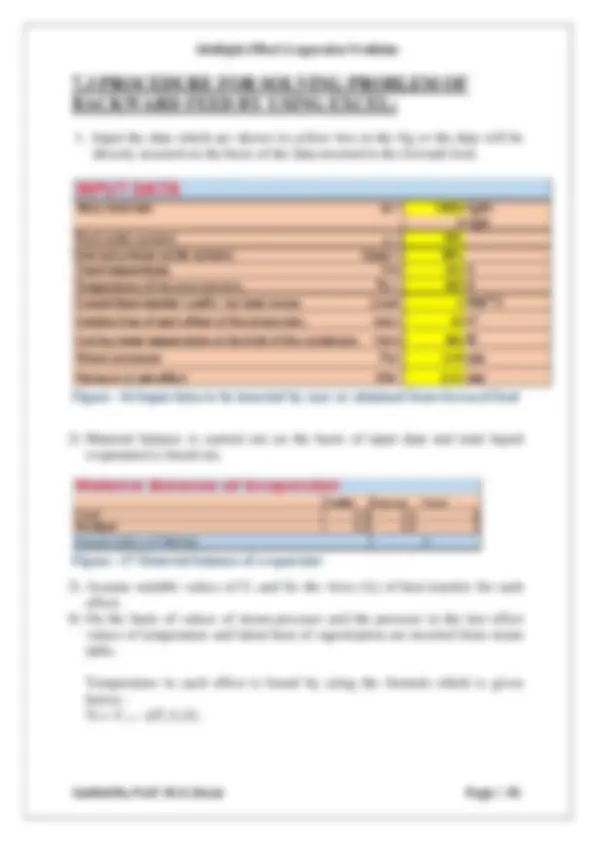
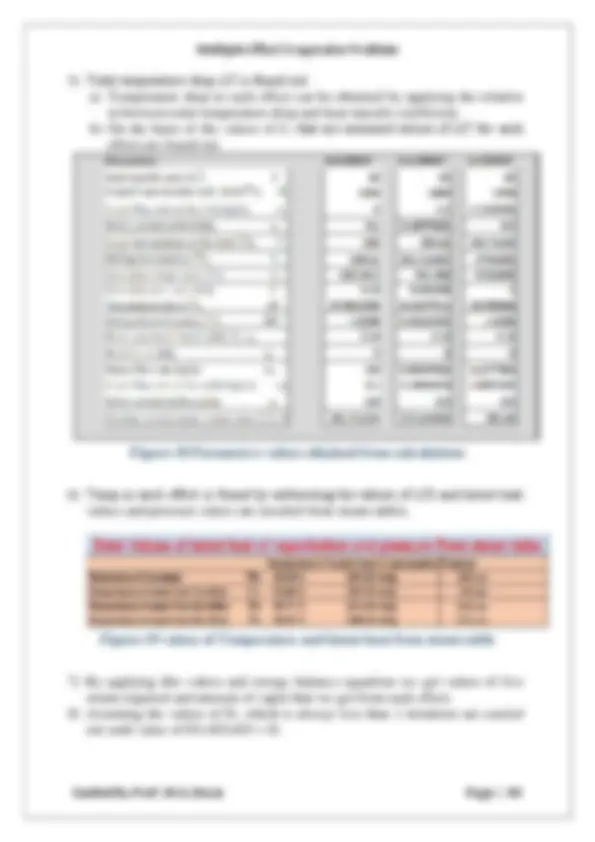
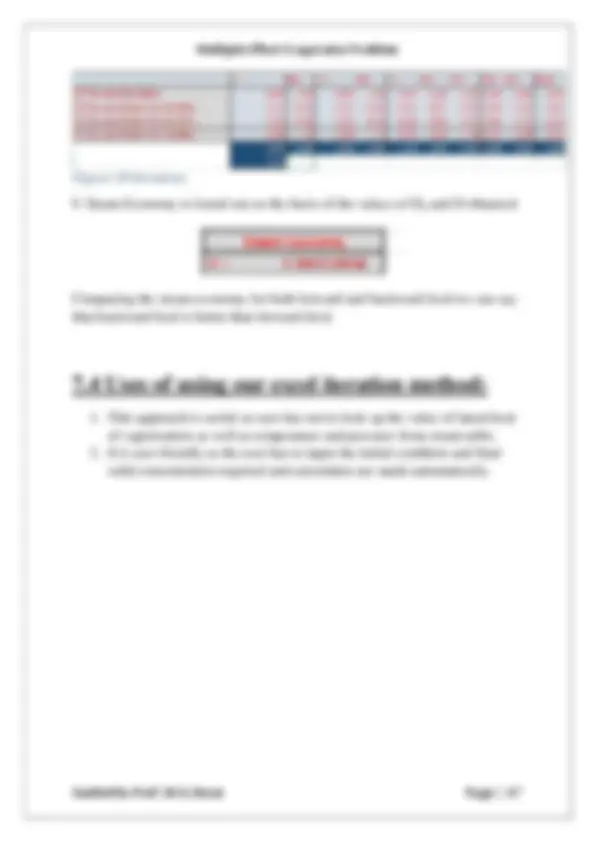
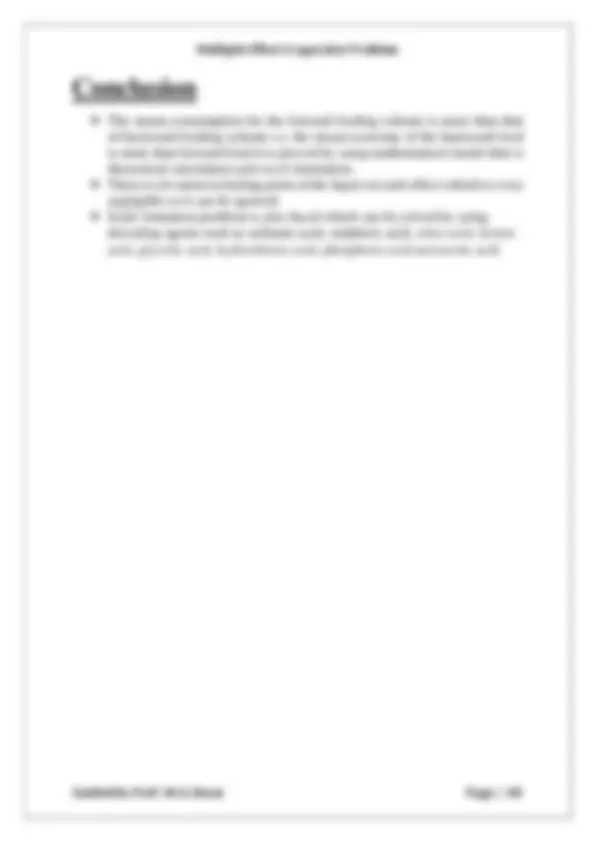
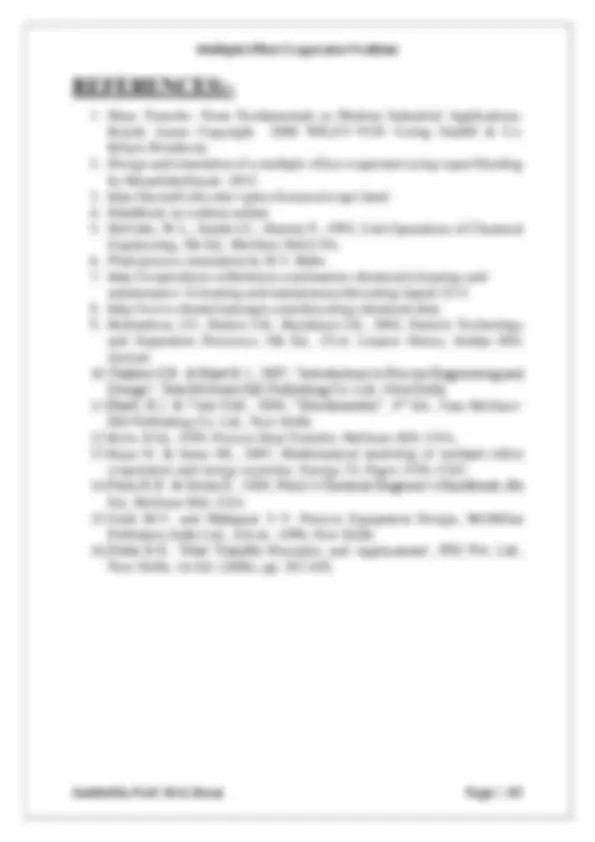
Estude fácil! Tem muito documento disponível na Docsity
Ganhe pontos ajudando outros esrudantes ou compre um plano Premium
Prepare-se para as provas
Estude fácil! Tem muito documento disponível na Docsity
Prepare-se para as provas com trabalhos de outros alunos como você, aqui na Docsity
Os melhores documentos à venda: Trabalhos de alunos formados
Prepare-se com as videoaulas e exercícios resolvidos criados a partir da grade da sua Universidade
Responda perguntas de provas passadas e avalie sua preparação.
Ganhe pontos para baixar
Ganhe pontos ajudando outros esrudantes ou compre um plano Premium
Comunidade
Peça ajuda à comunidade e tire suas dúvidas relacionadas ao estudo
Descubra as melhores universidades em seu país de acordo com os usuários da Docsity
Guias grátis
Baixe gratuitamente nossos guias de estudo, métodos para diminuir a ansiedade, dicas de TCC preparadas pelos professores da Docsity
CONCEITOS DE EVAPORAÇÃO DE MULTIPLO EFEITO
Tipologia: Resumos
1 / 49
Esta página não é visível na pré-visualização
