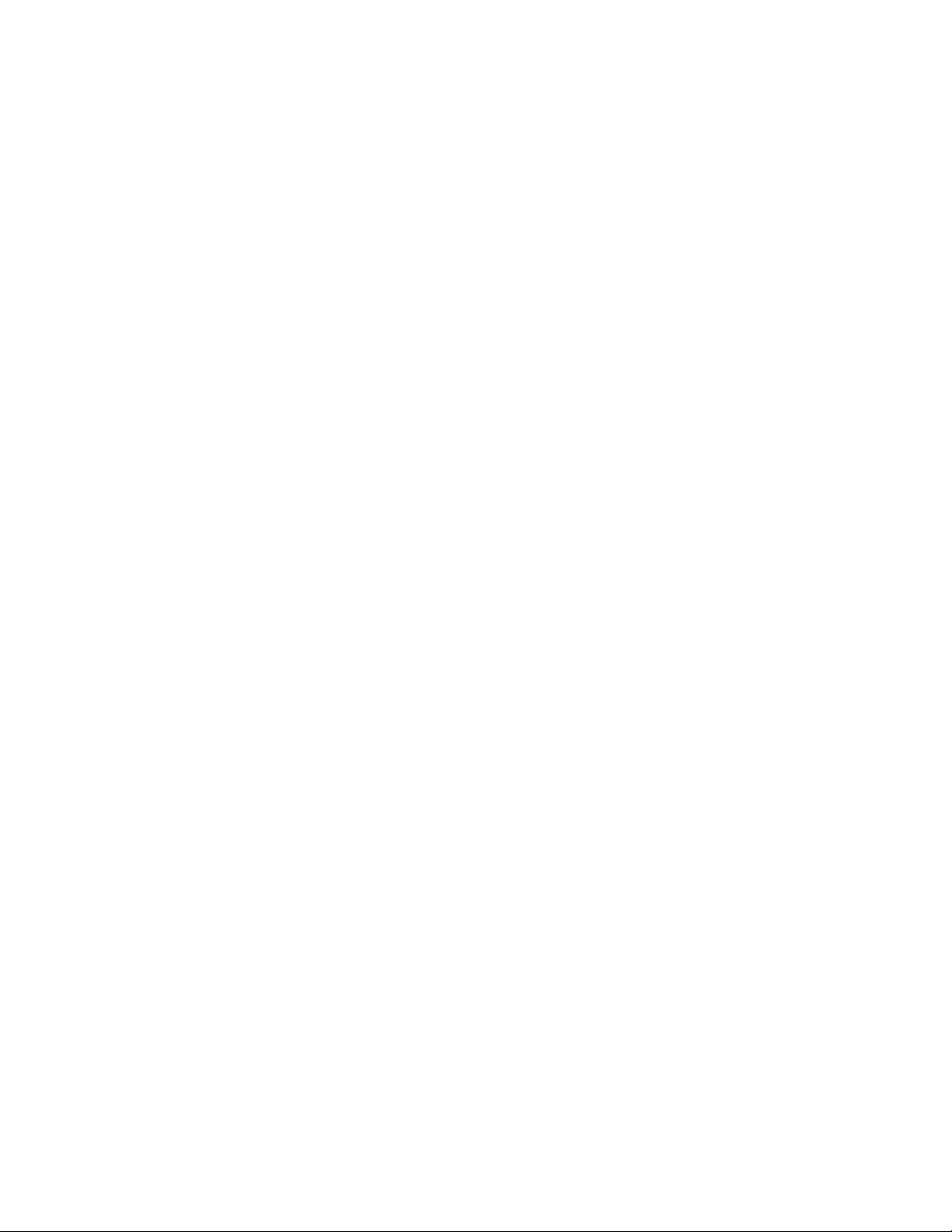
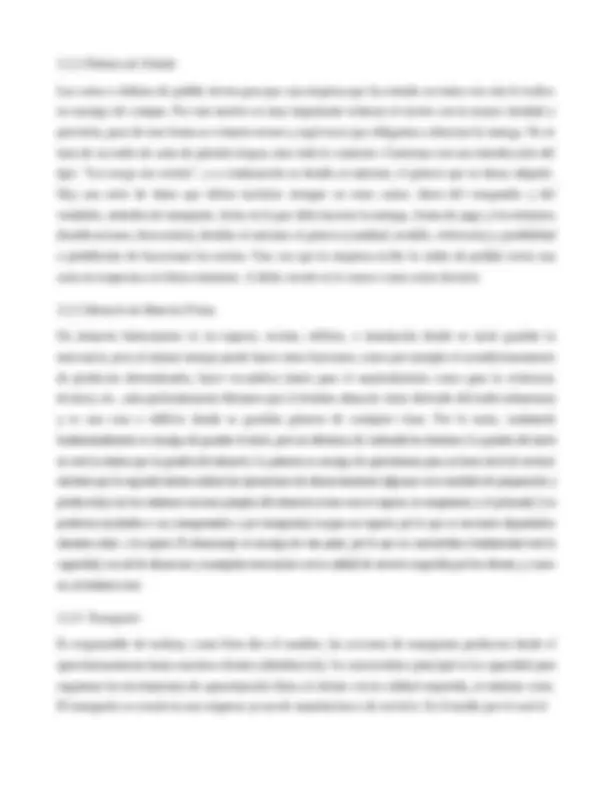
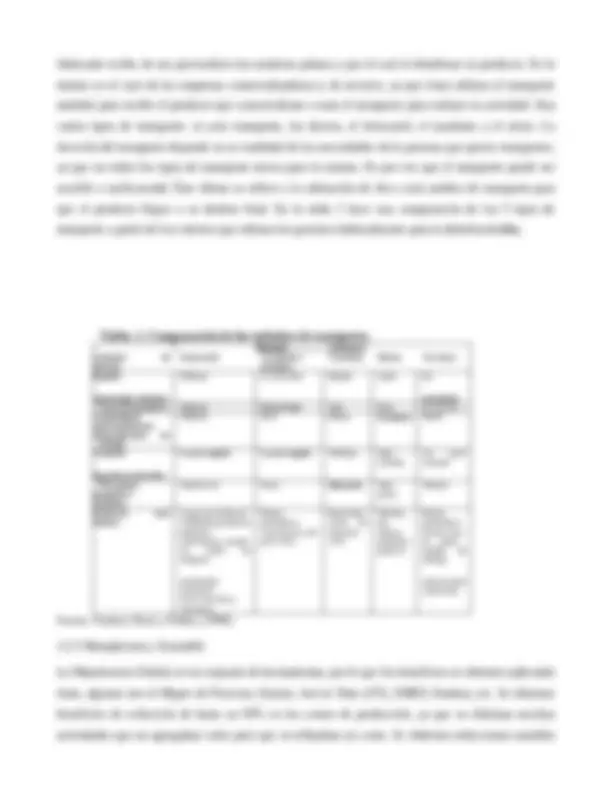
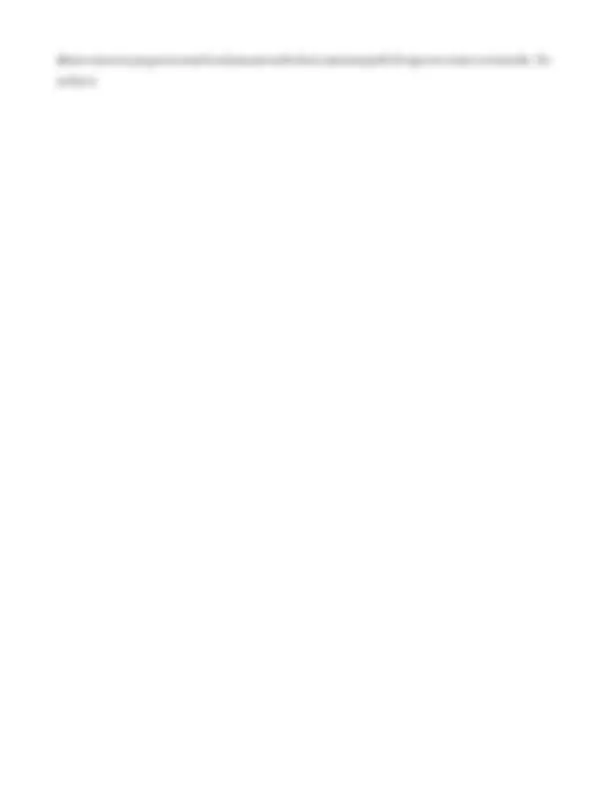
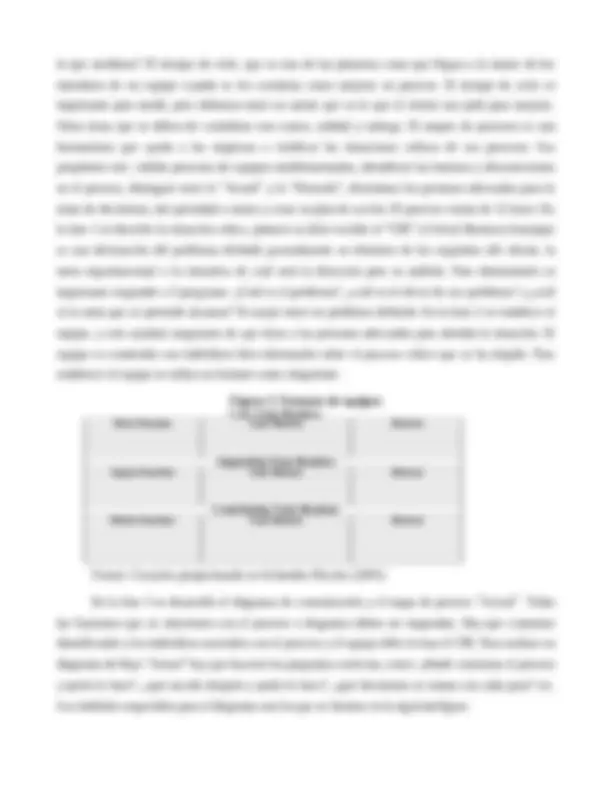
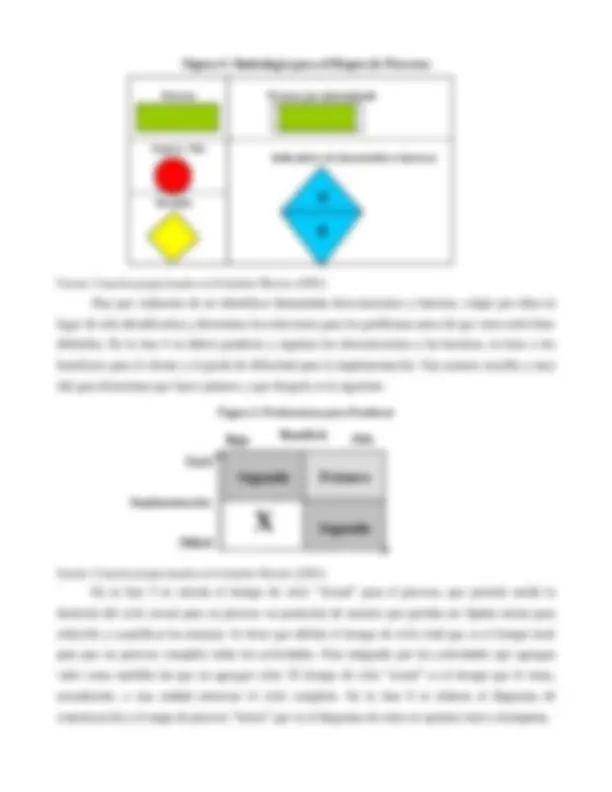
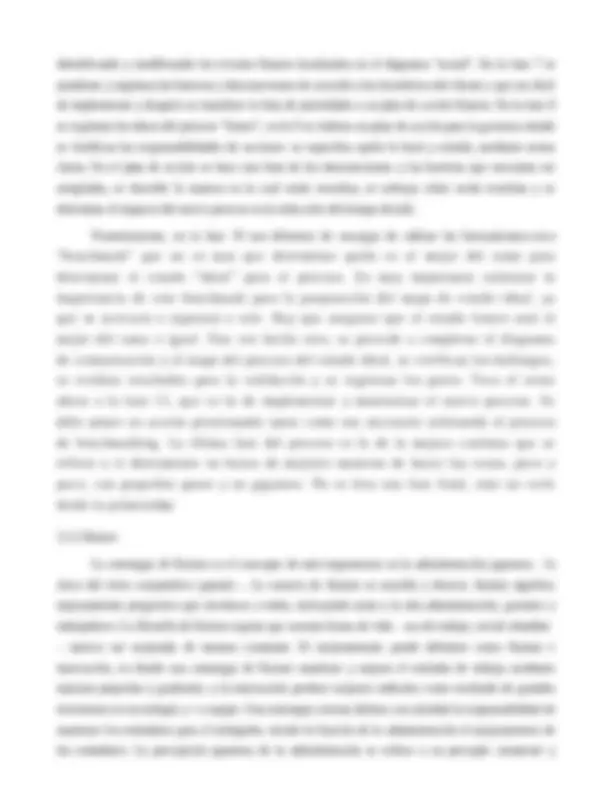
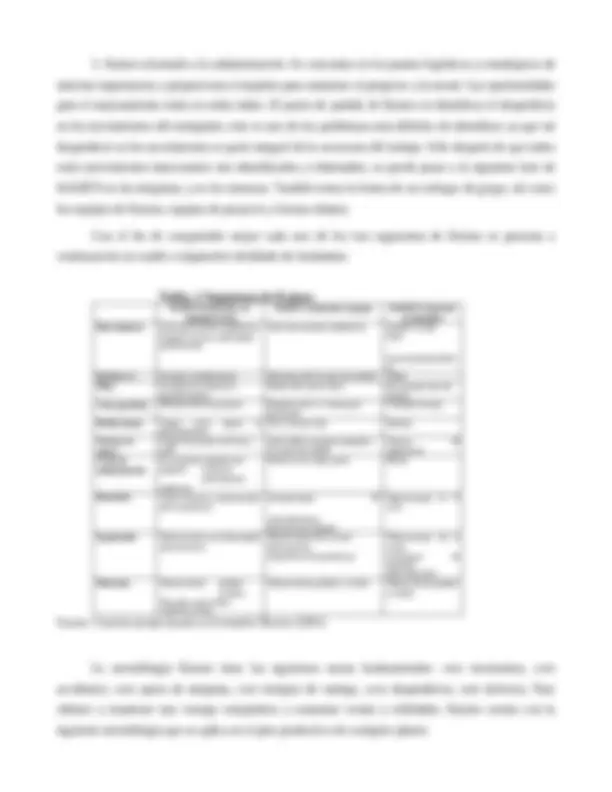
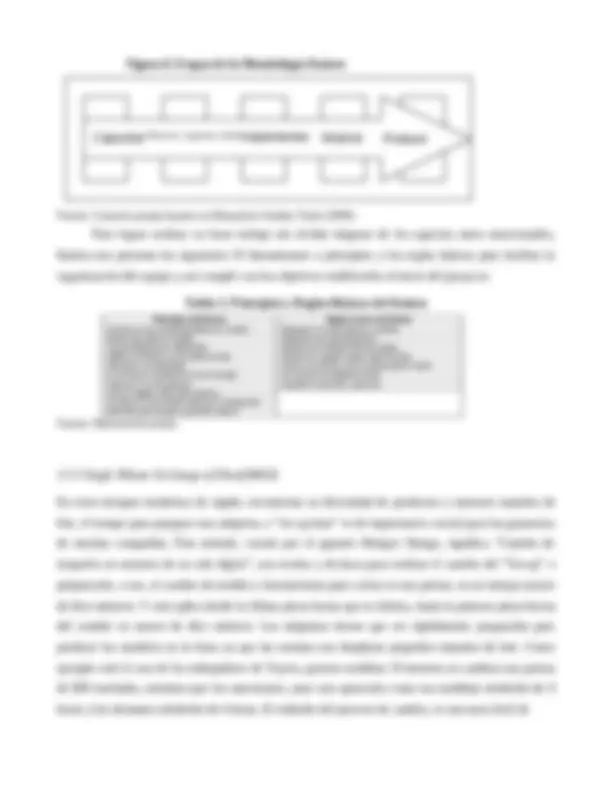
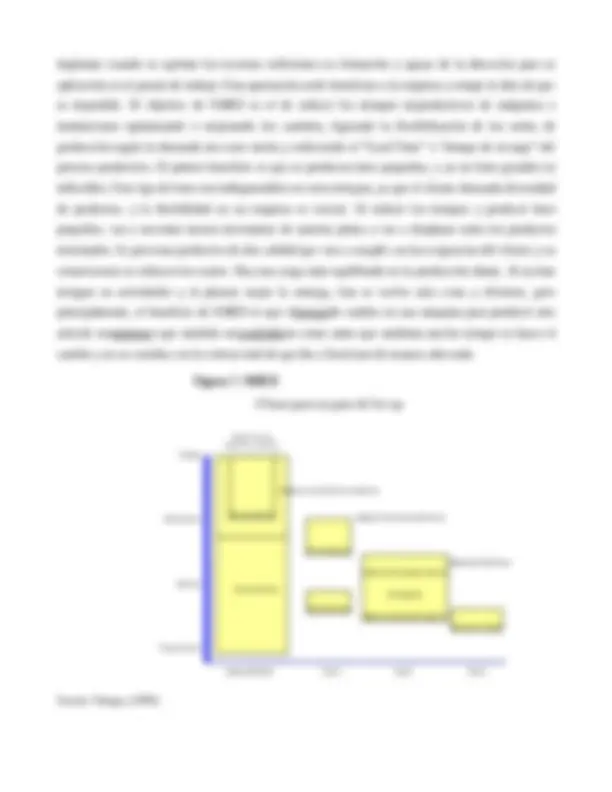
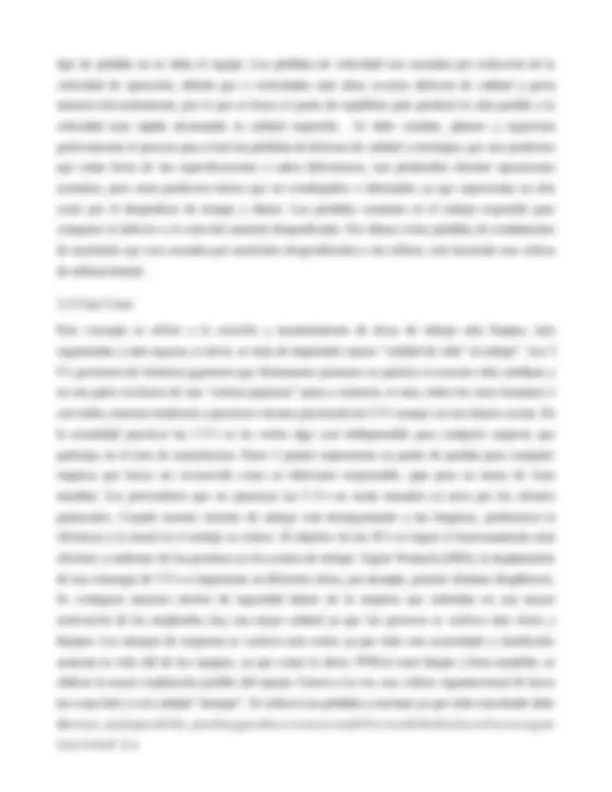
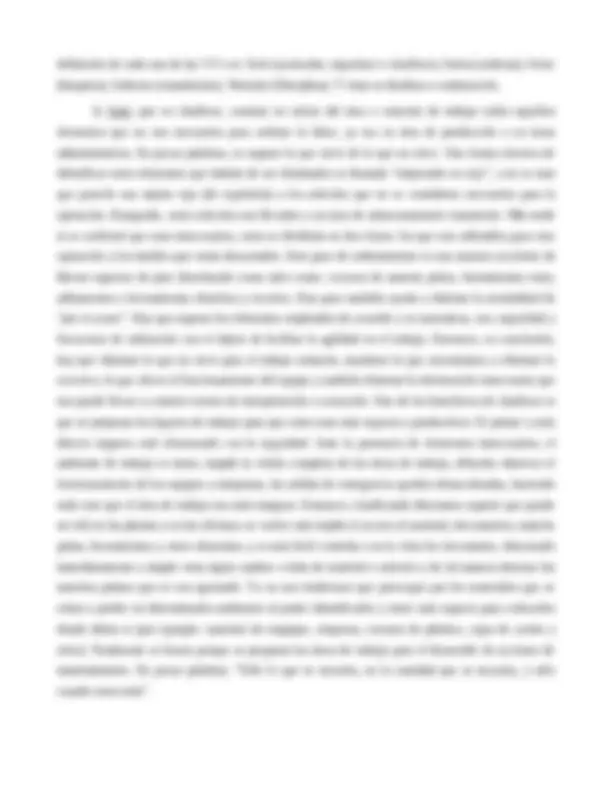
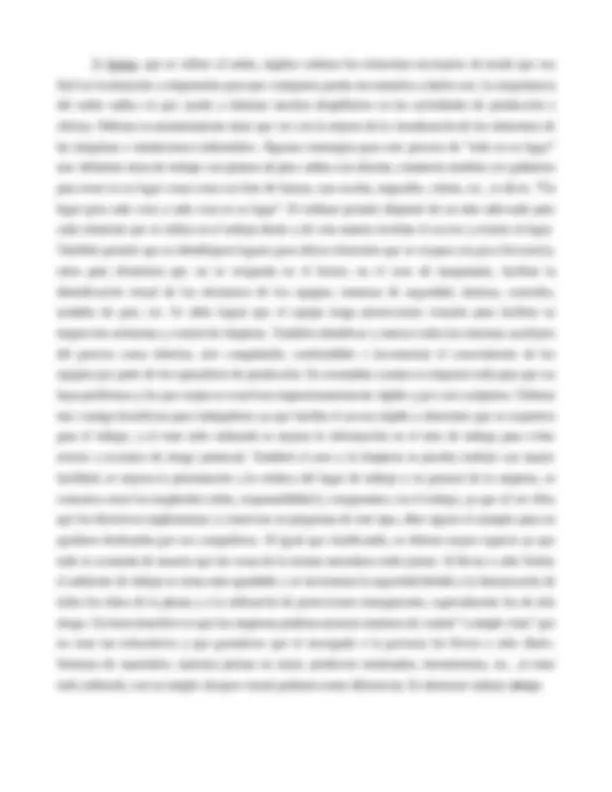
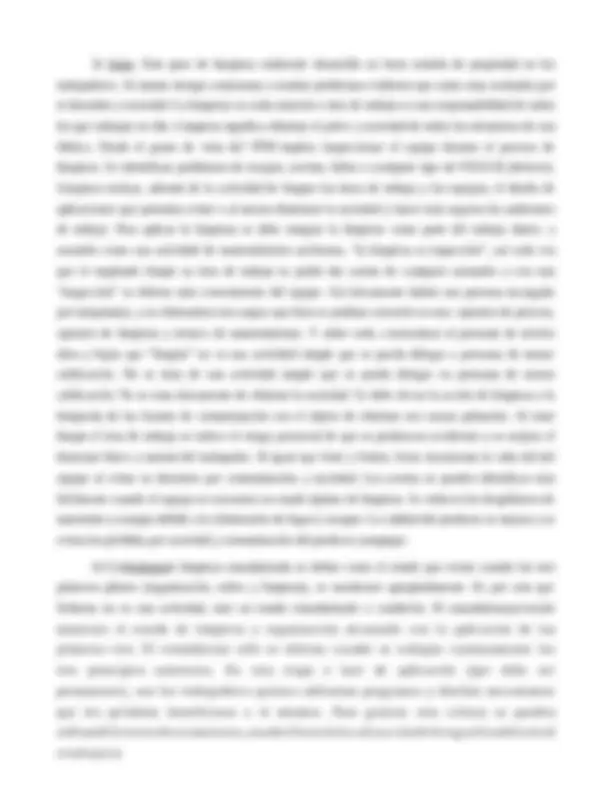
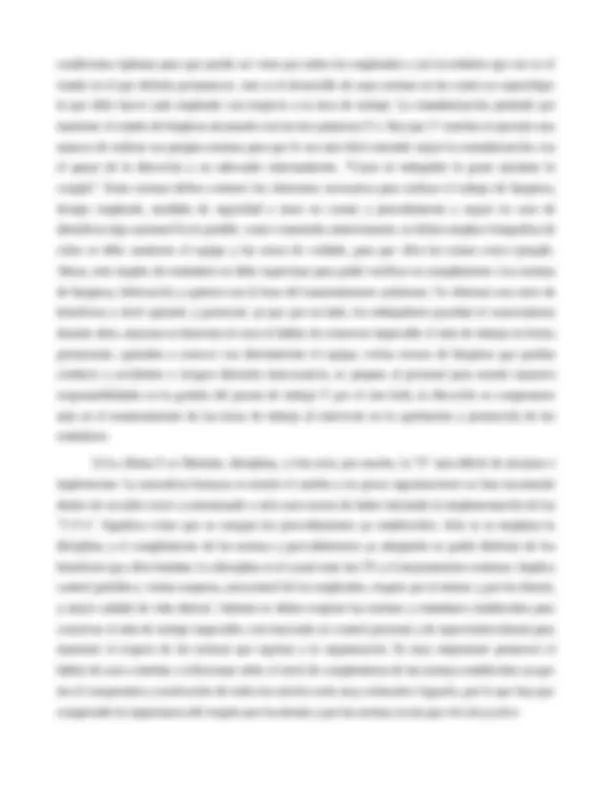
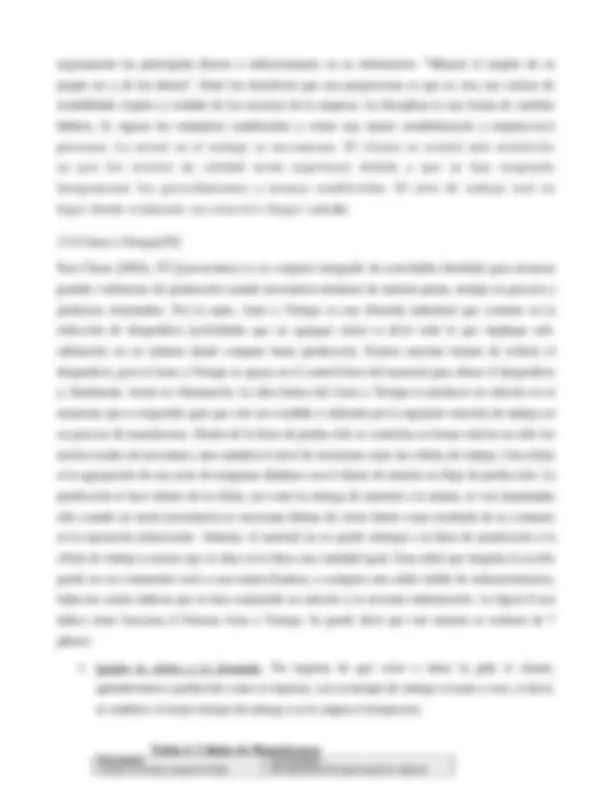
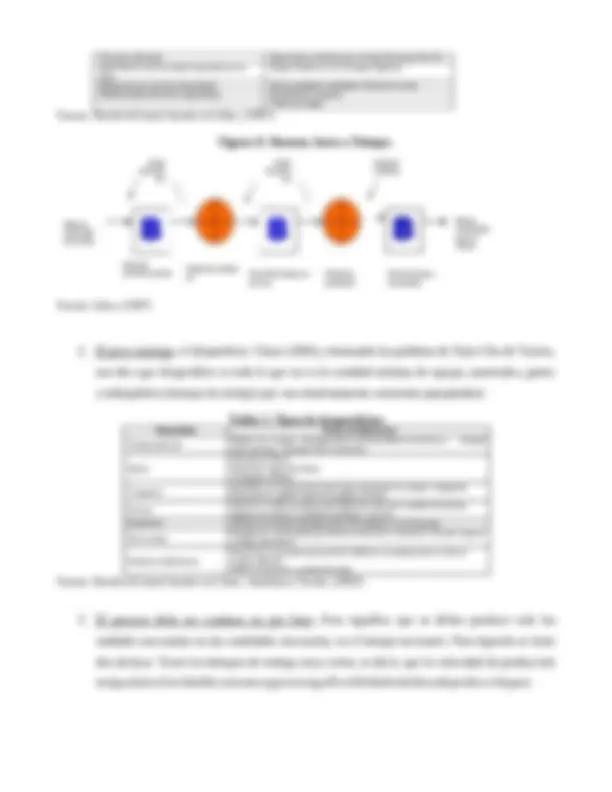
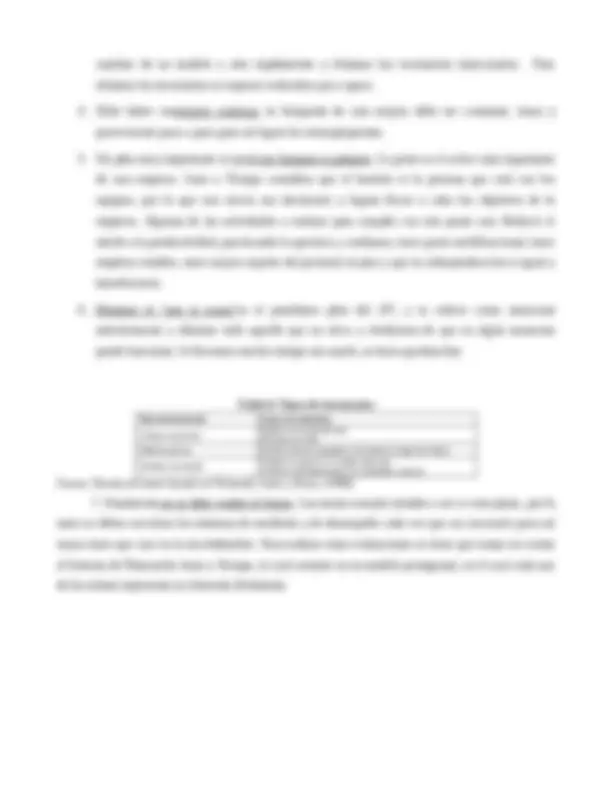
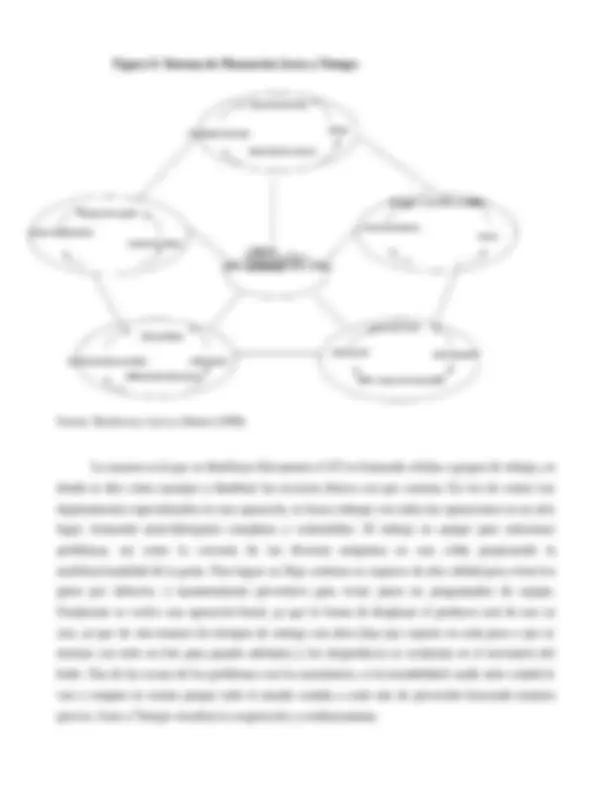
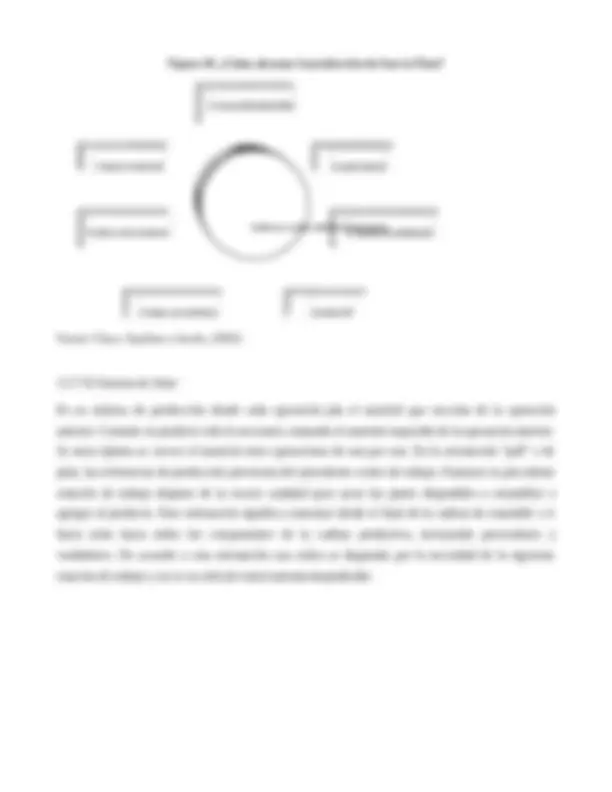
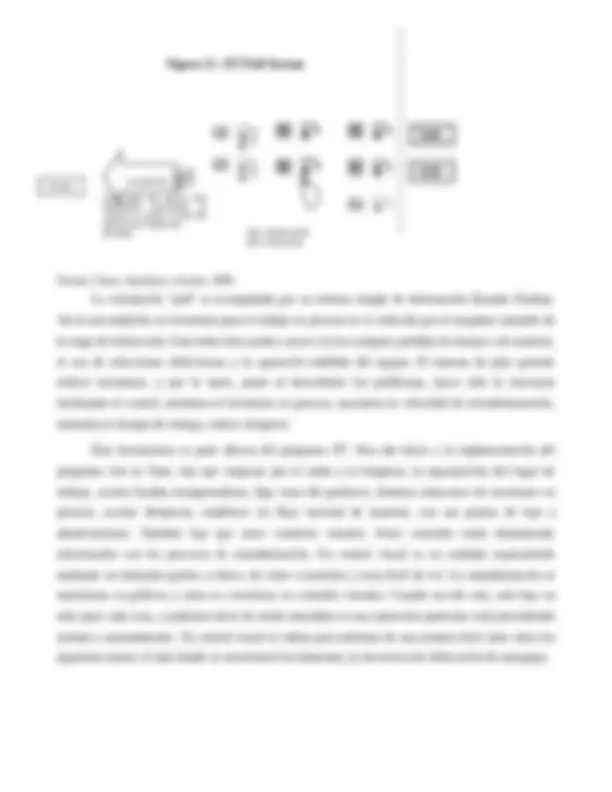
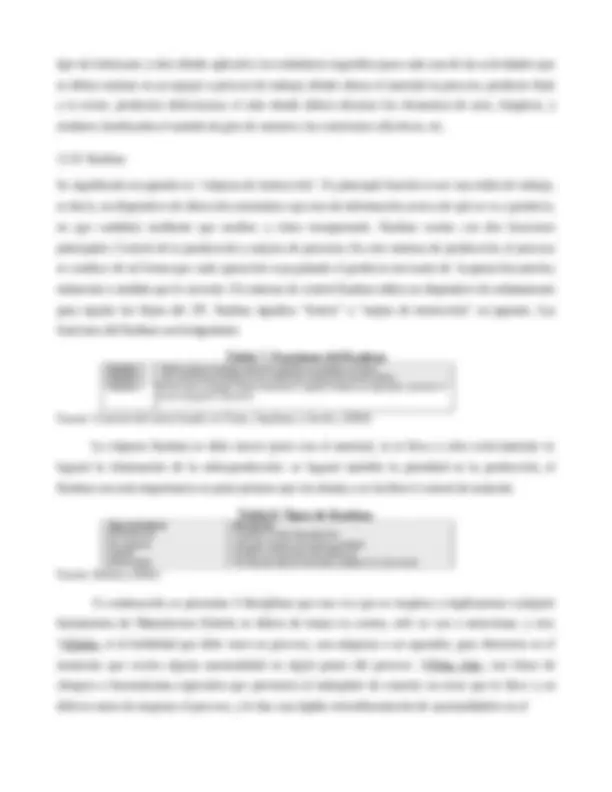
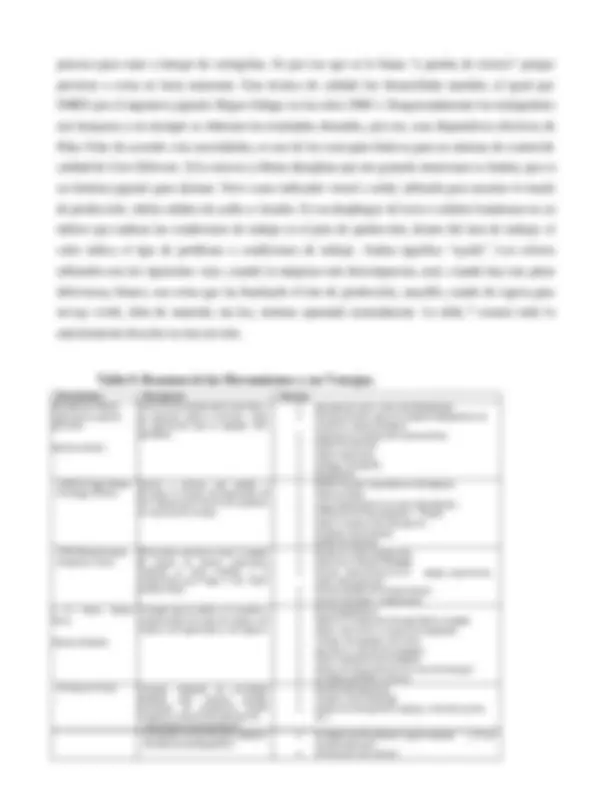
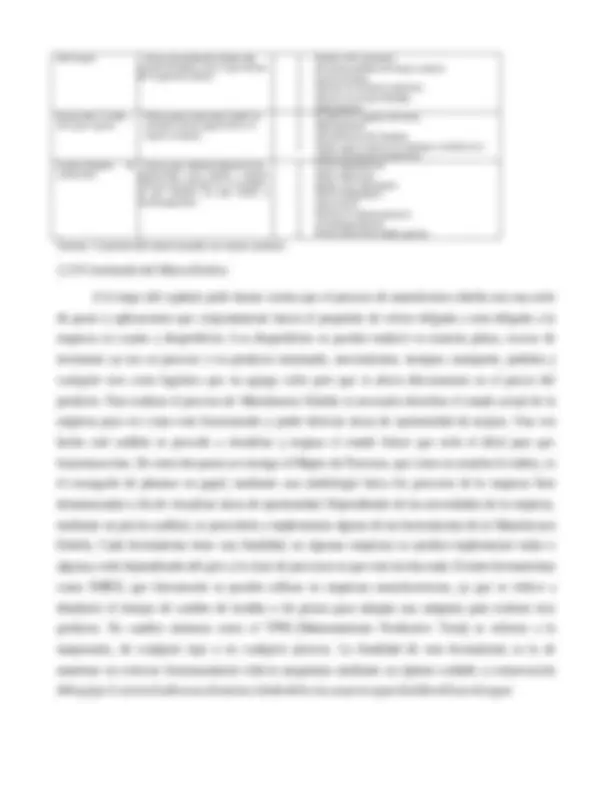
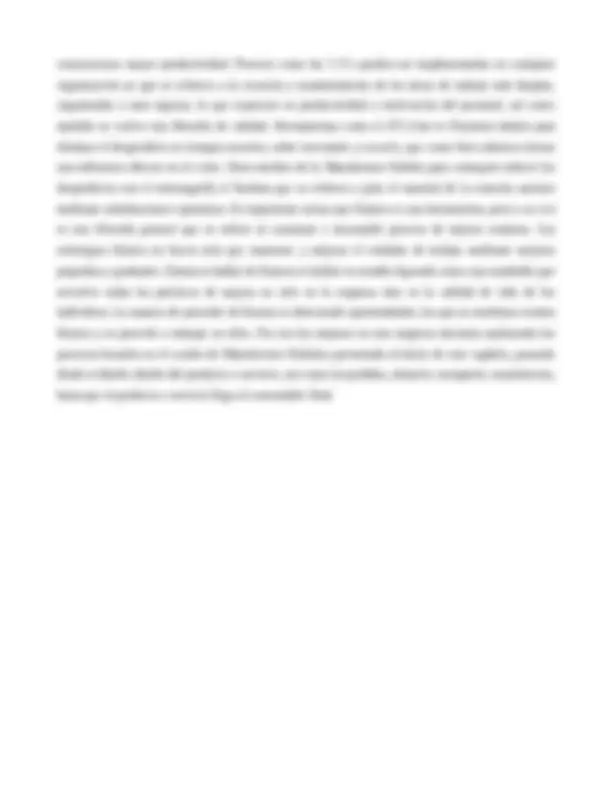
Prepara tus exámenes y mejora tus resultados gracias a la gran cantidad de recursos disponibles en Docsity
Gana puntos ayudando a otros estudiantes o consíguelos activando un Plan Premium
Prepara tus exámenes
Prepara tus exámenes y mejora tus resultados gracias a la gran cantidad de recursos disponibles en Docsity
Prepara tus exámenes con los documentos que comparten otros estudiantes como tú en Docsity
Los mejores documentos en venta realizados por estudiantes que han terminado sus estudios
Estudia con lecciones y exámenes resueltos basados en los programas académicos de las mejores universidades
Responde a preguntas de exámenes reales y pon a prueba tu preparación
Consigue puntos base para descargar
Gana puntos ayudando a otros estudiantes o consíguelos activando un Plan Premium
Comunidad
Pide ayuda a la comunidad y resuelve tus dudas de estudio
Descubre las mejores universidades de tu país según los usuarios de Docsity
Ebooks gratuitos
Descarga nuestras guías gratuitas sobre técnicas de estudio, métodos para controlar la ansiedad y consejos para la tesis preparadas por los tutores de Docsity
resumen de manufactura esbelta
Tipo: Resúmenes
1 / 32
Esta página no es visible en la vista previa
¡No te pierdas las partes importantes!
3.1 Introducción Tradicionalmente la teoría económica convencional ha considerado que el precio está determinado por las leyes de la oferta y la demanda, por lo que las empresas no pueden hacer nada para influir en los precios y lo único que les queda es trabajar para ser lo suficientemente productiva como para permanecer en el mercado. Sin embargo, a lo largo de la historia de las economías occidentales se ha visto que las empresas pueden aplicar estrategias que influyen no sólo en el precio sino en la estructura