
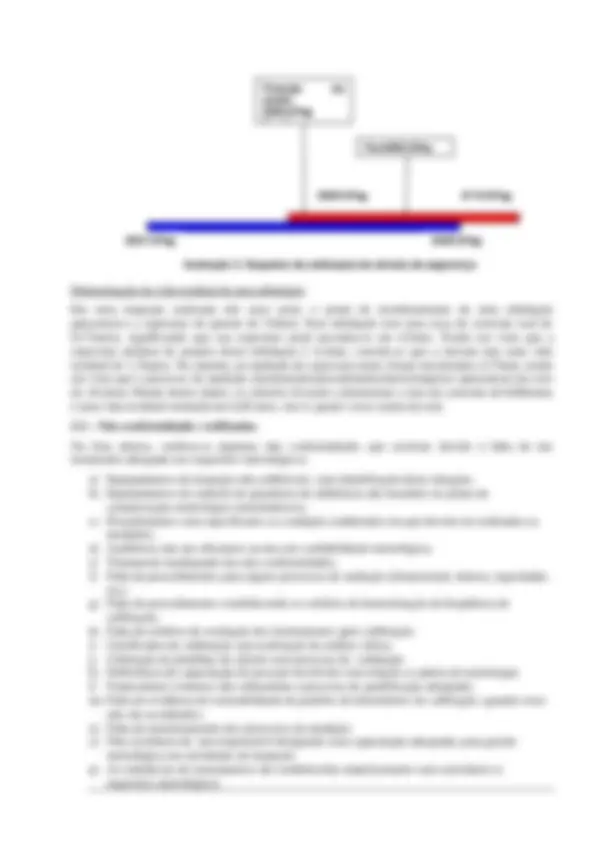
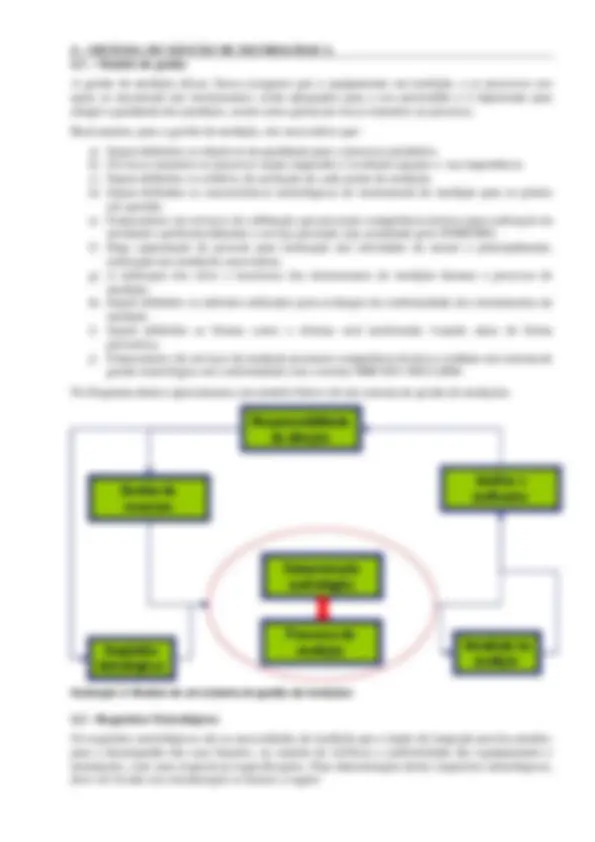
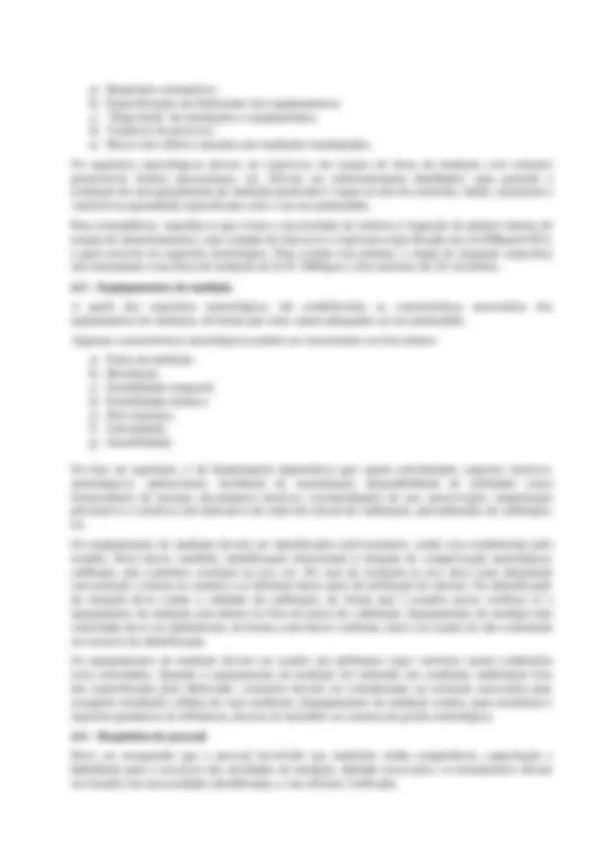
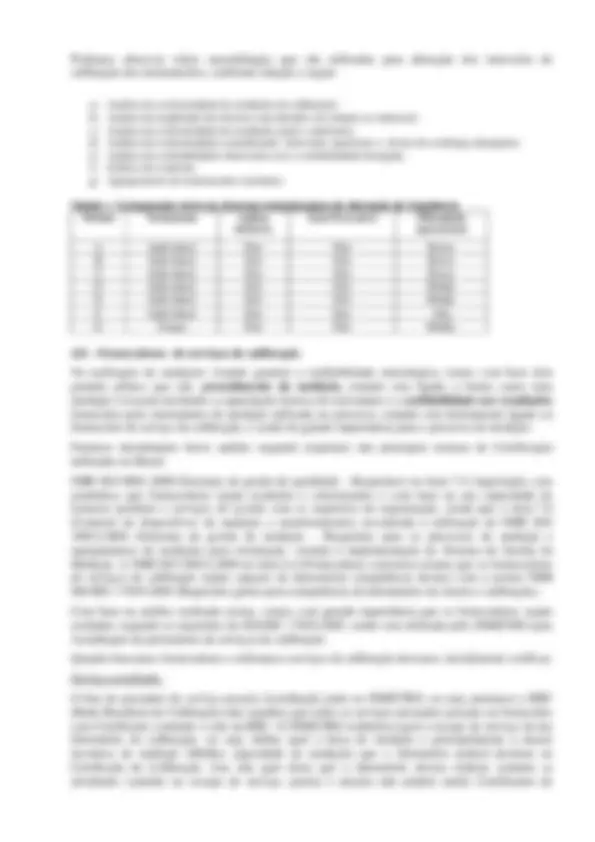
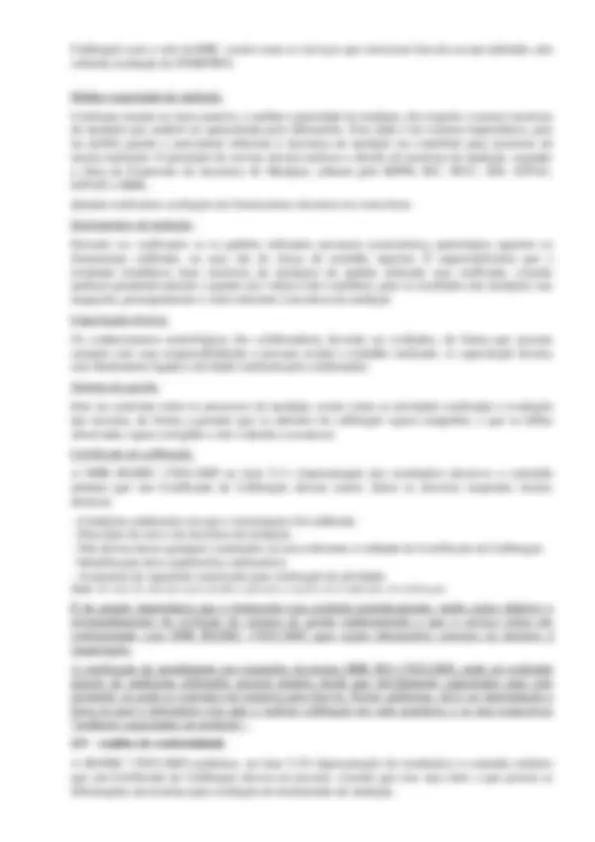
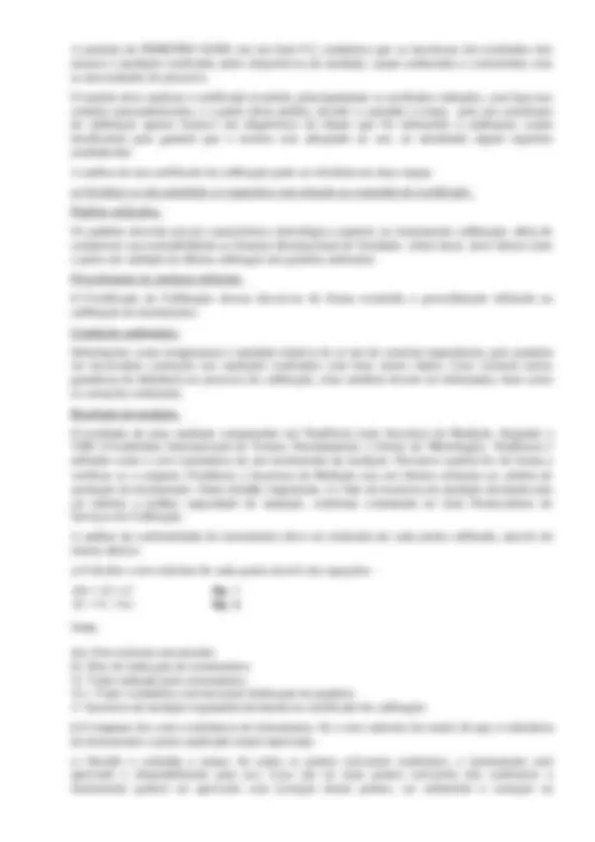
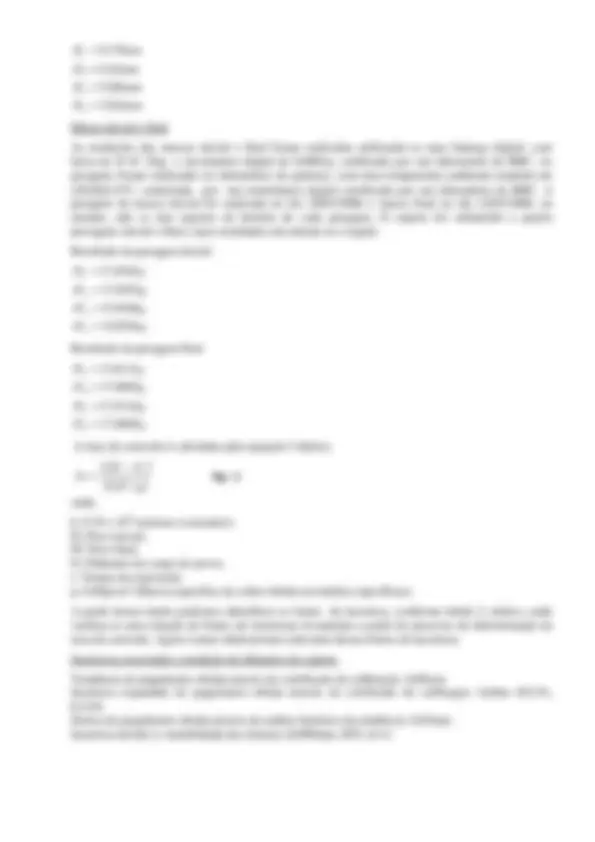
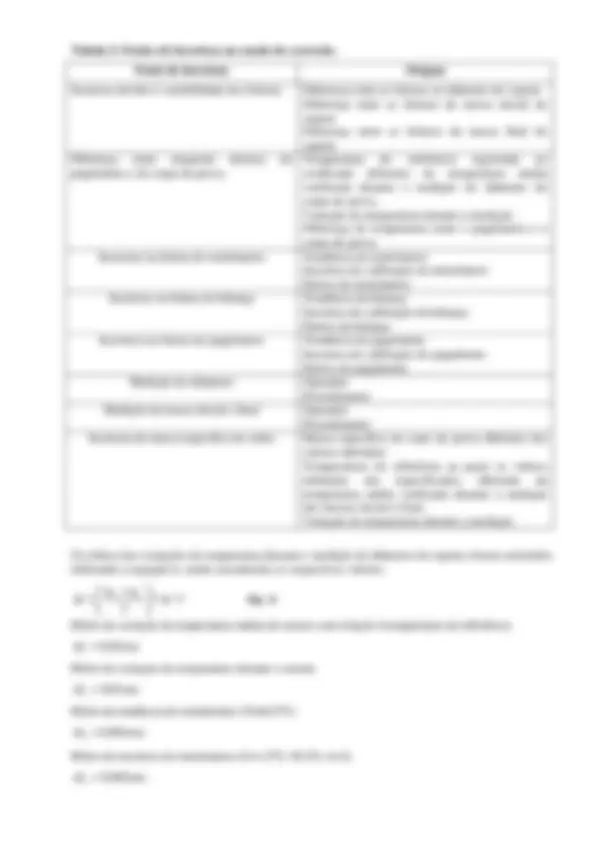
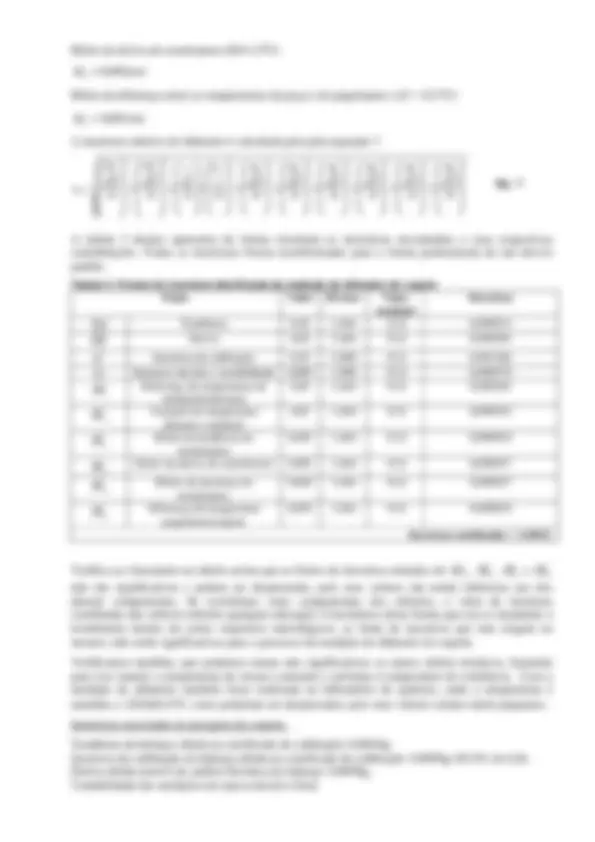
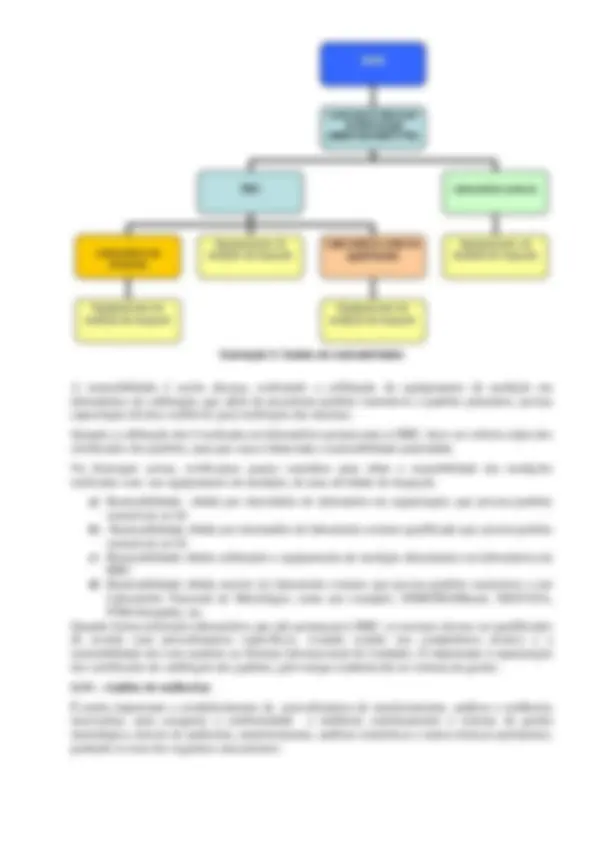

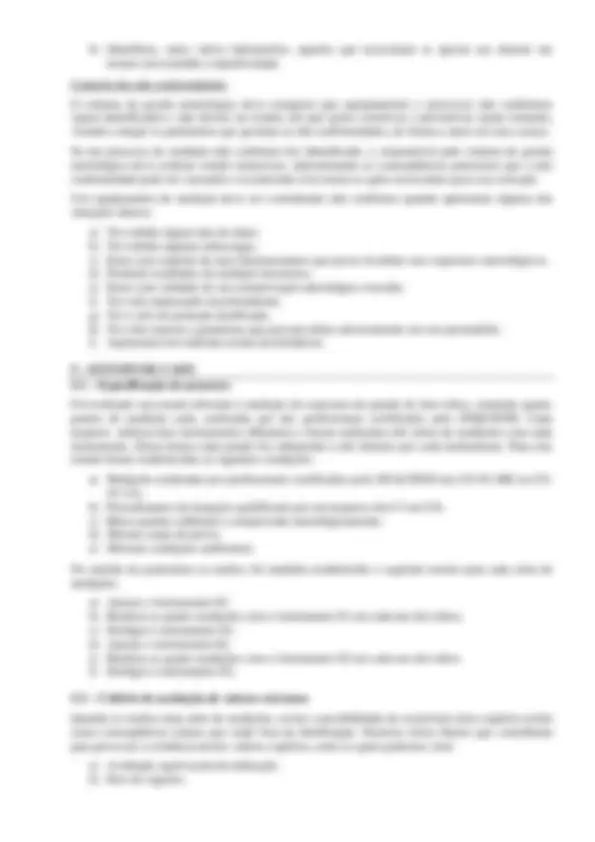
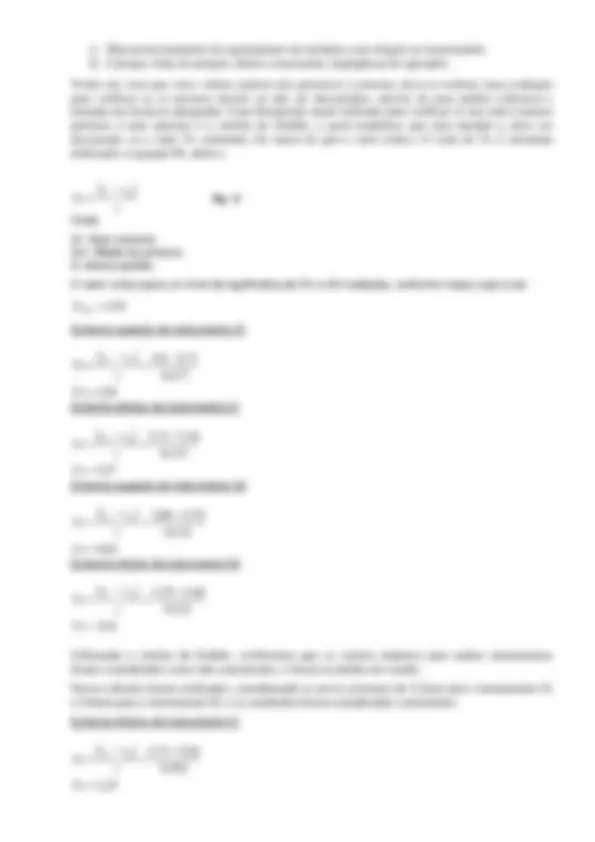
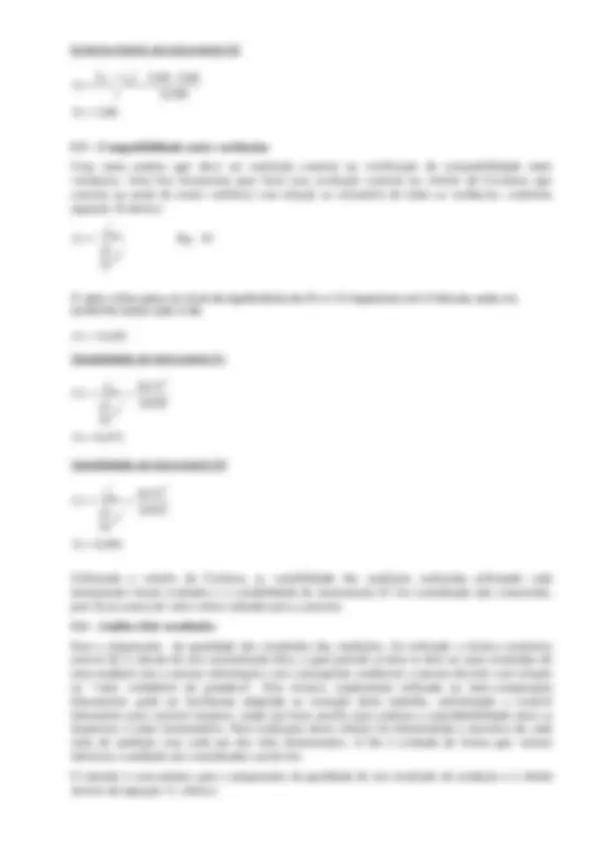
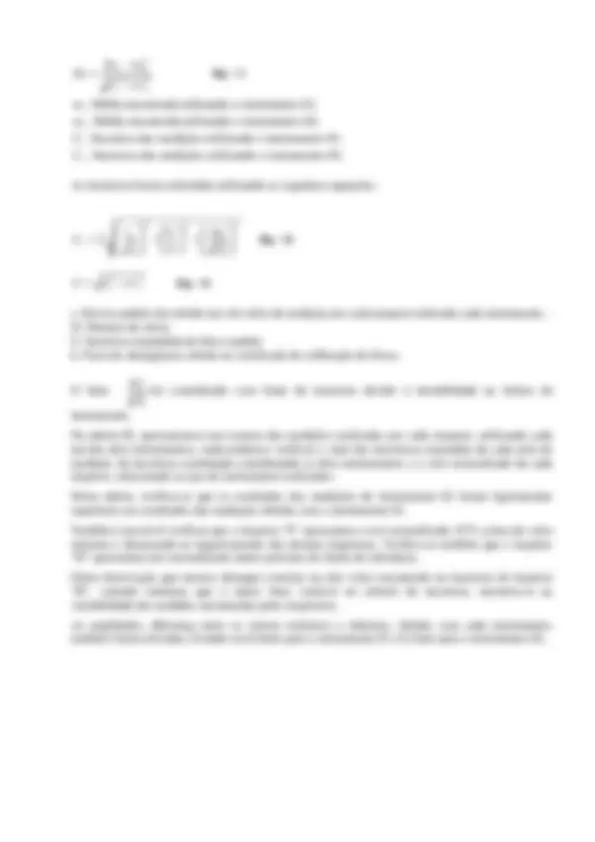
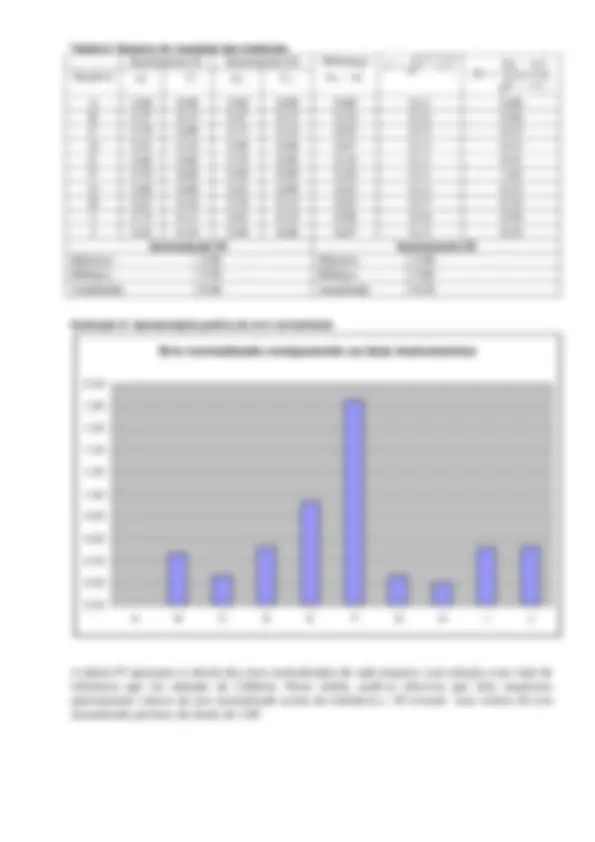
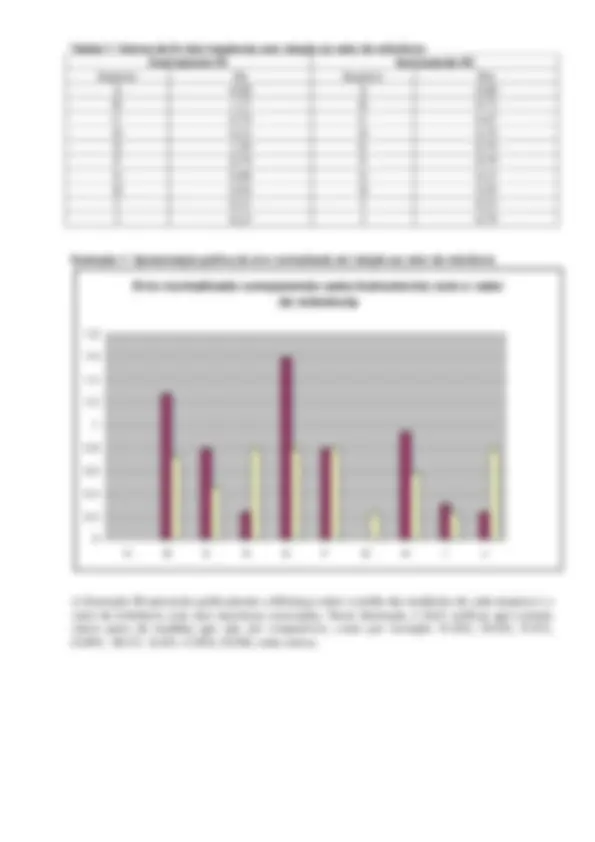
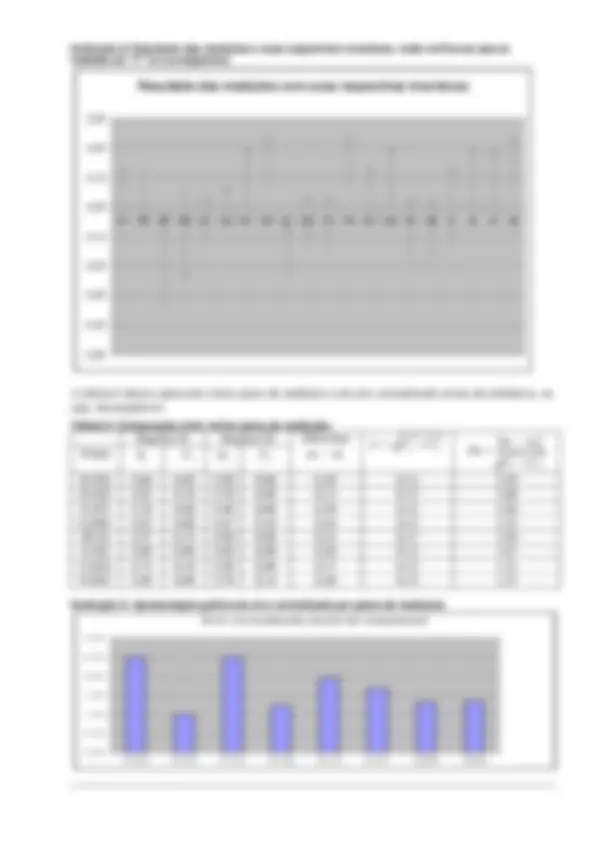
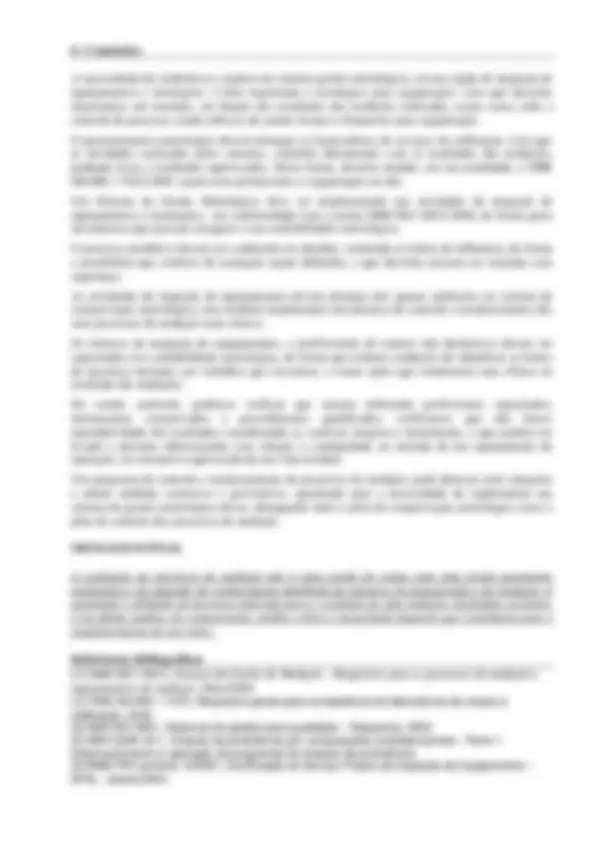
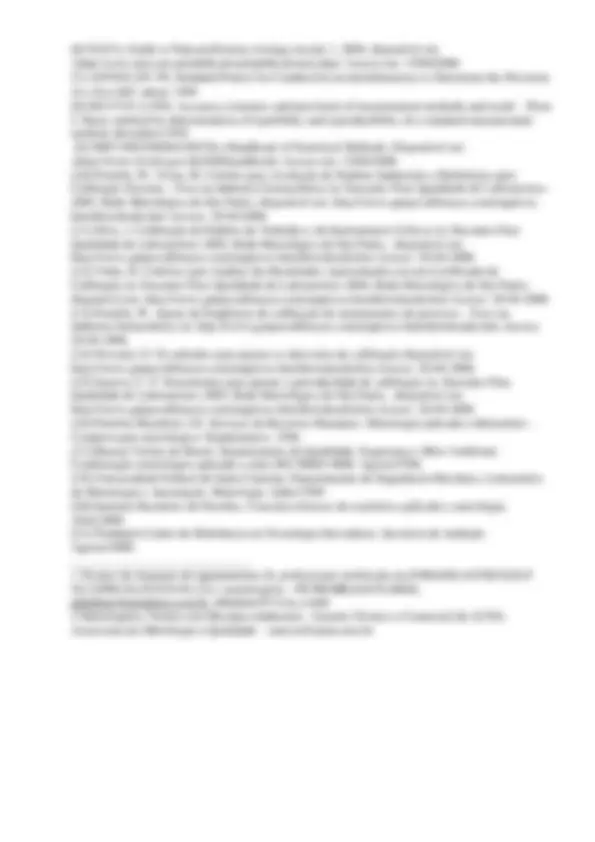
Estude fácil! Tem muito documento disponível na Docsity
Ganhe pontos ajudando outros esrudantes ou compre um plano Premium
Prepare-se para as provas
Estude fácil! Tem muito documento disponível na Docsity
Prepare-se para as provas com trabalhos de outros alunos como você, aqui na Docsity
