
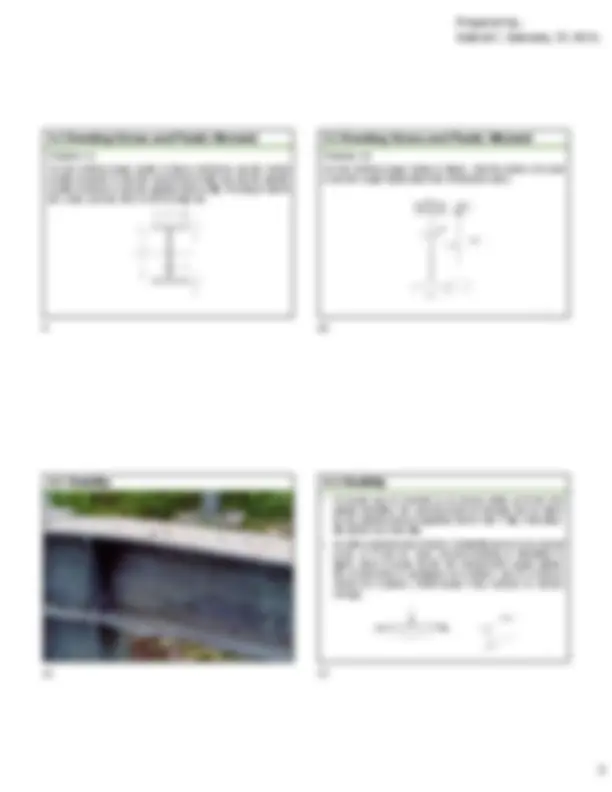
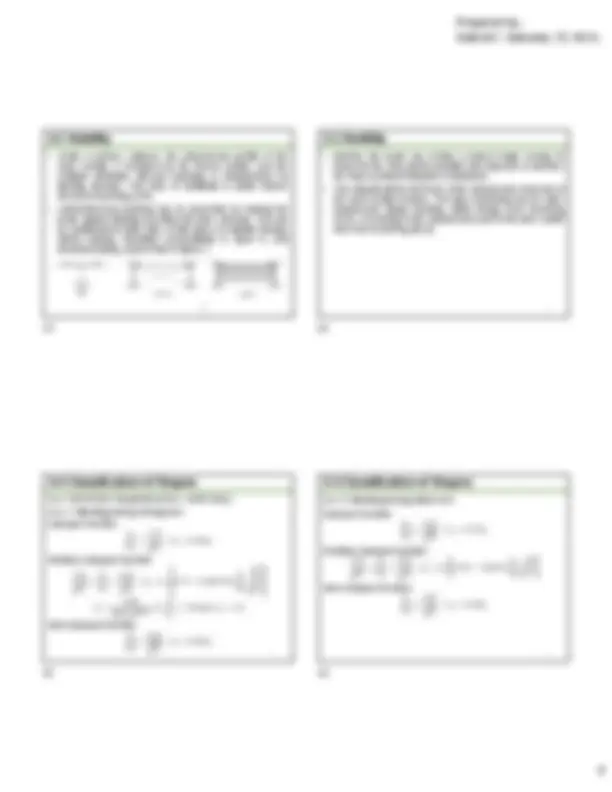
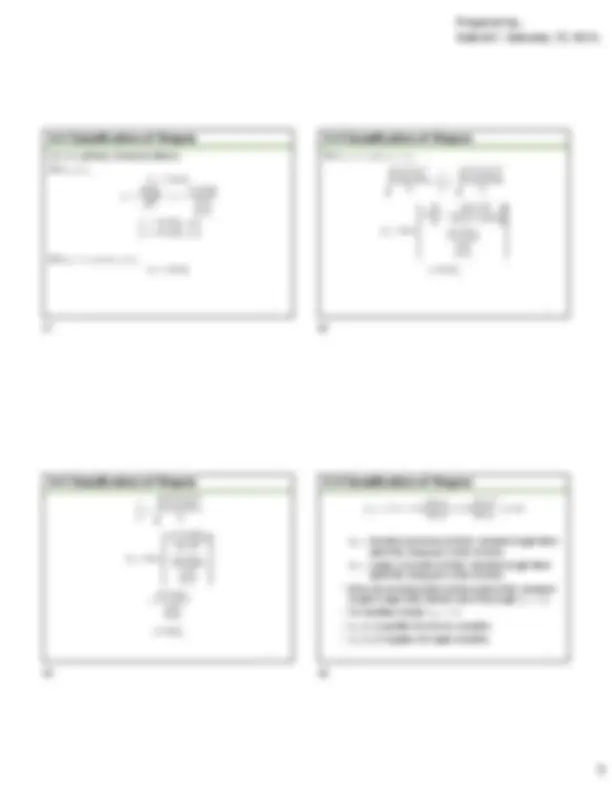
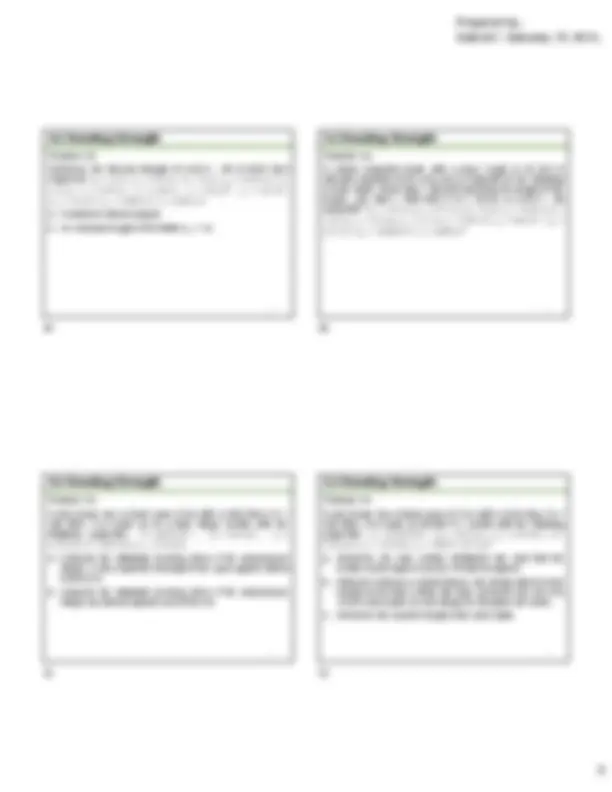
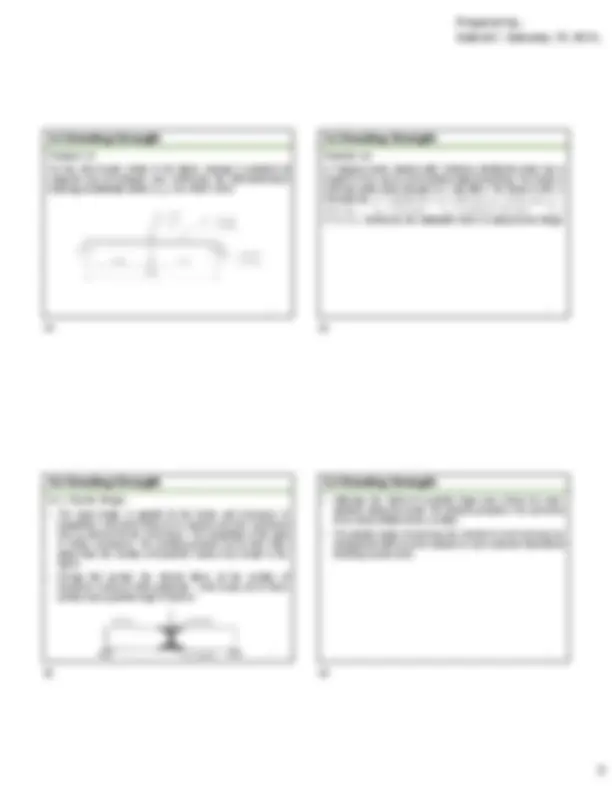
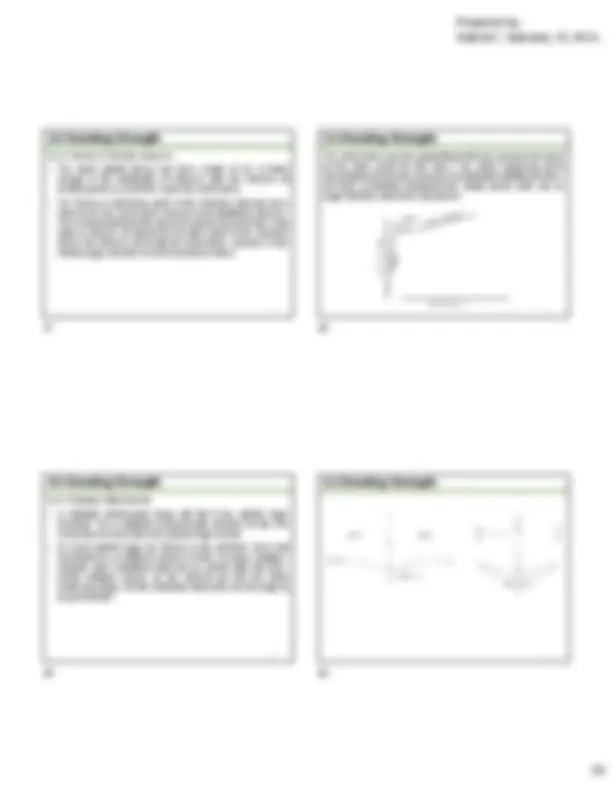
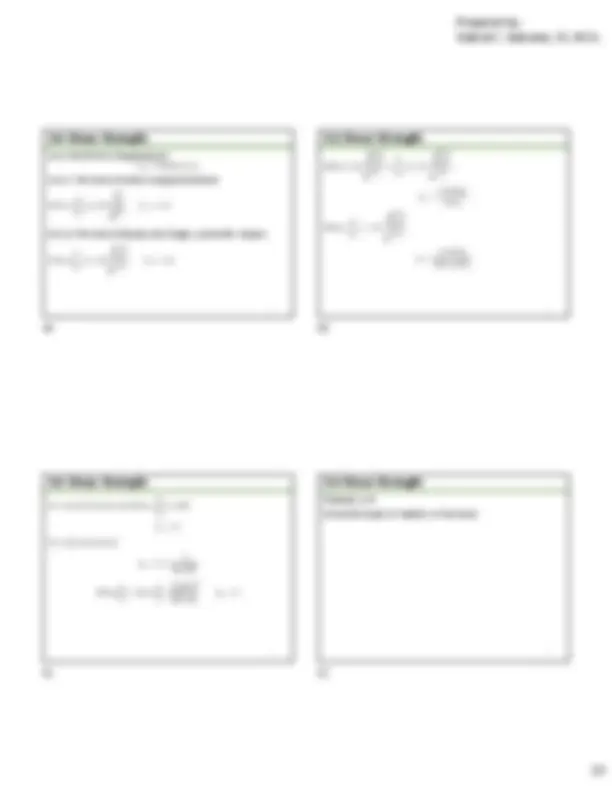
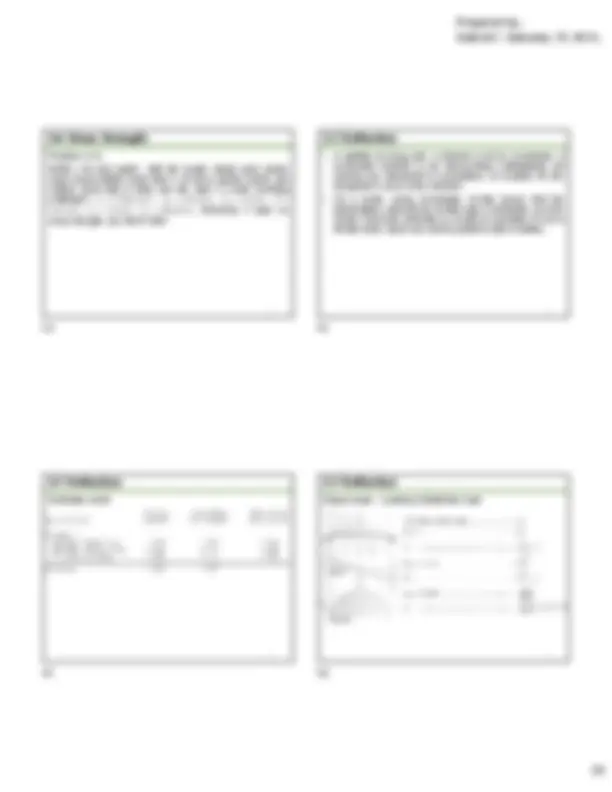
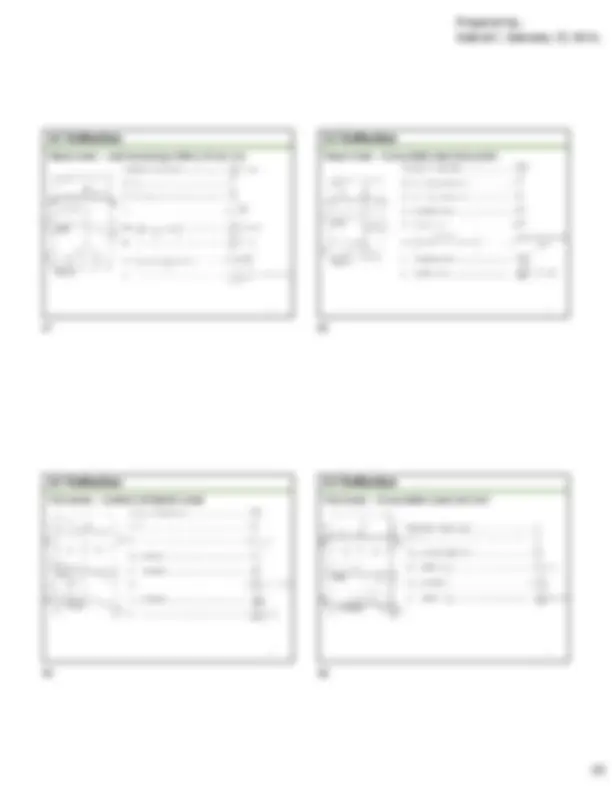
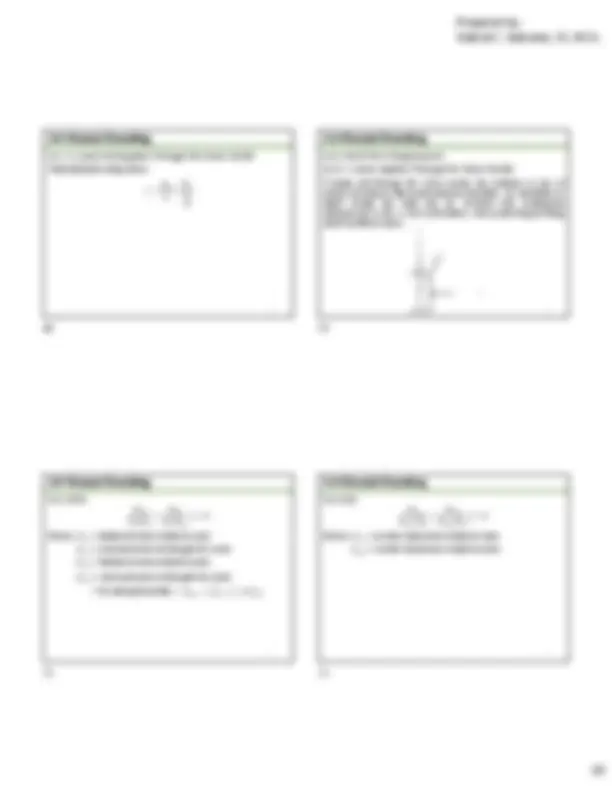
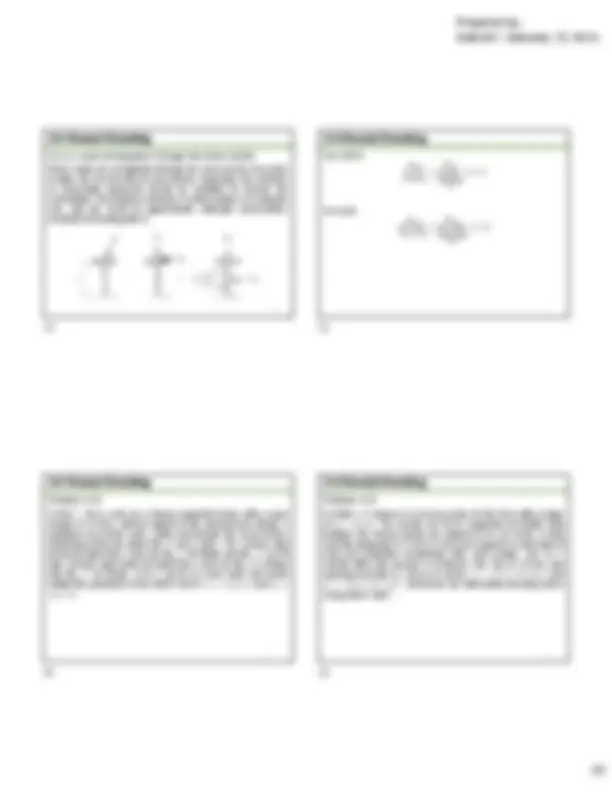
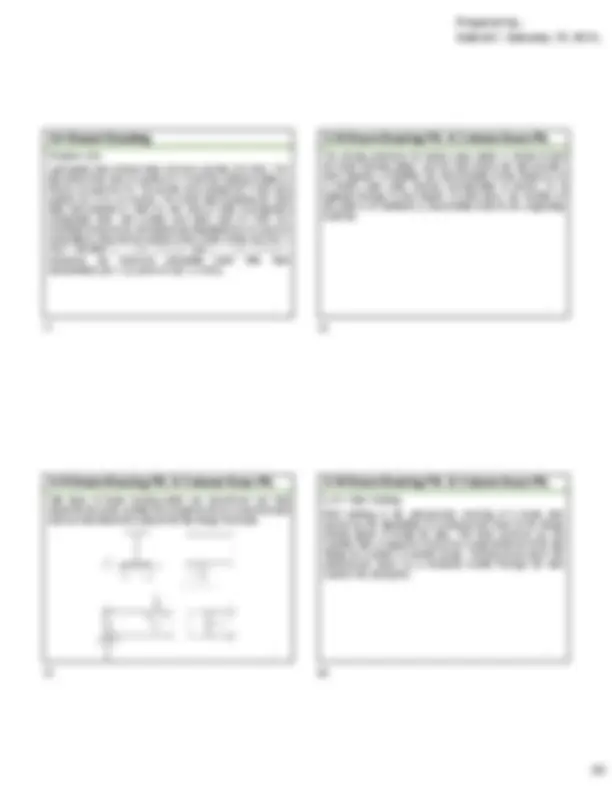
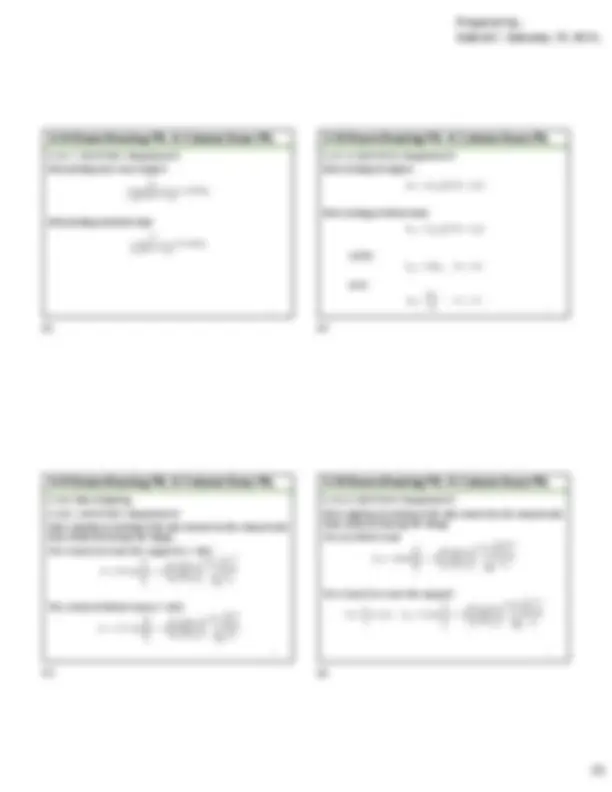
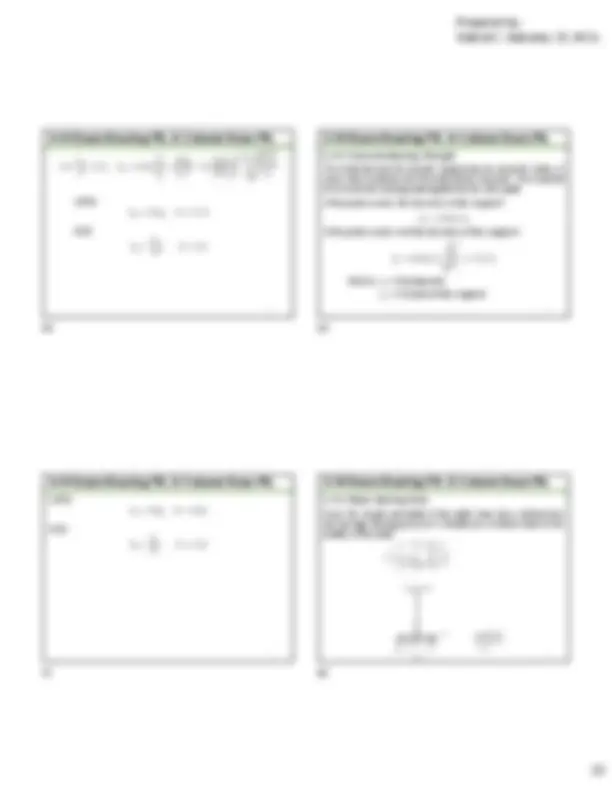
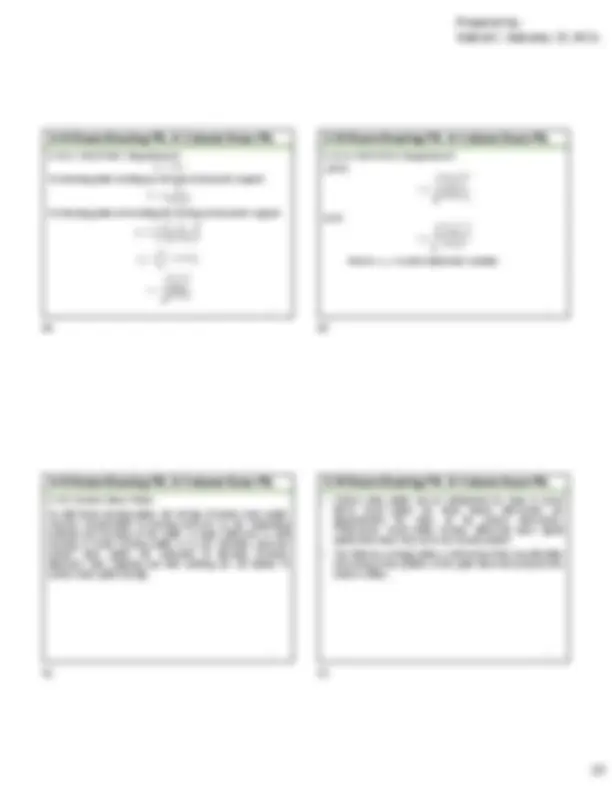
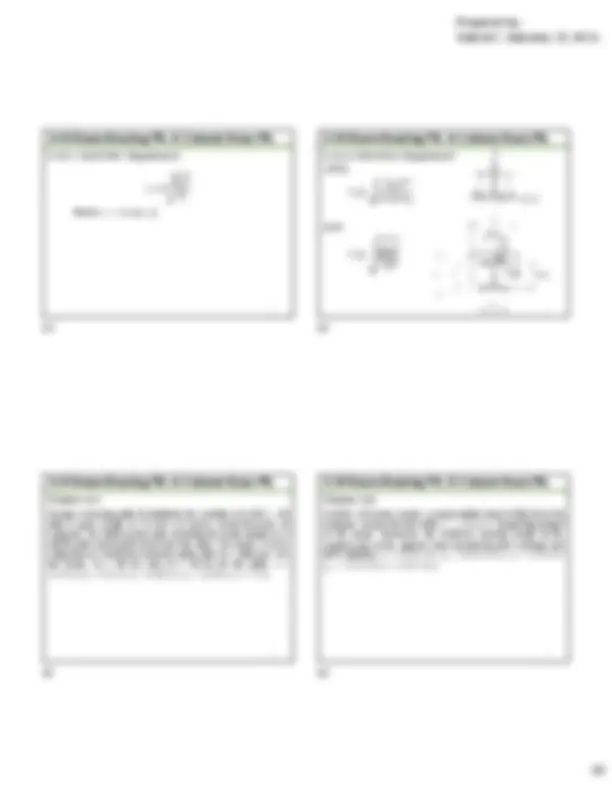