Não perca as partes importantes!
Submitted by
- Mrugesh M. Bhandari (110190105058) **- Umang M. Patel (110190105070)
In fulfilment for the award of the degree
Of
in
Government Engineering College, Valsad
ABSTRACT
During our visit to the ATUL LTD.,ANKLESHWAR we found in Multiple Effect
Evaporator plant that steam utility increases with the time for the production of
sodium sulfate.
Evaporators can minimize the production of regulated waste residues, and
increase the potential for recovering valuable materials from those wastes.
Multiple-effect evaporators (MEEs) are common to industries that concentrate
different products, regenerate solvents, or separate solid-liquid mixtures.
Since evaporation is the most energy-intensive stage in any industrial operation,
measures to reduce energy consumption in the evaporator are greatly beneficial
towards making an operation cost-effective.
Our aims are to find out the reason for the increase in steam utility, to find out its
suitable solution to reduce it out and simulation of Multiple Effect Evaporator. A
model for an evaporator used for the concentration of sodium sulfate solution is
developed using a set of non-linear equations derived from the mass and energy
balance relations. Excel is used for the designing of multiple effect evaporator
List of Figures
Sr. No.
(^1) Single effect evaporator 2 (^2) Multiple effect evaporator 4 (^3) Forward feed multiple effect evaporator 13 (^4) Backward feed multiple effect evaporator 14 (^5) Parallel feed multiple effect evaporator 15 (^6) Variables in evaporator, preheater, and flash box of effect i. 18 (^7) Forward-feed arrangement for a triple-effect evaporator 20 (^8) Backward-feed arrangement for a triple-effect evaporator 23 (^9) Boiling point elevation apparatus 27 (^10) Critical heat flux apparatus 29 (^11) Input data to be inserted by user for forward feed 34 (^12) Material balance of evaporator for forward feed 34 (^13) Parameters values obtained from calculations for forward feed 35 (^14) Values of Temperature and latent heat from steam table for forward feed
(^15) Iterations for forward feed 36 (^16) Input data to be inserted by user or obtained from forward feed for back ward feed
(^17) Material balance of evaporator for backward feed 37 (^18) Parameters values obtained from calculations for backward feed
(^19) Values of Temperature and latent heat from steam table for backward feed
(^20) Iterations for backward feed 39
List of Graph:
Sr. No. Graph Page No.
