
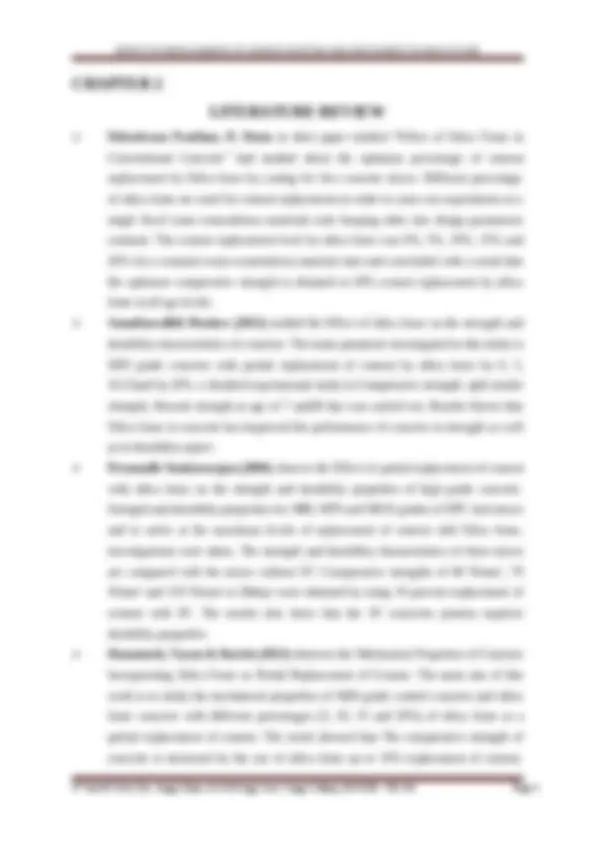
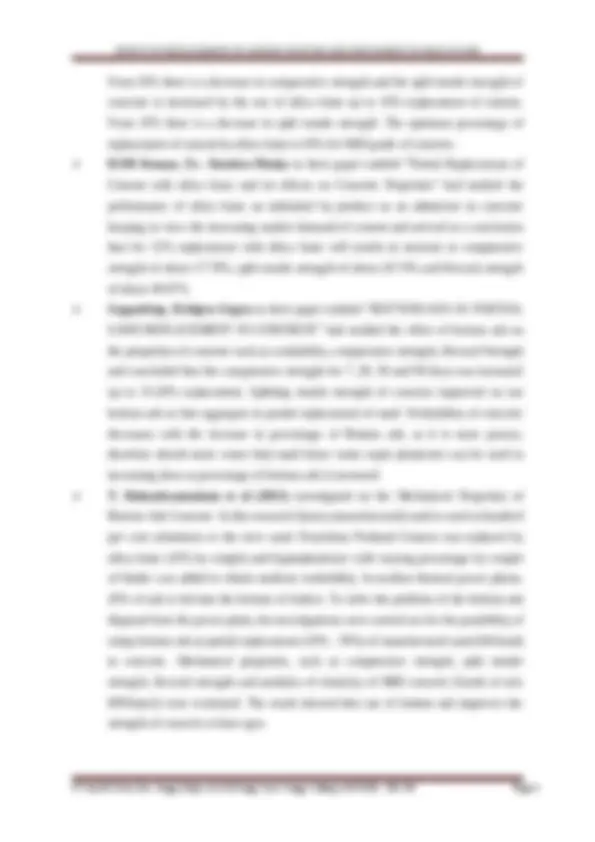
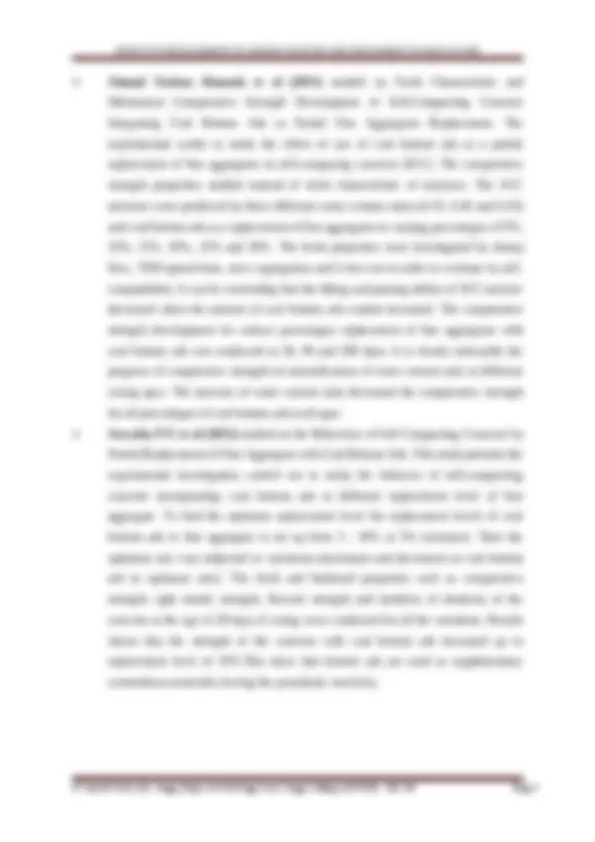
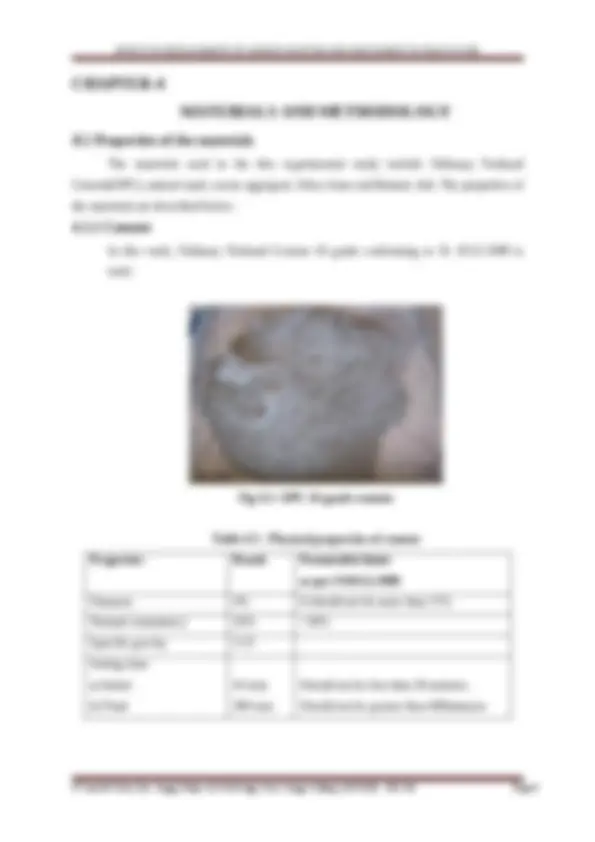

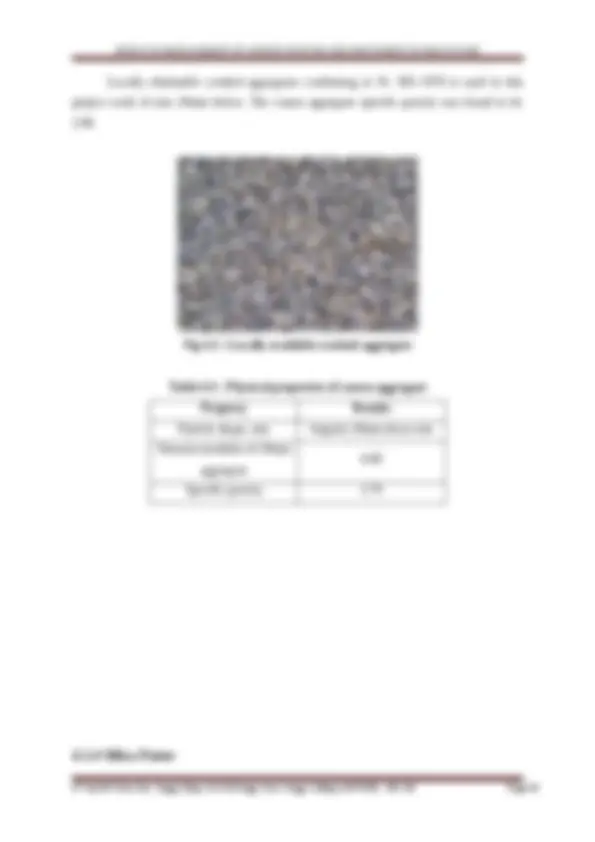
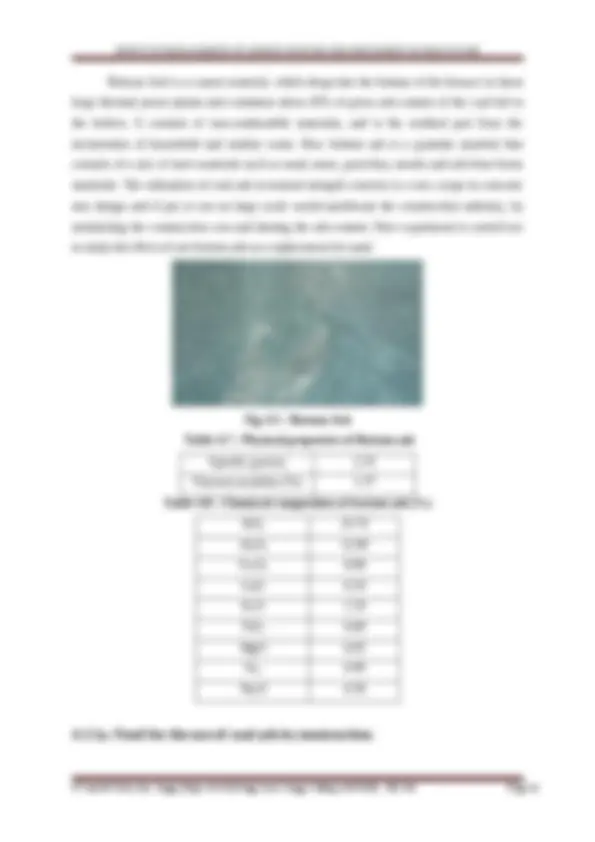
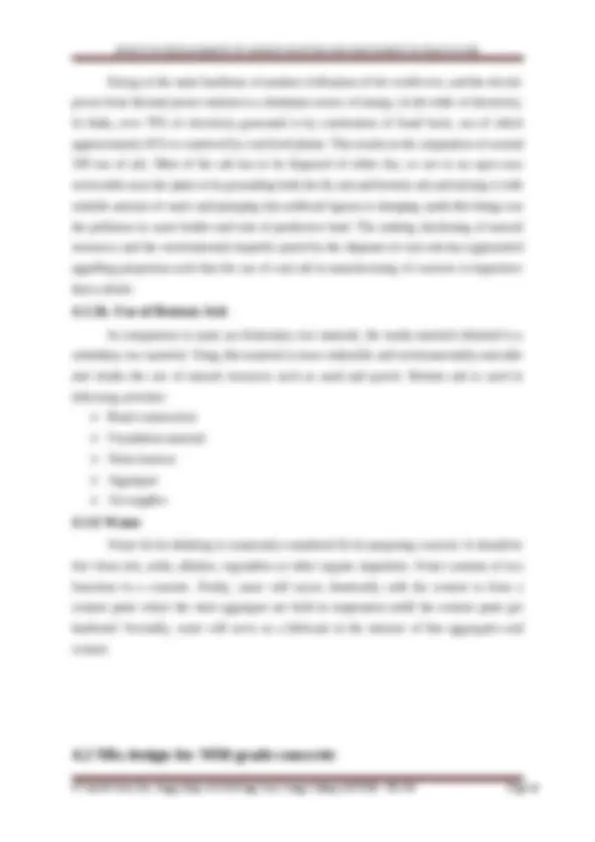
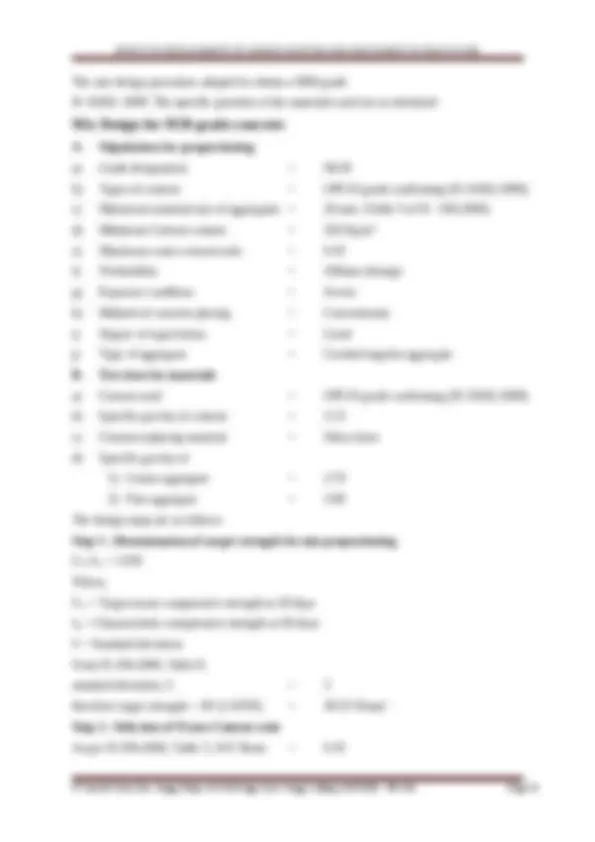
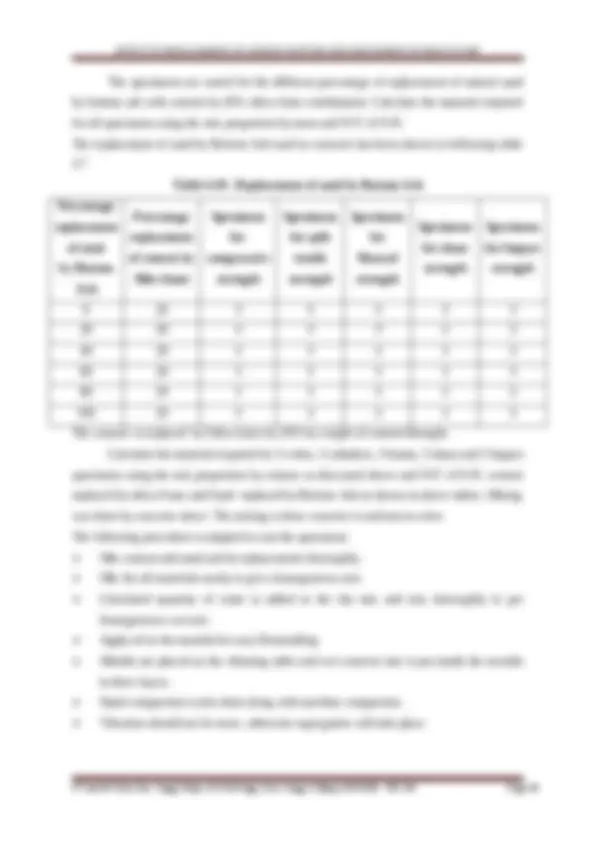
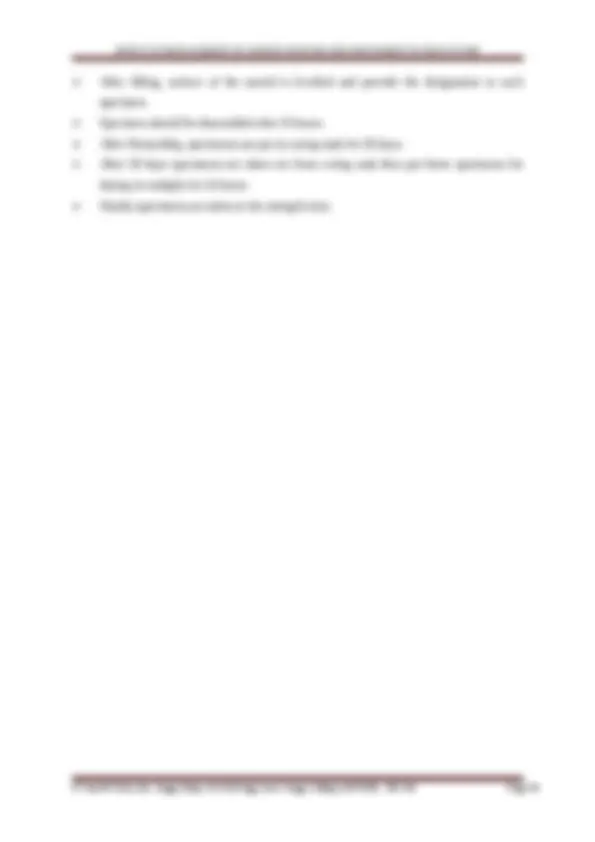
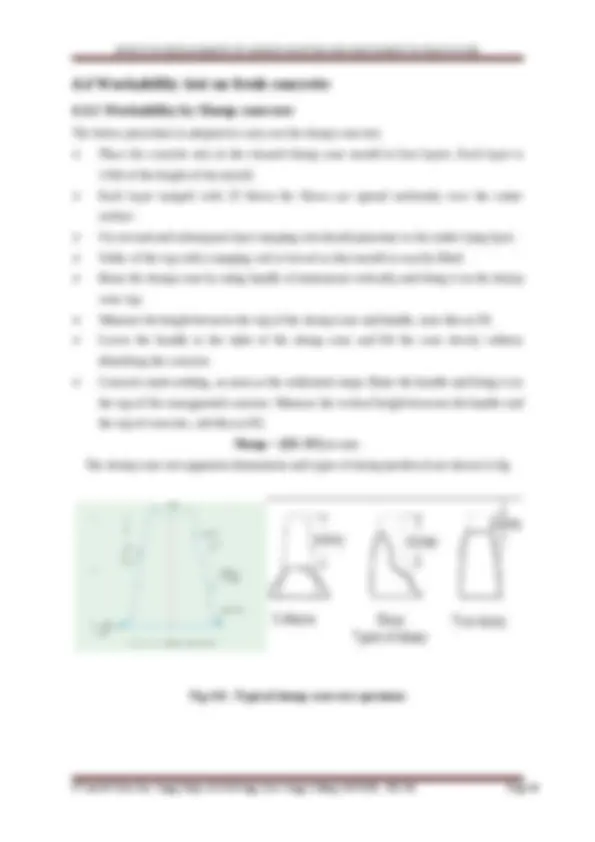
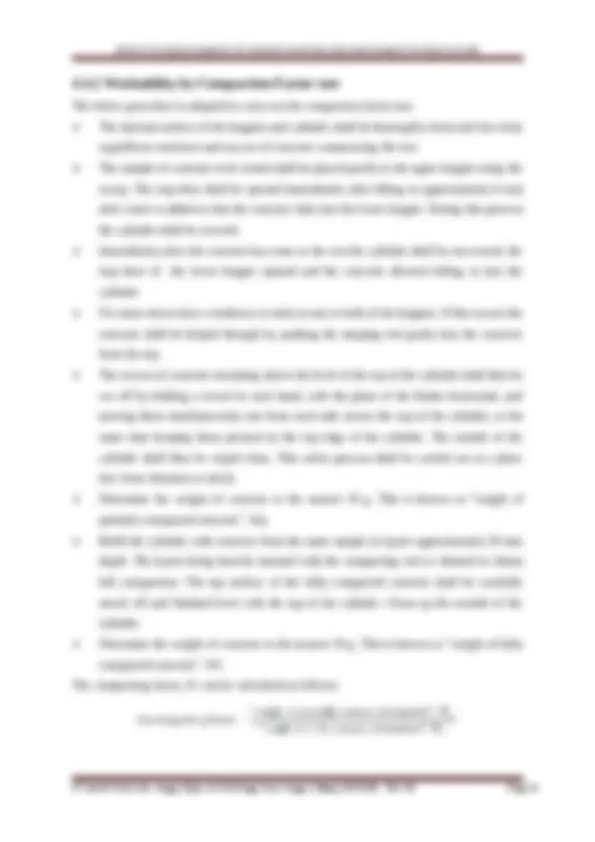
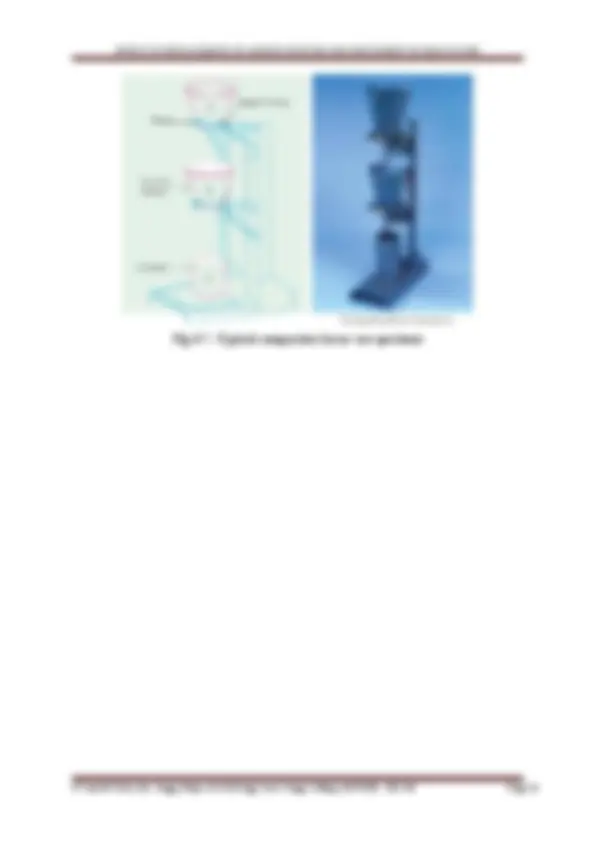
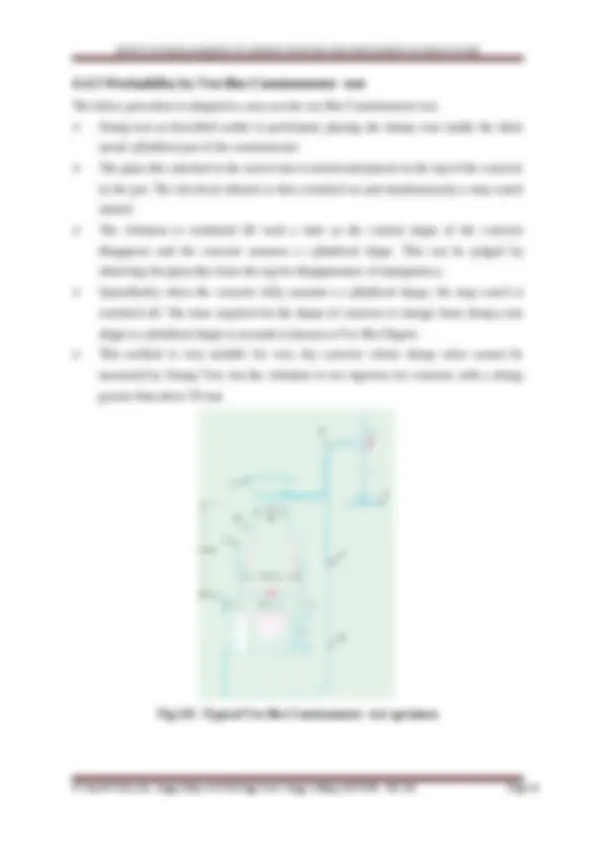
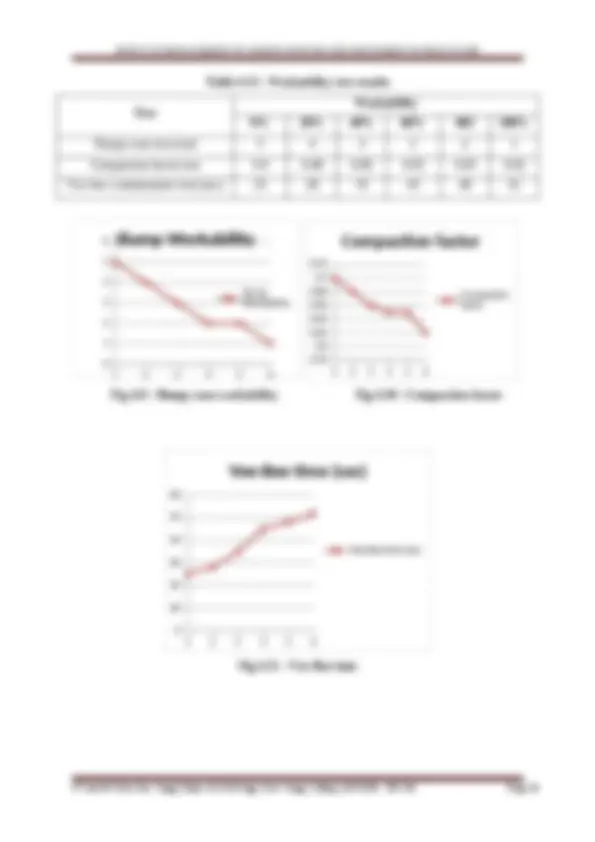
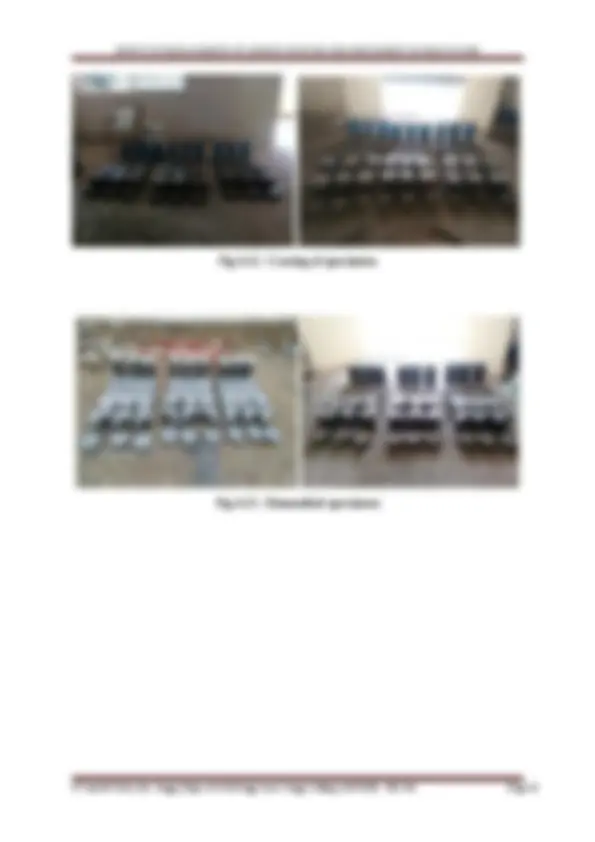
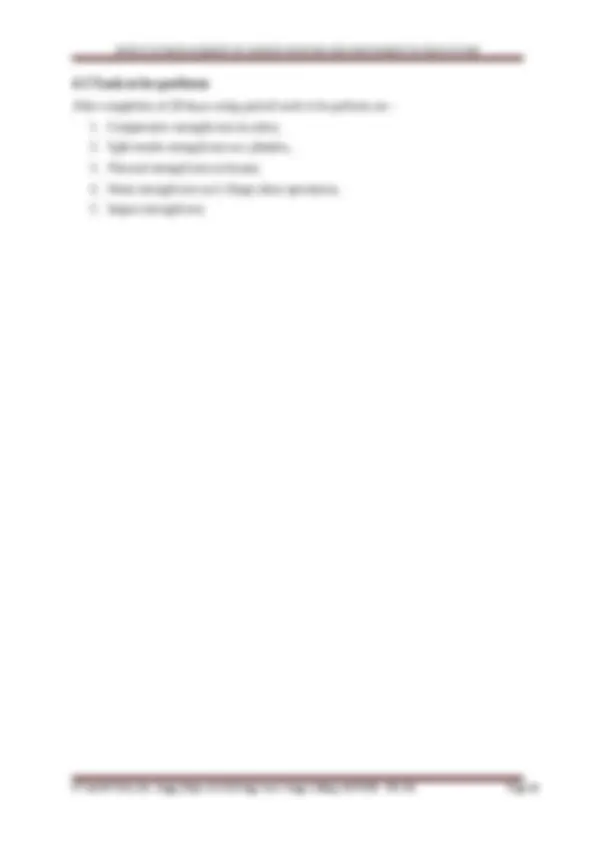
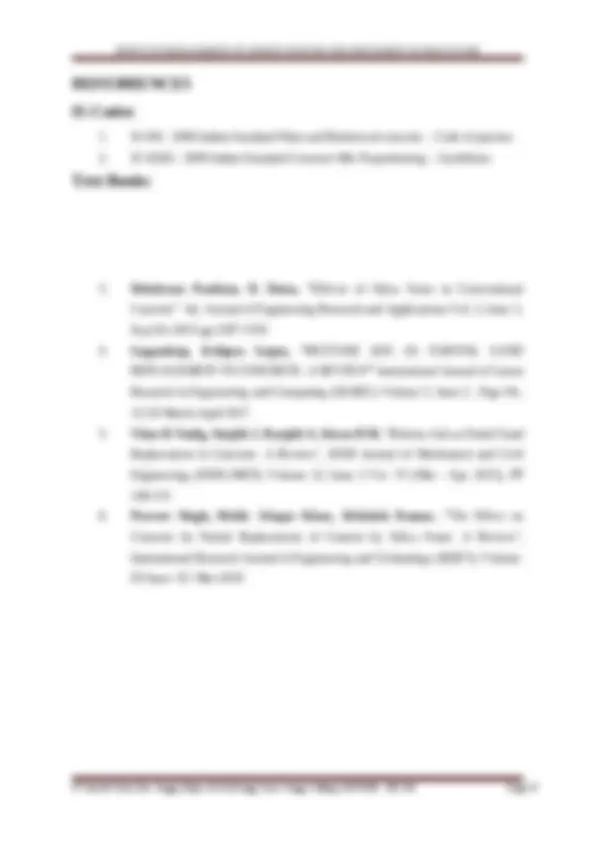
Study with the several resources on Docsity
Earn points by helping other students or get them with a premium plan
Prepare for your exams
Study with the several resources on Docsity
Earn points to download
Earn points by helping other students or get them with a premium plan
Community
Ask the community for help and clear up your study doubts
Discover the best universities in your country according to Docsity users
