
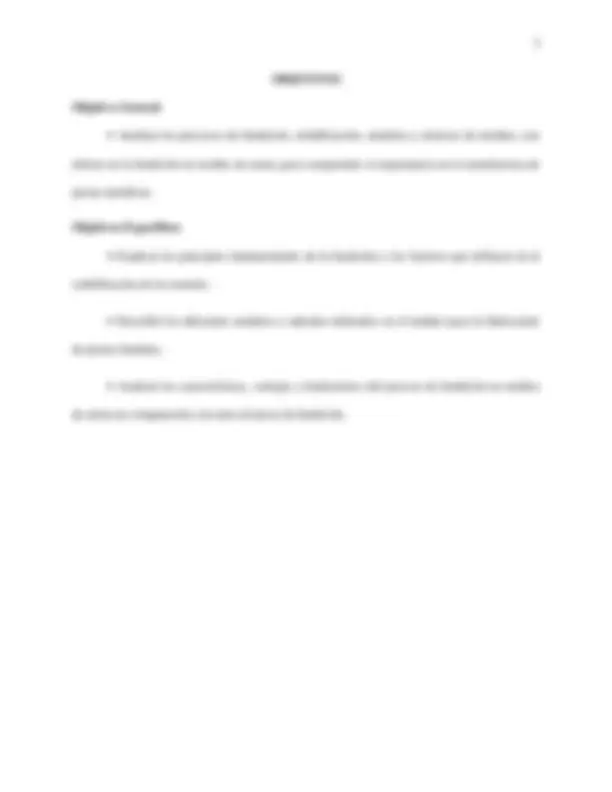
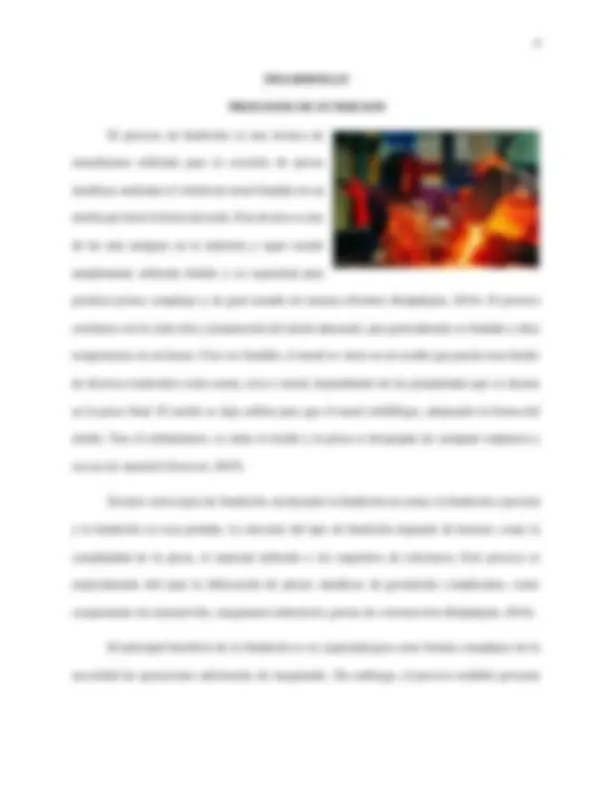
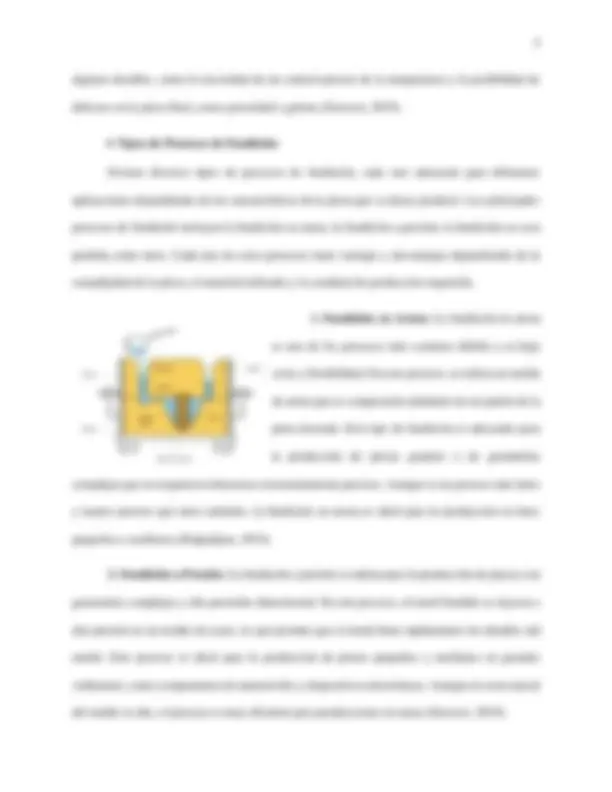
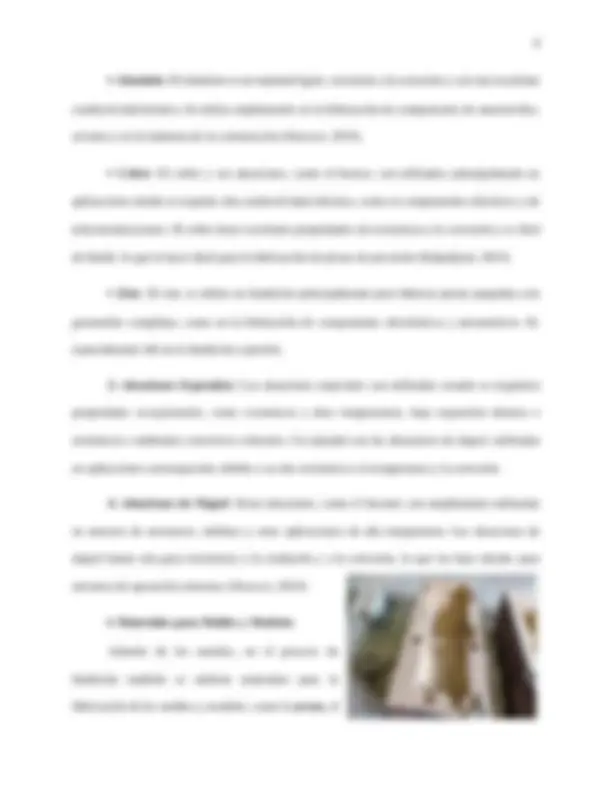
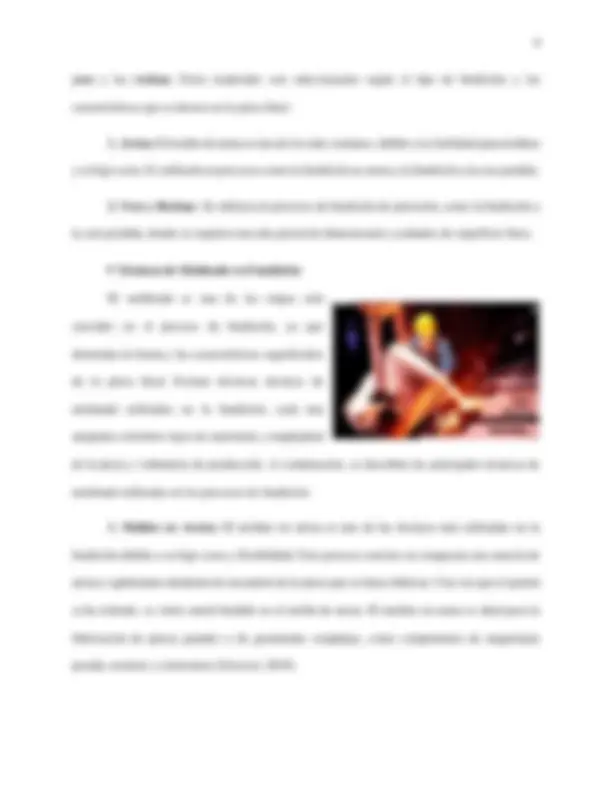
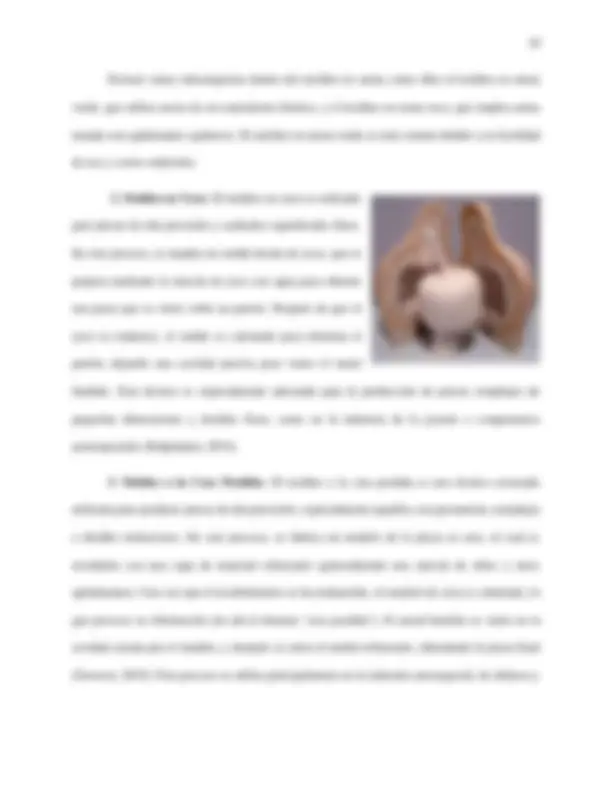
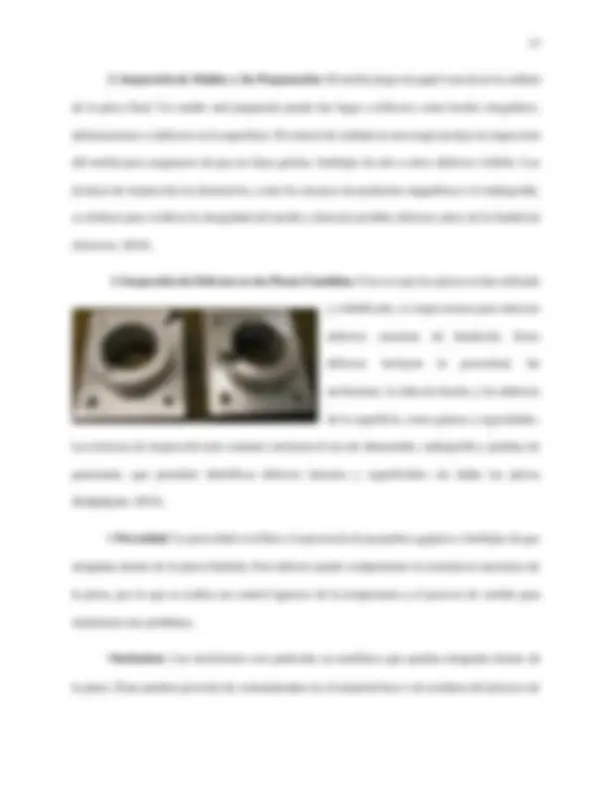
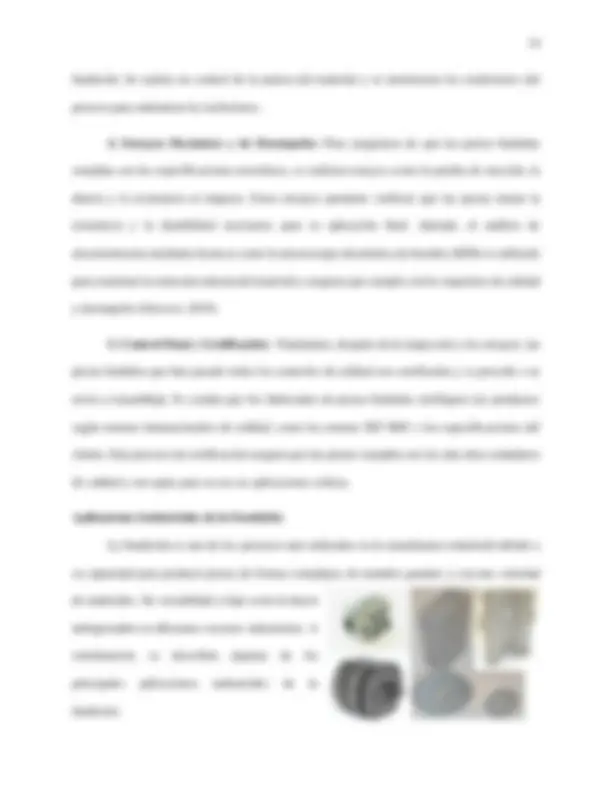
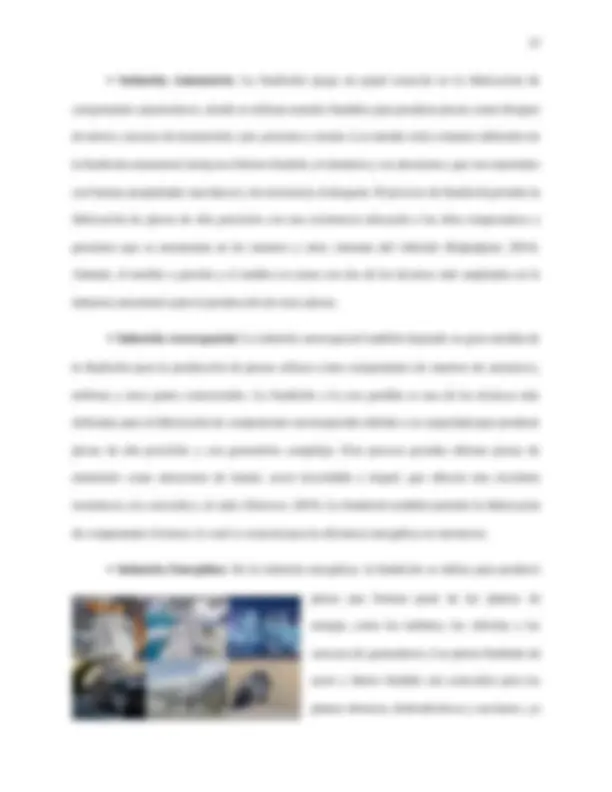
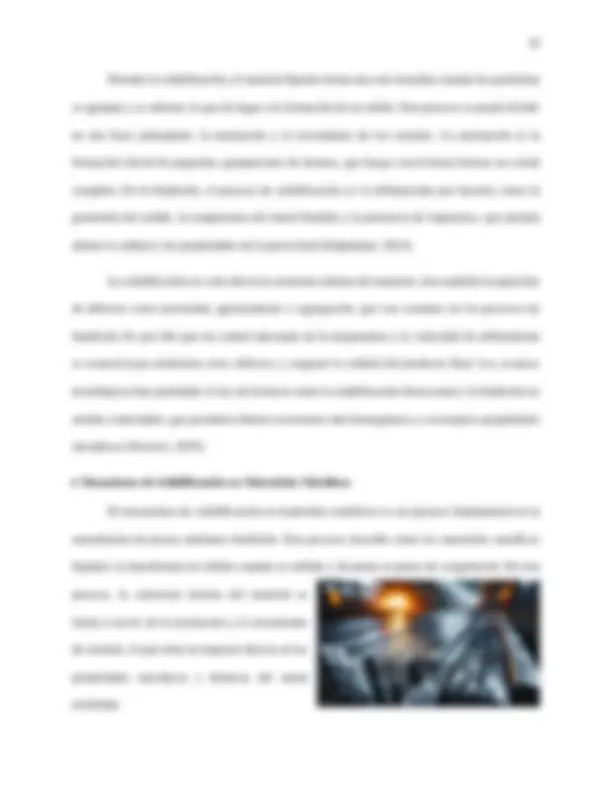
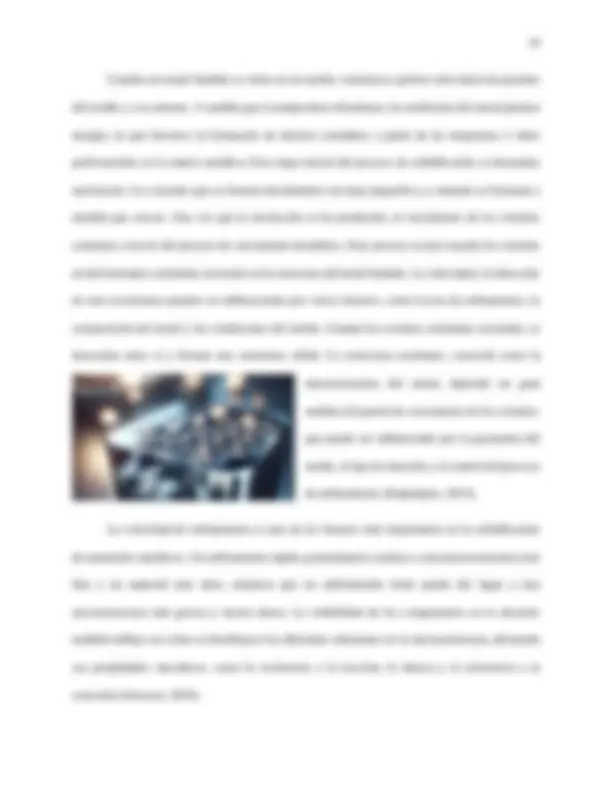
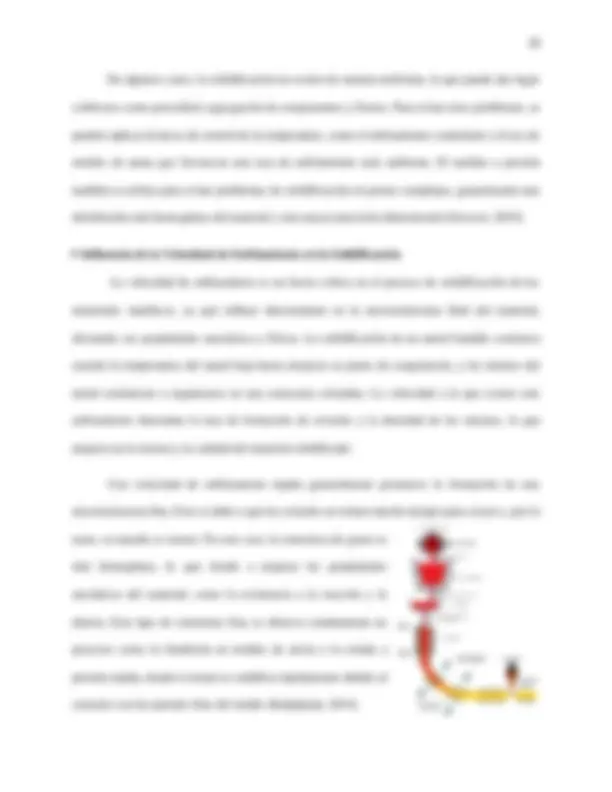
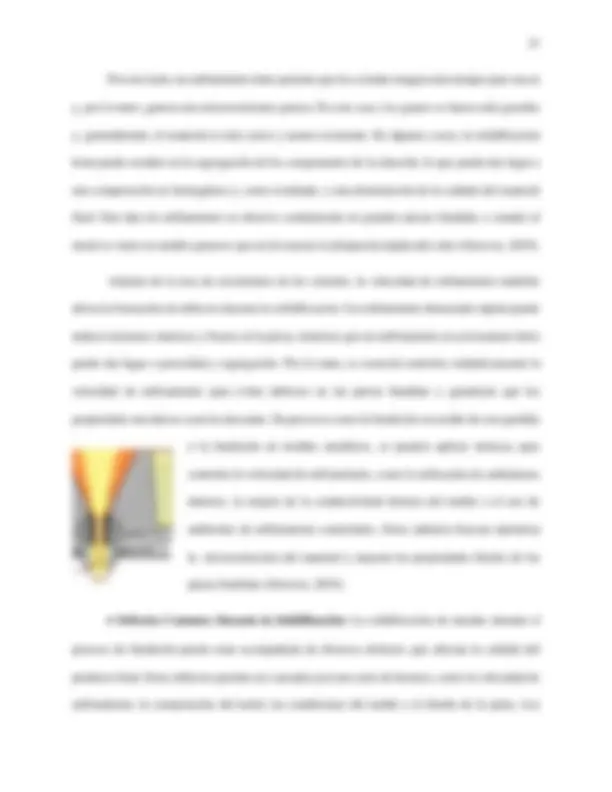
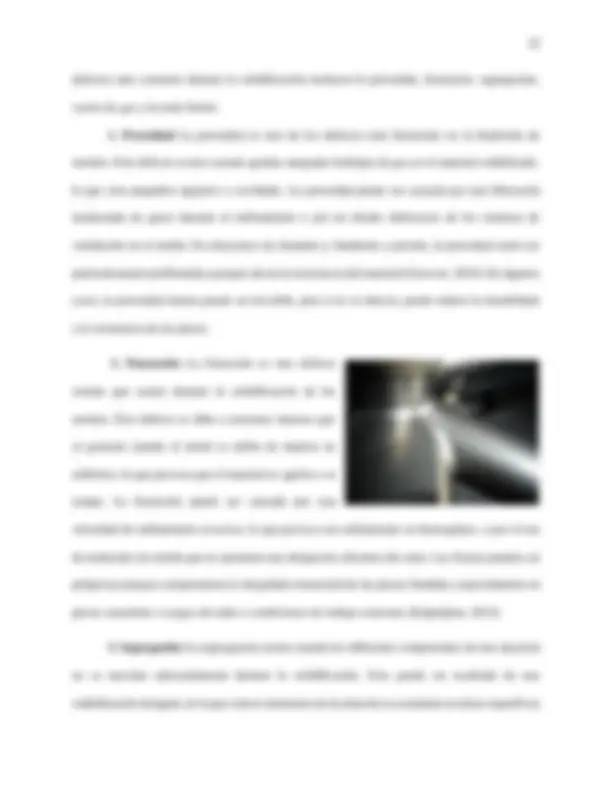
