
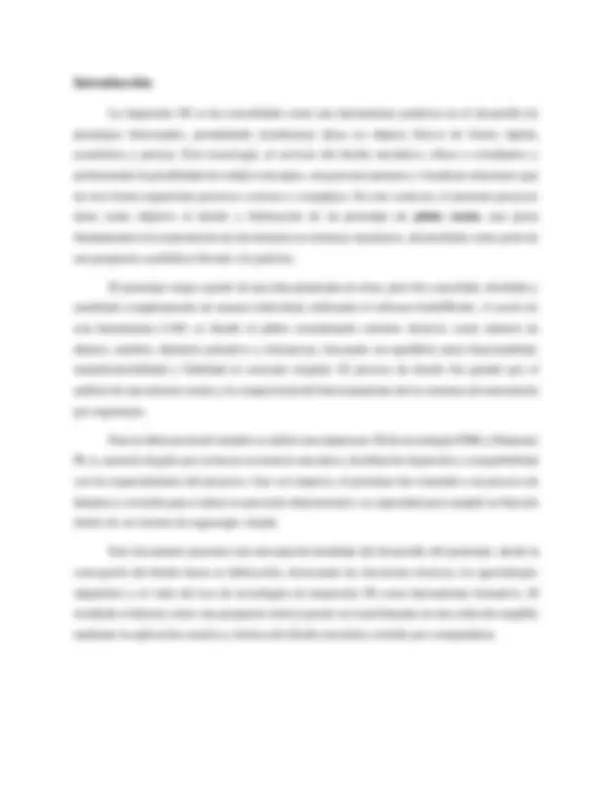
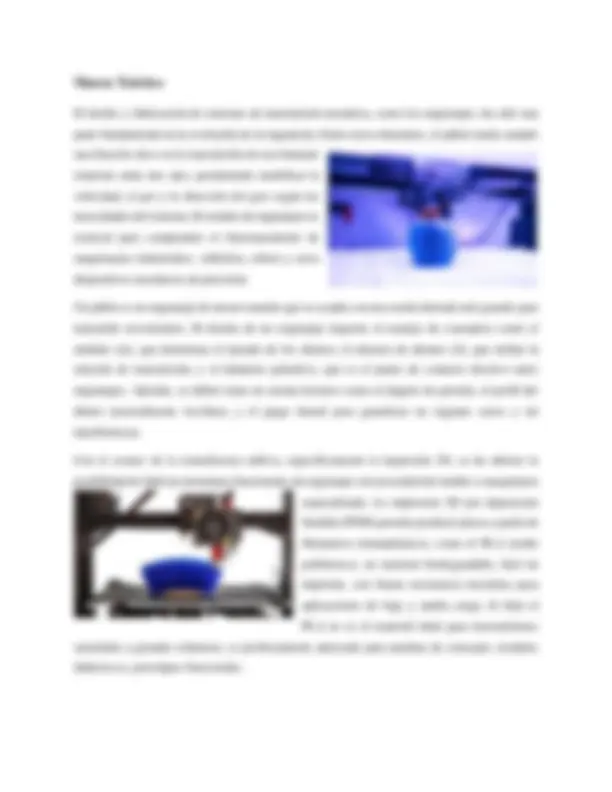
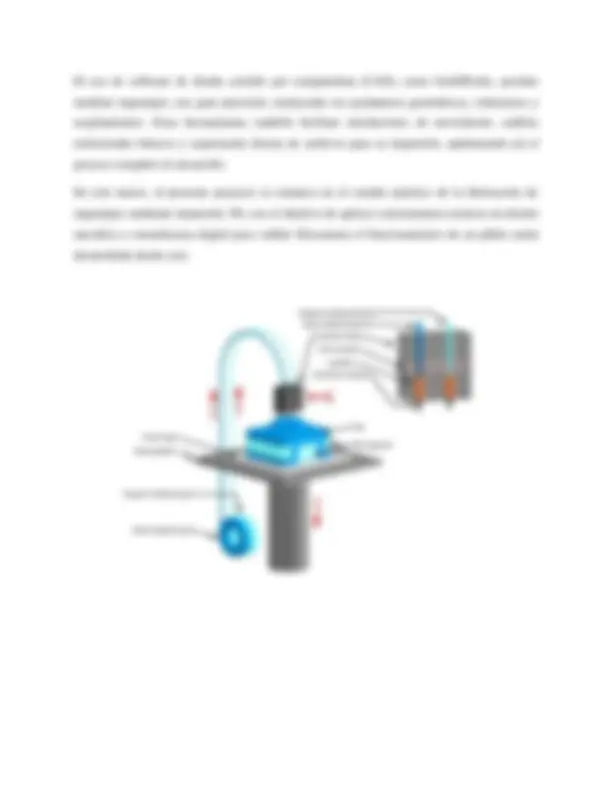
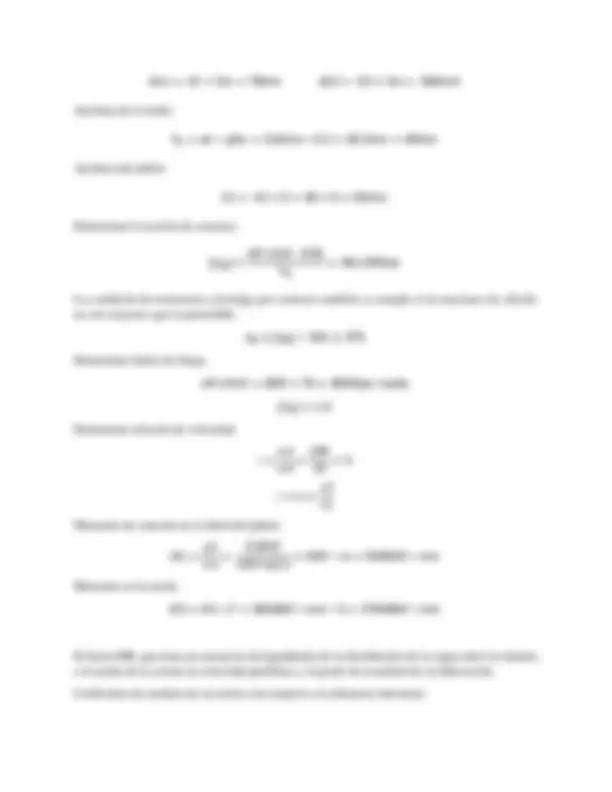
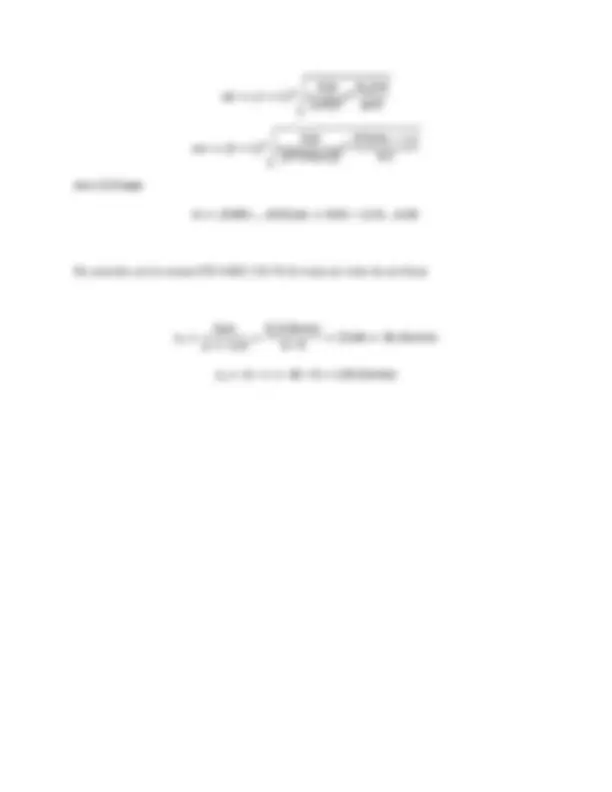
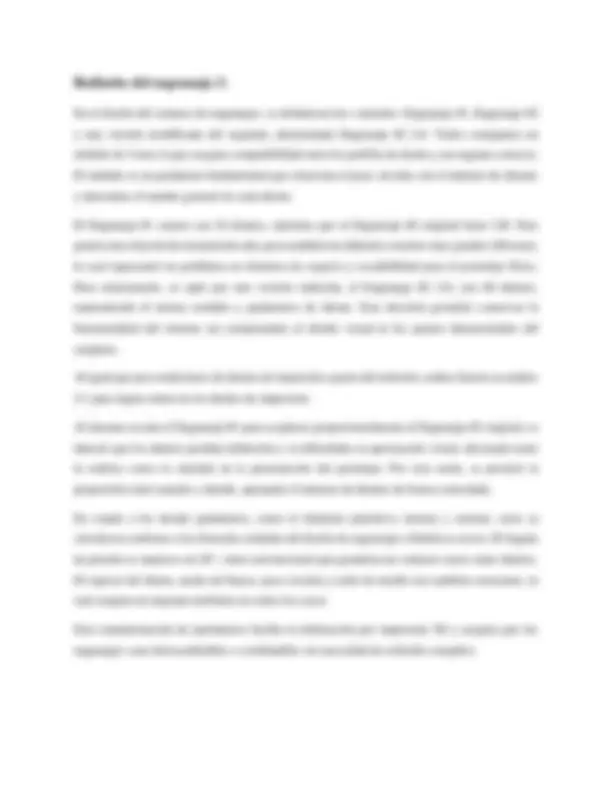
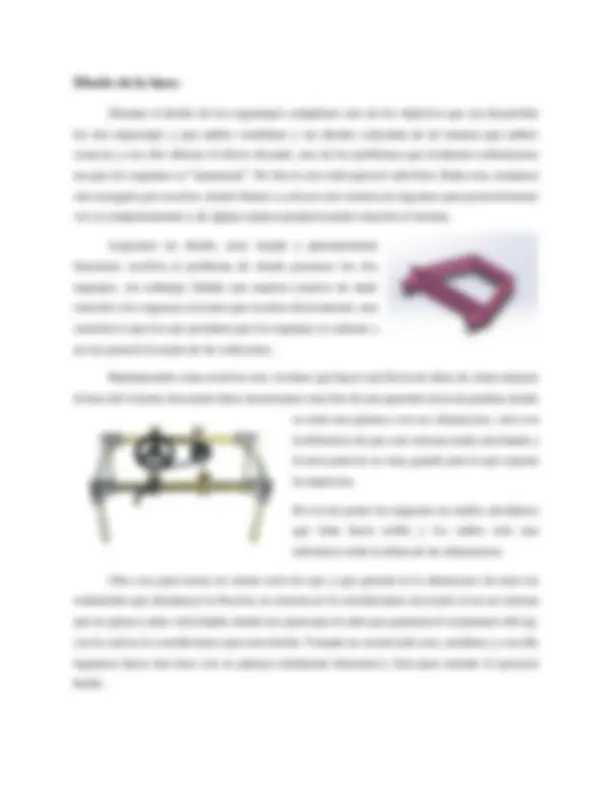
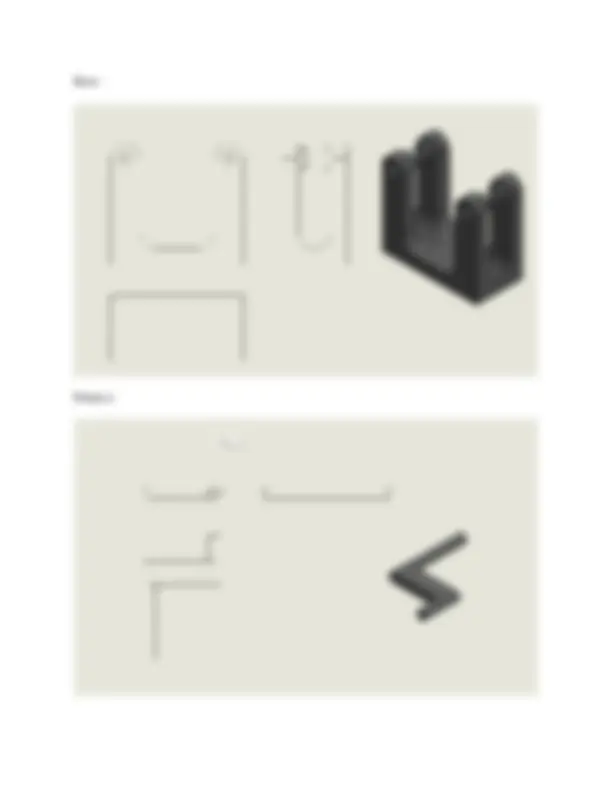
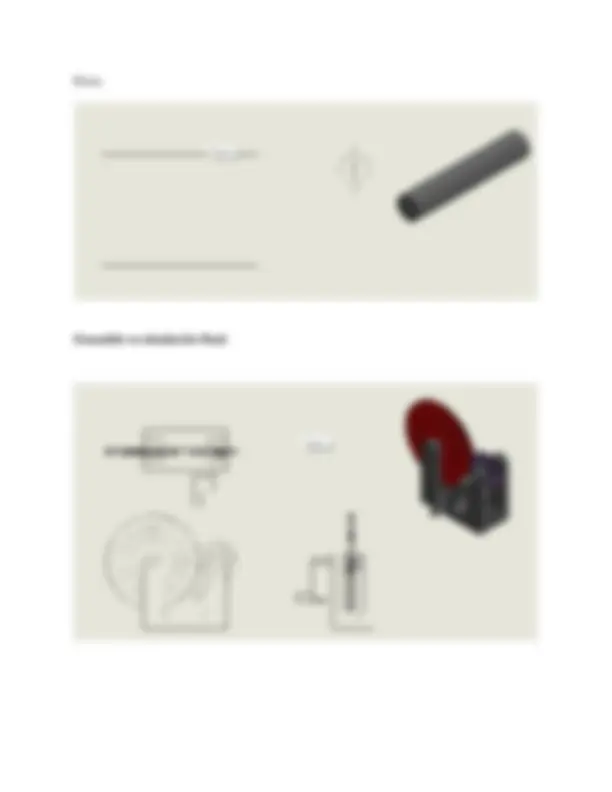
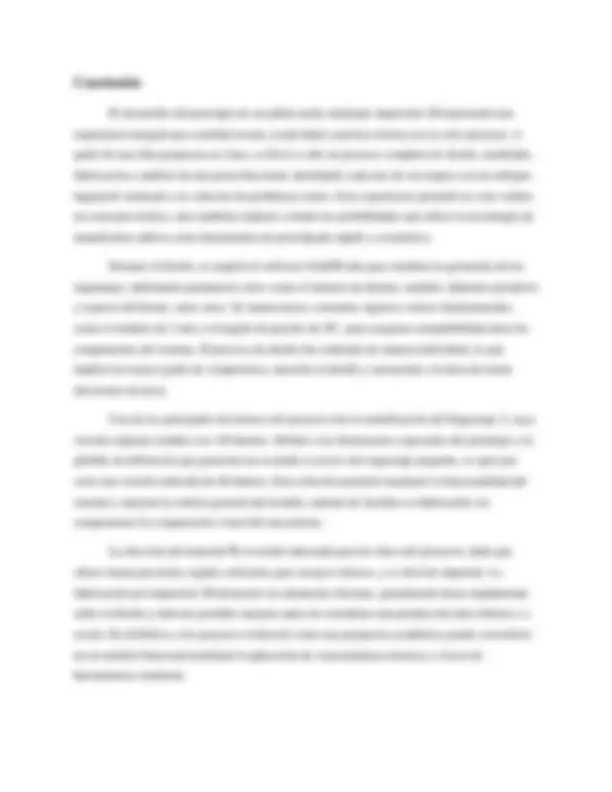