Free resources
Download our free guides on studying techniques, anxiety management strategies, and thesis advice from Docsity tutors
STUDY NOTES FOR PG STUDENTS, RESEARCH STUDENTS
Typology: Study notes
1 / 27
This page cannot be seen from the preview
Don't miss anything!
Cement and natural river sand are becoming scare resources all over the world because of its increasing demands day by day. The construction activities have increased in almost all the developing countries of the world. There always has been great effort in improving the quality and standards of the properties of concrete as a construction material. Concrete is a mix of ingredient of cement, fine aggregate, coarse aggregate and water. It can be molded into any shape in plastic stage. It is the composite material, most used for the construction of multistory buildings and various infrastructure developments area particularly in developing countries like India is more. The relative quantity of ingredients controls the property of concrete in wet stage as well as in hardened stage. Before two or three decades ago, the production of concrete for construction of building with OPC with the ease of availability of concrete ingredients irrespective of quality was in practice without considering the future of concrete structure. Now with the passage of time, in the modern era, investigations since last two to three decades made by Engineers and Scientists keeping in view the structural stability of structure which needs quality concrete with improved strength, durability and other characteristics of concrete. The demand of these characteristics derive the search for supplementary constituent materials. Search for any suitable material in partial replacement of cement and sand which is universally sustainable development and lowest possible environmental impact. Cement concrete is the most construction material today. We can say that we are living in the era of concrete. In general, fine aggregate used in concrete production of concrete is Natural River Sand. Now a days, natural resources like River Sand is exhausting gradually around the world. So, from the view point of protection of environment and saving natural resources, the construction industries are looks for the various alternative constituent materials for concrete