
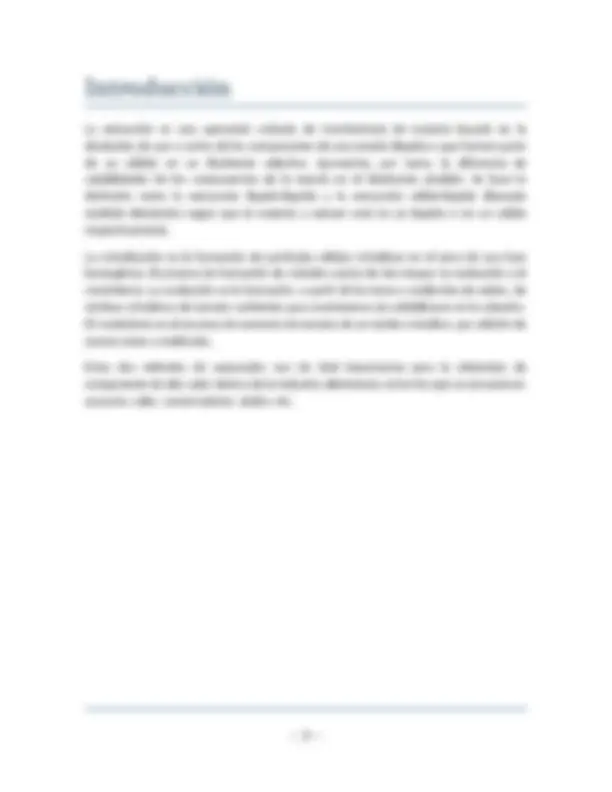
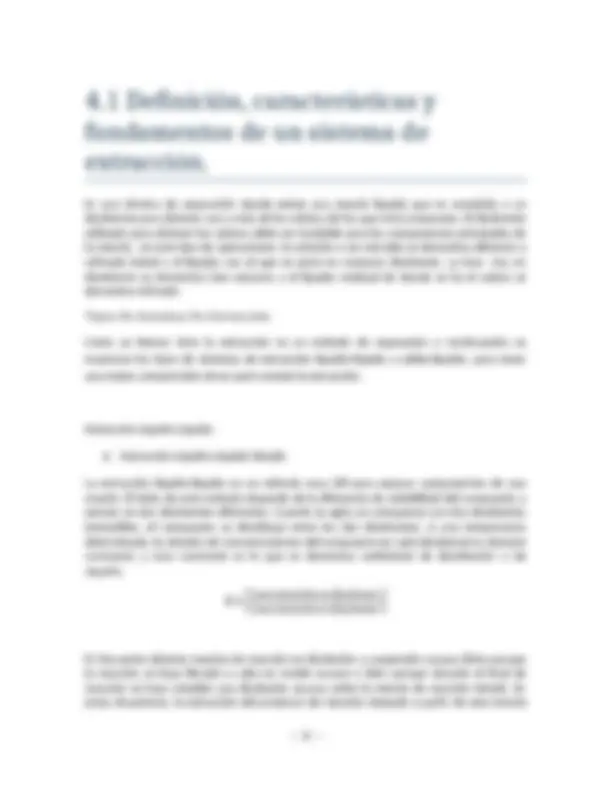
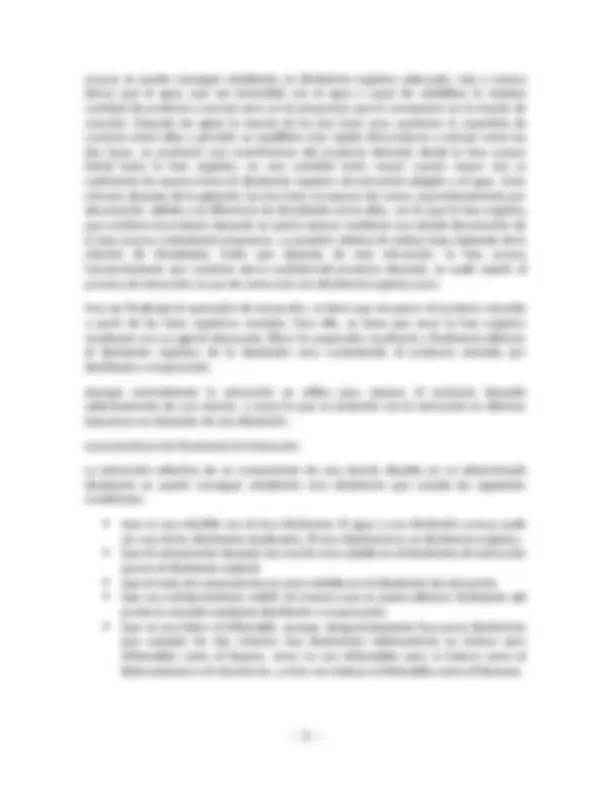
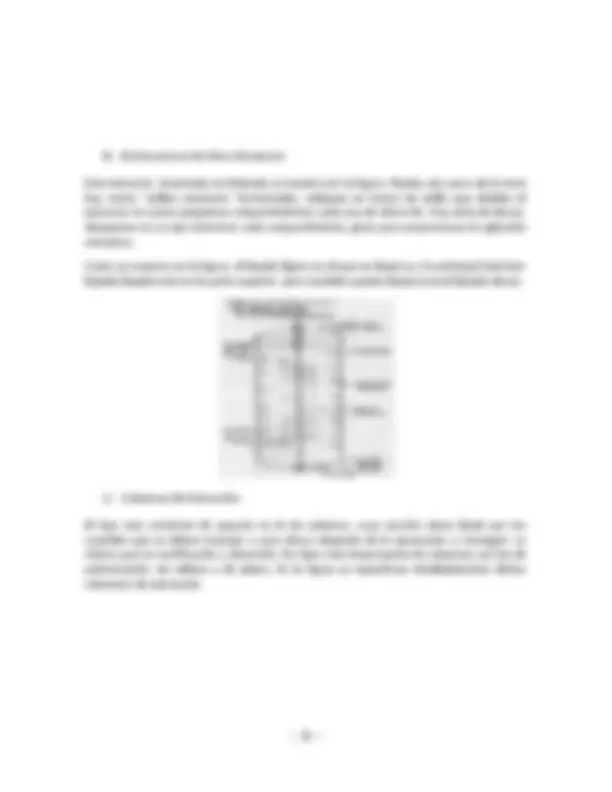
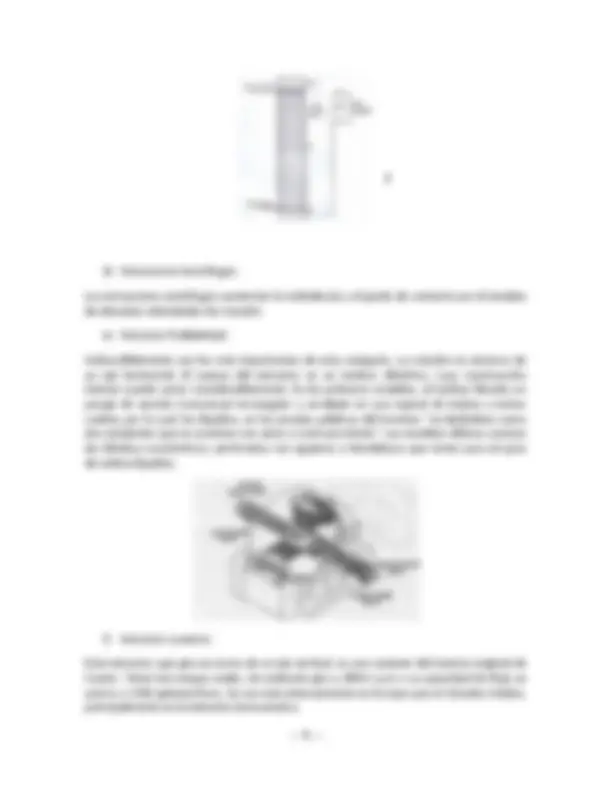
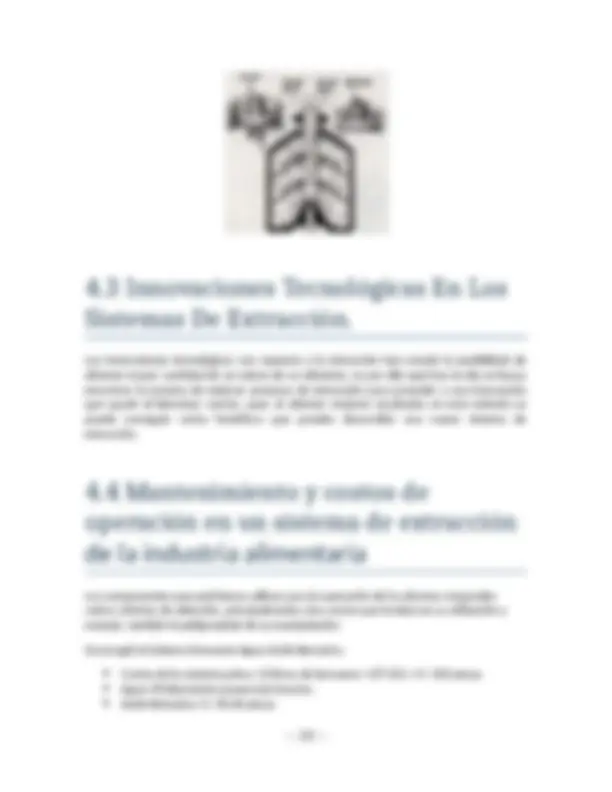
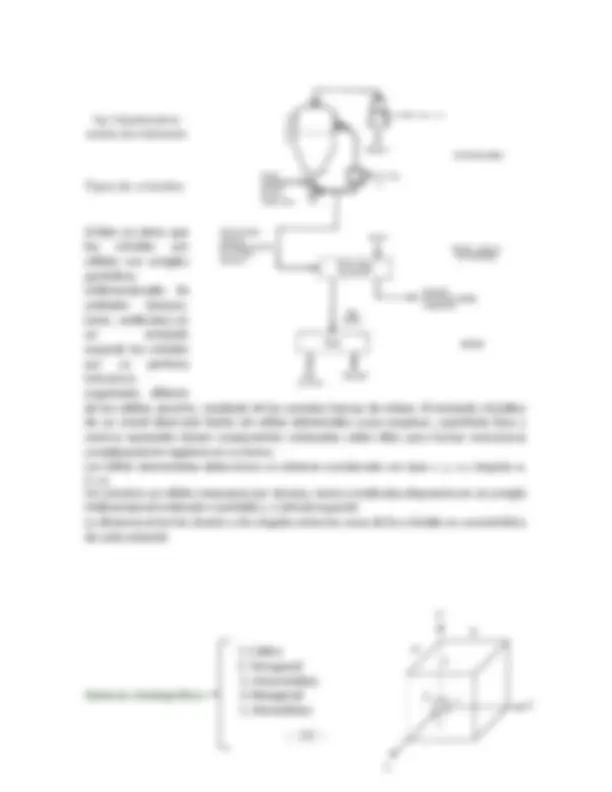
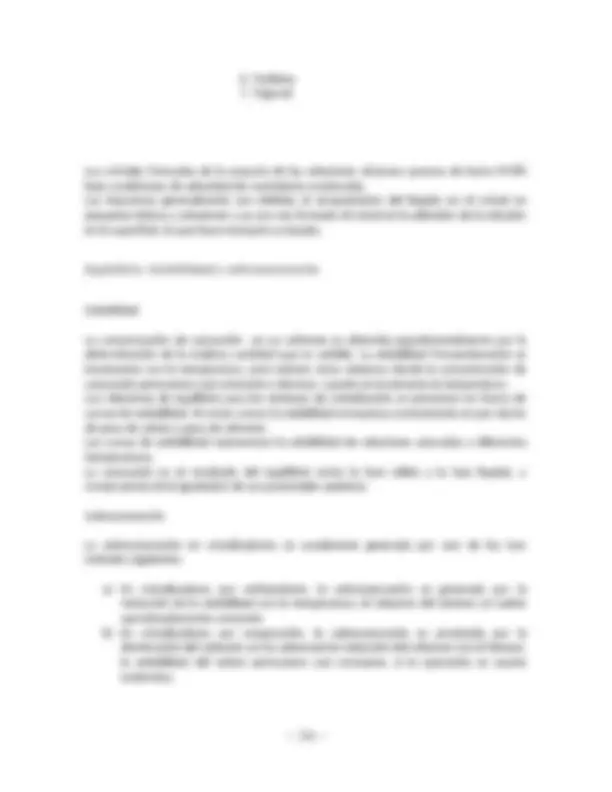
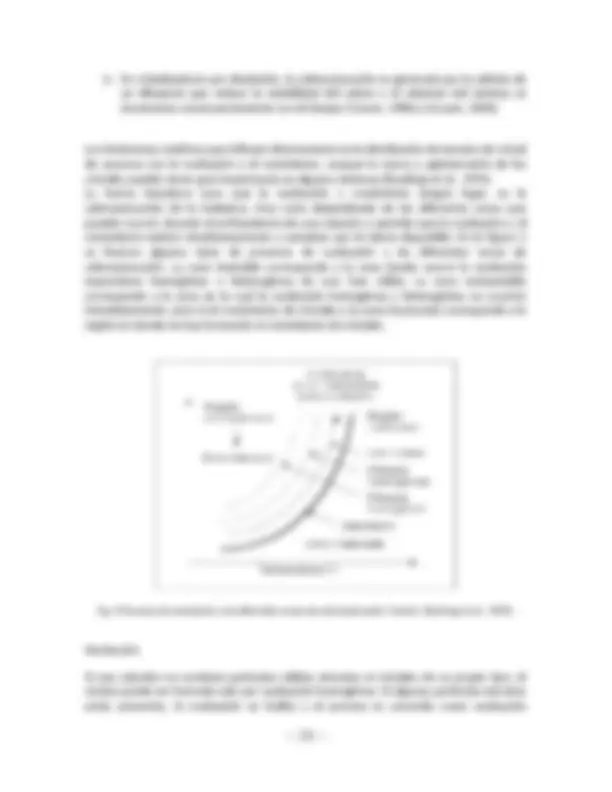
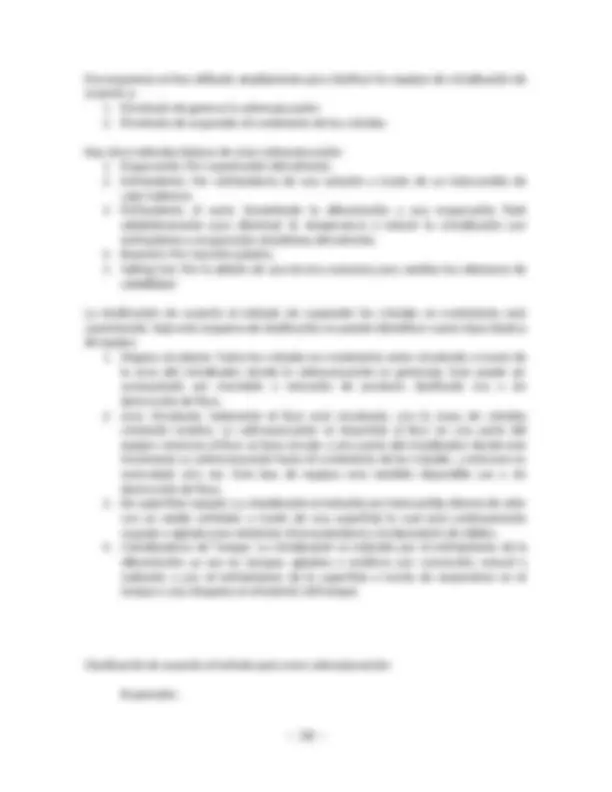
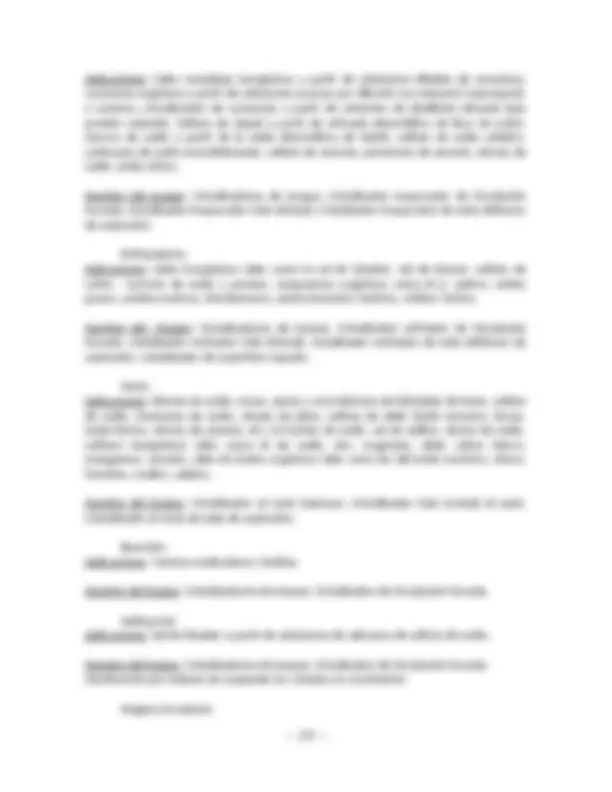
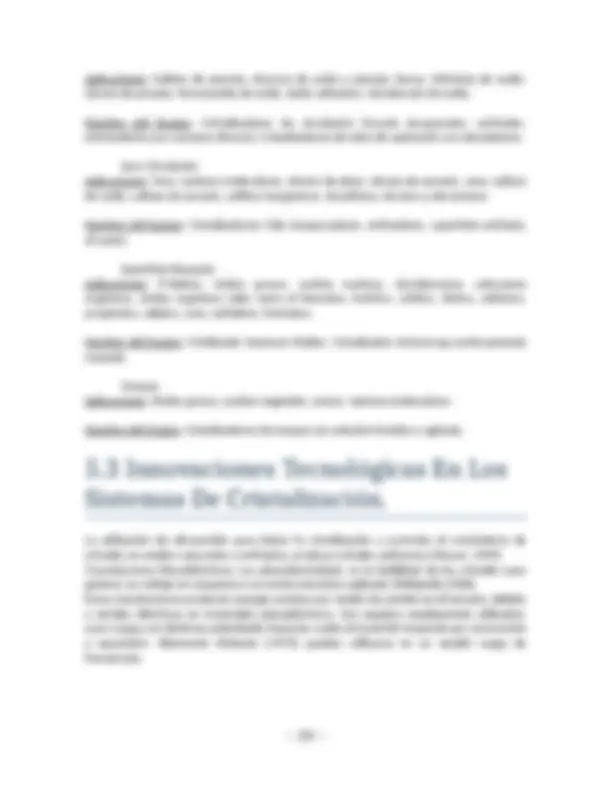
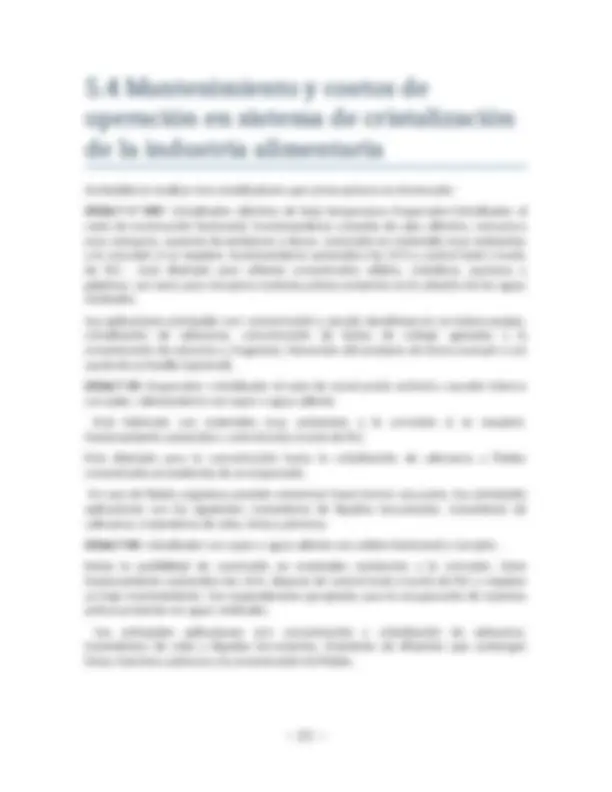
