
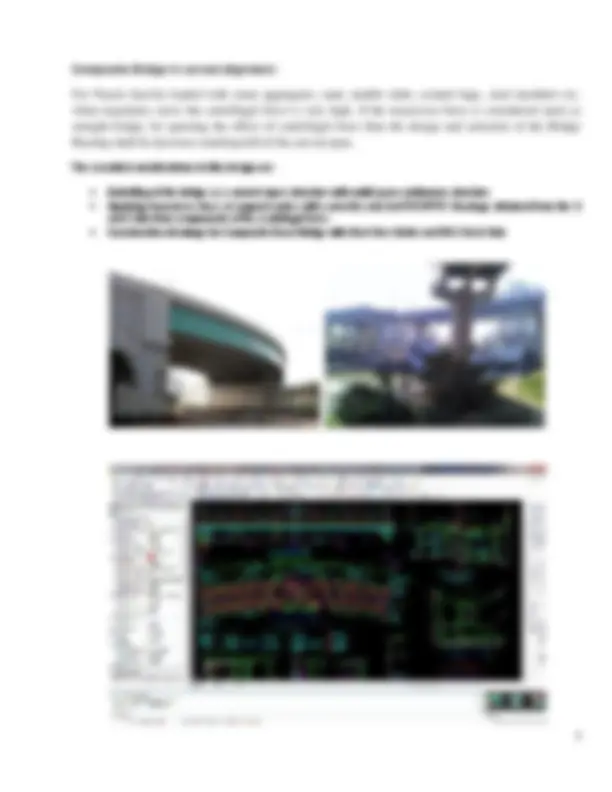
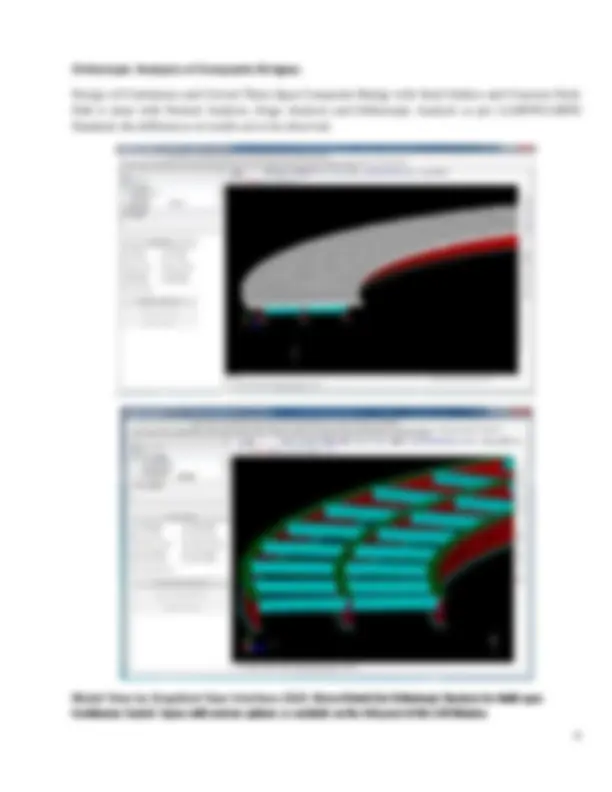
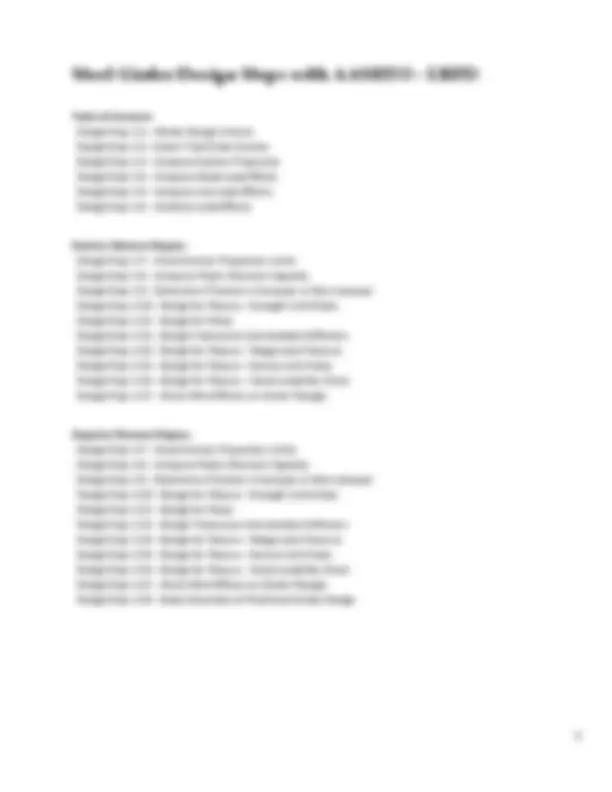
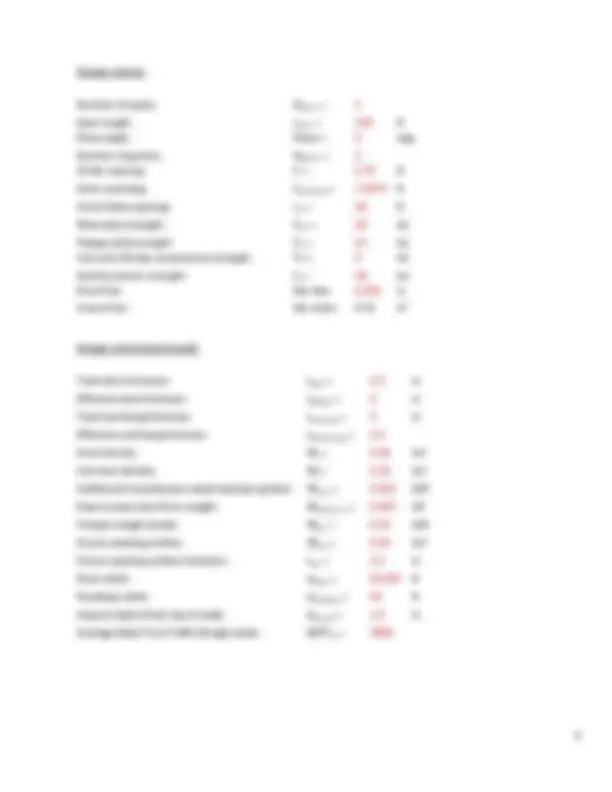
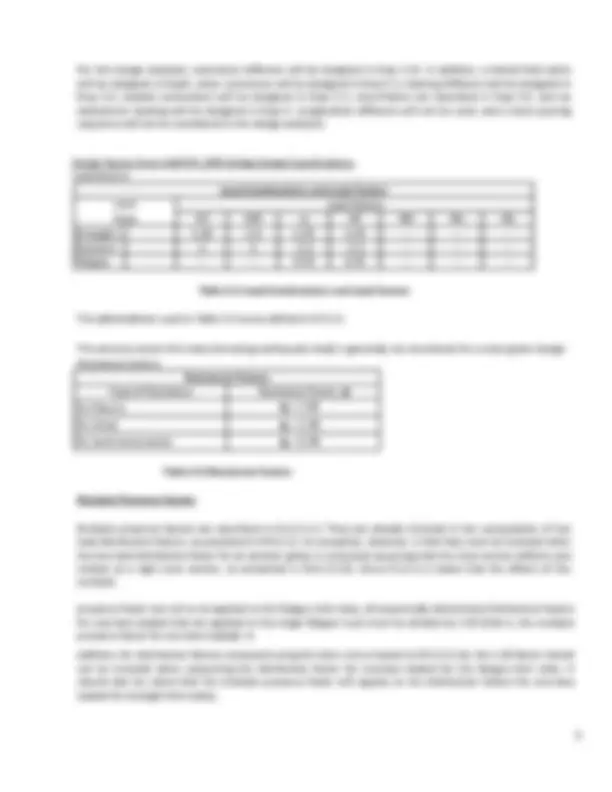
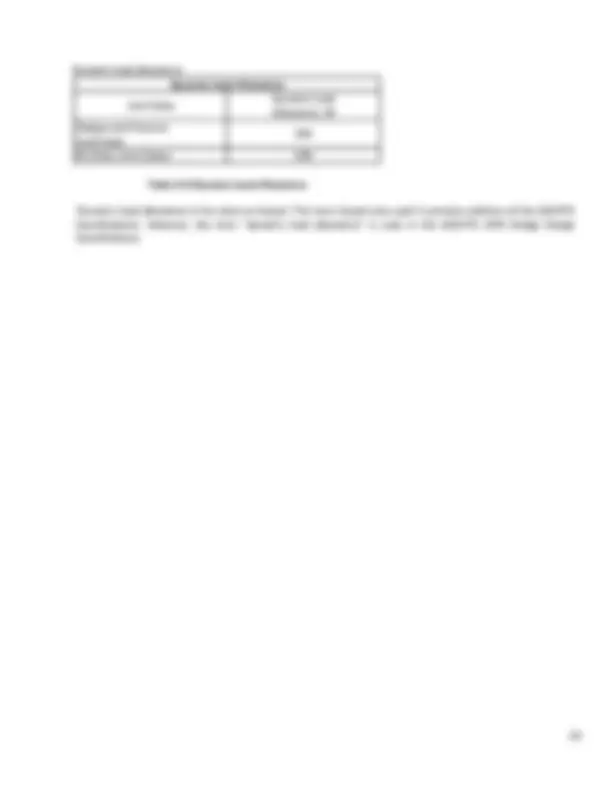
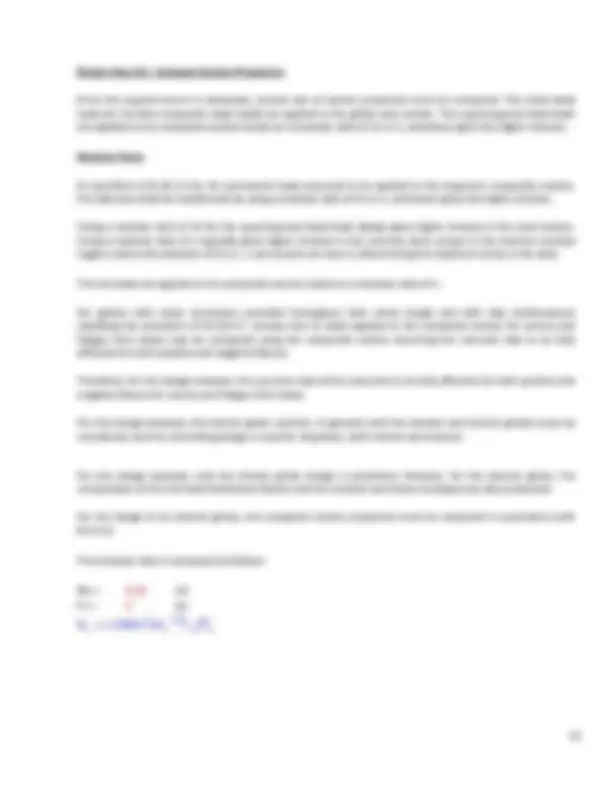
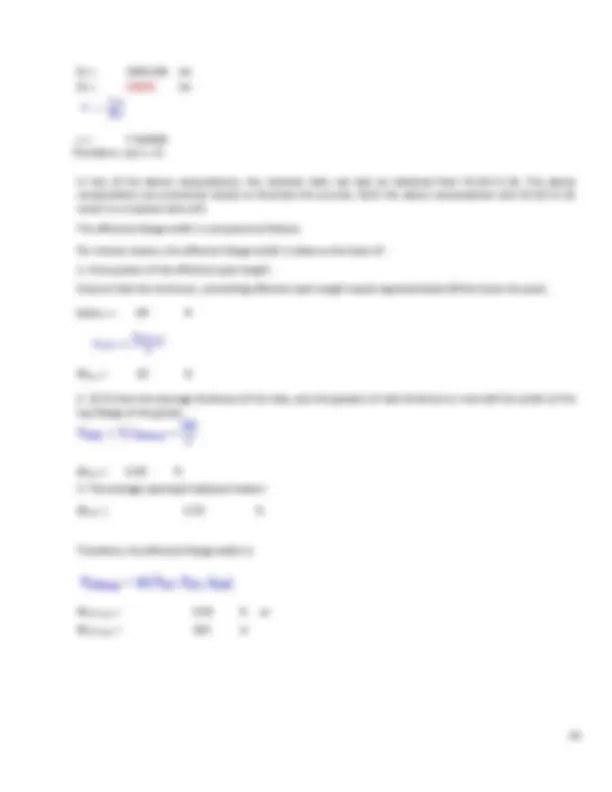
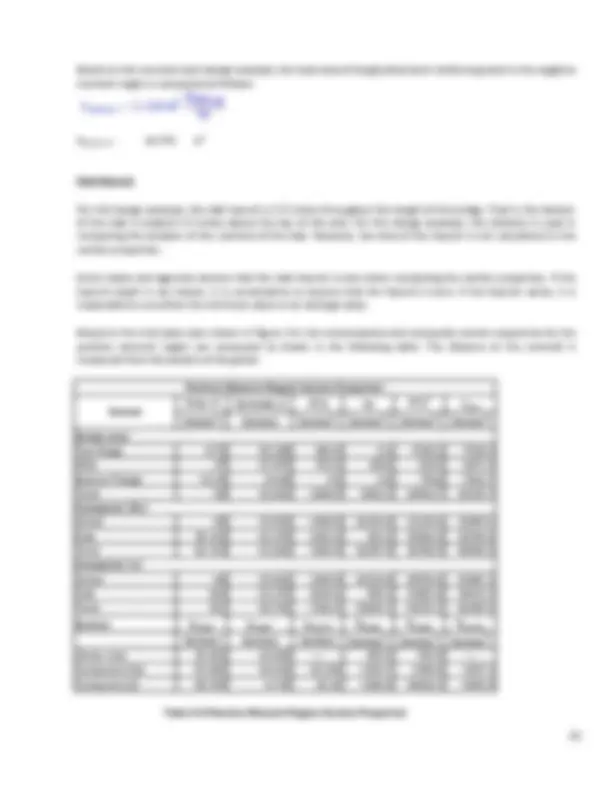
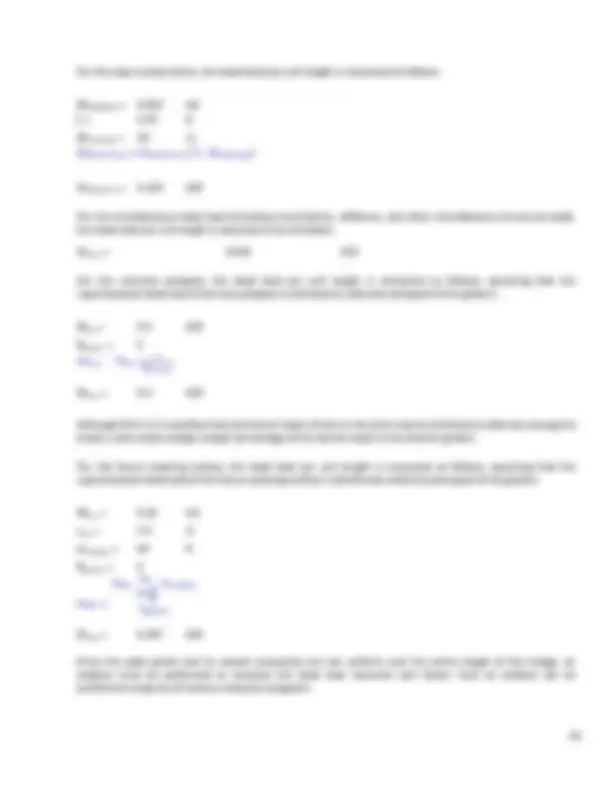
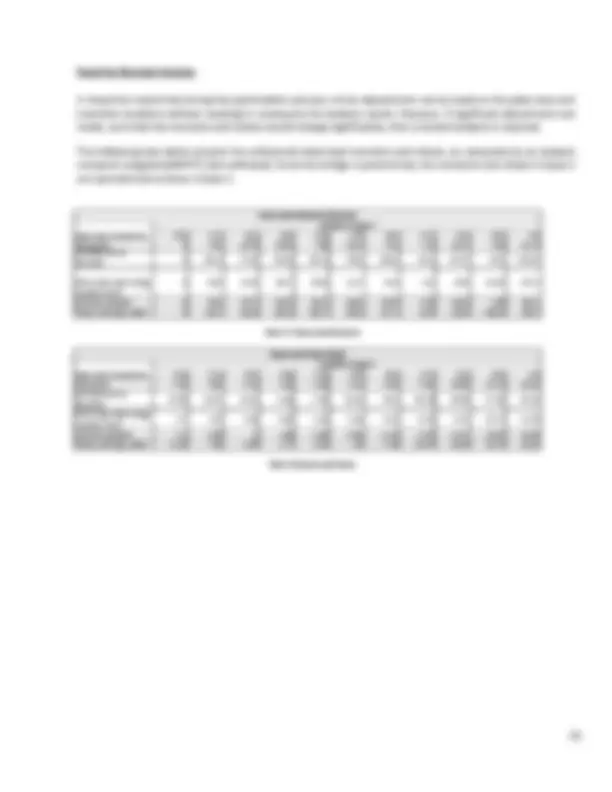
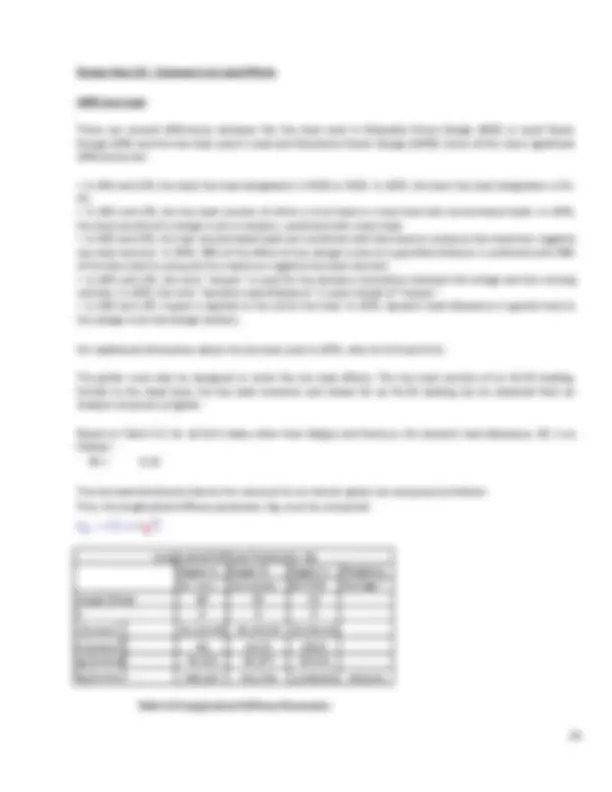
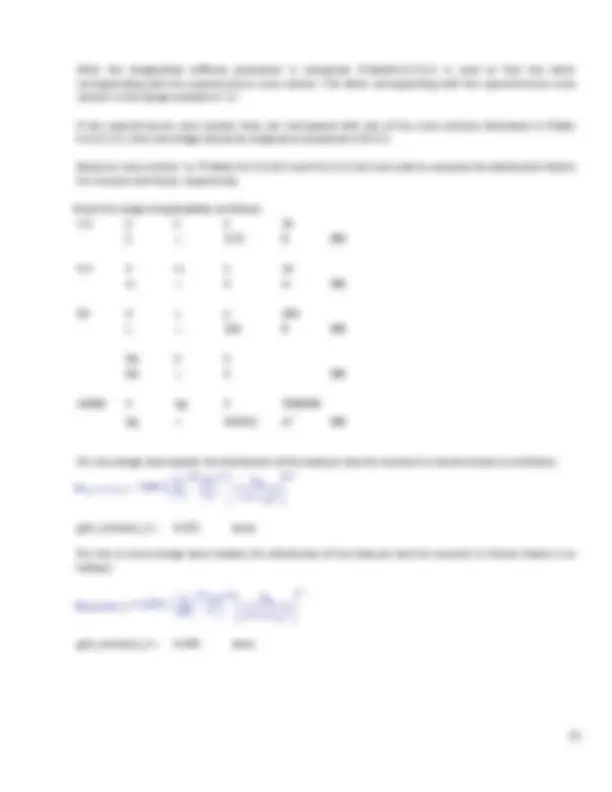
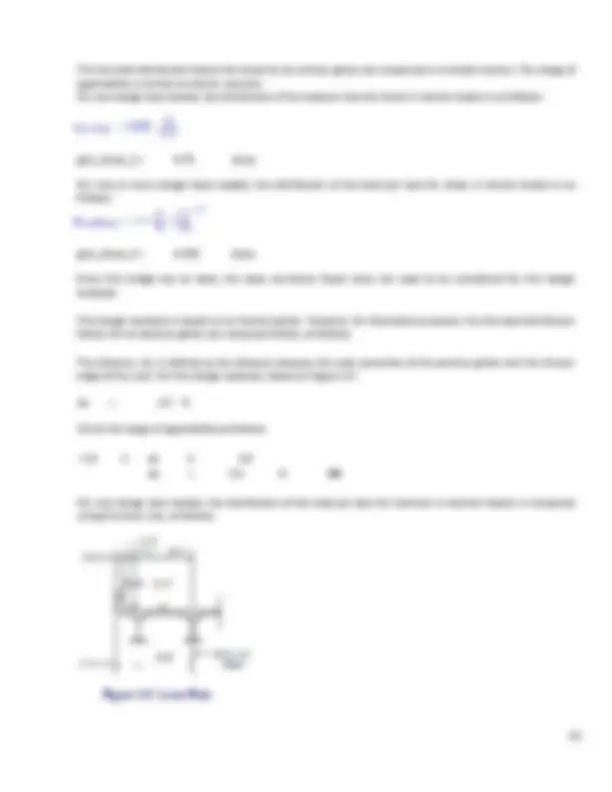
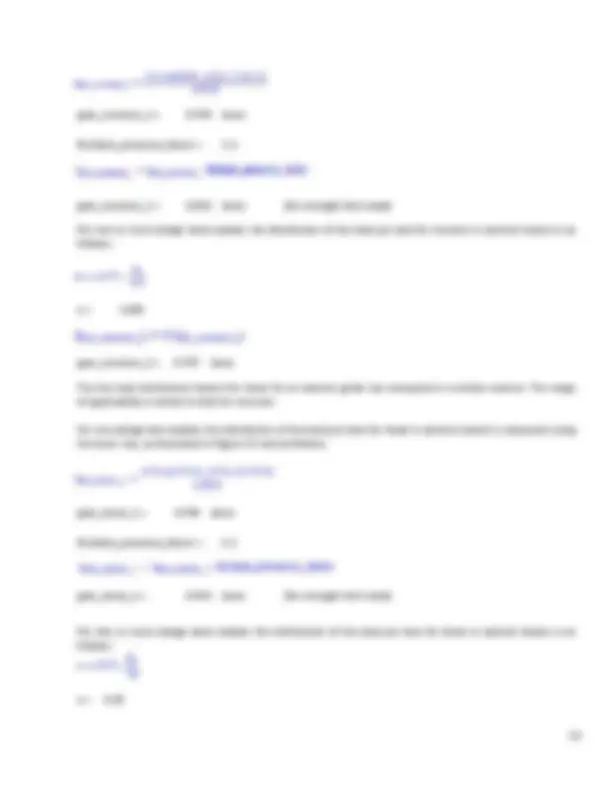
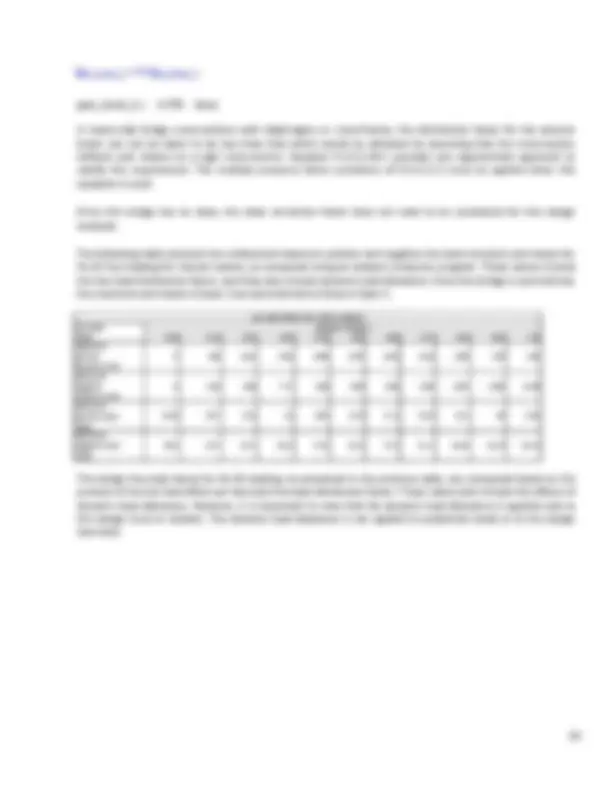
