
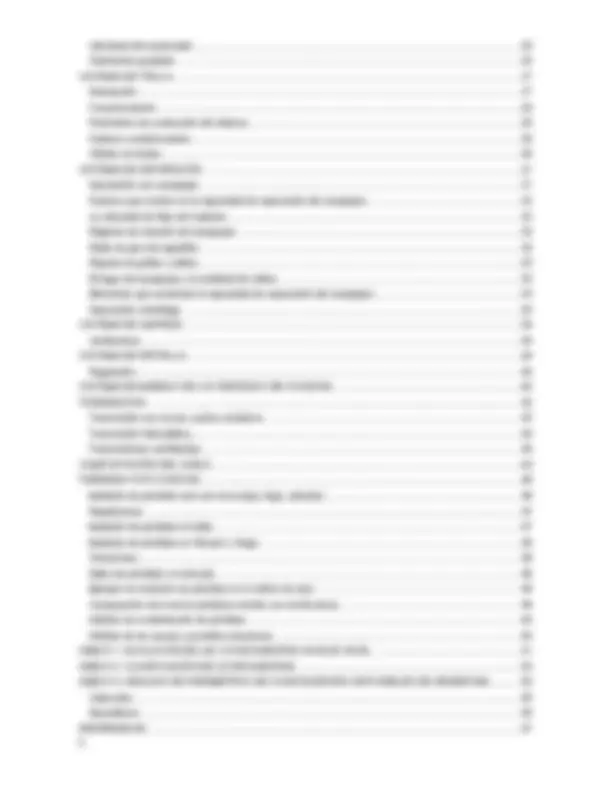
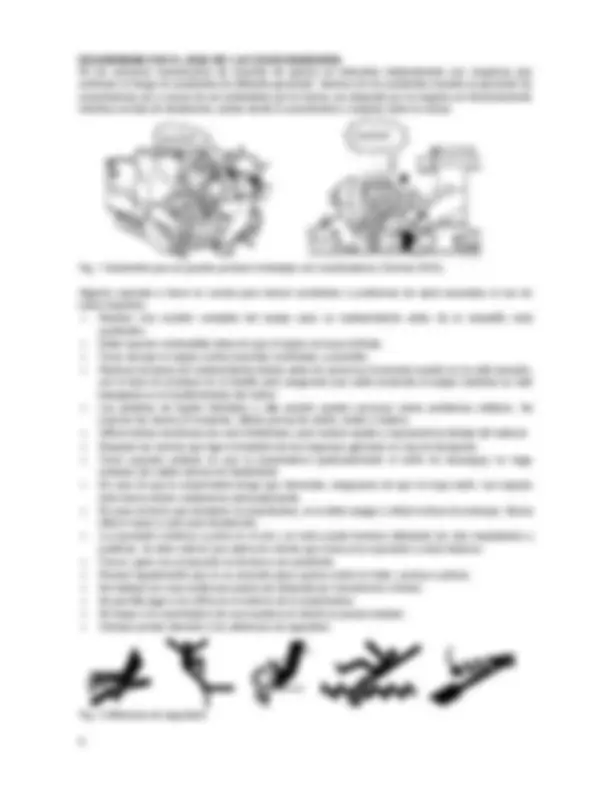
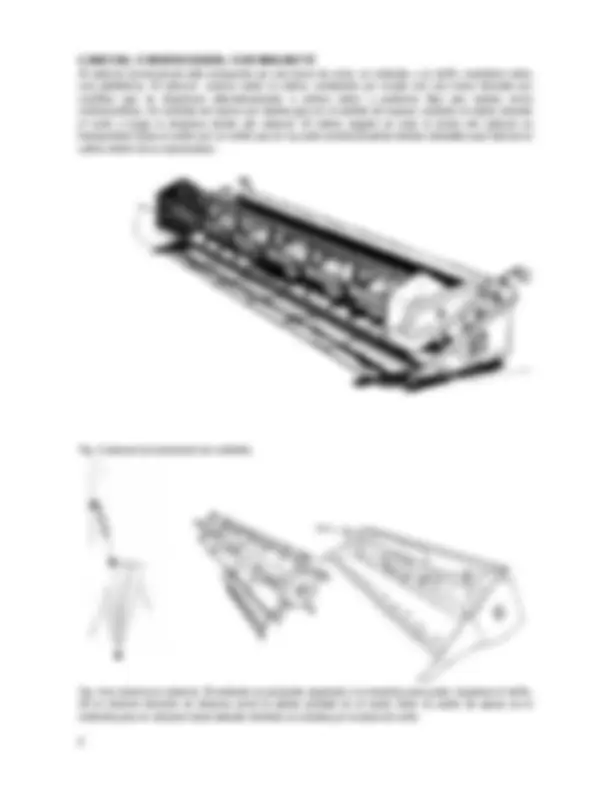
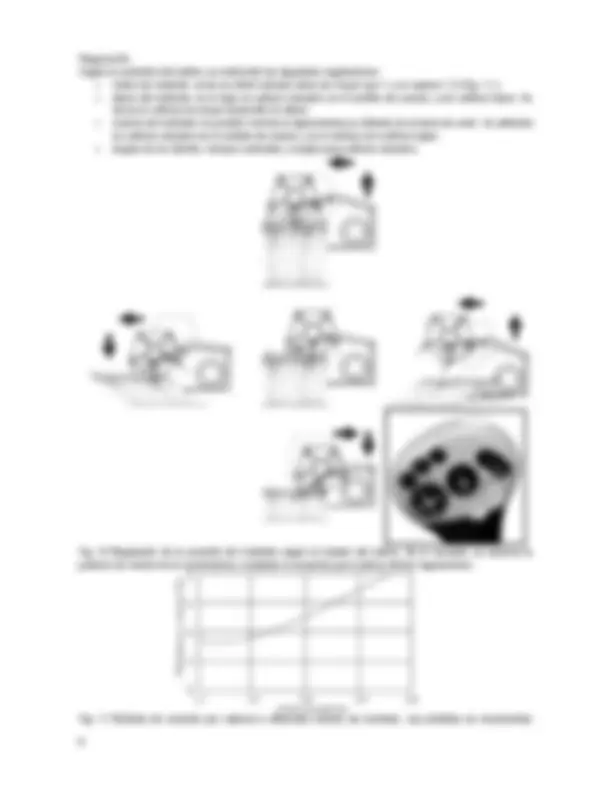
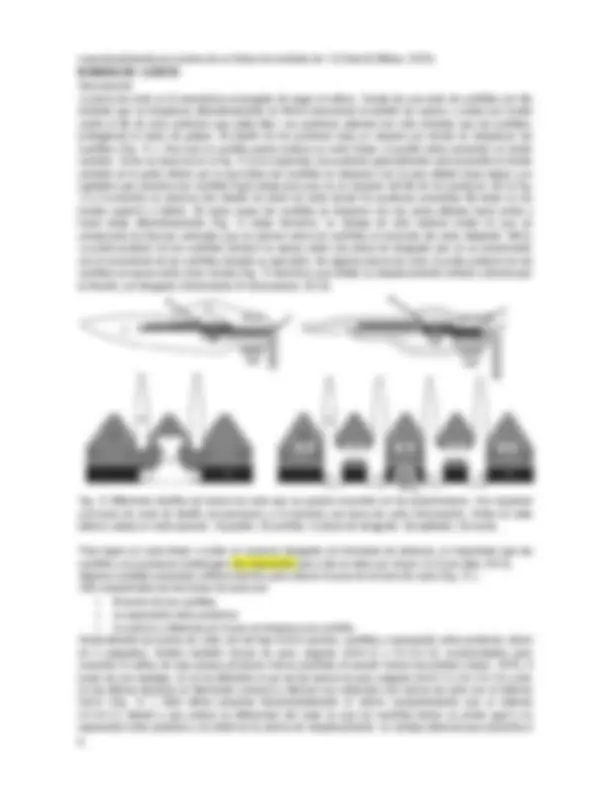
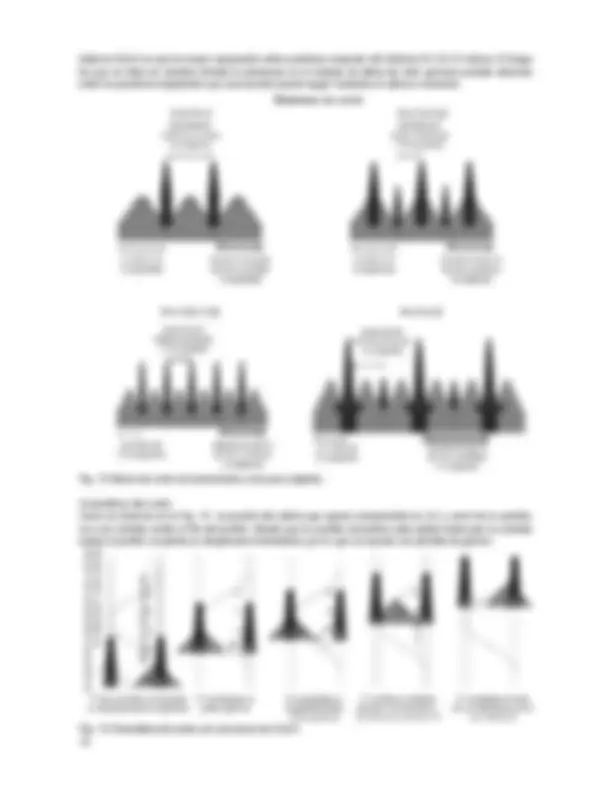
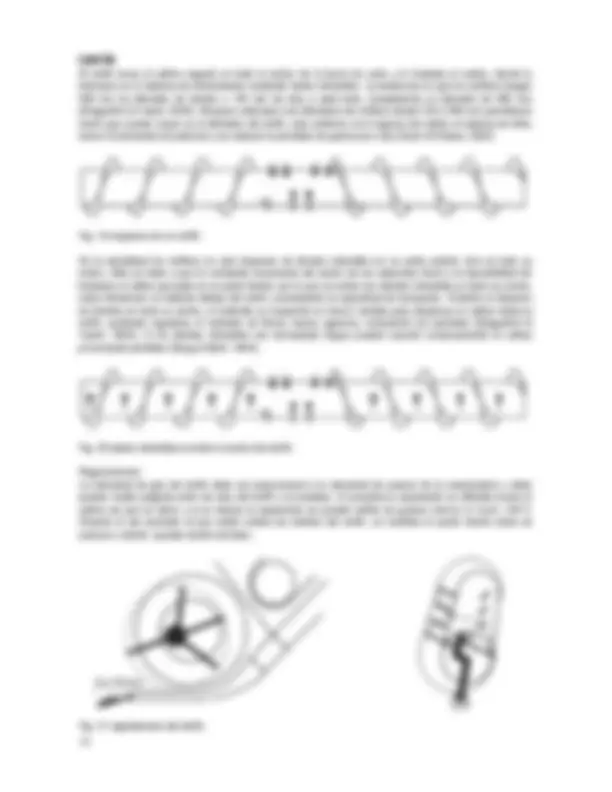
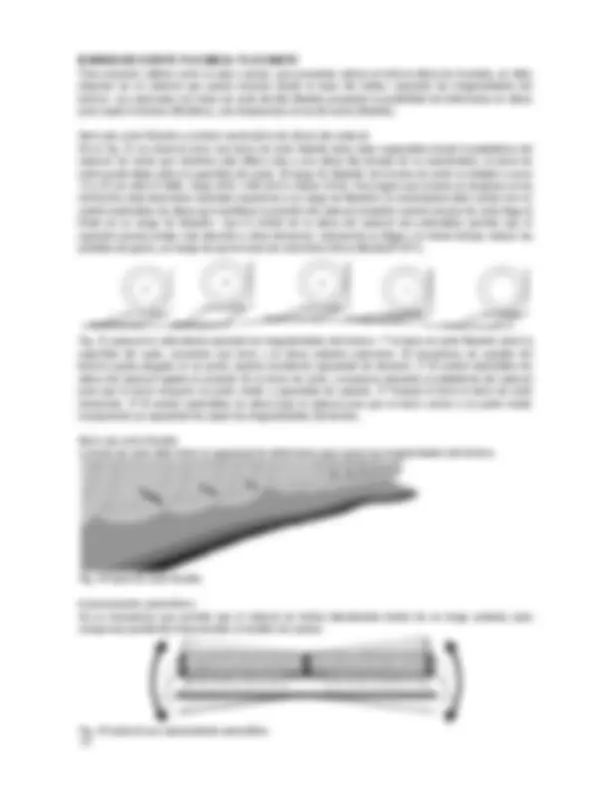
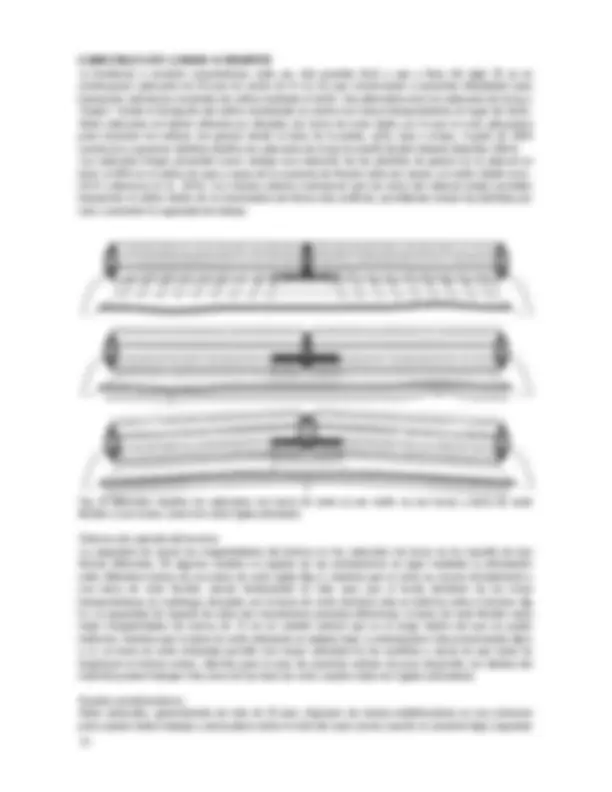
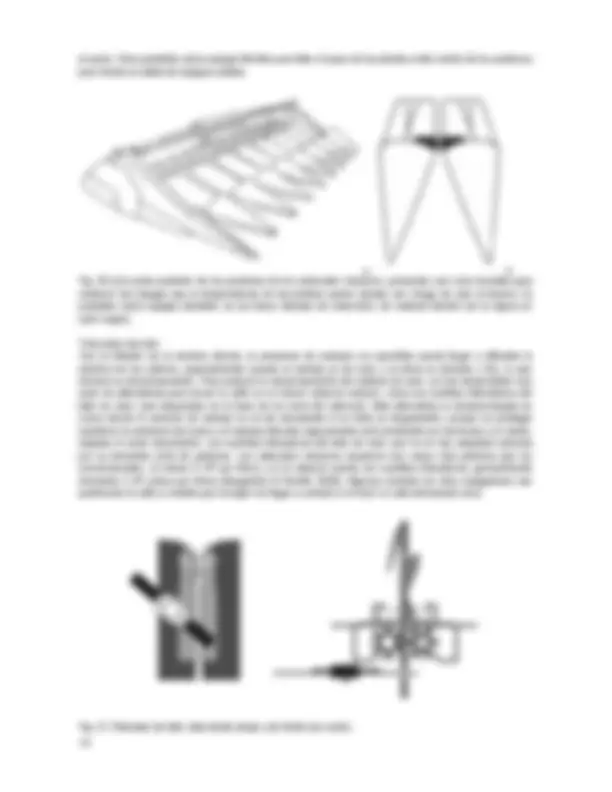
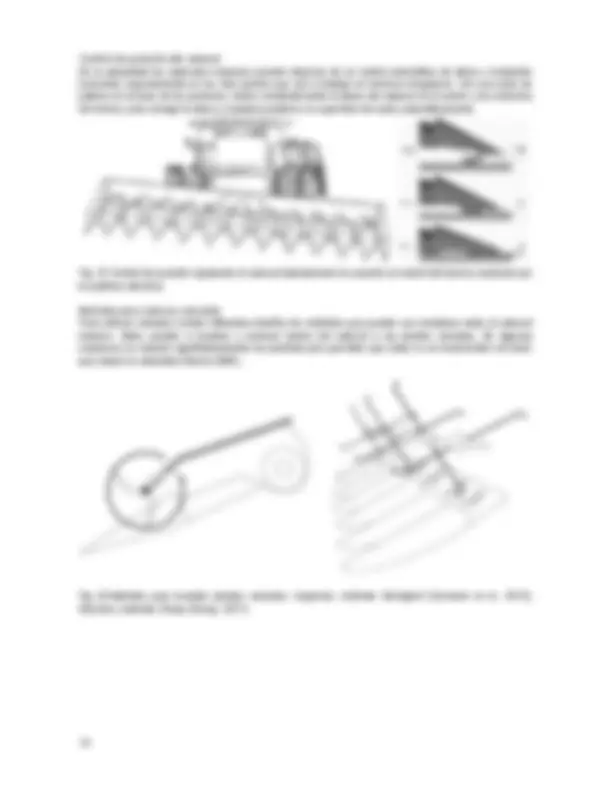
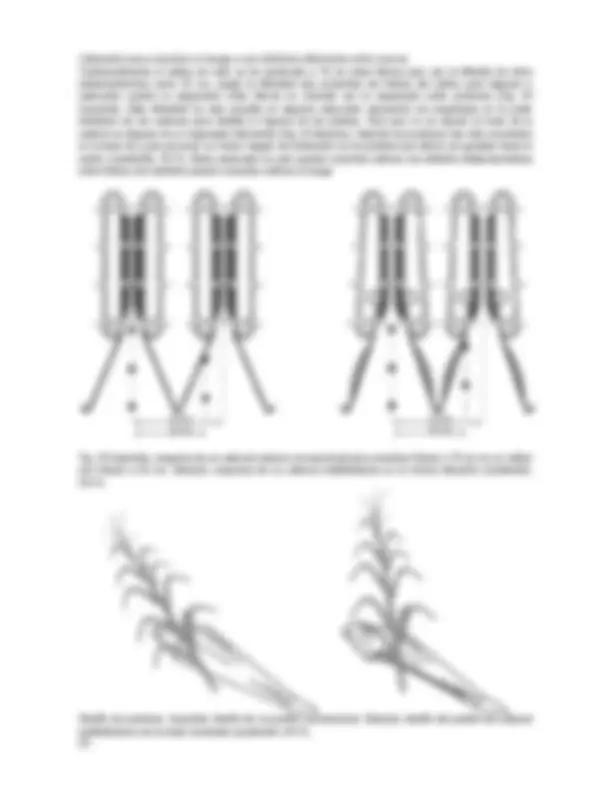
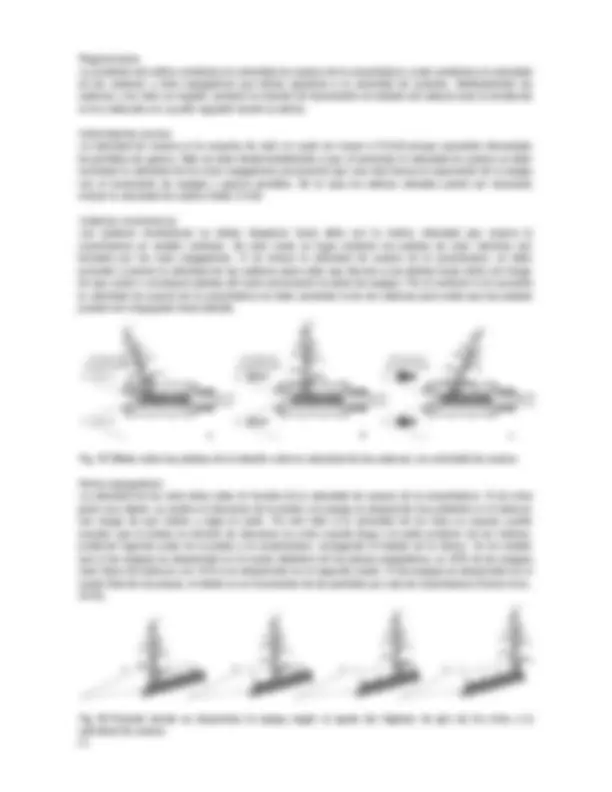
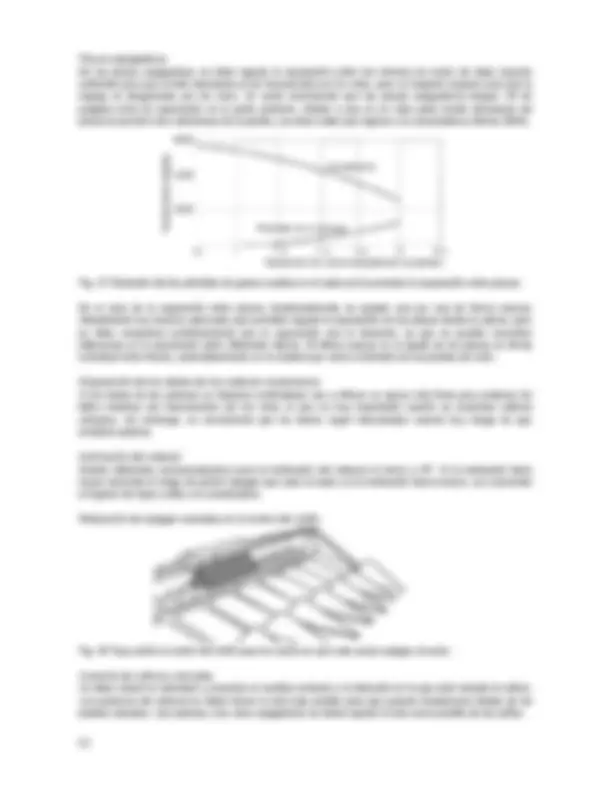
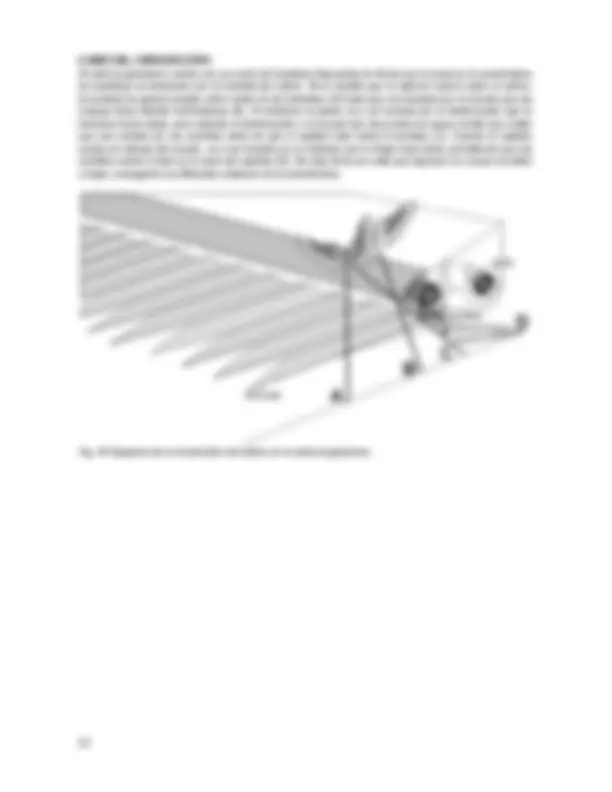
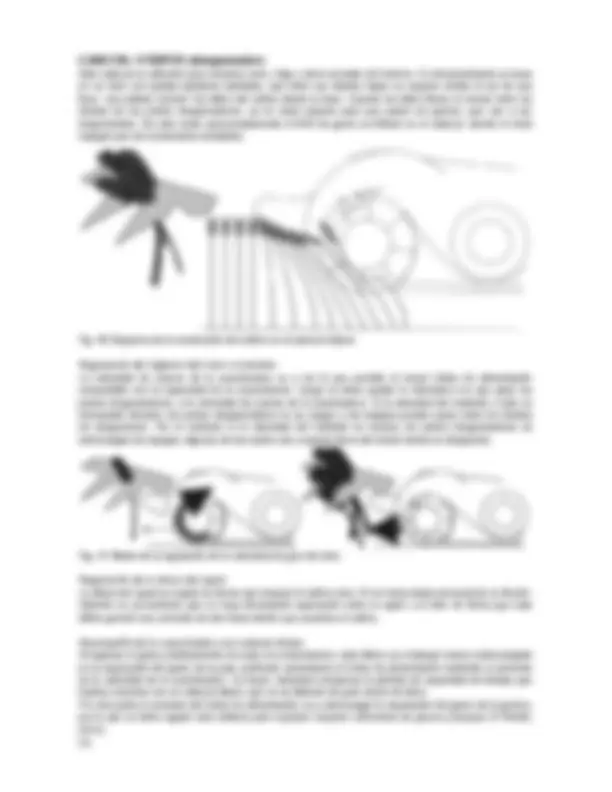
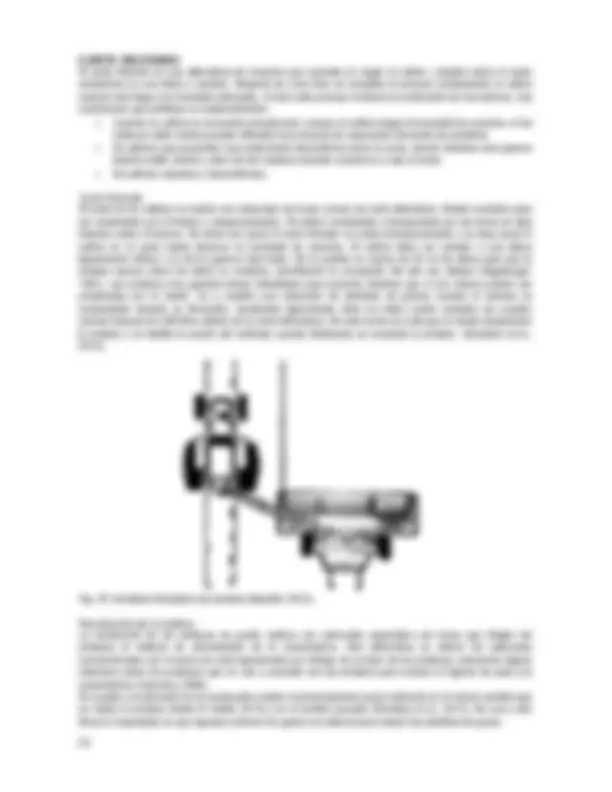
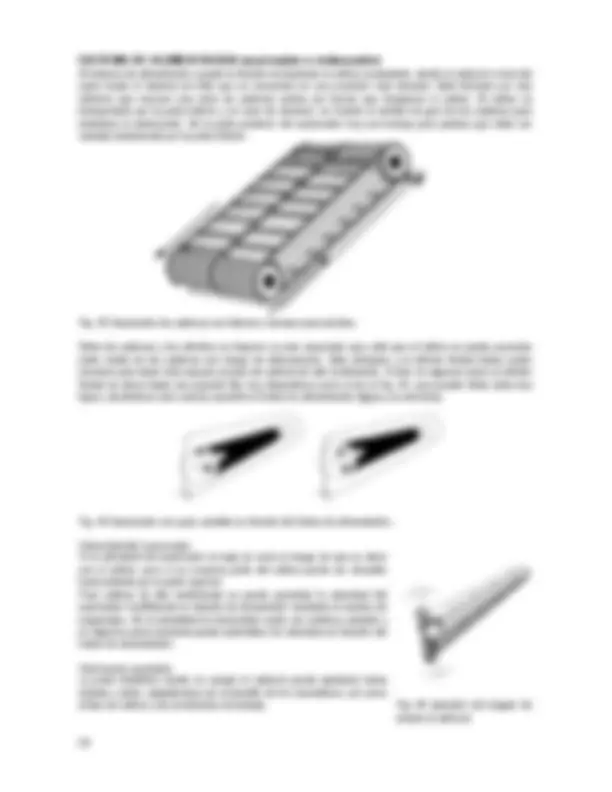
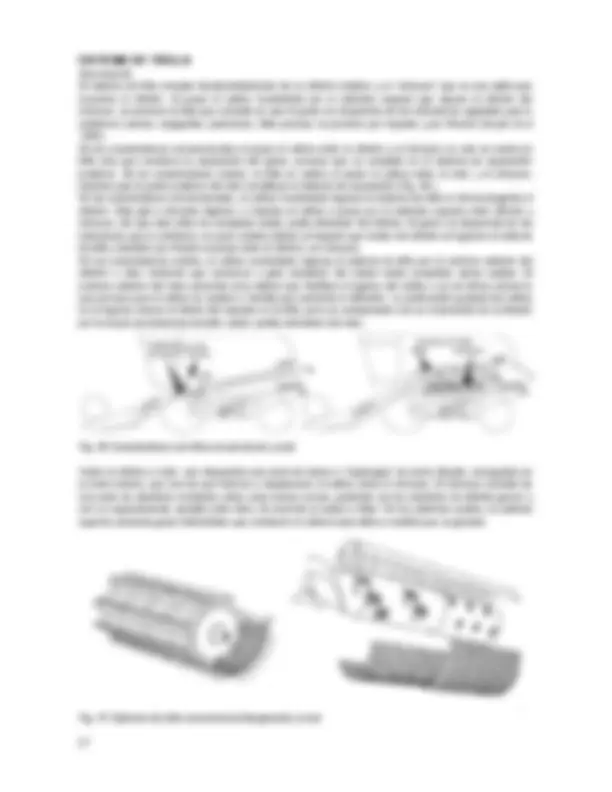
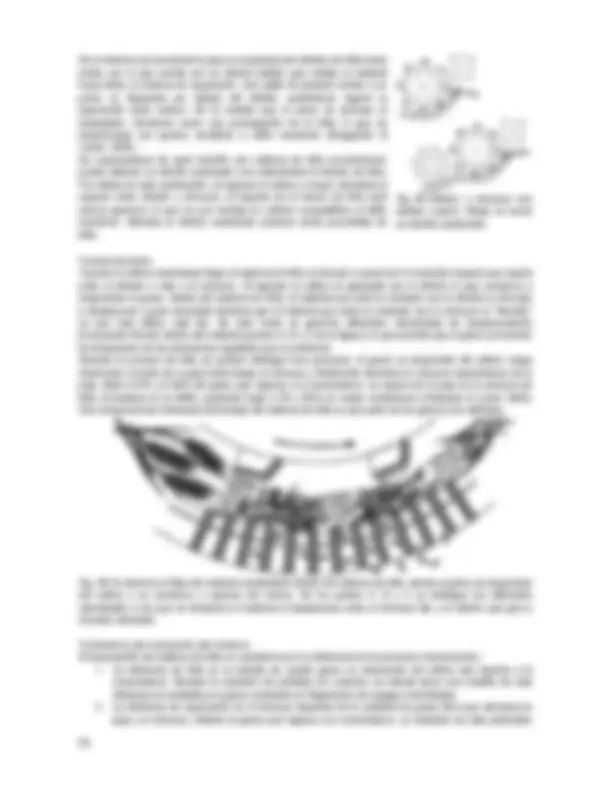
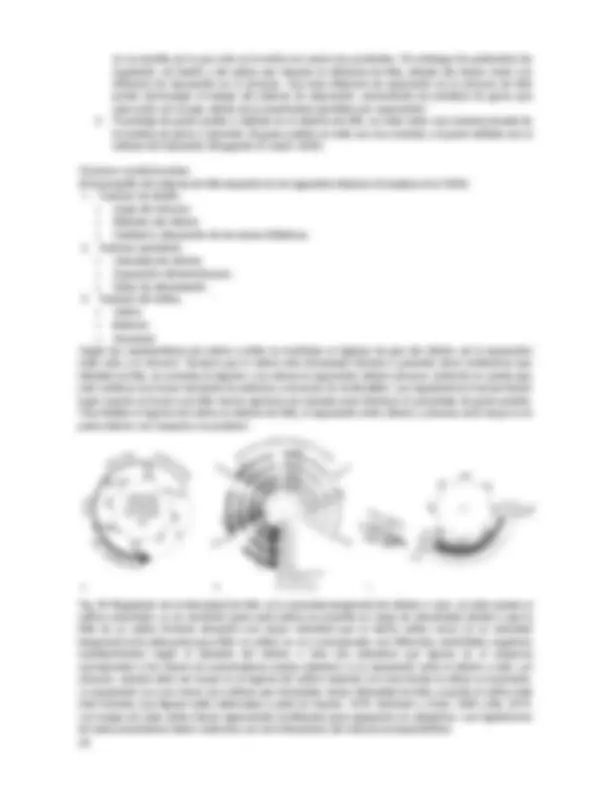
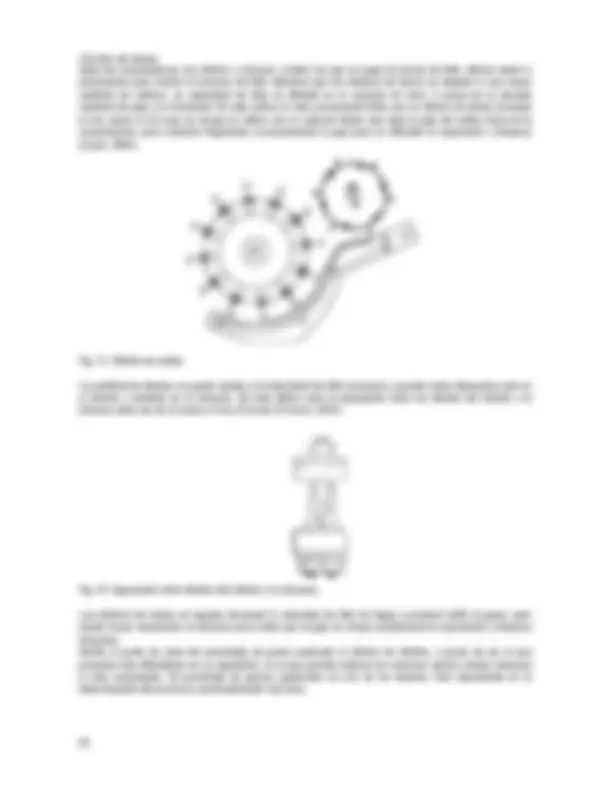
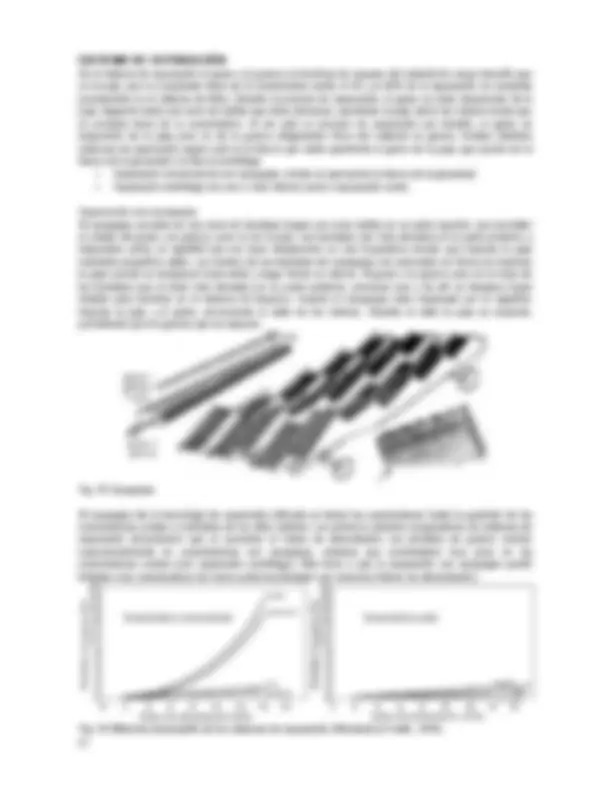
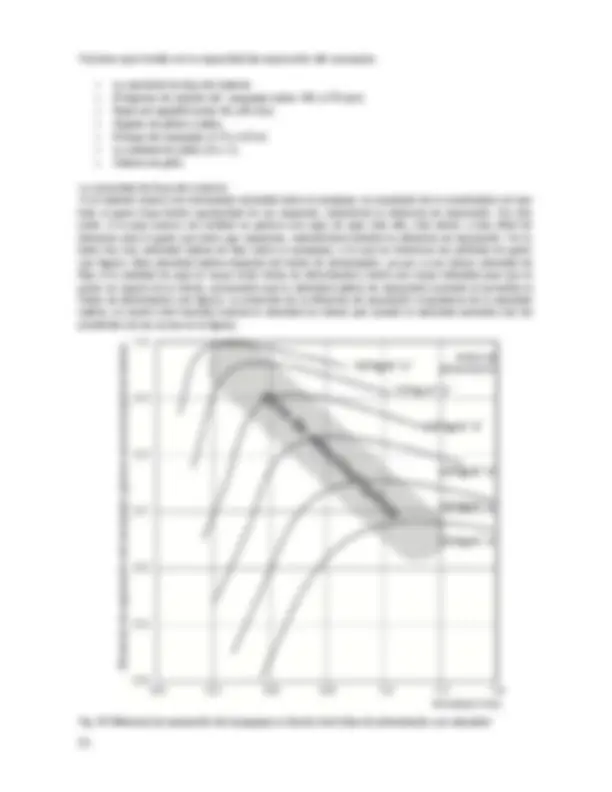
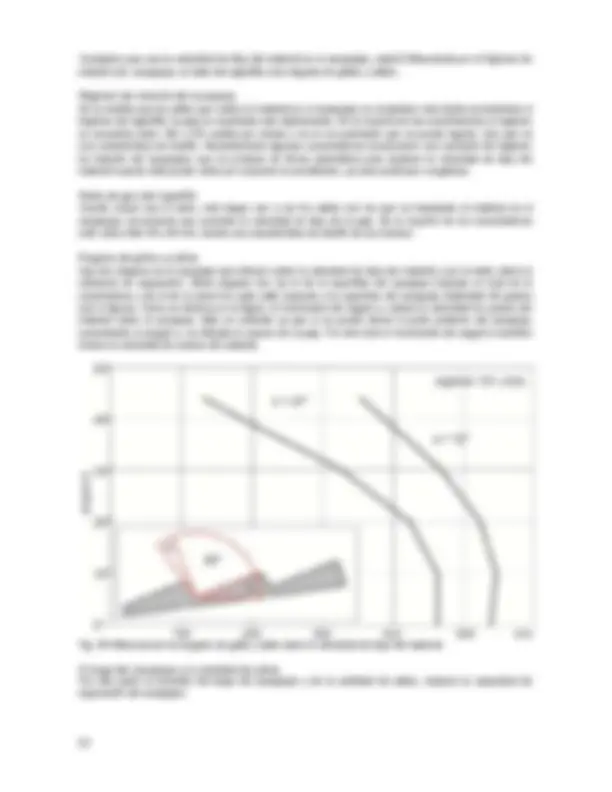
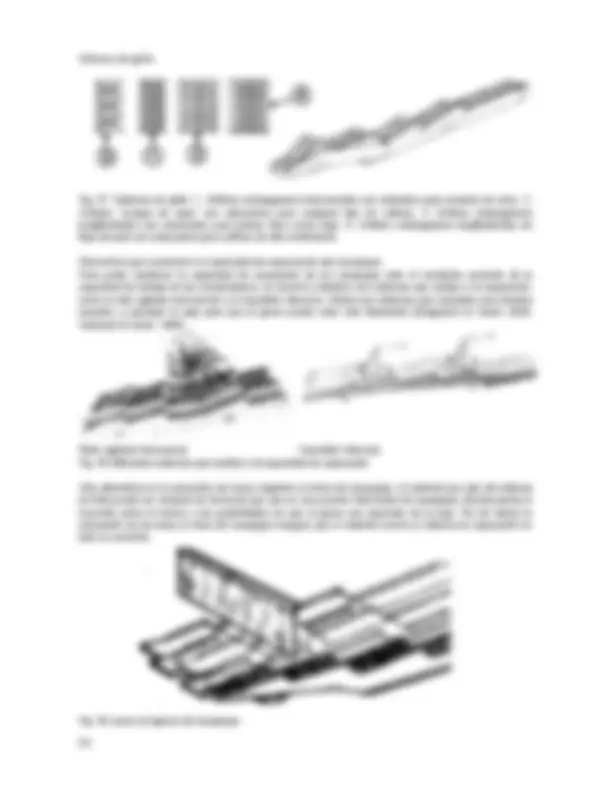

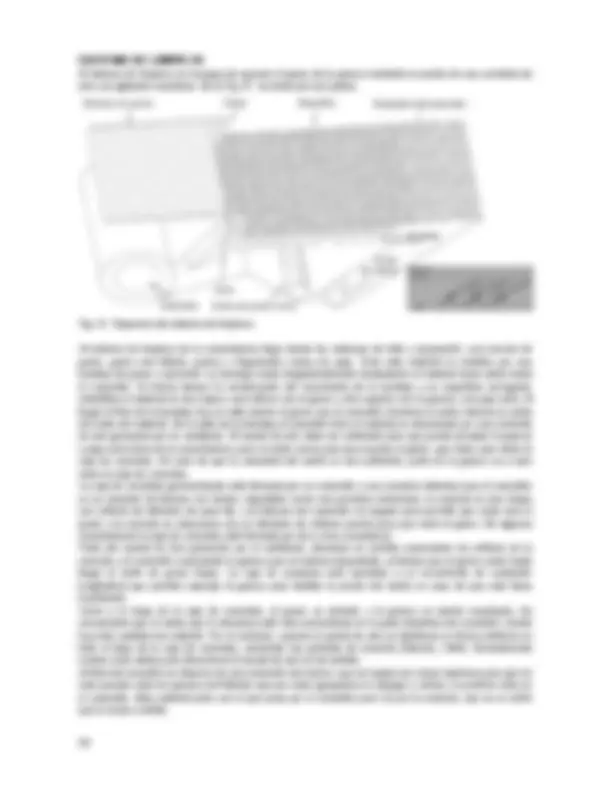
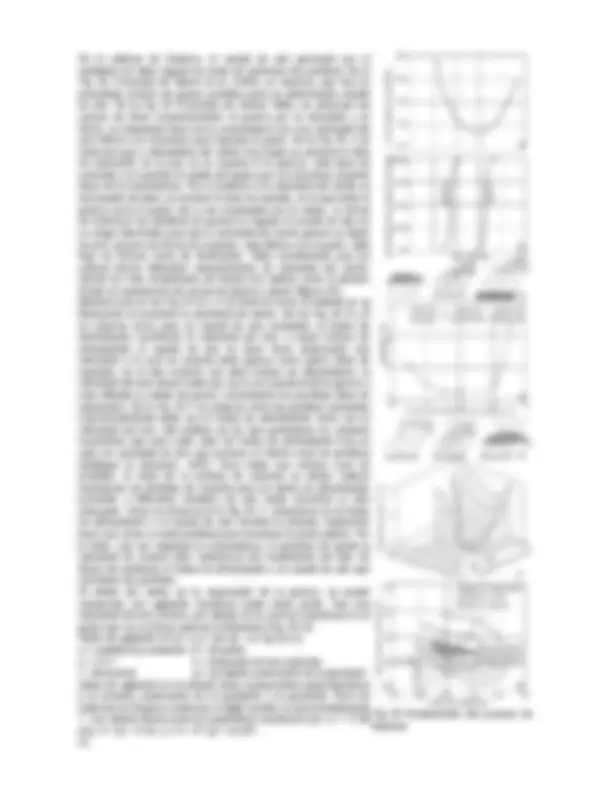
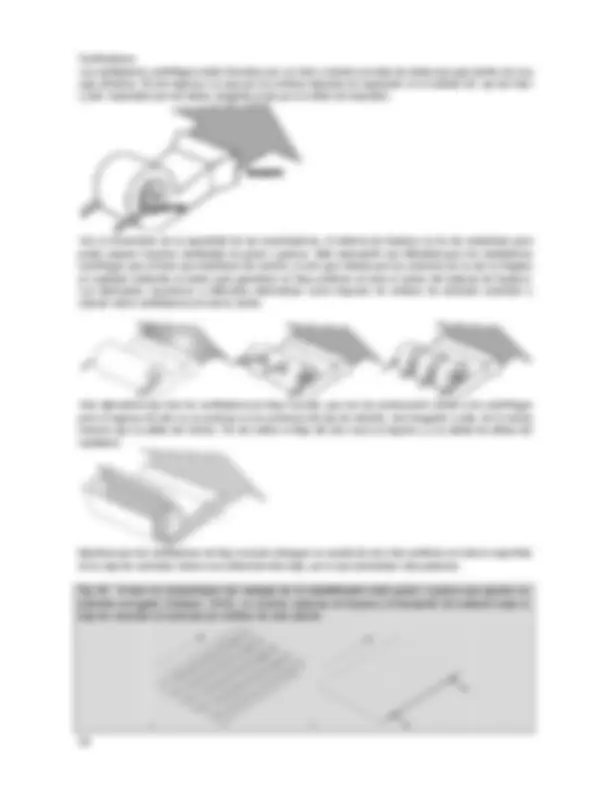
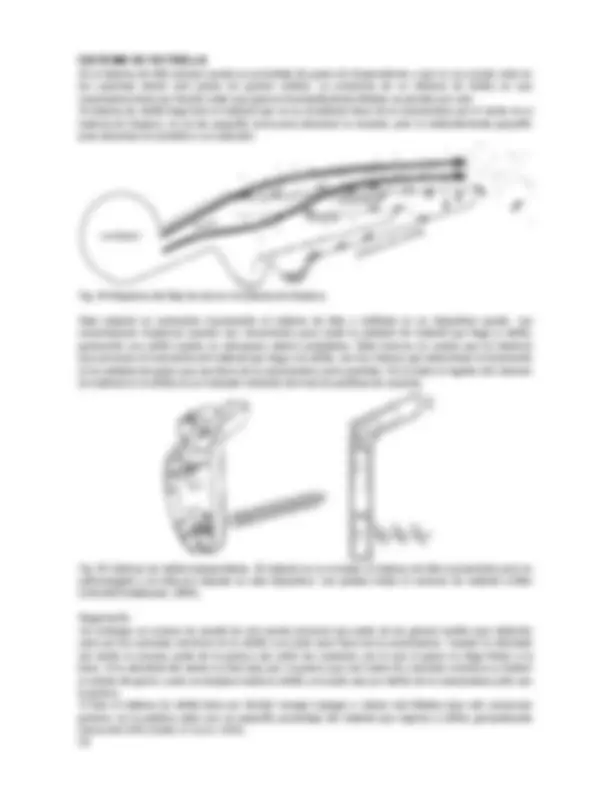
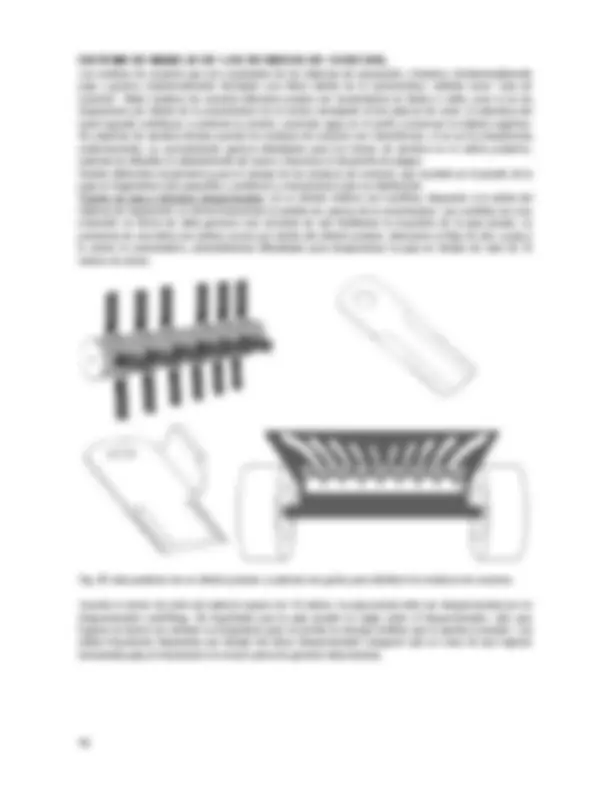
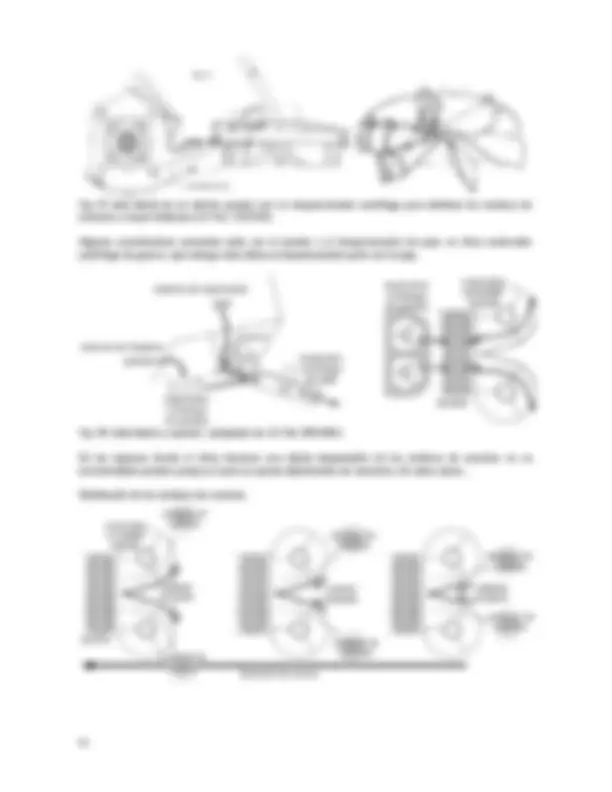
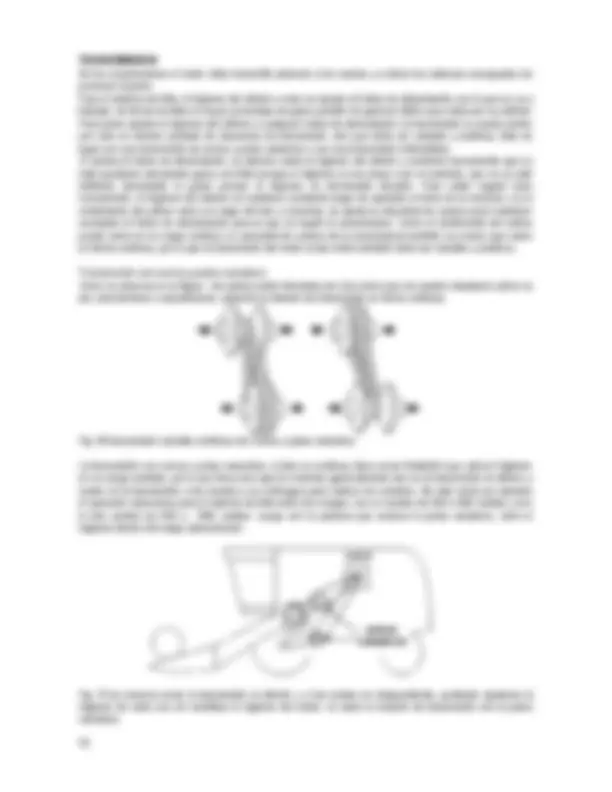
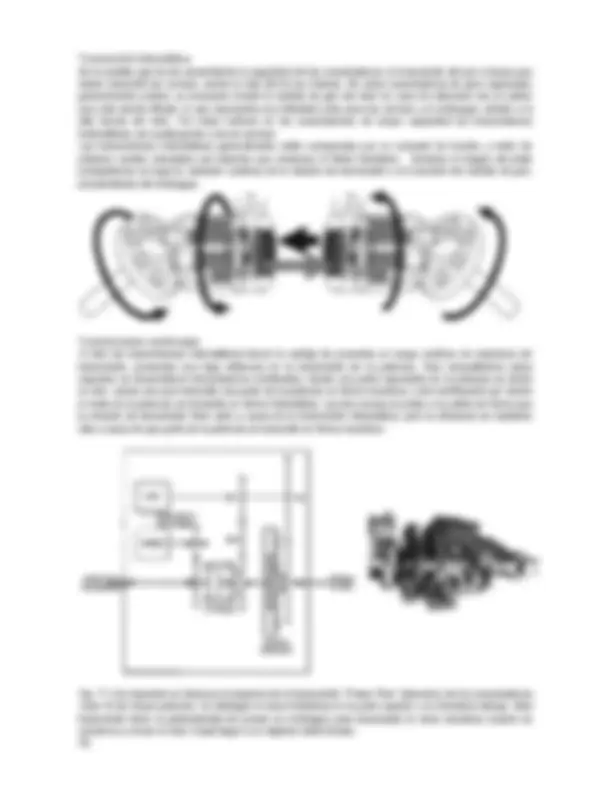
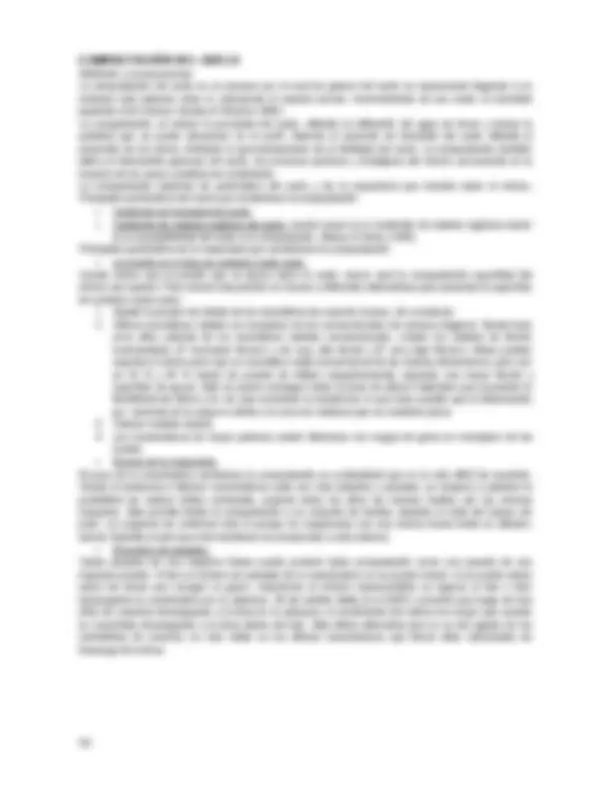
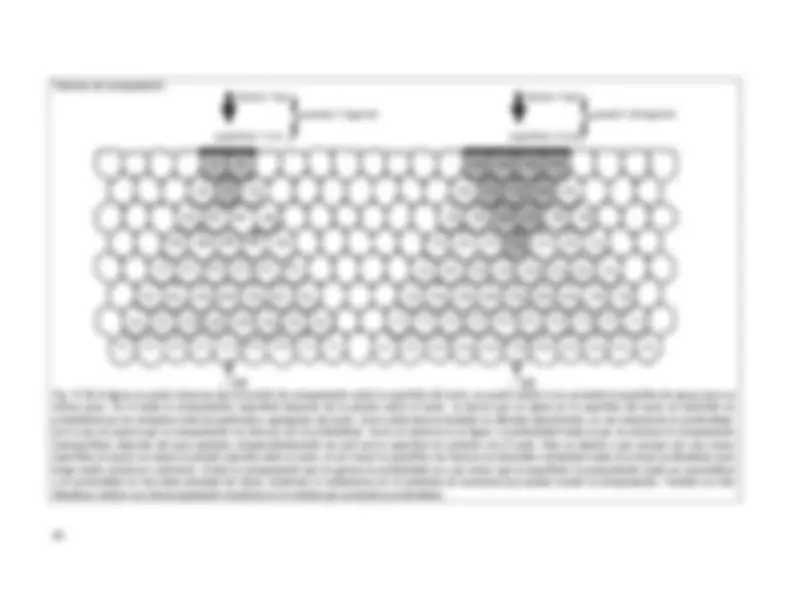
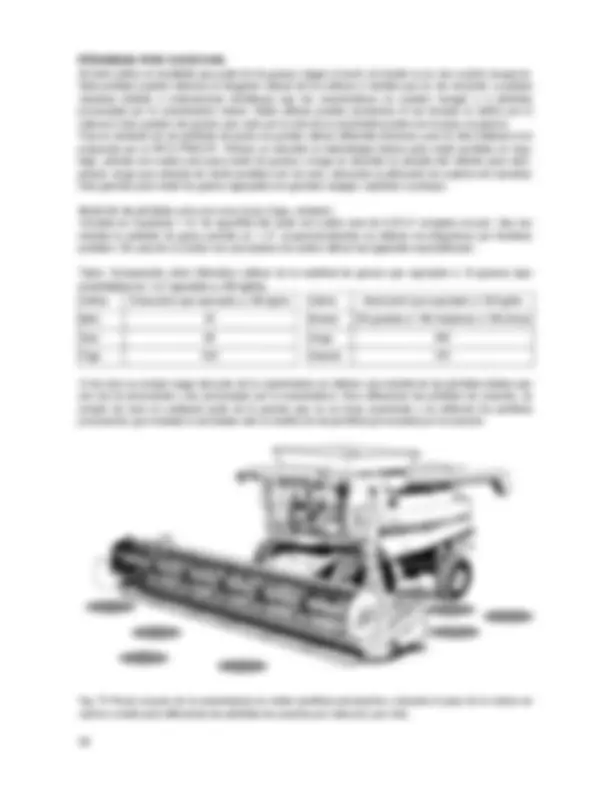
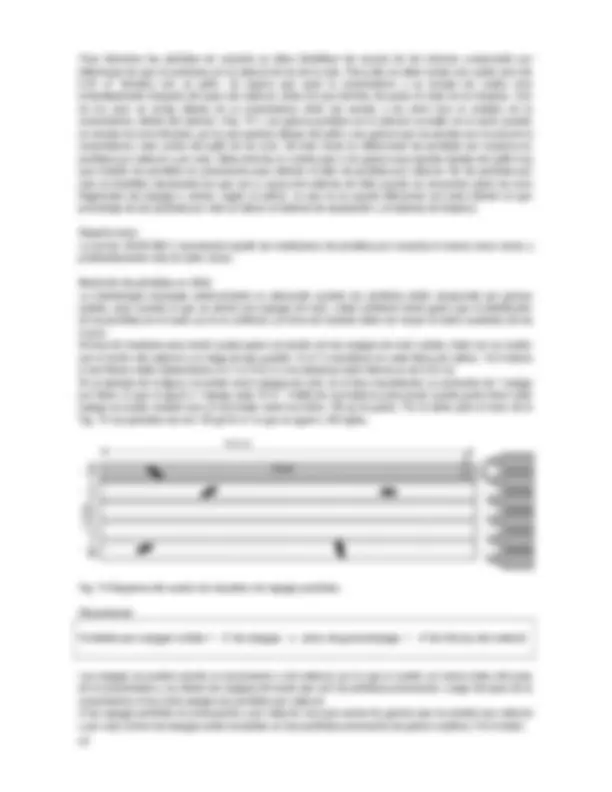
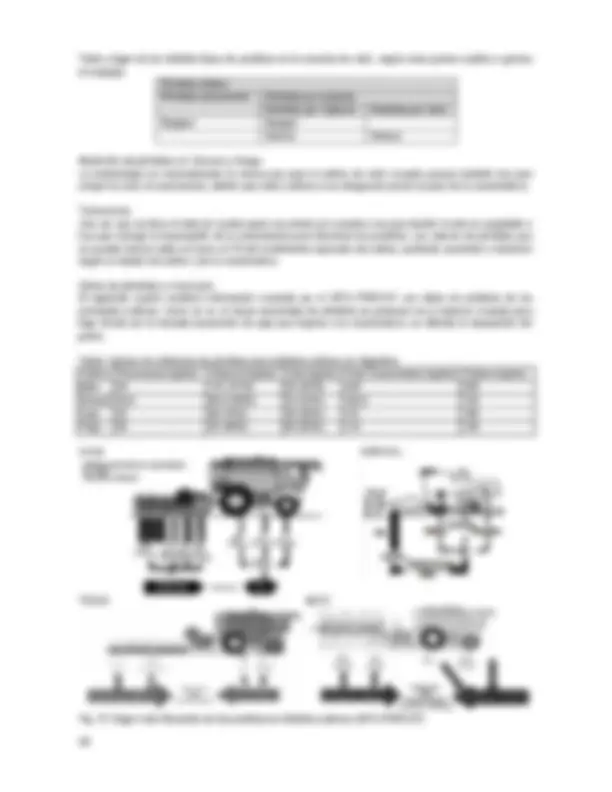