Evaporation is a widely used method for the concentration of aqueous solutions, involves the removal of solvent from a solution by boiling the liquor in a suitable vessel, generally an evaporator, and withdrawing the vapor. In majority of processes solvent is water. Evaporation is usually treated as the separation of a liquid mixture into a liquid product (concentrate or thick liquor ) and a vapor byproduct, although in special cases such as water treating and desalination, the vapor is the product instead of the thick liquor.
Evaporators are kind of heat transfer equipment where the transfer mechanism is controlled by natural convection or forced convection. If the solution contains dissolved solids, the resulting strong liquor may become saturated so that crystals are deposited or crystals can further be formed by using crystallization after concentrating the solution. Evaporation is a transport phenomenon in which vapors or vapor mixtures are in contact with the liquids, and a large amount of energy is released or absorbed with the phase change, which is known as the latent heat. Liquors which are to be evaporated may be classified as follows:
(a) Those which can be heated to high temperatures without decomposition, and those that can be heated only to a temperature of about 330 K.
Figure-1 Single effect evaporator
(b) Those which yield solids on concentration, in which case crystal size and shape may be important, and those which do not.
(c) Those which, at a given pressure, boil at about the same temperature as water, and those which have a much higher boiling point.
A characteristic of mass transfer in these phenomena is that it is always accompanied by an energy transfer (usually heat transfer) due to the phase change, and in this respect it is quite different from ordinary mass transfer, which is not accompanied by an energy transfer. Evaporation is achieved by adding heat to the solution to vaporize the solvent. The heat is supplied to provide the latent heat of vaporization and by adopting methods for recovery of heat from the vapor, it has been possible to achieve good steam economy. The normal heating medium is generally low pressure exhaust steam from turbines, special heat transfer fluids or flue gases are also used. The design of an evaporation unit requires the practical application of data on heat transfer to boiling liquids, together with a realization of what happens to the liquid during concentration. The material of construction of an evaporator may be any kind of steel. Special materials like copper, stainless steel, nickel, aluminium may be used depending upon the specific properties of the solution to be concentrated. The multiple effect evaporation system is formed by a sequence of single effect evaporators, where the vapor formed in one effect is used in the next effect. The vapor reuse in the multiple effect system allows reduction of the brine and the temperature to low values and prevent rejection of large amount of energy to the surrounding, which was the main drawback of the single effect system. If a single evaporator is used for the concentration of any solution, the vapor issuing out of it is condensed and discarded it is called a single effect evaporator system. If more than one evaporator is used in series for the concentration of any solution, the vapor coming out of one effect is used as a heating medium in the steam chest of the next effect, it is called a multiple effect evaporator system. Single effect evaporation is simple but the steam utilization is not effective, while multiple effect evaporators evaporate more quantity of water for the same amount of steam consumed in the evaporation process.
