
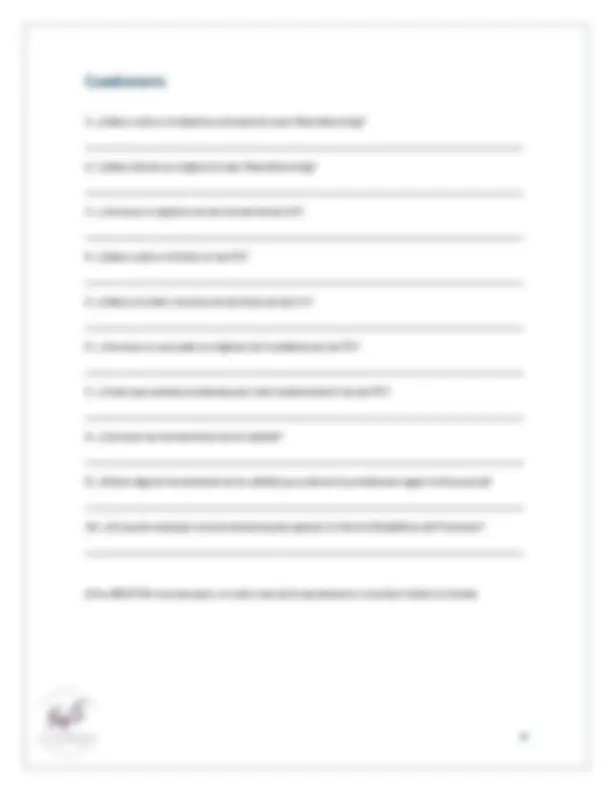
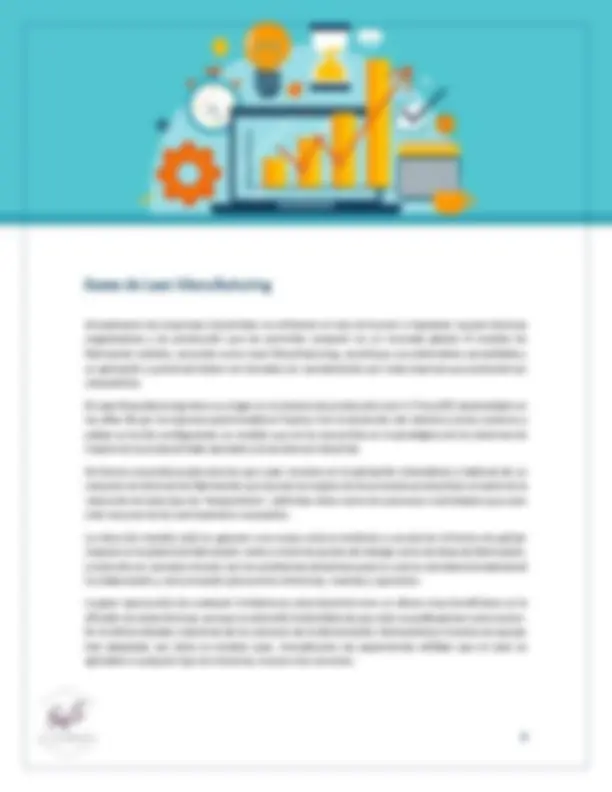
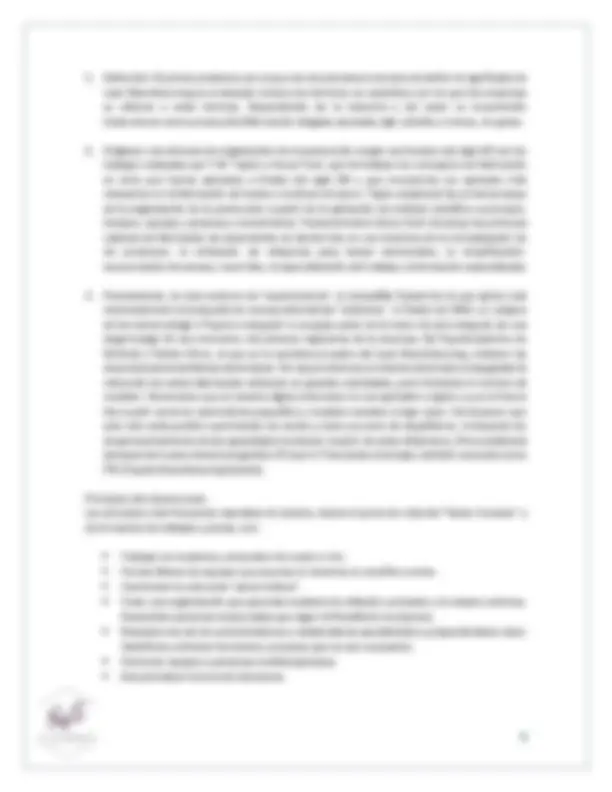
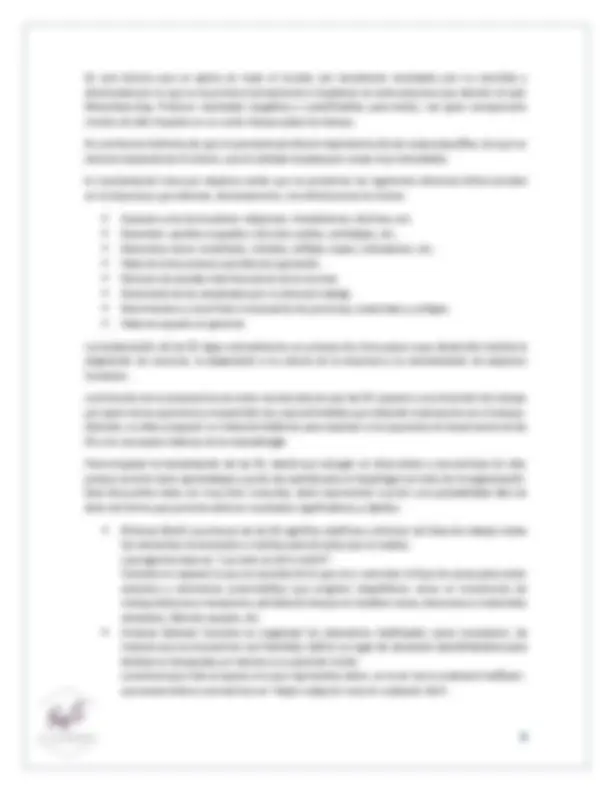
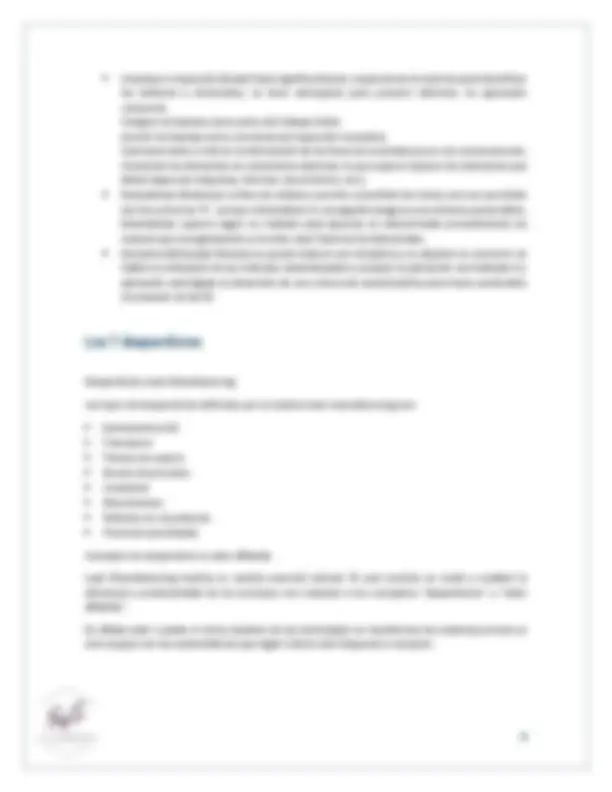
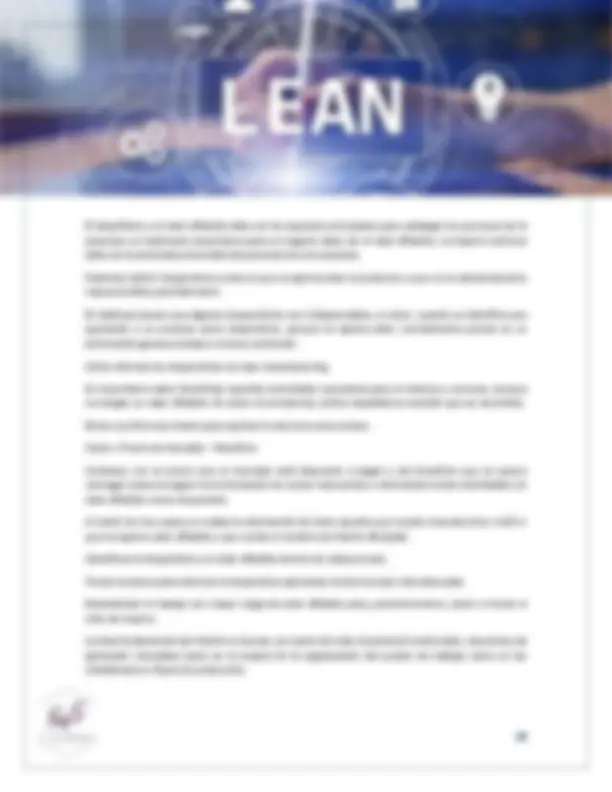
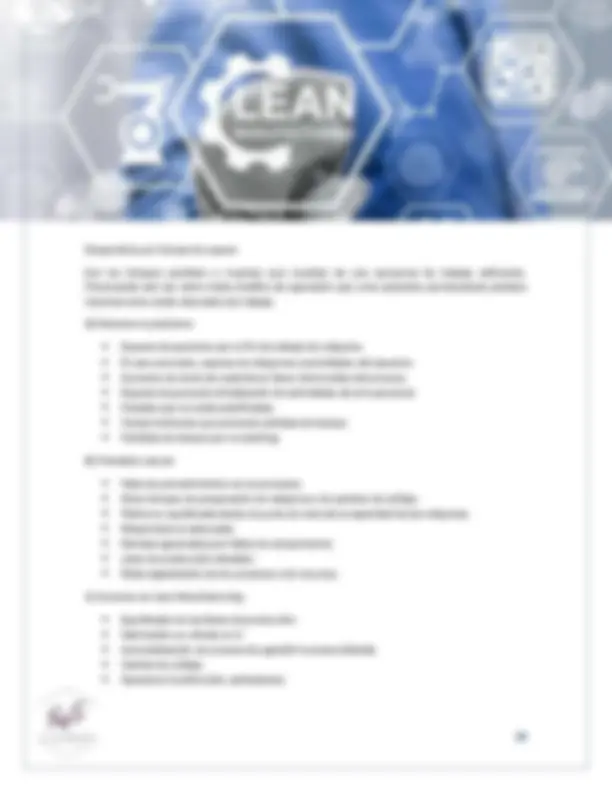
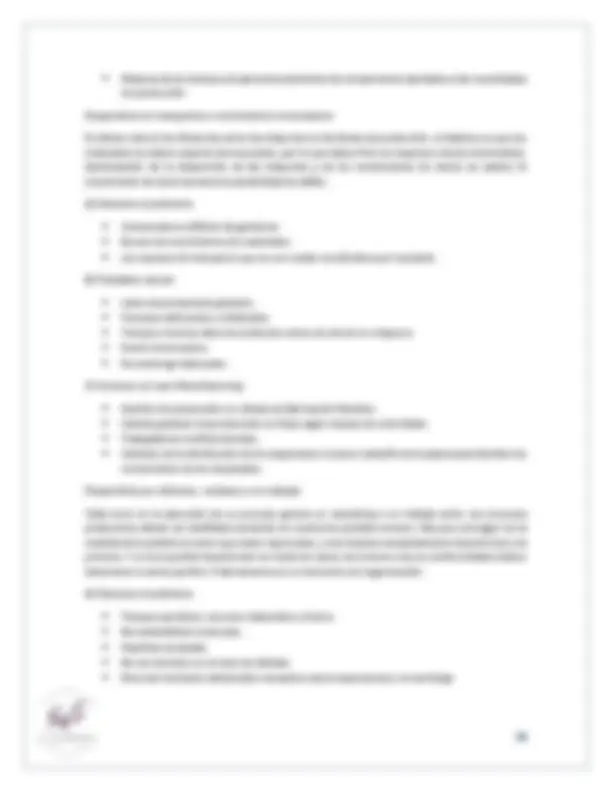
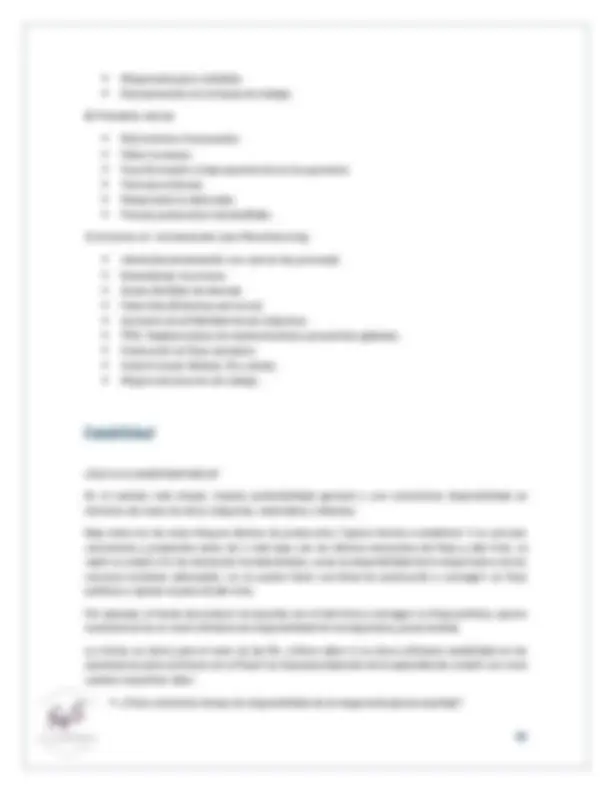
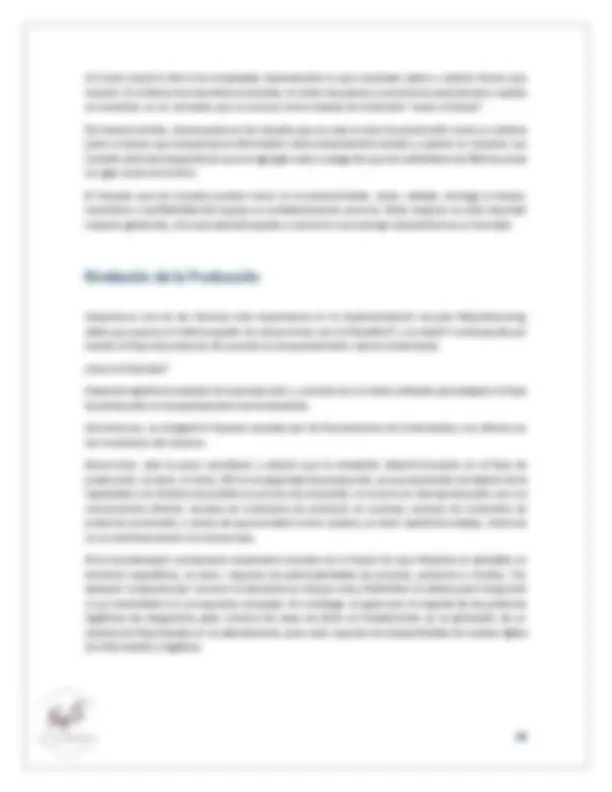
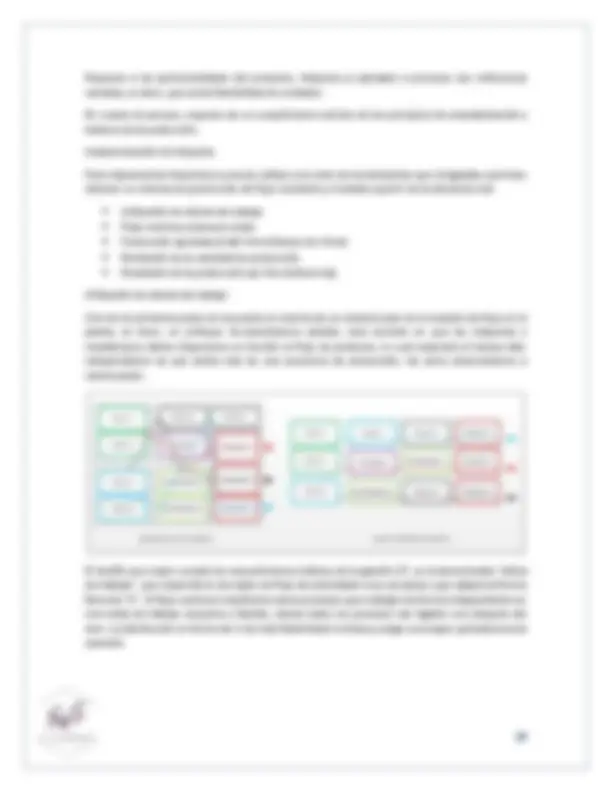
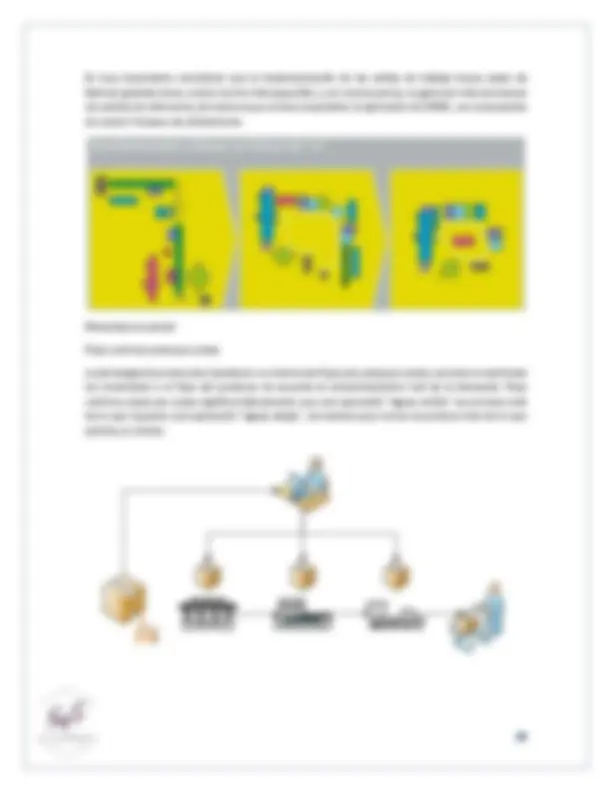
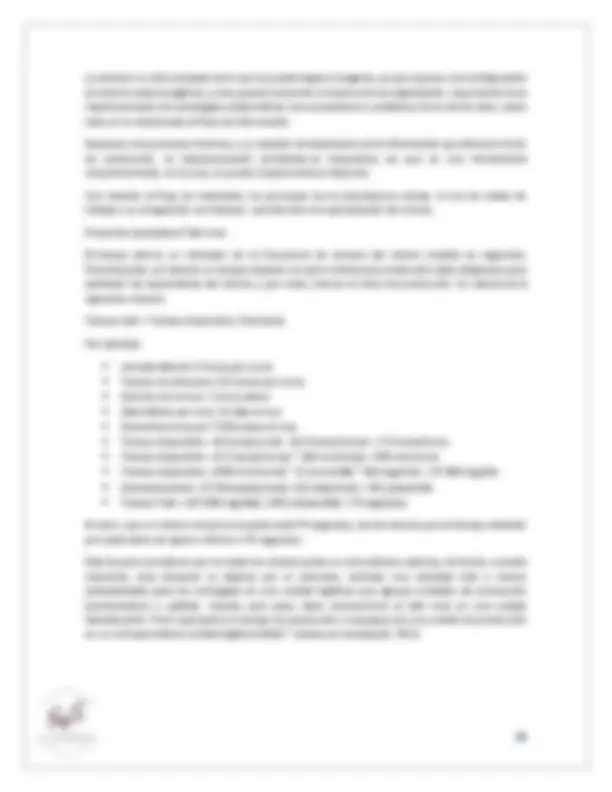
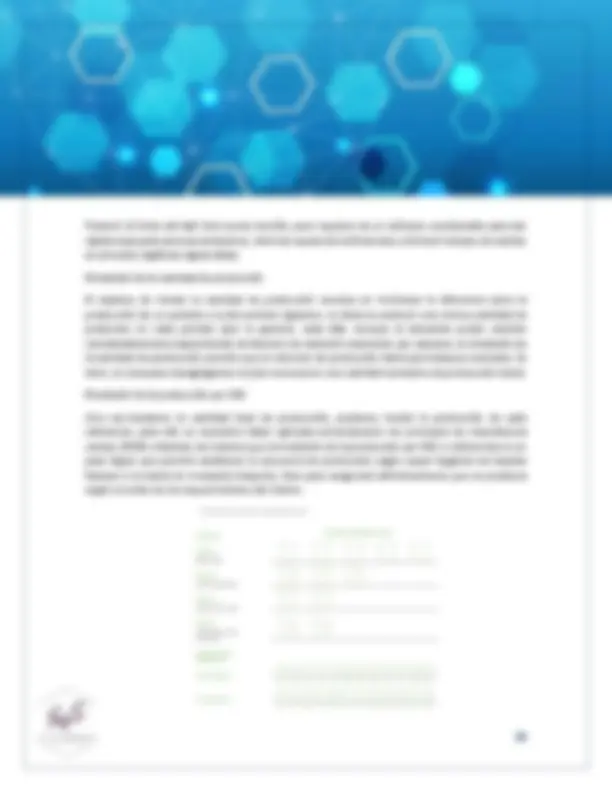
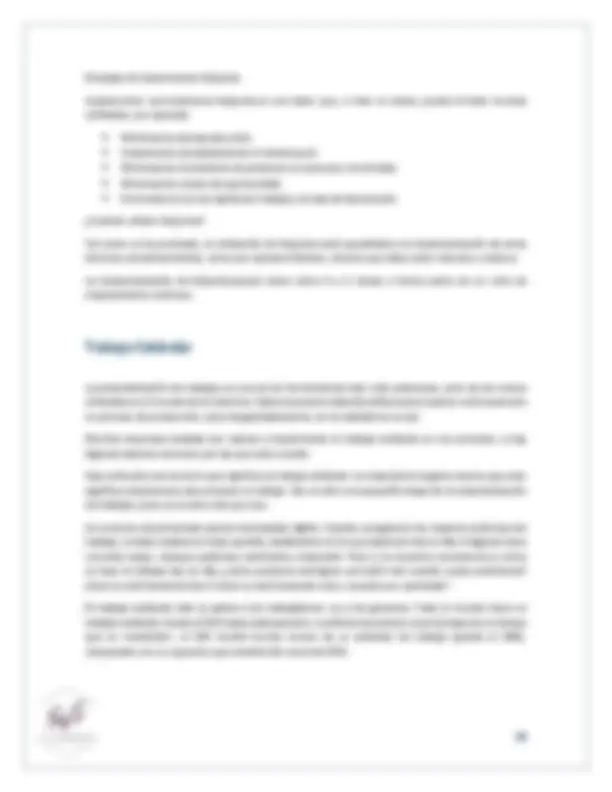
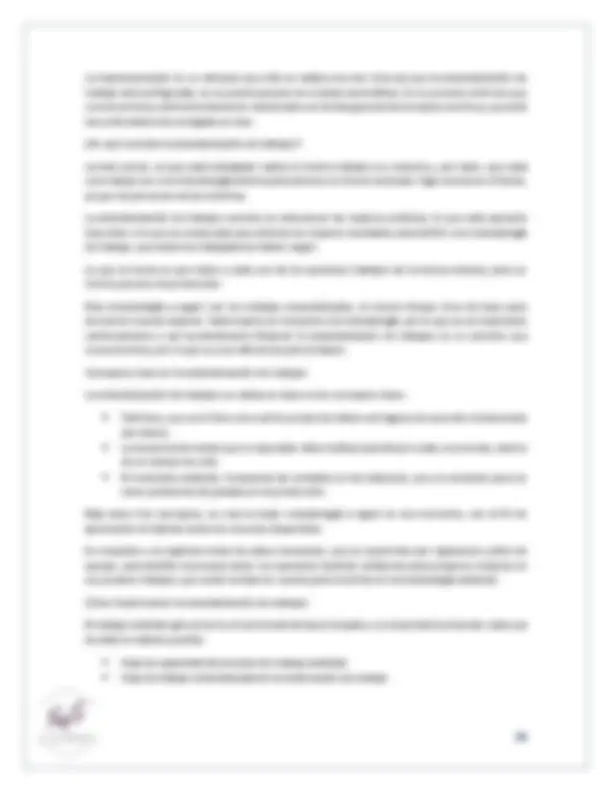
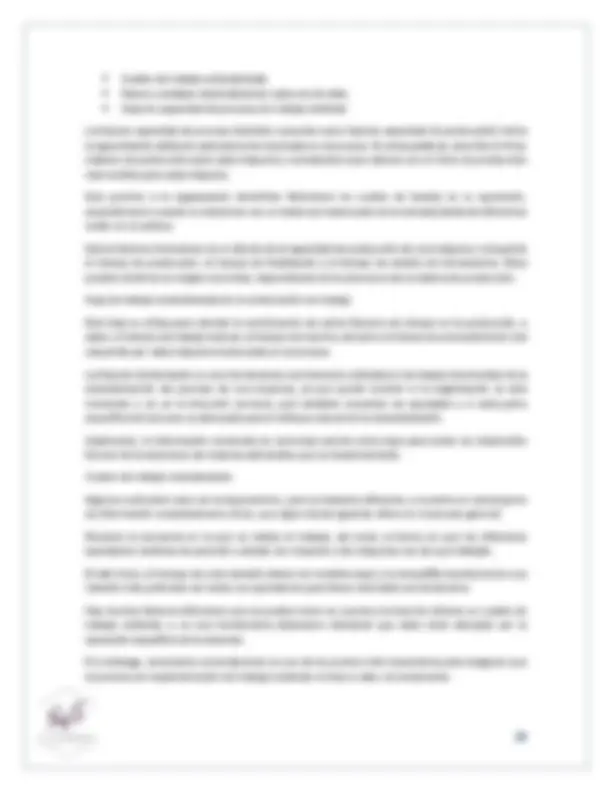
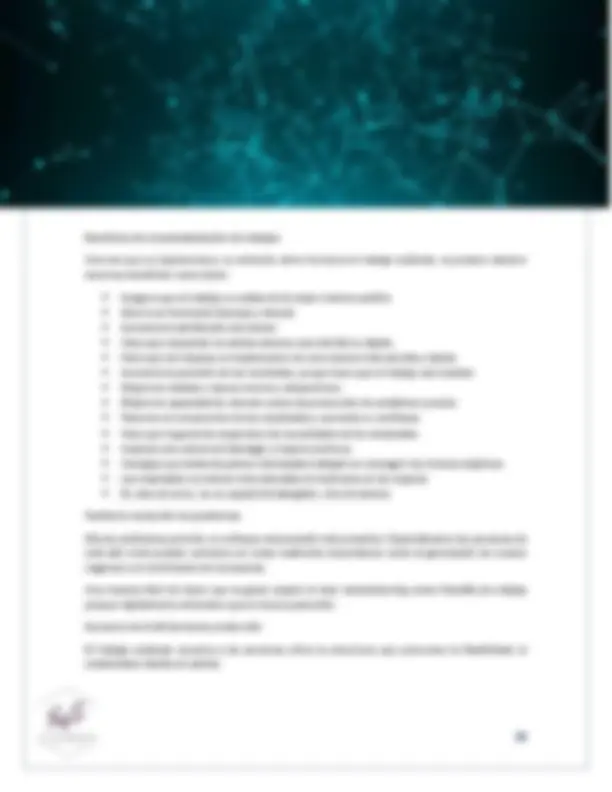
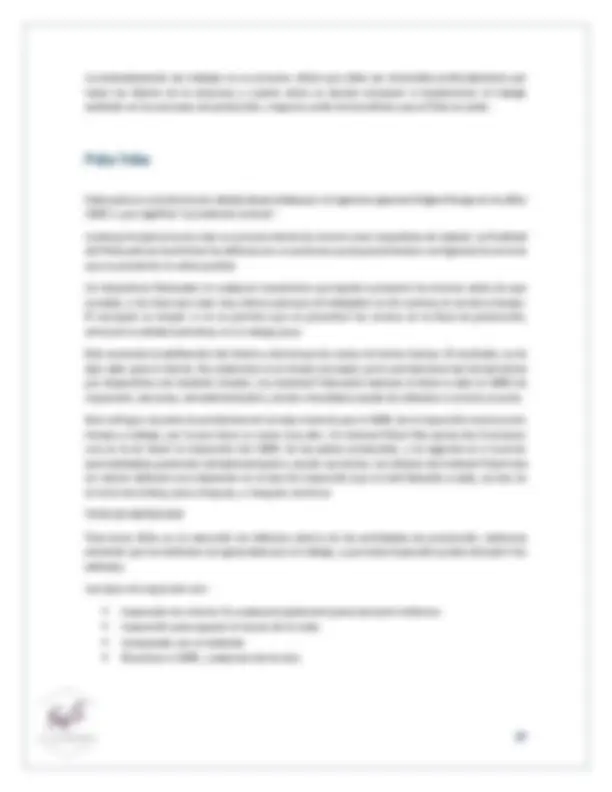
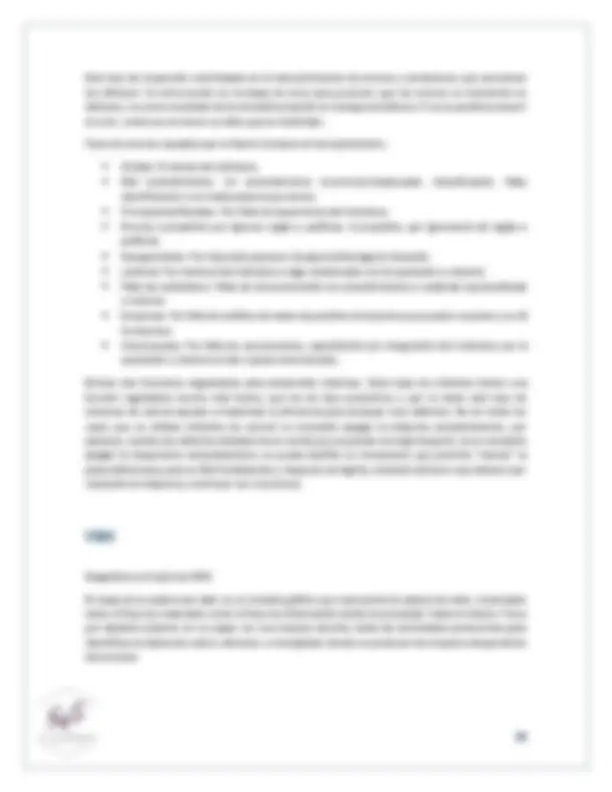
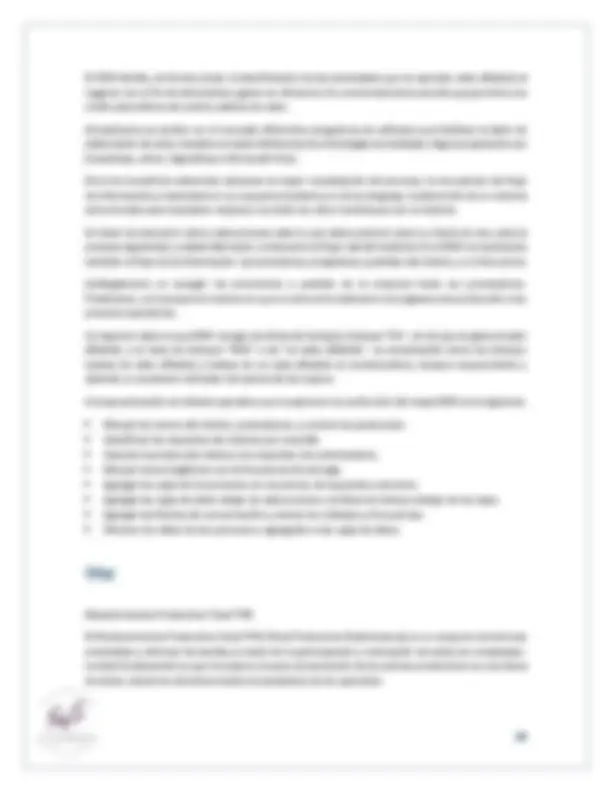
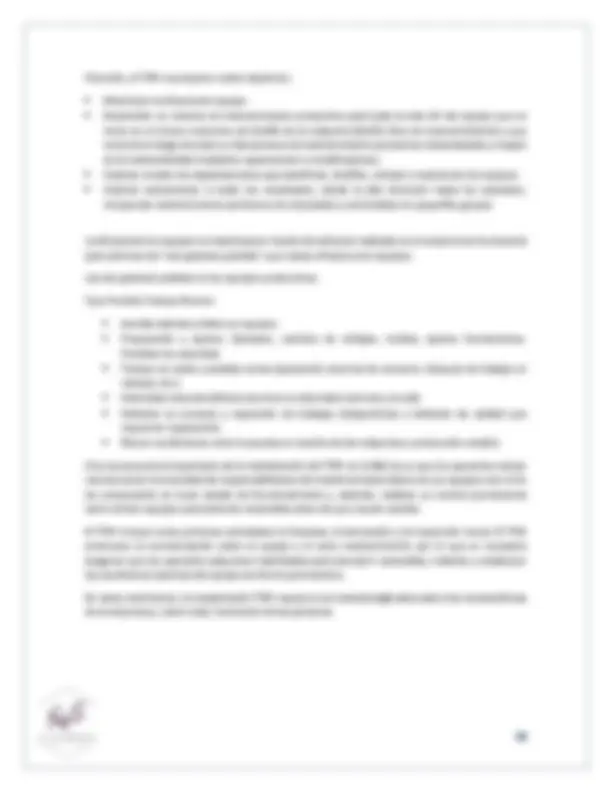
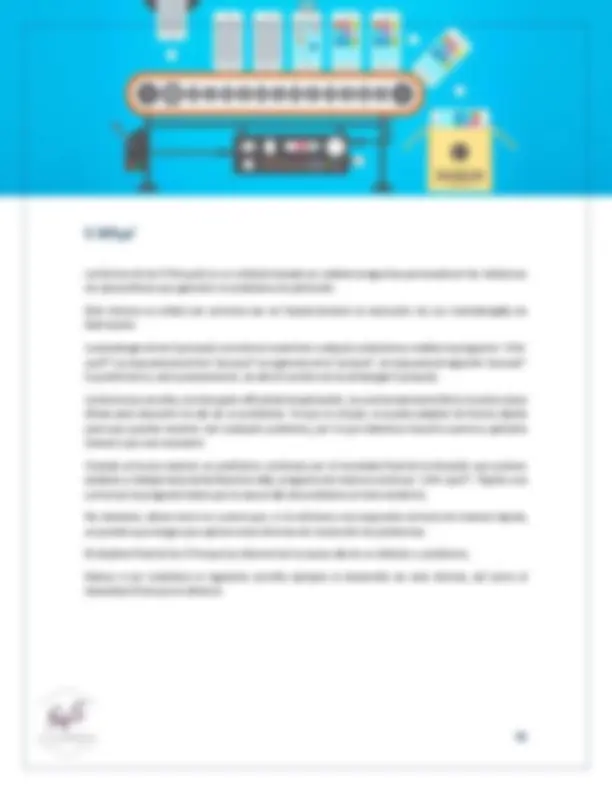
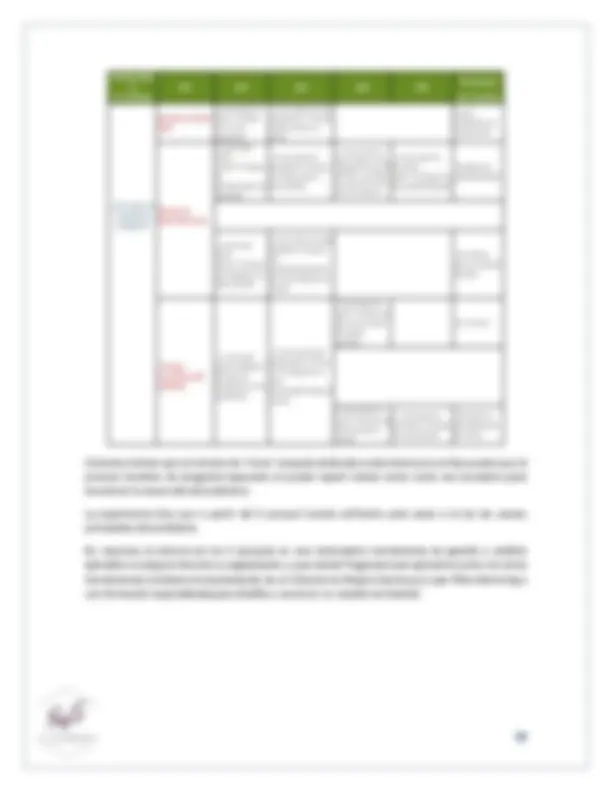
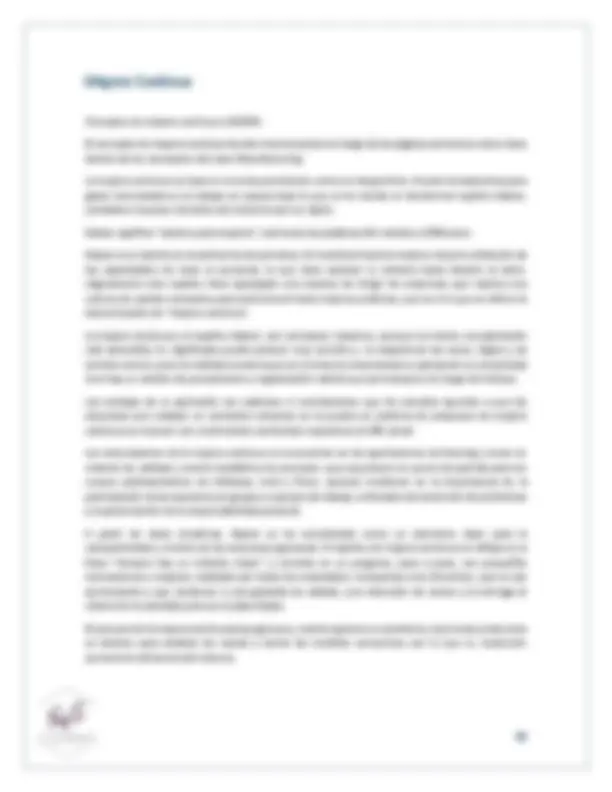
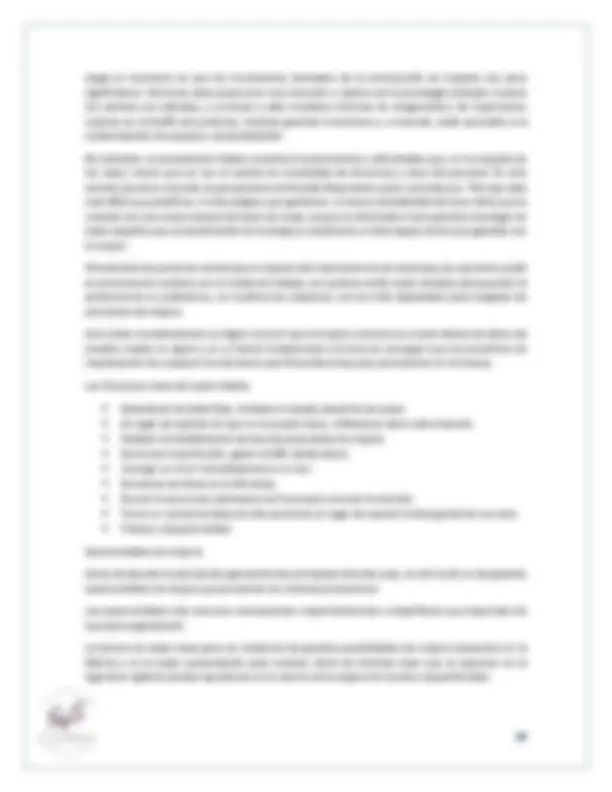
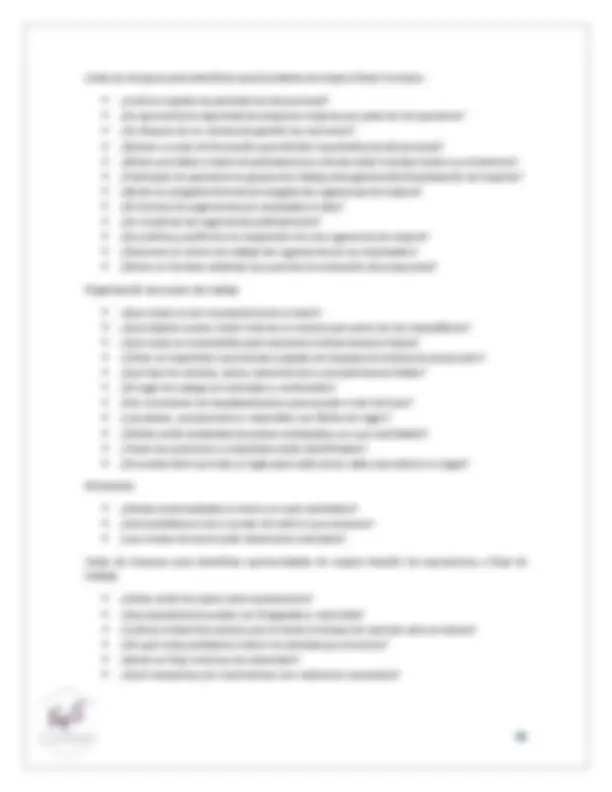
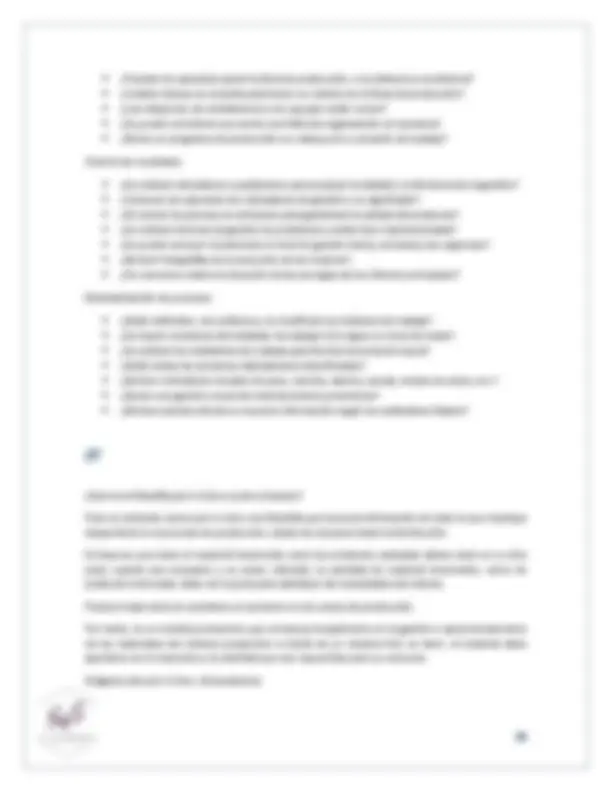
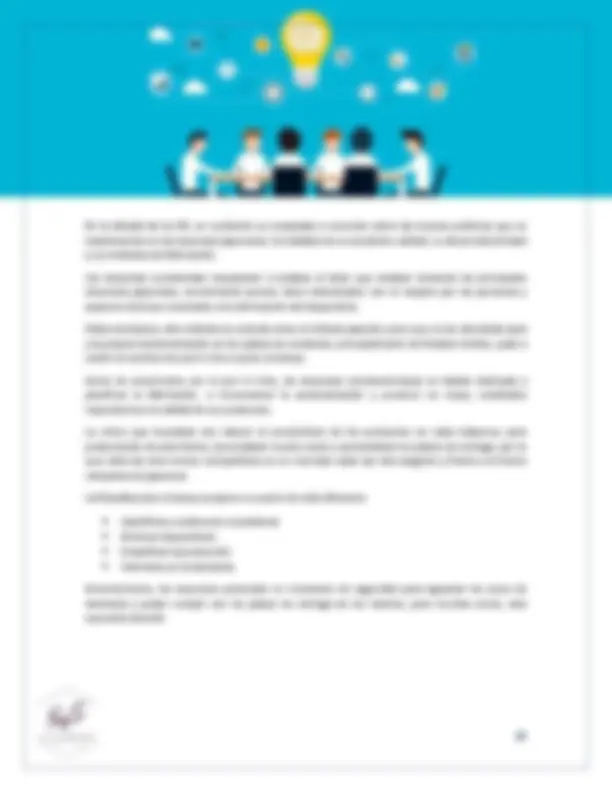
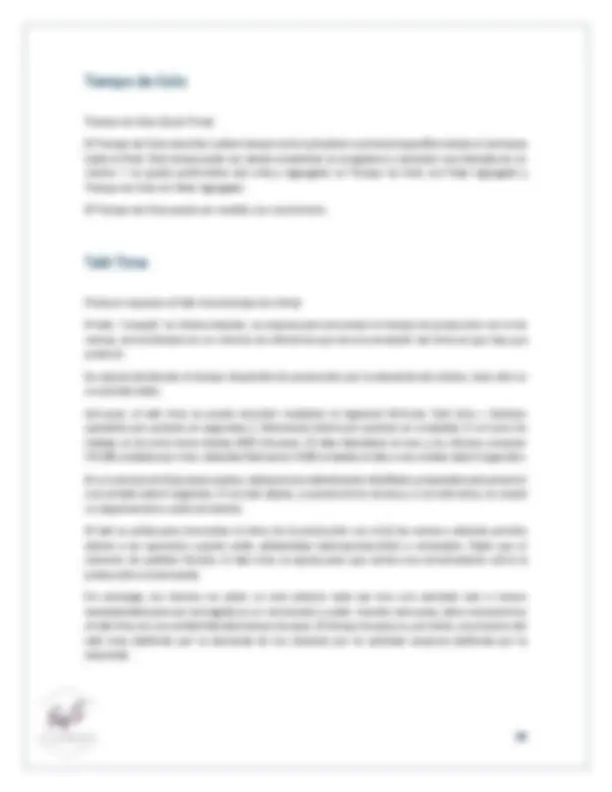
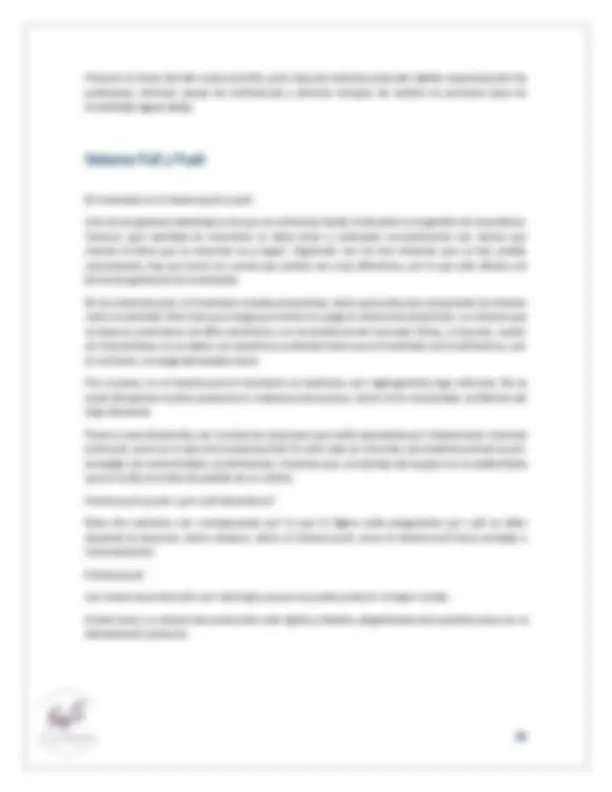
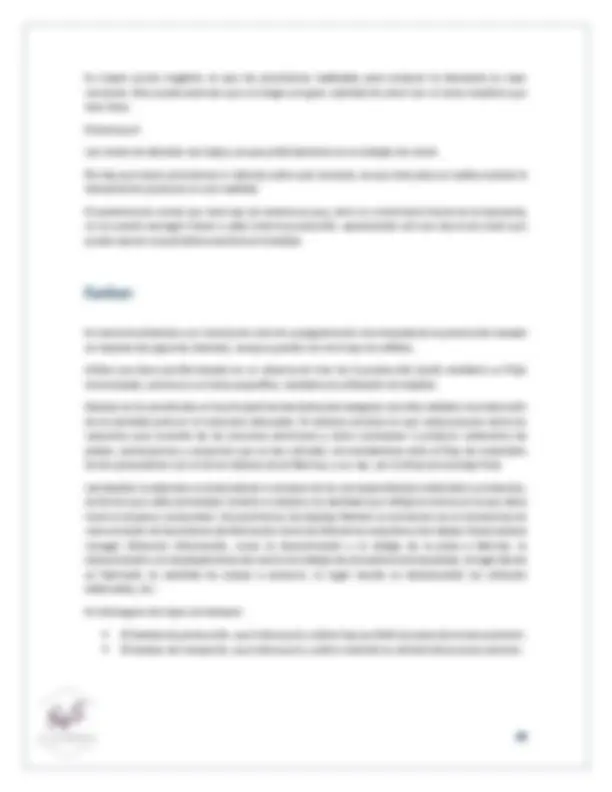
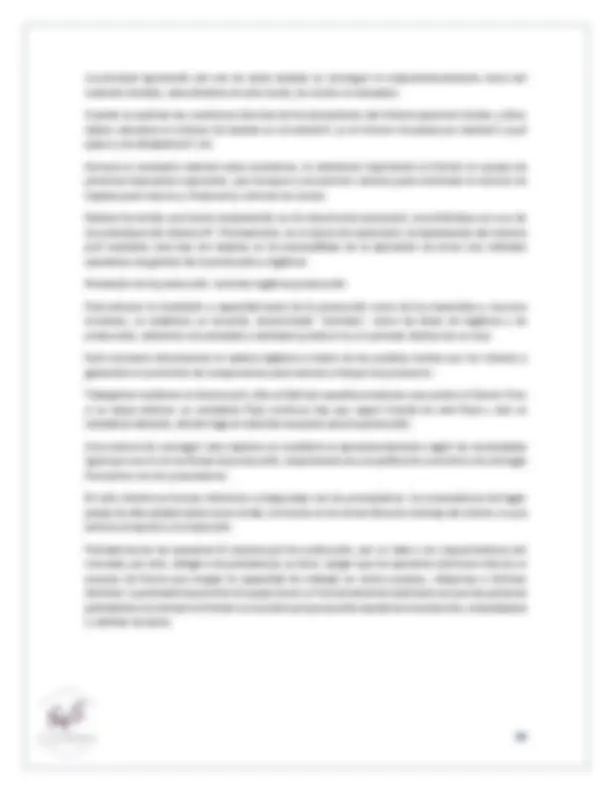
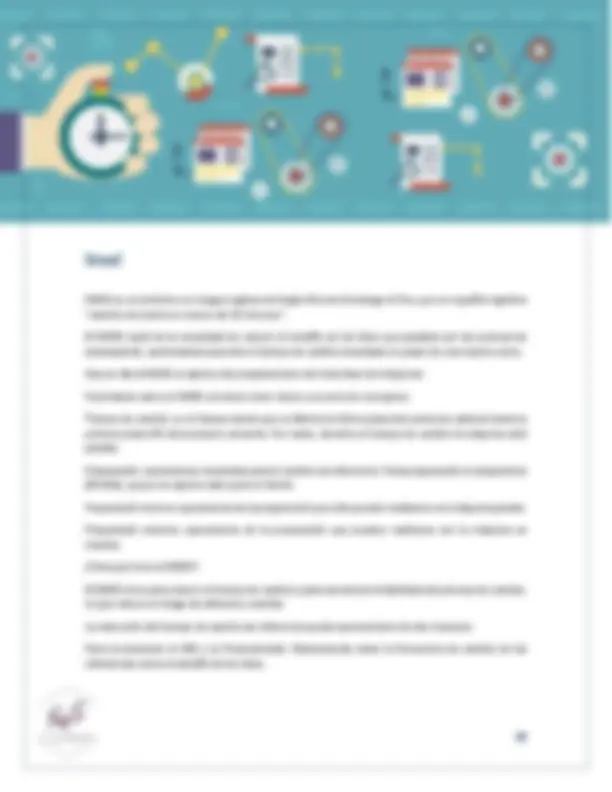
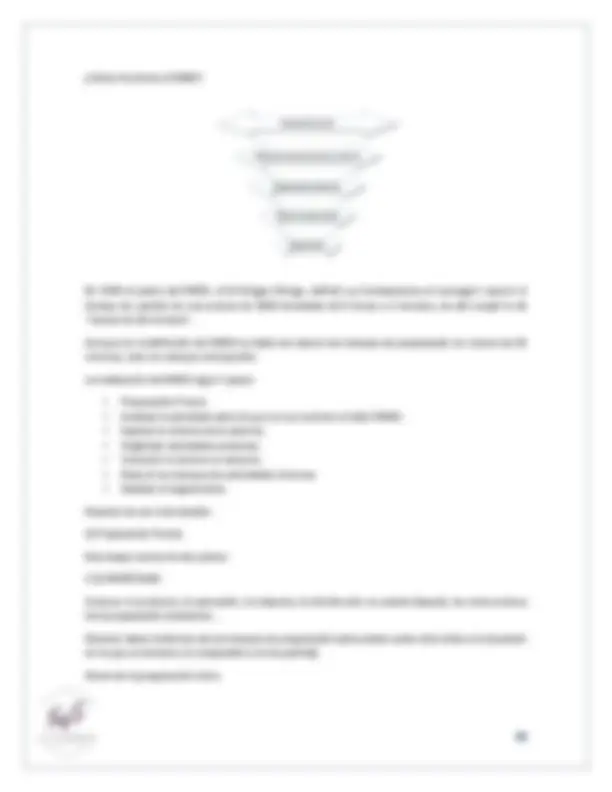
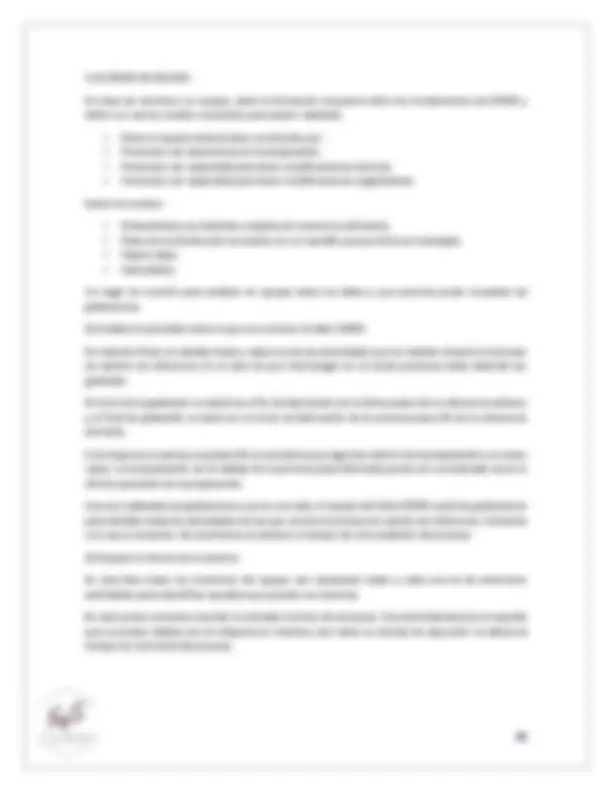
