
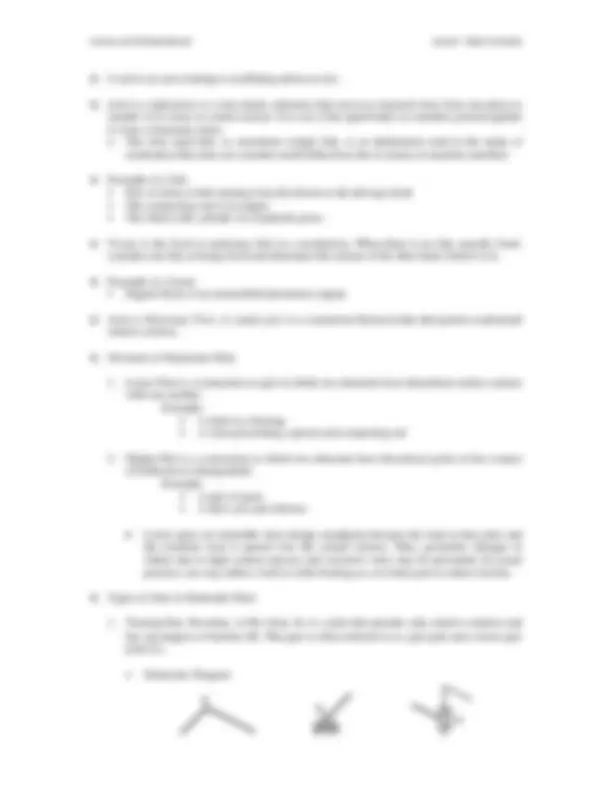
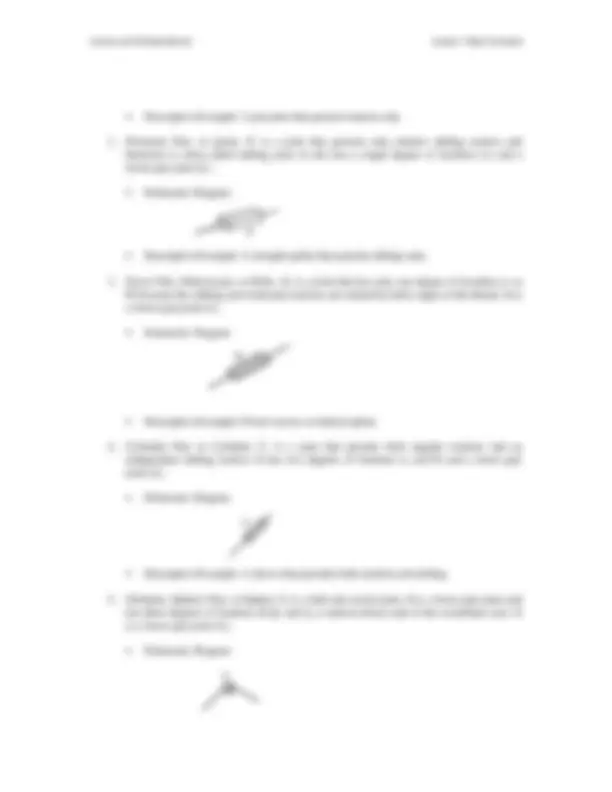
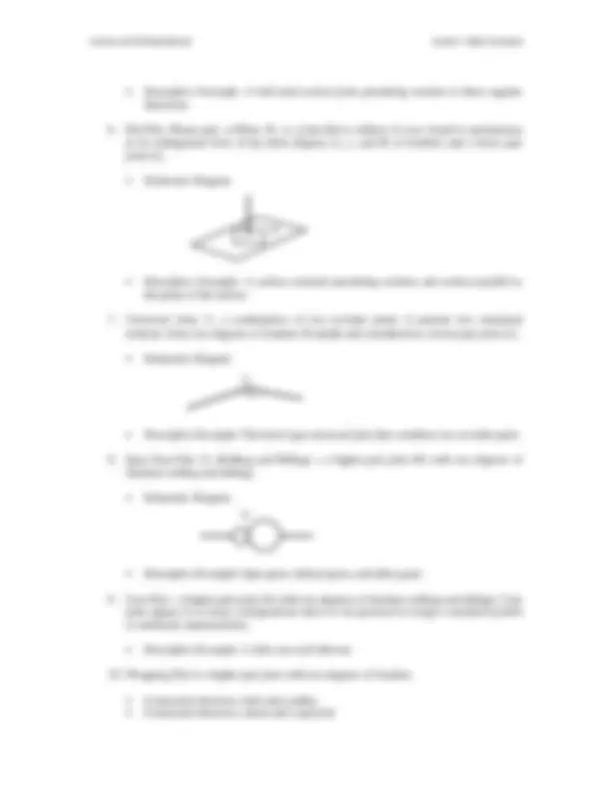
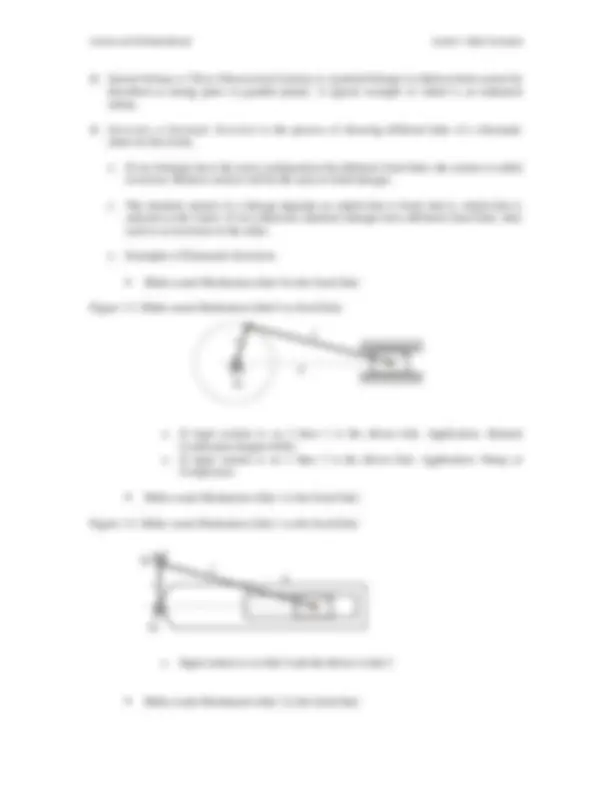
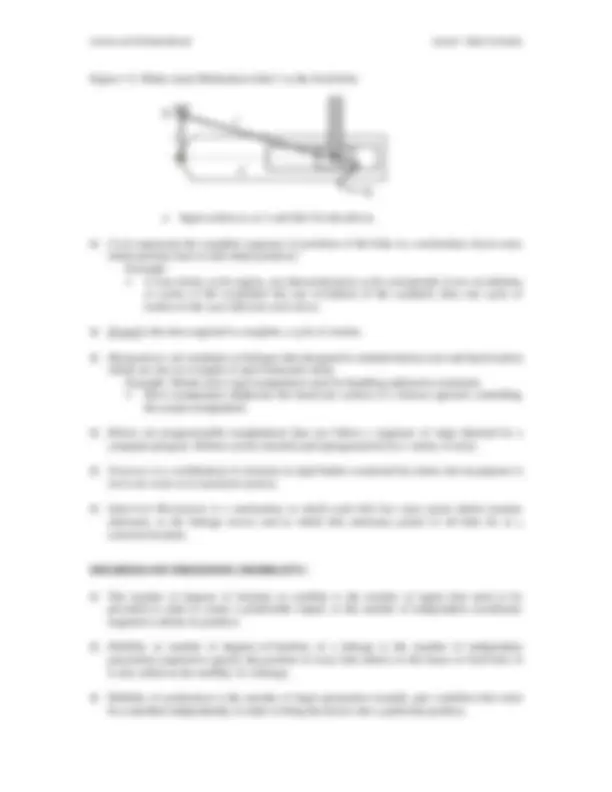
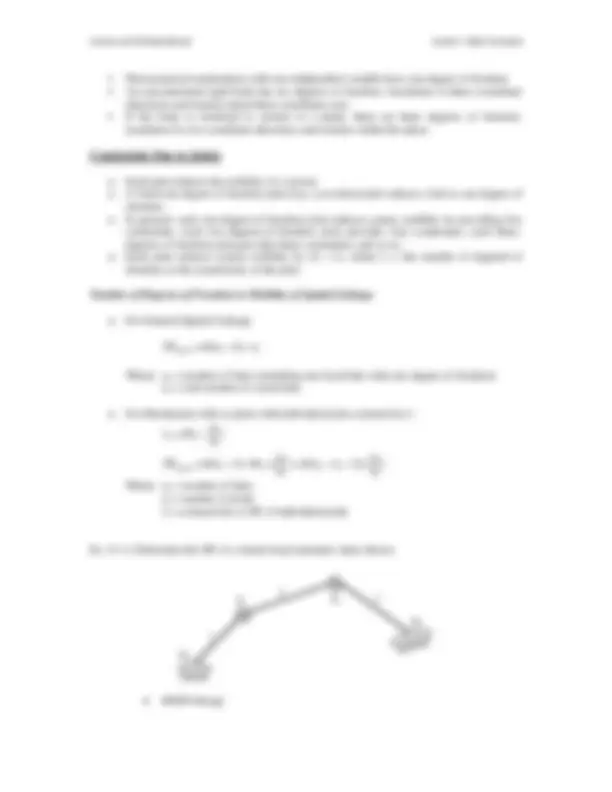
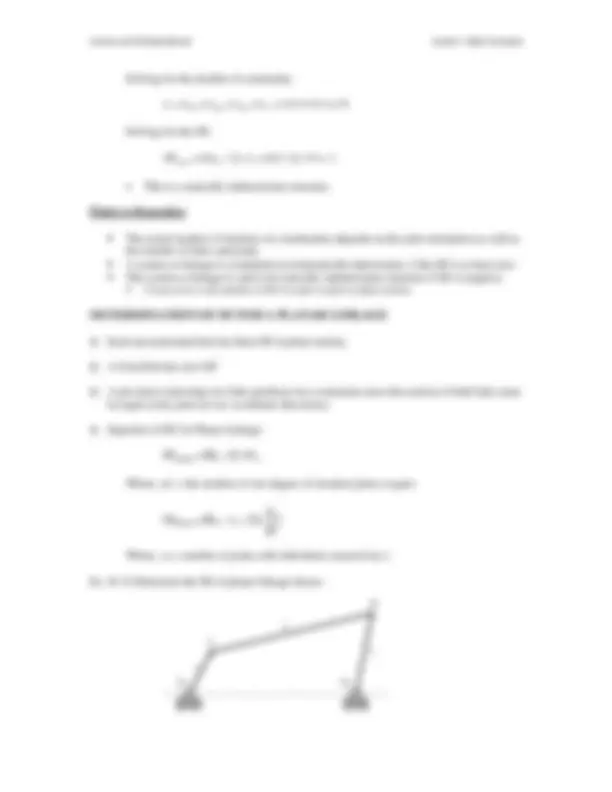
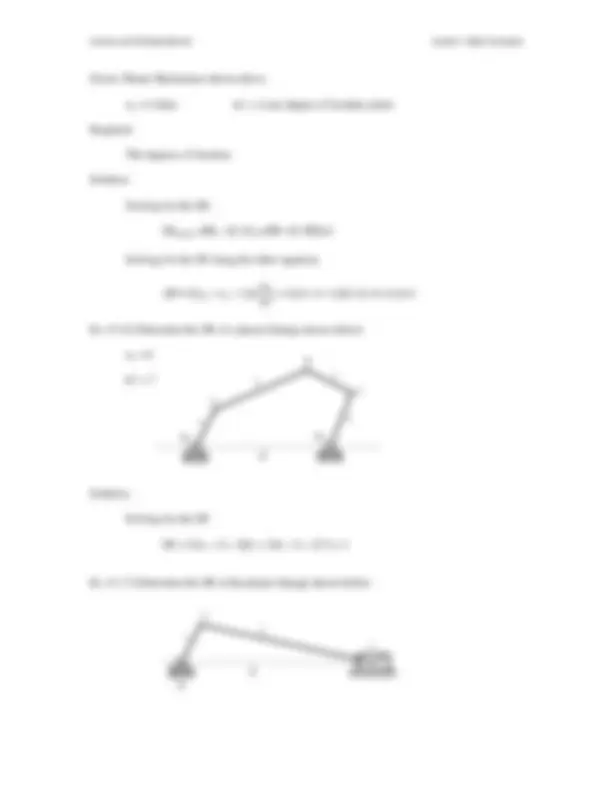
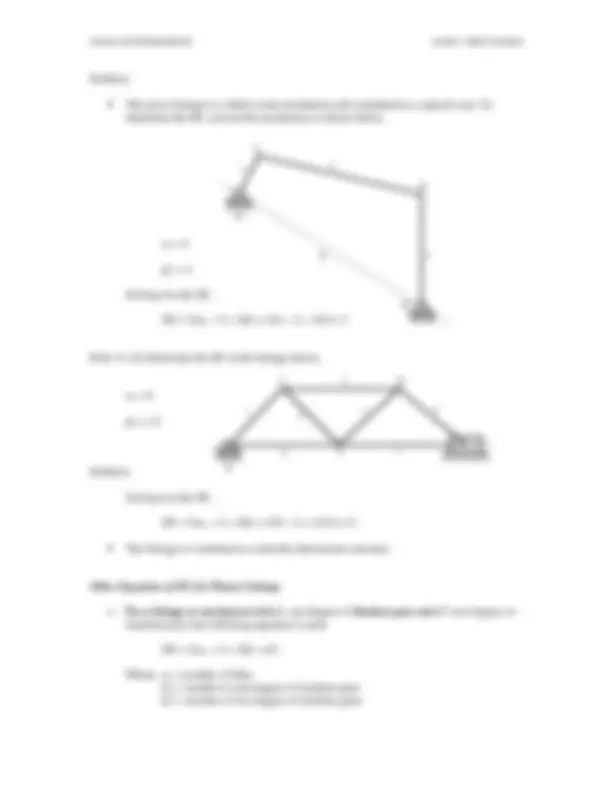
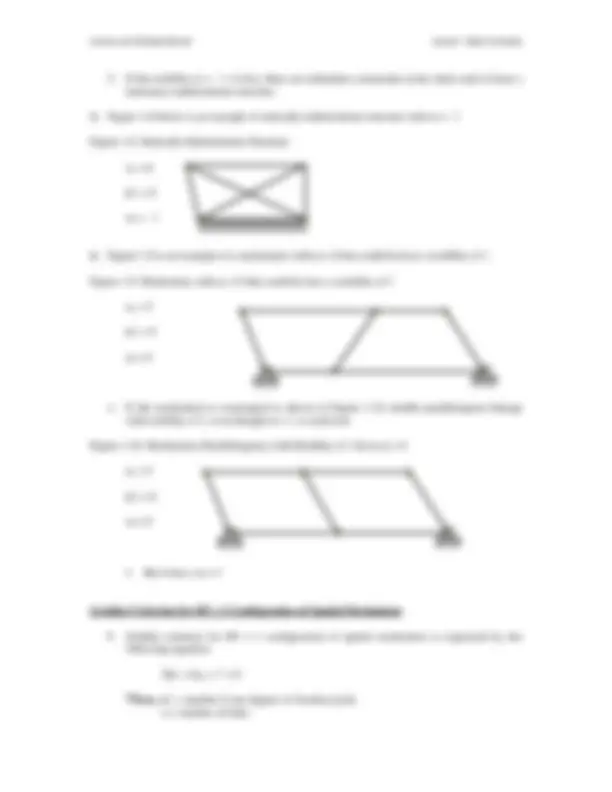
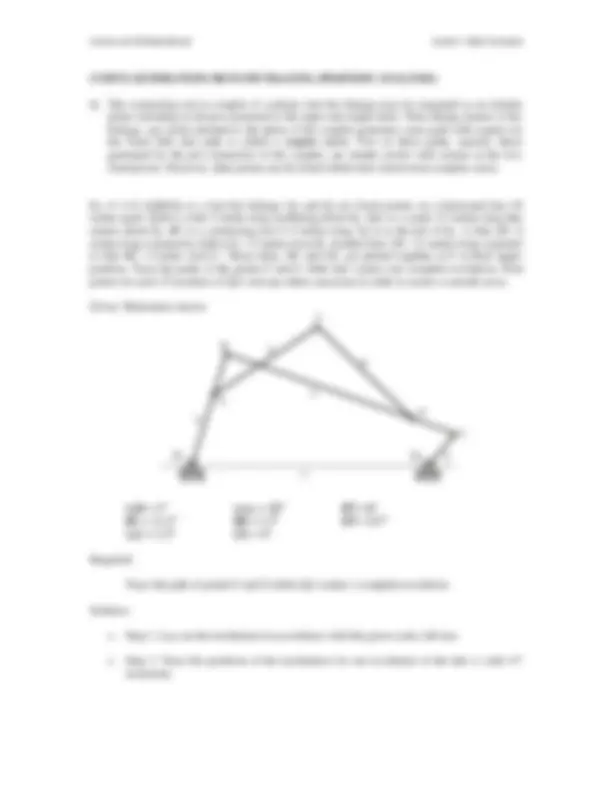
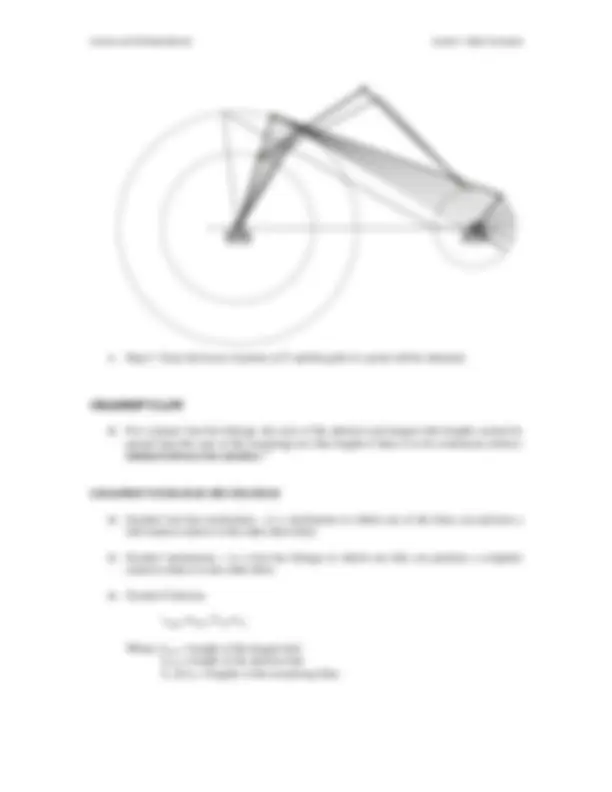
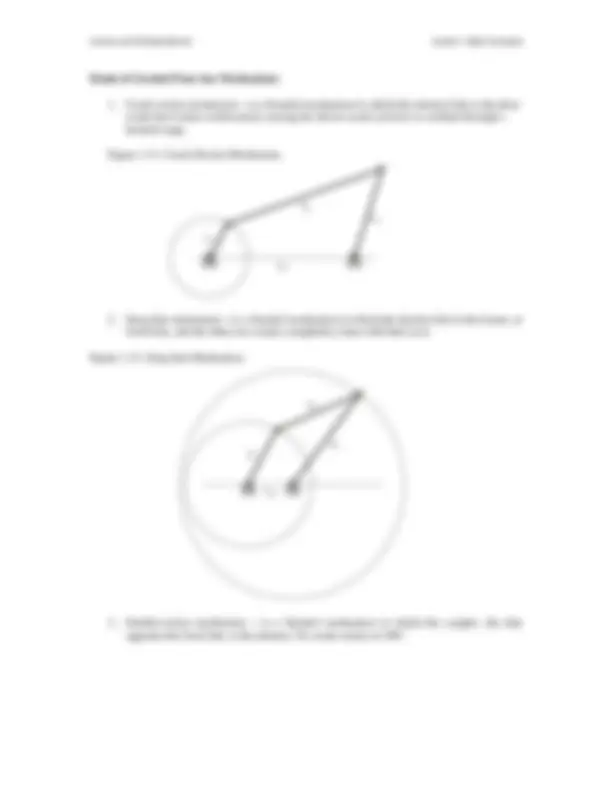
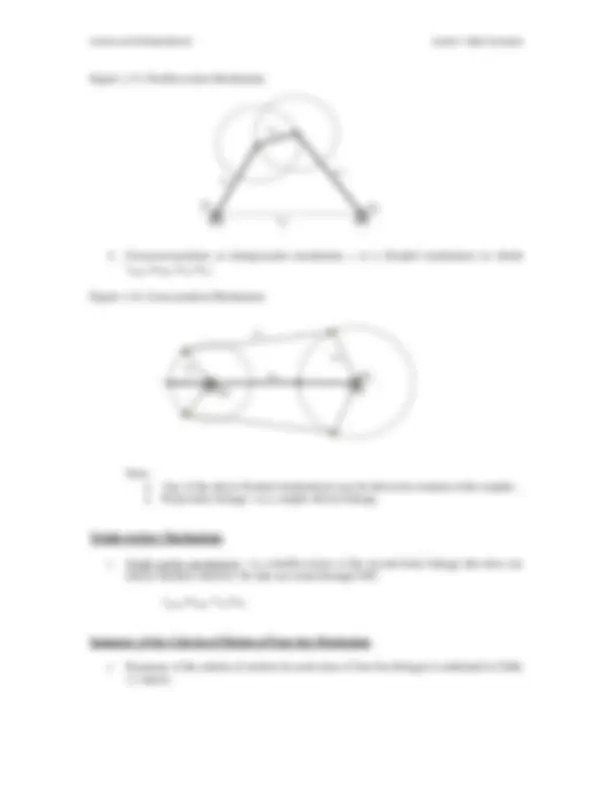
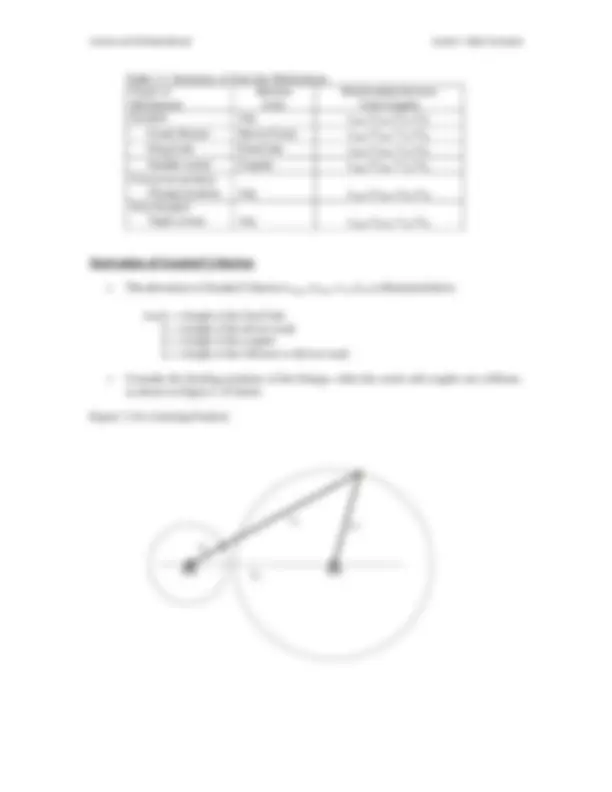
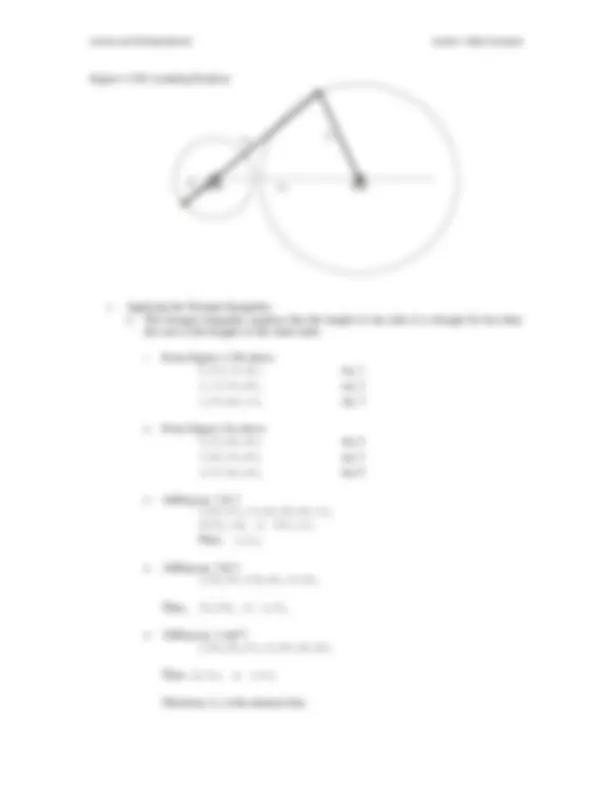
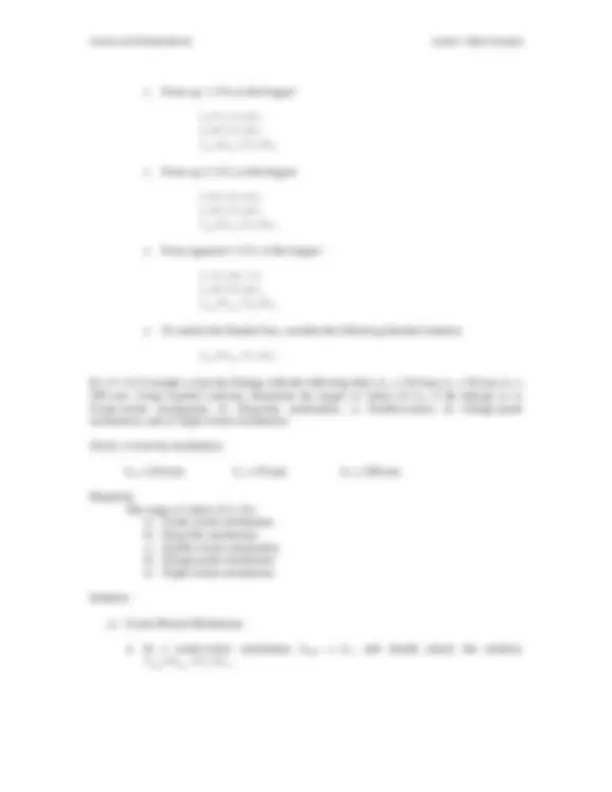
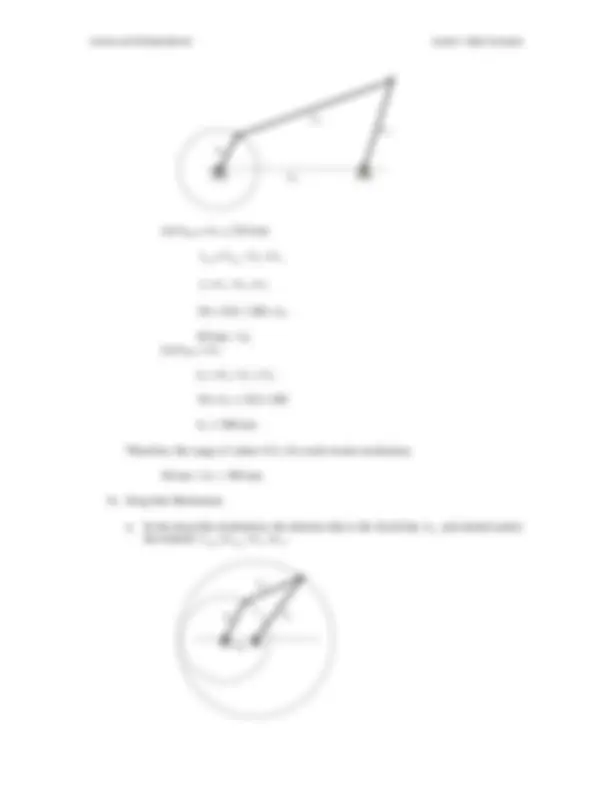
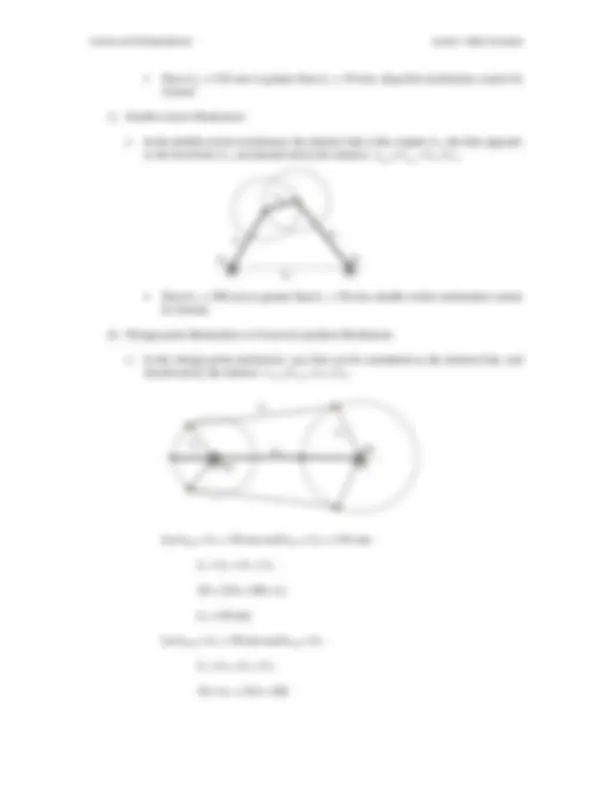
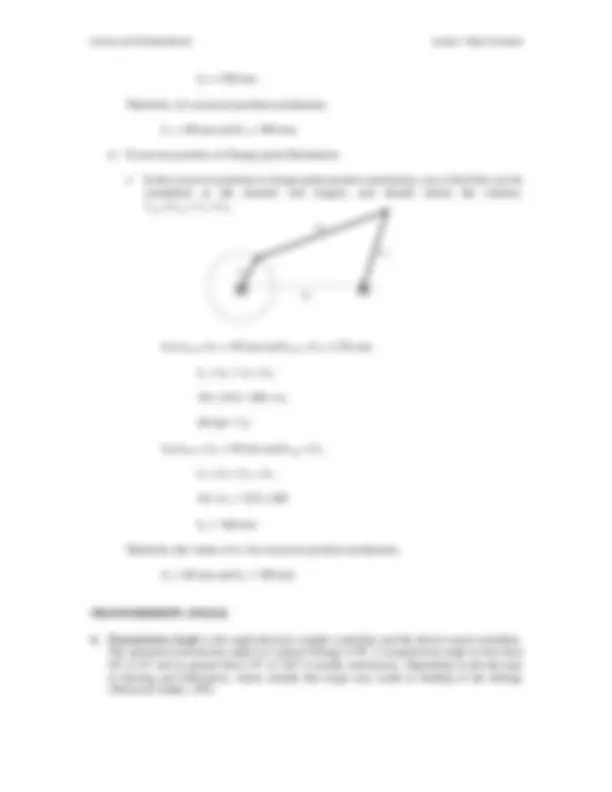
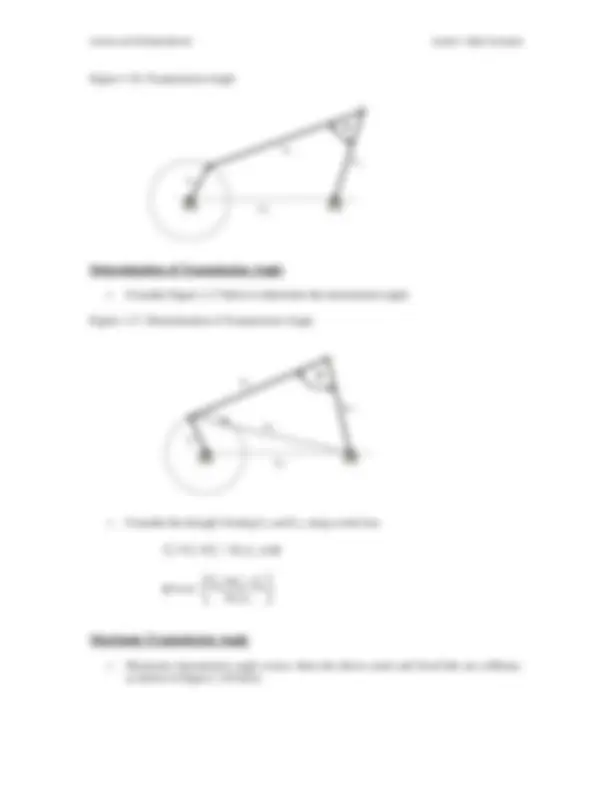
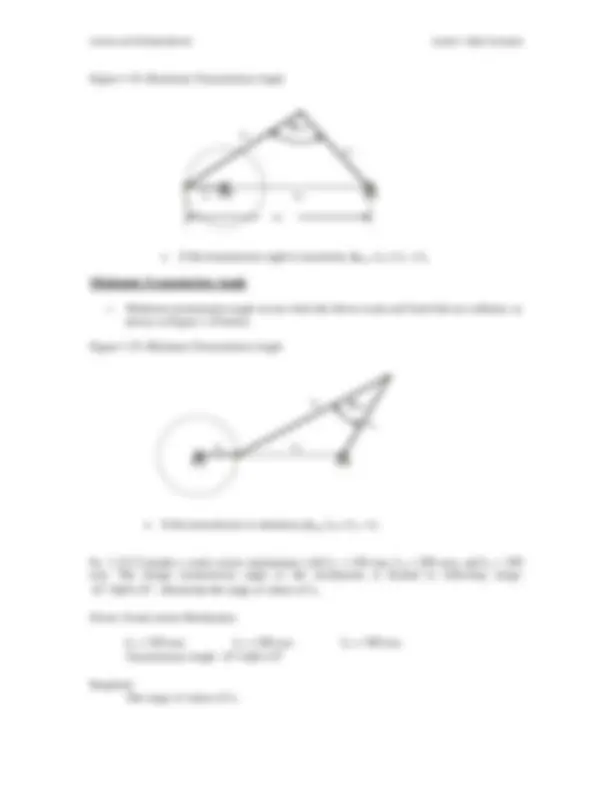
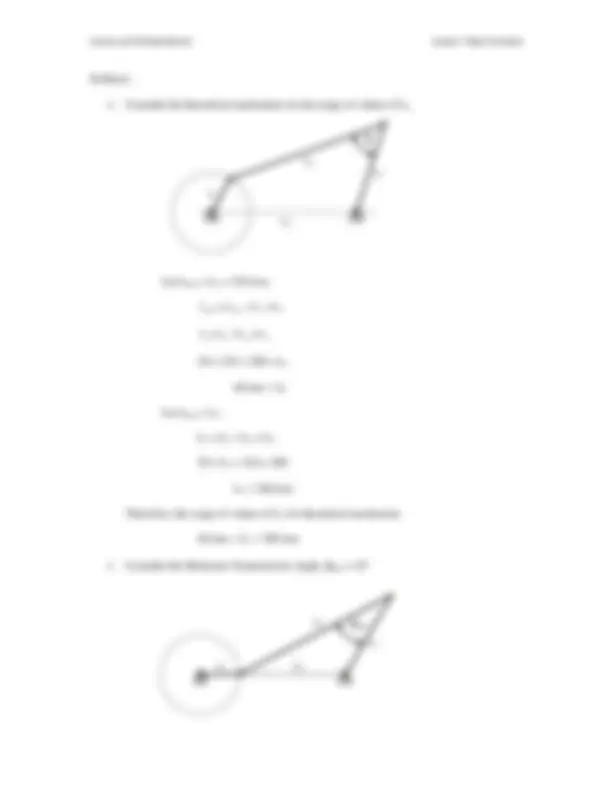
