
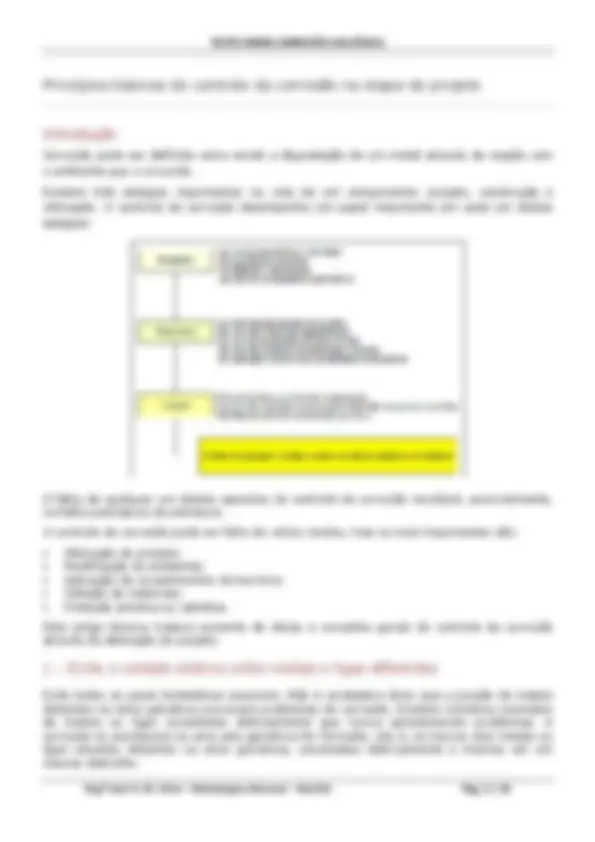
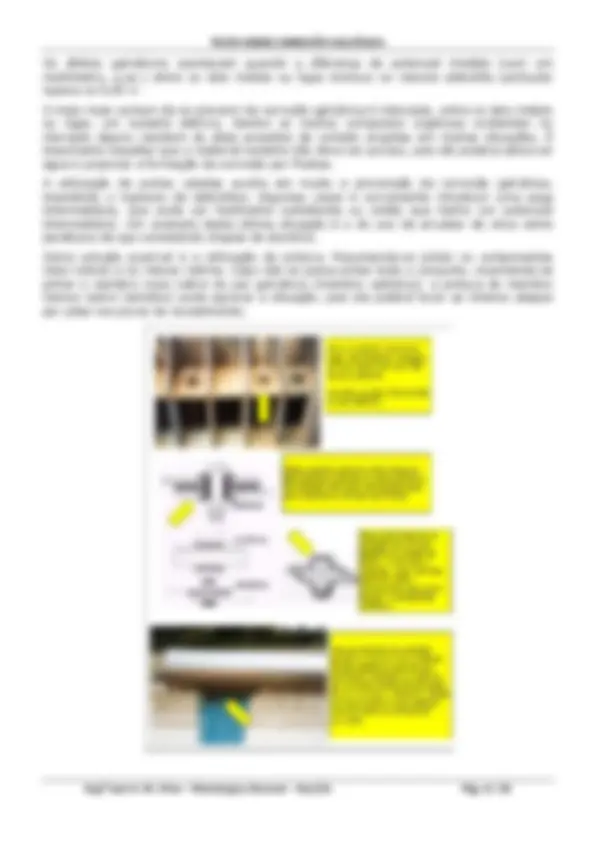
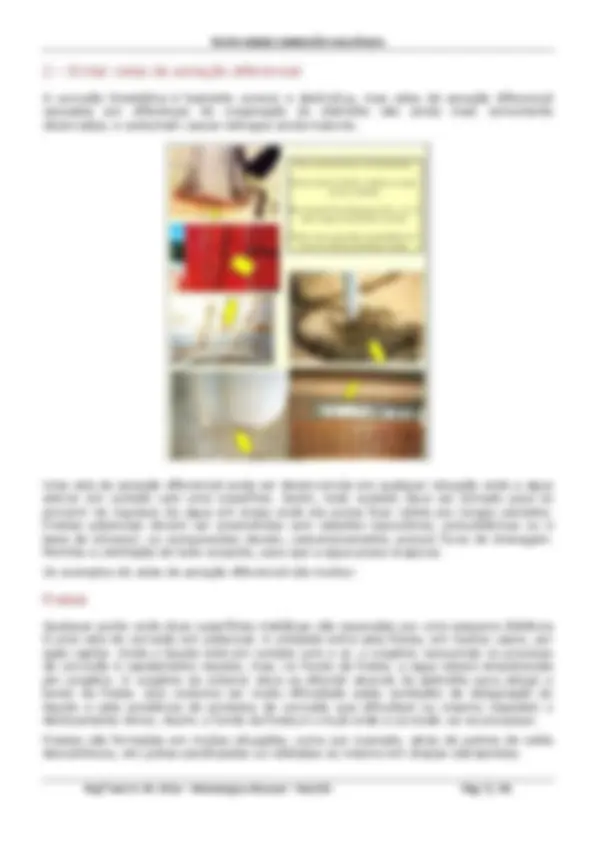
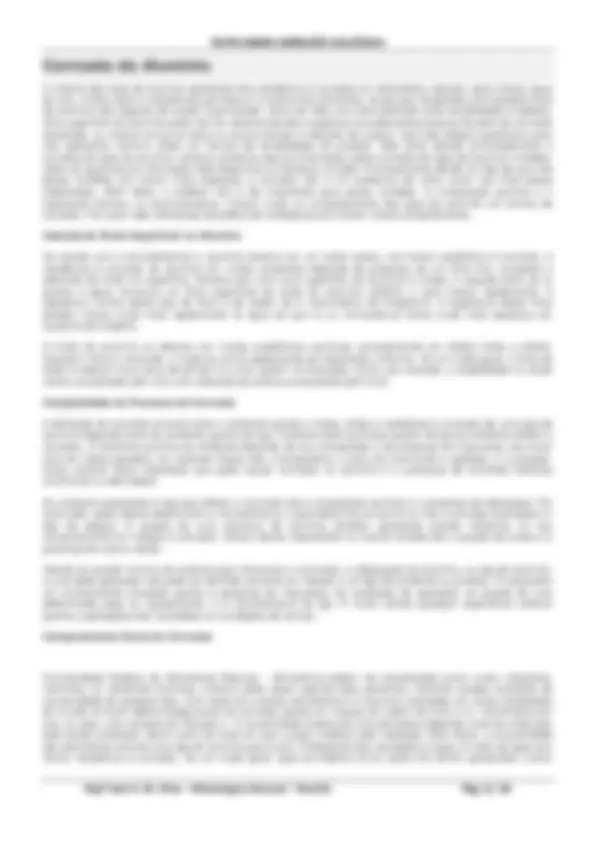
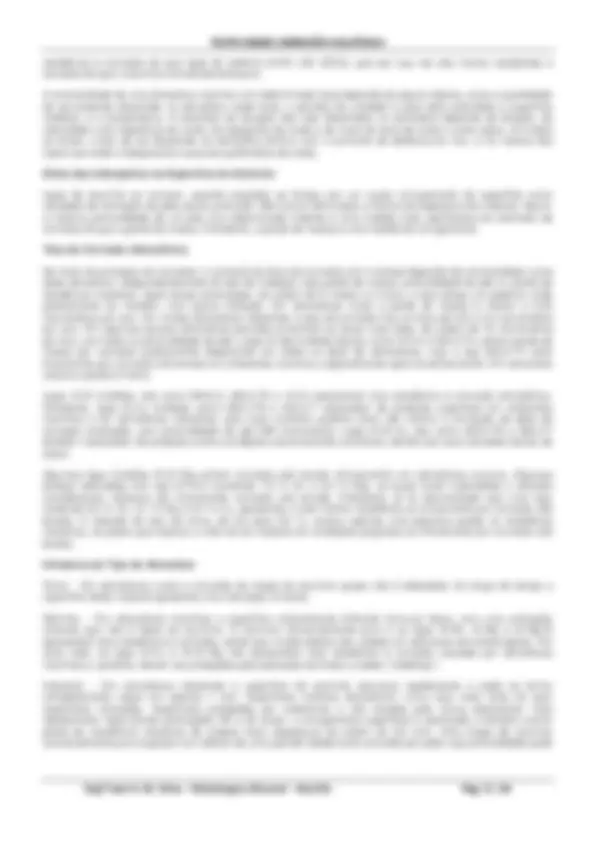
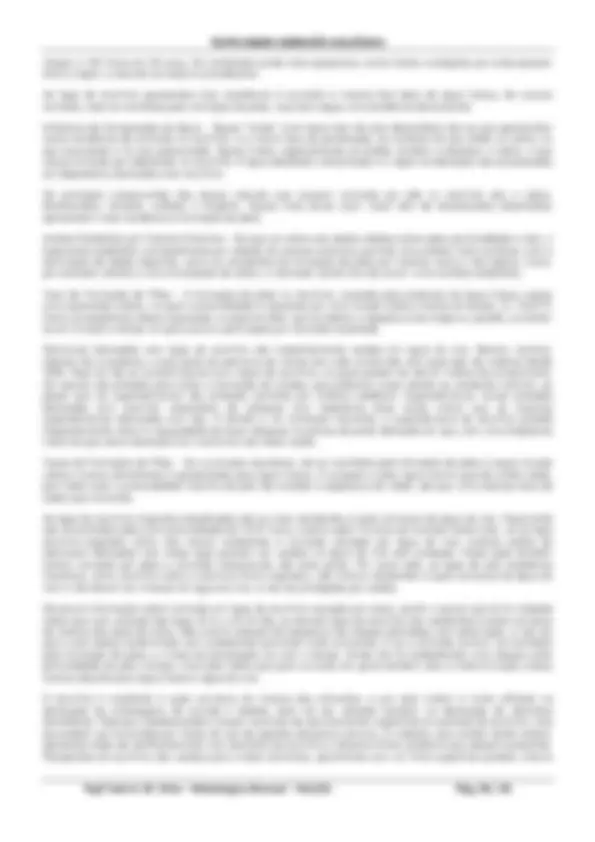
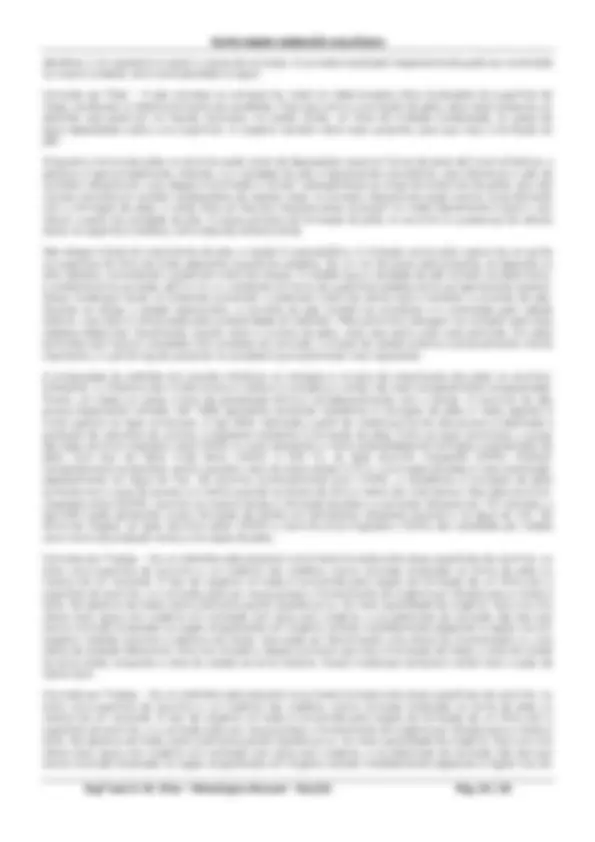
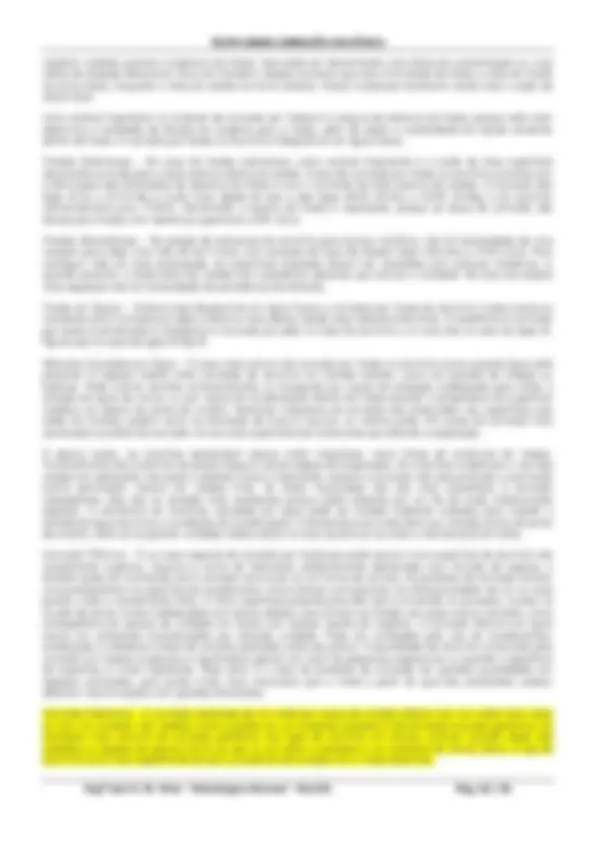
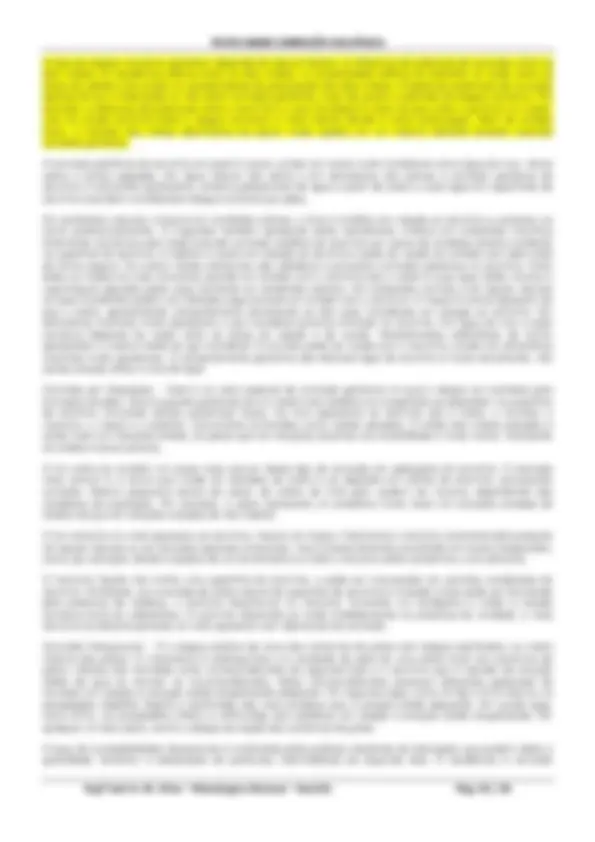
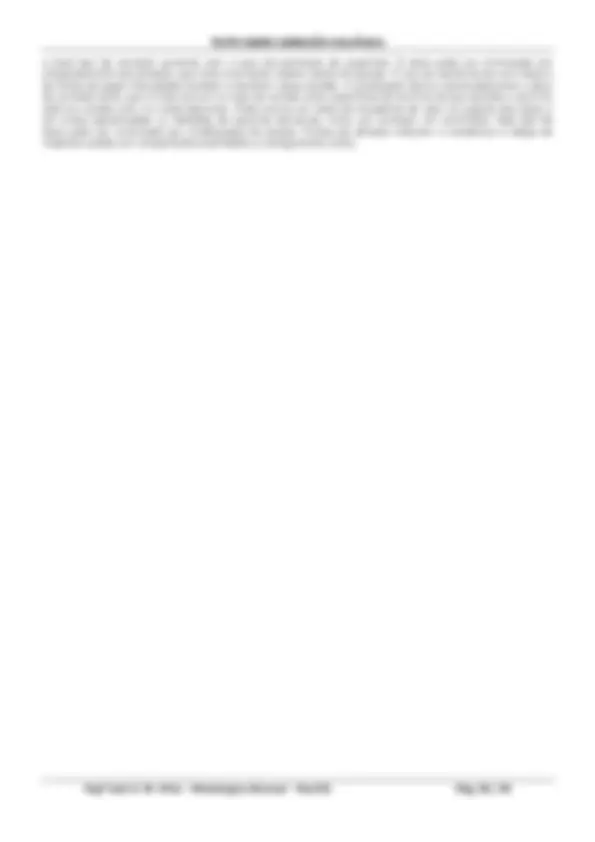
Estude fácil! Tem muito documento disponível na Docsity
Ganhe pontos ajudando outros esrudantes ou compre um plano Premium
Prepare-se para as provas
Estude fácil! Tem muito documento disponível na Docsity
Prepare-se para as provas com trabalhos de outros alunos como você, aqui na Docsity
Os melhores documentos à venda: Trabalhos de alunos formados
Prepare-se com as videoaulas e exercícios resolvidos criados a partir da grade da sua Universidade
Responda perguntas de provas passadas e avalie sua preparação.
Ganhe pontos para baixar
Ganhe pontos ajudando outros esrudantes ou compre um plano Premium
Comunidade
Peça ajuda à comunidade e tire suas dúvidas relacionadas ao estudo
Descubra as melhores universidades em seu país de acordo com os usuários da Docsity
Guias grátis
Baixe gratuitamente nossos guias de estudo, métodos para diminuir a ansiedade, dicas de TCC preparadas pelos professores da Docsity
A corrosão só acontecerá se uma cela galvânica for formada, isto é, se houver dois metais ou ligas situados distantes na série galvânica, conectados ...
Tipologia: Provas
1 / 18
Esta página não é visível na pré-visualização
Não perca as partes importantes!
2 – Evitar celas de aeração diferencial
Fabio Domingos Pannoni, M.Sc., Ph.D.