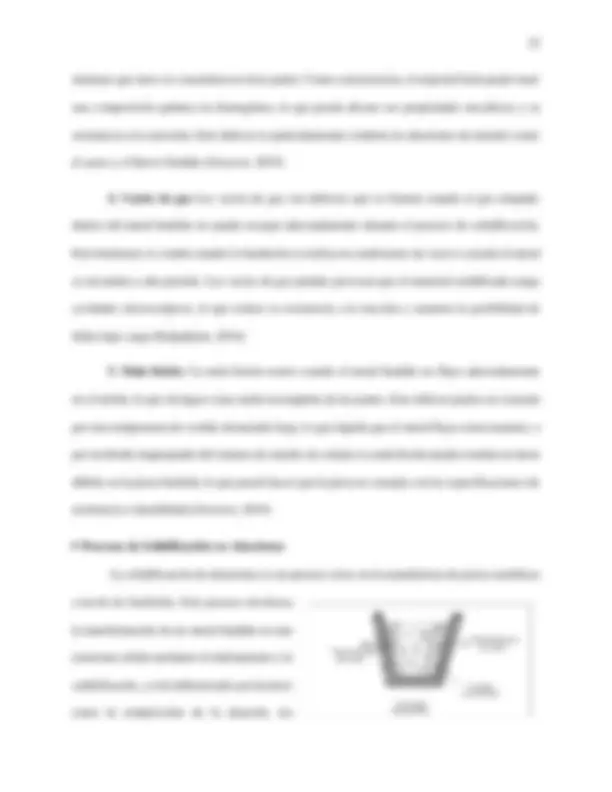
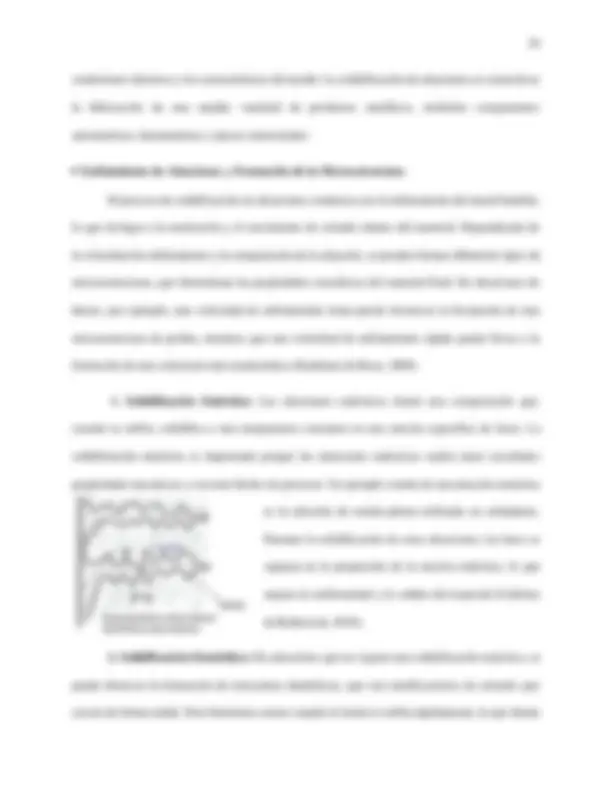
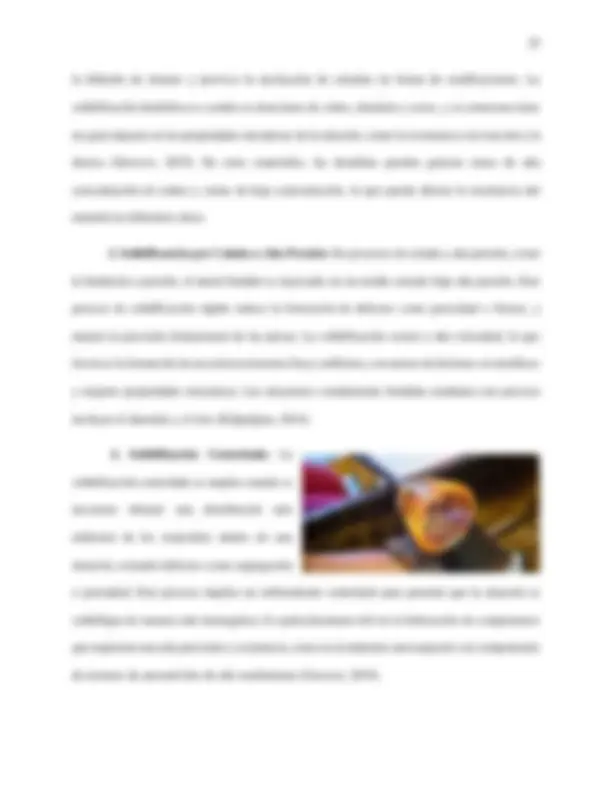
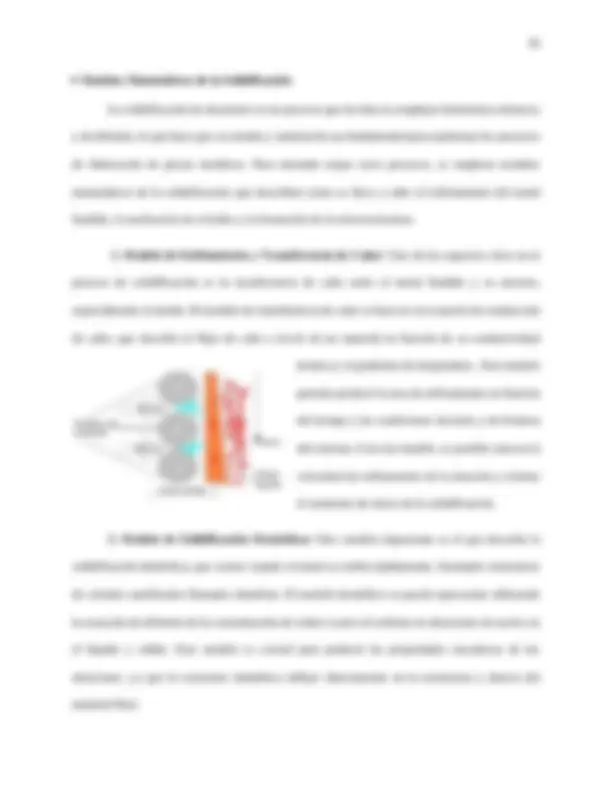
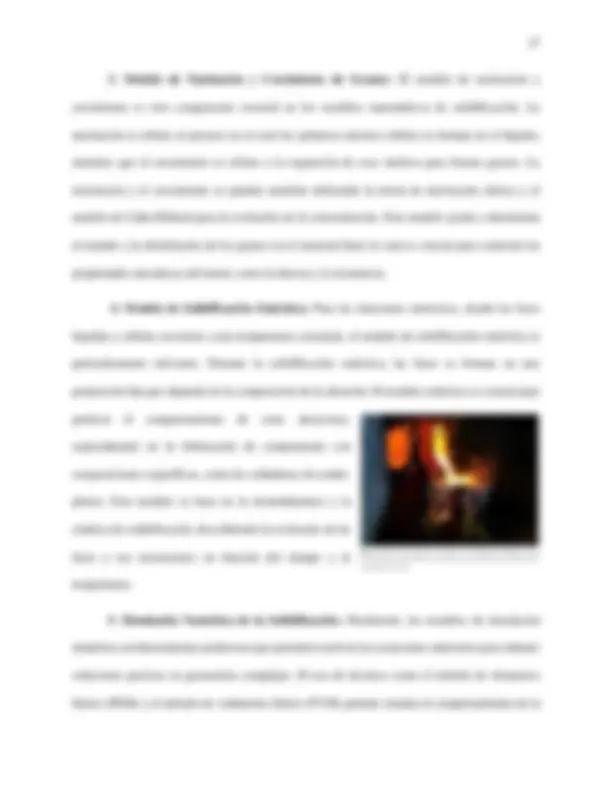
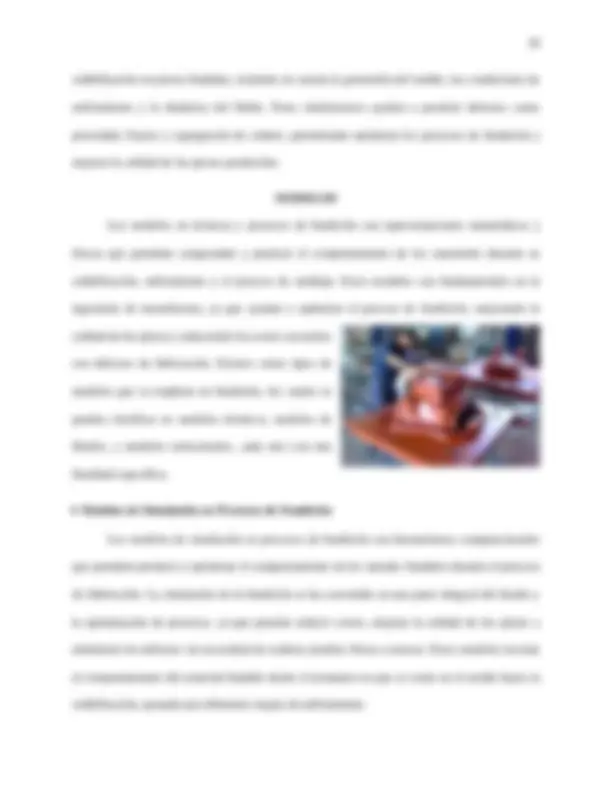
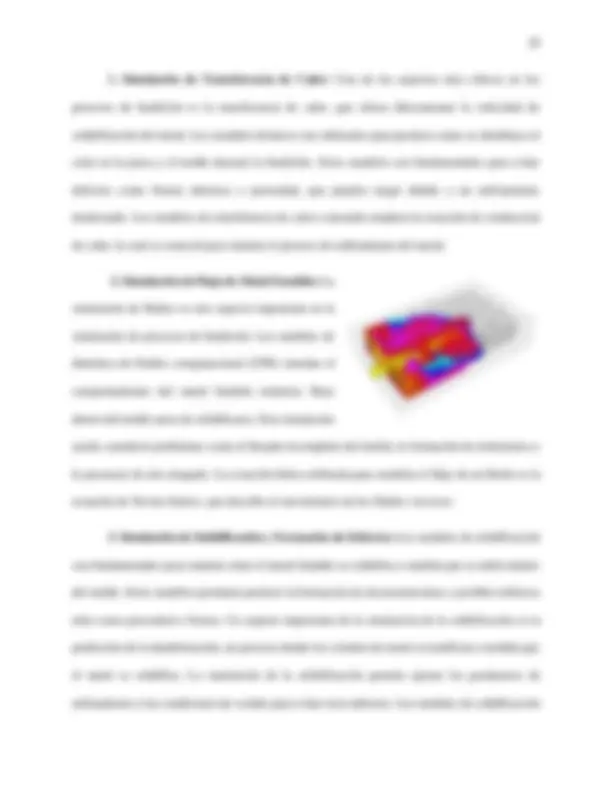
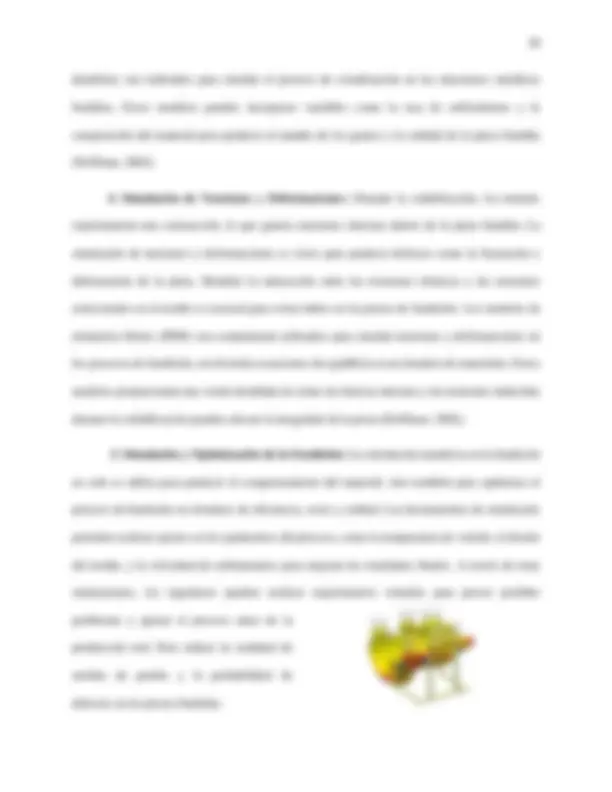
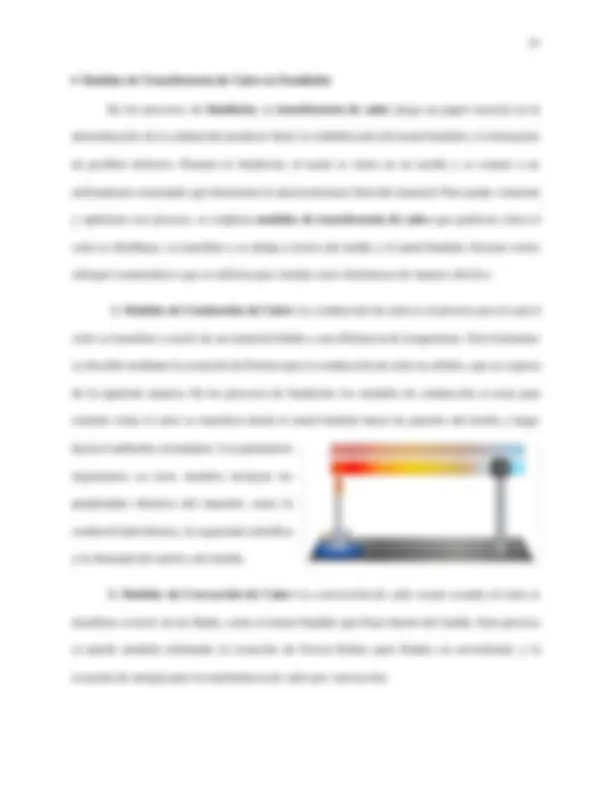
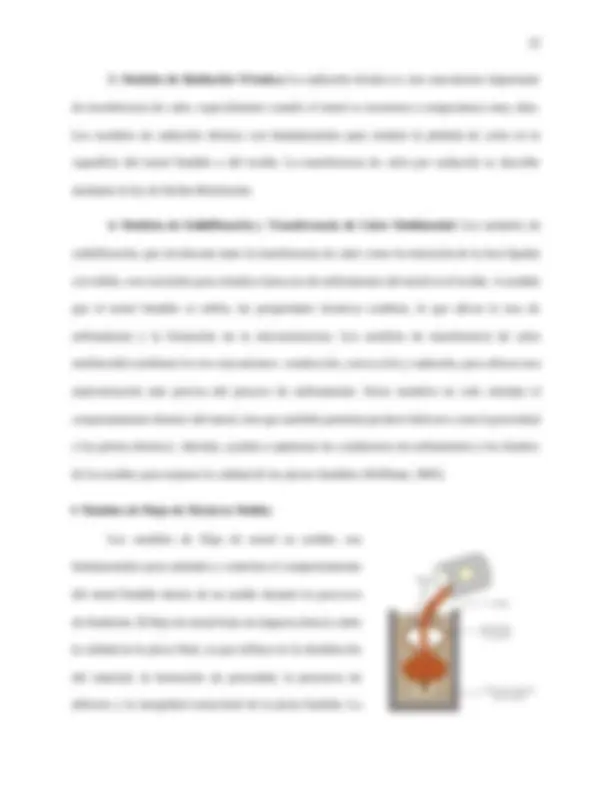
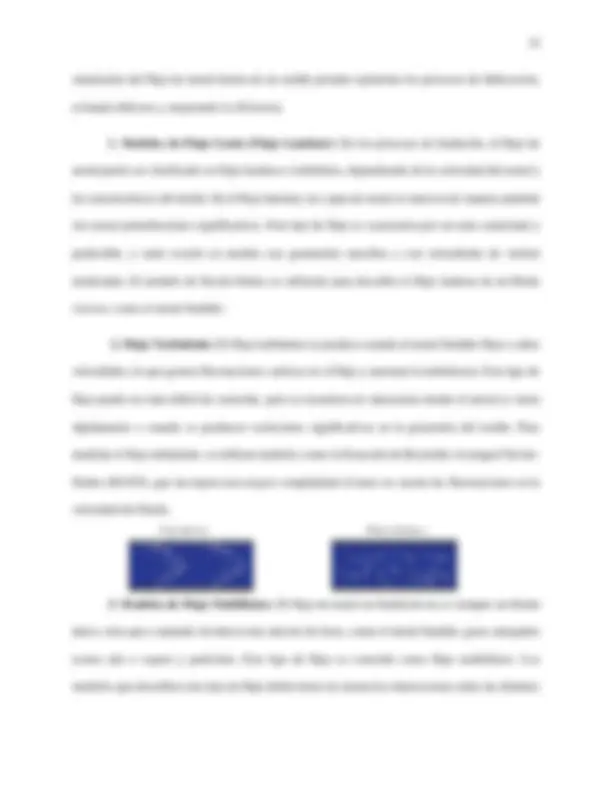
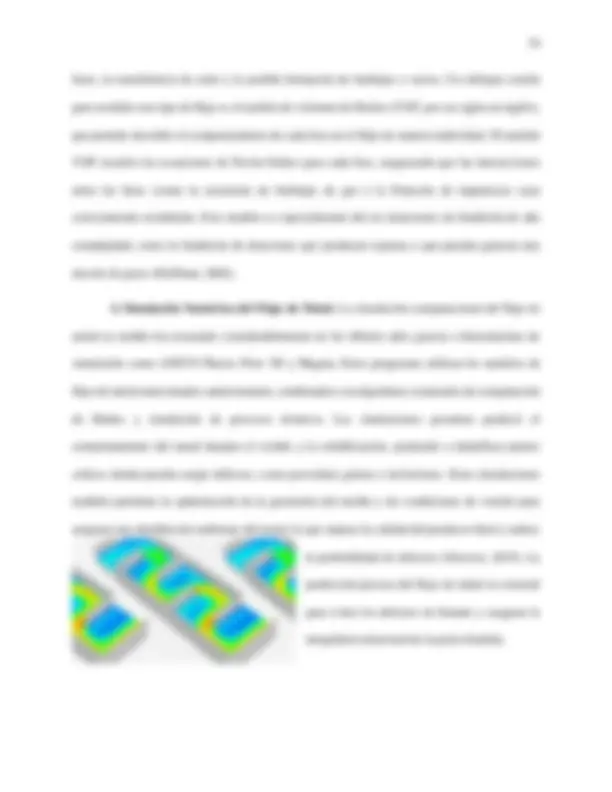
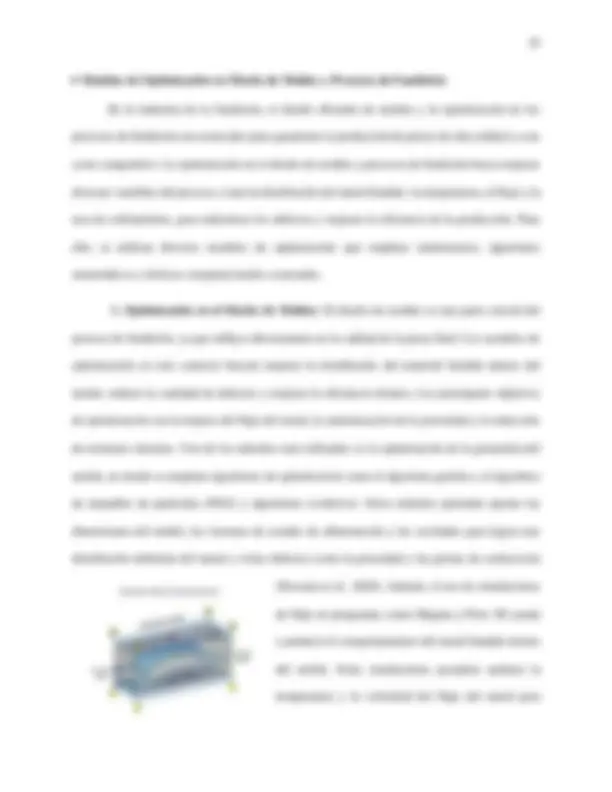
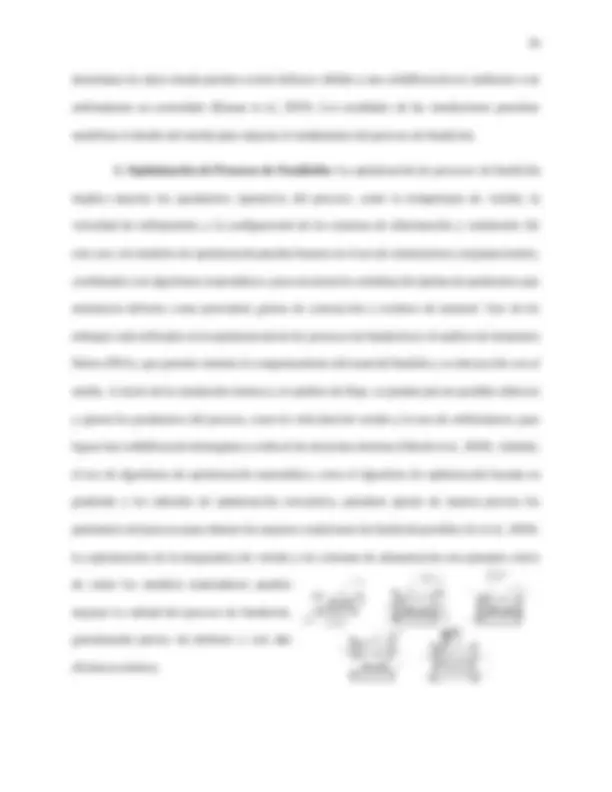