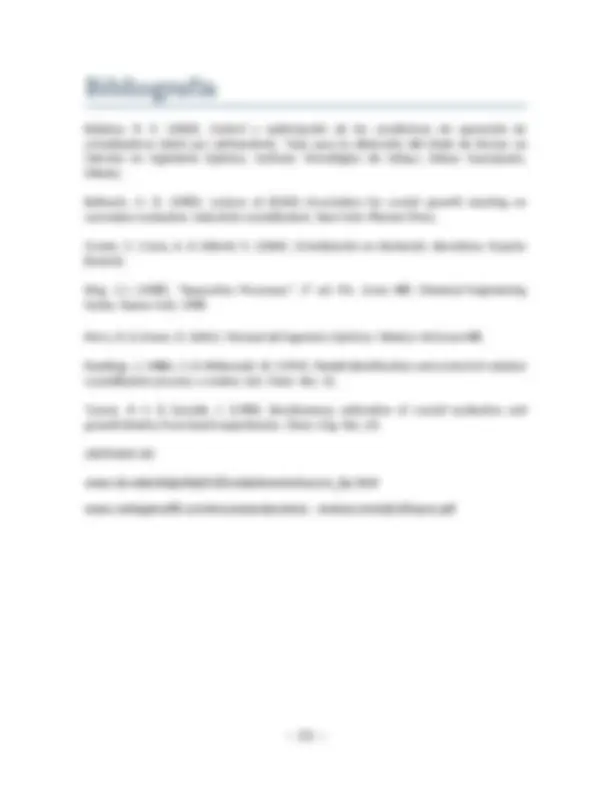
Prepara tus exámenes y mejora tus resultados gracias a la gran cantidad de recursos disponibles en Docsity
Gana puntos ayudando a otros estudiantes o consíguelos activando un Plan Premium
Prepara tus exámenes
Prepara tus exámenes y mejora tus resultados gracias a la gran cantidad de recursos disponibles en Docsity
Prepara tus exámenes con los documentos que comparten otros estudiantes como tú en Docsity
Los mejores documentos en venta realizados por estudiantes que han terminado sus estudios