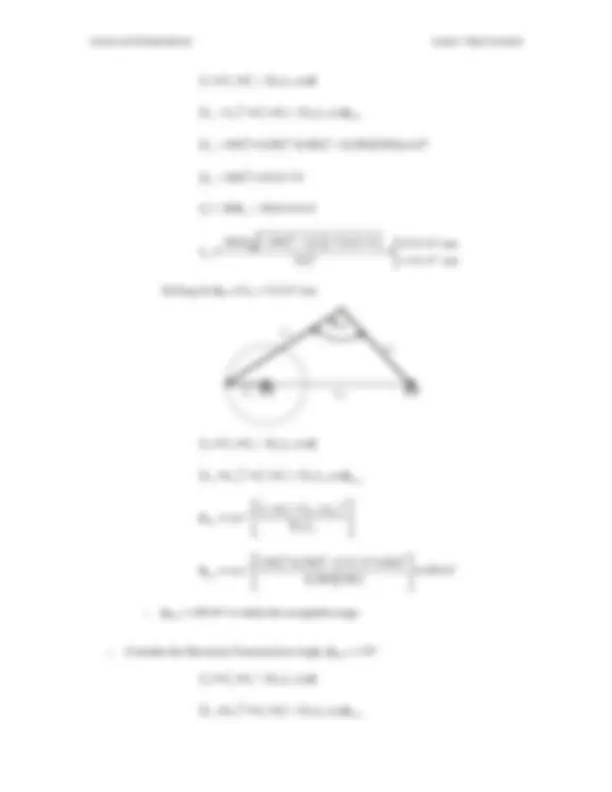
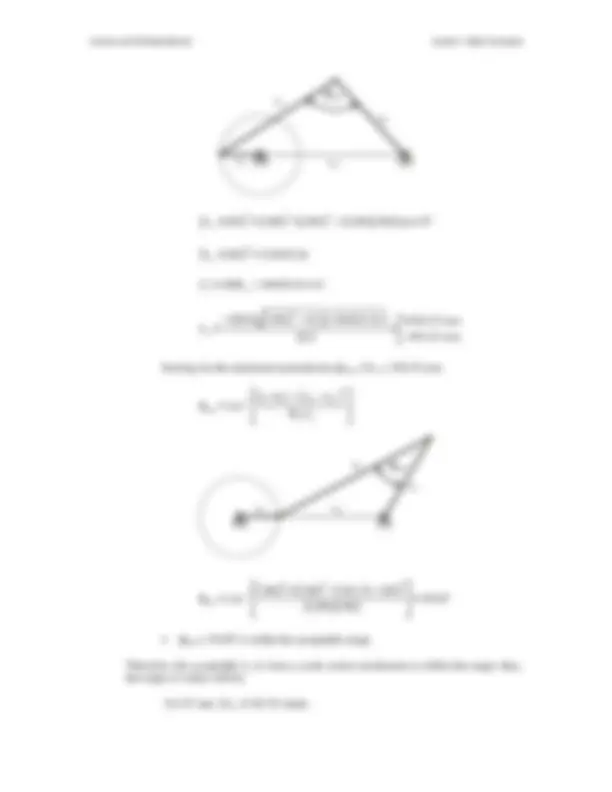
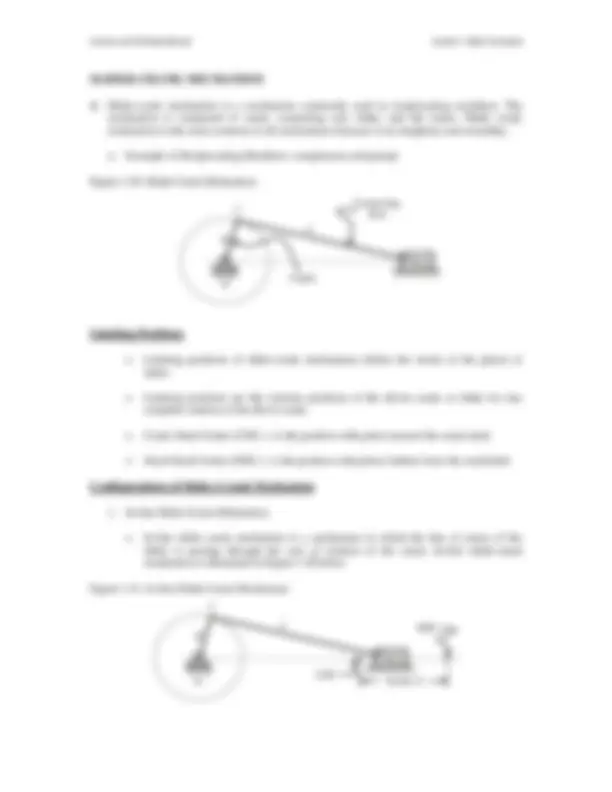
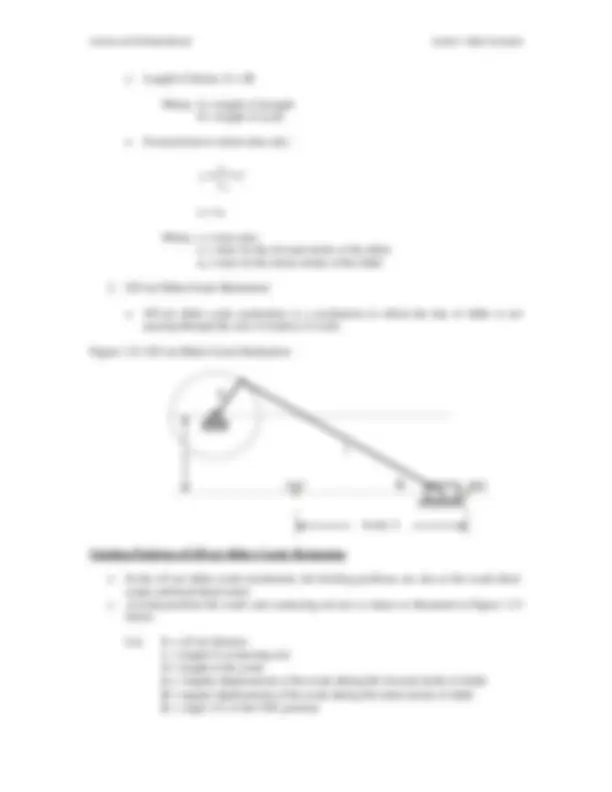
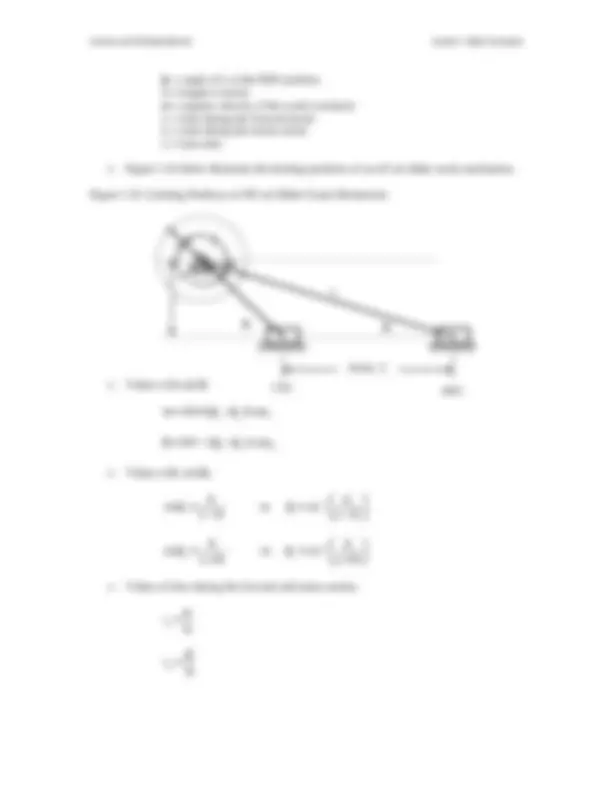
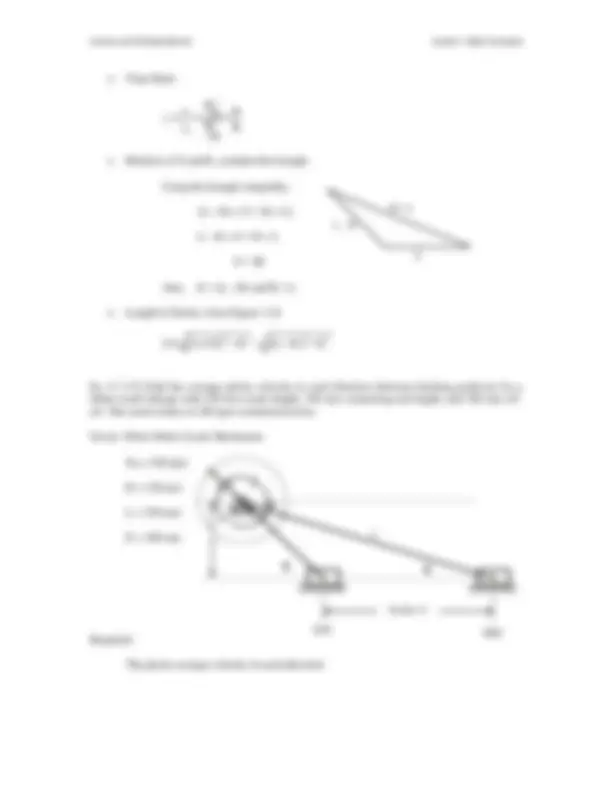
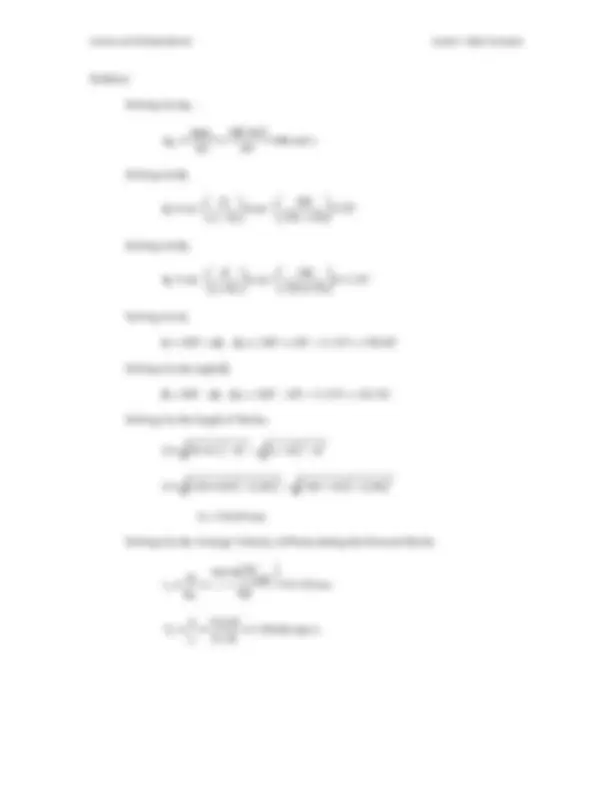
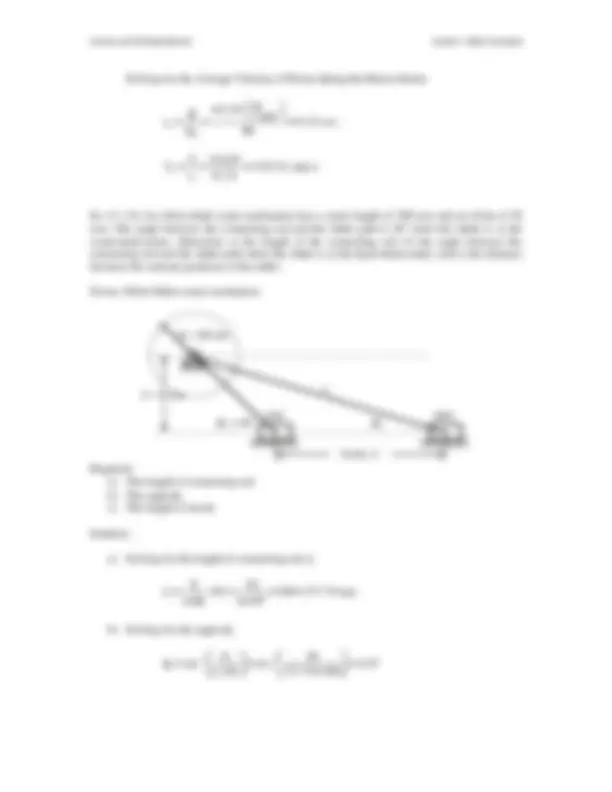
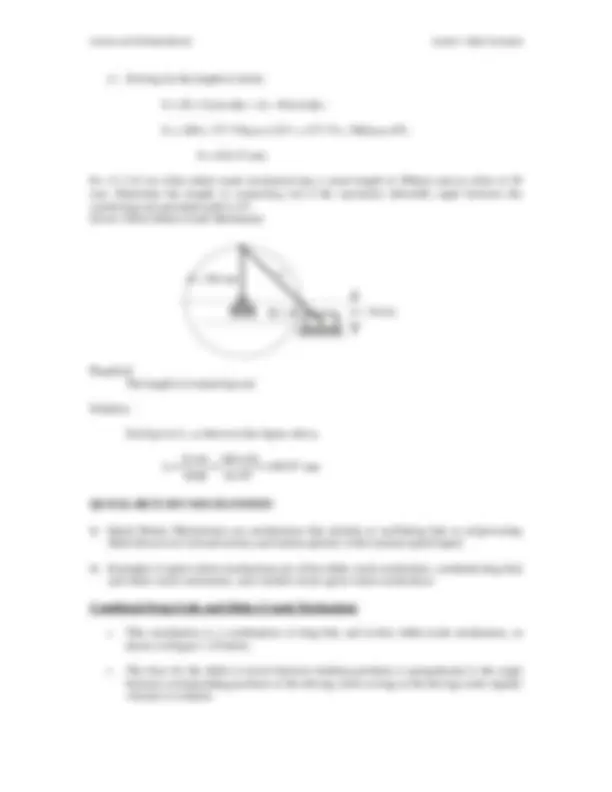
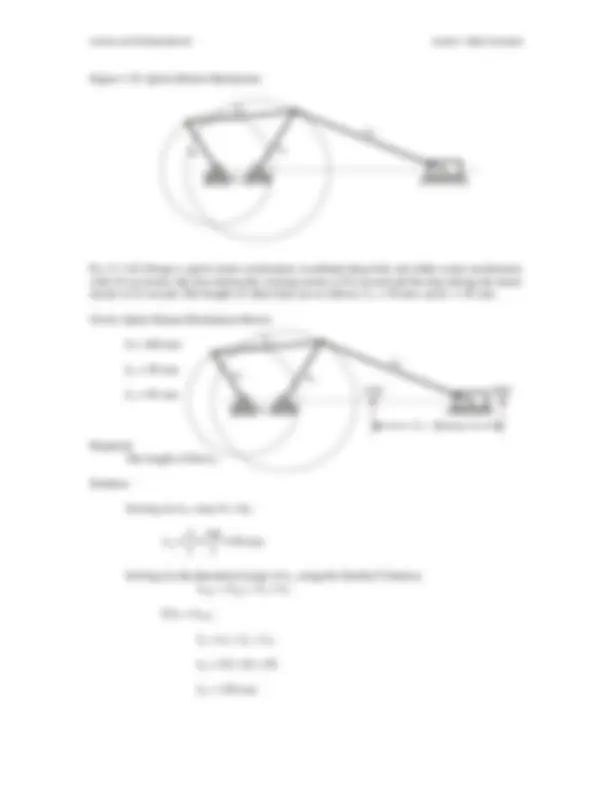
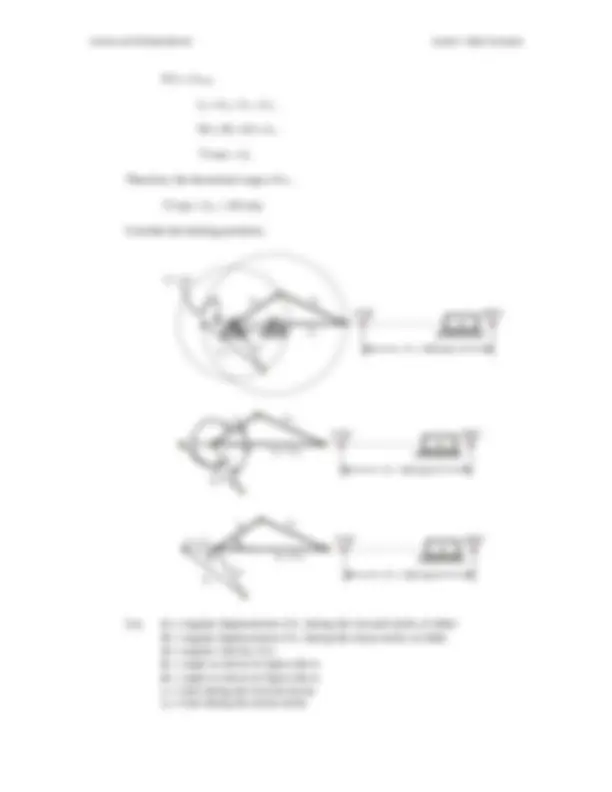
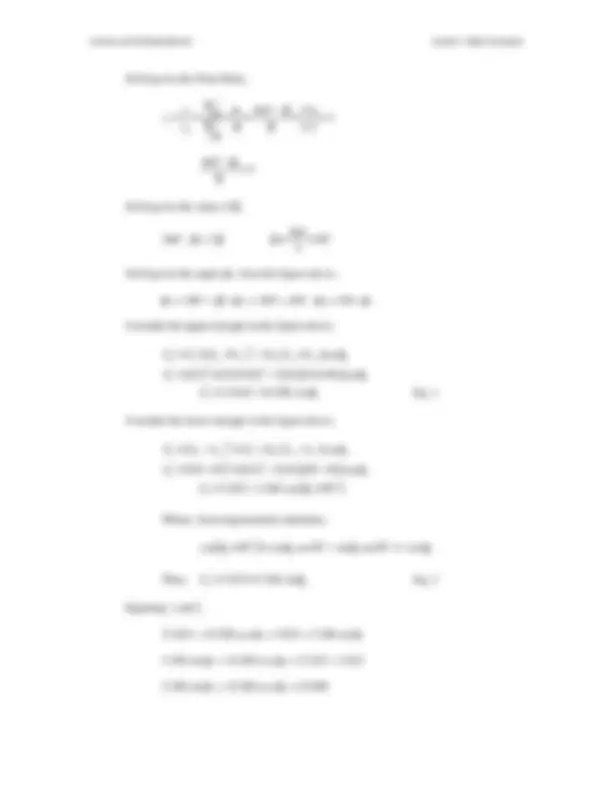
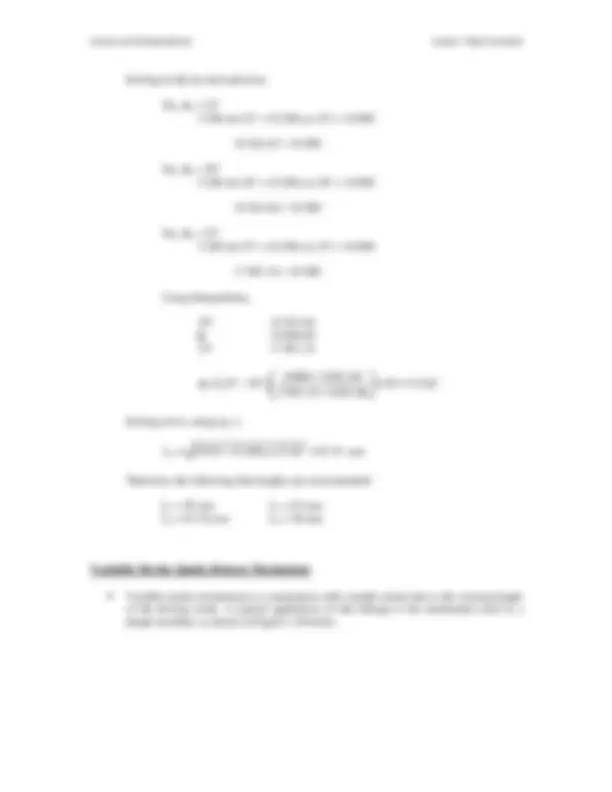
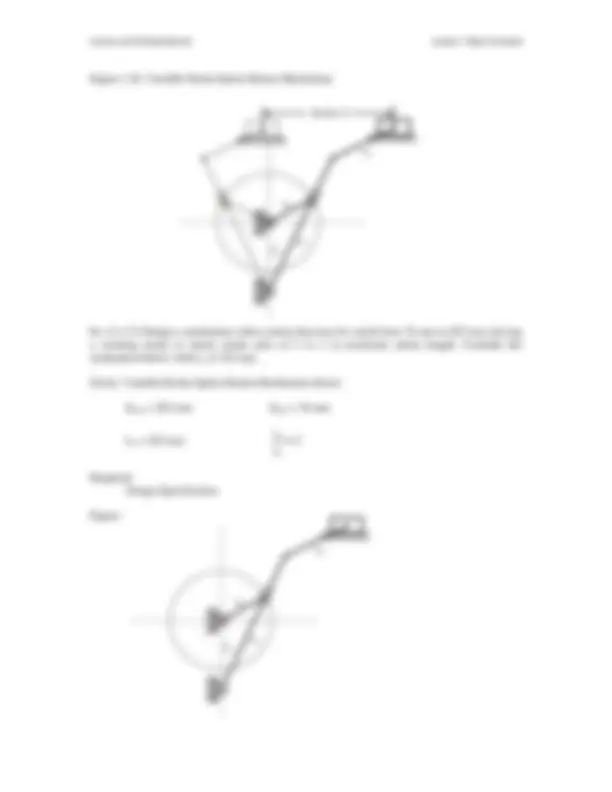
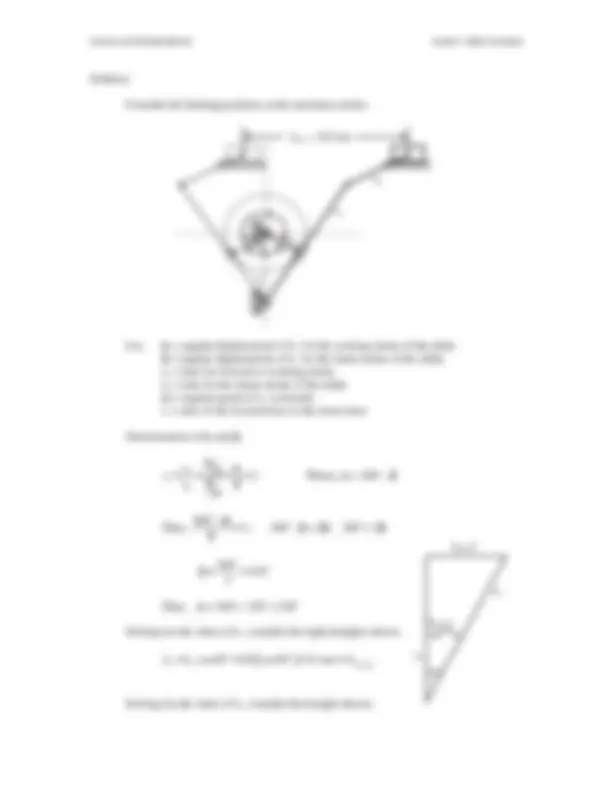
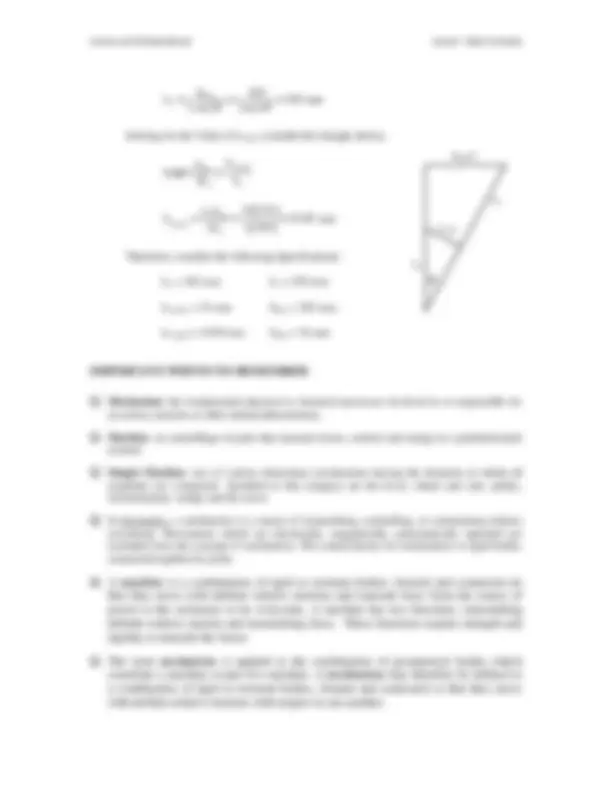
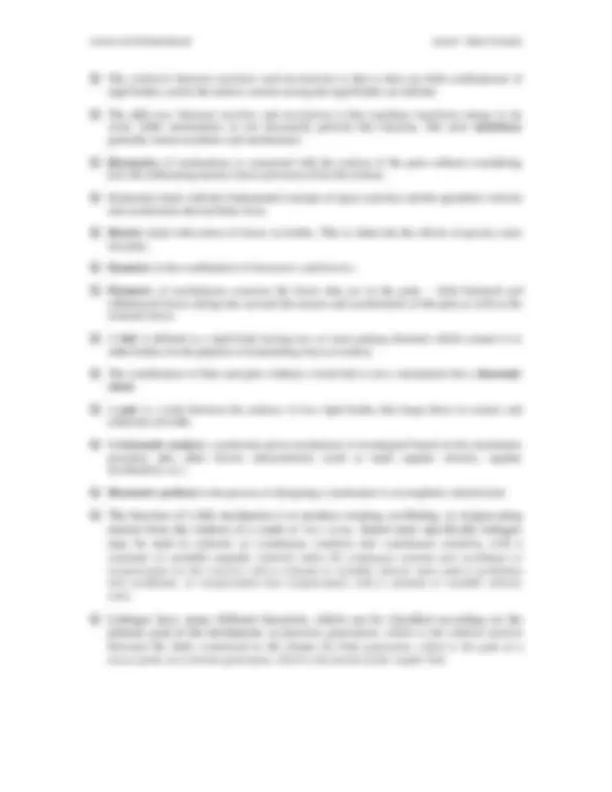

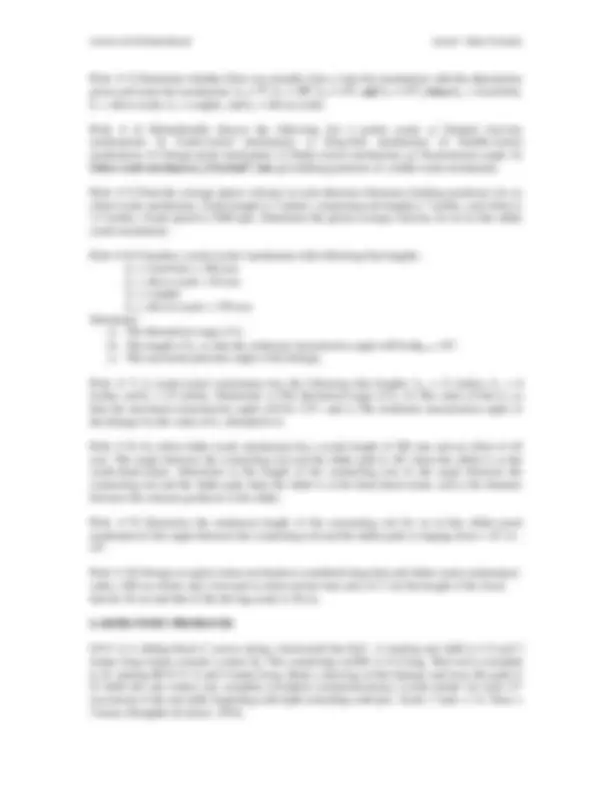
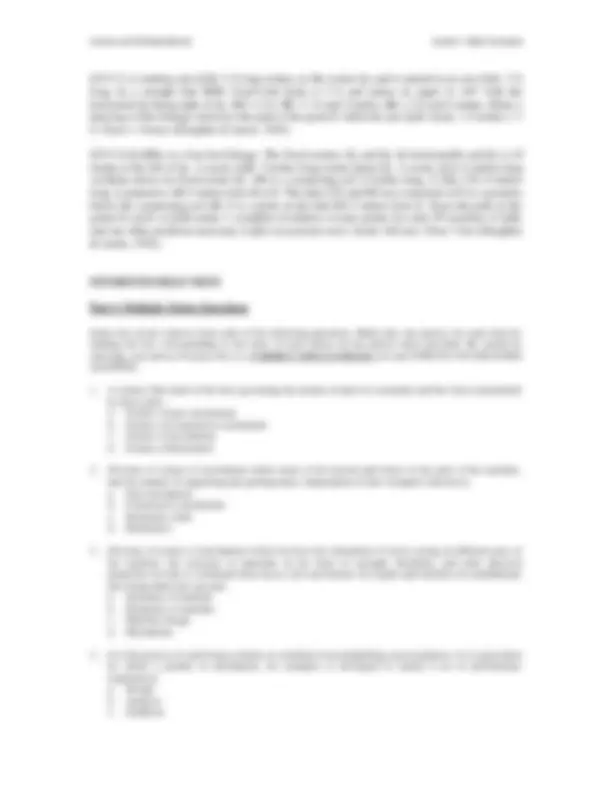
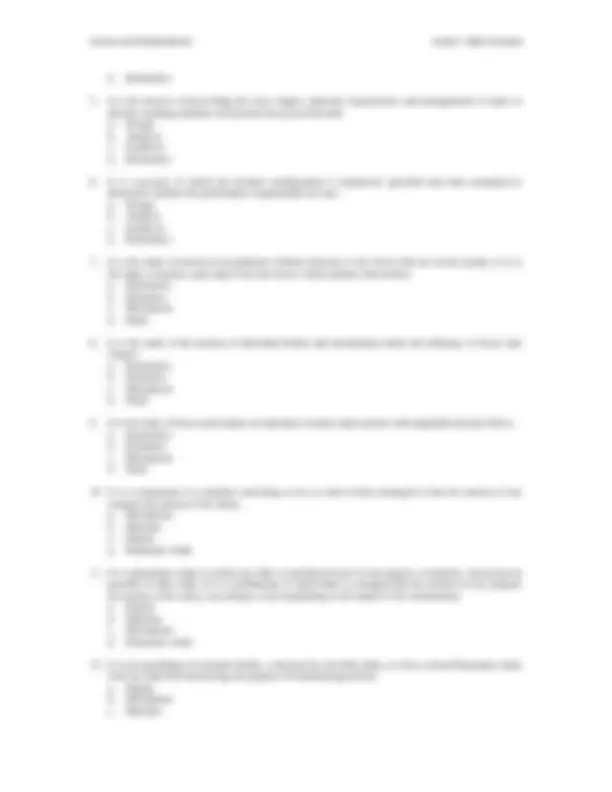
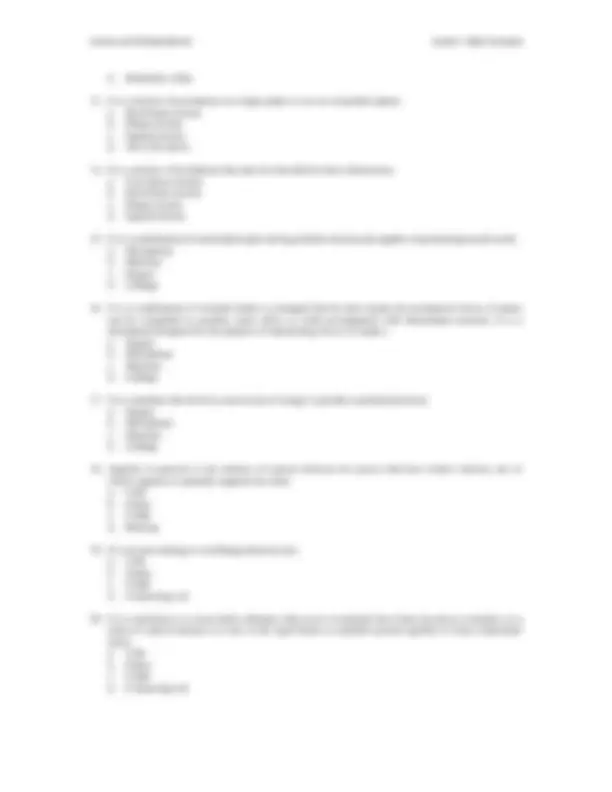
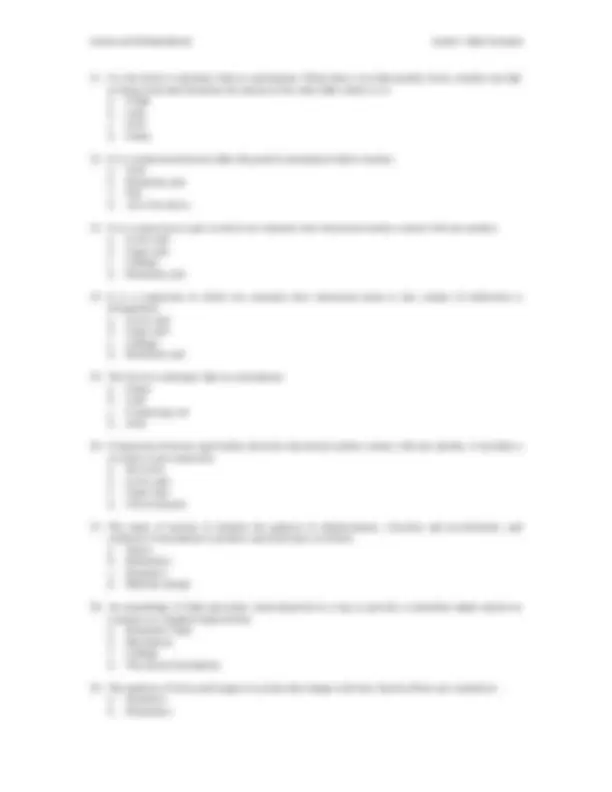