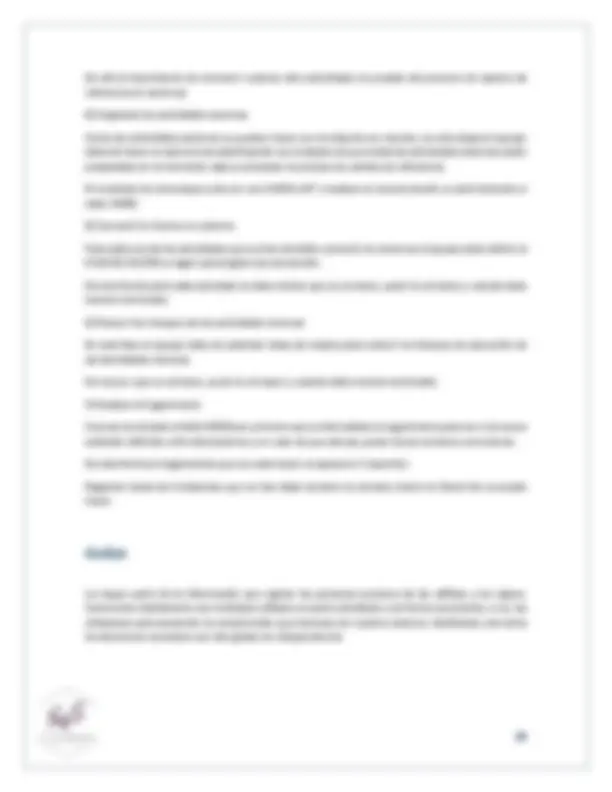
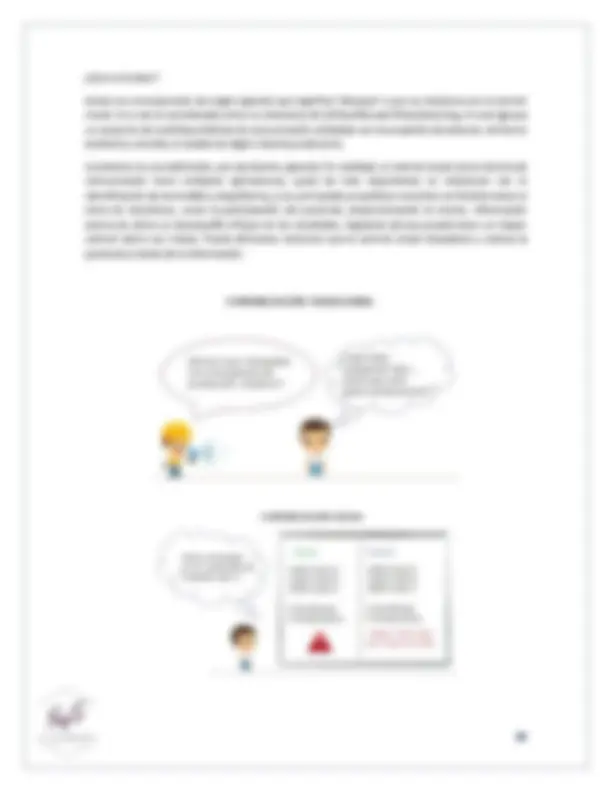
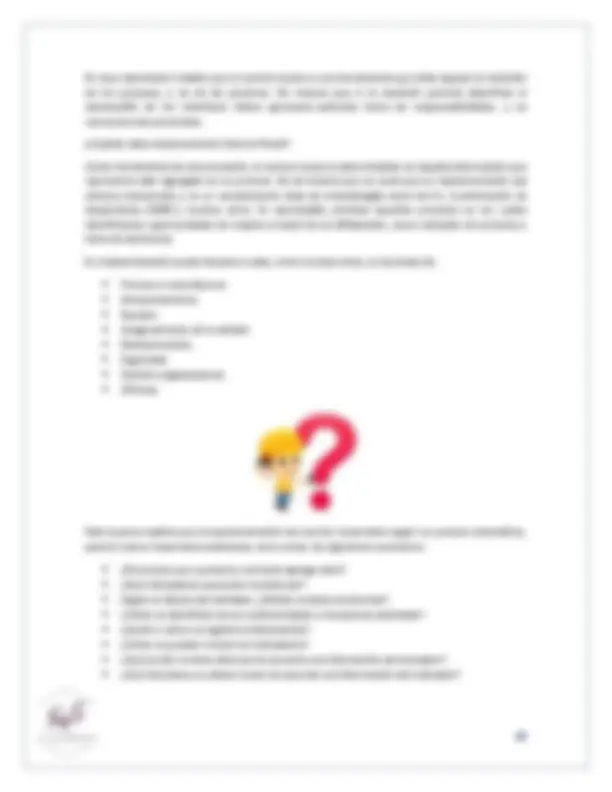
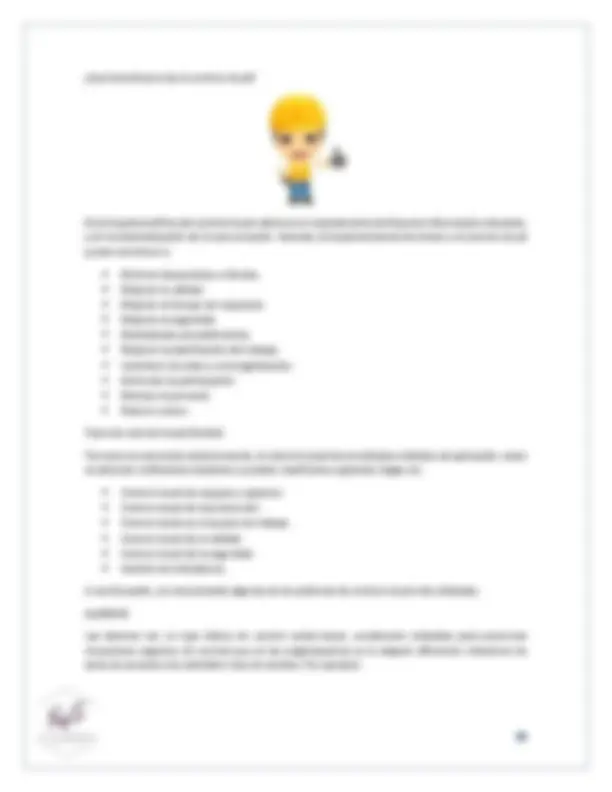
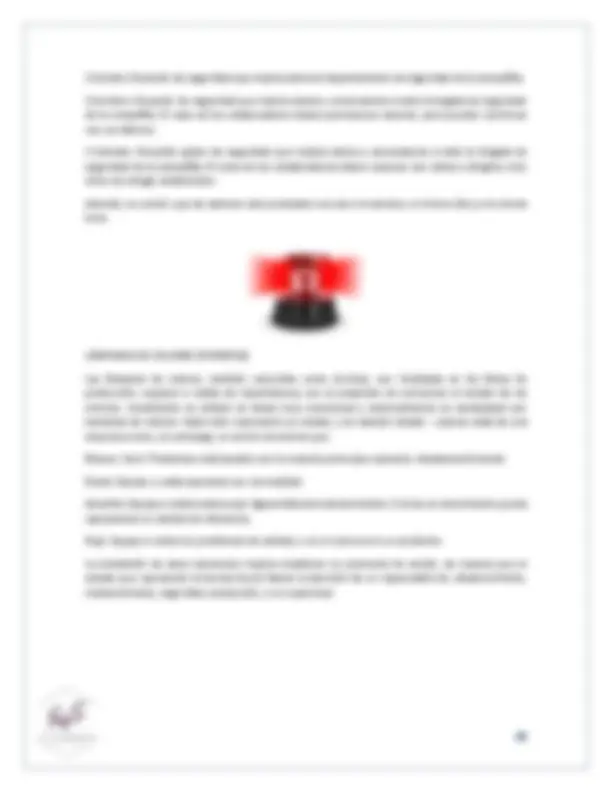
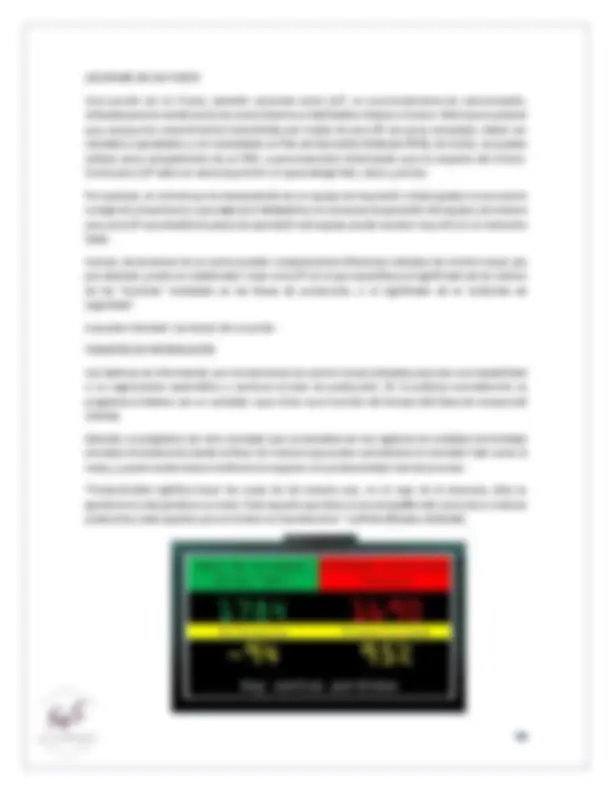
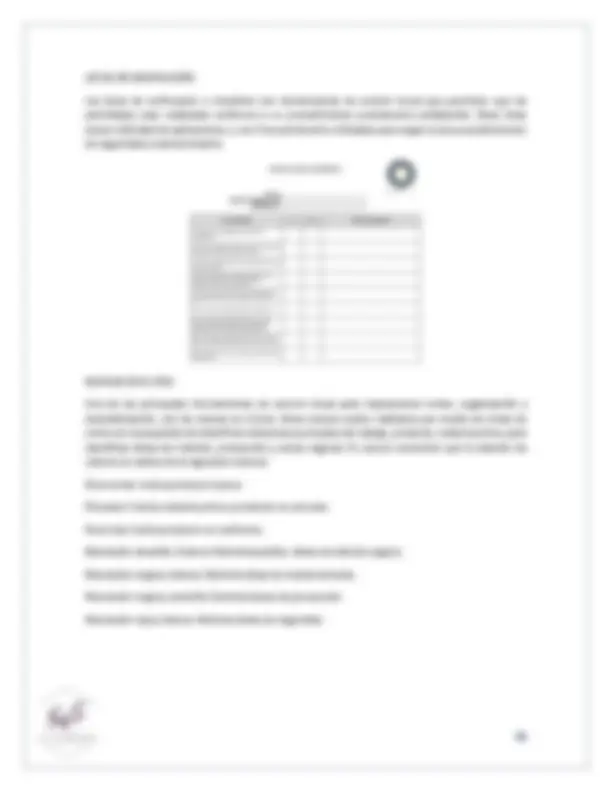
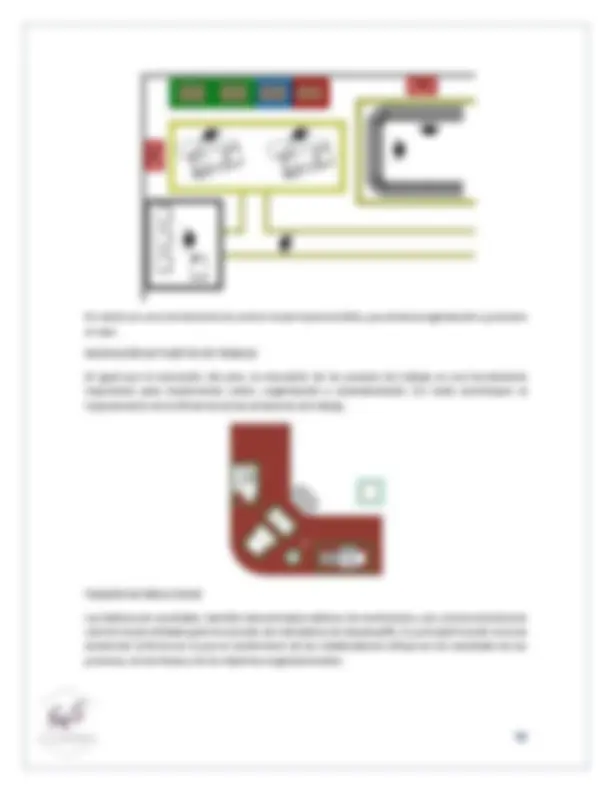
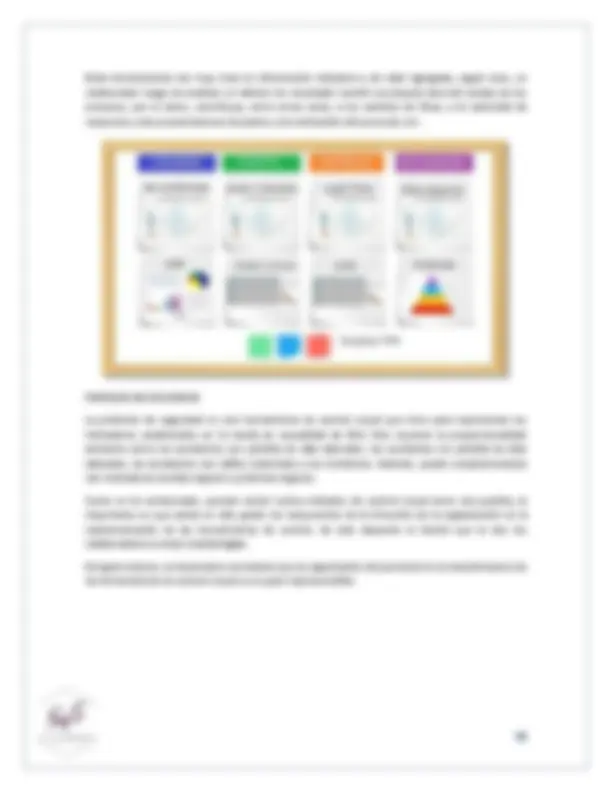
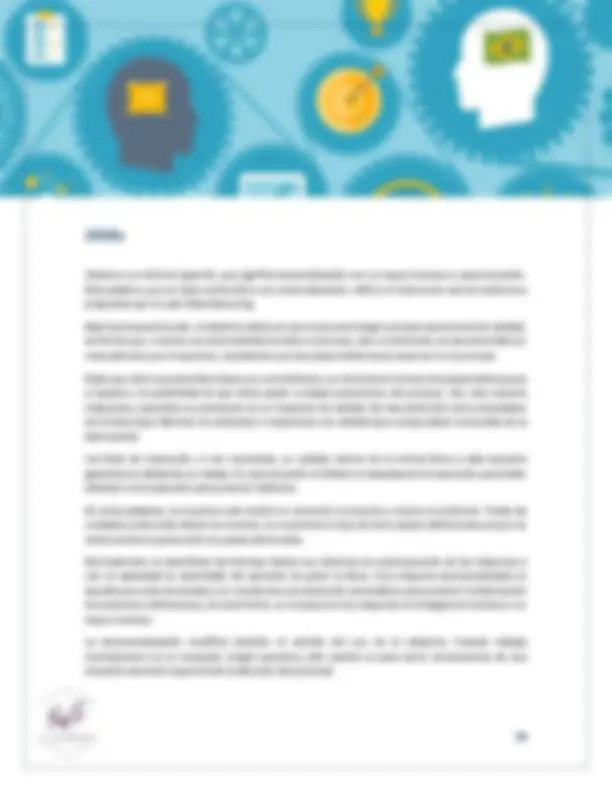
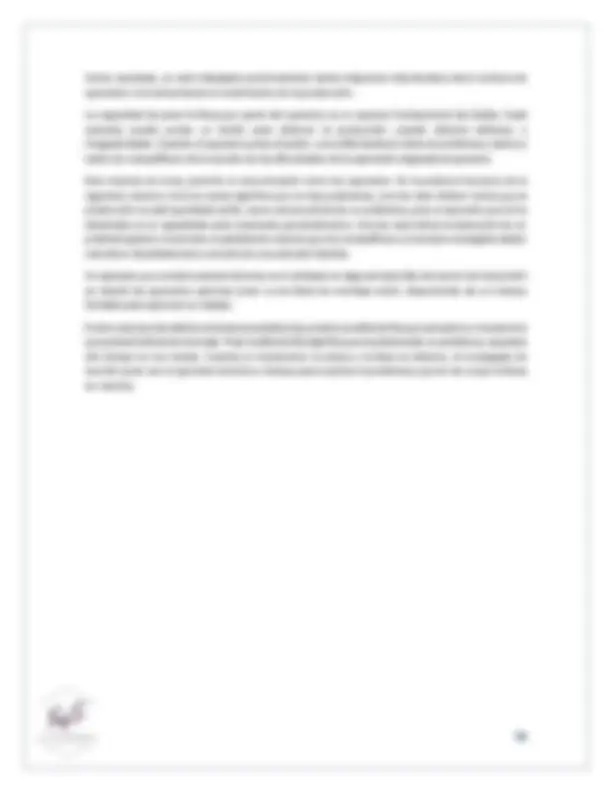
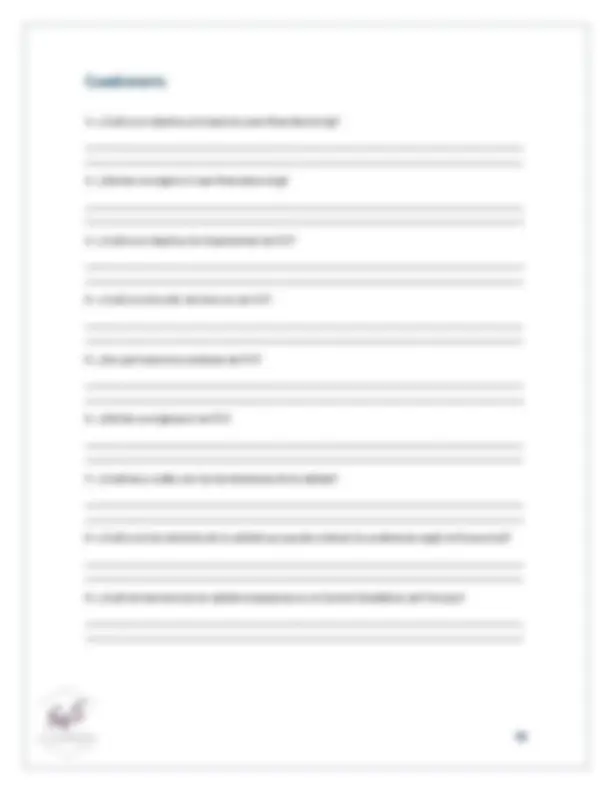
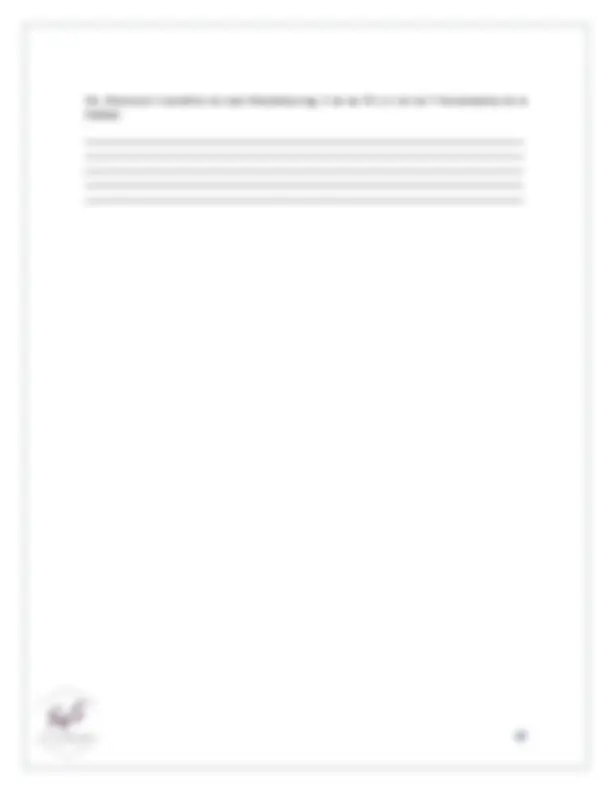
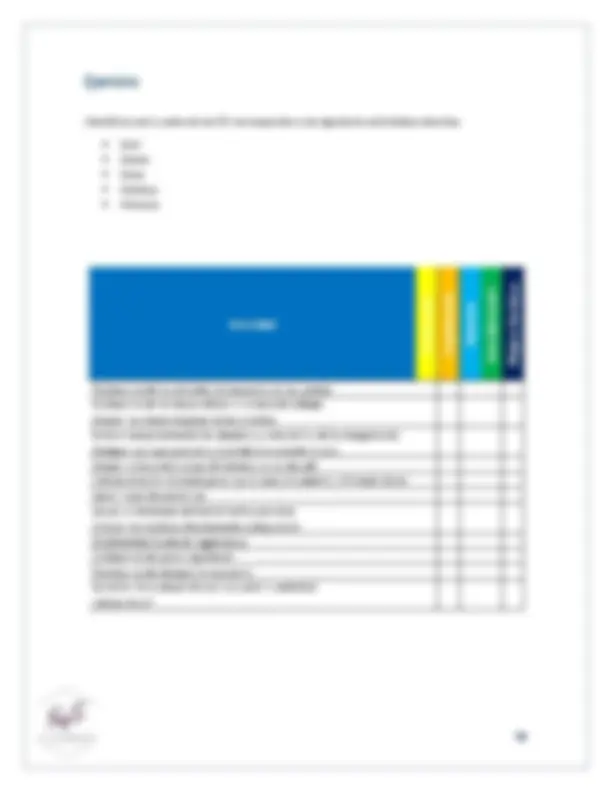
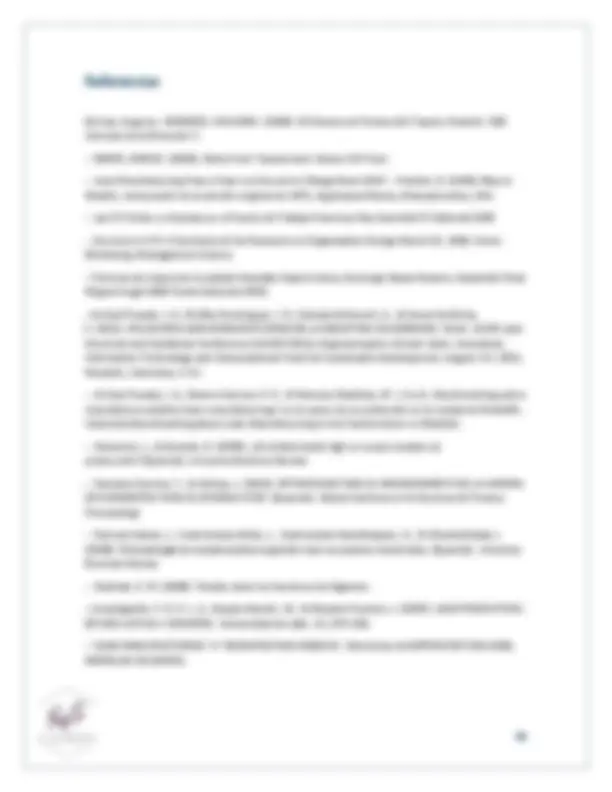
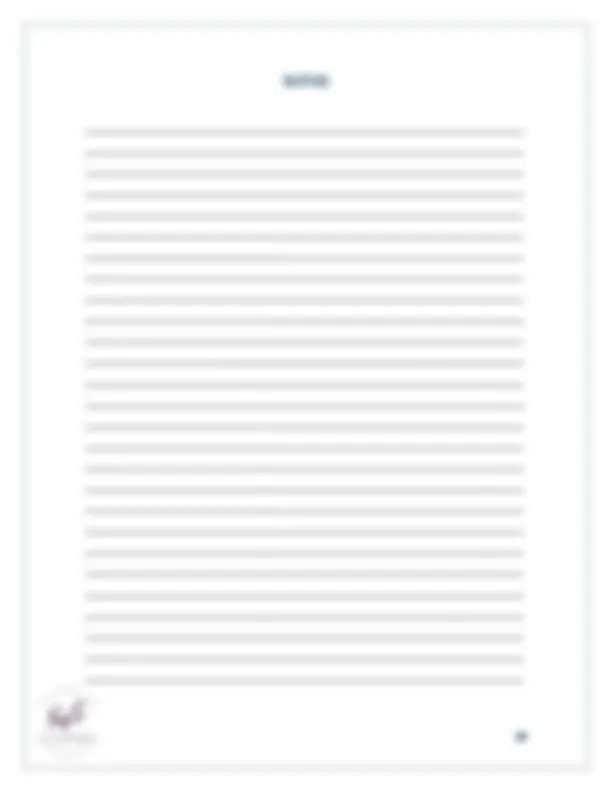
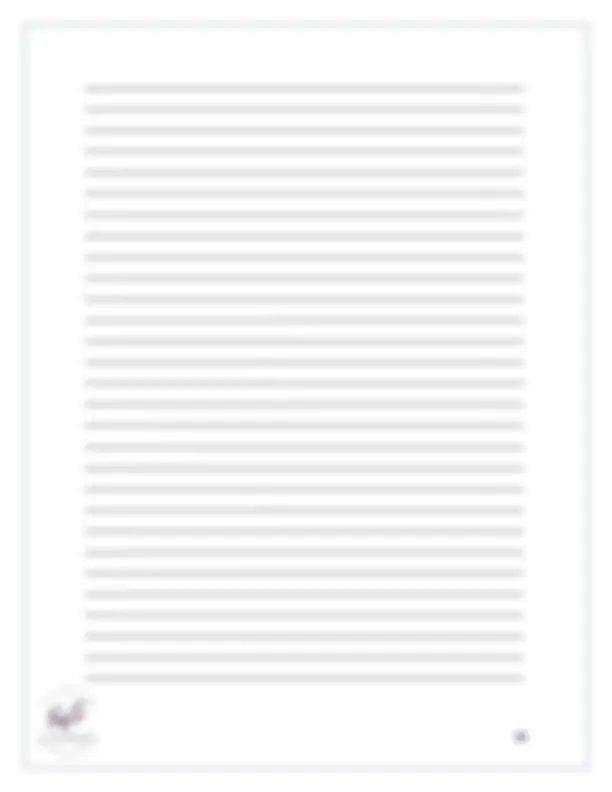
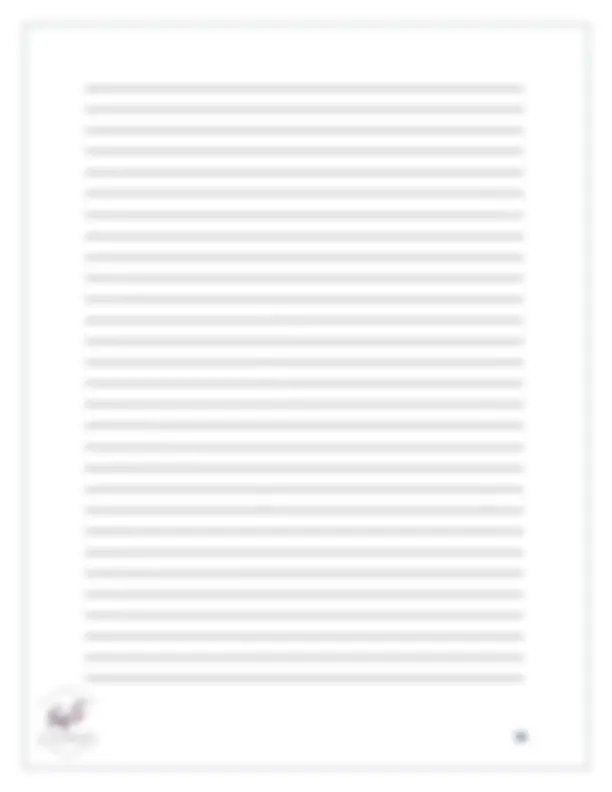
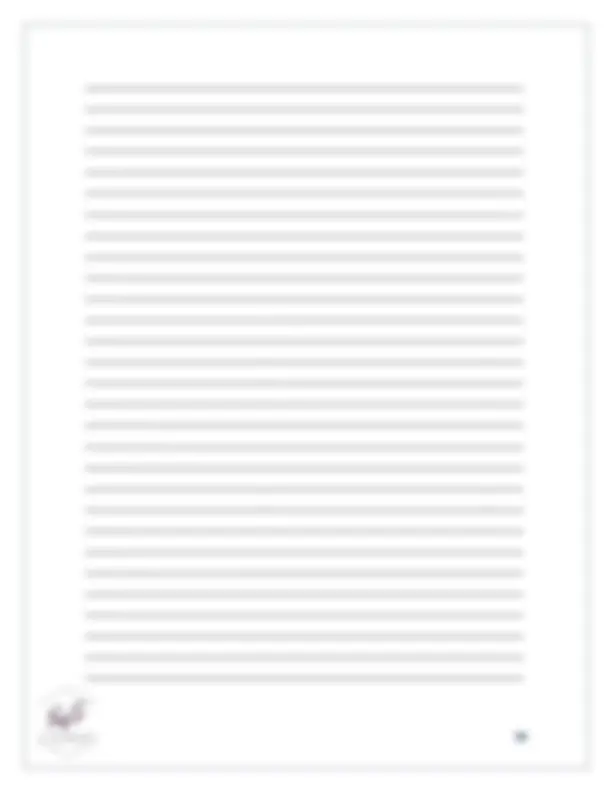
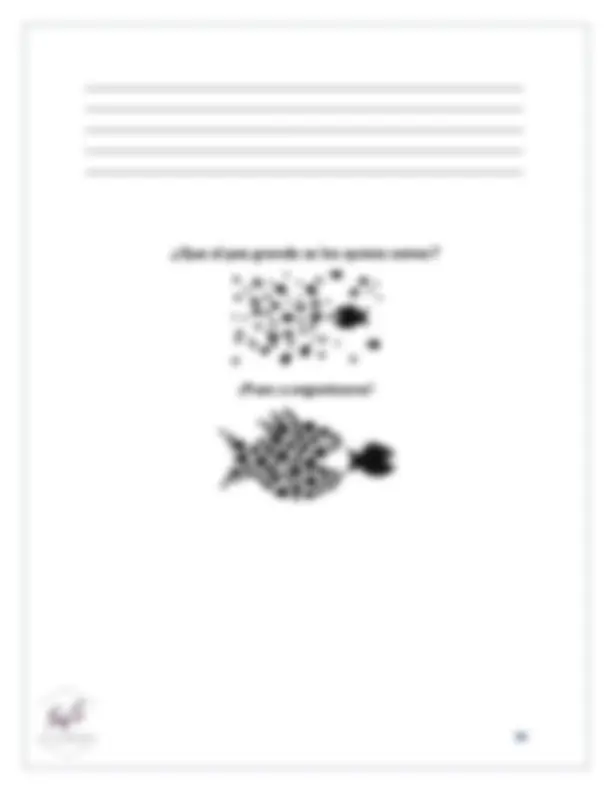
Prepara tus exámenes y mejora tus resultados gracias a la gran cantidad de recursos disponibles en Docsity
Gana puntos ayudando a otros estudiantes o consíguelos activando un Plan Premium
Prepara tus exámenes
Prepara tus exámenes y mejora tus resultados gracias a la gran cantidad de recursos disponibles en Docsity
Prepara tus exámenes con los documentos que comparten otros estudiantes como tú en Docsity
Los mejores documentos en venta realizados por estudiantes que han terminado sus estudios
Estudia con lecciones y exámenes resueltos basados en los programas académicos de las mejores universidades
Responde a preguntas de exámenes reales y pon a prueba tu preparación
