
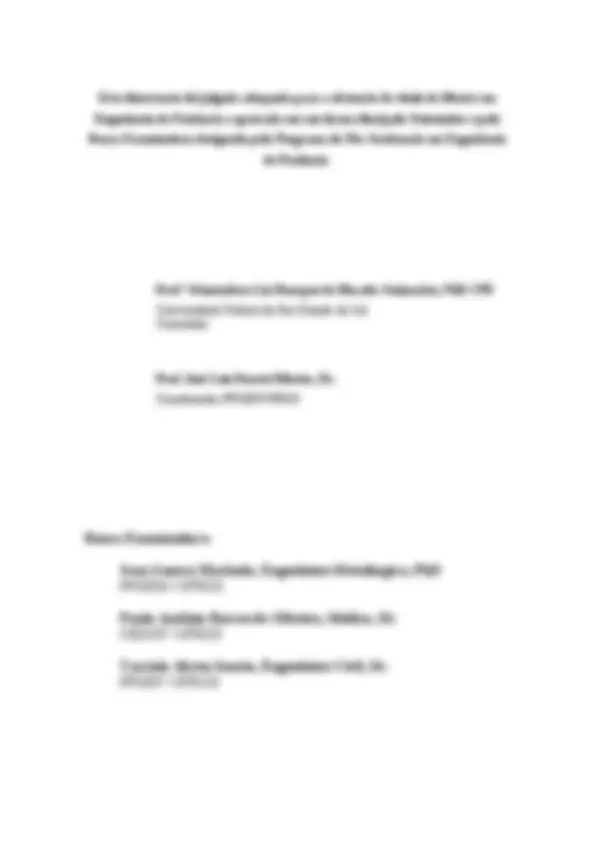
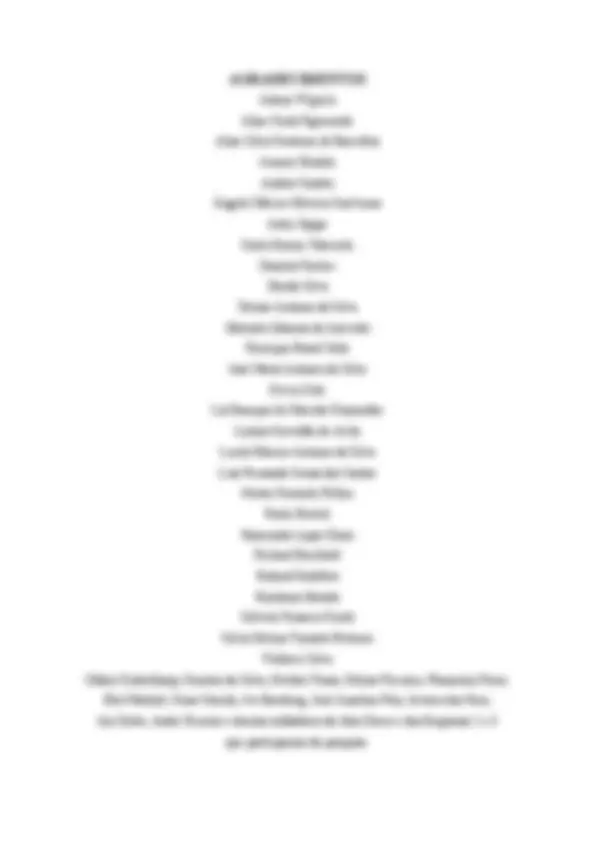
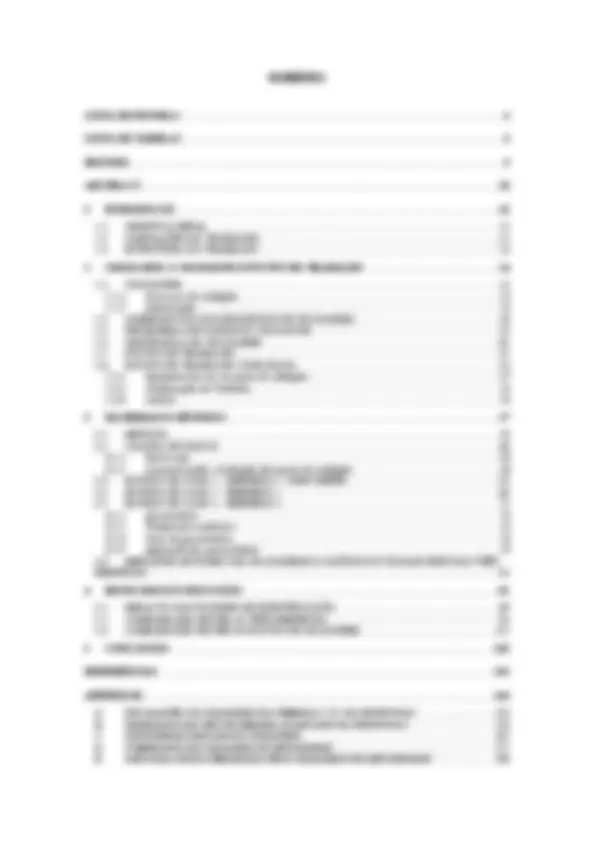
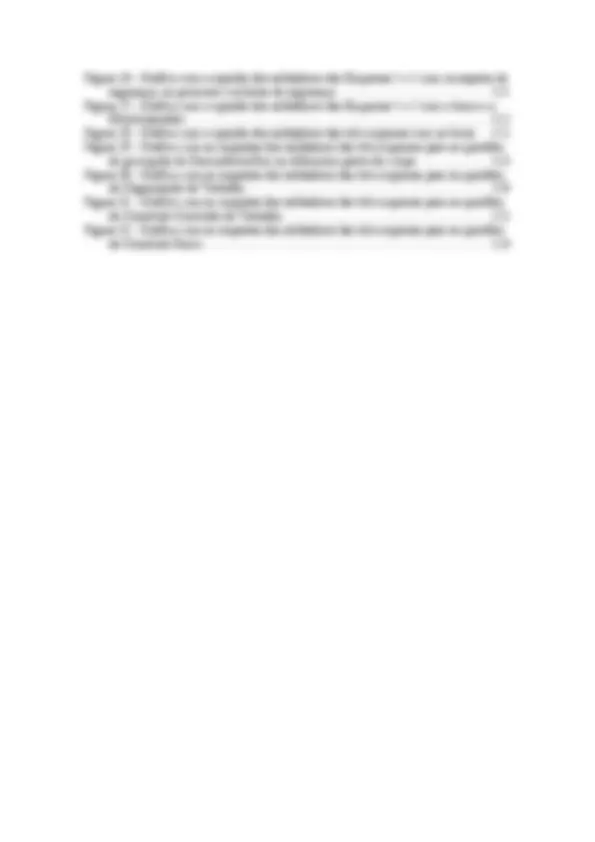
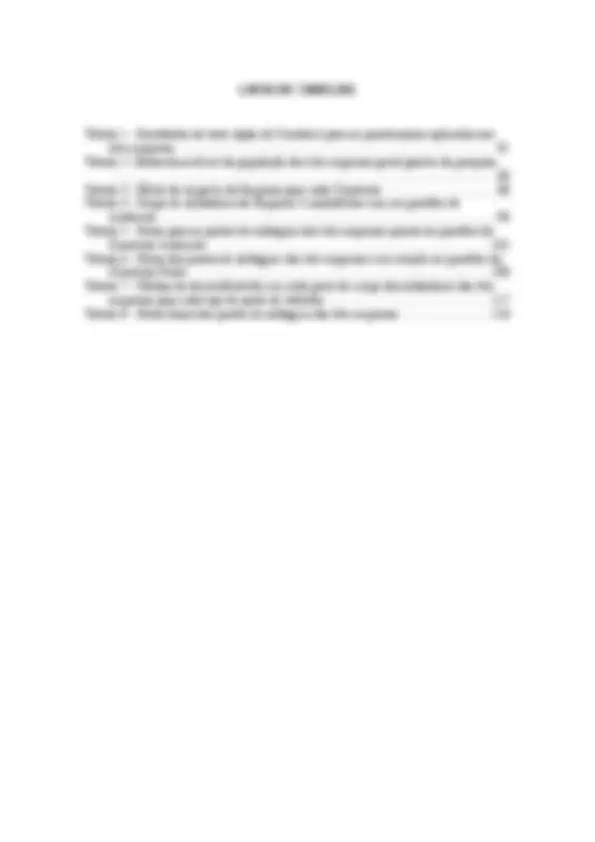
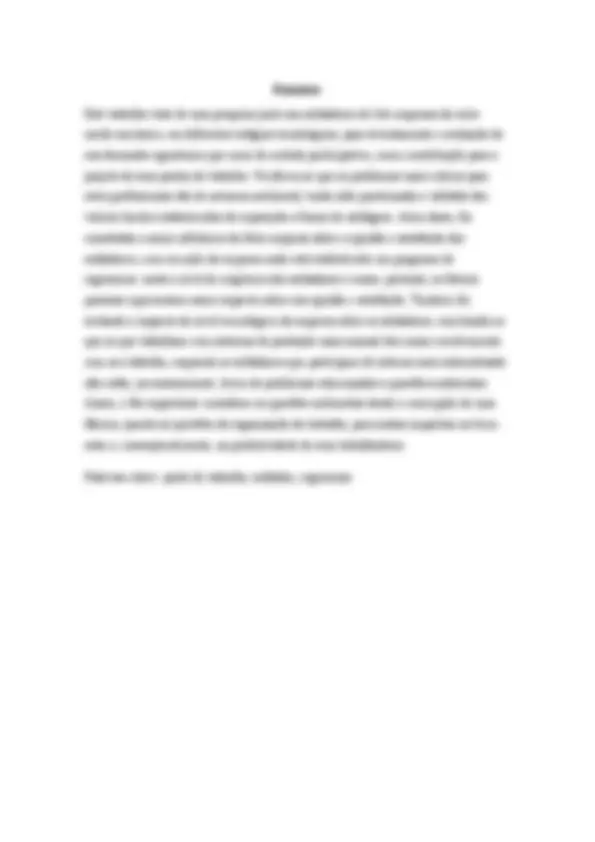
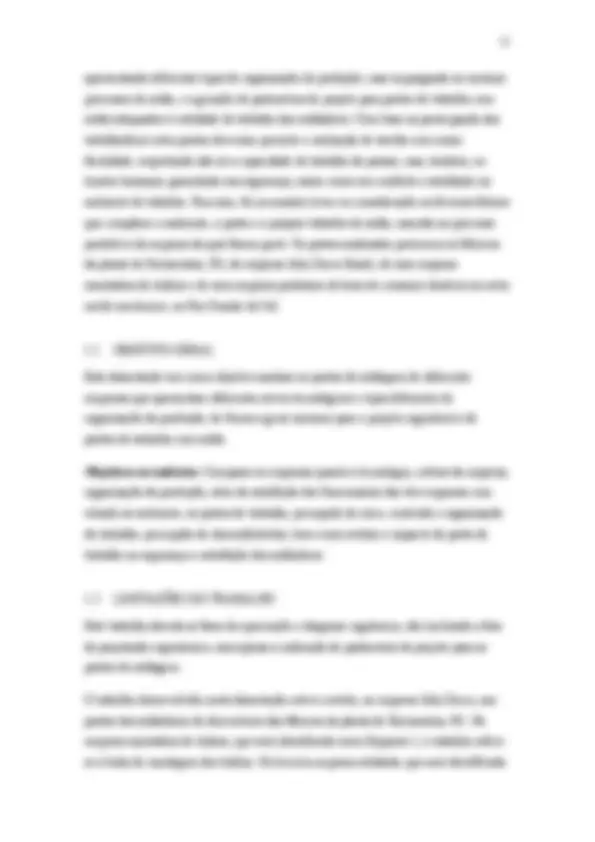
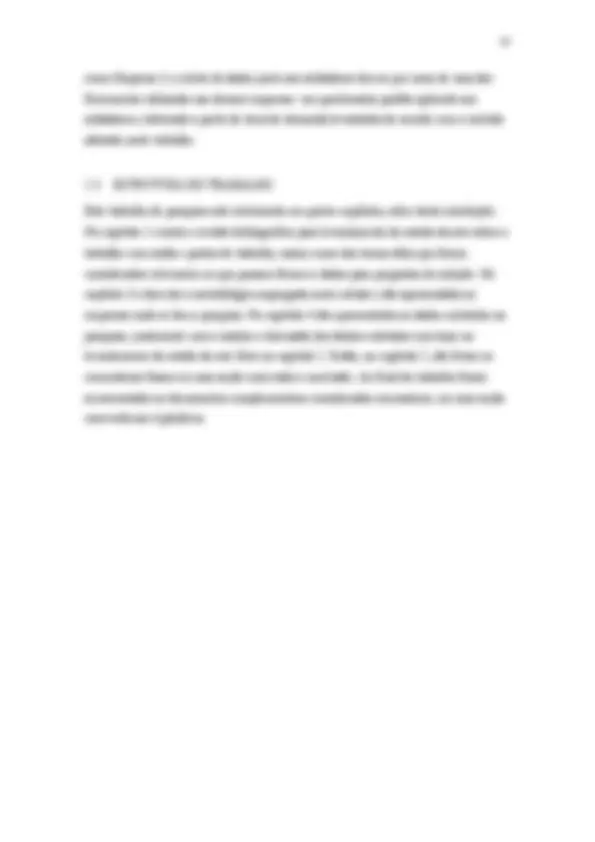
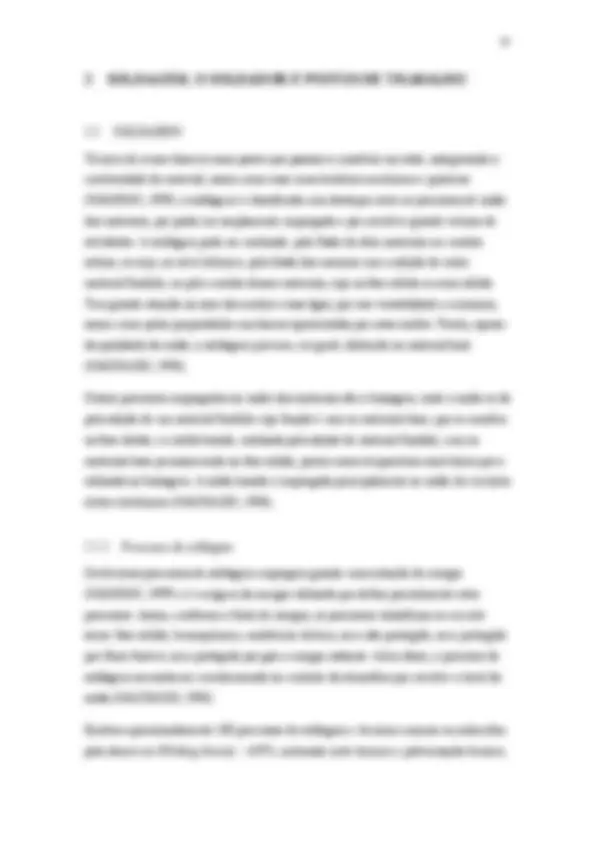
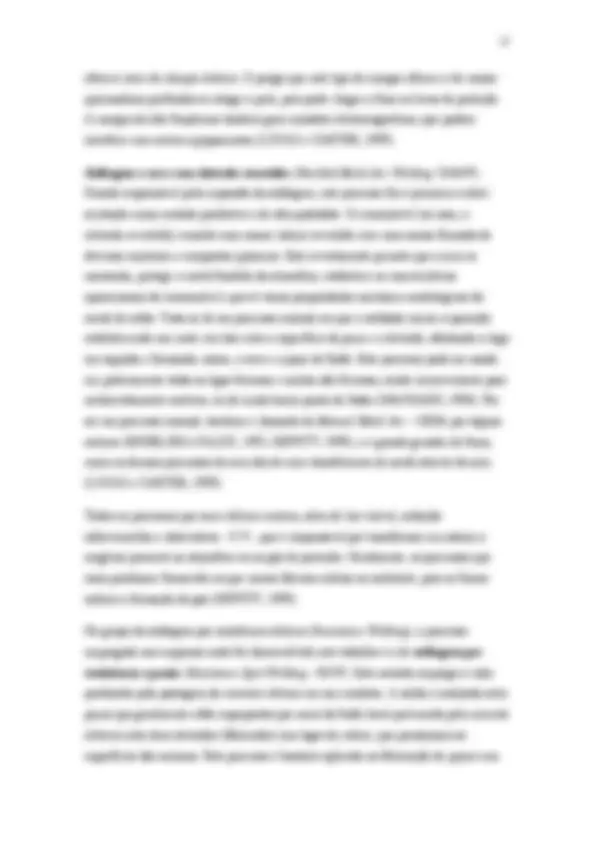
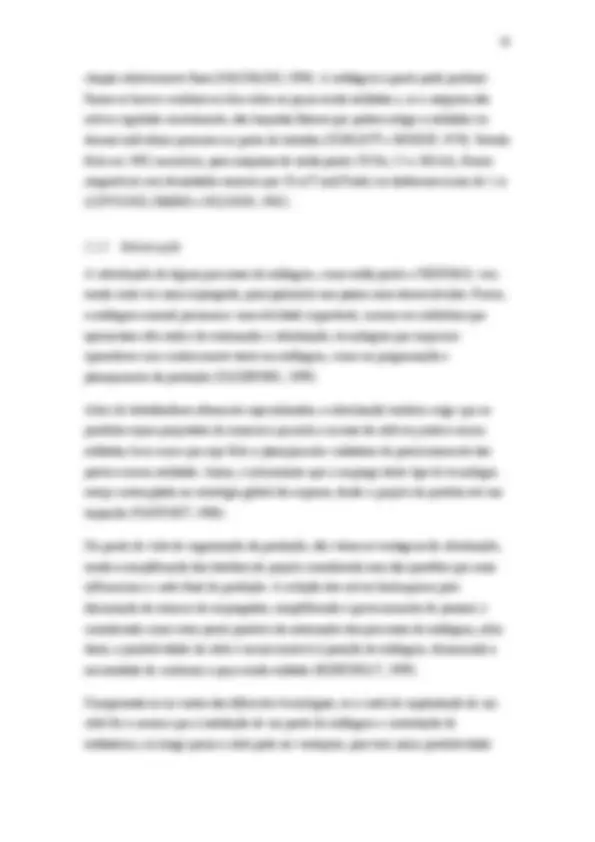
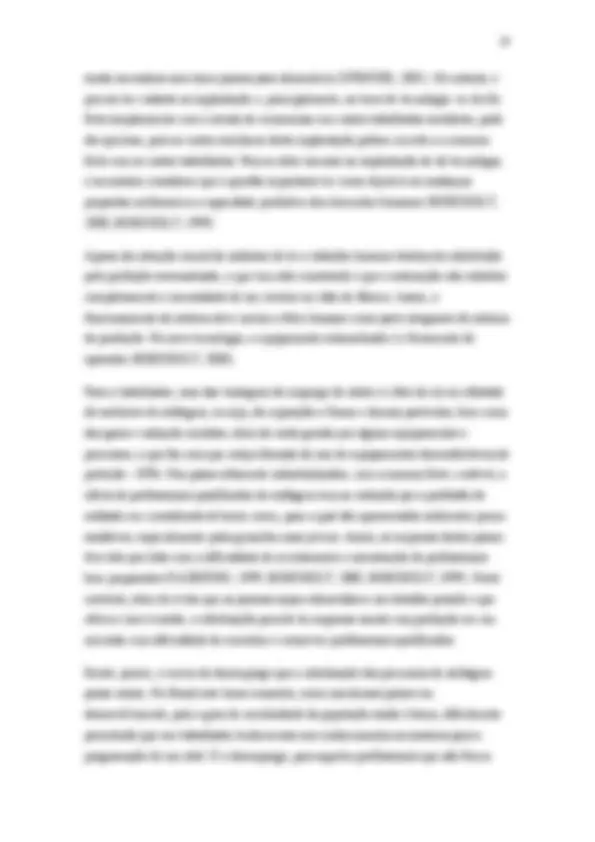

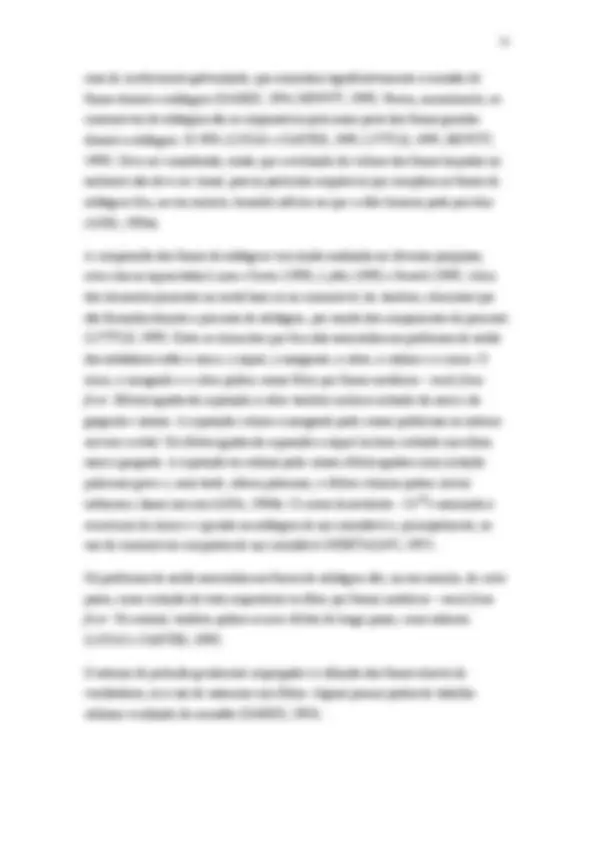
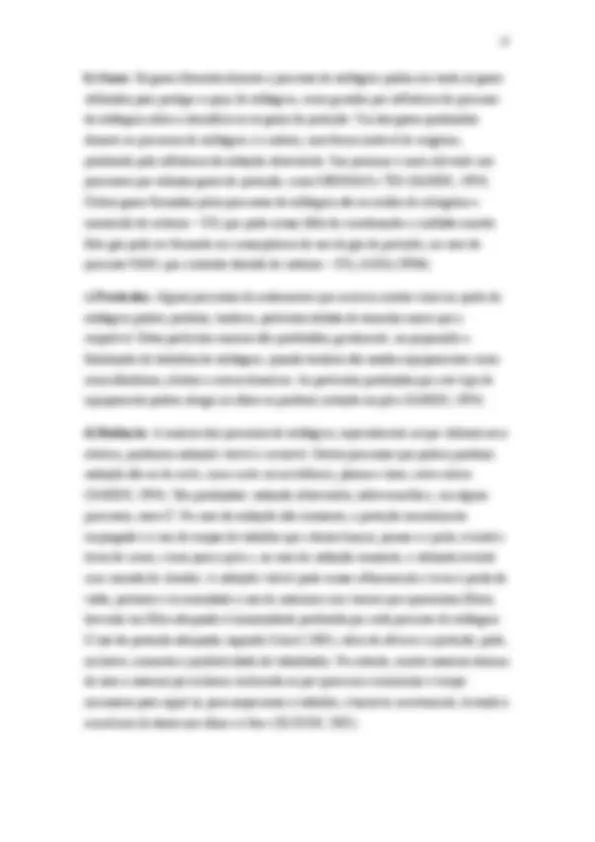