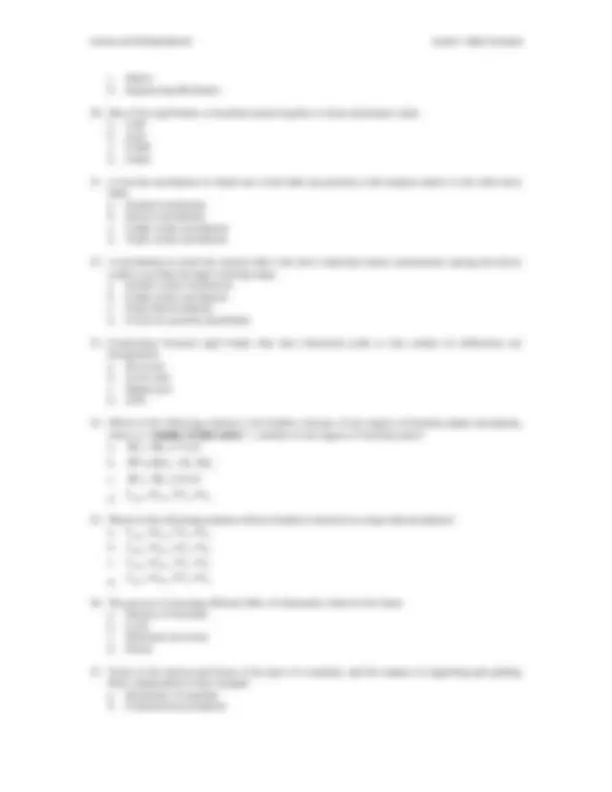
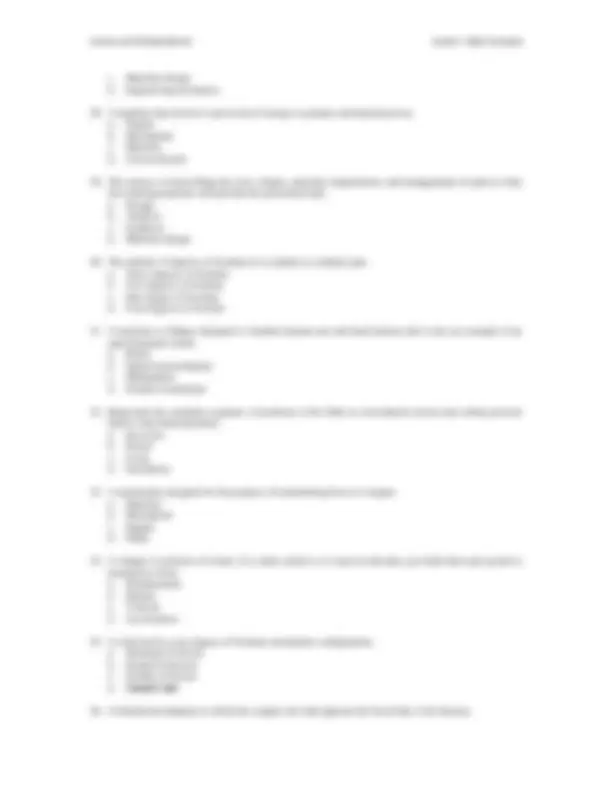
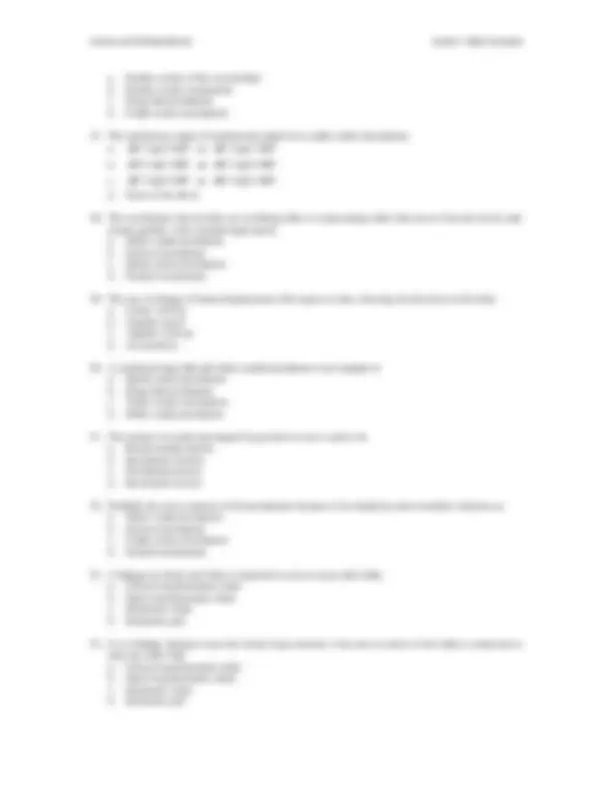
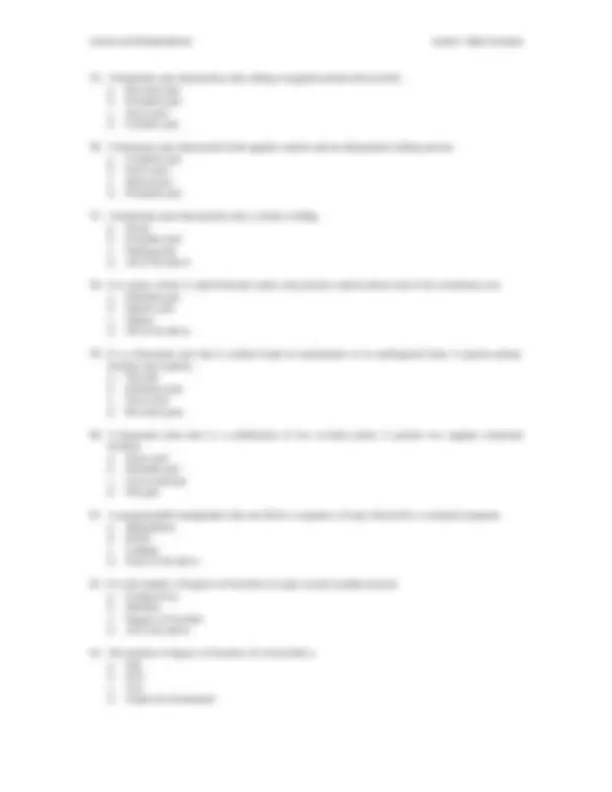
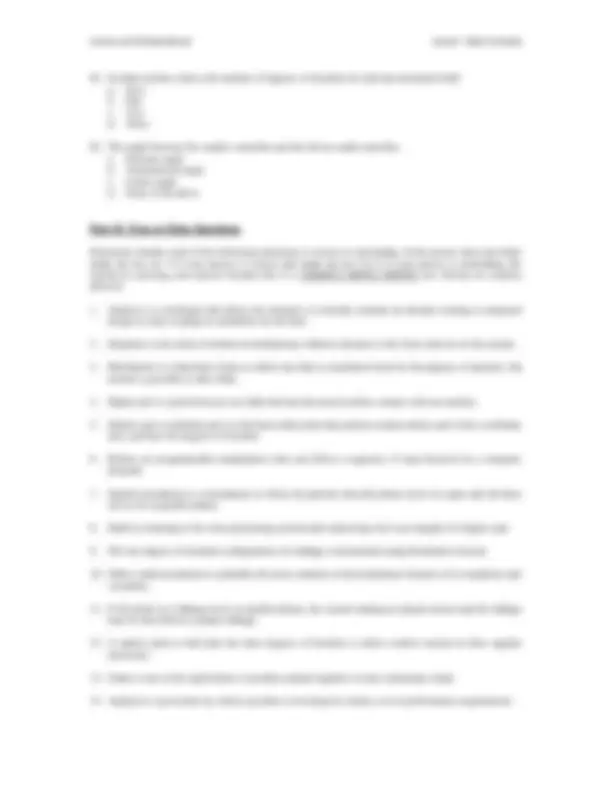

Study with the several resources on Docsity
Earn points by helping other students or get them with a premium plan
Prepare for your exams
Study with the several resources on Docsity
Earn points to download
Earn points by helping other students or get them with a premium plan
Community
Ask the community for help and clear up your study doubts
Discover the best universities in your country according to Docsity users
Free resources
Download our free guides on studying techniques, anxiety management strategies, and thesis advice from Docsity tutors
this is a document about Kinematics Lesson 1
Typology: Study notes
1 / 60
This page cannot be seen from the preview
Don't miss anything!