misma del mercado. Recientemente algunas empresas han desarrollado algunas herramientas estratégicas relacionadas con la eficiencia de los procesos que les ha permitido alcanzar una posición competitiva privilegiada en su industria, entre las que se encuentran lo que se conoce en inglés como Lean Manufacturing. (Henderson y Larco, 1999, p.19). El propósito de este capítulo es dar una descripción de la manufactura esbelta que servirá como referencia teórica para el resto de este estudio. Para ello en la sección dos se da un resumen de cada uno de los elementos que forman la manufactura esbelta. En la sección tres se detallan las herramientas que han ayudado a aplicar los elementos de esta filosofía. Este capítulo termina con algunas conclusiones. 3.2 Elementos de la ManufacturaEsbelta La Manufactura Esbelta es una filosofía utilizada en muchas partes del mundo que nace en Japón. Nace del sistema de Producción de Toyota, y fue concebida por William Edward Deming, Taiichi Ohno, Shigeo Shingo, Eiji Toyoda entre otros. La Manufactura esbelta es una serie de herramientas que le permiten a las empresas aumentar el valor de sus actividades mediante el mantenimiento de un ambiente de mejora continua que permite a la empresa reducir y eliminar todas las operaciones que no le agregan valor al producto, al servicio y a los procesos, tomando en cuenta siempre al trabajador. Específicamente, la Manufactura Esbelta reduce la cadena de desperdicios, así como el inventario y el espacio en el piso de producción, reduce las actividades de los sistemas de producción que no agregan valor, crea sistemas apropiados de entrega de materiales sin que se pierda tiempo, encuentra equivocaciones y mejora las tareas de manera que puedan ser más flexibles. Por lo tanto, uno de los objetivos principales de la Manufactura Esbelta es permitirles a las compañías reducir sus costos, mejorar los procesos, eliminar desperdicios, entregar más rápidamente sus productos terminados, aumentar la satisfacción de sus clientes, mantener un margen de utilidad aceptable y, en general, competirmáseficientementeen losmercadosinternacionalesy enfrentarconellolaglobalizaci ónde
Proveedores Customer los mercados. La Manufactura Esbelta cubre prácticamente todos las funciones y actividades de la empresa, desde el diseño y mejora de productos hasta la entrega del producto final a los clientes. Por lo tanto, los elementos tradicionales de la Manufactura Esbelta tienen que ver con diseño de nuevos productos y servicios, mejora de los productos ya existentes, órdenes de pedido, almacén de materia prima, transporte de materia prima, manufactura o ensamble, transporte de productos terminados, almacén de productos terminados, transporte de productos terminados a clientes y entrega de productos terminados a clientes. A continuación se explican cada uno de estoselementos. Figura 2. Manufactura Holística Diseño depro d. y/ oser v. Orden de pedido Almacén de materia prima Transporte Materia Prima Tecnología vehicular Área de producción y ensamble Operación Inspección Almacén Transporte Autocontrol ***Reduccion de *desperdicio. *Cero defectos. Células vinculadas Poka – Yoke
