
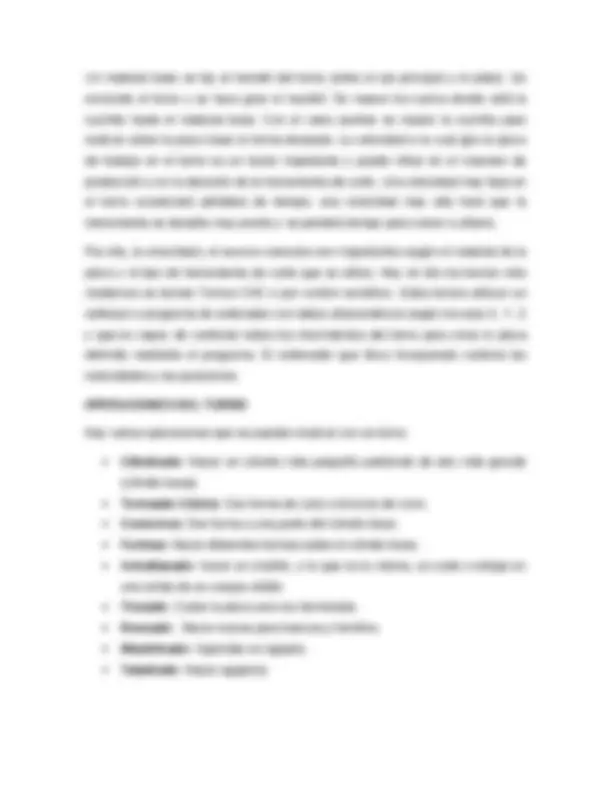
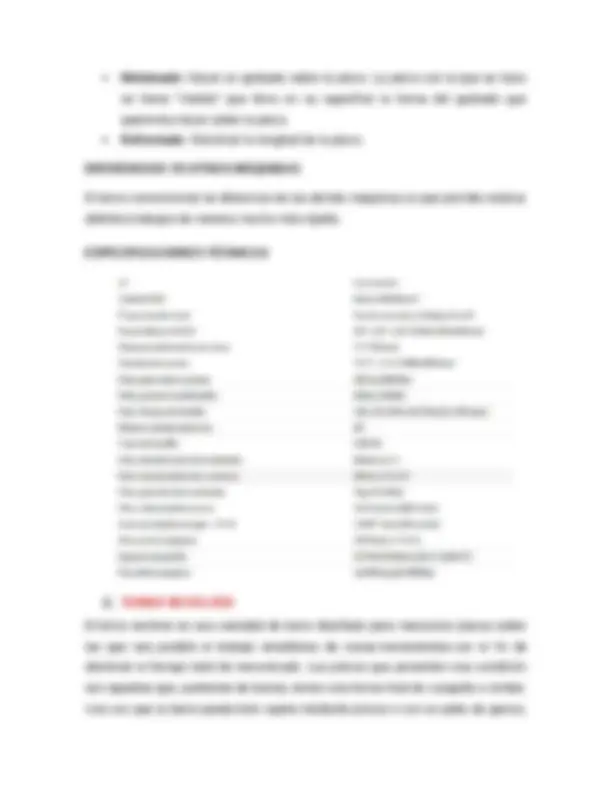
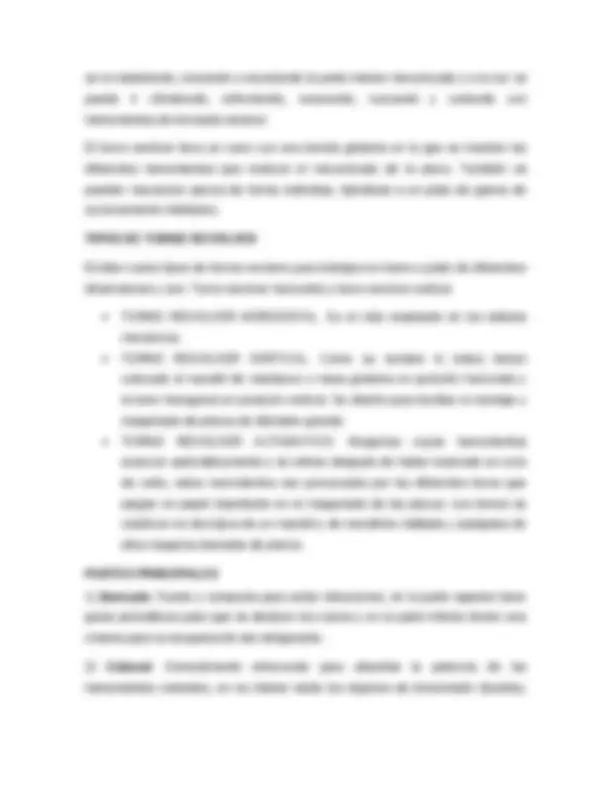
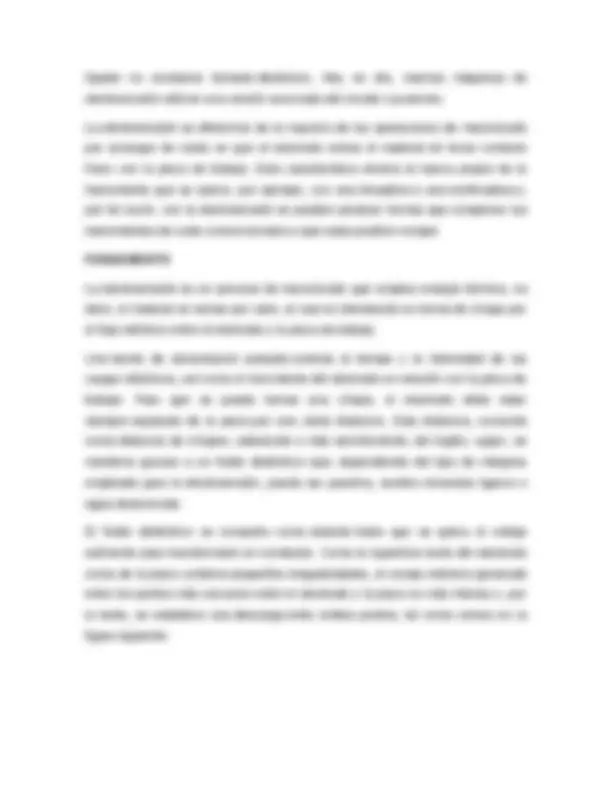
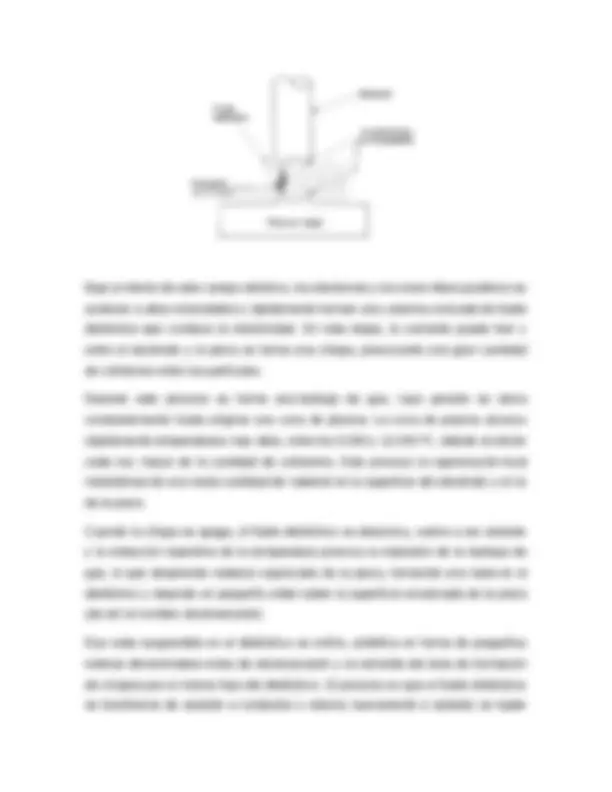
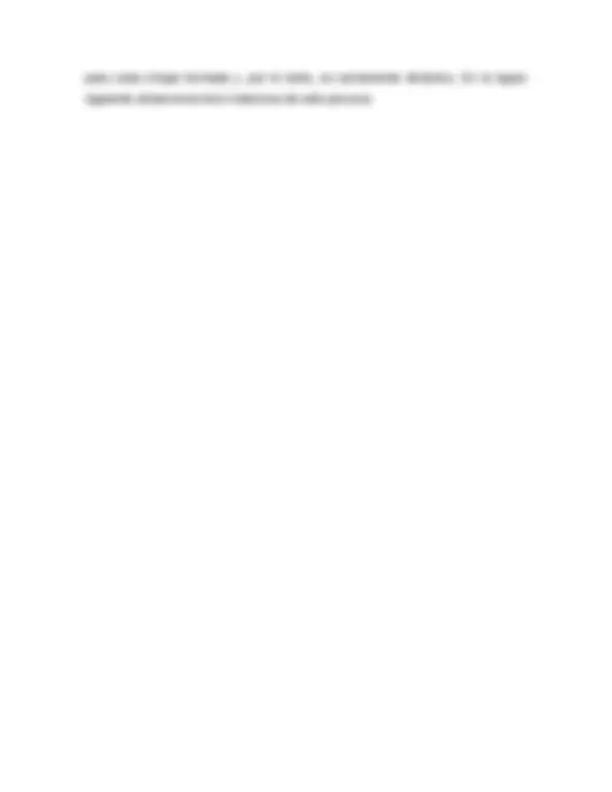
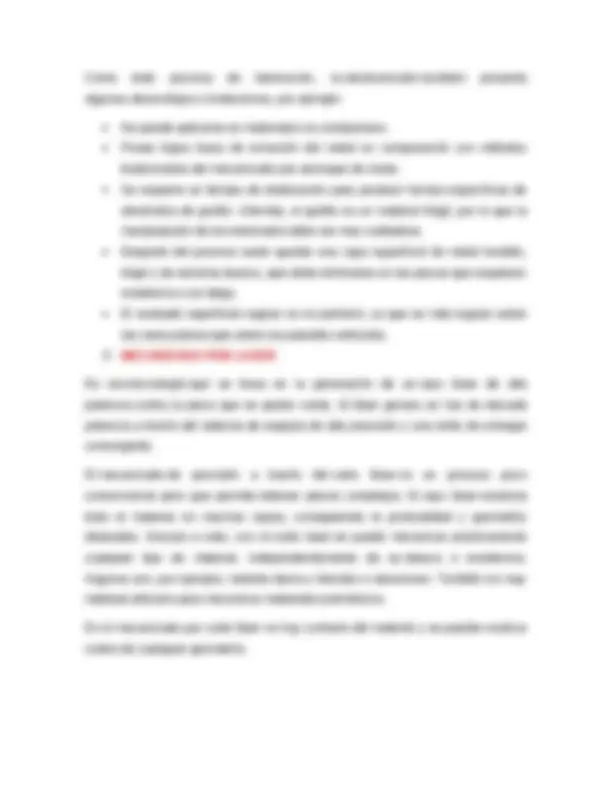
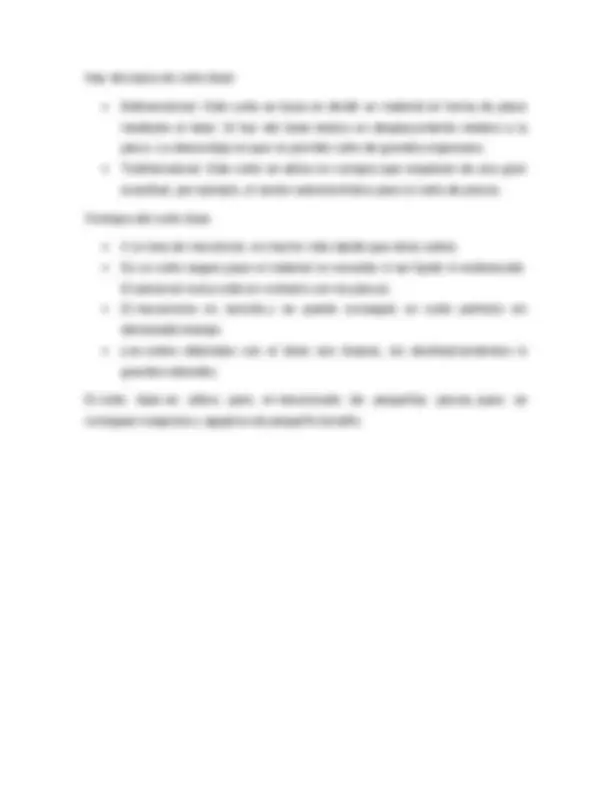
Prepara tus exámenes y mejora tus resultados gracias a la gran cantidad de recursos disponibles en Docsity
Gana puntos ayudando a otros estudiantes o consíguelos activando un Plan Premium
Prepara tus exámenes
Prepara tus exámenes y mejora tus resultados gracias a la gran cantidad de recursos disponibles en Docsity
Prepara tus exámenes con los documentos que comparten otros estudiantes como tú en Docsity
Los mejores documentos en venta realizados por estudiantes que han terminado sus estudios
