
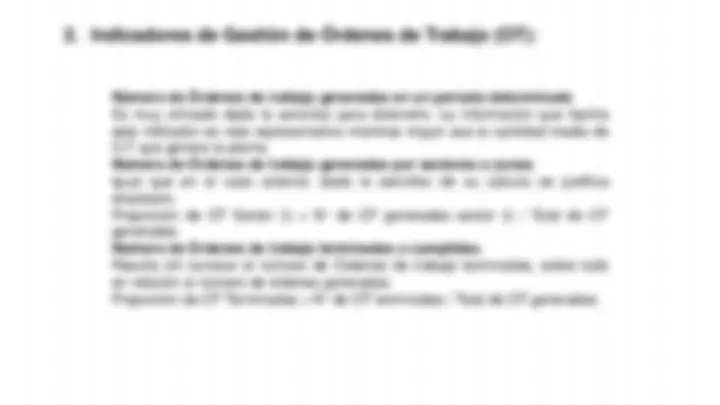
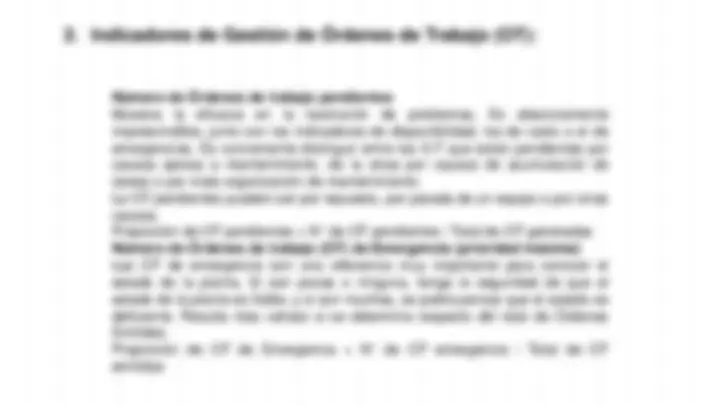
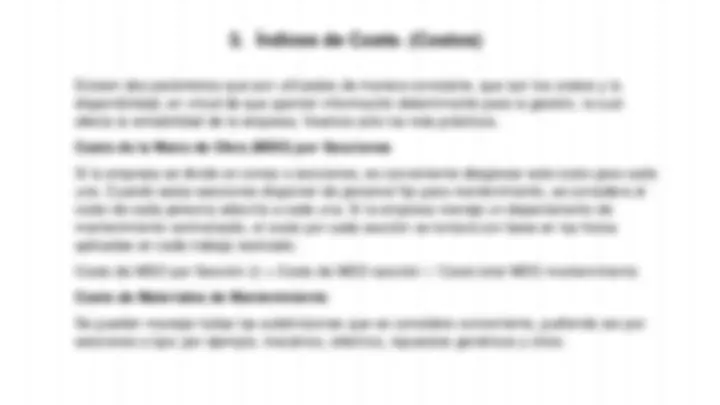
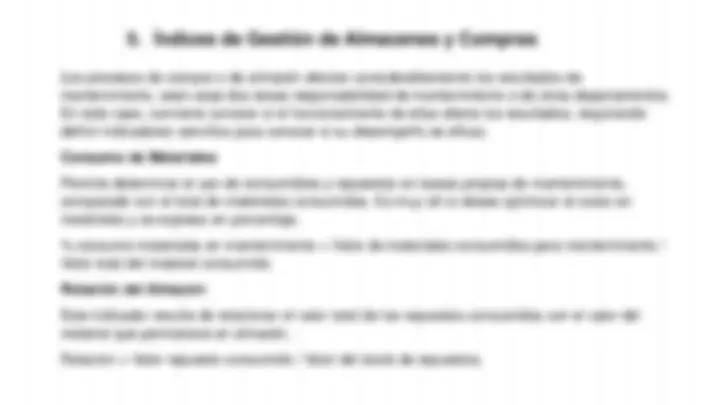
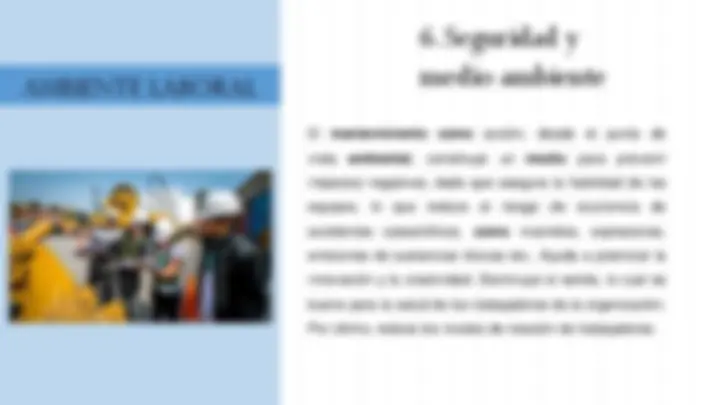
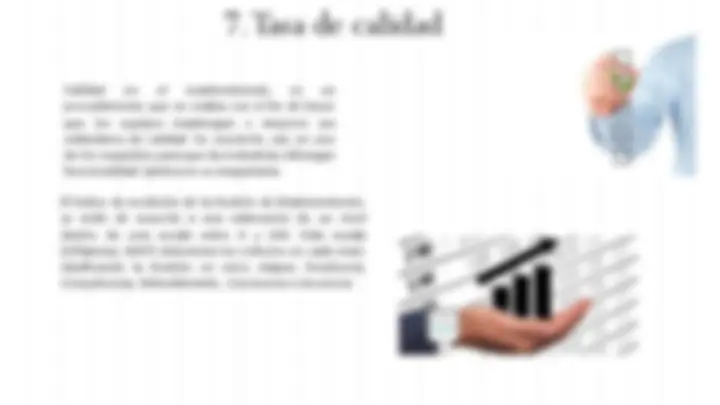
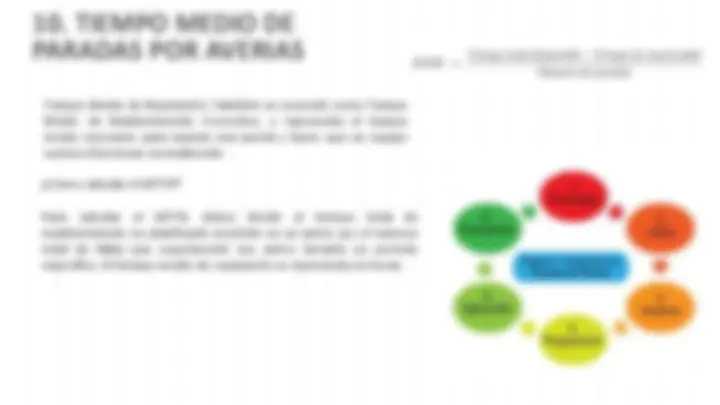
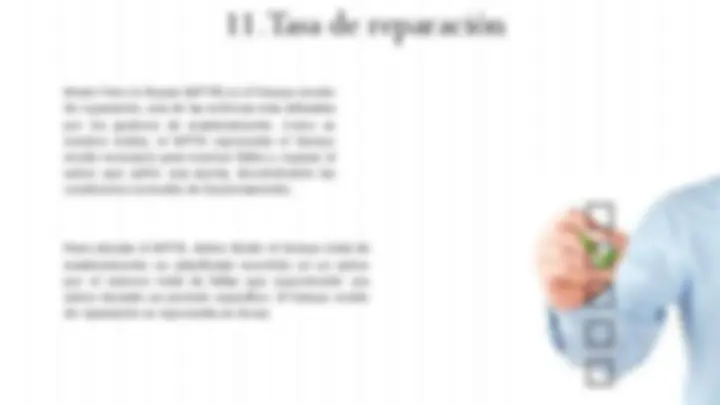
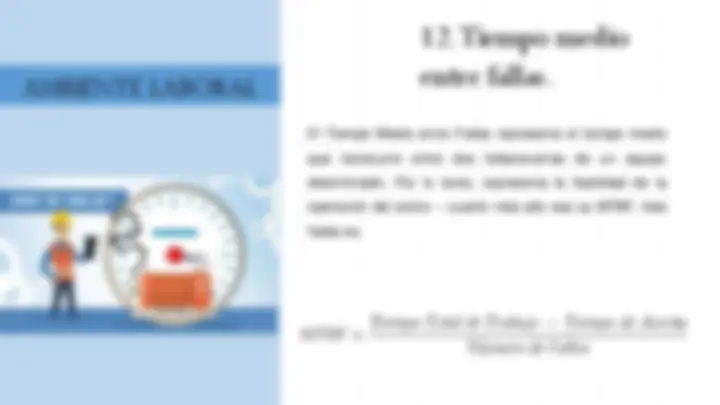
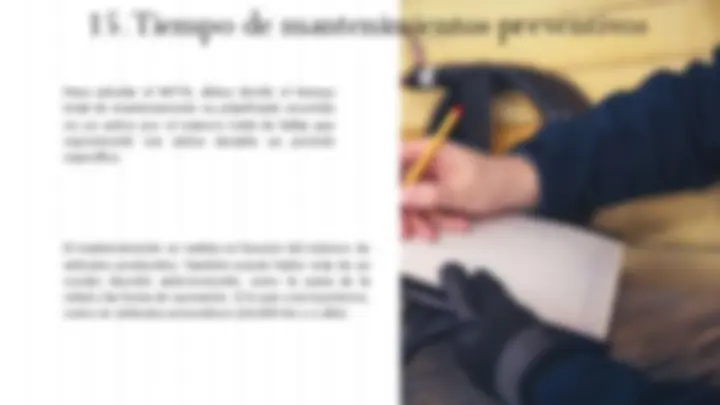
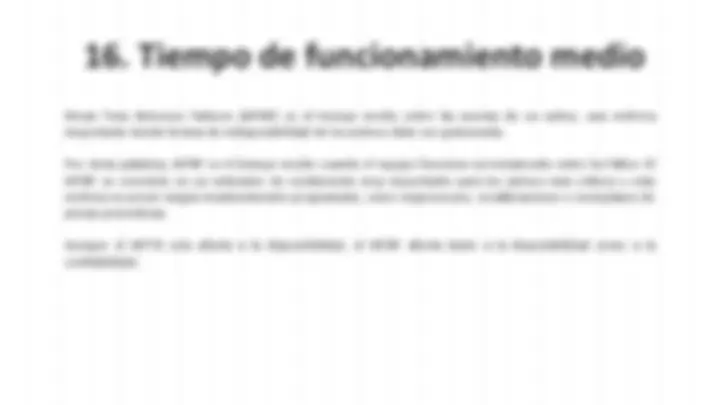
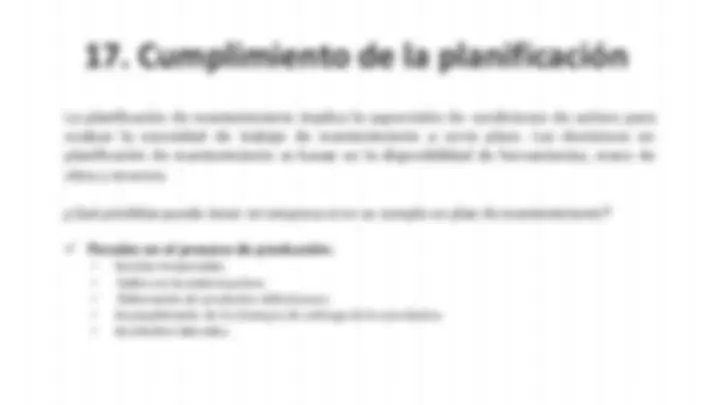
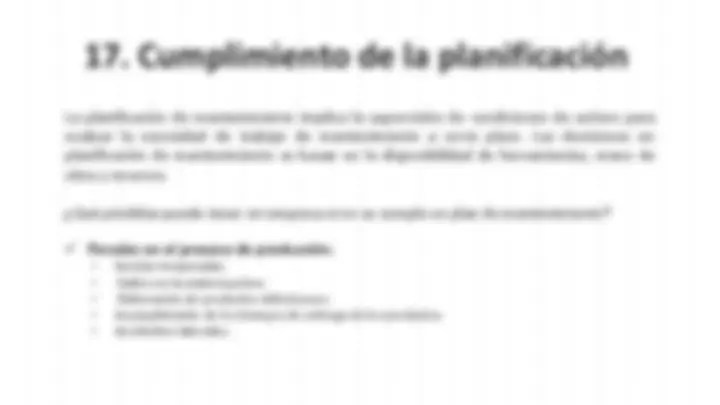
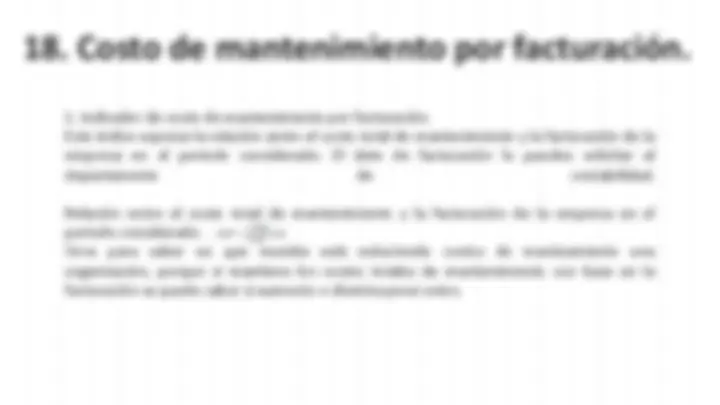
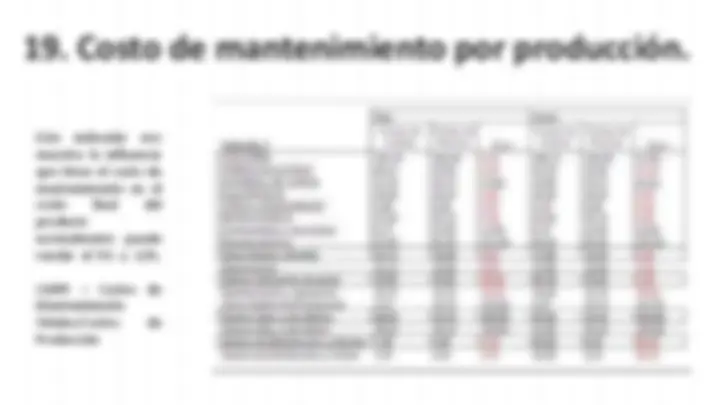
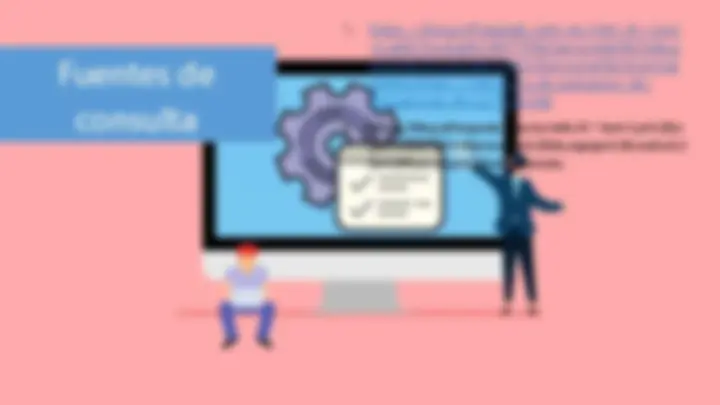
Prepara tus exámenes y mejora tus resultados gracias a la gran cantidad de recursos disponibles en Docsity
Gana puntos ayudando a otros estudiantes o consíguelos activando un Plan Premium
Prepara tus exámenes
Prepara tus exámenes y mejora tus resultados gracias a la gran cantidad de recursos disponibles en Docsity
Prepara tus exámenes con los documentos que comparten otros estudiantes como tú en Docsity