Os melhores documentos à venda: Trabalhos de alunos formados
Prepare-se com as videoaulas e exercícios resolvidos criados a partir da grade da sua Universidade
Responda perguntas de provas passadas e avalie sua preparação.
Ganhe pontos para baixar
Ganhe pontos ajudando outros esrudantes ou compre um plano Premium
Comunidade
Peça ajuda à comunidade e tire suas dúvidas relacionadas ao estudo
Descubra as melhores universidades em seu país de acordo com os usuários da Docsity
Guias grátis
Baixe gratuitamente nossos guias de estudo, métodos para diminuir a ansiedade, dicas de TCC preparadas pelos professores da Docsity
Trabalha apresentado XXIV CONAEV IEV e trata da importância da metrologia nas atividades de inspeção de equipamentos
Tipologia: Trabalhos
1 / 28
Esta página não é visível na pré-visualização
Não perca as partes importantes!
CONAEND 030 IMPORTÃNCIA DA CONFIABILIDADE METROLÓGICA NAS ATIVIDADES DE INSPEÇÃO DE EQUIPAMENTOS Paulo Cezar da Costa Lino Dunham^1 ,Marcio Machado^2 (b)
Copyright 2006, ABENDE Trabalho apresentado no CONAEND&IEV 2006, São Paulo, 2006 As informações e opiniões contidas neste trabalho são de exclusiva responsabilidade do (s) autor(es).
1 - SINOPSE No processo de inspeção de equipamentos realizam-se várias medições, cujos resultados são utilizados para tomadas de decisão. Tendo como base os resultados das medições, os equipamentos assim como as instalações, podem ser considerados em conformidade ou não, com relação às suas respectivas especificações. Um bom exemplo que se pode apresentar, encontra-se na estimativa da vida residual de um equipamento, a partir dos resultados das medições de espessura de parede. A qualidade principal dos instrumentos ou padrões de medição, consiste em apresentar resultados com a confiabilidade metrológica requerida, para a atividade a ser executada, ou seja, com o menor erro possível, assim como baixo valor da incerteza de medição; no entanto, todo instrumento por melhor que seja, apresenta erros e incerteza de medição e sua caracterização é de suma importância para que os resultados da medição, sejam determinados de forma segura e suas conformidades sejam definidas de forma clara e objetiva. Desta forma, a determinação dos erros e incerteza da medição dos instrumentos utilizados na inspeção, é de altíssima importância. Um sistema de gestão metrológica eficaz assegura que os instrumentos e processos de medição, sejam utilizados de forma adequada ao uso pretendido, visando alcançar a qualidade necessária para a realização de medições nas mais diversas inspeções, além de possibilitar o gerenciamento dos diversos riscos nos processos produtivos. Devido à falta de especialistas em metrologia nas atividades de inspeção de equipamentos de maneira geral, a gestão do sistema medição pode ficar relegada o segundo plano, colocando em dúvida os resultados das medições realizadas; desta forma, torna-se necessário que as atividades de inspeção de equipamentos e instalações, possuam um sistema de gestão de medição eficaz visando assegurar a confiabilidade dos resultados de suas inspeções.