❑ The Science of Mechanism treats of the laws governing the motion of parts of a machine and
the forces transmitted by these parts.
❑ Divisions of Science of Mechanism
parts of the machine, and the manner of supporting and guiding them, independent of
their strength.
acting on different pars of the machine; the selection of materials on the basis of strength,
durability, and other physical properties in order to withstand these forces, the
convenience for repairs and facilities for manufacture also being taken into account.
❑ Related Divisions of Problem in Designing Machine or in Studying the Design
proper motion.
❑ Synthesis is the process of contriving a scheme or a method of accomplishing a given
purpose. It is a procedure by which a product (a mechanism, for example) is developed to
satisfy a set of performance requirement.
❑ Design is the process of prescribing the sizes, shapes, material compositions, and
arrangements of parts so that the resulting machine will perform the prescribed task.
❑ Analysis – the technique that allows the designer to critically examine an already existing or
proposed design in order to judge its suitability for the task. It is not a creative science but
one of evaluation and rating of things already conceived. It is a process in which the product
configuration is tentatively specified and then examined to determine whether the
performance requirements are met.
❑ Kinematics is the study of motion in mechanisms without reference to the forces that act on
the system; or it is the study of motion, quite apart from the forces which produce that
motion.
❑ Dynamics is the study of the motion of individual bodies and mechanisms under the influence
of forces and torques.
❑ Static is the study of forces and torques in stationary systems (and systems with negligible
inertial effect).
❑ Mechanism is a component of a machine consisting of two or more bodies arranged so that