Estudia con lecciones y exámenes resueltos basados en los programas académicos de las mejores universidades
Responde a preguntas de exámenes reales y pon a prueba tu preparación
Consigue puntos base para descargar
Gana puntos ayudando a otros estudiantes o consíguelos activando un Plan Premium
Comunidad
Pide ayuda a la comunidad y resuelve tus dudas de estudio
Descubre las mejores universidades de tu país según los usuarios de Docsity
Ebooks gratuitos
Descarga nuestras guías gratuitas sobre técnicas de estudio, métodos para controlar la ansiedad y consejos para la tesis preparadas por los tutores de Docsity
Este documento proporciona una visión general de los procesos de extracción y cristalización, dos técnicas fundamentales en la industria. La extracción líquido-líquido y sólido-líquido se explican en detalle, incluyendo sus definiciones, características y fundamentos. Además, se aborda el proceso de cristalización, sus etapas de nucleación y crecimiento, y las propiedades de los cristales. Se mencionan diversas aplicaciones industriales de estos procesos, como la separación de hidrocarburos, la purificación de productos farmacéuticos y la obtención de sales inorgánicas. El documento también proporciona información sobre los equipos utilizados en la cristalización, como los cristalizadores de tanque y los cristalizadores evaporadores. En general, este documento ofrece una comprensión integral de estos procesos clave en la industria, lo que lo convierte en una valiosa herramienta de estudio y referencia para estudiantes y profesionales.
Tipo: Apuntes
1 / 22
Esta página no es visible en la vista previa
¡No te pierdas las partes importantes!