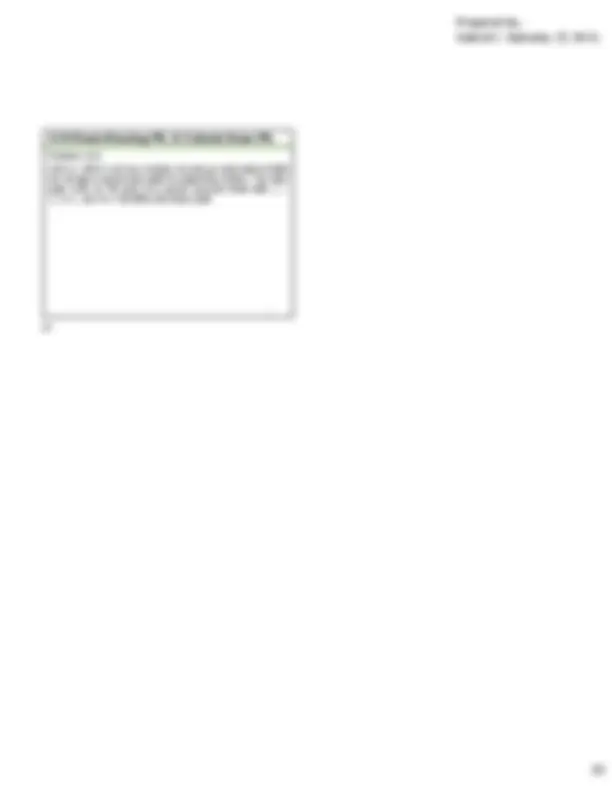
Study with the several resources on Docsity
Earn points by helping other students or get them with a premium plan
Prepare for your exams
Study with the several resources on Docsity
Earn points to download
Earn points by helping other students or get them with a premium plan
Community
Ask the community for help and clear up your study doubts
Discover the best universities in your country according to Docsity users
Free resources
Download our free guides on studying techniques, anxiety management strategies, and thesis advice from Docsity tutors