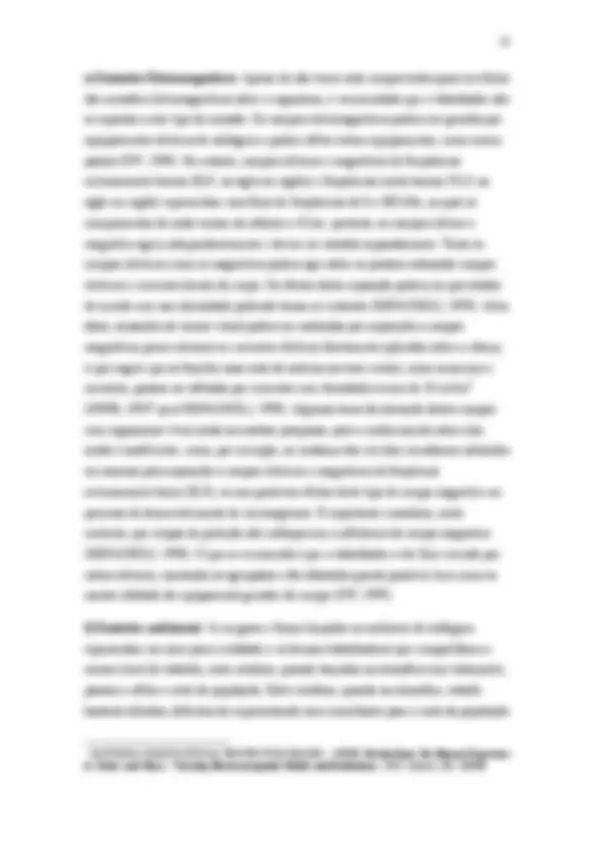
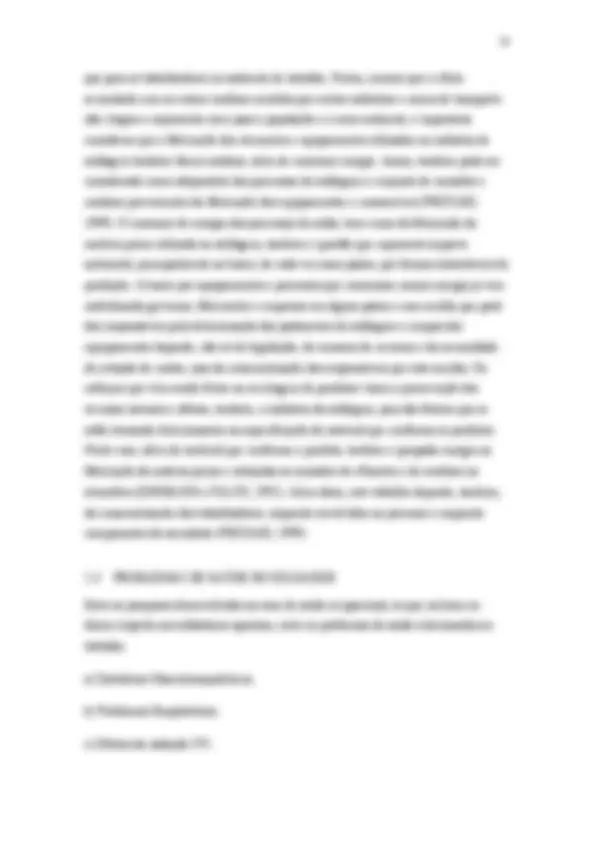

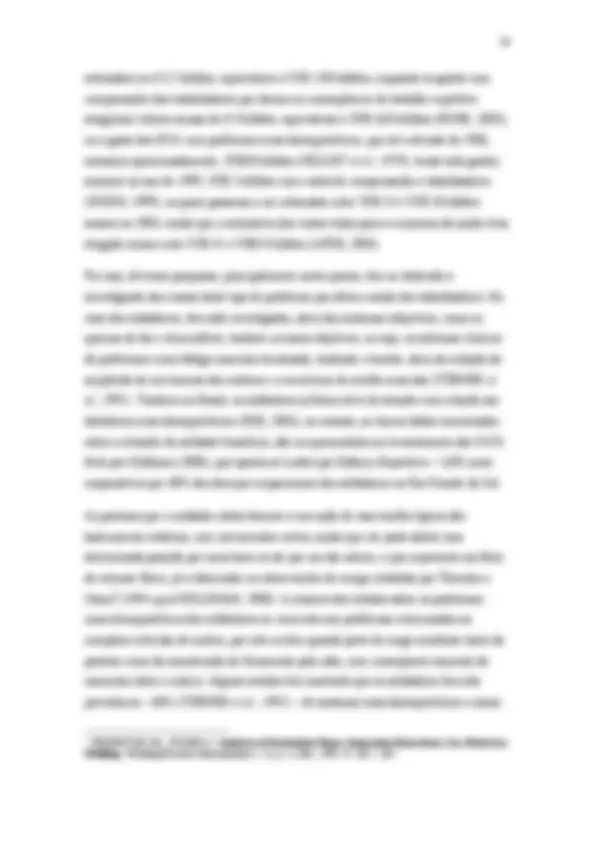
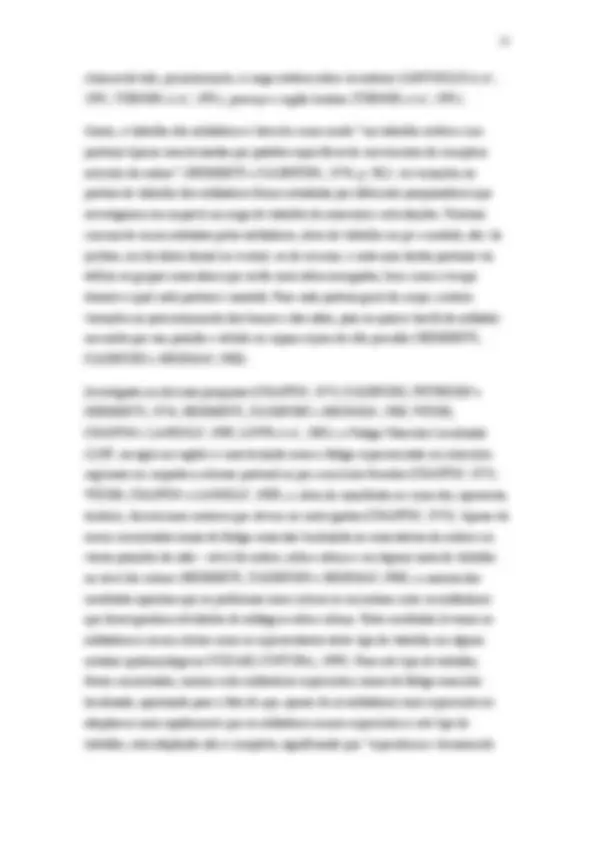
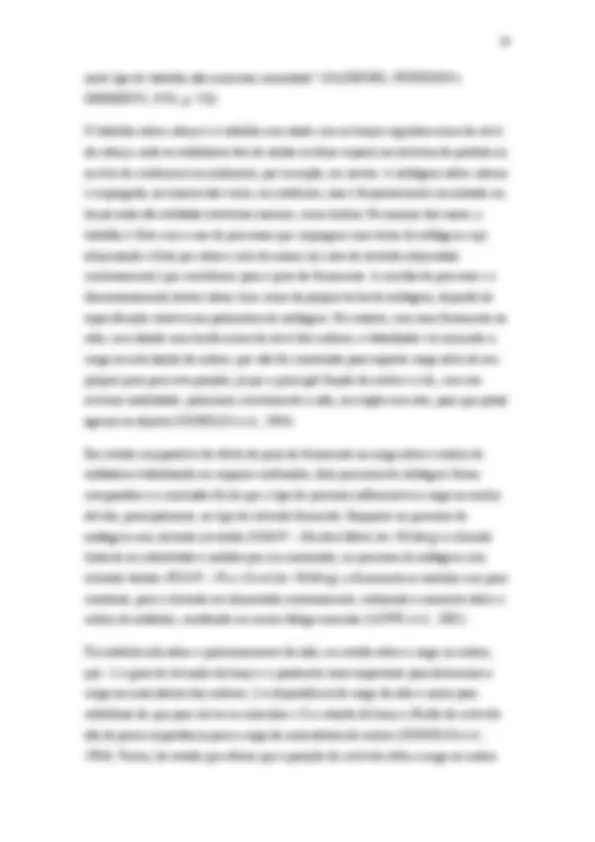
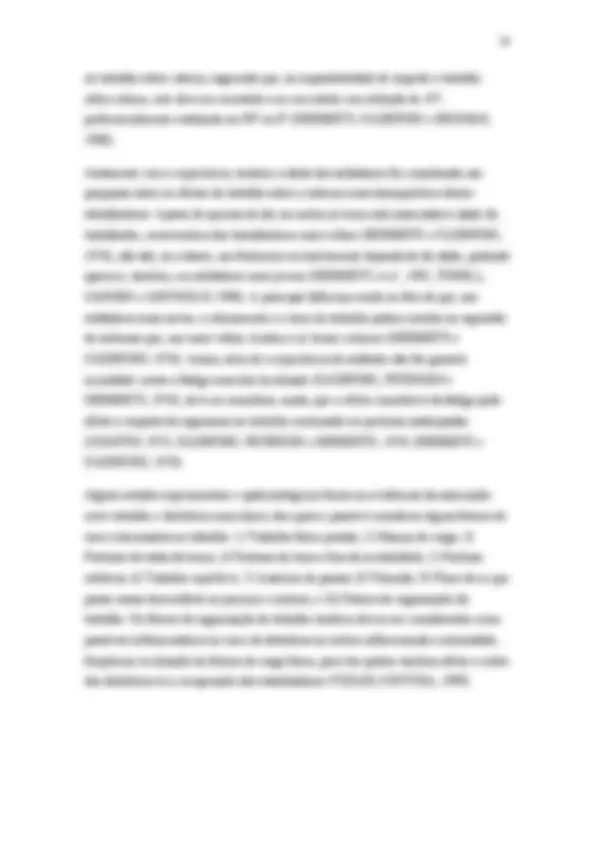
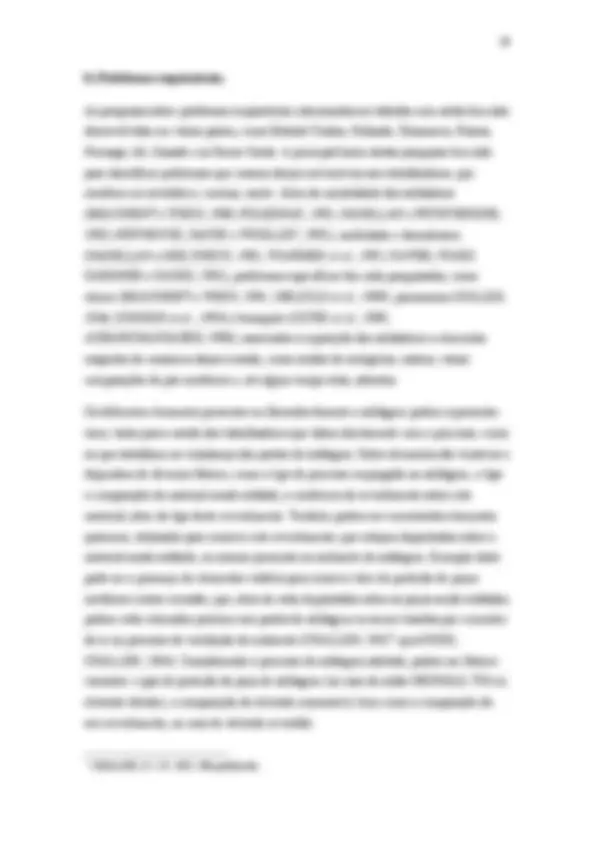
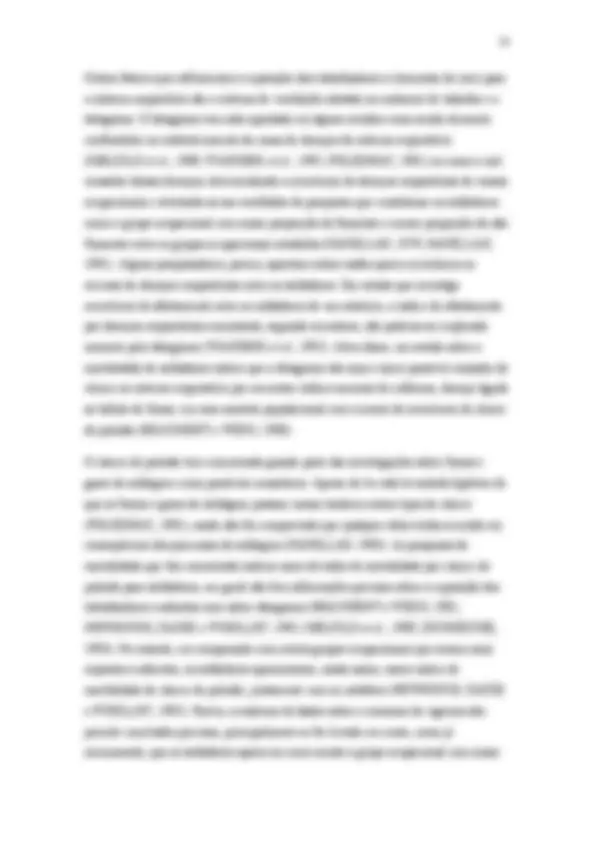
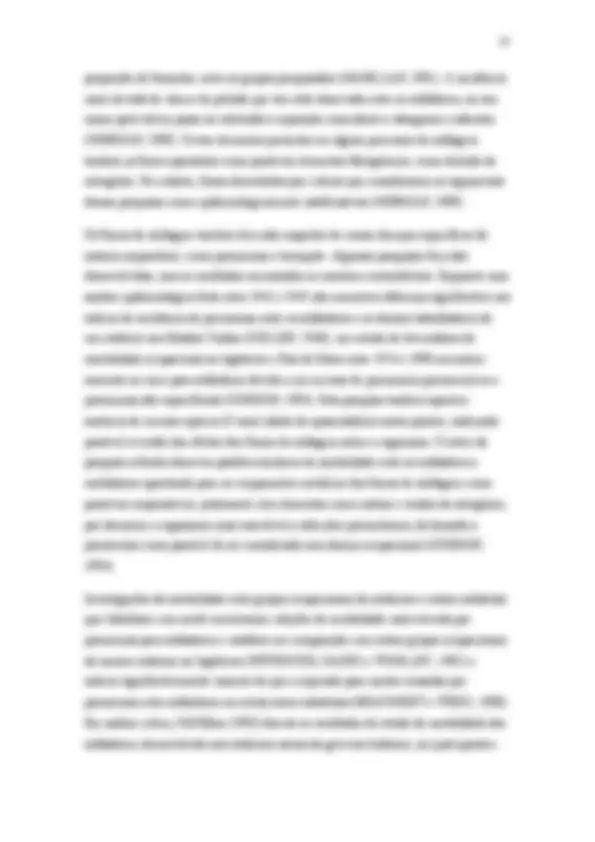
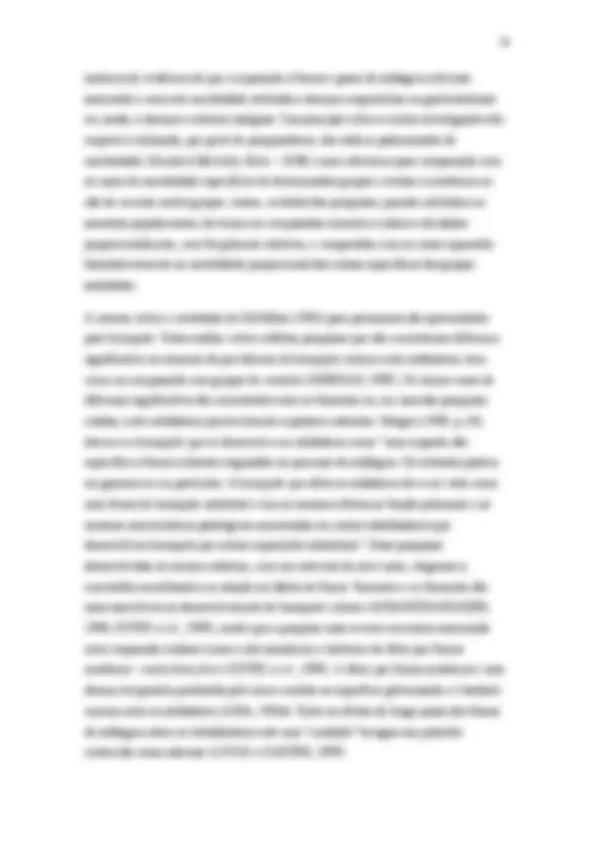
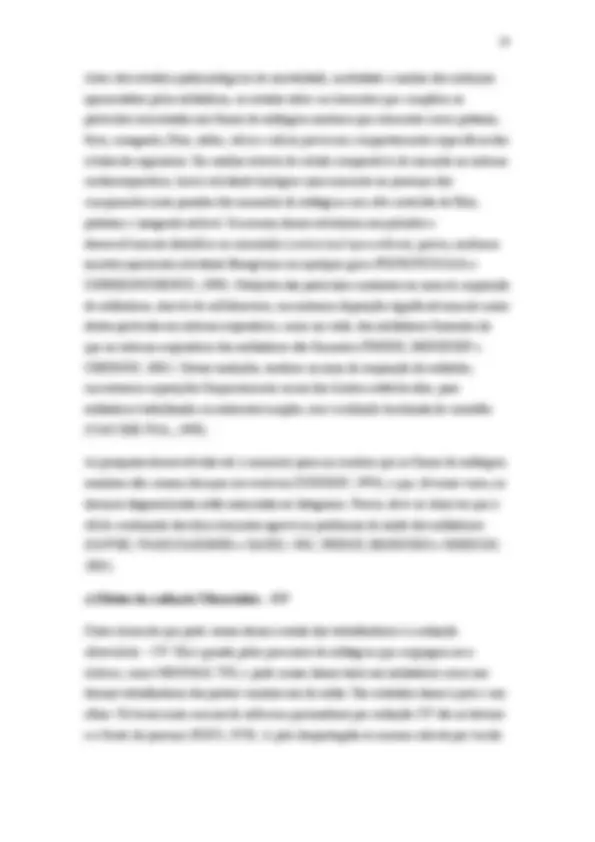
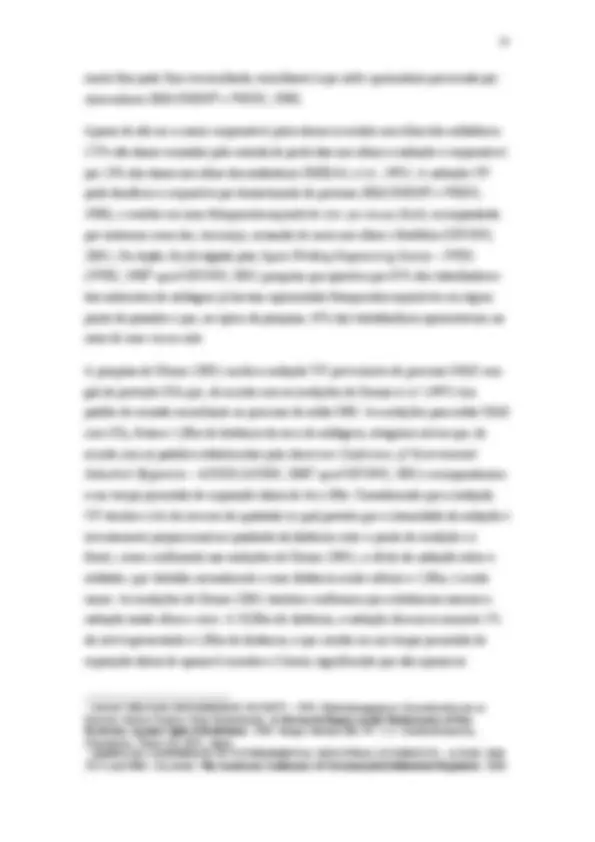
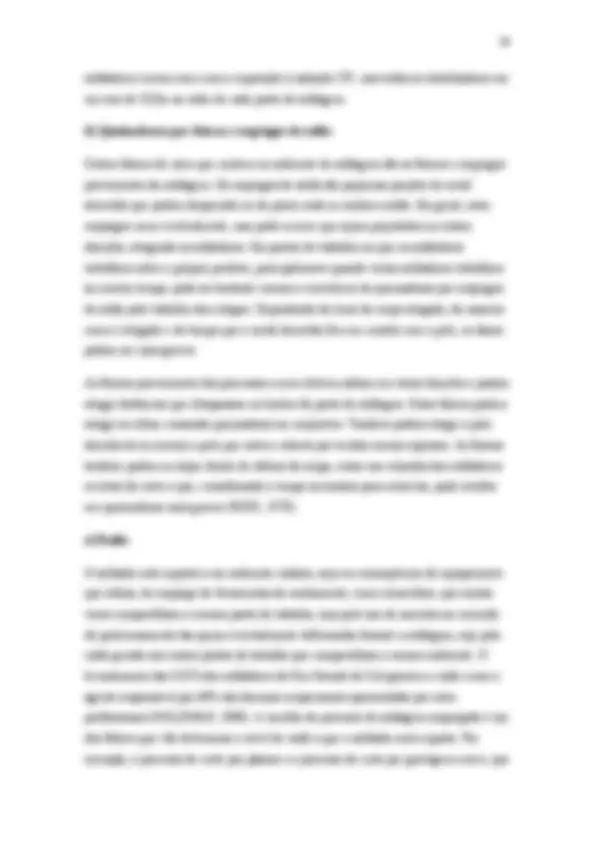

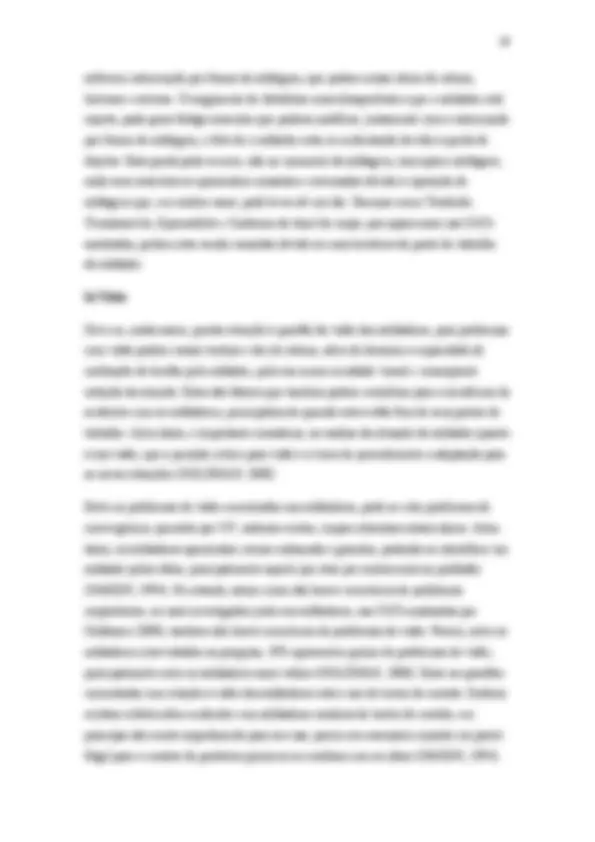
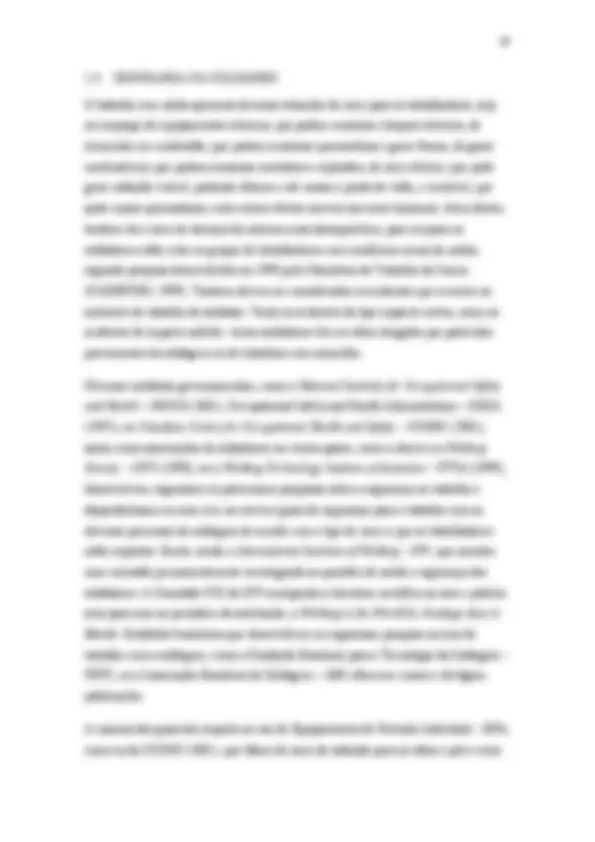
