
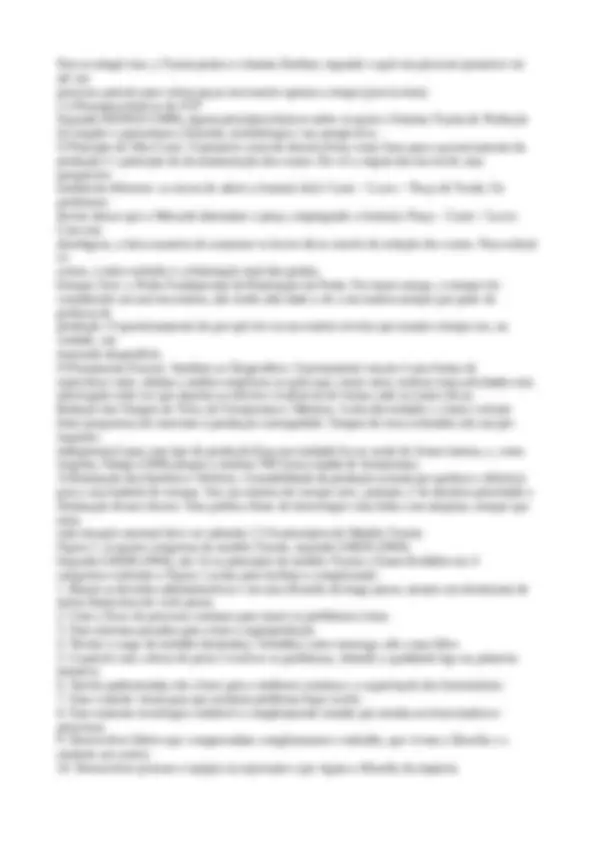
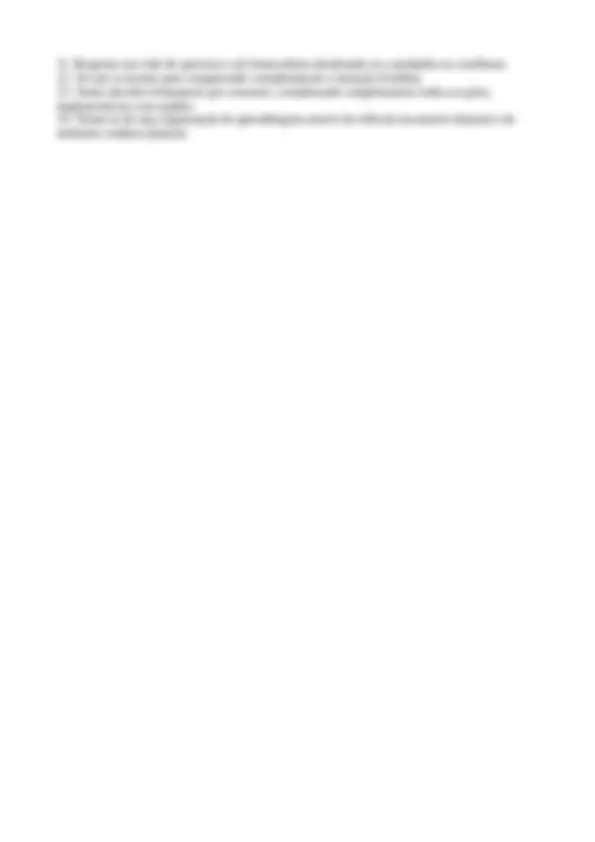
Estude fácil! Tem muito documento disponível na Docsity
Ganhe pontos ajudando outros esrudantes ou compre um plano Premium
Prepare-se para as provas
Estude fácil! Tem muito documento disponível na Docsity
Prepare-se para as provas com trabalhos de outros alunos como você, aqui na Docsity
Os melhores documentos à venda: Trabalhos de alunos formados
Prepare-se com as videoaulas e exercícios resolvidos criados a partir da grade da sua Universidade
Responda perguntas de provas passadas e avalie sua preparação.
Ganhe pontos para baixar
Ganhe pontos ajudando outros esrudantes ou compre um plano Premium
Comunidade
Peça ajuda à comunidade e tire suas dúvidas relacionadas ao estudo
Descubra as melhores universidades em seu país de acordo com os usuários da Docsity
Guias grátis
Baixe gratuitamente nossos guias de estudo, métodos para diminuir a ansiedade, dicas de TCC preparadas pelos professores da Docsity
Perdas - Perdas
Tipologia: Notas de estudo
1 / 4
Esta página não é visível na pré-visualização
Não perca as partes importantes!
