
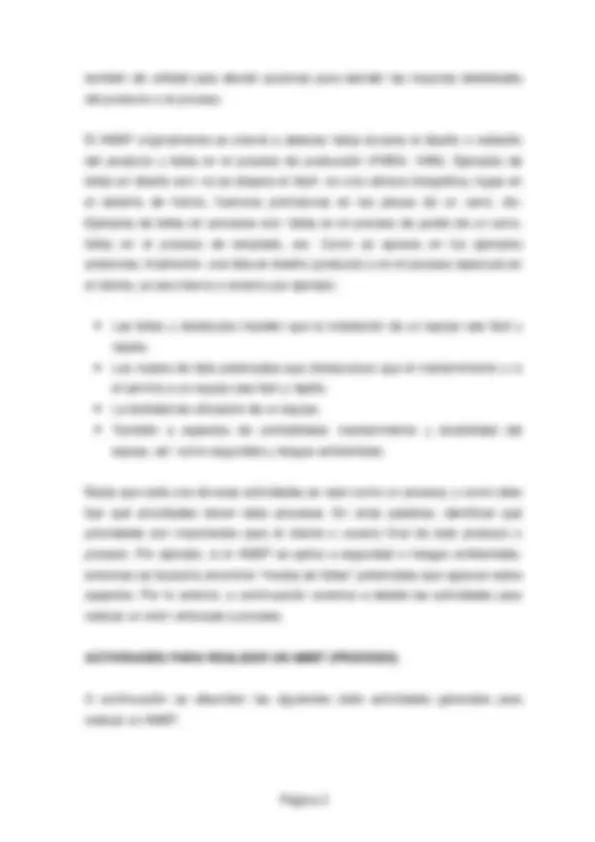
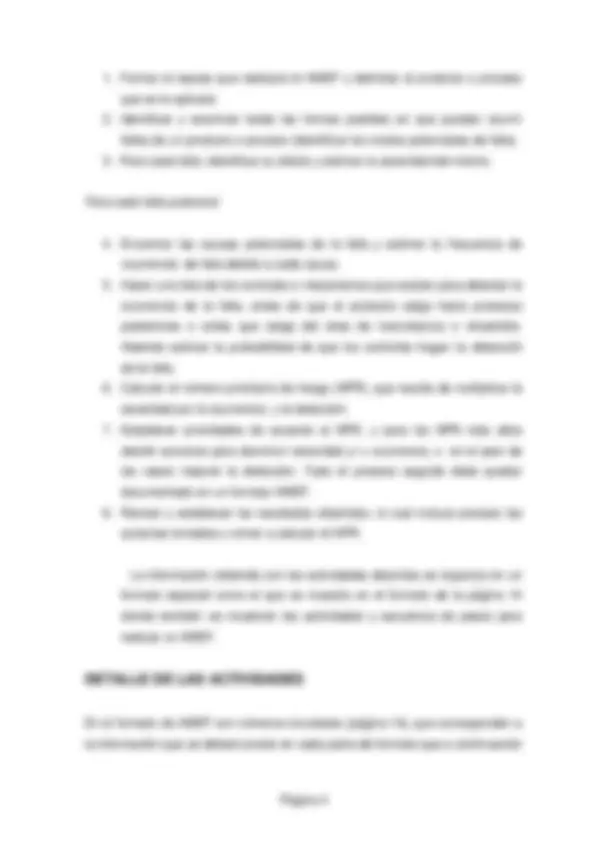
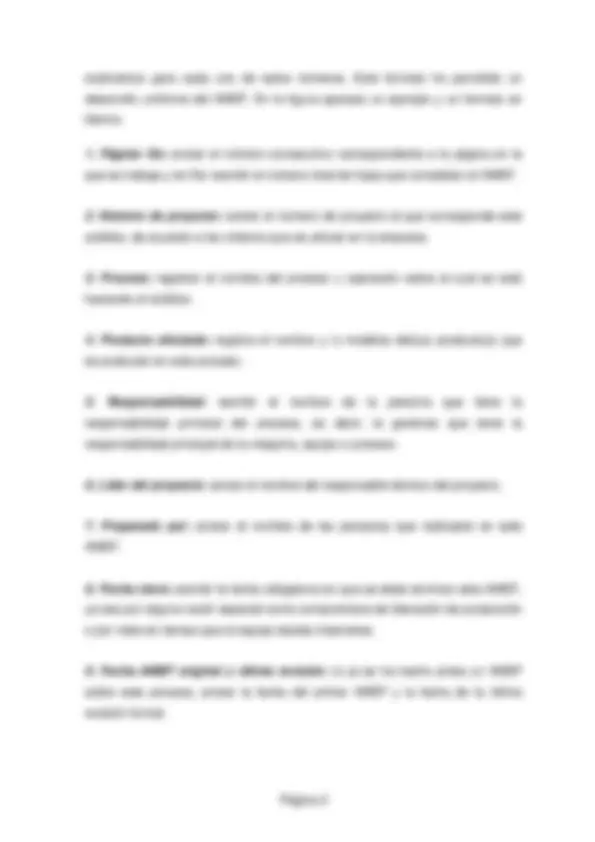
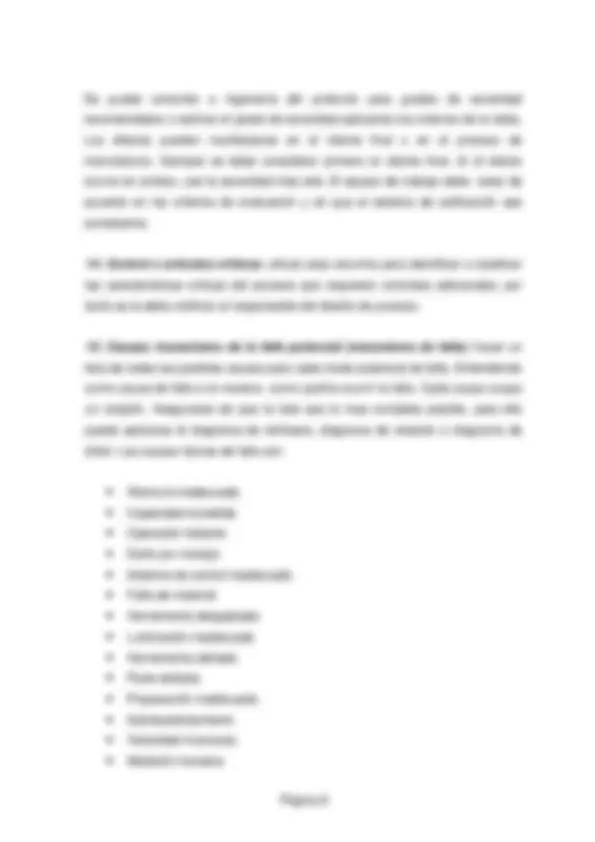

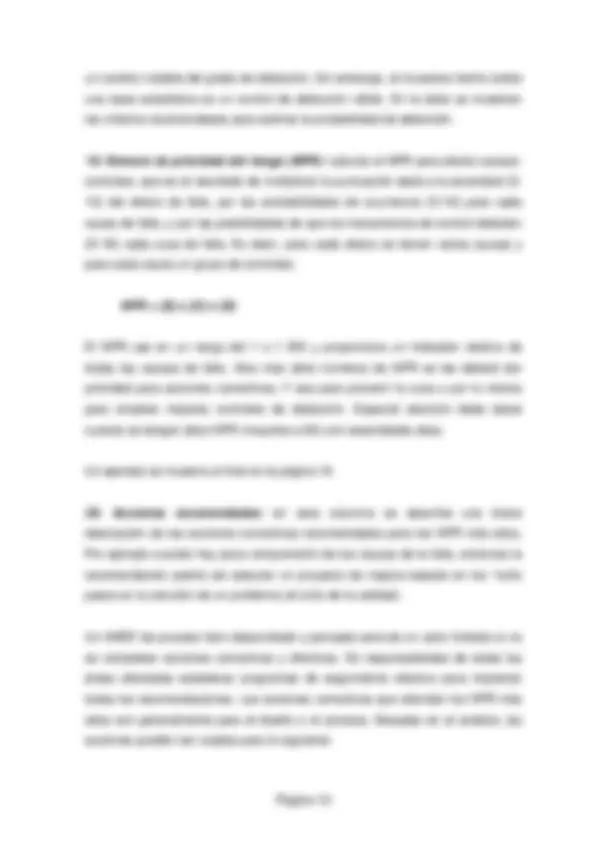
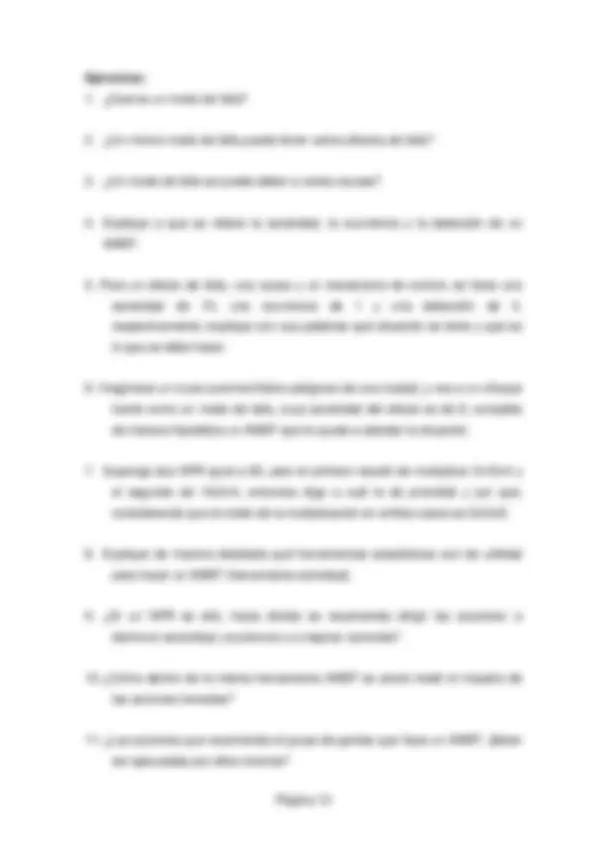
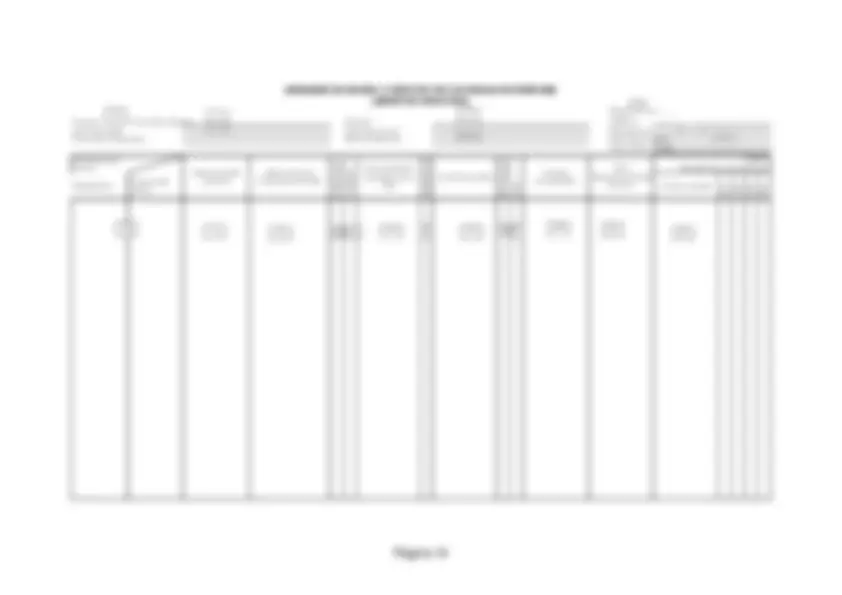
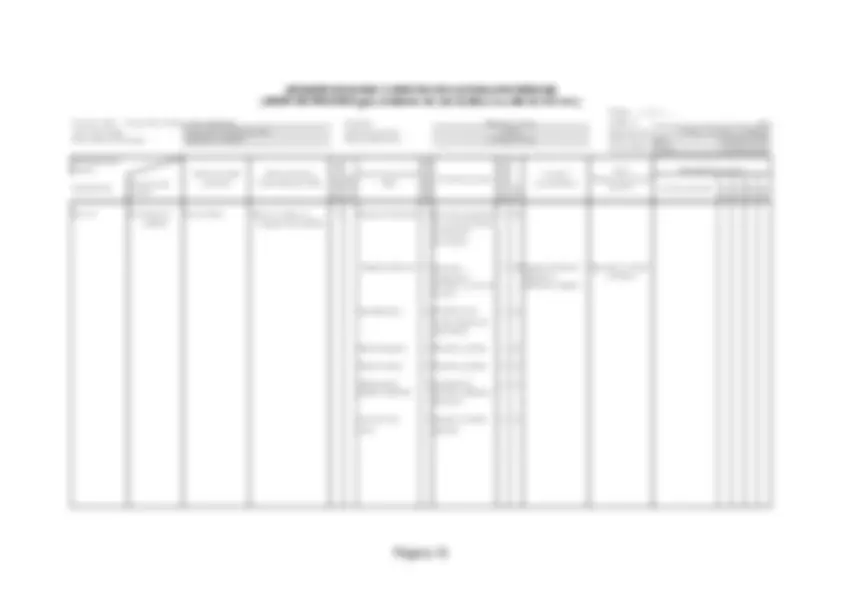
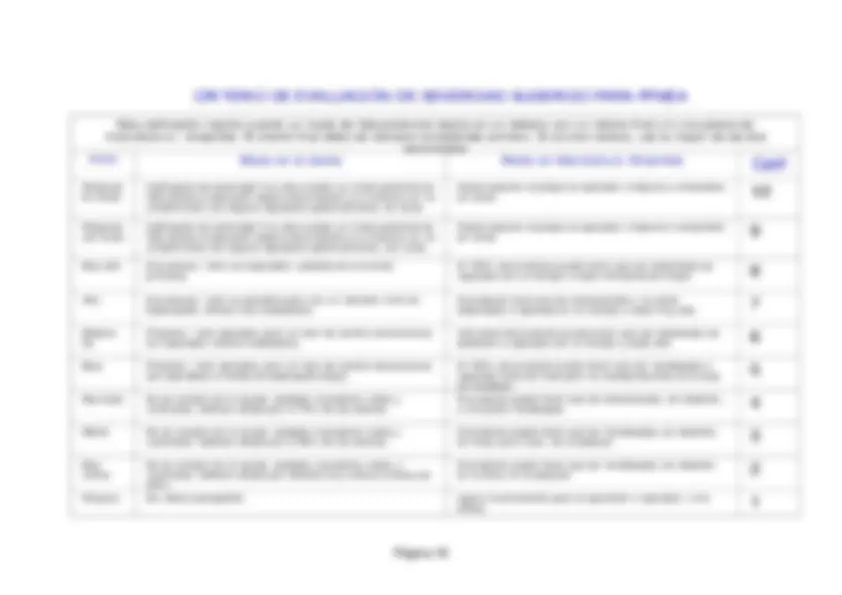
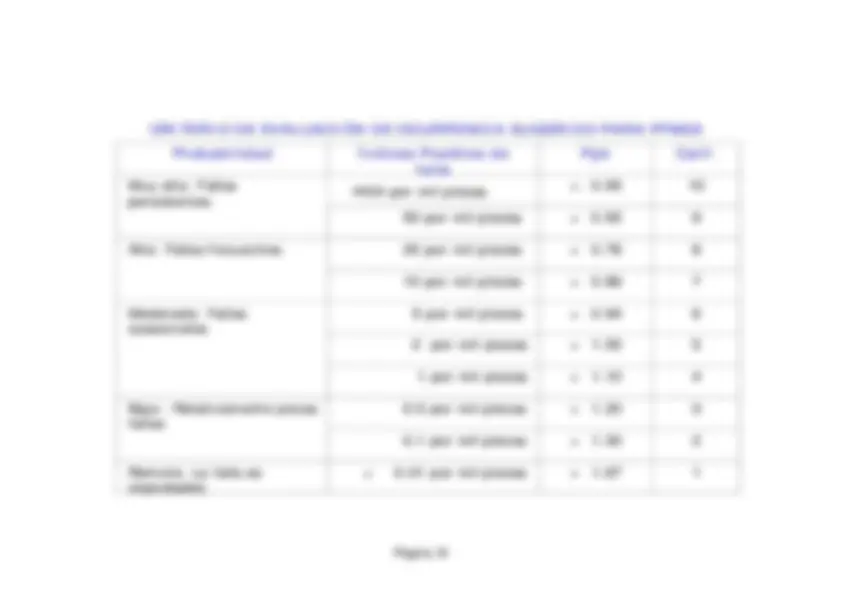
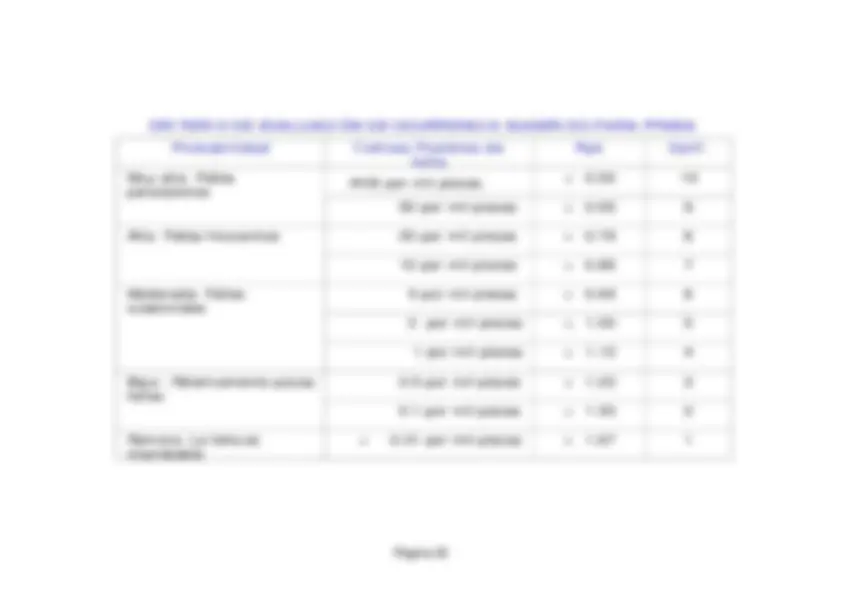
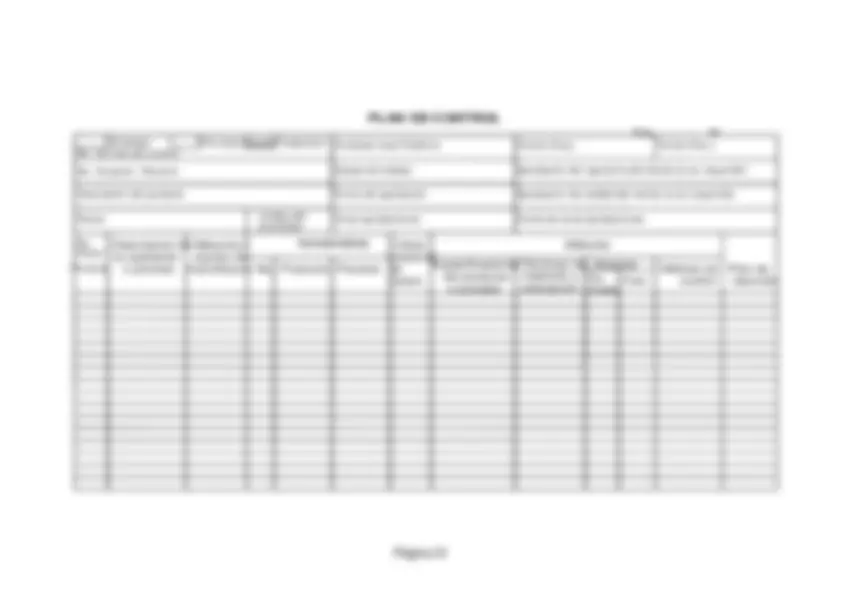
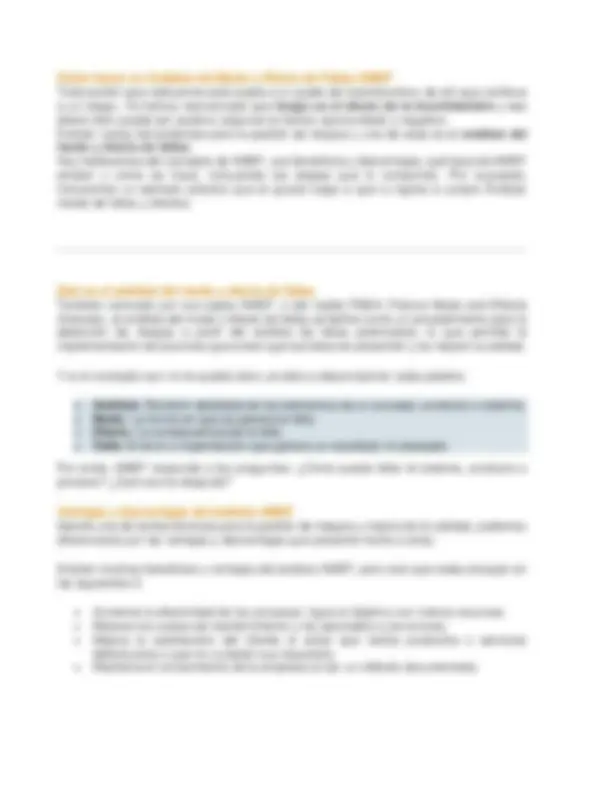
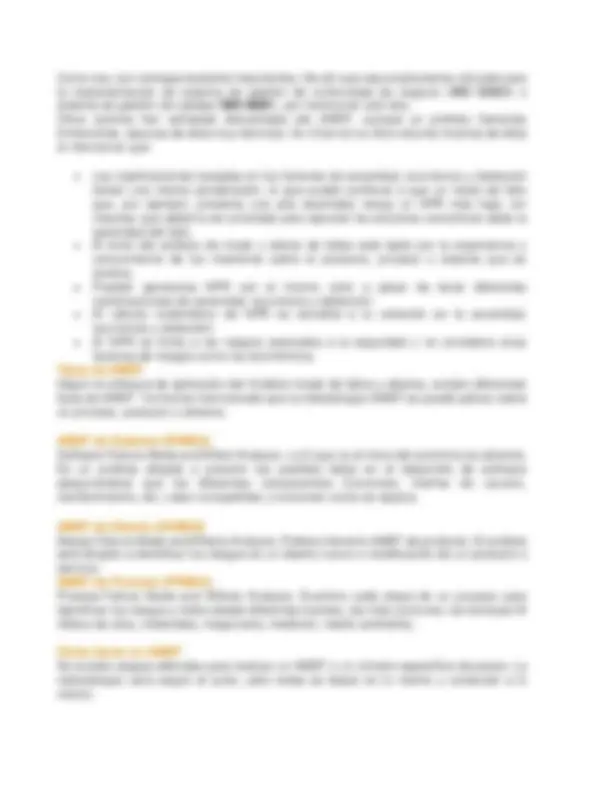
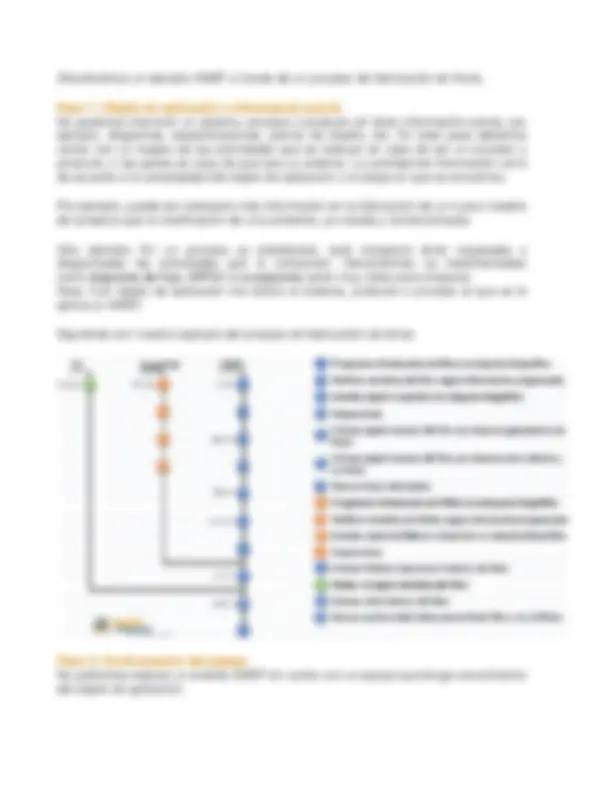
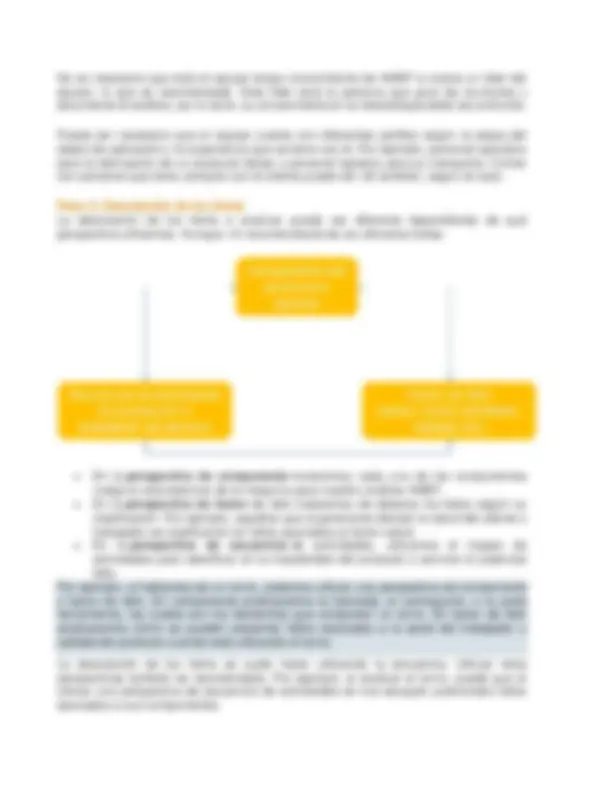
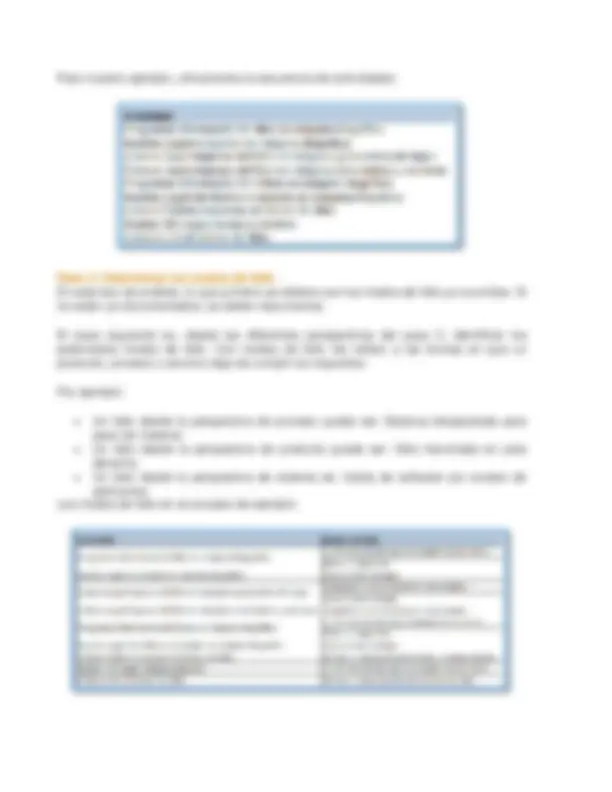
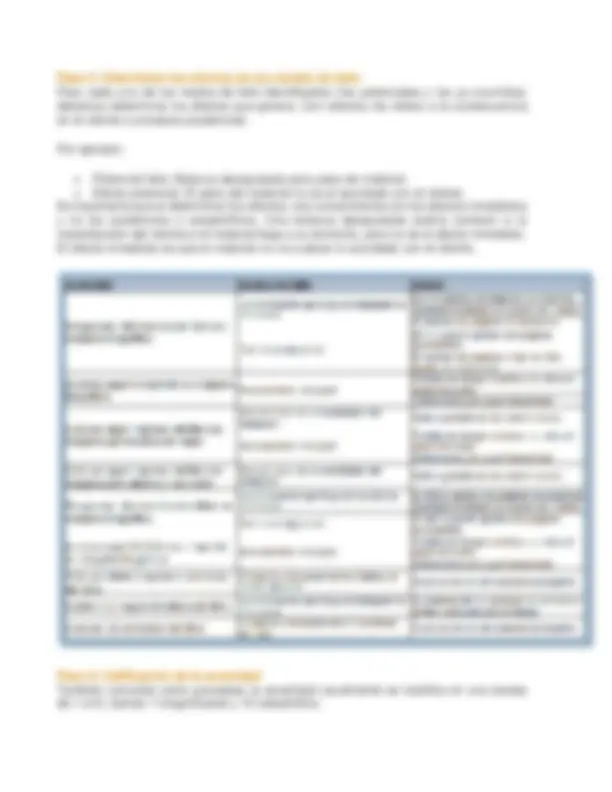
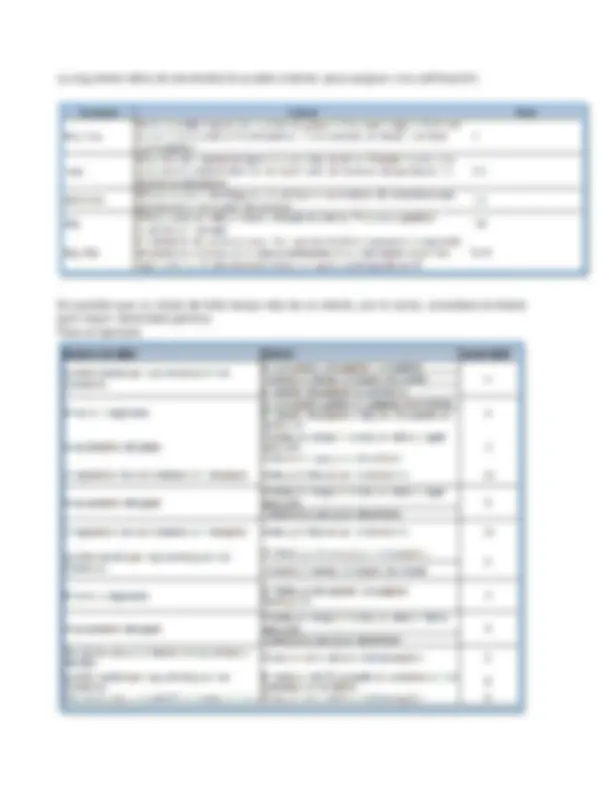
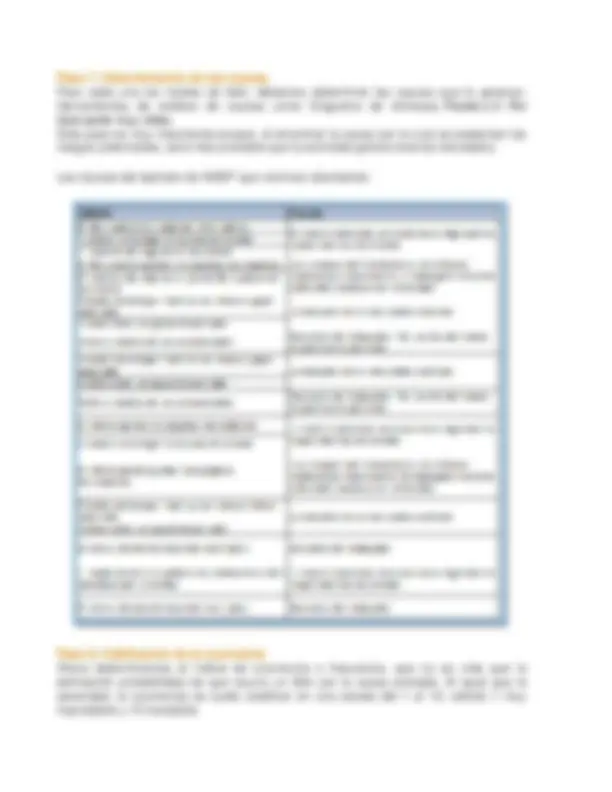
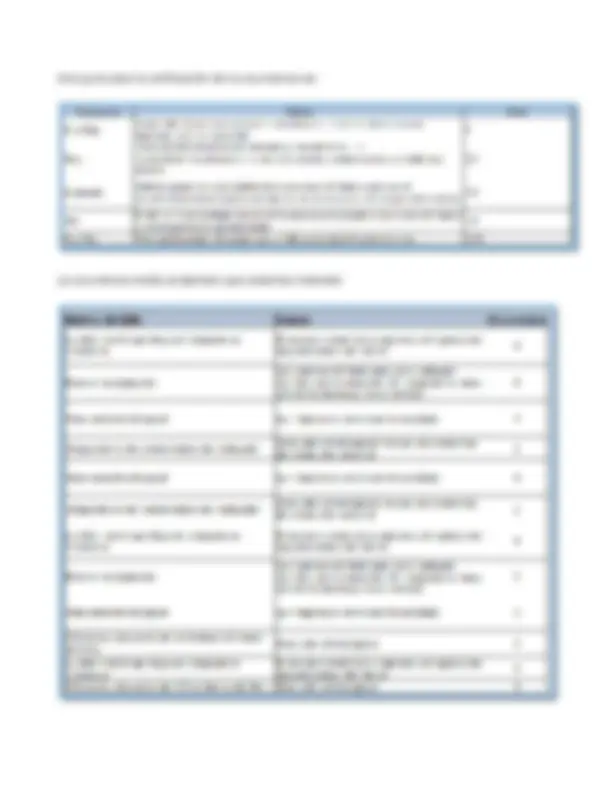
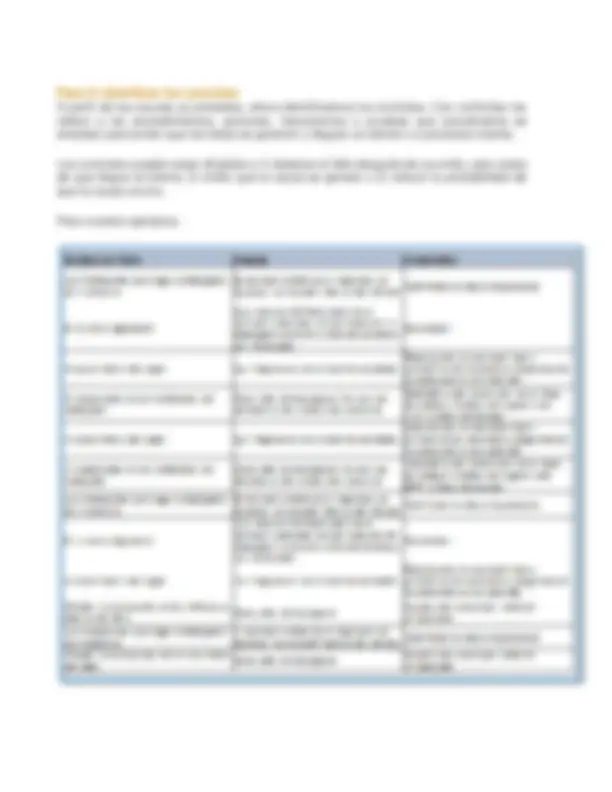
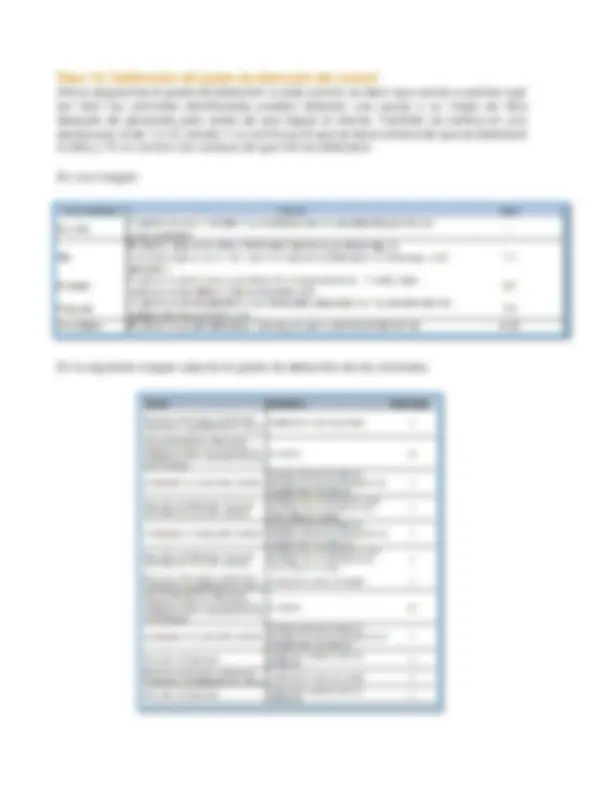
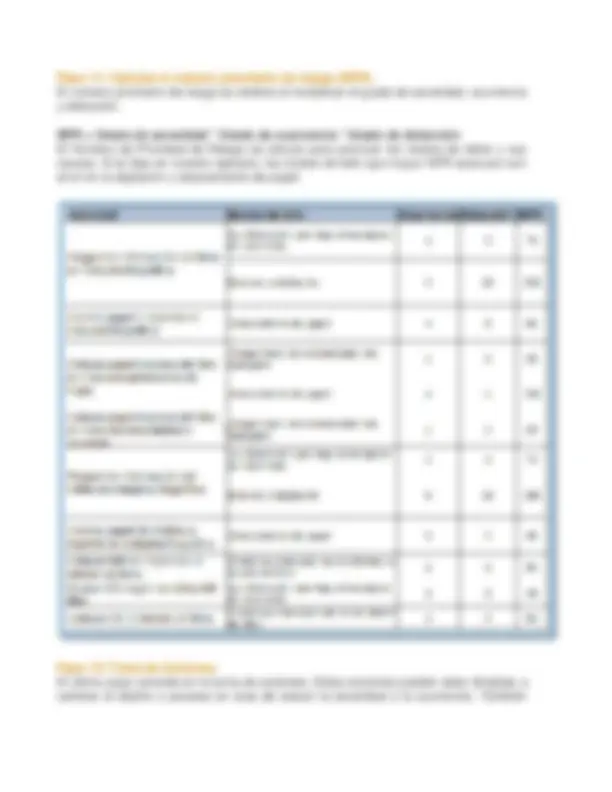
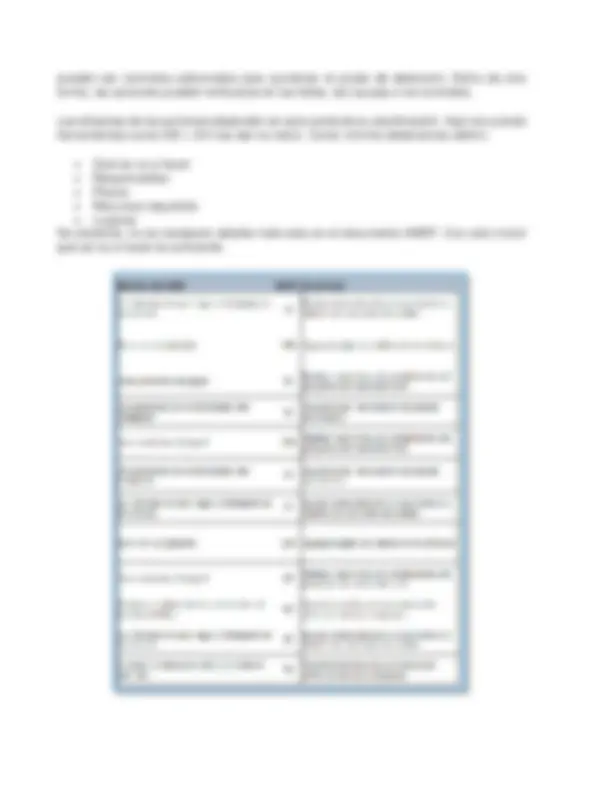
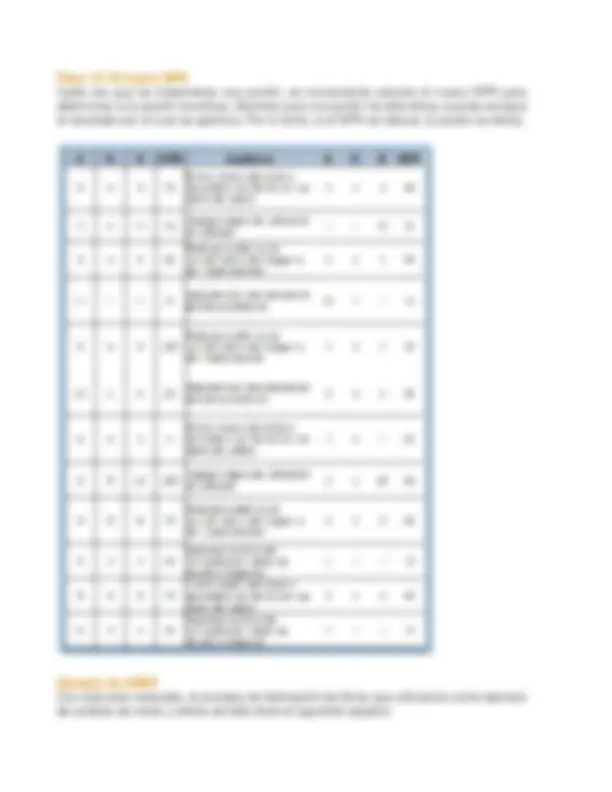
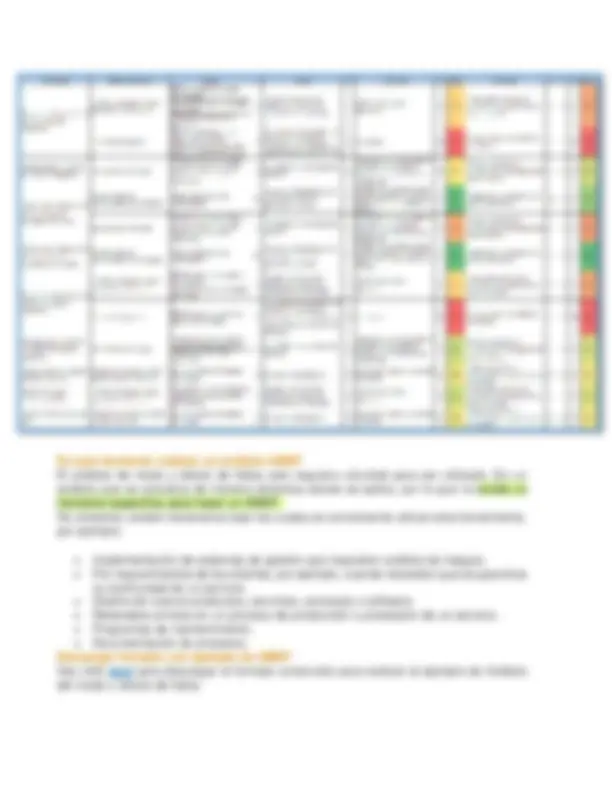
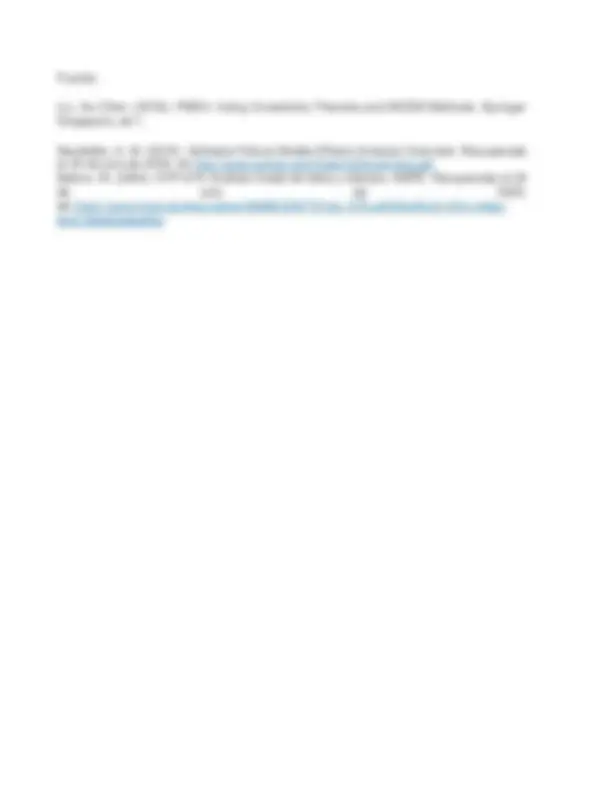