2 - INTRODUÇÃO O trabalho apresenta a importância da metrologia nas atividades de inspeção de equipamentos, mostrando que decisões equivocadas podem ser tomadas, em virtude de erros que venham acontecer nas medições que são realizadas nos ensaios não destrutivos e na inspeção de equipamentos de uma forma geral. Demonstra que estes erros podem ter sua origem nos aparelhos de inspeção, nos inspetores e nos processos de medição que são utilizados. Apresenta alguns exemplos que podem ocorrer, em virtude do conhecimento limitado em metrologia dos profissionais que atuam na área de ensaios não destrutivos e inspeção de equipamentos. Um estudo de caso realizado na UN-BSOL, utilizando dez profissionais certificados em medição de espessura é apresentado com resultados surpreendentes. Uma proposta de um sistema de gestão metrológica para as atividades de ensaios não destrutivos e inspeção equipamentos, é apresentada para debate da comunidade de inspeção de equipamentos.
3 – CONFIABILIDADE METROLÓGICA NA INSPEÇÃO DE EQUIPAMENTOS 3.1 – Características do sistema
Nas atividades de inspeção de equipamentos e ensaios não destrutivos, inúmeras medições são realizadas, onde poderão ser avaliadas grandezas de influência, como por exemplo, nível de luminosidade ou temperatura de uma superfície nos ensaios de líquido penetrante, partículas magnéticas, ultra-som, etc., ou podem ser utilizadas medições, cujos resultados são considerados para tomadas de decisão, como a pressão de abertura de uma válvula de segurança, a espessura de parede de um vaso de pressão, a dureza de uma peça soldada, etc. Os usuários de instrumentos de medição, nas atividades de inspeção, normalmente possuem um requisito para utilizar a inspeção, medições e testes o qual consiste apenas em atestar que os instrumentos estão calibrados, e desta
forma atender a fontes externas, tais como a portaria do INMETRO 16/2001, ISO 9000, entre diversas outras.
Muitos engenheiros e técnicos engajados nas atividades de inspeção, encaram a calibração como não agregante de valor a atividade relacionada, cujo único motivo de sua existência é para atendimento aos requisitos normativos. Tendo como base os parâmetros de rapidez, alta qualidade e baixo custo, a escolha normalmente recairá na rapidez e o menor custo possível, estando normalmente, mais preocupados com o atendimento à conformidade dos requisitos normativos, do que com a qualidade do processo de medição.
Atentamos para o fato, de que, uma confiabilidade metrológica deficiente, pode afetar a qualidade e confiabilidade dos resultados de uma inspeção, testes ou ensaios.
A seguir apresentamos alguns exemplos fictícios de medições, onde não são levados em consideração os fatores metrológicos.
Medição de espessura de um vaso
No projeto de um vaso de pressão, foi estabelecida uma espessura mínima na parede do casco de 15,0 mm. Na inspeção deste vaso, um profissional certificado pelo SNQC, encontrou o valor de 15,2mm e o vaso foi considerado aprovado sem restrição. No entanto, avaliando o processo de medição, verificou-se que a incerteza deste foi avaliada em U=±0,5mm (95,5%); de onde se conclui que a espessura do vaso pode encontrar-se no intervalo de [14,7 @ 15,7]mm, ou seja, existe uma probabilidade de a espessura encontrar-se abaixo do valor mínimo especificado.
Ilustração 1: Resumo esquemático da medição de espessura do vaso. ‘
Calibração de uma válvula de alívio de pressão
Uma válvula de segurança tem sua pressão de ajuste especificada em Paj=8300kPag±3%. Com isso esta PSV pode ser ajustada no intervalo de Pac=[8290 @ 8549] kPag. Durante o teste de bancada a PSV foi ajusta em 8500 kPag, valor que esta dentro das suas tolerâncias e a PSV foi liberada para operação. No teste foi utilizado um manômetro classe A1, com escala de 0 @ 21000 kPag. Na calibração deste manômetro foi encontrado um erro máximo de 210 kPag, na faixa entre 8000 @ 9000 kPag e este manômetro foi aprovado, pois o erro máximo encontra-se dentro da sua tolerância. Verifica-se, entretanto, que o valor da pressão ajustada em bancada pode encontrar-se na faixa de Pa=[8290 @ 8710] kPag, existindo uma probabilidade da válvula ter sido ajustada acima da tolerância permissível.
Espessura mínima especificada 15,0 mm
Espessura encontrada 15,2 mm
14,7 15,
Medidor de espessura E=0,0 mm U=±0,5mm
4.1 – Modelo de gestão
A gestão de medição eficaz, busca assegurar que o equipamento em medição, e os processos nos quais se encontram tais instrumentos, estão adequados para o uso pretendido e é importante para atingir a qualidade dos produtos, assim como gerenciar riscos inerentes ao processo.
Basicamente, para a gestão da medição, são necessários que:
a) Sejam definidos os objetivos da qualidade para o processo produtivo. b) Os riscos inerentes ao processo sejam mapeados e avaliados quanto a sua importância. c) Sejam definidos os critérios de aceitação de cada ponto de medição. d) Sejam definidas as características metrológicas do instrumento de medição para os pontos em questão. e) Fornecedores de serviços de calibração que possuam competência técnica para realização da atividade e preferencialmente o serviço prestado seja acreditado pelo INMETRO. f) Haja capacitação de pessoal para realização das atividades de ensaio e principalmente, realização das medições necessárias. g) A utilização dos erros e incertezas dos instrumentos de medição durante o processo de medição. h) Sejam definidos os métodos utilizados para avaliação da conformidade dos instrumentos de medição. i) Sejam definidas as formas como o sistema será monitorado visando atuar de forma preventiva. j) Fornecedores de serviços de medição possuam competência técnica e tenham um sistema de gestão metrológica em conformidade com a norma NBR ISO 10012:2004.
No Esquema abaixo apresentamos um modelo básico de um sistema de gestão de medições.
Ilustração 3: Modelo de um sistema de gestão de medições
4.2 - Requisitos Metrológicos
Os requisitos metrológicos são as necessidades de medição que o órgão de inspeção precisa atender, para o desempenho das suas funções, no sentido de verificar a conformidade dos equipamentos e instalações, com suas respectivas especificações. Para determinação destes requisitos metrológicos, deve ser levado em consideração os fatores a seguir:
a) Requisitos normativos; b) Especificações de fabricantes dos equipamentos; c) “Data book” de instalações e equipamentos; d) Variáveis de processo; e) Riscos dos efeitos causados por medições inadequadas.
Os requisitos metrológicas devem ser expressos em termos de faixa de medição, erro máximo permissível, limites operacionais, etc. Devem ser suficientemente detalhados, para permitir a avaliação de um equipamento de medição particular é capaz ou não de controlar, medir, monitorar a variável ou quantidade especificada com o seu uso pretendido.
Para exemplificar, suponha-se que exista a necessidade de realizar a inspeção de pintura interna de tanque de armazenamento, cuja camada de tinta teve a espessura especificada em e=(500μm±10%), a qual consiste no requisito metrológico. Para avaliar esta pintura, o órgão de inspeção especifica um instrumento com faixa de medição de (0 @ 1000)μm e erro máximo de 2% da leitura.
4.3 – Equipamentos de medição
A partir dos requisitos metrológicos são estabelecidas as características necessárias dos equipamentos de medição, de forma que estes sejam adequados ao uso pretendido.
Algumas características metrológicas podem ser encontradas na lista abaixo:
a) Faixa de medição; b) Resolução; c) Estabilidade temporal; d) Estabilidade térmica; e) Erro máximo; f) Linearidade; g) Sensibilidade.
Na fase de aquisição, é de fundamental importância que sejam considerados aspectos técnicos, metrológicos, operacionais, facilidade de manutenção, disponibilidade de utilidades como fornecimento de energia, documentos técnicos, recomendações de uso, preservação, manutenção preventiva e corretiva, um indicativo do intervalo inicial de calibração, procedimento de calibração, etc.
Os equipamentos de medição devem ser identificados univocamente, sendo esta estabelecida pelo usuário. Deve haver, também, identificação relacionada à situação de comprovação metrológica: calibrado, não conforme, restrição ao uso, etc. No caso de restrição ao uso, deve estar informado sua restrição e alertar ao usuário a se informar desta antes de utilização do mesmo. Na identificação da situação deve contar a validade da calibração, de forma que o usuário possa verificar se o equipamento de medição esta dentro ou fora do prazo de calibração. Equipamento de medição não controlado deve ser identificado, de forma a não haver confusão, entre seu estado de não controlado ou extravio da identificação.
