
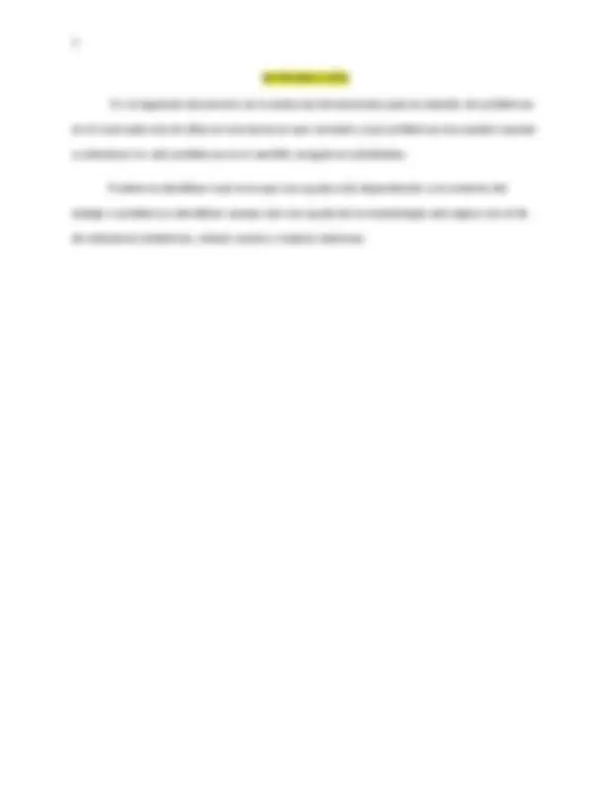
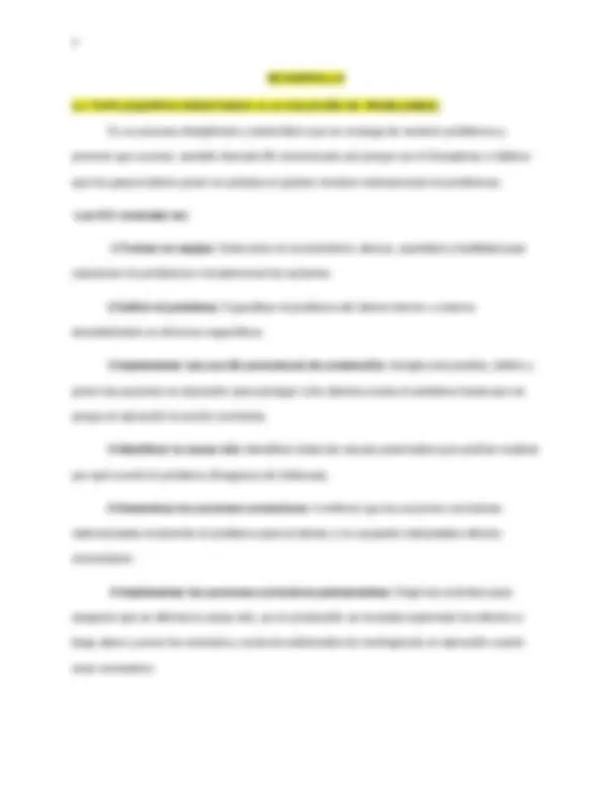
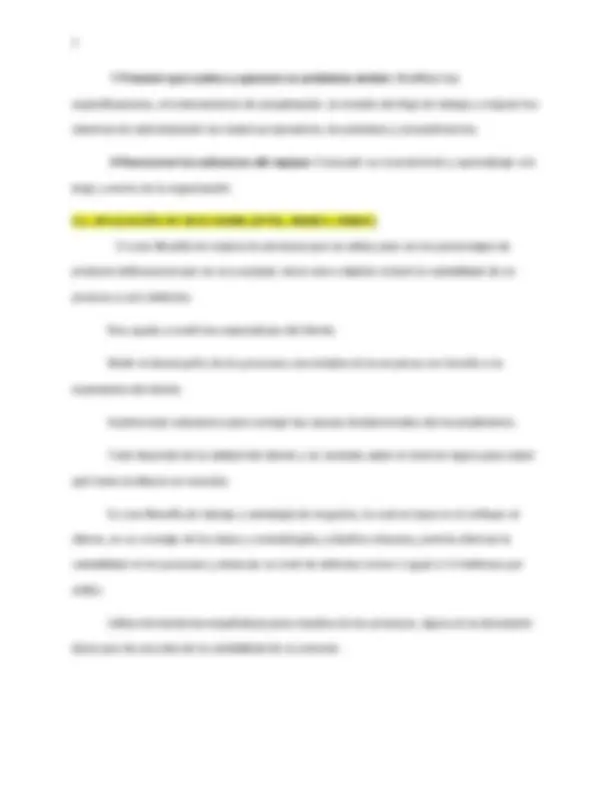
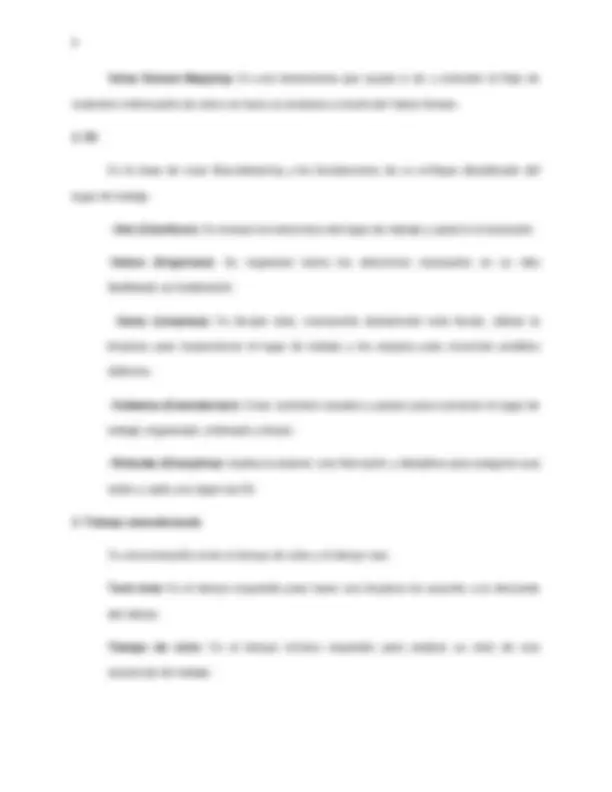
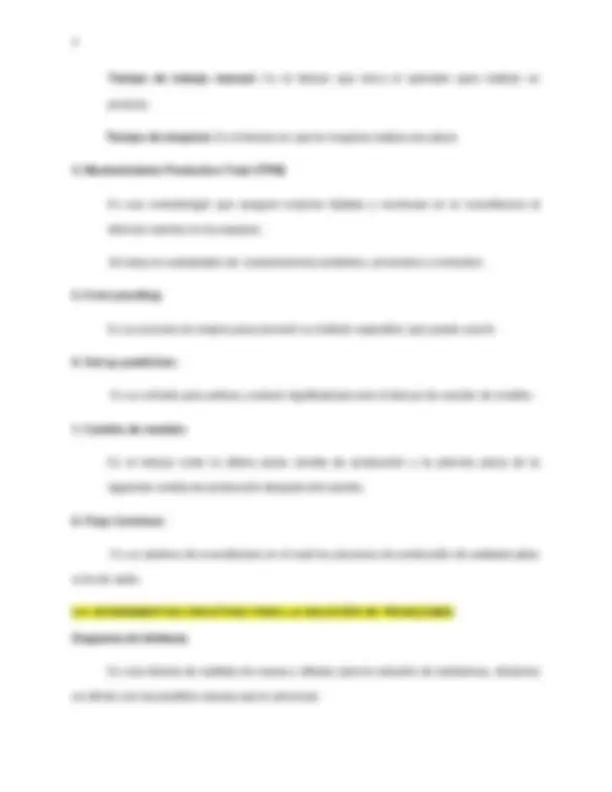
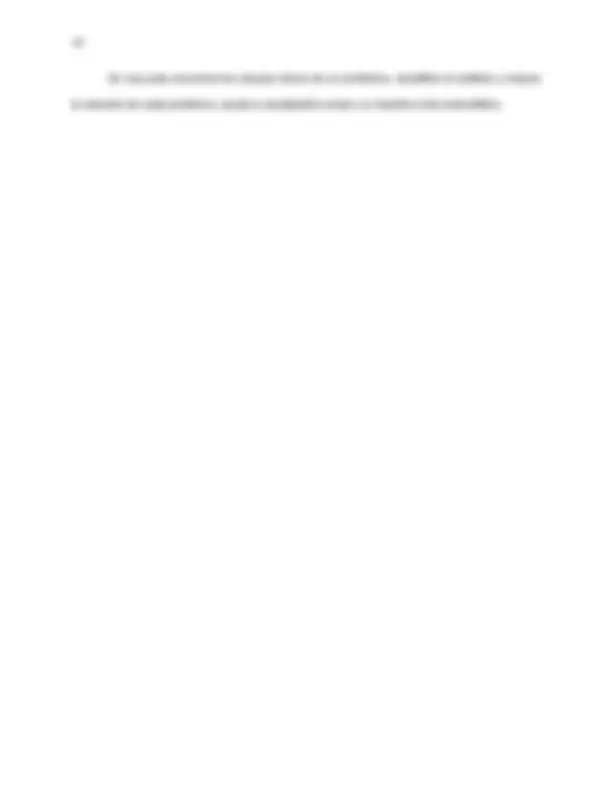
Prepara tus exámenes y mejora tus resultados gracias a la gran cantidad de recursos disponibles en Docsity
Gana puntos ayudando a otros estudiantes o consíguelos activando un Plan Premium
Prepara tus exámenes
Prepara tus exámenes y mejora tus resultados gracias a la gran cantidad de recursos disponibles en Docsity
Prepara tus exámenes con los documentos que comparten otros estudiantes como tú en Docsity
Los mejores documentos en venta realizados por estudiantes que han terminado sus estudios
Estudia con lecciones y exámenes resueltos basados en los programas académicos de las mejores universidades
Responde a preguntas de exámenes reales y pon a prueba tu preparación
Consigue puntos base para descargar
Gana puntos ayudando a otros estudiantes o consíguelos activando un Plan Premium
Comunidad
Pide ayuda a la comunidad y resuelve tus dudas de estudio
Descubre las mejores universidades de tu país según los usuarios de Docsity