fabricante recibe de sus proveedores las materias primas y por el cual el distribuye su producto. Es lo mismo en el caso de las empresas comercializadoras y de servicio, ya que éstas utilizan el transporte también para recibir el producto que comercializan o usan el transporte para realizar su actividad. Hay varios tipos de transporte: al auto transporte, los ductos, el ferrocarril, el marítimo y el aéreo. La elección del transporte depende en su totalidad de las necesidades de la persona que quiere transportar, ya que no todos los tipos de transporte sirven para lo mismo. Es por eso que el transporte puede ser sencillo o multi-modal. Éste último se refiere a la utilización de dos o más medios de transporte para que el producto llegue a su destino final. En la tabla 1 hace una comparación de los 5 tipos de transporte a partir de los criterios que utilizan los gerentes habitualmente para la distribuciónfísica. Tabla. 1. Comparación de los métodos de transporte. Métodode transporte Criterioss elección de Ferrocarril Vía fluvial y marítima Carretera Ductos Vía aérea Rapidez (entreorigen ydestino) Mediana La más lenta Rápida Lenta La másrápida Costo de transporte Mediano El más bajo Alto Bajo El más alto Confiabilidad enelcumplimiento delosprogramas de entrega. Mediana Poca Buena Excelente Buena Variedad deproductosofrecidos La más amplia La más amplia Mediana Muy limitada Un poco limitada Ubicaciones geográficas atendidas Muchísimas Pocas Ilimitadas Muy pocas Muchas Productos idóneos. más Largos recorridos de cantidades grandes de productos voluminosos, cuando los costos de tranporte sonelevados enrelación con el valor de la mercancía. Bienes perecederos voluminosos y de poco valor. Recorridos cortos de bienes de valor Petróleo, gas natural, productos pastosos. Bienes perecederos de alto valor, en quela rapidez de entrega essumamente importante. Fuente: Stanton, Etsen y Walter, (1996). 3.2.5 Manufactura y Ensamble La Manufactura Esbelta es un conjunto de herramientas, por lo que los beneficios se obtienen aplicando éstas, algunas son el Mapeo de Procesos, Kaizen, Just in Time (JIT), SMED, Kanban, etc. Se obtienen beneficios de reducción de hasta un 50% en los costos de producción, ya que se eliminan muchas actividades que no agregaban valor pero que si reflejaban un costo. Se obtienen reducciones notables
dei n v e n t a r i o y a q u e s e a n a l i z a l a m a n e r a d e ú n i c a m e n t e p e d i r l o q u e s e v a n e c e s i t a n d o. S e r e d u c e