Prepara tus exámenes y mejora tus resultados gracias a la gran cantidad de recursos disponibles en Docsity
Gana puntos ayudando a otros estudiantes o consíguelos activando un Plan Premium
Prepara tus exámenes
Prepara tus exámenes y mejora tus resultados gracias a la gran cantidad de recursos disponibles en Docsity
Prepara tus exámenes con los documentos que comparten otros estudiantes como tú en Docsity
Los mejores documentos en venta realizados por estudiantes que han terminado sus estudios
Estudia con lecciones y exámenes resueltos basados en los programas académicos de las mejores universidades
Responde a preguntas de exámenes reales y pon a prueba tu preparación
Consigue puntos base para descargar
Gana puntos ayudando a otros estudiantes o consíguelos activando un Plan Premium
Comunidad
Pide ayuda a la comunidad y resuelve tus dudas de estudio
Descubre las mejores universidades de tu país según los usuarios de Docsity
Ebooks gratuitos
Descarga nuestras guías gratuitas sobre técnicas de estudio, métodos para controlar la ansiedad y consejos para la tesis preparadas por los tutores de Docsity
El proceso de AMEF (Failure Mode and Effects Analysis), una metodología utilizada para la detección de riesgos y la implementación de acciones preventivas en el diseño y fabricación de productos. El AMEF permite identificar modos potenciales de falla y evaluar su gravedad, probabilidad y efectos, con el objetivo de reducir la cantidad de fallas y mejorar la calidad final. El documento incluye ejemplos de fallas en procesos y recomendaciones para controles actuales y acciones correctivas.
Tipo: Monografías, Ensayos
1 / 37
Esta página no es visible en la vista previa
¡No te pierdas las partes importantes!
Página 1
El AMEF es una herramienta clave para mejorar la confiabilidad de procesos y productos.
La metodología del análisis de modo y efecto de las fallas ( AMEF , FMEA, Failure Mode and Effects Analysis ), proporciona la orientación y los pasos que un grupo de personas debe seguir para identificar y evaluar las fallas potenciales de un producto o un proceso, junto con el efecto que provocan éstas. A partir de lo anterior, el grupo establece prioridades y decide acciones para intentar eliminar o reducir la posibilidad de que ocurran las fallas potenciales que más vulneran la confiabilidad del producto o el proceso.
