
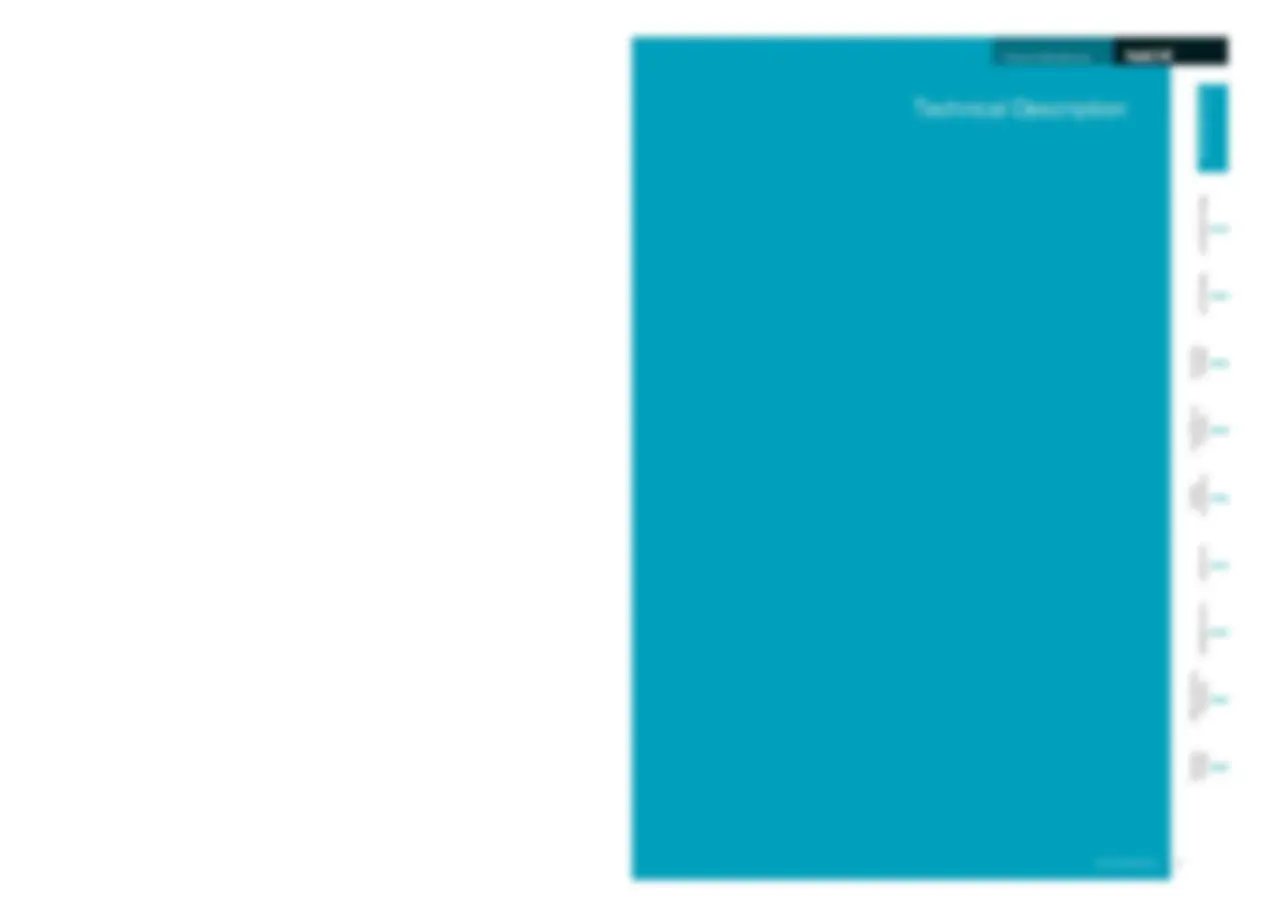
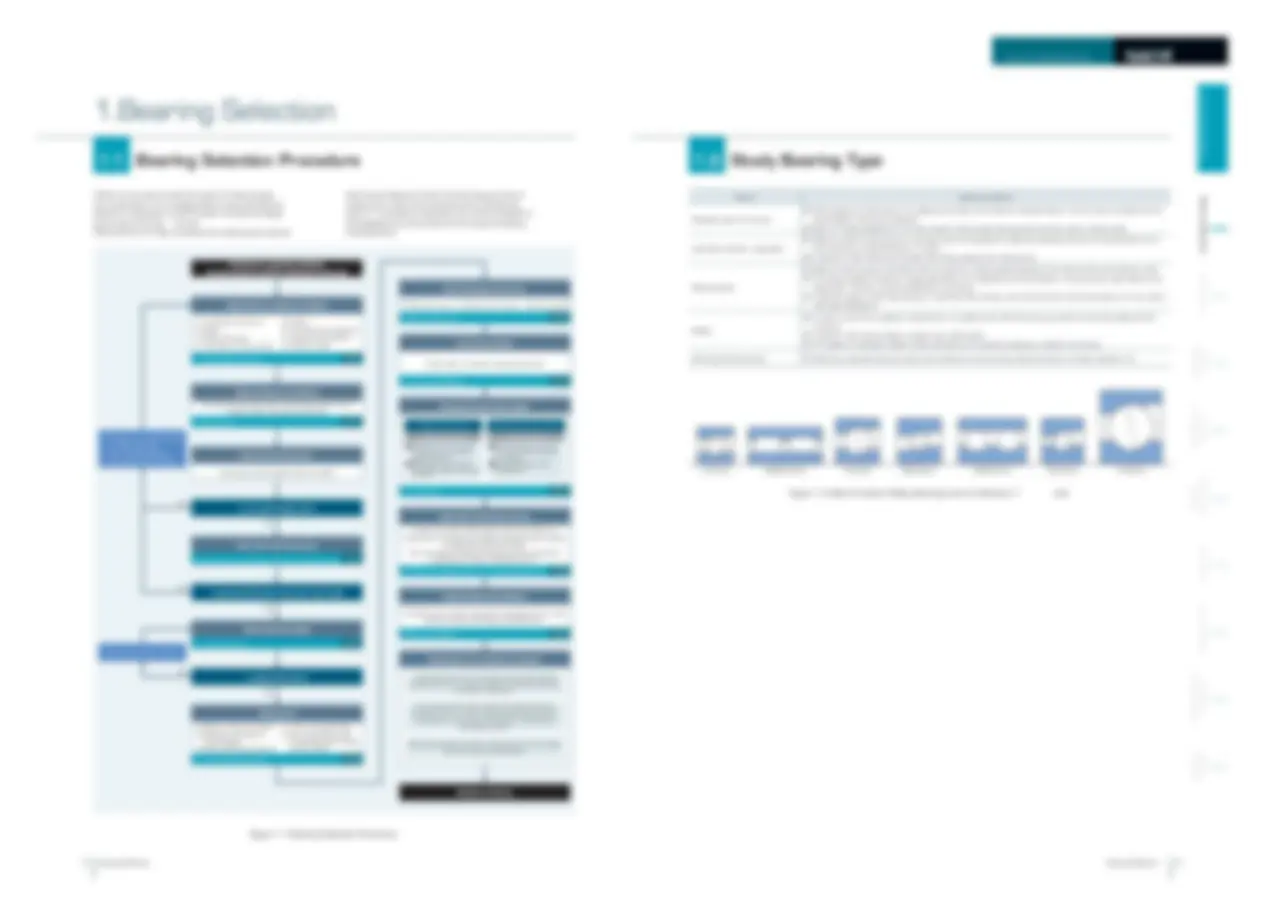
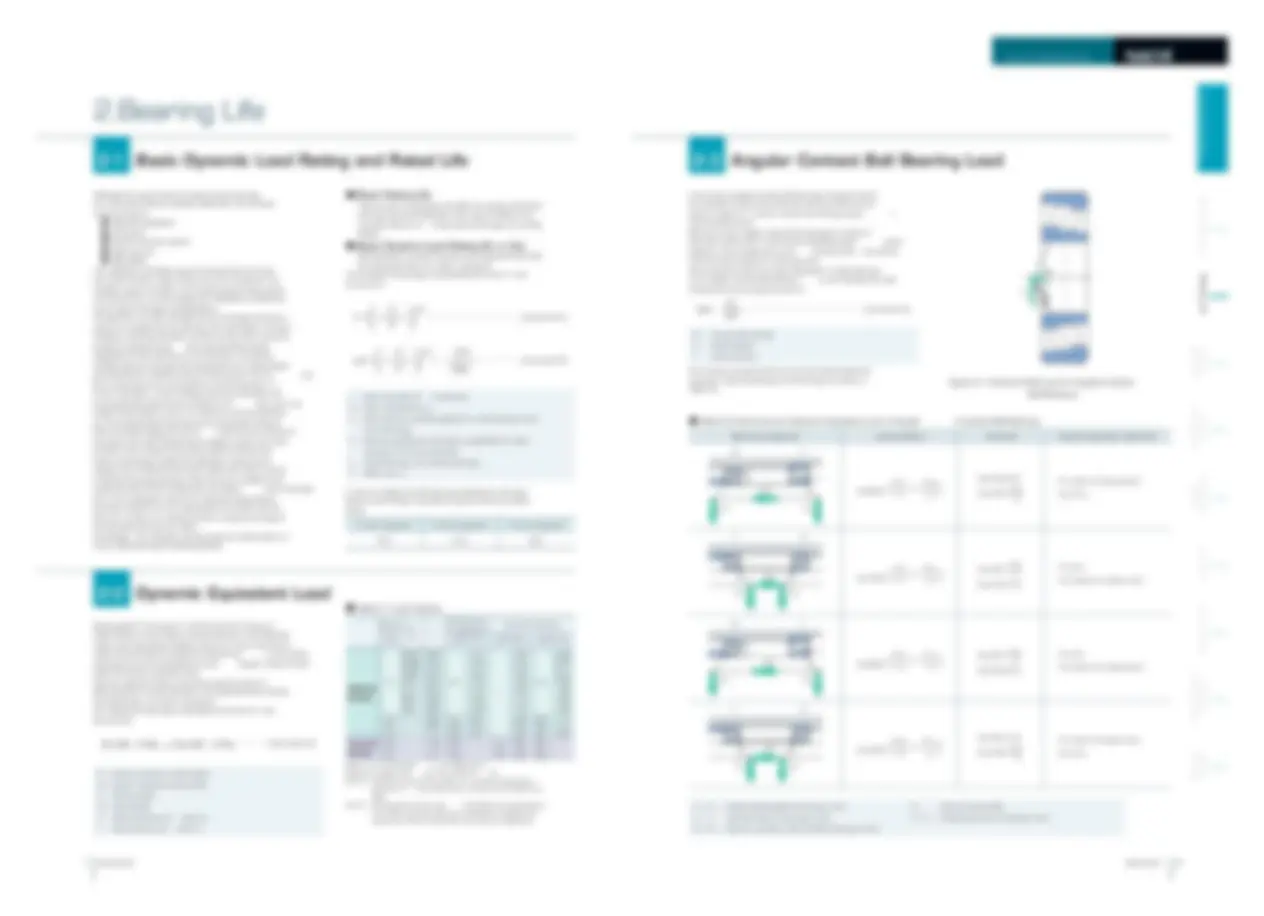
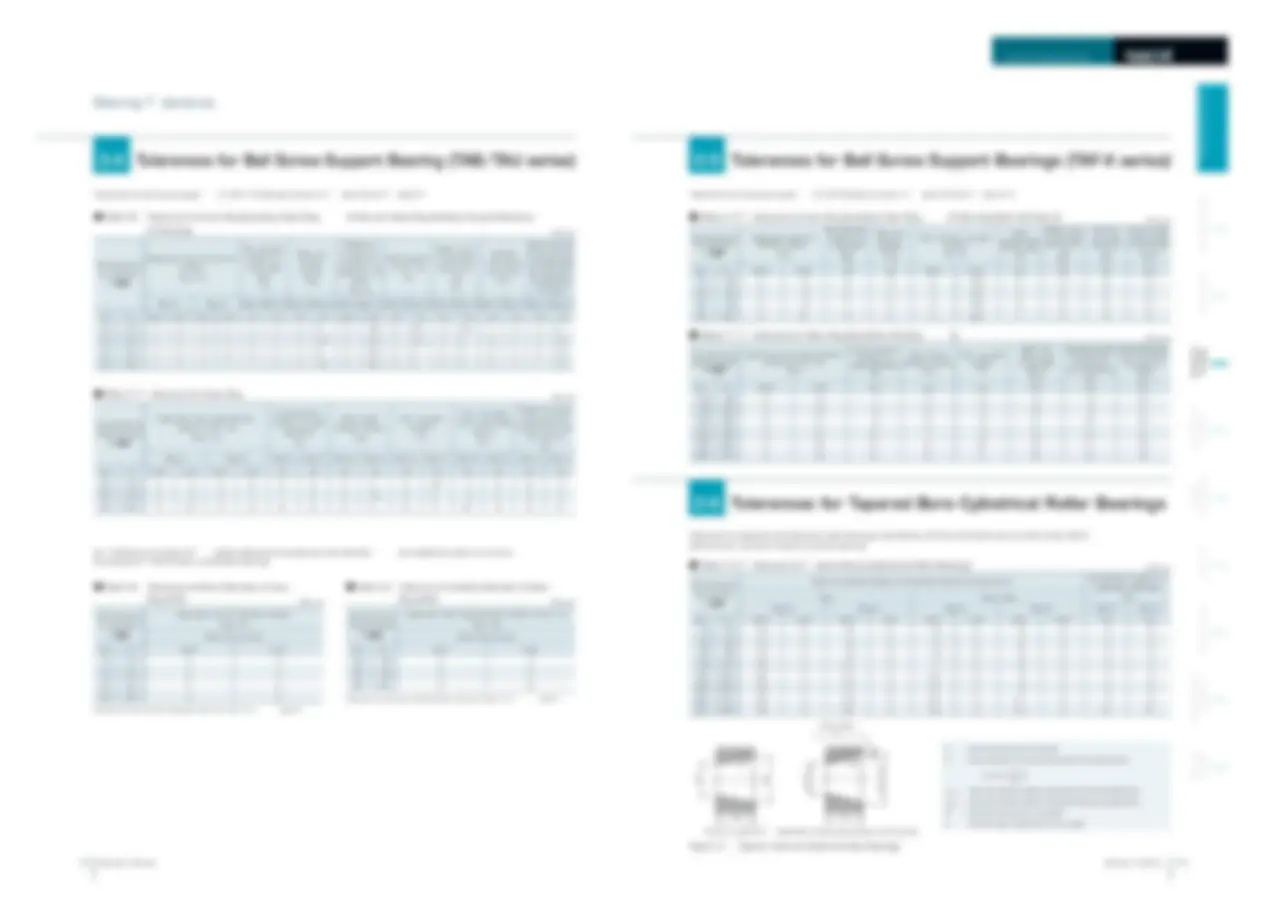
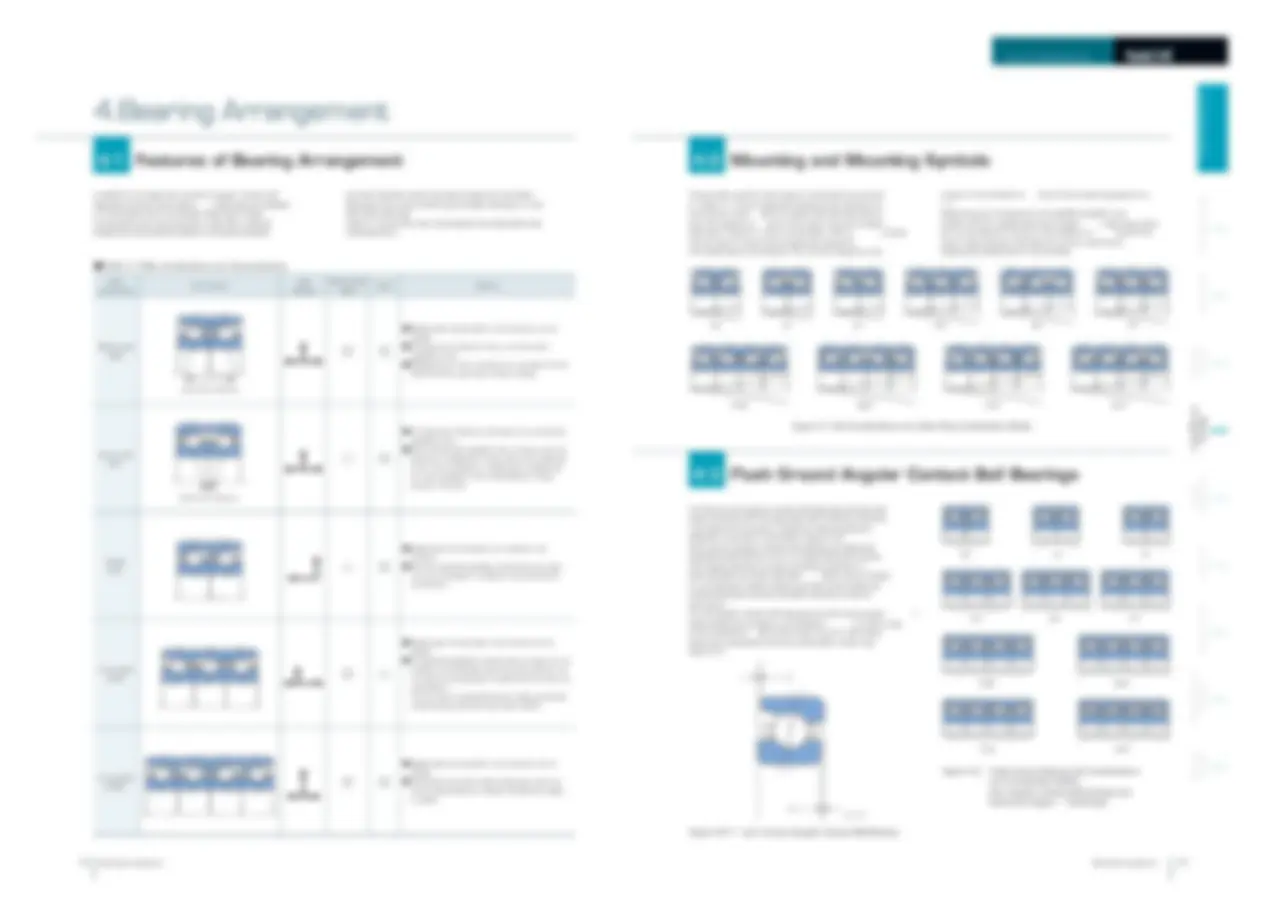
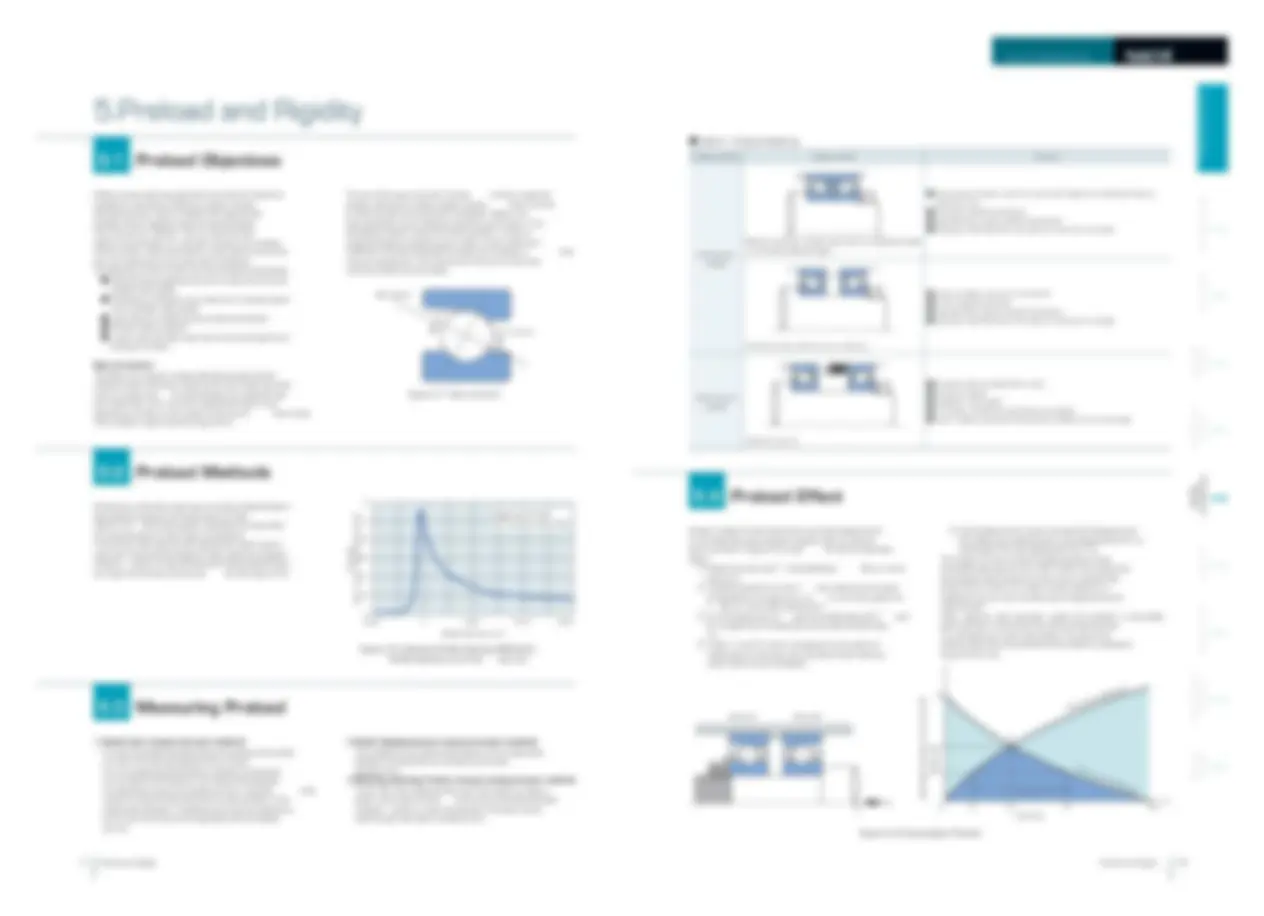
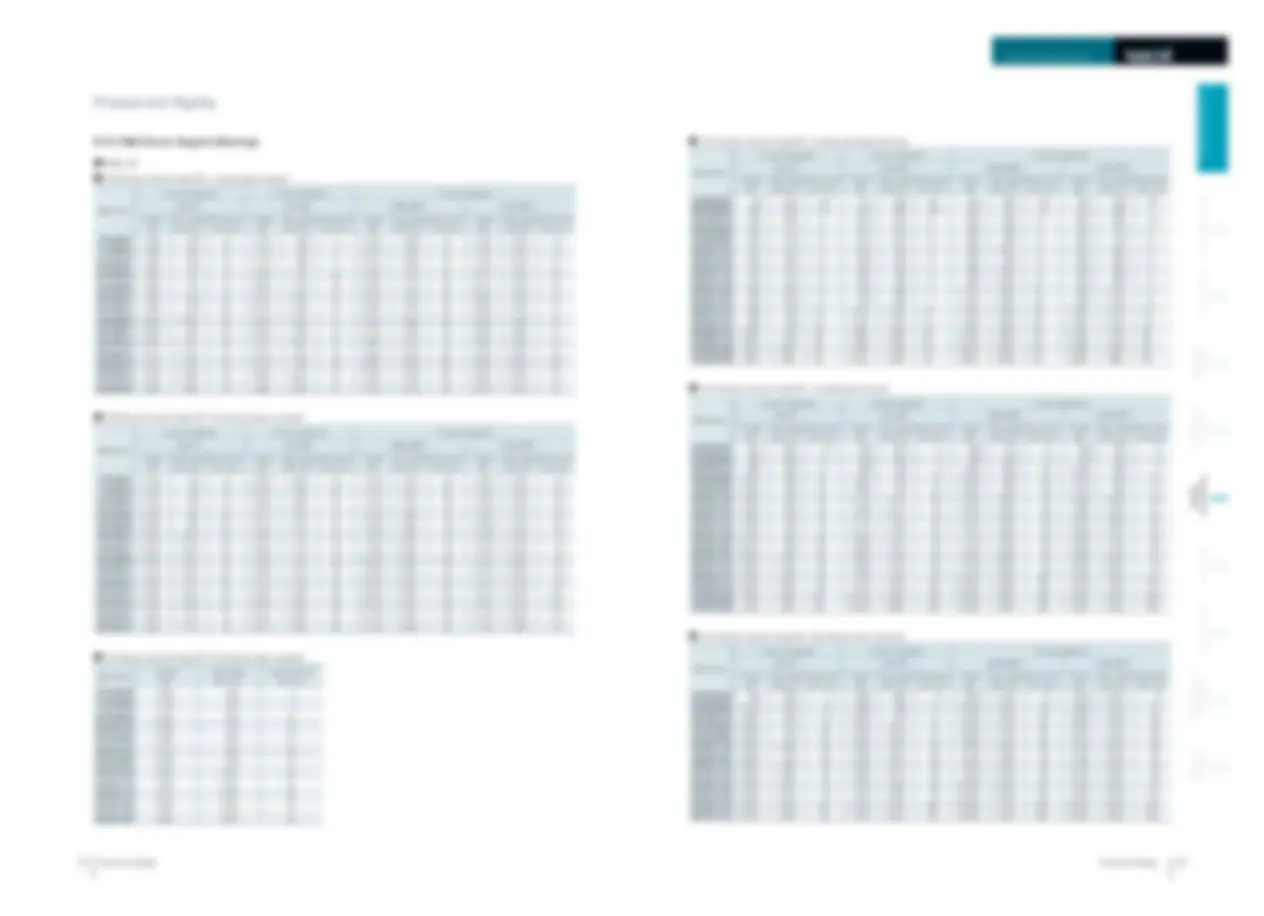
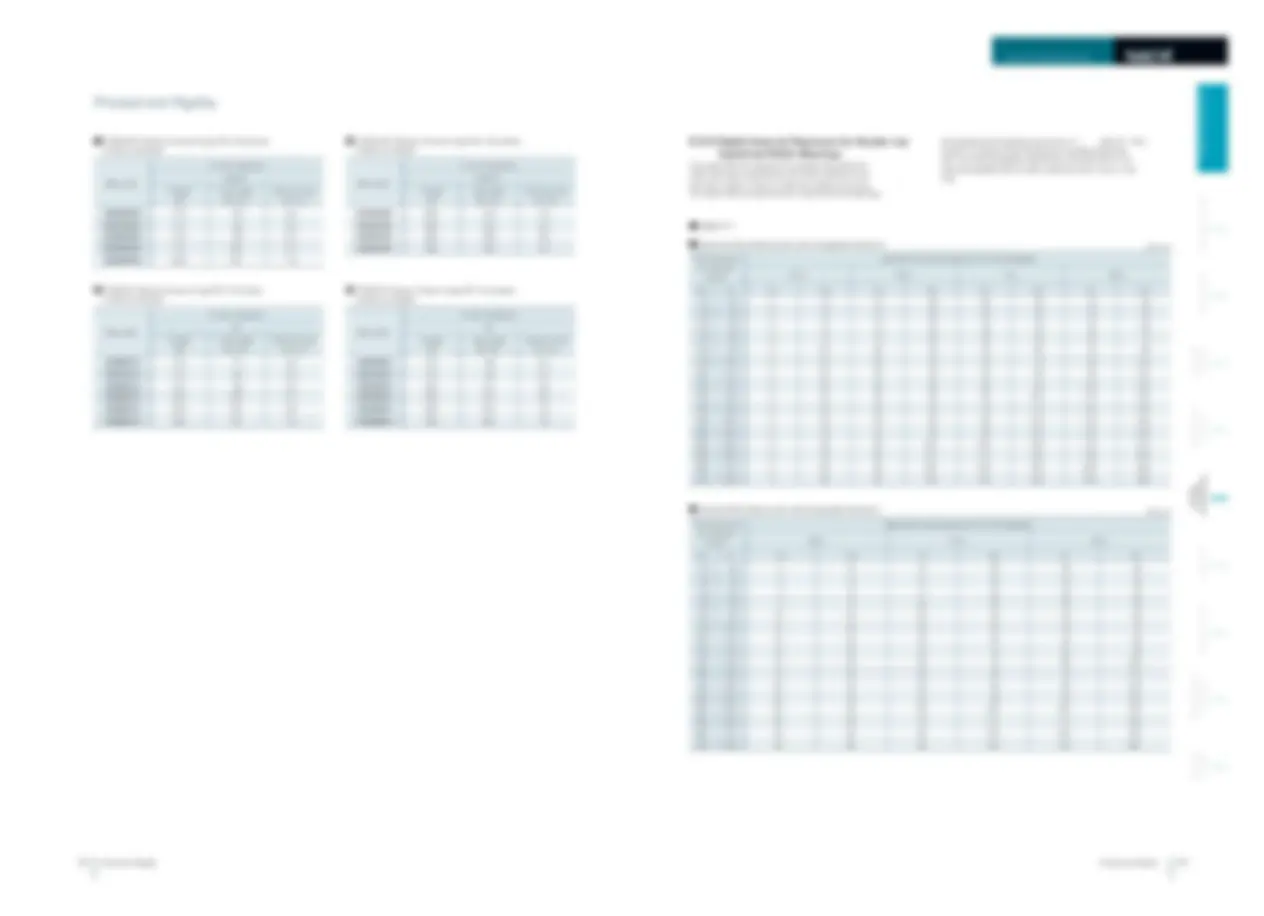
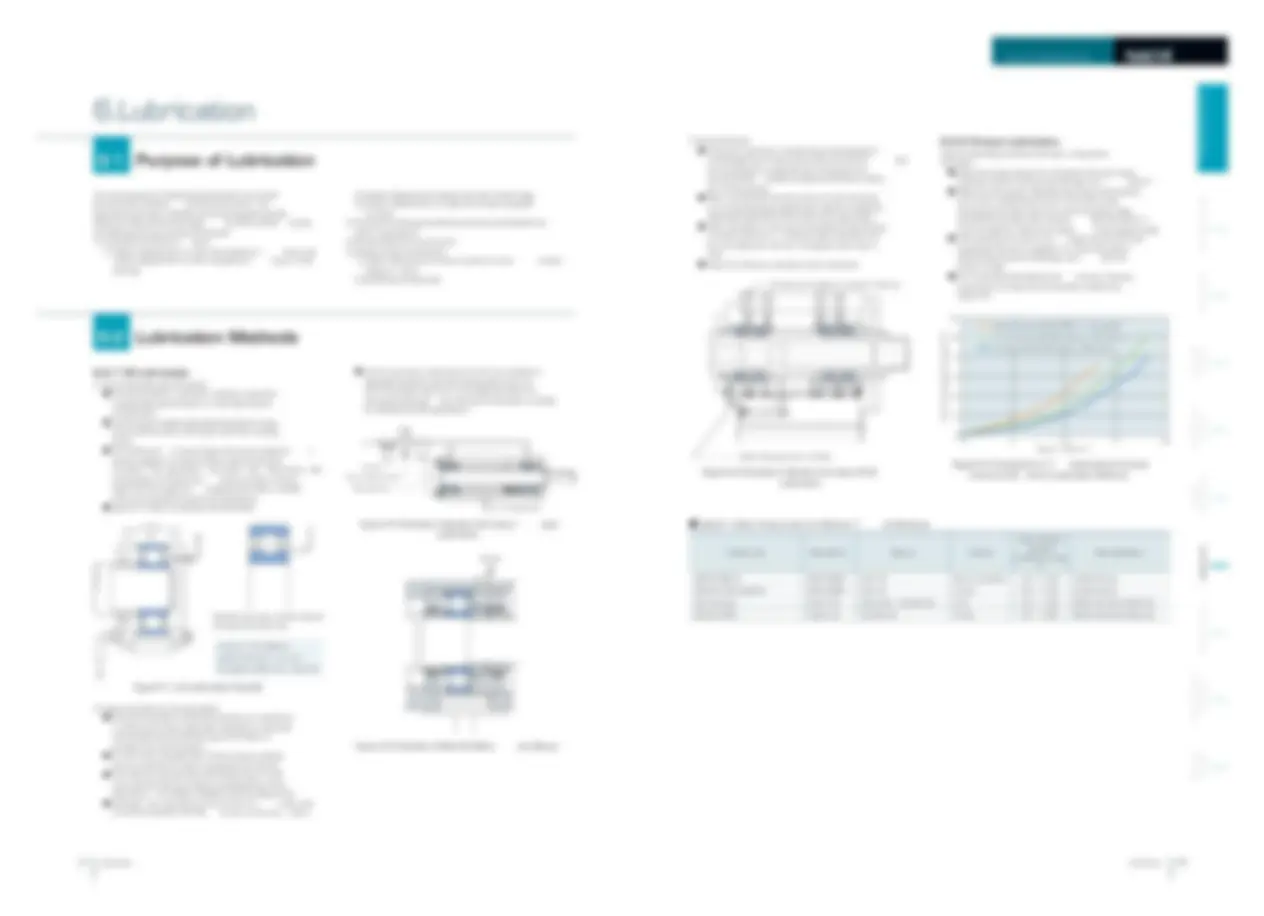