Prepara tus exámenes y mejora tus resultados gracias a la gran cantidad de recursos disponibles en Docsity
Gana puntos ayudando a otros estudiantes o consíguelos activando un Plan Premium
Prepara tus exámenes
Prepara tus exámenes y mejora tus resultados gracias a la gran cantidad de recursos disponibles en Docsity
Prepara tus exámenes con los documentos que comparten otros estudiantes como tú en Docsity
Los mejores documentos en venta realizados por estudiantes que han terminado sus estudios
Estudia con lecciones y exámenes resueltos basados en los programas académicos de las mejores universidades
Responde a preguntas de exámenes reales y pon a prueba tu preparación
Consigue puntos base para descargar
Gana puntos ayudando a otros estudiantes o consíguelos activando un Plan Premium
Comunidad
Pide ayuda a la comunidad y resuelve tus dudas de estudio
Descubre las mejores universidades de tu país según los usuarios de Docsity
Ebooks gratuitos
Descarga nuestras guías gratuitas sobre técnicas de estudio, métodos para controlar la ansiedad y consejos para la tesis preparadas por los tutores de Docsity
El documento en cuestión contiene información de manera resumida en cuanto a los mecanismos de piñón y rueda que puede ayudar al entendimiento del estudiante.
Tipo: Guías, Proyectos, Investigaciones
1 / 18
Esta página no es visible en la vista previa
¡No te pierdas las partes importantes!