producir por órdenes de los clientes, en vez de producir basados en pronósticos de ventas a largo plazo. Y finalmente hay que perseguir la perfección: una vez que una empresa consigue los primeros cuatro pasos, se vuelve claro para aquellos que están involucrados, que añadir eficiencia siempre es posible. Cabe mencionar que el esquema de manufactura esbelta presentado a principios del capítulo es una guía amplia de lo que una empresa de manufactura tiene que seguir para mejorar sus procesos. Este esquema se puede aplicar de igual manera a aquellas empresas que no son de manufactura pero que tienen otros procesos similares a los mencionados en éste. Más adelante en el cuarto apartado de la sección cuatro se explican los procesos en los que la empresa Llantiexpress, S.A. de C.V.incurre. 3.2.6 Entrega de Producto Terminado aClientes. Es este nivel cuando según lo acordado se hace la entrega del pedido al cliente. Debemos cuidar de cumplir con los requerimientos de la negociación, entregar la cantidad correspondiente con la calidad debida y en la fecha de entrega pactada al momento del trámite de la orden de pedido. 3.3 Herramientas de la ManufacturaEsbelta Los elementos de la manufactura esbelta se aplican a través de una serie de herramientas, entre las cuales destacan las siguientes: el mapeo de proceso, eventos Kaizen, SMED, TPM, las 5 S’s, Just inTime , Kanban y sistema pull , las cuales son de las más comunes, y por eso son éstas las que se van a describir a continuación. 3.3.1 Mapeo deProcesos En cada función, en cada organización, hay procesos de trabajo claramente definidos (y a veces no tan claramente definidos) que se tienen que seguir para coincidir con las expectativas del cliente. A menudo, la documentación para estos procesos no está disponible para otros empleados, terminando en la falta de comunicación o peores cosas. Los procesos son a menudo llenados con desperdicio y pueden hacer más lento el proceso o puede resultar en la producción de productos o servicios inferiores. Descubrir y remover el desperdicio de estos procesos ayuda a la organización a alcanzar metas para mejorar en áreas como el precio, calidad, entrega y por consiguiente entender mejor las necesidades de los clientes. Hay muchas herramientas usadas en los negocios para identificar fuentes de eliminación de desperdicio, éstas son conocidas también como herramientas de mejora continua, y una muy efectiva es el Mapeo deProcesos. Empecemos con definir un proceso. Un proceso es una secuencia de pasos repetibles que convierten entradas en salidas con valor para el cliente. Pero cuando analizamos los procesos, ¿qué es