Los mejores documentos en venta realizados por estudiantes que han terminado sus estudios
Estudia con lecciones y exámenes resueltos basados en los programas académicos de las mejores universidades
Responde a preguntas de exámenes reales y pon a prueba tu preparación
Consigue puntos base para descargar
Gana puntos ayudando a otros estudiantes o consíguelos activando un Plan Premium
Comunidad
Pide ayuda a la comunidad y resuelve tus dudas de estudio
Descubre las mejores universidades de tu país según los usuarios de Docsity
Ebooks gratuitos
Descarga nuestras guías gratuitas sobre técnicas de estudio, métodos para controlar la ansiedad y consejos para la tesis preparadas por los tutores de Docsity
Abarca pequeña explicación de lo siguiente: 1.Índice de Disponibilidad. 2.Indicadores de Gestión de Órdenes de Trabajo (OT). 3.Índices de Coste (Costos). 4.Índice de Mantenimiento Programado o Preventivo. 5.Índices de Gestión de Almacenes y Compras. 6.Seguridad y medio ambiente. 7.Tasa de calidad, Confiabilidad. 8.Rendimiento. 9.Tiempo medio de paradas por averías. 10.Tasa de Reparación. 11.Tiempo medio entre fallas. 12.Tiempo de mantenimientos preventivos. 13.Tiempo de funcionamiento medio. 14.Cumplimiento de la planificación- 15.Costo de mantenimiento por facturación. 16.Costo de mantenimiento por producción. (Incluye bibliografía)
Tipo: Diapositivas
1 / 24
Esta página no es visible en la vista previa
¡No te pierdas las partes importantes!
Calidad en el mantenimiento es un procedimiento que se realiza con el fin de hacer que los equipos mantengan o mejoren sus estándares de calidad. Se convierte, así, en uno de los requisitos para que las industrias obtengan funcionalidad óptima en su maquinaria. El Índice de medición de la Gestión de Mantenimiento, se mide de acuerdo a una estimación de un nivel dentro de una escala entre 0 y 100. Esta escala (Villamizar, 2007 ) determina los criterios en cada nivel, clasificando la Gestión en cinco etapas: Excelencia, Competencia, Entendimiento, Conciencia e Inocencia