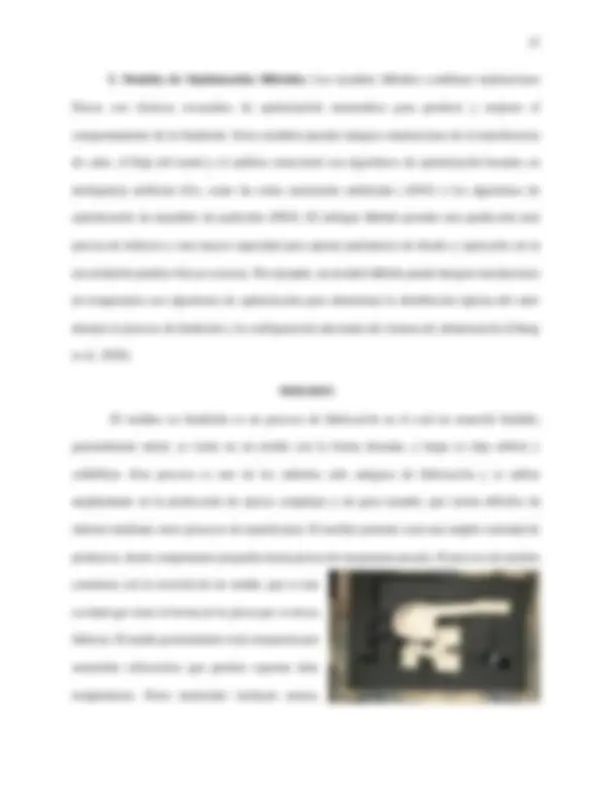
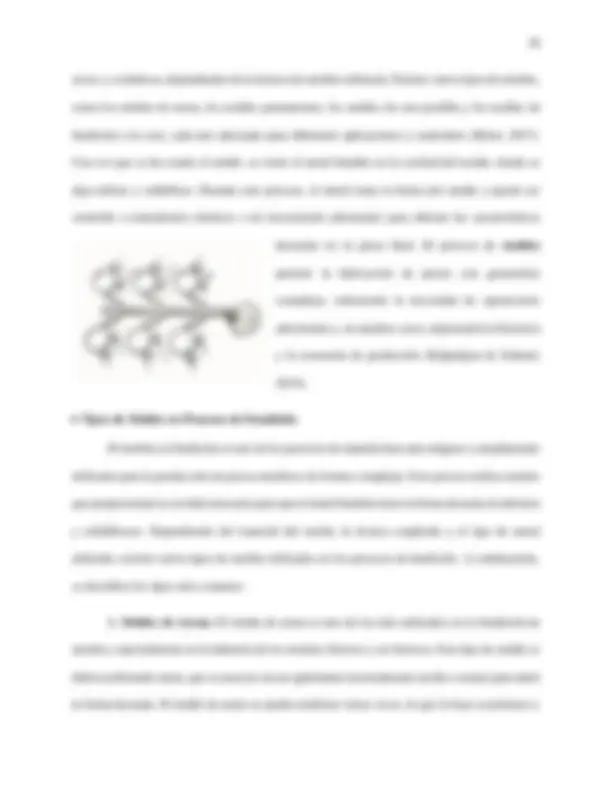
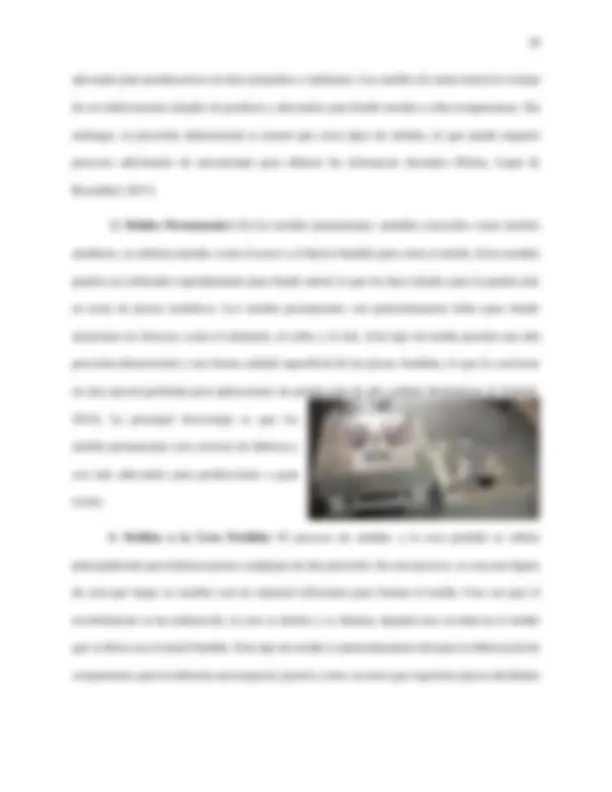
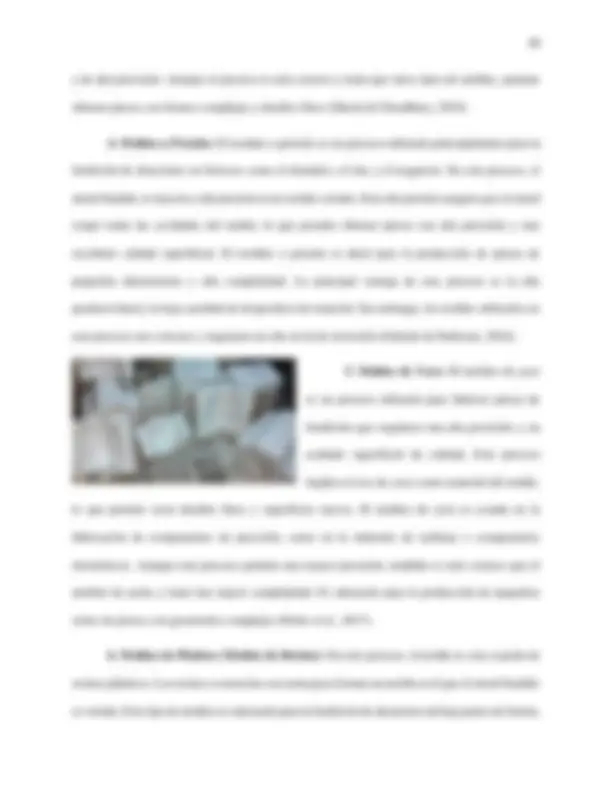
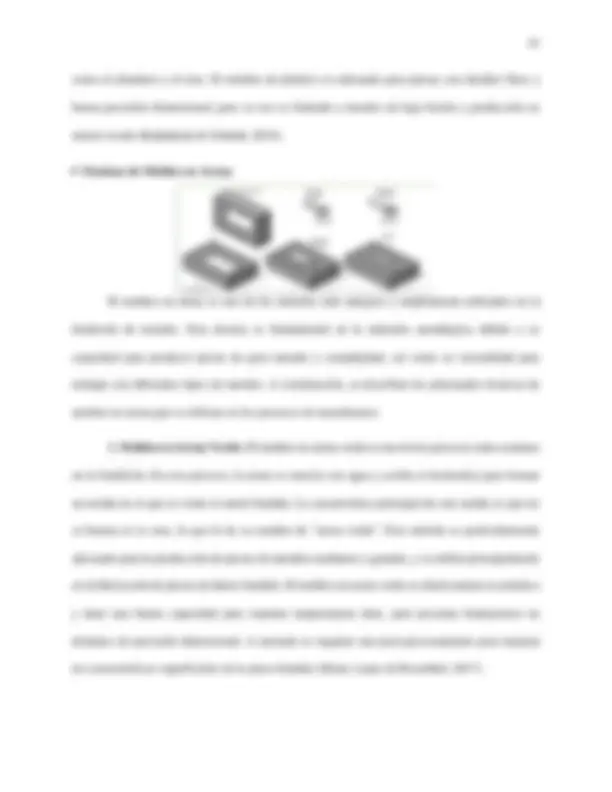
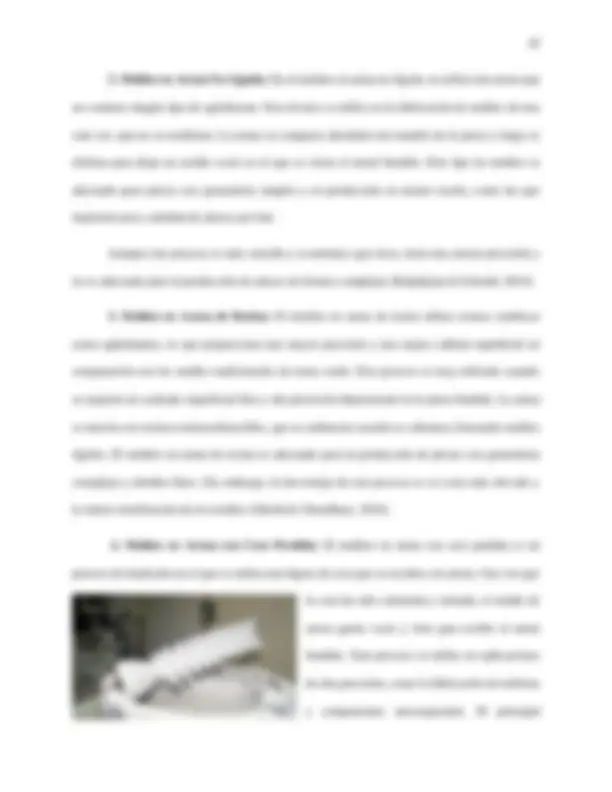
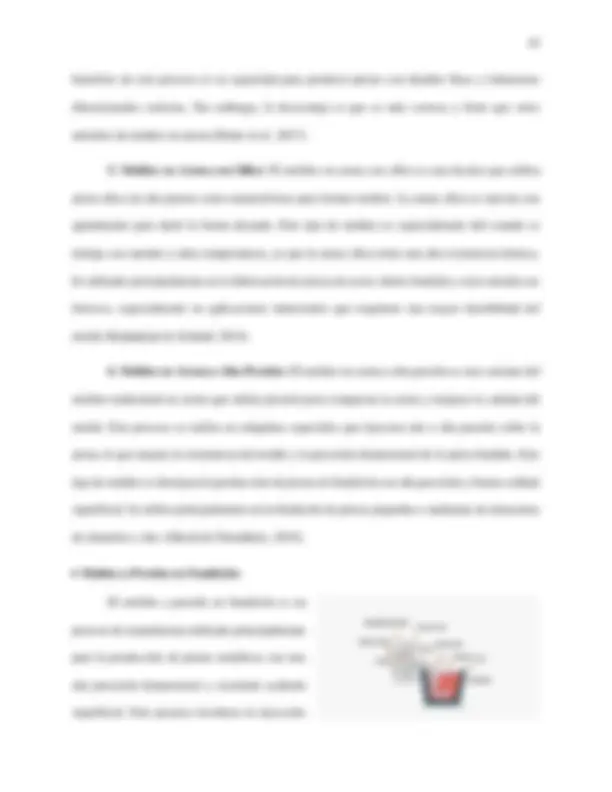
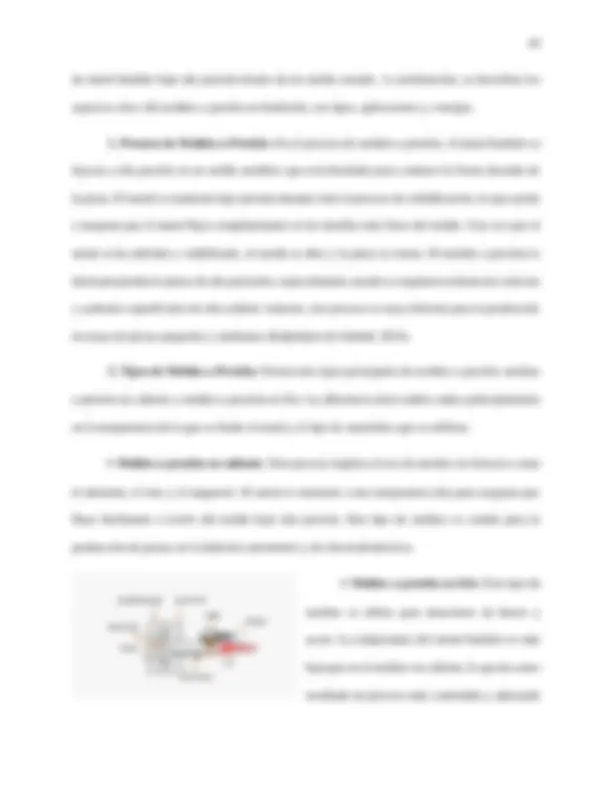
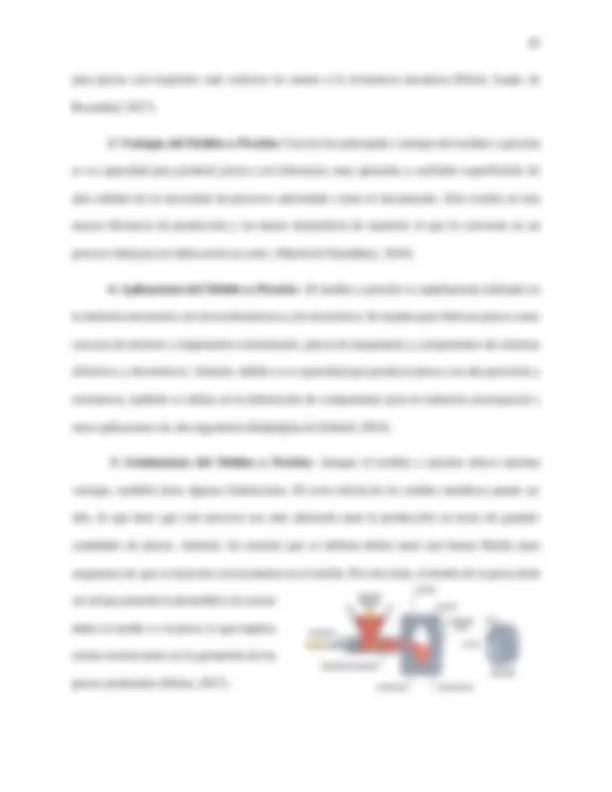
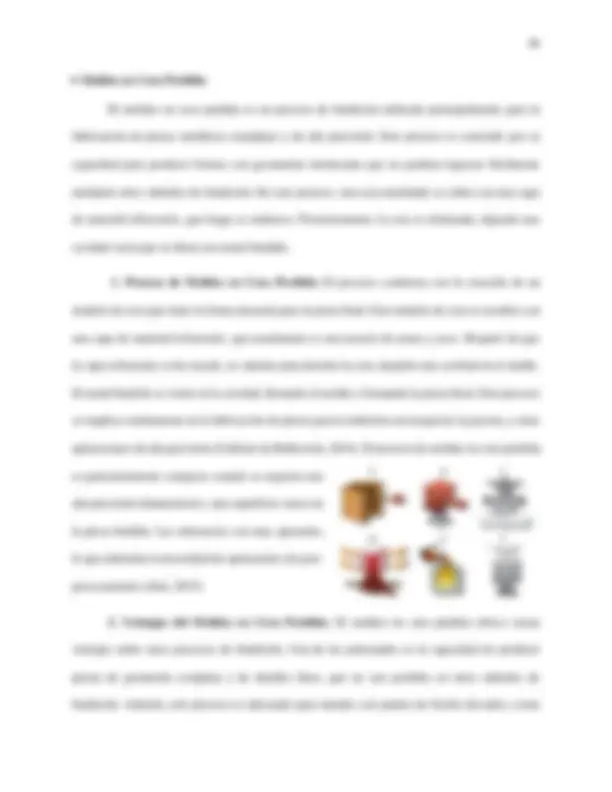
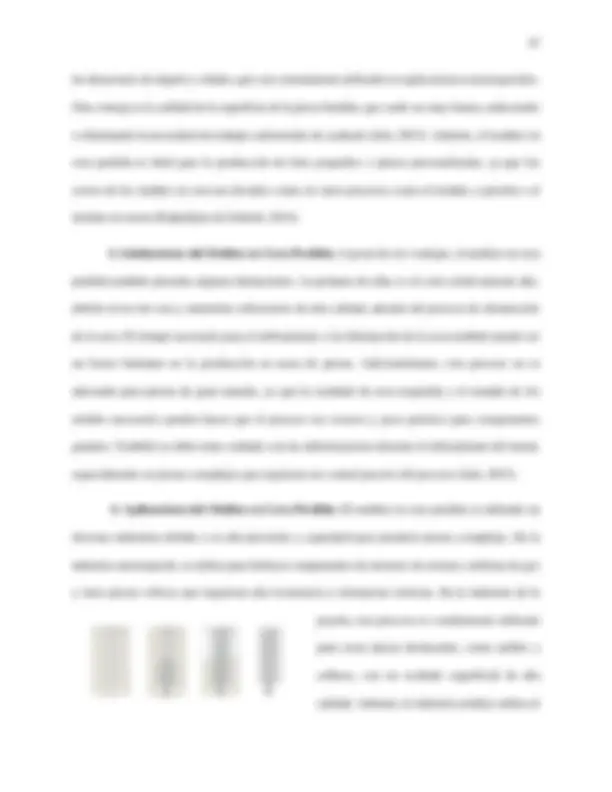
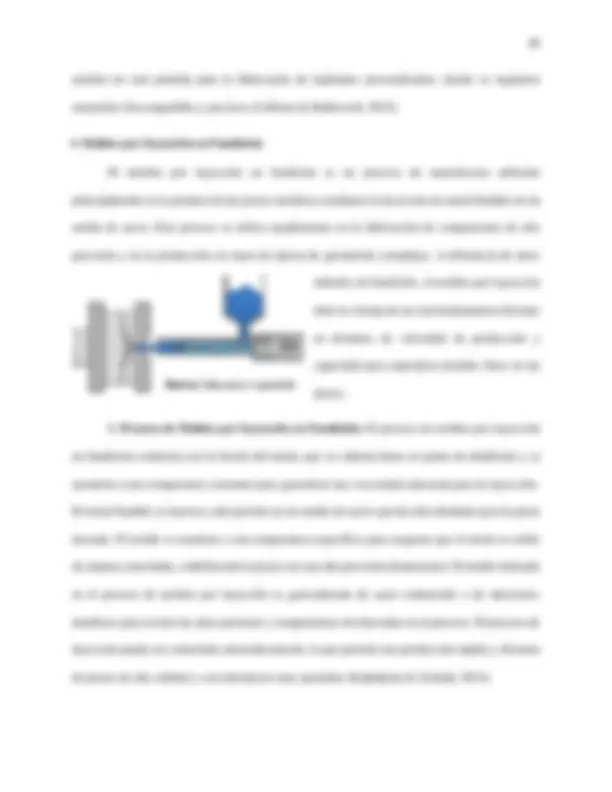
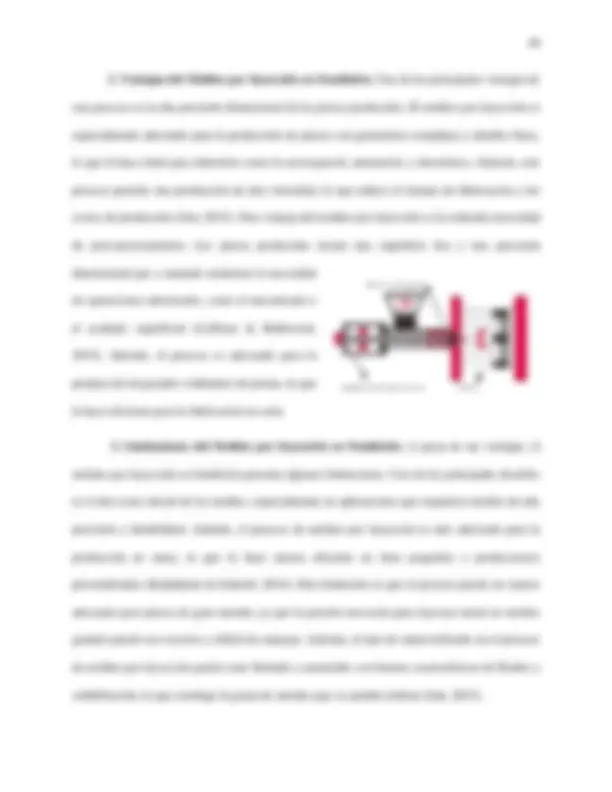
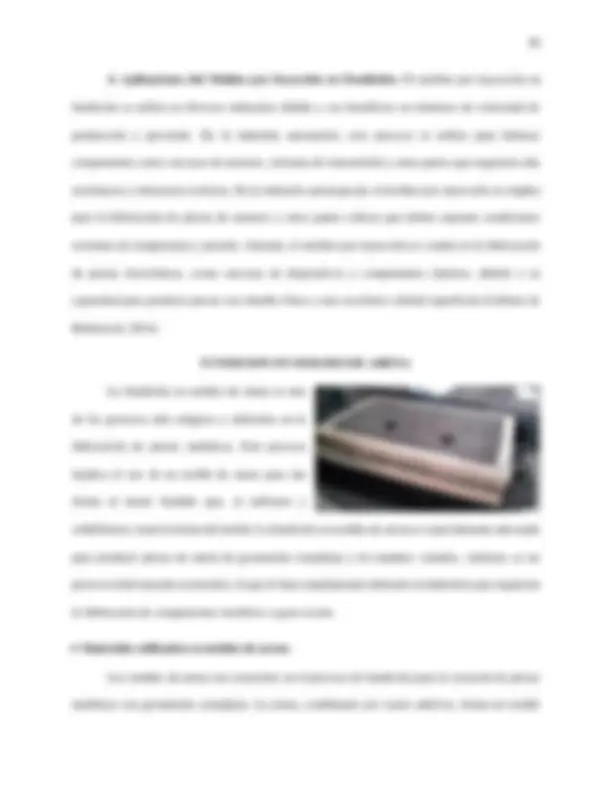
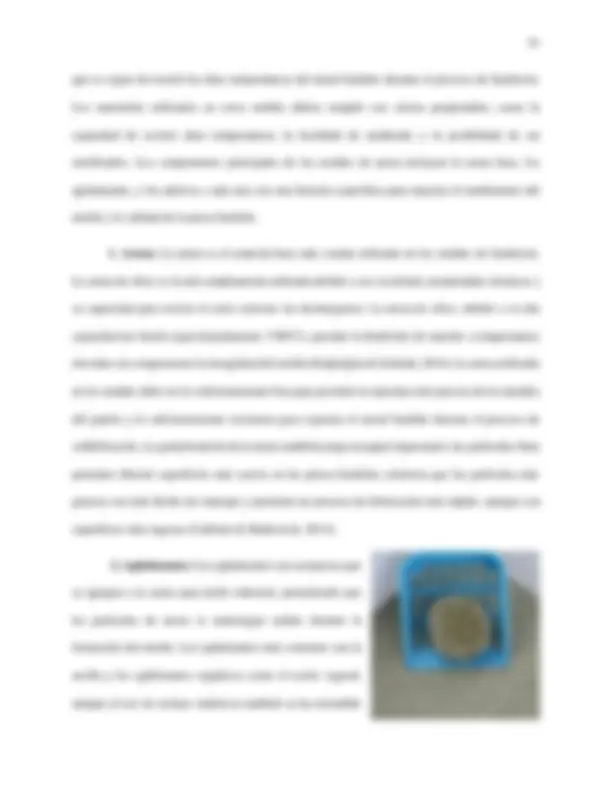
