
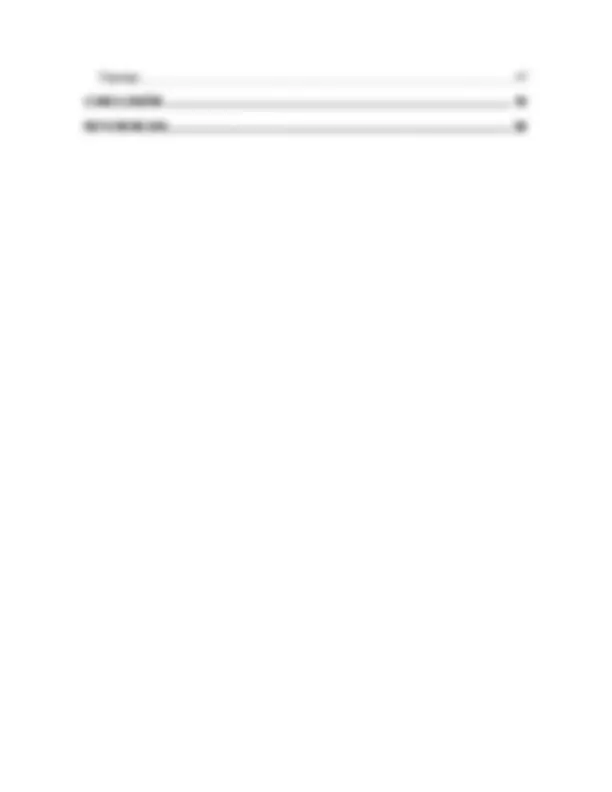
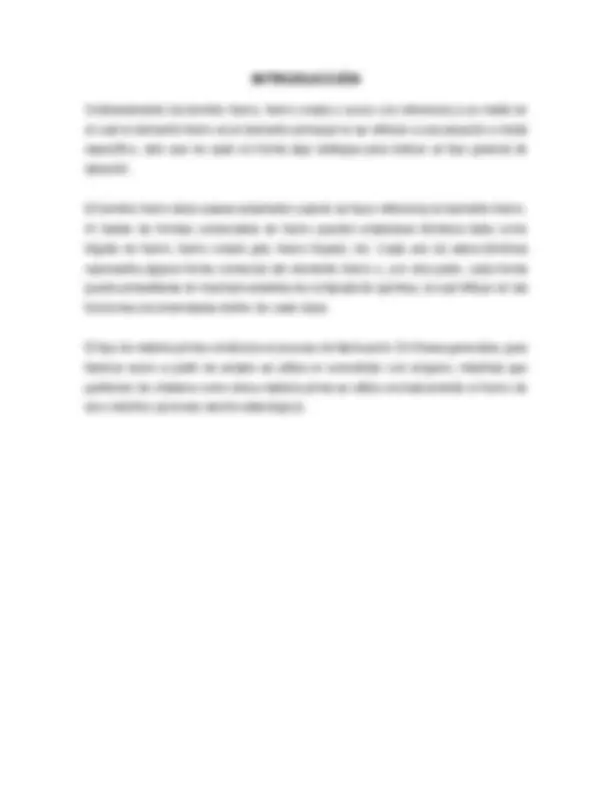
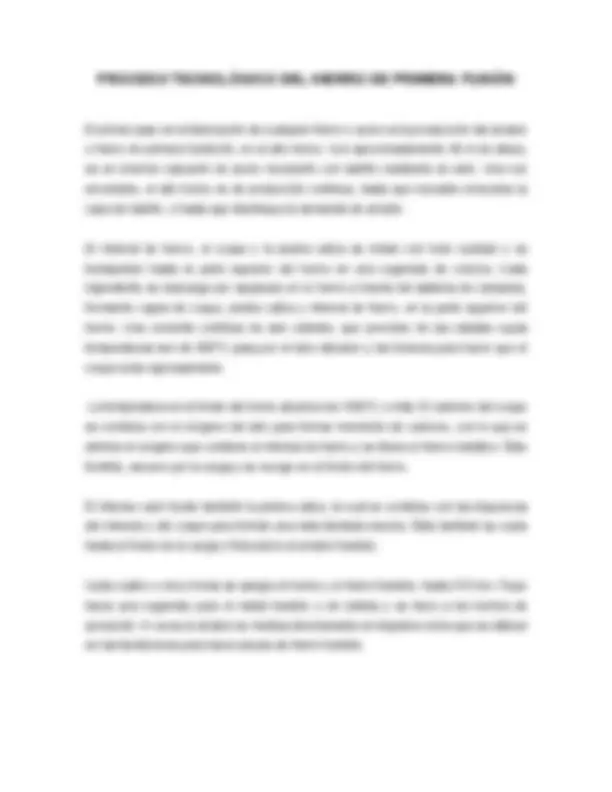
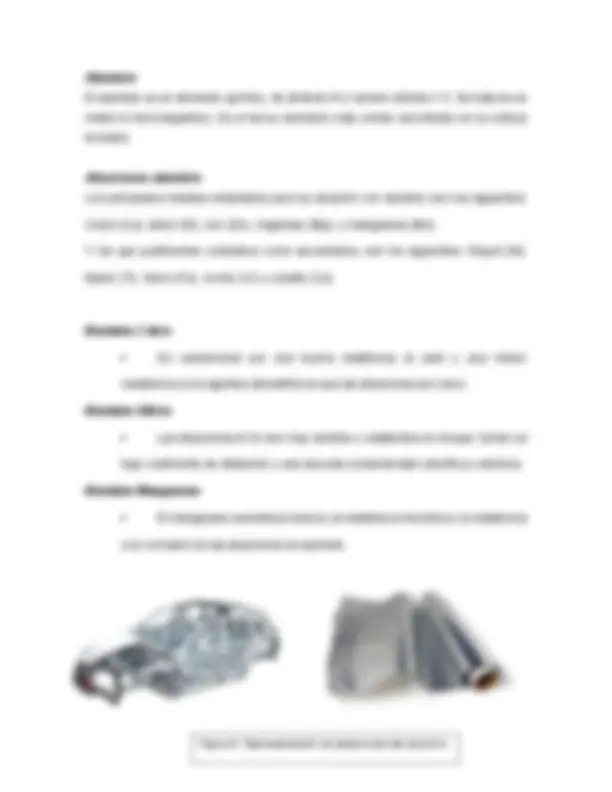
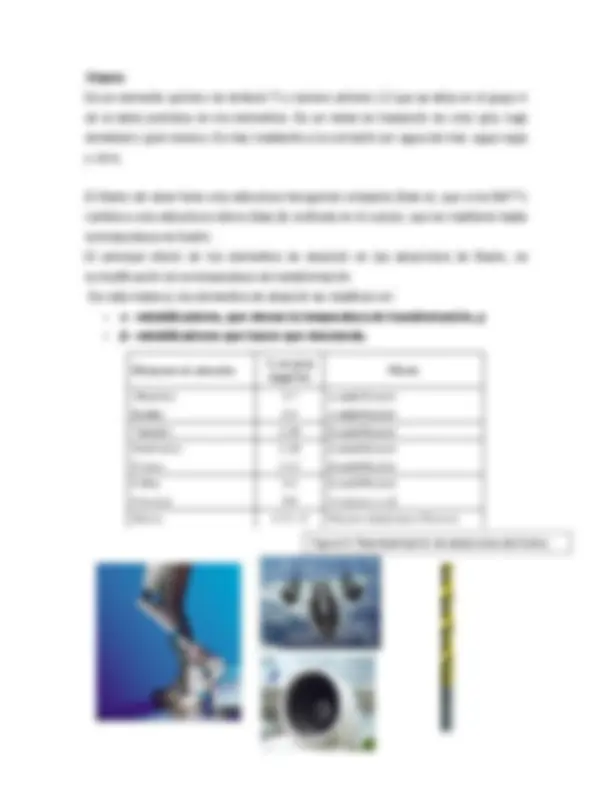
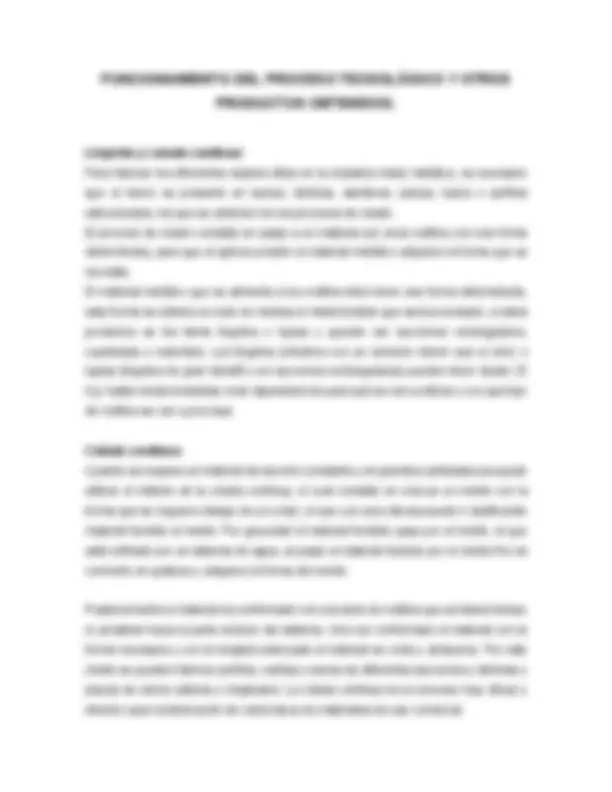
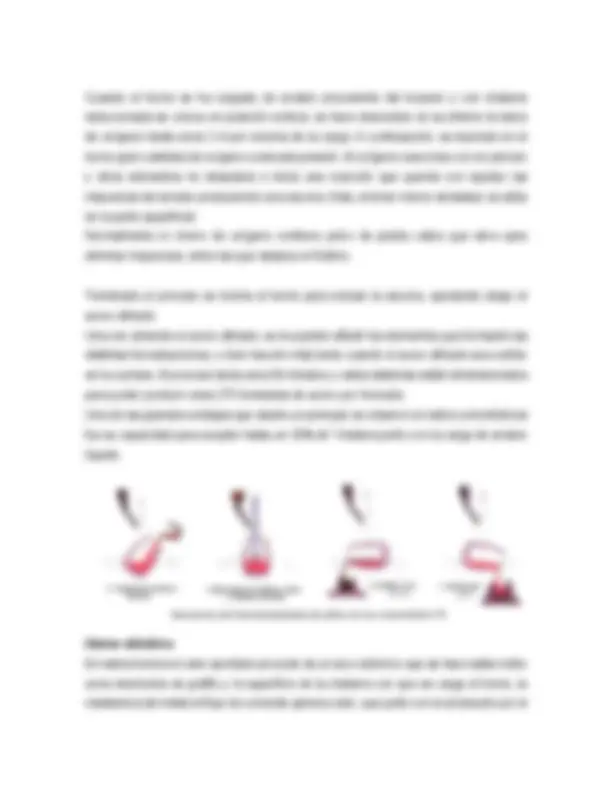
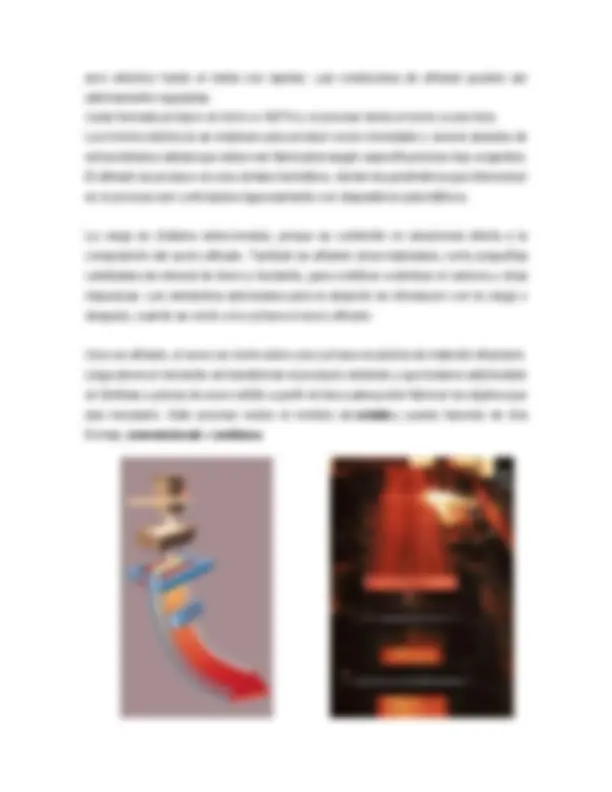
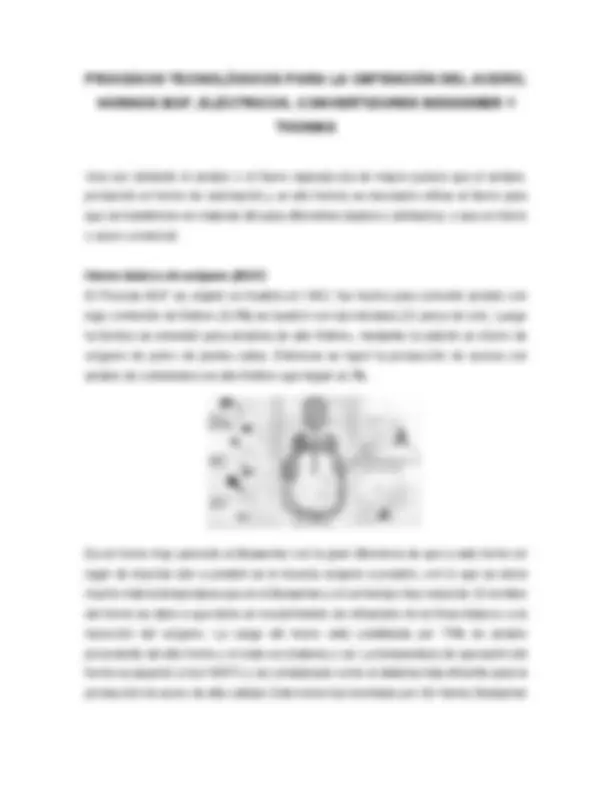
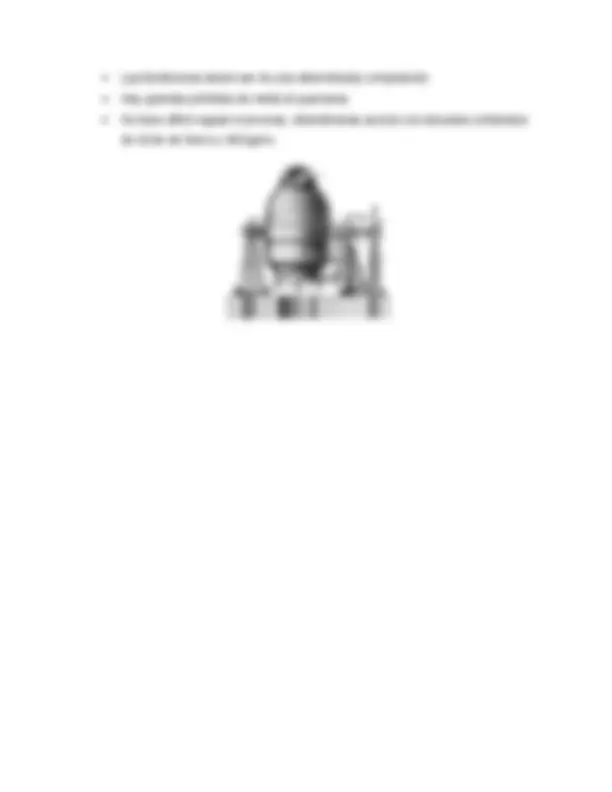
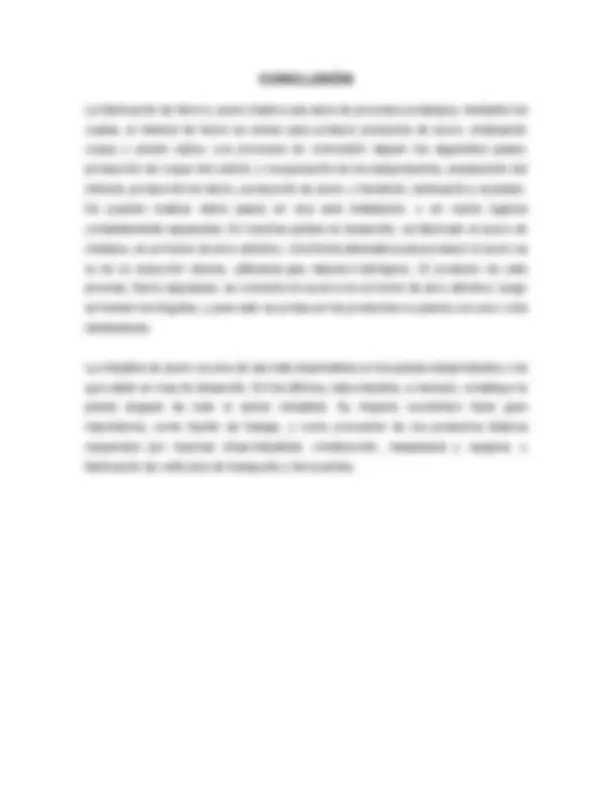
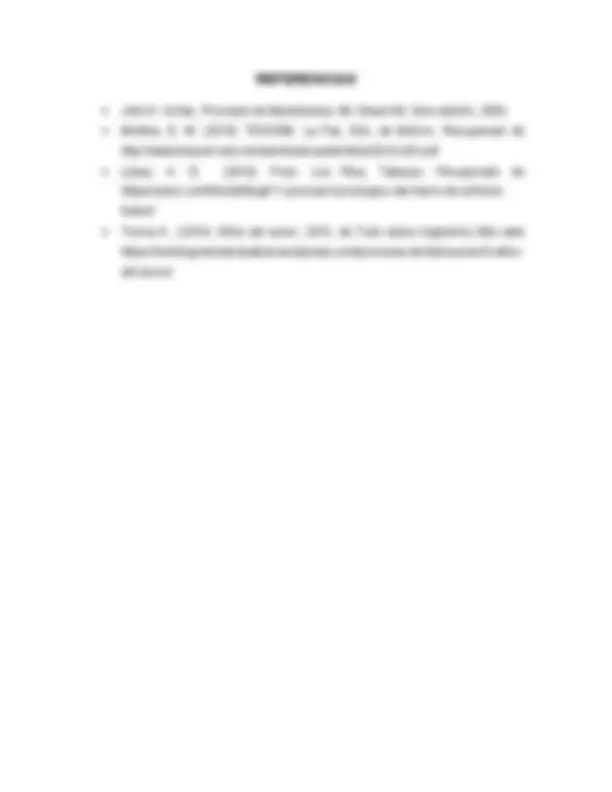
Prepara tus exámenes y mejora tus resultados gracias a la gran cantidad de recursos disponibles en Docsity