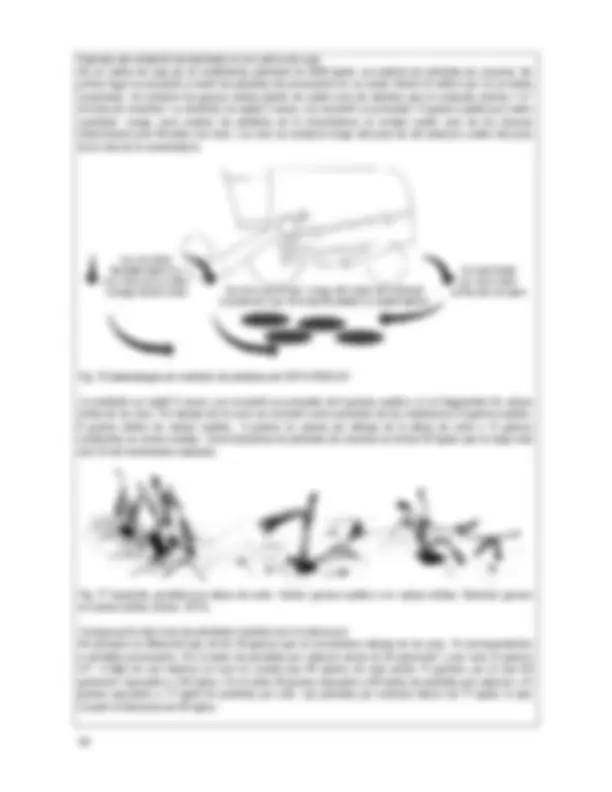
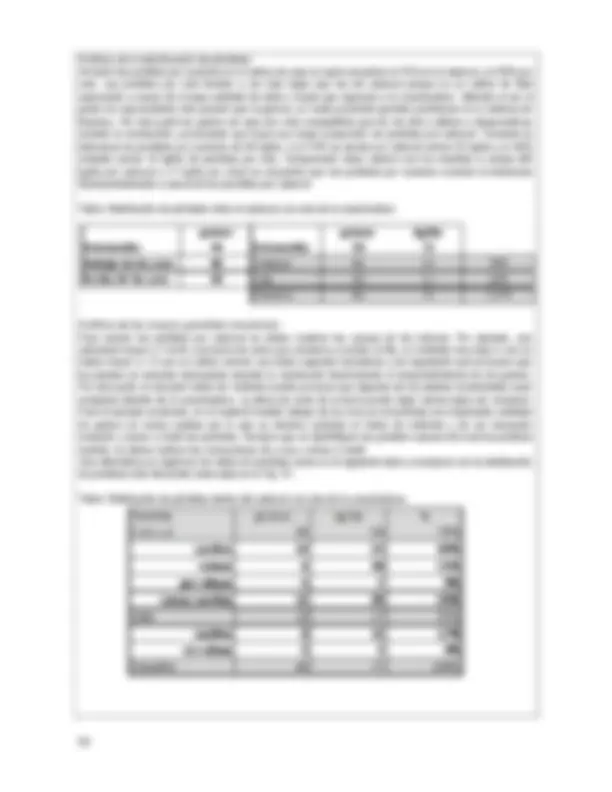
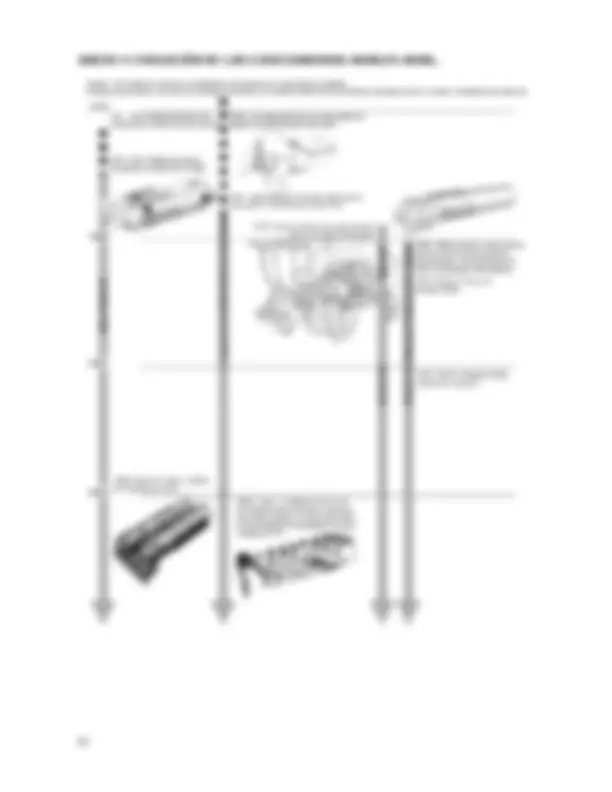
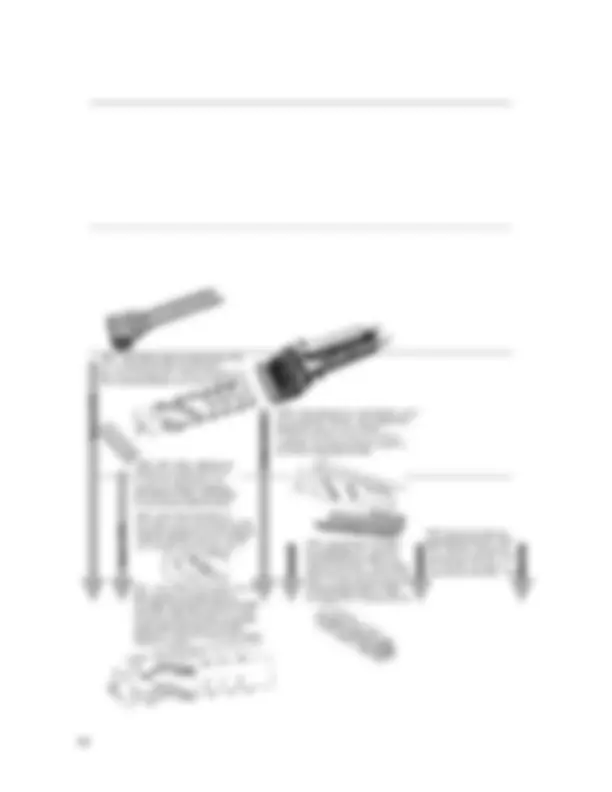
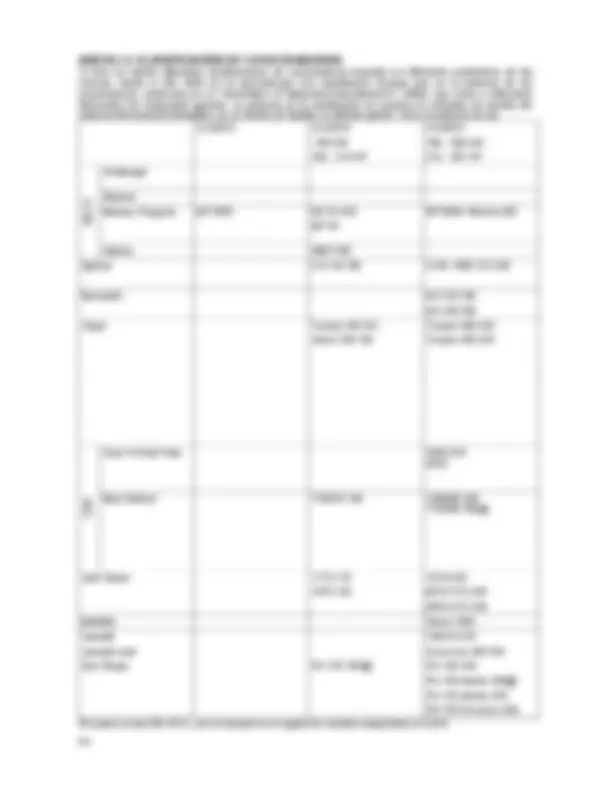
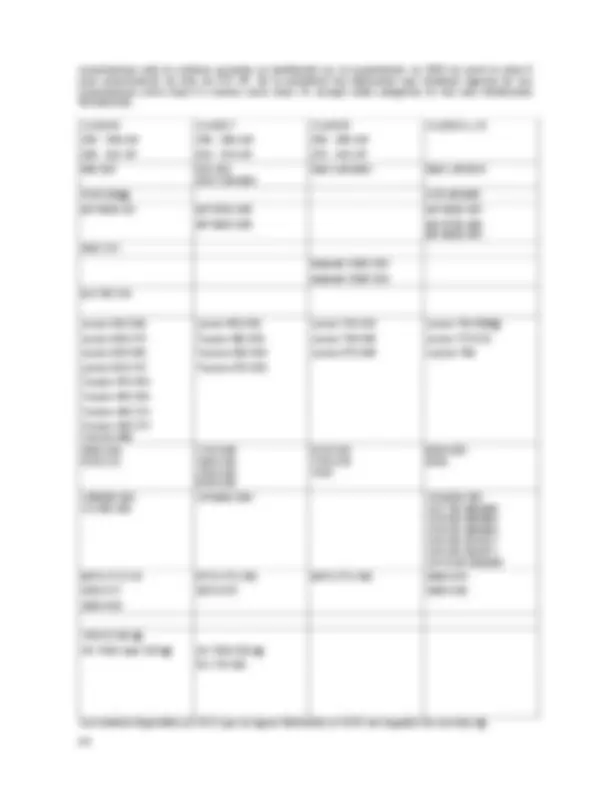
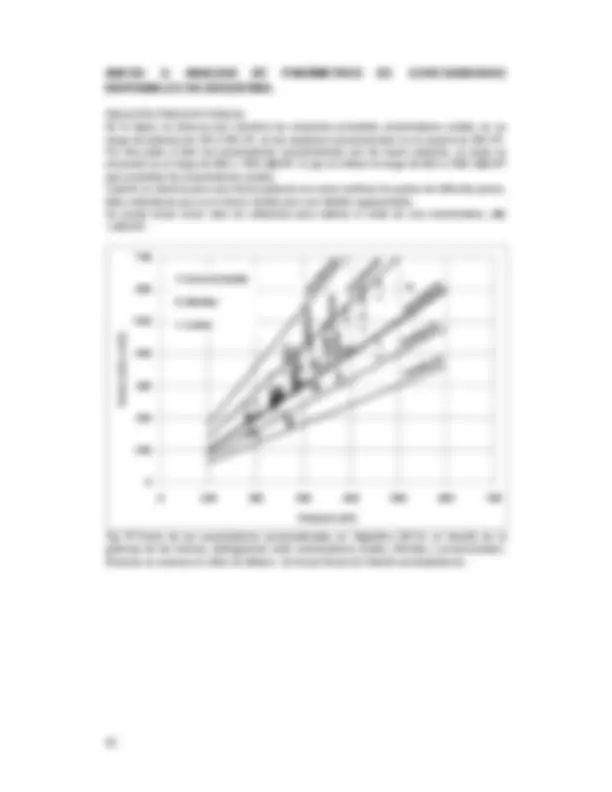
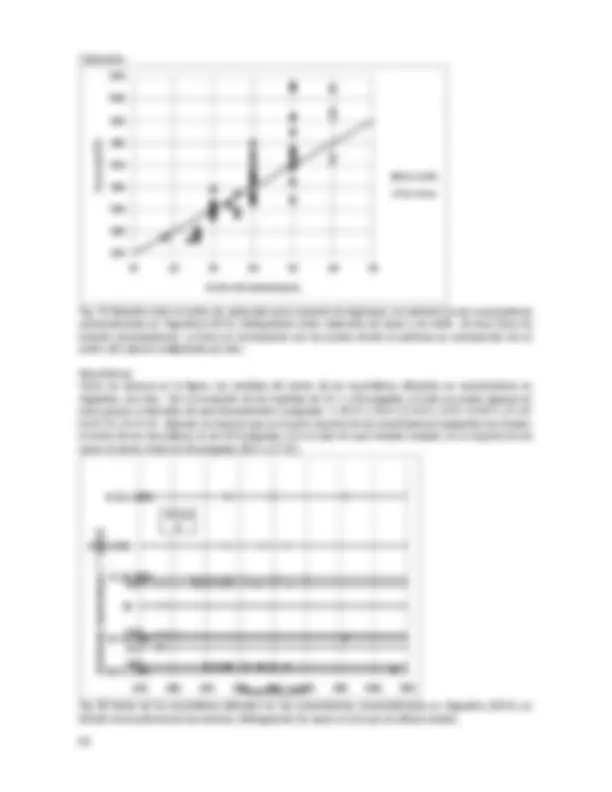
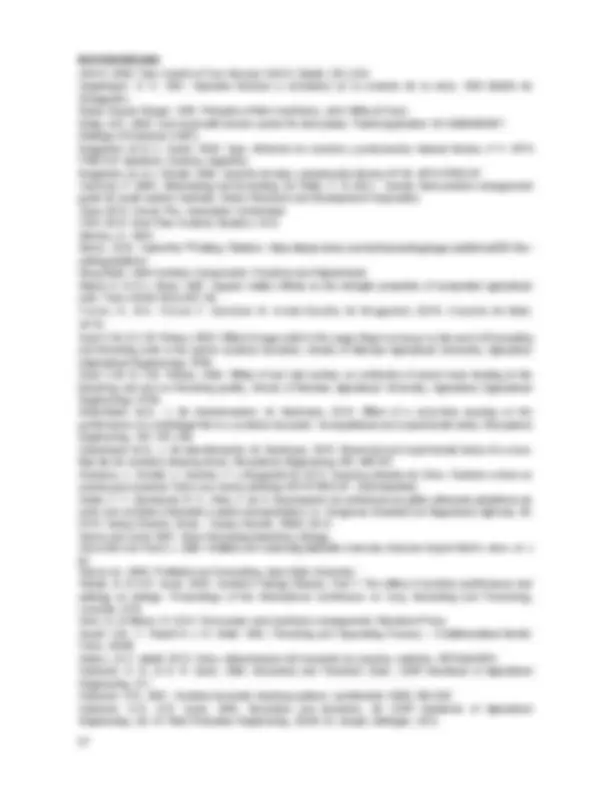
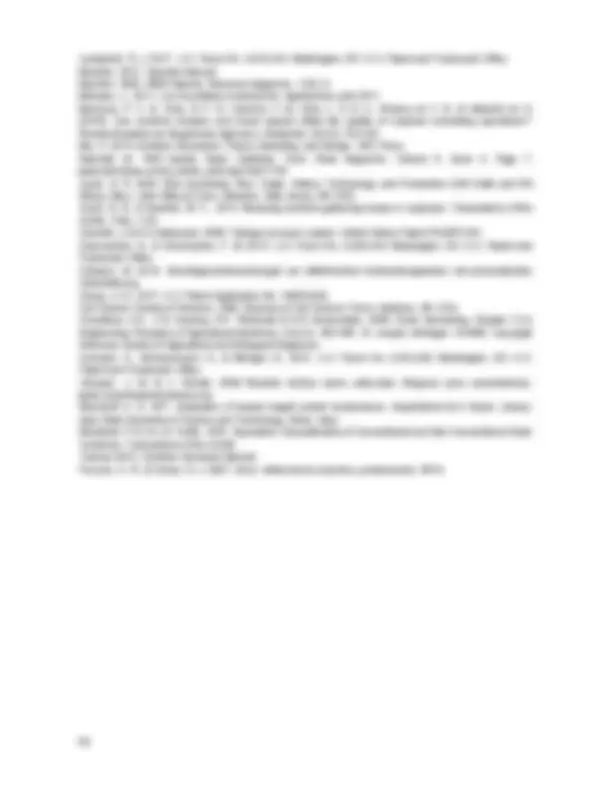
Prepara tus exámenes y mejora tus resultados gracias a la gran cantidad de recursos disponibles en Docsity
Gana puntos ayudando a otros estudiantes o consíguelos activando un Plan Premium
Prepara tus exámenes
Prepara tus exámenes y mejora tus resultados gracias a la gran cantidad de recursos disponibles en Docsity
Prepara tus exámenes con los documentos que comparten otros estudiantes como tú en Docsity
Los mejores documentos en venta realizados por estudiantes que han terminado sus estudios
Estudia con lecciones y exámenes resueltos basados en los programas académicos de las mejores universidades
Responde a preguntas de exámenes reales y pon a prueba tu preparación
Consigue puntos base para descargar
Gana puntos ayudando a otros estudiantes o consíguelos activando un Plan Premium
Comunidad
Pide ayuda a la comunidad y resuelve tus dudas de estudio
Descubre las mejores universidades de tu país según los usuarios de Docsity
Ebooks gratuitos
Descarga nuestras guías gratuitas sobre técnicas de estudio, métodos para controlar la ansiedad y consejos para la tesis preparadas por los tutores de Docsity
