
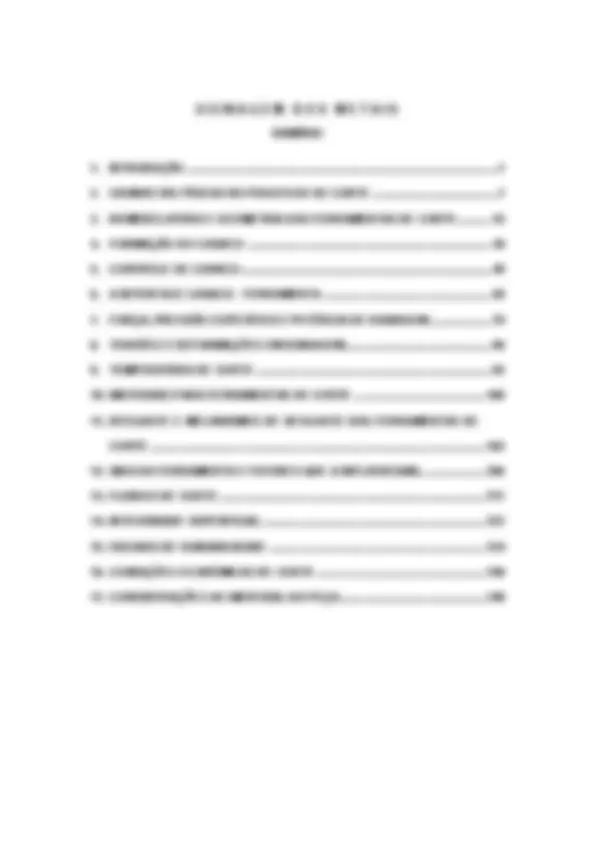
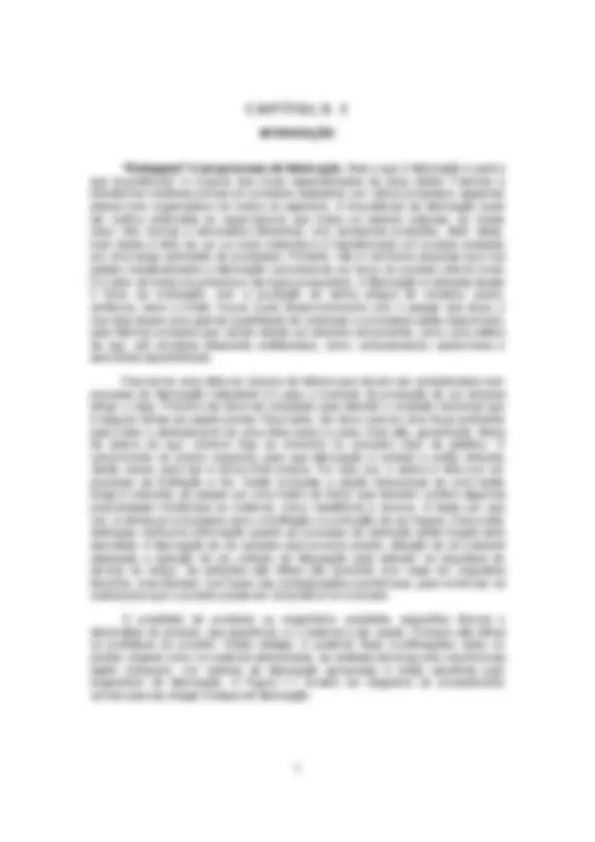
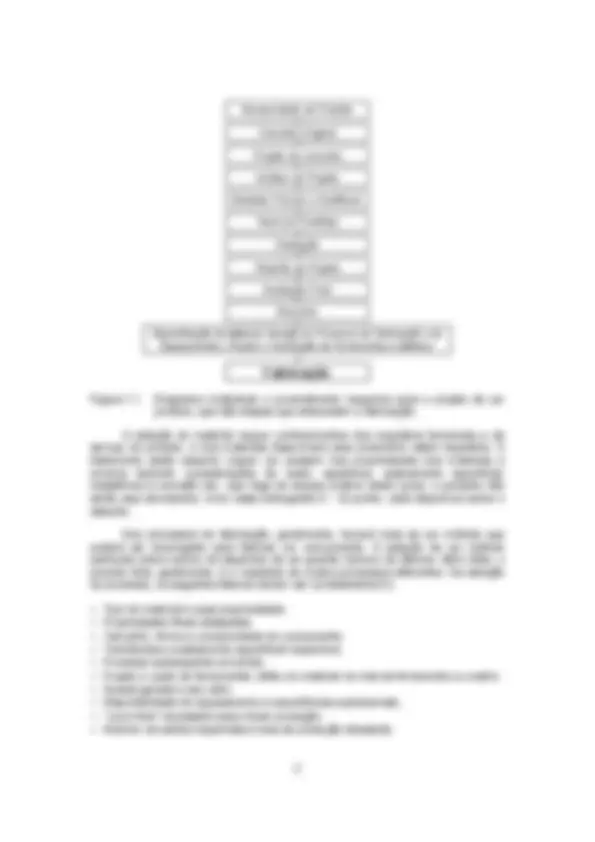
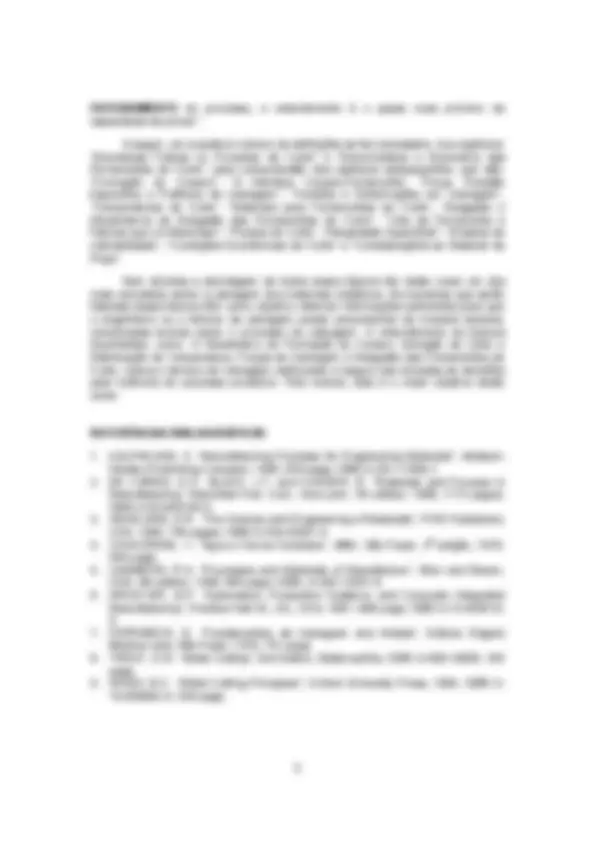
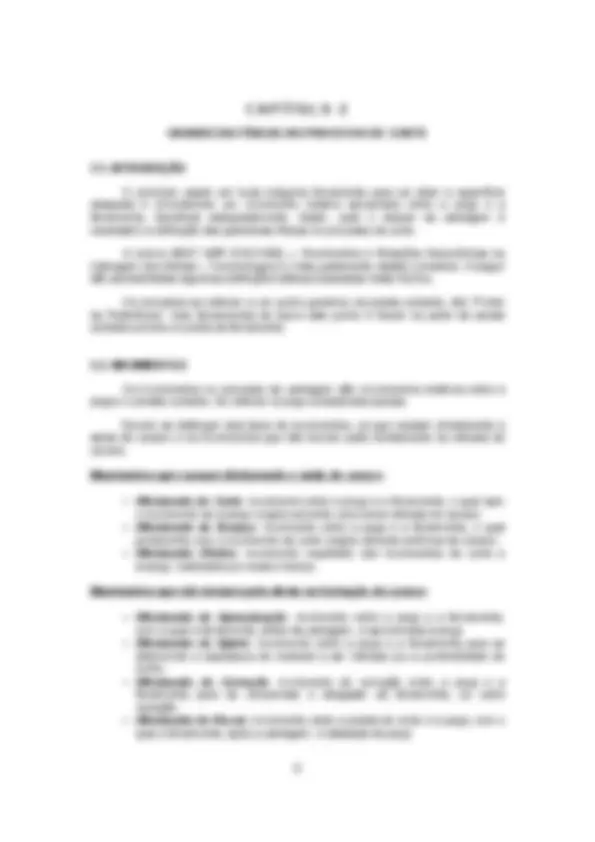
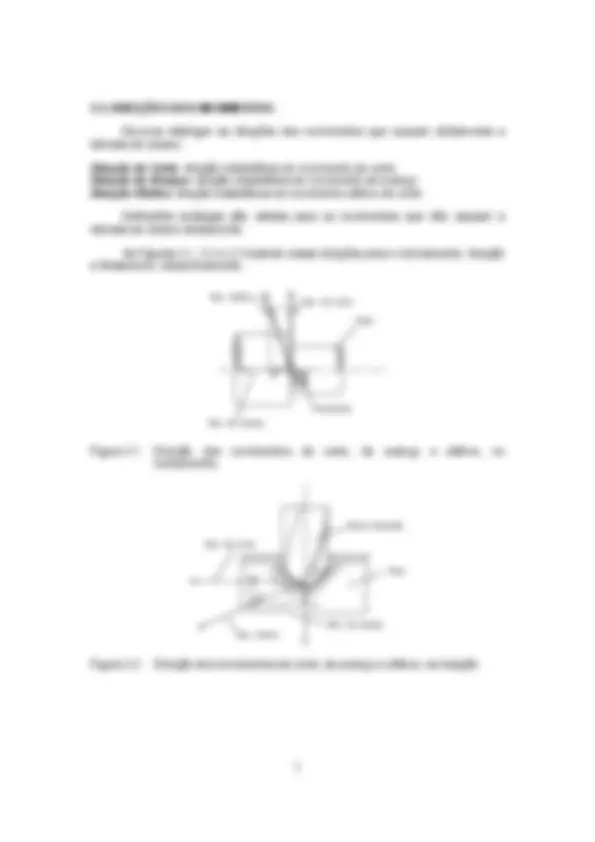
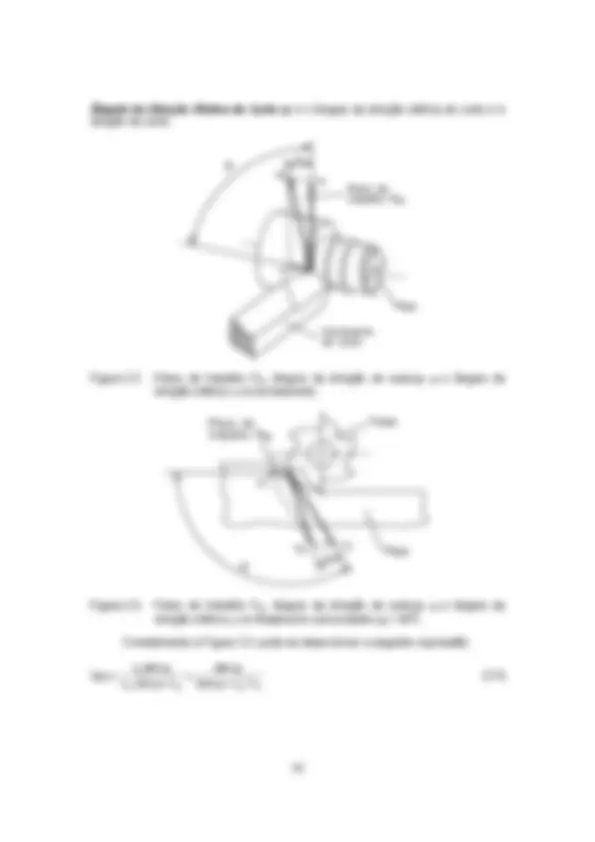
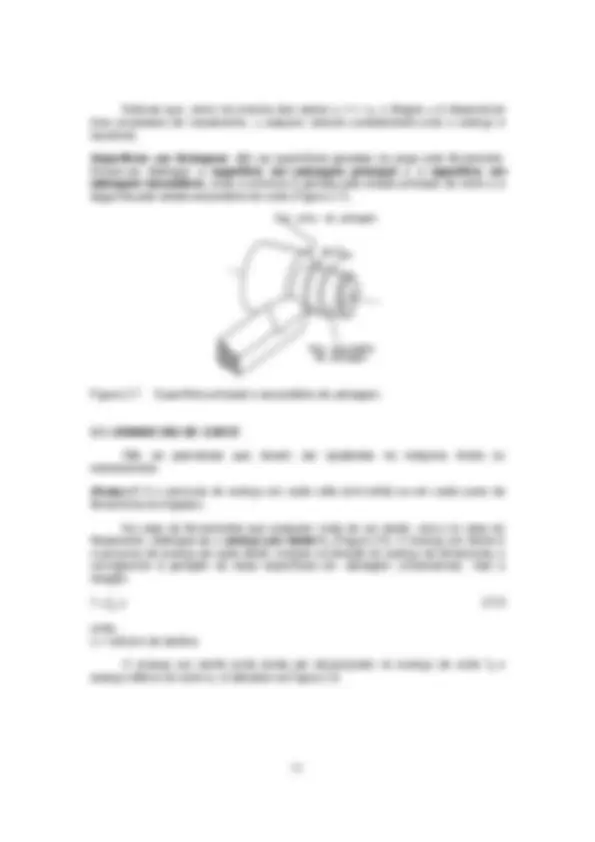

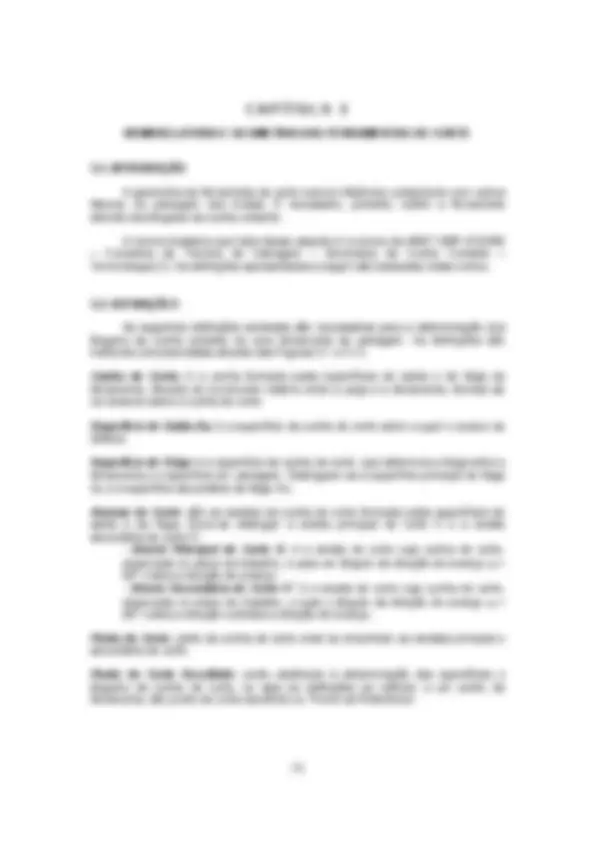
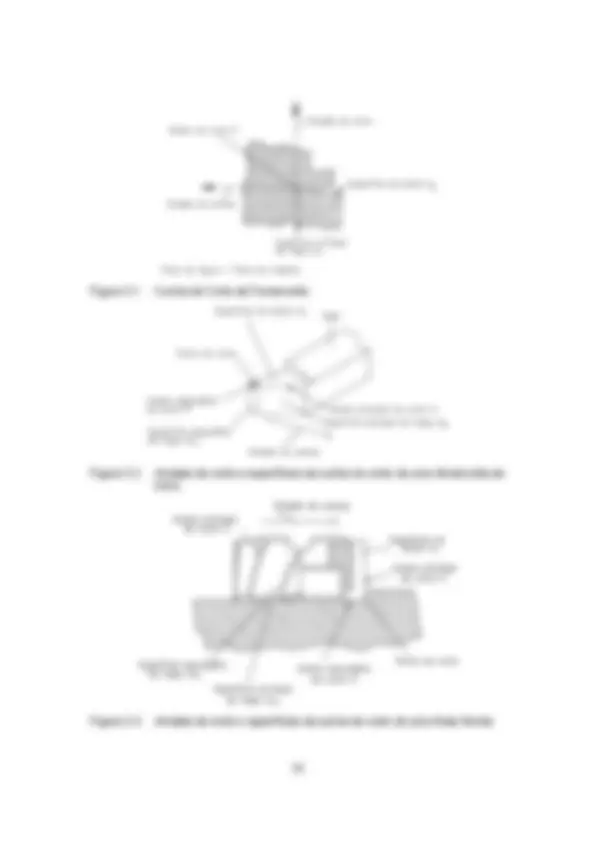
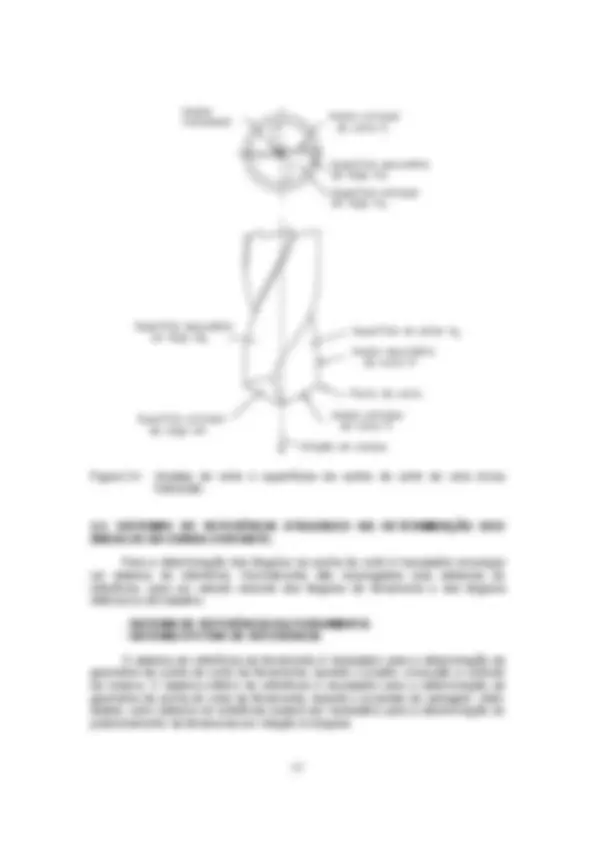
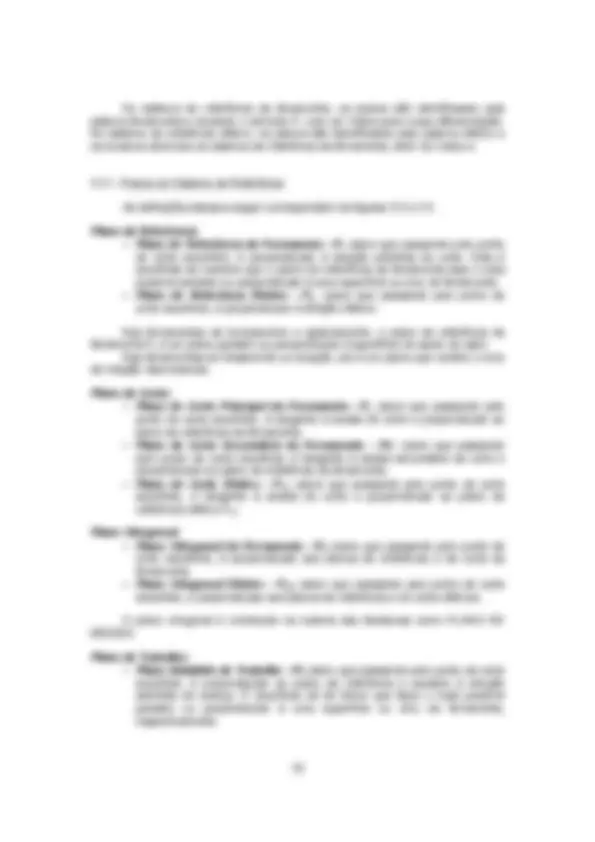
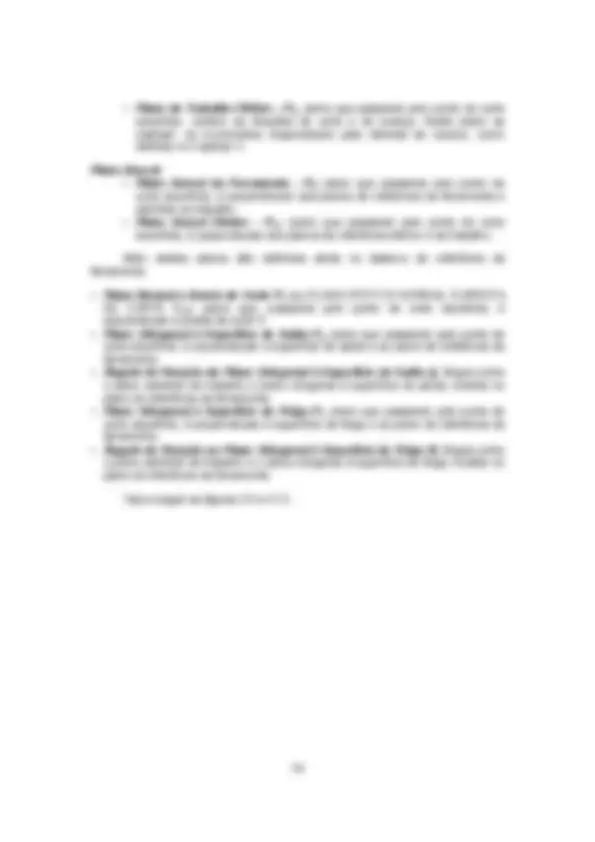
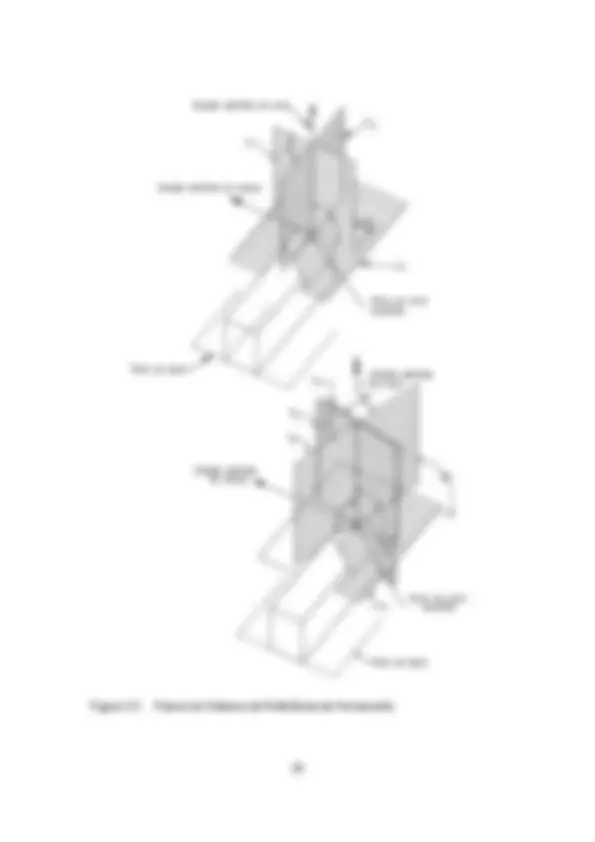