Estudia con lecciones y exámenes resueltos basados en los programas académicos de las mejores universidades
Responde a preguntas de exámenes reales y pon a prueba tu preparación
Consigue puntos base para descargar
Gana puntos ayudando a otros estudiantes o consíguelos activando un Plan Premium
Comunidad
Pide ayuda a la comunidad y resuelve tus dudas de estudio
Descubre las mejores universidades de tu país según los usuarios de Docsity
Ebooks gratuitos
Descarga nuestras guías gratuitas sobre técnicas de estudio, métodos para controlar la ansiedad y consejos para la tesis preparadas por los tutores de Docsity
Contiene algunas partes de los tipos de tornos y lo subí para descargar :))
Tipo: Resúmenes
1 / 14
Esta página no es visible en la vista previa
¡No te pierdas las partes importantes!
El torno convencional es una herramienta diseñada para mecanizar piezas que poseen formas geométricas. Estas máquinas hacen girar la pieza mientras varias herramientas que se encargan del corte se encarga de empujar la herramienta contra la superficie, cortándola de acuerdo con las especificaciones. Este tipo de herramienta es una de las más usadas debido a que permite realizar múltiples trabajos. Además, que, es de fácil uso ya que las herramientas suelen prepararse en líneas de tiempo bastante corta y de una forma muchísimo más simple. USOS COMUNES Pueden ser usados para infinidades de operaciones. No obstante, los usos más comunes que se suelen darle son los siguientes: refrenado, tornado cilíndrico, tornado cónico, corte de formas, corte de metal, etc. PARTES DEL TORNO Bancada : es su estructura y suele ser un gran cuerpo de fundición, sirve de soporte y guía para las otras partes del torno. Eje principal y plato : sobre este eje se coloca la pieza para que gire, en un extremo lleva un eje terminado en punta que es móvil, llamado contrapunto, para sujetar la pieza por un punto, en el otro extremo se sujeta la pieza con un plato. El plato se puede cambiar mediante el husillo. El torno dispone de varios platos para la sujeción de la pieza a mecanizar y que la hará girar en torno a un eje. La pieza queda sujeta por un extremo por el plato y por el otro por la punta del contrapunto. La pieza se coloca en el plato y se mueve el contrapunto hasta que apriete la pieza, el movimiento de corte y de la pieza lineales se hacen mediante los carros.
