
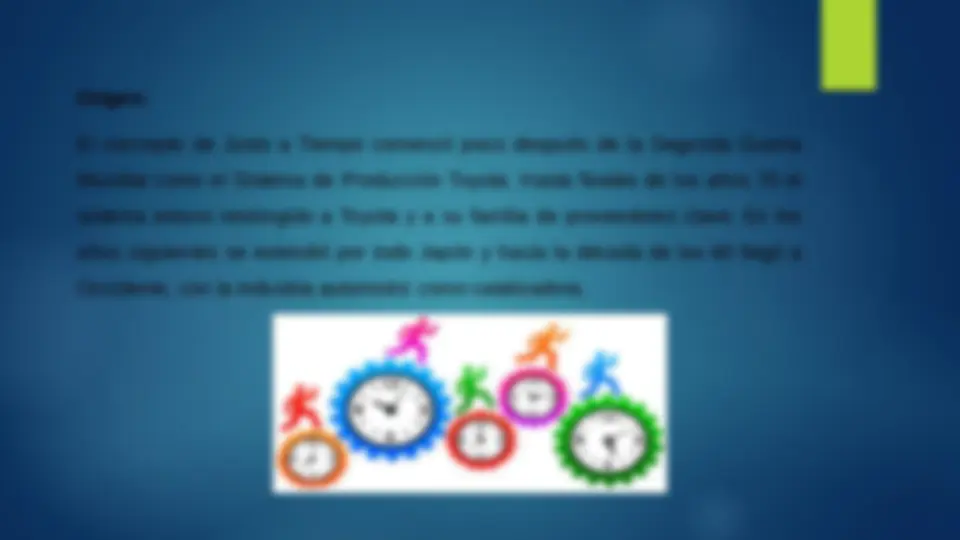
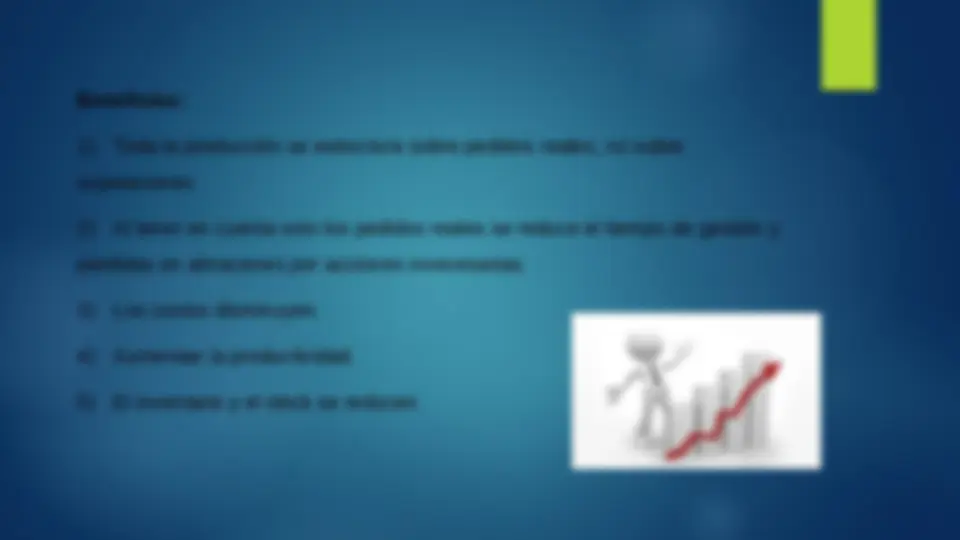
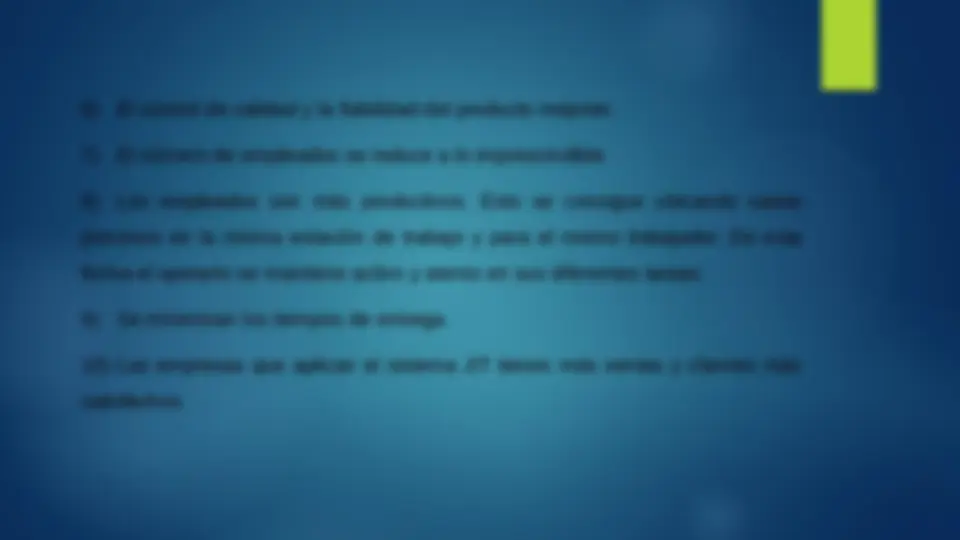
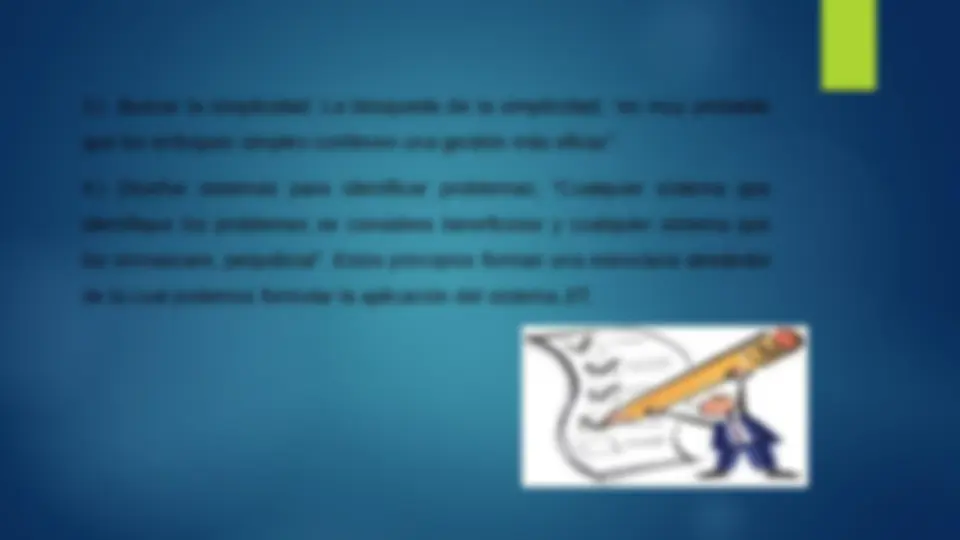
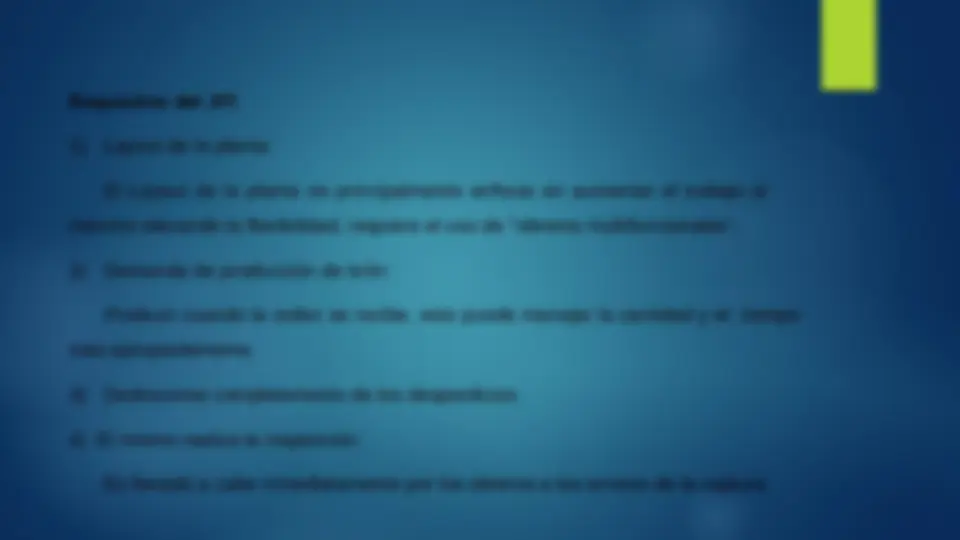
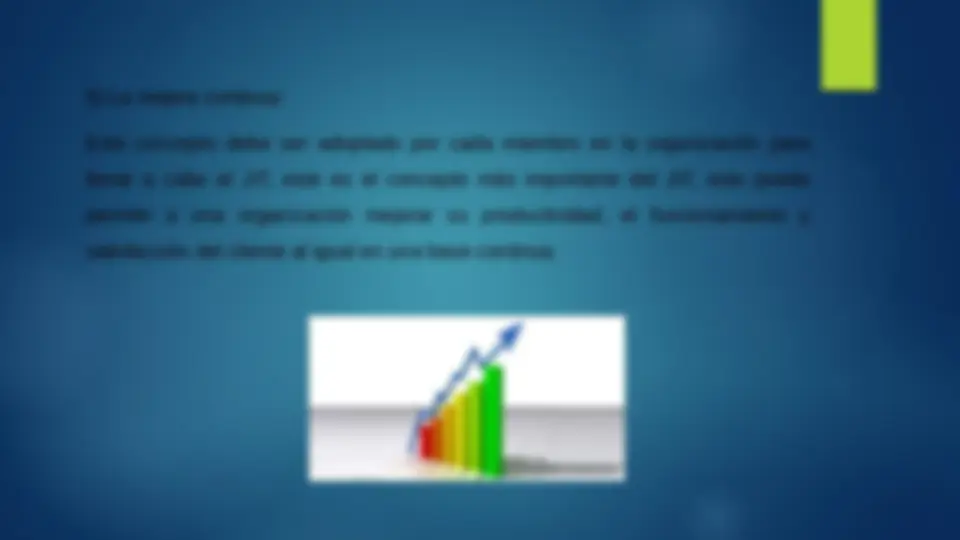
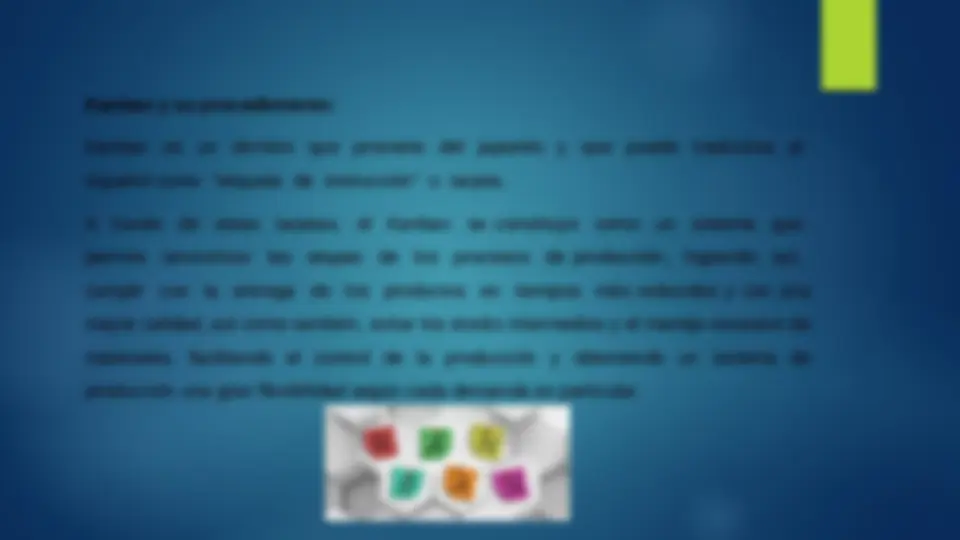
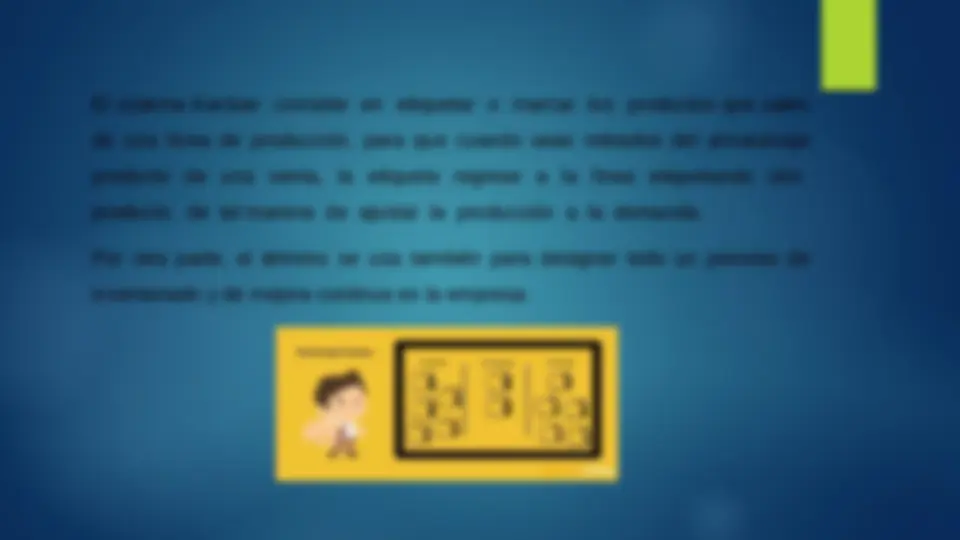
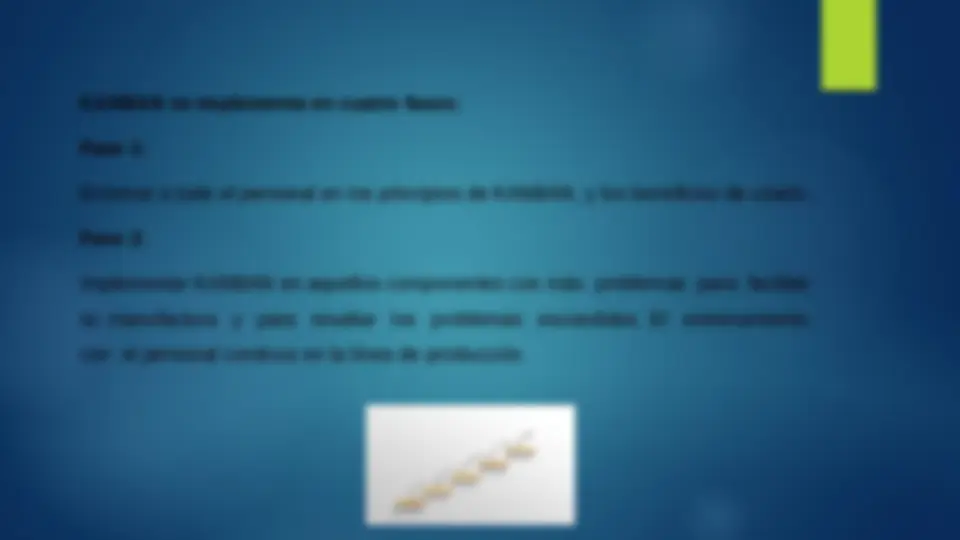
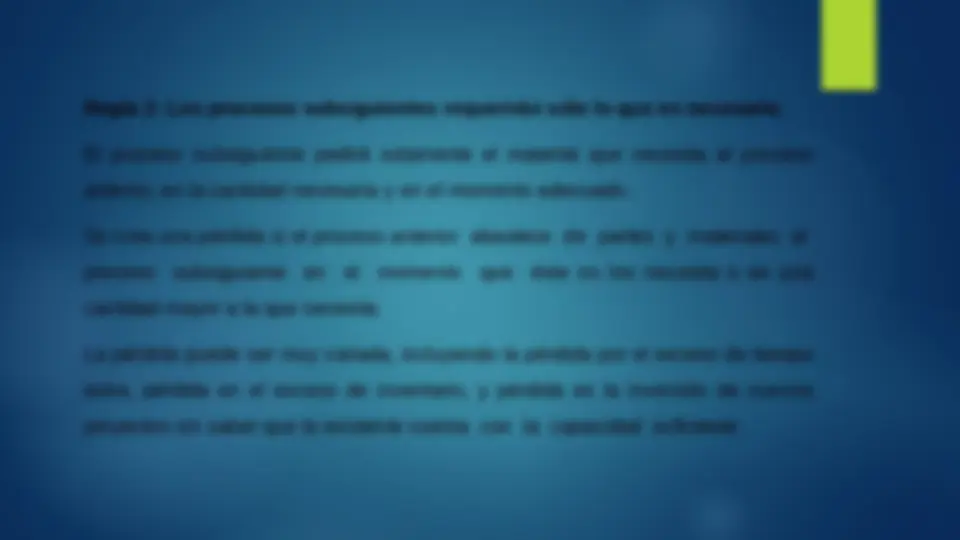
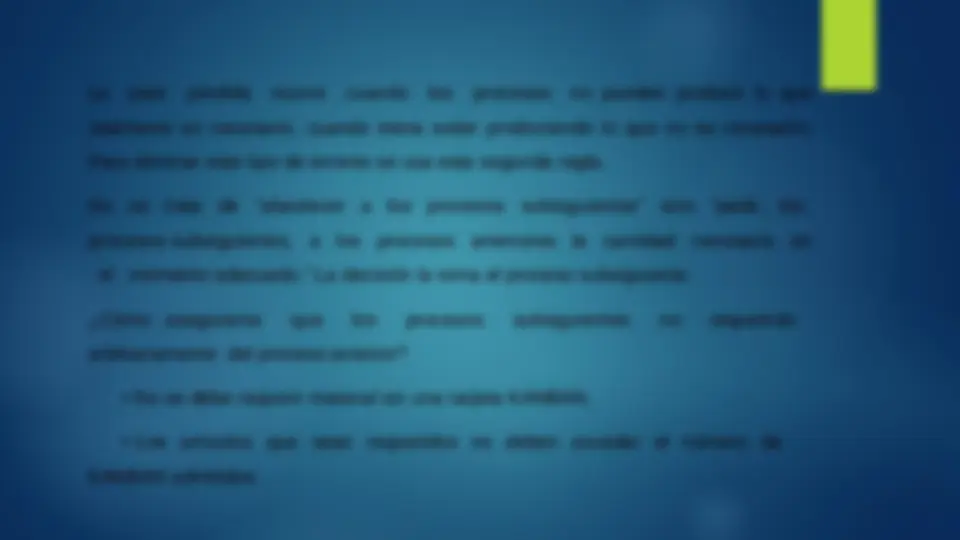
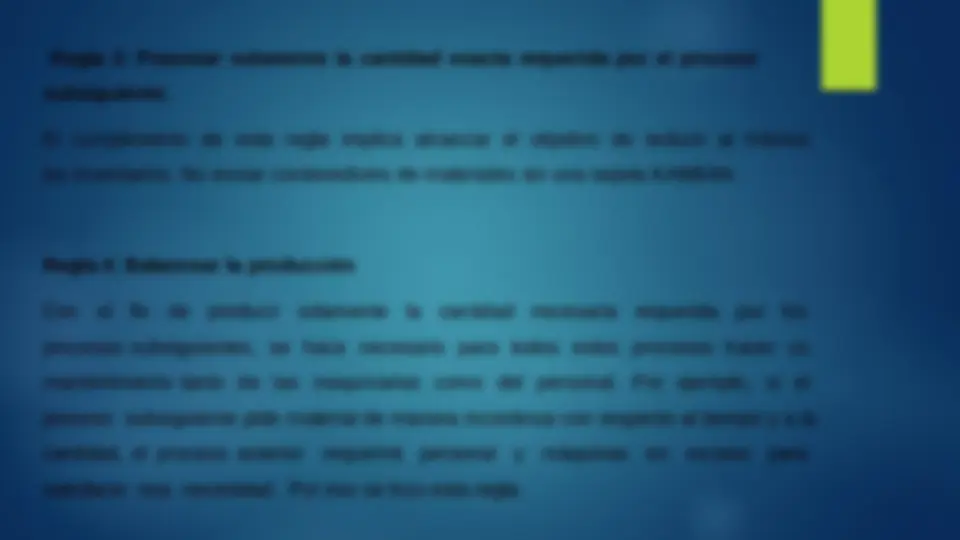
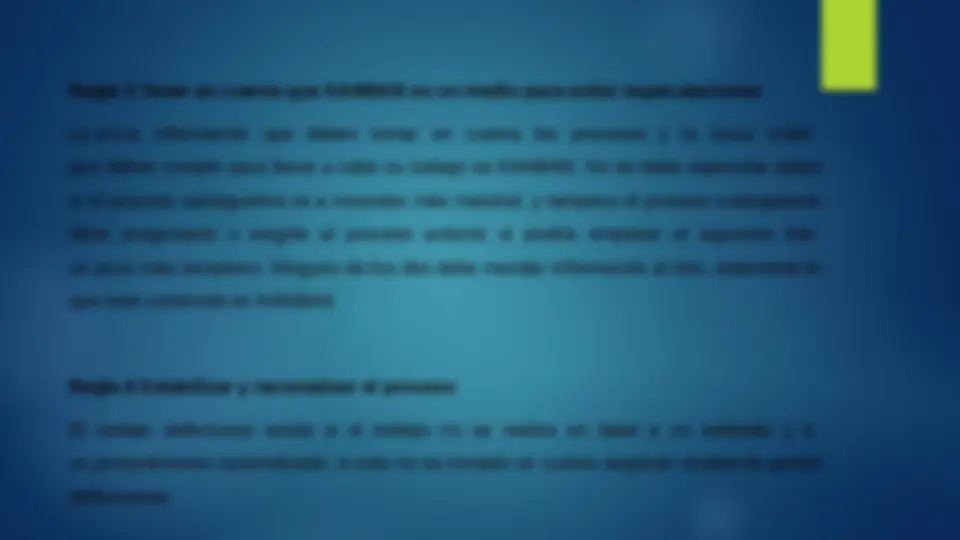
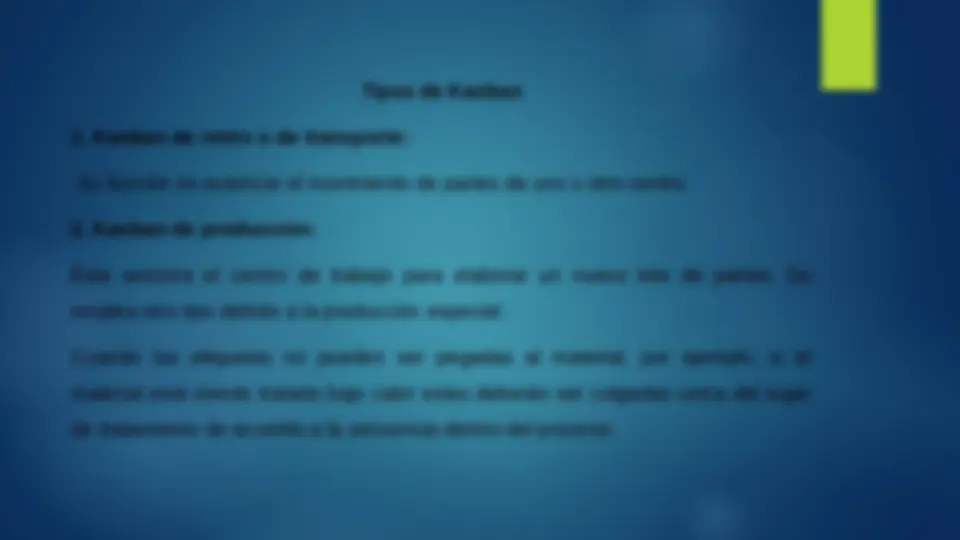
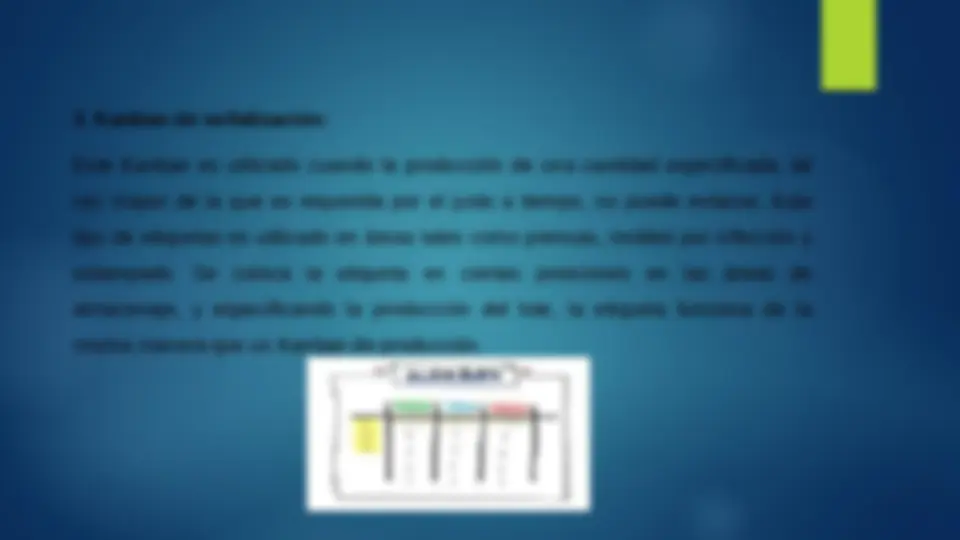
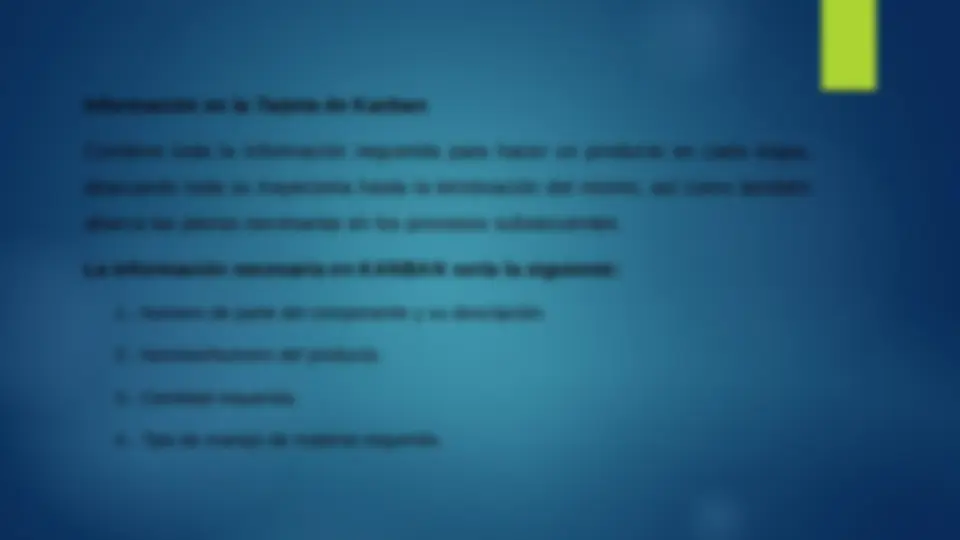
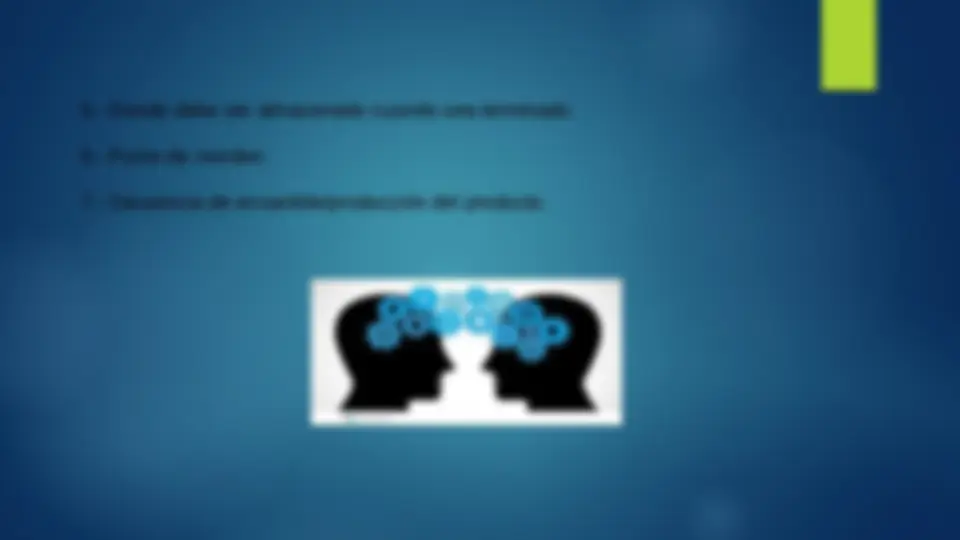
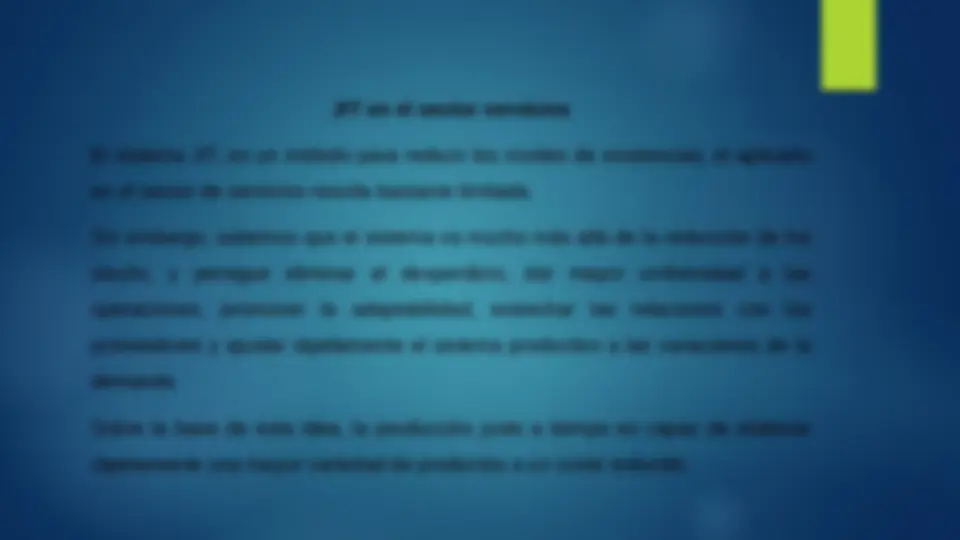
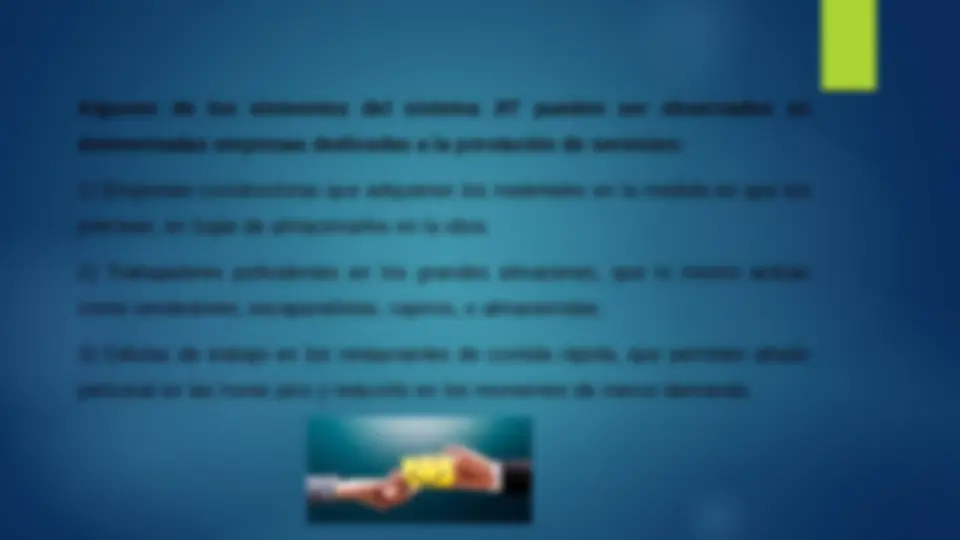
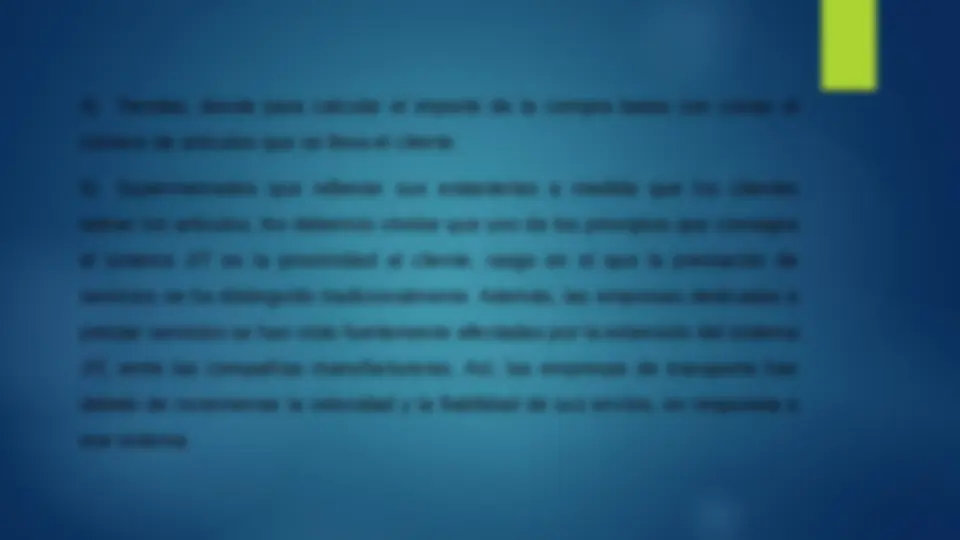
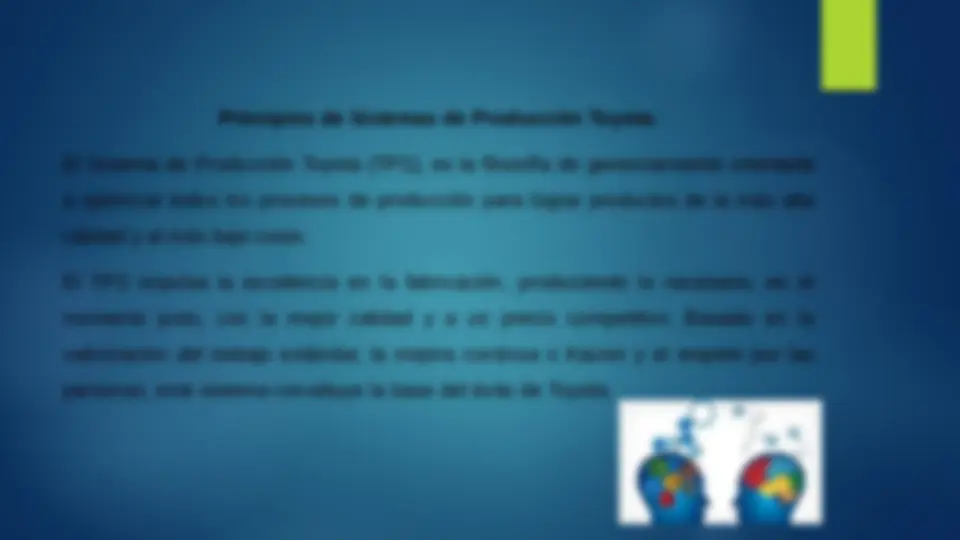
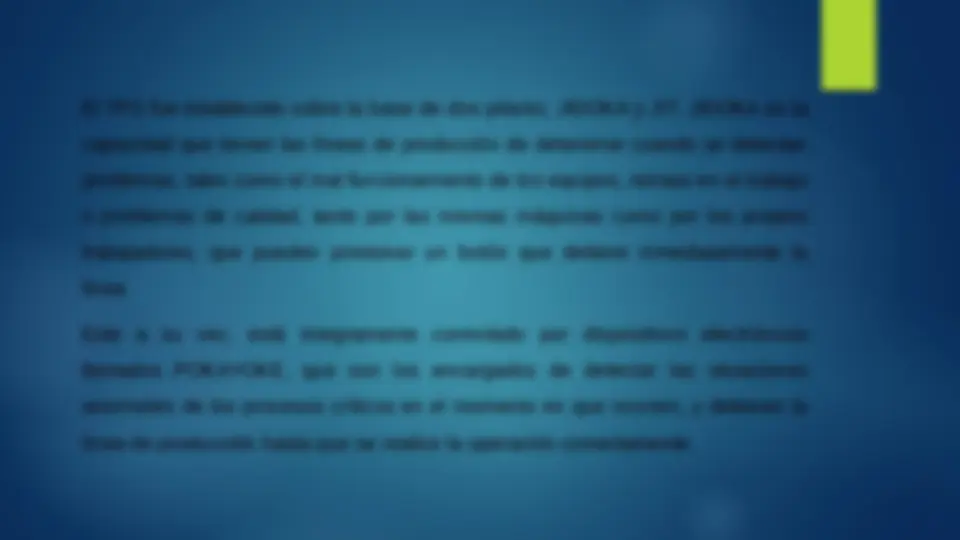