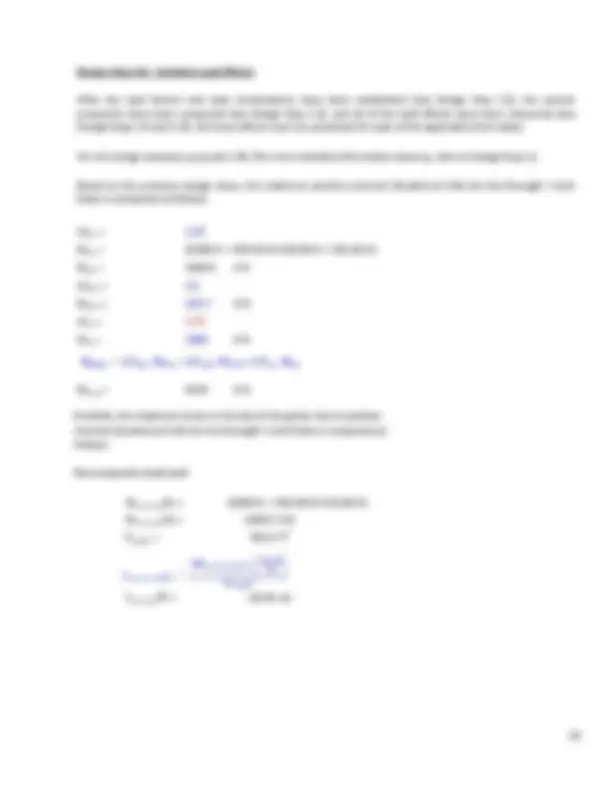
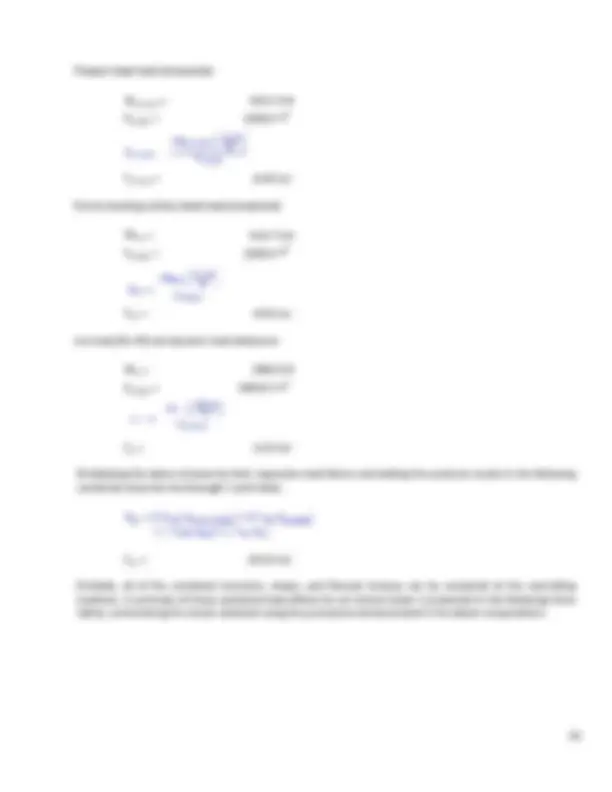
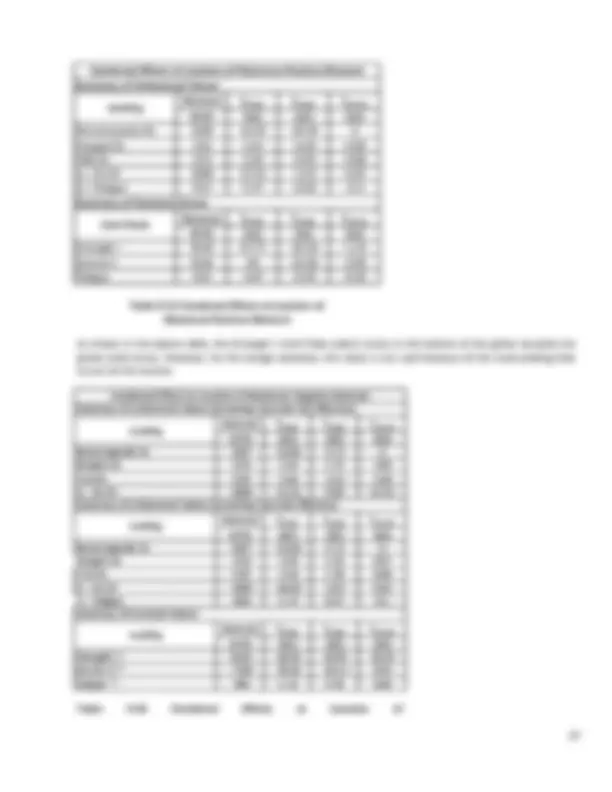
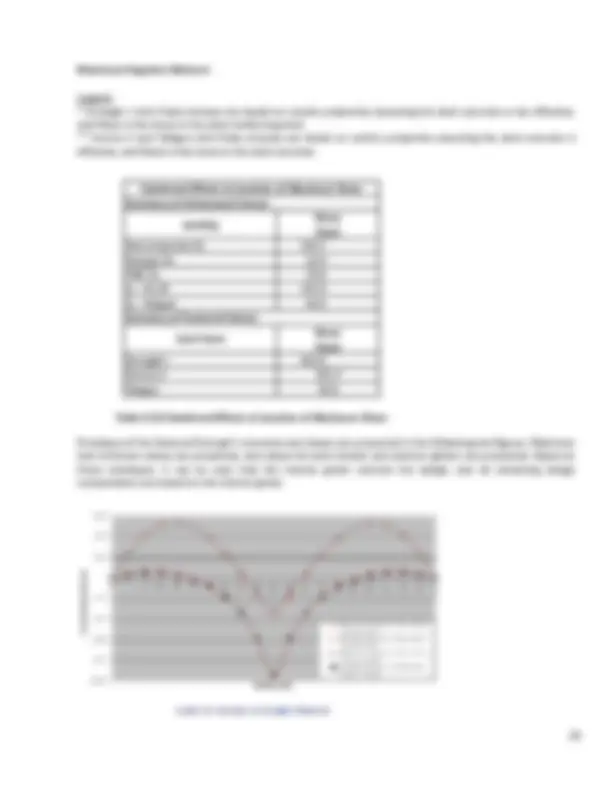
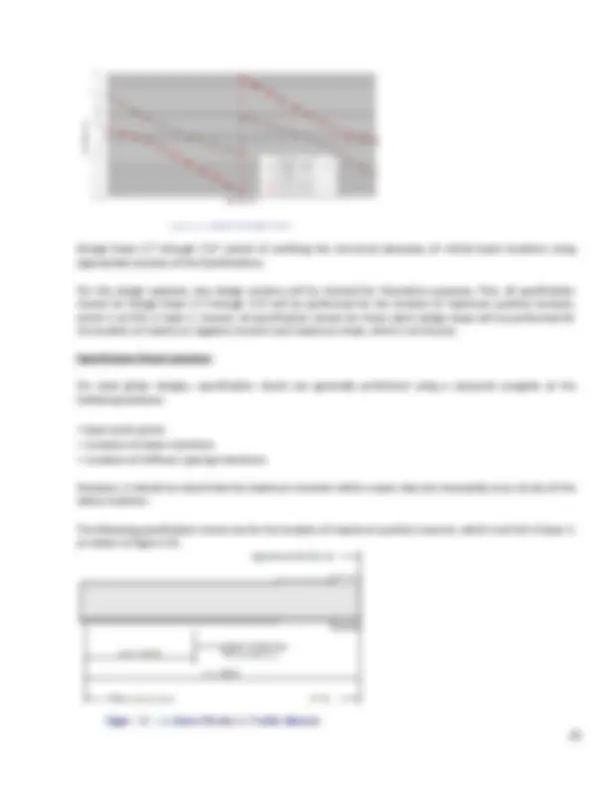
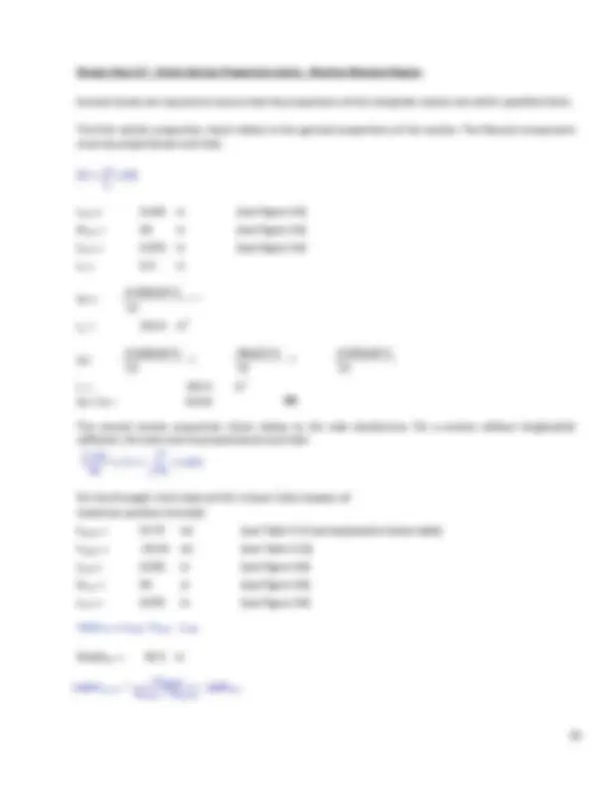
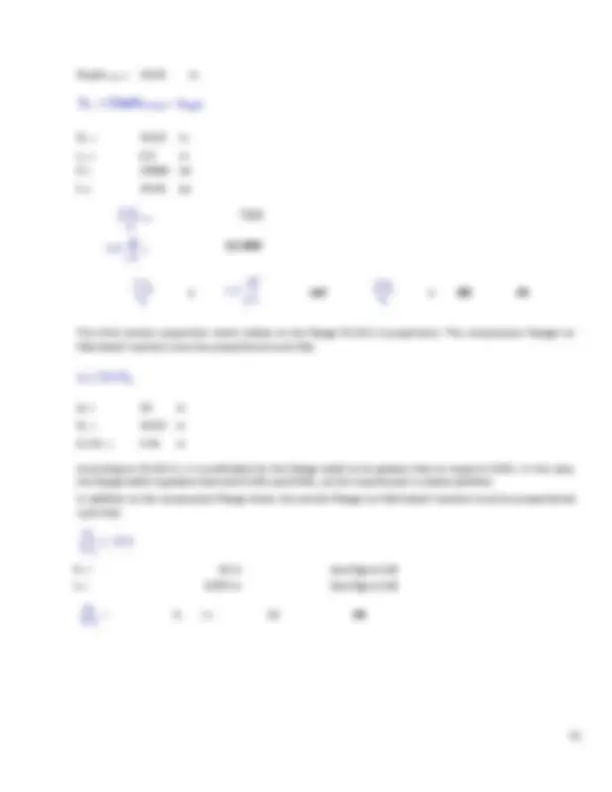
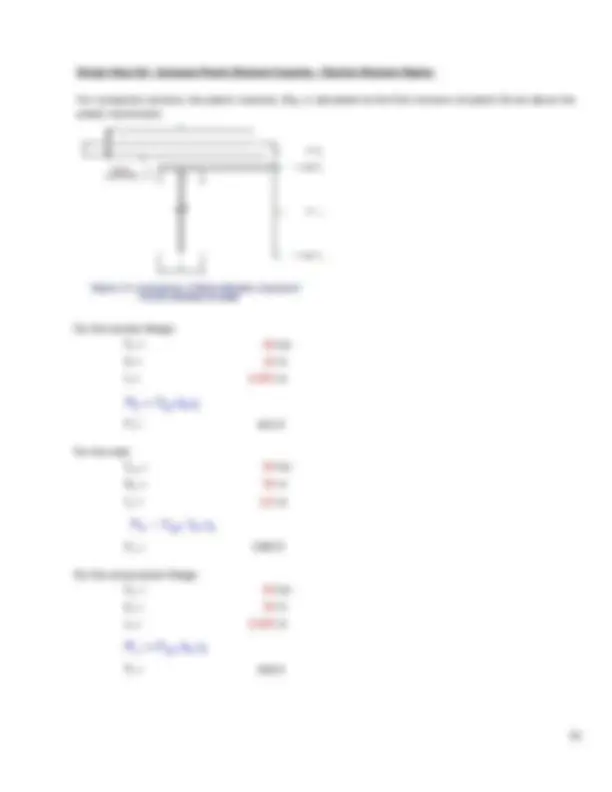
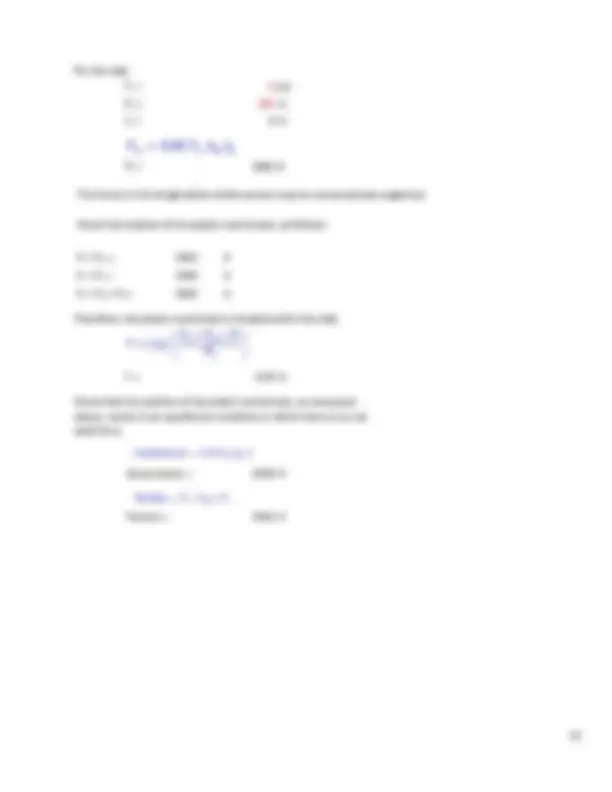
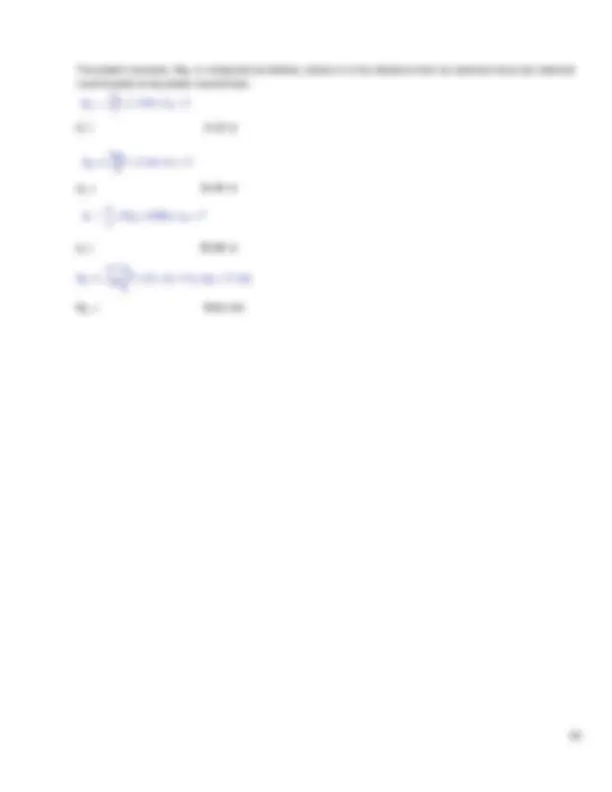
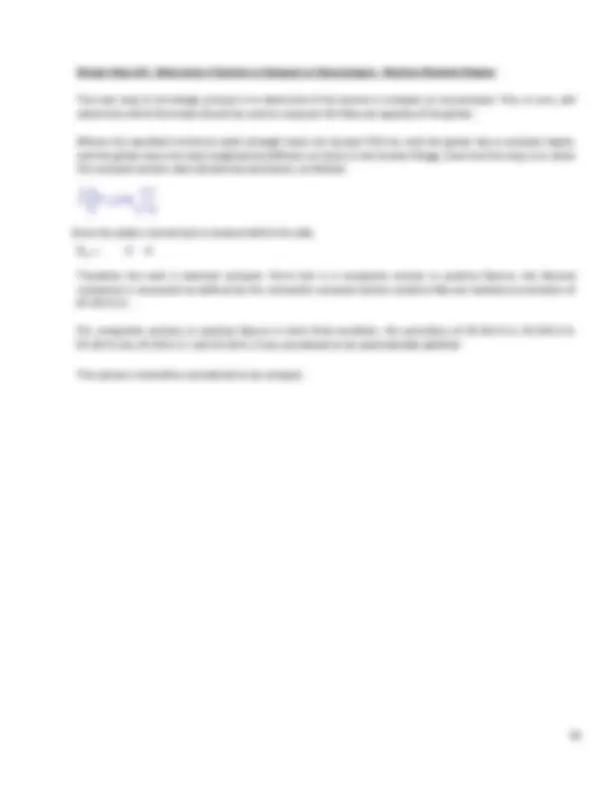
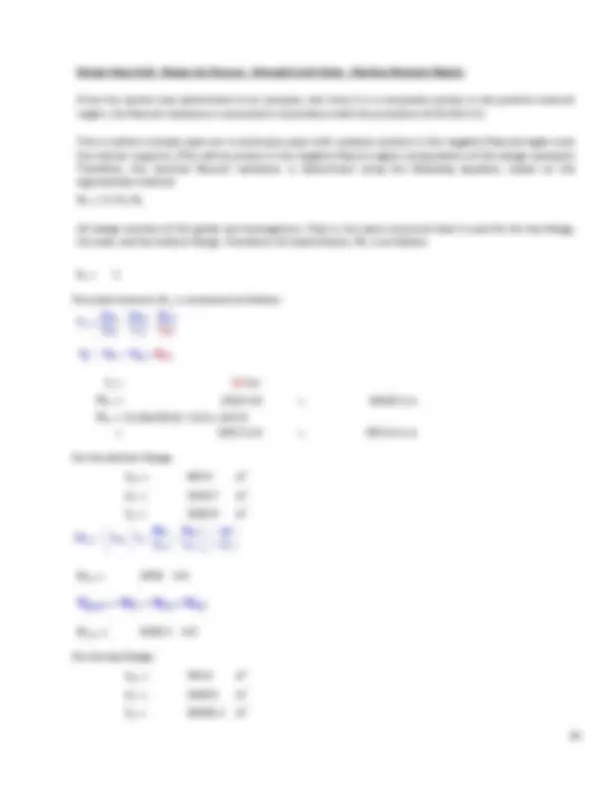
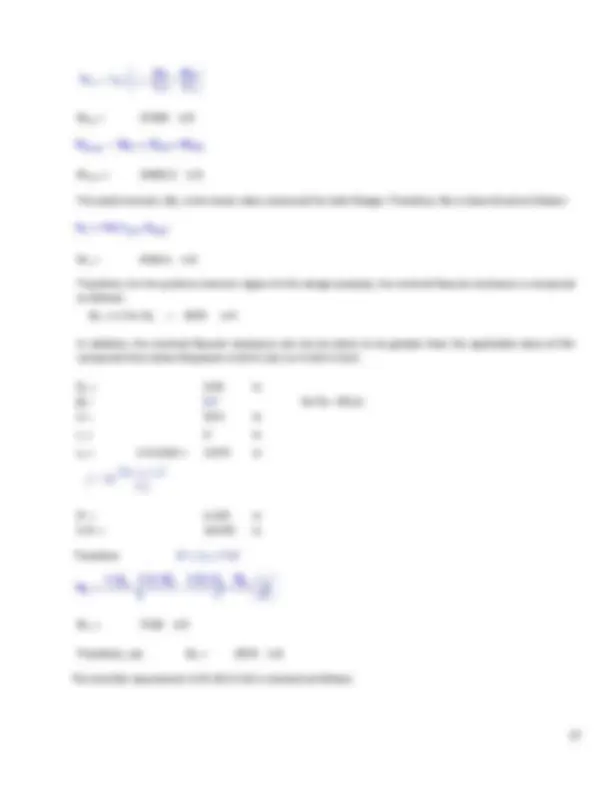
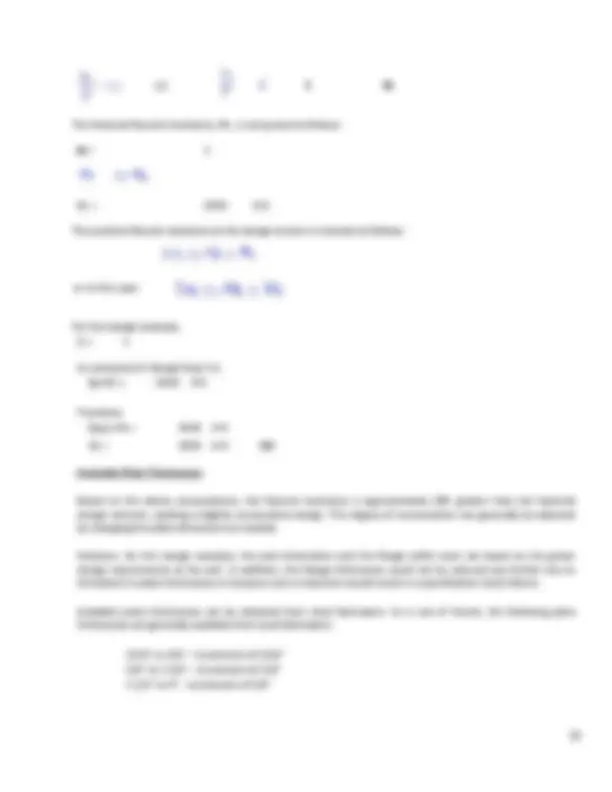
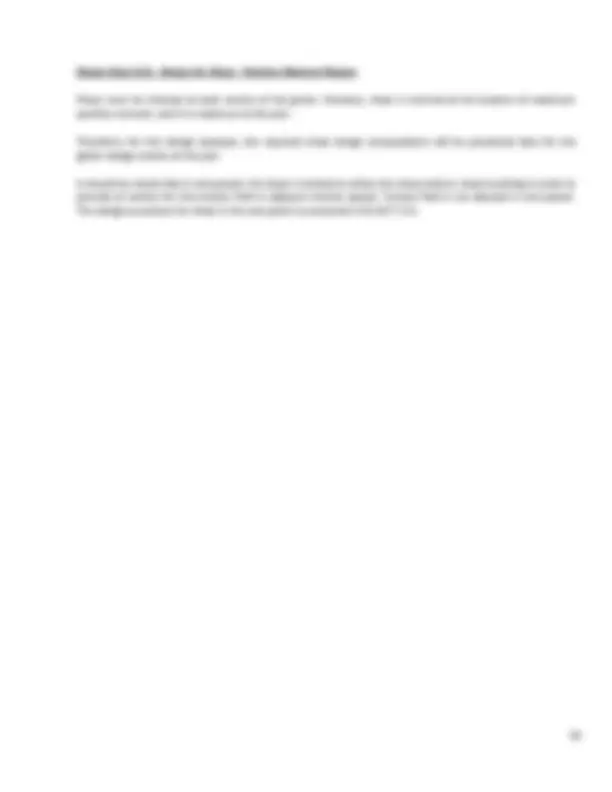