the motion of one compels the motion of the others.
❑ Mechanism is a kinematic chain in which one link is considered fixed for the purpose of
analysis, but motion Is possible in other links. It is a combination of rigid bodies so arranged
that the motion of one compels the motion of the others, according to a law depending on the
nature of the combination.
❑ Mechanism is an assemblage of resistant bodies, connected by movable joints, to form a
closed kinematic chain with one link fixed and having the purpose of transforming motion.
❑ Motion of Mechanism
❑ Machine is a combination of interrelated parts having definite motion and capable of
performing useful work.
❑ Machine is a combination of resistant bodies so arranged that by their means the mechanical
forces of nature can be compelled to produce some effect or work accompanied with
determinate motions. It is a mechanism designed for the purpose of transmitting forces or
torques.
❑ Examples of Machine Parts
belt pulleys, wheels, keys, collars, cylinders, pistons, connecting rods, piston rods, etc.
❑ Engine is a machine that involves conversion of energy to produce mechanical power.
Example: Crankshaft, connecting rod, piston, and cylinder of an automotive engine
❑ Bearing – applied, in general, to the surfaces of contact between two pieces that have relative
motion, one of which supports or partially supports the other.
❑ Bearing Arrangement according to the Relative Motion they will allow
▪ If one piece is fixed the surfaces of the moving pieces are called slides.
▪ Those of fixed pieces, slides or guides.
conoids, or flat disks.
▪ The surface of the solid or full piece is called a journal, neck, spindle, or pivot.
▪ For hollow or open piece, a bearing, gudgeon, pedestal, plumber-block, pillow block,
bush or step.
shape.
