
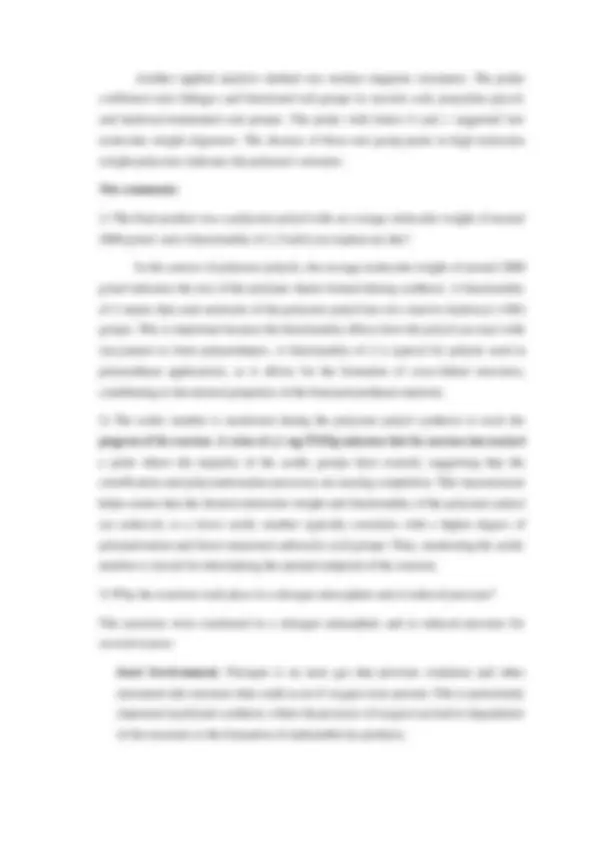
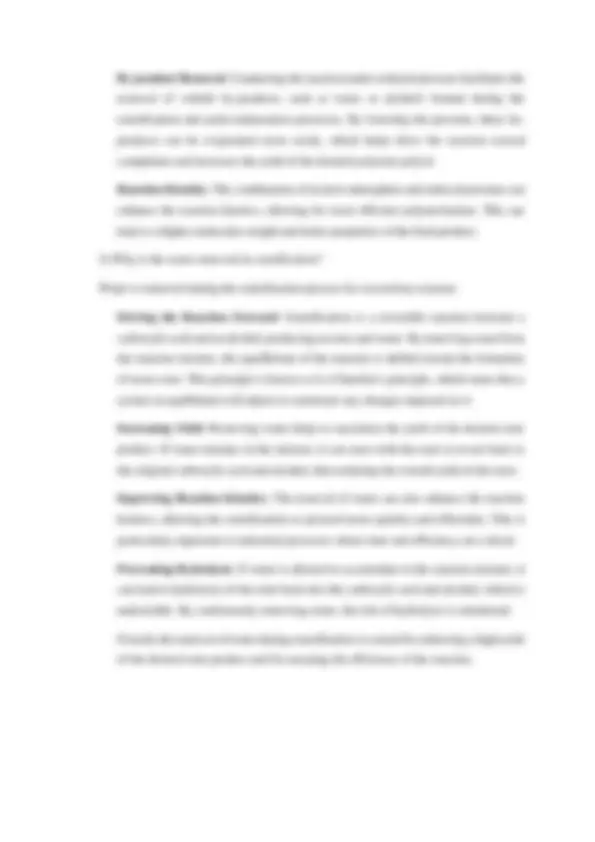
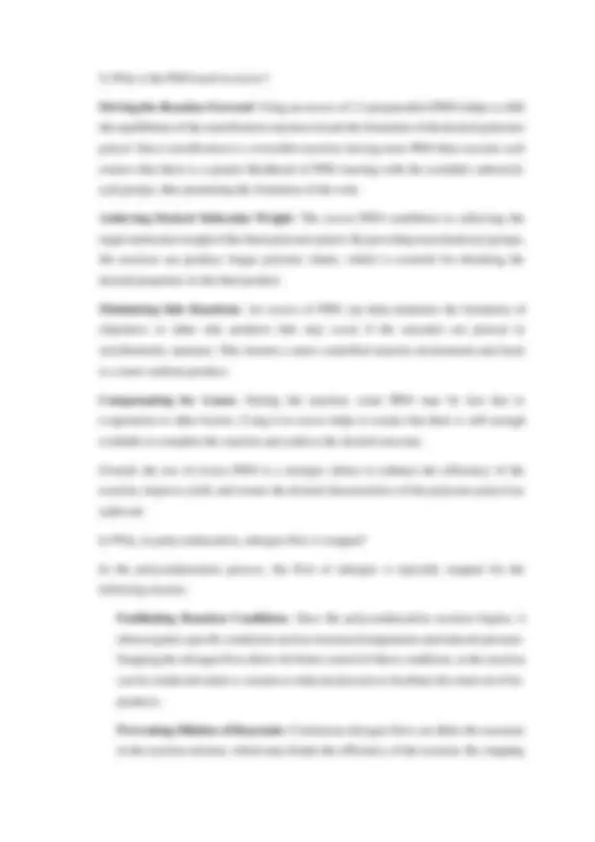
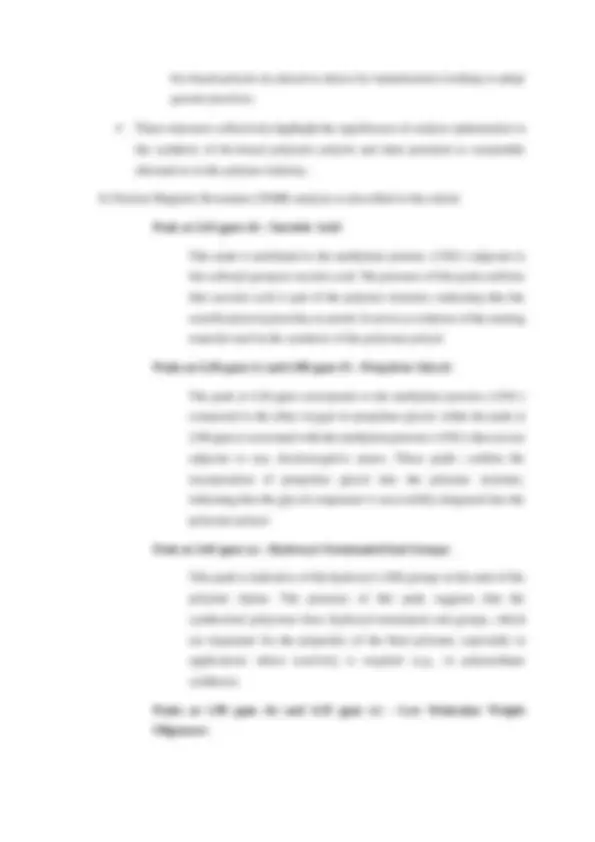
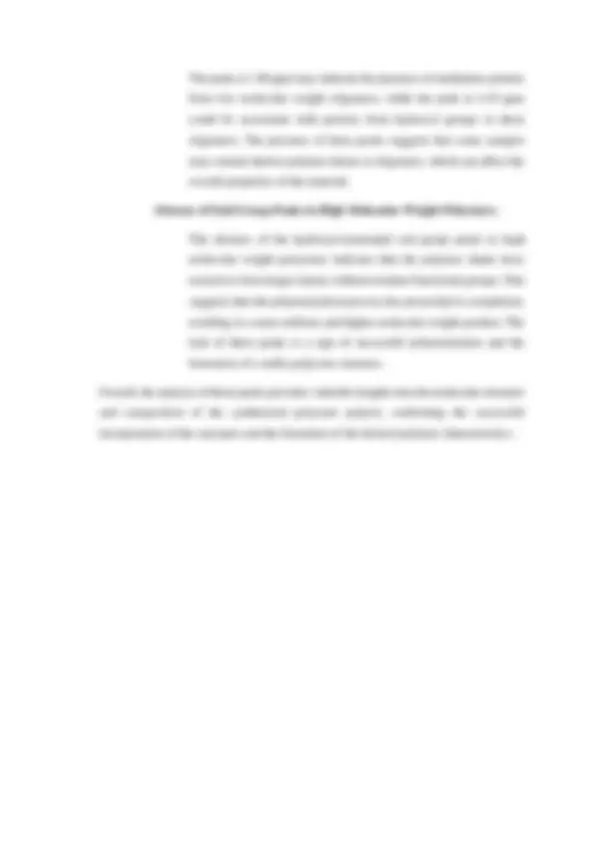
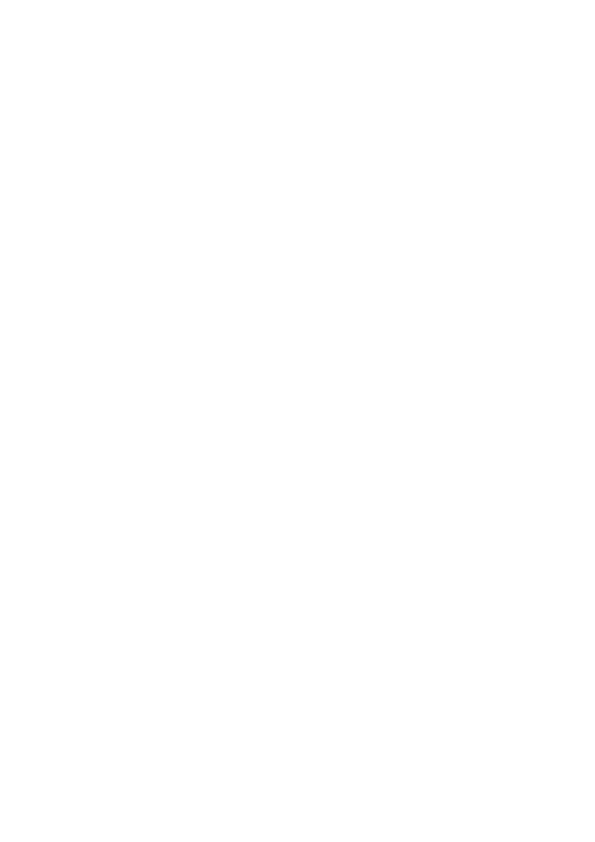
Study with the several resources on Docsity
Earn points by helping other students or get them with a premium plan
Prepare for your exams
Study with the several resources on Docsity
Earn points to download
Earn points by helping other students or get them with a premium plan
Community
Ask the community for help and clear up your study doubts
Discover the best universities in your country according to Docsity users
Free resources
Download our free guides on studying techniques, anxiety management strategies, and thesis advice from Docsity tutors
This document delves into the synthesis of bio-based polyester polyols using a two-step polycondensation process. It explores the influence of catalyst amount on rheological behavior and examines the reaction