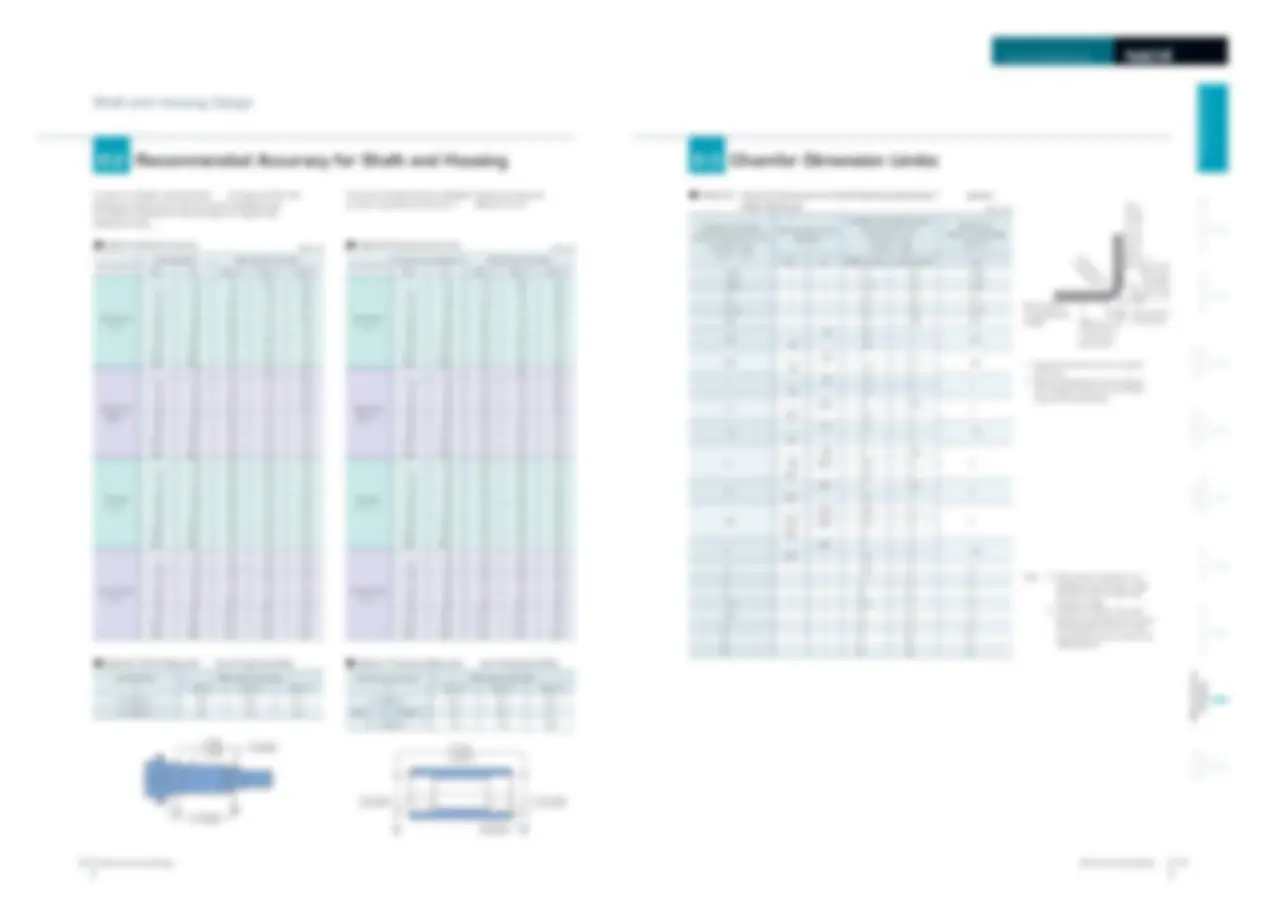
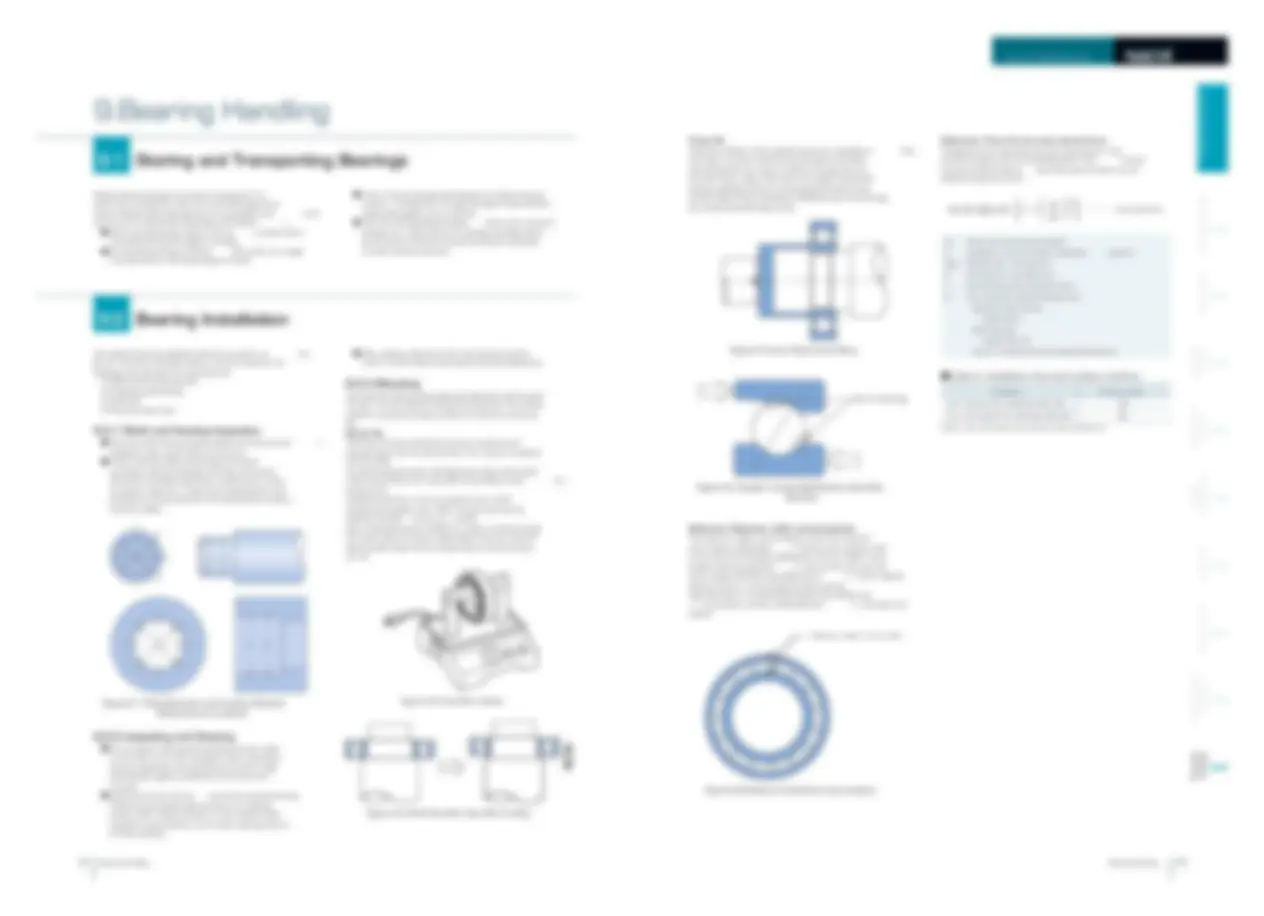
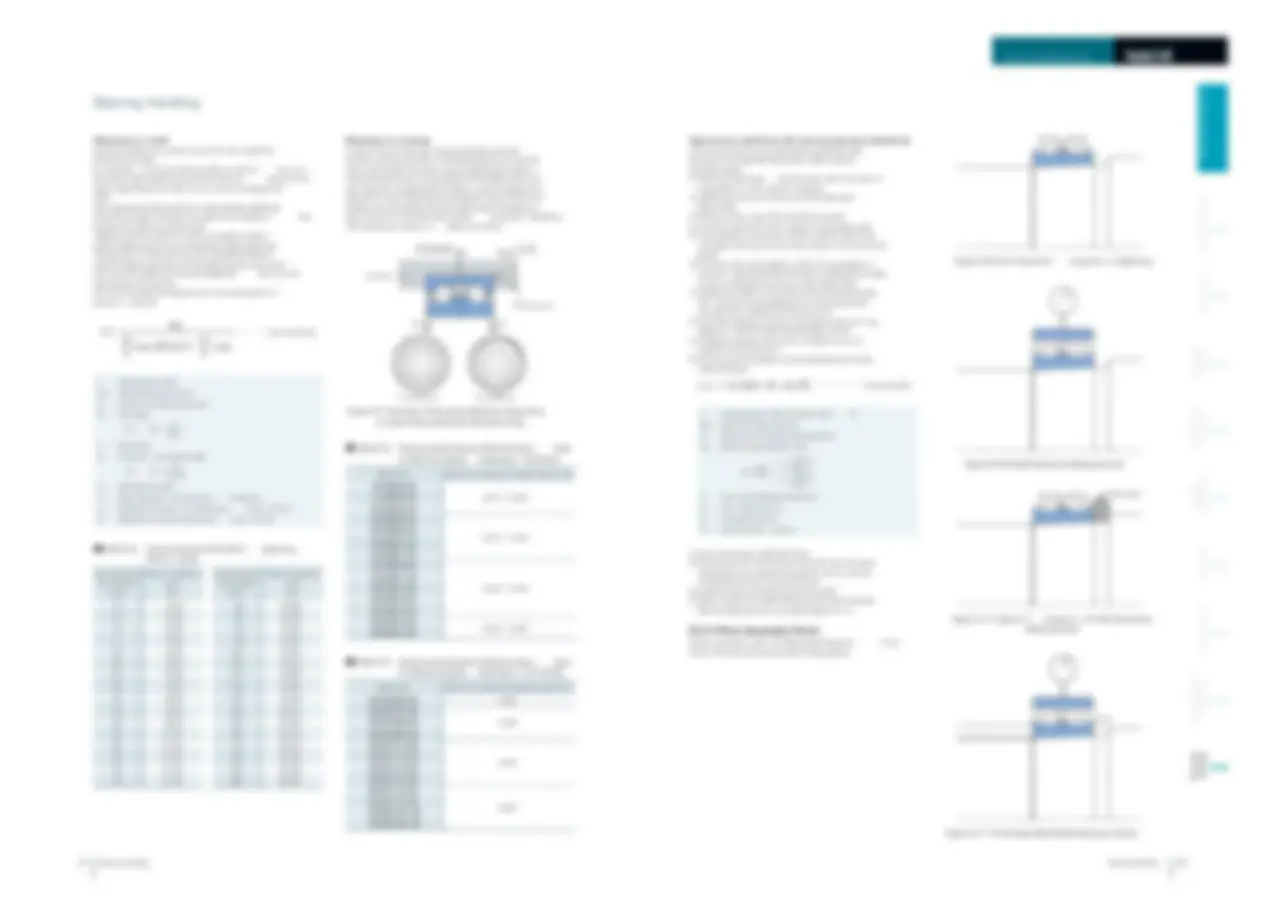
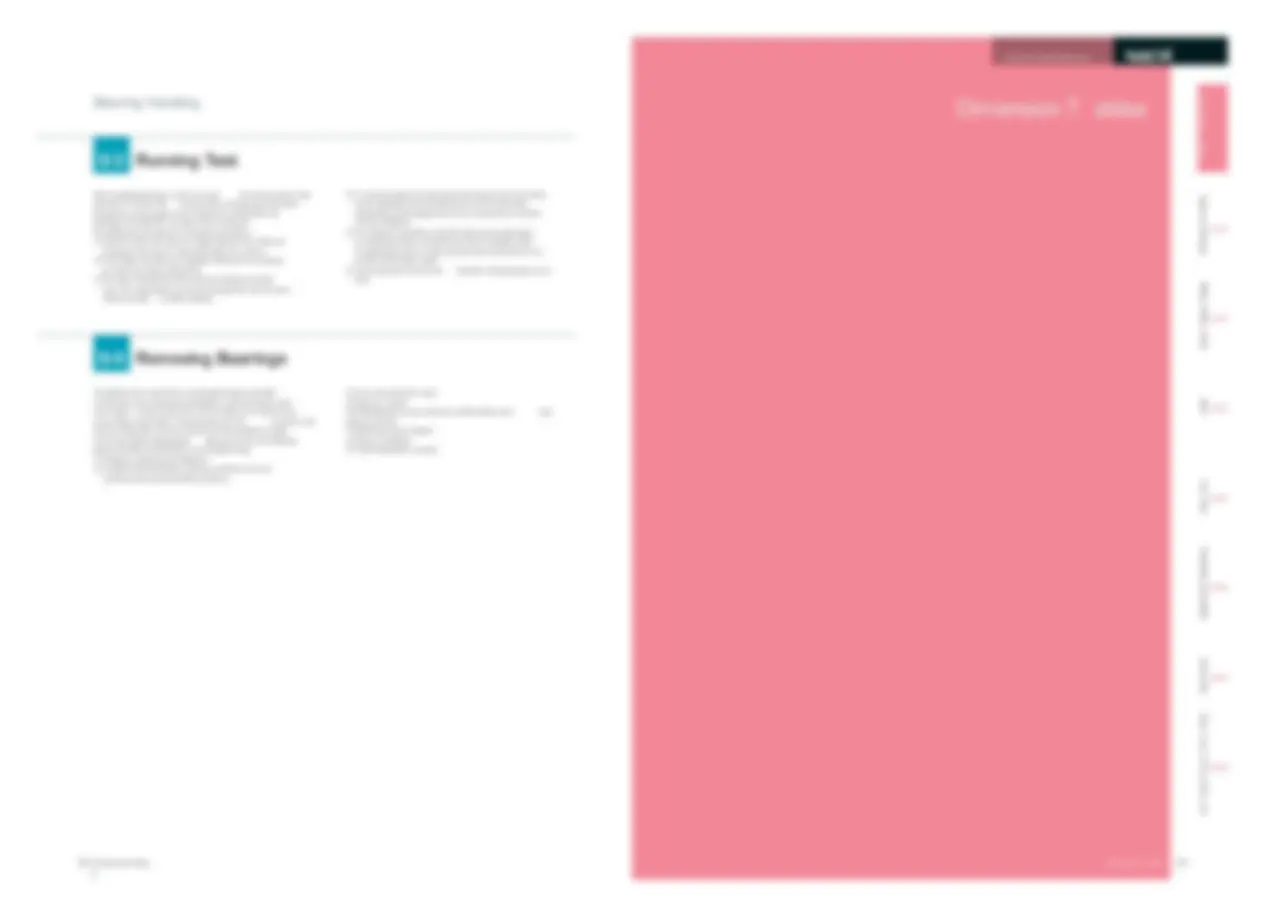
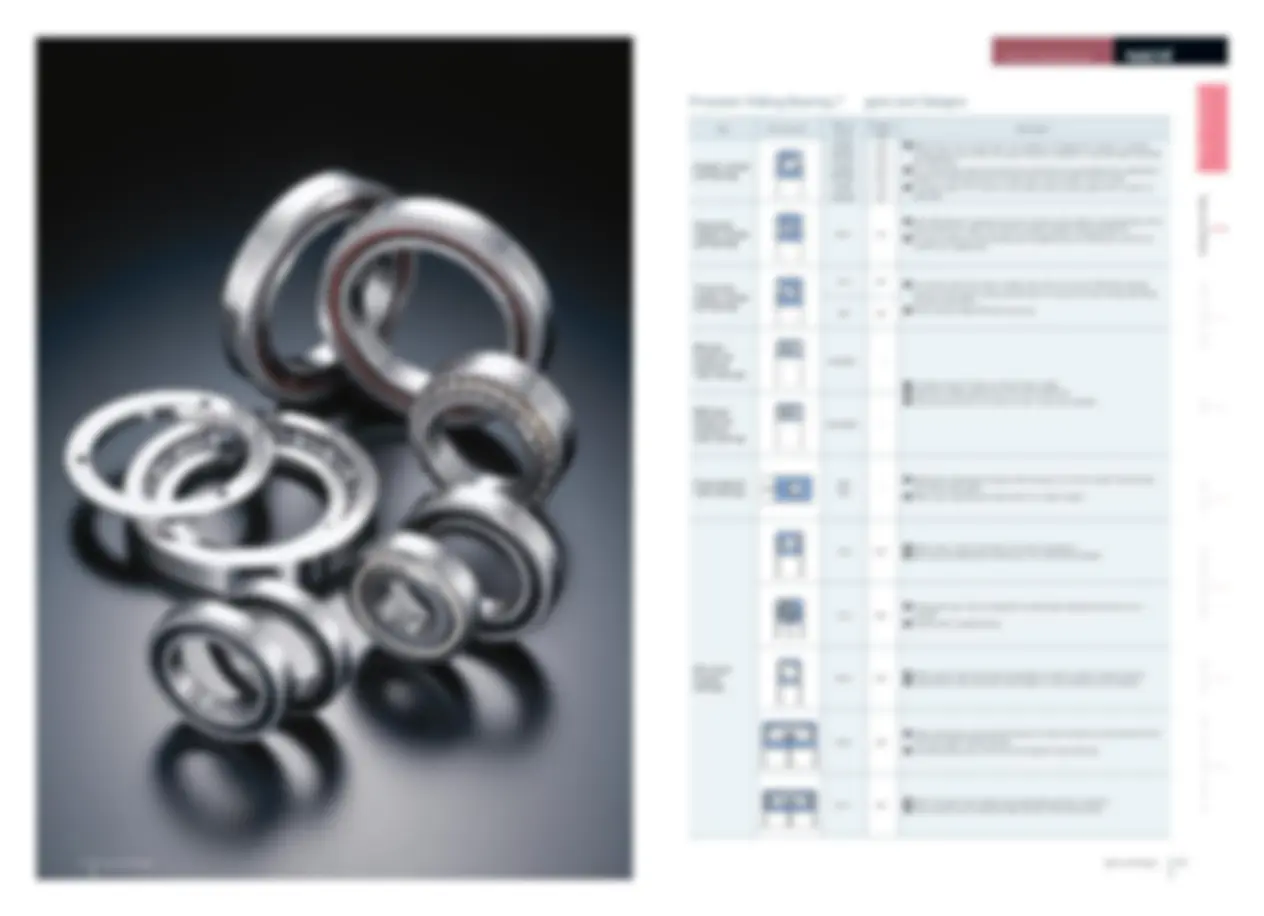
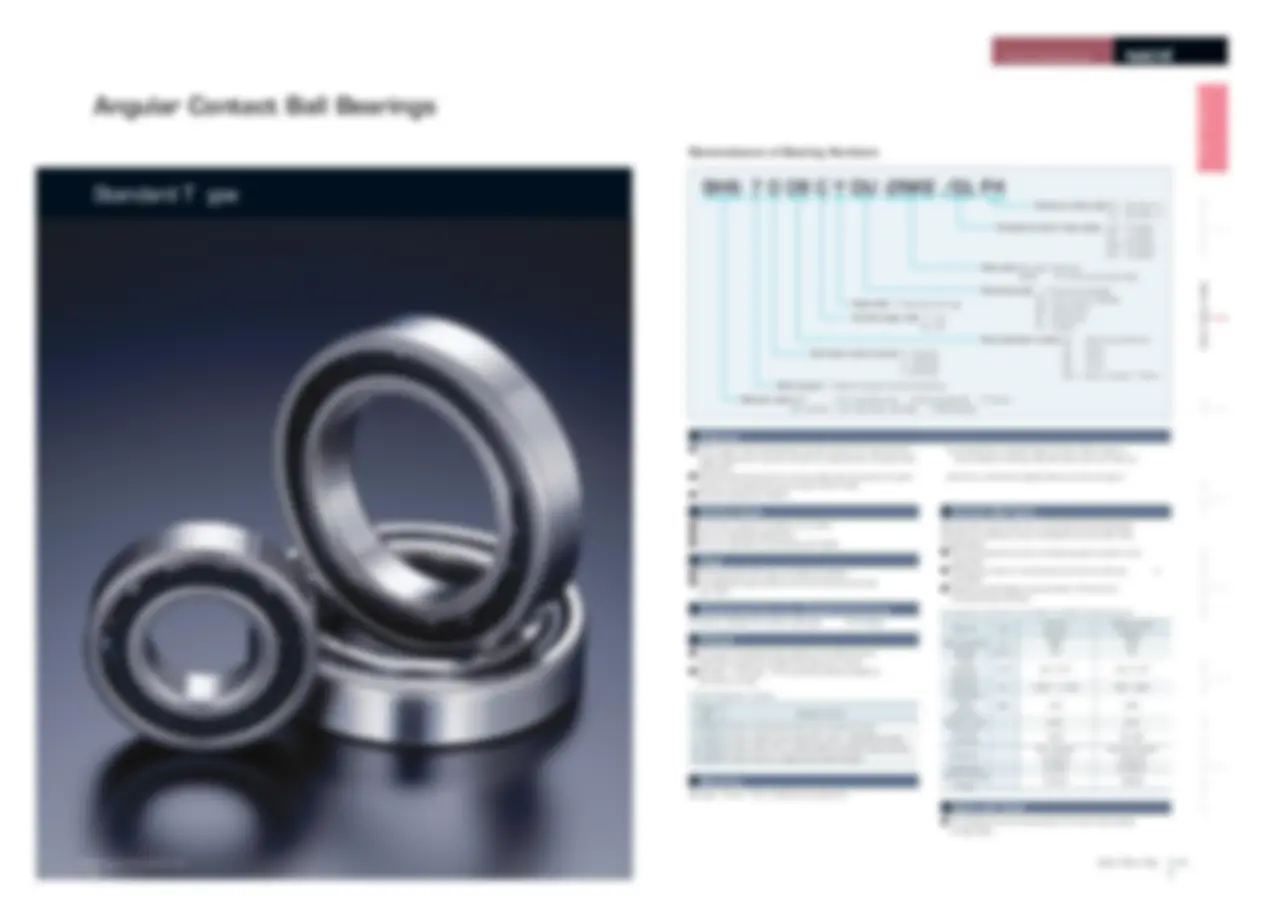
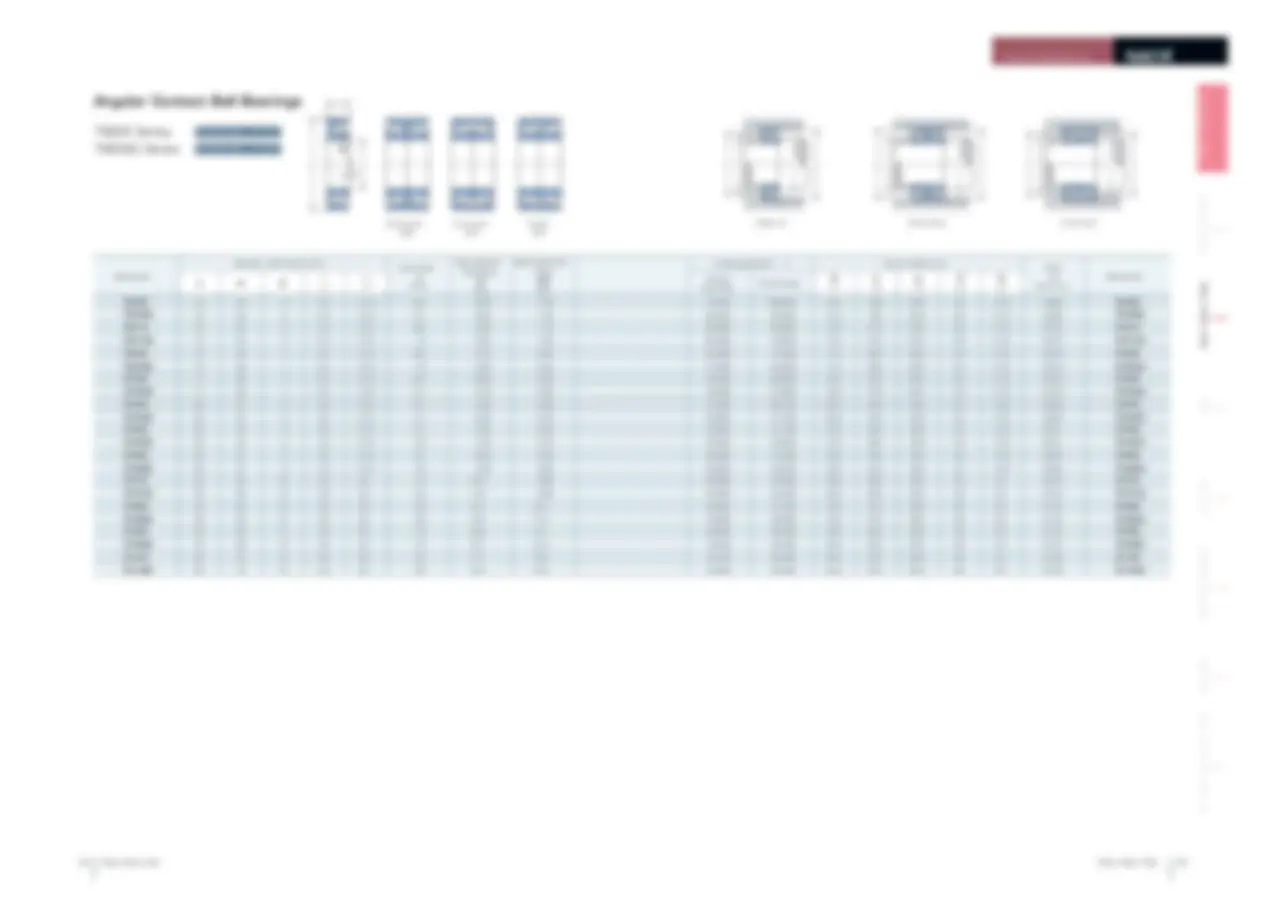
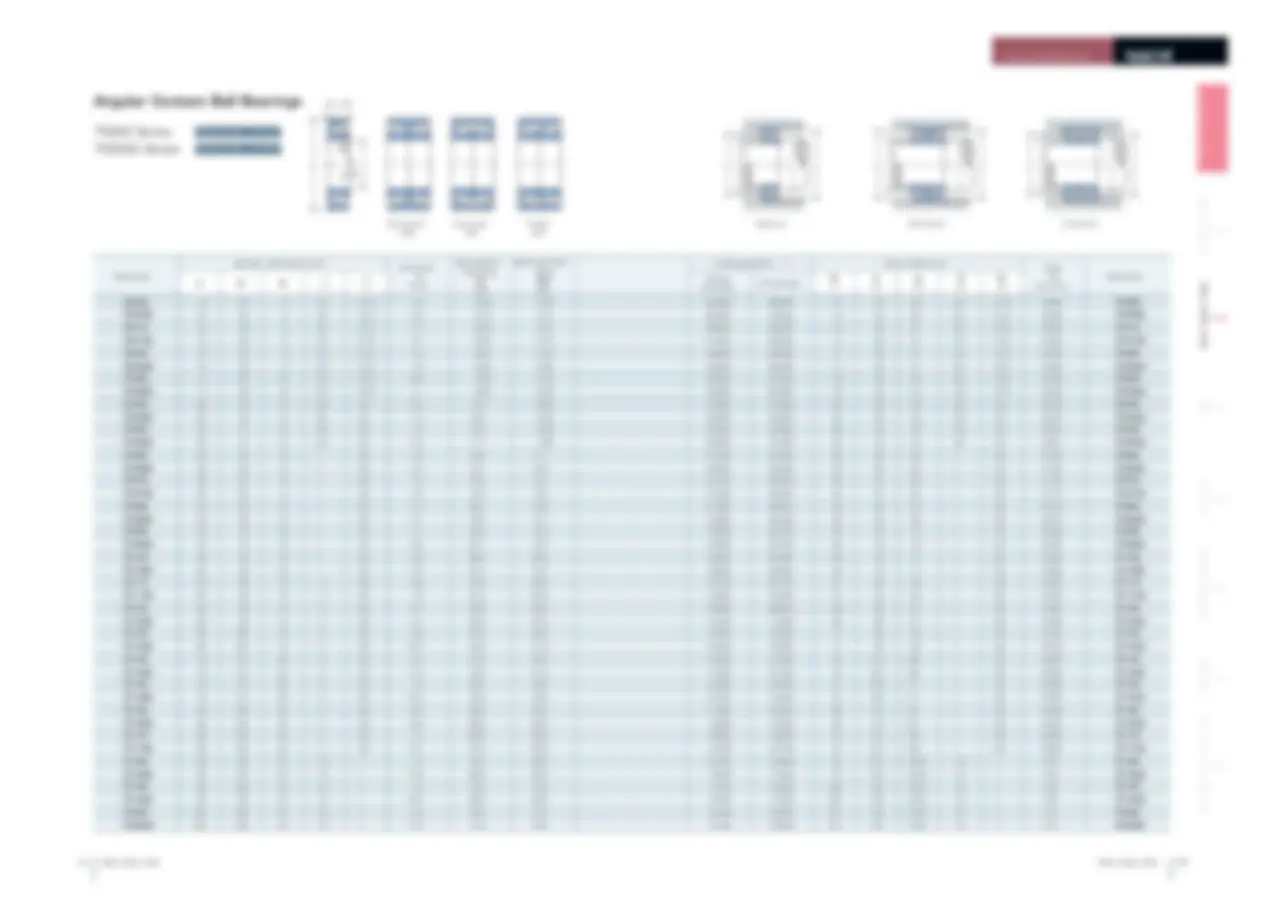
