
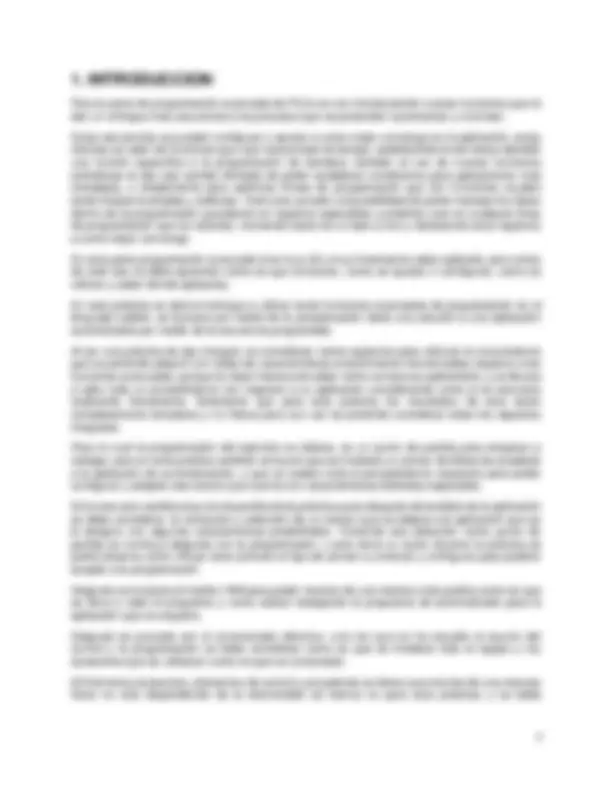
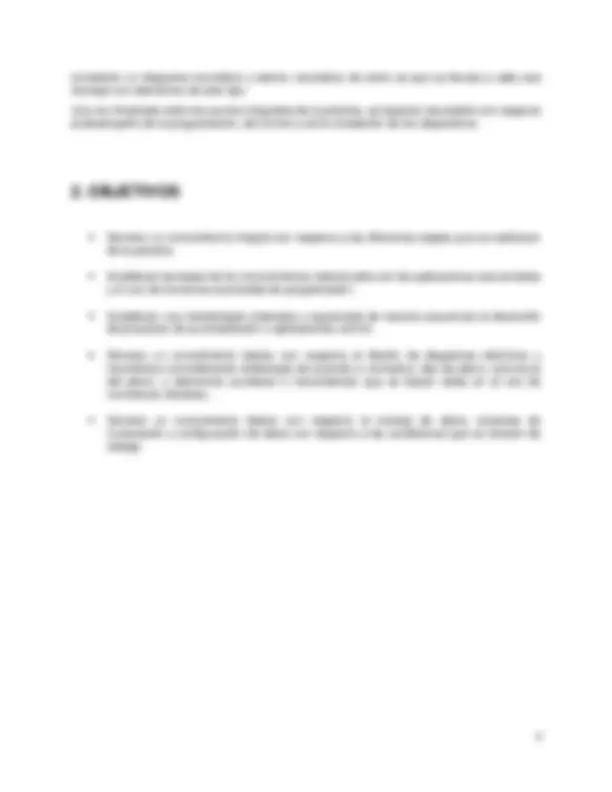
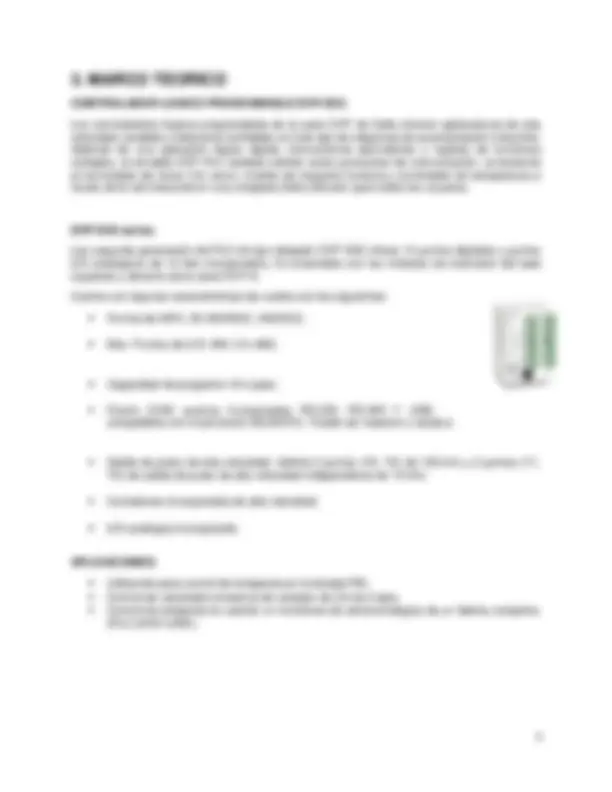
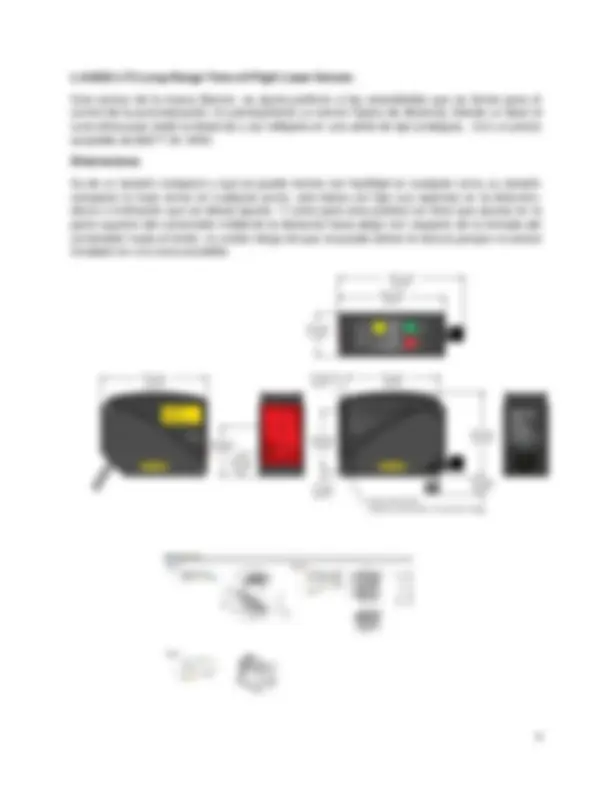
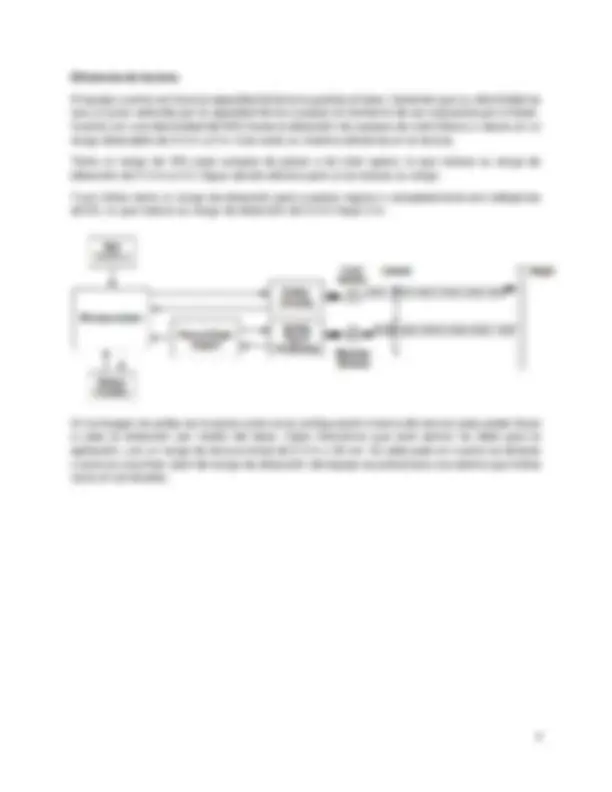
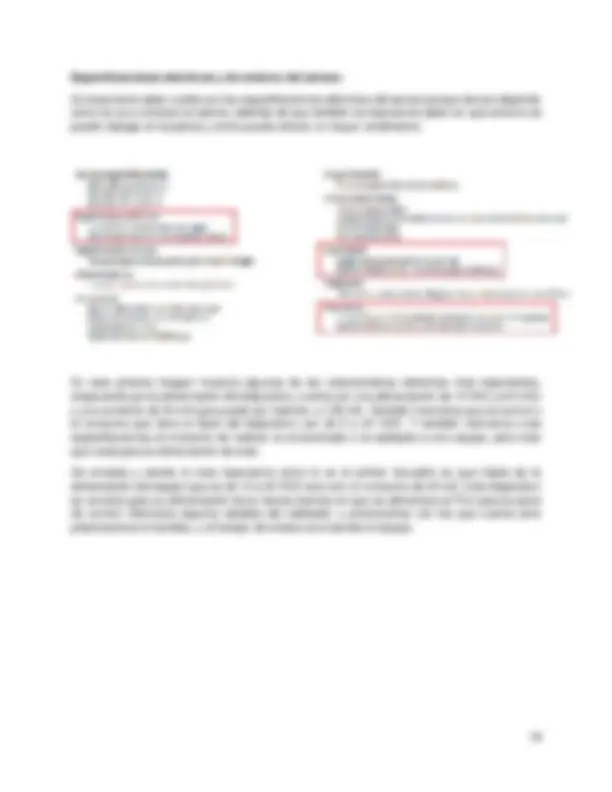

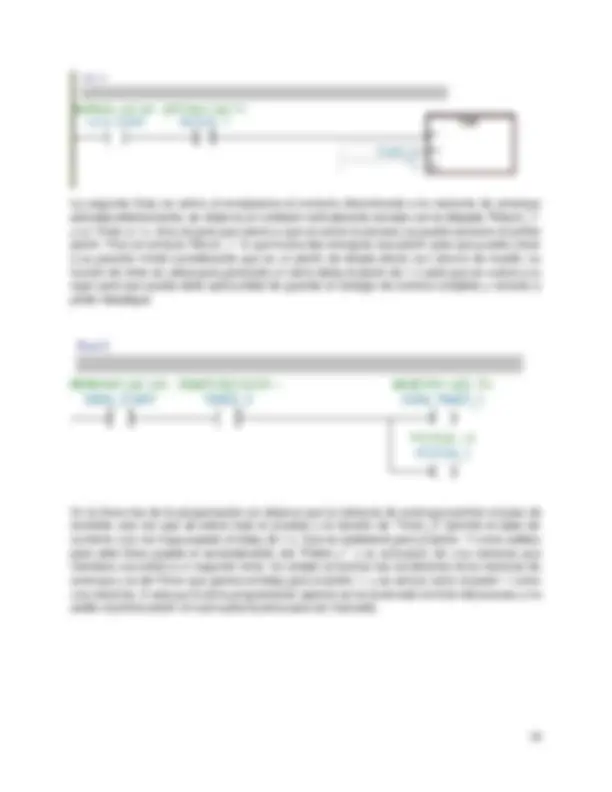
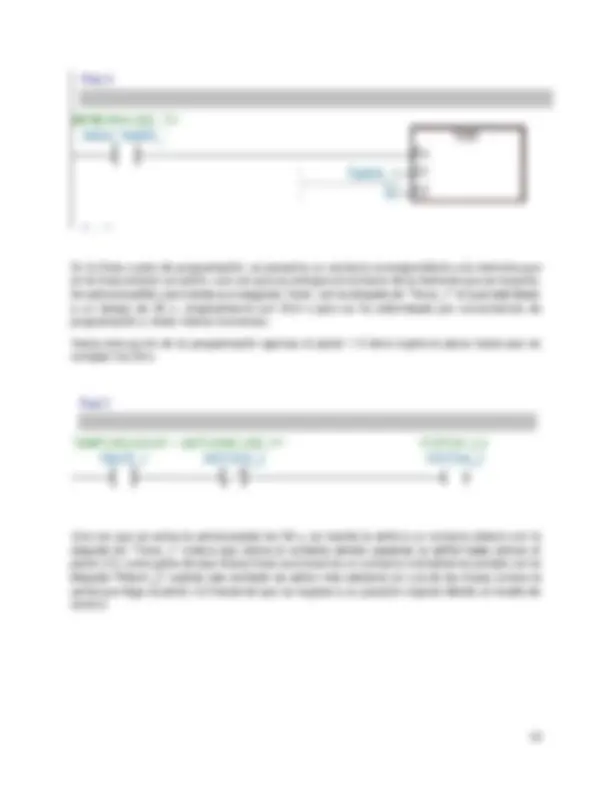
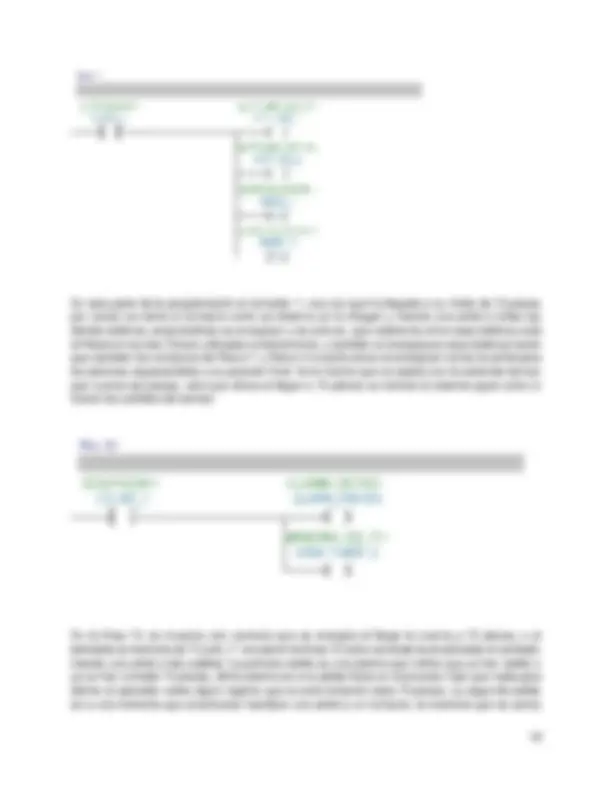
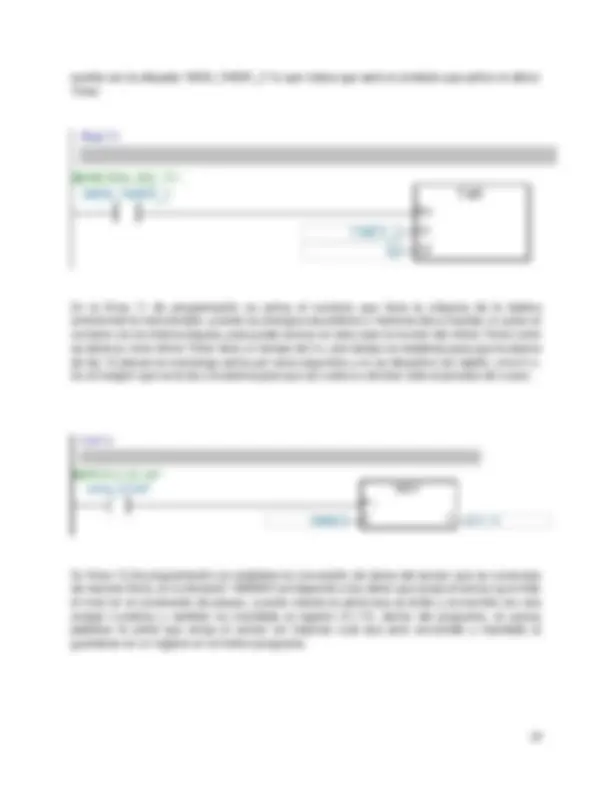
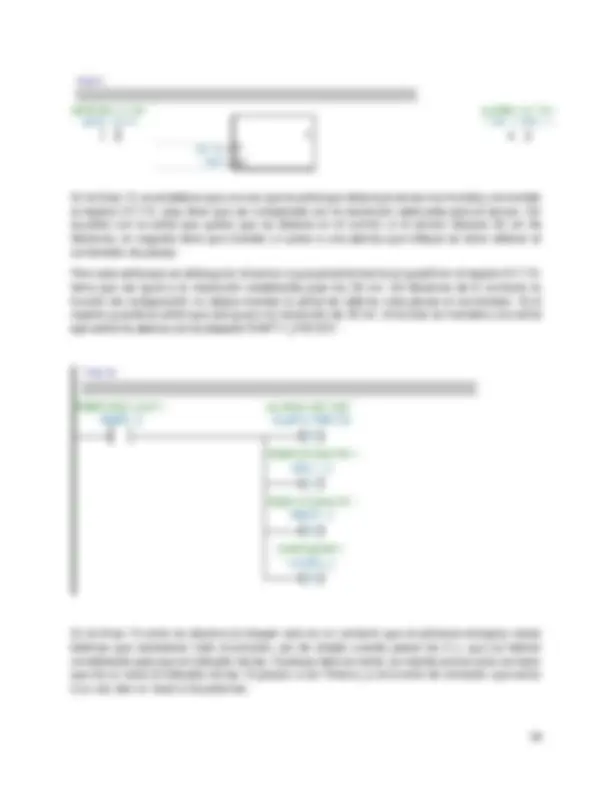