Este documento analiza las técnicas y sistemas de cosecha de cultivos, enfatizando en la trilla y separación de granos y paja. Se discuten aspectos como el número de barras en el sinfín, el diámetro del sinfín, el tipo de cabezales y su control de altura, sistemas de separación, y la eficiencia de trilla y separación. Además, se abordan los sistemas de cosecha de cultivos volcados y los diferentes diseños de cabezales.
Tipo: Monografías, Ensayos
1 / 58
Esta página no es visible en la vista previa
¡No te pierdas las partes importantes!
En los procesos mecanizados de cosecha de granos se interactúa habitualmente con maquinas que conllevan el riesgo de accidentes de diferente gravedad. Muchos de los accidentes durante la operación de cosechadoras son a causa de ser embestidos por la misma, ser atrapado por la maquina en funcionamiento mientras se trata de desatorarla, caídas desde la cosechadora o resbalar sobre la misma.
Fig. 1 Accidentes que se pueden producir al trabajar con cosechadoras (Yanmar 2016).
Algunos aspectos a tener en cuenta para reducir accidentes o problemas de salud asociados al uso de estas maquinas. Realizar una revisión completa del equipo para su mantenimiento antes de la campaña evita accidentes. Evitar reponer combustible antes de que el equipo se haya enfriado. Tener siempre el equipo contra incendios controlado y accesible. Realizar las tareas de mantenimiento diarias antes de comenzar la jornada cuando no se está cansado, con la llave de arranque en el bolsillo para asegurase que nadie encienda el equipo mientras se está trabajando en el mantenimiento del mismo. Las pérdidas de líquido hidráulico a alta presión pueden provocar serios problemas médicos. No