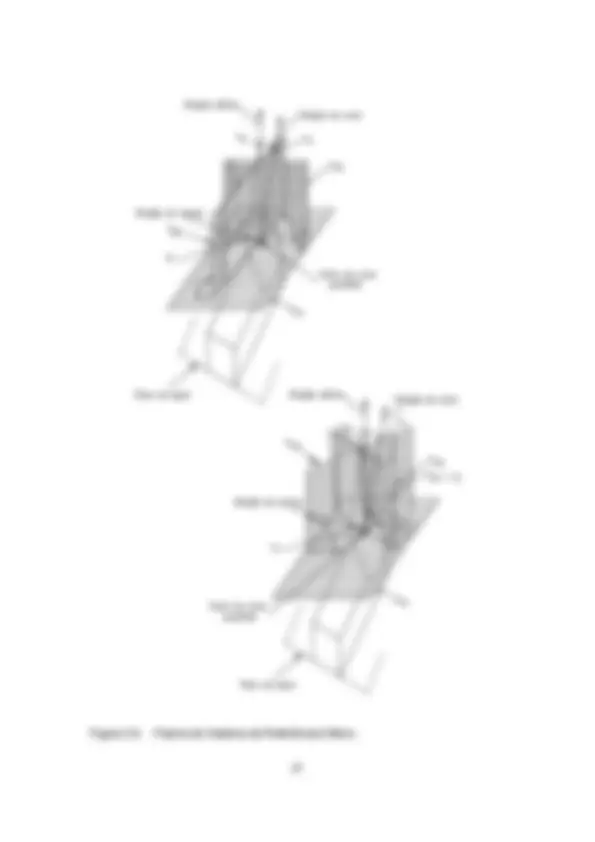
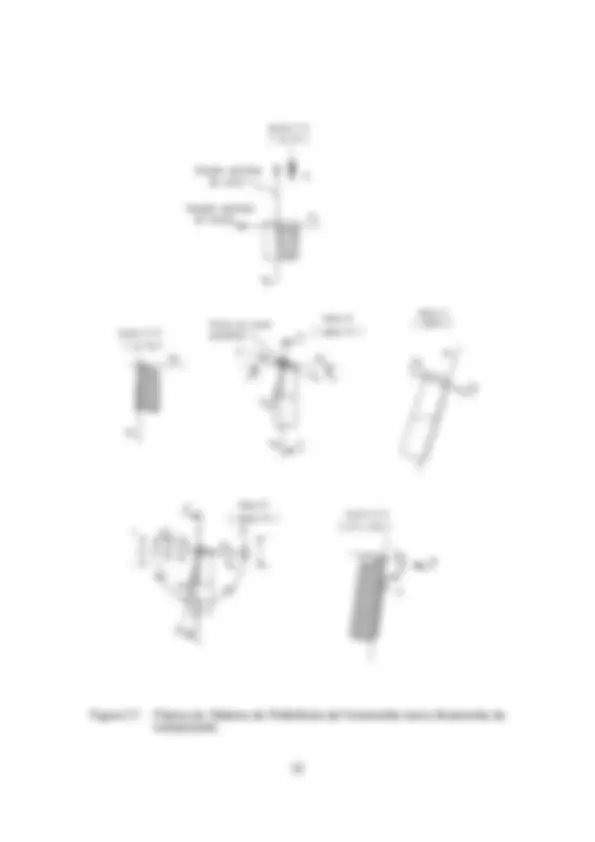
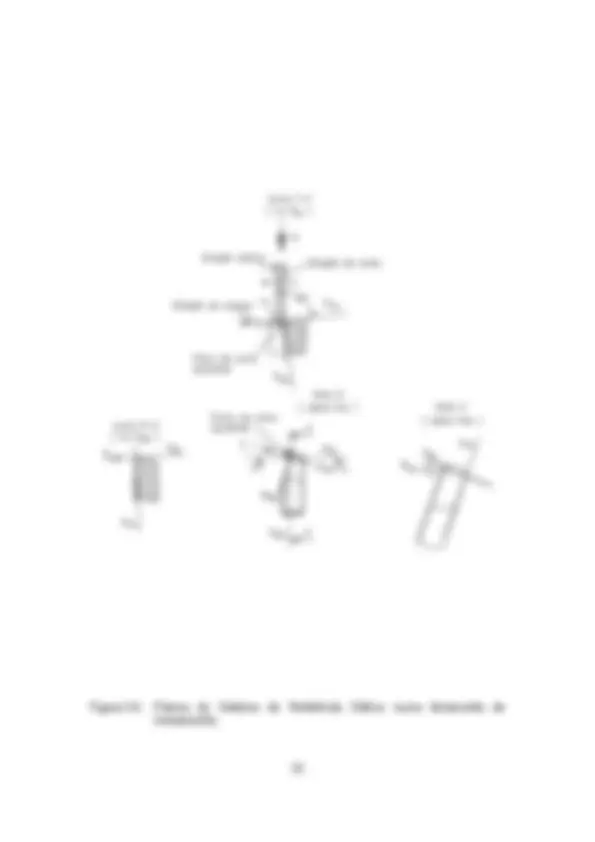
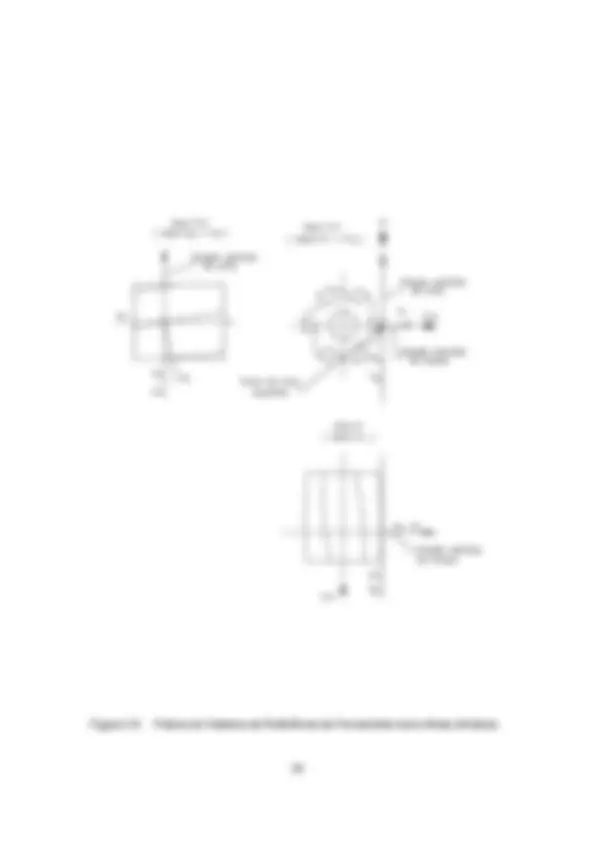
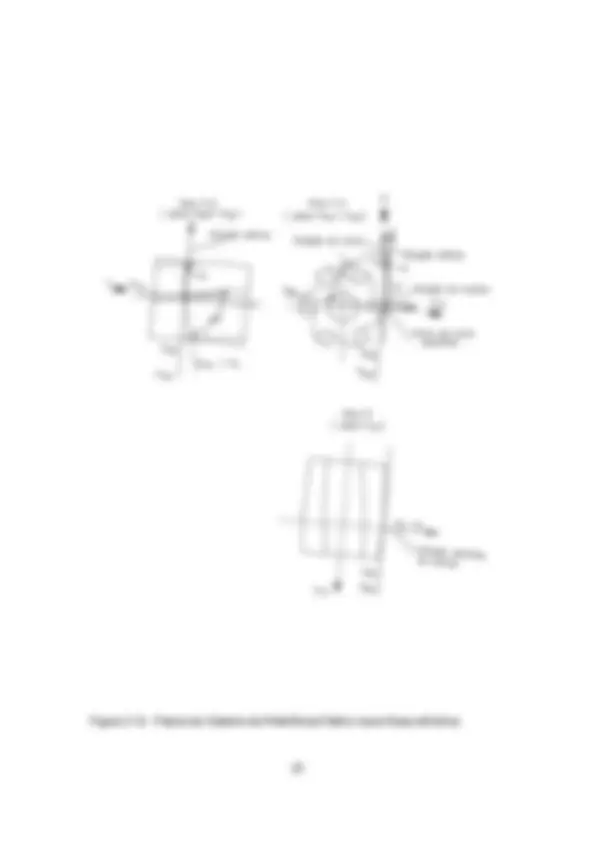
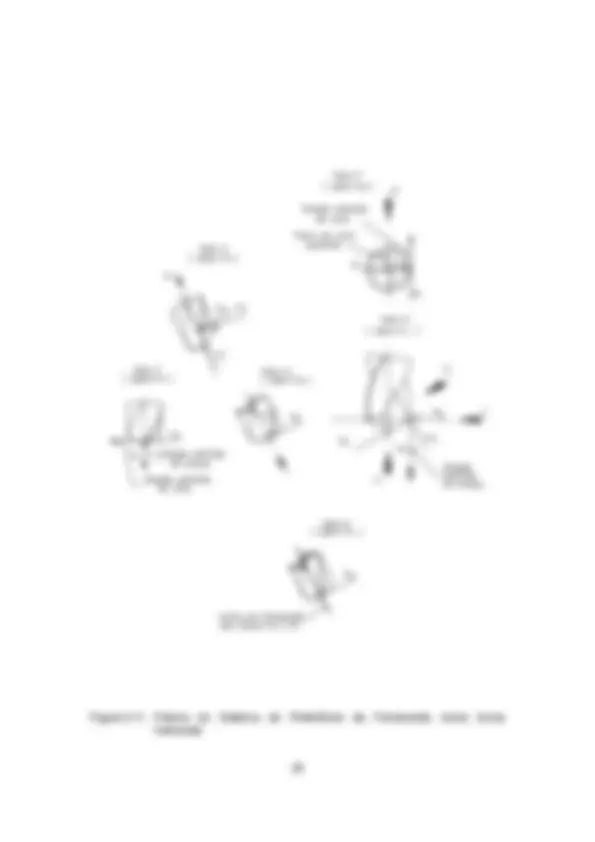
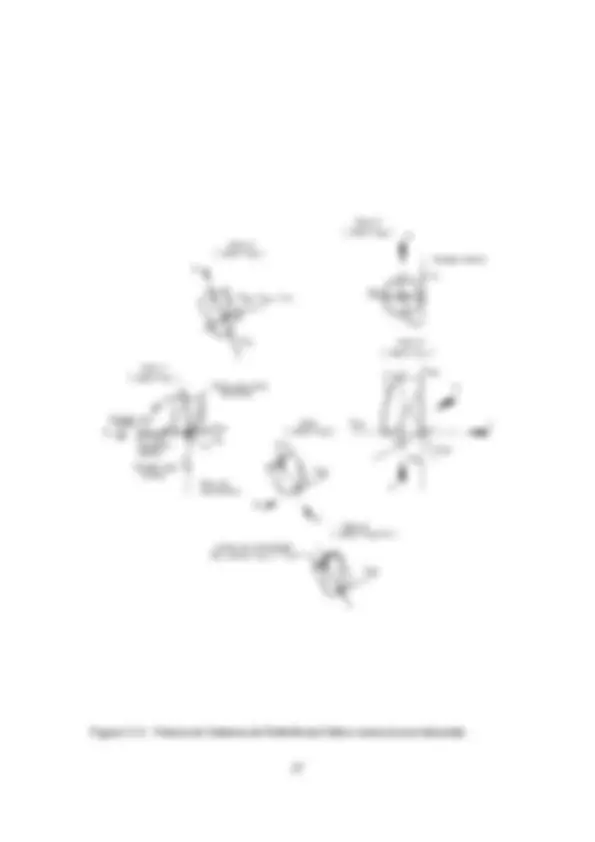
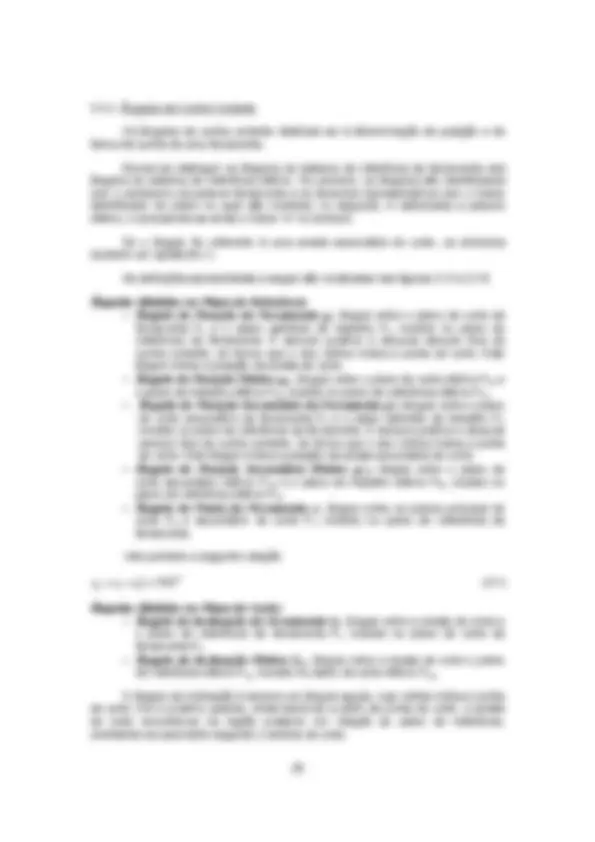
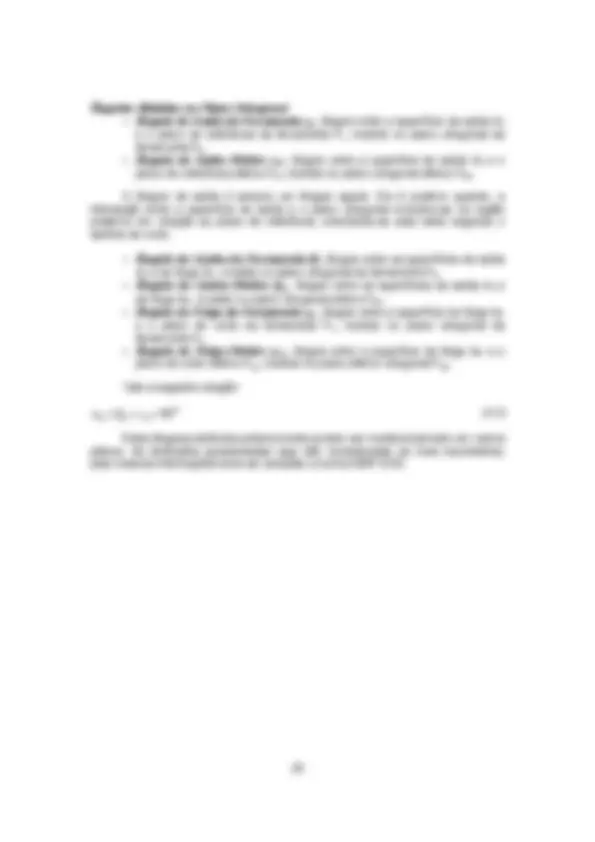
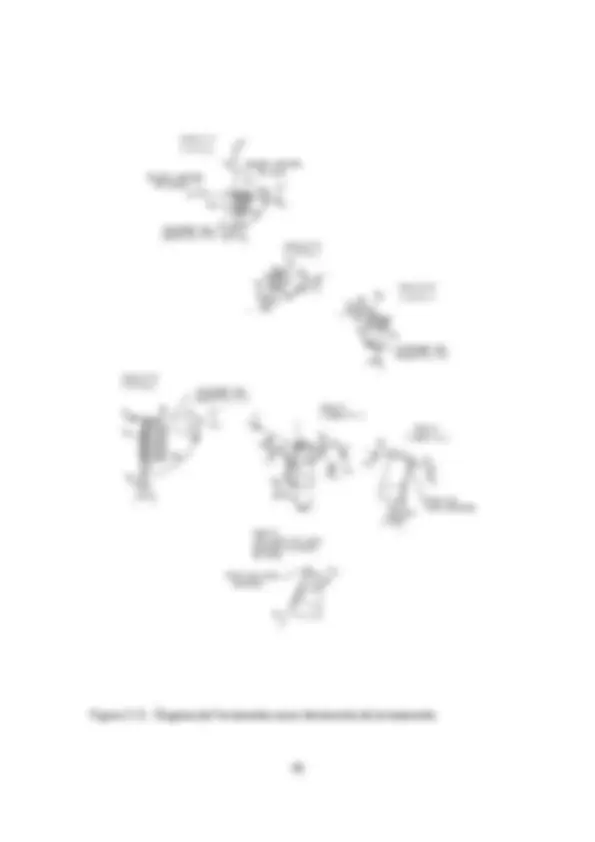

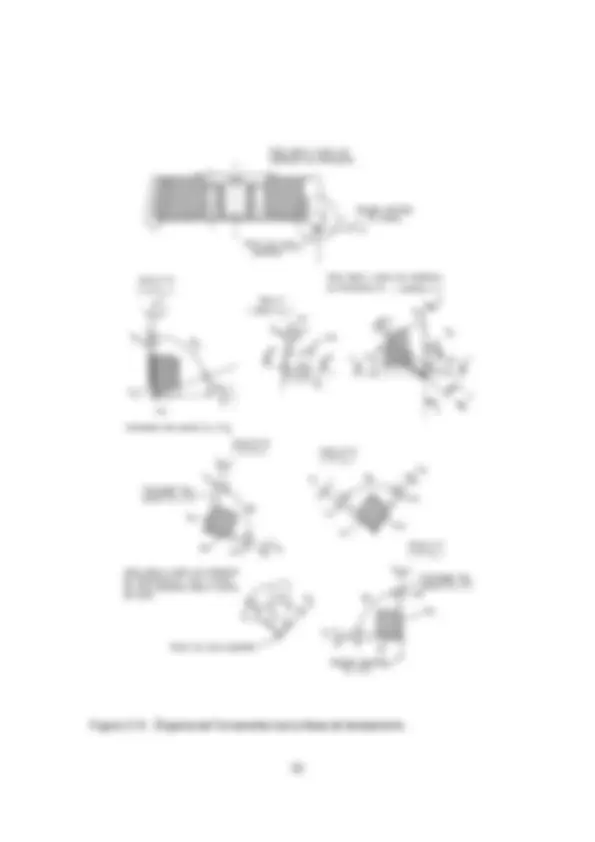
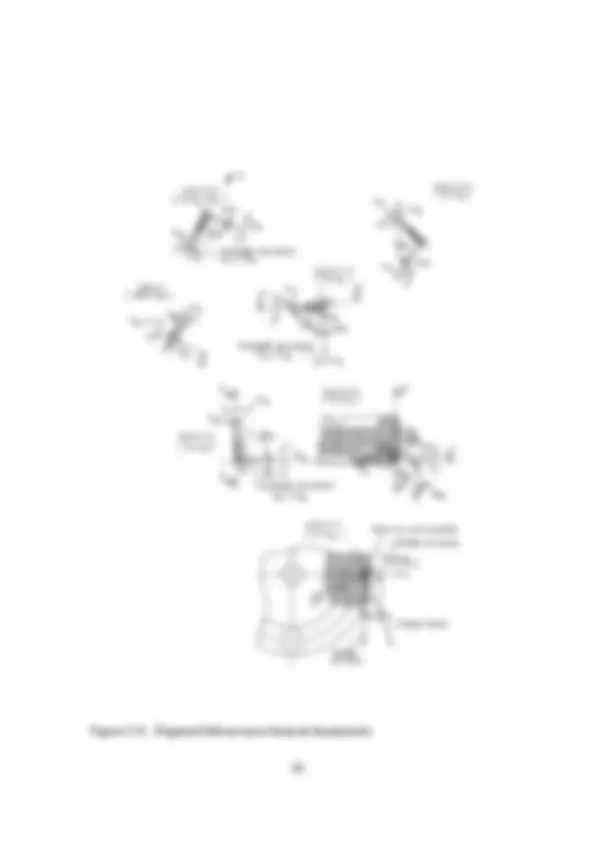
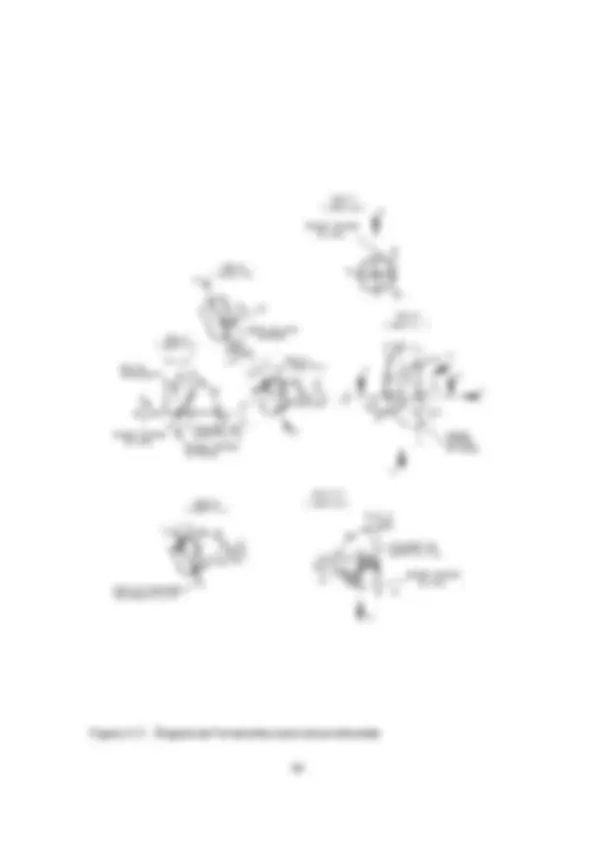
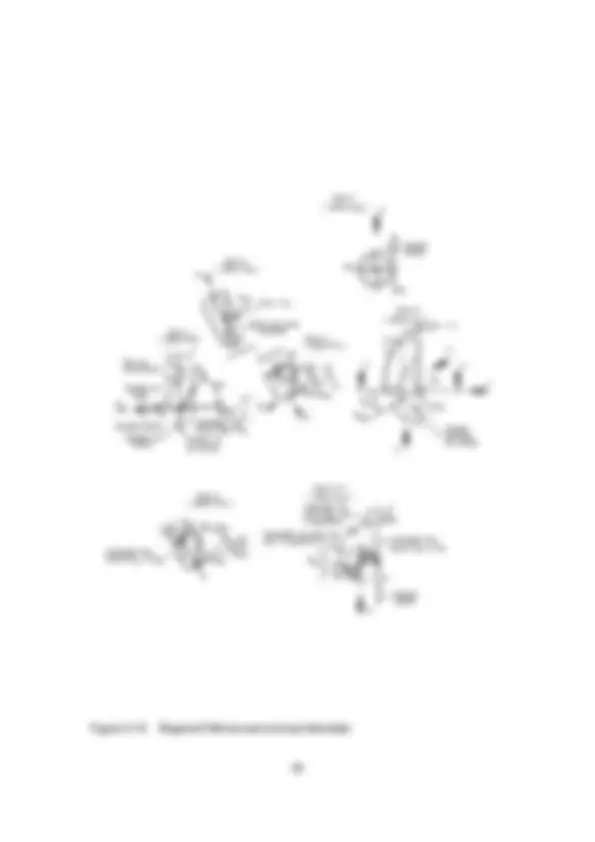