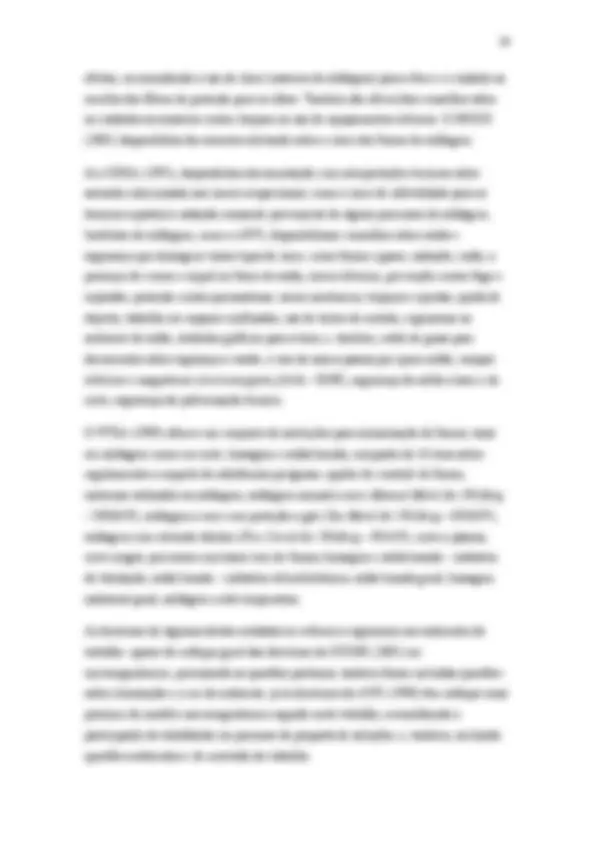
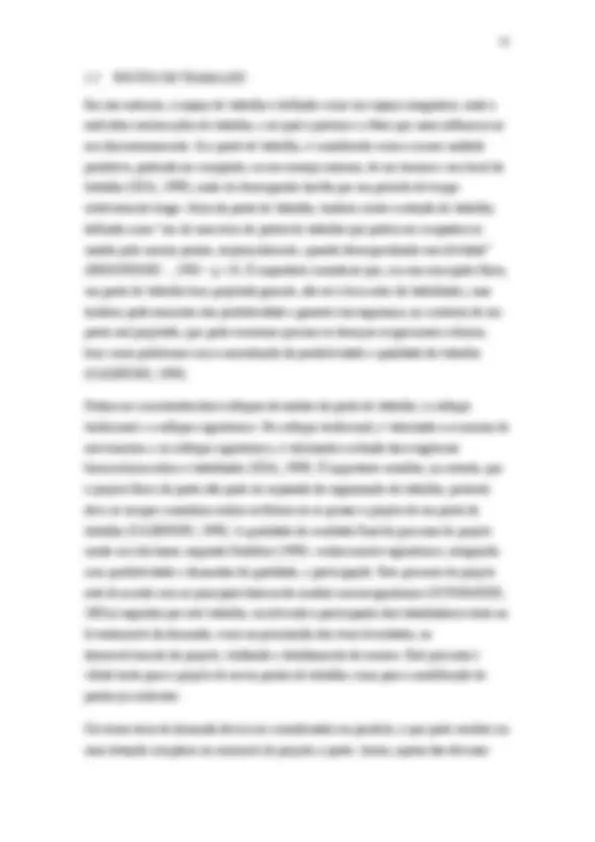
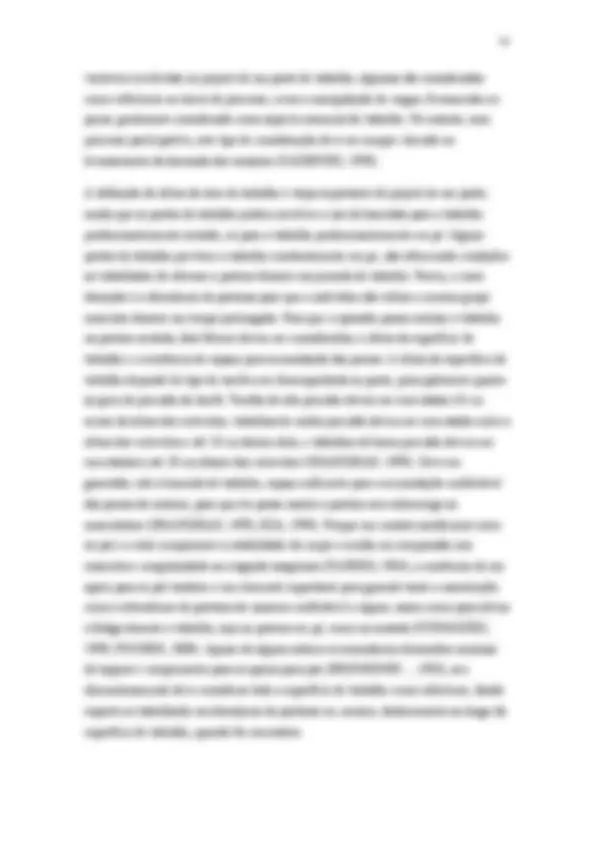
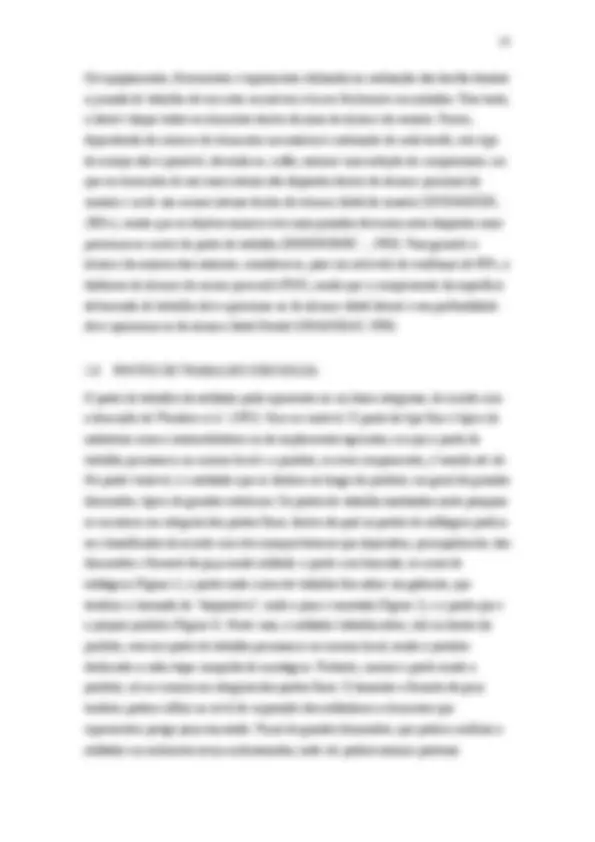
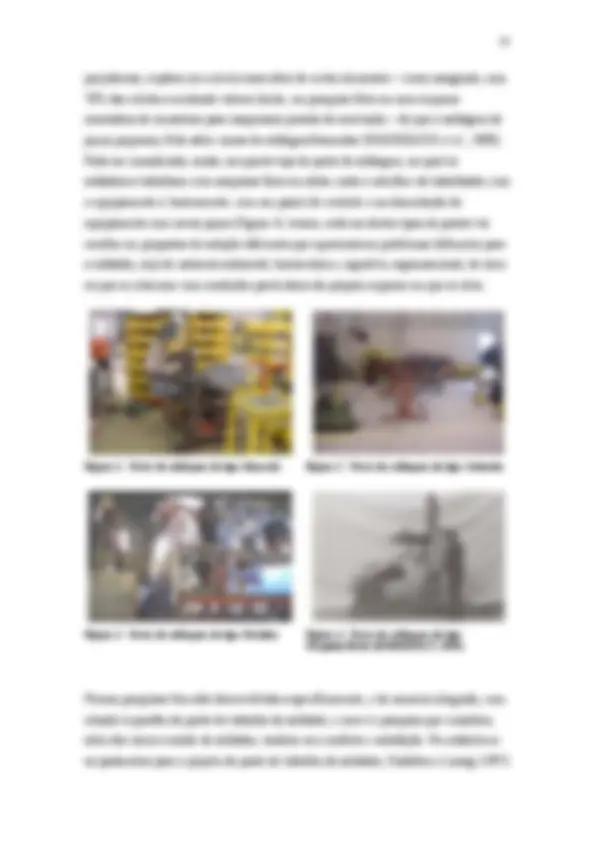
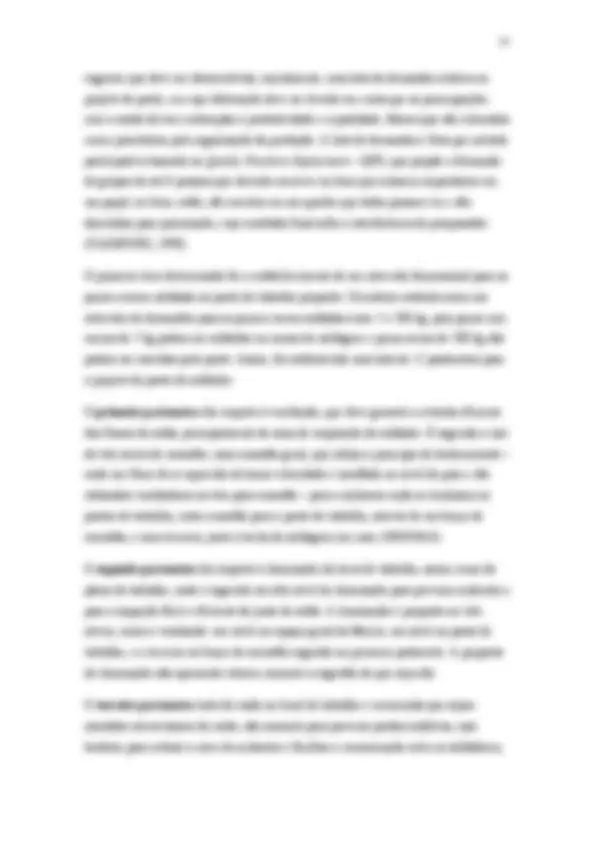
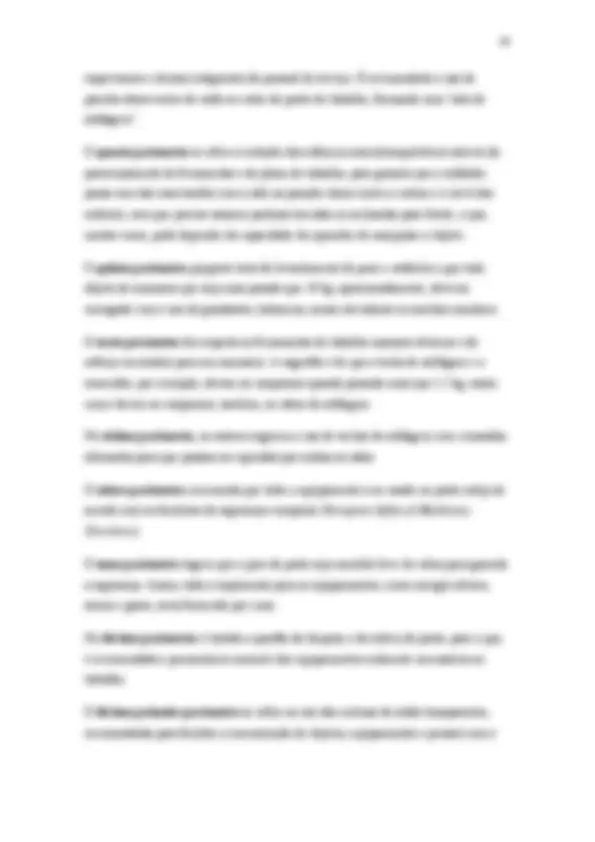
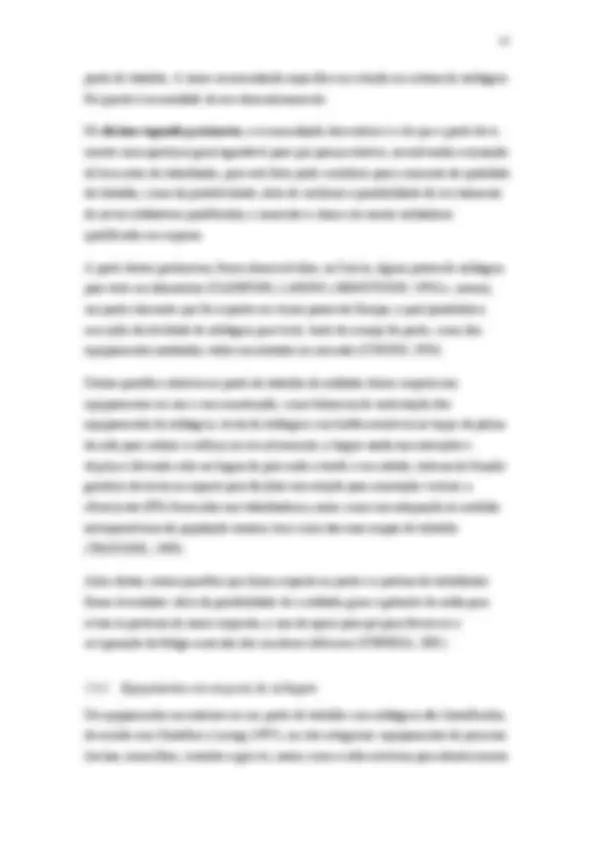
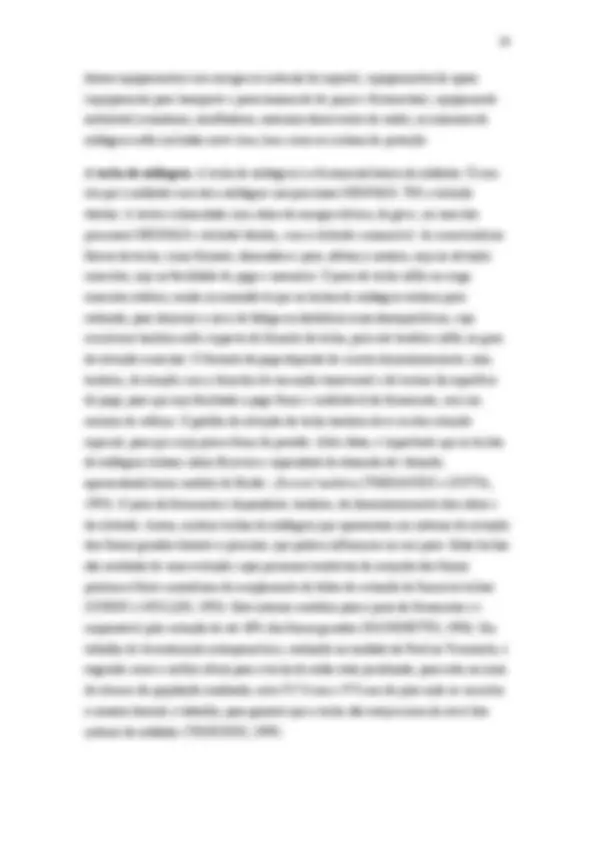
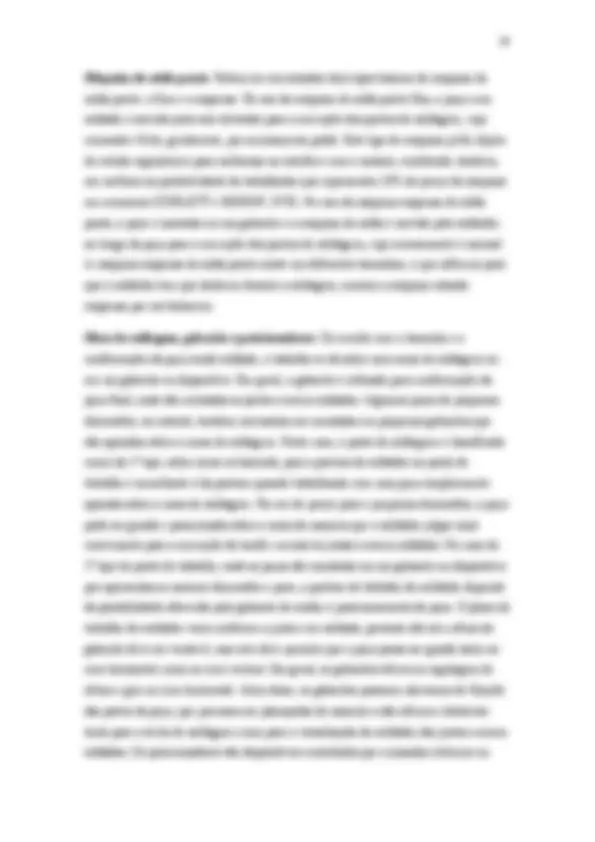
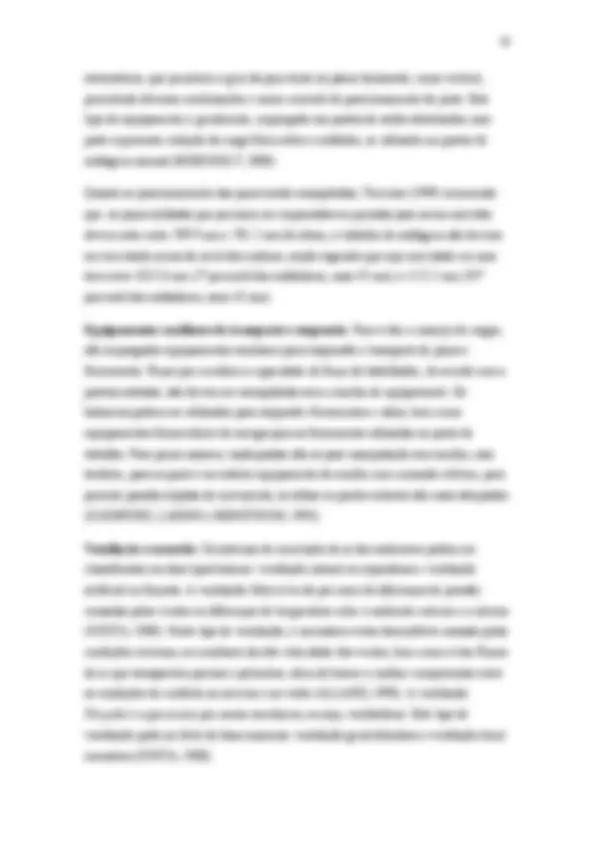
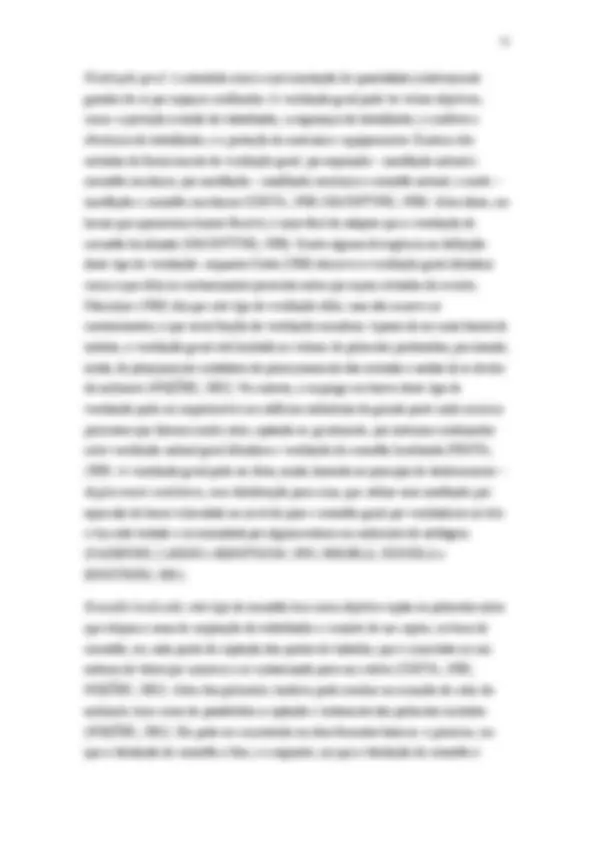
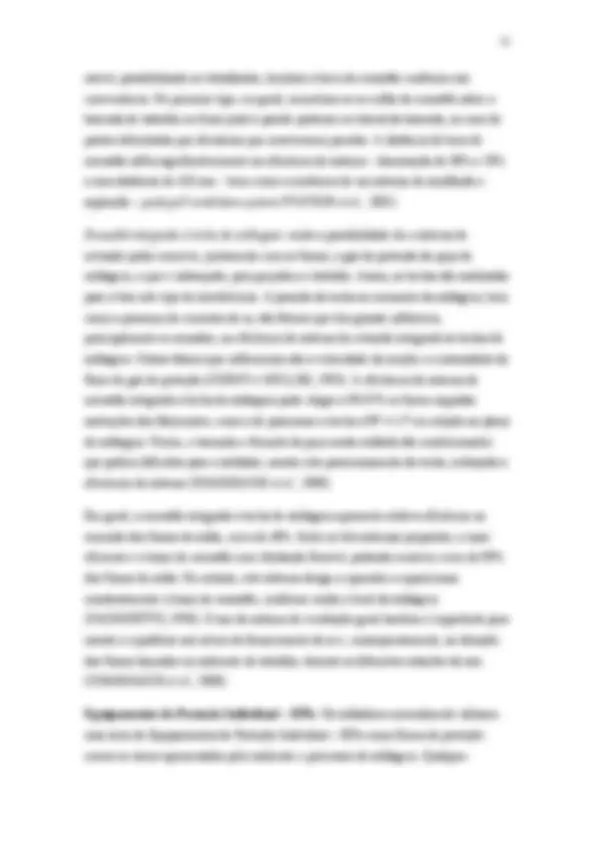
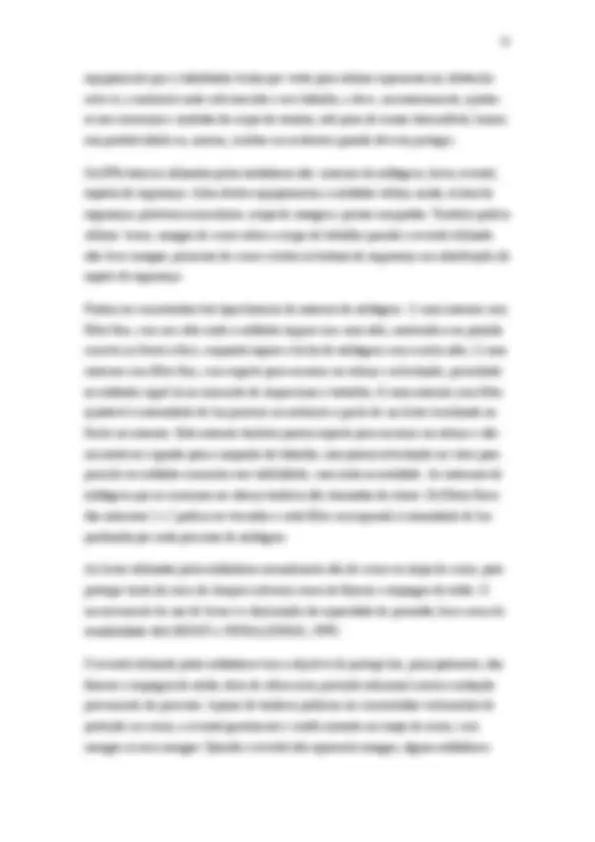