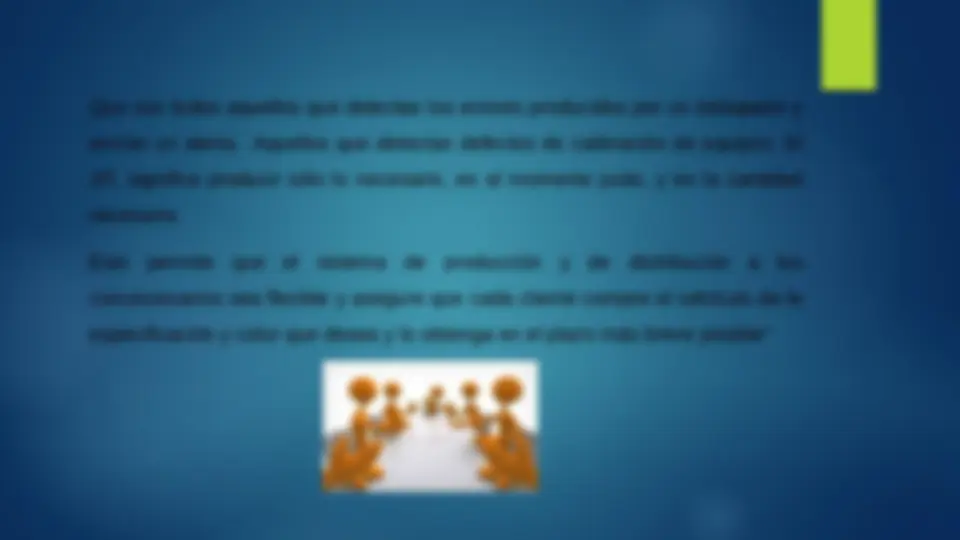
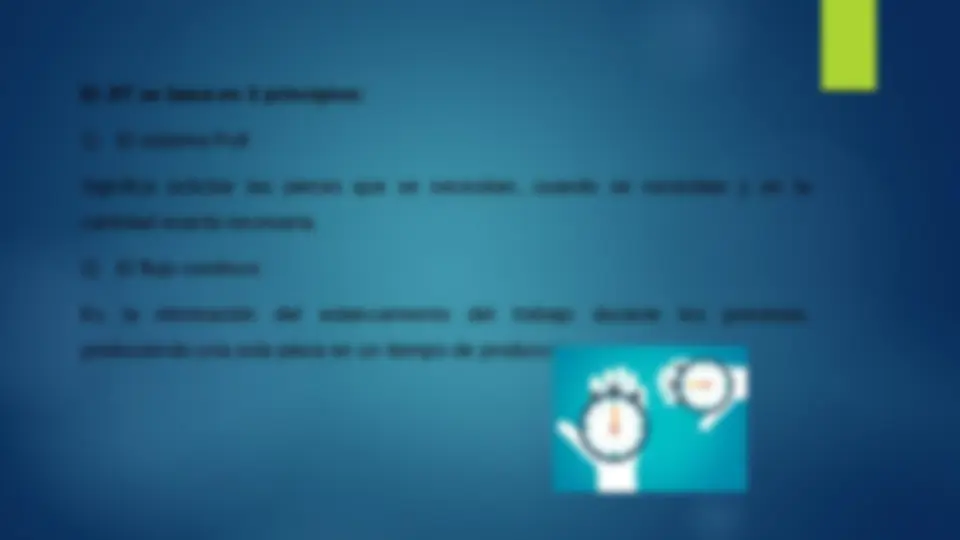
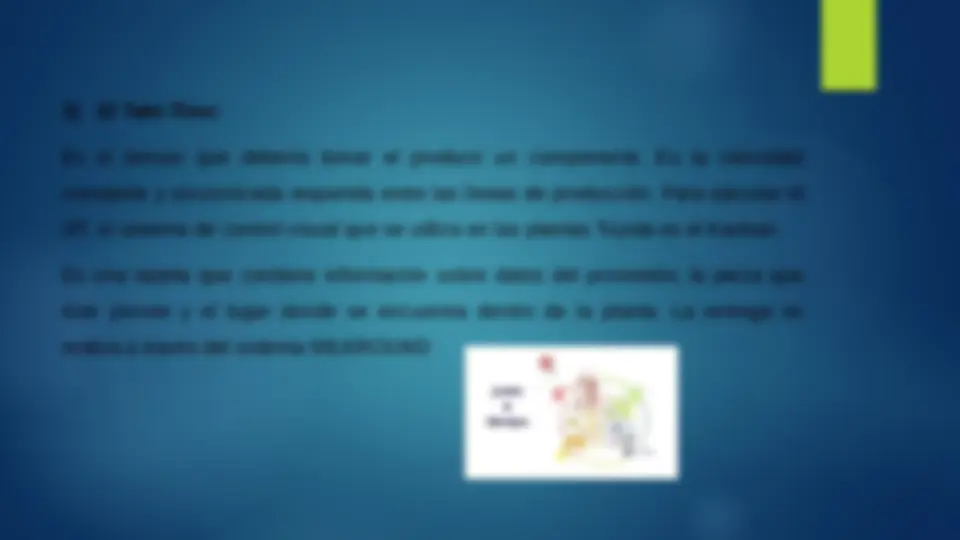
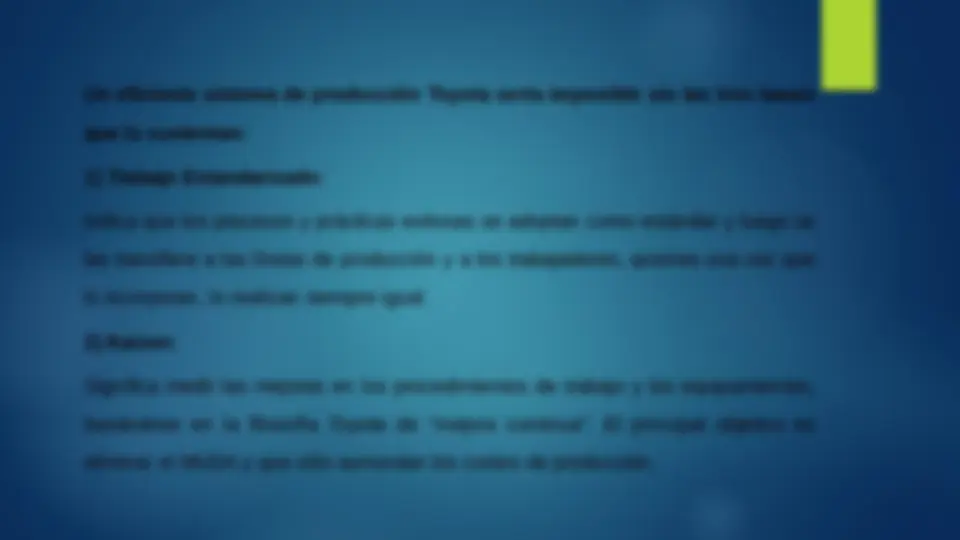
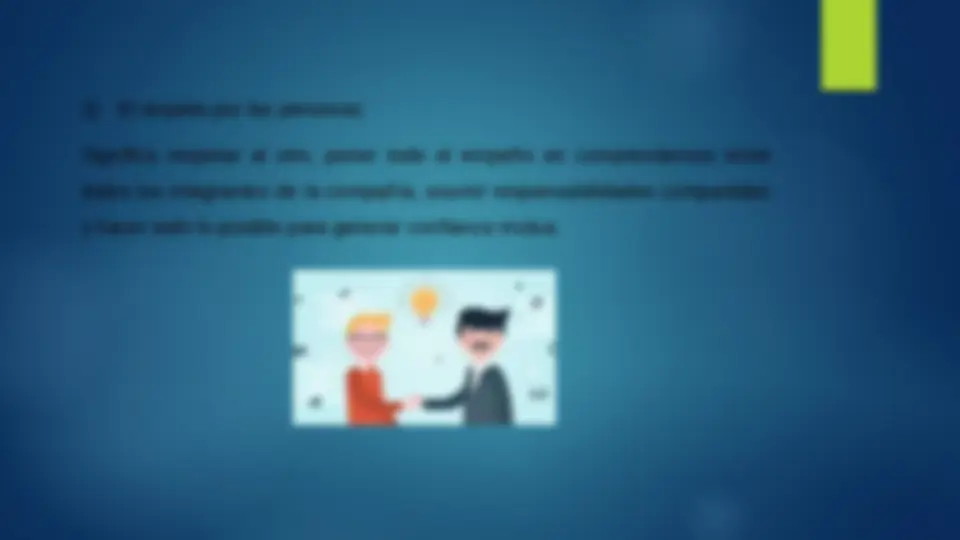
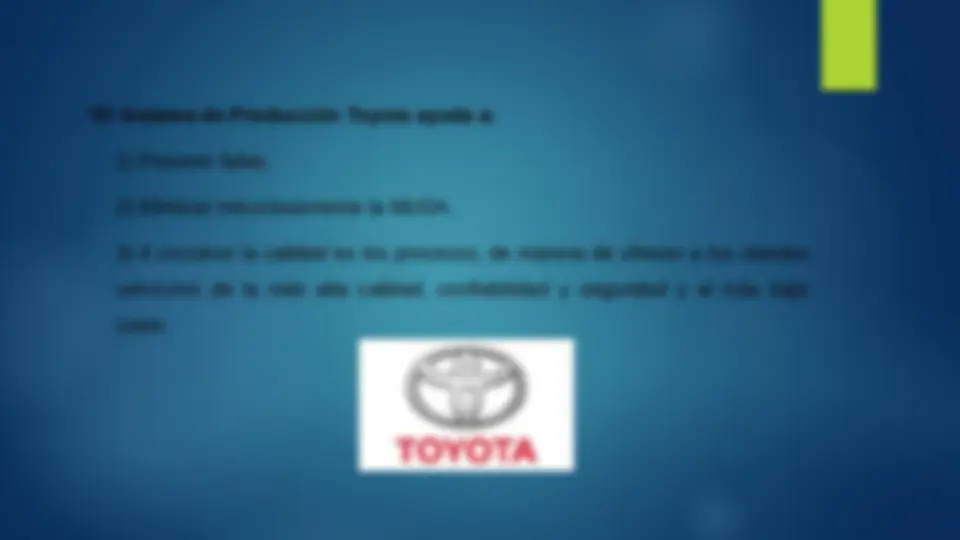
Prepara tus exámenes y mejora tus resultados gracias a la gran cantidad de recursos disponibles en Docsity
Gana puntos ayudando a otros estudiantes o consíguelos activando un Plan Premium
Prepara tus exámenes
Prepara tus exámenes y mejora tus resultados gracias a la gran cantidad de recursos disponibles en Docsity
Prepara tus exámenes con los documentos que comparten otros estudiantes como tú en Docsity
Los mejores documentos en venta realizados por estudiantes que han terminado sus estudios
Estudia con lecciones y exámenes resueltos basados en los programas académicos de las mejores universidades
Responde a preguntas de exámenes reales y pon a prueba tu preparación