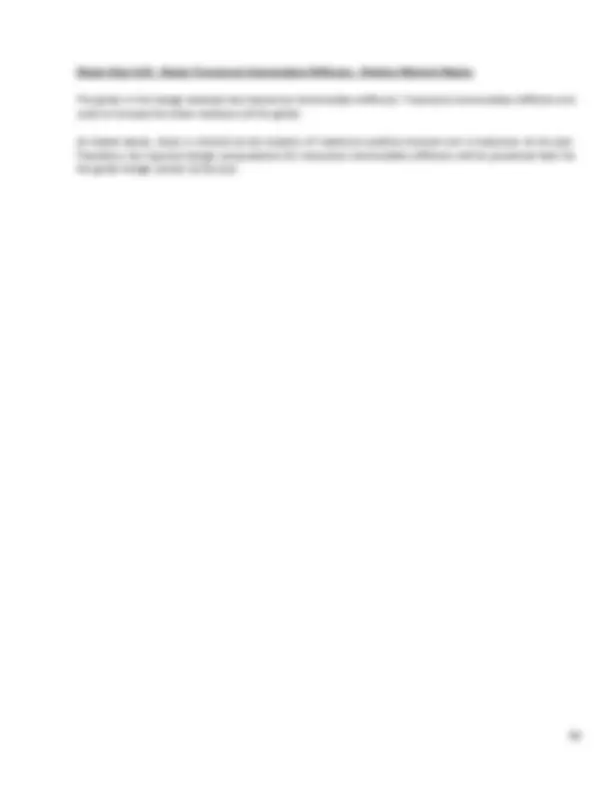
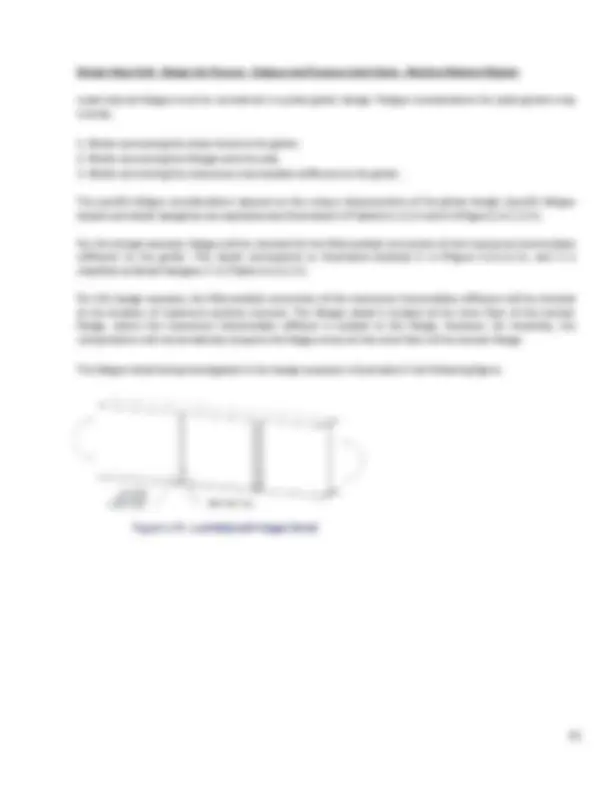
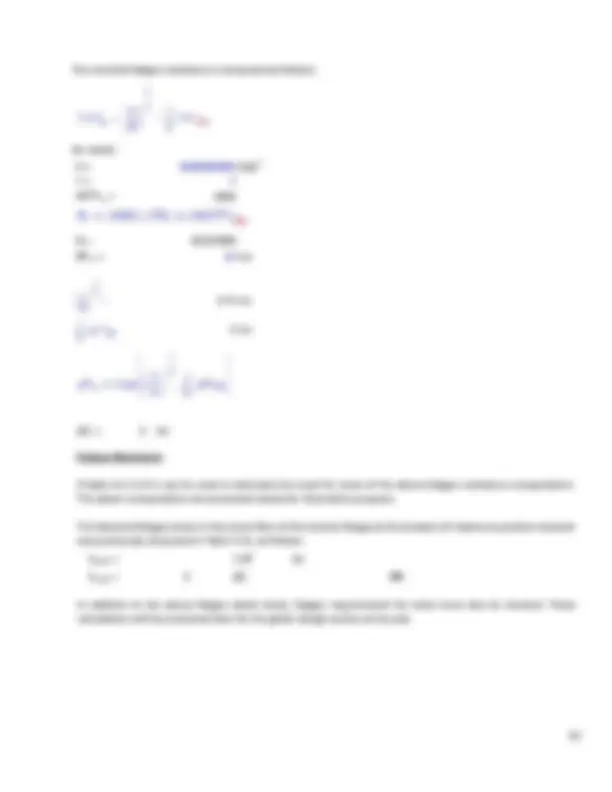
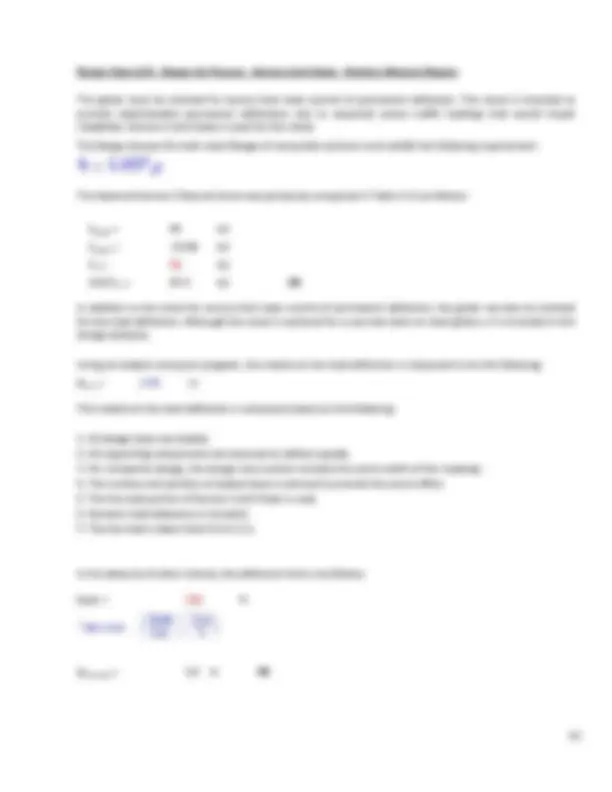
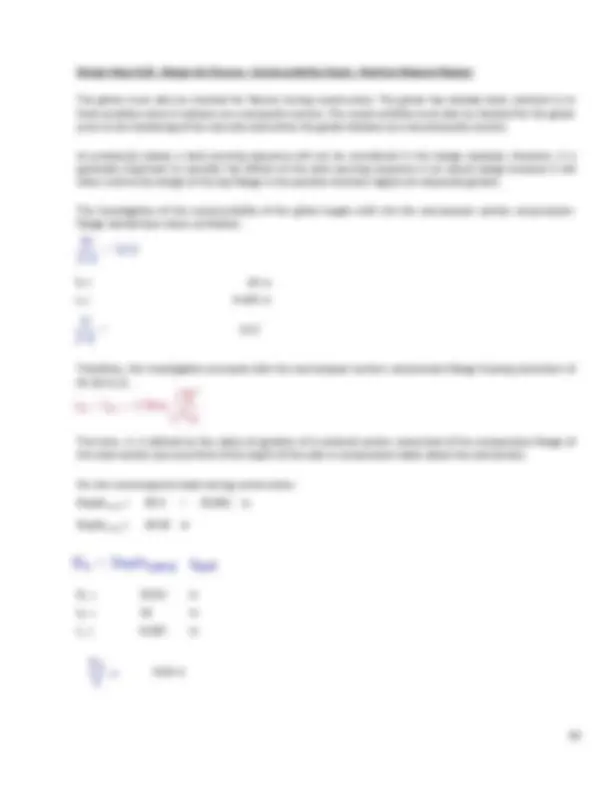
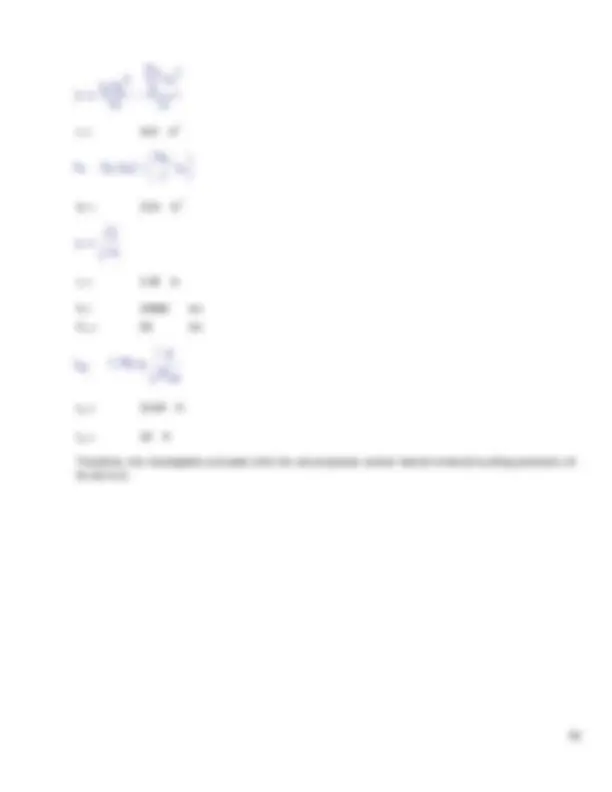
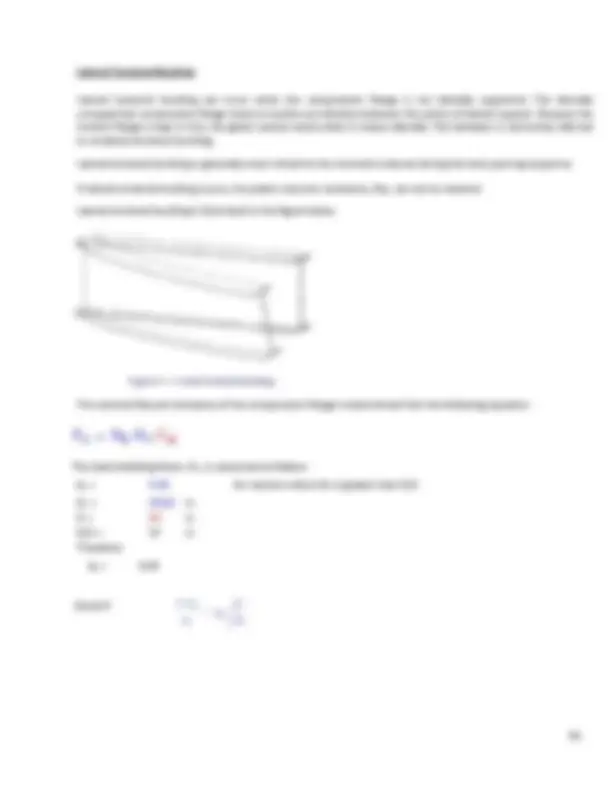
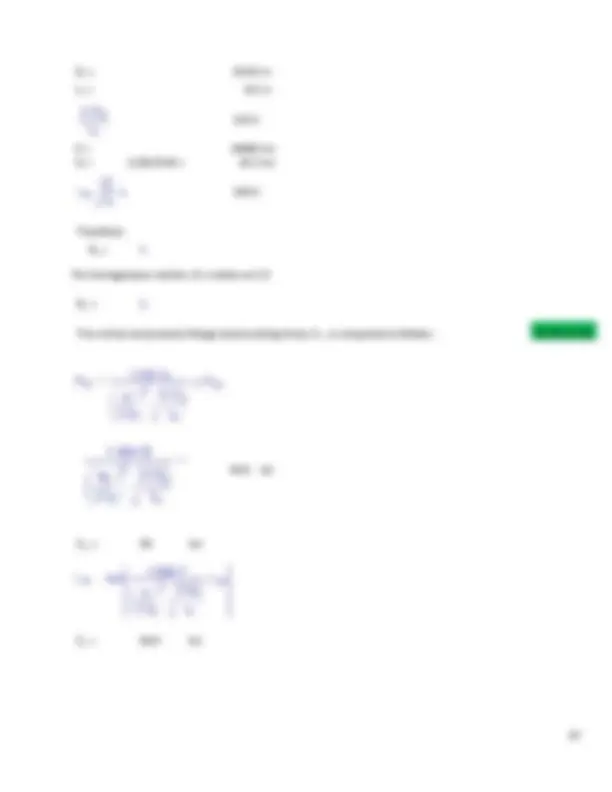
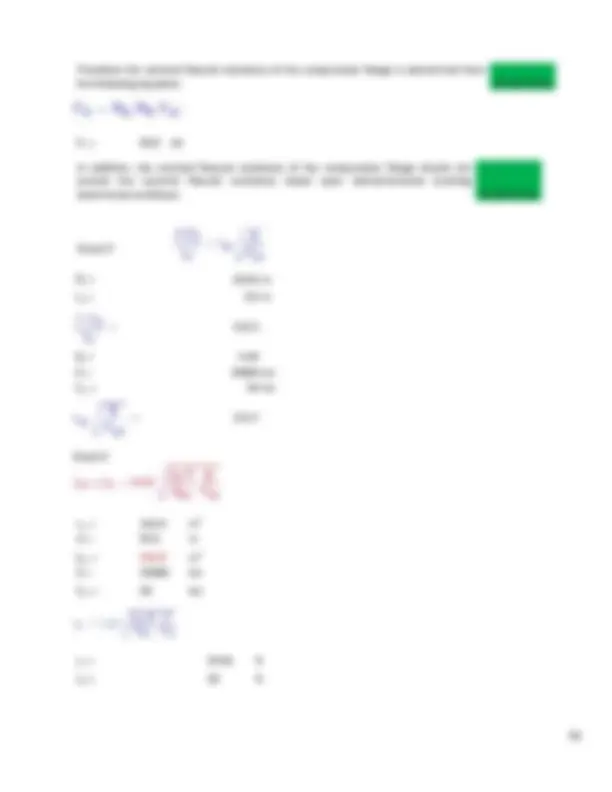
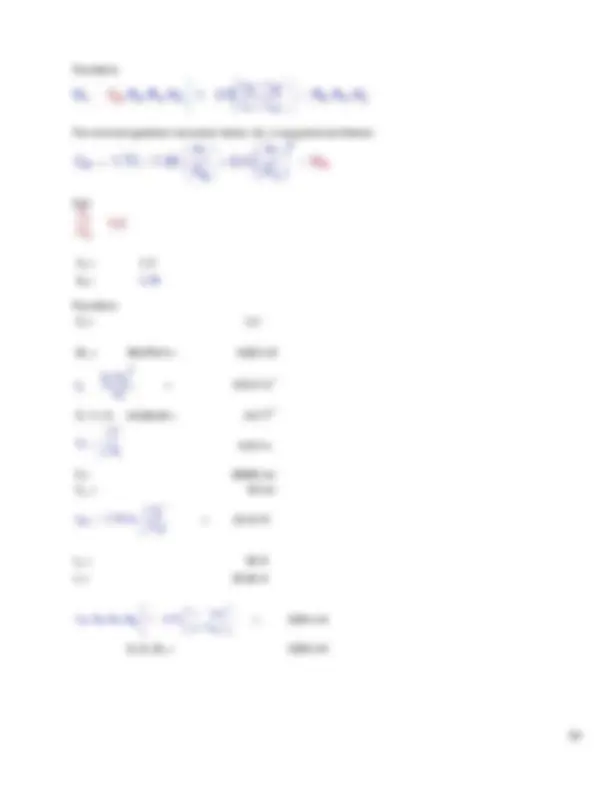
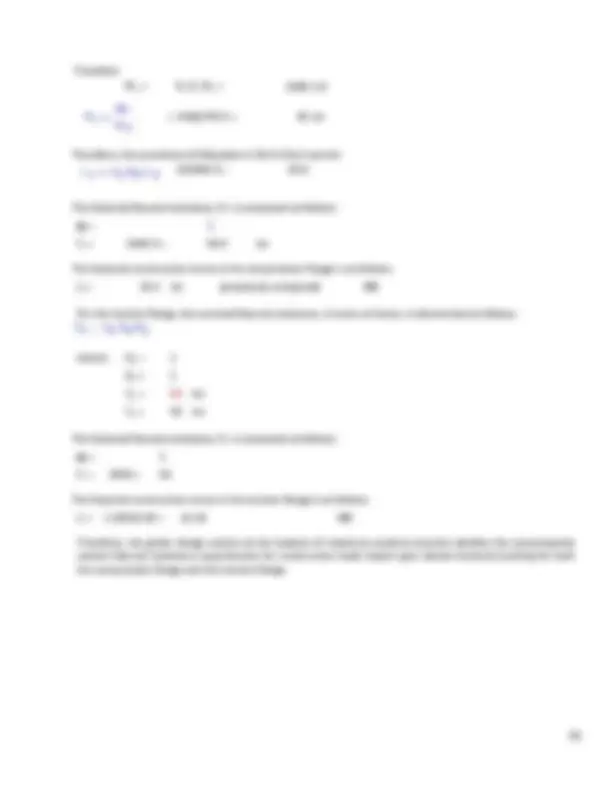
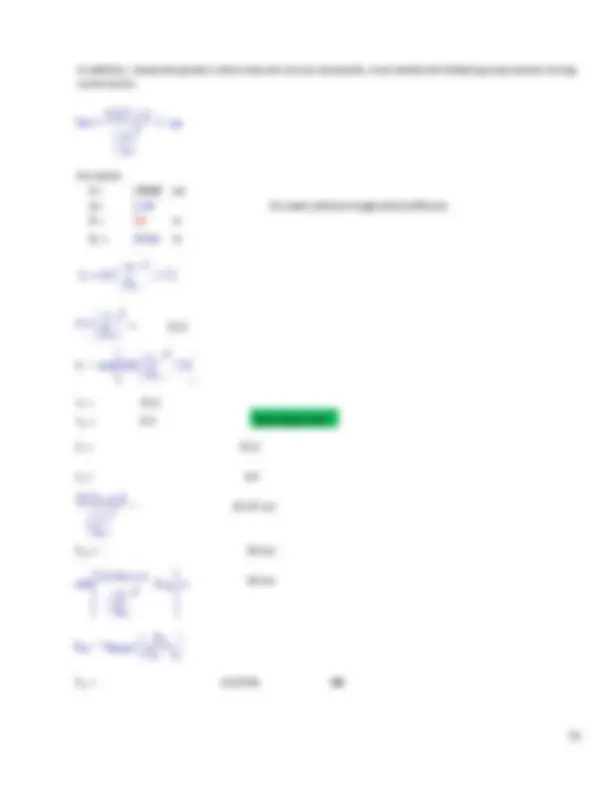
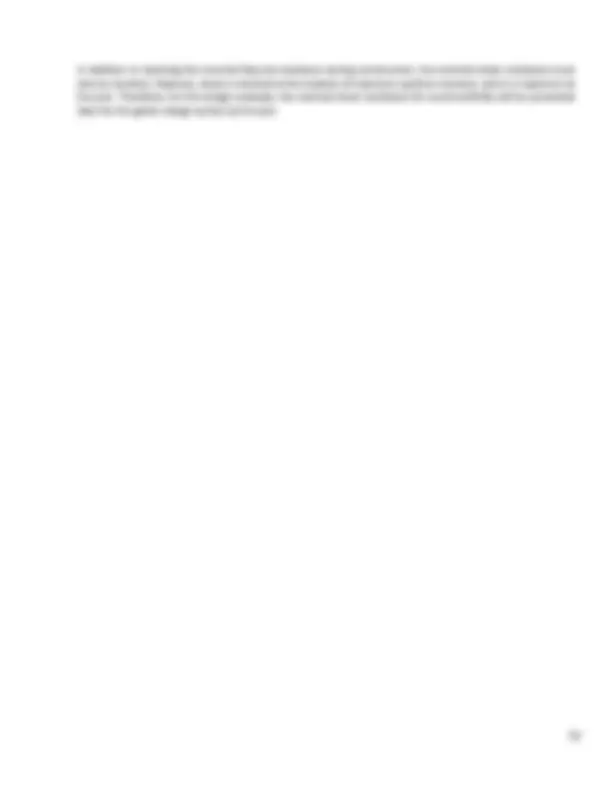

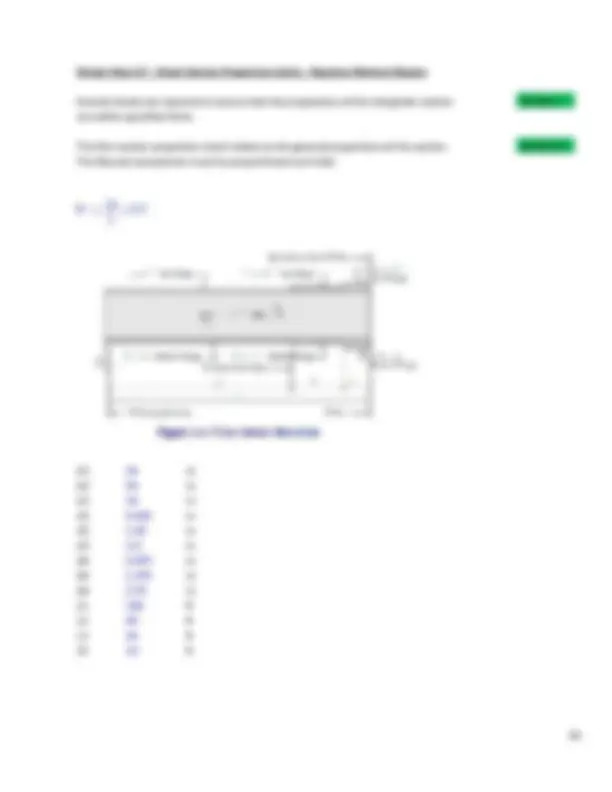
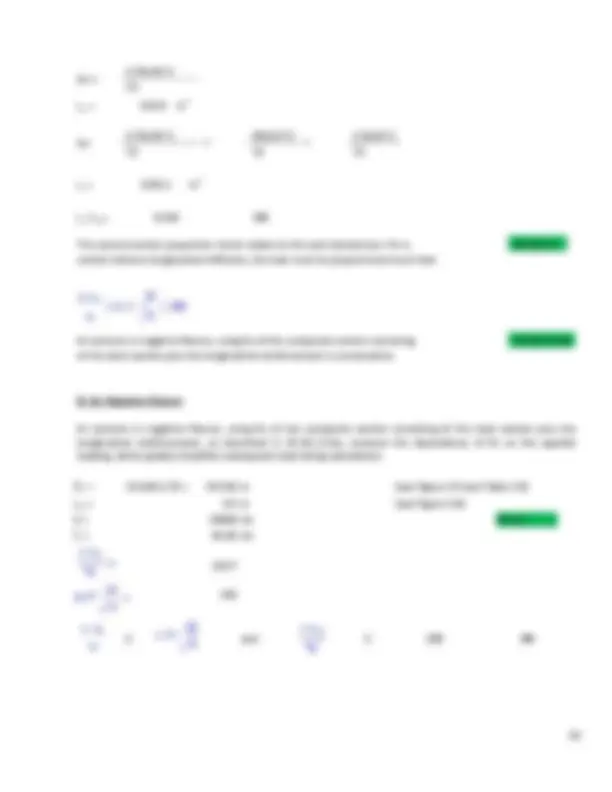
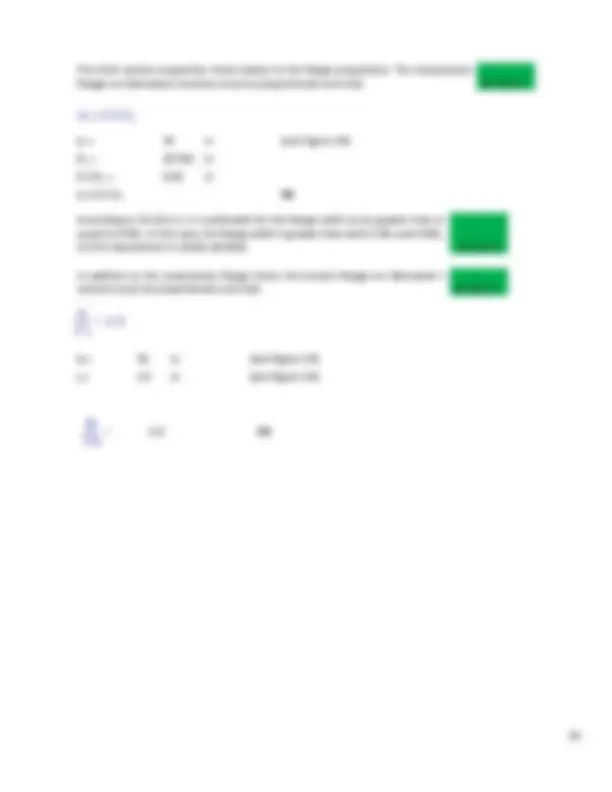