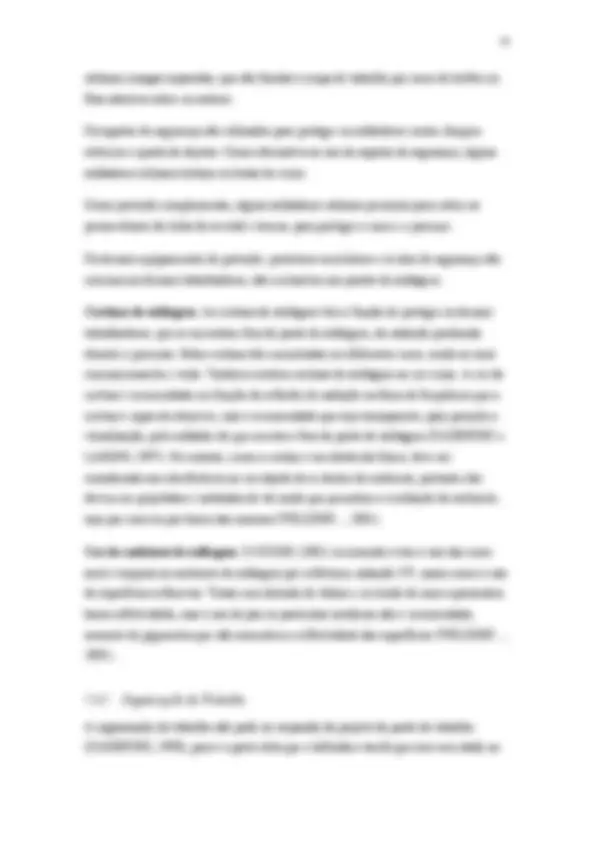
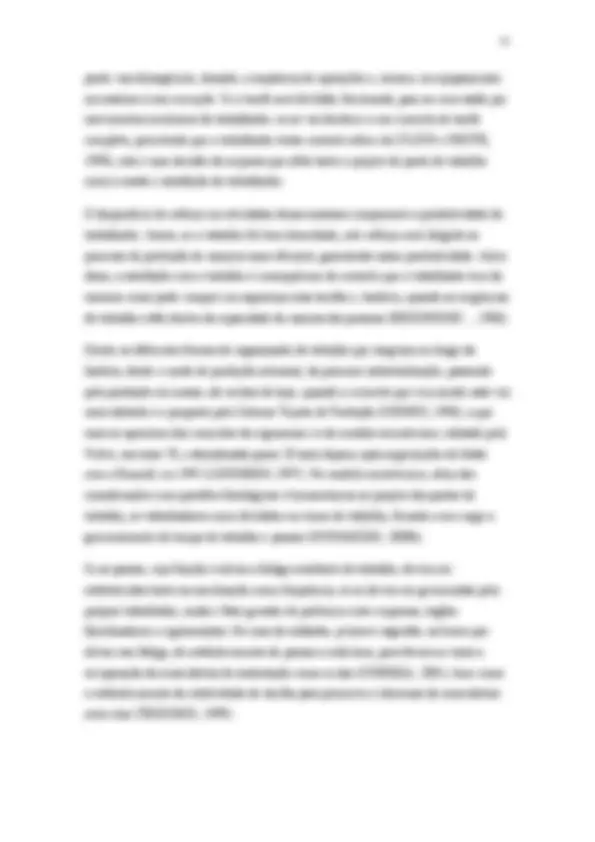
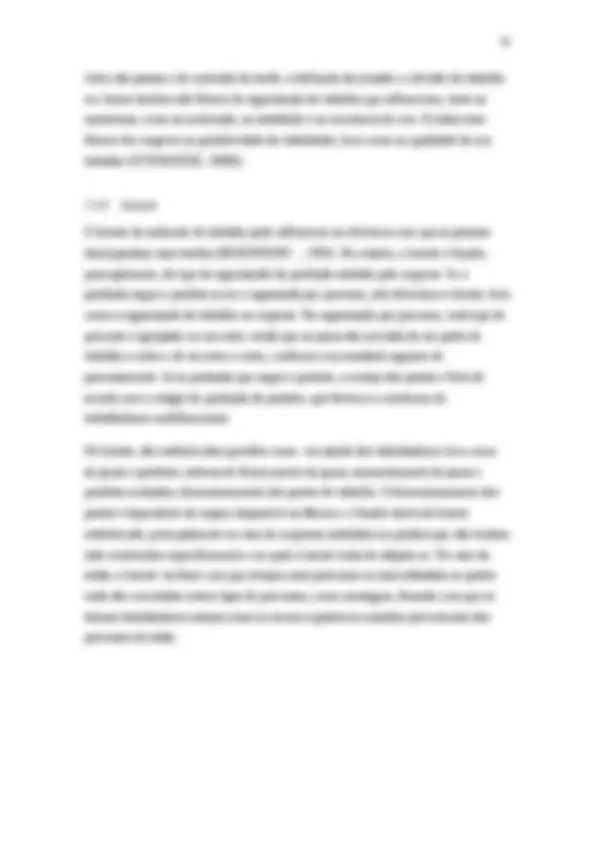
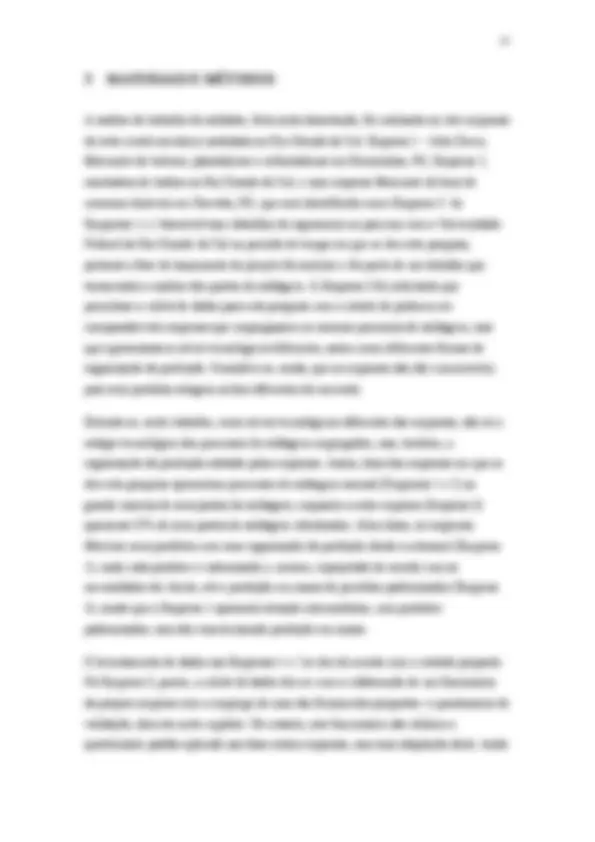
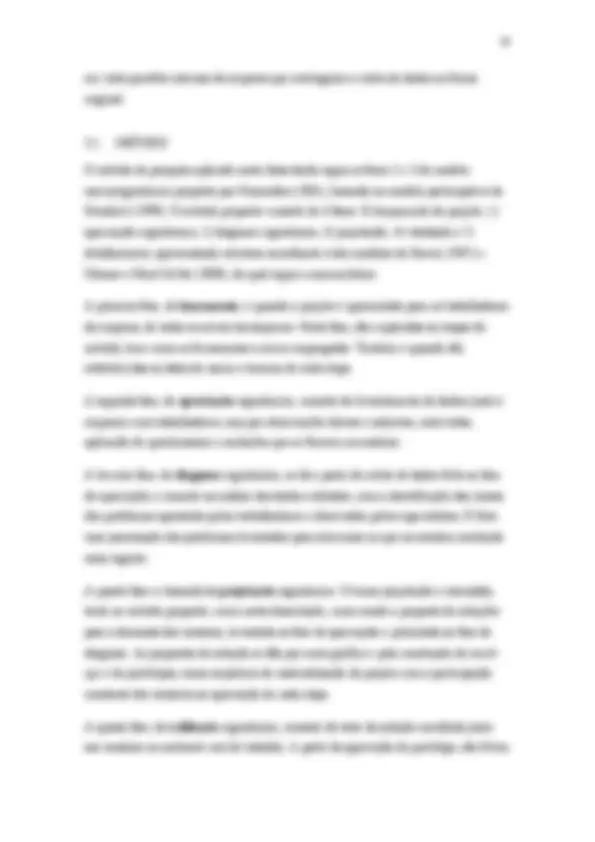
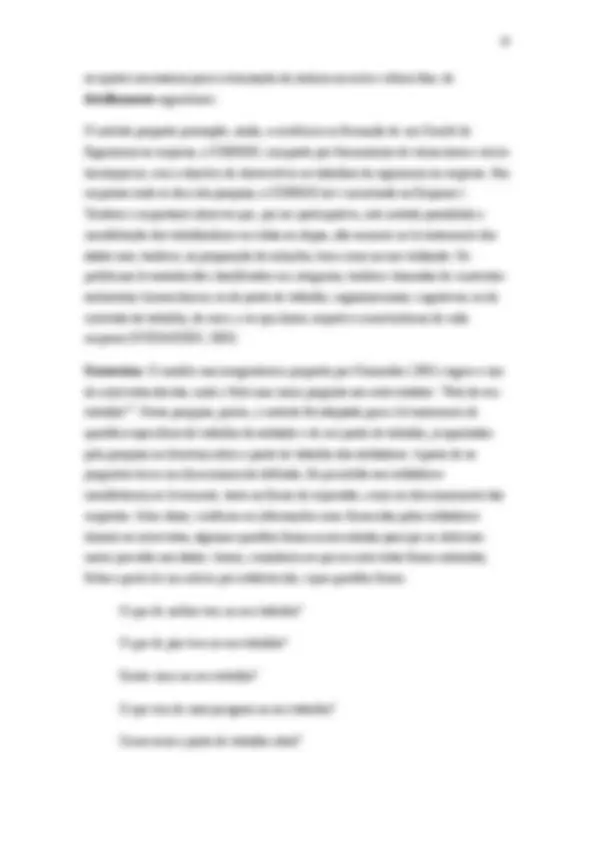
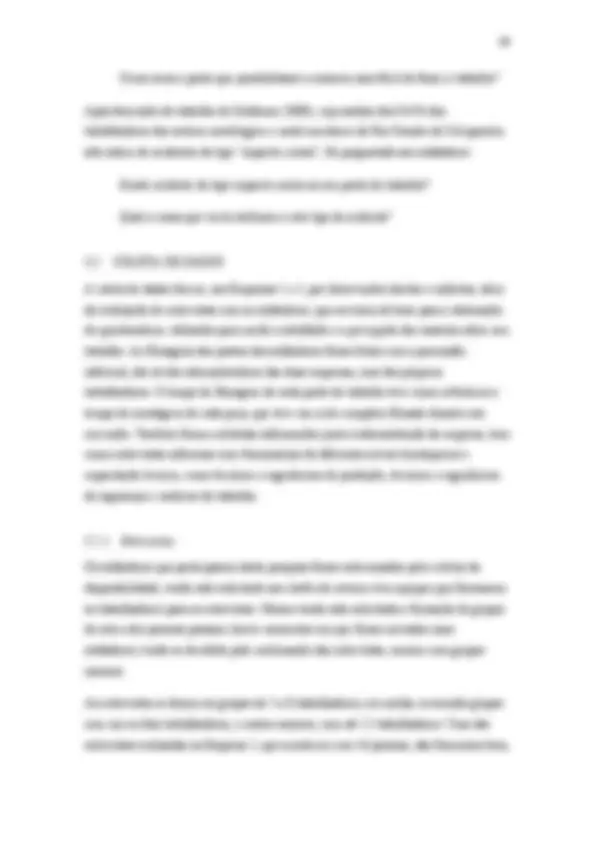
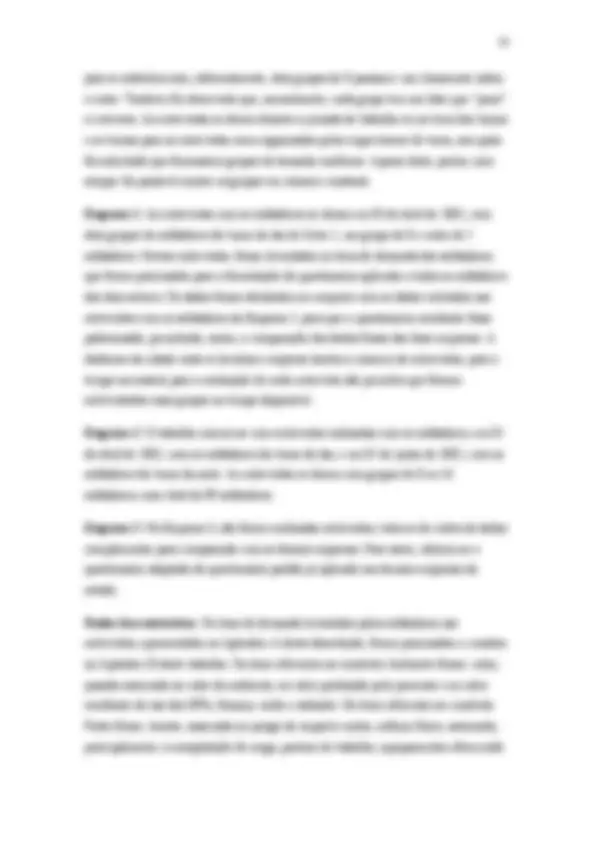
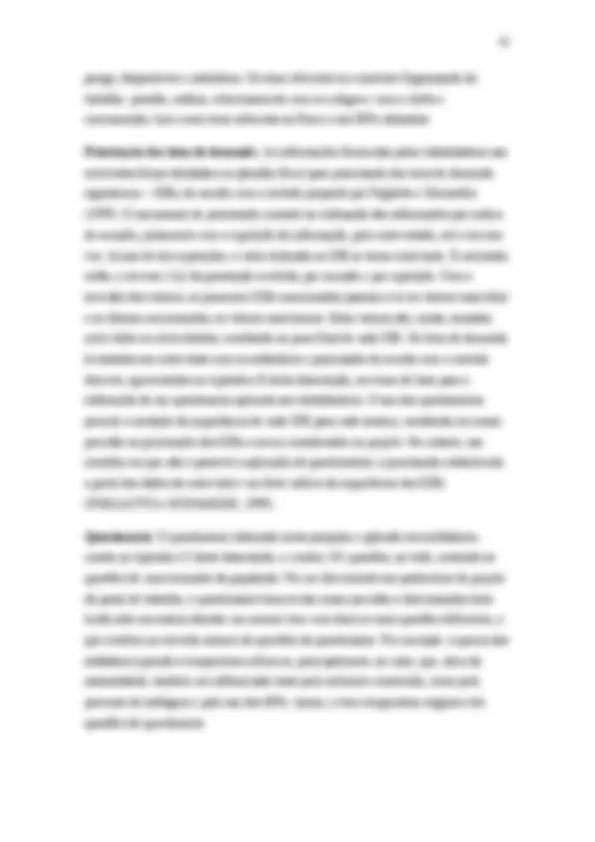
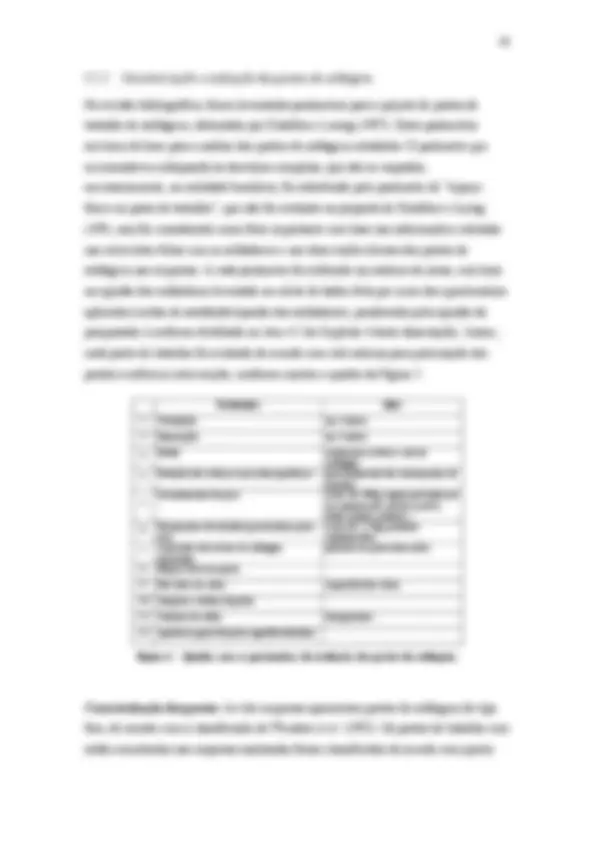
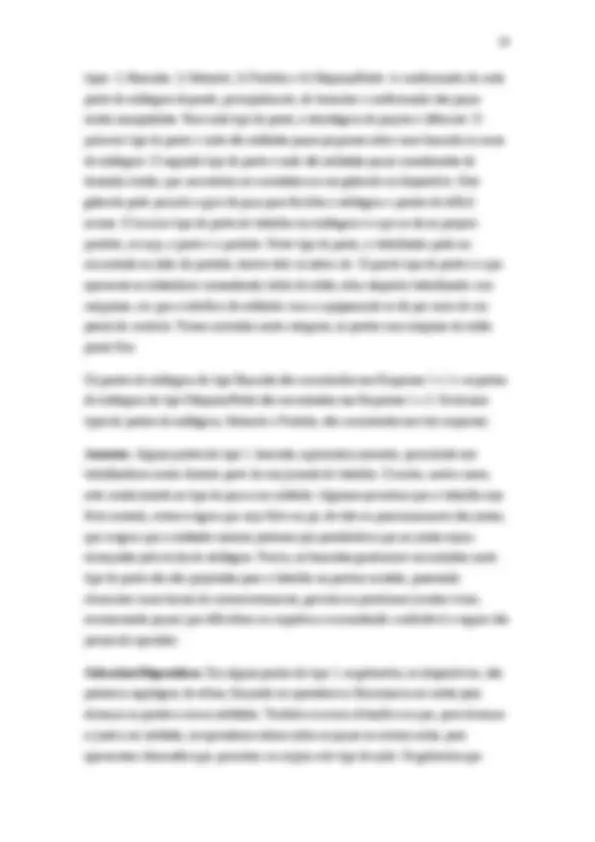
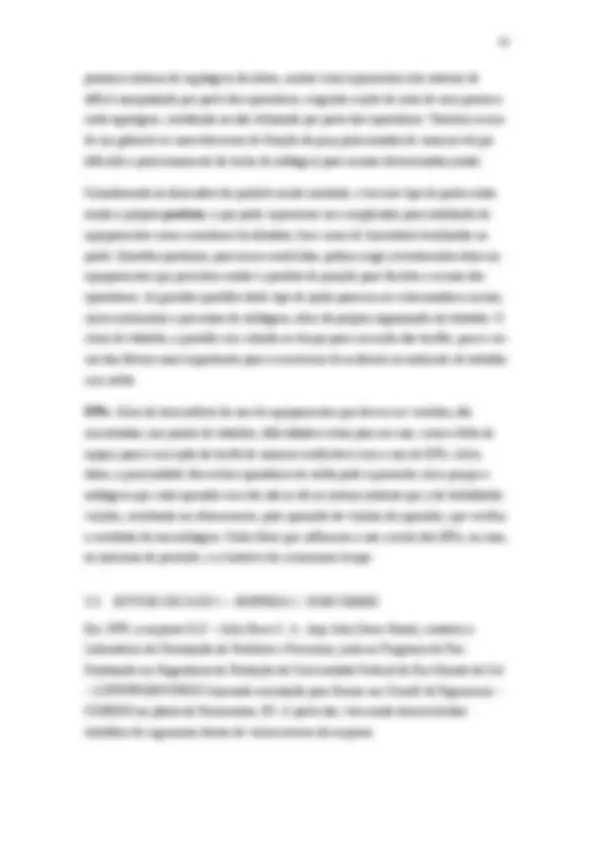
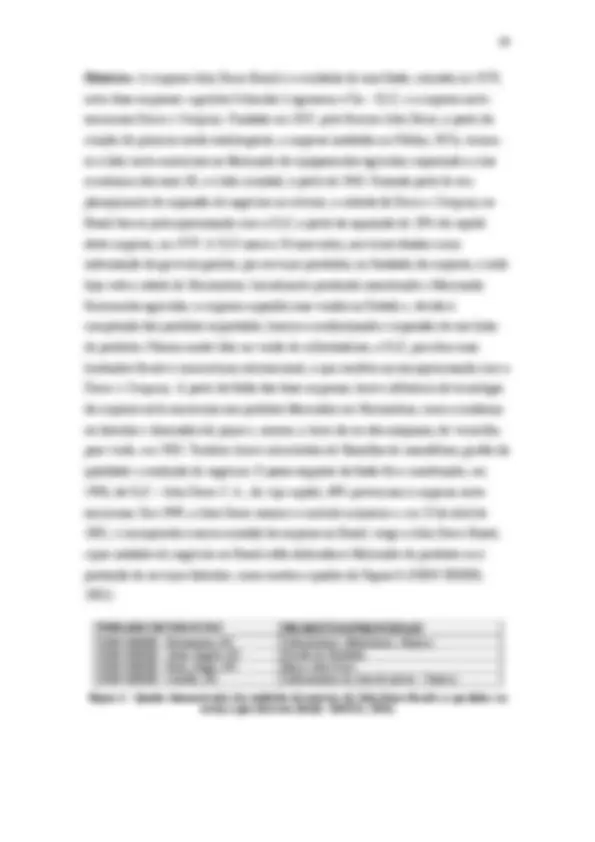
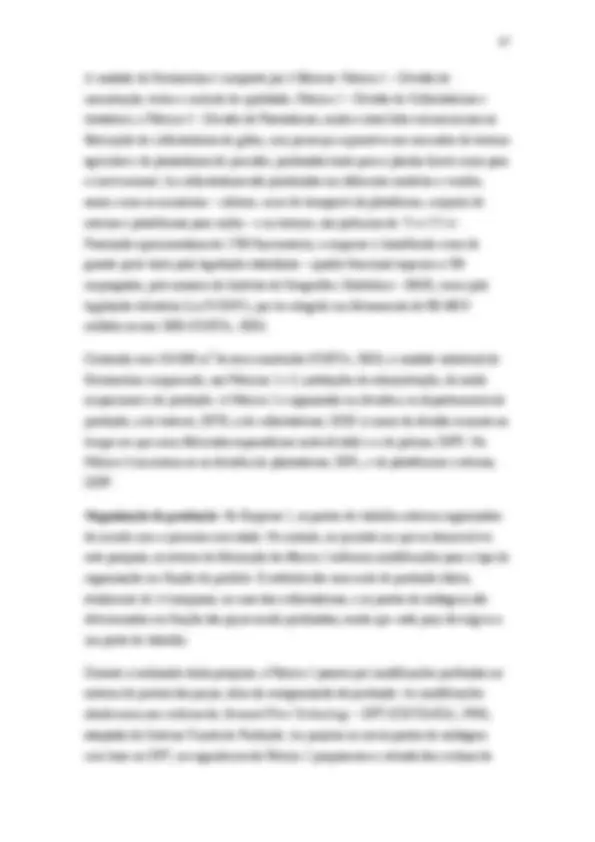
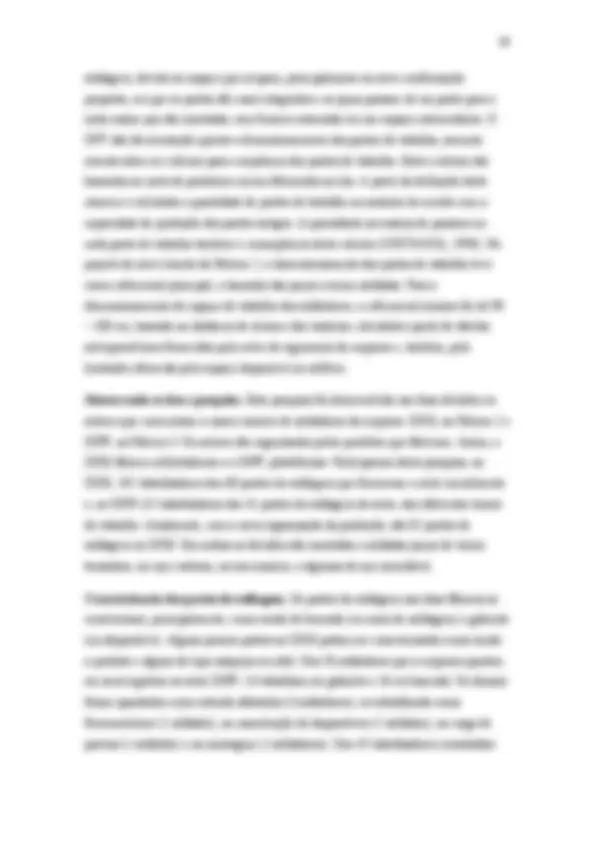