lo que medimos? El tiempo de ciclo, que es una de las primeras cosas que llegan a la mente de los miembros de un equipo cuando se les cuestiona como mejorar un proceso. El tiempo de ciclo es importante para medir, pero debemos tener en mente que es lo que el cliente nos pide para mejorar. Otras áreas que se deben de considerar son costos, calidad y entrega. El mapeo de procesos es una herramienta que ayuda a las empresas a clarificar las situaciones críticas de sus procesos. Sus propósitos son: validar procesos de equipos multifuncionales, identificar las barreras y desconexiones en el proceso, distinguir entre lo “Actual” y lo “Deseado”, determinar las personas adecuadas para la toma de decisiones, dar prioridad a metas y crear un plan de acción. El proceso consta de 12 fases: En la fase 1 se describe la situación crítica, primero se debe escribir el “CBI” ( Critical Business Issue) que es una declaración del problema definido generalmente en términos de los requisitos del cliente, la meta organizacional o la iniciativa de cuál será la dirección para su análisis. Para determinarlo es importante responder a 3 preguntas: ¿Cuál es el problema?, ¿cuál es el efecto de ese problema? y ¿cuál es la meta que se pretende alcanzar? Es mejor tener un problema definido. En la fase 2 se establece el equipo, y esto ayudará asegurarse de que tiene a las personas adecuadas para abordar la situación. El equipo es construido con individuos bien informados sobre el proceso crítico que se ha elegido. Para establecer el equipo se utiliza un formato como elsiguiente: Figura 3. Formato de equipos Core Team Members Direct Functions Team Members Alternate Supporting Team Members Support Functions Team Members Alternate Contributing Team Members Relative Functions Team Members Alternate Fuente: Creación propia basado en Schneider Electric (2001) En la fase 3 se desarrolla el diagrama de comunicación y el mapa de proceso “Actual”. Todas las funciones que se relacionan con el proceso o diagrama deben ser mapeadas. Hay que comenzar identificando a los individuos asociados con el proceso y el equipo debe revisar el CBI. Para realizar un diagrama de flujo “Actual” hay que hacerse las preguntas correctas, como: ¿dónde comienza el proceso y quién lo hace?, ¿qué sucede después y quién lo hace?, ¿qué decisiones se toman con cada paso? etc. Los símbolos requeridos para el diagrama son los que se ilustran en la siguientefigura:
identificando y modificando los eventos Kaizen localizados en el diagrama “actual”. En la fase 7 se ponderan y registran las barreras y desconexiones de acuerdo a los beneficios del cliente y que sea fácil de implementar y después se transfiere la lista de prioridades a un plan de acción Kaizen. En la fase 8 se registran los datos del proceso “futuro”, en la 9 se elabora un plan de acción para la gerencia donde se clarifican las responsabilidades