
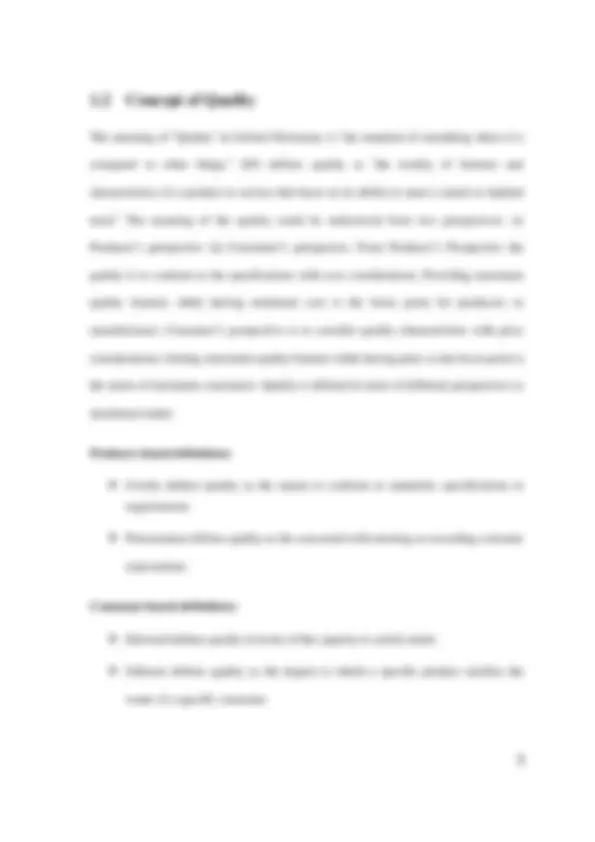
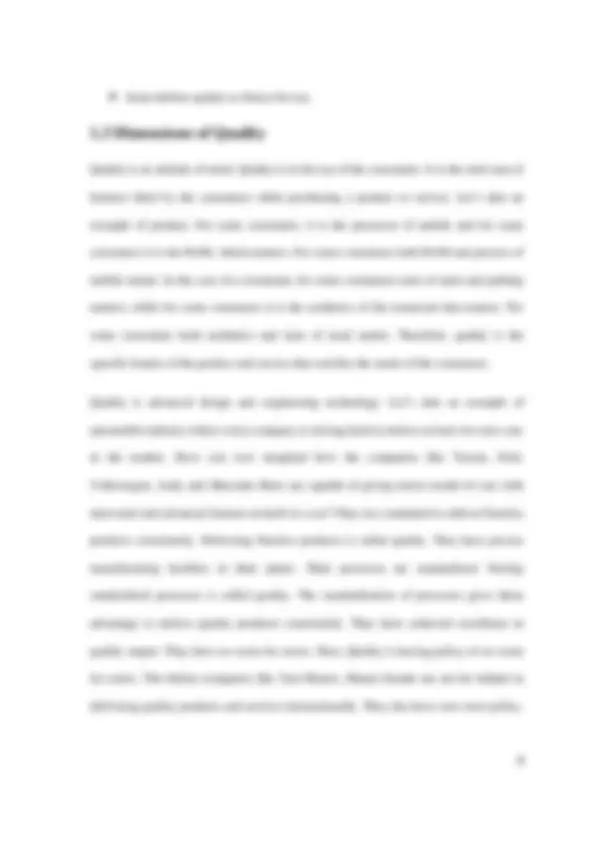
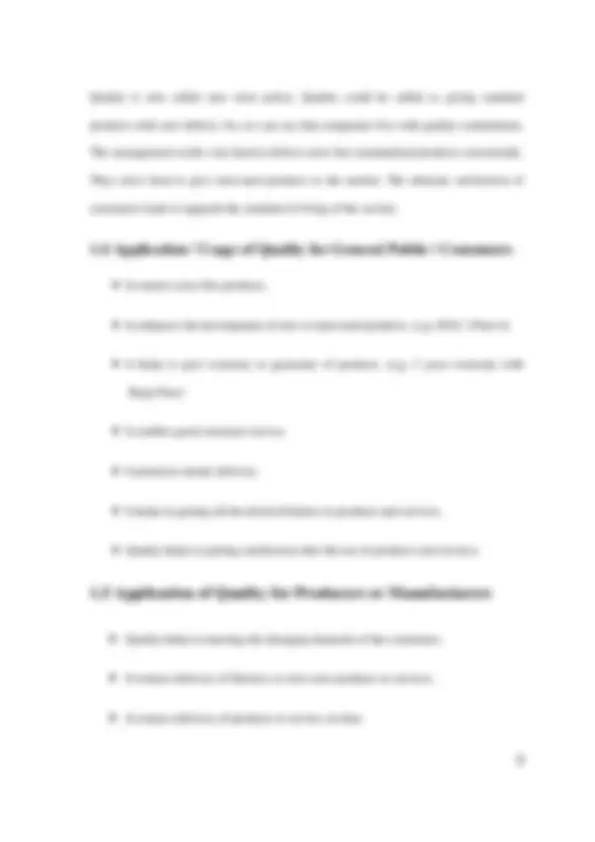
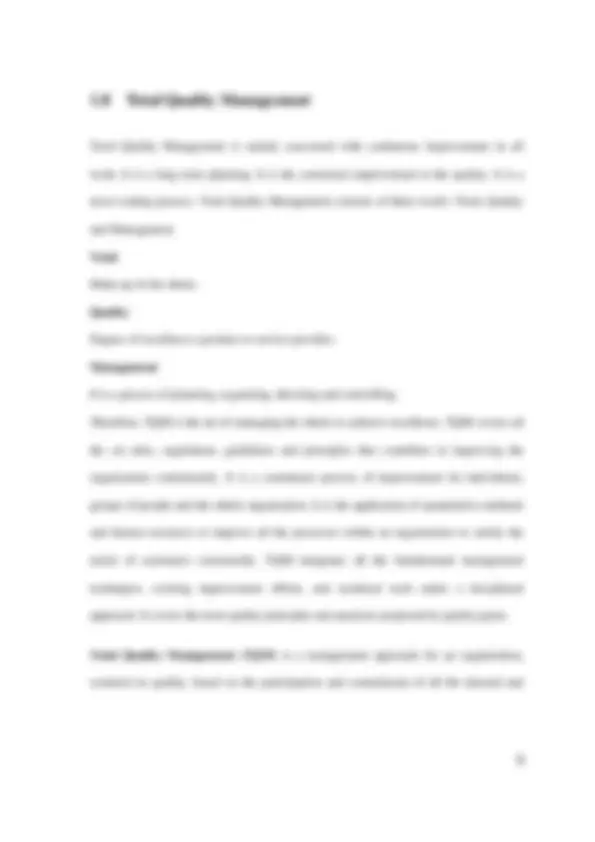
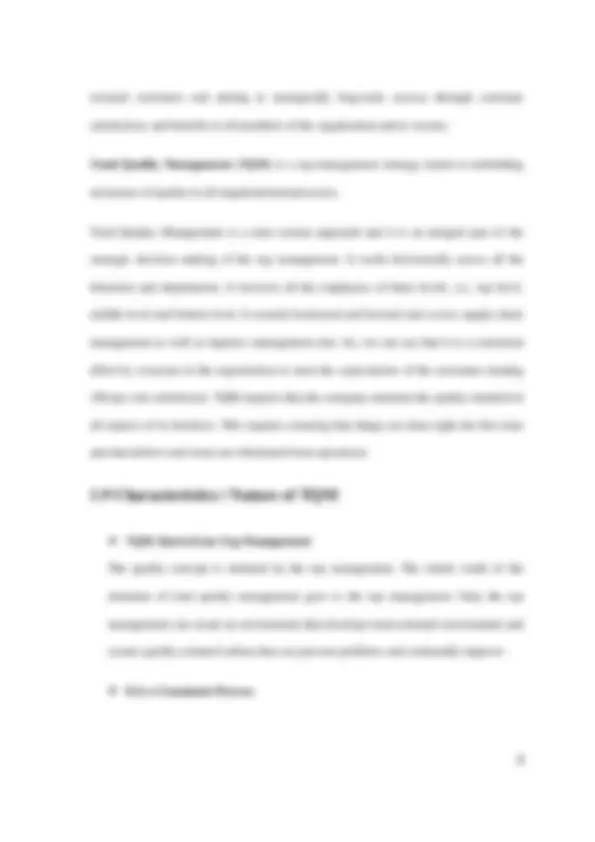
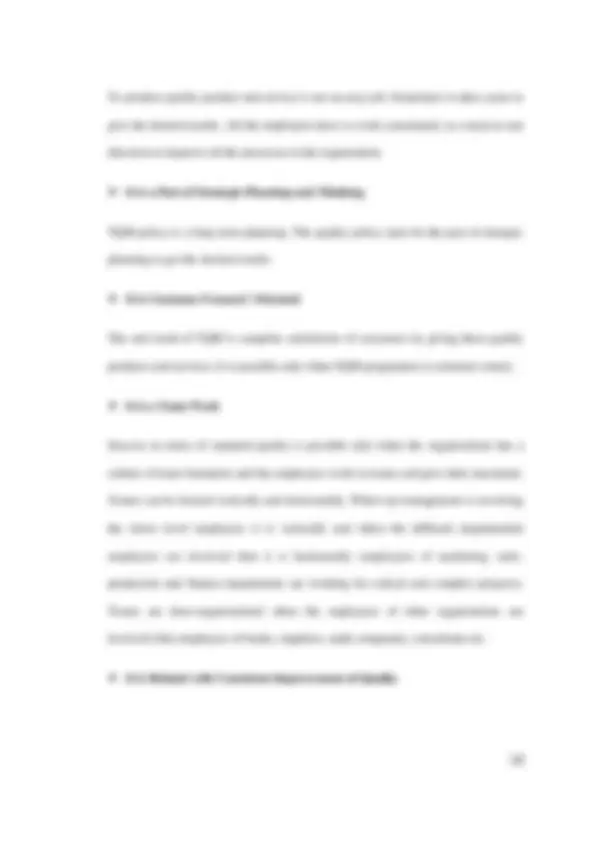
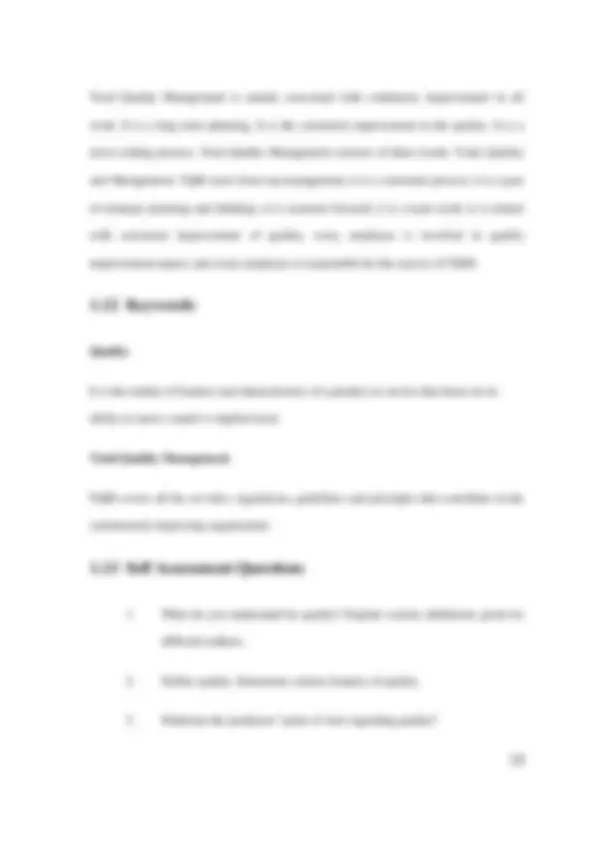
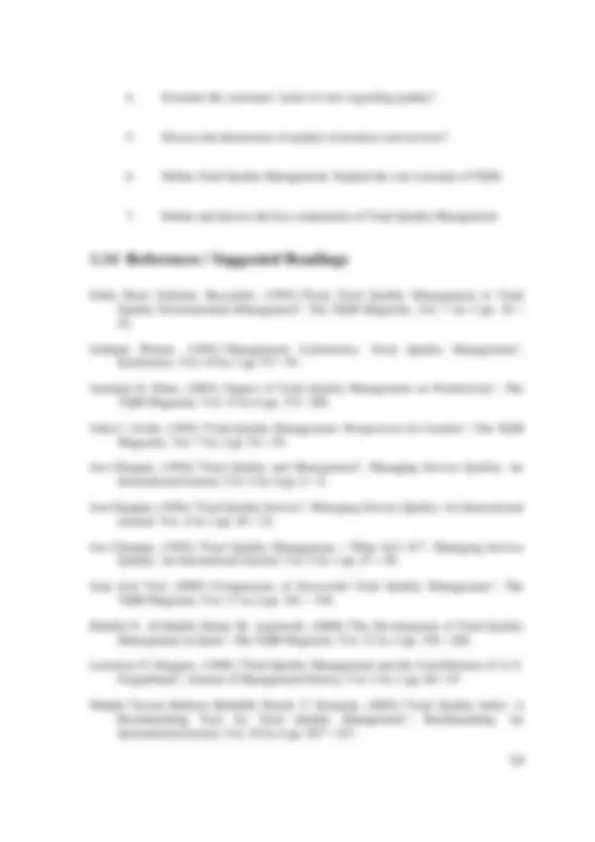
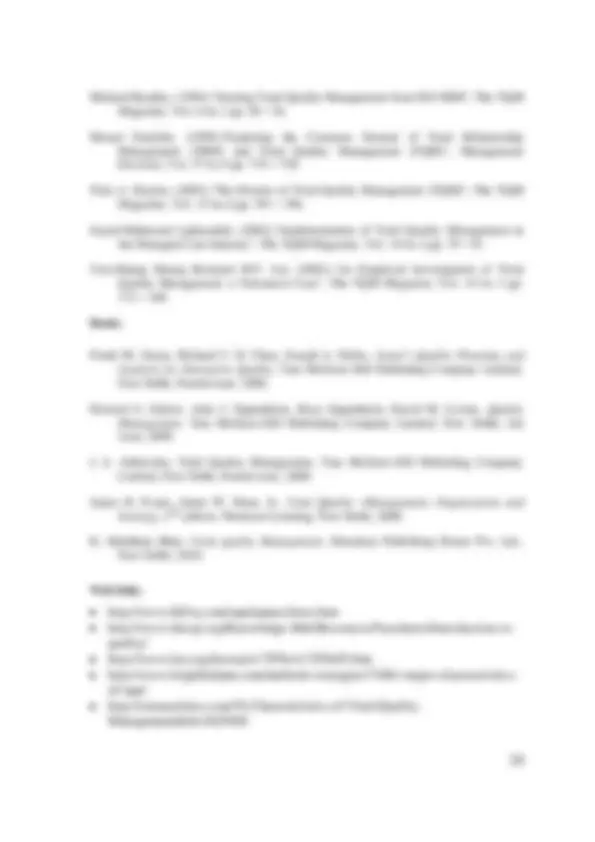
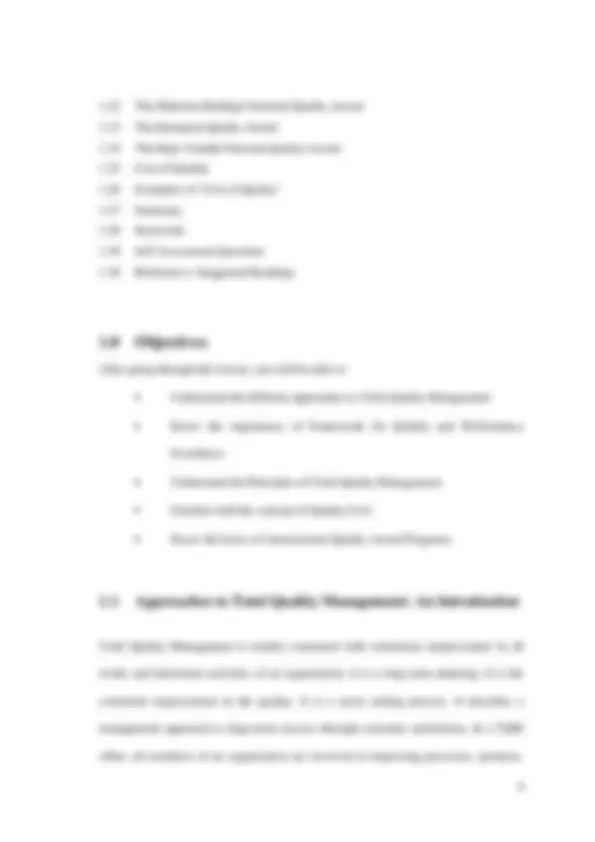
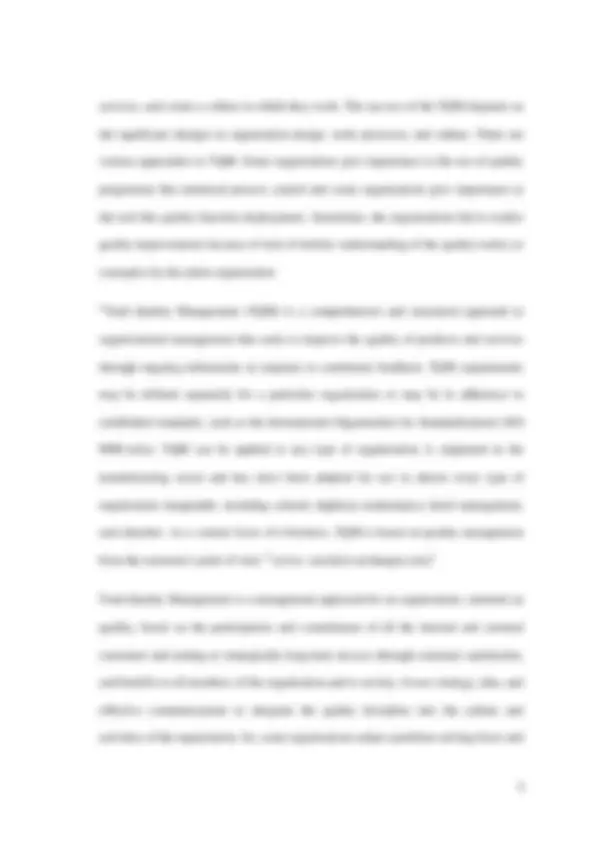

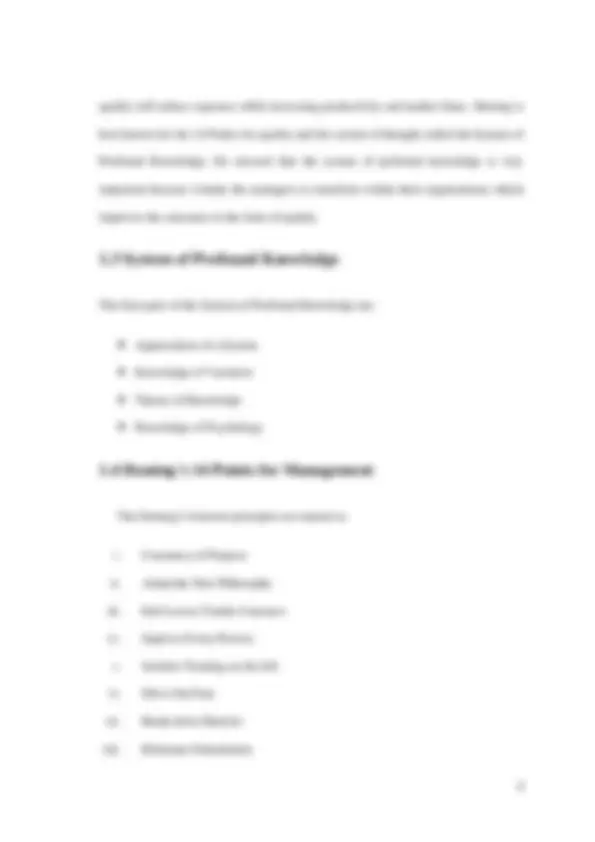
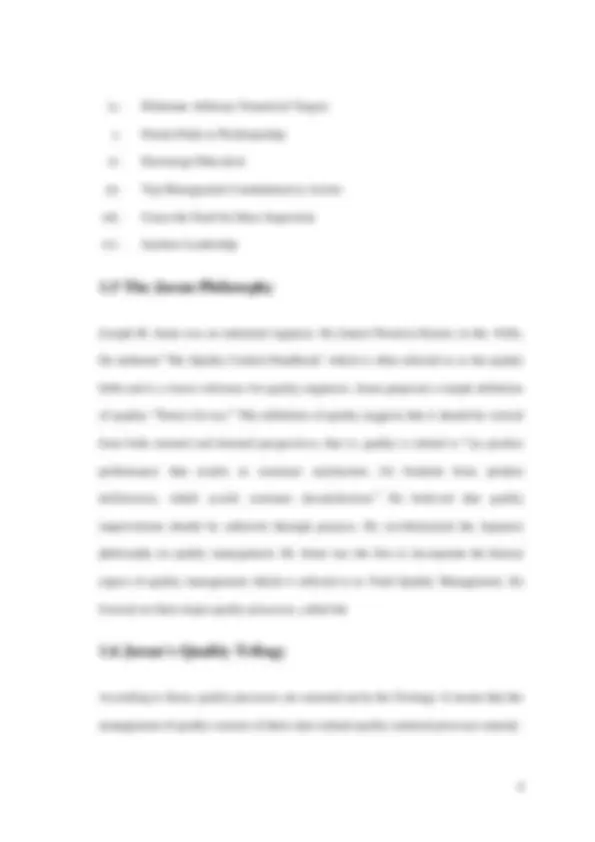
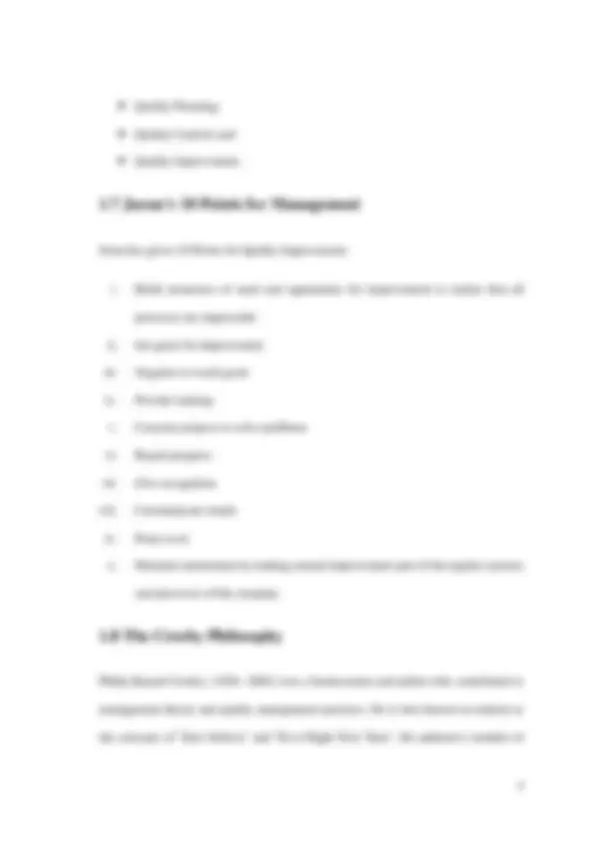

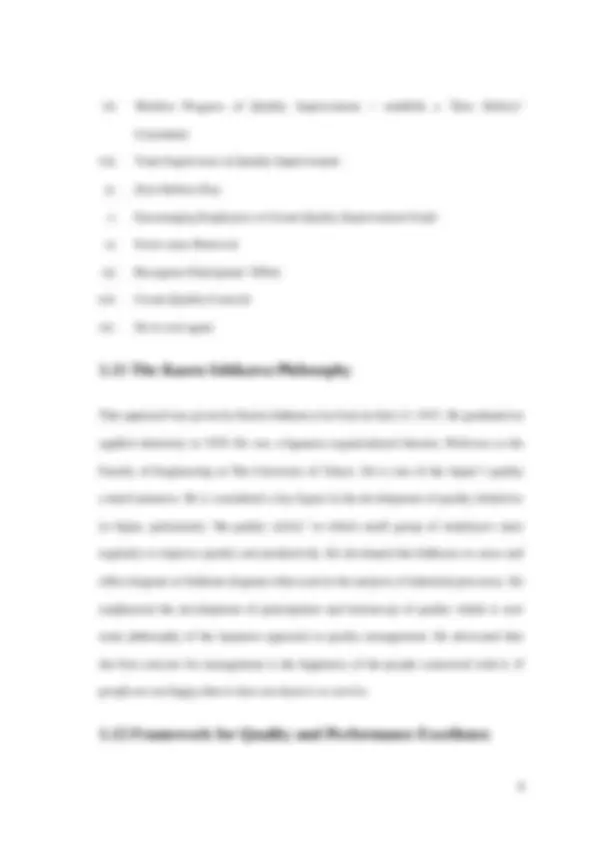
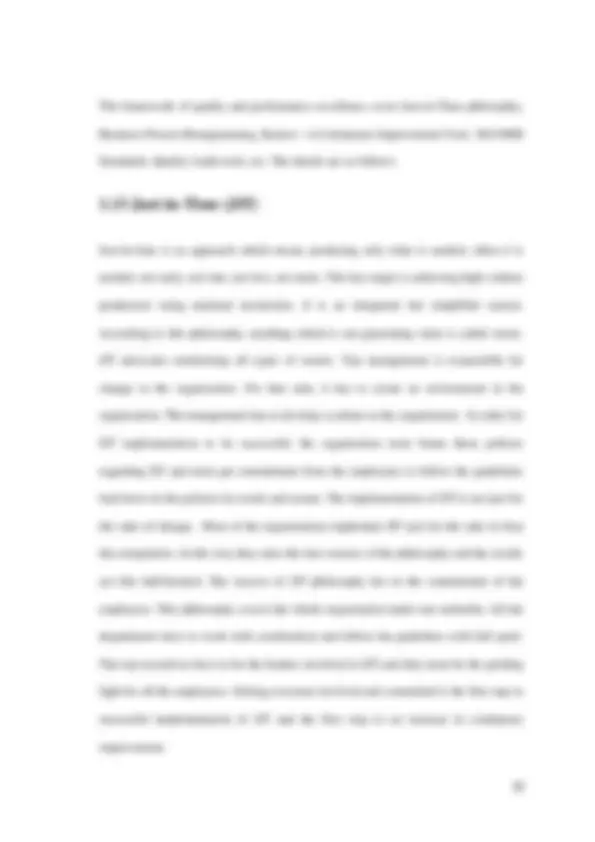
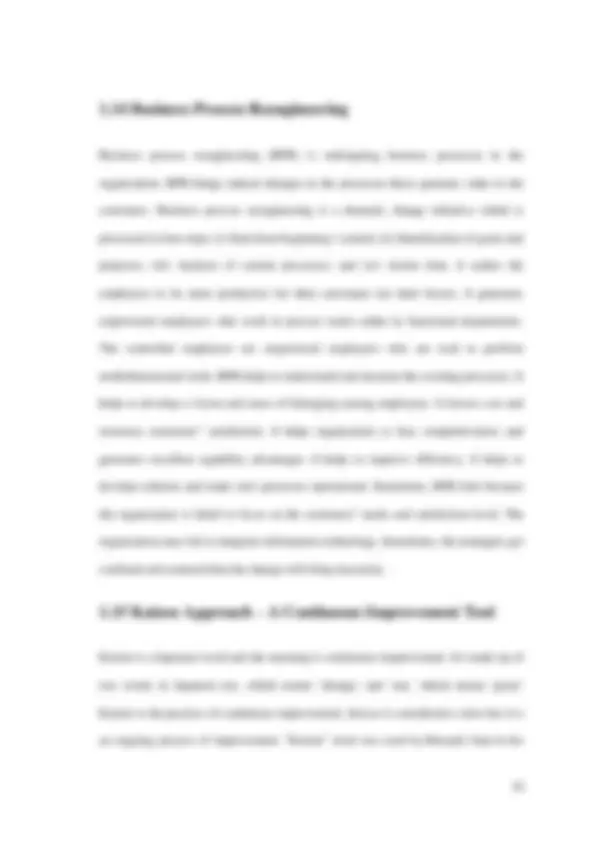
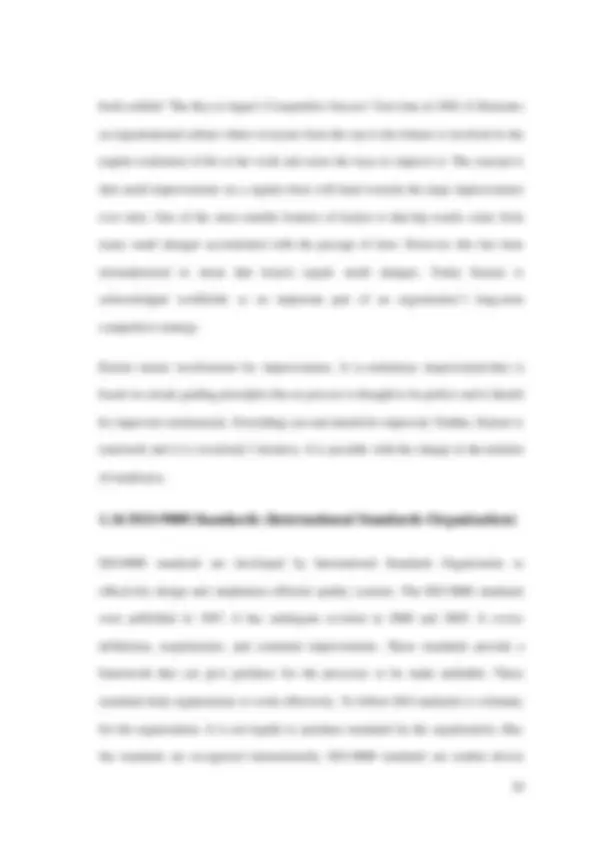
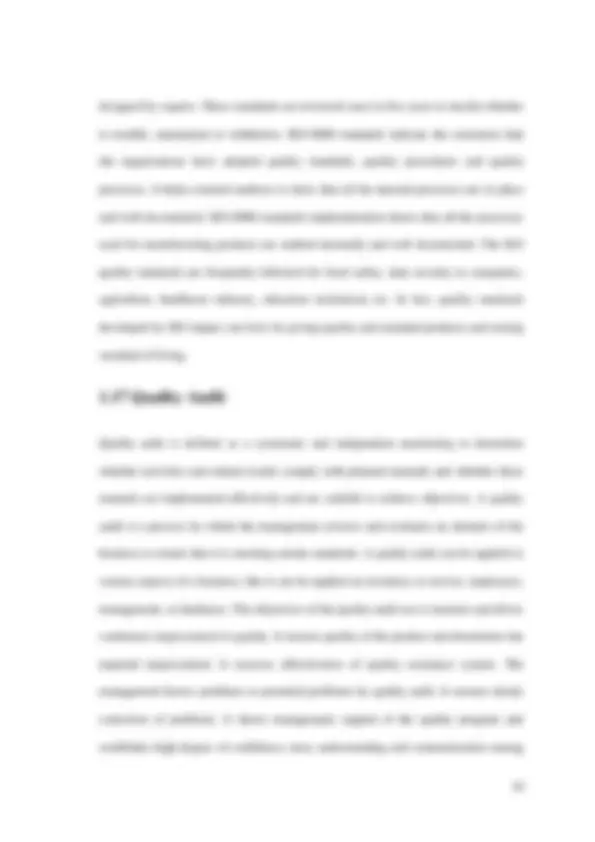
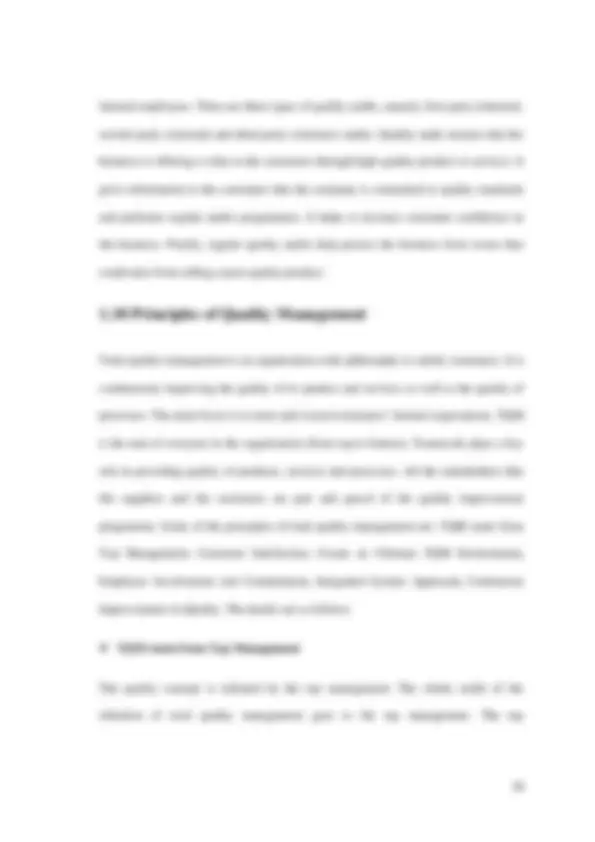
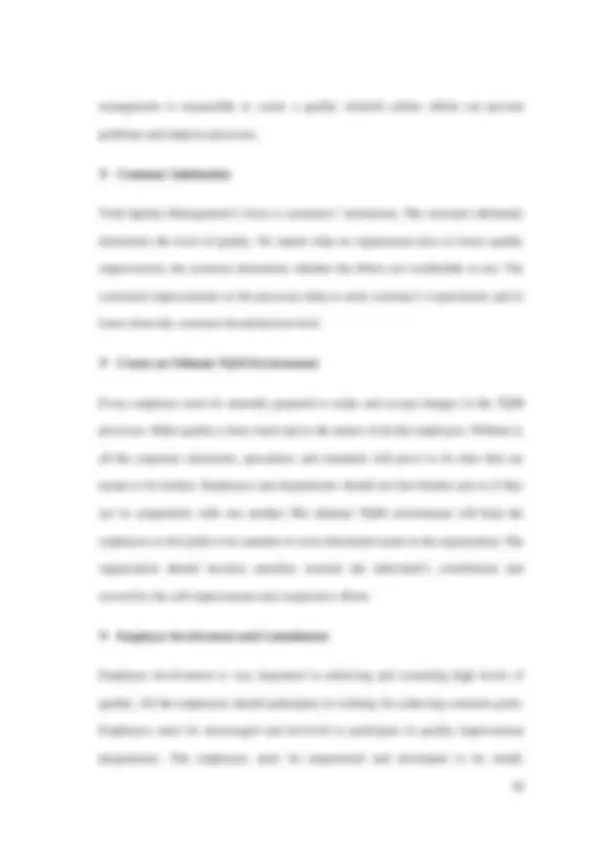
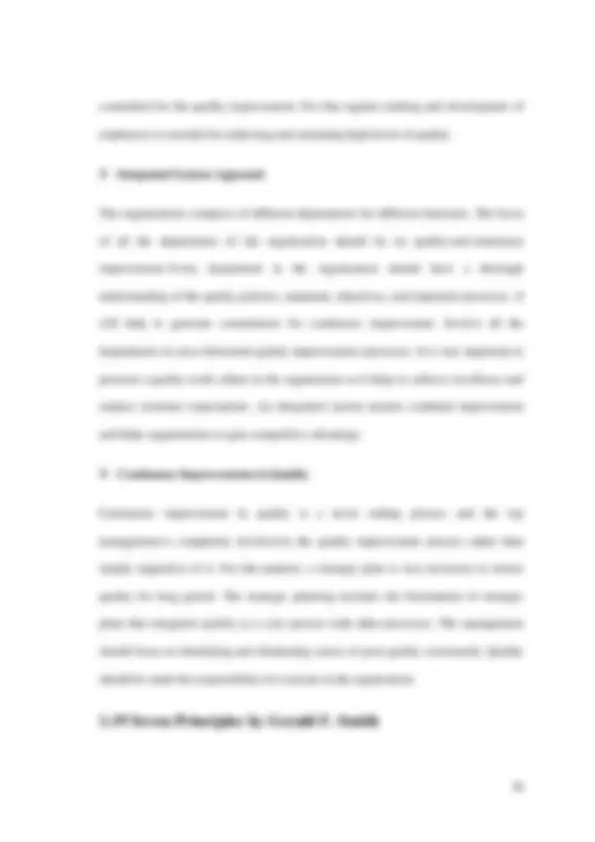
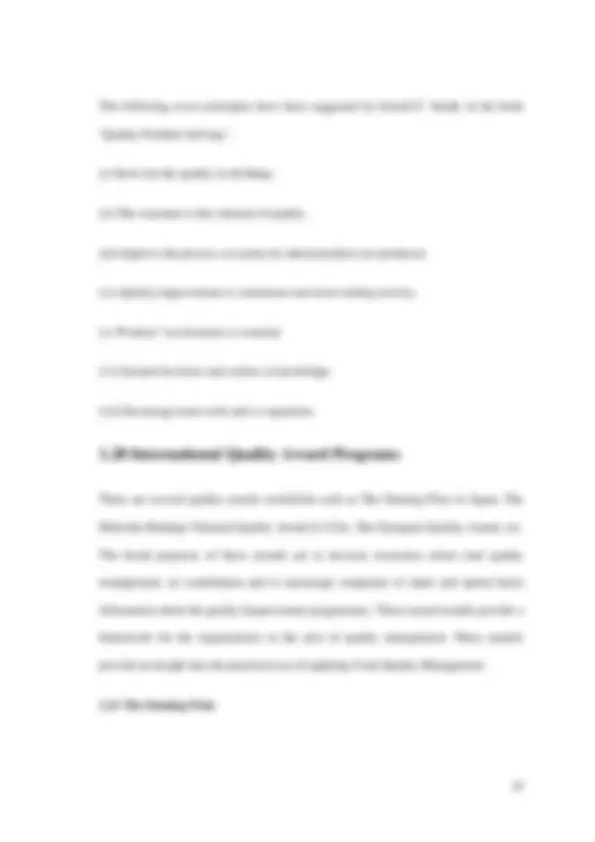
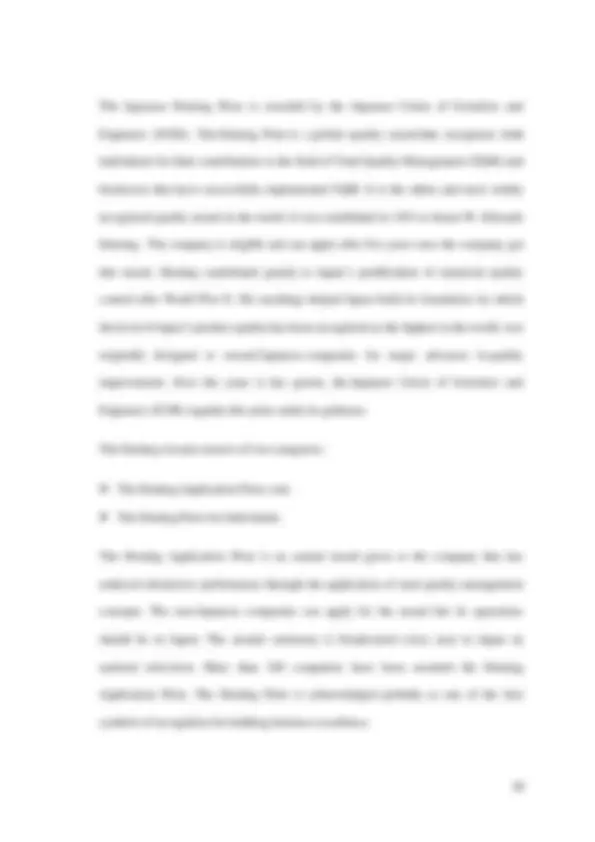
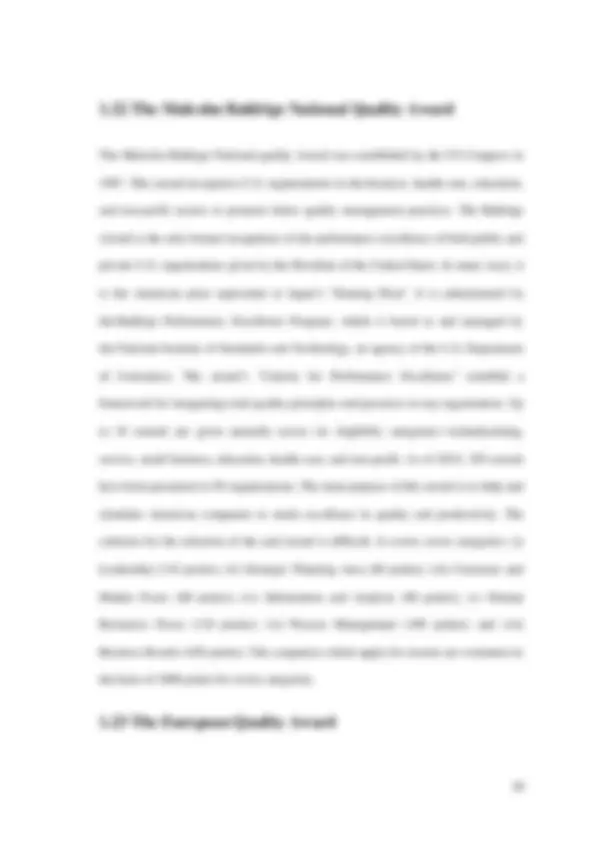
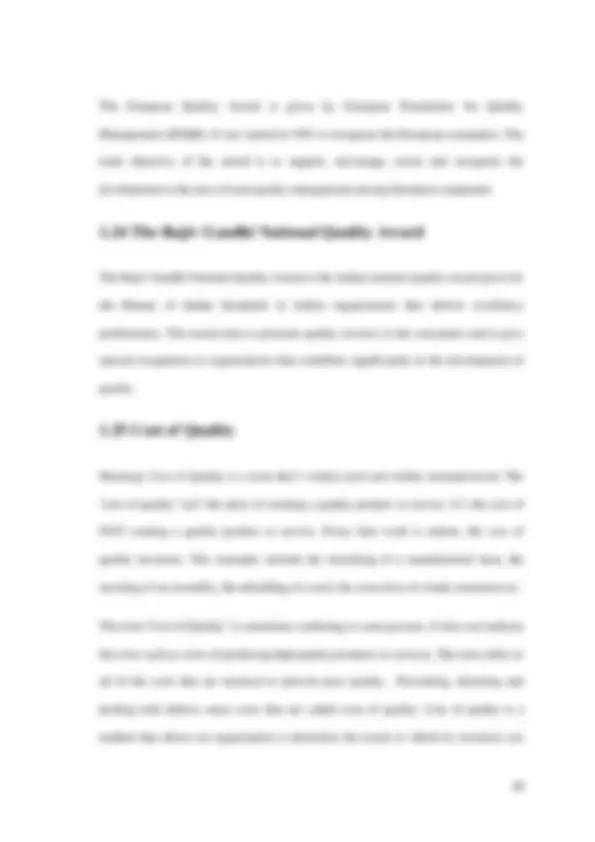
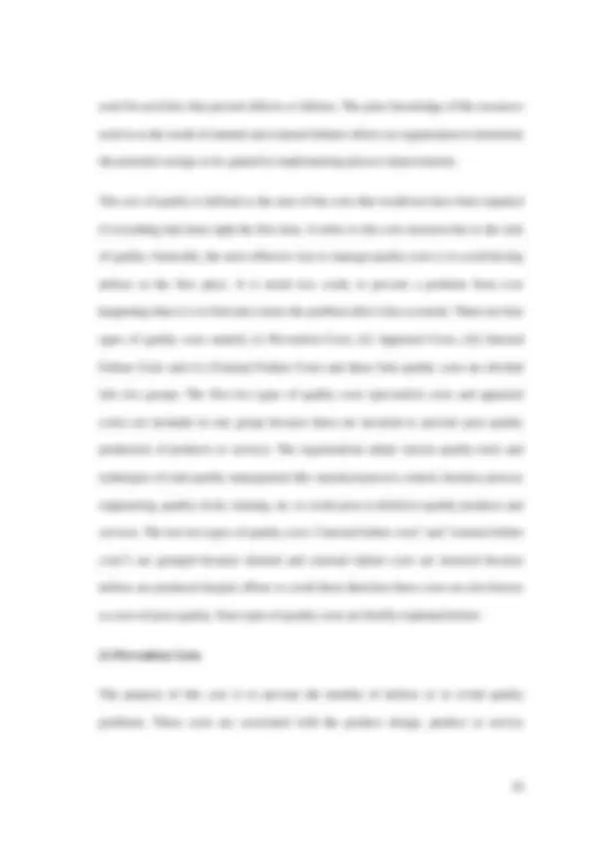
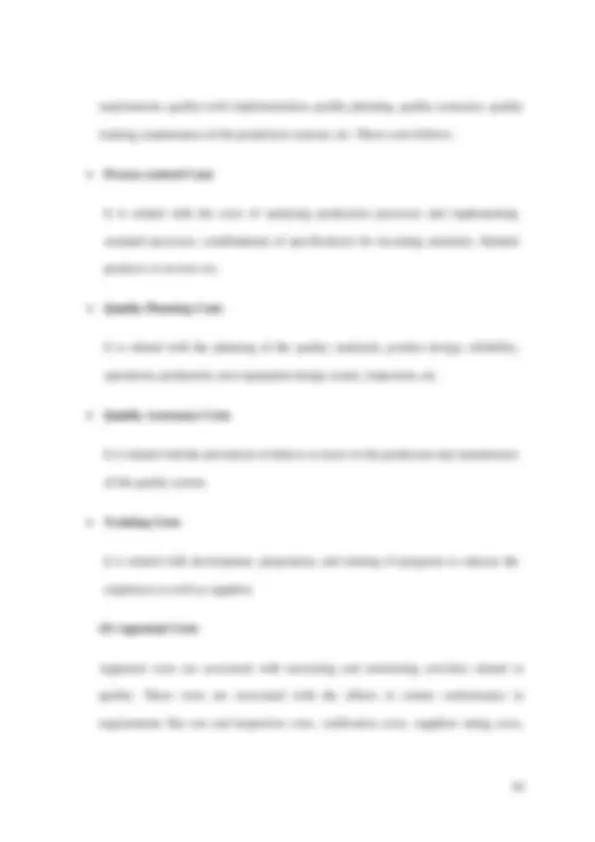
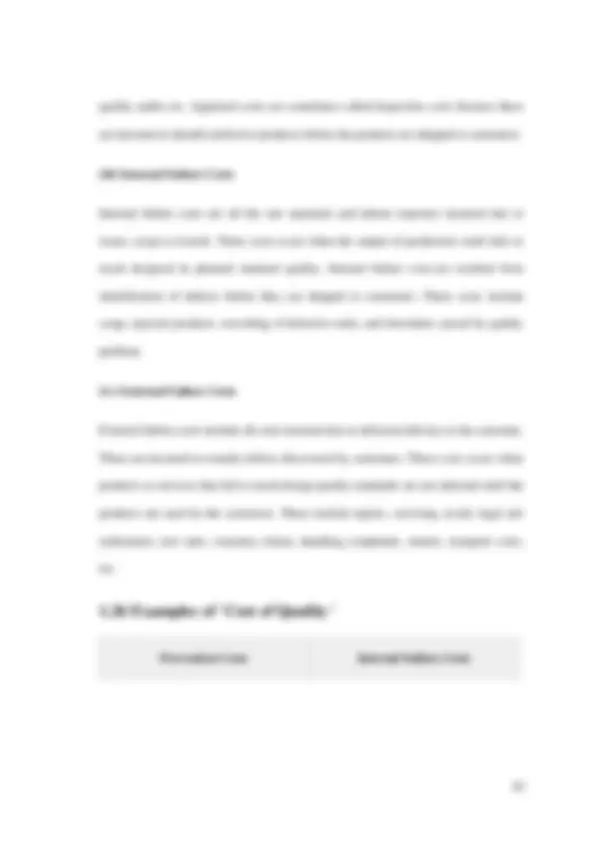
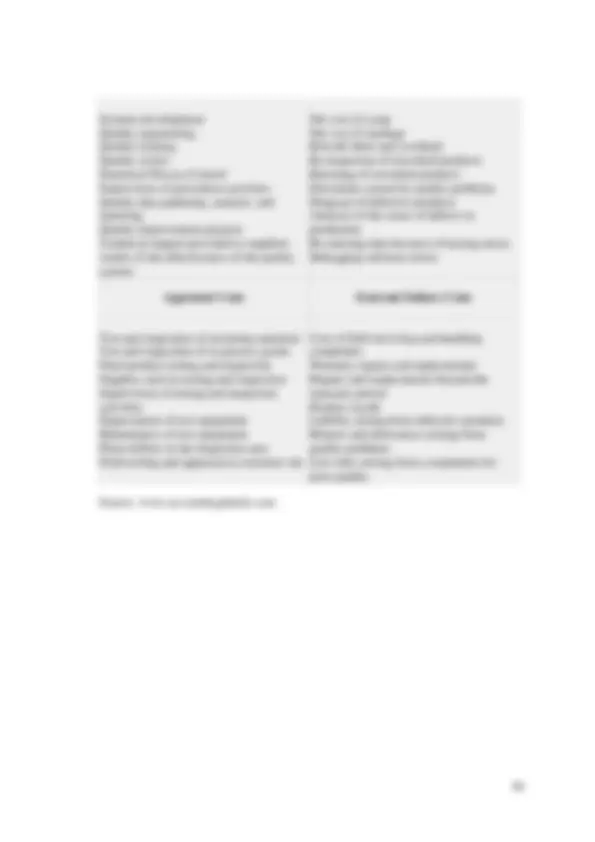
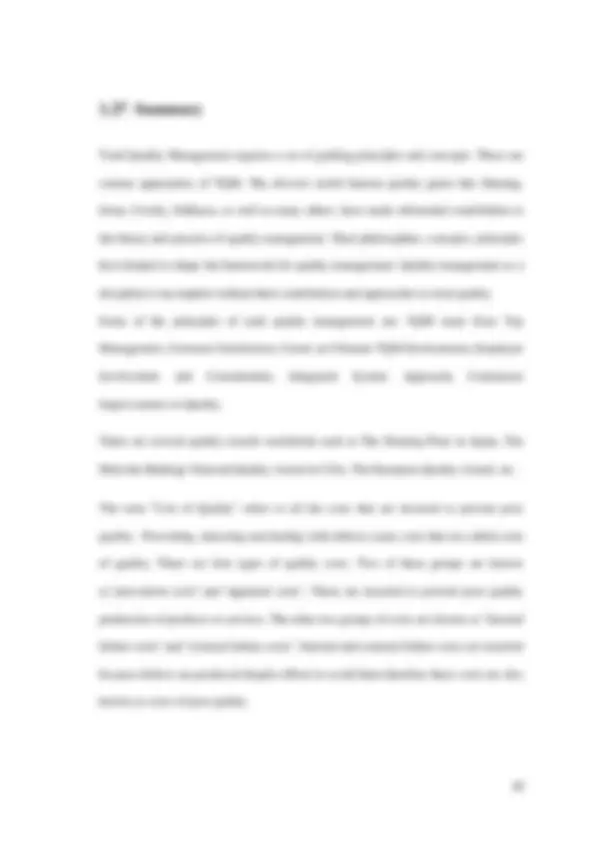
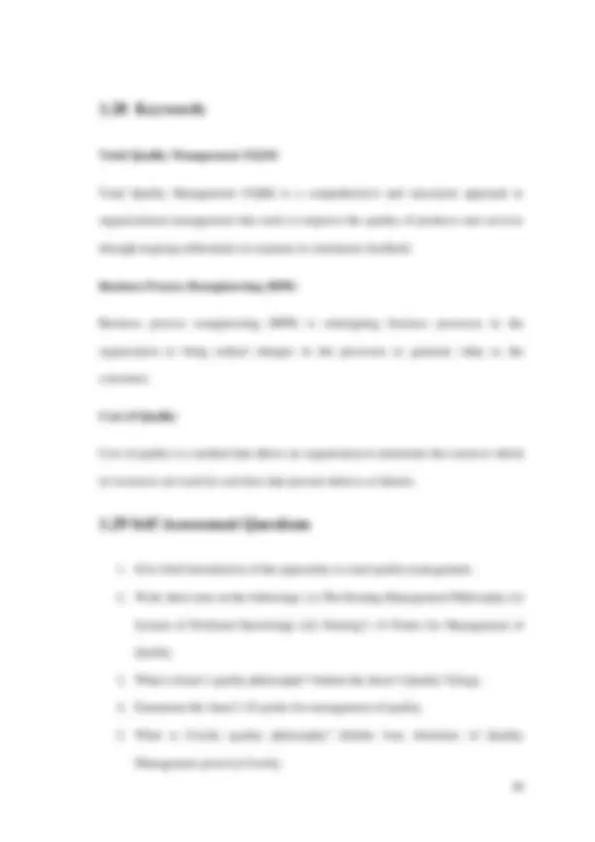
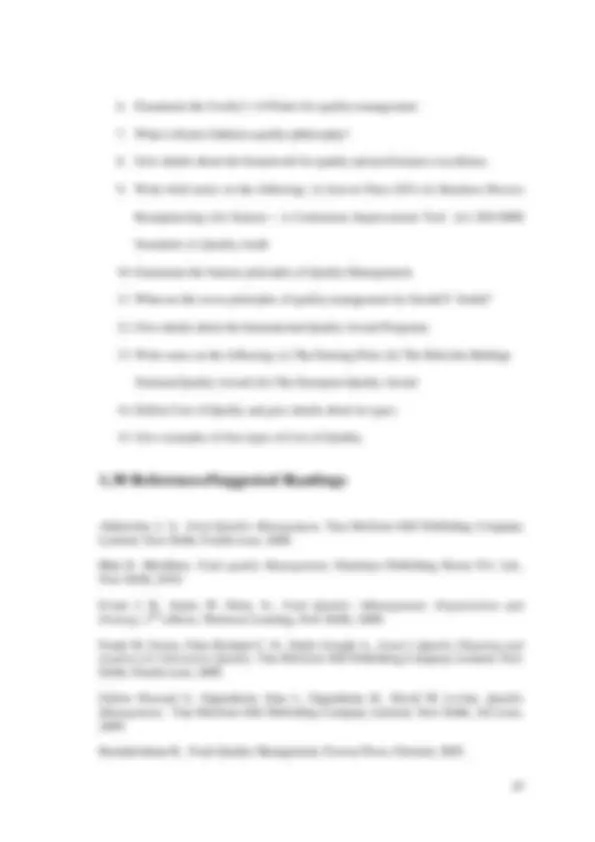
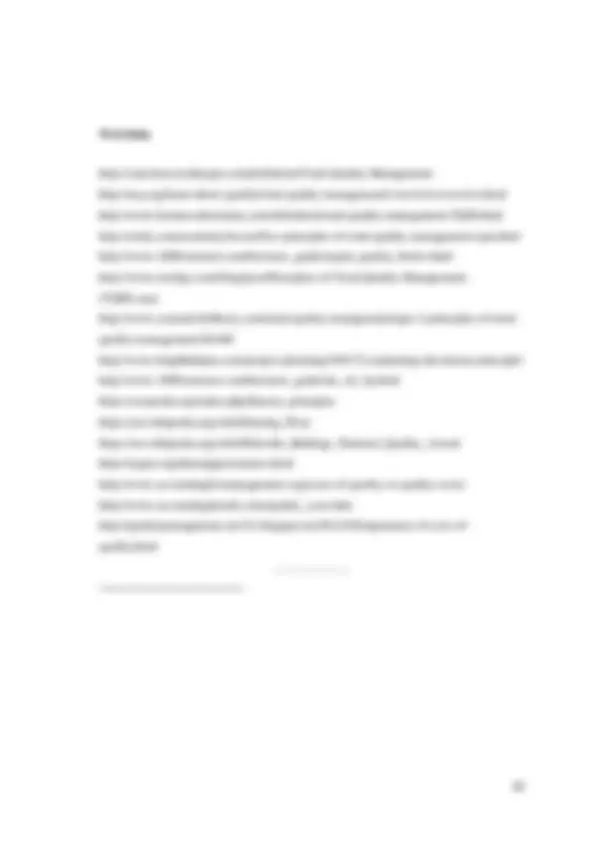
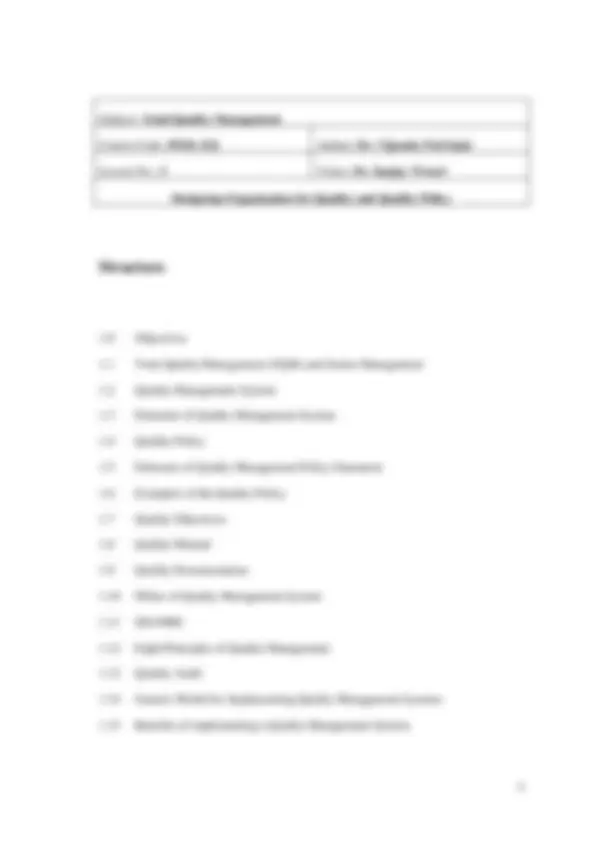
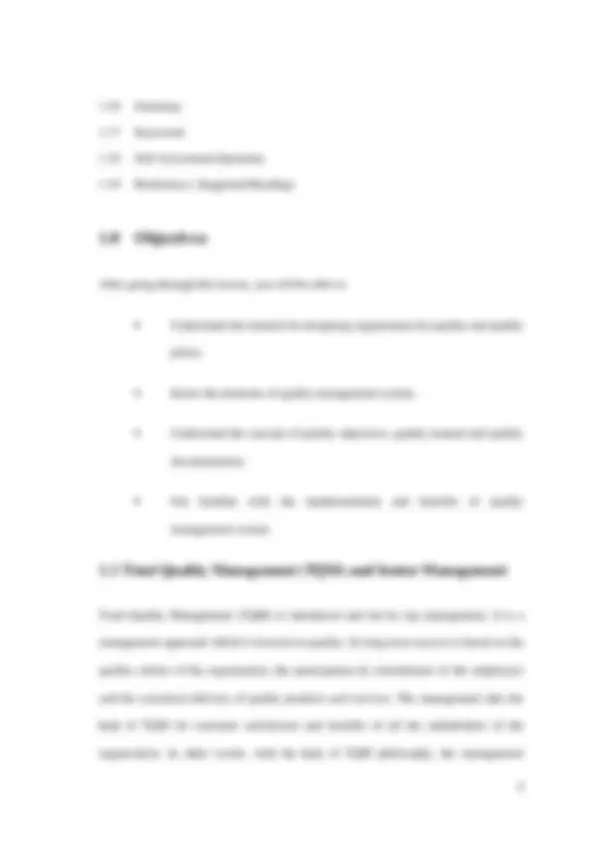
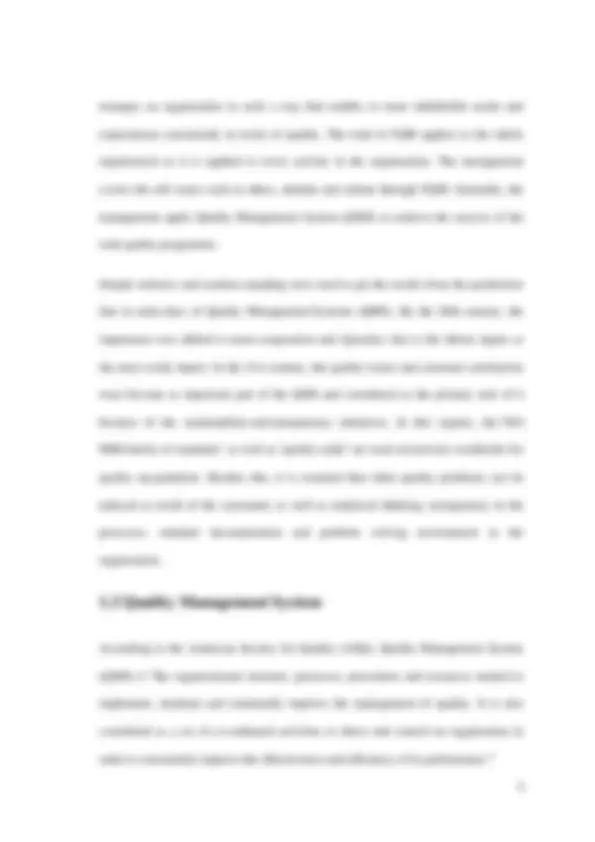
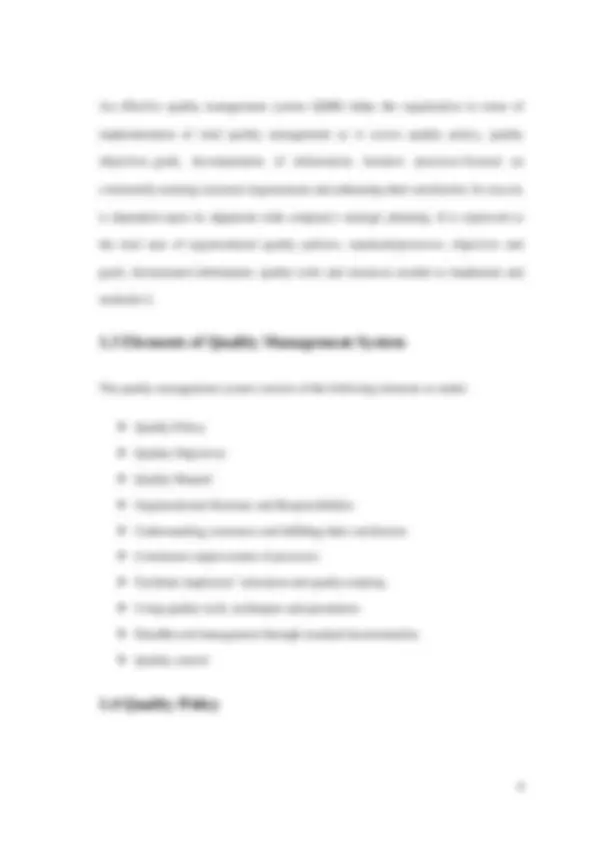
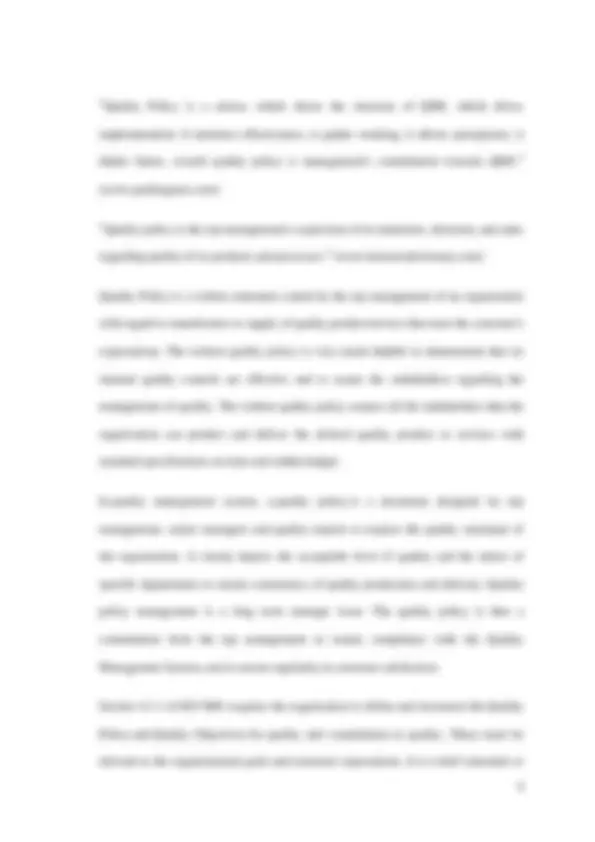
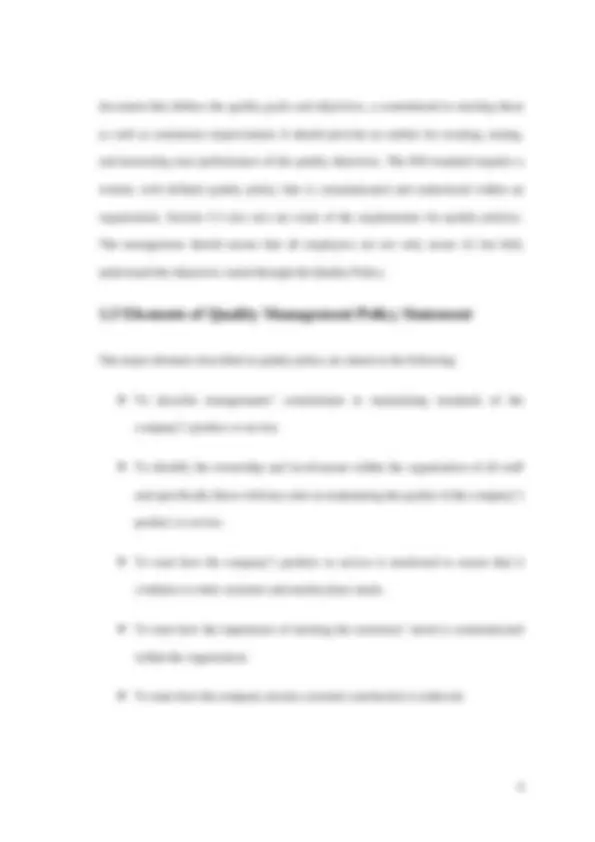
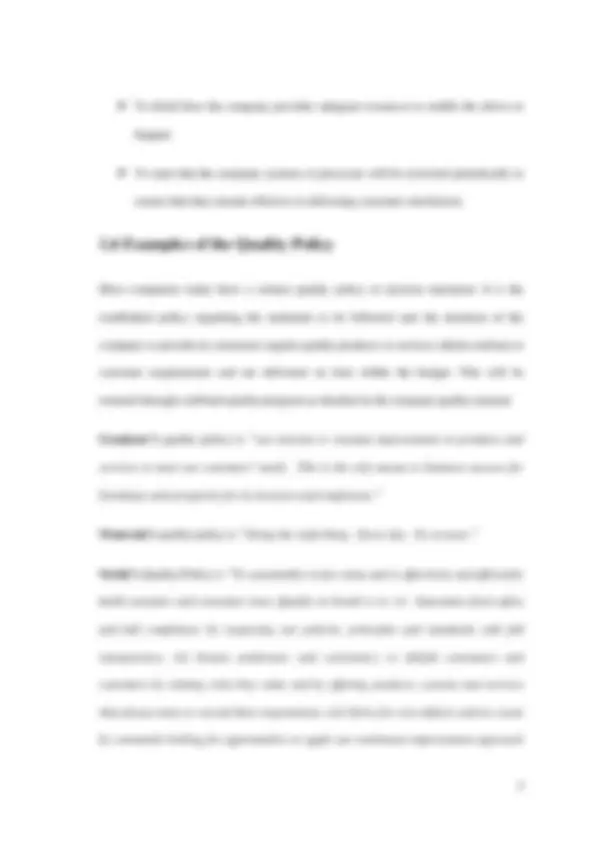
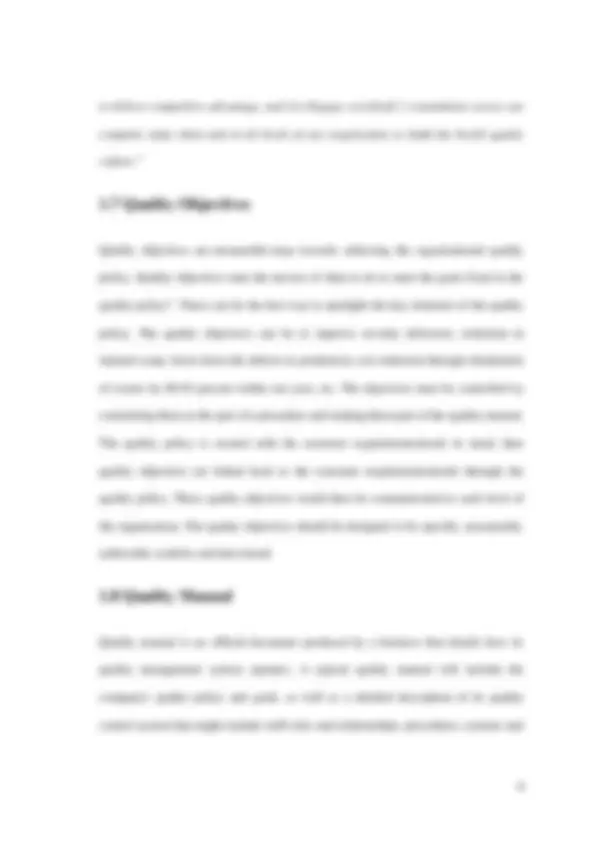
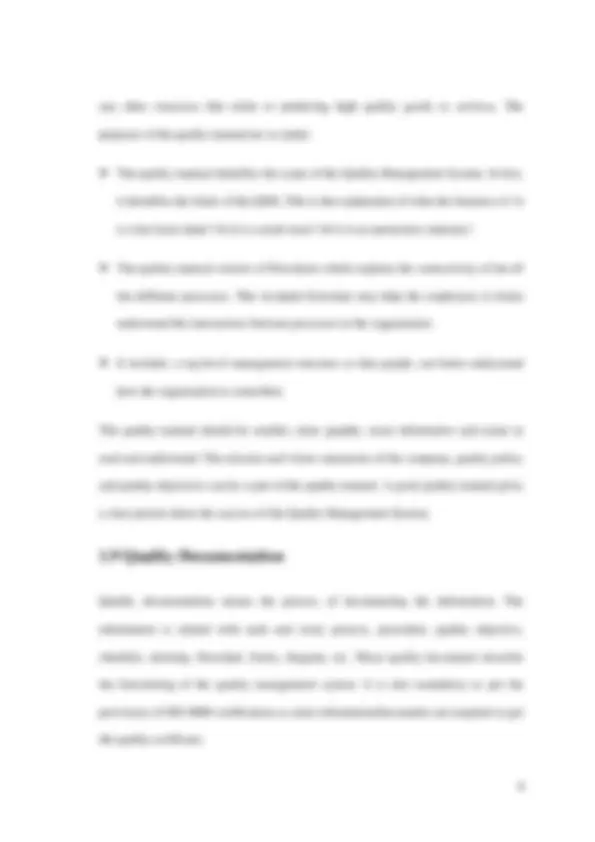
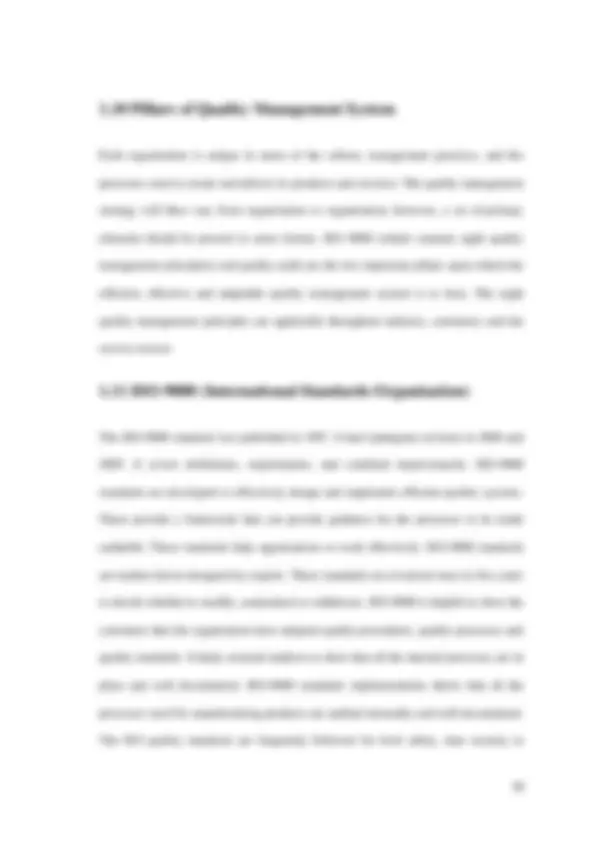
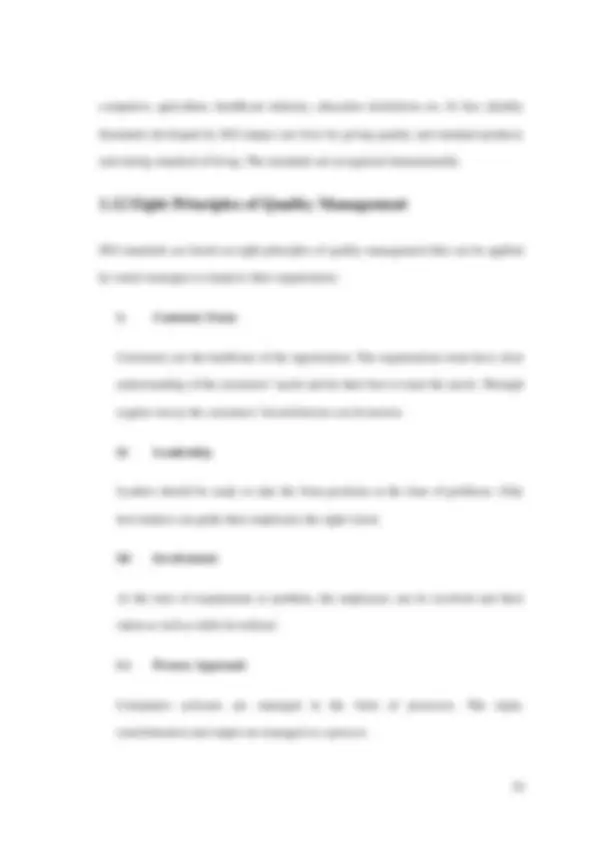
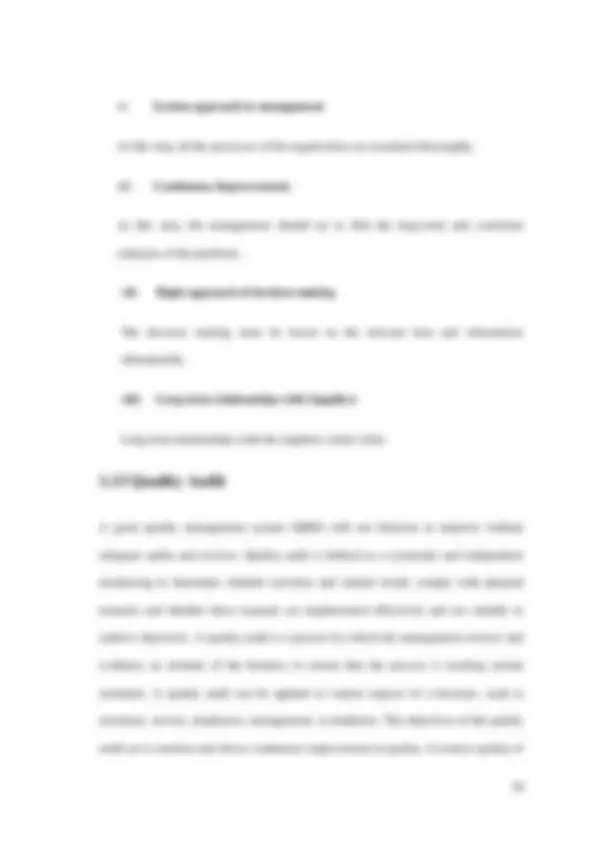
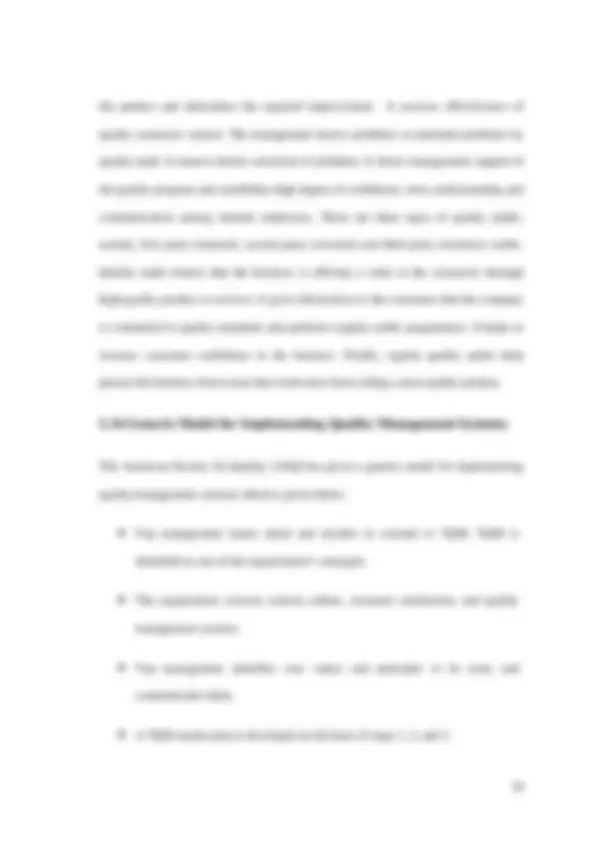
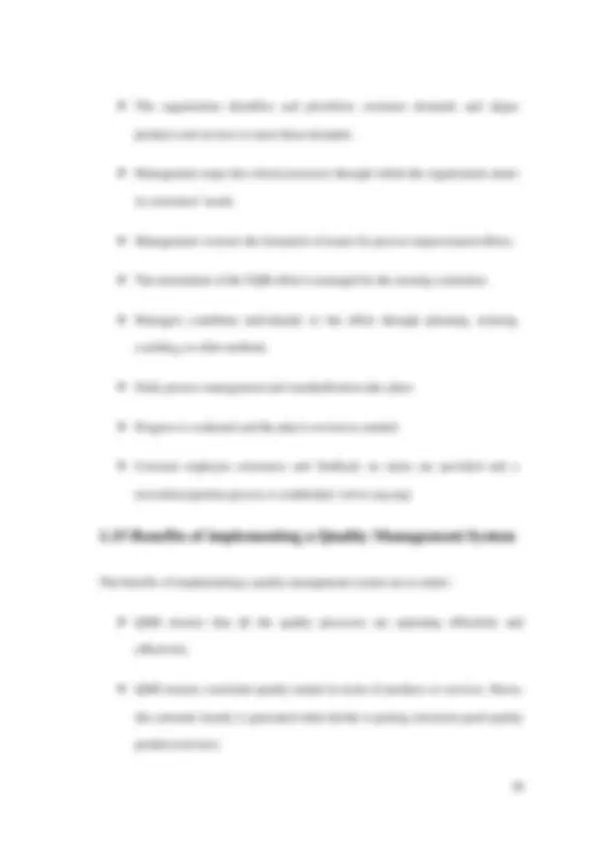
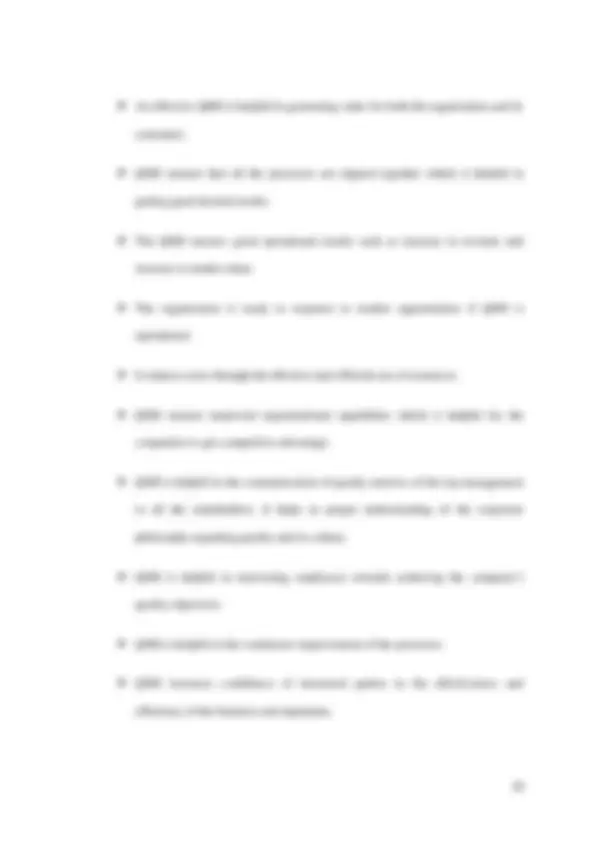
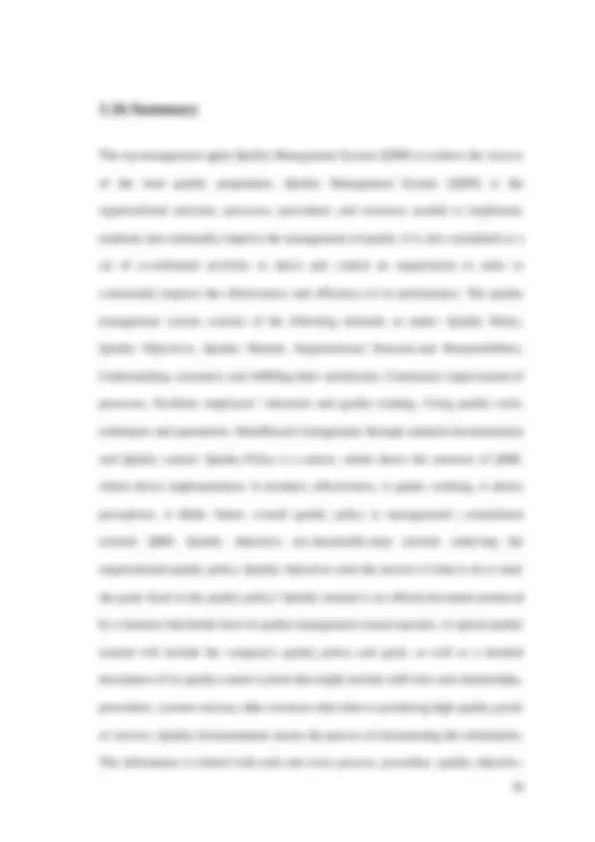
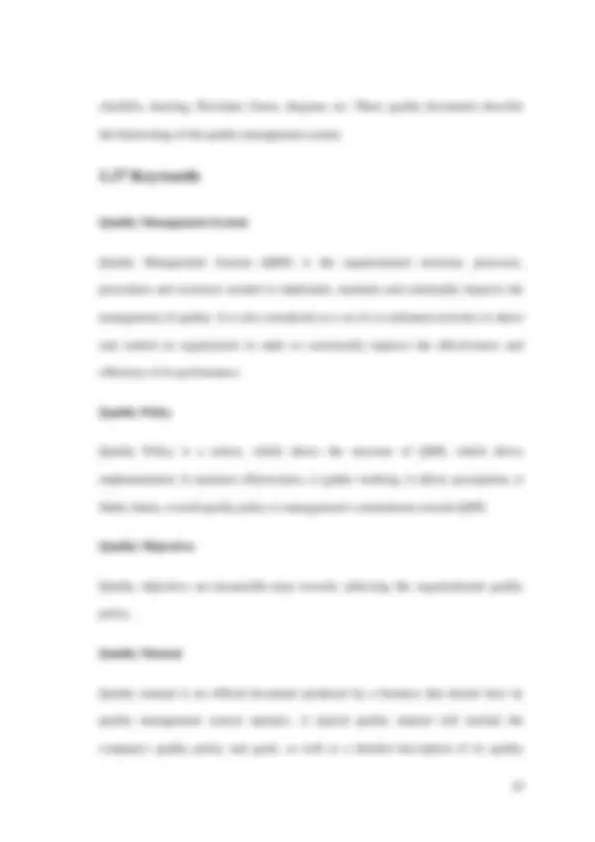
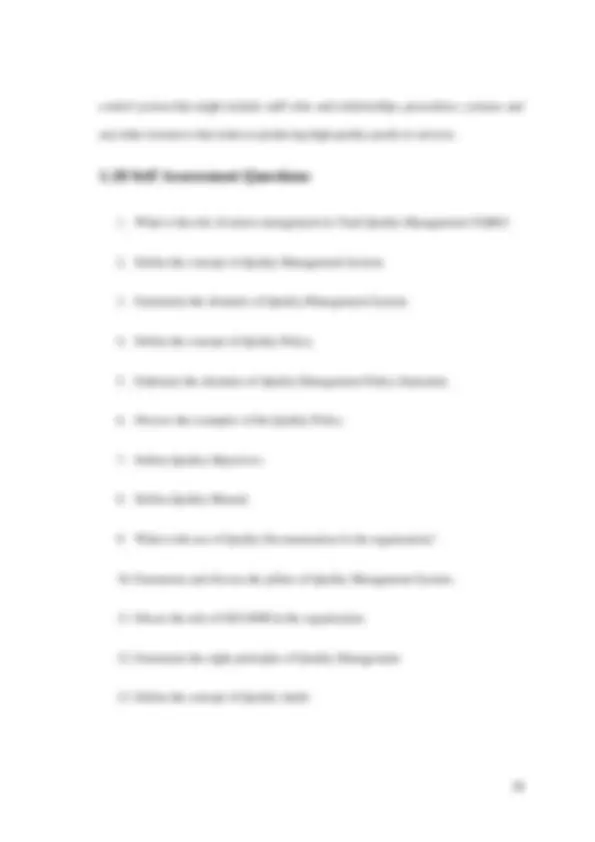
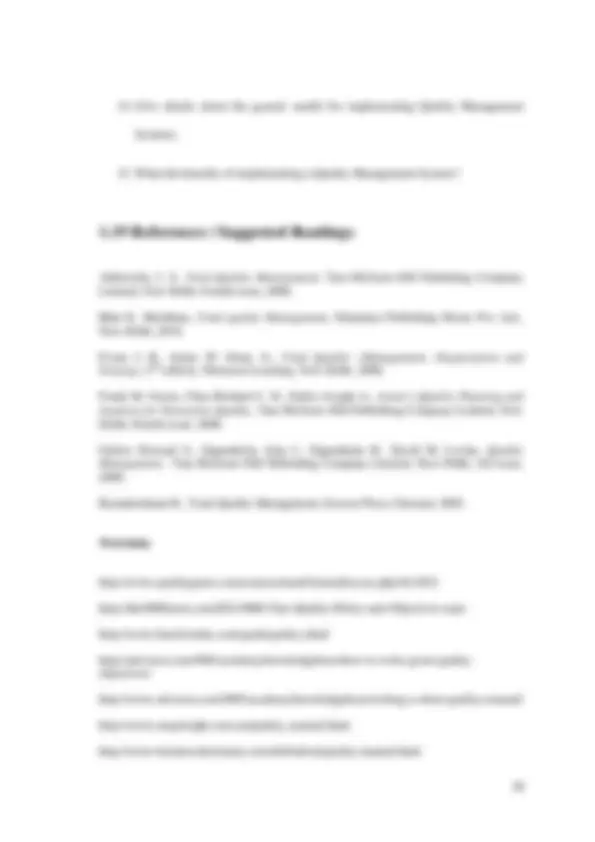
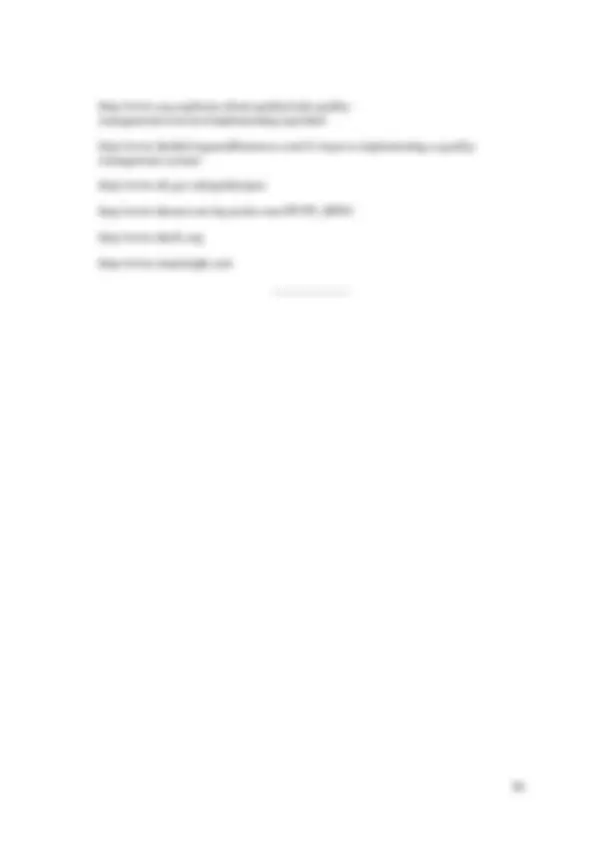
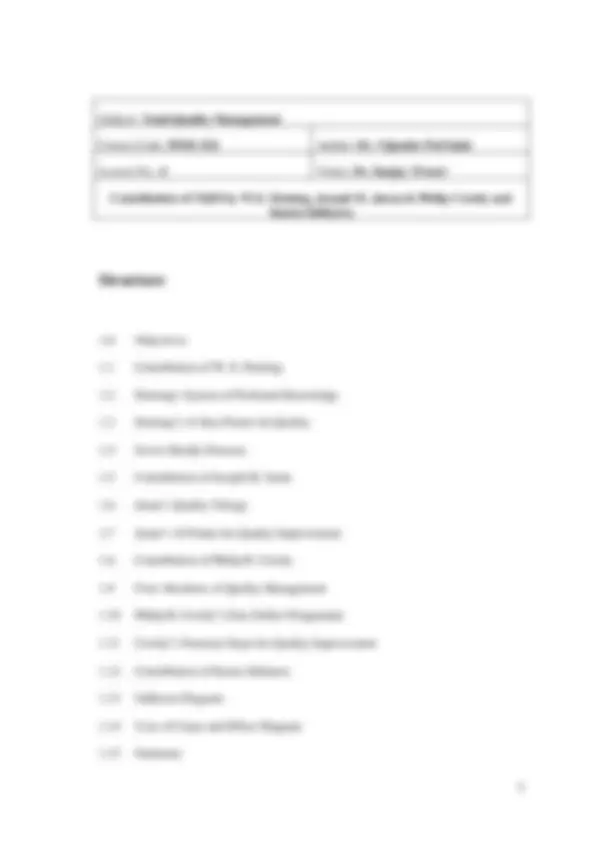
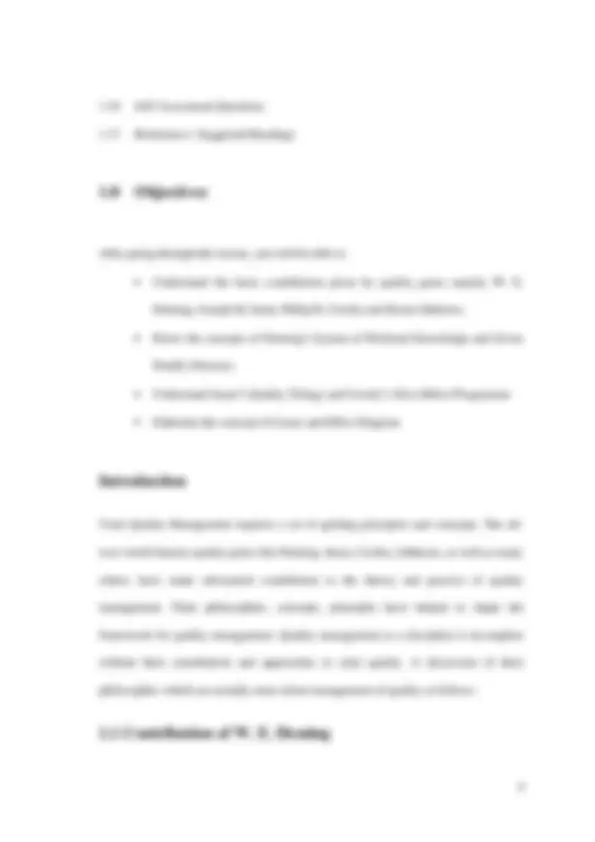
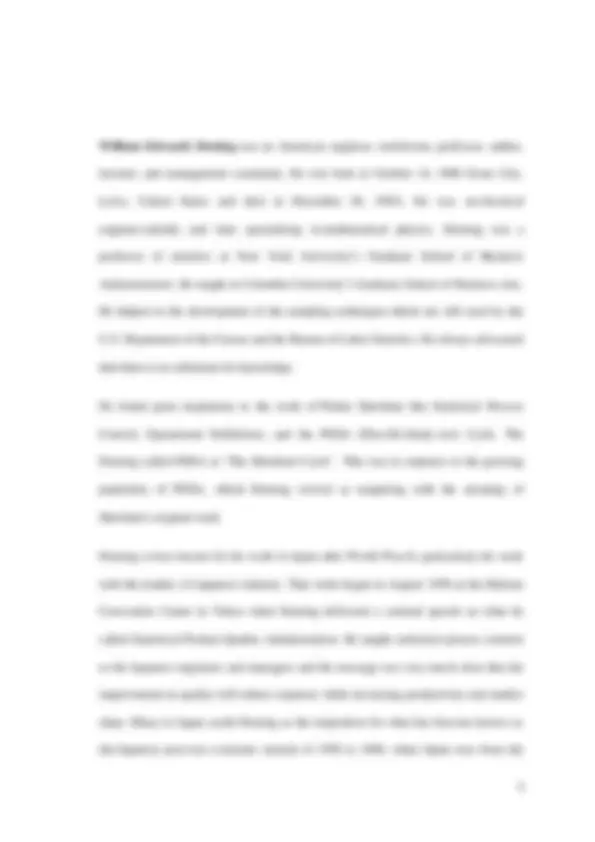
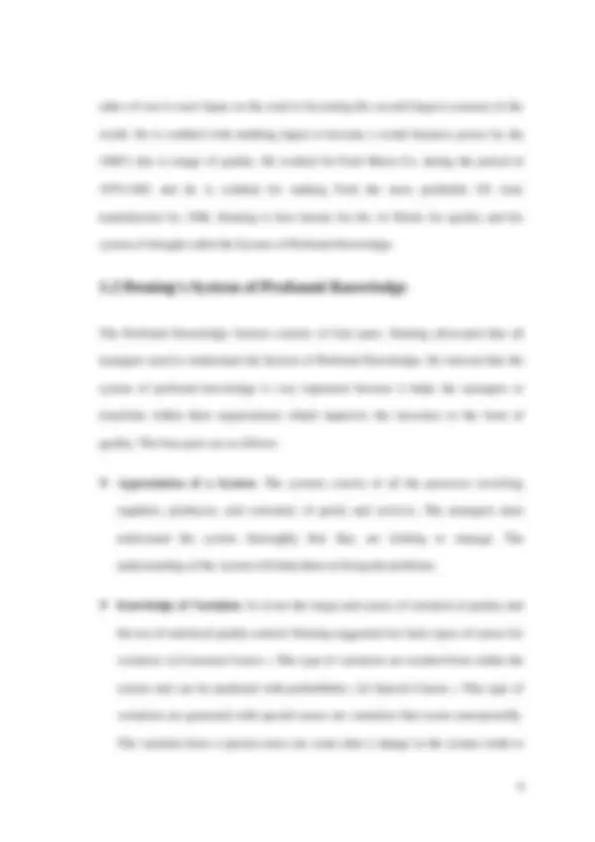
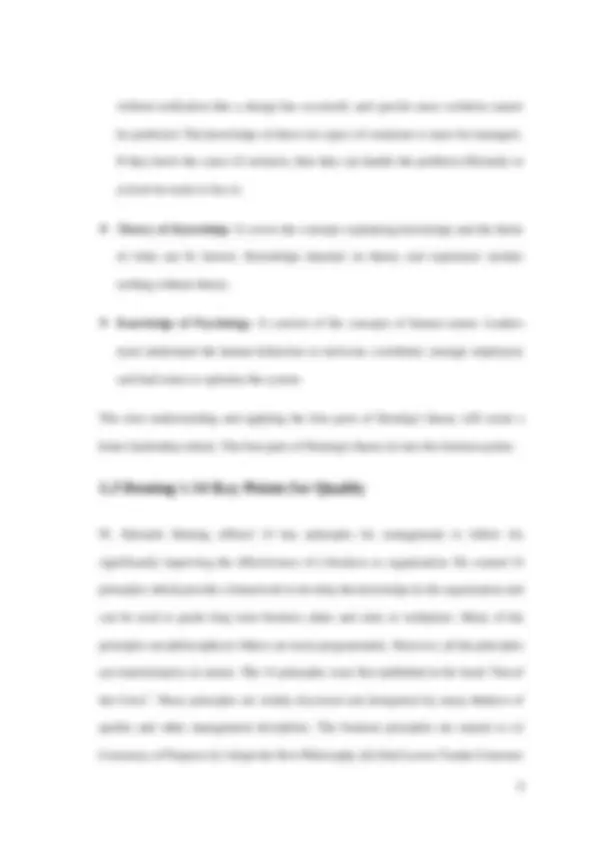
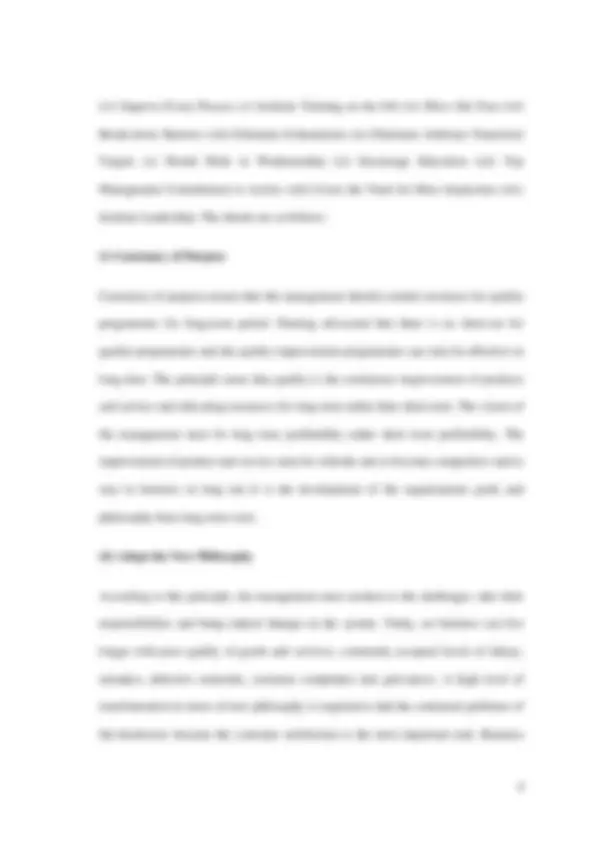
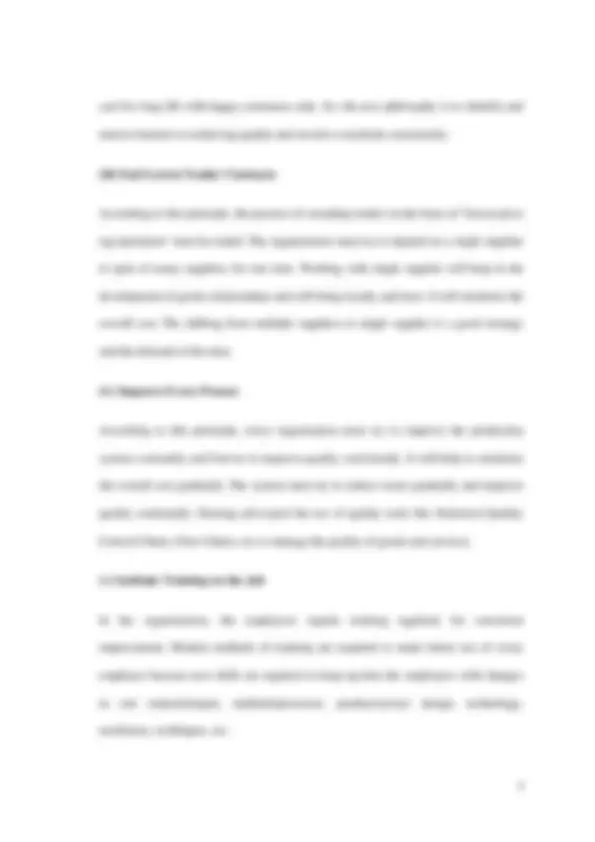
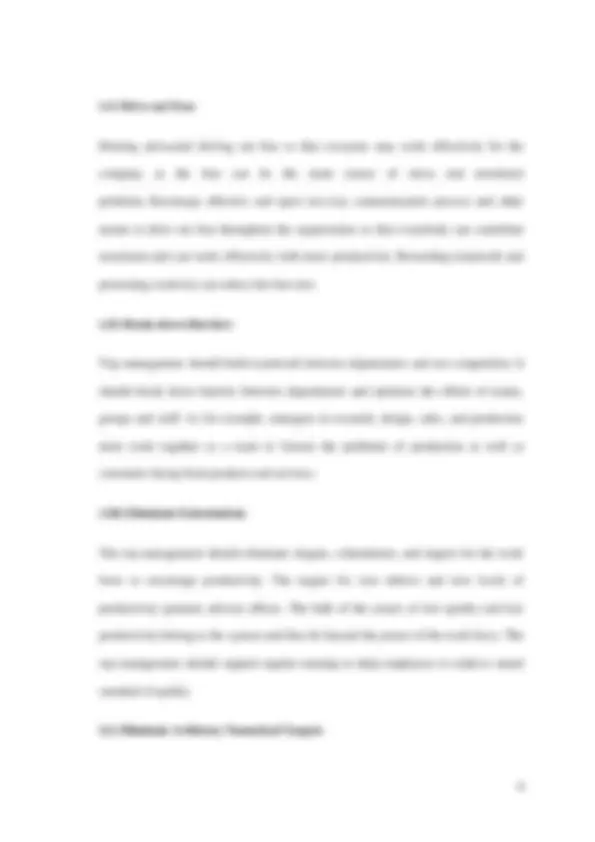
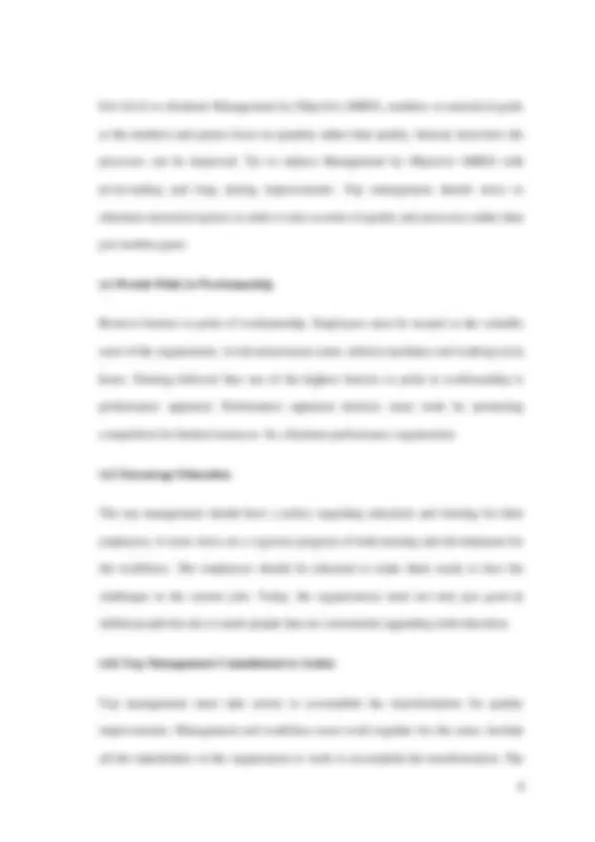
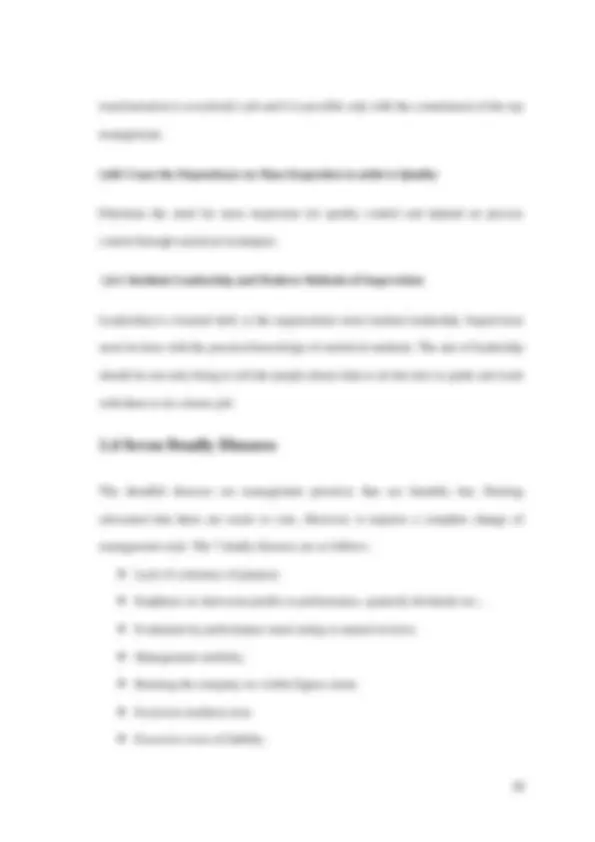
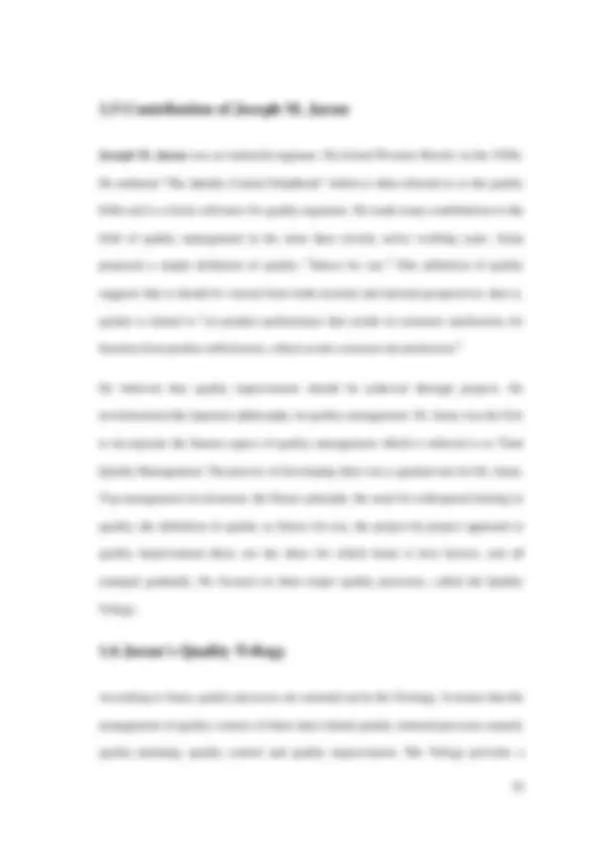
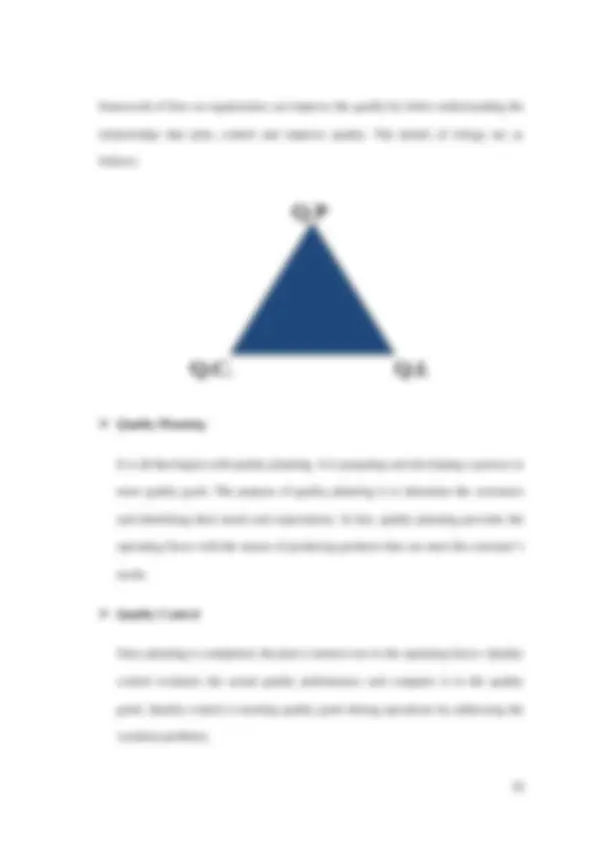