Flexural member design Bending stress and shear strength Lateral-torsional buckling considerations
Typology: Slides
1 / 25
This page cannot be seen from the preview
Don't miss anything!
Engr. Gabriel Gamana, M.Sc.
2 1.0 Introduction 2.0 Tension Members 3.0 Compression Members 4.0 Beams 5.0 Beam-Columns 6.0 Connections
3 4.1 Introduction 4.2 Bending Stress and Plastic Moment 4.3 Stability 4.4 Classification of Shapes 4.5 Bending Strength 4.6 Shear Strength 4.7 Deflection 4.8 Design 4.9 Biaxial Bending 4.10 Beam Bearing Plates and Column Base Plate
4
5
6
7 To be able to determine the nominal moment strength Mn, we must first examine the behavior of beams throughout the full range of loading, from very small loads to the point of collapse.
8 Plastic Moment Capacity 𝑀 = 𝐹௬𝑍 = 𝐹௬
Where A = Total cross-sectional area a = Distance between the centroids of half-areas Z = Plastic section modulus
13
14
15 4.4.1 NSCP 2001 Requirement (S.I. Units Only) 4.4.1.1 Bending Along Strong Axis Compact Section 𝑏 2 𝑡^ <^
Partially Compact Section 170 𝐹௬
70 then 𝑘 = 1. Non-Compact Section 𝑏 2 𝑡
16 4.4.1.2 Bending Along Weak Axis Compact Section 𝑏 2 𝑡
Partially Compact Section 170 𝐹௬
Non-Compact Section 𝑏 2 𝑡^ >^
17 4.4.1.3 Laterally Unbraced Beams For 𝐿 ≤ 𝐿 𝐹 = 0.66𝐹௬ 𝐿ଵ =
For 𝐿 > 𝐿 𝑎𝑛𝑑 𝐿 ≤ 𝐿௨ 𝐹 = 0.60𝐹௬