Gana puntos ayudando a otros estudiantes o consíguelos activando un Plan Premium
Prepara tus exámenes
Prepara tus exámenes y mejora tus resultados gracias a la gran cantidad de recursos disponibles en Docsity
Prepara tus exámenes con los documentos que comparten otros estudiantes como tú en Docsity
Los mejores documentos en venta realizados por estudiantes que han terminado sus estudios
Estudia con lecciones y exámenes resueltos basados en los programas académicos de las mejores universidades
Responde a preguntas de exámenes reales y pon a prueba tu preparación
Consigue puntos base para descargar
Gana puntos ayudando a otros estudiantes o consíguelos activando un Plan Premium
Comunidad
Pide ayuda a la comunidad y resuelve tus dudas de estudio
Descubre las mejores universidades de tu país según los usuarios de Docsity
Ebooks gratuitos
Descarga nuestras guías gratuitas sobre técnicas de estudio, métodos para controlar la ansiedad y consejos para la tesis preparadas por los tutores de Docsity
El proceso productivo del hierro y el acero, desde la extracción del mineral hasta la fabricación de lingotes y piezas. Se detalla el uso de hornos de altos furnos, convertidores LD y hornos eléctricos, así como los procesos de afino del acero. Además, se incluyen representaciones gráficas.
Qué aprenderás
Tipo: Resúmenes
1 / 20
Esta página no es visible en la vista previa
¡No te pierdas las partes importantes!
Fernando Loera Rivera
ALUMNO:
Rico Zamora Angel Fernando
Ordinariamente los termino hierro, hierro colado y acero con referencia a un metal en el cual el elemento hierro es el elemento principal no se refieren a una aleación o metal especifico, sino que se usan en forma algo ambigua para indicar un tipo general de aleación.
El termino hierro debe usarse solamente cuando se hace referencia al elemento hierro. Al hablar de formas comerciales de hierro pueden emplearse términos tales como lingote de hierro, hierro colado gris, hierro forjado, etc. Cada uno de estos términos representa alguna forma comercial del elemento hierro y, por otra parte, cada forma puede presentarse en muchas variantes de composición química, la cual influye en las funciones encomendadas dentro de cada clase.
El tipo de materia prima condiciona el proceso de fabricación. En líneas generales, para fabricar acero a partir de arrabio se utiliza el convertidor con oxígeno, mientras que partiendo de chatarra como única materia prima se utiliza exclusivamente el horno de arco eléctrico (proceso electro-siderúrgico).