Consigue puntos base para descargar
Gana puntos ayudando a otros estudiantes o consíguelos activando un Plan Premium
Comunidad
Pide ayuda a la comunidad y resuelve tus dudas de estudio
Descubre las mejores universidades de tu país según los usuarios de Docsity
Ebooks gratuitos
Descarga nuestras guías gratuitas sobre técnicas de estudio, métodos para controlar la ansiedad y consejos para la tesis preparadas por los tutores de Docsity
Explicación de la unidad 5 de justo a tiempo
Tipo: Diapositivas
1 / 36
Esta página no es visible en la vista previa
¡No te pierdas las partes importantes!
Este sistema también es conocido por los nombres: Método Toyota. Inventario Justo a Tiempo. JIT son las siglas del método en inglés (Just in Time). La metodología Justo a Tiempo es una filosofía industrial que puede resumirse en fabricar los productos estrictamente necesarios, en el momento preciso y en las cantidades debidas: hay que comprar o producir solo lo que se necesita y cuando se necesita.
Beneficios:
Características del sistema Justo a Tiempo: 1.) Poner en evidencia los problemas fundamentales: Reducir el nivel de las existencias, descubre los problemas, cuando los problemas surgen en algunas empresas, la respuesta era aumentar las existencias para tapar el problema. 2.) Eliminar despilfarros: Implica eliminar todas las actividades que no añaden valor al producto con lo que se reduce costes, mejora la calidad, reduce los plazos de fabricación y aumenta el nivel de servicio al cliente.
3.) Buscar la simplicidad: La búsqueda de la simplicidad, “es muy probable que los enfoques simples conlleven una gestión más eficaz”. 4.) Diseñar sistemas para identificar problemas: “Cualquier sistema que identifique los problemas se considera beneficioso y cualquier sistema que los enmascare, perjudicial”. Estos principios forman una estructura alrededor de la cual podemos formular la aplicación del sistema JIT.