Consigue puntos base para descargar
Gana puntos ayudando a otros estudiantes o consíguelos activando un Plan Premium
Comunidad
Pide ayuda a la comunidad y resuelve tus dudas de estudio
Descubre las mejores universidades de tu país según los usuarios de Docsity
Ebooks gratuitos
Descarga nuestras guías gratuitas sobre técnicas de estudio, métodos para controlar la ansiedad y consejos para la tesis preparadas por los tutores de Docsity
Este documento explora los principios fundamentales del lean manufacturing, centrándose en la implementación del trabajo estándar y la mejora continua. Se analizan conceptos como las siete mudas, las 5s, el takt time, la nivelación de la producción, la estandarización de trabajos y la importancia de la participación de los operarios en la mejora continua. El documento proporciona una visión general de las herramientas y técnicas utilizadas para optimizar los procesos de producción y aumentar la eficiencia.
Tipo: Guías, Proyectos, Investigaciones
1 / 64
Esta página no es visible en la vista previa
¡No te pierdas las partes importantes!
Actualmente las empresas industriales se enfrentan al reto de buscar e implantar nuevas técnicas organizativas y de producción que les permitan competir en un mercado global. El modelo de fabricación esbelta, conocido como Lean Manufacturing, constituye una alternativa consolidada y su aplicación y potencial deben ser tomados en consideración por toda