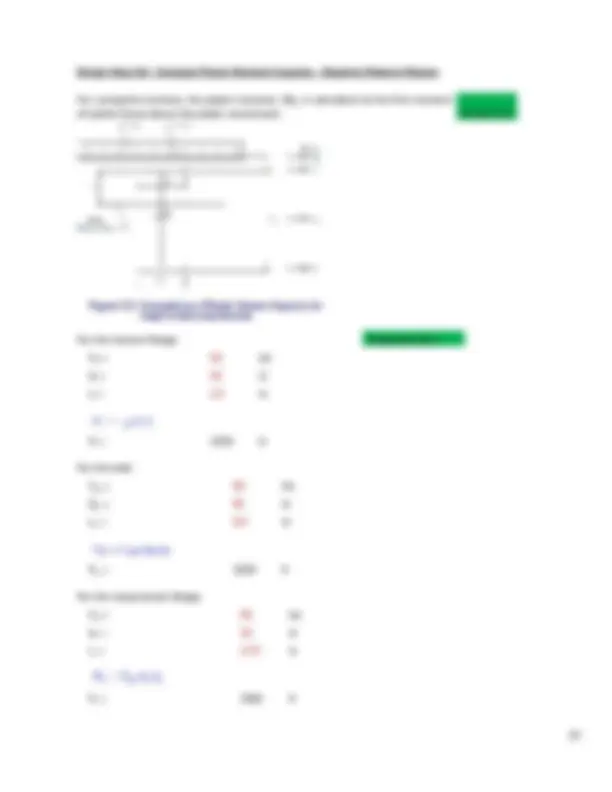
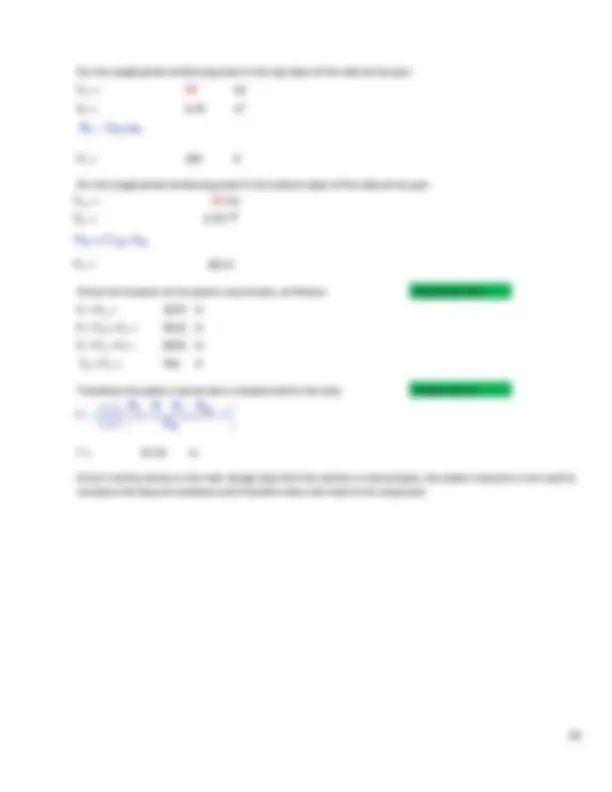
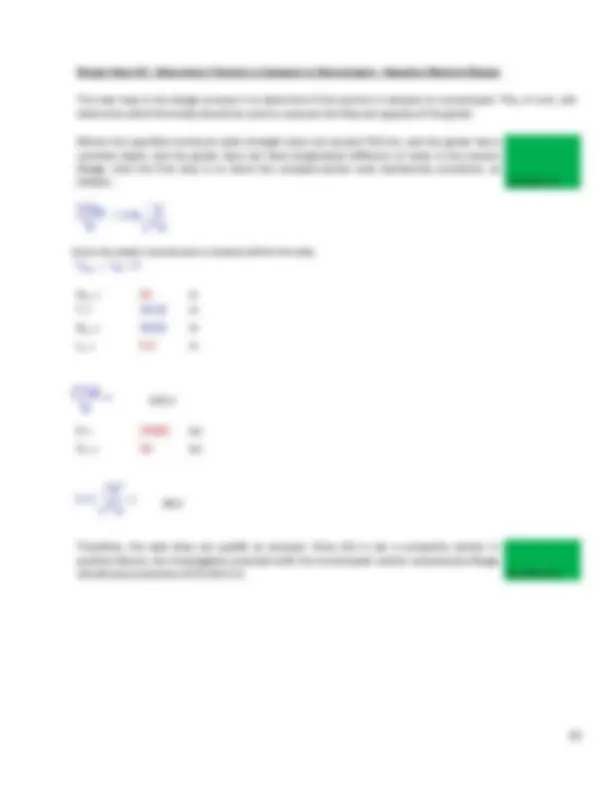
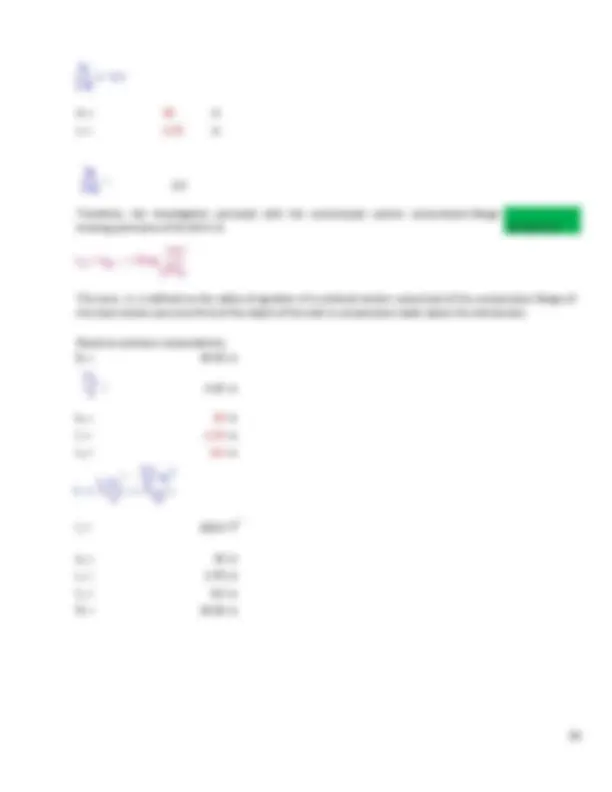
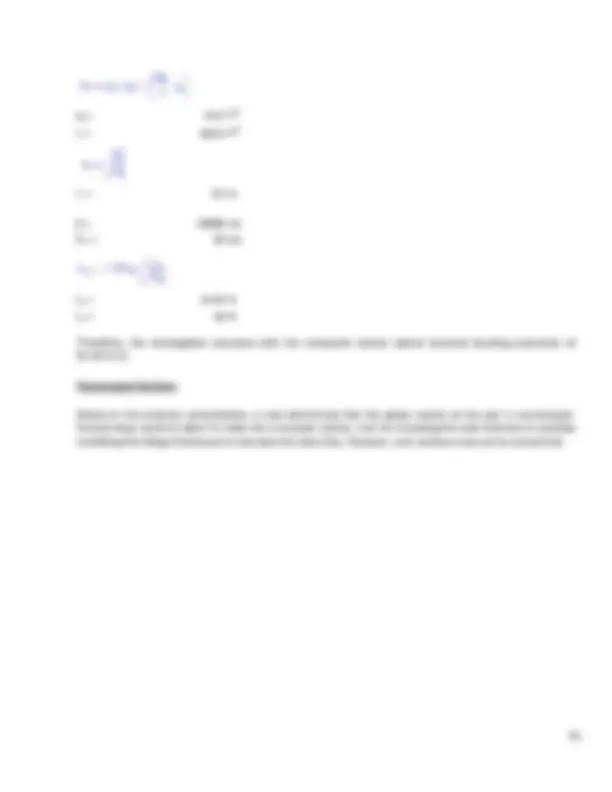
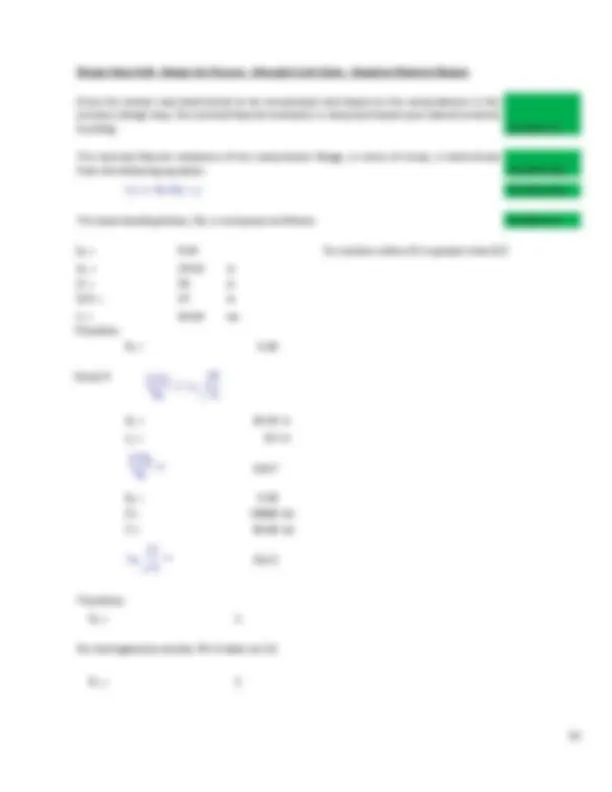
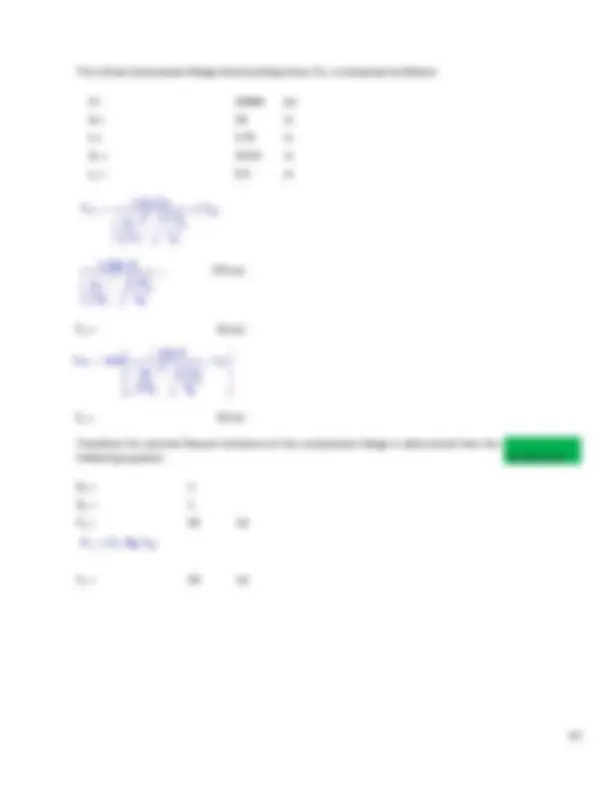
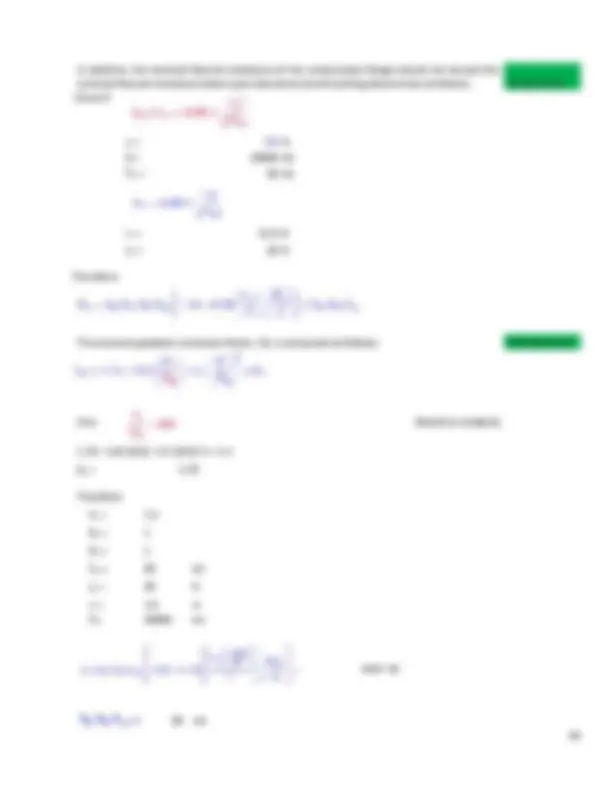
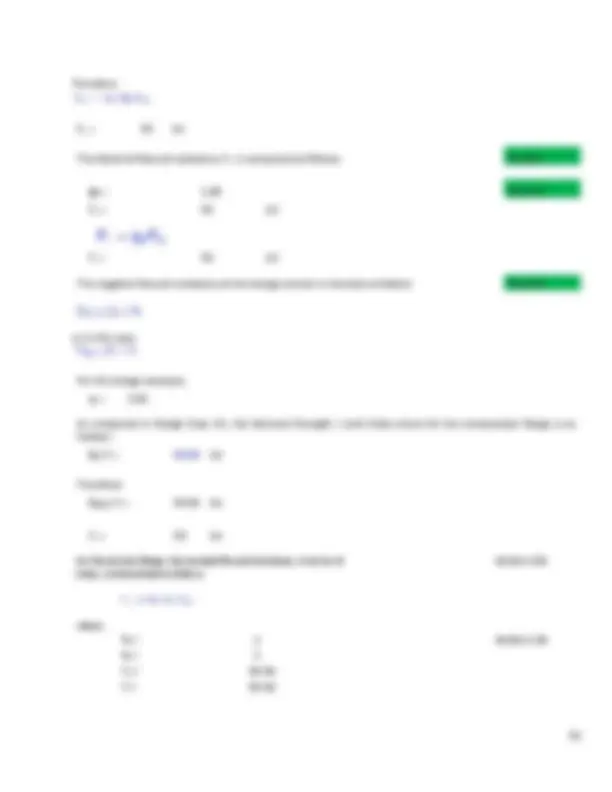
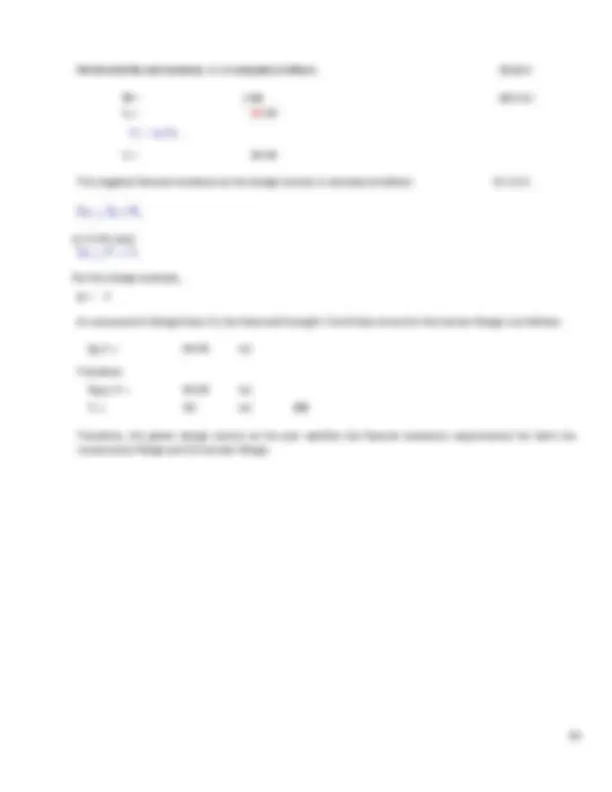
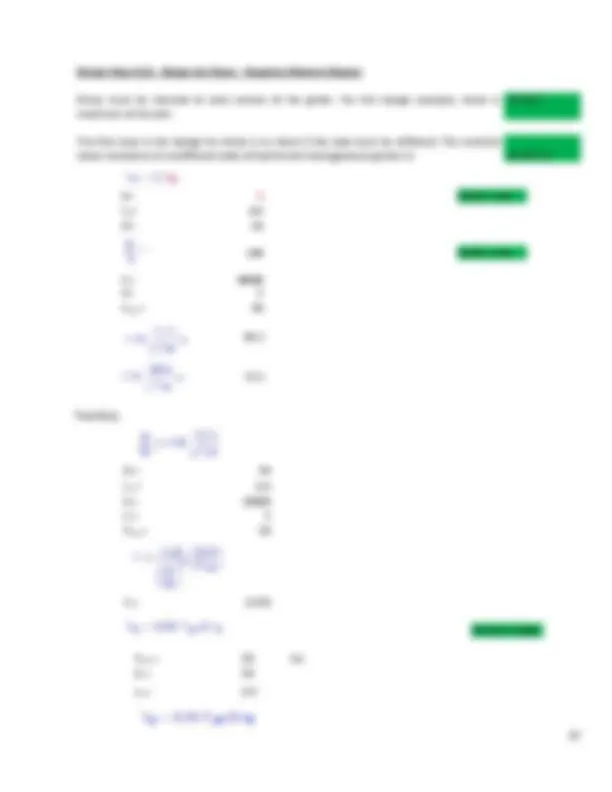
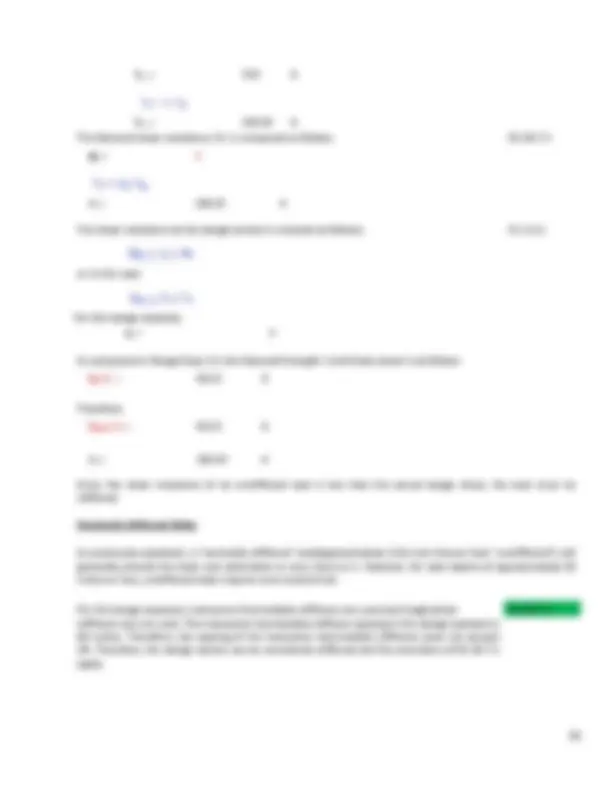
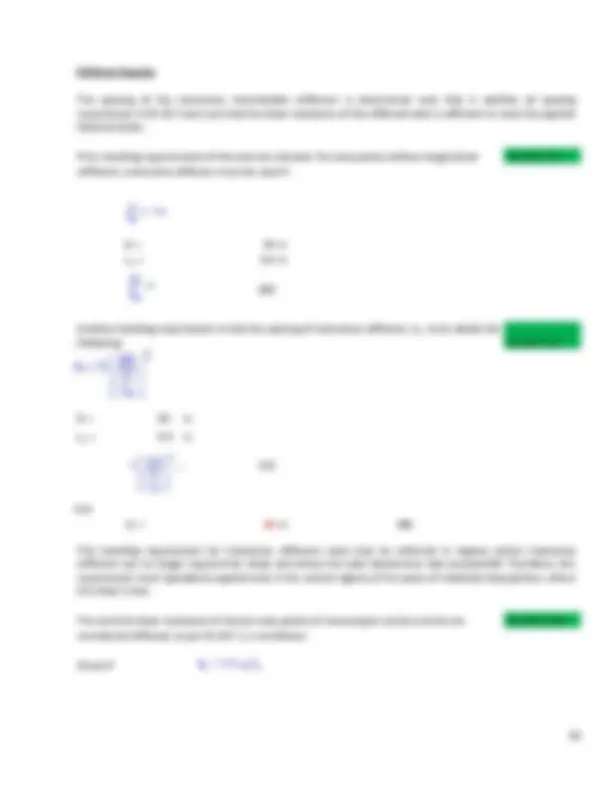
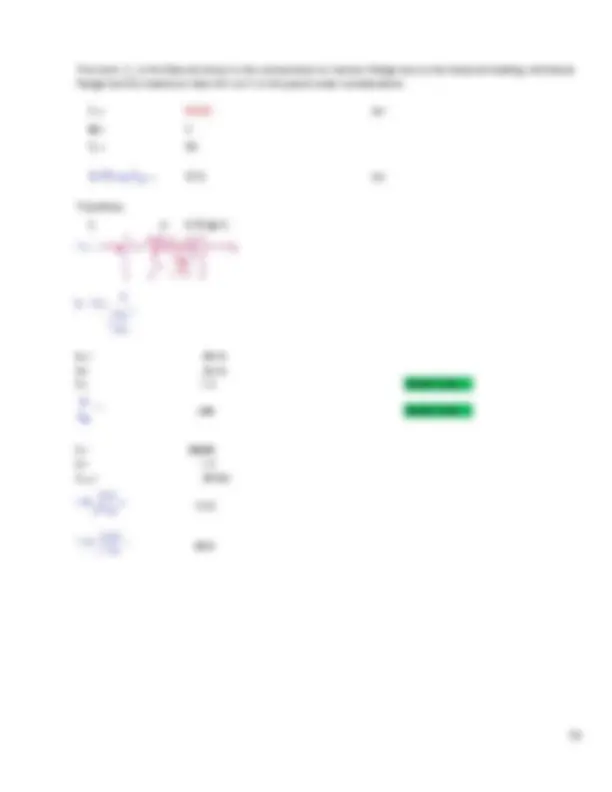
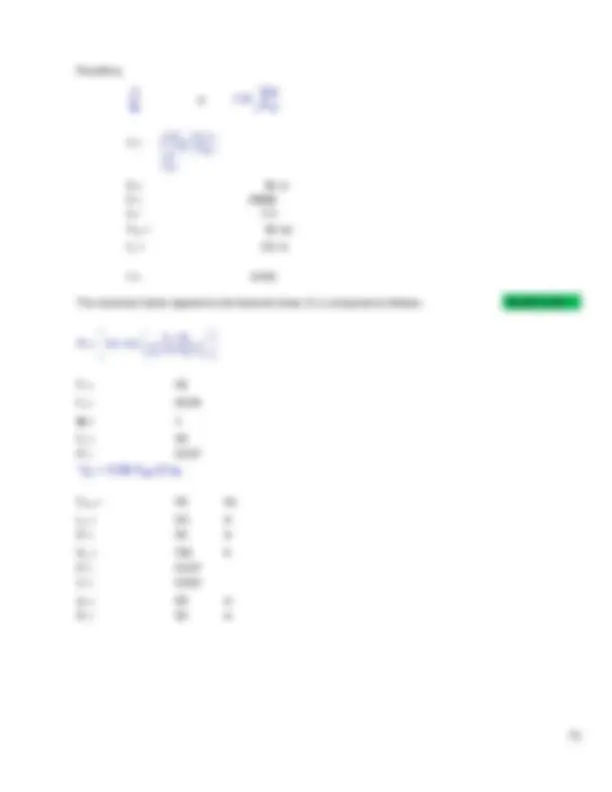
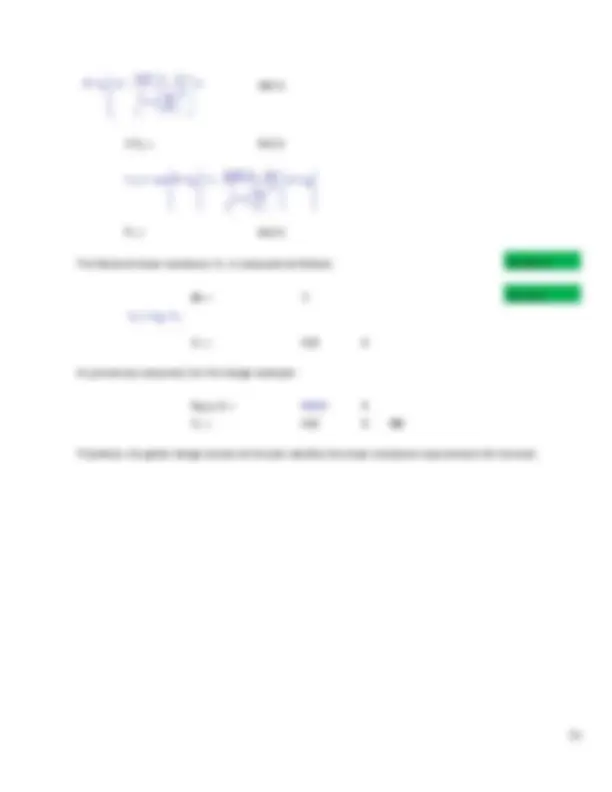