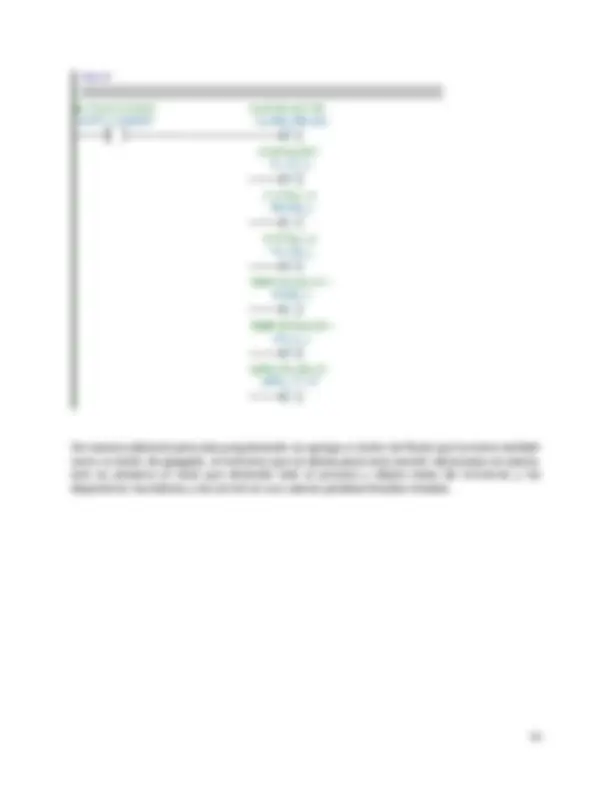
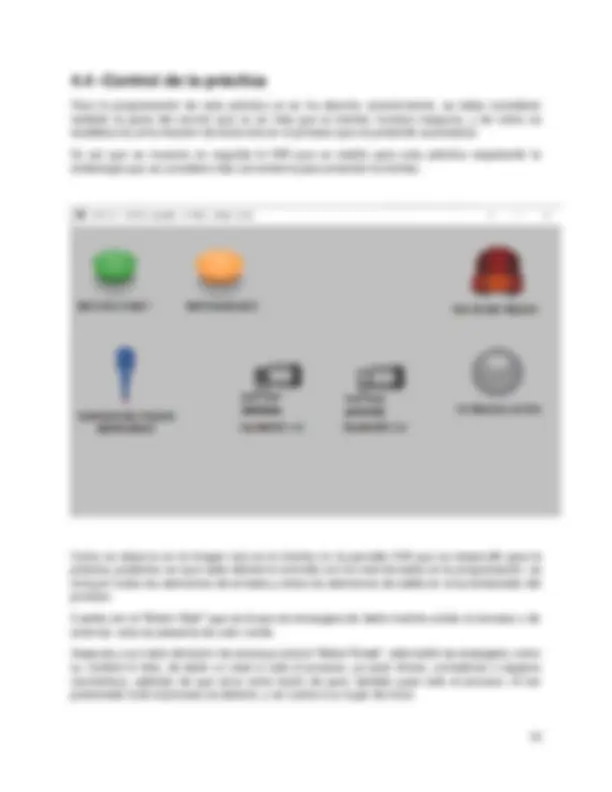
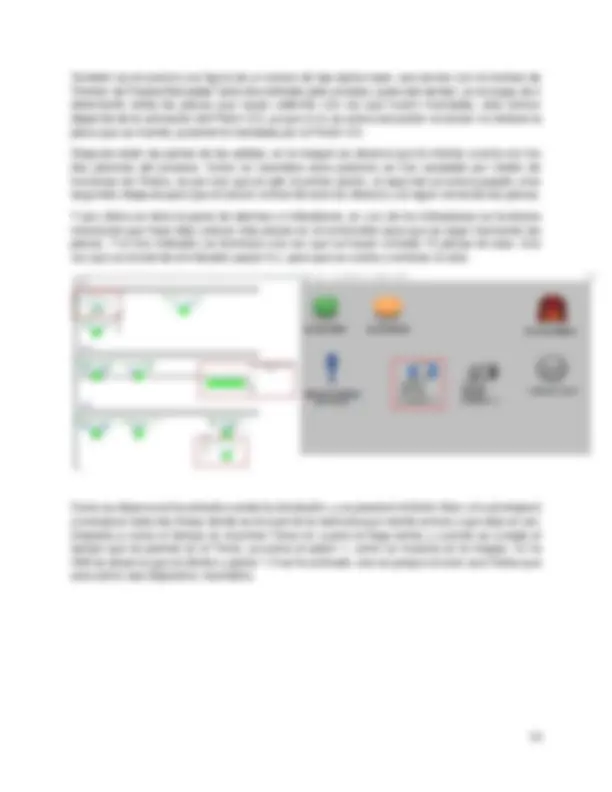
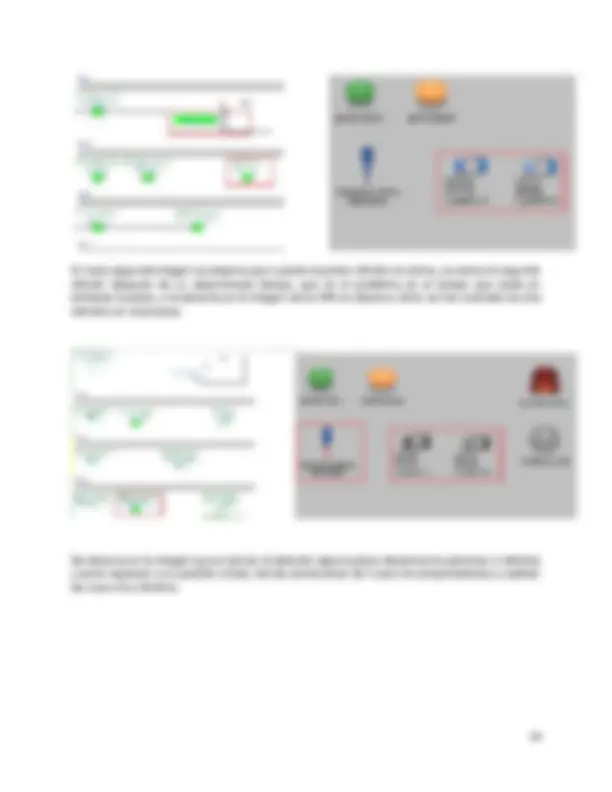
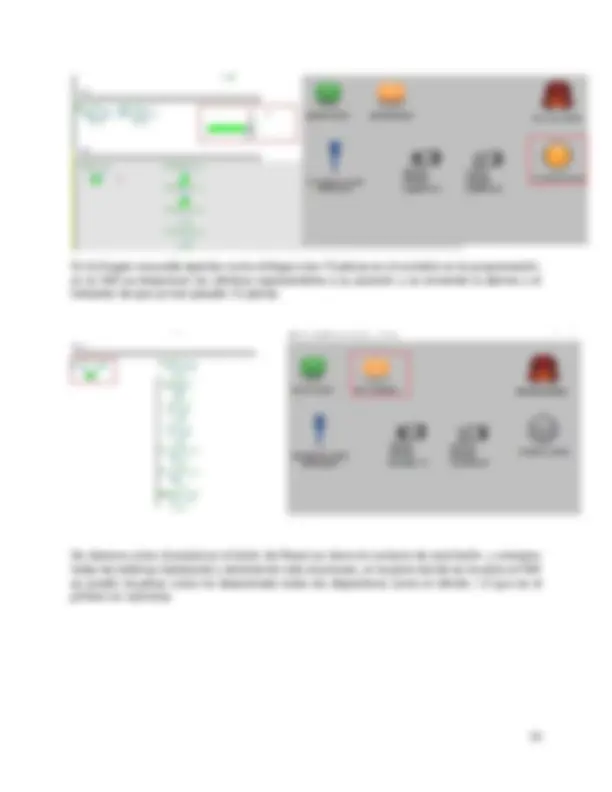
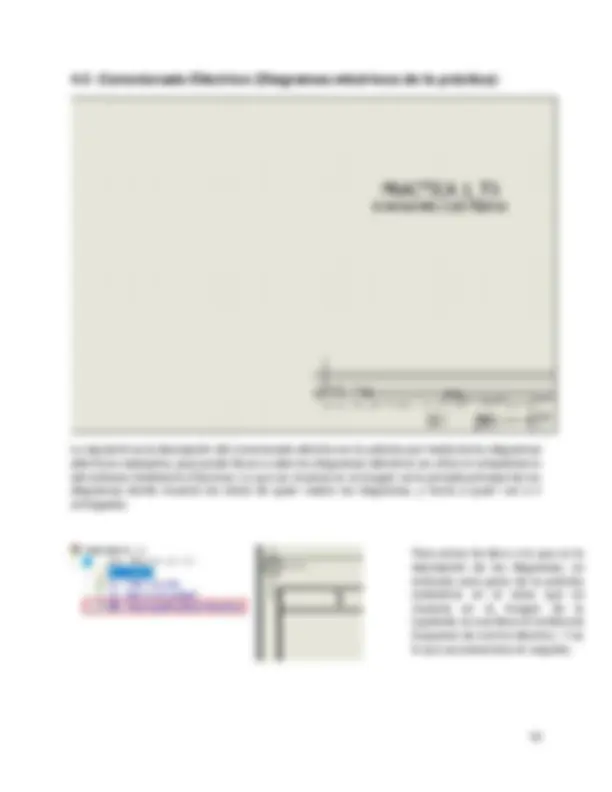
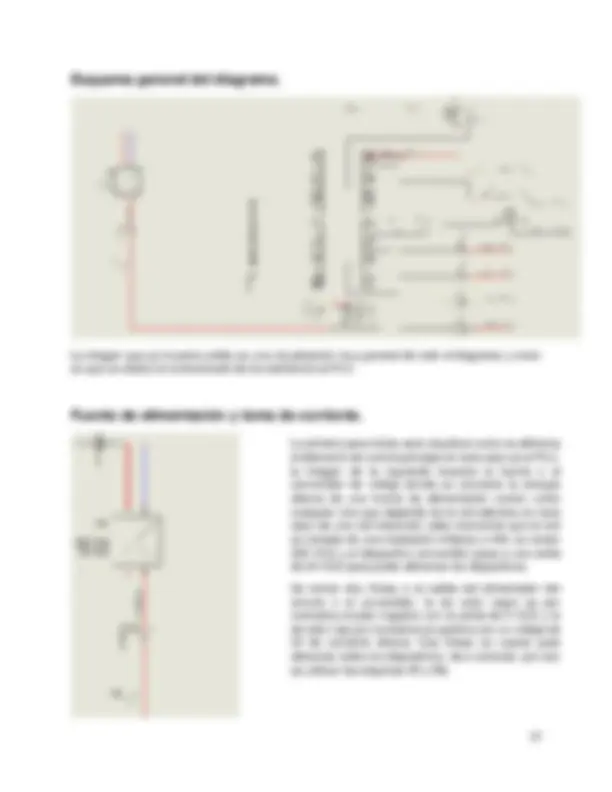
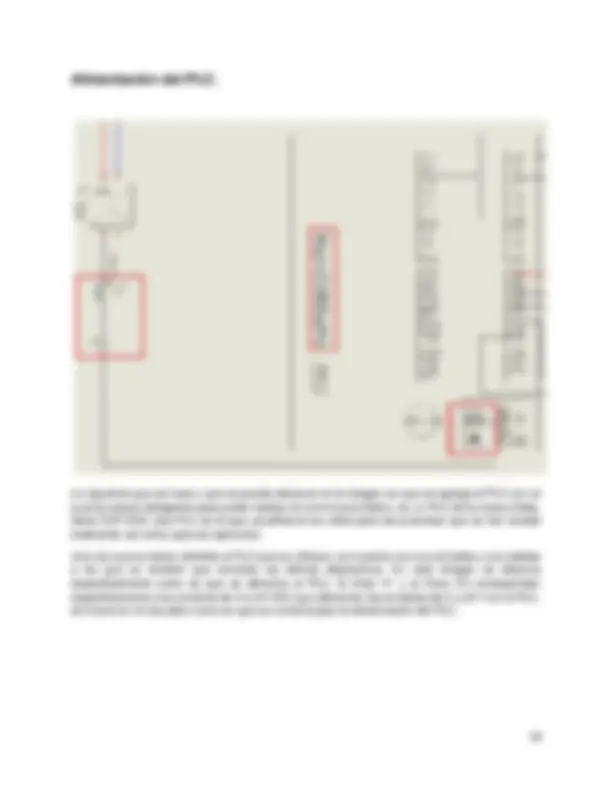
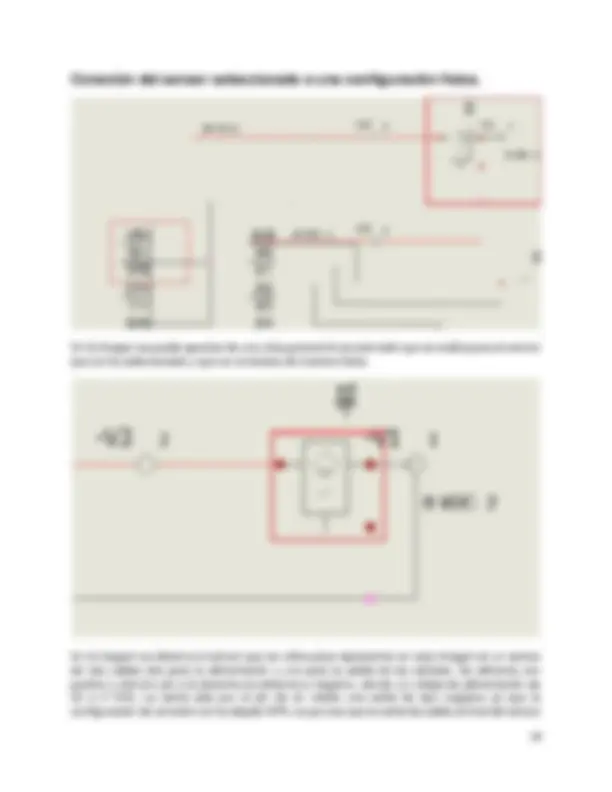
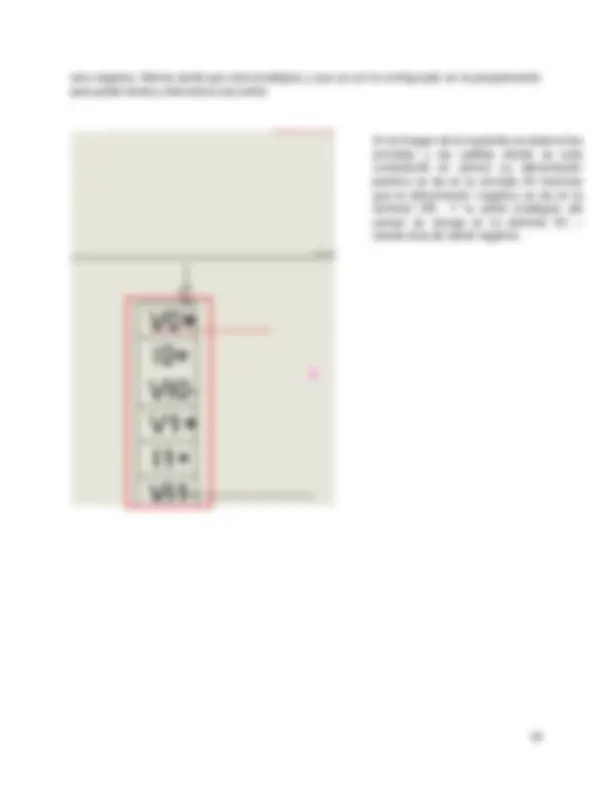
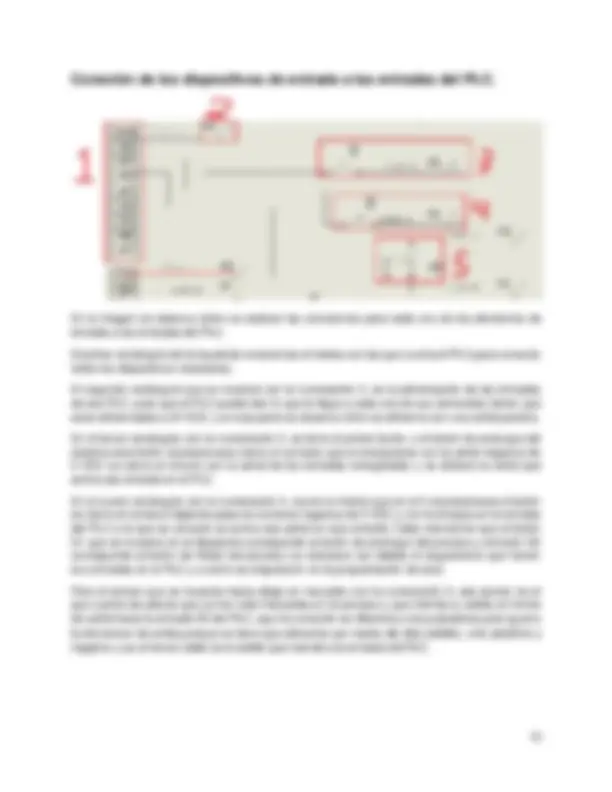
