
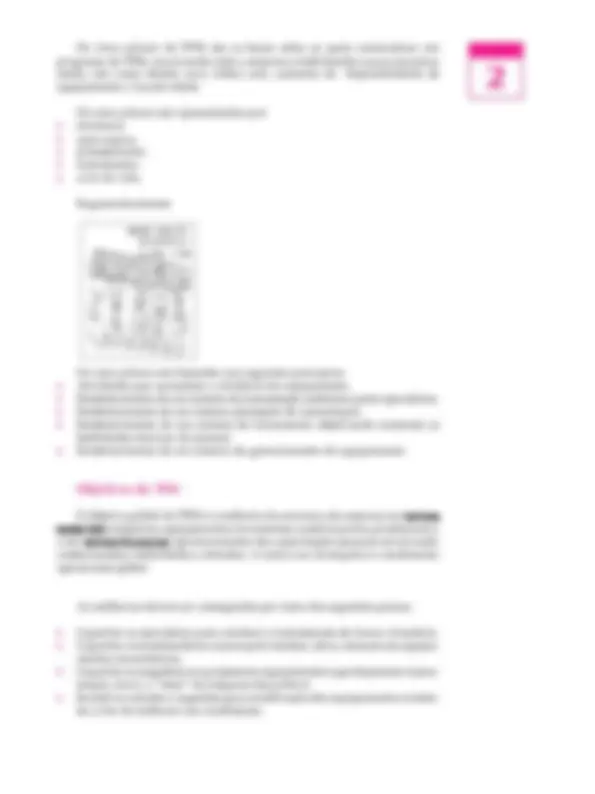
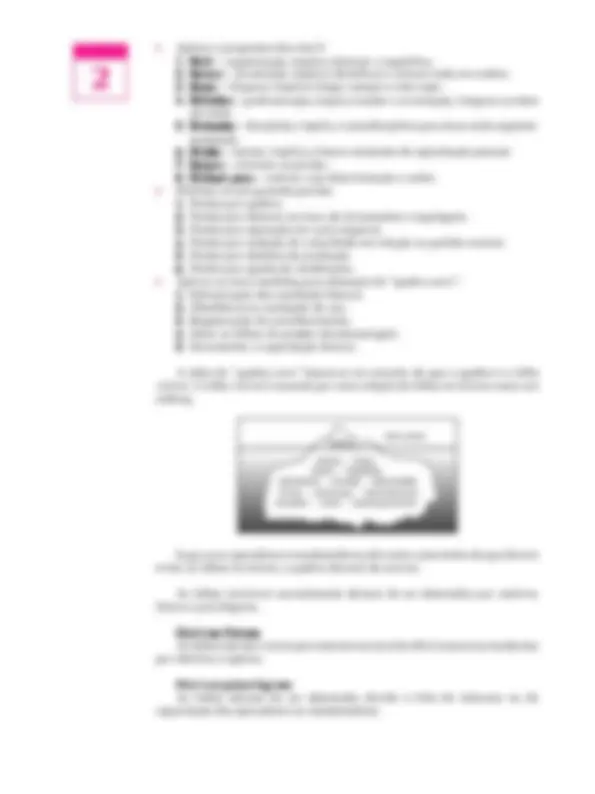
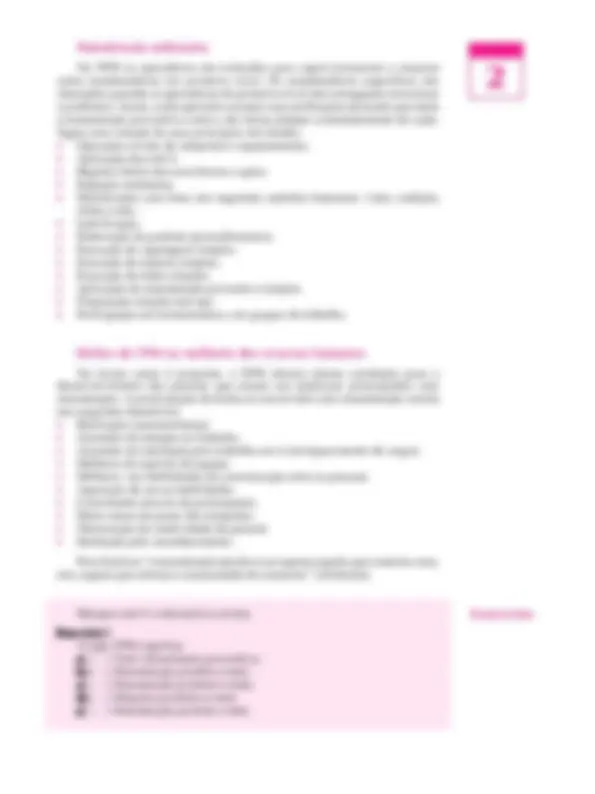
Estude fácil! Tem muito documento disponível na Docsity
Ganhe pontos ajudando outros esrudantes ou compre um plano Premium
Prepare-se para as provas
Estude fácil! Tem muito documento disponível na Docsity
Prepare-se para as provas com trabalhos de outros alunos como você, aqui na Docsity
Os melhores documentos à venda: Trabalhos de alunos formados
Prepare-se com as videoaulas e exercícios resolvidos criados a partir da grade da sua Universidade
Responda perguntas de provas passadas e avalie sua preparação.
Ganhe pontos para baixar
Ganhe pontos ajudando outros esrudantes ou compre um plano Premium
Comunidade
Peça ajuda à comunidade e tire suas dúvidas relacionadas ao estudo
Descubra as melhores universidades em seu país de acordo com os usuários da Docsity
Guias grátis
Baixe gratuitamente nossos guias de estudo, métodos para diminuir a ansiedade, dicas de TCC preparadas pelos professores da Docsity
TPM – Planejamento, organização, administração
Tipologia: Notas de estudo
1 / 7
Esta página não é visível na pré-visualização
Não perca as partes importantes!
A U L A
Durante muito tempo as indústrias funcio- naram com o sistema de manutenção corretiva. Com isso, ocorriam desperdí- cios, retrabalhos, perda de tempo e de esforços humanos, além de prejuízos financeiros.
A partir de uma análise desse problema, passou-se a dar ênfase na manuten- ção preventiva. Com enfoque nesse tipo de manutenção, foi desenvolvido o conceito de manutenção produtiva totalmanutenção produtiva totalmanutenção produtiva totalmanutenção produtiva totalmanutenção produtiva total, conhecido pela sigla TPMTPMTPMTPMTPM (total productive maintenance), que inclui programas de manutenção preventiva e preditiva.