FACULTAD DE INGENIERIA
Este proyecto consiste en el diseño, modelado y fabricación de un prototipo funcional
mediante tecnología de impresión 3D. El objetivo principal fue desarrollar a través del modelado
3D, un prototipo funcional del proyecto visto y resuelto con anterioridad, utilizando herramientas
de diseño asistido por computadora (CAD) y fabricación digital.
A lo largo del proceso, se utilizó el software Solidworks para el modelado 3D del
prototipo, teniendo en cuenta aspectos como dimensiones, ergonomía y funcionalidad.
Posteriormente, el modelo fue impreso con una impresora 3D de tecnología FDM utilizando
material PLA, bajo parámetros técnicos previamente establecidos.
Durante el desarrollo del proyecto se realizaron diversas pruebas y ajustes para mejorar la
calidad y funcionalidad del prototipo. Como resultado, se obtuvo una pieza funcional capaz de
cumplir con los requisitos propuestos, demostrando la eficiencia del proceso de diseño e
impresión 3D como herramienta rápida y accesible para la creación de soluciones físicas.
Tras la impresión, el prototipo pasó por un proceso de postproducción que incluyó
limpieza de soportes, lijado, ensamblaje y ajustes mecánicos. Posteriormente, se realizaron
pruebas funcionales para verificar el cumplimiento de los requisitos iniciales y se analizaron
posibles mejoras.
El resultado fue un modelo físico funcional que demuestra el potencial de la impresión 3D
como herramienta para el desarrollo ágil de prototipos. Esta metodología permitió iterar
rápidamente, reducir costos y validar conceptos de diseño de manera eficiente. El presente
documento detalla cada fase del proyecto, desde la idea inicial hasta la obtención del prototipo
final, aportando una visión completa del proceso de diseño y fabricación digital.
El diseño y fabricación de sistemas de transmisión mecánica, como los engranajes, ha sido una
parte fundamental en la evolución de la ingeniería. Entre estos elementos, el piñón rueda cumple
una función clave en la transmisión de movimiento
rotatorio entre dos ejes, permitiendo modificar la
velocidad, el par y la dirección del giro según las
necesidades del sistema. El estudio de engranajes es
esencial para comprender el funcionamiento de
maquinarias industriales, vehículos, robots y otros
dispositivos mecánicos de precisión.
Un piñón es un engranaje de menor tamaño que se acopla con una rueda dentada más grande para
transmitir movimiento. El diseño de un engranaje requiere el manejo de conceptos como el
módulo (m), que determina el tamaño de los dientes; el número de dientes (Z), que define la
relación de transmisión; y el diámetro primitivo, que es el punto de contacto efectivo entre
engranajes. Además, se deben tener en cuenta factores como el ángulo de presión, el perfil del
diente (normalmente involuta), y el juego lateral para garantizar un engrane suave y sin
interferencias.
Con el avance de la manufactura aditiva, específicamente la impresión 3D, se ha abierto la
posibilidad de fabricar prototipos funcionales de engranajes sin necesidad de moldes o maquinaria
especializada. La impresión 3D por deposición
fundida (FDM) permite producir piezas a partir de
filamentos termoplásticos, como el PLA (ácido
poliláctico), un material biodegradable, fácil de
imprimir, con buena resistencia mecánica para
aplicaciones de baja y media carga. Si bien el
PLA no es el material ideal para transmisiones
sometidas a grandes esfuerzos, es perfectamente adecuado para pruebas de concepto, modelos
didácticos y prototipos funcionales.
El uso de software de diseño asistido por computadora (CAD), como SolidWorks, permite
modelar engranajes con gran precisión, incluyendo sus parámetros geométricos, tolerancias y
acoplamientos. Estas herramientas también facilitan simulaciones de movimiento, análisis
estructurales básicos y exportación directa de archivos para su impresión, optimizando así el
proceso completo de desarrollo.
En este marco, el presente proyecto se enmarca en el estudio práctico de la fabricación de
engranajes mediante impresión 3D, con el objetivo de aplicar conocimientos teóricos de diseño
mecánico y manufactura digital para validar físicamente el funcionamiento de un piñón rueda
desarrollado desde cero.
1
2
𝐹
1
2
𝐹
Tensión permisible a la flexión:
𝐹 1
𝐹 2
La resistencia a la flexión de los dientes del piñón y de la rueda dependen de la relación.