exponer las manos al revisarlas. Utilizar piezas de cartón, metal o madera. Utilizar trabas mecánicas (no solo hidráulicas), para realizar ajustes y reparaciones debajo del cabezal. Respetar las normas que rigen el traslado de las maquinas agrícolas en vías de transporte. Tener especial cuidado en que la cosechadora (particularmente el sinfín de descarga), no haga contacto con cables aéreos de electricidad. En caso de que la cosechadora tenga que retroceder, asegurarse de que no haya nadie. Los espejos retrovisores deben mantenerse adecuadamente. En caso de tener que desatorar la cosechadora, se la debe apagar y retirar la llave de arranque. Nunca utilizar manos o pies para desatorarla. La exposición continua a polvo en el aire y el ruido puede terminar afectando las vías respiratorias y auditivas. Se debe valorar una cabina de mando que reduzca la exposición a estos factores. Frenar y girar con precaución en terrenos con pendiente. Revisar regularmente que no se acumule paja o granza sobre el motor, correas o poleas. No trabajar con ropa suelta que pueda ser atrapada por mecanismos móviles. No permitir jugar a los niños en el entorno de la cosechadora. No trepar a la cosechadora sin una escalera en donde se pueda resbalar. Siempre prestar atención a los adhesivos de seguridad.
Fig. 2 Adhesivos de seguridad.
El cabezal convencional está compuesto por una barra de corte, un molinete y un sinfín, montados sobre una plataforma. El cabezal avanza sobre el cultivo, cortándolo por cizalla con una barra formada por cuchillas que se desplazan alternativamente a ambos lados y puntones fijos