
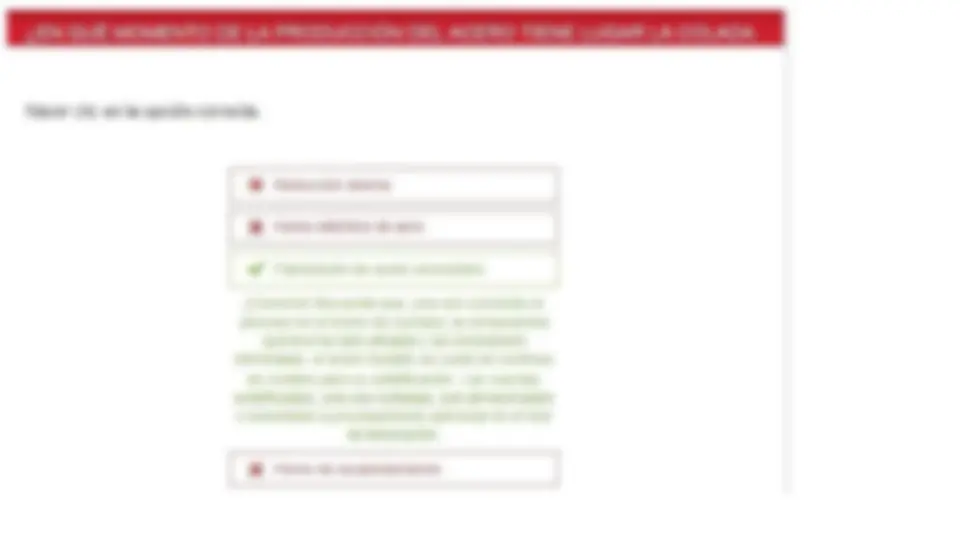
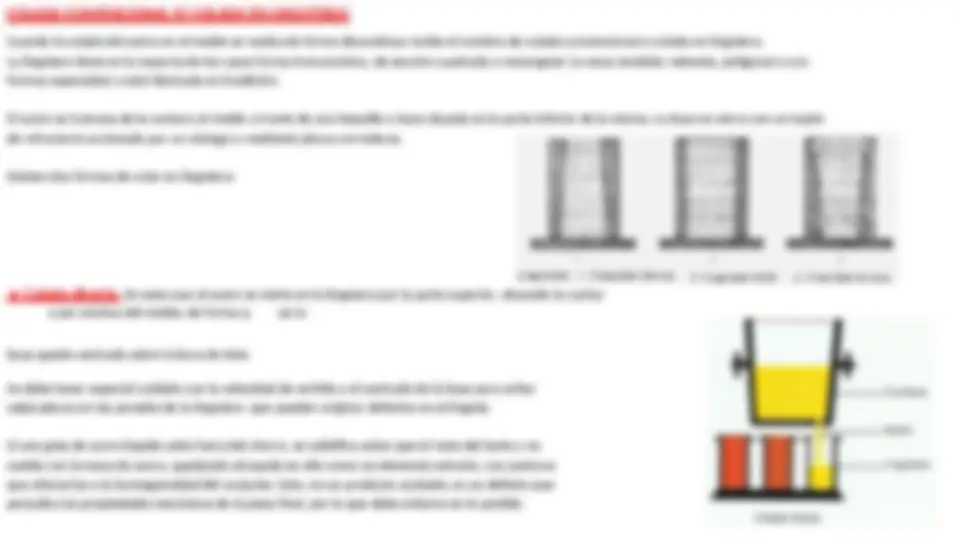
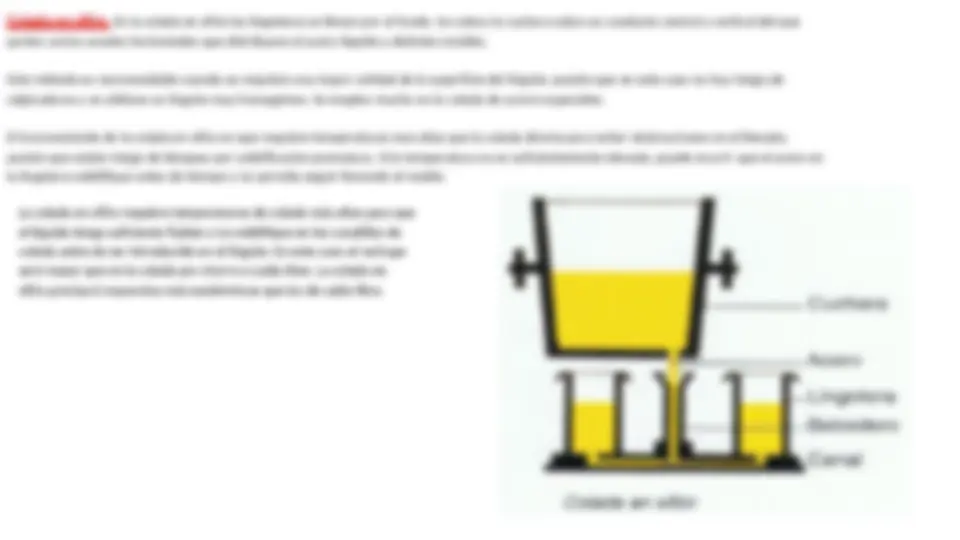
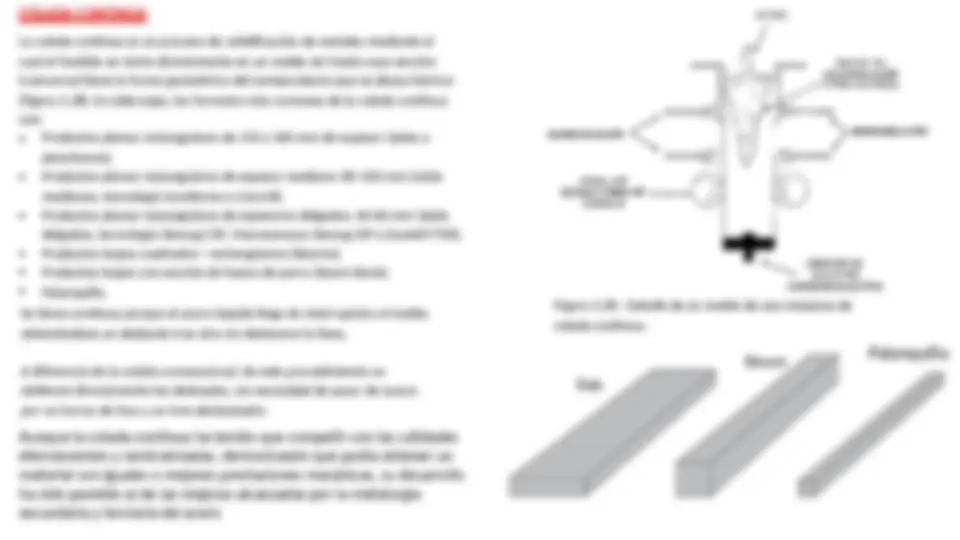
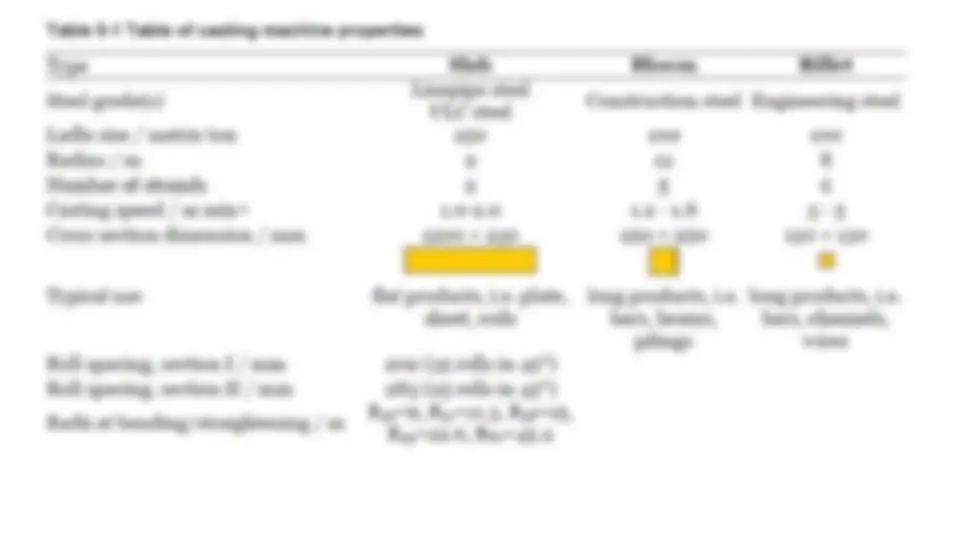
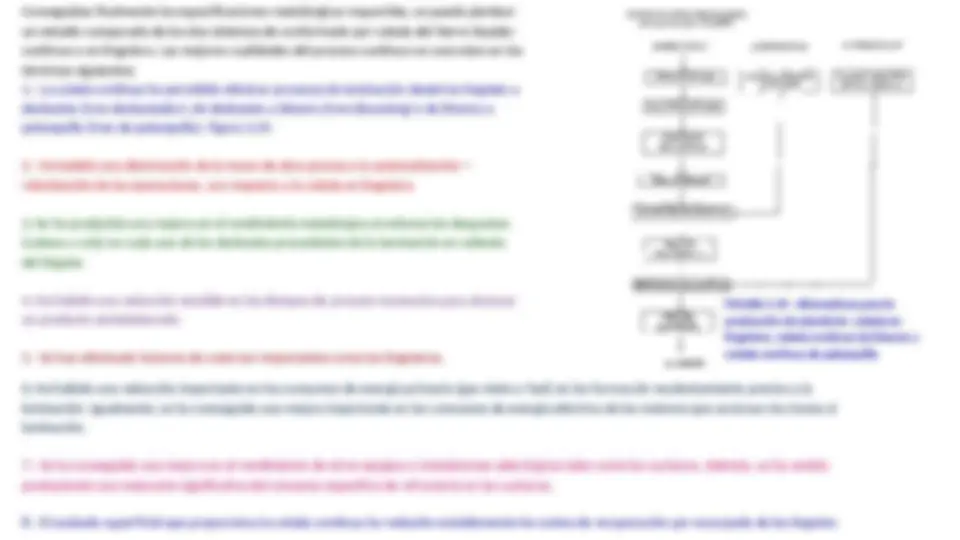
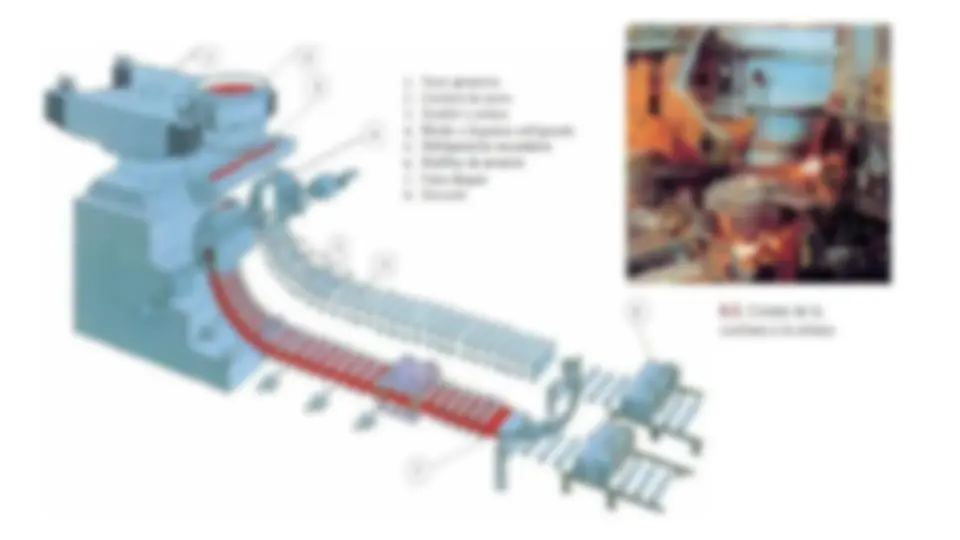
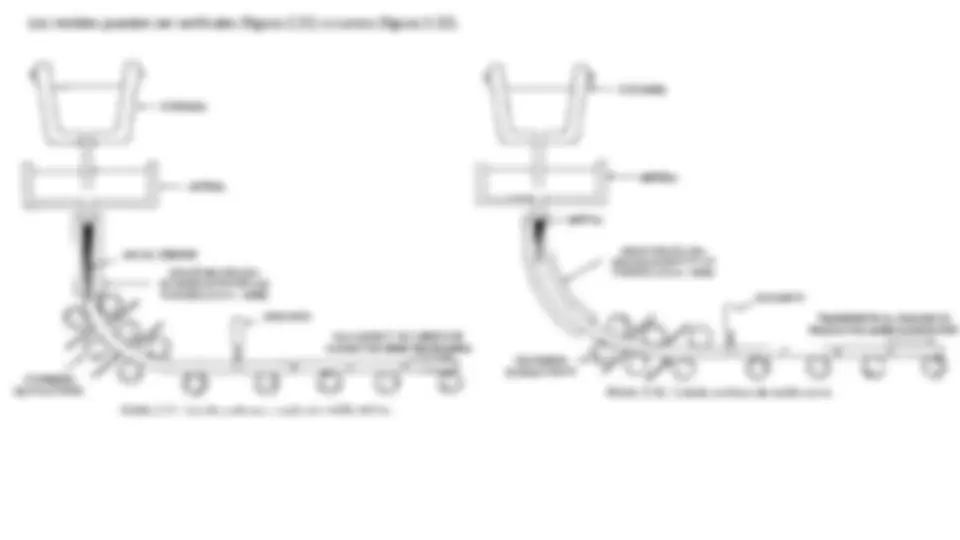
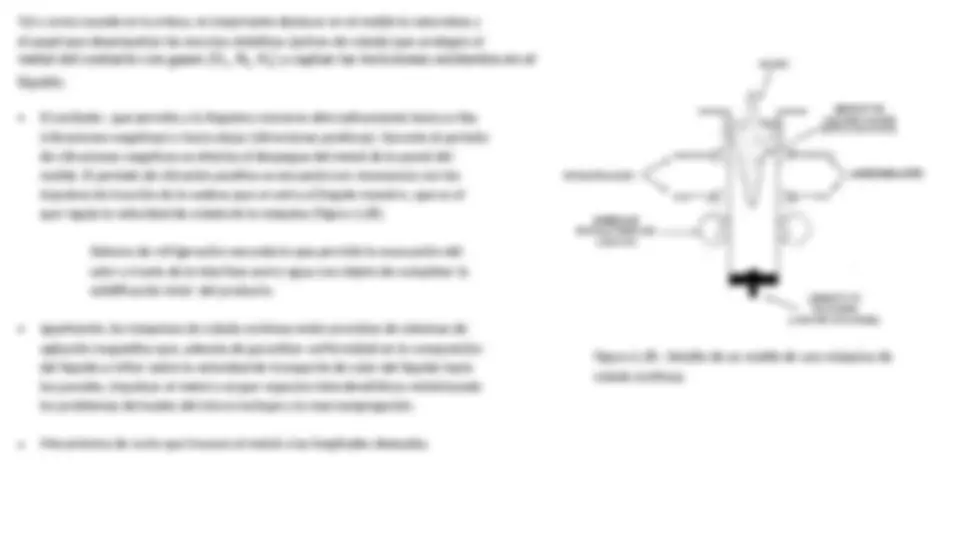
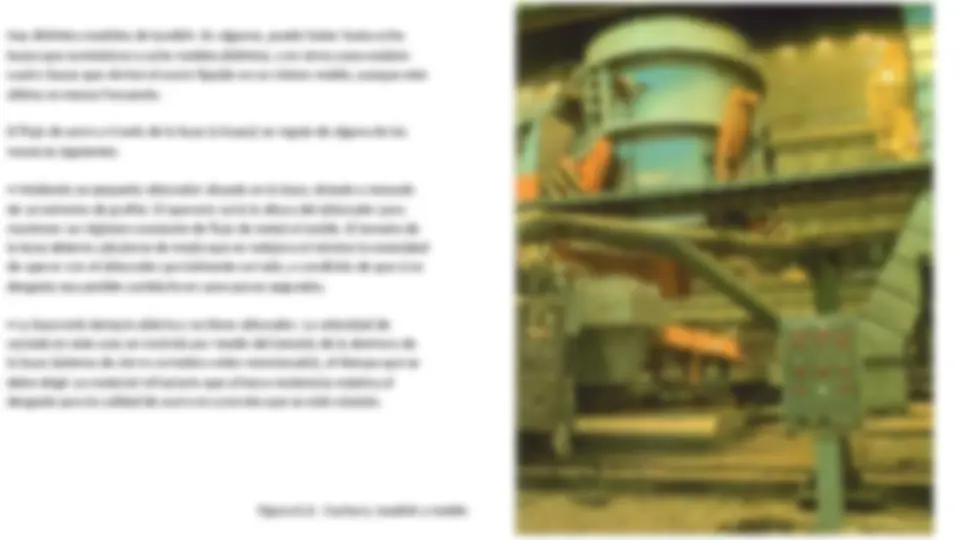
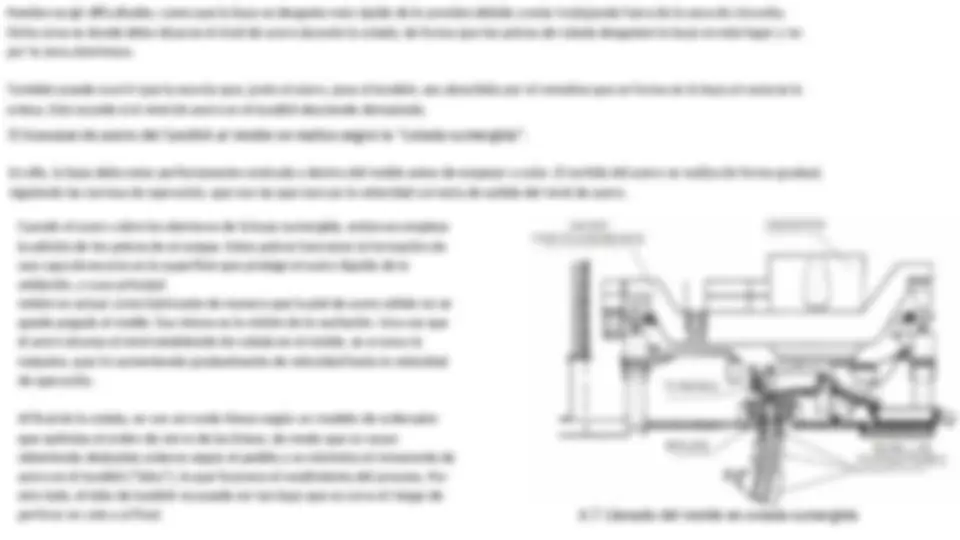
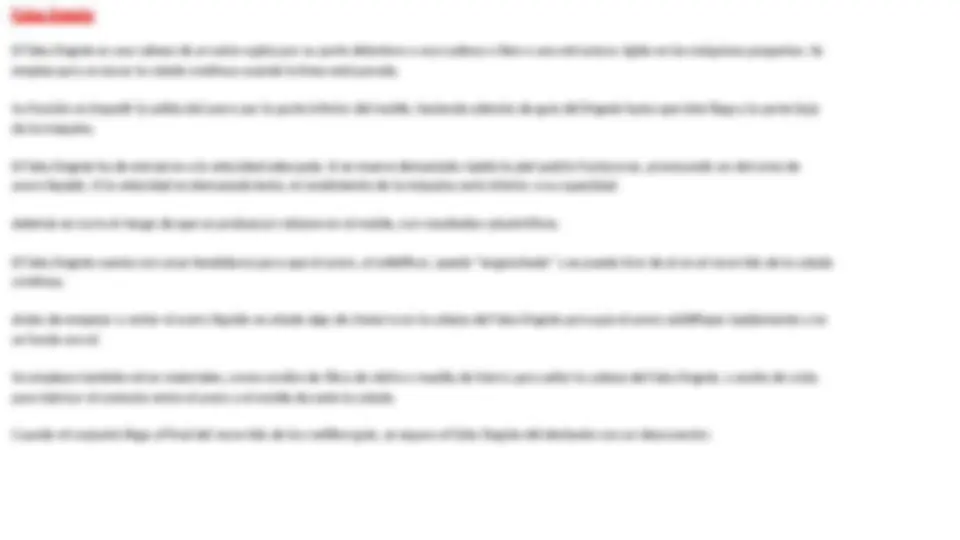
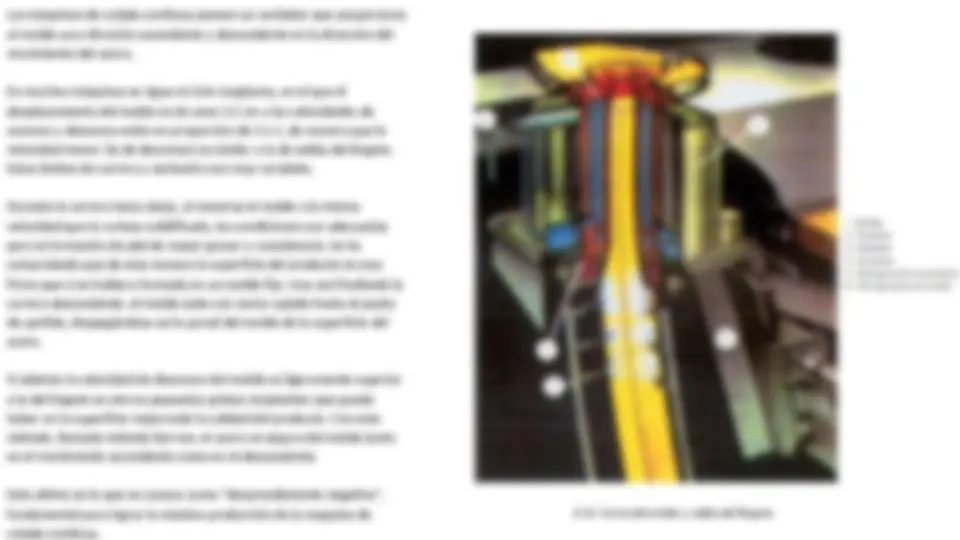
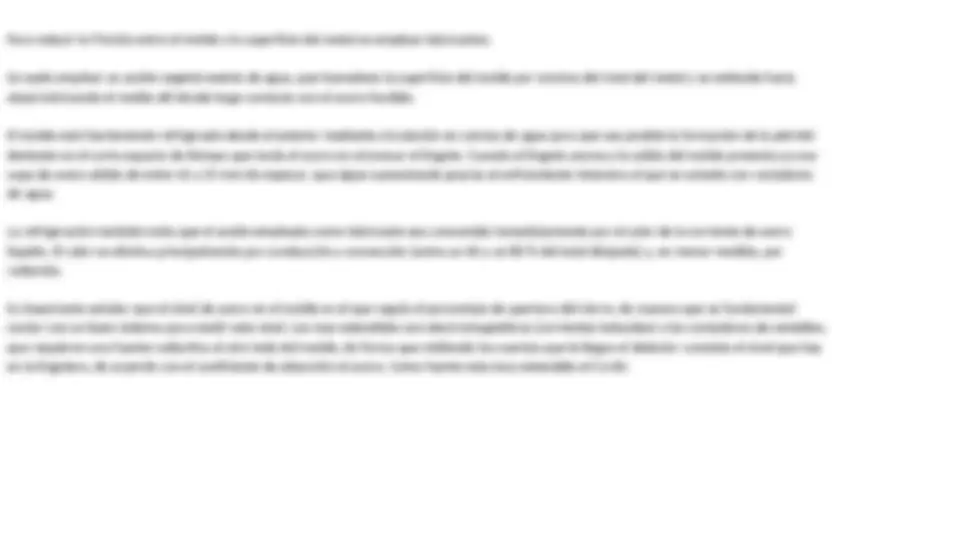
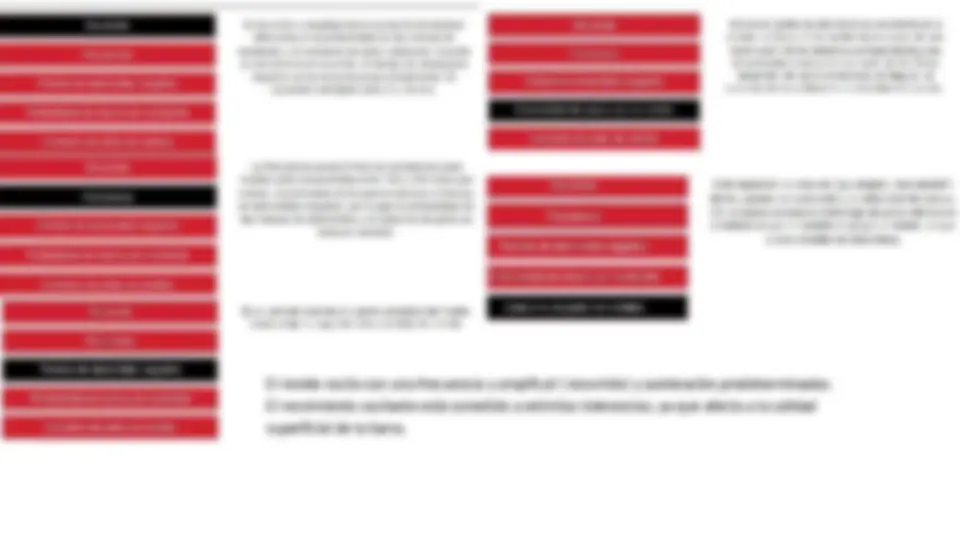
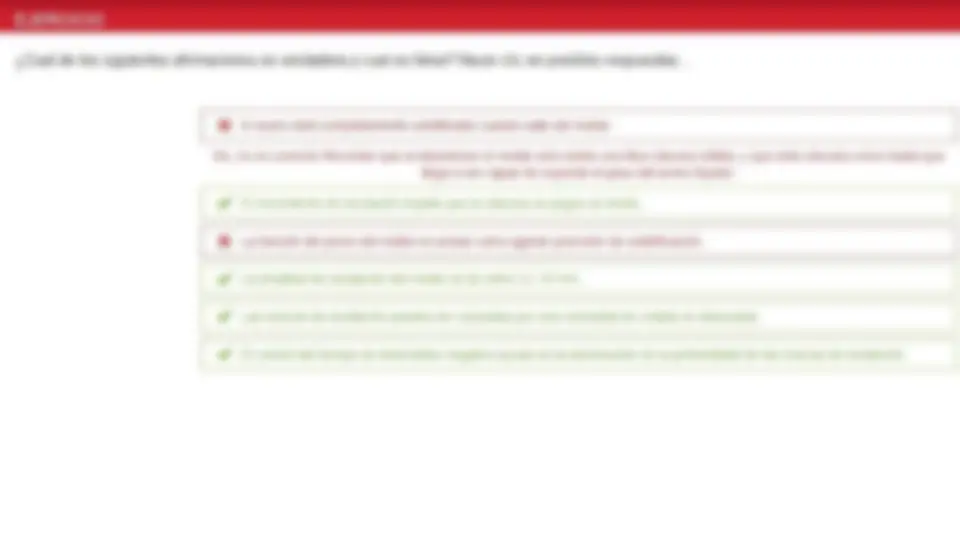
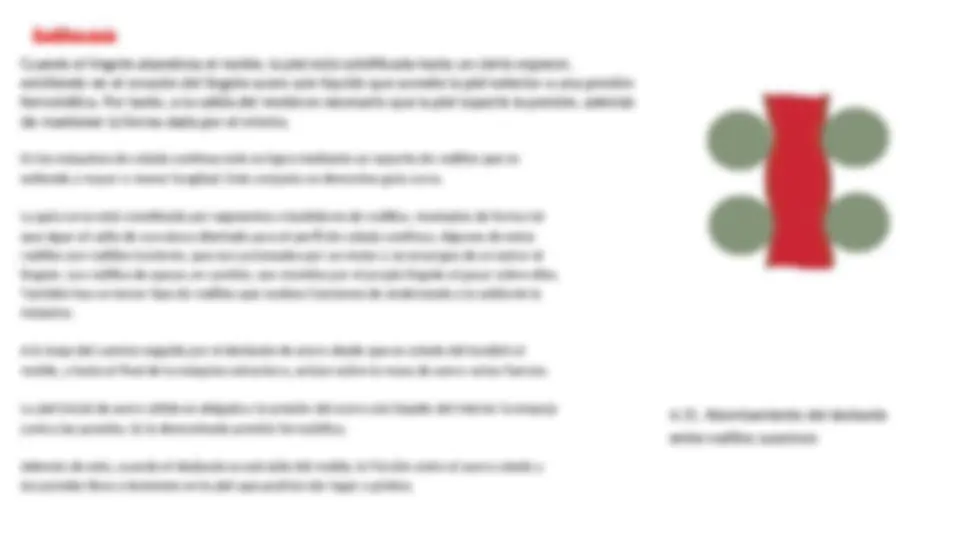

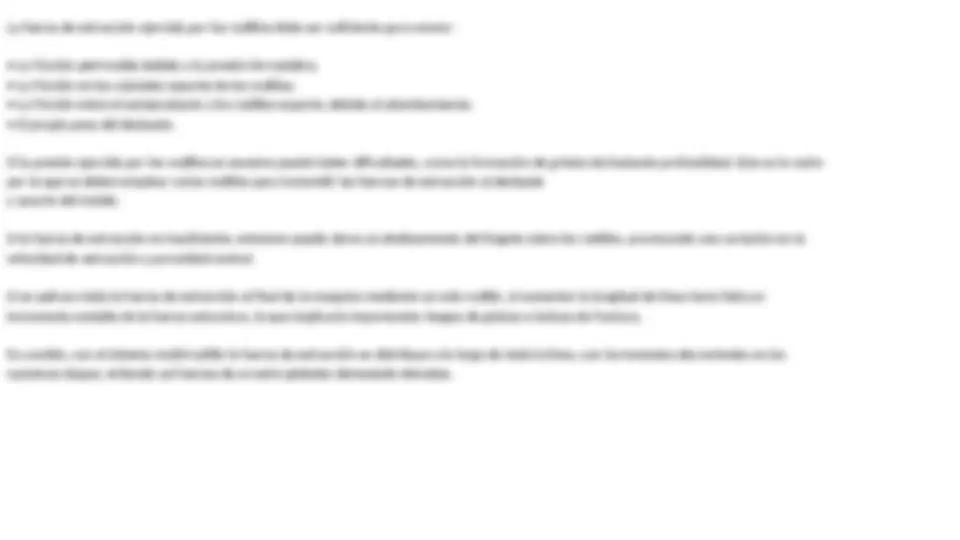
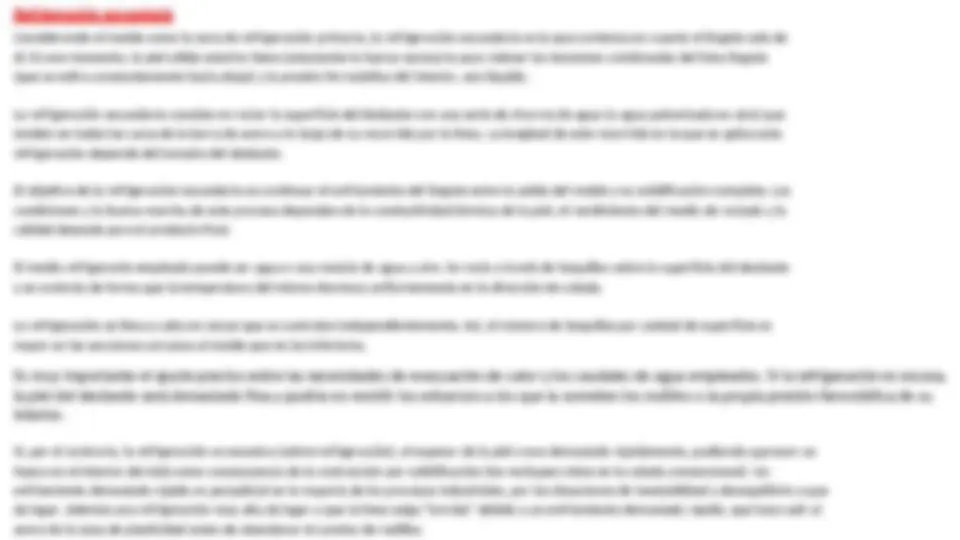
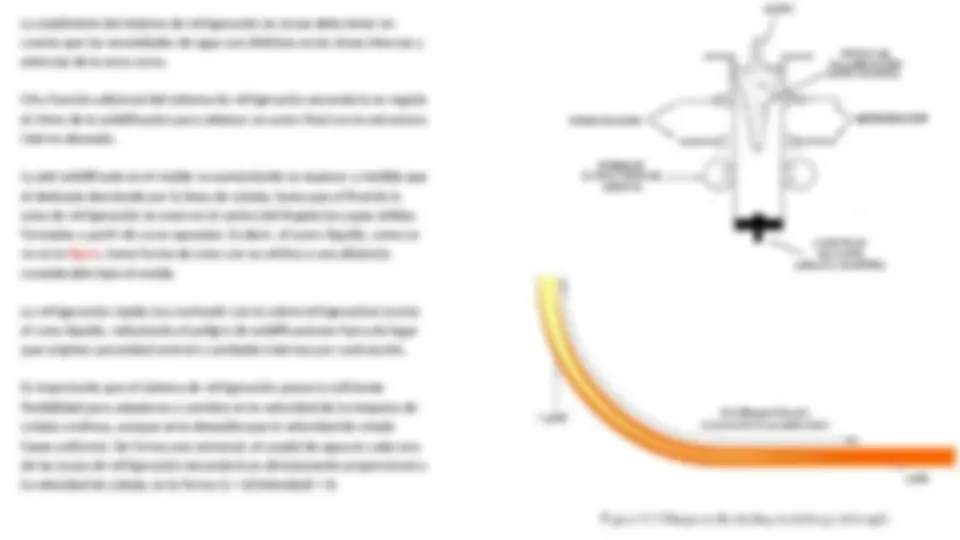
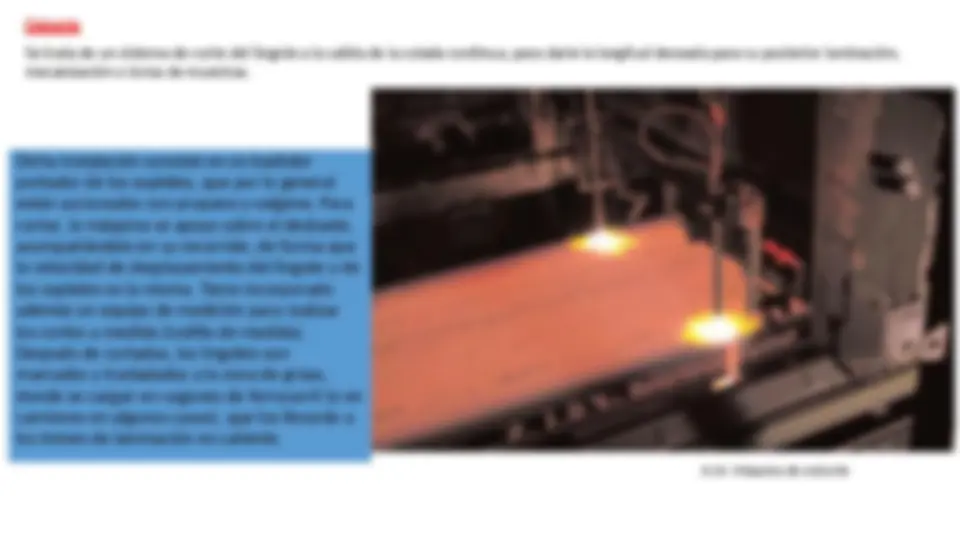
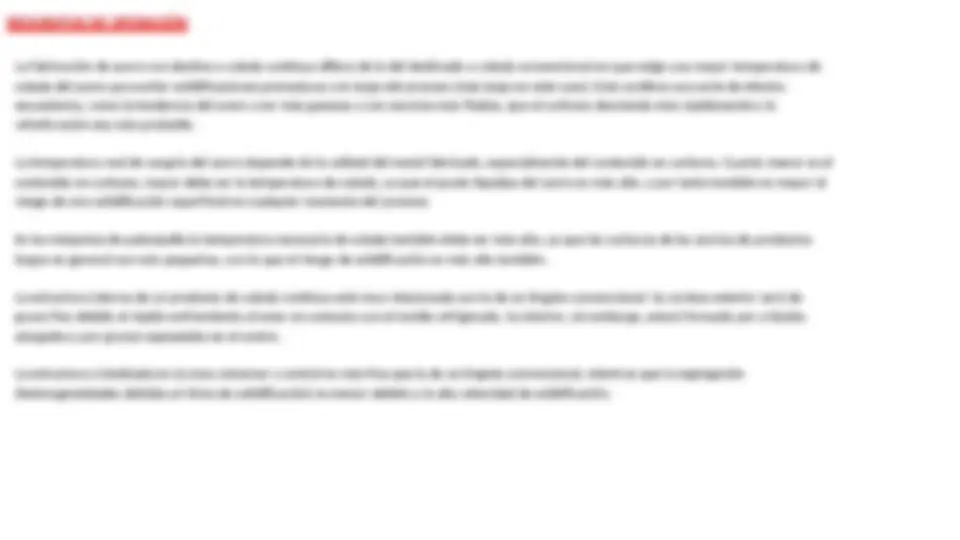
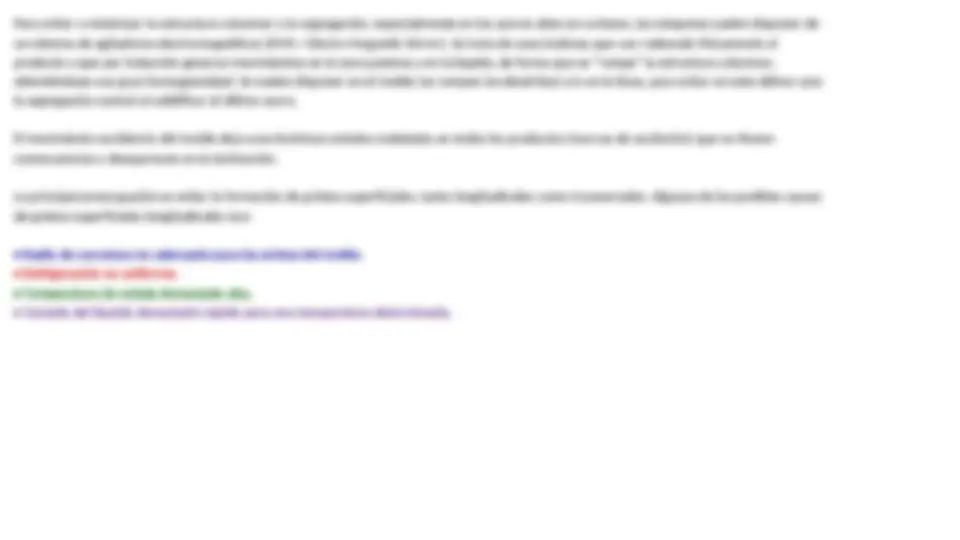
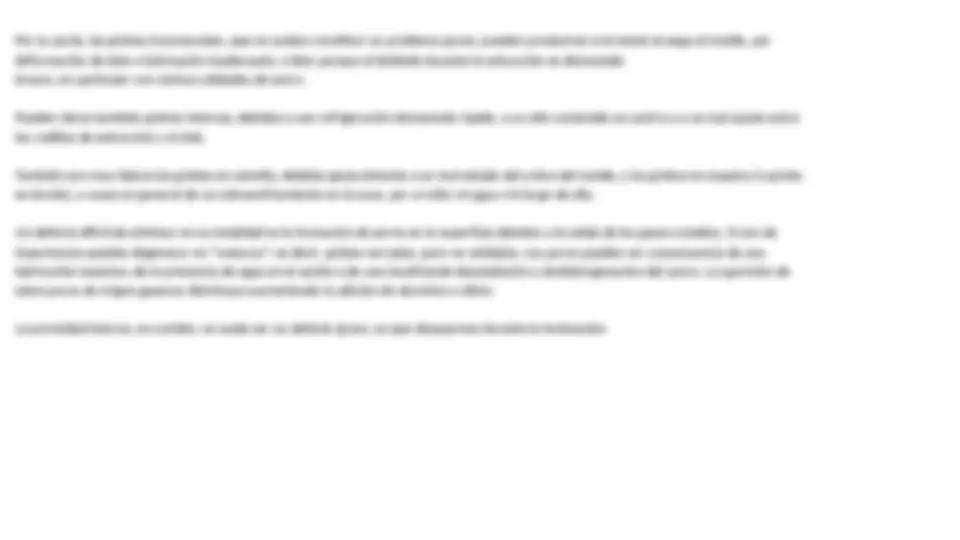
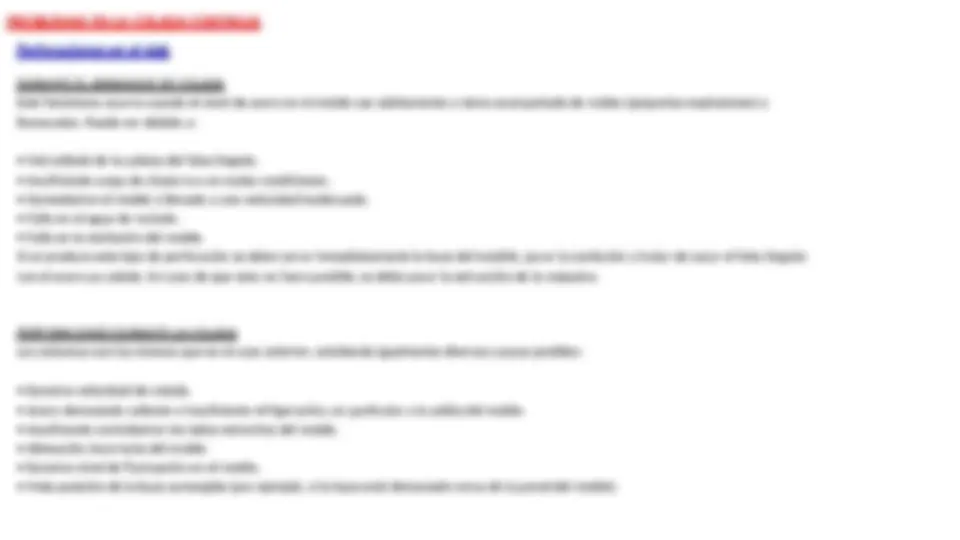
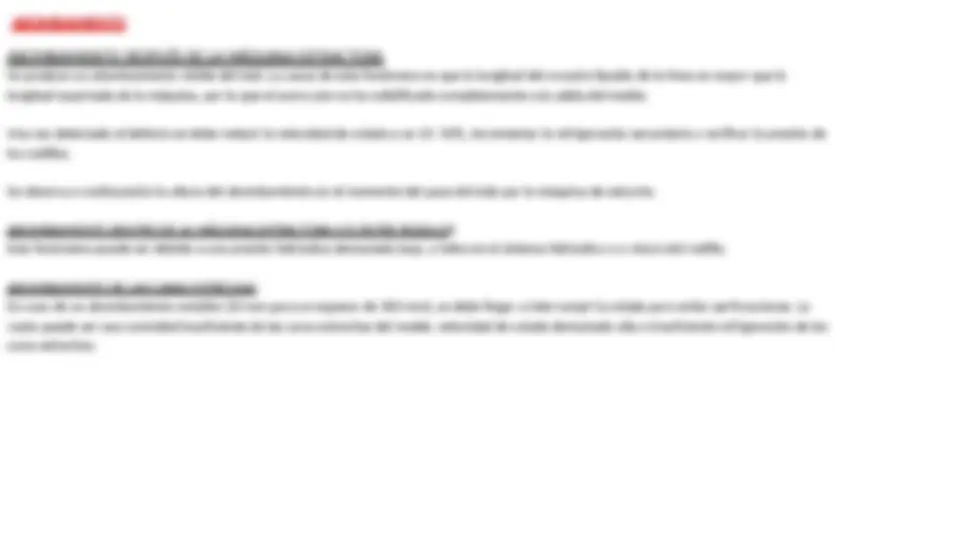