production. So, there is a need for the replacement of cement and sand in the concrete. In India, major portion of electricity is generated by burning coal resulting in the formation of ash. The ash content comes from the burning of coal has to be disposed as either in dry state or in wet state available open areas nearer the plant. These are open to atmosphere causes environmental pollution and loss of productive land. Substantial use of industrial by products save the cost and energy in addition to meet the requirement of environmental awareness. In the geourney of research, Silica fume, Fly ash, Ground granulated blast furnance slag etc are found most commonly used cementatious
materials in partial replacement of cement. The use of Silica fume as a cementatious material has increased in recent years because when mixed in certain proportions it enhances the properties of both fresh and hard concrete like durability, strength, permeability and compressive, flexural and tensile strength.
From 10% there is a decrease in compressive strength and the split tensile strength of concrete is increased by the use of silica fume up to 10% replacement of cement. From 10% there is a decrease in split tensile strength. The optimum percentage of replacement of cement by silica fume is 10% for M20 grade of concrete. RAM Kumar, Er. Jitendra Dhaka in their paper entitled “Partial Replacement of Cement with silica fume and its effects on Concrete Properties” had studied the performance of silica fume an industrial by product as an admixture in concrete keeping in view the increasing market demand of cement and arrived at a conclusion that for 12% replacement with silica fume will results in increase in compressive strength of about 17.76%, split tensile strength of about 20.74% and flexural strength of about 40.67%. Gagandeep, Kshipra Gupta in their paper entitled “BOTTOM ASH AS PARTIAL SAND REPLACEMENT IN CONCRETE” had studied the effect of bottom ash on the properties of concrete such as workability, compressive strength, flexural Strength and concluded that the compressive strength for 7, 28, 56 and 90 days was increased up to 15-20% replacement. Splitting tensile strength of concrete improved on use bottom ash as fine aggregate in partial replacement of sand. Workability of concrete decreases with the increase in percentage of Bottom ash, as it is more porous, therefore absorb more water than sand hence some super plasticizer can be used in increasing dose as percentage of bottom ash is increased. T. Balasubramaniam et al (2015) investigated on the Mechanical Properties of Bottom Ash Concrete. In this research Quarry (manufactured) sand is used as hundred per cent substitutes to the river sand. Pozzolona Portland Cement was replaced by silica fume (10% by weight) and hyperplasticizer with varying percentage by weight of binder was added to obtain medium workability. In modern thermal power plants, 20% of ash is fed into the bottom of boilers. To solve the problem of the bottom ash disposal from the power plant, the investigations were carried out for the possibility of using bottom ash as partial replacement (10% - 50%) of manufactured sand (M-Sand) in concrete. Mechanical properties, such as compressive strength, split tensile strength, flexural strength and modulus of elasticity of M60 concrete (Grade of mix 60N/mm2) were evaluated. The result showed that use of bottom ash improves the strength of concrete at later ages.