The energy consumption to evaporate an aqueous solution is fairly significant; therefore, in order to reduce the energy cost, systems such as multiple effect evaporation and thermal vapor recompression are often used. The steam consumption of the evaporator unit can be reduced by using the vapor from the first chamber to heat the second one. In such a system, the heat from the original steam fed into the system is reused in the successive effects. The thermodynamic principle of the multi-effect evaporator consists in a series of reboilers operating at different pressures; the water evaporated at one stage is condensed and used as the heat source for another stage. Due to its strong integration with the process, it is worth to analyze the integration of the multi-effect evaporator with the rest of the process. The objective of Multiple effect evaporator system is to concentrated the thin liquor of sodium sulfate to thick liquor which could be further be crystallized in a centrifuge to give a solid product. Large amount of water must be evaporated in order to maximize net calorific value in the boiler. The objective of this study has been to identify the opportunity of reducing the energy consumed in the evaporator section of a sodium sulfate salt producing plant in Atul ltd., Ankleshwar. Normally, all effects in an evaporator will be physically the same in terms of size, construction, and heat transfer area. Unless thermal losses are significant, they will all have the same capacity as well. Evaporator trains may receive their feed in several different ways. The feed order is not related to the numbering of effects. Effects are always numbered according to decreasing pressure (steam flow).
There are three main measures of evaporator performance:
Note that the measures are related, since Consumption = Capacity/Economy. Economy calculations are determined using enthalpy balances.
The key factor in determining the economy of an evaporator is the number of effects. The economy of a single effect evaporator is always less than 1..
Multiple effect evaporators have higher economy but lower capacity than single effect. The thermal condition of the evaporator feed has an important impact on economy and performance. If the feed is not already at its boiling point, heat effects must be considered. If the feed is cold (below boiling) some of the heat going into the evaporator must be used to raise the feed to boiling before evaporation can begin; this reduces the capacity. If the feed is above the boiling point, some flash evaporation occurs on entry.
Evaporators are integral part of a number of process industries namely Pulp and Paper, Chloro-alkali, Sugar, pharmaceuticals, Desalination, Dairy and Food processing, etc. Evaporators find one of their most important applications in the food and drink industry. The goal of evaporation is to concentrate a target liquid, and this needs to be achieved for many different targets today. One of the most important applications of evaporation is that on the food and drink industry. Many foods that are made to last for a considerable amount of time or food that needs a certain consistency, like coffee, need to go through an evaporation step during processing. It is also used as a drying process and can be applied in this way to laboratories where preservation of long-term activity or stabilization is needed (for enzymes for example). Evaporation is also used in order to recover expensive solvents such as hexane which would otherwise be wasted. Another example of evaporation is in the recovery of sodium hydroxide in Kraft pulping. Cutting down waste handling cost is another major application of evaporation for large companies. If up to 98% of wastes can be vaporized, industry can greatly reduce the amount of money that would otherwise be allocated towards waste handling. Evaporation is also used in pharmaceutical industry as to get a concentrated product and to improve the stability of the products. Evaporation is also used in the concentration of the sodium salts that are obtained as a by-product from the production of p-cresol. In an air-conditioning process, evaporation is used to allow the coolant, Freon, to evaporate from liquid to gas while absorbing heat.
Sodium sulfate is chemically very stable, being unreactive toward most oxidizing or reducing agents at normal temperatures. At high temperatures, it can be converted to sodium sulfide by carbothermal reduction:
Na 2 SO 4 + 2 C → Na 2 S + 2 CO 2
Sodium sulfate is a neutral salt, which forms aqueous solutions with pH of 7.Sodium sulfate reacts with sulfuric acid to give the acid salt sodium bisulphate.
