
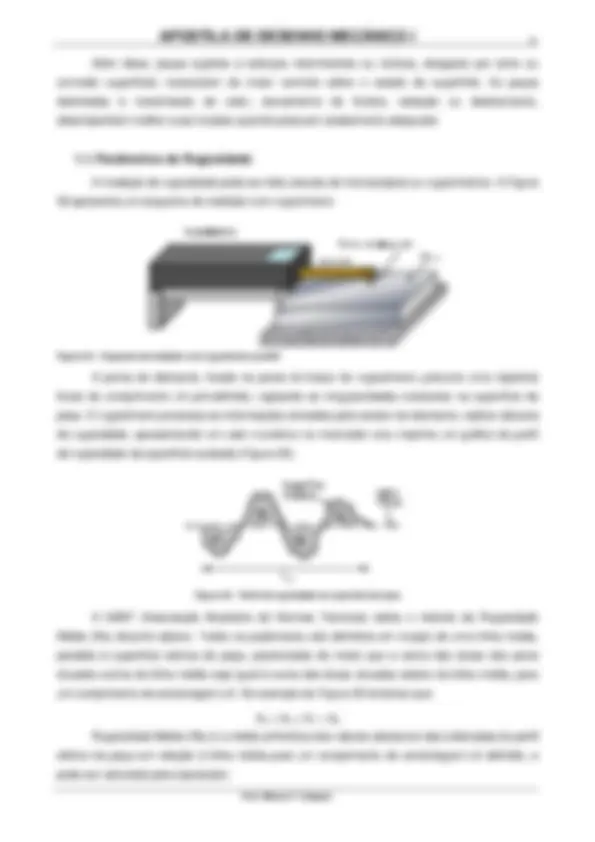
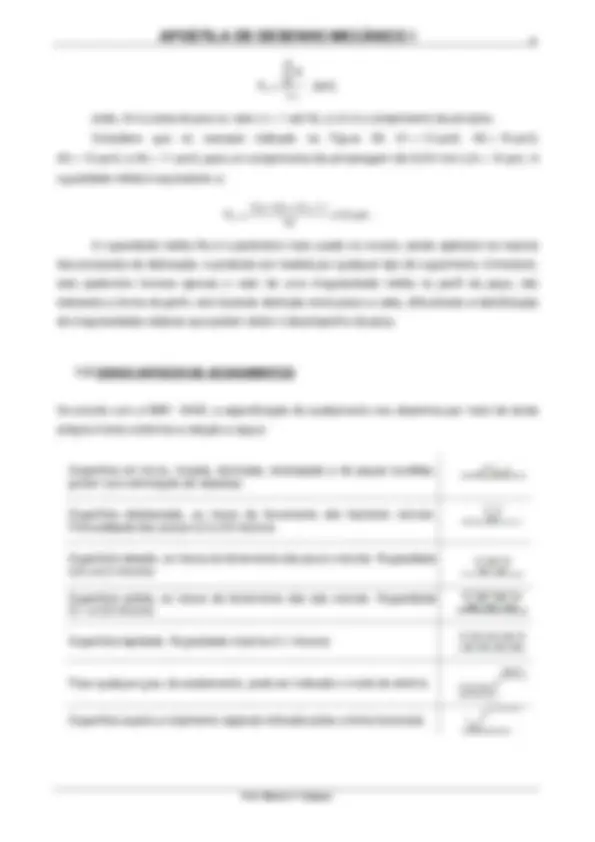
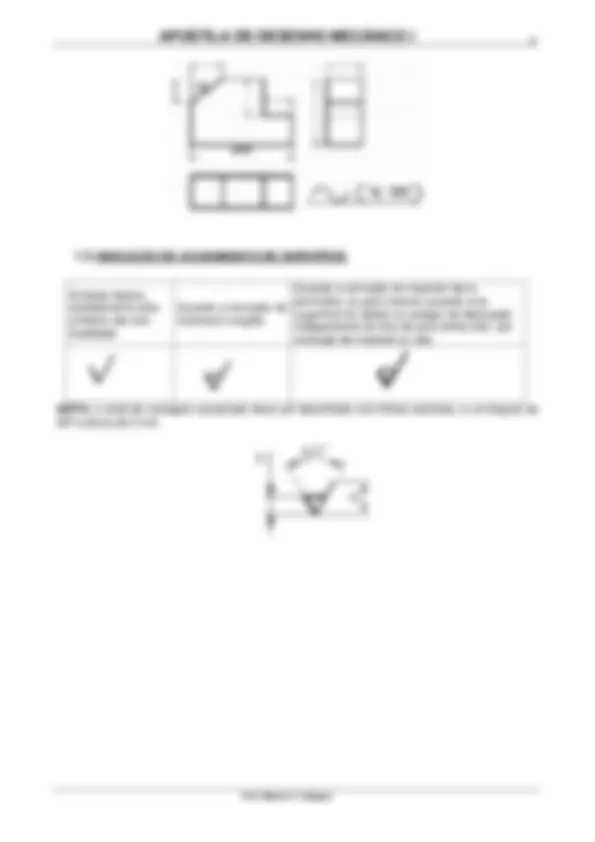
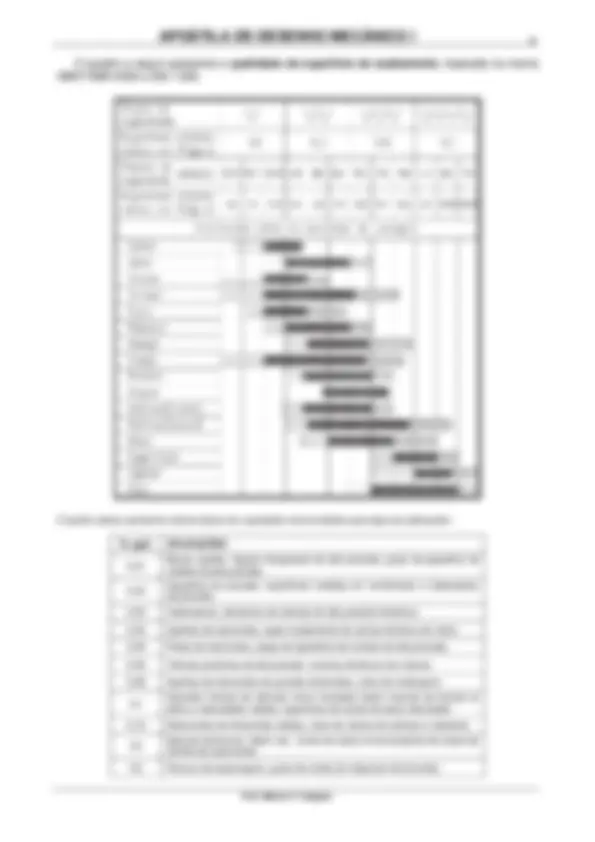
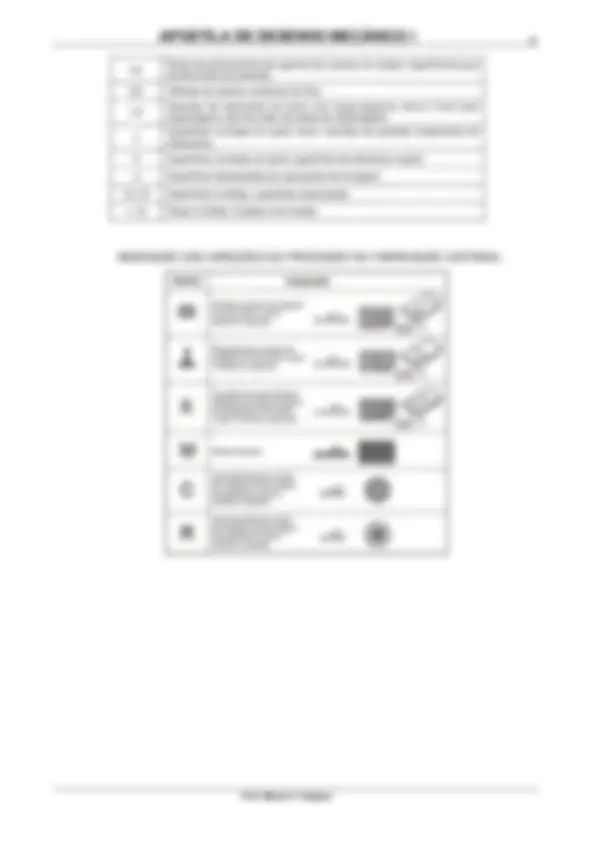
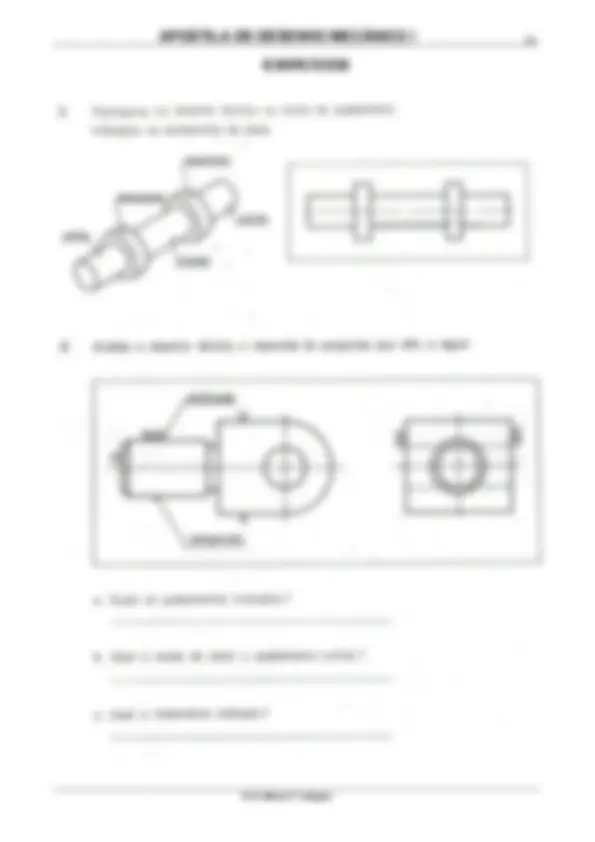
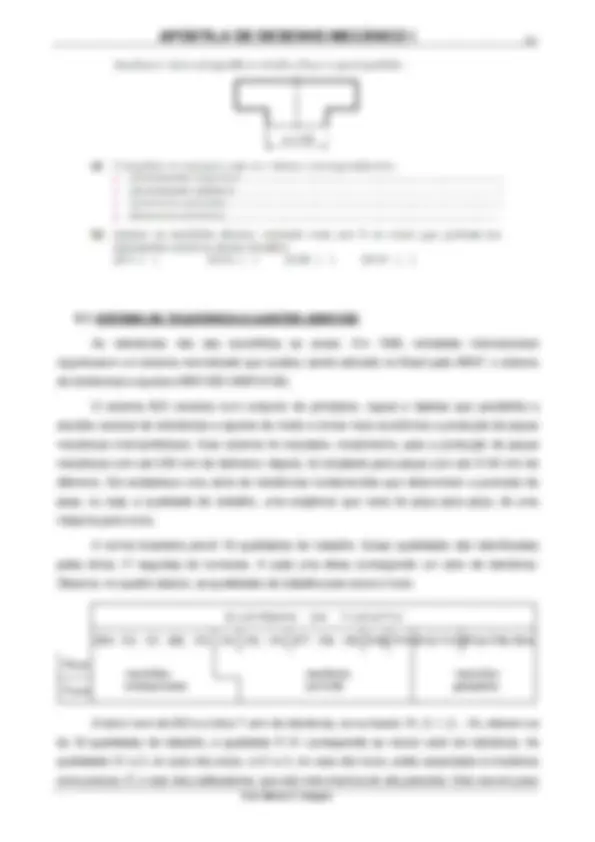
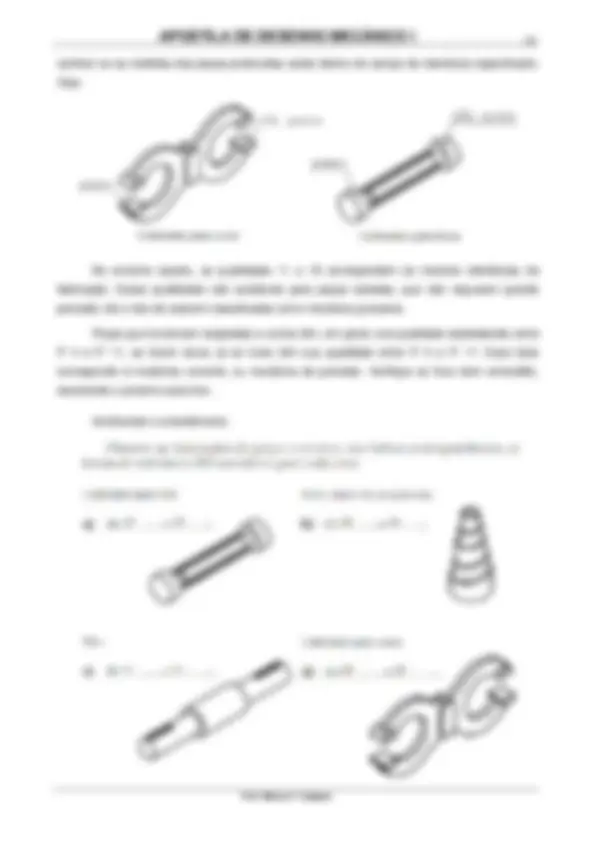