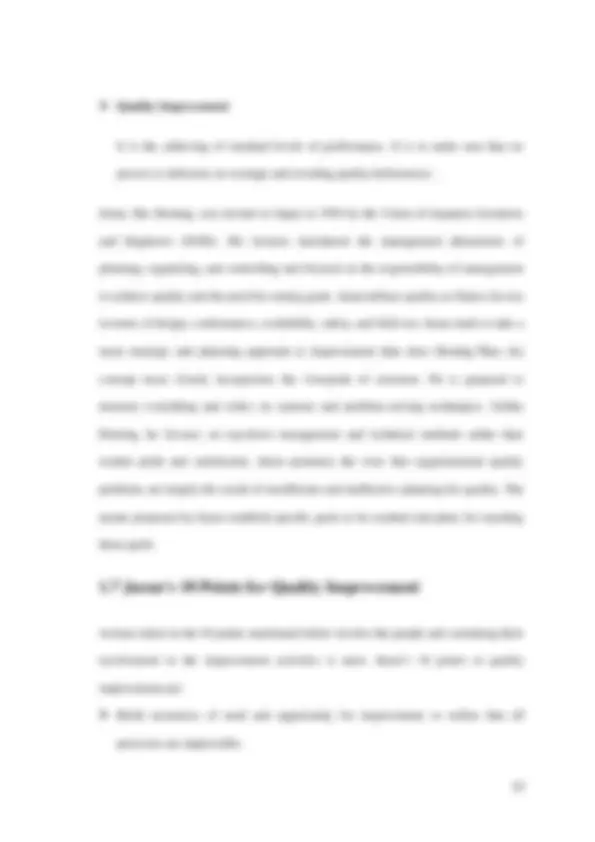
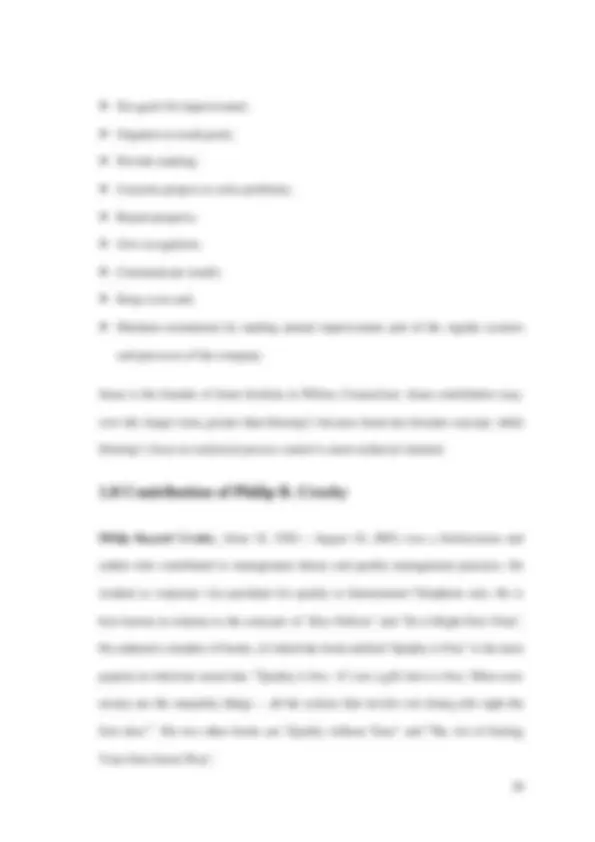
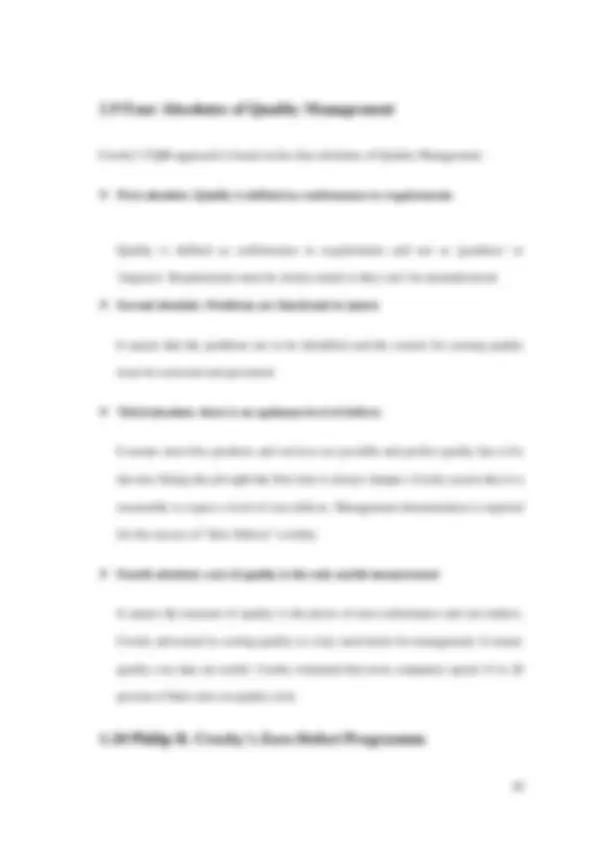
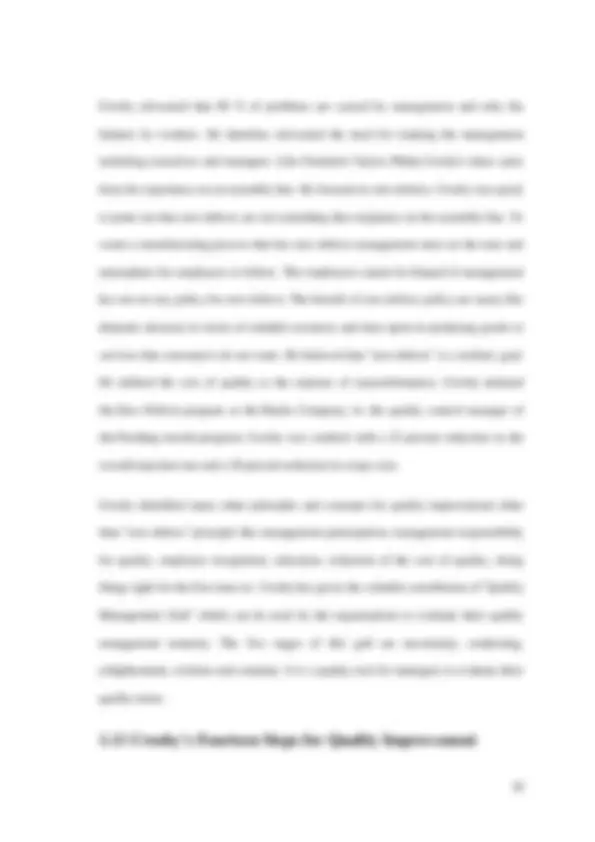
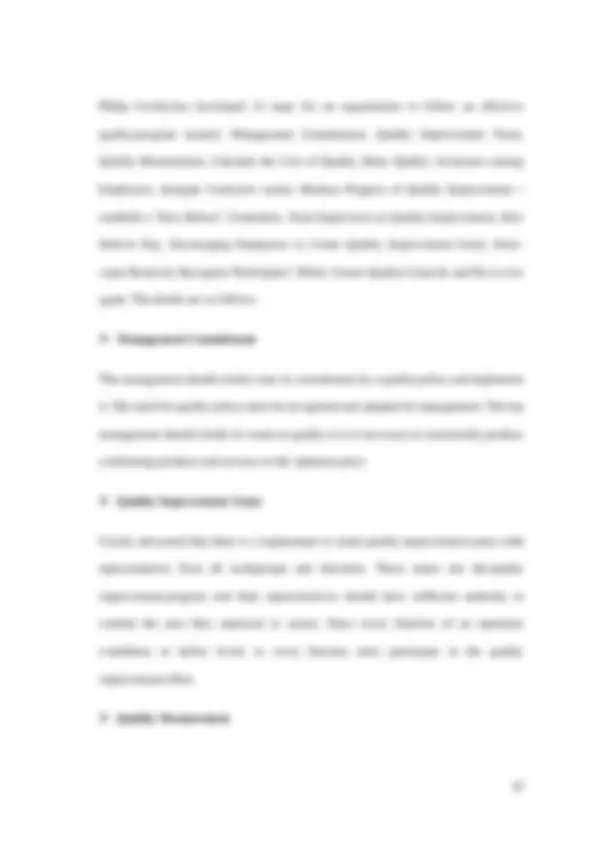
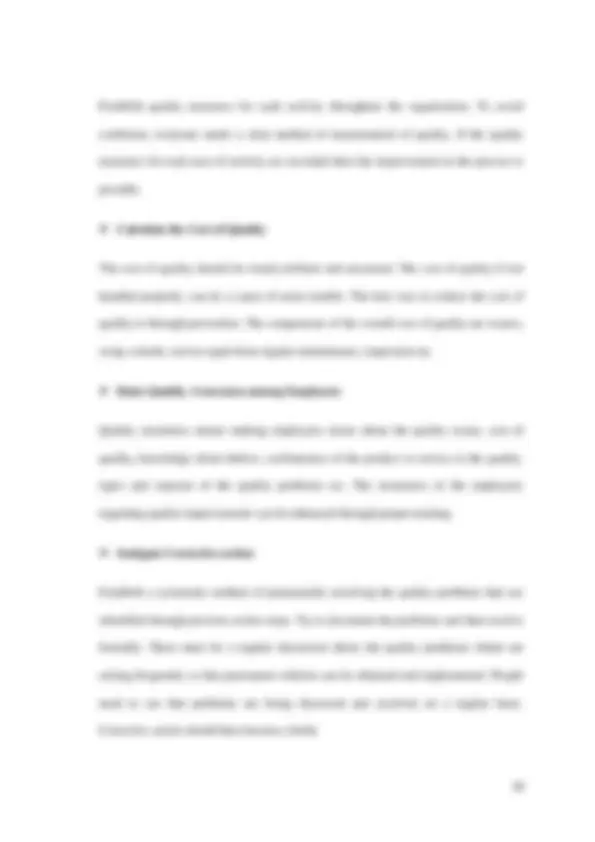
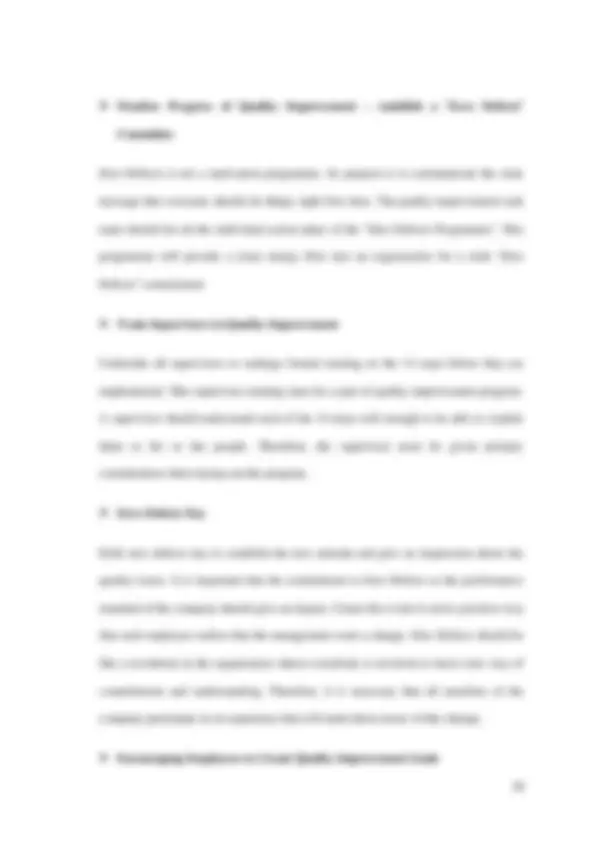
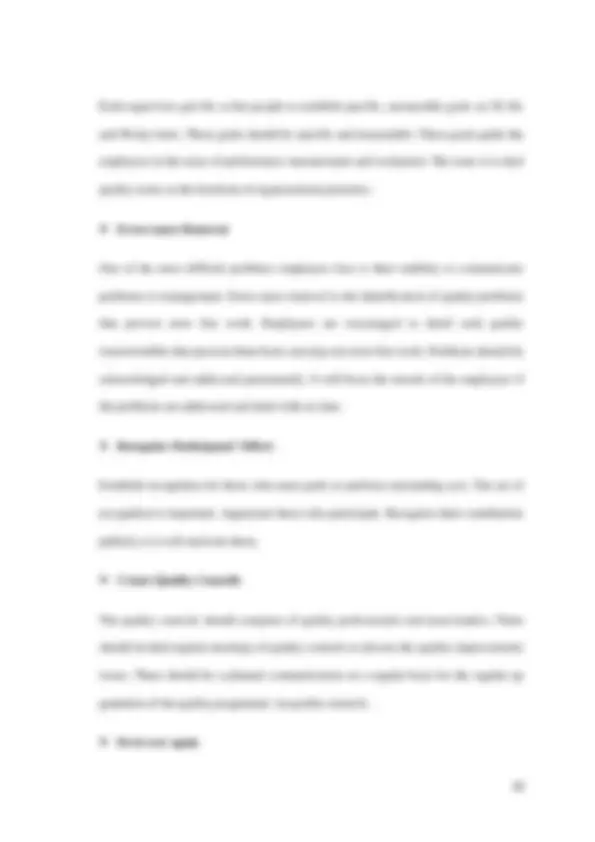
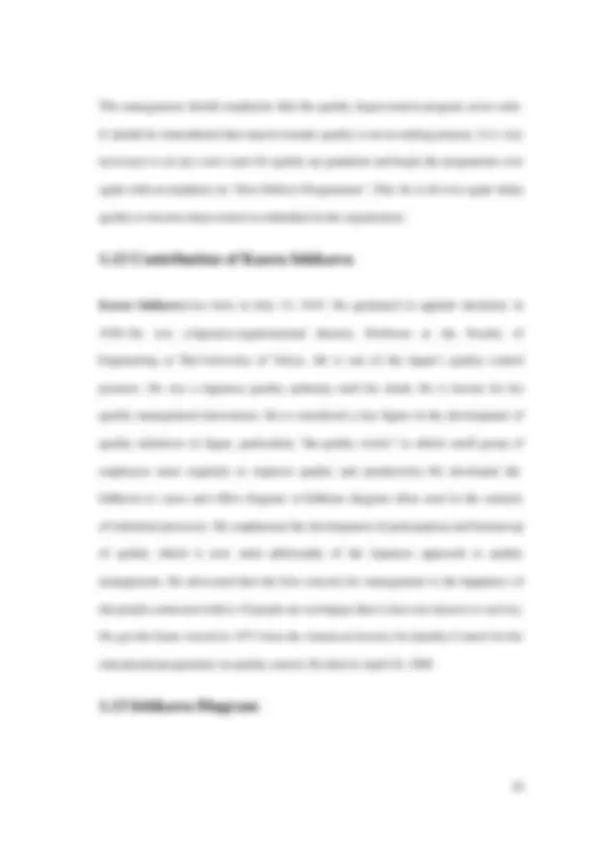
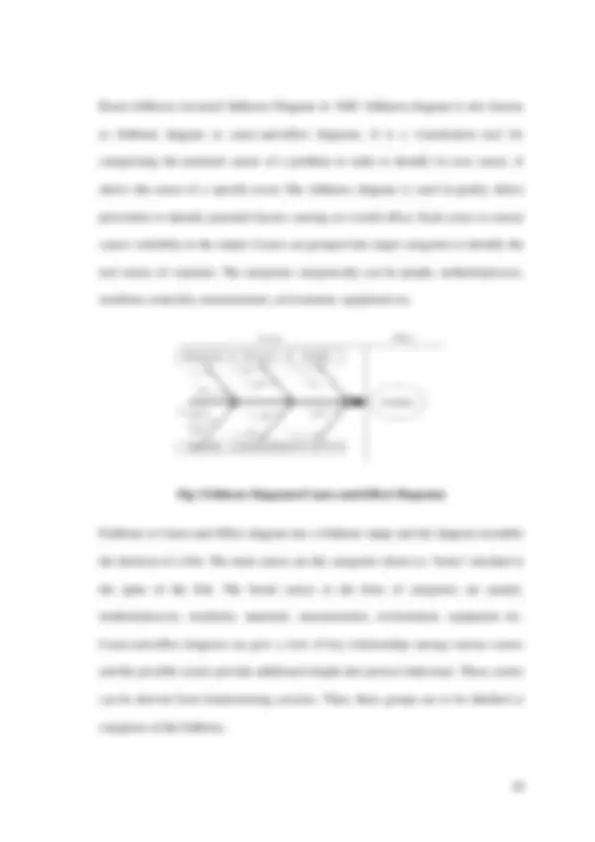
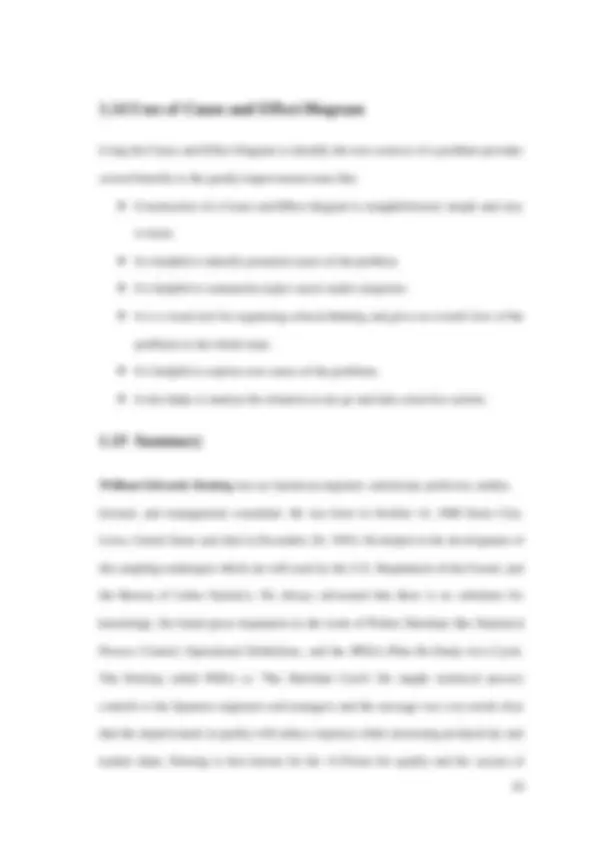
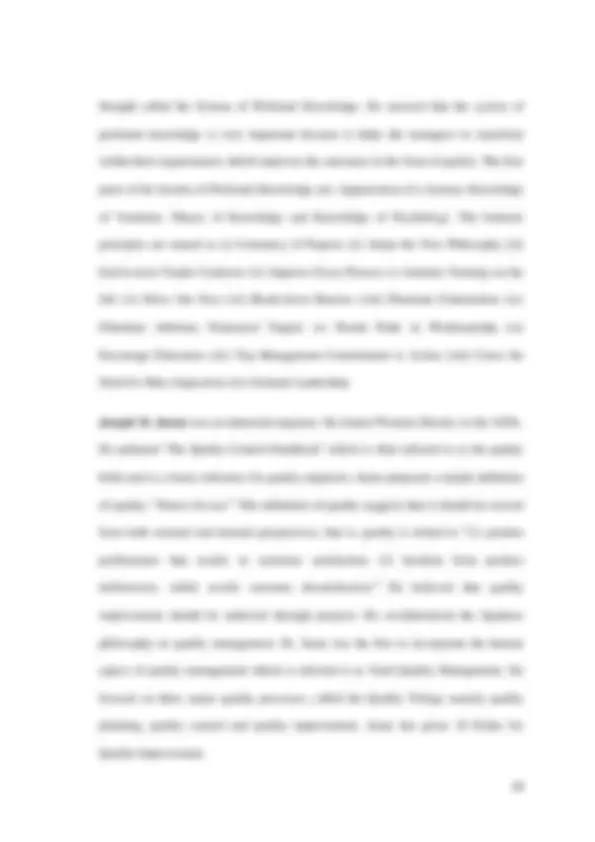
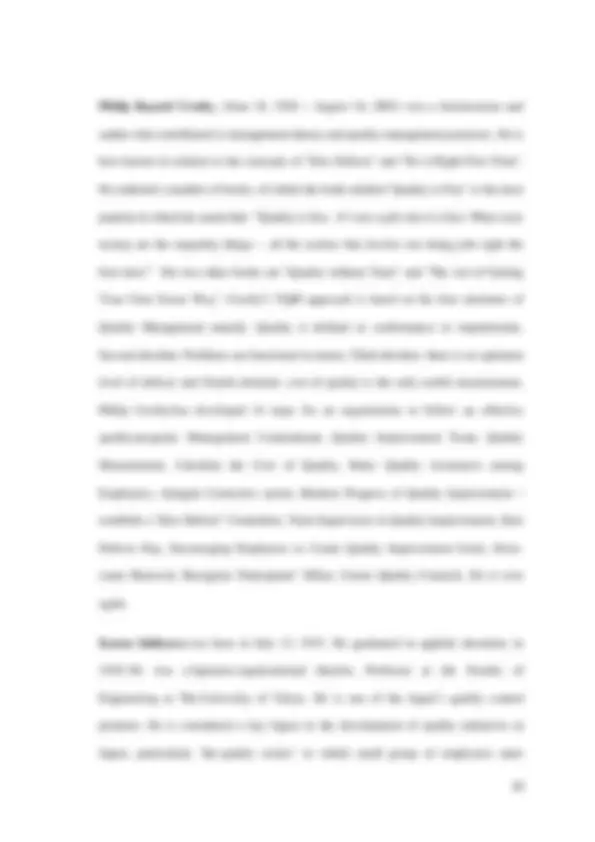
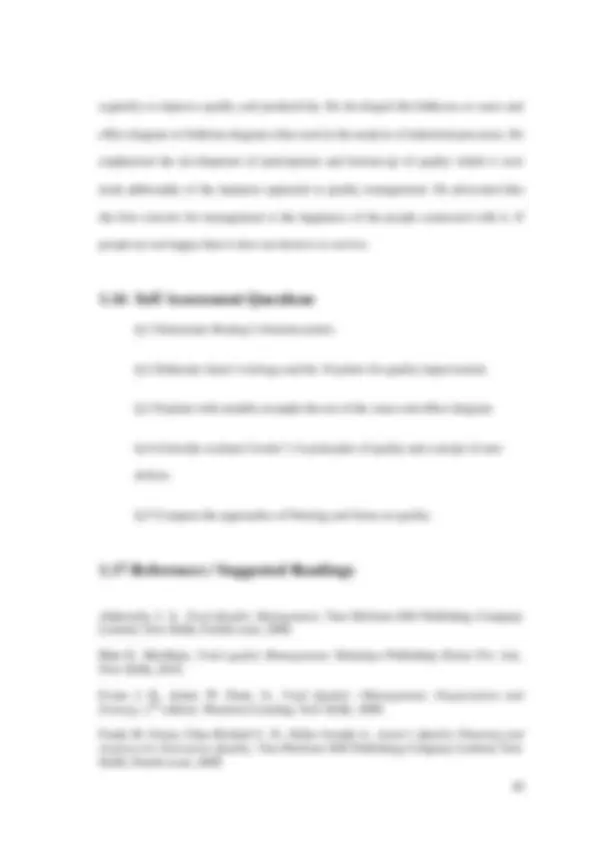
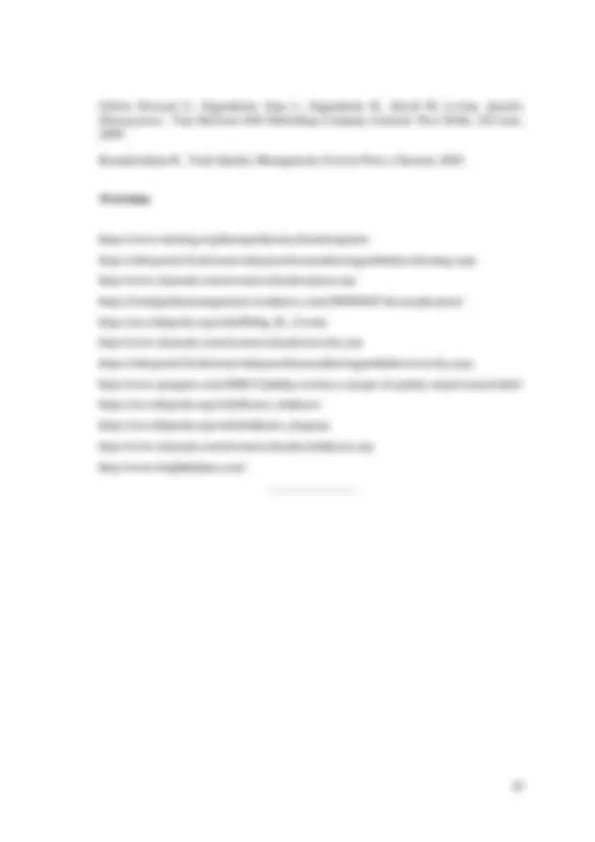
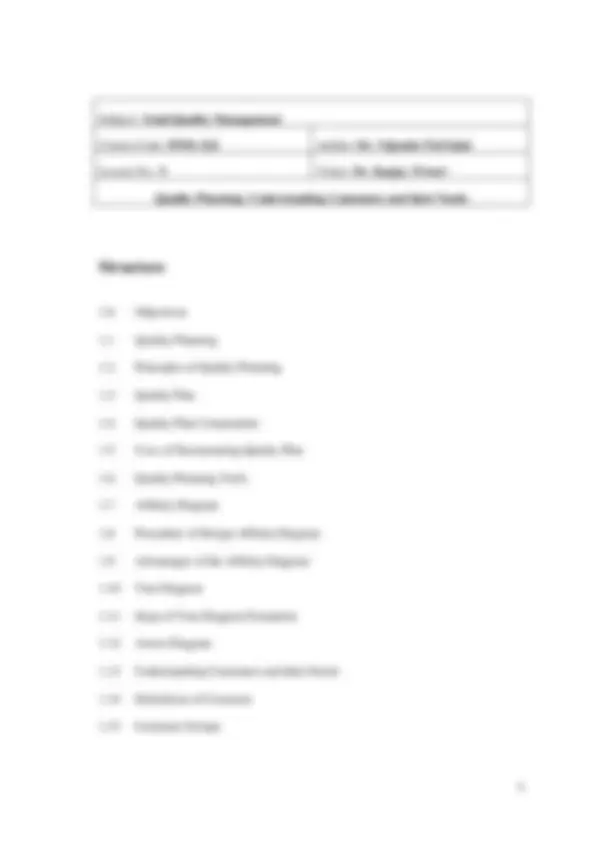
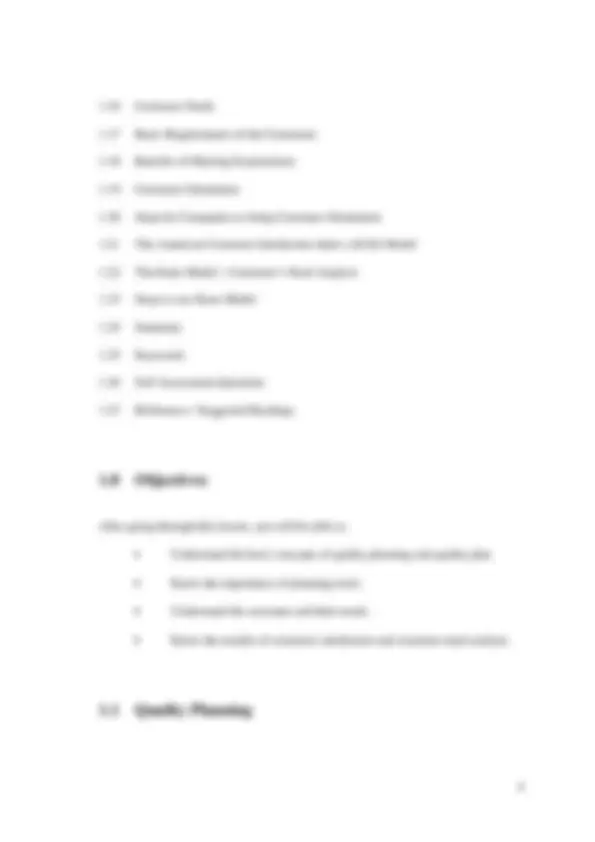
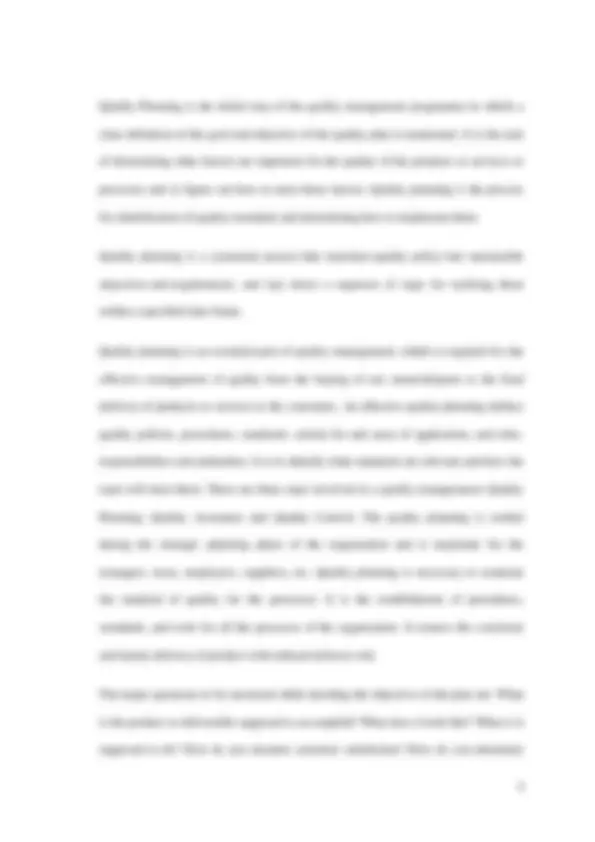
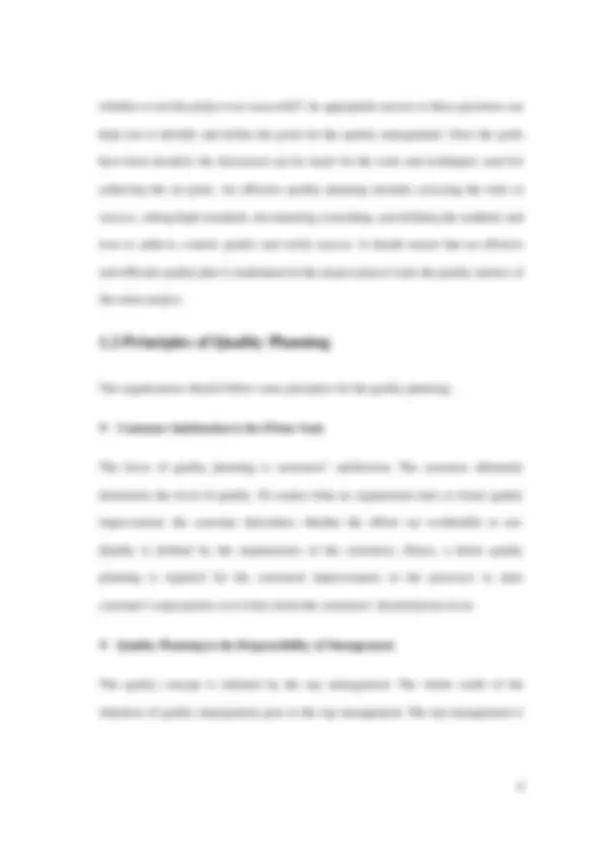
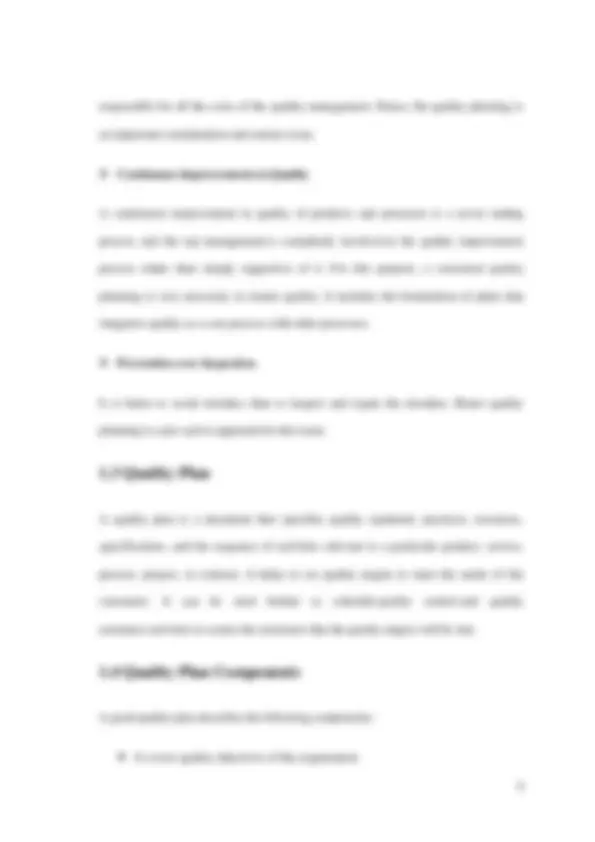
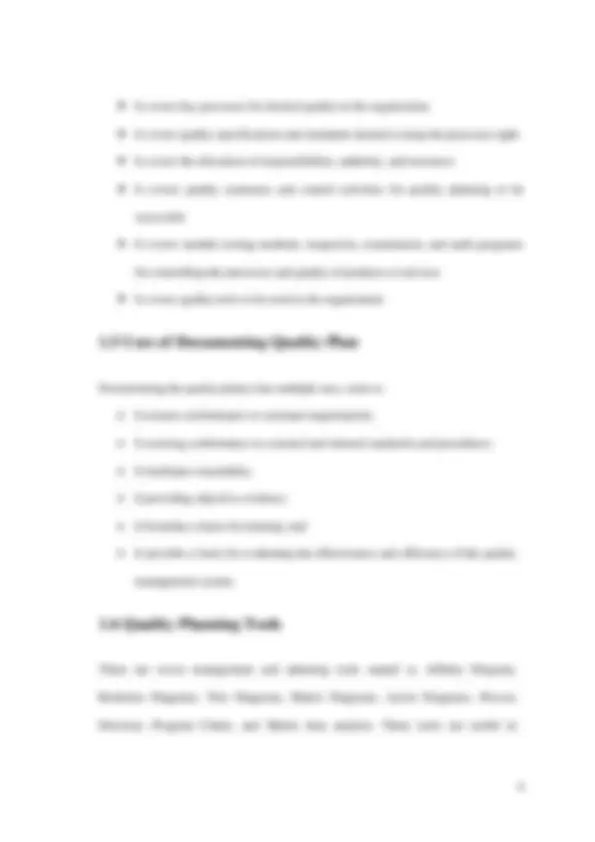

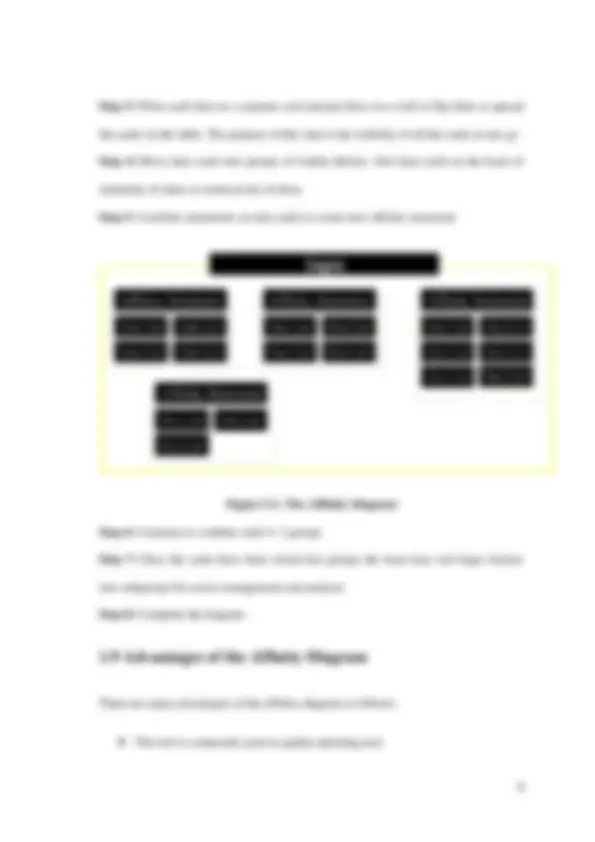
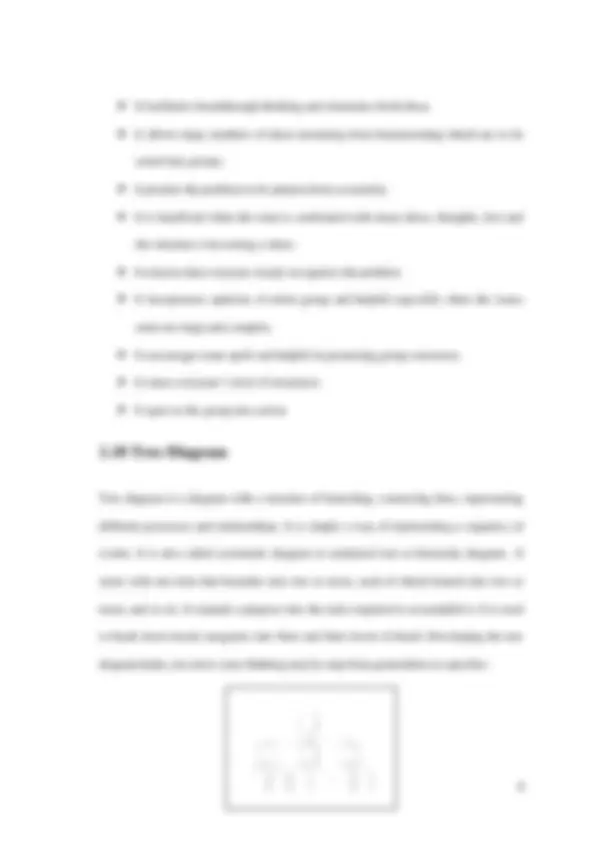
Study with the several resources on Docsity
Earn points by helping other students or get them with a premium plan
Prepare for your exams
Study with the several resources on Docsity
Earn points to download
Earn points by helping other students or get them with a premium plan
Community
Ask the community for help and clear up your study doubts
Discover the best universities in your country according to Docsity users
Free resources
Download our free guides on studying techniques, anxiety management strategies, and thesis advice from Docsity tutors
It is a summary of total quality management
Typology: Summaries
1 / 249
This page cannot be seen from the preview
Don't miss anything!
Subject: Total Quality Management Course Code: POM-324 Author: Dr. Vijender Pal Saini Lesson No.: 1 Vetter: Dr. Sanjay Tiwari Concepts of Quality, Total Quality and Total Quality Management
1.0 Objectives 1.1 Introduction 1.2 Concept of Quality 1.3 Dimensions of Quality 1.4 Application / Usage of Quality for General Public / Consumers 1.5 Application of Quality for Producers or Manufacturers 1.6 Factors affecting Quality 1.7 Quality Management 1.8 Total Quality Management 1.9 Characteristics / Nature of TQM 1.10 The TQM Practices Followed by Multinational Companies 1.11 Summary 1.12 Keywords 1.13 Self Assessment Questions 1.14 References / Suggested Readings
After going through this lesson, you will be able to: Understand the concept of Quality in day-to-day life and business. Differentiate between Quality and Quality Management Elaborate the concept of Total Quality Management