Os equipamentos de medição devem ser usados em ambientes cujas variáveis sejam conhecidas e/ou controladas. Quando o equipamento de medição for utilizado em condições ambientais fora das especificadas pelo fabricante, correções devem ser consideradas na extensão necessária para assegurar resultados válidos de suas medições. Equipamentos de medição usados, para monitorar e registrar grandezas de influência, devem ser incluídos no sistema de gestão metrológica.
4.4 – Requisitos de pessoal
Deve ser assegurado que o pessoal envolvido nas medições tenha competência, capacitação e habilidade para o exercício das atividades de medição. Quando necessário, os treinamentos devem ser focados nas necessidades identificadas, e sua eficácia verificada.
Os procedimentos e instruções de trabalho do sistema de gestão de metrológica devem ser documentados e validados assim como suas alterações. Uma instrução de trabalho pode consistir em uma lista de tarefas emitida conjuntamente com a ordem de serviço de calibração.
Programas de computador específicos para o controle de comprovação metrológica, pode ajudar a tornar o sistema mais confiável e agilizar todo o processo de controle. Existem vários programas comerciais destinados especificamente para esta atividade.
Os registros do sistema de gestão de medições devem ser controlados seguindo os mesmos critérios utilizados para controle dos documentos, sendo que, tais procedimentos de controle devem estabelecer a identificação, sistema de armazenamento, proteção, recuperação, tempo de retenção, responsabilidades, etc. Os certificados de calibração e seus resultados de avaliação devem ser mantidos por tempo suficiente, de forma a permitir análise histórica dos equipamentos de medição. Podem ser considerados registros do sistema de gestão metrológica:
a) Relatórios de medição; b) Relatórios de inspeção; c) Certificados de calibração; d) Relatórios de parecer técnico; e) Relatórios de auditoria interna e externa; f) Relatórios de qualificação de laboratórios externos.
4.6 – Comprovação metrológica
Entende-se por comprovação metrológica, o conjunto de atividades necessárias para assegurar que as características metrológicas do equipamento de medição, atendem aos requisitos metrológicos do processo de medição. A comprovação inclui a calibração, ajuste, re-calibração, análise crítica de certificado, avaliação de conformidade, marcação, preservação, etc. Através da comprovação metrológica, pode-se alcançar os seguintes objetivos:
a) Garantir que um equipamento de medição esta adequado ao uso pretendido; b) Melhorar e manter a qualidade de um sistema de inspeção; c) Atender exigências legais; d) Determinar propriedades metrológicas; e) Determinar tendências e incertezas; f) Determinar correções.
4.7 – Intervalo de comprovação
A característica principal no estabelecimento ou alteração dos intervalos entre calibração dos instrumentos, encontra-se na previsibilidade de desempenho do mesmo, de forma a garantir uma baixa probabilidade de utilização do instrumento fora das suas tolerâncias, com custos aceitáveis. Uma freqüência de calibração demasiadamente alta, pode gerar altos custos de manutenção, além de deixar o instrumento indisponível por um maior espaço de tempo. A freqüência de calibração com intervalos elevados, pode proporcionar perdas das características metrológicas dos instrumentos, em função de alteração de estabilidade ou desgaste, colocando em dúvida suas medições anteriores. Neste caso, pode ser necessária a reavaliação de todas as medições realizadas desde a última calibração.
No estabelecimento da freqüência de calibração, vários parâmetros devem ser levados em consideração, entre eles os que se segue:
a) Comportamento do instrumento ao longo do tempo. Estudo de tendência. b) Características metrológicas do instrumento (incerteza de medição, estabilidade, linearidade, etc); c) Severidade e freqüência de uso; d) Riscos e penalidades envolvidos na medição; e) Orientação dos fabricantes dos instrumentos; f) Experiência anterior com instrumentos semelhantes; g) Exatidão requerida na medição; h) Custos envolvidos.
Podemos observar várias metodologias que são utilizadas para alteração dos intervalos de calibração dos instrumentos, conforme relação a seguir.
a) Analise da conformidade do resultado da calibração; b) Analise da amplitude dos desvios encontrados em relação ao tolerável; c) Analise da conformidade do resultado atual e anteriores; d) Análise da conformidade considerando intervalos anteriores e níveis de confiança desejados; e) Análise da confiabilidade observada com a confiabilidade desejada; f) Gráfico de controle; g) Agrupamento de instrumentos similares.
Tabela 1. Comparação entre as diversas metodologias de alteração de freqüência Método Tratamento Análise histórica
Ação Preventiva Dificuldade operacional A Individual Não Não Baixa B Individual Sim Não Baixa C Individual Sim Não Baixa D Individual Sim Não Média E Individual Sim Não Média F Individual Sim Sim Alta G Grupo Não Não Média
4.8 – Fornecedores de serviços de calibração
Na realização de medições visando garantir a confiabilidade metrologica, temos com base dois grandes pilares que são: procedimento de medição, estando este ligado a forma como uma medição é executa incluindo a capacitação técnica do executante e a confiabilidade nos resultados fornecidos pelo instrumento de medição utilizado no processo, estando este diretamente ligado ao fornecedor de serviço de calibração, e sendo de grande importância para o processo de medição.
Faremos inicialmente breve análise segundo requisitos das principais normas de Certificação utilizadas no Brasil.
NBR ISO 9001:2000 (Sistemas de gestão de qualidade – Requisitos) no item 7.4 (Aquisição), esta estabelece que fornecedores sejam avaliados e selecionados e com base na sua capacidade de fornecer produtos e serviços de acordo com os requisitos da organização, sendo que o item 7. (Controle de dispositivos de medição e monitoramento) recomenda a utilização da NBR ISO 10012:2004 (Sistemas de gestão de medição – Requisitos para os processos de medição e equipamentos de medição) para orientação, visando à implementação do Sistema de Gestão de Medição. A NBR ISO 10012:2004 no item 6.4 (Fornecedores externos) orienta que os fornecedores de serviços de calibração sejam capazes de demonstrar competência técnica com a norma NBR ISO/IEC 17025:2005 (Requisitos gerais para competência de laboratórios de ensaio e calibração).
Com base na análise realizada acima, vemos com grande importância que os fornecedores sejam avaliados segundo os requisitos da ISO/IEC 17025:2005, sendo esta utilizada pelo INMETRO para Acreditação de prestadores de serviços de calibração.
Quando buscamos fornecedores e utilizamos serviços de calibração devemos, inicialmente verificar:
Serviço acreditado.
O fato do prestador de serviço possuir Acreditação junto ao INMETRO, ou seja, pertencer a RBC (Rede Brasileira de Calibração) não significa que todos os serviços prestados possam ser fornecidos com Certificado contendo o selo da RBC. O INMETRO estabelece qual o escopo de serviço de um laboratório de calibração, ou seja, define qual a faixa de medição e principalmente a menor incerteza de medição (Melhor capacidade de medição) que o laboratório poderá declarar no Certificado de Calibração. Isso não quer dizer que o laboratório devera realizar somente as atividades contidas no escopo de serviço, porém o mesmo não poderá emitir Certificados de
A portaria do INMETRO 16/001 em seu item 9.2, estabelece que as incertezas dos resultados dos ensaios e medições realizadas pelos dispositivos de medição, sejam conhecidas e consistentes com as necessidades do processo.
O usuário deve analisar o certificado recebido, principalmente os resultados relatados, com base nos critérios preestabelecidos, e a partir desta análise, decidir o caminho a tomar, pois um certificado de calibração apenas fornece um diagnóstico do objeto que foi submetido a calibração, sendo insuficiente para garantir que o mesmo esta adequado ao uso, ou atendendo algum requisito estabelecido.
A análise de um certificado de calibração pode ser dividida em duas etapas:
a) Verificar se são atendidos os requisitos com relação ao conteúdo do certificado:
Padrões utilizados.
Os padrões deverão possui característica metrológica superior ao instrumento calibração, além de comprovar sua rastreabilidade ao Sistema Internacional de Unidades. Além disso, deve deixar claro o prazo de validade da última calibração dos padrões utilizados.
Procedimento de medição utilizado.
O Certificado de Calibração devera descrever de forma resumida o procedimento utilizado na calibração do instrumento.
Condições ambientais.
Informações como temperatura e umidade relativa do ar são de extrema importância, pois poderão ser necessárias correções nas medições realizadas com base nestes dados. Caso existam outras grandezas de influência no processo de calibração, estas também devem ser informadas, bem como as correções realizadas.
Resultado da medição.