Ebooks gratuitos
Descarga nuestras guías gratuitas sobre técnicas de estudio, métodos para controlar la ansiedad y consejos para la tesis preparadas por los tutores de Docsity
Un análisis de las herramientas para la solución de problemas, incluyendo tops (equipos orientados a la solución de problemas), seis sigma (dfss, dmadv, dmaic) y lean manufacturing. Se explora la aplicación de cada herramienta, sus etapas, y su utilidad para la mejora de procesos, la reducción de costos y la optimización de la producción. El documento también incluye ejemplos prácticos y referencias bibliográficas.
Tipo: Guías, Proyectos, Investigaciones
1 / 12
Esta página no es visible en la vista previa
¡No te pierdas las partes importantes!
ALUMNO: Manzanarez Rivera Edwin Jacob GRUPO YB TEMA 3: SOLUCIÓN DE PROBLEMAS DE MANUFACTURA 10 DE OCTUBRE DE 2024 PRIMERA OPORTUNIDAD ÍNDICE INTRODUCCIÓN........................................................................................................................................... 3
Es un proceso disciplinado y sistemático que se encarga de resolver problemas y prevenir que ocurran, también llamado 8D denominado así porque son 8 Disciplinas o hábitos que los grupos deben poner en práctica si quieren resolver exitosamente los problemas. Los 8 D consisten en: 1 Formar un equipo : Debe tener el conocimiento, tiempo, autoridad y habilidad para solucionar los problemas e implementar las acciones. 2 Definir el problema : Especificar el problema del cliente interno o externo describiéndolo en términos específicos. 3 Implementar una acción provisional de contención: Arreglos temporales, definir y poner las acciones en ejecución para proteger a los clientes contra el problema hasta que se ponga en ejecución la acción correctiva. 4 Identificar la causa raíz: Identificar todas las causas potenciales que podrían explicar por qué ocurrió el problema (Diagrama de Ishikawa). 5 Determinar las acciones correctivas: Confirmar que las acciones correctivas seleccionadas resolverán el problema para el cliente y no causarán indeseables efectos secundarios. 6 Implementar las acciones correctivas permanentes: Elegir los controles para asegurar que se elimina la causa raíz, ya en producción se necesita supervisar los efectos a largo plazo y poner los controles y acciones adicionales de contingencia en ejecución cuanto sean necesarios.