A maioria das ligas de alumínio apresenta boa resistência à corrosão em atmosferas naturais, água fresca, água do mar, muitos solos e substâncias químicas e à maioria dos alimentos, sendo que recipientes com paredes finas de alumínio são capazes de resistir à perfuração. Deve ser feita uma clara distinção entre durabilidade e estética. Uma superfície de alumínio pode não ser atraente devido à aspereza causada pela presença de pites de corrosão localizada, ou mesmo tornar-se fosca ou escura devido à retenção de sujeira, mas este ataque superficial suave não apresenta nenhum efeito em termos de durabilidade do produto. Este texto aborda primordialmente a corrosão de ligas de alumínio, embora contenha alguma informação sobre corrosão de ligas de alumínio fundidas, sobre as quais pouca informação está disponível na literatura mundial. Provavelmente devido ao fato de que nas peças fundidas, por serem mais espessas a corrosão não é um problema tão sério como nas finas peças trabalhadas. Além disso, a estética não é tão importante para peças fundidas. A composição química e o tratamento térmico, ou termomecânico, influem muito no comportamento das ligas de alumínio em termos de corrosão. Por outro lado, diferenças de prática de fundição pouco influem nesse comportamento. Camada de Óxido Superficial no Alumínio De acordo com a termodinâmica o alumínio deveria ser um metal reativo, com baixa resistência à corrosão. A resistência á corrosão do alumínio em muitos ambientes depende da presença de um filme fino, compacto e aderente de óxido na superfície. Sempre que uma nova superfície de alumínio é criada, e exposta tanto ao ar quanto à água, forma-se um filme superficial de óxido de alumínio (Al2O3), o qual cresce rapidamente. A espessura normal desse tipo de filme é da ordem de 5 nanometros (50 Angstrom). A espessura desse filme protetor cresce muito mais rapidamente na água do que no ar, formando-se filmes muito mais espessos em ausência de oxigênio. O óxido de alumínio se dissolve em muitas substâncias químicas, principalmente em ácidos fortes e álcalis. Quando o filme é removido, o metal se corrói rapidamente por dissolução uniforme. De um modo geral, o filme de óxido é estável numa faixa de pH de 4,0 a 9,0, porém há exceções, como, por exemplo, a estabilidade no ácido nítrico concentrado (pH 1,0) e em hidróxido de amônia concentrado (pH 13,0). Complexidade do Processo de Corrosão A definição de corrosão envolve tanto o ambiente quanto o metal, então a resistência à corrosão de uma liga de alumínio depende tanto do ambiente quanto da liga. Variáveis tanto químicas quanto físicas do ambiente afetam a corrosão. A influência química do ambiente depende da sua composição e da presença de impurezas, tais como íons de metais pesados. As variáveis físicas são a temperatura, o grau de movimento e agitação, e a pressão. Outra variável física importante que pode causar corrosão no alumínio é a presença de correntes elétricas (contínuas ou alternadas). As variáveis associadas à liga que afetam a corrosão são a composição química e o processo de fabricação. Por outro lado, estes fatores determinam a microestrutura, a qual determina se ocorre ou não a corrosão localizada e o tipo de ataque. O projeto de uma estrutura de alumínio também apresenta grande influência no seu comportamento em relação à corrosão. Outros fatores importantes no mesmo sentido são o projeto de juntas e a presença de outros metais. Devido ao grande número de variáveis que influenciam a corrosão, a adequação do alumínio, ou liga de alumínio, a uma dada aplicação não pode ser definida somente em relação a um tipo de ambiente ou produto. É necessário um conhecimento completo quanto à presença de impurezas, às condições de operação, ao projeto de uma determinada peça ou equipamento, e à microestrutura da liga. É muito valiosa qualquer experiência anterior quanto a aplicações bem sucedidas em condições de serviço. Comportamento Geral em Corrosão Corrosividade Relativa de Atmosferas Naturais – Atmosferas podem ser classificadas como rurais, industriais, marinhas, ou industriais-marinhas, embora estes sejam apenas tipos genéricos, havendo amplas variações de corrosividade de qualquer tipo. Com base em ensaios atmosféricos no alumínio realizados em várias localidades do mundo já foram determinadas taxas de corrosão (perda em massa) da ordem de 0,03 a 4,1 micrômetros por ano, ou seja, uma variação de 160 para 1. A corrosividade relativa de uma atmosfera depende muito do metal que está sendo analisado, assim como do local em que a peça metálica está instalada. Além disso, a corrosividade das atmosferas varia de uma liga de alumínio para outra. A dispersão dos resultados é maior no caso de ligas com menor resistência à corrosão. De um modo geral, ligas do sistema Al-Cu (série AA 2XXX) apresentam menor
chegar a 152 micra em 52 anos. Em ambientes ainda mais agressivos, como túneis e estações por onde passam trens a vapor, a taxa de corrosão é considerável. As ligas de alumínio apresentam boa resistência á corrosão à maioria dos tipos de água fresca. Se ocorrer corrosão, esta se manifesta pela formação de pites, cuja taxa segue uma tendência decrescente. Influência da Composição da Água – Águas “moles” (com baixo teor de sais dissolvidos) são as que apresentam menor tendência de corrosão no alumínio, e a menor taxa de penetração, ao contrário do seu efeito no cobre, no aço escurecido e no aço galvanizado. Águas moles, especialmente as ácidas, tendem a dissolver o cobre, o que causa corrosão por deposição no alumínio. A água destilada e deionizada e o vapor condensado são processadas em dispositivos fabricados com alumínio. Os principais componentes das águas naturais que causam corrosão por pite no alumínio são o cobre, bicarbonatos, cloretos, sulfatos e oxigênio. Águas mais duras (com maior teor de bicarbonatos dissolvidos) apresentam maior tendência à formação de pites. Análise Estatística por Valores Extremos - No que se refere aos dados obtidos sobre pites (profundidade e etc), o tratamento estatístico, principalmente por método de valores extremos, permite uma análise mais confiável, com a eliminação de dados espúrios, como os resultantes da formação de pites por motivos raros e não típicos, como, por exemplo, devido a uma incrustação de cobre, o chamado “ponto fora da curva” numa análise estatística. Taxa de Formação de Pites – A formação de pites no alumínio, causada pela presença de água fresca, segue uma expressão cúbica, na qual a profundidade é expressa por uma função cúbica inversa do tempo: d = K(t)1/3. Como conseqüência dessa expressão, é possível dizer que ao dobrar a espessura da chapa ou parede, aumenta- se em 8 vezes o tempo no qual ocorre a perfuração por corrosão localizada. Estruturas fabricadas com ligas de alumínio são freqüentemente usadas em água do mar. Barcos, lanchas, cabines de cruzadores, e boa parte da estrutura de navios tem sido construída com esse tipo de material desde