El primer paso en la fabricación de cualquier hierro o acero es la producción del arrabio o hierro de primera fundición, en el alto horno. Con aproximadamente 40 m de altura, es un enorme cascarón de acero recubierto con ladrillo resistente al calor. Una vez encendido, el alto horno es de producción continua, hasta que necesite renovarse la capa de ladrillo, o hasta que disminuya la demanda de arrabio.
El mineral de hierro, el coque y la piedra caliza se miden con todo cuidado y se transportan hasta la parte superior del horno en una vagoneta de concha. Cada ingrediente se descarga por separado en el horno a través del sistema de campana, formando capas de coque, piedra caliza y mineral de hierro, en la parte superior del horno. Una corriente continua de aire caliente, que proviene de las estufas cuyas temperaturas son de 650°C pasa por el tubo atizador y las toberas para hacer que el coque arda vigorosamente.
La temperatura en el fondo del horno alcanza los 1650°C o más. El carbono del coque se combina con el oxígeno del aire para formar monóxido de carbono, con lo que se elimina el oxígeno que contiene el mineral de hierro y se libera el hierro metálico. Éste fundido, escurre por la carga y se recoge en el fondo del horno.
El intenso calor funde también la piedra caliza, la cual se combina con las impurezas del mineral y del coque para formar una nata llamada escoria. Ésta también se cuela hasta el fondo de la carga y flota sobre al arrabio fundido.
Cada cuatro o cinco horas se sangra el horno y el hierro fundido, hasta 315 ton. Fluye hacia una vagoneta para el metal fundido o de botella y se lleva a los hornos de aceración. A veces el arrabio se moldea directamente en lingotes cortos que se utilizan en las fundiciones para hacer piezas de hierro fundido.
Cobre Es el elemento químico de número atómico 29. Se trata de un metal de transición de color cobrizo (rojizo) y brillo metálico que, junto con la plata y el oro, forma parte de la llamada familia del cobre. El cobre es uno de los pocos metales que pueden encontrarse en la naturaleza en estado nativo.
Aleaciones Cobre El latón es más duro que el cobre, pero fácil de mecanizar, grabar y fundir. Es resistente a la oxidación, a las condiciones salinas y es maleable, por lo que puede laminarse en planchas finas. Su maleabilidad varía la temperatura y con la presencia, incluso en cantidades mínimas, de otros metales en su composición.
Las aleaciones en cuya composición predominan el cobre y el estaño (Sn) se conocen con el nombre de bronce. El bronce se emplea especialmente en aleaciones conductoras del calor, en baterías eléctricas y en la fabricación de válvulas, tuberías y uniones de fontanería.
Figura 2. Representación del cobre
Figura 3. Representación del bronce
Figura 4. Representación de aleaciones del cobre
Aluminio El aluminio es un elemento químico, de símbolo Al y numero atómico 13. Se trata de un metal no ferromagnético. Es el tercer elemento más común encontrado en la corteza terrestre.
Aleaciones aluminio Los principales metales empleados para su aleación con aluminio son los siguientes:
Cobre (Cu), silicio (Si), cinc (Zn), magnesio (Mg), y manganeso (Mn).
Y los que pudiéramos considerar como secundarios, son los siguientes: Níquel (Ni),
titanio (Ti), hierro (Fe), cromo (Cr) y cobalto (Co).
Aluminio-Cobre
Aluminio-Silicio
Aluminio-Manganeso
Figura 5. Representación de aleaciones del aluminio
Lingotes y colada continua: Para fabricar los diferentes objetos útiles en la industria metal metálica, es necesario que el hierro se presente en barras, láminas, alambres, placas, tubos o perfiles estructurales, los que se obtienen de los procesos de rolado. El proceso de rolado consiste en pasar a un material por unos rodillos con una forma determinada, para que al aplicar presión el material metálico adquiera la forma que se necesita. El material metálico que se alimenta a los rodillos debe tener una forma determinada, esta forma se obtiene al colar en moldes el metal fundido que será procesado, a estos productos se les llama lingotes o lupias y pueden ser secciones rectangulares, cuadradas o redondas. Los lingotes (cilindros con un extremo menor que el otro) o lupias (lingotes de gran tamaño con secciones rectangulares) pueden tener desde 25 Kg. hasta varias toneladas, todo dependerá de para qué se van a utilizar y con qué tipo de rodillos se van a procesar.