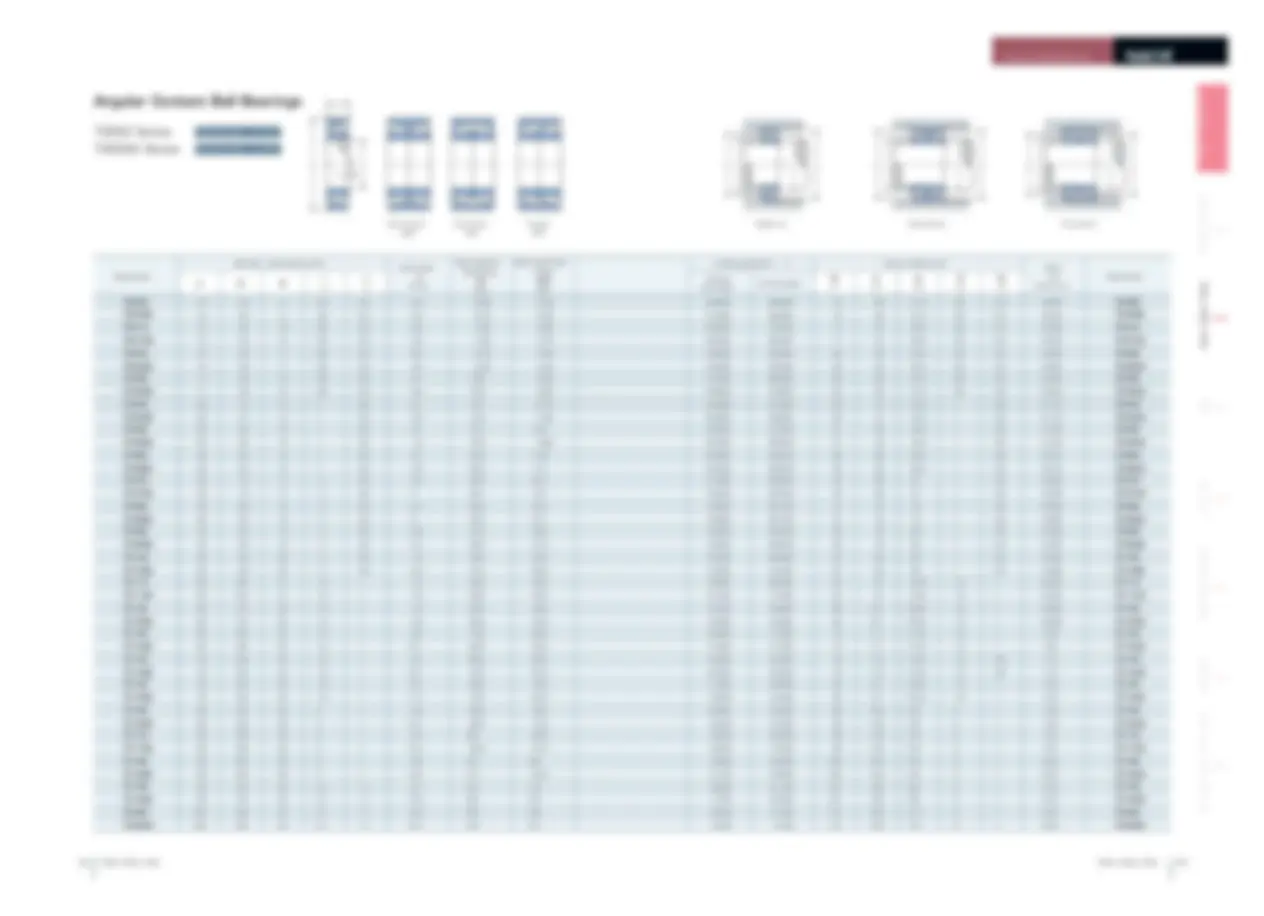
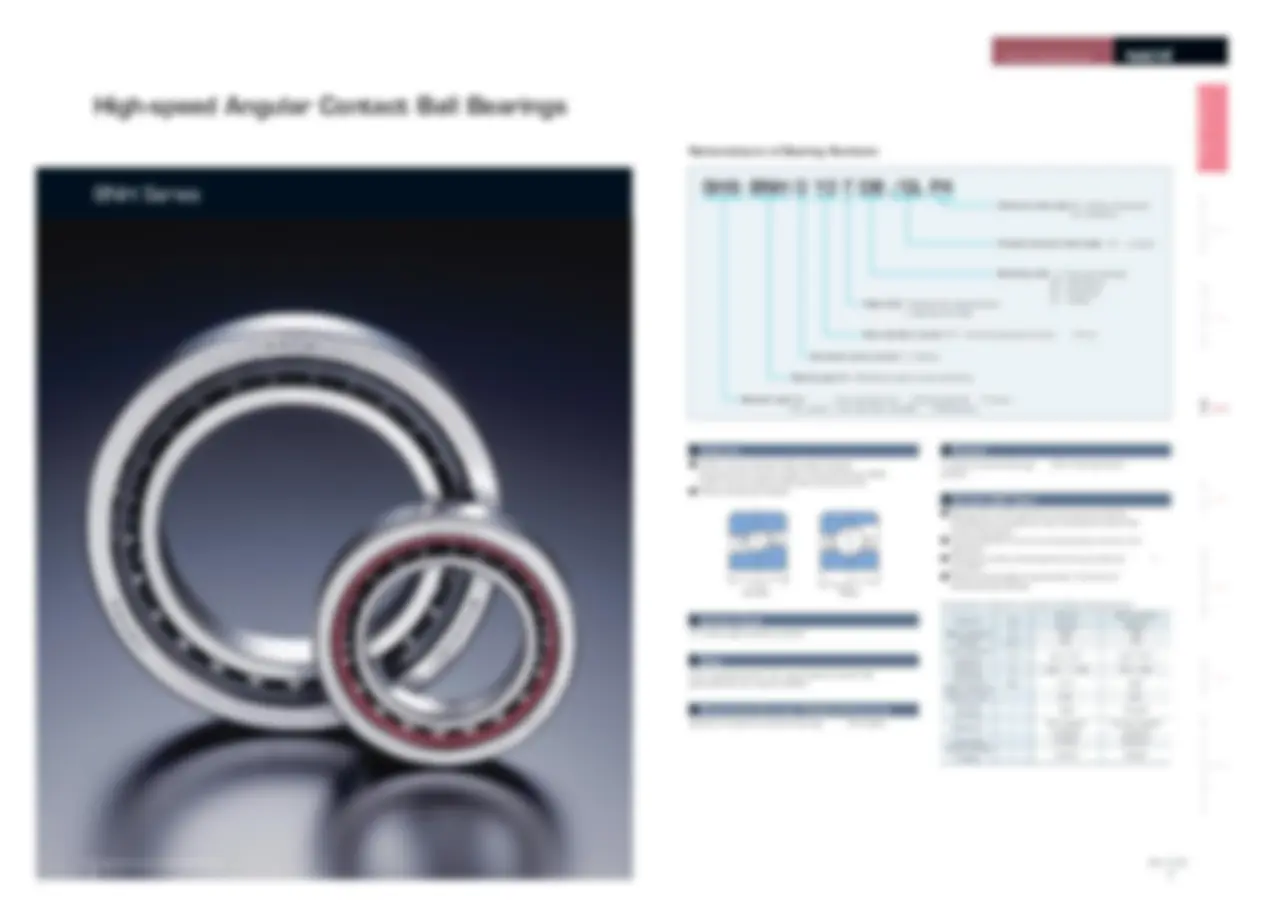
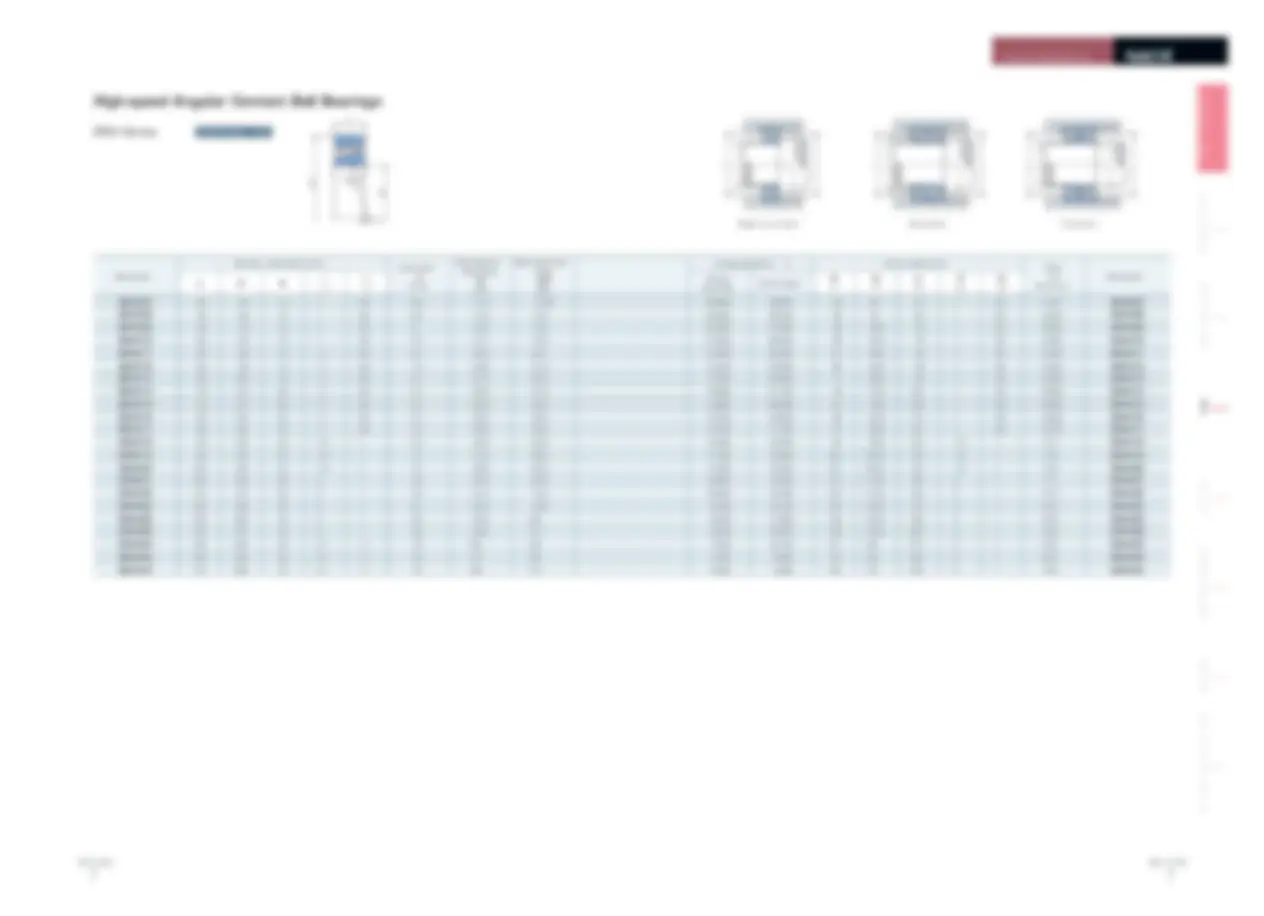
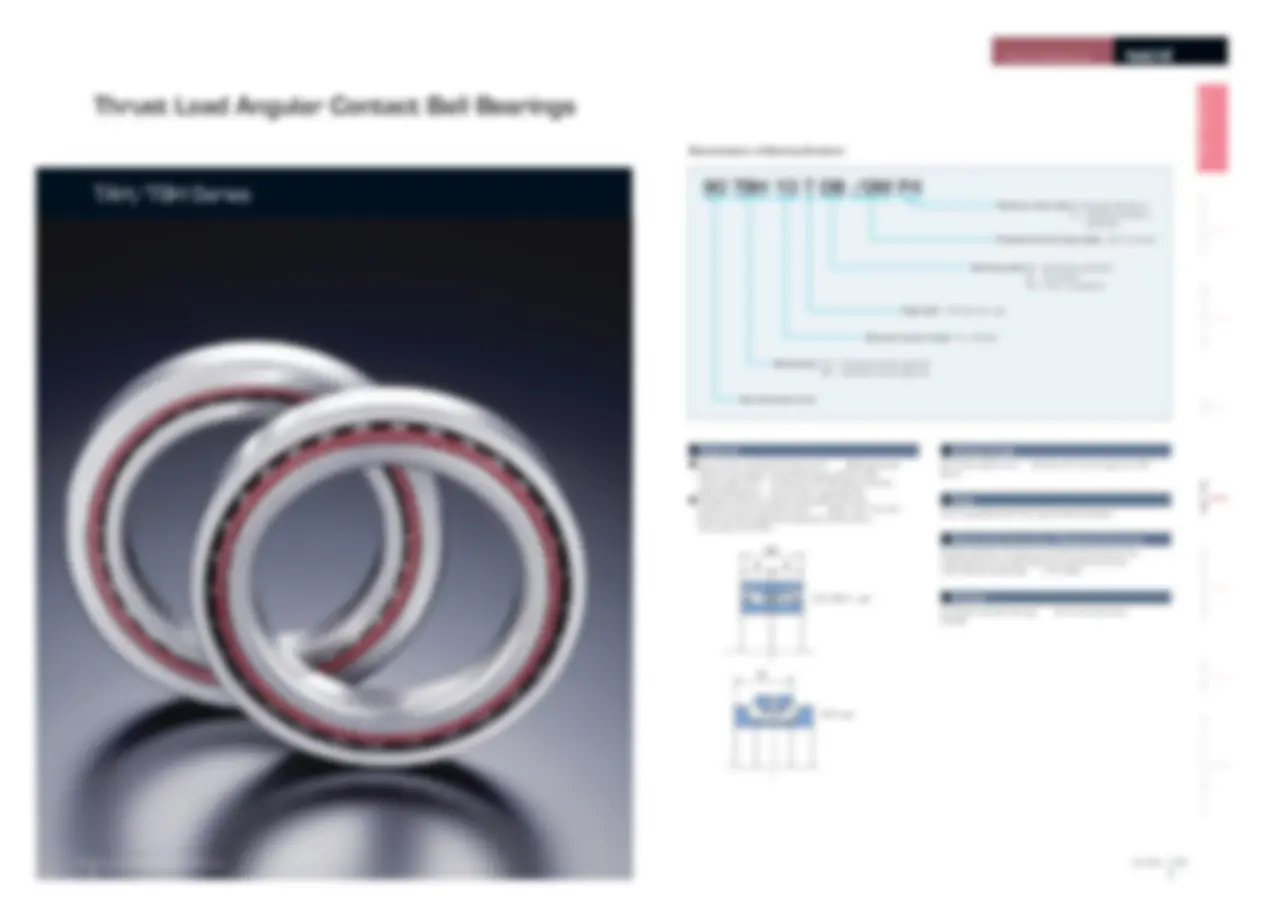
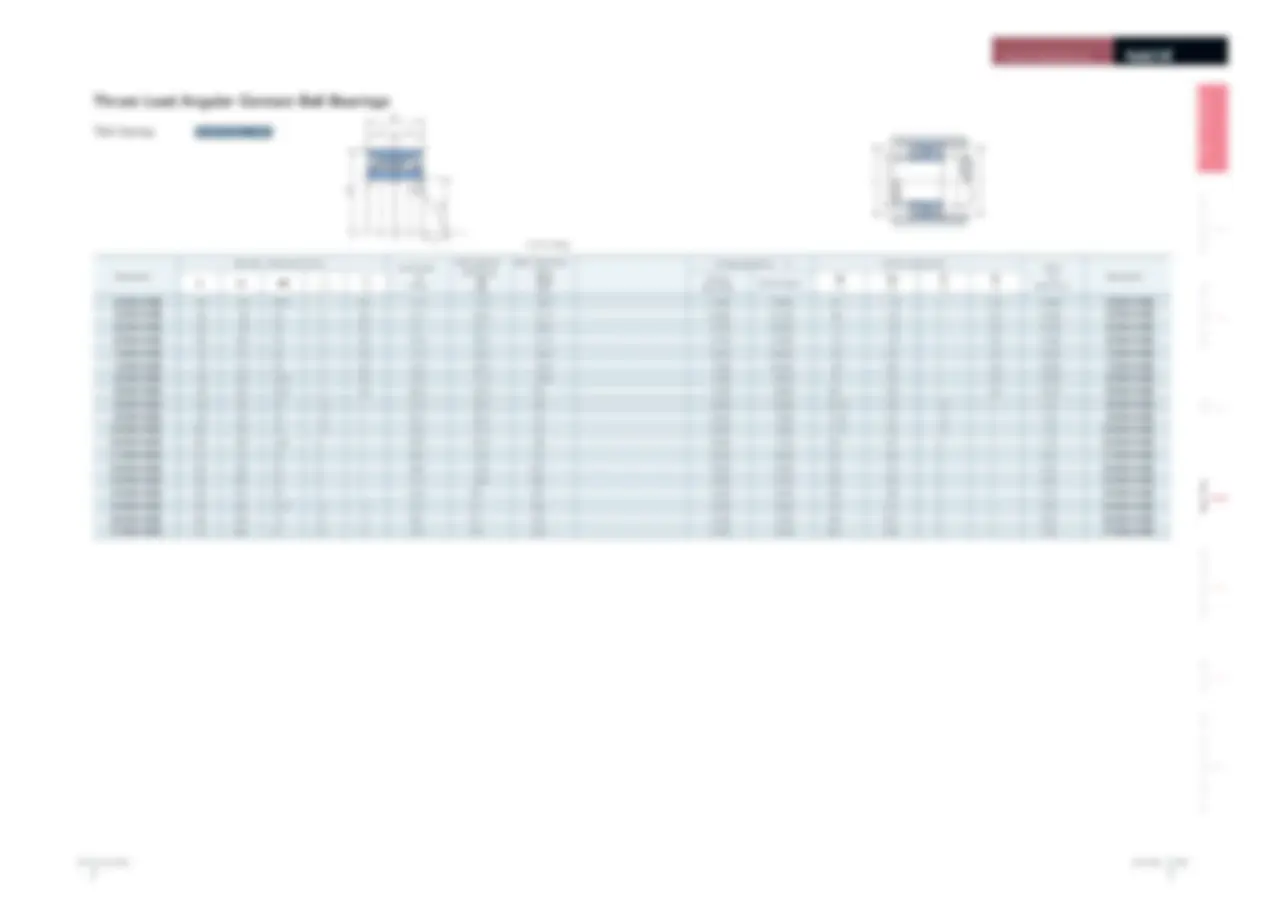
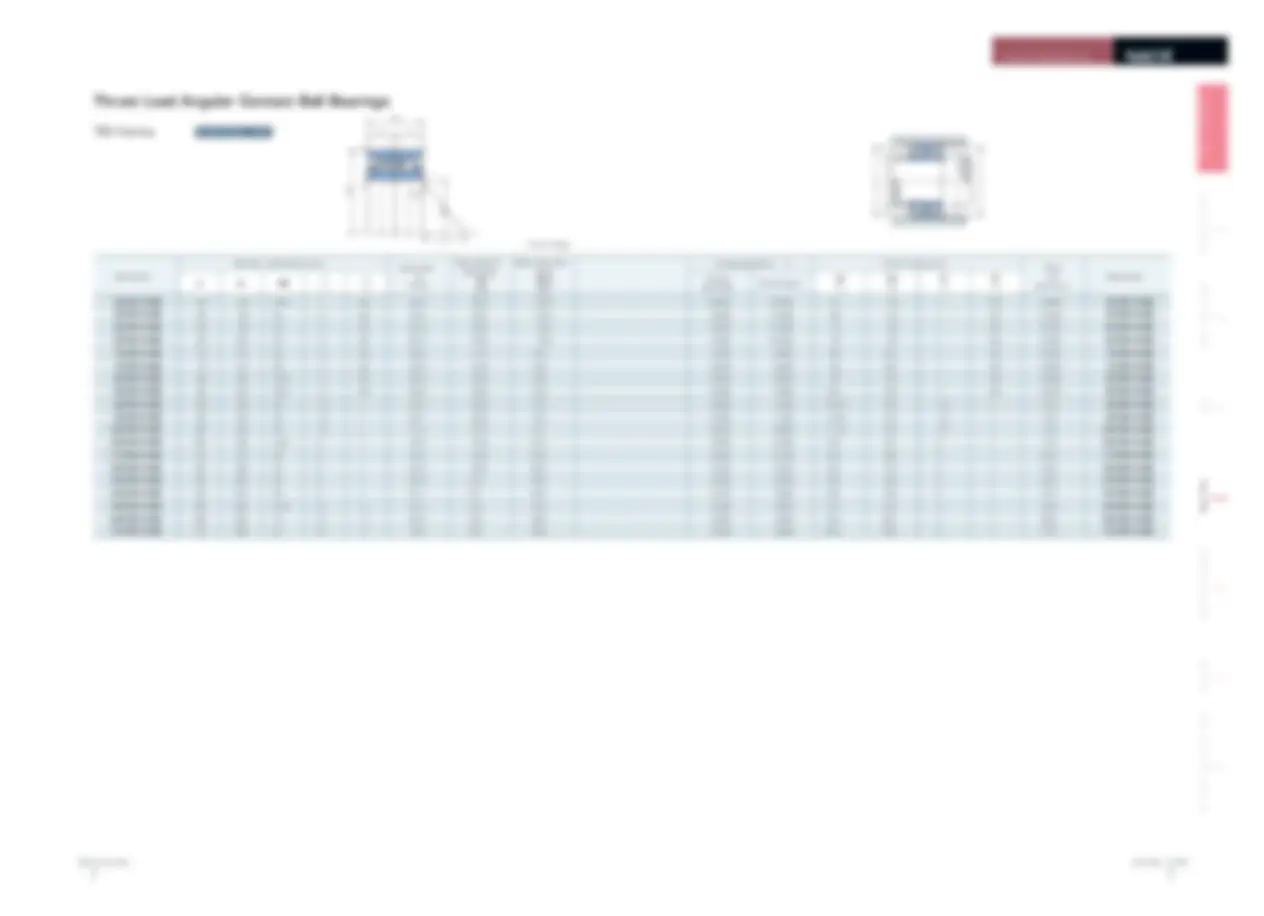

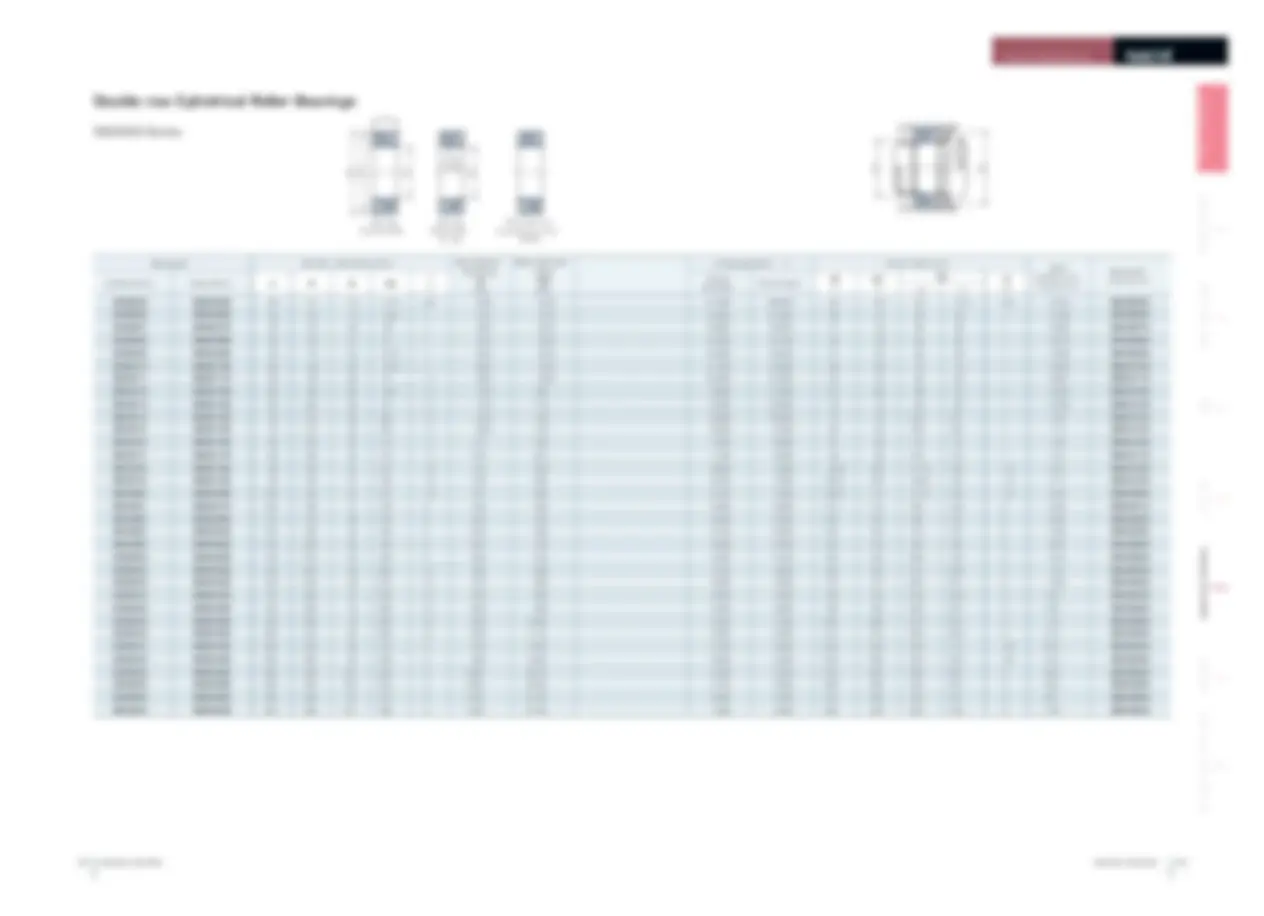
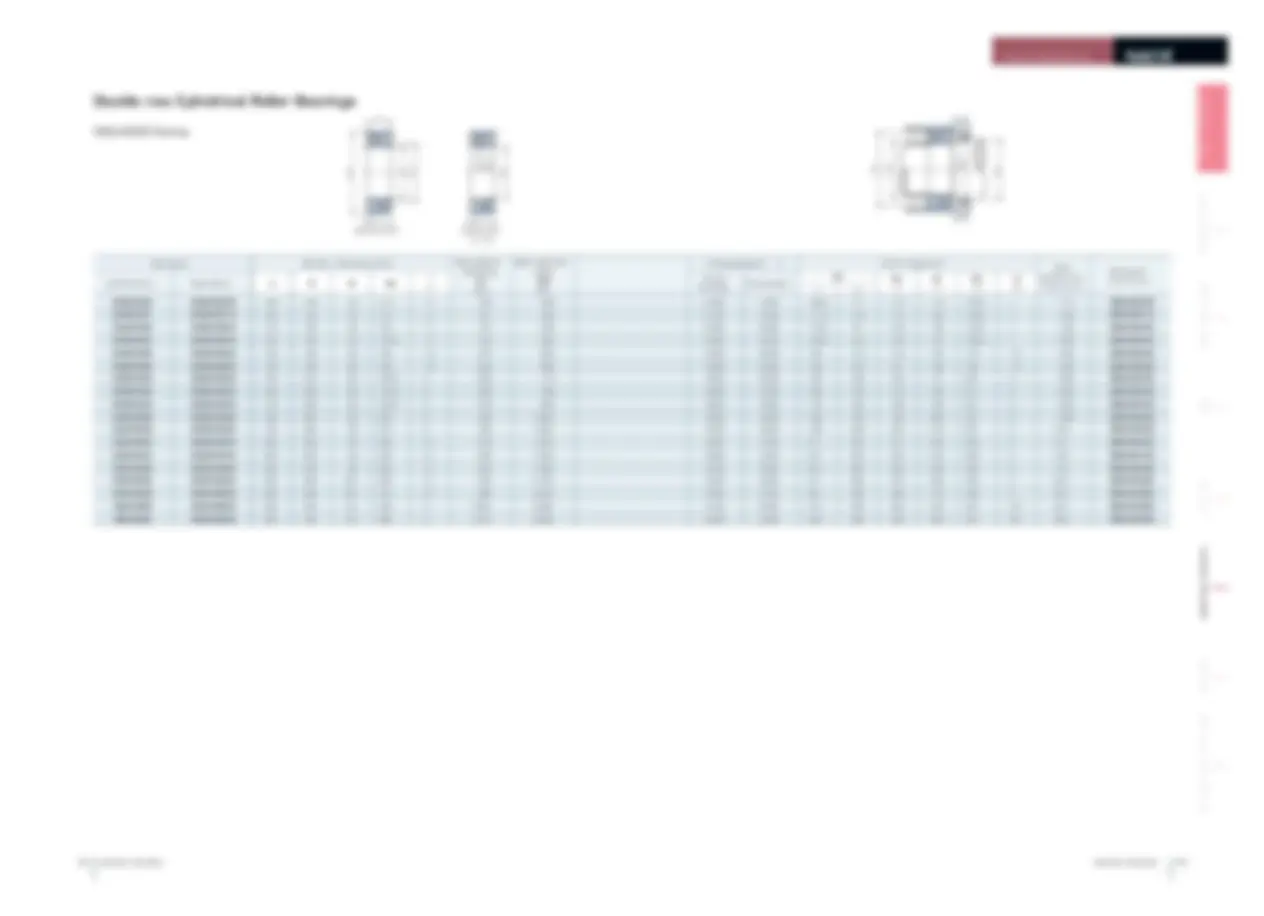
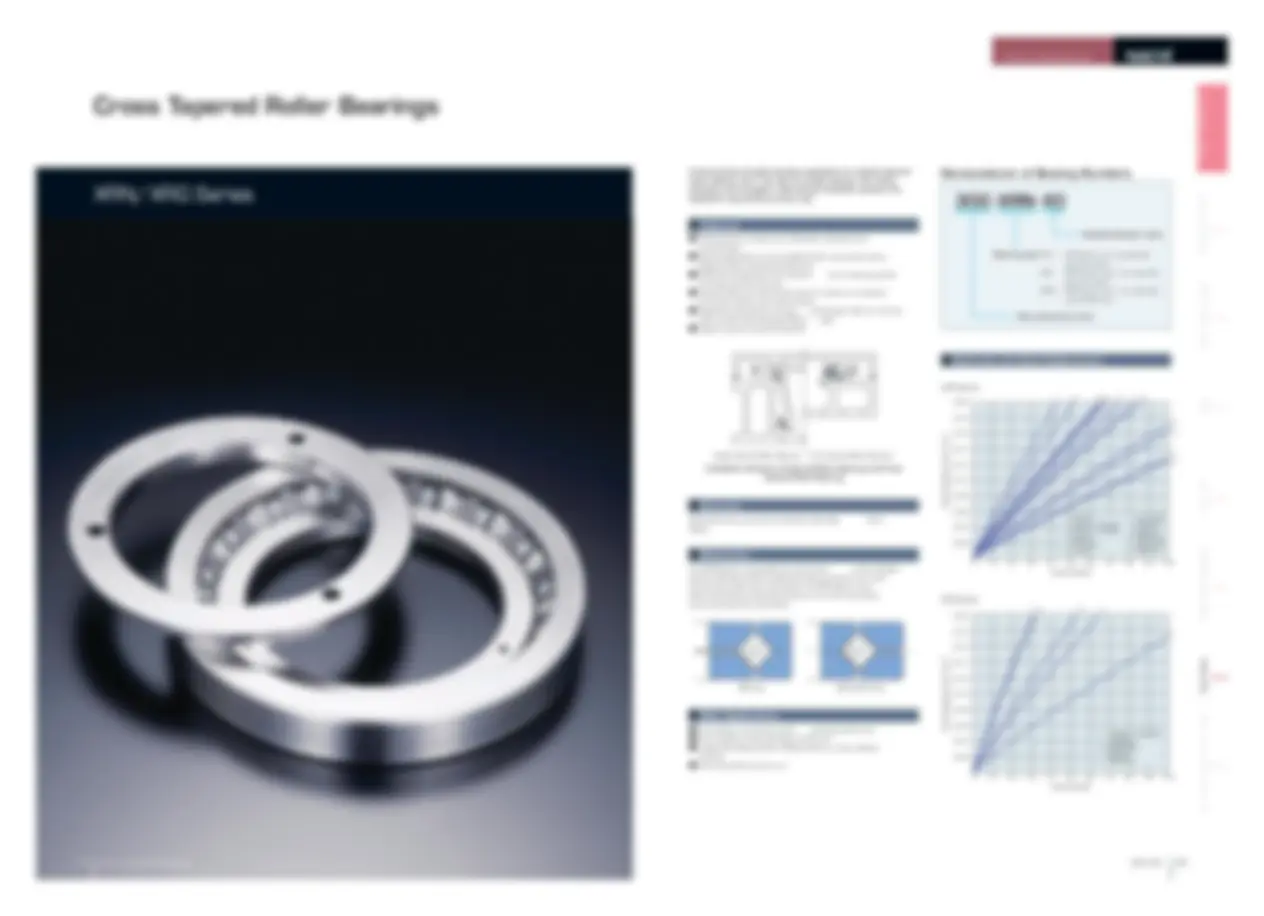