Ahmad Farhan Hamzah et al (2015) studied on Fresh Characteristic and Mechanical Compressive Strength Development of Self-Compacting Concrete Integrating Coal Bottom Ash as Partial Fine Aggregates Replacement. The experimental works to study the effect of use of coal bottom ash as a partial replacement of fine aggregates in self-compacing concrete (SCC). The compressive strength properties studied instead of fresh characteristic of mixtures. The SCC mixtures were produced by three different water cement ratios (0.35, 0.40 and 0.45) and coal bottom ash as a replacement of fine aggregates in varying percentages of 0%, 10%, 15%, 20%, 25% and 30%. The fresh properties were investigated by slump flow, T500 spread time, sieve segregation and L-box test in order to evaluate its self- compatibility. It can be concluding that the filling and passing ability of SCC mixture decreased when the amount of coal bottom ash content increased. The compressive strength development for various percentages replacement of fine aggregates with coal bottom ash was conducted at 28, 90 and 180 days. It is clearly noticeable the progress of compressive strength on intensification of water cement ratio at different curing ages. The increase of water cement ratio decreased the compressive strength for all percentages of coal bottom ash at all ages Aswathy P.U et al (2015) studied on the Behaviour of Self Compacting Concrete by Partial Replacement of Fine Aggregate with Coal Bottom Ash. This study presents the experimental investigation carried out to study the behavior of self-compacting concrete incorporating coal bottom ash at different replacement level of fine aggregate. To find the optimum replacement level the replacement levels of coal bottom ash to fine aggregate is set up from 5 - 30% at 5% increment. Then the optimum mix was subjected to variations (increment and decrement in coal bottom ash in optimum mix). The fresh and hardened properties such as compressive strength, split tensile strength, flexural strength and modulus of elasticity of the concrete at the age of 28 days of curing were conducted for all the variations. Results shows that the strength of the concrete with coal bottom ash increased up to replacement level of 10%.This show that bottom ash are used as supplementary cementitious materials, having the pozzolanic reactivity.
Concrete is a mixture of cement, aggregate and water. Sand is normally used fine aggregate that is derived from river banks. The utilization of river sand in constructions is also high due to its most use in concrete. In developing countries the usage of river sand is pretty high due to rapid infrastructural development which results in shortage of sand. Therefore, in developing countries identify substituent material to replace the natural sand in concrete. The utilization of waste materials it will decreases in environmental load & waste management cost, reduce the cost of production as well as concrete quality gets increasing. Now a day’s river sand is very costly material because of more constructional activities. Due to this situation, investigate began for alternative material to natural sand. The main objective of this investigational work is to determine the effect of partial replacement of natural sand by Silica fume and Bottom Ash on the properties of concrete. The percentage substitution of cement by Silica fume adopted in this experimentation is 20% and natural sand by Bottom Ash for 0%, 20%, 40%, 60%, 80% and 100%. The purpose is to study the possibility of using SF and BA to make a lightweight, high. performance and environmentally friendly concrete. The effect of SF and BA on the workability characteristics are studied through slump, compaction factor and vee-bee tests. The strength characteristics such as compressive, tensile, flexural, shear and impact strengths are studied. The work is carried out for M30 grade of concrete.
The materials used in the this experimental study include Ordinary Portland Cement(OPC), natural sand, coarse aggregate, Silica fume and Bottom Ash. The properties of the materials are described below.
In this work, Ordinary Portland Cement 43 grade conforming to IS: 8112-1989 is used. Fig 4.1: OPC 43 grade cement Table 4.1 : Physical properties of cement Properties Result Permissible limits as per IS 8112: Fineness 4% It should not be more than 11% Normal consistency 32% <34% Specific gravity 3. Setting time a) Initial b) Final 43 min 360 min Should not be less than 30 minutes Should not be greater than 600minutes
Locally obtainable crushed aggregates confirming to IS: 383–1970 is used in this project work of size 20mm below. The coarse aggregate specific gravity was found to be 2.68. Fig 4.3 : Locally available crushed aggregate Table 4.4 : Physical properties of coarse aggregate Property Results Particle shape, size Angular 20mm down size Fineness modulus of 20mm aggregate
Specific gravity 2.
Silica fume is a very fine noncrystalline material produced in electric arc furnace as a byproduct of silicon metal or ferrosilicon alloys. Silica fume has been known to us with different names such as micro silica, silica dust and condensed silica fume. Silica fume has a property that it behaves as a pozollana as well as cementatious material. One of the the most beneficial uses for silica fume is in concrete. Silica fume pozzolanic materials is found most suitable industrial product as to be used in concrete as partial replacement of cement. The optimum silica fume replacement percentage for obtaining maximum 28-days strength of concrete ranged from 5 to 20%. When pozzolanic materials are incorporated to concrete, the silica present in these materials react with the calcium hydroxide released during the hydration of cement and forms additional calcium silicate hydrate (C-S-H), which improve durability and the mechanical properties of concrete. When the fine pozzolana silica fume particles are added to the paste, a heat of hydration is observed resulting in the formation of pozzolanic material and calcium hydroxide. Due to large surface area silica fume gets densed packed in the paste of cement and aggregate reducing the wall effect in the transition zone between the paste and aggregate. Concrete having optimum percentage of silica fume shows increasing strength and durability of concrete. Fig 4.4 : Silica fume The physical properties of silica fume are as follows-
Bottom Ash is a coarser material, which drops into the bottom of the furnace in latest large thermal power plants and constitute about 20% of gross ash content of the coal fed in the boilers. It consists of non-combustible materials, and is the residual part from the incineration of household and similar waste. Raw bottom ash is a granular material that consists of a mix of inert materials such as sand, stone, porcelain, metals and ash from burnt materials. The utilization of coal ash in normal strength concrete is a new scope in concrete mix design and if put to use on large scale would ameliorate the construction industry, by minimizing the construction cost and abating the ash content. Here experiment is carried out to study the effect of use bottom ash as a replacement for sand. Fig 4.5 : Bottom Ash Table 4.7 : Physical properties of Bottom ash Specific gravity 2. Fineness modulus (%) 1. Table 4.8 : Chemical composition of bottom ash (%) SiO 2 33. Al 2 O 3 12. Fe 2 O 3 6. CaO 6. K 2 O 1. TiO 2 0. MgO 0. So 3 0. Na 2 O 0.