𝐹 1
𝐹 1
𝐹 2
𝐹 2
El cálculo de resistencia a la flexión debe realizarse para los dientes de la rueda puesto que para
ello es menor la relación hallada como factor de carga se toma KF = 2 y se procede a realizar el
cálculo:
𝐹 2
Se cumple la condición:
𝐹 1
𝐹 2
Distancia interracial real:
Dimensiones fundamentales del piñón y de la rueda.
Diámetro de los círculos de cabeza de los dientes:
Anchura de la rueda:
2
Anchura del piñón:
Determinar la tensión de contacto:
𝐻
ℎ
La condición de resistencia a la fatiga por contacto también se cumple si las tensiones de cálculo
no son mayores que la permisible.
𝐻
𝐻
Determinar límite de fatiga.
ℎ
Determinar relación de velocidad.
Momento de rotación en el árbol del piñón:
Momento en la rueda.
El factor KH, que tiene en cuenta las desigualdades de la distribución de la carga entre los dientes
o el ancho de la corona la velocidad periférica y el grado de exactitud de su fabricación.
Coeficiente de anchura de la corona con respecto a la distancia interaxial.
En el diseño del sistema de engranajes, se definieron tres variantes: Engranaje #1, Engranaje #
y una versión modificada del segundo, denominada Engranaje #2 2.0. Todos comparten un
módulo de 3 mm, lo que asegura compatibilidad entre los perfiles de diente y un engrane correcto.
El módulo es un parámetro fundamental que relaciona el paso circular con el número de dientes
y determina el tamaño general de cada diente.
El Engranaje #1 cuenta con 24 dientes, mientras que el Engranaje #2 original tiene 120. Esto
genera una relación de transmisión alta, pero también un diámetro exterior muy grande (366 mm),
lo cual representó un problema en términos de espacio y escalabilidad para el prototipo físico.
Para solucionarlo, se optó por una versión reducida, el Engranaje #2 2.0, con 60 dientes,
manteniendo el mismo módulo y parámetros de diente. Esta decisión permitió conservar la
funcionalidad del sistema sin comprometer el diseño visual ni los ajustes dimensionales del
conjunto.
Al igual que por condiciones de limites de impresión a parte del rediseño, ambos fueron escalados
2:1 para lograr entrar en los limites de impresión.
Al intentar escalar el Engranaje #1 para acoplarse proporcionalmente al Engranaje #2 original, se
detectó que los dientes perdían definición y se dificultaba su apreciación visual, afectando tanto
la estética como la claridad en la presentación del prototipo. Por esta razón, se priorizó la
proporción entre tamaño y detalle, ajustando el número de dientes de forma controlada.
En cuanto a los demás parámetros, como el diámetro primitivo, interno y externo, estos se
calcularon conforme a las fórmulas estándar del diseño de engranajes cilíndricos rectos. El ángulo
de presión se mantuvo en 20°, valor convencional que garantiza un contacto suave entre dientes.
El espesor del diente, ancho del hueco, paso circular y radio de entalle son también constantes, lo
cual asegura un engrane uniforme en todos los casos.
Esta estandarización de parámetros facilita la fabricación por impresión 3D y asegura que los
engranajes sean intercambiables o combinables sin necesidad de rediseño completo.
Diseño Original:
Parámetro Engranaje #1 Engranaje #
Número de dientes 24 120
Módulo 3 mm 3 mm
Diámetro Externo 78 mm 366 mm
Diámetro Primitivo 72 mm 360 mm
Diámetro Interno 66 mm 354 mm
Espesor del Diente 5 mm 5 mm
Ancho del Hueco 5 mm 5 mm
Paso Circular 9 mm 9 mm
Radio de Entalle 1 mm 1 mm
Ángulo de Presión 20° 20°
Rediseño:
Parámetro Engranaje #1 Engranaje #
Número de dientes 24.0 mm 60.0 mm
Módulo 1.5 mm 1.5 mm
Diámetro Externo 39.0 mm 183.0 mm
Diámetro
Primitivo
36.0 mm 180.0 mm
Diámetro Interno 33.0 mm 177.0 mm
Espesor del Diente 2.4 mm 2.4 mm
Ancho del Hueco 2.6 mm 2.6 mm
Paso Circular 4.7 mm 4.7 mm
Radio de Entalle .6 mm .6 mm
Ángulo de Presión 20° 20°
Durante el diseño de los engranajes cumplimos uno de los objetivos que era desarrollar
los dos engranajes y que ambos combinen y sus dientes coincidan de tal manera que ambos
avancen y con ello obtener el efecto deseado, uno de los problemas que temíamos enfrentarnos
era que los engranes se “amarraran”. No fue el caso todo pareció salir bien. Dado esto, teníamos
otra incógnita por resolver, donde íbamos a colocar este sistema de engranes para posteriormente
ver su comportamiento y de alguna manera proporcionarle rotación al sistema.