Nesta aula , vamos estudar a manutenção produtiva total ou, simplesmente, TPM.
A manutenção preventiva teve sua origem nos Estados Unidos e foi introduzida no Japão em 1950.
Até então, a indústria japonesa trabalhava apenas com o conceito de manu- tenção corretiva, após a falha da máquina ou equipamento. Isso representava um custo e um obstáculo para a melhoria da qualidade.
A primeira indústria japonesa a aplicar e obter os efeitos do conceito de manutenção preventiva, também chamada de PMPMPMPM (PMpreventive maintenance) foi a Toa Nenryo Kogyo, em 1951. São dessa época as primeiras discussões a respeito da importância da manutenibilidade e suas conseqüências para o trabalho de manutenção.
Em 1960, ocorre o reconhecimento da importância da manutenibilidade e da confiabilidade como sendo pontos-chave para a melhoria da eficiência das empresas. Surgiu, assim, a manutenção preventiva, ou seja, o enfoque da manutenção passou a ser o de confiança no setor produtivo quanto à qualidade do serviço de manutenção realizado.
A U L A
2
A U L A Na busca de maior eficiência da manutenção produtiva, por meio de um sistema compreensivo, baseado no respeito individual e na total participação dos empregados, surgiu a TPMTPMTPMTPM, em 1970, no Japão.TPM
Nessa época era comum: ∑ avanço na automação industrial; ∑ busca em termos da melhoria da qualidade; ∑ aumento da concorrência empresarial; ∑ emprego do sistema “just-in-time”; ∑ maior consciência de preservação ambiental e conservação de energia; ∑ dificuldades de recrutamento de mão-de-obra para trabalhos considerados sujos, pesados ou perigosos; ∑ aumento da gestão participativa e surgimento do operário polivalente.