Energy is the main backbone of modern civilization of the world over, and the electric power from thermal power stations is a dominant source of energy, in the order of electricity. In India, over 70% of electricity generated is by combustion of fossil fuels, out of which approximately 61% is contrived by coal-fired plants. This results in the origination of around 100 ton of ash. Most of the ash has to be disposed of either dry, or wet to an open area serviceable near the plant or by grounding both the fly ash and bottom ash and mixing it with suitable amount of water and pumping into artificial lagoon or dumping yards this brings out the pollution in water bodies and ruin of productive land. The untiring slackening of natural resources and the environmental imperils posed by the disposal of coal ash has approached appalling proportion such that the use of coal ash in manufacturing of concrete is imperative than a desire.
In comparison to sand, an elementary raw material, the sandy material obtained is a subsidiary raw material. Using this material is more endurable and environmentally amicable and eludes the use of natural resources such as sand and gravel. Bottom ash is used in following activities Road construction Foundation material Noise barriers Aggregate Art supplies
Water fit for drinking is commonly considered fit for preparing concrete. It should be free from oils, acids, alkalies, vegetables or other organic impurities. Water consists of two functions in a concrete. Firstly, water will reacts chemically with the cement to form a cement paste where the inert aggregate are held in suspension untill the cement paste get hardened. Secondly, water will serve as a lubricant in the mixture of fine aggregates and cement.
Adopt Water-Cement Ratio = 0. Step 3 : Selection of water content Referring to IS 10262-2009, Table 2, for coarse of size 20mm aggregate Maximum water content = 186 litre Therefore estimated water content = 186 + (6/100) = 197 litre Step 4 : Calculation of Cement content Water-Cement Ratio = 0. Cementitious material (Cement+S.F.) = 197/0.45 = 438 Kg/m^3 Minimum Cement content for severe exposure condition = 320 Kg/m^3 Hence the cement content is adequate. Increase of 10% Cementitious material content Cementitious material content = 438X1.10 = 481.8 Kg/m^3 Step 5 : Determination of volume of coarse and fine aggregate Referring to IS 10262-2009, Table 3, volume of coarse aggregate per unit volume of concrete corresponding to a maximum size of coarse of 20mm and fine aggregate corresponding to grading zone II and water-cement ratio of 0.45. Volume of coarse aggregate = 0. Volume of fine aggregate = 1-0.62 = 0. Step 6 : Mix calculation The mix calculation per unit volume of concrete shall be as follows. a) Volume of concrete = 1 m^3 b) Volume of cement = (Mass of cement/specific gravity of cement)/ = (481.80/3.15)X(1/1000) = 0.153 m^3 c) Volume of water = (Weight of water/specific gravity of water)/ = (197/1)X(1/1000) = 0.197 m^3 d) Volume of all in aggregate = [a-(b+c)] = [1-(0.153+0.197)] = 0.65 m^3 e) Mass of coarse aggregate = (d)xVolume of CAxSpecific gravity of CAx
= 1088.2 Kg f) Mass of fine aggregate = (d)xVolume of FAxSpecific gravity of FAx = 0.65X0.38X2.60X = 642.25 Kg Table 4.9 : Material ratios Materials Qtty Ratio Cement 481.80 1 Fine aggregate 642.25 1. Coarse aggregate 1088.20 2. Water-Cement ratio 0.45 0. Total volume = 0.33 m^3 Add 10% extra volume = 0.36 m^3 Density of concrete = 2500 Kg/m^3 Therefore volume of concrete = 0.36X2500 = 900 Kg Step 7 : Quantity Calculation Cement = (900X1)/(1+1.33+2.26) = 196.08 Kg Fine Aggregate = (900X1.33)/(1+1.33+2.26) = 260.78 Kg Coarse Aggregate = (900X2.26)/(1+1.33+2.26) = 443.14 Kg Water = (900X0.45)/(1+1.33+2.26) = 88.24 Ltr Silica Fume at 20% by weight of cement = 39.22 Kg Therefore cement qtty = 156.86 Kg Saving in cement qtty = 39.22 Kg
After filling, surface of the mould is levelled and provide the designation to each specimen. Specimen should be demoulded after 24 hours. After Demouldig, specimens are put in curing tank for 28 days. After 28 days specimens are taken out from curing tank then put those specimens for drying in sunlight for 24 hours. Finally specimens are taken to the strength tests.
The below procedure is adopted to carry out the slump cone test. Place the concrete mix in the cleaned slump cone mould in four layers. Each layer is 1/4th of the height of the mould. Each layer tamped with 25 blows the blows are spread uniformly over the entire surface. For second and subsequent layer tamping rod should penetrate to the under lying layer. Strike of the top with a tamping rod or trowel so that mould is exactly filled. Raise the slump cone by using handle of instrument vertically and bring it on the slump cone top. Measure the height between the top of the slump cone and handle, note this as H1. Lower the handle to the sides of the slump cone and lift the cone slowly without disturbing the concrete. Concrete starts settling, as soon as the settlement stops. Raise the handle and bring it on the top of the unsupported concrete. Measure the vertical height between the handle and the top of concrete, call this as H2. Slump = (H2–H1) in mm. The slump cone test apparatus dimensions and types of slump produced are shown in fig Fig 4.6 : Typical slump cone test specimen