Aplicar AMEF se ha vuelto un actividad casi obligada para garantizar que los productos sean confiables, en el sentido que logren funcionar bien el tiempo que se ha establecido como su periodo de vida útil, pero también cada día se hace más común su aplicación en muchos otros campos con el objetivo de detectar fallas potenciales y prevenirlas, y de esa forma reducir los tiempos de ciclo, mejorar la eficiencia de procesos, etc. Si un producto o un proceso se analizara como un edificio, aplicarles un AMEF es revisar sus cimientos y estructura, para asegurar que ambas sean confiables y seguras, para disminuir la probabilidad de que fallen. En éste sentido, un edificio, (proceso) no está realmente caracterizado, sino hasta que se le ha aplicado el AMEF, y a partir de éste se fundamentan acciones para su mejora integral.
La frecuencia con que ocurren las fallas junto con su severidad son una medida de la confiabilidad de un sistema. Mientras mayor sean éstas menor será tal confiabilidad. De ésta forma una tarea fundamental cuando se busca caracterizar y mejorar un proceso es aplicar la metodología del AMEF, con la idea de conocer mejor las debilidades (modos de falla potenciales) del producto o proceso y a partir de ahí generar soluciones a nivel proceso o rediseño de producto. Como se comentará adelante, las herramientas estadísticas serán de utilidad para establecer la frecuencia de fallas, los efectos y las causas más importantes y
Página 2
Página 4
Para cada falla potencial:
La información obtenida con las actividades descritas se organiza en un formato especial como el que se muestra en el formato de la página 14 donde también se muestran las actividades y secuencia de pasos para realizar un AMEF.
En el formato de AMEF con números circulados (página 14) , que corresponden a la información que se deberá anotar en cada parte del formato que a continuación
Página 5
explicamos para cada uno de estos números. Este formato ha permitido un desarrollo uniforme del AMEF. En la figura aparece un ejemplo y un formato en blanco.
1. Página/ De : anotar el número consecutivo correspondiente a la página en la que se trabaja y en De: escribir el número total de hojas que completan el AMEF. 2. Número de proyecto: anotar el número de proyecto al que corresponde este análisis, de acuerdo a los criterios que se utilizan en la empresa. 