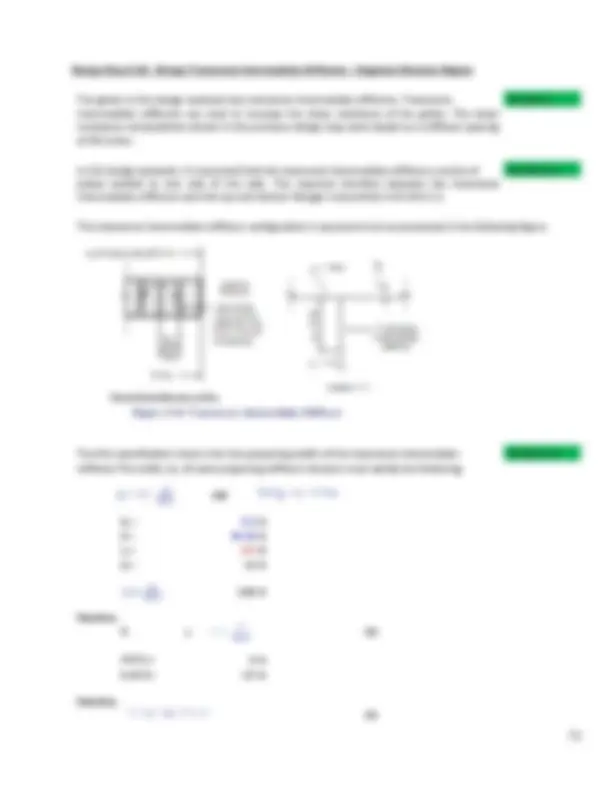
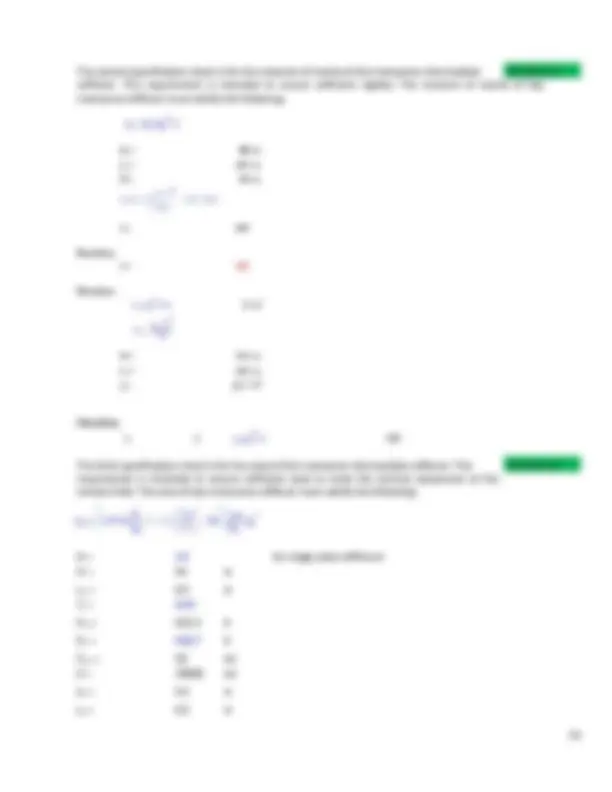
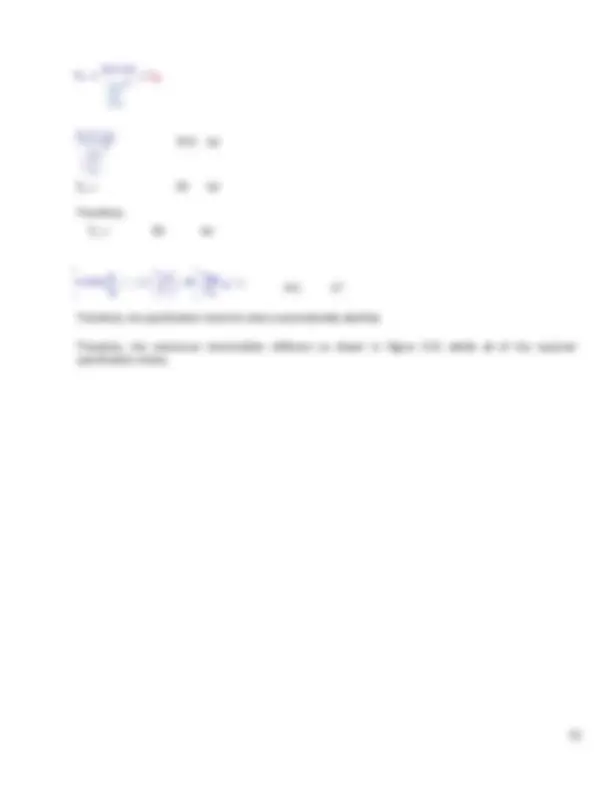
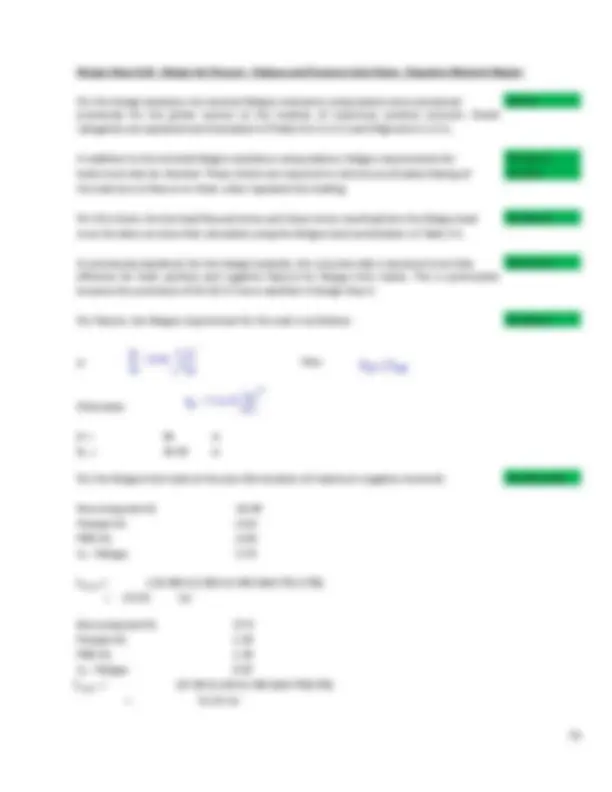
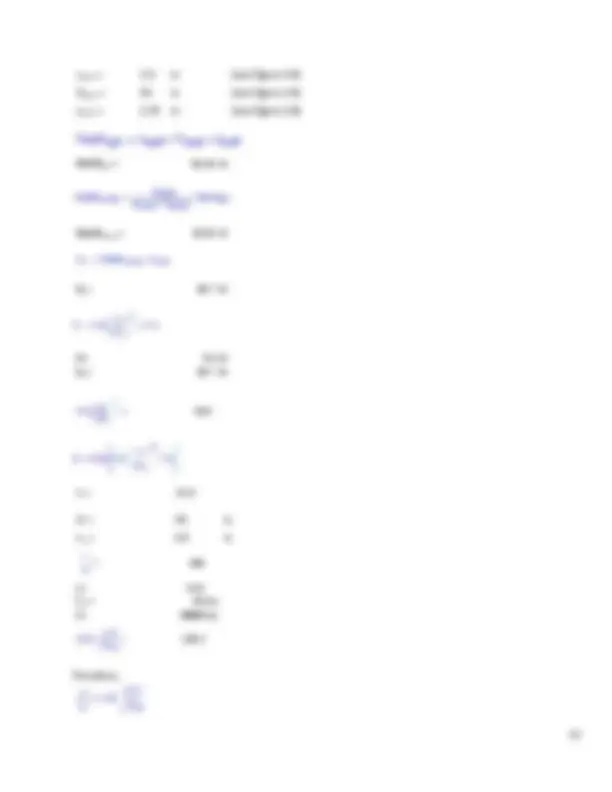
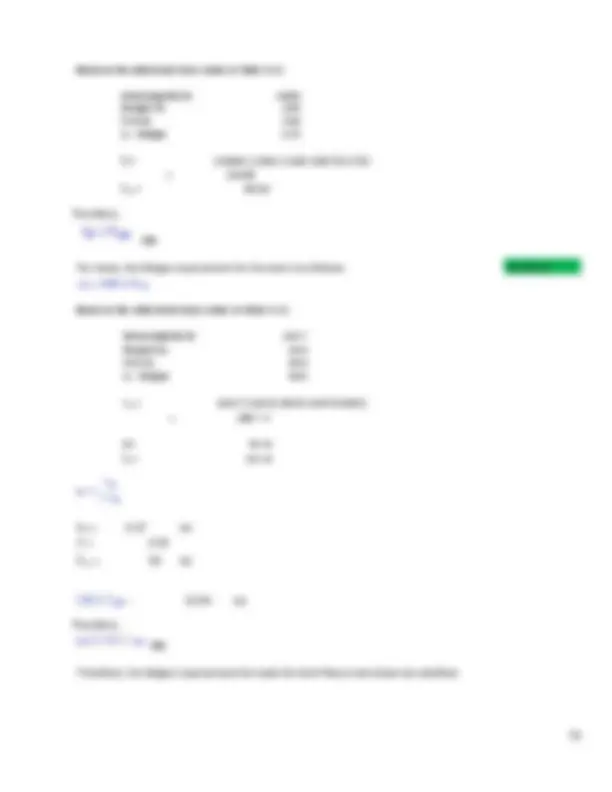
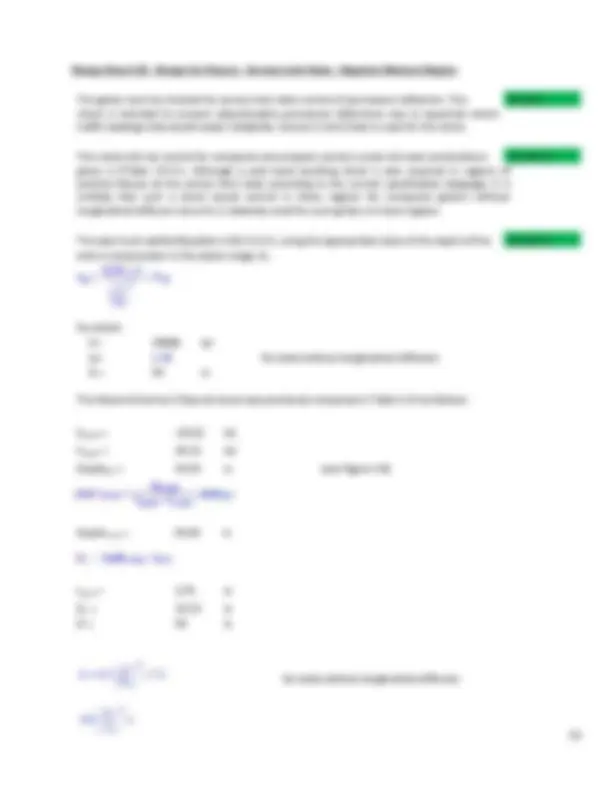
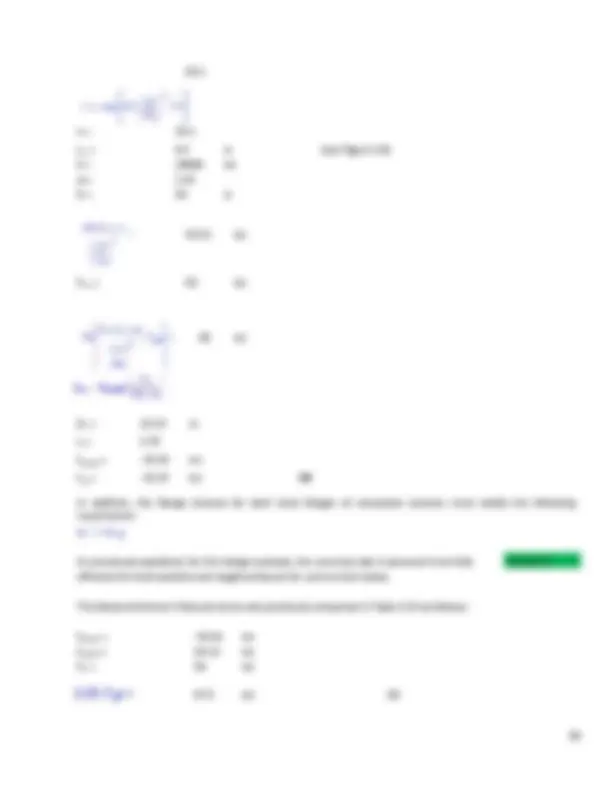
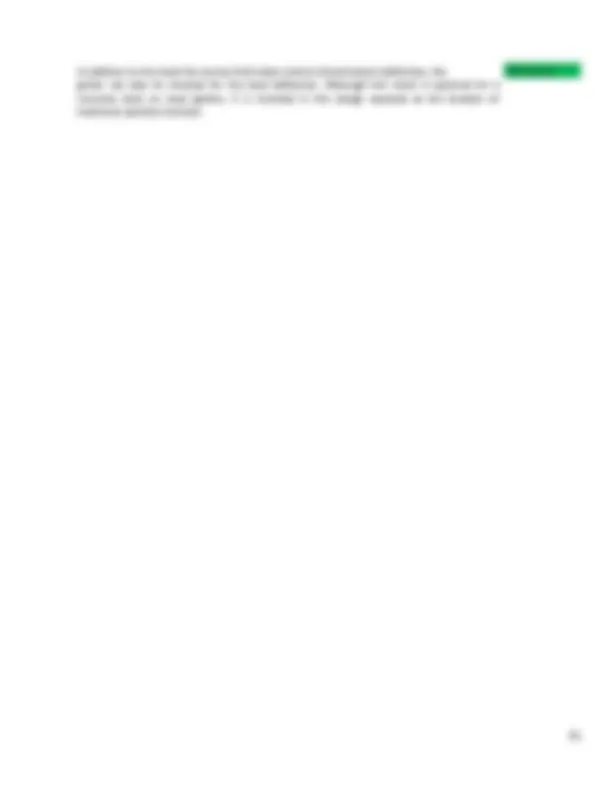
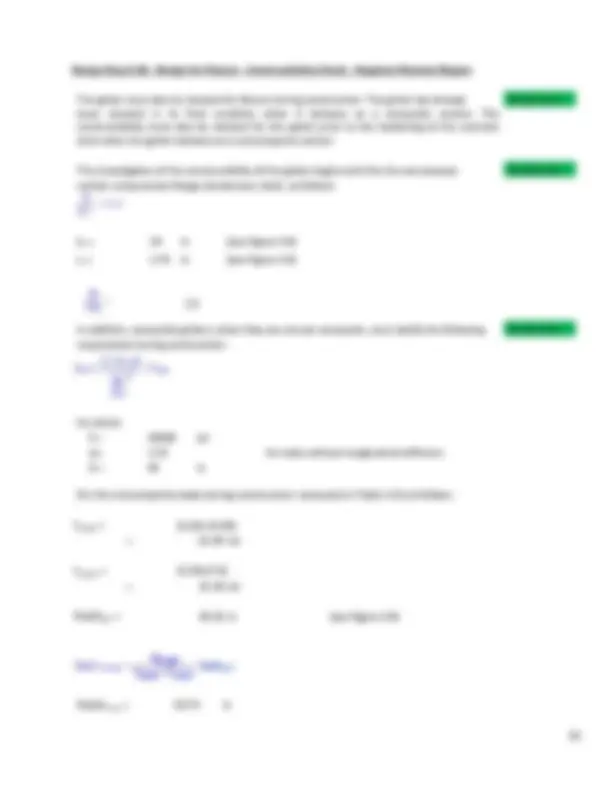
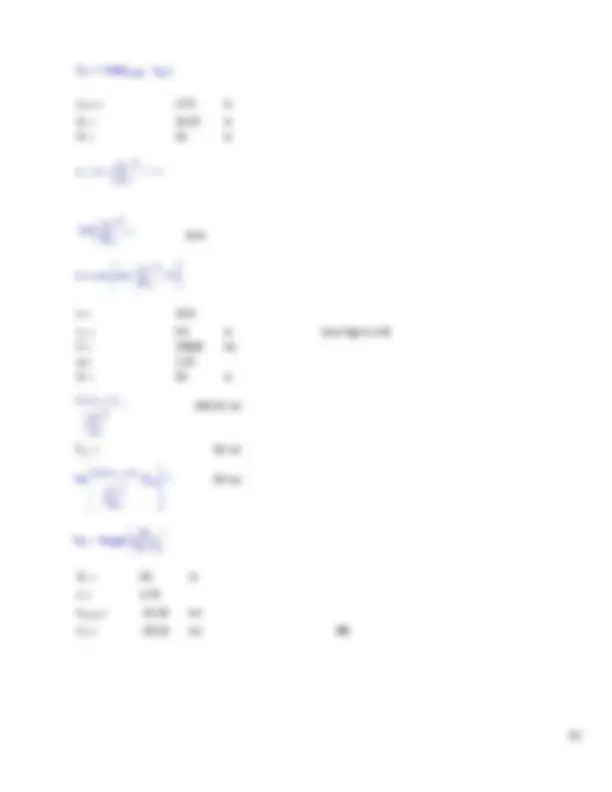
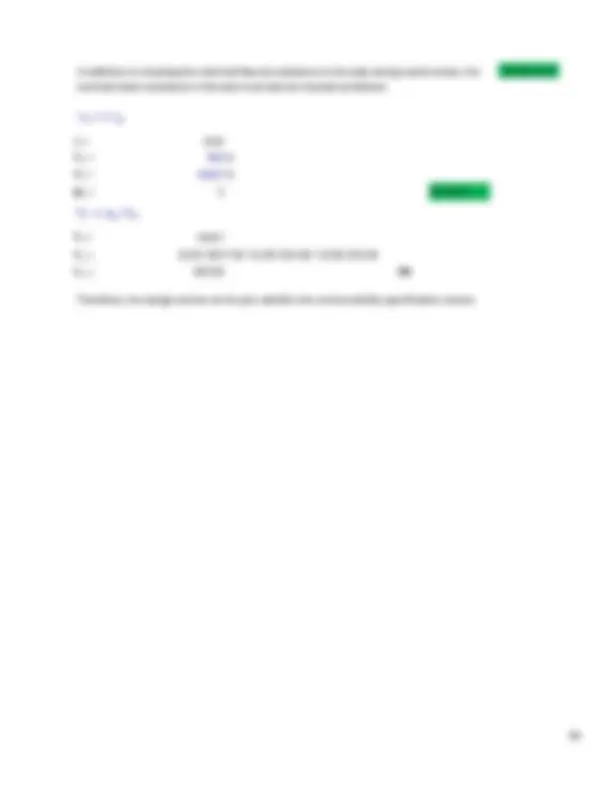
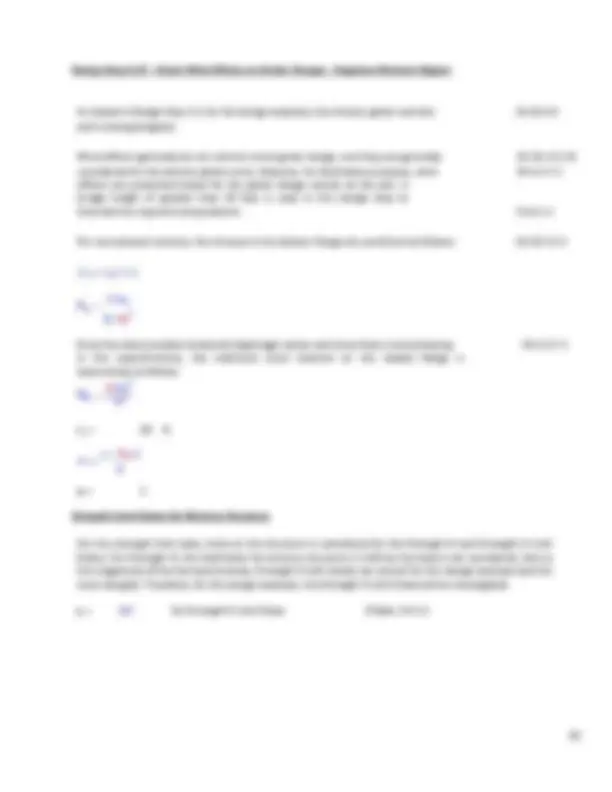
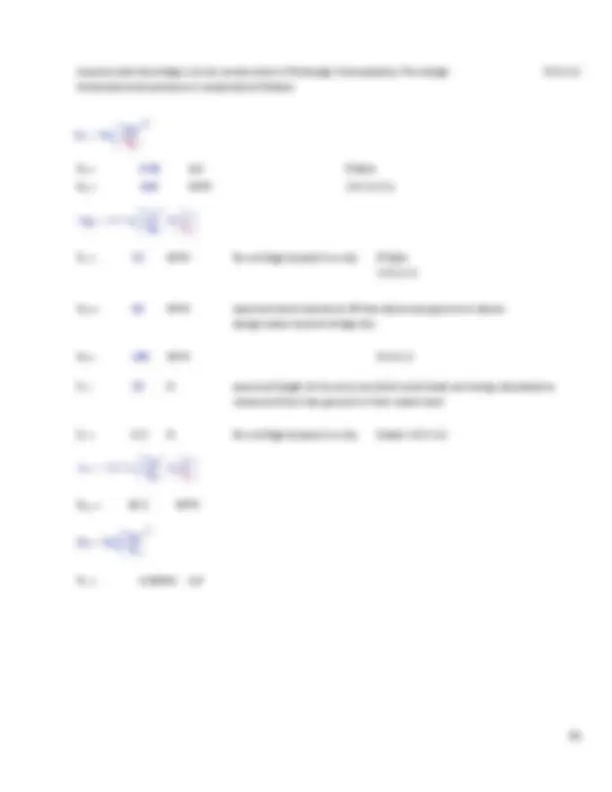
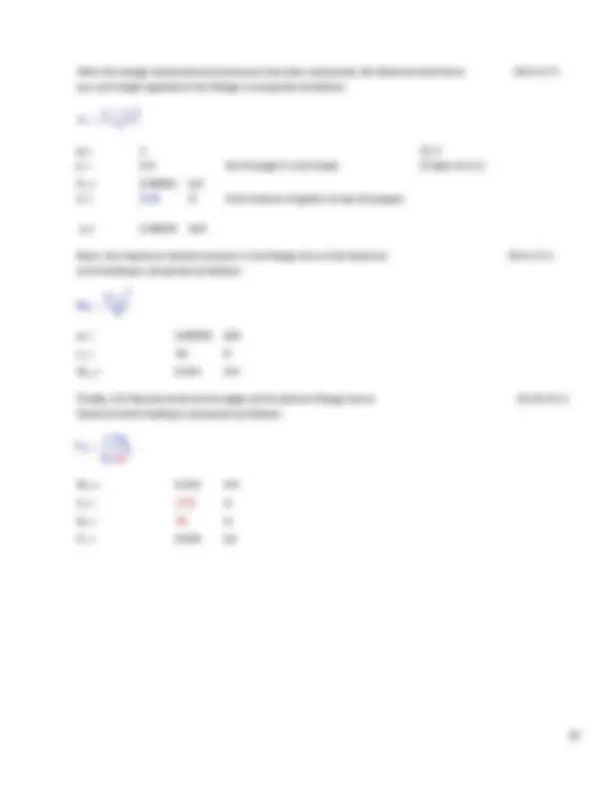
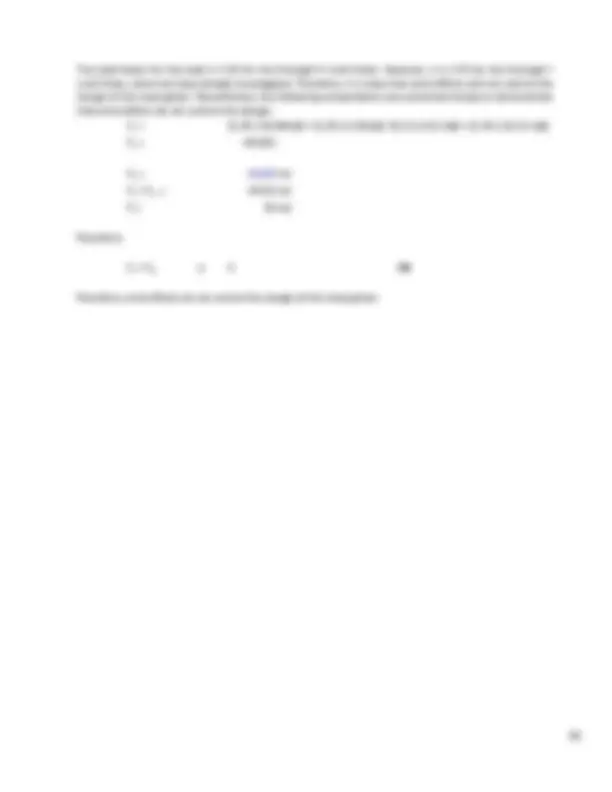