Colada continua: Cuando se requiere un material de sección constante y en grandes cantidades se puede utilizar el método de la colada continua, el cual consiste en colocar un molde con la forma que se requiere debajo de un crisol, el que con una válvula puede ir dosificando material fundido al molde. Por gravedad el material fundido pasa por el molde, el que está enfriado por un sistema de agua, al pasar el material fundido por el molde frío se convierte en pastoso y adquiere la forma del molde.
Posteriormente el material es conformado con una serie de rodillos que al mismo tiempo lo arrastran hacia la parte exterior del sistema. Una vez conformado el material con la forma necesaria y con la longitud adecuada el material se corta y almacena. Por este medio se pueden fabricar perfiles, varillas y barras de diferentes secciones y láminas o placas de varios calibres y longitudes. La colada continua es un proceso muy eficaz y efectivo para la fabricación de varios tipos de materiales de uso comercial.
Metalurgia de polvos: Se define como el arte de elaborar productos comerciales a partir de polvos metálicos. En este proceso no siempre se utiliza el calor, pero cuando se utiliza este debe mantenerse debajo de la temperatura de fusión de los metales a trabajar. Cuando se aplica calor en el proceso subsecuente de la metalurgia de los polvos se le conoce como sinterizado, este proceso genera la unión de partículas finas con lo que se mejora la resistencia de los productos y otras de sus propiedades. Las piezas metálicas producto de los procesos de la metalurgia de los polvos son producto de la mezcla de diversos polvos de metales que se complementan en sus características. Así se pueden obtener metales con cobalto, tungsteno o grafito según para qué va a ser utilizado el material que se fabrica.
El metal en forma de polvo es más caro que en forma sólida y el proceso es sólo recomendable para la producción en masa de los productos, en general el costo de producción de piezas producto de polvo metálico es más alto que el de la fundición, sin embargo, es justificable y rentable por las propiedades excepcionales que se obtienen con este procedimiento. Existen productos que no pueden ser fabricados y otros no compiten por las tolerancias que se logran con este método de fabricación
Figura 7 : Proceso de fundición continúa.
Cuando el horno se ha cargado de arrabio procedente del torpedo y con chatarra seleccionada se coloca en posición vertical, se hace descender en su interior la lanza de oxígeno hasta unos 2 m por encima de la carga. A continuación, se inyectan en el horno gran cantidad de oxígeno a elevada presión. El oxígeno reacciona con el carbono y otros elementos no deseados e inicia una reacción que quema con rapidez las impurezas del arrabio produciendo una escoria. Esta, al tener menor densidad, se sitúa en la parte superficial. Normalmente el chorro de oxígeno contiene polvo de piedra caliza que sirve para eliminar impurezas, entre las que destaca el fósforo.
Terminado el proceso se inclina el horno para extraer la escoria, quedando abajo el acero afinado. Una vez obtenido el acero afinado, se le pueden añadir los elementos que formarán las distintas ferroaleaciones, o bien hacerlo más tarde cuando el acero afinado sea vertido en la cuchara. El proceso tarda unos 50 minutos, y estos sistemas están dimensionados para poder producir unas 275 toneladas de acero por hornada. Una de las grandes ventajas que desde un principio se observó en estos convertidores fue su capacidad para aceptar hasta un 20% de "chatarra junto con la carga de arrabio líquido.
Horno eléctrico En estos hornos el calor aportado procede de un arco eléctrico que se hace saltar entre unos electrodos de grafito y la superficie de la chatarra con que se carga el horno, la resistencia del metal al flujo de corriente genera calor, que junto con el producido por el
arco eléctrico funde el metal con rapidez. Las condiciones de afinado pueden ser estrictamente reguladas. Cada hornada produce en torno a 100Tm y el proceso tarda en torno a una hora. Los hornos eléctricos se emplean para producir acero inoxidable y aceros aleados de extraordinaria calidad que deben ser fabricados según especificaciones muy exigentes. El afinado se produce en una cámara hermética, donde los parámetros que intervienen en el proceso son controlados rigurosamente con dispositivos automáticos.
La carga es chatarra seleccionada, porque su contenido en aleaciones afecta a la composición del acero afinado. También se añaden otros materiales, como pequeñas cantidades de mineral de hierro y fundente, para contribuir a eliminar el carbono y otras impurezas. Los elementos adicionales para la aleación se introducen con la carga o después, cuando se vierte a la cuchara el acero afinado.