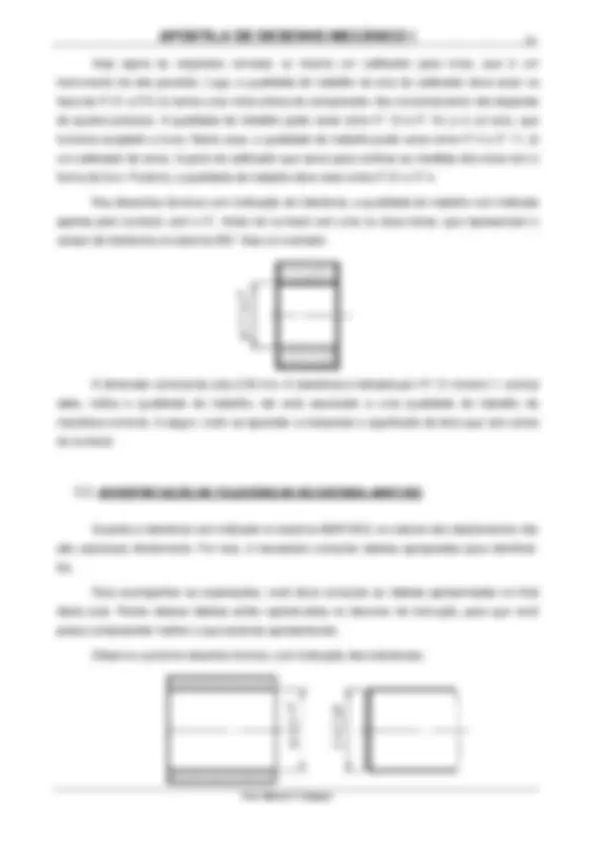
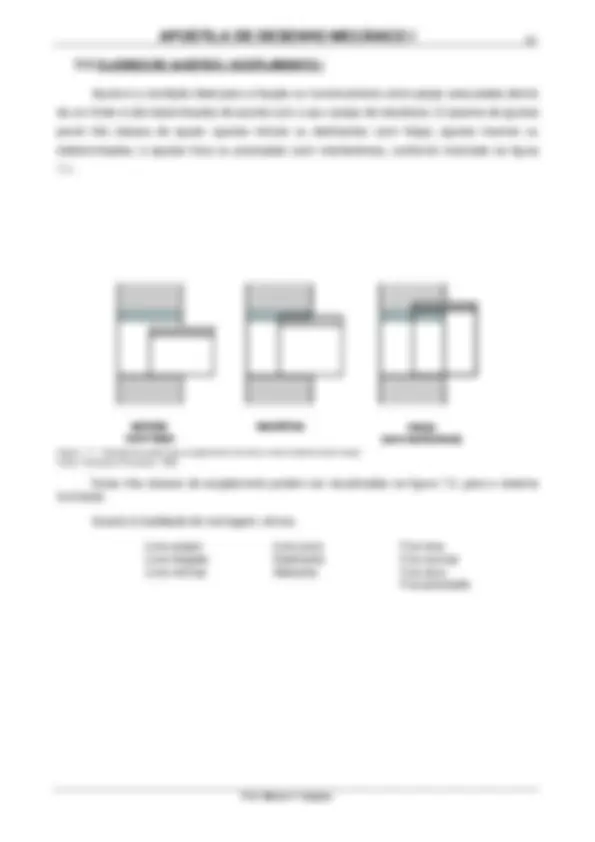
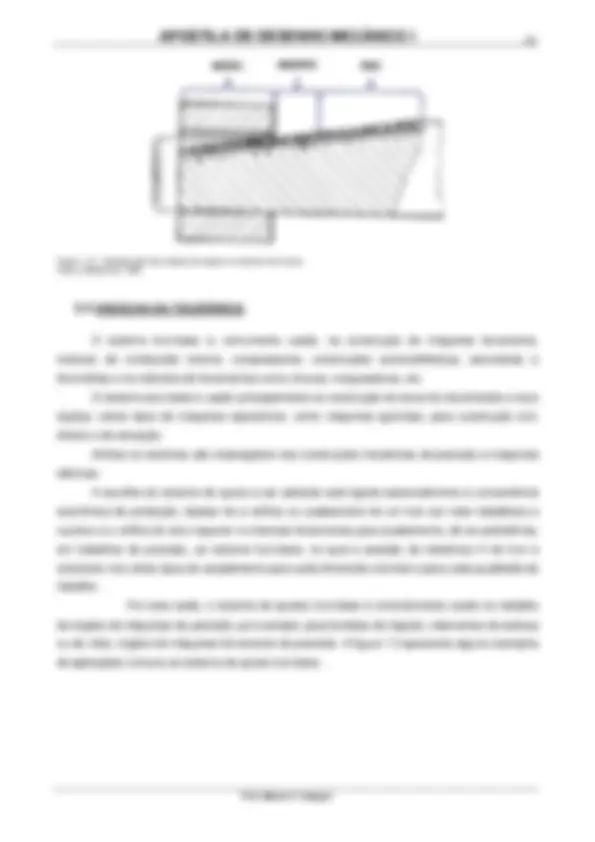

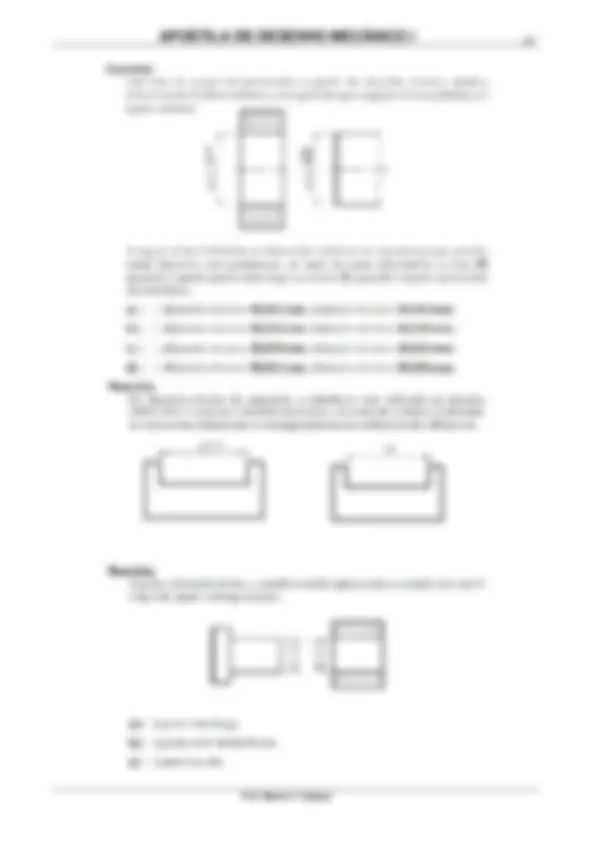
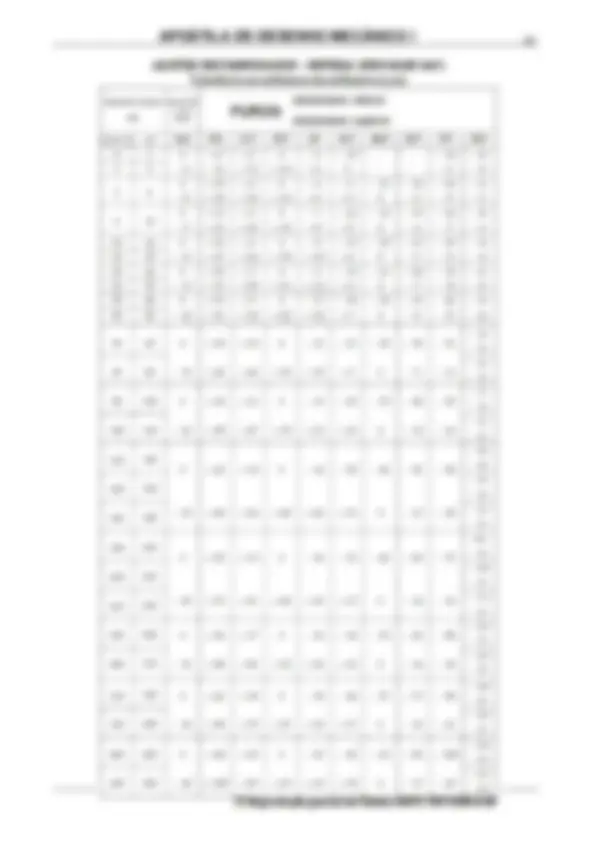
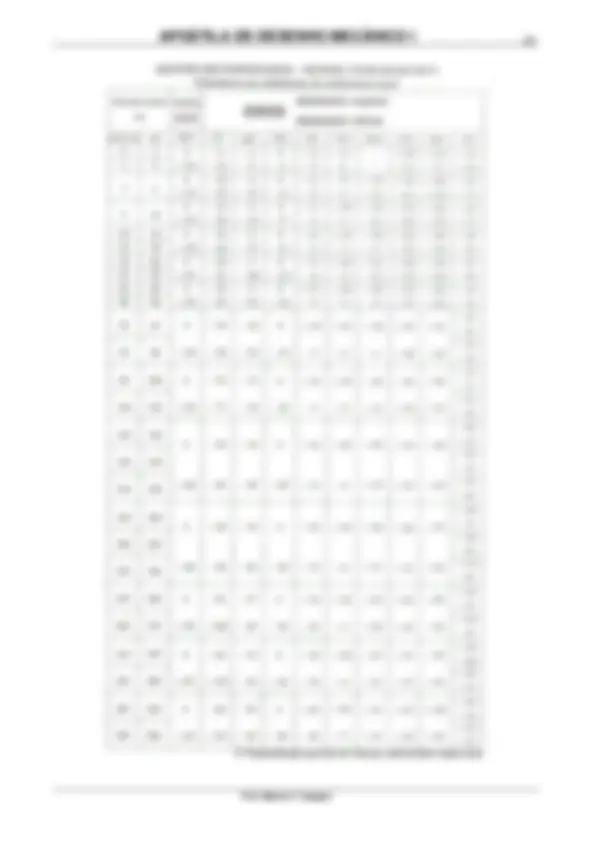
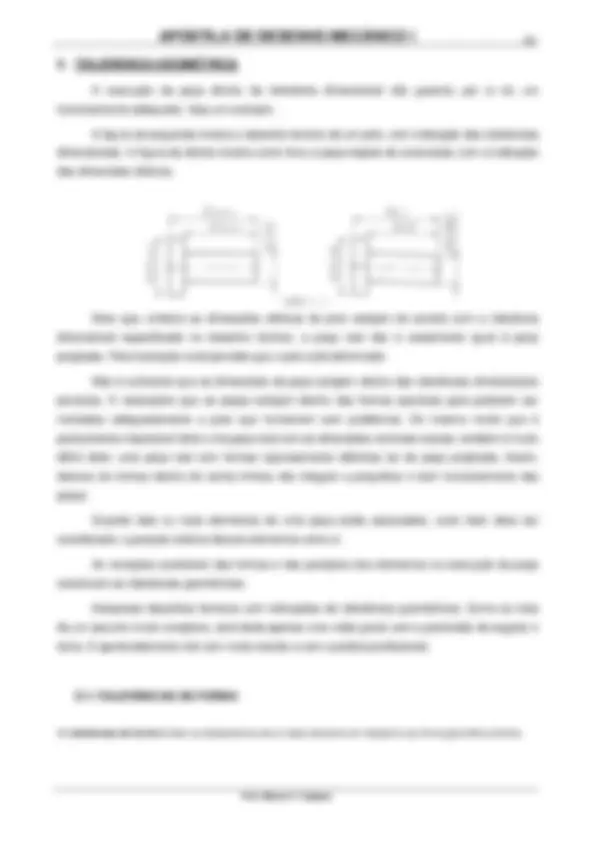