Carro Portaherramientas : son los carros que permiten desplazar la herramienta de corte, hay 3 carros diferentes: Carro Longitudinal o Principal : este se mueve a lo largo de la bancada o sea hacia la izquierda o a la derecha. Produce el movimiento de avance de la pieza, desplazándose en forma manual o automática paralelamente al eje del torno. Se mueve a lo largo de la bancada, sobre la cual se apoya. Sobre este carro está montado el carro transversal. Carro Transversal : se mueve hacia adelante o hacia atrás perpendicular al carro principal. Es utilizado para dar la profundidad. Se mueve perpendicularmente al eje del torno en forma manual, girando la manivela de avance transversal o embragando la palanca de avance transversal automático. Sobre este carro está montado el carro orientable o carro auxiliar. Carro Auxiliar o Portaherramientas : es una base giratoria a 360° y sirve principalmente para hacer conicidades o penetrar la herramienta con cierto ángulo. El carro auxiliar sólo puede moverse manualmente girando la manivela de tornillo para su avance. El buril o herramienta cortante se sujeta en la torreta portaherramientas que está situada sobre el carro auxiliar. La Torreta Portaherramientas : ubicada sobre el carro auxiliar permite montar varias herramientas en la misma operación de torneado y girarla para determinar el ángulo de incidencia en el material. Todo el conjunto de los carros, se apoya en una caja de fundición llamada Delantal o Carro Portaherramientas, que tiene por finalidad contener en su interior los dispositivos que le transmiten los movimientos a los carros. Caja Norton : sirve para ajustar las revoluciones de las velocidades mediante unas palancas que accionan un conjunto de engranajes que se encuentran en el interior de la caja. FUNCIONAMIENTO DEL TORNO
Moleteado: Hacer un grabado sobre la pieza. La pieza con la que se hace se llama "moleta" que lleva en su superficie la forma del grabado que queremos hacer sobre la pieza. Refrentado : Disminuir la longitud de la pieza. DIFERENCIAS VS OTRAS MÁQUINAS El torno convencional se diferencia de las demás maquinas ya que permite realizar distintos trabajos de manera mucho más rápida. ESPECIFICACIONES TÉCNICAS
2. TORNO REVOLVER El torno revólver es una variedad de torno diseñado para mecanizar piezas sobre las que sea posible el trabajo simultáneo de varias herramientas con el fin de disminuir el tiempo total de mecanizado. Las piezas que presentan esa condición son aquellas que, partiendo de barras, tienen una forma final de casquillo o similar. Una vez que la barra queda bien sujeta mediante pinzas o con un plato de garras,
se va taladrando, roscando o escariando la parte interior mecanizada y a la vez se puede ir cilindrando, refrentando, ranurando, roscando y cortando con herramientas de torneado exterior. El torno revólver lleva un carro con una torreta giratoria en la que se insertan las diferentes herramientas que realizan el mecanizado de la pieza. También se pueden mecanizar piezas de forma individual, fijándolas a un plato de garras de accionamiento hidráulico. TIPOS DE TORNO REVOLVER Existen varios tipos de tornos revolver para trabajos en barra o plato de diferentes dimensiones y son: Torno revolver horizontal y torno revolver vertical. TORNO REVOLVER HORIZONTAL. Es el más empleado en los talleres mecánicos. TORNO REVOLVER VERTICAL. Como su nombre lo indica tienen colocado el mandril de mordazas o mesa giratoria en posición horizontal y la torre hexagonal en posición vertical. Se diseño para facilitar el montaje y maquinado de piezas de diámetro grande. TORNO REVOLVER AUTOMATICO. Maquinas cuyas herramientas avanzan automáticamente y se retiran después de haber realizado un ciclo de corte, estos movimientos son provocados por las diferentes levas que juegan un papel importante en el maquinado de las piezas. Los tornos se clasifican en dos tipos de un mandril y de mandriles múltiples, cualquiera de ellos maquina elevadas de piezas. PARTES PRINCIPALES
de las operaciones más ejecutadas en el Torno, con el fin de obtener formas cilíndricas definitivas (ejes y bujes) o también preparar el material para otras aplicaciones. Refrentado: Refrentar es hacer en el material una superficie plana perpendicular al eje del torno, mediante la acción de una herramienta de corte que se desplaza por medio del caro transversal. Esta operación es realizada en la mayoría de las piezas que se ejecutan en el torno, tales como: ejes, tornillos, tuercas y bujes. El refrentado sirve para obtener una cara de referencia o como paso previo al agujereado. Agujero de centro: Hacer agujero de centro es abrir un orificio de forma y dimensión determinadas, con una herramienta denominada broca de central. Esta operación se hace, en general, en materiales que necesitan ser trabajados entrepuntas o entreplato y punta. A veces se hace agujero de centro como paso previo para agujerear con broca común.