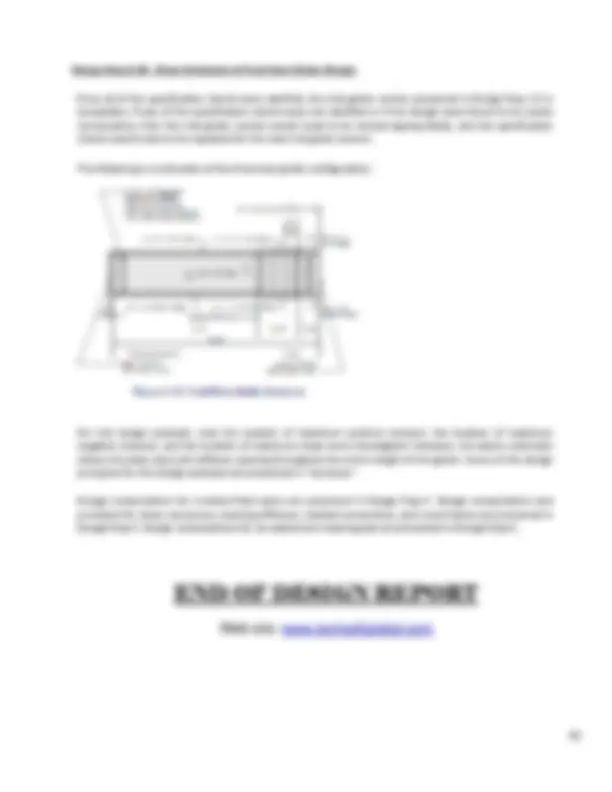
Study with the several resources on Docsity
Earn points by helping other students or get them with a premium plan
Prepare for your exams
Study with the several resources on Docsity
Earn points to download
Earn points by helping other students or get them with a premium plan
Community
Ask the community for help and clear up your study doubts
Discover the best universities in your country according to Docsity users
Free resources
Download our free guides on studying techniques, anxiety management strategies, and thesis advice from Docsity tutors
A detailed design procedure for a steel girder bridge, focusing on the positive and negative moment regions. It covers steps such as obtaining design criteria, selecting trial girder section, computing section properties, dead and live load effects, combining load effects, checking section proportion limits, computing plastic moment capacity, determining if the section is compact or non-compact, designing for flexure (strength, shear, fatigue and fracture, service, constructability), checking wind effects on girder flanges, and drawing the schematic of the final steel girder design. The document also includes tables and formulas for calculating various load effects and stresses.