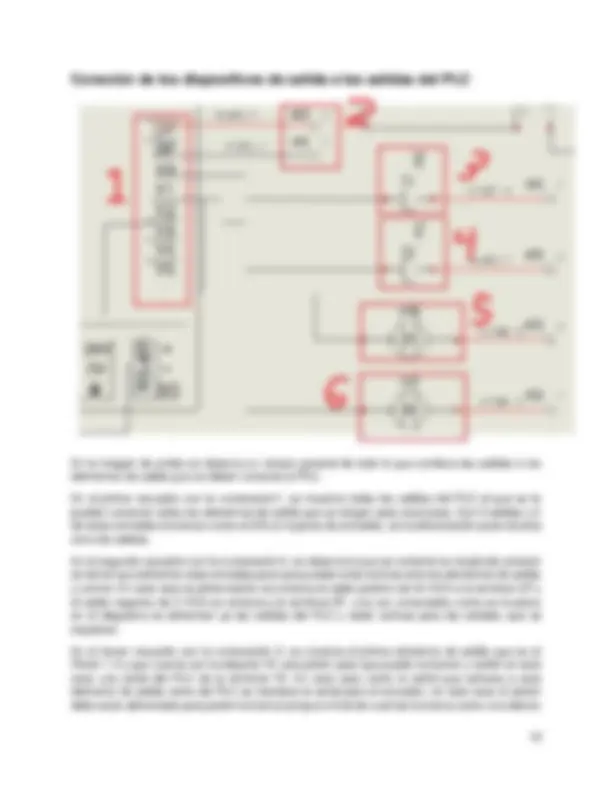
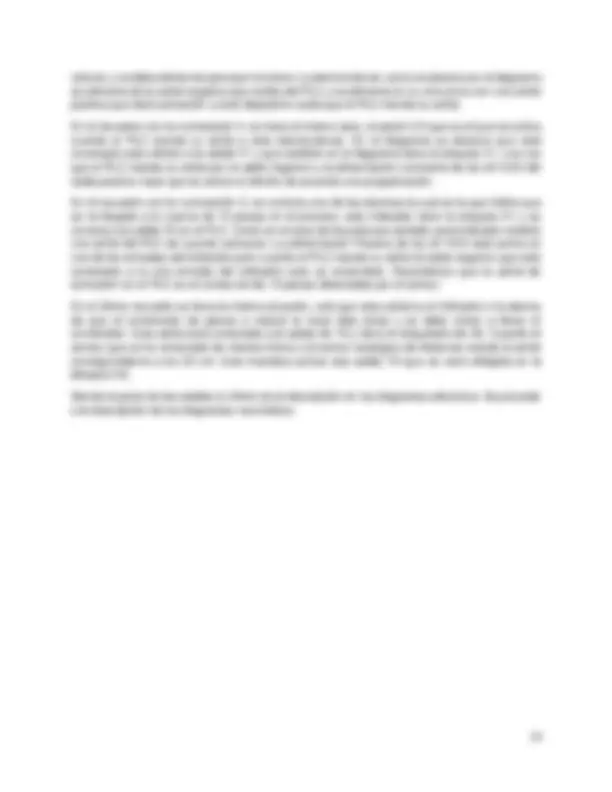
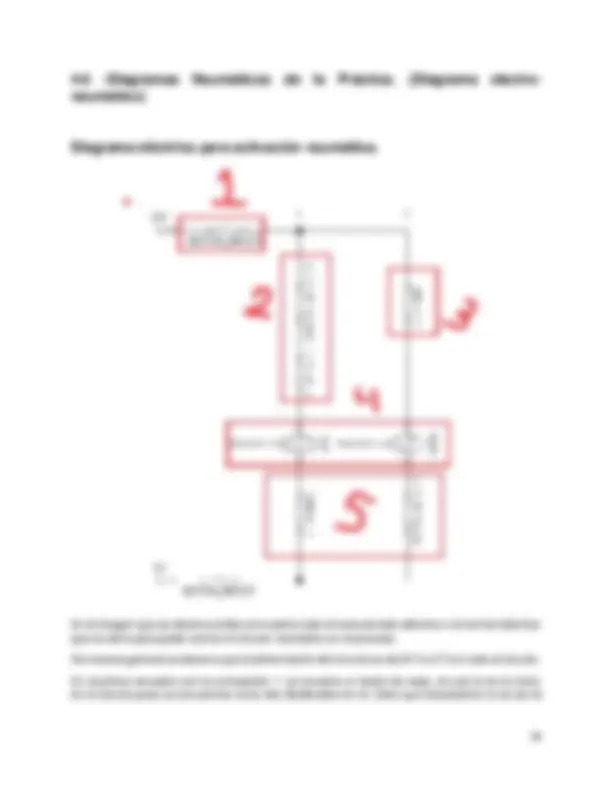
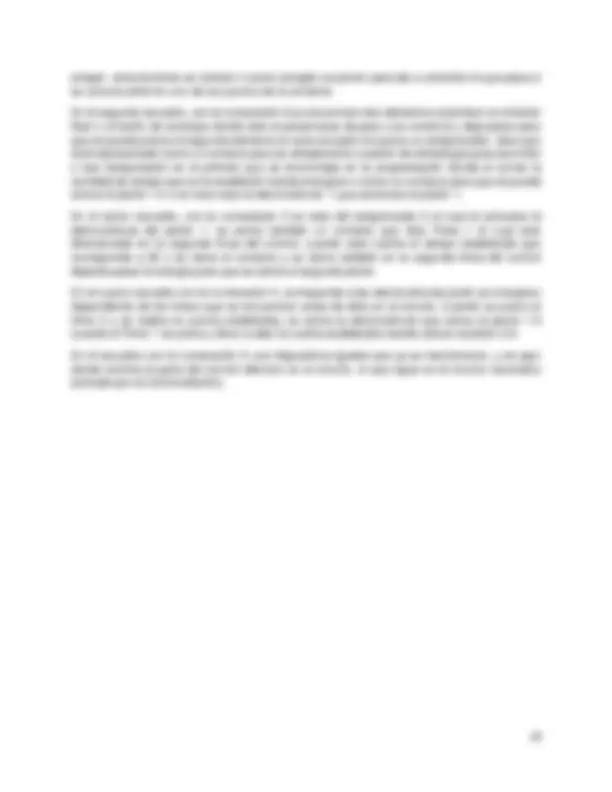
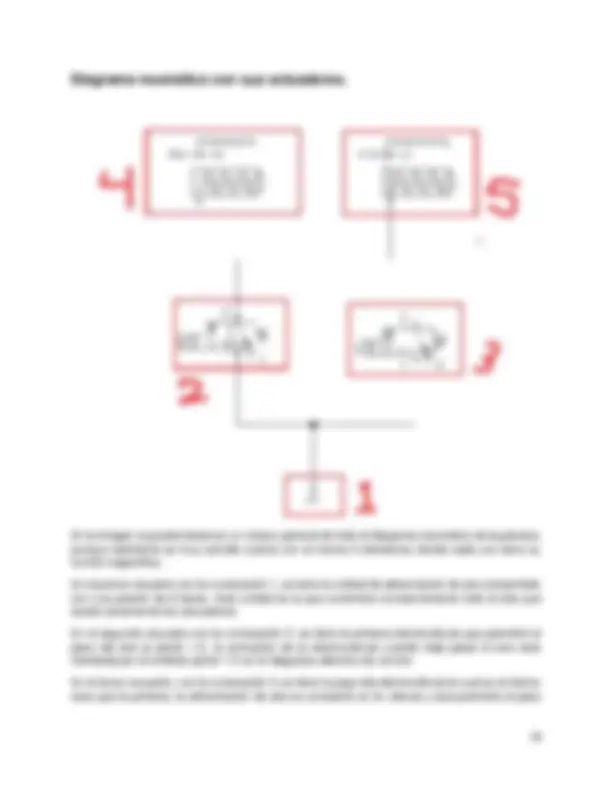
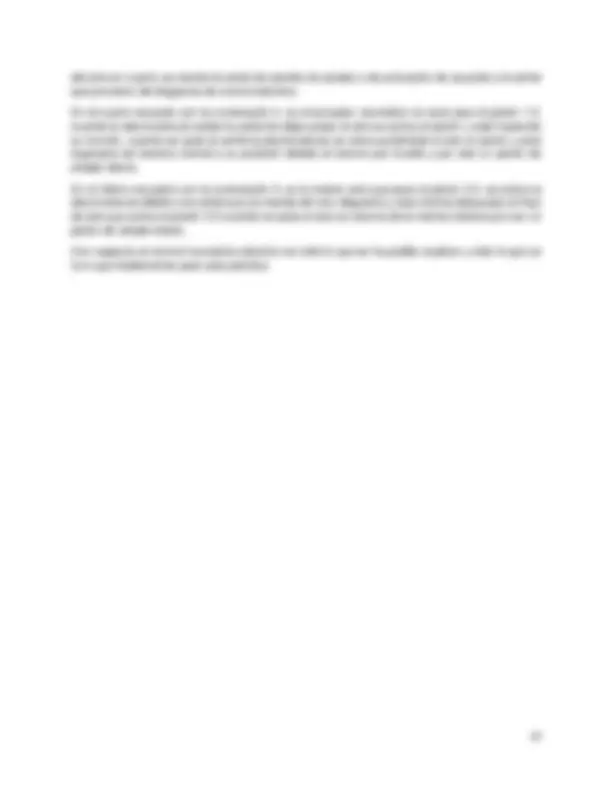
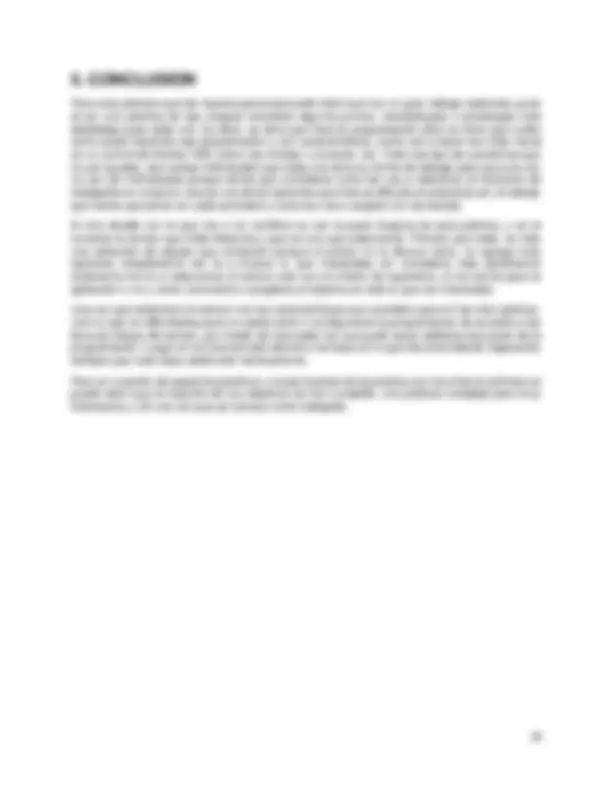
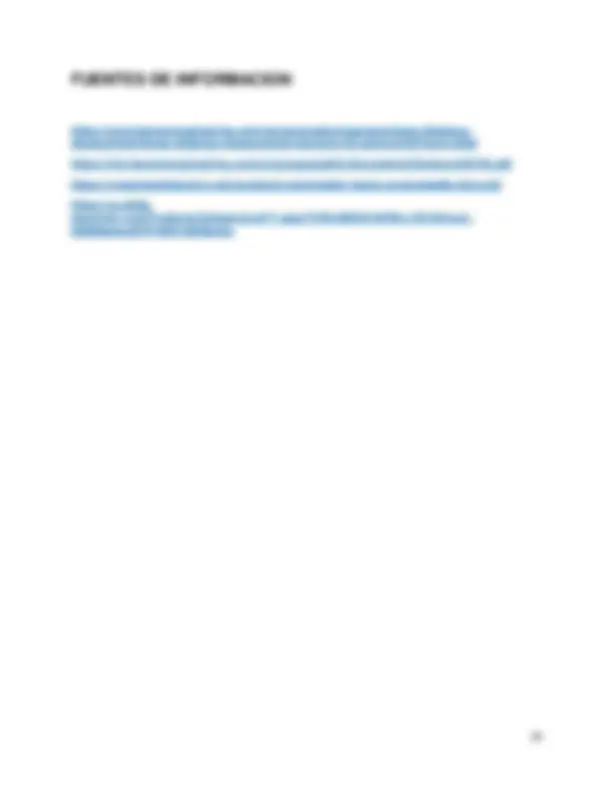
Prepara tus exámenes y mejora tus resultados gracias a la gran cantidad de recursos disponibles en Docsity
