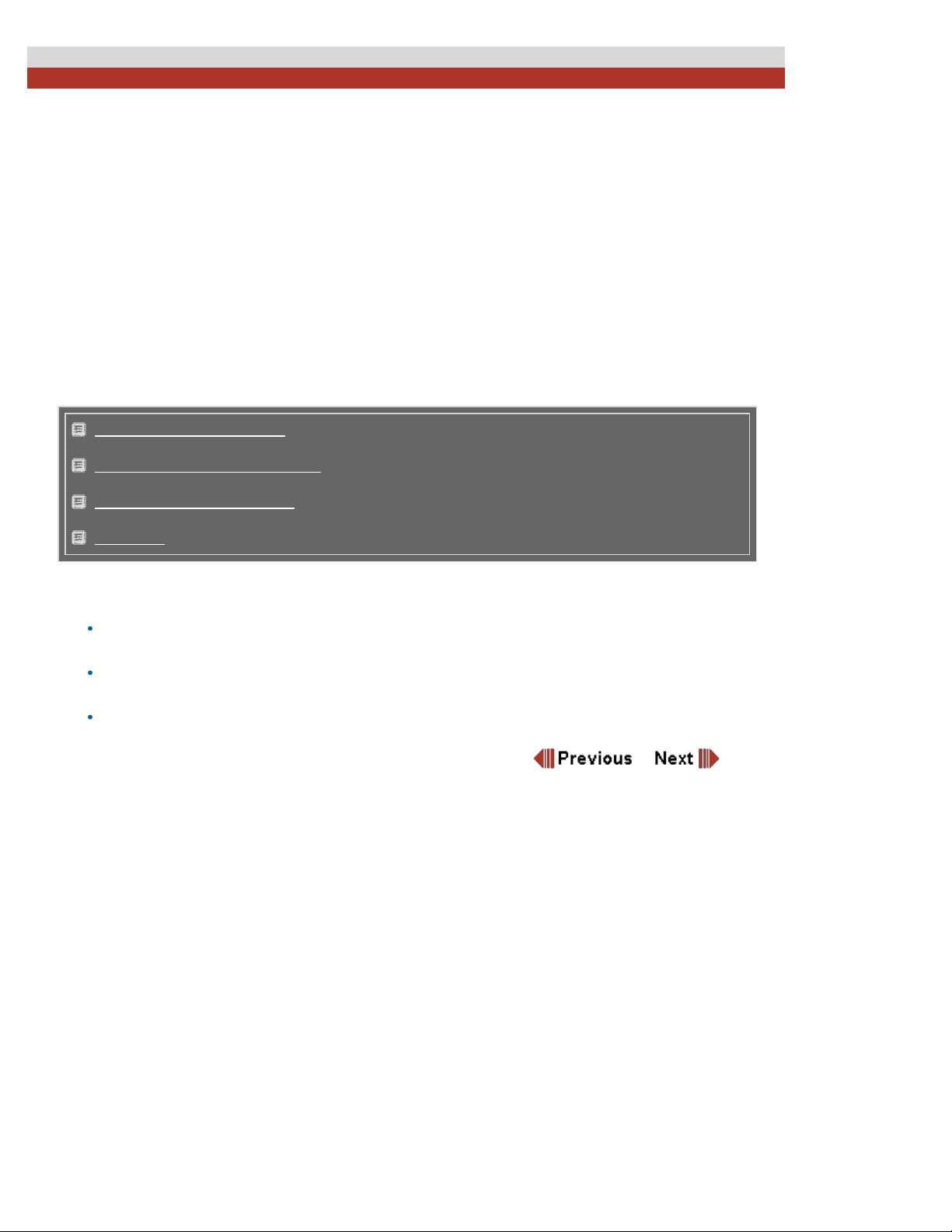
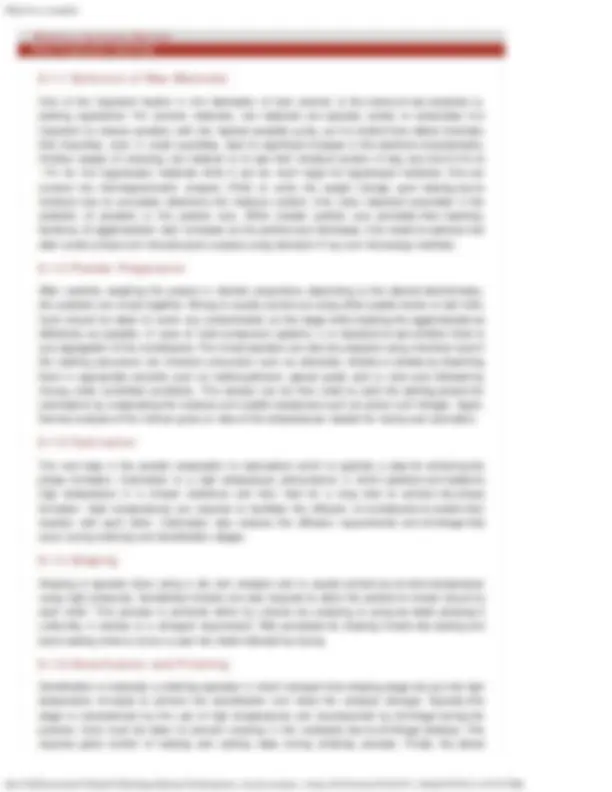
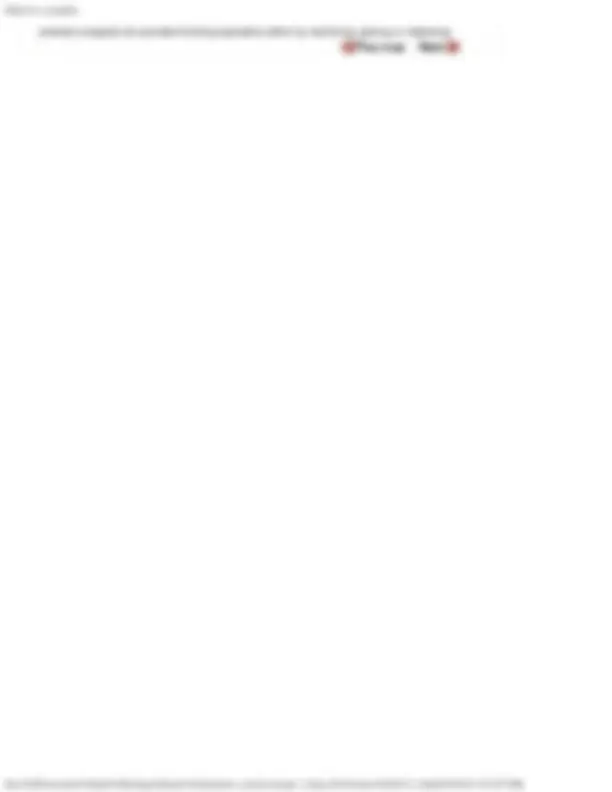
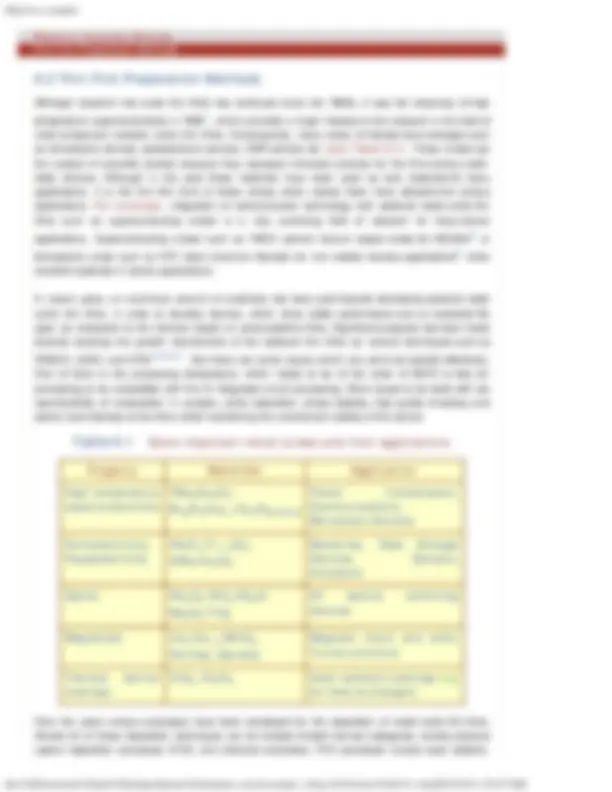
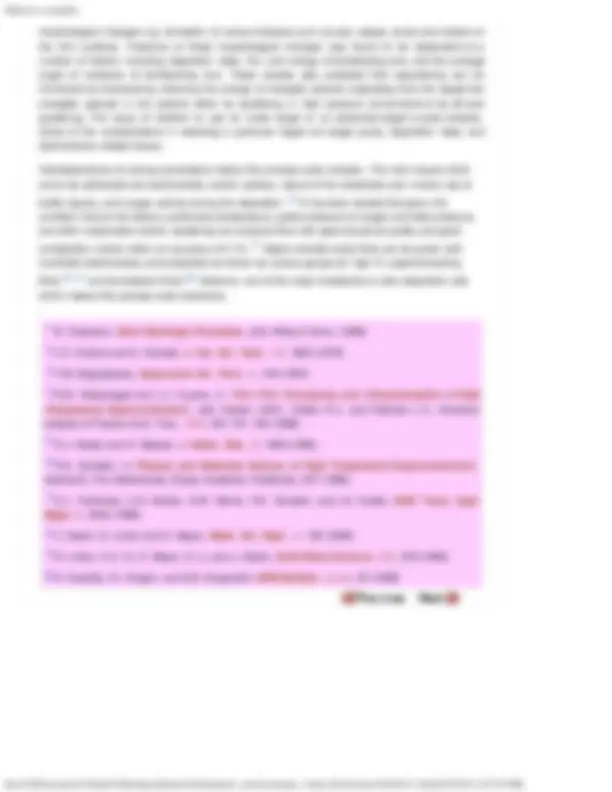
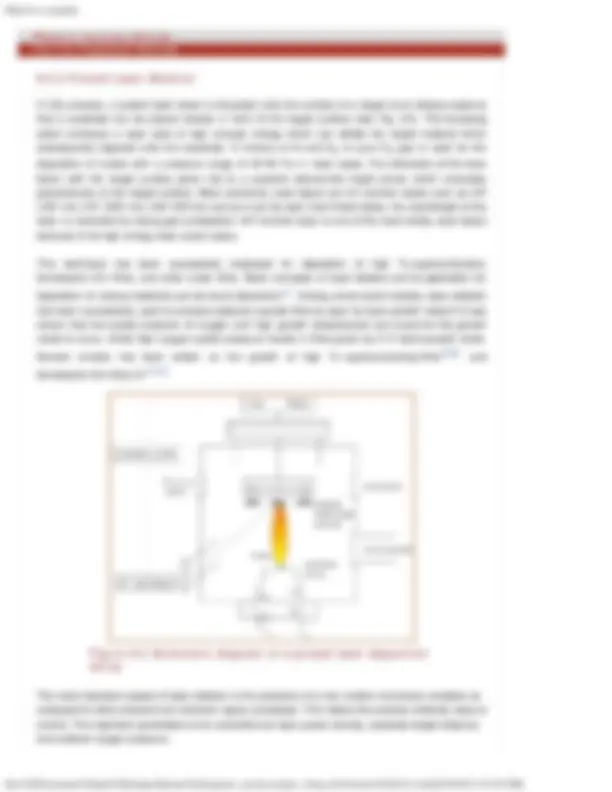
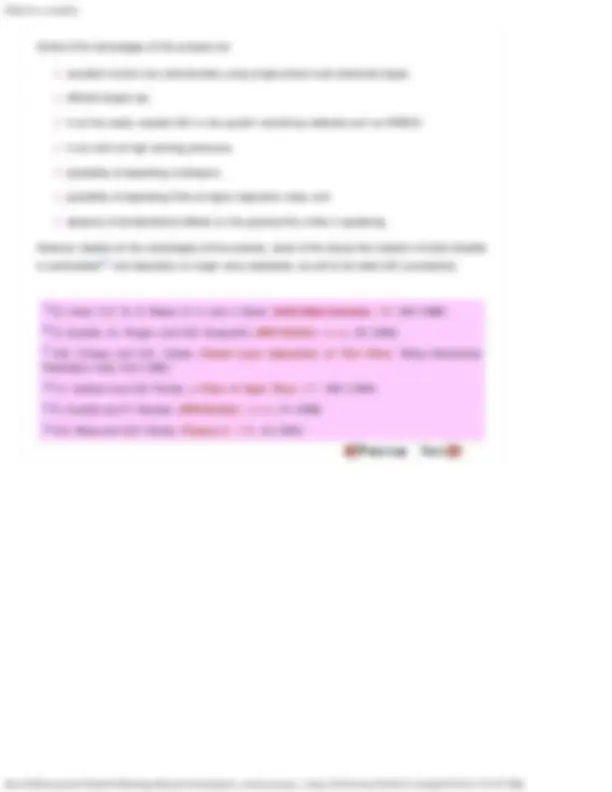
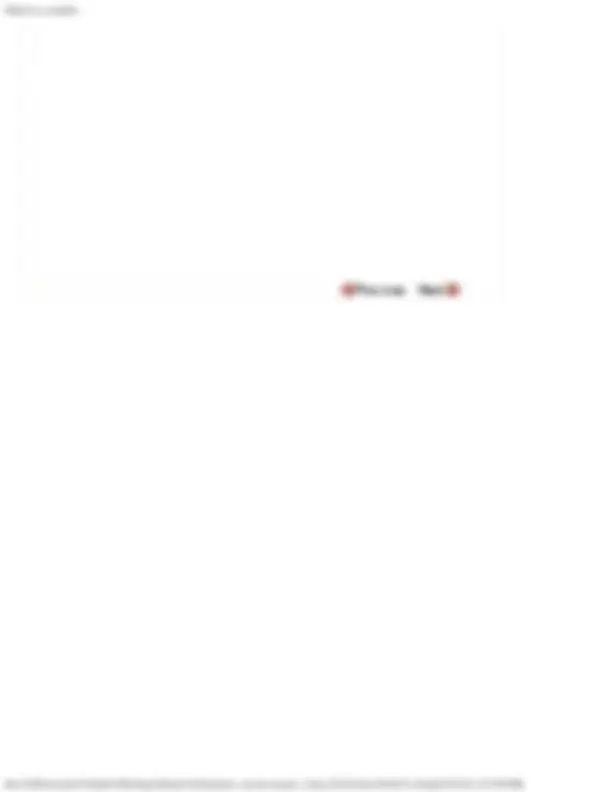