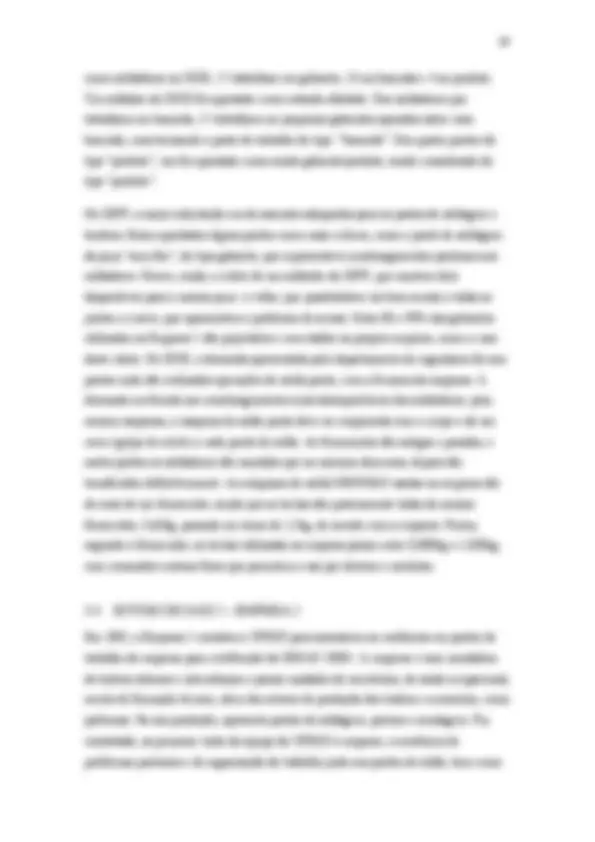
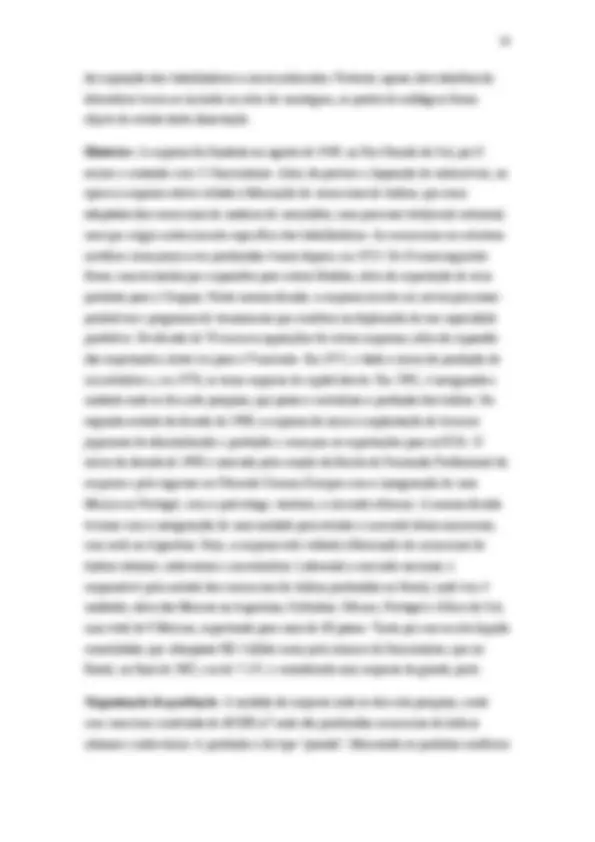
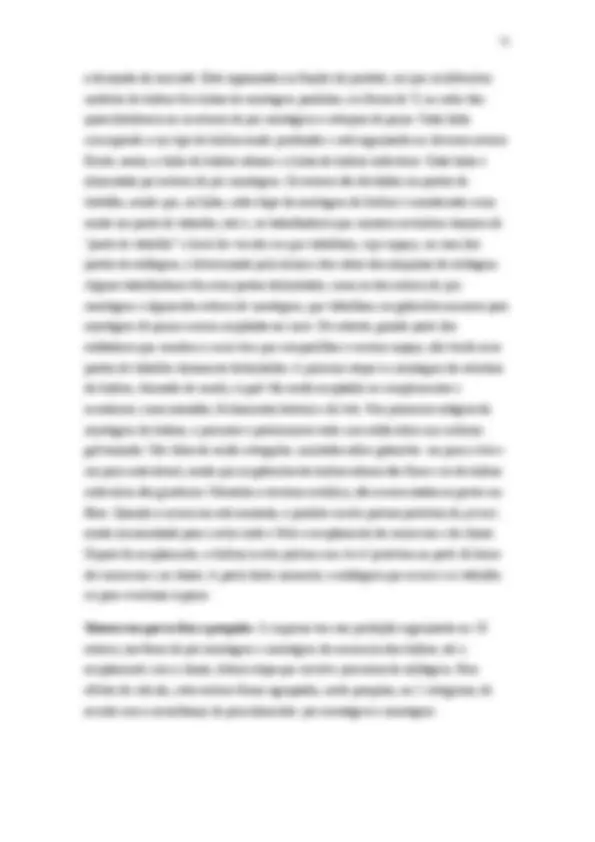
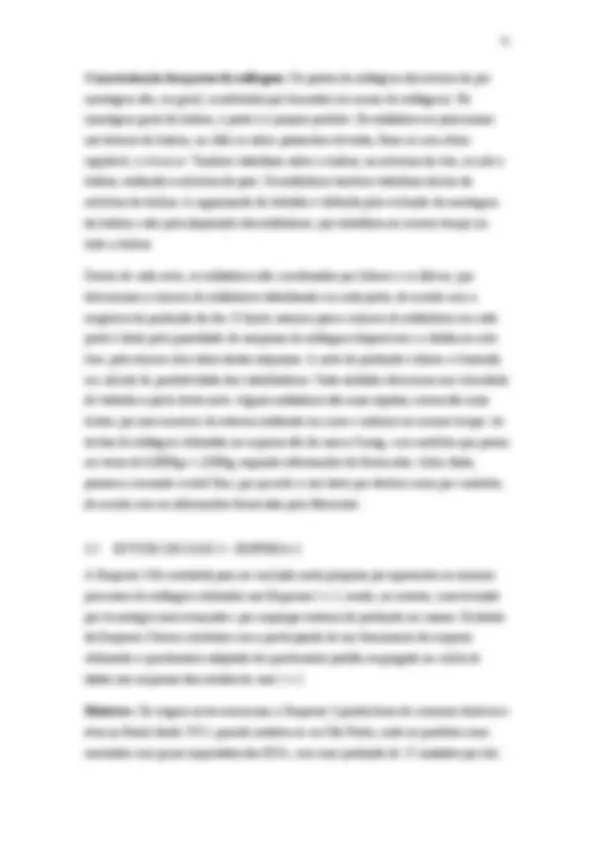
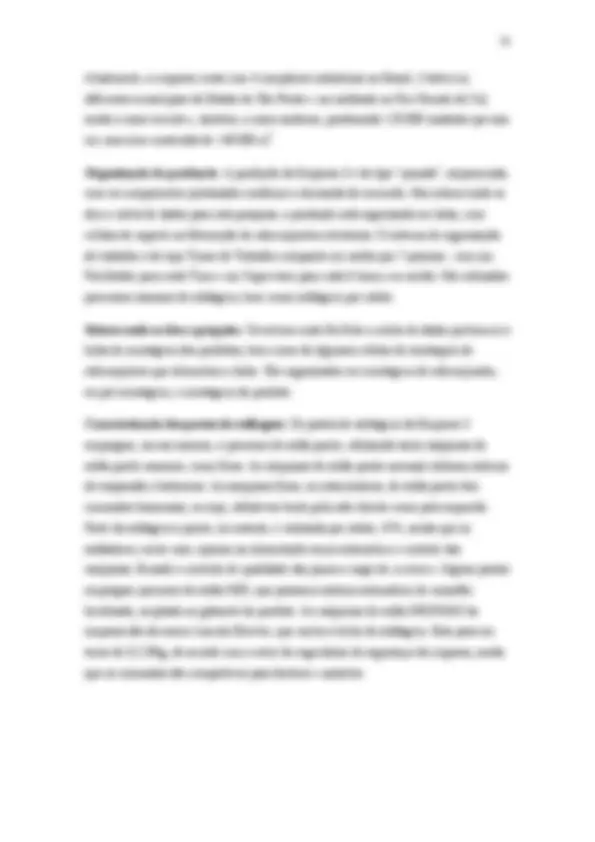
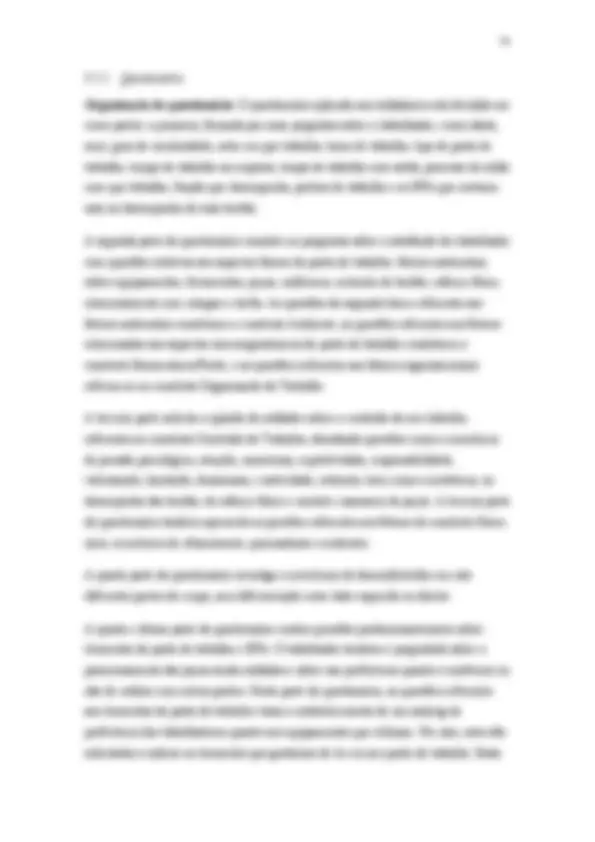
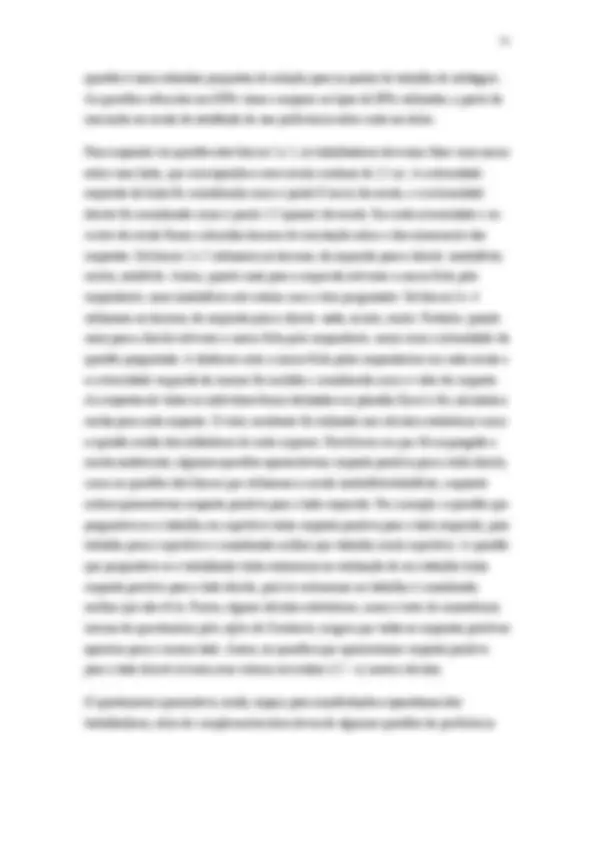
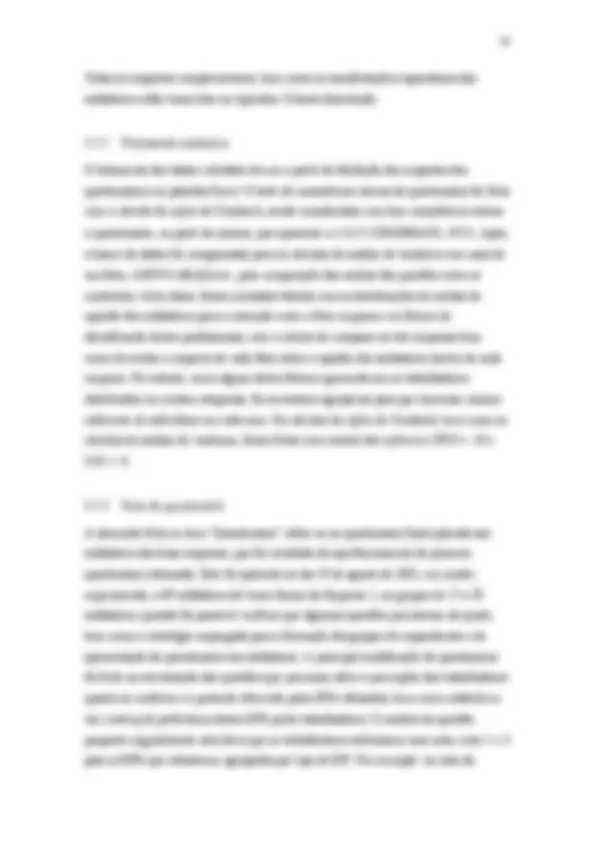
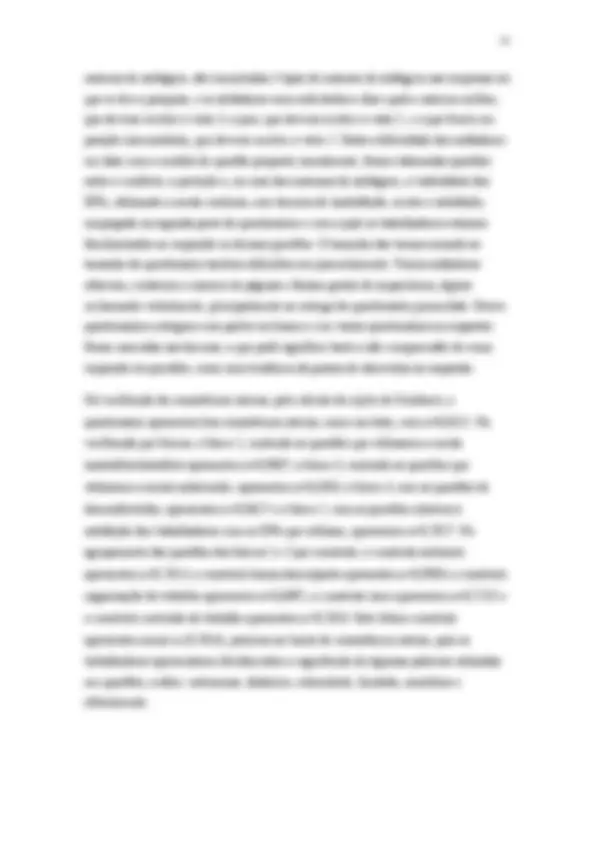
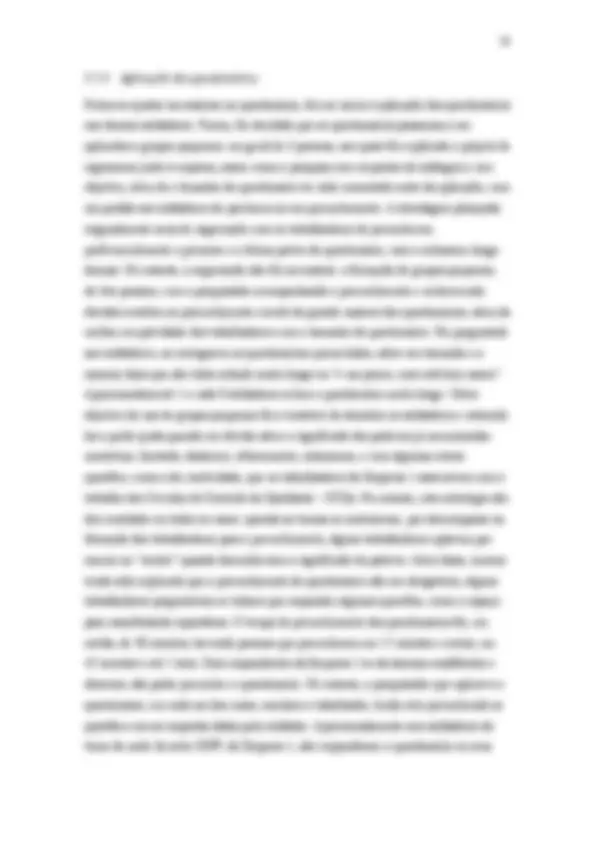
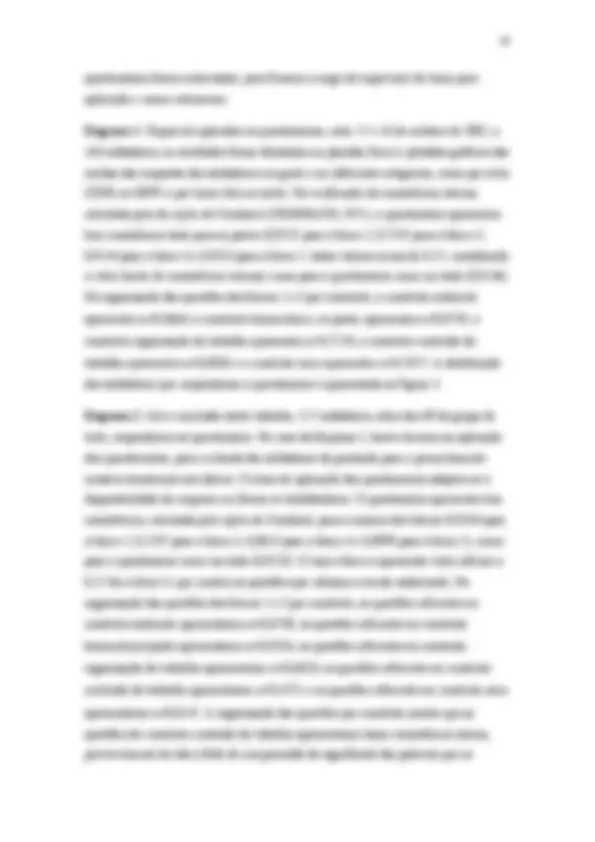
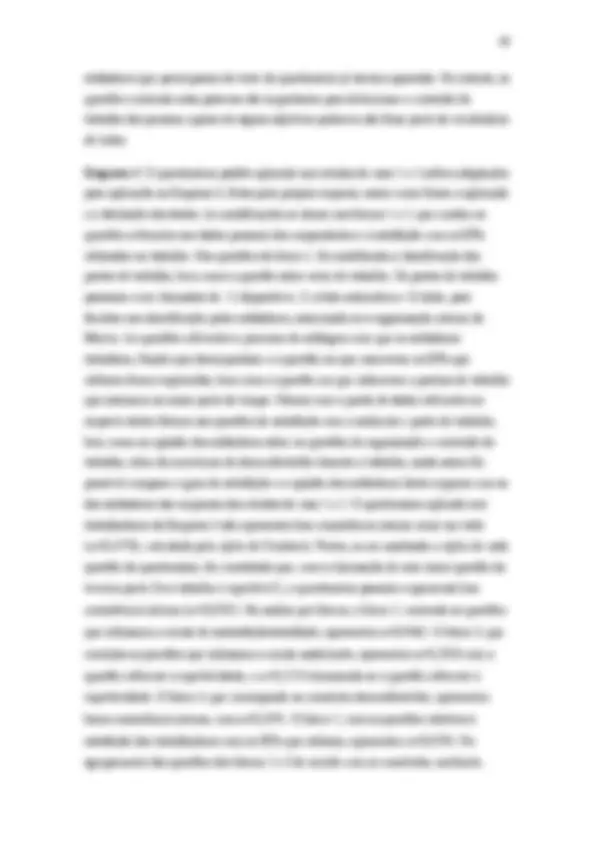
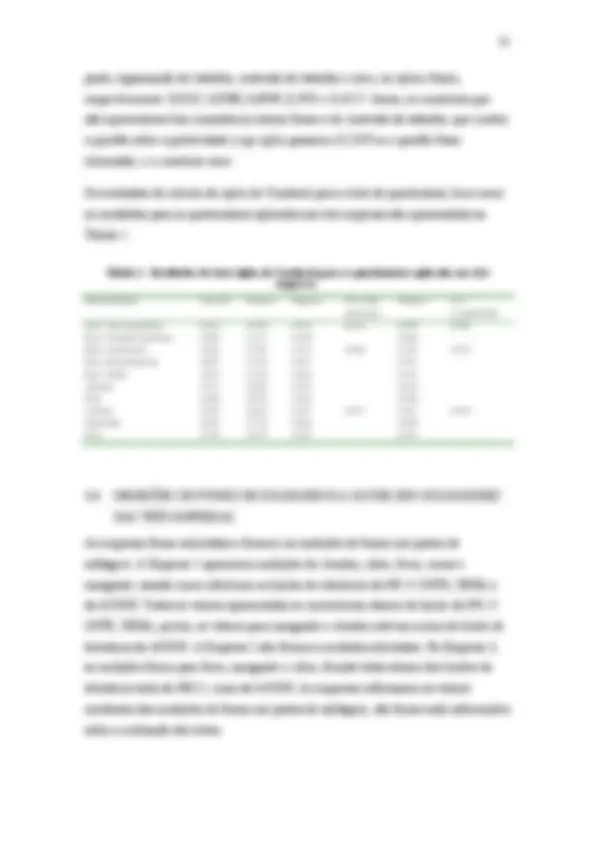
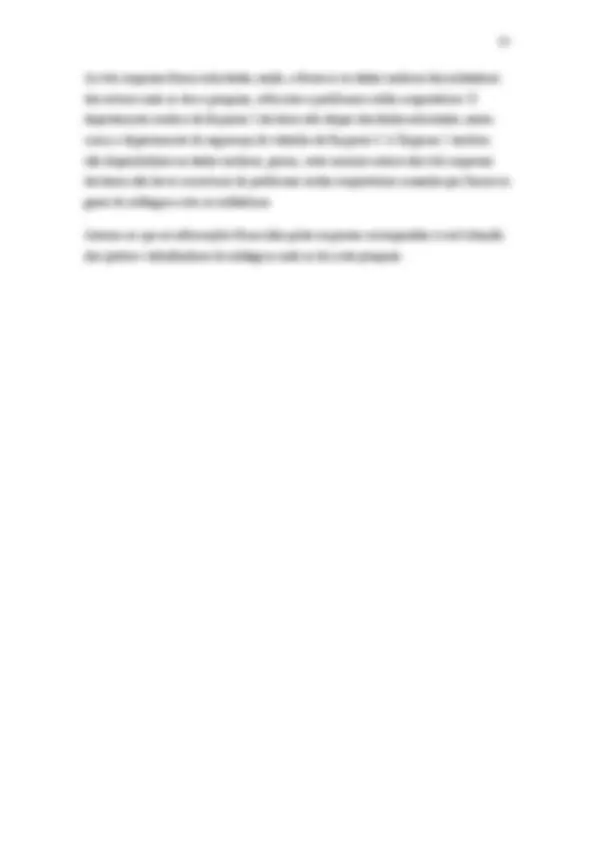