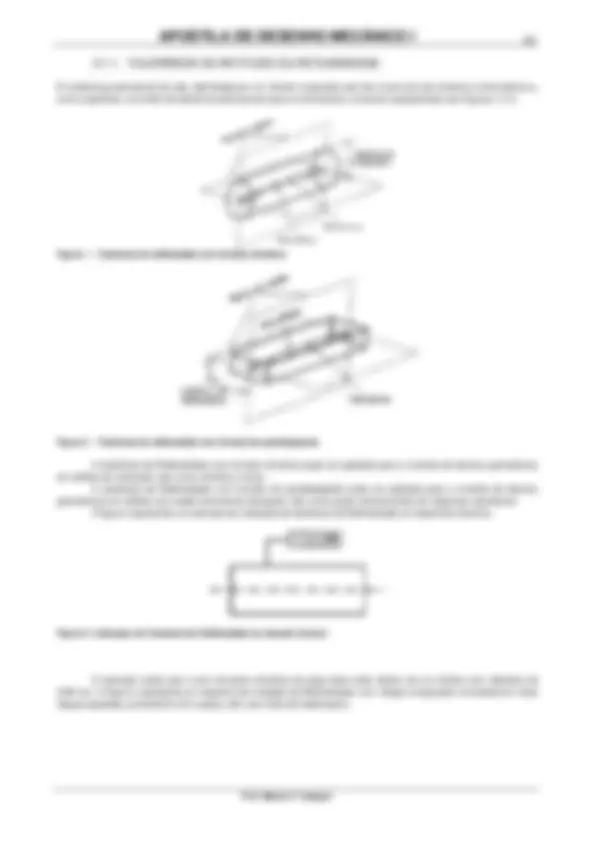
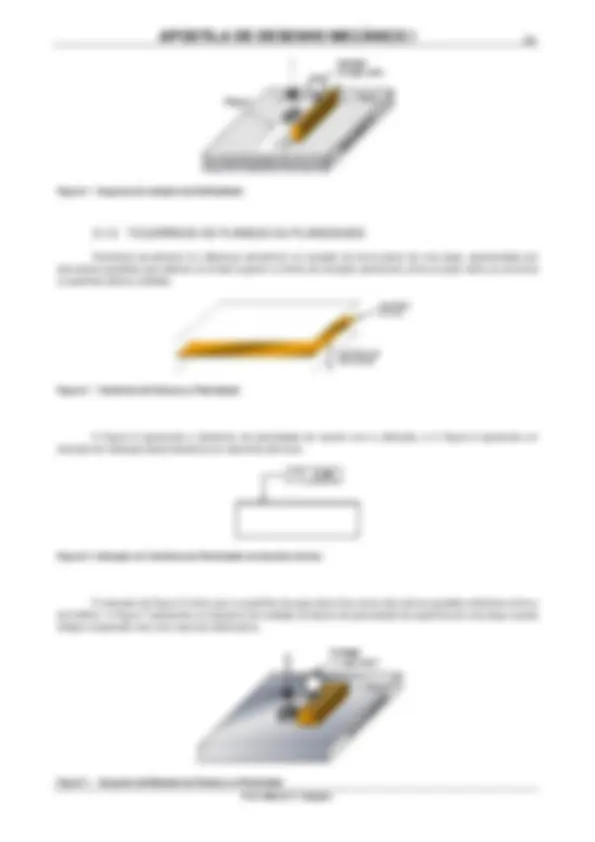
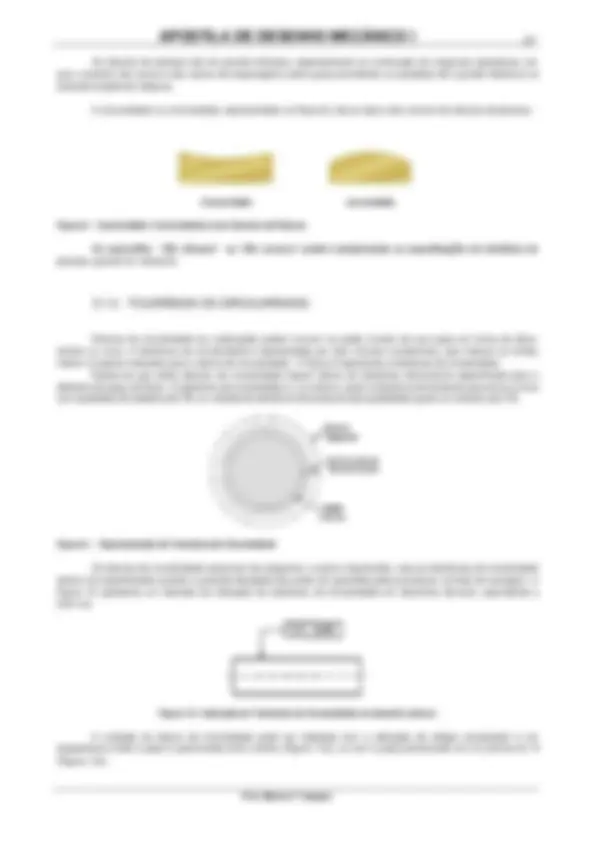
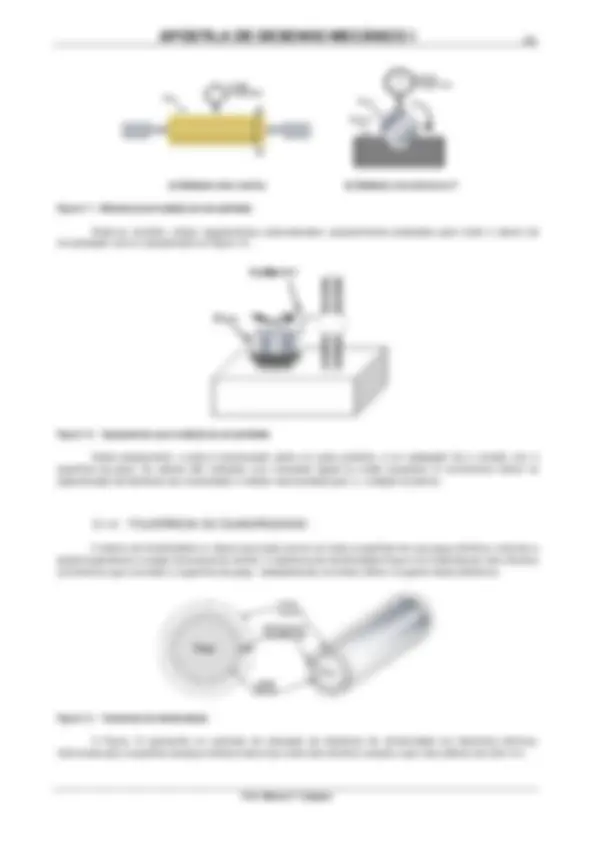
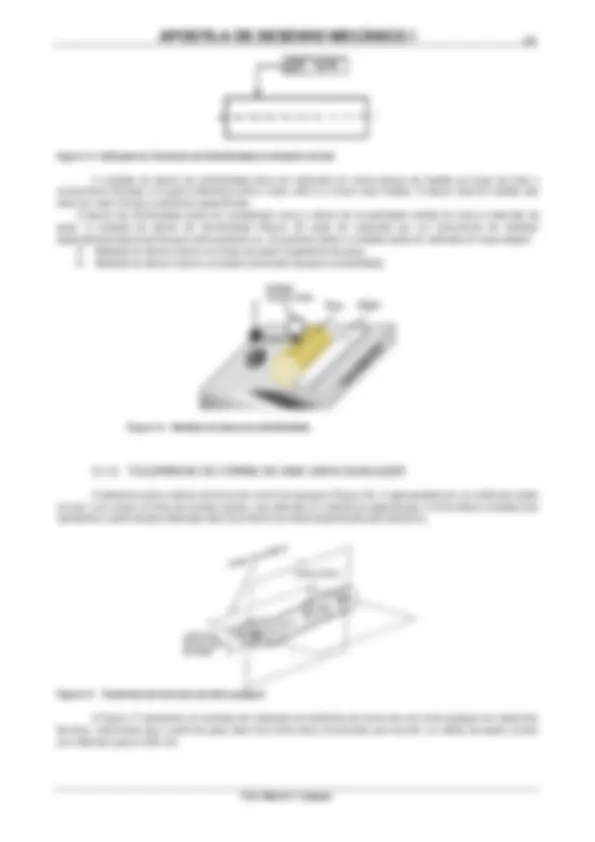
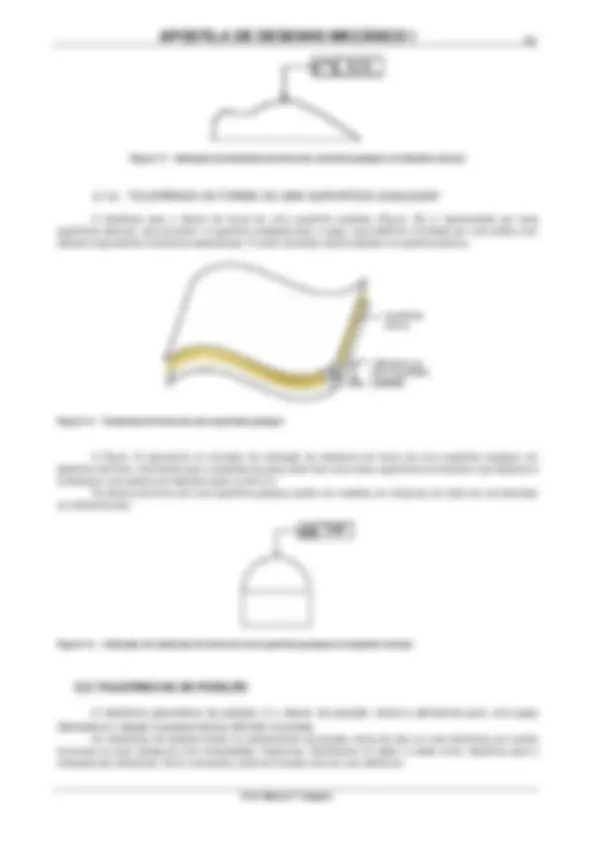
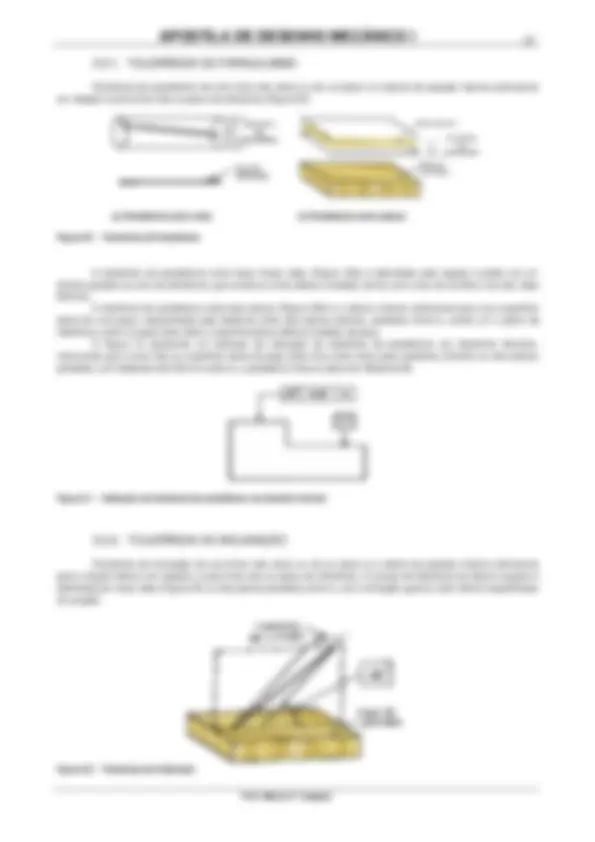
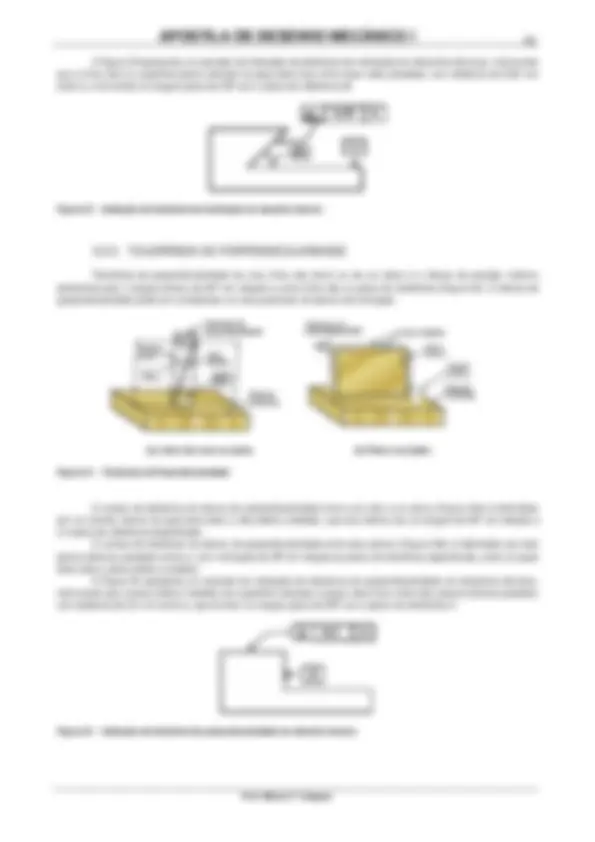