empresa que pretenda ser competitiva. El Lean Manufacturing tiene su origen en el sistema de producción Just in Time (JIT) desarrollado en los años 50 por la empresa automovilística Toyota. Con la extensión del sistema a otros sectores y países se ha ido configurando un modelo que se ha convertido en el paradigma de los sistemas de mejora de la productividad asociada a la excelencia industrial. De forma resumida puede decirse que Lean consiste en la aplicación sistemática y habitual de un conjunto de técnicas de fabricación que buscan la mejora de los procesos productivos a través de la reducción de todo tipo de “desperdicios”, definidos éstos como los procesos o actividades que usan más recursos de los estrictamente necesarios. La clave del modelo está en generar una nueva cultura tendente a encontrar la forma de aplicar mejoras en la planta de fabricación, tanto a nivel de puesto de trabajo como de línea de fabricación, y todo ello en contacto directo con los problemas existentes para lo cual se considera fundamental la colaboración y comunicación plena entre directivos, mandos y operarios. La gran repercusión de cualquier iniciativa en esta industria tuvo un efecto muy beneficioso en la difusión de estas técnicas, aunque se extendió la idea falsa de que solo se podía aplicar a este sector. En la última década, industrias de los sectores de la alimentación, farmacéutica o bienes de equipo han adoptado con éxito el modelo Lean. Actualmente las experiencias señalan que el Lean es aplicable a cualquier tipo de industria, incluso a los servicios.