Instituto Tecnológico Superior de Huatusco Ing. Industrias Alimentarias 602
4.1 Definición, características y fundamentos de un sistema de extracción. Es una técnica de separación donde existe una mezcla liquida que es sometida a un disolvente para obtener uno o más de los solutos de los que está compuesta. El disolvente utilizado para obtener los solutos debe ser insoluble para los componentes principales de la mezcla, en este tipo de operaciones, la solución a ser extraída se denomina alimento o refinado inicial y el líquido con el que se pone en contacto disolvente. La fase rica en disolvente se denomina fase extracto y el líquido residual de donde se ha el soluto se denomina refinado. Tipos De Sistemas De Extracción. Como ya hemos visto la extracción es un método de separación a continuación se muestran los tipos de sistemas de extracción liquido-líquido y solido-líquido, para tener una mejor comprensión de en qué consiste la extracción. Extracción Líquido-Líquido. A. Extracción Líquido-Líquido Simple. La extracción líquido-líquido es un método muy útil para separar componentes de una mezcla. El éxito de este método depende de la diferencia de solubilidad del compuesto a extraer en dos disolventes diferentes. Cuando se agita un compuesto con dos disolventes inmiscibles, el compuesto se distribuye entre los dos disolventes. A una temperatura determinada, la relación de concentraciones del compuesto en cada disolvente es siempre constante, y esta constante es lo que se denomina coeficiente de distribución o de reparto. K = Concentración en disolvente 2 Concentración en disolvente 1 Es frecuente obtener mezclas de reacción en disolución o suspensión acuosa (bien porque la reacción se haya llevado a cabo en medio acuoso o bien porque durante el final de reacción se haya añadido una disolución acuosa sobre la mezcla de reacción inicial). En estas situaciones, la extracción del producto de reacción deseado a partir de esta mezcla
acuosa se puede conseguir añadiendo un disolvente orgánico adecuado, más o menos denso que el agua, que sea inmiscible con el agua y capaz de solubilizar la máxima cantidad de producto a extraer pero no las impurezas que lo acompañan en la mezcla de reacción. Después de agitar la mezcla de las dos fases para aumentar la superficie de contacto entre ellas y permitir un equilibrio más rápido del producto a extraer entre las dos fases, se producirá una transferencia del producto deseado desde la fase acuosa inicial hacia la fase orgánica, en una cantidad tanto mayor cuanto mayor sea su coeficiente de reparto entre el disolvente orgánico de extracción elegido y el agua. Unos minutos después de la agitación, las dos fases se separan de nuevo, espontáneamente por decantación, debido a la diferencia de densidades entre ellas, con lo que la fase orgánica que contiene el producto deseado se podrá separar mediante una simple decantación de la fase acuosa conteniendo impurezas. La posición relativa de ambas fases depende de la relación de densidades. Dado que después de esta extracción, la fase acuosa frecuentemente aún contiene cierta cantidad del producto deseado, se suele repetir el proceso de extracción un par de veces más con disolvente orgánico puro. Una vez finalizada la operación de extracción, se tiene que recuperar el producto extraído a partir de las fases orgánicas reunidas. Para ello, se tiene que secar la fase orgánica resultante con un agente desecante, filtrar la suspensión resultante y finalmente eliminar el disolvente orgánico de la disolución seca conteniendo el producto extraído por destilación o evaporación. Aunque normalmente la extracción se utiliza para separar el producto deseado selectivamente de una mezcla, a veces lo que se pretende con la extracción es eliminar impurezas no deseadas de una disolución. Características Del Disolvente De Extracción: La extracción selectiva de un componente de una mezcla disuelta en un determinado disolvente se puede conseguir añadiendo otro disolvente que cumpla las siguientes condiciones. Que no sea miscible con el otro disolvente. El agua o una disolución acuosa suele ser uno de los disolventes implicados. El otro disolvente es un disolvente orgánico. Que el componente deseado sea mucho más soluble en el disolvente de extracción que en el disolvente original. Que el resto de componentes no sean solubles en el disolvente de extracción. Que sea suficientemente volátil, de manera que se pueda eliminar fácilmente del producto extraído mediante destilación o evaporación. Que no sea tóxico ni inflamable, aunque, desgraciadamente hay pocos disolventes que cumplan los dos criterios: hay disolventes relativamente no tóxicos pero inflamables como el hexano, otros no son inflamables pero sí tóxicos como el diclorometano o el cloroformo, y otros son tóxicos e inflamables como el benceno.
4.2 Equipos Elementos Y Tipos De Sistemas De Extracción. Equipos Utilizados Para La Extracción Líquido-Líquido Los equipos utilizados para la extracción dependen de la cantidad de alimento que se tenga, si la cantidad es pequeña bastara con el uso de unos cuantos utensilios de laboratorio pero si nuestros alimento es muy grande se tendrán que utilizar aparatos industriales, a continuación se nombran algunos de estos equipos utilizados en la industria moderna para tener una mayor conciencia de lo importante que es la extracción el hombre industrial.
1. Aparatos Mezcladores: El equipo para la extracción líquido-liquido depende de la forma en que se realice el proceso. Cuando el sistema está formado por estadios, hay dos fases bien diferenciadas: mezcla íntima y separación posterior que a su vez presentan aspectos diferentes según el proceso sea continuo o discontinuo. Los aparatos mezcladores, que consisten generalmente en tanques con dispositivos apropiados de agitación, deben proporcionar suficiente superficie de contacto durante un tiempo adecuado para que tenga lugar la transferencia de soluto. De los diversos tipos de aparatos empleados en la mezcla de materiales, los más utilizados en la extracción líquido-líquido son los agitadores y los mezcladores. a) Extractores Anulares Rotatorios: Estos extractores, de los que se muestra uno esquemáticamente en la figura, constan de un cilindro exterior estacionario, dentro del cual gira un cilindro concéntrico. El contacto liquido-liquido ocurre en el espacio anular entre los dos. Este es probablemente el tipo más simple de los extractores agitadores y ha despertado interés en el campo de los procesos con energía atómica por su sencillez y porque promete corto tiempo de residencia por etapa. Esto es necesario en la extracción de soluciones muy radioactivas para reducir al mínimo daños ala disolvente.
b) B) Extractores De Disco Rotatorio: Este extractor, inventado en Holanda se muestra en la figura. Fijados ala casco de la torre hay varios “anillos estatores” horizontales, tabiques en forma de anillo que dividen el extractor en varios pequeños compartimientos cada uno de altura Hc. Una serie de discos, dispuestos en un eje central en cada compartimiento, giran para proporcionar la agitación mecánica. Como se muestra en la figura, el líquido ligero es el que se dispersa y la principal interface liquido-liquido está en la parte superior, pero también puede dispersarse el líquido denso. c) Columnas De Extracción: El tipo más corriente de aparato es el de columna, cuya sección viene fijada por los caudales que se deben manejar y cuya altura depende de la separación a conseguir. Lo mismo que en rectificación y absorción, los tipos más importantes de columnas son las de pulverización, de relleno y de platos. En la figura se especifican detalladamente dichas columnas de extracción.