Typology: Lecture notes
1 / 89
This page cannot be seen from the preview
Don't miss anything!
Construction drawings for Composite Road Bridge with Steel Plate Girder and RCC Deck Slab
Orthotropic Analysis of Composite Bridges:
Model View by Graphical User Interface (GUI): View of Model for Orthotropic Analysis for Multi-span
Continuous Curved Spans with various options as available on the left panel of the GUI Window.
Steel Girder Design Steps with AASHTO - LRFD:
Table of Contents
Design Step 3.1 - Obtain Design Criteria Design Step 3.2 - Select Trial Girder Section Design Step 3.3 - Compute Section Properties Design Step 3.4 - Compute Dead Load Effects Design Step 3.5 - Compute Live Load Effects Design Step 3.6 - Combine Load Effects
Positive Moment Region:
Design Step 3.7 - Check Section Proportion Limits Design Step 3.8 - Compute Plastic Moment Capacity Design Step 3.9 - Determine if Section is Compact or Non-compact Design Step 3.10 - Design for Flexure - Strength Limit State Design Step 3.11 - Design for Shear Design Step 3.12 - Design Transverse Intermediate Stiffeners Design Step 3.14 - Design for Flexure - Fatigue and Fracture Design Step 3.15 - Design for Flexure - Service Limit State Design Step 3.16 - Design for Flexure - Constructability Check Design Step 3.17 - Check Wind Effects on Girder Flanges
Negative Moment Region:
Design Step 3.7 - Check Section Proportion Limits Design Step 3.8 - Compute Plastic Moment Capacity Design Step 3.9 - Determine if Section is Compact or Non-compact Design Step 3.10 - Design for Flexure - Strength Limit State Design Step 3.11 - Design for Shear Design Step 3.12 - Design Transverse Intermediate Stiffeners Design Step 3.14 - Design for Flexure - Fatigue and Fracture Design Step 3.15 - Design for Flexure - Service Limit State Design Step 3.16 - Design for Flexure - Constructability Check Design Step 3.17 - Check Wind Effects on Girder Flanges Design Step 3.18 - Draw Schematic of Final Steel Girder Design
Girder Spacing
Where depth or deflection limitations do not control the design, it is generally more cost-effective to use a wider girder spacing. For this design example, the girder spacing shown in Figure 3-2 was developed as a reasonable value for all limit states. Four girders are generally considered to be the minimum, and five girders are desirable to facilitate future redecking. Further optimization of the superstructure could be achieved by revising the girder spacing.
Overhang Width
The overhang width is generally determined such that the moments and shears in the exterior girder are similar to those in the interior girder. In addition, the overhang is set such that the positive and negative moments in the deck slab are balanced. A common rule of thumb is to make the overhang approximately 0. to 0.5 times the girder spacing.
Cross-frame Spacing
A common rule of thumb, based on previous editions of the AASHTO Specifications, is to use a maximum cross- frame spacing of 25 feet. For this design example, a cross-frame spacing of 20 feet is used because it facilitates a reduction in the required flange thicknesses in the girder section at the pier.
This spacing also affects constructability checks for stability before the deck is cured. Currently, stay-in-place forms should not be considered to provide adequate bracing to the top flange.
The following units are defined for use in this design example:
Design criteria:
Number of spans: Nspans = 1
Span length: Lspan = 120 ft
Skew angle: Skew = 0 deg
Number of girders: Ngirders = 5
Girder spacing: S = 9.75 ft
Deck overhang: Soverhang = 3.9375 ft
Cross-frame spacing: Lb = 20 ft
Web yield strength: Fyw = 50 ksi
Flange yield strength: Fyf = 51 ksi
Concrete 28-day compressive strength: f'c = 4 ksi
Reinforcement strength: fy = 60 ksi
Dia of bar Bar dia= 0.625 in
Area of bar Bar area= 0.31 in^2
Design criteria (continued):
Total deck thickness: tdeck = 8.5 in
Effective deck thickness: teffdeck = 8 in
Total overhang thickness: toverhang = 9 in
Effective overhang thickness: teffoverhang = 8.
Steel density: Ws = 0.49 kcf
Concrete density: Wc = 0.15 kcf
Additional miscellaneous dead load (per girder): Wmisc = 0.015 K/ft
Stay-in-place deck form weight: Wdeckforms = 0.015 ksf
Parapet weight (each): Wpar = 0.53 K/ft
Future wearing surface: Wfws = 0.14 kcf
Future wearing surface thickness: tfws = 2.5 in
Deck width: wdeck = 46.875 ft
Roadway width: wroadway = 44 ft
Haunch depth (from top of web): dhaunch = 3.5 in
Average Daily Truck Traffic (Single-Lane): ADTTSL = 3000
Dynamic load allowance:
Dynamic load allowance is the same as impact. The term impact was used in previous editions of the AASHTO Specifications. However, the term "dynamic load allowance" is used in the AASHTO LRFD Bridge Design Specifications.
Fatigue and Fracture Limit State
All Other Limit States
Table 3-3 Dynamic Load Allowance
Dynamic Load Allowance Dynamic Load Allowance, IM
Limit State
Design Step 3.2 - Select Trial Girder Section
Before the dead load effects can be computed, a trial girder section must be selected. This trial girder section is selected based on previous experience and based on preliminary design. For this design example, the trial girder section presented in Figure 3-4 will be used. Based on this trial girder section, section properties and dead load effects will be computed. Then specification checks will be performed to determine if the trial girder section successfully resists the applied loads. If the trial girder section does not pass all specification checks or if the girder optimization is not acceptable, then a new trial girder section must be selected and the design process must be repeated.
b1 = 14 ft d1 = 0.625 ft b2 = 14 ft d2 = 0.875 ft b3 = 14 ft d3 = 0.25 ft b4 = 14 ft d4 = 0.375 ft b5 = 14 ft d5 = 2.5 ft b6 = 14 ft d6 = 2.75 ft b7 = 0.5 ft d7 = 54 ft L = 120 ft L1 = 84 ft L2 = 24 ft L3 = 12 ft
For this design example, the 5/8" top flange thickness in the positive moment region was used to optimize the plate girder. It also satisfies the requirements of S6.7.3. However, it should be noted that some state requirements and some fabricator concerns may call for a 3/4" minimum flange thickness. In addition, the AASHTO/NSBA Steel Bridge Collaboration Document "Guidelines for Design for Constructability" recommends a 3/4" minimum flange thickness.
Design Step 3.3 - Compute Section Properties
Since the superstructure is composite, several sets of section properties must be computed. The initial dead loads (or the Non-composite dead loads) are applied to the girder-only section. The superimposed dead loads are applied to the composite section based on a modular ratio of 3n or n, whichever gives the higher stresses.
Modular Ratio
As specified in S6.10.3.1.1b, for permanent loads assumed to be applied to the long-term composite section, the slab area shall be transformed by using a modular ratio of 3n or n, whichever gives the higher stresses.
Using a modular ratio of 3n for the superimposed dead loads always gives higher stresses in the steel section. Using a modular ratio of n typically gives higher stresses in the concrete deck, except in the moment reversal regions where the selection of 3n vs. n can become an issue in determining the maximum stress in the deck.
The live loads are applied to the composite section based on a modular ratio of n.
For girders with shear connectors provided throughout their entire length and with slab reinforcement satisfying the provisions of S6.10.3.7, stresses due to loads applied to the composite section for service and fatigue limit states may be computed using the composite section assuming the concrete slab to be fully effective for both positive and negative flexure.
Therefore, for this design example, the concrete slab will be assumed to be fully effective for both positive and negative flexure for service and fatigue limit states.
For this design example, the interior girder controls. In general, both the exterior and interior girders must be considered, and the controlling design is used for all girders, both interior and exterior.
For this design example, only the interior girder design is presented. However, for the exterior girder, the computation of the live load distribution factors and the moment and shear envelopes are also presented.
For the design of an exterior girder, the composite section properties must be computed in accordance with S4.6.2.6.
The modular ratio is computed as follows:
Wc = 0.15 kcf
f'c = 4 ksi
Ec = 3834.254 ksi Es = 29000 ksi
n = 7. Therefore, use n = 8.
In lieu of the above computations, the modular ratio can also be obtained from S6.10.3.1.1b. The above computations are presented simply to illustrate the process. Both the above computations and S6.10.3.1.1b result in a modular ratio of 8.
The effective flange width is computed as follows:
For interior beams, the effective flange width is taken as the least of:
Spaneff = 60 ft
Weff1 = 15 ft
Weff2 = 8.58 ft
Weff3 = 9.75 ft
Therefore, the effective flange width is:
Weffflange = 8.58 ft or Weffflange = 103 in
Similarly, the noncomposite and composite section properties for the negative moment region are computed as shown in the following table. The distance to the centroid is measured from the bottom of the girder.
For the strength limit state, since the deck concrete is in tension in the negative moment region, the deck reinforcing steel contributes to the composite section properties and the deck concrete does not.
As previously explained, for this design example, the concrete slab will be assumed to be fully effective for both positive and negative flexure for service and fatigue limit states.
Area, A Centroid, d Ad Io Ay
2 Itotal (Inches^2 ) (Inches) (Inches^3 ) (Inches^4 ) (Inches^4 ) (Inches^4 )
ybotgdr ytopgdr ytopslab Sbotgdr Stopgdr Stopslab (Inches) (Inches) (Inches) (Inches^3 )^ (Inches^3 )^ (Inches^3 ) 28.718 30.532 --- 2278.2 2142.9 --- 37.766 21.484 30.484 2592.8 4557.7 3212. 46.702 12.548 21.548 2787.8 10376.2 6042. 32.668 26.582 31.082 2428.5 2984.5 2552.
Section
Top flange
Positive Moment Region Section Properties
Girder only:
Total
Girder Slab
Total
Section
Web
Bottom flange Total
Girder Slab
Composite (deck concrete using 3n):
Composite (rebar)
Composite (3n) Composite (n)
Composite (deck concrete using n):
Girder
Deck reinf. Total
Girder only
Composite (deck reinforcement only):
Design Step 3.4 - Compute Dead Load Effects
The girder must be designed to resist the dead load effects, as well as the other load effects. The dead load components consist of some dead loads that are resisted by the noncomposite section, as well as other dead loads that are resisted by the composite section. In addition, some dead loads are factored with the DC load factor and other dead loads are factored with the DW load factor. The following table summarizes the various dead load components that must be included in the design of a steel girder.
For the steel girder, the dead load per unit length varies due to the change in plate sizes. The moments and shears due to the weight of the steel girder can be computed using readily available analysis software. Since the actual plate sizes are entered as input, the moments and shears are computed based on the actual, varying plate sizes.
For the concrete deck, the dead load per unit length for an interior girder is computed as follows:
Wc = 0.15 K/ft^3
S = 9.75 ft
tdeck = 8.5 in
DLdeck = 1.036 K/ft
For the concrete haunch, the dead load per unit length varies due to the change in top flange plate sizes. The moments and shears due to the weight of the concrete haunch can be computed using readily available analysis software. Since the top flange plate sizes are entered as input, the moments and shears due to the concrete haunch are computed based on the actual, varying haunch thickness.
Need for Revised Analysis
It should be noted that during the optimization process, minor adjustments can be made to the plate sizes and transition locations without needing to recompute the analysis results. However, if significant adjustments are made, such that the moments and shears would change significantly, then a revised analysis is required.
The following two tables present the unfactored dead load moments and shears, as computed by an analysis computer program(AASHTO Opis software). Since the bridge is symmetrical, the moments and shears in Span 2 are symmetrical to those in Span 1.
0.0L 0.1L 0.2L 0.3L 0.4L 0.5L 0.6L 0.7L 0.8L 0.9L 1.0L 0 75.4 125.5 150.3 150 124.4 73.6 -2.5 -107.2 -244 421. 0 467.4 776.9 928.6 922.4 758.4 436.6 -43.1 -679.7 1472 2418.
0 68.8 114.3 136.7 135.8 111.7 64.4 -6.2 -99.9 -216.9 357.
Concrete parapets 0 93.9 157.2 189.9 192.2 163.8 104.9 15.5 -104.5 -255 436. Future wearing surface 0 113.7 190.4 230.1 232.7 198.4 127.1 18.8 -126.6 -308.9 528.
Table 3-7 Dead Load Moments
Location in Span 1
Dead Load Moments (Kip-feet)
Dead Load Component
Concrete deck & haunches
Other dead loads acting on girder alone
Steel girder
0.0L 0.1L 0.2L 0.3L 0.4L 0.5L 0.6L 0.7L 0.8L 0.9L 1.0L Steel girder 7.33 5.23 3.12 1.02 -1.08 -3.18 -5.29 -7.39 -10.06 -12.74 -16.
Concrete parapets 9.1 6.55 4 1.46 -1.09 -3.63 -6.18 -8.73 -11.27 -13.82 -16. Future wearing surface 11.02 7.93 4.85 1.77 -1.32 -4.4 -7.49 -10.57 -13.65 -16.74 -19.
Dead Load Shears (Kips)
Dead Load Component
Location in Span 1
Concrete deck & haunches 45.53^ 32.37^ 19.22^ 6.06^ -7.09^ -20.24^ -33.4^ -46.55^ -59.54^ -72.52^ -85.
Table 3-8 Dead Load Shears
Other dead loads actingon girder alone 6.7 4.76 2.83 0.89 -1.04 -2.98 -4.91 -6.85 -8.78 -10.72 -12.
Design Step 3.5 - Compute Live Load Effects
LRFD Live Load
There are several differences between the live load used in Allowable Stress Design (ASD) or Load Factor Design (LFD) and the live load used in Load and Resistance Factor Design (LRFD). Some of the more significant differences are:
For additional information about the live load used in LRFD, refer to S3.6 and C3.6.
The girder must also be designed to resist the live load effects. The live load consists of an HL-93 loading. Similar to the dead load, the live load moments and shears for an HL-93 loading can be obtained from an analysis computer program.
Based on Table 3-3, for all limit states other than fatigue and fracture, the dynamic load allowance, IM, is as follows: IM = 0.
The live load distribution factors for moment for an interior girder are computed as follows: First, the longitudinal stiffness parameter, Kg, must be computed:
Region A Region B Region C Weighted (Pos. Mom.) (Intermediate) (At Pier) Average *
Length (Feet) 84 24 12 8 8 8
I (Inches^4 ) 22,114.80 34,639.80 65,426.
A (Inches^2 ) 48 63.75 100. eg (Inches) 36.523 35.277 35.
Kg (Inches^4 ) (^) 689,147 911,796 1,538,481 818,
Longitudinal Stiffness Parameter, Kg
n
Table 3-9 Longitudinal Stiffness Parameter