para evitar o surgimento de pites. Além de embalagens para alimentos, o alumínio também é muito usado em embalagens para bebidas. O alumínio é completamente resistente à ação corrosiva de muitas substâncias químicas, enquanto em outras se dissolve uniformemente e rapidamente. Em algumas substâncias químicas, como o metanol ou o fenol, um traço de água (0,1 %) evita a corrosão, principalmente em altas temperaturas. Em outras, com, por exemplo, no SO líquido, um traço de água provoca corrosão. E a conjugação de substâncias diferentes, que isoladamente seriam inofensivas, pode causar corrosão no alumínio. Por exemplo, o ácido acético glacial é inócuo ao alumínio, mas com traços de mercúrio em dissolução pode causar corrosão por deposição no alumínio. A temperatura e o grau de agitação também exercem influência no comportamento do alumínio em corrosão causada por estas substâncias. Sempre que for desenvolvida uma nova aplicação importante para o alumínio seu comportamento em corrosão deve ser analisado em laboratório. Hidrocarbonetos Halogenados As ligas de alumínio em geral são resistentes à corrosão causada por hidrocarbonetos halogenados puros na maioria das condições, e particularmente à temperatura ambiente. Entretanto, alguns hidrocarbonetos podem produzir uma rápida taxa de corrosão ou mesmo uma reação violenta no alumínio. Devem ser estabelecidas condições de serviço em segurança antes que o alumínio seja usado em contato com qualquer hidrocarboneto halogenado. Os hidrocarbonetos halogenados podem ser decompostos por hidrólise se houver presença de água, ou por outros processos, produzindo ácidos minerais, como o ácido clorídrico. Esses ácidos corroem as ligas de alumínio ao destruir a proteção natural conferida pelo filme de óxido protetor. A corrosão das ligas de alumínio por esses ácidos podem promover reações nos próprios hidrocarbonetos, pois os haletos de alumínio formados pela corrosão são catalisadores para reações, como é o caso do AlCl3. Em alguns casos podem se formar compostos alcalinos de alumínio. Devido à rápida taxa de aquecimento, uma vez iniciadas a corrosão do alumínio e a reação do hidrocarboneto halogenado tendem a se tornar autocatalíticas. A reatividade das ligas de alumínio com os hidrocarbonetos halogenados geralmente decresce à medida que aumenta a estabilidade química desses hidrocarbonetos, geralmente disponível na literatura sobre termodinâmica. Assim, o alumínio é mais resistente aos hidrocarbonetos halogenados com flúor, seguidos por aqueles que contêm cloro, bromo e iodo em ordem de resistência à corrosão decrescente. O alumínio também é resistente à ação corrosiva de hidrocarbonetos halogenados altamente polimerizados, indicando o alto grau de estabilidade química deste tipo de substância. O comportamento das ligas de alumínio em contato com misturas de diferentes tipos de hidrocarbonetos halogenados, ou misturas destes hidrocarbonetos com outros compostos orgânicos, não pode ser inferido a partir do comportamento destes materiais com estas substâncias isoladas. Misturas de metanol e tetracloreto de carbono, por exemplo, resultam em rápida corrosão de algumas ligas de alumínio à temperatura ambiente, embora, isoladamente cada uma destas substâncias não apresentem o mesmo efeito. A resistência das ligas de alumínio à ação corrosiva de hidrocarbonetos halogenados tende a diminuir com o aumento da temperatura. A taxa da corrosão em muitos hidrocarbonetos halogenados líquidos permanece baixa até que p ponto de ebulição seja atingido. Em alguns tipos de hidrocarbonetos, a taxa é baixa ou inexistente mesmo nesta temperatura. Outros fatores que afetam a resistência a esse tipo de corrosão incluem a presença de um inibidor e a pureza do hidrocarboento halogenado. Aminas ou vários compostos heterocíclicos têm sido usados efetivamente como inibidores em certos casos. O alumínio finamente dividido, como no caso de pós e partículas finas em geral, não deve ser exposto a um hidrocarboneto halogenado. A possibilidade de ocorrer uma reação violenta, até mesmo uma explosão, aumenta quando o alumínio com elevada área superficial é exposto a um pequeno volume de hidrocarboneto halogenado, ainda mais quando esta operação é realizada sob pressão. Tubos de alumínio são utilizados para o transporte de substâncias refrigerantes à base de freon. Banhos desengraxantes de tricloroetileno são usados para limpeza de produtos de alumínio trabalhados mecanicamente. Estes banhos são comprovadamente eficientes nesta função, desde que um solvente estabilizado seja utilizado, evitando-se a acumulação de água e de finos de alumínio e descartando-se o banho quando for detectada a presença de ácido.
identificar o íon agressivo e assim a causa da corrosão. A corrosão localizada freqüentemente pode ser controlada ou mesmo evitada, como será abordado a seguir. Corrosão por Pites – O pite consiste na remoção de metal em determinados sítios localizados da superfície do metal, resultando no desenvolvimento de cavidades. Para que ocorra a formação de pites, deve estar presente um eletrólito, que pode ser um líquido volumoso, um sólido úmido, um filme de umidade condensada, ou gotas de água depositadas sobre uma superfície. O oxigênio também deve estar presente, para que haja a formação do pite. Enquanto a forma dos pites no alumínio pode variar de depressões rasas em forma de pires até furos cilíndricos, a abertura é aproximadamente redonda, e a cavidade do pite é ligeiramente hemisférica. Isso diferencia o pite da corrosão intergranular, cujo ataque é confinado a “túneis” subsuperficiais ao longo de contornos de grãos, que são visíveis somente em análise metalográfica de seções retas. A corrosão intergranular pode ocorrer conjuntamente com a formação de pites, e neste caso as fissuras intergranulares avançam no metal lateralmente e para o seu interior a partir da cavidade do pite. A causa primária da formação de pites no alumínio é a presença de células locais na superfície metálica, como descrita anteriormente. Nas etapas iniciais do crescimento do pite, a reação é autocatalítica. A iniciação ocorre pela ruptura de um ponto na superfície do filme de óxido adjacente à partícula catódica. Se um íon de cobre está presente, se deposita no sítio catódico, aumentando o potencial motriz da reação. À medida que a cavidade do pite (anodo) se desenvolve, o ambiente torna-se ácido (pH 3 a 4), e o ambiente em torno da superfície catódica torna-se ligeiramente alcalino. Essas mudanças locais no ambiente aumentam o potencial motriz da célula local e também a corrente do pite. Quando se atinge o estado estacionário, a corrente do pite mantém-se constante e é controlada pelo catodo externo, cuja área é influenciada pela condutividade do eletrólito. Pites próximos interagem ao competir pela área catódica disponível. Geralmente, quanto maior o número de pites, mais raso será o pite mais profundo. Em pites profundos que ficaram revestidos com produtos de corrosão, a função do catodo externo é provavelmente menos importante, e o pH do líquido presente na cavidade é provavelmente mais importante. A composição do eletrólito tem grande influência na iniciação e na taxa de crescimento dos pites no alumínio. Entretanto, a influência dos muitos ânions e cátions é complexa e ainda não está completamente compreendida. Porém, em todos os casos a taxa de penetração diminui consideravelmente com o tempo. O alumínio de alta pureza duplamente refinado (AA 1099) apresenta excelente resistência à formação de pites e neste aspecto é muito superior às ligas comerciais. A liga 3003, fabricada a partir de matéria-prima de alta pureza e destinada à produção de utensílios de cozinha, é bastante resistente à formação de pites. Entre as ligas comerciais, o grupo das ligas alumínio-magnésio (série 5XXX) é o que apresenta a menor possibilidade de formação e penetração de pites. Com teor de cobre muito baixo (inferior a 0,04 %), as ligas alumínio manganês (3XXX) mostram comportamento comparável, porém quando o teor de cobre atinge 0,15 %, a formação de pites é mais acentuada, especialmente em água do mar. No alumínio comercialmente puro (1XXX), a resistência à formação de pites aumenta com o grau de pureza e é melhor quando os teores de ferro e cobre são mais baixos. Nas ligas alumínio- magnésio-silício (6XXX), ocorrem ao mesmo tempo a formação de pites e a corrosão intergranular. Por