characteristics, including the use of nitrogen atmosphere and reduced pressure. The document also analyzes the ftir and nmr spectra of the synthesized polyols, providing insights into their molecular structure and composition. The study highlights the potential of these bio-based polyols as sustainable alternatives in the polymer industry.
Typology: Study notes
1 / 10
This page cannot be seen from the preview
Don't miss anything!
Study 2
- The title of the paper is 'Structure-Rheology Relationship of Fully Bio-Based Linear Polyester Polyols for Polyurethanes: Synthesis and Investigation,' by Paulina Parcheta and Janusz Datta.
reference. In the prepared samples, TPT concentrations ranged from 0.10% to 0.30%, with a 0.05% increase. As an experimental set-up, a three-neck glass flask was used as the reactor, equipped with key components, such as a mechanical stirrer, thermometer, and condenser. Experimental Overview- 2 Let’s talk about reaction characteristics.
By-product Removal : Conducting the reaction under reduced pressure facilitates the removal of volatile by-products, such as water or alcohols formed during the esterification and polycondensation processes. By lowering the pressure, these by- products can be evaporated more easily, which helps drive the reaction toward completion and increases the yield of the desired polyester polyol. Reaction Kinetics : The combination of an inert atmosphere and reduced pressure can enhance the reaction kinetics, allowing for more efficient polymerization. This can lead to a higher molecular weight and better properties of the final product.
distribution of polymer chains, allowing researchers to understand how the synthesis conditions (like catalyst amount) affect the final product. A well- defined molecular weight distribution is crucial for ensuring consistent performance in applications, particularly in the production of polyurethanes.
bio-based polyols an attractive choice for manufacturers looking to adopt greener practices.