de acciones: se especifica quién lo hará y cuándo, mediante metas claras. En el plan de acción se hace una lista de las desconexiones y las barreras que necesitan ser arregladas, se describe la manera en la cual serán resueltas, se subraya cómo serán resueltas y se determina el impacto del nuevo proceso en la reducción del tiempo deciclo. Posteriormente, en la fase 10 nos debemos de encargar de utilizar las herramientascomo “benchmark” que no es mas que determinar quién es el mejor del ramo para determinar el estado “ideal” para el proceso. Es muy importante enfatizar la importancia de este benchmark para la preparación del mapa de estado ideal, ya que se acercará o superará a este. Hay que asegurar que el estado futuro s erá el mejor del ramo o igual. Una vez hecho esto, se procede a completar el diagrama de comunicación y el mapa del proceso del estado ideal, se verifican los hallazgos , se evalúan resultados para la validac ión y se registran los pasos. Toca el turno ahora a la fase 11, que es la de implement ar y monitorear el nuevo proces o. Se debe poner en acción presionando tanto como sea necesario utilizando el proces o de benchmarking. La última fase del proceso es la de la mejora continua que s e refiere a ir diariam ente en busca de mejores maneras de hacer las cosas, poco a poco, con pequeños pasos y no gigantes. No es ésta una fase final, sino un ciclo des de la primera fase. 3.3.2 Kaizen La estrategia de Kaizen es el concepto de más importancia en la administración japonesa – la clave del éxito competitivo japonés -. La esencia de Kaizen es sencilla y directa: Kaizen significa mejoramiento progresivo que involucra a todos, incluyendo tanto a la alta administración, gerentes y trabajadores. La filosofía de Kaizen supone que nuestra forma de vida – sea de trabajo, social ofamiliar
mejorarl o s e s t á n d a r e s. K a i z e n e s l a e s e n c i a d e l a s p r á c t i c a s a d m i n i s t r a t i v a s j a p o n e s a s , y a s e a n d e
CapacitarObservar, organizar, definirImplementar Mejorar Producir Figura 6. Etapas de la Metodología Kaizen Fuente: Creación propia basado en Manual de Stanley Tools (2000) Para lograr realizar un buen trabajo sin olvidar ninguno de los aspectos antes mencionados, Kaizen nos presenta los siguientes 10 lineamientos o principios y las reglas básicas para facilitar la organización del equipo y así cumplir con los objetivos establecidos al inicio del proyecto. Tabla 3. Principios y Reglas Básicas del Kaizen Principios del Kaizen Reglas básicas de Kaizen Conservar una mentalidad abierta al cambio Mantener la mente abierta a cambios Pensar que querer es poder Mantener una actitud positiva No preocuparse por adelantado Generar un ambiente libre de culpas Hablar con datos, no con suposiciones Practicar el