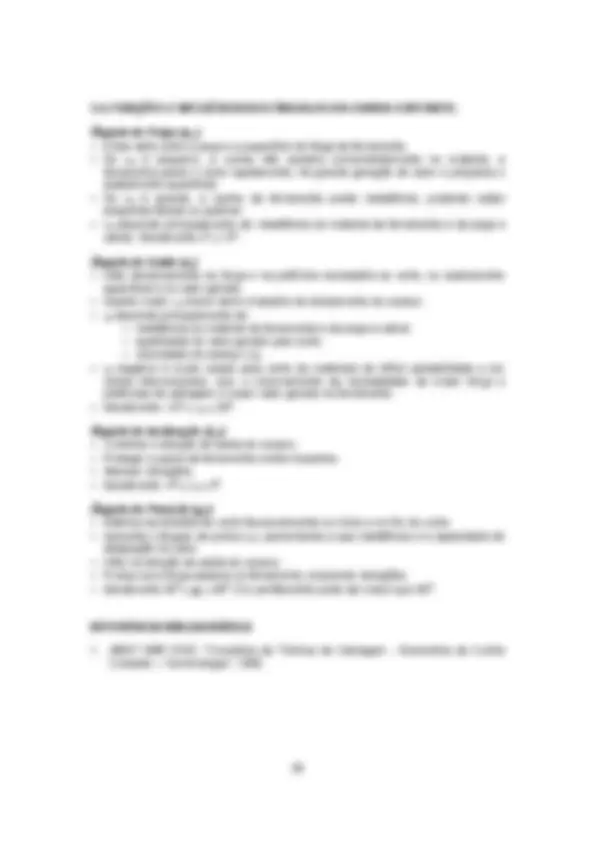
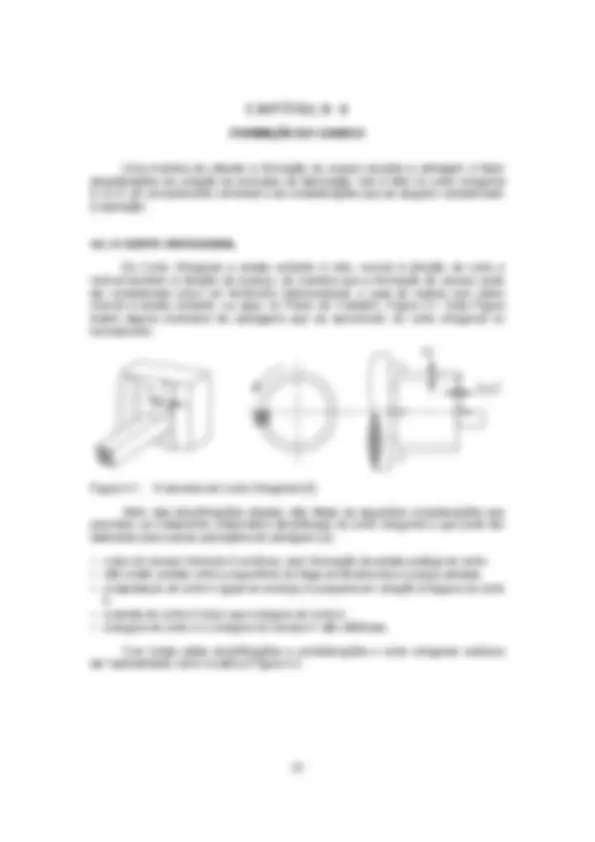

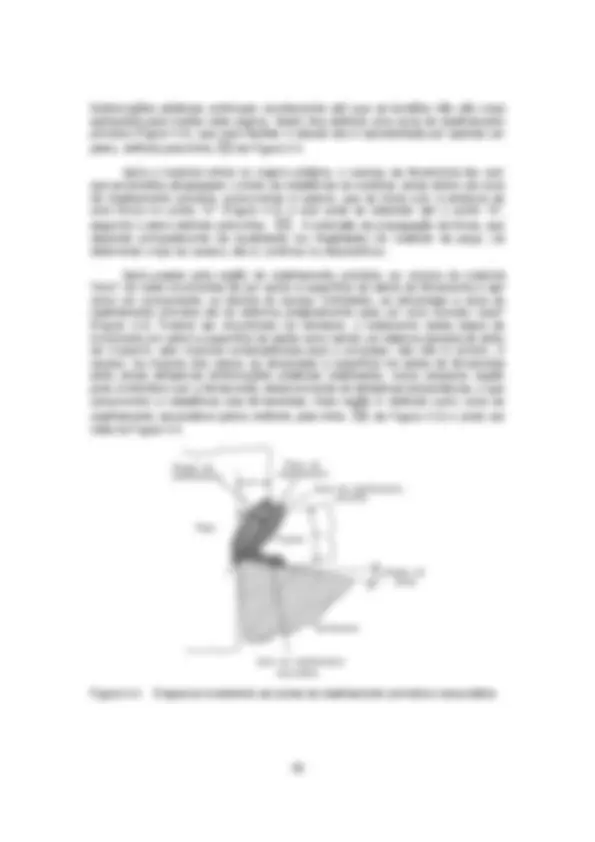
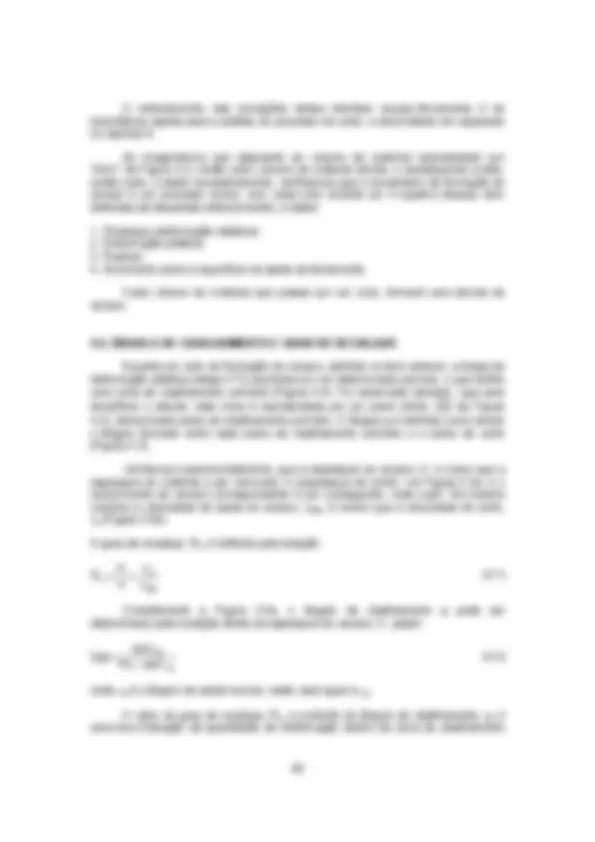
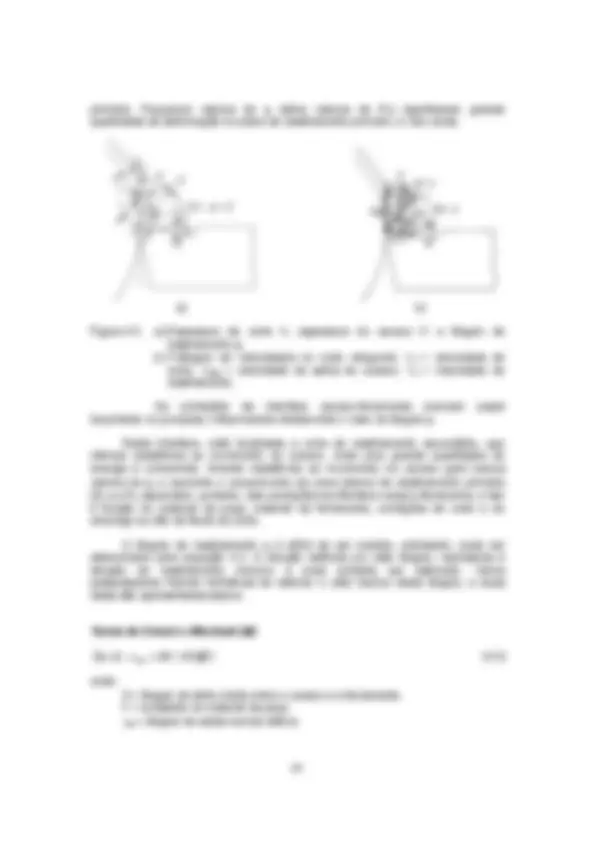
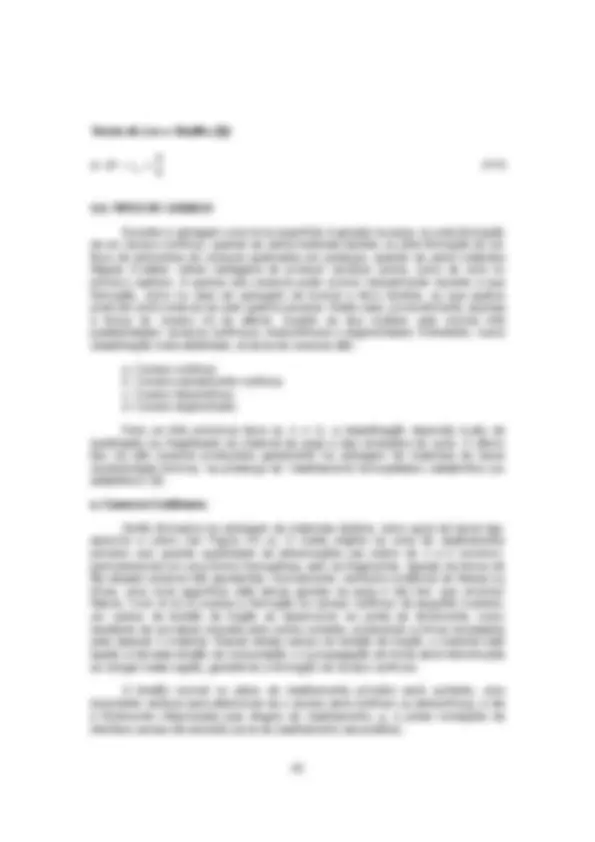
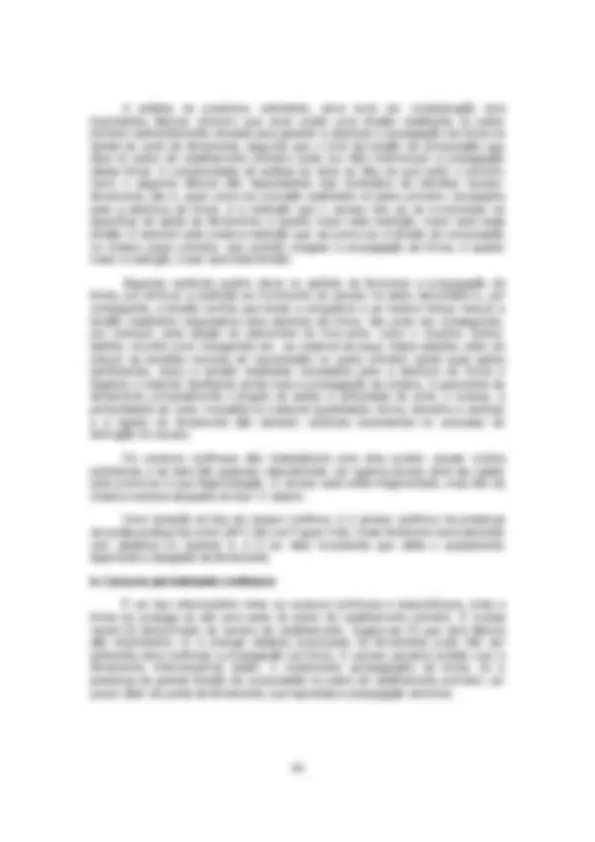
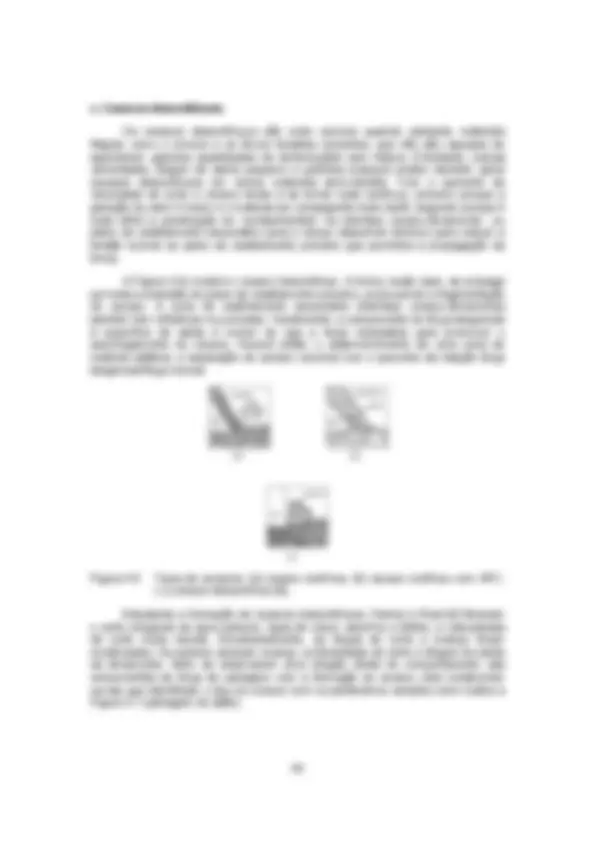
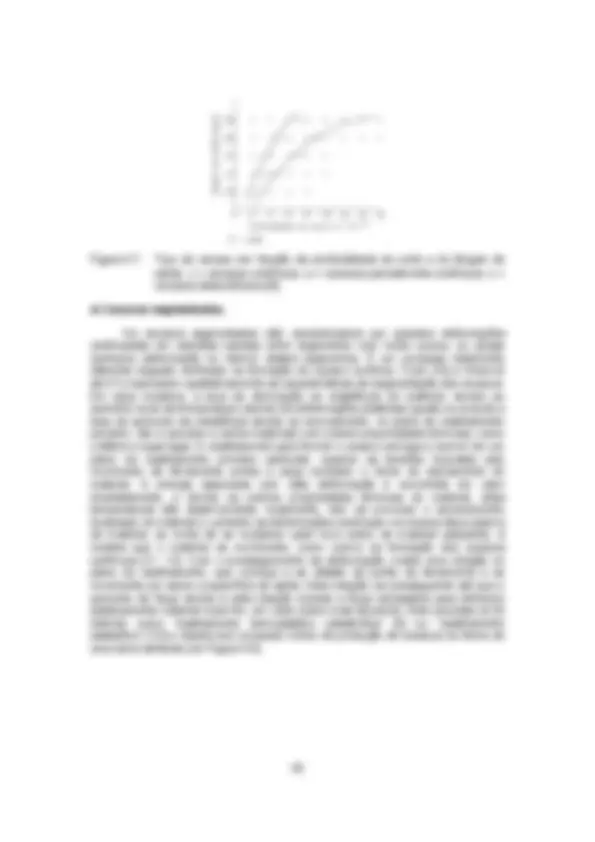
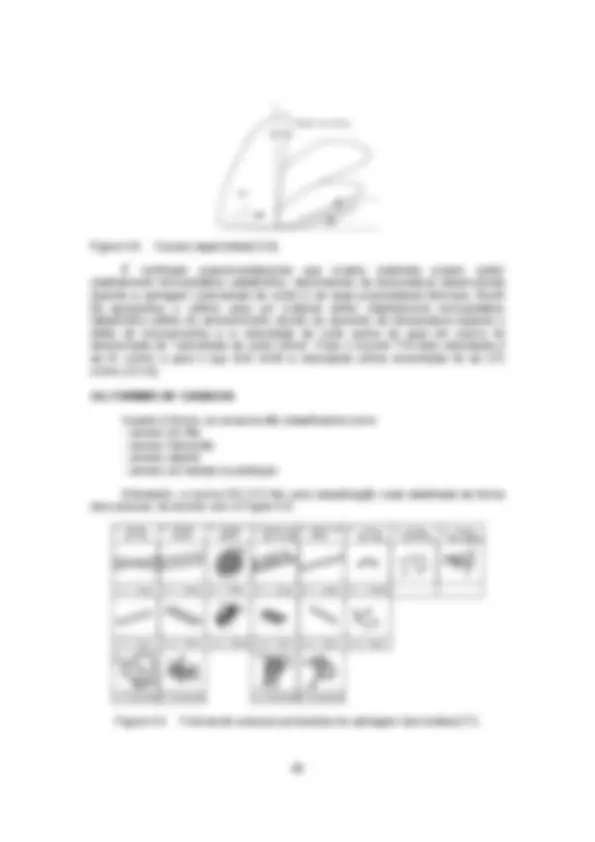
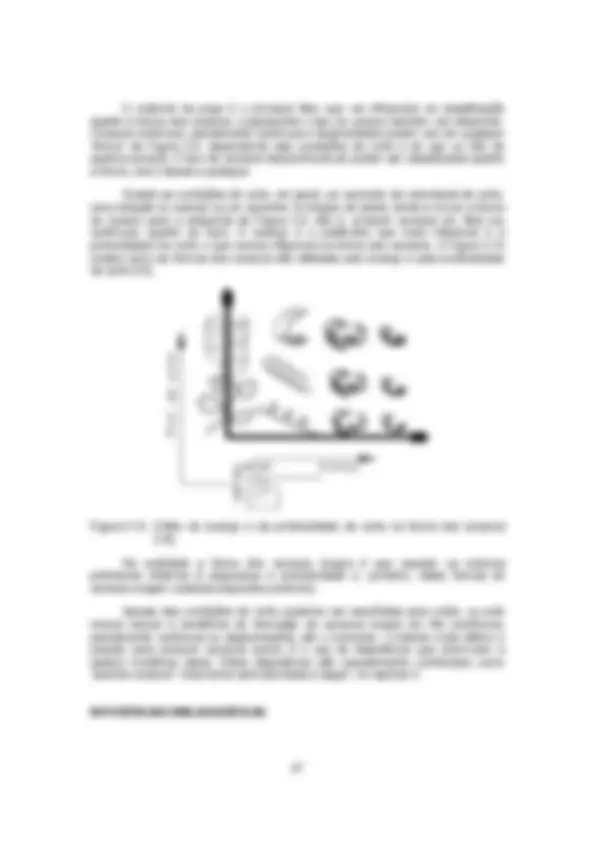
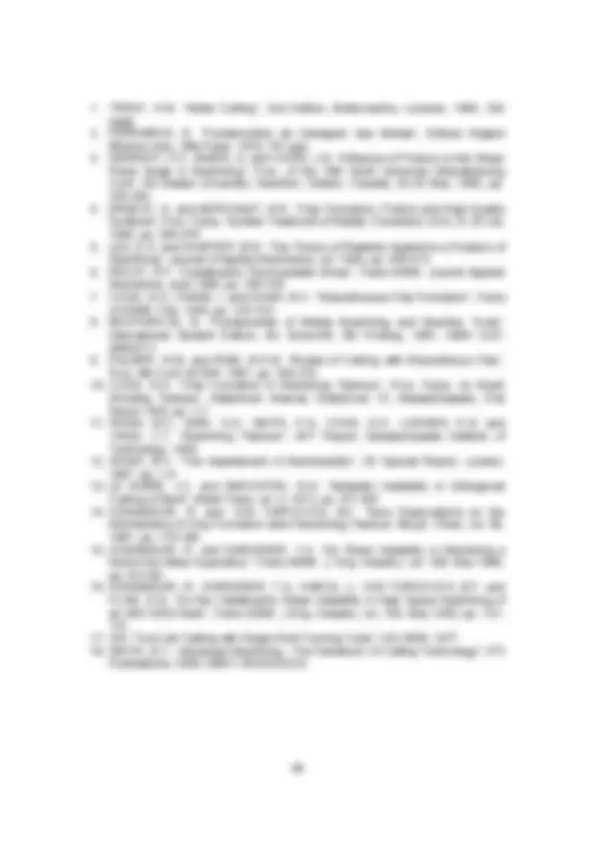
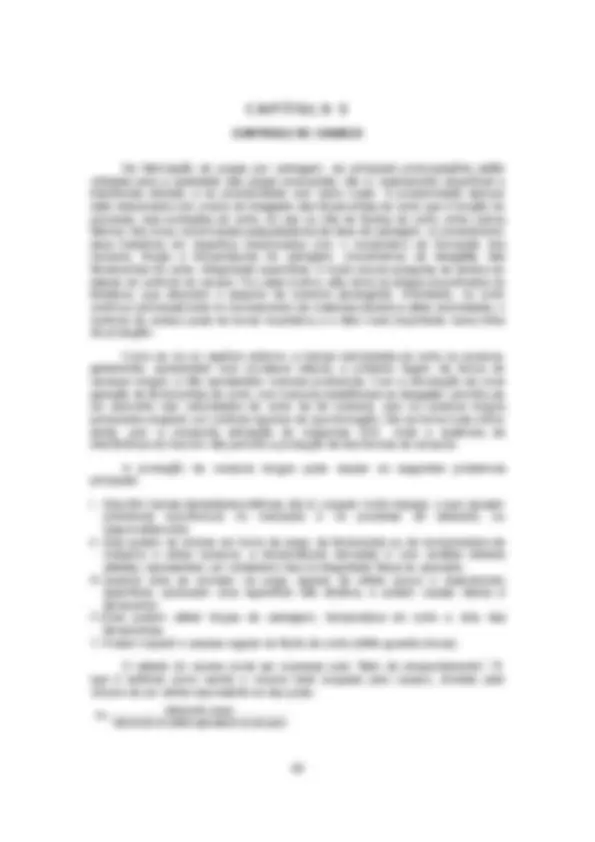
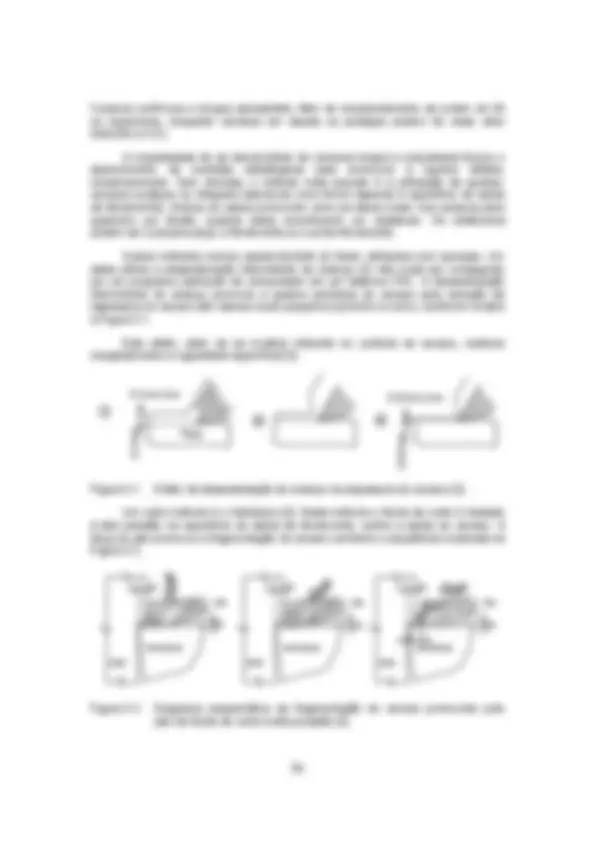