exemplo, a liga 6351 pode apresentar suave formação de bolhas em atmosferas industriais severas e na água do mar. Na forma de chapas, as ligas alumínio-cobre (2XXX) e alumínio-zinco-magnésio (7XXX) são revestidas por clades como forma de proteção contra a formação de pites. Corrosão por Frestas – Se um eletrólito está presente numa fresta formada entre duas superfícies de alumínio, ou entre uma superfície de alumínio e um material não metálico, ocorre corrosão localizada na forma de pites ou mesmo de um remendo. O teor de oxigênio na fresta é consumido pela reação de formação de um filme com a superfície de alumínio, e a corrosão pára por causa porque o fornecimento de oxigênio por difusão para a fresta é lento. Na abertura da fresta, tanto submersa quanto exposta ao ar, há maior quantidade de oxigênio. Isso cria uma célula local: água com oxigênio em contraste com água sem oxigênio, e os potenciais de corrosão são tais que ocorre corrosão localizada na região empobrecida em oxigênio (anodo) imediatamente adjacente à região rica em oxigênio (catodo) próxima à abertura da fresta. Isso pode ser denominado uma célula de concentração ou uma célula de areação diferencial. Uma vez iniciado o ataque corrosivo que leva à formação da fresta, a área do anodo se torna ácida, enquanto a área do catodo se torna alcalina. Essas mudanças favorecem ainda mais a ação da célula local. Corrosão por Frestas – Se um eletrólito está presente numa fresta formada entre duas superfícies de alumínio, ou entre uma superfície de alumínio e um material não metálico, ocorre corrosão localizada na forma de pites ou mesmo de um remendo. O teor de oxigênio na fresta é consumido pela reação de formação de um filme com a superfície de alumínio, e a corrosão pára por causa porque o fornecimento de oxigênio por difusão para a fresta é lento. Na abertura da fresta, tanto submersa quanto exposta ao ar, há maior quantidade de oxigênio. Isso cria uma célula local: água com oxigênio em contraste com água sem oxigênio, e os potenciais de corrosão são tais que ocorre corrosão localizada na região empobrecida em oxigênio (anodo) imediatamente adjacente à região rica em
oxigênio (catodo) próxima à abertura da fresta. Isso pode ser denominado uma célula de concentração ou uma célula de areação diferencial. Uma vez iniciado o ataque corrosivo que leva à formação da fresta, a área do anodo se torna ácida, enquanto a área do catodo se torna alcalina. Essas mudanças favorecem ainda mais a ação da célula local. Uma variável importante no contexto da corrosão por frestas é a largura da abertura da fresta, porque este valor determina a facilidade da difusão do oxigênio para a fresta, além de afetar a resistividade do líquido existente dentro da fresta. A corrosão por festas no alumínio é desprezível em água fresca. Frestas Submersas – No caso de frestas submersas, outra variável importante é a razão da área superficial ativamente corroída para a área externa efetiva do catodo. A taxa de corrosão por fresta no alumínio aumenta com a diminuição das dimensões da abertura da fresta e com o aumento da área externa do catodo. A corrosão das ligas Al-Cu e Al-Zn-Mg é muito mais rápida do que a das ligas 3XXX (Al-Mn) e 5XXX (Al-Mg) e do alumínio comercialmente puro (1XXX). Novamente a largura da fresta é importante, porque as taxas de corrosão são baixas para frestas com aberturas superiores a 254 micra. Frestas Atmosféricas – No projeto de estruturas de alumínio para serviço marítimo, não há necessidade de uma margem para obter uma vida útil de 5 anos, com exceção do caso de seções retas inferiores a 1016 micra. Para conseguir vida útil mais prolongada, as superfícies expostas devem ser revestidas com pinturas inibidoras, e, quando possível, a fresta deve ser selada com substância aderente que elimine a umidade. No caso de seções mais espessas não há necessidade de providência semelhante. Fresta em Águas – Embora seja desprezível em água fresca a corrosão por fresta do alumínio muitas vezes se manifesta como corrosão por pites, embora a taxa dessa reação seja relativamente lenta. A resistência à corrosão por fresta é semelhante à resistência à corrosão por pites no caso do alumínio, e é mais alta no caso de ligas Al- Mg do que no caso de ligas Al-Mg-Si. Manchas Causadas por Água – O caso mais comum de corrosão por fresta no alumínio ocorre quando água está presente no espaço restrito entre camadas de alumínio em contato estreito, como em pacotes de chapas ou bobinas. Pode ocorrer durante armazenamento ou transporte por causa de proteção inadequada para evitar a entrada de água da chuva, ou por causa de condensação dentro da fresta quando a temperatura da superfície metálica cai abaixo do ponto de orvalho. Manchas irregulares de corrosão são produzidas nas superfícies que estão em contato, podem variar na coloração de cinza a marrom, ou mesmo preto. Em casos de corrosão mais acentuada o produto de corrosão une as suas superfícies tão fortemente que dificulta a separação. E alguns casos, as manchas apresentam alguns anéis irregulares, como linhas de contornos de mapas. Provavelmente são contornos de poças d’água e várias etapas de evaporação. As manchas inviabilizam o uso das chapas em aplicações nas quais o aspecto visual é importante, embora a corrosão não seja profunda e raramente ocorra perfuração, mesmo em chapas finas. As áreas manchadas não são mais suscetíveis à corrosão subseqüente, elas são na verdade mais resistentes porque estão cobertas por um file de óxido relativamente espesso. A ocorrência de manchas causadas por água pode ser evitada mediante cuidados para impedir a entrada de água da chuva e condições de condensação. A temperatura do metal deve ser mantida acima do ponto de orvalho, tanto ao se garantir umidade relativa baixa no local, quanto ao se evitar o resfriamento do metal. Corrosão Filiforme – É um caso especial de corrosão por fresta que pode ocorrer numa superfície de alumínio sob revestimento orgânico. Assume a forma de filamentos aleatoriamente distribuídos com formato de espiras, e também pode ser conhecida como corrosão vermicular ou em forma de vermes. Os produtos de corrosão formam uma protuberância na superfície do revestimento, como colinas numa planície. As trilhas procedem de um ou mais pontos, onde o revestimento falha. O filme superficial propriamente dito não é envolvido no processo, exceto na função de prover zonas inadequadas com pouca adesão, que formam as frestas nas quais ocorre corrosão, como conseqüência do acesso da umidade em áreas com acesso restrito de oxigênio. A corrosão filiforme em geral ocorre em ambientes caracterizados por elevada umidade. Pode ser combatida pelo uso de revestimentos, anodização e inibidores à base de cromato aplicados antes da pintura. A quantidade de alumínio consumida pela corrosão em frestas é pequena e significativa apenas em caso de pequenas espessuras ou quando a aparência da superfície é muito importante. Mais sério é o caso de produtos de corrosão em grandes quantidades em espaços confinados, pois sendo muito mais volumosos que o metal a partir do qual são produzidos, podem distorcer mesmo seções com grandes dimensões. Corrosão Galvânica – A corrosão acelerada de um metal por causa de contato elétrico com um metal mais nobre ou com um condutor não metálico como a grafite em um ambiente condutor é denominada corrosão galvânica. Os exemplos mais comuns de corrosão galvânica nas ligas de alumínio em serviço ocorrem quando estas são soldadas ou ligadas de alguma forma ao aço ou ao cobre e expostas a um ambiente de névoa salina. A liga de alumínio corrói mais rapidamente do que na ausência de contato com o metal dissimilar.