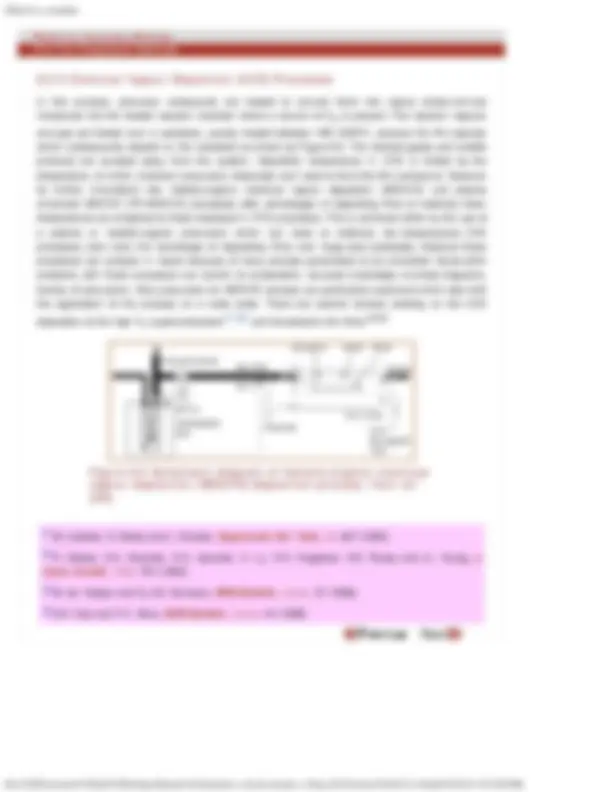
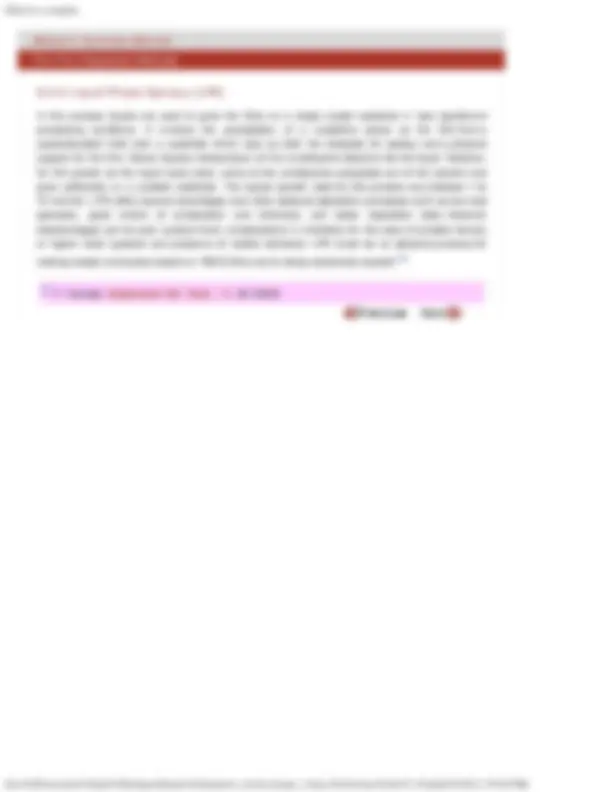
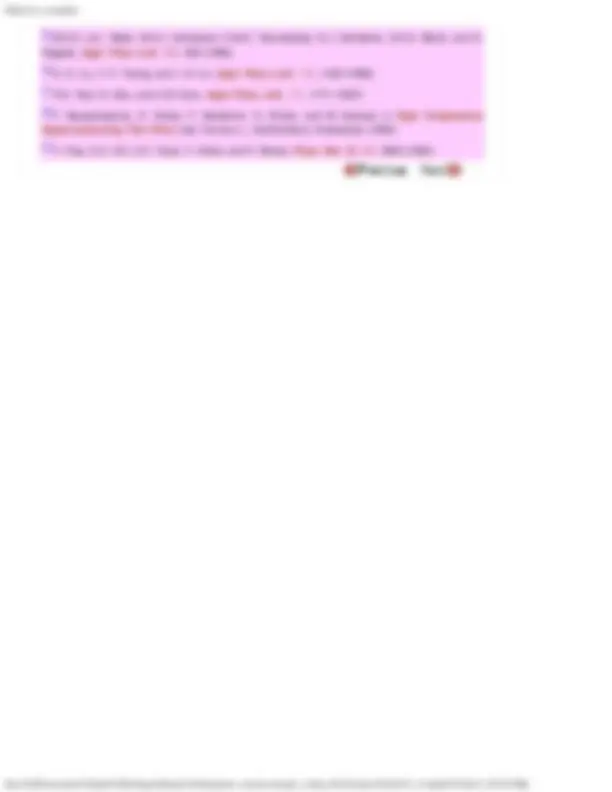
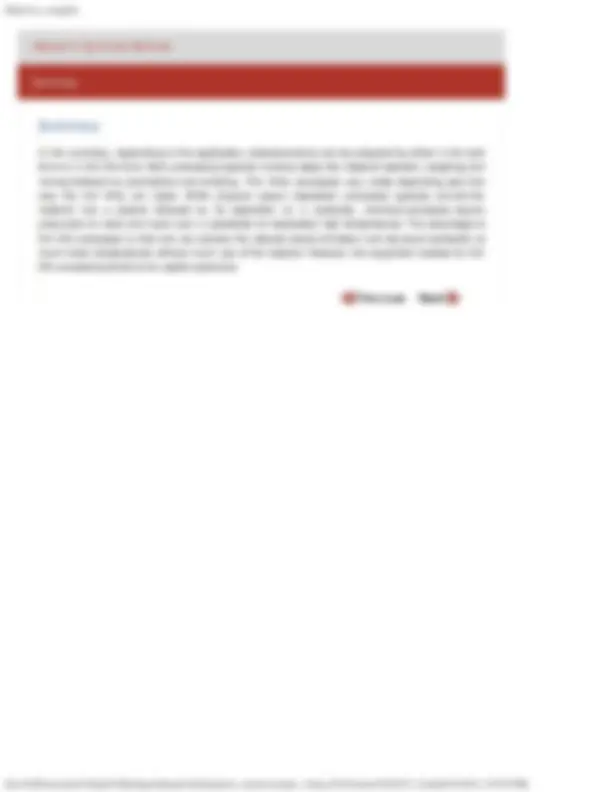
Study with the several resources on Docsity
Earn points by helping other students or get them with a premium plan
Prepare for your exams
Study with the several resources on Docsity
Earn points to download
Earn points by helping other students or get them with a premium plan
Community
Ask the community for help and clear up your study doubts
Discover the best universities in your country according to Docsity users
Free resources
Download our free guides on studying techniques, anxiety management strategies, and thesis advice from Docsity tutors
The main points are: Synthesis Methods, Bulk Preparation Methods, Film Preparation Methods, Film Deposition Issues, Selection of Raw Materials, Powder Preparation, Thermogravimetric Analysis, Densification and Finishing, Calcination
Typology: Study notes
1 / 19
This page cannot be seen from the preview
Don't miss anything!