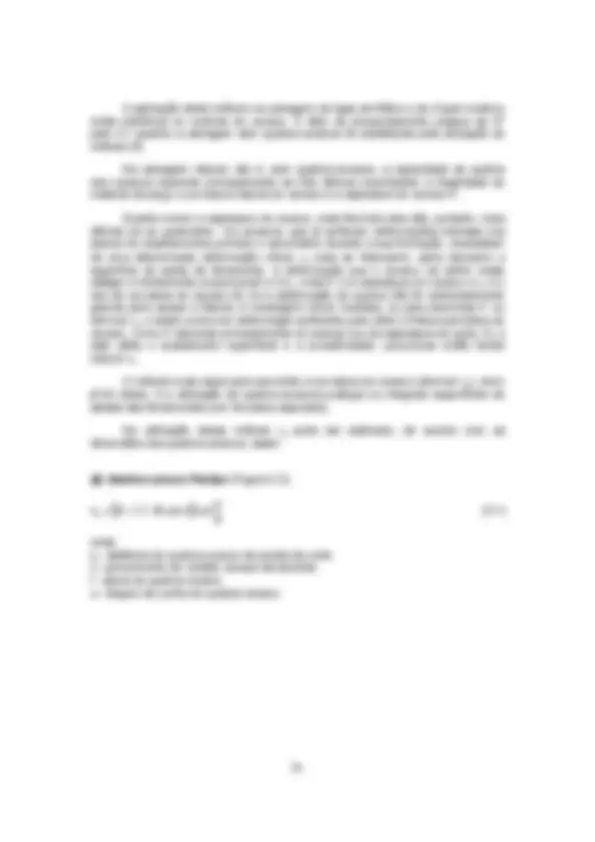
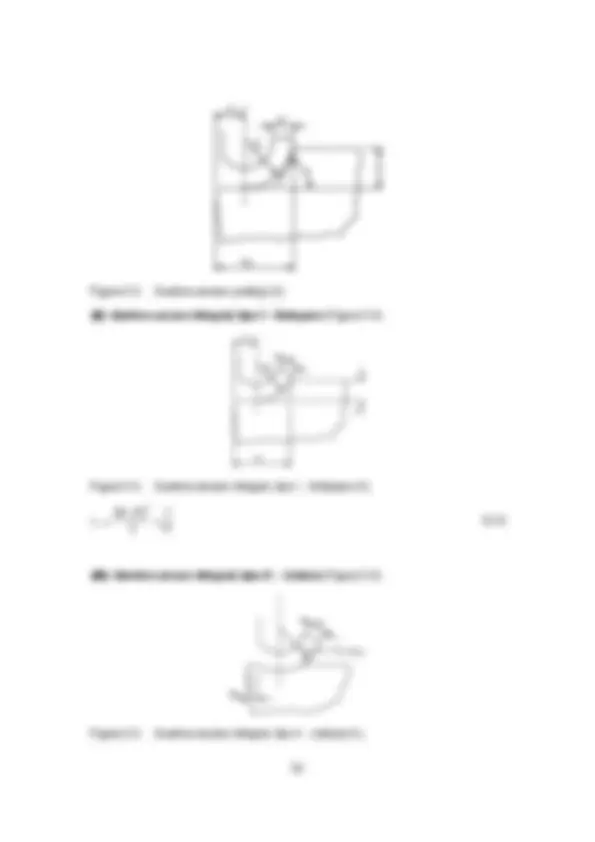
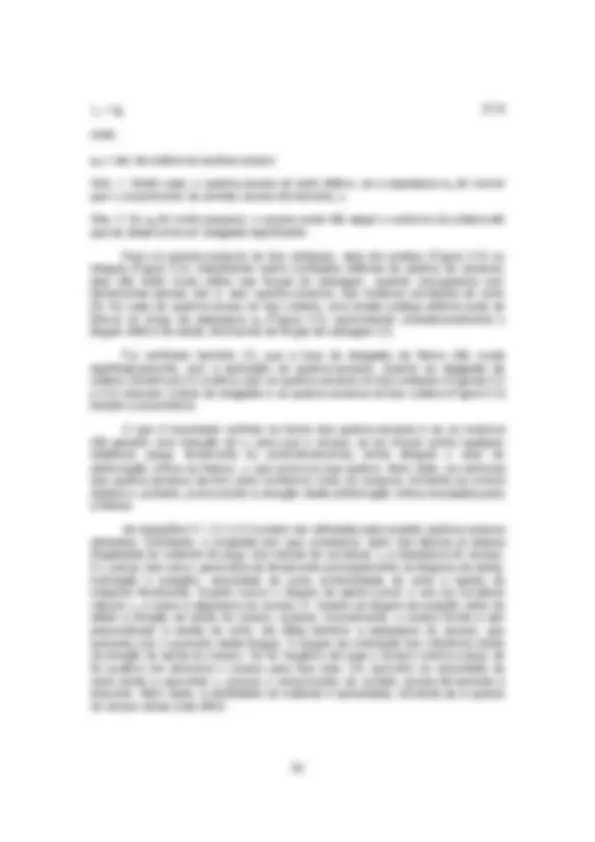
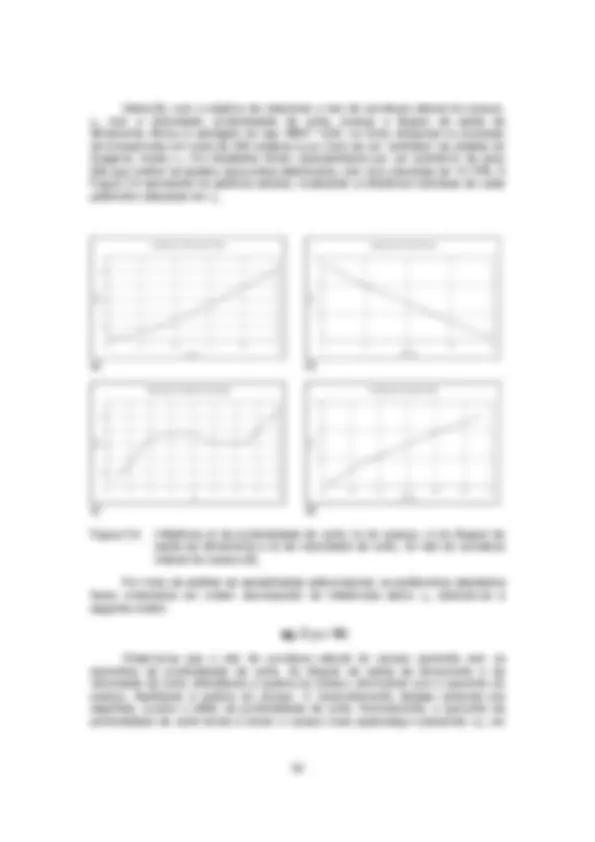
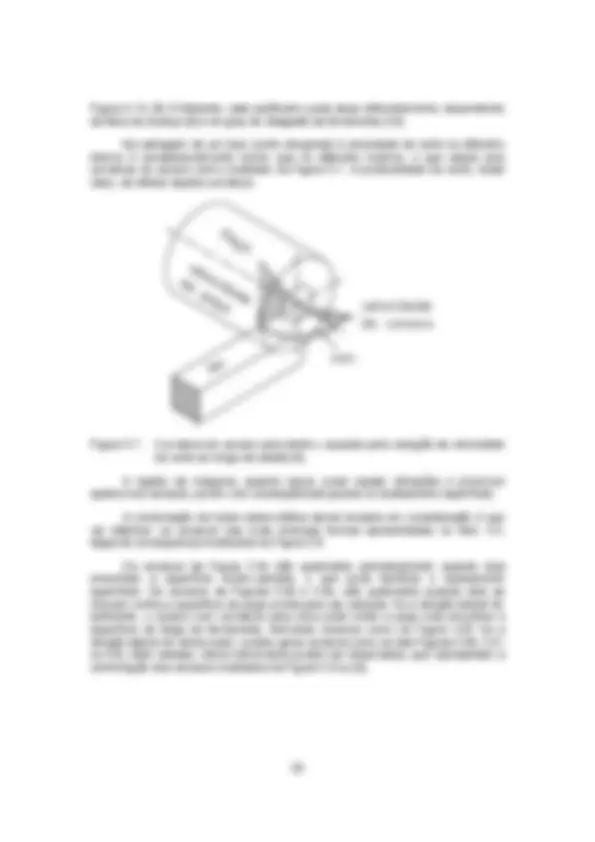

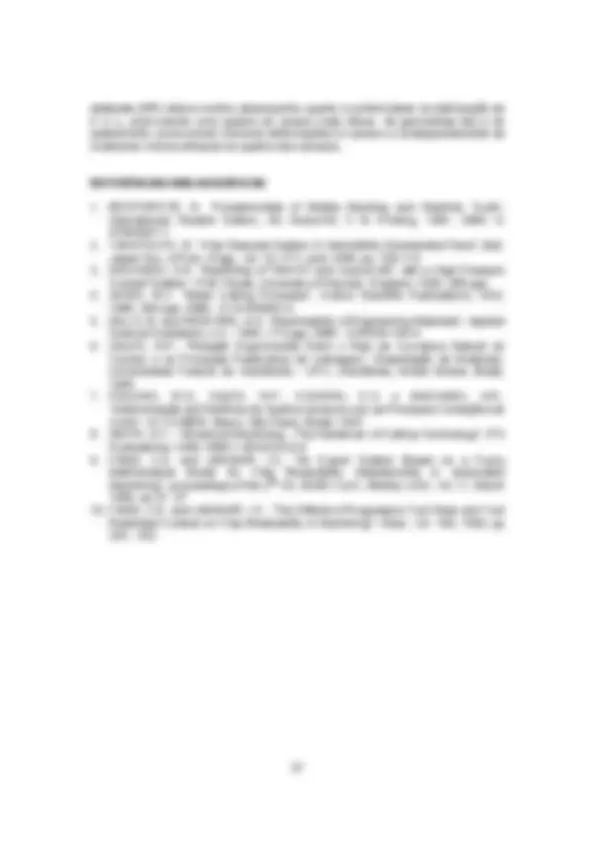
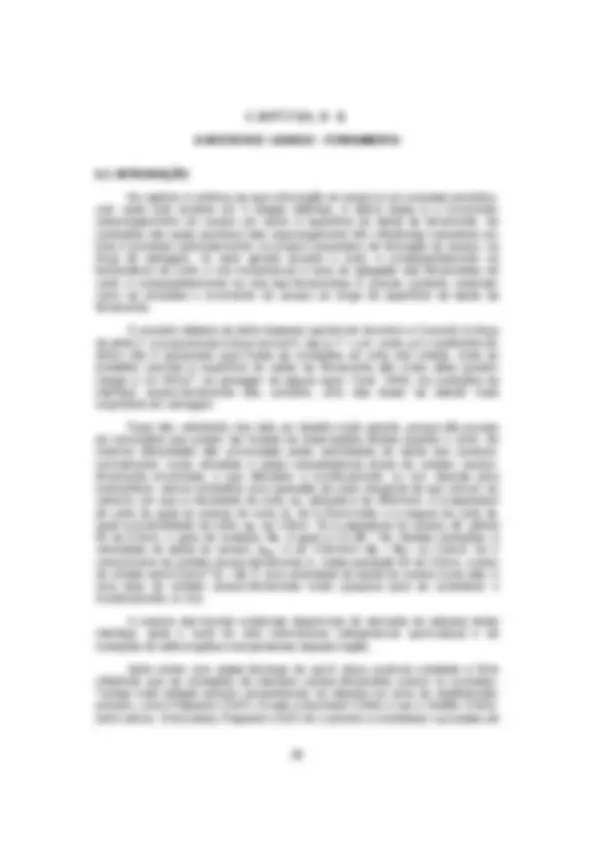
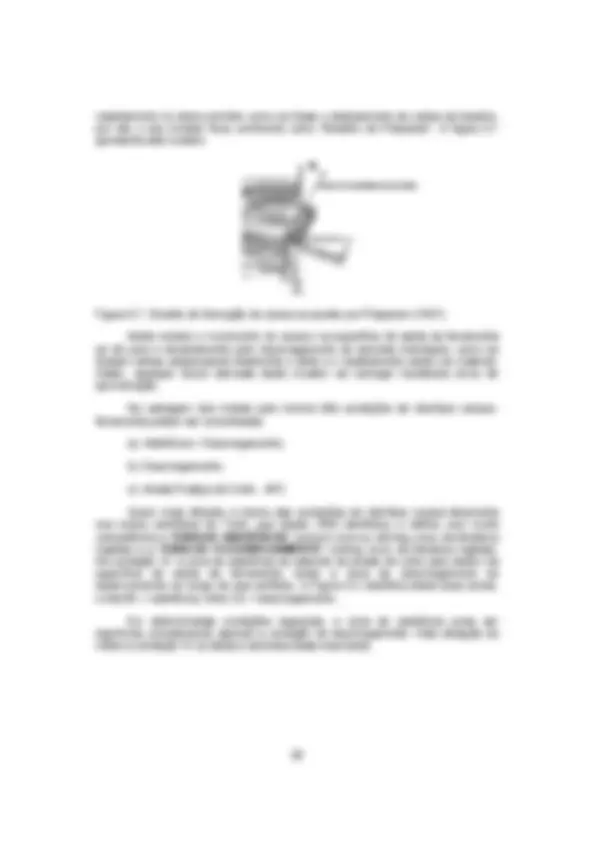
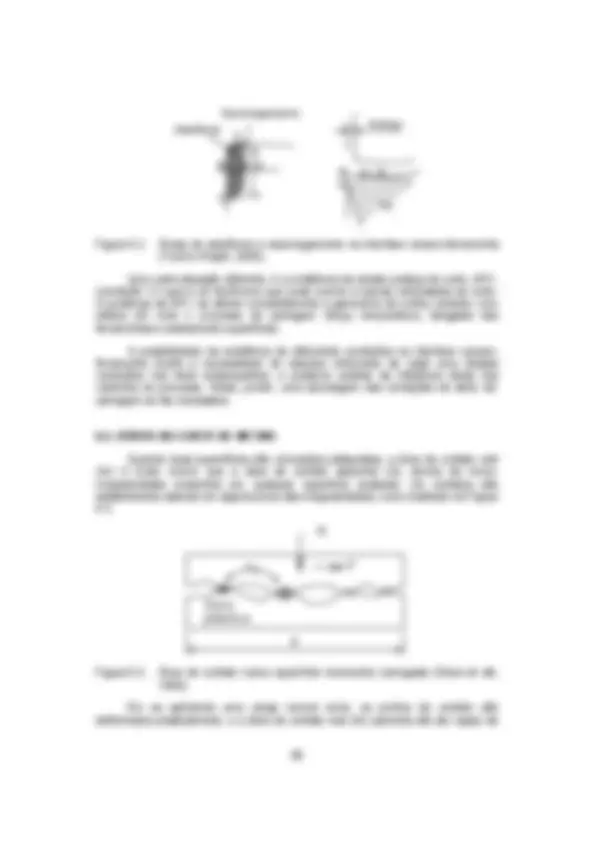
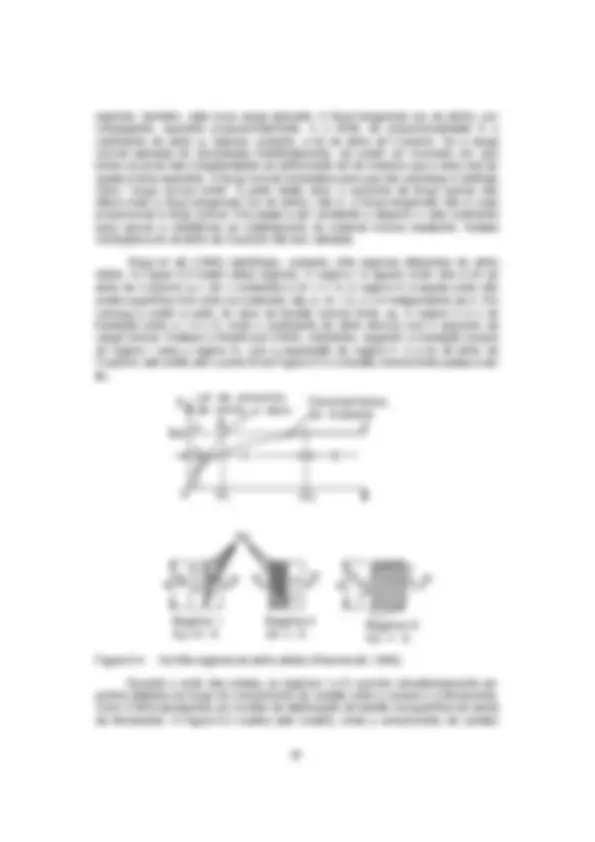
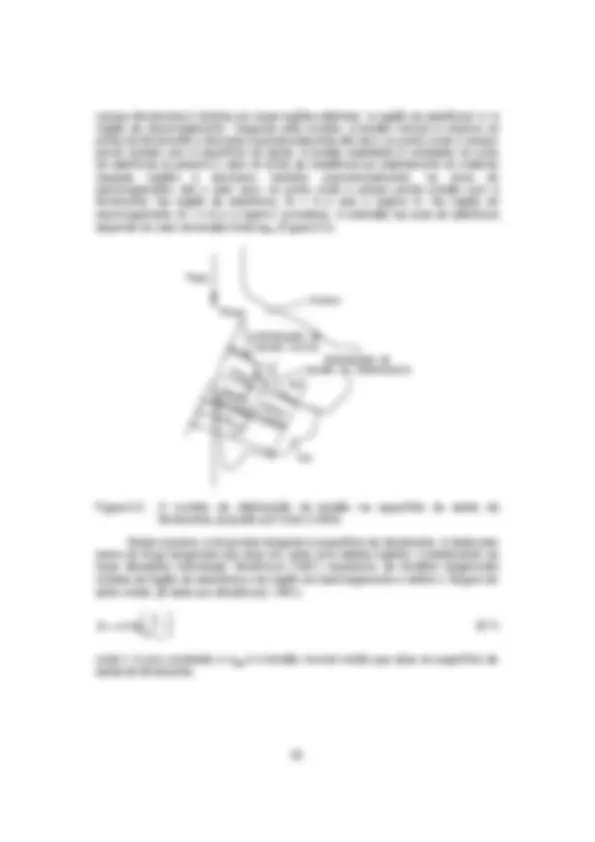
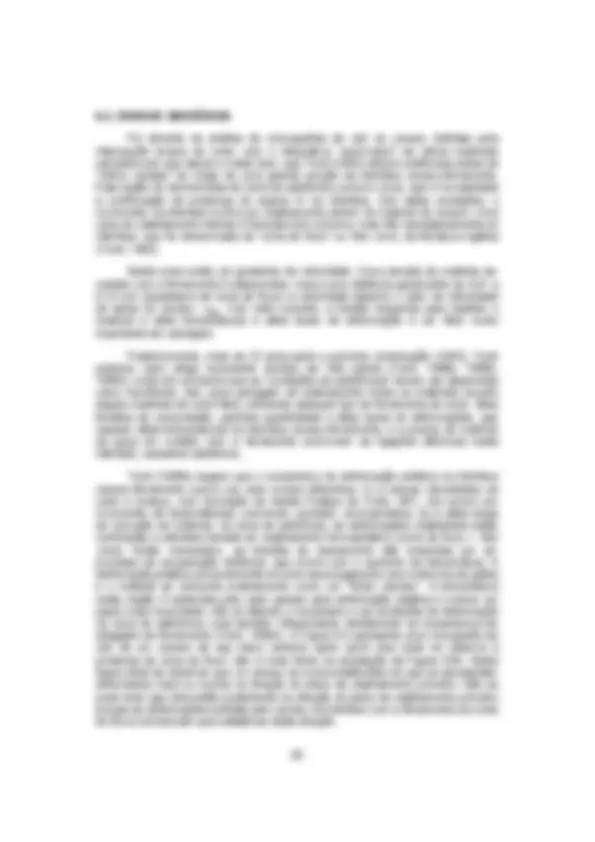
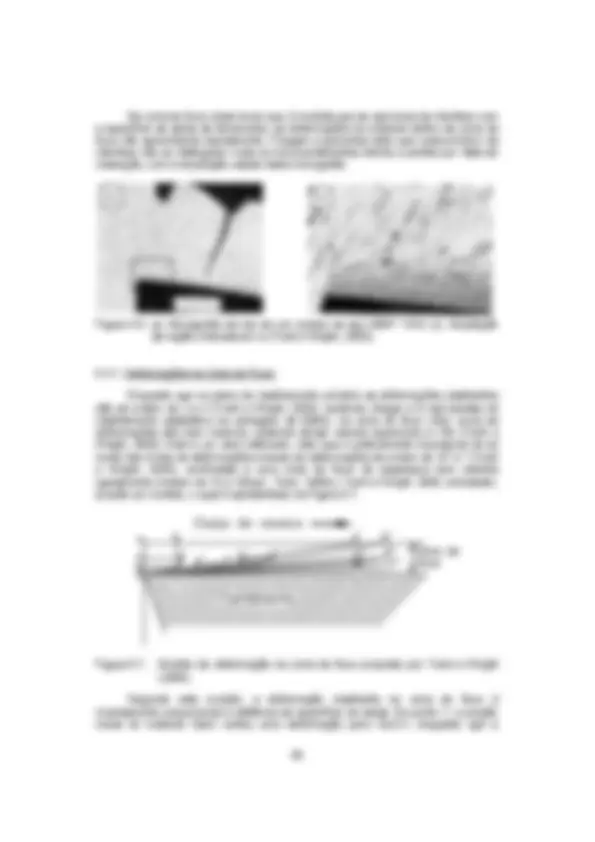
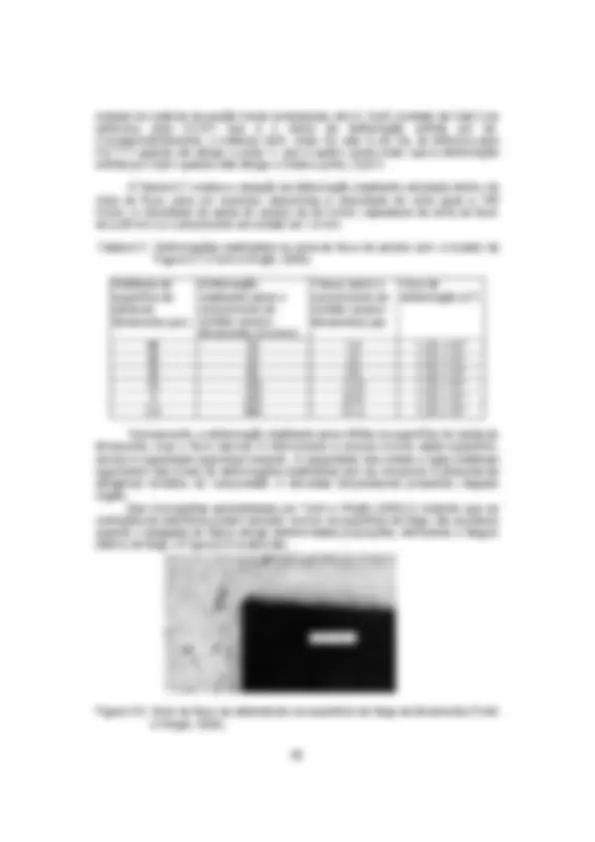