respeto mutuo todos los días Estimular la creatividad Tratar a los demás como se desea que lo traten Se alcanzará la perfección con el tiempo No existen las preguntas tontas Actuar en vez de protestar Entender el proceso y aplicarlo Usar el ingenio antes que el dinero Cambiar el movimiento inútil por el trabajo útil Recordar que siempre es posible mejorar Fuente: Elaboración propia 3.3.3 Single Minute Exchange of Dies(SMED) En estos tiempos modernos de rápido crecimiento en diversidad de productos y menores tamaños de lote, el tiempo para preparar una máquina, o “set up time” es de importancia crucial para las ganancias de muchas compañías. Éste método, creado por el japonés Shingeo Shingo, significa “Cambio de troqueles en minutos de un solo dígito”, son teorías y técnicas para realizar el cambio del “Set-up” o preparación, o sea, el cambio de moldes o herramientas para cortar en una prensa, en un tiempo menor de diez minutos. Y esto aplica desde la última pieza buena que se fabrica, hasta la primera pieza buena del cambio en menos de diez minutos. Las máquinas tienen que ser rápidamente preparadas para producir los modelos en la línea ya que las normas son desplazar pequeños tamaños de lote. Como ejemplo está el caso de los trabajadores de Toyota, quienes tardaban 10 minutos en cambiar una prensa de 800 toneladas, mientras que los americanos, para una operación como esa tardaban alrededor de 6 horas y los alemanes alrededor de 4 horas. El rediseño del proceso de cambio, es una tarea fácil de
3.3.4 Mantenimiento Productivo Total(TPM) Henderson (1999), en su libro, nos dice que TPM son las siglas en inglés de “Mantenimiento Productivo Total”, y que es un proceso que genera una relación directa entre mantenimiento y productividad, demostrando como el buen cuidado y conservación del equipo en óptimas condiciones, resultan en mayor productividad. TPM es un elemento clave en la Manufactura Esbelta ya que persigue un doble objetivo: cero caídas en producción y cero defectos, cuando esto se ha logrado, el periodo de operación mejora, los costos son reducidos, el inventario puede ser minimizado, y en consecuencia la productividad se incrementa. Para mejorar el mantenimiento de equipo, Japón utilizó de los Estados Unidos el concepto de Mantenimiento Preventivo. Más tarde siguió utilizando otrash e r r a m i e n t a s c o m o : m a n t e n i m i e n t o p r o d u c t i v o , p r e v e n c i ó n d e l m a n t e n i m i e n t o , e t c. É s t a s f u e r o n i m p l e m e n t a d a s a l a i d e o l o g í a j a p o n e s a d e d o n d e r e s u l t ó e l M a n t e n i m i e n t o A u t ó n o m o y a h o r a s e c o n o c e c o m o T P M ( M a n t e n i m i e n t o P r o d u c t i v o T o t a l ) , y q u e e s d e f i n i d o c o m o m a n t e n i m i e n t