O resultado de uma medição compreende em Tendência mais Incerteza da Medição. Segundo o VIM (Vocabulário Internacional de Termos Fundamentais e Gerais de Metrologia), Tendência é definido como o erro sistemático de um instrumento de medição. Devemos analisá-los de forma a verificar se o conjunto Tendência ± Incerteza de Medição esta nos limites referente ao critério de aceitação do instrumento. Outro detalhe importante, é o fato da incerteza da medição declarada não ser inferior a melhor capacidade de medição, conforme comentado no item Fornecedores de Serviços de Calibração.
A análise de conformidade do instrumento deve ser realizada em cada ponto calibrado, através do roteiro abaixo:
a) Calcular o erro máximo de cada ponto através das equações:
Em = Ei + U Eq: 1 Ei = Vi − Vvc Eq: 2
Onde,
Em : Erro máximo encontrado; Ei : Erro de indicação do instrumento; Vi : Valor indicado pelo instrumento; Vvc : Valor verdadeiro convencional (Indicação do padrão); U : Incerteza de medição expandida declarada no certificado de calibração.
b) Comparar Em com a tolerância do instrumento. Se o erro máximo for maior do que a tolerância do instrumento o ponto analisado estará reprovado.
c) Decidir o caminho a tomar. Se todos os pontos estiverem conformes, o instrumento será aprovado e disponibilizado para uso. Caso um ou mais pontos estiverem não conformes o instrumento poderá ser aprovado com restrição destes pontos, ser submetido à correção ou
reprovado e indisponibilizado para uso. Caso seja necessária a aplicação de curva de correção, a incerteza desta curva deve ser determinada e adicionada à incerteza da calibração do equipamento, e nova análise de conformidade devera ser realizada. A incerteza da curva pode ser determina utilizando-se e metodologia abaixo:
2
−
∑ n
Vi Vc uc Eq: 3
onde,
uc : Incerteza da curva; Vc : Valor atual obtido pela curva de correção; Vi : Valor indicado pelo instrumento; n : Número de pontos considerados.
2
2 c^2 uc k
= Eq: 4
onde,
Uc : Incerteza de medição após a correção; k : Fator de abrangência obtido no certificado de calibração.
Uma nova análise de conformidade será realizada, comparando-se a tolerância do instrumento com a incerteza corrigida.
Ajustes realizados no instrumento.
É muito importante que o prestador de serviço informe, quando aplicável, os valores encontrados antes a execução de ajuste, pois somente desta forma poderá ser possíveis à avaliação das medições realizadas e suas conseqüências.
4.10 – Transporte e armazenamento.
Devem existir procedimentos específicos para efetuar o uso, manuseio, transporte, armazenamento dos equipamentos de medição, de forma a prevenir contaminação, deterioração, desgaste prematuro, alterações de características metrológicas e proteger sua integridade. Os procedimentos devem individualizar equipamentos de medição que requer tratamentos mais criteriosos, como decantadores utilizados em inspeção por partículas magnéticas.
4.11 – Processo de medição
Embora a comprovação metrológica possa assegurar que as características metrológicas do equipamento de medição, atendam aos requisitos metrológicos do processo, não pode garantir a confiabilidade metrológica adequada deste processo. Mesmo com uso de equipamentos de medição que atendam aos requisitos do processo, o resultado da medição pode não ser confiável em virtude da utilização de procedimentos inadequados ou profissionais sem a capacitação necessária para o exercício destas medições. Desta forma, os processos de medição devem ser planejados, validados, implementados, documentados e controlados. Os processos de medição e suas grandezas de influência relacionadas aos processos e inspeção de equipamentos e instalações, também devem receber o mesmo tratamento dos processos de medição, utilizados para avaliação dos equipamentos.
Na especificação de um processo de medição de medição, deve-se incluir os seguintes parâmetros:
a) Relação dos equipamentos de medição e suas características metrológicas; b) Procedimentos de medição; c) Programa de computador para medição e cálculo; d) Condições de uso dos equipamentos de medição; e) Condições ambientais; f) Capacitação e habilidade dos executantes.
D mm
D mm
D mm
D mm
4
3
2
1
Massa inicial e final
As medições das massas inicial e final foram realizadas utilizando-se uma balança digital, com faixa de (0 @ 5)kg e incremento digital de 0,0001g, certificada por um laboratório da RBC. As pesagens foram realizadas no laboratório de química, com uma temperatura ambiente mantida em (20,0±0,3)°C, controlada por um termômetro digital certificado por um laboratório da RBC. A pesagem da massa inicial foi realizada no dia 20/01/2006 e massa final no dia 22/03/2006, no entanto, não se tem registro do horário de cada pesagem. O cupom foi submetido a quatro pessagens inicial e final, cujos resultados encontram-se a seguir:
Resultado da pesagem inicial
Pi g
Pi g
Pi g
Pi g
4
3
2
1
Resultado da pesagem final
Pi g
Pi g
Pi g
Pi g
4
3
2
1
A taxa de corrosão é calculada pela equação 5 abaixo.
. .. ρ
D^2 t
k P P Tx i f Π
= Eq: 5
onde,
k: 8,76 x 10^4 mm/ano (constante); Pi: Peso inicial; Pf: Peso final; D: Diâmetro do corpo de prova; t: Tempo de exposição; p: 8,89g/cm^3 (Massa específica do cobre obtida em tabelas específicas).
A partir destes dados podemos identificar as fontes de incerteza, conforme tabela 2, abaixo, onde verifica-se uma relação de fontes de incertezas levantadas a partir do processo de determinação da taxa de corrosão. Agora vamos dimensionar cada uma dessas fontes de incerteza.
Incertezas associadas a medição do diâmetro do cupom
Tendência do paquímetro obtida através do certificado de calibração: 0,05mm Incerteza expandida do paquímetro obtida através do certificado de calibração: 0,04m (95,5%, k=2,0) Deriva do paquímetro obtida através de análise histórica da tendência: 0,03mm. Incerteza devido à variabilidade das leituras (0,009mm; 68%; k=1)
Tabela 2: Fontes de incerteza na ensaio de corrosão.
Fonte de incerteza Origem
Incerteza devido à variabilidade das leituras Diferença entre as leituras no diâmetro do cupom Diferença entre as leituras da massa inicial do cupom Diferença entre as leituras da massa final do cupom Diferença entre expansão térmica do paquímetro e do corpo de prova.
Temperatura de referência registrada no certificado diferente da temperatura média verificada durante a medição do diâmetro do corpo de prova. Variação da temperatura durante a medição. Diferença de temperatura entre o paquímetro e o corpo de prova Incerteza na leitura do termômetro Tendência do termômetro Incerteza de calibração do termômetro Deriva do termômetro Incerteza na leitura da balança Tendência da balança Incerteza de calibração da balança Deriva da balança Incerteza na leitura do paquímetro Tendência do paquímetro Incerteza de calibração do paquímetro Deriva do paquímetro Medição do diâmetro Operador Procedimento Medição da massa inicial e final Operador Procedimento Incerteza da massa específica do cobre Massa específica do copo de prova diferente dos valores tabelados. Temperaturas de referência na quais os valores tabelados são especificados, diferente da temperatura média verificada durante a medição das massas inicial e final. Variação da temperatura durante a medição.
Os efeitos das variações de temperatura durante e medição do diâmetro do cupom, foram calculados utilizando a equação 6, sendo encontrados os respectivos valores:
l P^ C * t * l 2
α α Eq: 6
Efeito da variação da temperatura média do ensaio com relação à temperatura de referência:
∆ l (^) 1 = 0 , 02 mm
Efeito da variação da temperatura durante o ensaio.
∆ l (^) 2 = 0 , 01 mm
Efeito da tendência do termômetro (Td=0,5°C)
∆ l (^) 3 = 0 , 001 mm
Efeito da incerteza do termômetro (U=1,5°C; 95,5%, k=2)
∆ l (^) 4 = 0 , 002 mm
A incerteza da massa específica foi tirada em tabela técnica e desta forma vamos estimar sua incerteza em 0,05g/cm^3. Não existe registro dos horários em que as pesagens foram realizadas, mas apenas as suas respectivas datas. Desta forma, vamos estimar uma incerteza de 12h para sua contribuição.
A incerteza relativa do diâmetro é calculada pela pela equação 8.
2 2 1
(^222)
1
(^222)
12 12 2 4 12 12 2 4 12 12
ua
Df
Td
ua
Df
Td
u f f
b
f
b
f
i b
i
b
i
b
i
b
p ρ
ρ
Eq: 8
A tabela 4 abaixo apresenta de forma resumida as incertezas encontradas e suas respectivas contribuições. Todas as incertezas foram transformadas para a forma padronizada de um desvio padrão.