que actúan como contracuchillas. Un molinete de barras con dientes gira en el sentido de avance, sostiene el cultivo durante el corte y luego lo desplaza dentro del cabezal. El cultivo segado en todo el ancho del cabezal es transportado hasta el centro por un sinfín que en su parte central presenta dientes retractiles que fuerzan el cultivo dentro de la cosechadora.
Fig. 3 cabezal convencional con molinete.
Fig. 4 se observa el cabezal. El molinete se presenta separado a la derecha para poder visualizar el sinfín. En el extremo derecho se observa como la planta anclada en el suelo, tiene un punto de apoyo en el molinete para no volcarse hacia delante mientras es cortada por la barra de corte.
Dientes: En un cultivo normal, los dientes de los molinetes deben penetrar en el cultivo en posición vertical para hacerlo con la mínima resistencia, generando la menor alteración. Luego deben desplazarse hacia atrás manteniendo esa posición vertical para acompañar el cultivo cortado hasta el sinfín. Finalmente deben ascender en posición vertical para no impactar con el sinfín. Para mantener la misma posición durante todo este recorrido, tradicionalmente se ha recurrido a molinetes de dientes paralelos unidireccionales (Fig. 6 ). Este diseño generaba una zona triangular (en la figura sombreado de gris), donde el cultivo ya no era acompañado por los dientes y para llegar hasta el sinfín debía ser empujado por el cultivo cortado a continuación. Esto genera que con cultivos de escaso desarrollo vegetativo el ingreso del cultivo al sinfín se torna irregular. Los molinetes orbitales fueron diseñados para superar esa dificultad, al orientar los dientes hacia el sinfín, durante la entrega del cultivo (Fig. 6 ).