Logramos un diseño, muy simple y aparentemente
funcional, resolvía el problema de donde ponemos los dos
engranes, sin embargo faltaba una manera creativa de darle
rotación a los engranes sin tener que tocarlos directamente, otra
cuestión es que los ejes permiten que los engranes se salieran y
no nos pareció la mejor de las soluciones.
Replanteando como resolver esto, tuvimos que hacer una lluvia de ideas de cómo mejorar
la base del sistema, buscando ideas encontramos una foto de una aparente mesa de pruebas donde
se tenía una palanca con sus chumaceras, solo con
la diferencia de que este sistema usaba una banda y
la mesa parecía ser muy grande para lo que soporta
la impresora.
En vez de poner los engranes en medio, decidimos
que irían hacia arriba y los radios más una
tolerancia serán la altura de las chumaceras.
Otra cosa para tomar en cuenta sería los ejes y que girarán en la chumacera sin tener un
rodamiento que disminuya la fricción, en sistema no lo consideramos necesario al ser un sistema
que no girara a altas velocidades donde nos preocupe el calor que generará el rozamiento del eje,
con lo cual no lo consideramos para este diseño. Tomado en cuenta todo esto, medimos y con ello
logramos hacer una base con su palanca totalmente funcional y lista para simular el ejercicio
hecho.
Base:
Palanca:
Durante la impresión del proyecto se generan bases que ayudan al momento de imprimir, sin
embargo, estos deben de ser retirados para colocar de manera apta las piezas y que logren los
efectos que deseamos, este proceso lo hizo el operador de la impresora, con lo cual solo nos
correspondió lograr el ensamble adecuado. Algo que no tomamos en cuenta son los defectos de
los ejes al imprimirlos, con lo cual nos trajo problemas, se tuvo que lijar los ejes para lograr que
encajen y que giren sin problemas.
Finalmente, obtuvimos el resultado deseado:
La evaluación del prototipo de piñón rueda se realizó considerando aspectos funcionales,
dimensionales y visuales, con el objetivo de verificar la efectividad del diseño y la precisión del
proceso de impresión 3D. La pieza fue sometida a una inspección general tras la fabricación, así
como a pruebas de engrane básicas para validar su desempeño dentro de un sistema mecánico
simulado.
Desde el punto de vista dimensional, el prototipo impreso mostró una buena
concordancia con las medidas diseñadas en SolidWorks. Gracias al uso del material PLA y a
una configuración adecuada de la impresora (altura de capa, temperatura y velocidad), las
tolerancias se mantuvieron dentro de un margen aceptable para este tipo de fabricación, con
variaciones mínimas en diámetros y espesores. La geometría de los dientes fue reproducida de
forma satisfactoria, conservando el perfil involuta necesario para un correcto contacto entre
engranajes.
En cuanto a la funcionalidad, el prototipo fue ensamblado junto con sus engranajes
correspondientes, y se comprobó que el movimiento de transmisión se realizaba de manera
fluida y sin interferencias significativas. No se presentó desalineación ni desgaste durante la
prueba, lo cual sugiere que el acoplamiento entre dientes fue exitoso y que las dimensiones
clave, como el paso circular y el módulo, fueron bien aplicadas.
Uno de los puntos más relevantes en la evaluación fue la decisión de modificar el diseño
del Engranaje #2, reduciendo su número de dientes de 120 a 60. Este cambio resultó ser clave
para que el prototipo se ajustara a las limitaciones físicas del espacio disponible sin perder
claridad visual ni funcionalidad. El resultado fue un sistema más compacto y proporcional,
donde cada engranaje mantiene una presencia visual equilibrada y comprensible dentro del
conjunto.
Finalmente, el aspecto estético y de presentación también fue favorable. La impresión
resultó limpia, con buen acabado superficial para una pieza funcional, y sin defectos graves
como warping, stringing o capas desalineadas. Esto reafirma la capacidad de la impresión 3D
como medio efectivo para producir prototipos didácticos, útiles no solo para validar ideas sino
también para presentaciones técnicas o académicas.