3. Proceso: registrar el nombre del proceso u operación sobre el cual se está haciendo el análisis. 4. Producto afectado: registre el nombre y /o modelos del(os) producto(s) que se producen en este proceso. 5. Responsabilidad: escribir el nombre de la persona que tiene la responsabilidad primaria del proceso, es decir, la gerencia que tiene la responsabilidad principal de la máquina, equipo o proceso. 6. Líder del proyecto: anotar el nombre del responsable técnico del proyecto. 7. Preparado por: anotar el nombre de las personas que realizaste en este AMEF. 8. Fecha clave: escribir la fecha obligatoria en que se debe terminar este AMEF, ya sea por alguna razón especial como compromisos de liberación de producción o por meta en tiempo que el equipo decida imponerse. 9. Fecha AMEF original y última revisión: si ya se ha hecho antes un AMEF sobre este proceso, anotar la fecha del primer AMEF y la fecha de la última revisión formal.
Página 7
12. Efecto(s) de la falla potencial: se definen como los efectos del modo de falla, este efecto negativo puede darse en el proceso mismo, sobre una operación posterior o el cliente final. De esta forma, suponiendo que la falla ha ocurrido, en esta etapa se deben describir todos los efectos potenciales de los modos de falla señalados en el paso previo. Una pregunta clave para esta actividad es ¿qué ocasionará el modo de falla identificado? La descripción debe ser tan específica como sea posible. Las descripciones típicas de los efectos potenciales de falla, desde la óptica del consumidor final del producto, son:
y El producto no funciona y Eficiencia final reducida y Áspero y Calentamiento excesivo y Ruido y Olor desagradable y Inestabilidad y Mala apariencia
Mientras que desde la óptica de una operación posterior, algunos efectos potenciales típicos son:
y No abrocha y Pone en peligro a operadores y No se puede taladrar y No ensambla y No se puede montar y No se puede conectar
13. Severidad (S): estimar la severidad de los efectos listados en la columna previa. La severidad de los efectos potenciales de falla se evalúa en una escala del 1 al 10 y representa la gravedad de la falla para el cliente o para una operación posterior, una vez que esta falla ha ocurrido. La severidad solo se refiere o se aplica al efecto.