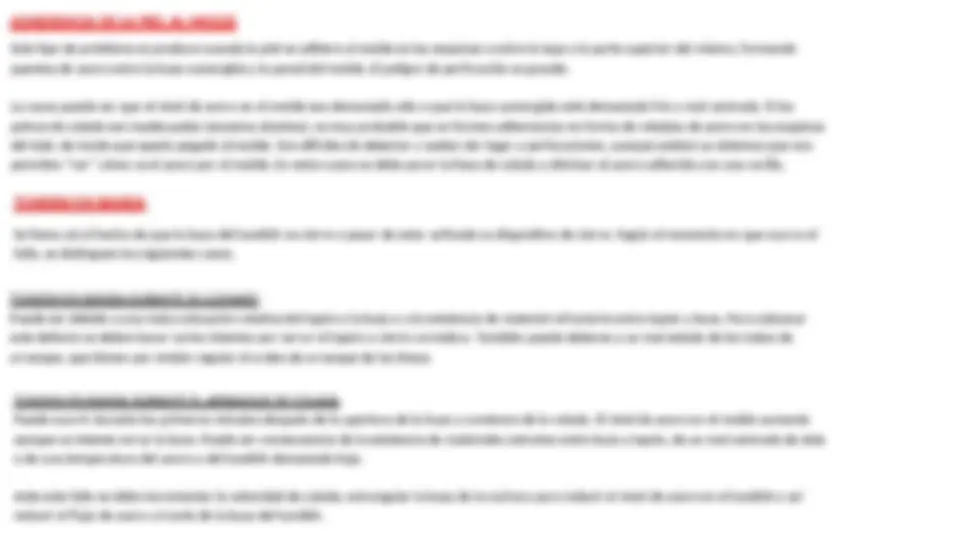
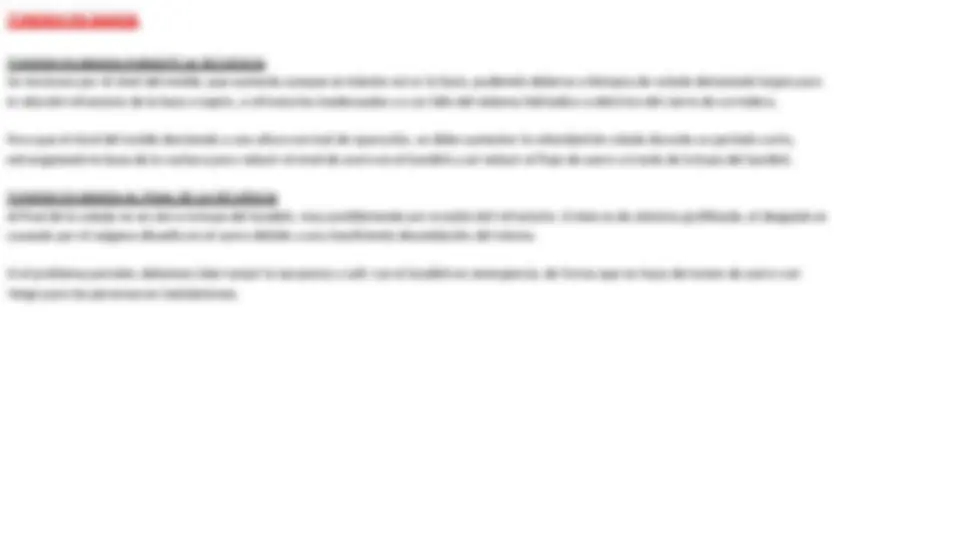

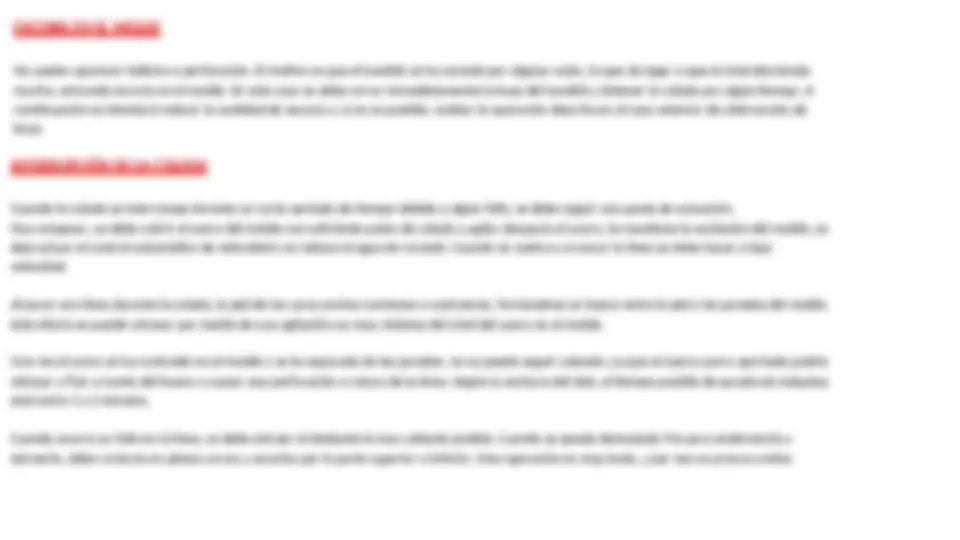
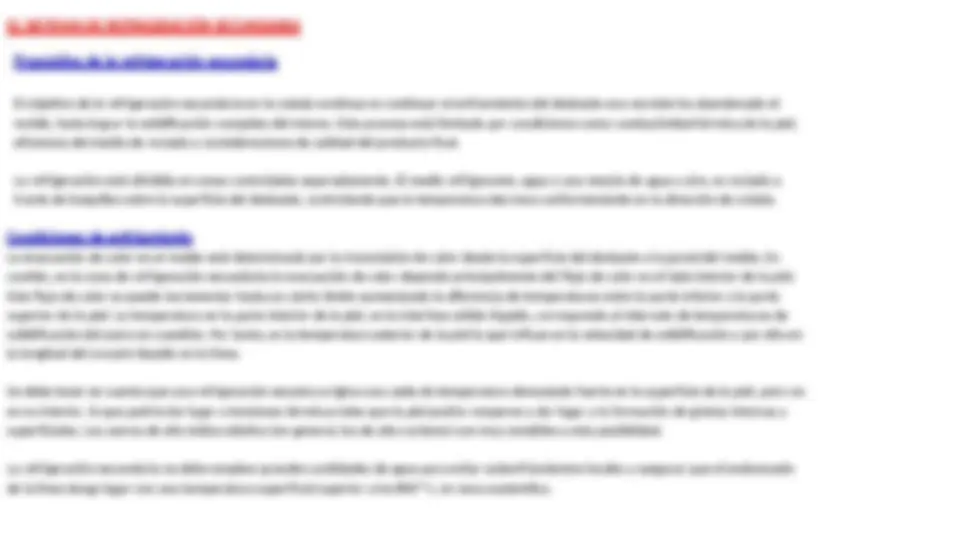
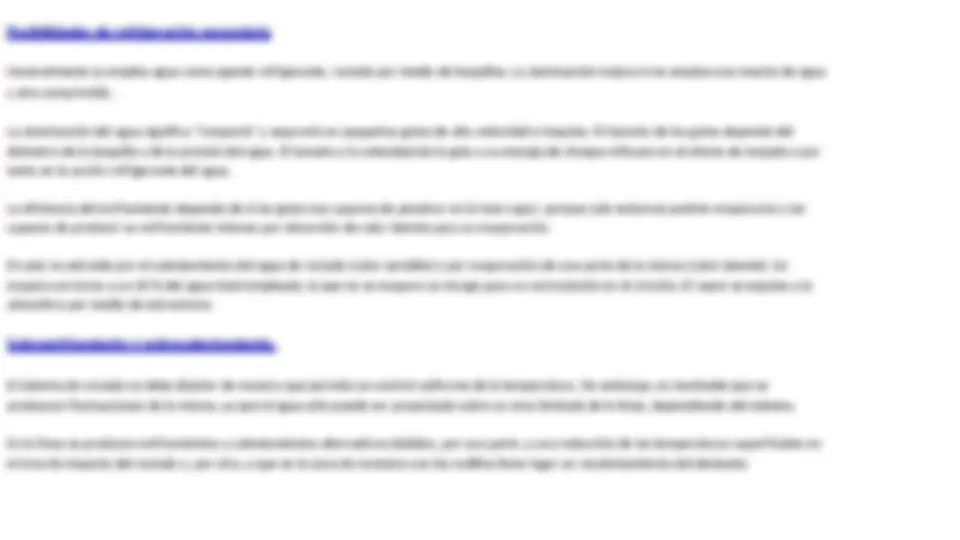
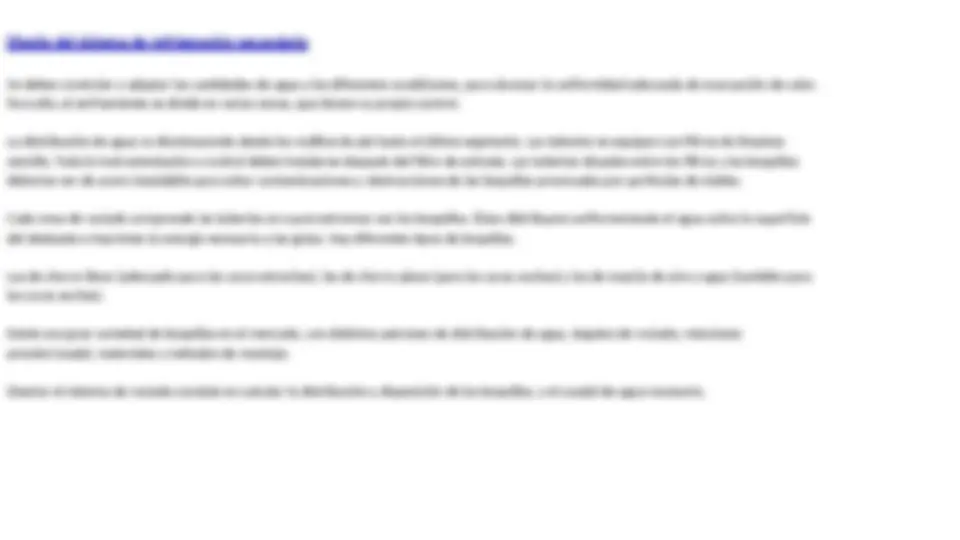

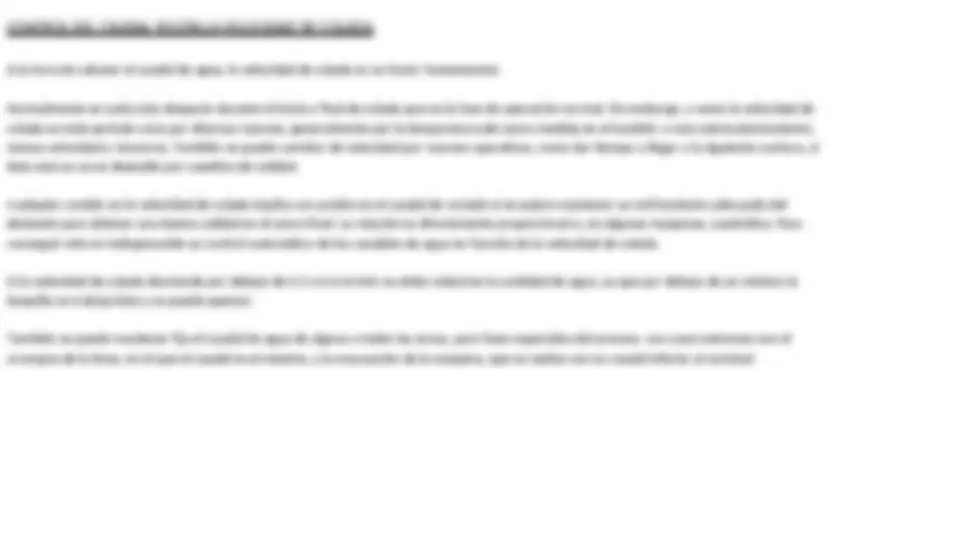
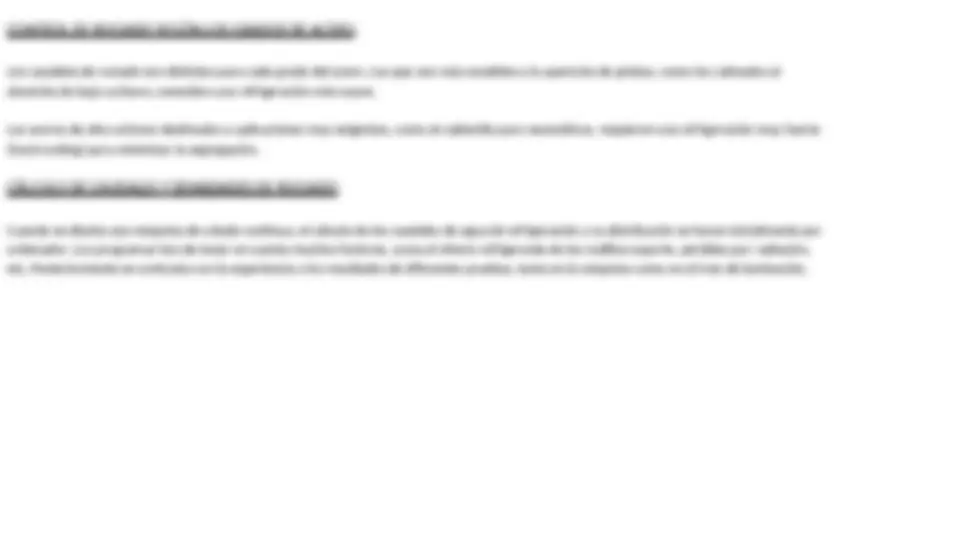
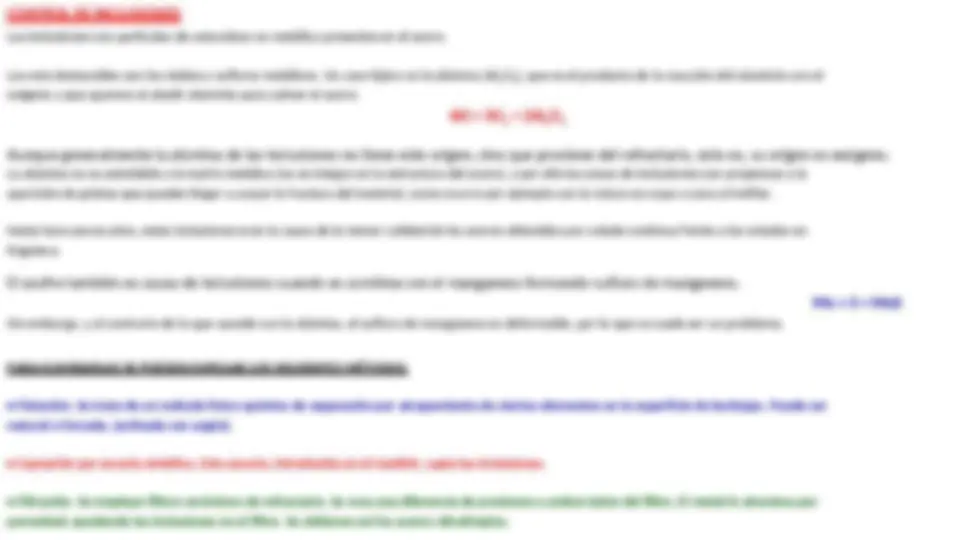
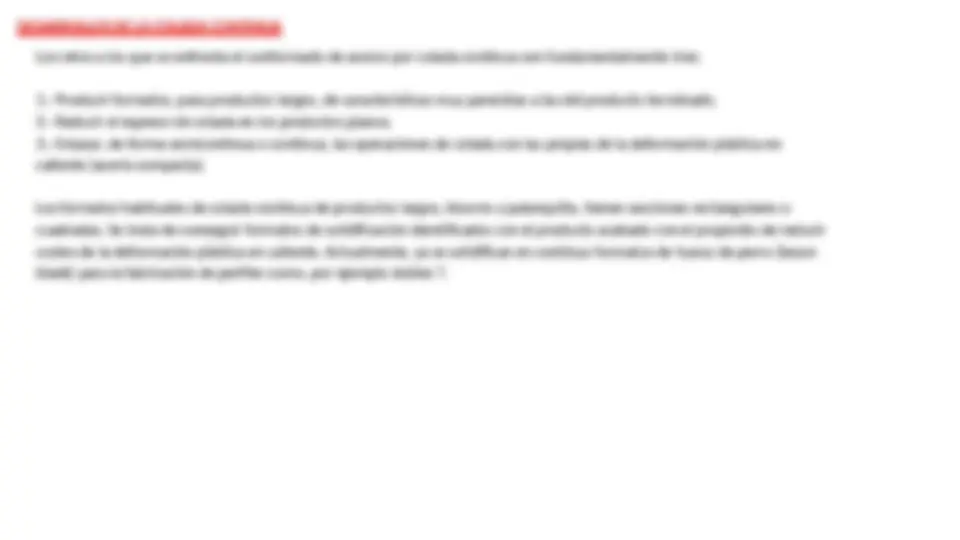
Estude fácil! Tem muito documento disponível na Docsity
Ganhe pontos ajudando outros esrudantes ou compre um plano Premium
Prepare-se para as provas
Estude fácil! Tem muito documento disponível na Docsity
Prepare-se para as provas com trabalhos de outros alunos como você, aqui na Docsity
Os melhores documentos à venda: Trabalhos de alunos formados
Prepare-se com as videoaulas e exercícios resolvidos criados a partir da grade da sua Universidade
Responda perguntas de provas passadas e avalie sua preparação.
Ganhe pontos para baixar
Ganhe pontos ajudando outros esrudantes ou compre um plano Premium
Comunidade
Peça ajuda à comunidade e tire suas dúvidas relacionadas ao estudo