While many properties of ceramics are dependent on defect equilibrium, microstructural features of material such as grain size, porosity etc also play very important role in determining the final properties. Both of these aspects depend heavily upon how these ceramics are processed. This is also affected by their physical dimensions and appearance i.e. whether they are in bulk form or thin film form. One of the major differences between thin films process and bulk processes is that typically bulk processes are treated as equilibrium processes while thin films processes are generally non- equilibrium phenomenon thereby altering the kinetics of phase formation. Typically we encounter that while bulk processing requires high temperatures for complete phase formation and densification, thin films can be made at much lower temperatures while achieving the desired phase as well as structural perfection. In this section, we will focus on a brief review of most common synthesis methods for fabricating the electroceramics, in both bulk as well as thin films form.
Introduction to Ceramics: W. David Kingery, H. K. Bowen, Donald R. Uhlmann, and Wiley Electroceramics: Materials, Properties, Applications: A. J. Moulson and J. M. Herbert, Wiley Material Science of Thin Films: Milton Ohring, Academic Press
By bulk material, we typically mean sample size of material more than a few hundred microns to a few mm and cms, even bigger. Figure one show a typical flow chart of the bulk preparation processes and are shown below. These processes are also explained briefly in the subsequent sections.
sintered compacts are provided finishing operations either by machining, glazing or metalizing.
file:///C|/Documents%20and%20Settings/iitkrana1/Desktop/new_electroceramics_14may,2012/lecture35(40)/35_4.html[5/25/2012 1:07:07 PM]
Although research into oxide thin films has continued since the 1960s, it was the discovery of high temperature superconductivity in 1986^1 , which provided a major impetus to the research in the field of multi-component complex oxide thin films. Consequently, many areas of interest have emerged such as ferroelectric devices, optoelectronic devices, CMR devices etc. (see Table 9.1). These oxides are the subject of scientific studies because they represent immense promise for the 21st century solid- state devices. Although in the past these materials have been used as bulk materials for many applications, it is the thin film form of these oxides which makes them more attractive for various applications. For example, integration of semiconductor technology with epitaxial metal oxide thin films such as superconducting oxides is a very promising field of research for many device applications. Superconducting oxides such as YBCO (yttrium barium copper oxide) for SQUIDs^2 or ferroelectric oxide such as PZT (lead zirconium titanate) for non-volatile memory applications^3 show excellent potential in device applications.
In recent years, an enormous amount of emphasis has been paid towards developing epitaxial metal oxide thin films, in order to develop devices, which show better performance over an extended life span as compared to the devices based on polycrystalline films. Significant progress has been made towards studying the growth mechanisms of the epitaxial thin films by various techniques such as RHEED, LEED, and STM. 4,5,6,7^. But there are some issues which are yet to be tackled effectively. One of them is the processing temperature, which needs to be of the order of 500°C or less, for processing to be compatible with the Si integrated circuit processing. Other issues to be dealt with are reproducibility of composition in complex oxide deposition, phase stability, high quality of epitaxy and atomic level flatness of the films whilst maintaining the commercial viability of the device.