Quality is a buzz word in our lives. When the customer is in market, he or she is knowingly or unknowingly very cautious about the quality of product or service. Imagine the last buying of any product or service, e.g., mobile purchased last time. You must have enquired about various features like RAM, Operating System, Processor, Size, Body Colour, Cover, etc. If any of the features is not available, you might have suddenly changed the brand or have decided not to purchase it. Remember, how our mothers buy fruits, vegetables or grocery items. They are buying fresh and look-wise firm fruits, vegetable and groceries. Simultaneously, they are very conscious about the price of the fruits, vegetable and groceries. So, by nature, we are inclined to get various features of products or services or these are supposed to be provided by the manufacturers. If we get the desired standard features in a product or service, we generally say that the quality of the product or service is up to the mark. It means the features of products and services give satisfaction. These features can be termed as quality characteristics. Cost considerations are also taken care of while measuring the quality considerations, but have you ever imagined how the producers or manufactures identify and provide these features of products and services?
Juran defines quality as fitness for use.
Quality is an attitude of mind. Quality is in the eye of the consumers. It is the total sum of features liked by the consumers while purchasing a product or service. Let’s take an example of product. For some consumers, it is the processor of mobile and for some consumers it is the RAM, which matters. For some consumers both RAM and process of mobile matter. In the case of a restaurant, for some consumers taste of meal and parking matters, while for some consumers it is the aesthetics of the restaurant that matters. For some consumers both aesthetics and taste of meal matter. Therefore, quality is the specific feature of the product and service that satisfies the needs of the consumers.
Quality is advanced design and engineering technology. Let’s take an example of automobile industry where every company is striving hard to deliver at least two new cars in the market. Have you ever imagined how the companies like Toyota, Ford, Volkswagen, Audi, and Mercedes Benz are capable of giving newer model of cars with innovated and advanced features in-built in a car? They are committed to deliver flawless products consistently. Delivering flawless products is called quality. They have precise manufacturing facilities in their plants. Their processes are standardised. Having standardised processes is called quality. The standardisation of processes gives them advantage to deliver quality products consistently. They have achieved excellence in quality output. They have no room for errors. Here, Quality is having policy of no room for errors. The Indian companies like Tata Motors, Maruti Suzuki are not far behind in delivering quality products and services internationally. They also have zero error policy.