Descubra as melhores universidades em seu país de acordo com os usuários da Docsity
Guias grátis
Baixe gratuitamente nossos guias de estudo, métodos para diminuir a ansiedade, dicas de TCC preparadas pelos professores da Docsity
pasos para colada continua y composicion para controlar variables fisiscas
Tipologia: Esquemas
1 / 47
Esta página não é visível na pré-visualização
Não perca as partes importantes!
Tras la metalurgia secundaria, el acero pasa a la etapa de solidificación, donde se obtienen generalmente semiproductos de sección constante que serán transformados posteriormente para darles la forma de la pieza final. Existen diferentes procesos de solidificación:
**- Colar el acero sobre moldes con la forma de la pieza final que se desea obtener (acero moldeado).
a por encima del molde, de forma q
Cuando la colada del acero en el molde se realiza de forma discontinua recibe el nombre de colada convencional o colada en lingotera. La lingotera tiene en la mayoría de los casos forma troncocónica, de sección cuadrada o rectangular (a veces también redonda, poligonal o con formas especiales) y está fabricada en fundición. El acero se trasvasa de la cuchara al molde a través de una boquilla o buza situada en la parte inferior de la misma. La buza se cierra con un tapón de refractario accionado por un vástago o mediante placas correderas. Existen dos formas de colar en lingotera:
- Colada directa. En este caso el acero se vierte en la lingotera por la parte superior, situando la cuchar ue la buza quede centrada sobre la boca de éste. Se debe tener especial cuidado con la velocidad de vertido y el centrado de la buza para evitar salpicaduras en las paredes de la lingotera que pueden originar defectos en el lingote. Si una gota de acero líquido salta fuera del chorro, se solidifica antes que el resto del baño y no suelda con la masa de acero, quedando atrapada en ella como un elemento extraño, con junturas que afectarían a la homogeneidad del conjunto. Esto, en un producto acabado, es un defecto que perjudica las propiedades mecánicas de la pieza final, por lo que debe evitarse en lo posible.
