
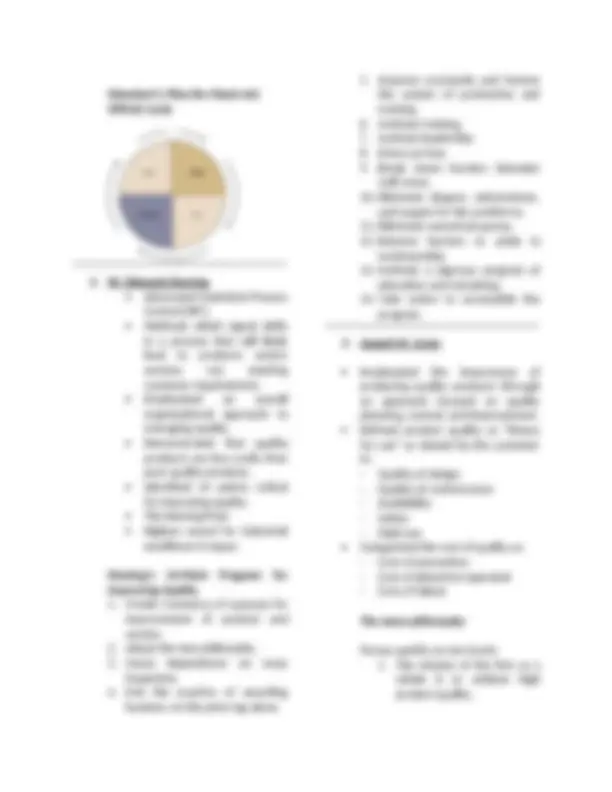
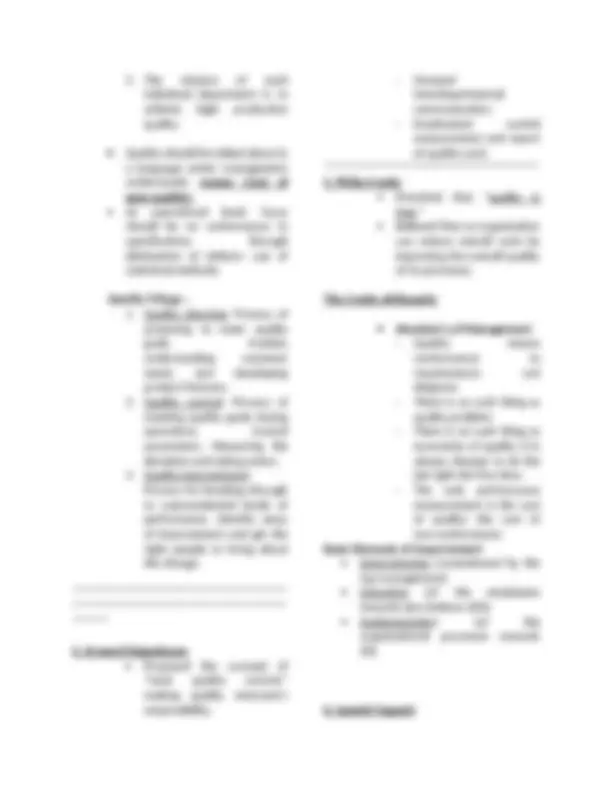
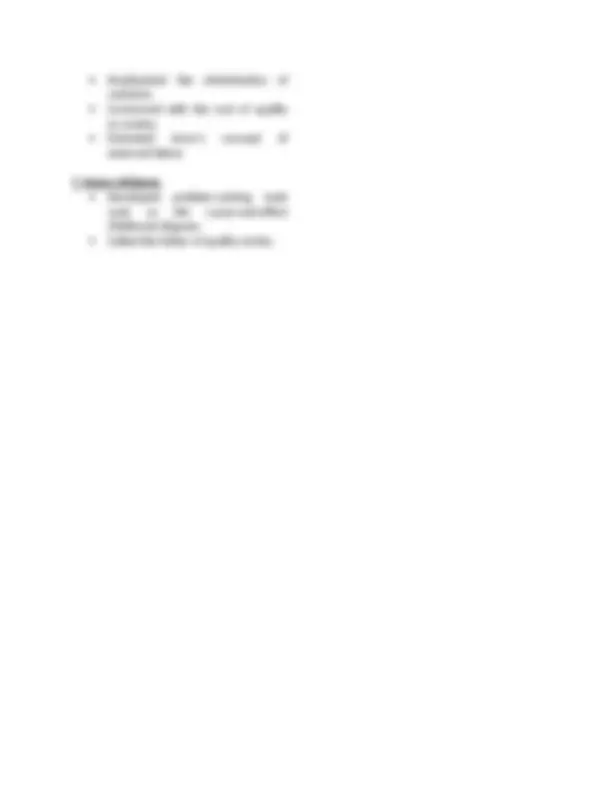
Study with the several resources on Docsity
Earn points by helping other students or get them with a premium plan
Prepare for your exams
Study with the several resources on Docsity
Earn points to download
Earn points by helping other students or get them with a premium plan
Community
Ask the community for help and clear up your study doubts
Discover the best universities in your country according to Docsity users
Free resources
Download our free guides on studying techniques, anxiety management strategies, and thesis advice from Docsity tutors
Quality perspectives Everyone defines Quality based on their own perspective of it. Typical responses about the definition of quality would include:
Typology: Cheat Sheet
1 / 5
This page cannot be seen from the preview
Don't miss anything!
Quality Management Concepts What is quality? Dictionary “Essential characteristic,” “Superior,” etc. “Quality is customer satisfaction,” “Quality is Fitness for Use.” What is TQM? A comprehensive, organization-wide effort to improve the quality of products and services, applicable to all organizations. What is a customer? Anyone who is impacted by the product or process delivered by an organization. External customer: The end user as well as intermediate processors. Internal customer: Other divisions of the company that receive the processed product. What is a product? The output of the process carried out by the organization. It may be goods How is customer satisfaction achieved? Two dimensions: Product features and Freedom from deficiencies. Product features – Refers to quality of design. Examples in manufacturing industry: Performance, Reliability, Durability, Ease of use, Esthetics etc. Examples in service industry : Accuracy, Timeliness, Friendliness and courtesy, Knowledge of server etc. Freedom from deficiencies – Refers to quality of conformance. Higher conformance means fewer complaints and increased customer satisfaction. (This is related to free from defects.) Reasons for quality becoming a cardinal priority for most organizations: Competition – Today’s market demand high quality products