El primer paso en el desarrollo del TPS consistió en identificar y establecer procedimientos para reducir mudas, originadas por trabajar mecánicamente ó por costumbre y se mantenían ocultas durante el proceso de producción, restando eficiencia al trabajo. Sobreproducción, producir más de lo pedido, teniendo productos terminados sin un destinatario definido (cliente). Esperas, tiempos desperdiciados de máquinas, personas y productos que no incorporan valor al producto final. Transporte, periodo de tiempo en el cual se mueve un producto sin adición de valor, (manipulación innecesaria). Inventarios, almacenamiento excesivo de materia prima que implica costos extras en el manejo y mantención. Exceso de movimiento, personal que se desplaza dentro de las áreas de trabajo sin añadir valor al producto final. Sobre procesamiento, más operaciones de las necesarias, excesivo número de pasos en el proceso productivo, debido a errores en la planificación operacional. Defectos, fallas y errores en el proceso de producción, para su corrección se debe efectuar trabajo adicional.
La herramienta 5S se corresponde con la aplicación sistemática de los principios de orden y limpieza en el puesto de trabajo que, de una manera menos formal y metodológica, ya existían dentro de los conceptos clásicos de organización de los medios de producción.
Es una técnica que se aplica en todo el mundo con excelentes resultados por su sencillez y efectividad por lo que es la primera herramienta a implantar en toda empresa que aborde el Lean Manufacturing. Produce resultados tangibles y cuantificables para todos, con gran componente visual y de alto impacto en un corto tiempo plazo de tiempo. Es una forma indirecta de que el personal perciba la importancia de las cosas pequeñas, de que su entorno depende de él mismo, que la calidad empieza por cosas muy inmediatas. Su implantación tiene por objetivo evitar que se presenten los siguientes síntomas disfuncionales en la empresa y que afectan, decisivamente, a la eficiencia de la misma: Aspecto sucio de la planta: máquinas, instalaciones, técnicas, etc. Desorden: pasillos ocupados, técnicas sueltas, embalajes, etc. Elementos rotos: mobiliario, cristales, señales, topes, indicadores, etc. Falta de instrucciones sencillas de operación. Número de averías más frecuentes de lo normal. Desinterés de los empleados por su área de trabajo. Movimientos y recorridos innecesarios de personas, materiales y utillajes. Falta de espacio en general. La implantación de las 5S sigue normalmente un proceso de cinco pasos cuyo desarrollo implica la asignación de recursos, la adaptación a la cultura de la empresa y la consideración de aspectos humanos. La dirección de la empresa ha de estar convencida de que las 5S suponen una inversión de tiempo por parte de los operarios y la aparición de unas