Fig. 6 a) molinete de dientes paralelos unidireccionales b) molinete de dientes orbital.
Numero de barras Cuanto mayor es el número de barras más continuo y uniforme es el ingreso del cultivo al sistema de trilla. Por otra parte el numero de barras no debería ser mayor a seis en cereales de invierno, para evitar que al penetrar en el mismo, agiten demasiado el cultivo provocando desgrane (Gach & Pintara, 2003). Bragachini & Casini (2005), recomiendan el uso de molinetes de seis barras en cultivos de soja de menor desarrollo vegetativo y de cinco barras en los de mayor desarrollo porque permiten un fácil ingreso del material con mayor desalojo. Fig. 7 molinetes de seis y cinco barras
Diámetro del molinete El diámetro del molinete no es un parámetro que influya significativamente en el trabajo de cosecha, siendo generalmente de un metro de diámetro (Gach & Pintara, 2003). Sin embargo un mayor diámetro de molinete en cultivos de gran desarrollo, puede facilitar la penetración de las barras y dientes. El diámetro suele variar entre 1,016 metros (40 pulgadas) en los cabezales con sinfín y 1,65 metros (65 pulgadas) en los cabezales con lonas (Miu 2015).
Fig. 8 influencia del diámetro.
Accesorios para recoger cultivos ralos En el caso de cosechar cultivos ralos, es probable que las plantas no puedan ser tomadas por los dientes del molinete. En ese caso se colocan en las barras del molinete, suplementos de lona o paletas plásticas.
Fig. 9 molinete con lonas para cultivos ralos (izq) paleta acoplable (der).