Elementos de un sistema JIT: La filosofía JIT cuenta con siete elementos: seis internos y uno externo: Internos: La filosofía Justo a Tiempo en sí misma La calidad en la fuente. Carga fabril uniforme Operaciones coincidentes Tiempo mínimo de alistamiento de las máquinas Kanban
Kanban y su procedimiento: Kanban es un término que proviene del japonés y que puede traducirse al español como “etiqueta de instrucción” o tarjeta. A través de estas tarjetas, el Kanban se constituye como un sistema que permite sincronizar las etapas de los procesos de producción, logrando así, cumplir con la entrega de los productos en tiempos más reducidos y con una mayor calidad, así como también, evitar los stocks intermedios y el manejo excesivo de materiales, facilitando el control de la producción y obteniendo un sistema de producción una gran flexibilidad según cada demanda en particular.
El sistema Kanban consiste en etiquetar o marcar los productos que salen de una línea de producción, para que cuando sean retirados del almacenaje producto de una venta, la etiqueta regrese a la línea etiquetando otro producto, de tal manera de ajustar la producción a la demanda. Por otra parte, el término se usa también para designar todo un proceso de inventariado y de mejora continua en la empresa.
Fase 3: Implementar KANBAN en el resto de los componentes, esto no debe ser problema ya que para esto los operadores ya han visto las ventajas de KANBAN, se deben tomar en cuenta todas las opiniones de los operadores ya que ellos son los que mejor conocen el sistema, es importante informarles cuando se va estar trabajando en su área. Fase 4: Esta fase consiste en la revisión del sistema KANBAN, los puntos de reorden y los niveles de reorden, es importante tomar en cuenta las siguientes