actividades que deberán mantenerse en el tiempo. Además, se debe preparar un material didáctico para explicar a los operarios la importancia de las 5S y los conceptos básicos de la metodología. Para empezar la implantación de las 5S, habrá que escoger un área piloto y concentrase en ella, porque servirá como aprendizaje y punto de partida para el despliegue al resto de la organización. Esta área piloto debe ser muy bien conocida, debe representar a priori una probabilidad alta de éxito de forma que permita obtener resultados significativos y rápidos. Eliminar (Seiri) La primera de las 5S significa clasificar y eliminar del área de trabajo todos los elementos innecesarios o inútiles para la tarea que se realiza. La pregunta clave es: “¿es esto es útil o inútil?”. Consiste en separar lo que se necesita de lo que no y controlar el flujo de cosas para evitar estorbos y elementos prescindibles que originen despilfarros como el incremento de manipulaciones y transportes, pérdida de tiempo en localizar cosas, elementos o materiales obsoletos, falta de espacio, etc. Ordenar (Seiton) Consiste en organizar los elementos clasificados como necesarios, de manera que se encuentren con facilidad, definir su lugar de ubicación identificándolo para facilitar su búsqueda y el retorno a su posición inicial. La actitud que más se opone a lo que representa seiton, es la de “ya lo ordenaré mañana”, que acostumbra a convertirse en “dejar cualquier cosa en cualquier sitio”.