parten varios canales horizontales que distribuyen el acero liquido a distintos moldes. Este método es recomendable cuando se requiere una mayor calidad de la superficie del lingote, puesto que en este caso no hay riesgo de salpicaduras y se obtiene un lingote muy homogéneo. Se empleo mucho en la colada de aceros especiales. El inconveniente de la colada en sifón es que requiere temperaturas mas altas que la colada directa para evitar obstrucciones en el llenado, puesto que existe riesgo de bloqueo por solidificación prematura. Si la temperatura no es suficientemente elevada, puede ocurrir que el acero en la lingotera solidifique antes de tiempo y no permita seguir llenando el molde. La colada en sifón requiere temperaturas de colada más altas para que el líquido tenga suficiente fluidez y no solidifique en los canalillos de colada antes de ser introducido en el lingote. En este caso el rechupe será mayor que en la colada por chorro o caída libre. La colada en sifón precisará mazarotas más exotérmicas que las de caída libre.
La idea inicial de colar de forma continua metales líquidos surge durante la primera mitad del siglo XIX. Los primeros proyectos ya incluían moldes refrigerados por agua, refrigeración secundaria, falso lingote, rodillos extractores y una máquina de corte de la línea. En 1933 Junghans desarrolla y patenta su sistema de oscilación del molde, lo que constituye un importante pilar para la aplicación de la colada continua a escala industrial. A partir de 1950 el desarrollo de la colada continua va a marcar una nueva era en el diseño de las nuevas acerías. Las máquinas de colada continua han ido evolucionando, pasando de las completamente verticales a las actuales, de menor altura, en las que el acero se solidifica con cierto grado de curvatura. Una vez en la zona horizontal de la línea, se endereza el desbaste y se corta a la medida. Es importante señalar que se debe calmar el acero en la metalurgia secundaria antes de ser llevado a la colada continua, puesto que en el caso de los aceros efervescentes la salida masiva de los gases ocluidos provocaría grandes vibraciones en la máquina y perforación del acero. No fue hasta que se desarrollaron suficientemente las técnicas de calmado del acero cuando se hizo posible aplicar la colada continua de forma generalizada. El rendimiento de los procesos de colada continua está en torno al 95 %, mucho mayor que el de la colada convencional o en lingotera, ya que en este caso no hay mazarotas que se deban recortar.
La colada continua es un proceso de solidificación de metales mediante el cual el fundido se vierte directamente en un molde sin fondo cuya sección transversal tiene la forma geométrica del semiproducto que se desea fabricar (figura 2.2 8 ). En siderurgia, los formatos más comunes de la colada continua son:
planchones). Productos planos rectangulares de espesor mediano: 80 - 100 mm (slabs medianos, tecnología Sumitomo o Conroll). Productos planos rectangulares de espesores delgados: 40 - 60 mm (slabs delgados, tecnología Siemag CSP, Mannesmann Demag ISP o Danieli FTSR). Productos largos cuadrados—rectangulares (blooms). Productos largos con sección de hueso de perro (beam blank). Palanquilla.