High temperature superconductivity
YBa 2 Cu 3 O 7 , Bi (^) mSr 2 Ca (^) n-1 Cu (^) n O (^) 2n+m+
Power transmission, Communications, Microwave Devices
Ferroelectricity, Piezoelectricity
Pb(Zr (^) x Ti^ 1-x )O^3 , SrBi 2 Ta 2 O (^9)
Memories, Data Storage Devices, Sensors, Actuators
Optics Nb 2 O 5 -SiO 2 -Na 2 O- Ba 2 O (^) 2- TiO (^2)
All optical switching devices
Magnetism (La (^) x Ca (^) 1-x )MnO 3 , Ferrites, Garnets
Magnets (hard and soft), Tunnel junctions
Thermal barrier coatings
ZrO 2 , Al 2 O 3 Heat resistant coatings e.g. for heat exchangers
Over the years various processes have been developed for the deposition of metal oxide thin films. Almost all of these deposition techniques can be broadly divided into two categories, namely physical vapour deposition processes (PVD) and chemical processes. PVD processes include laser ablation,
Sputtering is one of the effects in glow discharge processes when a surface is bombarded by energetic particles. In this process the target atoms are ejected by the bombardment of energetic species (usually inert gas ions) on it, as shown in Figure 9.2. The sputtered atoms travel through the plasma and undergo many collisions with the plasma species (electrons, neutrals, gas ions, and metals ions) and subsequently deposit on a strategically placed substrate. The substrate can be heated depending upon the nature of the deposition. Sputtering process can employ dc or rf power depending upon the electrical conductivity of the target. DC power can be used only for conducting targets where rf power can be used for both conducting and insulating targets. Usually a magnetic field (use of magnetron target) is employed to enhance the efficiency of plasma utilisation and sputter efficiency. This happens due to increased electron residence time in the plasma, improving the ion collision probability and thus larger discharge currents. Sputtering process using a magnetron is called magnetron sputtering. A complete description of glow discharge processes and their application to sputtering process can be found elsewhere.^11
Reactive sputtering can be used to prepare alloys or compounds, solid solutions, or a mixture. Reactive sputtering in a mixture of oxygen and argon has been a very important process for the deposition of oxides since the 1970s. Among one of the earlier studies, a mixture of argon (Ar) and oxygen (O 2 ) was used to deposit SiO 2 films from elemental Si target by reactive sputtering.^12 Application of RF sputtering facilitated the use of an oxide as the starting material and target, but given the variation in the sputter yields of different elements, the resulting films were not found to be stoichiometric.
Growth of oxides by sputtering involves different regimes depending upon the sputtering conditions. Work has shown that the nature of growth species changes from atomic to molecular as the sputtering gas pressure increases.^13 One major problem encountered in the sputtering of oxides is the resputtering of the growing film by negative ions and reflected neutrals14,15, leading to
morphological changes e.g. formation of various features such as pits, ripples, cones and craters on the film surfaces. Presence of these morphological changes was found to be dependent on a number of factors including deposition rates, flux and energy of bombarding ions, and the average angle of incidence of bombarding ions. These studies also predicted that resputtering can be minimized by thermalizing (reducing the energy of energetic species originating from the target) the energetic species in the plasma either by sputtering in high pressure environment or by off-axis sputtering. The issue of whether to use an oxide target or an elemental target is quite complex. Some of the considerations in selecting a particular target are target purity, deposition rates, and stoichiometry related issues.
Interdependence of various parameters makes this process quite complex. The main issues which are to be addressed are stoichiometry control, epitaxy, nature of the substrates (can involve use of
buffer layers), and oxygen activity during the deposition.^16 It has been studied that given the condition that all the factors, particularly temperature, partial pressure of oxygen and total pressure, are within reasonable control, sputtering can produce films with good structural quality and good
composition control within an accuracy of 0.1%. 17 Highly oriented oxide films can be grown with controlled stoichiometry and properties as shown by various groups for high Tc superconducting
films18,19^ and ferroelectric films.^20 However, one of the major drawbacks is slow deposition rate which makes this process quite expensive. .
(^11) B. Chapman, Glow Discharge Processes , John Wiley & Sons. (1980) (^12) J.C. Erskine and A. Csahati, J. Vac. Sci. Tech. , 15, 1823 (1978) (^13) Y.M. Boguslavsky, Supercond. Sci. Tech. , 4, 149 (1991) (^14) S.M. Rossanagel and J.J. Cuomo, in ‘ Thin Film Processing and Characterisation of High Temperature Superconductors’ , eds. Harper J.M.E., Colton R.J., and Feldman L.C., American Institute of Physics Conf. Proc., 165 , AIP, NY, 106 (1988) (^15) D.J. Kester and R. Messier, J. Mater. Res. , 8, 1928 (1993) (^16) R.E. Somekh, in ‘ Physics and Materials Science of High Temperature Superconductors’ , Dordrecht, The Netherlands, Kluwer Academic Publishers, 327 (1990) (^17) E.J. Tomlinson, Z.H. Barber, G.W. Morris, R.E. Somekh, and J.E. Evetts, IEEE Trans. Appl. Magn. 2 , 2530 (1988) (^18) J. Geerk, G. Linker and O. Meyer, Mater. Sci. Rept. , 4, 193 (1989) (^19) G. Linker, X.X. Xi, O. Meyer, O. Li, and J. Geerk, Solid State Commun. , 69, 249 (1989) (^20) O. Auciello, A.I. Kingon, and S.B. Krupanidhi, MRS Bulletin , June, 25 (1996)
Some of the advantages of this process are
excellent control over stoichiometry using single-phase multi-elemental target,
efficient target use,
it can be easily coupled with in-situ growth monitoring methods such as RHEED,
it can work at high working pressures,
possibility of depositing multilayers,
possibility of depositing films at higher deposition rates, and
absence of bombardment effects on the growing film unlike in sputtering.
However despite all the advantages of this process, some of the issues like creation of small droplets
or particulates^24 and deposition on larger area substrates, are yet to be dealt with successfully.