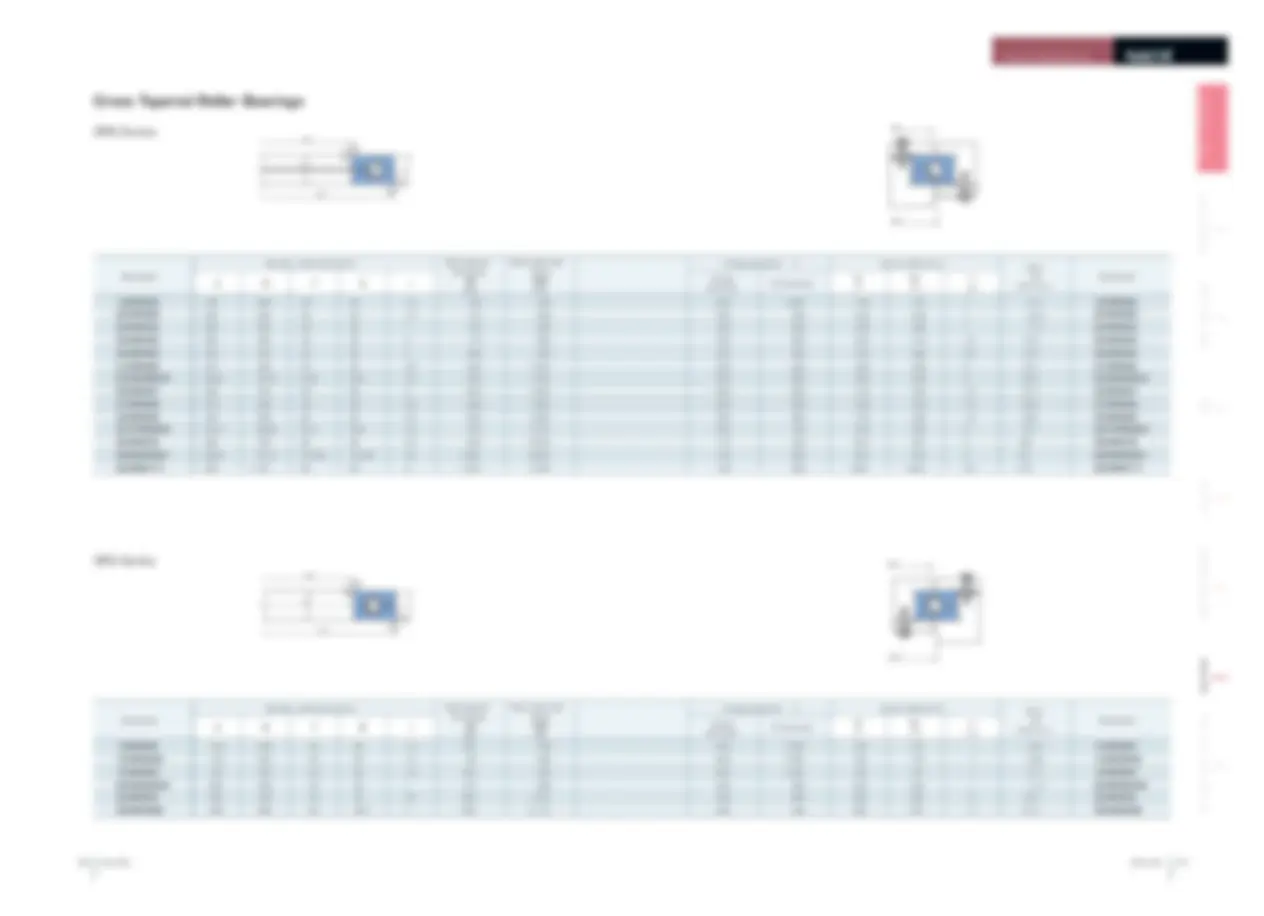
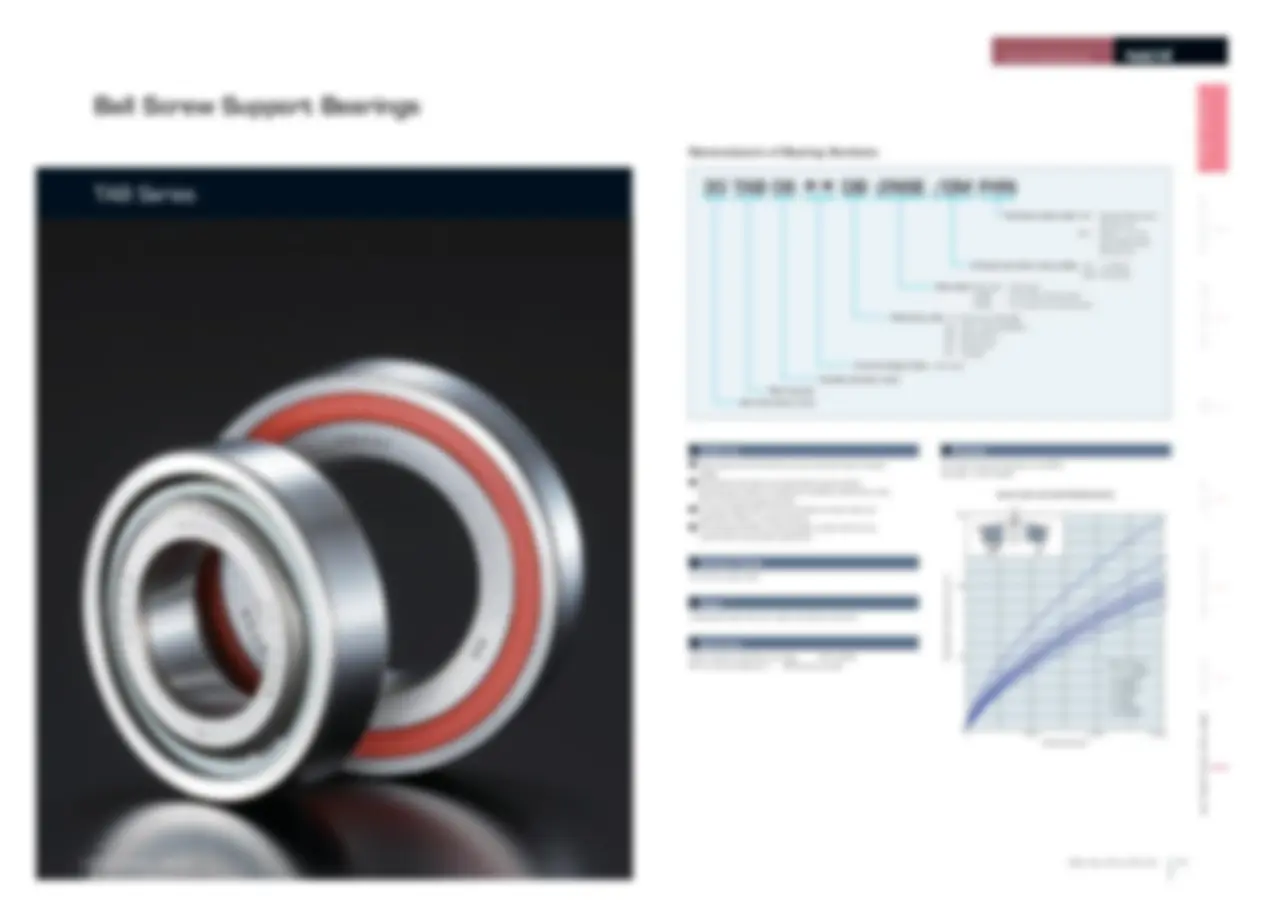
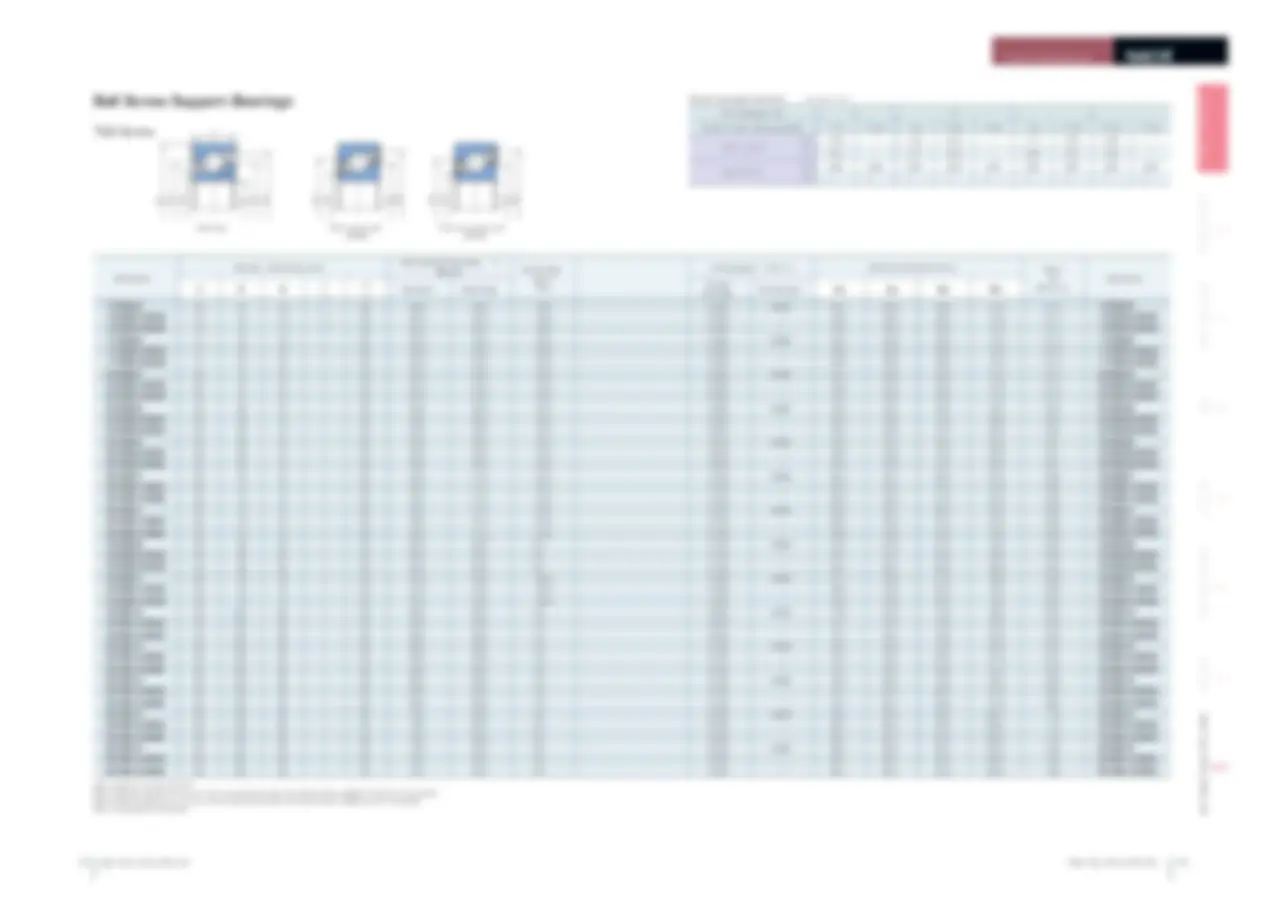
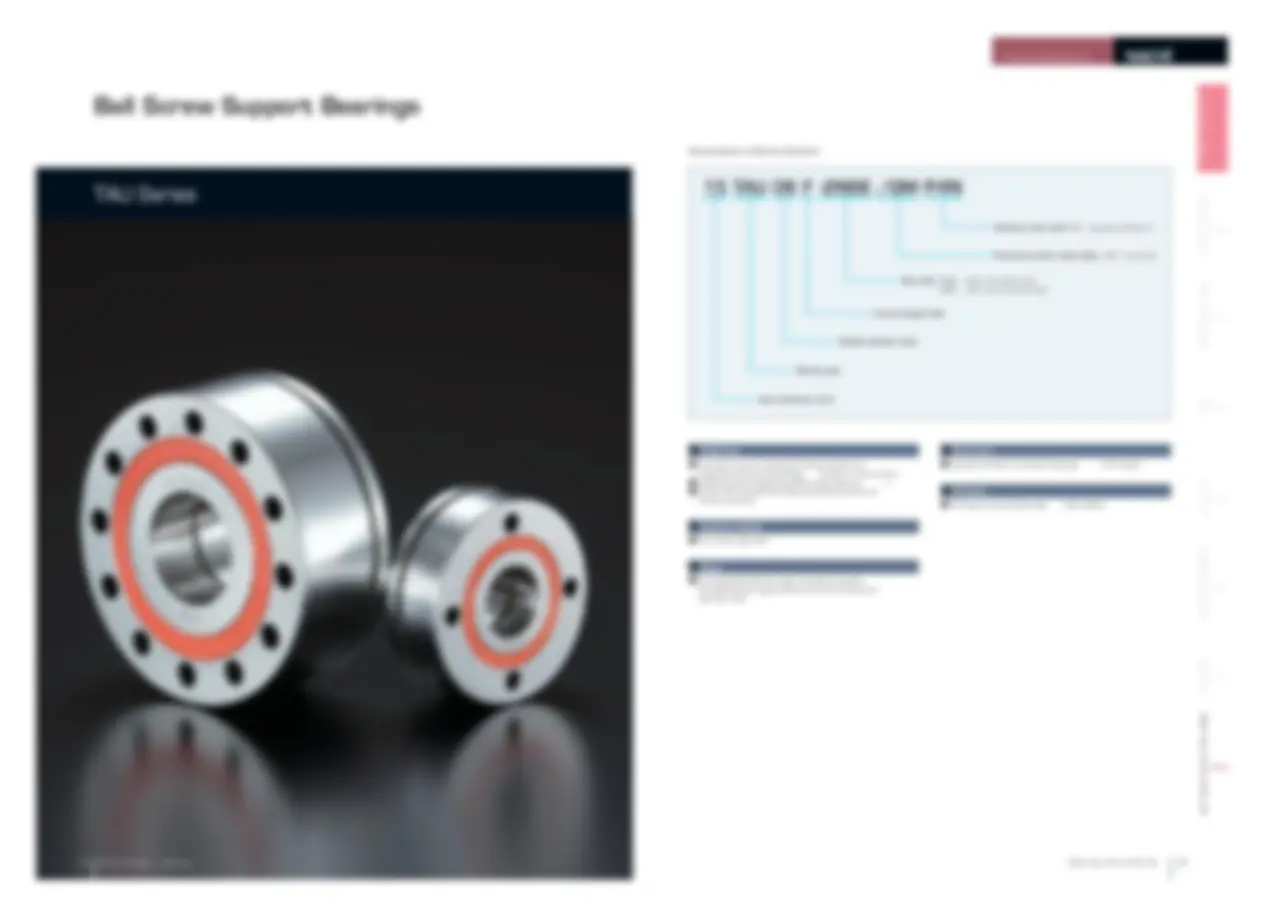
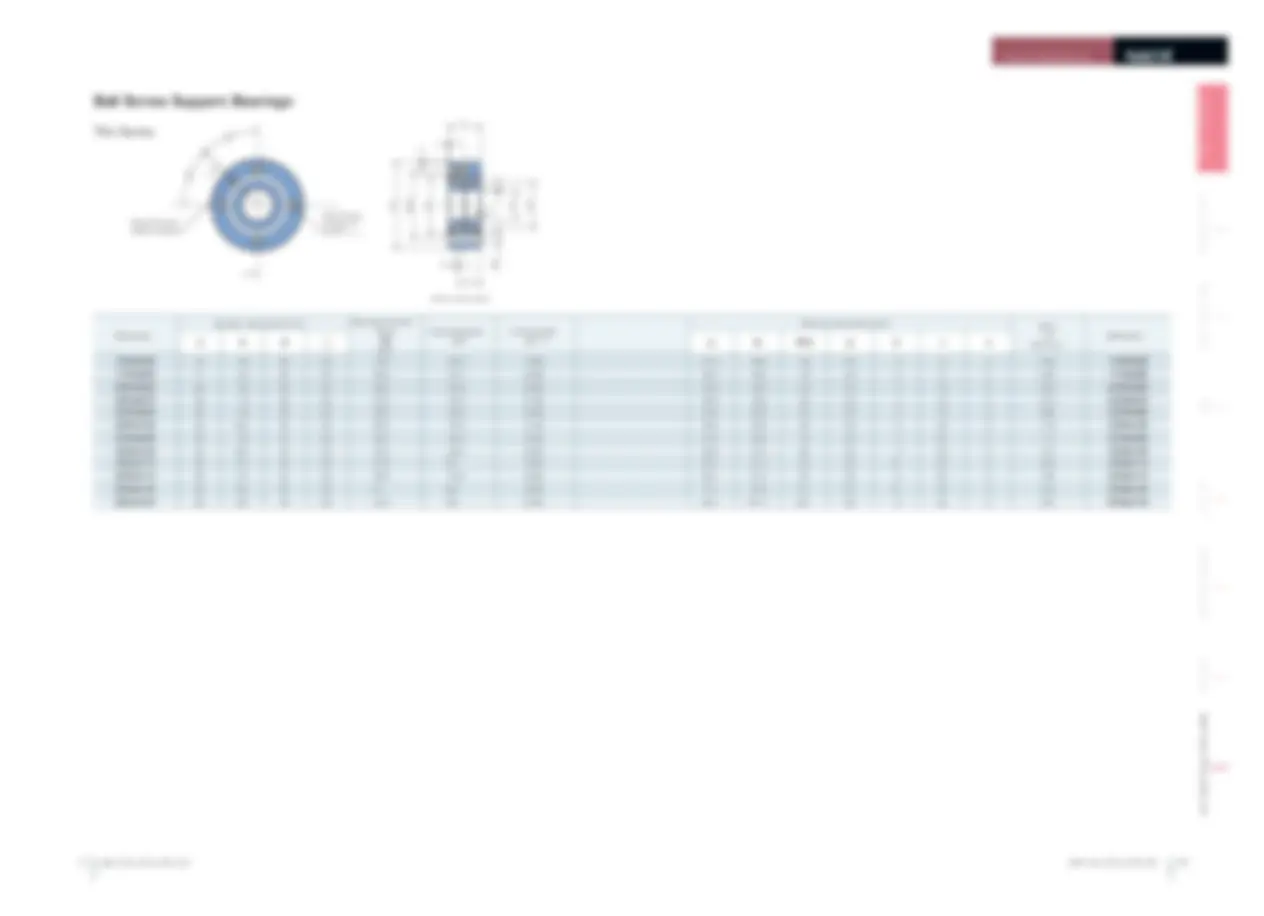
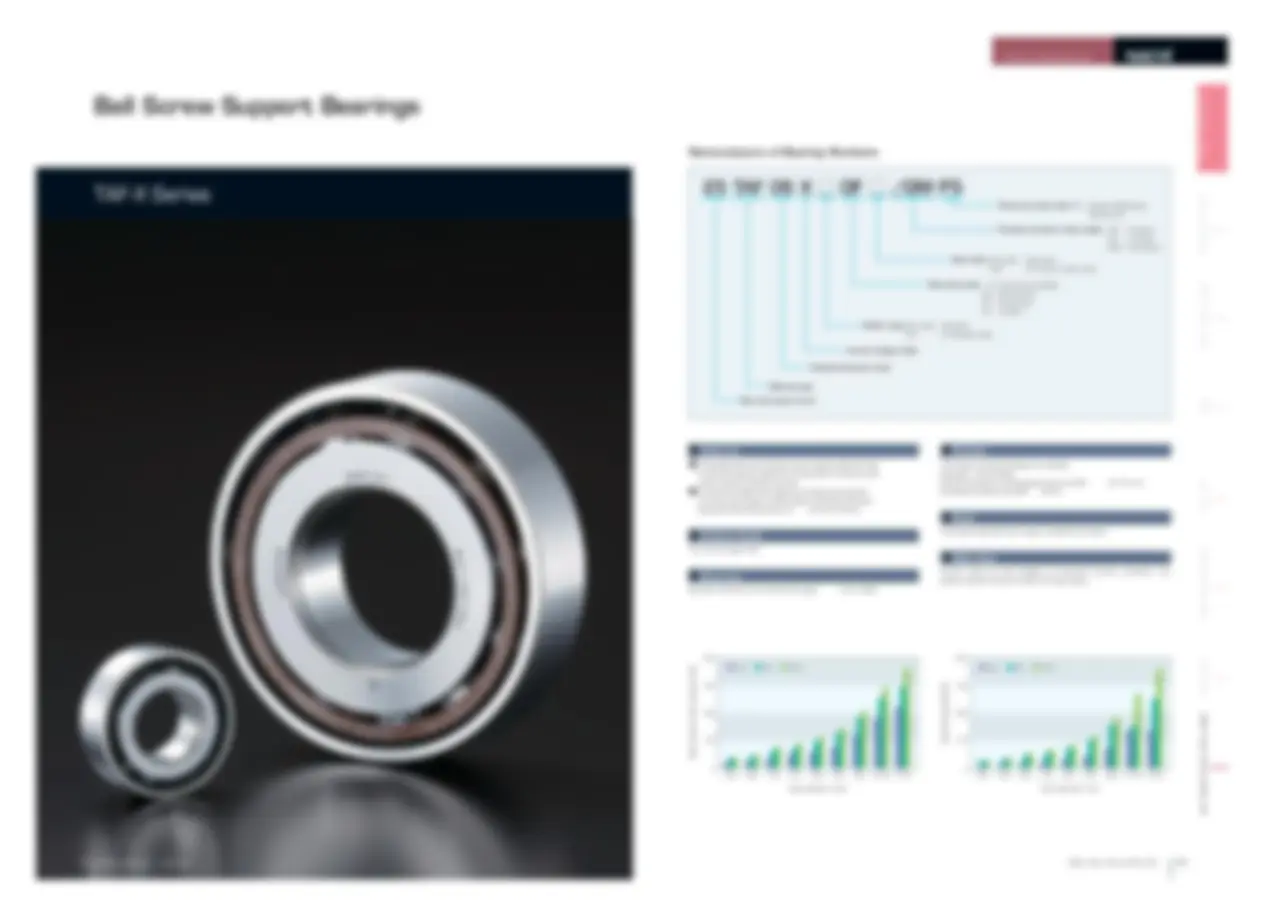
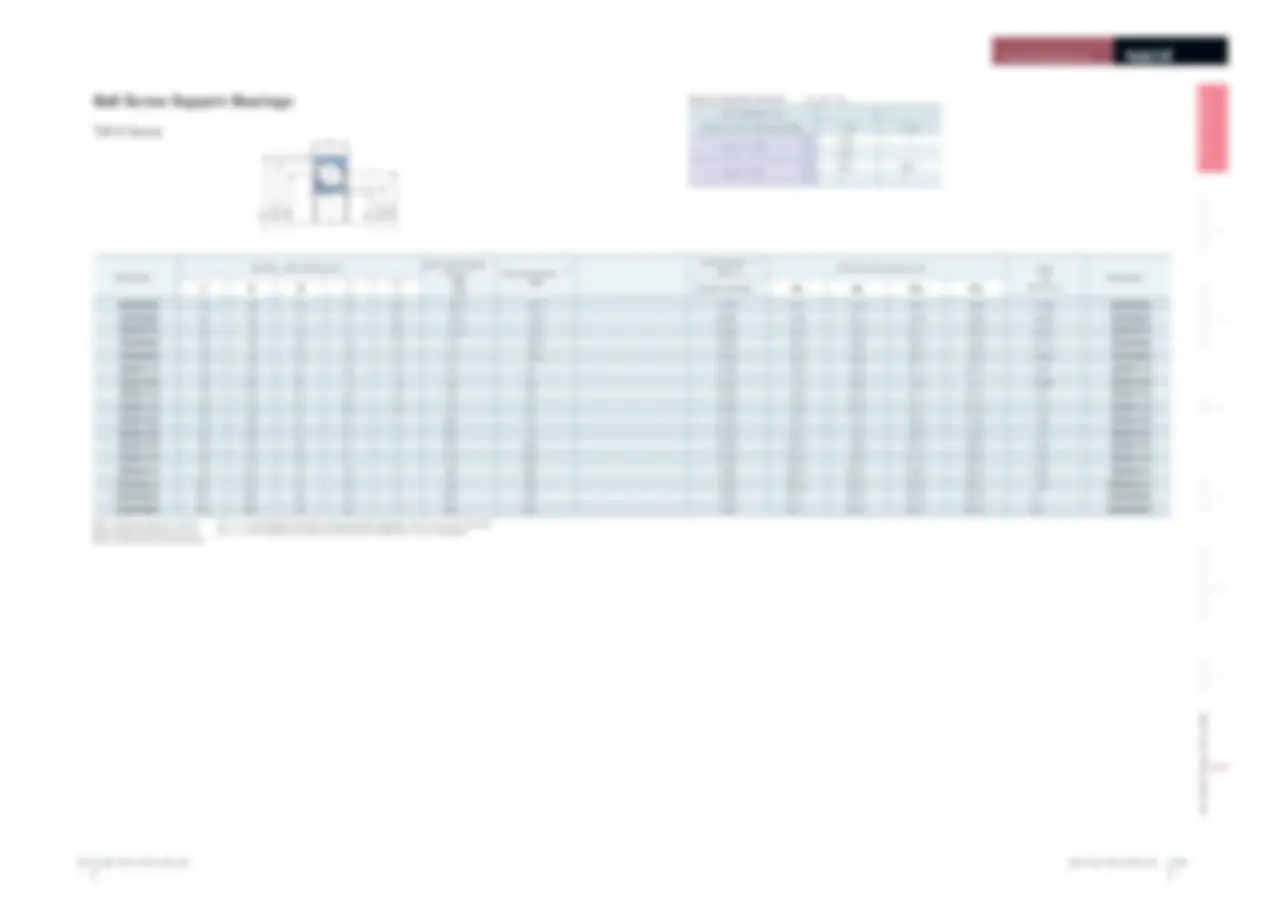
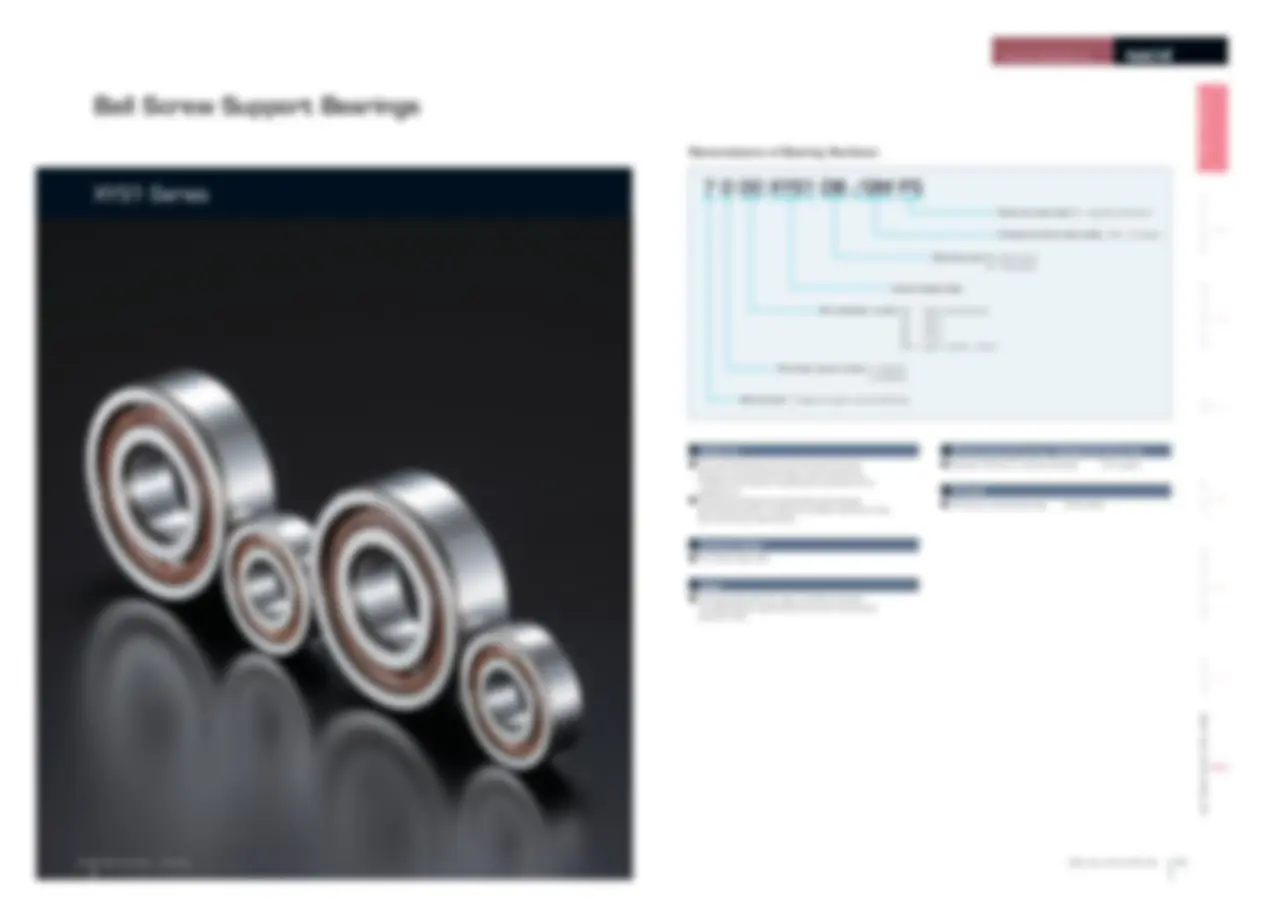
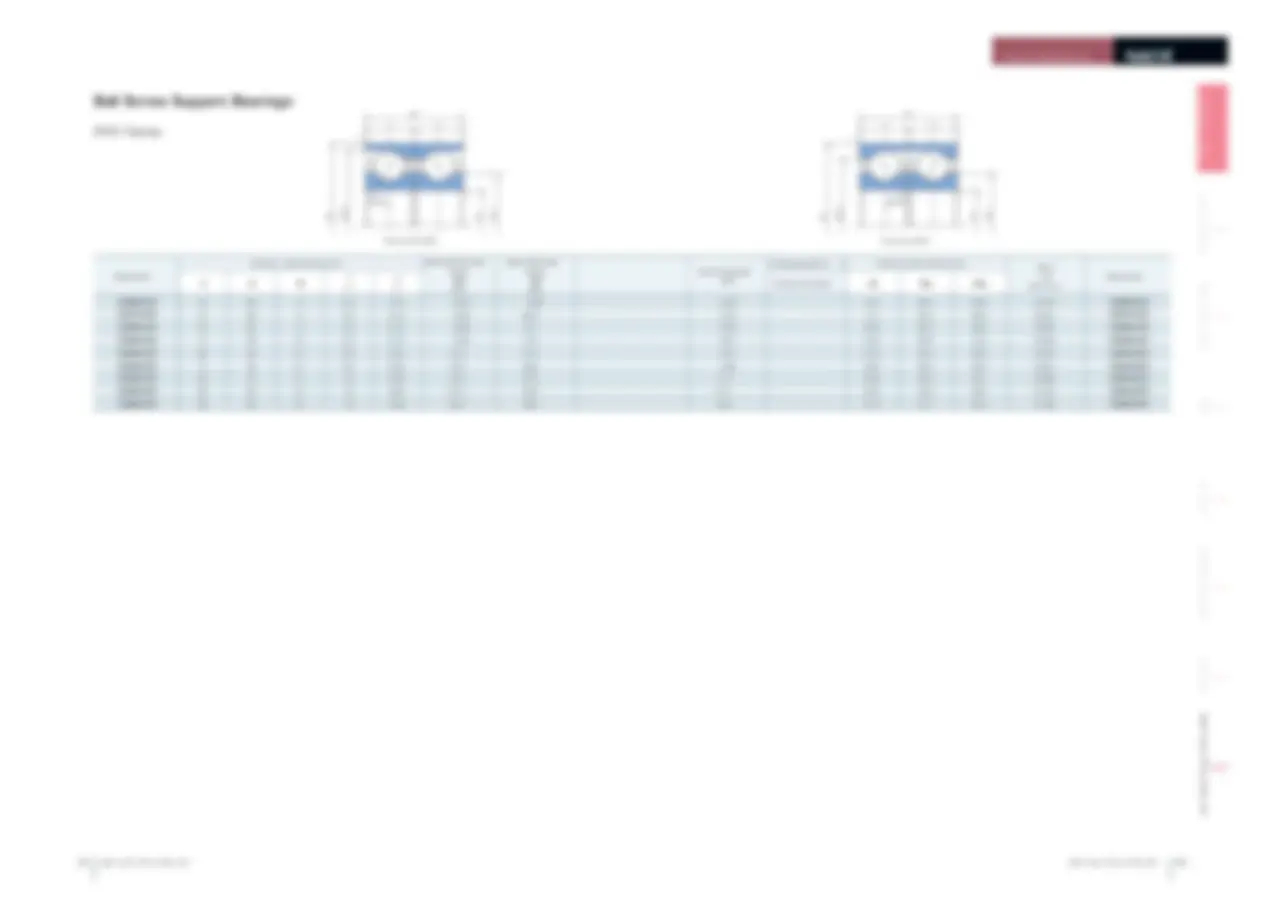