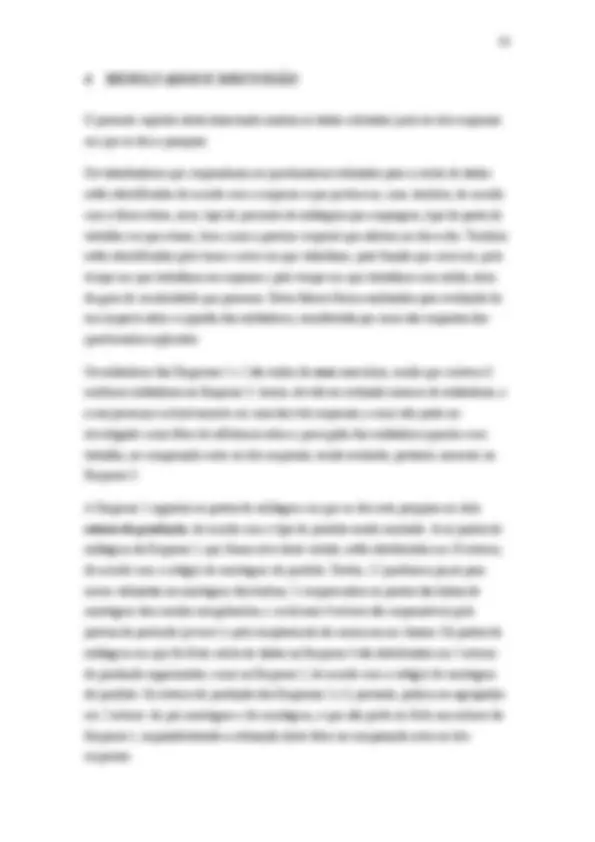
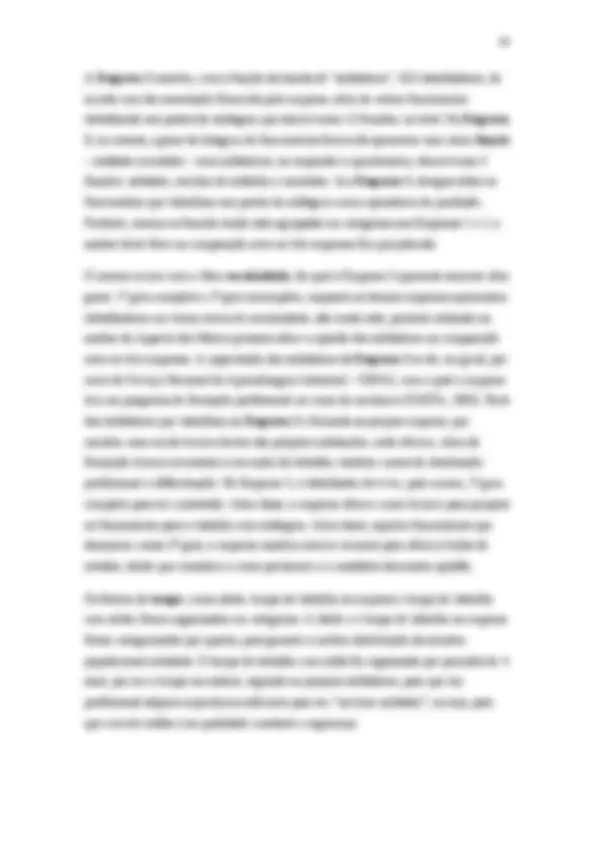
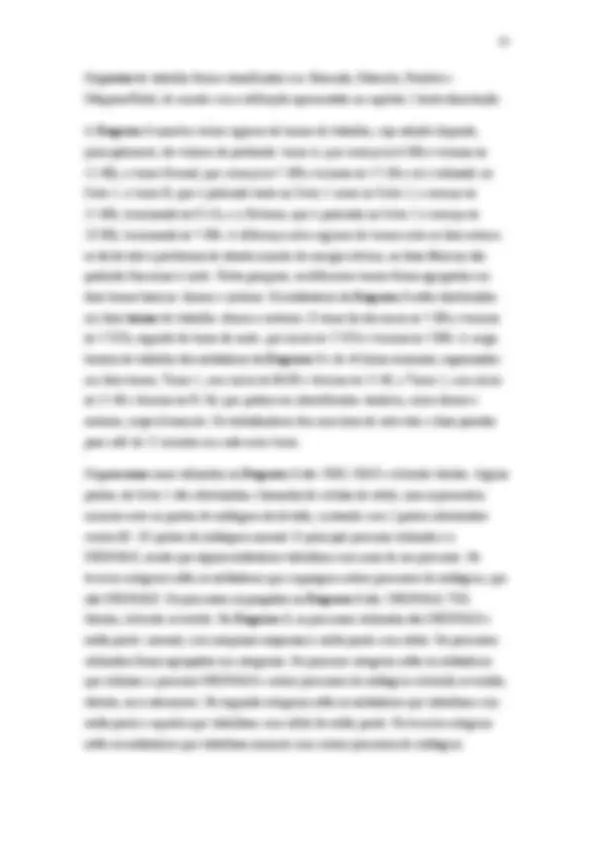
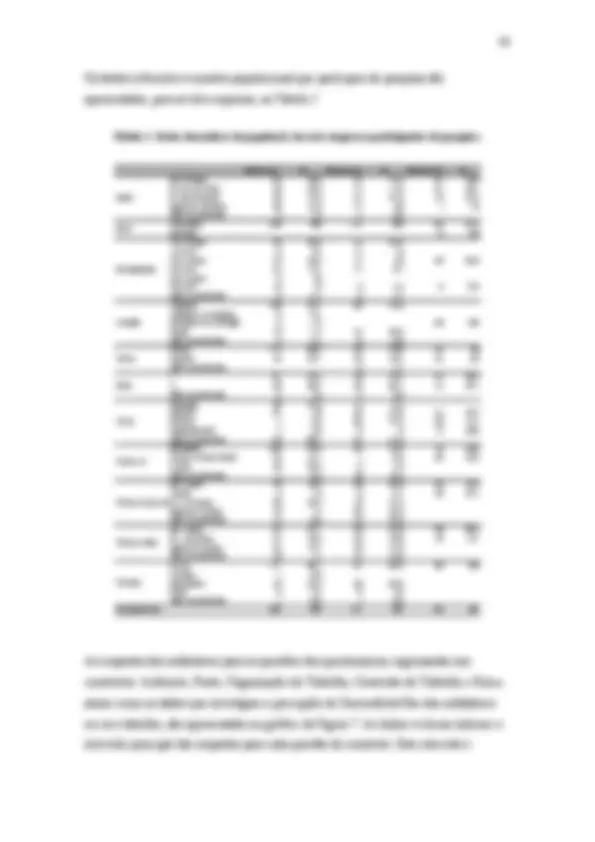
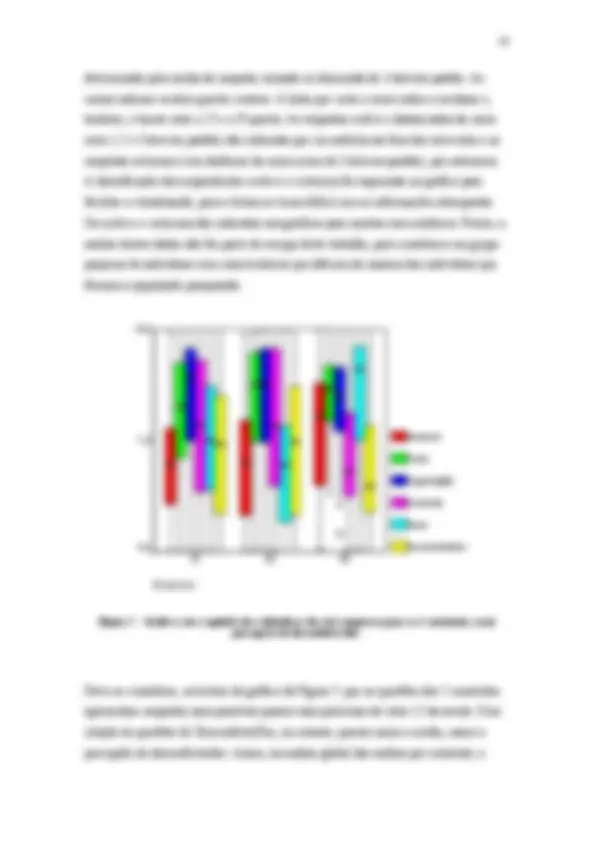
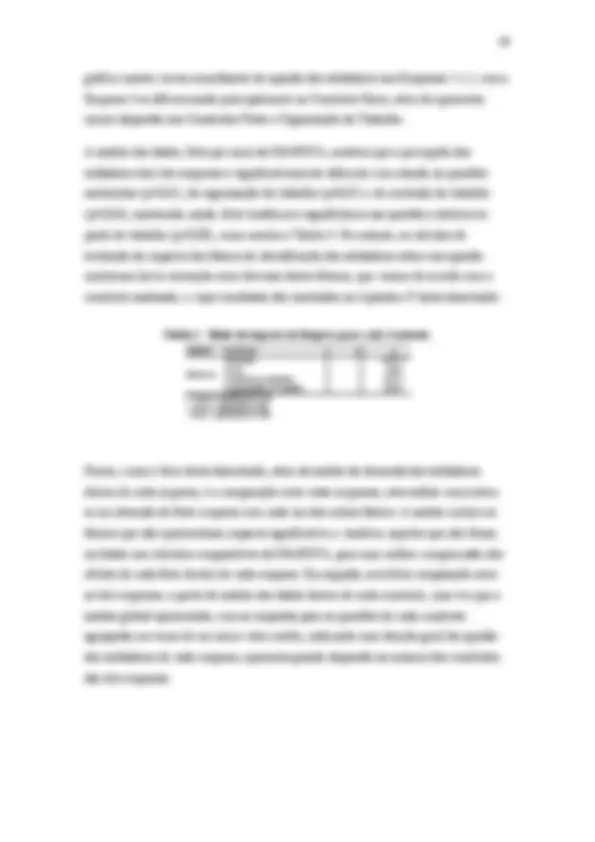
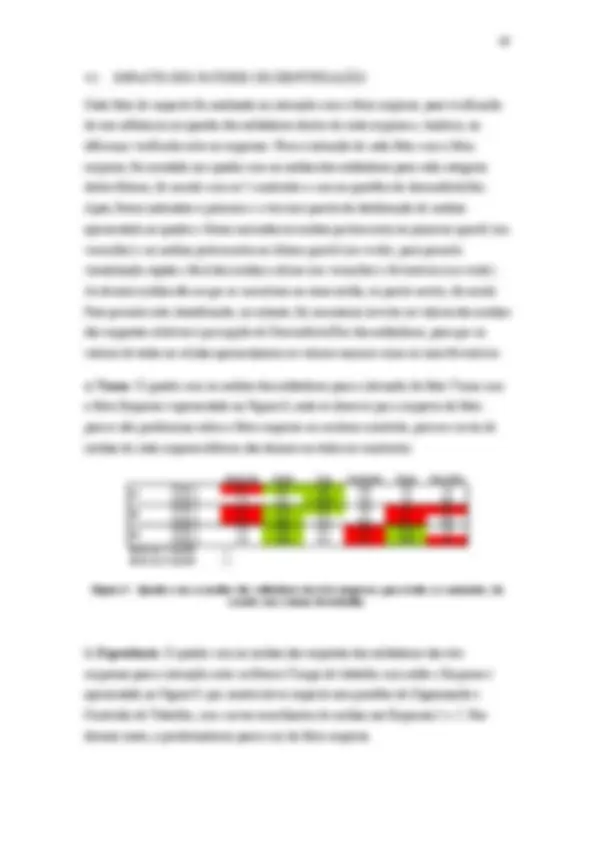
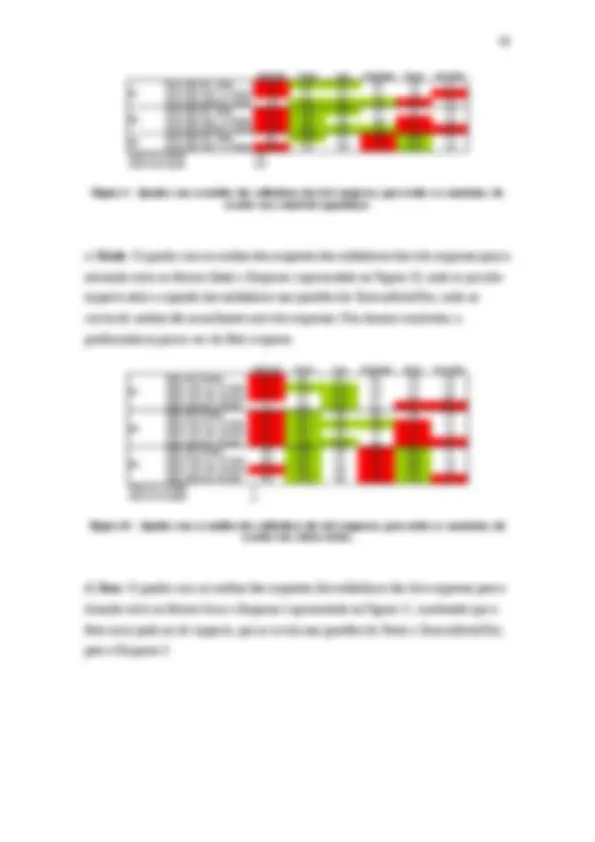
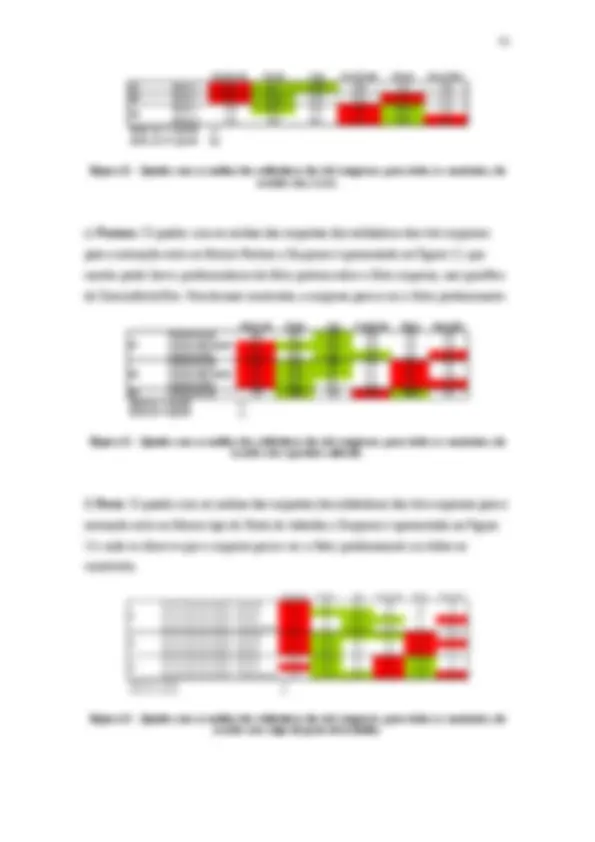
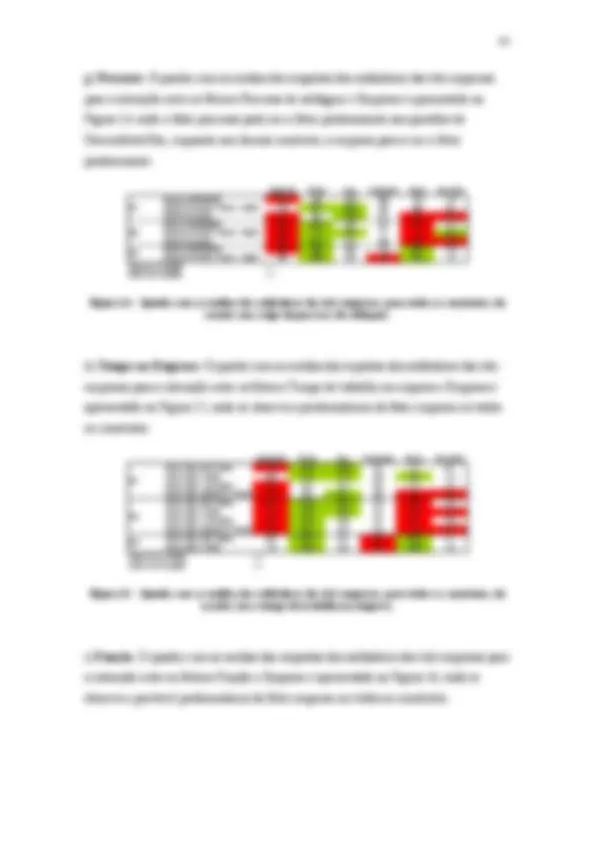
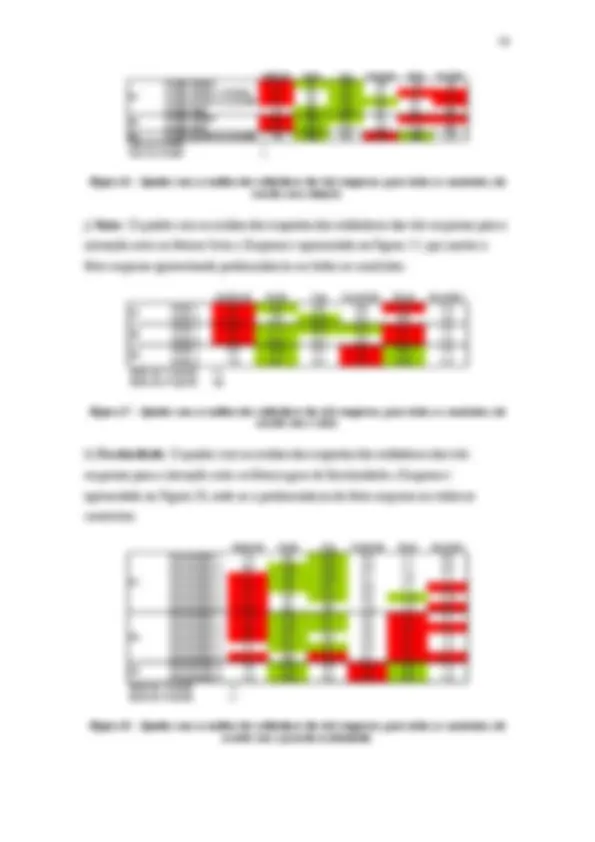
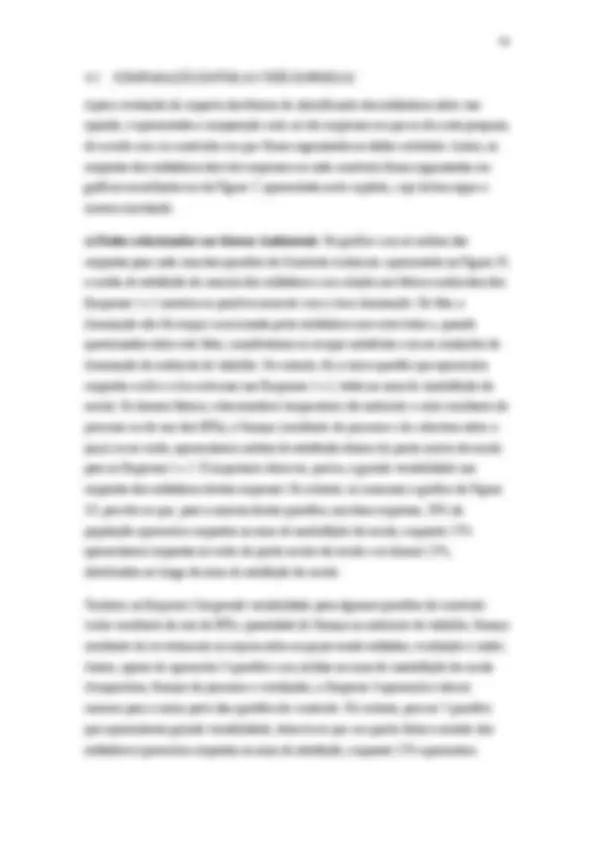
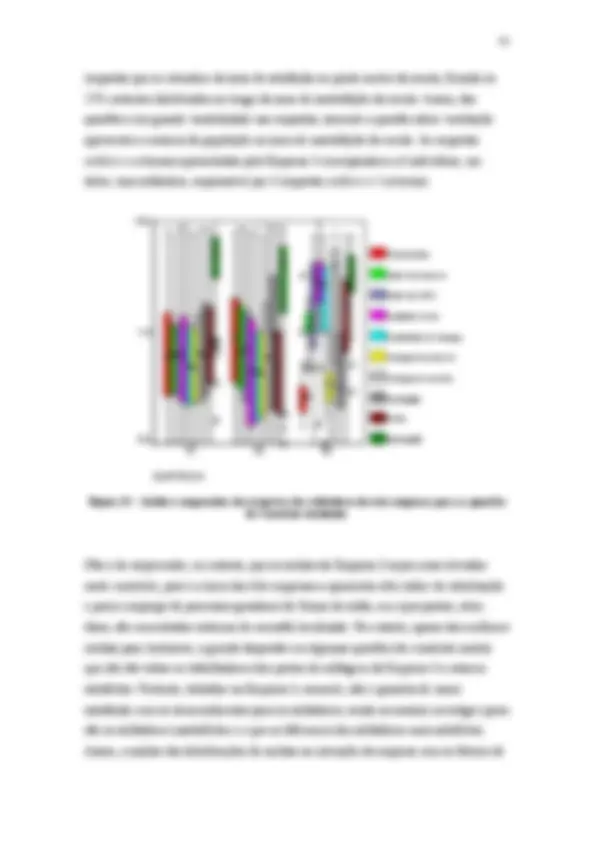
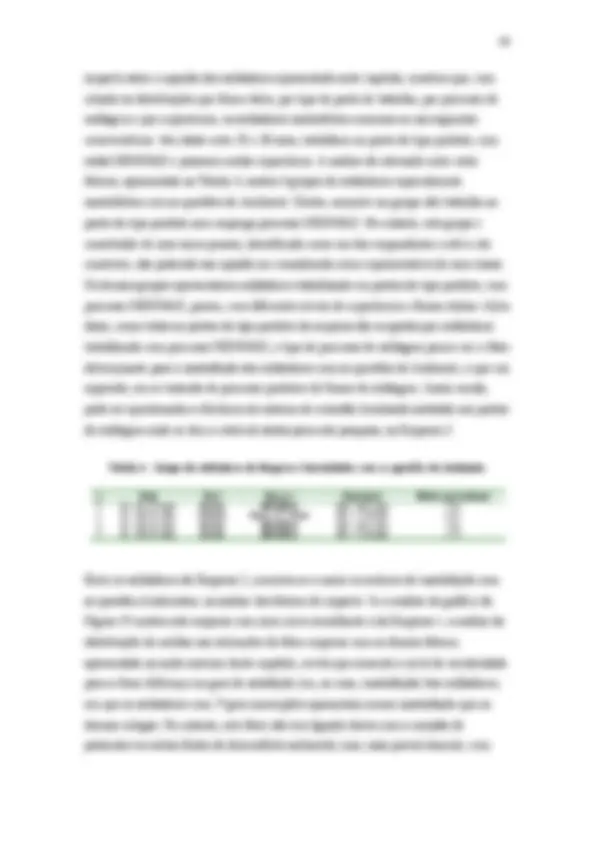
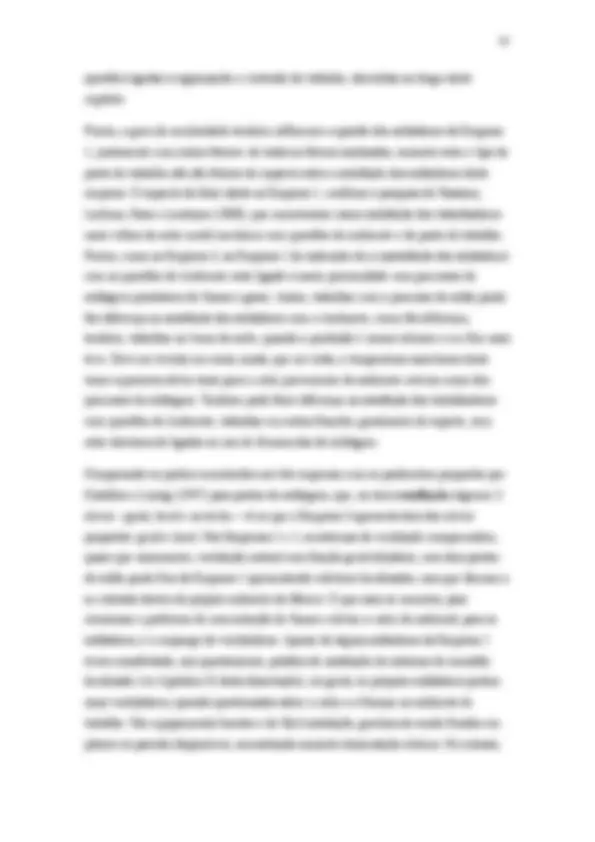