Una vez afinado, el acero se vierte sobre una cuchara recubierta de material refractario. Llega ahora el momento de transformar el producto obtenido y que todavía está fundido en láminas o piezas de acero sólido a partir de las cuales poder fabricar los objetos que sea necesario. Este proceso recibe el nombre de colada y puede hacerse de dos formas, convencional o continua.
a mediados de 1800, sólo que como en esa época la producción del oxígeno era cara se inició con la inyección de aire, con lo que surgió el convertidor Bessemer.
Horno de arco eléctrico Por lo regular son hornos que sólo se cargan con chatarra de acero de alta calidad. Son utilizados para la fusión de aceros para herramientas, de alta calidad, de resistencia a la temperatura o inoxidables. Considerando que estos hornos son para la producción de aceros de alta calidad siempre están recubiertos con ladrillos de la línea básica. Existen hornos de arco eléctrico que pueden contener hasta 270 toneladas de material fundido. Para fundir 115 toneladas se requieren aproximadamente tres horas y 50, kwh de potencia. También en estos hornos se inyecta oxígeno puro por medio de una lanza. Los hornos de arco eléctrico funcionan con tres electrodos de grafito los que pueden llegar a tener 760mm de diámetro y longitud de hasta 12m. La mayoría de los hornos operan a 40v y la corriente eléctrica es de 12,000 A.
Estos equipos tienen un crisol o cuerpo de placa de acero forrado con refractario y su bóveda es de refractario también sostenida por un cincho de acero, por lo regular enfriado con agua. Para la carga del horno los electrodos y la bóveda se mueven dejando descubierto al crisol, en el que se deposita la carga por medio de una grúa viajera. Estos equipos son los más utilizados en industrias de tamaño mediano y pequeño, en donde la producción del acero es para un fin determinado, como varilla corrugada, aleaciones especiales, etc.
Hornos Bessemer y Thomas El procedimiento Bessemer fue el primer proceso de fabricación químico que sirvió para la fabricación en serie de acero, fundido en lingotes, de buena calidad y con poco coste a partir del arrabio. Este procedimiento fue llamado así en honor de Henry Bessemer, quien obtuvo la patente en 1855 y la utilizó a través de la Henry Bessemer and Company, sociedad implantada en Sheffield, ciudad del Norte de Inglaterra.
El procedimiento fue descubierto de forma independiente en 1851 por William Kelly. El mismo también había sido usado fuera de Europa durante cientos de años, pero no a una escala industrial. El principio clave es la retirada de impurezas del hierro mediante la oxidación producida por el insuflado de aire en el hierro fundido. La oxidación causa la elevación de la temperatura de la masa de hierro y lo mantiene fundido.
Thomas Fue creado en 1878 por el inglés Thomas y se usa para hierros ricos en fósforo. El revestimiento de este convertidor se hace de dolomita, que es un material refractario compuesto de MgCO3.CaCO3.
La capacidad de estos convertidores es mayor que la de los Bessemer, pues a la materia prima empleada hay que agregarle cal. En este caso, el convertidor se calienta y se carga con la cal, después se vierte el arrabio y se suministra el aire.
Ventajas del acero logrado en convertidores
La fabricación de hierro y acero implica una serie de procesos complejos, mediante los cuales, el mineral de hierro se extrae para producir productos de acero, empleando coque y piedra caliza. Los procesos de conversión siguen los siguientes pasos: producción de coque del carbón, y recuperación de los subproductos, preparación del mineral, producción de hierro, producción de acero, y fundición, laminación y acabado. Se pueden realizar estos pasos en una sola instalación, o en varios lugares completamente separados. En muchos países en desarrollo, es fabricado el acero de chatarra, en un horno de arco eléctrico. Una forma alternativa para producir el acero es la de la reducción directa, utilizando gas natural e hidrógeno. El producto de este proceso, hierro esponjoso, se convierte en acerco en un horno de arco eléctrico; luego se funden los lingotes, y para esto se producen los productos no planos con una o dos laminadoras.
La industria de acero es una de las más importantes en los países desarrollados y los que están en vías de desarrollo. En los últimos, esta industria, a menudo, constituye la piedra angular de todo el sector industrial. Su impacto económico tiene gran importancia, como fuente de trabajo, y como proveedor de los productos básicos requeridos por muchas otras industrias: construcción, maquinaria y equipos, y fabricación de vehículos de transporte y ferrocarriles.