Quality is also called zero error policy. Quality could be called as giving standard products with zero defects. So, we can say that companies live with quality commitment. The management works very hard to deliver error free standardised products consistently. They strive hard to give innovated products to the market. The ultimate satisfaction of consumers leads to upgrade the standard of living of the society.
It ensures error free products. It enhances the development of new or innovated products. (e.g. HUL’s Pure it) It helps to give warranty or guarantee of products. (e.g. 2 years warranty with Bajaj Fans) It enables good customer service. It promises timely delivery. It helps in getting all the desired features in products and services. Quality helps in getting satisfaction after the use of products and services.
Quality helps in meeting the changing demands of the consumers. It ensures delivery of flawless or zero error products or services. It ensures delivery of products or service on time.
Quality management includes all the functions of the organisation to design and provide quality products and services which fulfils the needs of the customers and generate ultimate satisfaction. The core concept of quality management is quality planning, quality controlling and quality improvement. The traditional approach of quality management covers typical inspection aspect and the ‘do it right from the first time’ concept. The modern quality management covers all the concepts given by thinkers called Quality Gurus like W. Edwards Deming, Philip B. Crosby, Armand V. Feigenbaum, Kaoru Ishikawa, Joseph M. Juran and Genichi Taguchi etc.
Quality Planning
The first and foremost step in quality planning is to plan and know who your customer is, and what are his needs and wants. After optimising the product or service features, the organisation designs and develops the product or service. The next step is to standardise the processes so that the products or services can be standardised. The consistent production of desired quality products and services require high involvement and contribution of employees in planning.
Quality Control
It is a very important step in quality management. It requires extensive, proper and consistent training of employees so that errors can be controlled. Inconsistency in products and services can be avoided by using Statistically Process Control techniques.