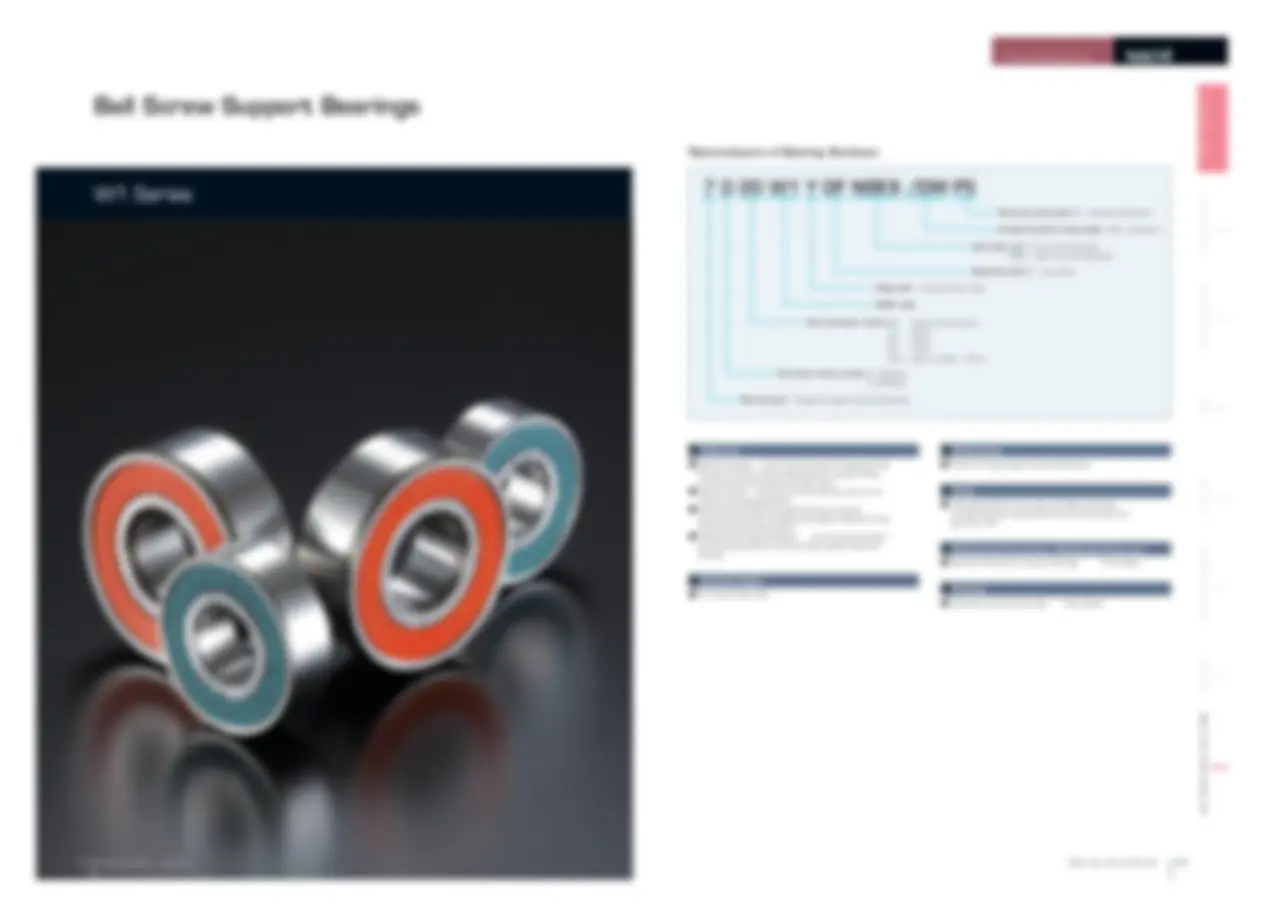
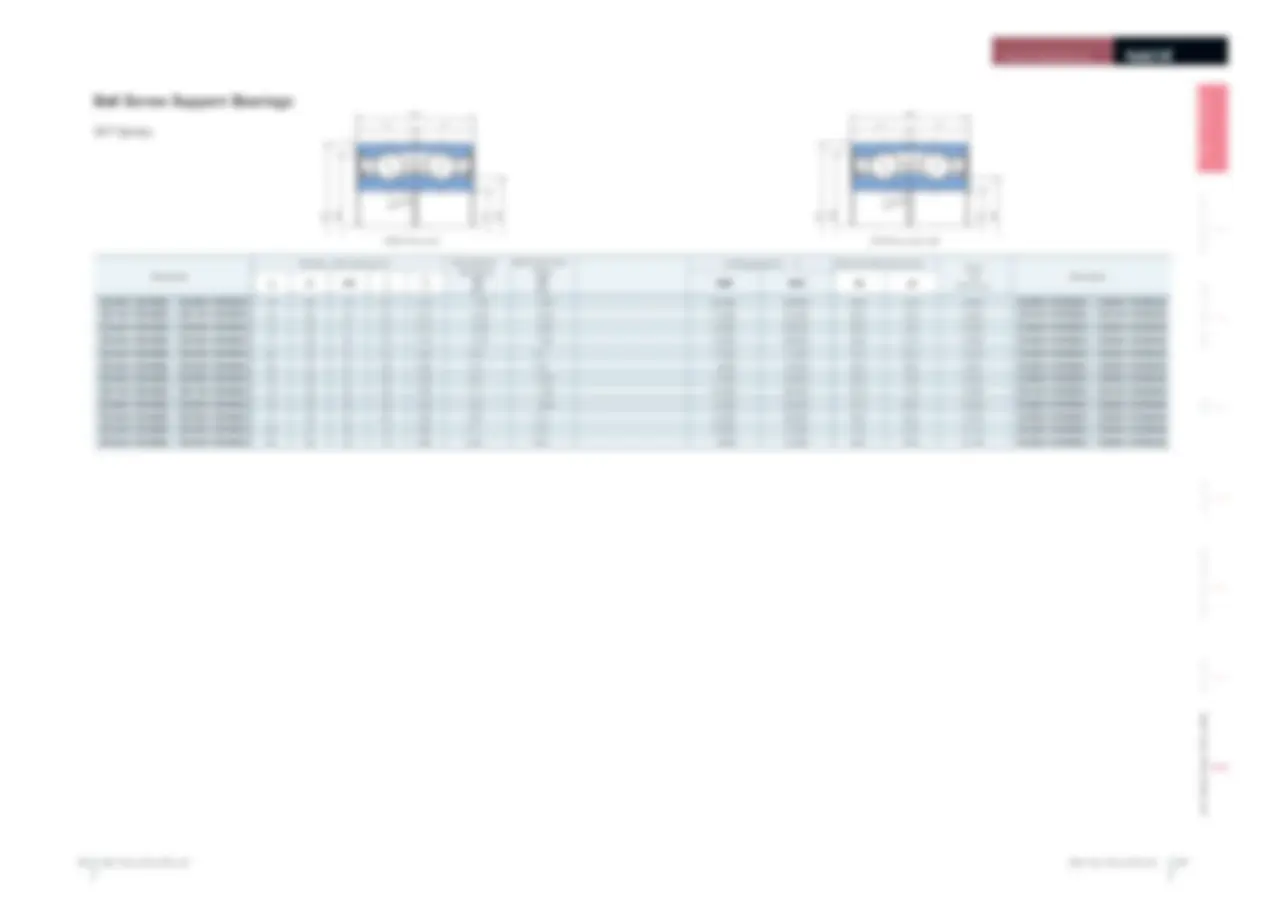
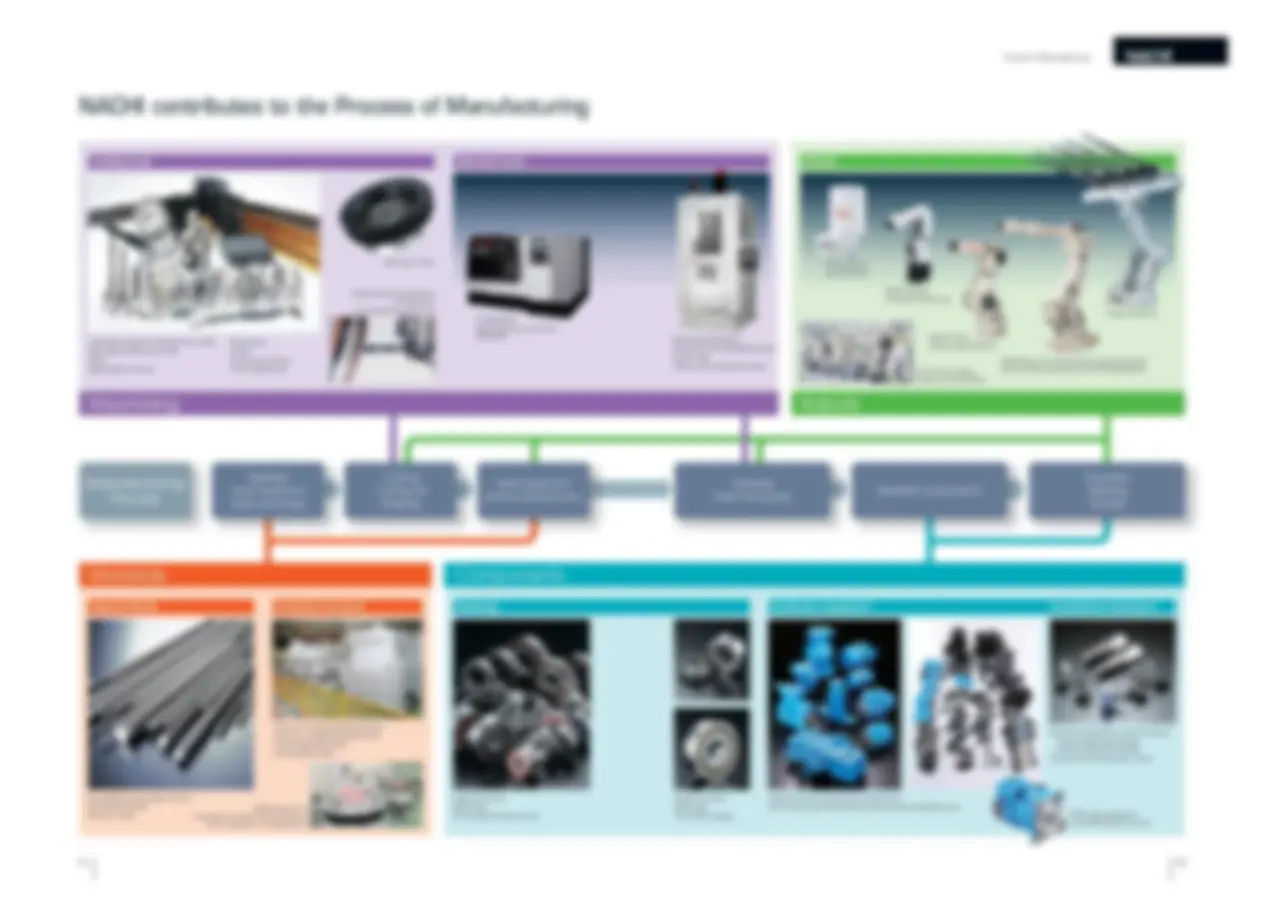
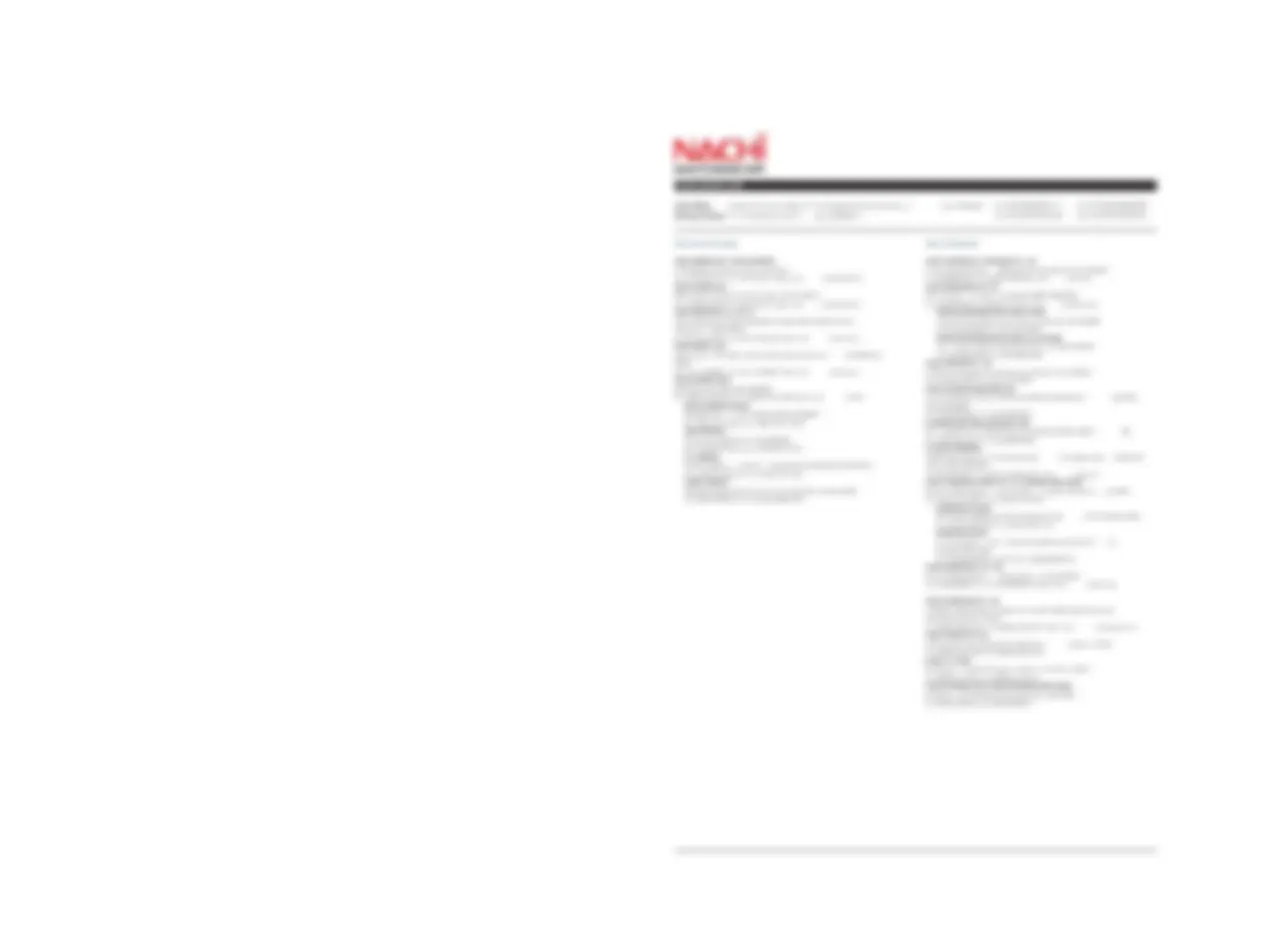
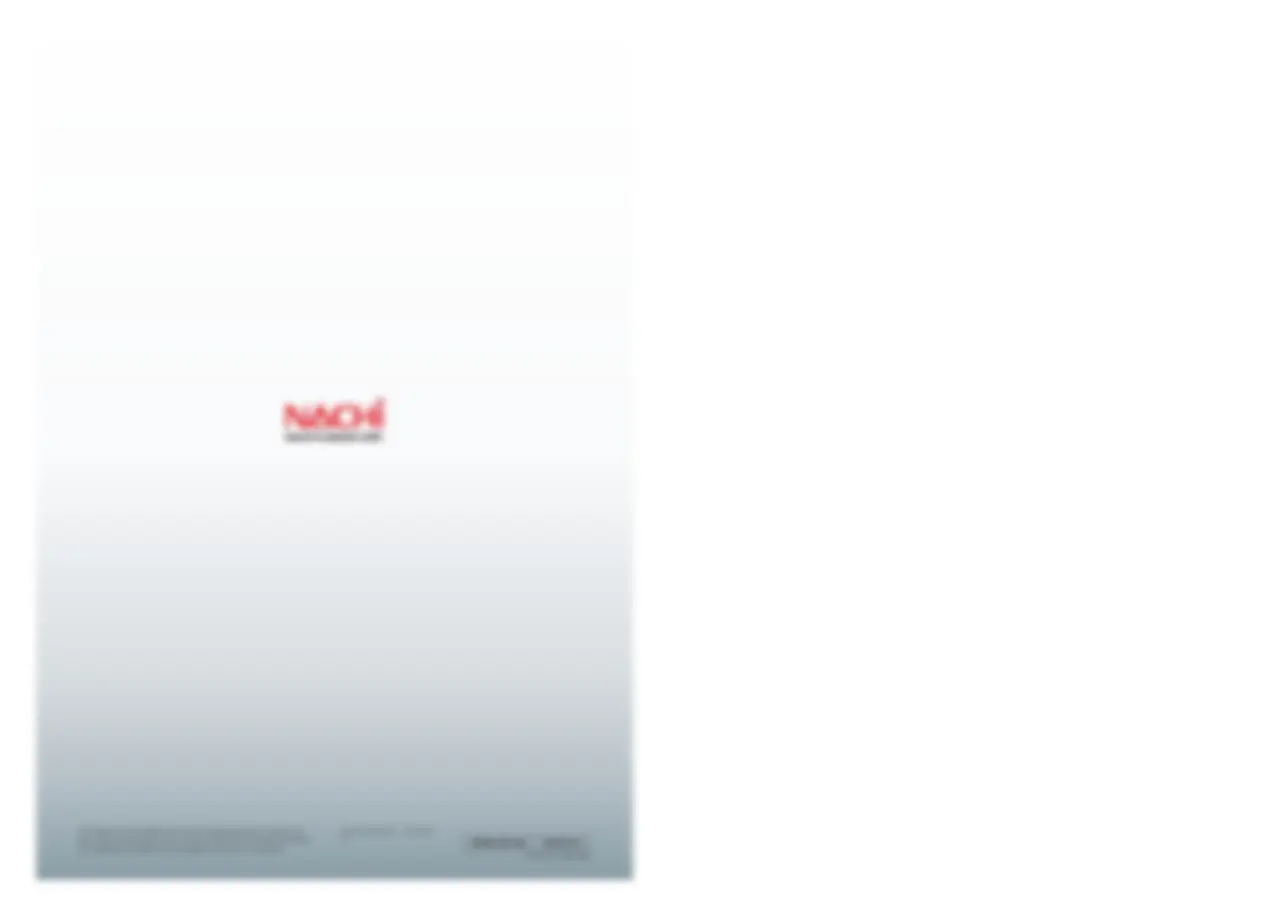
Estude fácil! Tem muito documento disponível na Docsity
Ganhe pontos ajudando outros esrudantes ou compre um plano Premium
Prepare-se para as provas
Estude fácil! Tem muito documento disponível na Docsity
Prepare-se para as provas com trabalhos de outros alunos como você, aqui na Docsity
Os melhores documentos à venda: Trabalhos de alunos formados
Prepare-se com as videoaulas e exercícios resolvidos criados a partir da grade da sua Universidade
Responda perguntas de provas passadas e avalie sua preparação.