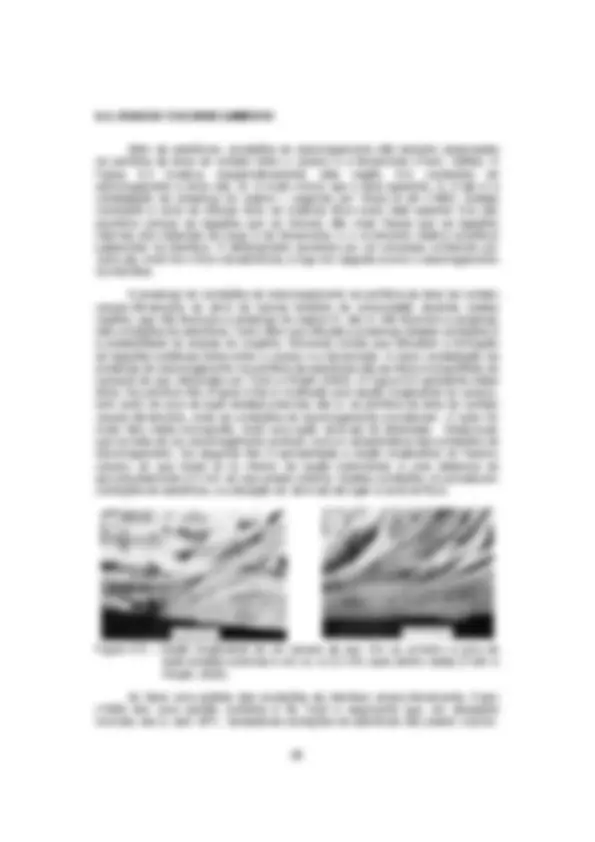
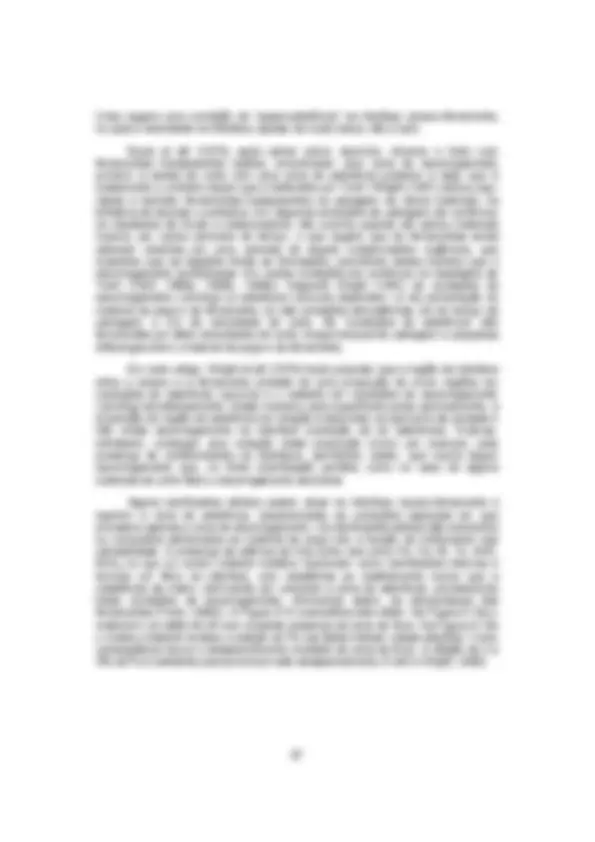
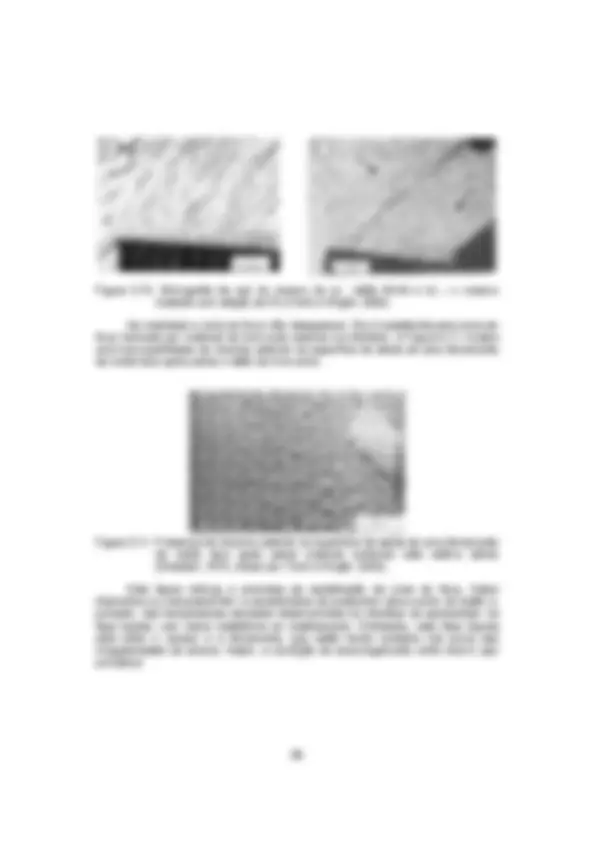
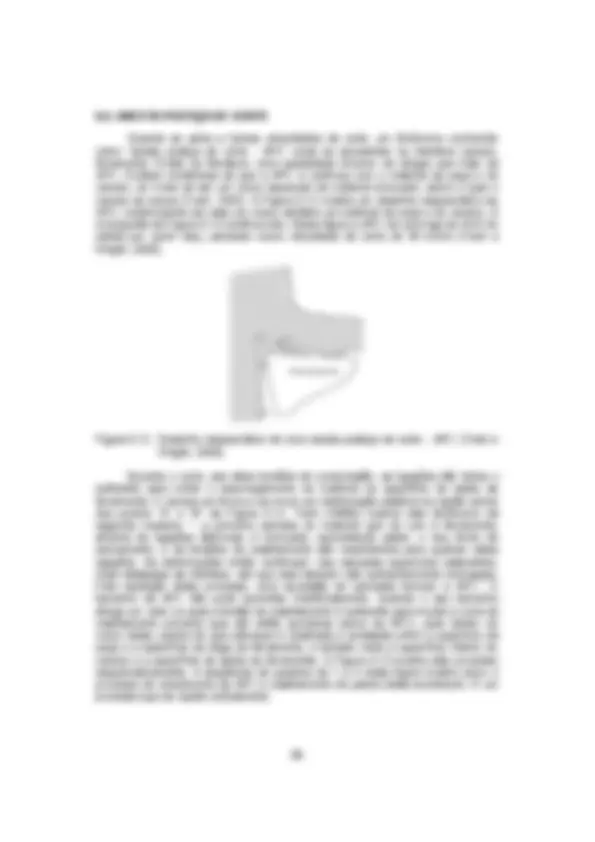
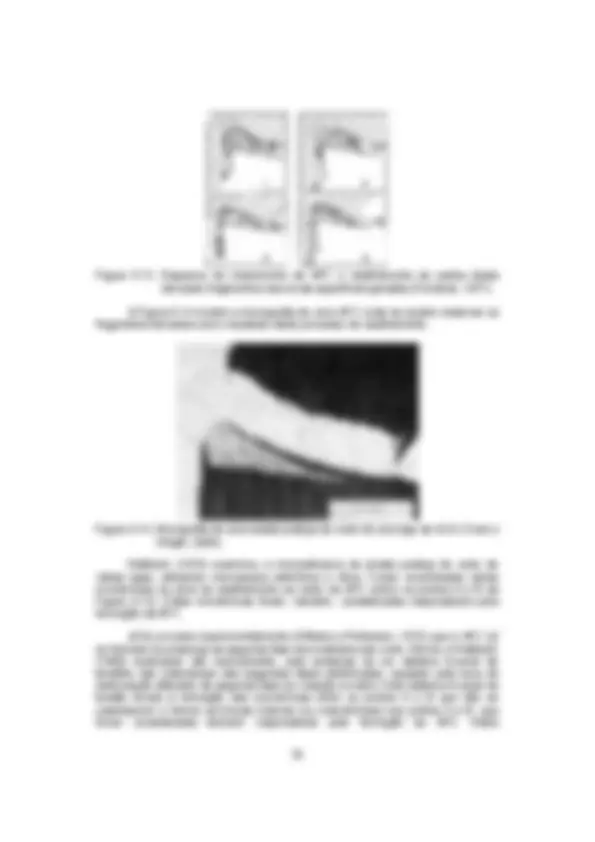
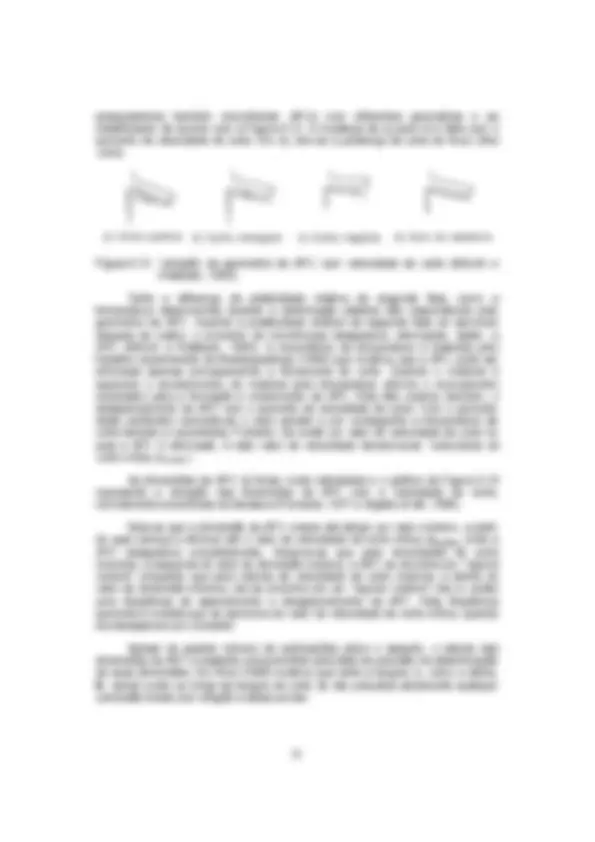
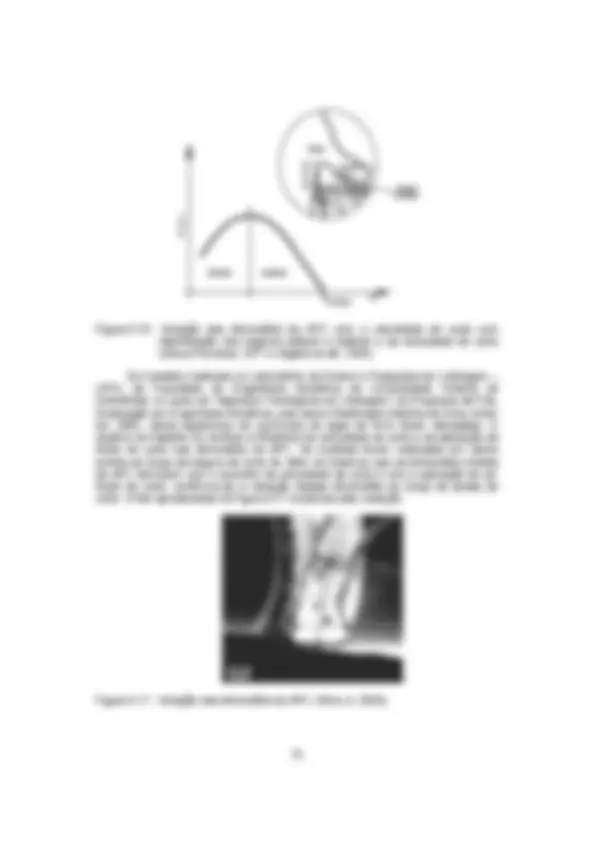
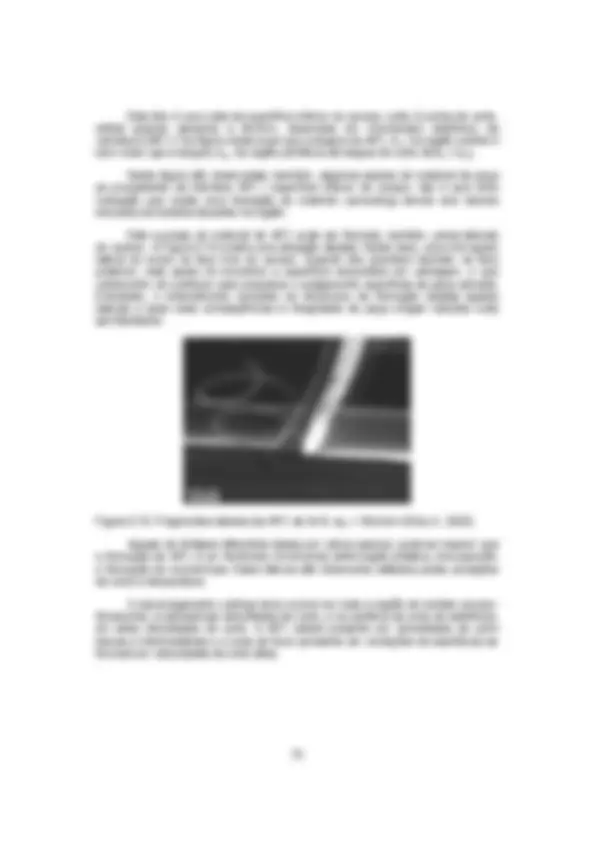
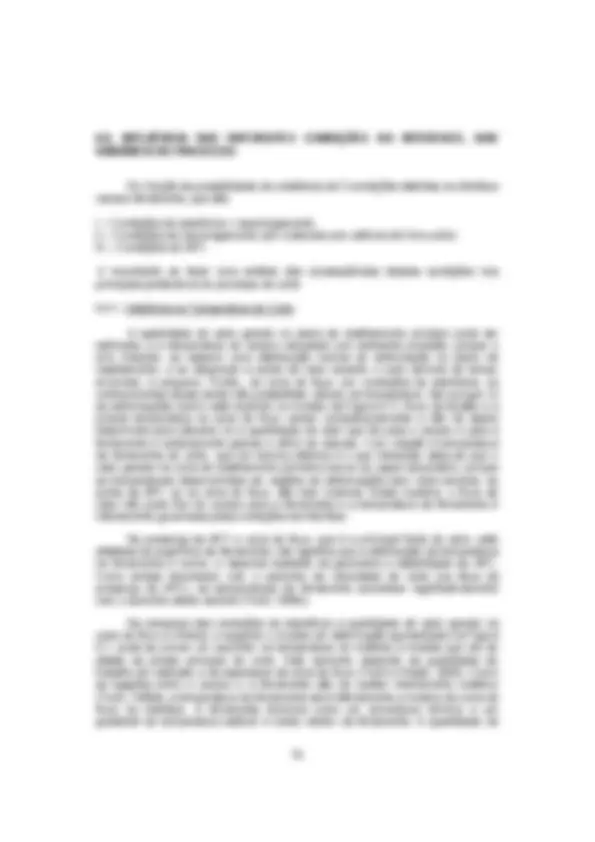
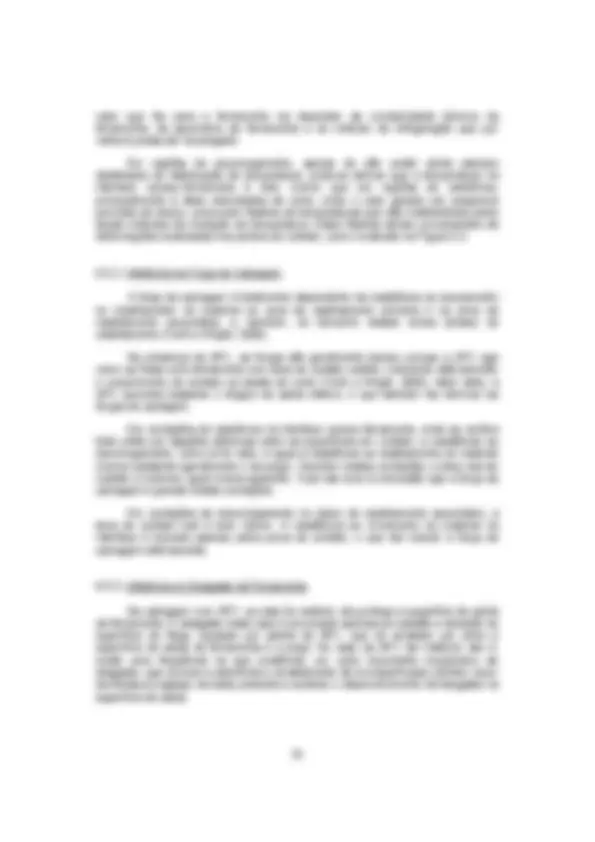
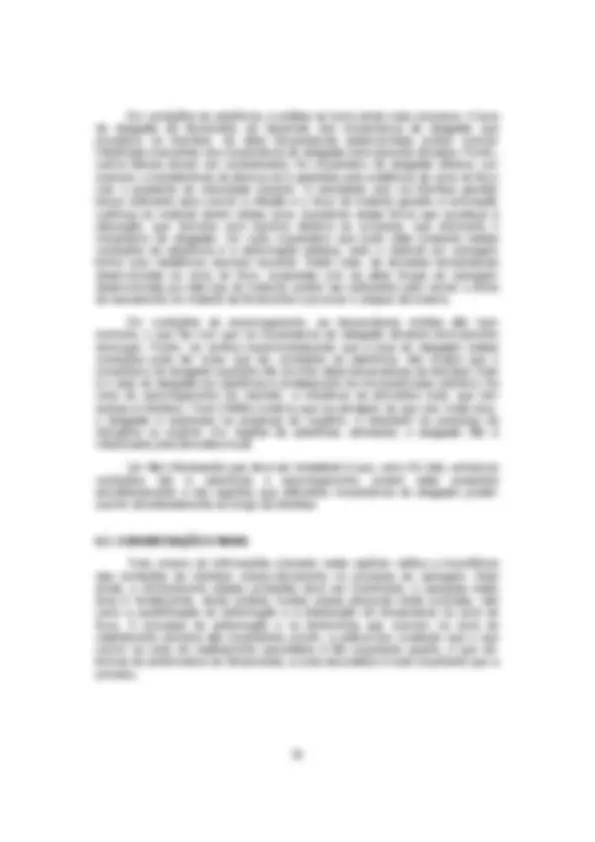
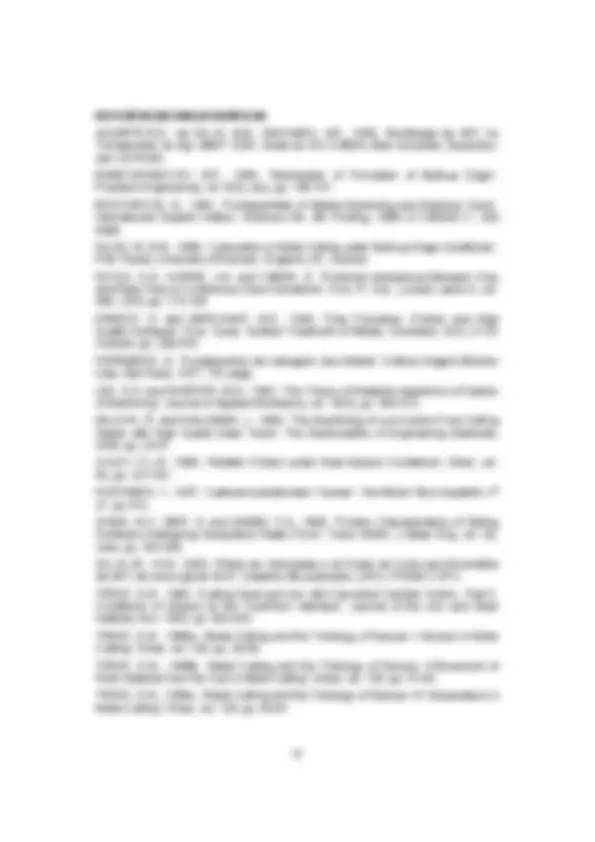
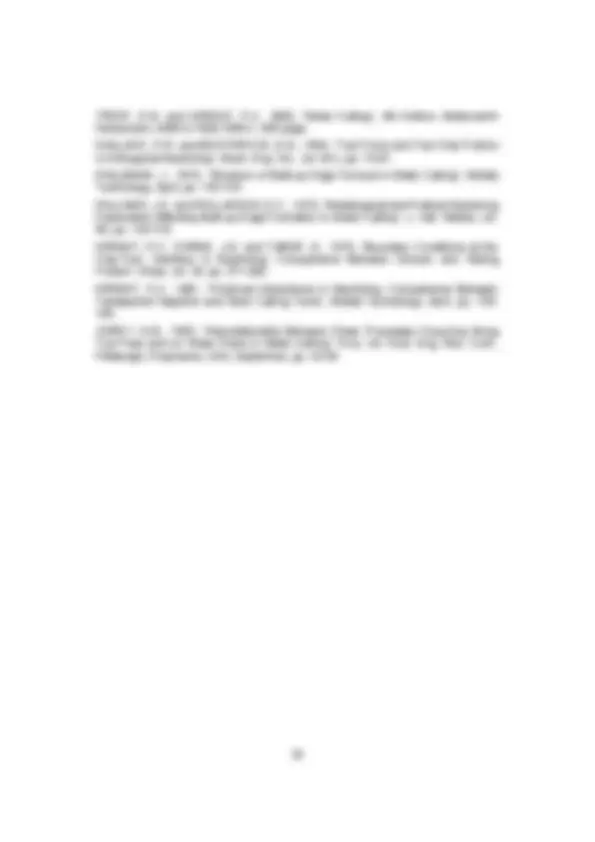
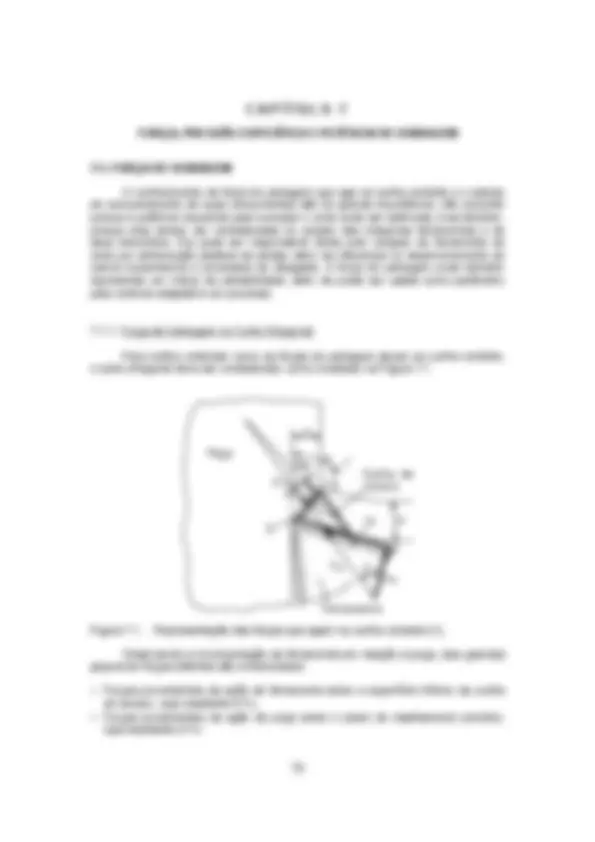