Total Quality Management is mainly concerned with continuous improvement in all work. It is a long term planning. It is the consistent improvement in the quality. It is a never ending process. Total Quality Management consists of three words: Total, Quality and Management Total Make up of the whole. Quality Degree of excellence a product or service provides. Management It is a process of planning, organising, directing and controlling. Therefore, TQM is the art of managing the whole to achieve excellence. TQM covers all the set rules, regulations, guidelines and principles that contribute in improving the organization continuously. It is a continuous process of improvement for individuals, groups of people and the whole organisation. It is the application of quantitative methods and human resources to improve all the processes within an organization to satisfy the needs of customers consistently. TQM integrates all the fundamental management techniques, existing improvement efforts, and technical tools under a disciplined approach. It covers the most quality principles and practices proposed by quality gurus.
Total Quality Management ( TQM ) is a management approach for an organization, centered on quality, based on the participation and commitment of all the internal and
To produce quality product and service is not an easy job. Sometimes it takes years to give the desired results. All the employees have to work consistently as a team in one direction to improve all the processes in the organisation.
It is a Part of Strategic Planning and Thinking
TQM policy is a long term planning. The quality policy must be the part of strategic planning to get the desired results.
It is Customer Focused / Oriented
The end result of TQM is complete satisfaction of customers by giving them quality products and services. It is possible only when TQM programme is customer centric.
It is a Team Work
Success in terms of standard quality is possible only when the organizations has a culture of team formation and the employees work in teams and give their maximum. Teams can be formed vertically and horizontally. When top management is involving the lower level employees it is vertically and when the different departmental employees are involved then it is horizontally (employees of marketing, sales, production and finance departments are working for critical and complex projects). Teams are inter-organisational when the employees of other organisations are involved (like employees of banks, suppliers, audit companies, consultants etc.
It is Related with Consistent Improvement of Quality
To deliver quality products and services is not an easy job. All the processes have to be developed and standardised by consistent improvement.