4.3 Innovaciones Tecnológicas En Los Sistemas De Extracción. Las innovaciones tecnológicas con respecto a la extracción han creado la posibilidad de obtener mayor cantidad de un soluto de un alimento, es por ello que hoy en día se busca encontrar la manera de mejorar procesos de extracción para proceder a una innovación que ayude al bienestar común, pues al obtener mejores resultados en este método se puede conseguir varios benéficos que pueden desarrollar una nuevo sistema de extracción. 4 .4 Mantenimiento y costos de operación en un sistema de extracción de la industria alimentaria Los componentes que podríamos utilizar para la operación de la columna responden varios criterios de selección, principalmente a los costos que involucran su utilización y manejo, también la peligrosidad de su manipulación. Se escogió el sistema Kerosene-Agua-Acido Benzoico. Costos de la materia prima: 35 litros de kerosene: 3.8*(35) = S/. 650 pesos Agua: El laboratorio posee este insumo. Acido Benzoico: S/. 83.00 pesos
Equipos Costo Unitario Unidades requeridas Total Bomba Centrifuga de 0.25 HP 100.00 2 200. Bureta para la cuantificación del ácido benzoico Tanque de almacenamiento de 45 litros de polímero. 40.00 2 80. Tanque de almacenamiento de 30 litros de polímero. 35.00 2 70. Válvulas de bola 5.00 6 30. Válvulas de compuerta 12.00 4 48. Tubería de PVC – HIDRO 10.00 1 10. Tubería de Acero Galvanizado Accesorios de plomería 40.00 1 40. Estructura de soporte para los tanques 30.00 1 30. El total de costos estimados en el equipo es de S/. 2500.00 pesos, y el costo de los insumos es de S/. 730.00 pesos, lo que suma S/. 3200.00 pesos mexicanos , para poner en funcionamiento el equipo según los cálculos.
Fig. 1 Esquema de un proceso de cristalización Tipos de cristales Si bien es cierto que los cristales son sólidos con arreglos periódicos tridimensionales de unidades (átomos, iones, moléculas) en un enrejado espacial, los cristales por su perfecta estructura organizada, difieren de los sólidos amorfos, resultado de las variadas fuerzas de enlace. El enrejado cristalino de un cristal ideal está hecho de celdas elementales cuyas esquinas, superficies lisas y centros espaciales tienen componentes ordenados sobre ellos para formar estructuras completamente regulares en su forma. Las celdas elementales determinan un sistema coordenado con ejes x, y, z y ángulos α, βy ɣ. Un cristal es un sólido compuesto por átomos, iones o moléculas dispuestos en un arreglo tridimensional ordenado o periódico, o retícula espacial. La distancia entre los átomos y los ángulos entre las caras de los cristales es característica de cada material.
heterogénea. Ambas nucleaciones, la homogénea y la heterogénea, toman lugar en ausencia de cristales de la propia solución y son colectivamente conocidas como nucleación primaria. Esto ocurre cuando la sobresaturación metaestable ΔCmet es obtenida en el sistema. En la cristalización comercial de la sacarosa en el tacho o cristalizador, se ha observado continuamente que la nucleación ocurre hasta en niveles muy bajos de sobresaturación ΔC<ΔCmet cuando existen cristales propios de la solución; por ejemplo, en la forma de fragmentos agotados o en el sembrado de cristales. Tales nucleaciones son conocidas como nucleación secundaria, la cual puede definirse como la nucleación que toma lugar solo por la previa presencia de cristales del material que empieza a ser cristalizado. Se sabe también que existen diferencias entre nucleaciones secundarias resultantes de contacto, rotura, abrasión, agotamiento y fraccionamiento de los cristales de azúcar. Algunos autores como (Grases, 2000) y (Botsaris, 1980), han clasificado el mecanismo de nucleación secundaria en aparente, verdadero y de contacto. La Figura 3 ilustra la clasificación de los mecanismos de nucleación. Fig. 3 Clasificación de la Nucleación. Fuente (Botsaris, 1980) Crecimiento El crecimiento de los cristales es un fenómeno cuya fuerza impulsora también es la sobresaturación. El crecimiento de un cristal es un proceso de adición capa por capa.