El despilfarro y el valor añadido debe ser los aspectos principales para catalogar los procesos de la empresa. Lo realmente importante para un negocio debe ser el valor añadido. La mejora continua debe ser la actividad primordial del personal de una empresa. Podemos definir desperdicio a todo lo que no aporta valor al producto o que no es absolutamente imprescindible para fabricarlo. Es habitual pensar que algunos desperdicios son indispensables, es decir, cuando se identifica una operación o un proceso como desperdicio, porque no aporta valor, normalmente pensar en su eliminación genera rechazo e incluso confusión. Cómo eliminar los desperdicios en lean manufacturing Es importante saber identificar aquellas actividades necesarias para el sistema o proceso, aunque no tengan un valor añadido. En estas circunstancias, dichos despilfarros tendrán que ser asumidos. Existe una fórmula simple para explicar la estructura de precios: Coste = Precio de mercado – Beneficio Iniciamos con el precio que el mercado está dispuesto a pagar y del beneficio que se quiere conseguir para conseguir la minimización de costes reduciendo o eliminando tantas actividades sin valor añadido como sea posible. A través de tres pasos se realiza la eliminación de todo aquello que resulte improductivo, inútil o que no aporte valor añadido y que recibe el nombre de Hoshin (Brújula): Identificar el desperdicio y el valor añadido dentro de cada proceso. Tomar acciones para eliminar el desperdicio aplicando la técnica Lean más adecuada. Estandarizar el trabajo con mayor carga de valor añadido para, posteriormente, volver a iniciar el ciclo de mejora. La idea fundamental del Hoshin es buscar, por parte de todo el personal involucrado, soluciones de aplicación inmediata tanto en la mejora de la organización del puesto de trabajo como en las instalaciones o flujos de producción.
Vamos a ir analizando cada uno de los desperdicios. Desperdicios por exceso en almacenamiento Permiten la existencia de productos muertos que sólo se detecta al realizar inventarios físicos. Pueden ser materiales o productos obsoletos. Todos los productos necesitan de cuidados, mantenimiento, vigilancia, contabilidad, gestión, entre otros, y entre más producto almacenado se tenga, más costo implica. No permiten tener una idea clara de los activos de los balances, puesto que si son productos obsoletos no deberían estar considerados como activos ni como una inversión en stock. El desperdicio por almacenamiento es la consecuencia de tener una mayor cantidad de existencias de las necesarias. El hecho de que se acumule material, antes y después del proceso, indica que el flujo de producción no es continuo. A) Detectar el problema Almacén excesivo. Contenedores o espacios individuales demasiado grandes. Poca rotación de stocks o existencias. Altos costes de almacenaje. Abundantes medios de manipulación (patines, carretillas elevadoras). B) Probables causas Procesos con pequeña capacidad. Cuellos de botella ocultos o descontrolados. Altos tiempos muertos en cambio o de preparación de máquina. Perspectivas de ventas erróneas. Sobreproducción. Re-trabajos por defectos de calidad del producto.
Desperdicio por tiempo de espera Son los tiempos perdidos o muertos que resultan de una secuencia de trabajo deficiente. Provocando asó con estos malos diseños de operación que unos operarios permanezcan parados mientras otros están saturados de trabajo. A) Detectar el problema Esperas de operarios por el fin de trabajo de máquina. El caso contrario, esperas de máquinas a actividades del operario. Aumento de stock de material en fases intermedias del proceso. Esperas de personal a finalización de actividades de otro personal. Paradas que no están planificadas. Tareas indirectas que provocan pérdida de tiempo. Pérdidas de tiempo por re-working. B) Probables causas Falta de procedimientos en los procesos. Altos tiempos de preparación de máquina o de cambios de utillaje. Planta no equilibrada desde el punto de vista de la capacidad de las máquinas. Maquinaria no adecuada. Retrasos generados por faltas de componentes. Lotes de producción elevados. Mala organización de los procesos o de recursos. C) Acciones en Lean Manufacturing Equilibrado de las líneas de producción. Fabricación en células en U. Automatización con presencia y gestión humana (Jidoka). Cambio de utillaje. Operarios multifunción, polivalentes.
Mejoras de los tiempos de aprovisionamientos de componentes ajustados a las necesidades de producción. Desperdicio en transportes o movimientos innecesarios Se deben reducir las distancias entre las máquinas en las líneas de producción, el objetivo es que los materiales no deben esperar entre puestos, por lo que deben fluir sin esperas o stocks intermedios. Optimización de la disposición de las máquinas y de los movimientos de stocks en planta. El movimiento de stock aumenta la posibilidad de daños. A) Detectar el problema Contenedores difíciles de gestionar. Exceso de movimientos de materiales. Los equipos de transporte que se ven vacíos moviéndose por la planta. B) Probables causas Lotes excesivamente grandes. Procesos deficientes e inflexibles. Tiempos muertos altos de productos antes de entrar en máquina. Stocks intermedios. Re-workings habituales. C) Acciones en Lean Manufacturing Gestión de producción en células de fabricación flexibles. Cambio gradual a la producción en flujo según tiempo de ciclo fijado. Trabajadores multifuncionales. Cambios de la distribución de la maquinaria e incluso rediseño de la planta para facilitar los movimientos de los empleados. Desperdicio por defectos, rechazos y re-trabajos Cada error en la ejecución de un proceso genera un reworking o un trabajo extra. Los procesos productivos deben ser diseñados teniendo en cuenta los posibles errores. Hay que conseguir en la medida de lo posible no tener que hacer reprocesos, y eso implica necesariamente hacerlo bien a la primera. Y si no es posible hacerlo bien en todos los casos, los errores o las no conformidades deben detectarse lo antes posible. Prácticamente en el momento de la generación. A) Detectar el problema Tiempos perdidos, recursos materiales y dinero. No estandarizar el proceso. Planificar al detalle. No ser estrictos en el nivel de Calidad. Recursos humanos adicionales necesarios para inspecciones y re-workings.
¿Dispone de suficiente material cada día para satisfacer las necesidades productivas? ¿Dispone de suficientes personas formadas para llevar los procesos actuales? ¿Dispone de unos métodos de trabajo definidos, tales como las instrucciones básicas de trabajo o estándares de trabajo? Si la respuesta es decididamente “no” a cualquiera de estas preguntas, deténgase y resuelva los problemas antes de seguir. Intentar hacer fluir el producto ajustándose exactamente a la demanda del cliente con personal no formado, poca supervisión o poco inventario disponible, es un billete hacia el desastre. Y al revés, no caiga en la trampa de usar estas preguntas como excusas para no avanzar. Por fortuna, los trabajadores suelen conocer bien su trabajo, si no tendríamos serios problemas. Sin embargo, en los años 50 Toyota aprendió unas técnicas básicas sobre la supervisión en la producción y cómo 4 seguir mejorando las habilidades y las capacidades de los equipos. Específicamente, adoptaron el programa de formación industrial que los Estados Unidos usaron durante la Segunda Guerra Mundial llamado Training Within Industry (TWI). El programa tenía tres cursos específicos de trabajo para los supervisores de producción, Job Instruction (Instrucción del Trabajo), Job Methods (Métodos de Trabajo) y Job Relations (Relaciones de Trabajo). Cada uno era un curso de 10 horas que enseñaba habilidades prácticas de supervisión. Instrucción del Trabajo (JI) enseñó a los supervisores cómo planificar, para disponer de los recursos humanos correctos que necesitaban para la producción, cómo desglosar trabajos para formar y cómo enseñar a la gente a actuar con seguridad, correctamente y conscientemente. Métodos de Trabajo (JM) enseñó a los supervisores cómo analizar trabajos y cómo hacer mejoras sencillas dentro de su área de control. Cada actividad se analizaba para ser mejorada. Los supervisores aprendieron a cuestionar porqué una actividad se hacía de una forma determinada y si esta actividad se podía eliminar, combinar con otra, reorganizar o simplificar. Relaciones de Trabajo (JR) enseñó a los supervisores a tratar la gente como individuos y a resolver los problemas humanos en la producción en vez de ignorarlos. Los 3 cursos juntos ayudaron a los supervisores a crear una rutina básica, disciplina y un sentido de justicia en los equipos. 50 años después, estos mismos cursos TWI y sus ideas centrales constituyen la base para formar a los supervisores y a los equipos de trabajo en Toyota.
¿Qué es una Fábrica Visual? Fábrica Visual es un concepto de manufactura esbelta que hace énfasis en la necesidad de colocar información crítica justo donde se necesita. El concepto de fábrica visual, que también se conoce como lugar de trabajo visual o gestión visual tiene como propósito colocar información crítica en las áreas físicas de trabajo mediante el uso de señalamientos, etiquetas, carteles, vitrinas y otros medios. Estos visuales ayudan a crear un entorno de trabajo más seguro y eficiente al eliminar la necesidad de capacitación repetitiva y supervisión constante. Los sistemas y dispositivos visuales desempeñan un papel fundamental en muchas de las más populares herramientas de manufactura esbelta, como 5S, Trabajo Estándar, Mantenimiento Productivo Total, Cambios Rápidos y Kanban. De hecho, Fábrica Visual sirve como un elemento clave para estas iniciativas, ya que asegura que las mejoras queden claramente visibles, que se comprendan con facilidad y que sean seguidas de manera consistente mucho después de que el evento kaizen o de mejoras rápidas haya terminado. ¿Cuáles son los beneficios de una Fábrica Visual? Las herramientas de comunicación visual ofrecen una variedad de beneficios sustanciales para la productividad y seguridad en el área de trabajo. Uno de los causantes principales de desperdicios son los déficits de información; los empleados simplemente carecen del conocimiento necesario para realizar sus actividades de manera eficiente y efectiva. Para encontrar la información que necesitan, los empleados con frecuencia pierden valioso tiempo buscando, esperando, recuperando, re trabajando. En una fábrica visual, la información que es crítica para el proceso de manufactura se coloca en el entorno físico. Los recursos visuales se colocan justo donde se necesitan y se pueden comprender con facilidad con sólo un vistazo.
Respecto a las particularidades del producto, Heijunka es aplicable a procesos con referencias variadas, es decir, que exista flexibilidad de unidades. En cuanto al proceso, requiere de un cumplimiento estricto de los principios de estandarización y balance de la producción. Implementación de Heijunka Para implementar Heijunka es preciso utilizar una serie de herramientas que integradas permiten obtener un sistema de producción de flujo constante y nivelado a partir de la demanda real. Utilización de células de trabajo Flujo continuo pieza por pieza Producción ajustada al takt time (tiempo de ritmo) Nivelación de la cantidad de producción. Nivelación de la producción por Sku (referencia). Utilización de células de trabajo Uno de los primeros pasos en la puesta en marcha de un sistema Lean es la creación de flujo en la planta, es decir, un enfoque de manufactura esbelta, esta consiste en que las máquinas e instalaciones deben disponerse en función al flujo de producto, lo cual mejorará el tiempo takt, independiente de que exista más de una secuencia de producción, tal como observaremos a continuación. El diseño que mejor cumple los requerimientos básicos de la gestión JIT, es la denominada “célula de trabajo", que responde al concepto de flujo de actividades muy cercanas y que adopta la forma física de “U”. El flujo continuo transforma varios procesos que trabajan de forma independiente en una celda de trabajo conjunta y flexible, donde todos los procesos van ligados uno después del otro. La distribución en forma de U da más flexibilidad a la línea y exige una mayor polivalencia del operario.
Es muy importante considerar que la implementación de las celdas de trabajo busca pasar de fabricar grandes lotes, a lotes mucho más pequeños, y en consecuencia, se generan más momentos de cambio de referencia, de manera que se hace imperativo la aplicación de SMED, con el propósito de reducir tiempos de alistamiento. Manufactura celular Flujo continuo pieza por pieza La estrategia de producción basada en un sistema de flujo pull, pieza por pieza, consiste en optimizar los inventarios y el flujo del producto de acuerdo al comportamiento real de la demanda. Flujo continuo pieza por pieza significa básicamente que una operación “aguas arriba” nunca hace más de lo que requiere una operación “aguas abajo”, de manera que nunca se produce más de lo que solicita un cliente.