Ganhe pontos para baixar
Ganhe pontos ajudando outros esrudantes ou compre um plano Premium
Comunidade
Peça ajuda à comunidade e tire suas dúvidas relacionadas ao estudo
Descubra as melhores universidades em seu país de acordo com os usuários da Docsity
Guias grátis
Baixe gratuitamente nossos guias de estudo, métodos para diminuir a ansiedade, dicas de TCC preparadas pelos professores da Docsity
Rolamentos de precisão para máquinas ferramentas
Tipologia: Esquemas
1 / 49
Esta página não é visível na pré-visualização
Não perca as partes importantes!
1-1 Bea ring Selection Procedure 5
1-2 Stu dy Bearing T ype 6
2-1 Basic Dynamic Load Rating and Rated Life 7
2-2 Dynamic Equivalent Load 7
2-3 Angular Contact Ball Bearing Load 8
2-4 Basic Static Load Rating and Static Equivalent Load 9
3-1 To lerances for Radial Bearings 10
3-2 To lerance for Thrust Load Angular Contact Ball Bearings (T AH/TBH Series) 12
3-3 To lerances for Cross T apered Roller Bearings 12
3-4 To lerances for Ball Screw Suppor t Bearing (T AB/T AU series) 13
3-5 To lerances for Ball Screw Suppor t Bearings (T AF-X series) 14
3-6 To lerances for T apered Bore Cylindrical Roller Bearings 14
4-1 Fea tures of Bearing Arrangement 15
4-2 Mounting and Mounting Symbols 16
4-3 Flush Ground Angular Contact Ball Bearings 16
5-1 Preload Objectives 17
5-2 Preload Methods 17
5-3 Measuring Preload 17
5-4 Preload Ef fect 18
5-5 Standard Preload and Axial Rigidity 19
6-1 Purpose of Lubrication 27
6-2 Lubrication Methods 27
7-1 Lim iting Speed Factors 31
8-1 Shaft and Housing Fits 32
8-2 Recommended Accuracy for Shaft and Housing 33
8-3 Chamfer Dimension Limits 34
9-1 Storing and T ranspor ting Bearings 35
9-2 Bea ring Installation 35
9-3 Running T est 39
9-4 Removing Bearings 39
5 Bearing Selection Bearing Selection 6
Figure 1.1 Bearing Selection Procedure
Factors Selection guidelines
Allowable space for bearings
● When designing a shaft system, the rigidity and strength of the shaft are important factors. The first step is to determine the shaft diameter, and the bore diameter. ● Figure 1.2 shows guidelines for the main precision rolling contact bearings types and sizes used in machine tools.
Load (type, direction, magnitude)
● Select the optimum bearing type in accordance with the magnitude of radial and axial load, direction of the load (either one or both directions), and level (vibration or shock). ● In general, a roller bearing has a greater load rating capacity than a ball bearing.
Rotating speed
● Select the bearing type in accordance with the maximum rotating speed specified for the machine where the bearing is used. ● The limiting speeds of bearings is largely depended on the magnitude of the load applied, running accuracy, cage material, and cage design. Therefore, careful consideration is necessary. ● In general, angular contact ball bearings or cylindrical roller bearings, which demonstrate minimal temperature rise, are used in high-speed applications.
Rigidity
● In order to improve the rigidity of rotational axis, the rigidity of the shaft and housing, as well as the bearing rigidity become important. ● In general, roller bearing rigidity is greater than a ball bearing. ● The rigidity of combination angular contact ball bearing is increased by applying a preload to the bearing. Mounting and dismounting ● Selecting a separable bearing increases work efficiency during mounting and dismounting for periodic inspection, etc.
79 Series NNU49 Series 70 Series BNH Series NN30 Series TAH Series 72 Series
Figure 1.2 Main Precision Rolling Bearings Used in Machine T ools
Performance, operating conditions, and environmental conditions demanded of bearings
Study bearing arrangement and types
Determine fit
Required Dynamic Load Rating
Select the degree of accuracy
Determining Preload
Study shaft and housing accuracy
Study handling and installation
Study design from maintenance viewpoint
Selection of bearing
Selecting the lubrication method Grease lubrication Grease and Oil Iubrication Sealed bearings Open bearings
Select bearing dimensions.
Basic static load rating check
Review operating speed
Is size within design limits?
Is operating load smaller than static load rating?
Is speed within limits?
Yes
Yes
Yes
No
No
No
1-2 Study Bearing Type
8-1 Shaft and Housing Fit
2 Bearing Life
3 Bearing Tolerance
5 Preload and Rigidity
8-2 Recommended Accuracy for Shaft and Housing
9 Bearing Handling
6 Lubrication
① Change from ball bearings to roller bearings. ② Use multiple bearings. ③ Use alternate dimension.
Review lubrication method
2-4 Basic Static Load Rating and Static Equivalent Load
7 Limiting Speeds
P.
P.
P.
P.
P.
P.
P.
P.
P.
P.
① Load direction and size ② Speed ③ Noise and torque ④ Horizontal or vertical shaft
① Outer or inner ring rotation ② Stationary, rotational or impact loading ③ Shaft and housing materials
Calculate the required dynamic load ratings based on load, rotation speed, and desired service life.
① Shaft axial run-out ② Vibration from rotation ③ Rotating speed
If high rigidity is required increase the preload.
In order to maintain performance of the main spindle in a machine tool, the accuracy of shaft and housing must be equal or higher than bearing accuracy. The recommended shaft and housing accuracy and surface roughness are shown in Tables 8.4 to 8.7.
Consider how to protect bearings from damage and dirt in the work environment, and design installation tools.
If the bearing service life is the same as or greater than the machine service life, consider a design or lubrication that does not require maintenance.
Monitoring equipment can help in predicting service life through heat and vibration measurements.
If the bearing service life or grease life is shorter than the machine service life, create a design that allows easy bearing replacement or easy grease replenishment, and define the maintenance interval.
Value analysis (Can standard parts be used?)
⑤ Rigidity ⑥ Axial bearing arrangement ⑦ Installation and removal ⑧ Vibration, shock
■ Prevent dirt, water, and other foreign matter from getting inside the bearing. ■ Maintenance is not required, since grease cannot be removedor added.
■ Countermeasures to keep dirt out, and to prevent oil/grease from leaking. ■ Design that allows grease replenishment.
④ Fixed or expansion (free) ⑤ Inner ring expansion due to centrifugal force at high rotation speeds
7 Bearing Life Bearing Life 8
● Basic Rating Life
● Basic Dynamic Load Rating (Cr or Ca)
L : Basic rating life (10 6 revolutions) Lh : Basic rating life (hours) C : Basic Dynamic Load Rating (N) (Cr for radial bearings, Ca for thrust bearings) P : Bearing Load (Dynamic Equivalent Load) (N) (Pr for radial bearings, Pa for thrust bearings) p : 3 (ball bearings), 10/3 (roller bearings) n : RPM: (min -1^ )
2-row arrangement 3-row arrangement 4-row arrangement 1.62 2.16 2.
Pr : Dynamic equivalent radial load (N) Pa : Dynamic equivalent axial load (N) Fr : Radial load (N) Pa : Axial load (N) X : Radial load factors (T able 2.1) Y : Axial load factors (T able 2.1)
● Table 2.1 Load Factors Nominal contact angle
iFa/ Cor e
Single row and DT combination DB and DF combination
X Y X Y X Y
Radial ball bearings
15°
0.015 0.
1
0.029 0.40 1.40 1.57 2. 0.058 0.43 1.30 1.46 2. 0.087 0.46 1.23 1.38 2. 0.12 0.47 1.19 1.34 1. 0.17 0.50 1.12 1.26 1. 0.29 0.55 1.02 1.14 1. 0.44 0.56 1.00 1.12 1. 0.58 0.56 1.00 1.12 1. 25° − 0.68 0.41 0.87 0.92 0.67 1. 30° − 0.80 0.39 0.76 0.78 0.63 1. 40° − 1.14 0.35 0.57 0.55 0.57 0. Thrust ball bearings
50° − 1.49 0.73 1 1.37 0.57 0.73 1 55° − 1.79 0.81 1 1.60 0.56 0.81 1 60° − 2.17 0.92 1 1.90 0.55 0.92 1 (Note 1) i = 2 for DB and DF , i = 1 for single and DT.
(Note 3) When the nominal contact angle is 15°, use linear interpolation to determine X, Y , and e values of iFa/Cor that are not included in the table. (Note 4) For high-speed use (dmn value > 800,000), the centrifugal force of the roller must also be taken into consideration in addition to the external load. Please consult NACHI concerning such applications.
Fa' : Induced axial load (N) Fr : Radial load (N) Y : Axial load factor
Figure 2.1 Induced Axial Load for Angular Contact Ball Bearings
● Table 2.2 Axial Load and Dynamic Equivalent Load of Angula r Contact Ball Bearings
Fr Ⅰ, Fr Ⅱ : Radial load (N) applied to bearings I and II YⅠ, Y Ⅱ : Axial load factors of bearings I and II Pr Ⅰ, Pr Ⅱ : Dynamic equivalent radial load (N) of bearings I and II
Fa : External axial load (N) XⅠ, X Ⅱ : Radial load factors of bearings I and II
11 Bearing T olerance Bearing T olerance 12
Bearing T olerance
● Table 3.2 T olerances of Outer Ring (JIS Class 5, Class 4, Class 2) (^) Unit: μm
Nominal bearing outside diameter
Single plane mean outside diameter variation of outer ring
Outside diameter deviation
Outside diameter variation in a single radial plane (1)
Mean outside diameter variation
Class 5 Class 4 Class 2 Class 4 Class 2 Class 5 Class 4 Class 2 Class 5 Class 4 Class 2
Over Incl. Upper Lower Upper Lower Upper Lower
Diameter series Diameter series 0,2 9 0,2 9 0,2 0,2 max max max Upper Lower Upper Lower max max max max max 18 30 0 -6 0 -5 0 -4 0 -5 0 -4 6 5 5 4 4 3 2.5 2 30 50 0 -7 0 -6 0 -4 0 -6 0 -4 7 5 6 5 4 4 3 2 50 80 0 -9 0 -7 0 -4 0 -7 0 -4 9 7 7 5 4 5 3.5 2 80 120 0 -10 0 -8 0 -5 0 -8 0 -5 10 8 8 6 5 5 4 2. 120 150 0 -11 0 -9 0 -5 0 -9 0 -5 11 8 9 7 5 6 5 2. 150 180 0 -13 0 -10 0 -7 0 -10 0 -7 13 10 10 8 7 7 5 3. 180 250 0 -15 0 -11 0 -8 0 -11 0 -8 15 11 11 8 8 8 6 4 250 315 0 -18 0 -13 0 -8 0 -13 0 -8 18 14 13 10 8 9 7 4 315 400 0 -20 0 -15 0 -10 0 -15 0 -10 20 15 15 11 10 10 8 5
Unit: μm
Nominal bearing outside diameter
Outer ring radial runout of assembled bearing
Variation of outside surface generatrix inclination with outer ring reference
Assembled bearing outer ring reference face runout with raceway (2)
Deviation of a single ring width
Outer ring width variation
Class 5 Class 4 Class 2 Class 5 Class 4 Class 2 Class 5 Class 4 Class 2 Class 5 Class 4 Class 2 Over Incl. max max max max max max max max max max max max 18 30 6 4 2.5 8 4 1.5 8 5 2.
Corresponds to the
the inner ring being matched with it.
(Note 1) Applies to open type bearings. (Note 2) Applies to ball bearings. Remark: The low outside diameter deviation of bearings in T able 3.2 does not apply within a distance from the ring face of 1.2 x r max of the chamfer.
3-2 Tolerance for Thrust Load Angular Contact Ball
Bearings (TAH/TBH Series)
3-3 Tolerances for Cross Tapered Roller Bearings
● Table 3.3 T olerance of Outside Diameter (^) Unit: μm Nominal bearing outside diameter
Outside diameter deviation
Over Incl. Upper Lower 50 80 -30 - 80 120 -36 - 120 180 -43 - 180 250 -50 - 250 315 -56 -
● Table 3.4 XRN Series Inner Ring and Outer Ring tolerances (^) Unit: μm
Bearing No.
Single plane mean bore diameter variation
Single plane mean outside diameter variation of outer ring
Upper Lower Upper Lower Upper Lower Radial run-out Sideface runout 150XRN23 0 -13 0 -15 +350 -250 7 7 200XRN28 0 -15 0 -18 +350 -250 7 7 250XRN33 0 -15 0 -18 +350 -250 7 7 250XRN35 0 -10 0 -13 +350 -250 9 9 300XRN40 0 -13 0 -15 +350 -250 7 7 310XRN42 0 -13 0 -15 +350 -250 7 7 0330XRN045 +25 0 +25 0 +350 -250 8 8 350XRN47 0 -13 0 -15 +350 -250 9 9 375XRN49 0 -13 0 -15 +350 -250 7 7 400XRN55 0 -13 0 -18 +350 -250 9 9 0457XRN060 +25 0 +25 0 +380 -380 9 9 580XRN76 +25 0 +38 0 +406 -406 10 10 0685XRN091 +38 0 +38 0 +508 -508 12 12 950XRN117 0 -75 0 -75 +750 -750 14 14
● Table 3.5 XRG (XRGV) Series Inner Ring and Outer Ring T olerances (^) Unit: μm
Bearing No.
Single plane mean bore diameter variation
Single plane mean outside diameter variation of outer ring
Upper Lower Upper Lower Upper Lower Radial run-out Sideface runout 130XRG23 0 -10 0 -15 +350 -250 6 7 140XRGV20 0 -13 0 -15 +350 -350 5 5 150XRG23 0 -13 0 -15 +350 -250 6 7 200XRGV028 0 -15 0 -18 +350 -350 7 7 320XRG43 0 -13 0 -15 +350 -250 7 7 480XRGV66 0 -45 -70 -100 +450 -450 11 11
13 Bearing T olerance Bearing T olerance 14
Bearing T olerance
3-4 Tolerances for Ball Screw Support Bearing (TAB/TAU series)
● Table 3.6 Tolerances for Inner Ring (Including Outer Ring W idth and Outer Ring Sideface Runout Reference to Raceway) (^) Unit: μm
Nominal bearing bore diameter
Single plane mean bore and bore variation
Bore diameter variation in a single radial plane
Mean bore diameter variation
Deviation of a single inner ring width (or a single outer ring width)
Width deviation of Inner ring
Radial runout of assembled bearing inner ring
Side face
reference to bore
Side face runout with reference to raceway of assembled bearing
assembled bearing
Class 5 Class 4 Class 5 Class 4 Class 5 Class 4 Class 5/Class 4 Class 5 Class 4 Class 5 Class 4 Class 5 Class 4 Class 5 Class 4 Over Incl. Upper Lower Upper Lower max max max max Upper Lower max max max max max max max max 10 18 0 -5 0 -4 4 3 3 2 0 -80 5 2.5 4 2.5 7 3 4 2 18 30 0 -6 0 -5 5 4 3 2.5 0 -120 5 2.5 4 3 8 4 5 2. 30 50 0 -8 0 -6 6 5 4 3 0 -120 5 3 5 4 8 4 6 2. 50 80 0 -9 0 -7 7 5 5 3.5 0 -150 6 4 5 4 8 5 7 2.
● Table 3.7 T olerances for Outer Ring (^) Unit: μm
Nominal bearing outside diameter
Single plane mean outside diameter variation of outer ring
Outside diameter variation in a single radial plane
Mean outside diameter variation
Outer ring width variation
Outer ring radial runout of assembled bearing
Variation of outside surface generatrix inclination with outer ring reference
Class 5 Class 4 Class 5 Class 4 Class 5 Class 4 Class 5 Class 4 Class 5 Class 4 Class 5 Class 4 Over Incl. Upper Lower Upper Lower max max max max max max max max max max 30 50 0 -7 0 -6 5 5 4 3 5 2.5 7 5 8 4 50 80 0 -9 0 -7 7 5 5 3.5 6 3 8 5 8 4 80 120 0 -10 0 -8 8 6 5 4 8 4 10 6 9 5
● Table 3.8 Tolerances for Bore Diameter of Inner Ring (P4F) (^) Unit: μm Nominal bearing bore diameter
Single plane mean bore diameter variation
Class 4 flush ground Over Incl. Upper Lower 10 18 0 - 18 30 0 - 30 50 0 - 50 80 0 - Tolerances for other than bore diameter conforms to Class 4 in T able 3.6.
● Table 3.9 Tolerance for Outside Diameter of Outer Ring (P4F) (^) Unit: μm Nominal bearing outside diameter
Single plane mean outside diameter variation of outer ring
Class 4 flush ground Over Incl. Upper Lower 30 50 0 - 50 80 0 - 80 120 0 - Tolerances for other than outside diameter conforms to Class 4 in T able 3.7.
3-5 Tolerances for Ball Screw Support Bearings (TAF-X series)
3-6 Tolerances for Tapered Bore Cylindrical Roller Bearings
● Table 3.10 T olerances for Inner Ring (Including Outer Ring W idth, Equivalent JIS Class 5) (^) Unit: μm
Nominal bearing bore diameter
Single plane mean bore diameter variation
Bore diameter variation in a single radial plane
Mean bore diameter variation
Outer and inner ring width variation
Width deviation VBS of Inner Ring
Radial runout of assembled bearing inner ring
Side face runout with reference to bore
Side face runout with reference to raceway of assembled bearing inner ring
Over Incl. Upper Lower max max Upper Lower max max max max 18 30 0 -6 5 3 0 -120 5 4 8 8 30 50 0 -8 6 4 0 -120 5 5 8 8 50 80 0 -9 7 5 0 -150 6 5 8 8 80 120 0 -10 8 5 0 -200 7 6 9 9
● Table 3.11 T olerances for Outer Ring (Equivalent JIS Class 5) (^) Unit: μm
Nominal bearing outside diameter
Single plane mean outside diameter variation of outer ring
Outside diameter variation in a single radial plane
Mean outside diameter variation
Outer ring width variation
Outer ring radial runout of assembled bearing
Variation of outside surface generatrix inclination with outer ring reference
Assembled bearing outer ring reference face runout with raceway
Over Incl. Upper Lower max max max max max max 50 80 0 -9 7 5 6 8 8 10 80 120 0 -10 8 5 8 10 9 11 120 150 0 -11 8 6 8 11 10 13 150 180 0 -13 10 7 8 13 10 14 180 250 0 -15 11 8 10 15 11 15 250 315 0 -18 14 9 11 18 13 18
● Table 3.12 T olerances for T apered Bores (Cylindrical Roller Bearings) (^) Unit: μm
Nominal bearing bore diameter
Mean bore diameter deviation at theoretical small end of a tapered bore Bore diameter variation in asingle plane radial plane
Class 5 Class 4 Class 5 Class 4 Class 5 Class 4 Over Incl. Upper Lower Upper Lower Upper Lower Upper Lower max max 18 30 +10 0 +6 0 +5 0 +3 0 3 3 30 50 +12 0 +8 0 +5 0 +4 0 4 3 50 80 +15 0 +9 0 +6 0 +4 0 5 4 80 120 +20 0 +10 0 +7 0 +5 0 5 4 120 180 +25 0 +13 0 +10 0 +7 0 7 5 180 250 +30 0 +15 0 +12 0 +9 0 8 6 250 315 +35 0 +18 0 +15 0 +11 0 9 9 315 400 +40 0 +23 0 +16 0 +12 0 12 12
Figure 3.1 Tapered Bores of Cylindrical Roller Bearings
Theoretical tapered bore Tapered bore with actual mean diameters at their deviations
φ d
α
α
φ d
1 φ(
d + Δd
)mp
φ(
d^1 +
Δd 1mp
)
Δd 1mp- Δd 1mp 2
17 Preload and Rigidity Preload and Rigidity 18
Gyro-moment
Ball rotation
Gyro-moment
Figure 5.1 Gyro-moment
① Axial load measurement method
② Axial displacement measurement method
③ Bearing starting friction torque measurement method
Figure 5.2 Cylindrical Roller Bearing (NN3020) Radial Clearance and Ser vice Life
0
-0.020 0 0.020 0.040 0. Radial clearance (mm)
Radial Load: 4710N (3% of dynamic load rating)
● Table 5.1 Preload Methods Preload methods Design example Features
Fixed-position preload
Method using either a duplex bearing with pre-adjusted preload or a dimension adjusted spacer
● Since bearing spread is used, the prescribed preload can be obtained simply by tightening a nut. ● Fit causes preload inconsistency. ● Heat generation causes preload inconsistency. ● Applying an axial load that is too great can cause loss of preload.
Preload adjustment method using nut tightening
● Uniform preload, even if fit is inconsistent ● Further tightening possible ● Heat generation causes preload inconsistency. ● Applying an axial load that is too great can cause loss of preload.
Fixed-pressure preload
Method using spring
● Constant uniform preload while running ● No loss of preload ● Suitable for high speeds ● In principle, one-direction axial load can be applied ● Inferior rigidity compared to fixed-position preload of the same preload
Figure 5.3 Fixed-position Preload
Bearing A Bearing B
Tw (^) O
Applied load Tw
Axial load
Ta
T-^ δ^ a curve of bearing A
T- δ a curve of bearing B
Tp Tb
Tpo
δ w
(Life=1 when radial clearance=0)
Life ratio
Axial elastic displacement amount
δ a
19 Preload and Rigidity Preload and Rigidity 20
Preload and Rigidity
● Table 5.2 Preload Factors for Multiple-row Arrangements 3-row arrangement 4-row arrangement FFB ・BFF FFFB ・BFFF FFBB ・BBFF 1.36 1.57 2
5-5 Standard Preload and Axial Rigidity
● Table 5.