El crecimiento solo puede ocurrir en la superficie del cristal y las resistencias involucradas en el crecimiento son la difusión del soluto hasta la superficie del cristal y la resistencia a la integración del soluto a la superficie del cristal. Una vez que los cristales han sido producidos por el proceso de nucleación, estos crecerán. El tamaño del cristal (frecuentemente el factor de mayor importancia) y la forma o hábito, son propiedades comunes del cristal relacionadas con el proceso de crecimiento. La pureza del cristal, perfección, dureza y la resistencia a la abrasión son otros parámetros que frecuentemente determinan las características de un cristal en particular. El proceso del crecimiento del cristal puede ser descrito por diferentes escalas: nivel molecular, microscópico y macroscópico. 5.2 Equipos, elementos y tipos de sistemas de cristalización. Debido a la amplia variedad de requerimientos para diferentes aplicaciones es raro encontrarse que equipos en diferentes sitios sean idénticos, sin embargo algunos principios básicos aplican para el diseño de cada unidad individual. Estos principios básicos son:
Aplicaciones: Sales complejas inorgánicas a partir de soluciones diluidas de amoniaco, sustancias orgánicas a partir de soluciones acuosas por dilución con metanol, isopropanol, o acetona, cristalización de sustancias a partir de solventes de ebullición elevada bajo presión reducida, Sulfato de níquel a partir de refinado electrolítico de licor de cobre, cloruro de sodio a partir de la celda electrolítica de NaOH, sulfato de sodio anhidro, carbonato de sodio monohidratado, sulfato de amonio, perclorato de amonio, nitrato de sodio, ácido cítrico. Nombre del equipo: Cristalizadores de tanque, Cristalizador evaporador de Circulación forzada, Cristalizador Evaporador Oslo (Kristal), Cristalizador Evaporador de tubo deflector de aspiración. Enfriamiento: Aplicaciones: Sales inorgánicas tales como la sal de Glauber, Sal de Epsom, sulfato de cobre , tartrato de sodio y potasio, compuestos orgánicos como el p- xyleno, acidos grasos, aceites marinos, clorobenceno, acidos benzoico, butirico, sórbico, bórico. Nombre del Equipo: Cristalizadores de tanque, Cristalizador enfriador de Circulación forzada, cristalizador enfriador Oslo (Kristal), cristalizador enfriador de tubo deflector de aspiración, cristalizador de superficie raspada. Vacío: Aplicaciones: Nitrato de sodio, mono, penta y octa hidratos de hidróxido de bario, sulfato de sodio, tiocianato de sodio, nitrato de plata, sulfato de níkel. Ácido tartarico, borax, ácido bórico, nitrato de potasio, di y tri fosfato de sodio, sal de anilina, citrato de sodio, sulfatos inorgánicos tales como el de sodio, zinc, magnesio, níkel, cobre, hierro, manganeso, amonio, sales de ácidos orgánicos tales como las del ácido tartárico, citrico, fumárico, oxalico, adipico. Nombre del Equipo: Cristalizador al vacío Swenson, Cristalizador Oslo (cristal) al vacío, Cristalizador al vacío de tubo de aspiración. Reacción: Aplicaciones: Tamices moleculares: Zeolitas Nombre del Equipo: Cristalizadores de tanque, Cristalizador de Circulación forzada. Salting Out: Aplicaciones: Sal de Glauber a partir de soluciones de salmuera de sulfato de sodio. Nombre del Equipo: Cristalizadores de tanque, Cristalizador de Circulación forzada. Clasificación por método de suspender los cristales en crecimiento: Magma Circulante:
Aplicaciones: Sulfato de amonio, cloruros de sodio y potasio, borax, trifosfato de sodio, nitrato de potasio, ferrocianida de sodio, ácido sulfamico, tetraborato de sodio. Nombre del Equipo: Cristalizadores de circulación forzada (evaporador, enfriador, enfriamiento por contacto directo). Cristalizadores de tubo de aspiración con desviadores. Licor Circulante: Aplicaciones: Yeso, tamices moleculares, nitrato de plata, nitrato de amonio, urea, sulfato de sodio, sulfato de amonio, sulfitos inorgánicos, tiosulfatos, cloratos y dicromatos. Nombre del Equipo: Cristalizadores Oslo (evaporadores, enfriadores, superficie enfriada, al vacío). Superficie Raspada: Aplicaciones: P-Xyleno, ácidos grasos, aceites marinos, clorobenceno, colorantes orgánicos, ácidos orgánicos tales como el benzoico, butírico, sórbico, bórico, sebácico, propionico, adipico, ures, naftaleno, formiatos. Nombre del Equipo: Cristlizador Swenson Walter, Cristalizador Armstrong continuamente raspado. Tanque: Aplicaciones: Ácidos grasos, aceites vegetales, azúcar, tamices moleculares. Nombre del Equipo: Cristalizadores de tanque con solución Estática o agitada. 5.3 Innovaciones Tecnológicas En Los Sistemas De Cristalización. La utilización de ultrasonido para iniciar la cristalización y controlar el crecimiento de cristales en medios saturados o enfriados, produce cristales uniformes (Mason, 1999). Transductores Piezoeléctricos: Las piezoelectricidad, es la habilidad de los cristales para generar un voltaje en respuesta a un estrés mecánico aplicado (Wikipedia 2006). Estos transductores producen energía acústica por medio de cambio en el tamaño, debido a señales eléctricas en materiales piezoeléctricos. Son equipos ampliamente utilizados; usan cargas con distintas polaridades hacia las cuales el material responde por contracción o expansión. Altamente eficiente (>95%) pueden utilizarse en un amplio rango de frecuencias.