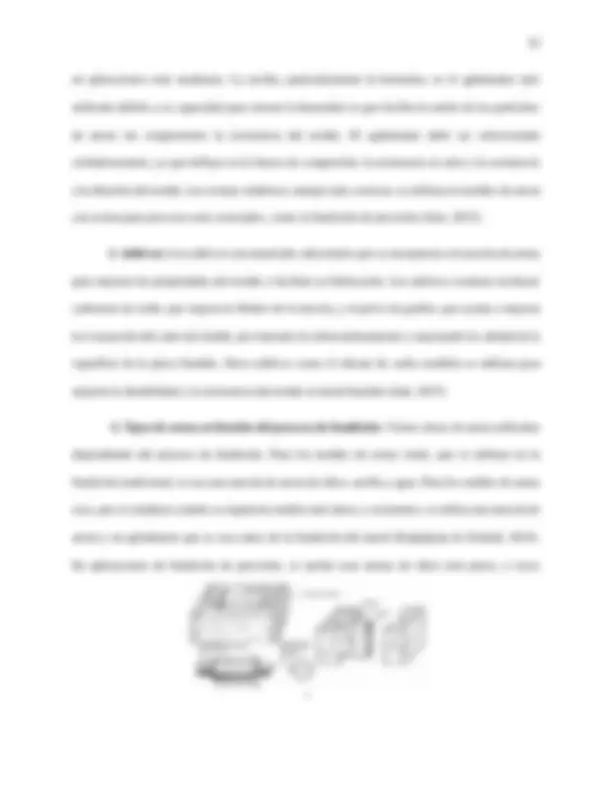
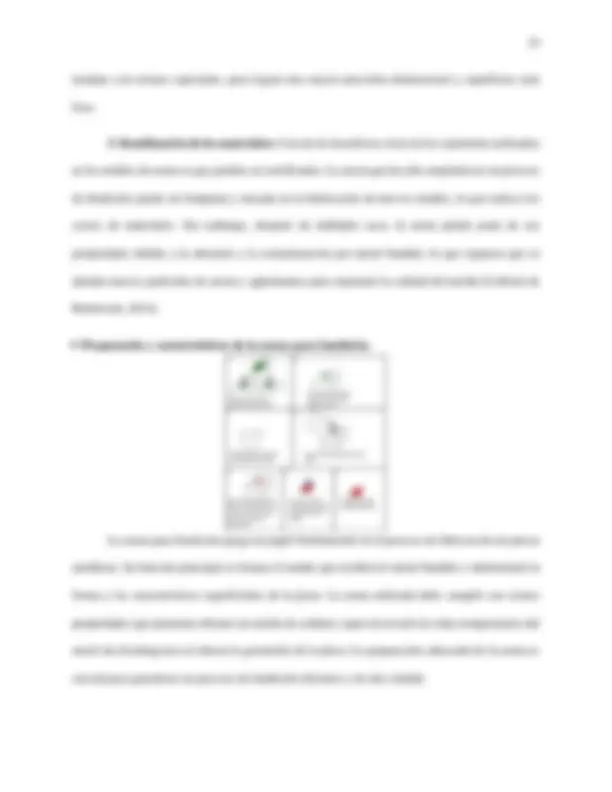
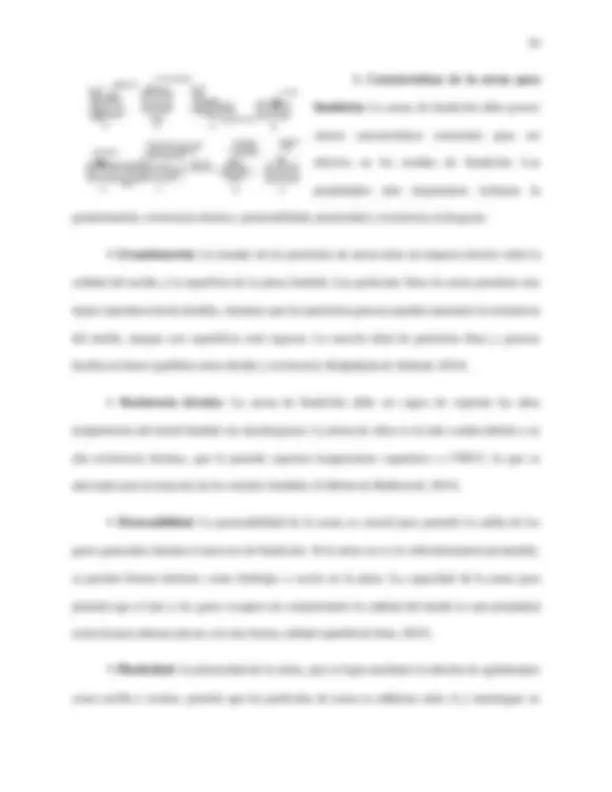
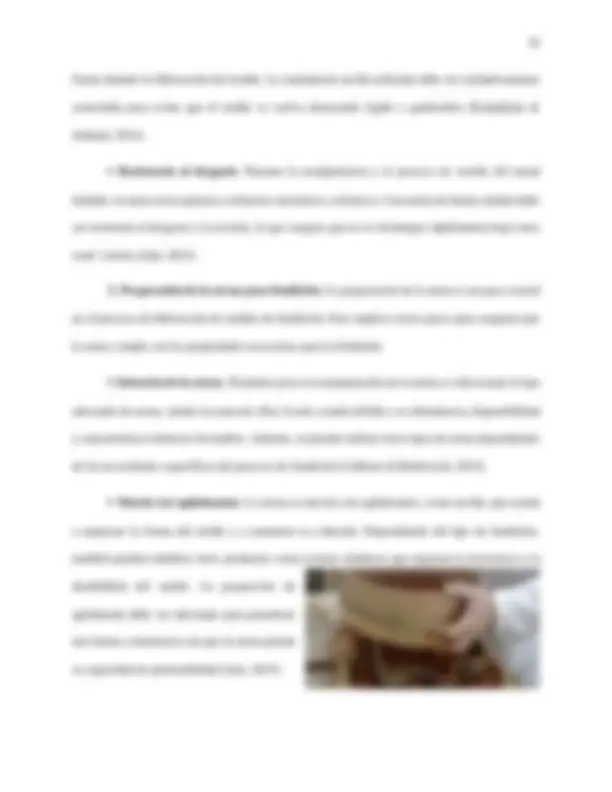
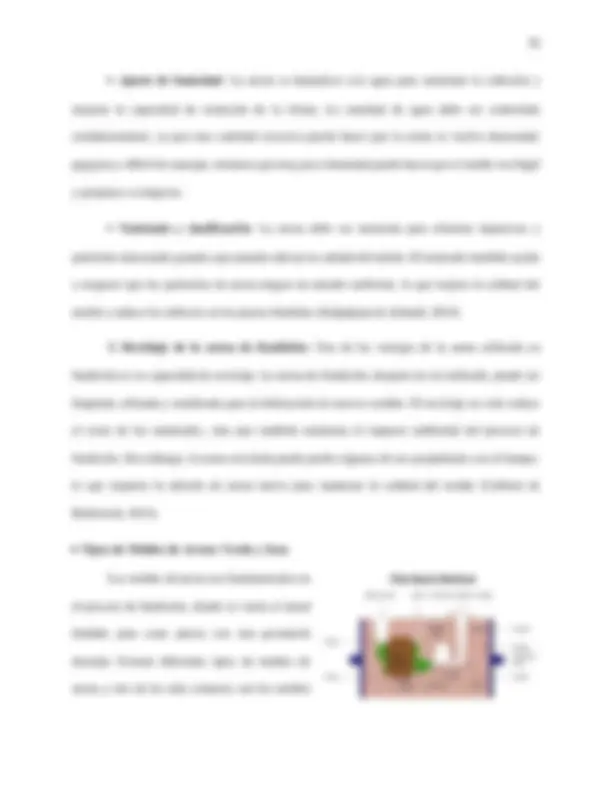
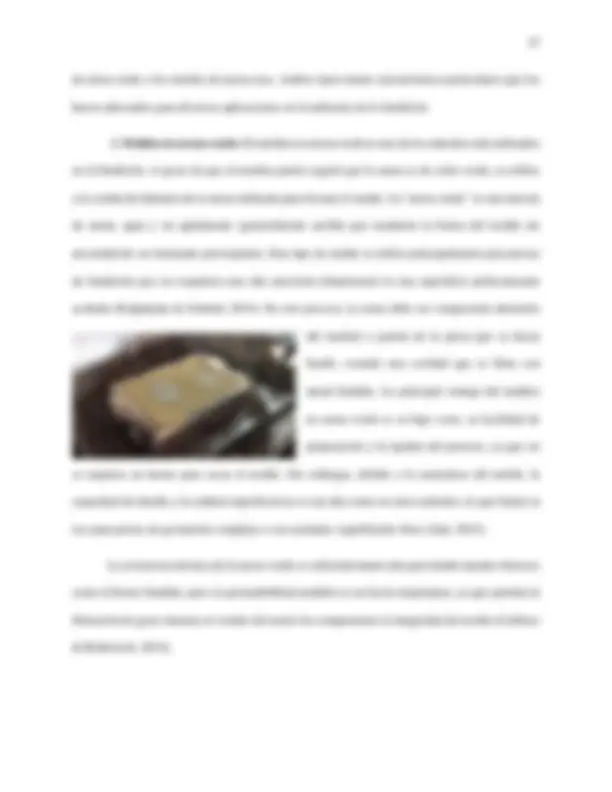
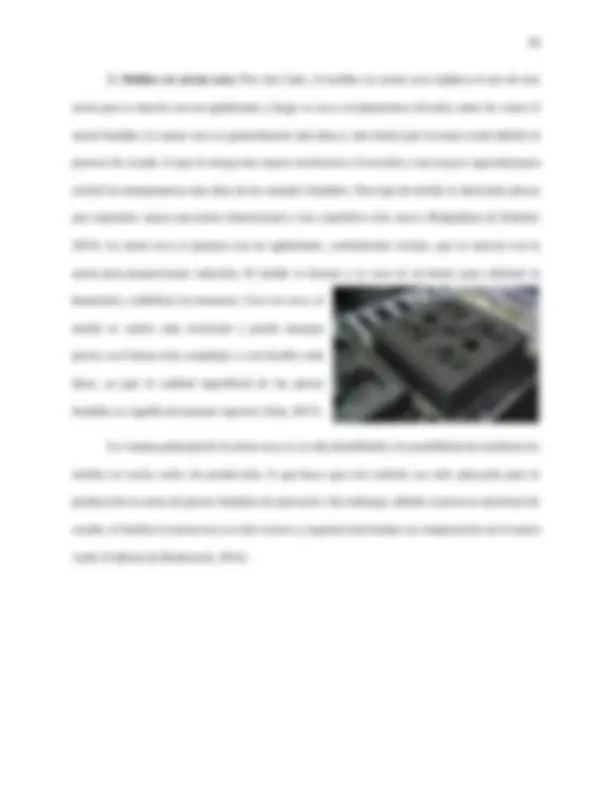
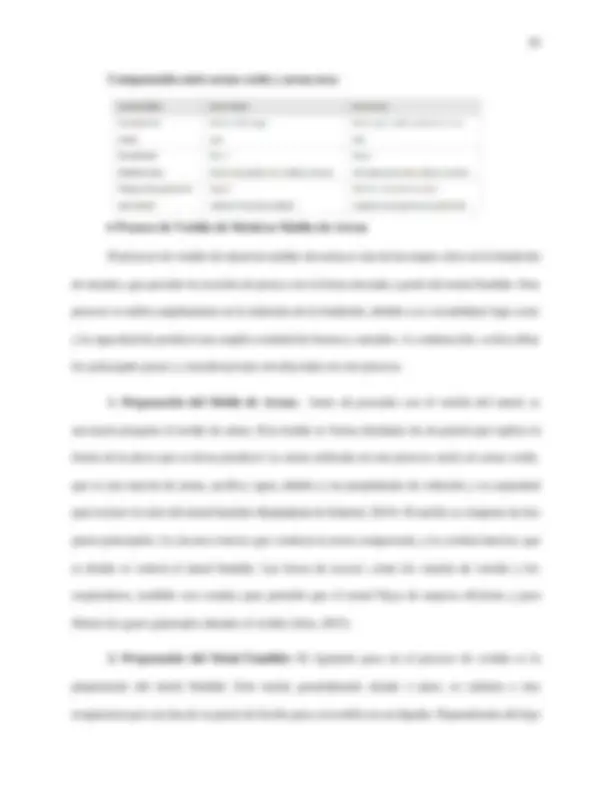
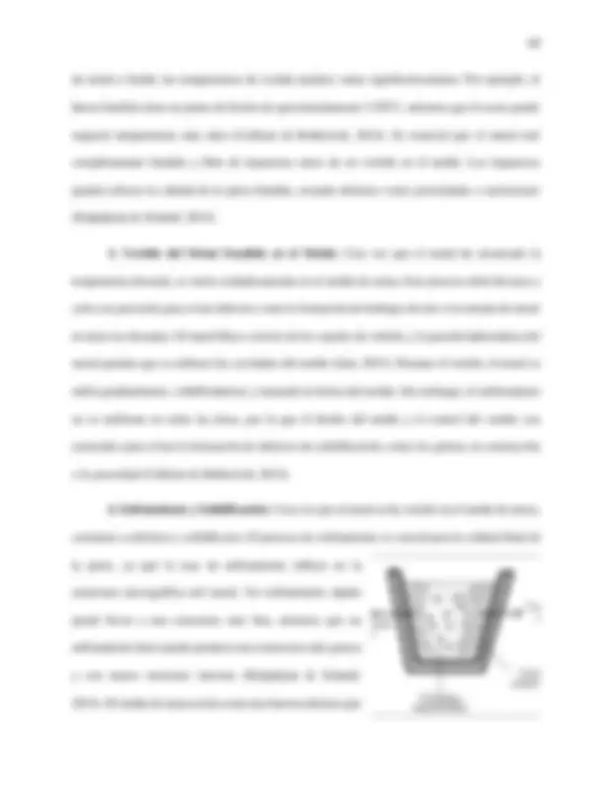
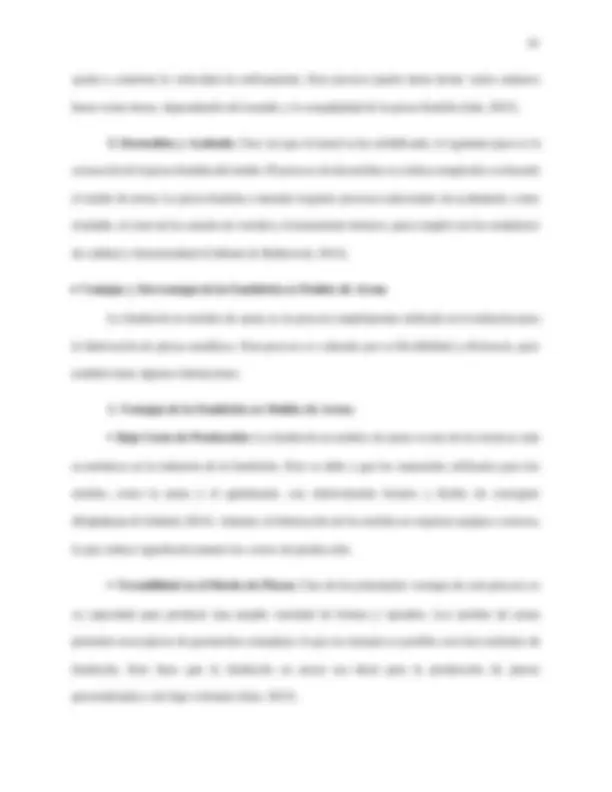
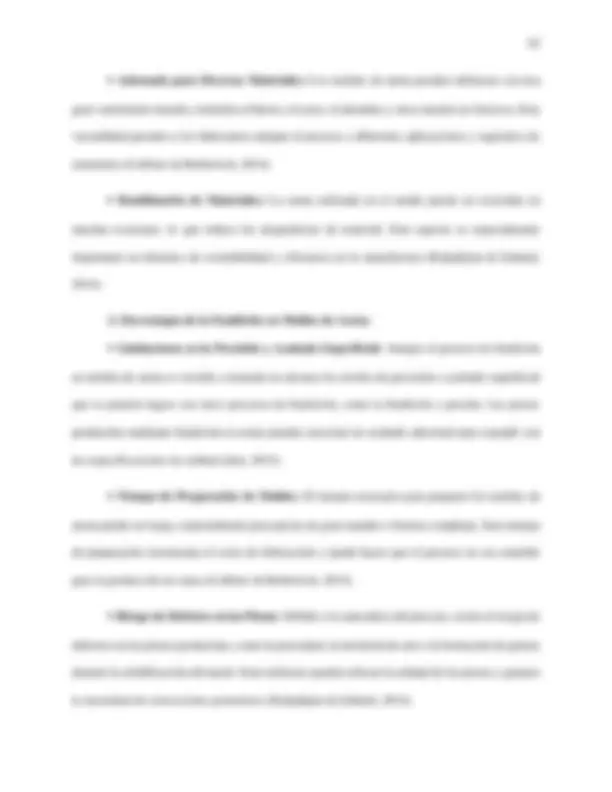
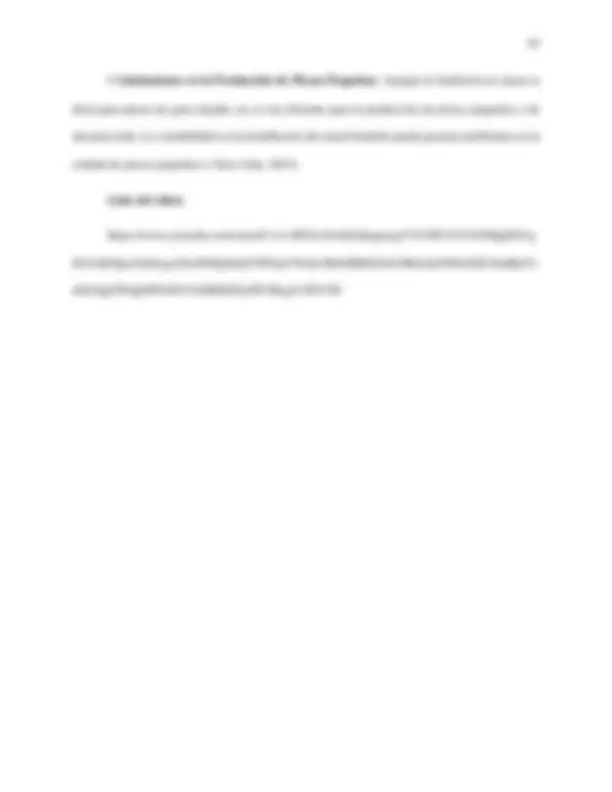
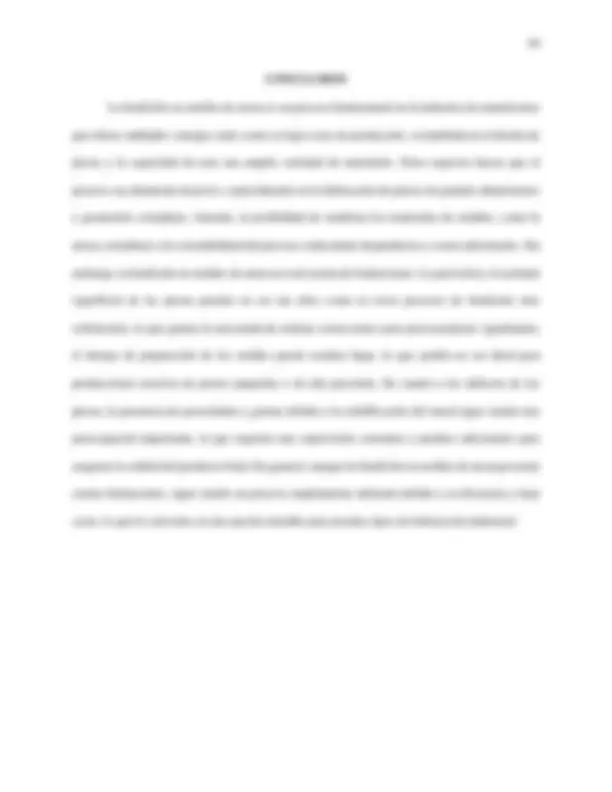
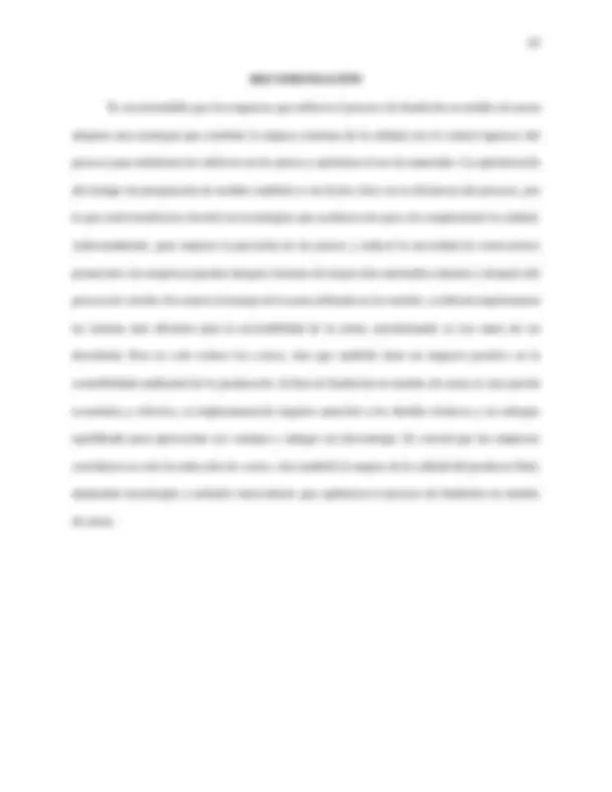