Every Employee is Involved in Quality Improvement Aspect
All the employees internal as well as external are involved in the TQM programme. Internal employees include all the employees included from top to bottom and external employees are suppliers, banks and other institutions which are involved in the TQM process.
Every Employee is Responsible for the Success of TQM
If all the employees are determined and committed for the quality products and services, then only quality could be delivered.
All the MNC’s like Sony, Toyota, Xerox, Motorola follow the Total Quality Management practices. The salient features of TQM approach followed by the best companies are as following: The companies create a sense of an environment of mutual trust, respect and dignity. The management act immediately on new ideas and suggestions. The companies are meeting and exceeding customers’ requirements and expectations on consistent basis. The companies hear and learn from the dissatisfied/unhappy customers and responsible for complete customer satisfaction.
Total Quality Management is mainly concerned with continuous improvement in all work. It is a long term planning. It is the consistent improvement in the quality. It is a never ending process. Total Quality Management consists of three words: Total, Quality and Management. TQM starts from top management; it is a consistent process; it is a part of strategic planning and thinking; it is customer focused; it is a team work; it is related with consistent improvement of quality; every employee is involved in quality improvement aspect; and every employee is responsible for the success of TQM.
Quality
It is the totality of features and characteristics of a product or service that bears on its ability to meet a stated or implied need. Total Quality Management
TQM covers all the set rules, regulations, guidelines and principles that contribute in the continuously improving organization.
Fabio Borri Giuliano Boccaletti, (1995),"From Total Quality Management to Total Quality Environmental Management", The TQM Magazine, Vol. 7 Iss 5 pp. 38 –
GerhardKybernetes, Vol. 24 Iss 1 pp. 55 Plenert, (1995),"Management – 59. Cybernetics: Total Quality Management",
Jamshed H. Khan, (2003),"Impact of Total Quality Management on Productivity", The TQM Magazine, Vol. 15 Iss 6 pp. 374 -380. John C. Groth, (1995),"Total Quality Management: Perspectives for Leaders", The TQM Magazine, Vol. 7 Iss 3 pp. 54 – 59. Jon Choppin, (1994),"Total Quality and Management", Managing Service Quality: An International Journal, Vol. 4 Iss 4 pp. 6 – 8. Jon Choppin, (1994),"Total Quality Service", Managing Service Quality: An International Journal, Vol. 4 Iss 3 pp. 49 – 52. Jon Choppin, (1995),"Total Quality ManagementQuality: An International Journal, Vol. 5 Iss 1 pp. 47 – What Isn – 49.’t It?", Managing Service