Todas essas ocorrências contribuíram para o aparecimento da TPMTPMTPMTPMTPM. A empresa usuária da máquina se preocupava em valorizar e manter o seu patrimônio, pensando em termos de custo do ciclo de vida da máquina ou equipamento. No mesmo período, surgiram outras teorias com os mesmos objetivos.
O quadro a seguir mostra a evolução do conceito de manutenção ao longo do tempo.
PERÍODOSPERÍODOSPERÍODOSPERÍODOSPERÍODOS^ ATÉATÉATÉATÉATÉ^ DÉCADADÉCADADÉCADADÉCADADÉCADA^ DEDEDEDEDE^19501950195019501950 DÉCADADÉCADADÉCADADÉCADADÉCADA^ DEDEDEDEDE^19501950195019501950 DÉCADADÉCADADÉCADADÉCADADÉCADA^ DEDEDEDEDE^19601960196019601960 DÉCADADÉCADADÉCADADÉCADADÉCADA^ DEDEDEDEDE^19801980198019801980
Estágio Manutenção Manutenção Manutenção Manutenção Conceitos corretiva preventiva do sistema produtiva total de produção (TPM)
Reparo corretivo x x x x Gestão mecânica da manutenção x x x Manutenções preventivas x x x Visão sistemática x x Manutenção corretiva com incorporação de melhorias x x Prevenção de manutenção x x Manutenção preditiva x Abordagem participativa x Manutenção autônoma x
2
A U L A ∑^ Aplicar o programa dos oito S: 1.1.1.1.1. SeiriSeiriSeiriSeiriSeiri = organização; implica eliminar o supérfluo. 2.2.2.2.2. SeitonSeitonSeitonSeitonSeiton = arrumação; implica identificar e colocar tudo em ordem. 3.3.3.3.3. SeisoSeisoSeisoSeisoSeiso = limpeza; implica limpar sempre e não sujar. 4.4.4.4.4. SeiketsuSeiketsuSeiketsuSeiketsuSeiketsu = padronização; implica manter a arrumação, limpeza e ordem em tudo. 5.5.5.5.5. ShitsukeShitsukeShitsukeShitsukeShitsuke = disciplina; implica a autodisciplina para fazer tudo esponta- neamente. 6.6.6.6.6. ShidoShidoShidoShidoShido = treinar; implica a busca constante de capacitação pessoal. 7.7.7.7.7. SeisonSeisonSeisonSeisonSeison = eliminar as perdas. 8.8.8.8.8. Shikari yaroShikari yaroShikari yaroShikari yaroShikari yaro = realizar com determinação e união. ∑ Eliminar as seis grandes perdas: 1.1.1.1.1. Perdas por quebra. 2.2.2.2.2. Perdas por demora na troca de ferramentas e regulagem. 3.3.3.3.3. Perdas por operação em vazio (espera). 4.4.4.4.4. Perdas por redução da velocidade em relação ao padrão normal. 5.5.5.5.5. Perdas por defeitos de produção. 6.6.6.6.6. Perdas por queda de rendimento. ∑ Aplicar as cinco medidas para obtenção da “quebra zero”: 1.1.1.1.1. Estruturação das condições básicas. 2.2.2.2.2. Obediência às condições de uso. 3.3.3.3.3. Regeneração do envelhecimento. 4.4.4.4.4. Sanar as falhas do projeto (terotecnologia). 5.5.5.5.5. Incrementar a capacitação técnica.
A idéia da “quebra zero” baseia-se no conceito de que a quebra é a falha visível. A falha visível é causada por uma coleção de falhas invisíveis como um iceberg.
Logo, se os operadores e mantenedores estiverem conscientes de que devem evitar as falhas invisíveis, a quebra deixará de ocorrer.