18 For 𝐿 > 𝐿 𝑎𝑛𝑑 𝐿 > 𝐿௨ 703270 𝐶 𝐹௬
19
20
ଶ ≤ 2. 𝑀ଵ = Smallest end moment of the unbraced length taken about the strong axis of the member 𝑀ଶ = Larger end moment of the unbraced length taken about the strong axis of the member
25 If the shape is noncompact because of the flange, the nominal strength will be the smaller of the strengths corresponding to flange local buckling and lateral torsional buckling. Flange local buckling For λ ≤ λ No Flange Local Buckling For λ < 𝜆 ≤ 𝜆 𝑀 = 𝑀 − 𝑀 − 0.7𝐹௬𝑆௫
26 Lateral-torsional buckling For 𝐿 ≤ 𝐿 No Lateral-torsional buckling For 𝐿 < 𝐿 ≤ 𝐿 𝑀 = 𝐶 𝑀 − 𝑀 − 0.7𝐹௬𝑆௫
For 𝐿 > 𝐿 𝑀 = 𝐹𝑆௫ ≤ 𝑀 𝐹 =
ଶ
27
𝑀௫ = Absolute value of maximum moment in unbraced segment 𝑀 = Absolute value of moment at quarter point of unbraced segment 𝑀 = Absolute value of moment at centerline of unbraced segment 𝑀 = Absolute value of moment at three-quarter point of segment 𝑅 = cross-section monosymmetry parameter = 1.0, doubly symmetric members
28
29 Problem 4- Determine the flexural strength of a W14 × 68 of A242 steel subject to: 𝑏 = 10 𝑖𝑛, 𝑡 = 0.72 𝑖𝑛, d = 14 𝑖𝑛, 𝑡௪ = 0.415 𝑖𝑛, k = 1.31 𝑖𝑛 , 𝑟௫ = 6.01 𝑖𝑛 , 𝑟௬ = 2.46 𝑖𝑛 , 𝐼௫ = 722 𝑖𝑛ସ^ , 𝐼௬ = 121 𝑖𝑛ସ^ , 𝑍௫ = 115 𝑖𝑛ଷ, 𝐶௪ = 5380 𝑖𝑛, 𝐽 = 3.010 𝑖𝑛ସ a. Continuous lateral support. b. An unbraced length of 20 ft with Cb = 1.0.