Juan José Tarí, (2005),"Components of Successful Total Quality Management", The TQM Magazine, Vol. 17 Iss 2 pp. 182 – 194. Khalifa N. Al-khalifa Elaine M. Aspinwall, (2000),"The Development of Total Quality Management in Qatar", The TQM Magazine, Vol. 12 Iss 3 pp. 194 – 204. Lawrence P. Huggins, (1998),"Total Quality Management and the Contributions of A.V. Feigenbaum", Journal of Management History, Vol. 4 Iss 1 pp. 60 – 67. Madjid Tavana Barbara Mohebbi Dennis T. Kennedy, (2003),"Total Quality Index: A Benchmarking Tool for Total Quality Management", Benchmarking: An International Journal, Vol. 10 Iss 6 pp. 507 – 527.
Subject: Total Quality Management Course Code: POM-324 Author: Dr. Vijender Pal Saini Lesson No.: 2 Vetter: Dr. Sanjay Tiwari Approaches of Total Quality & Cost of Quality
1.0 Objectives 1.1 Approaches to Total Quality Management: An Introduction 1.2 The Deming Management Philosophy 1.3 System of Profound Knowledge 1.4 Deming’s 14 Points for Management 1.5 The Juran Philosophy 1.6 Juran’s Quality Trilogy 1.7 Juran’s 10 Points for Management 1.8 The Crosby Philosophy 1.9 Four Absolutes of Quality Management 1.10 Crosby’s 14 Points for Management 1.11 The Kaoru Ishikawa Philosophy 1.12 Framework for Quality and Performance Excellence 1.13 Just-in-Time (JIT) 1.14 Business Process Reengineering 1.15 Kaizen Approach – A Continuous Improvement Tool 1.16 ISO-9000 Standards 1.17 Quality Audit 1.18 Principles of Quality Management 1.19 Seven Principles by Gerald F. Smith 1.20 International Quality Award Programs 1.21 The Deming Prize
services, and create a culture in which they work. The success of the TQM depends on the significant changes in organisation design, work processes, and culture. There are various approaches to TQM. Some organisations give importance to the use of quality programme like statistical process control and some organisations give importance to the tool like quality function deployments. Sometimes, the organisations fail to realize quality improvements because of lack of holistic understanding of the quality tool(s) or concept(s) by the entire organisation.
“Total Quality Management (TQM) is a comprehensive and structured approach to organizational management that seeks to improve the quality of products and services through ongoing refinements in response to continuous feedback. TQM requirements may be defined separately for a particular organization or may be in adherence to established standards, such as the International Organization for Standardization's ISO 9000 series. TQM can be applied to any type of organization; it originated in the manufacturing sector and has since been adapted for use in almost every type of organization imaginable, including schools, highway maintenance, hotel management, and churches. As a current focus of e-business, TQM is based on quality management from the customer's point of view.” (www. searchcio.techtarget.com)i