Bore diameter number
E preload (extra-light preload) L preload (light preload) M preload (medium preload) Preload (N)
Axial rigidity (N/μm)
Preload (N)
Axial rigidity (N/μm)
Preload (N)
Axial rigidity (N/μm) 00 5 10 15 15 30 20 01 7 12 20 18 40 24 02 8 13 25 21 50 28 03 8 13 25 21 50 28 04 15 19 40 27 80 36 05 15 19 50 33 100 43 06 15 21 50 36 100 48 07 25 28 70 41 140 56 08 25 28 80 44 155 60 09 35 35 100 53 195 70 10 35 35 100 56 195 72
Bore diameter number
L preload (light preload) M preload (medium preload) H preload (heavy preload) Preload (N)
Axial rigidity (N/μm)
Preload (N)
Axial rigidity (N/μm)
Preload (N)
Axial rigidity (N/μm) 00 20 33 88 59 196 82 01 20 33 98 65 216 90 02 29 42 108 67 235 94 03 29 42 118 74 255 102 04 59 65 235 107 490 149 05 69 69 265 120 560 169 06 78 78 294 134 628 190 07 88 88 323 147 785 212 08 88 98 412 165 1,000 244 09 98 109 470 188 1,040 260 10 118 118 520 208 1,140 284
Bore diameter number
E preload (extra-light preload) L preload (light preload) M preload (medium preload) H preload (heavy preload) Preload (N)
Axial rigidity (N/μm)
Preload (N)
Axial rigidity (N/μm)
Preload (N)
Axial rigidity (N/μm)
Preload (N)
Axial rigidity (N/μm) 00 20 13 50 20 100 29 145 37 01 20 14 50 21 100 31 145 39 02 20 15 50 23 100 34 145 42 03 20 16 50 25 100 35 145 43 04 50 23 100 33 195 48 295 59 05 50 26 100 36 195 50 295 63 06 50 27 100 38 195 53 390 75 07 70 33 145 46 295 64 390 75 08 70 34 145 49 295 68 590 98 09 70 34 145 49 295 68 590 98 10 70 36 145 51 295 70 590 100 11 100 43 195 56 390 78 785 112 12 100 43 195 58 390 82 785 115 13 100 47 195 61 390 85 785 123 14 145 57 295 75 590 105 1,170 149 15 145 57 295 77 590 107 1,170 153 16 145 57 295 75 590 105 1,170 149 17 195 65 390 89 785 125 1,470 171 18 195 65 390 87 785 121 1,470 165 19 195 68 390 91 785 125 1,470 171 20 195 70 390 93 785 127 1,470 173
Bore diameter number
L preload (light preload) M preload (medium preload) H preload (heavy preload) Preload (N)
Axial rigidity (N/μm)
Preload (N)
Axial rigidity (N/μm)
Preload (N)
Axial rigidity (N/μm) 00 39 39 118 62 314 95 01 39 44 127 67 343 104 02 49 49 157 83 353 118 03 59 59 216 98 520 144 04 59 59 274 110 608 152 05 108 83 392 140 804 187 06 118 91 441 158 892 208 07 127 98 539 174 1,156 236 08 147 113 617 193 1,176 256 09 216 135 745 213 1,646 300 10 225 141 784 224 1,744 317 11 314 157 1,040 254 2,078 341 12 333 167 1,098 268 2,205 362 13 363 191 1,225 299 2,450 402 14 392 196 1,460 332 3,010 443 15 412 206 1,530 348 3,155 464 16 529 230 1,900 373 3,880 504 17 549 239 1,990 390 4,080 530 18 676 260 2,185 405 4,600 555 19 706 272 2,300 427 4,810 580 20 745 287 2,400 445 5,050 608
23 Preload and Rigidity Preload and Rigidity 24
Preload and Rigidity
● Table 5.
Bearing No.
2-row arrangement 3-row arrangement 4-row arrangement DB/DF FFB/BFF FFBB/BBFF FFFB/BFFF Preload (N)
Axial rigidity (N/μm)
Starting torque (N ・cm)
Preload (N)
Axial rigidity (N/μm)
Starting torque (N ・cm)
Preload (N)
Axial rigidity (N/μm)
Starting torque (N ・cm)
Preload (N)
Axial rigidity (N/μm)
Starting torque (N ・cm) 15TAB04 1,080 540 10 1,470 800 11 2,160 1,080 16 1,700 1,020 12 17TAB04 1,080 540 10 1,470 800 11 2,160 1,080 16 1,700 1,020 12 20TAB04 1,080 540 10 1,470 800 11 2,160 1,080 16 1,700 1,020 12 25TAB06 1,665 757 15 2,260 1,130 20 3,330 1,510 30 2,610 1,430 23 30TAB06 1,665 757 15 2,260 1,130 20 3,330 1,510 30 2,610 1,430 23 35TAB07 1,960 933 20 2,670 1,390 27 3,920 1,870 40 3,080 1,760 31 40TAB07 1,960 933 20 2,670 1,390 27 3,920 1,870 40 3,080 1,760 31 40TAB09 2,600 1,000 30 3,540 1,490 41 5,200 2,000 60 4,080 1,890 47 45TAB07 2,060 981 20 2,800 1,460 27 4,120 1,960 40 3,230 1,850 31 45TAB10 2,990 1,107 35 4,070 1,650 47 5,980 2,210 70 4,690 2,090 54 50TAB10 3,140 1,163 40 4,270 1,730 54 6,280 2,330 80 4,930 2,200 62 55TAB10 3,140 1,163 40 4,270 1,730 54 6,280 2,330 80 4,930 2,200 62 55TAB12 3,530 1,358 45 4,800 2,020 61 7,060 2,720 90 5,540 2,570 70 60TAB12 3,530 1,358 45 4,800 2,020 61 7,060 2,720 90 5,540 2,570 70
Bearing No.
2-row arrangement 3-row arrangement 4-row arrangement DB/DF FFB/BFF FFBB/BBFF FFFB/BFFF Preload (N)
Axial rigidity (N/μm)
Starting torque (N ・cm)
Preload (N)
Axial rigidity (N/μm)
Starting torque (N ・cm)
Preload (N)
Axial rigidity (N/μm)
Starting torque (N ・cm)
Preload (N)
Axial rigidity (N/μm)
Starting torque (N ・cm) 15TAB04 2,160 735 15 2,940 1,080 20 4,310 1,470 30 3,430 1,320 25 17TAB04 2,160 735 15 2,940 1,080 20 4,310 1,470 30 3,430 1,320 25 20TAB04 2,160 735 15 2,940 1,080 20 4,310 1,470 30 3,430 1,320 25 25TAB06 3,330 981 20 4,510 1,470 27 6,670 1,960 40 5,200 1,910 30 30TAB06 3,330 981 20 4,510 1,470 27 6,670 1,960 40 5,200 1,910 30 35TAB07 3,920 1,230 25 5,300 1,770 35 7,840 2,350 50 6,180 2,300 40 40TAB07 3,920 1,230 25 5,300 1,770 35 7,840 2,350 50 6,180 2,300 40 40TAB09 5,200 1,320 50 7,060 1,910 68 10,400 2,550 100 8,140 2,500 80 45TAB07 4,120 1,270 30 5,590 1,910 40 8,240 2,550 60 6,470 2,500 45 45TAB10 5,980 1,470 60 8,140 2,160 82 12,000 2,890 120 9,410 2,790 95 50TAB10 6,280 1,520 65 8,530 2,260 88 12,600 3,040 130 9,810 2,940 100 55TAB10 6,280 1,520 65 8,530 2,260 88 12,600 3,040 130 9,810 2,940 100 55TAB12 7,060 1,770 70 9,610 2,550 95 14,100 3,480 140 11,100 3,380 110 60TAB12 7,060 1,770 70 9,610 2,550 95 14,100 3,480 140 11,100 3,380 110
Bearing No. Preload (N)^ Axial rigidity (N/μm)^ Starting torque (N ・cm) 15TAU06F 1,000 400 5 17TAU06F 1,180 450 5 20TAU06F 2,160 650 10 25TAU07F 2,350 750 15 30TAU08F 2,550 850 15 30TAU10F 4,310 950 30 35TAU09F 2,550 900 15 40TAU10F 3,230 1,000 20 40TAU11F 7,200 1,200 60 50TAU11F 4,210 1,250 30 50TAU14F 7,850 1,400 70 60TAU14F 4,980 1,300 40
Bearing No.
2-row arrangement 3-row arrangement 4-row arrangement DB/DF FFB/BFF FFBB/BBFF FFFB/BFFF Preload (N)
Axial rigidity (N/μm)
Starting torque (N ・cm)
Preload (N)
Axial rigidity (N/μm)
Starting torque (N ・cm)
Preload (N)
Axial rigidity (N/μm)
Starting torque (N ・cm)
Preload (N)
Axial rigidity (N/μm)
Starting torque (N ・cm) 25TAF05X 80 240 0.4 110 360 0.5 160 480 0.8 130 450 0. 25TAF06X 120 255 0.7 160 380 0.9 240 510 1.4 190 480 1 30TAF07X 180 345 1 240 510 2 360 690 2 280 650 1. 35TAF09X 270 410 2 370 610 3 540 820 4 420 770 3 40TAF09X 270 410 2 370 610 3 540 820 4 420 770 3 40TAF11X 410 510 3 560 760 4 820 1,020 6 640 960 4 45TAF10X 320 450 3 440 670 3 640 900 6 500 850 4 45TAF11X 410 510 3 560 760 4 820 1,020 6 640 960 4 50TAF11X 410 510 3 560 760 4 820 1,020 6 640 960 4 50TAF13X 550 600 5 750 890 7 1,100 1,200 10 860 1,130 8 60TAF13X 550 600 5 750 890 7 1,100 1,200 10 860 1,130 8 60TAF17X 890 780 10 1,210 1,160 13 1,780 1,560 20 1,400 1,470 15 80TAF17X 890 780 10 1,210 1,160 13 1,780 1,560 20 1,400 1,470 15 80TAF21X 1,390 930 20 1,890 1,390 25 2,780 1,860 40 2,180 1,760 30 100TAF21X 1,390 930 20 1,890 1,390 25 2,780 1,860 40 2,180 1,760 30 100TAF26X 1,960 1,000 30 2,670 1,490 40 3,920 2,000 60 3,080 1,890 50 120TAF26X 1,960 1,000 30 2,670 1,490 40 3,920 2,000 60 3,080 1,890 50
Bearing No.
2-row arrangement 3row arrangement 4-row arrangement DB/DF FFB/BFF FFBB/BBFF FFFB/BFFF Preload (N)
Axial rigidity (N/μm)
Starting torque (N ・cm)
Preload (N)
Axial rigidity (N/μm)
Starting torque (N ・cm)
Preload (N)
Axial rigidity (N/μm)
Starting torque (N ・cm)
Preload (N)
Axial rigidity (N/μm)
Starting torque (N ・cm) 25TAF05X 310 385 1.5 420 570 2 620 770 3 490 730 2 25TAF06X 460 390 3 630 580 4 920 780 6 720 740 5 30TAF07X 660 490 5 900 730 6 1,320 980 10 1,040 930 7 35TAF09X 1,000 495 10 1,360 740 10 2,000 990 20 1,570 940 15 40TAF09X 1,000 495 10 1,360 740 10 2,000 990 20 1,570 940 15 40TAF11X 1,550 795 15 2,110 1,180 20 3,100 1,590 30 2,430 1,500 25 45TAF10X 1,200 680 10 1,630 1,010 15 2,400 1,360 20 1,890 1,290 15 45TAF11X 1,550 795 15 2,110 1,180 20 3,100 1,590 30 2,430 1,500 25 50TAF11X 1,550 795 15 2,110 1,180 20 3,100 1,590 30 2,430 1,500 25 50TAF13X 2,070 920 25 2,820 1,370 30 4,140 1,840 50 3,250 1,740 35 60TAF13X 2,070 920 25 2,820 1,370 30 4,140 1,840 50 3,250 1,740 35 60TAF17X 3,350 1,180 45 4,560 1,760 65 6,700 2,360 90 5,260 2,230 70 80TAF17X 3,350 1,180 45 4,560 1,760 65 6,700 2,360 90 5,260 2,230 70 80TAF21X 5,200 1,030 90 7,070 1,530 120 10,400 2,060 180 8,160 1,950 140 100TAF21X 5,200 1,030 90 7,070 1,530 120 10,400 2,060 180 8,160 1,950 140 100TAF26X 7,500 1,800 150 10,200 2,680 250 15,000 3,600 300 11,800 3,400 235 120TAF26X 7,500 1,800 150 10,200 2,680 250 15,000 3,600 300 11,800 3,400 235
Bearing No.
2-row arrangement 3-row arrangement 4-row arrangement DB/DF FFB/BFF FFBB/BBFF FFFB/BFFF Preload (N)
Axial rigidity (N/μm)
Starting torque (N ・cm)
Preload (N)
Axial rigidity (N/μm)
Starting torque (N ・cm)
Preload (N)
Axial rigidity (N/μm)
Starting torque (N ・cm)
Preload (N)
Axial rigidity (N/μm)
Starting torque (N ・cm) 25TAF05X 780 550 4 1,060 820 6 1,560 1,100 8 1,220 1,040 6 25TAF06X 1,160 535 8 1,580 780 11 2,320 1,070 16 1,820 1,010 12 30TAF07X 1,660 650 15 2,260 970 17 3,320 1,300 30 2,600 1,230 20 35TAF09X 2,530 870 25 3,440 1,300 31 5,060 1,740 50 3,970 1,640 36 40TAF09X 2,530 870 25 3,440 1,300 31 5,060 1,740 50 3,970 1,640 36 40TAF11X 3,900 1,080 45 5,300 1,610 60 7,800 2,160 90 6,120 2,040 68 45TAF10X 3,050 975 30 4,150 1,450 40 6,100 1,950 60 4,790 1,840 47 45TAF11X 3,900 1,080 45 5,300 1,610 60 7,800 2,160 90 6,120 2,040 68 50TAF11X 3,900 1,080 45 5,300 1,610 60 7,800 2,160 90 6,120 2,040 68 50TAF13X 5,200 1,270 70 7,070 1,890 90 10,400 2,540 140 8,160 2,400 110 60TAF13X 5,200 1,270 70 7,070 1,890 90 10,400 2,540 140 8,160 2,400 110 60TAF17X 8,400 1,580 140 11,400 2,350 190 16,800 3,160 280 13,200 2,990 220 80TAF17X 8,400 1,580 140 11,400 2,350 190 16,800 3,160 280 13,200 2,990 220
25 Preload and Rigidity Preload and Rigidity 26
Preload and Rigidity
Bearing No.
2-row arrangement DB/DF Preload (N)
Axial rigidity (N/μm)
Starting torque (N ・cm) 7000XYS1 147 92 0. 7001XYS1 147 98 0. 7002XYS1 147 98 0. 7003XYS1 147 105 0. 7004XYS1 294 147 1.
Bearing No.
2-row arrangement DF Preload (N)
Axial rigidity (N/μm)
Starting torque (N ・cm) 7000W1Y 147 77 0. 7001W1Y 147 86 0. 7002W1Y 147 98 0. 7003W1Y 294 128 0. 7004W1Y 294 134 0. 7005W1Y 490 175 1.
Bearing No.
2-row arrangement DB/DF Preload (N)
Axial rigidity (N/μm)
Starting torque (N ・cm) 7203XYS1 294 140 1. 7204XYS1 490 169 3. 7205XYS1 490 188 3. 7206XYS1 490 196 4.
Bearing No.
2-row arrangement DF Preload (N)
Axial rigidity (N/μm)
Starting torque (N ・cm) 7200W1Y 147 82 0. 7201W1Y 147 82 0. 7202W1Y 294 118 0. 7203W1Y 294 118 0. 7204W1Y 490 153 1. 7205W1Y 490 169 1.
● Table 5.
Nominal bearing bore diameter d (mm)
Cylindrical bore bearing clearance (non-interchangeable) C1na C2na Cna C3na Over Incl. min max min max min max min max 24 30 0 10 10 25 25 35 40 50 30 40 0 12 12 25 25 40 45 55 40 50 0 15 15 30 30 45 50 65 50 65 0 15 15 35 35 50 55 75 65 80 0 20 20 40 40 60 70 90 80 100 0 25 25 45 45 70 80 105 100 120 0 25 25 50 50 80 95 120 120 140 0 30 30 60 60 90 105 135 140 160 0 35 35 65 65 100 115 150 160 180 0 35 35 75 75 110 125 165 180 200 0 40 40 80 80 120 140 180 200 225 0 45 45 90 90 135 155 200 225 250 0 50 50 100 100 150 170 215 250 280 0 55 55 110 110 165 185 240 280 315 0 60 60 120 120 180 205 265 315 355 0 65 65 135 135 200 225 295
Nominal bearing bore diameter d (mm)
Tapered bore bearing clearance (non-interchangeable) C9na C1na C2na Over Incl. min max min max min max 24 30 5 10 15 25 25 35 30 40 5 12 15 25 25 40 40 50 5 15 17 30 30 45 50 65 5 15 20 35 35 50 65 80 10 20 25 40 40 60 80 100 10 25 35 55 45 70 100 120 10 25 40 60 50 80 120 140 15 30 45 70 60 90 140 160 15 35 50 75 65 100 160 180 15 35 55 85 75 110 180 200 20 40 60 90 80 120 200 225 20 45 60 95 90 135 225 250 25 50 65 100 100 150 250 280 25 55 75 110 110 165 280 315 30 60 80 120 120 180 315 355 30 65 90 135 135 200
29 Lubrication Lubrication 30
Lubrication
● Table 6.2 Bearing Internal Space V olume
Bore diameter number
Bore diameter (mm)
Series 7900C 7900AC
Bearing No. Internal space volume [cc/ each] 15TAB04 3. 17TAB04 3. 20TAB04 3. 25TAB06 4. 30TAB06 4. 35TAB07 5. 40TAB07 5. 40TAB09 14 45TAB07 6. 45TAB10 15 50TAB10 16 55TAB10 16 55TAB12 19 60TAB12 19
Bearing No. Internal space volume [cc/ each] 25TAF05X 5. 25TAF06X 9. 30TAF07X 14 35TAF09X 26 40TAF09X 26 40TAF11X 44 45TAF10X 31 45TAF11X 44 50TAF11X 44 50TAF13X 70 60TAF13X 70 60TAF17X 149 80TAF17X 149 80TAF21X 285 100TAF21X 285 100TAF26X 488 120TAF26X 488
Bearing No. Internal space volume [cc/ each] 7000XYS1 0. 7001XYS1 0. 7002XYS1 1. 7003XYS1 1. 7004XYS1 2.
Bearing No. Internal space volume [cc/ each] 7203XYS1 2. 7204XYS1 4. 7205XYS1 5. 7206XYS1 7.
L : Grease life (hours) T : Bearing temperature (°C) S G : Life reduction factor based on grease type
Long life petroleum grease and silicon grease 0 Conventional petroleum grease 1. Diester and and low temperature grease 2.
S N : Life reduction factor based on rotation speed d : Nominal bearing bore diameter (mm) n : Bearing speed (min -1^ ) (dn) L : Bearing type-specific speed facto
Bearing type (dn) L Angular contact ball bearings 400, Cylindrical roller bearings 200,
S W : Load-specific life reduction facto C : Basic dynamic load rating (N) w : Bearing load (N)
31 Limiting Speeds Shaft and Housing Design 32
● Table 7.1 Limiting Speed Factors for Multiple Row Ball Be aring Combinations No. of bearings in set E preload (extra-light preload) L preload (light preload) M preload (medium preload) H preload (heavy preload) 2 rows 0.83 0.78 0.63 0. 3 rows 0.73 0.68 0.54 0. 4 rows 0.78 0.73 0.59 0.
● Table 8.1 Shafts and Recommended Fits (^) Unit: μm
Bearing type
Shaft diameter (mm)
Bearing accuracy class Class 5 Class 4/Class 2 Over Incl. Desired fit Shaft tolerance Desired fit Shaft tolerance
Angular contact ball bearings
10 18 0~2T h4 0~2T h 18 50 0~2.5T h4 0~2.5T h 50 80 0~3T h4 0~3T h 80 150 0~4T js4 0~4T js 150 200 0~5T js4 0~5T js
Cylindrical roller bearings (cylindrical bore)
25 40 − js4 − js 40 140 − k4 − k 140 200 − k4 − k Main spindle thrust bearing For all shaft diameters^ 0~6L^ h4^ 0~6L^ h Ball screw support bearings For all shaft diameters^ 0~10L^ h5^ 0~10L^ h
● Table 8.2 Housings and Recommended Fits (Fixed Side) (^) Unit: μm
Bearing type
Housing bore diameter (mm)
Bearing accuracy class Class 5 Class 4/Class 2 Over Incl. Desired fit Housing bore tolerance Desired fit Housing bore tolerance
Angular contact ball bearings
Cylindrical roller bearings Overall housing bore ± 0 K5 ± 0 K Main spindle thrust bearing Overall housing bore^ 30L~40L^ K5^ 30L~40L^ K Ball screw support bearings Overall housing bore^ 10L~20L^ H6^ 10L~20L^ H
● Table 8.3 Housings and Recommended Fits (Free Side) (^) Unit: μm
Bearing type
Housing bore diameter (mm)
Bearing accuracy class Class 5 Class 4/Class 2 Over Incl. Desired fit Housing bore tolerance Desired fit Housing bore tolerance
Angular contact ball bearings
Cylindrical roller bearings Overall housing bore ± 0 K5 ± 0 K Ball screw support bearings Overall housing bore^ 10L~20L^ H6^ 10L~20L^ H (Note) In T ables 8.1 through 8.3, "L" following a value indicates loose or clearance fit, while "T" indicates tight or inte ference fit
35 Bearing Handling Bearing Handling 36
Figure 9.4 Inner Ring Press Fitting
Risk of ball damage
Figure 9.5 Angular Contact Ball Bearing Assembly Direction
Maximum radial run-out surface
Figure 9.6 Maximum Radial Run-out Locations
2
Ka : Press fit force (removal force) (kN fk : Installation/removal condition coefficient ( able 9.1) Δde : Effective inter ference (mm) B : Nominal inner ring width (mm) d : Nominal bearing bore diameter (mm) di : Inner ring mean outside diameter (mm) Cylindrical roller bearing di=(D+3d)/ Other bearings di=(3D+7d)/ Here, D = Nominal bearing outside diameter (mm)
● Table 9.1 Installation/Removal Condition Coefficien Conditions fk (mean value) Inner ring press fit to cylindrical solid shaft 39 Inner ring removal from cylindrical solid shaft 59 (Note) V alues when shaft bore and shaft are thinly coated with oil.
Figure 9.1 Shaft Diameter and Housing Diameter Measurement Locations
Figure 9.2 Induction Heater
Figure 9.3 Shaft Shoulder Gap After Cooling
37 Bearing Handling Bearing Handling 38
Bearing Handling
F≈
F : Tightening force (N) Mn : Tightening torque (N·mm) d 2 : Thread nominal diameter (mm) β : Lead angle tan β = P πd 2 P : Pitch (mm) ρ : Thread sur face friction angle tan ρ = (^) cosμ α α : Half-angle of thread d n : Mean diameter of nut bearing sur face (mm)
● Table 9.2 Recommended Shaft Nut T ightening Force V alues Nominal bearing bore diameter (mm)
Shaft nut tightening force (N)
Nominal bearing bore diameter (mm)
Shaft nut tightening force (N) 10 1,500 80 19, 12 2,500 85 19, 15 2,500 90 19, 17 2,500 95 19, 20 4,900 100 19, 25 4,900 105 19, 30 4,900 110 19, 35 4,900 120 19, 40 9,800 130 19, 45 9,800 140 29, 50 9,800 150 29, 55 14,700 160 29, 60 14,700 170 29, 65 14,700 180 29, 70 14,700 190 29, 75 14,700 200 29,
Housing
2A clearance
Press-fit cover A A
Δ=0.010mm Δ=0.050mm Figure 9.7 Example of Raceway Deflection Depending on Outer Ring Clearance Reduction Gap
● Table 9.3 Recommended Clearance Reduction Gap V alues for Ball Screw Suppor t Bearings (T AB Series) Bearing No. (^) External ring clearance reduction gap Δ (mm) 15TAB04 DF 17TAB04 DF 0.010 ~ 0. 20TAB04 DF 25TAB06 DF 0.010 ~ 0.
● Table 9.4 Recommended Clearance Reduction Gap V alues for Ball Screw Suppor t Bearings (T AF-X Series) Bearing No. External ring clearance reduction gap Δ (mm) 25TAF06X DF 0. 30TAF07X DF 35TAF09X DF 0. 40TAF09X DF 40TAF11X DF
L’ : Average spacer width obtained in step ⑨ ΔR : Measured radial clearance Δ : Desired post-assembly radial clearance λe : External ring contraction ratio
λe (^) = DeD − 1 −( (^) DD^ eh ) 2
1 −( (^) DD h ) 2
D : Inner ring outside diameter (mm) D e : Inner ring bore (mm) D h : Housing bore (mm) δ : Outer ring inter ference
Figure 9.8 Inner Sub-unit T emporar y T ightening
Figure 9.9 Radial Clearance Measurement
Figure 9.10 Spacer T emporar y W idth Dimension Measurement
Block gauge
Figure 9.11 Final Assembly Radial Clearance Check