intergranular pode ser obtida pela aplicação de tratamentos térmicos que causem precipitação homogênea ao longo da estrutura dos grãos, ou ao restringir a quantidade de elementos de liga que podem causar este problema. Ligas nas quais não se formam microconstituintes de segunda fase nos contornos de grãos, ou aquelas que possuem potencial de corrosão similar ao da matriz (MnAl6) não são suscetíveis à corrosão intergranular, como é o caso das ligas 3003, 3004 e do alumínio comercialmente puro 1100. As ligas alumínio-magnésio (5XXX) contendo menos de 3 % de magnésio são bastante resistentes à corrosão intergranular. Em casos não comuns ocorre ataque intergranular na zona termicamente afetada de soldas após meses de exposição a temperaturas moderadamente elevadas (da ordem de 100 ºC), em soluções quentes e ácidas de nitrato de amônia (a cerca de 150 ºC), ou água potável quente (a 80 ºC). Para teores de magnésio mais elevados, a corrosão intergranular não ocorre quando estas ligas são fabricadas de maneira adequada e utilizadas à temperatura ambiente. Entretanto, certas ligas podem se tornar suscetíveis à corrosão intergranular após prolongada exposição em temperaturas elevadas, acima de 27 ºC. Este fenômeno é popularmente conhecido como sensitização. O grau de sensibilidade aumenta com o teor de magnésio, com o tempo de exposição à temperatura e com o grau de encruamento (trabalho mecânico de deformação plástica). As ligas Al-Mg-Si trabalhadas (6XXX) geralmente apresentam alguma susceptibilidade à corrosão intergranular. Com uma composição balanceada de magnésio e silício, que resulta na formação da fase Mg2Si, o ataque intergranular é menor e também inferior ao que ocorre nas ligas Al-Cu (2XXX) e Al-Zn-Mg-Cu (7XXX). Quando a liga Al-Mg-Si contém teor excessivo de silício (superior ao necessário para formar Mg2Si), aumenta a corrosão intergranular por causa da forte natureza catódica do constituinte insolúvel de silício. Nas ligas Al-Cu-Mg (2XXX), tratamentos térmicos que promovem precipitação seletiva nos contornos de grãos provocam susceptibilidade à corrosão intergranular. Já foi comprovado que o resfriamento rápido após o tratamento térmico de solubilização resulta em alta resistência à corrosão intergranular. Analogamente, o resfriamento lento pós-solubilização resulta em susceptibilidade intergranular. A corrosão intergranular em ligas Al-Zn-Mg-Cu (7XXX) também pode ser afetada por tratamento térmicos. O tratamento térmico, algumas vezes em combinação com a deformação mecânica, é utilizado para melhorar a resistência à corrosão intergranular. Corrosão por Esfoliação – A esfoliação, também chamada corrosão por camadas ou corrosão lamelar, é um tipo de ataque subsuperficial que ocorre ao longo de múltiplas trilhas paralelas à superfície do metal. O ataque ocorre geralmente ao longo de contornos de grãos (corrosão intergranular), mas também é observado ao longo de estrias de constituintes insolúveis que se distribuíram ao longo de planos paralelos na direção de trabalho mecânico. A esfoliação acontece predominantemente em produtos de pequena espessura e altamente deformados, com microestrutura de grãos alongados. A intensidade da esfoliação aumenta em ambientes ligeiramente ácidos e quando o alumínio está ligado a um metal dissimilar catódico. A esfoliação é caracterizada pela formação de “folhas”, ou camadas finas de metal ainda não corroído e camadas mais espessas de produtos de corrosão que aumentam o volume do material. Geralmente a esfoliação ocorre a partir de uma beirada cisalhada e se dirige para o interior do material. Quando é suave, assume a forma de bolhas com produto de corrosão se acumulando no centro. Neste caso inicialmente forma-se um pite que penetra para o interior até encontrar uma camada suscetível. O ataque então se transforma em penetração lateral com geração de produtos de corrosão volumosos que provocam o aparecimento de bolhas. A esfoliação não é acelerada pela aplicação de uma tensão e não leva ao trincamento por corrosão sob tensão. O alumínio comercialmente puro (1XXX) e as ligas alumínio-manganês (3XXX) são bastante resistentes à corrosão por esfoliação, mesmo em diferentes condições de processamento. Em ligas Al-Zn-Mg-Cu (7XXX) a resistência à corrosão por esfoliação pode ser aumentada pela realização de um tratamento térmico de superenvelhecimento (têmperas do tipo T7XXX em ligas trabalhadas), embora com perda de resistência mecânica da ordem de 5 a 10 %. Tratamentos térmicos que propiciem recristalização também podem ter efeitos semelhantes. Ajustes de composição química também podem ser benéficos nesse sentido. Trincamento por Corrosão sob Tensão – Sob a ação combinada de uma tensão trativa e de um meio corrosivo específico pode ocorrer a ruptura de alguns componentes fabricados com ligas de alumínio devido ao trincamento por corrosão sob tensão. Entretanto, a corrosão sob tensão se limita a ligas Al-Cu-Mg (2XXX) e Al-Mg (5XXX) contendo mais de 3 % de magnésio, e as ligas Al-Zn-Mg-Cu (7XXX). Raramente ocorre corrosão sob tensão em ligas Al-Mg-Si (6XXX). Não ocorre no alumínio comercialmente puro (1XXX), nas ligas Al-Mn (3XXX) ou nas ligas Al-Mg (5XXX) contendo menos de 3 % de magnésio. Ocorre em ambientes agressivos contendo cloretos e, em caso de maior susceptibilidade, ao ar úmido.