Com o recente anúncio que a Toyota passou a ser a maior montadora do mundo no primeiro trimeste de 2007 destronando a concorrente americana GM, que por 73 anos ocupava o posto, antecipando até as previsões dos analistas do assunto, fica mais importante a compreensão do Sistema Toyota de Produção (STP), a arma usada para alcançar o topo. Mas também, se tem notícias de que várias empresas, mesmo as japonesas, que tentam aplicar as técnicas como JIT, kanban, SMED, TPM, etc., não têm conseguido os resultados esperados. Dessa forma, torna-se necessário a abordagem sistêmica para que se possa compreender, adaptar e recriar o sistema de acordo com a realidade de cada empresa. LIKER (2004) obteve a resposta de Fujio Cho, então presidente da Toyota Motor Company, que aprendeu o Modelo Toyota com um dos seus criadores, Taiichi Ohno para o notável sucesso da Toyota: “ A chave para o modelo Toyota e o que a faz sobressair ser não é nenhum dos elementos individuais… Mas o importante é ter todos os elementos de unidos como um sistema. Eles devem ser postos em prática como todos os dias de uma maneira muito sistemática não isoladamente." WOMACK e JONES (1998) definem a produção enxuta como um processo de cinco passos: definir o valor do cliente, definir o fluxo de valor, fazê-lo "Fluir", a "Puxar" a partir do cliente e lutar pela excelência. 1.1 Os tipos de perdas Segundo SHINGO (1996) o Sistema Toyota de Produção (STP) “é um sistema que visa a eliminação tota de perdas”. Por muito tempo o STP foi confundido com o sistema Kanban que é um meiopara se chegar ao just-in-time (JIT) um dos pilares do STP. A Toyota identificou sete grandes tipos de perdas sem agregação de valor em processos administrativos ou de produção. Há um oitavo tipo de perda, incluído por LIKER (2004):
de pessoal e de estoque e com custos de transporte devido ao estoque excessivo.
peças. Geram-se perdas quando se oferecem produtos com qualidade superior à que é necessária.
durante o trabalho, tais como procurar, pegar ou empilhar peças, ferramentas, etc.
longas distâncias, criação de transporte ineficiente ou movimentação de materiais, peças ou produtos acabados para dentro ou fora do estoque ou entre processos.
acabados, causando lead-times mais longos, obsolescência, produtos danificados, custos de transporte e de armazenagem e atrasos.
substituir a produção e inspecionar significam perdas de manuseio, tempo e esforço.
automática ou que ficam esperando pelo próximo passo no processamento.
melhorias e oportunidades de aprendizagem por não envolver ou ouvir seus funcionários. 1.2 Just in Time e Autonomação Reafirmando a base do STP é a eliminação total do desperdício. Para atingir este objetivo, surgiram os pilares deste sistema, o JIT (just in time) e a Autonomação (automação agregada à autonomia). Just in time significa produzir o produto necessário na quantidade necessária no momento necessário. A relação entre clientes e fornecedores internos e externos é alterada, pois o fornecedor deverá proteger seu cliente de produtos somente na quantidade e no momento que esses forem utilizados pelo processo do cliente, o que implica entregas frequentes em quantidades pequenas, para que não haja a formação de estoques de matéria-prima e de produtos em processo. A propagação dessa atitude por toda empresa implicará em uma significativa redução de custo, como afirma MONDEN (1984): "Se o JIT é realizado em toda empresa, inventários desnecessários na fábrica são completamente eliminados, tornando almoxarifados e depósitos desnecessários. O custo de manter estoque é reduzido e a rotatividade do capital de giro aumentada". A automação pode ser interpretada como um controle autônomo de defeitos. Ainda de acordo com MONDEN (1984), apesar da autonomação envolver algum tipo de automação, ela não é limitado processo da máquina, e é utilizada em conjunto com a operação manual. É predominantemente uma técnica para detectar e corrigir defeitos de produção e através de um dispositivo para detectar anormalidades ou defeitos (poka-yoke), aliada a uma maior autonomia dada aos trabalhadores de chão de fábrica, que têm liberdade para buscar soluções para problemas de produção e até mesmo a possibilidade de parar linha ou a máquina quando a normalidade do defeitos ocorre. Desta forma, a automação apóia o JIT, pois impede fabricação de produtos defeituosos, elimina a superprodução e pára automaticamente no caso de anormalidades da linha, permitindo que a situação seja investigada. Outra vantagem da autonomação é a possibilidade de se valer do sistema operários não só para se evitar a produção defeituosa, e portanto, o desperdício, mas também para evitar que os problemas se repitam. 1.3 Produção em Massa versus Produção EnxutaSegundo OHNO (1997), fazer grandes lotes de uma única peça – isto é, produzir uma grande quantidade de peças sem uma única troca de matriz – ainda é hoje uma regra de consenso de produção. Esta é a chave do sistema de produção em massa de Ford. A indústria automotiva Americana tem mostrado continuamente que a produção em massa planejada tem o maior efeito na redução de custos. O Sistema Toyota de Produção toma o curso inverso. O slogan de produção é; “produção em pequenos lotes e troca rápida de ferramentas”. O Sistema Ford preconiza os grandes lotes, lida com grandes quantidades, e produz muito inventário. Por contraste, o STP trabalha com a premissa de eliminar totalmente a superprodução gerada pelo inventário e custos relacionados a operários, propriedade e instalações necessarias à gestão do inventário.