La confiabilidad en la industria es una de las aplicaciones de la Termografía que permite monitorear el comportamiento de cualquier Sistema Termodinámico en el tiempo. Este servicio y su metodología asociada puede ser aplicada a cualquier sistema termodinámico como: Motores, bombas, compresores, turbinas, etc
8. CONFIABILIDAD
Tiempo Medio de Reparación. También es conocido como Tiempo Medio de Mantenimiento Correctivo, y representa el tiempo medio necesario para reparar una avería y hacer que un equipo vuelva a funcionar normalmente. ¿Cómo calcular el MTTR? Para calcular el MTTR, debes dividir el tiempo total de mantenimiento no planificado invertido en un activo por el número total de fallas que experimentó ese activo durante un período específico. El tiempo medio de reparación se representa en horas.
10. TIEMPO MEDIO DE PARADAS POR AVERIAS
Mean Time to Repair (MTTR) es el tiempo medio de reparación, una de las métricas más utilizadas por los gestores de mantenimiento. Como su nombre indica, el MTTR representa el tiempo medio necesario para resolver fallos y reparar el activo que sufrió una avería, devolviéndole las condiciones normales de funcionamiento. Para calcular el MTTR, debes dividir el tiempo total de mantenimiento no planificado invertido en un activo por el número total de fallas que experimentó ese activo durante un período específico. El tiempo medio de reparación se representa en horas.
13. Seguridad y medio ambiente
14. Tiempo medio para reparaciones
Mean Time Between Failures (MTBF) es el tiempo medio entre las averías de un activo, una métrica importante donde la tasa de indisponibilidad de los activos debe ser gestionada. Por otras palabras, MTBF es el tiempo medio cuando el equipo funciona correctamente entre los fallos. El MTBF se convierte en un indicador de rendimiento muy importante para los activos más críticos y esta métrica no prevé ningún mantenimiento programado, como inspecciones, recalibraciones o reemplazos de piezas preventivas. Aunque el MTTR solo afecta a la disponibilidad, el MTBF afecta tanto a la disponibilidad como a la confiabilidad.