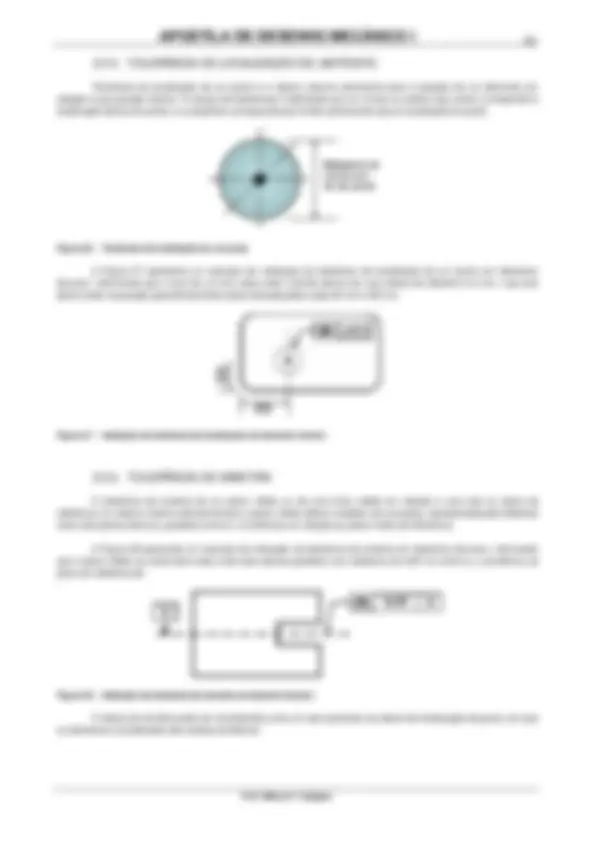
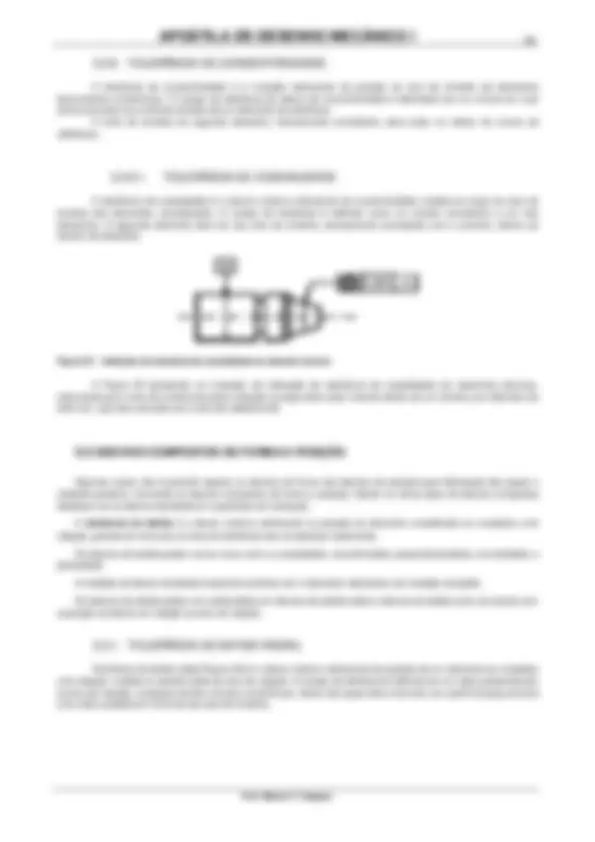
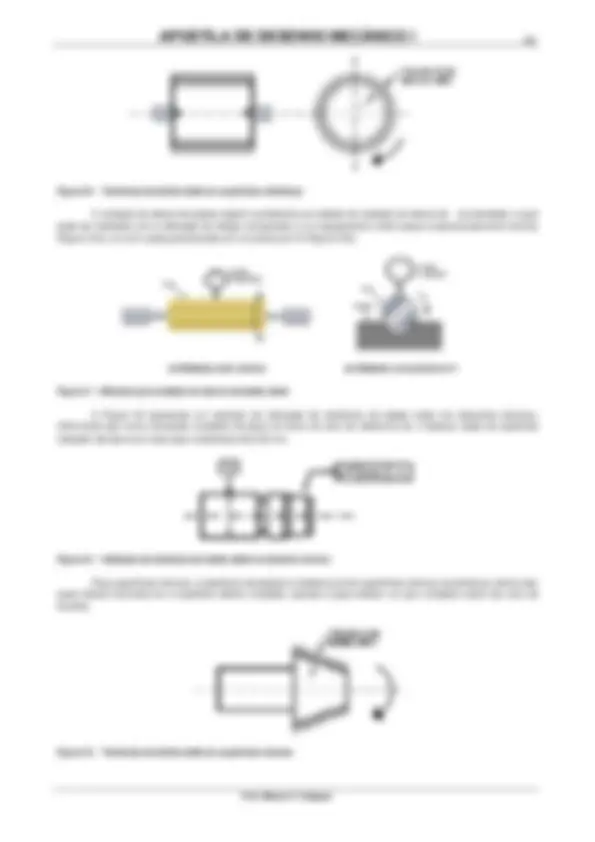
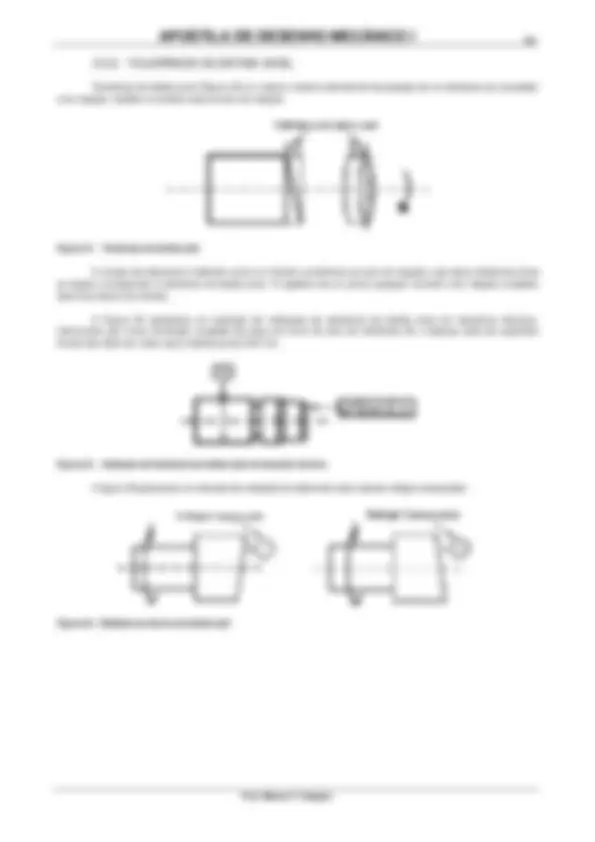
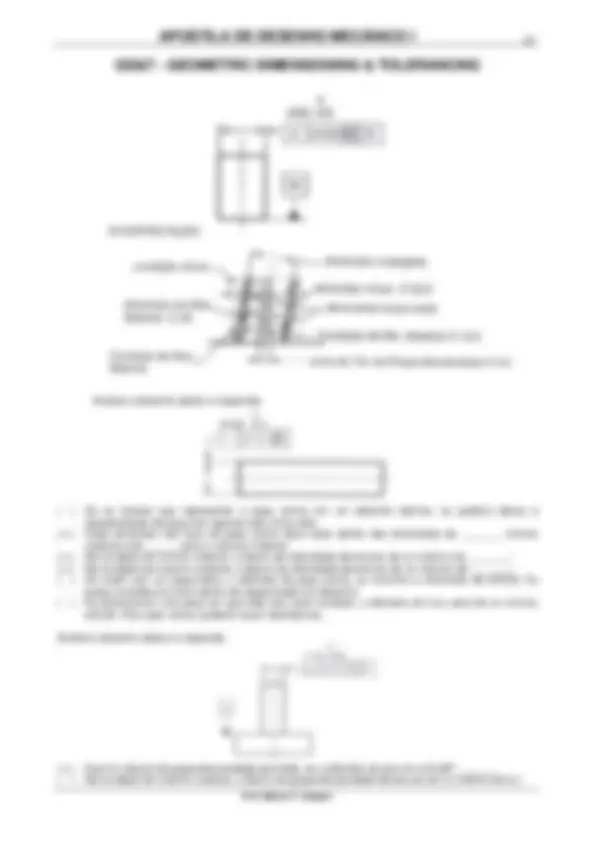
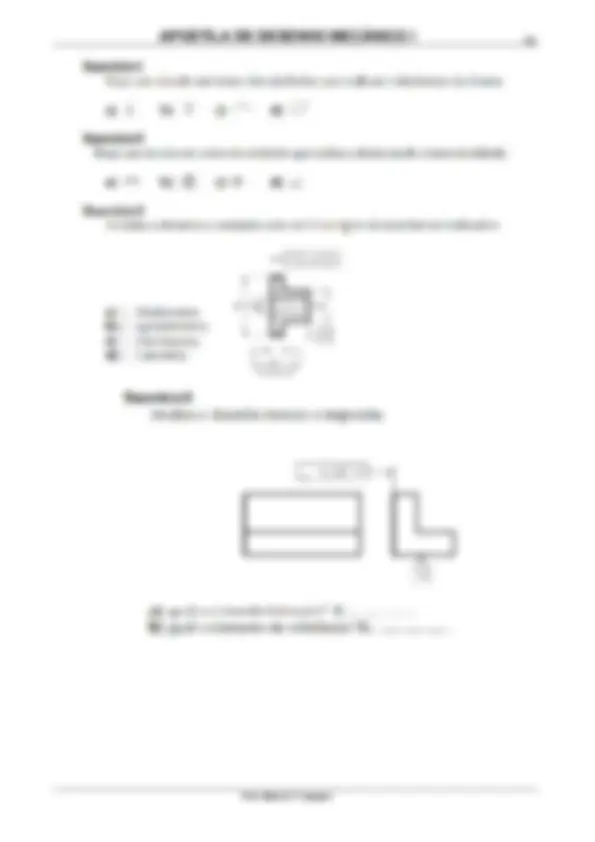
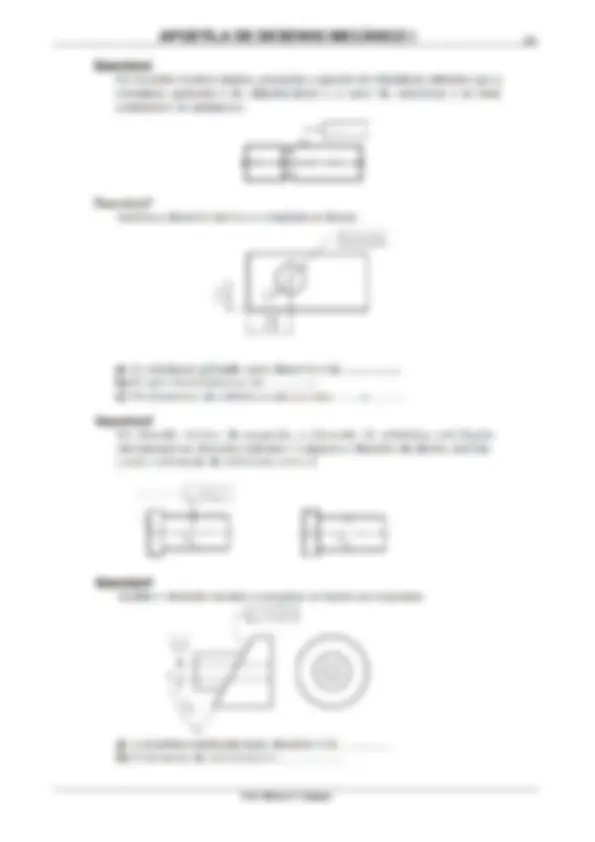