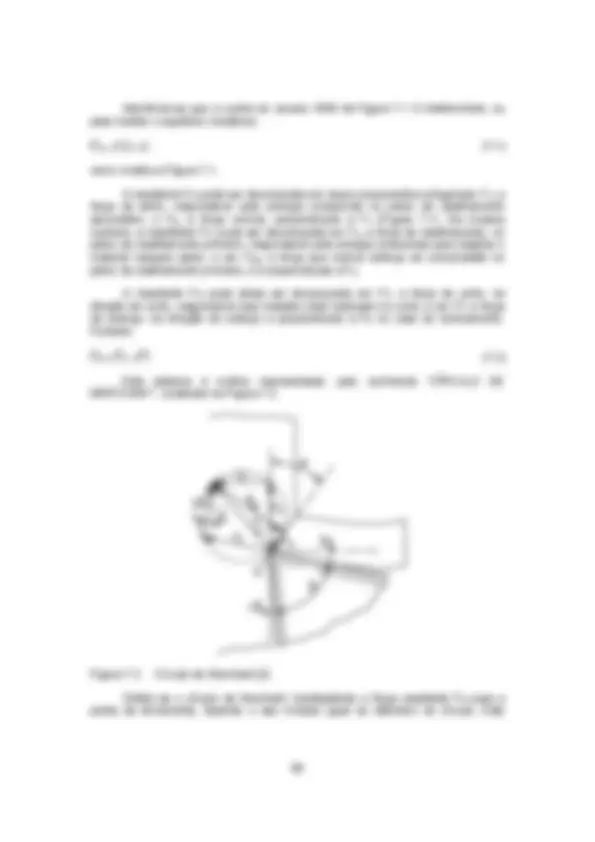
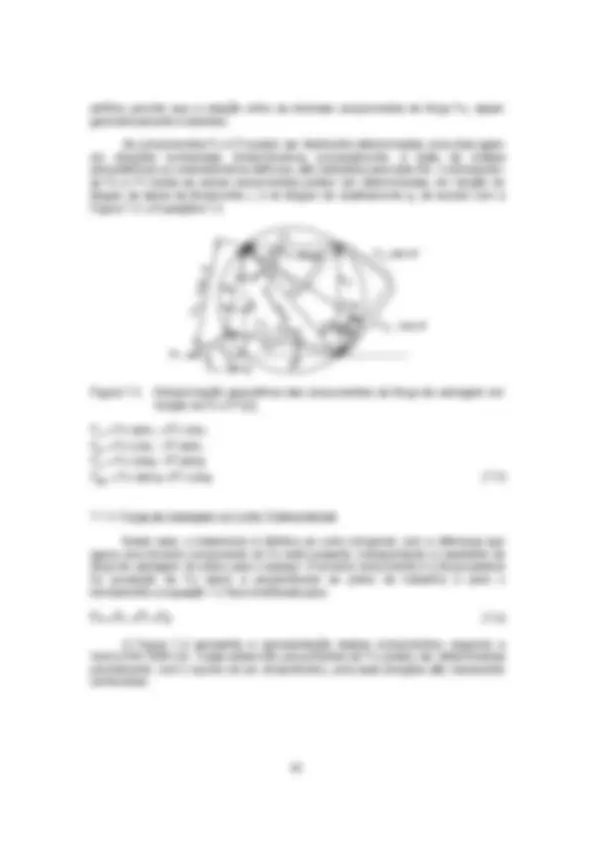
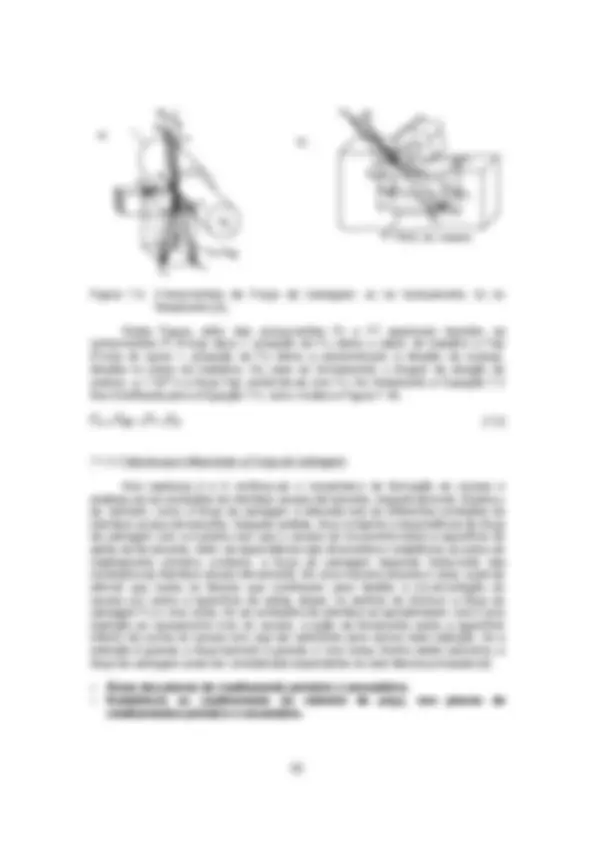

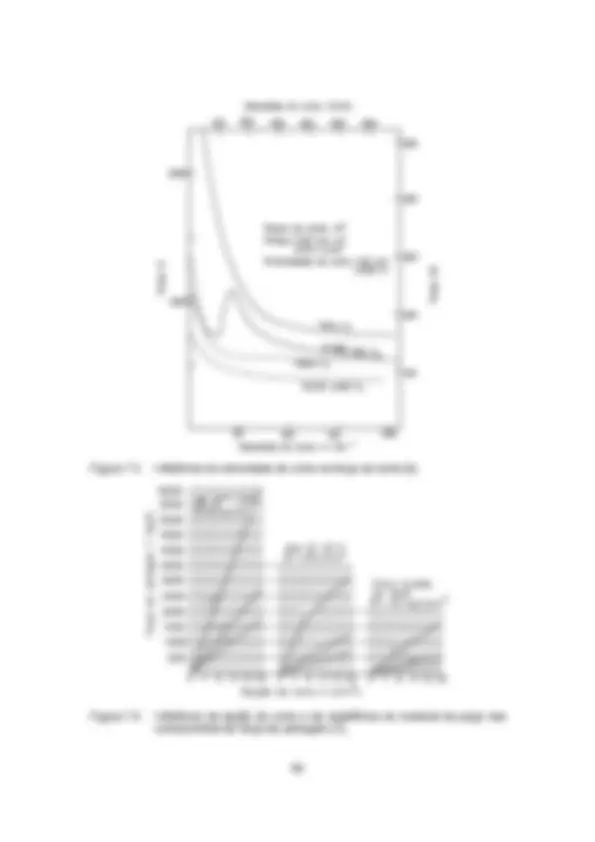


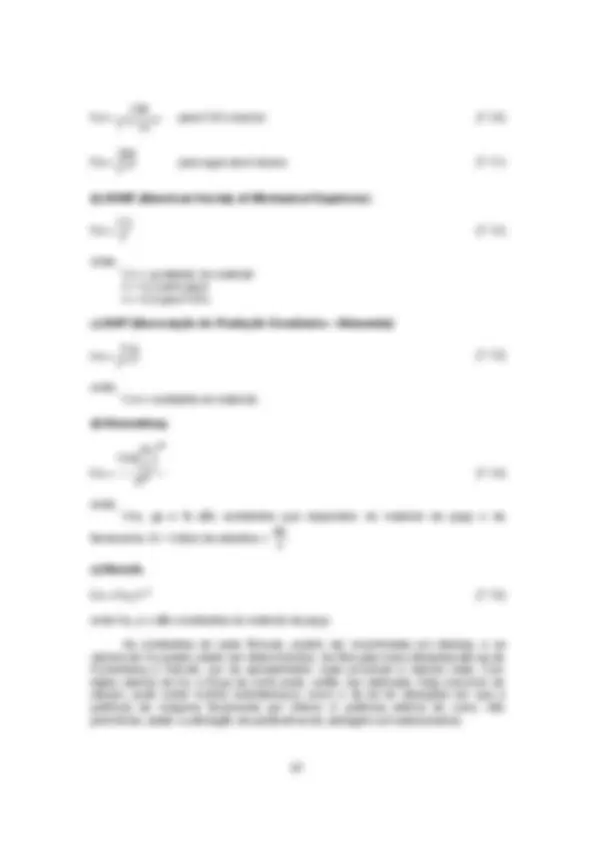
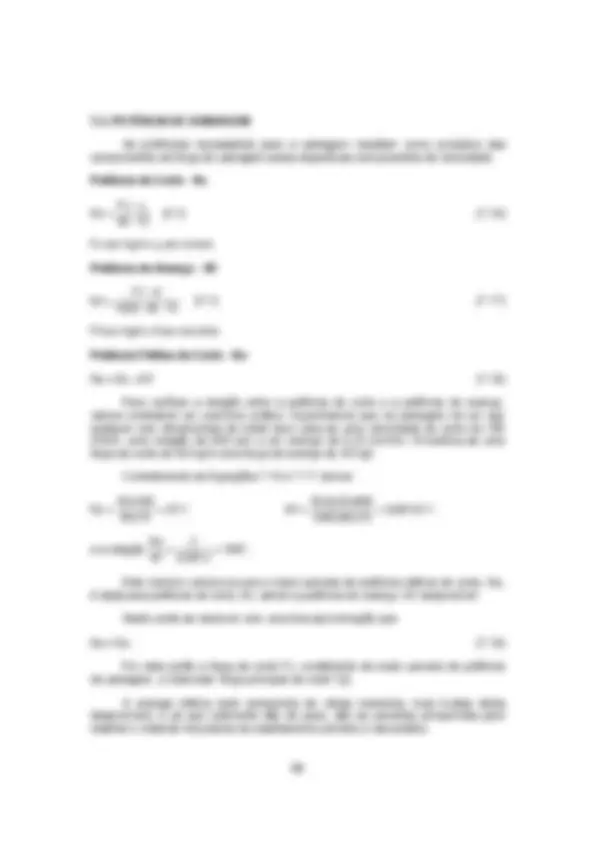
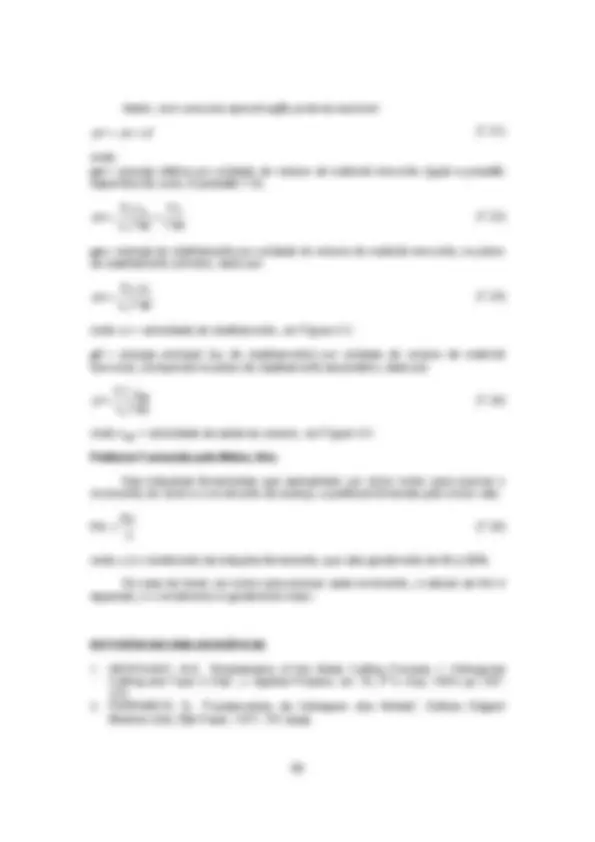
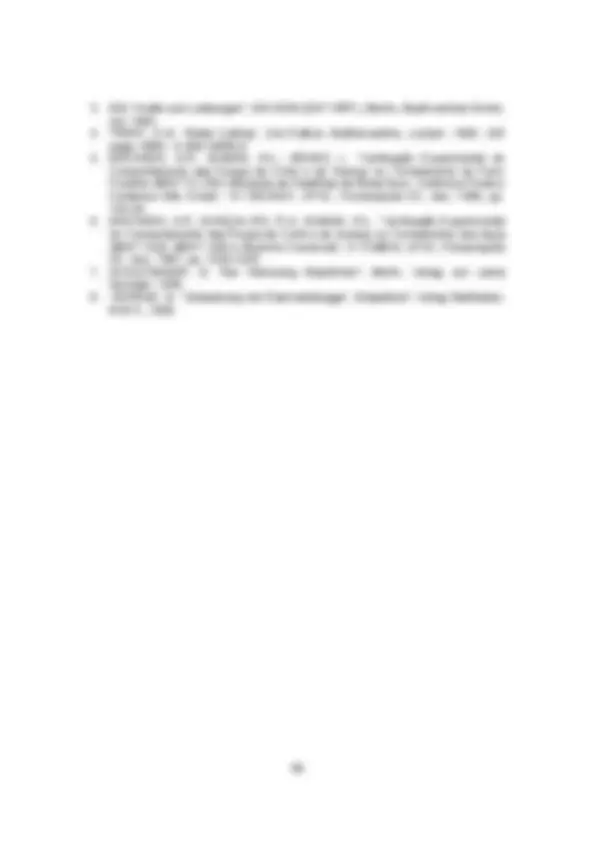
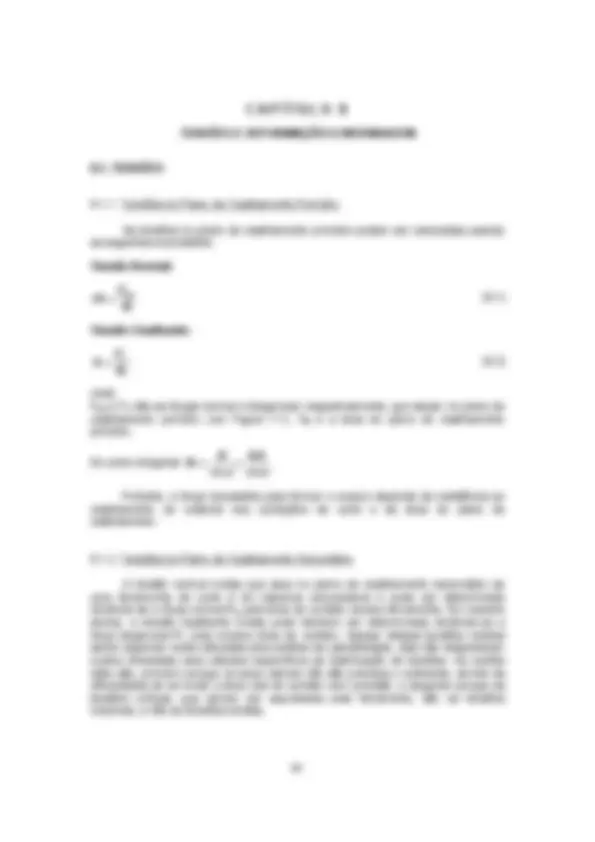
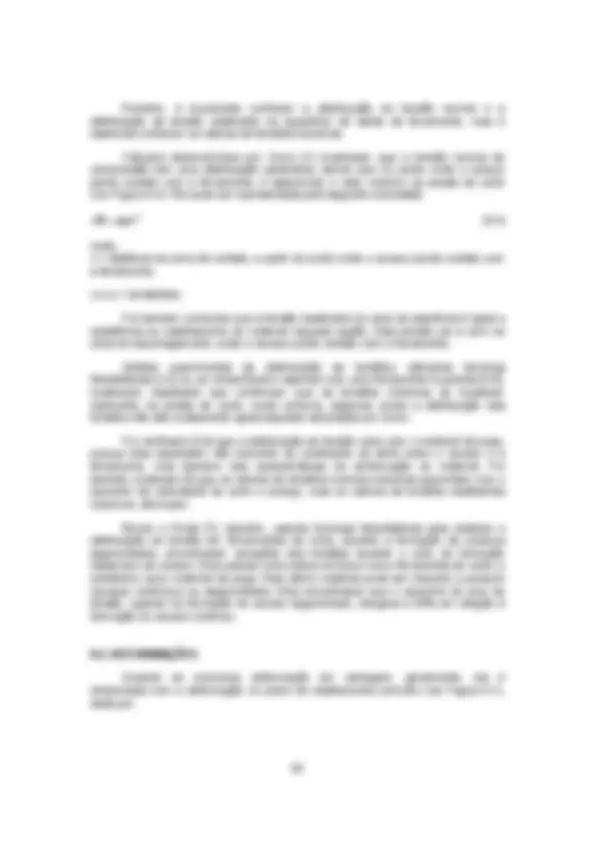
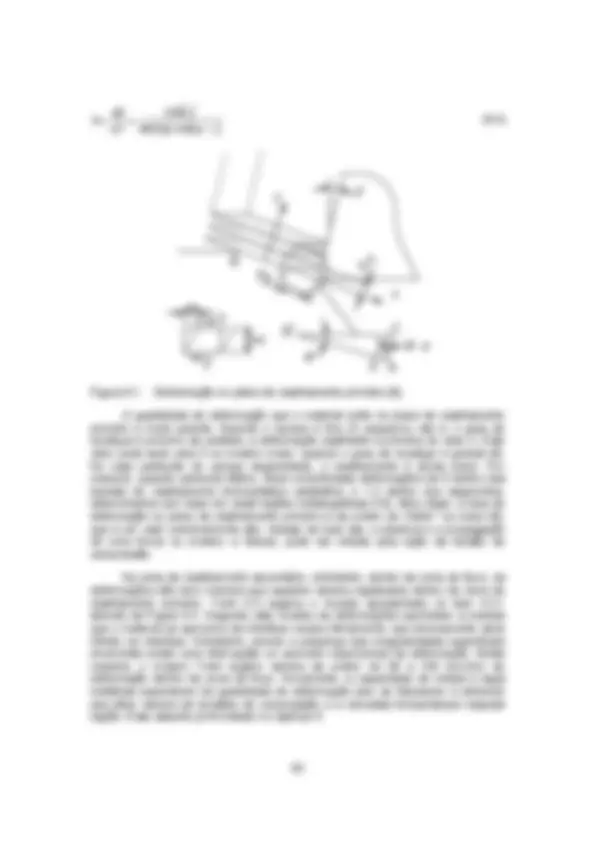
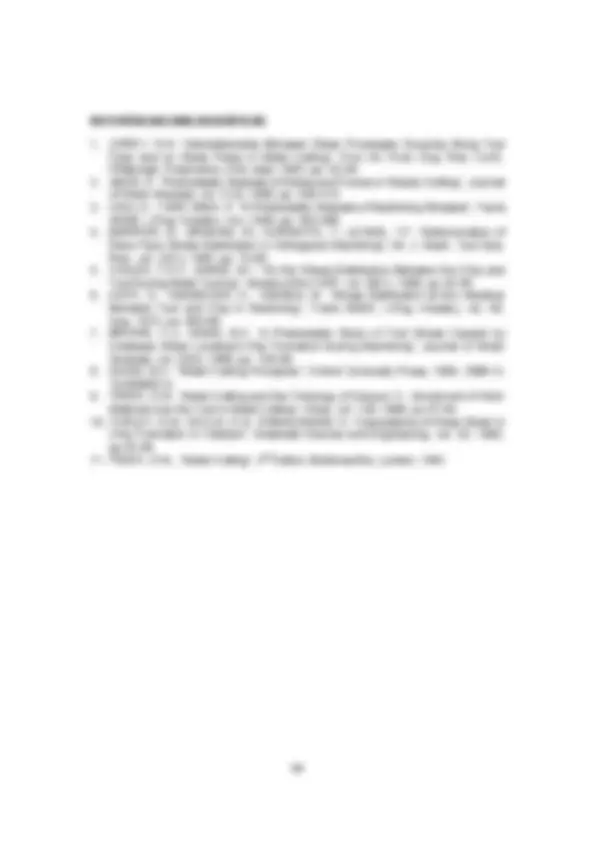
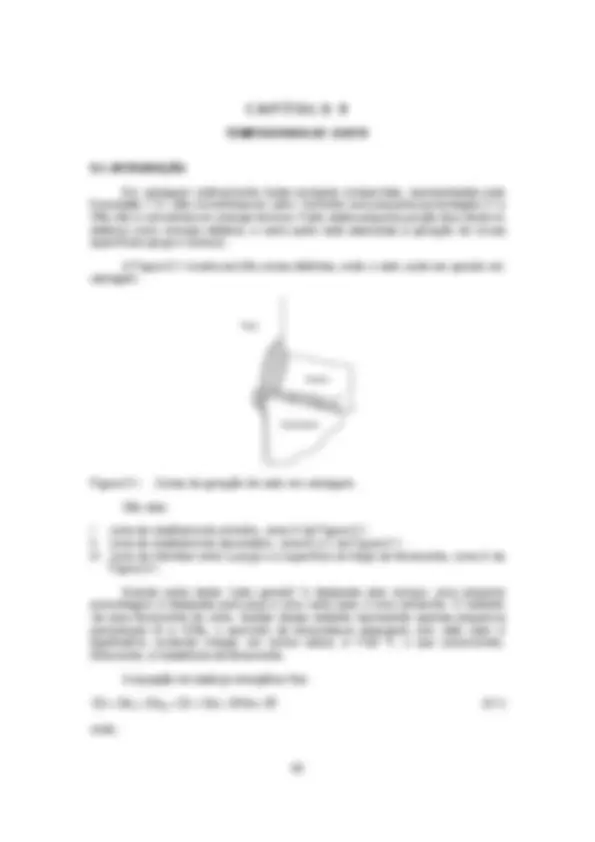
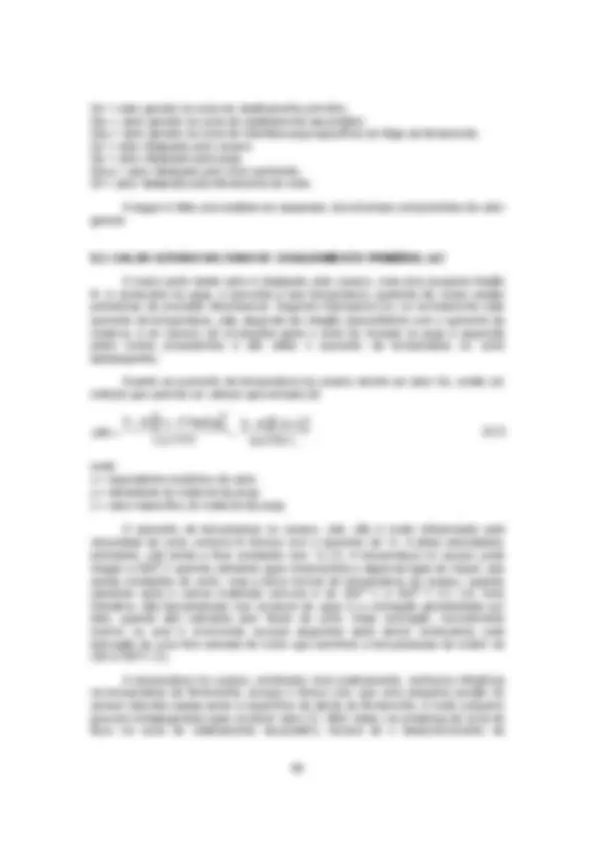