o p r o d u c t i v o i m p l e m e n t a d o p o r t o d o s l o s e m p l e a d o s , b a s a d o e n q u e l a m e j o r a d e l e q u i p o d e b e i n v o l u c r a r a t o d o s e n l a o r g a n i z a c i ó n , d e s d e l o s o p e r a d o r e s h a s t a l a a l t a d i r e c c i ó n. L o s o b j e t i v o s d e e s t e p r o g r a m a s o n m a x i m i z a r l a e f i c a c i a d e l e q u i p o , b u s c a n d o e l i n v o l u c r a m i e n t o g e n e r a l y t o t a l d e t o d o s p a r a l a i m p l e m e n t a c i ó n y e l i m i n a r f a l l a s y p é r d i d a s. L o s q u e p l a n e a n , d i s e ñ a n , u s a n o m a n t i e n e n e l e q u i p o t i e n e n q u e e s t a r i n v o l u c r a d o s ; c o m o d e c í a , d e s d e d i r e c t i v o s h a s t a o p e r a d o r e s d e l a s m á q u i n a s , p o r l o t a n t o t o d o s c o n o c e r í a n a l a p e r f e c c i ó n c u á n d o d a r l e s e r v i c i o a l e q u i p o y c ó m o m a n t e n e r l o e n b u e n e s t a d o. S e b u s c a t a m b i é n d e s a r r o l l a r u n s i s t e m a d e m a n t e n i m i e n t o p r o d u c t i v o q u e d u r e t o d a l a v i d a d e l e q u i p o , p a r a s a c a r l e e l m a y o r p r o v e c h o. E l T P M s e d e b e p r o m o v e r a t r a v é s d e l a m o t i v a c i ó n , e s t o l l e v a n d o a c a b o a c t i v i d a d e s a u t ó n o m a s d e p e q u e ñ o s g r u p o s , d o n d e s e p u e d a a t e n d e r m e j o r a c a d a i n t e g r a n t e y l a c o m p r e n s i ó n s e a m u c h o m e j o r , e x p l i c a n d o q u e l o s b e n e f i c i o s d e i m p l e m e n t a r e s t e p r o g r a m a s e r í a n p a r a todos. Las pérdidas por fallas, son causadas por defectos en los equipos que requieren de alguna clase de reparación. Estas pérdidas son por tiempos muertos y por los costos de las partes y mano de obra requerida para la reparación. La magnitud de la falla se mide por el tiempo muerto causado. Por otro lado se eliminan también las perdidas de setup y ajuste (SMED), ya que se reducen a lo mínimo el tiempo para hacer cambios en las condiciones de operación como empezar una corrida de producción o el empezar un nuevo turno de trabajadores. Estas pérdidas consisten de tiempo muerto y también pueden ser el cambio de moldes o herramientas, calentamiento y ajustes de las máquinas. Su magnitud
también se mide por el tiempo muerto. En general no se pueden registrar estas pérdidas directamente, por lo que se utiliza el porcentaje de utilización (100% menos el porcentaje de utilización), y en este
definición de cada una de las 5 S’s es: Seiri (acomodar, organizar o clasificar), Seiton (ordenar), Seiso (limpieza), Seiketsu (estandarizar), Shitsuke (Disciplina). Y éstas se detallan a continuación.