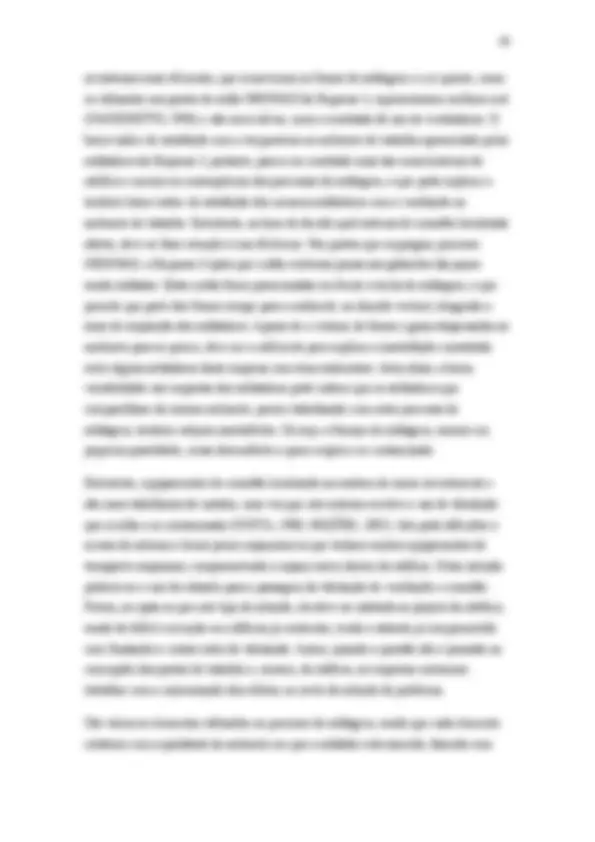
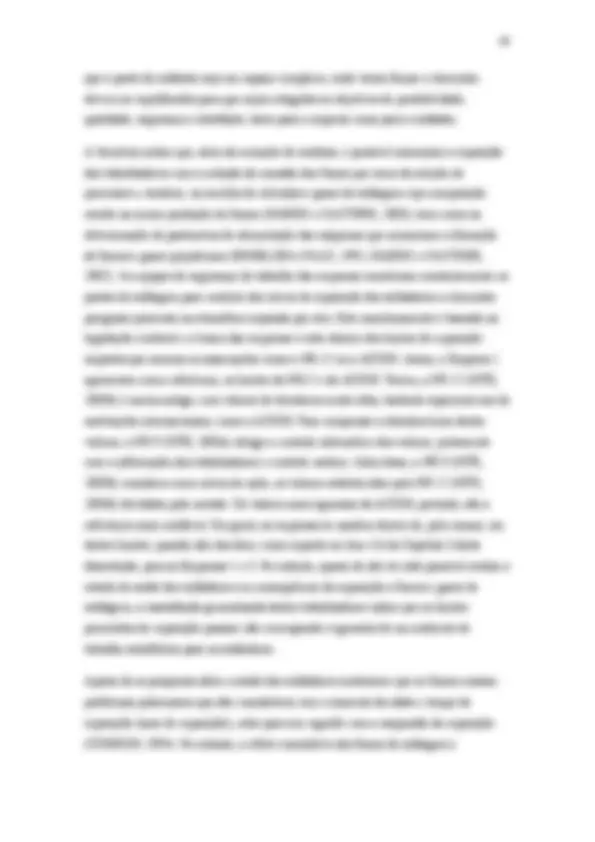
Estude fácil! Tem muito documento disponível na Docsity
Ganhe pontos ajudando outros esrudantes ou compre um plano Premium
Prepare-se para as provas
Estude fácil! Tem muito documento disponível na Docsity
Prepare-se para as provas com trabalhos de outros alunos como você, aqui na Docsity
Os melhores documentos à venda: Trabalhos de alunos formados
Prepare-se com as videoaulas e exercícios resolvidos criados a partir da grade da sua Universidade
Responda perguntas de provas passadas e avalie sua preparação.