Regulación Según la condición del cultivo, se realizarán las siguientes regulaciones: índice de molinete: como se indicó siempre debe ser mayor que 1 y no superar 1,5 (Fig. 11 ). altura del molinete: se lo baja en cultivos volcados en el sentido de avance y con cultivos bajos. Se eleva en cultivos de mayor desarrollo en altura. avance del molinete: la posición normal es ligeramente por delante de la barra de corte. Se adelanta en cultivos volcados en el sentido de avance y se lo retrasa con cultivos bajos. ángulo de los dientes: siempre verticales, excepto para cultivos volcados.
Fig. 10 Regulación de la posición del molinete según el estado del cultivo. En el recuadro se observa la palanca de mando de la cosechadora, resaltado el comando para realizar dichas regulaciones.
Fig. 11 Pérdidas de cosecha por cabezal a diferentes índices de molinete. Las pérdidas se incrementan
sistema 4x2x2 es que la mayor separación entre puntones respecto del sistema 3x1,5x1,5 reduce el riesgo de que en lotes en siembra directa la presencia en el rastrojo de tallos de maíz gruesos puedan atorarse entre los puntones impidiendo que esa sección pueda seguir cortando el cultivo a cosechar.
Fig. 13 Barras de corte convencionales y de paso angosto.
Cinemática del corte Como se observa en la Fig. 14 , la porción del cultivo que queda comprendida en el ir y venir de la cuchilla, va a ser cortada contra el filo del puntón. Desde que la cuchilla encuentra cada planta hasta que es cortada contra el puntón, la planta es desplazada inclinándola, por lo que se sacude con pérdida de granos.