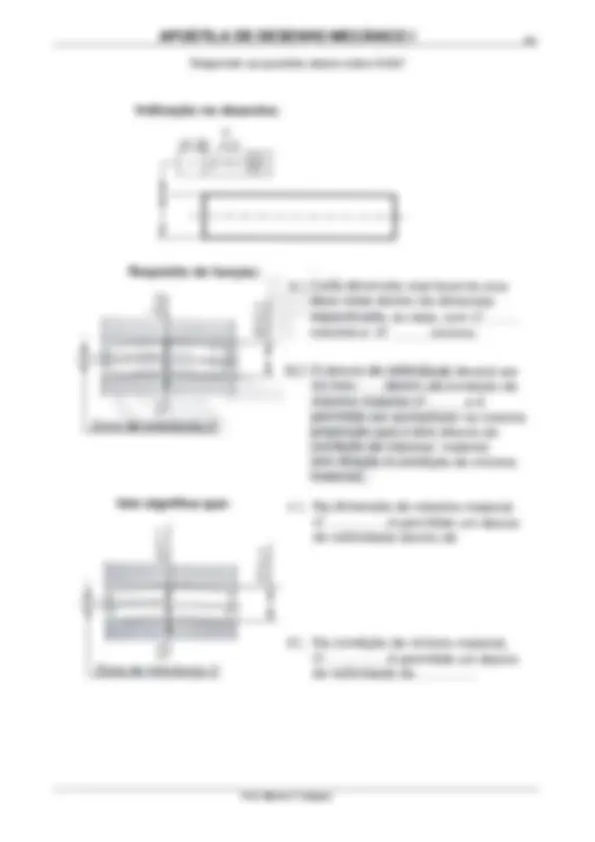
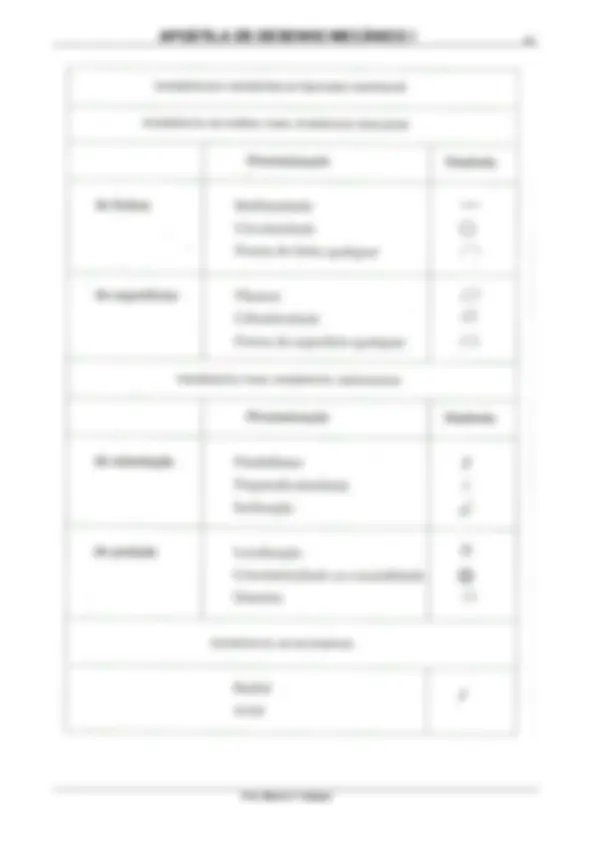
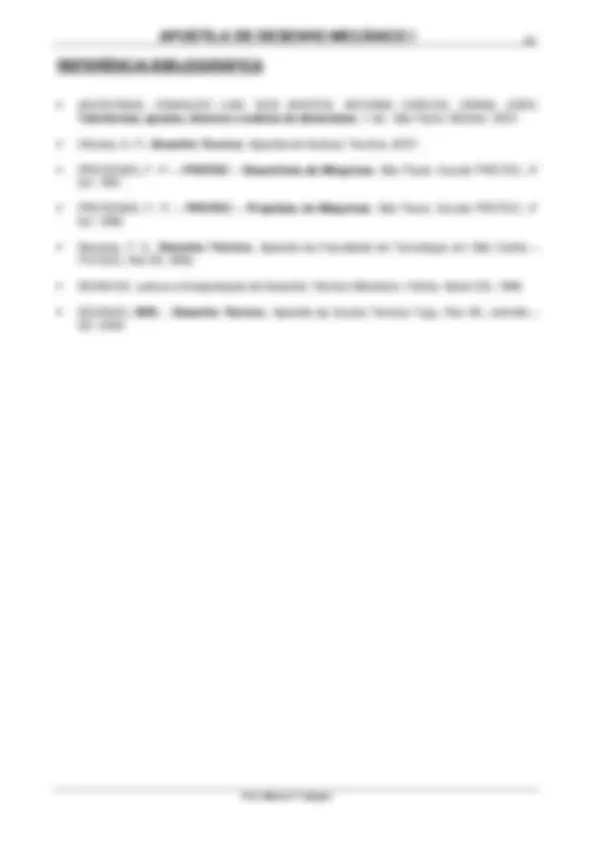
Estude fácil! Tem muito documento disponível na Docsity
Ganhe pontos ajudando outros esrudantes ou compre um plano Premium
Prepare-se para as provas
Estude fácil! Tem muito documento disponível na Docsity
Prepare-se para as provas com trabalhos de outros alunos como você, aqui na Docsity
Os melhores documentos à venda: Trabalhos de alunos formados
Prepare-se com as videoaulas e exercícios resolvidos criados a partir da grade da sua Universidade
Responda perguntas de provas passadas e avalie sua preparação.