Gana puntos ayudando a otros estudiantes o consíguelos activando un Plan Premium
Prepara tus exámenes
Prepara tus exámenes y mejora tus resultados gracias a la gran cantidad de recursos disponibles en Docsity
Prepara tus exámenes con los documentos que comparten otros estudiantes como tú en Docsity
Los mejores documentos en venta realizados por estudiantes que han terminado sus estudios
Estudia con lecciones y exámenes resueltos basados en los programas académicos de las mejores universidades
Responde a preguntas de exámenes reales y pon a prueba tu preparación
Consigue puntos base para descargar
Gana puntos ayudando a otros estudiantes o consíguelos activando un Plan Premium
Comunidad
Pide ayuda a la comunidad y resuelve tus dudas de estudio
Descubre las mejores universidades de tu país según los usuarios de Docsity
Ebooks gratuitos
Descarga nuestras guías gratuitas sobre técnicas de estudio, métodos para controlar la ansiedad y consejos para la tesis preparadas por los tutores de Docsity
En este documento se redacta el reporte de practica sobre cómo se utilizan o implementan funciones avanzadas en programación Ladder para un PLC en la interfaz de la marca Delta. Asimismo, como se hace un desglose de las actividades realizadas en la programación, se explica brevemente como se programa el control en una HMI y su conexionado de manera física por medio de diagramas multifilares.