Total Quality Management is a management approach for an organization, centered on quality, based on the participation and commitment of all the internal and external customers and aiming at strategically long-term success through customer satisfaction, and benefits to all members of the organization and to society. It uses strategy, data, and effective communications to integrate the quality discipline into the culture and activities of the organization. So, some organisations adopt a problem-solving focus and
concentrate on production as well as customer service processes. They adopt quality circles and team approaches. Some organisations concentrate on error prevention through continuous process improvement and business process reengineering.
Most of the successful companies have adopted unique approaches of total quality management according to their own requirements because one approach suitable for one organisation may be not suitable for another organisation. The reason is the difference in the culture. Every organisation has different culture. Total Quality Management requires a set of guiding principles and concepts. The all-over world famous quality gurus like Deming, Juran, Crosby, Ishikawa, as well as many others, have made substantial contribution to the theory and practice of quality management. Their philosophies, concepts, principles have helped to shape the framework for quality management. Quality management as a discipline is incomplete without their contribution and approaches to total quality. A discussion of their philosophies which are actually more about management of quality as follows:
William Edwards Deming (1900-1993) was an American engineer, statistician, professor, author, lecturer, and management consultant. He developed some sampling techniques which are still used by the U.S. Department of the Census and the Bureau of Labor Statistics. He always advocated that there is no substitute for knowledge. He found great inspiration in the work of Walter Shewhart like Statistical Process Control, Operational Definitions, and the PDSA (Plan-Do-Study-Act) Cycle. The Deming called PDSA as ‘The Shewhart Cycle’. He taught statistical process controls to the Japanese engineers and managers and the message was very much clear that the improvement in