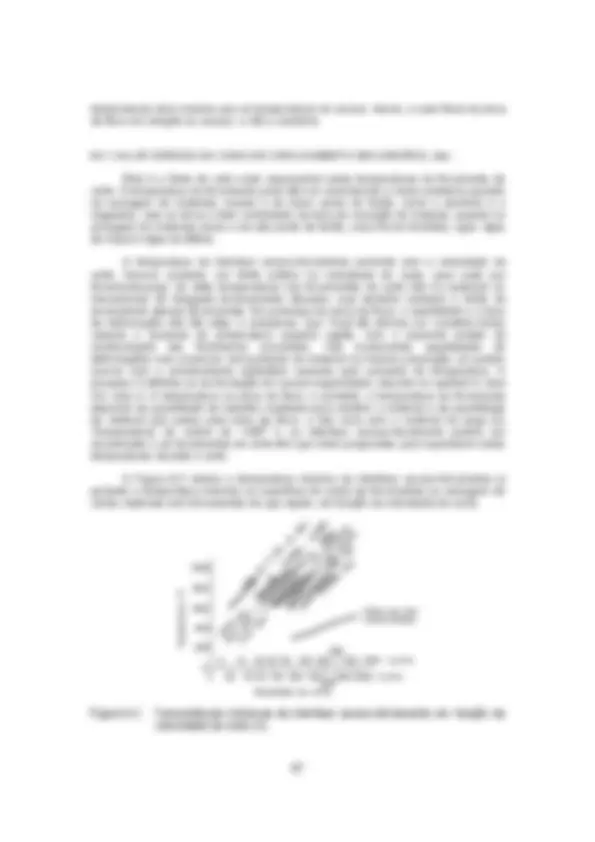
Estude fácil! Tem muito documento disponível na Docsity
Ganhe pontos ajudando outros esrudantes ou compre um plano Premium
Prepare-se para as provas
Estude fácil! Tem muito documento disponível na Docsity
Prepare-se para as provas com trabalhos de outros alunos como você, aqui na Docsity
Os melhores documentos à venda: Trabalhos de alunos formados
Prepare-se com as videoaulas e exercícios resolvidos criados a partir da grade da sua Universidade
Responda perguntas de provas passadas e avalie sua preparação.