A susceptibilidade das ligas de alumínio à corrosão sob tensão depende da microestrutura, a qual por sua vez é influenciada pelo tratamento/processamento prévio. A fragilização por hidrogênio é particularmente severa em ligas Al-Zn-Mg-Cu e em algumas ligas Al-Mg. Corrosão-Fadiga – Num ambiente corrosivo a curva S/N (tensão por número de ciclos) é deslocada para baixo, ou seja, para valores de tensão mais baixos num determinado número de ciclos, de tal modo que a corrosão-fadiga pode ser descrita como a falha de um metal sob a ação combinada de uma tensão cíclica atuante e um ambiente corrosivo, e o dano resultante é maior do que o que seria provocado pela ação corrosiva e pela fadiga isoladamente. Entretanto, geralmente é difícil diferenciar o aspecto visual da fadiga isolada do aspecto visual da corrosão-fadiga. As ligas de alumínio, assim como muito aços, apresentam resistência à corrosão-fadiga relativamente baixa, aproximadamente metade da resistência à fadiga ao ar e um quarto da resistência mecânica original do material. Surpreendentemente, a resistência à corrosão-fadiga de uma liga não é afetada significativamente pelo tratamento térmico, mesmo no caso das ligas endurecíveis por precipitação (Al-Cu (2XXX), Al-Mg-Si (6XXX) e Al-Zn-Mg-Cu (7XXX)). As falhas por corrosão-fadiga nas ligas de alumínio são caracteristicamente transgranulares, diferindo assim das falhas por trincamento por corrosão sob tensão, que são normalmente intergranulares. A corrosão localizada na superfície do alumínio, como a formação de pites, ou mesmo a corrosão intergranular, geram concentradores de tensões, reduzindo assim a vida em fadiga. Ao ar, a umidade relativa apresenta um pequeno efeito na vida em corrosão- fadiga das ligas de alumínio. Entretanto, para valores muito pequenos (umidade relativa inferior a 5 %), a vida em fadiga aumenta ligeiramente. Há pouca diferença no comportamento em corrosão-fadiga das ligas de alumínio para diferentes tipos de água, seja natural, desmineralizada, dura ou em salmoura. Isso é surpreendente, pois a corrosividade normal destas águas no alumínio varia bastante. Há pouca informação disponível sobre o efeito do processamento termomecânico no comportamento em corrosão-fadiga das ligas de alumínio. Não é possível garantir que uma determinada condição de processamento que proporciona boa resistência ao trincamento por corrosão sob tensão apresentará efeito igual ou semelhante com relação à corrosão-fadiga. Entretanto, é reconhecido o efeito benéfico da adição de cobre às ligas da série 7XXX (Al-Zn-Mg-Cu) no sentido de melhorar a resistência á corrosão-fadiga. O jateamento com partículas abrasivas, que aumenta a resistência à fadiga, provavelmente apresenta o mesmo efeito com relação à vida em corrosão-fadiga das ligas de alumínio, porém o jateamento não deve ser excessivo, o que poderia causar excessiva deformação plástica, que poderia causar susceptibilidade à esfoliação ou ao trincamento por corrosão sob tensão. Revestimentos protetores na superfície do material, inclusive pintura, também podem ser benéficos nesse sentido. A soldagem reduz tanto a vida em fadiga quanto a vida em corrosão-fadiga, mas o jateamento posterior aumenta a vida em corrosão-fadiga, principalmente quando sucedido por pintura. Cavitação – O dano por cavitação acontece quando um líquido turbulento forma bolhas que entram em colapso ao incidirem sobre a superfície da liga de alumínio, rompendo a camada passivada protetora de óxido, iniciando assim a formação de pites, que podem ser densos o suficiente para provocar o surgimento de uma certa aspereza na superfície do material, ou mesma encruá-la ao ponto de provocar corrosão-fadiga, além de arrancar pequenas porções de material devido ao impacto da ação mecânica. Assim, o dano por cavitação pode ser resultado da corrosão ou da ação mecânica, ou desses dois fatores atuando conjuntamente. Em casos de cavitação suave, provavelmente predomina a ação química, que não pode ser evitada por proteção catódica. Quando predomina a ação mecânica, , o dano só pode ser evitado pela eliminação da condição de cavitação, através de modificações no projeto do equipamento. Corrosão-Erosão – Quando um líquido passa por uma superfície de alumínio excedendo uma certa velocidade, podem se formar sulcos na superfície como resultado das ações química e mecânica. Em geral este fenômeno não corre quando a velocidade do líquido é inferior a 3 m/s. A corrosão-erosão e a cavitação apresentam certa similaridade e podem ocorrer conjuntamente. Apresentam como característica comum um mecanismo de dano na camada de óxido da superfície por ação mecânica, seguido por corrosão localizada. A perda de metal por corrosão pode ser acompanhada por perda de propriedades mecânicas, tanto por fadiga quanto por erosão. Os efeitos adversos da corrosão-erosão e da cavitação podem ser minimizados por diferentes métodos. A cavitação em bombas de água automotivas pode ser minimizada se o líquido de refrigeração contiver inibidores. Modificações de projeto e uso de inibidores podem evitar o acúmulo de óxidos em radiadores que causa corrosão nestes dispositivos. Corrosão-Atrito – É um processo de desgaste que produz pontos de abrasão e superfícies de alumínio que se movem deslizando em contato entre si num ambiente corrosivo. Estes pontos de abrasão assemelham-se a pites contendo pós pretos, que são pequenas partículas de óxidos de alumínio. Ocorre freqüentemente no transporte de pacotes de chapas, embora também possa ser observada em tubos empacotados com folgas. A susceptibilidade