Fig. 14 Cinemática del corte con una barra de 3x3x3.
La relación entre la velocidad de desplazamiento lateral de las cuchillas y la velocidad de avance de la cosechadora, queda plasmada en el índice de corte que no tiene unidades (Fig. 15 )
Fig. 15 Índice de corte. Las pérdidas del cabezal en el cultivo de soja se reducen con índices de corte cercanos a 1 (Quick, 1972).
Quick (1972), encontró que con índices de corte cercanos a 1 se reducían las perdidas por cabezal. A mayores índices de corte el impacto de la cuchilla contra las plantas, eleva significativamente las perdidas por desgrane. Por otra parte a menores índices de corte, las cuchillas avanzan una distancia mayor antes de cada corte, provocando una mayor inclinación de las plantas y el aumento de las perdidas por desgrane. En general la barra de corte suele ser accionada entre 500 y 600 rpm en la mayoría de los cabezales, por lo que las perdidas suelen ser más bajas a velocidades cercanas a los 5 km/h. Se recomienda que la velocidad de cosecha no supere los 7 km/h (Bragachini & Casini, 2005). En la Fig. 16 se observa el efecto de dos velocidades de avance sobre las pérdidas por desgrane.
Fig. 16 El aumento de la velocidad de avance incrementa la distancia que se desplaza una planta hasta que es cortada, provocando una mayor inclinación de la misma y un aumento de pérdidas de granos.
El sinfín toma el cultivo segado en todo el ancho de la barra de corte y lo traslada al centro, donde lo introduce en el sistema de alimentación mediante dedos retractiles. La tendencia es que los sinfines tengan 400 mm de diámetro de tambor y 130 mm de alas a cada lado, completando un diámetro de 660 mm (Bragachini & Casini, 2005). Ensayos realizados con diámetros de sinfines desde 220 a 560 mm permitieron medir que cuanto mayor es el diámetro del sinfín, más uniforme es el ingreso del cultivo al sistema de trilla, menor la demanda de potencia y se reducen la perdidas de granos por cola (Gach & Pintara, 2003).
Fig. 19 esquema de un sinfín.
En la actualidad los sinfines no solo disponen de dientes retractiles en su parte central, sino en todo su ancho. Esto se debe a que el constante incremento del ancho de los cabezales llevó a la imposibilidad de trasladar el cultivo apoyado en su parte frontal, por lo que al contar con dientes retractiles en todo su ancho, estos introducen el material debajo del sinfín, aumentando la capacidad de transporte. También al disponer de dientes en todo su ancho, el molinete es requerido en menor medida para desplazar el cultivo hasta el sinfín, pudiendo regularse el molinete de forma menos agresiva, reduciendo las perdidas (Bragachini & Casini, 2005). Si los dientes retractiles son demasiado largos pueden sacudir excesivamente el cultivo provocando pérdidas (Doug & Biehl, 1994).
Fig. 20 dedos retractiles en todo el ancho del sinfín.
Regulaciones: La velocidad de giro del sinfín debe ser proporcional a la velocidad de avance de la cosechadora y debe quedar media pulgada entre las alas del sinfín y la bandeja. Si aumenta la separación se dificulta mover el cultivo sin que se atore y si se reduce la separación se pueden dañar los granos (Hanna & Quick, 2007). Girando el eje acodado al que están unidos los dientes del sinfín, se modifica el punto donde estos se asoman y donde quedan dentro del tubo.
Fig. 21 regulaciones del sinfín.
Para cosechar cultivos como la soja o poroto, que presentan vainas en toda la altura de la planta, se debe disponer de un cabezal que pueda cosecha desde la base del cultivo, copiando las irregularidades del terreno. Los cabezales con barra de corte flexible flotante presentan la posibilidad de deformarse en altura para copiar el terreno (flexibles), y de desplazarse al ras del suelo (flotante).
Barra de corte flotante y control automatico de altura del cabezal En la Fig. 22 se observa como una barra de corte flotante debe estar suspendida desde la plataforma del cabezal, de modo que mientras este último esta a una altura fija tomado de la cosechadora, la barra de corte puede flotar sobre la superficie del suelo. El rango de flotación de la barra de corte es limitado a unos 15 a 22 cm (AGCO 2009, Claas 2018, CNH 2018 y Deere 2018). Para lograr que la barra se desplace al ras del terreno ante desniveles verticales superiores a su rango de flotación, la cosechadora debe contar con un control automático de altura que modifique la posición del cabezal completo cuando la barra de corte llega al límite de su rango de flotación. Que el control de la altura del cabezal sea automático permite que el operador pueda prestar más atención a otras funciones, reduciendo su fatiga y al mismo tiempo reduce las pérdidas de grano y el riesgo de que la barra de corte tome tierra (Woodruff 1971).
Fig. 22 cabezal en vista lateral copiando las irregularidades del terreno. 1º la barra de corte flotando sobre la superficie del suelo, encuentra una loma y se eleva evitando enterrarse. El mecanismo de copiado del terreno queda plegado en su punto superior perdiendo capacidad de elevarse. 2º El control automático de altura del cabezal registra la posición de la barra de corte y reacciona elevando la plataforma del cabezal para que la barra recupere su punto medio y capacidad de copiado. 3º Pasada la loma la barra de corte desciende. 4º El control automático de altura baja el cabezal para que la barra vuelva a su punto medio recuperando su capacidad de copiar las irregularidades del terreno.
Barra de corte flexible La barra de corte debe tener la capacidad de deformarse para copiar las irregularidades del terreno.
Fig. 23 barra de corte flexible.
Autonivelante automático Es un mecanismo que permite que el cabezal se incline lateralmente dentro de un rango acotado, para compensar pendientes transversales al sentido de avance.
Fig. 24 cabezal con autonivelante automático.
una mayor estabilidad y uniformidad en el corte. Cuando por las características del cultivo se debe cosechar al ras del suelo (por ejemplo soja), las ruedas estabilizadoras se rebaten, ya que toda la barra de corte se apoya sobre el suelo comportándose como flexible flotante.
Fig. 26 Las ruedas estabilizadoras se pliegan cuando el cabezal trabaja flotante y se bajan cuando el cabezal trabaja elevado para estabilizarlo.
Cuando por presencia de piedras o por requerimientos del cultivo, se necesario aumentar la altura de la barra de corte, esta se puede modificar variando la inclinación de los patines de la barra de corte
Fig. 27 El patín es la única alternativa para regular la altura de corte cuando el cabezal trabaja flotando.
Entrega del cultivo al acarreador Generalmente los cabezales draper, presentan una cinta transportadora central dispuesta longitudinalmente que fuerza el ingreso del cultivo dentro de la cosechadora, entregando el cultivo al acarreador. Al pasar el cultivo de las lonas laterales a la central, este cambia de dirección pudiendo frenarse, lo que genera riesgo de obturaciones. Para evitar estos inconvenientes es que la cinta central trabaja en un plano inferior de forma que el cultivo cae en esta última, disminuyendo el riesgo de que se frene. Un sinfín con dedos retractiles fuerza el ingreso al sistema de alimentación en todo su ancho.
Fig. 28 Distintos sistemas de entrega del cultivo al acarreador
Otro sistema reemplaza la cinta transportadora central por un piso fijo que igualmente se sitúa en un plano inferior a las cintas transportadoras laterales. También posee un sinfín de dedos retractiles pero de mayores dimensiones y en una posición más adelantada, ya que es el principal responsable del ingreso del cultivo al acarreador al no haber una cinta que lo transporte. Unas extensiones laterales del sinfín fuerzan el desalojo del cultivo de las cintas laterales al llegar a la parte central. El piso presenta una protuberancia que guía el cultivo que llega desde los laterales en un plano inferior y permite que el cultivo cortado en la parte central caiga sobre el anterior.
Descripción y funcionamiento El cabezal maicero está diseñado para cosechar solo las espigas, dejando el resto de la planta en el campo, para que no sobrecargue los sistemas de trilla, separación y limpieza de la cosechadora. Por el diseño de los cabezales, los cultivos se cosechan en la dirección en que fueron sembrados con los puntones avanzando entre medio de las hileras de cultivo. Cuando la distancia entre hileras en el cultivo no coincide con la separación entre puntones, se dificulta el ingreso de las plantas al cabezal con el incremento de espigas caídas al suelo. Los puntones del cabezal conducen las hileras del cultivo por entre medio de los mismos, hacia los mecanismos encargados de desprender las espigas de las plantas. Entre medio de los puntones unas cadenas con dedos fuerzan a las plantas a pasar entre medio de un par de rodillos que traccionan las plantas hacia abajo (Fig. 29 ). Debajo de las cadenas y por sobre los rodillos hay dos placas suficientemente separadas para que la caña baje sin atorarse, pero sin espacio para que pase la espiga. Esta última se desprende sobre las placas y es transportada hasta el sinfín por las cadenas. El sinfín que transporta las espigas desde los extremos hasta el centro del cabezal maicero, tiene un tubo o cilindro de diámetro reducido y espiras más amplias, para poder transportar las espigas de maíz, que ocupan mucho más espacio que otros granos. Debajo de los rodillos se encuentran unas placas gramilleras que tienen por función evitar que la maleza se pueda enrollar.
Fig. 29 Cabezal maicero
Los rolos espigadores en su extremo delantero presentan una punta cónica helicoidal para facilitar el ingreso de las cañas. A sí mismo cuando el diseño completo de los rolos es cónico, la velocidad tangencial de los mismos aumenta hacia atrás con el diámetro. Esto permite que la velocidad con que se baja la planta de maíz aumente gradualmente siendo mayor atrás para terminar de bajar la planta. Ademas de esta forma el diámetro del rolo aumenta a medida que el diámetro de la caña de la planta se reduce, facilitando el contacto entre los dos. Los puntones son diseñados con un ángulo bajo para facilitar su penetración debajo de cultivos volcados y en su porción posterior presentan una depresión para contener dentro las espigas sin riesgo de que caigan
Control de posición del cabezal En la actualidad los cabezales maiceros pueden disponer de un control automático de altura y nivelación horizontal, especialmente en los más anchos que van a trabajar en terrenos irregulares. Con una serie de patines en la base de los puntones, miden constantemente la altura del cabezal en el centro y los extremos del mismo, para corregir la altura y nivelarlo paralelo a la superficie del suelo automáticamente.
Fig. 32 Control de posición ajustando el cabezal lateralmente de acuerdo al control del terreno realizado por los patines (dercha).
Molinete para cultivos volcados Para cultivos volcados existen diferentes diseños de molinetes que pueden ser montados sobre el cabezal maicero. Estos ayudan a levantar y conducir dentro del cabezal a las plantas volcadas. En algunas ocasiones no reducen significativamente las perdidas pero permiten que estas no se incrementen sin tener que reducir la velocidad (Hanna 2008).
Fig. 33 Molinete para levantar plantas volcadas. Izquierda, molinete Geringhof (Surmann et al., 2015). Derecha, molinete Shoup (Shoup, 2017).
Cabezales para cosechar al sesgo o con distintas distancias entre surcos Tradicionalmente el cultivo de maíz se ha sembrado a 70 cm entre hileras pero con la difusión de otros distanciamientos como 52 cm, surgió la dificultad que presentan las hileras del cultivo para ingresar a cabezales cuando la separación entre hileras no coincide con la separación entre puntones (Fig. 34 izquierda). Esta dificultad ha sido resuelta en algunos cabezales separando los engranajes en la parte delantera de las cadenas para facilitar el ingreso de las plantas. Para que no se separe el resto de la cadena se dispone de un engranaje intermedio (Fig. 34 derecha). Además los puntones han sido recortados en la base (0), para provocar un menor ángulo de inclinación en las plantas que deben ser guiadas hacia el centro (Lambertini, 2017). Estos cabezales no solo pueden cosechar cultivos con distintos distanciamientos entre hileras sino también pueden cosechar cultivos al sesgo
Fig. 34 Izquierda: esquema de un cabezal maicero convencional para cosechar hileras a 70 cm en un cultivo con hileras a 50 cm. Derecha: esquema de un cabezal multidistancia en la misma situación (Lambertini, 2017).
Diseño de puntones. Izquierda: diseño de un puntón convencional. Derecha: diseño del puntón del cabezal multidistancia con la base recortada (Lambertini, 2017).