30 Problem 4- A simply supported beam with a span length of 45 feet is laterally supported at its ends and is subjected to the following service loads: Dead load = 400 lb/ft (including the weight of the beam). Live load = 1000 lb/ft. If Fy = 50 ksi, is a W14 × 90 adequate?: 𝑏 = 14.5 𝑖𝑛, 𝑡 = 0.71 𝑖𝑛, d = 14 𝑖𝑛, 𝑡௪ = 0.44 𝑖𝑛, k = 1.31 𝑖𝑛, 𝑟௫ = 6.14 𝑖𝑛, 𝑟௬ = 3.7 𝑖𝑛, 𝐼௫ = 999 𝑖𝑛ସ, 𝐼௬ = 362 𝑖𝑛ସ, 𝑍௫ = 157 𝑖𝑛ଷ, 𝐶௪ = 16000 𝑖𝑛, 𝐽 = 4.060 𝑖𝑛ସ
31 Problem 4- A steel beam has a simple span of 4m with a yield stress Fy = 400 MPa. It is made up to a wide flange section with the following properties; 𝐴 = 2690 𝑚𝑚ଶ^ , 𝑏 = 101 𝑚𝑚 , 𝑡 = 5.70 𝑚𝑚, d = 303 𝑚𝑚, 𝑡௪ = 5.10 𝑚𝑚. a. Compute the allowable bending stress if the compression flange is fully supported throughout the span against lateral movement. b. Compute the allowable bending stress if the compression flange has lateral supports only at its end.
32 Problem 4- A steel beam has a simple span of 12 m with a yield stress Fy = 250 MPa. It is made up W760x173 section with the following properties; 𝐴 = 22100 𝑚𝑚ଶ^ , 𝑏 = 267 𝑚𝑚 , 𝑡 = 21.6 𝑚𝑚 , d = 762 𝑚𝑚, 𝑡௪ = 14.4 𝑚𝑚, 𝐼௫ = 2060 × 10^ 𝑚𝑚ସ a. Determine the safe uniform distributed live load that the section could support. Assume full lateral support. b. Owing to unforeseen circumstances, the design load must be change to 56 kN/m uniform live load. Determine the size of a 10 mm cover plate on each flange to strengthen the beam. c. Determine the required length of the cover plate.
37 4.5.2 Theory of Plastic Analysis
38 The yield stress and the proportional limit are assumed to occur at the same point for this steel. The strain hardening could theoretically permit steel members to withstand additional stress, but from a practical standpoint the strains which arise are so large that they cannot be considered.
39 4.5.3 Collapse Mechanism
40
41 4.5.4 Virtual-Work Method The structure is assumed to be loaded to its nominal capacity, Mn, and is then assumed to deflect through a small additional displacement after the ultimate load is reached. The work performed by external loads during this displacement is equated to the internal work absorbed by the hinges. For concentrated force 𝑀 𝜃 = 𝑃𝑦 For distributed force 𝑀 𝜃 = 𝑤𝐿
42 Problem 4- Determine the collapse mechanism moment 𝑀 for the beam shown in figure
43 Problem 4- Determine the collapse mechanism load 𝑃 for the beam shown in figure
44 Problem 4- Determine the location of plastic hinge between the supports from the roller supports L
49 4.6.2 NSCP 2015 Requirement 𝑉 = 0.60𝐹௬𝐴௪𝐶 4.6.2.1 For web of rolled I-shaped members 𝑊ℎ𝑒𝑛
4.6.2.2 For web of doubly and singly symmetric shapes 𝑊ℎ𝑒𝑛
50
51
ଶ 𝑘௩ = 5
52 Problem 4- Check the beam in Problem 4-4 for shear
53 Problem 4- W350 x 90 steel girder with 8m length, simple span carries equal concentration dead load P at every quarter points and uniform dead load 5 kN/m and live load 7.2 kN/m including selfweight; 𝐴 = 11500 𝑚𝑚ଶ^ , 𝑏 = 250 𝑚𝑚 , 𝑡 = 16 𝑚𝑚 , d = 350 𝑚𝑚 , 𝑡௪ = 10 𝑚𝑚 , 𝐹௬ = 248 𝑀𝑃𝑎. Determine P base on shear strength. Use NSCP 2001
54
55 Deflection Limits
56 Simple beam – Uniformly Distributed Load
61 Problem 4- W350 x 90 steel girder with 8m length, simple span carries uniform dead load 5 kN/m and live load 7.2 kN/m including selfweight; 𝐴 = 11500 𝑚𝑚ଶ^ , 𝑏 = 250 𝑚𝑚 , 𝑡 = 16 𝑚𝑚 , d = 350 𝑚𝑚 , 𝑡௪ = 10 𝑚𝑚 , 𝐼௫ = 266 × 10^ 𝑚𝑚ସ^ , 𝐹௬ = 248 𝑀𝑃𝑎. Determine additional live load base on deflection 𝑦௪ = 𝐿/360.