Tabela 4: Fontes de incerteza identificas nas pesagens do cupom. Fonte Valor Divisor Valor nominal Incerteza
Ua i Variabilidade da pessagem inicial^ 0,0003^ 1,000^ 17,9551^ 0,
Ua (^) f Variabilidade da pessagem inicial^ 0,0004^ 1,000^ 17,9120^ 0,
Incerteza combinada: 0,
Verificamos que as fontes de incerteza da balança são pequenas e pouco significativas para o resultado final da medição. No entanto, as incertezas devido ao espaço tempo decorrido entre a pesagem inicial e final e a incerteza estimada da massa específica, consistem nas maiores fontes de incerteza do processo. Isto nos mostra que devemos melhorar o processo de forma a obter dados mais reais e assim diminuir estas fontes de incerteza.
Calculo da taxa de corrosão
Tx mm a
D t
k P P Tx i f
0 , 0250 /
2 2
=
U mm a
U k u u
Tx
Tx
Tx
Tx D b
Avaliação
Tx =( 0 , 0249 ± 0 , 0002 ) mm / a
Tabela 5: Classes de corrosão segundo a NACE RP 7556 Taxa de corrosão Classe <0,0250 Baixa 0,0250 a 0,1260 Moderada
0,1260 Severa
Ilustração 4: Diagrama da determinação da taxa de corrosão considerando a incerteza
Analisando o exemplo supracitado, sem considerar a incerteza do processo de medição, a taxa de corrosão seria avaliada como baixa; no entanto, pode ser verificado que existe uma probabilidade de a mesma encontrar-se na faixa de corrosão moderada, ficando claro a importância do controle de um processo de medição, de forma a determinar sua incerteza, para melhor tomar as decisões baseadas em resultados de medições. Após esta análise de incerteza o técnico responsável pelo ensaio de corrosão ainda poderia classifica-la como baixa, mas teria consciência dos riscos assumidos de a taxa de corrosão poder encontrar-se na faixa moderada. Salientamos entretanto que a incerteza poderia ser bem inferior se tivéssemos melhor controle sobre a incerteza do espaço de tempo do ensaio bem como da incerteza na determinação da massa específica. Salientamos, contudo, que muitas fontes de incerteza foram eliminadas em virtude das condições ambientais controladas e os instrumentos comprovados metrologicamente.
4.13 – Rastreabilidade
O sistema de gestão de medição deve estabelecer mecanismos que assegurem a rastreabilidade das medições, às unidades padrão do Sistema Internacional de Unidades (SI). Esta rastreabilidade é alcança, através de uma cadeia de calibração dos padrões hierarquicamente superior ao equipamento de medição, até alcançar os padrões primários. Em cada escala, o nível superior, deve- se manter a regra 4:1 a 10:1 entre a incerteza do equipamento de medição hierarquicamente inferior, com relação ao superior, isto é, a incerteza do equipamento de medição superior deve ser de (4 a 10) menor do que a incerteza do inferior.
No Esquema abaixo apresentamos um modelo básico com alguns caminhos para obter a rastreabilidade de um equipamento de medição.
0,
Tx=0,0249mm/a
0,
0,0247^ 0,
Análise crítica do sistema de gestão metrológico;
O responsável pelo sistema de gestão metrológica, deve realizar análises críticas periódicas, visando detectar, identificar e avaliar falhas, tomando as ações necessárias para suas correções.
Auditorias específicas para o sistema de gestão metrológica
a) Devem ser planejadas, implementadas e conduzidas auditorias internas periódicas, visando avaliar e assegurar conformidade do sistema de gestão metrológica com os requisitos especificados. Estas auditorias devem cobrir as atividades de comprovação metrológica com e processos de medição. As auditorias devem ser realizadas por equipe de auditores que não estejam envolvidos com as atividades do sistema de gestão metrológica, de forma que seja mantida sua independência e não existam influências e direcionamentos. Os auditores devem ser capacitados para realização da auditoria e pelo menos um auditor deve possuir conhecimentos metrológicos suficientes, possibilitando a avaliação dos processos. Temos verificado que muitas auditorias em sistemas de gestão metrológica são muito ineficazes, por estarem incluídas em um contexto maior (ISO 9000, SPIE, etc.) e por este motivo são muito superficiais e nada acrescentam para melhoria do sistema de gestão metrológica.
Monitoramento de processos de medição específicos
Os principais processos de medição devem ser monitorados periodicamente utilizando procedimentos específicos. O monitoramento tem como objetivo prevenir desvios dos requisitos metrológicos, assegurando a detecção e identificação das deficiências, de forma que sejam adotadas medidas para a pronta correção e prevenção de sua repetição.
A experiência prática demonstra que o resultado de medições, pode variar em função da variação de alguns fatores, por exemplo:
a) Operador; b) Equipamento utilizado; c) Calibração do instrumento; d) Condições ambientais; e) Procedimento de medição; f) Condições em que as medições são realizadas.
Desta forma, o monitoramento de processos de medição deve ser realizado, de forma a verificar a variação nos resultados das medições, quando um ou mais parâmetros são alterados. Por exemplo: pode ser verificado qual será a variação no resultado da medição de espessura de parede de um equipamento, quando as medições são realizadas por diferentes inspetores ou com diferentes instrumentos.
Ensaio de proficiência
Quando a atividade de inspeção utilizar laboratório da própria organização para realizar calibração em seus equipamentos de medição, é conveniente a realizados de programas de intra-comparações, de forma a verificar a homogeneidade dos seus resultados. Estes programas devem ser realizados através de procedimentos específicos, tendo como objetivos:
a) Analisar a consistência entre as medições realizadas pelos metrologistas ou a efetividade de treinamento; b) Estimar a grandeza das variabilidades devidas a fontes internas; c) Avaliar repetitividade e reprodutividade de processos de medição.
Quando a atividade de inspeção utilizar laboratório externo para realizar a calibração de seus equipamentos de medição, é conveniente a realização de programas de inter-comparações, de forma a verificar a homogeneidade dos seus resultados. Estes programas devem ser realizados através de procedimentos específicos, tendo como objetivo:
a) Determinar fontes de erros existentes entre laboratórios
b) Identificar, entre vários laboratórios, aqueles que necessitam se ajustar aos demais em termos em exatidão e repetitividade.
Controle das não conformidades
O sistema de gestão metrológica deve assegurar que equipamentos e processos não conformes sejam identificados e não devem ser usados até que ações corretivas e preventivas sejam tomadas, visando corrigir os parâmetros que geraram as não conformidades, de forma a atuar em suas causas.
Se um processo de medição não conforme for identificado, o responsável pelo sistema de gestão metrológica deve realizar estudo minucioso, determinando as conseqüências potenciais que a não conformidade pode ter causando e recomendar e/ou tomar as ações necessárias para sua correção.
Um equipamento de medição deve ser considerado não conforme quando apresentar alguma das situações abaixo:
a) Ter sofrido algum tipo de dano; b) Ter sofrido alguma sobrecarga; c) Estar com suspeita de mau funcionamento que possa invalidar seus requisitos metrológicos; d) Produzir resultados de medição incorretos; e) Estar com validade de sua comprovação metrológica vencida; f) Ter sido manuseado incorretamente; g) Ter o selo de proteção danificado; h) Ter sido exposto a grandezas que possam afetar adversamente seu uso pretendido; i) Apresentar erro máximo acima da tolerância;
5 – ESTUDO DE CASO
5.1 – Especificação do processo
Foi realizado um estudo referente à medição de espessura de parede de dois tubos, contendo quatro pontos de medição cada, realizadas por dez profissionais certificados pelo SNQC/END. Cada inspetor utilizou dois instrumentos diferentes e foram realizadas três séries de medições com cada instrumento. Desta forma cada pondo foi submetido a três leituras por cada instrumento. Para este estudo foram estabelecidas as seguintes condições.
a) Medições realizadas por profissionais certificados pelo SNAC/END em US-N1-ME ou US- N1-CL; b) Procedimento de inspeção qualificado por um inspetor nível 3 em US; c) Bloco padrão calibrado e comprovado metrológicamente; d) Mesmo corpo de prova; e) Mesmas condições ambientais.
No sentido de padronizar as tarefas, foi também estabelecido o seguinte roteiro para cada série de medições:
a) Ajustas o instrumento 01; b) Realizar as quatro medições com o instrumento 01 em cada um dos tubos; c) Desligar o instrumento 01; d) Ajustas o instrumento 02; e) Realizar as quatro medições com o instrumento 02 em cada um dos tubos. f) Desligar o instrumento 02;
5.2 – Critério de aceitação de valores extremos
Quando se realiza uma série de medições, existe a possibilidade de ocorrerem erros espúrios tendo como conseqüência valores que estão fora da distribuição. Existem vários fatores que contribuem para provocar a existência destes valores espúrios, entre os quais podemos citar:
a) Avaliação equivocada da indicação; b) Erro de registro;