(^19) G. Linker, X.X. Xi, O. Meyer, O. Li, and J. Geerk, Solid State Commun. , 69, 249 (1989) (^20) O. Auciello, A.I. Kingon, and S.B. Krupanidhi, MRS Bulletin , June, 25 (1996) (^21) D.B. Chrisey and G.K. Hubler, Pulsed Laser Deposition of Thin Films , 'Wiley-Interscience Publication, New York (1994) (^22) T.J. Jackson and S.B. Palmer, J. Phys. D: Appl. Phys. , 27, 1581 (1994) (^23) O. Auciello and R. Ramesh, MRS Bulletin , June, 31 (1996) (^24) D.S. Misra and S.B. Palmer, Physica C , 176, 43 (1991)
This process essentially involves evaporation of source material in a UHV environment and then deposition of the evaporated flux onto the substrate. Vacuum evaporation is a low energy process as compared to sputtering because energy of species reaching the substrate is very low, of the order of 0.5 eV. For deposition of oxides, reactive evaporation is a very important method. Reactive evaporation involves use of a reactive gas, O 2 , to maintain the correct oxygen stoichiometry of the film material while using elemental sources and also while using a compound source to compensate the loss of oxygen during the evaporation. The critical factors involved in the evaporation processes are vacuum level and the background oxygen pressure (pO 2 ) which are instrumental in controlling the impurity level and stoichiometry of the film. Among one of the early efforts on reactive evaporation, deposition of TiO 2 and Si 2 O 3 was successfully demonstrated.^25 Use of active oxygen has been shown to improve the film quality considerably. Epitaxial YBCO films have been deposited by MBE in the presence of an RF plasma discharge to generate reactive oxygen species at low temperatures (< 500°C) and improvement in film properties was observed.26^ Epitaxial DyBa 2 Cu 3 O (^) 6+x films were grown by MBE and it was shown that by controlling the local nucleation rate and lateral growth rate, it was possible to achieve layer by layer growth.^6 These processes can produce films with controlled stoichiometry and better epitaxy but at the cost of low deposition rates (of the order of 5-10 nm/m). Although these methods are complex in nature and expensive, they offer advantage of in-situ growth monitoring by RHEED/LEED.
(^25) E. Ritter, J. Vac. Sci. Tech. , 12, 225 (1966) (^26) H. Tsuge and N. Matsukara, IEEE Trans. Magn. , 27, 1009 (1991)
In this process, precursor compounds are heated to convert them into vapour phase and are introduced into the heated reaction chamber where a source of O 2 is present. The reaction vapours and gas are flowed over a substrate, usually heated between 400-1000°C, produce the film species which subsequently deposit on the substrate as shown by Figure 9.5. The residual gases and volatile products are pumped away from the system. Deposition temperature in CVD is limited by the temperature at which chemical precursors dissociate and react to form the film compound. However its further innovations like metallo-organic chemical vapour deposition (MOCVD) and plasma enhanced MOCVD (PE-MOCVD) processes offer advantages of depositing films at relatively lower temperatures as compared to those employed in PVD processes. This is achieved either by the use of a plasma or metallo-organic precursors which can react at relatively low temperatures. CVD processes also have the advantage of depositing films over large area substrates. However these processes are complex in nature because of many process parameters to be controlled. Some other problems with these processes are control of composition, accurate knowledge of phase diagrams, toxicity of precursors. Also precursors for MOCVD process are particularly expensive which also limit the application of the process on a wide scale. There are several reviews existing on the CVD deposition of the high T (^) C superconductors27.28^ and ferroelectric thin films. 29.
(^27) M. Leskela, H. Molsa and L. Niinisto, Supercond. Sci. Tech. , 6, 627 (1993) (^28) R. Hiskes, S.A. Dicarolis, R.D. Jacowitz, Z. Lu, R.S. Feigelson, R.K. Route, and J.L. Young, J. Cryst. Growth , 128, 781 (1993) (^29) M. de Keijser and G.J.M. Dormans, MRS Bulletin , June, 37 (1996) (^30) S.K. Dey and P.V. Alluri, MRS Bulletin , June, 44 (1996)
Even though thin film deposition of epitaxial metal oxides has been carried out since the 1960s and significant progress has been made on all fronts, yet there are some fundamental issues which are yet to be dealt with. To reduce the deposition temperature for depositing epitaxial films is the foremost challenge for most of the processing techniques, barring some chemical processes. Other aspects involve production of stable phases with precise composition and correct oxygen content, good structure and morphology of the films, high degree of desired orientation, and issues regarding the nucleation and growth of the films. Choice of device compatible and cheap substrates and deposition over larger area substrates are the main bottlenecks in the commercial success. The interdependence of various parameters, for example, processing temperature and epitaxy, poses serious questions about the choice of optimum conditions. In this section, it has been attempted to briefly elucidate these problems and the ongoing efforts to handle them.
Most of the metal oxides require high temperature for epitaxial growth, usually growth temperatures being 0.7-0.8Tm which is very high when compared to epitaxial growth temperatures of metals and semiconductors which fall usually between 0.2-0.5 T (^) m. These temperatures are very high when considering the processing compatibility with semiconductor circuit processing. The effect of deposition temperature is direct on the epitaxy, although it also depends upon the type of processes. Usually if the deposition temperature is lowered, then epitaxy deteriorates. But there are a few reports of deposition at lower temperatures by MOCVD processes 26 or evaporation processes 26 maintaining the desired orientation of the films. It has been shown for ion beam sputtered PZT films that bombardment of the growing film by low energy ions in ion beam sputtering and use of active oxygen species helps to reduce the crystallization temperature of PZT to some extent. But it is still not possible to deposit films at lower temperatures (below 500°C), with desired epitaxy, in processes like laser ablation or sputtering.