recomendaciones para el funcionamiento correcto de KANBAN: A) Ningún trabajo debe ser hecho fuera de secuencia. B) Si se encuentra algún problema notificar al supervisor inmediatamente.
Reglas de KANBAN: Regla 1: No se debe mandar material defectuoso a los procesos subsiguientes. El procesamiento de materiales defectuosos implica costos tales como inversión en materiales, equipo y mano de obra que no va a poder ser vendida. Este es el mayor desperdicio de todos. Si se encuentra un defecto, se deben tomar medidas antes que todo, para prevenir que este NO VUELVA A OCURRIR. Observaciones:
La peor pérdida ocurre cuando los procesos no pueden producir lo que realmente es necesario, cuando éstos están produciendo lo que no es necesario. Para eliminar este tipo de errores se usa esta segunda regla. No se trata de “abastecer a los procesos subsiguientes” sino “pedir, los procesos subsiguientes, a los procesos anteriores la cantidad necesaria en el momento adecuado.” La decisión la toma el proceso subsiguiente. ¿Cómo asegurarse que los procesos subsiguientes no requerirán arbitrariamente del proceso anterior?
Regla 3: Procesar solamente la cantidad exacta requerida por el proceso subsiguiente. El cumplimiento de esta regla implica alcanzar el objetivo de reducir al mínimo los inventarios. No enviar contenedores de materiales sin una tarjeta KANBAN. Regla 4: Balancear la producción Con el fin de producir solamente la cantidad necesaria requerida por los procesos subsiguientes, se hace necesario para todos estos procesos hacer un mantenimiento tanto de las maquinarias como del personal. Por ejemplo, si el proceso subsiguiente pide material de manera incontinua con respecto al tiempo y a la cantidad, el proceso anterior requerirá personal y máquinas en exceso para satisfacer esa necesidad. Por eso se hizo esta regla.