Ganhe pontos para baixar
Ganhe pontos ajudando outros esrudantes ou compre um plano Premium
Comunidade
Peça ajuda à comunidade e tire suas dúvidas relacionadas ao estudo
Descubra as melhores universidades em seu país de acordo com os usuários da Docsity
Guias grátis
Baixe gratuitamente nossos guias de estudo, métodos para diminuir a ansiedade, dicas de TCC preparadas pelos professores da Docsity
fala sobre regras e formas de denhar
Tipologia: Manuais, Projetos, Pesquisas
1 / 42
Esta página não é visível na pré-visualização
Não perca as partes importantes!
2
O desenho técnico, além de mostrar as formas e as dimensões das peças, precisa conter outras informações para representá-las fielmente. Uma dessas informações é a indicação dos estados das superfícies das peças. Acabamento: é o grau de rugosidade observado na superfície da peça. As superfícies apresentam-se sob diversos aspectos, a saber: em bruto, desbastadas, alisadas e polidas. Superfície em bruto é aquela que não é usinada, mas limpa com a eliminação de rebarbas e saliências. Superfície desbastada é aquela em que os sulcos deixados pela ferramenta são bastante visíveis, ou seja, a rugosidade é facilmente percebida. Superfície alisada é aquela em que os sulcos deixados pela ferramenta são pouco visíveis, sendo a rugosidade pouco percebida. Superfície polida é aquela em que os sulcos deixados pela ferramenta são imperceptíveis, sendo a rugosidade detectada somente por meio de aparelhos. Os graus de acabamento das superfícies são representados pelos símbolos indicativos de rugosidade da superfície, normalizados pela norma NBR 8404 da ABNT , baseada na norma ISO 1302. Os graus de acabamento são obtidos por diversos processos de trabalho e dependem das modalidades de operações e das características dos materiais adotados. Rugosidade são erros microgeométricos existentes nas superfícies das peças, provenientes do processo de fabricação, tais como ranhuras, sulcos, estrias, escamas e crateras. As ranhuras e sulcos são provenientes de marcas da ferramenta durante o avanço ou posicionamento da peça no processo de usinagem. As estrias e escamas formam-se na usinagem durante a retirada do cavaco. O controle da rugosidade torna-se importante quando aumenta a qualidade de fabricação (tolerância dimensional pequena) ao ponto de ocorrerem irregularidades na superfície da peça maiores do que a tolerância dimensional especificada (Figura 37).
Figura 37 – A Rugosidade e a Tolerância Dimensional
4
A
N a i^1 i L
A R
[m],
onde, Ai é a área do pico ou vale i (i = 1 até N), e LA é o comprimento da amostra. Considere que no exemplo indicado na Figura 39, A1 = 12 m2, A2 = 16 m2, A3 = 15 m2, e A4 = 11 m2, para um comprimento de amostragem de 0,010 mm (LA = 10 m). A rugosidade média é equivalente a:
Ra ^12 ^1610 ^15 ^11 5 , 4 m.
A rugosidade média Ra é o parâmetro mais usado no mundo, sendo aplicável na maioria dos processos de fabricação, e podendo ser medido por qualquer tipo de rugosímetro. Entretanto, este parâmetro fornece apenas o valor de uma irregularidade média no perfil da peça, não indicando a forma do perfil, nem fazendo distinção entre picos e vales, dificultando a identificação de irregularidades atípicas que podem afetar o desempenho da peça.
De acordo com a NBR - 6402, a especificação de acabamento nos desenhos por meio de sinais antigos é feita conforme a relação a seguir.
Superfície em bruto, forjada, laminada, estampada e de peças fundidas, porém com eliminação de rebarbas
Superfície desbastada, os riscos da ferramenta são bastante visíveis. Profundidade dos sulcos 6,3 a 50 microns
Superfície alisada, os riscos da ferramenta são pouco visíveis. Rugosidade 0,8 a 6,3 microns Superfície polida, os riscos da ferramenta não são visíveis. Rugosidade 0,1 a 0,8 microns
Superfície lapidada. Rugosidade máxima 0,1 microns
Para qualquer grau de acabamento, pode ser indicado o modo de obtê-lo.
Superfície sujeita a tratamento especial indicada sobre a linha horizontal.
5
Símbolo básico, isoladamente este símbolo não tem finalidade
Quando a remoção do material é exigida.
Quando a remoção do material não é permitida, ou para mostrar quando uma superfície foi obtida no estágio de fabricação independente do fato de esta tenha sido por remoção de material ou não.
NOTA: o sinal de usinagem atualizado deve ser desenhado com linhas estreitas, a um ângulo de 60º e altura de 5 mm.
7
Os símbolos e inscrições devem estar orientados de maneira que possam ser lidos tanto com o desenho na posição normal, como pelo lado direito. Se necessário, o símbolo pode ser interligado por meio de uma linha de indicação. O símbolo deve ser indicado uma vez para cada superfície e, se possível, na vista que leva a cota ou representa a superfície. Considere o seguinte exemplo:
Neste exemplo temos que 4 é o número da peça; N11 indica que a rugosidade máxima permitida no acabamento é de 25μm (0,025mm); N9 representado dentro dos parênteses e nas superfícies que deverão ser usinadas, indica rugosidade máxima permitida de 6,3μm (0,0063mm); N5 indica superfície usinada com rugosidade máxima permitida de 0,4μm (0,0004mm).
Exemplos de Aplicação:
Interpretação do exemplo a:
1 – é o número da peça
ao lado do número da peça, representa o acabamento geral, com retirada de material, válido para todas as superfícies. N8 indica que a rugosidade máxima permitida no acabamento é de 3,2μm (0,0032mm). Interpretação do exemplo b 2 é o número da peça. o acabamento geral não deve ser indicado nas superfícies. O símbolo significa que a peça deve manter-se sem a retirada de material. corresponde a um desvio aritmético máximo de 0,8μm (0,0008mm) e deve ser indicado sobre superfície desejada. corresponde a um desvio aritmético máximo de 6,3μm (0,0063mm), e deve ser indicada sobre a superfície desejada.