Tipo: Ejercicios
1 / 39
Esta página no es visible en la vista previa
¡No te pierdas las partes importantes!
considerar un diagrama neumático y electro neumático de cómo es que se llevara a cabo ese montaje con elementos de este tipo.
Una vez finalizado todos los puntos integrales de la práctica, se esperan resultados con respecto al desempeño de la programación, del control y de la instalación de los dispositivos.
2. OBJETIVOS
Generar un conocimiento integral con respecto a las diferentes etapas que se realizaron de la práctica.
Establecer las bases de los conocimientos relacionados con las aplicaciones secuenciales y el uso de funciones avanzadas de programación.
Establecer una metodología ordenada y organizada de manera secuencial el desarrollo de proyectos de automatización o aplicaciones control.
Generar un conocimiento básico con respecto al diseño de diagramas eléctricos y neumáticos (considerando simbología de acuerdo a normativa, tipo de plano, estructura del plano, y elementos auxiliares o herramientas que se basan todas en el uso de normativas oficiales).
Generar un conocimiento básico con respecto al manejo de datos, sistemas de numeración y configuración de datos con respecto a las condiciones que se ofrecen de trabajo.
3. MARCO TEORICO
CONTROLADOR LOGICO PROGRAMABLE DVP-SX2.
Los controladores lógicos programables de la serie DVP de Delta ofrecen aplicaciones de alta velocidad, estables y altamente confiables en todo tipo de máquinas de automatización industrial. Además de una operación lógica rápida, instrucciones abundantes y tarjetas de funciones múltiples, el rentable DVP-PLC también admite varios protocolos de comunicación, conectando el controlador de motor CA, servo, interfaz de maquina humana y controlador de temperatura a través de la red industrial en una completa Delta Solution para todos los usuarios.
DVP-SX2 series.
Las segunda generación del PLC de tipo delgado DVP-SX2 ofrece 14 puntos digitales y puntos E/S analógicos de 12 bits incorporados. Es extensible con los módulos de extensión del lado izquierdo y derecho de la serie DVP-S.
Cuenta con algunas características las cuales son las siguientes:
Puntos de MPU: 20 (8DI/6DO, 4AI/2AO).
Max. Puntos de E/S: 494 (14+480).
Capacidad de programa 16 k paso.
Puerto COM: puertos incorporados RS-232, RS-485 Y USB, compatibles con el protocolo ASCII/RTU. Puede ser maestro o esclavo.
Salida de pulso de alta velocidad. Admite 2 puntos (Y0, Y2) de 100 kHz y 2 puntos (Y1, Y3) de salida de pulso de alta velocidad independiente de 10 kHz.
Contadores incorporados de alta velocidad.
E/S analógica incorporada.
Utilizando para control de temperatura/ humedad PID. Control de velocidad constante de variador de CA de 2 ejes. Control de temperatura usando un monitoreo de señal analógica de un fabrica completa. (PLC EASY LINK).
Como se observa en la pieza se busca hacer el control de un proceso neumático y eléctrico. Es un contenedor de piezas las cuales se están marcando y se mandan a otro proceso de la planta. Suena sencillo pero esto conlleva una secuencia que se tiene que seguir y respetar para poder realizarse de la mejor manera.
En cuanto se arranca el sistema con un botón de inicio se activa un pistón el cual es el pistón 1.0, ese pistón mueve la pieza que se tiene que marcar y la mantiene sujeta durante 3.56 s. Pasando esos segundos, se activa el pistón 2.0 el cual pasa o saca la pieza de esa zona de marcado y la manda a otra operación del proceso. Para esto se ha instalado un sensor que detecta a la salida del pistón 2.0 para contar cuantas piezas han pasado ya, si se llega a un límite de 15 piezas se activa una señal de que va esa cantidad es como mantener un registro de lote de 15 piezas. También se debe instalar un sensor en la parte de arriba del contenedor de las piezas que alerte cuando estas piezas lleguen a una distancia determinada con respecto del fondo del contenedor y mande una alerta indicando que faltan piezas en el contenedor.
Como se puede observar es una aplicación sencilla donde se tiene que considerar la parte de las secuencias, si un elemento activa otro, que es lo que pasa y que es lo que sigue en las tareas, la idea es mantener la secuencia considerando los elementos neumáticos y electro neumáticos que se usaran en planta. Como parte adicional de la práctica se indica que la selección del sensor de distancia que mide el nivel del contenedor debe ser seleccionado y configurado para ser instalado en planta, es decir, una configuración real para un montaje real en planta.
4.2-Selección del sensor de distancia a aplicar en la práctica.
Como ya se había mencionado se debe elegir un sensor de distancia adecuado para poder ser montado en la parte alta del contenedor con el fin de mantener un control en el nivel de piezas.
El sensor más adecuado que se consideró para esta práctica, es un sensor óptico de distancia, con un rango aceptable de acuerdo a lo que pide la aplicación. Se considera uno salida analógica, para poder visualizar mejor la configuración en la programación y el conexionado. Considerando una marca aceptable y de buen precio así como las características técnicas para poder acoplar al control de la aplicación.
L-GAGE LT3 Long-Range Time-of-Flight Laser Sensor.
Este sensor de la marca Banner, se ajusta perfecto a las necesidades que se tienen para el control de la automatización. Es precisamente un sensor Óptico de distancia. Siendo un láser el cual utiliza para medir la distancia y así reflejarlo en una señal de tipo analógica. Con un precio accesible de $4577.35 MXN.
Dimensiones.
Es de un tamaño compacto y que se puede montar con facilidad en cualquier zona, su tamaño compacto lo hace entrar en cualquier punto, solo basta con fijar sus soportes en la dirección, altura o inclinación que se desee ajustar. Y como para esta práctica se tiene que ajustar en la parte superior del contenedor midiendo la distancia hacia abajo con respecto de la entrada del contenedor hacia el fondo, no existe riesgo de que se pueda alterar la lectura porque no estará instalado en una zona accesible.
Especificaciones eléctricas y de entorno del sensor.
Es importante saber cuáles son las especificaciones eléctricas del sensor porque de eso depende como se va a conectar en planta, además de que también es importante saber en qué entorno se puede trabajar en la planta y como puede ofrecer un mayor rendimiento.
En esta primera imagen muestra algunas de las características eléctricas más importantes, empezando por la alimentación del dispositivo, cuenta con una alimentación de 12 VDC a 24 VDC y una corriente de 24 mA que puede ser máxima a 108 mA. También menciona que el control o el consumo que tiene el láser del dispositivo van de 5 a 24 VDC. Y también menciona unas especificaciones al momento de realizar el conexionado o el cableado a otro equipo, pero más que nada para la alimentación de este.
De entrada y siendo lo más importante como lo es el primer recuadro es que habla de la alimentación del equipo que es de 12 a 24 VCD esto con un consumo de 24 mA. Este dispositivo se conecta para su alimentación de la misma manera en que se alimentara al PLC para la parte de control. Menciona algunos detalles del cableado, y protecciones con las que cuenta ante polarizaciones invertidas, y el tiempo de retraso al encender el equipo.