Na2SO4 + H 2 SO4 ⇌ 2 NaHSO 4
Sodium sulfate has unusual solubility characteristics in water. Its solubility in water rises more than tenfold between 0 °C to 32.384 °C, where it reaches a maximum of 497 g/L. Sodium sulfate is a typical ionic sulfate, containing Na+ ions and SO42− ions. The existence of sulfate in solution is indicated by the easy formation of insoluble sulfates when these solutions are treated with Ba2+ or Pb2+ salts:
Na 2 SO 4 + BaCl 2 → 2 NaCl + BaSO 4
Sodium sulfate is a very cheap material, approx. $30 per ton in 1970. The largest use is as filler in powdered home laundry detergents, consuming approximate 50% of world production. This use is waning as domestic consumers are increasingly switching to compact or liquid detergents that do not include sodium sulfate. Another formerly major use for sodium sulfate, notably in the US and Canada, is in the Kraft process for the manufacture of wood pulp. Organics present in the "black liquor" from this process are burnt to produce heat, needed to drive the reduction of sodium sulfate to sodium sulphide. The glass industry provides another significant application for sodium sulfate, as second largest application in Europe. Sodium sulfate is used as a fining agent, to help remove small air bubbles from molten glass. It fluxes the glass, and prevents scum formation of the glass melt during refining. The glass industry in Europe has been consuming from 1970 to 2006 a stable 110,000 tons annually. Sodium sulfate is important in the manufacture of textiles, particularly in Japan, where it is the largest application. Sodium sulfate helps in "levelling", reducing negative charges on fibers so that dyes can penetrate evenly. Unlike the alternative sodium chloride, it does not corrode the stainless steel vessels used in dyeing. This application in Japan and US consumed in 2006 approximately 100,000 tones.
The hydrate of sodium sulfate is known as Glauber's salt after the Dutch/German chemist and apothecary Johann Rudolf Glauber (1604– 1670), who discovered it in 1625 in Austrian spring water. He named it sal mirabilis (miraculous salt), because of its medicinal properties: the crystals were used as a general purpose laxative, until more sophisticated alternatives came about in the 1900s. In the 18th century, Glauber's salt began to be used as a raw material for the industrial production of soda ash (sodium carbonate), by reaction with potash (potassium carbonate). Demand for soda ash increased and the supply of sodium sulfate had to increase in line. Therefore, in the nineteenth century, the large scale Leblanc process, producing synthetic sodium sulfate as a key intermediate, became the principal method of soda ash production.
2.3 Production of Sodium sulfate:
The world production of sodium sulfate, mostly in the form of the decahydrate amounts to approximately 5.5 to 6 million tons annually (Mt/a). In 1985, production was 4.5 Mt/a, half from natural sources, and half from chemical production. After 2000, at a stable level until 2006, natural production had increased to 4 Mt/a, and chemical production decreased to 1.5 to 2 Mt/a, with a total of 5.5 to 6 Mt/a. For all applications, naturally produced and chemically produced sodium sulfate are practically interchangeable. Two thirds of the world's production of the dehydrate (Glauber's salt) is from the natural mineral form mirabilite, for example as found in lake beds in southern Saskatchewan. In 1990, Mexico and Spain were the world's main producers of natural sodium sulfate (each around 500,000 tones), with Russia, United States and Canada around 350,000 tons each. Natural resources are estimated at over 1 billion tones.
About one third of the world's sodium sulfate is produced as by-product of other processes in chemical industry. Most of this production is chemically inherent to the primary process, and only marginally economical. By effort of the industry, therefore, sodium sulfate production as by-product is declining. The most important chemical sodium sulfate production is during hydrochloric acid production, either from sodium chloride (salt) and sulfuric acid, in the Mannheim process, or from sulfur dioxide in the Hargreaves process. The resulting sodium sulfate from these processes is known as salt cake.
Mannheim: 2 NaCl + H 2 SO 4 → 2 HCl + Na 2 SO 4
Hargreaves: 4 NaCl + 2 SO 2 + O 2 + 2 H 2 O → 4 HCl + 2 Na 2 SO 4
The second major production of sodium sulfate are the processes where surplus sulfuric acid is neutralized by sodium hydroxide, as applied on a large scale in the production of rayon. This method is also a regularly applied and convenient laboratory preparation.[4]
2 NaOH (aq.) + H 2 SO 4 (aq.) → Na 2 SO 4 (aq.) + 2 H 2 O (l)
In the laboratory it can also be synthesized from the reaction between sodium bicarbonate and magnesium sulfate.
2 NaHCO 3 + MgSO 4 → Na 2 SO 4 + Mg (OH) 2 + 2CO 2