As falhas invisíveis normalmente deixam de ser detectadas por motivos físicos e psicológicos.
Motivos físicosMotivos físicosMotivos físicosMotivos físicosMotivos físicos As falhas não são visíveis por estarem em local de difícil acesso ou encobertas por detritos e sujeiras.
Motivos psicológicosMotivos psicológicosMotivos psicológicosMotivos psicológicosMotivos psicológicos As falhas deixam de ser detectadas devido à falta de interesse ou de capacitação dos operadores ou mantenedores.
2
Na TPM os operadores são treinados para supervisionarem e atuarem como mantenedores em primeiro nível. Os mantenedores específicos são chamados quando os operadores de primeiro nível não conseguem solucionar o problema. Assim, cada operador assume suas atribuições de modo que tanto a manutenção preventiva como a de rotina estejam constantemente em ação. Segue uma relação de suas principais atividades: ∑ Operação correta de máquinas e equipamentos. ∑ Aplicação dos oito S. ∑ Registro diário das ocorrências e ações. ∑ Inspeção autônoma. ∑ Monitoração com base nos seguintes sentidos humanos: visão, audição, olfato e tato. ∑ Lubrificação. ∑ Elaboração de padrões (procedimentos). ∑ Execução de regulagens simples. ∑ Execução de reparos simples. ∑ Execução de testes simples. ∑ Aplicação de manutenção preventiva simples. ∑ Preparação simples (set-up). ∑ Participação em treinamentos e em grupos de trabalho.
Na forma como é proposta, a TPM oferece plenas condições para o desenvolvimento das pessoas que atuam em empresas preocupadas com manutenção. A participação de todos os envolvidos com manutenção resulta nos seguintes benefícios: ∑ Realização (autoconfiança). ∑ Aumento da atenção no trabalho. ∑ Aumento da satisfação pelo trabalho em si (enriquecimento de cargo). ∑ Melhoria do espírito de equipe. ∑ Melhoria nas habilidades de comunicação entre as pessoas. ∑ Aquisição de novas habilidades. ∑ Crescimento através da participação. ∑ Maior senso de posse das máquinas. ∑ Diminuição da rotatividade de pessoal. ∑ Satisfação pelo reconhecimento.
Para finalizar “a manutenção não deve ser apenas aquela que conserta, mas, sim, aquela que elimina a necessidade de consertar” (Anônimo).
Marque com X a alternativa correta.
Exercício 1Exercício 1Exercício 1Exercício 1Exercício 1 A sigla TPM significa: a)a)a)a)a) (^ ) Total manutenção preventiva; b)b)b)b)b) (^ ) Manutenção preditiva total; c)c)c)c)c) (^ ) Manutenção produtiva total; d)d)d)d)d) (^ ) Máquina produtiva total; e)e)e)e)e) (^ ) Manutenção perfeita e total.
ExercÌcios
2
Exercício 6Exercício 6Exercício 6Exercício 6Exercício 6 A U L A Relacione a coluna 1 de acordo com a 2: Coluna 1Coluna 1Coluna 1Coluna 1Coluna 1^ Coluna 2Coluna 2Coluna 2Coluna 2Coluna 2 a)a)a)a)a) Seiri^ 1.1.1.1.1.^ (^ )^ Eliminar perdas. b)b)b)b)b) Seiton 2.2.2.2.2. ( ) Limpeza, limpar sempre e não sujar. c)c)c)c)c) Seiso^ 3.3.3.3.3.^ (^ )^ Arrumação. d)d)d)d)d) Seiketsu^ 4.4.4.4.4.^ (^ )^ Disciplina. e)e)e)e)e) Shitsuke^ 5.5.5.5.5.^ (^ )^ Treinar. f)f)f)f)f) Shido^ 6.6.6.6.6.^ (^ )^ Realizar com determinação. g)g)g)g)g) Seison^ 7.7.7.7.7.^ (^ )^ Eliminar o supérfluo. h)h)h)h)h) Shikari yaro^ 8.8.8.8.8.^ (^ )^ Padronização. 9.9.9.9.9.^ (^ )^ Conserto.