En esta segunda imagen se siguen mostrando las especificaciones más notorias del dispositivo, en el primer recuadro de la imagen se muestra los rangos de salida con los que cuenta el sensor, en sus dos modalidades analógicas y discretas. Además de mencionar los tiempos de respuesta de la señal con respecto a la configuración que se elija siendo 1 ms. La más alta y 100 ms. La más baja.
En el segundo recuadro muestra las condiciones de ambiente a las que se debe trabajar este equipo, menciona unos rangos de temperatura adecuados considerando la humedad para que no pueda haber un fallo en el equipo o el dispositivo, cuenta con protección IEC IP67, resaltando que tiene certificaciones que lo hacen eficiente el sensor ante algunos medios o entornos difíciles a los que se puede exponer en planta.
Y por último el tercer recuadro que es el más importante para esta práctica, pues es la parte de la configuración de salida del sensor, menciona que pueden ser dos formas de salir la señal ya sea que es una configuración NPN O PNP, siendo señal analógica o digital. Pero lo que más sirve de este apartado es que si la señal es analógica saber cuál es el valor de esa señal que para este caso puede ser en voltaje de 0 a 10 VDC o puede mandar una señal en corriente siendo un valor de 4 a 20 mA. Sin duda estos valores serán muy útiles al momento de la programación pues sirven como valor establecido para las conversiones que se tengan que hacer para poder realizar la discretizacion de la señal y obtener lecturas correctas.
4.3 -Programación y control.
Para esta práctica se hace uso del ISP soft. De la compañía DELTA, ya que se pretende utilizar un PLC de esta marca siendo el modelo DVP series SX2, es uno de los más adecuados en cuestión de aplicaciones de respuesta sincronizada y rápida para estas secuencias.
De la siguiente manera se ira explicando cada línea de programación ya realizada para que pueda comprenderse mejor la secuencia que se quiere plantear en este control.
Declaración de variables y memorias.
En la imagen de arriba se muestran todas la memorias y variables que se utilizaron para la programación realmente es pues como el etiquetado de todo lo que se utilizó para cada función. Hay algunas funciones o registros que no se definieron en este caso o al inicio ya que hubo algún conflicto con la declaración y era mejor no alterar más la programación.
Programación de la práctica.
En la primera línea de la programación se muestra el botón que se mencionaba en el ejercicio, el cual dará inicio al proceso, se puede considerar en el control y la interfaz un botón de tipo enclavado, pero en caso de que no sea así, se ha establecido una condición de Set en la activación del proceso.
La segunda línea se activa al energizarse el contacto direccionado a la memoria de arranque activada anteriormente, se observa un contacto normalmente cerrado con la etiqueta “Return_1” y un Timer a 1 s. Esto es para que previo a que se activó el proceso se pueda accionar el primer pistón. Pero el contacto Return_1 lo que busca des energizar ese pistón para que pueda volver a su posición inicial considerando que es un pistón de simple efecto con retorno de muelle. La función de timer se utiliza para generarle un cierto delay al pistón de 1 s cada que se vuelve a su lugar para que pueda darle oportunidad de guardar el vástago de manera completa y volverlo a poder desplegar.
En la línea tres de la programación se observa que la memoria de arranque permite el paso de corriente una vez que se activa todo el proceso y la función de “Timer_3” permite el paso de corriente una vez haya pasado el delay de 1 s. Que se estableció para el pistón. Y como salidas para esta línea puesta el accionamiento del “Piston_1” y la activación de una memoria que mandara una señal a un segundo timer. Es simple se activan las condiciones de la memoria de arranque y la del Timer que genera el delay para el pistón 1, y se activan tanto el pistón 1 como una memoria. A este punto de la programación apenas se ha accionado el inicio del proceso y ha salido el primer pistón el cual sujeta la pieza para ser marcada.
La siguiente línea es necesaria para activar una memoria, es la memoria con la etiqueta “MEM_COUNT_1” esta memoria se activa al iniciar activarse el timer 1 que era el de 36 s. Esta memoria activara más adelante la señal del contador de piezas detectadas gracias al sensor.
La memoria del contador 1, que se activó arriba da la señal para que se pueda energizar el sensor que cuenta las piezas que ya han sido marcadas y que va manteniendo el registro de estas piezas en el mismo contador. Aquí hay algo importante de mencionar, la memoria del contador 1, que se activó en la línea anterior permite la señal del sensor para que este pueda detectar, esto porque se plantea una situación en planta donde alguna persona u operador en planta haya pasado la mano cerca del sensor o por la zona de detección esto puede generar un mal conteo o una
desorganización en el registro, para evitar esta situación se plantea de esta manera la programación, de manera que pueda seguir una secuencia donde no se avanzara en el proceso hasta que se haya cumplido la condición anterior en la secuencia.
Otra cosa destacable en esta línea de programación es el Reset en los Timers, y la activación de los retornos de los pistones. Esto es para que cada que el sensor detecte una pieza marcada para sacar de esta parte del proceso, se reinicie de cierta manera el proceso inicial y los pistones puedan volver a su lugar para volver a realizar el ciclo. Claro que se está hablando de un tiempo muy rápido, es decir, la primera respuesta la recibe en menos de 1 s. el primer pistón la reacción de este pistón si es un poco más rápida, pero tiene el tiempo suficiente para reanudar el ciclo.
También se cuenta con una memoria del sensor, que al activarse también lo hará en otras líneas pero direccionada a esta memoria, que cada que se active activara también todos los contacto.
La memoria del contador 1 también está presente en esta línea siendo el contacto principal que brindara la energía a las demás funciones, después esta le memoria del sensor que se activara cada que el sensor detecte una pieza como se vio en la línea anterior. Por ultimo esta la función de contador la cual va llevando la cuenta de las piezas que van pasando por ese sensor y que previamente ya están marcadas.
cuenta con la etiqueta “MEM_TIMER_2” lo que indica que será el contacto que active el ultimo Timer.
En la línea 11 de programación se activa el contacto que tiene la etiqueta de la bobina anteriormente mencionada, cuando se energiza esa bobina o memoria iba a mandar un pulso al contacto con la misma etiqueta, para poder activar en este caso la función del último Timer como se observa. Este último Timer tiene un tiempo de 5 s. ese tiempo se establece para que la alarma de las 15 piezas se mantenga activa por esos segundos y no se desactive tan rápido, unos 5 s. Es el margen que se le da a la alarma para que se vuelva a reiniciar todo el proceso de nuevo.
En línea 12 de programación se establece la conversión de datos del sensor que se conectara de manera física, la numeración 16#0000 corresponde a los datos que arroja el sensor que mide el nivel en el contenedor de piezas, cuando manda la señal esa es leída y convertida con ese arreglo numérico y también es mandada al registro D1115, dentro del programa, en pocas palabras la señal que arroje el sensor sin importar cuál sea será convertida y mandada al guardarse en un registro en el mismo programa.
En la línea 13, se establece que una vez que la señal que detecta el sensor es movida y convertida al registro D1115, esta tiene que ser comparada con la resolución adecuada para el sensor. De acuerdo con la señal que quiere que se detecte en el control, si el sensor detecta 30 cm de distancia, en seguida tiene que mandar un pulso a una alarma que indique se tiene rellenar el contenedor de piezas.
Pero esta señal que se obtenga en el sensor y que posteriormente se guardó en el registro D1115, tiene que ser igual a la resolución establecida para los 30 cm. De distancia de lo contrario la función de comparación no dejara mandar la señal de rellenar más piezas al contenedor. Si el registro guarda la señal que sea igual a la resolución de 30 cm. Entonces se mandara una señal que active la alarma con la etiqueta “EMPTY_PIECES”.
En la línea 14 como se observa la imagen solo es un contacto que al activarse energiza varias bobinas que resetearan todo el proceso, asi de simple cuando pasan los 5 s. que se habían considerado para que el indicador de las 15 piezas diera la señal, se manda activar este contacto que da un reset al indicador de las 15 piezas, a los Timers y a la función de contador, que estos a su vez dan un reset a los pistones.