Figura 2.2 8 .- Detalle de un molde de una máquina de colada continua.
Se llama continua porque el acero líquido llega sin interrupción al molde, obteniéndose un desbaste tras otro sin detenerse la línea.
A diferencia de la colada convencional, de este procedimiento se obtienen directamente los desbastes, sin necesidad de pasar de nuevo por un horno de fosa y un tren desbastador.
Conseguidas finalmente las especificaciones metalúrgicas requeridas, se puede plantear un estudio comparado de los dos sistemas de conformado por colada del hierro líquido: continuo o en lingotera. Las mejores cualidades del proceso continuo se concretan en los términos siguientes: 1 .- La colada continua ha permitido eliminar procesos de laminación desde los lingotes a desbastes (tren desbastador), de desbastes a blooms (tren blooming) o de blooms a palanquilla (tren de palanquilla). Figura 2. 29. 2 .- Ha habido una disminución de la mano de obra gracias a la automatización— robotización de las operaciones, con respecto a la colada en lingotera. 3 .-Se ha producido una mejora en el rendimiento metalúrgico al evitarse los despuntes (cabeza y cola) en cada uno de los desbastes procedentes de la laminación en caliente del lingote. 4 .-Ha habido una reducción sensible en los tiempos de proceso necesarios para alcanzar un producto semielaborado. FIGURA 2. 29. -Alternativas para la producción de alambrón: colada en lingotera, colada continua de blooms y 5 .- Se han eliminado factores de coste tan importantes como las lingoteras.^ colada^ continua^ de^ palanquilla 6 .-Ha habido una reducción importante en los consumos de energía primaria (gas mixto y fuel) en los hornos de recalentamiento previos a la laminación. Igualmente, se ha conseguido una mejora importante en los consumos de energía eléctrica de los motores que accionan los trenes d laminación. 7 .- Se ha conseguido una mejora en el rendimiento de otros equipos o instalaciones siderúrgicas tales como las cucharas. Además, se ha venido produciendo una reducción significativa del consumo específico de refractario en las cucharas. 8 .- El acabado superficial que proporciona la colada continua ha reducido notablemente los costes de recuperación por escarpado de los lingotes
La máquinas de colada continua han ido evolucionando en su construcción pasando de las primeras completamente verticales (figura 2.30) hasta máquinas que han disminuido notablemente su altura, de forma que el semiproducto se cuela en una máquina de geometría curvada y solidifica con un radio determinado de curvatura, volviendo después de su solidificación a enderezarse para el corte final. La tendencia a la reducción de la altura de las instalaciones de colada continua ha llegado al máximo con las maquinas de colada continua horizontal. Las máquinas de colada continua horizontal funcionan con éxito desde 1966. En este año, Dawy-Loewy Ltd. instaló la primera máquina de este tipo en Gran Bretaña. Sus principales ventajas son:
Es el primer elemento de la instalación. En la torre se colocan las cucharas que proceden de metalurgia secundaria y que alimentan a la artesa o tundish. Cada torre tiene capacidad para dos cucharas (situadas opuestas una a la otra), cada una de ellas sostenida con dos brazos que la sujetan con firmeza y con un dispositivo de fijación que evita cualquier movimiento durante la colada. La torre dispone de movimientos de giro (36 0 º) y elevación independientes en cada brazo, de forma que puede alcanzar las posiciones de espera, colada y emergencia. Cuando la cuchara está en posición de colada, está suministrando acero líquido a la artesa, mientras que la cuchara opuesta a ella estaría en posición de espera. Cuando la primera cuchara está vacía, la torre gira 180 º y la segunda pasa a estar en posición de colada. Las cucharas deben calentarse para evitar choques térmicos (una gran diferencia de temperatura entre el acero líquido y la pared de la cuchara puede originar grietas en ésta) y homogeneizar la temperatura. Además, el acero podría solidificar en la propia cuchara si permanece en ella demasiado tiempo. El grado de calentamiento dependerá de la capacidad de la cuchara: cuanto mayor sea, mayor será la masa de acero que contiene y se enfriará más lentamente, por lo que la temperatura a la que hay que calentar la cuchara será menor. Por ejemplo, una cuchara de 100 t de capacidad se calienta a unos 700 oC, pero si la cuchara es de pocas toneladas hay que elevar la temperatura hasta los 1400 oC aproximadamente. Además es necesario mantener el calor del interior de la cuchara durante la colada a la artesa, operación que puede llevar un tiempo considerable por las exigencias de la colada continua. Para ello se puede cubrir la superficie del metal con una delgada capa de escoria u otro material aislante. Otra opción cada vez mas extendida es colocar una tapa en la cuchara a la salida de metalurgia secundaria, y no retirarla hasta que termina de colar en la maquina.
Se llama tundish o artesa al recipiente que recibe el acero líquido de la cuchara y lo distribuye por medio de las buzas a las líneas de colada, que generalmente son dos en las máquinas de slabs, tres o cuatro en las de blooms y de seis a ocho en las de palanquilla. El tundish actúa como acumulador de acero liquido, de forma que cuando hay que cambiar la cuchara, no se detiene el suministro de acero a la línea de colada. Como ventaja adicional, gracias al tundish se consigue una limpieza superior del acero, ya que parte de las inclusiones (refractario-exógenas y óxidos-endógenas) pasan a la superficie, siendo el acero libre de ellas el que se cuela al molde. La artesa esta constituida por una chapa de acero recubierta interiormente por refractario. En ella, el paso del acero al molde se controla por medio de una barra tapón o bien mediante el sistema de cierre corredera, cuyo porcentaje de apertura es regulado de forma continua por el nivel de acero en el molde, de forma que este se mantenga lo mas constante posible. El argón o el nitrógeno se emplean en el acoplamiento buza- tundish para inertizar, protegiendo así el chorro de acero del ataque atmosférico. Antes del inicio de la colada o la serie de coladas se sitúa el tundish en la zona de calentamiento, donde, mediante quemadores de gas, se eleva tanto su temperatura como la de la buza. Así se evita un choque térmico cuando se inicie la colada. El tundish esta montado sobre un carro que tiene movimiento de traslación y de elevación-descenso, para poder ser trasladado desde la zona de calentamiento hasta la de colada, bajo la torre de cucharas y sobre el molde. El movimiento de elevación hace posible colocar la buza corta (buza entre el tundish y el molde) dentro del molde. El carro esta equipado con un sistema de pesaje para poder conocer en todo momento el peso del acero en el interior del tundish, que facilita además la regulación del nivel de metal en el mismo.
Pueden surgir dificultades, como que la buza se desgaste más rápido de lo previsto debido a estar trabajando fuera de la zona de circonita. Dicha zona es donde debe situarse el nivel de acero durante la colada, de forma que los polvos de colada desgasten la buza en este lugar y no por la zona aluminosa. También puede ocurrir que la escoria que, junto al acero, pasa al tundish, sea absorbida por el remolino que se forma en la buza al vaciarse la artesa. Esto sucede si el nivel de acero en el tundish desciende demasiado.
En ella, la buza debe estar perfectamente centrada y dentro del molde antes de empezar a colar. El vertido del acero se realiza de forma gradual, siguiendo las normas de operación, que son las que marcan la velocidad correcta de subida del nivel de acero. Cuando el acero cubre las aberturas de la buza sumergida, entonces empieza la adición de los polvos de arranque. Estos polvos favorecen la formación de una capa de escoria en la superficie que protege el acero líquido de la oxidación, y cuya principal misión es actuar como lubricante de manera que la piel de acero sólido no se quede pegada al molde. Esa misma es la misión de la oscilación. Una vez que el acero alcanza el nivel establecido de colada en el molde, se arranca la máquina, que irá aumentando gradualmente de velocidad hasta la velocidad de operación. Al final de la colada, se van cerrando líneas según un modelo de ordenador que optimiza el orden de cierre de las líneas, de modo que se vayan obteniendo desbastes enteros según el pedido y se minimice el remanente de acero en el tundish (“lobo”), lo que favorece el rendimiento del proceso. Por otro lado, el lobo de tundish no puede ser tan bajo que se corra el riesgo de
El falso lingote es una cabeza de arrastre sujeta por su parte delantera a una cadena o bien a una estructura rígida en las máquinas pequeñas. Se emplea para arrancar la colada continua cuando la línea está parada. Su función es impedir la salida del acero por la parte inferior del molde, haciendo además de guía del lingote hasta que éste llega a la parte baja de la máquina. El falso lingote ha de extraerse a la velocidad adecuada. Si se mueve demasiado rápido la piel podría fracturarse, provocando un derrame de acero líquido. Si la velocidad es demasiado lenta, el rendimiento de la máquina sería inferior a su capacidad. Además se corre el riesgo de que se produzcan reboses en el molde, con resultados catastróficos. El falso lingote cuenta con unas hendiduras para que el acero, al solidificar, quede “enganchado” y se pueda tirar de el en el recorrido de la colada continua. Antes de empezar a verter el acero liquido se añade algo de chatarra en la cabeza del falso lingote para que el acero solidifique rápidamente y no se funda con el. Se emplean también otros materiales, como cordón de fibra de vidrio o masilla de hierro para sellar la cabeza del falso lingote, y aceite de colza para lubricar el contacto entre el acero y el molde durante la colada. Cuando el conjunto llega al final del recorrido de los rodillos-guía, se separa el falso lingote del desbaste con un desconector.