Ganhe pontos para baixar
Ganhe pontos ajudando outros esrudantes ou compre um plano Premium
Comunidade
Peça ajuda à comunidade e tire suas dúvidas relacionadas ao estudo
Descubra as melhores universidades em seu país de acordo com os usuários da Docsity
Guias grátis
Baixe gratuitamente nossos guias de estudo, métodos para diminuir a ansiedade, dicas de TCC preparadas pelos professores da Docsity
Uma análise detalhada das condições ideais de corte e da formação de cavacos durante o processo de usinagem de materiais. São abordados tópicos como a geometria e o material adequado da ferramenta de corte, a velocidade de corte e avanço ideais, o uso de fluidos de corte, a influência da rigidez da máquina-ferramenta, as diferentes formas de cavacos gerados e os fatores que afetam sua formação, como a velocidade de corte, o ângulo de saída da ferramenta e a profundidade de corte. Também são discutidos os efeitos da temperatura na interface cavaco-ferramenta, os mecanismos de desgaste das ferramentas de corte e as particularidades da usinagem de materiais de difícil usinabilidade, como as ligas de titânio. O documento fornece uma compreensão abrangente dos principais aspectos envolvidos no processo de usinagem de materiais, sendo relevante para estudantes e profissionais da área de engenharia mecânica e de materiais.
Tipologia: Notas de aula
1 / 260
Esta página não é visível na pré-visualização
Não perca as partes importantes!
8ª. versão, Abril de 2004
A idéia de realizar este trabalho surgiu após o meu retorno da Inglaterra em 1990, onde, durante os 4 anos anteriores, desenvolvi um programa de doutorado no Manufacturing Group da University of Warwick na cidade de Coventry, sob a orientação do prof. Dr. James Wallbank, mesmo pesquisador que veio mais tarde orientar também o prof. Marcio Bacci da Silva, com doutorado concluído em outubro de 1998. Assim que reassumi o posto de professor na Universidade Federal de Uberlândia, responsável pela disciplina de Usinagem na graduação em Engenharia Mecânica e uma outra similar na pós-graduação, senti muita dificuldade de continuar adotando o clássico livro “Fundamentos da Usinagem dos Metais” do saudoso prof. Dr. Dino Ferraresi, que até então era o insubstituível livro texto da disciplina. Esta obra continua sendo uma das mais valiosas referencias sobre o assunto de usinagem convencional na língua Portuguesa. Entretanto, ele foi elaborado no final da década de 60 e editado no início da década seguinte pela Editora Edgard Blücher Ltda. Mais de 30 anos, portanto, já se passaram, e neste período, novas técnicas e métodos de investigação foram desenvolvidos e importantes contribuições científicas foram publicadas. Os principais conceitos apresentados na obra do Prof. Ferraresi não mudaram, mas muito se aprendeu neste período e estes conceitos foram enriquecidos e, possivelmente, tornaram-se mais compreensíveis. Além disto, tópicos como materiais de ferramentas e fluidos de corte tiveram e vem tendo avanços tecnológicos consideráveis nos últimos anos o que exige constante atualização. Aproveitando parte de uma grande revisão bibliográfica que havia feito na Inglaterra no final da década de 80 e tendo como base conceitual os trabalhos do Dr. Trent, orientador de doutorado do prof. Wallbank e autor do livro “Metal Cutting”, editado pela Butterworths – Londres, já na sua terceira edição de 1991, considerado por mim a “Bíblia” dos profissionais da usinagem, resolvi então produzir algumas notas de aulas que, juntamente com as contribuições do Prof. Marcio Bacci da Silva se tornaram mais tarde este modesto trabalho. Desde o original de 1993, várias correções foram feitas. Na realidade, a cada nova impressão, corrigimos erros de ortografia e tentamos melhorar a redação. Nesta edição, a grande mudança está no capítulo 10 - Materiais para Ferramentas de Corte. O texto foi totalmente substituído, apresentando uma abordagem mais completa sobre o assunto, que na opinião dos autores, é a parte que mais se desenvolve com o avanço tecnológico. Devo citar que experiências práticas obtidas com profissionais da área substituiram muitas horas de estudo e consulta, que contribuíram sobremaneira pela fidelidade de informações apresentadas. Entre eles, destaca-se o dinamismo e a perspicácia dos Engos^ Antônio Maria de Souza Júnior da Fiat Automóveis S/A; Achille Sotírios de Liambos Júnior da Shell do Brasil S/A e Francisco Carlos Marcondes e João Carocela, da Sandvik do Brasil S/A, Prof. Marcus Antonio Viana Duarte (UFU), Prof. Gilmar Guimarães (UFU), Prof. Alexandre Mendes Abrão (UFMG) e Prof. Anselmo Eduardo Diniz (Unicamp). Agradeço muito a contribuição do técnico do LEPU – Laboratório de Ensino e Pesquisa em Usinagem da Universidade Federal de Uberlândia, Reginaldo Ferreira de Souza, responsável pela elaboração prática de todas pesquisas ali desenvolvidas que contribuíram para o enriquecimento de formação de idéias. Trabalho importante, também, tiveram a Srta. Maria das Graças Daud, na primeira edição deste texto e os técnicos desenhistas Márcio Mellazo e Júlio C.R. Ferreira na reprodução em AutoCAD de grande parte das figuras apresentadas. Finalmente, mas nunca menos importante foram as contribuições dos meus alunos e ex- alunos de graduação e pós-graduação. Todos, sem restrições, têm uma parcela de responsabilidade por este trabalho. Não poderia deixar, entretanto, de citar alguns nomes, pois eles foram responsáveis diretos por parcelas de diferentes conteúdos e informações aqui contidas. São eles Wisley Falco Sales, Marcelo Ferreira Motta, Jalon de Morais Vieira, Anderson Clayton Alves de Melo, Estevam Marcos de Souza, Júlio Romero Santos Fernandes, Eurípedes Barsanulpho Luz Júnior e Marcelo Fonseca Barbosa. Este último ainda foi responsável pelo árduo trabalho de editoração e diagramação desta apostila, tarefa executada com perfeição. Prof. Álisson Rocha Machado 30.03.
“Usinagem” é um processo de fabricação. Mas o que é fabricação e qual a sua importância? A maioria dos livros especializados da área define: Fabricar é transformar matérias primas em produtos acabados, por vários processos, seguindo planos bem organizados em todos os aspectos. A importância da fabricação pode ser melhor entendida ao observarmos que todos os objetos culturais, ao nosso redor, têm formas e dimensões diferentes, com raríssimas exceções. Além disso, todo objeto é feito de um ou mais materiais e é transformado em produto acabado por uma larga variedade de processos. Portanto, não é nenhuma surpresa que nos países industrializados a fabricação compreende um terço do produto interno bruto [1] (valor de todos os produtos e serviços produzidos). A fabricação é utilizada desde o início da civilização, com a produção de vários artigos de madeira, pedra, cerâmica, barro e metal. Houve muito desenvolvimento com o passar dos anos, e nos dias atuais uma grande quantidade de materiais e processos estão disponíveis, para fabricar produtos que variam desde um simples componente, como uma esfera de aço, até produtos altamente sofisticados, como computadores, automóveis e aeronaves supersônicas. Para se ter uma idéia do número de fatores que devem ser considerados num processo de fabricação Kalpakjian [1] usou o exemplo da produção de um simples artigo: o clipe. Primeiro ele deve ser projetado para atender o requisito funcional que é segurar folhas de papéis juntas. Para tanto, ele deve exercer uma força suficiente para evitar o deslizamento de uma folha sobre a outra. Eles são, geralmente, feitos de arame de aço, embora hoje se encontra no mercado clipe de plástico. O comprimento do arame requerido para sua fabricação é cortado e então dobrado várias vezes, para dar a forma final própria. Por sua vez, o arame é feito por um processo de trefilação a frio. Neste processo a seção transversal de uma haste longa é reduzida, ao passar por uma matriz de fieira, que também confere algumas propriedades mecânicas ao material, como resistência e dureza. A haste por sua vez, é obtida por processos como a trefilação e a extrusão de um lingote. Para evitar delongas, nenhuma informação quanto ao processo de obtenção deste lingote será abordada. A fabricação de um simples clipe envolve projeto, seleção de um material adequado e seleção de um método de fabricação para atender os requisitos de serviço do artigo. As seleções são feitas não somente com base em requisitos técnicos, mas também com base nas considerações econômicas, para minimizar os custos para que o produto possa ser competitivo no mercado. O projetista de produtos ou engenheiro projetista, especifica formas e dimensões do produto, sua aparência, e o material a ser usado. Primeiro são feitos os protótipos do produto. Neste estágio, é possível fazer modificações, tanto no projeto original como no material selecionado, se análises técnicas e/ou econômicas assim indicarem. Um método de fabricação apropriado é então escolhido pelo engenheiro de fabricação. A Figura 1.1 mostra um diagrama do procedimento correto para se chegar à etapa de fabricação.
Desenho Avaliação Final Revisão do Projeto ão Avaliação Teste do Protótipo Modelos Físicos e Analíticos Análise do Projeto Projeto do conceito Conceito Original Necessidade do Produto Especificação do Material; Seleção do Processo de Fabricação e de Equipamentos; Projeto e Construção de Ferramentas e Matrizes Figura 1.1. Diagrama mostrando o procedimento requerido para o projeto de um produto, que são etapas que antecedem a fabricação. A seleção do material requer conhecimentos dos requisitos funcionais e de serviço do produto, e dos materiais disponíveis para preencher estes requisitos. O tratamento deste assunto requer um passeio nas propriedades dos materiais e envolve também considerações de custo, aparência, acabamento superficial, resistência à corrosão etc., que foge do escopo prático deste curso, e portanto não serão aqui abordados. Uma vasta bibliografia [1 - 4] porém, está disponível sobre o assunto. Nos processos de fabricação, geralmente, haverá mais de um método que poderá ser empregado para fabricar um componente. A seleção de um método particular sobre outros vai depender de um grande número de fatores. Além disto, o produto final, geralmente, é o resultado de muitos processos diferentes. Na seleção do processo, os seguintes fatores devem ser considerados [1]:
Processos de Fabricação
ENTENDIMENTO do processo, e entendimento é o passo mais próximo da capacidade de prever”. A seguir, um exaustivo número de definições se faz necessário, nos capítulos: “Grandezas Físicas no Processo de Corte” e “Nomenclatura e Geometria das Ferramentas de Corte”, para compreensão dos capítulos subsequentes, que são: “Formação do Cavaco”, “A Interface Cavaco-Ferramenta”, “Força, Pressão Específica e Potência de Usinagem”, “Tensões e Deformações em Usinagem”, “Temperaturas de Corte”, “Materiais para Ferramentas de Corte”, “Desgaste e Mecanismos de Desgaste das Ferramentas de Corte”, “Vida da Ferramenta e Fatores que a Influenciam”, “Fluidos de Corte”, “Integridade Superficial”, “Ensaios de Usinabilidade”, “Condições Econômicas de Corte” e “Considerações ao Material da Peça”. Sem dúvidas a abordagem de todos esses tópicos faz deste curso um dos mais completos sobre a usinagem dos materiais metálicos. As maneiras que serão tratadas esses tópicos têm como objetivo oferecer informações suficientes para que o engenheiro ou o técnico de usinagem possa compreender de maneira simples, complicadas teorias sobre o processo de usinagem. O entendimento de tópicos importantes, como: O Mecanismo de Formação do Cavaco, Geração de Calor e Distribuição de Temperatura, Forças de Usinagem e Desgaste das Ferramentas de Corte, coloca o técnico de Usinagem estimulado e seguro nas tomadas de decisões para melhoria do processo produtivo. Pelo menos, este é o maior objetivo deste curso. REFERÊNCIAS BIBLIOGRÁFICAS
Deve-se distinguir as direções dos movimentos que causam diretamente a retirada de cavaco. Direção de Corte : direção instantânea do movimento de corte. Direção de Avanço : direção instantânea do movimento de avanço. Direção Efetiva : direção instantânea do movimento efetivo de corte. Definições análogas são válidas para os movimentos que não causam a retirada de cavaco diretamente. As Figuras 2.1, 2.2 e 2.3 ilustram essas direções para o torneamento, furação e fresamento, respectivamente. Figura 2.1. Direção dos movimentos de corte, de avanço e efetivo, no torneamento. Figura 2.2. Direção dos movimentos de corte, de avanço e efetivo, na furação.
Figura 2.3. Direção dos movimentos de corte, de avanço e efetivo, no fresamento discordante. 2.4. PERCURSOS DA FERRAMENTA NA PEÇA Percurso de Corte Lc : é o espaço percorrido pelo ponto de referência da aresta cortante sobre a peça, segundo a direção de corte. Percurso de Avanço Lf : é o espaço percorrido pelo ponto de referência da aresta cortante sobre a peça, segundo a direção de avanço. Nos casos em que haja movimento de avanço principal e avanço lateral, devem-se distinguir as componentes do percurso de avanço. Percurso Efetivo Le : é o espaço percorrido pelo ponto de referência da aresta cortante sobre a peça, segundo a direção efetiva do corte. A Figura 2.4 ilustra os percursos da ferramenta na peça. ae Figura 2.4. Percurso de corte Lc, percurso de avanço Lf e percurso efetivo Le para o fresamento discordante.
Ângulo da Direção Efetiva de Corte η : é o ângulo da direção efetiva de corte e a direção de corte. Figura 2.5. Plano de trabalho Pfe, ângulo da direção de avanço ϕ e ângulo da direção efetiva η no torneamento. Figura 2.6. Plano de trabalho Pfe, ângulo da direção de avanço ϕ e ângulo da direção efetiva η no fresamento concordante (ϕ > 90o). Considerando a Figura 2.5, pode-se desenvolver a seguinte expressão: tg v v v v v f f c c f η ϕ ϕ ϕ ϕ
sen
. cos sen cos /
Nota-se que, como na maioria dos casos vf <<< vc, o ângulo η é desprezível (nos processos de roscamento, η assume valores consideráveis pois o avanço é razoável). Superfícies em Usinagem : são as superfícies geradas na peça pela ferramenta. Devem-se distinguir a superfície em usinagem principal e a superfície em usinagem secundária , onde a primeira é gerada pela aresta principal de corte e a segunda pela aresta secundária de corte (Figura 2.7). Figura 2.7. Superfície principal e secundária de usinagem. 2.7. GRANDEZAS DE CORTE São as grandezas que devem ser ajustadas na máquina direta ou indiretamente. Avanço f : é o percurso de avanço em cada volta (mm/volta) ou em cada curso da ferramenta (mm/golpe). No caso de ferramentas que possuem mais de um dente, como no caso do fresamento, distingue-se o avanço por dente fz , (Figura 2.8). O avanço por dente é o percurso de avanço de cada dente, medido na direção do avanço da ferramenta, e corresponde à geração de duas superfícies em usinagem consecutivas. Vale a relação:
onde, z = número de dentes. O avanço por dente pode ainda ser decomposto no avanço de corte fc e avanço efetivo de corte fe, mostrados na Figura 2.8.
São grandezas derivadas das grandezas de corte, e são obtidas através de cálculos, Figura 2.10. Figura 2.10. Grandezas relativas ao cavaco, para arestas de corte retilíneas. Largura de Corte b : é a largura calculada da seção transversal de corte a ser retirada, medida na superfície em usinagem principal, segundo a direção normal à direção de corte. Em ferramentas com aresta cortante retilínea e sem curvatura na ponta, tem-se: b ap r
sen χ
χr é o ângulo de posição da aresta principal de corte. Largura Efetiva de Corte be : é a largura calculada da seção transversal efetiva de corte a ser retirada, medida na superfície em usinagem principal, segundo a direção normal à direção efetiva de corte. Pela Figura 2.10, têm-se:
b (^) e = b. ( −sen .cos (^) r) / 1 2 2 1 2 η χ (2.9) Espessura de Corte h : é a espessura calculada da seção transversal de corte a ser retirada, medida normalmente à superfície em usinagem principal e segundo a direção perpendicular à direção de corte. Em ferramentas com aresta de corte retilíneas:
Espessura Efetiva de Corte he : é a espessura calculada da seção transversal efetiva de corte a ser retirada, medida normalmente à superfície em usinagem principal e segundo a direção perpendicular à direção efetiva de corte. ( ) 2 1 /^2 r e 1 sen (^2) χ.tg η h h
Seção Transversal Efetiva de Corte A : é a área calculada da seção transversal de um cavaco a ser retirado, medida no plano normal à direção de corte. Seção Transversal de Corte Ae : é a área calculada da seção transversal efetiva de um cavaco a ser retirado, medida no plano normal à direção efetiva de corte. Na maioria dos casos: A = a (^) p. fc (2.12) A (^) e = a (^) p. fe (2.13) Em ferramentas sem arredondamento na ponta da aresta cortante: A = b. h (2.14)
Para maiores informações deve ser consultada a norma NBR 6162. REFERÊNCIA BIBLIOGRÁFICA
Figura 3.1. Cunha de Corte da Ferramenta. Figura 3.2. Arestas de corte e superfícies da cunha de corte de uma ferramenta de torno. Figura 3.3. Arestas de corte e superfícies da cunha de corte de uma fresa frontal.
Figura 3.4. Arestas de corte e superfícies da cunha de corte de uma broca helicoidal. 3.3. SISTEMAS DE REFERÊNCIA UTILIZADOS NA DETERMINAÇÃO DOS ÂNGULOS DA CUNHA CORTANTE. Para a determinação dos ângulos na cunha de corte é necessário empregar um sistema de referência. Normalmente são empregados dois sistemas de referência, para um estudo racional dos ângulos da ferramenta e dos ângulos efetivos ou de trabalho:
**- SISTEMA DE REFERÊNCIA DA FERRAMENTA