at low cost. Having `high quality’ reputation is not enough! Internal cost of maintaining the reputation should be less. Changing customer – The new customer is not only commanding priority based on volume but is more demanding about the “quality system.” Changing product mix – The shift from low volume, high price to high volume, low price have resulted in a need to reduce the internal cost of poor quality. Product complexity – As systems have become more complex, the reliability requirements for suppliers of components have become more stringent. Higher levels of customer satisfaction – Higher customers’ expectations are getting spawned by increasing competition. Relatively simpler approaches to quality viz. product inspection for quality control and incorporation of internal cost of poor quality into the selling price, might not work for today’s complex market environment.
Quality perspectives Everyone defines Quality based on their own perspective of it. Typical responses about the definition of quality would include :
4. Armand Feigenbaum Proposed the concept of “total quality control,” making quality everyone’s responsibility. Stressed interdepartmental communication. Emphasized careful measurement and report of quality costs
5. Philip Crosby Preached that “quality is free.” Believed that an organization can reduce overall costs by improving the overall quality of its processes. The Crosby philosophy Absolute’s of Management Quality means conformance to requirements not elegance. There is no such thing as quality problem. There is no such thing as economics of quality: it is always cheaper to do the job right the first time. The only performance measurement is the cost of quality: the cost of non-conformance. Basic Elements of Improvement Determination ( commitment by the top management) Education (of the employees towards Zero Defects (ZD)) Implementation (of the organizational processes towards ZD) 6. Genichi Taguchi
Emphasized the minimization of variation. Concerned with the cost of quality to society. Extended Juran’s concept of external failure.
7. Kaoru Ishikawa Developed problem-solving tools such as the cause-and-effect (fishbone) diagram. Called the father of quality circles.