**3. PROCESADORA
líquido no conductor llamado dieléctrico. Hoy en día, muchas máquinas de electroerosión utilizan una versión avanzada del circuito Lazarenko. La electroerosión se diferencia de la mayoría de las operaciones de mecanizado por arranque de viruta en que el electrodo extrae el material sin tener contacto físico con la pieza de trabajo. Esta característica elimina la fuerza propia de la herramienta que se ejerce, por ejemplo, con una fresadora o una rectificadora y, por tal razón, con la electroerosión se pueden producir formas que romperían las herramientas de corte convencionales o que estas podrían romper. FUNDAMENTO La electroerosión es un proceso de mecanizado que emplea energía térmica, es decir, el material se extrae por calor, el cual es introducido en forma de chispa por el flujo eléctrico entre el electrodo y la pieza de trabajo. Una fuente de alimentación pulsada controla el tiempo y la intensidad de las cargas eléctricas, así como el movimiento del electrodo en relación con la pieza de trabajo. Para que se pueda formar una chispa, el electrodo debe estar siempre separado de la pieza por una cierta distancia. Esta distancia, conocida como distancia de chispeo, sobrecorte o más sencillamente, del inglés, «gap», se mantiene gracias a un fluido dieléctrico que, dependiendo del tipo de máquina empleada para la electroerosión, puede ser parafina, aceites minerales ligeros o agua desionizada. El fluido dieléctrico se comporta como aislante hasta que se aplica el voltaje suficiente para transformarlo en conductor. Como la superficie tanto del electrodo como de la pieza contiene pequeñas irregularidades, el campo eléctrico generado entre los puntos más cercanos entre el electrodo y la pieza es más intenso y, por lo tanto, se establece una descarga entre ambos puntos, tal como vemos en la figura siguiente:
para cada chispa formada y, por lo tanto, es sumamente dinámico. En la figura siguiente observamos tres instancias de este proceso.
Como todo proceso de fabricación, la electroerosión también presenta algunas desventajas o limitaciones, por ejemplo: No puede aplicarse en materiales no conductores. Posee bajas tasas de remoción del metal en comparación con métodos tradicionales del mecanizado por arranque de viruta. Se requiere un tiempo de elaboración para producir formas específicas de electrodos de grafito. Además, el grafito es un material frágil, por lo que la manipulación de los electrodos debe ser muy cuidadosa. Después del proceso suele quedar una capa superficial de metal fundido, frágil y de extrema dureza, que debe eliminarse en las piezas que requieran resistencia a la fatiga. EI acabado superficial rugoso no es perfecto, ya que es más rugoso sobre las caras planas que sobre Ias paredes verticales.
Hay dos tipos de corte láser: Bidimensional: Este corte se basa en dividir un material en forma de place mediante el láser. El haz del láser realiza un desplazamiento relativo a la pieza. La desventaja es que no permite corte de grandes espesores. Tridimensional: Este corte se utiliza en campos que requieren de una gran exactitud, por ejemplo, el sector automovilístico para el corte de piezas. Ventajas del corte láser A la hora de mecanizar, es mucho más rápido que otros cortes. Es un corte seguro pues el material no necesita ni ser fijado ni enderezado. El personal nunca está en contacto con las piezas. El mecanismo es sencillo y se puede conseguir un corte perfecto sin demasiado trabajo. Los cortes obtenidos con el láser son limpios, sin deshilachamientos ni grandes rebordes. El corte láser se utiliza para el mecanizado de pequeñas piezas, pues se consiguen esquinas y agujeros de pequeño tamaño.