Ganhe pontos para baixar
Ganhe pontos ajudando outros esrudantes ou compre um plano Premium
Comunidade
Peça ajuda à comunidade e tire suas dúvidas relacionadas ao estudo
Descubra as melhores universidades em seu país de acordo com os usuários da Docsity
Guias grátis
Baixe gratuitamente nossos guias de estudo, métodos para diminuir a ansiedade, dicas de TCC preparadas pelos professores da Docsity
José Maria Antunes da Silva. Kevin Cole ... Este trabalho trata de uma pesquisa junto aos soldadores de três empresas do setor metal-mecânico, em diferentes ...
Tipologia: Exercícios
Compartilhado em 07/11/2022
4.5
(60)160 documentos
1 / 192
Esta página não é visível na pré-visualização
Não perca as partes importantes!
Porto Alegre, 2003
Simone Antunes da Silva
Trabalho de Conclusão do Curso de Mestrado Acadêmico em Engenharia como requisito parcial à obtenção do título de Mestre em Engenharia – modalidade Acadêmica – Ênfase em Gerência da Produção e Ergonomia
Orientador: Lia Buarque de Macedo Guimarães, PhD CPE
Porto Alegre, 2003
Adenir Wiprich Aline Kirsh Figueiredo Aline Silva Fontoura de Barcellos Amauri Brizola Anders Sundin Ângelo Márcio Oliveira Sant’anna Astor Zappe Carla Hiromi Takeuchi Daniela Fischer Danilo Silva Denise Antunes da Silva Gabriela Zubaran de Azevedo Henrique Brasil Salis José Maria Antunes da Silva Kevin Cole Lia Buarque de Macedo Guimarães Liziara Corvalão de Avila Lucila Ribeiro Antunes da Silva Luís Fernando Souza dos Santos Nestor Formolo Pellini Paulo Portich Raimundo Lopes Diniz Richard Boekholt Roland Kadefors Roselaine Batista Silvério Fonseca Kmita Sílvia Helena Tomatis Petersen Valdecir Silva Oldair Knebelkanp, Genésio da Silva, Getúlio Viana, Gilmar Piccinin, Flamarion Peres, Elói Marholt, César Camilo, Ivo Bamberg, José Anselmo Pais, Jovares dos Reis, Irio Dotto, André Ferreira e demais soldadores da John Deere e das Empresas 2 e 3 que participaram da pesquisa.
Figura 1 - Posto de soldagem do tipo Bancada .............................................................. 44 Figura 2 - Posto de soldagem do tipo Gabarito .............................................................. 44 Figura 3 - Posto de soldagem do tipo Produto ............................................................... 44 Figura 4 - Posto de soldagem do tipo Máquina/Robô (BOEKHOLT, 2000) ................. 44 Figura 5 - Quadro com os parâmetros de avaliação dos postos de soldagem. ............... 63 Figura 6 - Quadro demonstrativo das unidades de negócios da John Deere Brasil e os produtos ou serviços que oferecem (Fonte: KMITA, 2003). ................................. 66 Figura 7 - Gráfico com a opinião dos soldadores das três empresas para os 5 construtos, mais percepção de desconforto/dor. ....................................................................... 87 Figura 8 - Quadro com as médias dos soldadores das três empresas, para todos os construtos, de acordo com o turno de trabalho....................................................... 89 Figura 9 - Quadro com as médias dos soldadores das três empresas, para todos os construtos, de acordo com o nível de experiência. ................................................. 90 Figura 10 - Quadro com as médias dos soldadores das três empresas, para todos os construtos, de acordo com a faixa etária................................................................. 90 Figura 11 - Quadro com as médias dos soldadores das três empresas, para todos os construtos, de acordo com o sexo........................................................................... 91 Figura 12 - Quadro com as médias dos soldadores das três empresas, para todos os construtos, de acordo com a postura adotada. ........................................................ 91 Figura 13 - Quadro com as médias dos soldadores das três empresas, para todos os construtos, de acordo com o tipo de posto de trabalho........................................... 91 Figura 14 - Quadro com as médias dos soldadores das três empresas, para todos os construtos, de acordo com o tipo de processo de soldagem. .................................. 92 Figura 15 - Quadro com as médias dos soldadores das três empresas, para todos os construtos, de acordo com o tempo de trabalho na empresa. ................................. 92 Figura 16 - Quadro com as médias dos soldadores das três empresas, para todos os construtos, de acordo com a função........................................................................ 93 Figura 17 - Quadro com as médias dos soldadores das três empresas, para todos os construtos, de acordo com o setor. ......................................................................... 93 Figura 18 - Quadro com as médias dos soldadores das três empresas, para todos os construtos, de acordo com o grau de escolaridade. ................................................ 93 Figura 19 – Gráfico comparativo das respostas dos soldadores das três empresas para as questões do Construto Ambiente............................................................................ 95 Figura 20 - Gráfico com as médias das respostas dos soldadores das três empresas para as questões do Construto Posto. ........................................................................... 103 Figura 21- Gráfico com a opinião dos soldadores das Empresas 1 e 2 sobre as máscaras de soldagem. ......................................................................................................... 109 Figura 22 - Gráfico com a opinião dos soldadores das três empresas sobre a máscara de soldagem com sensor............................................................................................ 109 Figura 23 - Gráfico com a opinião dos soldadores das Empresas 1 e 2 com os aventais com mangas e sem mangas................................................................................... 110 Figura 24 - Gráfico com a opinião dos soldadores das três empresas sobre o avental sem mangas. ................................................................................................................. 110 Figura 25 - Gráfico com a opinião dos soldadores das três empresas com os sapatos de seguranças e com as perneiras. ............................................................................. 111
Figura 26 - Gráfico com a opinião dos soldadores das Empresas 1 e 2 com os sapatos de segurança, as perneiras e as botas de segurança................................................... 111 Figura 27 - Gráfico com a opinião dos soldadores das Empresas 1 e 2 com a touca e o filtro/respirador..................................................................................................... 112 Figura 28 - Gráfico com a opinião dos soldadores das três empresas com as luvas. ... 112 Figura 29 - Gráfico com as respostas dos soldadores das três empresas para as questões de percepção de Desconforto/Dor em diferentes partes do corpo. ....................... 113 Figura 30 - Gráfico com as respostas dos soldadores das três empresas para as questões de Organização do Trabalho................................................................................. 118 Figura 31 - Gráfico com as respostas dos soldadores das três empresas para as questões do Construto Conteúdo do Trabalho. ................................................................... 122 Figura 32 - Gráfico com as respostas dos soldadores das três empresas para as questões do Construto Risco. .............................................................................................. 124
Resumo
Este trabalho trata de uma pesquisa junto aos soldadores de três empresas do setor metal-mecânico, em diferentes estágios tecnológicos, para levantamento e avaliação de sua demanda ergonômica por meio de método participativo, como contribuição para o projeto de seus postos de trabalho. Verificou-se que os problemas mais críticos para estes profissionais são de natureza ambiental, tendo sido questionada a validade dos valores limites estabelecidos de exposição a fumos de soldagem. Além disso, foi constatada a maior influência do fator empresa sobre a opinião e satisfação dos soldadores, com exceção da empresa onde está estabelecido um programa de ergonomia: nesta o nível de exigência dos soldadores é maior, portanto, os fatores pessoais representam maior impacto sobre sua opinião e satisfação. Também foi avaliado o impacto do nível tecnológico da empresa sobre os soldadores, concluindo-se que os que trabalham com sistemas de produção mais manual têm maior envolvimento com seu trabalho, enquanto os soldadores que participam de sistema mais automatizado não estão, necessariamente, livres de problemas relacionados a questões ambientais. Assim, é tão importante considerar as questões ambientais desde a concepção de uma fábrica, quanto as questões de organização do trabalho, pois ambas impactam no bem- estar e, conseqüentemente, na produtividade de seus trabalhadores.
Palavras-chave: posto de trabalho, soldador, ergonomia
Abstract
The focus of this dissertation is the evaluation of the work developed by welders employed in three different metal industries with different technological levels. The research was carried out according to the methods of the participatory ergonomics to contribute to the welder´s workplace design. The critical problems were found to be of environmental nature, putting into question the validity of the established thresholds values for welding fumes exposition. The company was found to be the major influence on the welder’s satisfaction and general opinion although this was not the case of the only company which helds an ergonomics program: there, the individual issues impact more strongly the welder’s opinion and satisfaction. The evaluation of the impact of the company´s technological level lead to the conclusion that welders working at manual production systems have more involvement with their work, while welders working at more automated production systems are not necessarily free from environmental problems. Therefore, it is important to consider both the facility’s environmental issues and the work organization issues, as they impact the workforce welfare and, consequently, productivity.
Key-words: workplace, welder, ergonomics
apresentando diferentes tipos de organização de produção, mas empregando os mesmos processos de solda, e a geração de parâmetros de projeto para postos de trabalho com solda adequados à realidade de trabalho dos soldadores. Com base na participação dos trabalhadores estes postos deveriam permitir a realização de tarefas com maior facilidade, respeitando não só a capacidade de trabalho da pessoa, mas, também, os limites humanos, garantindo sua segurança, assim como seu conforto e satisfação no ambiente de trabalho. Para isso, foi necessário levar em consideração os diversos fatores que compõem o ambiente, o posto e o próprio trabalho de solda, inserido no processo produtivo da empresa da qual fazem parte. Os postos analisados pertencem às fábricas da planta de Horizontina, RS, da empresa John Deere Brasil, de uma empresa montadora de ônibus e de uma empresa produtora de bens de consumo duráveis no setor metal-mecâcnico, no Rio Grande do Sul.
Esta dissertação tem como objetivo analisar os postos de soldagem de diferentes empresas que apresentam diferentes níveis tecnológicos e tipos diferentes de organização da produção, de forma a gerar insumos para o projeto ergonômico de postos de trabalho com solda.
Objetivos secundários. Comparar as empresas quanto à tecnologia, cultura da empresa, organização da produção, além da satisfação dos funcionários das três empresas com relação ao ambiente, os postos de trabalho, percepção de risco, conteúdo e organização do trabalho, percepção de desconforto/dor, bem como avaliar o impacto do posto de trabalho na segurança e satisfação dos soldadores.
Este trabalho aborda as fases de apreciação e diagnose ergnômica, não incluindo a fase de projetação ergonômica, mas apenas a indicação de parâmetros de projeto para os postos de soldagem.
O trabalho desenvolvido nesta dissertação esteve restrito, na empresa John Deere, aos postos dos soldadores de dois setores das fábricas da planta de Horizontina, RS. Na empresa montadora de ônibus, que será identificada como Empresa 2, o trabalho refere- se à linha de montagem dos ônibus. Na terceira empresa estudada, que será identificada
como Empresa 3, a coleta de dados junto aos soldadores deu-se por meio de uma das ferramentas utilizadas nas demais empresas: um questionário padrão aplicado aos soldadores, elaborado a partir de itens de demanda levantados de acordo com o método adotado neste trabalho.
Este trabalho de pesquisa está estruturado em quatro capítulos, além desta introdução. No capítulo 2 consta a revisão bibliográfica para levantamento do estado da arte sobre o trabalho com solda e postos de trabalho, assim como dos temas afins que foram considerados relevantes ou que possam fornecer dados para propostas de solução. No capítulo 3 é descrita a metodologia empregada neste estudo e são apresentadas as empresas onde se deu a pesquisa. No capítulo 4 são apresentados os dados coletados na pesquisa, juntamente com a análise e discussão dos dados coletados com base no levantamento do estado da arte feito no capítulo 2. Então, no capítulo 5, são feitos os comentários finais em uma seção reservada à conclusão. Ao final do trabalho foram acrescentados os documentos complementares considerados necessários, em uma seção reservada aos Apêndices.
Esses processos estão organizados em treze grupos: 1) soldagem a arco elétrico; 2) soldagem em fase sólida; 3) soldagem por oxigás; 4) soldagem por resistência elétrica;
Nas empresas onde esta pesquisa foi desenvolvida, os processos empregados são: MIG ( Metal Inert Gas )/MAG ( Metal Active Gas ), TIG ( Tungsten Inert Gas ), solda tubular, solda ponto e solda com eletrodo revestido, todos processos de soldagem por fusão. Portanto, estes processos serão descritos mais detalhadamente. Todos os processos descritos têm em comum o consumo de energia elétrica, cuja proximidade faz com que os soldadores estejam expostos a risco de choques elétricos.
No grupo da soldagem a arco elétrico ( Arc Welding : AW), os processos empregados nas empresas analisadas são:
Soldagem a arco com eletrodo tubular ( Flux Cored Arc Welding : FCAW), processo que apresenta o consumível alimentado continuamente e contendo um fluxo fusível no seu interior, o que garante a execução das reações pirometalúrgicas, benéficas ao processo, sem impedir a soldagem em posições diferentes da horizontal e vertical, além da redução da contaminação do mesmo pela umidade e dejetos do ambiente. A proteção da poça de fusão também pode ser feita por gás, como no processo MIG/MAG (MACHADO, 1996). Por ser um processo de arco aberto, em que o metal do consumível é transferido através do arco para ser depositado na junta, a soldagem com eletrodo tubular – FCAW está entre os processos que produzem grande quantidade de fumo. Os fumos emitidos por este processo normalmente contêm quantidades significativas de cromo hexavalente – Cr VI, que exige medidas de controle mais rígidas (LUCAS e CARTER, 1999). Existem estudos, porém, que buscam a redução na emissão de fumos com modificação na especificação tanto da composição do fluxo fusível, quando do gás de proteção (HARRIS e CASTNER, 2002). Outra desvantagem apontada para este processo é a de produzir muitas faíscas (ENGBLOM e FALCK, 1992).
Soldagem a arco com proteção por gás e eletrodo consumível ( Gas Metal Welding – GMAW), tendo como variações a proteção por gás inerte, cujo processo é conhecido
como MIG ( Metal Inert Gas ); ou a proteção por gás ativo (oxidante), cujo processo é conhecido como MAG ( Metal Active Gas ). Neste caso, a soldagem é realizada por um arco elétrico, estabelecido entre um arame nu, continuamente alimentado, e a peça. A proteção do mesmo e da poça de fusão é realizada por gás que flui pelo bocal, tendo o arame no centro do fluxo. Geralmente, os gases utilizados são inertes, como argônio e hélio, ou do tipo oxidante, também denominado “ativo”, como CO 2 , ou argônio+CO 2 , ou argônio+O 2 , ou combinação destes três gases. A operação é semi-automática ou automática, podendo ser soldadas ligas ferrosas e não-ferrosas, sendo este processo considerado adequado para robotização (MACHADO, 1996). Assim como o FCAW, a solda MIG/MAG também é um processo de arco aberto com transferência de metal através do arco, estando, portanto, entre os processos que produzem grande quantidade de fumo. Os fumos gerados por estes processos normalmente contêm grandes concentrações do metal sendo depositado (LUCAS e CARTER, 1999). Além da escolha do eletrodo e da composição do gás de proteção, outros parâmetros de soldagem são a voltagem, a amperagem e o tipo de corrente elétrica, que pode ser contínua ou pulsada. A corrente pulsada oferece vantagens como a redução de fumos (HARRIS e CASTNER, 2002) e de faíscas, maior produtividade em certas aplicações e menor porosidade do cordão de solda, e é usada, principalmente para soldagem de alumínio e aço inoxidável (ENGBLOM e FALCK, 1992).
Soldagem a arco com proteção por gás e eletrodo não consumível ( Gas Tungsten Arc Welding – GTAW), que é conhecida como TIG ( Tungsten Inert Gas ). Este processo geralmente se destina à realização de soldas sobre peças de pequena espessura, no entanto, também é empregado sobre peças espessas quando for essencial a qualidade. O arco elétrico é formado entre um eletrodo não consumível (de tungstênio ou outros compostos com este elemento) e a peça. O eletrodo e a poça de fusão são protegidos por gás, geralmente inerte, que flui num bocal, envolvendo o eletrodo. O arco atua, portanto, somente como fonte de calor, sendo possível a adição manual de metal (no formato de varetas) ou automaticamente (na forma de arame fino) (MACHADO, 1996). É o único processo de arco aberto que não transfere material através do arco, resultando em menor produção de fumos (LUCAS e CARTER, 1999). No entanto, a produção de ozônio é maior, principalmente na soldagem de alumínio (HEWITT, 1999). A alimentação elétrica da solda TIG emprega energia elétrica de alta freqüência para iniciar e estabilizar o arco. Porém, por estar em um nível muito baixo de corrente, não
chapas relativamente finas (MACHADO, 1996). A soldagem a ponto pode produzir fumos se houver resíduos ou óleo sobre as peças sendo soldadas e, se a máquina não estiver regulada corretamente, são lançadas faíscas que podem atingir o soldador ou demais indivíduos presentes no posto de trabalho (CORLETT e BISHOP, 1978). Estudo feito em 1982 encontrou, para máquinas de solda ponto (50 Hz, 15 a 106 kA), fluxos magnéticos com densidades maiores que 10 mT (miliTesla) em distâncias acima de 1 m (LÖVSUND, OBERG e NILSSON, 1982).
2.1.2 Robotização
A robotização de alguns processos de soldagem, como solda ponto e MIG/MAG, vem sendo cada vez mais empregada, principalmente nos países mais desenvolvidos. Porém, a soldagem manual permanece uma atividade importante, mesmo em indústrias que apresentam alto índice de automação e robotização, tecnologias que requerem operadores com conhecimento tanto em soldagem, como em programação e planejamento da produção (KADEFORS, 1999).
Além de trabalhadores altamente especializados, a robotização também exige que os produtos sejam projetados de maneira a permitir o acesso do robô às juntas a serem soldadas, bem como que seja feito o planejamento cuidadoso do posicionamento das partes a serem soldadas. Assim, é interessante que o emprego deste tipo de tecnologia esteja contemplado na estratégia global da empresa, desde o projeto do produto até sua inspeção (PANISSET, 1986).
Do ponto de vista de organização da produção, são várias as vantagens da robotização, sendo a simplificação dos detalhes de projeto considerada uma das questões que mais influenciam o custo final de produção. A redução dos níveis hierárquicos pela diminuição do número de empregados, simplificando o gerenciamento de pessoal, é considerada como outro ponto positivo da automação dos processos de soldagem, além disso, a produtividade do robô é menos sensível à posição de soldagem, diminuindo a necessidade de contornar a peça sendo soldada (BOEKHOLT, 1999).
Comparando-se os custos das diferentes tecnologias, se o custo de implantação de um robô for o mesmo que a instalação de um posto de soldagem e contratação de soldadores, em longo prazo o robô pode ser vantajoso, pois terá maior produtividade
sendo necessária uma única pessoa para alimentá-lo (SPENCER, 2001). No entanto, é preciso ter cuidado na implantação e, principalmente, na troca de tecnologia: se ela for feita simplesmente com o intuito de economizar em custos trabalhistas imediatos, pode decepcionar, pois os custos auxiliares desta implantação podem exceder a economia feita com os custos trabalhistas. Para se obter sucesso na implantação de tal tecnologia, é necessário considerar que é questão importante ter como objetivo as mudanças propostas melhorarem a capacidade produtiva dos elementos humanos (BOEKHOLT, 2000; BOEKHOLT, 1999).
Apesar da intenção inicial da indústria de ter o trabalho humano totalmente substituído pela produção automatizada, o que tem sido constatado é que a automação não substitui completamente a necessidade de um cérebro no chão de fábrica. Assim, o funcionamento do sistema deve incluir o fator humano como parte integrante do sistema de produção. Na nova tecnologia, o equipamento automatizado é a ferramenta do operador (BOEKHOLT, 2000).
Para o trabalhador, uma das vantagens do emprego de robôs é o fato de ele ser afastado do ambiente de soldagem, ou seja, da exposição a fumos e demais partículas, bem como dos gases e radiação emitidos, além do ruído gerado por alguns equipamentos e processos, o que faz com que esteja liberado do uso de equipamentos desconfortáveis de proteção – EPIs. Nos países altamente industrializados, com economia forte e estável, a oferta de profissionais qualificados de soldagem tem-se reduzido por a profissão de soldador ser considerada de baixo status , para a qual são apresentados ambientes pouco saudáveis, especialmente pelas gerações mais jovens. Assim, as empresas destes países têm tido que lidar com a dificuldade de recrutamento e manutenção de profissionais bem preparados (KADEFORS, 1999; BOEKHOLT, 2000; BOEKHOLT, 1999). Neste contexto, além de evitar que as pessoas sejam submetidas a um trabalho pesado e que oferece risco à saúde, a robotização permite às empresas manter sua produção em um mercado com dificuldade de encontrar e conservar profissionais qualificados.
Existe, porém, o receio do desemprego que a robotização dos processos de soldagem possa causar. No Brasil este temor aumenta, como nos demais países em desenvolvimento, pois o grau de escolaridade da população ainda é baixo, dificilmente permitindo que um trabalhador tenha acesso aos conhecimentos necessários para a programação de um robô. E o desemprego, para aqueles profissionais que não forem