Página 8
Se puede consultar a ingeniería del producto para grados de severidad recomendados o estimar el grado de severidad aplicando los criterios de la tabla. Los efectos pueden manifestarse en el cliente final o en el proceso de manufactura. Siempre se debe considerar primero al cliente final. Si el efecto ocurre en ambos, use la severidad más alta. El equipo de trabajo debe estar de acuerdo en los criterios de evaluación y en que el sistema de calificación sea consistente.
14. Control o artículos críticos: utilizar esta columna para identificar o clasificar las características críticas del proceso que requieren controles adicionales; por tanto se le debe notificar al responsable del diseño de proceso. 15. Causas /mecanismo de la falla potencial (mecanismo de falla): hacer un lista de todas las posibles causas para cada modo potencial de falla. Entendiendo como causa de falla a la manera como podría ocurrir la falla. Cada causa ocupa un renglón. Asegurarse de que la lista sea lo mas completa posible, para ello puede aplicarse el diagrama de Ishikawa, diagrama de relación o diagrama de árbol. Las causas típicas de falla son:
y Abertura inadecuada y Capacidad excedida y Operación faltante y Daño por manejo y Sistema de control inadecuado y Falla de material y Herramienta desgastada y Lubricación inadecuada y Herramienta dañada y Parte dañada y Preparación inadecuada y Sobrecalentamiento y Velocidad incorrecta y Medición inexacta
Página 10
un cambio notable del grado de detección. Sin embargo, el muestreo hecho sobre una base estadística es un control de detección válido. En la tabla se muestran los criterios recomendados para estimar la probabilidad de detección.
19. Número de prioridad del riesgo (NPR): calcular el NPR para efecto-causas- controles, que es el resultado de multiplicar la puntuación dada a la severidad (S-
NPR = (S) x (O) x (D)
El NPR cae en un rango del 1 a 1 000 y proporciona un indicador relativo de todas las causas de falla. Alos más altos números de NPR se les deberá dar prioridad para acciones correctivas, Y sea para prevenir la cusa o por lo menos para emplear mejores controles de detección. Especial atención debe darse cuando se tengan altos NPR (mayores a 80) con severidades altas.
Un ejemplo se muestra al final en la página 10.
20. Acciones recomendadas: en esta columna se describe una breve descripción de las acciones correctivas recomendadas para los NPR más altos. Por ejemplo cuando hay poca comprensión de las causas de la falla, entonces la recomendación podría ser ejecutar un proyecto de mejora basado en los “ocho pasos en la solución de un problema (el ciclo de la calidad).
Un AMEF de proceso bien desarrollado y pensado será de un valor limitado si no se completan acciones correctivas y efectivas. Es responsabilidad de todas las áreas afectadas establecer programas de seguimiento efectivo para implantar todas las recomendaciones. Las acciones correctivas que atiendan los NPR más altos son generalmente para el diseño o el proceso. Basadas en el análisis, las acciones pueden ser usadas para lo siguiente:
Página 11
y Generar soluciones que eviten, prevengan o por lo menos reduzcan la probabilidad de ocurrencia de la falla, debido a la causa asociada. Estas soluciones deben ser a nivel proceso o diseño de producto. Las herramientas que se pueden utilizar para generar una buena solución son: metodología de los ocho pasos, diseño de experimentos, sistemas poka- yoke, o cartas de control. y En algunas ocasiones es posible reducir la severidad del modo de falla del producto modificando su diseño. y Para incrementar la probabilidad de detección se requieren revisiones al proceso. Generalmente, un aumento de los controles de detección es costoso e ineficaz para mejorar la calidad. Un incremento en la frecuencia de inspección en el departamento de calidad no es una acción correctiva positiva y debe utilizarse sólo como último recurso o medida temporal. y En algunos casos puede recomendarse un cambio en el diseño de una parte específica para ayudar a la detección. Pueden implementarse cambios en los sistemas de control actuales para incrementar la probabilidad de detección; sin embargo, debe ponerse énfasis en la prevención de defectos (es decir, reduciendo la ocurrencia), en vez de su detección; por ejemplo, teniendo un control estadístico de proceso en lugar de técnicas de muestreo al azar. Otra posibilidad es diseñar un mecanismo poka-yoke, que al integrarse al proceso mismo garantice la plena detección del defecto antes de que haya peores consecuencias.
21. Responsabilidad y fecha prometida para acciones recomendadas: especificar el área y personas responsables de la ejecución de las acciones recomendadas, con la fecha prometida para concluir tales acciones.
Página 13
Ejercicios:
Página 14
Página: ____ de _____
Proyecto: _______ Proceso:No. Nombre:
Producto
AMEF #:
Area responsable:
Líder del proyecto:
Preparado por:
Otras areas involucradas
Fecha de liberacion
Fecha Amef originalFecha Última revisión
Descripcion delprocesoIdentificación
Proposito delproceso
Acciones tomadas
SEV
OCU
DET
NRP
ANALISIS DE MODO Y EFECTO DE LA FALLA POTENCIAL
(AMEF DE PROCESO) Causa potencial omecanismo de la
falla
OCURRENCI
Controles actuales
Accionesrecomendadas
Modo de la fallapotencial
Efectos-Causa(s)Potenciales de la falla
SEVERIDAD
CRITICA
Area/ Responsable/Fecha
de cierre
Resultado de acciones
DETECCION
NPR
1
2
3
4
5
6
7
8
9
10
11
12
13
14
15
16
17
18
19
20
21
22
23
Página 16
Página: ____ de _____
Proyecto: _______ Proceso:No. Nombre:
Producto
AMEF #:
Area responsable:
Líder del proyecto:
Preparado por:
Otras areas involucradas
Fecha de liberacion
Fecha Amef originalFecha Última revisión
Descripcion delprocesoIdentificación
Proposito delproceso
Acciones tomadas
SEV
OCU
DET
NRP
Resultado de acciones
DETECCION
NPR
Area/ Responsable/Fecha
de cierre
Modo de la fallapotencial
Efectos-Causa(s)Potenciales de la falla
SEVERIDAD
DELTACausa potencial de la
falla
OCURRENCI
Controles actuales
Accionesrecomendadas
ANALISIS DE MODO Y EFECTO DE LA FALLA POTENCIAL
(AMEF DE PROCESO)
Página 17
Página: ____ de _____
Proyecto: _______ Proceso:No. Nombre:
Producto
AMEF #:
Area responsable:
Líder del proyecto:
Preparado por:
Otras areas involucradas
Fecha de liberacion
Fecha Amef originalFecha Última revisión
Descripcion delprocesoIdentificación
Proposito delproceso
Acciones tomadas
SEV
OCU
DET
NRP
Resultado de acciones
DETECCION
NPR
Area/ Responsable/Fecha
de cierre
Modo de la fallapotencial
Efectos-Causa(s)Potenciales de la falla
SEVERIDAD
DELTACausa potencial de la
falla
OCURRENCI
Controles actuales
Accionesrecomendadas
ANALISIS DE MODO Y EFECTO DE LA FALLA POTENCIAL
(AMEF DE PROCESO)
Página 19
Página 20
100 por mil piezas
Probabilidad
Índices Posibles de
falla
Ppk
Calif.
Muy alta: Fallaspersistentes
50 por mil piezas
Alta: Fallas frecuentes
20 por mil piezas
10 por mil piezas
Moderada: Fallasocasionales
5 por mil piezas
por mil piezas
1 por mil piezas
Baja : Relativamente pocasfallas
0.5 por mil piezas
0.1 por mil piezas
Remota: La falla esimprobable
0.01 por mil piezas