Because of the thin film growth processes in general being non-equilibrium in nature, it becomes very important to know about the phase evolution under a given set of process parameters and how a desired phase can be obtained if they are altered accordingly. This problem arises predominantly in terms of deposition temperature and oxygen activity. Most of the perovskite oxides are not only complex oxides, but they also have some specific oxygen level for desired properties e.g. superconducting oxides like YBCO. These complexities put enormous restriction on the processing conditions to produce the correct phase. The work of Feenstra et al.^32 on the effect of oxygen partial pressure and temperature on the stability of YBCO, gives a very good idea about operating windows for different processes.
Chemical complexity of these oxides also poses problems regarding the correct stoichiometry of the films. This is particularly difficult in sputtering because of the different sputter yields of different elements which cannot be controlled independently when using a compound target and due to resputtering effects on the growing film. This problem has been tackled by using multi-elemental targets.^10 Also each element has different collision cross section with the plasma species because of different atomic masses which leads to a complexity in the transport processes during sputtering. Laser ablation has emerged as one of the most promising processes to address this problem with
considerable success by using single compound oxide target and it has been demonstrated
successfully that films can be deposited without any loss of stoichiometry.^33
The choice of substrate is a very important factor in the growing epitaxial oxide films. It has been a matter of great concern in growing superconducting and ferroelectric oxide thin films. SrTiO 3 (100)
and MgO (100) have proven to be useful substrates for growing highly epitaxial films of YBCO. But moisture sensitiveness of MgO and high dielectric constant of SrTiO 3 makes them unattractive. They
are also expensive. Numerous other substrates have been tried such as LaAlO 3 , sapphire, NdGaO (^3)
etc. but the search is still on for the best which is inexpensive, should not react with the film at the film deposition temperature and should be able to give high quality epitaxial films with excellent
properties.^16 Ferroelectric thin films such as PZT have been grown epitaxially on platinised Si wafers (Pt/SiO 2 /Si) but films on Pt give very poor fatigue characteristics which is very important for
ferroelectric memory devices. This problem has forced researchers to look for other alternative electrodes such as LSCO, YBCO etc. but they have not yet fulfilled the promise because of some compromise required in other properties. These problems have been, to some extent, alleviated by the use of buffer layers. Buffer Layers act as intermediate layers between the substrate and film and minimise the various deleterious effects on epitaxy from factors such as mismatch in lattice parameters and coefficient of thermal expansion and interdiffusion of elements, and sometimes
promote crystallisation of the film.^34 Various^ materials have^ been used^ for^ this purpose such as
cerium oxide (CeO 2 ) for YBCO^35 , and strontium ruthenium oxide (SrRuO 3 ) for PZT^36 and resulted
in remarkable improvement in the device performance.
The structure of the epitaxial oxide thin films such as YBCO has been characterised by X-ray diffraction extensively and it has been found that the best films grown have rocking curve width of the
order of 0.15-20°.^9 This degree of orientation is acceptable but when compared to substrate, it shows that there is a lot of scope for further improvement. The better the epitaxy of the film, better is the surface roughness. STM studies reveal that films grown by layer by layer growth mechanism are
smoother than the films grown by 3-D island growth mechanism.^37 Stoichiometry control has also an important role to play in controlling the film structure. It was shown that by controlling the chemical composition correctly, films can be grown by layer by layer growth mode and this could also lead to
smoother surface.^38 The effect of atomic oxygen on the growth and surface roughness of YBCO films
grown on SrTiO 3 (100) by MBE process, has also been studied.^39 It was concluded that in the
presence of atomic oxygen and with careful control of process parameters (low pO 2 and low
deposition rate), it is possible to grow epitaxial films by 2-D growth mechanism and achieve atomically flat surfaces. So there are challenges to produce epitaxial oxide films with smoother surfaces and perfect orientation which require careful control of processing conditions.
(^32) R. Feenstra, T.B. Linemer, J.D. Budai and M.D. Galloway, J. Appl. Phys. , 69, 6569 (1991) (^33) B. Dam, J.H. Rector, J. Johansson, S. Kars, and R. Griessen, ‘ Stoichiometric Transfer of Complex Oxides by Pulsed Laser Ablation ’, E-MRS Spring Meeting, Cola 95, Strasbourg, May 22-26 (1995) (^34) G. Morris, ‘ Buffer Layers for High Temperature Superconductors’ , in High Temperature Superconductors, eds. Pouch J.J., NASA Lewis Research Laboratory Trans. Tech. Publications (1992)
In the summary, depending on the application, electroceramics can be prepared by either in the bulk form or in thin film form. Bulk processing typically involves steps like material selection, weighing and mixing followed by calcinations and sintering. Thin films' processes vary vastly depending upon the way the thin films are made. While physical vapour deposition processes typically convert the material into a plasma followed by its deposition on a substrate, chemical processes require precursors to react and crack over a substrates at moderately high temperatures. The advantage of thin film processes is that one can achieve the desired phase formation and structural perfection at much lower temperatures without much use of the material. However, the equipment needed for thin film processing tends to be capital expensive.