7 Prevenir que vuelva a aparecer un problema similar: Modificar las especificaciones, el entrenamiento de actualización, la revisión del flujo de trabajo y mejorar los sistemas de administración los sistemas operativos, las prácticas y procedimientos. 8 Reconocer los esfuerzos del equipo: Compartir su conocimiento y aprendizaje a lo largo y ancho de la organización. 3.2. APLICACIÓN DE SEIS SIGMA (DFSS, DMADV, DMAIC) Es una filosofía de mejora de procesos que se utiliza para ver los porcentajes de producto defectuosos que se va a aceptar, tiene como objetivo reducir la variabilidad de un proceso a cero defectos. Nos ayuda a medir las expectativas del cliente. Medir el desempeño de los procesos comerciales de la empresa con función a la expectativa del cliente. Implementar soluciones para corregir las causas fundamentales del incumplimiento. Todo depende de la calidad del cliente y se necesita saber el nivel de sigma para saber qué tanta confianza se necesita. Es una filosofía de trabajo y estrategia de negocios, la cual se basa en el enfoque al cliente, en un montaje de los datos y metodologías y diseños robustos, permite eliminar la variabilidad en los procesos y alcanzar un nivel de defectos menor o igual a 3.4 defectos por millón. Utiliza herramientas estadísticas para estudios de los procesos, sigma es la desviación típica que da una idea de la variabilidad de un proceso.
Define (Definir): ¿Cuál es el problema? Definir las necesidades del cliente y precisar los objetivos a conseguir, cuadrar el proyecto. Measure performance (medir): ¿Cuál es la capacidad del proceso considerado? Recolectar los datos representativos, medir la prestación, identificar las zonas de progreso. Analyze (analizar): ¿Cuándo, dónde y cómo se producen los defectos? Utilización de las herramientas analíticas y estadísticas para identificar las causas de los problemas. Improve performance (mejorar): ¿Cuáles son las soluciones de mejoría, cómo ponerlas en practica para alcanzar los objetivos del performance fijados? Identificación y puesta en práctica de las soluciones para eludir los susodichos problemas. Control performance (controlar): ¿Cómo guiar las claves variables para sostener y mantener la ventaja? Seguimiento de las soluciones establecidas. 3.3. HERRAMIENTAS LEAN MANUFACTURING Lean Manufacturing es una filosofía de gestión enfocada en la reducción de los ocho tipos de desperdicios (sobreproducción, tiempo de espera, transporte, exceso de procesado, inventario, movimiento y defectos, potencial humano sub-utilizado) en productos manufacturados. Las 8 herramientas de Lean Manufacturing:
1. VSM (Value Stream Mapping). Value Stream : Son todas las actividades en un negocio que son necesarias para diseñar y producir un producto y entregarlo al cliente final.
Value Stream Mapping: Es una herramienta que ayuda a ver y entender el flujo de material e información de cómo se hace un producto a través del Value Stream.
2. 5S Es la base de Lean Manufacturing y los fundamentos de un enfoque disciplinado del lugar de trabajo. -Seri (Clasificar): Se revisan los elementos del lugar de trabajo y quitar lo innecesario. -Seiton (Organizar): Se organizan todos los elementos necesarios en su sitio facilitando su localización. -Seiso (Limpieza): Es limpiar todo, mantenerlo diariamente todo limpio, utilizar la limpieza para inspeccionar el lugar de trabajo y los equipos para encontrar posibles defectos. –Seiketsu (Estandarizar): Crear controles visuales y pautas para mantener el lugar de trabajo organizado, ordenado y limpio. -Shitsuke (Disciplina): Implica mantener una formación y disciplina para asegurar que todos y cada uno sigan las 5S. 3. Trabajo estandarizado Es sincronización entre el tiempo de ciclo y el tiempo tact. Tack time: Es el tiempo requerido para hacer una limpieza de acuerdo a la demanda del cliente. Tiempo de ciclo: Es el tiempo mínimo requerido para realizar un ciclo de una secuencia de trabajo.
Se usa para encontrar las causas raíces de un problema, simplifica el análisis y mejora la solución de cada problema, ayuda a visualizarlos mejor y a hacerlos más entendibles.
El sistema de lean Manufacturing lleva a una empresa que lo implanta a niveles altamente rentables y competitivos. Las herramientas que el sistema ofrece permite modificar y mejorar en aquellas actividades y campos donde se aplique, pero es necesaria una estandarización del sistema que afirme y consolide todas las acciones que se realicen. La manufactura enfrenta la optimización de la producción, el mantenimiento de la calidad, la reducción de costos y la mejora continua de los productos y procesos.