▪ Descriptive Example: A pin joint that permit rotation only
therefore is often called sliding joint. It also has a single degree of freedom (x) and a
lower pair joint (L).
▪ Schematic Diagram
▪ Descriptive Example: A straight spline that permits sliding only.
) because the sliding and rotational motions are related by helix angle of the thread. It is
a lower pair joint (L).
▪ Schematic Diagram
▪ Descriptive Example: Power screws or helical spline
independent sliding motion. It has two degrees of freedom (x and ) and a lower pair
joint (L).
▪ Schematic Diagram
▪ Descriptive Example: A sleeve that permits both rotation and sliding
has three degrees of freedom (, , and ), a rotation about each of the coordinate axes. It
is a lower pair-joint (L).
▪ Schematic Diagram
C
P
H
S
▪ Descriptive Example: A ball (and socket) joint permitting rotation in three angular
directions
, is a joint that is seldom, if ever, found in mechanisms
in its undisguised form. It has three degrees (x, y, and ) of freedom and a lower pair
joint (L).
▪ Schematic Diagram
▪ Descriptive Example: A surface restraint permitting rotation and motion parallel to
the plane of the surface
motions. It has two degrees of freedom ( and ) and considered as a lower pair joint (L).
▪ Schematic Diagram
▪ Descriptive Example: The hook-type universal joint that combines two revolute pairs
freedom (rolling and sliding).
▪ Schematic Diagram
▪ Descriptive Example: Spur gears, helical gears, and other gears
pairs appear in so many configurations that it is not practical to assign a standard symbol
or schematic representation.
▪ Descriptive Example: A disk cam and follower
▪ Connection between a belt and a pulley
▪ Connection between a chain and a sprocket
P L
U
G
❑ Open-loop Kinematic Chain is a linkage failing to meet the closed-loop criterion; it has one
(or more) of the links is connected to only one other link.
❑ Linkage is any assemblage of rigid bodies connected by kinematic joints. Mechanisms and
machine may be considered linkage. It is restricted to kinematic chains made up of lower
pairs.
❑ Example of Linkage:
a. Three-bar linkage
b. Four-bar linkage
c. Six-bar lomkage
Figure 1.1. Four-bar linkage
Figure 1.2. Six-bar Linkage
❑ Planar Motion is a motion of points in a system that moves in parallel planes.
❑ Planar mechanism is one in which all particles describe plane curves in space and all these
curves lie in parallel planes.
❑ Planar Linkage is a linkage in which all links have parallel motion; a linkage that has planar
motion; it utilizes lower pairs only.
Example: Crank, connecting rod, and piston of an automotive engine.
L 0
L 1
L 2
L 3
Q 1 Q 2
Connecting rod or
Coupler
Crank (driver)
Crank (driven)
Frame or fixed link
A
B
L 0
L 1
L 2
L 3
Q 1 Q 2
Floating link or
Coupler
Crank (driver)
Crank (driven)
Frame or fixed link
A
B
C
D
L 4
Floating link or
Coupler
Slider
❑ Spatial linkage or Three-Dimensional Linkage is a general linkage in which motion cannot be
described as taking place in parallel planes. A typical example of which is an industrial
robots.
❑ Inversion or kinematic Inversion is the process of choosing different links of a kinematic
chain for the frame.
o If two linkages have the same configuration but different fixed links, the system is called
inversion. Relative motion will be the same in both linkages.
o The absolute motion of a linkage depends on which link is fixed, that is, which link is
selected as the frame. If two otherwise identical linkages have different fixed links, then
each is an inversion of the other.
o Examples of Kinematic Inversion
Figure 1.3. Slider-crank Mechanism (link 0 as fixed link)
o If input motion is on 3 then 1 is the driven link. Application: Internal
Combustion Engine (ICE)
o If input motion is on 1 then 3 is the driven link. Application: Pump or
Compressor.
Figure 1.4. Slider-crank Mechanism (link 1 as the fixed link)
o Input motion is on link 0 and the driven is link 2
0
1
Q 1
3
2
0
1
Q 0
2
3
Q 2
▪ Most practical mechanisms with one independent variable have one degree of freedom.
▪ An unconstrained rigid body has six degrees of freedom: translation in three coordinate
directions and rotation about three coordinate axes.
▪ If the body is restricted to motion in a plane, there are three degrees of freedom:
translation in two coordinate directions and rotation within the plane.
o Each joint reduces the mobility of a system.
o A fixed one-degree of freedom joint (say, a revolute joint) reduces a link to one degree of
freedom.
o In general, each one-degree-of-freedom joint reduces system mobility by providing five
constraints; each two-degrees-of-freedom joint provides four constraints; each three-
degrees-of-freedom joint provides three constraints; and so on.
o Each joint reduces system mobility by (6 – f i
), where f i
= the number of degreed of
freedom or the connectivity of the joint.
Number of Degrees of Freedom or Mobility of Spatial Linkage
o For General Spatial Linkage
( ) spatial L c
DF = 6 n − 1 −n
Where n L
= number of links (including one fixed link with zero degree of freedom)
n c
= total number of constraints
o For Mechanism with n J
joints with individual joint connectivity f i
i
n
c J i
i 1
n 6n f
=
= −
( ) ( )
J J
n n
spatial L J i L J i
i 1 i 1
DF 6 n 1 6n f 6 n n 1 f
= =
= − − + = − − +
Where n L
= number of links
n J
= number of joints
f i
= connectivity or DF of individual joints
Ex. # 1.1] Determine the DF of a closed-loop kinematic chain shown.
R 1
R 2
S 1
S 2
1
2
3
Solution :
For the number of links,
n 4
= 4 links
For the number of constraints,
n c
= n cR
n cS
n cS
n cR
Solving for the number of degrees of freedom, DF,
( ) ( ) spatial L c
DF = 6 n − 1 − n = 6 4 − 1 − 16 = 2 ans.
Other Solution:
( )
J
n
spatial L J i
i 1
DF 6 n n 1 f
=
= − − +
( ) ( )
spatial
DF = 6 4 − 4 − 1 + 1 + 3 + 3 + 1 = 2 ans.
o The RSSR mechanism above acts, for practical purpose, as one-degree-of-freedom
linkage if the degree of freedom that represents the rotation of link 2 about its own axis is
neglected.
Ex. # 1.2] Determine the DF of the RSUR mechanism below.
Solution:
Solving for the DF, ( )
spatial L c
DF = 6 n − 1 −n
Where,
c cR1 cS1 cU cR
n = n + n + n + n = 5 + 3 + 4 + 5 = 17
n L
= 4 links
Then, ( )
spatial
DF = 6 4 − 1 − 17 = 1 ans.
R 1
R 2
S 1
U
1
2
3
Solving for the number of constraints,
c cR1 cR 2 cR 3 cc
n = n + n + n + n = 5 + 5 + 5 + 4 = 19
Solving for the DF,
( ) ( )
spatial L c
DF = 6 n − 1 − n = 6 4 − 1 − 19 = − 1
▪ This is a statically indeterminate structure.
Points to Remember
the number of links and joints.
▪ Connectivity is the number of DF of a pair or joint in plane motion.
❑ Each unconstrained link has three DF in plane motion.
❑ A fixed link has zero DF
❑ A pin joint connecting two links produces two constraints since the motion of both links must
be equal at the joint (in two coordinate directions).
❑ Equation of DF for Planar Linkage
( )
planar L J
DP = 3 n − 1 − 2 n'
Where, n’ J
= the number of one-degree-of-freedom joints or pairs
( )
=
= − − +
J
n
i
planar L J i
DF n n f
1
3 1
Where, n J
= number of joints with individual connectivity f i
Ex. #1.5] Determine the DF of planar linkage shown.
O 1
O 2
A
B
1
2
3
Given: Planar Mechanism shown above
nL = 4 links n’J = 4 one-degree of freedom joints
Required:
The degrees of freedom
Solution:
Solving for the DF,
( )
( )
( = 3 − 1 − 2 = 34 − 1 − 24 )= 1
planar l J
DF n n'
Solving for the DF using the other equation,
( ) ( ) ( )
J
n
L J i
i 1
DF 3 n n 1 f 3 4 4 1 1 1 1 1 1
=
Ex. # 1.6] Determine the DF of a planar linkage shown below:
n L
n’ J
Solution:
Solving for the DF
DF = 3(n L
Ex. # 1.7] Determine the DF of the planar linkage shown below.
Q 1
Q 4
A
C
1
2
3
B
4
Q 1
A
1
2
3
B
Pair = lower pair, L
f i
Pair = lower pair, L
f i
Pair = lower pair, L
f i
Pair = lower pair, L
f i
ONE-DEGREE-OF-FREEDOM CONFIGURATION (Planar Mechanism)
o To determine a planar linkage with one-degree-of-freedom, the following equation is
used, known as Grubler Criterion.
2n’ J
Where, n L
& n’ J
must be positive and n L
must be an even number.
Ex. # 1.9] Determine the number of revolute joint for 2-bar linkage with DF = 1.
Solution:
Using the Grubler criterion,
2n’ J
( )
L
J
3n 4
n ' 1
Ex. 1.10] Determine the number of revolute joint of a linkage with 6 links and at DF = 1.
Solution:
Using the Grubler criterion,
( )
L
J
3n 4
n ' 7
= 6, n’ J
= 7, and DF = 1.
Kinematic sketch is shown in Figure 1.6 below.
Figure 1.6. Watt Linkage
o One of the links may be considered as the fixed link or frame.
= 6, n’ J
= 7, and
DF = 1. Kinematic sketch is shown in Figure 1.7 below
Figure 1.7. Stephenson Linkage
o One of the links may be considered as the fixed link or frame.
motion for the mechanism.
A
B
C D
E
F
G
❑ The connecting rod or coupler of a planar four-bar linkage may be imagined as an infinite
plane extending in all pin-connected to the input and output links. Then during motion of the
linkage, any point attached to the plane of the coupler generates some path with respect tot
the fixed link; this path is called a coupler curve. Two of these paths, namely, those
generated by the pin connection of the coupler, are simple circles with centers at the two
fixed pivots. However, other points can be found which trace much more complex curve.
Ex. # 1.11] Q 2
4
is a four-bar linkage. Q 2
and Q 4
are fixed centers on a horizontal line 10
inches apart. Q 2
B is a link 5 inches long oscillating about Q 2
4
C is a crank 2.5 inches long that
rotates about Q 4
. BC is a connecting rod 11.5 inches long. Q 2
is to the left of Q 4
. A link, EF, 6
inches long is pinned to Q 2
B at E, 1.5 inches from B. Another link, GF, 3.5 inches long is pinned
to link BC, 4 inches from C. These links, EF and GF, are pinned together at F in their upper
position. Trace the paths of the points F and G while Q 4
C makes one complete revolution. Find
points for each 15
o
position of Q 4
C and any others necessary in order to secure a smooth curve.
Given: Mechanism shown
2
2
4
4
Required:
Trace the path of points F and G while Q 4
C makes 1 complete revolution.
Solution:
o Step 1. Lay out the mechanism in accordance with the given scale, full size.
o Step 2. Trace the positions of the mechanism for one revolution of the link 4, with 15
o
increment.
Q 2
Q 4
E
B
C
G
F
o Step 3. Trace the locus of points of F and the path of a point will be obtained.
❑ For a planar four-bar linkage, the sum of the shortest and longest link lengths cannot be
greater than the sum of the remaining two link lengths if there is to be continuous relative
rotation between two members.”
❑ Grashof four-bar mechanism – is a mechanism in which one of the links can perform a
full rotation relative to the other three links.
❑ Grashof mechanism – is a four-bar linkage in which one link can perform a complete
rotation relative to the other three.
❑ Grashof Criterion:
max min a b
L +L L +L
Where, L max
= length of the longest link
min
= length of the shortest link
a
b
= lengths of the remaining links