8 O quadro a seguir apresenta a qualidade da superfície de acabamento , baseada na norma ABNT/NBR 8004 e ISO 1302.
O quadro abaixo apresenta valores típicos de rugosidade recomendados para algumas aplicações:
Ra ( m) APLICAÇÕES 0,01 Blocos padrão, réguas triangulares de alta precisão, guias de aparelhos demedida de alta precisão. 0,02 Aparelhos de precisão, superfícies medidas em micrômetros e calibradoresde precisão. 0,03 Calibradores, elementos de válvulas de alta pressão hidráulica. 0,04 Agulhas de rolamentos, super-acabamento de camisa de bloco de motor. 0,05 Pistas de rolamentos, peças de aparelhos de controle de alta precisão. 0,06 Válvulas giratórias de alta pressão, camisas de blocos de motores. 0,08 Agulhas de rolamentos de grandes dimensões, colos de virabrequim. 0,1 Assentos cônicos de válvulas, eixos montados sobre mancais de bronze outeflon a velocidades médias, superfícies de cames de baixa velocidade. 0,15 Rolamentos de dimensões médias, colos de rotores de turbinas e redutores. 0,2 Mancais de bronze, náilon, etc., cones de cubos sincronizadores de caixas decâmbio de automóveis. 0,3 Flancos de engrenagens, guias de mesas de máquinas-ferramentas.
10
EXERCÍCIOS
11
1 - Desenhe em duas vistas o BRAÇO de Ferro Fundido. Aplique o corte longitudinal sobre a nervura. Acab. Furos de 20 e 16 deve ser retificado, furo de 30 x 10 alisado, demais faces bruto de fundição. escala 1:1.
2 - Desenhe em duas vistas o BLOCO POSICIONADOR, faça o corte em desvio A B. Material Aço VC150, acab. base inferior alisada, as quatro faces laterais desbastadas com 12,5 μm, a face superior da peça e o furo de 20 mm retificada, demais faces desbastado com 50 μm. Escala 1:
13
As tolerâncias não são escolhidas ao acaso. Em 1926, entidades internacionais organizaram um sistema normalizado que acabou sendo adotado no Brasil pela ABNT: o sistema de tolerâncias e ajustes ABNT/ISO (NBR 6158).
O sistema ISO consiste num conjunto de princípios, regras e tabelas que possibilita a escolha racional de tolerâncias e ajustes de modo a tornar mais econômica a produção de peças mecânicas intercambiáveis. Este sistema foi estudado, inicialmente, para a produção de peças mecânicas com até 500 mm de diâmetro; depois, foi ampliado para peças com até 3150 mm de diâmetro. Ele estabelece uma série de tolerâncias fundamentais que determinam a precisão da peça, ou seja, a qualidade de trabalho, uma exigência que varia de peça para peça, de uma máquina para outra.
A norma brasileira prevê 18 qualidades de trabalho. Essas qualidades são identificadas pelas letras: IT seguidas de numerais. A cada uma delas corresponde um valor de tolerância. Observe, no quadro abaixo, as qualidades de trabalho para eixos e furos:
A letra I vem de ISO e a letra T vem de tolerância; os numerais: 01, 0, 1, 2,...16, referem-se às 18 qualidades de trabalho; a qualidade IT 01 corresponde ao menor valor de tolerância. As qualidades 01 a 3, no caso dos eixos, e 01 a 4, no caso dos furos, estão associadas à mecânica extra precisa. É o caso dos calibradores, que são instrumentos de alta precisão. Eles servem para
14
verificar se as medidas das peças produzidas estão dentro do campo de tolerância especificado. Veja:
No extremo oposto, as qualidades 11 a 16 correspondem às maiores tolerâncias de fabricação. Essas qualidades são aceitáveis para peças isoladas, que não requerem grande precisão; daí o fato de estarem classificadas como mecânica grosseira.
Peças que funcionam acopladas a outras têm, em geral, sua qualidade estabelecida entre IT 4 e IT 11, se forem eixos; já os furos têm sua qualidade entre IT 5 e IT 11. Essa faixa corresponde à mecânica corrente, ou mecânica de precisão. Verifique se ficou bem entendido, resolvendo o próximo exercício.
Verificando o entendimento:
16 O diâmetro interno do furo representado neste desenho é 40 H7. A dimensão nominal do diâmetro do furo é 40 mm. A tolerância vem representada por H7; a letra maiúscula H representa tolerância de furo padrão; o número 7 indica a qualidade de trabalho, que no caso corresponde a uma mecânica de precisão.
A tabela que corresponde a este ajuste tem o título de: Ajustes recomendados - sistema furo-base H7. Veja, a seguir, a reprodução do cabeçalho da tabela.
A primeira coluna - Dimensão nominal - mm - apresenta os grupos de dimensões de 0 até 500 mm. No exemplo, o diâmetro do furo é 40 mm. Esta medida situa-se no grupo de dimensão nominal entre 30 e 40. Logo, os valores de afastamentos que nos interessam encontram-se na 9ª linha da tabela, reproduzida abaixo:
Na segunda coluna - Furo - vem indicada a tolerância, variável para cada grupo de dimensões, do furo base: H7. Volte a examinar a 9ª linha da tabela, onde se encontra a dimensão de 40 mm; na direção da coluna do furo aparecem os afastamentos do furo: 0 (afastamento inferior) e + 25 (afastamento superior). Note que nas tabelas que trazem afastamentos de furos o afastamento inferior, em geral, vem indicado acima do afastamento superior. Isso se explica porque, na usinagem de um furo, parte-se sempre da dimensão mínima para chegar a uma dimensão efetiva, dentro dos limites de tolerância especificados.
Lembre-se de que, nesta tabela, as medidas estão expressas em mícrons. Uma vez que 1mm = 0,001 mm, então 25 mm = 0,025 mm. Portanto, a dimensão máxima do furo é: 40 mm + 0,025 mm = 40,025 mm, e a dimensão mínima é 40mm, porque o afastamento inferior é sempre 0 no sistema furo-base.
Agora, só falta identificar os valores dos afastamentos para o eixo g6. Observe novamente a 9ª linha da tabela anterior, na direção do eixo g6. Nesse ponto são indicados os afastamentos do eixo: -9/-25 O superior - 9mm, que é o mesmo que - 0,009 mm. O afastamento inferior é - 25 mm, que é igual a – 0,025 mm. Acompanhe o cálculo da dimensão máxima do eixo:
17
E agora veja o cálculo da dimensão mínima do eixo:
Finalmente, comparando os afastamentos do furo e do eixo concluímos que estas peças se ajustarão com folga, porque o afastamento superior do eixo é menor que o afastamento inferior do furo. No exemplo demonstrado, o eixo e o furo foram ajustados no sistema furo-base, que é o mais comum. Mas quando o ajuste é representado no sistema eixo-base, a interpretação da tabela é semelhante. É o que você vai ver, a seguir.
A dimensão nominal do eixo é igual à dimensão nominal do furo: 70 mm. A tolerância do furo é J7 e a tolerância do eixo é h6. O h indica que se trata de um ajuste no sistema eixo-base. Então, para identificar os afastamentos do eixo e do furo, você deverá consultar a tabela de Ajustes recomendados – sistema eixo-base h6. A tabela de ajustes recomendados no sistema eixo-base é semelhante à tabela do sistema furo-base. O que a diferencia são as variações das tolerâncias dos furos.
Primeiro, precisamos identificar em que grupo de dimensões se situa a dimensão nominal do eixo. No exemplo, a dimensão 70 encontra-se no grupo entre 65 e 80 (12ª linha). A seguir, basta localizar os valores dos afastamentos correspondentes ao eixo h6 e ao furo J7, nessa linha. Veja:
A leitura da tabela indica que, quando a dimensão do eixo-base encontra- se no grupo de 65 a 80, o afastamento superior do eixo é 0mm e o inferior é - 19mm. Para o furo de tolerância J7, o afastamento superior é + 18 mm e o afastamento inferior é -12mm.
19 MÓVELMÓVEL INCERTOINCERTO^ FIXOFIXO
Figura 7.2: Visualização das classes de ajuste no sistema furo-base Fonte: SENAI-ES, 1996
O sistema furo-base é, comumente usado, na construção de máquinas ferramenta, motores de combustão interna, compressores, construções automobilísticas, aeroviárias e ferroviárias e na indústria de ferramentas como, brocas, rosqueadoras, etc. O sistema eixo-base é usado principalmente na construção de eixos de transmissão e seus órgãos, vários tipos de máquinas operatrizes, como máquinas agrícolas, para construção civil, têxteis e de elevação. Ambos os sistemas são empregados nas construções mecânicas de precisão e máquinas elétricas. A escolha do sistema de ajuste a ser adotado está ligada essencialmente à conveniência econômica de produção. Apesar de a retífica ou acabamento de um furo ser mais trabalhoso e custoso e a retífica do eixo requerer numerosas ferramentas para acabamento, dá-se preferência, em trabalhos de precisão, ao sistema furo-base, no qual a posição da tolerância H do furo é constante nos vários tipos de acoplamento para cada dimensão nominal e para cada qualidade de trabalho. Por esta razão, o sistema de ajustes furo-base é correntemente usado no trabalho de órgãos de máquinas de precisão, por exemplo, para bombas de injeção, rolamentos de esferas ou de rolos, órgãos de máquinas ferramenta de precisão. A figura 7.3 apresenta alguns exemplos de aplicações comuns ao sistema de ajuste furo-base.
20
Figura 4.3: Principais aplicações do sistema de ajuste furo-base Fonte: SENAI-ES, 1996