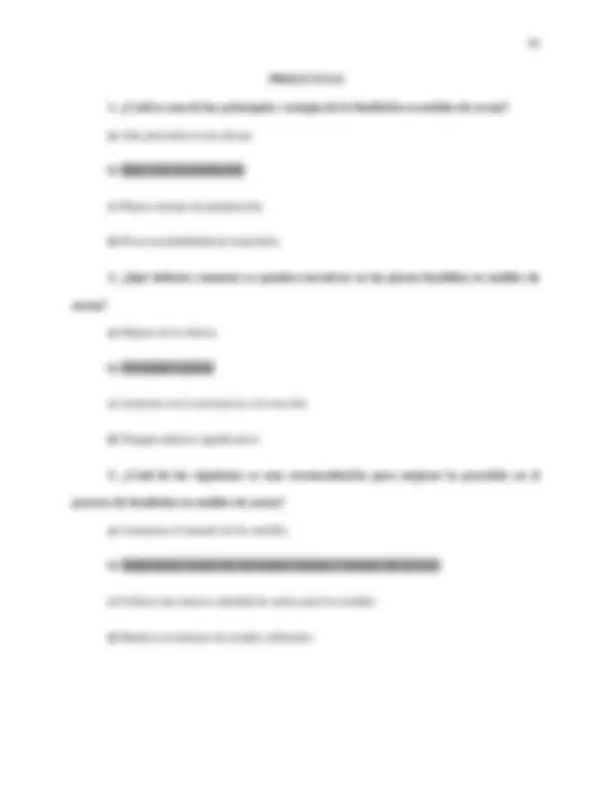
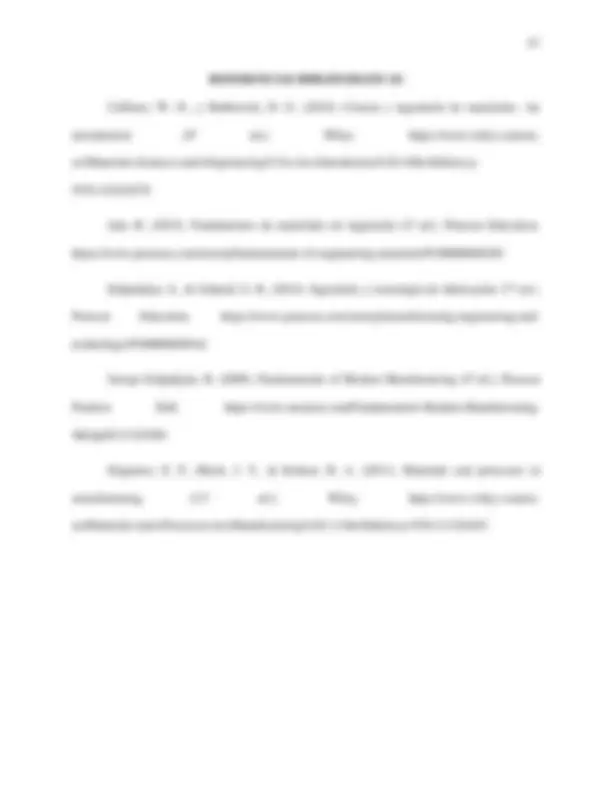
Prepara tus exámenes y mejora tus resultados gracias a la gran cantidad de recursos disponibles en Docsity
Gana puntos ayudando a otros estudiantes o consíguelos activando un Plan Premium
Prepara tus exámenes
Prepara tus exámenes y mejora tus resultados gracias a la gran cantidad de recursos disponibles en Docsity
Prepara tus exámenes con los documentos que comparten otros estudiantes como tú en Docsity
Los mejores documentos en venta realizados por estudiantes que han terminado sus estudios
Estudia con lecciones y exámenes resueltos basados en los programas académicos de las mejores universidades
Responde a preguntas de exámenes reales y pon a prueba tu preparación
Consigue puntos base para descargar
Gana puntos ayudando a otros estudiantes o consíguelos activando un Plan Premium
Comunidad
Pide ayuda a la comunidad y resuelve tus dudas de estudio
Descubre las mejores universidades de tu país según los usuarios de Docsity
Ebooks gratuitos
Descarga nuestras guías gratuitas sobre técnicas de estudio, métodos para controlar la ansiedad y consejos para la tesis preparadas por los tutores de Docsity
Una visión completa de la fundición en moldes de arena, un proceso de fabricación esencial para la producción de piezas metálicas. Se exploran los diferentes tipos de moldes, los materiales utilizados, los procesos de vertido y solidificación, así como las técnicas de optimización para garantizar la calidad y eficiencia del proceso. El documento también analiza los modelos de flujo de metal en moldes y los mecanismos de solidificación en materiales metálicos, proporcionando una base sólida para comprender los principios fundamentales de la fundición.