62 Beam design entails the selection of a cross-sectional shape that will have enough strength and that will meet serviceability requirements. As far as strength is concerned, flexure is almost always more critical than shear, so the usual practice is to design for flexure and then check shear.
63 Problem 4- Use A992 steel and select a rolled shape for the beam in figure. The concentrated load is a service live load, and the uniform load is 30% dead load and 70% live load. Lateral bracing is provided at the ends and at midspan. There is no restriction on deflection.
64 Problem 4- The beam shown in figure has lateral support at the ends only. The concentrated loads are service live loads. Use Fy = 50 ksi steel and select a shape using NSCP 2010 under LRFD. Do not check deflections.
65 Biaxial bending occurs when a beam is subjected to a loading condition that produces bending about both the major (strong) axis and the minor (weak) axis. Such a case is illustrated in figure below, where a single concentrated load acts normal to the longitudinal axis of the beam but is inclined with respect to each of the principal axes of the cross section.
66 The load passes through the shear center of the cross section. The shear center is that point through which the loads must act if there is to be no twisting, or torsion, of the beam. The location of the shear center can be determined from elementary mechanics of materials by equating the internal resisting torsional moment, derived from the shear flow on the cross section, to the external torque.
67 Sag Rod Supports Supported at both ends and at mid-span Supported both ends and at at middle-third Supported both ends at
68 4.9.1 NSCP 2001 Requirement 4.9.1.1 Loads Applied Through the Shear Center Interaction Value 𝑓௫ 𝐹௫
where; 𝑓௫ = ெ ௌೣ ೣ 𝑓௬ = ெ ௌ 𝐹௫ = 0.66𝐹௬ (For compact and laterally supported members) 𝐹௬ = 0.75𝐹௬ (For compact and laterally supported members)
73 4.9.2.2 Loads Not Applied Through the Shear Center When loads are not applied through the shear center of a cross section, the result is flexure plus torsion. If possible, the structure or connection geometry should be modified to remove the eccentricity. The problem of torsion in rolled shapes is a complex one, and we resort to approximate, although conservative, methods for dealing with it.
74 For LRFD 𝑀௨௫ 𝛷𝑀௫
For ASD 𝑀௫ 𝑀௫/Ω
75 Problem 4- A W21 × 68 is used as a simply supported beam with a span length of 12 feet. Lateral support of the compression flange is provided only at the ends. Loads act through the shear center, producing moments about the x and y axes. The service load moments about the x axis are MDx = 48 ft-kips and MLx = 144 ft- kips. Service load moments about the y axis are MDy = 6 ft-kips and MLy = 18 ft-kips. If Fy = 50 ksi is used, does this beam satisfy the provisions of the NSCP 2015? 𝑍௬ = 24.4 𝑖𝑛ଶ^ and 𝑆௬ = 15.7 𝑖𝑛ଶ
76 Problem 4- A C200 x 17 channel is used as purlins for the truss with a slope of 𝜃 = 18.43°. The purlins are to be supported at middle third between the trusses which are spaced 6.4 m on center. A clay roof tile weighing 0.77 kPa is used and support a snow load of 0.96 kPa projected horizontally from roof surface. Use Fy = 248.80 MPa and assume a minimum size rod of 16 mm and spacing of purlins is 1.90 m on center. 𝑆௫ = 133 × 10ଷ^ 𝑚𝑚ଷ^ and 𝑆௬ = 12.8 × 10ଷ^ 𝑚𝑚ଷ. Determine the total actual bending stress using NSCP 2001.
77 Problem 4- Light grade steel channel was used as a purlins of a truss. The top chord of the truss is inclined in 1:3 and the distance between trusses is equal to 3 m. The purlins has a weight of 71 N/m and spaced at 1.2 m on centers. The dead load including the roof load roof material is 1200 Pa, live load of 1000 Pa projected horizontally from roof surface and wind load of 1440 Pa. Coefficient of pressure at leeward and windward are 0.2 and 0. respectively. Sag roof are placed at the middle thirds and Fbx = Fby = 138 MPa. 𝑆௫ = 4.48 × 10ସ^ 𝑚𝑚ଷ^ and 𝑆௬ = 1.18 × 10ସ^ 𝑚𝑚ଷ. Determine the maximum interaction value from load combinations (DL + LL) and 0.75 (DL + LL WL).
78 The design procedure for column base plates is similar to that for beam bearing plates, and for that reason we will consider them together. In addition, the determination of the thickness of a column base plate requires consideration of flexure, so it logically belongs in this chapter. In both cases, the function of the plate is to distribute a concentrated load to the supporting material.
79 Two types of beam bearing plates are considered: one that transmits the beam reaction to a support such as a concrete wall and one that transmits a load to the top flange of a beam.
80 4.10.1 Web Yielding Web yielding is the compressive crushing of a beam web caused by the application of a compressive force to the flange directly above or below the web. This force could be an end reaction from a support or it could be a load delivered to the top flange by a column or another beam. Yielding occurs when the compressive stress on a horizontal section through the web reaches the yield point.