Tipo: Diapositivas
1 / 67
Esta página no es visible en la vista previa
¡No te pierdas las partes importantes!
Los procesos de fundición representan una de las técnicas más antiguas y fundamentales en la manufactura de piezas metálicas, permitiendo la producción de componentes con geometrías complejas y propiedades mecánicas adecuadas para diversas aplicaciones industriales. La fundición consiste en la fusión de un metal para luego verterlo en un molde, donde se solidifica y adquiere la forma deseada. Este procedimiento es ampliamente utilizado en la industria automotriz, aeroespacial, de construcción y manufactura en general, debido a su eficiencia y versatilidad en la producción de piezas de distintos tamaños y configuraciones. Uno de los aspectos clave en la fundición es el proceso de solidificación, que determina la estructura interna del material y, en consecuencia, sus propiedades mecánicas. Durante la solidificación, factores como la velocidad de enfriamiento, la formación de granos y la presencia de impurezas pueden influir en la calidad final de la pieza. Para optimizar este proceso, se emplean diversos modelos matemáticos y simulaciones que permiten predecir la microestructura del material y minimizar defectos como porosidades o contracciones. El moldeo es otra fase crucial en la fundición, ya que el molde define la forma final de la pieza y afecta su acabado superficial. Existen múltiples técnicas de moldeo, siendo la fundición en moldes de arena una de las más comunes debido a su bajo costo y flexibilidad. Este método consiste en la fabricación de moldes de arena compactada alrededor de un patrón, permitiendo la producción en serie de piezas con gran precisión dimensional. El estudio de los procesos de fundición y sus variables es esencial para mejorar la eficiencia y calidad de las piezas producidas, optimizando materiales, tiempos de fabricación y costos.
El proceso de fundición es una técnica de manufactura utilizada para la creación de piezas metálicas mediante el vertido de metal fundido en un molde que tiene la forma deseada. Esta técnica es una de las más antiguas en la industria y sigue siendo ampliamente utilizada debido a su capacidad para producir piezas complejas y de gran tamaño de manera eficiente (Kalpakjian, 2014). El proceso comienza con la selección y preparación del metal adecuado, que generalmente es fundido a altas temperaturas en un horno. Una vez fundido, el metal se vierte en un molde que puede estar hecho de diversos materiales como arena, yeso o metal, dependiendo de las propiedades que se deseen en la pieza final. El molde se deja enfriar para que el metal solidifique, adoptando la forma del molde. Tras el enfriamiento, se retira el molde y la pieza es despojada de cualquier impureza y exceso de material (Groover, 2019). Existen varios tipos de fundición, incluyendo la fundición en arena, la fundición a presión y la fundición en cera perdida. La elección del tipo de fundición depende de factores como la complejidad de la pieza, el material utilizado y los requisitos de tolerancia. Este proceso es especialmente útil para la fabricación de piezas metálicas de geometrías complicadas, como componentes de automóviles, maquinaria industrial y piezas de construcción (Kalpakjian, 2014). El principal beneficio de la fundición es su capacidad para crear formas complejas sin la necesidad de operaciones adicionales de maquinado. Sin embargo, el proceso también presenta
algunos desafíos, como la necesidad de un control preciso de la temperatura y la posibilidad de defectos en la pieza final, como porosidad o grietas (Groover, 2019).
propiedades físicas y químicas, y las aleaciones, que proporcionan características específicas para aplicaciones particulares.
1. Metales Ferrosos: Los metales ferrosos, especialmente el hierro y sus aleaciones, son los más utilizados en el proceso de fundición debido a sus propiedades de dureza, resistencia y facilidad para ser moldeados. El hierro fundido es uno de los materiales más comunes debido a su bajo costo y excelente fluidez, lo que lo hace ideal para piezas complejas. El acero fundido es utilizado cuando se requieren piezas con mayor resistencia y tenacidad, especialmente en la industria automotriz y de maquinaria pesada (Kalpakjian, 2014).
Existen varias subcategorías dentro del moldeo en arena, entre ellas el moldeo en arena verde, que utiliza arena sin un tratamiento térmico, y el moldeo en arena seca, que emplea arena tratada con aglutinantes químicos. El moldeo en arena verde es más común debido a su facilidad de uso y costos reducidos.
2. Moldeo en Yeso: El moldeo en yeso es utilizado para piezas de alta precisión y acabados superficiales finos. En este proceso, se emplea un molde hecho de yeso, que se prepara mediante la mezcla de yeso con agua para obtener una pasta que se vierte sobre un patrón. Después de que el yeso se endurece, el molde es calcinado para eliminar el patrón, dejando una cavidad precisa para verter el metal fundido. Esta técnica es especialmente adecuada para la producción de piezas complejas de pequeñas dimensiones y detalles finos, como en la industria de la joyería o componentes aeroespaciales (Kalpakjian, 2014). 3. Moldeo a la Cera Perdida: El moldeo a la cera perdida es una técnica avanzada utilizada para producir piezas de alta precisión, especialmente aquellas con geometrías complejas o detalles minuciosos. En este proceso, se fabrica un modelo de la pieza en cera, el cual es recubierto con una capa de material refractario (generalmente una mezcla de sílice y otros aglutinantes). Una vez que el recubrimiento se ha endurecido, el modelo de cera es calentado, lo que provoca su eliminación (de ahí el término "cera perdida"). El metal fundido se vierte en la cavidad creada por el modelo, y después se retira el molde refractario, obteniendo la pieza final (Groover, 2019). Este proceso se utiliza principalmente en la industria aeroespacial, de defensa y
en la fabricación de componentes médicos, donde se requiere una alta precisión y acabados de superficie finos.
4. Moldeo a Presión: En el moldeo a presión, el metal fundido es inyectado a alta presión en un molde cerrado, generalmente hecho de acero, lo que permite obtener piezas de alta precisión dimensional y con una excelente calidad de superficie. Este proceso es utilizado principalmente para la producción de piezas de pequeña y mediana escala, especialmente en la industria automotriz para componentes como carcasas de motores y partes del sistema de transmisión. El moldeo a presión ofrece una excelente relación costo-beneficio en la producción en masa, ya que permite producir piezas con tolerancias muy estrictas en un corto período de tiempo (Kalpakjian, 2014). 5. Moldeo en Fundición Centrifugada: El moldeo en fundición centrifugada utiliza la fuerza centrífuga para distribuir el metal fundido dentro del molde, lo que permite obtener piezas densas y uniformemente distribuidas. Este proceso es especialmente útil para la fabricación de piezas cilíndricas, como tubos, ruedas y otras formas tubulares, ya que la fuerza centrífuga asegura que el metal se distribuya de manera uniforme, eliminando las impurezas y logrando una mayor densidad en la pieza final. Este proceso se usa comúnmente en la industria de la construcción y en la fabricación de maquinaria pesada (Groover, 2019). Control de Calidad en Procesos de Fundición El control de calidad en los procesos de fundición es crucial para garantizar que las piezas producidas cumplan con los requisitos de diseño, especificaciones técnicas y estándares de
2. Inspección de Moldes y Su Preparación: El molde juega un papel crucial en la calidad de la pieza final. Un molde mal preparado puede dar lugar a defectos como bordes irregulares, deformaciones o defectos en la superficie. El control de calidad en esta etapa incluye la inspección del molde para asegurarse de que no haya grietas, burbujas de aire u otros defectos visibles. Las técnicas de inspección no destructiva, como los ensayos de partículas magnéticas o la radiografía, se utilizan para verificar la integridad del molde y detectar posibles defectos antes de la fundición (Groover, 2019). 3. Inspección de Defectos en las Piezas Fundidas: Una vez que las piezas se han enfriado y solidificado, se inspeccionan para detectar defectos comunes de fundición. Estos defectos incluyen la porosidad, las inclusiones, la falta de fusión y los defectos de la superficie, como grietas y rugosidades. Las técnicas de inspección más comunes incluyen el uso de ultrasonido, radiografía y pruebas de penetrante, que permiten identificar defectos internos y superficiales sin dañar las piezas (Kalpakjian, 2014).
fundición. Se realiza un control de la pureza del material y se monitorean las condiciones del proceso para minimizar las inclusiones.
4. Ensayos Mecánicos y de Desempeño: Para asegurarse de que las piezas fundidas cumplan con las especificaciones mecánicas, se realizan ensayos como la prueba de tracción, la dureza y la resistencia al impacto. Estos ensayos permiten verificar que las piezas tienen la resistencia y la durabilidad necesarias para su aplicación final. Además, el análisis de microestructura mediante técnicas como la microscopia electrónica de barrido (SEM) es utilizado para examinar la estructura interna del material y asegurar que cumple con los requisitos de calidad y desempeño (Groover, 2019). 5. Control Final y Certificación: Finalmente, después de la inspección y los ensayos, las piezas fundidas que han pasado todos los controles de calidad son certificadas y se procede a su envío o ensamblaje. Es común que los fabricantes de piezas fundidas certifiquen sus productos según normas internacionales de calidad, como las normas ISO 9001 o las especificaciones del cliente. Este proceso de certificación asegura que las piezas cumplen con los más altos estándares de calidad y son aptas para su uso en aplicaciones críticas. Aplicaciones Industriales de la Fundición La fundición es uno de los procesos más utilizados en la manufactura industrial debido a su capacidad para producir piezas de formas complejas, de tamaños grandes y con una variedad de materiales. Su versatilidad y bajo costo la hacen indispensable en diferentes sectores industriales. A continuación, se describen algunas de las principales aplicaciones industriales de la fundición.
que deben soportar condiciones extremas de temperatura y presión. Los componentes de las turbinas de gas, por ejemplo, requieren una excelente resistencia al desgaste y a la fatiga, lo que hace que la fundición sea una opción adecuada para su fabricación. Además, la fundición permite la producción de grandes piezas de manera más económica que otros procesos de manufactura, lo que resulta en una mayor eficiencia en la industria energética (Kalpakjian, 2014).
Además, la fundición de metales no ferrosos, como el aluminio, también se utiliza para fabricar sistemas de ventanas, puertas y otros componentes arquitectónicos (Groover, 2019).
Cuando un metal fundido se vierte en un molde, comienza a perder calor hacia las paredes del molde y a su entorno. A medida que la temperatura disminuye, las moléculas del metal pierden energía, lo que favorece la formación de núcleos cristalinos a partir de las impurezas o sitios preferenciales en la matriz metálica. Esta etapa inicial del proceso de solidificación se denomina nucleación. Los cristales que se forman inicialmente son muy pequeños y a menudo se fusionan a medida que crecen. Una vez que la nucleación se ha producido, el crecimiento de los cristales comienza a través del proceso de crecimiento dendrítico. Este proceso ocurre cuando los cristales recién formados continúan creciendo en la estructura del metal fundido. La velocidad y la dirección de este crecimiento pueden ser influenciadas por varios factores, como la tasa de enfriamiento, la composición del metal y las condiciones del molde. Cuando los cristales continúan creciendo, se intercalan entre sí y forman una estructura sólida. La estructura resultante, conocida como la microestructura del metal, depende en gran medida del patrón de crecimiento de los cristales, que puede ser influenciado por la geometría del molde, el tipo de aleación y el control del proceso de enfriamiento (Kalpakjian, 2014). La velocidad de enfriamiento es uno de los factores más importantes en la solidificación de materiales metálicos. Un enfriamiento rápido generalmente conduce a una microestructura más fina y un material más duro, mientras que un enfriamiento lento puede dar lugar a una microestructura más gruesa y menos densa. La solubilidad de los componentes en la aleación también influye en cómo se distribuyen los diferentes elementos en la microestructura, afectando sus propiedades mecánicas, como la resistencia a la tracción, la dureza y la resistencia a la corrosión (Groover, 2019).
En algunos casos, la solidificación no ocurre de manera uniforme, lo que puede dar lugar a defectos como porosidad, segregación de componentes y fisuras. Para evitar estos problemas, se pueden aplicar técnicas de control de la temperatura, como el enfriamiento controlado o el uso de moldes de arena que favorecen una tasa de enfriamiento más uniforme. El moldeo a presión también se utiliza para evitar problemas de solidificación en piezas complejas, garantizando una distribución más homogénea del material y una mayor precisión dimensional (Groover, 2019).